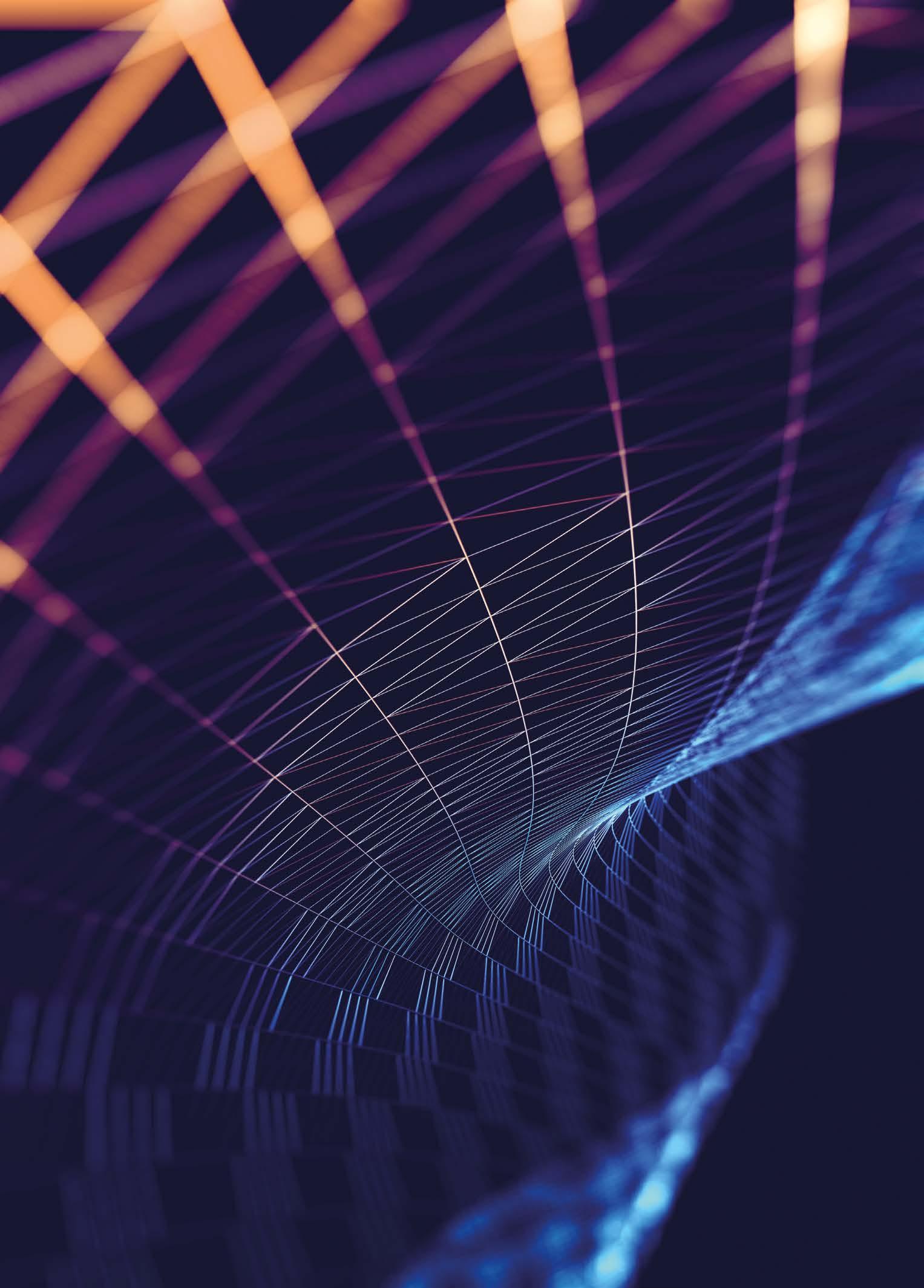
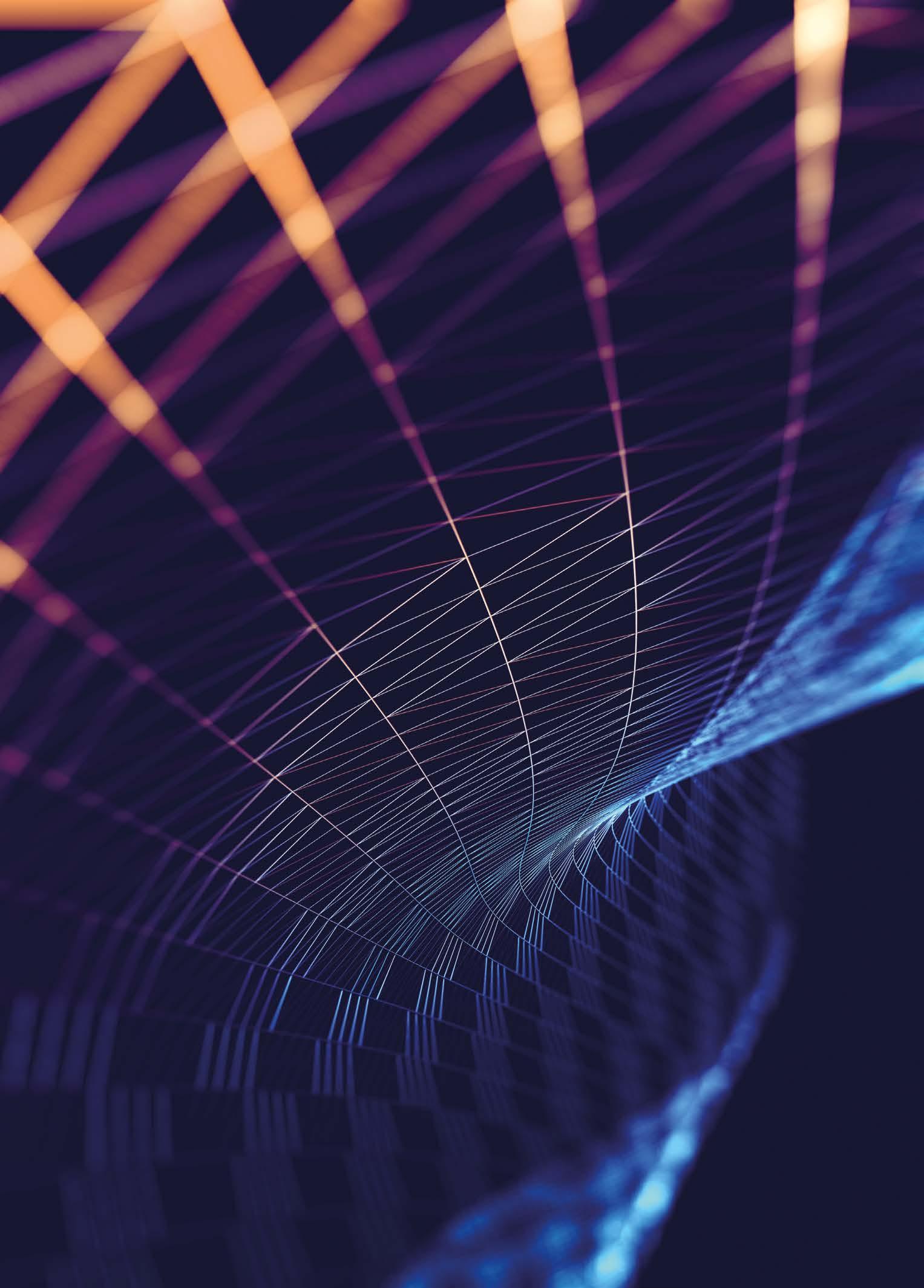
Inocart Powder Manual Coating Equipment
User-friendly and ergonomic manual powder gun
LIFETIME FINISH QUALITY: Long life waterfall durability and HV performance
BALANCED AND ERGONOMIC DESIGN: No repetitive strain damage, less fatigue
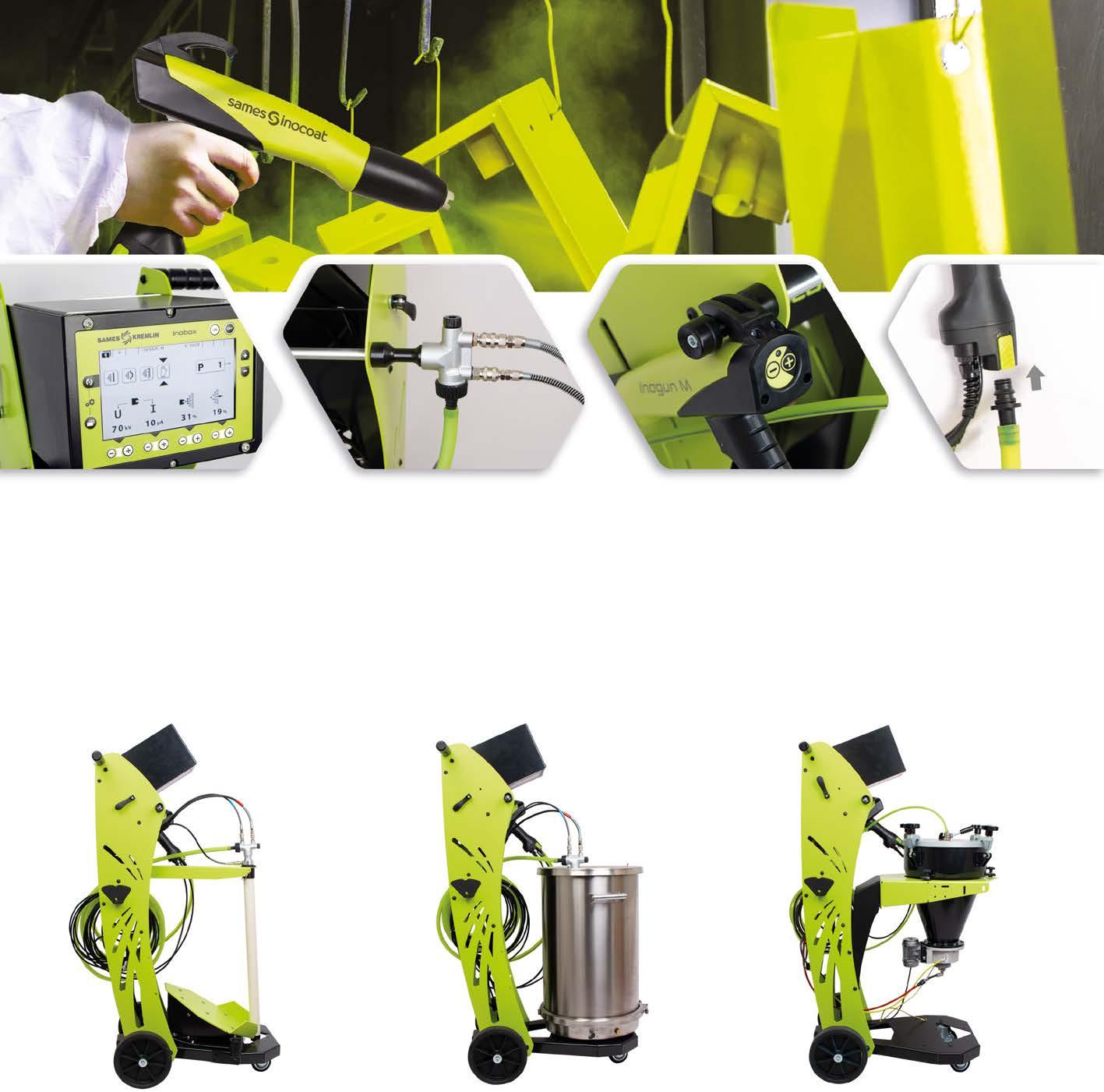
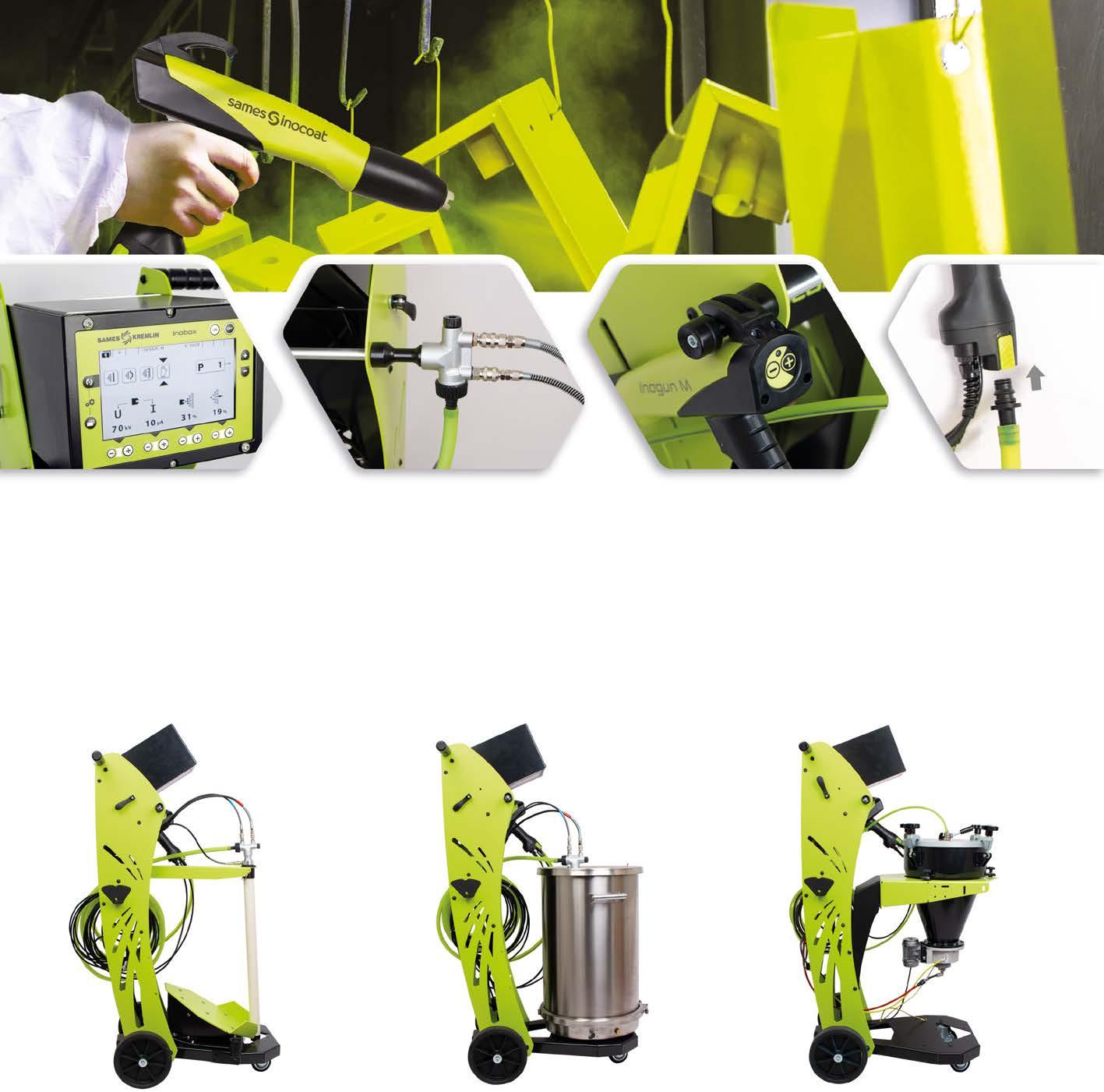

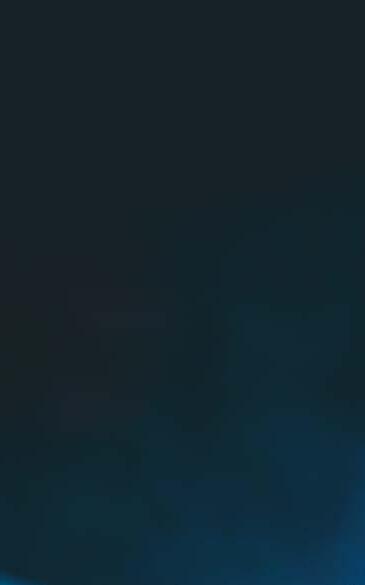
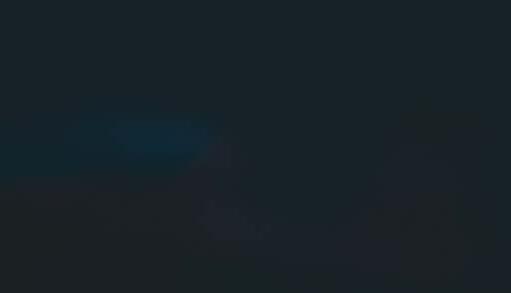
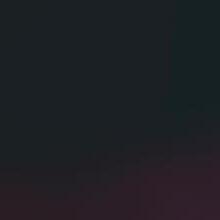
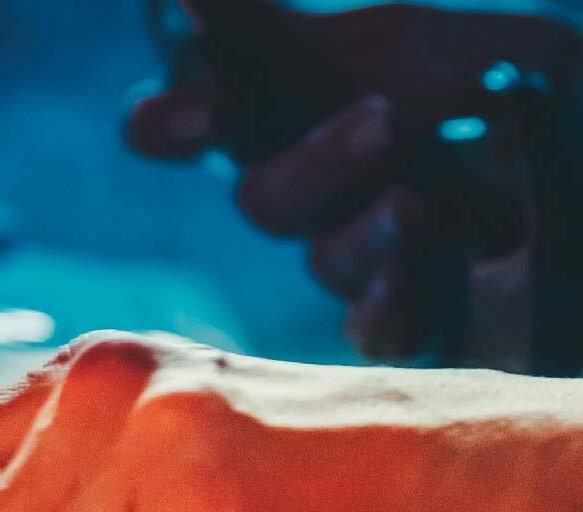
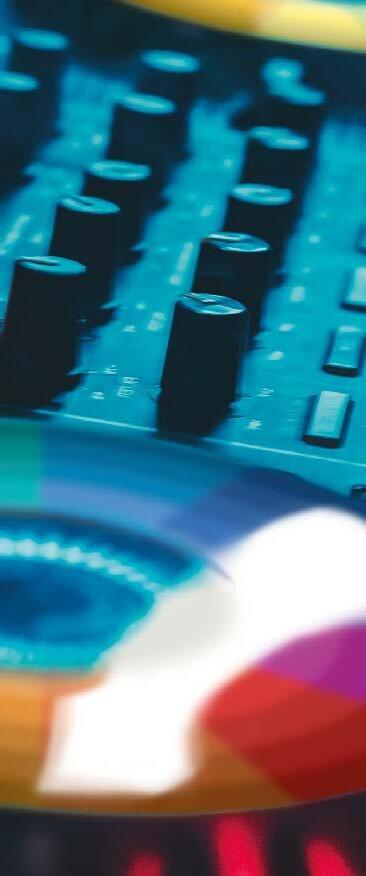
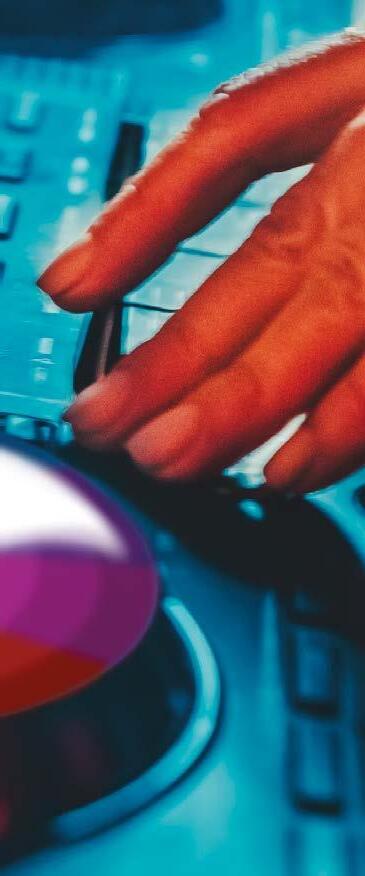

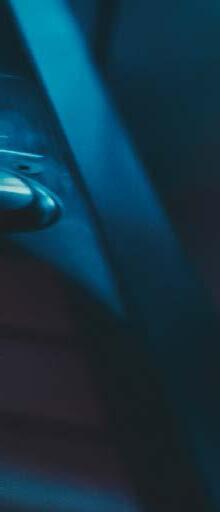
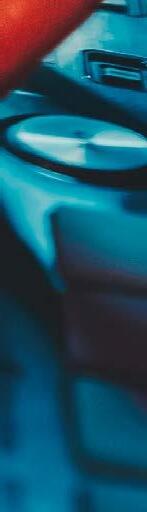
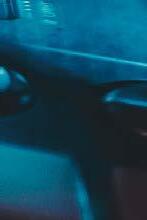
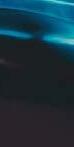
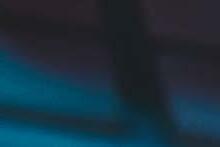

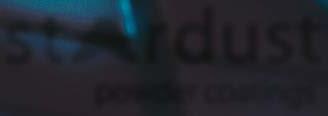

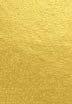
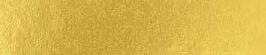
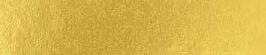






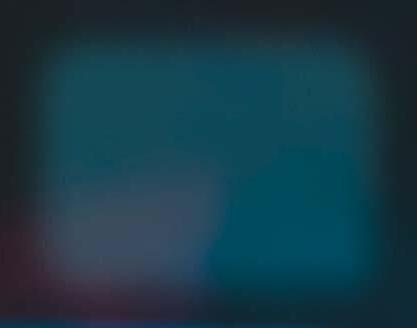



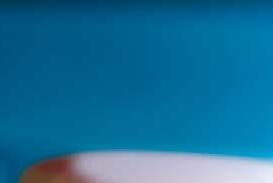
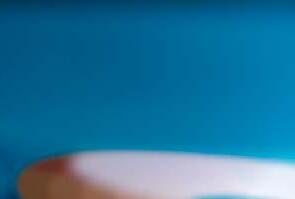

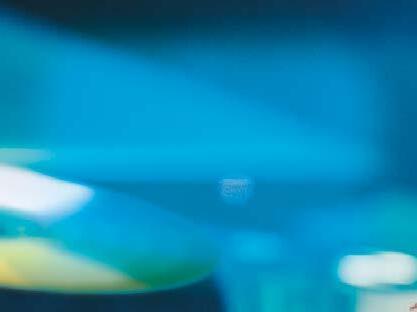
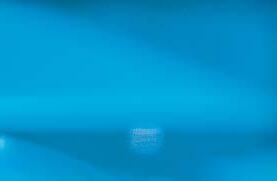

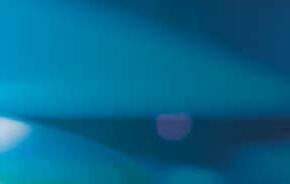
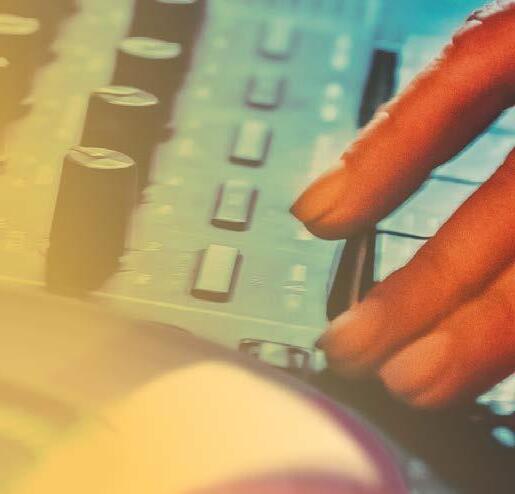
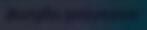
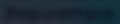



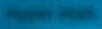
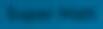


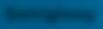











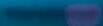

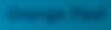



North America’s Largest Metal Forming, Fabricating, Welding and Finishing Event
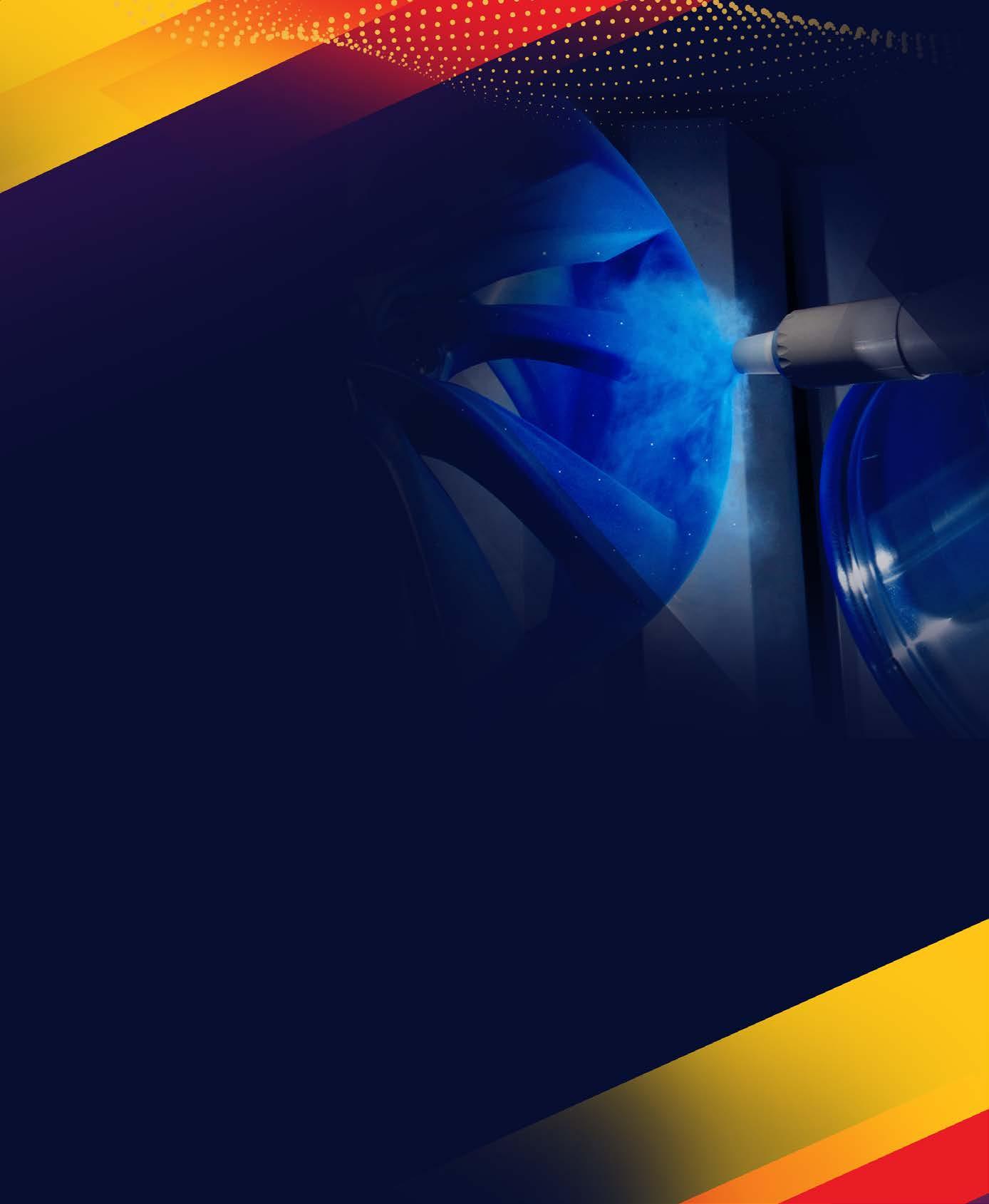
Driving Manufacturing Forward
Technology is advancing at a rapid pace. FABTECH brings the industry together to see the innovations transforming manufacturing.
Explore the latest trends, network with peers, and discover the solutions to take your business to the next level.
SEPTEMBER 11-14, 2023
Chicago, IL | McCormick Place
CLEAN IT. COAT IT. CURE IT.
CLEAN IT. COAT IT. CURE IT.
CUSTOM BUILT Engineered finishing systems: Blast, Pretreatment, Conveyors, Booths, applicators, robotics, and ovens.
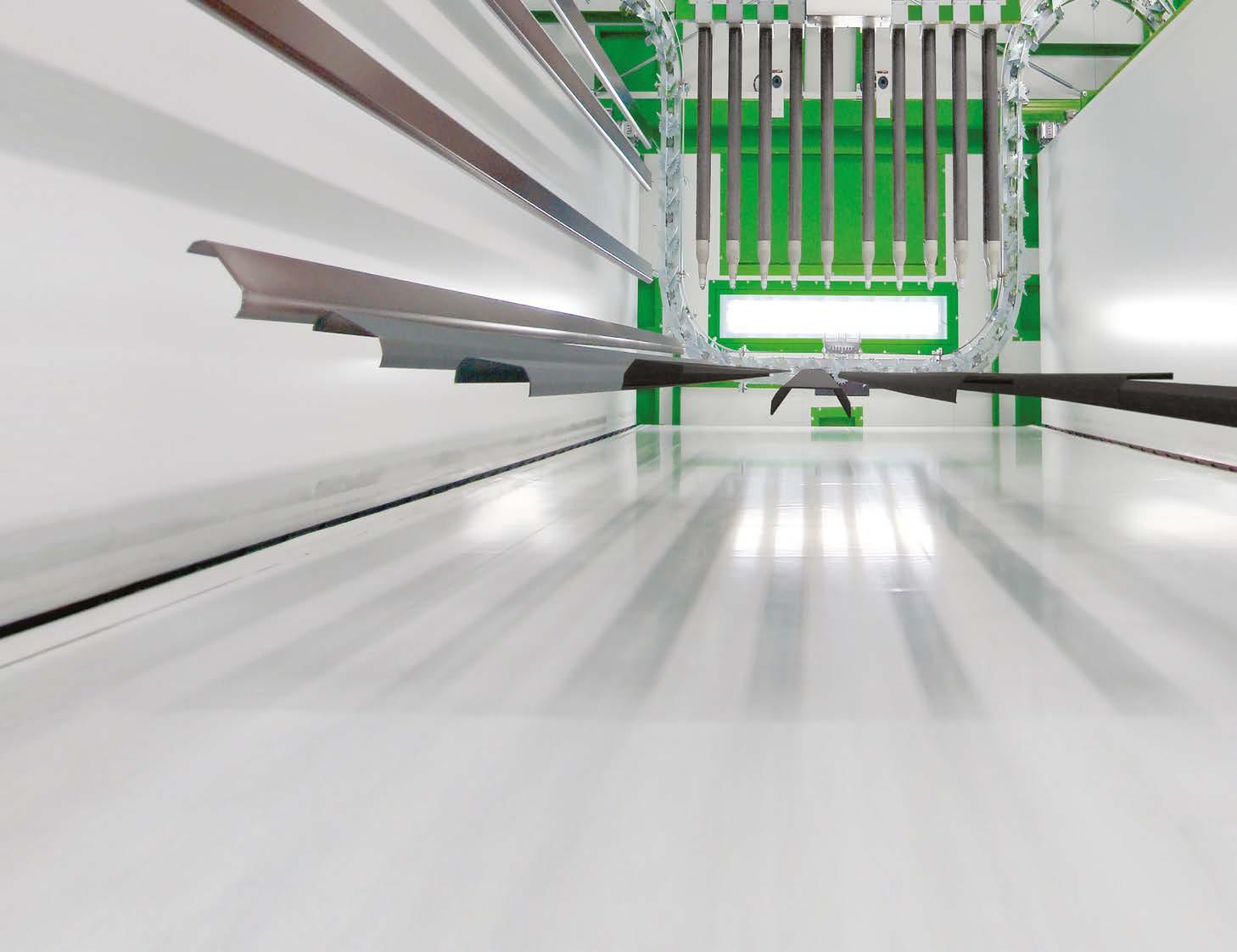
Total Finishing Systems is a leading designer and integrator of high-quality and complex industrial finishing systems. Whether you need an in-depth process analysis or require finishing equipment and components, our equipment exceeds expectations and our innovation and automation is industry leading.
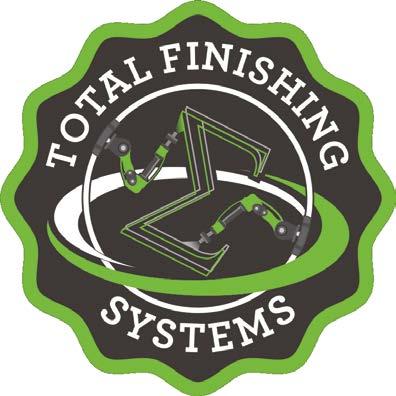
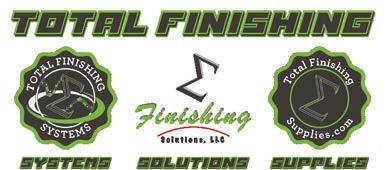
14
ADVANCEMENTS
ALIT Technologies lancia
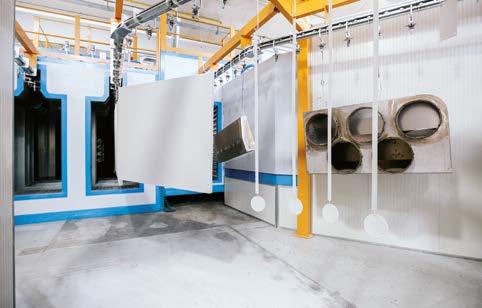

FASTRIP T2-120 MIX
36
HIGHLIGHT OF THE MONTH
Le tendenze di mercato del settore del trattamento acque industriali: l’analisi di Idrotecnica
50
FOCUS ON TECHNOLOGY
L’impianto di verniciatura a polvere del Gruppo ILTOM garantisce flessibilità produttiva riducendo al contempo i consumi energetici ed elevando le performance qualitative
31
62
WHERE WE HAVE BEEN
32 ADVANCEMENTS
Come ridurre la corrosione sugli spigoli utilizzando un primer di nuova generazione
40
e
FOCUS ON TECHNOLOGY
Nella Portugal Bike Valley la partnership vincente con il produttore di vernici in polvere alza l’asticella della qualità di finitura
46 ADVANCEMENTS
La differenza nel pretrattamento dell’alluminio per diverse ambientazioni climatiche basata sull’esempio di aziende di verniciatura certificate GSB
FOCUS ON TECHNOLOGY
Disporre del tempo del cliente valorizzandolo con un servizio all’avanguardia: la scommessa sul futuro del terzista di verniciatura
58 RESEARCH BREAKTHROUGH I rivestimenti cellulosici “invisibili” che mitigano la trasmissione superficiale degli agenti patogeni
60 ROAD TO 2050
EcoBell4: efficienza fino al 98% che consente di risparmiare importanti quantità di vernice e di prodotti per il risciacquo
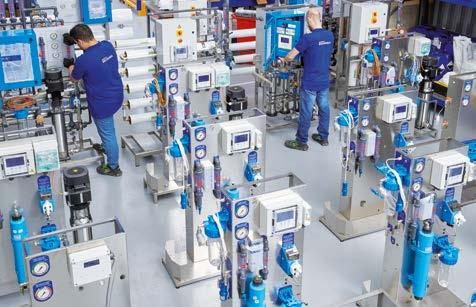
68 HIGHLIGHT OF THE MONTH
Lechler Tech: vernici industriali per ogni opportunità
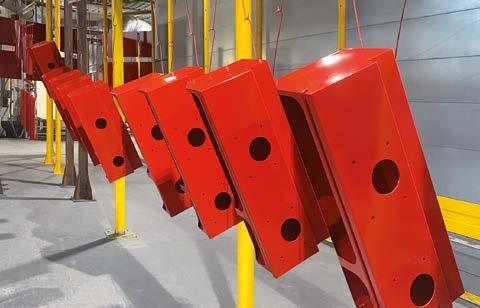
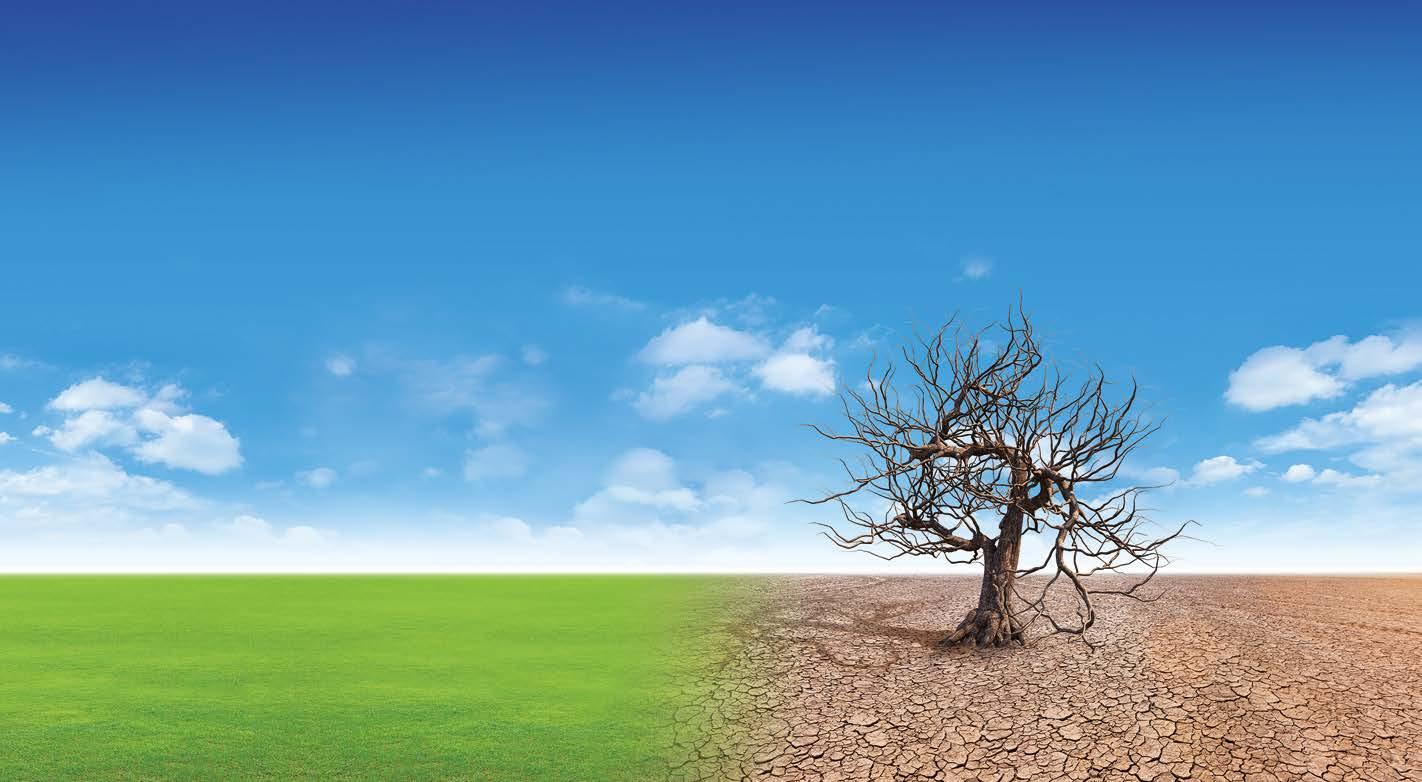

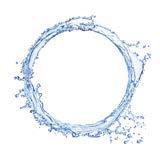
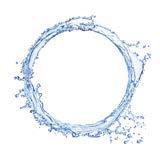
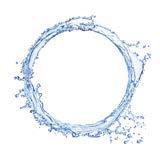
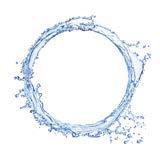
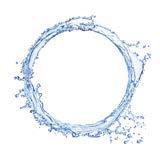
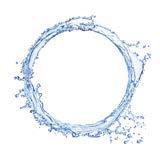
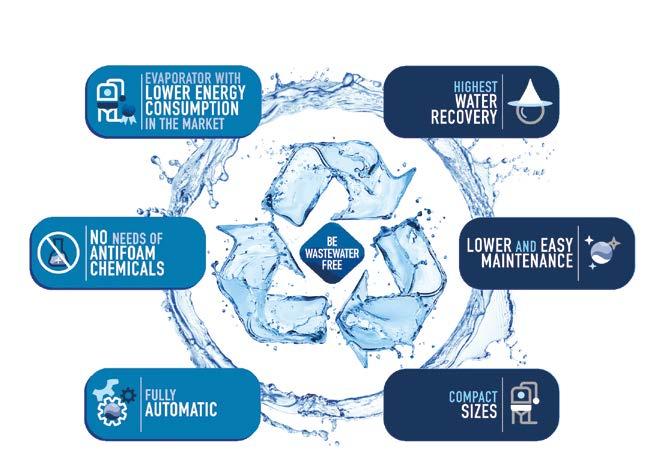
72
FOCUS ON TECHNOLOGY
Dimezzamento dei tempi di cambio colore e volume di polveri da smaltire ridotto di dieci volte: l’esperienza Nord Laser
84
ADVANCEMENTS
Più opzioni per la verniciatura di componenti per veicoli elettrici
96
ART WITHIN SURFACES
La simbiosi tra industria e design nella mostra “Red in Italy, i Colori del Rosso nel Design Italiano”
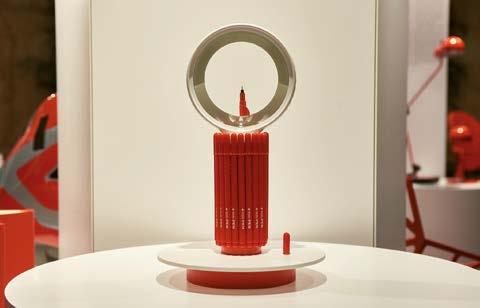
108
FOCUS ON TECHNOLOGY
T&G: la fidelizzazione di un partner per l’impiantistica di verniciatura segue la crescita dell’azienda
122 BRAND NEW
126 ADVANCEMENTS
Le nuove tecnologie dip-and-spin riducono il costo dei materiali e della manodopera nei processi di rivestimento dei metalli

130 SPECIALIZED TRAINING Ricerca, tecnologia e innovazione per un futuro industriale sostenibile

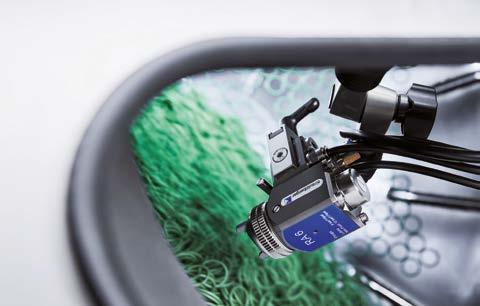
132 STANDARD&LEGISLATION
I criteri ESG: da valore aggiunto a requisito indispensabile per il mercato
134 MEETING THE INDUSTRY

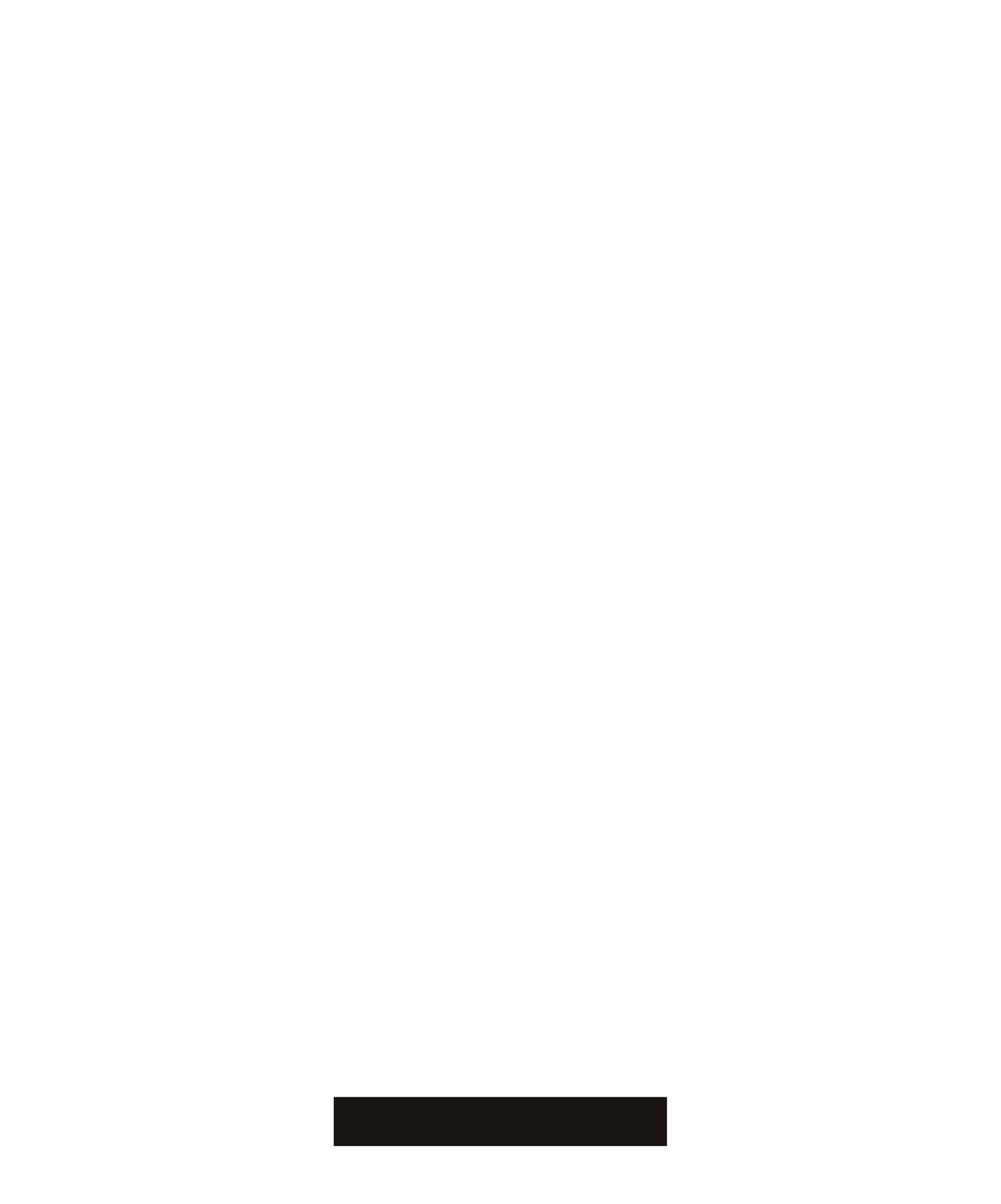

Quella in cui stiamo vivendo è definita da sociologi e filosofi come la società dell’informazione, un concetto familiare e caro a tutti coloro che – come me – hanno studiato le tecniche e le dinamiche della comunicazione. In questa società, i cui pilastri sono l’informatica e le telecomunicazioni, un bene immateriale come l’informazione prevale sull’industria e sul terziario. In quanto operatore del settore della comunicazione, e per di più di nicchia, sorge spontaneo chiedersi quale sia il ruolo dell’informazione specializzata nella società contemporanea, che colloca l’informazione in posizione centrale, attribuendole il ruolo di risorsa, fattore di sviluppo sociale ed economico, di crescita e di ricchezza culturale1
L’informazione tecnica specializzata, come quella che da quasi 15 anni ipcm® propone con le sue quattro riviste verticalizzate sui temi del trattamento delle superfici nell’ambito dell’industria in generale, dell’industria pesante e dell’automotive, è fonte di approfondimento, cultura industriale, conoscenza delle innovazioni. Quella di ipcm®, in modo particolare, è un’informazione che coglie l’essenza delle innovazioni e che le cala nella realtà industriale. Attraverso i nostri reportage effettuati presso gli utilizzatori finali di tecnologie per il trattamento delle superfici, la conversazione sulle innovazioni da astratta si fa concreta. Fotografa il mercato, le sue esigenze e le sue modalità di sviluppo, di crescita, di inserimento delle nuove tecnologie. Ne misura l’efficienza, l’efficacia, i vantaggi e gli svantaggi con un tono di voce il più possibile oggettivo. È un’informazione che si distacca dalla pulizia clinica degli articoli scientifici o tecnici scritti dai laboratori delle aziende. È un’informazione di qualità, verificata e verificabile, a volte anche scomoda perché apre a tecnologie disruptive, cioè di rottura con il passato, con il conosciuto. È un’informazione di prima mano, molto costosa per l’editore perché implica viaggi, trasferte, ore di lavoro. Ma è anche l’informazione più apprezzata dai lettori, che in essa riconoscono sé stessi, le proprie aziende e i propri bisogni. Questo tipo di informazione che proponiamo si presenta come una “polizza assicurativa” verso quel tipo di informazione nettamente pubblicitaria di cui molte riviste internazionali si nutrono.
Questo approccio verticale all’informazione, questa estrema specializzazione dei contenuti ci ha aiutato a costruire una community di lettori con i quali possiamo intavolare una conversazione che dalla rivista cartacea sconfina nei canali digitali, dai social media al sito web, che non sfruttiamo solo per mettere online le nostre riviste ma per fornire quotidianamente notizie di prima mano, espandere i contenuti fruibili sul cartaceo, per favorire il contatto tra le imprese, tra l’offerta e la domanda.
Con la speranza che voi, i nostri lettori, la nostra risorsa più preziosa, continuiate ad apprezzare questi contenuti ma anche a rivolgerci critiche costruttive, se necessario, o ad aprire dibattiti tecnici, vi auguro buona estate e buona lettura di questo numero estivo di ipcm®
1 Fonte: https://www.treccani.it/enciclopedia/societa-dell-informazione_%28Enciclopedia-della-Scienza-e-della-Tecnica%29/
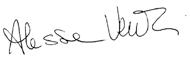
ERRATA CORRIGE
Sul fascicolo n. 78 a pag. 15 e sul nostro sito web è stato erroneamente riportato il termine “intumescente” invece di “ritardante di fiamma”. Ci scusiamo per l'errore con Axalta, Ibix e tutte le aziende coinvolte.
AkzoNobel Powder Coatings ha introdotto la piattaforma di e-commerce My Interpon Portal
My Interpon Portal migliora i servizi digitali di AkzoNobel, fornendo un accesso rapido e semplice alle informazioni sulle vernici in polvere.
AkzoNobel ha lanciato My Interpon Portal, una piattaforma digitale di e-commerce con caratteristiche e funzionalità avanzate che garantiranno ai clienti un accesso rapido e semplice alle informazioni e ai prodotti per la verniciatura a polvere.
La piattaforma di risorse online aiuta i verniciatori a scoprire la gamma di vernici in polvere Interpon nonché a sperimentare come i molteplici colori e trame performeranno, grazie a uno strumento di visualizzazione dei colori lightbox 3D. Infatti, la sua funzionalità consente ai clienti di navigare facilmente nel sito e cercare, trovare e confrontare centinaia di vernici in polvere.
“Questo lancio evidenzia ulteriormente l’impegno di AkzoNobel nei confronti dei clienti. Ci impegniamo nel semplificare il lavoro ai nostri acquirenti con strumenti pratici e supporto che ci rendono collettivamente più efficienti. Uno sviluppo significativo del nostro sito di e-commerce esistente, continueremo ad arricchire e migliorare le funzionalità di My Interpon Portal con nuove opzioni per aiutare i clienti
ad accedere alle vernici in polvere di cui hanno bisogno per i lavori più urgenti”, ha dichiarato Jeff Jirak, direttore dell’unità aziendale di AkzoNobel destinata alle vernici in polvere.
My Interpon Portal facilita la gestione degli ordini nuovi, in corso e ripetuti. Gli utenti possono visualizzare immediatamente i prodotti in magazzino, con i relativi dati tecnici scaricabili e la velocità con cui possono essere spediti. Inoltre, la funzionalità Track and Trace permette di verificare lo stato di avanzamento dell’ordine, mentre è anche possibile accedere, rivedere, stampare e archiviare le fatture passate e presenti.
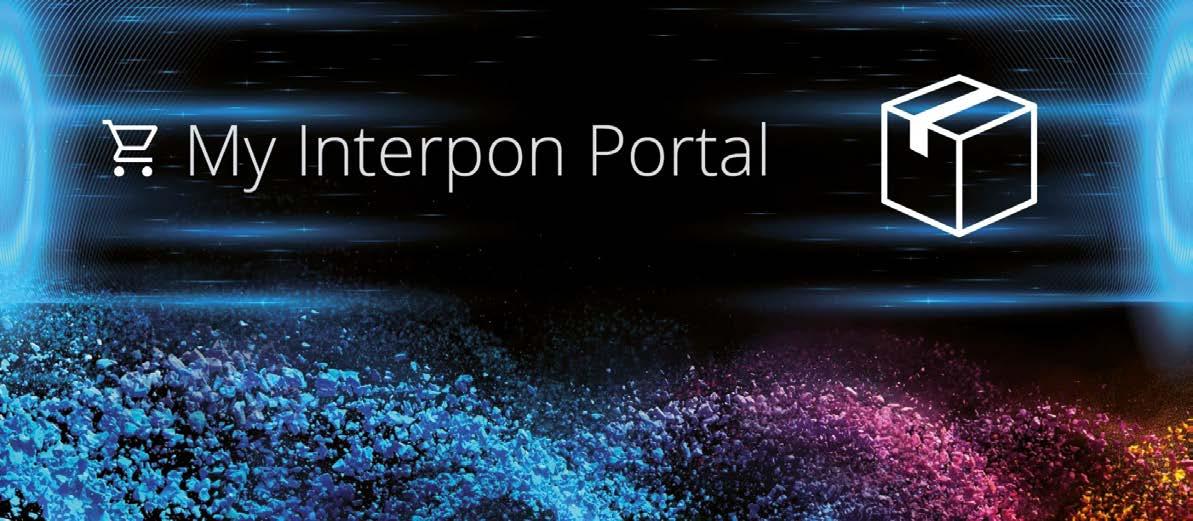
Il portale online è già attivo negli Stati Uniti, nel Regno Unito, in Germania e in Australia e nei prossimi mesi verrà implementato in Canada, Repubblica Ceca, Polonia, India e Nuova Zelanda.
Per maggiori informazioni: www.interpon.com
ChemQuest ha nominato Eric Casebolt come nuovo direttore
ChemQuest Group ha recentemente annunciato la nomina di Eric Casebolt come nuovo direttore dell’azienda. Casebolt ha una vasta esperienza nel dirigere società multinazionali e possiede una profonda conoscenza degli additivi impiegati nelle vernici, nel packaging e nell’edilizia. Quindi, fornirà supporto a ChemQuest incentrandosi sullo sviluppo di mercato, sull’innovazione dei prodotti e sui servizi strategici aziendali.
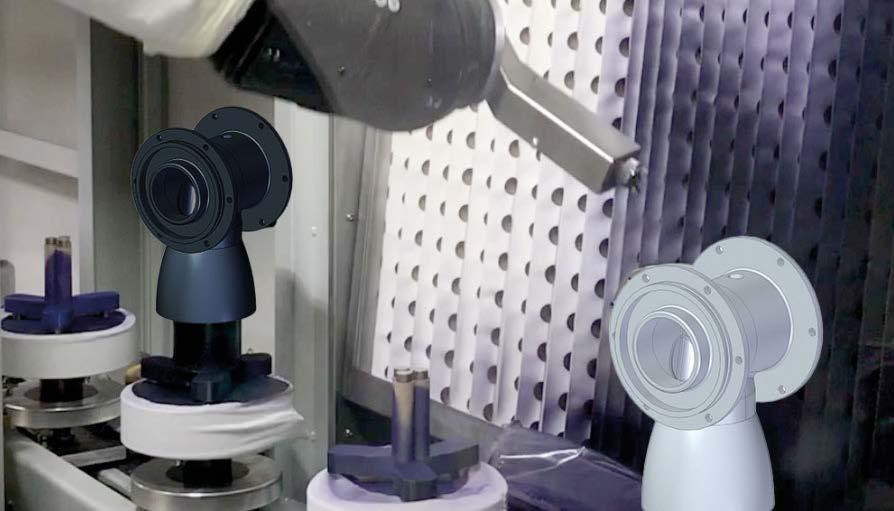
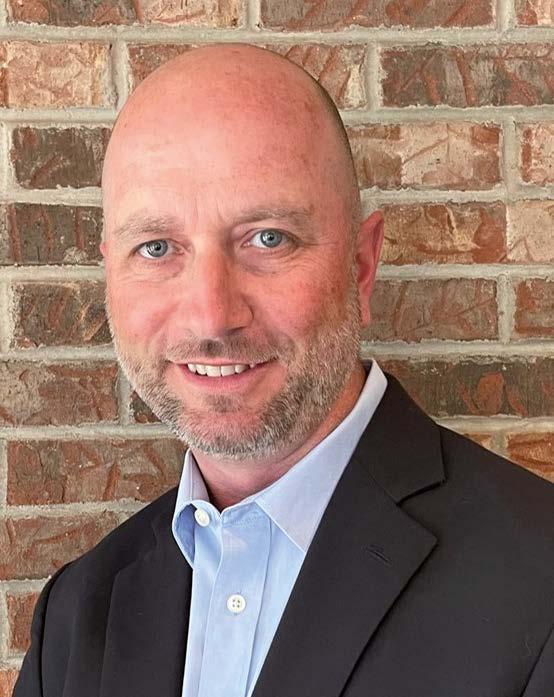
“Eric è un esperto, specialmente in sviluppo e strategia aziendale. Inoltre, prevedo che il suo lavoro di costruzione di pipeline innovative per svariate linee produttive porterà valore ai nostri team impegnati nello sviluppo dei prodotti presso il ChemQuest Technology Institute e il ChemQuest Powder Coating Research. Sono lieto di averlo in squadra”, ha dichiarato Daniel Murad, CEO di ChemQuest.
Il nuovo direttore di ChemQuest è in possesso di tre titoli importanti: una laurea in chimica alla University of Wisconsin Parkside, un master in chimica presso la DePaul e un MBA dalla Wake Forest University.
“Sono lieto e onorato di far parte del team di ChemQuest, un’organizzazione di consulenza di prim’ordine che fornisce all’industria chimica risorse e competenze impareggiabili. Non vedo l’ora di collaborare con il team e con i nostri clienti per aiutare le loro attività a crescere nei mercati che servono”, ha commentato Casebolt.
Per maggiori informazioni: https://chemquest.com
Eric Casebolt aiuterà ChemQuest a migliorare i servizi strategici aziendali per l’industria dei materiali speciali.
ABOUT PRODUCTS. IT’S A PROCESS.
challenge is different. And so are our solutions. We offer individualized finishing technologies, tailor-made for your application.
RMIT Europe parteciperà al progetto di ricerca ALCOAT per i rivestimenti in lega di alluminio
Il progetto ALCOAT svilupperà due nuove famiglie di rivestimenti in lega di alluminio riciclato come alternativa più sostenibile alla zincatura.
L’hub europeo dell’università globale di tecnologia, design e impresa RMIT ha recentemente annunciato di aver ricevuto la somma di € 272.500 per contribuire al progetto di ricerca ALCOAT, che mira a sviluppare rivestimenti in lega di alluminio come materiale più sostenibile in alternativa alla zincatura.
ALCOAT è un progetto di 42 mesi sponsorizzato dal Fondo di ricerca dell’UE per il carbone e l’acciaio (RFCS) che svilupperà due nuove famiglie di rivestimenti in lega di alluminio riciclato con un potenziale elettrochimico adattato chimicamente, al fine di creare un’alternativa allo zinco per la zincatura dei prodotti in acciaio.
L’acciaio è uno dei materiali metallici da costruzione più importanti grazie alle sue proprietà meccaniche, alla sua disponibilità e alla sua convenienza. Tuttavia, se non trattato, l’acciaio è suscettibile all’ossidazione e al successivo deterioramento, con segni rivelatori di danni come crepe e ruggine particolarmente diffusi in ambienti ricchi di umidità. La protezione dalla corrosione delle strutture in acciaio è quindi necessaria per allungare la durata di vita dei prodotti in acciaio e garantire il rispetto dei requisiti di sicurezza, prevenendo così il cedimento del materiale.
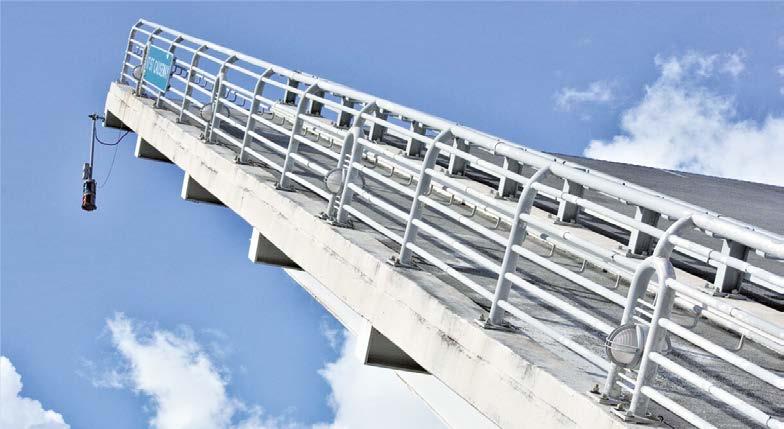
Sebbene lo zinco sia ampiamente utilizzato per proteggere l’acciaio dalla corrosione e sia molto efficace, è anche difficile da riciclare. Recuperare l’alluminio destinato allo smaltimento per impiegarlo come alternativa alla zincatura dei prodotti in acciaio assicurerà quindi rivestimenti dalle prestazioni efficienti e sostenibili per la protezione di pale eoliche,
navi e altre strutture esposte all’acqua marina e agli ambienti corrosivi, nonché per prodotti in lamiera d’acciaio per l’industria automotive, l’edilizia e la produzione di elettrodomestici. “L’alluminio di scarto è ampiamente disponibile ma, essendo contaminato da ferro e magnesio, è fragile e quindi inutilizzabile per molte applicazioni. Di conseguenza, è scartato o utilizzato per scopi di livello inferiore come i pellet”, ha affermato Ivan Cole, direttore della ricerca di RMIT Europa. “Tuttavia, l’alluminio è esattamente ciò di cui abbiamo bisogno per produrre un buon rivestimento per l’acciaio, poiché i contaminanti che contiene impediscono effettivamente la formazione di ossido. ALCOAT affronterà un problema di sostenibilità piuttosto che un problema di prestazioni”.
Si prevede che i rivestimenti in lega di alluminio sviluppati dal progetto porteranno numerosi vantaggi, come un tasso di
corrosione inferiore e un rischio ridotto di infragilimento da idrogeno. Saranno inoltre più leggeri, più sottili e più sostenibili data la riduzione della quantità di materie prime necessarie, aumentando così anche gli sforzi nell’economia circolare.
“L’utilizzo di materiali di scarto eviterà il processo ad alta intensità energetica di estrazione e lavorazione dello zinco vergine e il relativo impatto negativo per l’ambiente. Rispetto ai tradizionali processi per lo sviluppo del rivestimento, la procedura proposta da ALCOAT è altamente innovativa e avanzata e garantirà una drastica riduzione di tempi e costi”, ha concluso Cole.
Il progetto ALCOAT è coordinato dall’Università di Chimica e Tecnologia di Praga e inizierà il 1° settembre 2023.
Per maggiori informazioni: www.rmit.edu.au
La sede di Adapta Color diventa un’area cardio-protetta
Per migliorare la sicurezza del personale e dei visitatori, Adapta Color ha aggiornato il proprio piano di emergenza e primo soccorso.
Adapta Color è un’azienda spagnola produttrice di vernici in polvere da sempre attenta alla sicurezza dei propri dipendenti e dei collaboratori.
Per questo motivo, ha recentemente inaugurato una serie di iniziative con l’obiettivo di migliorare il proprio piano di emergenza e primo intervento presso la sua sede, situata a Peñiscola. Sono 65 i dipendenti e i dirigenti di Adapta ad aver ottenuto la certificazione del corso Supporto Vitale di Base - SVB e per l’utilizzo del defibrillatore esterno semiautomatico – DAE, approvato da EVES (Escola Valenciana d’Estudis per la Salut). Sono stati inoltre installati due defibrillatori esterni
semiautomatici e kit per controllare e gestire le ustioni e il sanguinamento, oltre che per il lavaggio oculare. L’attrezzatura contribuirà ad aumentare significativamente il tasso di sopravvivenza in caso di emergenza.

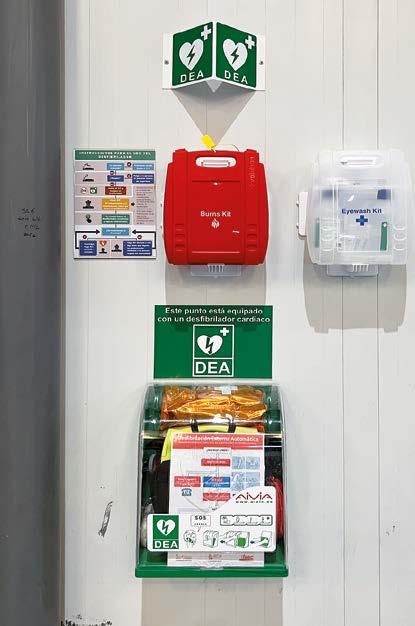
“A nome della direzione, vorrei ringraziare tutto il personale partecipante per il loro coinvolgimento e congratularmi con Ruth e Ximo di IRTA Asistencia Médica Integral S.L. per la loro professionalità e la formazione fornita”, ha dichiarato David Pellicer Roca, General Manager di Adapta Color S.L.
Per maggiori informazioni: www.adaptacolor.com
Hooks & CE Hooks

From the in-stock small and thin hook to the special hook Ø30 with EU certification and loading capacity calculation, for both small and heavy parts to be coated.
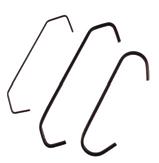
Evonik presenta l’additivo antiscivolo e antischiuma TEGO ® Rad 2550 per vernici e inchiostri a polimerizzazione UV
Il nuovo additivo sviluppato da Evonik fornisce resistenza allo scorrimento e al graffio nonché proprietà antischiuma e idrofobia per vernici e inchiostri a polimerizzazione UV e UV-LED.
Il ramo aziendale dedicato agli additivi per vernici di Evonik ha ampliato la gamma TEGO® Rad di acrilati siliconici su misura con TEGO Rad 2550, un nuovo additivo reticolabile liquido trasparente e a bassa viscosità che riduce efficacemente la tensione superficiale statica e dinamica nelle formulazioni convenzionali a polimerizzazione UV e LED.
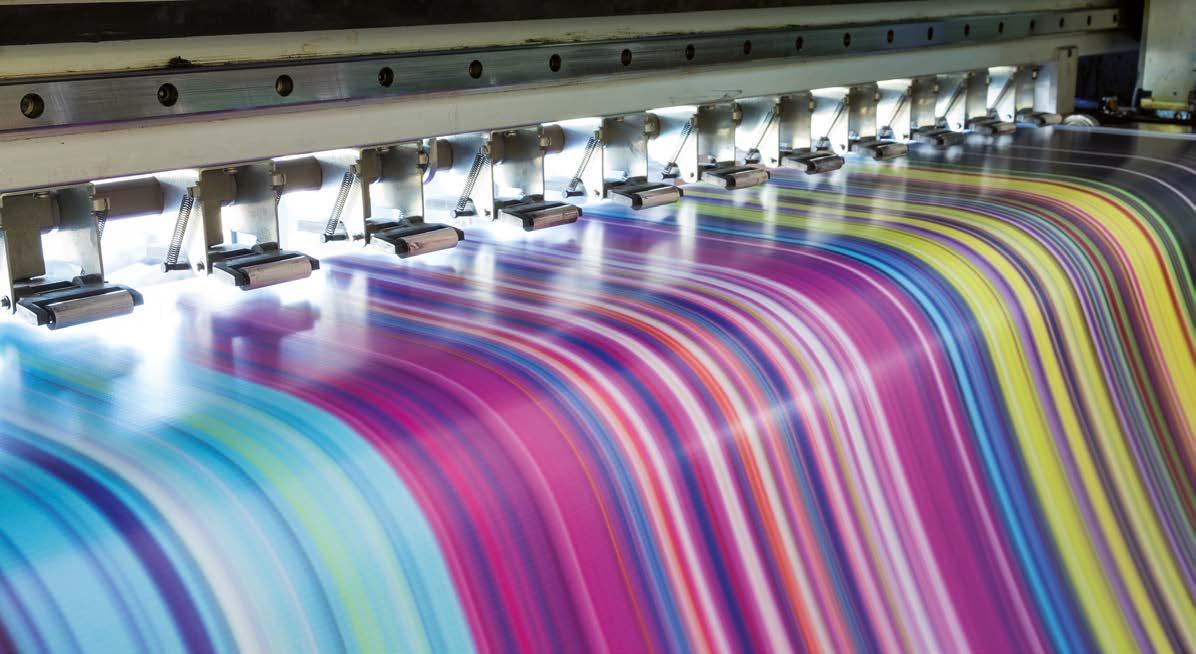
I prodotti acrilati consentono di minimizzare la migrazione e ottenere effetti molto pronunciati e duraturi. Il nuovo additivo per vernici, rivestimenti e inchiostri da stampa a polimerizzazione UV fornisce anche un basso coefficiente di attrito, un’elevata resistenza al graffio, buone proprietà antischiuma e l’abilità di creare superfici idrofobe. Inoltre, assicura un miglior livellamento, distensione ed apparenza e previene la formazione di crateri. Infine, permette ai formulatori di
creare prodotti con il livello desiderato di scorrimento, distensione e compatibilità.
“Grazie alle sue proprietà uniche, TEGO Rad 2550 è un additivo eccellente per la formulazione di vernici opache, di inchiostri pigmentati e di finiture per il legno applicate a rullo. Offre una prestazione reticolabile su misura. Per i formulatori di vernici e inchiostri, questo significa grande efficacia a lungo termine nel prodotto finale, elevata efficienza delle risorse e una soluzione sostenibile rispetto alle tecnologie alternative”, ha commentato Courtney Thurau, direttore del segmento di mercato globale dedicato agli inchiostri da stampa di Evonik Coating Additives.
Per maggiori informazioni: www.coating-additives.com/en
PPG fornisce a Satys un sistema e-coat per componenti aerospaziali

Satys utilizzerà il sistema di primer e-coat PPG AEROCRON™ per i componenti destinati all’industria aerospaziale.
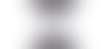
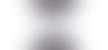
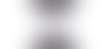
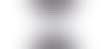




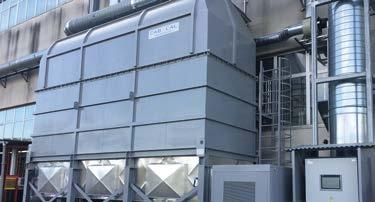


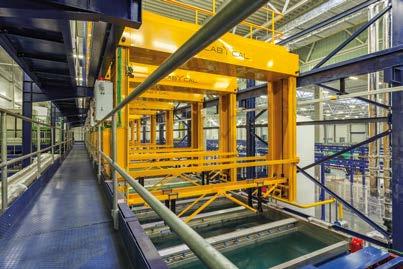
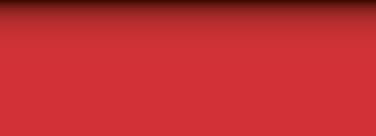
PPG – produttore internazionale di vernici e rivestimenti – ha recentemente annunciato una collaborazione con Satys, gruppo industriale francese operante nel settore aerospaziale e dedicato alla sigillatura, alla verniciatura e in generale ai trattamenti superficiali di componenti per il settore aeronautico. L’azienda fornirà il suo sistema di primer e-coat PPG AEROCRON™ a base acqua per lo stabilimento di Dugny. “PPG è orgogliosa di collaborare con Satys e fornire la sua innovativa tecnologia e-coat ai principali OEM del settore aerospaziale. I nostri clienti in Francia trarranno vantaggio dal sistema PPG Aerocron, che produce una finitura più uniforme sui pezzi dell’aeromobile, utilizzando meno vernice rispetto ai tradizionali sistemi applicati a spruzzo”, ha affermato Sam Millikin, direttore globale dei rivestimenti e dei sigillanti per la divisione Aerospace di PPG. Con il sistema Aerocron, i componenti metallici per il
mercato aerospaziale saranno immersi in una vasca da 8 m3 contenente un primer e-coat senza cromo – la più grande d’Europa – e caricati con corrente elettrica per applicare la vernice. Questo processo garantisce resistenza alla corrosione e agli agenti chimici, rispettando gli standard del settore, e fornisce finitura superficiale e spessore uniformi, senza gocciolamenti o colature nel film essiccato. Inoltre, la soluzione sostenibile di PPG rilascia pochi composti organici volatili e aiuta a ridurre il consumo di carburante grazie al risparmio di peso fornito dal minore utilizzo di vernice. “Siamo sempre alla ricerca di modi innovativi ed efficienti per migliorare la verniciatura degli aeromobili, oltre a contribuire alla decarbonizzazione dell’industria aerospaziale”, ha aggiunto Christophe Cador, presidente e CEO di Satys.

Per maggiori informazioni: www.ppg.com






Graco ha presentato la nuova pompa elettrica QUANTM a doppia membrana

La nuova pompa per applicazioni industriali e igieniche sviluppata da Graco è una soluzione leggera e di facile manutenzione per ambienti difficili.
Graco, produttore internazionale di apparecchiature per la gestione dei fluidi, ha recentemente annunciato il lancio della sua pompa elettrica a doppia membrana QUANTM™, una soluzione con una nuova struttura del motore elettrico. È adatta a quasi tutte le operazioni di trasferimento dei fluidi e offre un’ampia gamma di materiali di costruzione per supportare molteplici applicazioni industriali e igieniche, come la produzione di vernici, il trattamento delle acque e la lavorazione chimica.
“La pompa QUANTM non è una nuova versione di una vecchia tecnologia. Si tratta di un prodotto completamente innovativo, che cambia il funzionamento delle pompe negli impianti e in altre installazioni in tutto il mondo. Siamo entusiasti di aver creato un design avanzato ed estremamente efficiente, leggero e con costi di esercizio totali significativamente inferiori rispetto ad altre tecnologie. La pompa modernizza le operazioni, riducendo notevolmente i costi energetici. Ciò consente ai produttori industriali di proteggere e incrementare i margini e di contribuire significativamente al risparmio energetico, alla conformità
e alla gestione dell’ambiente”, ha affermato Bart Clerx, il responsabile del marketing per la regione EMEA di Graco. La nuova pompa è stata progettata per sostituire in modo altamente affidabile le attuali pompe pneumatiche o per la costruzione di nuovi impianti, in quanto può resistere ad ambienti industriali o igienici difficili grazie ai controlli integrati e all’assenza del riduttore, che la rendono leggera e di facile manutenzione. “Le nostre nuove pompe QUANTM sono la soluzione perfetta per aggiornare le pompe pneumatiche meno efficienti. Lo stesso eccezionale design autoadescante, di entrata in stallo, senza guarnizioni è indispensabile per le applicazioni in-process, i sistemi di riempimento e le applicazioni igieniche. I nuovi potenti motori e le trasmissioni FluxCore™ forniscono una coppia continua fino a 8 volte superiore alle basse velocità rispetto ai motori convenzionali. Inoltre, l’installazione plug-andplay consente di sostituire facilmente le pompe esistenti senza ulteriori investimenti o ristrutturazioni dell’infrastruttura”, ha concluso Clerx.
Per maggiori informazioni: www.graco.com
SONGWON collaborerà con KRAHN Italia per il ramo vernici
Grazie a un accordo distributivo, SONGWON rafforzerà la propria presenza nel mercato italiano delle vernici e dei rivestimenti.
Il fornitore internazionale di specialità chimiche e polimeri stabilizzanti SONGWON ha recentemente annunciato una collaborazione con KRAHN Italia per la distribuzione dei suoi prodotti per vernici e rivestimenti. A decorrere dal primo luglio di quest’anno, KRAHN Italia è il distributore esclusivo in Italia degli antiossidanti SONGNOX® CS, degli assorbitori UV SONGSORB® CS e degli stabilizzanti alla luce (HALS) SONGSORB® CS. L’azienda vuole rafforzare la propria posizione in Italia, che è ritenuta essere una delle principali regioni europee per il settore delle pitture e delle vernici.
“L’Italia è un mercato importante per noi e siamo molto lieti che un partner così esperto si unisca alla vasta rete di distributori globali di SONGWON. Siamo fiduciosi che l’esperienza di KRAHN Italia, le sue solide relazioni di mercato e il suo eccellente servizio clienti, combinati con i prodotti della SONGWON, ci aiuteranno a costruire e consolidare la nostra posizione di fornitore di fiducia di additivi per le pitture e vernici liquide in Italia”, ha affermato Simona De Gradi, direttrice delle vendite nella regione EMEAI di SONGWON. KRAHN Italia è specializzata nella commercializzazione e distribuzione di specialità chimiche. Offre ai suoi clienti una vasta gamma di prodotti di alta qualità, assistenza tecnica completa e supporto di laboratorio interno. Sfruttando la sua ampia conoscenza del mercato italiano delle vernici e dei rivestimenti, SONGWON beneficerà di un approccio di marketing del prodotto mirato e sostenibile.
“Siamo lieti di essere stati scelti per rappresentare SONGWON nel mercato italiano. Questa collaborazione commerciale rappresenta una grande opportunità per entrambe le aziende di collaborare attivamente e crescere, non solo per le nostre attività, ma anche per aggiungere valore per i nostri clienti in Italia. Espandere il consolidato portafoglio prodotti di KRAHN Italia con gli additivi per pitture e vernici di alta qualità di SONGWON non solo ci consente di soddisfare meglio le esigenze dei clienti, ma ci permette anche di aumentare la visibilità di SONGWON e di rafforzare la sua posizione nel mercato delle pitture e vernici in Italia”, ha dichiarato Enrico Bozzi, amministratore delegato di KRAHN Italia S.p.A.
Per maggiori informazioni: www.songwon.com
EQUIPMENT FOR powder coating
DESIGN
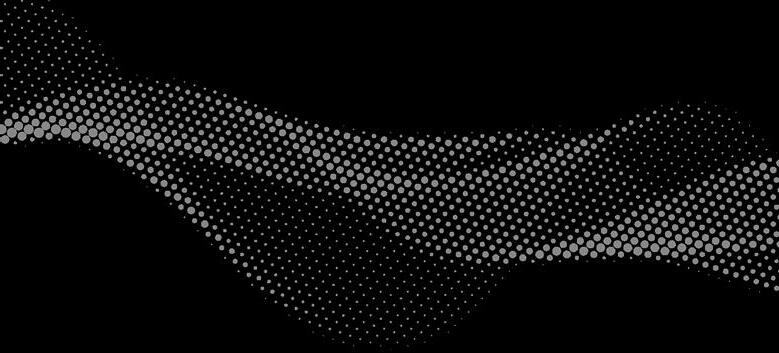
Our powder coating systems and accessories are designed and manufactured with the utmost attention to details
RESPONSIBILITY
We are loyal to the customer and to the product: we build a real relationship of trust and responsibility day by day
PROFESSIONALISM
We follow each customer from design to implementation, from installation to after-sales training
MADE
www.zeus-el.it
ADVANCEMENTS
ALIT Technologies lancia FASTRIP T2-120 MIX
A cura di ALIT Technologies
San Bonifacio (Verona), Italia info@alit-tech.com
ALIT Technologies ha annunciato il lancio di FASTRIP T2-120 MIX, il sistema di sverniciatura più compatto della gamma T2.
ALIT Technologies, azienda leader nella produzione di macchine e prodotti per il trattamento superficiale dei metalli, è lieta di annunciare il lancio di FASTRIP T2-120 MIX, un’evoluzione ancora più compatta del sistema T2, pensata per una rimozione efficace e rapida della vernice. Le aziende che effettuano internamente la verniciatura di manufatti metallici hanno, infatti, un’intrinseca necessità di sverniciare telai e ganci utilizzati per l’appensione dei pezzi oppure i manufatti che presentano difettologie. Al fine di offrire una soluzione tanto efficiente quanto ridotta nell’ingombro, ALIT Technologies ha sviluppato FASTRIP T2-
120 MIX, la macchina di sverniciatura più compatta della gamma T2. “La pluriennale esperienza accumulata da ALIT Technologies nel settore della sverniciatura è stata interamente trasferita nella macchina FASTRIP T2-120 MIX”, spiega Loris Rossi, CEO di ALIT Technologies. “In questo modello di macchina non sono presenti ultrasuoni ma l’azione meccanica dello sverniciante nei confronti della superficie da sverniciare viene effettuata grazie alla spinta idrostatica del miscelatore. Pertanto, FASTRIP T2-120 MIX si differenzia dal modello di punta FASTRIP T2-100 proprio per il fatto che gli ultrasuoni sono stati sostituiti dal miscelatore. Ciò
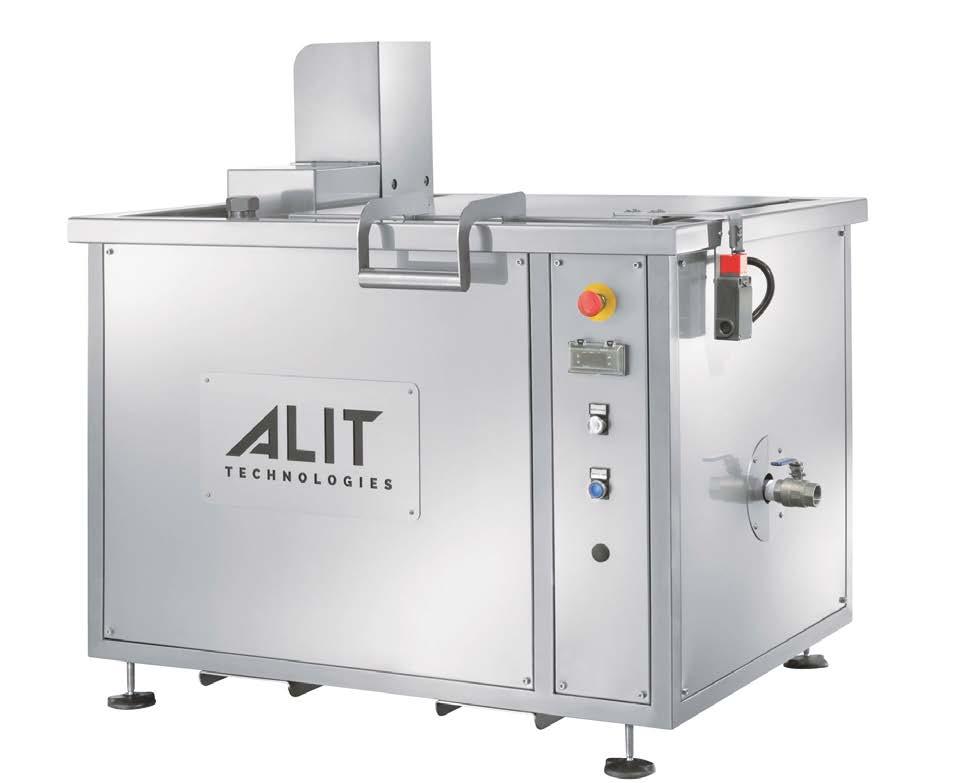
permette di avere una macchina più silenziosa ed in grado di operare anche con sverniciante maggiormente inquinato. Infine, l’assenza degli ultrasuoni permette l’uso di un’elettronica meno sensibile al calore sviluppato durante il normale esercizio della macchina. Complessivamente si è così ottenuta una macchina estremamente robusta, affidabile, sicura e ben funzionante”.
Il processo
Con FASTRIP T2-120 MIX la sverniciatura dei manufatti avviene mediante la loro immersione in una vasca contenente una soluzione liquida di sverniciante riscaldata e mantenuta sotto costante agitazione da un miscelatore a pale opportunamente progettato. Alla fine del ciclo di sverniciatura, il cestello contenente i manufatti viene estratto dalla vasca di processo e i materiali, dopo una fase risciacquo, possono essere normalmente riprocessati. Le fasi di processo sono schematizzate di seguito:
1. Riempimento del cestello con i manufatti da sverniciare;
2. Immersione manuale del cestello nella vasca
FASTRIP T2-120 MIX;
3. Sverniciatura;
4. Estrazione manuale del cestello;
5. Sgocciolamento sopra la vasca di sverniciatura;
6. Risciacquo esterno dei manufatti trattati.
Caratteristiche tecniche
FASTRIP T2-120 MIX è interamente realizzata in acciaio inox AISI 304 e si compone principalmente da:
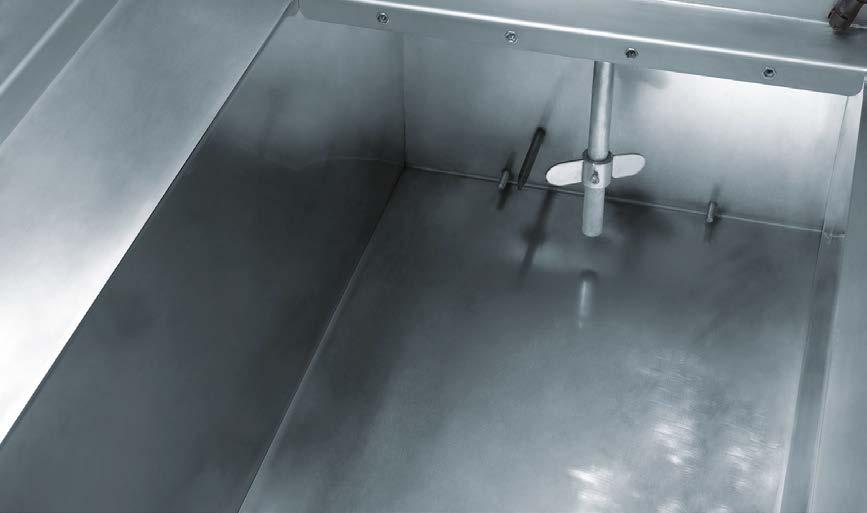
• Vasca di sverniciatura a sezione rettangolare con misure utili 450 x 700 x h300 mm circa e pareti di spessore 20/10, con un volume di riempimento di circa 120 litri. La vasca è dotata di valvola di fondo 1’’ in inox per lo svuotamento totale del liquido, di un sensore di temperatura del fluido sverniciante e di un sensore di livello del liquido. Nel corpo vasca è presente un manicotto superiore 2’’ utile per il raccordo ad eventuali sistemi di aspirazione.
• Mixer in acciaio posizionato sul lato corto della vasca, che mantiene il liquido costantemente in circolazione, garantendo una
maggiore efficienza di sverniciatura e migliori performance dell’impianto di riscaldamento. L’accoppiamento del motore con l’albero non è diretto, ma avviene attraverso un sistema di trasmissione cinghia-puleggia che preserva il motore sia dal riscaldamento diretto da parte del liquido che dai vapori dello sverniciante.
• Resistenze elettriche riscaldanti fissate esternamente alla vasca, che permettono di raggiungere una temperatura massima del liquido sverniciante di 80°C. La scelta di porre le resistenze esternamente evita il contatto diretto tra il liquido sverniciante e la fonte di riscaldamento, garantendo così i massimi standard di sicurezza.
• Coperchio interamente in acciaio, completo di isolamento termico e di una coppia di pistoni per agevolare le operazioni in manuale di apertura e chiusura. La chiusura del coperchio è sagomata in modo tale da raccogliere le condense formate su di esso durante il ciclo di sverniciatura.
• Elettroserratura che garantisce l’arresto del mixer in caso di apertura del coperchio.
• Quadro elettrico integrato e selettori elettromeccanici esterni per la gestione dei parametri di processo. Il quadro elettrico è
posizionato al di sotto della vasca ed è montato su di una slitta meccanica che ne permette l’estrazione in caso di ispezione o operazioni di manutenzione. È possibile regolare la temperatura del liquido, la temperatura delle resistenze, gestire l’elettroserratura e il mixer.
• Isolamento termico su tutti i lati della vasca, realizzato con lana di roccia ad alto coefficiente di isolamento.
• Pannellatura laterale in acciaio inox AISI 304 facilmente rimovibile in caso di operazioni di manutenzione.
ALIT Technologies
ALIT Technologies è un partner privilegiato di molte industrie ad alto posizionamento tecnologico operanti nel settore della verniciatura che necessitano di prodotti altamente efficienti per il pretrattamento di componenti metallici. Oltre al nuovo sistema di dosaggio e applicazione per la passivazione dei componenti metallici Drizzling, dalla propria sede in provincia di Verona ALIT Technologies è in grado di fornire anche innovativi impianti di sverniciatura chimica in linea con la serie Fastrip e formulati chimici ad elevate performance e basso impatto ambientale.
La rubrica “Chiedi all’esperto”
Kevin Biller kbiller@chemquest.comCiao Tu, grazie per il tuo messaggio. Credo di aver capito qual è il vostro problema. Indagherei su questi aspetti:
1. Dimensione delle particelle - questa è la proprietà più importante quando si tratta di efficienza di trasferimento. Domande: qual è la tua dimensione media (D50) delle particelle? Più importante, qual è la percentuale sotto i 10 micron e sopra i 100 micron? Come misuri la distribuzione dimensionale delle particelle? Come la controlli? Dovresti scegliere come target una dimensione media delle particelle dai 35 ai 40 micron e avere meno del 7% in volume di particelle inferiori a 10 micron. Inoltre, dovresti scegliere come target meno dell’1% in volume di particelle superiori a 100 micron.
La parola al nostro esperto Joe Powder, per risolvere i problemi più o meno classici della verniciatura a polvere in tutto il mondo, dal Vietnam al Sudafrica.

2. Qual è il peso specifico della tua polvere? È simile a quello del prodotto concorrente? È maggiore? Un peso specifico maggiore può ridurre l’efficienza di trasferimento, perdendo particelle per via della gravità (cadono sul pavimento della cabina).
Ciao Joe, ti ringrazio per averci fornito in passato delle soluzioni che ci hanno aiutato a migliorare i nostri prodotti in polvere. Cercheremo di imparare a svilupparli ulteriormente. Tuttavia abbiamo bisogno di un altro tuo consiglio. Stiamo lottando con i concorrenti del settore. Le condizioni di applicazione sono le stesse: stessa pistola, stesso voltaggio, stesso flusso, stessa velocità della linea. La resina nella formulazione è pari al 60-70% e utilizziamo uno speciale additivo antistatico, ma la nostra vernice in polvere produce uno spessore di 30-40 micron, mentre quella dell’azienda concorrente uno spessore di 60-70 micron.
Quale potrebbe essere il problema del nostro prodotto? Stiamo cercando di trovare la soluzione migliore, speriamo di ricevere i tuoi suggerimenti.
Cordiali saluti,
Tu NguyenAlphabet Coatings
Vietnam
3. Il tuo cliente quanto fa bene la manutenzione al suo sistema applicativo? Hanno una buona messa a terra sui ganci? Le pistole sono ben manutenute? Quanto spesso fanno manutenzione alle apparecchiature? È possibile che si verifichino problemi applicativi a causa di scarsa manutenzione a pistole, sistema di recupero e cabina. In ogni caso, io non sono un grande fan dell’aggiunta di additivi elettrostatici alle polveri. Credo sia come “mettere una pezza” e vi si dovrebbe ricorrere solo se tutte le alternative falliscono. Fammi sapere se hai altre domande. Un’ultima cosa, dove si trova la tua azienda? Sarebbe bello farvi visita un giorno.
Cordiali saluti, Joe Caro Joe, saluti da Johannesburg. Ho una domanda. Come posso rendere più fluide le mie vernici in polvere?
Grazie, Johann Kunneke
South Africa
Ciao Johann, aumentare la fluidità di una vernice in polvere, e in realtà di qualsiasi polvere, può essere complicato. Per i nostri lettori che non hanno familiarità con la fluidità, stiamo parlando del comportamento con cui una polvere consente all’aria di distanziare uniformemente le particelle l’una dall’altra. È una proprietà chiave nell’applicazione di vernici in polvere. In un sistema di applicazione polveri, la polvere sfusa viene introdotta in una tramoggia fluidificante. È un contenitore cilindrico o scatolare che ha sul fondo una piastra porosa in Teflon®. L’aria compressa passa attraverso questa piastra porosa per fluidificare o preparare la polvere per essere trasportata attraverso una pompa, quindi attraverso dei tubi flessibili e infine una pistola. La fluidità è fondamentale perché la polvere venga trasportata in modo uniforme nel sistema. Ora veniamo alla tua domanda Johann. Pochi fattori sono importanti nell’ottimizzazione della fluidità. Innanzitutto la distribuzione dimensionale delle particelle. Nota che ho scritto la “distribuzione” e non solo la dimensione. Ciò significa che prima devi gestire l’intera distribuzione dimensionale delle particelle. La cosa più importante è minimizzare le “fini”. Con fini si intendono le particelle inferiori a 10 micron di diametro. Meno è meglio e dovresti cercare di avere meno del 6 o 7% di particelle fini. Troppe particelle fini causano grumi, agglomerati e scarsa fluidità. Idem per le particelle grandi. Con grandi intendo circa 100 micron e oltre. Queste sono più difficili da muovere con l’aria compressa e quindi devono essere poche. Direi meno dell’1% di particelle sopra i 100 micron per ottenere la fluidificazione migliore possibile. Dopo aver definito la distribuzione dimensionale delle particelle è il momento di incorporare un additivo fluido o a miscela secca. Sono silici pirogeniche o allumina pirogenica e agiscono da cuscinetti a sfera tra le particelle di polvere. Tieni presente che poco fa molto. L’aggiunta deve essere fatta durante il processo di produzione della polvere, dopo il processo di estrusione. Tipicamente il materiale pirogenico viene aggiunto ai chip estrusi (scaglie) appena prima del processo di polverizzazione. Ciò assicura che gli agglomerati di silice pirogenica o allumina si disperdano uniformemente. In caso contrario possono formarsi pezzetti nel film in polvere finale. Un problema è che il materiale pirogenico può essere estratto dal sistema di macinazione e dal flusso di scarto che si deposita nel filtro a maniche. Alcuni produttori hanno escogitato dei modi per introdurre la silice dopo il processo di macinazione con una tecnica di deagglomerazione.
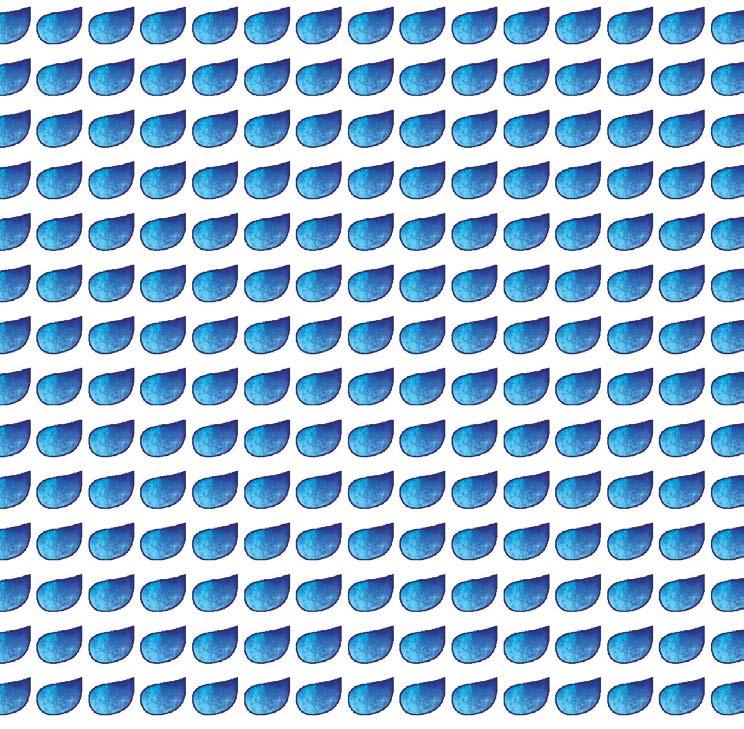
Ho scritto che poco fa molto – punterei a una concentrazione ben al di sotto dell’1%, direi vicina allo 0,2%. Spero di esserti stato di aiuto e che tu e i tuoi cari in Sudafrica stiate tutti bene.
Cordiali saluti, Joe PowderTurn key solutions for industrial wastewater treatment


Design and manufacturing of plants and chemicals for industrial wastewater treatment
Chemical-physical plants
Sludge treatment and compactor systems
Ion exchange demineralization systems and reverse osmosis systems
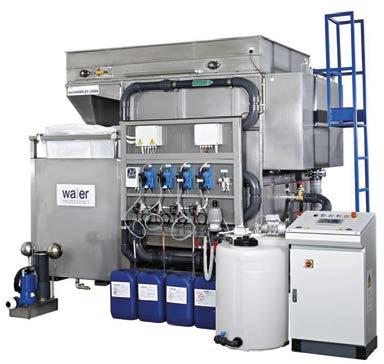
Oil separators
Filtering systems
Batch type systems
Flotation units
Chemicals and spare parts for water treatment
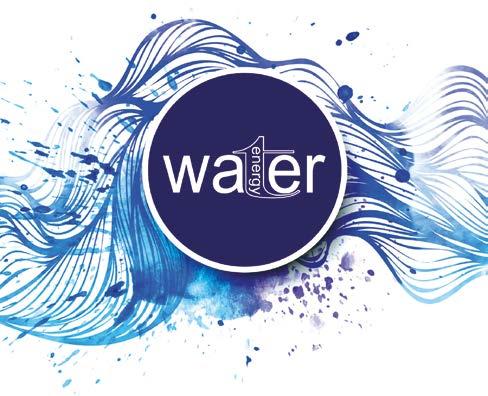
Technical service, support and maintenance of wastewater treatment plants

HIGHLIGHT OF THE MONTH
Cambio di look per Zeus Electrostatic System e per la sua gamma di prodotti
Da un’intervista con Massimo Ricci titolare di Zeus Electrostatic System

La nuova immagine coordinata, il restyling della gamma già presente sul mercato e il lancio di nuovi prodotti sono il frutto di una visione strategica volta a espandersi a livello internazionale e a proporre al mercato soluzioni di verniciatura a polvere all’avanguardia.
“Anche l’occhio vuole la sua parte ma la realtà è più profonda”.
È ciò che Massimo Ricci, titolare di Zeus Electrostatic System, azienda italiana specializzata nella progettazione e produzione di sistemi e accessori per la verniciatura a polvere, ha dichiarato durante l’intervista con ipcm®_International Paint&Coating Magazine. Per una piccola realtà rivolta al mercato nazionale, passare a un mercato internazionale significa agire su tutti gli aspetti aziendali; a livello mondiale
Zeus non è conosciuta e per essere percepiti come partner affidabili e di grande professionalità, oggigiorno è fondamentale che le imprese curino nel dettaglio non solo la qualità e l’efficienza dei propri prodotti, ma anche la propria corporate identity, ovvero l’insieme di elementi graficovisivi in grado di comunicare ai clienti i valori, la mission e l’identità stessa dell’azienda.
Partendo da questo concetto, Zeus, azienda con sede ad Argenta, in
provincia di Ferrara, ha intrapreso una serie di attività di marketing e comunicazione aziendale con l’obiettivo di migliorare il proprio posizionamento sul mercato a livello internazionale. La nuova immagine riflette l’evoluzione dell’azienda e in particolar modo la mission sempre più rivolta nel collocare al centro il cliente. Allo stesso modo, anche il portfolio di prodotti dell’azienda è stato oggetto di un restyling a livello tecnologico e grafico.
Nuova immagine coordinata, stessi valori di sempre
Il progetto di revisione dell’immagine coordinata nasce dopo un attento studio in collaborazione con un’agenzia di comunicazione del territorio e si pone l’obiettivo di rendere il brand Zeus più moderno e appetibile a livello internazionale. “Per un’azienda di piccole dimensioni come la nostra, il processo di internazionalizzazione può essere lungo e a volte tortuoso in quanto è necessario attuare una serie di cambiamenti organizzativi che coinvolgono ogni dipartimento dell’azienda – dal reparto produttivo al marketing”, afferma Massimo Ricci. “Dal punto di vista grafico, abbiamo deciso di mantenere intatto il logo dell’azienda e di dare una rifrescata ai colori e al design del sito web, dei profili social e del materiale promozionale, come brochure, cataloghi e inserzioni pubblicitarie grazie ad uno stile più accattivante e moderno in linea con le attuali tendenze di graphic design, che prediligono uno stile minimale e semplice, oltre che l’utilizzo di pochi colori in contrasto fra loro (in questo caso il rosso per il logo e gli highlights e il grigio antracite per gli sfondi).
Oltre alla comunicazione digitale e offline, il progetto ha anche coinvolto tutti i prodotti della gamma Zeus, il cui design è stato oggetto di un restyling tecnologico ed estetico con l’obiettivo di rendere sempre riconoscibile il brand.
“Il progetto di studio della nuova immagine coordinata è frutto della volontà di Zeus di espandere la propria presenza in nuovi mercati, soprattutto a livello europeo; tuttavia, nonostante questi cambiamenti, la direzione e tutti i collaboratori dell’azienda non hanno mai perso di vista l’identità e i valori fondamentali che ci contraddistinguono sin dalla fondazione dell’azienda negli anni ’70”, continua Ricci. “Seguiamo ogni cliente dal progetto alla realizzazione, dall’installazione alla formazione post-vendita; lo affianchiamo nel processo di acquisto, garantendo l’etica e la qualità dei nostri fornitori (tutti rigorosamente selezionati in Italia ed Europa) e consegniamo loro un prodotto totalmente made in Italy che in questi anni ci ha permesso di consolidare dei rapporti reali di fiducia e responsabilità reciproca con chi ci sceglie. Da tutto questo nasce, infine, il nostro nuovo payoff, di cui ci siamo dotati per la prima volta: Coating your world”.
La nuova serie di unità di controllo delle operazioni di verniciatura a polvere
Al fine di soddisfare tutte le esigenze dei professionisti coinvolti nelle operazioni di verniciatura a polvere, Zeus ha in progetto di lanciare una
gamma di sistemi di controllo della verniciatura a polvere di nuova generazione. “Questa nuova serie, chiamata J2, si andrà ad affiancare al modello J1 attualmente in produzione, e rappresenta un salto in avanti per quanto riguarda connettività e controllo. Per completare la gamma seguirà il progetto JE-asy rivolto a un mercato più semplice e a basso costo. I tre modelli sono caratterizzati infatti da diversi design, funzionalità tecniche e dalla presenza o meno di particolari accessori. L’unione di questi tre fattori ha reso possibile creare una serie che ci consentisse di soddisfare ogni esigenza in termini di produzione e costi”, afferma il titolare di Zeus.
J2, il prodotto di punta della nuova serie progettata da Zeus, che sarà lanciato sul mercato nei prossimi mesi, nasce da una collaborazione con un designer internazionale, che ha svolto un importante lavoro di ricerca al fine di ridisegnare un’interfaccia utente diversa dallo standard, con icone ricercate e con un layout moderno. L’unità di controllo elettrostatica J2 è caratterizzata da:
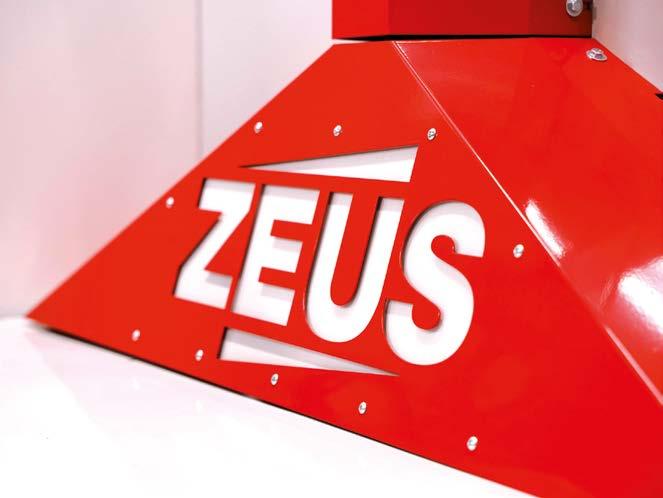
• interfaccia facile da usare e intuitiva grazie ad un touch screen da 7” pollici che consente di visualizzare tutte le informazioni e gli avvisi di sistema su un’unica schermata;
• moduli espandibili e facilmente integrabili in sistemi Industry 4.0;
• facile accesso alle metriche di processo per controllare e gestire la qualità e la produttività;
• possibilità di effettuare aggiornamenti software da remoto e in autonomia, senza la necessità di un intervento da parte di un tecnico Zeus.
Oltre ai nuovi moduli di comando è lunga la serie di novità che seguiranno nei prossimi mesi: segno di un’azienda dinamica e in continua evoluzione.
Total Finishing Systems presenta la nuova cabina di verniciatura a polvere con ciclone in PVC

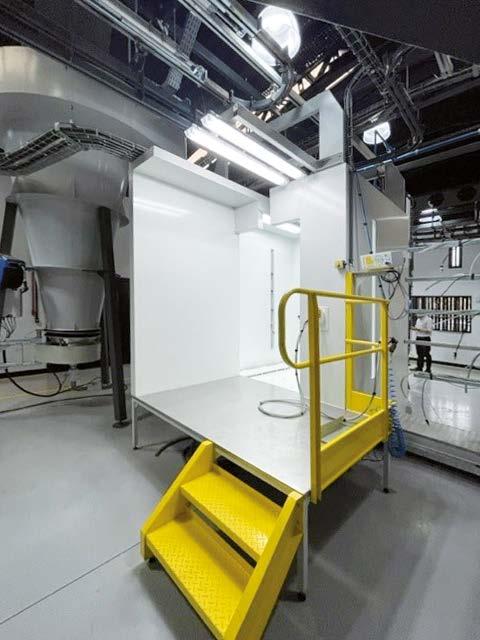
A Fabtech Chicago, che si terrà dall’11 al 14 settembre di quest’anno, Total Finishing Systems presenterà una nuova cabina di verniciatura a polvere con ciclone in PVC sviluppata in collaborazione con Erzinger.
Total Finishing Systems è lieta di annunciare l’espansione della propria collaborazione con Erzinger Equipment, produttore brasiliano di impianti di verniciatura, introducendo sul mercato americano le cabine di verniciatura a polvere con ciclone in PVC. Insieme alla nuova cabina, presenterà anche il sistema di controllo smart In-Line di ultima generazione, l’automazione dell’applicazione e i centri di distribuzione delle polveri. L’ampliamento della linea di produzione fornirà ai clienti nuove opzioni convenienti e sarà una soluzione completa per tutte le esigenze di verniciatura a polvere. L'azienda presenterà queste soluzioni a Fabtech Chicago, stand D40351 padiglione D, che si terrà quest’anno dall’11 al 14 settembre a McCormick Place.
A proposito di Total Finishing Systems
Attiva in tutto il Nord America, Total Finishing Systems è uno dei principali
progettisti e integratori di sistemi complessi e di alta qualità nel settore della verniciatura industriale. L’azienda, situata a Riverside (California, Stati Uniti), è specializzata nel settore della finitura delle superfici, dell’automazione dei processi dei materiali e delle installazioni sofisticate di rivestimento a liquido e a polvere, incluse le apparecchiature per il trattamento termico. Oltre al segmento impianti, la famiglia Total Finishing comprende: Total Finishing Solutions, specializzata nella fornitura di cabine di verniciatura a spruzzo, forni UV e IR, sistemi di sabbiatura e automazione industriale; Total Finishing Supplies, la divisione dedicata alla fornitura di tutti i materiali consumabili e le attrezzature necessarie per mantenere il funzionamento e l’efficienza degli impianti.
Per maggiori informazioni: https://totalfinishingsystems.com/
Your partner for green chemical processes



Chemtec’s mission is to update tradition.
Our revolutionary chemicals are designed to have a very limited environmental impact, to reduce consumption of resources and for a greater operational simplicity. With Chemtec technologies you can replace zinc&iron phosphate:

Want to use less energy, get rid of heavy metals and create a safer environment? Want to replace Zinc Phosphate?
Choose PRONORTEC
PRONORTEC nanotechnology is a new and innovative chemical process for multi-metal surface treatment, based on the use of organic Phosphorus compounds. It is a 1k process, it doesn’t need any additive to correct pH, nor any concentration of other metals. This process is highly revolutionary both for its ease of use and for the quality of results. It does not create any kind of sludge. It can be applied by spraying, immersion, or nebulization.
Choose TORAN 3®
Want to save energy, use no water, create no emissions and waste?
Want to replace Iron Phosphate?
Single-stage, room temperature multi-metal pre-treatment process, with no VOC emissions, no rinsing, no pre-degreasing, no creation of wastewater or sludge. The unique and innovative anhydrous process is based on organic high-boiling fluids and guarantees degreasing as well as immediate protection against oxidation, leading to excellent performances in the finishing cycle. The TORAN 3® treatment is a valid, less expensive alternative to phospho-degreasing and phosphating and passivating processes.
Choose WASTE WATER TREATMENT SYSTEMS
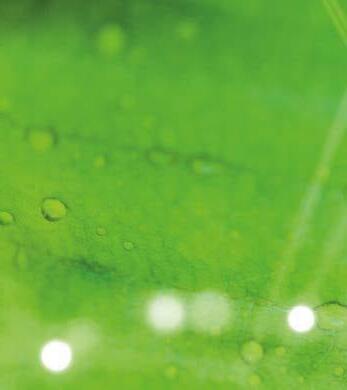
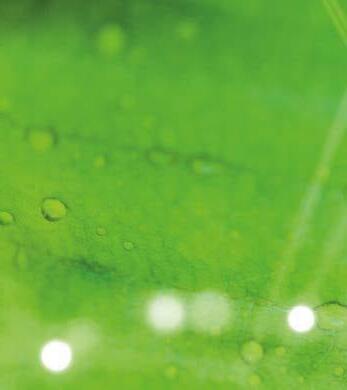
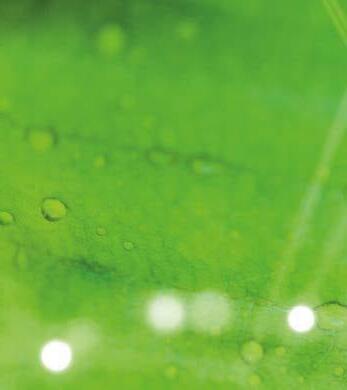
Want to save water, be more sustainable, create less waste?
The combination of Chemtec water treatment equipment (chemical-physical plant, skimmers, filters) with specific chemicals allows the purification and re-use of industrial polluted water in many different industrial applications. Water consumption is significantly cut and water discharge is no more a problem. Waste water are purified and re-circulated instead of discharged to meet the demand of circular economy.
Impact Coatings aprirà una nuova sede in Svezia nel 2024
La nuova sede accrescerà la capacità produttiva di Impact Coatings e includerà un laboratorio aggiornato per collaudare gli impianti e le tecnologie di verniciatura.
Impact Coatings ha recentemente annunciato di aver iniziato la costruzione di un nuovo stabilimento e di una nuova sede a Linköping (Svezia). I nuovi edifici sono adiacenti all’Università di Linköping e al Linköping Science Park, in prossimità dei suoi hotspot innovativi. L’azienda prevede di spostarsi nel corso del secondo semestre del 2024.
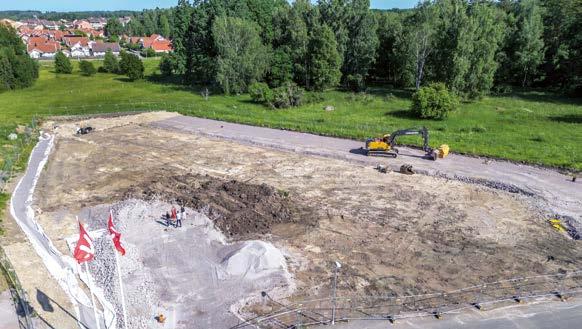
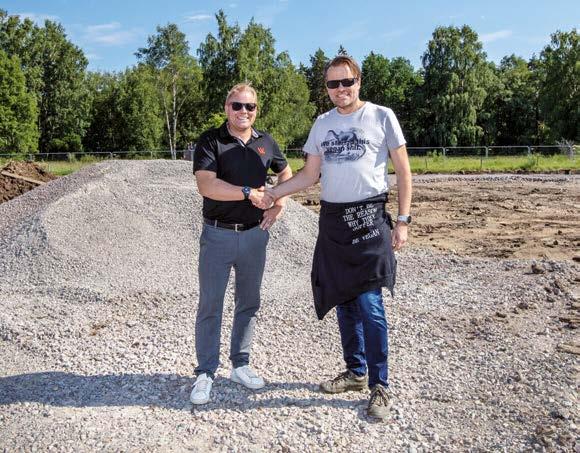
La nuova struttura sarà di circa 3.000 m2, duplicando l’attuale area produttiva e determinando così un aumento significativo della capacità di assemblaggio degli impianti di verniciatura nonché un ampliamento dello spazio per lo Swedish Coating Service Center.
Oltre che fornire una migliore capacità di supporto ai clienti e continuare la crescita delle operazioni aziendali, il nuovo polo svedese ospiterà anche nuovi uffici amministrativi, nuove sale conferenze, un laboratorio aggiornato, una zona di pre-produzione adibita alla pulizia e alla sabbiatura e un hub logistico. Inoltre, il Coating Service Center permetterà a Impact Coatings di effettuare delle prove sulle tecnologie di rivestimento oltre che fornire ai clienti maggiori informazioni sulle soluzioni complete di verniciatura in prima persona.
“Le nuove sedi sono un importante pezzo del puzzle nel nostro percorso di crescita. Grazie alla nuova e vantaggiosa sezione logistica e agli spazi produttivi ottimizzati situati nei moderni edifici, potremo continuare
ad attrarre i migliori talenti della regione e ad accrescere la nostra azienda nonché razionalizzare e automatizzare i nostri flussi produttivi. Aspetti chiave che sono in grado di supportare pienamente i settori in rapida crescita, che insieme a noi lavorano alla prossima generazione di soluzioni energetiche e di trasporto”, ha dichiarato Torbjörn Sandberg, CEO di Impact Coatings.
La costruzione della nuova sede sta avvenendo in stretta collaborazione con Wilzéns Fastighetsförvaltning, che possiederà e amministrerà la struttura. I lavori di costruzione del nuovo stabilimento si stanno svolgendo simultaneamente alla produzione del nuovo Coating Service Center di Shangai (Cina), mentre l’azienda sta anche pianificando la realizzazione di un altro sito negli Stati Uniti nel 2024.
“È gratificante realizzare questo progetto per Impact Coatings, considerando anche il loro impegno nel settore delle tecnologie green e l’impiego di metodi produttivi sostenibili, che va di pari passo con i nostri valori. Inoltre, vorrei anche elogiare il comune di Linköping per il ritmo veloce e l’atteggiamento positivo durante tutto il processo di pianificazione”, ha commentato Andreas Wilzén, CEO di Wilzéns Fastighetsförvaltning.
Per maggiori informazioni: www.impactcoatings.com
I nuovi impianti di granigliatura e verniciatura confermano Cos.Eco. azienda di eccellenza del Sud Italia
Monica Fumagalli ipcm®Essere un’eccellenza del Sud Italia significa coniugare innovazione ed ecosostenibilità in prodotti sempre più performanti: di seguito descriviamo il caso di successo di Cos.Eco., azienda pugliese al quarto posto a livello europeo per la produzione di veicoli ecologici, che ha scelto una granigliatrice OMSG per ottimizzare la preparazione del supporto e garantire maggiore adesione e durata al rivestimento applicato in un nuovo impianto di verniciatura Savim, rendendo al contempo più confortevole il lavoro dei propri collaboratori e con un occhio di riguardo sempre rivolto all’ecosostenibilità del processo produttivo.
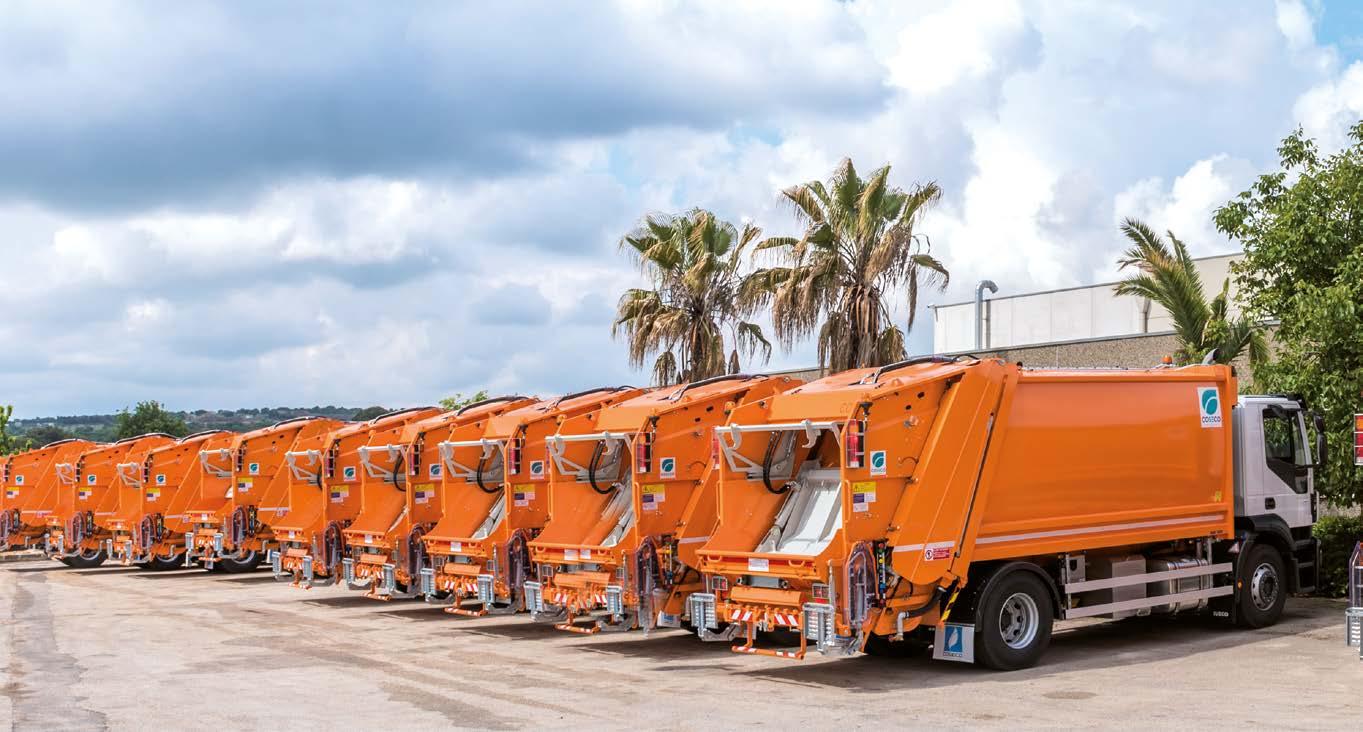
Secondo i dati recentemente aggiornati dal Parlamento Europeo, all’interno dell’UE ogni anno sono prodotte 2,2 miliardi di tonnellate di rifiuti1. Più di un quarto, il 27% circa, è rappresentato dai rifiuti solidi urbani, ossia gli scarti generati ogni giorno prevalentemente da privati cittadini, poi raccolti e trattati dai comuni.
1 https://www.europarl.europa.eu/news/en/headlines/society/20180328STO00751/ waste-management-in-the-eu-infographic-with-facts-and-figures
Secondo quanto riferisce il report, “dal 2018 al 2021, la quantità media di rifiuti urbani misurata per abitante è cresciuta nell’Unione Europea. Tuttavia, le tendenze possono differire da uno stato all’altro. […] Nonostante la produzione di rifiuti pro capite sia aumentata, il modo in cui gestiamo i rifiuti è migliorato - con un aumento del riciclaggio e del compostaggio, e una diminuzione dell’uso di discariche”. Tra gli obiettivi dell’UE in ottica di economia circolare c’è infatti quello di promuovere non solo la prevenzione della produzione di rifiuti ma anche il riutilizzo
dei prodotti ogni volta che sia possibile, dando quindi prevalenza alle istanze di riciclaggio, compostaggio e incenerimento. La stessa sensibilizzazione in ottica sempre più ecosostenibile caratterizza il settore dei veicoli per la raccolta e il trasporto dei rifiuti solidi urbani. Ci spiega infatti Giuseppe Debernardis, Amministratore Unico di una delle aziende italiane leader a livello nazionale e internazionale nella fabbricazione di mezzi per il trasporto dei rifiuti solidi urbani “Cos.Eco. Industrie Group Srl è specializzato nella progettazione, costruzione, commercializzazione e assistenza tecnica post vendita di attrezzature destinate alla raccolta, trasporto e smaltimento dei rifiuti solidi urbani, come compattatori, costipatori, vasche ribaltabili e lavacassonetti. Dal 2015 si occupa di eseguire all’interno la progettazione, la lavorazione delle materie prime, l’assemblaggio, la verniciatura ed il montaggio, con relativo collaudo di ogni singolo prodotto in un ciclo produttivo completo, completamente integrato ed ecologico: i nostri veicoli devono trasmettere
Cos.Eco. Industrie Group Srl è specializzato nella produzione di attrezzature destinate alla raccolta, trasporto e smaltimento dei rifiuti solidi urbani. Qui sotto, il nuovo reparto di verniciatura: a destra la granigliatrice OMSG e a sinistra l’impianto di verniciatura Savim.
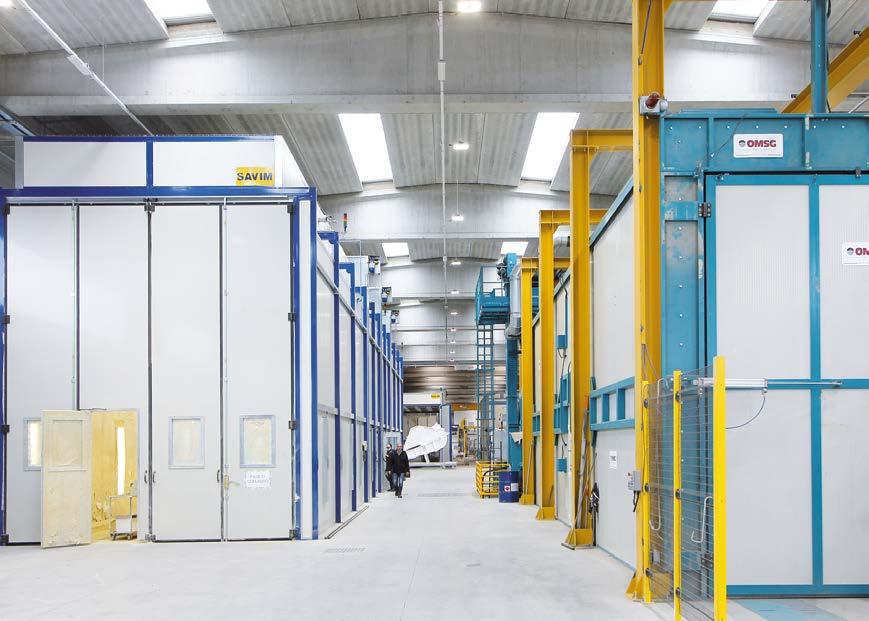
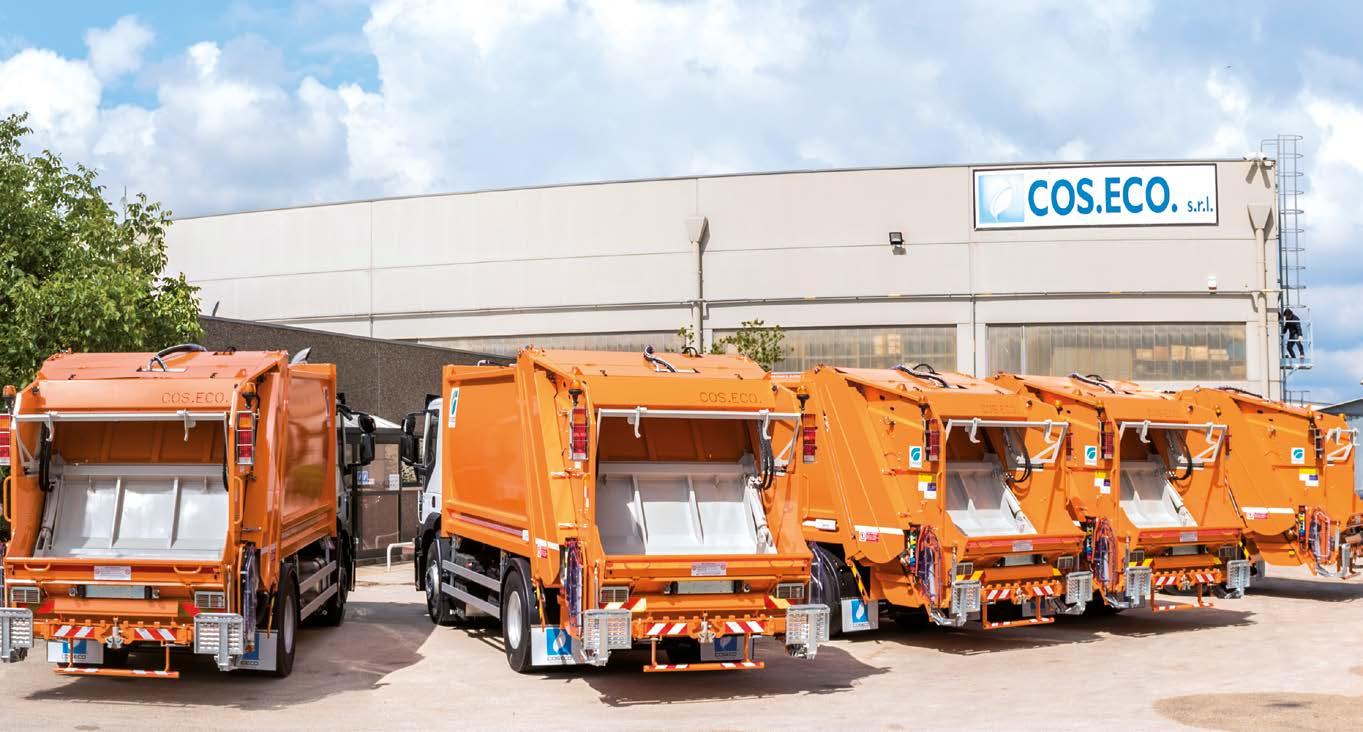
anche in termini di aspetto un’idea di pulizia e di sostenibilità, per questo motivo le fasi di preparazione del supporto e la verniciatura vera e propria risultano strategiche e, quando il collo di bottiglia di un ciclo manifatturiero come il nostro è identificato nella fase dei trattamenti superficiali, il problema va risolto con estrema urgenza”. Circa un anno fa l’azienda ha così rinnovato completamente il reparto di verniciatura dotandosi di una nuova granigliatrice automatica progettata e installata da OMSG – Officine Meccaniche San Giorgio di Villa Cortese, in provincia di Milano, e di un nuovo impianto di verniciatura fornito da Savim Europe Srl di Arbizzano (Verona).
Cos.Eco.: una storia di successo dal Sud Italia
La storia di questa azienda fiore all’occhiello del territorio produttivo delle Murge pugliesi ha preso avvio dallo spirito imprenditoriale di 2 uomini: Nicola Farella e Donato Debernardis, che negli anni Settanta fondarono ad Altamura la società DI.CAR. per la costruzione di attrezzature per il trasporto. Agli inizi degli anni Ottanta, dopo una grave battuta di arresto dovuta al terremoto del 1981 che mise in ginocchio le aziende lucane non più in grado di far fronte ai pagamenti dovuti, Nicola Farella decise di dedicarsi alla produzione esclusiva di veicoli municipali, tra cui compattatori, spazzatrici stradali e scuolabus. “E’ in questo periodo –racconta lo stesso Nicola Farella, recentemente nominato Cavaliere della Repubblica per l’impegno profuso in ambito professionale e sociale - che abbiamo deciso di vendere l’intero parco degli autotreni prima utilizzati
per il trasporto delle merci e di fondare Cos.Eco. Costruzioni Ecologiche Srl, trasferendone successivamente la sede da Altamura a Grumo Appula. Qui l’azienda ha infine abbandonato il settore dei trasporti per dedicarsi completamente alla produzione di attrezzature per l’ecologia”.
“Grazie alla continua innovazione tecnologica e alla cura che da sempre la nostra azienda pone in tutte le fasi di lavorazione – prosegue Farella – siamo riusciti ad affermarci anche a livello europeo, partendo da un territorio complesso come quello del Sud Italia, caratterizzato da numerose risorse, ma che a livello industriale ha ancora alcune lacune da colmare: un territorio al cui sviluppo Cos.Eco ha sicuramente contribuito creando un indotto di aziende che ruotano intorno alla nostra attività e offrendo numerosi posti di lavoro, tanto che oggi collaborano con noi 110 dipendenti attivi in uno stabilimento di 44 mila m2 di superficie. Siamo presenti in 40 nazioni che spaziano dai mercati più vicini come quelli del Nord-Europa, della Spagna e degli Emirati Arabi, fino a quelli più lontani, come Sudafrica, Singapore e Nuova Zelanda. Abbiamo costruito la nostra leadership nel tempo grazie a macchinari tecnologicamente avanzati, personale specializzato e alla cura che da sempre la nostra azienda dedica ai propri clienti in tutto il mondo”.
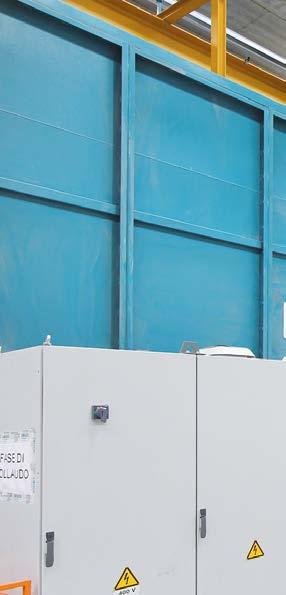
“Per garantire il livello di qualità dei prodotti e servizi” – continua Debernardis – “abbiamo ottenuto le certificazioni ISO 9001 e ISO 14001, che, oltre a certificare la qualità del prodotto, certificano la struttura organizzativa stessa, che ha integrato nel proprio sistema aziendale interno le regole per una gestione efficace con riferimento agli aspetti
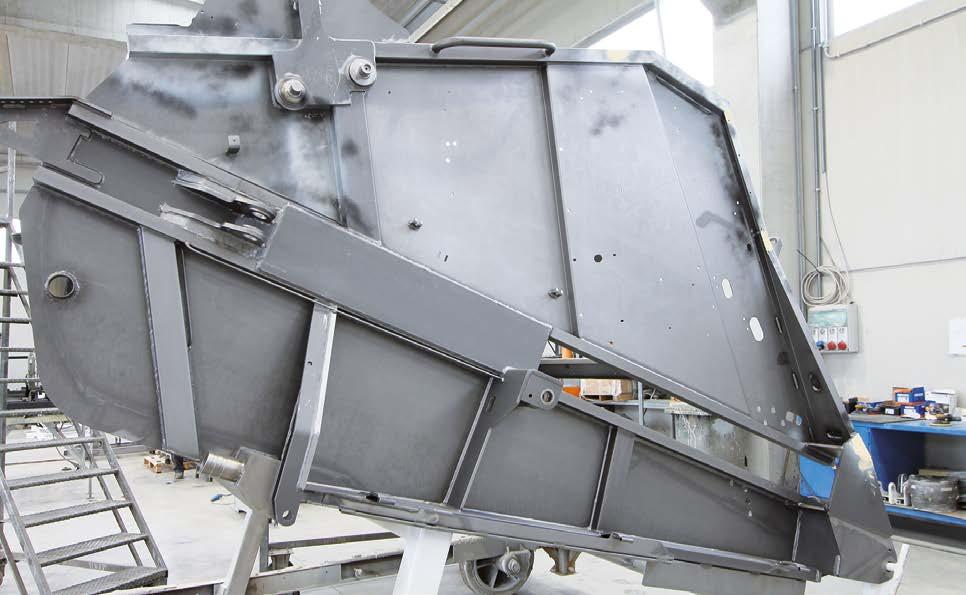
ambientali più significativi. Abbiamo inoltre ottenuto la certificazione dei materiali impiegati nella produzione, che attesta la qualità, le caratteristiche meccaniche e tecnologiche dei materiali stessi, come, per esempio, l’Hardox, uno degli acciai più resistenti in termini di abrasione, e gli acciai al carbonio S355, S275 e S355”.
Un ciclo produttivo completamente internalizzato

“Per risolvere il problema della difficoltà di reperimento di aziende terziste nel nostro territorio e per un maggior controllo del flusso di produzione abbiamo internalizzato tutte le fasi produttive, a partire dalle lavorazioni meccaniche di taglio, piegatura e saldatura fino ai trattamenti superficiali di granigliatura e verniciatura” – spiega Farella. Prima del pretrattamento meccanico, i pezzi sono lavati manualmente con l’idropulitrice per togliere gli oli delle lavorazioni e i depositi di materiali diversi derivanti dalla saldatura.
“Grazie a questo intervento di lavaggio” - prosegue Debernardis –“preserviamo anche la qualità della graniglia che rimane più pulita e può essere così recuperata. Per raggiungere il profilo di rugosità superficiale specificato, utilizziamo graniglia angolosa in acciaio”.
Da sinistra:
- Le dimensioni dei pezzi trattati possono raggiungere una lunghezza pari a 11 m.
- Panoramica dell’impianto di granigliatura.
GLOBAL SOLUTIONS FOR WATER TREATMENT
with a complete service that includes system design manufacturing, installation, technical support and chemicals
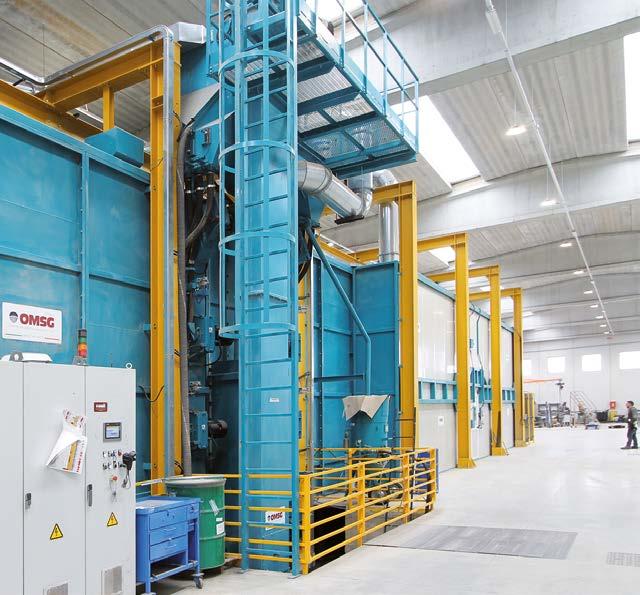
SPRAY BOOTHS WATER SLUDGE REMOVAL
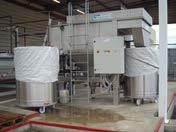
RESIN DEMINERALIZATION SYSTEMS
REMEDIATION OF CONTAMINATED SITES
BIOLOGICAL SYSTEMS
BATCH TREATMENTS
PHYSICAL-CHEMICAL SYSTEMS
ADSORPTION FILTRATION

REVERSE OSMOSIS
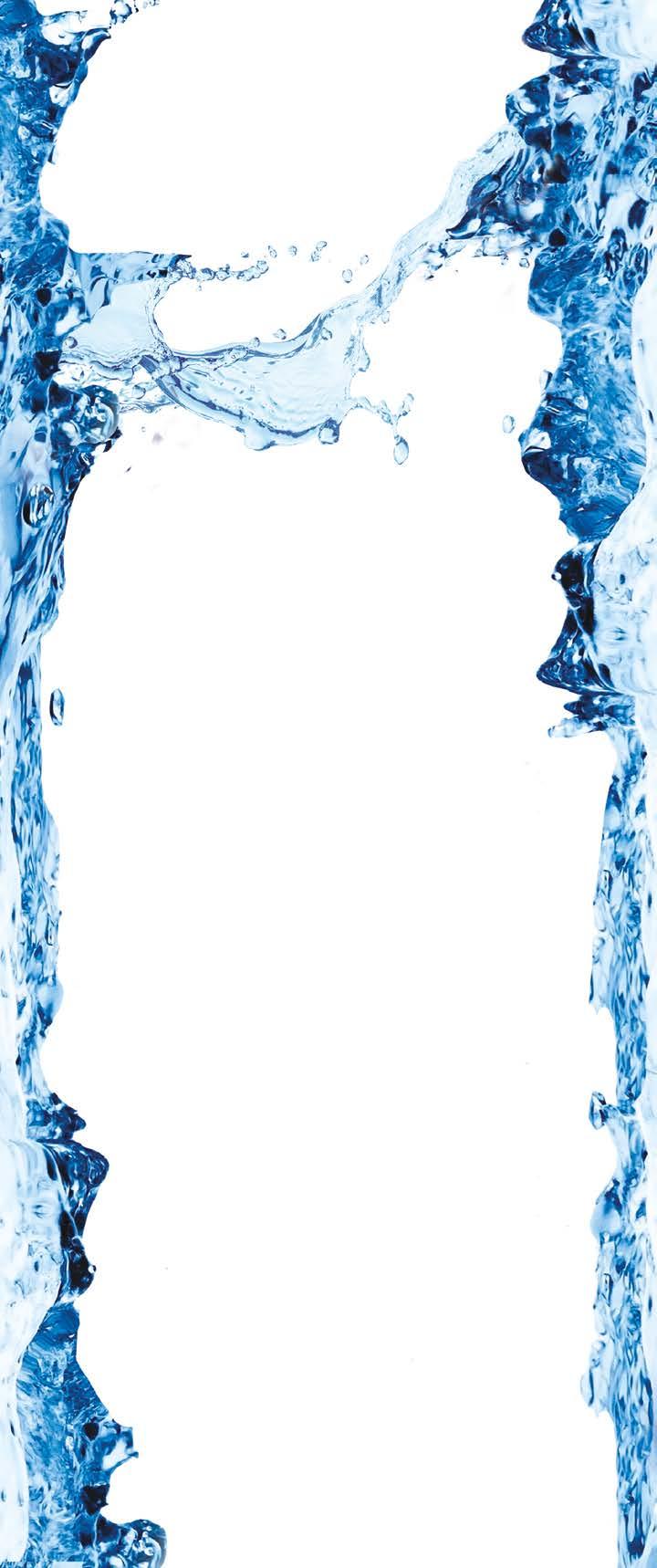
MEMBRANE SYSTEMS
EVAPORATORS
BIOGAS BIOMASS SYSTEMS
OIL SEPARATORS
DESANDERS
DESALINATION SYSTEMS
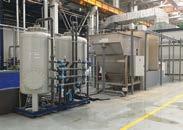
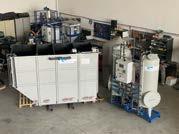
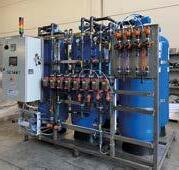
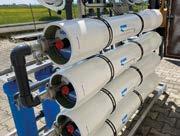
PYROCHAR
OTHER SYSTEMS
CHEMICALS
La nuova granigliatrice automatica a tunnel OMSG è stata installata circa un anno fa per risolvere un collo di bottiglia produttivo. “Prima effettuavamo un intervento di pretrattamento meccanico manuale, che non risultava agevole per i nostri collaboratori in termini di movimentazione, a causa del peso dei componenti di grandi dimensioni, e di applicazione, perché richiedeva la loro presenza fisica all’interno della camera di granigliatura. Adesso adibiamo la granigliatura manuale ai soli componenti di formato più piccolo e utilizziamo la granigliatrice automatica per pretrattare pezzi come i semirimorchi, che possono raggiungere dimensioni di 11 x 2,5 x 2,5 m”. Successivamente la superficie viene soffiata e la graniglia recuperata, prima del passaggio nell’impianto di verniciatura con cabina statica manuale. “Nel caso dell’impianto di verniciatura, invece, abbiamo escluso l’automazione perché i nostri componenti hanno conformazioni troppo diverse per poter sfruttare al meglio i vantaggi di un impianto automatico. Applichiamo vernici poliuretaniche liquide ad alto-solido in 3 mani con pistole WAGNER. L’impianto è costituito da diverse stazioni per l’applicazione del primer, l’asciugatura, la sigillatura e l’applicazione del topcoat che avviene in due mani. Dopo l’applicazione del primer, la sigillatura viene effettuata in una camera che può essere riscaldata, a seconda delle necessità, per l’evaporazione della vernice al solvente o la polimerizzazione del sigillante. Questa è infatti una delle caratteristiche più vantaggiose dell’impianto di verniciatura progettato e installato da
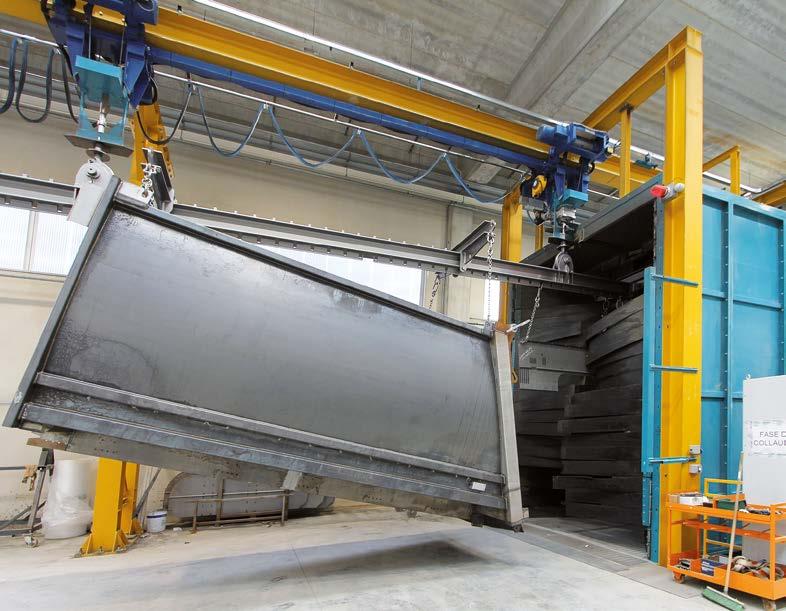
Savim: la sua compartimentazione tramite serrande mobili ci permette di riscaldare le singole zone alle temperature che ci servono in base alle operazioni che dobbiamo effettuare. Successivamente i pezzi passano nel forno di essiccazione dove sono lasciati ad asciugare a volte – grazie alle alte temperature tipiche della nostra zona - anche a temperatura ambiente, senza che sia necessario riscaldare”.
Le caratteristiche del nuovo impianto di granigliatura L’impianto automatico scelto per la granigliatura è un modello Tunnelblast 2535/16 H26 C.
“La sezione massima di granigliatura corrisponde a 2,5 x 3,5 m” –precisa Enzo Dell’Orto, CEO di OMSG. “L’impianto è dotato di 16 turbine monodisco con motore diretto da 7,5 kW di potenza cadauno. Il quadro elettrico è attrezzato con 16 Inverter per il controllo della velocità di rotazione delle turbine e la conseguente regolazione dell’energia cinetica dell’abrasivo in acciaio proiettato sul manufatto. Oltre agli inverter, la granigliatrice è dotata di speciali valvole di alimentazione della turbina, caratterizzate da un doppio cilindro pneumatico per la regolazione della portata dell’abrasivo alle turbine. La linea aerea, che ha una estensione esterna all’impianto di 12 m in ingresso e di 12 m in uscita, è composta da una coppia di paranchi di portata pari a 6000 Kg/cadauno”.
A valle del tunnel è installata una camera di sabbiatura manuale per ritoccare eventuali zone mascherate o sottosquadra non accessibili
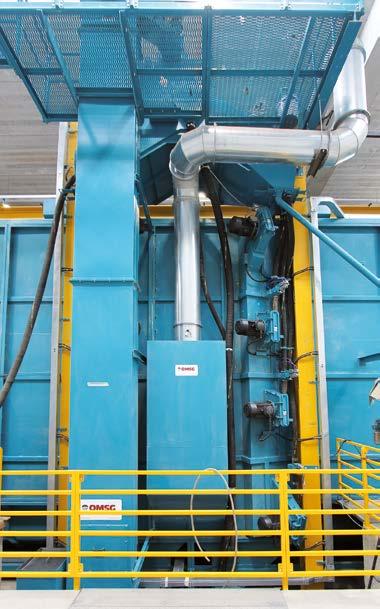
all’impatto diretto dell’abrasivo lanciato dalle turbine. La cabina di granigliatura manuale ha una lunghezza di 15 x 5 x 4,7 m. All’interno della cabina si effettuano anche le semplici operazioni di soffiaggio per rimuovere l’abrasivo depositato sui pezzi.
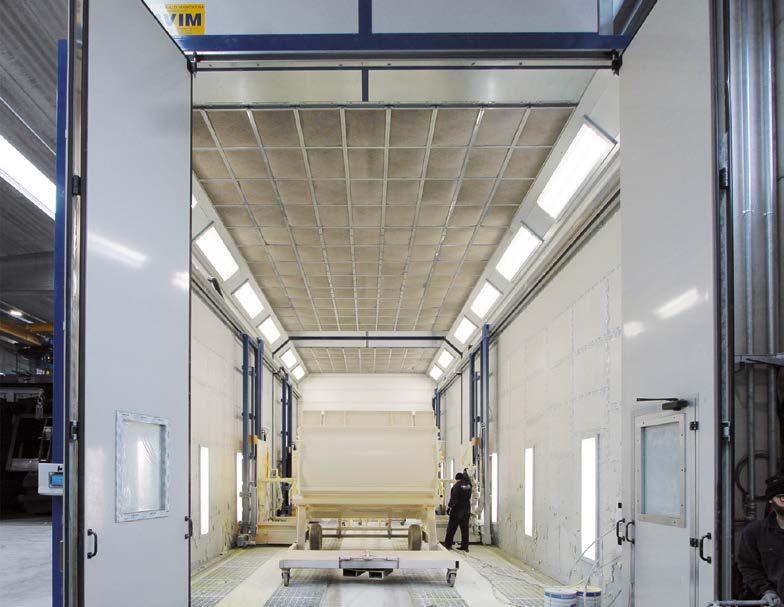
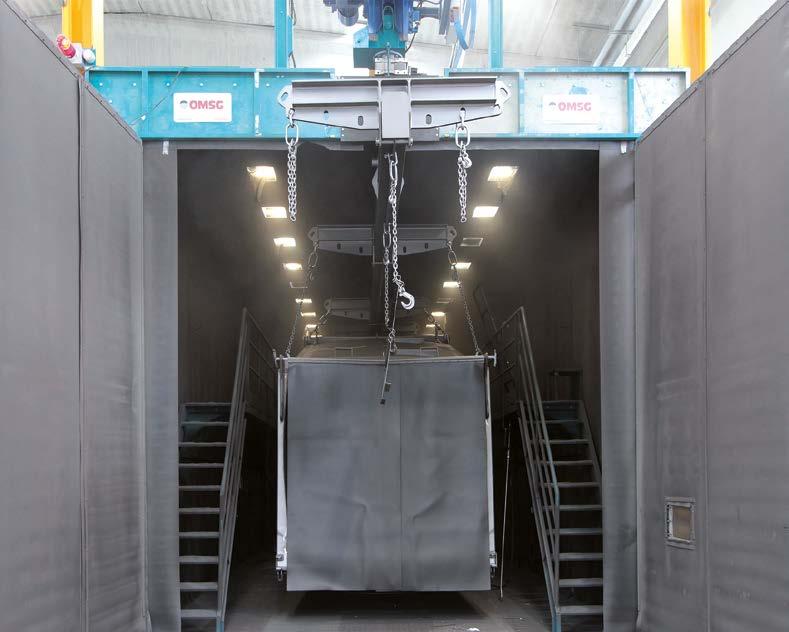
“L’intero impianto – prosegue Dell’Orto - è predisposto in ottica Industria 4.0. Il ciclo di lavoro è gestito tramite PLC e la macchina è dotata di sensori per il controllo dei livelli di abrasivo metallico nel separatore e della rotazione della puleggia inferiore dell’elevatore, di dispositivi di teleassistenza, di lettore del codice a barre e di controlli amperometrici digitali. Sia la granigliatrice a turbina sia la cabina manuale sono dotate di filtri a cartucce, realizzati con cartucce in poliestere antistatico e componenti ATEX: la macchina è attrezzata con un filtro da 20 mila m3/h, la cabina con uno da 7.500 m3/h”.
I vantaggi del nuovo binomio impiantistico
“Tra i vantaggi legati all’installazione del nuovo impianto di pretrattamento meccanico –prosegue Debernardis - c’è l’abbattimento delle tempistiche produttive. Oggi siamo in grado di produrre 2 compattatori al giorno, oltre a diversi componenti come le vasche realizzate in lamiera di acciaio o alluminio saldati a filo continuo e altri veicoli di dimensioni più piccole. Solo per l’intervento di granigliatura impieghiamo 20 min a fronte delle 5 ore circa della granigliatura manuale precedente. Anche se si tratta della nostra prima esperienza con una macchina OMSG non possiamo che ritenerci soddisfatti. Contestualmente all’aggiornamento del reparto di granigliatura abbiamo voluto realizzare un nuovo impianto di verniciatura perché il precedente era costituito da un’unica cabina in cui applicavamo il fondo e lo smalto. Per farlo ci siamo rivolti ad un’altra azienda solida con un profondo know how, la Savim di Arbizzano, in provincia di Verona. Quella di affidarci ad aziende con una solida struttura aziendale è stata una nostra precisa scelta: dobbiamo avere la garanzia che, nel caso
Da sinistra in alto in senso orario: La centrale vernici liquide WAGNER; un componente finito; uno dei compattatori realizzati da Cos.Eco.
Da sinistra: Nicola Farella, fondatore di Cos.Eco con Giorgio Casiello, responsabile dell’ufficio tecnico, e Giuseppe Debernardis.
sopraggiunga un problema impiantistico di qualsiasi genere, la soluzione sarà rapida ed efficace, perché per noi fermare l’impianto di granigliatura o verniciatura significa interrompere l’intero ciclo produttivo”.
Conclusioni
“Una gestione ambientale dei rifiuti più attenta – conclude Debernardis – è uno degli obiettivi che l’Unione Europea si è imposta entro il 2050. La strada è sicuramente tra quelle più difficili da percorrere, perché cambiare i metodi di raccolta utilizzati finora comporta modificare la mentalità non solo dei privati ma anche degli enti pubblici. Qualunque sia la strada che si sceglierà di percorrere, Cos.Eco è pronta ad affrontarla: oltre all’attenzione sempre alta all’impatto del nostro ciclo produttivo, già da tempo mettiamo a disposizione dei comuni i nostri
veicoli elettrici, che stanno avendo un’ottima diffusione. Abbiamo inoltre introdotto un nuovo compattatore per rifiuti movimentato a energia solare su nostro brevetto, dotato di un sistema interno di pesatura che ci ha permesso di abbattere i costi e l’impatto ambientale, azzerando il rumore e le emissioni. Questa continua ricerca di soluzioni innovative ed ecocompatibili è ciò che ha caratterizzato la storia della nostra azienda e la strategia imprenditoriale del nostro fondatore, Nicola Farella. La ricerca di soluzioni innovative passa attraverso la collaborazione con aziende competenti e solide come OMSG e Savim, con cui abbiamo aggiornato, ottimizzandolo, il nostro reparto di verniciatura: oggi da fase critica la verniciatura si è trasformata in una delle principali risorse produttive che ci hanno permesso di confermarci azienda di eccellenza del Sud Italia”.
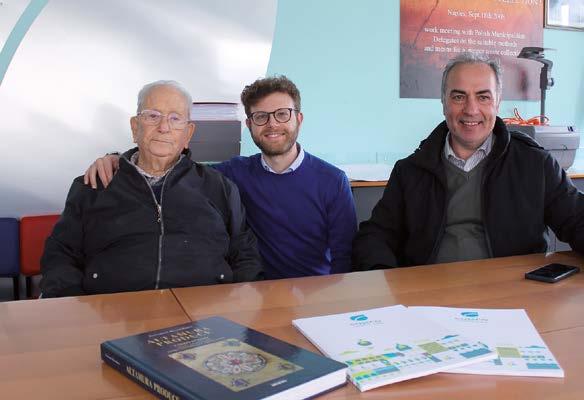
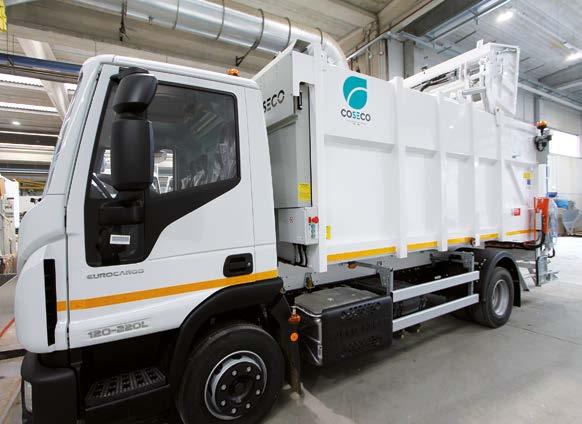

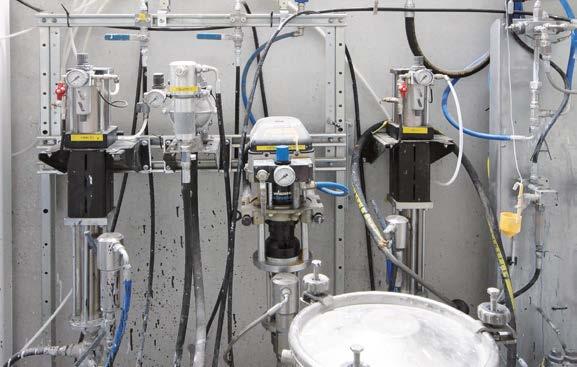
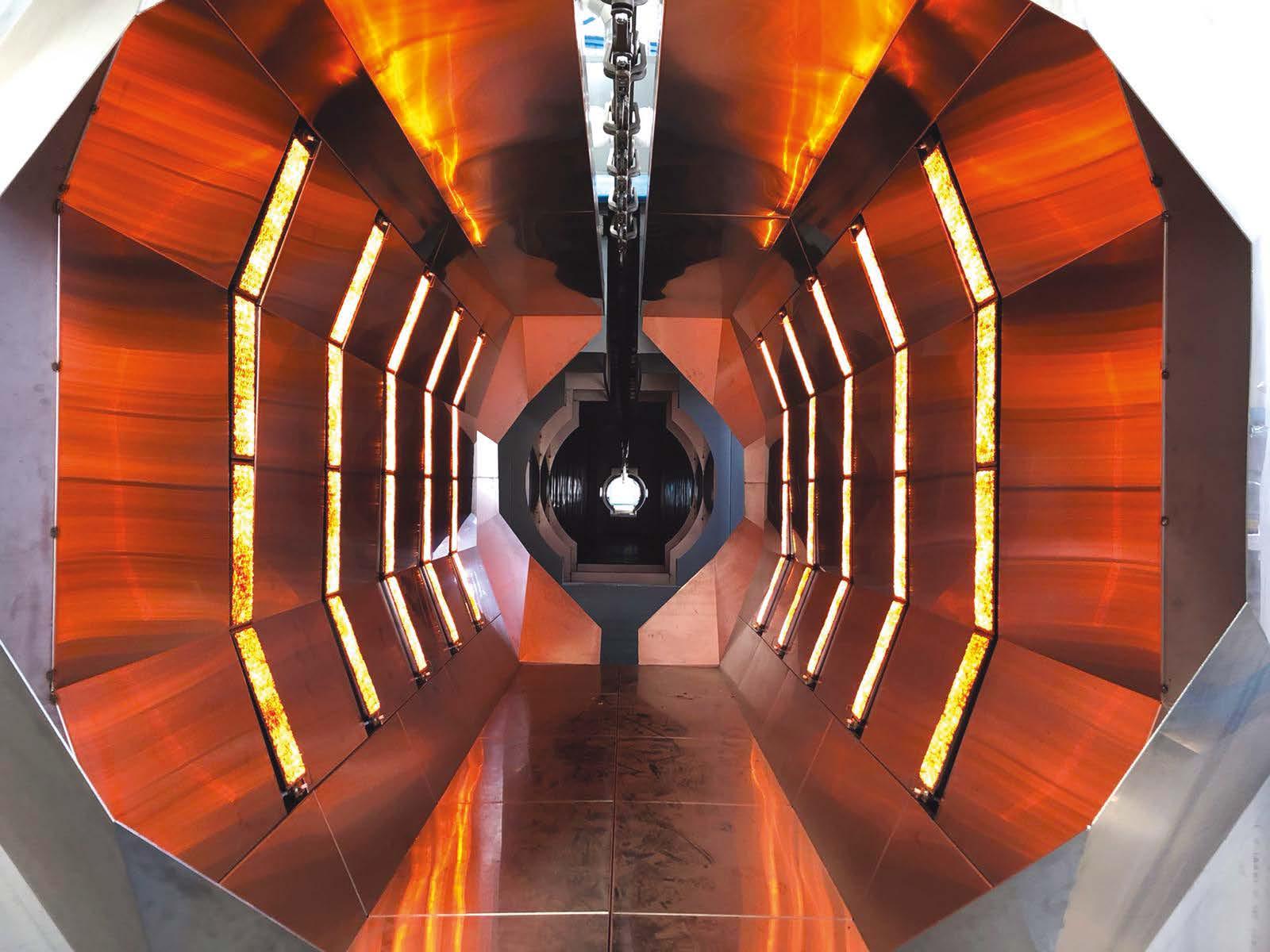
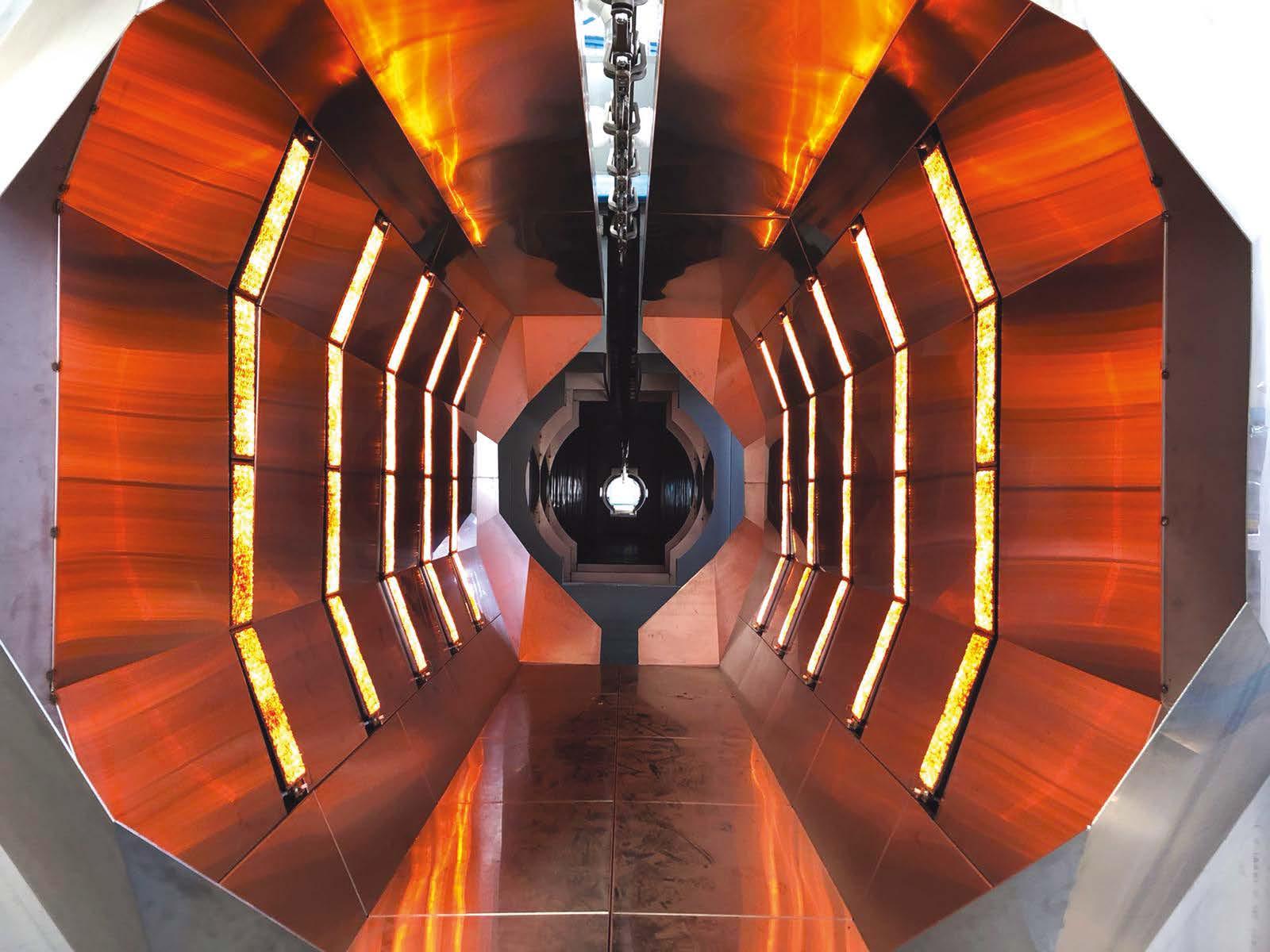
under the patronage of:







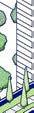


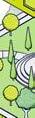



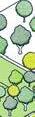











Products, networking, business and training.

WHERE WE HAVE BEEN
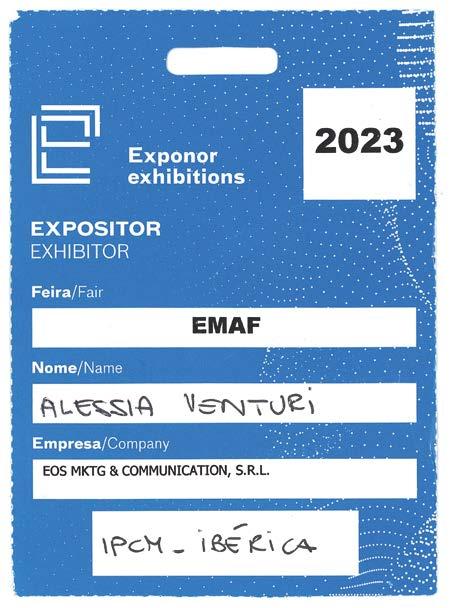
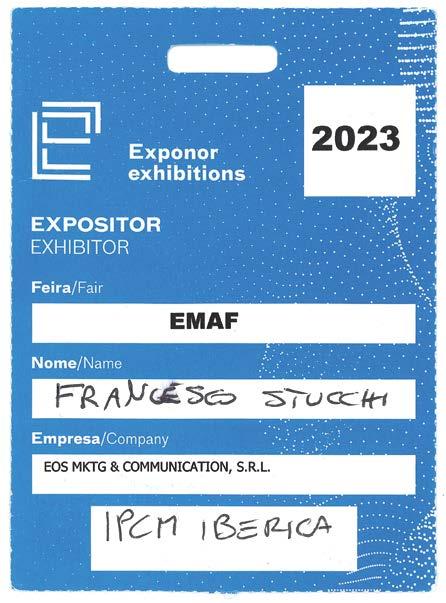
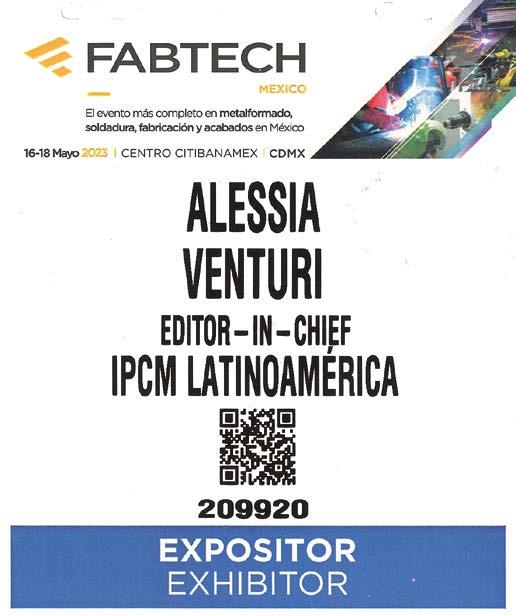

Come ridurre la corrosione sugli spigoli utilizzando un primer di nuova generazione
Andrea Perelli Pulverit Spa – Milano, Italia a.perelli@pulverit.itPulverit ha sviluppato “Endurance”, una serie di nuovi primer anticorrosivi che permettono di aumentare la resistenza alla corrosione, in particolar modo sui bordi dei manufatti.
Quanto costa la corrosione dei metalli? In un Paese industrializzato il costo attribuibile alla corrosione dei metalli è stimato intorno al 6-8% del PIL. Il che porta a stimare per l’intera Europa costi superiori a 750 miliardi di €/anno. Alla luce dei costi associati alla corrosione, riveste vitale importanza la durabilità dei prodotti. La corrosione del metallo inizia generalmente nei punti critici del manufatto e, una volta innescata, si diffonde nel resto del pezzo. Tra i punti critici possiamo individuare le aree dove il pezzo ha subito urti meccanici o graffi che hanno intaccato il film di vernice o gli spigoli vivi. Urti e graffi possono essere prevenuti attraverso una corretta manipolazione e/o un adeguato imballaggio dei manufatti. La criticità
relativa agli spigoli vivi, viceversa, è più difficile da arginare.
In quest’ottica, i laboratori Pulverit hanno sviluppato una serie di primer denominati Endurance, che consentono di aumentare la resistenza alla corrosione, in particolar modo sui bordi dei manufatti. La serie Endurance 16J0 realizzata attraverso la combinazione di una base epossidica leggermente raggrinzata con additivi ad effetto barriera e passivanti, garantisce un’eccellente copertura dei bordi, un’ottima protezione dalla corrosione e la sovraverniciatura del primer.
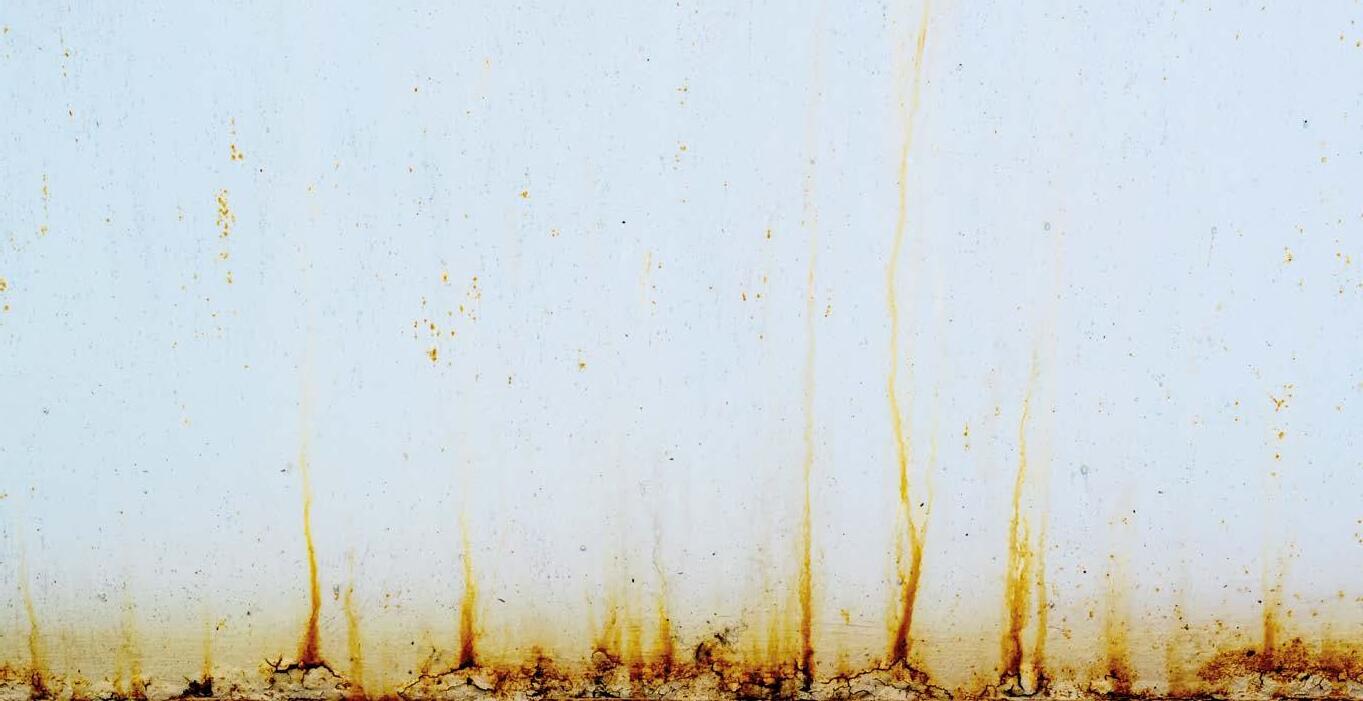
Le cause della corrosione sui bordi dei manufatti
Le cause principali della corrosione sui bordi possono essere diverse:
errori di progettazione del manufatto, un pretrattamento inadeguato o la difficoltà intrinseca delle vernici nella copertura degli spigoli vivi. Perché è difficile raggiungere un’adeguata copertura sui bordi? Da un lato abbiamo la difficolta di verniciare una superficie stretta e sottile e, dall’altro, la viscosità dei sistemi di verniciatura utilizzati. I primer tradizionali sono realizzati normalmente con sistemi epossidici lisci che, in quanto tali, tendono a scivolare sui bordi. Nelle figure 1 e 2 sono riportate le immagini al microscopio delle sezioni di alcuni prodotti verniciati con un primer tradizionale e una mano a finire (topcoat). Come si vede nella figura 1, lo spessore di vernice che si raggiunge sull’angolo è molto più basso rispetto alla parte piana. Tale differenza non può essere compensata dall’applicazione di un secondo strato, come si evince dalla figura 2.
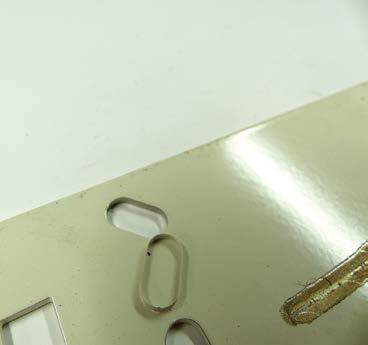
I primer Endurance
Per risolvere questo problema Pulverit ha realizzato i primer Endurance: la modifica della reologia del prodotto unitamente all’azione di particolari additivi consente di aumentare considerevolmente lo spessore di polvere sugli spigoli. Come si può vedere bene nella micro-sezione della figura 3, la protezione del bordo è ora completa: siamo passati da uno spessore di primer tradizionale inferiore a 10 µm della figura 1 a oltre 100 µm ottenuti con il primer Endurance di figura 3. Dopo aver applicato la seconda mano di vernice con lo stesso topcoat usato in precedenza, si può osservare nuovamente lo scivolamento della stessa vernice sui bordi (fig. 4); si evince pertanto che l’effetto protettivo deriva quasi esclusivamente dal primer Endurance.
I test che ne comprovano l’efficacia
Abbiamo fatto una prova di corrosione ciclica comparativa (KSP) utilizzando i due differenti primer su lamiere pretrattate con fosfatazione allo zinco e verniciate con il solo primer. I bordi non sono stati arrotondati meccanicamente. In entrambi i casi lo spessore del primer varia tra 70 e 90 µm.
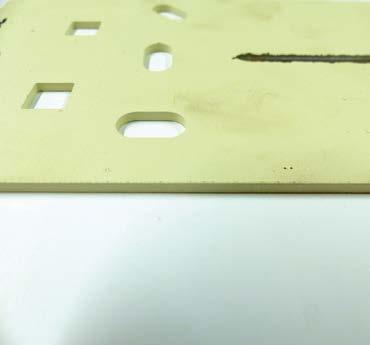
Alla fine del test sulla lamiera rivestita con il primer standard si nota un distacco completo del film di vernice nella zona dei fori così come l’inizio della corrosione sui bordi (fig. 5).
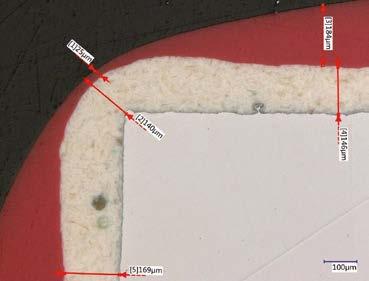
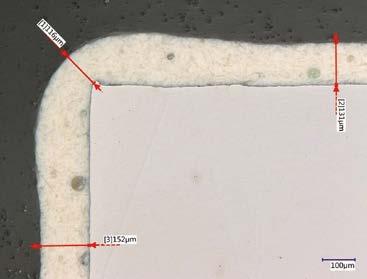
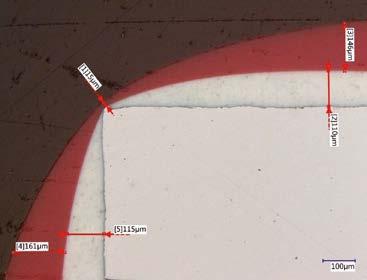
Viceversa, con il nuovo primer goffrato,16J, non è stata rilevata alcuna delaminazione del film dal supporto o
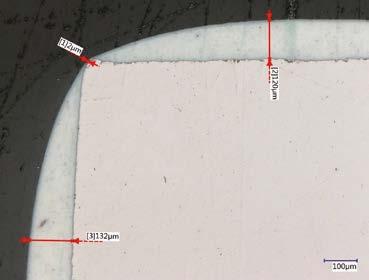
corrosione sui bordi (fig. 6). La durata del test KSP è stata di 720 ore. Più lo spigolo è “vivo” più è alta la criticità, per questo motivo abbiamo voluto fare un test estremo verniciando delle lamette da barba disponibili in commercio. Le lamette sono state verniciate sia a mano unica con un primer, che a doppia mano primer + topcoat: anche in questo caso le foto fatte al microscopio sono molto indicative.
Osservando le figure 7 e 8 (lamette verniciate con i soli primer) si vede che in figura 7 (primer standard) il bordo tagliente non è coperto dal primer tanto che la lama luccica, mentre in figura 8 il primer Endurance ricopre anche il bordo tagliente e la superficie risulta arrotondata.

Il risultato diventa ancora più chiaro quando si analizzano le immagini del taglio trasversale. Le figure 9 e 10 mostrano le lamette verniciate in doppia mano. In figura 9, nonostante la doppia mano sul bordo tagliente della lametta, lo spessore del film non è misurabile. Viceversa, con il primer Endurance 16J si raggiungono 61 µm anche sulla punta della lama (fig. 10). Ciò garantisce una protezione ottimale contro la corrosione dei bordi anche nelle condizioni più critiche. Infine, abbiamo voluto testare il nostro primer attraverso un test accelerato di corrosione NSS per oltre 2000 ore con un ciclo a doppia mano primer Endurance 16J0/0083 + topcoat poliuretanico RAL 7031 (pretrattamento fosfatazione di ferro ad alto spessore e passivazione senza risciacquo, Haug). Dopo 2000 ore, si vede una delaminazione sull’incisione compresa tra 0 e 1,5 mm e una corrosione, sempre sull’incisione, compresa tra 0 e 1,5 mm (fig. 11). Ottimo anche il risultato ottenuto sui bordi della lamiera dove non si osservano punti di corrosione (fig. 12).
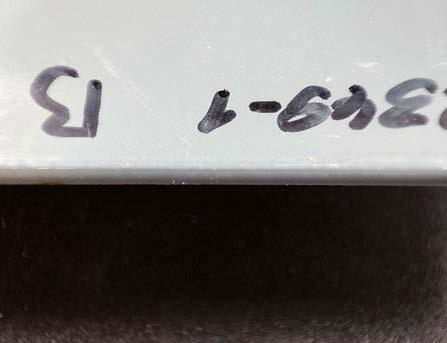
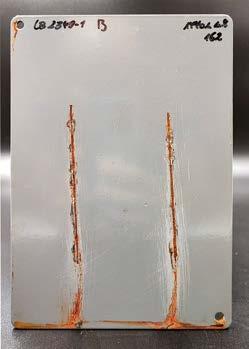
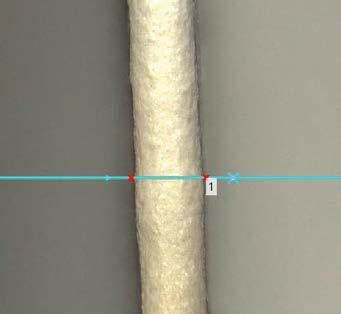
Conclusioni
Il primer Endurance 16J0 può essere parzialmente o totalmente polimerizzato prima dell’applicazione del topcoat secondo le esigenze del cliente. Qualora si utilizzi un topcoat raggrinzato può anche essere applicato bagnato su bagnato. Per il primer Endurance 16J0 abbiamo scelto due colorazioni 16J0/0083 RAL 1013 per colori tenui e 16J0/0463 RAL 7021 per colori scuri. Trattandosi di una raggrinzatura molto fine, il primer può essere riverniciato con qualsiasi topcoat liscio senza alterarne l’aspetto.
In sintesi, si può affermare che questo innovativo primer stabilisce un nuovo punto di riferimento nel campo dei primer anticorrosivi.
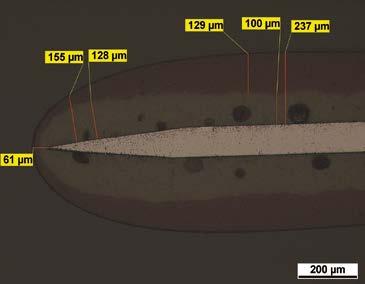

CHEMICAL MAKING SOLUTIONS
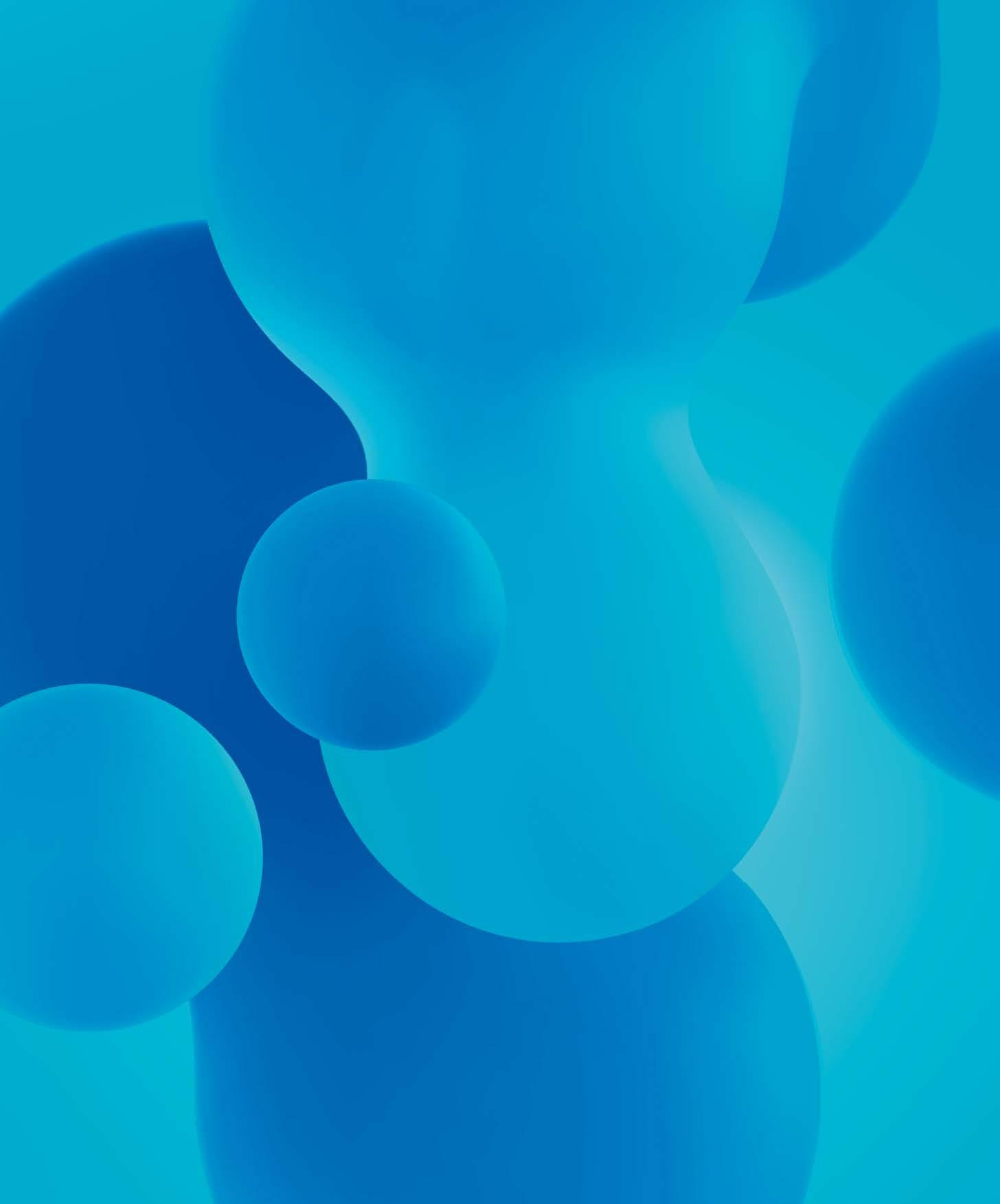
TRATTAMENTO ACQUE WATER TREATMENTS
SGRASSANTI INDUSTRIALI DEGREASERS
HIGHLIGHT OF THE MONTH
Le
tendenze di mercato del settore del trattamento acque industriali: l’analisi di Idrotecnica
Da un’intervista con Federico Marcenaro, CEO di Idrotecnica Srl
In questi primi 30 anni di storia, Idrotecnica, un’azienda italiana attiva nella produzione di impianti di purificazione e demineralizzazione acque industriali, ha collezionato una serie di importanti successi e traguardi: oltre ad essere una fra le prime aziende italiane a realizzare un impianto di trattamento ad osmosi inversa, l’azienda oggi fornisce i suoi prodotti in quasi tutto il mondo e si rivolge ad un numero sempre più significativo di comparti industriali. Abbiamo intervistato Federico Marcenaro, CEO dell’azienda, per individuare le tappe fondamentali della storia di Idrotecnica e analizzare le tendenze di mercato nel campo del trattamento acque.
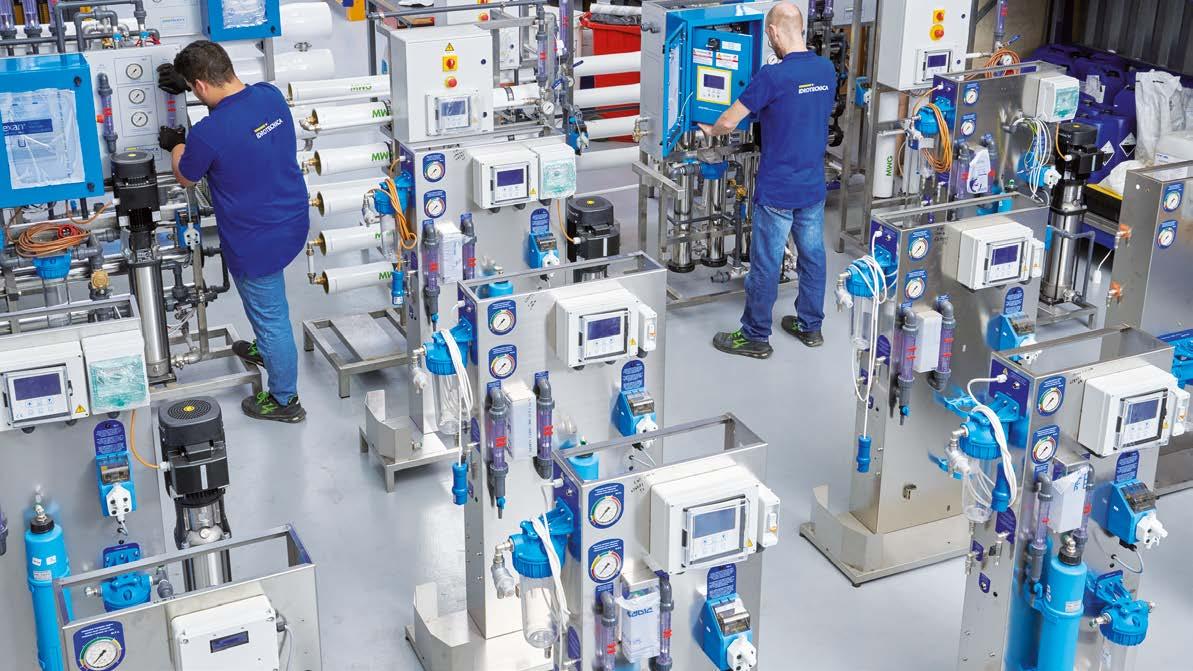
L’acqua è una risorsa fondamentale in molteplici comparti industriali e il suo trattamento consente di migliorare le prestazioni delle fasi di processo, oltre che di garantire maggiore protezione dell’ambiente. Purificare e/o demineralizzare l’acqua in ingresso ad un processo industriale tramite sistemi ed impianti realizzati ad-hoc è infatti un fattore di primaria importanza senza il quale si fermerebbe l’intero ciclo di produzione, comportando significativi fermi produttivi e conseguente aumento dei costi e delle tempistiche. Se caliamo il discorso nel settore dei trattamenti delle superfici,
il processo di demineralizzazione delle acque ricopre un ruolo imprescindibile nella fase di pretrattamento alla verniciatura in quanto l’impiego dell’acqua demineralizzata nell’ultimo stadio di risciacquo consente di aumentare la resistenza alla corrosione e migliorare l’adesione del prodotto verniciante. Tra i trattamenti più comuni di demineralizzazione dell’acqua vi sono l’osmosi inversa e lo scambio ionico. ipcm®_International Paint&Coating Magazine ha approfondito le principali caratteristiche e vantaggi di entrambi i processi in un’intervista con Federico Marcenaro, CEO di Idrotecnica Srl, Genova.
Chi è Idrotecnica
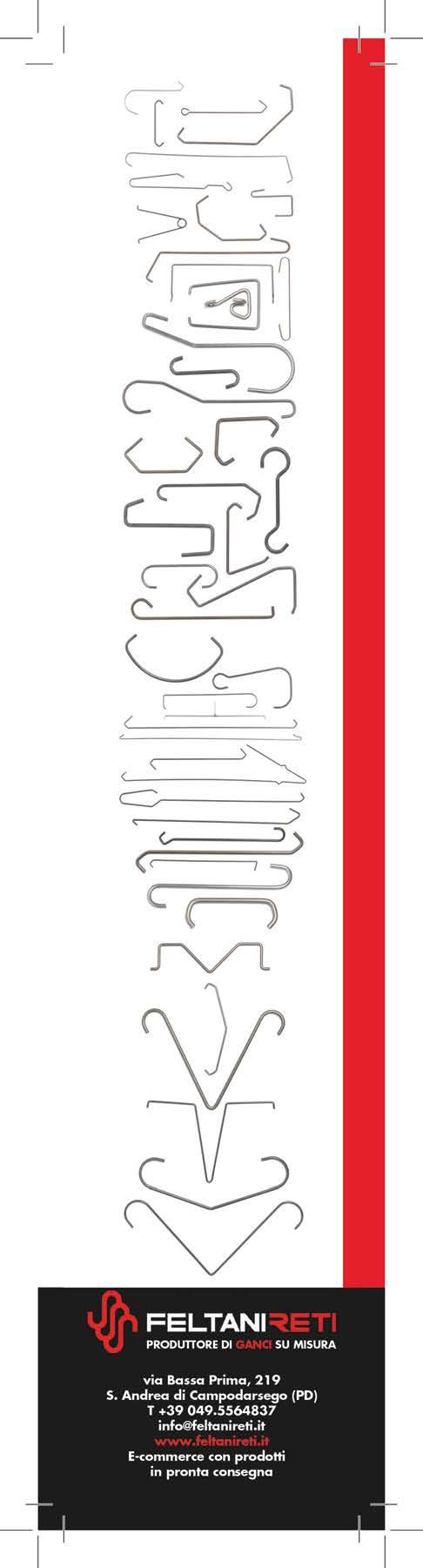
La storia di Idrotecnica Srl, azienda italiana specializzata nella produzione di sistemi di purificazione e demineralizzazione acqua, inizia nel 1991, già con un notevole bagaglio di esperienze e competenze maturate in precedenza dai suoi titolari, che decidono di mettere a disposizione le proprie competenze e il proprio know-how per progettare e realizzare soluzioni per il trattamento di acque industriali. L’azienda si specializza in particolar modo nella produzione di impianti a scambio ionico e ad osmosi inversa, diventando, nel 1993, una fra le prime aziende in grado di fornire al mercato italiano una tecnologia innovativa e in quel momento storico ancora poco conosciuta.

Da questo momento l’azienda inizia a collezionare una serie di importanti successi e traguardi: il continuo incremento della domanda consente a Idrotecnica di strutturarsi in modo più complesso, ad assumere progressivamente più personale tecnico e a trasferirsi in uno stabilimento più grande situato nel quartiere di Bolzaneto a Genova.
Nei primi anni 2000, Idrotecnica inizia ad esporre le proprie tecnologie alle numerose fiere ed eventi del settore organizzate a livello internazionale riuscendo a raggiungere nuovi mercati e settori industriali.
Oggi, gli impianti dell’azienda ligure raggiungono quasi ogni angolo del globo – dall’Europa all’America Latina, dall’Africa settentrionale all’Oceania; e servono svariate industrie, tra cui verniciatura, lavaggio industriale, cosmetica, farmaceutica, laboratori di ricerca e analisi.
La scelta di specializzarsi esclusivamente nel processo di demineralizzazione delle acque
Idrotecnica nasce con una filosofia ben precisa: specializzarsi su un unico core business, ovvero la demineralizzazione delle acque, e avere una profonda conoscenza tecnica dei settori di applicazione in cui gli impianti di demineralizzazione possono essere installati. “Questa scelta, che deriva dalla volontà di dedicare tutte le nostre competenze, il nostro tempo e le nostre risorse ad un unico comparto industriale, ci consente di offrire ai nostri clienti un servizio pre e post vendita rapido ed efficace. Il nostro team è infatti in grado di fornire supporto tecnico in meno di un’ora, anche in lingua inglese e in fusi orari differenti per le aziende che lavorano in altri continenti, oltre che spedire componenti di ricambio in circa 24 ore”. “Siamo estremamente consapevoli delle responsabilità che le nostre macchine ricoprono in quanto alimentano impianti che hanno un’importanza tecnica ed economica decisamente maggiore e per questo motivo investiamo quotidianamente nel nostro servizio di assistenza clienti e lavoriamo per sviluppare impianti estremamente semplici ed intuitivi nell’installazione e utilizzo, ma al tempo stesso robusti ed affidabili”.
Questa filosofia ha premiato Idrotecnica, consentendole di posizionarsi sul mercato come partner affidabile e di crescere costantemente nei suoi primi 30 anni di storia, presidiando sempre più settori industriali e mercati e fornendo i propri impianti ad un numero sempre maggiore di aziende.
Un’ampia gamma di impianti standard e personalizzati
Per soddisfare le esigenze dei clienti, il reparto produttivo di Idrotecnica è organizzato per realizzare impianti e apparati standard e su misura. La gamma standard di impianti di filtrazione e di demineralizzazione acque che sfruttano la tecnologia a scambio ionico e a osmosi inversa include circa 130 modelli differenti, che vengono consegnati nella maggior parte dei casi in meno di un mese (spesso in 1/2 settimane).
“L’estrema modularità e flessibilità dei nostri impianti ci consente di proporre la soluzione ideale in base alle esigenze produttive dei clienti. Qualora i modelli standard non soddisfino i requisiti di quest’ultimi, studiamo su misura la soluzione impiantista più idonea sia in termini di tecnologia sia di affidabilità e costi di gestione”.
La tendenza di mercato
“Nei primi anni ’90, Idrotecnica era una delle poche aziende italiane a credere nelle potenzialità della tecnologia a osmosi inversa, un principio fisico che all’epoca era ancora poco conosciuto e diffuso a livello industriale. Per decenni, svariati settori industriali hanno infatti continuato a preferire i demineralizzatori a scambio ionico. Tuttavia, negli ultimi anni, la nostra azienda sta riscontrando un aumento esponenziale della richiesta di impianti a osmosi inversa a scapito della tecnologia a scambio ionico in svariati comparti industriali, tra cui il settore della verniciatura”. Uno dei principali motivi che porta le aziende a prediligere il processo ad osmosi inversa è l’assenza di utilizzo di agenti chimici pericolosi come l’acido cloridrico e la soda caustica, garantendo maggiore sicurezza per l’ambiente e per l’operatore e facilitando le operazioni di smaltimento degli stessi. L’acqua prodotta a seguito del processo di osmosi inversa è infatti un’acqua che richiede una gestione molto più snella: la membrana semipermeabile che funge da filtro consente di rimuovere dall’acqua la quasi totalità delle sostanze in essa presenti permettendo quindi, con le giuste accortezze e con la consulenza di un tecnico competente, di affluire in fognatura senza ulteriori trattamenti.
Inoltre, le performance del processo ad osmosi inversa non dipendono né dalla presenza o meno di sali nell’acqua di alimento né dalla tipologia di acqua (dolce/dura): ciò lo differenzia dalla tecnologia a scambio ionico, le cui prestazioni sono correlate alla qualità dell’acqua di alimento. Il principale svantaggio dell’osmosi inversa rispetto allo scambio ionico, invece, riguarda il consumo di acqua in quanto i demineralizzatori a
scambio ionico sono in grado di eseguire un ricircolo dell’acqua all’interno del tunnel di lavaggio e di controllarne la conducibilità, riducendo drasticamente i consumi d’acqua.
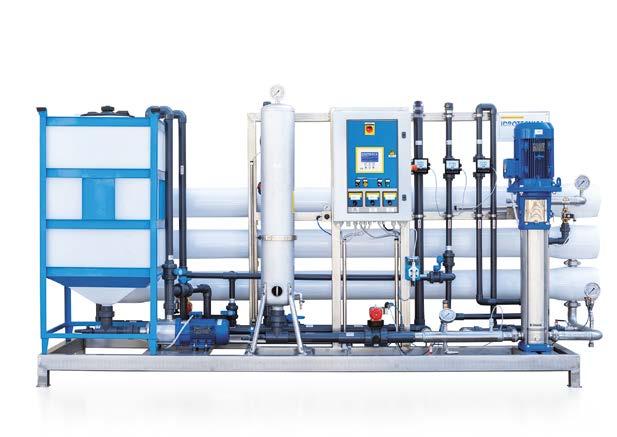
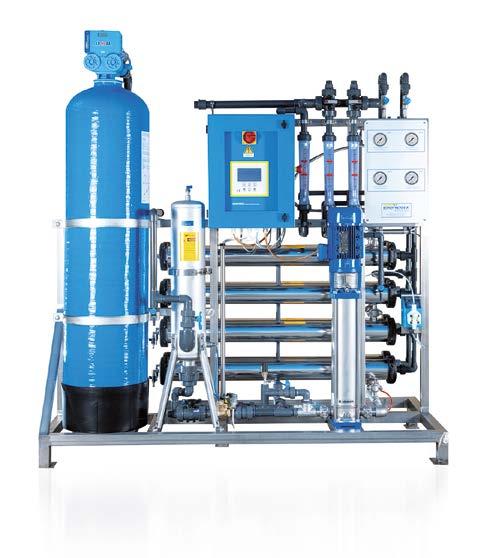
“Nonostante il mercato stia prediligendo il trattamento a osmosi inversa, Idrotecnica studia insieme al cliente la soluzione ideale tenendo in considerazione una serie di fattori, dal ciclo produttivo dell’azienda, dagli impianti installati all’interno dello stabilimento, alle competenze tecniche degli operatori e alle modalità di smaltimento dei prodotti”.
I progetti futuri
“Idrotecnica è un’azienda estremamente consolidata con un’importante esperienza, ma che mantiene un approccio fresco e dinamico tipico di una start-up e che si pone sin dall’anno della sua fondazione l’obiettivo di mettere il cliente e la sua soddisfazione al centro di ogni attività e progetto. Per questo motivo, l’aumento della domanda che abbiamo riscontrato negli scorsi anni e che continua ad essere in costante crescita ci porterà, nei prossimi mesi, ad assumere personale tecnico in grado di supportare le richieste dei clienti e di fornire loro un eccellente servizio di assistenza. Inoltre, per facilitare la gestione dei nostri impianti, abbiamo in programma di installare sistemi Industry 4.0 anche su impianti più economici e di dimensioni ridotte. Attualmente soltanto gli impianti più complessi sono dotati di soluzioni 4.0, ma crediamo che sia fondamentale fornire alle aziende e agli impiantisti che si interfacciano con il cliente finale la possibilità di gestire da remoto tutti i componenti che costituiscono l’impianto”.
E VOLUTION TO E -MOBILITY
Our 70 years experience in Surface Treatment is ready for the E-Mobility market.
Research, innovation, development.
In 70 years, our vision towards the future has never stopped. Today, Tecnofirma provides quality to the electric market which is the most evolving technology in the automotive industry. Our impregnation, cleaning and painting plants are the result of the constant commitment to offer cutting-edge solutions and products anytime, anywhere.
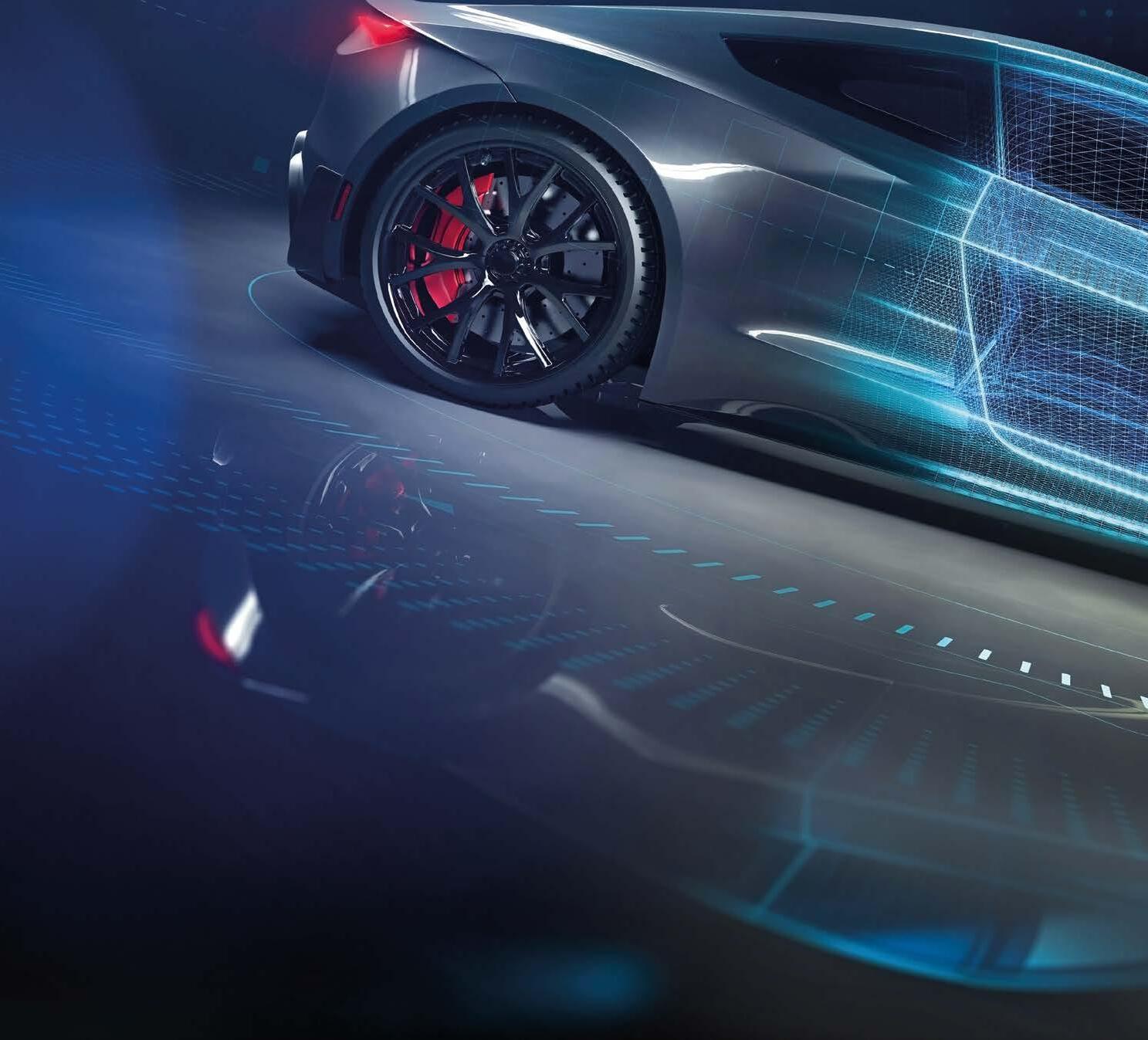
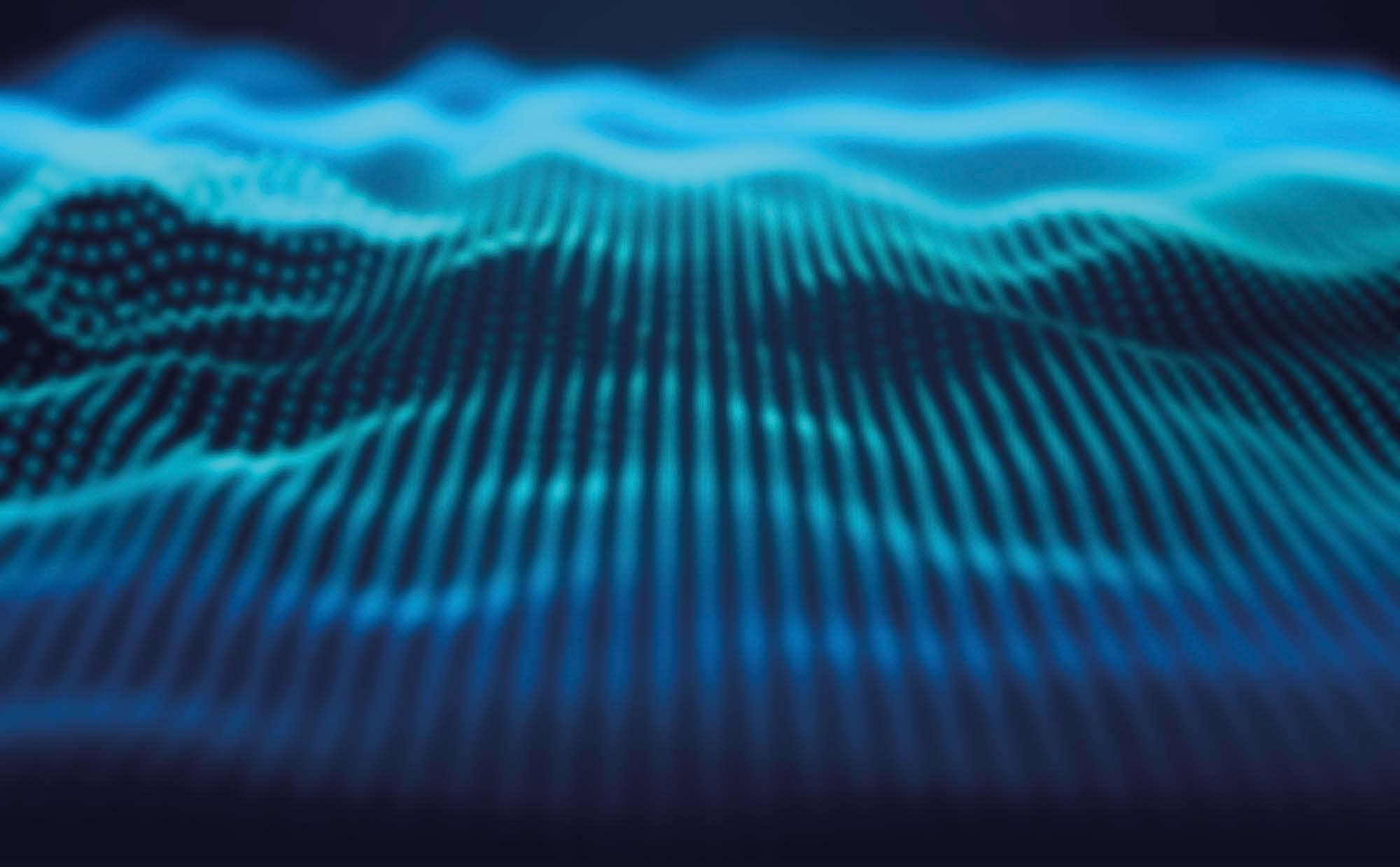
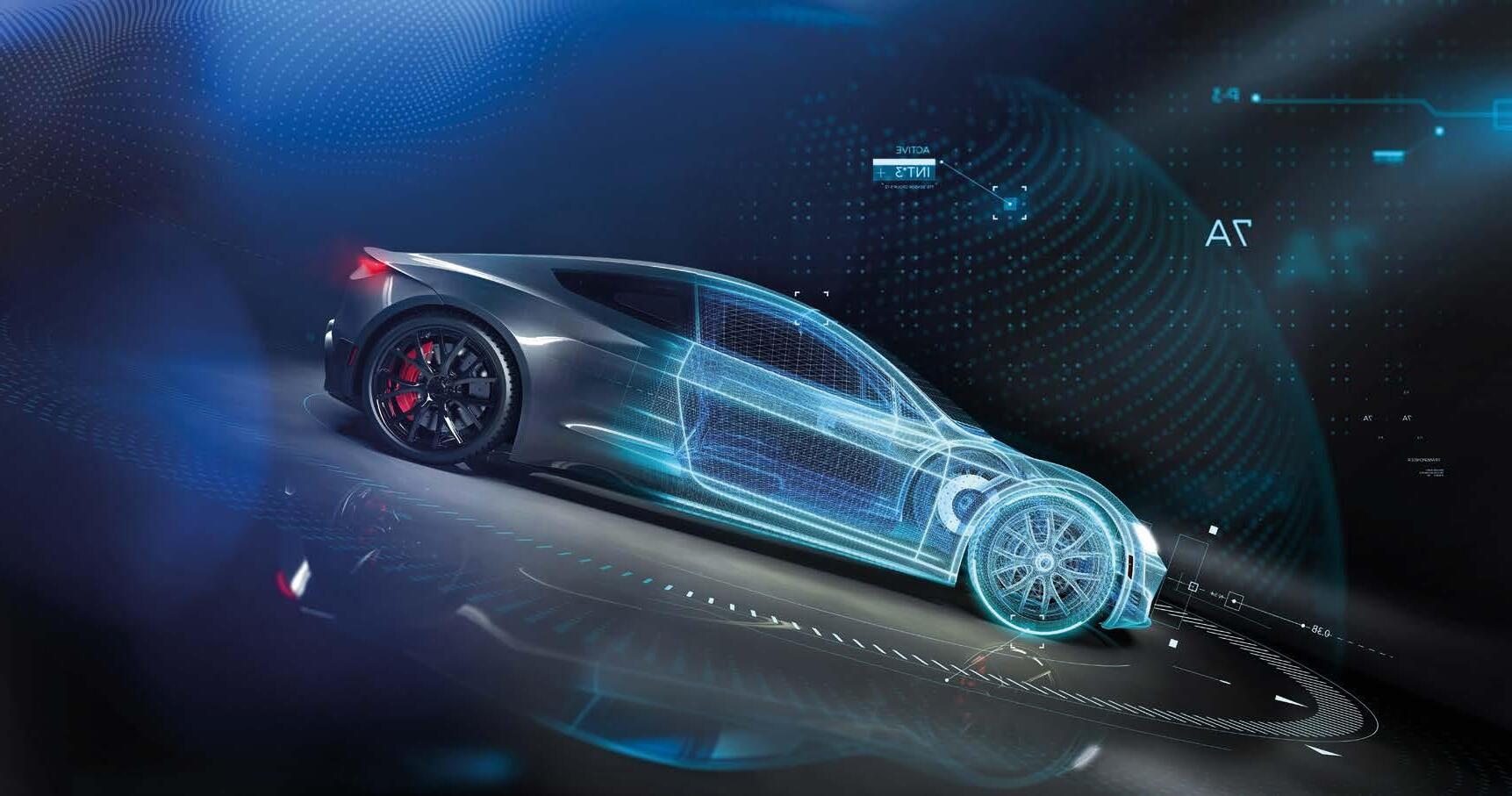
FOCUS ON TECHNOLOGY
Nella Portugal Bike Valley la partnership vincente con il produttore di vernici in polvere alza l’asticella della qualità di finitura
Sviluppo di vernici in polveri poliesteri e colour matching: questi sono gli strumenti di crescita che InCycles, azienda portoghese specializzata nell’assemblaggio e vendita di biciclette elettriche e tradizionali, ha consolidato insieme a uno dei propri fornitori di vernici, ST Powder Coatings, e con cui punta a cambiare il concetto di mobilità urbana, così come è stato inteso fino ad oggi, e l’apprezzamento del mercato verso manufatti verniciati a polvere invece che a liquido.
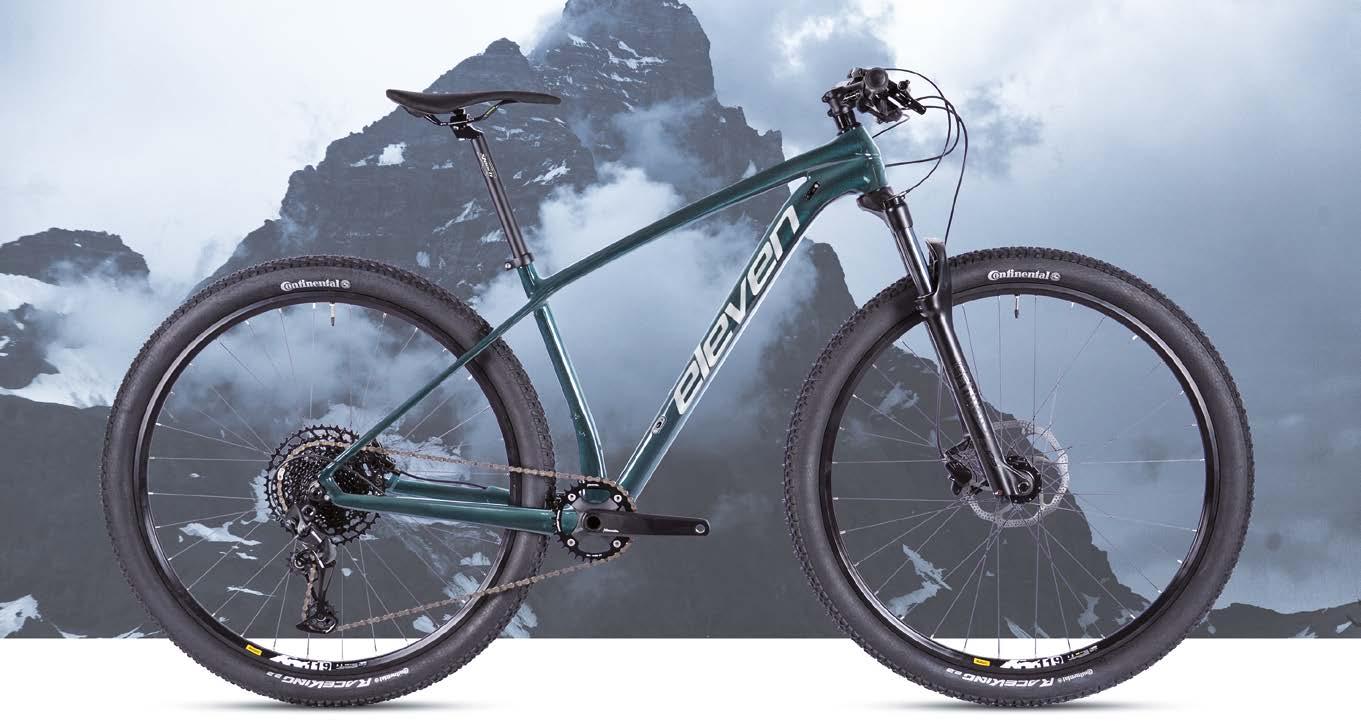
Lo scorso febbraio il Parlamento Europeo ha implementato in maniera decisiva la propria Cycling Strategy, incaricando la Commissione di raddoppiare il numero di chilometri destinati alle ciclabili in Europa entro il 20301. Secondo le principali associazioni del settore, questa mozione segna una svolta importante nello sviluppo di 1 https://www.europarl.europa.eu/doceo/document/B-9-2023-0102_EN.html
una politica più consapevole a livello europeo nei confronti di questa industria in rapido sviluppo. Secondo il comunicato stampa diffuso da ECF – European Cyclists’ Federation2, infatti, “l’invito segna il riconoscimento del ciclismo come modalità di trasporto a tutti gli effetti e risorsa industriale chiave per raggiungere gli obiettivi climatici a lungo termine 2 https://ecf.com/civicrm/mailing/view?id=5606&reset=1
e una produzione più pulita”. Il comunicato si conclude con un auspicio: “Tutti gli operatori dell’industria del ciclismo si augurano che la proposta di designare il 2024 come l’anno europeo del ciclismo […] incoraggi i governi nazionali a intraprendere ulteriori azioni come la riduzione delle aliquote IVA, moltiplicando le iniziative per promuovere l’uso della bicicletta e replicare il caso di successo della reindustrializzazione della ‘Portugal Bike Valley’ in altre regioni, con il sostegno mirato dei programmi di finanziamento europei”.
Il caso di successo citato si riferisce alla valle portoghese di Agueda, a sud di Porto, dove l’industria manifatturiera delle biciclette - in particolare delle e-bike – è diventato talmente fiorente da trasformare il Portogallo nel maggior produttore di biciclette nell’UE. Questa nazione di 10 milioni di abitanti, poco più del 2% della popolazione dell’Unione, produce un quarto delle biciclette del continente. Uno sviluppo che è la conseguenza di una crescente passione per il ciclismo in Europa - registrato in particolare dopo il periodo pandemico - e che ha modificato il concetto di mobilità urbana.

Per offrire un’idea di quanto questo settore abbia registrato uno sviluppo smisurato, proprio nel cuore della Portugal Bike Valley abbiamo visitato un’azienda che ha visto moltiplicare il proprio fatturato di 22 volte nel giro di pochi anni - dai 3 milioni di euro del 2018 ai 65 milioni dello scorso anno - e il numero dei propri dipendenti, da 15 a 300.
InCycles Bike Group di Agueda è specializzato nell’assemblaggio, verniciatura a polveri e distribuzione di e-bike e biciclette tradizionali sia per i più importanti marchi internazionali, sia con il proprio marchio “Eleven”.
Oggi la verniciatura delle biciclette riveste un ruolo sempre più importante all’interno del loro processo produttivo e l’attenzione alla sostenibilità dei prodotti utilizzati rientra nella visione di una produzione più pulita come quella auspicata dalla mozione del Parlamento Europeo. “Da circa 3 anni - spiega Pedro Conceição, General Manager di InCycles – abbiamo instaurato una partnership vincente con il produttore italiano di vernici in polvere ST Powder Coatings, che nel 2018 ha aperto una filiale a Maia, nel distretto industriale di Porto, non lontano dalla nostra sede. Fin dall’inizio le polveri hanno rappresentato la nostra principale scelta di finitura per due motivi: il primo è che sono caratterizzate da una maggiore resistenza in condizioni ambientali severe, che è un elemento chiave indispensabile soprattutto per i nostri interlocutori del Nord Europa, e, in secondo luogo, perché sono prodotti vernicianti ecocompatibili a zero emissioni di COV e completamente riciclabili e un numero sempre maggiore di clienti ritiene questo aspetto una discriminante per la scelta del proprio fornitore”.
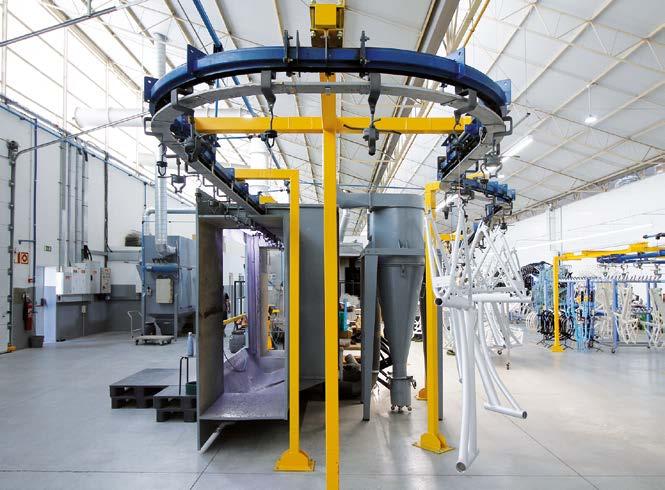
Il futuro è elettrico anche per le due ruote
“Stiamo cavalcando l’onda di questa crescita esponenziale della mobilità a due ruote – conferma Conceição – che sta attraversando attualmente l’Europa. Abbiamo puntato la nostra produzione sull’elettrificazione e ad oggi possiamo affermare che è stata la scelta vincente. Lo testimonia per esempio il fatto che uno dei progetti più importanti riguarda le e-bike da mettere a disposizione per il noleggio nelle più importanti città europee”. Proprio per far fronte al picco produttivo, recentemente l’azienda portoghese ha investito in una nuova struttura in cui ha accorpato la linea di verniciatura, le 4 linee di assemblaggio, di cui 3 dedicate alle e-bike e
una alle biciclette tradizionali, e le 6 linee dedicate alle ruote. Alberto Cardoso, direttore del reparto di verniciatura, ci spiega i principali passaggi del processo produttivo: “Riceviamo i componenti già granigliati e interveniamo con una carteggiatura manuale solo in caso di necessità. Passiamo quindi direttamente al reparto di verniciatura, dove i pezzi sono caricati sul trasportatore per essere condotti alla prima stazione in cui applichiamo manualmente la vernice in polvere. Passano quindi nel forno di polimerizzazione prima dell’applicazione delle decalcomanie all’acqua. Segue l’asciugatura, la rimozione delle maschere delle decalcomanie e l’applicazione del topcoat finale, che può essere lucido o opaco. Il ciclo di verniciatura si conclude con la polimerizzazione finale nel forno di cottura. A questo punto i pezzi sono pronti per essere trasportati al reparto di assemblaggio dove sono collocati su una delle 4 linee preposte, imballati e immagazzinati per la spedizione finale”.
Investire in verniciatura
“L’internazionalizzazione della nostra produzione – prosegue
Conceição - ha comportato non solo l’implementazione delle linee di assemblaggio, ma anche un investimento sempre più consistente nella linea di verniciatura a polveri installata 3 anni fa. La continua richiesta di rivestimenti superficiali di qualità è talmente forte che avremmo già voluto affiancarle un nuovo impianto, ma, purtroppo, la guerra in Ucraina e il conseguente outlook finanziario negativo a livello globale hanno – speriamo solo temporaneamente – fermato il nostro progetto. Il motivo per cui in questo momento è importante per noi puntare sulla verniciatura è che la qualità della vernice applicata sui componenti
provenienti dall’industria asiatica non soddisfa i requisiti minimi richiesti. Questo è uno degli aspetti per cui anche l’Unione Europea si sta muovendo con misure antidumping, derivate in gran parte dalla consapevolezza che anche nel settore delle 2 ruote dipendiamo in modo eccessivo dal mercato asiatico. Attualmente il 90% dei componenti che assembliamo nel nostro stabilimento hanno provenienza cinese”. La tendenza sta cambiando e, come testimonia la mozione del Parlamento Europeo, si spinge verso una produzione sempre più europea dei manufatti anche nel settore del ciclismo.
“Al momento attuale, quindi, la strategia che riteniamo vincente per affermarci in questo mercato complesso è quella di fornire le migliori performance di rivestimento possibile con 2 obiettivi principali: la qualità della finitura e la flessibilità della produzione”.
Una partnership perfetta per crescere
“Il primo contatto con ST Powder Coatings è stato determinante per la scelta del nostro fornitore di riferimento” – conferma Cardoso.
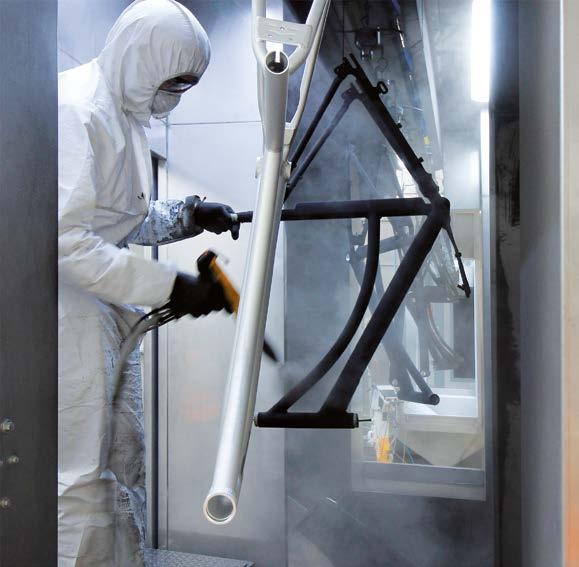
“Nonostante applichiamo anche vernici liquide per progetti speciali, sapevamo già che le polveri avrebbero rappresentato la soluzione perfetta, soprattutto per soddisfare i clienti del Nord Europa più esigenti dal punto di vista della qualità delle finiture e della loro resistenza in condizioni climatiche più severe di quelle sud-europee. Fino all’incontro con il produttore italiano utilizzavamo vernici epossidiche, ma, grazie ai test suggeriti dal suo team, abbiamo concluso che la chimica poliestere era più adatta per attribuire maggiore resistenza e durabilità in esterno alla finitura, soprattutto in condizioni di vicinanza al mare, di basse

temperature, di esposizione a neve o ghiaccio. “Le vernici in polvere poliestere – interviene José Carlos Manta, Direttore Generale di ST Powder Coatings Portugal - possono essere utilizzate sia in qualità industriale sia in qualità architettonica. La vernice poliestere è utilizzata in particolare per il rivestimento dei metalli destinati ad ambienti esterni proprio perché garantisce un’ottima resistenza agli agenti chimici e atmosferici e un’ottima ritenzione del colore. Nel caso specifico, InCycles utilizza come ciclo standard le polveri poliesteri industriali, mentre per esigenze specifiche le polveri poliesteri Qualicoat. Il nostro laboratorio formula e sviluppa polveri su richiesta specifica del cliente. Nella collaborazione con InCycles abbiamo cercato di sviluppare l’intero portfolio di tinte di cui avevano bisogno per trovare il perfetto accoppiamento di colore con i componenti verniciati a liquido provenienti dal mercato asiatico. Tuttavia, non è sempre facile trovare la tinta perfetta in polvere da abbinare al particolare effetto metallizzato, brillante e talvolta “chiassoso” ottenuto con le vernici liquide cinesi. Il colour matching con i rivestimenti già applicati sui componenti che InCycles riceve è una delle sfide più impegnative per il nostro team”. “ST Powder Coatings ha comunque trovato il giusto equilibrio –ribadisce Conceição – e, nonostante le difficoltà descritte, è riuscita a fornirci soluzioni di colour matching che soddisfano i nostri clienti. I primer e i topcoat a polvere forniti, anche quelli ad effetto metallizzato o speciale, restituiscono una finitura di basso profilo, meno vistosa rispetto alle vernici liquide di pari effetto o colore. Per questo stiamo cercando di convincere i nostri clienti a scegliere le vernici in polvere,
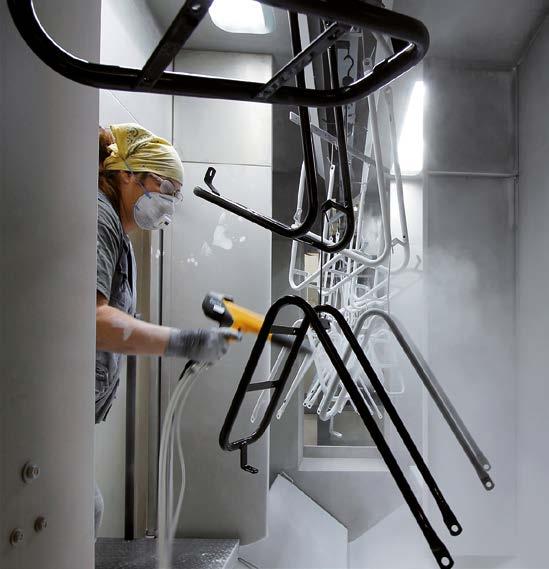
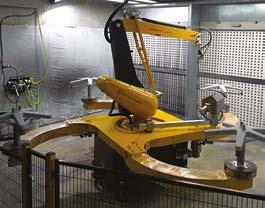

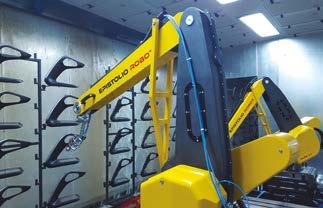


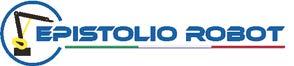
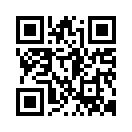
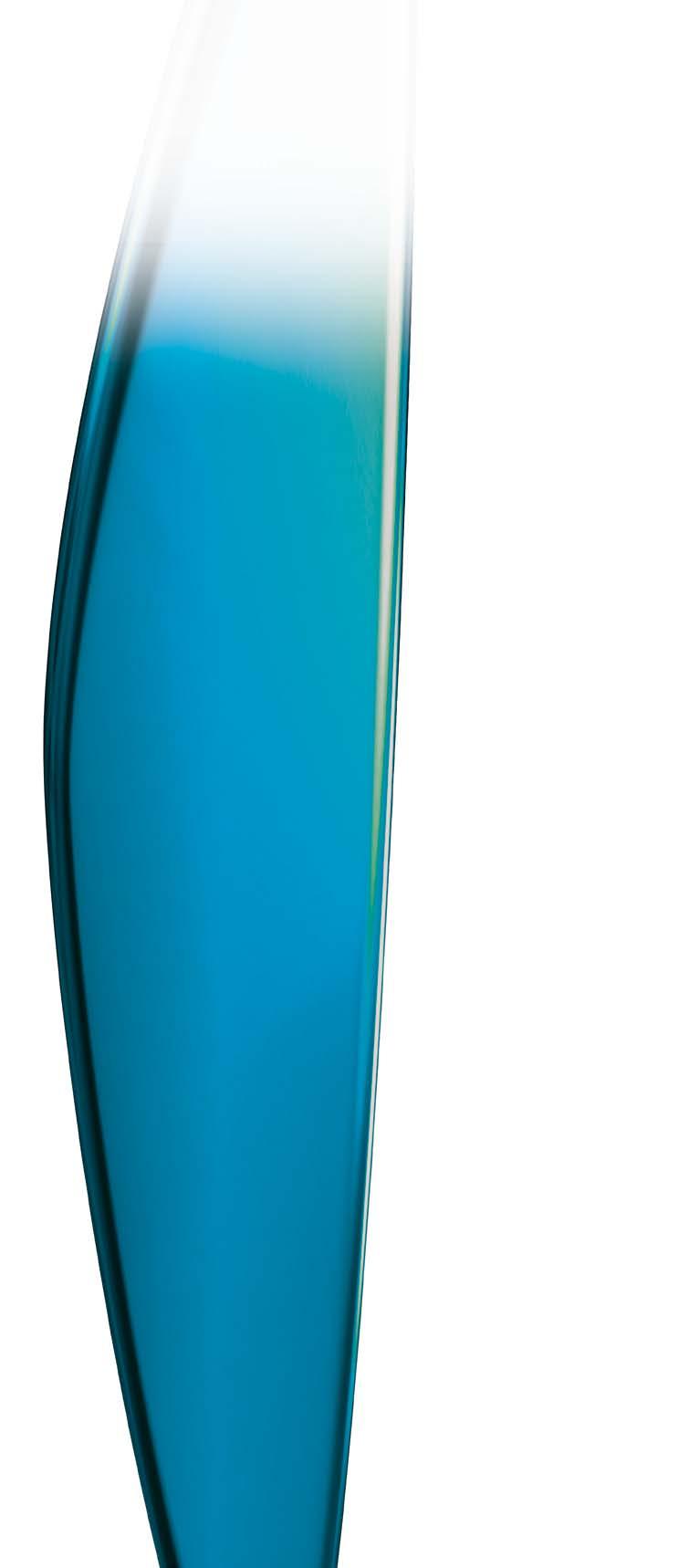
quando la tinta sviluppata da ST Powder Coatings si avvicina molto a quella liquida, e il riscontro che abbiamo dal mercato è al momento molto positivo. Oltre a questa estrema cura nella ricerca delle soluzioni più adatte alle nostre esigenze, ci sono altri aspetti che apprezziamo molto, come la rapidità e l’efficienza del servizio e l’attendibilità delle soluzioni proposte… penso che questo sia dovuto in parte anche all’esperienza nel campo della produzione e verniciatura di biciclette in cui l’Italia e il Veneto, in particolare, la regione di provenienza di ST Powder Coatings, rappresentano un punto di riferimento più che affermato”.
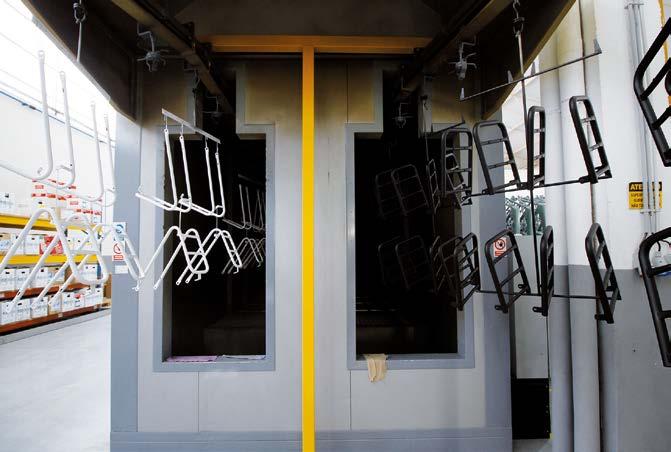
La bicicletta diventa protagonista di un cambio di mentalità sostenibile
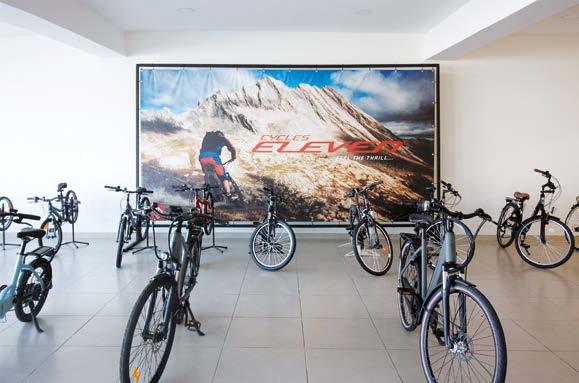
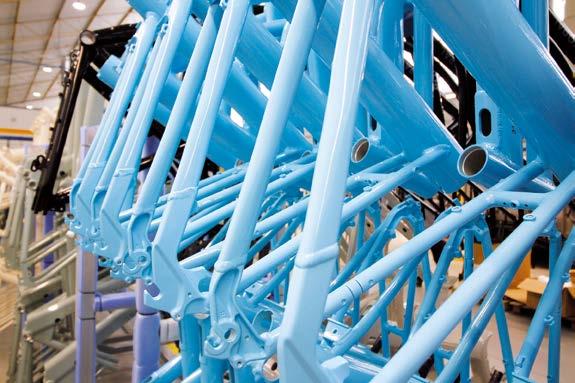
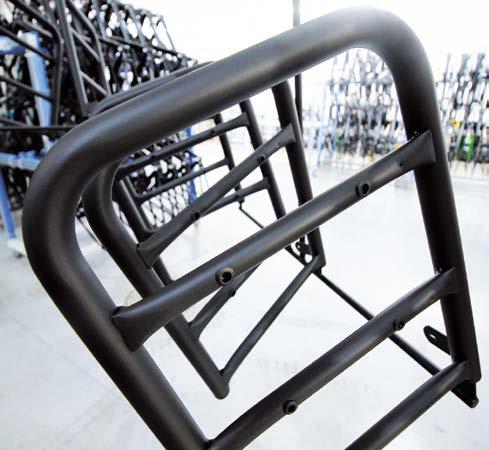
“Siamo fermamente convinti che l’uso quotidiano e l’accettazione della bicicletta come mezzo di trasporto – conclude Conceição – rappresenti
un’opportunità per implementare soluzioni di mobilità non inquinanti e sostenibili, alternative ai sistemi tradizionali, migliorando così la qualità della vita e le relazioni umane. L’obiettivo è quello di consolidare il cambio di mentalità già avviato, resosi necessario alla luce dell’attuale situazione economica mondiale, che vede nella limitazione dei prodotti a basso costo provenienti dal mercato asiatico una spinta alla crescita della produzione europea. InCycles è pronta per affrontare questa svolta con il supporto di partner competenti e flessibili come ST Powder Coatings ha dimostrato di essere, contribuendo in modo decisivo alla crescita della nostra azienda, dal momento che la verniciatura a polveri sta diventando un asset strategico sempre più determinante nelle scelte dei nostri clienti sia in termini di qualità di finitura sia in termini di sostenibilità”.
FASTRIP T2-120 MIX our brand new and most compact paint stripping system
FASTRIP T2-120 MIX uses the mechanical action of the paint stripper on the parts that is ensured by the hydrostatic thrust generated by a specially designed mixer.
• Rectangular tank in AISI 304 stainless steel, 450 x 700 x h300 mm, with 20/10 thick walls and a 1” bottom valve for easy emptying
• Steel mixer for continuous fluid circulation, enhancing paint stripping efficiency and heating system performance
• Motor is protected from heat and an electric lock that stops the mixer when the lid is opened
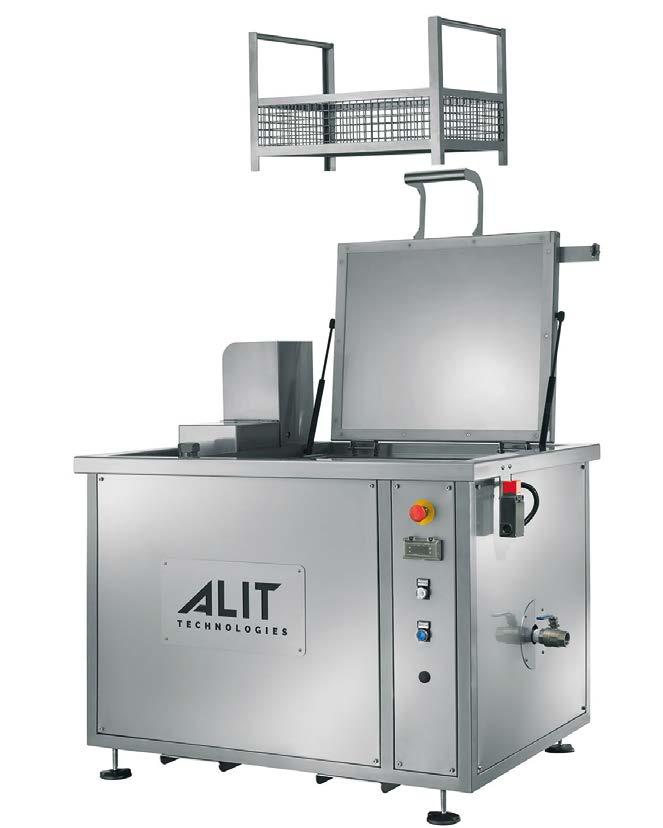
• Integrated control panel, removable lid with thermal insulation and pistons for easy access.
• Safety, efficiency, and superior quality.
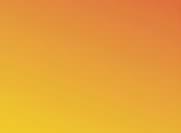

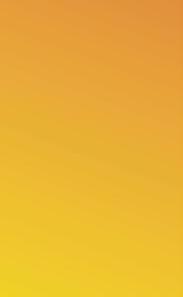

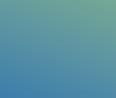
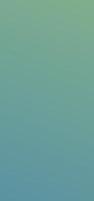
ADVANCEMENTS
Nel mercato delle vernici per alluminio vi è talvolta grande confusione quando si tratta di pianificare e scegliere il pretrattamento corretto.
Nel campo d’attività di GSB, dedicato alla garanzia della qualità della verniciatura su alluminio, acciaio e acciaio zincato nel settore dell’architettura, la questione del pretrattamento corretto per un particolare ambiente fa parte del lavoro quotidiano.
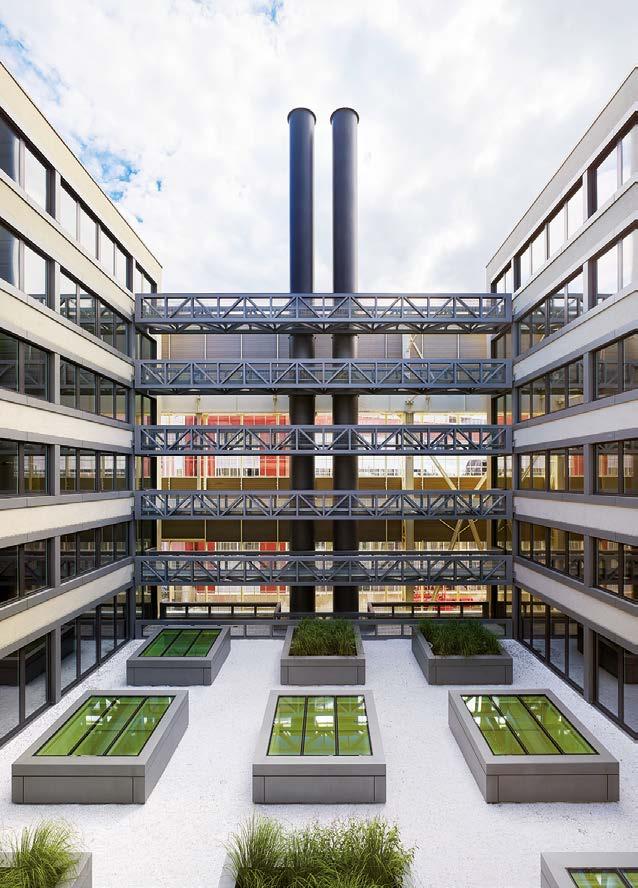
Il sistema di garanzia della qualità è stato sviluppato nel corso di decenni e comprende vari sigilli di qualità GSB per diverse aree applicative. Quindi, come è strutturato un sistema di garanzia della qualità rivolto ai rivestimenti per esterno mediante vernici in polvere e liquide?
Il sistema di garanzia della qualità GSB in sintesi
Il miglior modo di capire come scegliere il pretrattamento di una verniciatura per esterno è attraverso una rapida analisi con il sistema di garanzia della qualità GSB. Oggi ci limitiamo al substrato in alluminio.
Una verniciatura è conforme a GSB solo se è stata pretrattata con prodotti chimici di pretrattamento a base di cromo certificato GSB o esenti da cromo 6 in un processo complessivamente adeguato. In alternativa, è possibile eseguire il pretrattamento mediante pre-anodizzazione, ma ne parleremo più avanti. Inoltre, è obbligatorio che il processo di verniciatura sia realizzato da aziende del settore certificate GSB e che siano impiegate vernici a polvere o liquide (materiali di rivestimento) aventi la medesima certificazione.
Le ispezioni del verniciatore sono il fulcro della sicurezza della catena del processo di verniciatura. Gli istituti di prova autorizzati e indipendenti eseguono controlli alle aziende di verniciatura in possesso di certificazione GSB due volte l’anno e senza preavviso.
Qui non è il caso di dilungarsi troppo su quelli che sono considerati i test più restrittivi sul mercato dell’architettura per i prodotti chimici di pretrattamento e i materiali di rivestimento, ma piuttosto sulle ispezioni realizzate presso le aziende di verniciatura.
Categorie di corrosività e differenze nei sigilli di qualità GSB Ci sono vari sigilli di qualità, che si differenziano essenzialmente nei test di corrosione effettuati nell’ambito degli audit e il modo col quale sono valutati.
La differenza nel pretrattamento dell’alluminio per diverse ambientazioni climatiche basata sull’esempio di aziende di verniciatura certificate GSB
Nel caso di aziende di verniciatura certificate con Standard o Master Quality Seal senza un sigillo aggiuntivo, l’ispettore preleva dei pannelli campione dalla produzione come parte degli audit. Successivamente viene effettuato un test in nebbia salina acetica sui campioni (secondo ISO 9227).
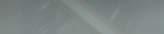

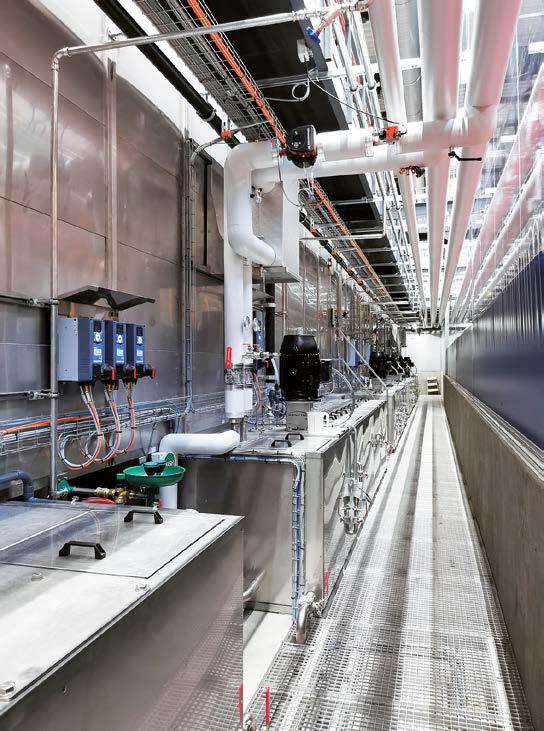
Il test dura 1000 ore, la delaminazione all’intaglio a T deve essere ad un massimo di dmax ≤ 1 mm e il grado di inclinazione deve essere di 0S(0). I rivestimenti applicati da verniciatori GSB Standard e Master Coaters sono la scelta ideale per ambienti caratterizzati dalla categoria di corrosività C3 (secondo ISO 9223).

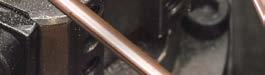

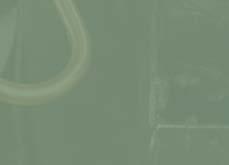

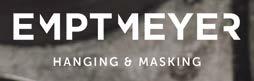



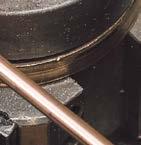

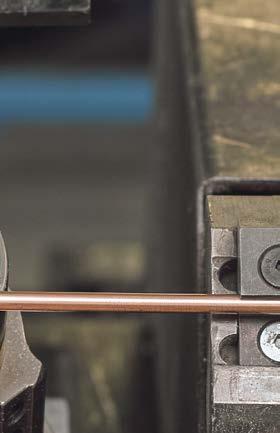

In aggiunta, ci sono i verniciatori GSB Master e GSB Premium che portano il sigillo supplementare Sea Proof. Oltre al test AASS, in questi casi è eseguita anche la prova di corrosione filiforme (secondo ISO 4623-2). Qui la lunghezza massima del filamento non deve superare i 2 mm. Oltretutto, c’è un valore speciale (F) per la corrosione filiforme calcolato dalla moltiplicazione della lunghezza media del filamento per la frequenza di comparsa del filamento e non deve superare 0,3. I rivestimenti degli applicatori GSB Master e Premium aventi il sigillo
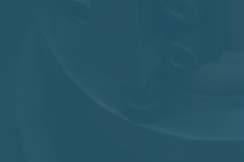
aggiuntivo Sea Proof sono utilizzabili in ambienti che potrebbero essere caratterizzati dalla categoria di corrosività C4 (secondo ISO 9223).

Ci sono poi i verniciatori GSB Master e GSB Premium che dispongono del sigillo supplementare Pre-anodisation Sea Proof Plus. Anche qui la lunghezza massima del filamento non dovrà superare i 2 mm. Tuttavia, la regolamentazione per il valore F è più stringente (F ≤ 0.1). In confronto ai verniciatori che non portano un sigillo aggiuntivo o quello supplementare Sea Proof, coloro che dispongono del sigillo Pre-anodisation Sea Proof Plus effettuano una pre-anodizzazione. La differenza tra anodizzazione decorativa e pre-anodizzazione è che in quest’ultima i pori rimangono aperti e perciò aiutano ad assicurare una buona adesione della vernice applicata in seguito.
Se un rivestimento si dovesse utilizzare in un ambiente potenzialmente caratterizzato dalla classe di corrosività C5, le aziende di verniciatura con il sigillo aggiuntivo Pre-anodisation Sea Proof Plus sarebbero la scelta ideale per portare a termine il lavoro. Solitamente un ambiente corrosivo di questo tipo si trova sulla costa, ad esempio, dove la concentrazione di sale nell’aria è elevata.
Quale categoria di corrosività si applica alla mia richiesta? Ma come sapete quale categoria di corrosività utilizzare per caratterizzare un ambiente? Ad esempio, ci sono mappe panoramiche che dividono i paesi in tipologie. Tuttavia, queste mappe sono utilizzabili solo come indicatori approssimativi. La corrosività dell’ambiente può variare di molto a livello locale, anche in aree piccole, ad esempio l’abrasione del rame dalle linee aree può aumentare la corrosività così come fabbriche industriali o strade ad alta percorrenza. L’unico metodo per determinare in modo affidabile la categoria di corrosività è analizzare dettagliatamente la posizione interessata insieme ad un esperto. ISO 9223 fornisce una linea guida per determinare la classe di corrosività basata sulla perdita di massa per alluminio, acciaio, rame e zinco nel primo anno di esposizione. Questo sarebbe il primo modo di stabilire la classe di corrosività e si effettua valutando la corrosione uniforme.
In questo caso, ISO 9223 dichiara che non è possibile determinare la corrosione uniforme e localizzata dell’alluminio per il primo anno mediante test all’aperto del campione, a causa del comportamento di passivazione e della diminuzione dei tassi di corrosione dell’alluminio nel tempo. Se non è possibile una valutazione basata sul grado di corrosione, ISO 9223 permette di determinare la categoria di corrosività basandosi sulle informazioni fornite dall’ambiente. Chiaramente questo lascia spazio all’interpretazione.
Ad esempio, se siete incerti tra le due categorie di corrosività, potreste optare per la categoria più alta successiva, specialmente se siete poco sicuri sulla corrosività di quell’ambiente in futuro. È anche importante considerare possibili cambiamenti futuri della corrosività di un ambiente, ad esempio la costruzione di nuove strade nell’area, le emissioni o l’apporto dato dal sale stradale possono aumentare il grado di corrosività.
In conclusione, le leghe in alluminio impiegate nell’edilizia (profili EN AW-6060 e EN AW-6063; per gli strati EN AW-5005/5005a e EN AW5754) possono essere lasciate in condizioni atmosferiche normali senza verniciatura e senza preoccuparsi di eventuali danni strutturali. Abbinare la verniciatura alla corrosività dell’ambiente ha uno scopo puramente decorativo nel caso dell’alluminio (per le leghe menzionate sopra).
“Abbinare la verniciatura alla categoria di corrosività” va ben oltre ISO 9223, la quale non tiene in considerazione le vernici. Questa è la ragione per cui GSB ha basato le raccomandazioni per le vernici sull’alluminio per vari ambienti sulle categorie di corrosività di ISO 9223.
La vernice è applicata: alcune parole sulla pulizia Ponendo che il progetto sia stato completato e che il processo di verniciatura sia stata pianificato correttamente e portato a termine, qual è il passo successivo? Una pulizia adeguata è estremamente importante e GSB fornisce raccomandazioni in merito agli intervalli di pulizia. Per i rivestimenti impiegati in progetti caratterizzati dalle categorie di corrosività C3 e C4, GSB raccomanda una pulizia all’anno. Per lavori in aree definite dalla categoria C5, GSB consiglia due pulizie all’anno. Questi intervalli di pulizia sono parte dei termini e condizioni generali di molti verniciatori GSB.
Un’ultima parola su ISO 9223 e un consiglio pratico
In sintesi, per la verniciatura dell’alluminio consigliamo quanto segue:
1. Determinare la corrosività dell’ambiente nell’area di utilizzo previsto.
2. Scegliere il verniciatore GSB basandosi sulla categoria di corrosività:
• GSB Standard o Master senza sigillo supplementare: C3
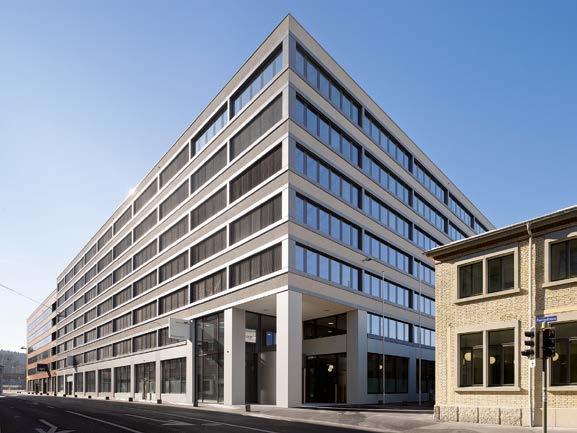
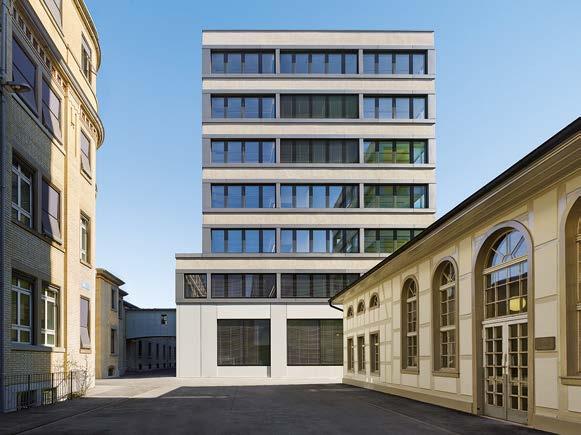
• GSB Master o Premium Coater con sigillo aggiuntivo Sea Proof: C4
• GSB Master o Premium Coater con sigillo aggiuntivo Pre-anodisation Sea Proof Plus: C5.

del Gruppo ILTOM garantisce flessibilità
produttiva riducendo al contempo i consumi energetici ed elevando le performance qualitative
Gabriele Lazzari ipcm®Il Gruppo ILTOM si è trasformato negli anni da una piccola realtà artigianale in una rinomata holding industriale attraverso una strategia di crescita dimensionale, sinergie produttive e investimenti innovativi. L’ultimo tra questi è il nuovo impianto automatico di verniciatura a polvere progettato e costruito da M.I. DUE, che consente all’azienda di gestire componenti di diverse dimensioni e geometrie garantendo qualità, riproducibilità e tempi di consegna rapidi.
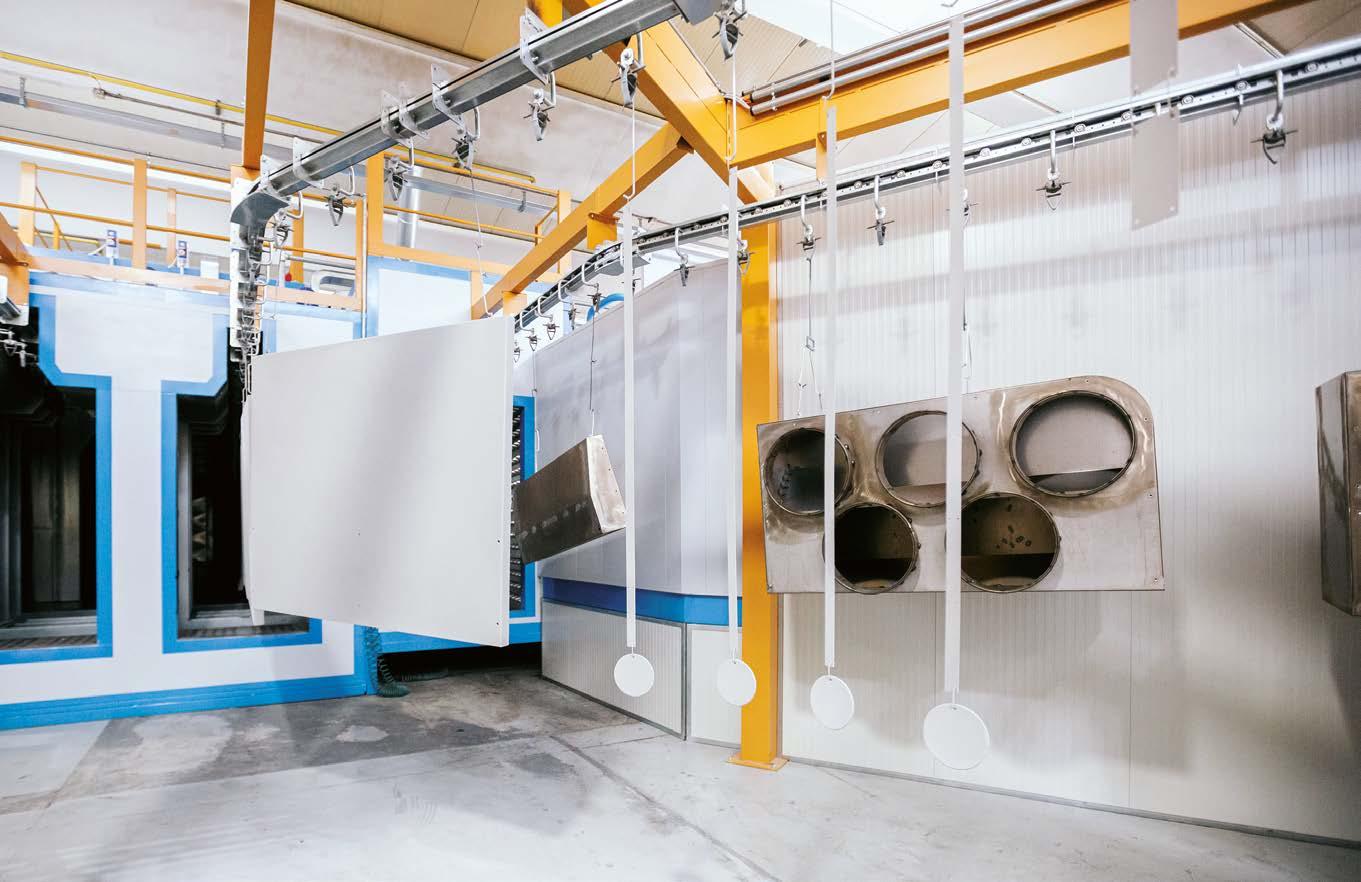
L’impianto di verniciatura a polvere
Al fine di soddisfare una realtà produttiva sempre più dinamica e globale e differenziarsi sul mercato rispetto ai concorrenti, una strategia molto diffusa è quella di implementare una catena di approvvigionamento e logistica altamente efficiente, basata su dispositivi intelligenti, tecnologie avanzate e processi perfettamente interconnessi che consentono di rispondere in modo tempestivo ed efficiente alle esigenze dei clienti.
In tal senso, il Gruppo ILTOM è un’azienda internazionale con sede a Romanengo (CR) che rappresenta una storia di successo italiana. Negli anni, l’azienda ha portato avanti una strategia di crescita incentrata sull’acquisizione di molteplici siti produttivi che sono stati aggiornati con soluzioni tecnologicamente avanzate ed interconnesse, al fine di garantire il rispetto dei medesimi standard qualitativi in tutte le sedi e poter soddisfare rapidamente ogni richiesta dei clienti. In questo modo, l’azienda ha raggiunto un notevole traguardo nel corso dell’ultimo anno, superando per la prima volta i 100 milioni di euro di fatturato. Il Gruppo ILTOM è una carpenteria industriale con clienti appartenenti a molteplici settori. L’azienda è inoltre fortemente impegnata nella sostenibilità ambientale. Pertanto, ha realizzato significativi investimenti nell’efficientamento energetico, con particolare attenzione alla riduzione dei consumi di gas.
Tenendo fede alla propria strategia aziendale, il Gruppo ha
recentemente investito in nuovo impianto di verniciatura a polvere progettato, costruito e installato da M.I. DUE S.R.L (Besana in Brianza, MB), che ha permesso a ILTOM di incrementare la capacità produttiva, riducendo al contempo i consumi energetici del 15% rispetto ad impianti tradizionali, sempre rispettando le stringenti specifiche tecniche imposte dai clienti.
ILTOM: una holding industriale a gestione familiare
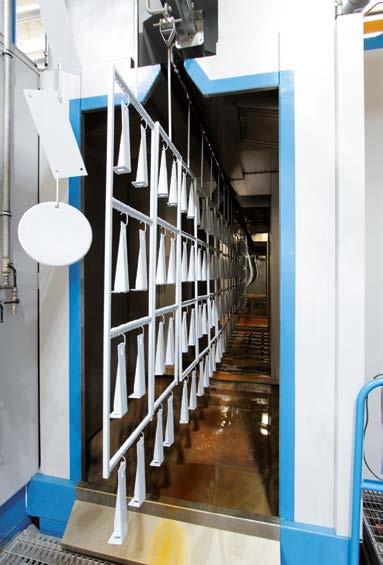
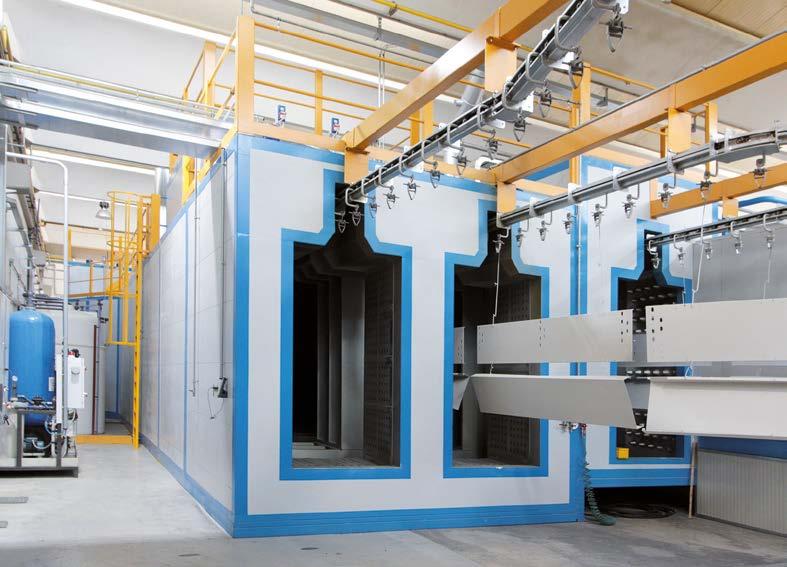
Il Gruppo ILTOM è una holding industriale ma a gestione familiare dedicata alla lavorazione della lamiera conto terzi. Fondata nel 1970 da Francesco Venturelli come piccola realtà, l’azienda si è evoluta negli anni grazie all’ingresso in società dei figli Luca e Pierangelo Venturelli nel 1996, che ne hanno a loro volta favorito esponenzialmente la crescita. Al fine di supportare i crescenti ritmi produttivi, ILTOM acquisì nel 2000 un nuovo stabilimento a Romanengo (CR), dove risiedono tutt’ora gli uffici e alcuni reparti produttivi dell’azienda. A seguito della crisi finanziaria del 2007, il Gruppo decise inoltre di espandersi anche sui mercati esteri, arrivando a commercializzare i propri prodotti in Francia (che rappresenta ora il 65% del fatturato), Svizzera, Ungheria, Polonia, Romania e altre nazioni extra-europee.
“La struttura aziendale del Gruppo ILTOM è il risultato di una strategia in cui sinergie produttive, crescita dimensionale, innovazione e qualità
sono state sempre considerate pre-condizioni per competere al meglio. Abbiamo cercato di procedere di pari passo, combinando l’aumento dei volumi interni con l’acquisizione di altre società che ci permettessero non solo di soddisfare velocemente le nostre esigenze produttive, ma anche di espanderci in nuovi settori o aree geografiche che in precedenza non eravamo in grado di presidiare”, esordisce Roberto Cagna, Purchasing and Supply Chain Manager di ILTOM Spa. “Tutte queste aziende sono state incorporate nelle logiche del nostro gruppo: il sistema gestionale SAP, le tecnologie produttive, i software di programmazione e le procedure di qualità sono infatti elementi caratterizzanti e comuni per tutte le società del gruppo. In questo modo, è stato possibile ottenere una certificazione di qualità di gruppo ed essere particolarmente flessibili nella gestione dei picchi di domanda. Al sorgere di eventuali problematiche produttive, infatti, possiamo smistare la produzione nelle varie sedi. L’investimento in un nuovo impianto di verniciatura commissionato a M.I. DUE, che ha sostituito una linea precedente non più in grado di soddisfare i requisiti di qualità e ripetibilità imposti, rientra quindi in questa logica: offrire un servizio completo ai nostri clienti internazionali, consegnando il pezzo finito e pronto per l’utilizzo in breve tempo e secondo standard qualitativi elevati”.
Dalla scelta della materia prima alla consegna del prodotto finito e imballato Attualmente il Gruppo ILTOM produce strutture e componenti per quadri elettrici, cabine elettriche, macchine utensili, distributori automatici di bevande e alimenti, impianti di climatizzazione e riscaldamento, veicoli industriali e agricoli e strumentazione medica e farmaceutica, oltre che per il settore nucleare e dell’elettronica. Fanno parte del core business la progettazione e la costruzione di stampi, la lavorazione meccanica di precisione della lamiera e la verniciatura a polvere.
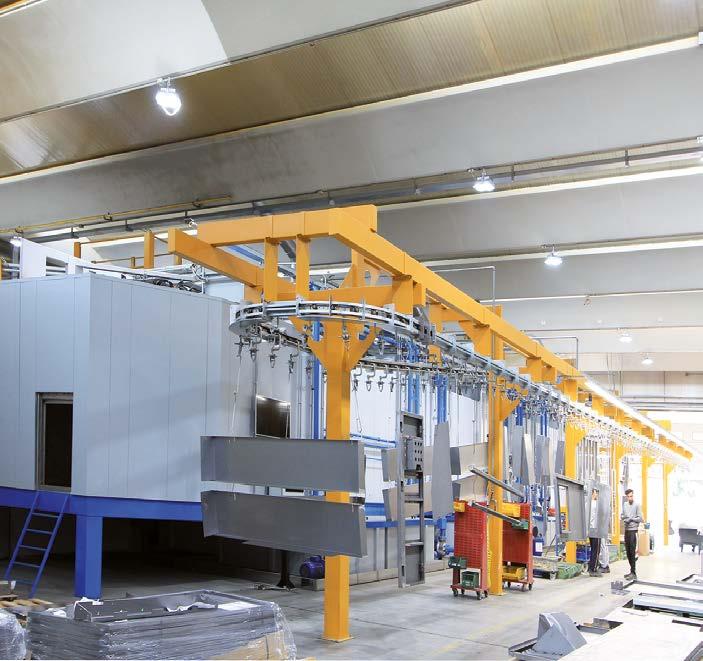
La produzione parte dall’acquisizione della materia prima, ovvero coils o fogli di lamiera di diverse dimensioni in acciaio decapata, lucida, zincata, elettrozincata e alluminata che, attraverso centri di lavoro con macchine a controllo numerico, sono soggetti a numerose lavorazioni meccaniche come, tranciatura, punzonatura, taglio laser

(sia fibra che CO2) e piegatura.

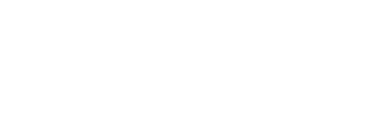
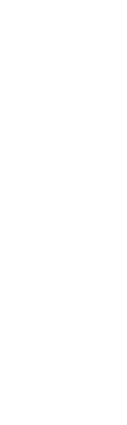
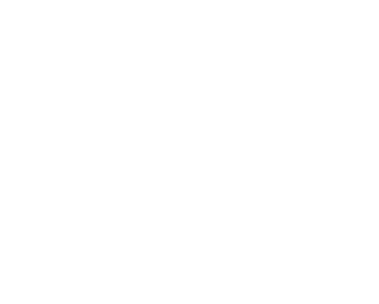
“Le richieste del mercato si stanno concentrando su lotti dai volumi produttivi sempre più piccoli con ordini just-in-time, pertanto il Gruppo ILTOM ha a disposizione differenti macchinari di ultima generazione e personale altamente qualificato in grado di rispondere a tutte le esigenze”, spiega Roberto Cagna.
Successivamente alle operazioni meccaniche avviene la saldatura e l’assemblaggio dei prodotti, a cui seguono la verniciatura a polvere e infine il montaggio e l’imballaggio dei codici finiti.
Molteplici impianti di verniciatura, medesime specifiche tecniche da rispettare
Il Gruppo ILTOM possiede una pluriennale esperienza nel settore della verniciatura industriale grazie ai molteplici impianti di verniciatura a polvere presenti nelle sue sedi produttive e in grado di trattare tutte le superfici metalliche, garantendo così la realizzazione di prodotti di alta qualità e resistenza alla corrosione.
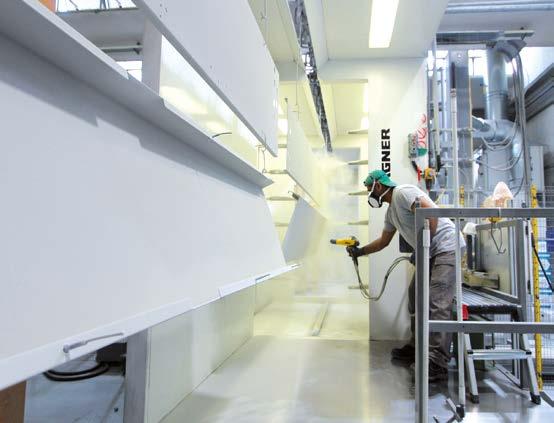

“Le vernici in polvere consentono di ottenere rivestimenti di elevata qualità per un’ampia gamma di superfici, conferendo un aspetto e una sensazione al tocco eccellenti, una lunga durata, un’elevata efficienza economica del processo e un uso sostenibile delle risorse, oltre a fornire un’ampia gamma di colori ed effetti superficiali. Per questo motivo disponiamo di linee di verniciatura negli stabilimenti di CMA, Paillet, Bruder Keller e Bresto in Francia e in quello di Fraven (Romania), oltre ai due impianti nella sede di Romanengo che ci permettono di garantire tempi di consegna molto brevi nonostante un magazzino ridotto”, continua Cagna. “Con tutti questi impianti a
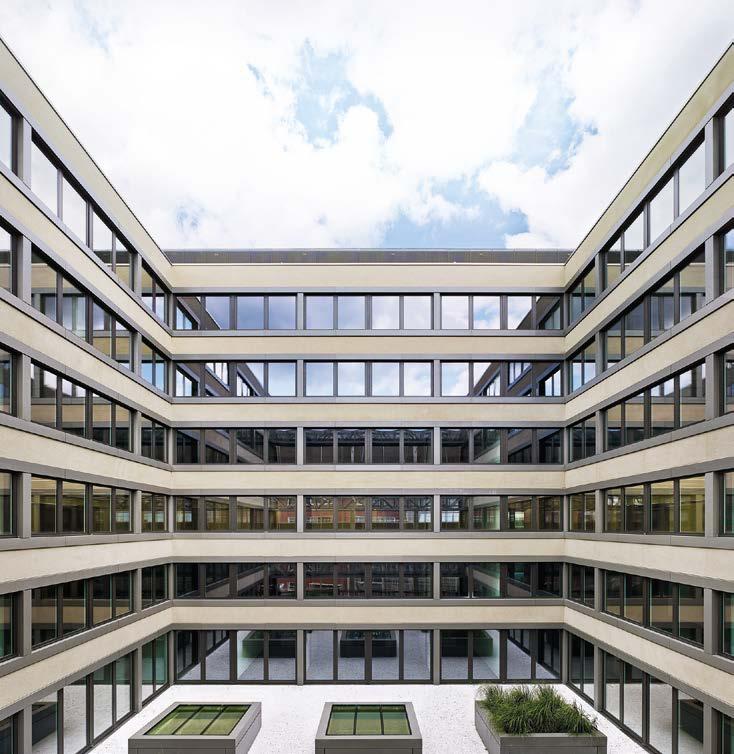
disposizione, è però essenziale monitorare costantemente il rispetto delle specifiche espresse dai clienti, al fine di garantire gli stessi livelli di qualità del rivestimento, uniformità dello spessore del film e ripetibilità dei risultati di verniciatura, a prescindere dal luogo in cui sono lavorati. Per esempio, il nostro principale cliente effettua degli audit sui nostri impianti e specifici esami di resistenza alla nebbia salina prima di consentirci di verniciare a polvere i loro interruttori di bassa e media tensione e i componenti per le cabine, i server e quadri elettrici”.
Il precedente impianto di verniciatura a polvere a disposizione del Gruppo ILTOM presso la sede di Romanengo prevedeva solamente tre stadi di pretrattamento e questo non assicurava il raggiungimento degli standard qualitativi richiesti dai clienti più esigenti. L’azienda nel 2022 ha pertanto deciso di investire nel nuovo impianto di M.I. DUE.
L’impianto automatico di verniciatura a polvere di M.I. DUE
M.I. DUE ha progettato, costruito e installato nell’agosto 2022 un impianto di verniciatura a polvere che prevede una zona di carico e scarico, dove l’operatore può inserire sulle bilancelle (dalla portata massima di 250 chilogrammi ciascuna) i molteplici componenti realizzati dal Gruppo ILTOM, dai piccoli particolari alle grandi carpenterie di dimensione massima di 900 x 2.000 x 4.000 mm. Il trasportatore monorotaia li conduce attraverso il tunnel di pretrattamento a spruzzo coibentato a sei fasi, dove i pezzi sono sottoposti a uno stadio di sgrassaggio alcalino seguito da due
risciacqui con acqua di rete, un risciacquo con acqua demineralizzata, una conversione con il prodotto nanotecnologico Oxsilan® e un ulteriore risciacquo finale con acqua demineralizzata. Dopo essere usciti dal tunnel di pretrattamento, i componenti passano in un’area di gocciolamento attrezzata con una pedana che consente di raccogliere l’acqua drenata dai pezzi e riutilizzarla. Dopodiché, le bilancelle sono condotte prima nel forno di asciugatura e successivamente nella cabina per l’applicazione della vernice in polvere. Attraverso un sistema intelligente di alimentazione e preparazione della polvere vergine di moderna concezione, questa cabina consente di effettuare il cambio colore in pochi minuti.
La cabina è equipaggiata con pistole automatiche, una postazione di preritocco con un robot antropomorfo con funzione di autoapprendimento di Lesta e una postazione di post-ritocco manuale. Dopo la polimerizzazione in un forno con doppio scambiatore e batteria a olio diatermico, i particolari sono infine condotti in un’apposita zona di raffreddamento (dove è anche possibile effettuare le operazioni di scarico) e poi completano il percorso sul trasportatore fino a ritornare nella zona di carico/scarico iniziale. In questo modo agli operatori è consentito di poter effettuare le varie manovre di scarico delle bilancelle in due punti distinti in modo da ottimizzare i flussi logistici e le attività di imballaggio successive.

A questo scopo, sull’impianto sono stati inseriti degli smart screen che forniscono le informazioni necessarie al personale aziendale inerenti alle modalità di imballo dei codici, eventuali controlli e indicazioni sulle fasi di lavorazione successive.
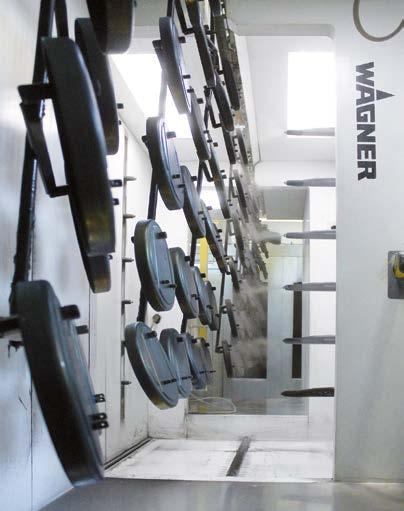
Risparmio energetico con i forni riscaldati con olio diatermico “L’impianto di verniciatura a polvere è entrato in funzione a pieno regime a fine settembre 2022. Abbiamo espressamente richiesto a M.I. DUE una soluzione che potesse rispettare i requisiti qualitativi imposti dai clienti ma che fosse al contempo anche ecologicamente sostenibile. Tutti i motori sono dunque sotto inverter e utilizziamo l’olio diatermico per riscaldare i forni e il tunnel di pretrattamento. In questo modo, siamo in grado di ridurre il consumo energetico del 15%,” interviene Gianluca Cremonesi, il responsabile del reparto di verniciatura del Gruppo ILTOM. Il riscaldamento dei forni dell’impianto è alimentato dunque da batterie a olio diatermico al fine di risparmiare gas, evitare l’utilizzo di bruciatori e di conseguenza eliminare la presenza di fiamme all’interno dello stabilimento. La caldaia, posizionata all’esterno del sito produttivo, scalda l’olio in ricircolo e lo invia alle batterie dei forni di asciugatura e polimerizzazione, dove si può regolarne la temperatura tramite termoregolatori e valvole modulatrici. Inoltre, uno scambiatore olioacqua riscalda anche le serpentine del tunnel di pretrattamento.




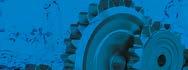
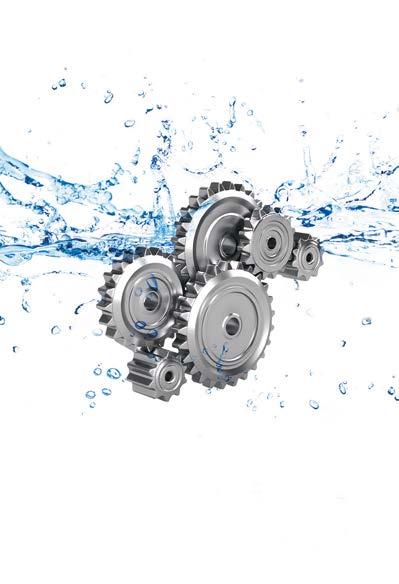
“Con l’olio diatermico è possibile mantenere la temperatura maggiormente stabile e regolarla con anche solo un grado di differenza, conferendo quindi una maggiore distensione al film di vernice e l’uniformità del colore durante la polimerizzazione. Su questo impianto abbiamo inoltre ragionato in ottica di recupero termico, quindi la caldaia è equipaggiata con un bruciatore molto efficiente e integra un sistema di recupero termico che sfrutta il calore dei fumi (300° C) per ottenere acqua calda utile a riscaldare la vasca di sgrassaggio alcalino. Pertanto, sono aumentati sia il risparmio energetico sia la sicurezza dell’ambiente di lavoro. Anche la manutenzione della caldaia risulta facilitata e non intralcia le operazioni produttive,” chiarisce Andrea Mattavelli, il progettista dell’ufficio tecnico di M.I. DUE che si è occupato dello sviluppo e della costruzione del nuovo impianto.




Flessibilità e riproducibilità con i robot ad autoapprendimento


L’azienda utilizza molteplici tipologie di vernici in polvere ed effettua in media otto cambi colore a turno. Pertanto, la flessibilità operativa dell’impianto è essenziale.


“Nel precedente impianto avevamo aggiunto un robot antropomorfo a cinque assi di Lesta con funzione di autoapprendimento e sistema di gestione RFID che abbiamo voluto mantenere anche in questo impianto, in modo da utilizzarlo per le operazioni di pre-ritocco di componenti dalle geometrie complesse come pezzi scatolati o con angoli e curvature particolari”, aggiunge Cremonesi. “L’operatore esegue i movimenti necessari per verniciare efficacemente il pezzo grazie ad un joystick ergonomico e il robot salva i dati, in modo da poterli replicare autonomamente. Inoltre, l’intero impianto è stato progettato in ottica 4.0, perciò attraverso un tablet presente nel reparto o anche con una app sui cellulari a disposizione del personale è possibile impostarne i vari parametri di funzionamento.
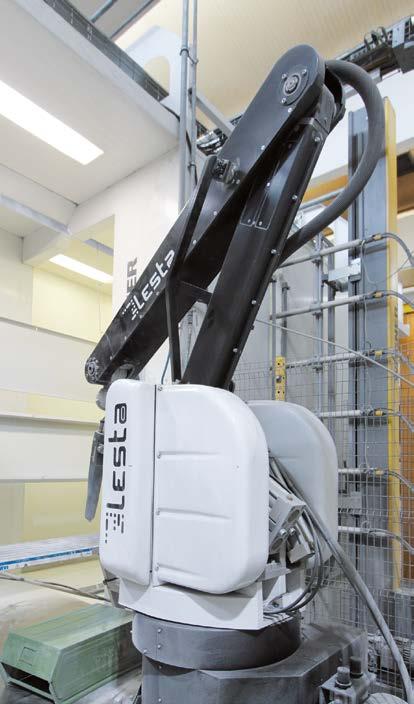


La collaborazione continuativa con M.I. DUE
La collaborazione strategica tra il Gruppo ILTOM e M.I. DUE non si è però limitata esclusivamente all’impianto di verniciatura installato nella sede di Romanengo. L’impiantista si è infatti occupato più volte dell’aggiornamento e della manutenzione degli altri impianti della società. Perciò, ILTOM ha deciso di affidarsi a loro per la realizzazione di un impianto di verniciatura in uno dei cinque stabilimenti produttivi dell’azienda in Romania.
“M.I. DUE si è sempre dimostrata professionale, affidabile e disponibile nel trovare la migliore soluzione alle nostre necessità. Per esempio, quando ci siamo spostati nel nuovo stabilimento rumeno, hanno smontato l’impianto di verniciatura e lo hanno immediatamente rimontato nel secondo sito, e, in nemmeno un mese, la produzione è ripartita senza inconvenienti. Quando la proprietà ha deciso di investire in un nuovo impianto per la sede italiana, dopo un approfondito benchmark, l’offerta di MI.DUE si è dimostrata la migliore in termini di proposta tecnica, tempi di installazione e assistenza. Il livello di personalizzazione che sono in grado di raggiungere e la competenza dei loro tecnici ci ha consentito di rispettare tutte le stringenti specifiche richieste dai nostri clienti, sia per verniciare componenti di grandi dimensioni come carpenterie per
condizionatori, caldaie e frigoriferi, sia per pezzi dalle geometrie ridotte più frequenti nell’industria dei distributori di bevande o nel mondo elettrico. Tutto questo diminuendo anche i consumi energetici e i conseguenti costi,” afferma Roberto Cagna.
Investimento vantaggioso e green
Oltre a permettere di raggiungere gli standard qualitativi necessari per soddisfare la variegata clientela del Gruppo ILTOM, il nuovo impianto di verniciatura a polvere di M.I. DUE possiede una capacità maggiore rispetto alla linea utilizzata in precedenza, pur richiedendo consumi energetici inferiori.
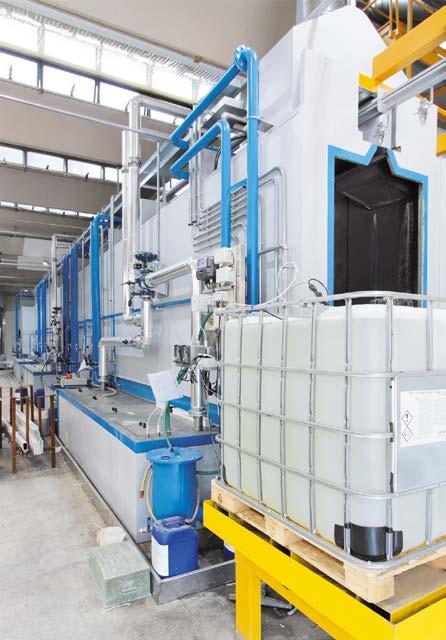
“Dotarci di un impianto con standard qualitativi molto più elevati e che potesse soddisfare tutti i requisiti della clientela era una necessità inderogabile, anche per il rischio di sovraccarichi dovuti a picchi di lavoro o guasti. Siamo completamente soddisfatti di questo nuovo capitolo della collaborazione con M.I. DUE in quanto siamo riusciti a incrementare la nostra capacità produttiva ed i nostri standard qualitativi riuscendo al contempo ad avere vantaggi economici (grazie alla riduzione dei consumi) e di sostenibilità green (grazie al recupero termico dei fumi)”, conclude Cagna.
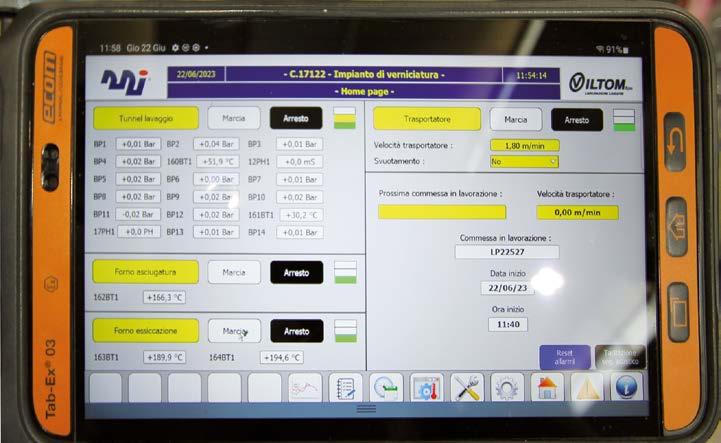
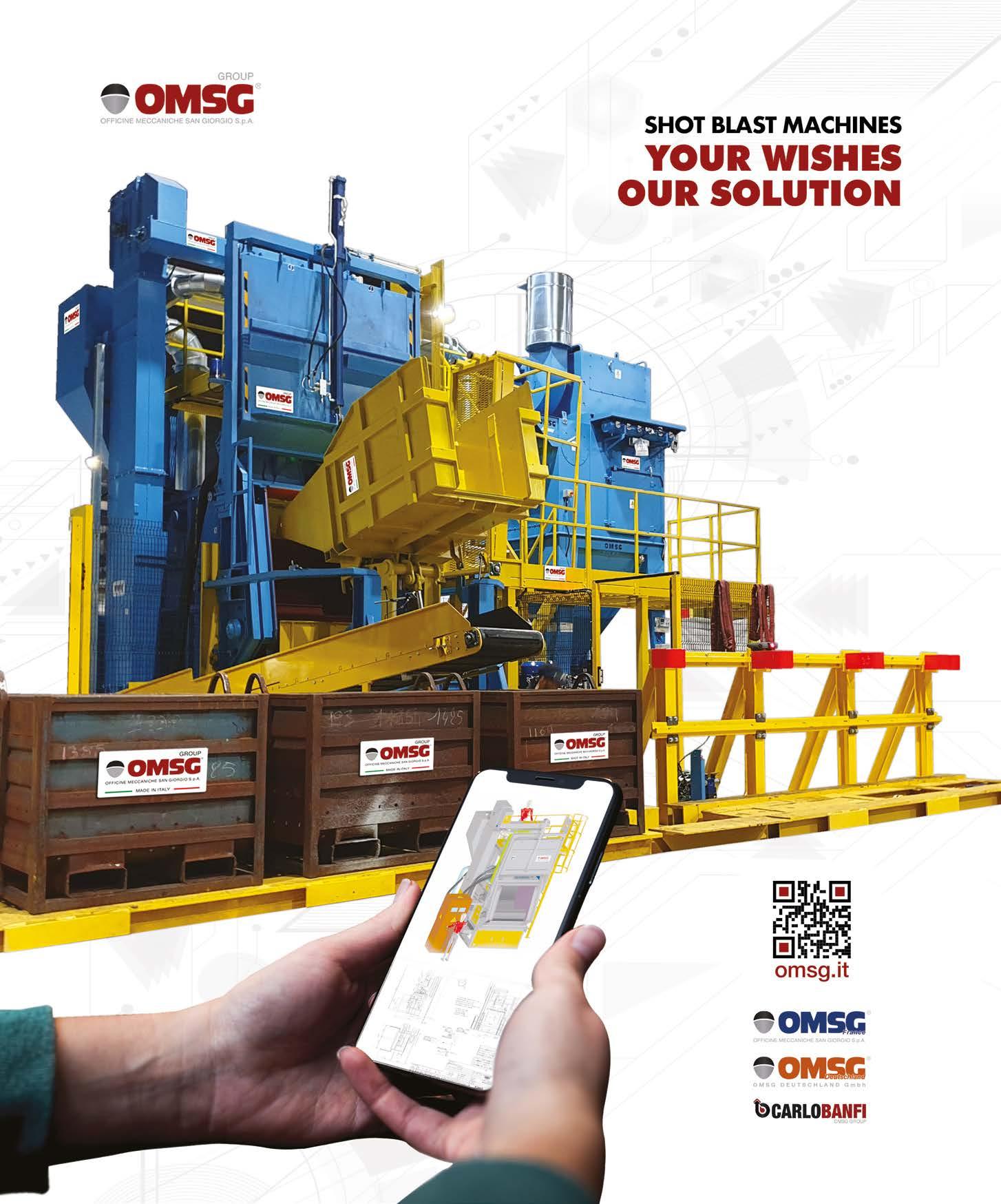
RESEARCH BREAKTHROUGH
I rivestimenti cellulosici “invisibili” che mitigano la trasmissione superficiale degli agenti patogeni
A cura dell’Università di Birmingham
Birmingham – Regno Unito
Un film sottile in fibra di cellulosa invisibile a occhio nudo e adatto all’impiego su oggetti ad alto contatto come maniglie delle porte e corrimani.
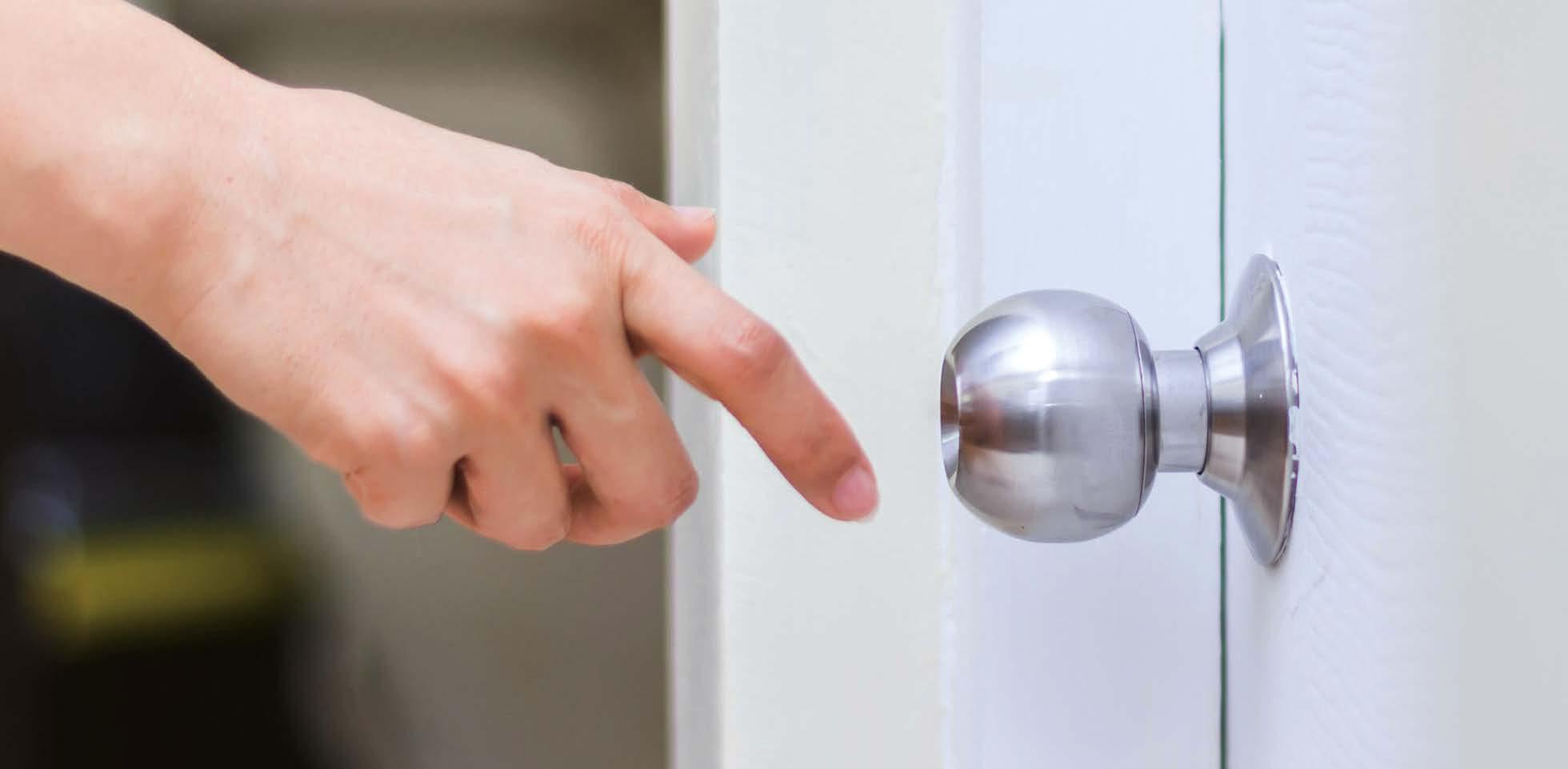
La ricerca ha confermato la stabilità del rivestimento, che non ha mostrato danni evidenti quando è asciutto e risulta di facile rimozione dalla superficie quando è bagnato, rendendolo adatto e conveniente per attività quotidiane di pulizia e di disinfezione. Lo studio1 ha mostrato che un film sottile di cellulosa può disattivare il virus SARS-CoV-2 nel giro di minuti, bloccare la crescita di batteri, tra cui l'E.Coli, e mitigare la trasmissione a contatto di agenti patogeni. Il rivestimento consiste in un film sottile in fibra di cellulosa che è invisibile a occhio nudo ed è resistente all’abrasione in condizioni asciutte, rendendolo adatto all’impiego su oggetti ad alto contatto come maniglie delle porte e corrimani.
1 https://pubs.acs.org/doi/10.1021/acsami.2c23251
Il prodotto è stato sviluppato dai team di scienziati dell’Università di Birmingham, dell’Università di Cambridge e FiberLean Technologies, che hanno lavorato ad un progetto finanziato da Engineering and Physical Science Research Council per formulare trattamenti2 per superfici in vetro, in metallo o laminate che garantirebbero protezione di lunga durata contro il virus COVID-19. Mentre i disinfettanti chimici convenzionali e la progettazione di superfici antivirali prendono di mira le proteine strutturali o gli acidi nucleici, i ricercatori, guidati dal professor Zhenyu Jason Zhang della scuola di ingegneria chimica di Birmingham, si sono concentrati nel fare asciugare le goccioline respiratorie, contenenti i virus, dalla forza capillare introdotta dalla struttura porosa.
2 https://www.birmingham.ac.uk/news-archive/2020/researchers-tackle-the-surfacetransmission-of-covid-19-in-new-partnership
Il virus COVID-19 è noto per rimanere attivo molti giorni su superfici come la plastica e l’acciaio inossidabile, ma solo per poche ore sulla carta. Il team, che ha esperienza in chimica delle superfici e in ingegneria della formulazione, ha studiato la struttura e le prestazioni di un rivestimento realizzato con cellulosa micro-fibrillata (MFC) fornita da FiberLean Technologies, il principale produttore internazionale di MFC per l’industria della carta e del packaging. I ricercatori hanno riscontrato che la natura porosa del film gioca un ruolo fondamentale: accelera il tasso di evaporazione delle goccioline d’acqua e introduce una pressione osmotica sbilanciata lungo la membrana batterica. Successivamente, hanno testato se il rivestimento potesse inibire la trasmissione superficiale di SARSCoV-2. Qui hanno trovato una triplice riduzione dell’infettività quando le goccioline contenenti il virus sono state lasciate sul rivestimento per 5 minuti e, dopo 10 minuti, l’infettività è scesa a zero. Al contrario, quando le goccioline contenenti SARS-CoV-2 sono state lasciate su una superficie di vetro, la loro infettività iniziale era inalterata dopo 10 minuti. Le prove antimicrobiche sono state ripetute con goccioline contenenti batteri (E.Coli e S.epidermidis) e, nuovamente, i ricercatori hanno notato riduzioni sostanziali nell’infettività a 1 ora e a 24 ore.
Gli esperimenti sono stati ripetuti con aerosol di saliva artificiale e qui
le analisi hanno suggerito che lo strato di cellulosa è anche efficace nel sopprimere il trasferimento da contatto degli aerosol respiratori.
“Il rischio di trasmissione superficiale, al contrario di quello da aerosol, deriva da grosse goccioline che rimangono infettive se atterrano su superfici dure, dove possono essere trasferite al tatto. Questa tecnologia di rivestimento superficiale impiega materiali sostenibili e potrebbe essere potenzialmente utilizzata in congiunzione con altri attivi antimicrobici per garantirne un effetto duraturo e a rilascio lento”, ha commentato il professor Zhang.
I ricercatori hanno confermato la stabilità del rivestimento grazie ai test di sfregamento meccanico, dove esso non ha mostrato danni evidenti da asciutto, ma di facile rimozione dalla superficie da bagnato, rendendolo adatto e conveniente per attività quotidiane di pulizia e di disinfezione.
L’Università di Birmingham Enterprise ha depositato una domanda di brevetto congiunta con FiberLean Technologies e l’Università di Cambridge coprendo una cellulosa micro-fibrillata che può disattivare i virus interrompendo l’involucro lipidico del virione.
Questo lavoro è finanziato dall'Unione Europea nell'ambito del progetto SUPREME (GA101058422).
Our potential customers
With over 50 ZLD plants installed all over the world, CIE is a leader company in Zero Liquid Discharge for metal finishing industry
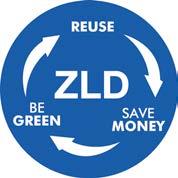
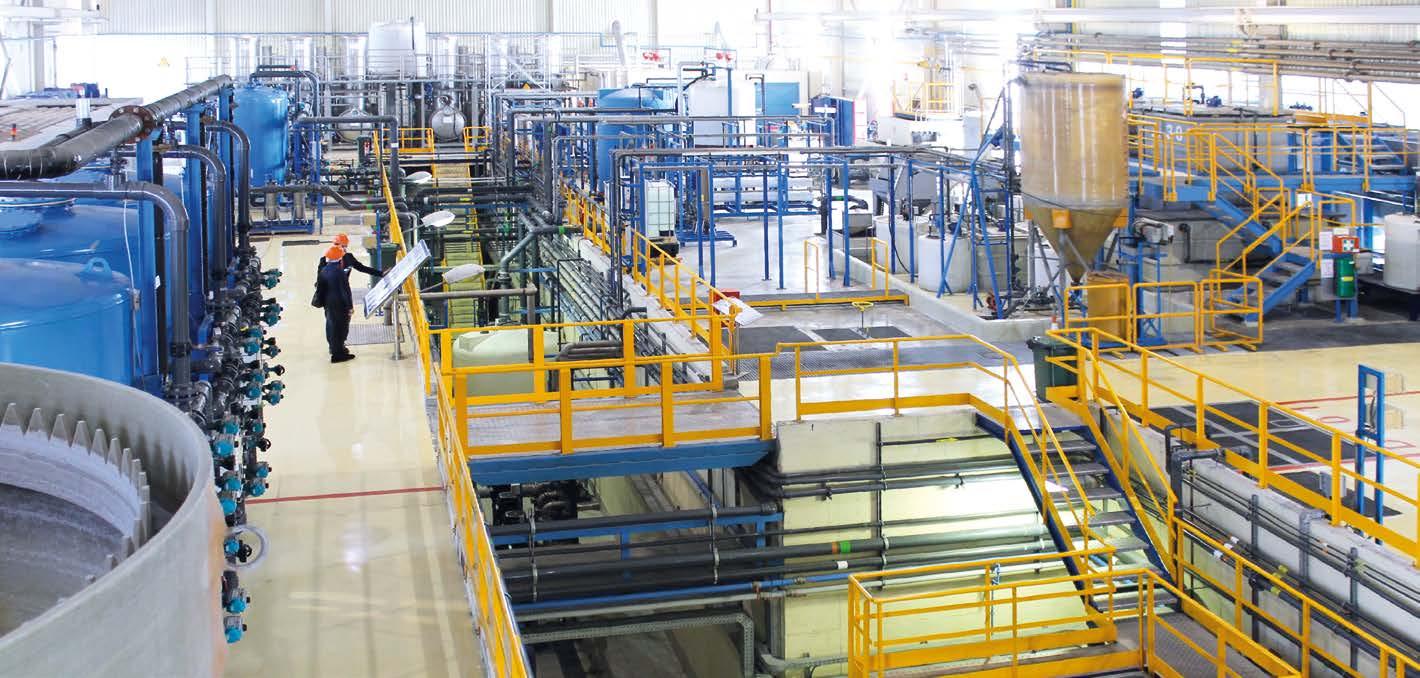
www.cieeng.com - info@cieeng.com



WASTE WATER TREATMENT PLANTS FOR


METAL FINISHING LINES
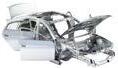


EcoBell4: efficienza fino al 98% che consente di
di vernice e di prodotti per il risciacquo
Dürr stabilisce nuovi parametri di riferimento nella produzione sostenibile con la sua nuova famiglia di polverizzatori rotativi ad alta velocità EcoBell4.
Una maggiore efficienza di applicazione della vernice riduce il consumo di materiali, risorse ed energia per processi più sostenibili. Con l’ultima generazione di polverizzatori rotativi
EcoBell4 Pro Hu con carica diretta ed EcoBell4 Pro Ux con carica esterna, Dürr sta raggiungendo nuovi traguardi. Per l’applicazione del trasparente, il polverizzatore rotativo ad alta velocità Dürr raggiunge un’efficienza di trasferimento compresa tra il 95% e il 98%, in conformità con la norma
DIN EN 13966-1. La velocità e la distanza di spruzzatura sono parametri di processo che ottimizzano l’efficienza di applicazione della vernice da parte del polverizzatore rotativo: entrambe sono ora significativamente ridotte in modo da aumentare l’impatto dell’alta tensione, pur mantenendo una portata elevata di vernice. L’aria di guida viene ridotta al minimo ed il controllo dell’alta tensione viene accuratamente regolato. Dürr sta attualmente testando l’implementazione di questo processo in un impianto di verniciatura vero e proprio del settore automobilistico in collaborazione con OEM interessati.
Anche gli impianti esistenti hanno il potenziale per essere equipaggiati con questa nuova generazione di polverizzatore rotativo ad alta velocità.
In che modo le misure adottate incidono sul processo Riducendo il volume dell’aria di guida ad un intervallo compreso tra 90 e 200 nl/min si ottiene un cono di spruzzatura più delicato. Insieme alla riduzione della velocità della tazza si riduce il consumo energetico. Contemporaneamente, una quantità maggiore di vernice raggiunge la scocca quando la distanza di spruzzatura viene ridotta a circa 100 mm. Due fattori contribuiscono a questo effetto: un programma di spruzzatura meno dispersivo e un campo elettrostatico potenziato tra la tazza e la superficie della scocca, circostanza questa che ottimizza l’utilizzo della forza elettrostatica attraverso una tensione costante. Di conseguenza, la vernice polverizzata raggiunge più efficacemente la scocca anziché disperdersi nell’aria della cabina. È possibile ottenere una velocità in uscita della vernice fino a 400 ml al minuto per conseguire gli spessori richiesti entro il tempo di ciclo previsto. EcoBell4 Pro Hu con carica diretta raggiunge quindi un’efficienza del 98%, per le applicazioni con rivestimento trasparente. L’utilizzo dei polverizzatori rotativi EcoBell4 Pro E con carica esterna per la verniciatura delle parti esterne genera un notevole aumento di efficienza per l’applicazione della mano di fondo, incrementandola dal 75 al 78% rispetto al modello precedente EcoBell3.
Il polverizzatore rotativo EcoBell4 Pro Ci per la verniciatura delle parti interne continua a raggiungere un’efficienza elevata ed impareggiabile, fino al 70%. Promuovendo le collaborazioni con gli OEM ed i fornitori di vernici presso il Centro Tecnologico Dürr, emergono ulteriori opportunità per migliorare l’efficienza e la qualità dell’applicazione di vernici.
Rapidi cambi di colore riducono il consumo di vernice e dei prodotti di risciacquo
Oltre ai progressi nel processo di verniciatura, le innovazioni tecniche nel design portano i polverizzatori rotativi ad alta velocità EcoBell4 ad un nuovo livello qualitativo. Questa nuova generazione migliora la flessibilità e l’efficienza per un processo più sostenibile. EcoBell4 consente cambi colore più rapidi rispetto a qualsiasi altro polverizzatore rotativo ad alta velocità presente sul mercato. Ciò è dovuto al fatto che la tecnologia brevettata a 4 aghi principali non consente soltanto di risparmiare tempo, ma riduce anche il consumo di vernice e dei prodotti di risciacquo, nonché le emissioni di composti organici volatili (VOC).
Ecco come funziona il principio: tre dei quattro aghi sono riservati esclusivamente ai colori utilizzati più di frequente. Tutti gli altri colori passano attraverso il quarto ago. I dati rilevati in condizioni reali del settore automobilistico dimostrano che oltre il 50% delle scocche è verniciato con i tre colori utilizzati più di frequente.
La tecnologia sfrutta questo fatto e fornisce i tre colori in modo permanente attraverso gli aghi principali, che si trovano direttamente dietro la tazza del polverizzatore. Quando è previsto un cambio di colore, il sistema può passare ad un altro ago nell’arco di 4 secondi, senza bisogno di risciacquare e pulire il canale. In questo modo si riducono tanto la perdita di vernice quanto il consumo dei prodotti di risciacquo associati ai cambi di colore. Qualora sia necessario applicare un colore usato meno frequentemente, questo si può alimentare facilmente tramite il quarto canale, mentre uno degli altri tre aghi continua ad applicare il colore principale. Ciò significa che ogni colore è disponibile per la scocca successiva in tempi molto brevi.
Ulteriori risparmi con il nuovo concetto di cabina di verniciatura
Rispetto al modello precedente EcoBell3 (1C), il consumo di vernice e dei prodotti di risciacquo è ridotto del 51% nella configurazione di linea
risparmiare importanti quantità
convenzionale. Ciò è positivo per l’ambiente e riduce al minimo i costi di processo. La nuova generazione di polverizzatori rotativi ad alta velocità è efficiente e sostenibile in combinazione con l’EcoProBooth. Considerando che la verniciatura interna ed esterna può essere eseguita in un’unica cabina, non solo i tempi di cambio colore sono più brevi, ma anche i tempi di movimentazione sono inferiori rispetto al processo in linea.
Il polverizzatore rotativo ad alta velocità universale EcoBell4 Pro Ux si abbina perfettamente all’EcoProBooth, adatto per applicazioni di verniciatura delle parti interne ed esterne della scocca e dei metallizzati. Utilizza un sistema unificato tazza / anello aria di guida ed un sistema di ricarica esterno per tutte e tre le operazioni di verniciatura.
La combinazione EcoBell4 Pro Ux ed EcoProBooth consente di risparmiare fino al 91% durante i cambi di colore, riducendo la perdita di vernice ed il consumo dei prodotti di risciacquo. “Si tratta di un progresso enorme. I calcoli relativi al nostro modello si basano su un impianto di verniciatura che utilizza 24 colori e vernicia 30 scocche ogni ora, 230 giorni l’anno su tre turni. La quantità di vernice risparmiata sarebbe sufficiente per verniciare ulteriori 15.600 scocche”, afferma Frank Herre, Responsabile “Application Technology Development” presso Dürr.
Solo quattro robot riducono i tempi di cambio colore e di manipolazione
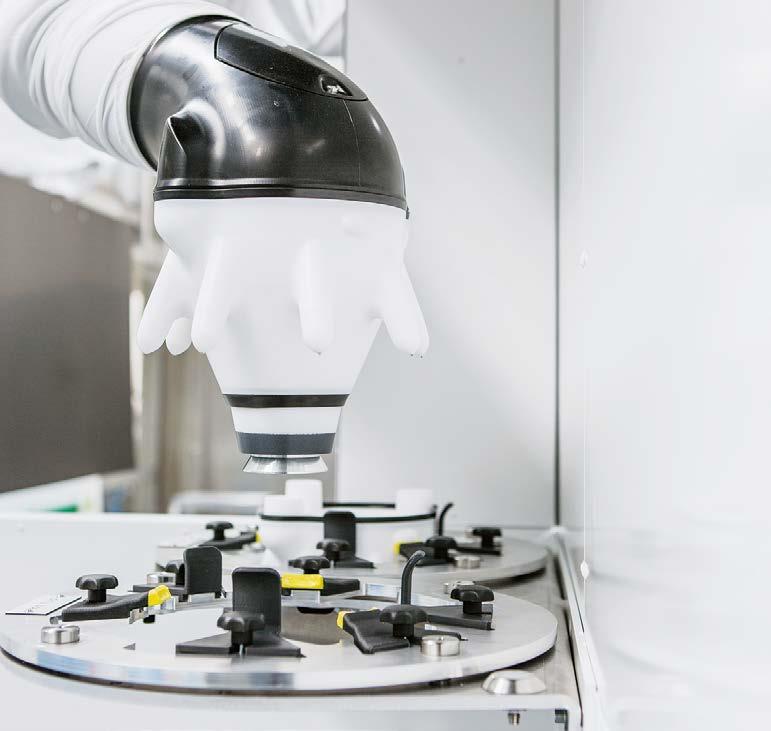
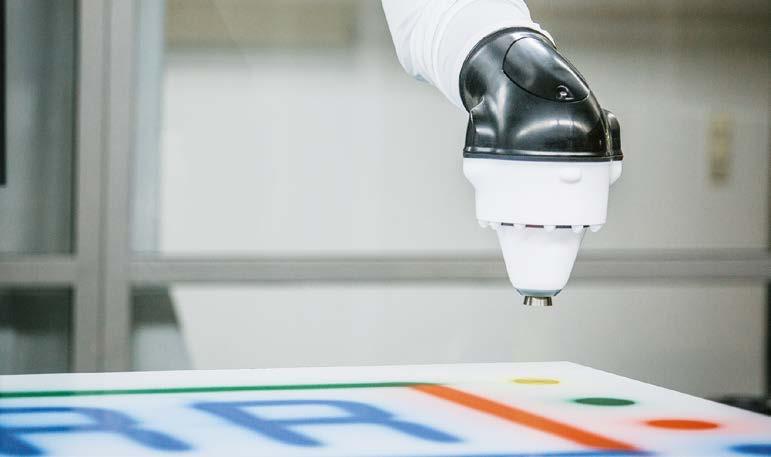
Il sistema comprende fino a quattro aghi principali, che soddisfano tutte le esigenze di verniciatura, dalla soluzione 4x1C per le mani di fondo alla soluzione 3x2C per i rivestimenti trasparenti.
Dürr offre dieci versioni di EcoBell4, adatte a tutte le applicazioni di verniciatura per le parti esterne ed interne delle scocche, con carica diretta o esterna. Per la prima volta, questa famiglia di prodotti comprende una versione base per applicazioni standard e una versione Pro per processi speciali quali 4x1C oppure 3x2C.
Disporre del tempo del cliente valorizzandolo con un servizio all’avanguardia: la scommessa sul futuro del terzista di verniciatura
Una concezione innovativa del terzismo di verniciatura basata sull’idea di offrire un servizio che non si esaurisce con la qualità della finitura del prodotto da consegnare al committente, ma che include la possibilità di gestire con dispositivi all’avanguardia il tempo produttivo che quest’ultimo mette a disposizione del terzista: questo è quello che emerge dalla nostra visita presso Tecnologie Galvaniche Innocenti, azienda di verniciatura a polvere conto terzi che ha recentemente integrato i dispositivi Gema Europe di ultima generazione allo scopo di proiettare il proprio processo produttivo nel futuro 4.0.

Con il termine “terzismo” si indica generalmente il servizio di un’azienda che effettua alcune fasi di lavorazione o l’intero processo produttivo per conto di una o più società altre. In genere, un’azienda si rivolge a una società “terza” affidandole la lavorazione di una parte del proprio prodotto per ottimizzare i costi di produzione, affrontare picchi produttivi difficili da gestire internamente oppure per affidarsi ad una struttura con tecnologie e competenze migliori o diverse rispetto alle proprie: quest’ultimo è il caso che nel terzismo di verniciatura si riscontra in percentuale più ampia. Il committente si affida al terzista con l’obiettivo di instaurare una partnership solida e affidabile e, oltre a sfruttarne il know how, richiede la gestione delle commesse nei tempi richiesti.
“Recentemente, soprattutto dopo il periodo pandemico, le tempistiche per la consegna dei componenti verniciati si sono ridotte drasticamente passando da 5 a 2 giorni lavorativi” – sottolinea Leonardo Innocenti, titolare di Tecnologie Galvaniche Innocenti Srl (Anagni, Frosinone) specializzata nella granigliatura e verniciatura a polvere e a liquido conto terzi di componenti di carpenteria
piccola, media e grande per i settori più diversi, dall’automotive all’aerospace, dall’architettura all’HVAC, all’industria in generale. “Per adattare il nostro stabilimento a queste nuove esigenze del mercato abbiamo deciso di attrezzarci con le ultime tecnologie 4.0, sfruttando gli incentivi governativi concessi alle PMI e rivolgendoci ai nostri fornitori storici di apparecchiature e soluzioni impiantistiche come Gema Europe Srl (Trezzano sul Naviglio, Milano) ed Euroimpianti (Valeggio sul Mincio, Verona)”.
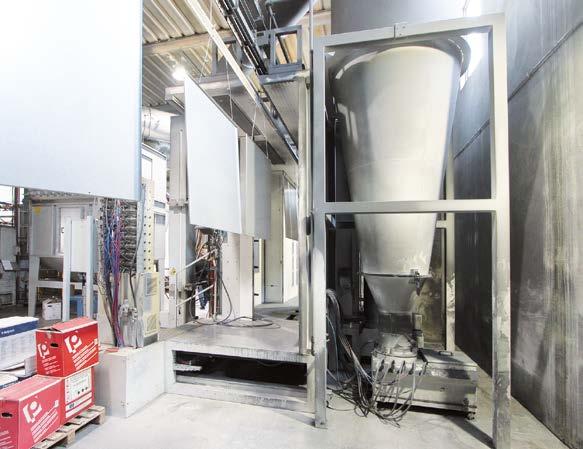

“Sono convinto che si debba guardare al servizio che offriamo come terzisti da un’altra prospettiva” – prosegue Innocenti. “Le aziende come la nostra non producono nulla ma gestiscono il tempo che i clienti ci mettono a disposizione per effettuare i trattamenti superficiali richiesti. Pensare di lavorare non solo nell’ottica di migliorare la qualità della finitura di un prodotto ma di ottimizzare il tempo produttivo dei committenti è sicuramente più difficile, ma, se riusciamo a farlo valorizzando questo servizio con gli strumenti impiantistici adeguati, siamo sulla strada giusta per vincere la nostra scommessa”.
Tecnologie Galvaniche Innocenti: dal dopoguerra alla quarta generazione, tutta al femminile
La storia di Tecnologie Galvaniche Innocenti ripercorre le tappe dello sviluppo del terzismo di verniciatura dal dopoguerra ai nostri giorni, con una particolarità: Leonardo Innocenti, che rappresenta la terza generazione della famiglia alla guida dell’azienda, è già affiancato dalle sue 3 figlie Cristiana, Giorgia e Fabiana, inserite rispettivamente nell’area amministrativa, in quella di produzione e programmazione e nella divisione commerciale di Tecnologie Galvaniche Innocenti.
“La storia della nostra azienda ha preso avvio da un piccolo laboratorio
di fabbro e verniciatore conto terzi creato dal mio bisnonno sul Tevere nell’immediato dopoguerra” – racconta Cristiana. “L’attività fu poi portata avanti dal nonno, che verso la fine degli anni Sessanta e l’inizio dei Settanta decise di trasferire la sede nella zona sud-est di Roma continuando il servizio di terzismo, ma specializzandosi nei trattamenti galvanici. Lo stabilimento in cui ci troviamo ora ad Anagni fu aperto nel 1995 per affiancare il servizio di verniciatura a polveri conto terzi a quello di galvanica della sede di Roma ancora attiva. Qui nel 2012 abbiamo introdotto un impianto per la verniciatura a liquido e uno per il decapaggio e la passivazione dell’acciaio inox che effettuiamo su richiesta di un singolo cliente del settore Oil&Gas. Oggi la nostra produzione riguarda per il 98% la verniciatura a polvere di qualsiasi tipologia di materiale ferroso; applichiamo raramente le vernici liquide e, in genere, su componenti per settori particolari, come quelli destinati alle caldaie, che devono essere in grado di resistere alle temperature più elevate. Per gli altri ambiti, è prima di tutto il nostro staff a suggerire la verniciatura a polvere, sia per i progressi che questa tipologia di vernici ha avuto nel corso del tempo, passando da un utilizzo prettamente industriale ad uno vastissimo che ha raggiunto anche settori inaspettati, come quelli sempre più esigenti dell’architettura e del design, sia per l’impatto ecosostenibile della loro applicazione”.
Il revamping dell’impianto di verniciatura a polvere automatico
“Questo stabilimento è attrezzato con tre impianti di verniciatura –prosegue Cristiana – uno per l’applicazione di vernici liquide e due per le polveri, di cui uno, manuale, è destinato ai componenti di carpenteria pesante di grandi dimensioni fino a 14 x 2,2 x 3 m di lunghezza e 5000
kg di peso movimentati da carrelli. L’altra linea a polveri è dedicata alla verniciatura automatica in serie di pezzi di medie e piccole dimensioni che opera attualmente a ciclo continuo, su 3 turni. Entrambe le linee sono state progettate e installate da Euroimpianti e, sempre in collaborazione con l’azienda veronese, grazie agli incentivi 4.0 abbiamo effettuato un revamping dell’impianto automatico, che, iniziato prima della pandemia, si è concluso nel 2022”.
Il progetto ha riguardato la modifica della struttura della linea, passando da un percorso ad anello che comportava un doppio passaggio dei componenti nel caso dell’applicazione del doppio strato a un layout ad “L”, che consente un ciclo più veloce e lineare, in cui sono stati integrati: una cabina esclusivamente adibita all’applicazione del fondo attrezzata con reciprocatori Gema già in uso, un forno ad aria calda per la gelificazione del fondo e la polimerizzazione della mano a finire e di una nuova cabina
Gema per l’applicazione del topcoat.
“Oggi l’impianto automatico è attrezzato con 3 cabine, una per il fondo, una per la finitura e una che in precedenza applicava la mano a finire in tutte le tinte, oggi adibita ai ritocchi manuali, ai piccoli lotti o all’applicazione delle tinte più problematiche in termini di cambio colore. Se prima con il doppio strato il tempo ciclo poteva raggiungere le 6 ore, oggi la nuova struttura e l’aggiunta della cabina ci permettono di effettuare il ciclo completo in 4 ore e mezzo”.
La cabina Gema di ultima generazione
“Tecnologie Galvaniche Innocenti ha scelto di installare una cabina MagicCylinder dotata di 10 pistole automatiche (5 per lato) e 4 manuali, con pompe in fase densa OptiSpray AP 01, del sistema laser scanner 3D per la lettura della conformazione dei pezzi in entrata e del centro polveri”
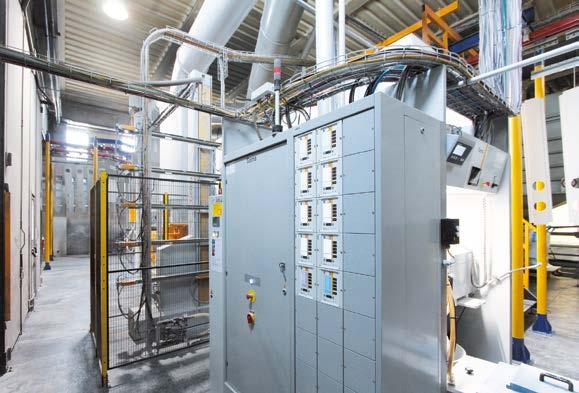
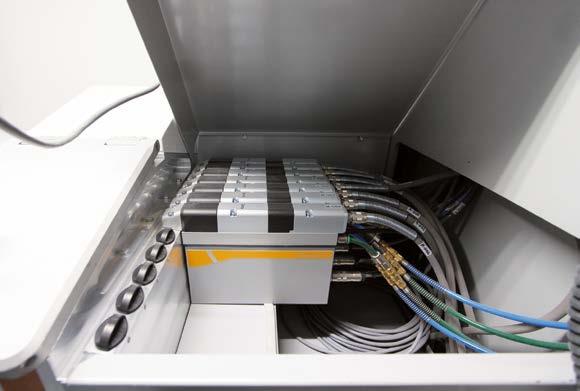

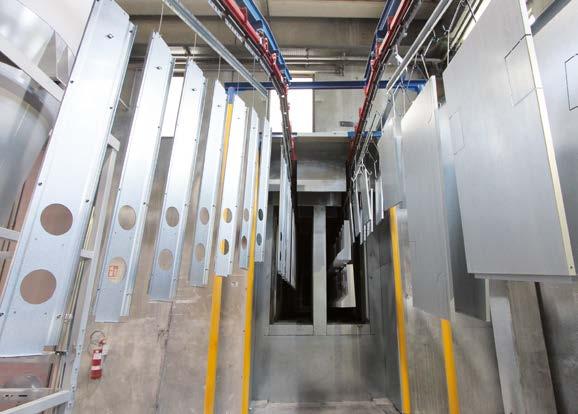
– spiega Claudio Sergenti, Area Manager presso Gema Europe. “Il design cilindrico della cabina garantisce accumuli di polvere ridotti per l’assenza di angoli dove questa potrebbe accumularsi e, quindi, una pulizia rapida, senza la necessità che l’operatore debba entrare al suo interno. Una delle particolarità di questa linea è l’installazione di un doppio ciclone che permette di gestire in modo ottimale le tinte chiare e quelle scure grazie alla maggior rapidità dei cambi colore e alla qualità della polvere che non rischia contaminazioni. Inoltre, il sistema di aspirazione EquiFlow crea condizioni di lavoro ideali in ogni sezione della cabina di verniciatura: un flusso d’aria regolare e omogeneo nell’area centrale garantisce condizioni ideali per l’applicazione ed evita la fuoriuscita di polvere dalla cabina”.

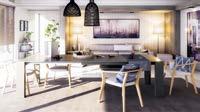
“In questa azienda – conclude Sergenti - la direzione ha voluto installare i migliori dispositivi possibili, ottimizzando la linea al massimo delle possibilità. L’intero sistema è interconnesso con il gestionale nel rispetto dei parametri Industry 4.0: questo permette loro di gestire le ricette di verniciatura in modo ottimale e valutare i report con i consumi giornalieri dei prodotti vernicianti e delle fonti energetiche”.
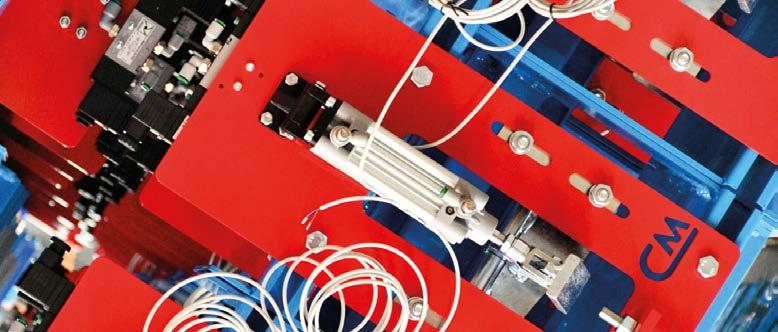
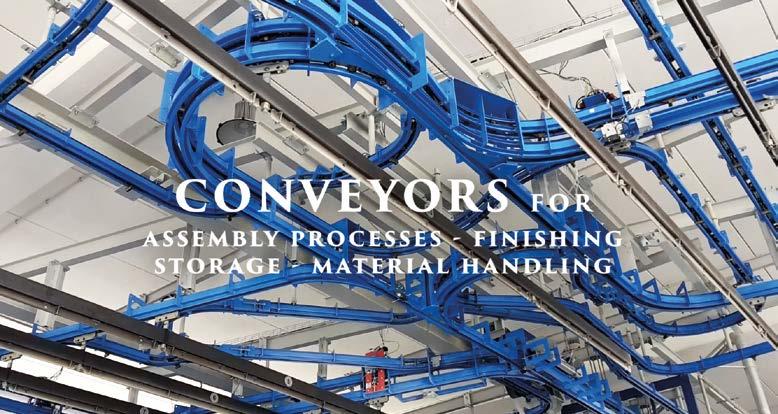
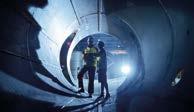
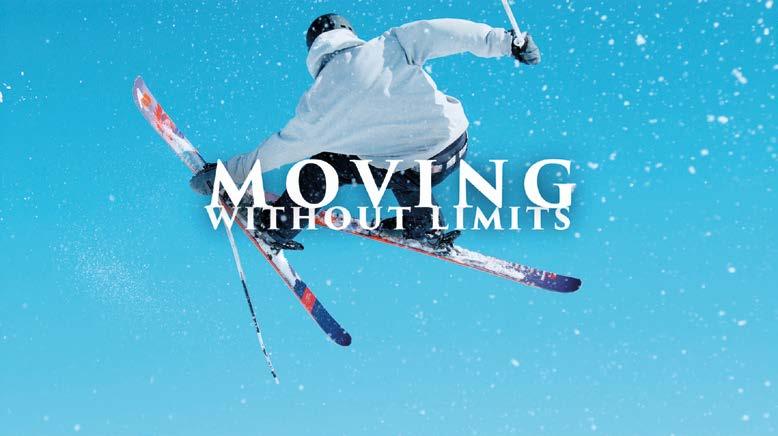
“Abbiamo investito sui dispositivi più avanzati presenti sul mercato –precisa Leonardo - allo scopo di garantire quella qualità di finitura che, se prima era richiesta come requisito minimo solo da determinate tipologie di clienti – in genere aziende medio-grandi di particolari settori come l’automotive o l’aerospace – oggi si ritrova specificata in qualsiasi capitolato insieme a richieste di finiture sempre più particolari che spaziano dal bucciato al corten, all’oro – le tendenze degli ultimi tempi. Accanto a requisiti di resistenza sempre più elevati, non si può più prescindere da una resa estetica di elevata qualità del rivestimento”.
I vantaggi della nuova cabina
“Tra i vantaggi che abbiamo rilevato con l’integrazione della nuova cabina e il nuovo layout dell’impianto automatico – afferma Cristiana – c’è la ripetibilità delle operazioni che ora, grazie alle ricette preimpostate, ci consente di avere uno standard di riferimento e, di conseguenza, una produzione più efficiente. L’automazione ha reso più semplice la gestione delle fasi di verniciatura perché la cabina non deve essere presidiata dall’operatore che può essere così adibito ad altre mansioni, come quelle più complesse richieste dall’impianto manuale. L’operatore è attivo nella sola cabina per il ritocco. Abbiamo dimezzato in questo modo la forza lavoro impiegata sulla linea automatica, passando da 4 a 2 operatori. Inoltre, l’impatto ambientale è minimo, il consumo di prodotto è ridotto per la possibilità di recuperare il 25% del prodotto, e lo smaltimento è pari a zero. Infine, la tecnologia in fase densa ci garantisce quell’uniformità del rivestimento durante la fase di applicazione che ne migliora la qualità estetica e soddisfa appieno le esigenze dei nostri clienti”.
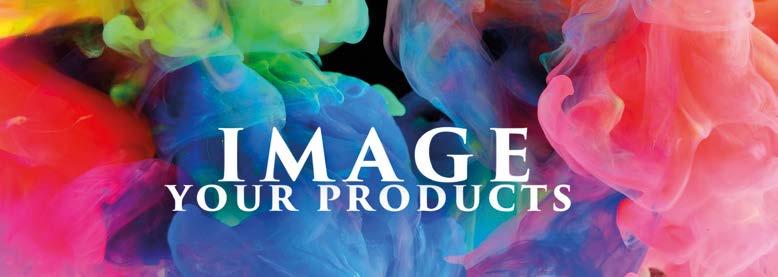
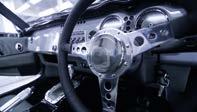
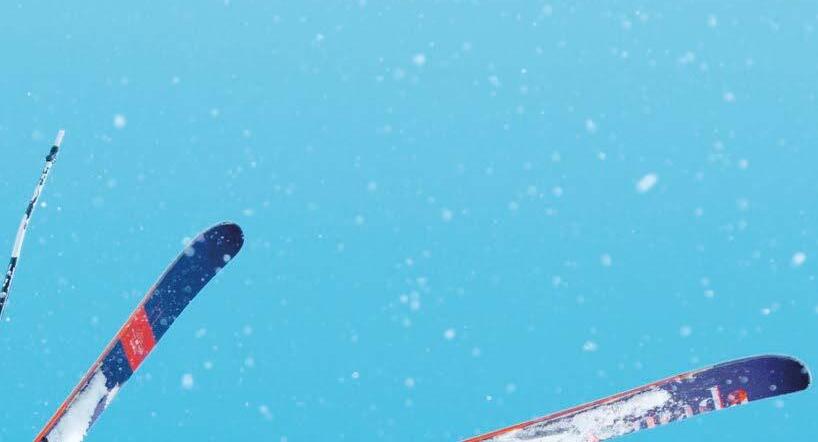
Una visione innovativa per vincere la scommessa sul futuro
“Dopo il periodo della pandemia, la nostra azienda ha avuto un picco produttivo legato all’esplosione del settore delle costruzioni che ci ha spinto a fare alcune valutazioni importanti” – continua Leonardo. “In un lasso di tempo brevissimo abbiamo triplicato i nostri collaboratori e investito nelle migliori tecnologie presenti sul mercato, come nel caso delle apparecchiature di Gema, un fornitore storico il cui know how è consolidato da molti anni. Il modello di cabina MagicCylinder rappresenta una delle soluzioni migliori e più innovative, abbinata al sistema di scansione 3D, a quello di aspirazione e alla tecnologia in fase densa. Con l’obiettivo di creare una struttura completamente gestita secondo i parametri dell’Industry 4.0, un altro dei progetti che abbiamo in conto di realizzare entro il prossimo anno è l’integrazione di robot per il pre e il post-ritocco. Al di là degli investimenti in ambito tecnologico, l’altro progetto su cui investo gran parte delle mie energie è quello di far crescere e continuare a formare questa nuova generazione che si sta sempre più inserendo in azienda: non parlo solo delle mie figlie che erediteranno l’impresa fondata da mio nonno, ma anche delle nuove figure professionali inserite, tra cui quella del commerciale che ha un ruolo strategico nel comunicare quello che facciamo e come lavoriamo ai potenziali clienti. Il messaggio che voglio trasmettere è che se sappiamo gestire al meglio il tempo che i nostri committenti ci mettono a disposizione stiamo mettendo le basi per vincere la scommessa sul futuro. Le tempistiche richieste per le consegne si riducono sempre di più e noi dobbiamo essere in grado di affrontare questi continui cambiamenti del mercato non solo con le tecnologie più innovative, ma anche con il giusto atteggiamento, per trasformarci in veri e propri partner dei nostri clienti e non rimanere meri prestatori d’opera”.
Dall'alto:
Una delle particolarità dell’impianto è il doppio ciclone che permette la gestione separata delle tinte chiare da quelle scure.
Un componente di grandi dimensioni verniciato sull’impianto manuale.
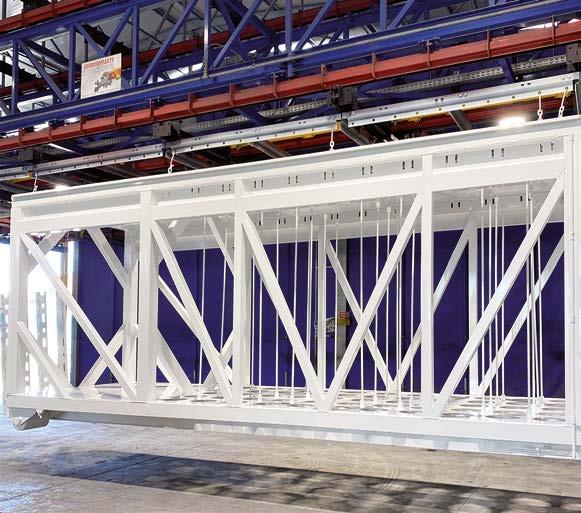
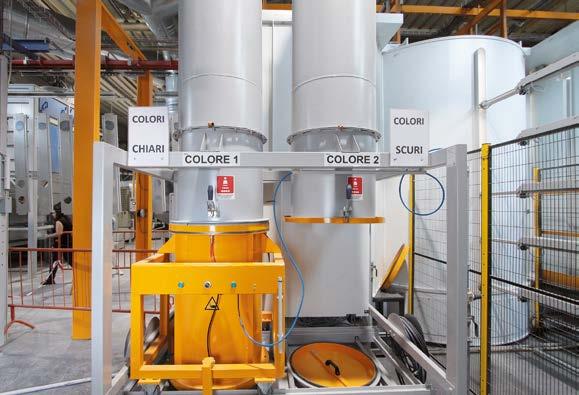
La quarta generazione alla guida di Tecnologie Galvaniche Innocenti: al centro Cristiana Innocenti con Giorgia (a destra nella foto) e Fabiana (a sinistra).
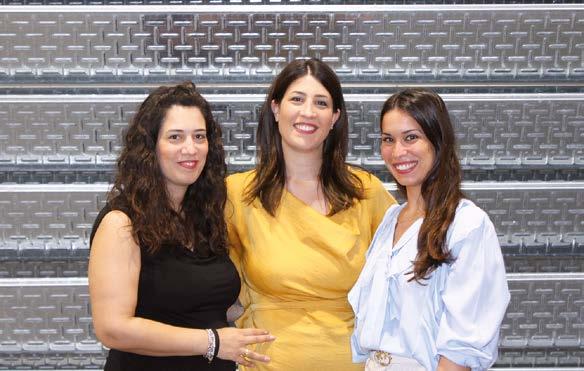
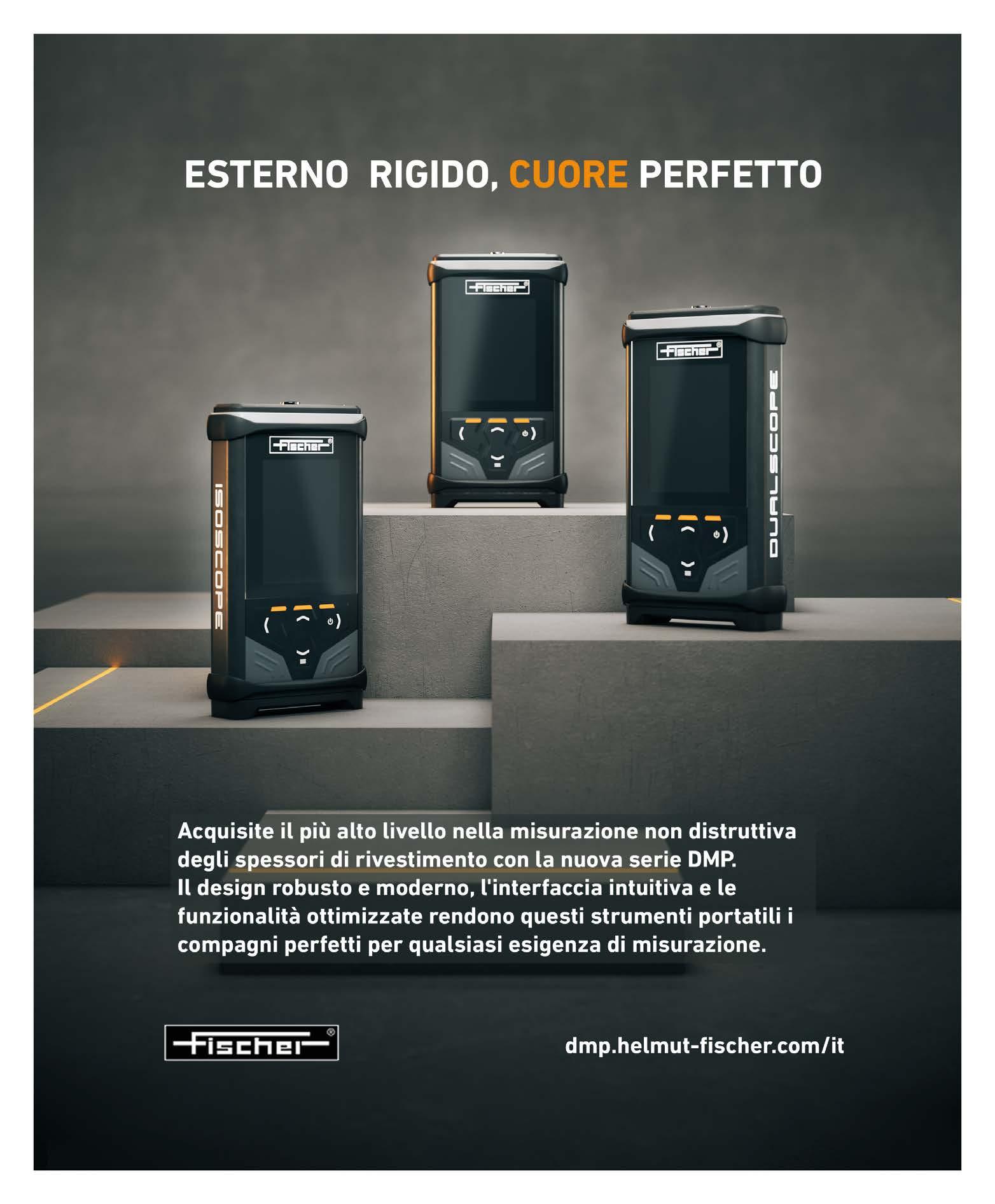
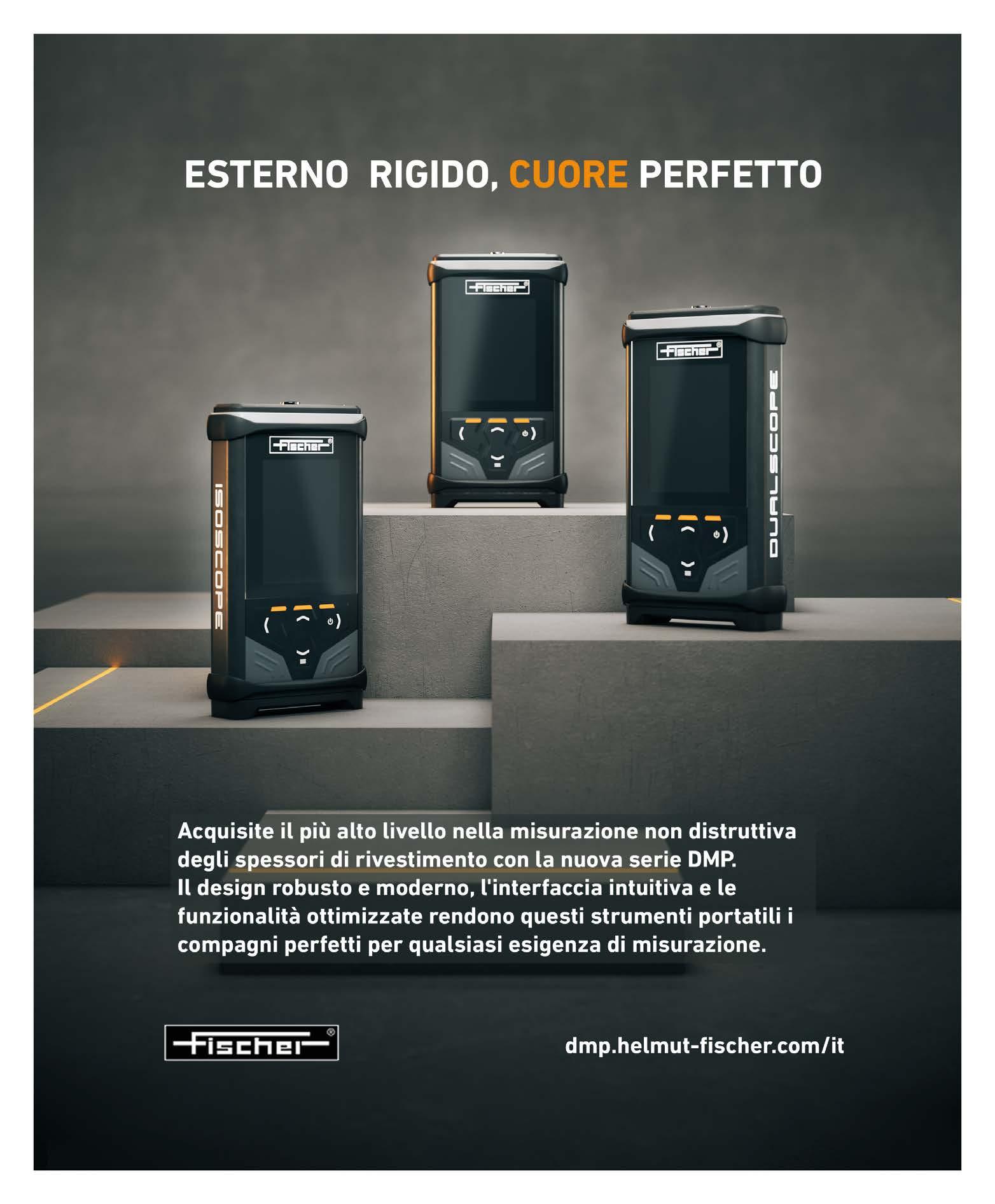
Lechler Tech: vernici industriali per ogni opportunità
A cura di Lechler Spa
Como - Italia info@lechler.eu
Non fa differenza su quale supporto si applica, fa differenza quale vernice si applica.
Che la verniciatura faccia la differenza migliorando le caratteristiche del supporto è ormai cosa nota, così come impreziosirlo e renderlo “accattivante” con le più svariate finiture, ma arrivare a riprodurre fedelmente lo stesso punto colore o effetto indipendentemente dalla tipologia del supporto stesso è spesso una necessità progettuale non semplice da soddisfare. Affrontiamo questo discorso con Lechler che ha fatto della replicabilità di colori e finiture su qualsiasi supporto che sia plastico o metallico, una meta e un punto di forza. Data la rifrazione della luce che modifica la percezione visiva del colore
su manufatti realizzati in materiali e forme diverse, in fase progettuale la questione va valutata e affrontata approfonditamente; Lechler per questo offre infinite soluzioni tecniche e coloristiche con cicli dedicati sia all’acqua che a solvente per tutti i settori come General industry, A.C.EAppliances And Consumer Electronics, Habitat, OEM - Original Equipment Manufacturer.
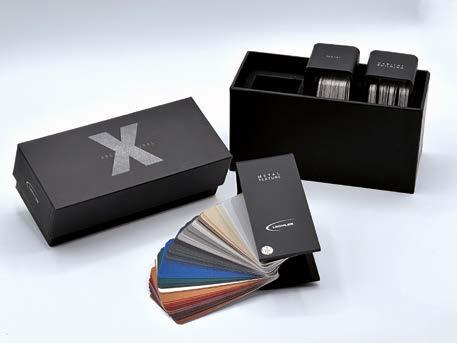
La ricchezza di soluzioni offerta da Lechler Tech abbraccia qualunque superficie e applicazione in ambito design, consentendo la progettazione di qualsiasi supporto e suggerendo finiture ricercate in grado di proteggere e impreziosire i manufatti nel tempo.
Tra i molteplici strumenti colore che Lechler mette a disposizione dei propri clienti, Architectural X è lo strumento più innovativo per il mondo della progettazione.

THE EASIEST WAY TO AUTOMATE YOUR PAINTING LINE
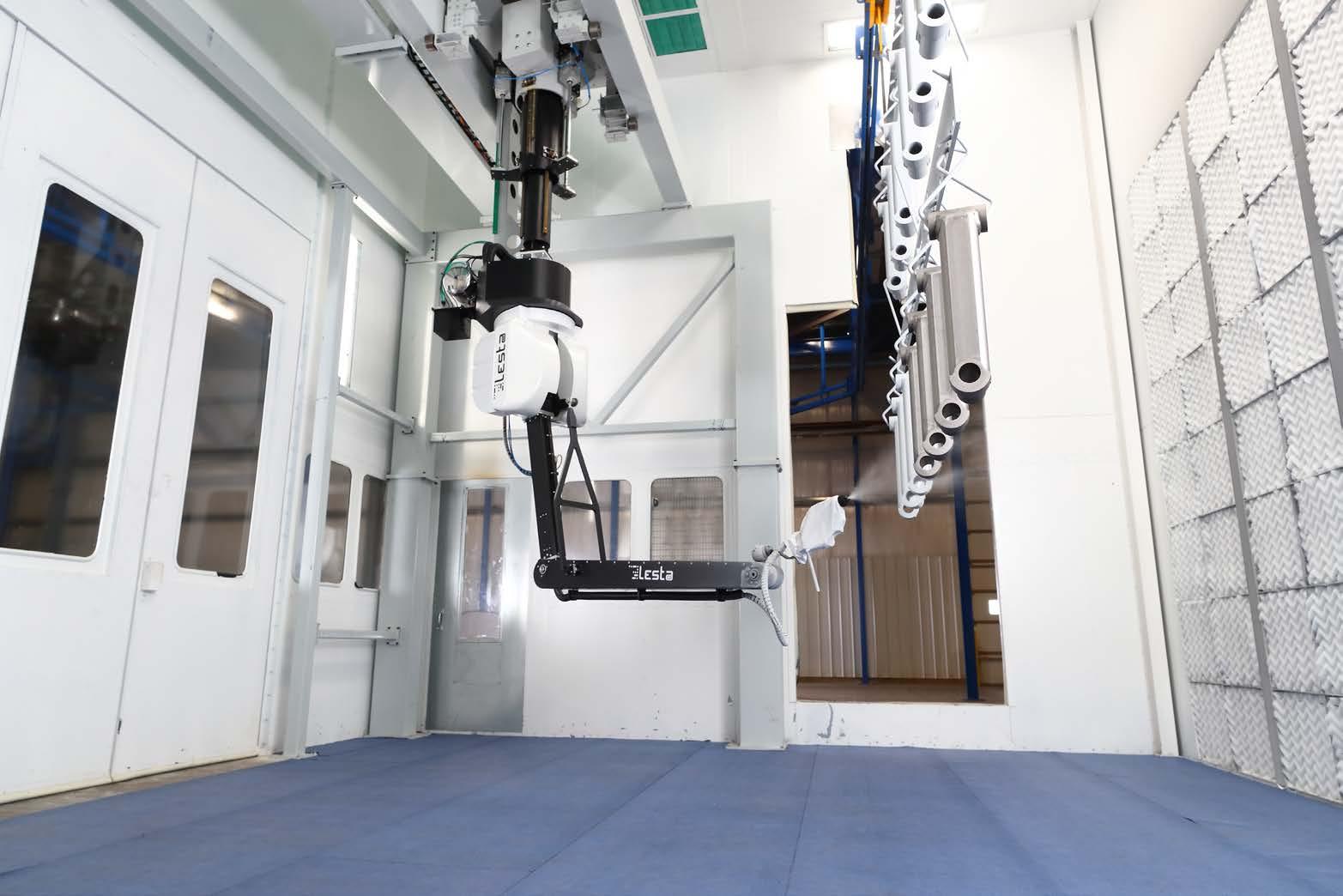
SELF-LEARNING ROBOT
1 OPERATOR REQUIRED
EUROPEAN ASSISTANCE
THE SCANNER RECOGNISES THE PARTS, THE ROBOT THEN PAINTS AUTOMATICALLY
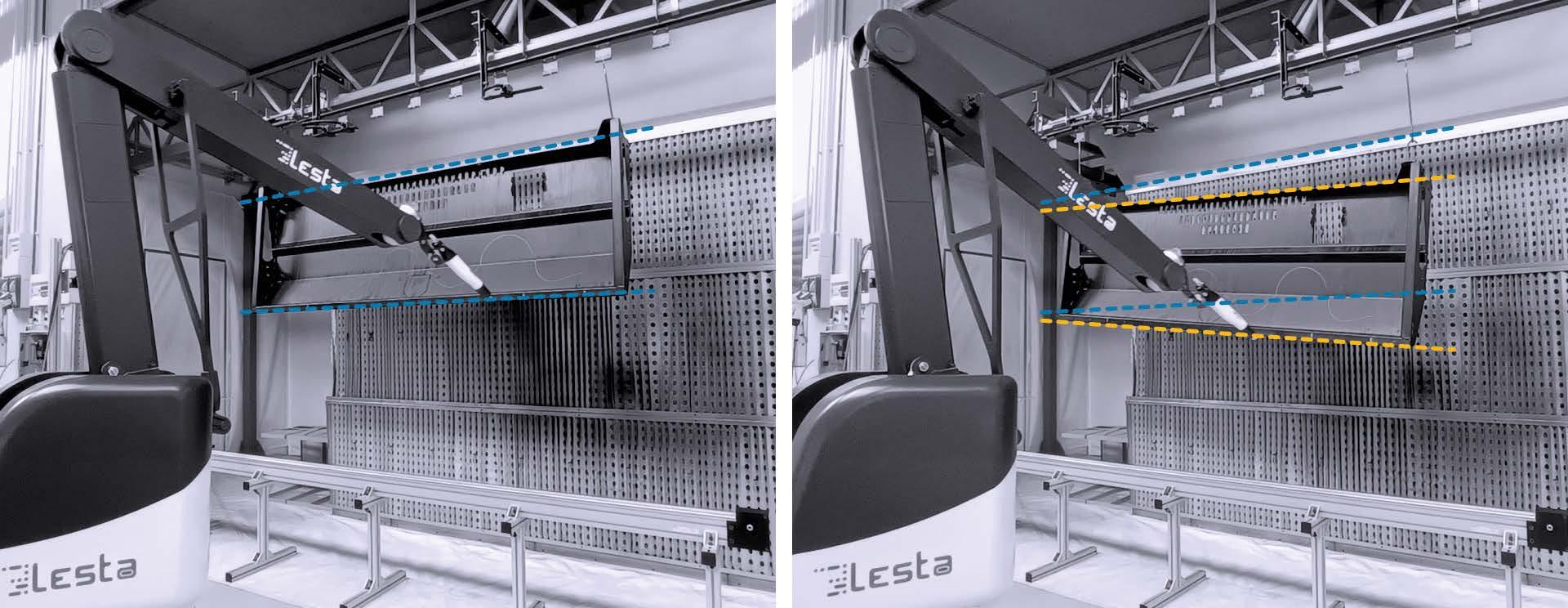

Tra i molteplici strumenti colore che Lechler mette a disposizione dei propri clienti, Architectural X è lo strumento più innovativo per il mondo della progettazione. Si compone di 3 mazzette di effetti che completano la proposta di effetti e finiture ad alto valore estetico conformi ai requisiti di bassa emissione di VOC con una proposta colore univoca per acqua e solvente. Le tre mazzette METAL, METAL TEXTURE, HABITAT BUILDING che compongono la collezione racchiudono la proposta completa di finiture per il mondo dell’Habitat con un’ampia scelta di colori metallizzati in versione lucida, opaca e texture. L’effetto materico rende tattile l’esperienza della finitura e permette di rispondere alle esigenze progettuali in ambito di architettura e design. In special modo la METAL TEXTURE rappresenta prodotti che applicati donano una fine struttura superficiale che permette di rendere materica e corposa la finitura riducendo la sensazione di “freddo” su supporti metallici e impreziosendo i materiali plastici grazie ad un elegante effetto metallizzato.
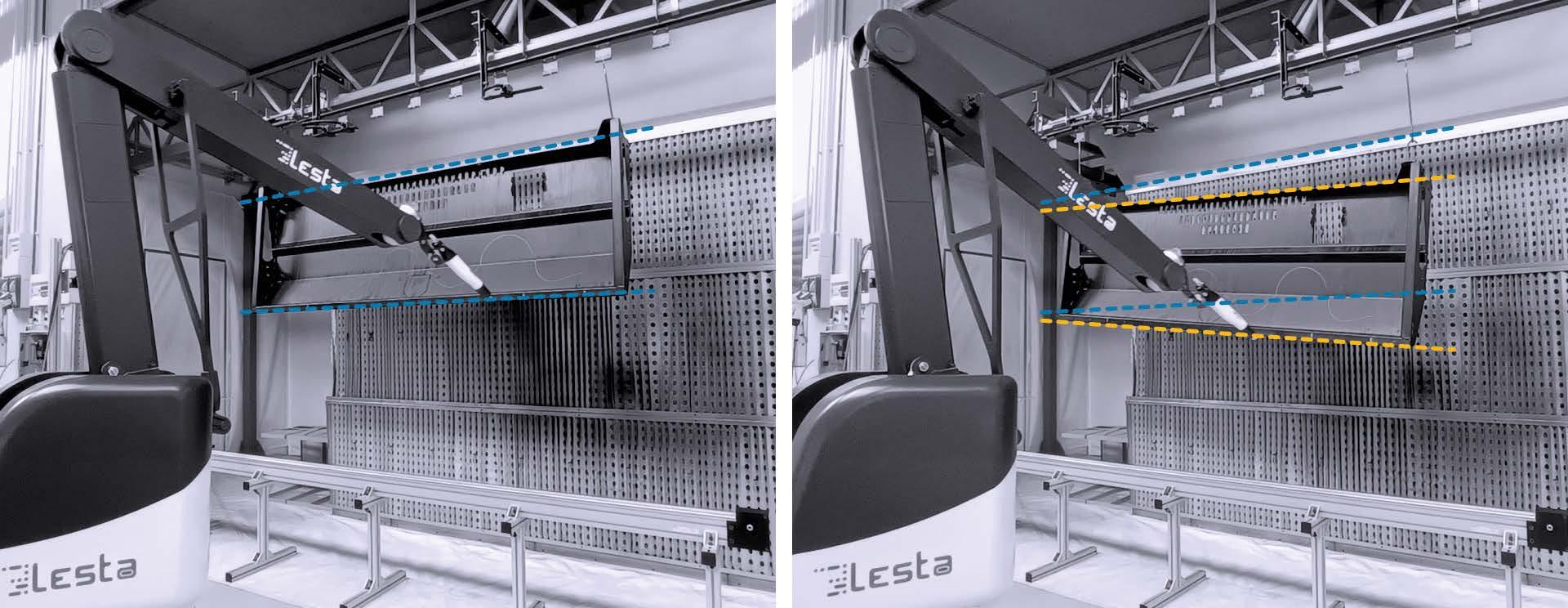
La texture consente inoltre di avere una superficie opaca più resistente allo sfregamento che maschera eventuali difetti del substrato.

Ideale per il mondo contract e dell’arredo, le colorazioni sono infatti in linea con le richieste del settore dell’architettura e del design di interior e di prodotto.
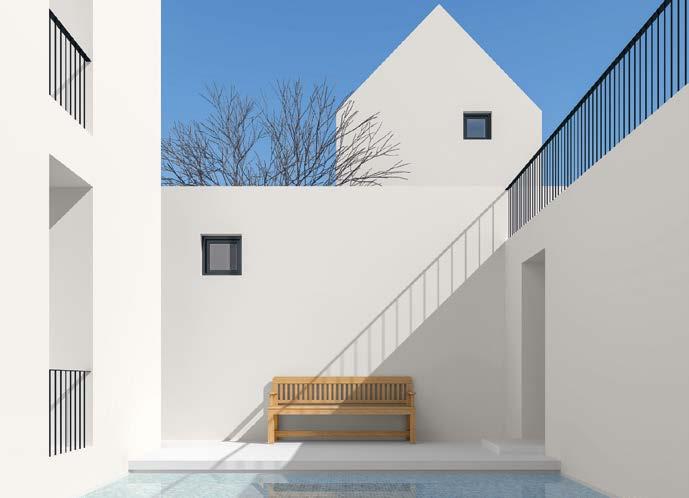
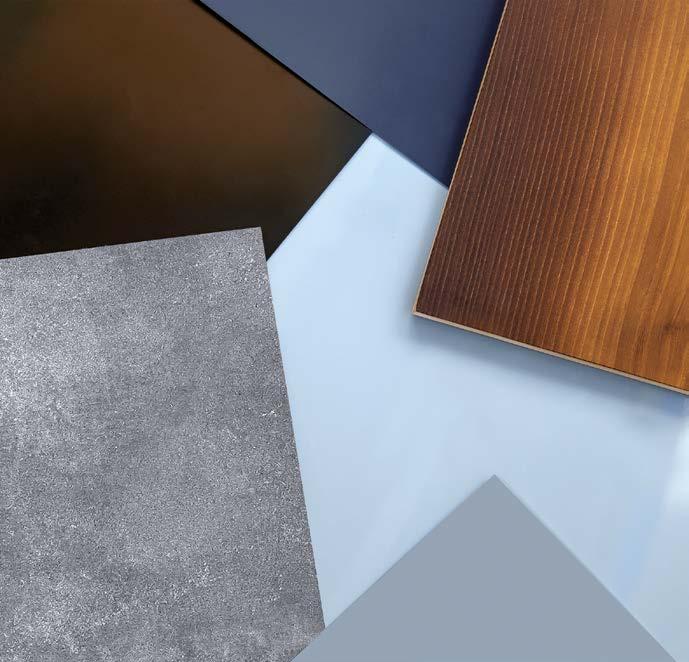
I binder scelti sono 29943 e YD943 in modo da dare coerenza di finitura sia su base solvente che acqua. Quest’ultima versione risulta inoltre conforme ai requisiti di VOC Emission internazionali per accrediti LEED, WELL e BREAM.
La collezione HABITAT BUILDING invece contiene colori e finiture evocativi dei materiali classici utilizzati in architettura per impreziosire le componenti plastiche (come ad esempio i serramenti in PVC) delle facciate facendole dialogare alla pari con gli altri elementi del contesto nella creazione dell’armonia d’insieme.
Proprio le soluzioni Lechler per la verniciatura dei profili in PVC sono certificate QB1 Profilés PVC revêtus e sono i cicli all’acqua con adesione diretta su PVC (Hydroframe Coat PVC Flex LH282) e nella versione a solvente con adesione diretta sia su plastica che su metallo (Framecoat PVC LS 282 e LS472, Plasticgrip 2K WS LS943).
1 Il marchio QB (“Qualità per gli edifici”) certifica la qualità, le prestazioni e l’affidabilità dei prodotti e dei processi di produzione e costruzione nel mondo dell’Habitat.
Il colore del vento: quando l’eolico diventa icona estetica
Intervista con Alberto Tessaro, Business Manager e fondatore di Enessere SrlDa tecnologie green contestate perché antiestetiche ad elementi di arredo urbano da installare in bella vista: grazie alle turbine eoliche ad uso domestico di Enessere, caratterizzate da linee sinuose ed eleganti e da suggestive tinte materiche, nasce una nuova cultura della sostenibilità.
L’energia eolica è tra le tecnologie rinnovabili più diffuse: secondo i dati riportati dall’IEA, l’International Energy Agency, nel 2022 l’energia elettrica prodotta dal vento è aumentata di 265 TWh (+14%) e l’eolico si è confermato la prima energia rinnovabile non idroelettrica con oltre 2100 TWh prodotti, più di tutte le altre tecnologie messe insieme1. Le turbine eoliche, tuttavia, così come altri dispositivi di generazione energetica, come i pannelli fotovoltaici per esempio, sono spesso al centro di discussioni perché ritenute antiestetiche nel contesto paesaggistico in cui sono collocate. L’azienda vicentina Enessere ha voluto rivoluzionare questa percezione, concependo un prodotto nuovo, dal design innovativo e dalle tinte accattivanti, un manufatto da valorizzare e non da nascondere: una turbina micro eolica verticale per produrre energia domestica pulita sfruttando il vento da
1 https://www.iea.org/energy-system/renewables/wind
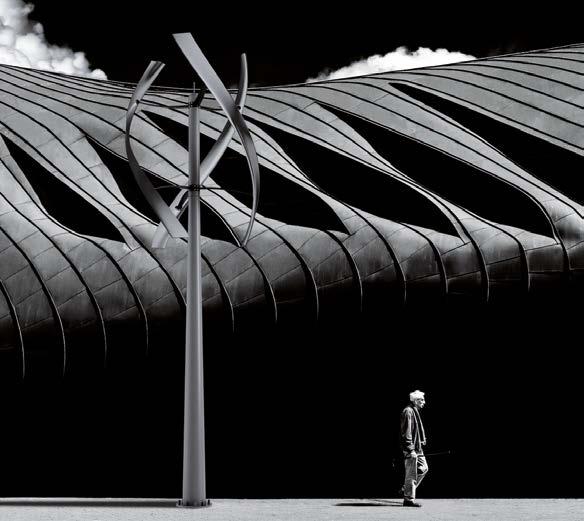

qualsiasi direzione provenga. Abbiamo intervistato il suo fondatore, Alberto Tessaro, per capire come il generatore eolico da dispositivo contestato perché ritenuto deturpante per l’ambiente si sia trasformato in un’icona estetica, quasi un elemento di arredo urbano.
Come è nata l’idea di valorizzare anche dal punto di vista estetico un manufatto per la produzione di energia elettrica come la pala eolica?
“Enessere è una giovane azienda fondata sul know how acquisito dal suo team nel settore dell’elettronica automotive. Si può dire che fin dalla nascita della nostra società avevamo in mente un progetto innovativo, senza precedenti in ambito energetico: abbinare lo sviluppo di una tecnologia avanzata per la produzione di energia elettrica domestica ad un design accattivante per realizzare un dispositivo che, oltre a garantire performance funzionali elevatissime, venisse esposto in bella vista e
non nascosto. A distanza di 10 anni dalla sua fondazione, possiamo affermare che Enessere ha centrato l’obiettivo grazie allo studio accurato della struttura che risulta lineare e sinuosa, dei materiali con cui realizzarla e delle tinte da applicare. Oggi i nostri piccoli eolici da 9m di altezza collocati nei giardini, nei parchi, nei paesaggi montani o sui lungomari si sono trasformati in “totem di sostenibilità”, un simbolo esibito con fierezza dai nostri committenti”.
Quali sono le peculiarità che rendono speciale questa turbina?
“Innanzitutto i materiali di pregio di cui è costituita: legno, acciaio inox e fibra di carbonio. La prima linea di turbine che abbiamo ideato si chiama “Hercules” e presenta una struttura portante in acciaio inox316 e vele rivestite da una fitta trama di lamelle in legno di Paulonia, per garantirne la perfetta aerodinamicità. La torre della nostra seconda linea “Pegasus” è invece realizzata in acciaio S355 N su cui applichiamo un triplo strato di vernice per proteggerne la superficie. La stessa vernice personalizzabile in diverse tinte è utilizzata anche per rivestire le vele, che sono dotate di una struttura in carbonio al pari delle razze che le sostengono. Questa possibilità di personalizzazione delle turbine con i colori scelti dal committente è la seconda importante caratteristica del nostro prodotto”.
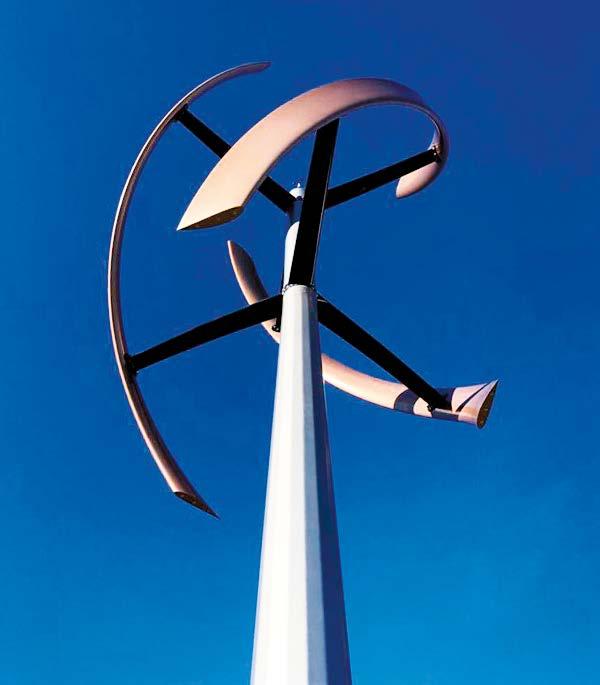
Perché il colore ha assunto un ruolo tanto strategico?
“Perché è anche attraverso il colore che un prodotto di questo tipo viene apprezzato. Oltre alle performance funzionali che garantiamo grazie alla nostra consolidata esperienza, abbiamo studiato insieme a
Francesca Valan, industrial designer specializzata nella progettazione di colori, materiali e finiture, e al nostro fornitore di vernici Lechler le tinte che meglio si adattano alle caratteristiche della pala, dopo aver scoperto che dare al cliente la libertà di scegliere la tinta che più preferisce, si trasforma spesso in un limite e non in un’occasione. Abbiamo così deciso di creare una cartella di colori tra cui è possibile selezionare quello più adatto per dialogare con il paesaggio creando una relazione cromatica in armonia con il luogo in cui la turbina sarà installata. Le vele delle turbine eoliche di Enessere riprendono infatti i colori del cielo e delle nuvole, le torri hanno colori neutri, caldi e freddi, che si intonano ai tronchi degli alberi e ai colori neutri della città. L’obiettivo era quello di proporre tinte “materiche” che richiamassero colori naturali e non “chiassosi”, in nome di quel ‘silenzio cromatico’ che volevamo ottenere con le nostre installazioni. Oggi le nostre torri dai colori materici (grafite, metallo, titanio) possono essere accostate a cinque tinte per le vele dai rimandi terreni e celestiali (seta, cielo, metallo, rame e spazio) in 6 combinazioni diverse”.
Come si svolge la verniciatura delle turbine?
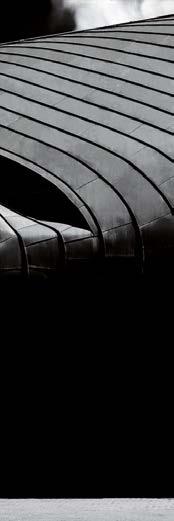
“Affidiamo la verniciatura in esterno e il nostro verniciatore utilizza lo stesso sistema applicativo manuale e a spruzzo utilizzato per il refinish automotive. Nel rispetto della normativa ISO 12944, soddisfa i requisiti del ciclo di verniciatura C5, una classe di verniciatura per ambienti molto corrosivi quali possono essere quelli dove sono esposti i nostri generatori a contatto con ambienti inquinati, condizioni di umidità e salinità dei paesaggi marini. Applica un ciclo tri-strato costituito da un primer protettivo, dalla vernice pigmentata scelta dal cliente e da uno strato di trasparente per la protezione contro i raggi UV. La qualità della finitura è equiparabile a quella della carrozzeria di un’auto, uniforme e piacevole alla vista, proprio perché il nostro eolico è un oggetto che deve integrarsi in particolari contesti paesaggistici, come quelli urbani. Per questo motivo abbiamo scelto di utilizzare vernici di tipo architettonico in grado di garantire una durata di vita del prodotto fino a 25 anni”.
Avete proposto al mercato qualcosa di veramente innovativo… “Mi piace pensare che Enessere non solo abbia ‘dato bellezza’ ad un manufatto considerato da sempre antiestetico, ma anche che, attraverso il colore, sia riuscita a creare una “cultura della sostenibilità” caratterizzata da turbine paragonabili a sculture di arte contemporanea - da esibire, quindi, e non da nascondere. Penso di poter concludere che, grazie a questo innovativo concept dei dispositivi per la produzione di energia rinnovabile, siamo finalmente riusciti a “colorare il vento”.
Dimezzamento dei tempi di cambio colore e volume di polveri da smaltire ridotto di dieci volte: l’esperienza Nord Laser
Alessia
Venturi ipcm®Un partner eccellente nella gestione della complessità. Queste sono le parole con cui Nord Laser Srl, carpenteria di Reana del Rojale, Udine, specializzata nella lavorazione di lamiere decapate e zincate per una varietà di settori industriali, definisce sé stessa. Dopo un processo di integrazione verticale della produzione durato anni, oggi l’azienda offre un servizio conto terzi completo di lavorazioni avanzate di carpenteria industriale, assemblaggio e verniciatura. L’investimento effettuato nel 2022 nel centro polveri di nuova generazione di Wagner ha decuplicato l’efficienza di verniciatura, garantendo un cambio colore senza intervento manuale, con tempi rapidi e costanti, l’accelerazione e l’incremento produttivo, la massimizzazione della qualità di finitura.
Nel 2022 Nord Laser ha investito in nuovo sistema applicativo, il centro polvere IPS di Wagner, che consente di pensare alla verniciatura con un punto di vista pari a quello utilizzato per le macchine utensili, incrementando la produttività, mantenendo standard qualitativi elevati, operando in modo semplice e diminuendo costantemente i tempi del cambio colore.

“Il plus di Nord Laser è semplificare le complessità grazie alla competenza strategica, all’approccio orientato alla risoluzione dei problemi del cliente e alla gestione delle criticità sviluppate in quarant’anni di storia” spiega Marco Bovolini, Presidente di Nord Group Spa, la holding cui fanno capo, oltre a Nord Laser, diverse aziende nei settori food, fitness e minerario.
“In Nord Laser ogni progetto è il racconto di una sfida etica, tecnologica e di innovazione. Nel corso degli anni, ci siamo strutturati per prepararci alla richiesta più inaspettata, ad accoglierla puntando a soddisfare il cliente, anche in termini di rapidità di consegna e di rispetto dei tempi di lavorazione pianificati. Per Nord Laser la puntualità è un valore essenziale” prosegue Bovolini. “La nostra idea di partnership è estremamente concreta, investe l’intero piano di sviluppo operativo e coinvolge il cliente in tutte le fasi di avanzamento: dalla co-progettazione alla condivisione degli obiettivi in una modalità di monitoraggio ciclica e saldamente integrata. In Nord Laser il cliente trova un servizio completo e verticalizzato in un unico fornitore, senza gli svantaggi di una supply-chain lunga e articolata”.
Dall’analisi alla produzione fino alla verniciatura e alla successiva spedizione: ogni fase è gestita per garantire al cliente prestazioni eccellenti.
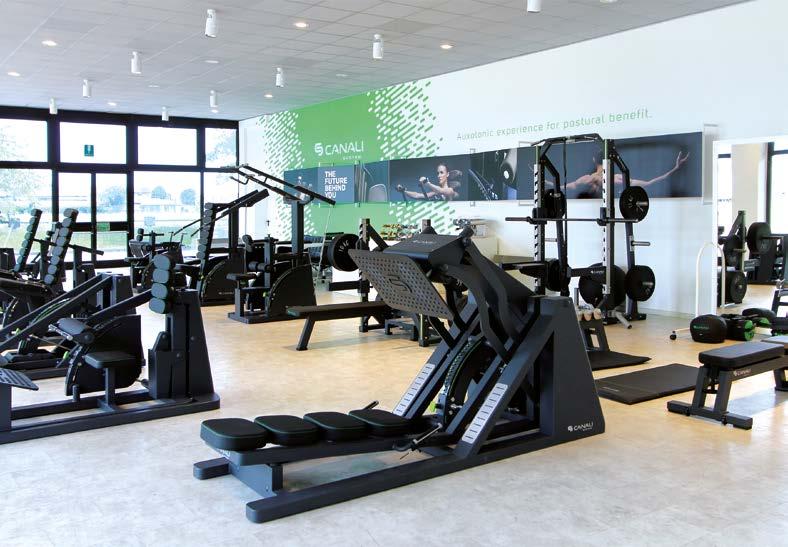
Proprio la verniciatura è stata oggetto di un importante investimento di capitale nel 2022 per il passaggio a un nuovo sistema applicativo, il centro polvere IPS di Wagner, che consente di pensare alla verniciatura con un punto di vista pari a quello utilizzato per le macchine utensili, incrementando la produttività, mantenendo standard qualitativi elevati, operando in modo semplice e diminuendo costantemente i tempi del cambio colore.
Dall’artigianalità degli anni 80 all’industrializzazione integrata dei 2000
La storia di Nord Group inizia nel 1984, quando Alessandro Bovolini fondò la Bovolini Snc

per l’esecuzione di lavori di saldatura e costruzione di manufatti di carpenteria leggera per il mercato locale. Negli anni l’azienda si è evoluta fino all’assetto odierno, dove la holding Nord Group Spa raggruppa sotto di sé altre quattro realtà aziendali, Nord Laser e tre start up: Canali System nel settore fitness, North Group Mining nel settore minerario, e Gabin nella ristorazione.
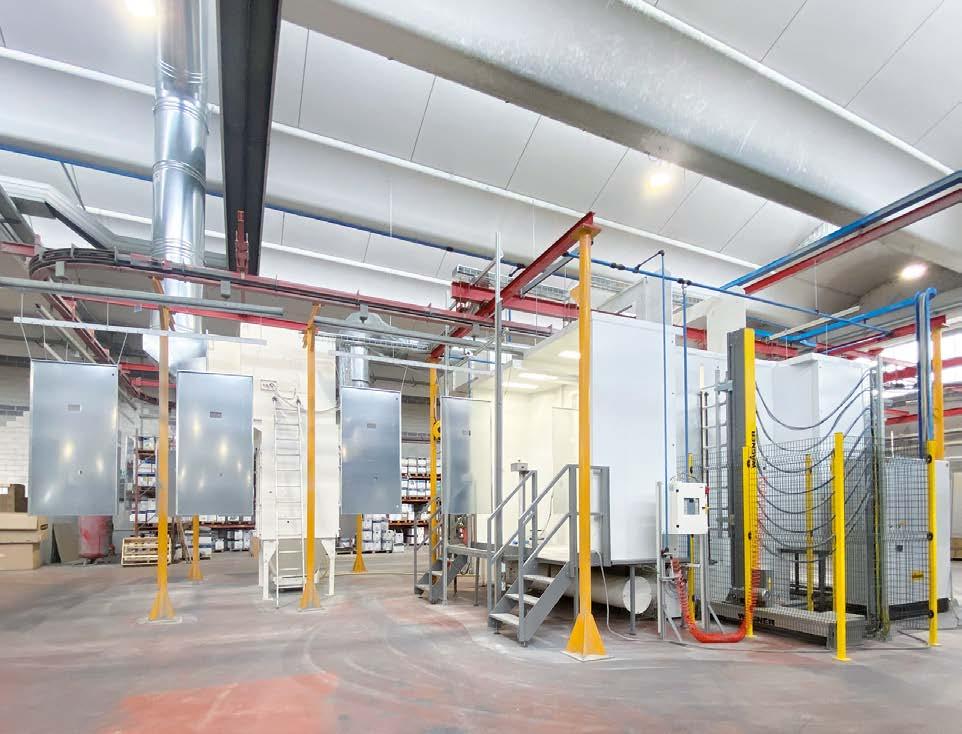
L’evoluzione di Nord Laser ha implicato il passaggio dalle pure lavorazioni di carpenteria manuale a un approccio sempre più tecnologico, dall’inserimento della prima punzonatrice passando per il taglio laser e altre macchine avanzate. Negli anni sono stati fatti diversi investimenti a livello di verticalizzazione della produzione fino all’integrazione della fase di verniciatura a polveri.
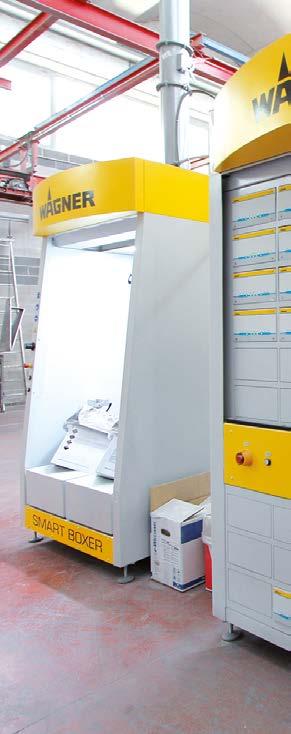
“Siamo un'azienda che lavora conto terzi ma abbiamo un ciclo produttivo molto verticalizzato: partiamo dalla materia prima, lamiera decapata o zincata, e forniamo parti di macchine o macchine complete, arrivando fino al collaudo della macchina finale, inclusa l’impiantistica elettrica a bordo macchina” prosegue Bovolini. “Amiamo definirci “il reparto produttivo dei nostri clienti”, i quali operano in vari campi, dall’industria dell’acciaio e dell’energia, all’industria tessile, del condizionamento, delle
macchine utensili, fino al mondo dell’arredamento e del fitness con Canali System, una delle aziende del nostro gruppo. Ciò significa che le specifiche tecniche e di qualità che dobbiamo rispettare variano molto a seconda del settore a cui un manufatto è destinato: spaziamo da specifiche prettamente funzionali, con elevati requisiti di resistenza alla corrosione, a specifiche dove il valore estetico è molto alto. In questo scenario, la nostra strategia è stata quella di verticalizzare la produzione per offrire ai clienti un servizio molto completo e la riduzione netta di tutti i costi di gestione di una supply-chain classica. Questo approccio, negli anni, ci ha premiato tanto che dal punto di vista commerciale stiamo cambiando il set-up dei nostri clienti, spostandoci sempre più verso aziende industriali.
Queste nuove esigenze comportano la necessità di una estrema flessibilità produttiva, di grande certezza dei tempi di realizzazione e della qualità. Questo ci ha portato a sofisticare gli strumenti di controllo di gestione: abbiamo introdotto un Enterprise Resource Planning (ERP) molto solido, un sistema di pianificazione e gestione della produzione aziendale, un MES per la raccolta dati, infine abbiamo puntato tanto sulla digitalizzazione e la 4.0, un approccio che interessa anche l’ultimo
investimento effettuato, quello nella cabina di verniciatura IPS di Wagner, che riteniamo rappresenti il nuovo benchmark nell’applicazione delle vernici in polvere”.

Un triennio di investimenti, protagonista la verniciatura
Negli ultimi 3 anni Nord Group ha investito circa 5 milioni di euro in nuove tecnologie, rinnovando il parco di macchine per il taglio laser e piegatura, creando un nuovo reparto interno di lavorazione meccanica, 5 postazioni robotizzate di saldatura e aggiornando l’impianto di verniciatura con una cabina di ultimissima generazione di Wagner.
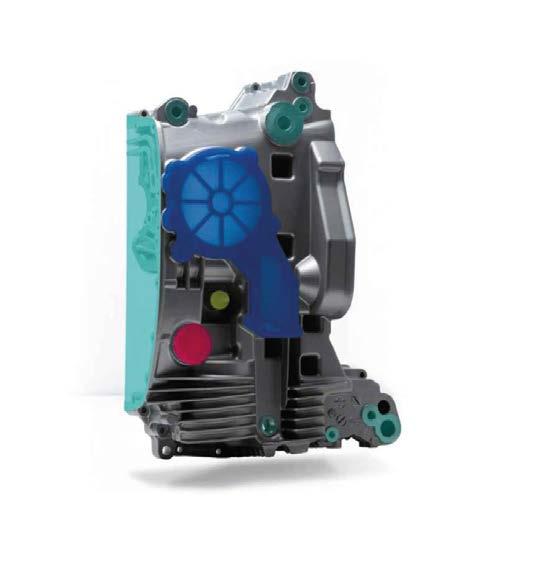
“Il nostro ciclo produttivo prevede taglio laser, punzonatura, sbavatura, piegatura, lavorazione meccanica, saldatura, verniciatura e assemblaggio finale. La verticalizzazione della fornitura di tutti questi servizi è una proposta commerciale vincente e la
verniciatura è una parte strategica di questa proposta: si tratta di un investimento di capitali alto, che richiede abilità, competenze e – appunto – capitali consistenti. Non tutte le aziende produttive sono disposte o sono in grado di integrare questo processo speciale al proprio interno” commenta Marco Bovolini.
Da sinistra:
La cabina di verniciatura Wagner con due postazioni per il ritocco pre- e post-verniciatura automatica, fa parte del sistema avanzato IPS di applicazione della vernice.
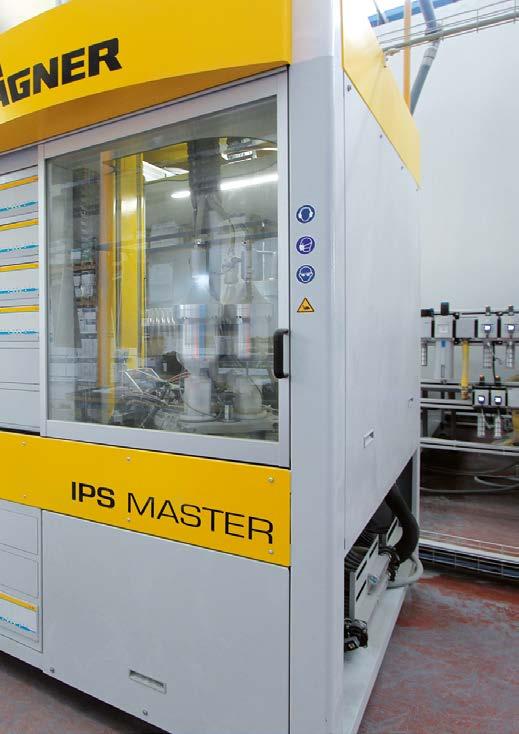
Vista generale del centro polveri IPS – Integrated Powder System che integra preparazione, alimentazione, dosaggio della polvere e cambio colore in un sistema completamente automatico.

Lo Smart Boxer, il sistema intelligente di alimentazione della polvere vergine nel ciclo di verniciatura, durante il cambio colore. Questo si attiva con la semplice pressione di un pulsante.
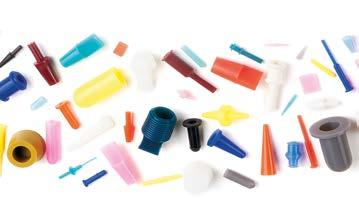
Nord Laser oggi è divisa in quattro stabilimenti da circa 5000 m2 ciascuno, la verniciatura occupa uno di questi con un impianto di verniciatura studiato da Imel nel 2000, una linea che può verniciare pezzi fino a sei metri di lunghezza, 2 metri di altezza e 1 metro di profondità. Due sono gli aggiornamenti più recenti effettuati su questo impianto. Il primo ha coinvolto il processo di pretrattamento, che da 5 stadi è passato a 7 stadi con sgrassaggio alcalino, risciacquo con acqua di rete, fosfatazione, risciacquo con acqua di rete, risciacquo con acqua demineralizzata, applicazione della passivazione nanotecnologica per nebulizzazione, ultimo risciacquo con acqua demi.
“L’esigenza alla base di questo aggiornamento era pretrattare con la medesima qualità entrambe le nostre materie prime: è noto che lo sgrassaggio alcalino lavora meglio sulla lamiera zincata mentre la fosfatazione è l’ideale per fare qualità sulla lamiera decapata” spiega Marco Bovolini.
“Inoltre, sulla lamiera zincata avevamo delle criticità di pretrattamento lungo il bordo tagliato al laser, sulla superficie di distacco fra parte zincata e parte tagliata. Per questo abbiamo anche introdotto una fase di sbavatura prima del pretrattamento chimico, al fine di arrotondare gli spigoli. Il nostro processo di verniciatura è certificato Qualisteelcoat.
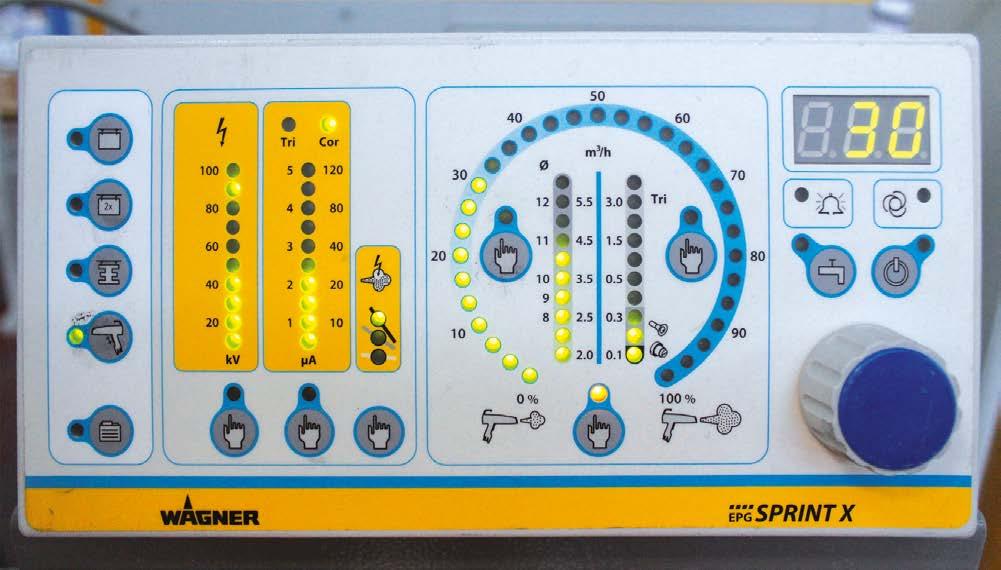
Garantiamo su lamierino zincato una classe 3C alta di resistenza alla corrosione con pretrattamento + uno strato di vernice. Riusciamo a raggiungere una classe C4 alta con l’applicazione di due strati di vernice in
polvere, ma al momento non vi è richiesta all’interno del nostro mercato”. “Questo aggiornamento del processo di pretrattamento è molto recente, la validazione con Qualisteelcoat è attualmente in corso” continua Bovolini. “L’altro aggiornamento invece, quello che ha portato dei vantaggi enormi in termini di efficienza della verniciatura, è la sostituzione della vecchia cabina di applicazione con il sistema di ultima generazione IPS di Wagner, un investimento che ha portato a una riduzione drastica dello smaltimento di polveri esauste, al dimezzamento dei tempi di fermo linea per il cambio colore e a un miglioramento della distensione e dell’omogeneità del rivestimento. In poche parole: estrema efficienza dell’applicazione”.
I vantaggi apportati da IPS
L’impianto di verniciatura di Nord Laser possedeva già una cabina automatica di applicazione polveri, che aveva subito un piccolo aggiornamento dei generatori elettrostatici per migliorarne l’efficienza. Tuttavia, lo smaltimento delle vernici esauste era ancora molto alto, nell’ordine delle 12 tonnellate l’anno su un consumo totale di 80-90 tonnellate. Nel 2021 Nord Laser apre una discussione con i potenziali fornitori di una nuova tecnologia di applicazione automatica, e sceglie di investire nel sistema avanzato IPS di Wagner, una soluzione completa e innovativa per ottenere risultati costanti di finitura, per un utilizzo completamente automatico: un nuovo approccio dell‘operatore al ciclo
di verniciatura, con un sistema che risponde a tutti i requisiti 4.0 e IoT, automatizzando attività fino ad ora totalmente manuali. “Fondamentalmente avevamo due benchmark del settore applicazione da paragonare, che se la giocavano sullo stesso livello. Con IPS, Wagner ha cambiato le carte in tavola” racconta Marco Bovolini. “Per la nostra vocazione tecnologica e per la volontà di essere sempre un passo avanti rispetto alla concorrenza, l’offerta IPS è stata scelta perché risolveva due problemi per noi molto importanti: il primo era il consumo di polvere, che aveva raggiunto un picco di 12-13 big-bag di polvere fine da smaltire all’anno; il secondo, i lunghi tempi di fermo catena per i cambi colore, che sono in media 6 al giorno. Quando Wagner ci ha presentato il sistema IPS, ci siamo subito resi conto che questo centro polvere di nuova generazione permetteva di gestire meglio il consumo di vernice nonché il layout del ventaglio di spruzzatura. Per Nord Laser sono stati determinanti i vantaggi in termini di gestione del processo produttivo, più che i vantaggi a livello estetico del rivestimento, su cui siamo meno sensibili poiché il 90% del nostro volume di verniciatura è costituito da manufatti industriali”.
“Tutti i centri polvere sul mercato hanno un elevato livello di automazione, le attività sono sequenziate dal sistema e non gestite dall'operatore.
NORD LASER, UN PARTNER CONCRETO
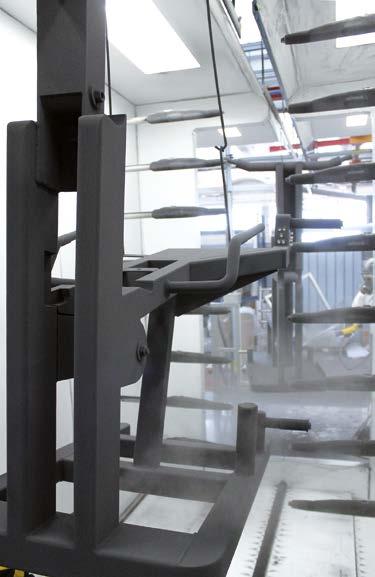

50.000 m2 di superficie, di cui 18.000 coperti
20 milioni di Euro di fatturato (anno 2022)
100 clienti nell'anno 2022
10.000 t di materiale lavorato
130 persone impiegate
Lavoro su 3 turni
Software 2D/3D Solidworks
Business Intelligence
Certificazioni Qualità
Lean Production
Con Smart Feeding Technology
l’alimentazione della polvere avviene grazie all‘utilizzo di un contenitore in pressione e di una valvola di dosaggio a controllo elettronico, e produce una nuvola morbida con poco overspray.
Con IPS l’operatore deve limitarsi alla pulizia della cabina e del ciclone: per tutto il resto è sufficiente premere un pulsante. Ciò ci ha consentito di definire con estrema precisione e costanza la tempistica di processo standard per il cambio colore” spiega Bovolini. “Con il centro polveri precedente, lasciavamo uno spazio sul trasportatore monorotaia di 12 bilancelle necessarie a garantire i tempi di cambio colore. A volte questo spazio non era sufficiente e la linea si fermava anche per 30-40 minuti. Con IPS abbiamo ridotto lo spazio sulla catena per il cambio colore a 6-7 bilancelle, ossia il 50% in meno rispetto a prima e senza fermi linea. A parità di prestazioni dell’impianto Imel, dati a consuntivo, il passaggio a IPS ci ha poi permesso di ridurre lo smaltimento di polvere a 1 bag, con un rapporto da 1 a 10 rispetto al precedente”.
“È innegabile che il sistema precedente fosse più “sprecone” in quanto non era attrezzato con una barra di lettura dei pezzi, dunque le pistole di verniciatura, 6 su ogni reciprocatore, erano sempre accese, con una dispersione di polvere notevole” interviene Venanzio Rosada, agente Wagner per il Friuli Venezia Giulia. “Tuttavia, anche inserendo una barra di lettura dei pezzi non avremmo ottenuto gli stessi risultati di diminuzione dei consumi perché IPS si differenzia per la gestione del recupero e della filtrazione dell’overspray di polvere, con una modalità di aspirazione e trasporto della vernice molto morbida, che riduce al minimo
la generazione delle polveri fini. Preciso che i dati raccolti sono a parità di fornitori di vernici in polvere, perché la costanza granulometrica della polvere svolge anch’essa un ruolo fondamentale nella creazione dei fini”.
“In sostanza IPS è un sistema di ultima generazione di alimentazione della polvere, che garantisce condizioni stabili nell‘alimentazione della polvere con sistema VACUM a mezzo bar di pressione e setacciatura a ultrasuoni pressurizzata” conclude Rosada. “IPS ha il massimo livello di automazione del cambio colore che non richiede presidio umano, con un controllo centralizzato di tutte le fasi del processo e la rilevazione dei consumi della polvere in tempo reale”.
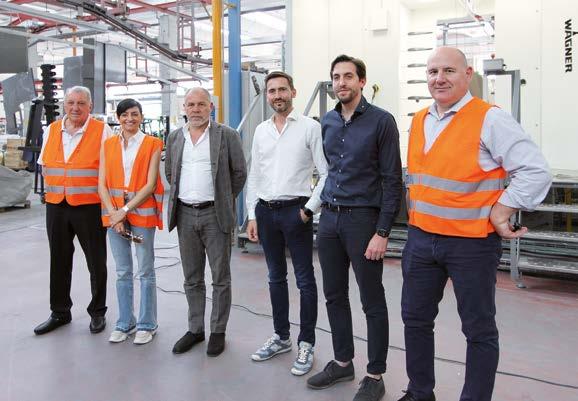
Un nuovo benchmark di mercato?
“Stiamo ancora lavorando per capire bene tutta la gestione dei parametri della cabina e per comprendere nel dettaglio il comportamento dell’alta densità di IPS al fine di ottimizzare la penetrazione di vernice nei particolari 3D” conclude Marco Bovolini. “Aver dimezzato i tempi di cambio colore per Nord Laser è stato fondamentale perché l’impianto è sempre saturo. È innegabile che l’investimento sia molto elevato, ma ritengo che anche il ritorno dell’investimento sia elevatissimo e i suoi tempi molto brevi. Senza contare che questa tecnologia potrebbe diventare un nuovo benchmark di mercato, con un valore residuo futuro molto alto”.
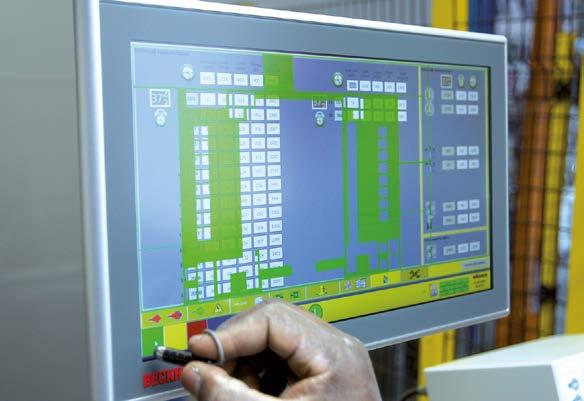
VERNICI E RIVESTIMENTI IN POLVERE POWDER COATINGS
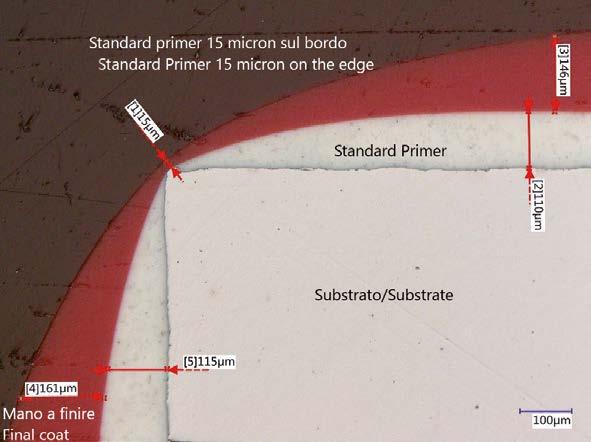
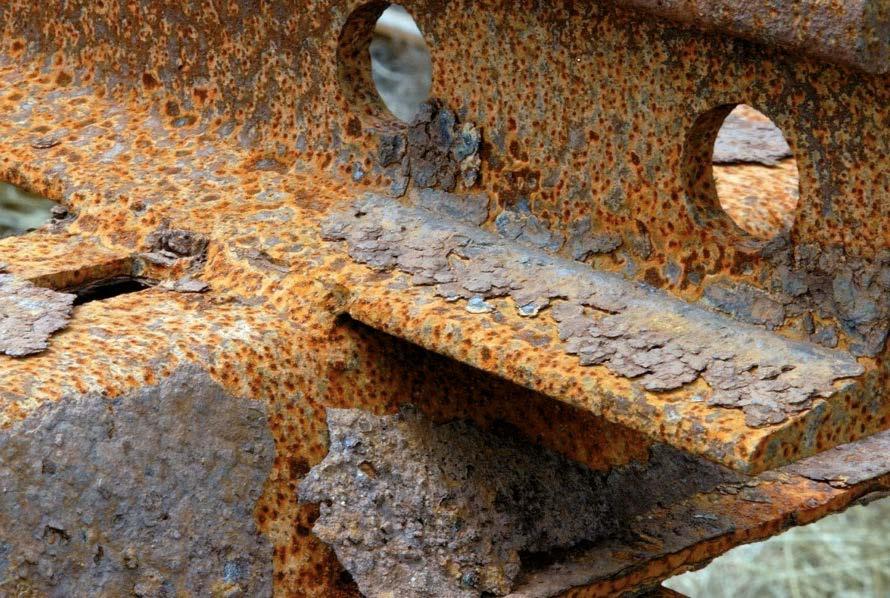
ENDURANCE
IL PRIMER COPRI SPIGOLI THE EDGE COVER PRIMER
ENDURANCE
La serie Endurance 16J0, realizzata con resina epossidica leggermente raggrinzata ed additivi ad effetto barriera e passivanti, garantisce un’eccellente copertura dei bordi e quindi un’eccellente protezione.
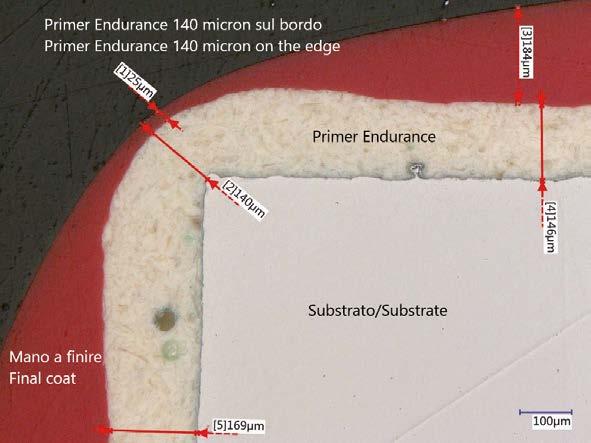
The Endurance 16J0 series, made with slightly fine textured epoxy resin and additives with a barrier and passivating effect, guarantees excellent edge coverage and therefore excellent protection.
Pulverit S.p.A. Italia
Via Carlo Reale, 15/4
20157 Milano-Italy
Tel +39 02 376751
email: pulverit@pulverit.it
Pulverit Polska Sp. z o.o.
ul. Strefowa 16
43100 Tychy-Polska
Tel. +48 32 329 14 11
email: biuro@pulverit.pl
Pulverit Deutschland GmbH
Im Wert 3
73563 Mögglingen- Deutschland
telef.: +49 7174 7193000
email: info@pulverit.de
Pulverit Iberia s.l.u.
c/ Caravis, 28, 1º 3ª
50197 Zaragoza
Tel. +34 607163259
email: iberia@pulverit.it
Le sfide dell’economia circolare all’industria della verniciatura e le risposte di Chemtec
Carlo E. Guidetti Chemtec Srl, Corbetta (Milano, Italia) info@chemtec.itLa popolazione mondiale è aumentata in maniera esponenziale negli ultimi decenni ed ha superato i 7 miliardi di persone. Diverse previsioni di sviluppo demografico indicano che nel 2050 la popolazione mondiale ammonterà a circa 10-11 miliardi di persone. E’ stato stimato che ad oggi nel mondo circa il 54% della popolazione viva in aree urbane e che aumenterà fino al 64% nel 2050. Le città sono responsabili del 70% circa delle emissioni di origine antropogenica, del 70% delle emissioni civili totali, del 50% della produzione globale di rifiuti e del 60% circa delle emissioni di gas serra1. Il Country Overshoot Day è il giorno dell’anno in cui un Paese va in debito ecologico, ossia ha utilizzato tutte le risorse naturali disponibili per l’anno in corso in rapporto alla capacità rigenerativa del territorio stesso. Si tratta, quindi, di un vero e proprio strumento di contabilità ambientale: ideato dal Global Footprint Network, utilizza i dati relativi alla biocapacità e all’impronta ecologica per determinare quando l’umanità, sia a livello globale che locale, arriverà ad utilizzare più risorse di quelle che in realtà possiede. Come si può notare in fig. 1, tutte le economie avanzate del pianeta consumano le proprie risorse entro i primi mesi dell’anno. Questi dati ci spiegano in maniera incontrovertibile che il sistema economico mondiale sta sfruttando troppo rapidamente le risorse che il nostro pianeta mette a disposizione. Si impone, quindi, un cambiamento di sistema globale per avviare un percorso in cui le nostre esigenze di vita si adattino alle risorse disponibili. In
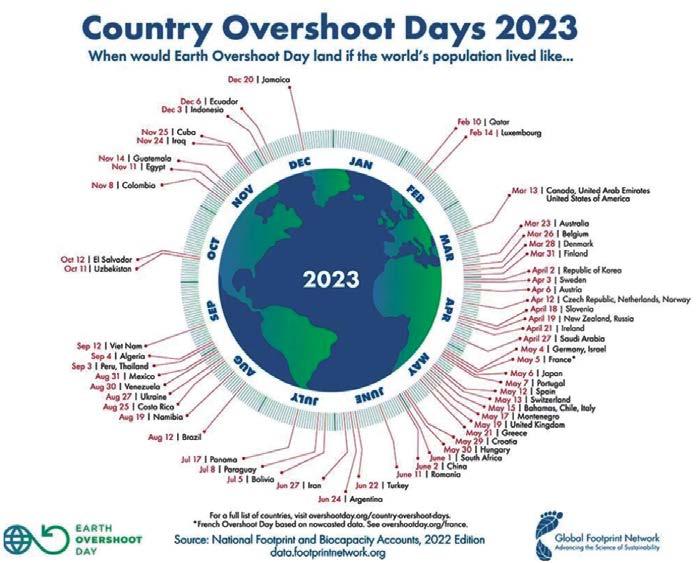
questo contesto, l’industria gioca un ruolo molto importante come grande utilizzatrice di risorse naturali (gas, acqua) e di energia e come creatrice di emissioni atmosferiche e solide.
Il passaggio da economia lineare a economica circolare
Il modello economico storicamente esistente, definito dagli studiosi “lineare”, prevede un ciclo molto semplice: prelievo di risorse dal pianeta, loro lavorazione per produzione di beni (spesso usando altre risorse e creando rifiuti all’interno del ciclo produttivo), commercializzazione e
utilizzo dei beni stessi e, a fine vita, smaltimento del bene. Questo sistema tradizionale è poco compatibile con l’attuale contesto ambientale e con le esigenze di cambiamento sopra descritte. Da qualche anno ormai, al modello economico lineare si contrappone un nuovo modello economico definito “circolare”, pensato per essere rigenerativo. In questo contesto, il modello di produzione promuove la minimizzazione dell’utilizzo delle risorse ambientali e delle emissioni nei processi produttivi. Il modello di consumo si basa sulla condivisione, il riutilizzo, la riparazione, il riciclo dei
materiali e dei prodotti esistenti al fine di ridurre sprechi e consumi di risorse. Le differenze fra i modelli economici classici e circolari sono riassunte nella figura 2
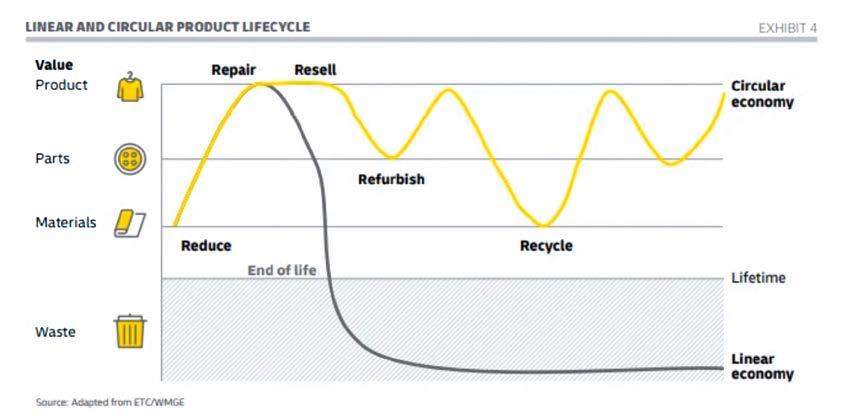
Economia circolare e le sfide per l’industria Il modello di economia circolare sviluppato anni orsono dalla Ellen MacArthur Foundation mostra come nel sistema circolare ogni bene venga prodotto utilizzando possibilmente energie rinnovabili, minimizzando l’utilizzo di risorse naturali e progettando un oggetto in modo che questo possa essere almeno parzialmente riparabile, riutilizzabile, ricondizionabile o riciclabile tramite semplici operazioni. Alcune conseguenze di questo modello economico sono già parte del nostro sistema: si pensi ad esempio al mercato degli smartphone o dei tablet ricondizionati. A partire da qualche anno, l’International Organization for Standardization (ISO) ha avviato un processo formale di regolamentazione per l’economia circolare, prevedendo standard attualmente in corso di elaborazione dalla serie ISO 59000.

A livello nazionale italiano, l’Ente Italiano di Normazione (UNI) ha adottato la norma tecnica UNI/TS 11820:2022, che permette a imprese e organizzazioni di misurare il proprio tasso di circolarità adottando criteri condivisi. L’attuale versione della specifica tecnica include 71 indicatori di circolarità, suddivisi in sei categorie: risorse e componenti, risorse energetiche ed idriche, rifiuti ed emissioni, logistica, prodotti/servizi e risorse umane.

E’ quindi chiaro che ci troviamo all’inizio di una fase transitoria dall’economia lineare a quella circolare. La capacità di adattarsi a tale cambiamento sarà uno dei fattori chiave nei prossimi anni per le imprese manifatturiere, quanto meno in Europa e nei mercati maturi del pianeta.
Aziende come Freitag2 sono citate dagli economisti come esempi di realtà capaci di sfruttare questa opportunità per creare nuovi business: Freitag realizza infatti borse e accessori partendo da teloni di camion riciclati, da bottiglie in PET o airbag di auto non scoppiati. Ma anche colossi del calibro di IKEA3 hanno iniziato a portare avanti iniziative importanti per il riutilizzo dei loro mobili e componenti.
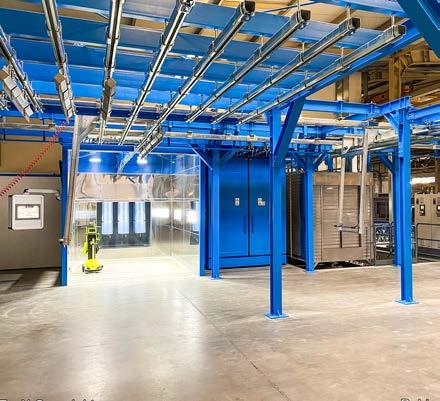
In questa nuova fase di modello economico circolare, le sfide che l’industria manifatturiera si trova a dover affrontare sono riassunte di seguito:
• minimizzazione dell’uso delle risorse ambientali: acqua e gas naturali
• riduzione drastica dei consumi energetici da fonti non rinnovabili
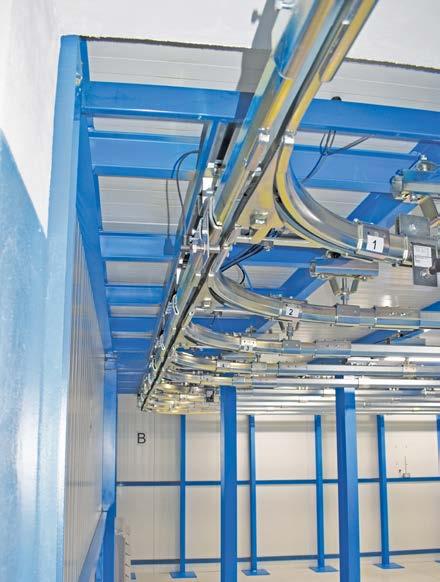
• eliminazione dell’uso di sostanze tossiche nei cicli produttivi

• riduzione della creazione di scarichi, reflui, sottoprodotti, scarti.
Ogni azienda produttrice che voglia anticipare i temi che la transizione all’economia circolare imporrà, dovrà
2 www.freitag.ch/it
3 www.ikea.com

inevitabilmente porsi questi obiettivi da gestire.
Le risposte di Chemtec alla transizione economica
Chemtec, azienda italiana con sede a Corbetta (Milano), specializzata nella formulazione, produzione, commercializzazione e applicazione industriale di prodotti chimici per il trattamento delle superfici pre-verniciatura e del trattamento per le acque industriali (chiare e di processo), si pone come partner strategico per accompagnare i propri clienti in questa transizione.
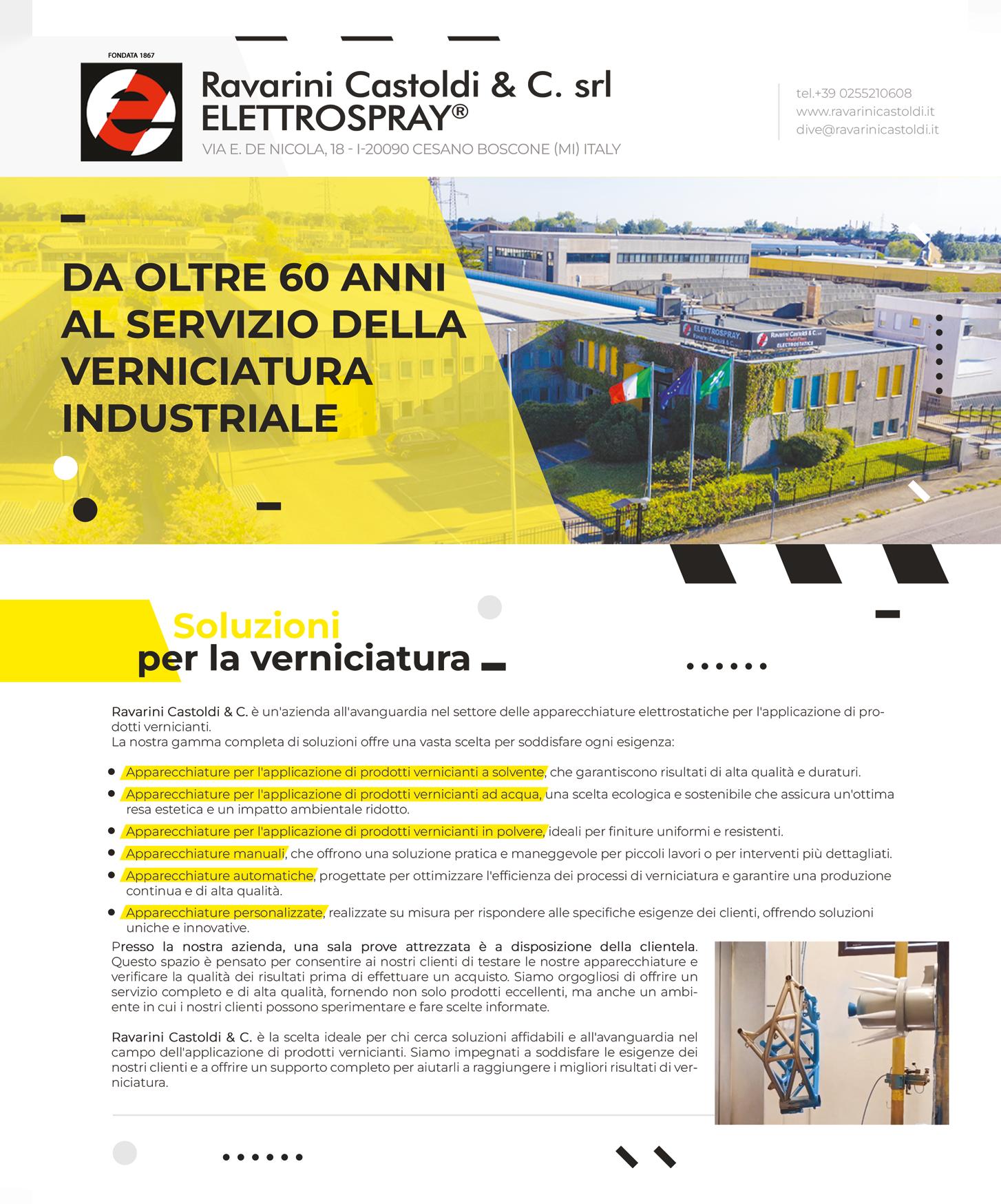
Trattamento dell’overspray Nell’ambito del trattamento dell’overspray delle cabine di verniciatura, ci sono due tecnologie disponibili: il filtro a secco o la cabina a velo d’acqua. A prescindere da qualsiasi valutazione di natura economica, in base ai principi dell’economia circolare sopra descritti, in molti casi la cabina a velo d’acqua è preferibile rispetto ai filtri a secco.
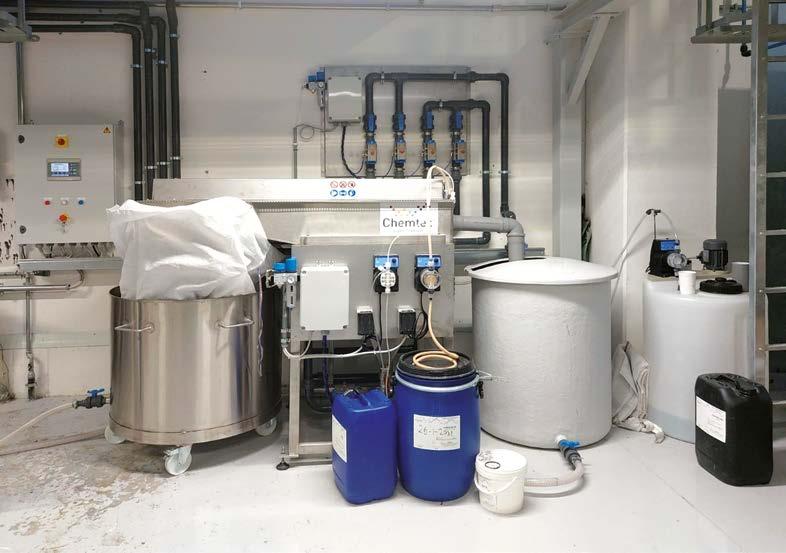
Nonostante le cabine a velo d’acqua utilizzino, appunto, l’acqua, attraverso l’uso di impianti specifici e di prodotti chimici appositamente
formulati (fig. 3) è possibile trasformare l’overspray della vernice in fango a basso contenuto di acqua (residuo secco pari a circa 60-70%), purificando l’acqua della cabina in maniera costante e continua ed evitandone i frequenti smaltimenti. Chemtec sta attualmente studiando una soluzione per riutilizzare questi fanghi, trasformandoli da rifiuti da smaltire a bye-products per il loro riuso come componenti di nuovi sistemi.
I filtri a secco impregnati di vernice sono invece dei rifiuti che devono essere eliminati senza poter dar loro una seconda vita.
Pretrattamento
Il processo di pretrattamento delle superfici metalliche alla verniciatura è una delle fasi a maggiore impatto ambientale del processo di finitura. I processi tradizionali consumano grandi quantità di acqua (centinaia o migliaia di m3 all’anno) ed enormi quantità di gas naturale e di energia elettrica per scaldare o movimentare grandi volumi di soluzioni acquose necessarie ai processi di lavaggio e fosfatazione. Queste, infine, creano fanghi solidi da smaltire periodicamente e vanne sostituite
con frequenza variabile mediamente da 1 a 4 volte all’anno. In base a quanto detto sopra, i processi tradizionali di lavaggio e fosfatazione difficilmente rispecchiano i parametri di economia circolare succitati. Chemtec propone processi nanotecnologici altamente innovativi per eliminare completamente o ridurre in maniera importante queste problematiche. Il TORAN 3, per esempio, è un’alternativa al fosfosgrassaggio che non contiene né usa acqua, non va scaldato, non genera fanghi né reflui di alcuna natura. Gli oli di lavorazione eliminati nella fase di sgrassaggio vengono incorporati nel processo, diventando un componente attivo dello stesso e rispettando così uno dei principi base dell’economia circolare, il riuso dei prodotti di scarto. Il processo nanotecnologico PRONORTEC consente di ridurre i consumi idrici, energetici e di gas naturale di circa il 40-60% rispetto ai processi tradizionali, sfruttando composti organici del fosforo, e, quindi, operando senza la presenza di alcun metallo pesante quale cromo, nickel, zirconio o titanio. Infine, la semplicità di utilizzo di questi processi garantisce una bassissima percentuale di scarti produttivi, aumentando l’efficienza e la qualità dei processi industriali.
Conclusioni
La fase di transizione del modello economico da lineare a circolare è già iniziata. Diverse grandi aziende hanno già adottato modifiche alla progettazione dei beni, ai processi produttivi e alla supply chain per riutilizzare e ricircolare i propri manufatti e ridurre al minimo l’uso di risorse ambientali. Le aziende che ad oggi non hanno ancora iniziato questo progetto o che stanno cercando soluzioni in questa direzione possono trovare in Chemtec e nei suoi processi tecnicamente innovativi un partner affidabile per affrontare insieme le sfide poste dall’economia circolare nei processi di verniciatura industriale.
L’autore desidera ringraziare sentitamente il Professor Andrea Urbinati dell’Università Liuc per la preziosissima collaborazione.
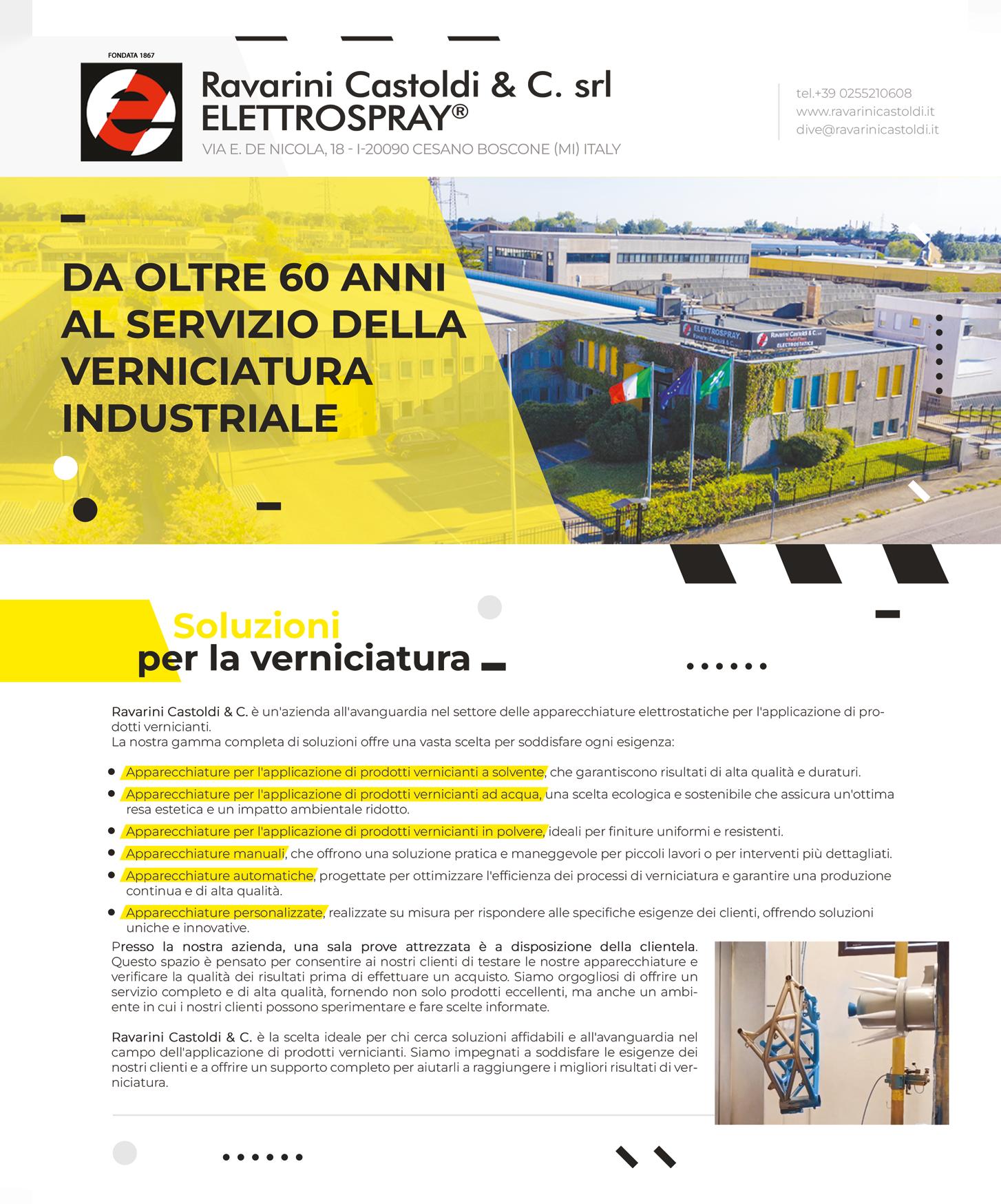
Più opzioni per la verniciatura di componenti per veicoli elettrici
Frank Siegel Walther Trowal GmbH & Co. KG, Haan - Germania f.siegel@walther-trowal.deLa domanda di sistemi di tenuta realizzati con elastomeri è in rapida crescita. Uno dei motivi principali è l’avvento della e-mobility. Per soddisfare le richieste di numerosi reparti verniciatura, Walther Trowal ha sviluppato la nuova Rotamat R 100. Confrontata con i suoi predecessori, questo modello di verniciatrice ha un volume utile praticamente raddoppiato. R 100 consente inoltre il rivestimento dei componenti di tenuta con una più ampia gamma di materiali quali diversi tipi di olio, cera e vernici a lenta asciugatura.
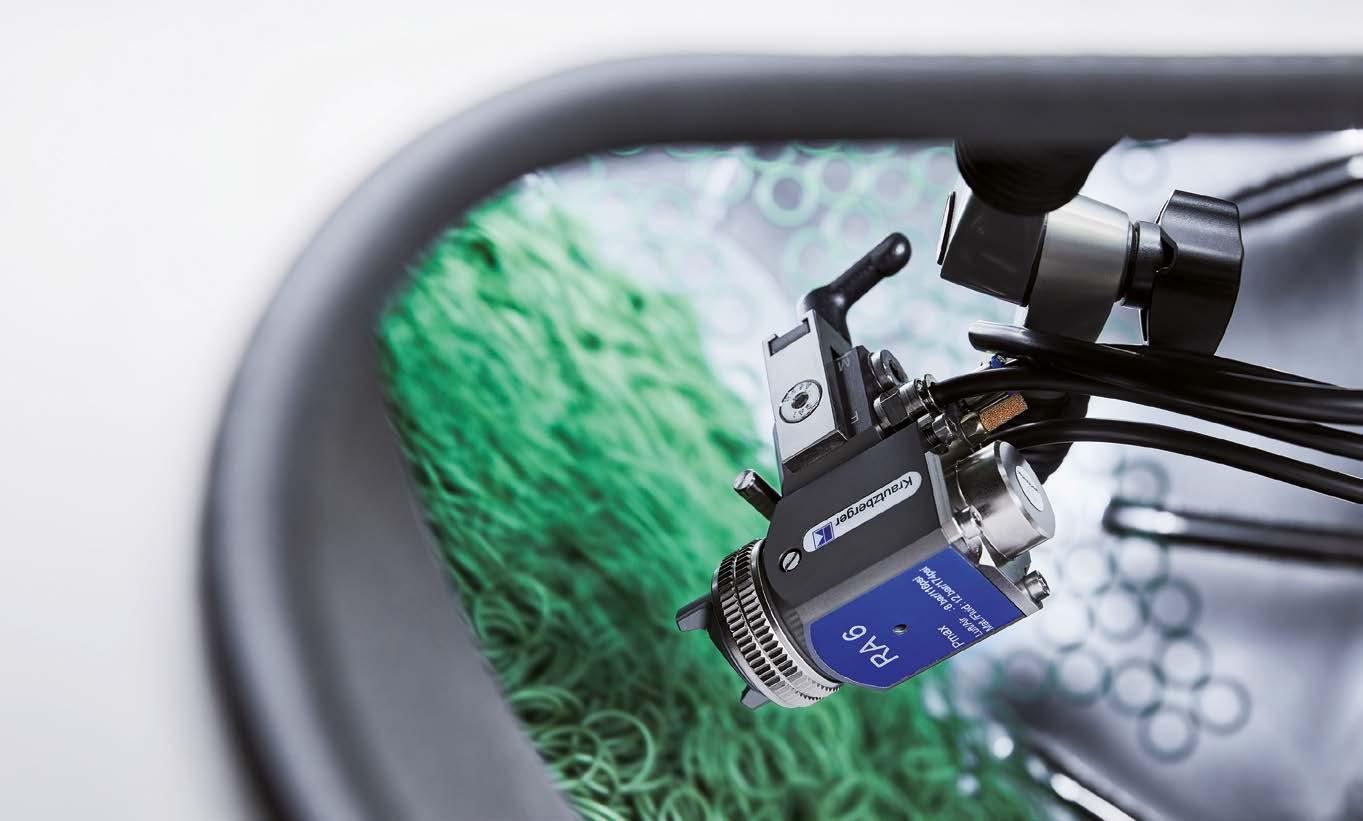
Le macchine Rotamat si sono affermate come soluzione ideale per la verniciatura di sistemi di tenuta elastomerici come gli O-ring con vernici anti-attrito. Sono utilizzate anche per la verniciatura di anelli metallici sottili – per esempio guarnizioni ad anello per alberi – con un agente legante.
Componenti più grandi e volumi produttivi più elevati
Per le loro trasmissioni e le loro batterie di accumulatori, i veicoli elettrici richiedono numerosi componenti di tenuta. Questi sono utilizzati non solo per le celle dell’accumulatore ma anche per il raffreddamento. Anche componenti quali i moduli di controllo per veicoli elettrici hanno i propri
Walther Trowal ottiene la precisione richiesta nel dosaggio dei materiali vernicianti grazie ad una tecnologia a sensori ultramoderna e ad una valvola elettropneumatica.
La nuova Rotamat R 100 permette di verniciare componenti con diametro fino a 300 mm. A destra, le macchine Rotamat durante la fase di assemblaggio finale presso lo stabilimento Walther Trowal di Haan.
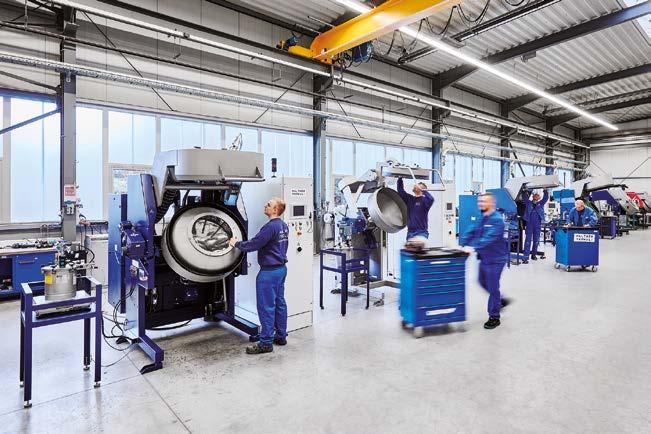
sistemi di raffreddamento con scambiatori di calore, nei quali si utilizzano componenti di tenuta con dimensioni fino a 300 mm. Presso i reparti verniciatura, che già gestiscono milioni di componenti, questo trend tecnologico ha creato il bisogno di sistemi di verniciatura con maggiori capacità di lavorazione. Per soddisfare questa necessità Walther Trowal ha sviluppato la nuova verniciatrice Rotamat R100. Con un volume utile di 160 litri e un carico utile di 100 kg può processare circa 1.000 guarnizioni in un unico lotto. Rispetto al suo predecessore R85 vernicia il doppio dei componenti – con lo stesso tempo ciclo e con un consumo energetico e un ingombro solo di poco maggiori. La prima R 100 sarà consegnata a breve ad un reparto verniciatura in Italia. Il diametro del tamburo rotante della R 100 è di 1.000 mm. Per coprire l’intero spazio interno del tamburo la macchina è dotata di due sistemi di spruzzatura.
Lavorazione di più tipologie di oli e cere
Un’altra tendenza tecnologica è l’aumento dell’uso di olio e cera per il rivestimento dei componenti di tenuta. Per esempio, nell’ingegneria medica le vernici vengono sostituite da olio di silicone come materiale di rivestimento predominante per gli elementi di tenuta di elevato valore. Per ovvie ragioni: gli oli siliconici sono più compatibili con il corpo umano. Poiché vengono applicati in strati sottili, ma richiedono una copertura della superficie estremamente omogenea, è essenziale un dosaggio preciso e con una tolleranza di soli pochi grammi.
Walther Trowal ottiene la precisione richiesta nel dosaggio con una tecnologia a sensori ultramoderna e con una valvola elettropneumatica. Ciò garantisce che la precisa quantità di materiale raggiunga la superficie del componente in un dato tempo. Il risultato è uno spessore omogeneo e una qualità di lunga durata.
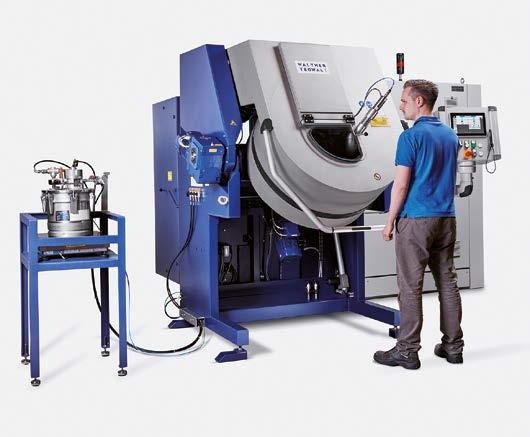
Utilizzo di più tipi di vernice
Diverse caratteristiche tecniche della nuova Rotamat permettono l’applicazione di un’ampia gamma di vernici. Alcuni tipi di materiale verniciante richiedono un rapido, a volte anche brusco, raffreddamento dei manufatti dopo la verniciatura. Per ottenere questo, Walther Trowal ha aggiunto un bypass per l’aria di scarico proveniente dal tamburo, che permette all’aria di bypassare l’unità di riscaldamento dopo la spruzzatura e che guida l’aria ambiente nel tamburo. Ciò impedisce che il calore residuo dell’unità di riscaldamento raggiunga i componenti verniciati. In questo modo non si appiccicano tra di loro e vengono scaricati dal tamburo come pezzi separati. Risultato: una maggiore resa di “qualità 1a”. Generalmente Walther Trowal equipaggia le macchine Rotamat con un sistema per l’aria di scarico a 4 stadi. Questo è composto da un filtro Papp a labirinto, un tappetino filtrante e due filtri a tasche. In questo modo i solventi presenti nell’aria di scarico non possono raggiungere l’ambiente. Questa soluzione ha dimostrato la sua efficacia e affidabilità in molte applicazioni.
Con alcuni tipi di vernice l’overspray richiede più tempo per indurire e diventare polvere secca. Per evitare che l’appiccicosa nebbia di overspray passi nel filtro e arrivi al sistema di scarico dell’aria, Walther Trowal ha ulteriormente ottimizzato la sua tecnologia di filtrazione. Se necessario, all’aria di scarico viene aggiunta dell’aria fresca, che fa raffreddare bruscamente le particelle di vernice residue. Queste sono poi trattenute in modo sicuro dal sistema di filtrazione di Rotamat – un beneficio notevole per la sicurezza degli operatori e per l’ambiente.
Elevato livello di automazione
L’inclinazione automatica del tamburo è un altro importante passo
verso l’automazione completa dei sistemi di verniciatura di Walther Trowal. Un produttore di componenti di tenuta ha riferito di dover regolare frequentemente l’inclinazione del tamburo durante il processo di verniciatura. Ha notato che i componenti non ancora verniciati presentavano delle caratteristiche di burattatura diverse rispetto ai componenti già verniciati. Fino ad oggi l’inclinazione del tamburo rotante era attivata da una guida elettromeccanica da avviare manualmente. Nella nuova Rotamat di Walther Trowal l’inclinazione del tamburo è completamente automatica e i rispettivi parametri di processo fanno parte dei programmi del PLC dedicati alle varie tipologie di manufatti. La macchina ora adatta automaticamente l’inclinazione del tamburo al tipo di rivestimento richiesto per ogni componente e funziona quindi in modo completamente automatico per tutta la durata del processo. Anche nelle attività che richiedono numerosi cambi di inclinazione, le uniche operazioni manuali sono il carico e lo scarico del tamburo rotante.
Maggiore stabilità del processo
Con il nuovo sistema di controllo del dosaggio di vernice, Walther Trowal è stata in grado di migliorare ulteriormente la stabilità di processo delle macchine Rotamat. Il nuovo sistema regola automaticamente la pressione di modo che, in diverse condizioni operative, la quantità specificata di materiale sia applicata con precisione alla superficie dei componenti.
Oltre alla sofisticata gestione della temperatura e al preciso flusso di aria fresca, il nuovo regolatore di pressione garantisce condizioni ottimali
nel tamburo rotante per tutta la durata del processo di verniciatura. Il nuovo sistema di controllo della pressione non solo migliora la stabilità complessiva del processo, bensì semplifica anche le operazioni di verniciatura.


Chi è Walther Trowal
Da olte 90 anni Walther Trowal produce e vende soluzioni modulari e personalizzate per affrontare le sfide più difficili nel campo del trattamento e della finitura delle superfici. Mentre inizialmente si concentrava sulla finitura in massa, nel tempo Walther Trowal ha continuamente ampliato la sua gamma di prodotti. Oggi l’azienda offre una vasta gamma di apparecchiature per la finitura di massa, la granigliatura e la verniciatura, per il lavaggio e l’asciugatura di una varietà di manufatti, nonché per la verniciatura di componenti piccoli prodotti in serie Walther Trowal sviluppa e implementa soluzioni complete: collegando e automatizzando vari moduli di lavorazione adatta la tecnologia di processo alle specifiche esigenze dei clienti. Questo include anche le apparecchiature periferiche come i sistemi di pulizia e di riciclo. Servizi completi come le prove di lavorazione con i manufatti dei clienti e il servizio globale di riparazione e manutenzione completano l’offerta dell’azienda.
Walther Trowal serve clienti in tutto il mondo, appartenenti a numerosi settori quali automotive, aerospaziale, ingegneria medica ed energia eolica.
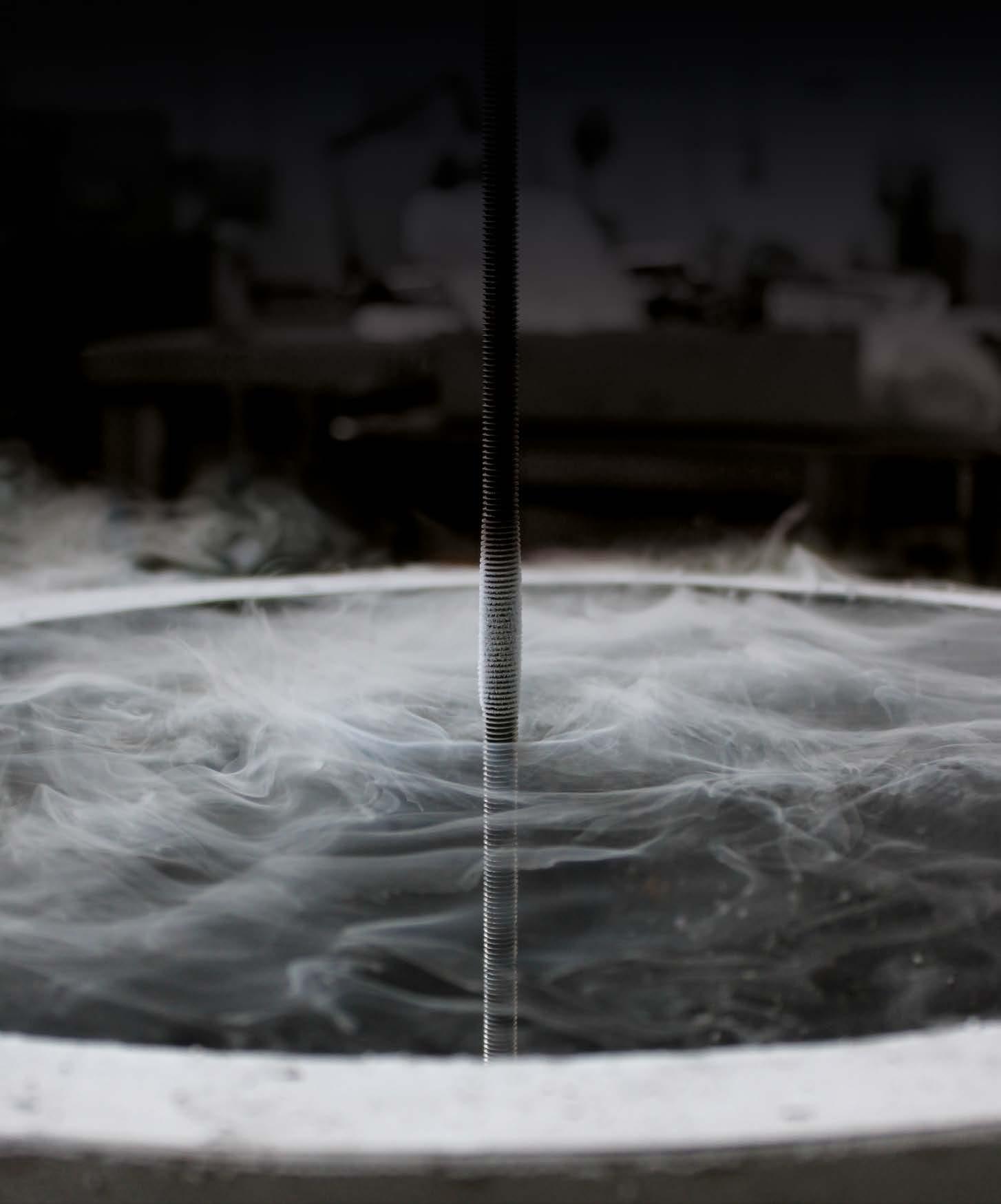

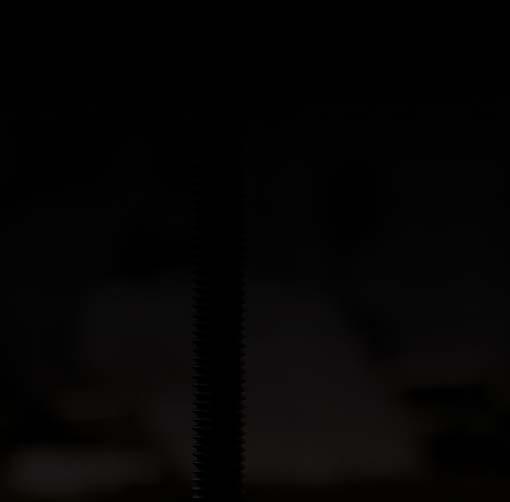
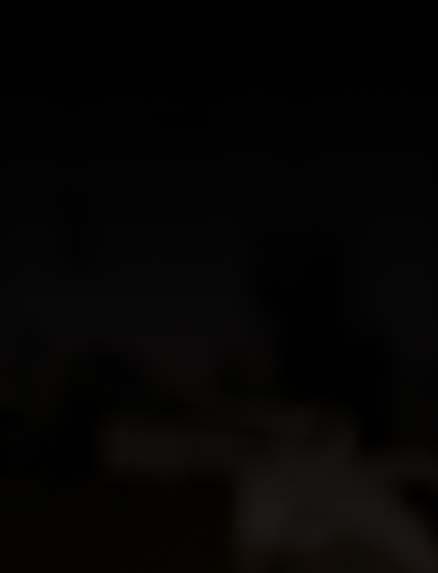


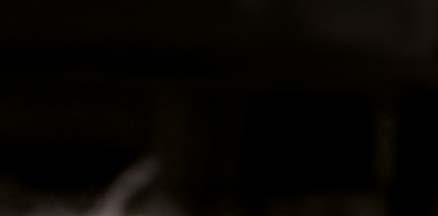
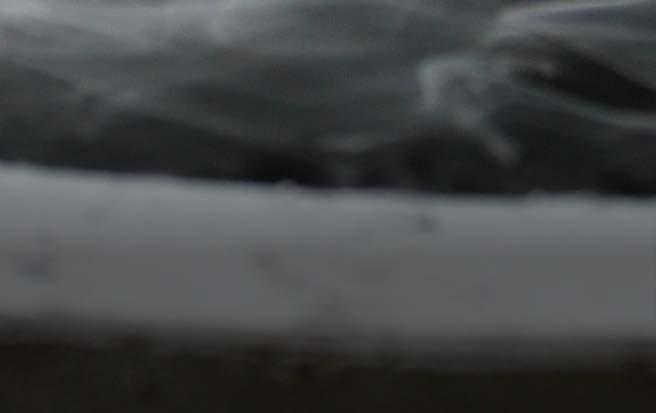
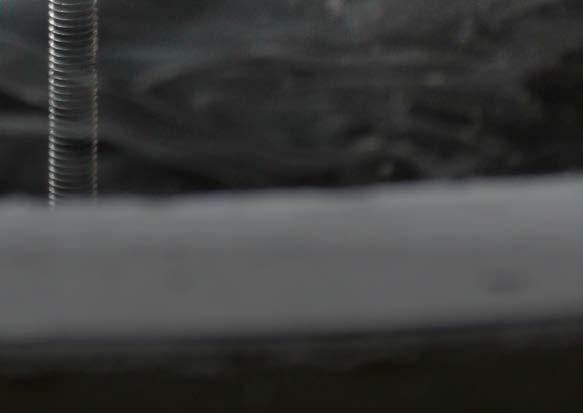
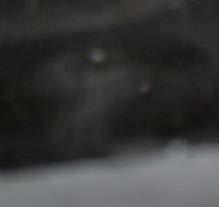
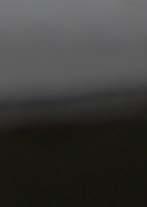

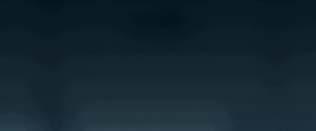
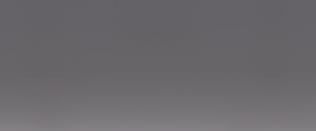
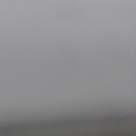
Brevi note sullo sviluppo di tecnologie orientate alla sostenibilità, grazie ad automazione, efficienza energetica, digitalizzazione e AI impiegate in un processo di verniciatura industriale
Alessandro Soba Verind Spa, Rodano (Milano) – Italia alessandro.soba@verind.itVERIND, parte del gruppo internazionale Dürr, progetta soluzioni tecnologiche innovative integrando know-how, ingegneria di sistemi industriali, apparecchiature ed eco-tecnologie specifiche per processi di verniciatura, rivestimento di superfici e trattamento delle acque reflue. Elemento comune di ogni sviluppo economico è l’energia e il suo consumo, da sempre declinati come motore dello stesso sviluppo. Un processo industriale è oggi analizzato in termini di energia, di efficienza, di rispetto ambientale con una visione tecnologica che indirizzi il processo produttivo a minimizzare i consumi di materia prima, migliorando il bilancio energetico complessivo e quindi gli sprechi e i costi.

La fase finale di un processo produttivo è normalmente la finitura superficiale: essa impatta sull’ambiente in termini di emissioni in atmosfera, creazione di rifiuti speciali ed inquinamento delle acque. È anche una fase energivora del processo produttivo, con elevati consumi di energia che impattano sull’ambiente in termini di riduzione delle risorse naturali.
Innovazione tecnologica, automazione, elaborazione dati derivati da sensoristica di campo integrata da logiche di digitalizzazione e AI è il mix di competenze che Dürr mette in campo per soddisfare gli attuali criteri di sostenibilità.
In questa logica, per linee di verniciatura ad alta produttività e a basso impatto ambientale, vengono oggi adottate innovative scelte ingegneristiche, allo scopo di:
• Ridurre i consumi energetici dei singoli processi
• Ridurre l’emissione globale di CO2
• Ridurre i consumi di prodotti impiegati e di materie prime
• Ridurre gli scarichi liquidi e gassosi
• Incrementare efficienza e qualità
• Ottimizzare il costo per unità prodotta
• Integrare automazione e digitalizzazione
• Incrementare l’efficienza attraverso la flessibilità.
Grazie all’innovazione e alla ricerca applicata, il gruppo Dürr ha sviluppato per il settore Automotive ed Industria importanti tecnologie.
Tecnologia elettrostatica EcoBell
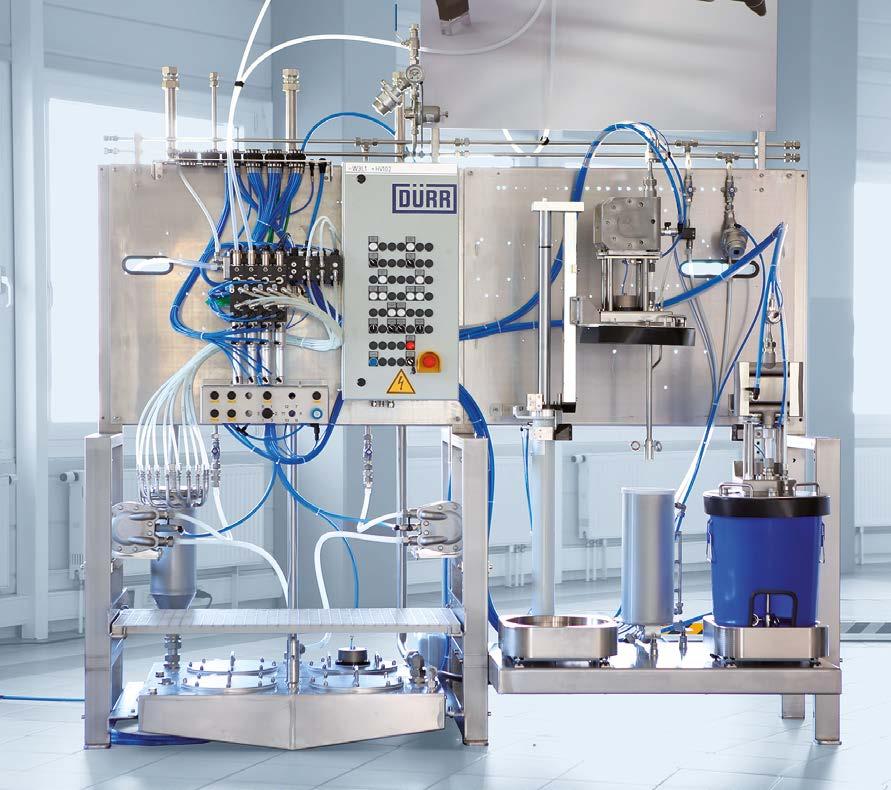
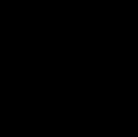

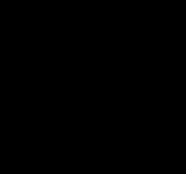

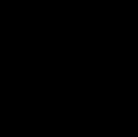

Questo polverizzatore rotativo con tecnica a 2 o 4 aghi e caricamento esterno compatto, ideale sia per l’impiego sulle linee automotive sia nel settore industria, garantisce massima qualità di rivestimento, minimo consumo di vernice, ridottissimi tempi di cambio colore. Esso soddisfa il risparmio di vernice nel processo di finitura di alta qualità e produttività, grazie all’effetto elettrostatico che assicura alti parametri di efficienza di trasferimento.
Tecnologia EcoSupply P
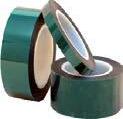
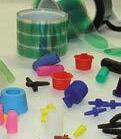
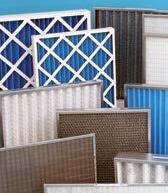

È un sistema di alimentazione della vernice standardizzato e modulare con tecnologia di raschiatura che può essere impiegato per le


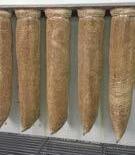


applicazioni di vernici a base di acqua e solvente. Per via del notevole aumento della varietà di colori sia nell’industria dell’auto e dei veicoli commerciali sia nell’industria in generale, da tempo non vengono solo applicati colori speciali e personalizzati mediante i sistemi a raschiatura, bensì anche colori per piccole serie. EcoSupply P soddisfa il risparmio di vernice e di prodotti di lavaggio nelle linee di produzione ove sono richiesti frequenti cicli di cambio colore. La vernice non utilizzata nelle tubazioni viene recuperata nel fusto vernice e riutilizzata.
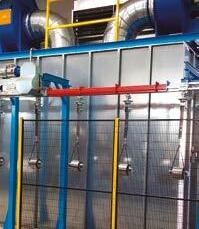

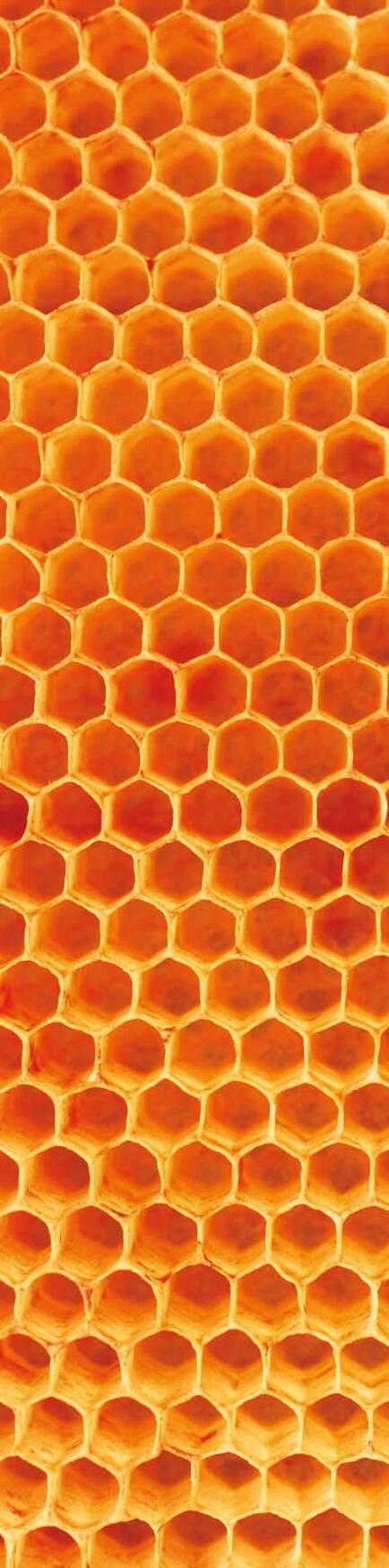
Tecnologia EcoPaint Jet - OFA (Overspray Free Application)
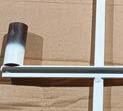
Livello di personalizzazione elevato: questa è la
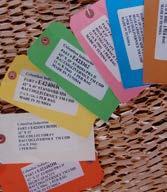
richiesta imperante che arriva dal mercato. Ne è un esempio la realizzazione di tetti bicolor nel settore dell’automotive o la creazione di strisce di design sui prodotti. EcoPaintJet è un sistema innovativo per la verniciatura automatizzata priva di overspray, una combinazione perfetta di robot, sistemi di misura e applicatori che garantisce un’applicazione selettiva della vernice. Il sistema di misura, attrezzato con sensori, misura la superficie da verniciare e invia i dati al software gestionale. Quest’ultimo calcola in modo costante in quali binari l’applicatore deve essere guidato sulla superficie e la quantità di vernice da dosare.
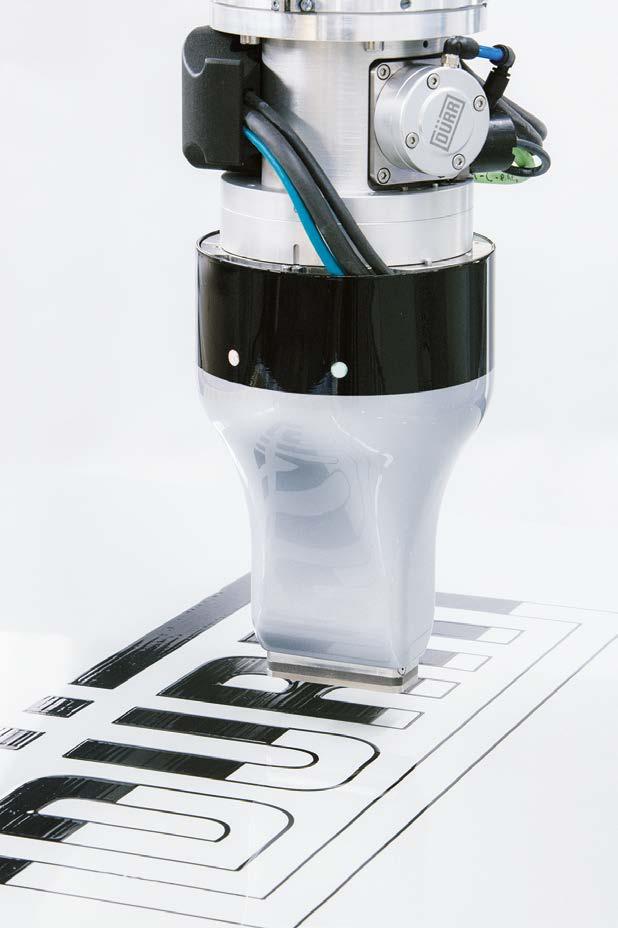
Essa soddisfa il risparmio di vernice nelle linee di produzione ove è richiesta per esempio la verniciatura di superfici bicolore. Il risultato ottenuto: assenza di overspray e di cicli operativi di mascheratura, riduzione dei consumi energetici del processo. Questa tecnologia consente un processo fortemente sostenibile.
Digitalizzazione del processo di verniciatura DXQ
L’obiettivo è applicare azioni di efficienza in tutte le fasi del processo di verniciatura per migliorare sistematicamente la produttività, ridurre i costi unitari mantenendo la massima qualità, integrando logiche di sostenibilità. DXQ è un potente strumento industriale che offre soluzioni per il funzionamento, l’analisi ed il controllo dei moderni impianti industriali. Esso consente di elaborare ed analizzare grandi volumi di dati per ottimizzare i processi consentendo così ampie ottimizzazioni del consumo energetico, maggiori tassi di produzione ed ordini intelligenti di ricambi volti a minimizzare l’impatto di manutenzioni preventive.
L’impegno per la sostenibilità
L‘impegno concreto di Dürr in ottica di sostenibilità si esplicita anche nella firma del Business Ambition for 1.5°C, iniziativa globale Race to Zero e Un Global Compact, e nella presentazione del Rapporto di Sostenibilità secondo lo standard GRI nonchè nella valutazione ECOVADIS del rating di sostenibilità.
There is a strength enclosed in the composition of Europolveri’s products, a formulation that determines their quality and which is reflected in the appearance and resistance of the treated surfaces
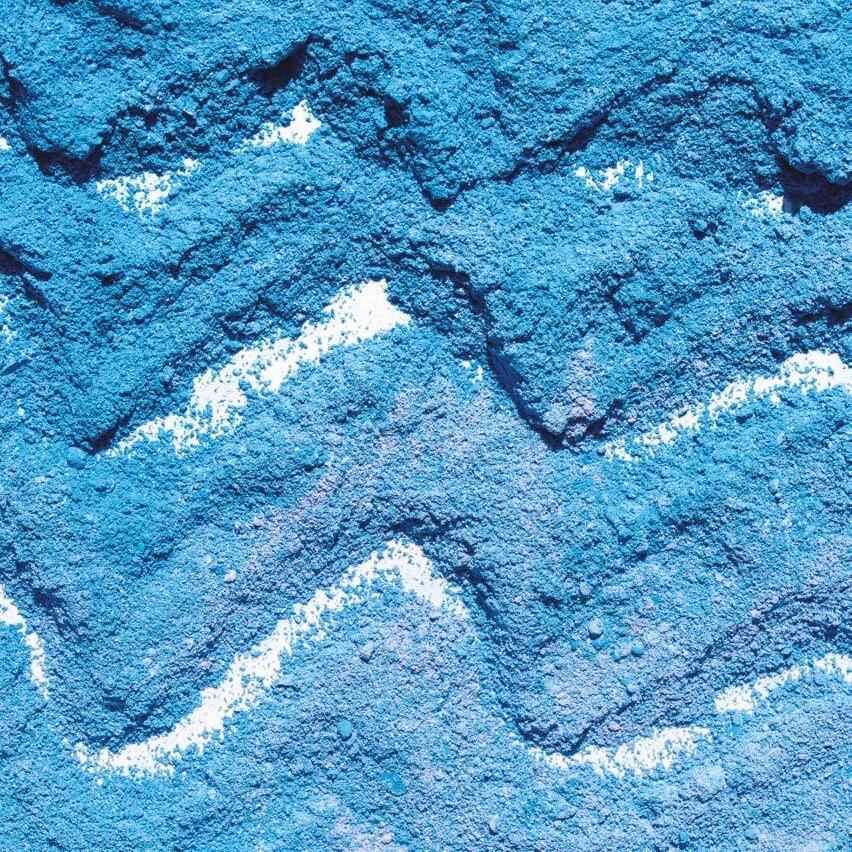
A quality that is never casual, but it is the result of a commitment to product development and industrial processes that have always been a guarantee of high resistance also in difficult enviroments

P o w e r i n s i d e d a d v a n c e d s o l u t i o n s f o r m e t a l s u r f a c e s t r e a t m e n t s i n c e 1 9 8 2


Eliminare la mascheratura dalle operazioni di verniciatura grazie ai laser
Guillaume Jobin Laserax, Quebec – Canada gjobin@laserax.comLaserax ha sviluppato un’innovativa soluzione laser che può sostituire la mascheratura manuale delle aree che devono essere protette prima della verniciatura.
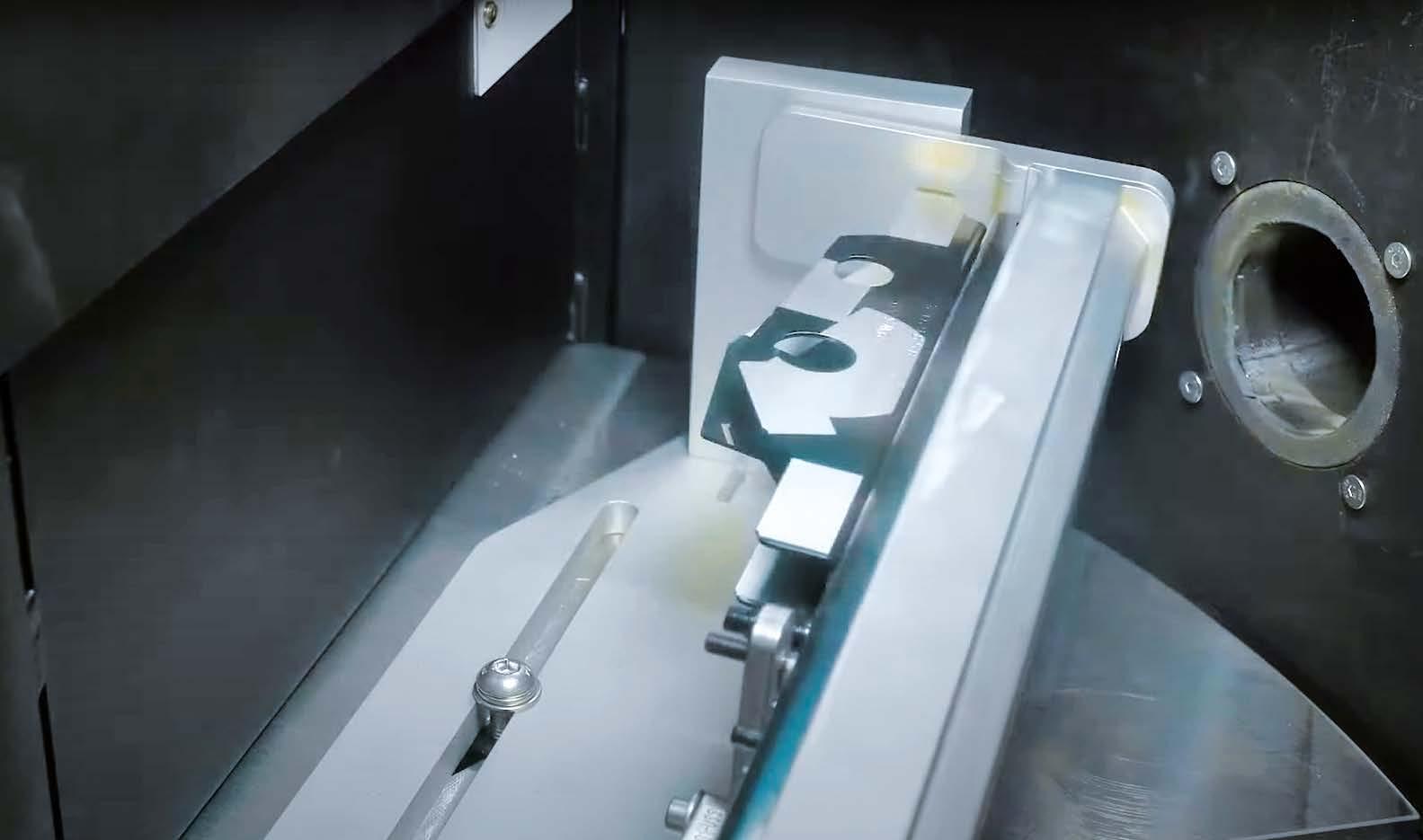
Nella verniciatura la mascheratura è ampiamente utilizzata per coprire o proteggere le aree di un manufatto che non devono essere verniciate. Le tecniche comuni includono l’applicazione di nastri specifici, tappi, cappucci e fissaggi per proteggere aree specifiche durante la verniciatura a polvere, la cataforesi e altre attività di verniciatura. La mascheratura può essere un processo che richiede tempo, specialmente nel caso di geometrie complesse. È anche costosa. I
materiali di consumo sono costosi e sono di solito applicati manualmente, il che richiede tempo e può portare a risultati disomogenei a causa di errori manuali. Per molti produttori la mascheratura è diventato un male necessario per garantire la qualità dei processi sequenziali. Nella saldatura le superfici devo essere prive di contaminanti che possano penetrare nei giunti. Nell’assemblaggio viti e bulloni aderiscono meglio alle superfici metalliche nude che a quelle verniciate.
Il laser come alternativa alla mascheratura
C’è un’altra opzione. La rimozione laser della vernice1 è un processo innovativo che permette ai produttori di eliminare la mascheratura. Anziché mascherare manualmente le aree che devono essere protette, i produttori possono semplicemente verniciare l’intero manufatto e poi usare il laser per rimuovere la vernice da aree specifiche. I laser sono caratterizzati da un controllo di precisione altamente efficiente, che riduce gli errori e garantisce che i componenti siano pronti per la successiva fase produttiva.
Rimozione della vernice con il laser: come funziona
Le vernici e i metalli hanno una soglia di ablazione2 — ovvero la temperatura alla quale vaporizzano in polvere e fumi.
I laser si possono utilizzare per portare le vernici alla loro temperatura di ablazione ed espellerle dalle superfici metalliche.
1 https://www.laserax.com/blog/coatings-removal 2 https://www.sciencedirect.com/topics/engineering/ ablation-threshold
Poiché la soglia di ablazione dei metalli è molto più elevata di quella dei rivestimenti, le vernici si possono rimuovere senza danneggiare lo strato sottostante. Il processo si svolge utilizzando un sistema che genera raggi laser, i quali trasportano grandi quantità di energia. Una parte di questa è assorbita dalla superficie, provocandone il surriscaldamento.
La velocità di rimozione laser dipende dal tipo di vernice, dal colore e dallo spessore. Per esempio, i rivestimenti più spessi richiederanno un’esposizione al laser più lunga oppure passaggi ripetuti. Inoltre, vernici diverse hanno soglie di ablazione diverse e colori diversi assorbono la luce laser con rapporti diversi. I produttori hanno bisogno di soluzioni di rimozione laser che si adattino alle loro esigenze. A seconda del processo e dei materiali usati, possono essere necessari laser più potenti per velocizzare l’ablazione.
I benefici della rimozione laser
La rimozione laser della vernice offre molti benefici rispetto ai tradizionali metodi di mascheratura.
Rimozione selettiva
I sistemi laser odierni forniscono una precisione al micron, che permette loro di rimuovere la vernice da aree specifiche senza influire sulle altre aree. Per esempio, i laser si possono usare per rimuovere le vernici dalle zone destinate alla saldatura e all’assemblaggio senza rimuoverle dalle aree circostanti. Con i loro spot più piccoli, i laser monomodali sono più precisi di quelli multimodali e sono più adatti quando è necessario “pulire” forme specifiche e ripetibili, specialmente nel caso di materiali più delicati o sensibili.
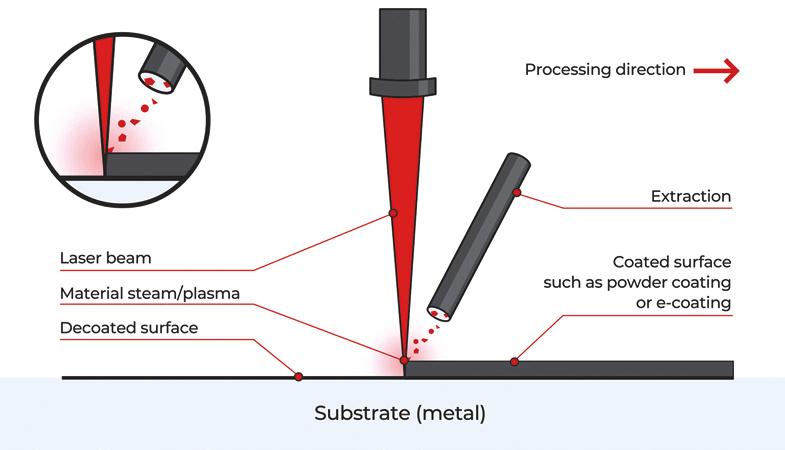
Velocità del processo
I laser velocizzeranno notevolmente il processo, eliminando la mascheratura manuale o automatica. Per i produttori ciò si traduce direttamente in una maggiore efficienza e produttività. Con i loro raggi più grandi, i laser multimodali sono l’ideale per trattare le aree grandi. Possono raggiungere anche potenze più elevate rispetto ai laser monomodali, consentendo una rimozione della vernice più rapida grazie al maggior apporto di energia.
Nessun danno
Gli abrasivi possono danneggiare le superfici metalliche nude, soprattutto se morbide o sottili. La rimozione laser della vernice è un’ottima alternativa quando gli abrasivi creano difetti. Essendo un processo senza contatto, elimina il rischio di danni meccanici al substrato. A differenza degli abrasivi, è possibile rimuovere la vernice senza influire sulla rugosità superficiale.
Migliore adesione
Il laser può rimuovere la vernice e allo stesso tempo creare una texture superficiale che aumenta l’attrito. Questo migliora l’aderenza dei sistemi di fissaggio meccanici durante l’assemblaggio. Si può anche utilizzare per migliorare l’incollaggio degli adesivi.
Processi uniformi e ripetibili
La mascheratura è inficiata dall’imprecisione, soprattutto quando eseguita manualmente. Non importa quanto siano precisi gli operatori, ci sarà sempre una certa differenza di applicazione. Anche gli operatori con esperienza commettono errori3, a causa della ripetitività delle operazioni. I laser non commettono errori. Sono programmati da un computer e dotati di strumenti per regolare il processo in base agli scostamenti individuati.
Automazione
più semplice
Rispetto alle alternative, i laser sono più semplici da automatizzare. A differenza della granigliatura abrasiva4, non ci sono polveri contaminanti da gestire, è necessaria poca manutenzione e il processo è interamente gestito da un computer.
Bassi costi operativi
Rispetto alle alternative, i laser hanno costi operativi molto più bassi. Una volta programmati, non richiedono operatori né materiali di consumo. Richiedono pochissima manutenzione e sono incredibilmente duraturi.
Più
sostenibili
La rimozione laser della vernice non richiedete prodotti chimici nocivi né genera rifiuti pericolosi. I sistemi a laser pulsato consumano poca energia e sono estremamente efficienti dal punto di vista energetico, diminuendo l’impronta ambientale. I laser lavorano inoltre in spazi compatti, riducendo lo spazio richiesto dall’attività produttiva e il consumo energetico.
Maggiore sicurezza
Le soluzioni laser odierne sono estremamente sicure. Grazie a un involucro di sicurezza e a un sistema di estrazione della polvere, gli
3 https://www.assemblymag.com/articles/97027-top-5-human-errors-in-manufacturing 4 https://www.cdc.gov/niosh/topics/blasting/default.html
operatori non devono indossare DPI nelle vicinanze dei raggi laser. Inoltre, non devono maneggiare sostanze chimiche o materiali pericolosi.
Limiti della rimozione laser della vernice
Il laser offre interessanti vantaggi. Tuttavia, ha alcuni limiti che i produttori dovrebbero conoscere. Tra questi:
• Rivestimenti più spessi: la rimozione laser funziona meglio con spessori dai 300 micron in giù. Quando sono maggiori, il processo può richiedere numerosi passaggi del raggio laser, riducendone l’efficienza. Il processo può essere comunque eseguito, ma richiederà più tempo.
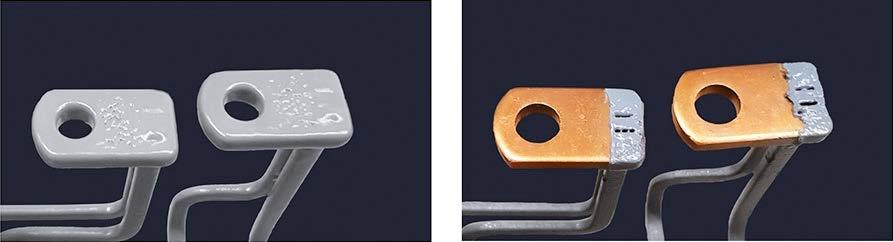
• Non funziona con tutti i tipi di vernice: i trasparenti e alcune vernici traslucide non assorbono la luce del laser in modo efficiente e sono quindi cattivi candidati per questo tipo di processo.
• Generazione di calore: alcuni materiali possono essere sensibili al calore del laser, creando potenziali danni o scolorimento.
• Filtrazione dei fumi: nell’involucro del laser è necessario un sistema di filtrazione ed estrazione dei fumi per prevenirne il rilascio nell’aria. Sebbene i laser richiedano poca manutenzione, la sostituzione del filtro è ancora manuale.
• Aree grandi: se la vernice da rimuovere copre un’area grande, possono essere necessari laser multipli per rispettare i tempi ciclo. Ciò fa aumentare rapidamente i costi e può dissuadere dall’acquisto di un laser.
• Forme complesse o componenti completi: la rimozione laser potrebbe non essere la soluzione ideale per geometrie complesse o componenti completi, poiché regolare spesso l’angolo del laser può essere meccanicamente impossibile.
• Spazio aperto: eseguire la rimozione laser della vernice in uno spazio aperto può essere complicato poiché le misure di sicurezza sono difficili da porre in essere. Tipicamente, la lavorazione laser si effettua in un involucro di sicurezza di classe 1 per contenere il raggio laser e i suoi riflessi.
Una soluzione innovativa per le operazioni di verniciatura
Negli ambienti produttivi odierni, nei quali è sempre più difficile reclutare e trattenere forza lavoro altamente qualificata, i laser possono automatizzare la maggior parte dei processi di mascheratura per sopperire alla carenza di manodopera. Questo tipo di efficienza sarà sempre più importante per i produttori. Un recente rapporto di Deloitte e del Manufacturing Institute riporta che negli Stati Uniti 2,1 milioni di posti di lavoro del settore manufatturiero potrebbero rimanere vacanti entro il 20305. Adottando questa tecnologia laser i produttori possono sbloccare il potenziale di significativi miglioramenti nell’efficienza, nella qualità e nella produttività.
5 https://www2.deloitte.com/us/en/insights/industry/ manufacturing/manufacturing-industry-diversity.html
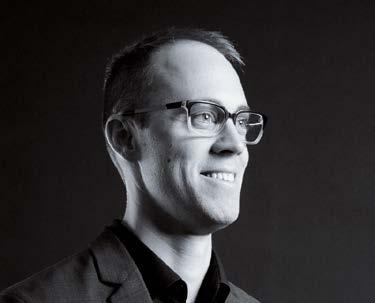
Il laser rappresenta un modo innovativo per gestire le operazioni di verniciatura e offre un futuro promettente, che apre la strada all’automazione e al miglioramento del controllo qualità, offrendo un vantaggio competitivo sul mercato.
L’autore
Formatosi come ingegnere meccanico, Guillaume Jobin ha oltre 10 anni di esperienza nell’automazione e nei sistemi di controllo. Presso Laserax ricopre il ruolo di Supervisore degli Specialisti Applicativi e supervisiona un team che analizza le esigenze dei clienti e che progetta le soluzioni laser più adatte a loro. È anche membro del Comitato Sostenibilità Aziendale.
GENERAL INDUSTRY
70 years of experience and innovation in surface finishing lines
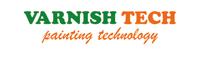

La simbiosi tra industria e design nella mostra “Red in Italy, i Colori del Rosso nel Design Italiano”
A cura di Hill + Knowlton Strategies per Campari Group
Il Ministero delle Imprese e del Made in Italy ha presentato ‘Red in Italy - I Colori del Rosso nel Design Italiano’, un progetto espositivo dedicato al rosso nel design Made in Italy ideato da Campari Group con il patrocinio di Altagamma.
Il 31 maggio scorso presso Palazzo Piacentini, sede del Ministero delle Imprese e del Made in Italy a Roma, è stata inaugurata ‘Red in Italy - I Colori del Rosso nel Design Italiano’, la mostra ideata da Campari Group, uno dei maggiori player internazionali nel settore degli spirit, con il patrocinio di Altagamma, la fondazione che dal 1992 riunisce le migliori imprese dell’Alta Industria Culturale e Creativa che promuovono nel mondo l’eccellenza, l’unicità e lo stile di vita italiani. Il progetto, ideato e curato da Francesca Valan con l’allestimento di FG Confalonieri, si propone di esplorare tutto ciò che ruota attorno al colore rosso (la cui storia ed evoluzione abbiamo analizzato sul fascicolo precedente di ipcm® in un articolo dedicato1, NdR) attraverso l’esposizione di una serie di oggetti simbolo del design Made in Italy e rappresenta lo stimolo per un confronto estetico e culturale.
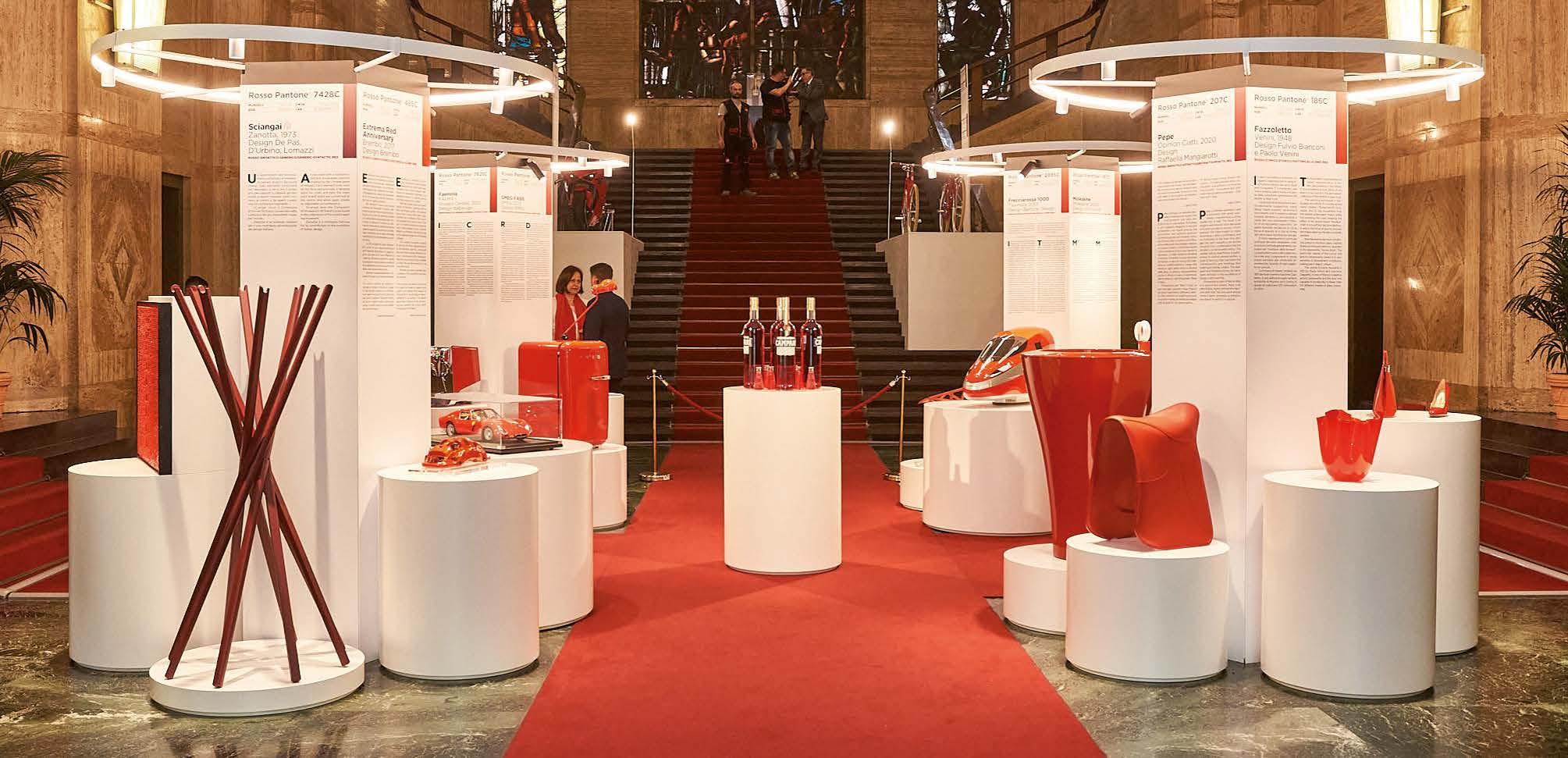
1 https://www.ipcm.it/it/open/ipcm/2023/81/178-180.aspx
“L’evento di oggi e l’inaugurazione della mostra “Red in Italy” sono particolarmente significativi per l’Italia, in un momento in cui il nostro Paese ha dimostrato di crescere di più rispetto alle economie occidentali. E il merito è delle nostre imprese” ha dichiarato il Ministro delle Imprese e del Made in Italy Adolfo Urso durante la cerimonia di inaugurazione. “Vediamo qui oggi riuniti esempi di eccellenza del Made in Italy, dal settore dell’alimentare a quello della moda, dal design all’automotive, riconosciuti in tutto il mondo per qualità e valore. Ringraziamo Altagamma e Campari Group per questo importante progetto che contribuisce a diffondere l’italianità e le nostre eccellenze in tutto il mondo.”
“La Mostra Red In Italy intesse un ideale fil rouge fra oggetti iconici di Aziende associate ad Altagamma portavoci dello stile di vita italiano
e della nostra capacità creativa ed estetica”, ha dichiarato Stefania Lazzaroni, Direttrice Generale di Altagamma. “Da oltre 30 anni Altagamma promuove l’eccellenza italiana: un comparto che vale 144 miliardi e dunque circa il 7,4% del PIL italiano. Siamo onorati di essere oggi al fianco del Ministero delle Imprese e del Made in Italy e di Campari Group, nostro Socio, in un’iniziativa dall’alto valore culturale che coinvolge marchi noti del design, dei motori e della moda. Un esempio virtuoso di cooperazione istituzionale all’insegna dell’intersettorialità, tratto distintivo della nostra Fondazione, e della valorizzazione dei nostri migliori talenti”. “Dopo un primo esordio a Bruxelles, nel 2019, siamo orgogliosi di aver portato Red in Italy in Italia, dove tutto è cominciato, e ringraziamo il Ministero delle Imprese e del Made in Italy e Fondazione Altagamma per aver creduto nella forza di questo progetto” ha dichiarato Sascha Cumia, Managing Director alla guida della divisione Europa Meridionale, Medio Oriente e Africa di Campari Group. “Questa mostra conferma il ruolo di rilievo di Campari come eccellenza italiana apprezzata in tutto il mondo, tra i simboli più riconoscibili del nostro stile di vita. Ma non solo, sottolinea il ruolo del nostro Gruppo come parte attiva nella promozione della cultura sul territorio italiano e all’estero”.
La mostra parte dal rosso iconico di Campari, da cui deriva una riflessione sul mondo dei rossi che hanno caratterizzato le civiltà a livello globale, per raccontare le creazioni di alcuni tra i più celebri designer del XX e XXI secolo che hanno contribuito alla costruzione simbolica dell’immagine dell’Italia all’estero, intrecciando non solo il design, ma anche l’arte, la cultura e la sociologia. Così come la storia di questo colore, ricchissima e sorprendente, che si è
evoluta insieme al pensiero e all’espressione dell’italianità nel mondo. Il percorso espositivo si snoda poi attraverso l’esplorazione di oggetti del design italiano accogliendo il visitatore in una vera e propria immersione nel colore, alla scoperta delle numerose eccellenze italiane caratterizzate dal rosso.
Insieme all’inconfondibile rosso Campari, presente con una bottiglia dell’edizione limitata creata appositamente per la mostra, prendono parte all’esposizione anche altri rossi simbolo del Made in Italy: Artemide, Brembo, Driade, Ducati, F.I.L.A. Fabbrica Italiana Lapis ed Affini, Ferrari, FontanaArte, Orsoni Venezia 1888, Gruppo Cimbali, Gufram, Magis, Moleskine, Alessi, Museo Kartell, Opinion Ciatti, Poltrona Frau, Rossignoli, Salvatore Ferragamo, Serralunga, Smeg, Stilnovo brand di Linea Light, Tecno, Trenitalia, Venini e Zanotta, oltre a Panzeri in qualità di sponsor tecnico per l’impianto di illuminazione della mostra.
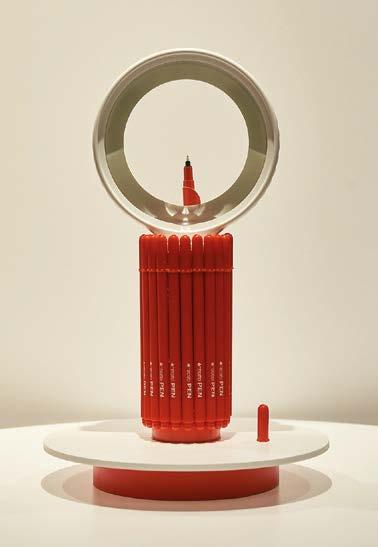
Guidata da Campari, l’esposizione Red in Italy aveva fatto il suo esordio a Bruxelles nel settembre 2019, per promuovere in modo integrato i marchi iconici del Made in Italy che hanno contribuito alla costruzione simbolica dell’immagine dell’Italia nel mondo. Il progetto curato da Valan con FG Confalonieri e con il coordinamento di Galleria Campari, si ispira al successo della mostra I colori del Rosso, organizzata presso gli spazi di Galleria Campari a Sesto San Giovanni nel 2015 in occasione di Expo Milano.
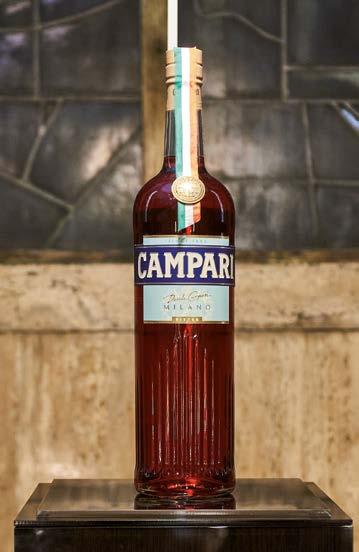
L’edizione romana di ‘Red in Italy - I Colori del Rosso nel Design Italiano’, ospitata dal Ministero delle Imprese e del Made in Italy, è rimasta aperta al pubblico nelle giornate di sabato 3, 10, 17 e 24 giugno 2023.
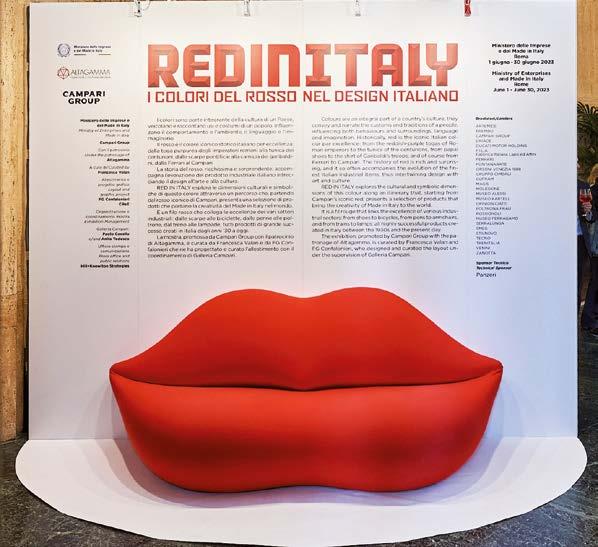
CEB investe sulla flessibilità e sulla riproducibilità con robot con funzione di autogenerazione dei programmi di verniciatura a polvere
Negli anni più difficili della crisi economica, CEB si è distinta per gli investimenti volti a migliorare la qualità e la velocità delle sue linee produttive. A distanza di sette anni dall’installazione di un nuovo impianto di verniciatura a polvere, ha scelto di incrementarne ulteriormente i risultati attraverso due robot di verniciatura di CMA Robotics in grado di autogenerare programmi di verniciatura tridimensionali attraverso il sistema AXPS-BOX.
CEB S.p.A. è un’azienda altamente specializzata nelle lavorazioni di carpenteria metallica di lamiera di ferro e acciaio inossidabile per la produzione di apparecchiature elettriche come armadi, cassette e banchi a leggio fondata nel 1980 a Montebello Vicentino (VI). L’esperienza professionale, le competenze tecniche, la flessibilità e la profonda conoscenza delle particolari dinamiche produttive e delle reali esigenze del settore ne hanno determinato la competitività, permettendole di proporre una gamma di soluzioni altamente differenziata ed accessoriata sull’intero territorio nazionale, fornendo sia prodotti di serie sia appositamente studiati per specifiche esigenze nel settore metallurgico, metalmeccanico ed alimentare – quindi sia posizionati in ambienti interni sia esterni. Oltre alla necessità di garantire la sicurezza e la resistenza dei propri prodotti, necessari per proteggere a lungo i circuiti elettrici, agli armadi di CEB è anche richiesta una finitura che possa offrire un livello estetico elevato e che sia in tinta con i colori principali delle strutture in cui si
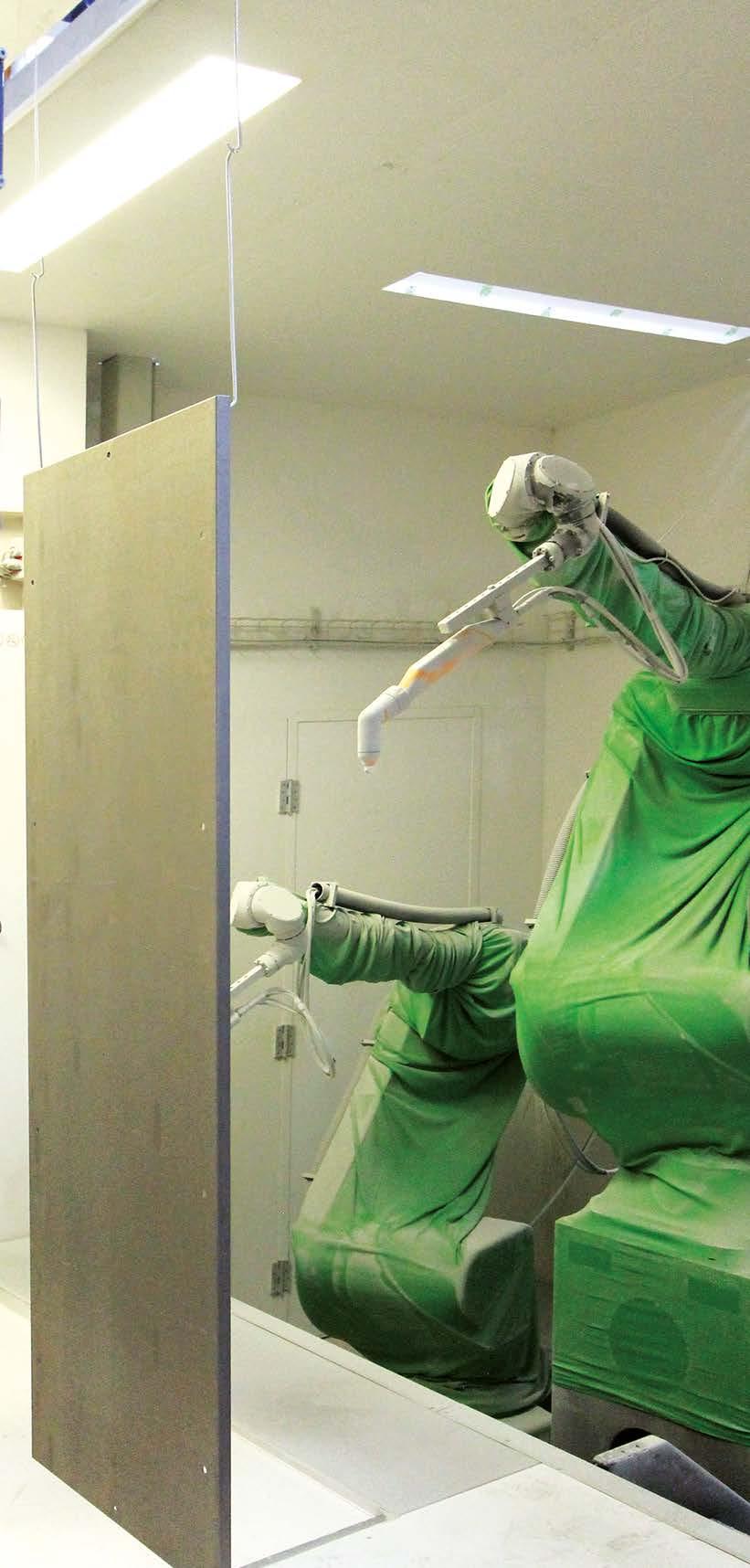
trovano. Di conseguenza, al fine di fronteggiare le crescenti richieste del mercato, l’azienda si è dotata nel 2016 di un moderno impianto di verniciatura a polvere progettato e costruito da Imel, già oggetto di un approfondito articolo realizzato per l’occasione1. In aggiunta, al fine di migliorare ulteriormente la qualità della propria offerta ed il lead-time, ha recentemente installato due robot antropomorfi della serie GR-680 con il relativo software e l’esclusivo sistema AXPS-BOX, che attraverso una scannerizzazione tridimensionale consente di identificare non solo la tipologia del pezzo in ingresso nella cabina ma anche la sua inclinazione e disposizione all’interno di essa, adattando di conseguenza il programma di verniciatura automatizzato e la sua traiettoria.
L’aggiornamento dell’impianto di verniciatura a polvere
I manufatti sono infatti caricati da un operatore sulle 31 bilancelle (con capacità massima di 5.500 x 1.000 x 2.200 millimetri per 500 chilogrammi) appese al trasportatore aereo birotaia di Futura Convogliatori Aerei (con velocità di processo di 2 metri al minuto) in modo da facilitarne lo sgocciolamento a seguito del processo di pretrattamento a spruzzo in un tunnel a cinque fasi (sgrassaggio
1 “Un sistema di applicazione polveri a garanzia di elevata produttività, risparmio di vernice e qualità costante per componenti di grandi dimensioni” di M. Fumagalli in ipcm®_International Paint&Coating Magazine n. 39.
alcalino a 55° C, risciacquo con acqua di rete, risciacquo con acqua demineralizzata, passivazione con il prodotto nanotecnologico Oxsilan® di Chemetall e risciacquo finale con acqua demineralizzata) e prima dell’ingresso del forno di asciugatura a 110° C.
L’impianto di verniciatura progettato, costruito e installato da Imel è dotato di due cabine automatiche MagicCylinder® EquiFlow di Gema con rispettivi reciprocatori per il cambio colore rapido, dove sono applicate le vernici in polvere epossidica e poliestere per le lamiere che andranno a comporre gli armadi collocati in esterno, quindi soggetti a condizioni ambientali difficili. Tuttavia, a causa della loro geometria complessa, era spesso necessario effettuare delle operazioni di pre-ritocco manuale. Attraverso il proprio impianto di verniciatura e i più recenti aggiornamenti delle tecnologie a sua disposizione, CEB è stata infatti in grado di incrementare la capacità produttiva. Di conseguenza, sono aumentati anche gli ordini di cassette, pannelli e particolari scatolati che presentano geometrie con molteplici rientranze, curvature e angoli.
La cabina destinata alla produzione multicolore è equipaggiata per il cambio colore rapido e iniettori con tecnologia Venturi, mentre la cabina monocolore è equipaggiata con le pompe di alimentazione delle vernici OptiSpray AP 01. In questa cabina sono stati recentemente installati i due robot antropomorfi della serie GR-680 di CMA Robotics.
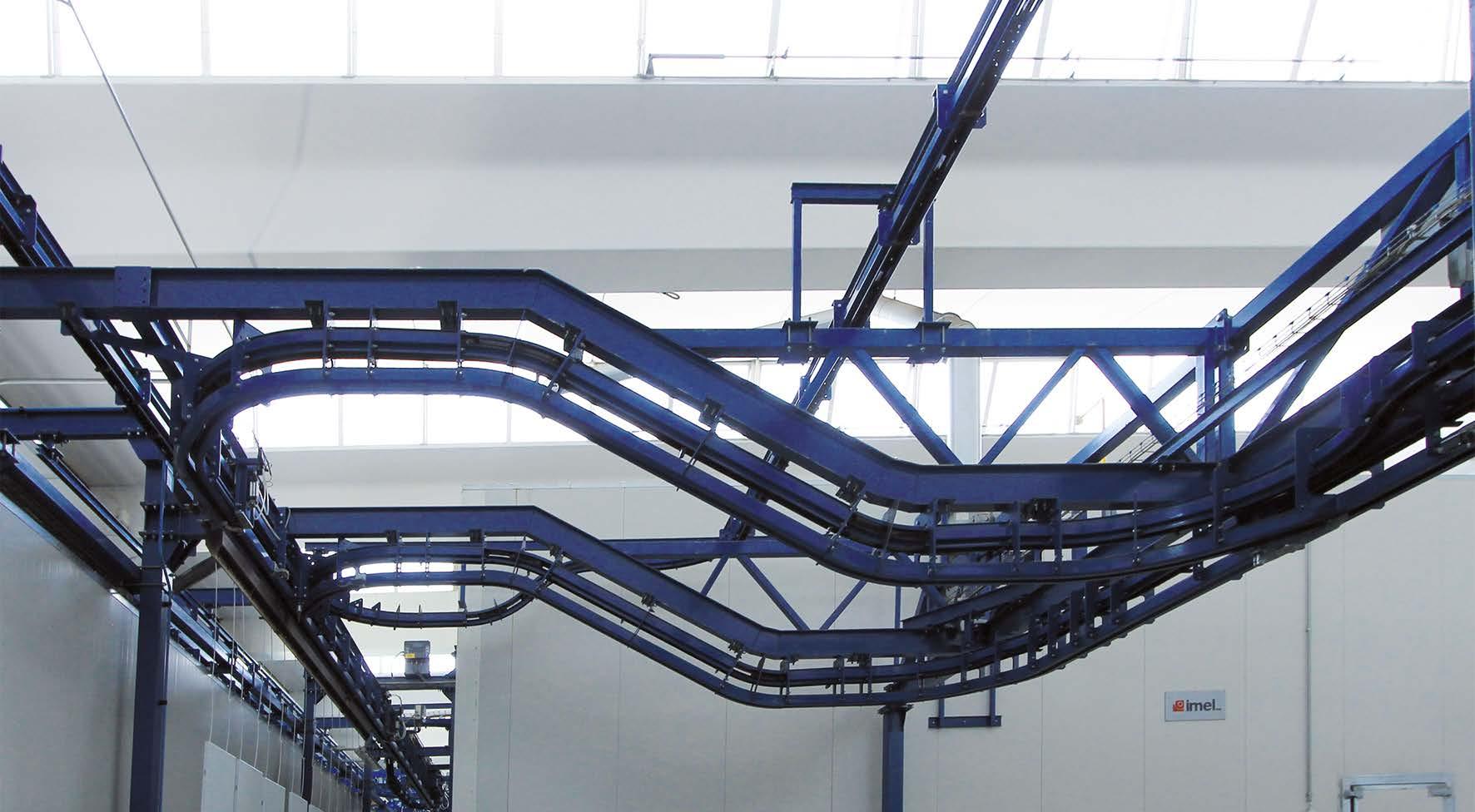
“Il processo di verniciatura di questi manufatti prevede una fase di preritocco della superficie interna che era in precedenza effettuata da due operatori specializzati, che però, dopo alcune ore di lavoro, accusavano un fisiologico calo delle prestazioni, diminuendo la velocità dei movimenti oppure aumentando la distanza tra la pistola di erogazione e il pezzo da verniciare. La qualità del rivestimento che vogliamo conferire deve però essere sempre elevata e soprattutto costante. Questa situazione provocava quindi dei ritardi per l’intera produzione, oltre allo spreco dei materiali. Abbiamo spiegato a Gema e Imel le nostre difficoltà e loro ci hanno suggerito di confrontarci con un produttore di robot antropomorfi per individuare la soluzione più adatta alle nostre esigenze,” afferma Silvano Biasin, il titolare di CEB.
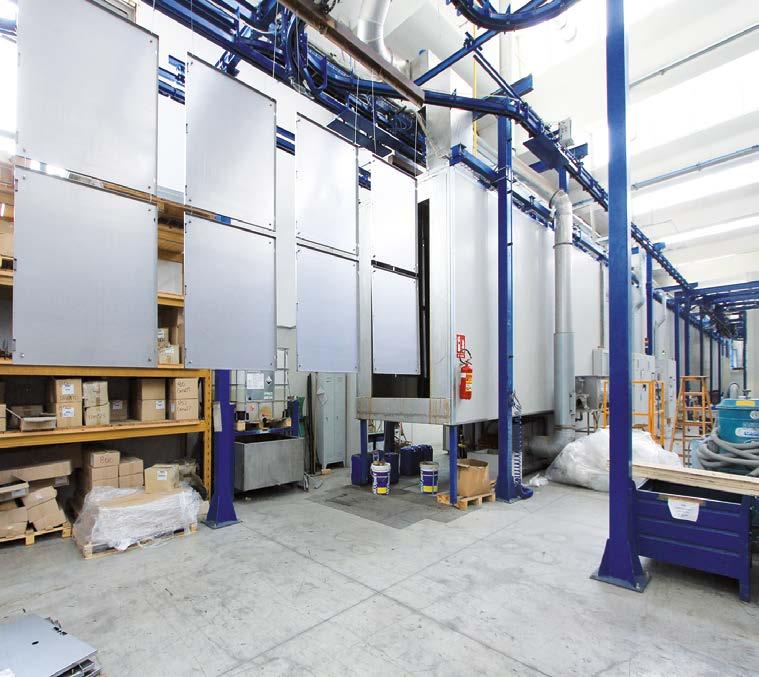
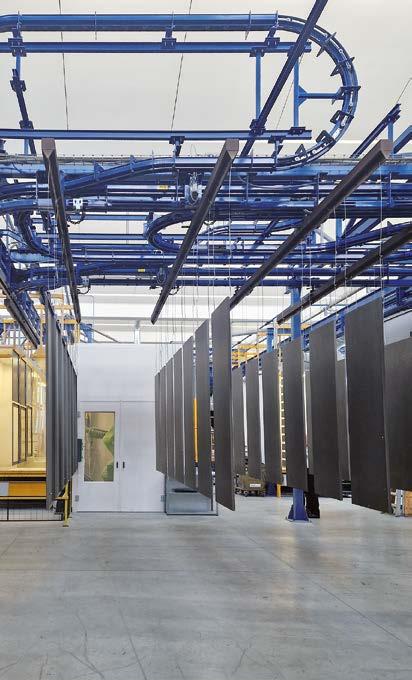
Robot con funzione di autogenerazione dei programmi di verniciatura
L’azienda ha quindi inviato alcuni campioni alla sede di Pavia di Udine (UD) di CMA Robotics, dove si sono svolti i test che hanno permesso al produttore di soluzioni automatizzate per la verniciatura di comprendere meglio le necessità di CEB. A giugno 2022 sono quindi stati installati due robot antropomorfi a controllo elettronico a sei assi in grado di
autogenerare i programmi di verniciatura tridimensionali attraverso il sistema AXPS-BOX.
I robot GR-680, come tutta la gamma prodotta da CMA Robotics, sono progettati per eseguire operazioni di spruzzatura di prodotti vernicianti in polvere, oppure liquidi, su superfici in metallo, legno e plastica e sono certificati da un ente esterno specializzato per operare in zona ATEX. Un’ulteriore caratteristica è la particolare configurazione del polso, che, tramite la rotazione di 360° di ogni singolo asse, permette di raggiungere agevolmente qualsiasi punto degli elementi in lavorazione.
Ogni robot può montare più pistole contemporaneamente o coppe rotanti ed integrarsi perfettamente con tutti i dispositivi di regolazione del flusso di aria e vernici mediante il sistema di controllo interno, il quale dispone di un software estremamente sofisticato ma allo stesso tempo di facile utilizzo e dotato di strumenti di diagnostica. “L’autogenerazione in 2D dei programmi di verniciatura è una funzione ormai assodata per la verniciatura di serramenti e telai, ma la progettazione di un sistema tridimensionale per rivestire queste tipologie di scatolati è stata una novità anche per noi. I componenti di CEB arrivano infatti nelle cabine appesi al trasportatore con inclinazioni variabili a seconda della loro dimensione e del loro peso, pertanto una normale scansione non avrebbe consentito al
robot di effettuare correttamente il programma di verniciatura assegnato a ciascuna tipologia di manufatto”, spiega Marco Zanor, il direttore delle vendite di CMA Robotics. “Tuttavia, non ci siamo scoraggiati e, dopo alcune prove, siamo riusciti a sviluppare una soluzione su misura per soddisfare tutte le necessità di CEB. Il dispositivo di lettura tridimensionale del pezzo posto all’ingresso della cabina non rileva infatti solamente la geometria del componente in arrivo, ma anche il suo grado di inclinazione e la sua posizione nello spazio. Il sistema AXPS-BOX utilizza quindi le regole impostate per autogenerare il programma di verniciatura in totale autonomia, consentendo di applicare la vernice in modo uniforme su tutte le superfici interne ed esterne”. In questo modo, a seguito anche delle ulteriori operazioni di verniciatura all’interno delle cabine di Gema, i manufatti presentano un rivestimento omogeneo e possono essere condotti prima
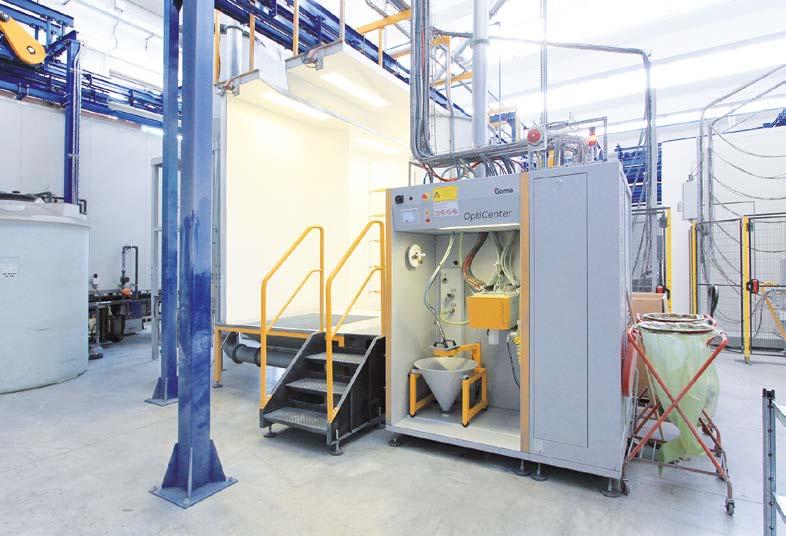
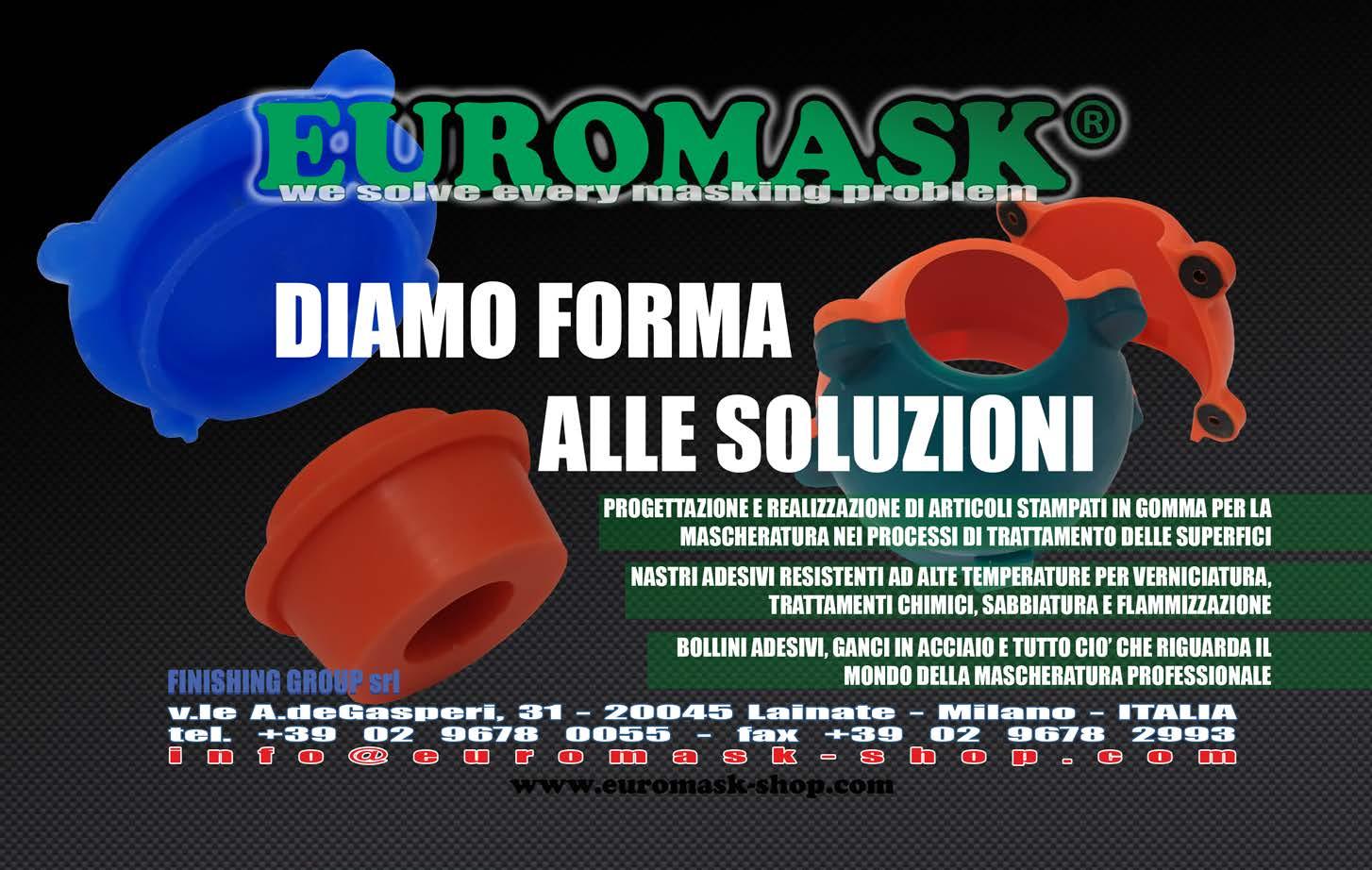
nel forno di polimerizzazione – dove sostano per venticinque minuti a 180° C – e poi nel polmone per il raffreddamento a temperatura ambiente. Infine, gli operatori scaricano i particolari, pronti per essere assemblati, imballati e spediti.
Verniciatura uniforme e riproducibile anche con geometrie complesse
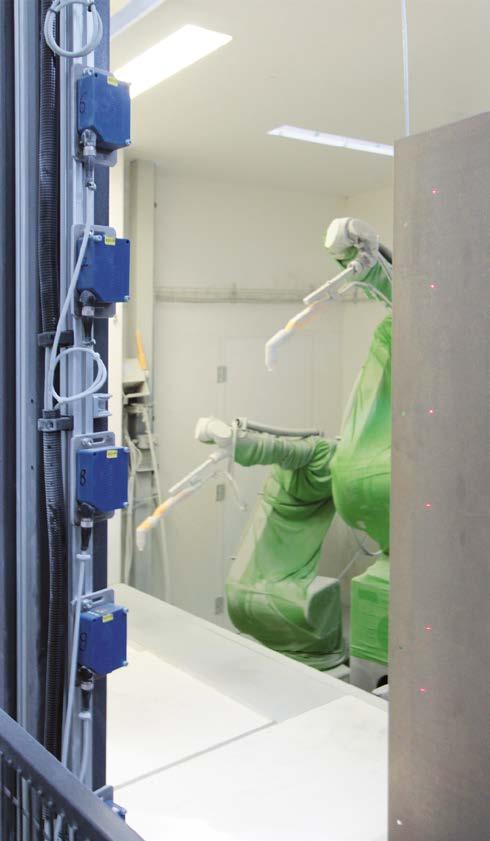
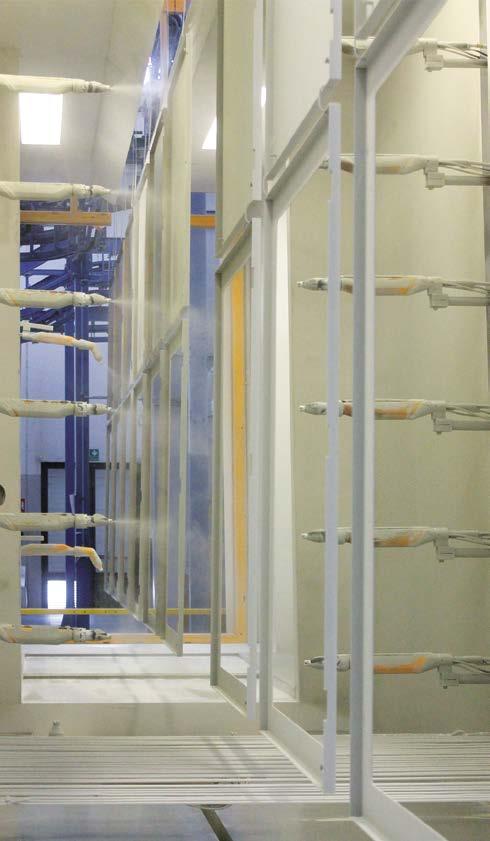
Attraverso questo investimento, CEB è dunque riuscita a migliorare il proprio flusso produttivo e la qualità dei componenti verniciati. In precedenza, per l’azienda era infatti necessario fermare la catena oppure effettuare operazioni di post-ritocco dopo l’assemblaggio dei pezzi.
“La cadenza produttiva è ora costante e il film di vernice applicato è maggiormente uniforme anche su geometrie complesse. Come dicevo, la stanchezza fisiologicamente insita in attività come la spruzzatura
manuale rendono difficile per l’operatore ripetere fedelmente la stessa gestualità per tempi prolungati. I due robot ci hanno permesso di mantenere l’operatività di 17 bilancelle all’ora con componenti che possono raggiungere anche i 2,20 metri di altezza. Inoltre, gli operatori precedentemente impiegati per questa fase di verniciatura sono ora dedicati alla fase di montaggio e imballaggio. In questo modo, non abbiamo solo velocizzato la verniciatura, ma l’intero flusso produttivo”, chiarisce Matteo Biasin, il responsabile di produzione di CEB.
“Non conoscevamo le potenzialità della funzionalità di questo nuovo sistema, ma ci siamo affidati alla professionalità di CMA Robotics e questa decisione ha dato i suoi frutti. Nello scorso articolo dissi che la produttività del nuovo impianto di verniciatura era ancora difficilmente valutabile considerato il poco tempo di attività, ma che alcuni dati come il risparmio sulla quantità di polvere impiegata e sulla velocità
e fluidità del processo di rivestimento fossero già evidenti. Lo stesso discorso vale anche per questo nuovo investimento: i robot di CMA sono pienamente operativi solamente da fine settembre 2022, ma già notiamo un aumento della qualità del film di vernice applicato e una riduzione delle risorse impiegate. Infatti, siamo già in contatto con Imel per poter comprendere come allungare la catena del trasportatore, al fine di creare più polmoni di accumulo ed ingrandire l’area di carico e scarico. Lo abbiamo già modificato recentemente, in modo da poter installare i due robot, e i tecnici di Imel si sono dimostrati disponibili ad ascoltare le nostre esigenze e ad implementare con rapidità le soluzioni più adeguate. Questo nuovo intervento ci potrebbe permettere di aumentare ulteriormente la redditività dell’intero impianto di verniciatura a polvere”, conclude soddisfatto Silvano Biasin.
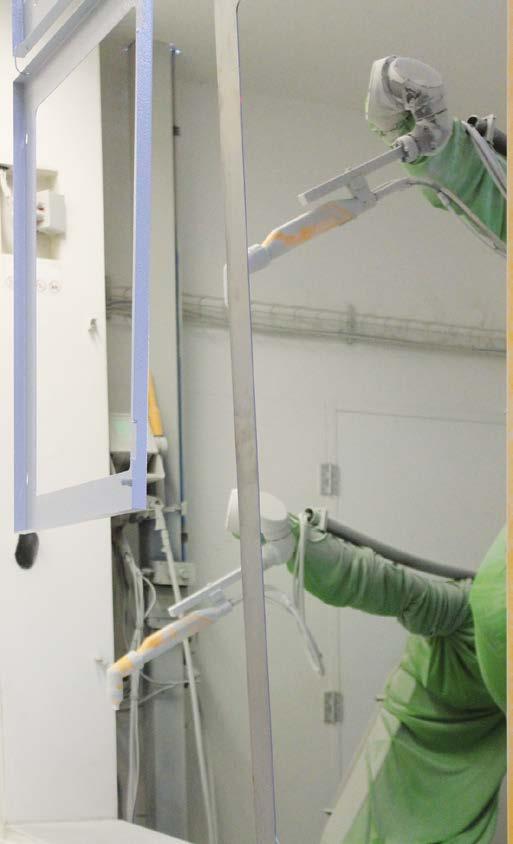






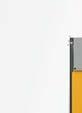


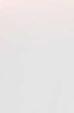


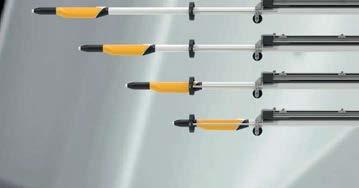
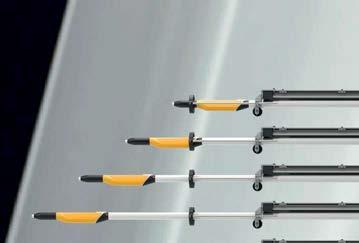
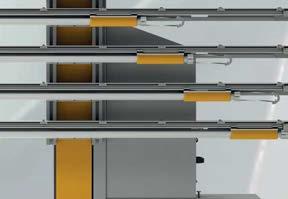
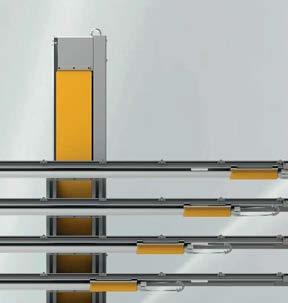



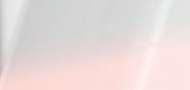



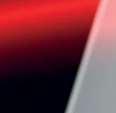


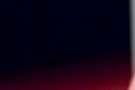









Sette test di qualità per i processi di verniciatura secondo Argos ST
A cura di Argos Srl Cambiago, Milano (Italia)
Per verificare la qualità dei processi di verniciatura effettuati, la sede Foresi del gruppo Argos ST elabora, su richiesta del cliente, report di misurazioni attraverso tre principali metodologie: test di adesione con prova di strappo su quadrettatura, misurazione dello spessore del trattamento e misurazione del gloss. Esistono, inoltre, altri quattro test di performance che possono essere eseguiti solo da laboratori certificati: la prova in nebbia salina, l’Alternate salt spray, l’immersione prolungata in acqua e l’Accelerated weathering test.
Verificare, su richiesta dei clienti, la qualità dei processi di verniciatura effettuati attraverso l’elaborazione di report e controlli. Questa, tra le altre, l’attività in capo alla sede Foresi del gruppo Argos ST, leader nei trattamenti superficiali, tra i quali rientrano anche tre tipologie di verniciatura industriale: cataforesi (o foresi), verniciatura a polvere e verniciatura a liquido, anche con liquidi ad alta temperatura. Questi trattamenti sono funzionali a prevenire la corrosione di materiali come ferro, acciaio e altre leghe, garantendone una maggiore resistenza: nello specifico, la verniciatura con liquidi ad alta temperatura consente alle parti metalliche sottoposte a temperature particolarmente elevate di mantenere una buona tenuta.
Misurare la qualità dei processi di verniciatura: le verifiche effettuate da Foresi

Tre sono le tipologie di controlli che Foresi adotta al suo interno per valutare la qualità dei processi di verniciatura effettuati: test di adesione con prova di strappo su quadrettatura, misurazione dello spessore del trattamento e misurazione della brillantezza.
• Il test di adesione con prova di strappo su quadrettatura è un metodo che consente, attraverso un apposito utensile a pettine e un nastro normato, di determinare la resistenza al distacco di vernici, pitture e rivestimenti rispetto ai supporti, attraverso la creazione di un reticolo ad angoli retti sulla superficie. Per procedere con la prova, occorre effettuare delle incisioni a reticolo che devono avere la stessa distanza tra loro, sia verticalmente che orizzontalmente, arrivando fino al substrato. Applicando il nastro adesivo sull’intera area di incisione e rimuovendolo energicamente è possibile determinare visivamente l’esito della prova: se nessun quadretto del reticolo si è distaccato, o se il distacco è limitato a un 5% della superficie e in corrispondenza delle intersezioni dei tagli, o ancora se la vernice si è staccata lungo i bordi dei tagli e alle intersezioni
del reticolo per un valore compreso tra il 5-15% dell’area, il processo di verniciatura sarà ritenuto idoneo, ma il supporto richiederà una preparazione prima di una nuova lavorazione. Se, invece, la vernice si è staccata lungo i bordi dei tagli, o nelle parti corrispondenti ai quadretti per un valore superiore al 15%, a seconda dell’estensione del danno, si dovrà procedere con una raschiatura parziale o totale della superficie, prima di una nuova verniciatura.
• La valutazione dello spessore: attraverso apposita strumentazione, permette di misurare lo spessore dei rivestimenti, sia sulle superfici lisce, sia su quelle ruvide.
• La misurazione della brillantezza con riflettometro Micro-Tri-Gloss
Byk-Gardner: perché un processo di verniciatura sia ritenuto di qualità deve necessariamente garantire una brillantezza costante e uniforme per qualsiasi prodotto trattato. Soprattutto in caso di prodotti multicomponente, un gloss uniforme è la prova dell’alta qualità del trattamento e, di conseguenza, del materiale finale ottenuto. Dunque, per misurare la brillantezza in modo oggettivo, si fa ricorso al glossmetro, che può essere utilizzato sia su vernici, sia su plastiche, ma anche su metalli a specchio.
Altri quattro test utili per la verifica della qualità
Esistono inoltre altri quattro test, eseguibili da laboratori certificati atti a verificare la qualità dei trattamenti di verniciatura: l’uso della nebbia salina
per monitorare la resistenza alla corrosione, i test di corrosione ciclici, il test di adesione dei trattamenti a seguito di un intervallo temporale di 24-48 ore di immersione in acqua e, infine, il test dell’invecchiamento accelerato:
• La prova in nebbia salina è un test standardizzato che permette di verificare quanto i rivestimenti superficiali riescono a proteggere il substrato dalla corrosione. I test di resistenza alla corrosione della cataforesi hanno una durata inferiore alle 500 ore, mentre per le applicazioni combinate di cataforesi e verniciatura a polvere i tempi di verifica si dilatano oltre le 500 ore. La verifica va effettuata all’interno di una camera in cui viene nebulizzata la soluzione salina di prova (5%NaCl) alla temperatura di 35° C; questo fa sì che la nebbia derivante ricrei un ambiente particolarmente corrosivo, che consente - a chiusura del test - di misurare il grado di corrosione del campione. Durante la prova possono essere registrati alcuni esiti parziali per monitorare l’avanzare del processo corrosivo.
• Esiste poi un test specifico denominato Alternate salt spray: simile alla prova appena prima descritta, questa misurazione si basa su un’alternanza di momenti in cui il materiale è esposto alla nebbia salina e momenti di riposo, così da simulare lo stress a cui è sottoposto il pezzo trattato nel corso del tempo. Questa alternanza può essere programmata dalla camera climatica, in modo da eseguire più cicli di durata variabile.
Painting excellence for every surface
Bringing your surface to perfection. Verind offers painting solutions from manual to automatic application, high-quality and easy to integrate.
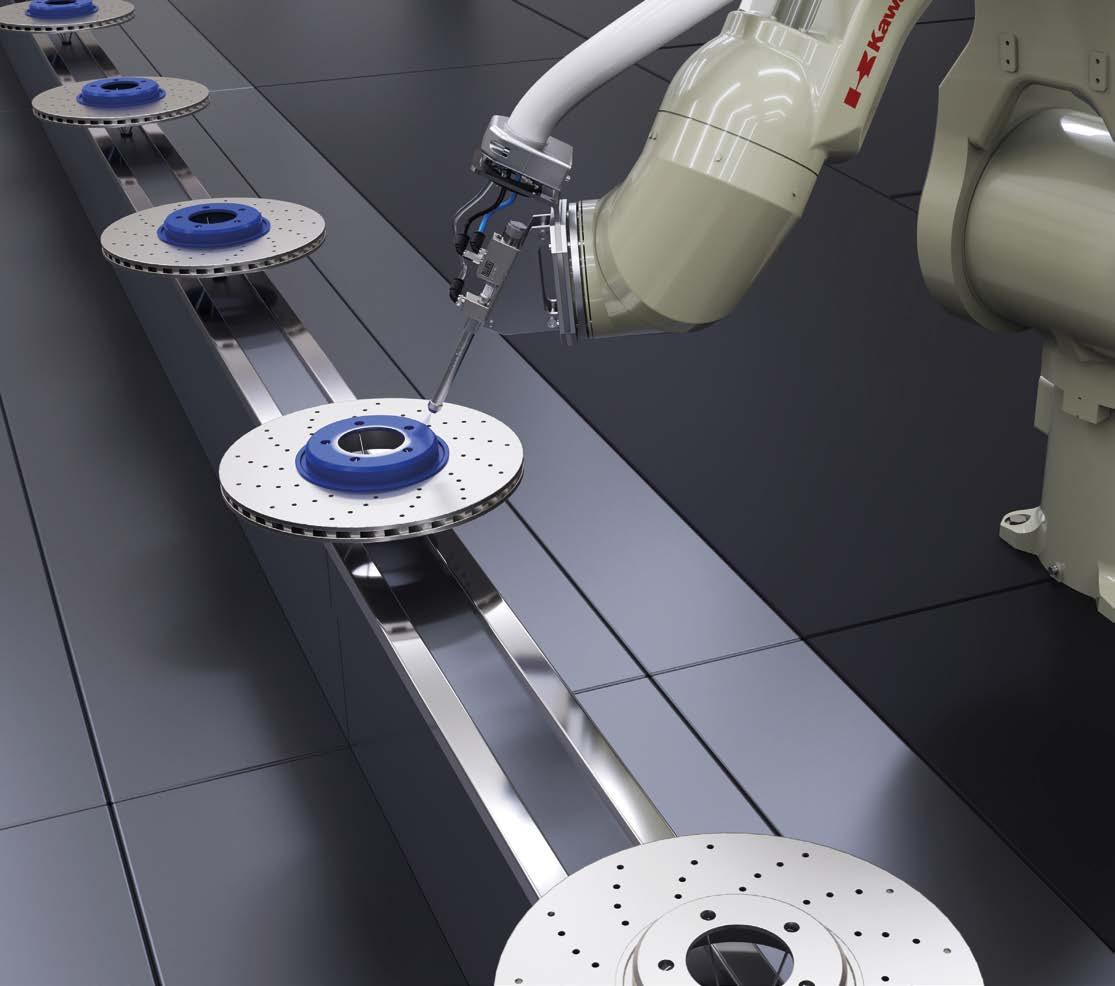

• Il test di adesione dei trattamenti si effettua lasciando immerso in acqua per 24-48 ore il particolare trattato. Successivamente a questo arco temporale si valuta il grado di adesione del trattamento.
• Infine, l’Accelerated weathering test, ossia il test per l’invecchiamento accelerato, permette di riprodurre in laboratorio - in un arco temporale molto limitato - quei danni che i materiali subirebbero se esposti per mesi e anni alla luce del sole, alla pioggia, alla rugiada. Per farlo, si fa ricorso ad apposite lampade UV: i materiali da testare sono così sottoposti non solo a temperature elevate e controllate, ma anche all’umidità.
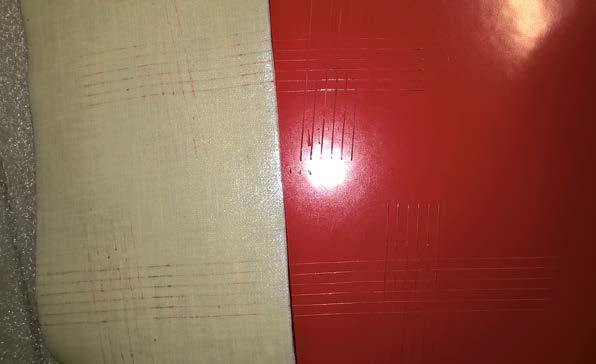
“I processi di verniciatura contribuiscono indubbiamente a una resa estetica, ma svolgono anche un importante ruolo funzionale” - commenta Guido Ghilardi, Amministratore Delegato degli stabilimenti Argos ST di Gonzaga e Borgaro Torinese. “Pur non essendo un laboratorio che può effettuare veri propri test ed emettere certificazioni, nella nostra sede effettuiamo delle prove, su richiesta dei clienti, che permettono di monitorare la validità dei processi di verniciatura che effettuiamo. Si tratta
di un’attività molto importante per noi, perché ci permette di garantire la qualità del nostro operato ed eventualmente correre ai ripari in caso di necessità”.
Argos Surface Technologies
Artefice il fondo di private equity Gradiente II, gestito da Gradiente SGR, nel 2020 nasce il nuovo Gruppo Argos Surface Technologies, che prende vita dall’unione di importanti realtà nel panorama dei trattamenti e dei rivestimenti superficiali, con l’ambizioso intento di creare una leadership nel settore. Nel 2020 il Gruppo prende avvio con le acquisizioni di Argos, Impreglon Italia e Aalberts ST. Nel 2021 il gruppo acquisisce le emiliane TSM (oggi Argos TSM), e Lualma Anodica (oggi Argos Lualma), e nel 2022 la bergamasca TEC.RI.MET, la mantovana FORESI. e la torinese Rotostatic. Il Gruppo vanta oggi nove stabilimenti: Gonzaga (Mantova), Origgio (Varese), Cambiago (Milano), Calcio (Bergamo), Opera (Milano), Monteveglio (Bologna), Imola (Bologna), Minerbio (Bologna) e Borgaro Torinese (Torino), con oltre 350 dipendenti e un fatturato che supera i 50 milioni di euro.

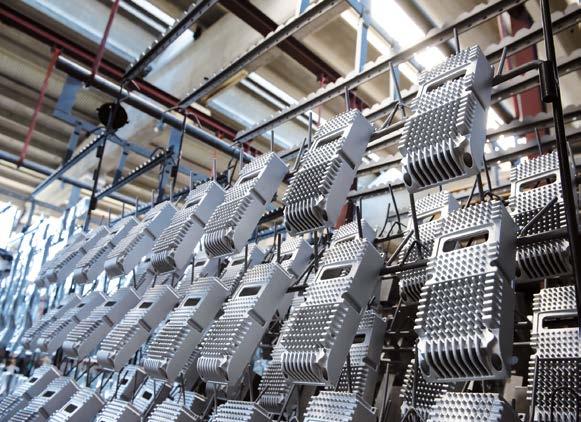
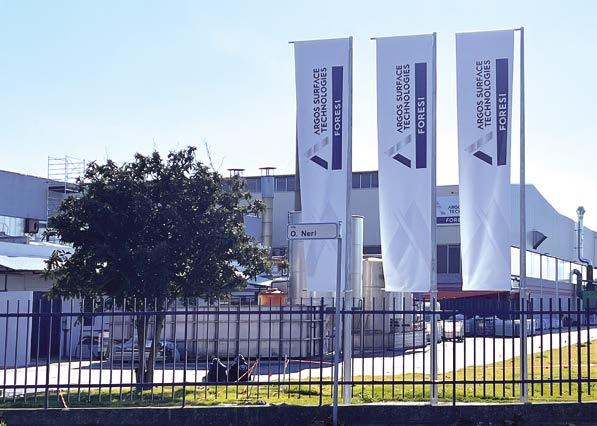
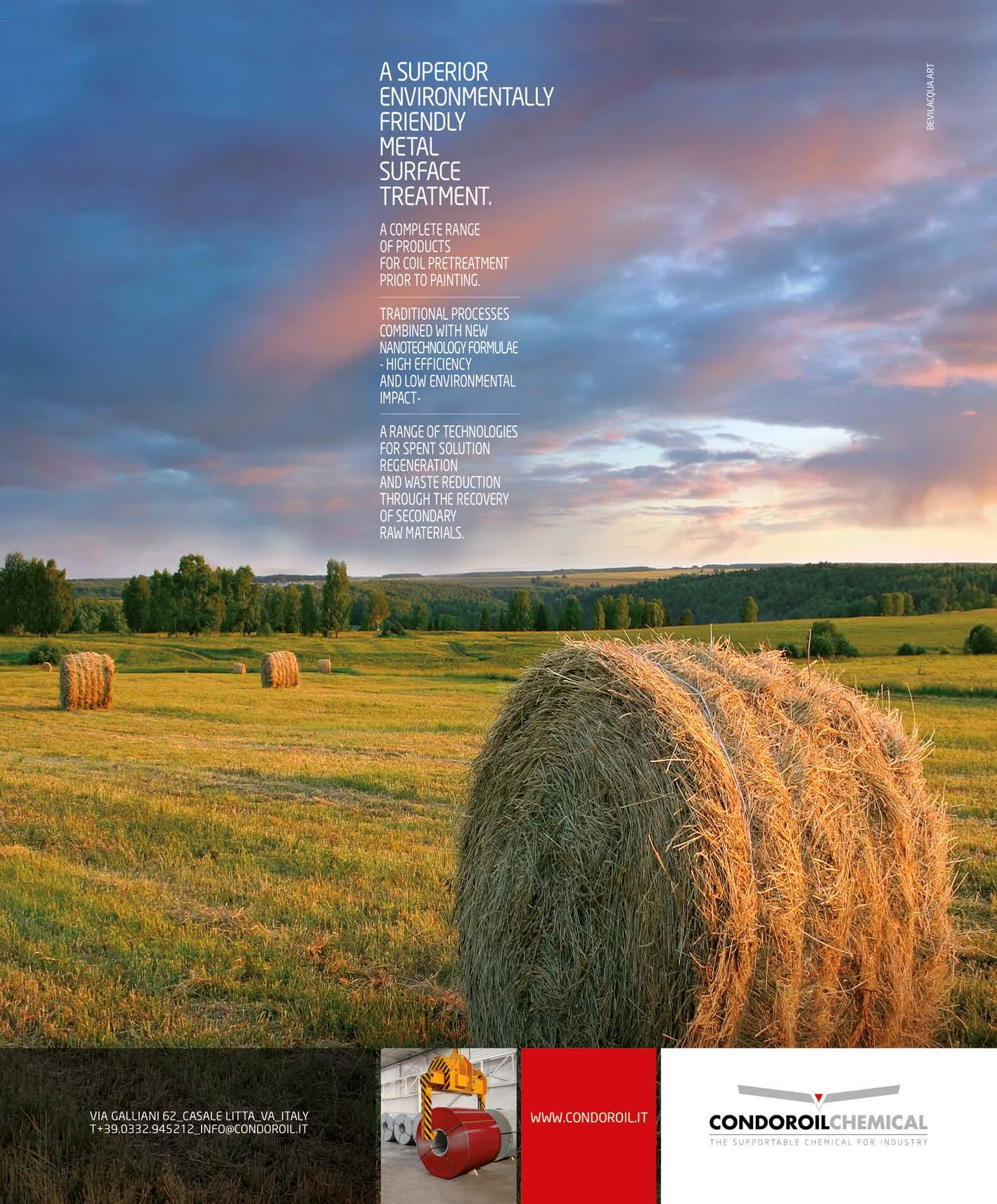
FOCUS ON TECHNOLOGY
T&G: la fidelizzazione di un partner per l’impiantistica di verniciatura segue la crescita dell’azienda
Alessia Venturi ipcm®
A un’azienda terzista di verniciatura servono tre cose per crescere: lo spirito imprenditoriale, la specializzazione in pochi settori, il giusto partner impiantistico. T&G di Castione di Loria, nel corso dei suoi 20 anni di storia, è riuscita a combinare tutti e tre questi elementi, contando sull’esperienza di Euroimpianti per la sua dotazione impiantistica.
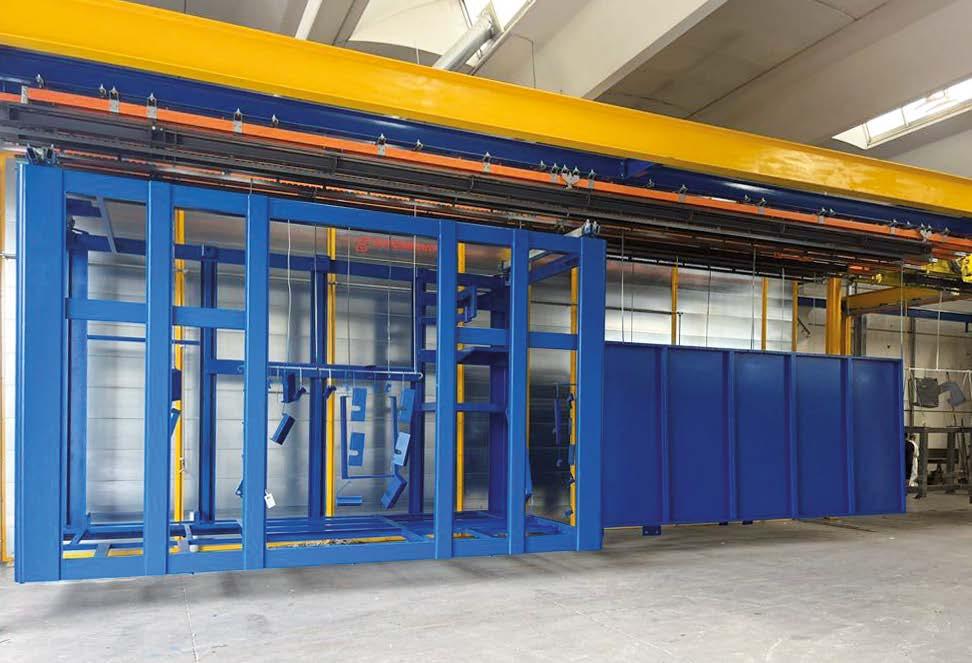
Lo spirito imprenditoriale è un atteggiamento mentale che cerca attivamente il cambiamento, l’innovazione e il miglioramento continuo. Audacia e rischio sono sinonimi di imprenditorialità. Avere uno spirito imprenditoriale, infatti, vuol dire assumersi la responsabilità, e quindi il rischio, delle proprie idee e delle proprie scelte nonché delle
ricadute che queste ultime avranno sulla propria impresa. Non tutti hanno spirito imprenditoriale, nemmeno gli imprenditori stessi. Ci sono poi persone che, al contrario, di spirito imprenditoriale ne hanno da vendere, come la coppia di soci Enrico Troisi e Luca Girolimetto, amici nella vita e colleghi di lavoro, che nel 2002 fondarono T&G Verniciatura
Industriale dopo un’esperienza da verniciatori presso un’altra azienda della zona.

In 20 anni, Enrico e Luca non si sono mai tirati indietro davanti alle sfide di crescita poste dal mercato e, con audacia e la voglia “di fare impresa”, hanno realizzato tanti investimenti per costruire quella che T&G è oggi: una della primarie realtà di verniciatura conto terzi a liquido e a polveri nel settore delle macchine utensili e dell’automazione, con tre capannoni a Castione di Loria, Treviso, 3 impianti di verniciatura a polveri, cabine di verniciatura a liquido per l’applicazione di cicli anticorrosivi, una granigliatrice automatica e una cabina di sabbiatura manuale.
Oltre allo spiccato spirito imprenditoriale dei soci, al successo di T&G ha contributo anche la partnership continuativa nel tempo con un’impiantista di verniciatura, Euroimpianti, e la totale fiducia posta nel suo titolare – Gianluca Baruffaldi – che ha accompagnato T&G nella crescita, agendo anche da consigliere e consulente dei due soci sulle tematiche di verniciatura.
Questa partnership ha portato T&G ad installare la gamma completa di impianti per la verniciatura industriale proposta da Euroimpianti, prima l’Eurocar, poi l’Euro90 automatico con trasportatore monorotaia e infine, pochi mesi fa, un Komby “ibrido” con traino automatico delle bilancelle progettato da Railtechniek.
“Ognuna delle linee di verniciatura modulari nella gamma proposta da Euroimpianti ben si adattava a soddisfare le nostre esigenze di crescita in un determinato momento del nostro percorso” commenta Enrico Troisi. “Guidati dall’esperienza di Gianluca abbiamo di volta in volta scelto l’impianto più adeguato, modificandolo o ibridandolo per personalizzarlo e calarlo nella nostra realtà produttiva. Oggi, questo assetto impiantistico ci consente di soddisfare una moltitudine di richieste di verniciatura per un settore come quello della meccanica e dell’automazione, che nella nostra zona (quella di Galleria Veneta, NdR) è molto fiorente, con tante attività manifatturiere che producono macchinari pesanti, dalle trivelle alle macchine per pastifici, che si affidano ai terzisti per la verniciatura dei componenti”.
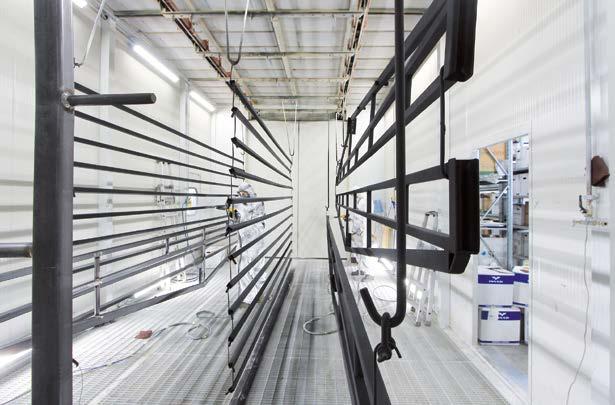
La storia di T&G
Fondata nel 2002 e operativa da marzo 2003, T&G ha offerto per i primi 5 anni solo la verniciatura a liquido, in un piccolo capannone di 400 m2. Il 2008 è l’anno della svolta e dell’approdo alla verniciatura a polvere, con il trasferimento in un nuovo capannone presso la sede attuale a Castione di Loria.
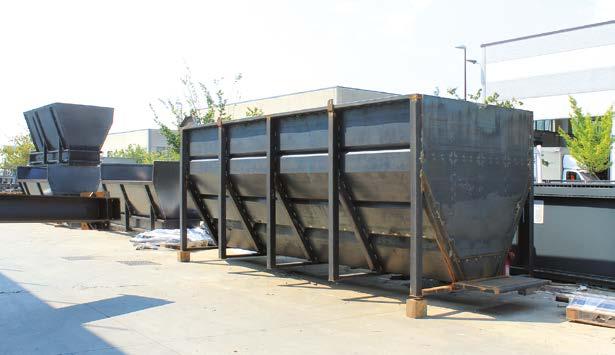
“A quell’anno risale il mio incontro con Gianluca Baruffaldi e l’inizio del nostro sodalizio per la verniciatura a polvere, con l’acquisto del nostro primo impianto, Eurocar 5, ossia con capacità di verniciare pezzi fino a 10 metri di lunghezza. Questo impianto ci ha dato la possibilità di verniciare a polvere sia componenti di piccole dimensioni
Dall'alto:
T&G vernicia manufatti di grandi dimensioni per primarie aziende che producono macchinari pesanti.
La cabina di verniciatura dell’impianto Eurocar.
Vista generale dell’impianto automatico Euro90.
sia manufatti più grandi, completando così la nostra offerta che già comprendeva la verniciatura a liquido con cicli prettamente anticorrosivi.
Sempre nel 2008, acquistammo anche una cabina di sabbiatura manuale per fornire una maggior qualità di rivestimento, sia a liquido sia a polvere, grazie al pretrattamento meccanico”.
“Nel 2013 meditammo di investire ulteriormente per espandere la gamma di servizi di trattamento superficiale” prosegue Luca Girolimetto. “Nell’arco di due anni acquistammo un nuovo capannone accanto al primo, per inserire un impianto di granigliatura automatico di OMSG, una Tunnelblast 3000x3000 con cabina di ritocco manuale, 16 turbine, inverter e pannello di controllo digitale. Nel 2016 decidemmo di trasferire in un terzo capannone le cabine statiche di verniciatura a liquido e di implementarle con altre cabine con filtrazione a parete, un plenum interno di immissione dell’aria e un sistema di estrazione e depurazione dell’aria in uscita. Contestualmente a questo trasferimento abbiamo anche revampato la cabina manuale di sabbiatura, dotandola fra le altre cose di tetto apribile per consentire l’entrata del carroponte in modo da poter trattare manufatti sempre più pesanti”.
“Crescevamo insieme ai nostri clienti e alle loro esigenze di trattamento superficiale” interviene Enrico Troisi. “Ciò che cambiava erano soprattutto le dimensioni dei pezzi da trattare. L’impianto Eurocar non bastava più, dunque investimmo in un Euro90 automatico che ci ha consentito di verniciare velocemente lotti sempre più numerosi di pezzi medi e piccoli”. “Infine, nel 2022 abbiamo scelto di inserire un terzo impianto di verniciatura a polvere per pezzi di grandi dimensioni, poiché la silhouette
massima dei pezzi verniciabili su Eurocar iniziava ad essere un limite alla crescita. Potevamo dirottare questa produzione sul liquido naturalmente, tuttavia la nostra strategia commerciale era portare quanto più possibile il cliente verso le polveri, limitando la verniciatura a liquido ai soli cicli anticorrosivi”.
Tre impianti per tre esigenze diverse di verniciatura Eurocar è l’impianto nella gamma Euroimpianti per la verniciatura industriale di grossi manufatti metallici per verniciare in modalità semiautomatica pezzi ingombranti e che, proprio per la loro dimensione, risultano difficilmente movimentabili per mezzo di un tradizionale trasportatore aereo monorotaia. Il sistema si avvale di un traslatore dei pezzi a passo per sostenere tutti i tipi di manufatti composto da due binari monorotaia collegati tra loro da un sistema di bilancelle. Questo speciale convogliatore trasla in automatico avanzando a passi temporizzati per l’esecuzione delle varie fasi di lavorazione lungo tutto il ciclo di verniciatura. “Eurocar era disponibile in varie taglie a seconda della lunghezza massima dei pezzi da verniciare. Noi scegliemmo la 5, ossia 10 m di lunghezza”, commenta Enrico Troisi, “ma successivamente all’installazione di Komby, abbiamo revampato Eurocar sostituendo la cabina di verniciatura, compattandolo e scalandolo a una taglia 3, ossia 6 metri di lunghezza massima pezzi. Il motivo è che il nuovo Komby ci dà la possibilità di verniciare manufatti di grandi e grandissime dimensioni, dunque Eurocar ha potuto diventare un impianto di taglia media, più rapido, per cambi colore frequenti”.

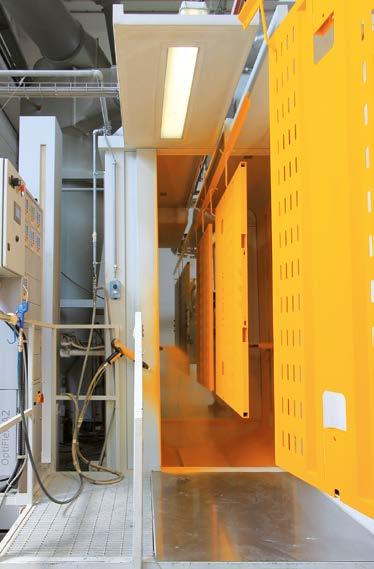
Euro90 è l’impianto per la verniciatura industriale a polveri dei semilavorati e dei manufatti metallici con le fasi di processo completamente automatizzate, un impianto di verniciatura costruito con componenti standardizzati per una consegna rapida e con un ottimo rapporto qualità/prezzo. Quello installato da T&G ha dimensioni massime dei pezzi di 3000 x 2000 x 80 mm con trasportatore monorotaia, tunnel di pretrattamento chimico, impianto di demineralizzazione, una cabina automatica di applicazione e forni di asciugatura e polimerizzazione.
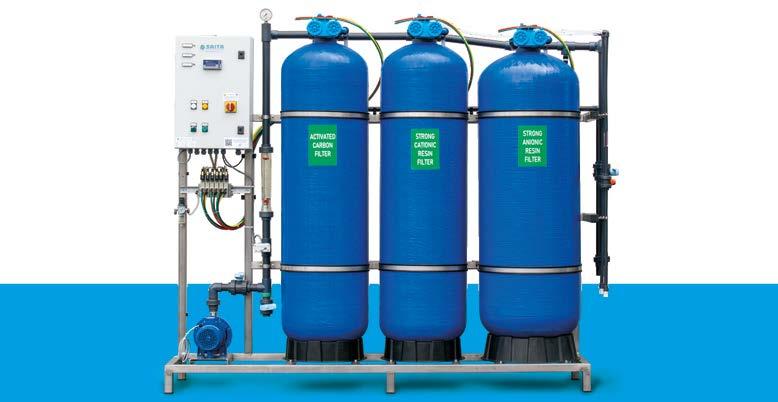
“L’investimento in un Euro90 ci ha consentito di aumentare il numero di clienti perché potevamo verniciare serie lunghe di pezzi in modo rapido ed efficiente” commenta Luca Girolimetto. “A breve aggiungeremo una seconda cabina automatica in linea, per dedicarne una al colore standard e una per i cambi rapidi di colore”.
All’inizio degli anni 20 del Duemila, a T&G si pone un altro problema: le taglie delle macchine costruite dai propri clienti diventano sempre più grandi, e le dimensioni di Eurocar, 10 metri di lunghezza, non bastano più.
L’investimento più recente è dunque una linea Komby, l’impianto per la verniciatura industriale in modalità manuale estremamente adattabile a pezzi metallici di diverse dimensioni, adatto alle piccole produzioni o ai ritocchi, grazie alla possibilità di caricare sul trasportatore aereo pezzi differenti da trattare con diversi colori e dimensioni. Inoltre, la modularità dei suoi componenti costruttivi permette di rivedere e modificare con moduli aggiuntivi il sistema di

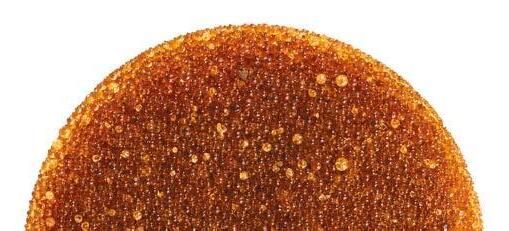

verniciatura nel tempo. Quello installato da T&G è un Komby con due moduli, applicazione e cottura della vernice, definito “ibrido”, poiché al posto del traslatore direzionale manuale, ha un monorotaia completamente automatizzato per la movimentazione di pezzi pesanti e di grosse dimensioni. Un carro aereo movimentato trasversalmente rispetto ai binari fissi che può portare fino a 4.000 kg distribuiti su 2 barre porta pezzo parallele. Le dimensioni delle barre di carico sono di 12.000 mm. Il sistema di trasporto è stato studiato dall’olandese Railtechniek, che ha realizzato anche 4 introduttori automatici a bordo carro per inserire, secondo ricette di lavoro preimpostate, le barre porta pezzo in entrambi i lati dell’impianto per realizzare differenti cicli di lavoro.
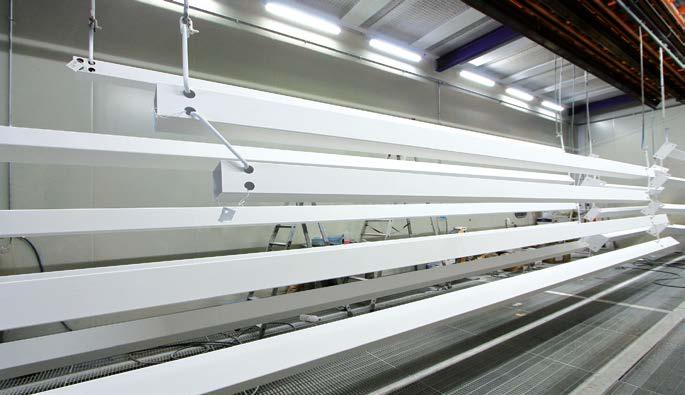
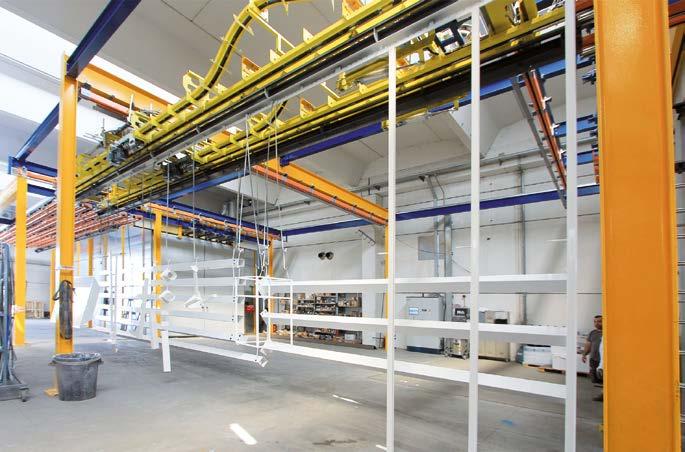
Conclusioni
“Nel corso della nostra carriera da imprenditori abbiamo sempre avuto come priorità investire nell’azienda, coccolare i clienti e fidelizzarli risolvendo loro dei problemi, in poche parole garantendo un servizio di alta qualità” conclude Enrico Troisi. “Oggi siamo in 45 e ci siamo specializzati nella verniciatura degli impianti di automazione e in generale di macchinari industriali. In questa specializzazione, ha giocato un ruolo importante l’avere sempre puntato sul pretrattamento meccanico, offrendo sia la sabbiatura manuale con garnet sia la granigliatura automatica con graniglia mista di ferro. Inoltre, dal momento che la formazione del personale è una criticità per aziende come la nostra, una volta ottimizzate le operazioni per una manciata di settori industriali, diventa antieconomico andare a conquistarne degli altri. T&G oggi è un terzista a tutto tondo, specializzato nei trattamenti superficiali di alta qualità e nell’applicazione di cicli di rivestimento sia a polvere sia a liquido con una vasta dotazione impiantistica in grado di soddisfare esigenze molto diverse tra loro. Siamo orgogliosi di ciò che è diventata la nostra piccola idea imprenditoriale”.
Dall'alto:
- Railtechniek ha studiato un sistema di trasporto unico nel suo genere per l’impianto Komby di T&G, sistema che rende il trasferimento dei pezzi fra i moduli operativi completamente automatico.
- La cabina di verniciatura manuale del Komby.
- Da sinistra Enrico Troisi, Alessia Venturi e Luca Girolimetto.
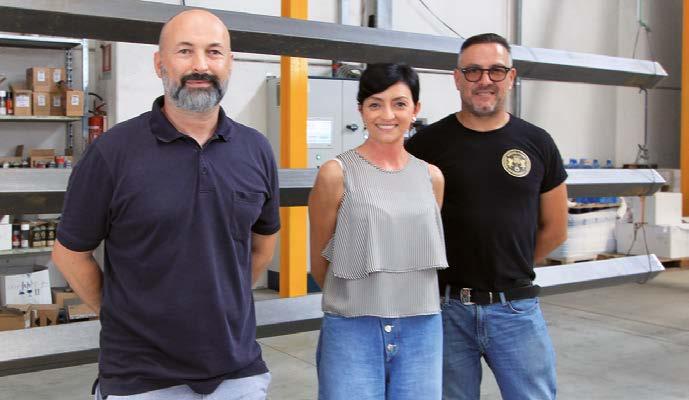
Super durable powder coating in anodized look
TIGER Drylac® Series 68 underscores the high demands of the architecture and facade industry on the performance of building envelops worldwide. The super durable product portfolio includes numerous anodized effects for smooth finishes in matte or flat matte aesthetics.
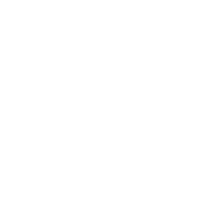
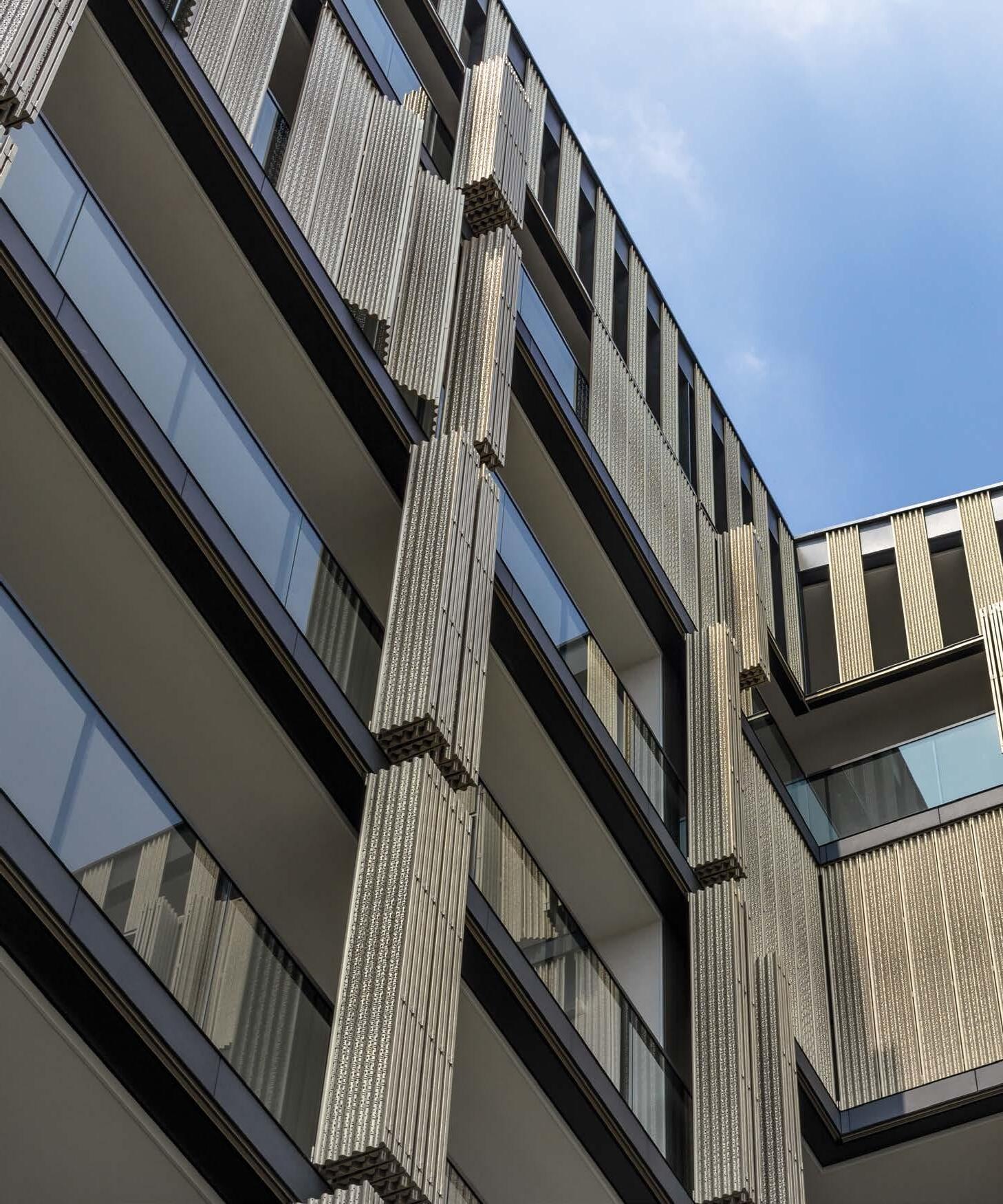
Your advantage: Not only aluminum, also steel and galvanized steel can be finished in a refined anodized look: cost-effectively, environmentally friendly and in just one coat. www.tiger-coatings.com
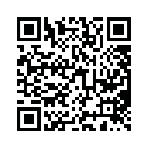
ART WITHIN SURFACES
AkzoNobel aiuta Southwest a celebrare la cultura hawaiana con Imua One
A cura di AkzoNobel Aerospace Coatings
Amburgo – Germania
L’aereo Boeing 737 MAX 8 di Southwest® Airlines è stato verniciato con diversi colori così da catturare il concetto culturale hawaiano di Imua.
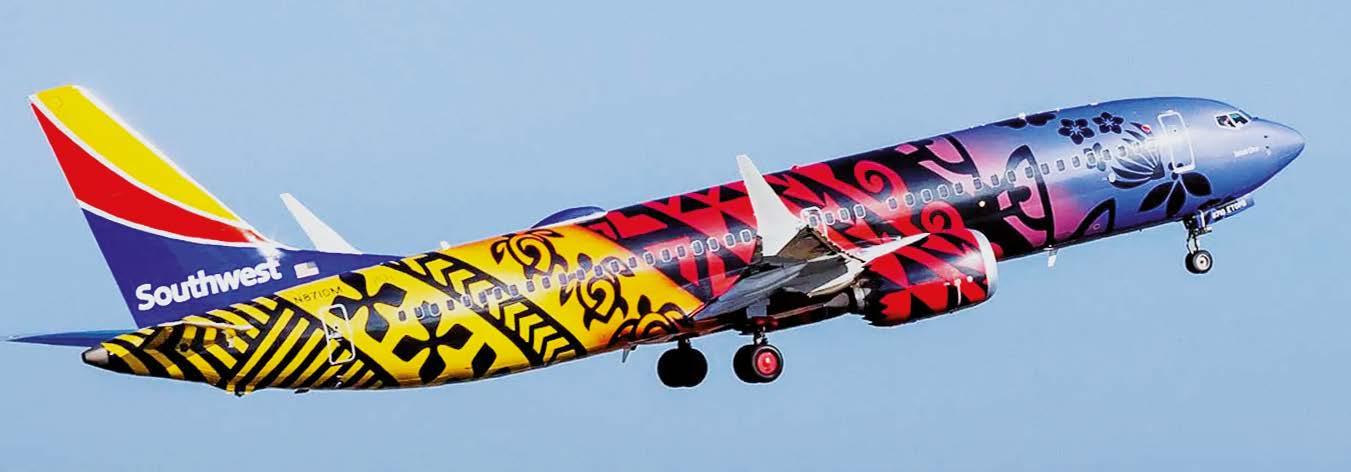
Ci sono livree speciali e livree che sono speciali per la compagnia aerea e per le persone che essa serve.
Quando Southwest® Airline ha voluto celebrare il quarto anniversario dell’azienda al servizio delle isole Hawaii, ha voluto creare un disegno unico che catturasse il concetto culturale hawaiano di Imua, che significa "in avanti", e la forza, il coraggio e lo spirito degli isolani.
Per il disegno di Imua One, la compagnia aerea ha collaborato con Osaki Creative Group con sede a Oahu e ha ricevuto assistenza da Herman Piikea Clark, un’artista nativo/Kanaka Maoli hawaiano, designer e ricercatore. Il design, su un Boeing 737 MAX 8 di Southwest, presenta una gamma di colori favolosi, compresi blu audaci, rossi caldi e giallo sunrise, con sfumature e adesivi che simboleggiano la transizione dalla notte al giorno e riflettono la storia del viaggio nel Pacifico sfruttando il sole, la luna e le stelle per navigare.
Per portare i propri disegni alla luce, la compagnia aerea si è rivolta ad AkzoNobel per la qualità delle sue vernici aeronautiche e per l’esperienza del suo Technical Services Team.
Il velivolo è stato ultimato in 17 giorni da un team composto da dieci
verniciatori che hanno lavorato a turni a Spokane, impiegando oltre 340 litri di vernici composte da 16 colori diversi.
Inizialmente, la livrea era stata verniciata di nero con una mano di Mica e una di clearcoat per fissarla in posizione e, successivamente, è stata levigata per fornire maggiore adesione ai colori speciali a seguire. Solo Graphix ha abilmente realizzato gli stencil pre mascherati, che sono stati successivamente applicati con la sola richiesta di lievi regolazioni. La facilità di utilizzo degli stencil, insieme alla velocità di impostazione dei materiali da verniciare, ha permesso il completamento del progetto due giorni prima del previsto.
Il disegno frontale (pre-mascheratura) è stato poi applicato sul nero e levigato, proseguendo con l’aggiunta di una vernice di colore blu e porpora insieme ad un’ulteriore mano di mica. Il design è stato sigillato con un clearcoat. Il team qualificato ha perfettamente gestito la sfida di mescolare l’arancione della sezione posteriore così da fornire l’effetto desiderato. Per la sezione centrale, le miscele di colore (da rosso ad arancio e da porpora a rosso) sono state completate contemporaneamente. Inoltre, ai design della sezione posteriore e
Custom-built painting installations
Macchine e impianti realizzati su misura
centrale è stata applicata un’ulteriore mano di mica sigillata con un clearcoat. Una volta completato il disegno, l’aereo è stato smascherato, lavato, soffiato per la rimozione dei detriti, virato e verniciato con le tre mani finali di trasparente. Sulla coda è stato applicato anche un ultimo strato di clearcoat. Durante l’intero programma, la vernice è stata applicata con facilità e non ha richiesto manodopera aggiuntiva. “La parte più difficile è stata la scelta di una Mica che funzionasse con i diversi basecoat. Abbiamo dovuto sviluppare altre cinque colorazioni in meno tempo rispetto allo standard nonché un colore supplementare creato sul posto durante la visita del cliente. Ciò ha richiesto un grande sforzo da parte del team di sviluppo del colore di Troy. Fortunatamente, ne è valsa la pena. Alla luce del giorno, l’aereo vive di vita propria, il disegno fluisce grazie alla dinamicità dei colori ed è strepitoso da vedere una volta appreso il significato dei simboli e cosa rappresentano per la popolazione delle Hawaii. Ha un significato speciale per tutti noi”, ha dichiarato Mike Suhara di AkzoNobel Aerospace Coatings, sostenendo che l’esperienza del team è stata cruciale per il successo del progetto.
vedere il processo di verniciatura del Boeing 737 MAX 8
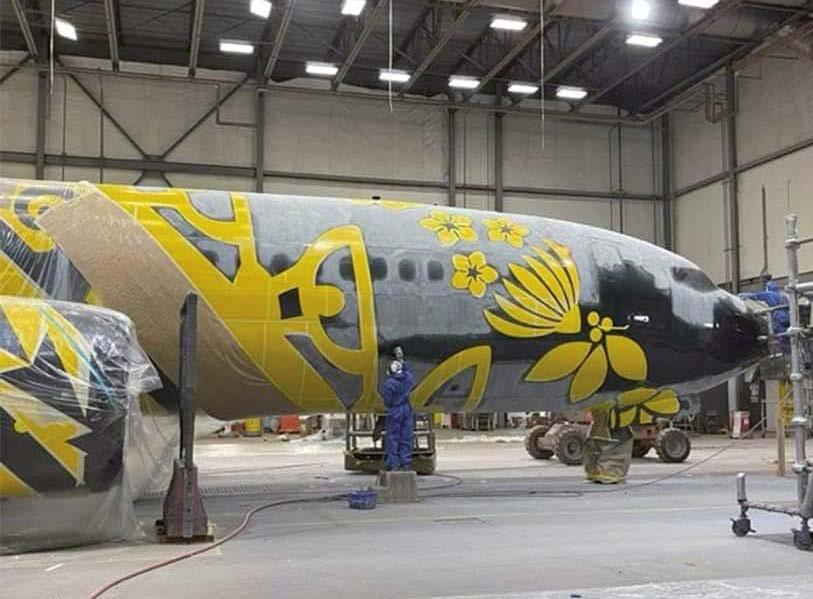
Shot blasting booths
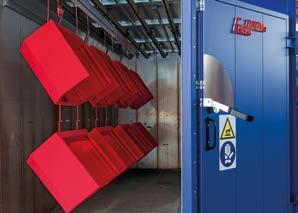

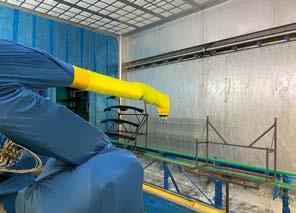
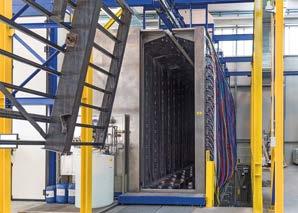
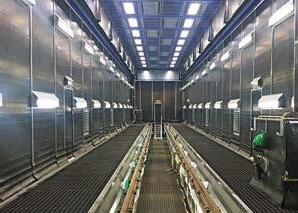
Cabine di sabbiatura
Washing tunnels
Tunnel di lavaggio
Liquid painting installations
Impianti di verniciatura a liquido
Powder painting booths Cabine di verniciatura a polvere
Curing ovens
Forni di cottura
Eurotherm S.p.A.
T +39 011 98 23 500 | M info@eurotherm.eu
Eurotherm Oberflächentechnik GmbH
T +49-7571-92795-10 | M germany@eurotherm.eu
Eurotherm France S.A.S.
T +33 (0) 7 89 37 56 88 | M france@eurotherm.eu
Eurotherm Benelux
T +33 (0) 6 47 44 96 27 | M dekergorlay@eurotherm.eu
ADVANCEMENTS
L’ultima generazione delle celle di dialisi CONDOROIL Stainless
A cura di CONDOROIL Chemical
Casale Litta (Varese), Italia info@condoroil.it
Le celle di dialisi sono fondamentali per la verniciatura cataforetica: Condoroil Stainless, divisione del gruppo Condoroil, ha sviluppato un nuovo concept di celle con caratteristiche innovative e pronte per qualsiasi esigenza del mercato.
L’azienda chimica CONDOROIL, fondata nel 1972 da Franco Zavattoni, vanta oggi 3000 prodotti a catalogo, 16 brevetti depositati e una gamma innovativa di tecnologie di recupero, rigenerazione e minimizzazione degli sprechi proposte a corredo dei formulati chimici. Lo stabilimento della società situato a Casale Litta, in provincia di Varese, ricopre una superficie complessiva di 10 mila m2, di cui 4 mila coperti, ed è costituito da 5 fabbricati con una capacità produttiva pari a 10 mila ton/anno. La divisione tecnica dedicata a ricerca e assistenza occupa mediamente il 35% dell’intera forza lavorativa e i laboratori chimici restano il fiore all’occhiello dell’intera struttura. Specializzata in soluzioni chimiche per la verniciatura industriale, la società offre un portfolio variegato che spazia dagli svernicianti ai prodotti per il trattamento acque, da quelli di pretrattamento fino ai prodotti per la verniciatura elettroforetica. In quest’ultimo ambito, la divisione Condoroil Stainless realizza celle di dialisi di ultima generazione utilizzate in tutto il mondo.
Le celle di dialisi CONDOROIL Stainless
Sono numerosissime le celle installate da Condoroil sia in Italia sia all’estero, a dimostrazione del fatto che le caratteristiche che la divisione R&D ha sviluppato per questa tipologia di prodotti sono in grado di soddisfare le molteplici e differenti esigenze dei clienti. Vediamo alcune di queste caratteristiche in dettaglio:
• la protezione: una rete ‘semirigida’ posizionata intorno alla membrana protegge quest’ultima dagli urti accidentali e, quindi, da eventuali danni.
In genere, scelgono questa opzione gli utilizzatori che necessitano di immergere nella vasca di cataforesi componenti con spigoli vivi, che oscillando possono urtare la cella.
• la ‘super’ lunghezza: ove necessario, la lunghezza della ‘membrana attiva’ può superare i 4 metri, soprattutto nel caso si debbano immergere nelle vasche componenti di autobus, TIR e mezzi di movimento terra.

• oltre gli standard: le celle T1 e T2, cioè con diametri dell’anodo corrispondenti a 1,5” e 2”, sono adatte per applicazioni industriali generali e sono in grado di offrire un ottimo rapporto membrana-anodo e di garantire la massima durata operativa possibile. La richiesta di questa tipologia di celle è sempre più spesso affiancata dalla domanda proveniente dal settore automotive di celle T3 e T5, che presentano un anodo dal diametro rispettivamente di 3” e 5” e che presentano l’ulteriore vantaggio di un numero di connessioni minore rispetto ai diametri inferiori.
Caratteristiche della cella di dialisi
La cella Condoroil con membrana a scambio ionico è realizzata mediante l’utilizzo di un foglio di polimero avvolto e saldato, che garantisce basse deformabilità e resistenza elettrica, ma una lunga durata e maggior intensità di corrente. Tale tipo di conformazione, dallo spessore minimo e, quindi, con limitata resistenza elettrica, sviluppa poco calore, che è la causa primaria dell’invecchiamento precoce della membrana stessa. La tendenza alla scarsa dilatazione, inoltre, evita il verificarsi di cortocircuiti da contatto tra membrana ed elettrodo.
Mentre nelle tradizionali celle il flusso di acqua entra nell’elettrodo
toccandolo fisicamente, nelle celle Condoroil scorre attraverso un tubo in plastica chiuso all’estremità opposta da un tappo atto ad evitare il ritorno di liquido nell’elettrodo. In queste celle tubolari, infatti, l’elettrolita viene flussato dall’alto all’interno dell’elettrodo e, risalendo dal fondo, esce dalla cella unitamente all’eccesso di elettrolita.

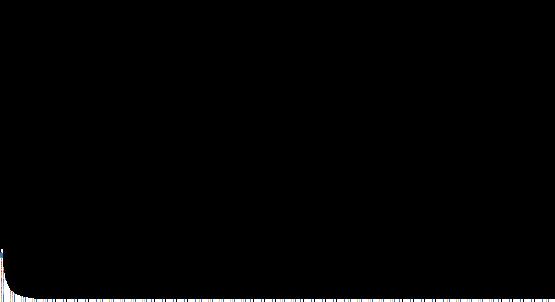
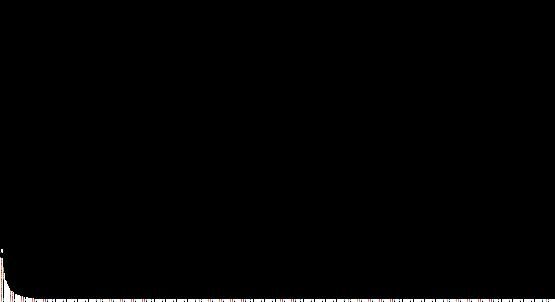
In caso di rottura dell’elettrodo, questa soluzione elimina il rischio di cammino preferenziale d’acqua, con conseguente accumulo di elettrolita nello spazio tra elettrodo e membrana. Un ulteriore vantaggio è rappresentato dal fatto che, nel caso di guasti e/o rotture, non è necessaria la sostituzione in toto del pezzo: queste celle permettono il solo cambio dell’elettrodo con conservazione della membrana.
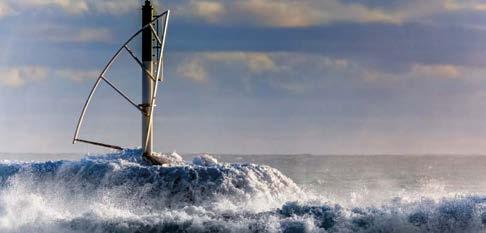

Inoltre, un altro benefit è determinato dalla soluzione di base sviluppata con la parte superiore aperta che permette una facile ispezione dell’interno e una manutenzione semplice. Soprattutto in caso di celle in pressione, è tuttavia possibile l’alternativa ‘Closed Top’, attraverso l’applicazione di un coperchio che viene collegato al circuito dell’acqua e al cavo elettrico.

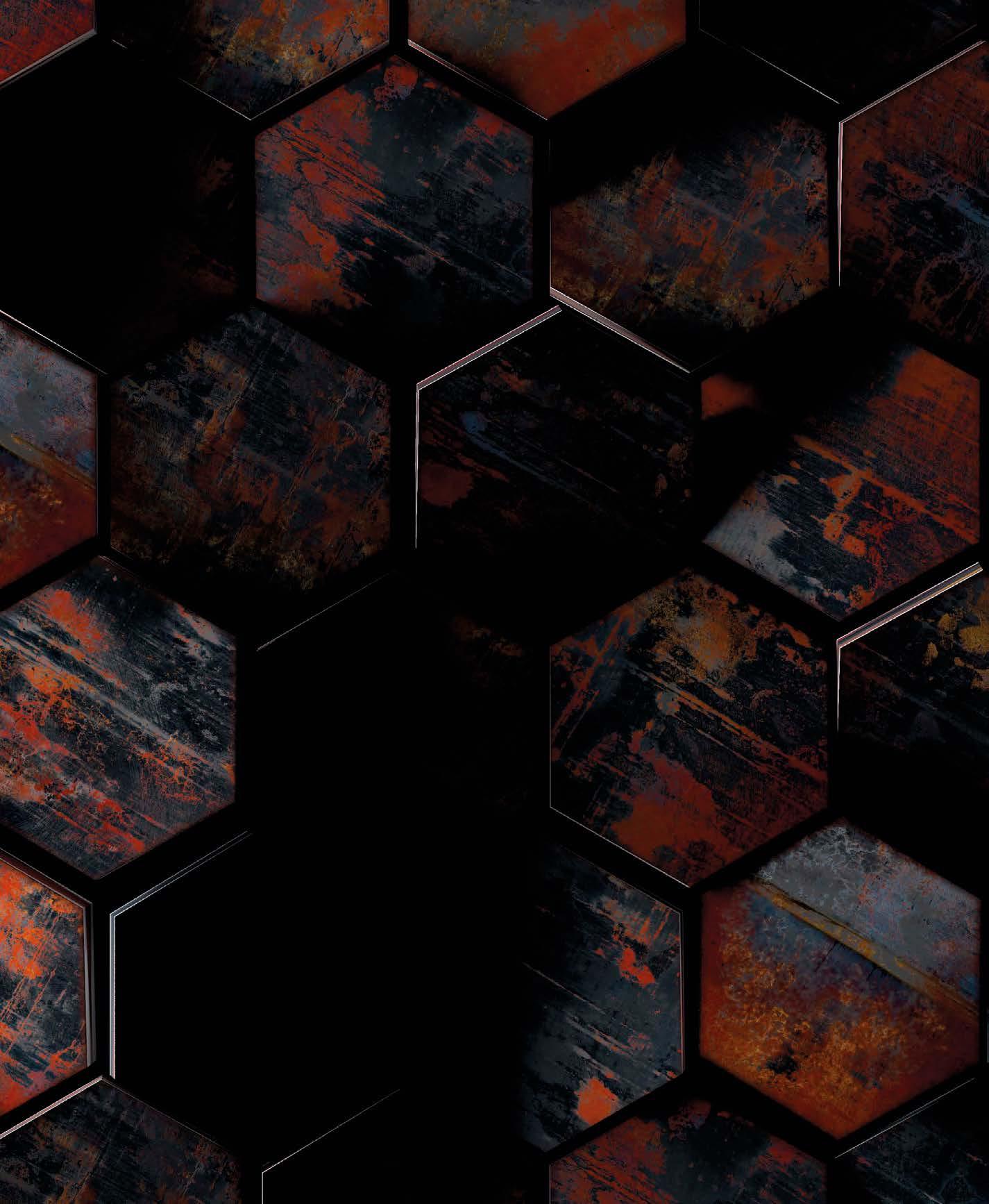
Anche in questo caso, la divisione Condoroil Stainless del Gruppo Condoroil si è dimostrata all’altezza delle richieste del mercato, ricercando e trovando soluzioni per celle di dialisi in grado di rispondere alle richieste più diverse e complesse, ottimizzando un prodotto fondamentale per il processo di verniciatura cataforetica.
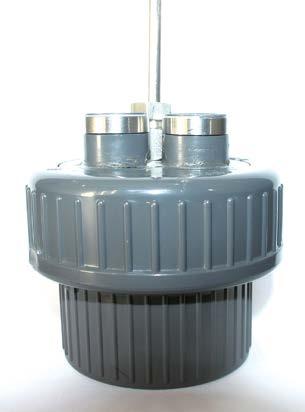
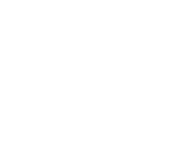
Da sinistra: la rete semirigida posizionata intorno alla membrana la protegge dagli urti accidentali; soprattutto nel caso di celle a pressione, il modello alternativo “Closed Top” permette di collegare il coperchio al circuito dell’acqua e al cavo elettrico.
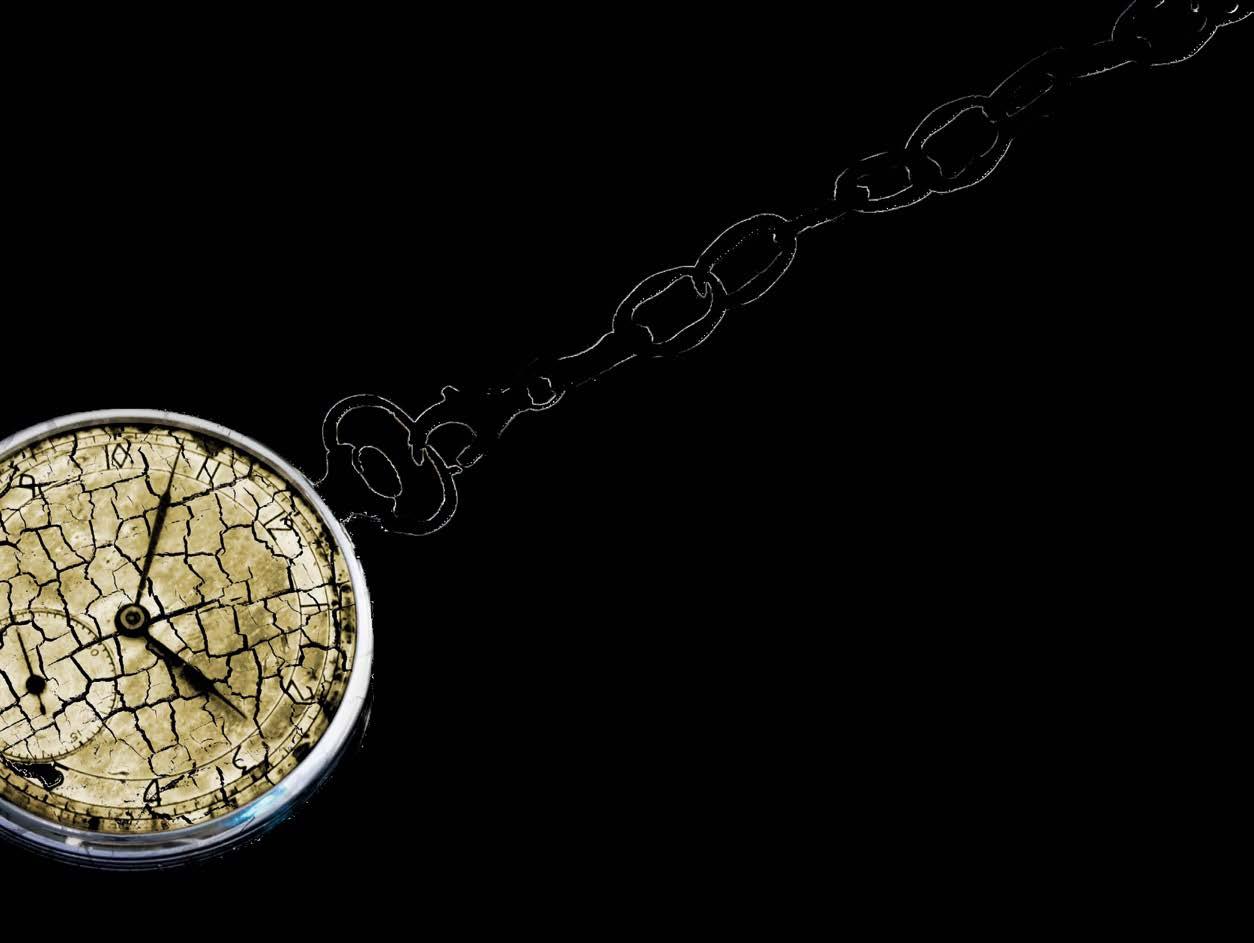
Verde ingannevole COLOUR STUDY
Monica Fumagalli ipcm®Da pigmento al veleno a bandiera dei movimenti ecologisti: il verde, colore della natura per eccellenza, è una delle tinte più difficili da sintetizzare e, forse per questo motivo, associato alla volubilità e all’inganno. Positività e negatività di un colore dalle molteplici sfumature.
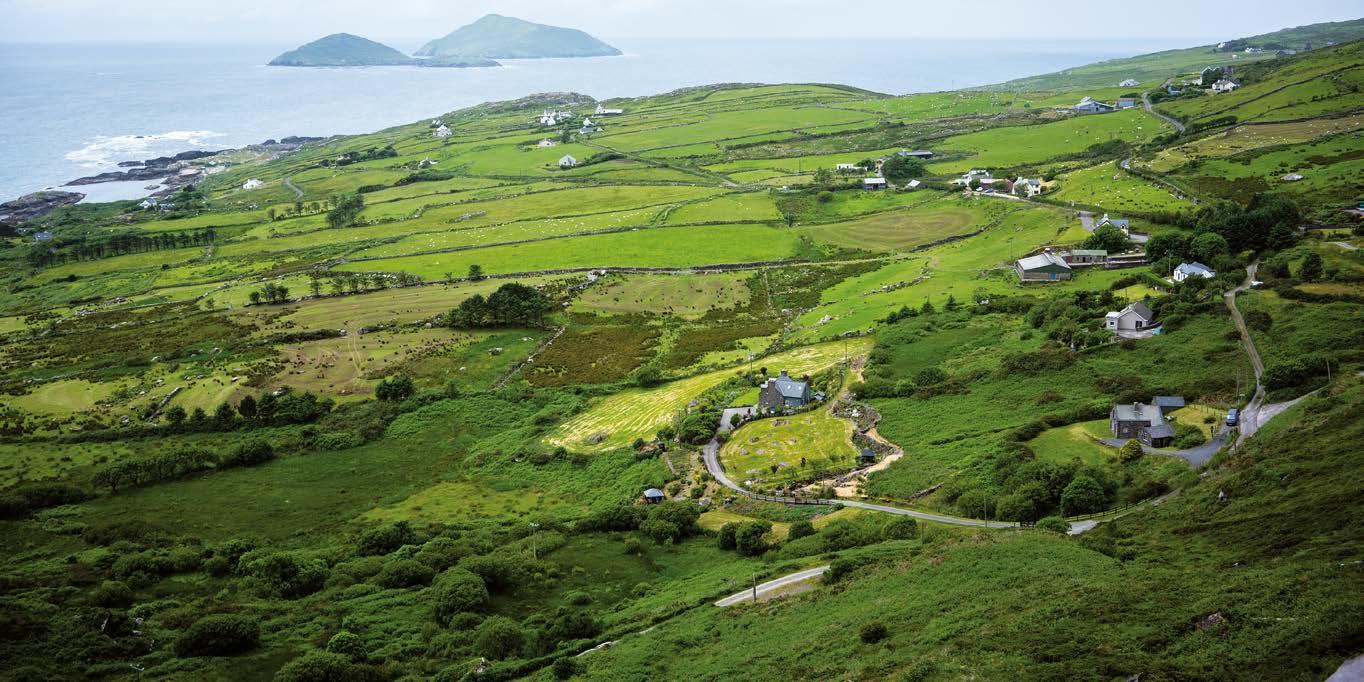
Il verde è il colore della sostenibilità e dell’ecologia per antonomasia, tanto che è ormai comune, in particolare nell’ambito della comunicazione tecnica nel settore dell’industria manifatturiera in cui lavoriamo, incontrare la definizione di azienda “green”. Si tratta però di un’associazione mentale ingannevole che richiama il mondo della natura e di ciò che risulta “pulito” per essa, perché il verde è una delle tinte più difficili da sintetizzare e il suo processo di produzione è tra i più complessi ed inquinanti, e lo stesso si può affermare per il suo smaltimento. Come dichiara infatti il chimico Michael Braungart in un’intervista di qualche anno fa al New York Times, “Il colore verde non potrà mai essere eco, a causa del modo in cui viene creato. È impossibile colorare di verde la plastica, o stampare con inchiostro verde su carta, senza contaminare. Ironico, vero?”1
1 https://www.nytimes.com/2010/04/05/arts/05iht-design5.html
Ottenuto dalla combinazione di giallo, il colore della gioia e del blu, il colore della tranquillità, il verde rimane comunque un colore positivo, proprio grazie alla sua connessione con la natura: il verde evoca sentimenti come rinascita, freschezza, vitalità e pace. Il verde favorisce il relax, ed ecco perché gli ambienti con elementi verdi sono pacifici e nutrono la mente, fino – si crede – a migliorarne la concentrazione. E’ anche il colore della speranza, della vitalità, della fertilità e dell’abbondanza. Nei semafori rappresenta il via libera, al contrario del colore rosso che obbliga a fermarsi. E’ tuttavia anche il colore dell’invidia, del diavolo medievale, della mancanza di risorse economiche (“essere al verde”), del disgusto e del veleno. Era un colore apprezzato fin nell’antichità, ma proprio perché difficile da ottenere, uno dei colori più problematici per la produzione artistica.
L’origine della parola “verde”
Il “verde”2 (in inglese “green”, in francese “vert”, in spagnolo e portoghese “verde” e in tedesco “grün”) era considerato dagli antichi una sfumatura di colore associata al giallo. Ce lo rivelano la radice indoeuropea ghel, che significava anche brillante, splendente, e il proto-germanico gewalz, che indicava appunto entrambe le tinte. Da qui sono nati i termini latini galbus (verde pallido) e galbinus (giallo).
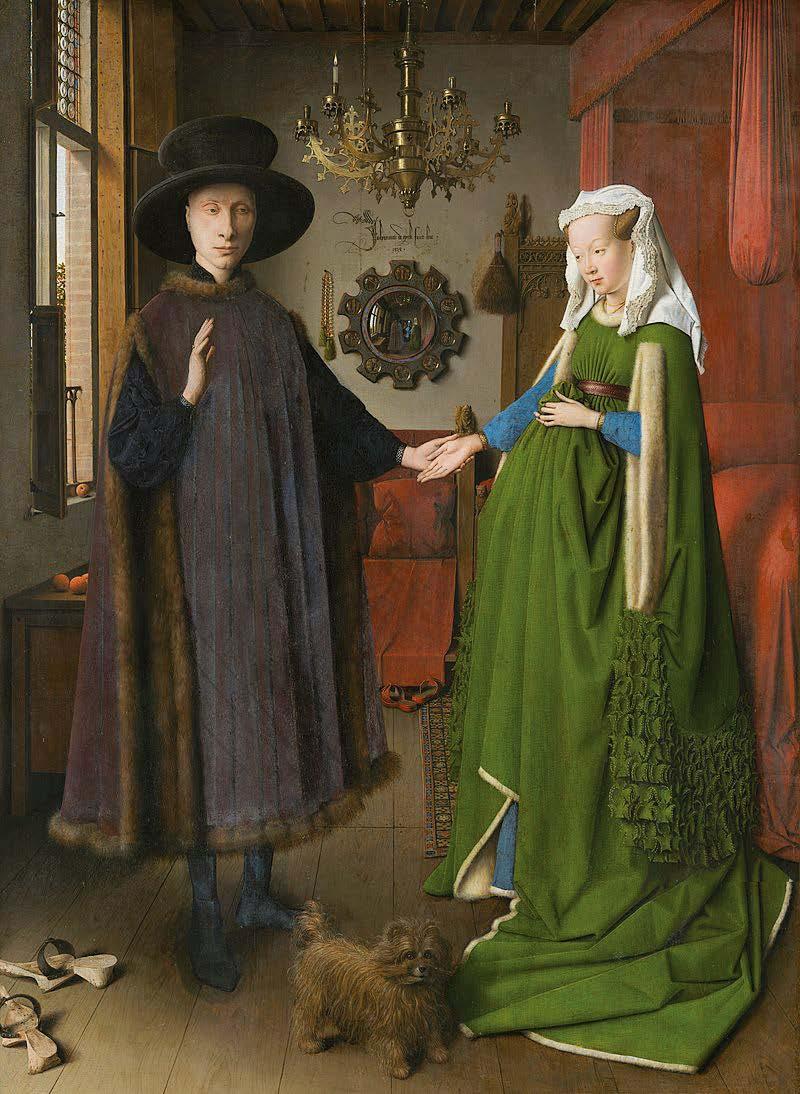
I primi a separare i due colori furono i greci: in greco antico, la stessa radice protoindoeuropea si è evoluta in khloròs, parola associata con meno ambiguità al verde pallido, tanto da diventare più tardi essa stessa radice di clorofilla.
Il termine italiano verde deriva quindi dal latino viridis, diventato poi virdis, che a sua volta era legato al verbo vireo, cioè germogliare, etimologicamente connesso a vigore, vegetare e vita (dalla radice protoindoeuropea weg-).
Lo stesso percorso è stato compiuto anche dal termine inglese “green”, derivante dal protoindoeuropeo ghreh- e dal protogermanico groniz, da cui si arriva, per nulla casualmente, anche al verbo grow (crescere).
Il verde nella storia antica
Al contrario del blu e del rosso, non c’è traccia di verde nelle pitture preistoriche, forse proprio perché sulle pareti delle grotte venivano utilizzati i colori trovati in natura, di cui non abbiamo più traccia. Le prime testimonianze dell’utilizzo di questa tinta risalgono a 5000 anni fa, quando gli antichi Egizi scelsero questo colore per rappresentare la vegetazione e la fertilità del Nilo, che inondava con le sue acque la terra rendendola rigogliosa. La divinità egizia Osiride era spesso rappresentata con la pelle verde, proprio per simboleggiare la rinascita e la fertilità. In alcune tombe dell’epoca sono state rinvenute tavolozze di trucchi per il viso di colore verde, ottenuto con la malachite, un minerale verde ricco di rame che veniva polverizzato e usato come pigmento: gli egizi avevano l’usanza di truccare il bordo degli occhi con la tinta verde per proteggersi dal male. La stessa credenza si ritrova per i defunti: piccoli amuleti di colore verde a forma di scarabei, realizzati in malachite, sono stati ritrovati all’interno delle tombe, probabilmente lasciati proprio con lo scopo di proteggere il defunto.
Oltre alla malachite, per ottenere la tinta verde venivano utilizzati pigmenti come il verdigris e il verde egizio: il verdigris era un composto di acetato di rame, ottenuto dalla corrosione del metallo, mentre il verde egizio era una miscela di malachite, azzurrite e altri minerali che veniva preparata sinteticamente.
Per colorare di verde i tessuti, prima venivano tinti di giallo con pigmenti a base di zafferano e poi imbevuti nella tintura blu ricavata dalle radici della pianta del guado.
2 www.linkedin.com/feed/update/urn:li:activity:7001092899694129152
Sfumature di verde nel Medioevo
Se nella Roma del Basso Impero i neonati erano avvolti in stuoie verdi per augurare loro una buona sorte, nel Medioevo questo colore era scelto dalle ragazze in cerca di marito che, poi, una volta sposate, lo indossavano come augurio di maternità. Ma, forse proprio a causa della sua instabilità nella tintura dovuta al processo di composizione difficoltoso, nel Medioevo il verde era anche associato all’inganno e all’astuzia e, quindi, rappresentava il colore del Diavolo, delle streghe e degli animali fantastici più spaventosi come i draghi, i serpenti mostruosi come l’idra e il basilisco, e le sirene.
Fin dai suoi primi giorni, il colore verde è stato associato all’Islam, perché legato ad una frase del Corano che recita: “coloro che abitano il paradiso indosseranno raffinati abiti di seta verde”. Così le moschee sono decorate in vari colori ma quasi sempre con toni verdi predominanti e le tombe dei santi sufi, la dimensione mistica dell’Islam, sono ricoperte di seta verde.
Ecco perchè la tribù del profeta Maometto aveva uno stendardo verde e quasi tutti i paesi islamici usano questo colore nelle proprie bandiere. Il verde mantiene il suo fascino controverso anche nella storia occidentale del secolo XV e XVI: la tradizione di buon auspicio del colore verde si conferma nel famoso “Ritratto dei coniugi Arnolfini” di Jan van Eyck (143435) in cui la donna raffigurata non è incinta, come si potrebbe indovinare a causa della foggia dell’abito, ma si pensa sia stata raffigurata in quella posizione e in verde come rito propiziatorio per una numerosa progenie.
Il verde al veleno
Il punto di svolta nella diffusione artistica – e non solo - di questo colore avvenne in epoca vittoriana, quando si diffuse l’usanza di ottenere la tinta verde aggiungendo arsenico, la sostanza altamente tossica che si ritiene causa del decesso dei numerosissimi che maneggiarono libri, giocattoli, oggetti decorativi o, solamente, dimorarono in stanze decorate con questo tipo di tintura3. Sia il verde di Scheele, messo a punto nel 1775 dal chimico svedese Carl Wilhelm Scheele, che ebbe subito un successo straordinario grazie alla sua intensità e resistenza alla luce, sia il verde di Parigi o verde di Schweinfurt, costituito da arsenico e piombo, di cui s’innamorarono i pittori impressionisti nel corso del XIX secolo, sono ritenuti i responsabili delle intossicazioni che costarono la salute o la vita dei molti entrati in contatto con i pigmenti verdi tossici. Solo per citare uno dei casi più famosi, la residenza di Napoleone Bonaparte in esilio sull’isola di Sant’Elena, Longwood House, aveva le pareti dipinte con questa tinta. Fu infatti Goethe, per primo, nella sua “Teoria dei colori”, a considerare la tinta verde “rasserenante” e a raccomandarne l’impiego nei locali destinati al riposo e al convivio e il movimento romantico della fine del 1700 a sdoganare il verde come colore della natura, dell’ecologia e dell’ambiente, così come è arrivato ai nostri giorni.
3 https://www.focus.it/cultura/curiosita/verde-arsenico-timore-mistero
Alcune curiosità
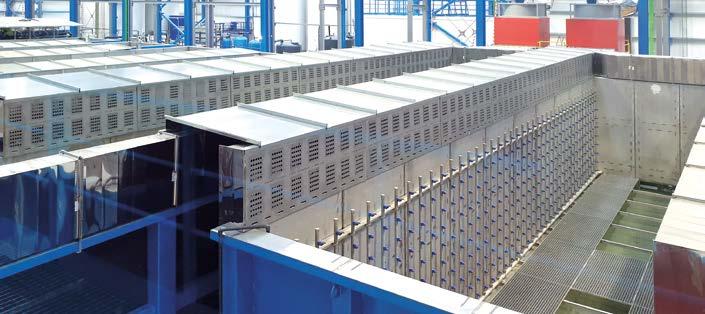
Alcune teorie sostengono che la casacca originale di Babbo Natale, prima dell’intervento di marketing commerciale di Coca-Cola4, fosse verde per richiamare l’origine “profana” della sua figura, collegata alla tradizione degli elfi che distribuivano i doni in alcuni Paesi del Nord Europa. Secondo il folklore d’Irlanda, l’sola verde per eccellenza, il verde è il colore preferito dalle fate.
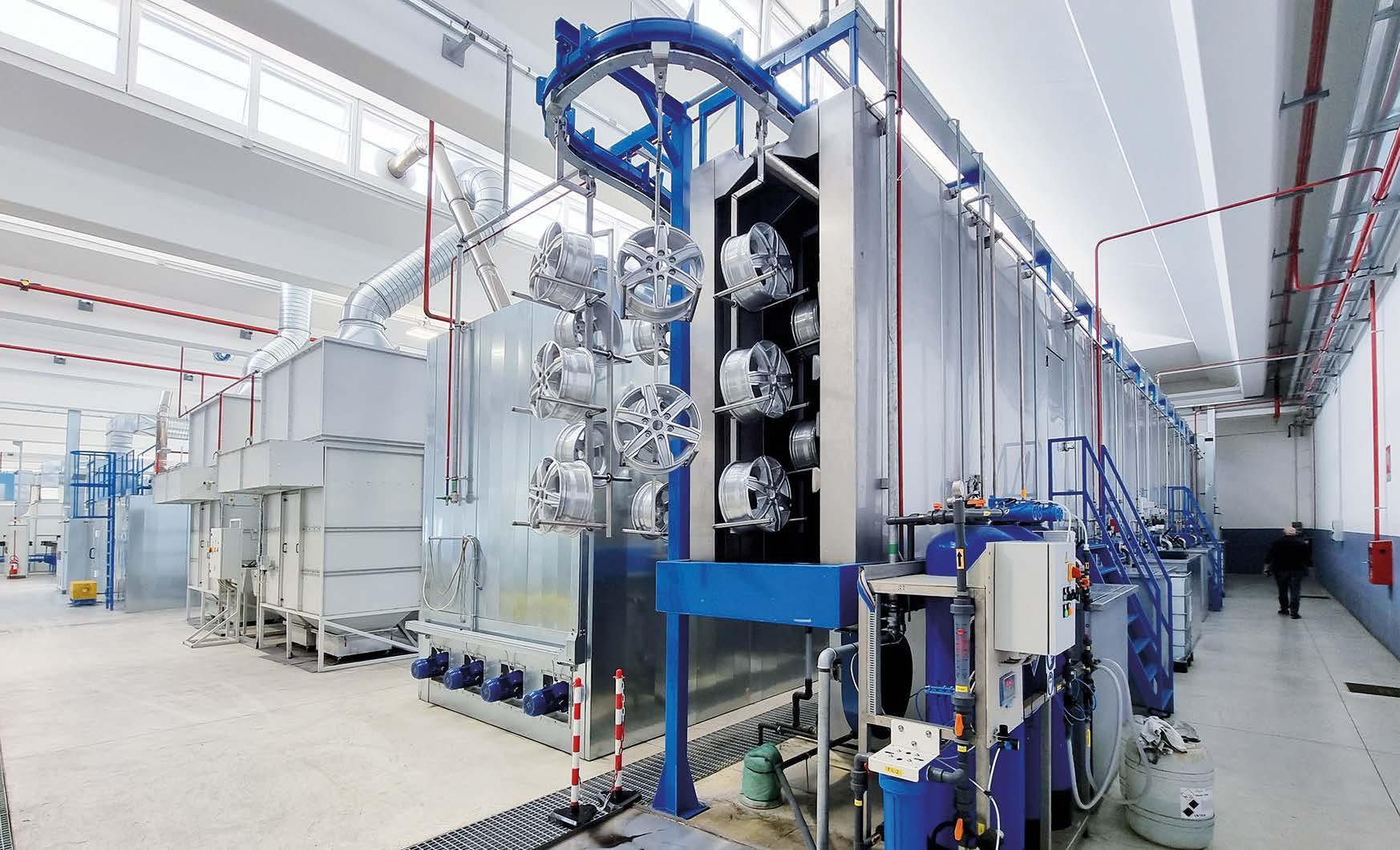
Ed ecco alcune connotazioni – forse più negative - del colore verde: per rappresentare il personaggio di “Disgusto” i creatori del film Pixar “Inside Out” hanno scelto il verde, accanto a Gioia (giallo), Tristezza (blu), Rabbia (rosso) e Paura (viola). Anche in questo caso l’ambivalenza del verde è confermata dal personaggio che, all’interno del concept emozionale del film diretto da Pete Docter e Ronnie del Carmen, ha comunque una valenza positiva perché permette alla protagonista di proteggersi dalle contaminazioni fisiche e sociali.
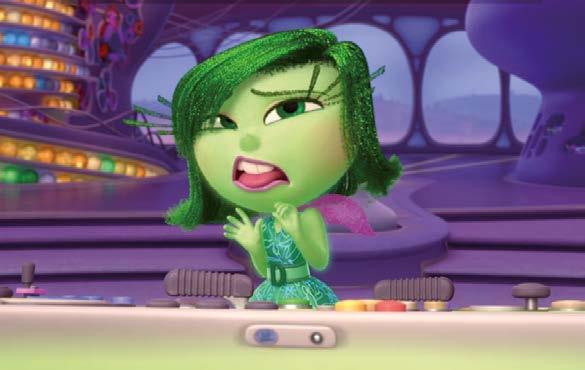
Un’ultima curiosità ci riporta ai problemi legati alla realizzazione di questo colore: sapevate perché la pelle dell’Incredibile Hulk è verde? Secondo i ben informati, nella rappresentazione originale di Hulk, Stan Lee voleva che fosse grigio. Ma, a causa di alcuni problemi di stampa delle prime copie dei fumetti Marvel, la figura di Hulk virava dal grigio al verde, che siamo abituati oggi a vedere nei fumetti e nei film.
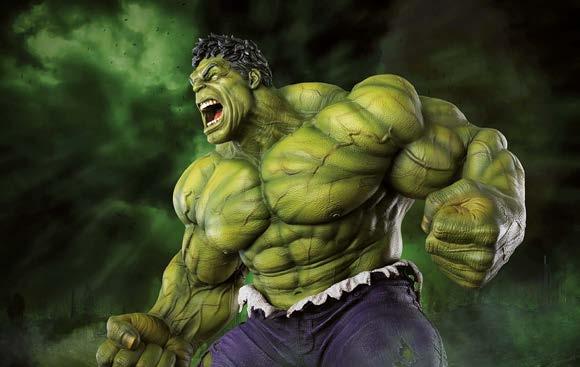
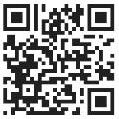
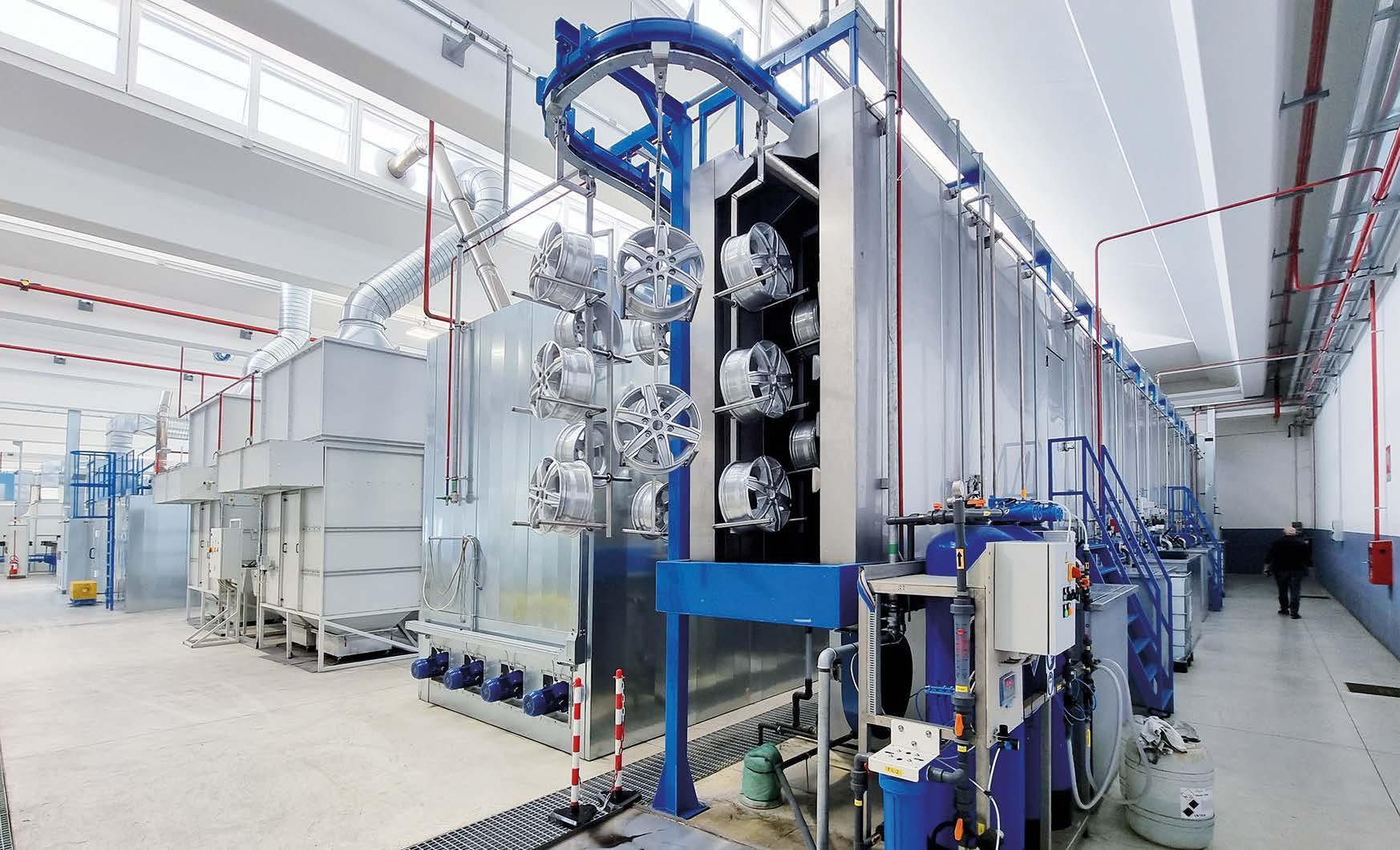
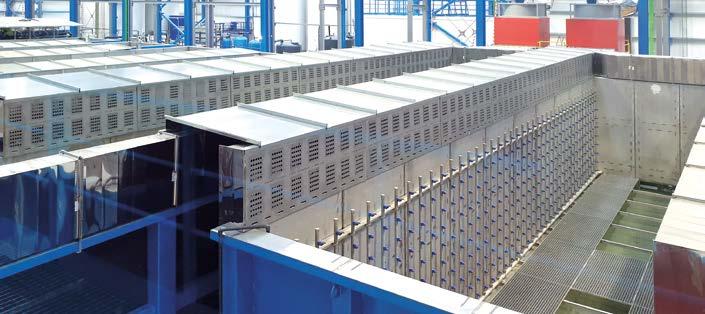
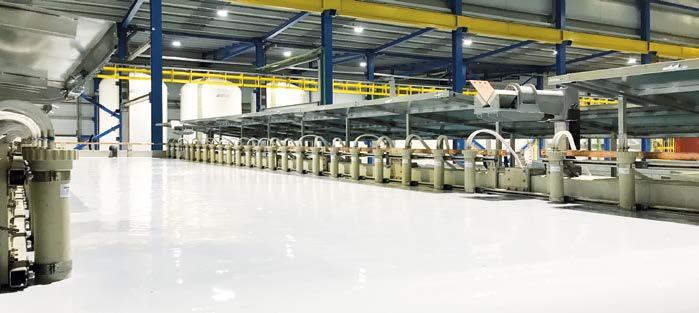

La traversata a nuoto dello Stretto di Messina: l’ultima impresa della squadra Verind

Lo sport è unione, condivisione e fatica per raggiungere un obiettivo comune: questo racconta l’esperienza di Matteo Minelli, Claudio e Francesca Orlando di Verind, che hanno compiuto la traversata a nuoto dello Stretto di Messina, dopo un anno di allenamenti insieme.
Lo scorso 12 giugno Claudio Orlando, Senior Manager Accounting & Controlling di Verind, sua figlia Francesca e Matteo Minelli, General Manager di Verind, hanno attraversato le incredibili acque blu dello Stretto di Messina, dove la leggenda mitologica di Scilli e Cariddi rivive ancora oggi.
La traversata è iniziata dalla costa siciliano presso Torre Faro e si è conclusa sulla spiaggia calabrese di Cannitello, proprio di fronte alla chiesa. Durante la traversata, le condizioni meteo sono cambiate repentinamente ed un fortissimo temporale ha accompagnato il gruppo per quasi tutta la nuotata, cessando solo in prossimità della costa calabra con l’uscita del sole. In totale, come testimoniato dall’orologio GPS di Matteo Minelli che ha registrato anche l’esatto itinerario seguito, la traversata è stata di 4.375 m, coperta in un tempo pari a 1:26’:04” per un totale di 3.444 bracciate.
“Sono appassionato di nuoto in acque libere ma, abitando a Milano, le opzioni per praticare questo sport sono poche” racconta Matteo Minelli
“Il mio collega Claudio Orlando condivide con me questa passione e ben presto, quella che era un’idea un po’ folle, nata chiacchierando in
azienda, si è concretizzata nell’obiettivo comune di attraversare a nuoto lo Stretto di Messina nel 2023. In un secondo momento si è aggiunta anche sua figlia Francesca, una ragazza molto sportiva”.
“Si tratta di un’esperienza che, per la sicurezza dei nuotatori, dal momento che lo Stretto ha un intenso traffico nautico e di mercantili, non può essere organizzata in autonomia ma serve l’appoggio di società sportive che si occupano della traversata, che forniscono le barche di appoggio che seguono i gruppi di nuotatori e che fissano, di concerto con la Capitaneria di Porto, delle date in cui è possibile effettuare la traversata. Claudio ed io abbiamo scelto il 12 giugno” prosegue Matteo Minelli.
“Purtroppo il meteo non è stato favorevole alla nostra impresa, perché il giorno si è aperto con il cielo coperto, che si è poi trasformato in una pioggia leggera e infine in una vera bomba d’acqua che ci ha colpito durante la traversata. Eravamo in poche persone, dunque abbiamo nuotato da soli, ognuno affiancato da una barca di supporto. Il briefing era molto semplice: nuotare seguendo la barca con lo sguardo ed evitare di guardare sotto, per non avere le vertigini date dal blu intenso e buio delle acque profonde dello Stretto.
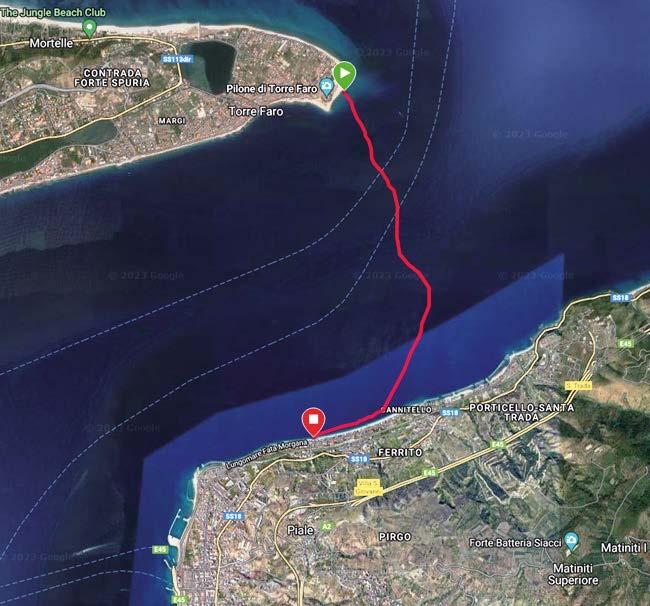
Abbiamo concluso la traversata con un tempo perfettamente in linea con quello dei nostri allenamenti in piscina, senza neanche provare un eccessivo affaticamento. Siamo arrivati alla spiaggia di Cannitello con il sole, dove ci hanno consegnato il Diploma che certifica il compimento della prova. Siamo tutti e tre molto soddisfatti di questa esperienza ma anche di tutto il percorso che abbiamo fatto insieme per prepararci”. “Lo scopo della traversata era quello di raggiungere un obiettivo comune, con allenamento e perseveranza ce l’abbiamo fatta: lavoriamo fianco a fianco da tanti anni e questa esperienza ci ha unito ancora di più.
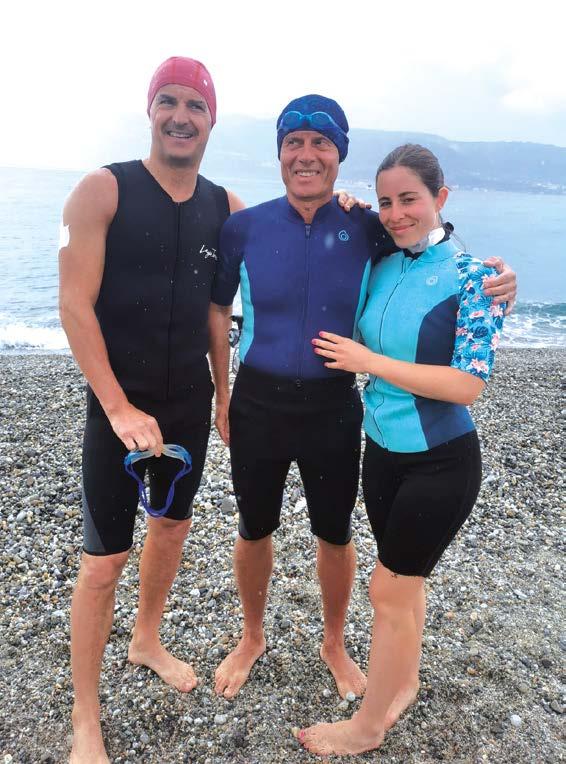
Il mio pensiero, appena toccato la sponda calabrese, è stato: noi siamo il team che ha unito l’Italia prima della costruzione del ponte sullo stretto”, conclude con un sorriso Matteo Minelli.
Per maggiori informazioni: www.verind.it
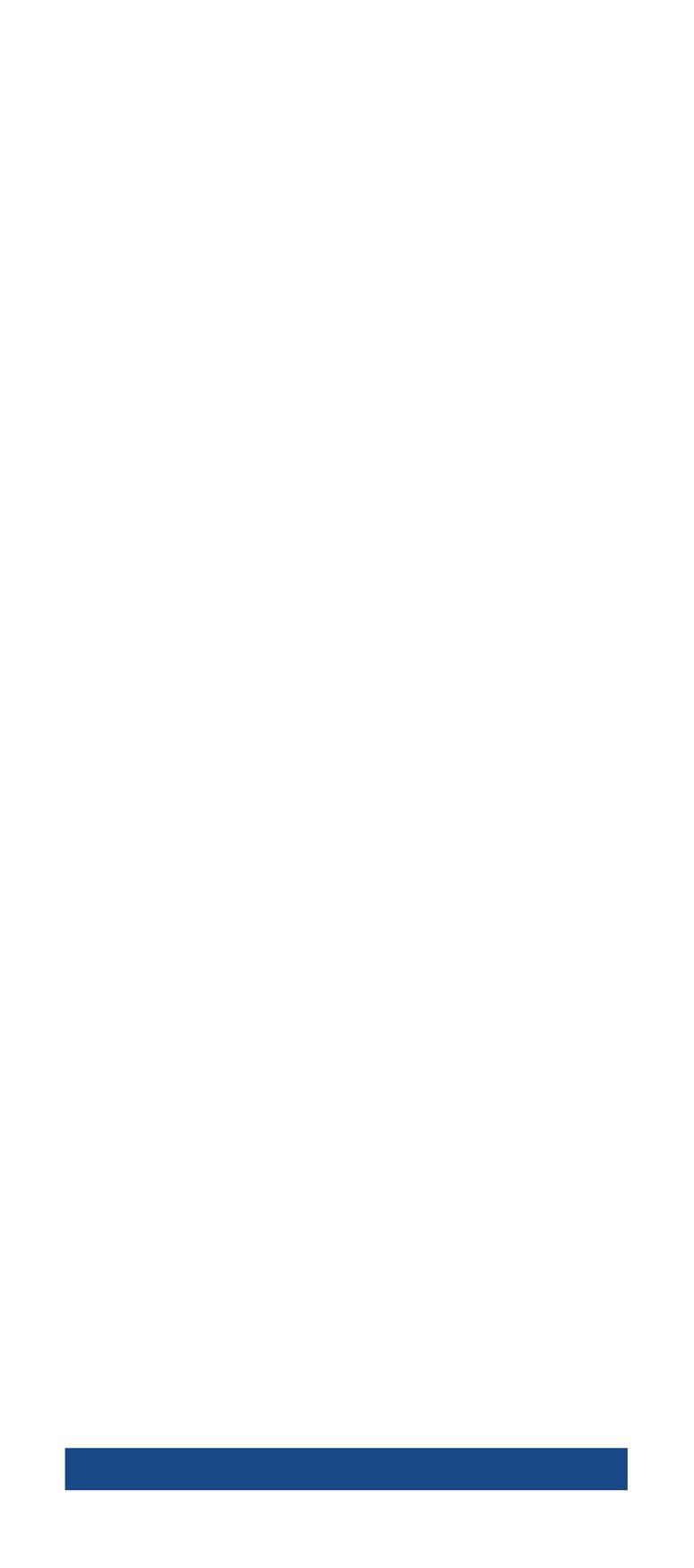
KANSAI HELIOS Austria ha assegnato ad
Anna Gruber il contributo di sponsorizzazione
KANSAI HELIOS Austria ha assegnato il suo contributo di sponsorizzazione ad Anna Gruber, che ha completato con successo la laurea in chimica applicata presso l’IMC Krems University.
Durante la cerimonia di laurea dell’IMC Fachhochschule Krems (l’Università di scienze applicate di Krems), KANSAI HELIOS Austria ha assegnato il suo contributo di sponsorizzazione ad Anna Gruber, che ha completato con successo il suo percorso di laurea in chimica applicata e ha mostrato un entusiasmo e un’iniziativa eccezionali durante la stesura della tesi. Il premio è stato consegnato da Hubert Culik – amministratore delegato di KANSAI HELIOS Austria – e dal Dr. Uwe Rinner, il direttore dell’Istituto.

KANSAI HELIOS Austria sostiene da molti anni il corso di laurea in lingua inglese in chimica applicata dell’università austriaca, poiché è gestito da professori provenienti sia dal settore accademico sia dall’industria chimica focalizzati su una formazione di base solida e orientata alla pratica,
fornendo così promettenti opportunità di lavoro per i neolaureati. La filiale con sede a Vienna (precedentemente nota come Rembrandtin Lack GmbH) è entrata a far parte del più ampio KANSAI PAINT Group nel 2017. I suoi portfolio principali includono moderni sistemi di protezione dalla corrosione e rivestimenti industriali innovativi per il segmento ACE e i veicoli ferroviari, nonché prodotti resistenti alle alte temperature e vernici per la segnaletica stradale. Attualmente conta 190 dipendenti, di cui più di un quarto nel reparto Ricerca & Sviluppo. Il premio permette di sostenere i futuri professionisti, che potrebbero entrare a far parte dell’azienda e aiutarla a continuare nella sua crescita.
Per maggiori informazioni: www.kansai-helios.at
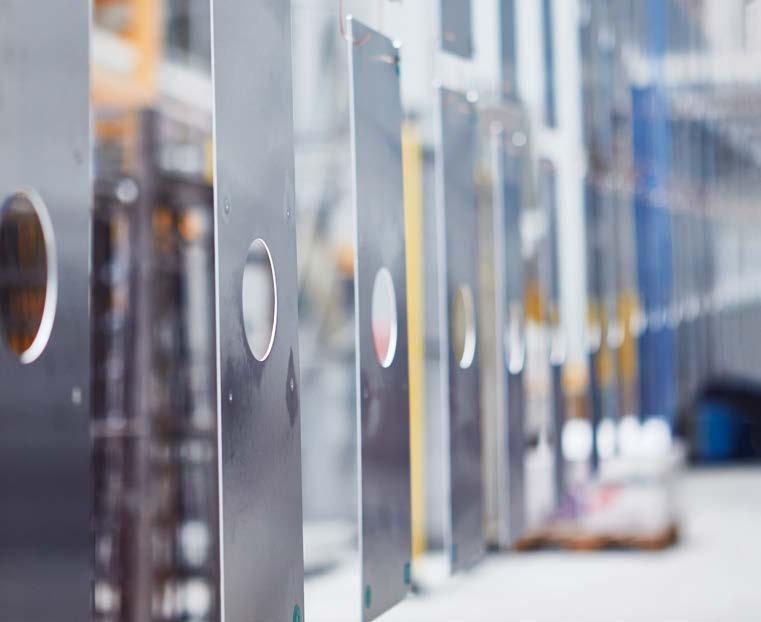
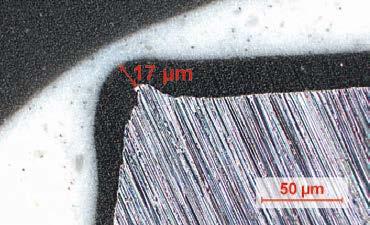

ADVANCEMENTS
Le nuove tecnologie dip-and-spin riducono il costo dei materiali e della manodopera nei processi di rivestimento dei metalli
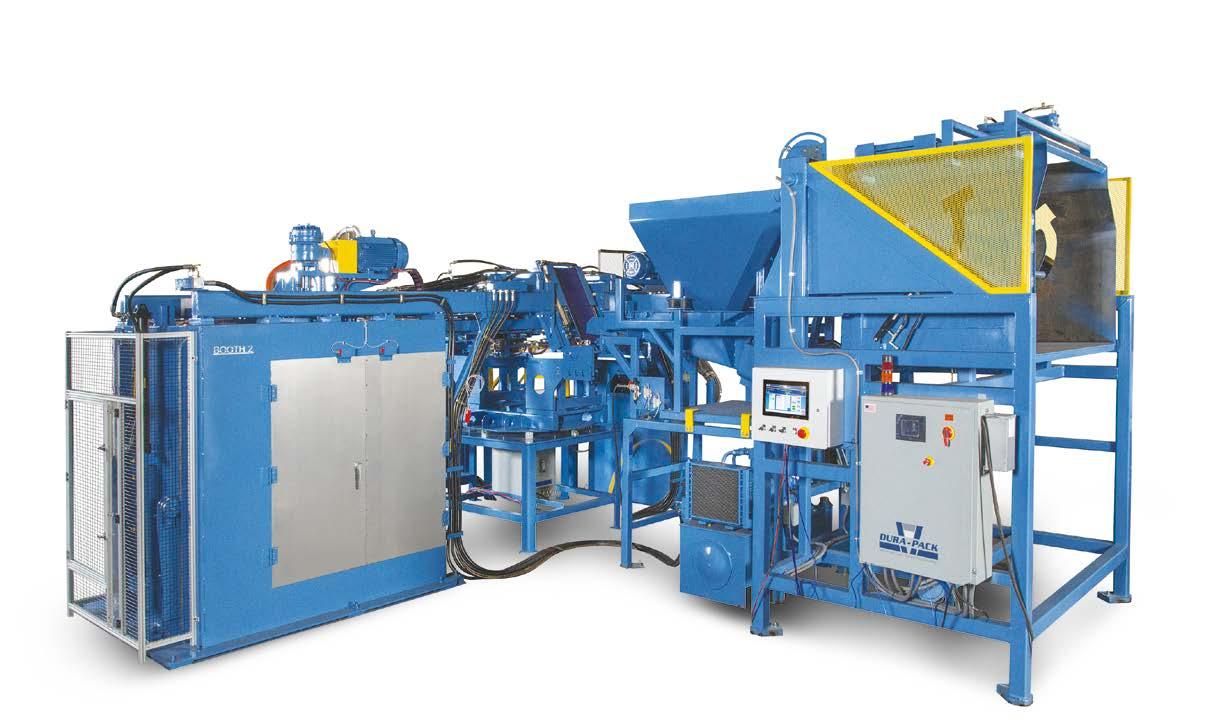
I recenti dissesti nella supply chain e la carenza di materiali hanno messo a dura prova ogni angolo del settore manifatturiero nordamericano e l’industria dei rivestimenti non fa eccezione. Dagli aumenti dei prezzi ai ritardi negli ordini, gli effetti della carenza di materiali non si possono sottovalutare. E come se ciò non bastasse, la persistente mancanza di manodopera continua a mettere alla prova la forza lavoro manifatturiera.
In un momento in cui ogni goccia di materiale verniciante e ogni ora di manodopera sono preziose, la riduzione degli sprechi e delle inefficienze operative è cruciale per il successo di qualsiasi processo di rivestimento e i nuovi sviluppi nelle tecnologie di verniciatura la rendono possibile.
Risparmio di manodopera, aumento della produttività, riduzione dei tempi di inattività
Secondo la National Association of Manufacturers, le aziende riferiscono che rispetto a qualche anno fa è più difficile del 36% trovare il giusto talento, nonostante l’alto tasso di disoccupazione. Si prevede che il divario
di competenze potrebbe portare a 2,1 milioni di posti di lavoro vacanti negli USA entro il 2030. Quando ogni lavoratore è prezioso, destinare più persone alla stessa mansione limita la capacità produttiva. I sistemi di rivestimento avanzati automatizzano l’intero processo – dal carico dei componenti fino al loro scarico – richiedendo una supervisione minima da parte dell’operatore. I sistemi si occupano dell’immersione dei manufatti, della rimozione di vernice in eccesso, dell’indurimento, del trasferimento da e verso l’unità di immersione e molto altro, e sono altamente programmabili per soddisfare le diverse esigenze di ogni processo. Ciò consente di “liberare” manodopera per dedicarla ad altre attività, combattendo così le difficoltà derivanti dalla carenza di forza lavoro. I sistemi automatizzati fanno risparmiare anche tempo. Sono dotati di sistemi di controllo touchscreen all’avanguardia, che semplificano l’utilizzo delle apparecchiature da parte degli operatori. Inoltre, tempi ciclo di immersione e centrifuga automatici di circa 2 minuti aiutano a mantenere costante l’attività. Nel caso in cui si verifichi un problema meccanico, la gestione dei guasti da remoto può accelerarne la risoluzione minimizzando i fermi macchina.
Ridurre il consumo di vernice
La Planetary Motion Technology introdotta recentemente da Forplan AG ha notevolmente migliorato il processo di rimozione della vernice in eccesso dai manufatti immersi. Il processo inizia con una pesatura automatica per garantire un carico coerente, con ogni lotto composto da due cesti di peso uguale. I due cesti insieme vengono immersi nella vernice inclinando e ruotando contemporaneamente, per garantire che tutti i componenti siano rivestiti. Dopo l’immersione dei manufatti, i cesti ruotano su loro stessi ad alta velocità e in modo planetario. Questa caratteristica garantisce un rivestimento uniforme e assicura che i componenti si muovano e si riorientino da soli per ottenere il miglior spessore possibile del rivestimento. La vernice in eccesso viene recuperata e reimmessa nella vasca di immersione per il riutilizzo. La tecnologia planetaria ha dimostrato di ridurre il consumo di materiale fino al 30%.
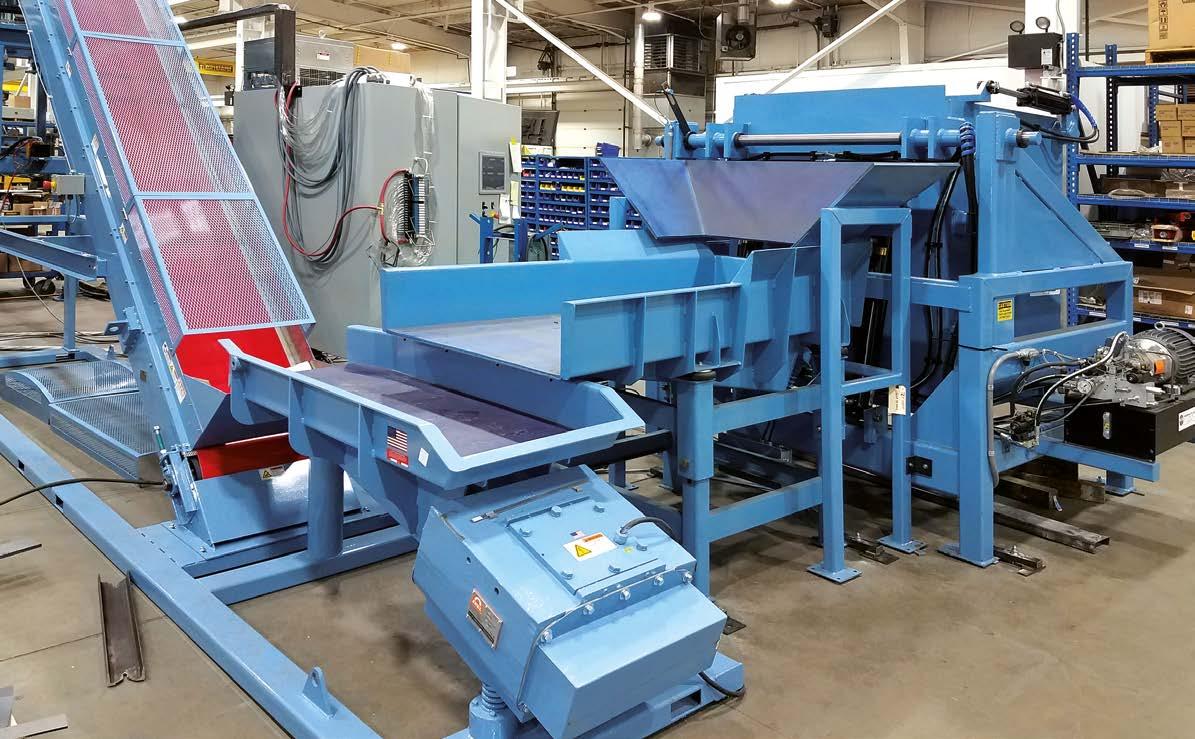
Risparmio di spazio e minore impronta di carbonio
Grazie a un migliorato e innovativo processo di indurimento, la nuova apparecchiatura richiede il 35% in meno di spazio rispetto ai tradizionali
sistemi dip-and-spin e può far risparmiare 285 t di CO2 rispetto alle comuni apparecchiature. Il ROI tipico per questo tipo di sistemi è inferiore a un anno.
Conclusioni
La domanda nel settore dei rivestimenti è in piena espansione. Secondo il “Paints and Coatings Global Market Report 2021”, si prevede che il mercato globale delle vernici e dei rivestimenti raggiungerà i 258, 45 miliardi di dollari nel 2025, con un tasso di crescita composto annuo del 4%. Con l’aumento della domanda è possibile che aumenti anche il costo dei materiali. Fortunatamente, i sistemi di rivestimento innovativi possono essere la chiave per risparmiare tempo, manodopera e materiali. I sistemi avanzati non solo aiutano ad affrontare le sfide future poste dalla turbolenza economica, bensì aiutano anche a massimizzare la crescita. Per fare il primo passo verso una produzione stabile e più sostenibile, è possibile consultare un esperto del settore o un produttore di fiducia per conoscere i benefici economici e ambientali delle nuove tecnologie planetarie dip-and-spin.
L’autore
Tim Hanna è Vicepresidente Sviluppo Aziendale e Direttore Vendite di STC DipSpin/PRAB. Grazie a un’esperienza trentennale nel settore, Tim ha una conoscenza approfondita del rivestimento dei componenti e delle esigenze dei clienti.
STC Dip Spin
STC Dip Spin ha costruito la sua prima macchina di rivestimento a immersione nel 1965. Quella macchina è in funzione ancora oggi. Da quel giorno STC lavora per creare le macchine di verniciatura più affidabili possibili. Nel 2020 STC ha collaborato con Forplan AG di Brugg (Svizzera), che offre una varietà di sistemi di verniciatura per componenti prodotti in serie – per manufatti sia sfusi che posizionati. Indipendentemente dal settore o dalle esigenze operative, STC offre una vasta gamma di apparecchiature affidabili, supportate da garanzie complete e da una competenza approfondita, e personalizzate per soddisfare le esigenze del cliente in ogni fase del processo.
I cesti ruotano su sé stessi per “centrifugare” i componenti immersi.
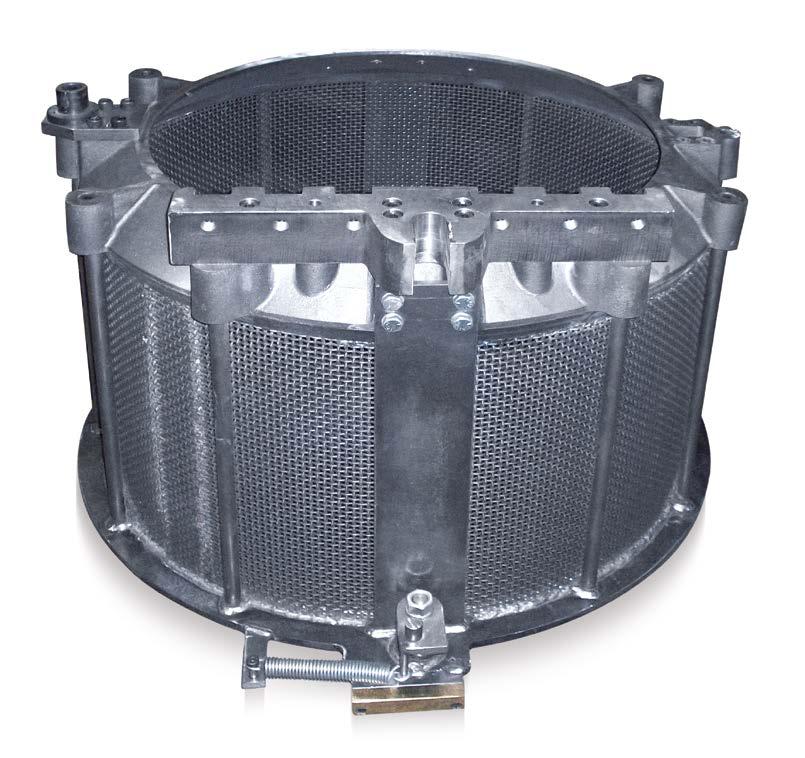
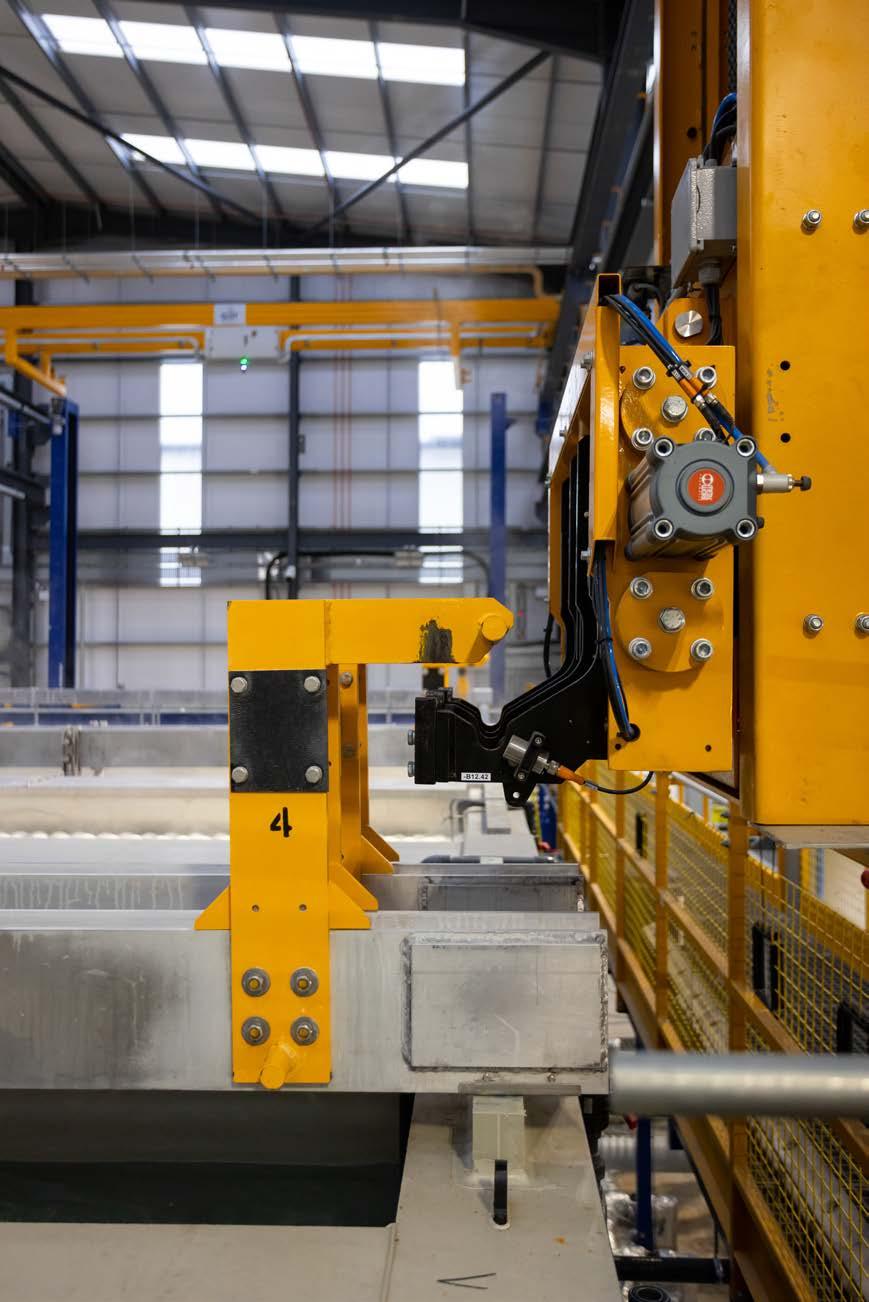
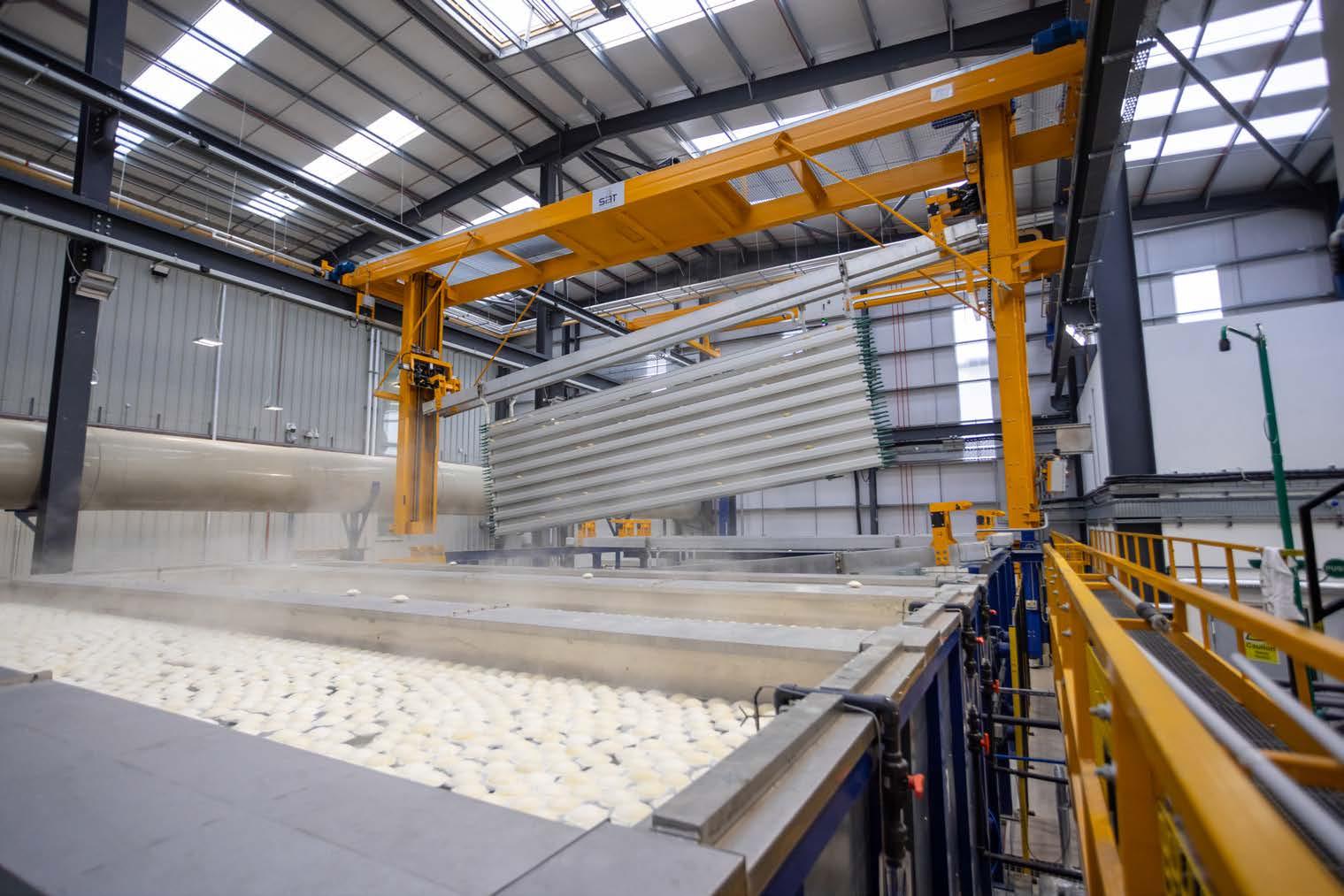

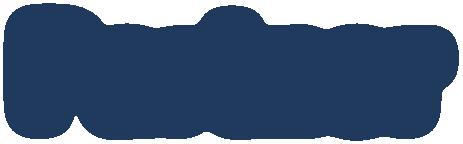
Ricerca, tecnologia e innovazione per un futuro industriale sostenibile
Alessandro Soba Verind S.p.A. – MilanoUno degli obiettivi più importanti per costruire le basi di un futuro industriale più moderno e sostenibile è consolidare il rapporto tra industria e università: il seminario svoltosi presso il Politecnico di Milano, con il contributo di Verind S.p.a. e PPG Srl, per il corso universitario “Advanced Organic Coatings” è la risposta giusta a questo scopo.
Con i mesi di maggio e giugno si è concluso il secondo semestre di lezioni presso il Politecnico di Milano, la più importante università italiana per la formazione tecnico-scientifica e tra i primi quindici atenei nella classifica di QS World University Rankings nella categoria Engineering & Technology1. Gli studenti del Corso di Studi per la Laurea Magistrale in Ingegneria dei Materiali e delle Nanotecnologie, volto a formare nuovi tecnici con un ampio spettro di conoscenze nei settori della produzione, trasformazione ed applicazioni dei materiali e in quello più innovativo delle nanotecnologie, hanno avuto l’opportunità di incontrare le aziende del settore della finitura superficiale.
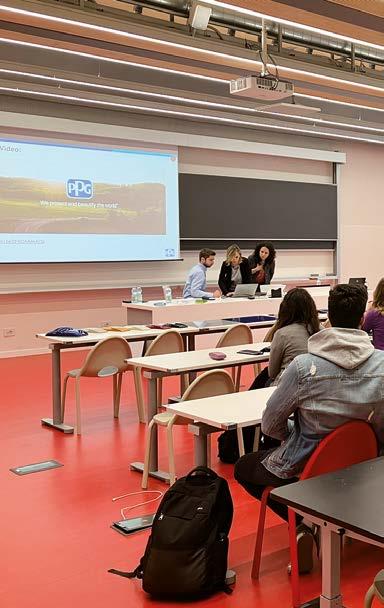
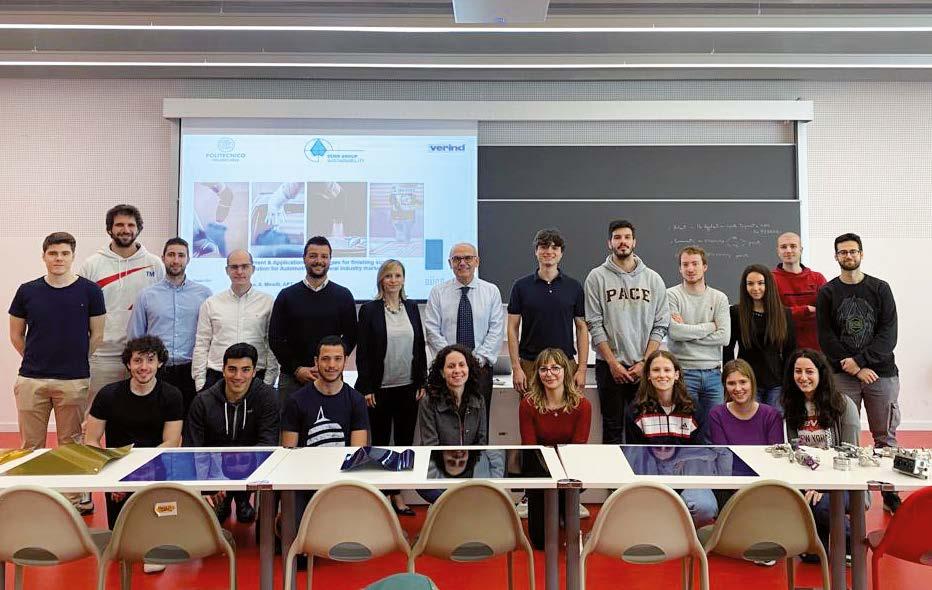
1 https://www.topuniversities.com/university-rankings/university-subject-rankings/2022/engineering-technology
Sono stati esaminati concept industriali per il settore automotive e industria relativi a:
• produzione dei prodotti vernicianti ed esame della qualità del film applicato, a cura di PPG
• tecnologie ed apparecchiature per applicare i prodotti vernicianti, a cura di Verind.
Il seminario tenuto in inglese da Alessandro Soba, di Verind S.p.A. (gruppo Dürr) e da Francesca Di Costanzo di PPG S.p.A (Quattordio, Alessandria) per il corso “Advanced Organic Coatings” ha rappresentato un esempio concreto dell’interazione tra studenti e aziende.
Gli studenti, guidati da Raffaella Suriano, professoressa associata del Dipartimento di Chimica, Materiali e Ingegneria Chimica “Giulio Natta”
del Politecnico, sono risultati particolarmente coinvolti e hanno posto numerose domande sia durante sia alla fine della lezione. “Sono state illustrate le tecnologie applicative Durr più attuali – ha spiegato Alessandro Soba - come il dispositivo elettrostatico EcoBell, il sistema per il dosaggio elettronico EcoDose 2k a mezzo di flussimetri massici Coriolis per vernici 2k e 3k, i sistemi PIG e Robot Process Arm, tutte soluzioni atte a ottenere risparmio nei consumi ed efficienza nel processo di verniciatura. Grazie ai video che mostravano linee e sistemi di verniciatura e rivestimento superficiale nel settore automotive e General Industry e alla presentazione in aula di apparecchiature specifiche per la verniciatura automatica e manuale, sono state affrontate tematiche attuali legate alle eco-tecnologie applicative in ottica di sostenibilità, efficienza e digitalizzazione di un processo di verniciatura”.
“In aula è stata presentata l’azienda PPG, leader globale nelle vernici, nei rivestimenti e nei materiali speciali” – ha dichiarato Francesca Di Costanzo, PPG Color Science Application and Quality Control Manager – “che, tramite i suoi due segmenti industriali Performance e Industrial Coatings, ha come finalità quella di ‘Proteggere e abbellire il mondo’. Nella mission aziendale 3 grandi drivers guidano i business: Innovazione, Sostenibilità e Colore. La tematica approfondita durante la sessione con gli studenti ha riguardato il Business Automotive OEM con tutte le linee prodotto comprese nel ciclo della verniciatura di una scocca, le relative funzionalità con un focus principale sulla caratteristica che le contraddistingue: il colore”. “Grazie alle interazioni continue in aula – ha proseguito Di
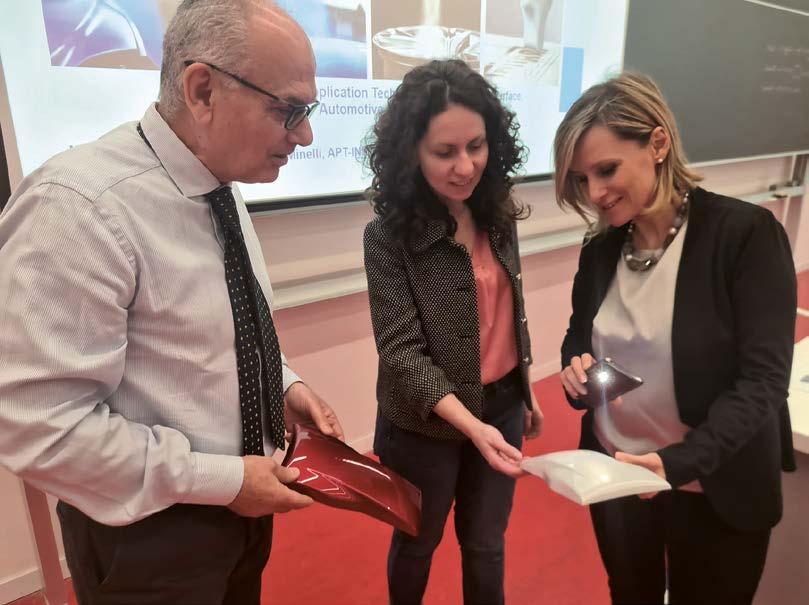
Costanzo - gli studenti insieme ai rappresentanti del Quality Control Lab dello stabilimento PPG di Quattordio, hanno potuto valutare e toccare con mano la parte pratica in cui sono stati riprodotti alcuni difetti, tipici della verniciatura (crateri, pinholing, sagging), o caratteristiche critiche che vengono testate in fase di controllo della qualità”.
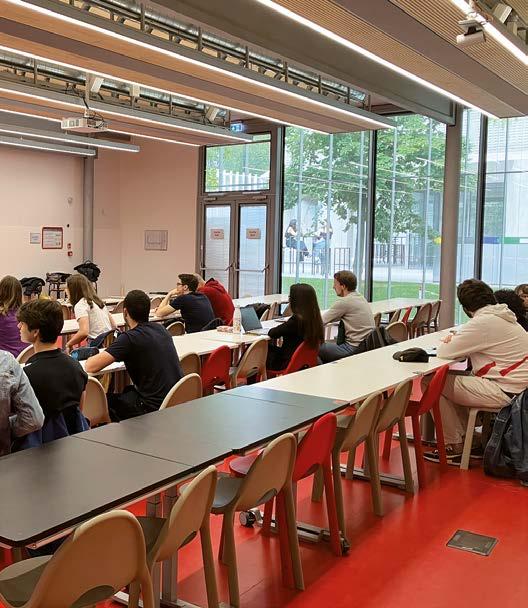
“L’incontro tra università e industria – ha concluso Raffaella Suriano - è stato possibile grazie alla collaborazione con PoliEfun, un’associazione del Politecnico di Milano che promuove la cultura d’impresa nel settore dei trattamenti superficiali2. PoliEfun incoraggia, infatti, il coinvolgimento delle figure industriali con il mondo accademico anche attraverso master in presenza e online come ISM10 (Industrial Short Master), giunto alla sua decima edizione, e TST2022, la conferenza digitale che l’anno scorso ha trattato argomenti come l’economia circolare e lo sviluppo di rivestimenti sostenibili bio-derivati, ottenuti riciclando gli scarti agricoli industriali come le bucce di pomodoro.
Grazie anche al supporto di PoliEfun, della Scuola di Ingegneria Industriale e dell’Informazione e del corso di Laurea in Ingegneria dei Materiali e Nanotecnologie, il corso di Advanced Organic Coatings nell’anno accademico 2022-23 ha dedicato il 40% delle ore di lezione alla didattica laboratoriale, in modo da corroborare ulteriormente le competenze e la preparazione tecnico-scientifica dei futuri ingegneri con esperienze pratiche e prove sperimentali”.
2 https://www.poliefun.com/
I criteri ESG: da valore aggiunto a requisito indispensabile per il mercato
Manuela Casali, UCIF – Unione Costruttori Impianti di Finitura, Milano, Italia info@ucif.netL’interesse verso ESG, acronimo per Environmental, Social e Governance, non è cosa recente. I temi della trasformazione ambientale e sociale sono da tempo al centro dell’interesse di aziende ed organizzazioni. Nel 2005 già si parlava di ESG, ma solo recentemente abbiamo a disposizione una grande abbondanza di dati che ci consentono di poter stilare report e statistiche. Quello che è cambiato in modo sostanziale è la comunicazione del rapporto che le aziende oggi hanno con i criteri ESG e la loro valorizzazione, fino a farne un fenomeno non solo reputazionale, ma anche e soprattutto commerciale. Ci si è resi conto che un numero sempre maggiore di consumatori indirizzano le proprie scelte secondo criteri etici: di qui l’immediata risposta in termini di monitoraggio e definizione di parametri che concorrono a creare vere e proprie classifiche delle organizzazioni più virtuose. E’ facile immaginare come da un parametro inizialmente utilizzato da grandi aziende che utilizzavano i parametri ESG per essere più attrattivi sul mercato ci si stia spostando sempre di più anche verso organizzazioni più piccole che utilizzano gli stessi criteri e parametri a testimoniare il proprio impegno ambientale, sociale ed etico.
A che punto siamo come comparto meccanico?
Sia che si tratti di grandi aziende sia che ci si riferisca, invece, ad aziende di dimensioni più contenute, oggi è sempre più diffusa la convinzione che le imprese in grado di produrre risultati positivi per ambiente e società siano anche più performanti sul lungo periodo nel raggiungere migliori risultati di business.
Sotto la lettera E di Environment si racchiudono i criteri e i valori ambientali e le aziende vengono valutate in base al loro comportamento nei confronti dell’ambiente: significa programmare investimenti e piani futuri nell’ottica della salvaguardia ambientale, sia da un punto di vista di infrastrutture aziendali sia da quello di progettazione di impianti sempre più green.
La lettera S identifica i valori determinati dall’impatto sociale, esaminando non solo i rapporti con i dipendenti, collaboratori, fornitori e clienti, ma in generale anche con la relazione che si stabilisce con il territorio in cui si opera, la comunità e le persone.
La G di Governance infine riguarda un tema difficile, quale quello della gestione aziendale – per tradizione in Italia ancora vista come qualcosa che va tenuta “riservata” e non comunicata all’esterno, se non per gli obblighi imposti dalla legge. I temi sotto osservazione per quanto attiene la Governance sono, per esempio, quelli relativi alla retribuzione dei dirigenti, il rispetto dei diritti degli azionisti e la trasparenza delle decisioni.
Stiamo parlando di temi nuovi? Certamente no, in passato abbiamo avuto già quelli che abbiamo chiamato “investimenti sostenibili”. La grossa differenza tra investimenti guidati da criteri ESG e investimenti sostenibili sta nella misurabilità dei primi: ogni sforzo fatto, ogni azione prodotta deve avere un ritorno positivo e misurabile dal punto di vista economico da parte degli investitori e non solo – oggi si parla sempre di più di un ritorno per la collettività e l’ambiente.
In più, i risultati prodotti, oltre ad essere misurabili, devono essere facilmente comprensibili e chiari. Gli effetti sull’ambiente esterno e sulle politiche sociali di un’azienda o un’organizzazione che lavora secondo i criteri ESG devono produrre risultati evidenti, portando concretamente migliorie e dati a supporto delle azioni intraprese. Nel medio periodo la raccolta di tutti questi dati porterà a stilare delle vere e proprie classifiche dove le aziende verranno messe a confronto su quanto dichiarato e quanto davvero eseguito con dati alla mano.
La convinzione che si va affermando sempre più è che un’azienda virtuosa, in grado di produrre risultati positivi per ambiente e società sarà anche un’organizzazione in grado di raggiungere ottimi risultati di business nel lungo periodo.

Le novità e gli sviluppi nel settore dell’alluminio al
12°
congresso mondiale
Aluminium Two Thousand
La prossima edizione di Aluminium Two Thousand organizzata in collaborazione con ICEB World Congress si svolgerà a Bologna presso il Royal Hotel Carlton dal 19 al 23 settembre 2023.


Più di 80 relatori “Aluspecialisti” altamente qualificati provenienti da aziende, università e associazioni di oltre 30 Paesi si sono dati appuntamento - come ormai avviene ogni due anni dal 1990 - per presentare a un pubblico specializzato e internazionale le tecnologie e le applicazioni più innovative nel campo dell’alluminio.
Aluminium Two Thousand è diventato un momento d’incontro insostituibile per tutti gli operatori del settore dell’alluminio (in materia di estrusione, fonderia, fusione, finitura e trattamento delle acque reflue).
Ma com’è nato? Lo chiediamo al suo ideatore, Walter Dalla Barba, CEO di Italtecno Srl (Fiorano Modenese), presidente di Interall e di Aluminium Two Thousand World Congress.
Walter Dalla Barba: “Negli anni Ottanta, partecipando ai congressi internazionali dedicati ai trattamenti superficiali e alle tecniche di estrusione, mi sono chiesto perché all’alluminio fosse riservato soltanto un posto fra i tanti, nonostante sia il terzo elemento dopo l’ossigeno e il silicio e il metallo più utilizzato, dopo il ferro, per la fabbricazione di
milioni di prodotti. Così, verso la fine del 1988, di ritorno dal congresso di Parigi Interfinish, parlando con un giornalista che collaborava con Italtecno da tanti anni, Velello Muratori, e con un altro mio socio, abbiamo deciso di organizzare noi un congresso che rendesse onore a questo nobile metallo: abbiamo stabilito la data della prima edizione, marzo 1990, e il titolo, Aluminium Two Thousand, visto che andavamo verso gli anni Duemila. Non potevamo sapere se sarebbero intervenute dieci o cento persone a Modena all’Hotel Raffaello, invece ne arrivarono circa duecento, nonostante qualche arabo avesse deciso di non venire perché nella nostra città “non c’era un hotel a cinque stelle”. Questo però mi fece capire che avevamo attirato un target di alto livello e che quindi il nostro congresso avrebbe dovuto rispondere alle aspettative, convocando manager e imprenditori delle più importanti industrie del settore in Italia e negli altri paesi produttori. E abbiamo avuto successo non solo dal punto di vista scientifico, ma anche per le attività collaterali che abbiamo organizzato: per trasferirci nel nord ovest della Sardegna, dove avremmo trascorso due giorni e due notti, avevamo prenotato
un aereo della Meridiana che abbiamo riempito subito, tanto da dover lasciare a casa alcune persone. E, dal 1990, tutte le iniziative che abbiamo offerto – dalla cena di gala alle gite e alle attività per accompagnatrici e accompagnatori, come la cooking class, che piace molto agli americani – sono state sempre più seguite e richieste”.
Chi sono i relatori del congresso?
Walter Dalla Barba: “A seconda degli argomenti, abbiamo convocato tecnici di aziende di estrusione, di anodizzazione, di verniciatura e di fonderia di alluminio, ma anche economisti, come il professor Cesare Garzia della Bocconi, che esporranno le loro analisi sull’andamento e le prospettive sia del settore dell’alluminio sia della congiuntura economica generale. Si parlerà dei differenti ambiti di applicazione degli estrusi, di problematiche delle leghe usate per i vari settori e dell’impiego dell’alluminio in architettura, nell’automotive, nei trasporti, nella bigiotteria e nell’arredamento. Tra l’altro al Salone del mobile abbiamo visto quanto l’alluminio stia diventando di tendenza nel design dei mobili sia in casa sia in ufficio. Sarà dato ampio spazio alle tecnologie innovative, in combinazione con la ricerca universitaria”.
A proposito, voi siete riusciti a fare incontrare università e industria attraverso la sinergia con l’International Conference on Extrusion and Benchmark (ICEB), il più grande evento in Europa legato ai più recenti sviluppi sulla tecnologia di estrusione e alla sua analisi tramite simulazione FEM. Quando
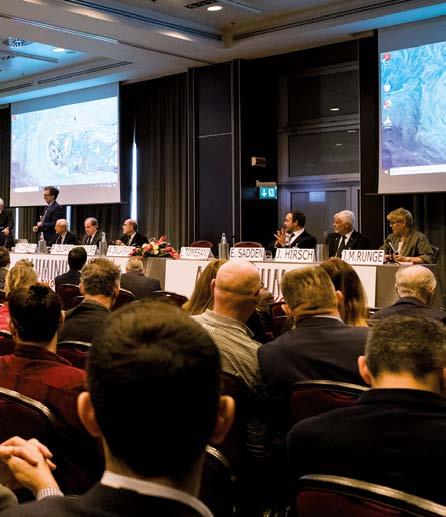
è incominciata la collaborazione con l’ICEB?
Walter Dalla Barba: “Tutto è nato nel 2003, quando alcuni ricercatori del Dipartimento di Ingegneria dell’Università di Bologna sono venuti al nostro congresso, che quell’anno si svolgeva a Roma. Quindi, a partire dalla 6° edizione, ospitiamo l’International Conference on Extrusion and Benchmark, un appuntamento a cui intervengono ricercatori di vari paesi, che prima si svolgeva in alternanza fra Bologna e Berlino. Per questo sono fiero di avere contribuito non solo a favorire il tanto auspicato scambio tra università e industria, in un contesto costruttivo e in un clima di amicizia fra ambiti differenti, ma anche di avere portato a Bologna un’eccellenza per gli studi sull’alluminio”.
Qual è il programma quest’anno?
Walter Dalla Barba: “Si terranno tre sessioni parallele per tre giorni interi di approfondimento di tutti gli argomenti nei dettagli, i cui papers saranno esaminati dal comitato scientifico del convegno, al fine di selezionare gli studi e le ricerche più innovativi, le più recenti applicazioni industriali e i casi di studio più interessanti. Inoltre, per assicurare un piacevole soggiorno a Bologna, si terranno eventi d’intrattenimento tutte le sere, una cena di gala, tour con accompagnatori, tour tecnici e un bellissimo tour sociale finale in città storiche e attraenti nei dintorni di Bologna, fra cui Ravenna, capitale dell’Impero Romano dal 408 al 476”.
Per maggiori informazioni: www.aluminium2000.com
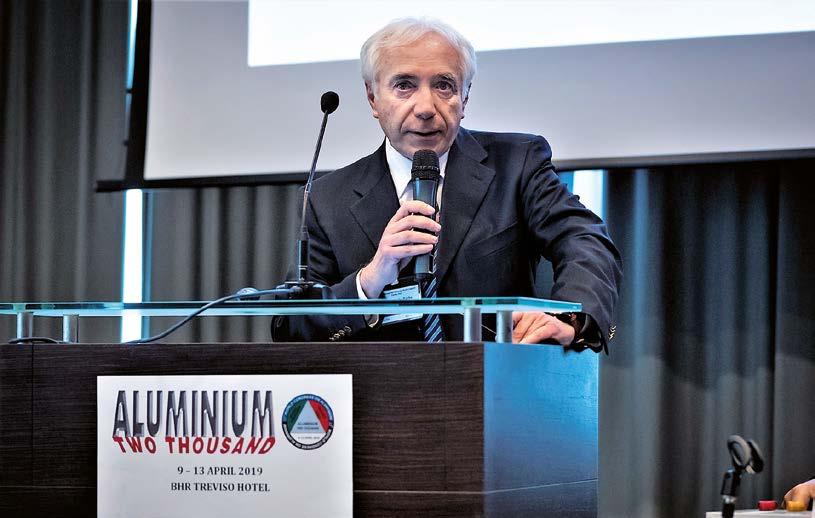
Chicago – Una città speciale per FABTECH
La prossima edizione di FABTECH si terrà a Chicago (IL, Stati Uniti) dall’11 al 14 settembre.
un’ampia gamma di argomenti tecnici per tutti i professionisti della finitura. “È incredibile come FINISHING Pavilion & Conference sia cresciuta da quando siamo diventati parte di FABTECH nel 2010. Lo sviluppo è stato fenomenale dal momento che CCAI è divenuta partner di FABTECH Finishing e siamo contenti che FINISHING Pavilion & Conference sia destinata a superare i nostri numeri precedenti alla pandemia, date le elevate richieste di registrazione all’evento”, ha dichiarato Anna Goyer, direttore esecutivo di CCAI. La formazione e l’educazione sono sempre state al primo posto nella missione di CCAI. Il programma della conferenza al FABTECH è la piattaforma perfetta che permette a CCAI di mostrare l’esperienza e la conoscenza dei membri e informare coloro che sono nuovi nel settore della finitura o chi desidera affinare le proprie capacità e acquisire nuove conoscenze. La traccia della conferenza FINISHING di CCAI comprende 27 sessioni che includono un ampio spettro di presentazioni tecniche, da quelle basilari alle quelle avanzate, affrontando argomenti di interesse per chiunque sia coinvolto nel settore della finitura. Vi sarà un altro highlight durante l’evento offerto nuovamente da CCAI che celebra la sesta edizione del FAB to FINISH Production Experience. Il programma offre ai partecipanti l’opportunità di vedere in prima persona la produzione di un manufatto, dalla fabbricazione alla fase di finitura, che prevede inizialmente il taglio laser e la piegatura di un prodotto campione e, successivamente, segue un percorso di produzione presso gli stand degli espositori aderenti al CCAI Corporate Member dove sperimenteranno il lavaggio, la verniciatura a polvere e la polimerizzazione del pezzo. Alcuni percorsi presenteranno la galvanica selettiva, mentre altri comprenderanno la misurazione dello spessore del rivestimento. Ogni anno questo programma cresce di popolarità dato il grande interesse mostrato dagli espositori e dai partecipanti.
Il programma della conferenza e gli espositori di Finishing a FABTECH 2023
FABTECH ritorna al McCormick Place di Chicago (IL) dall’11 al 14 settembre. Non c’è opportunità migliore per esplorare le ultime tecnologie, condividere conoscenze, formare una rete con i colleghi del settore e ottenere approfondimenti sui trend di finitura e di produzione che vi aiuteranno a prepararvi per ciò che vi aspetta. Tutto il necessario sulle operazioni di finitura è a vostra completa disposizione in un unico posto. A ridosso del quattordicesimo anniversario come partner di FABTECH, il FINISHING Pavilion and Conference di CCAI continua a crescere, offrire grandi innovazioni e importanti informazioni su tutti gli aspetti della finitura superficiale industriale. FABTECH fornisce una vastità di soluzioni tecnologiche nonché presentazioni guidate da esperti che coprono
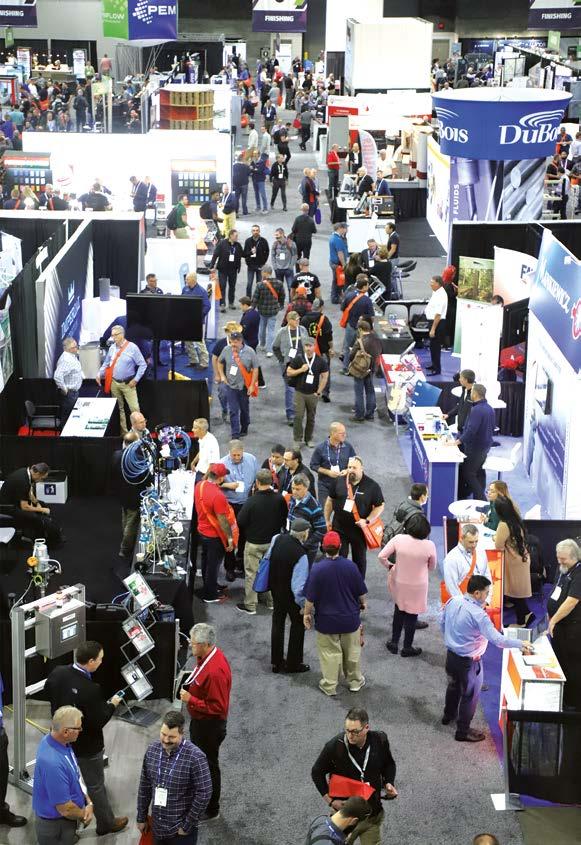
Prendete del tempo per recensire l’attuale programma della conferenza FINISHING e la sua lista degli espositori sul sito dell’evento. Per visualizzare le sessioni della conferenza, selezionare il tasto “Conference” in cima alla pagina principale e scorrere in basso fino a SESSION DETAILS. Assicuratevi di aggiungere il codice promozionale FINISHING 30 per risparmiare il 30% sulle vostre sessioni di finitura. Potete visualizzare la lista completa degli espositori di FINISHING visitando il sito web o selezionando la Exhibitor Directory sul sito di FABTECH per visualizzarne la planimetria e l’elenco. Il padiglione e le sessioni della conferenza sono situati presso l’edificio Lakeside Center.
Per maggiori informazioni: www.fabtechexpo.com
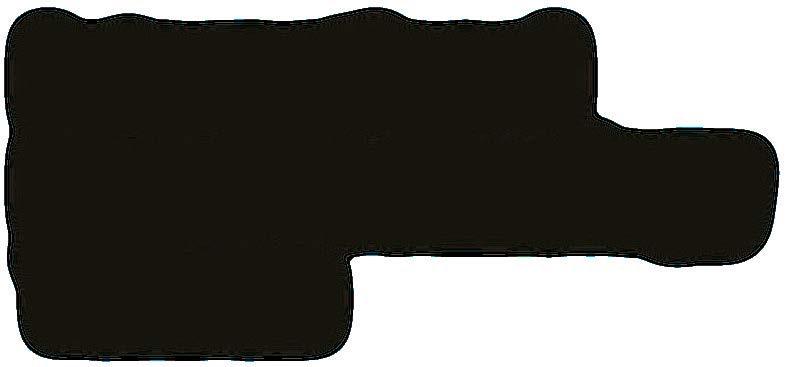
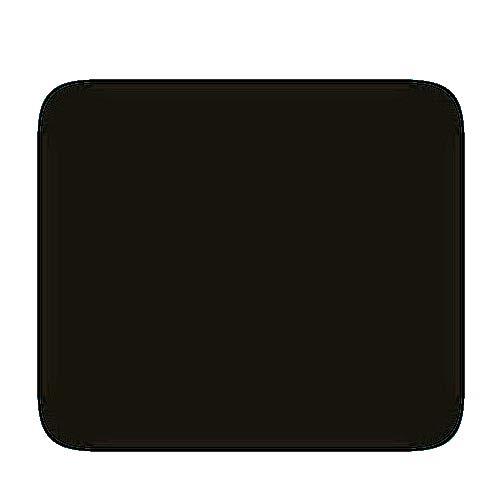

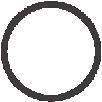

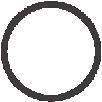

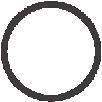

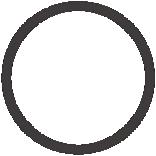
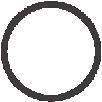

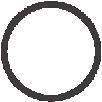
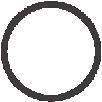
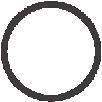

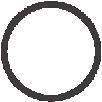
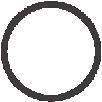
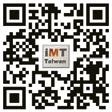
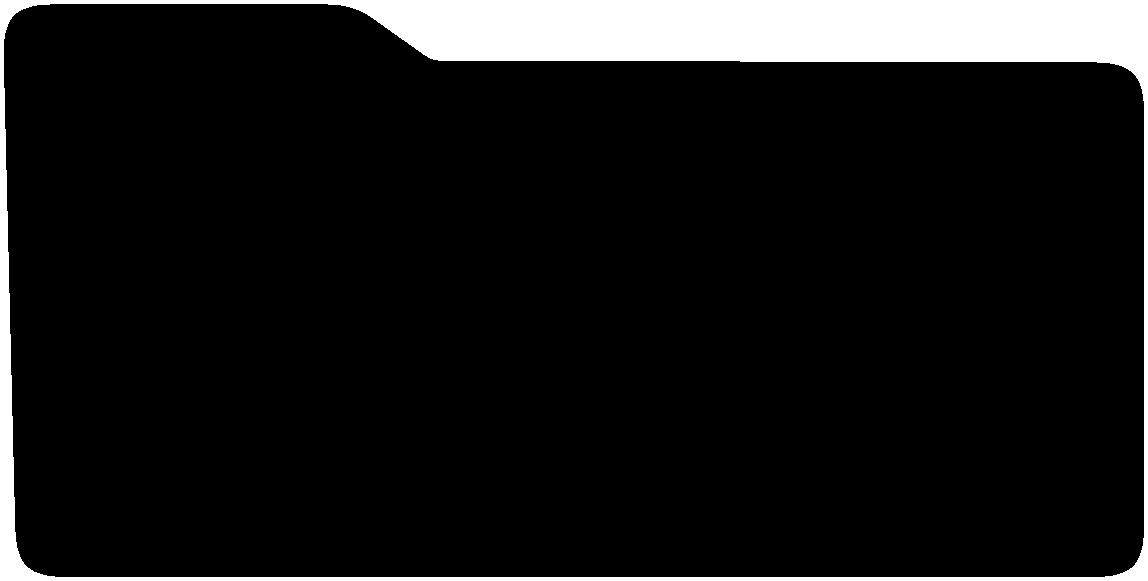
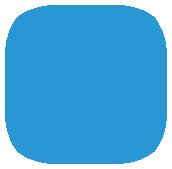



Tendenze attuali e future dei rivestimenti organici nel convegno organizzato presso l’Università di Trento
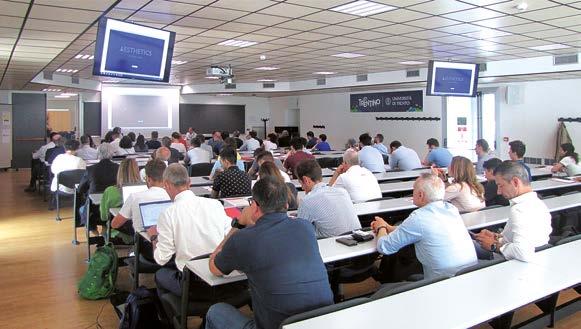
Il futuro dei rivestimenti organici in un convegno che ha riunito produttori e applicatori di vernici e il mondo universitario: il Dipartimento di Ingegneria Industriale dell’Università di Trento conferma il suo ruolo strategico nell’attività di ricerca e divulgazione scientifica delle informazioni più attuali a supporto dell’industria.
La prima sessione della giornata è stata inaugurata da Lorenzo Soldavini di PPG Italia (Milano), che ha presentato la relazione dal titolo “Vernici in polvere ad alte prestazioni per la protezione dalla corrosione”.
Maria Alba Fusco di Liberty Magona (Piombino, Livorno) ha proseguito la serie degli interventi con uno dal titolo “Reinventare l’acciaio per un futuro sostenibile”, sottolineando l’importanza dell’acciaio come scelta sostenibile, grazie alla sua possibilità di riciclo al 100%, e della ricerca e sviluppo di soluzioni per il risparmio energetico come quella studiata insieme al Laboratorio per mantenere il tetto degli edifici freddo con il rivestimento di un coil speciale.
“Applicazioni alternative per cataforesi” è il titolo della relazione di Gian Luca Gazzola di Arsonsisi (Lainate, Milano).
Lo scorso 20 giugno presso il Dipartimento di Ingegneria Industriale dell’Università di Trento si è svolto il convegno “Rivestimenti organici, la soluzione per la protezione e l’estetica: trend e novità nel settore”.
Moderato dal Professor Stefano Rossi, responsabile del Laboratorio Rivestimenti & anti Corrosione Industriale, che collabora da oltre 30 anni con aziende e centri di ricerca a livello nazionale e internazionale, il convegno è stato organizzato per fare il punto sulla situazione dei rivestimenti organici e per capire e discutere con i rappresentanti delle aziende partecipanti quali siano le sfide più complesse che questo settore dovrà affrontare in futuro.
“Protezione e resa estetica non bastano più – ha affermato Rossi durante il suo discorso introduttivo – “oggi ai rivestimenti si richiede altro: ridurre l’impatto ambientale trasformandosi in un prodotto sempre più green, utilizzare materie prime da fonti naturali o di riciclo, aggiungere proprietà diverse dalla semplice protezione dalla corrosione indirizzandosi verso i cosiddetti “smart coatings”, creare un’infinita possibilità di effetti fra colore e texture fino a comprendere non solo il senso della vista ma anche quello del tatto. Per utilizzare al meglio una vernice, non solo per motivi protettivi ma anche per quelli estetico-percettivi, risulta necessario conoscere le infinite possibilità che questo tipo di rivestimento ci offre. Ecco il motivo per cui il nostro Laboratorio ha sentito la necessità di organizzare questa giornata insieme ad alcuni partner industriali.”
La prima sessione del convegno si è quindi conclusa con la relazione di Giovanni Ciafrè di Renner Italia (Minerbio, Bologna): “Le vernici per legno: una questione di estetica, protezione e applicazione”.
Dopo la pausa caffè e la visita agli stand degli sponsor dell’evento di CO.FO.ME.GRA, Liberty Magona, Nikon, Merck e Pintarelli Verniciature, la seconda parte del convegno è proseguita con la relazione “Quale evoluzione ci possiamo aspettare per i rivestimenti classici per edilizia e anticorrosione?” di Gianfranco Di Tanna e Luciano Pau dell’Associazione AITIVA di Piacenza.
Tiziana Pintarelli di Pintarelli Verniciature (Lavis, Trento) ha sottolineato alcune problematiche dell’attività quotidiana del terzista di verniciatura nell’intervento dal titolo “Le vernici, il punto di vista dell’applicatore”. Prima della pausa pranzo, hanno concluso i lavori le due relazioni di Stefano Corrado di Merck (Milano) e di Francesca Valan di Valan Studio (Milano) con i titoli rispettivi di “Pigmenti e colori in movimento, un breve viaggio tra emozione e innovazione” e “Sostenibilità cromatica: i colori senza tempo”.
Nel pomeriggio per i relatori e partecipanti è stato possibile visitare i laboratori del Dipartimento attrezzati con le apparecchiature più avanzate per la caratterizzazione elettrochimica di superfici e rivestimenti, per l’invecchiamento accelerato, la resistenza all’abrasione delle superfici e la caratterizzazione microstrutturale.
Per maggiori informazioni: https://rb.gy/kv3uv
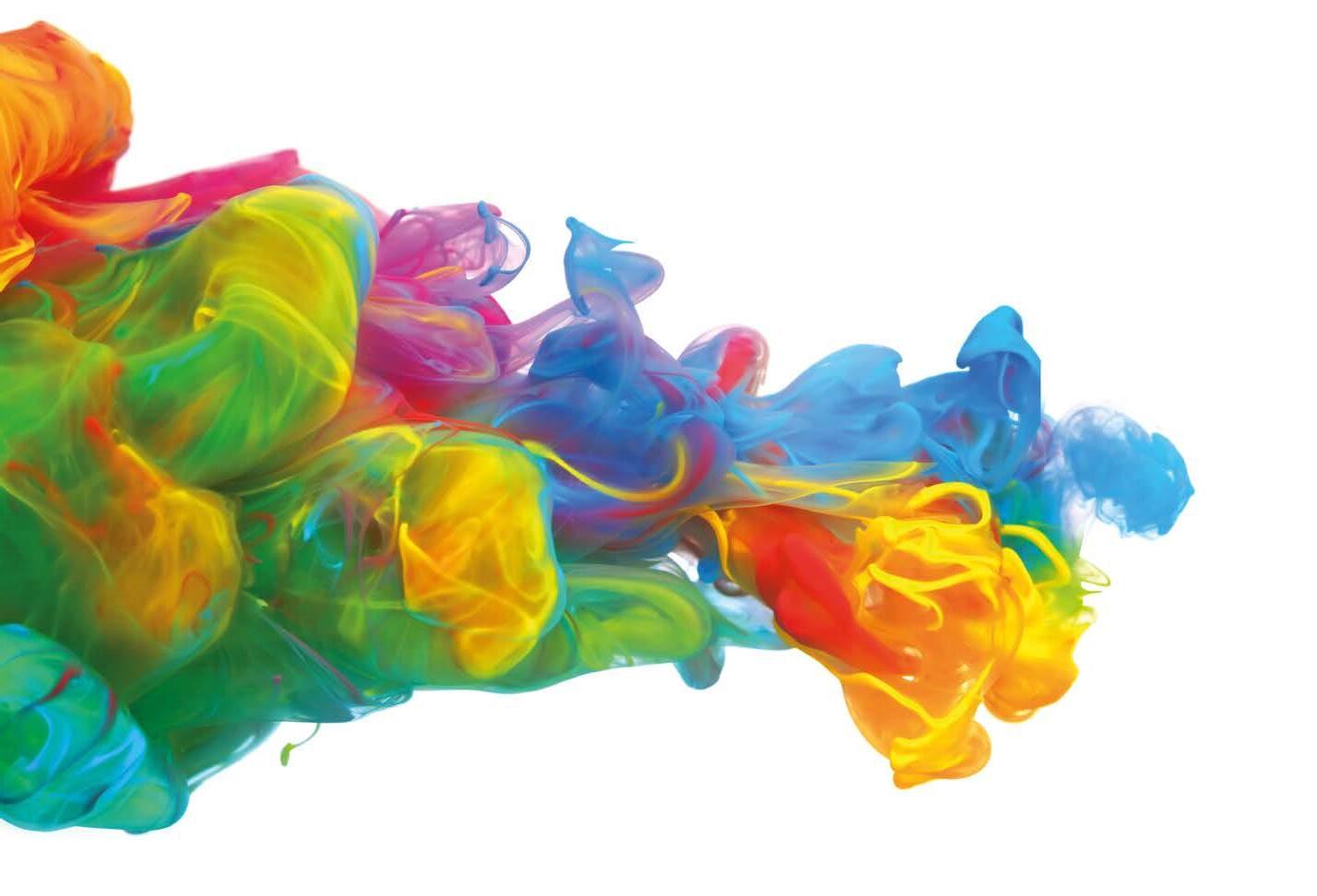
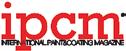

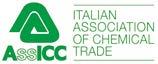
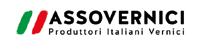
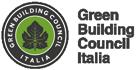
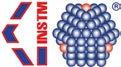
Redazione - Sede Legale:
Eos Mktg&Communication srl
www.eosmarketing.it - info@eosmarketing.it www.myipcm.com - info@ipcm.it
Via Pietro Mascagni, 8 - 20811 - Cesano Maderno (MB) - Italy Tel. +39.0362.503215 - Fax. +39.0362.1794768
EDITORIAL BOARD
Prof. Massimiliano Bestetti: Department of Chemistry, Material and Chemical Engineering, Politecnico of Milan –Section of Applied Chemistry and Physics
Prof. Paolo Gronchi: Department of Chemistry, Material and Chemical Engineering, Politecnico of Milan –Chemical Engineering Section
Kevin Biller: ChemQuest Powder Coating Research
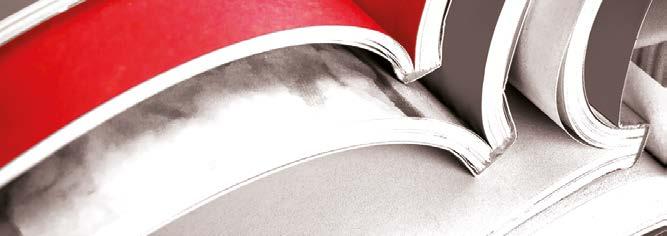
EDITOR IN CHIEF / DIRETTORE RESPONSABILE
ALESSIA VENTURI venturi@ipcm.it
EDITORIAL DIRECTOR / DIRETTORE EDITORIALE

FRANCESCO STUCCHI stucchi@ipcm.it
EDITORIAL OFFICE / REDAZIONE PAOLA GIRALDO giraldo@ipcm.it
MONICA FUMAGALLI fumagalli@ipcm.it
NICOLE KRAUS kraus@ipcm.it
MATTEO SOTTI sotti@ipcm.it
ILARIA PAOLOMELO paolomelo@ipcm.it
GABRIELE LAZZARI redazione@ipcm.it
EDITORIAL OFFICE AND GRAPHICS
ELISABETTA VENTURI grafico@ipcm.it
MEDIA SALES
FRANCESCO STUCCHI stucchi@ipcm.it
ILARIA PAOLOMELO paolomelo@ipcm.it
NICOLE KRAUS kraus@ipcm.it
CLAUS GÖRLICH goerlich@ipcm.it
The smart journal for surface treatments
This magazine is wrapped with a biodegradable and compostable film. Questa rivista è confezionata con un film biodegradabile e compostabile.
LAYOUT/ IMPAGINAZIONE ELISABETTA VENTURI
grafico@ipcm.it
PRINT/ STAMPA ROTOLITO SPA info@rotolito.com
Prof. Stefano Rossi: Material Engineering and Industrial Technologies, University of Trento - Product Design
Dr. Fulvio Zocco: Environment and quality
SUBSCRIPTION SERVICE - SERVIZIO ABBONAMENTI:
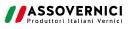
Sale only on subscription - Vendita solo su abbonamento E.mail info@ipcm.it
Subscription Rates 2023 - Tariffe Abbonamento 2023:
Annual subscription print + digital:
EMEA 110,00 € (postage included)
Rest of world 350,00 € (fast airmail shipping included)
Abbonamento annuale cartaceo + digitale:
EMEA 110,00 € (spese postali incluse)
Resto del mondo 350,00 € (spedizione via aerea inclusa)
Single copy: 15,00 € EMEA (postage included) - Rest of world (postage excluded)
Back issues: 30,00 € EMEA (postage included) - Rest of world (postage excluded)
Fascicolo singolo: 15,00 € EMEA (spese postali incluse) - resto del mondo (spese postali escluse)
Arretrati: 30,00 € EMEA (spese postali incluse) - resto del mondo (spese postali escluse)

Subscriptions can be made by bank transfer to the following account: Eos Mktg&Communication Srl IBAN IT97F0844033270000000084801 - SWIFT CODE CRCBIT22 or via payment online at: www.myipcm.com
Gli abbonamenti possono essere sottoscritti versando il relativo importo a mezzo b/b IBAN IT97F0844033270000000084801 intestato a eos Mktg&Communication Srl oppure con carta di credito direttamente dal sito www.myipcm.com
L’Iva sugli abbonamenti, nonchè sulla vendita di singole copie è assolta ai sensi dell’art.74 comma 1 lett. C DPR 633/72, DM 29/12/1989.
Registrazione al Tribunale di Monza N° 1970 del 10 Dicembre 2009Eos Mktg&Communication srl è iscritta nel Registro degli Operatori di Comunicazione con il numero 19244
POSTE ITALIANE S.P.A. – SPEDIZIONE IN ABBONAMENTO POSTALE –D.L. 353/2003 (CONV. IN L. 27/02/2004 N.46) ART. 1, COMMA 1 LOM/MI/4351

It is forbidden to reproduce articles and illustrations of “ipcm®” without authorization and without mentioning the source. The ideas expressed by the authors do not commit nor magazine nor eos Mktg&Communication S.r.l and responsibility for what is published is the authors themselves.
È vietata la riproduzione di articoli e illustrazioni di “ipcm®” senza autorizzazione e senza citarne la fonte. Le idee espresse dagli autori non impegnano nè la rivista nè eos Mktg&Communication S.r.l e la responsabilità di quanto viene pubblicato rimane degli autori stessi.
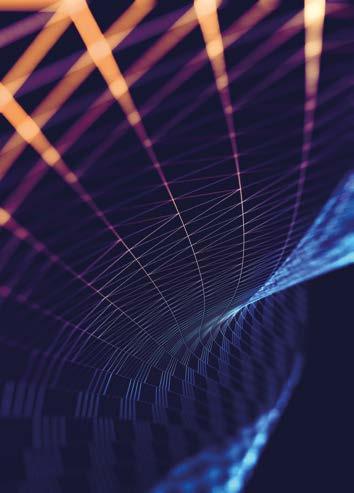
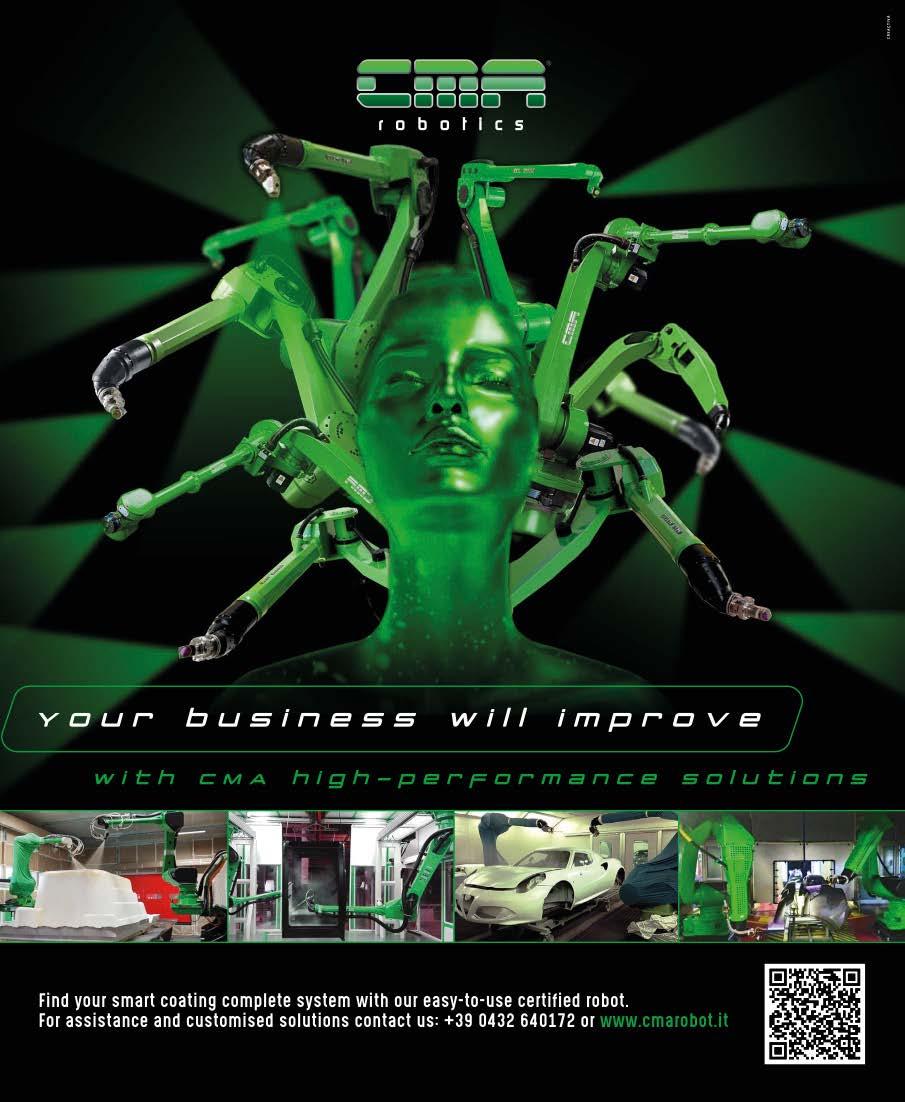
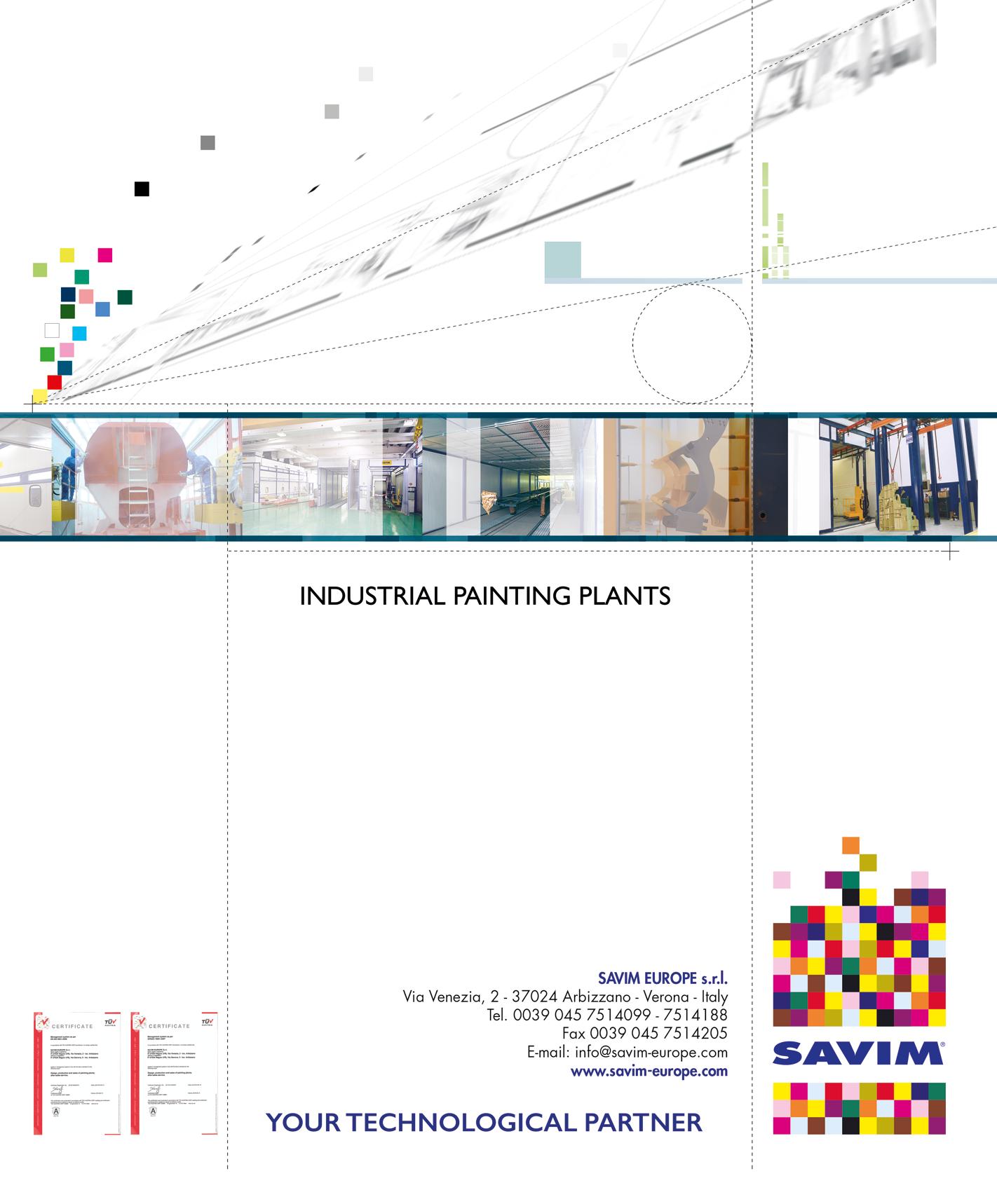