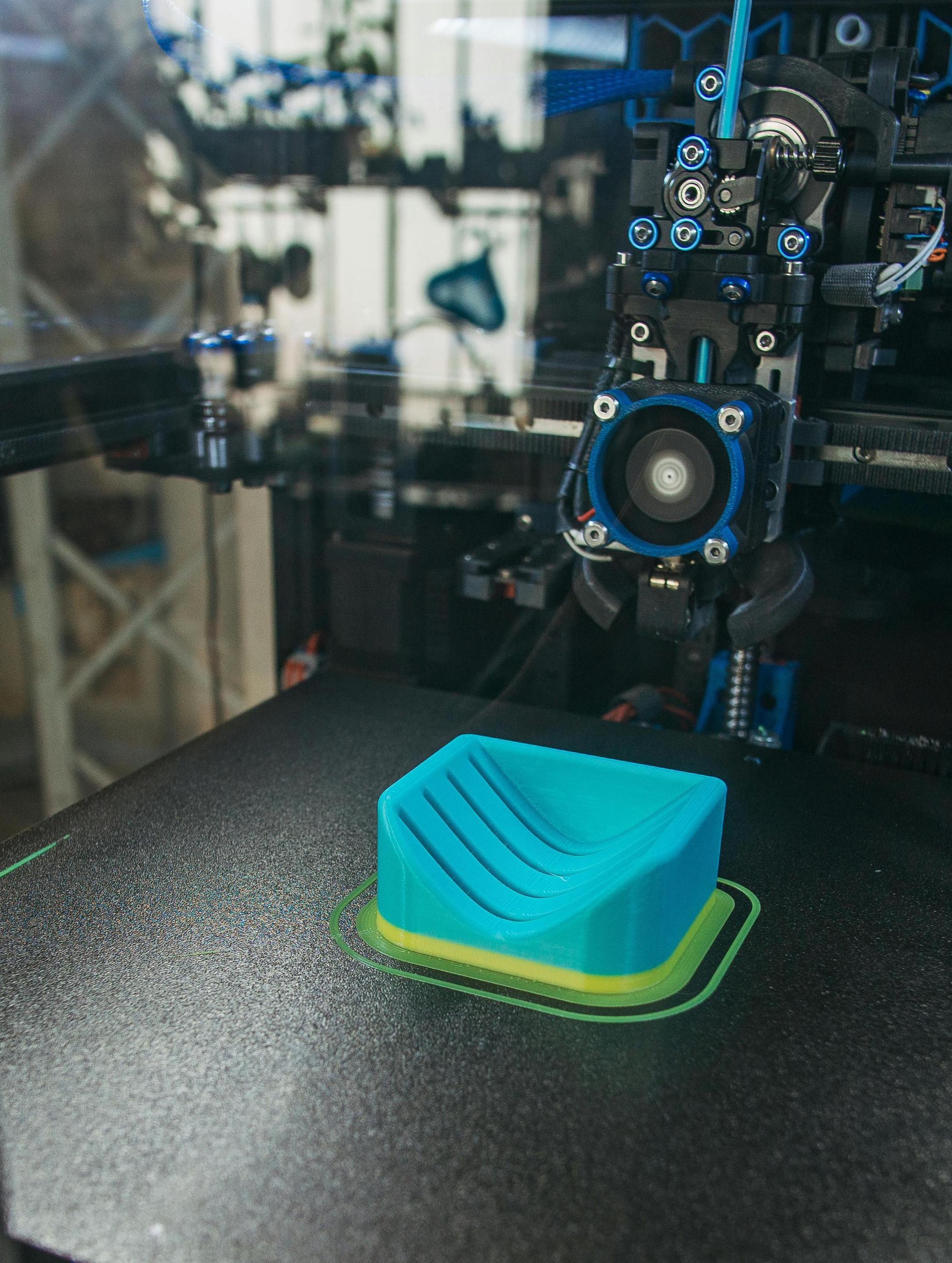
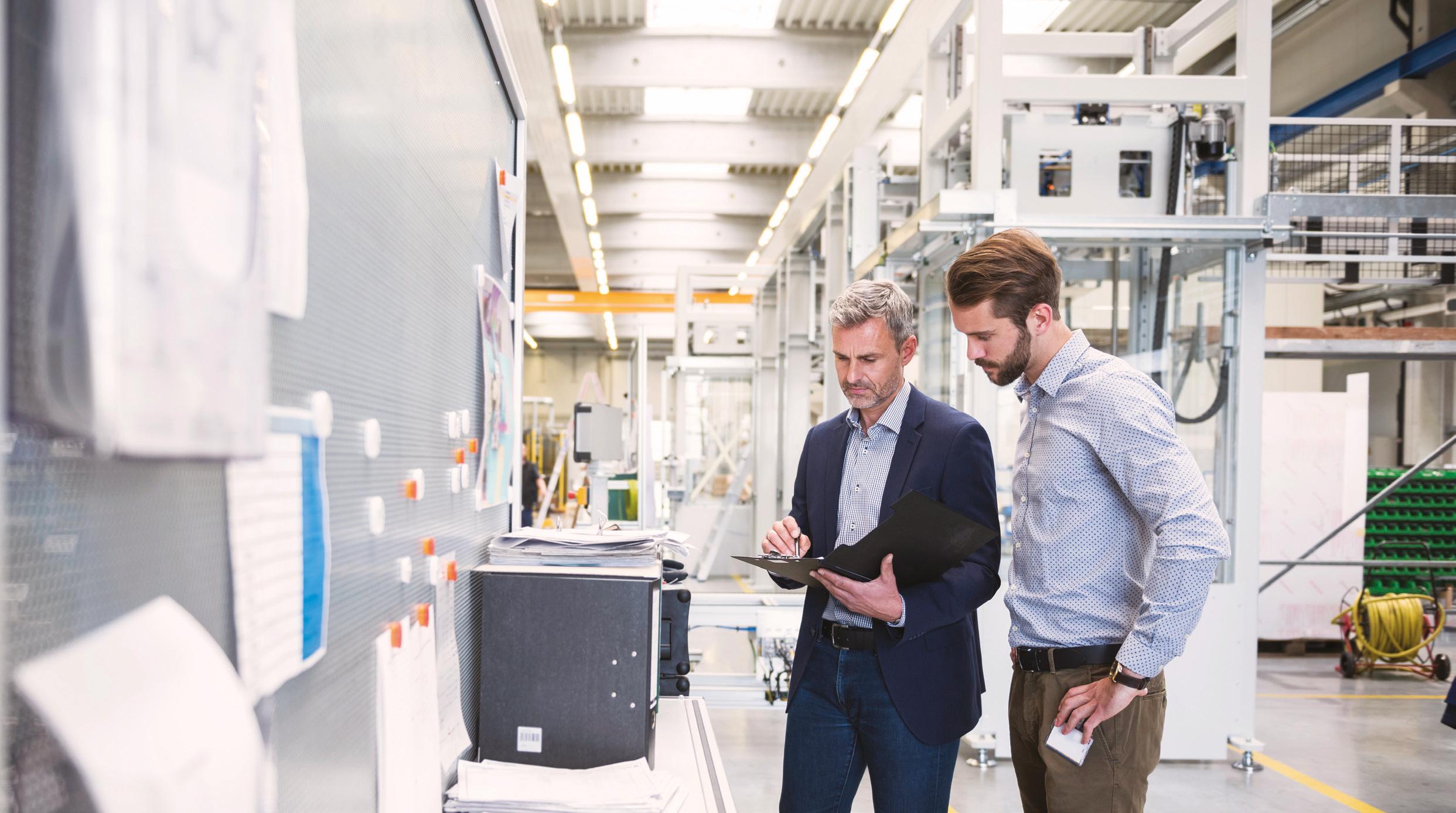
As one of the largest and most experienced insurance brokers in the world, Gallagher can offer you a complimentary review of your existing insurance programme. Our team can provide detailed insights on how your business benchmarks against others in the industry, identify potential coverage gaps and recommend the appropriate values and limits for your policies. Additionally, with improving market conditions, we may be able to highlight opportunities where you could save on costs.
CONNECT WITH A SPECIALIST TODAY.
For further information, please scan the QR code.
Editor
Paul Attwood editor@mpemagazine.co.uk
Senior Editorial Assistant
Sophie Weir editorial@mpemagazine.co.uk
Features Editor
Harry Peters editorial@mpemagazine.co.uk
Production/Design
Laura Whitehead laura@lapthornmedia.co.uk
Sales Manager
Charlotte Chapman charlotte@mpemagazine.co.uk
Accounts
Richard Lapthorn accounts@lapthornmedia.co.uk
Circulation Manager
Leo Phillips subs@mpemagazine.co.uk
Publishing Director
Maria Lapthorn maria@lapthornmedia.co.uk
Lapthorn Media Ltd
5-7 Ozengell Place, Eurokent Business Park, Ramsgate, Kent, CT12 6PB
Tel: 01843 808 102
UK Shoppers Call for More British-Made Products, Survey Finds Show Preview: Sneak Peek into UK Metals Expo 2025
James Newby, NMITE, on Redefining Higher Education for Industry Readiness Show Preview: Registration Opens For The PPMA Total Show® 2025
Aston University & MTC Form Partnership to Boost UK Manufacturing Innovation
Welcome to the latest issue of Manufacturing & Production Engineering magazine.
This edition previews three key industry events. First is IMHX 2025—the UK’s biggest logistics event—taking place 9–11 September at NEC Birmingham. Next is UK Metals Expo, the leading trade show for the metals supply chain, at the NEC on 10–11 September. We also look ahead to the PPMA Show, the UK’s largest processing and packaging machinery event, returning 23–25 September.
We also feature an interview with James Newby of NMITE on reshaping higher education for industry needs.
We hope you enjoy this issue. If you have news to share, please get in touch at editorial@mpemagazine.co.uk.
mpemagazine.co.uk
A recent YouGov poll commissioned by Made in Britain reveals nearly half of UK consumers want to see more domestically made products available in shops and online. Of the 2,000 respondents, 46% said they would be more likely to buy British if prices were more competitive, while 45% cited lack of availability as a barrier.
The findings come as new UK trade agreements with the US, EU, and India are expected to lower import costs and increase competition for domestic manufacturers.
Labelling also plays a role in purchasing decisions, with 44% of respondents saying clearer ‘Made in Britain’ branding would encourage them to buy UK-made products. One in five consumers said they would be more inclined to buy British if fewer imported goods were available in shops.
John Pearce, CEO of Made in Britain, said that while trade liberalisation could increase competition, consumer and retailer support will be more impactful than tariffs:
“Rather than relying on protectionist policies, we’re urging retailers to respond to public demand by stocking and promoting more British-made goods.”
Made in Britain, which represents over 2,160 UK manufacturers, supports members with a certified trademark recognised by 50% of UK adults. The organisation is backing a ‘Buy British’ campaign and has written to political leaders to advocate for greater visibility of UK-made products.
For more information on the Made in Britain campaign, visit the website: www.madeinbritain.org
Seco Tools has partnered with the Advanced Manufacturing Research Centre North West (AMRC) in Samlesbury, UK, on a project aimed at improving sustainability in machining through real-time data intelligence.
The collaboration focuses on capturing and analyzing machine and facility-level data to better understand energy consumption and environmental impact across three levels: the machining process, the machine environment, and the broader manufacturing facility.
The system tracks machine-level energy use, material consumption, and cutting fluid data, then translates this into real-time cost and CO₂ metrics using live grid carbon intensity factors. Environmental factors such as humidity and temperature are also monitored for their influence on energy efficiency.
By correlating machine behavior with environmental and facility conditions, the project seeks to uncover patterns that can drive carbon and cost reductions specific to each operation. The setup enables detailed power and emissions analysis of individual machining programs and supports lifecycle assessments across both Seco and third-party machines.
Future phases of the initiative aim to implement AI-powered feedback loops for real-time optimization of machining strategies, balancing productivity with environmental performance.
This project supports Seco’s broader goal of enabling sustainable manufacturing through data-driven insights and process automation.
Europe’s push for digitalised manufacturing has made the industry a prime cyberattack target, according to a new report from cybersecurity firm KnowBe4. Released on July 10, “Securing Manufacturing’s Digital Future” highlights how increased automation, smart factories, and interconnected supply chains have expanded the sector’s attack surface — leaving critical operations and intellectual property at risk.
The report reveals manufacturing remained the most targeted industry
for ransomware attacks from 2023 to 2024, citing its low tolerance for downtime as a key vulnerability. Even brief disruptions can cause severe financial losses and ripple effects across supply chains.
Among the findings:
• Confirmed data breaches in manufacturing surged by 89.2% between 2023 and 2024.
• Ransomware accounted for 47% of these breaches, with groups like LockBit and PlayCrypt frequently targeting European manufacturers.
• Social engineering attacks, including phishing, were responsible for 22% of breaches — underscoring the human element as a major security gap.
Javvad Malik, lead security awareness advocate at KnowBe4, stressed that many breaches stem from human error rather than technical flaws.
“Cyber resilience isn’t just about patching systems — it’s about equipping employees to recognise and stop threats before they escalate,” he said.
The report also showed the effectiveness of training in reducing risk. Over a year of consistent
Cyber resilience isn’t just about patching systems — it’s about equipping employees to recognise and stop threats before they escalate.
- Javvad Malik
security awareness training, phishing susceptibility dropped from nearly 32% to under 4%.
With the manufacturing sector increasingly vital to Europe’s economy, KnowBe4 warns that failure to address cyber risks now could lead to widespread disruption — not just within companies, but across supply chains and national infrastructure.
The UK Government’s new 10-year Industrial Strategy puts advanced manufacturing among its eight key sectors for economic growth, alongside industries like financial services, clean energy, and life sciences. Backed by promises of investment in digital transformation and skills, the strategy has been broadly welcomed by a manufacturing sector struggling with labour shortages, inflation, and supply chain disruption.
A key feature is a £40 million Robotics and Autonomous Systems (RAS) programme, aimed at establishing a network of Robotics Adoption Hubs. These centres will give manufacturers access to expertise, equipment, and support
to adopt robotics with lower risk — a critical step for many firms, especially SMEs, still lacking the digital maturity to embrace advanced technologies.
However, James Watson, Partner, and Rachel Noll, Data & AI Manager at IRIS at Argon & Co, stress that successful smart manufacturing demands more than just technology. It requires a structured journey towards operational visibility and data-driven decision-making.
That journey, they argue, starts with consistent operational metrics — even if captured manually — to enable visibility and highlight problem areas. The next phase involves automating data capture and using visual tools to spot trends. With a solid data foundation,
predictive analytics can then forecast potential issues, allowing firms to act before problems arise.
Prescriptive analytics follows, recommending specific actions based on historical patterns, though still relying on human oversight. Ultimately, the goal is a self-optimising system, where automated responses adjust operations in real-time.
Yet, no strategy or system works without people. Resistance to change remains a hurdle, and human judgment is critical to contextualising data. As Watson and Noll emphasise, the future of smart manufacturing relies on the right balance between human insight and machine intelligence — a challenge the new Industrial Strategy must help manufacturers overcome.
The ripple effects of global events have amplified economic volatility, heightening the risk of non-payment for businesses.
Nearly 50% of all B2B transactions in the UK are offered on credit, and recent statistics show 51% of B2B invoices are overdue, with 7% being a bad debt. This can place a growing concern on the financial health of a company if payments are not received on time, or not at all.
With many businesses under significant pressure to manage increasing expenses and find growth opportunities, Trade Credit insurance can offer a vital safety net to help protect against the uncertainties of non-payment and bad debts. It can also support businesses in other ways with managing their budgets, future business plans and corporate governance obligations, benefitting both investors and stakeholders. Colin Cunningham, Gallagher’s National Client Development Leader for Trade Credit, explains how Trade Credit Insurance can help protect your business.
Maintaining a steady cash flow is essential for operational efficiency and strategic planning. Trade Credit insurance can ensure that receivables are protected, offering companies the confidence to plan and invest without concerns regarding the repercussions of unexpected financial disruptions.
In every economic climate, whether stable or uncertain, Trade Credit Insurance can help safeguard your business against the risk of nonpayment, empowering you to trade with confidence, invest strategically, and grow sustainably.
— Colin Cunningham (pictured right), National Client Development Leader, Gallagher Trade Credit
Financial institutions may also view insured receivables favourably. When a business is found to have adequate protection against potential defaults on buyer payments, it enhances their creditworthiness. This can result in better access to financing and more favourable terms to support operations and the ability to seize opportunities with confidence.
As trade credit insurers track the financial health of companies, they can provide important, and early information and notifications on the likelihood of a customer default. This can assist a business to reduce exposure by avoiding further credit extensions to a particular supplier or buyer.
With Trade Credit insurance, companies can gain a competitive edge in the market by providing easier credit terms to their
customers and entering new markets, knowing they are appropriately protected against potential debt repayment defaults. This could help to solidify new customer relationships and facilitate market expansion.
A single instance of non-payment can trigger a chain reaction, commonly known as the ‘domino effect’. This occurs when the insolvency of one company raises the likelihood of other related companies, such as suppliers, debtors, and customers, to experience cash flow difficulties due to unpaid debts from the initial insolvency. This effect can be felt throughout the supply chain and take place over many years.
As one of the largest trade credit insurance brokers in the UK, we have a team of highly skilled and experienced specialists who understand the complexities of the market. With strong relationships with a wide range of reputable UK and global trade credit insurers, we can work with you to design a customised solution that aligns with your risk appetite and business objectives.
If you would like to speak to Colin and the team about Trade Credit insurance, please scan the QR code.
By Mark Withers, senior purchasing technician at King’s College London
The UK’s science sector faces a critical lab space shortage. This is especially true in the golden triangle region including London, Oxford and Cambridge. There are 6.4 million square feet of laboratories in the pipeline within the triangle, but it’s still not enough. Mark Withers, senior purchasing technician at King’s College London, explores how laboratories can adapt to ease the pressure, while industry must step up to meet the growing challenge.
A rising demand, a shrinking footprint
The government is pushing for the UK to become a ‘science superpower’, but infrastructure is not keeping pace.
There’s a strong push in personalised treatment and gene therapy, which involves modifying our own cells and genes. These manufacturing facilities need to be located close to the patient and in a controlled clean room environment.
- Jennifer Townsend
Several factors contribute to the shortage, but the most significant is the rapid growth of the scientific research sector. Scientific publications are increasing at an exponential rate of 5.6 per cent per year.
A surge in ‘mega-science’, that is large-scale, expensive research projects that rely on international collaboration, has only accelerated since the mid-20th century. Landmark initiatives like the Human Genome Project set a precedent for this kind of research, pushing demand for lab space in a direction that shows no sign of slowing.
As science advances, new specialisms continue to emerge, including clinical bioinformatics and clinical scientific computing. These fields add to the growing demand for research space.
“We’re seeing exciting treatments coming to the commercialisation stage that need to be manufactured” explained life sciences specialist Jennifer Townsend on the Intelligence Talks podcast.
“There’s a strong push in personalised treatment and gene therapy, which involves modifying our own cells and genes. These manufacturing facilities need to be located close to the patient and in a controlled clean room environment. It’s more conducive to carry this out domestically rather than relying on large global supply chains.”
The shift of the sector for domestically placed manufacturing reduces the research space available for research expansion. Retrofitting existing spaces is an option, but not always a realistic one. Costs can reach £500 to £4,000 per square metre. In a sector where budgets are already tight, the scientific community focuses heavily on efficiency, finding ways to make the most of the space they already have.
Scientific academia has long shared equipment, a collaborative mindset that helps maximise space and budget. Companies like UniGreenScheme collect, repair and resell lab equipment from across the UK. Instead of letting old instruments sit idle in storerooms, labs can offload unused items and free up much-needed space.
The scientific community is clear; if the UK is serious about becoming a science superpower, the spaces and systems supporting that ambition must be built with intelligence, efficiency and long-term flexibility in mind.
At King’s College London, its researchers are making full use of the scientific community’s collaborative spirit. When two of their X-ray machines went down, they reached out to the Natural History Museum, which offered access to its own facilities. This arrangement helped maintain research continuity while KCL worked to restore its own X-ray capacity.
Innovation from the inside out
The scientific industry is also responding to these spatial challenges. Compact equipment is the preferred choice for labs trying to do more with less. Hydrogenators that once took up four feet of fume hood space are now just one foot wide.
Footprint, not height, is often the constraint. Slim, tall designs use space more efficiently. IKA has begun to move in this direction with vertical vacuum pumps. Even something
as simple as placing a PC on top of equipment rather than beside it makes a difference. When computers are built into the equipment, the saving is even greater.
For smaller or startup labs, modular systems offer flexibility to expand gradually, based on space, budget and research needs. Eppendorf’s modular PCR machine is one example: it’s designed to scale over time, allowing labs to start small and build up as demand grows, rather than committing to an oversized system from the beginning.
Plug-and-play systems are also growing in popularity. Mobile equipment makes it possible to convert underused areas into functioning lab space. These setups are especially useful in teaching labs, where the space often needs to adapt day by day.
As demand continues to rise and space remains tight, adaptability is no longer a bonus but a requirement. The scientific community is clear; if the UK is serious about becoming a science superpower, the spaces and systems supporting that ambition must be built with intelligence, efficiency and longterm flexibility in mind.
To discover how the scientific community is col-LAB-orating on industry challenges, visit Lab Innovations on October 29 and 30.
By Dave Walsha, sales and marketing director at industrial gearbox manufacturer Electro Mechanical Systems
In Odense, Denmark, construction is underway on a new Large Structure Production (LSP) Centre. The facility will be dedicated to developing specialised automated equipment for heavy industry — a sector that has remained largely manual due to its harsh environments and the need for tools that can withstand extreme conditions while performing complex, high-force tasks. Here, Dave Walsha, sales and marketing director at industrial gearbox manufacturer Electro Mechanical Systems, explains why enabling the shift to automation starts with the right components.
Automation has transformed many industries by enabling faster production, improving consistency and reducing operational costs. However, sectors such as construction, shipbuilding and metal casting have yet to benefit fully. Unlike standard manufacturing environments, these sectors face harsh and unpredictable conditions, which have limited the feasibility of automation.
A 2018 McKinsey survey found that 88 per cent of heavy industry respondents planned to automate operations. Yet, progress has been slow. A 2024 Siemens
thought leadership piece suggests the challenge lies in developing equipment robust enough to operate in such environments.
Heavy industrial settings differ significantly from controlled factory floors. Equipment must endure dust, heat, moisture, shock and vibration — all of which can cause rapid degradation and system failure. To overcome this, automation in these sectors must be built from the ground up, beginning with custom components.
Gearboxes, which translate motion, torque and speed within systems, are crucial to automation. However, in heavy industry, offthe-shelf gearboxes often fail due to environmental and mechanical stresses like thermal fluctuation, particulates, and vibration. Custom gearboxes are therefore essential.
Designing a custom gearbox begins with analysing the application’s torque, speed, motion type and electrical needs. Then, environmental factors such as operating temperatures, dust or moisture exposure, and spatial constraints are considered. These determine material choices, sealing systems and gear tooth profiles — all tailored to ensure strength, wear resistance and efficient power transmission.
Engineers use CAD tools, gear modelling and thermal simulation to prototype and refine the design. The goal is to create a gearbox that withstands shock loads, minimises backlash and ensures long-term operational stability.
Custom gearboxes unlock automation’s potential in heavy industry. For instance, robotic gripper arms lifting large, hot or irregular components benefit from reinforced shafts, oversized bearings and low-backlash helical gears. These features absorb shock and provide precision, improving safety and reliability.
AGVs, increasingly used for internal logistics, must cope with heavy loads and uneven terrain. Custom gearboxes with high torque density and compact planetary stages allow AGVs to operate in tight spaces, on ramps and under load — extending automation’s reach.
CNC machines in heavy industry face constant vibration and heat while cutting hard metals. A custom gearbox with low thermal expansion materials and multi-stage gearing maintains cutting accuracy and component quality over long production runs.
The LSP Centre marks a key step toward automation in heavy industry — but real progress starts at component level. With the right gearbox, specialised automation becomes possible, even in the most demanding environments.
Bottom images: From Stone Junction/ EMS — stock.adobe.com
One of Sheffield’s newest manufacturers is helping to revitalise the city’s industrial capabilities with cutting-edge materials processing technology.
Sheffield Technology is winning a growing customer base, with some key projects being attracted back to the UK from overseas. The company is eager to leverage its ability to rapidly laser-cut materials up to 60mm thick— made possible by the company’s investment in a state-of-the-art 24kW Trumpf 5060 TrueDisk laser.
With fully automated material and part handling, this machine boasts a 6-metre by 2-metre plate capacity and can cut: Stainless steel, armour, carbon, and alloy steels – up to 60mm thick, Aluminium – up to 40mm, Copper – up to 16mm and Brass – up to 12.7mm.
Beyond laser cutting, Sheffield Technology’s extensive fabrication and machining capabilities include a
400-tonne, 5.1-metre press brake and automated cobot welding, allowing the company to deliver fully integrated manufacturing solutions.
Darren Mason, Works Director at Sheffield Technology, explained: “The big advantage for us is that we have truly disruptive technology. Our high-power laser operates at a scale and precision that challenges conventional thinking. While most lasers struggle beyond 30mm, we comfortably cut up to 60mm, allowing us to compete on both quality and cost with traditional heavy-duty processes, such as plasma & profile cutting.”
The company’s rapid expansion is reflected in its workforce growth, scaling from just 10 employees last year to 58 today, including four apprentices. With a firm commitment to developing future talent, Sheffield Technology plans to expand its apprenticeship program to pass on engineering skills that have defined the city for generations.
Darren commented: “We’re proud to be back in Sheffield, helping to underpin its metal processing history, and we trust the city will continue to attract work from across the country and beyond. Our capacities and state of the art equipment really do support continued competitiveness within the UK in this important sector, underpinning jobs for our young people in the years ahead.”
Sheffield Technology’s innovation and investment in advanced manufacturing can only support the city remaining at the forefront of British materials processing & manufacturing industry. Visit: www.sheffield-tech.com
HORIBA has opened a new Analytical Solution Plaza at MIRA Tech Park in Nuneaton, adding a UK-based hub to its global network of technical collaboration centres.
FANUC UK has named YMT Technologies as its official UK dealer for the ROBODRILL range of compact CNC machining centres. The partnership will see YMT support customers across the Midlands and southern England, particularly in sectors such as medical, aerospace, automotive, and electronics.
ROBODRILL machines are known for their high speed, accuracy, and compact design, making them suitable for precision tasks like drilling, milling, and cutting.
The appointment builds on an established relationship between the two companies, with YMT having previously integrated FANUC industrial robots into its CNC metal cutting solutions.
The 290 m² facility will serve as a resource across HORIBA’s business divisions, providing access to advanced analytical technologies for applications ranging from biopharmaceuticals and clean energy to advanced manufacturing, diagnostics, and environmental monitoring.
Opened by HORIBA Group Chairman and CEO Mr. Atsushi Horiba and British Ambassador to Japan, Her Excellency Julia Longbottom CMG, the centre is designed to support both commercial and research communities. A traditional kagami biraki sake barrel ceremony marked the occasion.
The site features demonstration zones by technology capability, a chemistry lab, and flexible event space. It will host feasibility studies, product trials, technical training, and STEM outreach activities.
Technologies on show include chemical imaging at micro and nano scales, spectroscopy, fuel cell and battery testing, particle analysis, water quality monitoring, and gas analysis for industrial and environmental use.
The Plaza will also offer contract analytical services, building on HORIBA’s existing
presence in the UK, where it employs over 800 people.
Located at MIRA Tech Park—home to over 1,500 specialists in areas such as autonomous systems, clean mobility, and AI—the facility is positioned to enable crosssector collaboration.
Dr. Simon FitzGerald FRSC, who leads the new centre, said the Plaza provides customers with “a gateway to the full breadth of HORIBA’s global technological capabilities.”
For more information about HORIBA in the UK, visit: www.horiba.com/gbr
Pictured from left to right: Managing Director of HORIBA MIRA and HORIBA Corporate Officer, Mr. Declan Allen, Envoy Extraordinary and Minister Plenipotentiary of Embassy of Japan, Mr. Masaki Ikegami, British Ambassador to Japan, Her Excellency Ms. Julia Longbottom CMG, Chairman and HORIBA Group CEO, Mr. Atsushi Horiba, and President of HORIBA UK and HORIBA Corporate Officer, Mr. Stuart Knight open HORIBA’s newest Analytical Solution Plaza in Nuneaton to give UK scientists ready access to the global company’s breadth of technological capabilities.
Quartzelec continues to strengthen its position as a trusted provider of electrical and mechanical engineering services across critical industries including power generation, transport, renewables, and industrial manufacturing.
Over the past year, the company has expanded its international presence, establishing a new subsidiary in Spain to improve service delivery within the EU and relocating its Middle East operations to a larger, betterequipped facility in Abu Dhabi. In Southeast Asia, efforts to grow its client base—particularly in the Philippines—are progressing strongly.
At home, Quartzelec remains committed to workforce development, increasing headcount and welcoming 30
new apprentices. Its in-house QuartzAcademy continues to deliver training in technical, safety, and leadership skills to support long-term capability building.
Despite ongoing global challenges, the business has maintained a clear focus on service quality, operational agility, and sustainable growth. Its decentralised model allows local teams to respond quickly to customer needs, supported by robust central functions.
Managing Director Stephen Morrison emphasised the company’s commitment to delivering engineering excellence while developing future talent and investing in capabilities that support longterm resilience and international growth.
The Must-Attend Event for Metal Manufacturers and Engineers this September at the NEC Birmingham
UK Metals Expo (www. ukmetalsexpo.com) returns 10 and 11 September 2025 at the NEC Birmingham, uniting the entire metals supply chain with the manufacturing and engineering community.
Since its 2022 launch, UK Metals Expo has become the essential meeting place for fabricators, stockists, production specialists, procurement teams, engineers, researchers, manufacturers, and policymakers. It’s where the industry comes together to collaborate, share ideas, and do business in a welcoming, engaging environment.
At UK Metals Expo 2025, you can meet face-to-face with leading suppliers and top technical experts ready to tackle your project challenges and deliver tailored solutions. Expect live machinery demos, automation, robotics, and AI-powered technology, plus cutting-edge materials, coatings, and processing systems.
This year’s event is bigger than ever, with over 320 exhibitors confirmed including Tata Steel, ArcelorMittal, Hydro Aluminium, Epicor, Marcegaglia, Outokumpu, Peel Ports, MEPS, Swiss Steel, Bystronic UK Ltd, KASTO Ltd, Metal Supermarkets, Steel Dynamics Group, Air Products Plc, Premier Steel Stockholding Ltd TW Metals UK and many more.
From primary production and processing to recycling, logistics, digital solutions, and advanced manufacturing, the Expo covers the entire value chain.
An Industry-Leading Speaker Programme
Spanning 4 themed theatres on the show floor, UK Metals Expo 2025 delivers
a packed seminar programme with practical solutions and strategic insights.
T. V. Narendran, Chair of the World Steel Association and CEO & Managing Director of Tata Steel, is confirmed as the headline keynote speaker. As one of the world’s most influential steel industry leaders, his public appearances in the UK are rare, making this a special opportunity for attendees to hear directly from the top about strategy, sustainability, and the future of steel.
Other top confirmed speakers include:
• Gareth Stace, Director General, UK Steel
• Nadine Bloxsome, CEO, Aluminium Federation (ALFED)
• Jon Bolton, Chairman, The Materials Processing Institute (MPI)
• Carles Rovira, CEO, 7 Steel UK
• Steve Morley, President, Confederation of British Metalforming (CBM)
• Carl Maitland, Senior Procurement Manager, JLR
• Nick Kemp, Head of Design, Brompton Bicycle
• Louise Slade, COO, DEEP Manufacturing
• Adam Amara, Chief Scientist, UK Space Agency
• Ed Bower, Advanced Technology Expert, Aston Martin Lagonda
• Marijn Rietveld, Head of Innovation, Hydro Aluminium AS
• Grant Adams, CEO, Sertec Group
• Michael Stacey, Award winning Architect & Author
• Michael Ward, CTO, Advanced Nuclear Research Centre
• Richard Prosser, Manufacturing Manager, Leonardo
• James Harwood, Sustainability Strategy Manager - Supply Chain, Jaguar Land Rover
These industry leaders ensure strong insight across automotive, aerospace, defence, energy, construction, advanced manufacturing and engineering.
• UK Industrial Strategy in Action
– How policy frameworks and procurement incentives are driving UK metals manufacturing investments.
• Low-Carbon Steelmaking – The shift to Electric Arc Furnace (EAF) production and design innovation to reduce steel use.
• Trade and Competitiveness –Addressing the impact of the Carbon Border Adjustment Mechanism (CBAM) and building resilient.
• Circular Economy and Scrap Recovery – Buy-back schemes, aluminium recycling, and achieving closed-loop production.
• Aluminium Sector Strategy and Recycling Investment – Building partnerships to scale UK aluminium recycling capacity and build a lowcarbon, UK-based supply chain.
• Advanced Manufacturing and Innovation – CNC, automation, robotics, AI-enhanced manufacturing and next-gen fabrication.
• Market Trends and Analysis –Insights into carbon and stainless steel stock markets.
• Skills and Careers – Including a dedicated Mentoring & Careers Day on 11 September to support workforce development.
Whether you manufacture it, work with it, procure it, shape it, or fabricate it, if metal is part of your world, you should attend UK Metals Expo, the leading trade show for the entire metals supply chain.
For the full agenda, exhibitor list, and free badge registration, visit www.ukmetalsexpo.com.
Celebrating its 40th anniversary this year, Waste Mission has an impressive track record of helping clients divert 100% of their waste from landfills through innovative solutions, making complex waste streams simple.
Waste Mission (formerly Alchemy Metals) simplifies waste management for manufacturers, collaborating with clients to create tailored solutions that achieve environmental goals.
Recent company case studies demonstrate a significant impact for manufacturers such as SRD Engineering, IPN (Inspired Pet Nutrition), and Trouw Nutrition.
Innovative Custom Portal
The team will be exhibiting at both UK Metal’s Expo and PPMA, demonstrating Waste Mission’s innovative Waste Management Portal. The portal is designed specifically for contracted customers, enabling them to manage
their waste more effectively than ever before, staying up to date with waste streams, compliance and ESG targets.
“These features are groundbreaking for our clients,” says Nicola Guest, Group Marketing Manager. “People have been blown away by the simplicity of use and the ease of understanding the data. Everything you need is at your fingertips and simplifies what has historically been a complex process, making sustainability simple.”
BG Steels Ltd was established in 2006 and has developed over the last 18 years to become the UK representation for many premier steel producers both in Europe and further afield. The products we supply, through our principals, are wide-ranging and well established.
Indeed, BG Steels with Lueling GmbH has now become the leading supplier of cold heading wire for fasteners in the UK and Ireland. Our growth over the years has been based on a thorough understanding of the
markets we serve backed up with solid management skills to ensure total supply chain solutions. The skill balance between our team is well-balanced with professional metallurgical qualifications and sound understanding of steel manufacturing and applications. Our business management skills ensure that customers needs are immediately grasped and can be matched to our principals’ product capabilities. With all our team skills, we ensure that both our customers and the companies we represent have a relationship of continuous improvement with the highest quality performances and secure source of supply.
Our product ranges are:-
• CARBON AND ALLOY COLD FORMING WIRES
• STAINLESS WIRES
• SPRING STEEL WIRES
• BRIGHT BARS
• HARDEN & TEMPERED STRIP
• FLAT & PROFILE WIRES
• LARGE DIAMETER HOT ROLLED AND FORGED BARS
• CLOSE DIE FORGINGS
www.bgsteels.co.uk
01433 631999
bj.hague@bgsteels.co.uk
As Sri Lanka's leading manufacturer and exporter of premium aluminum profiles, Alumex PLC delivers
SEPTEMBER 10-11 2025 | BIRMINDHAM, UK - HALL 12
In this interview James Newby, President and CEO of NMITE, outlines how the New Model Institute for Technology and Engineering is challenging long-held assumptions in engineering education.
From rejecting traditional lectures and exams in favour of immersive, hands-on learning to removing outdated entry barriers and embedding ethics and industry engagement at every level, NMITE is reshaping how engineers are trained in the UK.
As the sector faces mounting skills shortages, rapid technological change, and increasing demands for innovation, NMITE’s bold, locally focused, and industry-aligned model offers a compelling blueprint for the future of engineering education.
NMITE has been described as a “new model” for Higher Education – what inspired its founding and what makes it truly different from traditional engineering institutions?
NMITE was founded to challenge the status quo, with two main aims: firstly, to change the way engineers are trained and to produce graduate engineers who are work-ready and able to add value for their employers from day one. Engineering employers have long complained that graduates do not have the right skills to work effectively. Secondly, NMITE aims to drive the economic regeneration of a left behind region, our home county is Herefordshire (NMITE is in the city of Hereford) by producing more graduates locally – addressing critical skills shortages and providing opportunities for young people to find new routes into high value jobs.
We’re different because we put more real-world engineering into the programme rather than relying on traditional lectures. This delivers a completely different, hands-on experience for students and prepares them for work at an early stage of their career.
You’ve moved away from examination-led degrees in favour of course-led, handson learning – what are the advantages of this approach for both students and future employers?
Students learn by doing, not cramming, so they graduate confident, capable, and ready to work from day one. Employers get engineers who can hit the ground running and can collaborate across different disciplines.
Our students are trained in engineering studios, not classrooms, and mostly work as teams, meaning they learn to work well with others, identifying their own and team members’ strengths and motivations, and developing project management skills on the way.
Teamworking develops collaboration, critical thinking and problem-solving skills – all hugely important to employers of professional engineers.
This year, our first graduates are already making their mark on the world, with 100% of graduates seeking jobs already in work at some of the most prestigious engineering firms in the UK, including Balfour Beatty, Mondelēz and Kier.
Your students work directly with employer partners to solve realworld problems – can you share some standout examples of projects that have made a real impact?
Our students have worked on a range of projects, some of which tackle local challenges such as the development of early flood warning systems (Herefordshire is very prone to flooding). Some deliver humanitarian outcomes such as the creation of “pop up” accommodation for refugee camps and some work at the edge of knowledge in technology such as the development of new systems for navigating drones. Students work on projects that matter and that will find a real word application – not just theoretical engineering.
In essence, we encourage our students to include not just their knowledge of technology and applied science, but an awareness of societal needs and an understanding of 21st century global concerns. The ‘on-thejob’ training means that they learn to ask practical business questions and solve very real challenges.
The challenges we present to the students in the early modules are usually ones where experienced engineers can predict solutions. The later challenges, however, are often ones where the obvious technological solutions can also cause further problems and often even our employer partners have no clear idea of what the solution could be.
In this way, they learn to interact with our employer partners which gives them a chance to develop high-level communication skills that are highly valued in the workplace.
The new model has become a proven success. Since NMITE first opened its doors to students in 2021, it has demonstrated how a new model can offer something new to the university
In essence, we encourage our students to include not just their knowledge of technology and applied science, but an awareness of societal needs and an understanding of 21st century global concerns.
- James Newby
system and help young people, to become not just critical thinkers, but thinking doers. Since last year, applications are up 77%.
With NMITE offering flexible study paths, including accelerated degrees and Foundation Year options, how do you support students in choosing the path that best suits their needs?
We try to meet students where they are, not where the system expects them to be. Through personalised support and close mentoring, we help each student build a path that fits their goals and life. We also find that things often change so students might speed
up their path to a degree or slow it down.
We deliberately chose to remove the normal A Level maths entry requirement as a challenge to the assumption that capability in maths must be there at the point of admission. We know that there are many young people who have a passion for engineering but do not meet the entry requirements of maths and physics to enrol in engineering programmes at conventional universities, so these entry requirements are acting as a filter of talent, not an enabler, and misrepresenting the true potential of applicants. Our approach is to embed maths and physics in our engineering programmes.
Our Academic Skills and Knowhow (ASK) Centre is also a key component to the NMITE model. It exists as a drop-in and workshop space for students where they can come to ask questions and take part in support sessions. This enables transferable skills in mathematics, for example but also helps with study. There is also a strong focus on professional communications and writing.
How does NMITE prepare students to be ethically responsible engineers, and why is that increasingly important in today’s global context?
Ethics, sustainability and social impact are embedded from day one and included in all modules, not bolted on separately.
Today’s engineers must solve complex challenges responsibly, and we know that engineers have the power to do enormous good, but also great harm. So, we try to produce graduates that can build things but also know why they are building them.
What feedback have you received from industry employers about NMITE graduates, and how does that reflect on the success of your educational model?
Employers tell us our graduates are unusually work-ready: confident, team-focused and used to solving messy, open-ended problems. And our first cohort of graduates all found jobs. That’s exactly what we set out to achieve. Balfour Beatty partnered with NMITE in 2023 and since then, has been actively contributing to the curriculum with its experts talking to students, and engaging them in projects to enhance their practical experience and arm them with critical skills and industry knowledge that prepares them for a career in the industry. The students from NMITE that Balfour Beatty has taken on have really thrived.
You’ve spoken about the potential for a “small and local” model to address the engineering skills gap – what would it take to replicate NMITE’s approach in other parts of the UK?
There are several regions in the UK that could consider the surgical intervention of a small, specialist university. These include those areas where few young people go
NMITE has already established itself in the community as a centre for knowledge transfer and upskilling through its other business support programmes.
- James Newby
to university but where businesses are held back by the lack of skilled employees. There are about 50 such Higher Education “cold spots” in the UK. To replicate an institution like NMITE, a region would need a committed local authority and support from local businesses. Building new institutions from the ground up in such places is possible with a local coalition of willing partners.
NMITE holds Innovate UK’s Knowledge Base status – how are you using this to help unlock innovation-led growth for your business and industry partners?
It’s early days – the Knowledge Base status was achieved in April 2025. We plan to work with two or three local business partners in the next two years to extend and adapt our cuttingedge student projects into full KTPs
Knowledge Transfer Partnerships. We know this will inject fresh talent into local businesses and help innovation flourish where it’s often hardest to scale.
With final year student projects covering areas such as drones; a mechatronics attachment to a syringe to facilitate precise drug measurement; deployable mesh networks and low-cost robotics, NMITE is keen to ensure Herefordshire companies benefit from the potential offered by this new KTP programme.
With technology advancing rapidly, how important is knowledge transfer and upskilling for engineering professionals – and how is NMITE supporting this need?
It’s absolutely critical. NMITE works heavily in scanning the future skills needs of employers and those are changing more quickly now, than ever before. We’re building flexible, career-focused programmes to help professionals adapt, and a range of short courses to support businesses.
For a rural county like Herefordshire, often underserved in terms of access to high-level technical expertise, the KTP programme, for example, presents a gamechanging opportunity. It enables local companies to access fresh talent, cutting-edge research, and expert guidance—all aimed at boosting productivity, driving innovation, and stimulating economic growth.
NMITE has already established itself in the community as a centre for knowledge transfer and upskilling through its other business support programmes. These include the Innovation Programme for local businesses, as well as a series of professional development courses and an annual Future of Work Conference.
Looking ahead, what’s your vision for the future of engineering education in the UK, and how do you see NMITE shaping that future?
Engineering education must be delivered with a greater focus on work preparedness. It must also be opened to a much wider group of people to increase the diversity of the profession and to make it more future facing. NMITE’s model shows that it can be built locally from the ground up.
The Schmersal Group has designed a new safety light barrier especially for hygiene-sensitive uses in the food processing industry, such as milk and meat processing.
This version has evolved with the demands of standard cleaning operations in the industry as the sophisticated design helps to ensure IP69 degree of protection (protection against the ingress of water from high-pressure of steam cleaning).
The protective enclosure with external gaskets satisfies stringent standards and is designed to cope with frequent cleaning with water, foam, lyes, high-pressure or hot steam.
SCHMERSAL | Enigma Business Park Malvern, Worcestershire, WR14 1GL
www.schmersal.co.uk
uksupport@schmersal.com
3rd-4th September, 2025, Le Méridien Grand Hotel, Nuremberg, Germany
Reducing vehicle manufacturing costs to compete with lower-cost brands is the number one topic for automotive companies right now. The industry cannot wait 2-3 years – they need to start competing this year.
With this in mind, Automotive IQ are bringing manufacturing experts together for Reducing Cost of Automotive Manufacturing 2025, a laser-focused conference that will connect automotive manufacturers and experts as they share best practices, methodologies and tools to streamline automotive production, reduce costs, and adopt leaner processes.
Event Details:
• Taking place on 3rd-4th September, 2025
• Located at Le Méridien Grand Hotel, Nuremberg, Germany
• Speaker line-up led by ZF Group, BMW, Ford Motor Corporation, Nissan Motor Corporation, Bosch, Mercedes-Benz, Daimler Trucks and others.
• Download the agenda here to view all speakers & sessions
To help automotive companies navigate difficult market situations, leading OEMs, Tier-1 and Tier-2 companies will delve into the ways automotive companies need to adapt, innovate and position themselves to reduce the cost of automotive manufacturing and remain competitive while maintaining quality.
Experts will share case studies and best practices for reducing cost and lead time in key areas, new vehicle architectures and designs, opportunities for automation and leveraging insight from manufacturing data, integrating the latest innovations and AI tools for efficiency, implementing innovative materials, and much more.
Key Topics include:
• Detailed insight from major automotive OEMs and suppliers as they delve into practical measures to bring down cost of vehicle manufacturing.
• Analysing exactly what makes Chinese automotive OEMs so dominant right now.
• Assessing new and exciting developments that have been tested and proven from an
efficiency, reliability and durability point of view.
• Examining new processes and areas of improvement to make cost, quality and efficiency gains.
• An overview of the suppliers and latest innovations in manufacturing technologies and techniqueslearn the pros & cons of different tools without having to make an investment.
• As well as: additive manufacturing, how to apply digital twins, going agile to reduce waste, and much more!
Download the 2025 agenda for everything you need to know about the event, including a complete list of all the presentations and sessions, the stellar speaker line-up, ways to register, and more.
Interested in event sponsorship opportunities? Take a look at our Partnership Prospectus for more information.
If you have any further questions, please get in touch with the team at enquire@automotive-iq.com.
3–4 September 2025 | Le Méridien Grand Hotel, Nuremberg, Germany
3 What makes Chinese automotive companies dominant How
3. Explore real-world manufacturing case studies: Learn how ZF Group and Nissan Motor Corporation are leveraging AI in the development phase to reduce manufacturing costs. 12
1. Learn from Automotive manufacturing experts at the top of their game: Gain insights from industry leaders at Mercedes-Benz, Bosch, Nexteer Automotive, Ford Motor Company, BMW Group, Daimler Truck, and more.
2. Forge meaningful business connections: Learn from, collaborate with, and network among 80+ senior manufacturing experts from the world’s top vehicle manufacturers.
A sewer robot that inspects pipework and raises blockage alerts before flooding occurs is to be deployed in a live network for the first time.
Pipebot Patrol is a £1.8 million project, funded by the Ofwat Water Breakthrough Challenge, with Spring Innovation as the knowledgesharing partner.
As the first autonomous sewer robot of its kind in the world, Pipebot Patrol is designed to navigate and inspect miles of pipeline continuously over a 30-day period, pinpointing the precise location of blockages as they are beginning to form.
The project is managed by Northumbrian Water with partners Environmental Monitoring Solutions, Gateshead Council, Jet Aire, Minicam Group, Newcastle City Council, Southern Water, Sunderland City Council, Thames Water and the University of Sheffield’s School of Mechanical, Aerospace & Civil Engineering, leading on robot development.
Since the project launched in July 2024, the development team
After the fantastic progress already made, our team of technical specialists is approaching a key phase - deploying the Pipebot in a live sewer zone.
- Clive Surman-Wells
has designed, built and successfully tested the Pipebot in laboratory conditions. The next step is a sewer zone field trial, which will build understanding of how the robot operates under real conditions.
There are 40,000 incidents of sewer flooding each year in the UK, a high proportion of which are a consequence of blockages.
Historically, mitigating actions taken by utilities have been reactive, prompted by alerts to rising water levels in the network. This approach means it is often too late for a crew to be dispatched to clear the blockage before flooding occurs.
Pipebot Patrol enables proactive inspection and maintenance of networks through an array of advanced mobile sensors and realtime sewer data, captured as the robot moves through pipelines.
The data is analysed and presented in a user-friendly dashboard, which flags up potential blockages early, giving utilities time to take action before the sewer backs up and overflows.
As well as offering greater environmental protection, Pipebot Patrol aims to improve health and safety by minimising human exposure to sewers, deliver cost savings through fewer emergency callouts, support mapping of sewers for asset records and pave the way for future innovations in robotics.
Clive Surman-Wells, innovation partnerships manager for Northumbrian Water Group, said: “Pipebot Patrol is a game-changer for sewer management, presenting three completely new concepts in flooding avoidance - the mobile sensor array, continual patrolling and near real-time alerts on impending blockages, including location data.
“After the fantastic progress already made, our team of technical specialists is approaching a key phase - deploying the Pipebot in a live sewer zone.
“The learnings from the trials will help us move one step closer to being able to use robots at scale to reduce the risk of sewer flooding and prevent devastating harm to the environment and customer properties.
“We will actively share all progress and learnings with the rest of the sector in England and Wales.”
Totalkare’s ergonomic positioners are single or double column devices that enable the lifting and rotation of a product during welding and assembly operations.
With overall capacity from 2,000 - 90,000kg to suit, they are both compact and flexible.
The UK’s biggest processing and packaging machinery, robotics and industrial vision event, the PPMA Total Show®, is set to return to the NEC, Birmingham in September, with the show offering a host of opportunities and brand-new features for attendees.
Scott McKenna, Chief Operating Officer, said: “The PPMA Show® 2024 was a great success, and this year’s show will build on that, giving attendees access to cutting-edge technology and solutions to optimise performance, reduce costs, and future-proof their businesses.
The PPMA Total Show® 2025 will take place from 23-25 September, bringing together industry professionals from across the entire manufacturing spectrum offering networking opportunities, live equipment demonstrations, and valuable insight into innovative technologies.
The PPMA Show 2024 has been shortlisted as a finalist in the Best UK Trade Show category at The AEO Excellence Awards 2025. Organisers Automate UK have pledged to deliver a show that exceeds expectations this year, with an itinerary of expert speakers, a networking reception and a series of live demos to showcase the latest technology solutions.
This year, we’re offering visitors to chance to benefit and learn from expert-led seminars with relevant topics including sustainability, smart manufacturing, and operational efficiency...
The PPMA Show® 2024 was a resounding success, with more than 80% of visitors reporting that they discovered new solutions to enhance and support their businesses as a direct result of their attendance.
The 2025 show is now set to be bigger and better, with more than 350 exhibitors and 1,500 brands in attendance.
“This year, we’re offering visitors to chance to benefit and learn from expert-led seminars with relevant topics including sustainability, smart manufacturing, and operational efficiency, as well as dedicated networking opportunities throughout the course of the show.
“One of the standout successes of The PPMA Show® 2024 was Innovations Eleven – a brand-new live demo theatre, in which 11 selected exhibitors launched new technology directly to attendees, and we’re enhancing that experience this year.
“The PPMA Total Show® 2025 live demo theatre will be broadcast in real-time via PPMA Total Show TV, whilst expert-led daily innovation tours will be hosted for visitors to expand on the technology being showcased and its suitability for their business needs,” he added.
Attendance for The PPMA Total Show® 2025 is free, with registration now open.
To register, visit: www.ppmashow.co.uk.
Solweb Ltd is a custom software development business, based in Bournemouth, Dorset, that has clients all over the UK and in the USA. Born in the year 2000 and continuing to grow year on year, we have just celebrated our Silver Anniversary.
We primarily provide custom software, integrate business systems and provide automation services for clients who work in the manufacturing and engineering sectors. We also have developed several purposebuilt products since our inception, that allows our customers to further streamline their processes and save valuable time and money with the implementation of our software. All of our products and bespoke applications are designed to provide efficiencies within the business they are tailored for.
We also have a very high client retention rate, with some now having been with us over 20 years! We put this down to the robust and reliable nature of the software we build and the excellent aftercare support we provide once the software has been deployed. Our small, but exceptionally talented team of developers, monitor all supported software on our in-house monitoring system that allows them to identify any issue and frequently resolve before the client is even aware! Our support ticketing system, allows our clients to email in any time with any issues that they may have and our team always respond either on the same day or the next working day at the latest. 99.9% of support issues are resolved within 48 hrs. We know this is exceptionally higher than the industry
We primarily provide custom software, integrate business systems and provide automation services for clients who work in the manufacturing and engineering sectors.
standard, where recent stats showed average response times to support queries in our sector were 4-5 business days!
Now, with ever-increasing financial pressures on businesses, it is critically important for them to ensure that their operational costs are well-managed, so that they can remain competitive in their market place and continue to increase profits. When we build custom software for our clients, we tailor it specifically to their processes. This allows them to have software that is a perfect fit, without having to adapt their business to make “off the shelf” software suitable. This unique approach, allows clients to free up their
team from mundane manual tasks and proactively resource them elsewhere in their business, such as business development/sales.
We are exceptionally proud of what we have achieved to date and we all come in to work every day, looking to grow, innovate and achieve further success. We take a lot of care with our product development to ensure it will help our clients to achieve those important financial and time savings. We also spend a lot of time contacting and visiting our clients to make sure our software is working to its optimum level. It is this approach to how we operate our business, that allows us to help our clients grow their businesses. A winning formula that we hope continues for another 25 years!
Visit www.solweb.co.uk and see how we have helped businesses grow with our services.
By Simon Bowes, CVP of Manufacturing Industry at Blue Yonder
AI has emerged as a transformative force that is revolutionising the way supply chains operate. Until now, AI has primarily been used to improve the accuracy of demand forecasting. But this is just the starting point.
As the adoption of AI and machine learning (ML) models becomes more widespread, new applications are emerging that enable organisations to engage in next-generation demand planning practices that can truly elevate how they operate.
Supply chain disruptions remain the single most challenging issue impacting the operations of organisations today. Given the complexity of modern marketplaces, manual scenario planning is a tedious and time consuming task that often results in suboptimal decisions.
With so many data points and potential variables to consider, planners can easily overlook the key influencing factors that matter the most where forecast accuracy is concerned. For example, many planners failed to spot how the US presidential election would create a demand spike as consumers engaged in product hoarding before Donald Trump was even elected.
Far faster and more accurate than manual methods, today’s ML models are capable of both autonomously and dynamically configuring the best combination of variables to use in demand models. Powered by deep meta learning, these models enable planners to capture the complete value of unlimited data and unlock the speed of integrated ML.
Alongside eliminating guesswork and human bias from the process, this algorithmic approach ensures that variables can be rapidly reconfigured as market and business realities change.
Innovations such as generative AI now deliver fast access to data driven insights, as well as assisted decision-making and process automation. All of which dramatically improves the productivity and performance of planning teams.
These generative AI models enable planners to ask clarifying questions, request data, visualise influencing factors and assess the effectiveness of past decisions. They can also be trained on enterprise standard operating procedures, business processes and workflows
to provide highly contextualised and relevant responses to planner queries. There is no longer any need for planners to dig through multiple text-based resources to find answers to basic queries.
Finally, today’s AI-based training programmes can significantly reduce the time and effort required to cross-train planners and onboard new hires. Something that will significantly benefit organisations as they look to prepare the next generation of demand planners.
Gaining the competitive edge
As we’ve seen, recent AI developments are enabling companies to go beyond improving their forecasting accuracy to initiate agile and responsive supply chains capable of meeting the demands of today’s modern and highly dynamic marketplaces.
By giving demand planners the integrated demand and supply planning (IDSP) capabilities they need to model and optimise a 360-degree planning view in seconds rather than days, companies are now able to rapidly capitalise on new opportunities and resolve disruptions before cost and service outcomes are affected.
For organisations that want to thrive in today’s fast-evolving global commerce landscape, harnessing AI in the supply chain is fast becoming a necessity rather than a nice to have.
Baumer has launched the OT200, reportedly the smallest time-of-flight (ToF) sensor designed for applications with limited installation space. Measuring just 8 x 25.1 x 5.8 mm, the compact sensor offers reliable object detection and distance measurement even in challenging conditions.
The OT200 provides a detection range of up to 2.5 metres and a fast response time of 4 milliseconds.
It performs consistently across various surface types— including ultra-black, shiny, and reflective materials—making it suitable for diverse industrial uses.
Equipped with Baumer’s Sensor Suite software, the OT200 allows intuitive parameter setting and easy operation. Key applications include Automated Guided Vehicles (AGVs), where the sensor’s small size fits neatly within restricted spaces such as forklift forks, enabling precise width monitoring.
Emerson has introduced a new Dust Collector Monitoring and Control solution designed to enhance performance and environmental protection across industries such as cement, mining, chemicals, food, power, and utilities.
The solution integrates proven Emerson products—including ASCO™ pulse valves, pressure and particle sensors, PACSystems™ PLC, and Movicon™ SCADA—for automated filter cleaning, real-time diagnostics, and Floor-to-Cloud connectivity. This enables optimized pulse valve control, predictive maintenance, and remote monitoring, helping reduce energy consumption and compressed air waste.
By intelligently monitoring filter conditions and cleaning cycles, the system extends filter life by up to one year, potentially saving thousands of dollars. It also supports regulatory compliance by detecting failed filters early, preventing costly downtime and maintenance.
Samuele Oliva, Emerson’s product marketing manager, highlights the solution’s ability to deliver operational efficiency, reduce reactive maintenance, and provide accessible insights to plant personnel, all through seamless integration with existing automation systems.
Anritsu Corporation and Fujikura Ltd. have confirmed equivalent results in measuring intercore crosstalk within weakly coupled multi-core optical fibres using multiple methods. The findings were presented at the OptoElectronics and Communications Conference (OECC 2025) in Sapporo, Japan.
As demand for higher data transmission grows with AI and cloud services, existing singlemode fibres (SMF) are nearing their
physical limits. Weakly coupled multi-core fibres, containing multiple independent cores within a single fibre, offer increased capacity but face challenges with inter-core crosstalk—light leakage between cores that can degrade signal quality.
To address this, Anritsu and Fujikura evaluated crosstalk on a four-core fibre using four measurement techniques: two based on optical power meters and two employing Anritsu’s Optical
Time Domain Reflectometer (OTDR). The fibre tested, produced by Fujikura, has a standard 125 µm cladding diameter.
Results showed strong agreement across methods, with measurements within ±1.0 dB at the 1550 nm wavelength. This consistency means any of the four techniques can be applied reliably for research and development, manufacturing, or installation and maintenance tasks, depending on the specific application.
As battery energy storage systems (BESS) become increasingly integral to modern energy infrastructure, ensuring their safe operation is critical. While BESS plays a vital role in stabilizing renewable energy supply, they also present significant safety challenges — particularly around thermal runaway, a risk that requires precise monitoring and fast response.
Thermal runaway is a chain reaction that begins when a battery cell overheats. If left unchecked, it can spread to neighbouring cells, leading to fires that are notoriously difficult to control. Lithium-ion batteries, commonly used in BESS, are particularly susceptible to this phenomenon due to their high energy density. Causes range from electrical faults and physical damage to overheating in high ambient temperatures.
The rapid growth of grid-scale storage — which surged by more than 50% in 2024 alone — has only heightened the urgency for robust monitoring solutions. As installations
become larger and more widely distributed, operators face the challenge of maintaining visibility across complex systems and catching potential failures before they escalate.
Sensor Technology as a Frontline Defence
Thermal monitoring has emerged as a key safeguard, using infrared sensors to detect early-stage heat anomalies. These systems operate continuously, capturing real-time thermal data across battery stacks and enclosures. Unlike traditional fire detection systems, which often react only after smoke or flame is detected, thermal imaging provides a non-contact method to catch faults during their earliest, preignition phase.
Key features in modern thermal monitoring systems include:
• High-resolution thermal sensors – to identify small temperature differences across densely packed battery modules
• Wide field-of-view optics –enabling full system coverage with fewer cameras and no blind spots
• Edge analytics and smart detection – filtering out false alarms caused by reflections, weather, or maintenance activity
• 24/7 real-time operation – providing uninterrupted surveillance, critical for unmanned or remote installations
FLIR’s A500f and A700f Advanced Smart Sensor cameras are an example of this kind of system. With 640×480 thermal resolution, on-camera analytics, FSX® (Flexible Scene Enhancement) technology, and optional fields of view up to 80°, the platform offers continuous monitoring tailored to the demands of high-risk environments like BESS.
Integration with SCADA and industrial monitoring platforms allows alerts to be issued instantly to control rooms or mobile devices. Some systems also support automated shutdown or cooling procedures in the event of overheating, reducing the need for manual intervention.
The benefit is not just safety. Monitoring also supports operational efficiency. Early detection prevents downtime, protects infrastructure investments, and strengthens resilience as BESS continues to be deployed at scale.
As renewable energy capacity grows, so too does the demand for safe, reliable storage. Advanced thermal monitoring, backed by intelligent sensing and automated analytics, is proving to be a vital tool in managing the inherent risks of battery systems. For operators, it’s not just about spotting heat — it’s about gaining visibility, control, and confidence in a rapidly evolving energy landscape.
More information: www.teledyneflir.com
The one year IOA Diploma in Acoustics and Noise Control includes the General Principles of Acoustics, Laboratory and Experimental Methods, a project and two specialist modules chosen from:
• Bui ld i ng Acoustics
• Noise of Assessment nd a Regulation
• Noise: ronmental Envi Measu rement, Pred iction & C ontrol
• Noise a nd Vi bration C ontrol Engi neeri ng
FOR MORE INFORMATION:
www.ioa.org.uk E: education@ioa.org.uk T: +44 (0)300 999 9675
Established for more than 50 years, the Institute provides graduates and those with a proven interest in acoustics, the chance to become a recognised member of a vibrant and active global network with regular UK meetings and CPD
The Diploma is taught to candidates in centres across the UK and via distance learning tutorials, also facilitating candidates abroad – find out more at: www.i o a .o rg .uk/e d u c a ti o n-t ra inin g
Institute of Acoustics, Silbury Court, 406 Silbury Boulevard, Milton Keynes MK9 2AF
• Rugged and compact
• Easy to use
• Dust, splash or waterproof
• Data downloaded to PC
• Cost-effective
Plus 2
Rugged outdoor/industrial temperature/RH logger From £120 +VAT
Energy Logger
Non-invasive single & three phase power monitoring Full kit £995 +VAT
Tinytag Ultra 2
Accompanying probes are available for monitoring extremes of temperature, and for awkward to reach areas such as pipework.
For larger sites, the Tinytag Radio System automatically transmits data wirelessly, over Ethernet/LAN, or via mobile connection (4G).
Temp/RH for larger or remote sites
Bundles – 3 loggers/receiver/ software from £1,155 +VAT
System Indoor temperature & RH From £85 +VAT
Camozzi Automation and HAYLEY DEXIS | Fluid Power have joined forces to provide a fully integrated control panel for a materials processing facility, successfully completing the project in just four weeks.
The site, which produces aggregates, concrete, and recycled building materials, had experienced downtime and inefficiencies due to an ageing control panel prone to frequent breakdowns and requiring extensive maintenance. Having previously supplied a robust and reliable solution to the same customer, Camozzi and HAYLEY DEXIS were approached again to deliver a durable, high-performance upgrade.
A Camozzi representative and HAYLEY DEXIS Account Manager visited the site to assess the application and ensure a seamless replacement of the existing control panel. The goal was to quickly replace the incumbent panel while maintaining high operational efficiency and improving system durability and protection. With a clearer understanding of the customer’s operational needs, they created the custom panel solution.
The new panel replacement design featured a plug-and-play layout, offering easy installation and longterm durability for instrumentation and electrical components in the site’s demanding environment.
Custom CAD drawings were created based on the existing design to support a quick fit and reduce future maintenance requirements.
From concept to testing, the entire process was completed within four weeks of order placement. This rapid turnaround minimised plant downtime and allowed the customer to resume operations immediately. The new panel eliminated reliability issues and significantly boosted uptime, ensuring easier servicing and sustained performance.
This project highlights Camozzi and HAYLEY DEXIS’ commitment to fast delivery and engineering excellence. The customer’s decision to partner with them for a second installation is a testament to their trust in the efficiency and reliability of the previous solution. Both companies remain committed
to supporting industrial customers with durable, efficient pneumatic solutions—while continuing to drive innovation and excellent service.
Camozzi Automation is the UK arm of the global Camozzi Group, a leader in the design and manufacture of components and systems for industrial automation. With a heritage of engineering excellence and innovation, Camozzi Automation UK is headquartered in Warwickshire and serves a wide range of sectors, from packaging and food processing to life sciences, automotive, and beyond.
What truly sets Camozzi UK apart is its commitment to exceptional technical and customer support. The local team of experienced engineers works closely with customers to deliver fast, reliable advice and tailor-made solutions. Camozzi Automation UK’s is also renowned for its ability to manufacture bespoke cylinders rapidly in-house.
Camozzi Automation UK’s dedicated Automation Centre enhances its capability to deliver fully assembled pneumatic and electro-pneumatic control panels. From design to build, each project is handled in-house with a focus on quality, flexibility, and efficiency. This turnkey service allows customers to simplify installation, improve system integration, and reduce downtime – all backed by Camozzi’s trusted engineering expertise.
For tailored advice or to discuss your next automation project, contact our technical team at technical@camozzi.co.uk or call 024 7637 4114.
Emerson’s Appleton Group iron casting facility in South Milwaukee has received a 2025 Energy Excellence Award from Focus on Energy®, Wisconsin’s state-wide energy efficiency and renewable energy program. The award recognizes organizations demonstrating exceptional commitment to reducing energy use and costs.
Since partnering with Focus on Energy in 2017, the foundry has implemented a range of energy-saving measures, including upgrading air unit controls, replacing channel furnaces with induction melting furnaces, and switching over 800 fluorescent lights to industrial LED fixtures. These improvements save the facility over 10,000 megawatt-hours of energy and $1 million in annual costs,
while cutting emissions and energy consumption by about a third.
Erin Soman, managing director of Focus on Energy, praised the facility’s efforts: “Emerson’s foundry shows that even energy-intensive operations can be leaders in energy efficiency.”
John Schuster, plant manager at Emerson’s discrete automation business, said the award “highlights the dedication of our team to improve our environmental impact
and support cost reductions while moving toward a sustainable future.”
The Appleton foundry produces electrical fittings, enclosures, and cast products for electrical infrastructure, and stands as a notable example of industrial energy efficiency in Wisconsin.
For more information about Appleton electrical solutions from Emerson, please visit appleton.emerson.com/en-us.
Left to right: Doug Presny, CleanTech Partners; Joe Pater, Wisconsin Public Service Commission; Paul Kling, Focus on Energy; John Schuster, Emerson; Bob Axtell, Emerson; Bill Bolhuis, Franklin Energy; Chris Larson, Chris Jansen, Wisconsin State Senator, District 7; Jim Garbowski, WEC Energy Group. (Courtesy of Emerson)
OrganOx, a University of Oxford spinout, has been awarded the 2025 MacRobert Award by the Royal Academy of Engineering for its advanced organ preservation devices, which are helping to increase transplant rates and reduce waiting list deaths.
The company’s technology keeps livers and kidneys functioning outside the body for significantly longer than conventional cold
storage methods, enabling more transplants, reducing the need for emergency surgeries, and lowering healthcare costs. To date, the system has supported over 6,000 transplants across 12 countries, with some hospitals reporting transplant rate increases of up to 30%.
OrganOx has also developed a third device that provides extracorporeal liver support, or ‘liver dialysis’, using a donor organ to help patients in liver failure recover without needing a transplant.
The company’s devices operate at normal body temperature and replicate physiological conditions by perfusing organs with donor blood. They are fully automated, transportable, and suitable for clinical and surgical environments, including in-flight organ transfers.
OrganOx received the £50,000 prize at the Academy’s awards dinner on 8 July in London,
presented by Science Minister Lord Vallance. The MacRobert Award is the UK’s longest-running engineering prize, recognising innovations with commercial success and social impact.
Dr Alison Vincent, chair of the judging panel, said OrganOx’s “game-changing” innovation stood out among strong finalists Synthesia and Microsoft Azure Fibre.
Co-founder Professor Constantin Coussios said the technology was the result of two decades of work, adding: “Each quality-assured organ that has functioned effectively in our devices saves a life and gives patients and their families the gift of time and quality of life.”
The award adds OrganOx to a list of previous winners that includes engineering milestones such as the CT scanner and the world’s first bionic hand.
By Andrew Taylor, Managing Director at Specialist Glass Products
Glass machinery has experienced a significant transformation, from the traditional methods of the past to the automated processes we see today. The advancement of the machinery used in glass manufacturing now allows for increased efficiency and expert precision, helping to craft products that we use every day.
Andrew Taylor, Managing Director at Specialist Glass Products, reflects on the evolution of glass manufacturing, the technologies driving this change, and how this may shape the industry’s future in the years to come.
Helping to revolutionise the production of glass is the development of automated technologies, including CNC (Computer Numerical Control) Machinery. These developments enable exceptional precision in cutting, shaping, and edging glass, allowing for more complex and intricate designs.
Before the advancement of technology and machinery, the production of glass products heavily relied on a manual approach. This method was extremely timeconsuming, as craftspeople would use tools to carefully shape each piece of glass, often resulting in noticeable differences in shape and size.
The rise of automated technology in glass manufacturing has brought numerous benefits to manufacturers across the industry. A key benefit of using automated technologies in glass manufacturing
is increased productivity, as machines can operate continuously without requiring breaks. Furthermore, by automating specific tasks within the production process, tasks are completed more efficiently and quickly, enabling manufacturers to expand their production capabilities and meet the increasing demand for high-quality glass products.
The advancement of automation also enables glass manufacturers to produce glass products with extreme precision. This precision is crucial, as it enables the production of far more complex products, featuring intricate designs and shapes that were previously unattainable. With manufacturers now having the ability to create bespoke and accurate products, waste is significantly reduced, resulting in a more environmentally friendly method of manufacturing glass.
An example of this transformation in full effect is Specialist Glass Products’ new Systron proHD Vertical Glass Processing machine. The stateof-the-art machine enables the company to handle larger jumbo glass orders, measuring up to 6,000
mm x 3,210 mm. Additionally, they are the first company in the UK to acquire this machine in a jumbo size.
The new machine is multifunctional and can polish, grind, cut, and shape glass into various forms. Additionally, the automated services that the machine possesses enable the firm to streamline production processes, allowing the machine to produce higher-quality products more efficiently. It has already demonstrated its capabilities, helping to deliver on several projects, including this staircase, where the machine was used to craft 16 panels of 13.55mm toughened laminated glass.
Looking ahead to the future, there will be a growing emphasis on sustainable and environmentally friendly production practices. As machine technologies continue to advance, sustainability must be prioritised as these developments occur. Whether that be the creation of more energy-efficient machines or a focus on recycling and waste reduction practices, environmentally friendly processes must be a fundamental part of the glass industry.
The glass manufacturing industry has undergone significant changes with the development of automated machinery technologies. As demand for high-quality and innovative products continues to rise, manufacturers will continually identify new ways to improve efficiency, enhance product quality, and produce high-quality glass products sustainably.
Gundrilling and BTA deep hole drilling for highly productive shops.
Whether your shop needs on-center or off-center holes, specialized job shop work or fully automated production, UNISIG has a deep hole drilling solution with the accuracy and performance you need.
Take your shop’s production further - learn more at UNISIG.COM.
The International Materials Handling Exhibition (IMHX), the UK’s leading trade event for warehouse and intralogistics professionals, today announced its transition to a biennial format beginning with its 2027 event.
This strategic shift from its previous three-year cycle comes in direct response to overwhelming industry demand for more frequent networking and innovation showcases in the rapidly evolving materials handling sector.
IMHX 2025, scheduled for September 9-11 at the NEC Birmingham, will then start its new cycle and be back from 14 - 16 September 2027 in Hall 5 at NEC Birmingham.
“The decision to move IMHX to a biennial schedule reflects the accelerating pace of innovation in our industry,” said Chris Morley, Group Director – Maritime & Logistics at Informa. “With widespread automation, AI adoption and sustainability initiatives transforming warehousing and logistics at unprecedented speed, our stakeholders have clearly expressed the need for more regular opportunities to connect, showcase advancements and drive business growth.”
The transition to a biennial format represents our commitment to serving the evolving needs of the materials handling community.
The upcoming IMHX 2025 is expected to welcome approximately 10,000 attendees and over 300 exhibitors, including industry leaders such as Crown, Toyota Material Handling, Körber, Combilift, AutoStore, Exotec and Swisslog. The exhibition will feature the new Future Zone, presented in partnership with SEC Storage, showcasing cutting-edge technologies focused on renewables, warehouse optimisation and ecofriendly solutions.
Rob Fisher, Chief Executive Officer at the UK Material Handling Association (UKMHA), co-owners of IMHX, commented: “The transition to a biennial format represents our
commitment to serving the evolving needs of the materials handling community. This industry is a vital pillar of the UK economy and more frequent IMHX events will provide the consistent platform needed to support its continued growth and innovation. We’re excited about this new chapter and look forward to delivering even more value to exhibitors and visitors alike.”
The event will continue to offer its comprehensive free seminar programme covering smart technologies, environmental responsibility and operational excellence, while maintaining strong support from key industry associations including the Automated Material Handling Systems Association (AMHSA) and the UK Warehousing Association (UKWA).
Visitor registration for IMHX 2025 is now open, with free entry available to professionals from warehousing, distribution, supply chain, e-commerce, retail and manufacturing sectors at www.imhx.net.
• Explore new products & services
• Hear about future trends & tech
• Meet up with suppliers & colleagues
• Scan QR code for free registration Looking To Visit?
10,000+ ATTENDEES
300+ EXHIBITORS
WHAT DOES THE FUTURE HOLD FOR WAREHOUSE DESIGN AND INTRALOGISTICS?
Introducing the new IMHX Future Zone
With product demonstrations, talks and expert advice on future energy & future technology. Only at IMHX 2025!
80+ SPEAKERS
A cross-skilling pilot programme in Grangemouth and Aberdeen has successfully supported 15 oil and gas technicians in transitioning to roles in the wind energy sector.
The six-week initiative, developed by the Engineering Construction Industry Training Board (ECITB) in partnership with the Global Wind Organisation (GWO) and the Offshore Renewable Energy (ORE) Catapult, provided technical training across electrical, mechanical, and instrumentation disciplines, as well as wind-specific safety and turbine familiarisation.
Participants included employees from companies such as Wood, Petrofac, Semco Maritime and Ponticelli, alongside five former mechanical technicians from the Grangemouth refinery.
Several trainees have already secured roles in the wind industry, with others in interview processes.
The pilot recognised prior competence and aligned with the Connected Competence scheme and Energy Skills Passport, aiming to streamline retraining for skilled workers amid growing demand for wind turbine technicians.
Andrew Hockey, CEO of ECITB, said the programme supports a “just transition” by enabling twoway movement between oil and gas and wind sectors, helping to meet skills needs while maintaining safety and quality standards.
The training was delivered at Forth Valley and North East Scotland Colleges and by approved provider RelyOn, with practical elements completed at ORE Catapult’s Levenmouth demonstration turbine. It was fully funded by ECITB, with co-funding from the Scottish Government for the Grangemouth workers.
ECITB plans to expand the programme later this year based on feedback from participants, providers and employers.
Aston University and the Manufacturing Technology Centre (MTC) have launched a strategic partnership aimed at accelerating innovation and strengthening industrial impact across the UK manufacturing sector.
The collaboration will focus on Knowledge Transfer Partnerships (KTPs), a long-running UK governmentbacked programme that links academic research with business needs. Through these partnerships, Aston and the MTC will co-develop projects to support the adoption of new technologies, improve industrial processes, and enhance competitiveness—particularly among SMEs.
Aston University, which currently oversees 43 active KTPs, has been recognised in the top 20% of UK universities for business engagement, according to the latest Knowledge Exchange Framework.
Velocity Composites PLC has announced its adoption of the T-Level qualification programme to help build a pipeline of skilled technicians for its operations in the aerospace and advanced manufacturing sectors.
The company will offer placements to T-Level students as part of its workforce development
strategy, aiming to provide handson experience in composite manufacturing and related engineering disciplines. T-Levels are two-year technical qualifications, equivalent to A-levels, which include a minimum nine-week industry placement.
Newly appointed Chief Operations Officer Oliver Smalley is leading
the initiative. Smalley, who joined the company in February 2025, brings over a decade of experience in aerospace manufacturing and has previously led operational transformations across the UK and Europe.
“The T-Level programme allows us to actively shape future talent with the practical and theoretical skills needed for our industry,” Smalley said.
“It supports our strategy to scale efficiently while maintaining a highperformance workforce.”
CEO Jon Bridges described the move as a key part of the company’s growth plan:
The initiative will also support workforce development by embedding researchers into industry roles, where they will access MTC’s advanced facilities and benefit from expert mentoring.
More than half of engineering and manufacturing hiring managers globally — and 60% in the UK — say they’ve struggled to recruit in the past year, according to new data from Michael Page’s 2025 Talent Trends report. This comes despite nearly half (49%) of professionals in the sector globally, and 39% in the UK, actively seeking new roles.
The survey of nearly 4,000 professionals reveals a shift in candidate priorities, with UK respondents placing growing emphasis on work-life balance, wellbeing, and meaningful work — often above salary.
In the UK, 72% of engineering and manufacturing workers said they would decline a promotion to protect their wellbeing, while just 12% cited salary as their top reason for seeking a new role. By contrast, 83% prioritised worklife balance.
Trust in leadership is also under pressure, with 46% of UK professionals lacking confidence in leaders’ ability to balance business goals with employee wellbeing. Dissatisfaction with leadership is driving 42% of UK respondents to consider changing jobs.
The report highlights a growing demand for purposeful work, with 43%
Professionals are looking for more than a job — they want clarity on purpose, flexibility, and futurereadiness.
of UK professionals listing it as a top priority — a sharp rise from 26% last year and well above the global average of 33%. However, only 38% feel they can be their authentic selves at work.
Meanwhile, the use of AI tools is expanding across the sector. Globally, 43% of professionals now use AI in their roles, up from 24% last year. Among UK users, 71% engage with AI at least weekly. While many report increased productivity and job satisfaction, 62% globally say their organisations could do more to support AI integration.
Michael Page’s Ruth Hancock said the findings underline the importance of transparent communication around culture, leadership, and emerging technologies. “Professionals are looking for more than a job — they want clarity on purpose, flexibility, and future-readiness,” she said.
“As production ramps up, having a skilled workforce is essential. Investing in early career development supports both our operational needs and long-term competitiveness.”
Velocity Composites sees the integration of T-Levels as part of a wider commitment to operational efficiency and sustainability in its global operations.
For more information on the manufacture of composite materials and investment in manufacturing skills, visit here: www.velocity-composites.com
New research by the University Vocational Awards Council (UVAC) warns that planned government cuts to apprenticeship funding will leave UK employers with an estimated £214 million in additional training costs, with the manufacturing sector expected to be among the hardest hit.
From January 2026, the government will remove levy funding for Level 7 apprenticeships — equivalent to Master’s degrees — for apprentices aged over 21. UVAC data shows that 89% of current Level 7 apprentices fall into this age bracket, meaning the majority of learners will be affected.
The change comes despite continued growth in Level 7 uptake, with starts rising 13% over the past three years. These programmes are commonly used by manufacturers to develop future managers, technical specialists, and business leaders.
UVAC Chief Executive Dr. Mandy Crawford-Lee (pictured below) described the decision as a “major
blow” to the sector, warning it could widen the skills gap, hinder social mobility, and undermine economic growth.
“Removing funding for these apprenticeships signals a step back from supporting career progression at all stages,” she said.
The cuts follow years of stagnant funding for Level 7 apprenticeships, which have accounted for around 10% of the Department for Education’s apprenticeship budget. Critics argue the move contradicts broader economic aims, including Labour’s pledge to remove barriers to opportunity under its Industrial Strategy.
UVAC also pointed to research from the National Foundation for Educational Research showing that 90% of jobs are expected to require higher-level skills by 2035 — further reinforcing the role of advanced apprenticeships in workforce development.
The government has yet to issue a detailed response to the findings.
Energy company E.ON has partnered with STEM Returners for a second time to help professionals return to engineering and technology roles after a career break.
The 12-week programme offers hybrid placements at E.ON, with opportunities across engineering and tech. Participants will receive career coaching and mentoring through STEM Returners, and may be offered permanent roles at the end of the placement.
The initiative aims to address barriers faced by returners, particularly recruitment bias. According to STEM Returners’ research, those returning from career breaks—especially women—often struggle to re-enter the workforce despite having the right skills.
The renewed partnership follows a successful initial programme, which saw several returners move into permanent roles at E.ON, including Technical Product Engineer Nicola Kennedy.
The scheme is part of a wider effort to tackle industry skills shortages by supporting experienced professionals back into work.
To view STEM Returners’ opportunities, visit https:// stemreturners.com/liveprogrammes/
MSc - 1 year full time
time part time Certificate for CPD
MSc - 1 year full time
MSc - 2 or 3 year part time
PG Diploma • PG Certificate
MSc - 2 or 3 year part time
Short Courses for CPD
Designed
Designed
New research from Sulzer highlights significant inefficiencies across industrial pump fleets, identifying a major opportunity for energy savings and improved sustainability.
Despite pumps accounting for over 20% of industrial electricity use globally, many operators overlook their optimisation. The study, which analysed data from 464 pumps monitored over 12 months, found that 68% operated outside their preferred operating range (POR) for more than half of their runtime. Nearly half of the pumps ran outside this optimal range over 80% of the time, while 17% regularly operated in restricted zones — conditions
Tool machining specialist VOLLMER will debut several new technologies at EMO 2025 in Hanover, highlighting advancements in grinding, laser machining, erosion, and digital services.
Making its world premiere is the VGrind infinity linear, a flexible tool grinding machine designed for rotary tools made from materials including carbide, HSS, PcBN, and ceramics. Capable of producing tools with diameters from 0.2mm to 200mm, the machine supports automated, around-the-clock operation for batch production or special applications.
Also on display will be the VLaser 370, developed for precision machining of ultra-hard cutting materials like PCD and CVD diamond. Built for continuous operation with minimal manual intervention, it features high process stability and efficient extraction technology.
The VHybrid 260, combining grinding and erosion with dual vertically configured spindles, will demonstrate its ability to produce microtools down to 0.45mm with high precision and surface quality.
VOLLMER will also spotlight its Smart Hub digital platform, designed for real-time machine data collection and management. Integrated with AI-based tools, the platform aims to improve production transparency and efficiency.
Subsidiaries Loroch and ultraTEC innovation will feature at the stand, with Loroch showcasing its KSC 560-B saw blade sharpening machine and TC 720 measuring device, while ultraTEC presents its A20 C ultrasonic deburring system, capable of processing multiple components simultaneously with automated handling.
VOLLMER’s full line-up will be on Stand F26 in Hall 11.
that reduce efficiency, increase maintenance costs, and raise emissions.
These inefficiencies not only inflate energy consumption but also risk equipment lifespan and reliability. Sectors like oil, gas, and power saw the greatest inefficiencies, with downstream operators particularly affected.
Ravin Pillay-Ramsamy, Sulzer’s Services Division President, said, “Pumps are often taken for granted, yet our data reveals considerable value in reassessing their performance. With rising energy
costs, addressing pump inefficiency represents low-hanging fruit for many industries.”
To address this, Sulzer launched its Energy Optimization Service in April 2025, offering a complete solution from digital audits and retrofit implementation to ongoing monitoring. Compatible with pumps from any manufacturer, this service aims to help operators unlock energy savings and reduce emissions across sectors.
Sulzer’s full whitepaper, detailing sector and regional insights, is available for download here
A competition run by FANUC UK for students to design and manufacture trophies for the Enginuity Skills Awards has been won by MTC student Grace Peckett.
Celebrating the best in up and coming engineering and manufacturing talent, the Awards took place in London on 3 July 2025. As part of the company’s ongoing commitment to inspire and support the next generation of engineers, FANUC UK partnered with the Manufacturing Technology Centre (MTC) to host a competition to design and manufacture the trophies for the event.
Real-world manufacturing experience
A group of around 20 MTC students were tasked with creating their trophy design using CAD, before 3D printing a mock-up which they
presented to a team of judges. The top five entries were selected by the MTC and then invited to visit the FANUC UK headquarters in Coventry with their prototype trophies. Following a formal pitch by each finalist, a team of FANUC experts then chose their winner, awarding Grace Peckett the final honour.
The trophies were manufactured using the FANUC ROBODRILL compact CNC machining centre, while the event logo was EDM wired on the FANUC ROBOCUT machine. The materials used to create the final trophies were aluminium and brass.
To see the full list of winners of the Enginuity Skills Awards 2025, go to www.enginuity.org
Pictured: Competition winner MTC student Grace Peckett, sees trophy design come to life at Enginuity Skills Awards. Pictured with Oliver Selby, Head of Sales for FANUC UK.
For immediate benefits for efficient, safe primary containment
From day one, each Learner on EEMUA's MIPC® training builds a unique workbook of mechanical integrity know how – tailored to each Learner, site and company.
EEMUA's MIPC course develops practitioner-level engineers where they are needed – on-site and on top of industry developments and good practice in primary containment of hazardous substances, including for pressure systems.
Flexible, part-time, in-depth training for engineers whether on-site or on-call, each EEMUA Mechanical Integrity Practitioner Certificate course combines: live online classes; 1-1 sessions with subject expert Tutors; on-demand e-learning; and much more –all enhanced by Mentor support throughout.
Covers:
* Equipment Design Elements
* Asset Condition
* WSE
* Audit
* Reporting
* Risk and ALARP
* Legislative Environment
* Inspection and Test Techniques
* Postponement
* User Responsibilities and Competencies
* Feedback and * More.
Adapts to engineering needs of each individual Learner, their company, and their site/s – via a 2-hour Induction
Veolia has introduced a new treatment process for Aqueous Film Forming Foam (AFFF) fire suppressants containing PFAS (Per- and polyfluoroalkyl substances), ahead of the UK’s ban on these chemicals coming into effect in July 2025. The ban addresses the environmental and health risks of PFAS, which are bioaccumulative and toxic.
Veolia’s High Temperature Incinerator (HTI) at Ellesmere Port uses Environment Agency-approved incineration at 1100°C to safely destroy AFFF stockpiles, expected to total around 10,000 tonnes. The process achieves up to 99.999% efficiency, supported by rigorous emissions and residue monitoring.
Nicola Henshaw, Veolia UK’s Managing Director Hazardous, emphasises Veolia’s commitment to providing compliant PFAS management solutions aligned with its GreenUp strategy for environmental decontamination and sustainability. Beyond firefighting foams, Veolia’s HTI also treats PFAS-containing waste from diverse sectors including chemical manufacturing, construction, metal plating, and semiconductor production.
June 2025 regulatory change drives data integration and traceability focus
UK manufacturers of medical devices must now implement postmarket surveillance (PMS) systems under new regulations that came into effect on 16 June 2025. The Medical Devices (Post-market Surveillance Requirements) (Amendment) (Great Britain) Regulations 2024 align the UK with similar frameworks already adopted across the EU, US, and Australia.
to ensure compliance and protect patient safety. Injection moulding machines, temperature controllers, and robotics all play a role in capturing and transmitting production data into Manufacturing Execution Systems (MES), creating a digital record of each part produced.
Veolia’s BeyondPFAS programme integrates detection, treatment, and disposal services, offering tailored solutions to meet local regulations and customer needs. This initiative leverages Veolia’s centurylong expertise in hazardous waste management, supporting a safer, cleaner future amid tightening global PFAS regulations.
The new rules require manufacturers to monitor the safety and performance of medical devices once they are on the market. This includes collecting user feedback, tracking adverse events, and documenting any corrective or preventative actions. While the legal responsibility lies with the device manufacturer, component suppliers may also be affected depending on product classification and safety relevance.
Experts from Sumitomo (SHI) Demag highlight that traceability and real-time monitoring are now critical
Andy Jewell of Intouch Monitoring notes that MES platforms help meet compliance standards such as FDA 21 CFR Part 11 by enabling continuous process monitoring, audit readiness, and early detection of quality issues. Integration using open communication protocols like OPC UA is also key, ensuring different production systems can share data seamlessly.
Artificial intelligence is increasingly used to analyse data from MES and legacy systems, helping manufacturers identify deviations, automate reporting, and support regulatory submissions to the MHRA.
With rising regulatory scrutiny and shorter reporting windows for defects, the industry is shifting toward fully integrated, traceable production environments. Manufacturers are advised to review their digital capabilities and data infrastructure to ensure they can meet both current and future PMS obligations.
The Babcock Wanson Group has released a new brochure covering its many and varied sustainable solutions.
As a major international supplier of boiler rooms and associated equipment, operating in more than 13 countries, Babcock Wanson Group has become a major player when it comes to energy transition, offering increasingly carbon-free heat production solutions for industry.
The energy transition solutions deployed by the Group’s brands are built around four major pillars, which are explained within the new brochure: decarbonisation, energy performance, reduction of polluting emissions, and recovery & re-use.
For a copy of the new Babcock Wanson Group Sustainable Solutions brochure, go to www.babcock-wanson-group.com/our-solutions
www.contract-production.co.uk
Ray Penny has been appointed President of Mitutoyo Europe, becoming the first non-Japanese national in this role since the company’s European presence began 57 years ago. Penny, who started at Mitutoyo in 1986 as a UK service technician, has held multiple positions including Managing Director of Mitutoyo UK before taking on leadership of the entire EMEA region.
Penny aims to bring a more localized, agile approach to Mitutoyo Europe, aligning with the company’s mid-term management plan (2024–2029) and global “Vision 100” strategy for its centenary in 2034. A key focus is evolving Mitutoyo Europe into a “market-in” driven organization that anticipates customer needs to inform R&D in Japan.
Highlighting differences between the European and Japanese markets, Penny pointed to the strong aerospace and medical sectors in Europe and plans to expand automation and OEM integration services. His leadership style combines focus with openness, empowering teams while fostering motivation and retention amid current workforce challenges.
With nearly four decades at Mitutoyo, Penny is well-positioned to guide the company through a period of strategic growth and innovation across Europe, the Middle East, and Africa.
Dugard has expanded its team by appointing David Morning as Area Sales Manager to boost the company’s presence in the North East of England and Scotland. The South Coastbased firm has seen notable growth in these regions, and David’s appointment aims to further support its portfolio of leading machine tool brands.
David brings extensive industry experience, having started as an apprentice machinist at a subcontract machining company serving aerospace and MoD sectors.
He later transitioned to technical sales roles, supporting manufacturers across Scotland and Northern England with cutting tools, coolants, and workholding solutions. Most recently, he worked with a distribution company offering full-process solutions.
James Tan, who served as Managing Director of MAPAL Thailand since 2017, retired at the end of April. Effective immediately, Michael Loefflad, Managing Director of MAPAL KK in Japan, will oversee both Southeast Asian subsidiaries in a dual role.
James Tan has been a key figure for MAPAL in Southeast Asia for decades. Starting his career with MAPAL in 1995, he focused
on marketing German products across the region. He progressed to Technical Support Manager, providing training and support throughout Southeast Asia and played a vital role in establishing MAPAL operations in Malaysia and Indonesia. Since 2017, Tan led MAPAL Tooling Thailand, driving its growth through dedication and tireless effort.
Michael Loefflad, who has been Managing Director of MAPAL KK since January 2024, brings over 20 years of experience working in Asia. With his broad industry knowledge and leadership background, Loefflad is now responsible for managing MAPAL Thailand alongside his existing role in Japan, strengthening the company’s presence in Southeast Asia.
Pictured left: Now also Managing Director of MAPAL in Thailand: Michael Loefflad. He is already Managing Director of MAPAL Japan and now heads both positions at the same time.
©MAPAL
Danfoss has named Torben Christensen as Chief Financial Officer (CFO) of Danfoss Power Solutions, effective immediately. Christensen joins the Power Solutions Leadership Team and reports to President Daniel Winter, who previously served as CFO.
Based in Nordborg, Denmark, Christensen will lead financial strategy and oversee the Finance and Functions team, focusing on financial compliance, performance, and supporting strategic decisions during a period of strong growth and market challenges.
Bringing nearly 30 years of experience at Danfoss, Christensen has held key roles in Corporate Treasury and Global Services, managing areas such as logistics, finance, and procurement. Since 2017, he led Global Services and added the role of Chief Sustainability Officer in 2023.
He also serves on the boards of ProjectZero and STEAR, initiatives backed by the Bitten & Mads Clausen Foundation. Christensen holds a graduate diploma in finance and accounting.
The Building Controls Industry Association (BCIA) has appointed Ciaran Kelly as Technical Consultant and Rachael Zaidel Lamb as Marketing & Engagement Manager, underscoring its commitment to advancing the building energy management systems (BEMS) sector.
Ciaran Kelly brings over 14 years of international experience in building controls, having worked in manufacturing, system integration, and consultancy. In his new role, he will contribute to technical training content,
Quickparts has announced the appointment of Peter Jacobsen (pictured) as President of EMEA and Aidan O’Sullivan as President of the Americas, reinforcing its strategy to drive growth and improve regional responsiveness in on-demand manufacturing.
publications, and support the BEMS Controls Engineer Apprenticeship programme. Kelly emphasised the importance of education in improving BEMS design and performance to support energy efficiency and net zero targets.
Rachael Zaidel Lamb, a chartered marketer with more than a decade of experience in B2B marketing and events, will lead member engagement and communications. She will support BCIA’s mission to raise the profile of building controls and foster industry collaboration.
Jacobsen, based in Denmark, brings over 15 years of leadership experience in advanced manufacturing, having previously held senior roles at Nexa3D and Addifab. His focus will be on expanding Quickparts’ reach and capabilities across Europe, the Middle East, and Africa.
O’Sullivan, previously Quickparts’ Chief Transformation Officer, is based in the U.S. and brings more than two decades of experience in manufacturing operations, including senior positions at Shapeways and Kerry Group. He will now lead Quickparts’ operations across the Americas.
By Rob Beech, Director, Engineers Mate®
A leading UK kitchen manufacturer was facing persistent challenges with outdated pneumatic backplates controlling key stages of its cupboard assembly production lines. The system lacked colour-coded pipework, which made maintenance and fault-finding time-consuming. It also lacked an integrated monitoring system, which further complicated diagnostics.
Health and safety were growing concerns. Safety devices had been retrofitted over time, but the system as a whole lacked several critical safety features expected in modern industrial environments. The company needed a more reliable, efficient, and compliant solution.
Engineers Mate®, one of Camozzi Automation’s premium distributors and part of the IADA group, engaged Camozzi’s technical application team to develop a replacement solution for three initial units—two valve control backplates and one air preparation set.
A joint site visit allowed the teams to review the operational setup and
The whole engineering team
were very pleased with the quality of manufacture and the ease of installation.
discuss the customer’s technical and safety requirements. Camozzi proposed a redesign of the existing backplates, using original equipment documentation as a basis. The redesign would incorporate modern safety components, colour-coded pipework, and clear schematics to assist with future maintenance.
Working within space constraints, Camozzi’s team designed new backplates to match the original mounting points and physical dimensions, allowing for straightforward installation. Key enhancements included:
• Colour-coded tubing, tailored to the customer’s specifications for easier identification during maintenance.
• Dual Safemax MX monitored safety dump valves, compliant with ISO 13849-1 (Performance Level e), providing robust safety control over rod-lock cylinders.
• Custom-manufactured pneumatic cylinders, dimensionally equivalent to the original (non-ISO) components but produced in the UK as a costeffective alternative.
Following design approval, the upgraded components were assembled at the Camozzi Automation Centre and delivered as plug-and-play units to minimise disruption during installation.
The new backplates were successfully installed, tested, and commissioned by the manufacturer’s in-house team. The upgraded system delivered immediate improvements in both safety and energy efficiency. Reduced air leakage contributed to lower energy use and associated cost savings.
The compact, well-labelled layout improved access and simplified ongoing maintenance. Engineering staff reported the transition from the old panels to the new solution was smooth, with minimal downtime required.
Following the successful implementation, further discussions are in progress to roll out similar upgrades across the remaining nine machines and expand the pneumatic improvements site-wide.
“The whole engineering team were very pleased with the quality of manufacture and the ease of installation. Transitioning from the old, large panels to compact, welllaid-out new ones has been a great improvement,” the customer said.
For more information visit: engineersmate.com
Process improvement is like cycling. Everything runs more efficiently with the right partner.
Energy optimization is the key to sustainable production. As a strong partner for strategic energy management, we help you cope with rising energy costs and tighter environmental targets. We are at your side –uncovering the ways to save and be resourceful while maintaining safety, quality, reliability, and uptime.
Anritsu Corporation’s receiver test (SINK test) solution for the DisplayPort™ 2.1 standard has been certified by the Video Electronics Standards Association (VESA).
The solution pairs Anritsu’s Signal Quality Analyzer-R MP1900A with automated software from Granite River Labs (GRL) or Teledyne LeCroy to verify highspeed video transmission and
streamline calibration. This supports compliance testing for DisplayPort 2.1, which enables high-resolution video, including 8K, and is seeing growing adoption through integration with USB Type-C.
As testing for the evolving standard can be complex and timeconsuming, the certified solution aims to improve efficiency by automating setup and measurement procedures.
Chell Instruments has unveiled the 2432T, a high-accuracy, high-speed temperature scanner designed for industrial and aerospace environments.
Capable of measuring 32 thermocouple channels with corresponding cold junction temperatures, the 2432T supports multiple thermocouple types and outputs 32-bit engineering data via configurable protocols, including Modbus, iDDS, TCP/IP, and Netscanner® emulation. It is compatible with Chell’s pressure scanners and shares common communication protocols and accessories for streamlined integration across test systems.
Key features include real-time open circuit detection, impedance measurement, Power over Ethernet (PoE), and a rugged design tested to DO160G standards for use in harsh environments.
More details at www.chell.co.uk
More details available at: www.graniteriverlabs.com/en-us www.teledynelecroy.com
CGTech has released Icam Suite V26, introducing expanded automation features, improved diagnostics, and tighter integration with Vericut to streamline NC post-processing and simulation workflows.
The latest version features a new automatic rotary axis clamping algorithm and look-ahead capabilities for improved motion control at the start of operations. A new macro function, $FCLINFO(), enables faster, selective look-ahead of cutter location data, enhancing performance during toolpath analysis.
Diagnostic tools now include customizable message handling and color-coded severity indicators in both GENER and CERun.
Icam V26 strengthens its connection with Vericut through direct import of Vericut project data into the GENER panel, enabling the application of machine limits and tool lengths during post-processing. An Optimizer tab also allows feedrate optimization using Vericut Optimizer or Force before code generation, helping eliminate manual rework. More information at www.vericut.com.
binder has expanded its M9 circular connector portfolio, offering compact, robust solutions designed for applications where space is limited and connection reliability is critical. The 702, 711, and 712 series cover a range of use cases across industrial automation, medical technology, and test and measurement systems.
Designed for environments requiring both miniaturization and durability, the M9 connectors feature protection levels from IP40 to IP67, with options for shielded or unshielded, moulded or field-wireable variants. All series use a screwlocking mechanism to ensure a secure mechanical connection, even in mobile or vibration-prone installations.
• Series 711 offers IP40-rated connectors, suitable for standard environments, with both panel-
mounted and field-attachable options.
• Series 702 and 712 provide IP67 protection and shielding for more demanding environments. Series 702 includes overmolded versions with configurable cable lengths.
• All versions support 3 to 8 contacts, with metal or plastic housings depending on application requirements, such as EMC performance or weight sensitivity.
The M9 connectors are suited for signal and data transmission in compact control units, portable diagnostic devices, and sensor systems. They are also used in logistics and transport applications, including automated guided vehicles, where high ingress protection and compact form factors are essential.
binder employs automated manufacturing with strict tolerance controls to ensure the performance of the miniaturized components. Each connector undergoes extensive mechanical and electrical testing. The IP67 sealing system, used across several series, has been field-proven over decades.
Pictured left: The compact M9 connector portfolio combines a robust design with a wide range of flexible options for demanding applications. Image source: binder
Kongsberg Discovery is heralding a new age of efficient, simplified and sustainable pelagic trawling with the commercial launch of the breakthrough FS80 Trawl Sonar.
The compact, modular and multifrequency solution is the market’s first sonar system to combine net monitoring, intake profiling and bottom detection in a single unit, making the very latest sonar technology accessible to fishery operators, big and small.
Originally unveiled at Pacific Marine Expo (PME) in November last year, the innovation has now been put through its paces in extensive sea trails, with first class results.
The FS80 builds on the legacy of the enduringly popular FS70, which has been a trusted market leader for the past 20 years. Alongside
the upgrade in performance and integration, the new solution also supports a broad range of different telemetry cables, easing adoption for diverse customers.
A further innovation comes in its modularity; Kongsberg Discovery is on the cusp of launching the FH80 HUB, a central platform upon which modular components, such
as the FS80, can be based. This allows customers to “pick and mix” the optimal Kongsberg Discovery technology for their individual needs, giving them a unified, high performance trawling approach.
For further details please see www.kongsberg.com/discovery/ fish-finding/simrad-gearmonitoring-systems/simrad-fs80
Yorkshire Water has implemented Xylem’s CoMag® ballasted clarification system at its largest wastewater treatment works in Knostrop, Leeds, to meet stringent new phosphorus discharge limits set under the Environment Agency’s Water Industry National Environment Programme (WINEP).
Serving a population equivalent of 990,000, the Knostrop site required an upgrade to reduce phosphorus levels in treated effluent discharged into the River Aire—a waterway with numerous designated ecological protections. The new target was set at 0.4 mg/l total phosphorus.
The success at Knostrop has led to the selection of CoMag technology for another major site requiring phosphorus removal.
As part of a £60 million site upgrade, a single 32m CoMag clarifier was installed in 2023 to provide high-rate tertiary solids removal. The CoMag process uses magnetite—a dense, naturally occurring mineral—to increase the settling rate of flocculated solids. The system achieves up to 10 times faster settlement than conventional clarification and requires a fraction of the space: just 804 m² compared to the 14,136 m² that would be needed with traditional settlement tanks.
Commissioned in September 2024, the system now treats 75% of the site’s full flow-to-treatment (5,600 l/s), achieving an average phosphorus concentration of 0.25 mg/l—well below the regulatory threshold. During testing, levels as low as 0.1 mg/l were recorded.
The CoMag system’s magnetic recovery loop enables reuse of the magnetite, reducing operational costs and supporting Yorkshire Water’s sustainability goals. The success at Knostrop has led to the selection of CoMag technology for another major site requiring phosphorus removal.
More information: www.xylem.com
The River Deep Mountain AI (RDMAI) project has released its first suite of open-source artificial intelligence and machine learning (AI/ML) models aimed at improving water quality monitoring and pollution detection across the UK.
Developed through a cross-sector collaboration led by Northumbrian Water and funded by Ofwat’s Water Breakthrough Challenge, the models are designed to support river flow prediction, pollution source tracking, and hotspot mapping. The release marks the first major milestone for the project, which launched in July 2024.
The models have been built using data from a wide range of sources, including environmental sensors, satellite imagery, and citizen science initiatives.
Northumbrian Water is working alongside partners including ADAS, Anglian Water, Cognizant, Google, The Rivers Trust, WRc, Xylem, and others to develop AI-driven insights that can help improve the ecological status of UK rivers—only 14% of which currently meet Water Framework Directive targets.
Phase three of the RDMAI programme will focus on refining the tools, validating them in new catchments, and exploring national scalability. Updated versions of the models are expected to be released in November 2025.
The GitHub page for RDMAI can be viewed at https://github.com/ Cognizant-RDMAI
success will look after itself.”
We look after your marketing from start to finish!