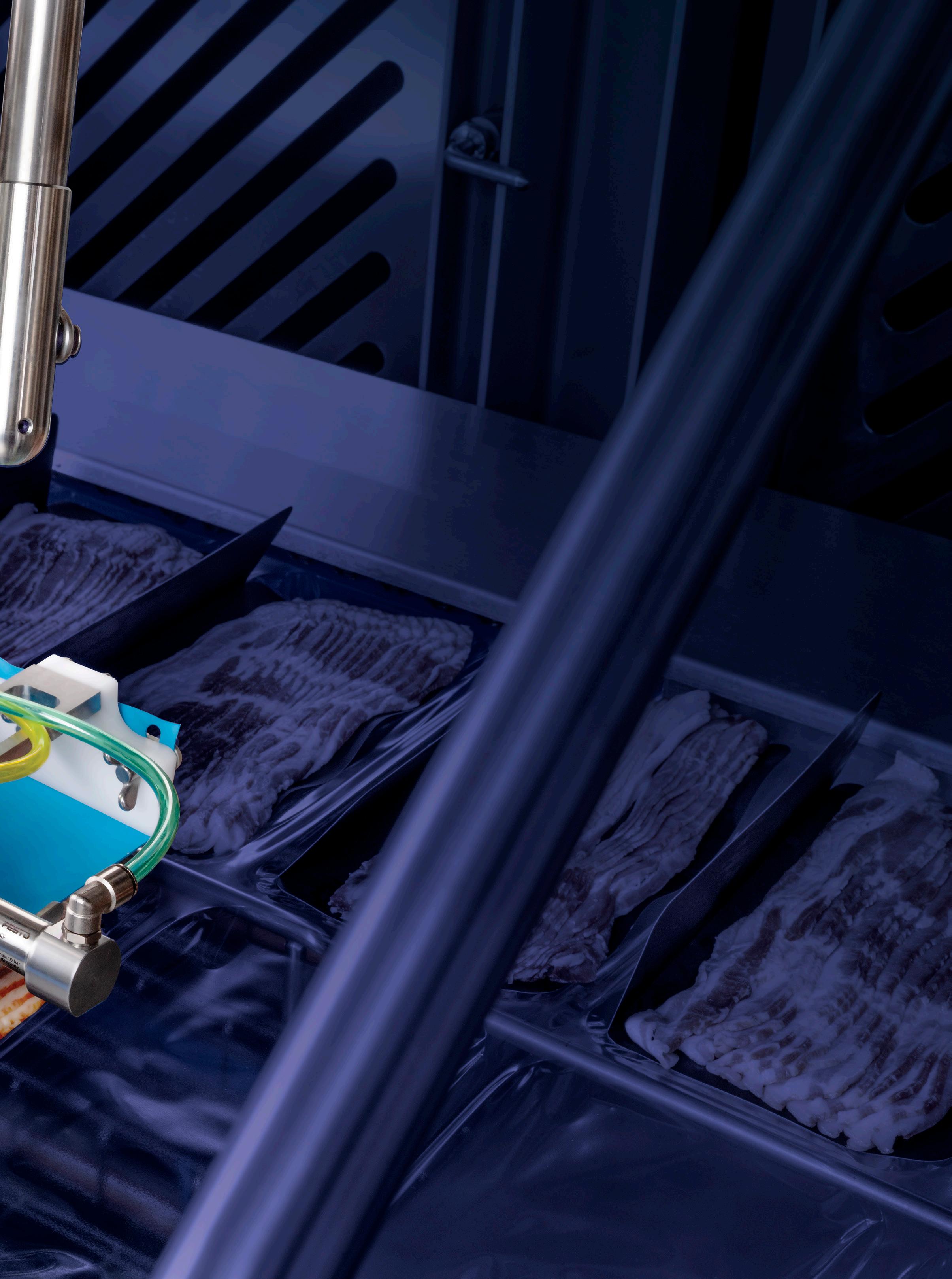
3 minute read
RAISING THE BAR FOR BETTER BACON
from JLS Magazine #3
From humble beginnings as a family-owned butcher shop to a modern robotic production line, today John F. Martin & Sons is making bacon better with JLS®. The Harrier automated bacon draft loading system from JLS is revolutionizing bacon packaging. Gone are the repetitive movements for line workers, while labor gaps are alleviated and efficiency is increased.
Though John F. Martin began selling meat over 8 decades ago, he started his family-owned butcher shop, John F. Martin & Sons, in Stevens, PA in 1961. Over 60 years later and in its fourth generation, the proudly American company has continued to grow over the years, while its commitments have remained the same. JFM is committed to providing quality meat and cheese products while promoting a safe environment for its employees to work in within the communities it operates.
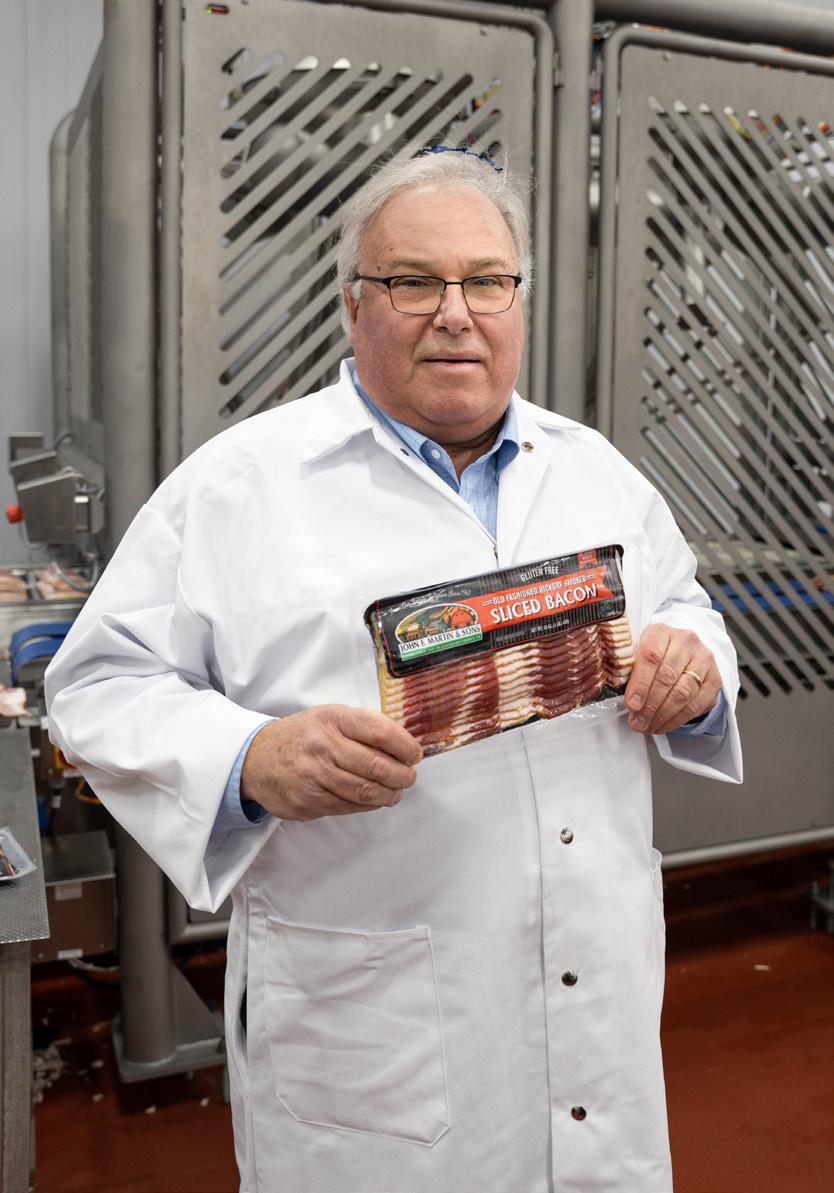
More Bacon, More Growth
JFM now has two locations–its flagship headquarters in Stevens, and its Womelsdorf, PA facility. The original Stevens facility has expanded over the years to its current size of 83,000 square feet and houses state-of-the-art processing and packaging operations. Its brand new 190,000 square foot facility in Womelsdorf is primarily used to accommodate its growing bacon line production needs.
As with many bacon producers, the demand for JFM’s bacon products has continued to grow year after year–so much so that the company needed to update its space in order to accommodate and respond to this increase in demand. In fact, at an average rate of 1.6% growth per year between 2018 and 2023, the market size of the bacon production industry in the US increased faster than the consumer goods and services sector overall.*
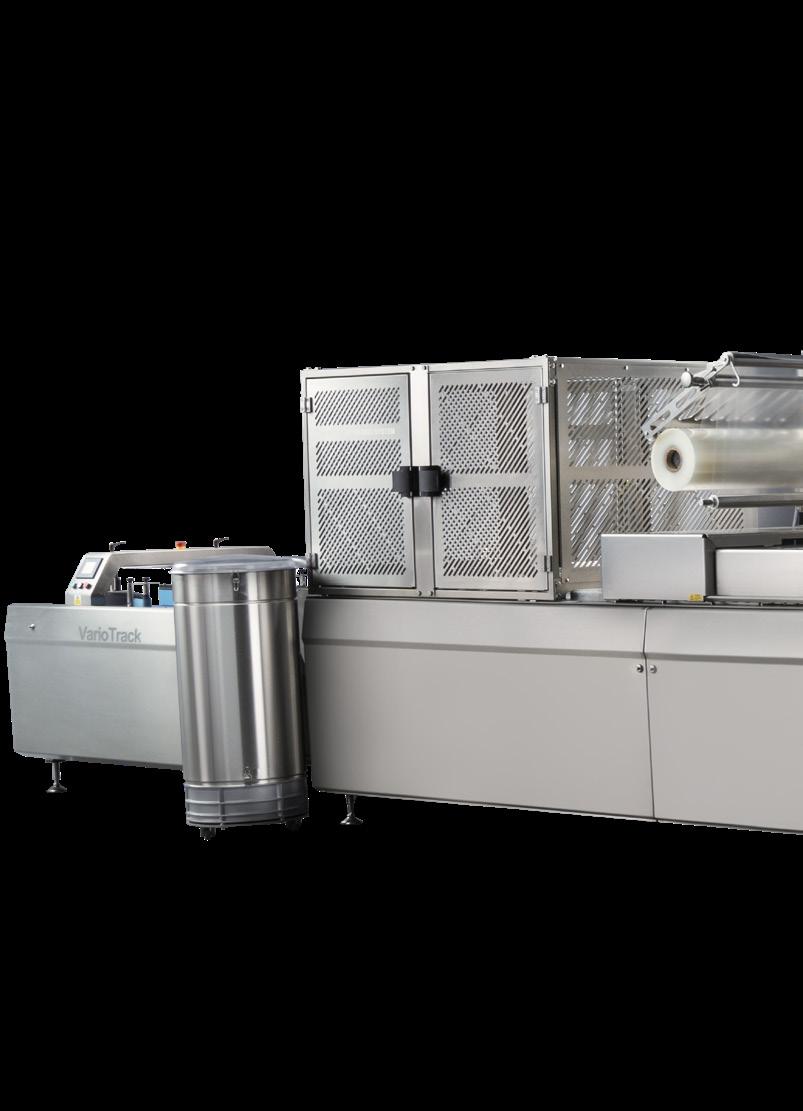
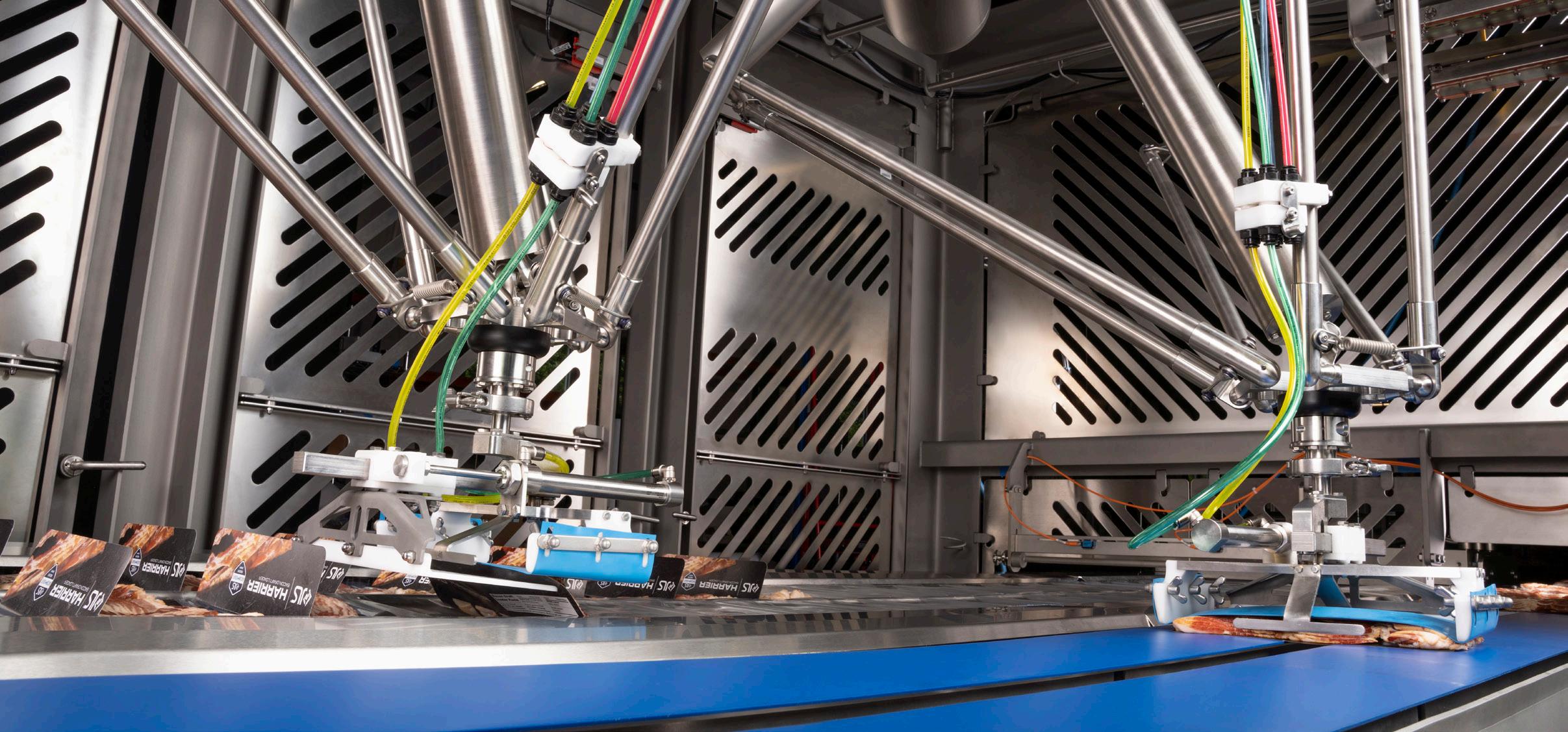
But with that growth have come challenges, and JFM isn’t alone.
Overcoming Challenges Through Partnership
“We expanded our building. And, we needed to grow our production,” said Tom Weber (pictured right), Director of Maintenance and Continuous Improvement at JFM. “But we also faced some challenges. The challenges were the availability of people, as well as finding technology that could help our team with hard tasks and increase our efficiency. We looked in the marketplace for ways to do that, and we found no equipment that existed. We found JLS and partnered with them to see if we could develop a piece of equipment that could solve our three problems.”
For JFM, it was important that the company chosen for this project was a true partner. Not only someone to work with, but someone to collaborate with, which is what led them to choosing JLS when seeking a solution for its bacon loading challenges. “That solution became the Harrier,” said Weber.
A New Solution to Common Problems
Together, JLS and JFM developed the Harrier, a revolutionary bacon draft loading system that automatically loads freshly sliced bacon drafts into thermoformers, effectively solving the challenges that are common for bacon producers. The Harrier eliminates hard tasks while improving food safety measures and increasing line efficiency.
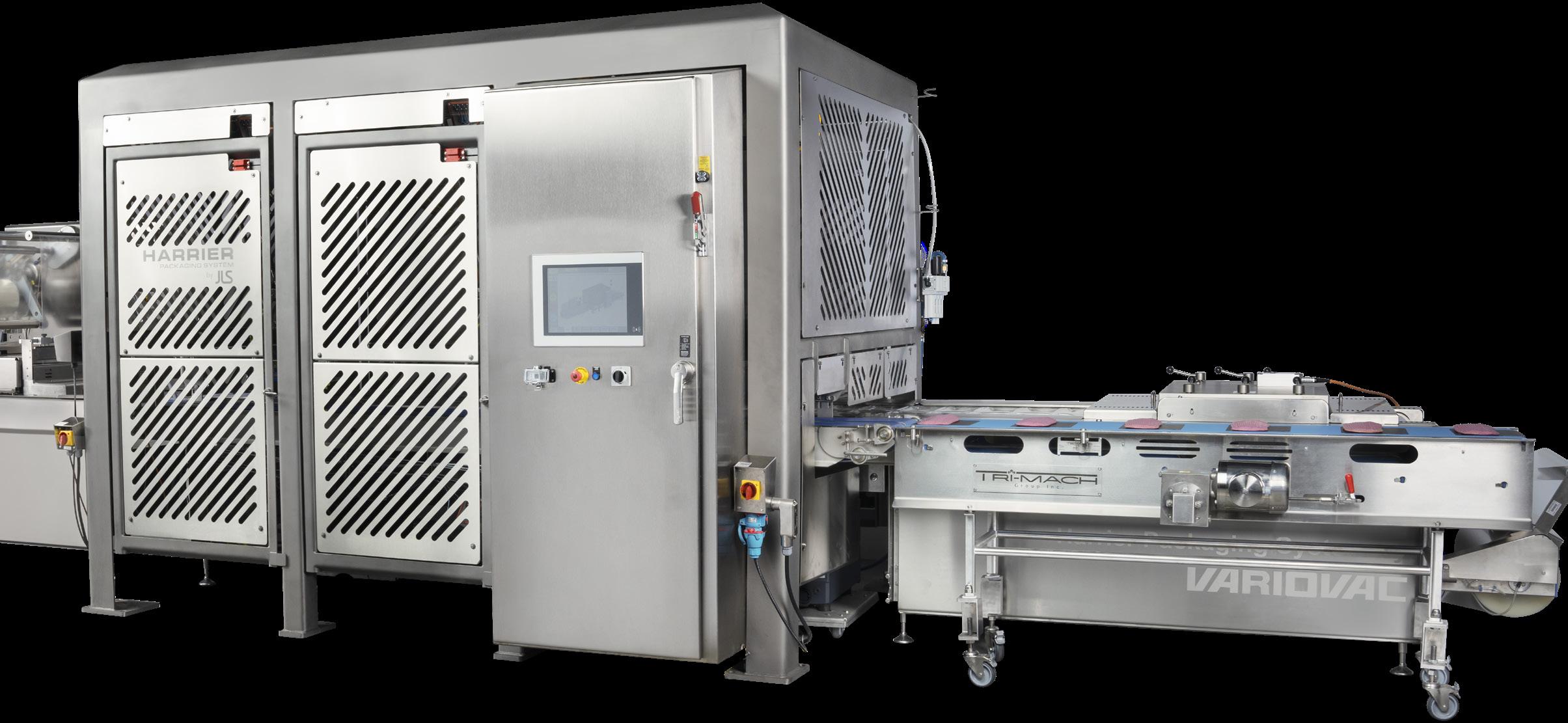
These efficiencies are supplemented with the addition of the JLS Osprey ® case packing system downstream of the Harrier. With sanitary end-of-arm tooling, the Osprey gently and accurately picks and loads the thermoformed pouches of bacon into cases at high speeds. High payload delta robots further improve line worker safety while increasing efficiencies.
Benefits Realized
Since installing this equipment, each of the challenges JFM originally sought out to solve has been mitigated. The company has been able to remove many of the hard tasks from its associates that work on the line every day, reduce the number of people required on the line, and have seen a growth in its overall efficiency and productivity.
But for JFM, at the heart of their experience was JLS’ aptitude for service and support, which helped JFM feel included along each step of the process. “JLS, while working on this with us, kept us well-informed about what was being tested, what they were working on, how it was going and what the challenges were,” said Weber.
What It’s Like Partnering with JLS
“Working with the folks at JLS was a good experience for everyone here at John F Martin. They kept us well informed about the progress we were making,” said Weber.
Perhaps even more importantly, “When we ran into difficulties,” he continued, “they stood behind their equipment and were certain that the issues were resolved and resolved timely through their engineering, manufacturing, R&D, even all the way up to the president. They really came in and made sure that we were comfortable with the equipment we were seeing, and it worked well.”
Together, the two companies overcame challenges, and have raised the bar for better bacon.
Innovation and Trust
“If I had to use only two words to describe JLS, they would be innovation and trust,” said Weber. “JLS showed their innovation in being able to develop and build the Harrier in the time they did. As well as trust. They’ve earned our trust by the way they installed it and with the people that worked on it.”
Source: https://www.ibisworld.com/industry-statistics/ market-size/bacon-production-united-states/