Senior Design
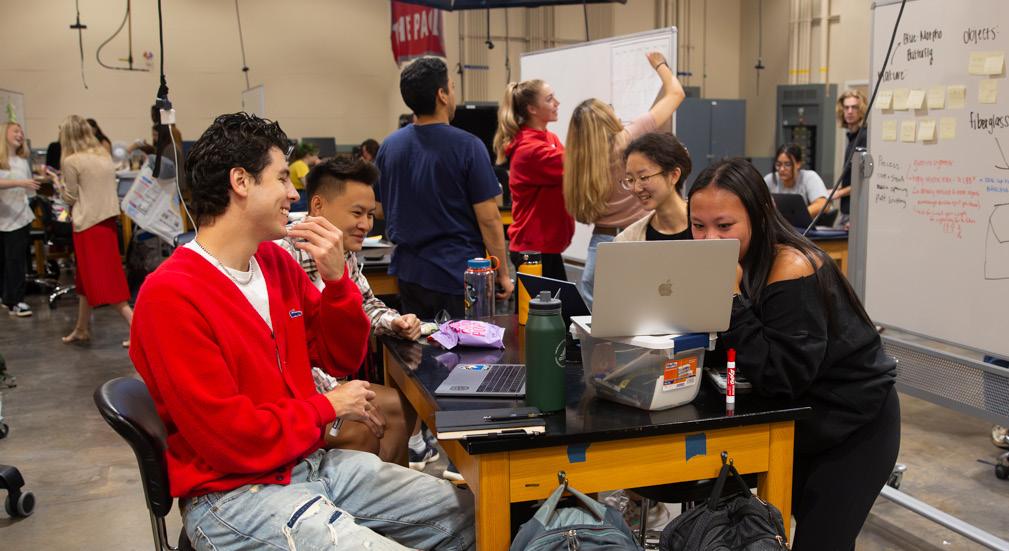
Amanda C. Mills (Ph.D., NC State University, Mechanical Engineering) is an assistant professor in the Department of Textile Engineering, Chemistry and Science at NC State University. Her focus is on developing innovative methods for electronics integration into textiles. She creates full system demonstration platforms to examine the impact of the textile on the device and vice versa. For example, this has included system level electronic designs and knit structure designs for human energy harvesting and physiological sensing.
Russell E. Gorga (Ph.D., Iowa State University, Chemical Engineering) was a full professor in the Department of Textile Engineering, Chemistry and Science at NC State University and was a former textile engineering program director. His main interests were in developing polymer nanocomposites with improved properties (mechanical and conductive) for a variety of functional applications.
Philip Bradford (interim co-director) (Ph.D., NC State University, Materials Science and Engineering) is a full professor in the Department of Textile Engineering, Chemistry and Science at NC State University. Through our Summer Textile Exploration Program, he discovered the field of textiles and received both his bachelor’s and master’s in textile engineering at the Wilson College of Textiles. His research group focuses on the synthesis and production of ultra-high aspect ratio carbon nanotubes (CNTs), and explores their wide range of applications such as composites, sensors, electrodes and filtration.
Bailey Knight (M.T., NC State University, Wilson College of Textiles) is a lab manager for Senior Design and for the Zeis Textiles Extension’s Prototype Lab. She supports students by providing them with the technology and knowledge to create soft-good prototypes and to conduct physical testing. She also helps students interface with the Zeis Textiles Extension labs as they request to have materials knit, spun, woven, dyed, finished and tested.
Connie Wong (B.S. Textile Technology, NC State University ‘23) is a graduate student in the M.S. in Textile Engineering program (May ‘24) at the Wilson College of Textiles. Her current research focuses on textile sustainability, specifically on the validity of current post-consumer textile recycling technology to further advance fiber-to-fiber recycling and textile circularity.
Savannah Strickland (B.S. Textile Engineering, NC State University ‘23) is earning an M.S. in Textile Engineering at the Wilson College of Textiles. Her current research is focused on sustainable dyeing techniques for sportswear apparel. Savannah is aiming to pursue material development or textile design within the sportswear or fashion industries.
Julia More (B.S. Textile Engineering, NC State University ‘23) is graduating in May with an M.S. in Textile Engineering at the Wilson College of Textiles. Julia is interested in pursuing a career in research and development within the field of textiles and is passionate about product development and finishing and dyeing. Her dream job would be to work for an athletic or outdoor company where she can combine her love of textiles and sports.
• William Barefoot, Weaving Lab Manager
• Jenna DeCandio, Knitting Lab Manager
• Jeffrey Krauss, Dyeing and Finishing Lab Manager
• Tim Pleasants, Spinning Lab Manager
• Teresa White, Physical Testing Laboratory Specialist
Allison Blanchard, Dr. Emiel DenHartog, Dr. Jeff Joines, Sara Kempin, Beth Palmer and the North Carolina Textile Foundation.
This capstone course in the Department of Textile Engineering, Chemistry and Science provides companies the opportunity to work with student teams to innovate in product and/or process development. In working with the student teams, companies explore materials property design, develop new directions for existing products or take their materials/product into a new marketspace. Our students utilize their expertise in engineering fundamentals, information systems, medical textiles, product development, supply chain management, testing and consumer behavior to solve a current product/process challenge. Through sponsored projects, student teams will learn project management and product design principles that leverage the global textile complex.
The purpose of this course is to deliver a ‘real-world’ experience that prepares students to solve open ended problems that they will face upon entering the workforce. The sponsored student team is expected to:
• Communicate effectively on the project problem, objectives and proposed solutions.
• Work efficiently in teams to deliver high-performing results.
• Assess, select and learn the latest and most appropriate technologies for project success and be able to adapt those technologies as needed.
• Analyze the project and solution from financial, economic, technical, ethical and commercial perspectives.
• Develop ideas with appropriate patent mapping and intellectual property assessment.
• Produce proof-of-principles prototype(s).
The annual Rice Bag Challenge is sponsored by Rise Against Hunger, an international organization that annually distributes millions of meals around the world through community meal-packing events. Each Senior Design team was given one week to create a useful prototype that would solve a problem in developing areas around the world using a maximum $10 budget and two, 50 pound rice bags. At the end of the week, each team pitched their product to a team of judges from Rise Against Hunger.
First Place: Team 5
Second Place (Tie): Team 6 and Team 8
While most sponsors spend an average of one to two hours per week on the project, many find interaction with the students to be the most rewarding aspect. Beyond that minimal time commitment, other expectations include:
• Helping define project scope and metrics for project success.
• Holding regular meetings with the team and providing specific project feedback.
• Providing technical mentoring and feedback on the team’s materials and process deliverables.
• Providing specific training on unique tools that are pertinent to the project.
• Providing coaching to help the student team reach the best solutions.
• It is important for the sponsor not to tell the team exactly what to do. This is an open-ended problem.
• Address any issues as they arise. If you encounter team issues or technical project issues, contact the program directors immediately.
• Encourage information sharing. Visit NC State and schedule times for the team to visit your company. Consider introducing the team to your company in mid-October and bringing them back at the end of March to present their hard work.
The project submission period is March 1 to July 1. Prior to submission, two short phone interviews are required with the Senior Design co-directors. This helps to identify the project scope and determine if the project fits well with our students’ skill sets. Sponsors are notified of project acceptance by August 20, and projects begin the first day of classes in mid-August.
Student teams are carefully selected based on their project interest, complementary skill sets and leadership style inventory. Each year, 45 to 60 students participate in the program, forming 12 to 18 teams of three to four students per team.
The rigorous Senior Design capstone program spans both fall and spring semesters. Course directors guide the teams through a design process to develop innovative products/processes that meet the projects’ defined criteria and constraints.
A required donation of $12,000 is due by the end of September. This contribution supports project expenses as well as strategic growth of the capstone lab space and program.
When a project is funded by a donation, NC State does not exert intellectual property (IP) ownership unless an NC State employee is involved; undergraduate students in this course are not NC State employees. The IP generated from the project is owned by the students unless otherwise agreed upon with the sponsor in the form of a non-disclosure agreement between the two parties at the onset of the project. Existing inventions and technologies are the separate property of the sponsor company or NC State. Sponsored research agreements are also available. Two public presentations by the team are made each year -- one in the fall semester and another in the spring semester. Teams are required to review content with the sponsor before this presentation.
The culmination of the course is a “Design Day” poster session generally held in April at NC State.
Sponsored by Hanesbrands and Champion, our project aims to innovate fleece fabric by incorporating non-traditional materials and/or processes. Our team seeked to emulate the appearance and comfort of their Champion Reverse Weave Hoodie fleece while implementing a novel component.
We collected several different commercial fleeces for benchmarking and tested their strength and hand. One of the more innovative fleeces we tested was a nonwoven hoodie from Nike called Nike Forward. Nike Forward fabric had comparable warmth and stiffness to the Reverse Weave Fleece, but a much higher bending rigidity. Our team took inspiration from the nonwoven aspect of Nike Forward, but looked to improve the flexibility and hand of the fabric. To achieve this, we settled on creating a layered fabric, with a skin-facing nonwoven layer for insulation and comfort, and an outer-facing knit layer for flexibility and visual appeal. An elastomer adhesive was used to laminate the knit and nonwoven layers together, while also adding a water repellent layer to the fabric.
Nonwovens are stiff and uncomfortable, so the majority of our time was spent on improving the nonwoven layer. We explored many different types of nonwoven fabric, including hydroentangled fabrics and carded fabrics. We also looked at processing steps after the nonwoven was created, such as patterned calendaring, sanding, tenting, and jet dying. However, during the lamination of the final layered fabric, most of the processing steps were negated when the nonwoven went through a heated press.
Our team finally settled on a carded needlepunch nonwoven because of the short fiber lengths in the fabric and high loft that can be achieved. A cotton/polyester blend was used as polyester adheres well to the elastomer adhesive and cotton provides a soft hand. We decided to use an interlock knit structure for the outer-facing layer because of its stable structure and similarity to the Reverse Weave. Our hybrid knit-nonwoven fabric exhibits comparable strength and acceptable comfort. Future testing could be done to improve the nonwoven layer, including an in-depth material analysis, blend percentages, fabric thickness, and fiber length.
Rachel Falkowski, Ysa Ferreria, Colin Kirila, Yuchen Zhou
Sponsored by Hanesbrands, we were tasked with re-engineering the Champion Reverse Weave Hoodie, specifically in the color black, to reduce the carbon dioxide equivalent (CO2e) emissions to achieve a net zero sum. Champion has been looking for a more sustainable alternative that appeals to a younger and more environmentally friendly audience.
Prior to this project, Champion did not have a full life cycle analysis (LCA) of their hoodie. We generated a full LCA of the hoodie and estimated its CO2e emissions from cradle to grave (from cotton cultivation to its disposal). The LCA started with collecting the raw material emission data, such as energy usage for synthesizing polyester and harvesting cotton. The next step was collecting emission data on the yarn manufacturing process. The processing stage (dyeing, finishing, cutting, sewing and packaging) of manufacturing the hoodie was the most impactful for emission data. Transportation was another highly influential factor in the hoodie’s LCA.
While analyzing the emissions of the Champion Reverse Weave Hoodie, our team began developing a prototype to eliminate elements and high emitting factors. Since we observed the dyeing process as the most influential, we decided to have an undyed prototype, but still looked into more sustainable alternatives to traditional dyeing, both in emissions and water consumption. Supercritical CO2 dyeing is a dyeing method that uses no water and requires very little energy when compared to its more traditional dyeing counterparts. After testing samples with this method, we were successful in dyeing the fabric a light sulfur color.
The all encompassing CO2e emissions for the Champion Reverse Weave Hoodie came out to approximately 5,233g of CO2e/hoodie. Our prototype is approximately 4,089g of CO2e/ hoodie, resulting in a 22% reduction. Outside of changing the manufacturing process we will implement offsetting practices for each hoodie sold. Two trees will be planted and tracked for 10-15 years to count as creditable offsets for each hoodie, resulting in a net -2,887g of CO2e/hoodie. Therefore our hoodie is not only carbon neutral, but carbon negative.
KJ Crenshaw, Kinkead Crotts, Kylie Scott, Tytianah Ward
HanesBrands has tasked our team to create a sock that is physically cool to the touch, addressing concerns regarding in-shoe temperatures to ensure wearer comfort throughout the day. In-shoe temperatures can reach up to 37°C with humidity reaching up to 96%, and each foot can produce up to one pint of sweat daily. Our goal has been to produce a sock that is cool to the touch to assist in thermoregulation and comfort.
We began with benchmark research on existing products and fiber technologies, selecting five socks for Q-max testing to measure heat transfer upon initial contact. This provided quantitative data to identify the coolest options. Raw materials were chosen based on the polymers of the top-performing socks and technical research, along with seven fiber technologies selected for their molecular composition, material properties, and fiber cross-sectional shape.
After analyzing benchmark products, we finalized the construction of our sock to ensure consistency during testing and for the eventual production of the final product. Our team developed two prototypes: an ankle sock and a crew sock, both featuring strategically positioned mesh panels and arch bands for enhanced performance and comfort.
Following Q-max testing, all of our benchmark socks and raw material knits were sent for thermal insulation testing using the Sweating Foot Manikin system. This system evaluates the heat and moisture management properties of the sock, giving us quantifiable measurables of comfort and heat stress.
Cross-analyzing data from Q-max and thermal insulation led us to select four top-performing materials. It was shown that Rayon outperformed all of the materials in Q-max and had one of the lowest thermal insulation values, so we decided to make Rayon consistent with our products. Three blended prototypes composed of Rayon and Aluminum, Rayon and Litrax L5, and Rayon and Nylon were created and underwent further testing.
Our final prototype will be a crew sock made with the best performing blend or individual fiber as determined by the last stage of testing. By utilizing this final stage of testing, the prototype will be one which was proven to outperform the benchmark and other fiber technologies.
Julia Heilmann, Madison Murry, Henry Phillips
For our senior design project, HanesBrands challenged us to create a monomaterial garment. Addressing NIST’s key challenges for the textile industry’s shift to a circular economy, this project aims to eliminate one of the most expensive and labor intensive steps of textile recycling –fiber sorting. Monomaterial garments allow for whole garment recycling without the need for deconstructing additional components.
After careful consideration, we opted for cotton as our monomaterial due to its alignment with Hanes’ brand identity and as it is a natural fiber. Most fleece hoodies are made from a cotton/ polyester blend that has been brushed, which allows the underside of the fleece to have a soft, fluffy texture. However, cotton is a cellulosic material that contains a high content of carbon, making it a highly flammable material. In a 100% cotton fleece, the air pockets within the structure provide fuel for fire to spread rapidly across the brushed fiber surface.
This poses such a high flammability risk that the government regulates all cotton raised surface fabrics under the Flammable Fabrics Act. Thus, we decided on a terry fabric which has as many desirable sweatshirt properties while still meeting flammability requirements. Another challenge we faced was seam strength. Cotton thread is typically weaker due to its short staple fibers, which is why polyester, a continuous synthetic filament, is most widely used for seams. To combat this, we chose to use a high-quality, long staple cotton thread that’s twice as thick as typical sewing thread. This resulted in seams that were so strong the fabric failed before the seams did. Our finalized garments feature several different knit structures that highlight the versatility of cotton. The cuffs, waistbands, and collars utilize a stretchy rib structure, while the body fabrics are made out of sturdier structures with heavier weights and higher insulation. We also incorporated more permeable knit structures under the arms to enhance comfort. Additionally, the aesthetics of the design, from appearance to hand and feel, were very crucial to the overall success of our monomaterial garments.
Rosie Fisher, Zimeng Li, Maddy Moore, Elizabeth Siu
Menstrual products have changed throughout the years, but the one element that has remained unchanged is the discomfort that can come from wearing them. Consumers are considering more environmentally friendly options for their menstrual products as the standard tampon and pad generate tons of waste and end up in landfills. The project scope was to provide the wearer with a more comfortable menstrual product, while also being reusable to cut down on overall menstrual product generated waste. Our main objective was to innovate a thinner novel core while maintaining the same levels of dryness and capacity. A secondary objective was to decrease the rinse time for the user after they are done wearing the underwear.
In the fall, we researched and identified a new core material structure that maintains both dryness and absorbent properties at the bottom to maintain capacity while making the overall core thinner. In the spring, we worked with the knitting lab and prototyping lab to develop our different prototypes. We also looked at the impact of different bluesign® approved wicking finishes at different levels. We did multiple trials of different fabric blends and different finishes in the Dyeing and Finishing Lab and sent finished samples to our sponsor to test impact on rinse time with real blood. In our lab, we tested the samples for capacity, wicking, and dryness. Throughout the year, we tested our benchmarking materials and our prototypes with saline and simulated blood to emulate both urine and menstrual blood. We worked with our sponsor to develop a simulated blood recipe that performed most similarly to real menstrual blood.
We made significant progress in developing a novel core for reusable menstrual and incontinence underwear. Our focus on enhancing moisture management while prioritizing comfort and sustainability led us to select samples and materials that performed best across various tests. We are excited about the potential impact of our work in improving user experience while reducing the environmental impact of menstrual and incontinence products.
Carlos Alonzo-Montufar, Leo Delgado, Paige Greener, Peighton Jones
Senior Design Team 6, sponsored by AFFOA, was tasked with creating a reliable abrasion resistance test method for electronic textiles (e-textiles), crucial for ensuring their durability across sectors like healthcare, sports, and fashion. Given the unique challenge posed by the integration of electronic components into traditional textile materials, a standardized and reproducible test method was essential to uphold e-textiles’ performance and longevity in real-world scenarios. The team prioritized reliability and reproducibility in their test method, emphasizing electrical and abrasion resistance measurements due to the complexity of e-textiles, which included conductive elements, interface layers, and flexible substrates.
To establish a robust foundation, the team conducted a comprehensive review of existing literature and methodologies. The group determined that the most suitable approach was to merge the ASTM D4966 Martindale Abrasion Test Method with ASTM D4496 D-C Resistance of Conductance of Moderately Conductive Materials.
Upon initiating the test method creation process, the team promptly identified potential challenges they would face and addressed them by deviating from the original Martindale Abrasion Test by modifying the setup of the abradant and sample, adopting the straight-line method for abrasion, and crafting a circuit to monitor and record resistance in real-time compared to cycles.
Once the team established a solid foundation for the test, they dived into creating samples. Initially, they produced samples by screen printing onto a TPU layer, which was then heat-pressed onto the fabric, but inconsistencies arose due to TPU’s elastic properties. The team then turned to embroidery samples for comparison, from which the obtained data was deemed reliable for assessing test reliability and reproducibility.
The team then focused on implementing the developed test method on their e-textile samples, validating the method, and gathering comprehensive data on the performance and wear patterns of different e-textiles. They aimed to achieve a reliable and reproducible methodology by conducting Gage R&R studies, utilizing advanced analytical tools such as Design of Experiments (DOE) and linear regression models, and refining their test method based on results. This iterative process underscored the team’s dedication to continuously improving their test method to meet rigorous scientific standards.
Logan Boyle, Jenna Diemel, Brigitte Gallagher, Colleen Sheridan
This year, we worked with a novel sustainable technology developed by Natural Fiber Welding called Clarus. Clarus is a yarn welding process that fuses the exterior fibers of a yarn to improve strength properties. Our sponsor, American and Efird (A&E), is looking to incorporate this technology into their signature pima cotton yarn, Anecot+, to improve its physical and chemical properties. We had the opportunity to perform physical testing on two different welded Anecot+ yarns, light and medium, that had different amounts of chemical weld applied.
To validate the extent to which this process improved A&E’s yarns, we performed a variety of physical testing on the greige Anecot+, light weld Anecot+, and medium weld Anecot+. Our tests were curated to the physical and chemical properties of most interest to A&E: strength, yarn diameter, elongation, and dyeability.
We decided on the best test methods to assess these properties, which was a blend of A&E’s in-house methods and known standards. Strength and elongation were both assessed using in-house test methods, while yarn diameter was measured using an ASTM standard. An investigation into dye properties required more trials until we settled on our preferred method of skein dying at a dye concentration of 1%, followed by a second overdye trial at a dye concentration of 3% shade. The decision to add an overdye trial was made due to Anecot+ being a thread that will traditionally be used in overdye applications. From this end-use application, we also decided to perform seam strength comparisons of the overdyed threads on a fabric. This gave us a snapshot of the performance of the welded yarn versus the Anecot+ at two different intersections for the product: greige and over-dying. Strength and elongation testing was repeated on the overdyed thread to examine possible differences between greige and treated thread.
The most important part of our project was becoming experts on the process our thread went through to better understand the effects chemical welding has on long-staple cotton. Our project gave us valuable exposure to physical testing, dyeing, and yarn wet processing.
Victor Alvarez Valverde, Megan Mae Dingle, Seongjin Kim, Sam Pan
Sponsored by Under Armour, our project was to redesign reflective yarns. With 76% of pedestrian accidents occurring at night, our goal was to provide a safe apparel alternative with a focus on developing reflective yarns. The current issue with reflective yarns revolves around the imbalance of high reflectance and high comfort, thus our project was based on maximizing both comfort and reflectivity of a yarn for applications in athletic baselayers.
Ideation ranged from biological mimicry of fish scales to altering the cross section of the yarn to maximize reflectance angles. We sought alternatives to traditional glass bead reflective yarns due to their abrasive hand. Drawing inspiration from industries like cosmetics and electronics, we experimented with integrating mica crystal structures at a yarn level due to their high refractive index.
Our yarn prototyping consisted of mixing mica crystals with binders and applying them to fabric samples. However, the mica crystals’ structure prevented the first prototype in achieving the desired reflective value.
Therefore, the shift in material selection led to the choice of aluminum beads due to their spherical structure. The spherical shape of the aluminum beads facilitated retroreflectivity, making them an excellent alternative to glass beads. Furthermore, the aluminum beads were softer to the touch, enhancing comfort and making them an ideal choice. Using a similar process to our previous prototype, we’ve not only enhanced reflectivity values but also improved comfort and hand. Testing followed performance sportswear standards for factors like air permeability, abrasion, washability, and fabric hand, alongside reflectivity tests meeting traffic standards. Testing was performed on all acquired benchmarks and prototypes with the highest focus being placed on the hand and reflectivity rating of the fabric.
Prior to senior design, our team had no experience with the full ideation process from concept to physical product, however, with consistent help from faculty and our sponsors, the project slowly took shape. Our team learned that an ambitious project gives unlimited space for innovation and creativity, something that was a guiding principle at an ideation and concept generation stage.
Leeanna Hines, Drew Lingerfelt, Brandon Russ, Kairas Williams
Synthetic fabrics are dominating the textile industry but dyeing polyester often involves toxic synthetic dyes and toxic chemicals, posing environmental hazards when improperly disposed of. Under Armour is taking an interest in increasing their corporate responsibility by reducing toxic chemicals and dyes in their dyeing project. For our Senior Design project, we are tasked with evaluating natural dyeing options for polyester that minimize the negative environmental impact of the dyeing process.
Our goal was to find at least 4 different natural dyes that show great lightfastness, crock fastness, and water fastness. We explored dye processes compatible with polyester, including traditional wet batch dyeing. In this process polyester had to be treated with a binder, called mordants, to allow for the natural colorants to attach to the fabric.
Mordants are common throughout the industry, but many use metal bases which are toxic and difficult to break down. We researched and discovered the chemical called potassium aluminum sulfate. This chemical acts as a salt for pickles, fruits, and vegetables and can be found at any local grocery store in the spice section. This chemical binds the dye onto the fabric creating a chemical bond on the surface of the fabric.
The next step of this process was to find natural dyes that could be used to dye polyester. Our group purchased 20 natural dyes from a company that produces its own natural dyes from materials like plants, flowers, fruits, insects, etc. After our dyeing process, we tested the dyes on lightfastness, crock fastness, and wash fastness. This would identify if our dyes stained or dyed the fabric. Our group was able to come up with 8 different dyes as follows: Marigold (yellow), Madder Root (yellow), Cape Jasmine (Blue), Gardenia Blue (Blue), Old Fustic (Brown), Gambir (Brown), and Mulberry Leaf (Green).
After the wet batch process, our group took our 8 dyes to see how well they dyed using a CO2 dyeing process. This takes supercritical CO2 and pressurizes it into a liquid, mixing it with the dye and dyeing the fabric. This process is very environmentally friendly since there is no water waste.
Kaleah Gaddy, Ashwaath Sathyanarayanan, Charlotte Willis
Sponsored by Sail2Shelter, a non-profit organization, the goal of our project was to find a new and useful way to reuse or repurpose old sailboat sails. The motivation behind this organization is to keep these sails out of landfills and warehouses, hoping to avoid an estimated 2,000 tons of waste solely from sails. Because of their mission, it was super important to us to keep in mind the environmental footprint of our project. At the start of the year, we moved through a process of ideation and conceptualization and recognized two main pathways we could take: breaking the sails down and repurposing them. However, after thorough research and experimentation, we determined that breaking them down wasn’t ecologically or economically viable and decided to move forward with repurposing the sails.
Ultimately, we decided on creating agricultural textiles for use as weed barrier protection as it was the most feasible under our time constraints. After acquiring sail material it was sent off to be perforated, meaning small holes were punched into the sails for drainage. Following prototype creation, we performed multiple tests to compare them to the fabrics currently on the market. For one of our tests we installed our fabric into a garden bed to test its effectiveness against weed growth.
Throughout this journey, we not only acquired technical expertise but also developed crucial teamwork, leadership, and project management skills. Engaging with industry professionals taught us effective communication strategies, while hands-on experience with textile testing machinery expanded our practical knowledge, preparing us for future careers or graduate studies. The combination of this technical knowledge as well as the experience of working with a team has really helped to bridge the gap between what we’ve learned in our classes and how we will effectively apply this knowledge moving forward. We’ve also learned that things don’t always go as planned but there are lessons in every roadblock we encounter. These lessons have led us to where we are today and have allowed us to succeed in our final product creation.
Tailor a Program to Fit Your Educational Goals
Three Specialized Curriculum Tracks
• Medical Textiles: Allows students to gain experience in the design and production methods for textile medical applications.
• Supply Chain Operations: Prepares students to manage the entire supply chain from raw materials to retail.
• Technical Textiles: Enables students to develop expertise and analytical skills needed to design and manufacture textiles for nonwovens and high tech applications.
One General Curriculum Track
• Textile Technology: Allows students the flexibility of designing their own interests or transferring from other programs or community colleges.
Dual Degree Options
• French Language Minors in a Variety of Disciplines
• Environmental Sciences
• Business Administration
• Statistics
• Arts Entrepreneurship
• Sports Science Accelerated Bachelor’s/Master’s (ABM) Program
• Five-year program that enables concurrent pursuit of a B.S. in TT and an M.S. in Textile Engineering for academically strong students.
The Advantages are Impressive
• Average starting salary: $66,000 in 2023.
• 95% of May 2023 B.S. degree recipients were working in a related field or continuing their education within six months of graduation (of 95% who reported).
• Small class sizes with < 1:25 professor-to-student ratio.
• Access to one of the largest college-based scholarship programs.
• Lifelong access to Wilson College’s Career Center via Wilson for Life.
• Undergraduate research with renowned and diverse faculty (go.ncsu.edu/ tecs-reu).
• Classrooms and labs that rival those in industry.
• Exciting summer internship opportunities: Adidas, DEVCOM Soldier Center, METXY, Technimark, Berry Global, Kohl’s, Nike, HanesBrands, Elevate Textiles, JB Martin, Mohawk, Lenovo, Intel.
• Many TT students are recipients of the Centennial scholarship program.
A Degree in TT Can Take You Anywhere
A Successful Professional Career
• Sample careers: materials developer, product designer, quality control engineer, R&D specialist, strategic sourcing manager, logistics manager, production project engineer, technical marketing manager, technical sales
• Athletics and Apparel: Nike, Adidas, The North Face, New Balance, Reebok, Levi’s, Fruit of the Loom, HanesBrands
• Healthcare / Medical Textiles: Medline, Secant Medical
• Homewares: Target, Kohl’s
• Government Agencies / Defense: United States Patent and Trademark Office, State Bureau of Investigation (SBI)
• Traditional Textiles: Milliken, Unifi, Parkdale Mills, Glen Raven, Springs Global
• Plus: SAS, All Trails, Lenovo, Cisco, Accenture, IBM, Wolfspeed Inc.Dual Degree Options Graduate School
• Textile Engineering: NC State
• Textiles: NC State Professional School
• Analytics Program: NC State
• Nursing School: Queens College
• Law: Campbell University
Tailor a Program to Fit Your Educational Goals
Three Curriculum Tracks
• Chemical Processing: Develop improved chemical processes for industries related to polymer and fiber fabrication.
• Information Systems Design: Learn how to use computer information systems to develop more efficient decision making.
• Product Engineering: Focus on designing new innovative products with this multi-disciplinary and flexible concentration.
Dual Degree Options
• TE / BME (Biomedical Engineering)
• TE / CHE (Chemical Engineering)
• TE / MSE (Materials Science Engineering)
• TE / CSC (Computer Science)
• TE / ISE (Industrial and Systems Engineering)
• TE / PCC (Polymer and Color Chemistry)
Minors in a Variety of Disciplines
Accelerated Bachelor’s/Master’s (ABM) Program
• Five-year program that enables concurrent pursuit of a B.S. and an M.S. in TE for academically strong students.
The Advantages are Impressive
• Average starting salary: $70,000 in 2023.
• 95% of May 2023 B.S. degree recipients were working in a related field or continuing their education within six months of graduation (of 96% who reported).
• Small class sizes with 1:30 professor-to-student ratio.
• Joint program between the Wilson College of Textiles and the College of Engineering (COE).
• More than 50% of TE students receive scholarships.
• Lifelong access to Wilson College’s Career Center via Wilson for Life.
• Undergraduate research with renowned and diverse faculty (go.ncsu. edu/tecs-reu).
• Classrooms and labs that rival those in industry.
• Only ABET-accredited textile engineering program in the United States.
• Only NC State engineering program that trains students in Lean Six Sigma Quality process improvement methodology.
• Exciting summer internship opportunities: Under Armour, Tesla, Lutron Electronics, ATEX, Cotton Inc., Elevate Textiles, Standard Textile, Phifer, Gore, Adidas, Cortland Biomedical, Sonoco, Medline, Contempora Fabrics, Smartwool, Nike, Stryker, UL.
• Sam Jasper was the second TE student awarded national Astronaut Scholarship Foundation Award.
• Won overall Engineering Senior Design Award for multiple years.
• Joseph Moo-Young was the third TE student to be selected for the prestigious COE Faculty Rising Senior Scholar program.
• Many TE students are recipients of the Park, Centennial, Goodnight, Shelton Leadership and Caldwell scholarship programs.
• Government Agencies / National Defense: NASA, The U.S. Army, Lockheed Martin, Natick, United States Patent and Trademark Office
• Athletics and Apparel: Nike, Adidas, Under Armour, The North Face, Lululemon, Patagonia, Levi’s, Peter Millar, HanesBrands
• Healthcare / Medical Textiles: ATEX, Merck & Co., Stryker, Medline
• Automotives: Tesla, BMW, Volvo Trucks, Nissan, Goodyear, Michelin
• Homewares: Home Depot, Lowe’s, Mohawk Flooring, Hunter Douglas
• Traditional Textiles: Milliken, Unifi, Elevate Textiles, SteinFibers
• Advanced Materials: Technimark, DuPont, Eastman, Honeywell
• Other Employers: SAS, All Trails, Lenovo, Cisco, Accenture, IBMOne General Curriculum Track Graduate School
• Materials Science Engineering: NC State
• Chemical Engineering: Georgia Tech, University of Florida
• Textile Engineering: NC State
• Biomedical Engineering: Duke University, Johns Hopkins University, NC State
• Industrial and Systems Engineering: Rensselaer Polytechnic Institute
• Polymer Science: NC State, UMass Dartmouth Professional School
• Analytics Program: NC State
• Dental School: UNC Chapel Hill
• MBA: Harvard, NC State, UNC Chapel Hill, Wake Forest University
• MHA: UNC Chapel Hill
• Medical School: UNC Chapel Hill, Wake Forest University
• Law School: UC Berkeley, UNC Chapel Hill, Wake Forest University