Evaluation
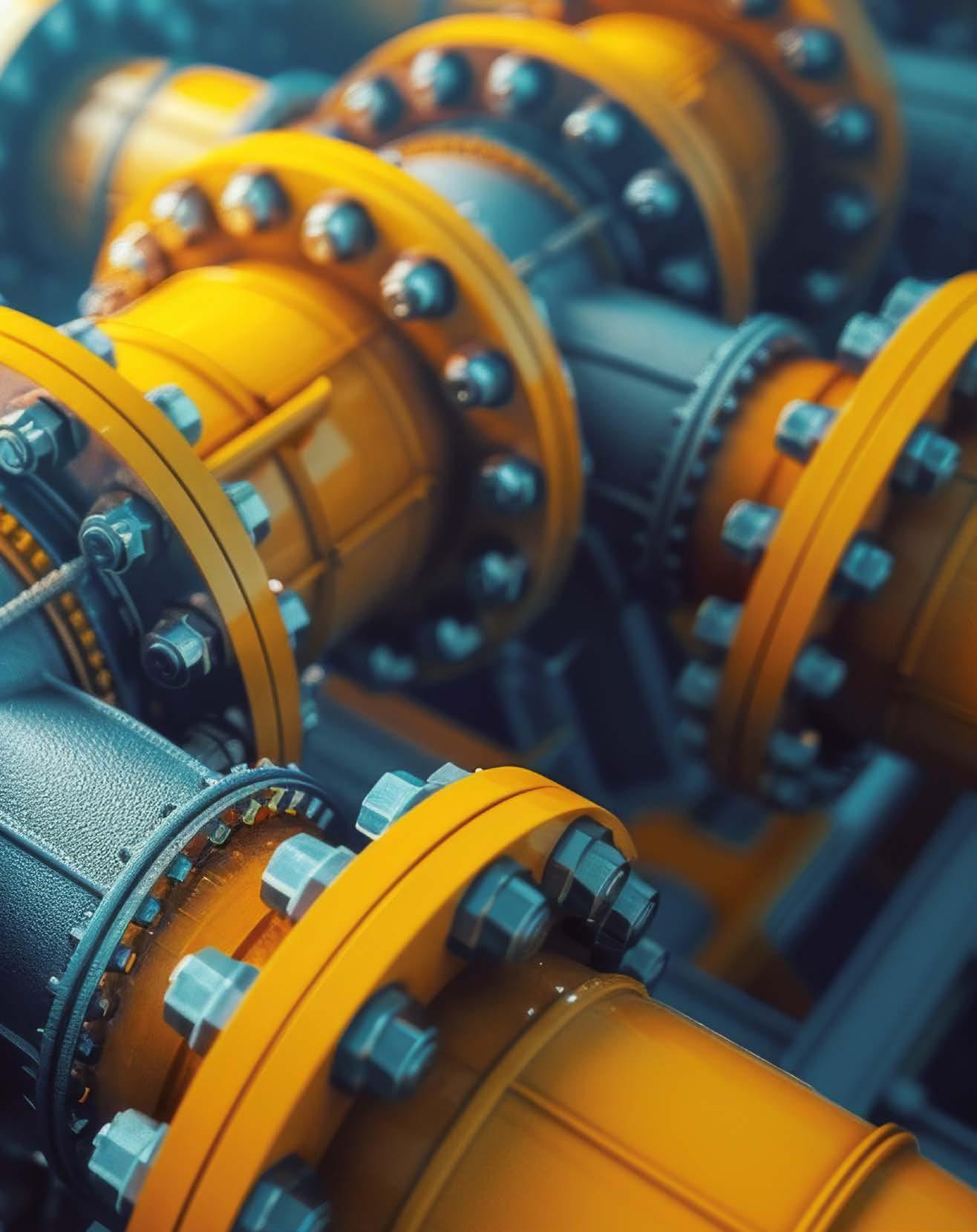
The
58
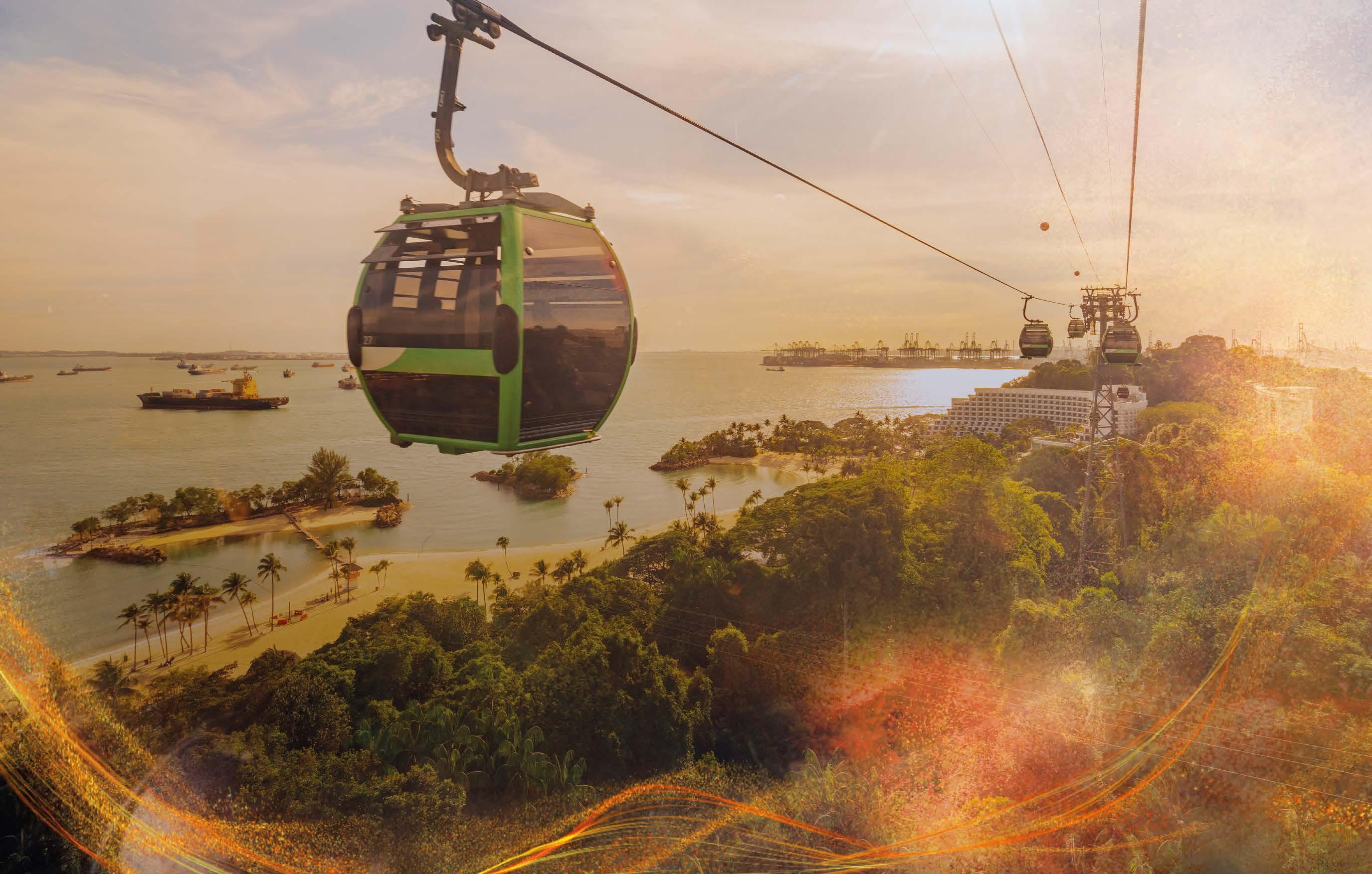
Evaluation
The
58
Corrosion can cause serious issues. Preventing corrosion, and protecting products, surfaces and structures from the damage it can cause is easy – but only if you know the right combination of coatings to choose. That’s where we come in. Interpon Redox takes the complicated science and makes it simple. It comprises a portfolio of tough and durable multi-layer powder systems to suit the widest range of substrates and applications, while our simple ‘System Finder’ helps you find the perfect combination for your particular project and deliver the ultimate corrosion protection. With thousands of colors to choose from, and the largest range of Ready to Ship products available, we’ve got the winning formula of colors, textures and finishes to ensure you remain unbeatable. Interpon. Your personal best.
All of the products within the Interpon Redox range are designed to be highly durable, delivering superior longevity for C4/5 environments compared to other coating solutions. Efficiency is also key: our products are easy to select – our guide is based on ISO 12944:2018 corrosivity categories – and similar easy to apply, with shorter curing times to enable projects to be completed on time, every time.
+39 0383 43345 - voghera@donelli.it
CX Plant - Via Francesco Somma, 32, 20012 Cuggiono (MI) +39 02 97240792 - cx@donelli.it
MXP Plant - Via Quarto, 48, 21010 Ferno (VA)
+39 0331 879174 - mxp@donelli.it Ravenna Plant - Via del Bragozzo, 7, 48122 Ravenna (RA)
+39 0544 436438 - eos@donelli.it
Wehaveworkedhardtoensureaunitarycustomer experience developing the “Donelli identity”. This is what you find in all 5 plants...
The energy sector is undergoing a profound transformation: traditional energy sources will continue to grow in the coming years despite their volatile price environment and the increasing market share gained by renewables. That is demonstrated by the launch of new investment projects worldwide, first of all in the Americas but also in the Middle East and Asia. According to Roland Berger’s report on Perspectives and strategic options for the operators of the Oil & Gas industrial valve sector1 – presented at the Valve Industry Think Tank 2023, an event that is a prelude to the fifth edition of the Industrial Valve Summit, to be held in Bergamo (Italy) on 15 and 16 May – in the two-year period 2023-2024, investments in new Oil & Gas plants are expected to grow by 16% over 2022, when the global situation stabilised after the rebound in 2021 from the significant contraction recorded in 2020.
control solutions, which is currently enjoying excellent development prospects in light of growing investment. Europe – with a focus on Italy, the leading country with a market share of over 30% – is the strongest continent in the production and export of industrial valves.
As strategic safety components of industrial power generation plants, where they ensure efficient and safe flows, these valves must undergo rigorous corrosion protection cycles to withstand exposure to aggressive environments, harsh operating conditions, and corrosive agents.
This April issue of Corrosion Protection includes a focus on innovations, studies, and successful application cases of corrosion prevention and protection technologies in the Oil & Gas sector and especially in the industrial valve sector, as this international magazine will once again be a media partner of Italy’s IVS - Industrial Valve Summit.
On the other hand, liquefied natural gas (LNG) is expected to face a general decline in investment. In contrast, global demand for hydrogen is growing: by 2030, announced green hydrogen projects worldwide are expected to reach a capacity of around 450 GW. Europe is going to be at the forefront of this global development in terms of both number of projects (468 compared to 60 in South America, the second in the ranking) and capacity (151 GW compared to 76 GW in North America). Nuclear power is also on the rise: currently, 58 reactors are under construction worldwide.
Uniting all these areas of the energy industry is the sector of industrial valves and flow
1 https://theenergyrepublic.com/ivs-summit-plays-central-role-inoil-gas-sector-bringing-together-delegations-across-the-world-lucapandolfi/
This April issue of Corrosion Protection includes a focus on innovations, studies, and successful application cases of corrosion prevention and protection technologies in the Oil & Gas sector and especially in the industrial valve sector, as this international magazine will once again be a media partner of Italy’s IVS - Industrial Valve Summit, the most important international event for industrial valve technologies and flow control solutions, an unmissable meeting point for the entire global supply chain.
Besides valve protection, in this issue, we also deal with new technologies for protecting pipelines, which are another critical component for the energy industry, and assessing the impact certain environmental conditions have on them.
Off-topic, there is also a wonderful insight into the “state of health” of the steel making up one of Europe’s symbols, the Eiffel Tower, and the presentation of a revolutionary product for cleaning high-voltage insulators.
Finally, we present a new, brilliant research study on the origin of corrosion.
Enjoy your reading.
The global coatings manufacturer Hempel A/S has recently introduced Hempatherm IC to control maintenance costs and manage corrosion under insulation (CUI). The new coating, seamless and with excellent film-building capabilities, offers superior protection and mitigation of CUI - significantly reducing the risk of water ingress and retention. Hempatherm IC consists of Hempatherm IC 170 and Hempatherm IC 175 and is designed to replace several conventional insulation coatings in the critical CUI temperature range. Furthermore, it provides both thermal insulation and CUI mitigation, thus maximising the service life of industrial equipment and assets. “Process industry operators are constantly looking for solutions that reduce the risk of CUI, while managing their personnel safety and energy consumption in a responsible way. They want robust solutions to minimise disruption and deliver long-term value. The Hempatherm IC system offers just that. It is designed with our customers’ need for energy conservation in mind, without the risk of associated CUI. Coatings provide a simple and elegant alternative to meet this requirement, while promoting cost competitiveness, productivity, and sustainability over its service life for all stakeholders across the value chain,” has stated Zechariah Lim, Product Manager CUI/High Heat & Insulation at Hempel. Hempel can provide superior insulation solutions for process control and energy saving thank to this new solution - thus enabling industries to achieve optimal operational performance, including:
Film with the highest thickness per layer compared to other
insulating coatings;
Prevents water entry and retention on insulated equipment, thus eliminating the risk of CUI;
Airgel filler provides low thermal conductivity, capable of replacing many types of conventional mechanical insulation in the critical CUI temperature range of -25°C up to 177°C;
Resistant to temperatures and cyclical fluctuations;
Non-flammable formulation allows safe application to hot surfaces for quick maintenance and ensuring assets are kept in service with minimal disruption to operations;
Easy installation without the need to handle the metal coating and applicable even on complex geometries;
Prevents solar heat accumulation with minimal thickness.
“Hempel is excited to be part of the market shift from mechanical insulation to an advanced insulation coatings system. Insulation coatings have over 25 years of proven performance, but up until now, limitations on coating film thickness have limited thermal insulation coatings as a comparative alternative. Our Hempatherm system provides one of the market’s highest film builds per coat, with a material engineered to maintain thermal performance over the service life, often in the range of 15-25 years,” has added David Hunter, Segment Development Manager, CUI/High Heat & Insulation at Hempel.
www.hempel.com
The global supplier of organic, inorganic and anti-corrosive pigments Heubach Group, affected by the recent condition on the Red Sea and Suez Canal, has passed on the surcharges that global carriers have imposed on their shipments.
“Heubach has been monitoring the situation closely in recent weeks and has adopted its business to ensure there is as little impact as possible on supply of our pigments, preparations and dyes. But the short-term changes and new routes adopted add not only additional time in transit, but also cost,” has stated Tyler Kilgannon, Senior Vice-President of Sales for Europe and the American regions. The price of the product has been supplemented with a temporary transport surcharge of between EUR 0.10/kg and EUR 0.25/kg for
pigments and preparations. This surcharge was calculated based on the logistics routes, the origin of the raw materials and the location of the plants. Furthermore, the price of the surcharge may increase or decrease depending on the escalation or conclusion of the conflict in the Red Sea. “After the logistic price increase in Europe and the Americas and recently also in Asia we are committed to keep all cost drivers under control and the impact on our customers at a minimum. But after significant reflection, we can no longer absorb these higher logistic costs”, has added Takayoshi Miyatani, Senior Vice-President of Sales for the AMEA region.
www.heubach.com
OCSiAl appoints Peter Cuneo as Chairman of the board of directors
OCSiAl, the global leader in the industrial synthesis of graphene nanotubes, announces the appointment of Marvel’s ex-CEO, Peter Cuneo, as Chairman of the Board of Directors. As President and CEO of Marvel Entertainment, Peter Cuneo orchestrated the legendary turnaround of a just-out-of-bankruptcy, struggling superhero franchise to an entertainment industry powerhouse, with the stock price rising from a low of $0.96 to $54 per share paid by Disney in 2009. Cuneo’s distinguished career also includes such roles as President and CEO of Remington Products, President of Black & Decker’s Security Hardware Group, and President of Bristol Myers Squibb pharmaceuticals group in Canada. He brings to OCSiAl his wealth of strategic leadership experience and a proven track record of investment in many industries. Cuneo said, “I am thrilled to be joining OCSiAl which has the potential to become a world leader in nanotechnology.”
Konstantin Notman, CEO of OCSiAl, commented, “I am delighted to welcome Peter to the Board. His depth of experience and strategic leadership are exactly what OCSiAl needs as it looks forward to the next steps in its rise from a unicorn tech company to a global player.” OCSiAl is dedicated to enhancing select properties of all base materials used by the global industry. The company develops universal nanotube solutions that allow its customers to add nanotubes to materials as part of standard manufacturing processes. Collaborating with customers and partners, OCSiAl creates new generations of nano-augmented materials and end products that have previously unattainable properties. These groundbreaking products set new market standards and will play a crucial role in accelerating the transition to a carbon-neutral future.
https://ocsial.com
Maintain steel integrity
Motivated by the toughest of conditions, we constantly seek to solve the problems that lie ahead. As a trusted maintenance partner, we offer innovative products and technologies that deliver exceptional performance for steel assets.
Support efficient operations
Reduce hazards and risk
Minimise environmental impact
jotun.com
PPG launched NEXEON 810 ultra-low friction antifouling coating
The international paints and coatings supplier PPG, through its Protective and Marine Coating Division, has launched NEXEON™ 810, an innovative copper-free antifouling coating developed with a strong emphasis on vessel performance, emissions reduction and sustainability. NEXEON™ 810 can reduce fuel consumption and greenhouse gas (GHG) emissions, enabling ships to sustain higher speeds, helping shipowners and operators remain compliant with the Organization’s Carbon Intensity Indicator (CII) requirements international maritime. As a matter of fact, the coating’s unique formula can achieve up to a 25% total reduction in greenhouse gas emissions and supports 60 days of downtime resistance with minimal loss of speed.
“PPG Nexeon 810 coating provides the ultimate combination of advanced coatings technology with improved vessel performance and responsible environmental protection. Thanks to PPG’s sustainably advantaged product development process, our customers can enjoy easier application and improved coating performance across the operating life of their vessels,” has stated Joanna van Helmond, PPG global product manager, antifouling coatings, Protective and Marine Coatings. NEXEON 810’s binder technology ensures controlled and predictable solubility, ensuring high performance throughout the operational life of the vessel. Furthermore, the coating’s copper-free technology features a significantly reduced biocide content, while its binding technology allows for gradual biocide release and close-to-surface use. Upon entering the water, the combined effects of sunlight and ocean bacteria trigger the decomposition of these organic biocides. Lastly, PPG’s new solution also allows for electrostatic application, a significant advantage that is not available in traditional antifouling coatings. Excellent transfer efficiency, achieved through electrostatic spraying, provides a uniform, ultra-smooth film as well as decreased overspray and waste - resulting in significantly reduced paint consumption and improved health and safety benefits compared to airless spraying.
www.ppg.com
At a major blue-chip nickel mine in Australia, Rezitech (authorised distributor of Belzona) has provided a full turnkey solution to combat corrosion under insulation on a tank. Within the space of 24 hours, the 9.5 m diameter tank, with a height of 2 metres from ground level, has been repaired and protected against corrosion thanks to the industrial composite wrap system Belzona SuperWrap II. The customer’s stainless steel feed tank exhibited corrosion under insulation and chloride-induced stress corrosion cracking. The company needed a solution that would restore the integrity of the substrate and protect the asset from future corrosion damage. Additionally, as the tank operates at high temperatures of around 70°C and handles highly corrosive media, the repair solution must be able to withstand harsh conditions. The customer placed their trust in the range of metal epoxy repair composites and industrial repair coatings offered by Belzona. Following an inspection by Heath Westell, Sales Engineer at Rezitech, the Belzona SuperWrap II composite wrapping system was specified. “This composite wrapping system consists of a fluid grade resin system, a custom-made hybrid reinforcing sheet made of glass fibre and carbon fibre, as well as a release film to compact and consolidate the application. The system is specially formulated to restore the strength of punctured, weakened and corroded pipes and tank walls, making it the ideal solution for long-term protection of the asset from corrosion under insulation. Additionally, due to the cold-curing properties of the composite winding system, this reduces the need for hot work, making it a reliable alternative to soldering,” said Heath Westell.
All traces of oil and grease contamination have been removed using a suitable Rezitech degreaser. In parallel, the surfaces were grit-blasted to provide a surface cleanliness compliant with ISO 8501-1 SA 2½, with a minimum rough corner profile of 75 μm. Once the surface was prepared, Belzona 9381 reinforcement sheet was first measured and moistened with Belzona resin and then applied to the areas to be repaired. Next, Belzona reinforcement sheets were applied to the tank in three layers, while compression film was added to the top of the application area.
The Belzona SuperWrap II composite wrapping system was rolled and compressed onto the surface of the tank using a roller, and then left to cure for approximately eight hours.
Lastly, by investing in Belzona’s composite wrap system SuperWrap II, the customer was able to successfully overcome the need to replace the corroded asset and extend its life for years to come - resulting in significant savings in both time and money.
www.rezitech.com.au/products/belzona
Sensorlink has been awarded a corrosion monitoring contract with Shell Trading and Shipping Company for the Northern Lights Joint Venture (JV).
The contract includes the provision of Swarm® UT sensors in CO₂ tanks onboard three ships currently under construction. Strategically installed at low spots of the tanks where water is most likely to accumulate, these sensors are designed to detect and monitor corrosion. They will provide online, high-accuracy wall thickness data directly to the ships’ control rooms, enabling early detection of corrosion.
Kjell Wold, Business Development Director at Sensorlink, said, “As part of the energy transition, there is an increase in the transportation of CO₂. While CO₂ itself is not corrosive, the presence of small amounts of water combined with contamination
Our shot blasting systems are made to measure. We take into account the available space, needs and objectives of our customers to structure a product that is functional and that responds to all processing requirements.
can lead to significant internal corrosion. We are enthusiastic to see that our technology and solutions also add value in targeted efforts to reduce greenhouse gas emissions.”
Shell is an international energy company with expertise in the exploration, production, refining and marketing of oil and natural gas, and the manufacturing and marketing of chemicals. The company uses advanced technologies and takes an innovative approach to help build a sustainable energy future.
Northern Lights delivers CO2 transport and storage as a service, enabling decarbonisation of European industrial emissions and facilitating carbon removal from the atmosphere. The company is a Joint Venture owned by Equinor, Shell, and TotalEnergies.
www.sensorlink.no
Eurotherm S.p.A. based in Turin, Italy
PLANT 1: 4.700 m2 of offices, metal work production and painting.
PLANT 2: 5.300 m2 for production, preassembling, warehouse and logistics.
Sherwin-Williams launched Repacor™ SW-1000 for offshore maintenance and repair
The international paints and coatings manufacturer Sherwin-Williams has recently launched Repacor™ SW-1000, an innovative 100% volume solids coating designed for safe, rapid, and economical steel structural maintenance tasks.
“Repacor™ SW-1000 is the result of a three-year research project to develop a coating solution that would simplify maintenance and repair work on offshore wind steel structures. This innovative new product has been developed with the safety of the applicator at the top of mind, as potentially dangerous high-level rope access coating applications can be made easier. Compared to the 2-3 layers needed with traditional technologies, it requires only a single layer coating, dispensed easily using a simple application gun, without the need for mixing,” has stated Claus Ackfeld, product manager at Sherwin-Williams.
Repacor™ SW-1000 is a one-coat solution that possesses all the properties of anti-corrosive coatings and durable finishes, with a dry film thickness of 500 microns. This solution could potentially mimic the original performance of structure coating systems used in offshore wind structures. In addition, Repacor™ SW-1000 also boasts a cure time of approximately four hours, faster than
alternative aerosol systems. The unique cartridge application process allows the applicator to work quickly and compactlyminimising packaging waste.
Repacor™ SW-1000 complies with NORSOK M-501, the offshore industry standard for coating material selection, surface preparation, application procedures and inspection of protective coatings, meeting the highest standards of anti-corrosion protection. It is also completely free of VOCs, carcinogenic, mutagenic and reprotoxic (CMR) substances.
“Repacor™ SW-1000 is transforming the maintenance and repair of wind turbines. However, although it is used predominantly offshore, it is also an excellent solution for onshore industrial environments if a simple to apply, high performance, durable and cost-effective coating is required. The fact that a single coat gives the same anti-corrosion and durability performance as a two or three coat aerosol system makes Repacor™ SW-1000 a genuine game changer,” has concluded Neil Wilds, global product director at Sherwin Williams.
Henkel has recently announced that it has completed the acquisition of Seal for Life Industries LLC, a company based in the United States of America and specialised in providing protective coating and sealing solutions for a broad variety of infrastructures in the renewable energy, oil and gas pipelines and water distribution sectors.
The signing of the transaction took place in February 2024. As infrastructure ages and sustainability gains ever more prominence, the necessity for repair solutions that enhance asset longevity is becoming more apparent. Consequently, maintenance and repair solutions for industrial, civil and municipal applications are gaining heightened importance.
The acquisition of certified protective coating technologies and the complementary applicator network seamlessly aligns with the expanding Maintenance, Repair and Overhaul (MRO) portfolio of Henkel, by introducing complementary repair solutions that significantly bolster the commitment to advancing the sustainability megatrends and facilitating advancements in retrofitting, smart maintenance and civil infrastructure development.
“MRO represent a pivotal growth sector for our organisation, presenting significant opportunities for pioneering solutions that protect, retrofit and digitally monitor infrastructure while advancing sustainability objectives. This strategic transaction represents another crucial milestone in our ongoing efforts to cultivate a robust growth platform within our MRO business to add more value to the operations of our customers and help them reach their targets,” has stated Kourosh Bahrami, the vice-president of Henkel.
“Coupled with the Critica Infrastructure acquisition closed in 2023 and our strong Loctite MRO solutions, we are well positioned to deliver on our strategy.”
Seal for Life operates on a global scale with a worldwide production network that comprises innovative coating and sealing solutions, including heat-shrink sleeves, viscoelastic coatings, epoxy and urethane paints and fire protection, insulation and sound-dampening solutions that allow to protect and retrofit several infrastructures, such as pipelines and piles.
www.henkel.com
The international chemicals supplier Evonik has recently launched Ancamine® 2844, an epoxy cure hardener designed for plural component spray applications.
As a matter of fact, this new highly-functional aliphatic amine-based hardener has ultra-fast curing properties and rapidly develops its properties in harsh conditions of low temperature and high humidity, as well as in marine and protective coating applications.
“Our focus has always been on innovation and performance and Ancamine® 2844 continues our track record of providing solutions that meet the evolving needs of our customers. With this latest curing agent, we are offering a product that not only enhances productivity for applications that require quick turnaround times, but also maintains the quality of the finish and protection, even Evonik developed a new hardener for protective and marine coatings
in the most demanding environments,” has stated Christian Schmidt, Head of the Crosslinkers business line of Evonik. The ultra-fast drying speed of Ancamine® 2844 allows for operations at temperatures as low as 5°C, making it ideal for winter coating applications.
The combination of low viscosity and load, with the high solids content, ensures easy application and a flawless finish. Additionally, the high chemical and corrosion resistance of Ancamine® 2844 effectively protects surfaces and can withstand salt spray testing with up to 3,000 hours of exposure – thus making it a robust solution for fast-curing protective and marine coatings.
https://corporate.evonik.com/en
DONELLI ALEXO INAUGURATES A NEW PLANT FOR APPLYING FBE POWDER LININGS ON OIL & GAS AND DRINKING WATER VALVES
byThe Donelli Group, a pioneer in corrosion protection since 1911, has opened an innovative factory in Ferno (Varese, Italy): Donelli Alexo MXP. Equipped with stateof-the-art technology, it will be the company’s hub for the application of powders, including FBE powder coatings, on valve, tank, and pipe internal surfaces and of liquid paints on both these components and actuators for the oil & gas and drinking water sectors.
In the petrochemical industry, valves play a key role in the extraction, transport, and refining of fluids because they ensure a safe and efficient flow. However, they are often exposed to harsh environmental conditions and aggressive corrosive agents. Such constant exposure can seriously compromise their structural and operational integrity, putting plant safety at risk and generating malfunctions that can cause costly and potentially dangerous operational interruptions. Corrosion protection is, therefore, a crucial factor that can never be underestimated as it is closely linked to the longevity and reliability of infrastructure.
In this scenario, companies specialising in corrosion protection clearly play a vital role. One of them is Donelli Alexo Srl, a company based in Cuggiono (Milan, Italy), which for decades has been offering anti-corrosion coating, fire protection, and insulation services for plants and structures in the energy, oil & gas, chemical, and offshore sectors. Recently, Donelli Alexo has further expanded its market presence by opening a new site in Ferno, in the province of Varese, just one year after its CX site, a satellite of the main one in Cuggiono. This expansion reflects the company’s commitment to meeting the growing needs of the industry through advanced and fully customised corrosion protection solutions. At this new location, Donelli Alexo can apply a wide range of coatings, including FBE linings, powders, and liquid paints, mainly on valves and actuators for the petrochemical and drinking water industries.
Established in 1911, the Donelli Group stands out in the field of protective and cosmetic-protective treatments for a wide range of substrates and infrastructures, including industrial, petrochemical, and chemical plants, power plants, and civil, residential, and commercial structures. It stands out especially for its state-ofthe-art technology, high quality standards, professionalism, and respect for the environment and operators’ safety.
Donelli Alexo, one of the eight companies that make up the Donelli Group, thanks also to the twenty-years experience and technicalcommercial collaboration of an external consultant, AMPP Senior Certified Coating Inspector Luca Calore, in recent years has been developing an FBE powder lining service for valves intended for contact with drinking water, in compliance with the main KIWA, AWWA, and WRAS standards, and with hydrocarbons up to 95 °C, in accordance with the most stringent specifications of end users such as SAUDI ARAMCO and SWCC (APCS-102A, APCS-102B, APCS-102C). It also coats the external surfaces of fittings with both single-layer FBE and double-layer FBE (DLFBE) solutions, with the possibility of also applying top coats with high abrasion resistance (Abrasion Resistant Overcoating, or ARO). “Over the years, our company has increasingly consolidated its presence in the market, becoming one of the leading players in the corrosion protection sector,” states Donelli Alexo CEO Alessio Trisolino.
“Just one year after the opening of the CX plant1 in Cuggiono (Milan, Italy), we inaugurated a new site in the province of Varese, near the international airport of Malpensa – hence its name, MXP. We had noticed a growing demand for the application of FBE powder products – this acronym stands for Fusion Bonded Epoxy – for the outer coating and inner lining of valves in a variety of industries, especially from companies operating in the Middle East, which is one of our main markets to date. Indeed, in recent years, our customers have been showing increasing interest in the FBE technology and entrusting us with more and more orders, including large ones. Therefore, to meet these demands and thanks to the experience gained at our primary plant in Cuggiono, where FBE coatings were already applied successfully, we decided to expand our production capacity by opening this new site,” says Trisolino.
“The achievement of this important milestone is part of a corporate strategy to position ourselves as the benchmark company in the corrosion protection sector. Especially when dealing with large orders, end customers are often concerned about delivery delays, which leads many of them not to rely
1 The technical description of the Donelli Alexo CX plant was published in issue no. 43 of ipcm®_ Protective Coatings: https://www.ipcm.it/en/open/protective-coatings/2022/43/24-31.aspx
exclusively on one coater but rather turn to several suppliers to mitigate potential delays and finishing quality issues.” However, Donelli Alexo has taken a different approach, structuring itself so that end customers see it as their one-stop shop. “With three sites devoted to valve coating, we can guarantee greater flexibility and reduce the risk of delivery delays. We optimise work by managing orders through all our plants, distributing them among the three sites or concentrating them in one depending on production requirements, thus ensuring greater adaptability and efficiency. End users also recognise and value process homogeneity among our plants, which translates into high consistency of the end products’ quality,” notes Trisolino.
Donelli Alexo’s core business is the surface treatment of valves intended for the petrochemical industry and for contact with drinking water. Before reaching the coating process, which takes place in a manual plant, each valve undergoes a series of critical steps. These include cleaning, degreasing, and a thorough mechanical surface preparation check, followed by a sandblasting stage, carried out also in one of the tunnel machines supplied by Cogeim (Casorezzo, Milan).
“At the end of the sandblasting process – using abrasives in different types and with different grain sizes depending on the surfaces to be treated and the specifications of the customer’s technical data sheets – we proceed with lining the inside of the valves by applying the Scotchkote™ FBE epoxy powder coating,” explains Alessio Trisolino.
The FBE powder application system was designed and installed by Eurotherm (Volpiano, Turin, Italy), a plant manufacturer that had already collaborated with Donelli Alexo in the past for the supply of the Cuggiono CX site’s coating line. “When we took over the Ferno plant, it was already equipped with a Eurotherm plant, which we decided to keep precisely because we were aware of the high quality of its technology and the skills of this company’s technical team. At the same time, we subjected it to a major revamping process, especially in terms of control devices, to ensure compliance with the most stringent specifications, such as those required by ARAMCO, with minimal tolerances for the dew point of the air used for powder application.”
Known for its effective corrosion protection properties, the Scotchkote™ FBE coating is mainly used for oil & gas pipelines, including their joints and, of course, valves. Depending on the intended use of such components, FBE coatings may require several processing steps.
“For valves intended for the petrochemical industry, we apply a phenolic primer after cleaning and grit blasting. This is followed by a pre-heating stage in an oven at the temperatures indicated by the product’s technical specifications. We then apply the FBE coating and end the process with an oven-curing phase.
Donelli Alexo’s valve lining cycle is a rigorous, tailor-made process designed to ensure optimal corrosion protection and long service life, in line with the specific needs of each customer and industry,” adds the CEO.
Another significant advantage of the Scotchkote™ XC-6171 product is the possibility of subjecting already coated valves to subsequent machining operations. “This means that we can apply the coating to the entire inner surface of the valves, including the sealing areas in contact with the fluid, and restore the finish with mechanical tooling operations. That distinguishes this product from many competitors as it also guarantees impermeability after machining, which is not always guaranteed by other certified products.”
KNOWN FOR ITS EFFECTIVE CORROSION PROTECTION PROPERTIES, THE SCOTCHKOTE™ FBE COATING IS MAINLY USED FOR OIL & GAS PIPELINES, INCLUDING THEIR JOINTS AND, OF COURSE, VALVES. DEPENDING ON THE INTENDED USE OF SUCH COMPONENTS, FBE COATINGS MAY REQUIRE SEVERAL PROCESSING STEPS.
For Donelli Alexo, Fusion Bonded Epoxy powder coatings are an advantageous solution for protecting both internal and external surfaces. “Although powders are an established technology for the lining of inner surfaces, we anticipate that they may also find fertile ground for the protection of outer surfaces. This fits in with our vision of the ecological transition since we expect powder coatings to completely replace solvent-based liquid products within five to fifteen years. However, we recognise that this change will take time as it is necessary to create an industrial culture that fully embraces this technology and its related processes,” says Marco Malandra, a board member and the coordinator of the technical and regulatory development office (ISO and Qualisteelcoat). “In addition to increased sustainability, powder coatings offer many advantages. Their durability is remarkable, reducing the need for frequent maintenance and its related costs and extending the service life of equipment and infrastructure. In addition, they can be applied electrostatically and in fluidised beds, enabling to coat even the most difficult-to-reach surface areas,” indicates Donelli Alexo’s CEO.
At its Ferno site, Donelli Alexo performs not only the FBE powder lining of valves’ internal areas but also the coating of their external surfaces with liquid-based paint products.
“After inner lining, the valves are shipped to the customer for machining (assembly, coupling, and so on) and then returned to us for outer coating. In the corrosion protection sector, very strict specifications govern 95% of projects. Therefore, customer specifications often determine the coating cycle and the paint products used.” “The plant we have installed at the new Ferno site is designed for manual coating and includes a cluster grit blasting machine supplied by Cogeim, a curing oven supplied by Eurotherm, and 6 manual coating areas, soon to become 9 as 3 more are currently being installed,” indicates Trisolino. The system can handle large-sized valves weighing up to 25 tonnes.
“We recently completed a very sophisticated project engineering-wise, involving the coating of 53 100-inch valves for the transport of drinking water in Mecca (Saudi Arabia).”
IN ADDITION TO INCREASED SUSTAINABILITY, POWDER COATINGS OFFER MANY ADVANTAGES. THEIR DURABILITY IS REMARKABLE, REDUCING THE NEED FOR FREQUENT MAINTENANCE AND ITS RELATED COSTS AND EXTENDING THE SERVICE LIFE OF EQUIPMENT AND INFRASTRUCTURE. IN ADDITION, THEY CAN BE APPLIED ELECTROSTATICALLY AND IN FLUIDISED BEDS, ENABLING TO COAT EVEN THE MOST DIFFICULT-TO-REACH SURFACE AREAS.
Every Donelli Alexo site has embraced the mission of pursuing continuous growth and researching ever-more advanced anti-corrosion products and processes. “We are committed to providing our customers with the highest coating quality and reliability, and this new plant tangibly embodies that commitment. The Ferno facility is also equipped with a traditional powder coating plant that will enable us to guarantee even higher quality standards,” states Trisolino. “We understand coating as much more than a mere protective solution. We intend to expand our range of services in the powder coating sector by exploring new international markets and applying three-coat systems to achieve aesthetic and protective results of the highest quality,” says the CEO of Donelli Alexo.
“To provide our customers with impeccable service, we are obtaining Qualisteelcoat certification and have already received ISO 9001, 14001, and 45001 quality, safety, and environmental certification for this plant. Our Donelli Alexo CX site in Cuggiono has also obtained ISO 9100 certification for the aerospace and military sectors. In addition, implementing advanced technologies to monitor each stage of the coating process guarantees uncompromising quality. Finally, the installation of state-of-the-art instrumentation such as differential scanning calorimetry (DSC) in our Cuggiono CX plant’s laboratory enables us to perform thermal analysis on coated samples directly in-house, demonstrating our commitment to ensuring the highest quality in every aspect of our work,” emphasises Marco Malandra. “These steps will enable us to provide our customers with an even higher level of quality within a shorter time frame, consolidating our position as their one-stop shop and point of reference for all their corrosion protection needs,” remarks Alessio Trisolino. ‹
Subsea oil and gas pipelines are frequently constructed by joining concrete-coated segments together. During construction, concrete-coated pipe may sit for six months to several years before installation. Capital spares are often ordered at the same time as the initial pipes but with a designed preservation life measured in decades of idle time. To ensure that these capital spares do not deteriorate prematurely, Cortec® shares several technologies and tips for preserving concrete-coated pipes from corrosion.
Subsea pipe spares are often stored near the coast due to material handling difficulties. An incredibly long storage period and an aggressive environment combine to pose a frequently overlooked risk for long-term integrity. Although the concrete coating will initially protect the outside of each steel pipe segment, the concrete will absorb moisture, chlorides, and carbon dioxide over time, eventually leading to corrosion. Extreme temperature swings and sporadic inspection intervals can exacerbate the problem. To complicate matters, the concrete coating makes it difficult to access and treat the OD (outer diameter) of the steel pipe.
Migrating Corrosion Inhibitor™ (MCI®) Technology is typically used to protect reinforcing metals embedded in concrete because of its ability to travel through concrete pores to reach the surface of the underlying metal. The same mechanism makes MCI® suitable for protecting the metal pipe OD of concrete-coated pipe. Migrating Corrosion Inhibitors applied to the outside of the concrete pipe can gradually migrate as much as several inches into the concrete to form a protective anticorrosive molecular layer on the steel OD.
Preservation of spare concrete-coated pipes should be done as soon as possible. Any delay gives moisture and chlorides a chance to start attacking the concrete and steel. Although preservation can be done later, additional rust removal and cleaning may be needed by then. In worst case scenarios, preservation may be neglected so long that corrosion compromises the integrity of pipe segments and new ones must be purchased, defeating the purpose of capital spares.
If integrity is confirmed and surfaces are clean, the concrete surface may be treated with MCI®-2020. This topical solution has the highest concentration of Migrating Corrosion Inhibitors compared to other surface applied corrosion inhibitors (SACIs) on the market. For further protection, a water repellent can be added to hinder the entrance of additional moisture and chlorides while trapping the MCI® inside. Alternatively, MCI®-2018, which contains MCI® in a 100% silane water repellent, can be used alone or (for maximum protection) in conjunction with MCI®-2020. Both MCI®-2020 and MCI®-2018 are certified to meet ANSI/NSF Standard 61 for use in drinking water system components, making them attractive for those laying pipeline in environmentally protected waters where dangerous leachates are a concern for sea life.
Often, several inches on each end of a subsea pipe are not coated with concrete. Here, MCI® CorShield® can be applied to protect the exposed metal. This water-based removable coating provides excellent protection in unsheltered outdoor environments and cures to a soft non-tacky film that eventually hardens. If the capital spares need to be installed, the coating can be removed with an alkaline cleaner, if desired.
The inner diameter (ID) of the pipeline segment should also be protected by fogging it with CorroLogic® Fogging Fluid VpCI®-339. This chemistry is similar to MCI® and migrates through void spaces to form a molecular protective layer that remains as long as the void stays closed. To meet this requirement and keep debris out, workers should cap the ends of each pipe segment with a material such as MilCorr® VpCI® Shrink Film, a heavy-duty plastic that also contains corrosion inhibitors. Once this is done, the spares can be left alone and checked once or twice a year.
Even though the need to install concrete-coated pipe spares may be unpredictable, these capital spares should remain on-call for emergency or routine replacement. Proper preservation helps oil and gas companies do so, keeping pipeline segments ready to use on short notice. ‹
Easy to apply, touch-safe, and eco-friendly new Evonik’s TEGO® Therm range to enhance the performance against CUI
The Coating Additives business line at Evonik has introduced a new series of high-performance granules and a heat-resistant binder specifically designed for thermal insulation coatings under the TEGO® Therm product range. When combined with a suitable primer, they provide improved corrosion protection and are effective in preventing corrosion under insulation (CUI) on metal structures. Alessia Venturi, Editor in Chief of Corrosion Protection Magazine, interviewed Niko Haberkorn, Global Head of Business Development
Industrial & Transportation Coatings at Evonik Coating Additives, to know future developments and potential applications of this new product range.
What are the requirements of the engineering, marine, and construction industries as far as thermal insulation is concerned?
In the engineering, marine and construction industries, thermal insulation must meet several critical requirements to ensure operational efficiency, durability, and safety. For chemical processing facilities, oil and gas operations, energy efficiency is essential. This involves minimizing energy losses in high and low temperature processes, which in turn reduces CO2 emissions and supports the sustainability of industrial processes while reducing energy costs. Thermal insulation systems should be easy to apply to keep maintenance costs low. This includes the ability to apply insulation without the need for shutdown and the ability to apply complex three-dimensional shapes, possibly by spray application. Another key factor is durability. Thermal insulation must be able to withstand extreme weather and temperature conditions over a long service life, maintain its effectiveness, and prevent moisture ingress that can lead to corrosion under insulation (CUI). And let’s not forget occupational safety as another important aspect of thermal insulation. Surfaces exposed to both extreme hot and cold temperatures, such as piping or vessels in industrial plants, must be adequately insulated to prevent unintentional contact injuries to workers. Moreover, it is essential that insulation materials utilized in the industrial, marine, and construction sectors possess fire-resistant and non-combustible properties to inhibit flame propagation and preserve structural integrity.
Can you please present Evonik’s TEGO® Therm product range?
Evonik’s TEGO® Therm range is a set of products designed to improve the performance of thermal insulation coatings (TICs). The range includes two types of microporous silica-based granules, TEGO® Therm HPG 4000 and TEGO® Therm HPG 6806, and a heat-resistant silicone-based binder, TEGO® Therm L 300. The granules feature a microporous structure, optimized density and superior hydrophobicity, all of which contribute to provide excellent insulating properties in coating formulations. In combination with the binder TEGO® Therm L 300, these granules enable high filler incorporation, robust adhesion to various substrates and long-term mechanical stability even at temperatures up to 250°C. Incorporating TEGO® Therm products into coatings allows to significantly reduce energy loss and make hot surfaces touch-safe, promoting a safer work environment. In addition, these coatings are userfriendly and can be easily applied to complex shapes, providing a more practical solution than traditional insulation methods such as mineral wool.
What are the corrosion protection performances of TEGO® Therm?
TEGO® Therm thermal insulation coatings, when combined with a suitable primer, provide improved corrosion protection and are effective
in preventing corrosion under insulation (CUI) on metal structures such as pipelines, vessels and other equipment. These coatings differ from conventional insulation systems, such as mineral wool, in that they help minimize the risk of CUI by preventing condensation. They maintain the surface temperature of the coating above the dew point, which helps prevent moisture buildup. In addition, the strong bond between the coating and the primer layer acts as a barrier, preventing moisture from penetrating and reaching the underlying metal surface, providing additional protection against corrosion.
Our TEGO® Therm coatings contribute to sustainability in several key ways. Firstly, they are waterborne, which means they have a low volatile organic compound (VOC) content. This is beneficial because it reduces the need for harmful solvents that can contribute to air pollution and have a negative impact on the environment. Moreover, the insulating properties of TEGO® Therm coatings lead to a decrease in energy consumption. By providing effective insulation, these coatings minimize heat loss from equipment and piping, which in turn reduces the amount of energy required to maintain desired temperatures. This energy efficiency translates into lower greenhouse gas emissions, as less fuel is burned to produce the necessary energy.
Evonik’s Life-Cycle Management team has conducted studies to quantify these energy savings in practical applications. The findings suggest that by using TEGO® Therm coatings on areas that are typically not insulated with traditional methods, such as valves and complex piping, there can be a substantial reduction
in energy loss. The result is a significant decrease in greenhouse gas emissions, which underscores the coatings’ contribution to environmental protection.
In summary, our TEGO® Therm toolbox offers solution for the formulation of long-lasting and effective insulation coatings, enabling a reduction in energy use and greenhouse gas emissions, and thus supporting global sustainability efforts.
The focus of the corrosion protection market is currently on ease of application, reduced curing time, reduced maintenance: what TEGO® Therm can offer to these respects?
Our TEGO® Therm range and its application in insulation coatings effectively supplements corrosion protection requirements, emphasizing ease of application, prevention of condensation and CUI, and therefore reduced maintenance needs. Thermal insulation coatings (TICs) based on TEGO Therm have been successfully implemented in a variety of applications across Evonik’s global production sites. With their low thermal conductivity and robust structural integrity, TEGO® Therm-based coatings are suitable for diverse applications, both indoors and outdoors.
The coatings are engineered to ensure touch safety, enhance energy efficiency, and prevent CUI. They are highly versatile and can be applied swiftly and effortlessly, even on complex surfaces. This streamlines the insulation process, cutting down on the time and effort typically required for application and significantly reducing the need for extensive maintenance. The result is a product that not only protects but also contributes to operational efficiency and longevity of the equipment it covers. ‹
Insulation Coatings based on TEGO® Therm components are easy to apply to all kinds of complex geometric shapes by time-saving spray application. The super insulation TEGO® Therm granules provide an outstanding low thermal conductivity characteristic, which significantly reduces the loss of energy. The coating also ensures personnel protection by reducing the surface temperature to an acceptable limit.
TEGO® Therm HPG 4000 are silica-based granules with superior low thermal conductivity, high hydrophobicity and reduced flammability:
Particle size d50 ~300 μm
Superinsulation properties
High hydrophobicity.
TEGO® Therm HPG 6806 is a finer powder which also provides excellent insulation functionality, enhances mechanical performance and features smooth & even surfaces of insulation coating:
Particle size d50 ~30 μm
Excellent insulation properties
Less thickening and easy incorporation in coatings.
TEGO® Therm L 300 is a liquid waterborne silicone hybrid binder with excellent heat & mechanical stability:
Liquid binder with solid content ≈50%
Broad compatibility with acrylic emulsions
Ambient film forming.
MI-PAC, a Spanish company specialising in complete solutions for civil works and physical branding, is one of the first applicators approved in AkzoNobel’s Interpon Redox Excellence network at the end of 2023, thanks to its excellent powder coating process that guarantees corrosion protection up to the C5H class.
Belonging to the Spanish network Redox Excellence –which means being approved as a certified applicator of AkzoNobel’s Interpon brand – is not just a matter of prestige but also of contributing to efforts to promote powder coatings and opening up new business opportunities. Indeed, Redox Excellence is the quality mark that certifies the application of anti-corrosion and functional coating systems on steel structures, and the applicators belonging to this network of excellence guarantee the application of corrosion protection products complying with resistance classes from C4H to C5H. Using AkzoNobel powder coatings is not enough to be part of the network: it is necessary to have implemented equipment
and processes that, by combining surface preparation, paint application, and quality control procedures, ensure corrosion specifications are achieved in compliance with ISO 12944. AkzoNobel’s powder coatings division directly selects this network of applicators, strategically distributed in several Spanish regions and communities. Offering complete solutions for civil engineering works and the creation and assembly of corporate image and physical branding elements since 1990, Obras y Montajes MI-PAC S.L. is currently the only company in the Castile-La Mancha community that has all the necessary processes, procedures, and skills to achieve the C5H resistance class with a powder coating line, without outsourcing any step.
MI-PAC can apply two-layer powder, two-layer liquid, and two-layer mixed (liquid primer and powder top coat) protective systems in accordance with customer requirements.
“In the late 1980s, in this area of Castile-La Mancha, there was much demand for the construction of service stations,” says Francisco Paco Sobrino, the founder’s son and the company’s current owner. “My father established this business with his partner Miguel de Toro in 1990, initially focussing on civil works and the production and installation of physical branding elements in service stations throughout the peninsula. Back then, everything was done on site: they had no specialised workshops where they could cut, machine, weld, and paint the metal components needed for the construction work or pre-assemble the physical branding materials required by the service stations. Hence, our idea to build such metal structures in a dedicated industrial hall and then bring the processed material to the construction site for faster assembly. Since then, MI-PAC has been striving for excellence in civil works and physical branding elements production and installation, combining state-of-the-art technology with creativity
to bring unique, visionary projects to life.”
“Our first 2,000 m2-wide premises were located in the urban core of Bolaños de Calatrava (Ciudad Real), where we began to produce all kinds of metal structures and corporate branding elements,” adds Paco Sobrino. “As we continued to grow, we moved to the Polígono Industrial El Salobral hub in 2000, expanding our infrastructure to 30,000 m2 with 7 factory halls covering 8,500 m2, where we carry out all our activities. In 2007, we integrated a powder coating plant, thus ultimately insourcing all stages of our production process.”
In particular, MI-PAC manufactures and paints any type of physical branding element, from furnishings and identifying marks to vehicle graphics, billboards, monoliths, and supports. In its premises in Bolaños de Calatrava, MI-PAC carries out its entire production process in-house, from design to shot blasting, from liquid to powder coating, and from milling, bending, and welding to electrical connections and graphic design.
OBRAS Y MONTAJES
MI-PAC S.L. IS CURRENTLY THE ONLY COMPANY IN THE CASTILE-LA MANCHA COMMUNITY THAT HAS ALL THE NECESSARY PROCESSES, PROCEDURES, AND SKILLS TO ACHIEVE THE C5H RESISTANCE CLASS WITH A POWDER COATING LINE, WITHOUT OUTSOURCING ANY STEP.
The finishing process of metal parts entirely performed in-house
“For iron, we can choose between mechanical pre-treatment in a manual shot blasting cabinet and chemical pre-treatment in a 5-stage tunnel: we mechanically pre-treat or clean each part depending on its coating needs and quality requirements. Aluminium components, on the other hand, are all subjected to cleaning. Subsequently, we apply a zinc-rich liquid or powder primer, depending on the material we are treating. For the application of the former, we have a double booth painting parts up to 20 metres in length. For the latter, we use an automatic plant with a monorail overhead conveyor, a 5-stage pre-treatment tunnel, a drying station, a pre-heating tunnel, an automatic application station with a manual touch-up booth, and a curing oven,” indicates Sobrino.
“This means that MI-PAC can apply two-layer powder, two-layer liquid, or two-layer mixed (liquid primer and powder top coat)
protective systems in accordance with customer requirements, the intended use of parts, the corrosion class to be achieved, and the type of substrate. Aluminium always undergoes chemical treatment and powder coating, whereas iron, if not galvanised, is subjected to mechanical or chemical pre-treatment, protection with a zinc-rich primer, and top coat application. As a rule, we use liquid corrosion protection systems for heavy workpieces that cannot be hung on the automatic plant’s chain, for small batches, and for anything that would not be sufficiently productive to powdercoat.”
MI-PAC has been collaborating with AkzoNobel Coatings, S.L.U. (Vallirana, Barcelona) since 2007. Such a longstanding collaboration has enabled both companies to profitably exchange skills and experience and mutually grow from a technical perspective.
MI-PAC is also one of the first applicators approved in the Interpon Redox Excellence network at the end of 2023 and is the only powder coating company in the Castile-La Mancha community that can achieve the C5H corrosion class on black steel with S.A. 2 ½-grade shot blasting.
MI-PAC’s work is highly customised, and the metal structures it produces can be installed in any environment, whether on the seafront or in the centre of Castile.
“MI-PAC can currently manage projects in both Castile-La Mancha and Andalusia, and also has contacts in the Madrid and Levante area,” notes Juan José Sánchez Maqueda, AkzoNobel sales representative in Castile. “It has achieved these results because it has all the necessary processes in place to apply verified protective systems capable of achieving a degree of resistance up to the corrosion class C5H in compliance with ISO 12944. Indeed, there is no need to apply many microns of paint, but it is important to have “weapons” available that can be combined to obtain effective corrosion protection finishes. As Paco mentioned, in particular, MI-PAC can perform chemical pre-treatment, mechanical pre-treatment, liquid paint application, powder coating application, pre-set quality control procedures, and a vertically integrated production process with very tight control over every step: in other words, everything necessary to provide the market with the guarantee of excellent corrosion protection.”
“In terms of powder coating products from the AkzoNobel range, MI-PAC usually works with the zinc-rich primer Redox P.Z., the barrier-effect epoxy primer Redox Plus, and Qualicoat Class 1 or 2 top coats for aluminium and iron,” states Juan José Sánchez Maqueda from AkzoNobel.
“We do not manufacture standard products,” explains Paco Sobrino. “We specialise in providing customised solutions: we support our customers from the development of their physical branding elements to their production and finishing. Our processes are highly customised, and the metal structures we produce can be installed in any environment. We can manufacture products to be placed as much on the seafront as in the centre of Castile. The
added value of our work is that we can cover all types of applications. Another advantage is that we have a supplier like AkzoNobel, which offers excellent service and top-quality products. We have never had a single problem with AkzoNobel’s coatings.”
Being approved as an Interpon Redox Excellence applicator was a further step towards quality for MI-PAC. “Besides prestige and the certainty of doing a good job, the biggest advantage of the Redox Excellence brand is the reputation it brings within the powder coating industry. Now, all companies in our area know they can count on us for any corrosion protection requirement up to the C5H class,” concludes Paco Sobrino. ‹
MI-PAC HAS ACHIEVED THESE RESULTS BECAUSE IT HAS ALL THE NECESSARY PROCESSES IN PLACE TO APPLY VERIFIED PROTECTIVE SYSTEMS CAPABLE OF ACHIEVING A DEGREE OF RESISTANCE UP TO THE CORROSION CLASS C5H IN COMPLIANCE WITH ISO 12944. INDEED, THERE IS NO NEED TO APPLY MANY MICRONS OF PAINT, BUT IT IS IMPORTANT TO HAVE “WEAPONS” AVAILABLE THAT CAN BE COMBINED TO OBTAIN EFFECTIVE CORROSION PROTECTION FINISHES.
Pacific Basin leads the largest adoption of graphene-based coating in the dry bulk segment ©
Pacific Basin has decided to apply XGIT-PROP, a sustainable graphene-based propeller coating developed by GIT Coatings, across its entire fleet.
In a proactive move towards energy efficiency and environmental sustainability, Pacific Basin, a leading dry bulk shipping company, has decided to apply a sustainable graphene-based propeller coating, XGIT-PROP, across its entire fleet. This innovative coating, developed by Canadian company GIT Coatings, has demonstrated the potential to enhance vessel performance by up to 4%, which also makes it a highly effective solution to improve CII and RightShip GHG ratings. Following successful application and observing positive results on one of its Supramax dry bulk vessels, Pacific Basin has started the rollout of XGIT-PROP across 40 vessels scheduled for dry dock maintenance in 2024.
This decarbonisation initiative marks the largest adoption of graphene-based propeller coating in the dry bulk segment, showcasing Pacific Basin’s leadership and strong commitment to sustainability through innovative solutions. It parallels the pioneering efforts of industry counterparts like Stolt Tankers and Eastern Pacific Shipping, amongst many others. Sanjay Relan, the General Manager of Optimisation & Decarbonisation at Pacific Basin, remarked, “Since 2007, we have been coating our vessels’ propellers with silicone paint to proactively maintain a smooth propeller surface and avoid the frequent need for polishing to recover lost performance. However, we have not been able to avoid edge damages to the silicone coating on the propellers, which requires the entire propeller coating to be stripped and reapplied at every docking. By adopting XGIT-PROP hard coating for our entire fleet, we are taking a proactive step towards more sustainable practices. We hope to maintain a damage-free, smooth propeller surface and improve efficiency
over longer periods. At a fleet-wide level, we anticipate significant reductions in both environmental impact and operational expenses.”
A biocide-free hard foul release coating, XGIT-PROP is designed to withstand the rigorous conditions faced by propellers, overcoming the shortcomings of conventional, biocide-based soft foul release coatings that release silicone oils and often peel away from propeller blades. Combining a strong adhesive primer with a hard foul release topcoat, XGIT-PROP ensures the propeller’s surface stays smooth over the drydocking cycle. In a fuel efficiency study conducted by Stolt Tankers in 2022, it was proven that XGIT-PROP has the potential to reduce fuel consumption by up to 4%. In addition to improved CII ratings, shipowners in the dry bulk sector are leveraging XGIT-PROP’s efficiency gains to improve their vessels’ RightShip GHG ratings. Maiko Arras, Director of Business Development at GIT Coatings, commented, “Collaboration with Pacific Basin marks another important milestone in our growth. While we have established fleet supply agreements with many other shipping companies, Pacific Basin stands out as the largest to fully integrate XGIT-PROP across a fleet of dry bulk vessels. We’re glad to see first movers selecting this innovative yet simple solution to drive the industry towards a sustainable future.”
The fleet agreement between Pacific Basin and GIT Coatings highlights the shipping industry’s ongoing shift towards sustainability. Faced with the need to meet environmental goals, reduce costs, and maintain efficiency, shipowners who are open to change can find help in innovative solutions like graphene-based coatings offered by GIT. ‹
Hydrogen atoms that penetrate inside the crystal lattice of metals and particularly steels can cause their fracture, leading to the phenomenon commonly known as "Hydrogen Embrittlement" (HE). This article examines the effects of environmental and mechanical parameters on the outcome of tensile tests conducted on cylindrical samples, employed to study HE susceptibility.
Hydrogen plays a relevant role in the decarbonization process that Europe started in the last decades. Its possible employment as a low-carbon footprint energy vector and energy storage means it is still considered a feasible option. During the first transition phase towards using this new energy vector, while no specific infrastructure for its transport is available, a small percentage of gaseous hydrogen could be blended with NG in the already dedicated transport and distribution network.
Several problems arise from such gas blending, particularly the compatibility of the existing pipelines with high-pressure hydrogen. In fact, it is well known that hydrogen, due to its electronic structure and small atomic size, can penetrate inside the crystal lattice of metals and particularly steels, endangering their integrity in several ways, which is commonly referred to as hydrogen embrittlement (HE).
To study the susceptibility of steel alloys to HE, there exist many different methods, which offer different kinds of information about their behaviour in the presence of a high-pressure hydrogen environment. This paper focuses on tensile tests performed on cylindrical samples, employed to study HE susceptibility. Tensile tests are indeed a very common way to study the hydrogen-alloy interaction under strain conditions.
The effects of environmental and mechanical parameters on the outcome of the tensile test will then be discussed, as well as the observations that can be deduced from the rich literature available on the subject, which is sometimes contradictory and, therefore, requires careful interpretation.
Introduction
Hydrogen plays a relevant role in the decarbonization process that Europe started in the last decades. Its possible employment as a low-carbon footprint energy vector and energy storage means it is still considered a feasible option. During the first transition phase towards using this new energy vector, while no specific infrastructure for its transport is available, a small percentage of gaseous hydrogen could be blended with NG in the already dedicated transport and distribution network. The percentage of hydrogen that can be mixed with NG at this first stage does not exceed 20%: first of all, to avoid the need to modify utilization equipment such as burners and boilers and, secondly, not to penalize the energy efficiency of
the whole transport system, taking into account that hydrogen carries about one-third of the energy of NG per unit volume with all other parameters (pressure, temperature and flow velocity) being equal. It is also known that molecular hydrogen can dissociate in its atomic form, penetrate and diffuse through steel, given its small size and electronic structure, causing a degradation of the mechanical properties of these materials, which is commonly referred to as hydrogen embrittlement (HE).
The industry, and in particular the chemical sector, has long experience in the production and use of hydrogen and hydrogencontaining gas mixtures; in fact, an estimated amount of hydrogen in the order of 1012 m3 (108 tons) is produced each year worldwide without detecting significant problems in its handling. However, it should be noted that, in the industrial plants mentioned before, low-grade steels (SMYS 52 ksi/360 MPa) with a low design factor (f=0,3-0,5) are used for hydrogen containment at room temperature and high pressure. On the contrary, in the case of the widespread use of hydrogen as an energy carrier, the use of higher SMYS steels with design factors approximately equal to those adopted today for NG will have to be envisaged to limit the problem of low energy density per unit volume.
In order to assess the suitability of new steels for use with hydrogen, numerous different types of tests can be employed, either provided for by international standards or proposed in the technical literature. These tests are carried out in a hydrogen environment of very high purity (99.9999%), with a very controlled
content of certain specific contaminants, such as oxygen or water, at the maximum pressure expected for actual operation and at ambient temperatures. The difficult experimental conditions, the need for complex instrumentation and the precautions to be taken in order to conduct the test under safe conditions make these tests very expensive, and only a relatively limited number of laboratories have the appropriate equipment and experience to carry them out. In this note, we will deal with the tensile test, which is in general very well known for the mechanical characterization of materials but which requires some specific considerations if it is to be used for the above-mentioned purpose. The tensile test is widely used in the technical literature for the evaluation of the behaviour of steels in a hydrogen gas environment, especially in the research phase where, as will be seen, it allows highlighting the effects of specific significant parameters on the response of metallic materials to the hydrogen environment. As far as standards are concerned, on the other hand, only ANSI/CSA CHMC 1 [1] provides for their use for the certification of materials with the possibility of using both smooth and notched specimens.
For smooth tensile specimens, the current literature states almost unanimously that hydrogen has no relevant effects on Yield Stress and Ultimate Tensile Stress. On the other hand, hydrogen clearly impacts ductility parameters. i.e. elongation (El) and reduction of area (RA). As can be observed in Figure 1, the
hydrogen test curves deviate from the reference curve in air only after reaching the UTS, when the necking begins and, within the volume of constricted material, the decohesion phenomena that will ultimately lead to fracture also begin. To assess the sensitivity of the material to hydrogen embrittlement, RA values in hydrogen and air are compared. Duncan et al. [3], also reporting data from other Authors, provide the following table of values of the tensile properties of four different materials (Table 1). As the table reads, the value of RA decreases in the presence of hydrogen for every alloy, between 14%-39% of its original value. Elongation at break, on the other hand, is much less sensitive to hydrogen presence. In one case (A516 steel), the material shows even higher elongation in hydrogen compared to air. Nanninga et al. [4], [5] performed similar tests on X52, X65 and X100 pipeline steels, obtaining respectively a RA ratio (RRA) of 0.50, 0.72 and 0.78 in hydrogen environment, with RRA being the ratio between the reduction of area in hydrogen environment (RAH) and the reduction of area in inert environment (RAR):
RRA is more severe for higher-grade alloys. Stalheim et al. [6], in tests on four materials, conclude that the material grade does not have a specific effect on embrittlement while the microstructure is more relevant: the best behaviour is with a microstructure of equiaxial ferrite plus approx. 10% acicular ferrite, while the worst
The difficult experimental conditions, the need for complex instrumentation and the precautions to be taken in order to conduct the test under safe conditions make these tests very expensive, and only a relatively limited number of laboratories have the appropriate equipment and experience to carry them out.
is with a ferritic/pearlitic microstructure.Now, we will delve into a rapid analysis of the two most impacting test parameters: hydrogen pressure and strain rate.
Partial pressure determines the total amount of hydrogen absorbed by the material when in equilibrium with the gaseous environment, if the metallic material has been in service for a sufficiently long time such that all the phenomena of absorption, diffusion, reaction with trap sites, etc. have reached their equilibrium conditions.
A typical trend of ductility as a function of hydrogen partial pressure is shown in Figure 2; ductility decreases rapidly
as hydrogen partial pressure increases until it reaches an approximately constant value in the cases presented for pH2 values of 5-10 MPa. Ductility loss in the presence of hydrogen is rather variable. Stalheim et al. [3] and Nanninga et al. [6] reported values around 50% for pressures above 10 MPa (Fig. 3), while Meng et al. [7] performed similar tensile tests on an X80 steel, reporting a decrease of El and RA up to 20% in the most severe conditions applied (pH2=60 MPa). Bertini et al. obtained similar El and RA reduction, never higher than 15%, when performing tensile tests on X52 smooth specimens pre-charged at 5, 10 and 15 MPa of gaseous hydrogen pressure. Although the results might be scattered, all these Authors agree on the fact that a hydrogen pressure increase leads to a decrease in ductility parameters El and RA; ductility decreases rapidly as hydrogen partial pressure increases until it reaches an approximately constant value, in the cases presented for pH2 values of 5-10 MPa.
Another test parameter that greatly influences the result is the strain rate applied during the test, as in the example in Figure 3 [2]. Usually, tensile tests with hydrogen are conducted as prescribed by ASTM G 192, “Standard Practice for Slow Strain Rate Testing to Evaluate the Susceptibility of Metallic Materials to Environmentally Assisted Cracking” [8].
This test was originally developed to study Stress Corrosion Cracking (SCC) phenomena, but it turned out to be also well suited to hydrogen embrittlement conditions where the phenomenon is controlled by the penetration and diffusion of hydrogen atoms into the metal, which are inherently slow processes; in an extremely slow test, therefore, solid-state diffusion phenomena are able to keep pace with and influence the dislocation generation and creep phenomena responsible for the plasticization of materials and ultimately of fracture processes. As can be seen in the example shown in Figure 4, the El of the material decreases as the strain rate decreases over a wide range from 5.5x10-1 to 5.5x10-7 s-1, but the most significant effects occur for strain rates below about 10-4 s-1, while the RA is relatively constant in the range of 5x10-3 to 5.5x10-7 s-1 rates with a decrease of 63-68% compared to the test in an inert environment (N2).
For notched tensile specimens, the matter is slightly different. In this case, the parameter employed for the evaluation of hydrogen embrittlement is notch tensile strength (NTS), defined as the ultimate tensile strength of the notched specimen, and the dominating parameter of the specimen’s geometry is its notch tip radius.
In the case of notched tensile specimens, the parameter employed for the evaluation of hydrogen embrittlement is notch tensile strength (NTS), defined as the ultimate tensile strength of the notched specimen, and the dominating parameter of the specimen’s geometry is its notch tip radius.
Song et al. [9] performed tensile tests on severely notched X70 samples with a notch tip radius of 0.083 mm. The tests were performed in He and 10 MPa hydrogen at different crossbeam displacement speeds.
The hydrogen embrittling effect reaches the maximum value for a displacement speed of 1x10-3 – 5x10-4 s-1, and in this interval, the NTSloss parameter, defined by the authors as:
NTSloss = (NTSHe – NTSH) / NTSHe x 100
assumed values between 13-15% (Fig. 4).
The ANSI/CSA CHMC 1 standard [1] defines the ratio (RNTS) between the average values of notch tensile strength in hydrogen (NTSH) and in inert environment (NTSR):
and for this parameter, it sets a lower limit of 0.90.
By the simple relation:
NTSloss = 100 – RNTS
we obtain RNTS = 85-87%, slightly below the acceptance threshold RNTS ≥ 90% required by the ANSI/CSA CHMC 1 standard. Nguyen et al. [10], [11], [12], on the same steel grade (X70), on notched specimens with a notch tip radius of 0.083 mm, but with a strain rate of 2x10-2 mm/s that does not comply with the prescriptions of the ANSI/CSA standard mentioned above, in an atmosphere of pure hydrogen at 10 MPa, obtained RNTS values of 0.97 with respect to air and 0.92 with respect to helium, demonstrating the critical relevance of test parameters on the results. The tests of these Authors, while critical for the aspects already pointed out, highlight the relevance of this parameter for the outcome of tests on notched specimens. Using radii of 0.083, 1.5 and 6 mm, they obtained the results shown in Figure 4 [11], where the “Stress Concentration Factor, Kt” is a parameter inversely related to the notch tip radius (r) and equal to 1.26, 1.82 and 5.59 for r values equal to 6, 1.5 and 0.083 mm, respectively (Figure 5).
The effect of the Kt factor significantly impacts the RRA parameter, which decreases to about 40/50% for severe notching, while, also for the reasons previously highlighted, the value of NTS loss is modest and always less than 5%.
One of the most widely employed ways to evaluate the HE susceptibility of steel alloys is to perform in-situ tensile tests on smooth or notched specimens. Some general considerations can be made:
When tensile tests are performed on smooth specimens, hydrogen does not cause any relevant modification to YS and UTS but only to ductility parameters, El and RA.
RRA can reach values up to 50% at a pressure of 10 MPa; RRA increases with the increase of the steel alloy’s mechanical properties.
RRA increase is particularly steep in the first 5 MPa of hydrogen partial pressure and slowly approaches an asymptotic value for higher pressures.
RRA also increases when the displacement speed decreases. For displacement speed values lower than 10-4 s-1, the RRA remains mostly constant. This is a direct consequence of the intrinsic speed of the solid-state diffusion of hydrogen.
When tensile tests are performed on notched specimens, hydrogen affects the ultimate tensile strength value, but the RNTS is always relatively low (≤ 15%), and it is difficult to directly correlate it to HE susceptibility. RRA is strongly dependent on the notch tip radius; lower notch tip radii lead to dramatically higher RRA when all the other conditions are kept constant. ‹
One of the most widely employed ways to evaluate the HE susceptibility of steel alloys is to perform in-situ tensile tests on smooth or notched specimens.
Bibliography
[1] “ANSI/CSA CHMC 1 - Test methods for evaluating material compatibility in compressed hydrogen applications - Metals.” 2014.
[2] I. Moro, L. Briottet, P. Lemoine, E. Andrieu, C. Blanc, and G. Odemer, “Hydrogen embrittlement susceptibility of a high strength steel X80,” Materials Science & Engineering A, vol. 527, no. 27–28, pp. 7252–7260, 2010, doi: 10.1016/j.msea.2010.07.027.
[3] A. Duncan, P. S. Lam, and T. Adams, “Tensile testing of carbon steel in high pressure hydrogen,” American Society of Mechanical Engineers, Pressure Vessels and Piping Division (Publication) PVP, vol. 6, pp. 519–525, 2008, doi: 10.1115/PVP2007-26736.
[4] N. E. Nanninga, Y. S. Levy, E. S. Drexler, R. T. Condon, A. E. Stevenson, and A. J. Slifka, “Comparison of hydrogen embrittlement in three pipeline steels in high pressure gaseous hydrogen environments,” Corros Sci, vol. 59, pp. 1–9, 2012.
[5] A. Nanninga, N., Levy, Y., Drexler, E., Condon, R., Stevenson, A., Slifka, “Tensile behavior of pipeline steels in high pressure gaseous hydrogen environments,” pp. 1–33.
[6] D. Stalheim, T. Bogges, C. San Marchi, B. Somerday, T. Boggess, and S. Jansto, “Microstructure and Mechanical Property Performance of Commercial Grade Api,” Proceedings of the 8th International Pipeline Conference, pp. 1–9, 2010.
[7] B. Meng et al., “Hydrogen effects on X80 pipeline steel in high-pressure natural gas/hydrogen mixtures,” Int J Hydrogen Energy, vol. 42, no. 11, pp. 7404–7412, 2017, doi: 10.1016/j.ijhydene.2016.05.145.
[8] “ASTM G 192-00 - Standard Practice for Slow Strain Rate Testing to Evaluate the Susceptibility of Metallic Materials to Environmentally Assisted Cracking,” 2006. doi: 10.1520/ G0129-00R06.2.
[9] E. J. Song, S. W. Baek, S. H. Nahm, and U. B. Baek, “Notched-tensile properties under high-pressure gaseous hydrogen: Comparison of pipeline steel X70 and austenitic stainless type 304L, 316L steels,” Int J Hydrogen Energy, vol. 42, no. 12, pp. 8075–8082, 2017, doi: 10.1016/j.ijhydene.2016.12.069.
[10] T. T. Nguyen, H. M. Heo, J. Park, S. H. Nahm, and U. B. Beak, “Stress concentration affecting hydrogen-assisted crack in API X70 pipeline base and weld steel under hydrogen/natural gas mixture,” Eng Fail Anal, vol. 122, no. December 2020, p. 105242, 2021, doi: 10.1016/j.engfailanal.2021.105242.
[11] T. T. Nguyen, J. Park, W. S. Kim, S. H. Nahm, and U. B. Beak, “Effect of low partial hydrogen in a mixture with methane on the mechanical properties of X70 pipeline steel,” Int J Hydrogen Energy, vol. 45, no. 3, pp. 2368–2381, 2020, doi: 10.1016/j.ijhydene.2019.11.013.
[12] T. T. Nguyen, N. Tak, J. Park, S. H. Nahm, and U. B. Beak, “Hydrogen embrittlement susceptibility of X70 pipeline steel weld under a low partial hydrogen environment,” Int J Hydrogen Energy, vol. 45, no. 43, pp. 23739–23753, 2020, doi: 10.1016/j.ijhydene.2020.06.199.
Heat resistant coatings are used for many applications covering multiple industries and segments. These coatings face various operational conditions and are applied on different substrates. The purpose of heat resistant coatings depends on the application, but some main categories are atmospheric corrosion protection and protection against corrosion under insulation (CUI). Further, when used for stainless steel, heat resistant coatings reduce the chances for chloride stress corrosion cracking (CSCC) and oxidation.
The performance of a heat resistant coating highly depends on the duration of exposure to heat and corrosive environments, and the substrate’s thermal expansion and oxidation process. Various substrates respond differently when exposed to heat. Differences in thermal expansion of the substrate and the coating may cause the coating to crack and/or delaminate from the substrate. Different metal substrates can also form a significant oxide layer on the surface between the coating and the steel that may lead to delamination. This calls for tailormade coating solutions that can not only withstand elevated temperatures and highly corrosive conditions, but also the thermally induced stresses caused by differences in thermal expansion. To cope with the oxidation process, Jotun states “where substrates allow” limiting the continuous operational temperatures for the heat resistant coatings to the substrates’ nature given limitations.
Heat resistant coatings for atmospheric corrosion protection of carbon steel, alloyed steel and stainless steel are important to protect against corrosion. This can be during the manufacturing phase until commissioning of e.g. a hydrocarbon processing industry plant, during production shutdowns and cyclic conditions during the operational phase. For such applications it is crucial that heat resistant coatings provide corrosion protection at ambient temperatures both before and after being exposed to high operating temperatures.
Heat resistant coatings are also frequently used as one of the few effective measures against CUI. CUI is known to be a high risk for all processing plants operating at elevated temperatures with insulated piping or processing equipment. For such applications, the heat resistant coatings must withstand elevated temperatures while also being exposed to highly corrosive environments. These environments are formed in the presence of moisture from water leaking through the insulation jacket/casing or condensation, combined with impurities and salts from the surrounding atmosphere and the insulation material. Above the boiling point of water, the surface of the piping will dry out, however, the insulation material surrounding the pipe may still hold moisture. Since many operations in process plants are cyclic, CUI challenges can often be encountered although the operating temperatures are above 100 °C. NACE SP0198 defines the CUI range from –4 to 175 °C [1]. Stainless steel is used for piping in process plants when operating conditions requires. This can either be because the operating temperature is above the temperature where the structural integrity and strength of carbon steel is reduced [2]. Stainless steel might also be preferred because the liquid or gas inside the piping is highly corrosive. Stainless steel is inherently well
protected against general corrosion; however, other forms of corrosion may occur under certain circumstances such as chloride stress corrosion cracking (CSCC). Heat resistant coatings are often used as a measure to protect stainless steel against different forms of intergranular corrosion by reducing the concentration of detrimental ions and molecules at the surface of the stainless steel substrate (e.g. chloride ions and oxygen, respectively).
In addition to the various corrosive environments heat resistant coatings must withstand and protect the substrate against, these materials also must perform under mechanical loads such as stresses induced by the difference in thermal expansion between the coating and the steel substrate. The thermal expansion of a heat resistant coating can be many times larger than the thermal expansion of the metallic substrate. This difference in thermal expansion will induce mechanical stresses predominantly at the steel-coating interface and will increase as a function of temperature.
The coating can only cope with these stresses by having sufficient internal strength and adhesion to the substrate to withstand the built-up stress. However, if the dimensional difference exceeds the coating material’s internal strength and/or the coating material’s ability to adhere to the substrate, the thermal expansion may cause the coating to crack and/or delaminate from the substrate. This calls for tailormade coating solutions that can not only withstand elevated temperatures and highly corrosive conditions, but also the thermally induced stresses caused by differences in thermal expansion.
Metals oxidize. The reaction between metals and oxygen is one of the simplest chemical reactions [3, 4]. The oxidation reaction is initiated by adsorption of oxygen on the metallic surface, followed by an initial transient stage where components in an alloy will oxidize. During the initial nucleation and growth, a thin oxide layer forms and covers the entire metal surface. Surface defects and impurities in the metal and/or the gas will influence the adsorption of oxygen, nucleation, and formation of the oxide.
The stability of an oxide, and thereby whether it will form or not, can be determined by considering the Gibbs free energy of the system [5]. A useful presentation of standard free energies for the formation of selected oxides is an Ellingham-Richardson diagram as shown in Figure 1. The most stabile oxides in such a diagram will be characterized by the most negative ∆G values. This information can be used to identify which element of an alloy that will form the most stable oxide and is thereby likely to act as a protective corrosion resistant oxide layer on the base alloy.
Although the thermodynamic stability of an oxide dictates whether it will form or not, the rate of oxidation and scale growth is given by the kinetics of the oxidation process. The kinetics of oxidation is highly temperature dependent, and the increase in oxidation rate as a function of temperature is often logarithmic. Isothermal high temperature oxidation is often following a parabolic rate law as most high temperature oxidation is limited by either cation or oxygen diffusion through the forming oxide scale [6]. So, the higher amount of a component that will easily form a stable oxide, e.g. chromium, the higher oxidation rate.
At the steel-coating interface there will initially be enough oxygen to the onset and progress of oxide scale formation. However, depending on the oxygen permeability of the coating and the composition of the steel alloy, the oxide scale growth can be reduced as time increases or continue following a parabolic growth rate. For temperatures of 200 °C and lower the oxidation at the steel-coating interface will be insignificant as coatings used in that temperature usually holds good barrier properties as well as the temperature not being high enough to sustain substantial oxide growth even for highly alloyed materials.
JOTUN SETS THE CONTINUOUS OPERATIONAL TEMPERATURE LIMITS BASED ON THE SUBSTRATE’S NATURAL HEAT RESISTANT
PROPERTIES AND STATE “WHERE SUBSTRATES
ALLOW” LIMITING THE CONTINUOUS OPERATIONAL TEMPERATURES TO THE SUBSTRATES’ NATURE
GIVEN LIMITATIONS. FOR SHORTER TIME PERIODS
A HEAT RESISTANT COATING MAY TOLERATE
HIGHER TEMPERATURES THAN THE GIVEN
CONTINUOUS OPERATIONAL TEMPERATURE LIMIT.
THE COMPANY IS ALSO EXTENDING THE TEST TIME FOR HEAT EXPOSURE TO 1000 HOURS TO BETTER REPRESENT IN-FIELD EXPOSURE.
However, at higher temperatures above 450 °C the oxide scale growth on highly alloyed stainless steels, meaning alloys with more than 17 wt. % of chromium, can continue as the coatings used for such conditions will have a higher permeability of oxygen due to the more porous structure the coating material due to lack of organic components.
Thorough testing and verification of Jotun’s findings with third party test institutes concludes that when stainless steel alloys containing enough chromium are exposed for an extensive duration to temperatures exceeding 450 °C and there is sufficient access to oxygen at the coating-steel interface, a continuous growth of oxide scale will form a significant oxide layer between the coating and the steel causing delamination regardless of the coating type or technology [7].
Most organic binder polymeric material compounds will start to be thermally degraded at temperatures above 230 °C, and at temperatures above 400 °C organic polymers will be decomposed [8]. Consequently, the remaining coating material after such decomposition of the organic polymeric binder structure will have an increased porosity. Increased coating porosity will increase the oxidation rate of the substrate.
A coating can perform for some time even if the surface of the steel has started to oxidize, however continued heat exposure will eventually result in delamination. Figure 2 shows cross cut and pull-off tests of a heat resistant coating on carbon steel (S355) after continuous exposure to 650 °C. The cross cut test result seems acceptable, however a pull off test reveals lack of adhesion between the oxidized carbon steel substrate and the coating. High temperature exposure over time will therefore likely result in complete delamination from a substrate with significant oxide scale formation, regardless of the coating type or technology. Consequently, Jotun sets the continuous operational temperature limits based on the substrate’s natural heat resistant properties and state “where substrates allow” limiting the continuous operational temperatures to the substrates’ nature given limitations. For shorter time periods a heat resistant coating
may tolerate higher temperatures than the given continuous operational temperature limit.
Jotun are also extending the test time for heat exposure to 1 000 hours to better represent in-field exposure. The performance of Jotun’s heat resistant coatings is verified by third party test institutes documenting 1 000 hours dry heat exposure and various tests for anti-corrosive properties on carbon steel, alloyed steeland various stainless steel-substrates.
The performance of a heat resistant coating highly depends on the duration of exposure to heat, corrosive environments, thermal induced stresses, and the substrate’s natural oxidation process. Jotun acknowledge that substrates respond differently to high temperature exposure and have therefore developed tailor made solutions to optimize performance on various substrates and temperatures, and to meet customers’ needs in the best way possible. ‹
References
[1] SP0198-2017, Control of Corrosion Under Thermal Insulation and Fireproofing Materials—A Systems Approach, 2017.
[2] Fire Design of Steel Structures: Eurocode 1: Actions on structures Part
1-2 – General actions – Actions on structures exposed to fire Eurocode 3: Design of steel structures Part 1-2 – General rules – Structural fire design.
[3] Kofstad, P. High Temperature Oxidation of Metals; Wiley, 1967.
[4] Young, D.J. High Temperature Oxidation and Corrosion of Metals; Elsevier, 2008; Vol.1.
[5] Ellingham, H.J.T.J.Soc.Chem.Ind., London 1944, 63, 125.
[6] Wagner, C.Z. Physik. Chem. 1933, B21, 25.
[7] Lai, G. Y. High Temperature Corrosion of Engineering Alloys; ASM International, 1990.
[8] Pielichowski, K. Thermal degradation of polymeric materials, 2005.
The SÄKAPHEN® cleaning system, consisting of SÄKA 80 and SÄKA 83 Cleaning Pastes and SÄKA 81 Silicone Grease allows easy cleaning and protection of ceramic, glass or plastic high voltage isolators. The long-lasting protection avoids flashovers and ensures improved safety levels.
Sher-Bar TEC for rebar increases corrosion resistance and bond strength with concrete, enhancing infrastructure longevity, safety and sustainability.
Sherwin-Williams Protective & Marine launched Sher-Bar TEC, a transformative new coating technology for the concrete industry. Designed for an array of construction applications and environments, the textured epoxy coating (TEC) redefines standards for rebar coatings, offering increased bond strength, damage tolerance and corrosion resistance for both horizontal and vertical concrete
projects. These properties enable improved asset longevity and reduced environmental impacts associated with construction and maintenance. “Sher-Bar TEC is a breakthrough in concrete and construction innovation,” says Jeffrey Rogozinski, Global Director of Functional Coatings for Sherwin-Williams Protective & Marine. “The textured epoxy coating has the potential to significantly extend the lifespan of critical infrastructure assets – offering a cost-effective solution that adds unprecedented value. With this novel TEC technology, Sherwin-Williams Protective & Marine is ushering in a new era of infrastructure protection and sustainability.”
As a secondary coating, Sher-Bar TEC provides added protection for the industry’s leading corrosion protection solution: epoxycoated rebar (ECR), which is commonly referred to as “green bar.” With a smoother surface than uncoated rebar, ECR results in reduced bond strength with concrete, necessitating the use of
more rebar in projects. This additional rebar adds costs and weight, as well as on-site rebar grid congestion when pouring concrete. These drawbacks have limited the use of ECR worldwide, leaving structures susceptible to corrosion and decay Sher-Bar TEC, with its textured elements, offers significant improvements over both ECR and uncoated rebar, known as “black bar.” Tests by independent labs and research universities have documented and demonstrated Sher-Bar TEC’s superior performance in bond strength, durability and corrosion resistance. The research led to the development of the new ASTM A1124/ A1124M-23 Standard Specification for Textured Epoxy-Coated Steel Reinforcing Bars, underlining the importance of TEC in the construction industry. According to a Wisconsin Department of Transportation study, Sher-Bar TEC can reduce rebar overlap by 10% to 60%, compared to black bar and ECR. This reduction helps to lower project weights, raw material costs and logistical expenses while also potentially allowing for the use of higher grades of concrete. Tests at the University of Illinois showed that cracks in concrete with Sher-Bar TEC-coated rebar were about half as wide as those with ECR bars – suggesting that less road salt and water will be able to infiltrate concrete and meet rebar where it could promote corrosion. Additional tests showed concrete with Sher-Bar TEC-coated rebar had lower levels of stress because the textured rebar was more engaged in the structure.
“Extensive testing has shown that Sher-Bar TEC is a unique and value-adding solution compared to existing rebar coatings and black bar,” says Anthony Del Percio, North American Sales Manager for Rebar, Valve and Traffic Markings for Sherwin-Williams Protective & Marine. “Its performance marks a significant leap
forward in the realm of concrete reinforcement.” Application of Sher-Bar TEC is also practical and efficient in highly controlled shop conditions. After coating the rebar with powdered fusion-bonded epoxy to create ECR, the powdered Sher-Bar TEC is immediately applied. The two layers cure simultaneously and form a seamless, monolithic coating that enhances barrier and durability properties to deliver superior corrosion resistance and damage tolerance. Additionally, the resulting texture restores the desired bonding interaction between the steel and concrete that is lost with smooth ECR surfaces.
Sher-Bar TEC also provides favourable sustainability impacts. Made with up to 30% upcycled materials redirected from landfills, Sher-Bar TEC supports environmentally friendly practices and promotes the potential use of alternative cementitious technologies that could reduce the significant carbon emissions associated with concrete production. ‹
Sher-Bar TEC, a transformative new textured epoxy coating technology from Sherwin-Williams Protective & Marine, provides a textured profile on rebar that’s similar to uncoated “black bar” (right), ensuring high bond strength with concrete while also delivering helpful corrosion resistance to extend the life of concrete assets.
The new Sher-Bar TEC from Sherwin-Williams Protective & Marine features enhanced bond strength with concrete compared to ECR, allowing grid congestion reductions and faster concrete pours compared to when using ECR.
The cleaning pastes SÄKA 80 and SÄKA 83 and the silicone grease SÄKA 81 developed by SÄKAPHEN GmbH offer three advantages in one product: through excellent cleaning, sealing, and protection, they can reduce the maintenance costs of ceramic, metal, resin, and plastic high-voltage insulators placed in highly contaminated and polluted environments by 75%.
High-voltage insulators are subject to ever-increasing chemical attacks from particulate matter, exhaust gases, corrosives, salts, and other airborne impurities such as sulphur dioxide or hydrofluoric acid, as well as erosion. Insulators with roughened, dirty surfaces, in particular, provide an ideal substrate for the growth of airborne contaminant deposits. Under dry conditions, such deposits reduce the devices’ insulating power; in the presence of condensation or wet substrates, a thin layer of water can form that favours the crystallisation of salts: once a high concentration of salts is reached, its combination with conductive solid particles leads to discharges, with severe consequences for plant operation.
The product range consisting of the SÄKA 80 and SÄKA 83 cleaning pastes and the SÄKA 81 silicone grease ensures rapid cleaning and protection of high-voltage insulators.
The SÄKA 80.750 paste can be applied with a cloth and only needs to be polished to achieve excellent surface waterproofing and protection.
The product range consisting of the cleaning pastes SÄKA 80 and SÄKA 83 and the silicone grease SÄKA 81, developed by SÄKAPHEN GmbH and distributed in Italy by Donelli Alexo Srl, ensures the rapid cleaning and protection of high-voltage insulators, preventing electrical discharges and guaranteeing increased operational efficiency and safety for operators. The result of extensive tests and practical experience, these products have been formulated to effectively clean and protect ceramic, glass, plastic, and metal insulator surfaces even after just one treatment. That is why their fields of application have expanded over the years to cover multiple sectors: power plants, steel mills, transformer stations, railway lines, and industrial plants.
The SÄKA 80.750 cleaning paste was formulated and designed to protect high-voltage insulators against electrical flash-over caused by the combination of dust and moisture in the atmosphere. In addition to enabling the removal of any paint drips from pylons and other equipment in the vicinity, it forms a protective film of UV-resistant silicone resin that does not dry and creates a hydrophobic layer sealing the treated surfaces. Maintenance cycles are thus extended, and costly downtimes are significantly reduced. The SÄKA 80.750 paste is therefore the ideal product for cleaning and waterproofing smooth and abrasion-resistant surfaces in one step: it can be applied with a cloth and only needs to be polished to provide waterproofing and protection. Solventfree and dermatologically tested, the SÄKA 80.750 cleaning paste is non-hazardous, and no special equipment or extensive personal
protection equipment (PPE) is needed during its application process. Therefore, it complies with regulations such as the following:
Regulation (EC) No. 1907/2006 (REACH);
Directive 67/548/EEC (dangerous substances);
Directive 1999/45/EC (dangerous preparations);
Annex I to Directive 76/769/EEC (component limitation and technical guidelines for dangerous goods);
German Technical Rules for Hazardous Substances TRGS 200, 220 (classification, identification of goods, preparation, products, and safety data sheets).
The SÄKA 83.750 cleaning paste was formulated and developed initially as a tailor-made solution for cleaning the delicate plastic, resin, and silicone insulators of company Uniper, mainly used in underground tunnels connecting power station generators with electrical substations, where components are exposed to high levels of dust and moisture that combine to form thick layers of contaminants. High-voltage insulators treated with the SÄKA 83.750 cleaning paste emit 35 kV at the point of partial
The SÄKA cleaning pastes are composed of oils that attack the layer of dirt, abrasives that pick it up, and greases that form a thin sealing layer on the treated surface.
discharge, compared to 32 kV when using common cleaners. Additionally, this product ensures a reduced loss factor of tan (δ) = 0.2%. It is also solvent-free and dermatologically tested. As it contains physiologically safe abrasives, oils, and greases, it is non-hazardous, and no special equipment or extensive personal protection equipment (PPE) is needed during its application process.
Developed through numerous long-term tests, the high-purity methylsiloxane-based silicone grease SÄKA 81.750 is the dirt-repellent sealant of SÄKAPHEN’s cleaning system, guaranteeing high protection in highly contaminated environments. Its unique viscosity properties, controlled through the presence of inorganic thickeners, prevent the formation of a water film on insulators in areas characterised by high humidity and high particulate contamination (such as areas polluted by fly ash or salts), protecting them against flash-over and irreparable damage by forming a uniform, abrasion-resistant, water-repellent protective layer.
This product can be applied with a soft brush or cloth to an approximate thickness of 0.3 mm (300 microns) and fully polished until the surface is non-stick and almost shiny, at operating temperatures ranging from -40 to +200 °C. As with the other products in this range, SÄKA 81.750 is solvent-free and contains physiologically harmless greases. Therefore, it is non-hazardous, and no special equipment or extensive personal protection equipment (PPE) is needed during its application process.
SÄKAPHEN, therefore, can meet the multiple needs of different, ever-evolving sectors and their corrosion protection requirements thanks to the constant development of high-quality materials and advanced application methods. Its system’s excellent resistance to the most aggressive acid and alkaline agents results in maintenance cost savings of up to 75%. The cleaning pastes and silicone grease of which it consists are therefore already used, as well as the power generation industry, in numerous markets including as follows:
Railway industry – Cleaning of traction unit insulators and warning signs;
Steel and cement production – Cleaning and maintenance of machinery and transformers subject to deterioration due to the deposition of contaminants and dust;
Biomass and wood chip power plants – Cleaning of electrical filters for dust removal.
The SÄKA cleaning pastes are composed of oils that attack the layer of dirt, abrasives that pick it up, and greases that form a thin sealing layer on the treated surface. The SÄKA silicone grease, on the other hand, is a pure grease mixture that creates a slightly thicker protective and sealing layer. Therefore, in environments with high humidity or atmospheric pollution conditions, for instance from particulate matter and pollen, it is possible to combine the cleaning paste SÄKA 80.750 with the silicone grease SÄKA 81.750 to provide ceramic insulators with additional protection, thus significantly reducing the electrical permittivity of their surfaces. On the other hand, the combined use of the sealing grease and the paste SÄKA 83.750 guarantees the same excellent results on plastic, resin, and silicone insulators. ‹
SÄKAPHEN GmbH is a family-owned company recognised internationally for the quality of its coating systems. Founded in Gladbeck (Germany) in 1954 and currently led by the third generation, it has unparalleled experience in the formulation, in-house laboratory development, and field application of corrosion protection products suitable for even the harshest environments and cleaning systems for high-voltage insulators. Through constant research and development, it continues to strive for excellence with customised, high-quality coating solutions capable of withstanding any operating conditions and meeting any customer requirements. With an extensive network of authorised applicators using its baked and cold-cured coatings and distributors of its insulator cleaning system, SÄKAPHEN serves customers all over the world, from Europe to Asia and from the Middle East to North America, enabling them to take full advantage of their assets effectively and economically through efficient resource consumption.
alfredo.rondinella@uniud.it
Due to its high susceptibility to corrosion, magnesium is used in a very limited industrial applications, even when it comes to resorbable materials like those used for biomedical devices. This study aims to explore how alkaline-based geopolymer coatings, with their inherent porosity, can be utilized to modulate the corrosion rate of magnesium.
Despite its excellent properties and light weight, the use of magnesium is severely limited in several industrial applications by its high corrosion susceptibility. Even in applications, such as those of resorbable materials, where corrosion is not necessarily a harmful phenomenon, the strong reactivity hinders the employment of this material. This work is concerned with investigating the effectiveness of alkaline-based geopolymer coatings to modulate, due to the inherent porosity of the coating, the corrosion rate of magnesium. The application of the geopolymer was carried out through an established dip-coating deposition procedure. The coating was characterized morphologically and chemically by SEM/EDXS analysis. The electrochemical behaviour, on the other hand, was studied first through potentiodynamic measurements and then through electrochemical impedance spectroscopy (EIS) in different aggressive environments.
Preliminary results indicate that in the short term, the geopolymer coating offers a reduction of the corrosion rate of magnesium, which is relevant for its application as resorbable material in biomedical devices.
Introduction
Despite its low density, strength-to-weight ratio, and excellent machinability, magnesium (Mg) is very susceptible to corrosion phenomena [1], [2]. Thus, its widespread use in engineering is severely limited by its very high reactivity [3]–[5], particularly in applications where Mg is exposed to aqueous environments. There are, however, some scenarios in which the corrosion phenomena are not completely detrimental to the application of
Mg, for instance bioresorbable medical implants [6]–[8] such as cardiovascular stents, bone fixations and sutures [9].
The use of a bioresorbable material in biomedical applications eliminates the need for surgical operations to extract materials that would otherwise remain indefinitely inside the human body. The corrosion rate must still be controlled, so that the resorption rate (and thus corrosion) is properly proportioned to the rate of healing of the biological tissue. Otherwise, there is a risk that the prosthesis will lose its properties before the complete healing occurs and that the hydrogen generated by the corrosion reaction will accumulate in the biological tissue [4], [10], [11].
Surface modification is crucial for regulating the corrosion rate of magnesium alloys, especially for prosthetic implants. Various techniques, such as hydrofluoric acid treatments, chemical deposition, organic coatings, and 3D printing of polymeric coatings, have been developed for this purpose [12]–[17]. While some treatments promote bone regeneration, they may lack long-term corrosion resistance. Conversely, certain coatings offer excessive protection, prolonging dissolution unsuitably for temporary implants [18]–[20]. Additionally, some methods require complex procedures or costly materials [18]–[20].
A possible solution for use in this context can be sought in alkaline-based geopolymer coatings. These materials consist of aluminosilicates formed through a polycondensation reaction in an alkaline environment. They possess an amorphous, polymerlike structure, are mostly inexpensive and can be produced by a simple sol-gel reaction [21]–[24]. The study of geopolymers began in the 1970s as a green alternative to Portland cement but, over the years, it has found several other applications including the biomedical field. They are biocompatible, antibacterial materials and offer excellent mechanical properties together with adjustable porosity [25]. The latter becomes crucial from the perspective of corrosion rate regulation.
This study investigates the effect of geopolymeric coatings in controlling the corrosion rate of the Mg. Given geopolymeric coatings inherent porous nature, they should facilitate gradual penetration of bodily fluids to provide protective functions without creating a complete barrier. The research focuses on evaluating the corrosion resistance of Mg samples coated with geopolymer in fluid environments mimicking bodily conditions. Geopolymer application involved a dip-coating process over AZ31 alloy preetched with hydrofluoric acid (HF). Morphological features were analysed through scanning electron microscopy (SEM) and stereoscopic microscopy. Corrosion protection was assessed using electrochemical impedance spectroscopy (EIS) and potentiodynamic polarizations.
Mg Samples preparation and geopolymeric formulation
The composition of the geopolymeric coating used in this work was optimized in a previous study [30] and used metakaolin as aluminosilicate source. It is obtained by mixing metakaolin powder (ArgicalTM-M 1200S, Imerys Performance Minerals, Paris, France), sodium silicate solution (Na2SO3, F.lli Mazzon, Vicenza, Italy), 8M sodium hydroxide solution (prepared using 98% sodium hydroxide pellets from Titolchimica Spa-Pontecchio Polesine, Ro-IT), and distilled water. The specific formulation of the geopolymeric coating, is detailed in Table I
Table I: Geopolymer reagents formulation.
Mg plates measuring 20x20x2 mm were utilized for this research. They underwent polishing using Silicon Carbide sandpaper ranging from 250 to 1200 grit, employing a grinder–polisher apparatus (FORCIPOL 300-1V grinder–polisher, Metkon, Turkey). Additionally, the samples were etched with a 10% v/v hydrofluoric acid solution (48% solution, Sigma-Aldrich, Missouri, USA) for two seconds to enhance coating adhesion. Subsequently, the samples were rinsed in distilled water to remove any residual acid. To prevent surface oxidation, the samples were then immersed in ethanol for storing and thoroughly dried using compressed air immediately before the dipping procedure. The geopolymeric coating was applied using a dip-coating
process. Following preparation, the plates were affixed to a moving support connected to the dip-coating system (KSV NIMA Dip Coater Single Vessel, Biolin Scientific, Vastra Gotaland County, Sweden), which operated at immersion and extraction rates of 100 mm/min with a contact time with the geopolymer solution of 60 seconds. After coating, the samples were air-dried for five hours at room temperature, followed by curing in an oven at 70°C for 12 hours. As specified above, the optimization of the coating and in particular its mechanical performance has already been achieved in previous work. Following those specifications, 3 depositions were made to obtain a multilayer coating. Before each additional layer was applied, the samples underwent immersion in demineralized water to improve adhesion with the subsequent layer. This immersion utilized OH ions in the water to promote the formation of chemical bridges. The resulting coating exhibited a porosity volume ranging from 0.04 to 0.05 cm3/g, with an average depth of at least 5.1 nm [24].
The morphology and composition of the coated samples were analyzed using scanning electron microscopy (SEM, ZEISS EVO 40 SEM, Zeiss Group, Jena, Germany) combined with energy-dispersive X-ray spectroscopy (EDXS). Cross-sectional examination of the coating was conducted to measure their thickness and evaluate the interface homogeneity. Electrochemical characterization tests were conducted on both uncoated and coated Mg substrates. The electrolytes used in the study are the following:
9 g/l NaCl solution;
Phosphate Buffer Solution (PBS)
Hanks Balances Salt Solution (HBSS); Corrosion measurements were conducted using a standard threeelectrode cell, with an Ag/AgCl (3M KCl) reference electrode and a Pt wire counter electrode. Experiments were carried out using a Metrohm Autolab PGSTAT30 Potentiostat/Galvanostat and Nova 2.1 software. Potentiodynamic polarization curves were generated from -0.100 V to 1 V (with respect to the OCP value, in the anodic direction) at 0.2 mV/s, and corrosion rates were calculated using the Tafel’s method. Electrochemical impedance spectroscopy (EIS) was performed at 0 h, 24 h, 192 h, and 360 h time intervals. EIS experiments employed a sinusoidal wave of 10 mA amplitude across a frequency range from 0.01 to 10 kHz logarithmically spaced (7 points per decade).
Figure 1 shows SEM images of the surface and of cross section of a coated specimen in panel (a) and panel (b), respectively. The surface morphology is homogeneous and no particular defects are visible. The cross-sectional view shows a coating with thickness of about 90 μm. It is possible to distinguish the interface between the different layers of the coating, each of which is highlighted by a dashed white line. Within the coating, unreacted metakaolin particles can be observed. This phenomenon is not unexpected, since the conversion of the starting powders is never complete. Such a low amount of unreacted particles does not affect the final properties of the coating for the purpose of slowing down corrosion.
The chemical composition of the coating, obtained by EDXS analysis of the areas shown in Figure 1, is shown in Table II. The presence of the chemical elements is justified by the starting
reagents. The coating has a nearly constant composition both in plan and cross-section, even between different layers.
Table II. Chemical composition of the geopolymer coating, obtained from analysis of the areas in Figure 1.
Before each additional layer was applied, the samples underwent immersion in demineralized water to improve adhesion with the subsequent layer. This immersion utilized OH ions in the water to promote the formation of chemical bridges. The resulting coating exhibited a porosity volume ranging from 0.04 to 0.05 cm3/g, with an average depth of at least 5.1 nm.
Figure 2 shows the polarization trends for magnesium samples in contact with NaCl, PBS and HBSS solution for both uncoated (panel a) and coated (panel b) samples.
Uncoated magnesium shows different polarization curves for the three solutions analysed. It can be seen from the graph that the NaCl solution is the most aggressive, as it is the one that generates the highest anodic currents, which are associated to higher corrosion rates.
The polarization trends for the coated magnesium samples after 10 min immersion in NaCl, PBS and Hanks’ solution are significantly lowered compared to the case of uncoated magnesium samples. This implies an increase in corrosion resistance due to the presence of the coating.
From the graphs it is possible to see that the anode branches have changed substantially, presenting a passivity range that indicates some protection by the geopolymer coating. All samples present a passivity breakdown, probably due to the initiation of pitting corrosion at those potentials.
Corrosion rates were derived by the Tafel’s method of Tafel lines. They are expressed in terms of current density per unit area in Table III. It can be seen that, when comparing uncoated and coated samples for each solution, the corrosion rates decrease. This phenomenon is particularly evident in the case of the NaCl solution, where the value of the corrosion rate becomes almost an order of magnitude smaller.
Table III. Average corrosion current density for coated and uncoated magnesium samples in contact with NaCl, PBS and HBSS, as calculated from Figure 2.
In Figure 3, the Nyquist diagrams over time for magnesium samples in contact with NaCl solution are shown.
It can be seen that, for the uncoated samples in Figure 3 (a), the impedance values are very low immediately after immersion (0 hours), which indicates high reactivity of the metal in accordance with the polarization curves.
After 24 hours of immersion the impedance values increase significantly, indicating a conspicuous decrease in the reactivity of the sample, probably due to the formation of a surface oxide/ hydroxide film. In the transition from 24 to 192 to 360 hours there is a gradual decrease of impedance values.
The shape of the loops is double semicircle, that is, with highfrequency capacitive loops followed by low-frequency capacitive
The polarization trends for the coated magnesium samples after 10 min immersion in NaCl, PBS and Hanks’ solution are significantly lowered compared to the case of uncoated magnesium samples. This implies an increase in corrosion resistance due to the presence of the coating.
loops. The first capacity loop at high frequency can be associated with charge transfer at the interface and double layer, while the second loop at low-frequency should be associated with the presence of oxides/hydroxides, which can lead to diffusive processes.
Conversely, Figure 3 (b) shows that immediately after immersion the impedance values for the coated samples are high, indicating very low metal reactivity. Increasing the immersion time, however, a conspicuous increase of the reactivity of the sample can be seen. In fact, there is a gradual decrease of the impedance values, which is evident for the measurements after 192 and
360 hours of immersion. This indicates a high corrosion rate for longer immersion times. Figure 4 shows the Nyquist plot for the uncoated and coated magnesium immersed in PBS solution, respectively in panel a) and b). It can be seen that the reactivity of the sample immersed in PBS follows the same trend observed for the tests in NaCl solution, i.e., at 0 hours of immersion the impedance values for uncoated samples are very low, at 24 hours of immersion the impedance values increase significantly and then gradually decrease for longer immersion times.
The 0-hour graph of the uncoated sample presents a highfrequency capacitive loop followed by a low-frequency capacitive one. The 24- to 360-hour diagrams present a purely inductive form. The inductive behaviour is usually attributed to adsorbed reactive phases [26].
Thus, initially the sample is found to be protected by a surface film that later dissolves. The surface film that imparts protection to the pure magnesium sample is probably due to the deposition of phosphate salts contained in the PBS solution [27]. The coated sample (cf. Figure 4 b)) indicates very low metal reactivity at 0 hours, which then grows very fast in the following hours.
The shape of the loops at 0 and 24 hours is flattened and slightly inductive with fairly high impedance values due to the presence of the coating. The inductive behaviour is usually attributed to adsorbed reactive phases. The loops for the magnesium sample immersed for longer times shrink significantly, indicating poor protection by the coating.
Figure 5 illustrates the behaviour of a Nyquist plot for uncoated and coated magnesium samples immersed in HBSS. It can be
seen that the reactivity of the uncoated sample immersed in Hanks’ solution follows the same trend found in PBS solution.
Figure 6 shows how the impedance modulus at 1 Hz changes over time for the magnesium samples immersed in the different solutions. From the impedance modulus plots in Figure 6, it can be seen that HBSS environment seems to be the least aggressive solution toward uncoated samples while PBS and NaCl solution are progressively more aggressive. The coating also seems to exert a more protective effect on samples that are immersed in HBSS solution. This trend is confirmed by the corrosion rates obtained from the polarization measurements (Figure 2 and Table III). For prolonged times, however, the values of electrochemical impedance measurements decrease to such an extent that they all appear to be identical. The comparison between the electrochemical impedance spectroscopy analysis
in Figure 3 to 6, shows that the coating is effective only in the first 24 hours of immersion. In fact, it can be seen that immediately after immersion in the testing electrolyte (0 hours) the impedance modulus has very high values for coated samples immersed in all three solutions. Whereas, after 24 hours of immersion there is a rapid decrease in the protective properties of the coating. This phenomenon may be due to the porosity of the geopolymer. In the instants after immersion, the geopolymer coating is wet only superficially; the electrolyte does not reach the metal substrate, which is therefore protected. Thereafter, the electrolyte begins to penetrate into the coating by capillarity, coming into contact with the metal. For long immersion times, magnesium samples coated with geopolymer are more active than uncoated samples. This phenomenon could be attributed to the coating. Generally, in Hanks and PBS solution, phosphates are deposited on the
surface of the metal samples, providing a film that hinders the action of chlorides, effectively protecting the underlying metal [28]. The geopolymer coating, however, hinders the deposition of phosphate salts, which makes the metal more susceptible to attack by aggressive species.
The objective of this work was to study the degradation of magnesium alloys and to test whether a geopolymer-type coating could allow controlled and uniform degradation of the metal substrate, in order to use magnesium for biomedical bioresorbable prostheses.
The geopolymer coating has a homogeneous morphology and composition;
For short periods of immersion, polarization and electrochemical impedance spectroscopy measurements showed that the coating was protective for all samples in the three solutions examined;
There is a gradual decline in the effectiveness of the coating over time. Electrochemical impedance spectroscopy measurements show that after 24 h of immersion, the geopolymer loses its protective ability due to the intrinsic high porosity of
the coating. Also, as time progresses, the coating causes the corrosion rate to increase compared to uncoated pure magnesium samples, especially in PBS and Hanks’ solution.
This work shows that, although there is a need for optimization of the coating porosity, geopolymer coatings are a promising possibility for modulating magnesium corrosion rates. ‹
The objective of this work was to study the degradation of magnesium alloys and to test whether a geopolymer-type coating could allow controlled and uniform degradation of the metal substrate, in order to use magnesium for biomedical bioresorbable prostheses.
References
[1] A. Atrens, M. Liu, N. I. Z. Abidin, and G.-L. Song, “Corrosion of magnesium (Mg) alloys and metallurgical influence,” in Corrosion of Magnesium Alloys, Elsevier, 2011, pp. 117–165.
[2] N. I. Zainal Abidin, D. Martin, and A. Atrens, “Corrosion of high purity Mg, AZ91, ZE41 and Mg2Zn0.2Mn in Hank’s solution at room temperature,” Corros. Sci., vol. 53, no. 3, pp. 862–872, Mar. 2011.
[3] G. L. Song and A. Atrens, “Corrosion mechanisms of magnesium alloys,” Adv. Eng. Mater., vol. 1, no. 1, pp. 11–33, Sep. 1999.
[4] G. Song and A. Atrens, “Understanding magnesium corrosion—A framework for improved alloy performance,” Adv. Eng. Mater., vol. 5, no. 12, pp. 837–858, Dec. 2003.
[5] E. Ghali, “Magnesium and Magnesium Alloys,” in Uhlig’s Corrosion Handbook, Hoboken, NJ, USA: John Wiley & Sons, Inc., 2011, pp. 809–836.
[6] A. Atrens, M. Liu, and N. I. Zainal Abidin, “Corrosion mechanism applicable to biodegradable magnesium implants,” Mater. Sci. Eng. B Solid State Mater. Adv. Technol., vol. 176, no. 20, pp. 1609–1636, Dec. 2011.
[7] N. I. Zainal Abidin et al., “The in vivo and in vitro corrosion of high-purity magnesium and magnesium alloys WZ21 and AZ91,” Corros. Sci., vol. 75, pp. 354–366, Oct. 2013.
[8] N. I. Zainal Abidin, A. D. Atrens, D. Martin, and A. Atrens, “Corrosion of high purity Mg, Mg2Zn0.2Mn, ZE41 and AZ91 in Hank’s solution at 37 °C,” Corros. Sci., vol. 53, no. 11, pp. 3542–3556, Nov. 2011.
[9] A. Atrens, G.-L. Song, F. Cao, Z. Shi, and P. K. Bowen, “Advances in Mg corrosion and research suggestions,” J. Magnes. Alloy., vol. 1, no. 3, pp. 177–200, Sep. 2013.
[10] G. Song and S. Song, “A possible biodegradable magnesium implant material,” Adv. Eng. Mater., vol. 9, no. 4, pp. 298–302, Apr. 2007.
[11] G. Song and A. Atrens, “Understanding magnesium corrosion. A framework for improved alloy performance,” Advanced.
[12] L. Mao, G. Yuan, J. Niu, Y. Zong, and W. Ding, “In vitro degradation behavior and biocompatibility of Mg–Nd–Zn–Zr alloy by hydrofluoric acid treatment,” Mater. Sci. Eng. C Mater. Biol. Appl., vol. 33, no. 1, pp. 242–250, Jan. 2013.
[13] A. Zomorodian et al., “Anti-corrosion performance of a new silane coating for corrosion protection of AZ31 magnesium alloy in Hank’s solution,” Surf. Coat. Technol., vol. 206, no. 21, pp. 4368–4375, Jun. 2012.
[14] Q. Zhao, X. Guo, X. Dang, J. Hao, J. Lai, and K. Wang, “Preparation and properties of composite MAO/ECD coatings on magnesium alloy,” Colloids Surf. B Biointerfaces, vol. 102, pp. 321–326, Feb. 2013.
[15] S. Hiromoto, M. Tomozawa, and N. Maruyama, “Fatigue property of a bioabsorbable magnesium alloy with a hydroxyapatite coating formed by a chemical solution deposition,” J. Mech. Behav. Biomed. Mater., vol. 25, pp. 1–10, Sep. 2013.
[16] A. Zomorodian, M. P. Garcia, T. Moura e Silva, J. C. S. Fernandes, M. H. Fernandes, and M. F. Montemor, “Corrosion resistance of a composite polymeric coating applied on biodegradable AZ31 magnesium alloy,” Acta Biomater., vol. 9, no. 10, pp. 8660–8670, Nov. 2013.
[17] N. Scharnagl, C. Blawert, and W. Dietzel, “Corrosion protection of magnesium alloy AZ31 by coating with poly(ether imides) (PEI),” Surf. Coat. Technol., vol. 203, no. 10–11, pp. 1423–1428, Feb. 2009.
[18] G. Song, “Control of biodegradation of biocompatable magnesium alloys,” Corros. Sci., vol. 49, no. 4, pp. 1696–1701, Apr. 2007.
[19] M. P. Staiger et al., “Summary of the panel discussions at the 2nd Symposium on Biodegradable Metals, Maratea, Italy, 2010,” Mater. Sci. Eng. B Solid State Mater. Adv. Technol., vol. 176, no. 20, pp. 1596–1599, Dec. 2011.
[20] G. L. Song, “Control of degradation of biocompatible magnesium in a pseudo-physiological environment by a ceramic like anodized coating,” Adv. Mat. Res., vol. 29–30, pp. 95–98, Nov. 2007.
[21] J. Davidovits, “Geopolymers: Ceramic-like inorganic polymers,” Journal of Ceramic Science and Technology, vol. 8, no. 3, pp. 335–350, 2017.
[22] H. Castillo, H. Collado, T. Droguett, M. Vesely, P. Garrido, and S. Palma, “State of the art of geopolymers: A review,” E-polymers, vol. 22, no. 1, pp. 108–124, Jan. 2022.
[23] N. Shehata, E. T. Sayed, and M. A. Abdelkareem, “Recent progress in environmentally friendly geopolymers: A review,” Sci. Total Environ., vol. 762, no. 143166, p. 143166, Mar. 2021.
[24] E. Furlani, E. Aneggi, A. Rondinella, M. Zanocco, L. Fedrizzi, and S. Maschio, “The Effect of the P/Si Ratio on the Preparation and Properties of Phosphoric Acid-Metakaolin Geopolymers,” Journal of Ceramic Science and Technology, vol. 12, no. 1, pp. 19–28, 2021.
[25] A. Rondinella et al., “Mechanical and antibacterial behavior of multilayered geopolymer coatings on Ti6Al4V alloys,” J. Mater. Sci., vol. 57, no. 39, pp. 18578–18588, Oct. 2022.
[26] S. Feliu Jr, “Electrochemical impedance spectroscopy for the measurement of the corrosion rate of magnesium alloys: Brief review and challenges,” Metals (Basel), vol. 10, no. 6, p. 775, Jun. 2020.
[27] L. Xu, E. Zhang, D. Yin, S. Zeng, and K. Yang, “In vitro corrosion behaviour of Mg alloys in a phosphate buffered solution for bone implant application,” J. Mater. Sci. Mater. Med., vol. 19, no. 3, pp. 1017–1025, Mar. 2008.
[28] M. Alvarez-Lopez et al., “Corrosion behaviour of AZ31 magnesium alloy with different grain sizes in simulated biological fluids☆,” Acta Biomater., vol. 6, no. 5, pp. 1763–1771, May 2010.
Rising up into the sky above Paris for 135 years, it is one of the most visited monuments in the world. Today, the Eiffel Tower is at the centre of much controversy related to its maintenance and its twentieth painting campaign, which is taking far longer than planned: the Dame de Fer is beginning to show its wrinkles.
The news has gone around the world – the six-day strike called by the employees of SETE, the Eiffel Tower operating company, between 19 and 25 February has called attention to an issue that those working daily in contact with the world’s most famous Iron Lady say has never been so dramatic: the corrosion of its puddle iron beams1
How is it that such a common problem with metal surfaces had never been highlighted so blatantly and in such a high-risk structure as the Eiffel Tower? To understand this, we need to take a few steps back.
Standing at over 300 metres high, the Eiffel Tower has been rising over the rooftops of the French capital since 15 May 1889, when it was opened to the public for the Paris Exposition, two years after its foundations were laid. Presented by two engineers from the Compagnie des Établissements Eiffel, managed by Gustave Eiffel, one of the most respected “iron architects” of the time, this project had won the competition held to create a monumental work that was unique in the world and bound to become one of the capital’s most interesting sights, in the intentions of the French government that selected the winning design. It was to stand for twenty years, just long enough for Gustave Eiffel to recoup the
1 Puddling was the first technique to obtain actual steel, which has a uniform carbon concentration in each part, between that of soft iron and that of cast iron, which is harder and more brittle. https:// en.wikipedia.org/wiki/Puddling_(metallurgy)
costs of building the structure, which he financed largely out of his own pocket, but it soon became an irreplaceable symbol of the city.
Let us look at some of its construction features in detail2:
Workshop drawings: 5,300;
Composition: 18,038 metal pieces and 2,500,000 rivets;
Total weight: 10,000 tonnes;
Metalwork weight: 7,300 tonnes;
Total cost: 7,800,000 gold francs;
Number of visitors: over 200 million since 1889;
Number of steps: 1,665 from ground level;
Pitch between the pillars at the base: 124.90 metres;
Spacing between pillars: 72.25 metres;
Width of the pillars: 26.08 metres.
Since its foundation, the Tower’s 250,000 m2-wide surface has been repainted every seven years, with a total of 60 tonnes of paint applied in an operation that lasts an average of 16 months at an average total cost of 3 million Euros. Its official website states that “The repainting campaign is an important event in the life of the monument and takes on a truly mythical nature, as with everything linked to the Eiffel Tower. It represents the lasting
2 https://en.wikipedia.org/wiki/Eiffel_Tower
The Eiffel Tower is composed of 18,038 metal pieces and 2,500,000 rivets.
Presented
by two engineers from the Compagnie des Établissements Eiffel, managed by Gustave Eiffel, one of the
most respected “iron architects” of the time, the project had won the competition held to create a monumental work that was unique in the world and bound to become one of the capital’s most interesting sights, in the intentions of the French government that selected the winning design.
quality of a work of art known all over the world, the colour of the monument that is symbolic of the Parisian cityscape, the technical prowess of painters unaffected by vertigo, and the importance of the methods implemented.3”
Already at the time of its construction, Gustave Eiffel emphasised the importance of its paintwork: “We will most likely never realize the full importance of painting the Tower, that it is the essential element in the conservation of metal works, and the more meticulous the paint job, the longer the Tower shall endure. This consideration is of special importance for the Tower, due to the small volume of each of its components, their low thickness, and the exceptional weathering to which they were exposed.4”
On average, therefore, the Iron Lady changes the colour of her “dress” every seven years. Venetian red was chosen for its first “dress”, applied directly in the Eiffel workshop in four coats of lead paint (minium), now banned but considered the best corrosion protection solution back then. Immediately after its inauguration for the Paris Exposition, it was coated with a thick layer of reddish brown paint and, later, in 1892, with an ochre brown product. In 1899, shortly before the 1900 World’s Fair, it turned yellow: five shades of this colour were applied, from yellow-orange at the
3 https://www.toureiffel.paris/en/the-monument/painting-eiffel-tower 4 ibidem
base to light yellow at the top. “The fact that these two early repainting campaigns were undertaken less than eleven years apart shows how important it was to Gustave Eiffel that the metal structure be protected, as this was the only way to ensure it could remain standing. Each repainting campaign was an opportunity to experiment with new products and compositions, entrusted to different companies (Société anonyme des gommes nouvelles et vernis in 1889, Georges Hartog & Cie in 1900) in order not only to improve the Tower’s protection, but also to offer a new understanding of this singular building.5” In 1907, when the Tower became permanent, Gustave Eiffel opted for the yellowbrown colour bound to cover it for forty-seven years. In 1954, the structure returned to its origins with a brownish-red colour, whereas the bronze-like shade by which it is now known, called “Eiffel Tower Brown”, was chosen in 1968.
This historical monument’s official website also presents a detailed analysis of the data and procedures involved in its coating process.
5 P.-A. Gatier, “La Tour Eiffel, une histoire de couleur” in “La Tour Eiffel sous toutes ses couleurs”, La lettre de l’Académie des Beaux-Arts numéro 95, pp. 28-33.
The
is currently undergoing its twentieth repainting campaign.
Here, we summarise the key figures of this monumental intervention work:
60 tonnes of paint;
about 50 painters, all of them specialists in work on metallic structures at great heights and on towers, and completely unaffected by vertigo;
the weight of eroded paint between two painting campaigns is estimated at 15 tonnes;
250,000 m² are repainted;
55 kilometres of safety line.
Each campaign is also an opportunity to check the building’s condition in detail and, if necessary, replace any corroded metal parts. The process’ scale and complexity require a rigorous method that includes as follows:
a preparatory stage to search for the most corroded areas;
paint stripping of these areas;
any structural repairs;
surface cleaning in preparation for the subsequent application phase;
application of an anti-rust primer;
second application to strengthen the rust-proofing;
application of a final coat.
Depending on its complexity, a painting campaign can last, on average, from eighteen months to more than three years
(except for the current one, which we will discuss later), with any interruptions being due to the weather, both in winter and summer – considering that it is impossible to paint on a substrate that is too cold and the paint does not adhere well in wet conditions. Two more interesting facts about the coating phase: painters still work today with the traditional methods used in Gustave Eiffel’s time, applying the paint mainly by hand with Guipon brushes – so much so that, hanging with harnesses from the structure while repainting it, they have become the iconic symbol of this operation. Moreover, three tones characterise the paint used, from the darkest one at the base to the lightest one on the top, to create a visual impression of uniformity when viewed from afar.
In 130 years, therefore, the Eiffel Tower has already been repainted 19 times. Its twentieth, complex painting campaign began in 2019. Intended to bring the structure back to the splendour of its early 20th-century golden “dress” for the Paris 2024 Olympics, it is however taking longer than planned due to numerous setbacks.
An article by Pierre-Antoine Gatier, the architect in charge of Historical Monuments whose company was entrusted with the management of this latest repainting campaign, states that this intervention “constitutes a new stage in the history of the Eiffel Tower, as we are also planning to strip the previous layers of paint
off and to restore the structure itself. This is a major turning point towards a new approach to conservation […] that aims to mitigate the expansive corrosion of ferrous materials. It also relates to an extraordinary cultural history surrounding the choice of colour and the Tower’s place in the larger urban landscape of Paris. The scientific approach implemented in the context of this 20th painting campaign thus integrates an adapted study methodology which combines analyses of historical data with scientific information gathered on site during complementary inspection campaigns. This method has allowed us to produce a detailed analysis of the history of the Eiffel Tower’s painting campaigns, with information on the colours used, their composition, manufacturers, applicators, the reasons for changes in colour, and so on.6”
After a nine-month break due to the pandemic, the campaign resumed in January 2022, only to be interrupted again due to the high lead level detected, generated by the removal of the previous 19 layers of paint. As an article in France Bleu stated, “Lead levels around the monument continue to be problematic. The technique called piquage, used to remove rusty layers of paint by collecting them in a large net, slowed down the work. The collection of the oldest paint layers released a large amount of lead.7” Lead is a carcinogenic agent, so piquage workers must wear suitable protective masks and take a decontamination shower at the end of each work shift.
The goal of the City of Paris was for the Eiffel Tower to be recoated entirely for the start of the Paris 2024 Olympics, but work is now planned to be suspended for the duration of the competition and only resumed at the end of the Games.
In the initial plans, as mentioned, the Eiffel Tower was to stand in the Paris sky for only twenty years: its dismantling should have taken place in 1909, but long before that, despite initial scepticism often translated into outright hostility, the Dame de Fer had already won the hearts, and eyes, of Parisians – and the whole world. Indeed, its dismantling would have solved, albeit drastically, one of the most severe problems afflicting its metal structures: corrosion. Gustave Eiffel himself had stated that ‘identifying and stopping the spread of rust is the biggest challenge to the construction’s longevity” and identified a possible solution in frequent maintenance, suggested to keep the structure in good condition for as long as possible. In particular, some defects that had never surfaced before, such as rust stains and widespread
6 ibidem
7 https://www.francebleu.fr/infos/culture-loisirs/paris-la-tour-eiffel-va-etre-partiellement-repeintepour-les-jo-2024-4579556
cracks, came to light due to the delays in the last repainting work. This was the situation noted and denounced by workers on strike in February, who were concerned about the structure’s degradation, even visible to the naked eye. The strike, which blocked tourists’ access to one of the most famous monuments, obviously had an international echo that sparked a debate.
Already in a June 2022 article, the weekly publication Marianne provocatively wondered whether, after watching Notre Dame burn, Parisians would witness another catastrophe: the collapse of their symbol, the Eiffel Tower8. “According to several confidential reports (three confidential surveys carried out between 2010 and 2016, Ed.),” the article read, “the most famous French monument has been in a very degraded state for several years, and its maintenance leaves much to be desired.” One reported testimony was certainly not reassuring: “In emergency cases (for damaged surfaces, Ed.), on certain areas, a coat of paint is simply applied over existing layers that are flaking off. That is heresy.”
The problem stressed by many is that the Eiffel Tower would need a complete renovation but is currently undergoing a simple cosmetic makeover in anticipation of this year’s Olympics. The cost of this campaign, during which one-third of the monument would have had to be dismantled to apply two new layers of paint, amounts to 60 million Euros.
However, the unforeseen events we mentioned have meant that
8 https://www.marianne.net/societe/mal-en-point-rouillee-la-tour-eiffel-va-t-elle-tomber
In 130 years, the Eiffel Tower has already been repainted 19 times. Its twentieth, complex painting campaign began in 2019. Intended to bring the structure back to the splendour of its early 20th-century golden “dress” for the Paris 2024 Olympics, it is however taking longer than planned due to numerous setback.
only 3% of the construction is going to be repainted before the major sporting event that will turn the world’s cameras towards Paris. According to the Guardian, “The company that oversees the Tower, SETE, which is 99%-owned by the city hall, is reluctant to close it for a long period because of the tourist revenue that would be lost. The Tower receives about 6 million visitors in a typical year, making it the fourth most visited cultural site in France after Disneyland, the Louvre, and the Palace of Versailles. Its Covidenforced closure in 2020 led to a loss of €52m in income.9” The British newspaper continued this analysis by pointing out that in a 2014 report, expert paint company Expiris found the Tower had cracks and rusting, and only 10% of the newer paint on the Tower was adhering to the structure. “Even if the general state of the anti-corrosion protection seems good to the eye, this can be misleading. [...] It cannot be envisaged to plan for a new application of a coat of paint that will do nothing but increase the risk of a total loss of adhesion in the system10.” A third report in 2016 found 884 faults, including 68 that were said to pose a risk to “the durability” of the structure. According to many experts, therefore, the current repainting campaign would be a palliative, whereas the Tower would need a far more radical intervention to protect it from the wear and tear of time.
Architect, engineer, and historian Bertrand Lemoine, however, is more optimistic: according to him, “the enemy of iron is corrosion, caused by water and air that gradually oxidise iron exposed to
9 https://www.theguardian.com/world/2022/jul/04/eiffel-tower-riddled-with-rust-and-in-need-ofrepair-leaked-reports-say
10 ibidem
A forward-looking, effective intervention strategy is needed for the Eiffel Tower. It is impossible to think of Paris, and France, without this old Lady – with strong bones but weak armour – and without what it has been representing throughout its long history as the symbol of modern and industrial engineering in the transition between the 19th and 20th centuries.
open air”, but “if it is repainted, the Eiffel Tower can last forever”11. The same opinion is held by Kako Naït Ali, a materials engineer and corrosion specialist, who explained in an interview that corrosion is the natural degradation of iron, but there is nothing dramatic about it12. “We should be vigilant in areas where it has a structural impact. The areas where rust is most visible are not necessarily those where its presence is the most problematic: between rivets, for example, it is not visible. If corrosion were to affect the area of a rivet, the resulting deformations could create gaps and allow air and water to pass through, further exacerbating the problem.” At the same time, Naït Ali emphasises that the monument cannot
11 https://www.toureiffel.paris/en/news/130-years/how-long-can-tower-last
12 https://lanouvellerepublique.fr/a-la-une/corrosion-sur-la-tour-eiffel-il-faudrait-completement-ladecaper
be left in this state. “If we wanted to keep it as long as possible, we would have to disassemble and repaint it completely. The building is covered with 3 mm of paint: the 19 layers applied over one another since its construction. In many areas, old paint and corrosion traces are removed manually before applying the new coating layer. It is the resulting irregularity of the substrate that produces the marbling-like visual appearance under the paint. It is not ideal for sustainability, either,” said the expert.
The photos of the Dame de Fer’s corroded parts taken and posted by striking workers and visitors went around the web, raising alarmed and concerned reactions. However, those responsible for the twentieth painting campaign reassured the success of this
latest intervention, explaining its related difficulties in an interview with franceinfo13. “This is the first time we have dismantled the Tower. It is an incredible success to have been able to realise this project,” emphasised Pierre-Antoine Gatier, referring to this technological feat. The dismantling work was all the more difficult as it was necessary to deal with the lead in the Tower’s coating: “We had to reinvent all the implemented techniques, redefine all work protocols. This was expensive,” explained the architect. He then added, “After the paint stripping operation carried out at the end of the pandemic, the iron we brought back to the surface is in an exceptional state of preservation. As for corrosion, it is strictly superficial and does not call into question the solidity of the iron parts.” Magazine Marianne’s article also mentioned the existence of 68 parts subjected to reporting out of a total of over 18,000 pieces. However, Gatier replied that, “These are secondary elements. There is no urgency regarding these repairs.”
The franceinfo article also quotes Bernard Giovanonni, SETE’s technical advisor from 2009 to 2016, who drew up the three reports mentioned by Marianne at the company’s request. “We are lucky: the Eiffel Tower is made of puddle iron, a material on which corrosion is less aggressive. The main structure of the Eiffel Tower endures.”
The percentage of the Tower repainted to date is 60% and includes “the outer faces of the four pillars, the decorative arches, and almost the entire spire,” SETE told franceinfo. Pierre-Antoine Gatier hopes to “finish painting all the exterior faces of the Tower” by the start of the Olympic Games. Afterwards, the work is scheduled to resume to paint the lower interior faces, the parts where the coating is most damaged, in 2025-2026. According to SETE, the twenty-first painting campaign, scheduled for after 2026, will include a new paint stripping phase, particularly on the decorative arch between the south and west pillars.
In the pages of this magazine, we have repeatedly emphasised the consequences of corrosion and the high costs involved in restoring damaged structures. The circumstances we have described by quoting some concerned testimonies from French and international media indicate that a forward-looking, effective intervention strategy is needed for the Eiffel Tower. It is impossible to think of Paris, and France, without this old Lady – with strong bones but weak armour – and without what it has been representing throughout its long history as the symbol of modern and industrial engineering in the transition between the 19th and 20th centuries. ‹
13 https://www.francetvinfo.fr/vrai-ou-fake/vrai-ou-faux-la-tour-eiffel-est-elle-dans-un-etat-dedelabrement-avance_6381535.html
AkzoNobel Intersleek® 1100SR coating successfully reduced costs and carbon emissions
Performance data from ships show that the coating Intersleek 1100SR® developed by AkzoNobel helped to reduce fuel bills by $8 billion and emissions by 41 million tons.
Back in 2013, when the Marine and Protective Coatings business of AkzoNobel launched the Intersleek 1100SR® coating, the pioneering product sent shockwaves rippling through the industry. It was the first biocide-free fouling control coating in the whole world to feature patented slime release technology that could tackle micro-fouling on the hulls of the ships. It has since set the standard for foul release technology, having been applied to more than 3,000 vessels. The product works by removing any slime built up during docking, which is then released when the vessel travels through the water. This helps to significantly reduce drag, improve fuel efficiency and reduce CO2 emissions.
As a matter of fact, real-world performance data compiled from ships coated with Intersleek 1100SR over the past ten years shows that the coating has slashed ship fuel bills by $8 billion and reduced 41 million tons of CO2 emissions.
“Our groundbreaking Intersleek range has set new standards for efficiency, performance and sustainability in the marine industry when it comes to biocide-free performance,” has stated Chris Birkert, AkzoNobel’s Marine Coatings Segment Manager. “The numbers are even more impressive when you look at overall performance data that has been compiled over the last two decades. Together with our customers, Intersleek has the largest foul release track record, gathered from 20 years of vessel performance data that proves our coatings have helped save ship owners $19.6 billion dollars in fuel costs and 103 million tons of CO2 to help them hit carbon targets.”
The positive impact being made on the industry by Intersleek is making an important contribution to the company’s ambition of reducing carbon emissions across its full value chain by 50% (absolute) by 2030, taking 2018 as baseline. It is indeed part of its efforts to become a carbon neutral company by 2050. The International Marine Organization (IMO) has similar ambitions. In 2023, it announced new carbon targets for the fleet, which include a 20% reduction in emissions by 2030, a 70% reduction by 2040 – compared with 2008 levels – and the ultimate goal of net zero emissions by 2050.
Demand for AkzoNobel high-performance biocide-free technology has therefore risen steeply in the past 18 months as ship owners work to cut CO2 emissions to comply with new carbon regulations and look for proven solutions. ‹
by Binghamton University, State University of New York Binghamton (NY), United States
Binghamton University collaboration with University of Pittsburgh, Brookhaven National Laboratory offers a new view of everyday chemical reaction
When water vapour meets metal, the resulting corrosion can lead to mechanical problems that harm a machine’s performance. Through a process called passivation, it also can form a thin inert layer that acts as a barrier against further deterioration. Either way, the exact chemical reaction is not well understood on an atomic level, but that is changing thanks to a technique called environmental transmission electron microscopy (TEM), which allows researchers to directly view molecules interacting on the tiniest possible scale.
Professor Guangwen Zhou — a faculty member at Binghamton University’s Thomas J. Watson College of Engineering and Applied Science (Binghamton, NY, United States) — has been probing the secrets of atomic reactions since joining the Department of Mechanical Engineering in 2007.
Along with collaborators from the University of Pittsburgh and the Brookhaven National Laboratory, he has studied the structural and functional properties of metals1 and the process of making “green” steel. Their latest research, “Atomistic mechanisms of water vapor induced surface passivation,”2 was published in November 2023 in the journal Science Advances. Co-authors included Binghamton PhD students Xiaobo Chen, Dongxiang Wu, Chaoran Li, Shuonan Ye and Shyam Bharatkumar Patel, MS ‘21; Na Cai, PhD ’12; Zhao Liu, PhD ’20; Weitao Shan, MS ’16, and Guofeng Wang from the University of Pittsburgh; and Sooyeon Hwang, Dmitri N. Zakharov and Jorge Anibal Boscoboinik from the Brookhaven National Laboratory.
1 https://www.binghamton.edu/news/story/3766/new-materials-research-sees-transformations-at-an-atomic-level 2 https://www.science.org/doi/10.1126/sciadv.adh5565
The cost of repairing corrosion worldwide is estimated at $2.5 trillion a year, which is more than 3% of the global GDP, so developing better ways to manage oxidation would be an economic boon. Additionally, understanding how a water molecule’s hydrogen and oxygen atoms break apart to interact with metals could lead to clean-energy solutions.
In the paper, Zhou and his team introduced water vapour to clean aluminium samples and observed the surface reactions. “This phenomenon is well-known because it happens in our daily lives,” he said. “But how do water molecules react with aluminium to form this passivation layer? If you look at the [research] literature, there’s not much work about how this happens at an atomic scale. If we want to use it for good, we must know, because then we will have some way to control it.” They discovered something that had never been observed before: In addition to the aluminium hydroxide layer that formed on the surface, a second amorphous layer developed underneath it, which indicates there is a transport mechanism that diffuses oxygen into the substrate. “Most corrosion studies focus on the growth of the passivation layer and how it slows down the corrosion process,” Zhou said. “To look at it from an atomic scale, we feel we can bridge the knowledge gap.” The cost of repairing corrosion worldwide is estimated at $2.5 trillion a year, which is more than 3% of the global GDP — so developing better ways to manage oxidation would be an economic boon. Additionally, understanding how a water molecule’s hydrogen and oxygen atoms break apart to interact with metals could lead to clean-energy solutions, which is why the U.S. Department of Energy funded this research and Zhou’s similar projects in the past.
“If you break water into oxygen and hydrogen, when you recombine it, it’s just water again,” he said. “It doesn’t have the contamination of fossil fuels, and it doesn’t produce carbon dioxide.”
Because of the clean-energy implications, the DOE regularly has renewed Zhou’s grant funding over the past 15 years.
“I greatly appreciate the long-term support for this research,” Zhou said. “It’s a very important issue for energy devices or energy systems, because you have a lot of metallic alloys that are used as structural material.” ‹
Two immersive days of captivating talks delivered by industry experts.
Connect with visionaries shaping tomorrow's maritime landscape. 2-DAY CONFERENCE
Stay ahead of the curve with insights from leading maritime professionals.
Boris Miksic, a Croatian-American entrepreneur and owner of Cortec® Corporation, has received special recognition for 50 years of dedicated work at NACE-International, the largest global organization focusing on developing standards for corrosion prevention.
Cortec® is a global corrosion inhibitor manufacturer and a leader in green corrosion protection technologies. This valuable recognition confirms Mr. Miksic as one of the leading global experts in the field of VCI/VpCI corrosion inhibitors.
Patented Vapour phase Corrosion Inhibitors are revolutionary technology that simplifies corrosion protection and is ideal for keeping enclosed void spaces such as packages, equipment internals, or structural metal cavities, corrosion-free. This technology is designed to save time, money and offer more thorough, reliable, and easier-to-use protection than a variety of other metals preservation strategies.
Boris Miksic is a Croatian-American
who immigrated to the USA in the 1970s, where he founded Cortec® in his garage. From modest beginnings in Hugo, Minnesota, Cortec® grew into the world’s leader in VpCI®/MCI® corrosion protection technology. With its 9 plants, warehouses, and laboratories, Cortec is the world’s largest producer of VCI, VpCI®, and MCI® products and services. It operates in over 100 countries and is the world’s largest privately held company involved in corrosion and environmental protection. “I have dedicated my life to developing new green technologies in the corrosion industry, and this award is a great honour. All my investments have a sustainability focus, and my vision from the beginning was to develop environmentally
safe solutions. Our plants operate on the circular economy principle, and we recently started utilizing our energy resources by installing solar power plants,” says Miksic. “Most of our products are bio-based and recyclable. We reprocess them in-house, significantly reducing the amount of waste for disposal. This is how we demonstrate not only responsibility towards our customers but also toward our communities. For me, this is equally important. Cortec®, is an example of a modern company that is based on sustainability principles,” he adds.
The Cortec® Corporation’s headquarters in St. Paul, Minnesota (United States).
In his rich 50-year career, he received 66 patents and played an important role in the National Association of Corrosion Engineers (NACE, now AMPP). He has won numerous awards, chaired NACE symposiums and working groups, helping to develop numerous industrial testing standards. His discoveries on vapor-phase corrosion inhibitor technology have been published in various scientific journals.
In the early 2000s, Miksic launched production in his home country Croatia, which experienced significant expansion. Today, Croatian plants supply not only Europe but also a large part of Asia. Boris Miksic is very pleased with how business is developing in Europe: “EcoCortec®- our sustainable, solar-powered production complex, located in the green fields of the Baranja region, made Croatia one of the
central points in Europe for manufacturing and exporting green corrosion inhibitors worldwide” he states.
The event entitled CORROSION 2024Conference and Exposition was organized earlier this month by NACE International. During the event, NACE’s recognition for long-standing work and achievements in the field of corrosion protection was awarded to Boris Miksic. He received this honourable recognition at a grand ceremony held at the World War II Museum in New Orleans. Over the past 50 years, Boris Miksic issued 66 patents and played a significant role in the National Association of Corrosion Engineers (NACE, now AMPP). He has won numerous awards, chaired NACE symposiums and working groups, and helped develop numerous industrial testing standards. His
“I have dedicated my life to developing new green technologies in the corrosion industry, and this award is a great honour. All my investments have a sustainability focus, and my vision from the beginning was to develop environmentally safe solutions”.
discoveries on vapour-phase corrosion inhibitor technology have been published in various scientific journals. Miksic’s vision of pushing boundaries towards sustainability in the industry is prevalent today. More and more companies are following Cortec’s example and turning towards environmentally responsible technologies. “My mission was, and still is, to always be one step ahead. I promoted the importance of green anticorrosion solutions when it was still something that very few were considering. Today, it has become the gold standard in our industry. After many years of hard work advocating for sustainability, I am pleased to see great progress,” concludes Miksic. ‹
see what makes SMM the #1 smm-hamburg.com/trailer
smm-hamburg.com
the leading international maritime trade fair
3 – 6 sept 2024 hamburg
The
Jotun, the Norwegian multinational company specialising in the production of protective and anti corrosion coatings for the marine and industrial sectors, held a full-day seminar dedicated to its new Jotachar JF750 XT product and its application on 6 February. The event took place at the Continental Hotel & Restaurant in Osio Sotto (Bergamo, Italy), intended in particular for engineers, maintenance managers, safety and fire officers, consultant specifiers, applicators, asset owners, plant managers, and all operators responsible for fire and corrosion protection. The seminar aimed to provide a detailed presentation of this
new coating, developed to protect critical steel structures against hydrocarbon fires, alongside a series of in-depth debates on aspects such as fire scenarios, industry regulations, terminology, and application equipment. After the speeches, a practical demonstration of the products application process and characteristics was organised. This took place at the premises of one of the best known applicators of corrosion protection coatings for the petrochemical, offshore, naval, civil, and food sectors, Lena Anticorrosione Srl, where it was demonstrated how quickly and easily the product can be applied.
Jotachar JF750 XT1 is an intumescent coating developed for passive hydrocarbon fire protection of oil and energy plants installed in all types of environments. It has been extensively tested in extreme weather conditions worldwide – including the world’s only test station for paints and coatings in the Arctic but also desert and subtropical environments. A third-party certified that the material can protect structural elements in carbon steel, aluminium, hot-dip galvanised steel, and stainless steel substrates against fire.
The first session of the seminar featured speeches delivered by the following professionals:
Epoxy Intumescent Specialist Alessandro Formenti, offering technical support for both onshore and offshore projects, including the qualification and training of applicators for the correct installation of the Jotachar brand’s intumescent products;
Roberto Baruzzo, Global Key Account Manager of the Energy segment and responsible for the retention, management, and development of strategic customers globally;
Nicolay Dinspel, Head of the Energy and Infrastructure segments for Jotun Germany and Regional PFP Manager;
Alberto Cecinati, Sales and Technical Assistance Manager at Graco Specialised Distributors in Southern Europe and an expert in 2K Protective Coating applications, who closed the first part of the seminar.
1 https://www.ipcm.it/en/post/jotun-launched-intumescent-coating-tested-in-arctic-station.aspx
The second session saw the participants move to Lena Anticorrosione’s premises for a practical demonstration. This familyrun company is known in Italy and abroad for the quality and flexibility of its service, as it can apply a wide range of protective coatings on both small, light, and easy-to-handle components and large, heavy, and complex structures, particularly pipes, joints, valves, filters, tanks, and metalwork fabrications for chemical and petrochemical plants (offshore, onshore, underwater), the food industry, power plants, and nuclear, geothermal, and wind power plants.
During the workshop, an operator applied Jotachar JF750 XT to a medium-sized component with a Graco XM PFP plural application pump, demonstrating the ease of application of Jotun’s new coating to the participants, who appreciated how easy the material is to apply and how efficient the whole process was.
“Seminars which combine both theoretical content and the opportunity to wittnes practical demonstrations are a well-established concept of Jotun’s communication strategy,” explains Vaira Vesnaver, Marketing Specialist - Jotun Europe. “Our aim is to provide customers with the theoretical basis needed to fully understand the application possibilities of a new product, and also to gain hands-on experience of a material's performance, by providing the opportunity to witness a live application process. We are very interested in the opinion of users, and gathering their feedback immediately after the presentation of a product adds value to our collaboration, while at the same time enabling us to provide important customer feedback to our Global Intumescent R&D Facility based in Flixborough, UK. Our Intumescent R&D teams develop and test new materials which are designed and developed according to the needs of different markets. Indeed, Jotun Europe Sales is a cluster present in 6 nations, which, despite sharing some common requirements, are characterised by country-specific certification systems, approvals, and regulations, thus requiring targeted product development.
“We plan to roll-out these combined educational and practical seminars several times each year across several geographic areas, making them easily accessible for our customers. We also really value the interaction, ideas and the exchange of information that come from meeting this way. The success of this seminar is tangible proof of that.”
From the top: A moment during the seminar; One of Lena Anticorrosione’s coating departments; The application of Jotun’s new coating during the workshop.
The fifth edition of IVS - Industrial Valve Summit, the most important international event dedicated to industrial valve technologies and flow control solutions promoted by Confindustria Bergamo and Promoberg, will take place in Bergamo (Italy) from May 14th to 16th, 2024.
The session will kick off on the morning of May 14 with the early opening of the pavilions reserved for exhibitors, a novelty introduced to generate a valuable networking opportunity for the protagonists of IVS 2024. Highlight of the day is the opening conference of the Summit, where the event will be officially kicked off and where institutions, guests of honour, decision-makers and high-profile experts will take the floor.
In the afternoon, the extensive IVS scientific programme will start. A space that has proven over the years to be an agora where change can be interpreted and the latest technological innovations can be explored, identifying, and analysing the challenges of the sector. To support the development of the scientific calendar, the Summit organisers have created two
additional conference rooms in Hall C. IVS 2024 includes 52 sessions including conferences, round tables, workshops, case studies and laboratories, providing a plan that is more than 50% greater than the 34 in-depth technical events of IVS 2022.
On May 15 and 16, the trade fair will go live and the halls will open their doors to the international valve community. Following the two-day exhibition, there will be a further opportunity for foreign delegations attending the fair to meet the players in the extended oil and gas supply chain on Friday May 17. The organisers have fuelled qualitative growth for the 2024 edition, increased the number of scheduled appointments in the trade fair programme and enriched the side events, taking the Industrial Valve Summit from a two-day exhibition to a full-fledged valve week.
The fifth edition of the event takes place two years after IVS 2022 and continues on the path of growth that has marked it since the first edition.
The Summit organisers are predicting record numbers for IVS 2024, starting with the companies taking part in the exhibition.
There will be more than 310 exhibitors, of which the international component is growing strongly, with more than 20% foreign companies. The number of visitors is also expected to grow, with more and more countries expected to arrive in Bergamo, representing all continents.
Despite the travel restrictions in force in some areas of the world and the delicate global scenarios, IVS 2022 welcomed 12,000 visitors (+12% compared to 2019) from more than 60 countries.
IVS hosted almost 300 exhibiting companies (+17% on 2019), from 12 countries: Italy, Germany, Great Britain, the United States of America, France, South Korea, Spain, the Netherlands, Belgium, South Africa, Turkey and the Czech Republic. These numbers tell how IVS has established itself as an essential showcase for the entire supply chain connected to industrial valves and flow control. The synergies with ICE (the Agency for the promotion abroad and internationalisation of Italian companies), AVR ANIMA (the industrial trade association representing Italian companies in the valves and fittings sector) provide a great stimulus for the increase in high-level international presence, Confindustria Assafrica &
Mediterraneo (the Confindustria international office that supports Italian companies in their growth path in Africa and the Middle East) and SACE (the insurance-financial group directly controlled by the Ministry of Economy and Finance, specialised in supporting companies and the national economic fabric).
The partnerships will bring international delegations comprising institutional representatives, entrepreneurs, decision makers, speakers and specialised operators to the fair. The organisers have invited over 100 qualified end-user buyers of primary standing and international EPCs. A distinguished parterre that can interface with operators from the entire energy sector, giving rise to moments of exchange and discussion. In addition, through an operational collaboration with UNIDO ITPO Italy (the Italian Office for the Promotion of Technology and Investment of the United Nations Industrial Development Organisation), IVS confirms the participation of a delegation of entrepreneurs and representatives of Iraqi institutions.
https://industrialvalvesummit.com
AMPP, the Association for Materials Protection and Performance, is a global community of professionals dedicated to materials protection through the advancement of corrosion control and protective coatings. It protects infrastructure and assets worldwide through member and workforce education and credentialing, company accreditation, technological innovation, and global standardization. AMPP connects its global audience at the local level by creating local chapters, and hosting industry and technology-specific events such as conference, seminars, and exhibits. Recently, the Association proudly announced the formation of its 100th chapter with the inclusion of three new branches: Kentucky, Iraq and Australia. For almost 10 years, AMPP Italy Chapter (formerly Nace Italia Milano Section) has been organizing events and meetings to promote the exchange of knowledge and ideas in corrosion control and to create a network involving representatives from the industry and institutions. For the third time since its foundation, AMPP Italy is organising its Conference & Expo, which will take place from 9th to 11th June 2024 at the Genoa’s Porto Antico, in the structure called “Magazzini del Cotone”, as per past editions. This year, the conference will be focused on the motto “Sharing knowledge, the way forward! An international event for corrosion prevention.”
After the years of the pandemic event, it will be a unique opportunity to return to share and discuss in person the latest news and guidelines on topics related to corrosion, its prevention and protection. The main topics covered will concern coatings, cathodic protection, the choice of materials in the petrochemical sectors and refineries, the use of chemical products and the use of highly corrosion-resistant steels. Obviously, the AMPP Italy Conference will also talk about hydrogen and renewable sources, so there will be no shortage of technical-scientific sessions dedicated to the topics of corrosion resistance of the materials used in these sectors. The event is an opportunity for technical discussion between researchers, technicians, engineers, producers and users, owners of structures, sector associations and producers of materials for the world of anti-corrosion.
www.amppitaly.org
Accadueo, the international event for water professionals organized by BolognaFiere Water&Energy - BFWE, expands and arrives for its 17th edition in Bari (Italy). Starting this year, Accadueo will be hosted at Bari’s Nuova Fiera del Levante in evennumbered years, providing a platform to strengthen strategic and industrial alliances in the water service sector among companies, operators and institutions of the Central South Italy and the countries bordering the Mediterranean. The seventeenth edition of Accadueo is scheduled for November 27-28, and will continue its traditional presence in Bologna in odd-numbered years. The event will feature exhibition areas alongside conference and training events. It will therefore discuss reuse, digitization, desalination, irrigation, recovery, purification and all those innovative technologies that contribute to minimizing water losses, ensuring the continuous supply of quality drinking water and modernizing infrastructure with a view to the circular economy.
All these topics have always been addressed at Accadueo, and this year in Bari they will be dropped into the reality of the area: the central-southern region faces specific challenges and potentials;
with a few exceptions, generally, its water service is less efficient and has higher water losses compared to Northern Italy. The aim is to collaboratively explore the underlying causes of water inefficiencies and to identify actionable solutions.
Focus will be made on the functioning of various water services in the single regions and the opportunities arising from collaboration with countries in the Mediterranean Basin. Accadueo will also be an opportunity to strengthen relations and dialogue between managers, regions and municipalities of Central-Southern Italy, overcoming the current excessive fragmentation. Additionally, there will be updates on funding from the PNRR and Italian and European policies that are reshaping the sector towards alternative models.
The exhibition area will offer a firsthand look at the latest innovations showcasing cutting-edge technologies and materials used by the companies committed to modernizing the water service.
“Given the great success of the three-day event in Bologna in October, BFWE has decided to explore new chances in the Central South Italy by planning this new stop in Puglia. The goal is to help companies and operators seize all the opportunities offered by the territory. The Bari event is also a chance to promote greater dialogue between regional and municipal administrations for a more efficient and less fragmented management of the water service”, says Paolo Angelini, CEO of BFWE.
“We are very pleased to host such an important event as Accadueo. Our goal is to develop synergies with specialized trade exhibitions of high added value. Accadueo deals with a fundamental and vital theme for all of us: the protection of a precious asset like water from the perspective of a sustainable and circular economy. As Nuova Fiera del Levante, we can offer a vision of the Southern economy and we can be a Mediterranean hub, fostering dialogue between Europe and all the countries of the Mediterranean Basin, the Balkans, Africa, and the Middle East.” comments Gaetano Frulli, President of Nuova Fiera del Levante.
“After the successful experience of Mecspe, we decided to hold Accadueo in alternate years in Bari as well, confident that this theme will generate keen interest among economic operators and institutions. With this new event, we confirm and strengthen an important industrial partnership that we are sure will be successful”, said Gianpiero Calzolari, president of BolognaFiere.
www.accadueo.com/en
Baku Energy Week will take place in June
The Baku Energy Week will take place from June 4th to 6th in the city of Baku, combining three prestigious events under one brand. As part of the Baku Energy Week, the 29th International Caspian Oil & Gas Exhibition Caspian Oil&Gas, the 12th Caspian International Power and Green Energy Exhibition Caspian Power and the 29th Baku Energy Forum will be held.
Baku Energy Week is held with the support of the Ministry of Energy of the Republic of Azerbaijan and SOCAR. This event has become an important platform for cooperation in the oil, gas and energy sector for 29 years. The participation of the President of Azerbaijan, Ilham Aliyev, in the opening ceremony of the Baku Energy Week in 2023, as in previous years, is an indicator of the high status of the event. Following the event’s inauguration, President Aliyev applied postage to the commemorative stamps released during Baku Energy Week in commemoration of the centenary of the birth of Great Leader Heydar Aliyev. Greeting letters were sent by the President of the United States of America, Joseph Biden, and the Prime Minister of Great Britain, Rishi Sunak. Cristina Lobillo Borrero, Director for Energy policy: strategy and coordination at the European Commission, spoke at the opening ceremony, as well. Traditionally, high-ranking guests - heads of state structures, companies operating in the energy field, heads of diplomatic missions of foreign countries in Azerbaijan visited Baku Energy Week. By the Decree of the President of the Republic of Azerbaijan, Ilham Aliyev, 2024 was declared the “ Green World Solidarity Year” in Azerbaijan. This significant event will also be reflected in the event program of the Baku Energy Week.
Among the main themes of the Caspian Oil&Gas exhibition are business opportunities in the oil and gas industries, strategies for large-scale carbon capture, utilization, and storage, digitization in energy, and more. Simultaneously with the Caspian Oil&Gas exhibition, the Caspian International Power and Green Energy Exhibition “Caspian Power” will be organized. The exhibition program includes offerings from international and local companies in the field of energy and the use of renewable energy sources.
The Baku Energy Week will conclude with the Baku Energy Forum, which will address energy issues of importance to both Azerbaijan and the entire Caspian region.
The Zero Waste program, which is a set of principles
aimed at preventing waste, will be implemented during the forum: printed materials will be replaced with electronic media as much as possible, with the foodstuff optimal use principle will be implemented under the international Zero Food Waste initiative. The Baku Convention Center, where the event will be held, was built in an ecological concept. Centrally installed solar panels save on energy usage costs.
The event attracts many sponsors. This year’s sponsors of Baku Energy Week are companies like ABB, ADNOC, AIQ, Ansaldo Energia, AZFEN, Baku Steel Company, bp, Caspian Drilling Company, Caspian Marine Services, Deloitte & Touch, GAP Construction, GL, INPEX, KOLIN Construction, Masdar, Nobel Energy, Photomate, SEE BREEZE, SLB, TEKFEN, TotalEnergies, Turkiye Petrolleri, Uniper. The Boston Consulting Group acts as an intellectual partner of the Baku Energy Forum.
The Baku Energy Week is actively supported by Azerbaijan Association of Exhibition Organisers (ASTA) in 2024, as in the previous year. The organization, which has been operating for a year, already includes more than 40 members. The member companies have more than twenty years of experience in holding large international events. ASTA actively cooperates with state institutions, business sector and public organizations to ensure high-level organization of events within the framework of congress and exhibition activities held in Azerbaijan.
The organizers of the Baku Energy Week are Iteca Caspian and Caspian Event Organisers in collaboration with ICA Events and CEM FZ LLC as international partners.
https://bew.az/
From 20 to 22 March, the European wind industry met in Spain for WindEurope’s Annual Event on onshore and offshore wind energy. 12,000+ people attended our event, together with 516 exhibitors across the buzzing halls of the Bilbao Exhibition Centre. This year there was also a strong attendance of students with 500 of them who came along. This was the perfect time for the European wind industry to share new insights, strengthen ties, and show its determination to drive Europe’s energy transition. WindEurope returned to Bilbao for the third time. And the impact of our event is only getting greater for the Basque Country. The WindEurope 2024 Annual Event generated more than €30mn to Spain’s gross domestic product.
The theme of this year’s event was “Our wind, our value”. Across 80+ sessions we heard from 425 speakers – policymakers, industry leaders, financial experts , NGOs, community representatives and academics. We learnt about wind energy’s value creation for Europe in a range of areas – and how it supports European values too. The European wind industry has boosted employment in Spain by creating a total of 39,000 jobs. The wind sector creates wider economic benefits. It provides 0.5% of Spain’s GDP. Wind energy improves Spain’s energy security and reduces the need for expensive fossil fuel imports. Wind energy generation covers 24% of Spain’s electricity demand - making it the leading sources of renewable electricity. Representatives of local Spanish municipalities explained the positive impact wind
farms have on local communities and municipal budgets. They described how wind energy can help revitalise deprived rural areas. Spain wants to install up to 3GW of offshore wind by 2030 and become a technology leader for particularly floating offshore wind. Bilbao and the Basque Country will play a leading role in this process. Spain’s very first floating offshore wind turbine feeding electricity into the grid, the DEMOSath project, is spinning of the coast of Bilbao. The upcoming offshore wind sector will further strengthen the international importance of Bilbao and the role of the port of Bilbao as a leading European logistics hub for wind energy
Securing Europe’s technology leadership
European manufacturing of wind turbines is indispensable for Europe’s energy security and for competitive electricity prices. Europe must expand its wind energy supply chain. Today’s factories cannot produce the volumes of new turbines, substations and cables we need to install to reach the EU’s climate and energy security targets. The European Union has understood: the EU Net Zero Industry Act will increase Europe’s manufacturing capacities. Last year the EU also published a Wind Power Package with 15 immediate actions to support the European wind industry. The WindEurope Annual Event 2024 explored how EU Member States can implement these excellent actions and what else is needed to ensure Europe remains a technology leader and innovation hub for wind energy. The wind industry is turning a corner. Permitting is improving. New investments are up and auction volumes are reaching record levels. Some examples: Germany alone permitted 7.5 GW of new onshore wind last year, and they’re going to auction 15 GW of onshore wind in 2024. Europe invested €48bn in new wind farms last year – a more than 50% increase on 2022, with a major recovery in offshore wind investments. The upcoming EU elections will decide over Europe’s future energy plans. During a TV-debate format on the first day of the 2024 event politicians from different European party families presented their views on Europe’s future energy system. It’s now of crucial importance that the incoming European Commission continues the path towards a decarbonised energy system by 2050. Wind energy will have a central role to play in this. Today wind is 19%of all electricity consumed in Europe. By 2050 the EU wants it to be at least 50%.
The next WindEurope Annual Event will take place in Copenhagen from 8-10 April 2025.
https://windeurope.org/annual2025/
From 8 to 11 April 2024, Berlin hosted the 19th annual Pipeline Technology Conference (ptc), bringing together more than 1,000 attendees from 51 countries, representing a global forum for discussions on the future of pipeline technology. This year’s conference and exhibition marked a significant milestone in the event’s history, attracting delegations from 98 pipeline operating companies. “The Pipeline Technology Conference has once again proven to be the premier gathering for the global pipeline community. ptc 2024 provided a comprehensive platform for pipeline operators and industry professionals to explore the latest technological advancements and tackle the current and future political, economic, and technical challenges facing the industry worldwide,” said Dennis Fandrich, Chairman of the Pipeline Technology Conference and Member of the Management Board of the organizing EITEP Institute. Highlights from the conference included a series of highlevel discussions on topics such as the resilience of energy infrastructure in complex geopolitical landscapes, the role of digital transformation and AI in optimizing pipeline operations, innovative strategies for managing methane emissions, and a focus on Germany’s ambitious hydrogen core network plans. The event also featured technical sessions across six tracks, delivering insights into cutting-edge developments in pipeline technology.
This year’s ptc also featured an ever-growing exhibition with 92 exhibitors from around the globe, highlighting the latest technologies and services in the pipeline sector. Marian Ritter, Member of the Management Board of the EITEP Institute, emphasized the exhibition’s importance: “The expanding scope of the ptc Exhibition mirrors the dynamic advancements in the pipeline industry and provides an invaluable platform for networking and knowledge exchange. Exhibitors praised the good discussions and are confident that opportunities will arise from them. We have already confirmed many bookings for 2025 and plan to enlarge the exhibition area.”
The event saw significant contributions from young professionals, with the involvement of technical students and members of Young Pipeline Professional communities around the globe, highlighting the industry’s focus on nurturing the next generation of pipeline experts. This year’s conference further emphasized the role of diversity within the industry with the Global Women in Pipeline initiative, which connected and inspired women through a series of talks and networking opportunities.
The 20th Pipeline Technology Conference will take place from 5 to 8 May 2025 again in Berlin.
www.pipeline-conference.com
Parliamentary State Secretary at the Federal Ministry for Economic Affairs and Climate Action Stefan Wenzel giving his keynote speech on “The German Hydrogen Core Network - Status of Planning”.
EDITOR IN CHIEF
ALESSIA VENTURI venturi@ipcm.it
EDITORIAL OFFICE
PAOLA GIRALDO giraldo@ipcm.it
MONICA FUMAGALLI fumagalli@ipcm.it
MATTEO SOTTI sotti@ipcm.it
ILARIA PAOLOMELO paolomelo@ipcm.it
GABRIELE LAZZARI redazione@ipcm.it
MEDIA SALES
FRANCESCO STUCCHI stucchi@ipcm.it
ILARIA PAOLOMELO paolomelo@ipcm.it
NICOLE KRAUS kraus@ipcm.it
CLAUS GÖRLICH goerlich@ipcm.it
GRAPHICS
ELISABETTA VENTURI grafico@ipcm.it
TRANSLATIONS
CHIARA FOPPA PEDRETTI chiara.foppapedretti@gmail.com
JONA SRL | www.jonasrl.it
EDITED BY
Eos Mktg&Communication srl
Via Pietro Mascagni, 8 - 20811 Cesano Maderno (MB) - Italy
Tel. +39.0362.503215 - Fax. +39.0362.1794768
www.eosmarketing.it - info@eosmarketing.it | www.myipcm.com - info@ipcm.it
EDITORIAL DIRECTOR
Marco Ormellese, Politecnico of Milan
EDITORIAL BOARD
Annalisa Acquesta, University of Naples
Francesco Andreatta, University of Udine
Mehdi Attarchi, Senior Materials & Corrosion Specialist
Andrea Balbo, University of Ferrara
Hadi Beirami, Cathodic Protection Certified Specialist
Maria Bignozzi, University of Bologna
Stefano Caporali, University of Florence
Marco Cattalini, AMPP Italy Chapter Chairman
Eos Mktg&Communication Srl - IBAN IT97F0844033270000000084801 - SWIFT CODE: CRCBIT22 or online payment at: www.myipcm.com an ipcm® magazine
Jérôme Crouzillac, BAC Corrosion Control
Marina Delucchi, University of Genoa
Sergio Lorenzi, University of Bergamo
Tullio Monetta, University of Naples
Tomáš Prošek, University of Prague
Edoardo Proverbio, University of Messina
Stefano Rossi, University of Trento
Monica Santamaria, University of Palermo
SUBSCRIPTION SERVICE
Sale only on subscription e-mail: info@ipcm.it
Subscription Rates 2024
Annual subscription printed + digital:
EMEA € 80,00 (postage included)
Rest of world € 250,00 (fast airmail shipping included)
Single copy: € 20,00 EMEA (postage included) - Rest of world (postage excluded)
Back issues: € 40,00 EMEA (postage included) - Rest of world (postage excluded)
Subscriptions can be made by bank transfer to the following account:
Be sure to take part in the world’s biggest and most important business platform for the onshore and offshore wind industry!
• Meet up with 1,500 exhibiting companies from 40 countries across 10 halls
• Get in touch with the key decision makers of the international wind energy sector
• Visit the first-rate conference programme on 4 stages in the halls free of charge
• Two days dedicated to recruiting – for career starters, specialists and career changers windenergyhamburg.com