Ortlieb’s Bottling House StudyCase2021 Whole Life-CycleBuildingAnalysis

The renovation into an architectural office preserved the original structural system (steel columns, beams, and roof trusses), concrete floor, envelope, terra cotta tile finishes, and select terra cotta interior partitions. The major changes during the renovation included a full replacement of windows, full replacement of the roof thermal and moisture layers, and the addition of raised access floors and interior partition walls. These modifications aimed to decrease the building’s projected energy consumption and increase thermal comfort for building occupants using a mixed mode system and natural ventilation.
PROJECT OVERVIEW
Included Model Scope: Substructure, superstructure, enclosure, non-structural partitions, and finishes as modeled in Revit. To account for the savings associated with reuse and retrofit, the environmental impacts for the Manufacturing and Construction phases (LCA Module A) are excluded for materials retained from the original building.
KieranTimberlake 2CASE STUDY Ortlieb’s Bottling House Ortlieb’s Bottling House
When applied to the scale of a full building, WholeBuilding Life Cycle Assessment (WBLCA) can evaluate the embodied environmental impacts associated with the manufacturing of materials, the construction and demolition of the building, and the disposal of the materials after their use. At KieranTimberlake, WBLCA serves to help a project team make decisions to reduce the embodied environmental impacts of the project.
The final embodied carbon intensity of the building is 123 kg CO2 /m2 /yr, a noteworthy improvement over the Carbon Leadership Forum’s (CLF) 2017 baseline for new construction office buildings of 410.4 kg CO2 /m2 , based on (283) models, and also a significant reduction from the baseline for office renovation of 386.4 kg CO2 /m2 , based on 7 models.
To understand the full carbon impacts of building operations and construction, KieranTimberlake uses Life Cycle Assessment (LCA) to evaluate the embodied environmental impacts of building materials and assemblies. When paired with energy modeling, LCA is an important tool to help identify strategies to decarbonize our projects. LCA models measure impacts according to a range of categories, including global warming, acidification, eutrophication, smog formation, ozone depletion, and the depletion of non-renewable resources.
WBLCA METHODOLOGY
Excluded Model Scope: Railings (<1% by mass), casework, furniture, MEP, landscape elements, and site work.
This study considers the environmental impacts associated with the renovation of a historical beer bottling plant-turned-architectural office space, both by and for, KieranTimberlake. The building is a 2-story, 60,000 sq. ft. standalone building in Philadelphia, PA. The construction system includes a braced steel frame infilled with concrete floors wrapped in a multi-wythe, non-load-bearing masonry envelope. Between uses, the building was vacant for 30 years.
INTRODUCTION TO LCA AT KIERANTIMBERLAKE
LCA Scope: Modules A1-4, B2-5, C2-4, D. To account for the savings associated with reuse and retrofit, the environmental impacts for the Manufacturing and Construction phases (LCA Module A) are excluded for materials retained from the original building.
LCA Software and Version: Tally® version 2017.06.15.01 Reference Building Life: 60 years Biogenic Carbon: Included Module D Credits: Included
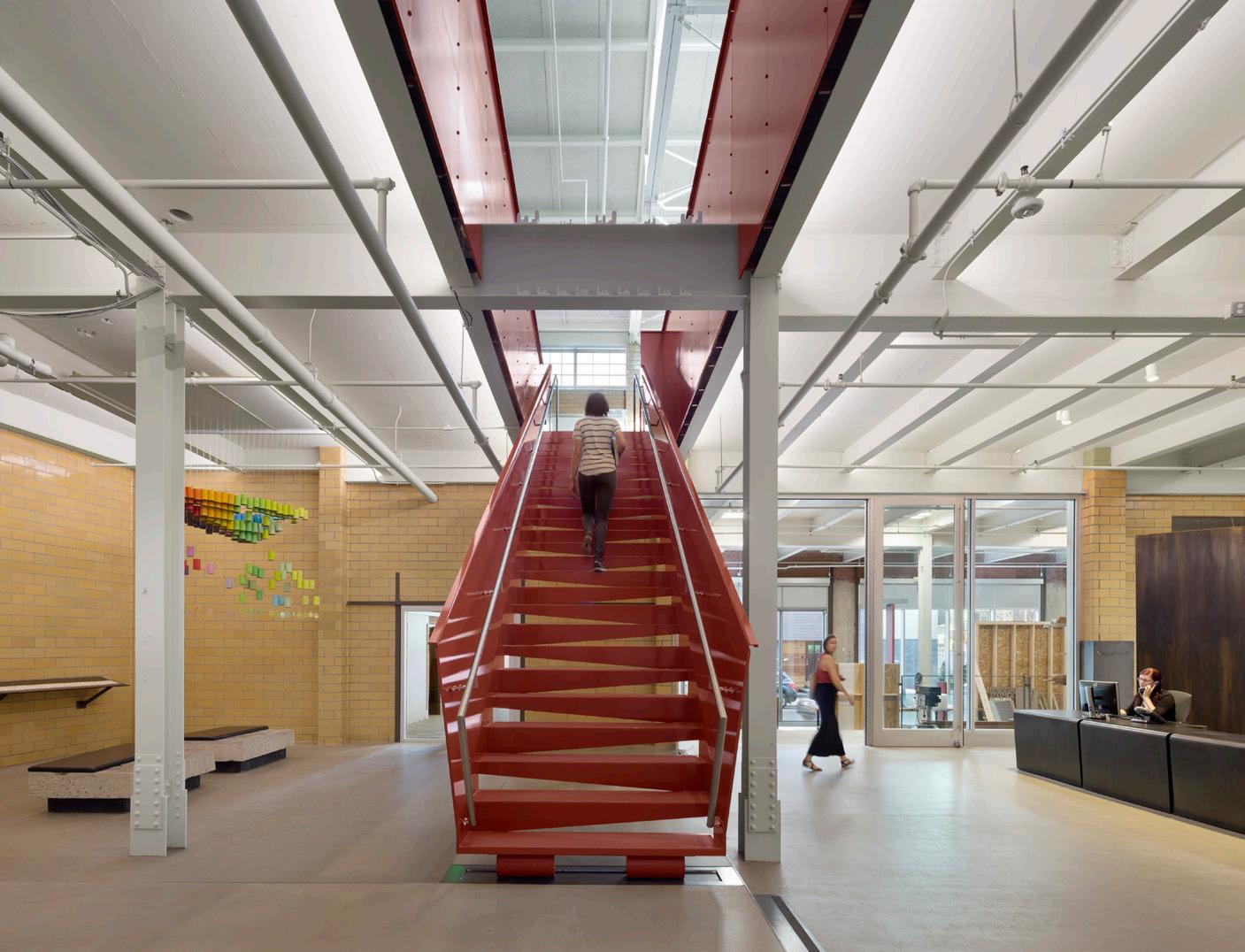
The building has two types of finish flooring in the building, a carpeted raised access floor on the second story that creates a plenum space for air circulation by the low-velocity HVAC system, and a self-leveling concrete skim coat for the exposed concrete flooring on the first story. Although the raised access floors are the most significant single contributor to embodied carbon—contributing a fifth of the total embodied carbon associated with the renovation—the system cannot be considered in isolation. This plenum flooring allows for the reduction of materials used in HVAC circulation that is not accounted for in the traditional scope of HVAC and allows for the implementation of an HVAC system that has lower energy demand, reducing the operational carbon of the building.
Windows not only fill the studio with light, they open and close on a schedule to let in fresh air and reduce reliance on the air conditioning system.
KieranTimberlake 3CASE STUDY Ortlieb’s Bottling House PROJECT FINDINGS
While structural and envelope components such as concrete foundations, concrete floor slabs, and steel structural frames are typically manufacturingintensive, they also have long life spans, require little maintenance, and can be mostly refurbished and reused when a building is renovated. Because the renovation reused as much of these existing elements as possible—including all foundations, most of the building’s superstructure—metal and concrete accounted for only 26% of the building’s mass and 14% of its global warming potential (GWP). In contrast, if the same building were to be re-built today, the concrete and metal would be 65% of the building’s mass and 57% of its embodied carbon.
The renovation impacts came primarily from the windows, amounting to almost a quarter of the embodied carbon. Other embodied carbon hotspots came from the skylight panels (made of glass fiber reinforced plastic) and the EPS insulation in the roof. These two materials had the highest embodied carbon, at 9% and 7%, respectively. Both materials are made of fossil fuels using energy-intensive production processes, and both are difficult to recycle at the end of their lives, ending up in landfills. Interestingly, the addition of operable windows, skylights, and increased roof insulation also form the foundation of the project’s energyefficiency upgrades, allowing for increased natural ventilation and daylight, and allowing for reductions in air conditioning and lighting loads over the building’s lifetime.
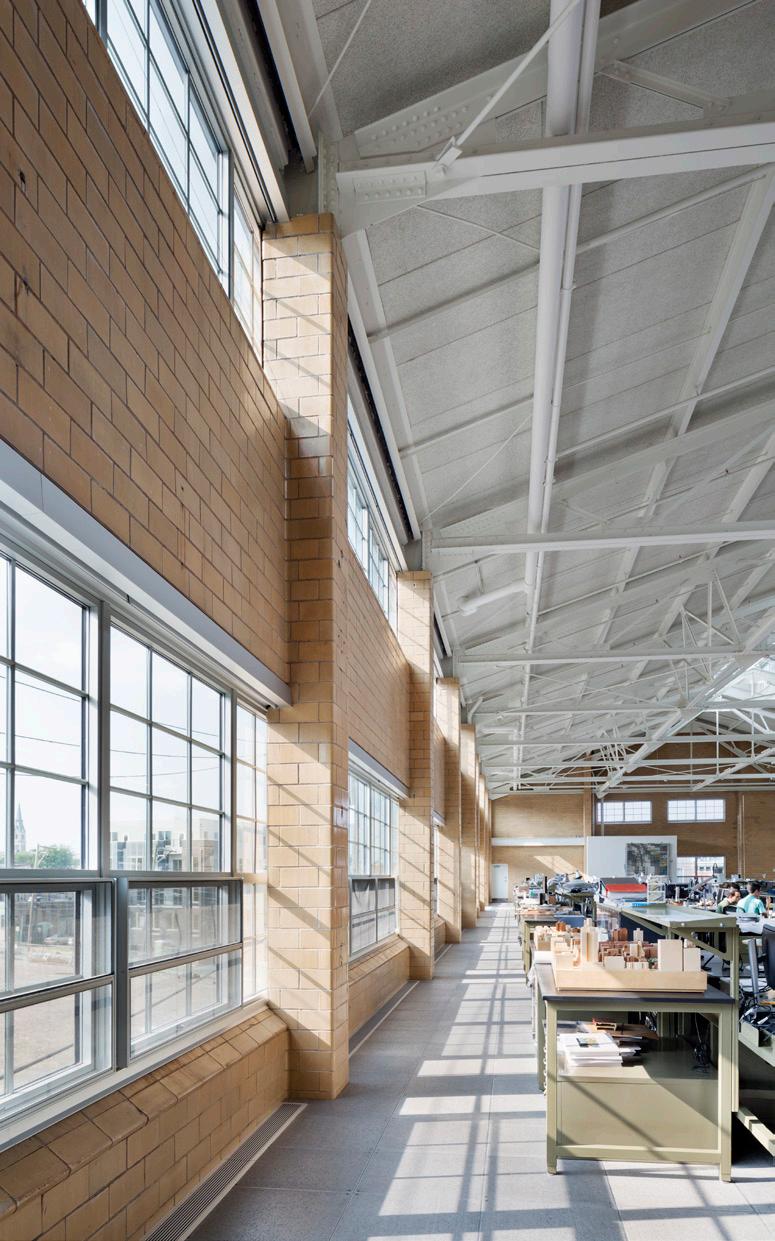
LCA RESULTS
STUDY Ortlieb’s Bottling House
KieranTimberlake 4CASE
• Assessing operational and embodied carbon holistically can yield improved results for both. In this case, a new-construction building meeting 2030 Challenge requirements would have to operate for 183 years to catch up to the carbon savings of the renovation of Ortlieb’s Bottling House.
Life Cycle Assessment is an emerging practice. We view every WBLCA as an opportunity to reduce embodied carbon and evolve our practice, and we hold ourselves to the highest standard while conducing WBLCA. In the interest of ongoing improvement of our efforts and promoting LCA across the profession, this project helped us mature our practice in the following ways:
• Whenever possible, assess structural and envelope systems for refurbishment, repurposing, and renovation before demolition
This WBLCA advanced KieranTimberlake’s understanding of the magnitude of environmental benefits associated with renovating existing buildings. In particular, it highlighted the embodied carbon savings that can be made when structural systems and envelope systems can be saved and reused. Although the majority of projects may not have the opportunity to repurpose an existing structure in total, KieranTimberlake has learned first to ask how structural elements may be refurbished, repurposed, and renovated before determining that demolition will be required for new projects. For example, some projects might have opportunities for select reuse of foundations or of select steel components.
Figure 1 Building compontents’ roles in the renovation’s overall embodied environmental impacts, reported by CSI Division. Note the relatively small impact of concrete. Because the renovation reused all foundations and most of the building’s superstructure, metal and concrete accounted for only 26% of the building’s mass and 14% of its global warming potential (GWP).
OPPORTUNITIES FOR IMPROVEMENT
7% 6% 6% 21%7% 4% 8% 24% 10% 7% 5% 16% 26% 13% 11% 13% 5% 7% 17% 8% 14% 7% 12% 28% 21% 29% 6% 26% 30% 7% 36% 29% 40% 53% 42% 39% 59%100%90%80%70%60%50%40%30%20%10%0% AcidificationPotential(kgSO2eq) EutrophicationPotential(kgNeq) Global(kgCO2eq)PotentialWarming Ozone(CFC-11eq)PotentialDepletion Smog(kgO3eq)PotentialFormation PrimaryDemandEnergy(MJ) Mass(kg)Total 09 - Finishes 08 - Openings 07 - Thermal 06 - Wood/Plastics/Composites 05 - Metals 04 - Masonry 03 - ConcreteMass21%5%5%7%59%Total(kg) 09 - Finishes 08 - Openings and Glazing 07 - Thermal and Moisture Protection 06 - Wood/Plastics/Composites 05 - Metals 04 - Masonry 03 - Concrete
09 - Finishes 08 - Openings and Glazing 07 - Thermal and Moisture Protection 06 - Wood/Plastics/Composites 05 - Metals 04 - Masonry 03 - Concrete
In 2019, the Ortlieb’s office building had a total energy use intensity (EUI) of 38.6 kBtu/sf. This energy demand was a little over half electricity, with 1,492,327 kBtu of on-site electricity demand, and the remainder from natural gas, with a demand of 1,134,438 kBtu on-site. Within the Philadelphia energy grid, this energy is typically supplied by PECO for electricity and PGW for gas, with a carbon intensity of 128 kg CO2/MBtu and 60 kg CO2/MBtu, respectively.
5CASE STUDY
Ortlieb’s Bottling House
KieranTimberlake
A low-velocity HVAC system prioritizes thermal comfort of building occupants rather than heating the entire space, further reducing operational carbon.
This building has a minimal operational energy demand, due to efforts to increase access to diffuse natural light throughout the floorplan and use of efficient HVAC system that prioritizes thermal comfort of building occupants rather than heating the entire space. Each of these operational energy demand reductions directly relates to new materials, and in turn, embodied carbon emissions associated with building renovation and construction. Although the operational energy savings equates to a lower overall carbon contribution of the building, a “total carbon” approach to structural design, material selection, and systems design, which includes both the embodied carbon and the operational carbon impacts as a whole, provides better insight into the overall performance of the building and potential trade-offs between operational and embodied carbon.
Although KieranTimberlake, as the tenant, has decided to reduce operational carbon intensity through a power purchase agreement sourcing the majority of electric power from a solar provider, a newly built office building could make the same arrangements. Therefore, we will use the typical grid intensity to compare the total carbon of the renovation against that of a new construction office building.


Total carbon intensity of the Ortlieb’s Bottling House compared to a new building that meets the requirements of the 2030 Challenge in kg CO2 /m2 Years of operation
0 1,000400200100300500600700800900
KieranTimberlake 6CASE STUDY Ortlieb’s Bottling House REFERENCES 1 Simonen, K., Rodriguez, B., Barrera, S., Huang, M., (2017) CLF Embodied Carbon Benchmark Database, database. Available at http://hdl.handle. 2net/1773/38017.ISO14040-14044:2006, Environmental Management – Life Cycle Assessment. EN15804 – Sustainability of construction works –Environmental product declarations – Core rules for the product category of construction products. 3 Zero Tool, “Zero Tool: Calculate Baseline and Target,” accessed 7/24/2020, https://zerotool. org/zerotool/. PHOTOS Cover: Chris Leaman Others: Michael Moran/OTTO CONTACT Efrie 841KieranTimberlakeEscottNorthAmerican Street Philadelphia, PA 19123 (215) efriedlander@kierantimberlake.com922-6600
60
New
NEW BUILDING COMPARISON Figure 2
• This study shows the significant environmental benefits of renovating an existing building. It also highlights how challenging it would be to replicate these benefits in a new construction scenario, since reusing large amounts of concrete and steel was vital to minimizing our environmental impact.
New embodiedOrtlieb’sembodiedbuildingcarbonBottlingHousecarbon Ortlieb’sbuilding 120 180
Using the typical Philadelphia energy grid, the operational carbon intensity of the renovated Ortlieb’s Bottling House in 2019 was 4.35 kg CO2/m2/yr. A new building that meets the requirements of the 2030 Challenge would have an operational carbon intensity of just 2.78 kg CO2/m2/yr. However, a new building is not necessarily the better environmental choice. Consider that the embodied carbon of the new building is 410.4 kg CO2/m2, while the renovated Ortlieb’s is 123 kg CO2/m2. For the new construction building to catch up to the renovated Ortlieb’s Bottling House’s total carbon intensity, it would have to operate (with no significant renovations or additions) for 183 years.
TotalintensitycarboninkgCO2/m2 New embodiedOrtlieb’sembodiedbuildingcarbonBottlingPlantcarbon
•
0 1,000400200100300500600700800900 New embodiedOrtlieb’sembodiedbuildingcarbonBottlingHousecarbon New Ortlieb’sbuilding 60
LESSONS LEARNED
• It is essential to consider embodied carbon and material selection in combination with operational carbon to reduce total carbon when attempting to minimize environmental impact. Deep energy retrofits of existing buildings are an important strategy for decarbonizing the building sector. More research and case studies are needed to evaluate the payback period of upfront carbon emissions (from embodied carbon associated with renovations building materials) required to achieve operational carbon reductions. 120 180