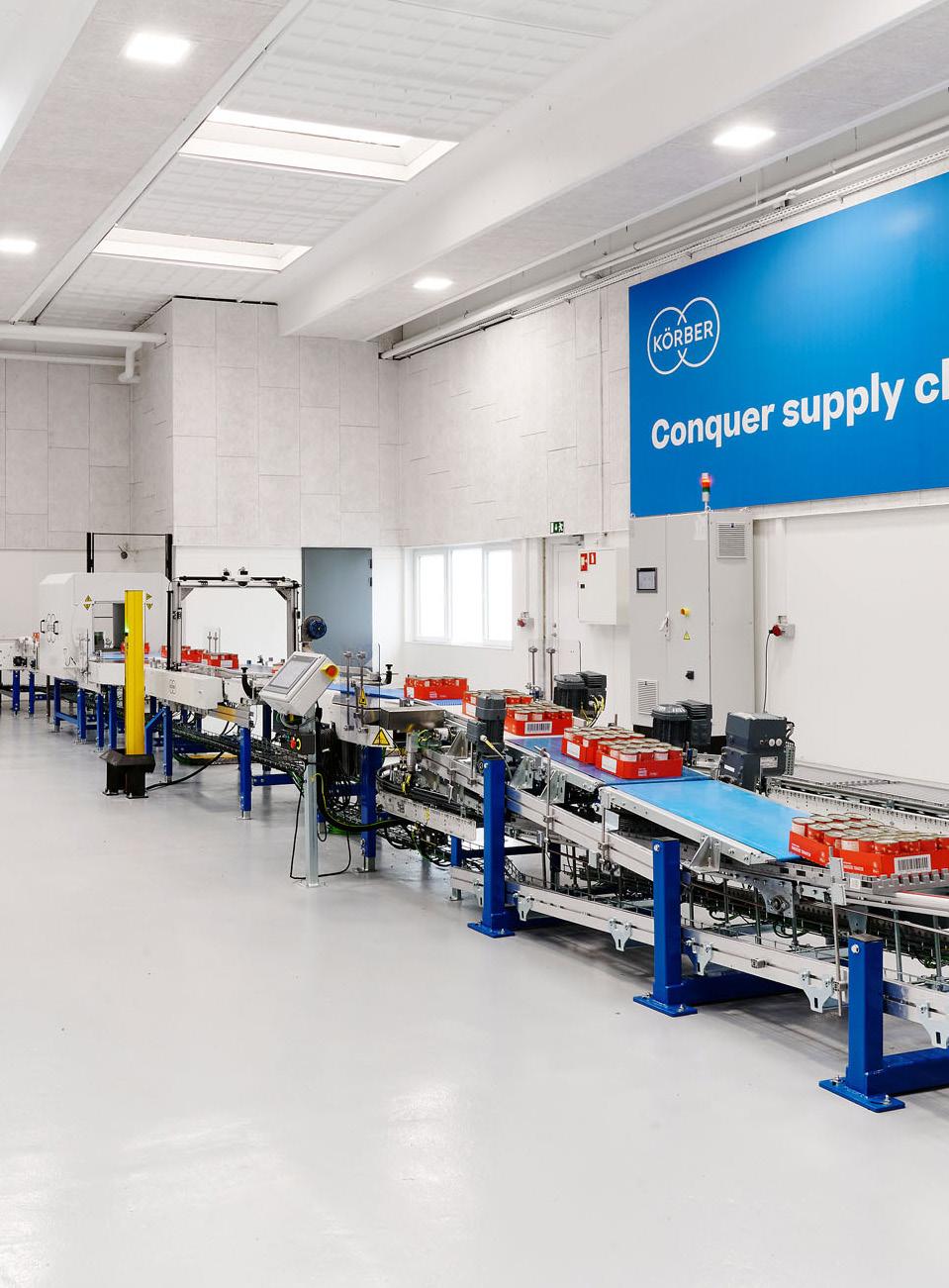
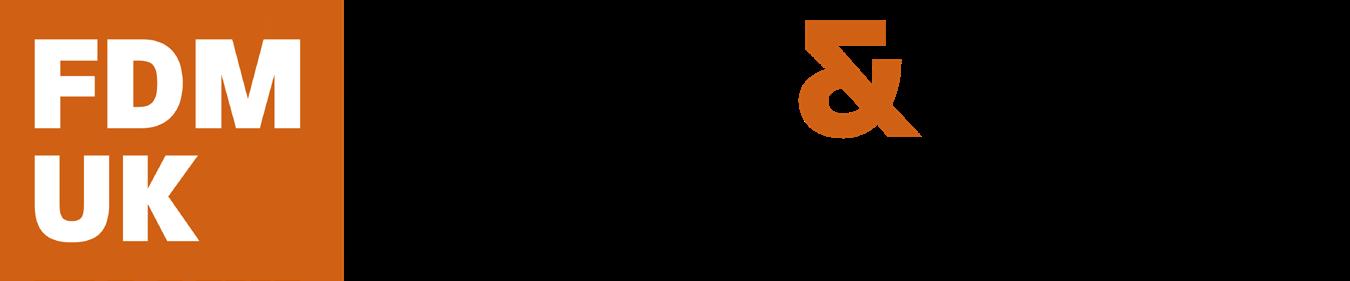
Oakley are the UK’s leading design, build and fit out partner for growing SME food manufacturers.
Oakley’s turnkey approach to factory design, build and fit out means that, as the business owner, you can focus on growing your business, without the stress, distraction and risk that often accompanies an expansion project.
expansion plans… delivered
01843 808 117 www.fdm-uk.co.uk
Distilling
Welcome to the latest issue of Food & Drink Manufacturing UK Magazine.
In this edition we hear from Valpak’s chief executive, Steve Gough. Steve has warned that the plastic packaging tax still has a “long way to go” to boost circularity, following news that the tax has raised £208m in the first three quarters.
We bring news of the upcoming exhibition, London Packaging Week. An exciting event being held at Excel, London on 21 & 22 September 2023.
According to the World Health Organization (WHO), consuming contaminated food results in an estimated 600m people falling ill every year, leading to 420,000 deaths. We cover a story about new global guidance from BSI, their study identifies that the common factor in food safety incidents, quality failures and recalls is people rather than failures of machinery or technology.
We hope you enjoy this issue and as always, if you have any news that you would like to feature, please email details to editorial@fdm-uk.co.uk.
Every effort is made to ensure the accuracy and reliability of material published in Food & Drink Manufacturing UK however, the publishers accept no responsibility for the claims or opinions made by advertisers, manufactures or contributors. No part of this publication may be reproduced or transmitted in any form or by any means, mechanical, electronic (including photocopying) or stored in any information retrieval system without the prior consent of the publisher.
Hilton Food Group plc has announced the appointment of Steve Murrells CBE as Group Chief Executive Officer. The company also published its preliminary results for the 52 weeks ended 1st January 2023, which underlined its volume and revenue growth against a volatile backdrop.
Murrells will assume the role from 3rd July 2023, and will join the Group Board at the same time. He succeeds Philip Heffer, who has decided to stand down from the Board and step back from running the company after almost 30 years with Hilton Foods, including the past five years as Group CEO. Heffer will remain with the business as co-founder and advisor to the Hilton Foods Board.
Steve Murrells’ connection to the business dates back almost 30 years, when he was one of Hilton Foods’ first customers and commercial partners at Tesco. After serving as CEO of Tulip Ltd from 2009 to 2012, Steve was appointed as CEO of Co-op Food, where he oversaw a turnaround in performance and repositioned the business as a leading convenience player.
This was followed by five years as Group CEO of Co-op Group, leading the business through the Covid-19 pandemic, repositioning the Group’s Insurance and Probate businesses, and growing its online capabilities.
Murrells was appointed Commander of the Order of the British Empire (CBE) in the 2022 New Year Honours for services to the food supply chain. He also currently acts as an advisor to Noble Foods Ltd.
The Institute of Food Science and Technology (IFST) has announced that Sterling Crew has been elected as the new President of the organisation, effective immediately. Sterling has worked and led in the sector for over 35 years.
IFST is the leading professional body for those involved in all aspects of food science and technology, with members from government, industry, and academia.
As President, Crew will lead the Institute in its mission to promote the advancement and application of food science and technology for the benefit of the public.
“We are delighted to welcome Sterling as our new President,” said Tim McLachlan, chief executive of IFST. “His extensive experience in the food industry, coupled with knowledge of food enforcement and his dedication to advancing food science and technology, make him the ideal person to lead IFST in the years to come.”
Murrells was appointed Commander of the Order of the British Empire (CBE) in the 2022 New Year Honours for services to the food supply chain. He also currently acts as an advisor to Noble Foods Ltd.
The FSA has launched a 12-week consultation seeking views from local authorities and district councils, food business operators, third-party assurance organisations for food safety, professional awarding bodies for environmental health and trading standards, trade unions and other interested groups.
The FSA Board endorsed the headline policy and principles to evaluate success for a modernised
FHDM. It is now seeking stakeholders’ views.
“We want people to have food they can trust. So we want to make sure local authorities and district councils can target their resources as effectively as possible as we develop a food hygiene regulatory model that is fit for the future.
“The consultation ends on 30th June 2023, so we would encourage all those who have an interest in this to respond over the next twelve weeks.”
WRAP and WWF have secured commitment from Aldi, Co-op, Lidl, M&S, Morrisons, Sainsbury’s, Tesco, and Waitrose, who represent around 80% of UK grocery retail market share, to a two-phased programme.
The first phase, in 2023, will ensure consistent measurement and reporting of their scope 3 GHG emissions, building on the WRAP Scope 3 GHG measurement and protocols in May 2023, and the piloting of these with 17 businesses across the food supply chain.
All comments and views should be included in the consultation response form and emailed to hygienemodelreview@food.gov.uk The consultation will close at 23:59 on Friday 30th June 2023.
Nestlé and private equity firm PAI Partners have set up a joint venture for Nestlé’s frozen pizza business in Europe.
Nestlé will retain a non-controlling stake with equal voting rights alongside PAI Partners. The transaction is subject to employee consultations and the approval of regulatory authorities and is expected to close in the second half of 2023. Financial details are not being disclosed.
Climate action NGO WRAP and WWF-UK have joined forces with eight of the UK’s largest retailers to standardise measurement and reporting of GHG emissions from food and drink, and drive action on cutting the environmental impact of food and drink.
The group estimates that food and drink consumed in the UK is responsible for around 35% of territorial emissions. Its Retailer Net Zero CAP (Collaborative Action Programme) aims to take the sector towards Net Zero at the pace it says is needed to meet existing commitments and mitigate the devastating effects of climate change.
It will also focus on scoping high-impact areas for collaboration to accelerate progress on reducing GHGs from the huge amount of food that is sold in UK supermarkets. Phase 2, from 2024, will take action on these high-impact opportunities, and the investments needed to collaborate and meet targets. The programme will build an assessment of the action currently being undertaken by retailers on key areas of GHG mitigation and identify gaps. Using the Courtauld Commitment 2030 as a preexisting governance vehicle, with widespread buy-in across the UK food sector, the programme will drive action on addressing these gaps.
Nestlé’s pizza business spans several countries across Europe, with an annual turnover of around CHF 400 million. Pizzas are currently distributed under the Wagner, Buitoni and Garden Gourmet brands, including in Germany, Italy, France, Spain, Switzerland, Portugal, Austria, Belgium and The Netherlands. The business will be headquartered in Germany and led by a strong and experienced management team. It will operate two manufacturing facilities, in Nonnweiler, Germany, and Benevento, Italy.
This partnership follows the creation of Froneri in 2016, a highly successful joint venture with PAI Partners. Today, Froneri is a global leader in ice cream with iconic brands and world class category expertise.
The proposed partnership will only cover Nestlé’s frozen pizza business in Europe. Nestlé’s leading pizza business in the United States is not part of the scope and remains integral to Nestlé’s frozen food operations there.
New collaboration with 8 UK supermarkets to drive action on cutting climate impact of UK food and drink
Food manufacturing specialist Wrights has announced a £1.3m investment in a fleet of environmentally friendly vehicles.
The three-site manufacturer which supplies and distributes sweet and savoury bakery products and ready meals into the hospitality and retail sectors as part of The Compleat Food Group, has invested in eight new vehicles which are fuelled by Compressed Natural Gas (CNG) bringing, what it claims will be a 95% saving in carbon emissions.
The new fleet includes heavy duty tractor units which tow trailered loads,
typically transporting frozen goods to customers across the UK; rigid vehicles and shop vehicles which transport items baked in Crewe to local shops and businesses across the North West.
The Group’s Crewe-based Health, Safety & Environmental Compliance manager Paul Strangwood said:
“We are working hard to get ahead of the government-set target of reducing carbon emissions by 2030. This is a mission which sits alongside our wider Group’s Environmental, Social and Governance targets which include a commitment here in Crewe of making a 50% reduction of our 2021 carbon emission levels by 2030 and a 90% reduction on 2021 carbon emission levels by 2035.”
Grocery price inflation rose by 17.3% in the four weeks to 16th April 2023, down marginally on the 17.5% recorded in the previous four weeks according to the latest data from Kantar. Take home grocery sales grew by 8.1% over the month to mid-April.
Fraser McKevitt, head of retail and consumer insight at Kantar, said: “The latest drop in grocery price inflation will be welcome news for shoppers but it’s too early to call the top.
“We’ve been here before when the rate fell at the end of 2022, only for it to rise again over the first quarter of this year.
“We think grocery inflation will come down soon, but that’s because we’ll start to measure it against the high rates seen last year.
“It’s important to remember, of course, that falling grocery inflation doesn’t mean lower prices, it just means prices aren’t increasing as quickly.”
The three largest grocers continued to grow at similar rates in the 12 weeks to 16th April 2023. Asda led the pack with sales up 8.8% year on year, giving the retailer a 14% share of the market. Tesco and Sainsbury’s weren’t far behind with their
sales increasing by 8% and 8.7%, claiming 27% and 14.9% of the sector respectively.
Morrisons’ sales continued to increase, and it now holds an 8.7% share of the market. Co-op’s market share stands at 5.7%, with sales growing by 2.7% in the latest 12 weeks. Waitrose’s sales increased by 3.2%, its best performance since June 2021, pushing its market share to 4.5%. Iceland matched the 12week market growth rate of 9.4%, maintaining its level of share at 2.2%. Ocado outpaced the overall online market, increasing sales by 8.7%.
The latest drop in grocery price inflation will be welcome news for shoppers but it’s too early to call the top.
Optimise your cleaning and maintenance, improve production automation, and access out of reach places and remove hazardous dust and fumes.
Total industrial vacuum solutions from Nilfisk
Clean air specialist Filtermist has introduced an exciting new range of Kerstar KEVA Premium industrial vacuum cleaners that include patented filter cleaning technology for the safe and efficient collection of hazardous dust, debris and workplace particles that pose a health and safety risk to employees. Regarded as the perfect all-rounder for your manufacturing facility, the new modular KEVA Premium series is ATEX certified, making it ideal for applications as diverse as powder coating, pharmaceutical, food processing, additive manufacturing, woodworking and much more.
What sets the impressive KEVA Premium Type H cleaner apart from its rivals is the ability to safely and effectively collect hazardous dust particles using a 3-stage filtration system that resides on the negative side of the powerful 230V 50Hz (1150w Max / 1000w Mean) electronically commutated brushless motor.
From a technical perspective, both KEVA Premium vacuums incorporate the renowned Kerstar 230V 50Hz (1150w Max / 1000w Mean) electronically commutated brushless motor.
From a health and safety perspective, the KEVA Premium vacuums are classed as Category 3 equipment, making them suitable for applications in Dust Zone 22 – an atmosphere where air and flammable dust can be explosive. With three stages of filtration that includes two conical M class filters at the first stage, an oversized, metal cased H14 Grade HEPA absolute filter at the second stage and a conductive fabric filter assembly at the third stage, the new vacuum series can achieve a filtration efficiency of 99.995%. Safety is further assured by the robust stainlesssteel construction and conductive rollers that eliminate any hazard potential in safety-critical areas, with additional 2m earthing clamp for added protection.
With two models in the new Premium range, the KEVA Premium CBS (continuous bagging system) and the Keva Premium 50L (50 litre drop down collection container), a key advantage is the new conical filtration system. The M and H14 Dust Class filter units incorporate a new mechanical cleaning system that simply requires a pull on an external lever to undertake fast and efficient filter cleaning. The patented mechanical control enables a reliable, reverse pulsation cleaning action on the first stage filtration system, helping the filters retain maximum efficiency. Contrary to a common ‘shaker’ mechanism for filters, this unique cleaning method prevents undesired wear issues caused by shaking. Cleaning the filter in seconds, the patented system on the new KEVA Premium series eliminates the need for dismantling the vacuum and manually cleaning the filters. This not only saves valuable time, but in instances where hazardous dust is collected, it helps
to protect the health and well-being of staff. Furthermore, the ability to frequently, quickly and safely clean the filter prolongs the life of the HEPA filter by up to 50%, reducing operational costs with fewer changeovers. This ease of filter cleaning also ensures that the maximum suction volume of 210M3/h is maintained for extended periods.
The KEVA Premium CBS has been developed with an ingenious bagging system at the base of the unit. This enables users in pharmaceutical and other particularly hazardous environments to safely collect, bag and remove contaminants without ever risking contact with the particulate. Perfect for environments that demand the highest levels of hygiene, safety and staff protection from potentially carcinogenic or harmful waste, the KEVA Premium CBS minimises exposure to any contaminant whilst the quick-change bag system maximises vacuum running hours. Alongside the KEVA Premium CBS is the 50L unit. With a fully enclosed stainless steel collection drum, the KEVA Premium 50L is the perfect unit for a wide variety of industry applications.
From a technical perspective, both KEVA Premium vacuums incorporate the renowned Kerstar 230V 50Hz (1150w Max / 1000w Mean) electronically commutated brushless motor. They also include a stainless-steel roller carriage, 2m earthing clamp, cyclone separator, a 10m connection cable, a flashing LED blockage warning indicator and vacuum pressure gauge that notifies the operator of any potential filter blockages. For customers working in particularly challenging environments, Filtermist can provide a host of optional equipment such as anti-static suction hoses, floor nozzle box, anti-static accessories, carbon fibre high reach pole sets and more.
For further details, please visit www.kerstar.com. You can contact our team of experts to find out more on 01952 290500 or email sales@filtermist.com
In the current climate, maintenance management teams are facing numerous challenges, and delivering solutions and new processes to deal with things is not easy. Teams are being pushed to work to tighter budgets, discover ways to reduce energy consumption, effectively monitor condition measurements, keep tabs on which critical parts are on back order and impacted by supply issues, and much more. All this whilst continuing to ensure production uptime, equipment and asset availability, and compliance.
SSG Insight have lived and breathed maintenance management side-by-side with our customers through all sorts of global challenges, over the last forty years. We have seen maintenance evolve alongside equipment and process developments. We understand what maintenance teams are up against now and we are here to help. We firmly believe technology is the answer, and it is why our vision is a future where humanity and technology can work in harmony together.
In the meantime, living in the here and now, let’s take all the uncertainty from your maintenance headaches mentioned above, and create predictability.
What does creating predictability from uncertainty look like? Here’s a snapshot:
• Prevent downtime
• Drive visibility
• Improve performance
• Ensure compliance
• Optimise asset life cycles
• Enhance resource utilisation
• Empower workforces
• Measure & track conditions
• Integrate business systems
• Facilitate sustainability measures
In climates like the one now, businesses and teams need agility, that cleverness, sharpness, and quickness, to help solve maintenance challenges. It is the perfect time to discover Agility CMMS, the maintenance and asset management software that helps alleviate your challenges whilst connecting your assets and parts, people, and processes.
• Effective job deployment
• Self-allocation of work
• Access job details & documentation
• Complete risk assessment electronically
• Issue & return parts
• Less admin & paper
• Easy image & signature capture
• Full audit trail & compliance
Over the last decade or so, the benefits of aseptic filling technology compared to traditional hot filling techniques have become well known in the food and drink sector. The benefits in terms of product quality have been well documented and discussed. However, the environmental benefits, both in terms of energy consumption and typical life cycle analysis of this packaging method are less understood.
A number of Life Cycle Analysis (LCA) studies have shown that aseptic filling techniques using ultra heat treatment (UHT) systems of pasteurisation or sterilisation, which are based on heat
exchangers, generally have lower environmental impacts. This is down to two main factors: the packaging used in the two different processes and the energy footprint of the process itself.
The thermal processing of food and drink products, and the production of the relevant packaging have significant environmental impacts. However, despite this there have been few studies looking at the energy footprint and other environmental impacts of these processes.
Aseptic filling provides robust product quality, minimal thermal impact on the beverage, and greater bottle design flexibility with the ability to use lighter
The use of heat exchangers for pasteurization and cooling as part of aseptic filling provides significant energy savings
weight PET bottles or cartons. In contrast, hot filling requires a higher energy requirement, has a thermal impact on the beverage itself, and has less flexibility of bottle design than aseptic filling.
In an aseptic (cold fill) system, the product is pasteurised or sterilised using UHT systems and then cooled immediately. It is then placed in the packaging which has either been presterilised (or is sometimes sterilised at filling). Heat exchangers are generally used for both the heating and cooling processes, enabling very efficient heat transfer and the use of heat regeneration to minimise the overall energy requirement. In these situations, ‘considerable energy is saved by using the hot product’s heat to pre-heat the cold one, and vice versa.
In a hot filling system, the product is pasteurised or sterilised (using heat exchangers or other thermal technologies). The packaging is then filled at a high temperature (typically between 80 and 92 °C) which has the result of sterilising the packaging. The packaging is then tilted or agitated to ensure complete contact with the hot product and the temperature is maintained for a specified period, such as two minutes. After this the packing and the product are cooled. How this is done, and how soon after filling the process is carried out, depend on the product and the packaging. Typical methods include blast tunnels, falling water coolers or even cold storage.
While the initial capital investment in an aseptic system is often higher than for a comparable hot fill system, aseptic systems have lower daily operational costs (e.g., less energy usage) and allow for the use of lighter weight PET bottles. As a result, the Total Cost of Ownership (TOC) of an aseptic system is lower than for a hot fill system.
Aseptic filling has a lower GHG footprint than hot filling
In practice there are many different types of packaging used in both systems, although in general terms board-based cartons and light-weight PET bottles are used with aseptic systems, while hot fill machines are associated with heavier PET bottles, glass or cans.
In an effort to accurately compare the environmental impact of both systems, some researchers compared aseptic and hot fill systems based on the production of 500 ml PET bottles of orange juice. Because a thicker gauge of plastic bottle is required to withstand the higher temperatures in hot filling
systems, more plastic is used (in this example 24 g for hot filling versus 16 g for aseptic filling). As a result, the greenhouse gas (GHG) emissions associated with the packaging are 80.4 g CO2e per bottle for the hot fill process, compared to 61.8 g CO2e per bottle for aseptic filling – a saving of 23.1%.
The difference in energy consumption between the two systems is due to different heat treatment, filling and cooling methods has often been ignored by researchers.
Typical methods include blast tunnels, falling water coolers or even cold storage.
- Matt Hale
One typical (and totally inaccurate) observation is, ‘the energetic matrix was assumed to be the same for all systems.’ This is patently untrue, as other studies have shown that ‘There are several advantages to aseptic processing and packaging over traditional pasteurisation. Advantages include extended shelf life [and] lower energy costs.’
Where the energy footprint of aseptic filling has been compared to hot filling techniques, it has shown that, ‘the product treatment in hot filling appears to have higher impacts die to the higher energy requirement that occurs during the warming and the chilling phases’ and, ‘in hot filling systems the heat of the treated product cannot be recovered.’
Some of the benefits are less clear cut than may be supposed and vary according to the heating medium source (such as steam), as well as the electrical and compressed air consumption of different system components. However, using heat exchangers with energy recovery provides significant energy savings.
Despite these complications, using the same 500 ml PET bottles of orange juice example above, GHG emissions associated with energy consumption by the process were 31.6 g CO2e per bottle for the hot fill process, compared to 24.4 g CO2e per bottle for aseptic filling – a saving of 5.32%. While this may seem small, when applied up to a theoretical production of 250 million bottles per year, this represents a saving of more than 1,500 tonnes of CO2e each year.
Based on our experience of thermal processing systems around the world, at HRS we believe that the GHG impacts of hot filling technology are in fact higher than this. There are a number of different techniques used to cool product and packaging after hot filling, and not all of these are as energy efficient as the chilled-water drench described in the above study. For example, where cold rooms are used, their overall cooling efficiency is low and the electrical energy requirements are significant.
As energy prices around the globe rise rapidly, and the need to take action on climate change intensifies, more and more food and drink manufacturers are looking to reduce the energy costs of their production processes. Switching from hot fill to aseptic production lines is increasingly attractive, and for new lines, the arguments for adopting aseptic techniques are clear.
As the scientific studies above show, overall GHG savings of 24.9 g CO2e per bottle are possible, something that is far from significant. To discuss how the HRS range of heat exchangers, pasteurisation and sterilisation technologies, and complete aseptic treatment and filling systems, can help your business to realise these monetary and environmental savings, please contact us.
For more information:
www.hrs-heatexchangers.com
As energy prices around the globe rise rapidly, and the need to take action on climate change intensifies, more and more food and drink manufacturers are looking to reduce the energy costs of their production processes.
- Matt HaleOrange juice produced via aseptic filling has a lower greenhouse gas (GHG) footprint than that produced with hot filling techniques
Across the globe, enough food is produced to feed 10 billion people, yet hunger and famine still prevail. Each year, around 931 million tonnes of food is wasted following production and processing; of this, 569 million tonnes (61%) is consumer waste, and 118 million tonnes (13%) comes from retail.
Sustainable development and fighting climate change are directly related to reducing food waste. As such, the UN Sustainable Development Goals include a target to halve this by 2030 – but all aspects of the value chain will have to invest and play their part if we are to achieve this aim.
Lee Metters, Group Business Development Director, Domino Printing Sciences, discusses the role that 2D codes could play in helping to cut food waste by providing more information on the location and age of food products.
2D codes can be instrumental in helping brands to gain more insight into their products and improve customer experience by providing information on goods and services –but the benefits of 2D codes do not stop there.
Unique and batch-level 2D codes can be embedded with information to link physical products to their supply chains, allowing brands to collect and share data, track products, and better manage recalls.
While other connective technologies, including RFID tags, can offer many of the same benefits, 2D codes are one of the most practical solutions available today. Creating and printing 2D codes is cheap and easy, and the technology required for scanning and accessing data is readily available and wellestablished.
At the retail level, including product expiration data within 2D codes can enable retailers to improve inventory management, by tracking the quantity of sellable stock on the shop floor and in the warehouse. This information can be used to remove items from shelves that are past their expiration date, or indeed prevent items with longer sellor use-by dates being placed on the shop floor before older produce is sold.
Inventory management can be tedious and time-consuming, but with the help of 2D codes, it can be done faster
and more efficiently. It also allows businesses to dynamically adjust the price of specific product batches to incentivise purchasing short-life products and further reduce waste.
Dynamic pricing is a retail strategy designed to respond to changes in the market – also known as algorithmic pricing – which involves using an algorithm to calculate the optimal price for a product or service.
Dynamic pricing is often used in ecommerce, with companies reducing prices when demand is low and increasing prices when demand is high. It can also be used to tempt consumers to buy products or services they have viewed but not bought, with a price discount applied to encourage a sale.
In stores where 2D codes are used for stock management and at the point of sale (POS), dynamic pricing can be used to encourage consumers to buy products nearing their expiration date. While a standard, linear barcode will only allow a POS system to retrieve a universal product code (UPC), a 2D code can link to much more granular product information, allowing retailers to adjust prices for specific product batches.
Including batch-level data within scannable POS codes allows retailers to update the prices for specific batches to incentivise purchasing. It’s a win-win from a sustainability, and a profitability perspective – retailers reduce food waste by selling products instead of throwing them away, while boosting profit margins.
In recent years, several retailers – such as Woolworths in Australia, and Meny in Norway and Denmark – have trialled dynamic pricing models through datecontaining 2D codes on own-brand produce. Third-party providers have also emerged to offer dynamic pricing infrastructure, including shelf labels and POS systems, such as Wasteless, an Israeli start-up using expiry dates and stock data to calculate the optimal
It’s a win-win from a sustainability, and a profitability perspective – retailers reduce food waste by selling products instead of throwing them away, while boosting profit margins.
- Lee Metters (Pictured Left)
product price in real-time, with product data embedded within a 2D code.
The end consumer can also gain from the inclusion of additional information within 2D codes. With dynamic pricing models like those described above, consumers can benefit from more competitive pricing and enjoy discounts on items with a reduced shelf life.
In addition, research suggests that consumers are becoming more au fait with the idea of scanning 2D codes to
access product information. A recent study from Cornell University looked at replacing date codes on milk with scannable QR codes that would provide a best before date when scanned by a smartphone. During the twomonth study, over 60% of customers purchased milk with the QR code rather than a traditional best before date.
Equipping products with 2D codes also opens opportunities for further Internet of Things (IoT) applications and integration into smart home systems. Smart fridges and personal assistants equipped with technology to download information on products from a scannable 2D code – or from shopping data obtained directly from the retailer – could use the data to provide a household inventory, meal plans, and waste-saving tips.
This may sound futuristic, but innovative tech companies are already releasing smart home systems to help consumers fight food waste. In 2019, Samsung launched the Family Hub,
a smart fridge with a built-in internal camera designed to pick up the best before date from fresh produce and advise when food is approaching its expiration.
As the benefits and relevance of 2D codes become more prevalent throughout the food production supply chain – from manufacturing execution, logistics and traceability, retail stock management, and consumer awareness – the time to act is now.
While the application of this technology may seem still to be in its infancy, the rate of adoption looks set to increase rapidly, to which the amount of investment and innovation bears witness.
For retailers and manufacturers yet to think about the role that 2D codes could have in your business, there has never been a better time to invest – the market (and competitors) is undoubtedly moving in this direction.
The end consumer can also gain from the inclusion of additional information within 2D codes.
- Lee Metters
There are two types of plastics cycles: pre-consumer and postconsumer recycling. The waste generated during the production and processing of plastics is collected, reprocessed if necessary and used again in production together with the new plastic. This is called pre-consumer recycling. The advantages here are the short distances, as the plastic is often reprocessed internally, and that the production waste is clean and its chemical composition is known to the producer.
In post-consumer recycling, the waste from end consumers is reused. In many countries, plastic waste is collected separately: e.g. the deposit return of bottles or the yellow bag in Germany and Austria. The collected material is sorted, washed and processed into granulate – also known as postconsumer recyclate. Products can then be made again from this recyclate. For example, old fishing nets are turned into watering cans for children. PET bottles can be recycled to produce new bottles. Compared to production from
new PET, this saves up to one tenth of CO2 emissions.
The circular economy is not yet completely round
Recycling is still a complex and expensive process that requires energy and emits greenhouse gases. In addition, recycled material is often of lower quality than virgin plastic. The use of recyclate in production may fail to meet quality and hygiene requirements. However, wherever possible, recycled material should be used.
In addition, recycling starts long before production. When developing their packaging, design teams must consider mind how a plastic product can later be successfully recycled. Only if consumers can easily separate the individual components of the packaging, can they be further reused in a circular economy.
The trade in used machinery is a step in the cascade use of machinery and thus
a contribution to the circular economy in machinery and plant engineering sector. Every used machine saves considerable amounts of greenhouse gases and raw materials compared to new production. With around 55,000 machines and operating equipment that are auctioned annually at the industrial auction house Surplex, the CO2 reduction amounts to around 1,300 t every year. Plastics processors will find what they are looking for on Surplex.com, where regular auctions of machines and inventory for plastic processing take place, offering companies the ideal opportunity to make their production even more sustainable.
In many countries, plastic waste is collected separately: e.g. the deposit return of bottles or the yellow bag in Germany and Austria.
London Packaging Week will again assume its rightful place at the epicentre of the packaging industry later this summer, but in a brand-new home - the world-famous ExCeL Centre in London.
London’s premier international convention and events venue, situated on the historic Royal Victoria Dock’s northern quay, will host four co-located events –Packaging Premiére, PCD, PLD, and Food & Consumer Pack – held on 21 & 22 September.
Event organiser, Easyfairs, is delighted to secure such an iconic venue. The docks continue to draw people and produce from all over the world some 167 years after their opening.
As one of the world’s most connected venues, the ExCel offers more space, extra parking, and improved transport links. With more convenient hotels, London Packaging Week promises an enhanced visitor experience for the thousands of anticipated visitors.
“We’re already fielding an increased number of enquiries from people wanting to find out what opportunities might lie within this showpiece event for their business,” said Renan Joel, Managing Director, Packaging at Easyfairs.
“There’s a reason London Packaging Week remains the beating heart of a global network of brands, innovators, designers and creators – its credentials in breaking down what the next 12 months and beyond have in store for the world of package design, branding, and material innovation, are second to none.”
PROPER snacks healthy foods founder Cassandra Stavrou, wellbeing guru Liz Earle MBE, and Candy Kittens confectionary co-founder Jamie Laing have also been revealed as the first confirmed headline speakers, with more very exciting names set to be confirmed soon. The full content programme is set to be released in early June.
The four shows combine to capture the inspiring free-spiritedness of the art and fashion worlds and blend them with the cutting-edge science and technology of packaging to create a unique showcase.
Packaging Premiére is focused on the future of luxury packaging. It matches visitors from the ExCel Design – combines the world’s most cutting-edge cosmetics packaging solutions under one roof. Meanwhile, PLD focuses on Premium and Luxury Drinks packaging, connecting designers, specifiers, and buyers across the premium beverage industry. Completing the event is Food & Consumer Pack, which highlights the latest innovations in the food and FMCG sector and attracts global brands and manufacturers.
“Exhibitor slots have begun to fill up rapidly, with some of the biggest names in the food, BPC, premium, and luxury packaging industries already on board,” added Joel.
“LPW is renowned as one of the premier exhibitions for sustainable and stylish packaging solutions worldwide.
“Top luxury brands will once again walk the floor of the ExCel on the lookout for sophisticated packaging that prioritises their environmental commitments while adhering to aesthetic expectations.”
Over 5,000 expected visitors will have access to over a hundred of the best packaging suppliers and innovative solutions in design, sustainability, branding, e-commerce and more!
Registrations for attendees will open shortly.
To register interest in visiting, or to enquire about exhibiting at the show, visit londonpackagingweek.com today.
Leading multi-format event organiser Easyfairs has committed to taking the packaging sector’s temperature in the coming weeks by launching a brand-new survey.
London’s vibrant home for packaging innovation and design, London Packaging Week, is seeking to canvas the opinion of suppliers, designers, packaging developers, marketers, and founders, as it continues to identify the major forces and emerging trends that will reshape luxury over the next decade.
The five-minute, 10-question survey looks into which influential brands, organisations, and external factors are making waves - from manufacturing to consumerism.
Renan Joel, Managing Director, Packaging at Easyfairs, said: “This is an opportunity to help shape an already renowned event and allow us to continue creating a dynamic and inspirational offering that drives packaging innovation, business and connections at the heart of the UK’s luxury and consumer products markets.
“Unequivocally, our performance is contingent on the quality of our listening. It qualifies us to connect the dots between trust and relationships, whether between individuals, an organisation and its customers, or stakeholders.
“It enables us to look audiences in the eyes and guarantee a level of interest they relish.”
LPW, scheduled to take place on September 21 and 22 at the ExCel London, will, no doubt, be awash with of brands, innovators, designers and creators looking to study what drives the success of prestige brands innovating to come up with a league of creative and sustainable solutions.
“Packaging matters more than ever,” added the Easyfairs chief. “In a world of disparate alternatives, consumers choose to express themselves with brand choices that reflect their values.
“London’s vibrant home for packaging innovation and design will walk you through the entire immersive process, where the right materials and shapes are matched to the desired sensory cues
that trigger a positive response in the consumer’s mind. Quite simply, there is no other exhibition or observer of the luxury industry whose insights are more useful, accurate and packed with smart predictions for the packaging sector. LPW will, once again, show that it understands the mindset that creates luxury’s timeless value.”
The short survey comprising 10 key questions can be found here, and Easyfairs is encouraging key businesses and media outlets to share far and wide.
matters more than ever. In a world of disparate alternatives, consumers choose to express themselves with brand choices that reflect their values.
We don’t mince our words. Krehalon is proud to launch its recycle-ready KreCycle PP™ films for all flowrap and thermoforming applications, available in the UK, Ireland and selected European Markets.
100% recycle ready Weight reduction opportunities v standard films.
Plug and play set up. Excellent clarity. Perfect for all mince types and cheese applications.
Full print options available.
Thinner. Stronger. Lighter.
Want to know how?
The growing emphasis on sustainability in nearly all sectors has placed the packaging industry under scrutiny. As a critical component of the global economy, the packaging sector holds significant environmental implications. In the pursuit of sustainable packaging, a holistic approach is necessary, encompassing aspects such as material selection, carbon footprint reduction, and the development and implementation of government policies that foster a circular economy. This article provides a comprehensive examination of the key themes and challenges surrounding packaging and recyclability and delves into their connections with prevailing environmental concerns and policies.
The three main elements of environmentally sustainable packaging are Resource Planning, Carbon Reduction, and Waste Reduction. Resource planning aims to cut waste by encouraging reusability through material choices which facilitate reuse and efficient recycling. Carbon Reduction strives to lower the impact of greenhouse gas emissions by considering the entire carbon lifecycle of packaging, from manufacturing to consumer behaviour. Grasping an understanding of the stages in the lifecycle with the largest carbon emissions enables those areas to be addressed through the initiation of programmes such as utilising renewable energy for production or enhancing transportability through alterations in packaging dimensions or form. Waste Reduction aims to lower waste volume through strategies like
waste prevention, reuse, recycling, and composting. This can be achieved through material minimisation, recyclable or compostable designs, and reusable packaging systems. Using alternative packaging materials, such as recycled paper, biodegradable polymers, and plant-based options, can also decrease the carbon footprint of packaging.
One method to advance sustainable packaging solutions is through the establishment of regulations and policies that inform decision-making among businesses. Making the environmental impact of a diverse array of materials and products transparent can encourage manufacturers to choose more sustainable options. Environmental Product Declarations (EPDs), for instance, can provide valuable data for comparisons. Nevertheless, the current EPD system contains technical documentation that is difficult to evaluate, whilst there is a shortage of available EPDs. To tackle this problem, it is critical to make these evaluations more accessible to the general public.
There is also a need for more sophisticated guidance in evaluating the emissions associated with different disposal techniques. Presently, the emission factors provided by the UK Department for Business, Energy & Industrial Strategy inadvertently provide incentive for organisations to prefer landfill disposal of plastic rather than recycling. To address this issue, an effective strategy should focus on pinpointing opportunities to
Despite efforts to manage plastic waste recycling, a notable gap persists in the UK between recycling rates of paper/cardboard (71%) and plastic packaging (44.1%). To address this, the UK government introduced a tax in 2022 targeting plastic packaging with less than 30% recycled content.Nathan D. Wood Dr Aaron Yeardley Natalie Bavis Dr Torill Bigg
decrease carbon emissions specifically from recycling processes themselves. This may encompass investments in cutting-edge recycling technologies, enhancement of sorting and separation procedures, and the investigation of pioneering recycling methodologies for a diverse array of materials.
Besides transparency on the environmental impact of materials, incentives and regulatory measures play a vital role in promoting sustainability. The UK, for example, has taken a leading role in implementing environmental policies such as the ban on plastic microbeads and limitations on single-use plastic items. These policies are important in addressing both the impact on resource use and environmental plastic pollution. The implementation of policies encourages consumers and businesses to adopt sustainable alternatives.
Despite efforts to manage plastic waste recycling, a notable gap persists in the UK between recycling rates of paper/cardboard (71%) and plastic
packaging (44.1%). To address this, the UK government introduced a tax in 2022 targeting plastic packaging with less than 30% recycled content. This strategic tax measure is designed to provide businesses with an economic incentive to incorporate recycled plastic materials into their packaging, thereby fostering increased waste plastic recycling and collection rates, and ultimately reducing waste destined for landfill or incineration. The tax is projected to increase recycled plastic utilisation by 40% and result in carbon savings of nearly 200,000 tonnes during 2022-2023.
Furthermore, in light of the pressing demand for enhancing the recyclability of packaging materials, the UK Government has introduced the concept of ‘Extended Producer Responsibility’ (EPR). As of January 2023, businesses have been mandated to collate data pertaining to their packaging to comply with EPR regulations, with a registration deadline of 2024, at which point fees shall become payable to the
environmental regulator. By holding packaging manufacturers responsible for non-recyclable materials, EPR is anticipated to lead to a shift towards reusable or recyclable materials, thus fostering a circular economy.
It is imperative to create informed and balanced policies in order to circumvent potential pitfalls while meeting sustainability objectives and goals. Certain measures may inadvertently encourage bad behaviours, such as an increase in landfill disposal to reduce the measured carbon footprint of companies who conduct yearly carbon assessments. Policymakers must carefully evaluate the potential consequences of their actions to ensure that they do not result in counterproductive outcomes. Another challenge is the potential for ‘greenwashing’ or the practice of making misleading claims about the environmental benefits of a product or service. Policymakers and industries must remain vigilant against greenwashing and promote transparency.
Glad tidings often follow trials; many auspicious negotiations nestle an ultimatum; great rewards are inextricable from great risks; and environmental action comes with legal obligations. The world has welcomed 2023 with enormous anticipation as much as pressing demands for concerted climate action, a great portion of which involves the complex world of packaging. From sweeping bans to labelling specifications, the European packaging field is transforming rapidly as more and more governments are recognising the long-term benefits of EPR. It is only the first month of a new year and a dizzying number of laws are already in force.
Several countries have taken their turn in transforming EU directives on single-use plastics into domestic laws. As of the first day of the new year, Andorra has banned such products as plastic straws and polystyrene containers to promote reusable alternatives. France’s Environment Code has entered a new phase as throwaway boxes and single-use cutlery are now banned from restaurants and cafes, joining in the Code’s various measures to eliminate nation-wide use of singleuse products since 2021.
France’s Environment Code has entered a new phase as throwaway boxes and single-use cutlery are now banned from restaurants and cafes, joining in the Code’s various measures to eliminate nation-wide use of single-use products since 2021.
Since the 5th of January, Italy has initiated the first stage of its EPR requirement for manufacturers and importers of designated singleuse products, with producers and distributors of disposable plastic tobacco filters being now obligated to implement a producer responsibility scheme and undertake relevant awareness campaigns; a similar requirement has been enforced in Cyprus as part of an amendment to the country’s Law on Waste. Transposing EU into domestic law, Poland has amended its act on the management of packaging and packaging waste to charge producers with a packaging fee and require each single-use plastic product to bear a visible and indelible mark.
Yet more laws and amendments are in place. Spain’s much-awaited Plastic Tax is now in force, and 0.45 euros are due on any non-recycled plastic contained in non-reusable packaging, semi-finished plastic products, and products containing plastic intended to allow the closure, marketing, or presentation of nonreusable containers. Germany’s major packaging act, VerpackG, has mandated that retailers, restaurants, and distributors of “to-go” food delivery offering plastic food packaging and beverage cups inform consumers of reusable options for takeaway meals and drinks that can replace single-use packaging. Going a step further, Luxembourg’s amendment to the Law on Waste requires restaurants to serve meals and drinks consumed on-site in reusable containers and with reusable cutlery.
Greece has officially extended the scope of its existing EPR scheme to additional disposable plastic products, such as beverage cups and food containers, as well as requiring producers to participate in or organise a Collective Alternative Management System for packaging waste.
Spain’s muchawaited Plastic Tax is now in force, and 0.45 euros are due on any non-recycled plastic contained in non-reusable packaging, semi-finished plastic products, and products containing plastic intended to allow the closure, marketing, or presentation of non-reusable containers. Germany’s major packaging act, VerpackG, has mandated that retailers, restaurants, and distributors of “to-go” food delivery offering plastic food packaging and beverage cups inform consumers of reusable options for takeaway meals and drinks that can replace single-use packaging.
Hungary has prohibited all beverage cups from being placed on the market and single-use plastic fast food containers from being offered to consumers free of charge.
In addition to these major changes, more laws have been enforced with the advent of 2023 and further legislation is expected to roll in within the next weeks and months. Although this legal onrush is an exciting sign of a timely rise in environmental awareness across Europe, making sense of the logistics behind how obligated companies are from now on expected to design and distribute their products on a day-to-day basis can be daunting. If you expect your company to be impacted by sweeping shifts in 2023’s packaging world, reach out to Ecoveritas and our global EPR team will advise you on your obligations.
Get in touch with us today to learn more about our exclusive EPR Matrix. Please speak to one of our advisors on +44 (0)1865 502176 or email us at info@ecoveritas.com.
We stay ahead of a constantly moving consumer world by being agile, innovative and passionate about the possibilities of packaging.
From design, tooling manufacturing to extrusion and thermoforming, we take care of everything in-house.
Working each day to be part of the solution, not part of the problem.
Because we know the huge role we play in creating a world that our children – and their children – can enjoy.
That’s why we do more than simply excel at packaging.
We take packaging personally.
We are members of:
The global thin-wall packaging market is projected to grow, driven by the increasing demand for lightweight and customer-friendly packaging.
The global thin-wall packaging market is forecast to grow due to increasing demand for lightweight and customerfriendly packaging. The market is expected to expand at a compound annual growth rate (CAGR) of 4.6% from 2020 to 2030.
This is according to a new report from Research and Markets, which also highlights the role of advanced technologies and the growth of the food and beverage industry in driving market growth.
Thin wall packaging refers to plastic packaging or parts with a wall thickness of less than 0.8mm, which is used in many different sectors such as dairy products, frozen goods, fruit and vegetables, and meats, Market and Research says in a release.
The study found the thin-wall packaging market is driven by the growth of the food and beverage industry, which has increased the demand for packaging solutions that can preserve the quality and freshness of products.
The report also notes the adoption of advanced technologies such as injection moulding and thermoforming has led to the production of thinner and lighter packaging materials.
Asia Pacific will dominate the market
Asia Pacific is expected to dominate the thin-wall packaging market due to the increasing population, urbanisation, and changing lifestyles, which have led to a rise in demand for packaged food and beverages.
The EU’s proposed Packaging and Packaging Waste Regulation (PPWR) could lead to higher carbon dioxide emissions and increased costs, according to a new study.
New research has found the European Union’s (EU) proposed Packaging and Packaging Waste Regulation (PPWR), which includes strict reusable packaging targets by 2030, could have unintended consequences. The study, which analysed data from various sources, found that reusable solutions could result in higher carbon dioxide emissions and increased costs for consumers.
The research compared the environmental impacts, economic effects, and societal implications of paper-based packaging currently used in food takeaway and e-commerce in Belgium and Germany with those of reusable plastic packaging if the PPWR reuse targets were applied.
The researchers concluded the use of reusable plastic packaging could result in up to 160% more carbon dioxide emissions for food takeaway and up to 40% more for e-commerce and explained this is as per the findings of a McKinsey article, which was one of the sources of the research.
Europe is also expected to witness significant growth in the market due to the region’s strict regulations on the use of plastics, which have encouraged the adoption of eco-friendly and recyclable packaging materials.
The report highlights some of the key players in the global thin wall packaging market, including Amcor Limited, Berry Global Inc., Huhtamaki Oyj, and Sealed Air Corporation. These companies are focusing on product innovation and development to meet the growing demand for sustainable packaging solutions.
Furthermore, the high operating costs associated with reusable packaging would likely result in higher costs for consumers, the researchers said. Transport would be the primary driver for both carbon dioxide emissions and costs, as reusable packaging needs to be transported back to the producer after delivery or purchase.
A more sustainable and costeffective option
The research suggests that recycling paper and board packaging is a more sustainable and cost-effective option.
The report’s assumptions for reusable plastic packaging represent a best-case scenario, assuming that plastic recycling will experience a rapid development in the future and that plastic packaging will be reused more times than is currently the case.
The report also notes the adoption of advanced technologies such as injection moulding and thermoforming has led to the production of thinner and lighter packaging materials.
Seal Packaging has introduced Infinity TopSeal™, a revolutionary and sustainable solution for food delivery businesses and foodservice caterers from restaurants to pubs and garden centres to the healthcare sector.
Last year, Seal Packaging was acquired by experienced industry professionals Kevin Curran and Sally Gabbitas, as a vehicle to launch new ranges of innovative and sustainable packaging. Their stated aim is to help their clients achieve net zero by ensuring the sustainability of its products’ raw materials, usage, and end-of-life, to protect the environment.
“At Seal Packaging, our mantra is ‘Packaging with Integrity’ and we are always seeking sustainable solutions which deliver as many operator and end-user benefits as possible,” says Kevin Curran.
The future of sustainable packaging for food-to-go
“Infinity TopSeal is a truly revolutionary packaging solution, which ticks so many boxes. Available with single or double compartments, these microwavable fully recyclable trays keep food hotter for longer, while staying cool to the touch. They weigh less than traditional sealable options – as the material they are made from is over 60% air – and they therefore have a low carbon footprint. In short, Infinity TopSeal from Seal Packaging represents the future of sustainable top-seal packaging for food-to-go.”
Mono-material
Infinity TopSeal is a mono-material foodservice packaging solution, and is therefore 100% recyclable.
The tray is made from expanded polypropylene (EPP), and the heatsealable film lid is made from polypropylene film. EPP was developed by Klöckner Pentaplast (KP) – a global leader in materials manufacturing, headquartered in Luxemburg, with 31 facilities worldwide.
“We are pleased to have partnered with Klöckner Pentaplast, as they are one of the most proactive and innovative materials manufacturers on the global market,” says Kevin Curran.
EPP is a sustainable replacement for expanded polystyrene (EPS) which was the favoured material for making takeaway food trays and clamshell burger boxes for many years. Many retailers have already ceased using EPS and from October this year, in England, all foodservice packaging made from EPS will be banned, while a ban applied in Scotland since June 2022.
Easy-to-use, and a drop-in replacement from rigid PP containers, Infinity TopSeal can be used with existing sealing equipment, so requires no additional investment.
Secure delivery of takeaway food
Infinity TopSeal is ideal to use for food delivery businesses. EPP has
exceptional insulating properties –keeping food hotter for longer by more than 10°C, compared with alternative packaging solutions. It has a low heat transfer rate, retaining heat inside the packaging while keeping the outside cooler to the touch.
As a plastic, this packaging is naturally water-resistant with no need for extra coatings or additives to keep it stable and robust to maintain food quality. It also offers best-in-class resistance to the acids, alkalis and hot oils found in many foods and sauces. This quality helps food retain heat and cuts down the risk of leakage and odour transfer.
Sealed at source, Infinity TopSeal also provides perfect tamper-evidence, which guarantees food security and delivery integrity. It ensures hygiene and eliminates the potential for tampering or product loss during delivery, which reassures customers and protects a food outlet’s reputation.
“Using Infinity TopSeal from Seal Packaging can also make a significant contribution to reducing food waste,” says Sally Gabbitas. “In factory and office canteens, at the end of each meal service, caterers can now hygienically portion and seal left-overs to freeze and use later, while in educational establishments, portioned left-overs can be sealed and sold to students. In healthcare, Infinity TopSeal enables the creation of dietand allergen-safe meals in bulk which can then be portioned, sealed and chilled or frozen for later use.”
“We are so proud of this innovative and unique sustainable packaging solution,” concludes Kevin Curran. “We launched Infinity TopSeal at the Hotel, Restaurant and Catering Show at ExCel in March and the reaction has been really exciting, with dozens of operators wanting to introduce it as soon as possible. We know that they’ll want to share all the positive benefits with their end-user customers, and to ensure that consumers understand their role, the packaging is embossed with the phrase ‘Recycle Me’.”
“Infinity TopSeal from Seal Packaging represents the future of sustainable packaging for food-to-go.”
Using Infinity TopSeal from Seal Packaging can also make a significant contribution to reducing food waste.
Uber Eats in Central London has begun a trial offering customers the option to order their takeaway in reusable containers in a bid to tackle single use packaging.
Bringing together various businesses, the project will test and measure how localised doorstep at-home collections of reusable packaging can increase the uptake of reuse systems and improve convenience.
When placing their orders, Uber Eats customers can opt-in to receive their food in reusable packaging. Once they’ve enjoyed their meals, all they need to do is scan a QR code, select a day for collection (from as early as next day to no later than 3 weeks later), give the containers a simple rinse and await collection.
All collections are low or no emissions, made by couriers using bikes, electric cars or vans. The trial will run for six months with a group of restaurant partners on the food delivery app Uber Eats and will be managed by Again, a reusable packaging supply chain company.
Participating restaurants are located withing a 5km radius of the Again facility in Kennington Park. Various incentives will be tested throughout the trial to measure what motivates customers to engage with reusables
(opt-in rate) and what motivates them to return the packaging (return rate). Again, who manages the trial, is one of six winning projects chosen by the £1.4 million Bring It Back Fund launched by Hubbub and Starbucks to fund trial innovative new solutions and systems for sustainable packaging in the food and beverage industry.
Matthew Price, Uber Eats general manager, UK and Ireland, said: “We know consumers care about the impact that their decisions have on the environment, and we are delighted to be part of this innovative trial which is another step in our mission to do our part in helping the food delivery ecosystem transition to a cleaner and greener future.”
Matt Kennedy, founder and chief executive at Again said: “Today, reusable packaging is too inconvenient for everyday customers. We’re excited to be partnering with the Bring it Back Fund to explore how we can make it really simple for customers to return packaging by trialling a new logistic service that will collect directly from customers’ doors. As we look ahead to 2030, we see that household collections will pay will play a pivotal role in the scale-up of reusable packaging. Once vehicles are collecting from households, new products, new retailers and new meal delivery platforms are incremental. We are creating an exciting future of low-cost household takeback for all products.”
Valpak’s chief executive has warned that the plastic packaging tax (PPT) still has a “long way to go” to boost circularity, following news that the tax has raised £208m in the first three quarters.
Steve Gough was responding to the latest figures from HMRC, which show that quarterly data totalled £72m and £70m through the first two quarters of recognised receipts. In addition, the third quarter raised a further £66m.
Gough said: “The government’s new PPT was designed to stimulate a shift from the production and use of virgin plastics to an increasingly high proportion of recycled plastic.That the level of tax paid has surpassed government estimates should act as a warning that we have a long way to go on improving the circularity of plastic packaging. There is a clear economic incentive to increase recycled plastic packaging production in this country with growing demand for these more sustainable materials, particularly given the majority of this demand is currently being serviced from abroad.
“On a business level, increasing numbers are becoming aware of their responsibilities around packaging compliance. Companies need to urgently put in place in strategies around plastic packaging that not only meet regulatory demands – now and in the future – but also continue the drive to a circular economy. Alongside the financial nudge from this tax and building on the excellent work already achieved in reducing singleuse materials, we hope to see further progress in the production and use of recycled plastic packaging.”
With sustainability and the rising cost-of-living being at the forefront of the media, Rotech have been looking at ways in which their innovative solutions can help food and drink manufacturers reduce their waste, while also shedding excess pounds spent on their coding and marking processes.
Targeting troublesome areas with TIJ
The waste produced by coding and marking technologies, and the recyclability of such waste, can vary drastically, and should be a key consideration for manufacturers looking to reduce their environmental impact.
The waste produced by our favoured technology, thermal inkjet (TIJ) against that produced by other technologies commonly seen in food & drink production environments, thermal transfer (TTO) and continuous inkjet (CIJ) is substantially less – the only
disposal component is an easily recyclable ink cartridge.
Manually hand labelling or stamping date and batch codes onto packaging can be a time-consuming, labourintensive process, one that often results in mislabelled or printed packs that have to be thrown away, a waste of both product and the manufacturers time.
By automating the process with the RF Lite, manufacturers can see productivity levels rise dramatically; the compact system can feed and print up to 400 packs per minute, freeing up skilled workers for other tasks.
Misprinted packs also become a thing of the past. The RF Lite accurately feeds product through to the printer, which triggers at the same point on each pack, producing a quality, clear print each time – a print automatically
generated by the printer’s intuitive iDesign formatting software.
Shed pounds and aid recyclability by printing direct to the box
Rotech’s large area printers allow for information previously carried on a label to be reliably printed directly onto outer cases and boxes at high speed.
As a result, you save costs on consumables, printing, and the need for an application system. With the ability to print a barcode to the required standard, the savings of direct box printing are substantial.
Lastly, due to the adhesives and ink used, labelled boxes can be more difficult to recycle. However, when boxes are directly printed, their composition remains unchanged so they can continue to be widely recycled.
Could Rotech help with your transformation?
Speak with our experts today to talk about how we can work together to reduce your waste while subsequently helping you to save money, without compromising on quality or efficiency.
For any further information on Rotech, or any one of our solutions, visit our website www.rotechmachines.com
Rotech’s large area printers allow for information previously carried on a label to be reliably printed directly onto outer cases and boxes at high speed.
Do you know how many new workers are needed to enter the manufacturing sector annually to meet demand? The estimate from the government sits at around 168,000. And that’s to just meet needs by 2024.
Where are we at? According to a recent study by Nineteen Group, 78% of industrial companies in the UK are finding it ‘harder’ or ‘much more complex than usual’ to source the employees they need. 57% of those in engineering are finding populating roles a challenge, sitting at 42% for both manufacturing and technical.
That doesn’t feel too encouraging when all three elements integrate within our sector, right? As a manufacturing MD, I understand and relate to the stats all too well. Not least because our modern world still assumes that a day at the office – or should I say, factory – is labour-intensive, with heavy-lifting activities clouded by dust.
While certain roles are concentrated to the warehouse floor, there’s a swarm of new roles that aren’t.
Industry 4.0 specialists. Data and analytics experts. Digital twin operators.
Our sector’s brimming with state-ofthe-art technology that promises to keep manufacturing relevant in the 21st century and beyond. But it’s missing the people that can take us there.
Make UK’s an example of an organisation targeting energy into overhauling the pre-historic image of manufacturing that many potential employees share. Though to me it seems that we’re yet to have our real breakthrough moment, it’s not actually all doom and gloom.
Apprenticeship starts were up 8.6% in 2021/22 compared to 2020/21. 349,190 apprentices began practical routes into careers, with just over 14% (49,100) relating to engineering and manufacturing technologies. Could it be that single word, ‘technologies’, where the cause for real change lies?
Robotics, automation, digitalisation –we’re churning out R&D in technologies every single day that work to stimulate efficiencies across industry and supply chains. Amazon’s been using an AI model that’s learnt from real-world customer complaints data on product damage to choose the optimum package for a product. There’s already been a 24% reduction in shipment damage and 5% cut in shipping costs. Proof’s in the pudding that it opens the floor to leaner ways of working.
And it’s this out-of-the-box thinking we need to raise the profile of. Who raised the case to adopt AI at Amazon? Whether there was an internal lightbulb moment or a stellar pitch, it’s a huge call to switch-up an operation that receives 18.5 orders per second, shipping around 1.6 million packages a day. To continue to drive forwards, we need to employ critical-thinkers and problem-solvers who recognise the scope of the task. And who can swing the doors wide open to the seemingly unlimited opportunities they can accommodate.
That brings me onto my next point. We can’t attract without being seen. Other sectors live and breathe social media –ours should be, too. Potential applicants aren’t just scoping out our websites before they hit ‘apply’. They’ll also be looking at our LinkedIn feeds, recent Tweets, Instagram posts...
It comes back to raising the profile of what we actually get up to behind the shutters.
Our sector’s brimming with state-of-the-art technology that promises to keep manufacturing relevant in the 21st century and beyond. But it’s missing the people that can take us there.
Louise O’Brien
• A time-lapse of the state-of-the-art machinery that operates on the factory floor.
• Before, during, and after photo series that show the intricacies involved in guiding concept and design through to final product.
• ‘A day in the life of’ videos that showcases the variety of work our talented employees take on during their 9 to 5.
Everyone can say a role’s this or that. But not everyone can show it. And that’s our URP (unique recruiting point).
It makes sense, then, that culture’s my final point. 51% of survey respondents named applicants opting for ‘jobs where they can work remotely’ and offer a ‘more sustainable work-life balance’ as some of the most significant reasons that roles are proving hard to fill. Is it really out of the realm of possibility to transition manufacturing to a working model that’s more the norm for 2023?
I don’t think it is. It’s not just recruitment that our industry’s struggling with, it’s retention too. Looking after the employees you already have is key to attracting those you don’t. Despite recruitment agencies singing your company’s praises or a host of 5* employee reviews on Glassdoor, word of mouth’s still one of the most influential ways to attract new faces. After all, employee satisfaction is the free PR tool that’s easily forgotten.
And with that comes pressure to integrate remote, or at least hybrid, working patterns. We can do it – we just need a new mindset. Take your local GP – that’s a role we long-associated as face-to-face. But 4 in 10 appointments now take place remotely.
It’s the same in manufacturing, especially as the sector embraces and evolves with tech.
Like remote monitoring equipment status that’s updated in real-time. Or using virtual reality to assist with design visualisation that doesn’t require everyone to be in the same room.
Obviously, there are limits and there’s also some preference for physical work. There’s something about being next to the 3D printer as it engineers your prototype, and not many of us have those hanging around at home! But what’s important here is the initiative to think wider than the confinements of the warehouse.
Flexibility can be achieved not just where you work, but when you work, too. We’ve done it – we now start at 7am instead of 8am, finishing at 4pm rather than 5pm Monday to Thursday. Why? We recognised our employees were fed up with getting stuck in rush-hour traffic, feeling as though they’d lost 30-60 minutes of their day. By opening earlier and closing earlier, we’ve cut
out unnecessary idling. Our staff feel as though they’ve got back time to do the things they want to be doing. Without work getting in the way.
Even more, our working week ends at 1.30pm sharp on Fridays. Staff get more time to make the most of the weekend or catch up on ever-growing piles of ‘life admin’. And in return, we’ve got a content workforce. Employee satisfaction is reflected in the products we produce and ripples around our company as a whole. And works to accommodate the next generation of manufacturers who are making significant employment decisions based on the modern work-life balance.
The only way is up for demand for our next era of employees. Their digital capabilities and imaginative mindsets are in prime position to propel the next line of production. It’s now up to us to put on the show that attracts them there.
Louise O’Brien is the Managing Director of Greyhound Box, trusted supplier of corrugated cases. Specialising in consultation, bespoke design, and expert manufacturing of packaging, all solutions are sustainability-centric. Greyhound Box prides itself on operational efficiencies for environmentallyresponsible processes and products.
The only way is up for demand for our next era of employees.Louise O’Brien (pictured right)
Tech advancements such as sophisticated sensor technology, Artificial Intelligence (AI) and faster microprocessors are conspiring to make line-scan camera technology a compelling option in a host of new areas.
Inline quality control of web printing processes is one of the most established fields of application for line-scan imaging - these fast cameras can often be found inspecting printed sheets or textiles for defects such as ink spot marks, embossing defects and misregistered colours.
Beyond the printing industry, however, their use has been limited to niche pockets of application. In the electronics industry, for example, line-scan cameras are deployed for inspecting printed circuit boards, and in the food industry, they can be found on nut sorting lines, scanning product flows as they cascade in a curtain past the camera.
Essentially, in scenarios where a moving, continuous material needs to be analysed for faults or defects, linescan cameras will generally provide a better solution than conventional areascan cameras, owing to fundamental differences between the two cameras.
Area-scan cameras capture the data for an entire image in one go and the dimensions of the resulting image correspond to the number of pixels on the sensor. Line-scan cameras, on the other hand, use a single row of light-sensitive pixels to constantly scan moving objects at a high frequency, capturing lots of ‘slices’ of an image which it then combines to construct the final image.
Because of this, area-scan cameras are not as suited to very fast web based applications but are easier to install and use than line-scan cameras, making
them ideal for straightforward machine vision tasks.
That said, the advent of bigger, faster and more sensitive area-scan sensors means that it is not unusual to see a CMOS area-scan sensor being used where a line-scan camera would have been the default option. The ability to adjust the active area on the sensor means that a line-scan camera can be emulated in some cases.
The complexity of implementing line-scan cameras can be off-putting.
Although capable of higher speed processing, line-scan cameras are more complicated and costly to install, mainly because the line rate of the camera must be synchronised to the speed of the object being detected.
Tech progress drives line-scan camera uptake
However, tech advancements in the last few years have meant that industries such as food, pharmaceuticals, e-commerce and logistics can no longer afford to ignore the performance advantages of line-scan cameras.
Advancements in Image Signal Processors (ISPs) are facilitating higher quality and faster processing of 3D images in more demanding environmental and lighting conditions. This enables the cameras to detect more critical detail and capture higher resolution images.
For example, HIKROBOT, represented by Scorpion Vision in the UK and Ireland, earlier this year launched a 16K line-scan camera that is capable of detecting minute defects in PCB, EV battery, semiconductor, print and film inspection applications.
At the same time, system designers are harnessing GPUs (Graphics Processing Units) from the gaming industry for image processing. This PC graphics hardware can reduce algorithm and data processing time and enables the use of AI-powered analysis.
Using AI to improve pattern matching capabilities improves and accelerates inspection performance. The combination of advanced image sensor technology and AI is enabling line-scan cameras to infer increasingly complex insights from the vast amounts of vision data they capture.
Sophisticated sensor technology has also provided solutions to the problem of adjusting the line rate to match the
The scanning unit incorporates two 3D Stinger cameras built into enclosures with internal polarised light sources, an arrangement that enables robust acquisition of images on reflective surfaces.
- Paul Wilson
speed of the material under inspection, enabling accurate, meaningful 3D analysis of the image at high frequencies using software algorithms.
Scorpion Vision has recently designed an AI-powered line scanning system to inspect IQF burgers for visual abnormalities and defects. The bespoke system, which incorporates two Scorpion 3D Stinger cameras above and below the conveyor belt, ensures that every single burger that passes through the line is visually perfect - to meet the increasingly stringent presentation demands of both consumers and retailers.
The camera system will check each frozen burger is exactly the correct shape and size, shows no signs of discolouration, freezer burn or ice crystal formation and is free from unsightly visual abnormalities such as large lumps of fat.
There are two reasons why a line-scan camera is the best solution for this application. Firstly, the inspection needs to take place while the frozen burgers are being transported to a robotic pick & place packing system on a very fast moving conveyor belt. An area-scan camera would not be able to perform the required imaging at this high speed. The linescanning system designed by Scorpion is able to locate, inspect and measure the burgers in real time.
Secondly, an area-scan camera would only able to image the surface that faces upwards, not the underside of the burger. With the line-scan system, the burgers are passed over a very narrow gap between two conveyors and two cameras (one above and one below the conveyor) build up a 3D image of the complete burger as it passes over the gap.
The scanning unit incorporates two 3D Stinger cameras built into enclosures with internal polarised light sources, an arrangement that enables robust acquisition of images on reflective surfaces. Scorpion Vision’s proprietary AI-optimised software analyses these images in realtime for reference features that have been established through deep learning, and any burgers that exhibit abnormalities are immediately rejected from the line.
This is only the start of what is possible when AI is combined with fast scanning technology, but it demonstrates how AIenabled line scanning systems are breaking new ground in inspection speed, accuracy and repeatability.
Measuring conductivity in smaller sized production facilities especially in the food and pharmaceutical industries demands the most compact, yet robust sensors and the new BAUMER PAC50 process sensors meet these critical requirements. These ultra-compact sensors set new standards and are based on the proven performance and durability of their ‘bigger brother’ the Baumer AF14/5 conductivity sensor.
Due to continued requests from customers for increasingly smaller components to fit into tight production lines these sensors feature a housing measuring just 60mm, with the potential for reducing the display size even further down to 32mm x 25mm. IO-Link is also a standard feature.
Despite their compact design the sensors deliver high temperature stability up to 140ºC allowing them to be specified for permanent use, even in CIP (Cleaning-inPlace) and SIP (Sterilisation-inPlace) systems. Their robustness and durability is largely due to an innovative one-piece sensor tip design which means optimum resistance to strong and or frequent temperature fluctuations, compared to other sensors which typically feature a two-piece tip.
Experience shows that many sensors have lower temperature
limits (typically 100ºC) and lower resistance to chemicals. This is why PAC50 sensors have a sensor tip made entirely of highperformance plastic polymer or ketone (PEEK) which offers much better resistance to chemicals and higher temperatures. Another important feature is the all stainless steel sensor housing with all parts laser welded ensuring optimum resistance to all ambient conditions outside the pipe.
PAC50 in its H version complies with EHEDG (European Hygienic Equipment Design Group) hygiene standards as required for many food, beverage and pharmaceutical applications. They are also 3-A certified and all media contacting parts are FDA certified. Like other Baumer sensors, IOLink is a standard feature allowing the collection of secondary data, such as temperature for process monitoring and communication to control devices. This means users can quickly and easily parameterise the sensor prior to and during operation – even when the sensor is integrated via an analogue interface. Furthermore, to optimise flexibility the dual channel feature allows users to operate the PAC50 via analogue or digital channel, or even both in parallel.
More here: baumer.com/gb/ en/new-level-sensor-to-detecteven-process-water/n/levelmeasurement-baumer-plp70
Ultra-compact sensor for optimum conductivity measurement
Schaeffler’s OPTIME wireless condition monitoring solution saves a leading food and biochemicals plant in South East Asia 30,000 euros per year by preventing unplanned machine downtime on a variety of rotating equipment. The plant benefits from the early detection of equipment failures, as well as more precise trend data and increased reliability of the monitoring solutions.
With its diverse markets and customers, the food and biochemicals company must always ensure that its machines run smoothly, therefore the company has been using Schaeffler’s offline and online monitoring solutions for their most critical machines. However, in searching for a comprehensive condition monitoring solution, the plant’s maintenance team decided on the OPTIME wireless condition monitoring solution, which met their increasingly demanding applications.
Sustainable products such as bioplastics are becoming increasingly important. At the biochemical plant, complex fermentation processes are carried out to produce derivative acid (e.g. lactic acid) which customers use in a variety of ways such as a food additive for bakeries, breweries and confectionery products, as well as for biodegradable packaging. During the production process, the machines are subjected to extreme stress, therefore production throughput must be optimised in order to avoid unplanned machine downtime.
The expansion of the plant in recent years presented a new challenge for maintenance – loose meshing of the machine gears. This meant tremendous stress on the gears and resulted in accelerated wear and tear and a risk of incorrect lubrication. Therefore, the maintenance
management team turned to Schaeffler for a comprehensive solution.
Easily scalable, wireless solution
Working together with the customer and understanding the demanding needs of the application, Schaeffler’s experts recommended OPTIME, an easily scalable wireless condition monitoring solution consisting of wireless sensors, a gateway and digital services based on proprietary Schaeffler algorithms. The gateway receives data from the sensors and transfer it to the Schaeffler cloud. OPTIME automatically detects any problems, issues the appropriate alarms and provides information on the possible cause of the problem. Condition monitoring expertise on the part of the customer is not required as this knowledge is already fully integrated into OPTIME.
A total of 50 OPTIME sensors were installed on a variety of pumps and gearboxes, as well as cooling tower fans and refrigeration compressors. With this solution, the majority of machines (157 pieces of equipment in total) are continuously monitored online.
Within a year of usage, OPTIME had detected a total of 17 faults, including
five serious ones. The savings of 30,000 euros were calculated based on the prevention of six days (144 hours) of unplanned downtime per year. Coupled with Schaeffler’s wired condition monitoring solution, SmartCheck, and offline measuring system, a comprehensive monitoring solution has been implemented at the plant.
An application engineer at the biochemical plant commented: “We’ve been using condition monitoring solutions from Schaeffler for years. Each solution provides us with the protection we need for our machines. SmartCheck is used for individual critical units and has saved us from some unplanned downtime. OPTIME enables us to implement comprehensive monitoring in our plant.”
OPTIME is part of the Schaeffler Lifetime Solutions portfolio, which offers a comprehensive range of products, services and solutions for industrial maintenance. It is designed to support maintenance engineers over the entire lifetime of a machine.
Website: www.schaeffler.co.uk
OPTIME enables us to implement comprehensive monitoring in our plant.
Accurate and reliable temperature data is essential for the integrity of the food industry and the safety of consumers.
Tinytag Data Loggers are robust, reliable and highly accurate measuring devices for monitoring temperature and humidity during food processing, storage and cold chain distribution.
Tinytag use simple technology that’s easy-to-use, easy-to-manage and conveniently versatile to help businesses gather vital temperature data at every stage of the food supply chain.
Improve temperature management
Tinytags can aid quality and food safety inspections (including compliance with HACCP regulations) by providing evidence of conditions that’s easyto-read and readily available in userfriendly data logging software, Tinytag Explorer.
Monitoring with data loggers can indicate the need to replace old or faulty equipment, stabilise temperature conditions in refrigerated areas or improve insulation in packaging, helping you to streamline product storage.
Save energy, save money
Temperature data loggers can help to identify the efficiency of heating and cooling equipment, helping businesses to pinpoint where to save energy and save money across their operation.
Data you can trust
Tinytag data loggers bring over three decades of manufacturing experience from an ISO 9001 and ISO 14001 accredited UK manufacturer, Gemini Data Loggers UK Ltd.
Certifiable instrument accuracy through our in-house Calibration Service that’s traceable to National Standards means you can put extra trust in the reliability of your data – and prove it to auditors.
Versatile data logging: portable data loggers
Compact, portable and easy-to-use Tinytag data loggers (temperature, relative humidity and energy consumption) provide a flexible solution for monitoring food processing and cold chain compliance. Tinytags are battery-powered, self-contained devices and have configurable LED alarms for notifying temperature breaches.
The Tinytag Connect system of Radio and LAN (Ethernet) data loggers brings you convenient wireless temperature and relative humidity monitoring at an affordable price and is ideal for use in warehouses and refrigerated storage and distribution, where central data management presents a significant –time-saving – advantage. Mix-and-match Radio and LAN loggers according to infrastructure requirements, get real-time data access and receive email alerts when temperatures are out of range to take fast corrective actions.
Tinytag DI is the secure software for Tinytag data loggers. With Tinytag DI, you can control who has access to your data loggers by managing user access levels. You may also set up groups according to location or department to assign data loggers to the relevant teams. An audit log ensures accurate and consistent data, providing a record of critical events and any changes made to the loggers.
You don’t get a second chance to make a first impression, and this saying is never more important than when it comes to your product labels.
The boring (but vital) part of food labelling is the information intended to help your customers become savvy about their choices. The front, back, sides and even the top and bottom of food packaging is filled with information on what the food contains and provides a guidance in their selection process. The laws around food labelling in the UK have largely been retained from the EU legislation on the provision of food to consumers. The laws outline the information which must be provided to customers when purchasing and stipulates how this information is presented.
The impact of your labels, however, goes far beyond the legal requirements and all manufacturers know that the visual aspect of the labelling of their product is equally as important.
The label must be easy on the eye but also grab the attention of the consumer, your product needs to stand out among all of your competitors, to be the chosen one.
The overall design of your label, the colours you choose and the information you provide will all go a long way in positioning your product in the eyes of the consumer, but of equal significance, is your choice of label supplier. A great label design communicates the quality and character of your product, but this can all be destroyed by a poorly printed label on a poorly selected material.
When choosing a manufacturer to print your labels, you will want to choose a company who have not only been established for a long period of time but also who have a comprehensive knowledge of the industry and the products involved.
If you feel you have found a manufacturer, request a sample pack of their existing work, which should show
a strong presence in your industry and a range of products and finishes. From this, you will be able to make a decision on whether the quality of their product meets your expectations.
When speaking with the manufacturer, consider asking about their colour management system and in-house studio capabilities. Ask about their experience in the industry and other companies they have supplied. Ask about their quality management system and if they have ISO9001. Ask about their capabilities and the total number of colours they can print. Ask about their printing techniques and whether they can supply flexo, litho or digital or a range of these. Ask. Ask. Ask.
This is your first chance to make a first impression, so when selecting your label partner, you want to leave no stone unturned, or rather, no label unstuck.
A great label design communicates the quality and character of your product, but this can all be destroyed by a poorly printed label on a poorly selected material.
You don’t get a second chance to make a first impression...
With the launch of a new depalletization system, Körber Supply Chain becomes the first supplier of automated logistics solutions to offer a total turn-key solution for the separation of goods from pallet to tray. The goal is to fully automate and eliminate risks and sudden downtime in the sorting process.
New research shows that sudden stops and interruptions in the supply chain are the biggest concern for almost 90% of the companies surveyed within among others retail trade, consumer goods, and industrial production. This is one of the reasons why close to half of these companies expect to increase investments in strengthening their supply chain – including technology that ensures increased flexibility, transparency, and an overview.
To meet the market’s challenges, Körber Supply Chain has now, as the first supplier in the industry, developed a total solution to manage the sorting of products from pallets to trays.
The solution is called Downstream. It is a de-palletizing system that separates each pallet layer into individual items, which can be turned and tilted to fit into trays and prepared for further distribution through a conveyor belt.
It is not straightforward to break down pallets into trays in a fully automated solution with the large variety of products handled by many companies. The overview is lost, when one mistake results in sudden downtime, creating an inefficient sorting process. Therefore, a reliable and durable automated logistics system was needed, which ensures higher productivity and stability and is future-proof in relation to new products, says René Kahr, Product Manager at Körber Supply Chain.
The pallet to tray solution has been part of Körber Supply Chain’s portfolio for a few years, but the new version is a natural development by the tech company.
The pallet to tray solution has been part of Körber Supply Chain’s portfolio for a few years, but the new version is a natural development by the tech company. The latest version is more intuitive and adaptable, thus decreasing potential downtime in the process.
De-palletizing from pallet to tray is not affected by unique product packaging designs, slip sheets, or changes in the assortment, which are otherwise the classic culprits for errors and downtime.
When there are changes in packaging and assortments, problems arise in automated logistics. We now make the complex easy, and our system effortlessly sorts a pallet into smaller packages for distribution. In addition, the system can be integrated into other integrator solutions, while our software can be adapted to the individual distribution center’s quantities and sizes, explains René Kahr.
He explains that Downstream is estimated to be able to sort up to 2,400 items per hour, with sorted packages being redistributed and loaded onto a tray with one to six items on each tray.
At Körber Supply Chain, one of the main goals is “digital enablement”. The goal is to help companies improve productivity and operations by implementing digital solutions. The pallet to tray solution is an AI-based solution that, with data tracking of the individual products throughout the entire process, 100% automatically transforms whole pallets into separate items on trays without manual intervention. The objective is to help to move companies towards a much more efficient operation.
There doesn’t exist a turnkey solution on the market about the redistribution from pallet to tray. With the new Downstream, we are closing that gap. It will help optimize operations, save resources, and remove uncertainty in an automated logistics process at distribution centers.
The solution has already been sold to some of the leading players, so we know there is a need for the solution in several markets. The potential is high, says Ralph Korsbæk, Head of Sales of Product Solutions at Körber Supply Chain.
More information about Downstream: https://www. koerber-supplychain.com/ supply-chain-solutions/ supply-chain-materialhandling/layer-pickers/ downstream-equipment/
There doesn’t exist a turnkey solution on the market about the redistribution from pallet to tray. With the new Downstream, we are closing that gap. It will help optimize operations, save resources, and remove uncertainty in an automated logistics process at distribution centers.
A continuing surge in contracts within the booming Scotch whisky industry has led specialist process engineers and sustainability experts, Briggs of Burton, to open a new Scottish hub.
A continuing surge in contracts within the booming Scotch whisky industry has led specialist process engineers and sustainability experts, Briggs of Burton, to open a new Scottish hub.
Since 2010, when Briggs of Burton completed its first Scottish project with Loch Lomond Distillery, the company has seen tremendous growth. The Scotch whisky sector saw global exports hit £6 billion in 2022 and Briggs of Burton announced today the opening of its new office in Moray, in the heart of whisky country. The office will lead 6 new projects in Speyside, whilst servicing major existing clients including the Glenlivet, Glenfiddich, Dalmunach and Mortlach distilleries, as well as managing a large number of new enquiries.
Rob Buxton, Managing Director at Briggs of Burton, commented: “Expanding into Morayshire, the ancestral home of the distilling industry, felt like the natural progression for Briggs of Burton, given its longstanding history of work within Scotland. We are working on contracts ranging from £3m to £30m and the new
office will support ongoing growth, create at least 10 jobs and reduce our carbon footprint by bringing our expertise closer to clients. Briggs of Burton has extensive experience in delivering distillery projects in key spirit producing regions and this new premises will allow us to further deepen our knowledge of the Scotch whisky industry as well as support jobs and investment.”
The firm has secured premises at Forres Enterprise Park, home to over 100 acres of beautifully landscaped grounds and sustainable buildings in a thriving community of manufacturing, engineering and technology businesses.
Briggs of Burton already owns Scottish copper still manufacturer McMillan - a significant force in the domestic and worldwide supply of copper distilling and stainless steel process equipment - which is based in Prestonpans, approximately eight miles east of Edinburgh. Originating from Burton on Trent, Briggs of Burton is a UK success story, specialising in delivering safe, high-quality process engineering in an environmentally sustainable way to help distilleries
reach their decarbonisation targets. The company is designing, expanding and building new distilleries around the world, covering North America, Central America, Europe, Africa, Australia, Japan and China.
Briggs of Burton’s impressive portfolio of clients include William Grant & Sons, Diageo and Chivas. The firm recently partnered with Ardgowan Distillery to lead the design, build and engineering of their carbon negative distillery. Briggs of Burton is also supporting Brown-Forman to double its production capacity at its iconic GlenDronach distillery in Aberdeenshire by implementing operational energy efficiencies and supplying traditional Scottish copper distillation equipment.
The firm recently partnered with Ardgowan Distillery to lead the design, build and engineering of their carbon negative distillery.
Handling operations are now the most popular application for industrial robot purchases, representing 52% of UK installations in 2021 . But as well as speed and dexterity, today’s manufacturers are also looking to maintain rigorous hygiene standards when automating their handling applications. To this end, FANUC has launched two new ultra-hygienic additions to its renowned SCARA pick-and-place robot range: the cleanroom-standard, pedestal-mounted SR3iA/C three-axis and SR-6iA/C four-axis robots. Ideal for replacing manual labour in handling tasks, they also boast novel anti-contamination features, meeting the highest safety and hygiene standards in even the most challenging food, pharma and general manufacturing settings.
Standing for Selective Compliance Articulated Robot Arm, the latest SCARA models from FANUC sport a white epoxy coating as opposed to the yellow usually associated with the brand. This is not an aesthetic choice; the white coating provides extra durability. Certified to IP54-rated levels of protection against ingress of water, dust or other contaminants, the new models are perfectly suited for use in situations that require thorough clean down, also meeting ISO Class 5 cleanroom standards. Specially designed bellows that protect the critical spindle during cleaning eliminate another potential hygiene headache for operators, while NSF-H1 certified grease and anti-rust bolts are also available.
Besides their ultra-hygienic properties, the new SCARA models also offer a compact footprint, allowing for the integration of smaller workcells with no loss of performance. Their 360-degree envelopes allow integrators to exploit the full reach of the robots within smaller cells, also minimising physical interference with nearby devices or work areas. Services including power supply, solenoid valves and pneumatic airlines are fully integrated within the robot arm, further helping to reduce interference contours and snagging.
Despite its compact footprint, the SR-3iA/C boasts a 3kg payload, a 400mm reach and a maximum pushdown force of 150 Newtons. Meanwhile, the SR-6iA/C has a 6kg payload, a 650mm reach and a maximum push-down force of 200 Newtons. High speed comes as standard with both models, too. Depending on the application, up to 120 cycles/minute is possible, with
no loss of precision: the robots are accurate to ±0.01mm in the linear axes and 0.004O wrist rotation. The wrist also offers ±720O of motion and 3,000O/second speed, with continuous rotation as an option.
FANUC’s SR-3iA/C and SR-6iA/C are also completely compatible with the company’s latest R-30iB Compact Plus controller. The web-based user interface, which employs FANUC iRProgrammer software, delivers fast, intuitive, platform-independent set-up capabilities, with teaching and programming provided via a tablet or PC. No specialist tools or interface units are required. Average power consumption is 0.25kWh in the case of the SR-3iA/C, and 0.35kWh for the SR6iA/C, running on 200-230V single-phase power supply.
Both robots are fully equipped for standard, static operations but can, optionally, be fitted with fully integrated FANUC iRVision visual detection and iRPickTool systems for intelligent tracking of goods on a moving conveyor.
keeping unchanged its properties with our scalable pilot production system:
• for R&D:
1x PEF chamber for solids & creams and 1x coax PEF chamber for liquids;
• for pilot production: two in line coaxial chambers at same or different optimally enhanced pulsing using batch or direct flow through processing.
Broadest changeable SPEF parameters:
• Pulse rates in Hz: 4, 20, 100, 500, 4-125;
• Pulse lengths in μs: 2,5, 5, 10, 50, 2,5-20;
• electrical fields 5-50kV/cm;
• selectable pulsing time 1s-9h;
• 25kV 2kW pulser, up to 10kW options;
• overcurrent protection is build-in with a reset;
• convenient in use, simple to maintain, safe!
Pulse shapes:
• positive rectangular,
• fronts/tails ~1 µs;
• ~5% flat at 50µs:
V(t) & I(t) at 25kV >
Inactivation of bacteria in juices with this system can reach 3-6 logs at 250l/h and 2-4 logs at 500 l/h with one or both coax chambers. Plus, its unique set of broad pulsing values with up to 50kV/cm fields allows finding optimal parameters for your future costeffective production system.
Wek-Tec offers to evaluate or to develop your optimal PEF process which work can be credited to your possible purchase of our system. This work is done at our place with a bio-support from a local certified food lab as explained here.
Our PEF and PUV pilots have been successfully used past 23 years worldwide and brought valuable scientific results referenced in various academic and in industrial publications. to fill in our contact form
PEF sterilizes by stretching bacteria up to its ruptures by electrical fields with 20- 50kV/cm strength delivered by sharp square pulses.
More in details.
As it was independently shown with our PL system by the Baxter Corp. on UV resistant spores of B. Pumilos. Why so is in this chart and its clarifications:
The effectiveness of PL from identical to continuous UVC light #1 region progresses to region 2 with more and more accelerated DNA damage.
In the region 3 bacteria and spores also are disintegrated by overheating from all UV spectra plus to some extend with the visible light. For that light pulses have to be very intense, short and rapid.
For pharma companies our achievements open opportunities to sterilise transparent liquids in thin clear transparent glass vials or plastic bags.
To reach your objectives we offer to select optimal parameters for your application with these two systems. Or to sell you those. The tests results will also to design and to construct full-scale production PL sterilization tunnels or systems also for other usages:
Our UV tunnel for powders in a flow-through sanitation or its photo-chemical modifications (e. g. by UVB enriching the D2 vitamin in mushroom powders) is designed for up to 100kg/h and for further adjustments as per data from your powder evaluation on our Vortex >
We offer evaluation tests at our place or can sell such Vortex. It allows a cost-effectively to reduce micro-organisms at 1-2 logs & more.
< in Vortex powders are moved around a UVC lamp by a forced air flow with the Oxygen being replaced with the Nitrogen gas.
Wek-tec e. K. looks for a capable partner to mutually benefit from our IP and suppliers.
With our systems & services come benefits of German manufacturing and legal standards.
As part of any Food processors HACCP program, validation of cook and chill processes is a critical and significant task, taking time, effort, and resources.
PhoenixTM have developed a thru-process temperature monitoring technology specifically for this task, designed to meet the challenges of the food processing market. Ideal for the validation process for any new cook regime, new product, or annual process certification. Whether performing an oven survey “oven mapping to identify cold spots” or validating the cook under production conditions, the thruprocess profiling solution gives you the accuracy, efficiency, and reliability you need to satisfy your HACCP demands.
As its name suggests, thru-process profiling is the method by which product and or process temperature is monitored throughout the complete cook / chill process. The data logger
making the physical temperature measurement, with multiple thermocouples, travels safely with the product through the process. Protection from process conditions such as heat, steam, water, and oil is provided by a suitably designed thermal barrier.
The thermal barrier provides robust protection to the data logger to prevent damage but also ensure that it maintains a safe operating temperature to give accurate temperature readings. Monitoring of continuous conveyorised linear and spiral ovens and semicontinuous or rotational batch cooks is feasible where the use of external recorders with trailing thermocouples is tedious, completely impractical, and possibly unsafe.
Employing the thru-process principal, process monitoring can be performed under true production conditions without compromising line productivity .
At the heart of the thru-process monitoring system is the PhoenixTM data logger. The PhoenixTM NT data logger range has been designed specifically for the challenges of monitoring food processing applications with an IP67 case design protecting from moisture. Type K or Type T data logger options allow accurate measurement of both cook and chill processes (Type T measurement range -200 °C to 400 °C).
Data logger and thermocouple correction factors can be applied to the recorded data logger data to maximise measurement accuracy. PhoenixTM offer a range of thermal barriers to suit the process type, duration, and temperatures. Even if a standard thermal barrier cannot meet the process requirements, PhoenixTM can often custom design a unique solution to suit.
Monitoring core temperatures of food products can be a challenge and getting
it right or wrong can have a significant influence on the data collected and therefore any decisions or conclusions made.
PhoenixTM offer a range of different designs of thermocouple to suit different product types and sizes. The needle thermocouples ensure you can measure the true core/cold spot of the product accurately and repeatably. Fitted with standard miniature thermocouple sockets, the data logger is also compatible with other generic commercially available thermocouple designs.
Employing the thru-process temperature monitoring principle provides the food technologist with a complete temperature profile of the cook process from start to finish. This information is like the Cook DNA giving full details of the product and or process temperature which is invaluable to allowing validation of the Cook CCP.
From a temperature profile it is possible to accurately quantify product safety (pasteurisation) knowing both the temperature, and time at temperature, of the product.
From the profile graph you can see instantaneously the variation in
product temperature at any point in the process either at different locations on the product (whole chicken) or different product positions within the cooker, cooking rack or across a mesh belt.
The PhoenixTM Thermal View Food Software provides a comprehensive suite of analysis tools to convert the raw profile temperature data into useful process information. The analysis tools include the ability to calculate Fo/Pu
values for the process against target micro-organisms.
For a typical chicken cook process the lethality parameters for Listeria Monocytogenes (Tref 70 °C, Dt 16.2 s and Z value 7.5 °C) can be input to automatically and accurately calculate for each monitoring point the number of decimal reductions of the pathogen achieved during cook to meet CCP limits.
The information gathered, further to process validation, can be used to allow informed process problem solving and optimisation to maximise product quality, yield, process productivity and efficiency.
Contact PhoenixTM to help Find, Fix and Forget your Food Cook Problems!
Employing the thruprocess temperature monitoring principle provides the food technologist with a complete temperature profile of the cook process from start to finish.
Linx Printing Technologies, laser and CIJ coding & marking equipment manufacturer, has been helping its customers to overcome counterfeiting issues and brand identity theft by providing them with permanent laser marking solutions.
Linx’s laser machines, carefully selected to suit customer needs, production set up and output requirements, apply a permanent code BBD, batch codes, QR codes, and others, to help with traceability and provide a distinct, permanent way of branded marking on the product. Installed by highly qualified engineers to ensure maximum safety and operational efficiency, Linx lasers can be used to etch on multiple substrates, such as metal, plastic, glass, or cardboard.
Irish Distillers, Ireland’s leading supplier of spirits and wines and producer of some of the world’s most well-known and successful Irish
whiskeys, are using Linx CSL30 and CSL60 lasers to ensure brand identity and anti-counterfeiting of their Jameson whiskey.
To prevent their best-selling product from being falsified, Irish Distillers were looking for a solution to add a distinctive mark onto their bottles that would be very hard to replicate.
Linx have been given the challenge of finding a way to apply a unique stamp of approval directly onto three different substrates at the same time as bottles move through production process and has developed a bespoke solution using
their laser machines. The permanent coding was required, the challenge was to do it at their highest production speeds. These demanding production volumes fall under Linx’s capabilities and outside capabilities of others, which makes Linx a market leading application supplier for super-fast production environments.
Only original Jameson whiskey bottles have their bottle distinctively marked with stamp of approval that goes over the seal, glass and label perfectly aligned, highly visible and permanent.
To find out more about Linx’s coding and marking equipment, or to discuss your needs, please visit www.linxglobal.com, call us on 01480 775223 or email uksales@linx.co.uk. We always welcome a challenge!
Irish Distillers were looking for a solution to add a distinctive mark onto their bottles that would be very hard to replicate.
A food safety culture that prioritizes people and supports collaboration in manufacturing facilities, food service businesses, restaurants or retail stores can help improve quality, minimizing the risks of contamination or recalls, while also benefiting productivity and talent retention.
New global guidance from BSI, developed through consensus with industry giants including Walmart, McDonald’s, PepsiCo, HelloFresh, Kerry Foods and 3M, and published this week, identifies that the common factor in food safety incidents, quality failures and recalls is people rather than failures of machinery or technology. Equally, when issues occur, people are the key to avoiding recurrence.
According to the World Health Organization (WHO), consuming contaminated food results in an estimated 600m people falling ill every year, leading to 420,000 deaths. A desire to tackle this led to a round-table discussion at the 2019 International Association for Food Protection (IAFP) Annual Meeting, then ultimately the creation of an industry steering group. The resulting document, Developing and sustaining a mature food safety culture (PAS 320), is designed to guide organizations of all sizes across food, beverage and retail to create a culture where people are prioritized, all employees embrace food safety, take responsibility for reporting issues, and are empowered to initiate change.
Relevant to anyone from manufacturers and factory workers to restauranteurs and baristas, the guidance has been published by BSI following extensive sector discussion on food safety culture, including what it is, how to measure it and how to ensure continuous improvements.
The document defines food safety culture as the ‘shared values, beliefs and norms that affect mindset and behaviour toward food safety in, across and throughout an organization’.
It notes that creating and maintaining a strong culture that preserves quality and reduces risk requires management commitment and a mindset that safety is the responsibility of everyone at every stage of the food supply chain. Culture is also highlighted as key for employee retention, improving quality and decreasing contamination risk by decreasing turnover rate.
PAS 320 includes steps on identifying gaps and then implementing a plan for change. It makes recommendations related to leadership; the organization’s vision, mission, values and policy; organizational structure; responsibilities, accountabilities and authorities; guiding coalition team; interested parties; change champions; influencers; and food safety documentation. The guidance also includes advice on how prioritizing people in the sector not only supports improved food safety, but also brings other benefits including investment return, business performance improvement, reduction of the costs associated with poor quality, and enhanced efficiency.
In the UK, this comes in the wake of the passing of ‘Natasha’s Law’, which requires organizations providing food to include full ingredients labelling on pre-packed for direct sale foods in order to protect allergy sufferers and give them confidence in the food they buy. It follows the UK’s departure from the European Union, which means that packaging and labelling is now led in the UK by the Food Standards Agency.
Neil Coole, Director, Food and Retail Supply Chains, at BSI, said: “A positive food safety culture that prioritizes people and gives everyone a stake in driving quality can have a transformative effect and help reduce the risk that comes from unsafe food. This starts with leadership taking steps to turn ambition into action in order to build and sustain continuous improvements across their organization and the wider supply chain.
“Ultimately, moving from seeing food safety culture as a compliance issue to an investment in people can offer huge benefits for individuals, organizations and society as a whole.”
Scott Steedman, Director General, Standards, BSI, said: “It is tragic that so many lives are lost globally every year to contaminated food. This is something nobody in the industry can ignore and urgent steps to change this are required. We understand that the common factor in food safety related risks is people, and it is an organisations culture towards food safety that presents the opportunity for continuous improvement. PAS 320 provides the guidance to empower people to make a positive impact on the future of the food industry.
“Enabling a robust food safety culture is vital for enhancing quality and safety across the food sector. Strengthening understanding of what best practice looks like and how everyone in the food sector can play a role, by enhancing global consistency and offering clarity, can help food sector organizations accelerate change and support the realization of quality and food safety ambitions. This new standard on food safety culture can build confidence in the global food industry and offer longterm benefit for everyone.”
Positive food safety culture that prioritizes people ‘key to reducing risk of contamination or recalls’
Ultimately, moving from seeing food safety culture as a compliance issue to an investment in people can offer huge benefits for individuals, organizations and society as a whole.
BST are proud to be the original pioneers in metal detectable plastic technology and are the driving force in the UK combatting the issue of plastic contamination in food production worldwide. We specialise in metal detectable, x-ray visible, shatter resistant, and antimicrobial food safe products, utilised across all food sectors to reduce the risk of foreign body contamination.
Brain S Teasdale (BST) founded the company in 1985 and initially focused on providing engineering supplies to UK bakeries, before inventing the concept of metal detectable products and the world’s first detectable pen. BST remains a family business, now headed by John S Teasdale since Brian’s retirement in 2002.
Detectable products are now an integral part of food safety and
HACCP procedures worldwide. As new regulations and legislations have highlighted the necessity for detectable, food safe products in the food industry, it is becoming increasingly important to show due diligence in the prevention of plastic and rubber contamination. BST focus on producing high quality detectable products, less susceptible to wear and therefore less likely to end up contaminating food in production. Should a BST detectable item break or be dropped into food production, fragments as small as 5mm³ can be detected by metal detection or x-ray inspection systems and automatically be rejected from the production line.
The food industry aside, BST products are high quality, ergonomic, and a wide range of the products are antimicrobial and so are also suited to environments of high-risk cross
infection such as medical areas, reception areas, open plan offices, and call centres.
Website: www.bst-detectable.com
BST Detectable Products are the original pioneers in metal detectable plastic technology.
Since 1985 BST have refined our materials to increase both performance and the range of products available to the food industry.
BST detectable products are developed using highly advanced food grade materials, tested on x-ray inspection and metal detection systems, produced in hygienic environments and migration tested to the FDA and EU standards for food contact.
Our products are designed to be as safe as possible for food production environments and if we don’t have what you need, then we can use our stocked materials to make it for you, through our network of injection moulders, machinists, and extruders.
Detectable products are now an integral part of food safety and HACCP procedures worldwide. As new regulations and legislations have highlighted the necessity for detectable, food safe products in the food industry, it is becoming increasingly important to show due diligence in the prevention of plastic and rubber contamination.
Having engineered some of the most reliable x-rays on the market, the newest in-line Raptor X-Ray, Pipeline X-Ray and Apollo machines from Fortress Technology Europe all deliver cleanability, supreme hygiene standards and food protection assurance in bucket loads. With not a loose wire or hanging cable in sight!
Utilising the highest-spec food x-ray technologies, all three machines within the Fortress X-Ray range minimise cleaning and set up times to increase plant productivity. Yet, also give producers of fresh, chilled and frozen wrapped and unpackaged products the added assurance of exceptional brand safety by ensuring cross contact contaminations are tightly controlled.
Reassuringly, the frameworks on all Fortress X-Ray inspection systems are IP69k rated. With no trailing cables, they are fully protected against dust and other particulates, to withstand high-pressure, high-temperature jet sprays, wash-downs or steam-cleaning procedures.
Fortress x-ray electrical panels are all IP65k-rated. This means they are all dust tight and are protected against low-pressure water jets when using a nozzle.
Another unique feature on the conveyor x-ray range is the protective acrylic window. With the radiography beams fully contained, food operatives can work alongside the machines and see packs travelling through the system. Users can instantly spot product spillages and action accordingly, without feeling like their personal safety is being compromised.
Fortress Commercial Manager Jodie Curry explains: “Having a clear side removes the mystery and fear factor, especially when there’s a stainless steel box with a big radiation sign on the side.” An extra benefit of this visibility is it removes the need for bulky safety guards. Removing these to access machines can add another layer of complexity for machine cleaning notes Jodie.
Magnetic x-ray curtains, the easy clean tight fitting conveyor, IP69k sensors and bevelled surfaces further speeds up repeatable cleaning and sanitation tasks, highlights Jodie.
Describing in more detail the easyclean conveyor concept, Jodie adds: “Our unique conveyor features a quick release for disassembly of the deck, belt, motor and rollers, saving valuable time, money and labour to provide the ultimate in hygiene peace of mind.
During the sanitisation process, machine operators simply unclip and disconnect the conveyor motor and lift out the entire assembly.”
The ‘no tool’ maintenance innovation, which features on all three models, including the X-Ray Pipeline, is another massive time-saver. As well as stopping operatives fiddling with screws, nuts, bolts etc. and using incompatible tools that could damage the machine, it eliminates the risk of accidently contaminating food with a stray component.
Rather than using unhygienic stickers and labels, all safety symbols, industryapproved markings and the machine nameplate are laser-etched directly onto every Fortress X-Ray steel cabinet.
Average clean times on all machines should now take a matter of minutes, suggests Jodie. “When sanitation employees have open areas and smooth surfaces to work with, they can more efficiently access and clean equipment to reduce machine downtime and prevent cross contact contamination.”
Rather than air conditioning, passive airflow technology is used maintain a regulated filament temperature in the X-Ray cabinet, never exceeding the constant 30°C. Additionally, an electric servo driven reject system eliminates the used of compressed air. All of which can help to reduce running costs and maximise efficiency.
Modular by design and automatically incorporating every retailer COP that exists, the Raptor X-Ray and Apollo X-Ray machines can be integrated with a Checkweigher to create a high performance x-ray combination inspection system. The electronics can also be fully integrated with upstream flow wrapping or packaging machines and controlled via a single HMI.
Having a clear side removes the mystery and fear factor, especially when there’s a stainless steel box with a big radiation sign on the side.
- Jodie Curry