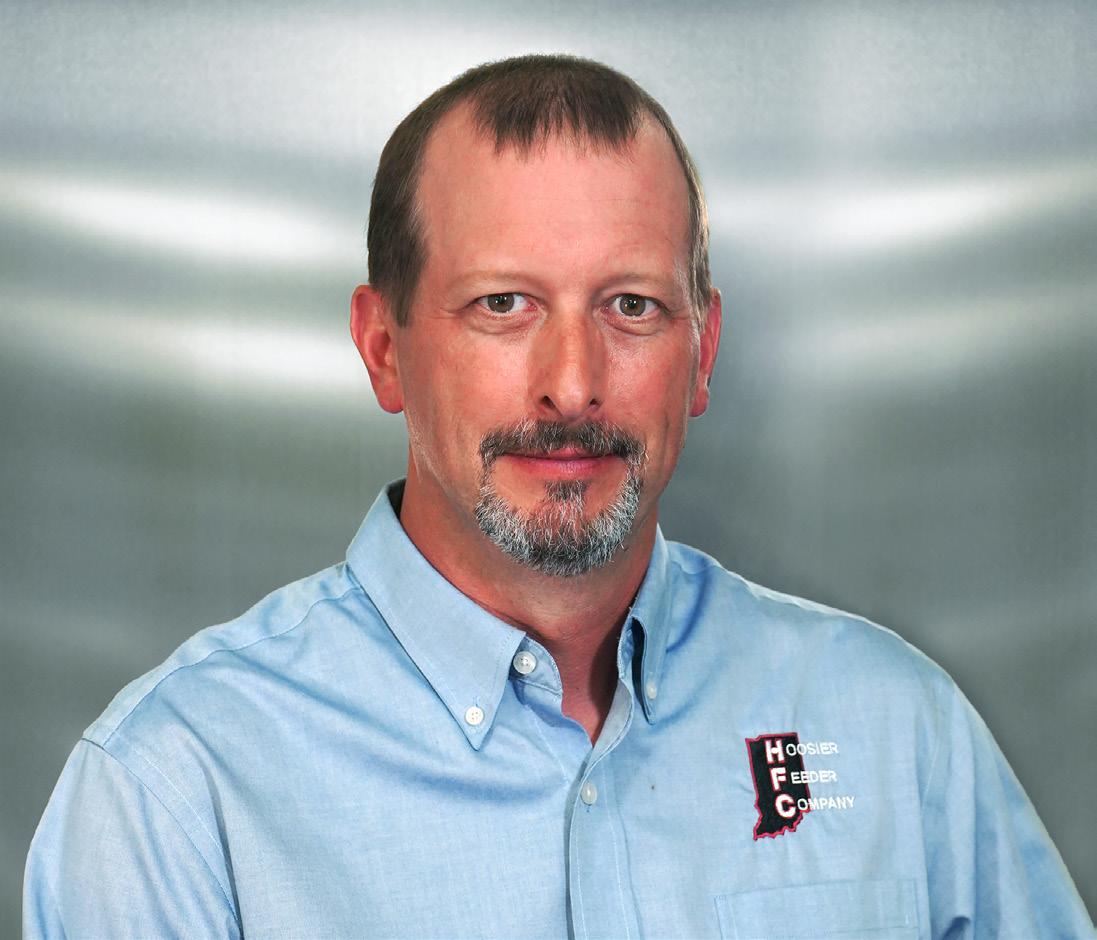
2 minute read
Collaboration & Innovation Drive Partnership
from JLS Magazine #3
SCHOMBERT: We provide orientating conveyor systems that take products from bulk and singulate or orientate for downstream processes. We also provide bulk storage hopper elevators that meter product into the conveyor systems on demand.
Q:What sets you apart from others?
SCHOMBERT: Our team puts a lot of passion into taking care of the customer. Our focus is on innovation and capabilities that allow us to take on unique projects. We love to innovate and are constantly looking for ways to solve unique problems and challenges. Our team goes beyond providing an offthe-shelf conveyor; we provide an engineered solution.
Q:When did Hoosier’s relationship start with JLS® and what does it mean to your team?
Greg Schombert, CEO of Hoosier Conveyor Company
Schombert has over 25 years of experience providing automation solutions to a variety of industries including food processing, bakery, and industrial automation. He is CEO of Hoosier Conveyor Company, a custom conveyor solutions provider; and President & CEO of Hoosier Feeder Company, a leader in vibratory and centrifugal feeder bowl systems. He co-founded both companies in Knightstown, IN.
SCHOMBERT: Our relationship started in 2019 at an industry event. A conversation at dinner turned into a wonderful partnership with an industry-leading company. One of the things that makes our partnership so successful is that we focus on similar goals and industries. Both organizations understand the importance of putting the customer first.
It’s so important to have confidence in the companies you partner with, and we have that with JLS. We enjoy that JLS is best-in-class. We strive to be the best and we feel that we can do that together. JLS doesn’t look to cut corners, they look to build industry-leading equipment and solve the complex challenges of handling protein in harsh environments.
Q: Why are your orientating conveyor systems a good match for JLS?
SCHOMBERT: Food safety is our highest priority. Our focus is on making the units hygienic and keeping consumers safe. We continually meet with customers, document, and address concerns, and reevaluate and improve our designs. We give special consideration to eliminating any cracks, crevices and flat surfaces to prevent contamination or opportunities for bacteria to grow. Collaborating with JLS and end users while being open to feedback has driven us to refine our conveyor systems to be what we feel are among the most hygienic conveyor solutions available in the market today.
Q: What are some unique applications you have collaborated with JLS on?
SCHOMBERT: We’ve collaborated on so many amazing applications–from sandwich rolls, candy bars, sauce packets, sausages, meat sticks, corn dogs, granola bars, sausage chubs and many more.
The sandwich rolls application was notable because it significantly helped the customer improve their process and meet demand. We developed a conveyor solution that orientated and singulated the product before it went into the slicer. This automated solution helped reallocate labor and improve output.
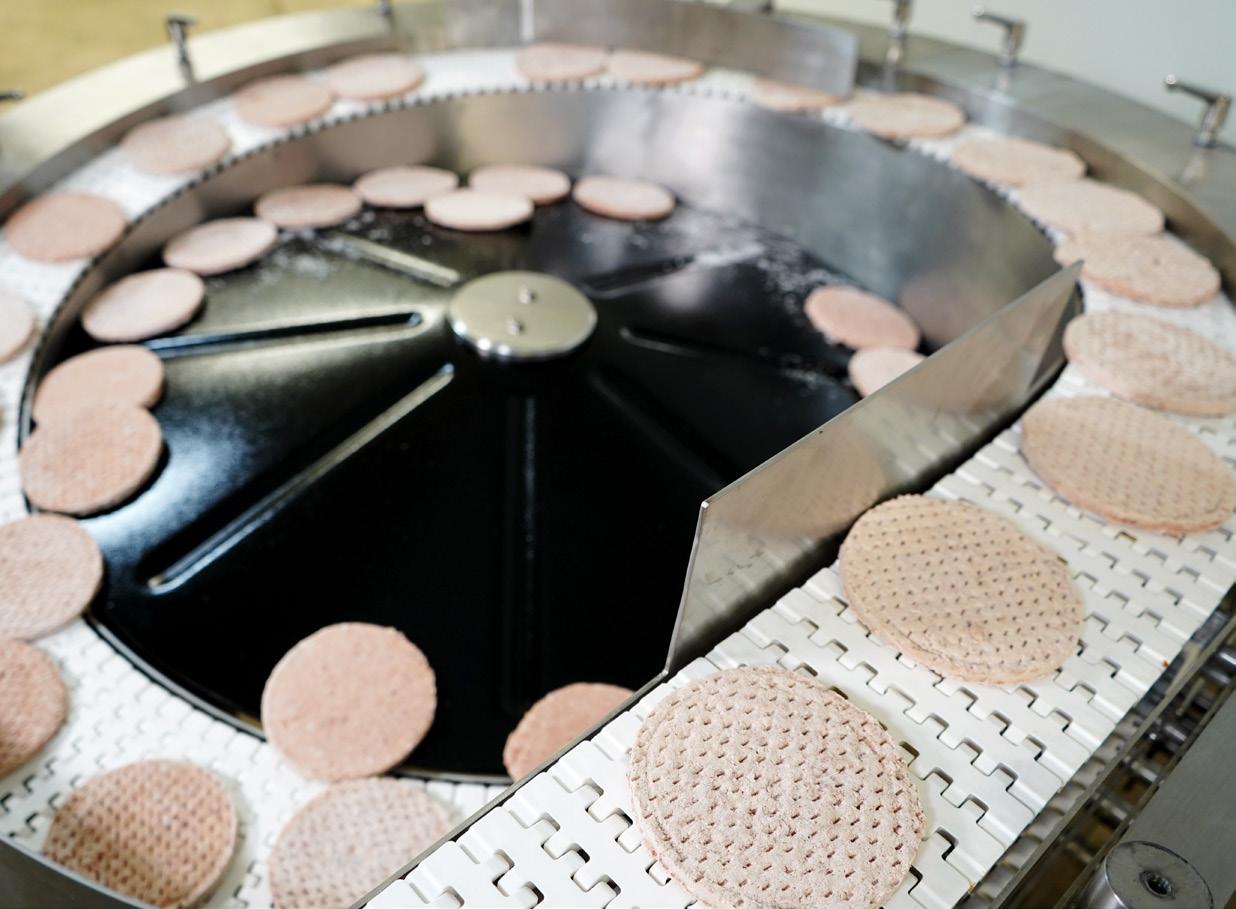
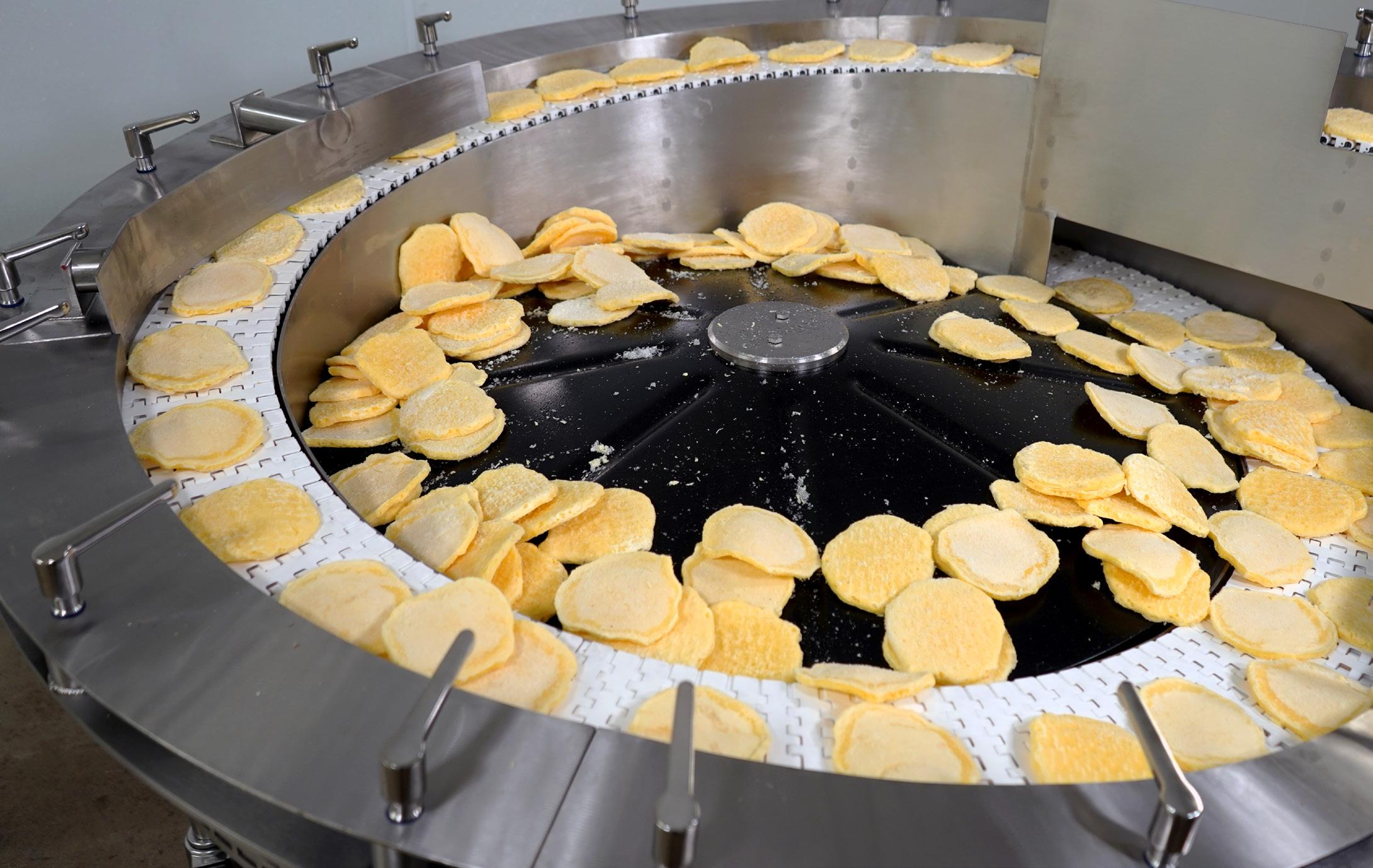
We don’t like to guess what the solution will be. We look to JLS if it is something unique and we’re not familiar with it, get samples and do in-depth testing to make sure we are addressing major challenges early in the process before committing to a solution we haven’t figured out yet. Upfront testing adds a tremendous amount of value and controls costing throughout the process. It’s important to us that we build efficient equipment with minimal scrap rate.
Q:If you could describe your partnership with JLS in two words, what would those words be and why?
SCHOMBERT: Mutually beneficial. We’re collaborative, working to improve our customer’s processes and efficiency. We’re committed to seeing each and every project through. JLS doesn’t approach a project or problem in anything but a collaborative manner. It’s always, “What is the path forward?” Our relationship helps our customers and that benefits us. From the first unit we sold to JLS to what we have now, we have grown leaps and bounds, and our systems are better because of the collaboration. Together, we’re focused on continuous improvement and finding new solutions, leading the industry in innovation.