FOOD & DRINK PROCESSING & PACKAGING
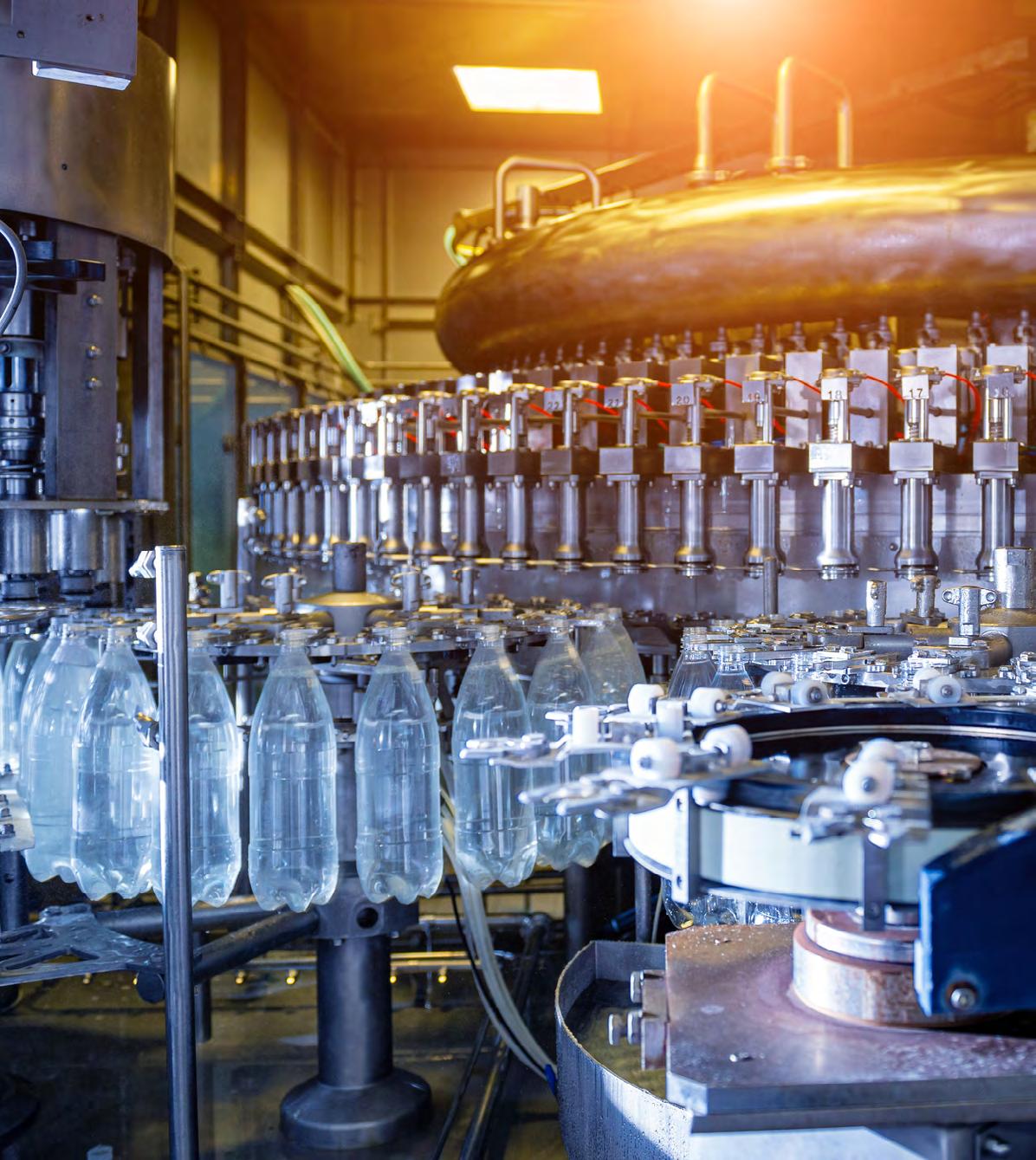
Beardow Adams develops new eco-friendly, semipressure sensitive labelling adhesive
Quality stands proud for UFP with Ishida X-ray/checkweigher combination
Beardow Adams develops new eco-friendly, semipressure sensitive labelling adhesive
Quality stands proud for UFP with Ishida X-ray/checkweigher combination
Whether it’s pasta, meat, vegetables or milk, food and beverage products must reach the market fast, fresh, and in the best possible condition.
Enabling high throughput and consistent quality, robotic automation offers the ideal solution. Suitable for tasks including picking, packing, palletizing, cutting and slicing, robots are proven to transform output and flexibility and make workers more productive by assisting with heavy and repetitive tasks.
Discover how robots could transform your business: https://bit.ly/ABBRobotsFoodandBeverage
by
Strong PulsedElectrical
Fieldsof juices & wines or honey & creams keeping unchanged its properties with our scalable pilot production system:
• for R&D:
1x PEF chamber for solids & creams and 1x coax PEF chamber for liquids;
• for pilot production: two in line coaxial chambers at same or different optimally enhanced pulsing using batch or direct flow through processing.
Broadest changeable SPEF parameters:
• Pulse rates in Hz: 4, 20, 100, 500, 4-125;
• Pulse lengths in μs: 2,5, 5, 10, 50, 2,5-20;
• electrical fields 5-50kV/cm;
• selectable pulsing time 1s-9h;
• 25kV 2kW pulser, up to 10kW options;
• overcurrent protection is build-in with a reset;
• convenient in use, simple to maintain, safe!
Pulse shapes:
• positive rectangular,
• fronts/tails ~1 µs;
• ~5% flat at 50µs: V(t) & I(t) at 25kV >
PEF sterilizes by stretching bacteria up to its ruptures by electrical fields with 20- 50kV/cm strength delivered by sharp square pulses: more in details.
Inactivation of bacteria in juices with this system can reach 3-6 logs at 250l/h and 2-4 logs at 500 l/h with one or both coax chambers. Plus, its unique set of broad pulsing values with up to 50kV/cm fields allows finding optimal parameters for your future cost-effective production system.
Wek-Tec offers to evaluate or to develop your optimal PEF process which work can be credited to your possible purchase of our system. This work is done at our place with a bio-support from a local certified food lab as detailed here.
Our PEF and PUV pilots have been successfully used past 23 years worldwide and brought valuable scientific results referenced in various academic and in industrial publications.
as proven on our PUV system by Baxter Corp. with UV resistant spores of B. Pumilos.
Clarifications:
the sterilization effectiveness of Pulsed UV light increases with its power from identical to the continuous UVC light by low pressure Mercury vapor lamps to turning on accelerated DNA damages possible only for more and more intense UV pulses. Further increases of pulse power in w/cm² enters the PUVD region where the joint power of UV and also of the visible light pulses physically disintegrate all bacteria and spores.For this process to happen, these pulses have to be very short, intense and rapid. It makes it possible to sterilize vaccines in vials, clear-packed food items, etc.
For pharma companies our achievements open opportunities to sterilise transparent liquids in thin clear transparent glass vials or plastic bags.
To reach your objectives we offer to select optimal parameters for your application with these two systems. Or to sell you those. The tests results will also to design and to construct full-scale production PL sterilization tunnels or systems also for other usages
Our UV tunnel for powders in a flow-through sanitation or its photo-chemical modifications (e. g. by UVB enriching the D2 vitamin in mushroom powders) is designed for up to 100kg/h and for further adjustments as per data from your powder evaluation on our Vortex >
We offer evaluation tests at our place or can sell such Vortex. It allows a cost-effectively to reduce micro-organisms at 1-2 logs & more.
< in Vortex powders are moved around a UVC lamp by a forced air flow with the Oxygen being replaced with the Nitrogen gas.
Wek-tec e. K. looks for a capable partner to mutually benefit from our IP and suppliers.
With our systems & services come benefits of German manufacturing.
MILO is made from the goodness of milk, malt barley and cocoa and packed with essential vitamins and minerals. Owned by Switzerland-based Nestlé, the MILO brand has been popular in Southeast Asia, Australia and worldwide for decades. It is one of many products manufactured at Nestlé’s plant in Singapore, where the company has operated since 1912. MILO® is an essential in many Singaporean households and continues to be in the forefront in meeting their evolving tastes and the need for healthier and more nutritional products
The Singapore plant produces and packages MILO drink powder in formats including tins and easy-open, easy-pour sachets that are formed and filled on a high-speed rotary filler. Upstream of the sachet filler is a metal
detector that scans the powder to identify contaminants. Detection of a contaminant, called a “strike,” triggers the metal detector to divert a portion of the powder stream into a collection bag. Workers then inspect the rejected powder to verify that the contaminant was removed, and log the incident into a quality-assurance report. This had been a cumbersome process until a flexible screw conveyor smoothed the flow to the metal detector.
The metal detector originally sat directly below the surge hopper that discharged the MILO powder via gravity through a butterfly valve. “When the valve opened, often one large chunk of powder would
flow through the metal detector which wasn’t fast enough to reject the whole chunk,” says Sean Phua, engineering manager. As a result, some portion of the powder—and possibly the contaminant— passed through the metal detector and into a flexible screw conveyor that transferred it to the sachet filler. That would force operators to halt production.
With production halted, the operators would run the flexible screw conveyor in reverse to empty all the powder in flight. That powder, along with the rejected material, was then hand-sieved and dissolved with water to find the contaminant and “determine whether we had a real or a false strike.” It was messy and the interruptions reduced packaging productivity, Phua says.
He learned that the operation would improve if the powder could free fall into the metal detector in a steady stream. One possible solution would be to add a rotary valve under the surge hopper, but lack of headspace made that impossible, Phua says. Instead, Flexicon recommended offsetting and raising the metal detector, allowing room to add a new flexible screw conveyor to feed powder to the metal detector in a steady, controlled flow. Flexicon Singapore provided the new conveyor to accommodate spatial constraints and throughput requirements.
The conveyor is 1.5 m (59 in.) long and includes a spiral enclosed in a 90 mm (3.5 in.) diameter outer tube made of ultrahigh-molecular-weight polyethylene. The screw—the only moving part that contacts the product—ensures that the powder does not pack, cake or separate.
The conveyor includes a 150 mm (5.9 in.) diameter inlet flange and charging adapter that connects under the surge hopper’s butterfly valve. From there, the powder is transported at a 41-degree angle and discharges into the metal detector through a 150 mm (5.9 in.) diameter downspout. The conveyor’s 2.2 kW (1.3 hp) drive turns at a constant speed to transport about 720 kg (1,587 lb) of powder per hour for 20 hours a day. Level sensors at the conveyor’s inlet and discharge are linked to the sachet filler’s controls, enabling both units to operate in sync.
According to Phua, the new flexible screw conveyor has streamlined the operation. “All strikes are rejected before the powder enters the original flexible screw conveyor to the sachet filler,” he says, “eliminating false rejections and manual clearing of powder from the conveyor.” His colleagues in the quality-assurance department welcome the improvement. “Because we have more positive rejection from the metal detector, quality assurance people have less worry about contaminants not being rejected.”
More reliable rejection boosts productivity by increasing sachet filler uptime and reducing incident reporting, while conserving product. “Previously, large chunks were being rejected. Now as a freefall, less powder is flowing, which reduces product loss by a good amount,” he concludes.
Level sensors at the conveyor’s inlet and discharge are linked to the sachet filler’s controls, enabling both units to operate in sync.
Throughout history, consumer trends rise and fall; closely reflecting the general consensus of the time. One of the most significant developments of the last 15 years is the rise of the conscious consumer. Affecting all industries and the companies within them, the societal goal of improving sustainability has influenced the packing of products in a multitude of ways; from the materials used, to how products are packed. Which is where Cerulean comes in.
Our FPS range including our new FPS120s is the future of tube packing. These packing machines are simply and robustly constructed whilst incorporating the latest control and display technology.
The FPS-300s is still the most compact, high speed machine in the market, and is characterised by its fast and simple set up, with box and tube size changeovers typically being achieved in under 20 minutes, allowing the Cerulean FPS-300s to meet the flexible requirements of the modern tube making environment. After rigorous testing to prove successful use of recycled tubes on the packing machines, they are perfect for your eco-friendly manufacturing facility.
The fast-moving-consumer-goods industry’s efforts to promote sustainability are led by a focus on high recyclability and recycled content. With 60% of commitments by FMCGs including an aim to increase recyclability up to 100%, and 14% going above and beyond to promote change e.g. partnering with suppliers to reduce consumption and increase substitutes. The significance of using recycled material is clear.
The actions of these companies are justified from numerous consumer
surveys which all arrive at the same conclusion. An example of this is a survey carried out by McKinsey & Company in the US to find out whether consumers will pay for greener alternatives; across all enduse segments, 60 to 70 percent of consumers said they would pay more than the current price for sustainable packaging. With this willingness to pay more being relatively equally distributed across all end-use segments.
Another way Cerulean are helping you uphold your greener ethos is by offering retrofitting to your existing FPS instruments. This option to add new features to a previous model is a more cost effective and energy efficient way of getting the latest technologies within the tube packing space.
Learn more about Ceruleans approach to sustainable development here: Our Approach | Cerulean
The fast-movingconsumer-goods industry’s efforts to promote sustainability are led by a focus on high recyclability and recycled content.
Is sustainability the key driver influencing the packing industry of today?
Cerulean launched the FPS-120s low-speed tube packing system in June 2022 as a low cost alternative to the FPS-300s.
Capable of hygienically packing a variety of tube types directly from the tube maker into cartons at speeds of up to 120 tubes per minute. The FPS-120s offers a user friendly colour touch screen, enabling the user to control set up, packing options and store all settings in a library for quick change over and later use.
Compatible with all Cerulean Tube Infeed Conveyors (TIC) and with the ability to choose left or right-hand carton entry as well as offering alternative tube size kits, the FPS-120s is a flexible solution for your tube packing needs.
World-wide support; we are your global, local supplier.
Are you open-minded when it comes to replacing your warehouse equipment?
Impact Handling and Cat® Lift Trucks can offer you radically different products with game-changing effects on your profitability.
If you’re looking to replace, for instance, a platform stacker, the obvious approach is to choose another platform stacker. From the constantly innovating Cat® warehouse range, we can certainly find you a similar but superior new model. But would you consider choosing something other than a platform stacker to do the job? In some cases, the gains will be much greater.
Impact highlights a new generation of Cat stand-in and sit-on stackers and power pallet trucks.
First, these trucks allow you to increase the storage capacity – and hence the money-making potential – of your warehouse. Next, they boost your productivity, by moving more pallet loads per hour. Finally, they reduce your lift truck fleet’s total cost of operation in various ways.
Taking the Cat NSR12-20N2(I) stand-in stacker range as an example, compared to platform models, stand-in trucks have a smaller footprint. What’s more, they lift higher – going up to 7 metres, depending on model and mast choice. It means you can make your aisles narrower and your racking taller, to fill more of your valuable warehouse space. Using the optional folding side stabilisers, which add extra residual capacity, you can also stack heavier loads at each level.
One time-saving advantage over platform trucks is obvious: there’s no need to keep stopping to fold and unfold platforms and sidebars. Others result from stand-in truck operators’ increased sense of confidence and empowerment.
The operator is fully enclosed and protected, so there’s no fear of a shoulder, arm or leg banging into a racking column or other hard structure. From the operator’s central standing position, he or she also has a clearer all-round view. In addition, there are automated aids for speed and stability control. As a result, operators feel safe to drive faster. Meanwhile, the high manoeuvrability, advanced technology and precise handling of the trucks
makes every task quicker and smoother.
Further productivity gains have been made through ergonomic, high-comfort design which enhances user satisfaction and performance. This is another area in which the designers have extended their long-established world leadership in stand-in lift truck development.
The operator compartment is vibrationfree, comfortable, quiet and very easy to enter and exit. These factors, together with ergonomically designed controls, minimise stress, strain and fatigue. Operators feel better, work more productively and are less likely to need sick leave.
While improved storage efficiency and work rates boost income, the new trucks also reduce overall expense. For a given volume of pallet load movement, the stand-in stacker concept requires less labour and fewer trucks. Quite simply, the operators can do the work in a shorter time.
One time-saving advantage over platform trucks is obvious: there’s no need to keep stopping to fold and unfold platforms and sidebars.
Your businesses can additionally save on fleet investment by taking advantage of the stand-in stackers’ multi-role versatility. For example, they are suitable for replacing reach trucks in some situations. Their lifting matches that of many reach models, but they cost less and will work in tighter spaces. As well as stacking and retrieving goods, their uses may extend to order picking and to horizontal transport over both long and short distances.
Cat lift trucks also typically make TCO savings through their durability, low maintenance needs and high energy efficiency. For even lower ongoing costs, and continuous operation without battery changes, the trucks can be specified with lithium-ion technology.
Along with the stand-in stackers, Impact offers a new Cat stand-in power pallet range: NPR20-30N2. At first glance, the only obvious difference is that the power pallet trucks have no mast. Most features and benefits are shared. Again, the major sales arguments relate to increased storage
efficiency, productivity, and cost savings.
Cat stand-in power pallets are designed for fast internal transport of heavy and long loads. This may involve anything from short shuttle runs to large distances. They provide an efficient answer to intense demands, including multi-shift truck use. Their key applications include production areas, warehouses, and cross-docks.
For even greater ergonomics and comfort, in the most tiring of jobs, there are Cat sit-on trucks. Cat NSS1620N2(I) sit-on stackers and NPS2030N2 sit-on power pallets ease the strain of long and heavy shifts. Like their stand-in equivalents, they also enable fuller use of warehouse space, boost throughput and reduce TCO.
In addition to a comfortable suspension seat, they feature anatomically supportive and positionally adjustable armrests. These place the driver’s hands perfectly for easy reach of the mini steering wheel and fingertip hydraulic controls. Other luxuries include the
option of electrically adjustable floor height for a perfect driver fit.
Cat stackers and power pallet trucks provide a great illustration of how this manufacturer’s constant innovation gives more choice and better results. From the comprehensive Cat line-up, , Impact’s expert sales teams will identify the ideal model and specification for your situation. We will then maintain its productivity levels and TCO savings through our first-class national support network.
www.impact-handling.com
With the rapid increase of energy costs, businesses are looking at reducing their electricity usage while maintaining comfortable and compliant conditions for products and staff. UK based EcoCooling offers a cost-effective cooling solution for food storage and processing facilities. With blanket or spot cooling options available, evaporative cooling offers a flexible approach to process or people cooling that can be easily retrofitted to the majority of buildings.
Evaporative cooling adds humidity to the air, which can be beneficial to some food storage environments such as bakeries, wine and chocolate producers, cereal manufacturers and more, with some of the leading UK brands utilising our equipment for the processing or packing facilities, including Subway, Hotel Chocolate, Premier Foods, Greggs and many more.
As part of a balanced ventilation system, evaporative cooling is achieved through the natural process of direct evaporation of water into supply air, which is extremely effective in temperate climates like the UK. Air supply temperatures off the coolers do not exceed 25C, without the need to utilise any refrigerant technology.
Even on the hottest days, a standard unit covering a 250m2 area or spot cooling a 15m diameter zone can operate at a cost less than 22p in electricity and 2p in water per hour, based on service costs of £0.19/kWhr and £1.90/cum respectively (2023 figures). This gives an energy saving of 90% on an equivalent refrigeration-based system with a 35kW cooling load.
An additional benefit of an evaporative cooling-based solution is the cost of installation, which is a fraction of that of the equivalent refrigeration system.
Evaporative cooling is extremely beneficial in a bakery environment. The humidity levels keep the bread fresh and don’t dry it out, unlike traditional air conditioning which is extremely dry and can often shorten the lifecycle of fresh produce, so it is highly effective for bakery cooling.
Premier foods were looking for a cost-effective bakery cooling strategy for their Barnsley site. Evaporative cooling can guarantee cool supply air of below 25°C all year round in the UK, making it the perfect solution for those wanting to reduce temperatures in their bakeries. 12 down discharge EcoCoolers were supplied and fitted to 12 existing Air Handling Units (AHU’s) on the roof of Manor Bakeries, Barnsley to provide cooling for the bakery. The existing refrigeration based cooling system has been decommissioned and the packaging area is now solely cooled using the EcoCooling Evaporative cooling system.
Following commissioning the system was tested and monitored, the following performance figures were recorded for the facility:
EXTERNAL AMBIENT = 23°C (WARM SUNNY CLEAR DAY)
AIR TEMP OFF COOLER = 16.6°C
AIR VOLUME THROUGH COOLER = 4.47M3/S
PRESENT COOLING CAPACITY = 34KW PER COOLER
TOTAL SYSTEM CAPACITY = 12 COOLERS
X 34KW = 408 KW
www.ecocooling.co.uk
Planned closures of factories and production lines are a perfect time to ensure equipment is operating safely and efficiently. If your business is operating a seasonal shut-down, Filtermist can help your team with essential maintenance and repairs of your industrial extraction systems.
Our team of P601/02 qualified engineers are on hand throughout the summer to visit your site and provide servicing and maintenance, as well as thorough examination and testing of Local Exhaust Ventilation (LEV) systems - giving you peace of mind that your workforce is protected from exposure to hazardous airborne contaminants and your business is operating in compliance with relevant HSE regulations.
All industrial air filtration and extraction equipment performs best with regular preventative maintenance. Benefits include increased efficiency, less production downtime, and reduced costs.
Our skilled engineers can carry out internal and external inspections of all of your LEV equipment, checking for cracks, defects and poor filtration. Our team can also review your process and by referring back to your original commissioning reports, can ensure the system is still operating as well as it was on the day that it was installed. If it’s not operating at its best, then our engineers can identify faults and recommend and implement changes to get your equipment back on top form.
Filtermist engineers will look for:
• Cracks, defects and poor filtration from your filter unit
• Dust bypass from a process – is your dust getting into places it really shouldn’t be?
• Blinded, burst or cracked filter cartridges and bags
• Duct issues such as a faulty swarf arrestor, blockages or defects
• Fan efficiency – looking at the rotators, unusual vibrations, alignment and impeller issues
• Operation of other auxiliary parts on your equipment such as shaker motors, drums and bearings
We can also calibrate differential pressure gauges, digital screens and ensure visual indicators are operating correctly.
For more information visit www.filtermist.co.uk, contact the Aftermarket Team on 01952 290500 or email sales@filtermist.com.
Since the invasion of Ukraine in February 2022, prices for electricity, gas and oil have rocketed. The situation on the world’s energy markets remains tense, with the high costs a huge financial burden for both consumers and industry. There is an increasing demand for alternative solutions to secure an economical supply of energy in the long term. This is where KHS comes in with its package of shrink tunnel conversions. With it, the Dortmund specialist for filling and packaging systems enables its clients to convert their existing machinery to a number of different forms of energy.
The customers can opt for conversion
from one source of energy to another –from natural gas to electricity or liquid gas, for instance. They also have the option of switching the system between two types of gas or flexibly converting it to electricity. Conversion back to a gas supply can then be performed by the customer as required. This significantly reduces dependence on a single source of energy and increases the security of supply.
Conversions are available for practically all existing shrink tunnels and are installed by KHS specialists specifically trained for the job. There is usually no change in machine control for the operating personnel. With the reversible option the setup is changed by the customer either digitally in a matter of minutes using a selector switch on the HMI or by changing a module over (this takes just a few hours).
Website: www.khs.com
Email: presse@khs.com
There is an increasing demand for alternative solutions to secure an economical supply of energy in the long term.
Your KHS system for efficient water bottling.
From the preform to the packaged PET bottle, our lines not only considerably save on energy but also on materials and maintenance costs. One such system is our compact InnoPET TriBlock Aqua M, which forms, labels, and fills single-serve bottles especially efficiently. At a rate of up to 82,000 bottles per hour it also saves time. This is what we call efficiency right down the line! khs.com/water
Beardow Adams has developed a new adhesive for labelling, that supports the move towards greater sustainability in the packaging and labelling sectors.
The new adhesive, BAM 2537, allows returned bottles to be washed in a caustic solution, separating them from their labels, as well as the adhesive, before being returned to the market. This reuse loop can take place between ten to fifteen times, before the bottle is fully recycled – drastically, helping to reduce the number of single-use plastics in use today.
The innovative semi-pressure sensitive formulation, BAM 2537 works on all types of containers, but especially with highly carbonated bottles as it provides a more aggressive bond, resistant of the stresses caused by the expansion of PET bottles under pressure.
Its residual tack also allows labels to be pressed back into the desired position should the label peel away, satisfying both, manufacturers who need to protect their brands, and end-users who benefit. The adhesive is suitable for low- and high-speed running machines (an average of 26,000 bottles per hour), and easily produces the required adhesion between PET-label and PETbottle.
Fully aligned with the growing introduction of deposit return schemes, BAM 2537 is approved by circular economy bodies, Returpack and PETCycle, and forms part of an eco-friendly range of adhesives from Beardow Adams that also includes bio-based, vegan friendly, and pallet stabilisation adhesives.
BAM 2537 is also FDA approved, allowing it to be used in the manufacturing of food and drink labelling and packaging.
If you would like more information regarding our semi pressure sensitive labelling adhesive, please contact marketing@beardowadams.com
www.beardowadams.com
The new adhesive, BAM 2537, allows returned bottles to be washed in a caustic solution, separating them from their labels, as well as the adhesive, before being returned to the market.
T-T’s clean water booster sets are designed to match the pressure demands of any application, with larger bespoke sets and fixed or variable speed options available. Scan the QR code to learn more
*Residual current is the difference between the current flowing into and out of a circuit. i.e. the difference is the amount of current leaking to earth.
Unfamiliar with the term leakage (residual*) current ? This is the current that leaks to earth from live conductors and electrical equipment. Leakage current is an indicator of the health of an electrical system (heartbeat / pulse). Increases in leakage current indicate developing problems with the electrical system and or electrical equipment - an early warning! Don’t wait for a fuse, circuit breaker to disconnect the electrical supply. You do not for example wait for pressure to exceed a critical level and shut down the production, you monitor it constantly. So why not monitor electrical leakage?
Efficient and effective production is synonymous with the health of the production line. We monitor changes in temperature, vibration, pressure, sound etc to identify developing issues,
enabling earlier intervention. The cost benefits of monitoring leakage current , compared to the cost of lost production due to sudden power loss, damage to electrical equipment and personal safety are easy to quantify for individual sites.
Electrical systems leak electricity to earth, this is a characteristic of electricity and electrical insulation. Leakage currents associated with electronic equipment such as speed
control invertors, EMC filters, motion control for positioning and robots, are significantly higher in value than conventional electrical equipment and more complex. Increases in operational leakage current above the norm (design level), indicate a change in electrical insulation quality e.g. a developing fault in electrical equipment and cables.
Periodic electrical inspections, including simple insulation tests carried out with the production line shutdown give a basic snapshot of the electrical health. They do not reflect what is happening when the production line is running or between tests.
If we checked the leakage current flowing in the main protective conductor during production line operation , this would be the sum of all the individual leakage currents associated with the production line, excluding any currents leaking to earth via other paths/metal work etc. Questions to ask: Is this value normal? Is it higher or lower than last week, yesterday or has it just increased by 25% in the last few minutes? What is the distribution of the leakage current associated with individual manufacturing cells, robots ? Is there a developing problem with one of the cells, which will result in a protection device tripping, leading to a partial or complete production stoppage? Spot checks of this nature have limited value in the production environment.
Continuous monitoring of leakage currents at critical points within a production line and or at manufacturing cell level, enable the identification of trends and consequently early warning of developing faults. This approach (condition monitoring) has recognised cost benefits within the modern and well managed production environment moving from a reactive (fix it when its broke approach) to managed intervention (red flag – plan to check and repair as appropriate).
Developments in predictive maintenance, associated with shared data, IIoT, ML, AI (Industry 4) at the top end, are enablers for high level management and control through condition monitoring and installation forecasting regarding future installation behaviour. Existing production line automation may not fully embrace the Industry 4 benefits, without major upgrades to hardware and software.
Product developments such the e. Guard residual current monitoring system from Doepke, enable the adoption of a fully scalable bundle, with 5 levels of performance:
Basic Level 1, using free Doepke software enabling clear visualisation of the complex leakage currents within a system, offering evaluation, and monitoring of < 20 RCMs on a PC, plus alarm email messaging.
Moving through the levels adds additional
features e.g. Level 5 – bespoke software incorporating machine learning, customer meta data, hyperparameters, developed in conjunction with the Customer’s Engineering and IT project team.
e. Guard permanently monitors the residual currents in an electrical installation and therefore offers comprehensive surveillance of their status. Smart residual current sensors positioned at critical points in the system, manufacturing cells and or items of equipment, enable the early identification of issues within specific locations.
This results in timely and planned intervention by electrical staff to conduct essential checks and repairs. The aim, reduce downtown, catastrophic equipment failures and associated production line losses. For further information please contact Doepke on sales@doepke.co.uk.
www.doepke.co.uk
Efficient and effective production is synonymous with the health of the production line.
Cardboard box manufacturer Reedbut Group operate across three UK-based sites, producing sustainable bespoke packaging solutions for a wide range of industries and sectors.
The Reedbut Group design team works directly with customers, developing the perfect box to deliver food items safely and securely. BRCGS certified with an ‘A’ rating for direct food contact, Reedbut Group strives to adhere to the global standard of quality to ensure customers from the food and drink sector can buy from them with confidence.
Among the food and drink packaging solutions on offer, Reedbut Group can design and manufacture letterboxfriendly postal boxes, corrugated cardboard delivery crates, shelf ready packs (SRPs), window-patched boxes and more. Each cardboard box is designed with sustainability in mind, utilising water-based inks for printing, and developed around the product itself to minimise empty space.
Reedbut Group have been creating custom printed packaging for drinks and alcohol for many years, delivering for briefs including single bottle packs, multipacks, gift packaging and point-ofsale displays.
From biscuits and cupcakes to vegetables and deli produce, Reedbut Group can manufacture the perfect box to make sure goods arrive safely. Perishable items are protected, maintaining shelf-life and reducing food waste, and breakable containers are kept secure during transit.
SRPs have been proven to increase product presence in a crowded retail environment. Combining an outer transit box with a point-of-sale display unit, this bespoke packaging can both protect food and drink products and enhance visibility.
Inhouse window patching applies a thin film to a die-cut window in any box, creating a food-safe barrier which eliminates the need for bags. Customers can get a taste of the contents combined with the knowledge that they’re wellprotected.
With over 46 years of industry experience, Reedbut Group offers a wide range of cardboard packaging options, all of which can be designed bespoke for your product needs and printed inside and out to make your branding shine.
Each cardboard box is designed with sustainability in mind, utilising water-based inks for printing, and developed around the product itself to minimise empty space.
Kecolhaveover25yearsofexperienceinhandlingall typesofviscousproductsinthefood,pharmaceutical andcosmeticsmarkets,aswellasgeneralindustrial
With CAPEX conditions restricting response time to unscheduled process and production downtime, Axium Process, specialists in liquid filtration solutions, have launched a new service that can now be funded through OPEX channels. Designed to meet a range of liquid processing concerns, Axium’s UF & RO2Go rental plants meet industrial scale demand for many different industries including pharmaceutical, food, beverage, dairy and water recycling. The systems are built on tried-and-tested technology and have been developed for rapid deployment with minimal operator training, allowing them to be up and running in a matter of hours following installation. Offering great flexibility, and backed by extensive technical expertise, Axium’s rental range can fulfil high-priority requirements swiftly, while reducing capital expenditure risk by allowing the technology to be assessed over the long term.
For further information, please contact: Derek Davies
Axium Process, Hendy Industrial Estate, Swansea, SA4 0XP Tel: 01792 883 882 | Email: derek.davies@axiumprocess.com info@axiumprocess.com
KHD specialises in providing conveyor belt steam cleaning solutions for the Food Industry. With 25 years experience of developing portable and fixed conveyor belt steam cleaning systems, KHD has the most useful and effective product range available. KHD systems are in use by big brand names around the world. KHD machines are powerful tools that work within existing cleaning regimes to enable operators to do their job better, faster and more effectively.
SUSTAINABLE CLEANING
KHD provides environmentally responsible solutions, producing designs that have the widest possible use within a factory. Portable solutions quickly adjust so they can be used on multiple conveyors in a factory. KHD devices clean primarily with steam and without chemicals, harnessing industrial steam power that uses very little water, typically 15-30 litres of tap water per hour.
The Fixed Conveyor Belt Cleaning Systems use steam and vacuum to clean and sanitise conveyor belts and are suitable for use during production. The lightweight cleaning heads are quick and easy to remove for cleaning. Designed for use in conjunction KHD portable 3-phase steam generators, the systems are also suitable for use with factory steam supply. Available for both single or double sided cleaning this innovative and
flexible system can be fitted to a wide range of existing or new conveyor belts.
KHD Technology is a design led company. Alongside standard products KHD also provides bespoke solutions, selling direct to end users and to OEMs including conveyor equipment manufacturers.
Why choose industrial dry steam cleaning over other cleaning methods? You need to have a rigorous cleaning regime in place, opting for an innovative dry steam cleaning approach offers greater benefits.
It’s quicker, easier and cheaper, Traditional cleaning methods tend to involve consumables in the form of chemical cleaning agents, and require a lot of labour and time. The amount of
time cleaning takes has a direct impact on productivity – the longer a conveyor line is out of action for cleaning, the less product can be processed and dispatched.
It’s better for the environment (and you) Avoiding the use of chemical-based cleaning products, which can be toxic to the environment has additional benefits to cost saving. The quantity of water needed (and the energy required to heat it) to use and wash away chemical cleaners is excessive compared to the amount of water required for steam cleaning.
Further product details, images and video are available at www.KHDtechnology.com
Keith Handy +44 (0)7966 447770
Telephone: +44(0)1785 811443
Email: sales@khdtechnology.com
KHD provides environmentally responsible solutions, producing designs that have the widest possible use within a factory.
There are countless sizes and types of conveyors in food manufacturing. No two factories are the same and cleaning is o:en ;me-consuming, difficult and tedious. Crea;ng a por@olio of steam cleaning products has to address a complex array of factors, including: food type, size, speed, duty cycle, belt type, local environment, power supply, cleaning regime. The list goes on.
For over 25 years KHD has been developing an ever expanding por@olio of belt steam cleaners, to provide quick and easy to use solu;ons for food factories around the world.
From dedicated fixed systems to portable belt cleaners, we design and manufacture systems to handle the widest range of cleaning tasks.
• Reduce down;me
• Speed up cleaning
• Improve quality
• Free-up manpower
• Reduce energy
• Reduce water
• Chemical free
We can show you how effecRve KHD products are by demonstraRng on your conveyor. Contact us for details.
Gellert freeze dryers are the perfect solution for manufacturers looking for a reliable and scalable option for regulated food production. With a notable shift towards the freeze-dried product market, manufacturers and consumers alike are recognizing the benefits of this process. By reducing, or removing, the need for cold chain handling, manufacturers can reduce transportation and storage costs, and as freeze-dried material is much lighter than frozen or refrigerated product, this further lowers costs. Additionally, freeze dried products not only take less energy and cost to store, but they also maintain the biological benefits and flavours of the raw product whilst extending shelf life.
Gellert freeze dryers offer a controlled and repeatable manner for in-situ freeze drying directly on the shelves, ensuring the product maintains its shape, structure, and nutritional value. Gellert has developed a range of freeze dryers with ease of scale-up, user requirements, and operation in mind, making them versatile and popular in the industry.
Some of the beneficial features of Gellert equipment include AutoDry, an intuitive feature that allows users to input their desired temperature differential between the product, sample, and shelves, ensuring the sample can be dried using the AutoDry feedback mechanism,
optimizing drying cycles. The chamber, condenser, shelves, and shelf stack can all be constructed from 316L stainless steel for product contact, and a hybrid cooling system is also available on larger equipment, to utilize defrost water by re-heating via the freeze dryer compressors, saving energy and costs.
The most common applications that Gellert’s freeze dryers are used for include: -
• smart foods e.g., supplements and nutraceuticals
• food and beverages
• dairy products
• fruits and vegetables
• pet food and pet treats
All Gellert systems are manufactured in Europe and strictly adhere to compliance regulations such as F-gas.
Biopharma Group is the exclusive distributor of Gellert freeze dryers across the UK, Ireland, and France. Both Biopharma Group and Gellert are well respected and renowned companies, combining years of lyo industry experience. This winning combination allows the Biopharma Group team to help you select the best freeze dryer to meet your specific need and Gellert has accrued a high level of practical experience and in-house expertise, developing an array of different models and configurations to satisfy a broad range of food production purposes.
Contact Biopharma Group’s product specialists to discuss your requirements or request more information.
www.biopharma.co.uk
freeze dried products not only take less energy and cost to store, but they also maintain the biological benefits and flavours of the raw product whilst extending shelf life.
The installation of an Ishida DACS-G checkweigher and metal detector combination at leading Polish confectionery manufacturer ZPC Otmuchów has helped the company to double production capacity for its range of jellies packed into jars, providing both an important quality check and valuable production data that helps to minimise product giveaway.
Supplied by Ishida’s Polish agent Fenix Systems, the new checkweigher and metal detector are working in conjunction with a 14-head Ishida midrange multihead weigher, which packs the jellies into jars from 90g to 210g in size. While the metal detector ensures there is no metal contamination in the product, the checkweigher confirms that every jar is within the permitted weight range. Importantly, the checkweigher is also able to feedback to the multihead
weigher information on overweight packs. This enables the parameters of the multihead to be adjusted to further improve the accuracy of each weighment and keep over-weights as low as possible.
The feature is part of Ishida’s proven Ishida Data Capture System (IDCS), a powerful software that captures and manages data from every pack that passes over the checkweigher. This provides in-depth real time performance monitoring that identifies opportunities for performance improvement and enhancement throughout the line to deliver increased Overall Equipment Effectives (OEE).
The DACS-G-S015 model is the fifth checkweigher to be installed by ZPC Otmuchów, and the company also has eight Ishida multihead weighers in operation at its four manufacturing plants. The reliability and excellent performance of its existing equipment, together with operator familiarity with the checkweighers, were key reasons for the selection of the latest checkweigher.
“All our Ishida checkweighers utilise the IDCS and are therefore interconnected, so it was important that our new Ishida checkweigher could be part of this, in addition to being well-known to our people on the shopfloor,” explained Dawid Lampka, Production Manager at ZPC Otmuchów.
“The checkweighers are practically maintenance- and trouble-free. In the event of any problem, we can count on the support from Fenix Systems. Importantly, issues can usually be remotely diagnosed and solved.”
The new line incorporates one of ZPC Otmuchów’s existing multihead weighers to mirror the existing line for jellies, both operating at around 30 jars per minute. The lines are in operation 24/7.
The sticky nature of the sugar-coated jellies makes them difficult to handle and control in an automated weighing operation. To counter this problem, the Ishida multihead weighers incorporate a special C4 coating which prevents the
products from sticking to the contact parts. This ensures a consistent flow of jellies throughout the weigher.
“The use of the C4 material has been crucial, as the solution has allowed us to significantly improve our processes,” confirmed Dawid Lampka.
The proven accuracy of the Ishida multihead weighers installed at ZPC Otmuchów has ensured consistent pack weights and minimum product giveaway.
“Our contact with Ishida is excellent,” he concluded. “When we bought our first models, we received full operation and maintenance training. And as well as receiving ongoing support when needed, they are also in attendance when we have any external inspections of the
equipment for weights and measures legislation.”
Established in 1946, ZPC Otmuchów is one of Poland’s leading producers of sweets, including chocolate candies, halva, marshmallow, hard and filled candies, gummies, bars, breakfast cereals and salty snacks. The company’s portfolio includes two main brands, Odra and Freeyu, with listings in major domestic and international retail chains, and it also provides comprehensive product solutions for private label and B2B operations. The Group is also a partner in the development of innovative products for large international corporations, including pharmaceutical companies.
www.ishidaeurope.com
The use of the C4 material has been crucial, as the solution has allowed us to significantly improve our processes
The business relationship between SATO and ALTech has gone from strength to strength for over 30 years, built on a cornerstone of trust, mutual growth and innovation. And the latest chapter in this success story came under two months ago, when the new S84 86NX smart print engines were delivered from SATO.
Rory Horton-Smith, Managing Director of ALTech UK, shares his insights on the impact they have already had on ALtech labelling processes and the future of the partnership.
SATO, a global leader in auto-ID and labelling solutions, recently launched the innovative S84/86NX smart print engines, designed for automation and on-site usability. Equipped with Application-Enabled Printing (AEP), they offer enhanced customization and improved performance in harsh industrial environments. The partnership between SATO and ALTech, spanning over three decades, is testament to the benefits of these ground-breaking print engines in food labelling automation.
Rory Horton-Smith, Managing Director of ALTech UK – the UK subsidiary of ALTech, shares his insights on how SATO’s S84/86NX smart print engines have boosted their operational capacity, highlighting the key role of the AEP functionality: “This additional intelligence provides us with the ability to provide solutions that used to be difficult.”
Thanks to AEP, for example, warehouse operators can directly connect to weigh scales, automate weight input and print from programmable logic controllers (PLCs), halving the reprogramming time required.
The SATO print engines have streamlined ALTech’s customers operations, providing reduced labour costs and enhanced operational efficiency. Automating labelling processes has allowed these companies to focus on boosting productivity and saving costs. The autolabelling abilities of the print engine provide enhanced real-time traceability and extra intelligence that breaks new ground. Rory highlights the benefits of real-time updates, saying: “From a
traceability perspective, the intelligence of the printer potentially allows recording of the label printed (e.g. to a network file) as well as just printing it, for example”
The S84/86NX print engines are designed for demanding industrial environments, resistant to solvents and water and ideal for factories and warehouses where extreme temperatures and varying conditions are the norm. Features like the open cover sensors and stronger hinges and nip rollers add durability, extending the product’s lifespan in the 24/7 ecommerce fulfilment era. With SATO’s preventative maintenance service, SOS, users can remotely monitor the status of their print engines on a single dashboard, eliminating downtime and keeping operations running smoothly.
Rory also commends the seamless retrocompatibility of the SATO print engine with existing setups and its emulation. Scope to integrate the new print engines effortlessly makes the transition from older labelling solutions smoother and more efficient.
All of which means the SATO-ALTech partnership continues to flourish, thanks to a shared commitment to innovate and remain ahead of the curve. The SATO S84/86NX smart print engines, with their advanced features and flexibility, have proven invaluable in addressing complex challenges for ALTech and their customers in the food labelling automation industry. As both companies look to the future, they will continue to provide cutting-edge solutions and set the pace in the market, revolutionizing food labelling processes and enhancing efficiency in the sector.
www.satoeurope.com
“This additional intelligence provides us with the ability to provide solutions that used to be difficult.”
Providing supreme accuracy, SATO printers are designed with high-speed data rates and right-first time tagging capabilities to meet the needs of the most complex business environment
With improved flexibility, usability, connectivity and reliability, our flagship print engines are now equipped with next level SATO innovation, eclipsing all previous expectations.
Efficient and accurate labelling using thermal transfer technology. Packaging materials can be integrated into existing lines, and have features like automatic label detection and variable data printing for traceability and safety
Designed for the most demanding environments, the series is available inboth 4” and 6”, direct thermal/thermal transfer solutions Ideal for printing text data, barcodes, RFID tags and labels Its unrivalled versatility in performance is due to its excellent capabilities in emulation, PC-Less printing through Simple Stand Alone Mode or more complex AEP autonomous applications, alongside fast throughput and print speed
Book your demonstration today
Address : Valley Road, Harwich, Essex, CO12 4RR
Mailbox : enquiries-uk@sato-global.com
Website: www satoeurope com
SR-TEK transparent vessels have become increasingly popular in the food and drink industry due to their unique properties that provide numerous benefits for processing and packaging applications. These vessels are made from high-performance plastics or toughened glass and are designed to offer excellent transparency and durability, making them an ideal solution for a variety of applications in the food and drink industry.
One of the primary uses of SR-TEK transparent vessels is for storing and transporting food and drink products. These vessels offer excellent transparency, allowing for easy visual inspection of the contents. This is particularly useful for products that require high levels of quality control, such as juices and other beverages. Additionally, their high quality make them resistant to corrosion and chemical damage, ensuring that the contents are protected from external factors that could compromise their quality.
Another significant benefit of SR-TEK transparent vessels is their ability to withstand low and high temperatures. These vessels can be used for applications such as sterilization and pasteurization analysis, where low or high temperatures are necessary to ensure the safety and quality of the products. They are also ideal for use in hot-fill processes, where the vessel is filled with a hot liquid product, such as soup or sauce, and then sealed to prevent contamination.
The durability and toughness of SR-TEK transparent vessels make them ideal for use in the packaging of food and drink products. They can be used for developing new techniques of conservations, aging analyses of products such as fish, meat, condiments, sauces, and dressings. Additionally,
the high-performance materials used in SR-TEK vessels make them suitable for use in a range of packaging formats, including jars, bottles, and pouches.
Another significant advantage of SR-TEK transparent vessels is their compatibility with a range of processing and packaging technologies. They can be used in conjunction with a variety of filling, capping, and labeling equipment, making them a versatile solution for food and drink manufacturers.
In conclusion, SR-TEK transparent vessels offer a range of benefits for the food and drink industry. Their transparency, durability, and temperature resistance make them ideal for storing, analysing, transporting, and packaging a variety of products. With the increasing demand for high-quality food and drink products, SR-TEK vessels will continue to play an essential role in the industry.
The durability and toughness of SR-TEK transparent vessels make them ideal for use in the packaging of food and drink products
The incorporation of CBD into foods – as well as cosmetics and pharmaceuticals – is becoming one of the fastest-growing trends in the process industry. A variety of different products such as beverages, gummies, snacks and baked foods containing CBD oil are now available. Silverson mixers are increasingly being used for R&D and small scale production in this emerging market.
The latest ‘short’ in the 30 second guide video series, focuses on why Silverson mixers are ideal for the incorporation of CBD oil into a variety of different products. Silverson mixers offer unrivalled versatile and as all Silverson mixers are supplied with interchangeable workheads, one mixer can be used for several applications, making them ideal for manufacturers who produce more than one CBD oil based product.
Hart Door Systems, the original British manufacturer of the high-speed door concept, is confident that there are considerable prospects for another successful year for the Speedor brand.
“Our management team led by Nick Hart as managing director and David Mason as sales director has just delivered a very good year when there have been many uncertainties in the UK economy and wider afield.
“In that challenging business environment, we have had many successes at home and abroad not just through the Speedor range of highspeed doors but through our range of high-quality shutters. Both these leading brands have had additional variants introduced such as Speedor ECO and our Typhoon shutters,” says Doug Hart, chairman, Hart Door Systems.
“The breadth of offer created by the choice of solutions for industry and commerce has cemented our presence in the UK market and globally. The fundamentals delivered by Hart are quality throughout manufacture to installation as well as service back-up to comply with changing national and international safety standards.
“We are also cognisant of Climate Change issues and the need to keep both Hart’s and our clients’ carbon footprints to a minimum by using the latest manufacturing technology to streamline the manufacturing process. Where possible we would use recyclable materials.”
Looking more closely at Speedor ECO, this high-speed door complements Hart’s very successful Speedor Storm, Speedor Mini and sub brands such as Speedor Conveyor and Speedor Cleanroom, further
strengthening Hart’s overall high-speed door offer.
Speedor ECO is a new mid-range variant suitable for external use up to Class 3 and available up to 5m x 5m size whereas the Speedor Mini is for internal use only to a maximum 4m x 4m size. The focus with these two Speedor options is on lower price and high-speed doors that can be tailored to meet clients’ budgets.
Mr Hart says: “With the new Speedor ECO being a mid-priced high-speed
door variant with state-of-the-art direct drives and controls which are BSEN safety compliant, the ECO offers single or variable speed motor, heavy fabric and hand chain operation if necessary.
This adds to ECO’s many other features such as safe operation, reliability, and ruggedness. “We have always had quality as our prime driver and our success with new variants, not just in high-speed doors but shutters such as our new Typhoon range, the fundamentals are quality throughout manufacture to installation and service
to comply with changing national and international safety standards,” says Mr Hart.
“Without doubt there is demand for a mid-priced high-speed door variant such as ECO and given our considerable experience, we are the ones to deliver it,” he adds. “ECO will appeal to companies requiring a high-speed door solution but within a tight budget. It is for frequent use, high traffic situations where low maintenance is a priority.
“In all cases across our range of brands, we comply with the new code of practice announced by the DHF Door Hardware Federation and we are ever mindful of post installation maintenance costs. So, while Mini and ECO cater for less demanding environments, Speedor Storm’s increasing success is based on its improved, rugged, design predominately for external use up to 8m x 6m/6m x 8m) often in robust operating conditions with high wind loads.
“We have always had quality as our prime driver and our success with new variants, not just in high-speed doors but shutters such as our new Typhoon range, the fundamentals are quality throughout manufacture to installation and service to comply with changing national and international safety standards.”
Hart Door Systems, now in its 75th
year, is a global business supplying a range of door and shutter systems to sectors such as automotive, agriculture, communications, consumer foods, energy, environment, exports, food, logistics, manufacturing, power, sport, transport and utilities.
Contact www.hartdoors.com
t: 0191 214 0404
sales@hartdoors.com
Without doubt there is demand for a midpriced high-speed door variant such as ECO and given our considerable experience, we are the ones to deliver it.
In manufacturing, efficiency is key to success. Improved efficiency results in greater productivity, less waste, fewer hours lost to downtime and lower costs. This is why automated technology such as sack-filling machines and palletisers is so valuable – these machines feature specialist gripping heads to handle items with speed and precision.
The gripping heads found on palletisers are designed to hold bags, sacks and packages securely, allowing them to be moved quickly and efficiently without causing damage. Different gripping heads are available for handling different products and the most appropriate one will depend on the item’s shape, size, weight and handling requirements.
Common gripping heads may be vacuum operated, feature side clamps or magnets, or use a combination of all three.
Where there is a flat top surface, such as on boxes and cartons, a vacuum gripper is often used. However, at PALpack, we prefer to use a physical mechanical gripper, for reasons from changes in porosity to stability. All of PALpack’s palletisers are designed so that there are no change parts for different pack types.
World-leading manufacturer Lita offers gantry-style Cartesian palletisers which can pick and place items, often in complex pallet patterns. Several different gripping heads are available for handling different products. Because of the different gripping heads, both can handle RSC cases and shrink-wrapped packs of varying sizes and Robodue can also manage jerry cans.
machines feature specialist gripping heads to handle items with speed and precision.
Suitable for handling RSC cases, shrink wrapped packs, metal drums, bags, and sacks, Logico by Lita features a single arm with different gripping heads for different products. They can insert pads between layers and handle empty pallets as well as move packages.
Different types of bags or sacks have different handling requirements and gripper heads can be designed accordingly. Europack’s rotating beam palletisers have a 360o rotating gripper head that can be changed to suit
different packages, while combined heads can deal with more than one type of product.
Using sack-filling and palletising technology along with specific gripping heads improves processes, saving time, reducing manual labour and helping manufacturers to improve their overall operations. PALpack can supply not only sack palletisers, but also VFFS sack filling machinery.
For more information about PALpack’s automatic palletising solutions, please visit www.palpack.co.uk.
These
PALpack work with our UK and Irish clients to offer practical, technical advice on automated palletising. With over 25 years' experience in the field, we understand all levels of food and beverage production, from low-speed, simple operations, to super high-speed, complex, multi-product manufacturing. PALpack are agents for top-of-the-range machinery supplied by European manufacturers
Since our machine was installed, our line efficiency has improved dramatically, with little or no downtime recorded for technical issues, and their aftersales service is the best we have had from anyone in the 16 years of bottling production. I thoroughly recommend PALpack to anyone looking for some automatic palletisation on their production lines
Europack invented the rotating beam palletiser. Manufactured using only the highest quality components such as Siemens and SMC, these simple and easy-to-use palletisers have an extremely small footprint, with prices starting from as little as €60k.
VAI has designs, produces and supplies automatic and semi-automatic sack filling solutions, with machines that are used for decades. Their highly reliable solutions are made bespoke to customer requirements
One of the world’s most experienced and established manufacturers of automatic palletisers, Lita specialise in conventional medium to highpaced palletisers. These include Cartesian palletisers, layer palletisers and de-palletisers, as well as pallet de-stackers and layer card applicators
As part of any Food processors HACCP program validation of cook and chill processes is a critical and significant task taking time, effort, and resources.
PhoenixTM have developed a thru-process temperature monitoring technology specifically for this task designed to meet the challenges of the food processing market. Ideal for the validation process for any new cook regime, new product, or annual process certification. Whether performing an oven survey “oven mapping to identify cold spots” or validating the cook under production conditions, the thruprocess profiling solution gives you the accuracy, efficiency, and reliability you need to satisfy your HACCP demands.
As its name suggests thru-process profiling is the method by which product and or process temperature is monitored throughout the complete cook / chill process.
Monitoring of continuous conveyorised linear and spiral ovens and semi-continuous or rotational batch cooks is feasible where the use of external recorders with trailing thermocouples is tedious, impractical, and unsafe.
Employing the thru-process principal process monitoring can be performed under true production conditions without compromising line productivity .
At the heart of the thru-process monitoring system is the PhoenixTM data logger.
The PhoenixTM NT data logger range has been designed specifically for the challenges of monitoring food processing applications with an IP67 case design protecting from moisture. Type K or Type T data logger options allow accurate measurement of both cook and chill processes. The data logger itself can operate between -40 °C to 80 °C with a data logger accuracy of ±0.3 °C operating below +50 °C.
Data logger and thermocouple correction factors can be further applied to maximise measurement accuracy.
PhoenixTM offer a family of thermal barriers to suit the process type, duration, and temperatures of a wide range of cook regimes.
An extensive range of different thermocouple types is also available to suit different product types , sizes and monitoring demands.
The PhoenixTM Thermal View Food Software provides a comprehensive suite of analysis tools to convert the raw profile temperature data into useful process information. The analysis tools include the ability to calculate Fo/Pu values for the process against target micro-organisms.
The information gathered, further to process validation, can be used to allow informed process problem solving and optimisation to maximise product quality, yield, process productivity and efficiency.
Contact PhoenixTM to help Find, Fix and Forget your Food Cook Problems!
Further Information
LensConnect … Zoom, Focus & Iris remote-controllable from PC Introducing the award-winning computar LensConnect Series
Precise adjustment of Focus & Iris USB connector standard Inspection while moving focus
• Easy Installation
• High Resolution at any position
• Superb stopping accuracy
Connection Diagram
• Outstanding repeatability
• Low voltage and current
• Superior and versatile interface computar-global.com
With the advancement of power electronic components in general gives rise to increased heat dissipation, resulting in more hotspots within control cabinets where traditional methodology of construction is employed. Separating the wiring from the components allows for free air movement, resulting in passive cooling within the cabinet.
A live on-site test was conducted to prove effectiveness of this approach. The first cabinet was equipped with a traditional back plate and cooled using an air conditioning system with a 1.5 kW heat loss. In the second cabinet a 1.45kW heat exchanger was fitted, and the mounted components were separated from the wiring using the Lutze AirSTREAM wiring frame. (shown in figure 1).
Measurements were taken for six hours at a time in each cabinet. The measurements were carried out over two days, with 10 sensors recording the ambient and internal temperatures. In the cabinet using the back plate the temperatures fluctuated between 29 degrees C and 43 degrees C. In the cabinet using AirSTREAM, the temperatures fluctuated between 30 degrees C and 34 degrees C (as shown in figure 2). The test demonstrated that using AirSTREAM can achieve noticeable cooling and a consistent climate inside the control cabinets. This not only protects the components but reduces the amount of energy needed to cool the cabinets.
Visit https://www.luetze.com/en-gb/airstream-climb-c for more information.
An Ishida X-ray inspection system and checkweigher combination has played a key role in enabling one of the UK’s leading contract packing companies to implement a new packaging solution for a major customer.
Universal Flexible Packaging, based in Leicester, UK, is a long-term partner of leading Asian-inspired food brand Itsu. Itsu wanted to reduce the amount of packaging for its premium noodle cup range with a new cup and foil sealed lid. However, this meant quality checks using traditional metal detectors would not be possible, and for a filling and packing system where the majority of the equipment is built of stainless steel, X-ray provided the best solution for both brand and consumer protection.
While X-ray inspection technology delivered effective quality control, the challenge was to keep the lightweight cups upright. With most other X-ray solutions, cups would topple as they pass through the protective curtains to enter the inspection chamber.
Ishida’s solution was to use its entrylevel IX-EN-2463 X-ray inspection system with a lower 50kV voltage and
remove the protective curtains. As the pots enter the chamber an extended guarding provides full protection from the X-ray process without the need for the curtains.
“We have a longstanding working partnership with Ishida, so they were the obvious choice for this particular application,” said Steve Potter, Universal Flexible Packaging’s Engineering Manager.
“As well being able to come up with a suitable solution, the company’s IX-EN X-ray inspection system was very competitively priced.”
The IX-EN is integrated with Ishida’s DACS-G checkweigher, which provides
The installation and integration with the rest of the line was seamless, and both machines have proved very reliable and easy to operate.
a final weight check to ensure that all ingredients in the pot are present. The system incorporates Ishida’s Retail Reject Confirmation (RRC) software that checks and confirms that any outof-spec products or packs have been successfully removed from the packing line, in line with individual UK retailer quality standards and codes of practice. Two reject bins identify packs rejected by either the X-ray or the checkweigher.
“The installation and integration with the rest of the line was seamless, and both machines have proved very reliable and easy to operate,” said Steve Potter.
The Ishida X-ray and checkweigher combination is handling two designs of pot at around 80 packs per minute and is in operation for up to 24 hours a day, five days per week. Importantly for Universal Flexible Packaging, the system has helped to increase efficiencies on the line.
A further benefit of the Ishida IX-EN is its ability to identify other types of foreign bodies, such as glass, ceramics and stones. While it is highly unlikely that such items would be found in the cups, this capability adds a further level of quality assurance to Universal Flexible Packaging’s operations in line with its BRC AA* accreditation.
The latest quality control system joins the existing seven multihead weighers and 15 checkweighers currently in operation across Universal Flexible Packaging’s two factories in Leicester.
“Ishida has been a reliable partner for us for many years,” concluded Steve Potter. “As well as the quality of the equipment, we know that in the event of a problem or the need for a spare part, we will always receive a fast response. It is reassuring to have a large global company that is still able to deliver a personal, localised service for its customers.”
www.ishidaeurope.com/en
Handling an abrasive or viscous liquid is often one of the most demanding applications a pump can experience.
The inability of such fluids to flow well under gravity, suspension of sharp particles which can cut seals or gaskets creating leaks and solid concentrations which can reduce pumping efficiency, often mean that only a handful of pump technologies exist to handle such a requirement.
Whilst often there can be more than one solution for transferring an abrasive or viscous solution, selecting the right pump for the process application can often mean the difference between lowest life time cost, or a lifetime of problems!
A client approached us with an application to transfer ceramic resin from containers to machines. This was a new process and they wanted to ensure any unit supplied could handle sharp solids without experiencing wear or failure as part of a robust manufacturing process.
The customer had various existing pumps on site, but were concerned that when handling the ceramic resin, premature damage may be incurred to the pump or internal parts.
We worked with the customer to obtain an overview of the process and once the specifics of the process were understood we determined that a peristaltic pump which transfers fluids at low speeds via a reinforced natural rubber hose was the correct solution. With a maximum operating speed of only 29 revolutions per minute, it would ensure that ceramic particles would not be given enough energy or velocity to cause damage to either internal parts, pipework or seals.
Peristaltic pumps not only operate at very low speeds, but as they are seal
The pump will transfer ceramic resin which is around 1000cst at up to 800Litres an hour, well within the pumps performance range meeting process requirements.
less there are not prone to leaks when handling abrasive media as is found with other pump designs.
The pump will transfer ceramic resin which is around 1000cst at up to 800Litres an hour, well within the pumps performance range meeting process requirements.
4 Reasons why a Peristaltic Pump was the best solution:
1. Slow pump operation ensured sharp particles were not transferred at high velocities which could damage pipework or the pump.
2. Variations in viscosity means flow rates would not be affected due to its positive displacement design.
3. The Unit can run dry or with higher
concentrations of solids without damage.
4. As the unit is seal less and contains a single wearing part, maintenance can be performed with ease, with very little experience, and only 1 spare part is required – a hose.
Additionally, the pump was supplied with 2 spare reinforced hoses, ensuring should maintenance be required in the future, they are on hand for maximum reliability in a hazardous environment.
If you have a process requiring the pumping of abrasive solid laden fluids, or have aging process equipment that is holding back your plant, contact us on 01773 302 660 or visit www.northridgepumps.com to see how we can help.
Optimise performance with specialist support
Whether you’re dealing with clogging, separation, downtime, or other issueit’s costly. Time wasted troubleshooting and lower production mean missed targets and less profit. A sanitary pump is the solution but choosing the right one feels like stepping into a minefield. You know what you need it to do but with so many options, it’s difficult to know which is best for your process and parameters.
+ Accelerated stator wear
+ Clogging
+ Changes to fluid consistency
+ Clean-in-place and sterilise-in-place hygiene issues
+ Crushing of sensitive products
+ Inconsistency in finished product
+ Inaccurate transfer of flavourings or ingredients
+ Liquid separation
+ Seal wear or failure
EXAMPLE PRODUCTS:
+ Abrasive mixtures
+ Creams, milk & ice cream
+ Edible oils & fats
+ Fish & meat
+ Fruits eg. cooked apples, plums, berries, grapes
We’ve been engineering sanitary pumps for sectors such as distilling, brewing, food manufacturing/processing, and more, for 20+ years. We understand industry-specific processes and know what it takes to optimise performance through better-suited pump design - giving you complete peace of mind.
EXPERT GUIDANCE:
Our expert engineers understand your process and guide you through the options, so you can confidently select the most suitable sanitary pump.
Want to optimise performance sooner? Speak to one of our specialists.
+ Grains & seeds
+ Pastes & purees
+ Syrups, juices & alcohols
+ Vegetables & peelings
+ Waste eg. trimmings, packaging & offcuts
+ Sheer sensitive liquids
+ Solid laden or viscous mixtures
In recent years, the manufacturing industry has undergone a significant transformation, driven in part by advances in high-mix, low-volume (HMLV) manufacturing. This trend has impacted the entire supply chain operation, from procurement to sales. Here, Adnan Khan, business development manager at Beckhoff Automation UK, discusses how manufacturers can leverage technology to manage their supply chain effectively, save on costs, and deliver products to customers on time and in the way they want it.
HMLV manufacturing involves producing a variety of products in small quantities. This approach allows manufacturers to cater to individual customer needs and preferences while minimising inventory costs. However, it also presents significant challenges to supply chain operations. Each product requires unique components, which can make it difficult to manage inventory and track products throughout the process.
To meet the evolving demands of their customers, numerous HMLV manufacturers are embracing increased automation. However, conventional fixed automation products can be excessively costly or lack flexibility. Automation suppliers are now addressing this gap in the market with solutions that provide flexibility, modularity, a small physical footprint, and mobility. This is made possible by onboard software intelligence, more lightweight and responsive hardware, and low-code/no-code applications.
The Beckhoff XTS linear transport system is an instance of such a solution. It is a flexible conveyance technology that
empowers manufacturers to handle diverse product combinations and packaging formats on a single line, without requiring any mechanical changeovers.
The XTS comprises configurable motor modules that are assembled into a continuous track, which can take on various shapes such as circular, rectangular, or complex, curved geometries based on the requirements of the specific application. The movers on the XTS have the ability to operate autonomously, allowing them to accelerate, brake, and adjust their speed independently.
They can also form groups and synchronise with other equipment such as conventional conveyors. Manufacturers can process a larger variety of products without needing to expand their facilities due to the XTS’s configurable track, which conserves floor space and facilitates software-based changeovers.
Manufacturers in the global confectionery industry face numerous trends that can change rapidly, necessitating the production of many different products that require packaging in a wide range of packages and pack sizes.
Cereal bars are a prime example of the diverse range of products in the confectionery industry. They are available
in various flavours and packaging formats such as single-serve portions, variety packs, multi-packs, and family packs, with different numbers of bars in each pouch. The bars themselves can differ in length and width and may require packaging in various box sizes and shapes based on retailers’ needs. To meet these demands, high-speed packaging systems with rapid format changeover capabilities are essential.
Traditionally, supply chains require individual and manual changeovers of movers for each packaging format. However, with the XTS, this can be done at the push of a button through its corresponding software functionality, resulting in significant time savings and improved overall machine efficiency.
The trend of HMLV manufacturing has brought about new challenges and opportunities for manufacturers, particularly in managing their supply chains effectively. However, with the development of innovative automation solutions like the XTS, manufacturers can address these challenges while also providing more customised products and reducing inventory costs.
Linear transport systems allow manufacturers to handle diverse product combinations and packaging formats on a single line, resulting in improved efficiency and time savings. As the manufacturing industry continues to evolve, the adoption of these advanced automation technologies will likely become increasingly essential for manufacturers looking to stay competitive and meet the changing demands of their customers.
Walk round any manufacturing business in the UK and you’ll see constant reminders of safety at work. It’s high on the agenda for all successful companies. At a recent site visit to Smurfitt-Kappa in Norfolk, the attention to safety was tangible in every aspect of our time there, from top to toe PPE; green lights, red lights; clearance to walk in certain areas; the requirement to ‘go the long way round’ to keep us safe; to reminders and updates on information boards, corridors and more.
As the supplier of instant buildings we are invited on site to organisations of all sizes to have meetings, undertake site surveys and make essential checks way before our site teams arrive to even begin the build project. Our approach to health and safety means that not only are we looking after our people but we are also working in tandem with our customers, respecting and reflecting their requirements.
Working with our customers’ health and safety criteria can often mean we need to adapt as, depending on their industry sector, there might be additional things to factor in. We’ve worked airside at airports, within
nuclear power stations, in schools during term time and even at a wind farm in Taiwan. All of these environments have called for additional risk assessments and safety measures as well as integrating any further requests from the customer. There is also the need to risk assess and support all equipment and plant being used on a build. Each piece of kit needs to be checked and supported with paperwork – in close partnership with the qualified (and experienced) operating member of the team, our health and safety standards and all in context at the client site – taking into consideration any additional points to note there.
“It was refreshing to work with a business for whom health and safety was an automatic process - it reinforced my belief that we had chosen a supplier who does things properly”
commented Matt Dakin, Commercial Manager of Universal Fabrications.As Operations Director I am focused on safety around the clock – for every person involved with every project - and on a day-to-day basis in and out of our own premises. We have a very successful initiative that has become part of the Smart-Space culture which we call the ‘No Surprise Rule’. It ensures that the senior management team is made aware of all safety concerns or incidents within 15 minutes of them occurring. It gives us the opportunity to review, investigate and implement improvements, no matter how small, to support our constant journey to zero harm.
Of course Smart-Space has been installing buildings of all types and sizes, in all sorts of conditions and for different uses for well over thirty five years. We have a dedicated safety team, train all staff who work on site, and have a number of industry standard accreditations. Maintaining that reputation and continuing to put our people and customers first means we also ‘go the long way round’ and will always do so.
Visit Smart-Space at smart-space.co.uk or email Sales Director Jason Lynock at jason@smart-space.co.uk
Talk to our friendly, professional, experienced team - we can advise on the best options from a range of solutions. Our British supply chain and directly employed teams means we are quick and reliable. We are also completely flexible: you can hire or purchase (or switch whenever you like) and you can off-hire at any time. We do everything - from building only to turnkey solutions (and everything in between).
Polypropylene (PP) pots incorporating 50% recycled material from Berry Superfos are helping Norway’s largest dairy company TINE achieve its sustainability strategy.
TINE has converted the packaging for two of its Rømme products and one of its sour creams from polystyrene (PS) to PP pots with 50% recycled material, calculated using the mass balance approach, certified by the International Sustainability & Carbon (ISCC PLUS) system.
TINE’s head of sustainability Bjørn Malm said: “At TINE, we want all our packaging to be made of renewable or recycled material by 2025. Our new packaging solution for Rømme and sour cream is an important step towards our goal.”
Rømme is a dairy product best described as a fusion of sour cream and cream, used to create tasty dressings, dips, porridge and other dishes. TINE has introduced the pots using recycled PP (rPP) for its Rømme 300g Lettrømme 17%, 300g Seterrømme 35% and 300g Creme Fraiche 35%. Gradually, rPP will also be phased in on six other products in pots. In the long run, TINE is planning to use rPP for its entire portfolio of products for cooking, in line with the EU’s target for 50% of all plastic packaging to be recycled in 2025, rising to 55% in 2030.
“If we are to reach the EU goals, it is evident that both Norway and all other EU countries must increase material recycling by tens of thousands of tonnes in the years to come,” said Bjørn Malm. “Switching from PS to PP is a good way of contributing to this since a larger share of PP than PS is recycled.
PP is a material with a lower climate footprint than PS because, among other things, it has a lower melting point and is therefore less energy intensive.
Therefore, we are very pleased to have successfully converted to 50% rPP based on the mass balance approach for three of our main products.
“PP is a material with a lower climate footprint than PS because, among other things, it has a lower melting point and is therefore less energy intensive,” he continued. “Add to this the fact that 50% of the PP in our new pots consists of recycled PP (rPP), then we have improved the climate footprint of the pots quite a bit and we save 110 tonnes of virgin fossil plastic material.”
In addition, TINE points out that PP cups
are more robust than PS ones which, in turn, increases user functionality for the customer.
Berry Superfos worked closely with TINE in the development of the new pots. Brand manager for TINE’s cooking assortment Camilla Løken said:
“Our collaboration with Berry Superfos has been very good, well focused and highly valued throughout the project. With a positive and helpful attitude and thanks to its ISCC PLUS certified site in Lidköping, Sweden, Berry Superfos made the conversion in a short time and showed great flexibility related to design deadlines and delivery of packaging on time to our facilities. Berry also followed up on large-scale testing at our productions facilities and has assisted during the test runs. In short, we are very satisfied with our collaboration.”
For more information on Berry’s range of solutions for the dairy industry, visit www.berryglobal.com/en/markets/ food/dairy
Whether you’re building cables as part of your product, or checking cables for your equipment maintenance program, automated testers allow you the convenience of accuracy, speed, traceability and more.
As a specialist supplier of ATE to NASA and the Nobel Prize-Winning Ligo R&D team, we understand the importance of being able to depend on fast, accurate and precise cable testing equipment.
Our CableEye® wiring analyzers are used for countless test applications of products destined for a broad range of sectors. Whether you’re an R&D engineer designing cables, a production worker checking hundreds of cables an hour, or an engineer maintaining robotic machinery, the unique CableEye graphic wiring display tells you what you need to know clearly and immediately. Its signature easy-to-interpret color-coded graphics instantly identifies not only when there is a fault, but what type and where.
Graphically see missing or shorted conductors, miswired cables, reversed diodes,
twisted-pair errors, and backward connectors. Check shorts, opens, miswires, components, leakage-current, and insulation resistance in one step. Know in an instant, exactly which conductor and pins are the issue. Then, print crystal-clear test results with the wiring schematic from your fully traceable test data.
Easily automate your tests to your specifications and, as needed, rapidly identify the wiring of unknown cables.
Testing your cables, wire harness assemblies, and backplanes is only part of the solution. By combining test, fault location, design, documentation, labeling, database storage, and automation in one instrument, your CableEye® test and management system covers all the bases. www.camiresearch.com
Fats, oils and grease (FOG) are an ever-increasing problem, causing almost three quarters of blockages in UK sewer networks. Fog-rich waste from food processing manufacturers, restaurants, fast food establishments and consumers results in a £100m spend by the UK water industry to clear blockages.
FOG blockages, commonly known as ‘Fatbergs’, are gaining increased media coverage. Preventive measures are costly, so education is necessary to change public behaviour in disposing of FOG waste. Initiatives like Unblocktober were launched to raise public awareness and help reduce the amount of fats, oils and greases being put down our drains.
Regulation (Water Industry Act 1991) dictates that FOG must not be discharged into the sewer network and traditionally this is prevented in food establishments with the use of grease traps (Building Regulations 2000 Approved Document H). However, grease traps are highly inefficient, require regular cleaning and are subject to rodent infestation.
Industrial food companies experience similar problems but their impact on the sewer network is more visible and easier to police. FOG recovery and removal has long been a major component of a food manufacturers wastewater treatment plant, but effective removal has not always been achievable and failures can result in breach of environmental permits, fines and even prison.
Smart Storm, a leading UK wastewater company have designed and manufactured an innovative solution to FOG issues. Trade marked as The Greasebuster, it is a highly efficient alternative to traditional methods of removing FOGs from wastewater tanks and systems and removing the need for grease traps and interceptors.
www.smartstormgroup.com
The Greasebuster uses a unique material to attract non-polar liquids such as fats, oils and greases onto a extraction belt whilst rejecting water. The Greasebuster sits in a reception tank, which continuously rotates through the surface collecting up to 99% of FOGS up to 20m3/day. An adjustable paddlewheel breaks up the surface and pulls the FOG onto the belt. Speed control and belt attack angle are also fully adjustable for different FOG types – which are then scraped off the belt and deposited into an IBC or other suitable containers.
John Duffy, Founder and Manging Director of Smart Storm, says “We are firm believers in prevention is better and cheaper than the cure. We observed the remedial work being done to clean up blockages, listened to customers in the food industry and came up with The Greasebuster concept. It has been very well received by food manufacturers, particularly where solid waste is a problem and oil skimmers and interceptors have failed.”.
Image 1 Solid Fatberg fully blocking London Sewer Image 2 Fatberg compositionMettler-Toledo Product Inspection has launched a new software update for its M30 R-Series metal detection systems designed to offer practical improvements that can help boost productivity and make compliance easier. The highly innovative SENSE™ software offers increased metal detection security and performance capabilities at an affordable price and addresses multiple food safety regulations and standards facing manufacturers all over the world.
“This next level in SENSE™ is a huge leap in the metal detection field,” said Rob Stevens, Metal Detection Systems Product Inspection Specialist, MettlerToledo. “By automating the processes further, we can now offer our customers a game-changing way to future-proof their production lines, resulting in less room for human error and more consistent productivity and efficiency.
The digitalisation of data reporting and storing also offers manufacturers the chance to improve their green credentials at a time when increased sustainability is so fundamental. We are looking forward to sharing this new technology with our customers and prospects at Interpack in May.”
Where the upgraded SENSE™ metal detector software really stands out is in the future-proof benefits available to manufacturers and co-packers. The new software enables the M30 R-Series metal detection system to automatically integrate with ProdX™ data management software. This results in streamlined processes, automated reporting of inspection activities and easy data collection in real-time at the touch of a button, plus simplified and paperless data storage and quick retrieval of information. The intelligence
that can be gleaned from the reported information supports full visibility and transparency of the product journey and helps digitalise food safety compliance.
For easy filtering of historic Performance Monitoring Routine (PMR) testing information, SENSE™ software provides PMR Log and Report capabilities and functionality to help improve operational efficiencies. This efficient digital process offers instant retrieval of data which can be used easily to assist with management reporting. It also helps to improve production line efficiency and makes the process far less susceptible to human error.
With an innovative PMR Wizard, the system offers an end to end, structured and guided performance test process, from initiation to reporting, including test due alerts, a guided test
process wizard and test frequency and scheduling.
The software has the ability to set up products using imperial or metric units and the facility to customise the HMI language at an individual user level therefore offering flexibility to manufacturers across the globe.
The smart SENSE™ software also offers a range of automation capabilities. Automatic product set-up allows for high detection sensitivity to detect all types of ferrous and non-ferrous metal contaminants and stainless steel contaminants and, by default, reduce any existing operational challenges. With no operator intervention required, human errors are greatly reduced, helping to ensure increased functionality and improved productivity. This improved automation uses no paper records as
of SENSE™ to gain access to the new features. All new units purchased will automatically have the latest SENSE™ software.
The M30 R-Series is the first product family from Mettler-Toledo built around the leading-edge SENSE™ software technology, bringing new levels of intelligence and innovation to metal detection. Visitors to Interpack 2023 will be able to view and get a live demonstration of the M34R and M33R
which are part of the M30 R-Series product line, on the Mettler-Toledo booth located at A60 in Hall 11 at the Messe Düsseldorf, Germany.
For more information, click here or visit www.mt.com/md-m30-rseries-pr
Where the upgraded SENSE™ metal detector software really stands out is in the future-proof benefits available to manufacturers and copackers.
Looking back to 2021, it was easy to consider compressed air as something of a ‘free’ resource. Energy prices were low and manufacturers generating compressed air for one area of their factory could utilise it in another area for next to zero marginal cost. However, since energy prices began their upwards journey, compressed air is no longer the cheap commodity it once used to be.
In 2022, the British Compressed Air Society (BCAS) conducted research into the extent of compressed air use in UK industry. They found that 70% of UK industry uses compressed air in some form or another and that on average, 30% of a business’s entire energy costs could be attributed to compressed air generation.
Using figures from the (then recent) UK Energy-related products policy study, conducted by ICF in May 2021, they calculated the combined energy usage for the mid-point of all industrial compressor technologies over their lifetime at 11.71 TWh. Based on the current UK average non-domestic electrical unit cost of 12.49p/kWh at the time, the figures were substantialequating to £1.475 billion being spent by UK companies to generate the compressed air their businesses rely on.
Add to this the fact that on average 32.9 per cent of this energy was being wasted through leaks and inefficient practices - equivalent to £485.43 million in wasted electricity spend - and we began to understand the extent of which this presents a problem for UK manufacturing.
Skip forwards to today and the Department of Business, Energy and Industrial Strategy (BEIS) has recently published its figures for UK average nondomestic electricity costs for the final
quarter of 2022. This figure now stands at 24.56p/kWh according to statistics, but it is estimated that many industrial tariffs are now reaching as high as 50.73p/kWh as of January 2023.
If we use the Government’s current published figures as a starting point and adjust the BCAS research for today’s prices, we find that £2.943 billion is being used to generate compressed air in the UK. At a loss rate of 32.9%, that’s almost £1 billon of wasted energy every year in the UK, equivalent to £2.62 million every single day.
This staggering figure may come as a surprise to many of the UK’s manufacturers who have until recently worked on an ‘out of sight, out of mind’ policy when it comes to monitoring exactly what is going on within their compressor houses. It’s with this in mind that industry veterans Thorite recently launched their ‘Behind Closed
Doors’ campaign, urging businesses to gain a better insight into what their compressors are actually doing for them. From scheduled leak testing to automatic shut off valves, datalogging to flow control and monitoring, the options for saving energy are numerous and the results are astonishing.
While energy savings in the past might have been outweighed by the cost of fixing leaks, thanks to the latest energy prices, the return on investment to combat inefficiencies is now months, not years. Not to mention the opportunity to reduce carbon emissions by up to 3.2 tons per year - a consideration that companies can’t help but be aware of.
With all things considered, isn’t it time your company found out what is happening behind closed doors?
Bearings using cylindrical rolling elements, such as IKO’s range of standard needle roller bearings, ensure smooth rotation around the load axis when loaded properly. These bearings are widely used in the rotating parts of production machinery where compactness, high rigidity, and high rotational accuracy are all key requirements.
Alinear rail and carriage system is many a design engineers first choice for transporting a load, and for good reason. It provides a rugged and precise solution that is inherently self-aligning, offers high load handling capabilities, and can operate in some of the most challenging environments. But the temptation to over-engineer a system can add significant cost to a project, while asking a vendor to supply a non-standard arrangement can dramatically lengthen the lead time.
This is where IKO Nippon Thompson’s in-house design and adjustments service becomes invaluable, with the UK team of applications engineers able to suggest design amendments that can reduce lead times from months to days, and/or remove significant cost from a project. Mark Ross, technical sales engineer at the company’s Milton Keynes UK headquarters, says: “There are a wide range of things we can do at local level, from the everyday to the more unusual, to deliver an application-specific solution, providing a key service that can save UK customers time and money.”
our various global locations, and we can tap into that free stock and have it delivered within a couple of days,” says
stroke length, but then bumped up the rail and carriage dimensions to accommodate the required load? Perhaps they’ve even ended up with a design that uses non-standard length carriages.
“By adjusting the rail and carriage dimensions, we can often find a much more cost-effective approach, selecting more appropriate and standard products or better cost products,” he continues. “We can play
Mark.
“From there we have the in-house capabilities to modify standard products to meet specific customer requirements.”
Examples include cutting rail to specific length at the simplest level, or changing the e-dimension –the measure from the end of the rail to the first mounting hole. “As standard, this e-dimension would be half the normal hole pitch, but that might not suit the application,” Mark explains.
A prime example is the company’s ability to assess the key parameters in a project, and look at what can be easily amended without compromising the performance criteria, so that the project can be serviced from the company’s free stock. “For any supplier, manufacturing a system to order is going to take time, but IKO Nippon Thompson will always have standard products available as free stock at
Applications with complex loads can lead to rapid wear and damage of a standard bearing. In this case, IKO’s crossed roller bearing range (CRB) might be a wise choice. This specialised design consists of V-shaped raceway rings holding cylindrical rolling elements with crossed orientations at right angles to each other. Due to the crossed arrangement of the cylindrical rollers, these bearings can support both axial forces and radial forces as well as tilting moment loads and any complex loads by means of a single bearing. As a result, designs involving two ball bearing positions can be reduced to one single bearing.
A number of types are offered, such as slim, super-slim, high rigidity models to be pressed on to a shaft or into a housing, as well as a model with mounting bolts (pictured below), which facilitates easier mounting.
Cylindrical rolling elements, combined with the design of the bearing structure, improve rigidity compared to using ball bearings. According to IKO, its CRB is three to four times more rigid than a double-row angular-contact ball bearing, as well as offering a more compact cross-sectional dimension.
And these bearings are available in many
Such adjustments and amendments can be important time savers for customers, particularly when they are building a prototype as proof of concept. But IKO Nippon Thompson’s design services can also save customers significant amounts of money, for example when it is clear that the design engineer has over-specified the project, perhaps as a belt and braces approach to meeting particular lifespan requirements.
“We can quickly drill down to the customer’s most important considerations and then look at how that impacts on the rail and carriage dimensions,” says Mark. “By talking through load and stroke requirements, that might lead us to propose alternative carriage lengths. For example, has the designer opted for a shorter carriage to increase
sizes. The highest load rating in the catalogue is 2,640kN. IKO has helped with larger applications, such as radar towers on ships, which use the bearings in setting azimuth accuracy.
More than £3.5m of product stock is kept centrally in Milton Keynes, a significant portion of which is freely available for general sale.
“We’re flexible; we get product in and monitor that so it’s always here, or at worst on its way from the factory, so customers can maintain their manufacturing requirements,” says Technical Sales Engineer Mark Ross. All the company asks for is regular communication, so that variations in
with parameters such as preload to see if this provides a better way to meet specific application criteria. Or we can butt together standard rails to deliver longer, non-standard lengths at given profile dimensions without impacting precision.
supply, for example, can be adjusted for.
“In addition, we can add seals and scrapers to protect the rolling elements on some product types, as well as offering different coating options to protect against rust or to alter the products’ aesthetic appearance if that’s a requirement too. The addition of rail caps can also be a further simple (yet cost-effective) way to increase the longevity of the system, and is something which, whilst basic, is often overlooked.”
All of this comes hand in hand with the capability to provide CAD drawings and models, and to port those designs straight into customers’ models.
IKO Nippon Thompson is conscious, too, of the cost of logistics for its customers, and so can supply pre-packaged sets to reduce packaging, handling and stock management. And then there is the company’s on-site training in addition to its telephone and web video support.
And if an urgent stocking need arises unexpectedly, IKO can draw on global stocks. That is just another way in which IKO is helping customers satisfy their production commitments, even for specialised items such as crossed roller bearings.
“It’s all part of a service that means we are much more hands-on with our customers than perhaps other suppliers are willing or able to be,” concludes Mark. “We want to be more involved because it benefits all of us – we get to deliver the most appropriate solution and customers get time- and cost-saving benefits.”
In addition to these crossed roller bearings, IKO manufacture a wide range of other radial, linear, & mechatronic products including cam followers, rail & carriage combinations, crossed roller ways, precision slide units, linear bushings, & ball splines ….. to name but a few
Contact IKO UK today to discuss your motion control needs.
Email: enquiries@iko.co.uk
Tel: 01908 566144
Website: www.ikont.eu/en
We’re flexible; we get product in and monitor that so it’s always here, or at worst on its way from the factory, so customers can maintain their manufacturing requirements
We talk to the experts at IKO Nippon Thompson about how linear rail and carriages can be easily adjusted and modified, and how projects can be redesigned around standard products, to save customers time and money
Engineers and technicians working in the food and drink processing and packaging industries are well aware of the possible consequences of tools going missing. Foreign object damage (FOD) is a threat in any manufacturing or line maintenance workplace, especially those where food or drinks are being produced.
Keeping track of every tool and item of equipment presents a major challenge, making professional tool storage and management more important than ever. Snap-on Industrial’s Level 5™ automated tool management system constantly tracks every tool, advising with voice announcements which tools have been removed or when they are returned, ensuring greater protection against FOD.
It also enables engineers and technicians to find every tool they need quickly, saving time and easing stress.
Major benefits of the system include:
• No individual tool scanning required;
• No RFID tags to install or replace;
• No limitations on tool size: from ¼” screwdriver bit upwards;
• Intuitive interface, via touchscreen;
• Audible voice confirmation of tool removal and replacement;
• Automatic locking for maximum security;
• Errors announced and displayed to indicate incorrect tool position or advise when a drawer is not closed.
Says Richard Packham, Director UK & Europe for Snap-on Industrial: “Snap-on’s automated system takes tool management to an entirely new level. The ability to monitor several boxes from one central computer offers managers a huge time saving advantage.”
For more information visit: www.snapon-industrial.co.uk; call (01536) 413904 or e-mail: industrialuk@snapon.com
Industrial process heating equipment and solutions specialist Babcock Wanson has supplied a new TPC-B Thermal Fluid Heater to Crisp Malt to replace the existing Babcock Wanson heater that has been in operation for an incredible 30 years!
Crisp Malt, a British malting company dating back to 1870, supplies high quality English, Scottish and Organic malts to award-winning breweries and distilleries across the globe. Crisp Malt combines traditional and modern malting techniques at its sites in England and Scotland. An important part of the process is the drying of the malt. At its Fakenham site, a Babcock Wanson Thermal Fluid Heater has been performing this task for the past 30 years. Having well and truly served its purpose, a replacement was required and the company naturally returned to Babcock Wanson. A new TPC 6000B Thermal Fluid Heater was recommended, based on its reliability, high efficiency and large output.
The TPC 6000B is the largest Thermal Fluid Heater in the TPC-B range. These fully automatic coil type, multi-pass heaters come complete with integrated burner, control system and safety devices. They provide optimal distribution of the heat, high fluid velocity in the exchange tubes and continuous flow monitoring to ensure long thermal fluid and system life and the highest level of safety.
The new TPC 6000B Thermal Fluid Heater installed at Crisp Malt
offers several advantages over its elderly predecessor, including improved controls, Human Machine Interface and overall efficiency, plus a considerable reduction in emissions to comply with current regulations.
The TPC 6000B Thermal Fluid Heater was supplied by Babcock Wanson along with new pumps and valves.
Whilst the new heater was being produced, Crisp Malt took advantage of Babcock Wanson’s Thermal Fluid Heating system rental service. Two ‘plug and play’ TPC 2000B Thermal Fluid Heaters were delivered to site and set up by Babcock Wanson’s experienced commissioning engineers to guarantee production.
Following the installation of the new heaters, a full service agreement has also been implemented.
Babcock Wanson offers a complete range of products and services for boiler houses and other process heating needs, from steam boilers, thermal fluid heaters, rapid steam generators and hot water boilers to VOC and odour treatment by thermal oxidation, water treatment or process air heating solutions. The company aims to help optimise customer’s energy production with high quality products and efficient service.
For more information, please contact Babcock Wanson on 020 8953 7111 or info@babcock-wanson.com or go to www.babcock-wanson.com
“It is not the strongest of the species that survives, nor the most intelligent that survives. It is the one that is most adaptable to change.”
Charles Darwin
In our uncertain environment, energy adaptability is key. When it comes to process heating, Babcock Wanson offers more choice and flexibility to achieve your decarbonisation goals, reduce your fuel bill and allow for energy diversification.
Cognex Corporation (NASDAQ: CGNX), a leader in industrial machine vision, has released the In-Sight® 3800 Vision System. Designed for high-speed production lines, In-Sight 3800 offers an extensive vision toolset, powerful imaging capabilities, and flexible software to deliver a fully integrated solution for a wide range of inspection applications.
“The In-Sight 3800 offers twice the processing speeds of previous systems, performing tasks like a quality inspection in as little as one-third of a blink of the eye,” said Lavanya Manohar, Vice President of Vision Products. “This added power allows users to maximize throughput and accommodate faster lines while delivering the high accuracy that they have come to expect from the In-Sight product line.”
This new system is embedded with a comprehensive set of vision tools that includes Artificial Intelligence
(AI)-based edge learning technology and traditional rule-based algorithms. Easy-to-use edge learning tools solve tasks with high variability and are set up in minutes with just a handful of training images. The industry-proven
rule-based tools are well-suited to solve deterministic tasks with specific parameters.
Customers have begun using the In-Sight 3800, with impressive results.
“When we selected Cognex, we were under the assumption that the processing time of the In-Sight 3800 would be 30% faster than the current In-Sight 7900 vision system being used,” said Nicolas Chomel, Technology Development Director at SIDEL, a leading provider of equipment, services and complete solutions for packaging consumer products. “However, during qualification tests, the In-Sight 3800 proved to be 50% faster in our application.”
In-Sight 3800 is powered by In-Sight Vision Suite software, a common platform
across all In-Sight products, which offers both EasyBuilder® and Spreadsheet development environments. The intuitive, point-and-click EasyBuilder interface guides users step-by-step through the development process, making it ideal for simple or common applications, while the robust spreadsheet interface enables finetuning of job parameters for advanced or highly customized applications.
“Flexible development options allow users to easily modify their application for new or changing requirements,” said Manohar. “In doing so, In-Sight 3800 offers a scalable solution for addressing both current, and future, factory automation needs.”
For more information, visit: www.cognex.com/in-sight-3800 or call +44 121 296 5163.
The In-Sight 3800 offers twice the processing speeds of previous systems, performing tasks like a quality inspection in as little as one-third of a blink of the eye.
COVAL offers manufacturers a range of vacuum grippers suitable for handling of parts of various sizes, weights, and materials. This gripper range has been extended with the latest CMS HD series multistage vacuum pumps, developed by COVAL. With this enhancement, the new generation of grippers meets the demands of Industry 4.0 with greater robustness, communication, and modularity.
COVAL’s range of vacuum grippers is based on two complementary solutions. The CVGL is characterized by its lightness and great adaptability. It is available as standard in several lengths, power ratings, and gripping interfaces.
The MVG, on the other hand, offers the possibility of configuring the gripper to allow it to be perfectly adapted to each application by determining the length, width, gripping interface, and vacuum generator while guaranteeing extreme lightness. It offers a tailored solution that integrates perfectly with handling robots.
COVAL’s new generation of vacuum grippers now incorporate the latest CMS HD series of vacuum pumps.
These pumps have a heavy-duty design for high reliability even in harsh environments (IP65), capable of ensuring 50 million cycles. A factor of the pump’s longevity is their modular design which allows specific configurations and targeted maintenance of specific parts to optimize repairability.
As a result, the new generation of CMS HD multistage pumps adds to
the vacuum grippers´ reliability and adaptability.
The new COVAL vacuum grippers offer a choice of three multistage vacuum pump configurations, depending on the needs of the integrator or end user: nonpiloted, piloted, and communicating.
The communicating configuration, which makes the vacuum grippers easier to use and parameterize, is obtained by integrating the CMS HD VX version of the multistage pump.
The VX pump version features an IO-Link communication interface, compliant with the international IEC 61131-9 standard, for fast and cost-effective installation, continuous diagnostics, centralized parameterization, and
efficient communication with higherlevel protocols (EtherNet/IP, PROFINET, EtherCAT, etc.).
It can also support a Human Machine Interface (HMI) with NFC interface, enabling the operator to read and modify setup parameters and diagnostics from a mobile device (Android or iOS) using the dedicated COVAL Vacuum Manager app.
With these pump capabilities, the new generation of COVAL vacuum grippers become even more versatile and perfectly compatible with the robot systems at the heart of Industry 4.0.
Thanks to their great modularity and ease of integration in all contexts, CVGL and MVG vacuum grippers can be found in many industries: packaging, plastic, metal, and wood for handling porous and non-porous objects.
Qualities that make the difference:
• Solutions adapted to each process
• Configurable vacuum grippers
• Robustness, longevity, and economy of use
• Vacuum grippers with communications capability for Industry 4.0
www.coval-international.com
With these pump capabilities, the new generation of COVAL vacuum grippers become even more versatile and perfectly compatible with the robot systems at the heart of Industry 4.0.
When the world’s largest beverage can manufacturer was experiencing regular, unexpected production stoppages due to the premature failure of spray-head bearings in its coating machines, the company turned to the expertise of NSK. Recommending NSK deep groove ball bearings featuring VV series non-contact seals helped the plant to eliminate failures and achieve impressive annual savings of€240,000.
The food and beverage industry is extremely demanding, not least because production line stoppages can prove expensive in all kinds of applications. Manufacturing aluminium cans for soft, isotonic, and alcoholic drinks is no exception, particularly when the company happens to be the world’s largest beverage can manufacturer.
Repeat failures of the spray-head spindle bearings in the factory’s can-coating machines was causing significant disruption to production and costly downtime on a high-volume production
line. The company tasked NSK with resolving the issue.
Expert NSK engineers conducted a full evaluation of the application, including comprehensive bearing and grease analysis. From this activity it was possible to deduce that the bearings were seizing due to the ejection of bearing grease by high-pressure air needed for the process. Inadequate bearing seals were failing to prevent this unwanted effect.
As part of a complete value proposal, NSK recommended the adoption of its deep groove ball bearings with VV series non-
contact seals and C3 internal clearance geometry. Offering high performance in contaminated environments, this innovative configuration seals effectively without increasing either torque or operating temperature. Notably, the noncontact lip design reduces bearing drag, an important advantage where power loss is critical.
The NSK solution resulted in excellent grease retention while still allowing highpressure air flow through the bearing as part of the machine’s operating procedure. Most importantly of all, the can manufacturing plant witnessed a dramatic increase in bearing life: from 7 to 110 days of operation, after which routine maintenance took place.
The customer is benefitting from extended bearing life, alongside increased productivity and reduced maintenance costs, resulting in annual savings of €240,000.
The NSK solution resulted in excellent grease retention while still allowing high-pressure air flow through the bearing as part of the machine’s operating procedure.
Carrying out maintenance and repair work can be challenging when making sure machines are safe. Dold’s solution to this –the SAFEMASTER STS safety switch and key transfer system – has been developed to cope with rough operating conditions in mind and provide an enhanced level of safety for your team.
THE CHALLENGE
When ensuring the machine is safely switched off, depending on the application, an additional safety release signal must first be received by the control panel before access can be granted. This functionality is imperative in order to avoid accidents. These could be caused by, for example, run on movements of the machine or elevated temperatures. Only when criteria are met and the system is safe may the access doors for the cleaning process be opened.
THE DOLD SOLUTION
With SAFEMASTER STS, predefined processes can be enforced for ensuring the safety of personnel before triggering a system restarting, which then makes it safe to enter an area. For plants such as mixers and vessels, this is ensured by forced key transfer. SAFEMASTER STS offers two shutdown
alternatives: Power Interlocking and Control Interlocking. The possibility of mechanically and wirelessly safeguarding entrances and safety doors saves installation cost and increases the availability and ergonomics of the system.
The Safemaster STS difference -
• Highly robust stainless steel design
• Wireless protection
• Modular, expandable system
• For safety applications up to Performance Level e / Category 4
In short - SAFEMASTER STS from Dold combines the advantages of safety switches, guard locks, key transfer and command functions in a single system. The new fibre reinforced polymer (FRP) variant, with its sleek functional design and its ability to be
combined with established stainless steel systems brings a reliable solution to rough environmental conditions.
Going a stage further, Dold have a handheld solution in their SAFEMASTER range to give another layer of security when accessing hazardous areas. While calibrating machines or remedying problems, the wireless enabling switch from the SAFEMASTER W range is the ideal companion for your safety.
It switches off in the event of any dangerous activity in just a fraction of a second, through a lightweight, ultra-compact hand-held transmitter and a radio safety switch with safety-oriented outputs. The signal transmission via radio of up to 800 mtrs and infra-red unit registration ensures that only systems in the field of vision of the hand-held transmitter can be activated.
When it comes to safety, Dold are constantly evolving their range to harness new technologies to assist in improved security and ultimately, safer ways for you to work. For detailed information on the specs and variations available on all these products, head to www.dold.co.uk
Manufacturing and reuse of timber pallets increased significantly according to the most recent survey commissioned by the Timber Packaging & Pallet Confederation (TIMCON) and the research arm of the Forestry Commission, Forest Research.
The UK Wood Pallets & Packaging Market survey showed that UK manufacturers produced an estimated 48.6 million in 2021, up 8.3 per cent from 44.9m the previous year. These manufacturers repaired and sold on for reuse a further 16.2m pallets, up from 15.6m in 2020. Overall, pallet repair was down slightly, at 48.1m, compared with 49m the year before. The annual survey is based on a questionnaire answered by TIMCON members, who manufacture approximately 80 per cent of the 50 million new pallets produced in the UK every year.
Commenting on the figures, TIMCON
President John Dye said: “It is encouraging to see that this report shows a substantial uplift in the number of new pallets manufactured. While there was a small drop in the reported number of pallets inspected and repaired, this number is still similar to the number of new pallets – and I would expect to see it start to rise again in the months ahead, and also be boosted by the formal implementation of the UK Government’s eagerly awaited reuse incentive in 2025.”
Dye added that the manufacturing increase has led to corresponding growth in sawmilling output into the pallet and packaging sector of around 13 per cent, to 1.61m3. He also noted that employment in the pallet and packaging industry had risen to 4,221, a year-on-year increase of 23 per cent.
The report was presented to TIMCON’s general meeting held in Manchester during March, which also heard updates on TIMCON’s work with the UK Government, including the recent consultation on the
reform of existing Packaging Waste Regulations and the new Extended Producer Responsibility (EPR) for Packaging Waste, due to come into force in 2025. As a result of this work, said Dye, Defra announced earlier this year that it was still considering the recycling target for wooden packaging and, rather than setting recycling targets for wooden pallets, it is now considering options for reuse obligations before recycling.
Thomas Hare of environmental consultant Valpak gave a further update on the expected timeline for implementing the EPR for packaging, which he said would significantly increase admin and was expected to generate a £1.7 billion in total annual costs for obligated businesses.
FEFPEB President Rob van Hoesel and General Secretary Fons Ceelaert attended the meeting. Ceelaert gave an overview of the latest developments in European environment-focused legislation as part of the European Green Deal, including the EU Circular Economy Action plan to reduce net greenhouse gas emissions by at least 55 per cent by 2030. He said the wooden pallet and packaging industry was engaging with the review of packaging and packaging waste regulations (PPWR) and that FEFPEB now has an PPWR taskforce to manage the process and highlight the “unique contribution of the sector to a sustainable world.”
Charlie Law, Sustainability Director at
Timber Development UK, presented the timber industry’s Net Zero Roadmap to the meeting. Timber Development UK signed up to the SME Climate Hub Commitment in January 2022, pledging to support its members in halving greenhouse gas emissions before 2030 and achieving netzero emissions by 2050.
Law highlighted that timber related industries in the UK are responsible for around 1.58 million tonnes of territorial CO2 emissions annually, around 0.35 per cent of the country’s total. This, he added was ‘very low compared to other industries’, such as steel (12m t, 2.7 per cent of the total) or concrete (7.3m t, 1.5 per cent of the total). He said that it was essential to measure product flows in every timber industry in order to start reducing carbon emissions, something he added the pallet and packaging sector ‘has a really good handle on’.
The TIMCON meeting heard updates on the organisation’s other work, including its collaboration with the NWPCA in the US, and the Global Wood Packaging Forum and engaging with the UK government on issues such as sourcing workers from overseas and the post-Brexit Windsor Framework.
Dye was among the members of the pallet and packaging sector who said goodbye and thank you to TIMCON Past President Gil Covey, who is retiring from the industry at the end of April, after 33 years. Covey also served as FEFPEB President for more than 10 years before becoming Treasurer of the organisation, and is currently NonExecutive Director of James Jones & Sons (Pallets and Packaging) Ltd.
TIMCON has just relaunched its website at www.timcon.org. The new site includes information on the wooden pallet and packaging business, news and resources for members.
celebrates its 1 billionth 1,000,000,000 daily disposable contact lens made in the UK and sold direct around the world for half the price of competing brands from 20p delivered.
Ondine Biomedical, a Canadian life sciences company, reported that photodisinfection being developed for food processing demonstrated high efficacy against key food-borne pathogens. Results of the proof-of-concept study confirmed 4-5 log (up to 99.999%) elimination of pathogens commonly found on hard surfaces in meat processing facilities, as well as those directly located on fresh-cut chicken, beef, and pork meat.
Bacterial contamination in the meat industry significantly impacts consumers, workers, animals, community well-being, and industry profitability. Consuming meat contaminated with harmful bacteria can cause illness and death, with over 400,000 people globally dying each year from eating contaminated food. This damages public health and leads to loss of consumer confidence in meat products which can significantly impact profitability across the meat industry.
Conducted in collaboration with Chinook Contract Research, the Ondine Biomedical program identified four food-safe photosensitizers –compounds which eliminate pathogens when exposed to a specific wavelength of light. The photosensitizers were screened against the bacterial organisms Salmonella enterica (Salmonella) and MRSA (Methicillin-resistant Staphylococcus aureus), grown and tested as biofilms. Results showed that the photodisinfection process was able to achieve complete elimination of all Salmonella enterica biofilms (>99.999%), and a 99.999% (5-log) reduction of MRSA biofilms in several different food safety models
1 https://www.who.int/news-room/fact-sheets/detail/food-safety 2 >5 log10 CFU (colony forming units) reduction.
www.vanepercy.com
Trayforma BarrPeel by Stora Enso is a new, easy-peeling board material for vacuum skin packs enabling packaging fresh food on recyclable paperboard trays. Trayforma BarrPeel supports brand owners’ sustainability ambitions by reducing plastic to less than 10% of the tray.
Trayforma BarrPeel by Stora Enso is a sustainable barrier-coated paperboard material for pressed trays -- an ideal solution for vacuum packaging cold cuts, single portion meats, fish, and cheese. It consists of 90% renewable wood fibers, keeping plastic usage to a minimum and significantly reducing the packaging’s carbon footprint. Vacuum-sealed skin packaging extends the shelf life of fresh food, thus limiting environmental impact by preventing food waste.
The special surface of Trayforma BarrPeel material allows the overlaying polymer skin film to be easily peeled, providing packagers with an affordable solution that satisfies the increasing consumer demand for sustainable packaging materials.
“With Trayforma BarrPeel, we improve environmental performance on two levels: protecting food to provide a longer shelf life, and reducing the share of fossil-based materials,” says Jaana Keskitalo, Technical Account Manager, Trayforma & Barriers at Stora Enso. “We’re especially proud that we can achieve this while also providing a great user experience. This easily peelable tray material lets consumers enjoy their product with minimal effort.”
Already commercially available, this combination of sustainability performance and high functionality is resonating with manufacturers. We will also be showcasing Trayforma BarrPeel at Interpack, 4-10 May, Messe Düsseldorf, Hall 9, stand B20. Read more about Trayforma products here
With Trayforma BarrPeel, we improve environmental performance on two levels: protecting food to provide a longer shelf life, and reducing the share of fossilbased materials.
The president of the National Farmers’ Union (NFU) has warned that the UK could face a heightened risk of vegetable shortages this year, as the domestic farming sector struggles to adapt to extreme weather and higher costs. While the UK will always need some food imports, the NFU has issued the stark warning that shortages could become more common if the government doesn’t act. Here, David Strain, technical director at integrated automation systems specialist, Technidrive, joins this debate.
As extreme weather events become more common, it’s imperative that we focus on building resilient domestic food supply. At Technidrive, we have long supplied integrated automation solutions to the farming sector. We’ve spoken to farmers directly who have reiterated that they are facing challenges related to cost and production feasibility.
The economics for British growers are even less favourable this year due to ever-increasing energy prices. This has made heating greenhouses more expensive. In response, the NFU has launched a strategy designed to boost UK fruit and vegetable production and minimise future supply chain disruption.
The strategy sets out ten policies to enable long-term growth and ensure the ongoing fresh supply of produce on supermarket shelves. The plan calls for boosting of sustainable energy supplies, an improvement in access to skilled labour, investments in productivity and greater supply chain fairness.
One area that we’d particularly like to see focus on is technological investment to increase productivity in farming. We’re not suggesting that technology should replace governmental change. However, in an already challenging environment, could automation provide that much needed buffer?
One area where automation is certainly making an impact is in combating the labour shortage. Farmers have long reported either high labour costs, or limited access to it altogether.
At Technidrive, we’ve witnessed first-hand how bespoke automation can increase efficiency gains. We worked with propagator firm, John Gabbie & Sons based in County Down, Northern Ireland, to develop an automated cart system.
The firm germinates and grow plants until they are large enough to handle. These plants are then distributed to farmers, who grow and sell them to supermarkets.
John Gabbie & Sons has several greenhouses that are up to half an acre in size and split up into bays. These bays are up to ten metres wide and 16 metres long with walkways for forklifts and tractors.
Before deploying automation, an operator needed to drive a tractor or a forklift along the pathway to move bays of plants through the greenhouses. The plants were then physically carried to the end of the bay to be boxed. As with many traditional farming practices, this process was labour intensive.
The automated cart system designed by Technidrive runs along railings in each walkway, removing the need for manual labour. Not only does this speed up the process, but it also reduces the space needed for each walkway, allowing the company to pack more product in the greenhouse.
While this is just one isolated example, by making technological investment more accessible to agricultural businesses, we can support long-term growth in our domestic food production sector. As extreme weather incidents increase, it’s even more important to make efficiency gains wherever possible. It’s clear that our empty supermarket shelves are only the tip of the iceberg.
For further information about Technidrive’s bespoke automation systems visit the website or talk to a specialist today.
www.technidrive.co.uk
Harnessing the power of artificial intelligence, Minesoft Origin is a patent intelligence solution that empowers today’s pioneers to make their own discoveries at speed and with accuracy, enabling them to focus on developing world-enhancing innovations.
Patent searching, made simple with AI. Get started today at minesoft.com
In a hygiene-sensitive manufacturing environment stainless steel components are true all-rounders: easy cleaning, no adhesion of dirt, germs or detergents, permanent cleanliness. They are also corrosion-resistant, durable, temperatureresistant, low-maintenance, hygienic and economical.
Find these products in our full range with more than 70,000 parts in THE BIG GREEN BOOK 2022