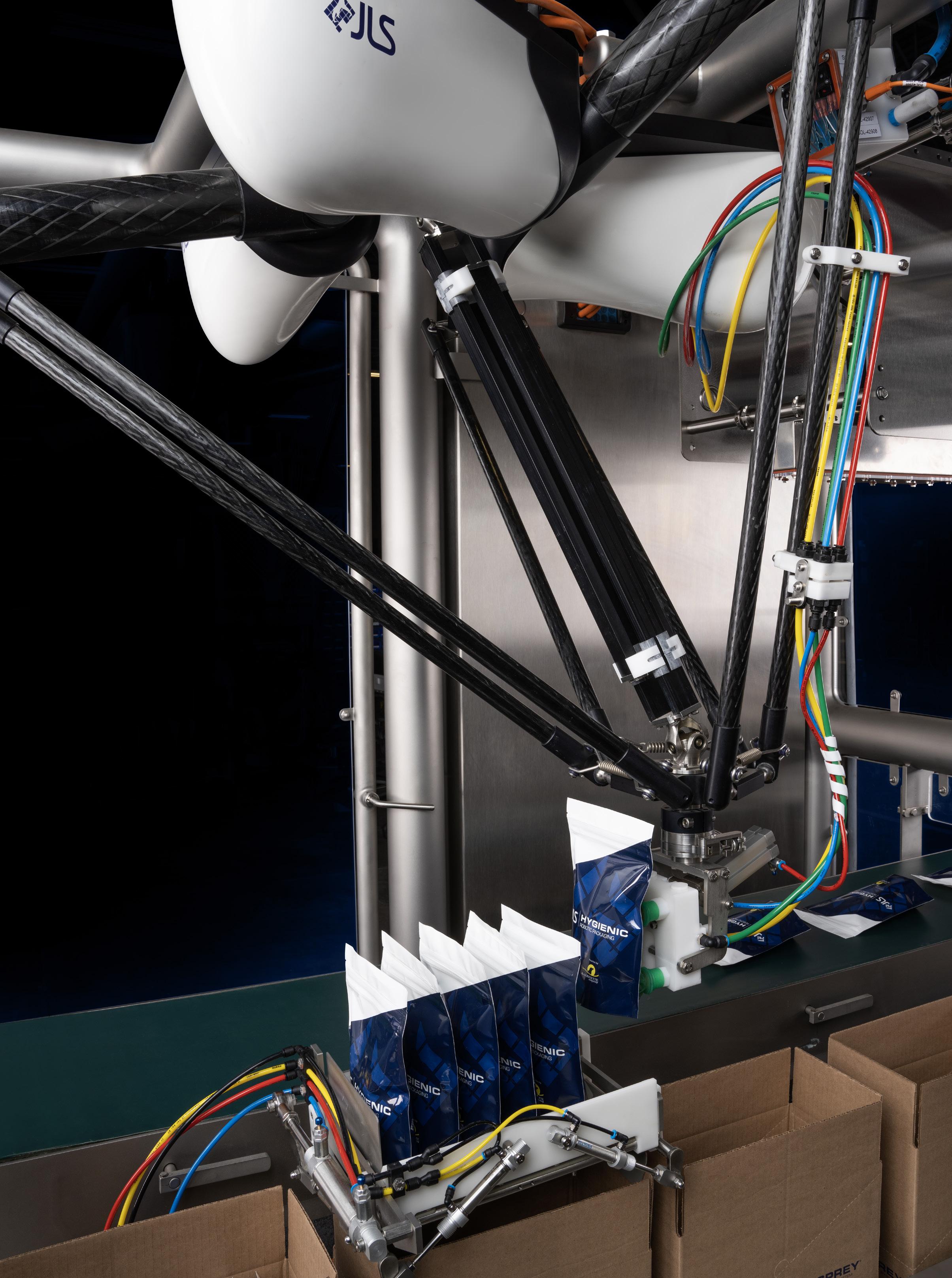
2 minute read
PERFORMANCE SOARS
from JLS Magazine #3
With Sanitary Robotic Case Packing System
Osprey ® optimizes production while keeping products safe
From food safety to labor shortages, food manufacturers are facing greater challenges than ever before. One solution is to automate their case packing operations to not only keep up with demand and growth, but also fill labor gaps.
Aligned with the rest of JLS’ product portfolio, the Osprey vision guided robotic case packer is the ultimate solution to these challenges. The Osprey offers a small footprint that allows food manufacturers to maximize the potential of their floorspace while also benefiting from sanitary features. Enhanced with features that help meet strict sanitary requirements, the Osprey provides rapid changeover with the flexibility inherent with vision guided solutions as well as the hygienic design that JLS® is known for.
Sanitation Made Simple
Recognizing the demands of food packaging, the Osprey’s hygienic design allows it to be located adjacent to washdown areas. An all stainless steel construction is standard and features smooth, continuous welds, sloped surfaces on enclosures and an open design that allows for easy entrance and access to all parts for cleaning and maintenance. Other washdown features include high-payload delta robots, motorized rollers on conveyors with standoffs, stainless steel conduit and attention to detail to eliminate human and food risks.
And, featuring our sanitary, proprietary Vacuum On Board™️ (VOB) technology, which was developed in tandem with Penn State University, sanitation is as simple as a tooless end-of-arm tool changeover. This makes the Osprey ideal for a wide variety of applications in meat, dairy, bakery and other markets where hygienic design is a requirement.
Developed to facilitate the use of highspeed vacuum generators in primary and secondary food packaging equipment and applications, our VOB has no moving parts and is virtually clog-free by nature, turning production floor nightmares into production floor ease. The vacuum’s turn on/off time is greatly reduced and problematic vacuum hoses are eliminated.
Built-In Versatility
Versatile by design, the Osprey easily integrates into existing lines or helps automate manual case packing processes, providing savings on floorspace and the ability to reallocate labor.
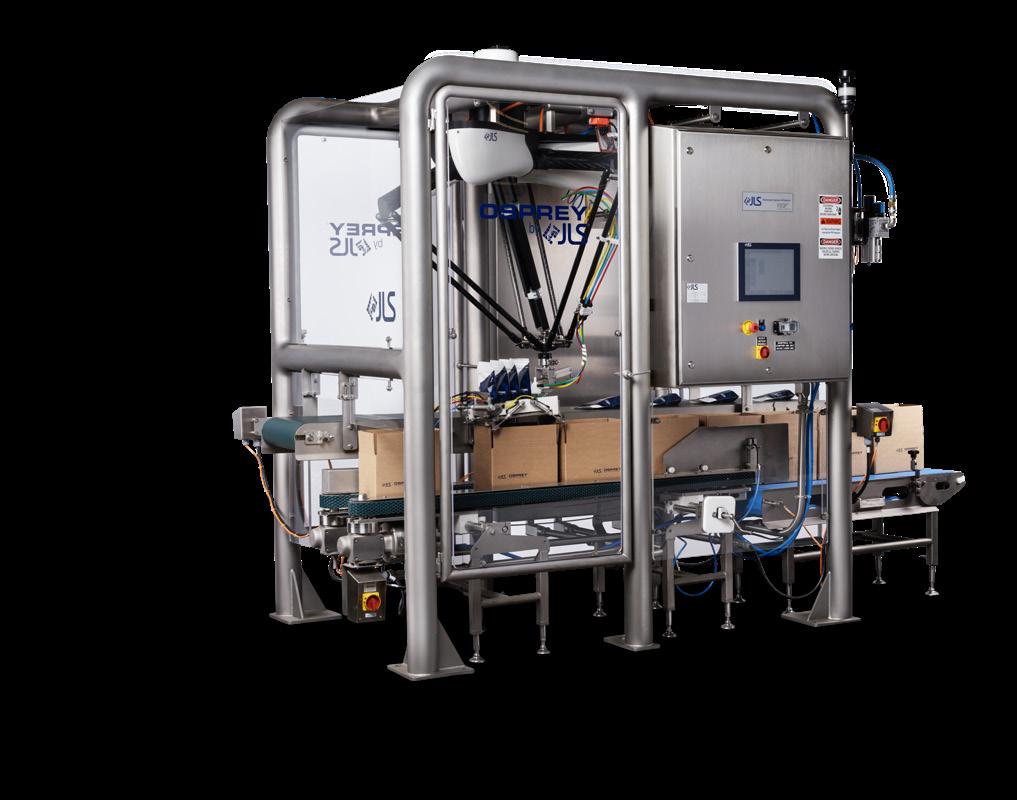
Although initially designed and optimized to be downstream of a thermoforming machine, the Osprey is well suited to handle a variety of other products and packages. In fact, Osprey handles just about any package you can think of, including stand-up pouches in flat or vertical orientation, large foodservice bags, MAP trays, thermoformed pouches, chub packs, clamshells and more.
The Osprey also features patented and proprietary end-of-arm tooling that easily handles meat and poultry, frozen foods, bakery products, cheese and more. Tooling options are designed to fit your specific application and include vacuum, robotic grippers and paddle lifters.
But the Osprey’s versatility doesn’t stop there, whether you need to load RSC or retail-ready cases, or both, the Osprey is the answer for case packing versatility.
Eliminate Leakers
The Osprey’s optional proprietary PIVT (Package Integrity Validation Technology) automatic leak detection system eliminates leaky packages and reduces waste.
to 160 packages per minute. The system is ideal for packages that contain brine such as hot dogs, sliced luncheon meats and sausages. Once a package is picked, PIVT simply detects the leak, drops the package and rejects it from the system. No more leakers, no more waste.
Small Electrical Footprint
Featuring standard controls from B&R Automation, the Osprey uses less parts and smaller control cabinets than similar systems by integrating motion, logic and HMI into one controller. By using only one hardware element and one software element, it eliminates several parts, including electrical components and software interfaces.
The more control cabinets, cables and wires you have, the more potential for harborage points where pathogens, food particles, and other potential contaminants can build up. The Osprey’s compact design and reduction in electrical components is just one reason why it is the most sanitary case packing option available on the market.
Ready to Soar with Oprey?
The Osprey’s sanitary, versatile design allows for labor reallocation and space savings while offering complete flexibility. By keeping labor gaps and food safety concerns at bay, the Osprey helps food production soar and business grow.
PIVT uses a combination of vacuum, vision and other sensors to find package seal con tamination, leaks and pinholes at speeds up