StudyCase2021 Whole Life-CycleBuildingAnalysis OpenHome
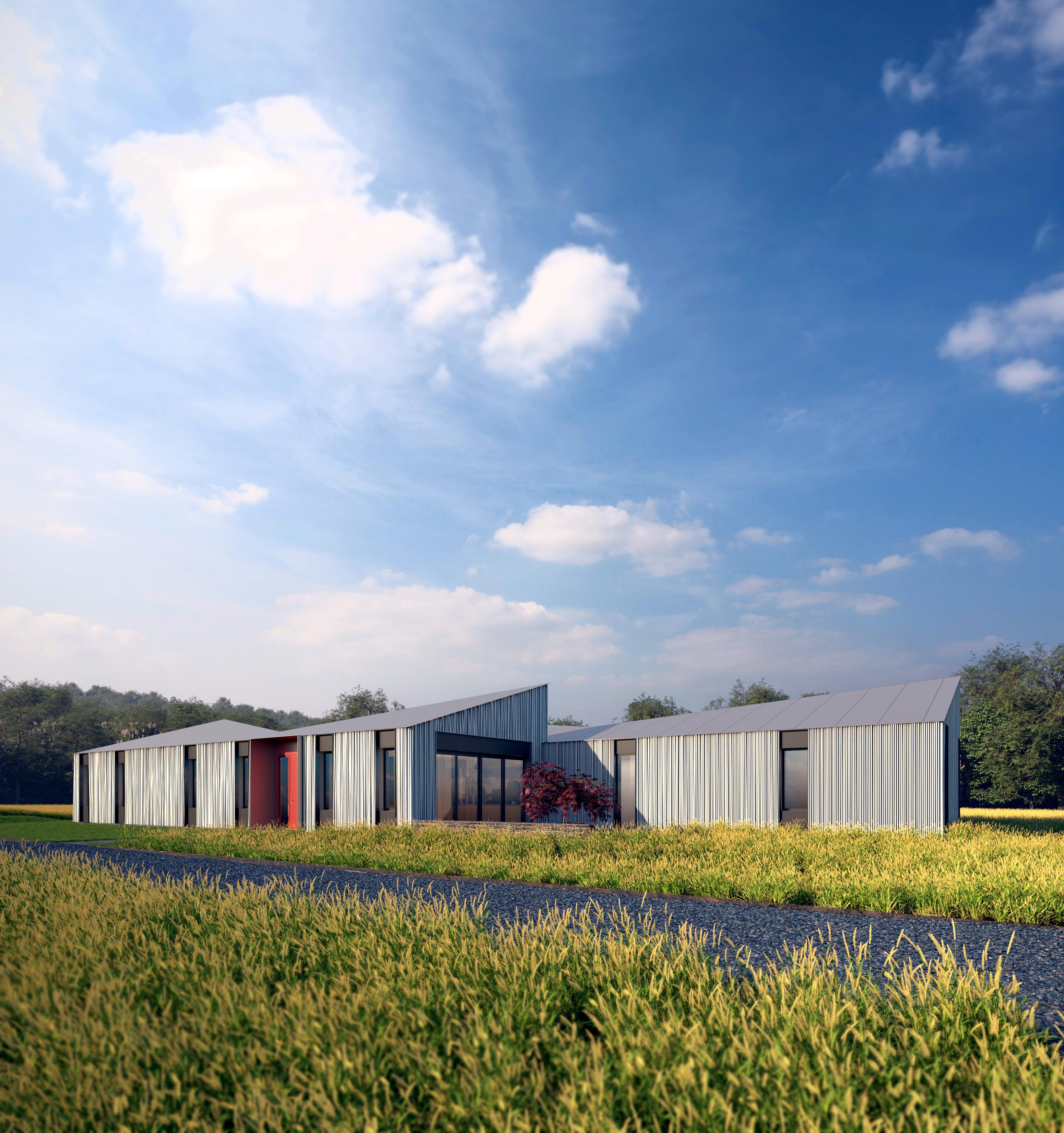
This project is KieranTimberlake’s first to identify a pathway to net-zero embodied carbon, done in collaboration with the project’s off-site fabricator, Bensonwood. The design team approached the goal of net-zero embodied carbon using two primary strategies: reducing the quantity of high embodied carbon materials, and increasing the use of carbon sequestering materials.
KieranTimberlake
2CASE STUDY OpenHome OpenHome
To understand the full carbon impacts of building operations and construction, KieranTimberlake uses Life Cycle Assessment (LCA) to evaluate the embodied environmental impacts of building materials and assemblies. When paired with energy modeling, LCA is an important tool to help identify strategies to decarbonize our projects. LCA models measure impacts according to a range of categories, including global warming, acidification, eutrophication, smog formation, ozone depletion, and the depletion of non-renewable resources.
OpenHome is a system for constructing customizable prefab homes created in collaboration with Bensonwood, a builder of timber-frame houses and highperformance architectural components. The system is designed to meet the requirements of the Passive House Standard, making it energy-efficient (and therefore low operational carbon) with superior air quality and acoustics.
WBLCA
INTRODUCTION TO PROJECT
INTRODUCTION TO LCA AT KIERANTIMBERLAKE
LCA Scope: Modules A1-4, B2-5, C2-4, D. Included Model Scope: Superstructure, substructure, enclosure, interior partitions, and finishes for single-family home, as modeled in Revit Excluded Model Scope: Casework, furniture, MEP, landscape elements, and site work LCA Software and Version: Tally® version 2020.06.09.01 Reference Building Life: 60 years Biogenic Carbon: Included Module D Credits: Included
The first WBLCA modeled on the project served to identify the significant contributors of embodied carbon, with a whole-building embodied carbon intensity of 364 kg CO2 /m2
KieranTimberlake’s OpenHome system can be customized according to the climate, landscape of the site, and preferences of the owner. The baseline prototype is 3,653 sq. ft., with three bedrooms, three and a half bathrooms, a home studio space, kitchen, media room, living room, and dining room. Without the purchase of carbon offsets, the final embodied carbon intensity of the buildings is 84 kg CO2 /m2 , a remarkable improvement over the Carbon Leadership Forum’s 2017 baseline for single-family residential buildings of 315 kg CO2 /m2 , based on 23 models.
When applied to the scale of a full building, WholeBuilding Life Cycle Assessment (WBLCA) can evaluate the embodied environmental impacts associated with the manufacturing of materials, the construction and demolition of the building, and the disposal of the materials after their use. At KieranTimberlake, WBLCA serves to help a project team make decisions to reduce the embodied environmental impacts of the project. METHODOLOGY
PROJECT FINDINGS
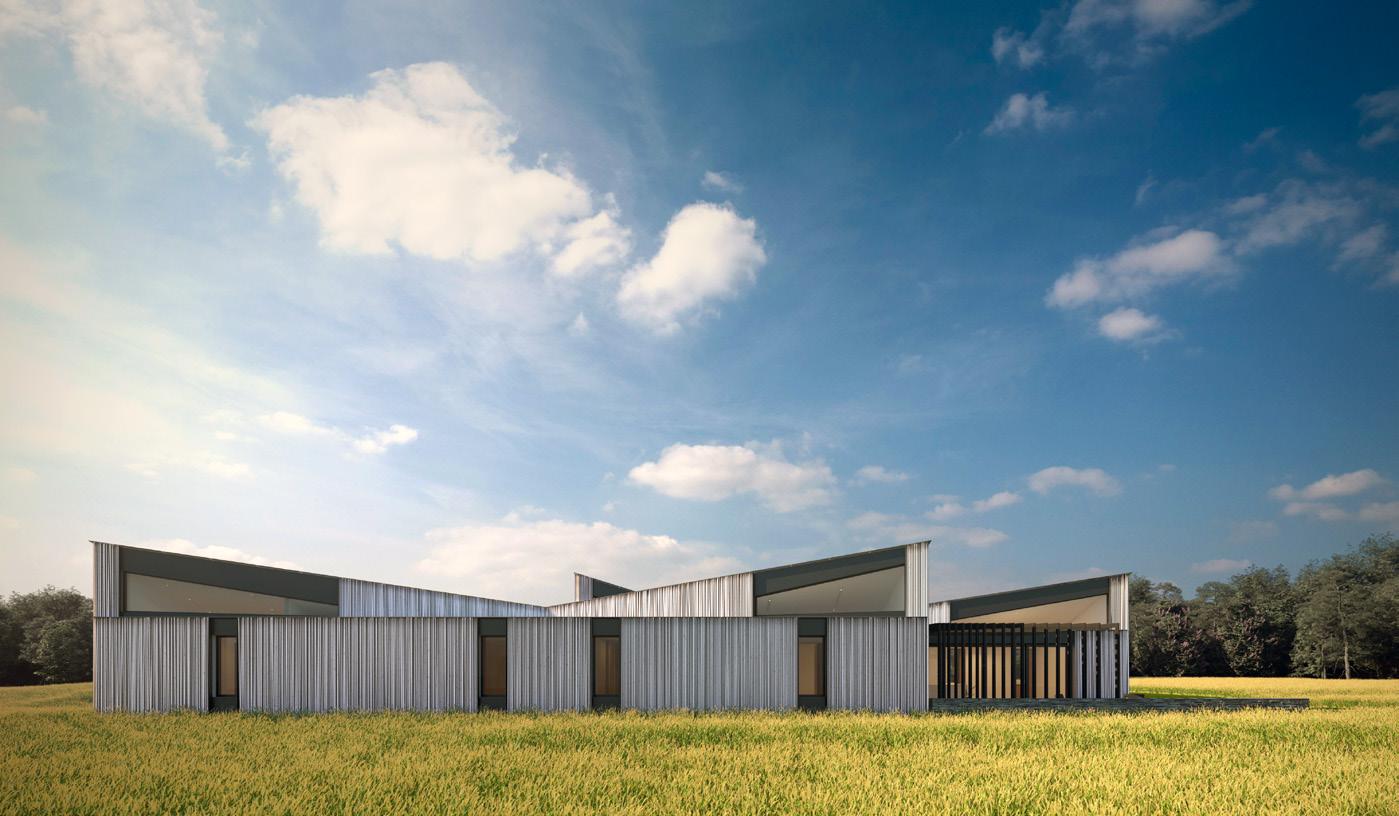
KEY STEPS IN OPTIMIZATION
15025035030040020010050 (CARBONOFFSETS) PLASTICS,WOOD, COMPOSITES+THERMAL+MOISTURECONCRETEMETALSOPENINGS+GLAZINGFINISHESINTENSITYCARBONEMBODIED CO2/m2kg • Structure: Wood framing • Foundations: Concrete slab with concrete footings • Envelope: Wood rainscreen with aluminum panel accents • Insulation: bio-based and mineral wool • Foundations: Optimize foundation system to reduce quantity of cement and rebar • Fnishes: use porcelain instead of slate tile to reduce need for grout and mortar • Interior: use MDF and wood panel instead of gypsum • Envelope: use metal-clad OSB for metal accents • Insulation: cellulose insulation for interior acoustic partitions • Foundations: Prefabricated insulative walls using metal framing replace CIP concrete • Foundations: use wood framing instead of rebar for strength • Foundations: use wood framing and composite wood I-joists for floor assembly structure • Envelope: Use reclaimed wood for the rainscreen • Envelope: use contrasting hardwood for accents instead of aluminum panel • Envelope: use wood shingle for roof instead of standing-seam metal • Purchase offsets 240 364 187 Bio-BasedSelect CementReduce BASELINEEarly SD 122 FoundationsOptimize 104 ReclaimedUseMaterials 84 (0) Net Zero KieranTimberlake 3CASE STUDY OpenHome Key steps in the optimization included (1) reducing cement content, including in the concrete for the foundations and in the mortar for the interior tiled areas; (2) adding more bio-based materials to act as “carbon sinks” to sequester carbon; (3) optimizing the foundation system to remove the concrete footings and reduce the concrete in the foundation walls; and (4) using reclaimed materials when possible for any wood that is not carbon-negative over its lifecycle. 1 2 3 4
Figure 1 Graphs show one the path to achieve netzero embodied carbon for a version of the product that includes a crawl space in the foundation system. In the baseline, the largest contribution to embodied carbon came from the cement used in the foundation system and the thick-set mortar for interior tiles. Building on previous experience with embodied carbon reductions, KieranTimberlake first suggested optimizing the concrete mix to reduce cementitious content. The design team also targeted a reduction of the cement content in the interiors through a change to the tile size and type to reduce cement content in the mortar, and through replacing some of the floor areas using tile with a finished wood floor, keeping tile only to areas where functionally necessary. These first steps reduced the project’s embodied carbon intensity by 34%, to approximately 240 kg CO2 /m2 . While this represented a significant reduction, the foundation system still contributed a large portion of the building’s embodied carbon impacts.
Although this team made significant reductions in the embodied carbon of the building, reaching net zero embodied carbon still required a minimal purchase of carbon offsets in order to offset the embodied carbon associated with the glazing. High-performance insulated glazing units with triple-pane glazing have a significant amount of embodied carbon associated with them. Occupant health OpenHome’s flexible design system stacks and arranges pre-designed elements to create a unique home.
• Lack of appropriate bio-based insulation materials for parts of the envelope system means we must continue evaluate emerging bio-based products as they become available
The next design iteration looked to increase the volume of bio-based, carbonsequestering materials. This included reducing the thickness of metal panels by increasing the OSB structural support, increasing the amount of cellulose insulation for higher acoustic partition performance, and replacing gypsum panels with MDF.
KieranTimberlake 4CASE STUDY OpenHome
Although the combination of Iteration 1 (Reference Figure 1, “Reduce Cement”) and Iteration 2 (Figure 1, “Select Bio-Based”) created a reduction of embodied carbon by almost 50% compared to the baseline case, the design team recognized that there were very few further optimizations that could be made with the current approach to the structural system. This spurred the team to investigate alternative approaches to the foundation structure that would still meet the requirements for Passive House operational energy performance while significantly reducing the concrete quantity. In reviewing foundation systems used for Passive House in Germany, the team identified three options that allowed for wooden slab framing with minimal concrete around a large volume of insulation, resulting in a further reduction of embodied carbon from the baseline by another 35% (shown in Figure 1 as “Optimize Foundations”).
Life Cycle Assessment is an emerging practice. We view every WBLCA as an opportunity to reduce embodied carbon and evolve our practice, and we hold ourselves to the highest standard while conducing WBLCA. In the interest of ongoing improvement of our efforts and promoting LCA across the profession, this project helped us mature our practice in the following ways:
• Although material optimization can yield significant carbon savings there is a limit as to how much carbon can be saved without causing detrimental impacts on design until manufacturing for certain materials, like glazing, improves
• Balancing occupant health and comfort with carbon investment meant optimizing glazing size and placement
OPPORTUNITIES FOR IMPROVEMENT
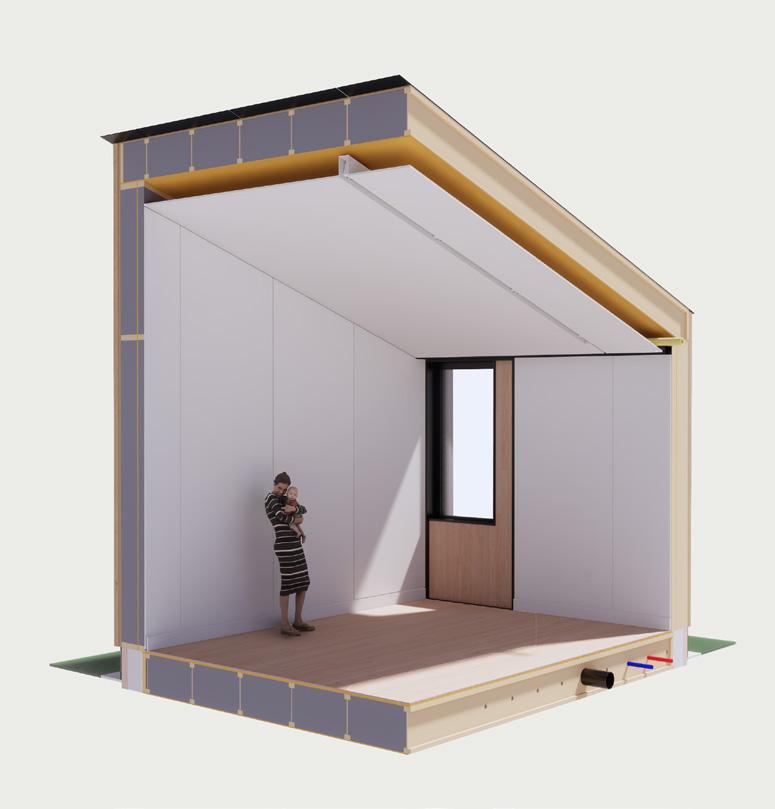

KieranTimberlake 5CASE STUDY OpenHome REFERENCES 1 Simonen, K., Rodriguez, B., Barrera, S., Huang, M., (2017) CLF Embodied Carbon Benchmark Database, database. Available at http://hdl. 2handle.net/1773/38017.ISO14040-14044:2006, Environmental Management – Life Cycle Assessment. EN15804 – Sustainability of construction works – Environmental product declarations – Core rules for the product category of construction products. PHOTOS Cover: Chris Leaman Page 3: Michael Moran Photography Inc. CONTACT Efrie 841KieranTimberlakeEscottNorthAmerican Street Philadelphia, PA 19123 (215) efriedlander@kierantimberlake.com922-6600
• Although bio-based materials can work to offset some of the smaller sources of embodied carbon, the use of carbon-intensive materials—such as concrete, glass, and metal— need to be minimized to reach reduction targets.
and comfort demand access to natural light, fresh air, and views to the outdoors.
• Targeting Net Zero challenged the team to move beyond our typical, known embodied carbon reduction techniques to radically re-think the foundation system approach.
Balancing these needs against the embodied carbon investment of glazing requires optimization of glazing size and placement to maximize its effect while minimizing glazing area.
In order to achieve Passive House levels of operational energy performance, the current iteration of OpenHome still uses mineral wool as one of the insulation materials in the envelope system as there are still locations in the envelope where bio-based products are not an appropriate substitute. As improved bio-based products become available on the architectural market, design teams need to continually evaluate them for effectiveness as replacements for traditional building materials.
LESSONS LEARNED
• MEP systems are an important factor when considering substantial shifts in building material selection, as radiant systems and thermal massing strategies will not work with all building materials.
• Starting embodied carbon reductions in very early design phases allowed the team to make big moves such as shifting the approach to the foundations—actions that cannot be taken after building and structural systems are finalized.
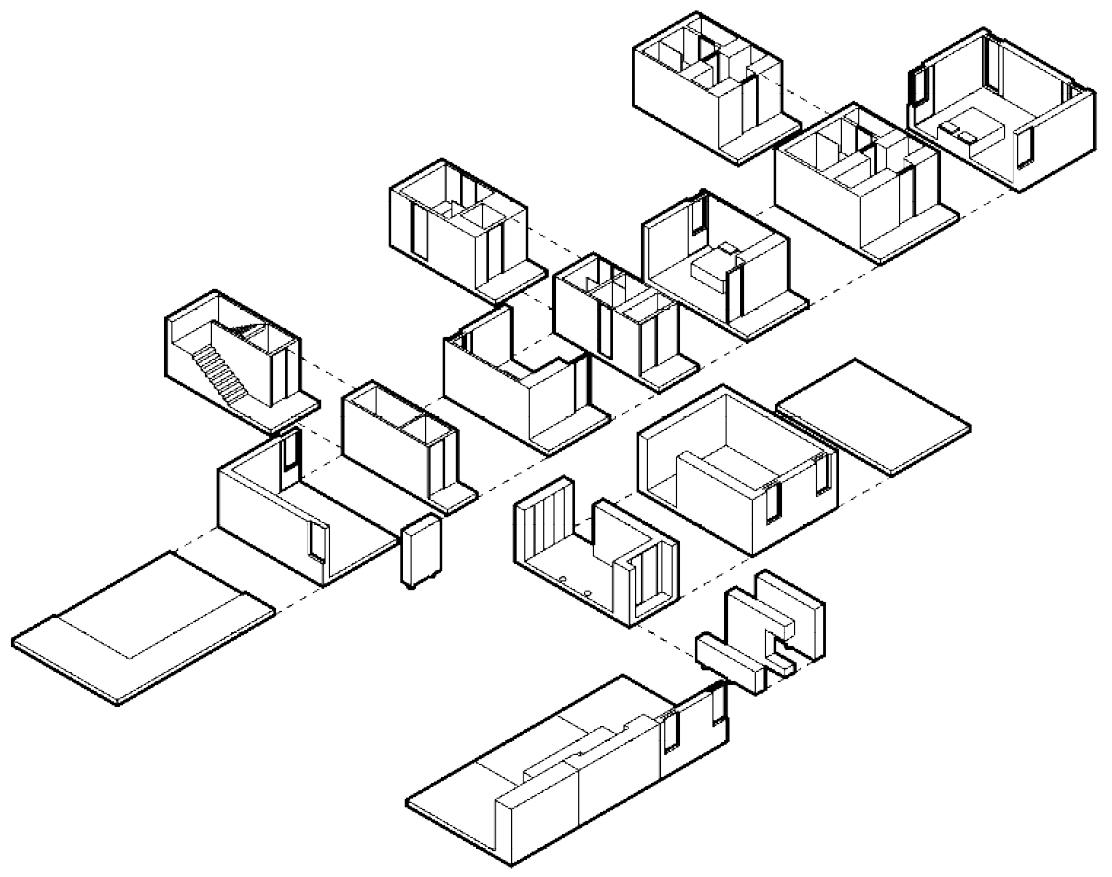