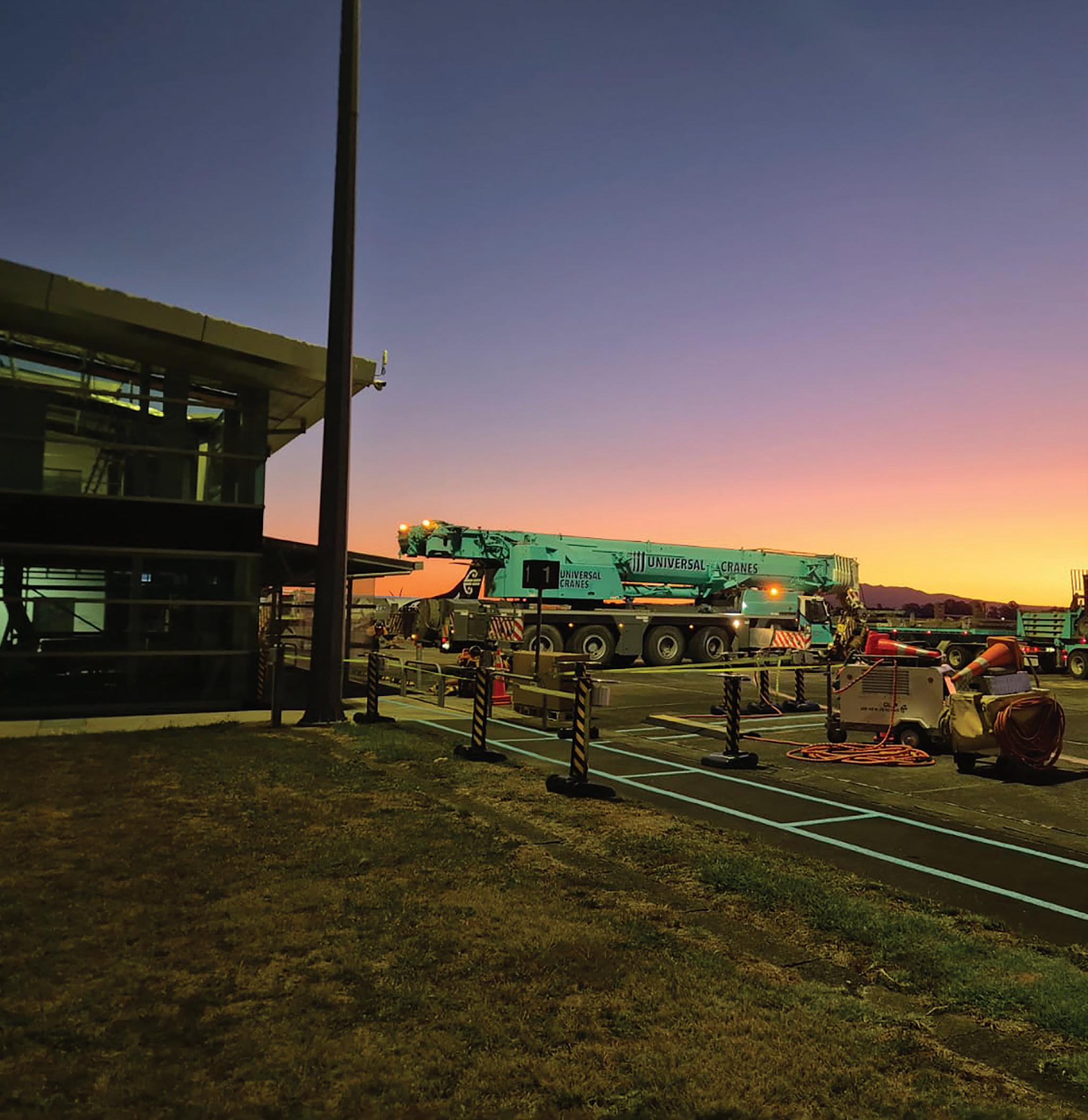

Get more from your machine with Komatsu Utility Excavators –tough, reliable and ready to work.
For a limited time, take advantage of our 1.99% finance rate, plus enjoy the confidence that comes with *4 years / 4,000 hours of factory-backed warranty ** – helping you stay productive and protected for longer.
Workplace Safety Solutions is an NZQA-approved training facility that offers quality driver training with on and off site options available. Our trainer/assessor in Rotorua has extensive industry experience, providing proven industry credibility.
Where
Dr Brian Guo, Associate Professor of Engineering at the University of Canterbury, discusses the future of AI in engineering
Ironclad investment Is a steel-framed home right for you? 42 Ute pursuit
The BYD Shark 6 is causing a commotion 46 System overhaul? Clearer pathways needed for apprenticeships
This issue of Elevate celebrates the return of trans-Tasman flights to the Waikato for the first time in 13 years – the $5m terminal transformation and what touchdown means for the region.
We deep dive consent statistics to find out where is booming – and where isn’t – as well as examining the region’s biggest developer and exploring the impact
of the drop in construction cost inflation.
There’s also a look at the new hybrid ute creating waves in a diesel-dominated market, we visit Hamilton’s first 6-star energy rated building, and tackle the thorny issue of swearing on the worksite…
8011
- (03) 961 5088 jarred@markat.co.nz
Ann - Design
Mundy - (03) 961 5075 amber@markat.co.nz
961
Angela Elley - (03) 961 5184
By Ben O’Connell
There were 34,062 new homes consented in Aotearoa New Zealand in the year ended March 2025, down 3.3% compared with the year ended March 2024, according to new figures released by Stats NZ.
In the year ended March 2025, the North Island recorded 23,570 new home consents, a decrease of 7.1% compared with the year ended March 2024. Yet the South Island saw a 6.4% increase over the same period, reaching 10,491 new homes consented.
Economic indicators spokesperson Michelle Feyen said the increase in the South Island was driven by higher numbers of new homes consented in Otago, Tasman, and Canterbury compared with the same period last year. Take Queenstown as a prime example, a booming southern town now home to some of New Zealand’s richest.
“In the 12 months to March 2025, 2,556 new homes were consented in Otago – the highest number ever recorded for the region.”
Internal migration plays a quieter but still meaningful role in reshaping our housing landscape. Affordability, lifestyle, and remote working opportunities continue to lure North Islanders south; Kiwis in general are moving from larger, more expensive urban areas to quieter, more affordable towns.
Domestic outflows can put pressure on regional infrastructure, schools, and healthcare systems not originally designed to support
rapid growth. Yet commercial and residential construction remains in decline.
In February, Michelle Feyen remarked that the annual number of new homes consented has been plateauing for nine months. Residential property values echo this standstill.
“Residential property values continue to bubble up and down slightly from month to month but have been kept virtually motionless as a whole throughout the first quarter of 2025,” QV operations manager James Wilson said on the release of the latest House Price Index.
“Although interest rates have reduced markedly, buyers
In the year ended March 2025, the North Island recorded 23,570 new home consents, a decrease of 7.1% compared with the year nded March 2024. Yet the South Island saw a 6.4% increase over the same period, reaching 10,491 new homes consented.
are still finding the current economic climate to be a challenge. Job worries and a rise in unemployment are causing many to be cautious and play it safe right now, which is understandable. This is one factor that has helped to keep the brakes on throughout the first quarter of 2025 – a sizeable surplus of properties for sale is another.
“It seems sellers are out in force across Aotearoa today. You don’t have to walk very far around the neighbourhood these days to see a ‘for sale’ sign. Ample properties for sale and a lack of meaningful competition are helping keep prices really flat for now. That’s no bad thing, as firsthome buyers continue to make up a larger share of the market overall.”
“When the economy does eventually recover and all the excess stock that is available for sale on the market today is sold, that’s when we will see some more sustained home value growth. It could be a while yet.”
It’s official. Hamilton Airport is re-joining the ranks of international gateways.
Starting in June 2025, transTasman travel is back on the departure board, with Jetstar announcing direct flights to both Sydney and the Gold Coast.
These will be the first international commercial flights out of Hamilton in more than a decade. The final trans-Tasman flight departed the tarmac on October 27, 2012, when Virgin Australia wrapped up its Brisbane service, ending 18 years of regular international connectivity. Since then, Hamilton Airport has served only domestic routes.
Now, the runway is once again preparing to welcome overseas travellers. Jetstar, a subsidiary of Qantas, will operate three return flights
per week to the Gold Coast and four return flights per week to Sydney, perfectly timed to launch ahead of New Zealand’s mid-year school holidays.
For Waikato Regional Airport Ltd (WRAL) chief executive Mark Morgan, it’s the culmination of more than a year’s hard work.
Speaking at a celebration marking the announcement, he says, “It’s been hard, complex work, in a very sensitive commercial environment, and we are thrilled to have pulled this off. The benefits for the entire region – not just passengers – are huge. Analysis indicates the flights will boost the regional economy by about $45 million per year. That’s fantastic for everyone; this is not just about the airport, it’s a great day for the region.”
The numbers speak volumes. Economic modelling suggests the flights will inject around
$45 million into the regional economy annually, with over 100,000 additional passengers expected to pass through the terminal each year. That growth will directly lead to the creation of around 60 new airport-based jobs and countless others indirectly throughout the region.
The return of international services is expected to be a game-changer for the Waikato. Whether it’s tourism, business, education or visiting friends and family, easy access to Australia opens up a host of new possibilities for both residents and visitors.
Nicola Greenwell, general manager of Hamilton & Waikato Tourism, is ecstatic. “This is fantastic news, brilliant. Australian visitors already account for 19 per cent of our international visitor spend in the region. Now, with direct flights into Hamilton Kirikiriroa, we become even more accessible, and this is
fantastic news for the mighty Waikato, for the central North Island and beyond,” Greenwell said.
The announcement comes hot on the heels of news about two new hotels being built in Hamilton, adding further momentum to the region’s tourism and hospitality industries.
For Jetstar, this move is part of a much wider expansion strategy across Aotearoa. Jetstar Group CEO Stephanie Tully says the airline is in a period of “unparalleled growth.”
“As the country’s only lowcost airline, Jetstar provides critical competition in New Zealand and helps keep travel affordable for Kiwis, with one million domestic fares selling for less than $100 in the past year alone.
“With consistently low fares and improved reliability,
there’s never been a better time to give Jetstar a go.”
Once the flights commence, Jetstar will become the fourth carrier to operate out of Hamilton Airport, joining Air New Zealand, Sunair, and Originair.
Terminal transformation underway
To prepare for international operations, Hamilton Airport is undertaking a $5 million refurbishment of its northern terminal. Work began in late 2024, and while the airport underwent a major seismic strengthening and upgrade in 2022, further modifications
are required to meet customs, security, and biosecurity requirements.
This isn’t just a paper shuffle and paint job. In a major milestone moment, contractors recently pulled an all-nighter to install critical equipment for international departures.
Starting at 7pm and working through to 5am, a large section of the terminal roof was peeled back so that two massive X-ray screening machines, a body scanner, and supporting infrastructure could be craned into place. The machines, one of which weighs approximately 2.5
As the country’s only low-cost airline, Jetstar provides critical competition in New Zealand and helps keep travel affordable for Kiwis, with one million domestic fares selling for less than $100 in the past year alone.
With consistently low fares and improved reliability, there’s never been a better time to give Jetstar a go.
tonnes, were carefully lowered into the building using cranes. Once that delicate job was done, new air conditioning units were installed on the roof.
Hamilton Airport chief executive Mark Morgan explains, “We needed the crane gone from the airport apron, where planes park, before flights arrived, so timing was key. It was a tight, logistical exercise involving builders, roofers, crane operators, air conditioning contractors and our own team, and it went well. Even the weather played ball.”
The airport team will next install the baggage carousel, currently en route to New Zealand from India. The work remains on schedule, and Morgan is confident everything will be ready in time for Jetstar’s inaugural Sydney flight on Monday, June 16.
Importantly, no changes are required to the runway itself. Hamilton’s runway has always been long enough to accommodate trans-Tasman flights, and the aircraft chosen for the routes, the 188-seat Airbus A320 Neo, fits the bill perfectly.
The resurrection of international service has been a collaborative effort involving WRAL, Jetstar, and numerous local and national agencies. Barry Harris, chair of the WRAL Board of Directors, is proud of what’s been achieved.
“There have been a lot of moving parts to this on both sides of the Tasman, and it’s taken a lot to pull it together,” he says. “We congratulate Mark’s team for what they have achieved and congratulate Jetstar too for
recognising the Waikato represents a huge opportunity.”
He’s equally optimistic about the future. “Hamilton Airport is in good shape financially, and that’s allowed us to identify opportunities and go after them. The resurrection of international fights is great for the airport but more importantly, it’s great for the wider region and for the travelling public.”
For many locals, the news has sparked nostalgia for a time when heading overseas didn’t mean driving to Auckland first. The return of international flights makes travel more accessible and opens up possibilities for families, businesses, and tourists alike.
The move also reflects a growing confidence in regional air infrastructure. As populations grow and tourism rebounds postpandemic, secondary airports like Hamilton are increasingly being seen as viable hubs, not just overflow for major centres.
The story of Hamilton’s return to international skies is one of persistence, vision, and smart investment. From long nights under crane lights to high-level negotiations behind closed doors, the effort to bring back trans-Tasman flights has paid off.
Come June 2025, when that first Jetstar flight from Sydney touches down, the Waikato will once again be part of the international flight map. And for Hamilton Airport, it’s the beginning of a new chapter.
• Homes & Apartments
• Commercial Facilities
• Insurance Industry
• Schools & Aged Care Facilities
• Subsistence Housing
• Water Utilities
• Rural & Agriculture
• Local Government
• Building Codes
AquaTrip is a permanently installed Leak Detection System with an integrated automatic Shutoff Valve.
It functions as a Water Trip Switch, constantly monitoring all the plumbing pipes, fittings and water using appliances on the property.
If it detects a leak, a tap left running or some other plumbing failure, it will shut off the water automatically, to minimise water damage, prevent excess water bills and save water.
You can easily turn the water back on when required.
AquaTrip is a permanently installed Leak Detection System with an integrated automatic Shutoff Valve. Shop in-store at one of our accredited retailers or shop online for NZ-wide shipping, including Auckland, Tauranga, and Wellington. We stock both commercial and residential water leak detection systems to protect your home or commercial property from accidental flood damage has never been easier.
Premium Water Leak Detection Systems Protect your home from costly water leaks, install an Aquatrip water safety trip.
Aquatrip water leak detection systems essentially functions as a Water Trip Switch, constantly monitoring all the plumbing pipes, fittings and water using appliances on the property.
If it detects a leak, a tap left running or some other plumbing failure, it will shut off the water automatically, to minimise water damage, prevent excess water bills and save water. You can easily turn the water back on when required.
It can detect the difference between your normal water use and a plumbing leak or tap left running by mistake, protecting your entire plumbing system.
It is easily programmable to suit your home and lifestyle.
¼07 5520322
ºleo@aquatrip.co.nz
í5 Bristol Avenue, Brookfield, Tauranga
Ôwww.aquatrip.co.nz
By Ben O’Connell
Hamilton City Council data shows that Kāinga Ora built more homes in the city than any other developer in 2024.
The news comes from an Economic Development Committee meeting agenda, which said residential construction industry growth was “driven” by the government housing provider. The report described 2024 as “a tough year for construction,” with a need for more affordable homes and land to improve feasibility.
Consents data for the year to December 2024 show that 801 new housing consents were lodged, down 23%; 613 homes were under construction, down 26%; and 908 new home consents were granted, down 25%. The number of “consents lodged is still very low, although the September and December quarters saw improvement,” the report reads. “There is unlikely to be any real jump in consents granted.”
The stable figures are not positive. The number of homes under construction has also plateaued at a low level, though it is not falling further, the report continues. “Consents granted appear to have stabilised [to] just over 200 dwellings per quarter.”
The industry sentiment towards Kāinga Ora is mixed. Over the years, some local professionals have told the media that they are thankful it is keeping the construction industry in
Consents data for the year to December 2024 show that 801 new housing consents were lodged, down 23%; 613 homes were under construction, down 26%; and 908 new home consents were granted, down 25%.
The number of “consents lodged is still very low, although the September and December quarters saw improvement,” the report reads. There is unlikely to be any real jump in consents granted.
Hamilton afloat. With private developers scaling back due to high costs and low feasibility, Kāinga Ora projects have helped keep tradespeople employed.
Others are fearful that the agency is squeezing out other developers, that the scale and government backing of Kāinga Ora risk pushing out smaller developers, making it harder
for private firms to compete for land and resources. There is an undoubted need for more affordable housing, but some stakeholders fear that over-reliance on a single public developer could limit diversity in housing supply and design or reduce opportunities for innovation in the private sector.
Per the government’s direction, Kāinga Ora is on track to
build and purchase over 1000 new homes in the Waikato region between 2023 and 2025. “We’re looking to bring the benefits of urban intensification, like green spaces, playgrounds, increased safety, and a stronger sense of community, to more areas,” says Mark Rawson, Regional Director Waikato of Kāinga Ora, of the housing provider’s regional plan.
“This plan isn’t just about the buildings. It’s about ensuring our customers can maintain their connections to the community and support networks. By redeveloping in areas where we already have homes, we’re helping people stay connected to the places and people they know.”
At Sparky Direct, we don’t just provide services – we build partnerships. Our journey in the realm of trade services and construction solutions is defined by a passion for innovation, a commitment to quality, and a genuine understanding of our clients’ aspirations.
Founded with a vision to be industry experts and a mission to offer the best possible solutions to our clients, Sparky Direct has evolved into a trailblazing force in Electrical, HVAC, and Solar services. We commit ourselves to continuous learning, adaptability, and unwavering dedication to enhancing the services that we provide.
Meet the Team:
Behind every successful project is a team of dedicated
professionals who bring it to life. Our team is a tightknit family of experts, each contributing their unique talents and experiences to create extraordinary outcomes. From skilled electricians to ingenious HVAC specialists and visionary solar engineers, our collective strength lies in our diversity. But we are more than just a team of technical experts. We are listeners, problem solvers, and partners in your journey. We take the time
to understand your project’s intricacies, challenges, and dreams. We believe that every project is a collaboration, where your vision is our guiding light.
Empathic Approach:
At Sparky Direct, we don’t just see blueprints; we envision the spaces you aim to create. We understand that each project carries its own narrative – a story of innovation, functionality, and sustainability. Our empathic approach allows us to tailor our solutions to your unique needs, ensuring that every wire, duct, and solar panel aligns perfectly with your goals.
Beyond Services:
Our commitment transcends delivering services; it extends
to crafting experiences. When you choose Sparky Direct, you gain a partner who is as invested in your project’s success as you are. We are with you every step of the way – from conceptualization to completion – providing guidance, insights, and solutions that elevate your project to new heights while keeping your budget in mind.
In a world where innovation meets compassion, and technical expertise meets human understanding, Sparky Direct is your trusted ally. Let’s build not just structures, but legacies. Welcome to Sparky Direct – where your vision ignites our passion.
Amohia Ake, the new ACC Centre
developed by Tainui Group Holdings on Collingwood Street in Hamilton, has achieved a landmark distinction as the first building in the city to receive a 6 Star NABERSNZ energy rating from the New Zealand Green Building Council.
This prestigious certification, the highest possible under the NABERSNZ system, recognises exceptional energy efficiency in office buildings.
Out of more than 150 buildings rated under NABERSNZ across the country, Amohia Ake is now one of just six nationwide to attain the top-tier 6 Star rating. The building uses approximately 80% less energy than a typical New Zealand office building - a significant achievement in sustainable design and operation.
Andrew Eagles, Chief Executive of the New Zealand Green Building Council, described the rating as a milestone for the Waikato region.
He said Amohia Ake sets a new benchmark for energyefficient buildings in New Zealand, benefiting both
Out of more than 150 buildings rated under NABERSNZ across the country, Amohia Ake is now one of just six nationwide to attain the top-tier 6 Star rating. The building uses approximately 80% less energy than a typical New Zealand office building - a significant achievement in sustainable design and operation.
its tenants and the wider community. He credited the accomplishment to the shared vision of Tainui Group Holdings and ACC, noting that prioritising efficient building use can deliver long-term gains.
The development, owned by Tainui Group Holdings and leased to ACC, reflects the Iwi organisation’s commitment to sustainability and environmental guardianship. Acting CEO Richard Jefferies said the achievement aligns with the Iwi’s core value of kaitiakitanga (stewardship), and demonstrates their dedication to reducing
energy use and creating environmentally responsible buildings.
“This rating reflects our focus on sustainable development and the high performance of the buildings we deliver. We’re proud to support our tenants and the community by setting a new standard for energy-efficient design,” Richard said.
The building’s success is also attributed to a close collaboration with consulting engineers from Beca. Ben Masters, Sustainable Buildings Team Lead at Beca, explained that the building’s fully-electric design - completely free of
gas or fossil fuels for heating and hot water - was key to its high energy performance.
Masters added that Amohia Ake’s smart design reduces pressure on the electricity grid. Its high-performance building envelope helps minimise heating and cooling demand, while energy-efficient systems and post-occupancy optimisation further reduce energy consumption.
These features not only slash emissions but also deliver meaningful cost savings for both Tainui Group Holdings and ACC.
With over 800 ACC staff now based in the building, the benefits extend well beyond efficiency. Stewart McRobie, ACC’s Deputy Chief Executive for Corporate and Finance, said the organisation is proud to work in a building that supports environmental goals while enhancing operational outcomes.
“This building helps us lower our carbon footprint and reduce energy costs, which ultimately contributes to our mission of supporting the wellbeing of whānau and communities across Aotearoa,” Stewart said.
“We look forward to continuing our partnership with Tainui Group Holdings and supporting a more sustainable future.”
DANPALON’s performance is certified by rigorous testing from worldwide institutions. It offers a new concept in glazing providing outstanding performance and flexibility in design. Use Danpalon for roofing, facades or partitions, internally and externally
In the heart of Waikato, Pump & Electrical Services Ltd stands as the best of the best in pump and electrical solutions, offering a large selection of services designed to meet every need.
Whether it’s domestic, industrial, or agricultural requirements, our expertise covers the installation, maintenance, and repair of a wide array of systems, including milking machinery, water pumps, and electrical equipment.
Your trusted partner in pump and electrical solutions
At Pump & Electrical Ltd, we understand the importance of efficient water systems and electrical services. Our team, based out of Hamilton and Huntly, is renowned across
Waikato for their dedication and expertise. With a commitment to quality and reliability, we provide everything from UV treatment systems to complex installations for large-scale operations.
Comprehensive services for every requirement
Our offerings are diverse to ensure optimal performance and convenience:
• Pump sales and service: We handle everything from light residential needs to heavy industrial setups
• Milking systems: Improve your dairy operations with our advanced milking systems
• Water treatment: From filtration systems to full-scale water treatment, we ensure your water is clean and safe
• Irrigation solutions: Maximising your water efficiency with state-of-the-art irrigation systems
• Emergency repairs: Our 24/7 service ensures we are always there when you need us, minimising downtime and avoiding potential losses.
• Expertise: Our team of professionals have years of experience and is equipped with the knowledge to handle any challenge
• Quality: We use only the best products and the latest
technology to ensure your systems run smoothly
• Customer service: We believe in building lasting relationships with our clients, offering aftersales support that truly makes a difference.
Don’t let pump and electrical issues disrupt your home or business. Contact Pump & Electrical Services Ltd to discuss your needs and find out how our solutions can bring efficiency and peace of mind to your operations. Our team is ready to provide you with the best products and services in Waikato.
Call us at 07 846 0678 or visit us in Hamilton for a consultation.
Whether you need a unit for a single worker or your whole crew for a couple of nights or longer term – Mercury Bay Holiday Park offers a full range of basic or self-contained cabins to suit all budgets.
Everything you need for your next big job.
Everything you need for your next big job.
Contact us today to find out more.
¼07 866 5579
º info@mercurybayholidaypark.co.nz
í121 Albert Street, Whitianga
Ôwww.mercurybayholidaypark.co.nz
Based in Tauranga and Taupo, we serve the Bay of Plenty, Waikato, and Central North Island with top-notch scaffolding services.
PROVEN EXPERTISE & PROBLEM-SOLVING SKILLS
EFFICIENCY & VERSATILITY
COMMITMENT TO SAFETY & CUSTOMER FOCUS
INNOVATIVE SOLUTIONS & CONTINUOUS IMPROVEMENT
The building and construction industry in New Zealand has experienced a marked slowdown in cost inflation, signalling a significant shift from the heightened levels of recent years.
Cost inflation has slowed dramatically due to reduced pressures in the sector, improved supply conditions, and falling commodity prices, according to a new report from industry research company Macromonitor.
The new report, New Zealand Construction Cost Trends, provides detailed cost escalation projections for all categories of construction inputs in New Zealand. Construction cost inflation, which reached a peak of 14% in 2021/22, has significantly slowed to just 0.44% in the year to December 2024. This is the lowest annual inflation rate since June 2020, when it stood at just 0.40%.
“While declines in some costs are evident, a full reversal to pre-2021/22 price levels is unlikely. Instead, construction costs are expected to stabilise and grow at more normal rates, but from the current elevated base,” according to the report’s author, Macromonitor Economist Abdul Hannan.
The report highlights that falling prices for key materials, such as steel and oil, have been pivotal in easing overall construction input costs. Improvements in global and local supply chains have also contributed to reducing inflationary pressures, as logistical disruptions that once strained the industry have steadily diminished.
“Additionally, a decline in construction activity, particularly in the residential sector, has further alleviated demand-driven cost increases,” says Mr. Hannan.
“The labour market has also softened, with slower wage growth and reduced labour demand contributing to the easing of inflation. This reflects broader trends in the domestic economy, where tighter monetary policies and weaker demand conditions have created a more balanced cost environment,” adds Mr. Hannan.
The report also notes persistent challenges in some areas. Construction equipment costs have
continued to rise sharply, creating ongoing upward pressure on costs.
“While some cost pressures persist, we anticipate that overall inflation will stabilise gradually and grow at more sustainable rates,” says Hannan. “However, global factors such as U.S. tariff policies could impact import prices, posing a risk to future cost trends.”
Macromonitor forecasts a 3.5% rise in total construction costs in 2025 and 2.2% in 2026, aligning with a gradual return to long-term growth trends.
Data from this chart is available upon request. Please contact Abdul Hannan at 02 9869 8844 or abdulhannan@ macromonitor.com.au.
For more information about this report visit: www.macromonitor.com.au/ new-zealand-constructioncost-trends/
Macromonitor is an Australian industry research and forecasting company with a commitment to providing high quality information to industry.
We Fix & Service Truck Curtains, 24/7
We are committed to high quality repairs. Fifita has the right equipment and experience to locate, repair & replace truck curtains quickly & effectively.
Truck Rips & Repairs | Certifying your Truck Curtains | Roof Holes, Floors, Poles Pelmet Rubber, Ratchets, | Instillation of New Curtains, Strap N Go Systems.
LET’S GET YOU BACK ON THE ROAD AGAIN
021 294 7096 | liviela@fifita.co.nz | www.fifita.co.nz
The Bolt Shop was established in 2000 under the direction of Director Geoff Smith with a wealth of fastening and technical experience. The team is prepared to support you with your project requirements and take on challenging issues.
The University of Auckland Formula SAE Team and its F:SAE:47 Projects are proudly sponsored by The Bolt Shop Team.
As Child Safety Advocates, we also support the New Zealand Police Managers Guild Trust.
Our Products:
• Mild Steel Bolts
• High Tensile Bolts
• Tapping Screws
• Rivets
• Nuts
• Machine Screws
• Threaded Rod
• Socket Head
• Drills
• Hardware
• Stainless Steel Bolts
• Washers
• Wood Screws
• Masonry
• Taps & Dies
• Consumables
• Tools
Glenfield
191B Archers Road, Glenfield, North Shore City
Phone: 09 441-9425
Mon-Fri: Open 7:30am to 5:00pm Sat: Open 8:30am to 12:00pm gfsales@boltshop.co.nz
Wiri
23 Ash Road, Wiri, Auckland City
Phone: 09 262-2944
Mon-Fri: Open 8:00am to 5:00pm
wirisales@boltshop.co.nz
the owner of a small
Since joining the YourLocal franchise in 2019, we have had the privilege of servicing over to 3000 properties across the Waikato.We have built some great relationships with our customers, someof whom we have serviced for 6 years.
The basics of business are what we hold to, such as clear communication, honoring a quote, doing the job with integrity and treating each property and person with respect. These are all things we strive for here at Your Local Housewash and Pest Control Hamilton and Waikato, and have seen, upheld and outworked during our time in business.
We have been named Franchise of the Year in 2020 and 2022, and received the 2021 Aspiring to Excellence award, each at their respective
annual franchise conference. In 2023 we received our first external award, the Entrepreneur award from the Waikato Pacific Business Network. I am really proud to have received all of these awards as they fit well with our ethos. We want to do the best work possible for our customers.
We are apart of the exterior cleaning industry association and the pest management association of New Zealand. And are also totika certified as well as now working along side a local council
in providing our exterior cleaning and pest control services.
Our team love a yarn at the end of a job, readily share their knowledge and enjoy what they do. As a business, we are fully insured and offer a 100 percent money back guarantee on most services. We are confident that we can provide you with exceptional service.
Rick Johnson, from LINK Business Brokers, boasts an impressive history of business sales in the Construction and Trades sector. Known for his experience and expertise, Rick has proven he can navigate the intricate challenges in the business sales process to secure optimal outcomes. His exceptional communication, unwavering transparency, and absolute professionalism are widely acknowledged and appreciated by his previous clients. Rick’s clients benefit from his tailored approach, insider knowledge, and extensive network of contacts. Operating from the Hamilton/Waikato office, Rick’s network extends across the broader Waikato/Bay of Plenty region and into Auckland, Taranaki, Hawkes Bay and Manawatu.
Rick has successfully facilitated the sale of numerous companies and specialises in brokering small to mediumsized businesses valued between $500k-$10million. Rick proudly holds the distinction of being LINK’s top broker in the Waikato region and ranks among the elite 5% of LINK brokers globally. His achievements have been recognised with a collection of awards and accolades across his 10-plus years with the company.
For those seeking to buy or sell a business in the Construction and Trade Services industries, there’s no broker better for the job than Rick Johnson.
What my clients say:
“He guided us professionaly through the whole experience to a successful sale... His progessionalism was outstanding and with his ability to inspire respect and cooperation, he guided both parties through the whole process. Thank you Rick, it has been a pleasure to work with you.”
Rick Johnson LINK
BROKER M 021 991 485 E rick.johnson@linkbusiness.co.nz
After discovering 3D printing technology around three years ago, the team at Iconic Construction quickly became intrigued.
They approached QOROX before starting a new childcare facility in Hamilton, and after seeing the benefits of 3D printed concrete during a visit to the QOROX showroom, decided to update and reconsent a project in order to give it a try themselves.
“From that initial meeting, I guess we fell in love with it, we thought it was really cool and were so impressed with what could be designed, and knew straight away how innovative it is and how we could use it building in New Zealand,” says Johnny Gordon, General Manager at Iconic Construction.
The recently completed 3D-printed home in Brymer Heights, Rotokauri, took 99 days to complete and was designed by Waikato-based architects, The Architecture People. The homes features include an open-plan living area, curved walls, three bedrooms, two bathrooms, and one and a half garage spaces.
Johnny says that all of the 36 walls of the home were printed off-site in the QOROX factory, which took a total of 24 hours of printing time over ten days to complete, and were then brought onto the site.
The recently completed 3D-printed home in Brymer Heights, Rotokauri, took 99 days to complete and was designed by Waikatobased architects, The Architecture People
“One of the key benefits is around the time it takes to build a house, so with this build, we started on the 23rd of July, and we had a code of compliance, which means you have council sign off on the build, and this was issued on the 12th of December, so it took us four and a half months to build the house.”
Because this was Iconic Construction’s first architecturally designed house using 3D printing, there was a lot of learning going on for the whole team, “but we still think that was really fast. We’re
aiming to improve this with the ultimate goal of getting the build schedule down to around three months to build a 170 square metre house.”
One challenge that stood out to Johnny was the foam that goes inside the walls and serves as insulation, which he says was overfilled. “There was quite a bit of excess foam that required removing when the panels were placed on site.
We’ve reviewed this and come up with an improved system for how the walls will be insulated in the factory moving forward, so this doesn’t happen again.
“There has been a ton of learning for all involved on this build, and it’s a matter of taking those learnings, so we keep learning and developing an efficient system.” The 3D home is predominantly constructed of concrete, featuring concrete floors and walls, and also has a traditional timber trussed roof system. Johnny says that, due to the floors and walls, the longevity of the home surpasses that of the standard New Zealand home.
“You may need to replace windows, kitchen, and roofing, but you need to do that with any house. The longevity of the house is going to be multigenerational for families to be able to live in for hundreds of years rather than only a few generations before the house is demolished.
“That’s a really neat thing that happens in Europe a lot, they’ve got three, four-hundred-year-old houses that are concrete and stone, and the same with Asia, but here in New Zealand we don’t really have that, we build timber framed houses that only have a certain lifespan which is relatively short.”
While completing this build, there was significantly less waste than would be generated when completing a standard build, Johnny said. “With a build of this size, which is 167 square metres, you usually have up to three skips of waste; we only had one skip of waste, and then we had a lot of stuff that we took to recycling.” QOROX also 3D printed a curved seat for us that was placed in the garden, and rather than sending the excess foam from the walls to landfill, Johnny says
Since opening the home to the public, the team have had about 700 people through so far, as some events are coming up in the calendar. Johnny says the response has been overwhelmingly positive, and that “people have come in and said it’s way better than they thought, and they are really impressed by it and love the curves in the walls.
they used some of the excess foam to place in the middle of the of the 3D concrete printed seat.
Since opening the home to the public, the team have had about 700 people through so far, as some events are coming up in the calendar. Johnny says the response has been overwhelmingly positive, and that “people have come in and said it’s way better than
they thought, and they are really impressed by it and love the curves in the walls.” Johnny adds that there has been a small percentage that haven’t liked the 3D printed line look on the walls, “although you’ve got the option of plastering the walls if you want to, which is an additional cost though.
“We have been really happy with the public’s response, and the challenge for me is to
be able to convert that from people liking it to wanting to build out of it.” Iconic Construction has become a regional partner with QOROX, the company that brought the technology to New Zealand in 2020, and is excited to introduce 3D printing to the construction industry.
Johnny says that they have also brought another robot, which is located in Christchurch, as they want to be able to build 3D-printed houses in the South Island as well.
“We are early adopters of this technology, and we are excited to bring it to the market in New Zealand with QOROX.”
Swearing has become so much a part of our culture that many probably hardly notice it. The odd F-bomb seems to slip into our daily conversations as regularly as asking what is for dinner, but what if the language we take for granted isn’t as harmless as it seems?
Swearing on the worksite serves several functions, and not all of them are negative. In many cases, it’s simply a form of venting – an instinctive release when things go wrong. When you’re working in high-pressure, physically demanding environments, frustration is inevitable. A welltimed expletive can act as a release, letting off steam in the moment and helping workers reset without slowing down. According to Psychiatrist.com, swearing signals an area of the brain known as the amygdala to release adrenaline. This release of hormones subsequently leads to a soothing effect.
Then there is the camaraderie factor. Studies suggest that the use of profane language can lead to tighter emotional and social bonds and a harmonious environment. Swearing can act as social glue on the jobsite – a sort of form of trust that indicates a close bond. Shared banter, even if laced with mature language, can
Swearing on the worksite serves several functions, and not all of them are negative.
In many cases, it’s simply a form of venting – an instinctive release when things go wrong. When you’re working in high-pressure, physically demanding environments, frustration is inevitable.
create a sense of team identity and mutual understanding. In this sense, it’s not much different from sports teams or corporate teams, where intense environments give rise to blunt, unfiltered speech.
But while swearing can unite, it can also divide. The line between bonding and bullying can be thin. The use of profanity can be used to humiliate, and when strong language is turned toward individuals, especially
repeatedly, it can quickly change from expressive to oppressive. What’s considered “normal” banter to one might feel hostile or alienating to another, especially if there are differences in age, gender, background, or experience.
Efforts to improve inclusion and mental health on worksites are starting to gain momentum, but language and how we casually communicate remain a blind spot. A culture that tolerates – or even celebrates
– aggressive or explicit speech may inadvertently reinforce the idea that only certain types of people “belong.”
So where is the line? It’s not about banning swearing altogether; not many would want a site free of all colourful language and character. But being aware of the intent and impact of our language is really important. Swearing used to blow off steam or share a laugh is one thing. Swearing used to intimidate, belittle, or exclude is something else entirely.
Any sort of construction or trade is a team sport. Like any good group, communication is key. And while the occasional F-bomb and outburst of mature language might fly, the way we speak on site should reflect the kind of environment we are trying to build on the worksite.
We provide skip bins and hook bins to the construction industry at reasonable rates. We are super reliable and responsive. We are uniquely placed to help you to meet waste reduction targets as we sort all materials we collect from site and divert what we can from going to landfill. What We Can Do For You:
Classify and weigh all materials from building sites
Produce detailed reporting on volumes of diverted waste
Simplify waste minimisation plans required for building consents
By Ben O’Connell
Associate Professor in the Department of Civil and Natural Resources Engineering at the University of Canterbury, Dr Brian Guo lists three adjectives that will shape the future of engineering: digital, sustainable, and resilient.
“It’s a pretty awesome time to be in the field!” he exclaims. “In a nutshell, the future of engineering is all about using cool tech, protecting the planet, and building things that can stand up to whatever life throws at us.
“First, digital,” he says. Whether it’s AI, 3D printing, or smart sensors, engineering is more tech-driven than ever. “These tools are helping us design and build things faster, smarter, and with way more precision. It’s like giving engineers superpowers to solve problems we couldn’t tackle before.”
Brian says this is where automation and AI come in. Faster, more accurate, and of higher quality, embracing these technologies means getting more done with less human effort. This might mean robots handling bricklaying or site inspections, and AI optimising project schedules and reducing waste. “These technologies can take over repetitive, time-consuming, or physically demanding tasks, freeing up people to focus on more
it—30 years ago, jobs like ‘app developer’ or ‘data analyst’ didn’t even exist. The key is to adapt and upskill. Governments, industries, and educators need to work together to make sure people are prepared for these changes.”
The construction industry could benefit from robots and cobots (collaborative robots) to handle repetitive and hazardous construction work, such as on masonry walls, prefab elements assembly, and interior finishing. But these bots cause safety concerns when you consider how workers interact with them in shared workspaces.
It’s a pretty awesome time to be in the field! he exclaims.
In a nutshell, the future of engineering is all about using cool tech, protecting the planet, and building things that can stand up to whatever life throws at us.
creative, strategic, and highvalue work.”
When I asked David whether you and I are right to fear automation and AI, he admitted that, like many, he’s wrestling with it too. “If automation, robots, and AI can improve productivity, then I believe the general public should embrace and adapt to these changes rather than fear them.
“New Zealand, like many countries, has a low productivity issue. What
does that mean? Basically, it means we’re not getting as much output from the work we put in compared to other countries. Low productivity leads to slower economic growth, which in turn means lower salaries and fewer resources for things like healthcare, education, and infrastructure. It’s a big deal.”
He says that while some roles will indeed change or disappear with the rise in automation, history shows new tech means new opportunities. “Think about
Brian has been working with UC Doctoral student Zhe Zhang and A/Prof Goh Yang Miang (National University of Singapore) to address the emerging safety issue of human-robot collaboration in construction. They immerse workers in virtual reality to test their situational awareness and determine what safe robotics systems on construction sites actually look like. The immersive, realistic approach is a significant step toward successful hazard recognition performance. Robots work with and around humans, and never the opposite, after all.
“The bottom line is this: automation isn’t about replacing humans—it’s about making us more productive. And in a country like New Zealand, where productivity is a major challenge, embracing these technologies could be a game-changer. It could lead to higher wages, better-
Sustainable building isn’t just a trend—it’s a smarter way to build for the future. It’s about balancing cost, performance, and environmental impact to create spaces that work for people and the planet.
quality work, and a stronger economy. So instead of fearing automation, we should see it as a tool to help us build a brighter future.”
Sustainable
“Second, sustainable—this is a huge one.” Engineers are at the forefront of sustainability, making and maintaining our green built environment. Whether it’s life cycle assessments or renewable energy systems, David says the field is all about creating solutions that don’t just work for us now, but also leave a better world for future generations.
“The building industry contributes to greenhouse gas emissions (30%), energy consumption (40%), and waste (32%) worldwide.”
There are many misconceptions about sustainable building practices: too expensive, not worth the effort, too complicated, worse on performance, and only for experts. Brian says the truth is that sustainable building is more accessible every day.
“A lot of folks assume that going green means spending a ton of money upfront, but they don’t always see the long-term savings. For example, energy-efficient buildings might cost a bit more to design and build, but they save heaps on power bills over time. It’s an investment that pays off.
“People sometimes think that eco-friendly materials or designs are less durable or functional, but that’s just not true. In fact, many sustainable materials are just as strong, if not stronger, and they often come with added benefits, like better insulation or improved air quality.”
And it’s not just about the environment. “While protecting the planet is a huge part of it, sustainable practices also focus on creating healthier, more comfortable spaces for people. Things like natural lighting, better ventilation, and non-toxic materials make buildings nicer to live and work in.”
Another research project that Brian is involved with explores energy retrofitting school buildings nationwide to reduce energy use and greenhouse gas emissions. It looks at the relationship between lifestyle cost and assessment, energy consumption, and thermal comfort to identify the optimal retrofit package that balances environmental and economic goals. Decisions regarding school buildings in New Zealand are never straightforward. This research aims to support decision-making processes for the education sector, which will contribute to the bigger picture of achieving New Zealand’s 2050 net-zero carbon emission target.
“Both projects highlight two big values for the future of engineering: sustainability and human-centric tech design. The school retrofit project focuses on cutting energy use and emissions in buildings, showing how engineering can help fight climate change and hit net-zero goals.
“The VR project uses immersive tech to make construction robots safer for workers, putting people first when designing new systems. Both projects show engineering’s role in creating a greener, safer future.
“Sustainable building isn’t just a trend—it’s a smarter way to build for the future. It’s about balancing cost, performance, and environmental impact to create spaces that work for people and the planet.”
“And finally, resilient— our world is facing more challenges, like climate change, natural disasters, and even pandemics. Engineers are focusing on designing infrastructure and systems that can bounce back from these shocks. Whether it’s buildings that can withstand earthquakes or cities that can handle floods, resilience is key to keeping communities safe and functional.”
New Zealand has a strong, innovative reputation for innovation, especially when it comes to sustainability and resilience, he says. Given
www.canterbury.ac.nz
our unique environment and the challenges we face, like earthquakes and climate change, we’ve become world leaders in designing disasterresistant structures.
Resilience isn’t just a buzzword here; it’s a necessity. From seismic strengthening to climate-adaptive design, New Zealand engineers are constantly finding ways to future-proof our built environment.
Looking at the industry overall, there’s room for improvement. “One of the biggest opportunities is in research and development. Compared to other countries, New Zealand’s investment in academic research for civil and construction engineering is relatively low. If the government were to increase funding in this area, it could make a huge difference.
“This investment could focus on key areas like technology, automation, sustainability, and industry resilience—all of which align with our national strategy to improve productivity.”
The industry faces massive challenges. Higher building costs and economic uncertainty mean hesitance to start new projects, so fewer opportunities for construction companies and engineers. This has a ripple effect.
“Fewer projects mean less work, and that leads to the last issue—job losses. Unfortunately, when the industry slows down, people lose their jobs, and that’s been really hard on a lot of skilled workers and their families.”
Brian says there have already been many changes in his field since his PhD in 2012. “The next decade will bring even more transformation.
“We’ll see a lot more work on digitalisation, automation,
The industry faces massive challenges. Higher building costs and economic uncertainty mean hesitance to start new projects, so fewer opportunities for construction companies and engineers. This has a ripple effect.
Fewer projects mean less work, and that leads to the last issue—job losses.
and sustainability—these are already big topics, but they’ll become even more critical as we tackle global challenges like climate change and resource scarcity.
Human-robot collaboration and the ethical implications of AI will also be huge areas of study, especially as these technologies become more integrated into our daily lives and industries.”
The latest information from the front lines of industry, media, technology, and commerce.
In line with this, Brian expects education and training to look very different, with a focus on interdisciplinary skills like coding, data analysis, and systems thinking. “Virtual and augmented reality could become standard tools for teaching and research, allowing students and academics to simulate complex scenarios and visualise datain new ways.”
The same goes for researchers. “With so much information and technology at our fingertips, the real challenge will be identifying the right problems to solve and framing them in a way that leads to meaningful solutions.” He predicts openaccess journals will become the norm, bridging the gap between academia and industry and making research more inclusive and impactful.
“At the same time, I think the academic community has started valuing quality over quantity when it comes to publications. Instead of focusing on how many papers someone has published, we’ll care more about the depth, originality, and real-world impact of their work.”
For six decades, Dimond® Roofing has played a leading role in shaping New Zealand’s roofing and cladding industry, transforming both residential and commercial communities through innovative solutions and a steadfast commitment to quality.
Since our inception, our mission has remained clear: to deliver exceptional products and services that not only protect and enhance buildings, but also foster lasting relationships within the communities we serve.
Our reputation as an industry leader is built on a steadfast dedication to quality. Every
Dimond roof is manufactured to the highest standards, with strict adherence to AS/NZS 2728, the NZMRM Code of Practice, and other relevant industry benchmarks. This ensures that every project we undertake is built to last—delivering unmatched protection, performance, and peace of mind for our customers.
At Dimond® Roofing, we believe that innovation drives excellence. Our team of industry experts continually seeks out new technologies and sustainable practices, ensuring that our solutions remain at the fore front. Customer satisfaction is at the heart of everything we do, and our enduring presence in the industry is a testament to the trust our clients place in us.
Environmental responsibility is woven into the fabric of Dimond® Roofing. We are proud to have achieved the prestigious Global GreenTag™ GreenRate™
Customer satisfaction is at the heart of everything we do, and our enduring presence in the industry is a testament to the trust our clients place in us.
“Level A” Certification, highlighting our commitment to reducing our carbon footprint and supporting green building initiatives.
As we celebrate 60 years of excellence, Dimond® Roofing remains dedicated to delivering trusted and quality cladding and roofing solutions with sustainable practices—today, and for many years to come.
By Ben O’Connell
With over 30,000 homes built in New Zealand every year, it’s no wonder the industry battle between timber frames and steel frames is intense.
Members of the timber team say that steel homes have a larger carbon footprint, poor thermal performance, can be susceptible to corrosion and rust, transmit sound more readily within the home, and make your Internet connection spotty, among other reasons.
Supporters of steel frame homes list enhanced fire resistance, design flexibility, and resistance to pests, mould growth and decay as some of the material’s advantages.
Still, interest in light gauge steel frame (LGSF) homes is growing, accounting for 6% of the homes built in New Zealand. Most of our roofs are steel, so why not the frame, too? Greg Jones is the deputy chair of NASH, the National Association of Steel Frames Housing. He refutes many of the common
arguments against steel homes, some of which have fallen as the industry has developed.
One such example is thermal performance. Greg says this is resolved by mandating the level of installation used in a steel-framed home.
“Thermal transfer is not solely a steel frame issue; timber is prone to this,” he says. “Take a look around next autumn and look for the shadows of the studs on the exterior walls of timber homes... that’s thermal transfer.”
Greg cites a current NASH project on moving light gauge steel frame homes into the next generation. “There are some exciting products that can improve efficiency and fit in with the machine manufacturing accuracy of LGSF,” he says.
Another concern about steel frames is that ‘tinny feeling’, but as an LBP carpentry, Greg says there’s nothing tinny about steel framed homes: they fully comply with the New Zealand Building Code, and once the house is lined, there’s no real way of knowing.
Members of the timber team say that steel homes have a larger carbon footprint, poor thermal performance, can be susceptible to corrosion and rust, transmit sound more readily within the home, and make your Internet connection spotty, among other reasons.
He notes that sound transfer needs to be considered no matter what material is used. “Sound does travel through steel, but we aren’t building a railroad,” he remarks. “Using good design and materials that absorb, isolate or deflect sound is essential to creating a liveable environment.
And we cannot ignore money. NASH says that though LGSF can be more expensive than other materials at first, its long-term benefits prove more cost-effective. “In general, we are on par to 10% cheaper than our timber counterparts,” Greg says, especially when you consider every component of a timber frame, down to the last brace and purlin.
Also saving the client, steel frames are typically built quickly, meaning efficiency,
schedule certainty, and pre-punched services, which save time and onsite mess. Builders aren’t as tired at the end of a day working with steel over timber frames.
Greg advises anyone considering a steel home to align with an architect and NASH fabricator. Finding industry experts is crucial. A full 3D model project render will be made so that you can manipulate and see how the rooms will look.
“We are experts in modular building, so plans and details are comprehensive without being incomprehensible,” he says. “Be aware of the hold timber has on our industry and what that means to the information you have been gathering while doing your due diligence.”
x
If you’ve ever wondered what would happen if you blended the practicality of a work ute with the performance of a sports car and the efficiency of an electric vehicle (EV), then the BYD Shark 6 might just be what you’d imagine.
This plug-in hybrid ute is setting a new standard in New Zealand’s traditionally dieseldominated pickup market.
Performance that surpasses expectations It’s fair to say that, as the first plug-in hybrid ute to hit Kiwi shores, the BYD Shark 6 has made a strong impression. The Launch Edition Premium AWD model, which sits alongside heavyweights like the Ford Ranger Sport 2.0 and Toyota Hilux SR5 Cruiser, packs a punch with a combined power output of 321kW from its 1.5-litre turbocharged petrol engine paired with dual electric motors.
The result? An impressive 650Nm of torque and acceleration from 0 to 100km/h in just 5.7 seconds – figures that might make even some sports cars envious.
But the Shark 6 is more than just a powerhouse on the road. It offers up to 100km of pure electric range and a combined range of 800km, making it a great option for long trips or city
commutes. The towing capacity, while not matching diesel rivals at 2,500kg with trailer brakes, is still more than adequate for most needs.
Cutting-edge hybrid technology
At the heart of the Shark 6 is its Super Hybrid technology. This cutting-edge powertrain combines a 1.5-litre turbocharged engine with dual electric motors, achieving performance akin to a 4.0L V8 engine but with far fewer emissions.
With the EHS (Electric Hybrid System) and a dedicated all-wheel-drive powertrain, it offers a thrilling driving experience without sacrificing fuel efficiency.
The BYD Blade Battery, a lithium-ion phosphate (LFP) battery, ensures longer-lasting power, increased range, and improved safety compared to traditional designs. This battery technology makes the Shark 6 a true game-changer in the world of hybrid utes.
As you’d expect, the Shark 6 is packed with modern tech. The V2L (vehicle-to-load) function allows the ute to transform into a mobile power station, making it ideal for powering tools on
job sites or providing electricity in off-grid locations.
Inside, the Shark 6 features an impressive 10.25-inch LCD instrument panel and a rotating 15.6-inch adaptive screen that provides a futuristic and intuitive driving experience. The cabin is designed with comfort in mind, offering heated, ventilated, and electrically adjustable front seats, as well as rear seats that recline by 27 degrees – a feature rarely seen in traditional utes.
Beyond its performance, the Shark 6 doesn’t skimp on comfort. The interior blends luxury with utility, offering what you could say is a refined experience in a traditionally rugged segment, ensuring a comfortable ride, whether you’re navigating city streets or heading out for an adventure.
The Shark 6 integrates the ultra-high safety Blade Battery along with a high-strength steel frame, thanks to BYD’s CTC technology, ensuring occupants are protected in the event of a collision. The vehicle also comes with a range of advanced safety features, including hill hold control, vehicle dynamic control, and hill descent control, providing enhanced peace of mind for drivers.
The BYD Shark 6 is something entirely new for the New Zealand ute market, bridging the gap between traditional ute capability and the modern demand for hybrid efficiency.
While its towing capacity might not match that of its diesel counterparts, the Shark 6 offers impressive performance, genuine electric-only range, and a suite of innovative features that make it a compelling choice for city tradies, lifestyle buyers, and anyone looking to reduce their carbon footprint without sacrificing utility.
Competitively priced against high-spec traditional utes, it delivers a sophisticated blend of power, technology, and efficiency that could very well reshape what people expect from a modern ute.
For those ready to embrace electrification without compromise, the Shark 6 is worth serious consideration.
Premium Launch
Edition: $69,990
EV Range: Up to 100 km
Fuel Economy: 2.0/100km
Combined Range: Up to 800 km
from BYD.
www.agrisolar.co.nz
1.2kw Victron Off Grid Solar Package for Sheds/Workshops Led lighting and charging power tools Installed Package $8,000
2.4kw Off Grid Solar Package for Tiny House/Shed/Workshop Installed Package $18,000
5kw Victron Off Grid Solar Package for 1-3 Bedroom house or Lifestyle shed Installed package $30,000 :
8kw Victron Off Grid Solar Package for 2-4 Bedroom House or Lifestyle Shed Installed Package $50,000 :
12kw Victron Off Grid Solar Package for 3-5 Bedroom House or Lifestyle shed Installed package $68,000
5kw Grid Tied packages from $12,000 : 8kw Grid Tied packages from $18,000
Are you looking to enhance the safety, security, and style of your Waikato/South Waikato home?
Look no further than South Waikato Garage Doors, the only local Matamata/South Waikato Garage door company in the region. With 46 years in business, we are dedicated to providing top-quality garage doors that not only protect your home but also elevate its aesthetic appeal.
At South Waikato Garage Doors Ltd, we pride ourselves on offering an extensive range of garage doors to suit every need. Whether you’re in the market for sectional doors, tilta doors, roller
doors, or even commercial and industrial options, we have you covered. Our rural garage door solutions and comprehensive range of garage door parts ensure that we can meet any requirement.
Our installation service is second to none, guaranteeing a seamless and professional experience from start to finish. We don’t just install; we also service and repair all makes and models of garage doors and automatic openers. This means you can rely on us for
all your garage door needs, ensuring they remain in perfect working condition for years to come.
We are dedicated to providing top-quality garage doors that not only protect your home but also elevate its aesthetic appeal.
At South Waikato Garage Doors Ltd, we stand by our commitment to quality. We offer professional service with a team of qualified staff, ensuring every job is completed to the highest standards. We use only the
best materials to guarantee durability and performance. Our skilled installers take care to leave your premises tidy upon completion. Your satisfaction is our priority, and we go above and beyond to exceed your expectations.
Transform your home with a stunning new garage door from South Waikato Garage Doors Ltd. Contact us today for a free quote and experience the difference that quality and local expertise can make. Call us at (07) 888 8715 or visit us at Shed 2 – 12 Short St, Matamata 3400.
For safety, security, and style, trust South Waikato Garage Doors Ltd – where excellence is just a call away.
By Ben Kennedy
New Zealand’s apprenticeship system is falling short in providing clear pathways for young people entering the workforce.
Only 6% of school leavers pursue apprenticeships, while nearly twice as many—11% of 16- to 19-yearolds—are not engaged in employment, education, or training. A new report from The New Zealand Initiative, Trade Routes: Charting New Pathways from Secondary School to Industry Training, highlights systemic weaknesses and calls for urgent reforms.
The report reveals that vocational education in New Zealand is fragmented, with no structured pathway equivalent to university preparation. “Schools are primarily geared toward university-track education, even though only about onethird of school leavers enrol in degree programmes,” says Dr. Michael Johnston,
the report’s author. He argues that New Zealand’s system fails to integrate apprenticeships into mainstream education, leaving many young people without a clear direction.
Johnston points to Germany’s ‘dual training’ apprenticeship system, which, in contrast, sees nearly half of all school leavers enter workplace-based training. Approximately 93% of those trainees graduate, and threequarters are immediately employed by the companies where they trained. Ultimately, New Zealand’s weak apprenticeship uptake, combined with a high number of young people disengaged from education and work, is indicative of a significant waste of human potential.
The cultural and structural barriers
One of the biggest challenges to apprenticeship growth in New Zealand is a deep-seated cultural bias toward university education.
University degrees are widely regarded as the superior pathway, a perception reinforced by parents, teachers, and schools. The secondary school curriculum is designed primarily to prepare students for university, offering little structured support for those interested in vocational training.
Johnston argues that this bias is further embedded by the qualifications system.
“The University Entrance qualification illuminates the way to university, but there is no qualification to do the same for trades,” he notes. The report suggests that an equivalent qualification, such as a Certificate of Trades Preparation, could help place vocational training on equal footing with university education.
Another challenge is the lack of coordination between secondary education and industry training. While initiatives such as Trades Academies and the Gateway program provide opportunities for students to gain industry experience,
they function as fragmented “add-ons” rather than forming a cohesive pathway. The Trade Routes report suggests that these initiatives should be unified under a single, structured vocational education pathway. Fixing the system
The Trade Routes report outlines several key reforms that could improve apprenticeship pathways in New Zealand. Among them is a recommendation to restructure Workforce Development Councils, which currently oversee standard-setting for industry training. The report suggests that Workforce Development Councils should be reconstituted with members elected by industry bodies rather than appointed by government ministers. This would increase their accountability and ensure that vocational education aligns with employer needs.
Another recommendation is to establish cooperative arrangements between secondary schools,
Continued over page >
Use the most cost effective and easiest job site in New Zealand. Now with a new and improved website making things even easier, ensuring you get quality applicants, every time!
Purchase 1 ad (for 1 month) for $157+gst or unlimited ads for 12 months for $1597+gst
100% money back guarantee if you don’t think it’s the best money you’ve spent all year, plus we’ll give you another 12 months free!
Include your company profile so applicants can see why they want to work for you! (once again, other companies charge for this)
allowing them to specialise in different educational pathways. This would mean that some schools could focus on university preparation while others develop strong vocational training programs. Johnston believes this approach could help normalise apprenticeships as a mainstream option rather than a fallback for students who struggle academically.
BusinessNZ has also voiced support for greater investment in apprenticeship training. Chief Executive Phil O’Reilly has praised the government’s efforts to boost funding and incentives for apprenticeships. However, he warns that “higher educational content will need to complement – not replace – practical elements of the training.” Employers, he argues, need a system that produces wellprepared apprentices with hands-on experience.
changes target apprenticeship completion
The Government has introduced two major policy changes for 2025 that could impact apprenticeship retention and completion rates.
First, changes to the Fees Free program will shift funding from the first year of study to the final year of training. Under the new system, apprentices who have not previously used Fees Free funding may have their last year of study covered, with fees reimbursed up to $12,000 upon completion. This adjustment is aimed at reducing dropout rates and ensuring more apprentices reach their qualifications.
Germany’s dual training apprenticeship system is frequently cited as a model of success, with half of all school leavers entering workplace-based training.
The program combines structured classroom learning with paid, on-the-job training, ensuring that apprentices develop industry-specific skills while gaining practical experience.
Second, the Apprenticeship Boost program will be refocused on first-year apprentices in high-demand sectors. From January 2025, employer subsidies will only be available for apprentices in industries deemed crucial to New Zealand’s economic growth, including construction, engineering, agriculture, and food production. While some see this targeted funding as a positive step, critics warn that it could leave other industries struggling to attract apprentices.
Could New Zealand adopt the German model?
Germany’s dual training apprenticeship system is frequently cited as a model of success, with half of all school leavers entering workplace-based training. The program combines structured classroom learning with paid, onthe-job training, ensuring that apprentices develop industry-specific skills while gaining practical experience. Johnston acknowledges that fully replicating Germany’s system in New Zealand is neither politically nor culturally realistic. However, he believes key elements— such as closer industryschool collaboration, a clear apprenticeship qualification, and stronger financial support—could be
successfully adapted to the New Zealand context. One potential model for reform comes from Australia’s ‘Busy Schools’ initiative, which helps students transition into the workforce. Busy Schools provides workreadiness education, part-time internships, and structured pathways into apprenticeships. Johnston suggests that a similar approach in New Zealand, possibly through the 2025 charter school initiative, could provide clearer routes into vocational training.
Economic and social benefits
Expanding and strengthening apprenticeships would not only benefit young people but also address pressing economic challenges. New Zealand faces ongoing skills shortages in key industries such as construction, manufacturing, and agriculture. A more robust apprenticeship system would help fill these gaps while reducing youth unemployment.
Furthermore, apprenticeships offer young people a financially viable alternative to university study. Unlike university students, who often accumulate significant debt, apprentices can earn while they learn, gaining work experience without
taking on student loans. This makes apprenticeships particularly attractive for hands-on learners and those who struggle in traditional academic settings.
A stronger apprenticeship system would also improve industry engagement in education. Employers directly involved in training programs can ensure that graduates possess the skills needed in the workforce. This reduces the mismatch between education and industry needs, leading to better employment outcomes.
Addressing New Zealand’s apprenticeship gap will require coordinated action from government, schools, and industry leaders. Education policy must shift to place apprenticeships on an equal footing with university education. Schools must promote vocational pathways as a respected and viable option for students. Employers must be given incentives to take on apprentices and invest in training programs.
Johnston believes that systemic reform is necessary to change the perception of apprenticeships. “If clearer pathways from school to industry training were established as a serious option for all students, esteem for industry training would gradually improve,” he argues.
With recent policy changes and growing pressure for reform, the opportunity to reshape New Zealand’s apprenticeship system is now.
• SOLAR ENERGY PLANNING
• FULL SYSTEM DESIGN
• SOLAR SYSTEM QUOTATION
• SOLAR PREWIRE SERVICES
• FULL INSTALLATION SERVICES
• BATTERY BANK REPLACEMENT
• FULL COMPLIANCE
With a long and successful career in real estate, Glenda has built a reputation for delivering outstanding results across both lifestyle and residential markets. Specializing in high-value properties, she applies the same dedication, professionalism, and attention to detail to every client, ensuring that each transaction is handled with care and expertise, regardless of the property’s price point.
Living in the Hinuera Valley with her husband, Mark, on their family dairy farm, Glenda has a deep connection to the local community and a firsthand understanding of rural living. Her background in agribusiness, combined with her National Certificate in Agribusiness Management, equips her with unique insights into the needs of lifestyle property buyers and sellers.
Originally from South Africa, Glenda moved to Matamata in 1997 and has had a diverse and accomplished career. She started as a legal
secretary specializing in conveyancing before advancing to a registrar role within the Labor Court system. She later spent two decades in the optical industry, qualifying as a contact lens technician and dispensing optician.
In 2006, Glenda transitioned into real estate, drawn to the dynamic nature of the industry and the opportunity to help clients achieve their property goals. After taking time to raise her family, she re-licensed and joined Bayleys Matamata, where she continues to thrive. Her extensive professional background enables her to navigate complex transactions with confidence, while her warm and approachable manner ensures a seamless experience for buyers and sellers alike.
If you’re looking for a real estate professional with proven expertise, local knowledge, and an unwavering commitment to achieving the best results, Glenda is the trusted choice.