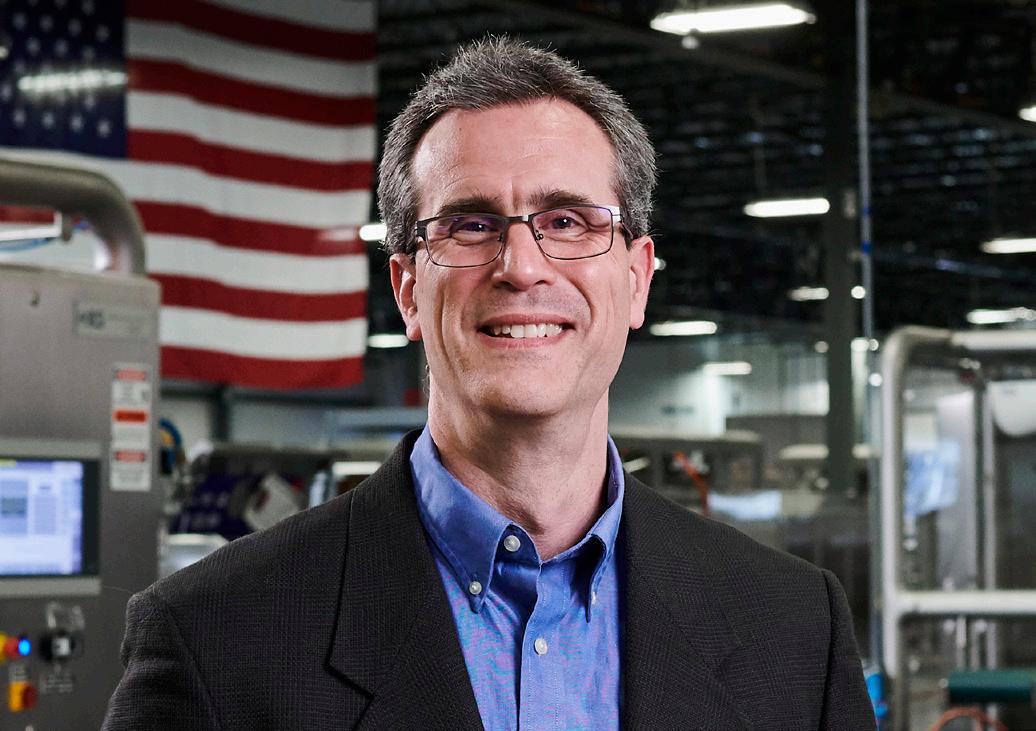
3 minute read
Case Packing Innovation Takes Flight
from JLS Magazine #3
An in-depth look at how the vision for the Osprey® case packing system came to be other components such as air cylinders, product guides, proximity switches and photo-eyes. This results in a reduction in operator effort and potential errors during changeover as well as less effort for maintenance to manage all of the various mechanism adjustments and potential failure points. A typical example of our approach is to pick several packages in series from a flat conveyor belt and then place them on the fly into a case without a need to buffer or guide the packages or manipulate the case flaps. Optimized tool design allows this approach to work effectively whether handling flexible or rigid packages.
Q:JLS has become the standard on hygienic design. What are the main hygienic features of the Osprey?
Q:When was the Osprey developed and what problem were you looking to solve?
HAFNER: Osprey development began in 2011. Although we had delivered case packing systems previously, they were handled as custom vision-guided robotic solutions. We wanted to develop a product line to handle a wide range of case packing applications efficiently and take advantage of reusable engineering content. Although customization is not uncommon on Ospreys, our customers still benefit from proven core design elements.
Q: What are the main benefits of the Osprey compared to typical mechanical or even other robotic case packers?
HAFNER: Our robotic implementation focuses on making maximum use of robotic capabilities while minimizing the number of
HAFNER: By far, our biggest hygienic feature is simplicity. Any component we can eliminate from our design is one less item to clean and worry about. We aggressively push to streamline our concepts to achieve this result. We also continually review and refine our design to improve the hygienic characteristics of the remaining components by paying attention to potential harborage points, surface finishes, seals, etc. Many of the design features we develop for primary product handling filter down to the Osprey and further improve its hygienic design.
Q:In 2018, JLS switched its standard controls platform to B&R. What was the main motivating factor(s) to switch to this platform and what problems has that solved for your customers?
HAFNER: Before switching to B&R controls, we were using a conventional robot and controller along with a PLC to accomplish machine control. We were starting to struggle with conveyor tracking performance, and robot CPU processing power limits along with many minor headaches. The architecture made it difficult to develop an ideal user interface since much of the data which would be helpful to display was located in the robot controller (sometimes several controllers), rather than the PLC. We were hitting limits on the amount of data we could effectively pass between the multiple devices.
Switching to B&R immediately resolved our major pain points. The common controller eliminates any communication between a robot controller and PLC since there is only one device. The increased processing power allows us to handle more than 5 times the number of robots on a single controller. The increased power also means that we can focus on improving performance rather than optimizing code to reduce CPU load. Our HMI has improved and expanded dramatically. Much more diagnostic information is available now, and it is tailored to the user whether it is an operator, a maintenance person or a JLS technician. Flexibility to control recipe parameters also increased significantly so that creation of new recipes is no longer reliant on engineering support.
Q:Likewise, JLS turned to Codian as your standard delta robots. What was the main motivating factor in making that switch and how has that benefited your customers?
HAFNER: Codian offers a tremendous range of products to cover different hygienic requirements, payloads, axis count, and reach, and they do this with an emphasis on quality and robust design. This allows us to select the optimal robot mechanical components for the customer’s requirement. Whether packing hundreds of pounds of product per minute in large packages or cycling over 100 packages per minute on small items, Codian offers an appropriate robot.
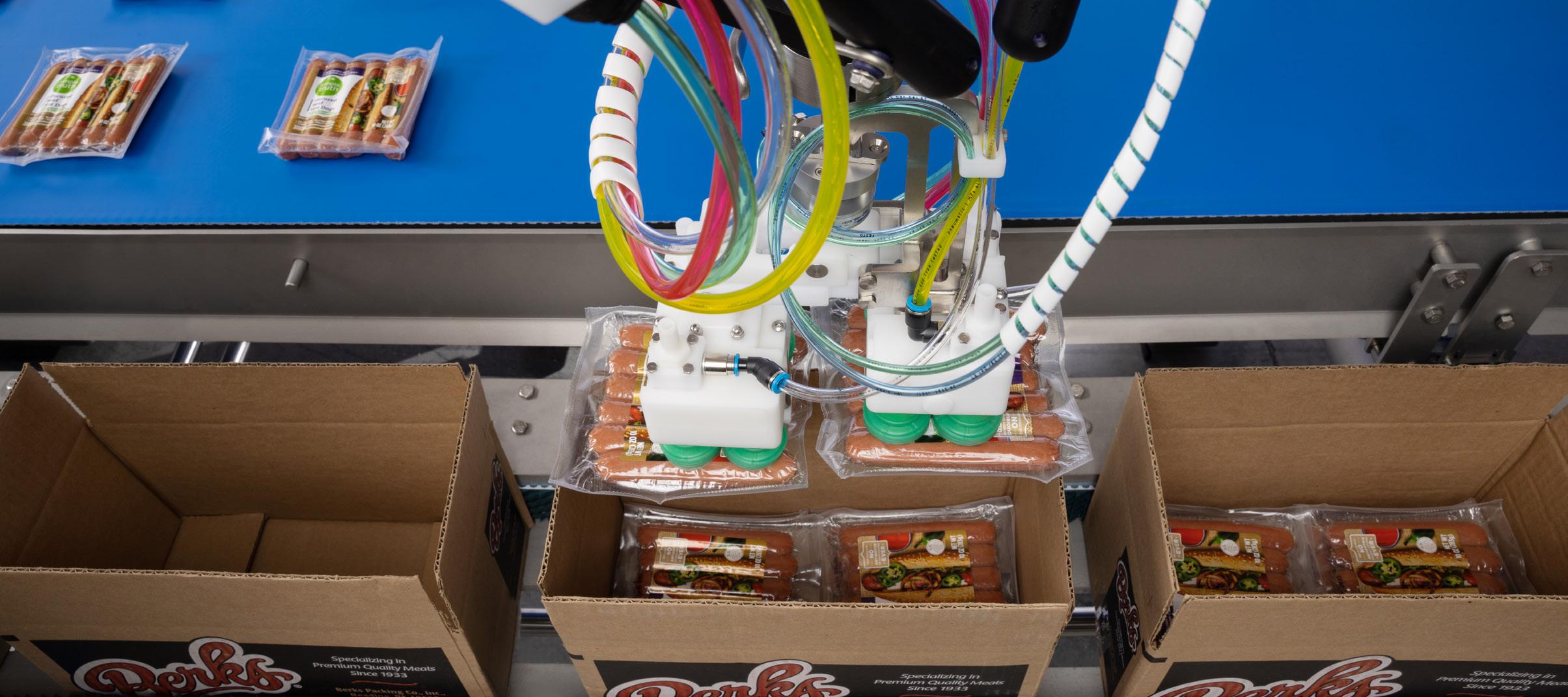
Q:While the Osprey is clean, open, and simpler than typical case packers, it’s also the most versatile. Tell us a little about your vision and thought process when you added vertical pack capability.
HAFNER: In addition to our focus on clean design, we also emphasize building equipment with a compact footprint. Many case packers implement vertical pack by adding extra robots or additional stages alongside the typical machine. These changes increase footprint, sometimes dramatically. The Osprey FLEX adds vertical pack capability with no impact on the already compact standard Osprey design. We also wanted to maintain the ability to provide quick changeover, so the Osprey FLEX uses a cassette system which is easily interchanged and without operator adjustments.
Q:
Not to spill the beans, but what is on the horizon for taking the Osprey to the ‘next’ level?
HAFNER: You know I’m not authorized to answer this question, but I would recommend visiting JLS at one of our upcoming shows to learn more.
Greg Schombert Hoosier Conveyor Company
Q:What types of products does Hoosier manufacture for the meat industry?