Senior Design
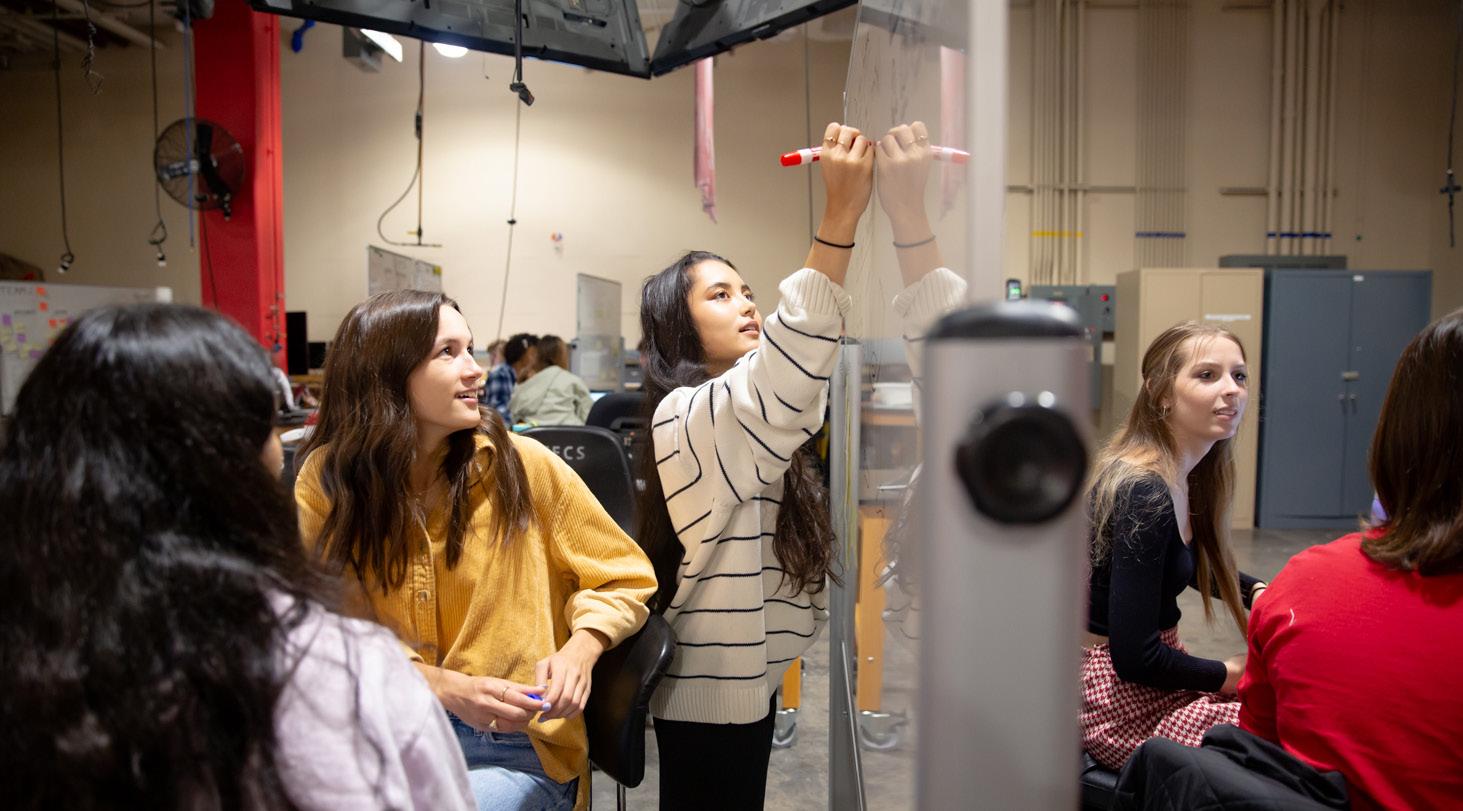
Russell E. Gorga (Ph.D., Iowa State University, Chemical Engineering) is a professor in the Department of Textile Engineering, Chemistry and Science at the NC State University and former program director of textile engineering. His main interests lie in developing polymer nanocomposites with improved properties (mechanical and conductive) for a variety of functional applications.
Before coming to NC State, Dr. Gorga was a postdoctoral associate at MIT where he worked on improving the strength of brittle polymers (such as poly (methyl methacrylate)). In addition, Dr. Gorga worked as a research engineer at Union Carbide Corporation from 1997 through 2000, where he focused on structure-property relationships of semi-crystalline polymers for high strength
Amanda C. Mills (interim co-director) (Ph.D., NC State University, Mechanical Engineering) is an assistant research professor in the Department of Textile Engineering, Chemistry and Science at the NC State University. Her focus is on developing innovative methods for electronics integration into textiles. She creates full system demonstration platforms to examine the impact of the textile on the device and vice versa. For example, this has included system level electronic designs and knit structure designs for human energy harvesting and physiological sensing.
Claire Henson (B.S. Textile Engineering, NC State University is earning an M.S. in Textile Engineering at the Wilson College of Textiles. She is a passionate advocate for sustainability in the textile industry, with a specific focus on sustainable materials. Claire will be graduating in May 2023 and plans to pursue a role in sustainable material development.
Emily Odykirk (B.S. Textile Technology, NC State University) is a master’s student studying textile engineering at the Wilson College of Textiles. Her research focuses on moisture management and new testing methods for wicking and cooling efficiency, and she also serves as a laboratory assistant in the TPACC Fabric Comfort Evaluation Lab.
Laura Potok(B.S. Textile Engineering, NC State University, B.A. Chemistry, Meredith College) is pursuing her Master of Science in Textile Engineering and a Master of Textiles at the Wilson College of Textiles. Laura’s research interests include dyeing and finishing, as well as sustainable garment design. Outside of being a TA for senior design, Laura enjoys swimming, cycling and making homemade sweatshirts for every holiday.
•Jenna DeCandio, Knitting Lab Manager
•William Barefoot, Weaving Lab Manager
•Tim Pleasants, Spinning Lab Manager
•Jeffrey Krauss, Dyeing and Finishing Lab Manager
•Teresa White, Physical Testing Laboratory Specialist
TECS Admin staff, Allison Blanchard, Joyce Cole, Beth Palmer, Dr. Joines, Dr. DenHartog and the North Carolina Textile Foundation.
This capstone in the Department of Textile Engineering, Chemistry and Science provides companies the opportunity to work with student teams to innovate in product and/or process development. In working with the student teams, companies explore materials property design, develop new directions for existing products or take their materials/product into a new marketspace. Our students utilize their expertise in engineering fundamentals, information systems, medical textiles, product development, supply chain management, testing and consumer behavior to solve a current product/process challenge. Through sponsored projects, student teams will learn project management and product design principles that leverage the global textile complex.
The purpose of this course is to deliver a ‘real-world’ experience that prepares students to solve open ended problems that they will face upon entering the workforce. The sponsored student team is expected to:
•Communicate effectively on the project problem, objectives and proposed solutions.
•Work efficiently in teams to deliver high-performing results.
•Assess, select and learn the latest and most appropriate technologies for project success and be able to adapt those technologies as needed.
•Analyze the project and solution from financial, economic, technical, ethical and commercial perspectives.
•Develop ideas with appropriate patent mapping and intellectual property assessment.
•Produce proof-of-principles prototype(s).
The annual Rice Bag Challenge is sponsored by Rise Against Hunger, an international organization that annually distributes millions of meals around the world through community meal-packing events. Each Senior Design team was given one week to create a useful prototype that would solve a problem in developing areas around the world using a maximum $10 budget and two, 50 pound rice bags. At the end of the week, each team pitched their product to a team of judges from Rise Against Hunger.
This year we judged in 2 sessions:
Session 1 Winner: Team 2
Session 2 Winner: Team 11
While most sponsors spend an average of one to two hours per week on the project, many find interaction with the students to be the most rewarding aspect. Beyond that minimal time commitment, other expectations include:
• Helping define project scope and metrics for project success.
• Holding regular meetings with the team and providing specific project feedback.
• Providing technical mentoring and feedback on the team’s materials and process deliverables.
• Providing specific training on unique tools that are pertinent to the project.
• Providing coaching to help the student team reach the best solutions.
• It is important for the sponsor not to tell the team exactly what to do. This is an open-ended problem.
• Address any issues as they arise. If you encounter team issues or technical project issues, contact the program directors immediately.
•Encourage information sharing. Visit NC State and schedule times for the team to visit your company. Consider introducing the team to your company in mid-October and bringing them back at the end of March to present their hard work.
The project submission period is March 1 to July 1. Prior to submission, two short phone interviews are required with the Senior Design co-directors. This helps to identify the project scope and determine if the project fits well with our students’ skill sets. Sponsors are notified of project acceptance by August 20, and projects begin the first day of classes in mid-August.
Student teams are carefully selected based on their project interest, complementary skill sets and leadership style inventory. Each year, 45 to 60 students participate in the program, forming 12 to 18 teams of three to four students per team.
The rigorous Senior Design capstone program spans both fall and spring semesters. Course directors guide the teams through a design process to develop innovative products/processes that meet the projects’ defined criteria and constraints.
A required donation of $10,000 is due by the end of September. This contribution supports project expenses as well as strategic growth of the capstone lab space and program.
When a project is funded by a donation, NC State does not exert intellectual property (IP) ownership unless an NC State employee is involved; undergraduate students in this course are not NC State employees. The IP generated from the project is owned by the students unless otherwise agreed upon with the sponsor in the form of a non-disclosure agreement between the two parties at the onset of the project. Existing inventions and technologies are the separate property of the sponsor company or NC State. Sponsored research agreements are also available. Two public presentations by the team are made each year -- one in the fall semester and another in the spring semester. Teams are required to review content with the sponsor before this presentation.
The culmination of the course is a “Design Day” poster session generally held in April at NC State.
Sail to Shelter, a non-profit organization and sponsor of this team, is committed to keeping racing sails from piling up in landfills by giving them a second life. Sail racing’s high level of competition results in the disposal of sails after just a few uses. To keep up with this demand, over 3 million square yards of sail fabric are produced each year, and 97% of that ends up in landfills. Our team’s task was to repurpose woven polyethylene terephthalate (PET) sails into a product that can be used for humanitarian aid.
PET sails are a highly durable and water resistant woven material that are coated and impregnated with a melamine-based mixture. One of the first questions this project proposed was, do we want to pursue recycling or repurposing this material? We decided to pursue both paths.
For recycling, we were planning to melt down the sails due to the thermoplastic properties of PET and turn them into yarn that could then be knit into blankets or sleeping bags. Through research and experimentation, we eventually found that vegetable oil is a promising solvent for the coating and impregnations, giving the material the ability to melt.
The bulk of our project was spent repurposing the sail material. We brainstormed many ideas relating to humanitarian aid. We defined measurables for each product, conducted background research on current products and made design iterations. We ultimately decided to pursue the semipermanent structure and inflatable bed. We tested and analyzed the material’s air permeability, water resistance, flame resistance and comfort, as well as the tensile strength and air permeability of different seams.
Our shelter prototype is a spacious, water resistant tipi shaped structure made up of triangular panels of sail material held together with industrial sewing and water-resistant seam tape. The material is padded with an environmentally conscious, flame resistant coating to insure the safety of refugees. Our inflatable bed prototype is made up of two rectangular cut sail pieces that are calendered (heated and pressed) to improve the softness, sono bonded together, then calendered again to make the seams air tight. The bed can be inflated with or without electricity to accommodate different circumstances.
Athletic apparel brand Oya Femtech Apparel, wanted to redesign the insert for the crotch of their “Happy Vagina” leggings, which are meant to comfortably absorb and retain feminine fluids for the wearer during movement. The insert needed to be foldable, removable and washable, while still maintaining its performance and integrity. The insert design Oya was using at the time was made up of three primary layers: one for comfort and wicking, one for absorbency, and one for waterproofing. We established that we could improve the performance of the insert not only by using higher performing materials, but also by altering the construction method of the insert.
Our team began the project by ordering a variety of benchmarking products from varying brands to determine the industry standards for wearable absorbent products. Through our research, we discovered a variety of technical textiles that address our performance concerns and then ordered them for their respective test methods. We combined the fabrics that performed best in their category and combined them into three different prototypes, based on their compatibility with three different construction methods: laser cutting, seam tape, and ultrasonic welding.
When we practiced these methods, we found that laser cutting was unable to properly attach the layers and that seam tape application was incompatible with the insert shape. Ultrasonic welding became our main construction method for our final three prototypes because it successfully welded a clean cut edge around the insert. We ultimately developed three prototypes:
- Prototype 1a had a 65% polyester, 35% nylon sports jersey treated with silver as the wicking layer, a 100% polyester microfiber terry cloth for the absorbent layer, and a 100% polyester ECO-PUL silver-treated fabric for the waterproof barrier fabric layer.
- Prototype 1b had the same absorbent and waterproof layers with 94% polyester 6% spandex Gridface fabric for the wicking layer.
- Prototype 2 had a 100% polyester REPREVE Interlock Knit wicking layer, an absorbent layer made up of cotton, tencel, bamboo viscose, polyester, and nylon, and a waterproof layer of bamboo viscose, polyurethane, organic cotton, and polyester.
All three prototypes performed significantly better than the benchmark products, including Oya. Of these prototypes, prototype 2 performed better than prototype 1b, and prototype 1b performed better than prototype 1a. However, each prototype performed well enough to provide with Oya three different options for redesigning their insert.
In 2011, OSHA reported that nearly fifty-percent of injuries reported among nurses were musculoskeletal injuries (Occupational Safety and Health Administration, 2011). Strains and sprains are most common, but more serious injuries like disc herniations and rotator cuff tears are risks to all medical staff that lift patients using the current industry standard of log rolling, in which the patient is physically rolled to the side while devices are placed under them. This additionally increases risk for patient injuries as a result of spinal rotation.
The Textile Patient Elevator Project, sponsored by Stryker, challenged our team to engineer solutions to lifter and patient injuries as they relate to patient transfer. The goal of this project is the elimination of the log rolling method and subsequent elevation of the patient from the ground to stretcher or bed level.
Through the ideation and prototyping process, our team created three prototypes: the sliding bar, the inclined spineboard, and an inflatable device. After thorough testing and evaluation of the prototypes, the Sliding bar prototype was selected for further development. This prototype functions by using thin steel bars, attached to both sides of a nonwoven sheet. The steel bars on one side of the nonwoven sheet are slid beneath the patient’s natural arches of their neck, back and knees. Once the bars are pulled entirely below the patient, the nonwoven sheet follows under the patient. The steel bars from both sides of the sheet are then attached to a hoyer lift, or another lifting device. The Spunbond-MeltblownSpunbond (SMS) nonwoven sheet used in this device was selected for its combination of strength, sterility, and disposability.
Solar harvesting yarns are a promising solution for renewable energy in various applications. Phifer Incorporated partnered with our Senior Design team to develop a process for creating a fiber-based photovoltaic (PV). We were tasked with creating a circular substrate capable of generating energy.
After a thorough literature review, we determined that an organic photovoltaic design was the most suitable option. The team designed multiple apparati to apply the necessary coatings and to test the yarn at the final stage of the process. Through a combination of literature review and trial and error, the team created solution formulas for each PV chemical.
The coating procedure is a multi-step process, and our team faced several challenges regarding the application procedure. However, we addressed and solved most of these challenges to create a working PV yarn.
We hope our work prepares future Senior Design students to finish this project. The project demonstrates the potential for creating renewable energy solutions through innovative textile engineering techniques.
Our sponsor, Hanesbrands, challenged us to develop a fabric for hoodies and sweatshirts with increased levels of protection for school-aged children without making the hoodies uncomfortable to wear. Our team narrowed the scope down to cut-resistance and abrasion-resistance. Serving as our ‘comfort’ baseline material, the Hanes Reverse Weave® fabric is composed of 82% cotton and 18% polyester. Our team added ultra-high-molecular-weight polyethylene (UHMWPE) to improve protection performance.
In response to the project scope, our team researched commercial cut-resistant products and analyzed how their yarn composition and fabric structure influenced their cut performance. Based on our findings, we narrowed down our ideas into multiple prototypes, ranging in complexity and innovation: core-spun interlock knit, plated jersey knit, 3-ply interlock knit, nonwovens interlock knit, and self-stitch interlock knit.
After our prototyping session, we conducted physical tests to evaluate comfort and protection levels based on our measurables: cut resistance, abrasion resistance, launderability, hand, tear strength, air permeability, and pilling. Based on our results, we were able to pinpoint ways to further refine our prototypes moving forward. Our project’s next step is garment design, which will include a notification device that will allow the wearer to send an alert to their parents or guardians if needed. Throughout this course, we have developed valuable skills in regards to teamwork, including communication, time management and presenting.
Our team, sponsored by Hanesbrands, was tasked with creating a performance level gaming garment for both the professional eSports player and the average gamer that provides posture and wrist support without losing its comfortability. We first did extensive research of products marketed as gamer apparel to see what customers were buying. During ideation, we brainstormed ideas and split them into three subcategories: the hood, the body and the arm. With advice from our sponsor, we decided to focus on adding wrist and back support to our final garment.
As we began prototyping, Assistant Professor Gloria Hwang helped us modify the original Champion gaming hoodie pattern to incorporate our new design. This involved changing the underside panels of our garment to include a more breathable and wicking material to provide more comfort to the gamer. We also tested each aspect of the hoodie to make sure our design decisions were justified. Looking into arm and wrist compression, we did testing on fabric elasticity and pressure testing to compare it to other products on the market. We next looked into comfort and breathability, which included moisture management and air permeability testing to prove the fabric construction we chose.
Our team has learned a lot about the design process from idea to prototype to final product. Through our testing and evaluation process we learned how to interpret results and present them in a more approachable way. Being engineers and technologists, we had no background in the design side of textiles, so it was important to always be open to learning a new skill for the project.
Our team was tasked with developing a sleep promoting garment for Hanesbrands. Sleep is an incredibly broad and subjective matter, so initially we had to narrow down our scope and determine what we wanted to target. We ultimately decided to focus on temperature and overheating while sleeping. We ultimately decided to develop a garment intended to keep the user cool, dry and asleep for longer without interruption.
Over the course of this project we researched fibers, fabrics and finishes that could be used for that purpose. We also used benchmark products from both Hanesbrands and other companies to determine which fabrics and finishes would be optimal for staying cool, dry and comfortable. To assess these qualities we performed a series of tests to measure air permeability and moisture management, moisture vapor transmission rate and more.
After testing, results showed that knitted cotton and lyocell would be the best combination for these measurables and for cost efficiency. After determining the blend that would be used, we manufactured three different blend combinations of those two fibers (50/50, 67/33 and 33/67). For each fiber blend combination, we tried out three knit structures (links-links knit, mesh knit and single jersey knit) to develop nine samples in total. Air permeability and moisture management testing displayed results that suggested 50/50 mesh and 50/50 links-links were the best fit for our garment.
With our fabrics narrowed down we wanted to apply a temperature adaptive evaporative cooling chemical finish to the fabrics for increased cooling and wickability. Two finishes were applied to smaller scale samples and subsequently tested and validated.
Our final prototype sleep garment is made up of a lyocell/cotton blend in both link and mesh knit structures with a temperature adaptive finish applied.
To help combat the environmental impacts of home laundering, Hanesbrands Inc. and Champion tasked our group with modifying the Champion Powerblend hoodie to withstand being worn longer between washes.
Because the Powerblend hoodie is such an iconic staple item in the Champion brand, we had to ensure that the essence of the classic Powerblend hoodie was left intact. That meant maintaining the comfort, aesthetic and price of the existing product.
As a result, some of our proposed changes, such as detachable parts of the hoodie or a cuff taper to reduce the possibility of staining on the sleeves, were ruled out due an increase in production costs or a decrease in comfort of the hoodie. We had to learn to simultaneously prioritize form and function. Throughout our project, we not only performed testing to ensure the efficacy of our changes in decreasing the need for washing – such as stain resistance, reduced bacterial content and increased breathability – but also to ensure that the comfort and durability of the garment remained uncompromised.
Our final prototype is a hoodie treated with BacShield antimicrobial finish on the inside and Daikin Unidyne XF 5003 stain resistant finish on the outside. We added a breathable underarm panel constructed from a knitted mock mesh. We also placed a decorative tag prominently on the garment to remind the wearer of the “wash less” capabilities of the hoodie. The resulting prototype will not need to be washed as frequently as the existing Powerblend hoodie, while still maintaining the product’s reputation for comfort and affordability.
Historically, nylon takes decades to degrade and leaves behind a legacy of microplastics which are major pollutants of water, air and ground environments. To improve sustainability, U.S. Army DEVCOM challenged our team to find a biodegradable polymer replacement for nylon to be used in a variety of their textile products.
For this project, our team investigated three biodegradable nylon options which utilize additives and other technologies to increase the biodegradation rate of the polymer. We evaluated these three polymer replacements based on their biodegradability and fabric performance using a benchmark of the preexisting standard U.S. Army fabric and continuous filament nylon woven to the same specification as the prototypes.
The yarns were placed into a biodegradation test for approximately one month, with weekly monitoring and regulation, and mechanically tested in yarn and fabric form. The samples were woven into a plain weave fabric to test their fabric performance against the nylon benchmark fabric. Extra tension had to be applied during the warping and drawing in process to combat the impact of texturing and high elastic recovery of the yarns.
In this project, our team learned how to utilize our engineering skills in troubleshooting sourcing various yarns with specifications, understanding the effect of texturing yarns for the weaving process and normalizing data so that the evaluation of the performance of each yarn would be accurate. Additionally, we learned how to use limitations, such as timeline and access to necessary resources, to create a modified biodegradability test which increased microorganism activity and provided direct visibility of the degradation process. Based on preliminary results, our team has decided that Amni Soul Eco and CiCLO enhanced nylon would be two great alternatives for the nylon in U.S. Army fabric. The mechanical properties and biodegradation of the two fibers has shown promise for future applications. We also recommend looking into fabric degradation, as we only examined yarn degradation during this project.
Our project, High Speed Moisture Transfer, sponsored by U.S. Army DEVCOM is focused on redesigning the current cold weather-base layer uniforms. In their day to day operations, our soldiers are being put in cold, uncomfortable and potentially more dangerous situations as sweat is being trapped within their base layer uniform. We have learned so much throughout this project, such as specifications required for U.S. Army garments, wicking/moisture management techniques, 3D modeling software, various standardized tests and teamwork.
We conducted background research and benchmark testing both in the Senior Design Lab and in the Textile Protection and Comfort Center on the current base layer uniforms and other competing product technologies we selected as our benchmark products.
From our background research and meetings with various professors/professionals we decided to move forward with constructing a knit garment, plaited with a wool/nylon blended yarn and various polyester yarns. We originally tested three samples: 80/20 wool/nylon plaited with Sorbtek, 80/20 wool/ nylon plaited with Coolmax, and 80/20 wool/nylon plaited with a Coolmax/Thermolite blend.
Through working with Jenna DeCandio in the Knitting Lab at the Wilson College of Textiles, we constructed the prototypes with a plaited, single jersey knit design that uses chevron ‘channels’ designed to draw the moisture from high sweat areas and move it to other more breathable parts of the garment on the sides of the body. Through use of our “colored water” benchmark test and MMT testing we were able to successfully test our prototypes and narrow down our design to a 80/20 wool/nylon blend plaited with Sorbtek. Our design not only wicks away moisture from the body, but also is durable and less flammable than the current base layer uniform.
Gildan’s product development team is constantly pursuing innovative ways to accelerate timelines and reduce the carbon footprint of their design process. One innovation that Gildan believes could help accelerate their sock prototyping process is the TS-1800, a state-of-the-art digital yarn dyeing system. This technology, created by an Israeli company called Twine Solutions, can quickly dye polyester yarn samples in a variety of colors without using any water in the dyeing operation. Our Senior Design team’s goal was to determine whether this novel technology could help Gildan accelerate their color development process and reduce yarn and water waste.
Our team delivered a technical analysis, a productivity analysis and a business feasibility assessment to Gildan. The goal of the technical analysis was to understand the capabilities and limitations of the yarn dyeing system. We learned how to operate the system and collected data on color matching, uniformity, colorfastness, repeatability and general machine limitations. The productivity analysis aimed to quantify the time, yarn and water required by the TS-1800 in order to develop quantities of dyed yarn sufficient for Gildan’s sock prototyping (and in the correct color). We compared these values to a simulation of the traditional disperse dyeing process, which uses package dyeing. Finally, we prepared a business assessment that addressed the question: is the machine worth the investment? We detailed the advantages and disadvantages of adopting this novel technology, as well as recommendations for Twine Solutions regarding how they could work to improve their product to be competitive in the global market.
As the shoe industry continues to evolve, it is more important than ever to prioritize breathability to maximize athletes’ comfort and performance. Our project was sponsored by Under Armour, and we were tasked with understanding what “breathability” really means – and making a shoe upper centered around it. Ultimately, “breathability” is the sweet spot of both air permeability and evaporative resistance (how air convects to evaporate sweat).
Our ideation process was inspired by life around us, from bike shoes to car hoods. Initially, we looked to use phase change material core-spun yarn for our prototype (what we called the “Icepack Shoe”), but after learning more about mechanical cooling, we opted for a design that takes advantage of an athlete’s stride to take in the most air possible for maximum convection (an iteration we called our “Moon Shoe”).
During the fall semester, we collected benchmark data from three Under Armour performance shoes. The shoes were tested at the Wilson College’s Textile Protection and Comfort Center (TPACC), using its hot plate to mimic the results of their sweating foot to analyze evaporative resistance and thermal heat transfer. We also disassembled the shoes to conduct air permeability tests and used both data sets to determine which shoe performed the best overall.
In January, we immediately ordered spacer mesh for our design and began to knit different samples for our upper. This was followed by a great deal of testing. Most of our time was spent analyzing our data and determining the relationship between air permeability and evaporative resistance so that we could select our final prototype structure. Finally, we were able to knit our upper so that we could last it to an outsole to create a finished, and breathable, shoe.
Through this project, we dove deep into the world of footwear heat management technology and were able to dabble in creating some technology of our own. We learned a tremendous amount about heat transfer from feet to shoes, defined breathability in working terms, and identified a relationship between air permeability and insulation. All these findings boiled down to the ultimate conclusion that the most “breathable” shoe would need to have a very thin upper as well as an air layer within the shoe which could be translated to extra room in the toe box.
Our Senior Design project was sponsored by Pine Bluff Arsenal (PBA), a small U.S. Army installation located in Arkansas that works alongside the Department of Defense to provide products and services for military use. For this project we worked on process optimization for ghillie suits, a type of camouflaged uniform used by snipers for disguise.
We focused specifically on the head drape component of the suit, which is used to cover the back and upper body. Our goal is to present PBA with a design and process that can be incorporated into their current layout that will help reduce production time and labor costs.
Over the better part of a year, our group researched and discovered various ways to improve the current flow of the head drape composition. Ranging from reverse engineering to hands-on sewing, we determined the best way to refine the process was to create a simulation and focus on the details of current work instructions. Through this project, we learned the importance of detail and how that translates to impacts on production. This importance was evident in the amount of specifics needed to create our simulation program, Simio, to its entirety with data entry to get an attainable result along with specifics for the work instructions and standard operating procedures to assemble the head drape. We have utilized this program for process and machinery optimization. Recommendations on the process will then be made based upon statistical and comparative analyses on the experimental production runs.
Throughout the past year, we have been working on a project for American Merchant Inc., aimed at optimizing processes and reducing costs at their towel manufacturing facility in Bristol, Virginia. The project was aimed at finding real-time changes to improve their position in the industry. The goal was to find ways to improve efficiency, increase productivity, and ultimately reduce costs in order to keep production in the United States.
To better understand the project, we began by conducting a thorough process analysis. This involved observing the production process, collecting data on cycle times and other key metrics, and conducting interviews with workers and managers. From this analysis, we were able to identify several areas for improvement.
We used Simio software to understand the current product flow and simulate and test new models for overall layout as well as cut/sew to determine if improvements can help increase throughput and reduce labor costs. Using Simio allowed the team to create accurate dimensions of the factory and test efficiencies, as well as determine if any changes to the production process were viable, before making recommendations. We focused on creating standard operating procedures (SOPs) for every process to improve quality and accountability as well as workflow and operator issues. Creating SOPs would also make it easy to replicate processes, and employees at each location could use the same operating manual to identify how to perform a standard procedure.
Furthermore, our team did a lot of research and provided American Merchant with a detailed comparison list of the top textile and manufacturing ERP systems that would work best for the plant based on their needs as well as an ERP selection checklist and manufacturing ERP requirement template for their future search and implementation. Implementing an ERP system would significantly help optimize business activities and processes for optimal performance.
Wireless Charging is a growing market, with an estimated 2.2 billion mobile phones to be ‘Qi’ enabled by 2026. Of the 1 billion current wireless charging phones, about 130,000,000 have the capability to send a charge through ‘battery share’ functionality. Through my work in Senior Design, I took this functionality and developed a garment that powers wearable devices wirelessly via your phone. Think of a shirt that charges implants, or pants that have your phone in one pocket, charging earbuds in the other. The wireless charging receiving garment bridges the gap between comfort and powering personal devices, taking advantage of phones being by our side.
The main deliverables of my project include an engineered coil design that is secured to a warpknit open mesh and covered by a nylon/elastane compressive layer. The resulting material is then secured to a cotton/polyester shirt in the form of a patch pocket. The two fabrics work to hold the coil taut to the phone while in the pocket, ensuring that the wireless charging connection is not interrupted while the user is performing daily activities. The geometry of the coil is designed to be large enough that while the phone is in the pocket it will be able to receive the phone’s charge.
Through the course of the fall and spring semesters, four types of coils were initially made, being 3D printed, weft-knit inlay, laser cut, and embroidered. What I found was that embroidering conductive yarns in the bobbin provided a superior, and repeatable, design while the fabric maintained a degree of flexibility. From this, I constructed three iterative prototypes that were evaluated using the constraints of electrical properties, flexibility, wash and abrasion resistance. Thanks to the testing equipment and materials in the Senior Design lab, I was able to make rapid-decisions on essential subsystems of my project.
Cultural eutrophication is one of the most important environmental issues being faced today. As human activities have radically increased the concentration of nutrients, primarily nitrogen and phosphorus, in bodies of water, harmful algal and bacterial blooms are becoming increasingly common. These blooms cause red tides, toxic water and massive die-offs of marine ecosystems, ultimately making the waters almost completely devoid of life. This process has massive implications for fisheries, marine biodiversity and climate change.
One way that cultural eutrophication can be stopped is by removing the nutrient pollution from the water directly. The vast majority of current solutions involve large installations and earthenworks projects which do not integrate well into the natural environment and can not be mass produced.
Floating wetland islands are a commonly used technology for removing harmful nitrogen and phosphorus compounds from waterways that can get around many of the negative aspects of nutrient removal systems. These islands work by floating on any body of water and actively locking nutrients away in macroscopic plant biomass. However, these islands are still not perfect; issues include massive labor requirements, high costs, considerable maintenance requirements and poor plant retention. All of these problems can be solved by redesigning these islands around a textile-based system.
My project looked at how a textile-based floating wetland island can be implemented and which textile parameters are important in ensuring an effective end product. By conducting growth experiments with different fabrics of varying dominant hole size and seed placement, a predictive statistical model can be developed to better understand the ideal characteristics of the cladding material for the textile-based wetland islands. Determining these characteristics will help these textile-based wetland islands to not only perform as well as their traditional counterparts, but also overcome their shortcomings. The continuation of this project can hopefully lead to a textile-based wetland island that is optimally designed, and which can be used all over the world to combat cultural eutrophication to bring life back to our destroyed aquatic environments.
Tailor a Program to Fit Your Educational Goals
• One General Curriculum Track
- Textile Technology - Allows students the flexibility of designing their own interests or transferring from other programs or community colleges.
• Three Specialized Curriculum Tracks
- Supply Chain Operations - Prepares students to manage the entire supply chain from raw materials to retail.
- Medical Textiles - Allows students to gain experience in the design and production methods for textile medical applications.
- Technical Textiles - Enables students to develop expertise and analytical skills needed to design and manufacture textiles for nonwovens and high-tech applications.
• Dual Degree Options
- French Language
• Minors in a Variety of Disciplines
- Environmental Sciences
- Business Administration
- Statistics
- Arts Entrepreneurship
- Sports Science
• Accelerated Bachelor’s Master’s (ABM) Program
- Five-year program that enables concurrent pursuit of a B.S. in TT and M.S. in TE for academically strong students academically strong students.
The Advantages are Impressive
• Average starting salary: $58,500 ($45k - $93k*) in 2017.
• 96% placement in 2015, 97% placement in 2014, 93% placement in 2013 graduating classes.
• Small class sizes with < 1:25 professor-to-student ratio.
• Access to largest college-based scholarship program.
• Lifelong access to Wilson College’s Career Center.
• Undergraduate research with renowned and diverse faculty.
• Classrooms and labs rival those in industry.
• Exciting summer internship opportunities: Ralph Lauren, HanesBrands Inc., Smithsonian Institute, Under Armour, Unifi, Glen Raven, American & Efird, Limited Brands, Spanx Inc., Kohls, Shaw Industries, Cotton Inc., Eastman Chemical, International Textile Group, Michael Kors, Milliken, PGI, Spanx and Precision Fabrics.
• Courtney Bolin interned at The Smithsonian Institute.
• Centennial Scholarship Recipients.
• Rigorous open-ended problem solving.
• Industry and government sponsored projects: Nike, HanesBrands Inc., U.S. Army, Under Armour, Patagonia, Firestone, VF, Gildan, Willow Wood, Eastman, NASA, Saab Baracuda, Monterey Mills, Cotton Inc. and Gryppers.
• Industry and government sponsored projects: Nike, HanesBrands Inc., US Army, Under Armour, Patagonia, Firestone, VF, Gildan, Willow Wood, Eastman, NASA, Saab Baracuda, Monterey Mills, Cotton Inc. and Gryppers.
• Biometric feedback shirt, Energy harvesting textiles, Realistic bite sleeve for canine training, 3-D fabric for prosthetics, Advanced flame retardant apparel, Wading/ submersion fabric durability, Quick to market textiles, Advanced camouflage surface treatments, Cooling vest for firefighters and Textile composites for structural beams.
Tailor a Program to Fit Your Educational Goals
• Three Curriculum Tracks
- Information Systems Engineering - Design systems to make better decisions that improve people’s lives.
- Chemical Processing - Develop chemical processes to make the world a better place.
- Product Engineering - Design new innovative products to solve the world’s challenges.
• Dual Degree Options
- TE/BME (Biomedical Engineering)
- TE/CHE (Chemical Engineering)
- TE/MSE (Materials Science Engineering)
- TE/CSC (Computer Science)
- TE/ISE (Industrial and Systems Engineering)
- TE/PCC (Polymer and Color Chemistry)
• Minors in a Variety of Disciplines
• Accelerated Bachelor’s Master’s (ABM) Program
- Five-year program that enables concurrent pursuit of a B.S. and M.S. in TE for academically strong students.
The Advantages are Impressive
• Average starting salary: $58,210 ($45k - $80k) in 2017.
• 98% placement in 2015, 96% placement in 2014, 97% placement in 2013 graduating classes.
• Small class sizes with 1:30 professor-to-student ratio.
• Joint program between the Wilson College of Textiles and the College of Engineering (COE).
• More than 50% of TE students receive scholarships.
• Lifelong access to Wilson College’s Career Center.
• Undergraduate research with renowned and diverse faculty.
• Classrooms and labs rival those in industry.
• The top ABET-accredited textile engineering program in the United States.
• Only NC State engineering program that trains students in Lean Six Sigma Quality process improvement methodology.
• Exciting summer internship opportunities: Nike, PGI, HanesBrands Inc., The North Face, Target, Patagonia, Uni-fi, Tempur Sealy, Limited Brands, Technimark, Deutsche Bank, Eastman Chemical Company, Natick, SAS and PGI Aachen University (Germany).
• Sam Jasper becomes the second TE awarded national Astronaut Scholarship Foundation Award in 2016.
• Won overall Engineering Senior Design (2014, 2015).
• Joseph Moo-Young becomes the third TE to win the prestigious COE faculty rising senior scholar in 2014.
• Park, Centennial, Goodnight, Shelton Leadership and Caldwell Scholarship Recipients.
• Emily McGuinness NSF Graduate Fellowship in 2017.
• Rigorous, open-ended problem solving.
• Industry and government sponsored projects: Nike, HanesBrands Inc., U.S. Army, Under Armour, Patagonia, Firestone, VF, Gildan, Willow Wood, Eastman, NASA, Saab Baracuda, Monterey Mills, Cotton Inc. and Gryppers.
• Biometric feedback shirt, Energy harvesting textiles, Realistic bite sleeve for canine training, 3-D fabric for prosthetics, Advanced flame retardant apparel, Wading/ submersion fabric durability, Quick to market textiles, Advanced camouflage surface treatments, Cooling vest for firefighters and Textile composites for structural beams.