RISE TO NEW DIMENSIONS
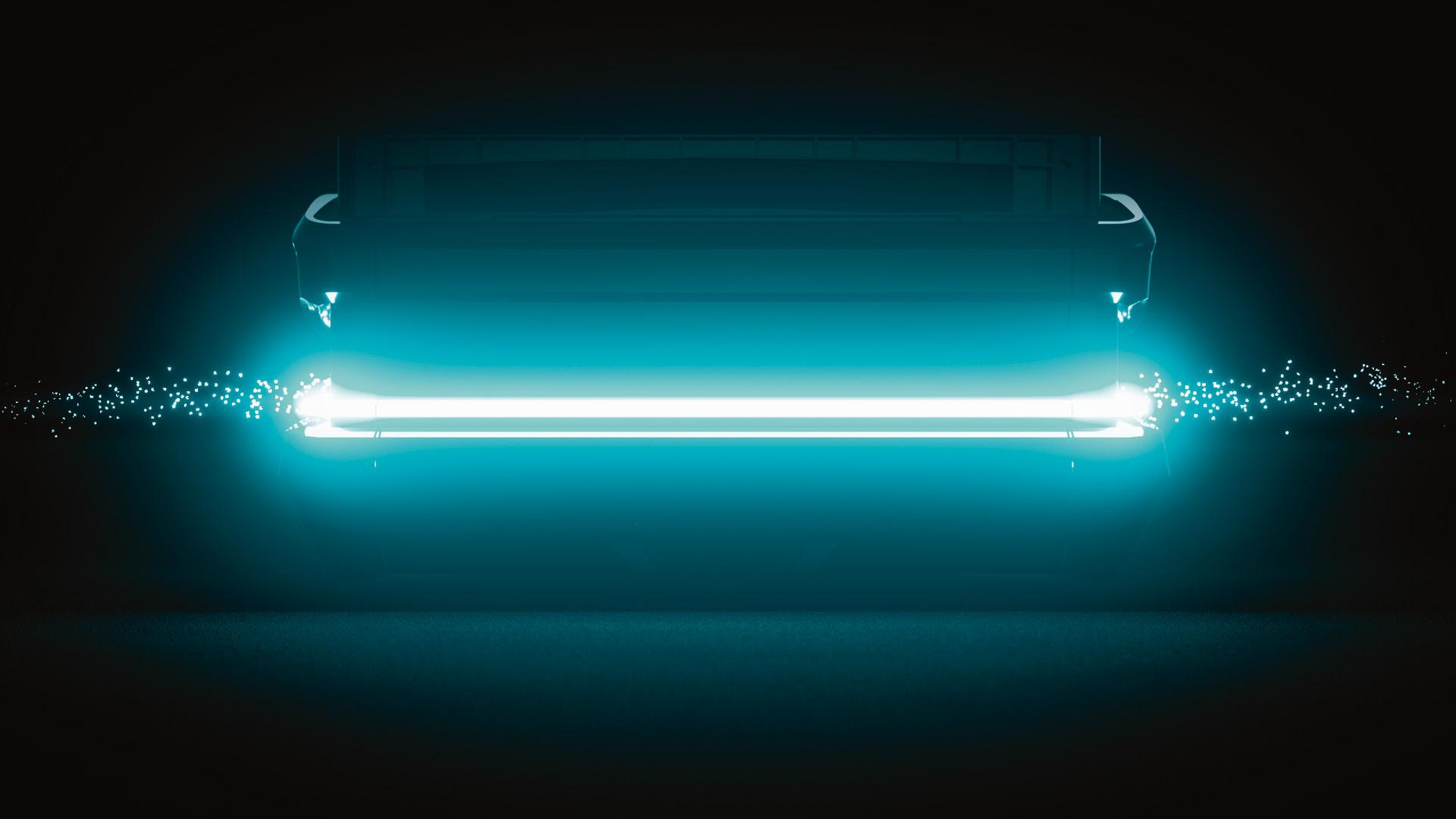
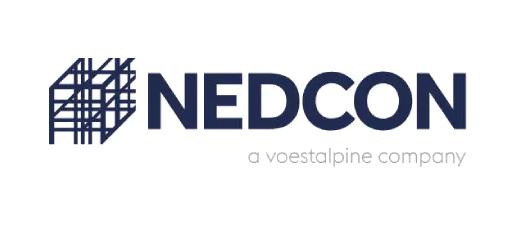
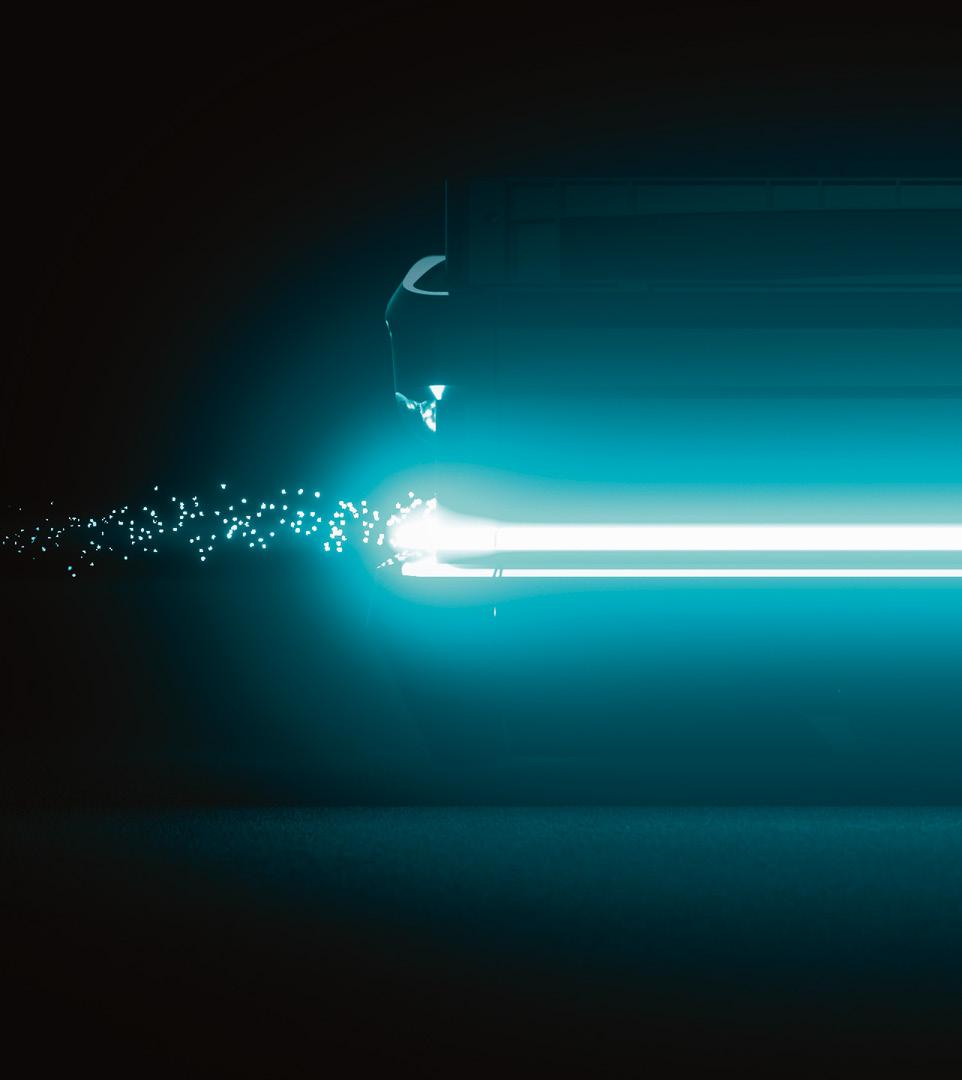
An industry-leading provider of intelligent automation solutions for intralogistics and manufacturing, KNAPP operates across 62 locations worldwide. Andreas Salznig, COO of KNAPP North America, discusses the company’s recent award-winning innovations and future aspirations
Writer: Lily Sawyer | Project Manager: Poppi Burke
Largely driven by technological innovation, socioeconomic fluctuation, and shifting consumer expectations, global supply chains have been undergoing significant transformations over the past five years.
Post COVID-19 pandemic consumer behaviors saw an acceleration of digital transformation and e-commerce, fueled by machine learning (ML) and artificial intelligence (AI).
“KEY TO OUR SUCCESS IS THE FACT THAT ALL OUR TECHNOLOGIES SEAMLESSLY INTEGRATE WITH ONE ANOTHER, OFFERING EXCEPTIONAL FLEXIBILITY”
– ANDREAS SALZNIG, COO, KNAPP NORTH AMERICA
As such, an emerging preference for online shopping, coupled with increasing labor shortages, began to push companies toward automation, particularly in warehousing and logistics.
Andreas Salznig, COO of KNAPP North America, remarks, “Today, the widespread adoption of robotics and automation has become essential for maintaining operational efficiency.”
Meanwhile, green logistics continues to gain momentum, with numerous opportunities for greater sustainability emerging across supply chains.
As a value chain tech partner, KNAPP’s activities in North America include designing, developing, and manufacturing intelligent warehouse systems, alongside point of sale and last mile logistics solutions.
Of the 2,000+ automation installations KNAPP oversees globally, a growing proportion of these are in North America –including major customers such as Walmart, who partnered with KNAPP to build four ultra-modern fulfillment centers, with a fifth on the way.
“Whatever complexities our clients need to solve, within our portfolio
we can offer the right technology and solution to handle it, from pallets to single pills,” Salznig adds.
Having become a trusted, stable partner for its clients in the healthcare, retail, fashion, food, wholesale, manufacturing, and e-commerce sectors over the years, KNAPP is ideally positioned for continued growth and success.
Driven by its company-wide motto ‘rise to new dimensions,’ KNAPP seeks to embody this theme in its everyday products and processes.
Andreas Salznig, COO:
“Sustainable logistics is all about efficiency – doing the right thing at the right time, utilizing the equipment in the right way, and using energy efficiently.
“KNAPP’s bot-solutions are built in a way that they can use latent energy when braking or climbing down a rack to recharge batteries, as with AeroBot. In this way, energy is recycled into the battery.
“Sustainability through digitalization in logistics is only possible with software as integrated intelligence. That’s why we at KNAPP view the warehouse management system (WMS) as the ‘central nervous system’ of a warehouse.
“An efficient WMS can offer benefits such as clean warehouse processes, reduced resource usage and errors. Interconnected software then opens the door for other solutions like transport management systems, data analysis tools, or packaging optimization solutions.
“To realize highly efficient system solutions, data-analytics is necessary to provide the required information. Trained AI models, meanwhile, help us to forecast future orders days in advance and prepare systems for peakscenarios.”
For readers unfamiliar with Monoflo International, can you share an overview of your company and the solutions you provide?
Monoflo International is a leading North American manufacturer specializing in high-performance, reusable transport packaging solutions. With over 50 years of experience, Monoflo produces injectionmolded plastic containers, trays, pallets, and bulk containers engineered to precise specifications for automated storage and retrieval (ASRS) and general use applications. Monoflo serves industries such as retail, e-commerce, manufacturing, automotive, processed food, wholesale bakery, and general distribution. Our solutions are designed to seamlessly integrate into high-speed automated systems, offering options like RFID tracking, barcode labeling, prototyping, and ASRS induction services—all with a focus on repeatable quality, long-term durability, and sustainability through recyclable and reusable products.
What role do Monoflo’s products play in highperformance automation systems like KNAPP’s?
Monoflo’s products are built for precision, durability, and reliability, making them ideally suited for highperformance automation systems like those developed by KNAPP. Our containers and trays are designed to exact dimensional tolerances to ensure flawless performance within automated environments. Features such as conveyor-friendly bottoms, reinforced corners, and pin up bottom lifter plates help reduce system jams, increase throughput, and maintain reliability. These design attributes ensure that Monoflo’s products move smoothly through high-speed systems, minimizing
downtime while supporting speed and efficiency in these highly demanding operations.
How do design and material choices in your containers impact the overall efficiency, durability, and reliability of automated warehouse systems? (chance to incorporate sustainability impact)
Monoflo’s containers are carefully engineered using high-quality resins like polypropylene (PP), high-density polyethylene (HDPE), and Electro-Dissipative ESD-safe materials, chosen for their strength and longevity in rigorous environments. Structural features like doublewall corners and hybrid bottoms enhance load stability and reduce wear during conveyor use. Ergonomic touches—such as molded handles, barcoding zones, and fire-vent sidewall designs—further support handling and safety. These thoughtful material and design decisions result in containers that are not only cost effective and durable but also sustainable, as every unit is 100% recyclable and part of a closed-loop system that includes end of life buy-back and environmentally friendly plastic reprocessing options.
customization or innovation
Monoflo takes a collaborative approach to customization, engineering containers that precisely match the design use application, dimensional, and performance requirements of our partner’s automation system. This includes tailoring footprints to regional or application-specific standards, such as 600×400 mm,
650×450 mm, or 800mm x 600mm containers, and even custom sizes for unique use cases. Innovations include in-mold RFID tags, integrated barcodes and/or QR codes for real-time system operation and tracking, as well as specialized features like internal divider systems, drain holes, lids, lifter plates, and ergonomic access points. These customizations ensure that every product supports seamless integration and optimal flow within automated environments.
How does Monoflo stay ahead in terms of design, manufacturing precision, and product durability for automated environments?
Monoflo maintains its competitive edge by investing in high-pressure, high-speed injection molding technology, robotic automation, and ISO 9001:2015-certified quality systems. Our ability to quickly prototype and iterate on designs allows us to rapidly bring precise, system-compatible products to market. With a track record of millions of deployed containers and trays across multiple industries, Monoflo combines field-proven experience with continuous product evolution—evident in the release of innovations like FM-compliant drain holes and next-generation container designs. Our commitment to precision manufacturing ensures that each product consistently performs in the most demanding automated environments.
What trends do you see shaping the future of containerized automation, especially in sectors like retail and e-commerce?
Containerized automation is rapidly evolving, especially in retail and e-commerce sectors where speed, accuracy, and sustainability are paramount. One major trend is the widespread adoption of smart containers embedded with RFID and scannable codes to support real-time tracking, inventory accuracy, and order delivery accuracy. Another is the shift toward circular supply chains, where durable, reusable, and recyclable containers help companies meet ESG goals. Additionally, there is growing demand for modular and collapsible designs that reduce, empty storage, and return logistics costs and warehouse footprint. As systems become more complex, containers must also
support multi-SKU handling through features like internal dividers and mini-tote formats that increase existing cube utilization.
What’s next for Monoflo—are there new product innovations or partnerships on the horizon?
Monoflo is advancing its leadership in automation by delivering engineered container solutions built for high-performance intralogistics systems. Its latest product innovations—such as automation-optimized totes, modular divider systems and pallet systems—are designed to seamlessly integrate with AS/RS platforms, conveyor networks, and robotic picking systems across a wide range of industries. Solutions are engineered with reinforced bases, FM Global-compliant drain holes, and optional features like welded or hybrid bottoms, integrated divider slots, and custom RFID or barcode tagging to ensure smooth, reliable performance in highspeed, 24/7 operations.
To better serve automation providers and end-users, Monoflo is also expanding its manufacturing and logistics footprint. With facilities in Winchester, Virginia, and Ottawa, Kansas, and a growing presence in León, Mexico, the company is positioned to shorten lead times by moving closer to its partners across North and Latin America.
Complementing its innovation and growth is a deep commitment to sustainability. Monoflo supports a circular supply chain with fully recyclable products, in-house reprocessing capabilities, and product buy-back programs that extend the life and value of every container. Looking ahead, Monoflo will continue to collaborate with system integrators and warehouse automation leaders to deliver precise, durable, and scalable container and pallet solutions that power the next generation of automated fulfillment.
“WE STRIVE TO MAINTAIN OUR POSITION AS A BEST-IN-CLASS LEADER IN TECHNOLOGICAL SOLUTIONS”
– ANDREAS SALZNIG, COO, KNAPP NORTH AMERICA
Flexibility is at the forefront of this objective, with agile solutions and the ability to grow and adapt to ongoing challenges and changes in consumer behaviors being key priorities.
“We are proud to have a portfolio of products that allow us to consistently provide the best possible solutions –technically and economically – based on our customers’ requirements. Together, we rise to new dimensions, allowing our partners to do so by improving their service quality and delivery times,” Salznig remarks.
When it comes to supporting its customers, no matter the performance level, storage location, or service required, KNAPP is on hand to deliver tailormade solutions.
Reflecting on KNAPP’s recent
participation in the global supply chain conference ProMat 2025, where key speakers from the company spoke on the technology needs of hyperlocal markets, Salznig discusses how ‘one size does not fit all’ when it comes to providing logistics solutions.
“Every logistics solution must be designed in a way that, while addressing today’s requirements and operational pain points, is flexible and agile enough to be adapted in the future.”
Since it is nearly impossible to predict how end-customer needs will evolve over time, Salznig points out how it is vital to build a solution which enables growth, reactivity, and adaptation.
For example, KNAPP’s AeroBot system is an innovative solution that redefines automated storage and retrieval with unmatched flexibility, efficiency, and the highest storage density.
“Currently, solutions that provide an easier entry to automation and are flexible enough to adapt rapidly to market conditions are in demand,” adds Salznig.
Always open to developing new products and solutions, KNAPP’s ongoing focus remains on developing the broadest portfolio of technologies on the market, allowing it to address all market requirements with the optimal technical system solution while remaining cost-effective.
“Key to our success is the fact that all our technologies seamlessly integrate with one another, offering exceptional flexibility,” continues Salznig.
AWARD-WINNING SOLUTIONS
Offering a new level of efficiency to storage and retrieval processes, AeroBot recently received the Best
THE WORLD OF STORAGE IS CHANGING RAPIDLY. GROWING SECTORS, NEW MARKETS AND CHANGING CUSTOMER EXPECTATIONS REQUIRE INNOVATIVE SOLUTIONS. FOR NEDCON THIS MEANS THAT WE NOT ONLY DELIVER WHAT IS NEEDED TODAY, BUT ABOVE ALL THINK ALONG ABOUT WHAT WILL BE CRUCIAL TOMORROW. FROM SMART, EFFICIENT AND SCALABLE WAREHOUSE SOLUTIONS TO SUSTAINABLE PRODUCTION – WE ARE READY TO ADD VALUE WITH OUR EXPERTISE.
USA production facility
Automation and robotization
Improve efficiency, fast and reliable delivery while maintaining flexibility and scalability.
Knowledge and experience NEDCON has decades of experience with projects in automated warehouses.
• AeroBot – With the introduction of AeroBot at Promat 2025, the company has added a small footprint, high-density 3D shuttle that can operate independently outside of the shuttle rack structure. AeroBot’s seamless integration with the entire portfolio of hardware and software is a distinct differentiator.
• Evo Shuttle – KNAPP’s 1D and 2D shuttle systems form the heart of a modern warehouse, which can be seamlessly integrated into any logistics system with customized software and ergonomic workstation solutions.
• KiSoft – The company’s logistics software suite, KiSoft, is the central intelligence that ‘brings it all together’. The software not only covers vertical integration, such as machine control, warehouse control, and warehouse management, but it also makes horizontal integration possible along the entire value chain – all the way to the point of sale or end customer – supported by analytics and transport management.
• Open Shuttle - Free-moving shuttles supply workstations and deliver totes, cartons, or pallets while driverless vehicles can deliver volumes of up to 2,800 pounds.
• Pocket Sorter – Highly effective for order selection, packing, and sorting, this technology is space efficient and easily integrates with KNAPP’s supplementary goods-to-person technologies. With the ability to consolidate hanging and flat-packed goods, it is ideally suited for retail, fashion, e-commerce, omni-channel, and returns operations. The latest model automates pocket loading and unloading, offering seamless solutions for e-commerce and distribution.
• Pick-it-Easy Robot – AI-driven technology with various grippers and intelligent object recognition enables KNAPP’s Pick-it-Easy Robot workstation to handle a broad range of items in diverse sectors. The robot learns continuously, informing a cloud-based database which, in turn, increases overall system performance.
• Pick-it-Easy Workstations – These efficient, ergonomic goods-to-person workstations are the right choice for empowering and retaining labor. Various tasks can be handled at workstations, including order picking, returns processing, inventory, repacking, consolidating goods, or value-added services.
SatBot to handle load carriers up to 35 kilograms for quadruple-deep storage, powered by KiSoft software for seamless integration with WMS and warehouse control systems, making it ideal for e-commerce, microfulfillment, and manufacturing.
“In short, AeroBot delivers fast, scalable, and intelligent automation –making it a future-ready solution for modern intralogistics,” Salznig adds.
Alongside the award-winning AeroBot, KNAPP’s pocket solutions, such as PocketEngine, are lowering costs, increasing performance, and enhancing services in terms of order fulfilment.
A highly standardized solution, PocketEngine allows for fast installation and realization, while its ability to eliminate time-consuming specification processes means it can offer reduced costs.
Meanwhile, a pocket structure can be installed overhead without interrupting activities on the ground, which means it can easily be integrated at any given brownfield site without disrupting ongoing operations.
Product award at LogiMAT 2025 in Stuttgart, Germany.
Salznig elaborates, “We’re thrilled with what AeroBot has achieved. At its core, it features autonomous robotics with light detection and ranging (LiDAR) navigation and friction drive
technology, enabling movement in all directions up to 12 meters high without using any chains or gears.
“That means we have the simplest possible racking solution with zero maintenance requirements!”
Each AeroBot also carries a
“Pocket solutions provide a complete sequence for packing stations, enabling an efficient and fast packing process with very low error rates,” says Salznig.
In addition, KNAPP’s latest deployed pocket solution – the so-called ‘selfopening pocket’ – allows it to operate a 100 percent automated packing and picking system.
“We can directly and automatically drop products into totes and preerected cartons, offering a ‘zero touch’ approach,” Salznig adds.
In addition to its work with e-commerce and fulfillment centers, KNAPP has also developed an automated and prescriptionspecific vial filling system for the pharmaceutical sector, establishing a standardized system for mail order
and central fill pharmacy applications.
“Besides our own pill dispensing and counting technology, our KiSoft stack covers all necessary pharmacy processes and reduces operational errors to a minimum,” Salznig explains.
As such, the company is offering scalable system solutions based on the number of prescriptions being handled daily.
The solution can also be completed using tote conveyors and technologies designed for unit-of-use, including an automated storage and retrieval system (AS/RS), an A-frame, or a KNAPP store to prepare ready-made orders including pre-packaged medication.
By increasing the level of automation, KNAPP can optimize staff utilization while also lowering operating costs.
“Cost savings are the main driver of pharmacy automation, with accuracy and labor challenges also contributing.
KiSoft and automation streamlines fulfillment, saving time and optimizing logistics,” Salznig adds.
As a privately-owned company that stands for sustainable and organic growth, KNAPP spends a significant portion of its budget on R&D to continually innovate.
“We strive to maintain our position as a best-in-class leader in technological solutions,” Salznig asserts.
Looking ahead, the company aspires to elevate customer satisfaction and service, aiming to conclude every project with a satisfied client – an aspiration that Salznig believes is particularly well reflected in its North American operations.
Salznig concludes, “We grow together with our customers, since their successful business case is our best reputation and the foundation for long and ongoing relationships in the industry.
“I’m confident that the North American market has many opportunities for us, and with that, we are always looking for talent to join us!”