
www.nzmanufacturer.co.nz
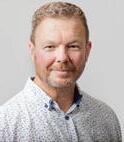
The role of digital skills training in NZ’s manufacturing industry.

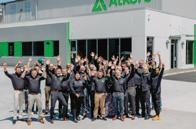
New
factory a game changer.
www.nzmanufacturer.co.nz
The role of digital skills training in NZ’s manufacturing industry.
New
factory a game changer.
The Southland Engineering and Manufacturing Cluster, a pioneering collective dedicated to transforming Southland’s industrial landscape, has identified key themes within the industry, emphasising collaboration and innovation as primary drivers for growth.
Led by Brendan Gray, the Engineering and Manufacturing Cluster is working to transform Southland into a united industrial hub for the engineering and manufacturing sector.
Dean Addie, Chair of the Southland Engineering and Manufacturing Cluster, underscores the importance of collaboration within the industry, stating, “Our core objective is to ensure sustainable growth in engineering and manufacturing throughout the region. By fostering collaboration among industry players, we showcase the incredible capabilities of our region and empower our regions to bid for large engineering and manufacturing contracts with confidence.”
The cluster is an initiative introduced from Just Transitions; a government supported initiative to develop an economic road map for Southland as it navigates the uncertainty of the future of New Zealand Aluminium Smelter.
The Cluster has an important role to support local contracting firms to transition from reliance on NZAS business and participate fully in new economic opportunities, while also supporting existing major industries.
Brendan Gray, Southland Engineering Cluster Manager, expressed his enthusiasm for supporting the engineering
community, saying, “It has been enlightening working with industry, understanding the needs and desires of the engineering and manufacturing community to fully support their transition and growth into a new era of business opportunities.”
The cluster’s recent findings highlight a true desire within the industry to collaborate and work together, coupled with an understanding and acceptance of the need to innovate, pivot, or change to foster growth.
In an exemplar of collaboration, five key players within the Southland engineering community are joining forces to explore new energy opportunities. They will be attending a symposium next week to delve into collaboration potential and opportunities for the region, further solidifying Southland as a beacon of collaborative excellence within the engineering and manufacturing sector.
Gray has been connecting with industry and understanding the needs and pain points for the sector and comments on the key findings, “It’s positive to see genuine desire to work together and grow our sector.
The themes that have emerged are not surprising, but it is positive to see the active participation and widespread understanding that collaboration and innovation is central to our sectors growth.”
3 Versions to choose from. Only buy the tools that you need. Solid Parts Sheetmetal Parts Assemblies
NZ
The leading supplier of the BIGGEST names in Automation
Energy Chain
Flexible Cables
Secure supply of energy and data to moving industrial equipment.
• Large size range
• Vertical travels
• Energy tubes
• Hygienic chains
• Solutions for long travel
• Guide troughs
• Readychain
• Robotic, 3D
• Circular movement
Flexible Conduits
HUGE range of high quality flexible cables
• Control cables
• Single cores
• Data cables
• Sensor/Actuator
• Intrinsically Safe
• VSD/EMC cables
• Halogen Free cables
• High temperature
• Harsh Conditions
• Crane cables
• Profibus cables
• Bus/DeviceNet
• Solar cables
• Instrumentation
• Flat cables
• Curly cords
Connectors
Largest range of flexible conduits for cable protection
• Conduits
• Conduit fittings
• Divisible systems
• Jumbo systems
• Conduit Accessories
• Braided cable protection
• Fire barrier solutions
• Food and beverage
• EMC systems
• Ex, ATEX, IEC EX
Safety
Industrial connectors for many industries
• Rectangular multipole connectors from ILME
• Single pole Powerline connectors from TEN47
• EPIC connectors from Lapp Group
• M23 circular connectors from Hummel
• Circular connectors specifically for the entertainment/stage lighting industry from Socapex
Sensors
Safety engineering solutions from EUCHNER
• Multifunctional Gate Box MGB
• Transponder-coded safety switches
• Electromechanical safety switches
• Magnetically coded safety switches
Sensor technologies for automation
• High-Precision Laser Distance Sensors
• Ultrasonic Sensors
• Inductive Sensors
• Fluid Sensors
Cluster identifies key themes: Collaboration and innovation at the forefront.
EDITORIAL
Technology supports productivity.
BUSINESS NEWS
Innovative approach pays off.
SMART MANUFACTURING
How a data driven approach will achieve operational excellence.
Canterbury plant set to turbocharge pet food manufacturing.
Unleashing manufacturing potential: AspectPL MES transforms SME operations.
3D printed titanium structure shows supernatural strength.
Unlocking Potential: The Role of Digital Skills Training in New Zealand’s Manufacturing Industry.
SUSTAINABILITY
Yes, greenwash matters to manufacturers too!
WOMEN IN BUSINESS
Andrea Broughton, Arotec Diagnostics Ltd.
ANALYSIS
NZ Manufacturing - Connecting for Prosperity.
DEVELOPMENTS
New Hamilton factory a game changer.
ANALYSIS
Clearing the Way: Accelerating Industry 4.0 Adoption through Global Benchmarking.
PRODUCTIVITY
The Productivity Dilemma – don’t wait for the government.
If we’re all so busy, why isn’t anything getting done?
Curing the productivity disease.
WORKSHOP TOOLS
Advanced parting at a 90-degree angle. Servo motors in integration-friendly designs.
Wenglor - Accurate angle measurement in press brakes.
SUPPLY CHAIN
Embracing technology in the manufacturing supply chain.
THE LAST WORD Urban Plus.
Kirk Hope Is Chief Executive of BusinessNZ, New Zealand’s largest business advocacy body He has held a range of senior positions at Westpac and is a barrister and solicitor
Ian Walsh
Ian is a Partner, Argon & Co. NZ, a master black belt improvement specialist and global lean practitioner. He is passionate about improving productivity and helping to create world class New Zealand businesses.
Dr Barbara Nebel
CEO thinkstep-anz Barbara’s passion is to enable organisations to succeed sustainably. She describes her job as a ‘translator’ – translating sustainability into language that businesses can act on.
Lewis oodward
Is Managing Director of Connection Technologies Ltd, Wellington and is passionate about industry supporting NZ based companies, which in turn builds local expertise and knowledge, and provides education and employment for future generations.
Brett O’Riley
EMA chief executive Brett O’Riley has a background in technology and economic development. Brett actually grew up with manufacturing, in the family business, Biggins & Co. He currently holds board roles with Wine Grenade and Dotterel Technologies and is also on the NZ Film Commission board.
Insa Errey
Insa’s career has been in the public and private sectors, leading change management within the energy, decarbonisation, and sustainability space. Insa holds a Chemical and Biomolecular BE (Hons) from Sydney University. She is a member of the Bioenergy Association of NZ and has a strong passion for humanitarian engineering, working with the likes of Engineers Without Boarders Australia.
Insa is a member of Carbon and Energy Professionals NZ, been an ambassador for Engineering NZ's Wonder Project igniting STEM in Kiwi kids and Engineers Australia Women in Engineering, increasing female participation in engineering.
PUBLISHER
Media Hawke’s Bay Ltd, 121 Russell Street North, Hastings, New Zealand 4122.
MANAGING EDITOR
Doug Green
T: +64 6 870 9029
E: publisher@xtra.co.nz
CONTRIBUTORS
Holly Green, EMA, Business East Tamaki, Ian Walsh, Dr. Barbara Nebel, Adam Sharman, Catherine Lye, Jane Finlayson John Luxton, Andrew Bayly, Paul Clark Andrea Broughton, Scott Adams, Rebecca Reed
ADVERTISING
T: + 64 6 870 9029
E: publisher@xtra.co.nz
DESIGN & PRODUCTION
:kim-jean:
E: kim.alves@xtra.co.nz
WEB MASTER
Julian Goodbehere
E: julian@isystems.co.nz
PUBLISHING SERVICES
On-Line Publisher
Media Hawke’s Bay Ltd
DIGITAL SUBSCRIPTIONS
E: publisher@xtra.co.nz Free of Charge.
MEDIA HAWKES BAY LTD
T: +64 6 870 9029
E: publisher@xtra.co.nz
121 Russell Street North, Hastings NZ Manufacturer
ISSN 1179-4992
Vol.15 No.2 March 2024
Copyright: NZ
are necessarily agreed to by the editor or publisher of NZ Manufacturer and, whilst all efforts are made to ensure accuracy, no responsibility will be taken by the publishers for inaccurate information, or for any consequences of reliance on this information. NZ Manufacturer welcomes your contributions which may not necessarily be used because of the philosophy of the publication.
The year is ticking along. Government has finished its 100 - day plan of forty-nine key policy areas (ideas) to deal with and Australia wins the cricket. We need a new VIP plane, the ferries breakdown and the PM can’t live in his Wellington residence (of choice).
So it’s business as usual?
Every area of life in NZ is screaming out for assistance and every day there seems to be another major problem on the horizon. I have an idea: how about some of these ‘problems’ be relegated in the daily news instead of making them headline issues?
But then, of course, what would go on Page 1? Something positive, a non-newspaper seller. How about that?
Changing the pace, Adam Sharman from Dsifer, in his article on Page 21, says that “as organisations look for productivity gains, competitive advantages in agility scalability and sustainability, more and more are looking to technology to support, augment or accelerate their operations.
“A recent report from Westpac identified that, whilst digital tech adoption is growing, New Zealand’s manufacturers have room to adopt these technologies and boost their productivity and the contribution of the manufacturing sector to New Zealand’s GDP.”
It’s a hard road to walk this one, especially when only 20% of business leaders have the tech skills to get ahead. So, let’s support the likes of the EMA, Advanced Manufacturing Aotearoa, proponents of the Digital Manufacturing Challenge, The Smart Manufacturing Showcase and Callaghan Innovation who are all trying to get us up to speed, assist with productivity and get us over the line for a better future ahead.
These organisations will be appearing at EMEX 2024 at the end of May in Auckland and when you visit the show, go see them, have a chat and you might realise the issues that concern you and your company about technology aren’t so difficult after all.
As a nation, we can keep on moving forward George Costanza style: but this doesn’t make much business sense to me!
New FinTech offers an alternative to big bank overdrafts at about half the cost.
New locally-owned FinTech start-up, Taxi, is giving Kiwi businesses access to a new form of funding at half the cost of big bank overdrafts – a gamechanger for small businesses who, on average, experience negative cashflow for four months of the year.
Powered by IRD-approved intermediary Tax Traders,
Taxi utilises smart technology to unlock funding supported by the billions of underutilised pre-paid provisional tax paid by 250,000+ Kiwi businesses.
NZIER Principal Economist Michael Bealing has calculated that the more accessible cash and lower borrowing costs provided by Taxi will have a measurable impact on both individual business productivity and the economy as a whole.
“It’s widely accepted that small-to-medium sized businesses (SMEs) make a significant contribution to the New Zealand economy. On average, SMEs experience negative cashflow for four months a year, which prevents growth and entrepreneurialism.
“Having improved access to funds, and at significantly reduced costs, makes it easier for businesses to smooth out fluctuations in cashflow, invest in productivity improvements, and support innovation. Taxi has the potential to make a tangible difference to individual businesses that could in the long run stimulate the economy as a whole,” says Michael.
Taxi has achieved this by developing software to provide access to key benefits of the New Zealand tax system that have, until now, only been available to large corporates with expert taxation, legal and financial specialists.
For Taxi co-founders Nicola Taylor and Josh Taylor, this has been more than a decade-long journey.
“In our experience at Tax Traders, only a small number of large businesses with significant resources have been accessing funding using New Zealand’s
unique tax framework in this way. We’re a team of accountants and tax experts on a mission to change that and unlock these benefits for all Kiwi businesses.
“We understand how important it is for businesses to have enough capital to grow and the Auckland lockdowns showed us first hand that successful businesses still need access to cash to help ride out the tough times. It was in the lockdown of 2021 that we knew we needed to develop Taxi to help more Kiwi businesses.
“The result is that Taxi currently offers a 7.09% per annum rate on any money borrowed and charges a monthly access fee that is also lower than most bank overdraft fees. Taxi backs SMEs; we understand their world and we’re in their corner. We are here to provide businesses with real options to grow and expand, and access funding with dignity. We built Taxi to provide a meaningful alternative to a big bank overdraft, one that is easy and affordable,” says Nicola Taylor.
NZIER calculations show that savings on overdraft costs alone could easily exceed $50 million annually and that is money that will stay in New Zealand.
For
Nicola Taylor and Josh Taylor, this has been more than a decade-long journey.
On a mission to digitise New Zealand’s supply chain, “Orderlink,” an Auckland based startup, founded by Nar Singh and Braedyn Mackay, is making waves with its innovative approach to streamline communication and data exchange between buyers and suppliers.
With over a decade of experience in the supply chain industry and the support of Callaghan Innovation, Nar Singh and Braedyn Mackay identified a prevalent challenge: the inefficiency and lack of integration in the communication between buyers and suppliers.
Purchase orders, dispatch confirmations, and invoices exchanged as PDFs through emails led to enormous amounts of labour intensive administrative work.
Processes that the duo thought deserved to be automated.
“We found businesses were often dealing with incomplete information, causing delays and hindering decision-making in manufacturing. We were also witnessing high levels of expenditure on urgent airfreight of raw materials. In solving this problem, we have created a centralised source of truth for both medium and large enterprises to manage their inbound supply chains efficiently.
“We want to minimize the risk of production delays, enabling manufacturing sites to meet deadlines consistently and enhance their customer satisfaction while reducing expenditure on urgent airfreight.”Braedyn Mackay, Co-Founder.
To tackle this challenge, Orderlink has introduced a groundbreaking solution by seamlessly integrating buyers’ ERP systems with its platform. This integration enhances the capabilities of ERP (Enterprise Resource Planning) systems, providing features like Smart Order Management, Stakeholder Collaboration, Shipment Tracking, Document Extraction, Receipt Reconciliation, and Invoice automation.
Gain real-time control over your purchase orders with our Smart Order Management dashboard. Receive automated status updates and have all your orders in one centralized platform. Access and store crucial order documents directly on the dashboard enabling effortless order management.
An all-in-one platform facilitating communication among buyers, suppliers, freight forwarders, colleagues, third-party logistics providers (3PLs), and contract manufacturing facilities. Orderlink categorizes collaborators into different roles, such as Admin, Member, and Editor, each with distinct access levels tailored to their responsibilities within the order process.
Experience real-time visibility into your shipments with our advanced tracking capabilities. Unlike traditional methods that focus on vessel and container numbers, our platform takes tracking to the next level. Users can monitor shipments down to the granular level of purchase order items, providing detailed information on quantities and ensuring a comprehensive view of the shipment’s progress.
Utilise an efficient artificial intelligence tool that scans purchase orders, dispatch confirmations, delivery dockets, and invoices in various file formats such as PDF, XML, ePUB, and more. This tool ensures quick extraction of data from email attachments, converting them into digital formats instantly upon arrival in your inbox and presenting the information directly within the Orderlink platform.
Streamline inventory management even when receiving orders at third-party logistics providers or contract manufacturing facilities. With Orderlink’s Receipt Reconciliation feature, you can effortlessly manage incoming orders and their documentation remotely. The platform enables automatic receipt of orders via Orderlink, eliminating the need to sift through emailed files from external parties.
Orderlink’s platform extracts invoice data seamlessly and integrates with your accounts payable system, automating the completion of bills. This approach ensures efficiency and accuracy, significantly reducing the manual effort traditionally required for entering invoice details manually.
With these features Orderlink aims to eliminate all manual interventions, achieve a 99% shipment ETA accuracy, reduce total monthly purchases, and lower air freights costs. They thereby enable their customers to optimize stock levels and achieve healthier cash flows.
“We see Orderlink as the central hub for all things supply chain. What Xero did for accounting we aim to do for supply chain.” Nar Singh, Co-Founder & CEO.
Looking ahead, Orderlink is concentrating on expanding exclusively within the New Zealand market. Firm in their belief that the local market provides substantial opportunities, the team is committed to making it their sole focus.
Grounded in the principle of prioritising users, Orderlink ensures that user satisfaction remains paramount while navigating the expansion within the New Zealand market.
Many Kiwis have good instincts, or just good common sense, for our decision making. We might not be experts in all fields but we’re good enough to get by, and with a bit of focus we can adapt. We are, for example, certainly quite expert at managing rugby games from our couch: what combinations work, how to play against the opposition, and how much the interference of the TMO is destroying the game.
But it would also be generally true that we are not so good with facts and data, where we often have high levels of distrust combined with a generally low level of competency in creating and utilising data.
Whenever my consulting firm, Argon & Co, is asked to help a company to improve operational performance we always ask for data: how many projects and what scale, how many different services and products, how much waste, and how much margin.
Then we ask for more data, and we will keep asking for more data until we have a clear idea of how much work is ahead of us because it usually does not take long before the well of data dries up and this is especially so with operational performance data.
This lack of collecting and utilising data is one of the direct causes of our very low position on the OECD productivity (GDP per hour worked) list.
If I am asked by a manufacturing company what is the best digital solution for them, my response is that the first step is to use digital, or automated, methods to collect and manage operational performance data to pick up process throughput, waste, and speed to deliver.
Though the world of digital is more exciting if it involves automation using Robots or applying artificial intelligence or building digital twin models, anything at this higher level is based on having a good data foundation.
Clearly, a robot is an expensive mistake if it does not improve productivity so we have to have the data to make decisions whether the cost will be outweighed by the benefits.
And, unfortunately, it is not as simple as just hiring a data analyst to perform some magical insight, which only provides temporary benefit. A more certain outcome would be to apply the following approach that Argon & Co have successfully utilised thousands of times across hundreds of companies: IDEX which stands for Integrated Daily Execution, which is based on utilising data holistically.
The physical process at the centre of IDEX for a manufacturing company is the full end-to-end process from sales through to a customer signing receiving the product. Each stage creates data which can be utilised to better inform other stages.
What IDEX illustrates is that data alone is not sufficient for operational excellence. For data driven management to be effective it requires at a minimum, the following four capabilities:
1. Position data at the heart of your daily decision-making with a focus on the small number of key indicators that create a direct link between real-time variation and a business objective.
2. Training and empowerment of your operational performance focused teams to be able to make change based on their knowledge of processes and people.
3. Mentoring of operational managers in this new decision-making methodology which will take practice, and preparedness for mistakes to enable learning.
continued on Page 27
Global pet food brands starved of opportunities to manufacture in New Zealand will soon have access to a new state-of-the-art canning facility.
Built by an experienced team of pet food entrepreneurs, the ultra-modern Canterbury factory will each year make 30 million cans of high-value cat and dog food, adding significantly to an industry generating over $NZ300 million in exports annually.
Set to open next month, the plant established by Riverlands Foods Limited is a first for New Zealand. It will produce exclusively for their clients’ brands, removing a logjam that limited New Zealand as a go-to destination for third-party manufacturing.
While other plants exist, they’re either very small, running at full capacity making their own brands, or in long-term contracts for a small number of large clients, meaning smaller and innovative brands can’t make their pet food in New Zealand.
“Not producing our own brand gives us a real point of difference. All customers are treated equally. It also provides us with flexibility to meet the changing market demands such as different product textures and formulations,” Michael Dance, General Manager of Riverland Foods, says.
New Zealand is known for its high-class ingredients and strong country brand and reputation, leaving pet food companies frustrated they couldn’t make product here.
Dance and colleagues, all veterans of the pet food industry, spied the manufacturing gap in New Zealand, so in 2022 began developing plans for the Hornby facility.
“With global sales of cat and dog food at $US58 billion ($NZ95 billion) predicted to more than double by 2030, there is huge demand for access to modern manufacturing facilities which are both adaptable and innovative,” Dance adds.
“Initial investment in the project exceeds $NZ30 million but further funds are committed for future staged development.”
Alongside Dance, the team driving Riverlands includes Head of Operations Tom Coughlan, Quality Assurance Officer Sarah Morris, and Site Manager Chris Gourlie. Coughlan, Dance and Gourlie are all former managers of New Zealand pet food company Ziwi.
Coughlan, who ran a meat processing business before switching to pet nutrition, is looking forward to providing high-quality cat and dog food made
from the best ingredients in the South Island.
“We chose Christchurch because of its proximity to processing plants and quality raw materials,” Coughlan says, adding that mainly rural Canterbury is a strategic location for New Zealand’s top meat processors.
Dance said that over 95 percent of the plant’s output will be sent overseas, boosting value-added exports and aligning with the coalition government’s aim for New Zealand to become an “export powerhouse” by focusing on an economy that enables wealth creation and maximises added value before exporting.
Petfood manufacturing has been identified by consecutive governments’ reports as a high emerging growth industry within the food and beverage sector[1].
Commissioned by MBIE, the 2021 Coriolis report concluded New Zealand’s pet industry had low production costs, high productivity people and farming systems, and was located close to growth markets in Australia and Asia.
“Riverland Foods is leveraging this growth, working alongside pet food technicians to create new recipes and textures for products while engaging with researchers and nutritionists to ensure all decisions are based on quality data and science,” Dance said. “A key point of difference is our in-house research and development kitchen for testing product concepts cost-effectively and quickly before scaling up to commercial production. “
Another Riverlands’ advantage is its ability to quickly adjust recipes as demand changes for cat food, with various cats preferring different textures such as
mousse, pate or chunky-with-gravy styles.
All of these textures have a different ‘mouth feel’ and for cats that’s really critical, Dance says.
“Because cats can whimsically change whether they like a texture or not, a cat will stop eating one texture in preference to another, forcing the pet food company to stock a range of textures - or they lose a customer.
“Riverlands’ ability to make many different textures gives brand owners the opportunity to hold on to their customers within their brand.”
Dance says Riverlands is attending global trade shows, in discussion with brand owners in North America, Asia and Australia to manufacture their products, and a member of the New Zealand Pet Food Association.
Pet Food Association Executive Director Richard Brake said the addition of world-class production capacity is very welcome.
Pet food exports have quadrupled in less than a decade, increasing from $75 million a year in 2014 to $320 million in 2023.
“Retail-ready petfood exports have been growing very strongly for some time. Growth is at 17.4% into North America and 25.3% into Asia.” Brake says.
“A recent plateau in exports was caused by production capacity constraints and most recently the effects of Cyclone Gabrielle on East Coast manufacturers, but the addition of Riverlands’ factory will further boost New Zealand pet food exports.”
[1] Taking New Zealand Pet Food Exports to a Billion — Coriolis Research
Industry 4.0 refers to the fourth industrial revolution taking place right now. This revolution is driven by the convergence of digital technologies such as the Internet of Things (IoT), robotics, artificial intelligence (AI), augmented and virtual reality, 3D printing and more. Adopting these technologies is enabling manufacturers to enhance their performance, output, monitoring, quality and control on a global scale.
The challenge for New Zealand businesses starting out on their Industry 4.0 journey is knowing when, how and what technologies to adopt to improve efficiency, quality, documentation, business intelligence and sustainability.
This Government initiative enables Kiwi manufacturers to experience Industry 4.0 technologies first-hand via nationwide showcase events, manufacturing site visits, interacting with and learning from industry leaders.
The Smart Factory Showcase is a free, interactive session designed to demystify and break down Industry 4.0 with a world leading NZ example. The session will highlight how incorporating smart technologies improves efficiencies, productivity, connectivity, solves common manufacturing issues and streamlines systems and processes. The Showcase provides an ideal introduction to kick-start or progress your own Industry 4.0 journey.
This event is designed for CEO’s, Digital Technology Managers, Operations Managers, Design Engineers and Managers seeking an in-depth understanding of the latest available technologies for businesses. It is a valuable forum to get buy-in from stakeholders and the events are relevant across all sectors. Teams are encouraged to attend together.
The Smart Factory Showcase highlights Nautech Electronics’ Auckland facility and what the future of advanced manufacturing looks like – You will be inspired, gain powerful insights to enhance your manufacturing agility and be armed with the knowledge to join the Industry 4.0 revolution.
It can really help by providing concrete examples of how you can actually apply this stuff and get value from it, and network with others to find out what they’re doing to implement Industry 4.0
Mitchell Sanson, Engineering Manager, Hansa ProductsFeaturing
The Employers and Manufacturers Association (EMA), with ACC’s support, are working on behalf of the manufacturing sector to develop an industry-led health and safety plan to prevent harm and reduce workplace injuries.
EMA Head of Advanced Manufacturing, Jane Finlayson, says manufacturing has one of New Zealand’s highest rates of workplace injury, with fatality rates that are significantly higher than those is Australia.
“Too many people are being hurt at work.
Manufacturing is one of the country’s largest employers, employing more than 10 percent of New Zealand’s workforce. It is also a large employer of the Māori and Pasifika workforce, both of whom are over-represented in the rate of injury prevalence and workplace fatalities,” says Jane.
“If we want to reduce New Zealand’s high rate of workplace injury, which is estimated to cost the country $4.4 billion every year, then we need to
focus on harm prevention in manufacturing.
“To achieve this, over the next seven months we are doing the exploration work to produce an industry-led Manufacturing HSW Action Plan that provides the next steps for reducing harm and preventing injury, in the manufacturing sector.
“The first phase of this work will see the project team examining the research around what works and engaging with manufacturers, unions, iwi, academics, and other stakeholders across the country to identify the opportunities available and to better understand the experiences and challenges of those working in the sector.
“This work will form the foundation for an evidence-backed action plan of practical interventions and initiatives – including use of new technology, workplace design, workforce development and leadership capability – which can be leveraged to reduce workplace harm in the manufacturing sector.”
with other sectors, to lead, coordinate and deliver the action plan.
“We want all manufacturing workers to go home safe every day. Unfortunately, the rate of workplace injury in the manufacturing sector is among the highest in New Zealand, costing ACC an average of over $50 million every year in acute injury costs,” says Iain.
“We know that we can make a difference by working alongside industry and have seen significant success in partnering with the construction sector to establish Construction Health and Safety New Zealand (CHASNZ), which is raising the standard of health, safety and wellbeing in construction.
“This provides a potential blueprint for the manufacturing sector, which has been consistently identified as a priority sector in addressing workplace harm. We welcome the EMA’s proactive approach to lead the first phase of the project to act as a coordinator bringing the sector together to start this
Callaghan Innovation has announced the expansion of the Industry 4.0 nationwide showcase, with the addition of the LMAC Group as partner.
The LMAC Group has built a new mobile showcase experience focused on digital technologies designed to help New Zealand companies harness
Sean Doherty, Callaghan Innovation Product Manager – Industry 4.0 says, “We are excited to bring a new mobile showcase experience on stream to further demystify what is Industry 4.0, and show New Zealand manufactures that it’s not just about the tech, but how the tech enables greater
Digital transformation is an ongoing process so we can expect to see breakthrough trends continuing to shape society. But how will these trends impact robotics and automation and what can the manufacturing industry expect to see in 2024?
AI is transforming the world of software development, making it cheaper, faster, and more effective. Software is a key component of automation, and with AI, software developers will be able to create more customised and optimised solutions for various tasks and challenges.
If software development has sometimes felt like digging with a shovel, the introduction of AI is like bringing two horses and a plough to the process. However, automation expertise will remain a scarce and valuable resource in the process of AI revolutionsing manufacturing.
It has been interesting and perhaps surprising to see AI changing the lives of office workers before it touches working practices in most factories. The benefits of machine learning will reach more manufacturers in 2024.
After all, the technology is already there – we have many partners developing applications using AI to allow our robots to perform more complex and diverse functions. For example, AI allows robots to have human-like perception, handle variation, move parts precisely, adapt to changing environments, and learn from their own experience.
With time, these capabilities will lead to unprecedented flexibility, quality and reliability in manufacturing.
Developments in robotics software will enable more sharing and reuse
Robotics software is the glue that binds users to their mechanical counterparts - a digital connectivity that transcends physical interaction.
Software developments are enabling a new dimension of collaboration - connecting the people that use robots. 2024 will see software developments leading to new levels of sharing and reusability.
Imagine a world where, instead of reinventing the wheel, we leverage existing software assets— components, interfaces, algorithms—across multiple applications.
It’s a principle that already underpins our UR+ partner ecosystem, streamlining innovation and reducing time-to-market. I can’t wait to see this evolve next year.
The future of manufacturing is intricately linked to IT/ OT integration as data will underpin innovation and efficiency. Research shows that the manufacturing industry has been at the forefront of adopting
cloud-based software services and we are already seeing some customers use these to enhance quality, cost efficiency, and predictability.
That makes me confident that 2024 will see the growth of data-driven logistics and manufacturing systems.
Many still have an outdated view of the cloud merely being a data collector and backup function, as we know if from our private lives. But the real potential and power doesn’t lie in storing data or even in linking machines.
The real transformative leap comes when cloud-based software services connect humans and machines and thus help manufacturers simplify complex processes and make smarter decisions.
The benefits of this digital evolution are significant. Remote access to manufacturing data enables quick responses to issues and continuous automation improvement.
With dynamic systems now essential, trusted cloud technologies offer the latest in security and state-of-the-art services. Industrial Internet of Things (IIOT) companies highlight this progression, promising improved efficiency and reduced downtime through Overall Equipment Effectiveness (OEE) visualization and predictive maintenance.
As we approach 2024, manufacturers stand to gain from these advancements, achieving higher quality, reduced downtime, better predictability, and cost optimization.
This transition is a strategic necessity, supporting the shift towards high-volume, high-mix production, resilient supply chains, competitive data utilization, and sustainability goals.
Earlier this year, Interact Analysis looked at projected growth rates in robot shipments across industries. The stand-out projected growth area? Logistics, where Interact Analysis put the projected CAGR for collaborative robot (cobot) shipments at 46% for 2023-2027. I’m not surprised as the market for non-industrial applications is growing fast.
Like manufacturing, many logistics companies face serious labor shortages while pressure is increasing as a result of globalisation, e-commerce and complex multichannel supply chains.
More logistics, warehouse and distribution centres will turn to automation next year to provide services faster and with greater accuracy.
To take an example - facing the challenge of surging e-commerce demands, one logistics company we worked with revolutionised its fulfilment centre with collaborative robots, resulting in a 500% surge in efficiency and order accuracy.
The automation system, adept at processing thousands of orders daily, particularly excelled during peak periods, like Black Friday, where a robot managed up to 4,400 orders in one day with just a small crew for replenishment.
Robots– and the smart use of data – are poised to revolutionise logistics businesses across the whole value chain from incoming packages to outbound logistics.
The pace of development is robotics remains impressive - I look forward with great anticipation to another exciting year of progress.
Snack bar and wholefood ball manufacturer Tasti Products Limited has chosen Plex, by Rockwell Automation as its new integrated smart manufacturing and business process solution.
Tasti Products will migrate to Plex’s cloud-based solutions, implementing Plex ERP (Enterprise Resource Planning), including Plex’s world-class MES (Manufacturing Execution System), to drive their New Zealand-based operations.
Recognising their legacy ERP system could no longer support an expanding business, Tasti Products searched a smart manufacturing solution that would allow the company to scale in size and improve the speed in which business analytics could be performed. Tasti sought a manufacturing solution that was cloud-based and could offer end-to-end digital transformation.
With the ability to offer world-class food safety and its established presence in the food and beverage industry, Plex will provide Tasti Products with a connected plant floor, digital product tracking capabilities, and real-time data to support the company as it continues to grow and flourish.
As a cloud-based platform, Plex enables future-focussed food and beverage manufacturers like Tasti to achieve real-time integration, high levels of availability and flexibility, cybersecurity, and scalability.
Food and beverage manufacturers can – and often do – use different platforms for monitoring, tracing, and tracking, but with the Plex Smart Manufacturing Platform, all three work in harmony to provide real-time data, which can be used
for genealogy reporting, recalls, audits, and analytical insights.
The Plex implementation marks a new era for Tasti Products, as the Plex Manufacturing Excellence System digitises facility operations and offers much-needed structural support for the company’s exciting and vibrant growth.
In the realm of manufacturing, digital transformation is no longer a luxury exclusive to large enterprises. Today, modern Manufacturing Execution Solutions (MES) like AspectPL are revolutionising operations for SMEs across Australia and New Zealand.
Before the advent of solutions like AspectPL, SME manufacturers faced daunting challenges. Lack of connectivity between shop floor operations and ERP systems led to operational blind spots. Production metrics were elusive, leaving businesses struggling to forecast accurately and plan efficiently.
Manual data collection processes resulted in wasted time and hindered analysis for continuous improvement. Downtime recording was often sporadic and outdated, inhibiting the identification of root causes and impeding lean manufacturing initiatives.
The competitive landscape demanded heightened productivity, yet traditional methods fell short in providing the clarity and real-time insights necessary for success.
AspectPL: Bridging the gap between shop floor and ERP
AspectPL emerges as a game-changer, seamlessly bridging the gap between shop floor operations and ERP systems. Its unique connectivity ensures instant access to critical information for all stakeholders, eliminating the need for physical reconnaissance through production facilities.
Whether deployed via cloud or on-premise, AspectPL offers a simple yet powerful solution that yields remarkable returns on investment.
The efficacy of AspectPL is exemplified by the success story of Alto Hamilton Dairy (part of PACT Group Limited), a prominent dairy packaging manufacturer. By implementing AspectPL, Alto Hamilton achieved an impressive 10% increase in Overall Equipment Effectiveness (OEE) within just 12 months.
This improvement is impressive, as each 1% of OEE improvement can translate into substantial financial gains.
AspectPL empowered Alto Hamilton to measure and optimize OEE, streamline scheduling, control labour and machine utilization, enhance traceability, and ultimately, boost productivity.
The transition from traditional manufacturing processes to AspectPL-enabled operations brought about a paradigm shift. Scheduling became centralised and dynamic, facilitated by live updates and digital interfaces.
Real-time manufacturing data empowered informed decision-making and facilitated a culture of measurement and improvement. Automatic integration between ERP and MES systems ensured seamless data flow, enhancing communication and collaboration across shifts.
AspectPL not only addressed existing challenges but also unearthed opportunities for further optimization, driving continuous improvement initiatives and maximizing plant productivity. www.aspectpt.com
A 3D printed ‘metamaterial’ boasting levels of strength for weight not normally seen in nature or manufacturing could change how we make everything from medical implants to aircraft or rocket parts.
RMIT University researchers created the new metamaterial – a term used to describe an artificial material with unique properties not observed in nature – from common titanium alloy.
But it’s the material’s unique lattice structure design, recently revealed in the journal Advanced Materials, that makes it anything but common: tests show it’s 50% stronger than the next strongest alloy of similar density used in aerospace applications.
Lattice structures made of hollow struts were originally inspired by nature: strong hollow-stemmed plants like the Victoria water lily or the hardy organ pipe coral (Tubipora musica) showed us the way in combining lightness and strength.
However, as RMIT’s Distinguished Professor Ma Qian explains, decades of trying to replicate these hollow ‘cellular structures’ in metals has been frustrated by the common issues of manufacturability and load stress concentrating on the inside areas of the hollow struts, leading to premature failures.
“Ideally, the stress in all complex cellular materials should be evenly spread,” Qian explained.
“However, for most topologies, it is common for less than half of the material to mainly bear the compressive load, while the larger volume of material is structurally insignificant.”
Metal 3D printing provides unprecedented innovative solutions to these issues.
By pushing 3D printing design to its limits, the RMIT team optimized a new type of lattice structure to distribute the stress more evenly, enhancing its strength or structural efficiency.
“We designed a hollow tubular lattice structure that has a thin band running inside it. These two elements
together show strength and lightness never before seen together in nature,” said Qian.
“By effectively merging two complementary lattice structures to evenly distribute stress, we avoid the weak points where stress normally concentrates.”
The team 3D printed this design at RMIT’s Advanced Manufacturing Precinct using a process called laser powder bed fusion, where layers of metal powder are melted into place using a high-powered laser beam.
Testing showed the printed design – a titanium lattice cube – was 50% stronger than cast magnesium alloy WE54, the strongest alloy of similar density used in aerospace applications. The new structure had effectively halved the amount of stress concentrated on the lattice’s infamous weak points.
The double lattice design also means any cracks are deflected along the structure, further enhancing the toughness.
Study lead author and RMIT PhD candidate Jordan Noronha said they could make this structure at the scale of several millimetres or several metres in size using different types of printers.
This printability, along with the strength, biocompatibility, corrosion and heat resistance make it a promising candidate for many applications from medical devices such as bone implants to aircraft or rocket parts.
“Compared with the strongest available cast magnesium alloy currently used in commercial applications requiring high strength and light weight, our titanium metamaterial with a comparable density was shown to be much stronger or less susceptible to permanent shape change under compressive loading, not to mention more feasible to manufacture,” Noronha said.
The team plans to further refine the material for maximum efficiency and explore applications in higher-temperature environments.
While currently resistant to temperatures as high as 350 C, they believe it could be made to withstand temperatures up to 600 C using more heat-resistant titanium alloys, for applications in aerospace or firefighting drones.
As the technology to make this new material is not yet widely available, its adoption by industry might take some time.
“Traditional manufacturing processes are not practical for the fabrication of these intricate metal metamaterials, and not everyone has a laser powder bed fusion machine in their warehouse,” he said. “However, as the technology develops, it will become more accessible and the printing process will become much faster, enabling a larger audience to implement our high-strength multi-topology metamaterials in their components. Importantly, metal 3D printing allows easy net shape fabrication for real applications.”
Technical Director of RMIT’s Advanced Manufacturing Precinct, Distinguished Professor Milan Brandt, said the team welcomed companies wanting to collaborate on the many potential applications. “Our approach is to identify challenges and create opportunities through collaborative design, knowledge exchange, work-based learning, critical problem-solving and translation of research,” he said.
One million ‘Introduction to AI’ scholarships available to Australians
Artificial intelligence (AI) ‘scholarships’ are now on offer to one million Australians, in a bid to increase the nation’s literacy of a technology estimated to be worth $4 trillion to the economy by the early 2030s.
The free ‘Introduction to Artificial Intelligence’ microskill course is provided by the National AI Centre (NAIC), coordinated by Australia’s national science agency – CSIRO, and the Institute of Applied Technology Digital (IATD).
The course will provide a non-technical introduction to AI fundamentals and is designed for people at the beginning their AI literacy journey.
This makes it ideal for workers seeking to upskill, individuals starting their career in AI, and small to medium business owners.
With many small to medium enterprises (SMEs) grappling with the challenge of adopting AI, NAIC Director Stela Solar said the course is the perfect opportunity for business owners to build their AI understanding.
“SMEs make up over 98 per cent of Australia’s economy, and ‘Introduction to AI’ is their opportunity to learn how they can use this revolutionary technology to enhance their operations, services, and market competitiveness,” Ms Solar said.
Council of Small Business Organisations Australia (COSBOA) CEO Luke Achterstraat welcomed the introduction of the course, praising its ability to provide small businesses with the knowledge needed to unlock AI’s vast opportunities.
“Small businesses are a main source of innovation in Australia - they are entrepreneurs who try new ideas, test new products and usually back themselves with their own capital.
“This microskill course will help build confidence and competency for small businesses as they navigate the AI landscape.”
Director of IATD Operations Helen Fremlin said the accessibility of the course will empower Australians nation-wide to advance their AI understanding.
“No programming or computer science background is required for students to enrol, and the virtual nature of this course facilitates an easier path for Australians to upskill in AI, whenever and wherever they choose.”
Available now through IATD, the two-and-a-halfhour course will cover:
• What AI is
• Common AI terminologies
• The challenges and risks of using AI
• Common misconceptions
• Real-world applications of AI
• Australian AI case studies
• Advice from industry experts to start your career in AI
Students will receive a certificate of completion upon finishing the course.
“Unlocking potential: The role of digital skills training in New Zealand’s manufacturing industry”-David O’Connor, Commercial Manager, The Learning Wave
In the rapidly evolving landscape of global industry, the New Zealand manufacturing sector finds itself at a crucial juncture. As technological advancements redefine traditional paradigms, embracing digital transformation – and upskilling the digital capability of the workforce - becomes not merely a choice but an essential strategy for survival and growth.
There has been much written about the significant need for our New Zealand businesses to prioritise investment in digital technologies. This investment isn’t just about staying afloat; it’s about thriving in an increasingly competitive landscape, and we totally agree that this ongoing investment is vital.
Yet, while investing in cutting-edge hardware and software is crucial, it’s only part of the equation. At the core of this transformation lies the workforce – their ability to effectively utilise digital tools will define the sector’s competitiveness and resilience moving forward.
Currently, the New Zealand manufacturing sector is grappling with a significant skills gap in digital capabilities. Our clients continue to affirm this and as more technology is introduced to their business, they are quickly identifying a broader range of workers who lack the digital mindset and digital skills required to operate advanced machinery, analyse data, or collaborate in digital environments.
What is even more surprising is that according to KPMG’s 2023 CEO Outlook report, this gap impedes digital transformation for 78% of Kiwi CEOs, yet less than half are addressing it.
We are seeing a growing interest from manufacturers for training programmes that focus on digital upskilling, and a focus on planning for skills training of their workforce alongside their technology investments. While many of our clients have already identified key work groups that need training, we are hearing from the sector that many are still unsure of where to start, how best to understand their current digital capability, and what training packages are available.
Having worked in the digital upskilling space over the past 7 years with a broad range of manufacturing businesses we know that effective digital skills training isn’t just about learning to use a specific piece of software or a new system; it’s about cultivating a digital mindset. This involves being open to discovery, embracing technology’s potential, and fostering a culture of learning and adaptation. Learning practical skills such as critical thinking and problem-solving supports employees in navigating the complexities of the digital landscape. Contextual skills, focused on workplace systems and devices, ensure adaptability in evolving workplaces.
Not only is the training having a direct impact on digital confidence and digital capability but also enables businesses to increase staff engagement and conversations around ongoing technology transformation and benefits to staff. Feedback from one of our clients who embarked on a digital skills training programme in 2021 shows the real impact prioritising training and the investment in your people. “due to their increased digital skills we have been able to have conversations with them about the systems change coming - these conversations would not have been possible 6 months ago”
Tailored Digital Skills training solutions, such as those developed in collaboration with Make NZ, and LMAC Consulting, and have the support of Hanga-Aro-Rau, and Te Pukenga Competenz are available to the sector and have been developed to enhance digital skills at all levels of a business and empower the workforce to embrace Industry 4.0 solutions confidently.
Autodesk Informed Design is a cloud-based solution that connects design and manufacturing workflows to streamline the building design and construction process.
Informed Design allows architects to work with customisable, pre-defined building products that yield valid results and manufacturers to share their products with design stakeholders.
Informed Design unlocks industrialised construction – the application of manufacturing principles to the built environment – and will help transform the architecture, engineering, construction and operations (AECO) industry.
The AECO industry is facing rising pressure to accommodate growing populations, urbanisation and a global housing crisis. For example, nearly 100,000 new affordable homes need to be built every day to house an estimated three billion people by 2030. Additionally, the industry faces pressure to improve its sustainability; construction is one of the most wasteful industries in the world and it’s responsible for nearly 40 per cent of global CO2 emissions.
“The way the AECO industry works today is not sustainable or scalable. For the industry to keep pace, it needs to build more, faster and more sustainably. The answer is industrialised construction,” said Ryan McMahon, director and general manager, Informed Design at Autodesk.
“Autodesk Informed Design connects design and make from day one and brings industrialised construction workflows to reality. Our solution is unique because it empowers architects to design with certainty and validate their plans in real-time, while product managers and engineers can share accurate manufacturing information with design teams. As a result, projects are completed quicker, with higher quality and generate less waste.”
Informed Design is part of Autodesk’s Design and Make Platform environment, which includes cloud-connected software solutions that unite teams,
data and workflows across entire project lifecycles to deliver better, faster outcomes.
With Informed Design, Autodesk is ushering the AECO industry towards an industrialised setup that embeds sustainability throughout. Informed Design is available globally as a free add-in for two of Autodesk’s industry solutions:
Autodesk Informed Design for Revit allows design professionals to design with known-manufacturable building products for unparalleled certainty and quality. This add-in for Revit 2024 provides improved design quality, increases workload capacities and reduces errors and rework. Capabilities include:
• Template discovery: Explore building product templates to seamlessly incorporate manufacturing-level detail into your design files.
• Customisation: Tailor building products to align with your building’s requirements, enabling compliance with the manufacturers’ specifications.
• Certainty: Confirm design decisions are accurate and manufacturable to reduce project risk and prevent errors.
Autodesk Informed Design for Inventor enables product managers and product engineers to align their manufacturing capabilities with customer requirements. This add-in for Inventor 2024 provides a more streamlined design and manufacturing process. Capabilities include:
• Seamless collaboration: Collaborate with designers by creating parametric models of your building products and confirm that only compliant versions are used.
• Powerful Building Information Modeling (BIM) content creation: Define BIM content to confirm your building products meet project requirements and are compatible with other components and industry standards.
• Streamlined product documentation: Simplify the generation of product documentation at
scale and generate the necessary outputs for fabrication.
Green Canopy NODE, a construction technology company tackling the housing and environmental crises, has been using early access versions of Informed Design for Revit and Inventor to improve its building design and engineering processes:
“Autodesk Informed Design has shown that there’s a way to bring customised details, good aesthetics and quality engineering into a product that can be mass produced,” said Benjamin Hall, senior product manager, Green Canopy NODE.
“Designing with constraints doesn’t curb my creativity – it gives me choices I know will work. And that is good for the planet, the building’s inhabitants and for the building industry.”
International Data Corporation (IDC), the premier global provider of market intelligence, advisory services, and events for the information technology, telecommunications, and consumer technology markets, shared its perspective on the benefits of connecting workflows with Informed Design:
“Through a connected, bidirectional digital thread and sharing of data across the AECO ecosystem of partners, it is easier to optimise supplier performance and deliver quality products and services that complement the overall design of a building,” said Jeffrey Hojlo, Research Vice President, Future of Industry Ecosystems & Energy Insights.
“With Informed Design, Autodesk enables AEC organisations to streamline the connection between asset design and the BIM process.”
New Relic, the all-in-one observability platform for every engineer, has launched, for general availability, New Relic live archives. By storing historical logs alongside other logs and telemetry data within the New Relic Data Platform, live archives allows instant access to historical logs and eliminates the need to rehydrate, reload, re-index, or move data to multiple locations.
It maintains historical logs in an active and enhanced state, which allows engineering teams to instantaneously address regulatory requests, thereby minimising compliance risks. At one-fourth the cost of other long-term log storage solutions, live archives allows engineers to store historical logs for up to seven years, making it one of the most affordable compliance solutions on the market.
IT and engineering teams have historically been faced with limited options for long-term log storage. As a result, teams are left to decide between
Peter Marelas, New Relic Chief Architect, Asia Pacific and Japanhot storage solutions that are easy to use but prohibitively expensive or cold storage solutions that are excessively toilsome and often lead to hidden costs and surprise bills when historical logs need to be moved into an active state.
Most log data is unused until it’s needed and some data is only needed for compliance purposes or pulled for postmortem analysis, However, the need to access data quickly when it is required and in a cost-effective way is in demand, and any solution that offers both is a win for users.
With an industry-wide need for a better way to retain logs to meet regulatory requirements, live archives provides a fast, easily accessible, long-term logs storage solution that helps organisations be better prepared to manage their compliance risks.
Key capabilities and benefits include:
• Access instantly: Query and analyse historical logs instantly – all stored within the New Relic
Data Platform – with the same familiar log management experience as operational logs.
• 1/4th lower costs: Avoid paying for ingress and egress (i.e., moving historical log data in and out of the cloud to analyse), indexing, reformatting, or the need to operate additional logs tools.
• Eliminate toil: Retain historical logs for up to seven years in an active and enriched state and streamline the process to store and access historical logs, removing the need to rehydrate, reload, re-index, manually intervene, or move data to multiple locations or tiers to analyse.
• Setup in 30 seconds: Easily define which logs to store via a simple New Relic Query Language (NRQL) rule, using your current logs to decide what to route to live archives, without needing a new log collector.
‘Greenwashing is a marketing issue. What it’s got to do with manufacturers?’
A lot, actually. Many consumers (wholesale and retail) want to understand the environmental impacts of the products they buy – and every product is manufactured somewhere.
So the claims you make about your products to your customers, or that your customers make about your products to their customers, need to stand up to scrutiny.
Is my claim true? Is it accurate? Is it specific to my product? Can I prove it? Or is it ‘greenwash’ – a vague, meaningless statement that suggests you’re doing more to protect the environment than you are?
In 2021 the International Consumer Protection and Enforcement Network carried out a global sweep of more than 500 websites that promote products and services. More than 40% appeared to be using greenwashing as a marketing tactic.
Scrutiny from consumer organisations and climate activists is growing globally and prosecutions continue to rise. Major retailers including H&M have been forced to backpedal on sustainability claims made about the products they sell.
Your manufacturing business has probably spent years and a lot of money building your reputation and brand. Look after them! Promising an ‘eco’ benefit that you can’t back up can damage both. (Social media is relentless.)
Regulators have greenwash in their sights. The financial penalties are large. Companies convicted of greenwashing face fines of up to $600,000 in Aotearoa New Zealand and more in Australia.
Tip 1: know your numbers
If you want to claim that your product is ‘low-carbon’ or ‘uses less water’, make sure you can back these statements up with data. Start by setting a baseline (where you are now). For example, carry out a Life Cycle Assessment (LCA) to understand your product’s environmental impacts (e.g. the greenhouse gases they emit).
• Minimise compliance response time: Quickly meet regulatory requirements with log queries that are readily available for critical legal discovery and compliance audit requests.
“The breadth and diversity of the Asia Pacific region poses an added challenge for organisations
An LCA measures impacts across every stage of a product’s lifecycle from the raw materials used to make it to its ‘end-of-life’.
Use this data to set targets to reduce your impacts (without increasing others), track your progress, compare your products with competitors’ products – and communicate credibly. No greenwash here!
Council® (FSC®) certification for its tissue products.
Tip 2: tell the truth – the whole truth
Your claims must be truthful, accurate and specific. For example, if you state that your product is ‘made from recycled materials’, make sure you can specify how much of the materials were recycled. If you claim your product is ‘recyclable’, make sure the countries it is sold in have facilities to recycle it. Context matters. Don’t cherry pick what you communicate (‘low-carbon packaging!) to draw attention from the ‘big issues’ (say, a product that contaminates local waterways).
Tip 3: speak your truth clearly
While marketing buzzwords like ‘natural’, ‘eco-friendly’, ‘green’ or ‘sustainable’ trip off the tongue, they’re too vague to be meaningful. (Arsenic is a ‘natural’ product too.) Use language that is simple, clear and precise.
Tools like Environmental Product Declarations (EPDs) will help you communicate clearly and credibly. Manufacturer Red Stag’s EPDs tell the environmental story of its timber products over their life cycles. EPDs use LCA data, meaning they are ‘science-based’.
They are independently verified, publicly available and follow a simple format that your customers can understand. EPDs are often compared with the nutrition labels on food products.
Tip 4: get a third-party certification
Consider a science-based, independent label or certification to help prove your environmental claims. There are many to choose from. Kawerau manufacturer Essity has gained Forest Stewardship
seeking to comply with varying regulations around log retention,” said New Relic Chief Architect, Asia Pacific and Japan Peter Marelas.
“New Relic live archives enables engineering teams to access historical logs promptly to respond to regulatory requests, reducing compliance risks. At a
The Sustainable Business Network has a list of certifications relevant to businesses in New Zealand. If you sell to Australia, check out the Ecolabel Index.
Tip 5: compare with care
If you want to talk about your product being ‘the most sustainable on the market’ or ‘lower carbon’ than competitors’, you must be able to back this up. (There are rules for comparing LCA studies.)
Tip 6: delve into your supply chain
Before you make claims, check your supply chain. Don’t risk your reputation by associating with suppliers who deplete rare resources or practise modern slavery.
Tip 7: help your customers review their supply chains
Your customers may do due diligence on their suppliers too, including your business. Strengthen your relationship by showing them your data and certifications.
Tip 8: speak up!
The fear of being accused of greenwash can lead to ‘greenhush’ (saying too little). For example, some businesses making great strides to reduce their greenhouse gas emissions are unwilling to talk about their work.
If you’re becoming more sustainable and have data to prove it, share the good news! This will help you engage your team, suppliers and customers to make faster progress. You’ll also stand out from your competitors and attract customers and investors who share your values.
www.thinkstep-anz.com
fraction of the cost of other log storage solutions, live archives offers APAC organisations a truly cost-effective compliance solution in an increasingly complex regulatory environment.”
Live archives is now available to users worldwide for US$0.005 GB per month until September 1.
I am Workstream Leader for native Human derived antigens that we purify at Arotec Diagnostics Ltd. I manage a team of 8 alongside two other workstreams (Animal Derived and Recombinant Antigens). We prepare highly purified proteins that our customers use in diagnosing specific autoimmune diseases.
What challenges does the job present to you?
Every protein behaves differently, so it is important to recognise the particularities of each one and be mindful of anything that may cause the protein to become unstable or degrade.
We want the customer to have consistent product, so its important that the quality is maintained throughout the manufacturing process. This is dependant on our source material, the equipment that we use, and the people we employ to carry out the purification process.
How come your interest in the field of antigens?
I have always enjoyed working in fields that focus on health and well-being, and this position allows me indirectly assist with helping people get a diagnosis, which hopefully will lead to a more effective management system for their condition and a better quality of life.
As leader of a team of Production Scientists, at AROTEC Diagnostic’s you must be well organised?
It is critical that we are well organised; we have a Production schedule that is based on manufacturing particular proteins to meet customers needs when they require it; we also need to ensure we have the adequate resources (equipment and staff).
It can be a bit like playing Tetris at times! I find keeping routines helpful both within the workplace and homelife as a way to stay on top of things.
What are developments in this field that you are observing?
And how do they impact society?
With autoimmune disease, autoantibodies are produced by the immune system to one or more of an individual’s own proteins, essentially turning the immune system on itself. Incidences of autoimmune diseases have been steadily increasing for the past several years, due to a range of factors such as the environment, stress, viral challenges; sometimes people suffer for many years before getting a diagnosis.
Autoantibodies can often be detected years before physical symptoms are evident; if we are able to keep our customers well stocked, it ultimately helps to diagnose more people, hopefully sooner.
New diseases are continually being identified, and its important that we keep developing new and useful antigens to reach more people.
International Women’s Day is here. Does it have special meaning for you?
I am encouraged that there is so much more information around the changes that occur during perimenopause and menopause, and that it is not as hidden away as it was for our mothers and grandmothers, the majority of whom suffered through this time of life silently.
Who or what inspires you?
Amanda Palmer – Singer, songwriter, artist – I really admire her creativity, honesty, and her vulnerability. I also love to travel and experience other ways of life; it helps to have an adventure to plan, big or small and have that to look forward to.
Favourite quote?
‘Calm blue ocean’ -Miss Hoover, The Simpsons. This always helps to calm me down when things start to get hectic.
Last book read?
Frida: Style Icon. Frida Kahlo was such a colourful person, and I admire how she used her personal style to express herself. I really enjoy biographies and autobiographies, learning about what drives inspiring people.
If not this field, what other career might have you chosen?
Archaeologist – I was a big fan of Indiana Jones growing up.
Only 14% of all our engineers are women. We want to change that.
It’s no secret that New Zealand’s manufacturing sector is struggling. Sales adjusted for inflation have been in negative territory for a while, while the much-watched PMI suggests that sector very much in the “bust” part of the cycle. And with the economy set to slow further, there are few signs of an imminent turnaround.
Manufacturers have responded by going back to what they know. They’ve cut jobs, cut hours, frozen new hirings and clamped down on overheads. Some have rationalised product lines and canned projects, especially those that don’t deliver immediate benefits. Others have looked at how to retain their best customers, as well as coming up with ways to hold on to critical staff.
These measures mostly represent a short-term fix. They are critical for survival.
But they also ignore a fundamental problem facing the sector and that relates to its vulnerability to changes in the economic cycle. Fixing that is about increasing the resilience of the sector.
There are two areas where manufacturers should focus on. The first is boosting the resilience of their supply chain chains – if they stop working or are significantly disrupted, manufacturers are in big trouble. The second is on operations – an inability to maximise operational efficiencies implies a loss of competitiveness which could prove terminal.
Thankfully, advances in digital technology offer a way forward. That includes state-of-the-art software that allows for better communication, Cloud computing for more efficient data storage, artificial intelligence (AI), and data analytics to help make better decisions, as well as robotics, sensors, and Industry Internet of Things (Iiot) to automate processes.
These technologies are making it possible for manufacturers to see every part of the supply chain, and track products in real time as they progress along the value chain. They allow manufacturers to not only have full visibility of their supplier’s suppliers and their customer’s customers, but also understand the inter-dependencies that exist between them.
But that is just the start. They are also helping manufacturers move away from global procurement models. Customer demands for more responsive services, rising wages in previously low wage economies and volatile freight transport costs
are prompting a move -towards near-, friend and onshoring of productive capacity.
At the same time, leading manufacturers are using digital technology to move from traditional linear supply chains to tech-driven supplier networks that incorporate an ever-larger number of supplier partners. Diversification and building in contingency have become commonplace, evidenced by a shift away from “just-in-time” to “just-in-case” logistics. Predictive analytics now inform how much inventory should be held.
And that’s not just happening overseas. According to a 2023 report by Sense partners, 23% of the nearly 100 New Zealand firms surveyed were preparing for shocks by diversifying their supply base, while 14% were in the process of onshoring and near-shoring.
The changes don’t stop there. Class leading manufacturers are also deploying digital technologies to make their supply chains smarter and faster. Automation, driven by AI, robotics, Iiot and sensor technology are transforming supply chains, with 45% predicted to be autonomous by 2035.
These same technologies are also changing how these manufacturers produce things. The move is away from machine-based assembly lines towards smart factories that rely on digital technologies to automate the production process.
What counts here is how these technologies work together to reduce costs, improve quality, minimise negative externalities such as carbon emissions and waste, and increase the responsiveness of productive capacity to changing customer demands.
These shifts are already underway. Smart factories are increasingly common in the US and Aisa Pacific regions. Europe follows some way behind. According to Callaghan Innovation, New Zealand lags at least a decade behind Europe.
That’s not to say that manufacturers in New Zealand are not investing in digital technologies. The larger ones are, although this tends to be more about achieving greater efficiencies from existing operating setups rather than using digital technologies to transform how they operate. Very few firms in New Zealand have gone that far.
Indeed, the reality is that the majority of the 23,000 firms that call the manufacturing sector home, are reluctant adopters of digital technology. That reluctance is clearly reflected in the Stats NZ
Business Operations survey, which shows that New Zealand’s manufacturers are using increasingly older equipment.
They are not just lagging their international peers in this regard; they are also falling behind other sectors in the New Zealand economy.
There are many reasons for this. Finance is one, especially for smaller cashflow dependent firms. It’s not just the cost of machinery that needs to be considered, but also the cost of lost output between its commissioning and putting it into production. Adopting new technologies is also disruptive, especially if it involves a new operating model.
A lack of wherewithal is another factor, with digital skills and competencies always in short supply. Other manufacturers just cling to the tried and trusted. That’s especially so for independent family-owned manufacturing operations.
Addressing these issues is key if the sector wants to build resilience and position itself for the upturn that will inevitably come.
To achieve that manufacturers should be looking to educate themselves about the benefits and opportunities that new digital technologies and smart factories can deliver. They should also be getting an assessment of their digital readiness –these form the basis for transformation plans that close the gap to best practice.
The final step is to put these plans into action. That will require investment, not just in digital infrastructure and machinery, but also in the workforce, which will have to come to terms with operating in an increasingly automated environment.
We hope many manufacturers will make the transition to a digital future, although it’s likely that some won’t. Over time, these firms will lose competitiveness to manufacturers that have managed to transition.
They will either fall to the wayside or be consumed by others looking to add competencies, skills, and capabilities to their existing repertoires.
What do the Waterview Tunnel, City Rail Link, Auckland Harbour Bridge and the Christchurch Convention Centre all have in common? Their building service supports are constructed and seismically braced using the world’s most flexible, all-purpose metal framing system.
The manufacturer, Atkore Unistrut, opened a new state-of-the-art factory and distribution centre in Hamilton last week which will increase production capability and enable the design and manufacture of bespoke engineered solutions.
The opening also coincides with the company’s 100-year anniversary.
David Hardy, New Zealand General Manager, says the double milestone highlights the huge success the modular framing system has had in the construction industry over the last 100 years.
“Atkore Unistrut’s Strut System eliminates the need for welding and drilling. It is easily adjustable and reusable and is the industry standard to support heating, ventilation and air conditioning systems,
cable containment, pipework and create seismic bracing systems,” explains Hardy. “There’s a little bit of Unistrut in every industrial and commercial building in New Zealand.”
“The new manufacturing and distribution facility will increase our capacity to serve the construction market across New Zealand allowing us to undertake larger and more complex projects within quicker time frames. This includes our ability not just to supply but to install our product as well. We have a dedicated construction team that supports contractors nationwide.”
The new $20million, 6000 square metre site at Horotiu, 13 kilometres north of Hamilton city centre, joins existing sales offices in Auckland, Wellington and Christchurch.
As well as the increased floor space to house additional machinery, including a $400,000 laser cutter, the new facility allows for the provision of prefab support frames and modular assembly for building services. With an inhouse mechanical engineer, Atkore Unistrut can also offer a portfolio of services, especially with seismic engineering.
“Even though Unistrut products are fundamentally used in industrial applications, in recent years, the trend for retail and cafes to have an industrial look with exposed services, Unistrut has played into that, providing not just a functional solution but offering an architectural style,” says Hardy.
“As the market leader in cable containment we manage the entire product lifecycle, from product design to manufacture and installation.”
With the company’s heritage founded in the United States, architect, Charles Attwood, came up with the ingenious concept, in the 1920s. He created a channel support system with curved pyramid edges followed by a spring nut with serrated slots. This resulted in a complete box section support that could be built into a frame support. The tightening up of these nuts would then allow more framing to be added to the original support, with the absolute certainty that the strut could not lose its shape.
From this original idea, it could be calculated what weight each section could support and if further support was required. No drilling was required, just the addition of more spring nuts and further lengths of Unistrut channel supports.
This has proven to be an absolute game changer for the construction industry.
Having contributed to many of the country’s largest construction and infrastructure jobs, Atkore Unistrut is looking forward to its latest project – providing cabling containment and infrastructure components for the long-awaited Te Kaha Christchurch sports stadium. Product for the stadium and the new Dunedin Hospital will be among the first to be manufactured at the new Hamilton site.
Atkore is a global leader in electrical, safety and infrastructure solutions which are used to power and protect the world, including electrical conduit and fittings, cable and cable management systems, infrastructure products, and safety and security products. The company acquired Unistrut in 1995.
Looking for a marketing edge?
As organisations look for productivity gains, competitive advantages in agility scalability and sustainability, more and more are looking to technology to support, augment or accelerate their operations.
A recent report from Westpac identified that, whilst digital tech adoption is growing, New Zealand’s manufacturers have room to adopt these technologies and boost their productivity and the contribution of the manufacturing sector to New Zealand’s GDP.
Through our work with manufactures in New Zealand and the UK, it is clear that, whilst most organisations understand the value and the imperative of digitisation, the roadmap to achieve it can be overwhelming.
A quick Google search can pull up examples like Ocado’s lights-out warehouses and it can be a seemingly impossible task to achieve that level of digitisation Most companies both globally and locally are grappling with the concept of Industry 4.0 and the value it could bring for them.
For these companies, questions such as What is Industry 4.0, and how can it benefit my company?
Where should I start? What are my gaps today and where are the opportunities tomorrow? remain unanswered.
To help organisations start to unpick these questions, there are tools to help cut through the complexity and develop an industry 4.0 transformation plan that is specific to their business. In this article we will provide an overview of a tool that is gaining traction around the world. The Smart Industry Readiness Index (SIRI).
The Smart Industry Readiness Index (SIRI) Framework and an accompanying Assessment Matrix tool were therefore developed to help organisations assess their readiness and prioritise the highest impact interventions in industry 4.0 adoption.
The SIRI Framework covers the 3 core building blocks (Process, Technology, and Organisation) critical to achieving future-ready facilities, and the Assessment Matrix tool is designed to strike a balance between technical rigour and practical applicability.
The Assessment Matrix also defines the end states and the intermediate steps needed for continual improvement. Collectively, the SIRI Framework and Assessment Matrix tool aim to equip companies with practical knowledge about:
What Industry 4.0 is and the tangible benefits it could yield; The maturity levels of their organisations and facilities; and How they can improve in a targeted and incremental manner.
Today, SIRI has been adopted internationally by both multinational corporations and SMEs, with thousands of manufacturing companies across more than 30 different countries having completed the Official SIRI Assessment (OSA).
In 2020, the World Economic Forum announced a proposal to accelerate the adoption of SIRI as the international standard for Industry 4.0 benchmarking and transformation.
The SIRI Framework consists of three layers. The topmost layer is made up of the three fundamental building blocks of Industry 4.0: Process, Technology, and Organisation. Underpinning the building blocks are eight pillars, which represent critical aspects that companies must focus on to become future-ready organisations.
The third and final layer comprises 16 dimensions that companies should reference when evaluating the current maturity levels of their facilities. Organisations are assessed against each of the 16 SIRI dimensions by a certified SIRI assessor who works with organisations to build awareness about Industry 4.0 and collaboratively engage teams to understand and evaluate the organisation.
During the engagement, an expert in digital transformation within manufacturing spends
2-3 days with the organisation to:
1. Build awareness, understanding and alignment across the team on the latest Industry 4.0 and Advanced Manufacturing concepts
2. Assess the organisation’s readiness for Digital Transformation and identify quick wins
3. Benchmark the business globally and at an industry specific level, helping the organisation to understand how they can best compete.
4. Create a high-level Technology roadmap, built around proven change management practices to show the practical next steps for the business to take
New Zealand has adopted the SIRI assessment as a tool to support our manufacturing industry drive innovation and productivity through Industry 4. Through Callaghan Innovation, 200 manufacturers can access a free SIRI assessment with a certified assessor.
Organisations with under 150 employees can apply for this free assessment through Callaghan Innovation at Smart Factory Assessment: Industry 4.0 | Callaghan Innovation. Organisations with more 150 employees can also access the SIRI assessment by approach an assessment partner directly.
New Zealand business have been slower to take up Industry 4.0 opportunities and risk finding themselves at a growing competitive disadvantage as they could be consumed by more tech savvy competitors.
Tools like the Smart Industry Readiness Index provide the starting point and the roadmap support our businesses accelerate their productivity and stay ahead of the competition.
Engineers have seen average salary increases of 7.8% over the past year to $124,000, as shown by the latest remuneration survey from Engineering New Zealand Te Ao Rangahau.
Chief Executive Dr Richard Templer says the 2023 results show the profession has grown on the previous year but there are “real challenges” faced by the industry. He says uncertainties surrounding government projects are negatively impacting the profession.
“We are aware of firms having to reduce staff numbers because of the cancellation or delay of projects. We need central and local government to rapidly agree on priorities and recommence work on these important projects,” he says.
In the longer term, Aotearoa needs about 2,500 new engineers every year to keep up with growth, but Engineering New Zealand estimates domestic
tertiary institutions are currently only graduating about 2,000 engineers annually.
Templer says immigration can help but not solve the problem. “We operate in a globally competitive market. There’s a global shortfall of engineers, and a greater long-term demand for engineers here in Aotearoa than supplementary immigration can provide,” he says.
The usual pathway into engineering requires a foundation in science and maths. But over the last decade, the number of students challenging NCEA in chemistry, physics and maths has declined by up to 25%.
Templer says it’s time for New Zealand to “unlock opportunities in the education system to grow the pool of engineers”, and that Engineering New Zealand and industry organisations have written to the Minister for Education to express their shared
concern and desire to partner with government to find solutions.
He says Engineering New Zealand’s programme the Wonder Project – which helps inspire students to pursue careers in science, technology, engineering and maths – recently lost its long-standing government funding.
“Engineers are needed to help solve some of society’s most pressing issues like mitigating and adapting to climate change, ensuring we have clean water and a safe and resilient built environment – as well as endless possibilities at the frontier of digital engineering, food production, healthcare, and space exploration,” says Templer.
“Our latest remuneration survey confirms prospects are bright for young people choosing a career in engineering,” he says.
In his maiden speech last year, the Prime Minister stated that New Zealand “for the last thirty years has been suffering from a productivity disease”.
As the inaugural Minister for Manufacturing, I have been uniquely put in the role to help administer the cure, and some may even say a doctor to help treat this unproductive ailment!
The treatment began this year when I met for the first time with my ministerial Manufacturing Productivity Advisory Group which I have established to assist me with liaising with this sector. The group comprises around forty business leaders from across the manufacturing sector, covering a wide range of businesses and manufacturing specialities from Northland to Southland.
The meeting was convened in Auckland to address some of the root causes of our manufacturing productivity challenges and explore avenues for improvement.
What I have asked of the group is not to advise yet again another manufacturing plan, but rather to identify some high-impact but easy-to-implement initiatives that I can readily action.
The intent is that once I have completed that, we will reconvene and identify the next set of three to five initiatives.
The reason for this tactical approach is that there has been too much talking and planning and not enough achieving meaningful outcomes. In other words, too much hui, not enough do-ey.
Automation technologies, smart manufacturing, advanced manufacturing – all these are critical, now more than ever, for us to meet our nation’s manufacturing needs. And by using these, we can support our other vitally important sectors: energy,
agriculture, health, biotech, the list goes on.
Investment is vital. A stark reality revealed by recent reviews of the sector show the subpar state of our manufacturing equipment. Only 35 per cent of manufacturers have up-to-date core equipment, positioning manufacturing at the bottom rung among all industries nationwide.
It’s a glaring issue that will require concerted efforts to modernise and upgrade our infrastructure.
Innovation within the industry will serve multiple purposes. Firstly, it will shatter preconceived notions about what manufacturing really is. Gone are the days of manufacturing being an antiquated, polluting process. We are currently at the beginning of the Fourth Industrial Revolution, Industry 4.0, and need to utilise all the opportunities available to us from it.
Manufacturing can and should be a high-tech, efficient, eco-friendly sector at the forefront of our economy.
Innovation will begin to address the perceptions of what it means to work in manufacturing. We need to rebrand the industry as vibrant and forward-thinking, which will help attract top talent and investment to fuel industry growth.
We have not invested enough into skills, research and development, and innovative technologies at even nearly the same rate as other OECD partners across the world.
Support for investment and skill development must be pursued in tandem. From current practice we know that one won’t work without the other; that
talent is required to help kickstart the introduction of digital technologies for businesses. We need to be creating these positions and opportunities now. Higher-wage, higher-growth economies are going to be what underpins Kiwis’ futures.
Ultimately, we want our labour productivity to rise. New Zealand hasn’t seen an increase in capital intensity for over a decade, and this must change. We need initiatives to support young people into training; we need to simplify industrial relations legislation to cut red tape and encourage more hires; and open up our immigration settings.
Streamlined R&D processes would go a long way to encourage further technological uptake.
Collaboration and partnership are key to addressing these challenges. My Manufacturing Productivity Advisory Group will continue to be an important forum for business leaders to come together, share insights and address challenges, charting a course towards a brighter future for New Zealand’s manufacturing sector.
Right here, right now New Zealand SME owners are well-positioned to boost productivity within their own operations, even amidst broader societal or governmental challenges in addressing productivity issues.
This capacity for internal transformation is critical for driving business growth and setting a benchmark for productivity improvement.
Embracing digital transformation is a key strategy for SMEs. By integrating technology into daily operations, such as project management tools, CRM systems, and cloud-based accounting software, businesses can streamline processes, reduce manual tasks, and free up time for strategic development. Additionally, leveraging digital marketing can significantly enhance visibility and customer engagement.
Investing in employee engagement and skill development is another avenue for boosting productivity. Cultivating a culture that values continuous learning and improvement, through
training opportunities and mentorship programs, can increase team motivation and efficiency. When employees feel valued and are equipped with necessary skills, their contribution to business success is amplified.
Process optimisation is essential for eliminating inefficiencies and reducing waste. Adopting continuous improvement principles to focus on maximising customer value while minimising non-essential activities can help SMEs stay competitive and agile.
Focusing on customer needs and maintaining a dialogue through feedback mechanisms can lead to improved service or product offerings and higher satisfaction rates.
This customer-centric approach can provide valuable
insights for innovation and business development. Lastly, fostering a culture of innovation encourages the exploration of new ideas, diversification of product lines, and sustainable business practices.
Being open to change and willing to take calculated risks can uncover new growth opportunities and productivity enhancements.
By leveraging technology, valuing their teams, optimising processes, focusing on customers, and embracing innovation, SME owners in New Zealand can significantly increase their businesses’ productivity, serving as exemplars of internal initiative in productivity improvement.
Waiting for the government to “do something” is called hope and hope is not a strategy.
Have you ever asked why it’s so difficult to get things done in business today—despite seemingly endless meetings and emails? Why it takes so long to make decisions—and even then not necessarily the right ones?
You’re not the first to think there must be a better way. Many organisations address these problems by redesigning boxes and lines: who does what and who reports to whom.
This exercise tends to focus almost obsessively on vertical command relationships and rarely solves for what, in our experience, is the underlying disease: the poor design and execution of collaborative interactions.
In our efforts to connect across our organisations, we’re drowning in real-time virtual interaction technology, from Zoom to Slack to Teams, plus group texting, WeChat, WhatsApp, and everything in between. There’s seemingly no excuse to not collaborate.
The problem? Interacting is easier than ever, but true, productive, value-creating collaboration is not. And what’s more, where engagement is occurring, its quality is deteriorating. This wastes valuable resources, because every minute spent on a low-value interaction eats into time that could be used for important, creative, and powerful activities.
• Decision making, including complex or uncertain decisions (for example, investment decisions) and cross-cutting routine decisions (such as quarterly business reviews)
• Creative solutions and coordination, including innovation sessions (for example, developing new products) and routine working sessions (such as daily check-ins)
• Information sharing, including one-way communication (video, for instance) and two-way communication (such as town halls with Q&As)
When you’re told you’re “responsible” for a decision, does that mean you get to decide? What if you’re told you’re “accountable”? Do you cast the deciding vote, or does the person responsible? What about those who must be “consulted”?
Sometimes we are told input will be reflected in the final answer—can a decision be vetoed if input is not fully considered?
It’s no wonder one of the key factors for fast, high-quality decisions is to clarify exactly who makes them. Consider a success story at a renewable-energy company. To foster accountability and transparency, the company developed a 30-minute “role card” conversation for managers to have with their direct reports.
As part of this conversation, managers explicitly laid out the decision rights and accountability metrics for each direct report.
The result? Role clarity enabled easier navigation for employees, sped up decision making, and resulted in decisions that were much more customer focused.
Routine working sessions are fairly straightforward. What many organisations struggle with is finding innovative ways to identify and drive toward solutions. How often do you tell your teams what to do versus empowering them to come up with solutions?
While they may solve the immediate need to “get stuff done,” bureaucracies and micromanagement are a recipe for disaster.
They slow down the organisational response to the market and customers, prevent leaders from focusing on strategic priorities, and harm employee engagement.
Take Haier. The Chinese appliance maker divided itself into more than 4,000 microenterprises with ten to 15 employees each, organised in an open ecosystem of users, inventors, and partners (see sidebar.
This shift turned employees into energetic entrepreneurs who were directly accountable for customers. Haier’s microenterprises are free to form and evolve with little central direction, but they share the same approach to target setting, internal contracting, and cross-unit coordination.
Empowering employees to drive innovative solutions has taken the company from innovation-phobic to entrepreneurial at scale.
Since 2015, revenue from Haier Smart Home, the company’s listed home-appliance business, has grown by more than 18 percent a year,
topping 209 billion renminbi ($32 billion) in 2020. The company has also made a string of acquisitions, including the 2016 purchase of GE Appliances, with new ventures creating more than $2 billion in market value.
Successful empowerment, counterintuitively, doesn’t mean leaving employees alone. Empowerment requires leaders to give employees both the tools and the right level of guidance and involvement. Leaders should play what we call the coach role: coaches don’t tell people what to do but instead provide guidance and guardrails and ensure accountability, while stepping back and allowing others to come up with solutions.
Haier was able to use a variety of tools—including objectives and key results (OKRs) and common problem statements—to foster an agile way of working across the enterprise that focuses innovative organizational energy on the most important topics. Not all companies can do this, and some will never be ready for enterprise agility. But every organisation can take steps to improve the speed and quality of decisions made by empowered individuals.
TechRentals® is an IANZ endorsed Calibration Laboratory
We offer both IANZ Endorsed and Traceable Calibrations of test and measurement equipment inluding:
Danfoss Power Solutions, a leading global supplier of mobile and industrial hydraulics as well as electric powertrain systems, has partnered with Australian crane manufacturer Franna to improve the performance of its MAC 25 crane.
With the PVG 48 proportional valve at the heart of the work and steering subsystems, Danfoss is delivering a reliable, precise, future-proof solution.
Franna, a Terex brand, is a leading manufacturer of pick and carry cranes with a rich heritage of design and engineering excellence.
For more than 40 years, Franna has been a leader in the Australian market, and today its products are at work in more than 30 countries across the globe.
Franna’s MAC 25 mobile articulated crane features a maximum lifting capacity of 25 tonnes (27 tons) and a maximum boom length of 18.4 meters (60 feet). The crane offers maximum safety, excellent roadability, intuitive operation, and unmatched versatility.
True to the company’s heritage, the crane’s design has been tested, proven, and continuously improved over the years.
In 2021, Franna began looking at other options for the MAC 25 crane’s main control valve. The company required a solution that was precise, reliable, and future proof to accommodate increasingly sophisticated electronic control systems.
The Danfoss PVG 48 proportional valve, then in development, emerged as the superior solution.
PVG 48 is a pre-compensated proportional control valve for applications requiring flow rates of up to 180 liters per minute (47.6 gallons per minute).
The latest member of the PVG load-sensing valve family, PVG 48 is ideal for machines such as wheel loaders, aerial lifts, and cranes in which precise flow and controllability are essential.
Danfoss launched the PVG 48 valve to the general market in June 2023 with Franna as a key pilot customer. On the MAC 25, the valve turns operator joystick inputs into quick, accurate boom movement.
The PVG 48 valve integrates easily with electric actuators, sensors, and digital controls, opening a range of possibilities. One of them is to automate certain machine functions so the crane assists – or even takes over from – the operator. Such a function
can be advantageous in many situations, particularly when instant reaction is required to ensure safety. With the change to PVG 48, Franna also switched to Danfoss counterbalance valves. Together with PVG 48, they ensure smooth and safe activation of the crane’s boom.
Bourke adds that initial feedback from crane operators using MAC 25 with a PVG 48 and Danfoss counterbalance valves is positive, too.
The Danfoss PVG 48 proportional valve is already at work in more than 100 of Franna’s MAC 25 cranes throughout Australia.
We.EV is rolling out fully installed smart chargers from global IoT leader Teltonika, making reliable, attractive home charging solutions accessible to EV drivers across New Zealand.
We.EV, a subsidiary of WEL Networks, is diversifying its charging offerings to include residential EV charging, helping balance demand on the national grid and enhancing electric fleet vehicle battery life. Drivers of company vehicles can gain the convenience of installing the same type of charger at home that they use at work.
The selection of Teltonika’s 7.4kW Teltocharge for its
compact European design and reliability supports We.EV’s strategy to future-proof residential energy connections. The smart charger’s app allows drivers to control what time of day to charge their EVs and whether to use grid or solar power.
We.EV is making the smart charger and installation available nationwide for a limited, introductory price beginning at $1595 including GST. The Teltocharge’s native solar integration means that drivers with home solar generation could potentially charge their car for free.
“With the introduction of fully installed Teltocharge smart chargers, We.EV is setting a new standard in home EV charging,” says Sam Montgomerie, Product Manager at We.EV.
“Home charging is the most convenient way to charge an EV, while prolonging vehicle battery life and safeguarding the national grid as the country moves to more sustainable transport.”
“We are delighted to extend our relationship with We.EV to enable home charging at scale, providing drivers with a smart charger that’s straight forward to install, offers greater control over energy usage, and enhances the aesthetics of any home,” says Kestutis (Kes) Grauslys, CEO of Teltonika Australia. The Teltocharge features a swappable Accoya wood front plate and four additional color front plates. Teltonika devices also enable We.EV’s commercial charging operations.
Precisely bent sheets are required in a wide range of applications, for example in the automotive industry and shipbuilding. The wenglor sensoric group offers the ideal sensor solution for maximum precision in inline bending angle measurement:
The MLSL1xxS50 uses laser triangulation to measure metal parts to the precise second to ensure consistent pressing results. The MLSL is mounted on the press brake and reliably detects all surfaces and provides relevant angle information.
Seamlessly integrated into the software of standard control system manufacturers, the sensor can be connected easily via Plug & Play and put into operation and adjusted directly. The corresponding interface also enables integration of the sensor with other manufacturers.
The sensor’s optical angle measurement is aimed directly at the sheet metal and can therefore be used for all combinations of upper tools.
The MLSL1xxS50 also ensures consistent results for different batches of sheet metal production, different materials, different bending directions to the rolling direction and slightly fluctuating sheet thicknesses. Through direct integration into the control system, predefined parameters determine the specifications of the bending process, which can be readjusted immediately.
The MLSL1xxS50 sensors can monitor various work steps and bending operations along the press. With long components in particular, the angle can be precisely checked over the entire length. To increase production capacity, multiple sensors can be used simultaneously to speed up measurements. An Ethernet connection connects sensors and control, ensuring seamless communication.
Highlights at a glance:
• Fully integrated with the systems of the most common control manufacturers
• Plug and play connectivity
• Compact, lightweight and robust
• Large measuring range
• Stable measurement results regardless of surface finish
• Spot or continuous measurements www.treotham.com.au
Fully integrated, accurate angles and precise: The MLSL from the wenglor sensoric group for accurate inline measurement of the bending angle.
These new frameless motors are available in compact sizes with an outer diameter of 100 mm or 112 mm –as well as in three different lengths, namely 30 mm, 60 mm and 120 mm. A PT1000 and a PTC temperature sensor are integrated every time, to protect against thermal overload and enable constant monitoring of the drive temperature.
The modular motor system also provides enormous design flexibility due to the choice between small or large hollow shafts as well as voltage classes for 60 VDC and 600 VDC / 750 VDC. Furthermore, the cyber kit line medium is compatible not only with Wittenstein cyber motor’s cyber simco drive 2 servo drive but also with other standard servo drives worldwide.
The modularly configurable frameless motors in the cyber kit line medium series are optimally adaptable to specific tasks and operating conditions owing to the large number of possible variants. This opens up numerous innovative design options for highly dynamic drive solutions in OEM machines.
cyber kit line medium bridges the performance gap in a range of applications
The motors, which can also be used as direct drives, are both frameless and bearingless. With their compact dimensions and reduced weight, they are just perfect for direct, space-saving integration into machines.
Thanks to the hollow-shaft concept cable, compressed air, vacuum, fiber optic and laser feedthroughs for gripping elements or sensors, among others, can be elegantly implemented when only limited space is available. The frameless servo motors are no less impressive in use, setting benchmarks in terms of torque density and dynamics.
As far as performance is concerned, the cyber kit line medium bridges the gap very neatly between the successful cyber kit line small and cyber kit line large series of frameless motors.
Collaborative and industrial robotics, machine tools, packaging technology, actuators for assembly, transfer and handling systems, testing and measuring machines or tasks in semiconductor manufacturing are typical applications for these highly dynamic and robust servo motors.
CoroCut QD Y-axis tools are optimised to enable improved surface quality, reduced vibration and higher blade stiffness.
Unlike conventional parting-off tools that align
with the X-axis of the machine tool, Y-axis parting operates on a different principle. By rotating the insert pocket 90 degrees and aligning it with the Y-axis brings several benefits.
The upgrade to the CoroCut QD improves surface quality, creates less vibration compared to conventional parting off — resulting in less noise — as well as the parting off of much larger diameters than what is currently possible with conventional methods.
Additionally, shifting the resultant load to the strongest section of the blade creates six times higher blade stiffness, enabling increased feed and longer overhangs without losing stability.
More specifically, the blades have been upgraded to have no Y offset, meaning easier programming and increased stroke. The blades also have a stop surface that serves two important application needs — preventing the blade from being pushed into the adaptor and enabling easier set-up.
New encoder module for cyber® kit line small
Wittenstein has simultaneously introduced a new encoder module for the cyber kit line small that can be built in as an option for four different feedback signals.
It provides >16 bit system accuracy as well as repeatability of <± 0.1°and ships in two versions: either with BiSS-C and SSI interfaces or for incremental and Hall signals. In combination with the cyber® simco drive 2 servo drive, the frameless motors in the smallest series with an integrated encoder module are the perfect system solution for 48 VDC applications.
Conventional parting off uses feed motion along the X-axis, which means the cutting force is directed through the weakest section of the blade,this can lead to deformation and instability.
By rotating the insert pocket 90 degrees and using the Y-axis, the cutting force is shifted down through the complete blade length, resulting in an increased blade stiffness of up to 600%.
CoroCut QDY is ideal for parting off in turning centres and multi-task machines with Y-axis. This includes parting off in sliding head machines, large diameters of up to 120 millimeters (mm), and long overhangs to reach between main and sub chuck.
So, when there is the need to part off or machine deep grooves without compromising process security or machining efficiency, the upgraded CoroCut QDY solution is the perfect choice.
www.sandvik.coromant.com
After a tumultuous period for global supply chains, manufacturers are turning to software solutions and big data to fully understand existing and future business challenges.
Darren O’Connor, Körber Director of Solutions ANZ, explains how Software-as-a-Service and Warehouse Management Systems can help maintain reliable flow of goods, increased material availability and efficient distribution processes.
In recent years, more pressure has been applied to progressing New Zealand’s onshore manufacturing capability.
As the COVID-pandemic demonstrated, global manufacturing strategies are often vulnerable to supply chain challenges, such as natural disasters, geopolitical factors and shipping disruptions. While local production is essential for New Zealand’s manufacturing prosperity, completely foregoing the cost-effectiveness and availability of offshore materials isn’t feasible.
Furthermore, it is more difficult for a smaller, more isolated nation such as New Zealand to compete with the buying power on the world stage.
New Zealand’s local manufacturing industry plays an increasingly crucial role in ensuring robust supply chains for local production. The pandemic has provided an opportunity for better education around supply chains, to open up more efficient network flows, connections and materials handling.
Industry 4.0 has ushered in a new level of digital efficiency to modern supply chains, with an ability to track, visualise, simulate and automate decisions quickly and effectively.
The pandemic accentuated a movement which was already gaining momentum – the need for manufacturers to embrace data-heavy supply chains. If businesses aren’t vertically integrated, they will find it time consuming and costly to pass data around internally and with partners, running the risk of falling behind in an uber competitive market.
Manufacturing is a broad spectrum, with types of products and customers varying greatly dependent on the sectors they serve. Therefore, each business requires a highly specialised supply chain process to support the larger degree of customisation required by today’s end customer.
Manufacturers face a balancing act of maintaining overall volumes by fulfilling larger numbers of orders with keeping costs down, which has placed an onus on efficiency across the supply chain.
We see this with new lean manufacturing strategies such as Build-to-Order and Build-to-Stock –Build-to-Order products are linked to a specific sales order, whereas Build-to-Stock products are based on sales projections or anticipated customer demand.
In an ideal world, manufacturers should have all their focus on what they do best: manufacturing. By integrating supply chain software solutions with cutting-edge voice directed workflows and specialised automation equipment, manufacturers can focus on their core competencies.
Industry 4.0 – also known as the fourth industrial revolution – has changed manufacturing and the wider business world, with cloud-based software enabling businesses to control key information and processes via a single platform.
In a SaaS delivery model, a vendor provides web-based access to applications through a subscription pricing model. The vendor takes responsibility for delivering the solution as a complete service: the WMS application, the underlying system – hardware and software – system maintenance, updates, backups, support and IT security.
This eliminates the need for customers to buy, deploy, maintain and support both the IT infrastructure and the WMS application.
Specialised cloud operations have governance processes interweaved within them. This capability means manufacturers can constantly monitor the health and performance of systems on the workshop floor.
As manufacturers are aware, machine downtime has disastrous consequences, so monitoring tools allow teams to easily find and connect the causes of issues in complex IT systems and trace them back to their cause, while providing superior system visibility for all involved IT operations and support personnel.
Visibility is just as crucial outside the warehouse, as supply chain transparency has become a strategic imperative for manufacturing businesses. In complex, global supply webs, end-to-end visibility is foundational to resilience, agility and delivering customer promises.
Without visibility, manufacturers are flying blind, unaware of disruptions until bottlenecks or delays become a reality.
New technology such as automated sensors, Internet of Things devices, blockchain ledgers, and control towers are illuminating operations in real-time.
Manufacturers can now spot delays as they emerge across supplier tiers, production lines, and distribution routes - then respond with agility before small issues become major disruptions.
Here, supply chains become proactive, rather than reactive, and products flow at the speed of customer demand, not at the speed of the next disruption.
Every workshop floor is different, so Körber places an emphasis on solutions being flexible and extendable with incremental functionality.
All core technology should be interconnected, which allows for true visibility throughout the supply chain, from the orders coming in, to the trucks being loaded.
Manufacturing’s relationship with supply chain has been riddled with challenges in recent years, but now the COVID dust has settled, an opportunity exists to take charge.
Some manufacturing customers are looking for a point of difference to separate themselves from
competition, while some are looking to stabilise and recover losses.
Whatever the solution, manufacturers are beginning to recognise how integral supply chain flexibility and awareness is to their overall success.
Brendan Gray and Dean Addie, represented the Southland Engineering and Manufacturing Cluster, in a two-day symposium in the Hunter Valley, Australia. The Hunter New Energy Symposium takes place annually in Newcastle, NSW, drawing industry leaders from across Australasia.
Both individuals were joined by other fellow members of the Southland business community, united in their pursuit to enhance understanding and foster collaboration in hydrogen development as a new energy opportunity for Southland.
Together, they are absorbing insights and engaging in discussions that hold the potential to significantly influence the future energy landscape of Southland.
The other attendees included Daryl Cook of EIS Group, Craig McKenzie of HWR Hydrogen and My Transport, and Hoani Cooper of NES Ltd. Craig McKenzie from HWR and My Transport was positive about the future and the immense potential and transformative power of hydrogen technology in shaping a sustainable future.
“We have a real opportunity here. There is a large body of work already being done, and collectively, we can make some real impact and speed up the pace to move towards a more sustainable future.”
For Brendan Gray, the symposium was not only an opportunity to gain invaluable knowledge about the hydrogen and energy industries, but also a chance to explore collaborative opportunities with industry peers.
continued from Page 8
He sees the event as a catalyst for fostering collaboration and innovation among the participating companies, which will be vital for driving sustainable development in Southland.
Gray emphasises the importance of understanding future trends and workforce development, recognising their crucial role in preparing the region for emerging opportunities.
Dean Addie echoes Gray’s sentiments, highlighting the symposium’s role as a crucial platform for industry players to come together, not only to gain insights into new energy opportunities but also to explore collaborative ventures.
Addie saw the event as an opportunity to showcase Southland’s collective capabilities and empower the region to bid for large engineering and manufacturing contracts with confidence through joint efforts.
He emphasised the importance of collaboration and innovation in driving growth throughout the region, ensuring its readiness to embrace the challenges and opportunities of the future.
Both Gray and Addie are optimistic about the potential positive outcomes for the Southland region
as a result of their collaborative attendance at the symposium alongside the other key companies. They anticipate gaining a deeper understanding of policy implications, major projects, and investments that will impact the region, ultimately driving greater economic growth, industry collaboration, and increased public and private investment.
As they engaged in conversations related to hydrogen and energy readiness, they were confident that Southland is poised to solidify its position as a beacon of collaborative excellence within the engineering and manufacturing sector, leading the way toward a brighter and more sustainable future for the region.
What is Urban Plus’s point of difference in the property market?
Urban Plus is a multi-faceted property management and development company, predominantly focused on the delivery of social and public housing outcomes and developing and releasing housing for first-home buyers and owner-occupiers.
We are owned by Hutt City Council, operate as a Council Controlled Organisation (CCO) and were established in 2007.
We are also proud to be one of the few large-scale developers in Wellington delivering Homestar rated homes for market release.
What is a Homestar 6 rated home?
Homestar is an independent rating tool for residential houses which is administered by the New Zealand Green Building Council (NZGBC). It effectively provides a common framework to assess and measure the sustainability of participating homes across New Zealand.
It does this by allocating points for homes that meet specific performance benchmarks (i.e. thermal performance, water sensitive design, waste reduction etc) and then uses these points to benchmark homes against their scoring criteria.
NZGBC identifies Homestar 6 rated homes as being easier to keep warm and healthy, more cost effective to run, and more environmentally friendly than a home built to the Building Code.
Why are these homes only for first home buyers and/or owner occupiers?
Two reasons:
Firstly, during the buoyant property market of 2020-21 we knew that speculation was common with many off-plan purchases being
resold shortly after completion for a profit.
To the extent possible, we didn’t want to contribute towards this speculation and believed that limiting sales to first-home buyers and/or owner-occupiers was likely to limit the extent of speculation on our homes.
Secondly, in 2022 our shareholder (Hutt City Council) commissioned research into the quality of life amongst local residents and found significant differences in the reported wellbeing between owner-occupiers and renters. While we acknowledge that rental housing plays an important role in our housing continuum, selling to first home buyers and/ or owner occupiers represents our attempt to support more individuals make the transition from rental housing to owner-occupied housing – hopefully supporting an improvement in the quality of life of residents.
You recently launched a new development in Lower Hutt. How can homeowners save money by purchasing these homes?
That’s right, we’ve recently launched a residential housing development in Lower Hutt which we believe could save homeowners up to $4,000 a year in living costs.
The development is located on Brook Street in Waterloo and includes twenty new twoand three-bedroom townhouses. It’s being marketed exclusively towards first-home buyers and owner-occupiers, with homes priced from just $649,000.
All homes are new, turn-key, fee simple homes with innovative custom designs built and manufactured locally and all come with a 10-year structural warranty. Completion is currently expected in late-2024.
It has been estimated that a 6 Homestar rating provides annual energy savings of up to $500 per household. It gives purchasers confidence that their homes use less energy and water and that the materials used to build the homes have a lower environmental impact.
In addition to the energy and water savings, ANZ Bank is currently offering interest rate reductions of up to 1% for homeowners purchasing a Homestar 6 rated home which could save homeowners thousands of dollars per year on their mortgage repayments.
Can you provide a specific example of savings a homeowner
could achieve by purchasing an Urban Plus Homestar 6 rated house?
If you take an example of a house purchased for $880,000 with a 20% deposit and 30-year loan term, we estimate that homeowners could save up to $3,863 on their repayments in the first year.
We know that every dollar counts during the current cost of living crisis, and UPL is hoping that the financial savings associated with Homestar will better enable families to purchase a warm, dry and environmentally friendly home of their own.
What is so unique about this particular development?
It is unique because this is one of the only developments in the region offering Homestar rated houses for market release. This sees us place a huge focus on sustainability throughout the design and build and encourages the minimisation of waste and use of responsibly sourced materials.
We know buyers are much more aware and conscious of the environmental factors. Our listing agent CK & Co tell us they are coming across more and more buyers who are looking for homes that not only meet their practical needs, but also align with their values and beliefs around sustainability and environmental responsibility. A Homestar certification should give them the confidence that your home will be more sustainable, as well as easier to keep warm with lower running-costs.
Why do we need to be building more Homestar houses in New Zealand?
Homestar delivers more than just a financial benefit to purchasers. New Zealand has a well-documented housing shortage, but we feel what is often underreported is that we also have high levels of substandard housing which causes a myriad of issues.
For example, we have the second-highest rate of asthma in the world, which is exacerbated by our poor quality housing stock. We believe that good quality and thermally efficient homes help to reduce heating costs and improve our collective health and wellbeing.
,http://www.urbanplus.co.nz/
Manufacturers focused on