

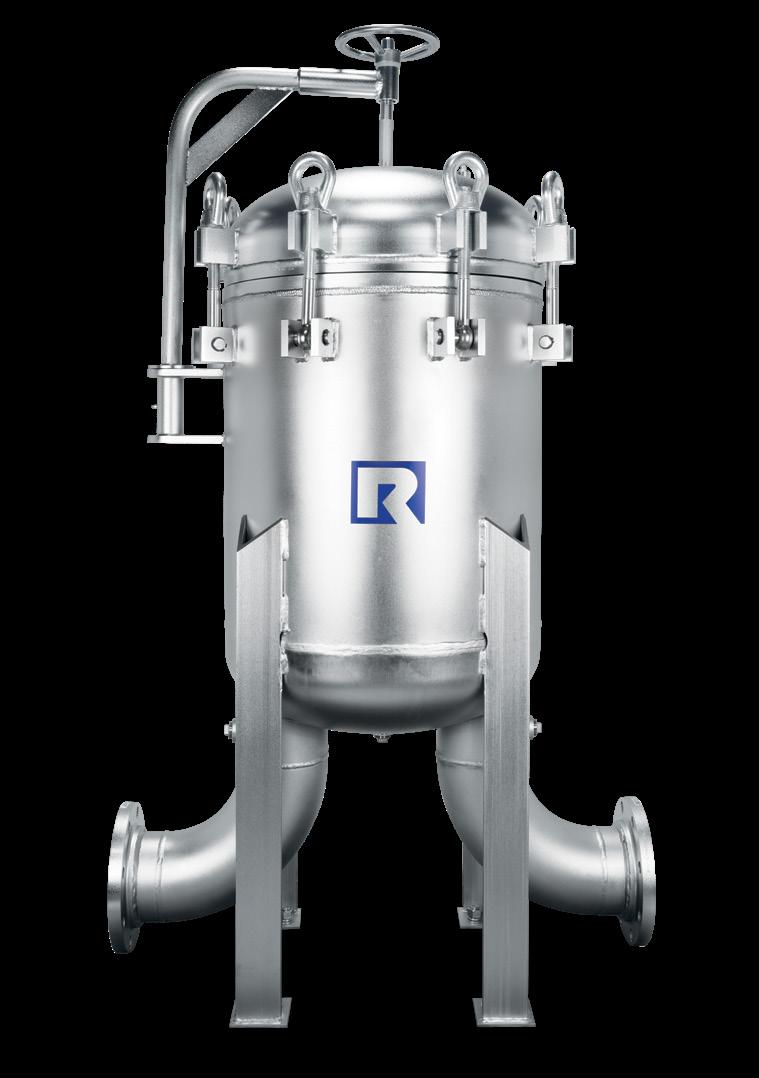
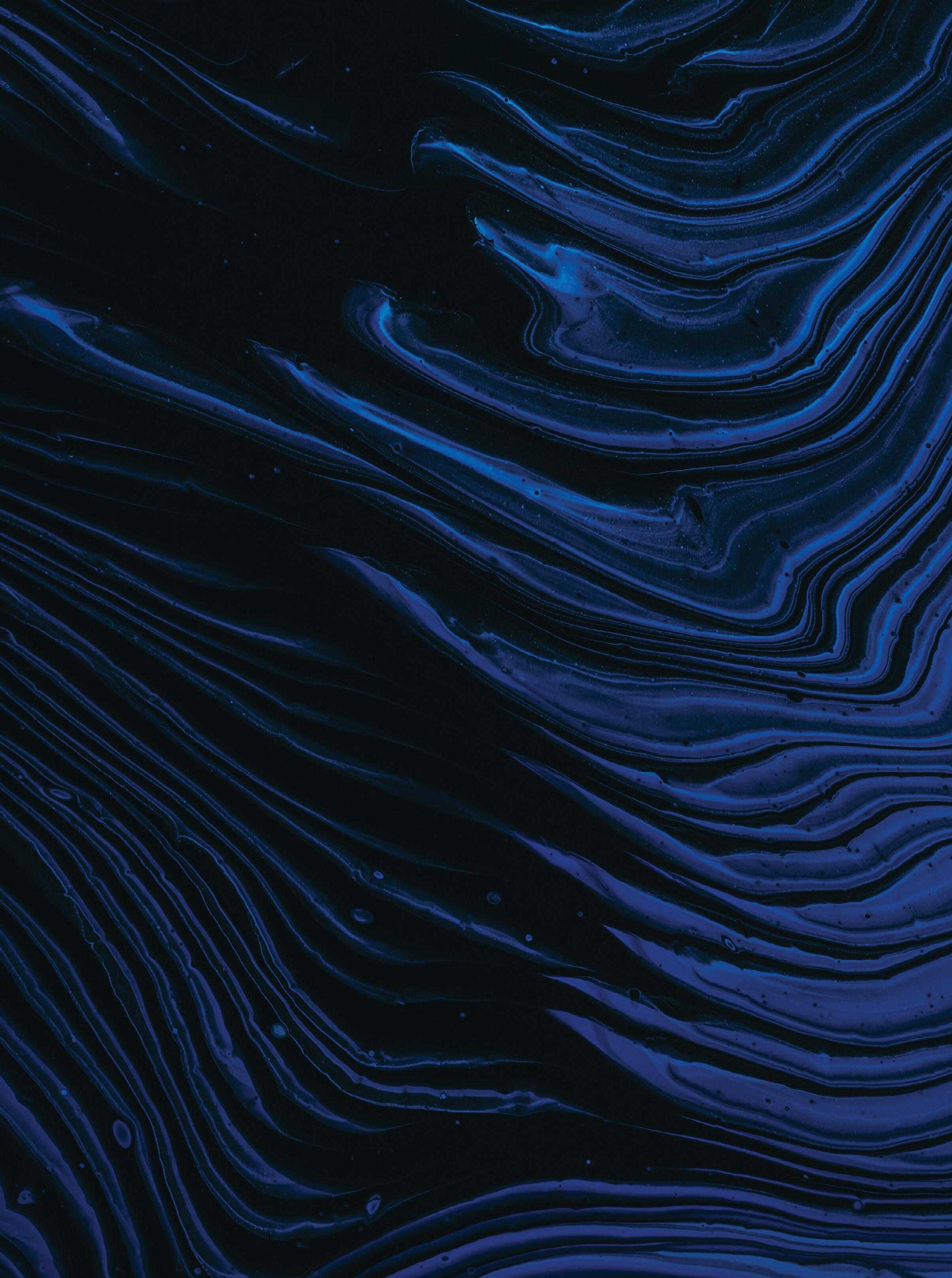

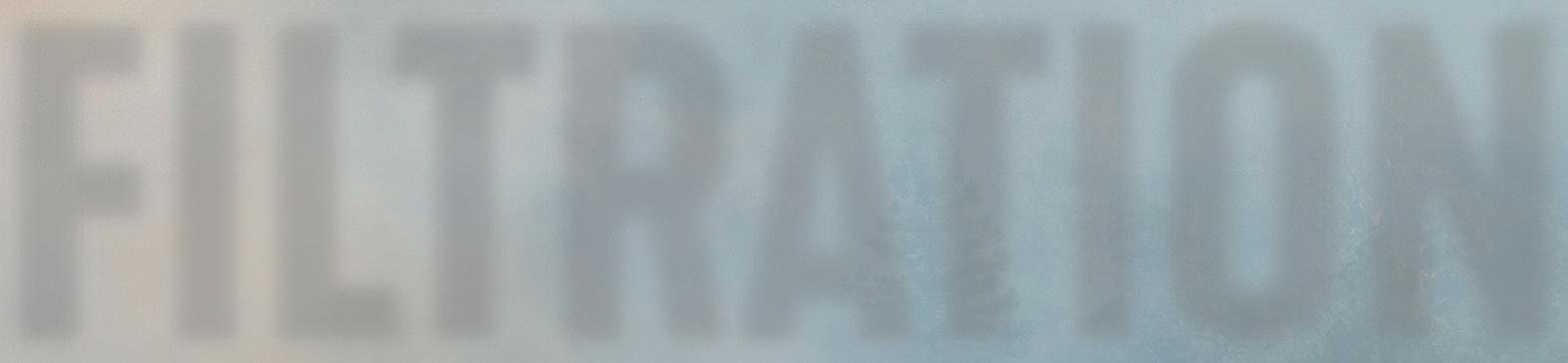
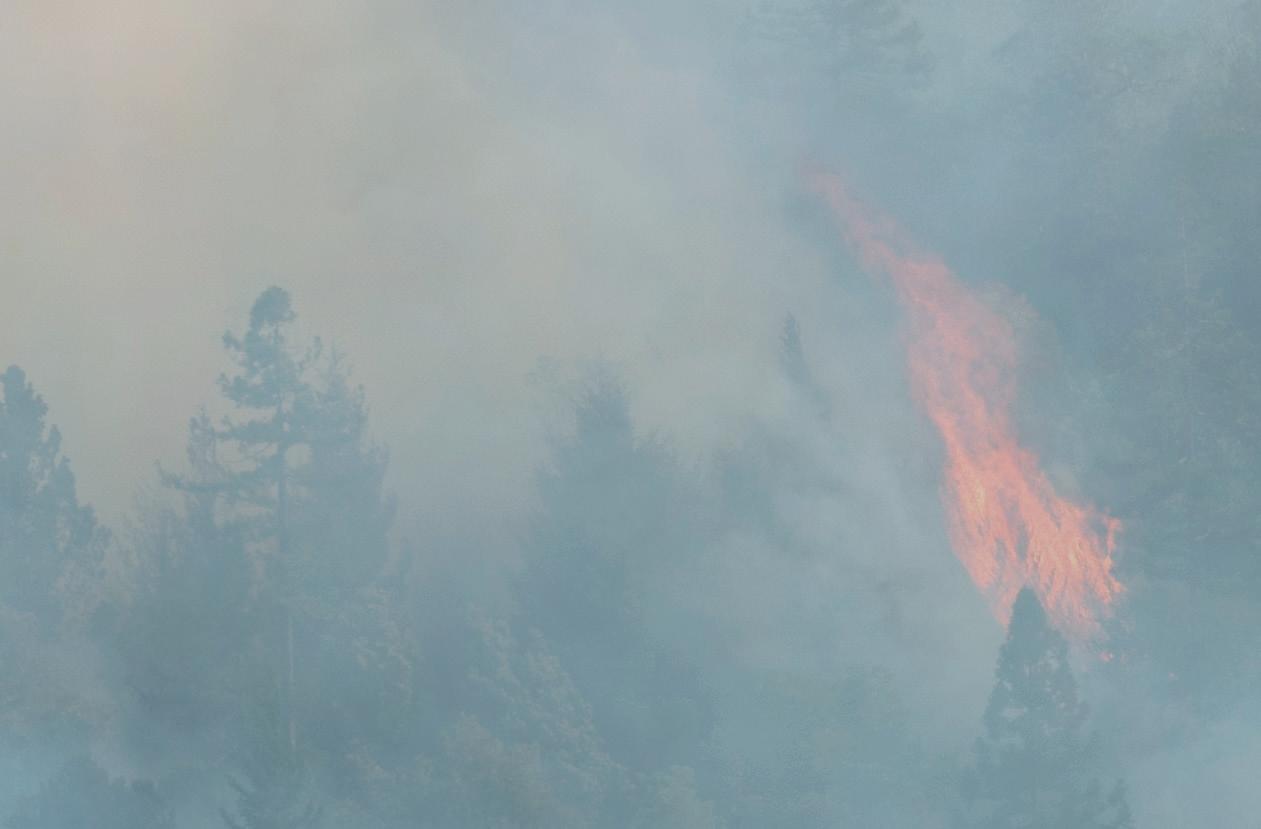
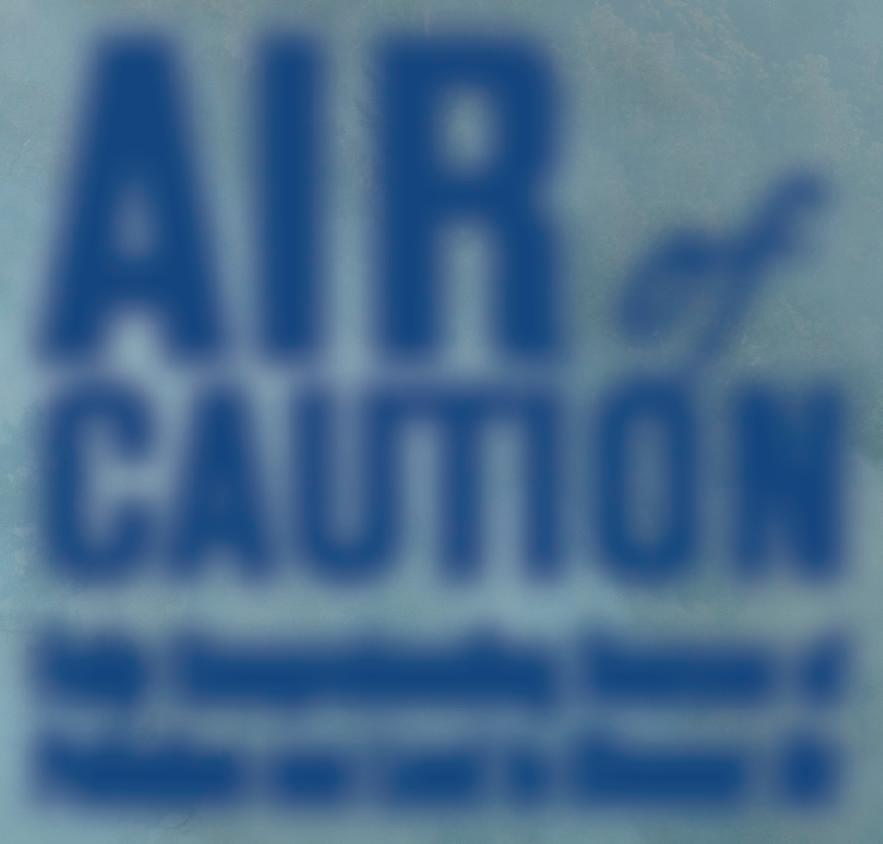
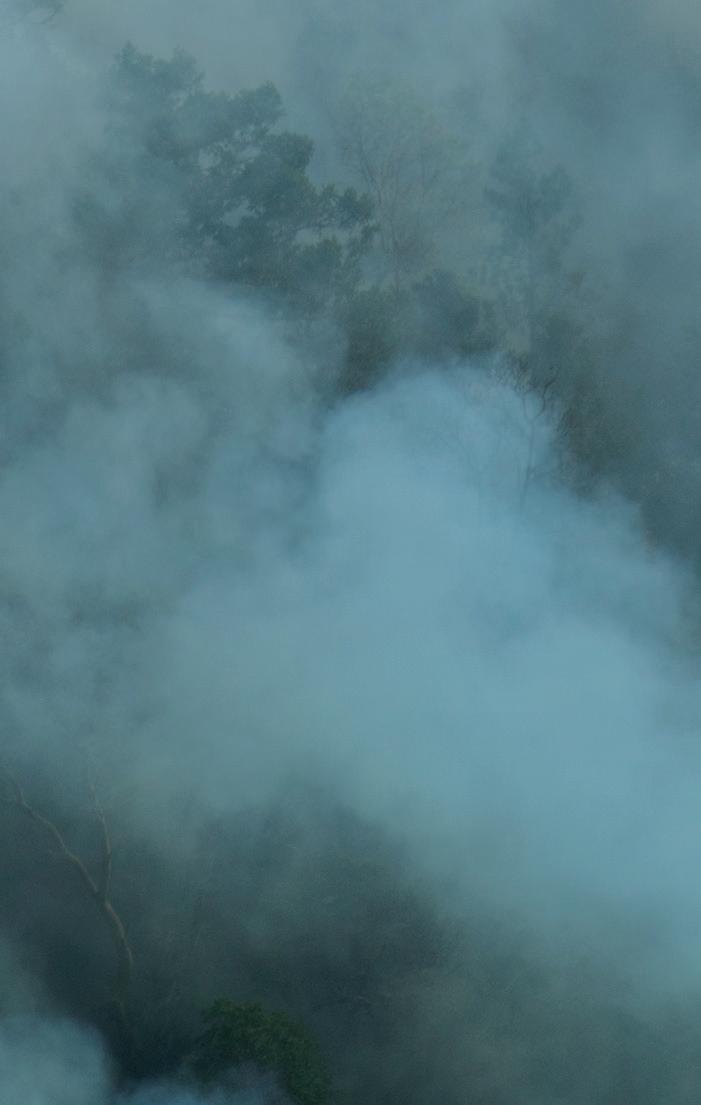
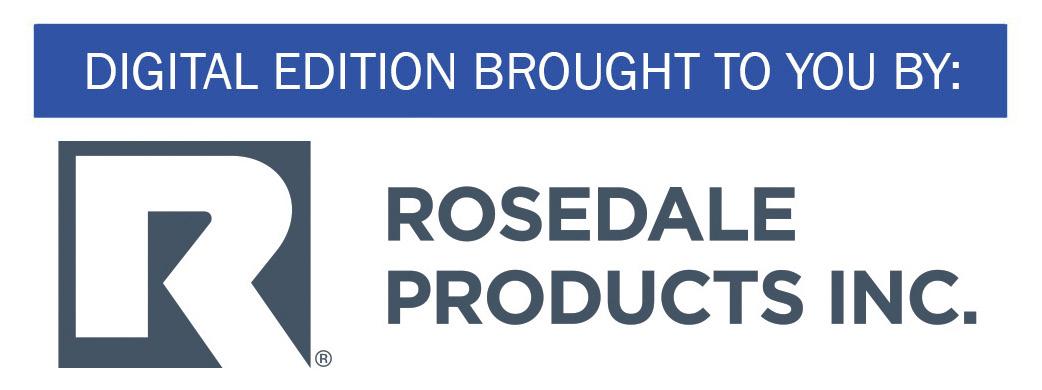
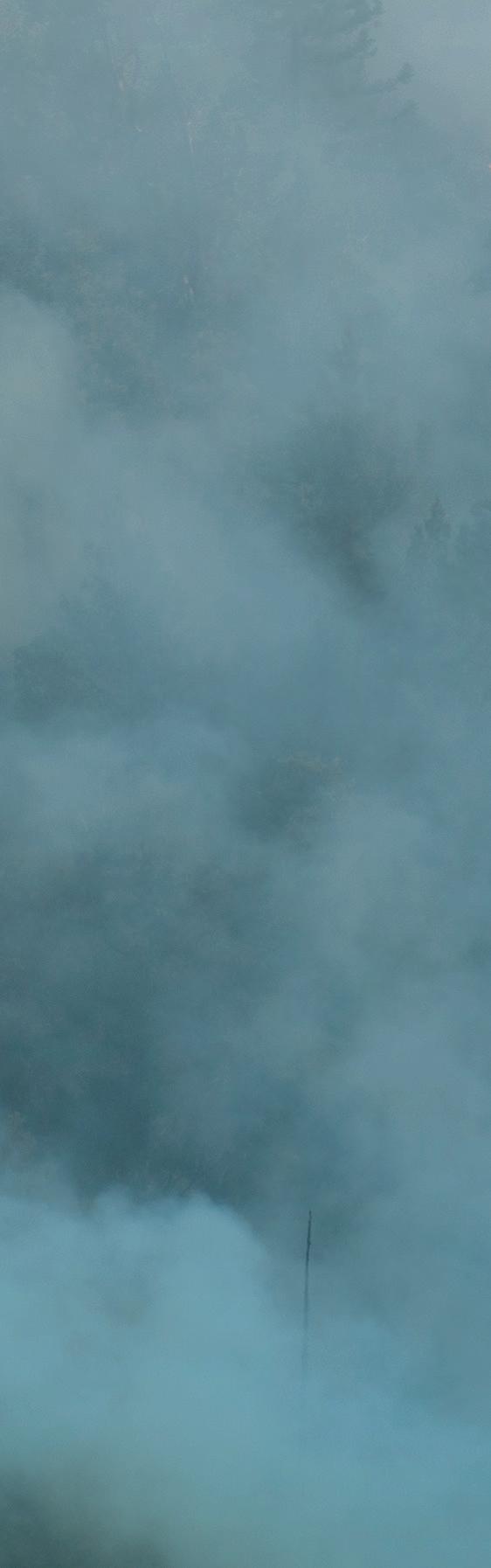
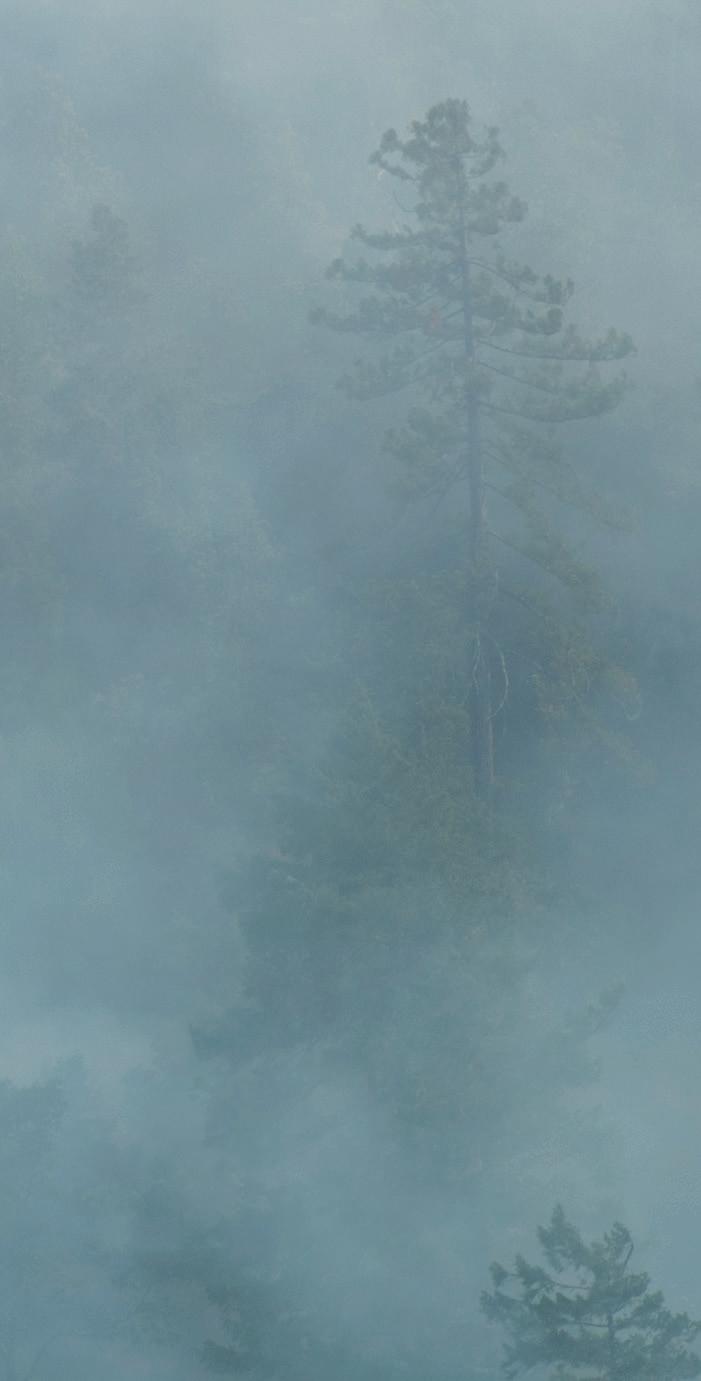
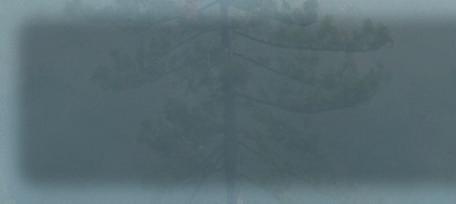

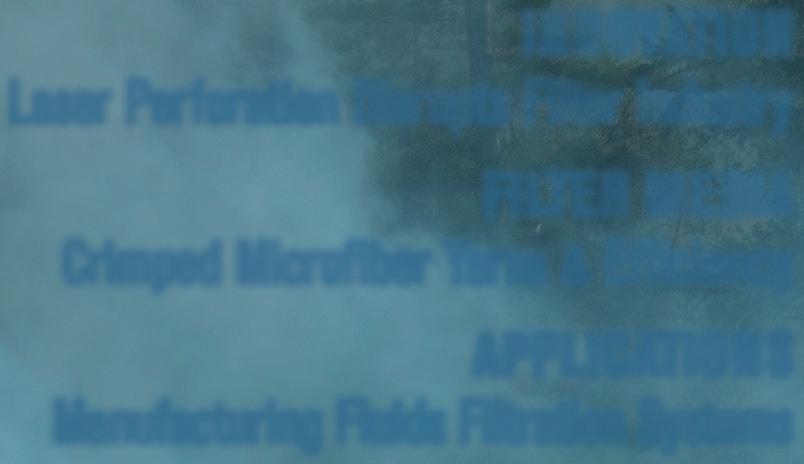

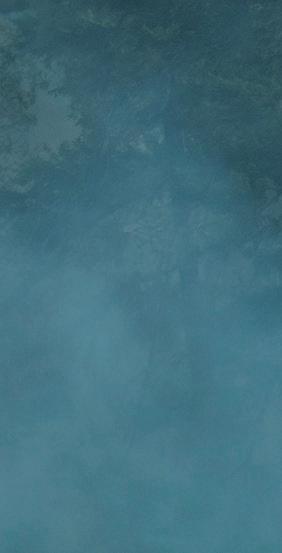
At
Infinity Core TM isn’t just a new product for 2024, it’s a revolution in filtration.
Seamless construction core
99% nickel composition
Patented mandril-based process allows for endless designs
To learn more, visit beverlin.com or call us at 616.949.5990
Solution Centers
Bringing Innovation to the Industry
Berry Global Pall Rosedale
Restoring Planetary Health with Carbon Capture
By Caryn Smith, IFN Chief Content Officer
Show Preview: INTERPHEX 2024
A Building Envelope of Peril
By Dr. Iyad Al-Attar
Breathing Easy: A Breakthrough Solution for Indoor Air Quality
By Greg Rankin
Laser Perforation Disrupts the Filter Industry
By Luca Longoni
Does Staying Indoors Protect Against Wildfire Smoke?
By Tanya Shirman Ph.D. and Sissi Liu
Efficient Air Filter Media of Crimped Microfiber Yarns
By Lukas Hermann M. Eng.
Closed Loop Arrangements
By James J. Joseph
Viewpoint
Constructing Ecosystems for Clean Air
By Caryn Smith, IFN Chief Content Officer & Publisher
Tech Spotlight
Reducing Risk of Airborne Bacterial
Infections Caused by Air Filtration Systems
Tech Notes
New Technology Briefs
Tech Talk
Unravelling Particle Deposition on Fibers and Formation of Dendrites
By Felix Swamidoss
True Cost
Capturing Opportunities
By Bob McIlvaine, President, The McIlvaine Company Movers & Shakers
Industry News & Notes
Caryn Smith
Chief Content Officer & Publisher, INDA Media csmith@inda.org
Sissi Liu
Co-founder and CEO, Metalmark Innovations, PBC sissi@metalmark.xyz
Dr. Iyad Al-Attar
Visiting Academic Fellow School of Aerospace, Transport, & Manufacturing, Cranfield Univ. i@driyadalattar.com
Lukas Herrmann M. Eng. ProVentecs GmbH, Research and Development Engineer Lukas.Herrmann@proventecs.de
Greg Rankin, Rankin PR +1 323.490.5791 greg@rankinpr.com
James J. Joseph Industry Consultant, Liquid Filtration
+1 757.565.1549 josephmarketing120@gmail.com
Luca Longoni
Technical Sales Manager IPG Photonics Linkedin.com/in/luca-longoni
Dr. Felix Swamidoss
Head of Research & Development Spectrum Filtration, India felix@spectraco.in
Dr. Tanya Shirman
Co-founder and VP of Materials, Metalmark Innovations, PBC tanya@metalmark.xyz
Bob McIlvaine
President, The McIlvaine Company
+1 847.784.0013 rmcilvaine@mcilvainecompany.com
With our extensive knowledge in production of the innovative SOLTECH “Mini Pleat” Systems, and over 20 years of contract pleating with our revolutionary glue bead technology.
We offer the following services to our customers:-
MINI-PLEAT-GLASS
Mini-Pleat: H.E.P.A., ULPA & ASHRAE
Pleat heights 1/2” to 12” upto 39” wide. Interrupted beads, many configurations.
MINI-PLEAT-SYNTHETIC
Mini-Pleat: H.E.P.A. & ASHRAE
Pleat heights 3/4” to 4” upto 25” wide. Interrupted beads, many configurations.
We can incorporate the following features in your elements:
Seal - allowing economical frame sealing
- multiple packs
IDEA®25 is a gathering of the international nonwovens industry to discuss the future of nonwoven materials, their applications, and how they will shape both form and function in various market sectors.
Attend – Experiencing IDEA®25 provides a unique opportunity to see, touch and feel innovations in person. Meet and create new business with the professionals and companies behind these developments.
Exhibit – Showcasing your company at IDEA®25 inspires brand owners and brand marketers as they interact with your materials, technologies and processes. Partner with industry leaders to create new products with the intent of recycling, reusing and repurposing…for a healthier planet.
CSMITH@INDA.ORG
+1 239.225.6137
Our goal is a delightfully diverse, safe, healthy, and just world, with clean air, water, soil and power – economically, equitably, ecologically and elegantly enjoyed.
Discussions on air quality controls are dominated by carbon emissions. Last year, TIME magazine named William McDonough, an architect, chemist and globally recognized leader in sustainable development and design, to the inaugural TIME100 Climate list, recognizing innovative leaders driving business climate action. His iconic architectural designs are renowned, like the Ford River Rouge truck plant, featuring North America’s largest living roof, and the NASA Sustainability Base, which generates more energy than it consumes and uses 90% less water than comparable structures.
His expertise includes carbon capture. “Climate change is the result of breakdowns in the carbon cycle caused by us: it is a design failure. Anthropogenic greenhouse gases in the atmosphere make airborne carbon a material in the wrong place, at the wrong dose and wrong duration. It is we who have made carbon a toxin. In the right place, carbon is a resource and tool,” McDonough says in his blog, emphasizing that being carbon neutral is not enough, we must work towards carbon positivity.
Start-up innovators are flocking to the carbon capture space. For instance, the Energy Monitor reports that Graphyte, a startup backed by Bill Gates’ climate solutions accelerator Breakthrough Energy, opened a factory that turns carbon-rich biomass waste from nearby paper mills into bricks – ‘carbon
— William McDonoughcasting’ – that are safely stored underground, removing atmospheric carbon dioxide.
Articles in this IFN explore the filtration industry’s role in carbon capture, building for clean air, and understanding environmental impacts on indoor air filtration.
On page 16, I interviewed David Gory, CEO of one carbon capture start-up, Airbuild. They are ingeniously utilizing rooftop solar panels to grow algae to capture carbon, create sellable biomass, and improve energy efficiency.
On page 31, Metalmark Innovations share research surrounding environmental impacts on indoor air quality. Using wildfire smoke as a variable on HVAC filter media effectiveness, they highlight the importance of MERV ratings to develop healthy air solutions.
Dr. Iyad Al-Attar continues his series on page 21, calling for higher levels of collaboration in the filtration industry to address a holistic solution to air filtration design. And on page 26, North Carolina State University researchers share a ground breaking air filtration technology that offers 99.9% efficiency in smoke and pathogen air removal.
As industry takes a proactive role in their sector, it contributes to collective change. McDonough says, “Sustainability takes forever. And that’s the point.”
Caryn Smith
Chief Content Officer & Publisher, INDA Media, IFN
R. Vijayakumar, Ph.D., Chair
AERFIL
Tel: +1 315-506-6883
Email: vijay@aerfil.com
Rahul Bharadwaj, Ph.D.
Lydall Performance Materials
Tel: +1 603-953-6318
Email: rbharadwaj@lydall.com
Tom Justice, CAFS, NCT ZENE, LLC Filtration
Tel: 757-378-3857
Email: justfilter@yahoo.com
James J. Joseph
Joseph Marketing
Tel/Fax: +1 757-565-1549
Emai: josephmarketing120@gmail.com
Wenping Li, Ph.D.
Agriltech Research Company
Tel: +1 337-421-6345
Email: wenpingl@agrilectric.com
Ernest Mayer, Ph.D.
E. Mayer Filtration Consulting, LLC
Tel: +1 302-981-8060
Email: ernestmayer6@gmail.com
Robert W. McIlvaine
The McIlvaine Company
Tel: +1 847-784-0013
Email: rmcilvaine@mcilvainecompany.com
Rishit R. Merchant
Parker Hannifin
P: +1 (805) 604-3519
E: rishit.merchant@parker.com
Thad Ptak, Ph.D.
TJ Ptak & Associates
Tel: +1 414-514-8937
Email: thadptak@hotmail.com
IFN is the leading source for the dialogues, debates and innovations across the full spectrum of filtration and separation applications and processes.
If you would like to utilize your expertise to help shape the content in the IFN , consider applying for the IFN Editorial Advisory Board. We welcome participation through input on trends and innovations, new story ideas and overall thought leadership. This is a collaborative board that meets quarterly to discuss the state of the industry. Send an email to Caryn Smith at csmith@inda.org for consideration.
Conference Features
•3 Plenary Presentations
•Expo Hall
•Student Poster Competition
•Monday Evening Networking Reception (additional fee)
•Two Panel Sessions – New for FiltCon 2024
•Filtration Short Courses (additional fee)
•Industry Tours (additional fee)
•Four Tracks – Solid/Liquid, Air/Gas, Prof. Chase (1-day), Energy Track (1-day)
NEW FOR 2024: Latest & Greatest Product Preview (reservations required)
Plenary Speakers
Additive Manufacturing and Membranes for High Performance
Dr. Rigoberto Advincula University of Tennessee
Mr. Trey Hamblet Industrial Info Resources
Panel Moderators
Carbon Capture (Energy Aspect)
Dr. Wu Chen Retired
Dr. Imad Khalek Southwest Research Institute
The Confluence of Sustainability and Performance in Filtration Media Made with Biobased Materials
Mr. Koen Bastiaens Natureworks, LLC
Anovel nanoparticle spray coating process has been shown to all-but eliminate the growth of some of the world’s most dangerous bacteria in air filtration systems, significantly reducing the risk of airborne bacterial and viral infections. That’s the principal finding of a recently published study, led by researchers from IMDEA Materials Institute in collaboration with scientists from the Networking Biomedical Research Centre in Respiratory Diseases (CIBERES) and Rey Juan Carlos University (URJC) in Madrid, Spain.
The study, Control of microbial agents by functionalization of commercial air filters with metal oxide particles, tested various spray coatings of silver (Ag2O), copper (CuO) and zinc (ZnO) oxides as low-cost antiviral and antibacterial filters when applied to commercially available air filtration systems.
In their most promising result, the authors found that both the Ag2O and CuO compounds used were shown to have a total antiviral activity (greater than 99%), with the Ag2O filter extract also demonstrating a complete prevention of targeted bacterial growth throughout the 24hour incubation period measured by the study.
The study’s findings could prove relevant in preventing the spread of a wide number of respiratory infections. However, researchers focused specifically on the antimicrobial properties of metal oxide particles against two specific respiratory pathogens: Streptococcus pneumoniae and Pseudomonas aeruginosa.
“S. pneumoniae and P. aeruginosa are considered among the top 5 bacterial pathogens
leading to death worldwide,” explained IMDEA Materials researcher Dr. Mónica Echeverry-Rendón. “S. pneumoniae is the major cause of community acquired bacterial pneumonia, acute otitis media in children and non-epidemic meningitis.”
“P. aeruginosa, meanwhile, is commonly associated with recurrent exacerbations associated with chronic infections in patients with cystic fibrosis and bronchiectasis.”
The study was conducted in conjunction with Spanish air filter manufacturer Venfilter, which supplied five commercially available filters for testing.
While the study’s initial results are extremely promising, further testing will need to be conducted to confirm and evaluate the findings.
“Overall, this work presents a partial preliminary evaluation of spray-coating as a lowcost, simple and versatile post-manufacturing process of air filters that can be applied to commercial purposes,” concluded Dr. Echeverry-Rendón.
“However, although the achievements reached up to this point are very significant at a scientific level, there is still a long way to go before it will be possible to commercialize them at an industrial level.”
“Different aspects and further tests will need to be considered in future works ... so that a complete characterization of coating effectiveness and filter performance, over time, and using real-size filter prototypes with sealed frames, can be carried out.”
Alongside Dr. Echeverry-Rendón, researchers involved in the study included IMDEA Materials’ Prof. Javier LLorca and Dr. Juan José Vilatela, Dr. De-Yi Wang, Dr. Miguel Vazquez-Pufleau and Dr. Bruno Ribeiro, exIMDEA Materials’ researcher and current URJC professor, Dr. Antonio Vázquez López, and CIBERES’ Mirella Llamosí and Drs. Julio Sempere, José Yuste and Mirian Domenech.
This investigation was supported by the project MAMAP, funded by the REACT-EU call from the Comunidad de Madrid and the European Regional Development Fund, by the project (MAD2D-CM)-IMDEA Materials funded by the Community of Madrid and by the Recovery, Transformation and Resilience Plan and by NextGenerationEU from the European Union and by the Marie Sklodowska Curie Fellowship SUPERYARN (grant number: 101029091). In addition, this study was partially supported by the research grant project PID2020-119298RB-I00 funded by MICINN/ AEI/10.13039/501100011033.
materials.imdea.org
For details on how to submit your company’s technology for consideration as a “Technology Spotlight” in IFN , contact Ken Norberg at ken@filtnews.com or +1 202.681.2022.
ABB has launched its technology solution for the cold block stage of the brewing process to further support breweries in their operational efficiency and in the adoption of digital solutions.
The cold block stage of the brewing process involves fermentation and maturation, yeast management, filtration, bright beer tanks (BBT) area, cleaning in place (CIP), and all secondary processes. These are the stages at which variations in recipe and flavor can be managed and introduced, which is particularly important to brewers. ABB uses modular automation, digital capabilities, simulation technology, and advanced process control (APC) to ensure the solution will support customers’ current challenges and future developments.
It will benefit customers who require a solution to improve and optimize their processes, reduce their energy and water consumption, and increase productivity. The solution is based on the ABB Ability™ System 800xA® distributed control system (DCS).
With its primary focus on breweries, ABB Ability™ BeerMaker provides users with a technological package of ready-made and tested master recipes, processes, templates, and objects that can be easily adapted to their needs by using a variety of configuration/recipe parameters and control schemes. Brewmasters receive a powerful production tool that imposes no limits on their production schedules or creativity. www.abb.com
Willow Industries, the leader in cannabis decontamination technology and microbial control services, announced the launch of WillowAir, an air filtration system designed to capture and remove airborne contaminants, providing safer workplaces for employees and a direct solution to one of the main factors in contaminated product: air quality.
Addressing the industry’s heightened need for employee safety, Willow Industries has engineered a science-backed and cost-effective solution to the evolving needs of the industry. The WillowAir system effectively counters inhalation hazards of ground cannabis dust, respiratory irritants, airborne pathogens like Aspergillus, and overall health risks in cultivation environments. As a multifunctional system, WillowAir plays an equally crucial role in combating the pervasive threat of airborne contaminants affecting plant quality, product safety, and regulatory compliance. By lowering exposure to microbial burden and cross-contamination, the system proactively maintains a clean environment throughout upstream processes. www.willowindustries.com
Ahlstrom is investing in a new production line for molecular filtration media in Turin, Italy. Air quality in closed environments such as buildings and vehicles is a major concern in many areas of the world. In this context, particulate filter media play an important role in removing solid particles and aerosols from the air. Molecular filter media are used in complement, removing gaseous pollutants, including volatile organic compounds, inorganic gases (such as sulfur dioxide, nitrogen oxides, ammonia), and odors, and delivering the cleanest air to people and processes.
The new line is being designed to produce the highest-performance adsorbent materials for premium filtration applications, including next-generation cabin air and fuel cell air intake, as well as a complete range for HVAC and cleanrooms. It will enable Ahlstrom to offer superior solutions for customers and support their industrial filtration application development as well as the transition to electric vehicles.
The investment is made in synergy with Ahlstrom’s Fine Fiber platform in Turin, which will be upgraded to produce HEPA filtration layers. Fine Fiber media can be combined with molecular filtration materials also to deliver the best protection against the finest particles. www.ahlstrom.com
Amazon Filters has become the first industrial filter maker in the UK to use polypropylene manufactured from renewable resources in the production of meltblown filter media. The Surrey-based manufacturer has launched sustainable polypropylene versions of its flagship ranges SupaSpun II, SupaGard, Contour and VisClear II.
These filters are widely used in critical liquid filtration processes in industries such as municipal water, oil and gas, food and beverage, chemicals and coatings, and pharmaceuticals. Traditionally, monomers sourced from fossil fuels have been the base media feeding into the polymers involved in polypropylene manufacturing.
But now, under a “mass balance approach” developed by Vienna-headquartered Borealis, a world leader in polymer development and manufacture, a proportion of the fossil-derived propane can be replaced by an identical volume of sustainable monomers that are tested to ensure the same level of quality. Amazon Filters’ product variations involve Borealis’ Bornewables polymers made from sustainably sourced renewable feedstocks. They are derived solely from waste and excess vegetable oils such as used cooking oil and residues from vegetable oil processing.
The approach has already been used in polypropylene manufacture by early adopters in the Netherlands, including in the production of medical face masks and other filter media. Describing the process, Amazon Filters Managing Director Neil Pizzey said raw waste vegetable oil collected from restaurants and the food industry is used to make the monomers that feed into the polypropylene manufacturing process in the same way as monomers sourced from fossil fuels. www.amazonfilters.com
Biotech Fluidics AB of Sweden announced a new range of multilayer stainless-steel filters for larger bore elevated temperature and corrosive processing applications. Benefiting from proprietary “Closed Edge Technology” these unique PORO–FRIT™ filters deliver an unmatched even flow through profile even at the filter edges.
The filters are available in a wide range of diameters from 20-200 mm, with a porosity between 2 and 20 microns. These multilayer sintered wire mesh filters are self-standing and inherently stable. Delivering market leading performance, these filter elements can lower your costs by providing longer on-stream life and years of trouble-free service. In addition, Biotech Fluidics multilayer stainless-steel filters are easily cleaned thereby reducing your disposal costs. www.biotechfluidics.com
United Kingdom Aston University will establish the Aston Institute for Membrane Excellence (AIME), a globally unique, cross-disciplinary institute to develop novel biomimetic membranes, after receiving a major grant of £10m from Research England.
AIME will be led by Professor Roslyn Bill, from the School of Biosciences, with co-lead Professor Paul Topham from the department of Chemical Engineering and Applied Chemistry (CEAC).
Membranes, both biological and synthetic, are hugely important in many sectors. For example, the world’s top ten selling human medicines all target proteins in biological membranes, while synthetic polymer membranes are used in the US$100bn/year water purification industry. The team behind AIME believes that the full potential of membranes will only be realized by an interdisciplinary group spanning biology, physics and chemistry that can investigate membranes holistically.
www.aston.ac.uk
Pall Corporation, a leading provider of filtration, separation and purification solutions, has introduced SepraLYTE™ liquid/gas coalescers, an innovative solution designed to meet the increasing demand for efficient separation of electrolyte aerosols from gas in green hydrogen production processes.
Leveraging advanced separation technology, SepraLYTE coalescers excel in the separation of water or electrolyte aerosols (30% potassium hydroxide solution) from hydrogen, ensuring the purity of hydrogen produced from electrolysis processes. They are highly suitable for a wide range of separation applications where minimal pressure drop is crucial for downstream processes.
These coalescers feature Pall’s proprietary melt blown media technology, which achieves outstanding liquid mist separation with low differential pressure. The compact design incorporates coalescer media that ensures compatibility with various chemical applications. Other key advantages of SepraLYTE liquid/gas coalescers is their ease of maintenance, compact size and waste reduction.
Utilizing SepraLYTE liquid/gas coalescers, customers gain significant advantages over conventional separation products. These advantages include reliable, consistent, and verifiable separation performance, high gas flow and liquid removal in a compact cartridge, which allow for smaller systems with low capital, operating, and maintenance costs. www.pall.com
At Berry, we leverage our unmatched global capabilities, sustainability leadership, and deep innovation expertise to serve customers of all sizes around the world. Harnessing the strength in our diversity and industry leading talent of 47,000+ global employees across more than 300+ locations, we partner with customers to develop, design, and manufacture innovative products with an eye toward the circular economy. The challenges we solve and the innovations we pioneer benefit our customers at every stage of their journey.
With over 35 years of experience manufacturing filtration media, Berry Global’s products have become the industry standard in the pleat support and filter layers for air, liquid, and gas applications. Berry Global’s proprietary technologies deliver unique material solutions for challenging customer needs. Whether using our unique REEMAY® spunbond PET technology in vaccine manufacturing, or TYPAR® spunbond PP nonwovens in water filtration to create safe drinking conditions, customers trust our proven filtration solutions.
Our filtration capabilities encompass a wide range of specialty materials, process technologies, and state-of-the-art innovation centers.
• Reemay®
• Meltex™
• Typar®
• Air Filtration
• Industrial Filtration
• Water Filtration
• Automotive Filtration
• Food & Beverage Filtration specialties@berryglobal.com
Carbon capture, utilisation and storage (CCUS) is regarded as a key part of the global strategy for reaching net zero by 2050 and is set to play a vital role in mitigating the adverse effects of climate change. Legislative mandates on reducing emissions and incentives for carbon removal are increasing across the world.
With a surge in the use of CCUS, it is more important than ever to be aware of the challenges involved with capturing, processing and storing carbon. Harmful impurities including sulfur dioxide, nitrogen oxide, oxygen and water in the carbon dioxide stream cause operational issues, reduced carbon capture efficiency, critical equipment damage, unscheduled downtime and increased maintenance costs. If the carbon dioxide is not purified to the right level when being transported – either for storage in geological reservoirs or for making new products – there is also a threat of corroding pipelines and unwanted side reactions. Proactive contaminant removal can therefore provide a good return on investment.
As decarbonisation projects continue to accelerate, filtration and separation technology will play a critical role across the value chain of CCUS. This particularly applies to absorptive (solvent-based) carbon capture, which is currently the most commonly used CCUS method. This is primarily because it is more economical and at a more mature stage of development than other existing methods such as cryogenics and chemical looping.
The compression and storage of carbon dioxide is a key part of the CCUS process, with CO2 needing to be compressed to reduce its volume for efficient transportation and processing. As compressors are highly sensitive to contaminants, which can quickly cause corrosion and lower compressor yields, it is vital to sup-
port them with the right technology.
High tech coalescers, for example, can be used to boost compressor operation and reliability by removing carry-over liquids (oil that seeps past the separator filter into the discharge piping), free water (condensation) and particulate matter (a mixture of solid and liquid droplets). When compressed carbon dioxide is sent though long pipelines to underground reservoirs for storage, it can also contain solid contaminants which can foul the reservoir. Installing high efficiency particulate filters at the reservoir inlet is necessary to solve this issue.
It is clear that carbon capture is vital to a wider energy transition vision and meeting global net zero emissions. While carbon capture technology has been around
for decades, there needs to be a massive ramp up in CCUS projects to meet climate targets by 2050. More investment in CCUS technology is required, with filtration and separation applications playing a key role in maintaining high carbon capture efficiency and reliable equipment operation, as well as meeting safety regulations.
Collaboration between tech suppliers, industry and governments is going to be pivotal in providing a sustainable and economic solution to meet these needs.
www.pall.com
Rosedale Products, Inc. is a leading technology developer in the field of liquid filtration systems and waste minimization products for customers around the globe. With more than 50 years of experience, Rosedale offers an exceptional product line that includes high-performance filtration solutions for multiple industries. Rosedale technicians help customers find the best, most cost-effective approaches to their filtration needs.
Rosedale product lines set the industry standard in versatility and reliability and includes bag and cartridge filters, basket strainers, automatic back washing filters, filter cartridges, and many special application products. Together with ongoing consulting, troubleshooting, and support from our team of in-house experts, Rosedale provides comprehensive solutions for every critical industry filtration need.
Rosedale is committed to your vision. Rosedale manufactures industrial filtration products for virtually any industry where liquid and gas flows are present.
With a vast product line that suits many needs, as well as the flexibility to customize standard products. Rosedale’s sales staff has knowledge of many industrial practices, giving customers the confidence that their filter solution is the best available for their specific need. The most popular products are bag filters, pleated cartridge filters, and basket strainers. Rosedale High Flow horizontally mounted filter vessels are setting the industry standard with containing 1 to 31 large pleated cartridges in 40 or 60 inch lengths. The High Flow product line boasts flow rates of up to 400 gallons per minute for each element in select applications.
Whatever your filtration application, Rosedale Products, Inc. offers a product designed to meet your needs. From filters that accept high-efficiency filter cartridges to filter bags, Rosedale products deliver superb performance at an exceptional value.
Innovation + Design + Experts.
Rosedale Product Offering:
• High-Flow Housings
• Single/Multi-Bag Housings
• Polypropylene Housings
• Indicating Filter
• Centrifugal Separators
• Backwashing Systems
• Coolant Filter Systems
• High Capacity Elements
• Filter Bags
Call 800.821.5373 or write us today at filters@rosedaleproducts.com for more information.
t Rosedale Products
Backflush Filter Assembly (U.S. Patent No. 11,904,261).
Airbuild is a company driven by the vision of transforming the world through the power of algae. Led by David Gory, Chief Executive Officer, the team includes John Bucur, Chief Sustainability Officer, Richard Mariita, Chief Science & Technology Officer and James Davis, Founding Principal Engineer. Their mission is rooted in developing and deploying algae-based carbon capture solutions that are scalable, affordable, and accessible to communities around the globe. Their venture is driven by personal experience with the effects of environmental hazards that plague the world’s sustainability. Airbuild started as an LLC in 2021, but officially restructured and relaunched as a C corp last year.
Using a patented and proprietary carbon removal process that is hosted in a solar panel and employs the most efficient biological organisms – microalgae – each of Airbuild’s solar-driven panel solutions removes more carbon dioxide than 15 trees. The efficiently sized panels, at 5 ft x 4 ft and 6 inches deep, sequester carbon at the rate of 150 kg per year, with solar generation at 450 watts.
With embedded solar cells, there is no compromise for the productivity of roof space, as they contribute to energy efficiency of the building on which they are hosted. The Airbuild panel generates renewable energy to meet organizational needs. It goes one step further to utilize water filtration, where algae produces oxygen that allows aerobic bacteria to break down organic contaminants in water and takes up excess nitrogen and
phosphate in the process. What remains is an algae biomass that then can be commercialized by selling it to companies that use it in their products, many of which are recognizable name brands.
While the concept is in final testing phases with the University of Massachusetts, they are working towards a massproduced product in test scenarios with companies that are already on board to adopt.
International Filtration News spoke with David Gory on the concept and company. It is one to watch.
International Filtration News: Let’s take a step back and in your words, describe carbon capture and why is it an important emerging technology?
David Gory: The easiest way to explain the need is, it’s all about plus minus. The way the planet stays at the same temperature is simple science. As we breathe, carbon gets released by humans, then nature through photosynthetic organisms converts the carbon into oxygen while the ocean and rocks just capture it.
Over the course of industrialization, trees were destroyed to build our muchneeded infrastructure, which has caused a release of more carbon than other elements including the ocean, the rocks, the mountains, and the plants are able to capture. So, now there is an imbalance. We are aware of it; we see the effects from here in the state of California, to all around the world, evident in highly unusual weather patterns. I’m from Nigeria, where I spent the first 16 years of my life before attending college in the United States. My parents, who are still there, often comment on insane weather patterns, as well as the significant temperature difference from, say, 10 years ago to today.
The idea of carbon capture is to take in the excess carbon from the environment, to return the temperature and environmental balance to what it was preindustrialization.
IFN: What is the background of you and your team, and how did it originate?
Gory: I have a bachelor’s degree in mechanical engineering, a master’s degree in business administration and another in cybersecurity, which in no way, shape, or form relates to this project.
When studying at Cleveland State University, I met one of the former co-founders, who left the company last year. I was an undergraduate and he was in graduate school, and we became close friends. Fast forward two years later, he had started his career and I was in my master’s program. We reconnected. He mentioned starting a company with John Bucur with the mission to restore planetary health. He connected me to John, we had immediate synergy, and I joined the team.
John’s idea stemmed from his undergraduate study of business sustainability at Arizona State University. His interest was in green roofs and the impact they have on the environment. The limitation of green roofs is that they are too heavy for the zones that need them the most –industrial and commercial zones. His mission was to exponentially increase their potential and decentralize carbon sequestration by engineering a solution to solve that problem.
As a team, after analyzing many materials for the project, ultimately we decided to utilize algae because of its many unique properties, yet none of us are biologists. We struck gold bringing on Dr. Richard Marita, PhD, a micro-biologist with multiple degrees, two patents, and published in multiple publications. Before Richard, our trial and error in the lab kept bringing us back to the drawing board. When Richard joined the team, in six months we got to a final product that we are currently testing with the University of Massachusetts.
What makes Richard unique is, like me, he’s someone who has felt the direct impact of industrial pollution in his native country. In Nigeria, we had to drink water out of wells because the natural water sources are polluted by industries. The terrible air quality leads to low quality of life for the citizens in that environment. But the person who felt it more was him; he lost his mother and his sister to waterborne diseases. This has been a motivating factor to find solutions for decentralized water filtration to preserve public health. He has started two NGOs giving aid to Kenya and Ukraine in their time of need through water filtration. The second he told me that story, I knew he was the right person. I love his passion, his drive, and I believe with him we will succeed.
IFN: Describe the product under development.
Gory: Imagine a solar panel, on the outside, we have solar cells that generate energy. And on the inside, we grow algae. To get the algae to live in that solar panel, is where the IoT and automation comes in. We control the entire environment inside the panel by pumping air from the environment into the algae, which draws in the carbon and releases oxygen. In the overall process, we engineer a route
to also detoxify grey water (wastewater that would end up in a septic and sewer system and can eventually end up in water bodies) from the building.
For water detoxification, the algae removes the nitrogen and phosphate that are harmful to aquatic life, plants, and humans. Algae absorbs them and releases clean water that can be sent into a water stream.
We route the cleaned grey water release for alternative purposes, such as irrigation. Also, the solar panel generates as much energy as a traditional solar panel.
IFN: The membrane is a bio-product; are you farming the algae in the solar panel?
Gory: We put the algae into the panel and then begin pumping in the grey water. The algae multiply aggressively, as it feeds on the grey water and carbon. Within hours, the algae starts growing and the panel gets greener. And you can visually see the effect as it multiplies over days. In approximately 12 to 30 days, it fills the entire panel and the algae is ready for harvest.
IFN: What happens to the algae in the panel?
Gory: There’s an automated system that harvests about 80% of the panel’s algae. Then, more grey water is pumped in and
continues the cycle of growth. Right now, we’re testing with a centrifuge that separates the water from the algae biomass. The water gets routed to an irrigation system. And the biomass is harvested as a raw material that can be used to produce other fascinating things. For us, it is a waste material, but to others it is a raw material that can be monetized and sold to other industries to make kitchen counter tops, biodegradable ceramics, green hydrogen, ink for pens, plastics, and even coffee cups, you name it. We’re working with these kinds of companies to be a supplier of this raw material.
IFN: How does this work in the business side of your operation?
Gory: The way we structured our business plan, the panel belongs to the customer. We sell the panels, charge a monthly subscription for harvest and data management, and take a transaction fee for algae biomass and carbon credit sales on our marketplace.
IFN: Is there a working model of your concept and what are the obstacles so far?
Gory: We are still in final testing and hope to be ready for our testing partners to install their panels soon. As proof of concept, in 2013 in Hamburg, Germany, a company called Cellparc actually integrated algae into our built environment.
The idea is to keep the algae in motion. If you keep if you let algae settle, then it starts sticking to things, so there’s always sustained airflow, and we’re continually annoying the cells. This is where the genius of Richard comes in with innovation to prevent biofilm and reduce maintenance. It works as a full system, currently being fine-tuned in the lab with automation and ML.
IFN: To clarify, the solar panels act as filtration and HVAC elements, and carbon capture agents?
Gory: Our panels help with grey water filtration, carbon capture for the environment, and energy generation for the building. By regulating the heating and cooling temperature of the building, we believe it would reduce the amount of energy they’re consuming. Most buildings will have a traditional HVAC system, but they can supplement their energy with solar power.
IFN: Tell us about your affiliation and support from the Techstars program.
Gory: Techstars is the world’s most active pre-seed investor; their acceptance rate is less than that of Harvard. We got lucky enough to be accepted into the inaugural class of Techstars San Diego powered by SDSU. We learned so much about building a business out of an idea, because that’s all we had at that point.
We received pre-seed funding from them, learning under the wings of great mentors Ryan Kuder, Andy Ballester, and Vidya Dinamani to name a few, and tapped into that network to guarantee our success.
IFN: Your mission is to make a global impact, how do you see that happening?
Gory: The way we see the ability to grow this in any country is the way we incentivize them. We designed a business plan that’s driven by passive profit. Reduced energy costs may not be enough of a motivation. So, on our end, we added the benefit of a passive revenue stream from the algae biomass, as well as the carbon credits. Companies from day one could generate passive revenue, which would help their bottom line. And that's how we plan to incentivize them.
We are currently having conversations with some international companies on pilots with the product. So far, the reception has been great. Right now, we’re targeting industries, but eventually we plan to target governments, as well.
IFN: How do you see working with construction/ building industries to build a sustainable building from the ground up?
Gory: We currently have a letter of intent for collaboration with an architectural firm and are working to become a resource for other architects who could pitch this concept for new buildings. The whole idea is, yes, we can integrate with existing buildings. But, if you utilize this in new building design, you can increase efficiency and lower the cost savings for installation.
It is pretty much an either/or – instead of routing your pipes to go left, you route them to go right, send water through our panels, and then take the pipes left.
IFN: Where are you in the overall process now?
Gory: Once we achieve third-party validation from the lab, where it is working great, we plan to take it out to the field to get real world validation, where we hopefully break it a couple times to fine tune it. Then, we are ready to pilot with our
committed customers; we have several right now here in the U.S. and India who have committed to pilot the panels for continued validation.
We’re currently in conversations with three ports on the West Coast to field test over six to eight months. Hopefully, the impact of the product is felt from day one and our collaborators in the field will want to commercialize it across their portfolio.
IFN: Being emerging technology, carbon capture is taking shape in many ways. Why do you think your product is feasible on a global scale?
Gory: People say, a drop of water makes a mighty ocean. Right now, the existing solutions for carbon capture are all centralized. There’s a big direct air capture plant in the middle of nowhere that’s performing this direct air capture of carbon and sequestering it underground.
We believe that if we could have little drops – 50 panels here, 100 panels here,
200 panels there – on every building, we could make an impact on a multi-gigaton scale, which is going to be the largest ever in terms of carbon capture. And that will
accelerate the impact. For us, it’s an allhands-on-deck type of problem. Those who are doing a centralized system are great. They’re working on their solution, which is much needed, while we are still working on it on a smaller scale, which is needed as well.
The added features of onsite water filtration and energy generation are the secret sauce that we are mixing to differentiate ourselves from other emerging solutions and hopefully positively impact quality of life.
We believe that carbon capture is the future because scientists are predicting that the Earth will or could be destroyed in a finite amount of time. Fixing this is of utmost importance to us, you know, not just for ourselves, but for future generations.
This is all about restoring planetary health and fixing environmental mistakes that were made.
To learn more about the vision of Airbuild, visit their website at www.airbuildinc.com.
The leading global pharmaceutical and biotechnology event INTERPHEX, will descend on New York City April 16-18, 2024, for the annual gathering of industry professionals, where attendees can “Experience Science through Commercialization.” Notable new features at this year’s event are learning labs and other display pavilions where visitors can experience new inventions and processes through live displays.
The organizer expects more than 8,000 industry professionals to attend the three-day event at the Javits Center. Attendees will be able to source new products from more than 450 exhibitors, while attending a curated conference and unparalleled networking events.
INTERPHEX 2024 is introducing new features to enhance the attendee experience. There are five notable new additions:
INTERPHEX Conference in the Learning Lab: Attendees have the option to purchase a conferee badge that grants access to the Learning Lab, a brand-new area on the show floor. This transformative event enriches the meeting experience by offering technical and scientific sessions led by experts in areas such as
inspection, formulation, cell and gene advancements, pharma 4.0, and automation.
AI in Pharma Pavilion: As the pharmaceutical industry embraces technological advancements, INTERPHEX presents the “AI in Pharma Pavilion.” Here, exhibitors showcase cutting-edge solutions related to artificial intelligence, a transformative wave shaping the future of pharmaceuticals.
Innovation Technology Gateway Pavilion: Building on its launch in 2023, this pavilion serves as the portal to global pharmaceutical technologies. Attendees can witness live demonstrations from even more exhibitors, showcasing the latest technology across the entire pharmaceutical product development lifecycle.
New Exhibitors Pavilion: Industry professionals seeking the newest products, services, and turnkey solutions can explore the offerings from new vendors at the show. This sought-after destination provides fresh perspectives and solutions.
Additional Tech Theater Stage: Due to popular demand, an additional Technical Theater will be available on the Show Floor. Leading exhibitors will present and demonstrate their latest technological advancements, providing valuable insights for all attendees.
Designed in collaboration with the American Association of Pharmaceutical Scientists (AAPS) and curated by scientists volunteering on the independent INTERPHEX Scientific Programming Advisory Committee, this year’s INTERPHEX Conference will consist of presentations, quick fires, keynotes, and late-breaking sessions that help conferees understand the latest science and its business applications while fostering connectivity and offering a unique opportunity for participants.
“We are especially excited for this year’s INTERPHEX,” said Event Director Douglas
Lugo. “In addition to a dynamic marketplace filled with top and emerging brands and the return of many popular programs, we are introducing the Learning Lab, home to the new conference. INTERPHEX will have more curated content, be scientifically qualified, and provide relevancy and interconnectedness between track offerings. Conferees will also have various new perks within the Learning Lab – making this experience fundamentally different than anything we’ve offered in the past.”
“The Scientific Programming Advisory Committee has developed a comprehensive program for the INTERPHEX Conference that emphasizes current scientific talking points within the pharmaceutical sector,” AAPS Executive Director Tina Morris, Ph.D., said. “At AAPS, we are enthused with the program as it touches on so many areas of science. No matter where your science falls on the product development lifecycle, there is something for you.”
Filtration plays a crucial role in pharmaceuticals and biotechnology, and a slew of filtration companies will be displaying filters for clean rooms, testing services, dispensers, separation and other compliance services. No less than 117 speakers will be at the event discussing products, technologies, AI, material handling, and manufacturing to name a few.
AAPS is a non-profit association of more than 7,000 scientists and professionals employed in academia, industry, regulatory, and other research related to the pharmaceutical sciences worldwide. Its mission is to advance the capacity of pharmaceutical scientists to develop products and therapies that improve global health.
www.interphex.com
Climate change is an insidious problem whose definition is elusive and for which definitive solutions may be lacking, as Frank Incropera[1] indicates in his book, Climate Change: A Wicked Problem . Positioning humanity to resolve climate change challenges requires an intrinsic understanding of our environmental status quo. We are running amuck with current anthropogenic emissions, and possessing advanced filtration technologies does not justify the current pollution actions. Eventually, embracing sustainability becomes the only way forward as “business as usual” models can risk our existence, particularly if we continue with current polluting conduct and linear economic endeavors.
The air we breathe consists of particles emitted from natural events such as sandstorms, volcanoes, forests, sea spray, and anthropogenic sources, which refer to those emitted by human activities. [2,3] Atmospheric air is full of microscopic particles, which can be health hazardous and thus considered a specific type of air pollution. The dynamic mixture of atmospheric solid and liquid particles emitted from various sources poses a significant challenge for filter performance prediction. Therefore, it is difficult to generalize the atmospheric air’s physical and chemical characterization, challenging installed air filters that rely on outdoor air. Consequently, it is typical for actual filter performance to deviate from laboratory test reports, which can be due to location sensitivity and
filter loading with various atmospheric pollutants. The interaction between particle characteristics such as concentration, size, distribution, shape, and filter media properties also impacts filter loading and performance. Investigating such interaction helps predict the filter's lifetime and performance in terms of the rise in pressure drop and the efficiency filters provide before replacement.
To avoid living in a building envelope of peril, fibrous filters (Figure 1) are called upon to capture unwanted particles before introducing outdoor air indoors. Fibrous filtration is commonly used in many filter applications such as HVAC, automobiles, sewage plants, and the intake of land-based gas turbines (Figure 2). Fibrous air filters used in HVAC applications rely on depth particle deposition on filter fibers where the feed concentration is low, and filter porosity is high (Figure 3).
Fiber size distribution and adjacent fibers (Figure 4), dendrite formation (Figure 5), fiber shape (Figure 6), and charge influence the loading of filters.[4] Ultimately, filter efficiency and dominant capture mechanisms depend upon many interrelated factors such as aerosol size, density, face velocity, media porosity, filter media, and particles’ physical and chemical characteristics. Failing to understand the interplay among all these parameters can lead to surface deposition on a depth filter media (Figure 7), thus reducing its lifetime and leading to pre-mature clogging.
Ultimately, pre-filtration can be pivotal in lowering particle concentration and adjusting particle size distribution to facilitate further depth deposition. Appropriate pre-filter selection can extend the stationary filtration stage, where particle deposition causes a negligible rise in the installed filter's pressure. Engineered multistage filtration utilizing pre-filters helps maintain
the filter’s permeability (Figure 8), and extends its lifetime while ensuring a sustainable performance.
Globally, the built environment uses one-fifth of all the electricity used in buildings for space cooling.[6] That represents 26% of global energy-related emissions, highlighting tremendous energysaving opportunities to lower their environmental footprint.[7] Therefore, appropriate employment of aerodynamic filters and performance prediction accompanied by sustainable operation and maintenance of HVAC systems are paramount to meeting energy efficiency targets.
Anthropogenic emissions alter ambient conditions surrounding HVAC and filtration systems and impact their predicted performances differently. Outdoor air pollution can further challenge the installed HVAC and filtration systems and spark additional complexities in managing and measuring IAQ and conducting professional maintenance practices while adhering to energy efficiency goals. Exposure to various pollutant types and high concentrations can severely load air filters. Inappropriate filter installation and leakage lead to pollutant deposits on
the cooling/heating coils, compromising the heat transfer mechanism on the one hand but also changing the dynamics of filter loading on the other hand. Furthermore, high moisture levels and particle concentrations can reduce the filter’s permeability,
EQUIPMENT:
• Pleat Welding
• Ring Welding
• Laminators (Ultrasonic/ Thermal/ Adhesive)
• Slitters (Ultrasonic/ Laser/ Mechanical)
• Traverse/ Spiral winders
• Hollow fiber/ Memb rane Lines (Lab/ Pilot Scale)
• Custom Mac hines
TECHNOLOGY:
• Ultrasonics
• CO2 Lasers
• RF Welding
• Hot Air/ Wedge
• Band Sealing
• Adhesive Dispensing
• Impulse Welding
We employ our 70 years of web handling experience to benefit our customers. Contact Chase Machine today for your equipment needs!
Addressing global air quality complexities requires scientists, policymakers, and industry leaders to work together to enable communities to embrace responsible and sustainable living in healthy building envelopes. Catchy “sustainability” slogans and “green and clean” planet wishful thinking will not amount to much if we lose track of resolving air quality challenges.
impeding HVAC equipment to deliver the required thermal comfort and ventilation flow rates.
The overall objective of filtration for HVAC systems is to render the filtered air fit-for-purpose given the application. However, it is challenging to improve air quality if chronic filter failure is the norm in a typical HVAC system operation and maintenance. Figure 9 shows pleat deformation and rupture of a depth filter installed in a typical air handling unit, leading to leakage and efficiency degradation. Inappropriate maintenance and attempting to regenerate a disposal fibrous filter by compressed air damages the filter media and will never allow the filter to be reset to its original efficiency. Furthermore, squeezing mechanical air filters in limited spaces within air-handling units lowers the efficiency ceiling that can potentially be achieved. Ultimately, such limitations impede any attempt to provide sustainable filter performance to enhance air quality, failing to give spaces for higher filtration efficiency through multistage filtration against targeted pollutants. Appropriate filter selections should look be-
yond particle capture and the sole reliance on mechanical filters, which requires an engineering approach to provide sustainable air filter performance.
Dust removal immediately comes to mind whenever air filtration is addressed, as if dust is the only harmful contaminant to our respiratory systems. Minimal emphasis, at best, is placed on contaminants in the atmosphere, such as radon, soot, carbonaceous particles, greenhouse gases and bioaerosols. We must step back to gain a broader perspective of the contaminants surrounding us, requiring thorough characterization analysis to make appropriate filter selections.
Today, the premise of proper filter selections should look beyond particle capture to entail similar filtration solutions for gases and bioaerosols. However, engineering and employing fitfor-purpose filtration systems should be only one of many foci. We must ask ourselves why we are polluting horrendously and spending tremendously on filtration and other mitigation technologies to re-capture what we just emitted.
The performance characteristics of air filters are efficiency, performance, and lifetime during operation. To ensure such operation is sustainable, we need to go the extra mile and employ online measurement of air filter performance, which can prove invaluable in monitoring its efficiency, not just the rise in pressure drop. Ultimately, that would grant data-driven decisions based on feedback loops for an optimal operational lifetime. Particle deposition on diffusers, cooling/heating coils, and eventually onto our lungs indicate that poor or no filtration was entertained. Failing to comprehend the risk of inhaling polluted air raises a red flag about our readiness to avail filtration technologies to confront particle and virus transmission through HVAC equipment. No wonder pandemics do not come along with wake-up calls; they swiftly storm cities, economies, building
envelopes, and our respiratory systems, leaving the surviving to bury loved ones and abandon their built environment.
Although air filtration is not the leading cause of poor indoor air quality (IAQ), filters are frequently sought to tackle IAQ ills. The demand for more stringent filtration standards, tweaked measures, and approaches to filter testing, installation, and performance is rising. However, crafting standards alone without air quality policies and incentive programs for concrete implementation leaves much to be desired. Sound planning, relevant standards, and assiduous guidance to adroit compliance and implementation should be the order of the day to deliver clean air to humanity equally, successfully, and sustainably.
Clustering people in polluted cities cannot be celebrated, and the solution to the rising tide of air pollution cannot lie simply in a filtration delirium to chase every airborne particle. Embracing sustainability is everyone’s business, and bringing about change requires everyone in every sector to make their fair share of contributions. Air quality inclusion is a core undertaking in sustainable urban development so we can collectively live, grow, and urbanize without polluting. Addressing global air quality complexities requires scientists, policymakers, and industry leaders to work together to enable communities to embrace responsible and sustainable living in healthy building envelopes.
Catchy “sustainability” slogans and “green and clean” planet wishful thinking will not amount to much if we lose track of resolving air quality challenges. Today, the increasing population in cities and anthropogenic emissions deteriorate air quality and provide the ideal conditions for diseases to spread, vary, and thrive. It is naive to think that pandemics like SARS-CoV-2 will be once-in-a-generation events, and vaccinations and employment of high-efficiency filters alone would poise infectious diseases for defeat. Humanity must embrace efficient processes and modern infrastructure and depend on responsible policymakers and
individuals to tackle the dismayingly long list of challenges over the following decades. Environmental degradation, global warming, and proliferating pandemics hinder our ability to respond to these challenges, which will require scientific and engineering breakthroughs and will be critical for future generations. A paradigm shift is imperative to attain and maintain healthy environments filled with clean air as we transition to pandemic-proof cities.
Ultimately, ascending the air quality heights entails engaging HVAC and their associated filtration systems to respond to any variation in IAQ. Buildings’ system adaptivity based on humancentric concepts and observance of energy efficiency do not have to be mutually exclusive. Enshrining air quality governance within legislation hold immense promise to drive change toward building envelope designs that enhance the well-being of human occupants far and beyond conventional settings.
Dr. Al-Attar is a mechanical engineer and an independent air filtration consultant. He is a Visiting Academic Fellow in the School of Aerospace, Transport, and Manufacturing at Cranfield University, consulting for air quality and filter performance relevant to land-based gas turbines. Dr. Al-Attar is also the strategic director, instructor, and advisory board member of the Waterloo Filtration Institute. In 2020, Eurovent Middle East appointed Dr. Al-Attar as the first associated consultant for air filtration. Recently, he became the Indoor Air Quality (IAQ) patron for EUROVENT. With engineering degrees (BSc, MSc, Ph.D.) from the University of Toronto (Canada), Kuwait University, and Loughborough University (UK), respectively, he is now reading for an MSc in sustainable urban development for air quality inclusion at the University of Oxford. His expertise is on the design/performance of high-efficiency filters for HVAC and land-based gas turbine applications, focusing on chemical and physical characterization of airborne pollutants.
1. Incropera, F.P., 2016. Climate change: a wicked problem: complexity and uncertainty at the intersection of science, economics, politics, and human behavior. Cambridge University Press.
2. EPA, 2005. Review of the national ambient air quality standards for particulate matter: policy assessment of scientific and technical information. OAQPS Staff Paper.
3. Hinds, W.C. and Zhu, Y., 2022. Aerosol technology: properties, behavior, and measurement of airborne particles. John Wiley & Sons.
4. Wakeman, R., 2007. The influence of particle properties on filtration. Separation and Purification Technology, 58(2), pp.234-241.
5. Al-Attar, I.S., 2011. The effect of pleating density and dust type on performance of absolute fibrous filters (Doctoral dissertation, Loughborough University).
6. IEA (2018), The Future of Cooling, IEA, Paris https://www.iea. org/reports/the-future-of-cooling, License: CC BY 4.0.
7. IEA (2023), World Energy Outlook 2023, IEA, Paris https://www. iea.org/reports/world-energy-outlook-2023, License: CC BY 4.0 (report); CC BY NC SA 4.0 (Annex A).
While the need for effective air filtration technologies has long been recognized, traditional solutions such as high-efficiency particulate air (HEPA) filters and ultraviolet light (UVC) devices have demonstrated limitations in providing comprehensive pathogen removal and deactivation, particularly during COVID-19. In response to these challenges, North Carolina State University (NC State) researchers have developed a groundbreaking air filtration technology – SPAR (Smoke and Pathogen Air Removal), formerly known as FIL-TEX, that offers a viable alternative for the 21st century.
For decades, HEPA filters have stood as the gold standard in air filtration. Their impressive 99.9% efficiency in capturing small particles and pathogens has made them a staple in healthcare, education, transportation, and other settings. However, HEPA filters have inherent drawbacks. They excel at capturing pollutants but fall short in deactivating bacteria and viruses, making filter replacement a potentially hazardous endeavor.
Dr. Warren Jasper, a professor at NC State, explains, “Because HEPA filters merely capture particulates and pathogens and focus them in one place, there is a strong likelihood that any collected bacteria or viruses will be re-aerosolized when replacing the filter.”
Furthermore, HEPA filters are typically positioned within air handling systems, which limits their effectiveness. Even when added to an air purifier, they fail to offer widespread protection. “Essentially, HEPA filters are often placed too far away to provide protection to areas where people are congregating,” Jasper says.
Ultraviolet light disinfection technologies (UVC) have gained popularity for their ability to deactivate live pathogens by destroying their DNA. However, just like HEPA filters, UVC systems have their own set of challenges including potential health risks such as headaches and skin cancer for individuals overexposed to UV
light. Furthermore, integrating UVC technologies with HVAC systems can increase operational and maintenance costs due to higher power requirements and costly bulb replacements.
Recognizing the limitations of these decades-old technologies, NC State researchers embarked on a mission to develop a cutting-edge solution that addresses the unique challenges of today’s world. “Filtration of airborne particulates can be divided into two camps – active and passive. We decided to take the best
SPAR technology is built on a foundation of woven, knit, or non-woven structures. Within these structures, non-conductive yarns are combined with conductive yarns that serve as electrodes. When voltage is applied to these conducting yarns, they generate a non-thermal plasma (NTP).
performance characteristics from passive technologies that capture particulates and active technologies that purify the air and combine them into a single, more modern air cleaning solution,” Jasper says.
The result of their innovative endeavor is SPAR, which represents a fusion of the finest attributes of HEPA filters and UVC devices, encapsulated within a flat, lightweight, non-thermal plasma-enhanced textile. This innovative textile filter excels at both capturing and killing bacteria, viruses, and other contaminants, boasting an impressive 99.9% efficiency.
SPAR technology is built on a foundation of woven, knit, or non-woven structures. Within these structures, non-conductive yarns are combined with conductive yarns that serve as electrodes. When voltage is applied to these conducting yarns, they generate a non-thermal plasma (NTP).
Non-thermal plasma, often referred to as cold plasma, represents an electrically energized state of matter that remains cool to the touch. It is composed of a partially ionized gas that reacts with pathogens, chemicals, odorants, and other contaminants, converting them into harmless oxidized forms. When airborne pathogens pass through the SPAR filter, the NTP reacts with the sheath membrane of the microorganisms, deactivating the virus or destroying the cell wall of the bacterium, effectively eliminating airborne pathogens while safely collecting them.
Essentially, SPAR operates as a magnet that attracts, deactivates, and removes unwanted contaminants from the air, all without emitting any additives or substances into the environment.
The need for an air filtration technology that can eliminate aerosolized pathogens
is now more evident than ever, particularly in confined spaces where people frequently gather. Dr. Frank Scholle, Associate Professor of Biological Sciences at NC State, explains, “While good air circulation helps reduce the likelihood of the transmission of airborne viruses and bacteria, effective filtration is crucial in locations where there is not much air turnover and in which we pack a lot of people.”
To validate the efficacy of SPAR, researchers in Scholle's virology lab conducted extensive testing. They introduced an aerosolized coronavirus, genetically similar to the virus responsible for COVID-19 infections, into a laboratoryscale tunnel with SPAR situated between the inlet and outlet. Air samples collected before and after passing through SPAR demonstrated impressive post-filtration effectiveness, with nearly a 3-log reduction in infectious virus, equivalent to up to 99.7% effectiveness.
Following the successful tests at NC State, SPAR underwent independent analysis at CREM Co Labs, a specialized R&D laboratory focusing on antimicrobial testing. The results were equally compelling, with SPAR proving its ability to remove over 99.9% of airborne viruses, including COVID-19, and 99.9% of airborne bacteria like staph, while deactivating 98% of viruses found on the filter's surface.
SPAR's versatility extends beyond pathogens. It has demonstrated rapid absorption of continuous smoke and particulates such as oil, carbon, soot, ash, and tar in enclosed spaces where venting is not feasible, making it a versatile air cleaning technology with numerous potential applications.
The SPAR filter can be crafted from various fabrics, including cotton, polyester, polypropylene, Kevlar, and others. Its lightweight, flat design, with a thickness of only about 2 mm, facilitates high airflow while requiring minimal power consumption. This versatility allows for integration into various air cleaning devices and systems, including wall- or ceiling-mounted units and HVAC systems.
Currently, SPAR technology is available through Stitch Partners, which holds the intellectual property license from NC State. Manufacturers of air cleaning devices can incorporate SPAR as a component in the development of new or existing systems.
For more information, contact Stitch Partners by phone at (978) 880-3783, via email at info@stitchpartners.com or visit https://stitchpartners.com.
Greg Rankin is a Houston-based freelance writer with more than 20 years of experience writing about the HVAC industry, mechanical engineering, and clean technology.
Fiber lasers are the tool of choice for precision metal work. For metal cutting applications, fiber lasers dominate due to their combination of speed, flexibility and precision. The advent of handheld welding solutions promises to quickly grow laser’s share over traditional techniques due to similar advantages. Years ago, the aerospace industry adopted laser drilling for perforating high performance metal parts to improve thermal performance. Now, advances in the productivity and precision of fiber laser drilling have begun to disrupt the industrial filter industry (Figure 1).
Filters are porous devices which remove impurities as material passes through. The quality of the filtered product relies on the uniformity and cleanliness of the filter holes. Lasers are a non-contact drilling technique which has no mechanical wear associated with tooling, so excellent hole uniformity is maintained over a lengthy fabrication process covering a large surface. In many cases, the smaller the holes, the better the filtering. Lasers are particularly suited to drilling holes < 100 µm diameter, which are challenging dimensions for traditional alternatives like chemical etching or mechanical punching (Figure 2).
Sustainability policies create new, demanding applications for high performance filters which laser drilling is uniquely able to fulfil. Plastic recycling plants melt incoming garbage, then pass the liquid through a sequence of filters, before re-solidifying the filtered material into recycled plastic pellet feedstock. Products made of recycled plastic, for example PET water bottles, must meet the
high standards of the food and beverage industry. Laser-drilled filters featuring hole diameters in the 60-80 µm range are a field proven solution meeting these high standards.
Drilling of common materials like stainless steel is accomplished by focusing an intense fiber laser beam to a spot
diameter as small as 40µm. The intense laser melts and vaporizes the metal at a high rate with excellent consistency. High pressure nozzles direct gas which efficiently remove liquid and gaseous metal enabling the laser to drill deeper. In a short amount of time, usually just a few tens of microseconds, the laser punctures the backside, and the hole is complete. The laser is turned off, quickly repositioned, and the process repeats. In this manner, filters numbering millions of holes are fabricated at great speed with outstanding precision and uniformity. An excellent feature of laser drilled holes is the natural taper, meaning the exit diameter on the backside is smaller than the input side. This creates a useful funneling effect, while resisting harmful backflow through the filter.
Laser drilling is a flexible technique able to employ multiple methods to optimize hole quality and throughput. The simplest is single shot drilling in which a single burst of energy penetrates the entire sample thickness. Single shot is the highest throughput technique, enabling a modulated laser to produce hundreds of holes per second.
Multi-shot, or percussion drilling, utilizes multiple laser bursts to minimize the overall thermal impact of the energy required to puncture the substrate. Percussion drilling is often accomplished
Laser drilling easily penetrates stainless steel with high surface hardnesses.
Laser drilling creates highly tapered holes, minimizing back-pressure and risk of hole blind.
in concert with a galvanometric scanner and pulsed lasers which provide tens or hundreds of thousands of shots per second. This technique is most popular for microfabrication, where precision and quality requirements trump throughput. By repeatedly scanning the laser over multiple spots, high quality holes are created with minimal heat affected zone. The throughput challenges of multi-shot drilling are somewhat offset by its ability to create many holes in parallel (Figure 3).
A third technique called trepanning moves the laser energy in a spiral trajectory around the perimeter, resulting in a hole which is cut, rather than drilled. Trepanning is desirable for larger holes, because no energy needs to be expended to remove center material from the cut-out area. When trepanning, the laser spot may be moved either using mechanical or optical means. Large diameter holes of excellent quality are realized, but generally at a slower rate than is achieved by single shot or percussion drilling methods.
Throughput is maximized when “on the fly” techniques are employed, but precise timing is required (Figure 4). On the fly continuously moves the drilling head optic over the sample, without stopping to drill each position. By avoiding the inertia loss of stops and starts, on the fly maximizes laser utilization and drilling rate.
Filter fabrication is normally accomplished using parallel rows drilled by rastering the laser beam across the substrate in continuous motion. To ensure precision spacing and hole quality across the entire filter, heat input from the laser must be managed, else the substrate’s thermal expansion may bow upwards. The outer regions of the substrate are clamped to
Train with the nonwoven experts! Excel in your career with one of these world-class courses designed for newcomers and seasoned nonwovens professionals alike.
Spunbond Technology
March 19-21
Intermediate Nonwovens
April 30-May 3 & October 15-19
Elementary Nonwovens
May 7-8 & September 10-11
Nonwoven Fabric Property Development and Characterization
June 4-7
WIPES Academy
June 17-18
Fiber and Filament Extrusion Fundamentals
July 24-27
Nonwoven Product Development and Innovation
August 13-16
Absorbent Hygiene Course
August 27-29
ensure the substrate does not shift laterally. Striking a delicate but repeatable balance between precision, quality and throughput is the filter driller’s art.
For more information, visit: inda.org/training
Questions?
Contact the Registrar registrar@inda.org
T: +1 919 459 3724
Selecting the correct laser, machine and perforation technique depends on substrate material type, thickness, hole diameter requirements. Powerful laser sources capable of single shot drilling are preferred for throughput sensitive tasks, especially in the case of thicker substrates and larger hole diameters which better resist the thermal load placed by the laser energy. The LaserCube driller is able to cover the full range of single shot, multishot and trepanning techniques by providing a single, flexible platform. On the fly drilling of small (<100µm diameter) holes in substrates up to 1mm thick can manufacture filters having 500,000+ holes on a tight pitch at speeds of 300-500 holes per second. When set up for thicker (up to 1.5mm) material, larger (e.g. 200µm diameter) holes may be created at a rate up to 75 holes per second. The fiber laser is a flexible source. Important features like hole diameter, taper and pitch are easily altered by adjusting laser and machine parameters. Unlike traditional methods, laser drilled hole features may be changed on the fly enabling a tool to drill multiple hole types on a
single substrate without a tool change. Machines, such as the LaserCube provide this complete functionality over a 1 m2 metal working area. Fiber laser drilling of high quality holes is possible on stainless steel or Hastelloy sheet with thicknesses up to 10 millimeters while maintaining throughput up to 300 holes per second. The laser drilling machine incorporates cutting capability such that at the end of the process the filter outline is separated from the substrate, enabling the operator to unload a completed filter (Figure 5).
Filters fabricated using fiber lasers are increasingly adopted due to their numerous advantages. No alternative technique can realize tiny holes with excellent uniformity at extremely high throughput. For either sustainable manufacturing, or simply better manufacturing, filters fabricated using fiber lasers are an increasingly attractive solution.
Luca Longoni is a technical sales manager at IPG Photonics specializing in pulsed laser applications like drilling, marking, engraving and cleaning. He earned a Mechanical Engineering at Politecnico of Milan in 2003. His began his career by designing laser micro-maching tools before taking on a number of customer facing roles. His interests culminated with the introduction of the Lasercube Driller tool which addresses the need of filters fabricators for a cost effective, high performance drilling technology.
The wildfire season kicked off early this year, with infernos raging from Texas to Australia. The Texas Panhandle and parts of Oklahoma are now recovering from the recordbreaking devastation of the Smokehouse Creek wildfire – the largest fire in Texas history that has already consumed a staggering million acres. Massive wildfires have become annual events, starting earlier and lasting longer. Meanwhile, wildfire smoke travels by wind, affecting air quality, visibility, and atmospheric chemistry of places thousands of kilometers away from the original locations of wildfires.
In June 2023, in the wake of 500 ongoing wildfire events in Canada, heavy smoke and particulate emissions blanketed major parts of the northeast and northcentral United States, resulting in some of the most polluted days on record and affecting some 122 million people. In late June 2023, the smoke crossed the Atlantic, reaching Europe, and furthering its impact.
Wildfire projections indicate an impending shift to a temperature-driven global fire regime in the 21st century, creating an unprecedentedly fire-prone environment globally and increasing health risks, as well as societal and economic burdens. With the rise in global wildfire activities, maintaining indoor air quality (IAQ) is critical for ensuring safe and healthy building occupancy. Such a rapidly emerging requirement points to the need for climate adaptation and demands science-based climate resilience solutions that balance human health with building energy efficiency, climate footprint, and other sustainability parameters.
Biomass burning emits large amounts of toxic trace gases and particulate matter (PM) into the atmosphere. According to the EPA's National Emissions Inventory (NEI) estimate from the EPA, wildfires and prescribed burns are the largest source of PM2.5 emissions in the U.S, accounting for as much as ~30% of total emissions across the continental U.S., and up to half of total PM2.5 on an annual basis in the Western U.S., compared with 9.2% from transportation sources.
The exact composition of a wildfire’s smoke depends on numerous factors, including the incinerated material (e.g., type of biomass, building materials, plastics, waste, etc.), the conditions under which it is burnt, ambient temperature, and weather conditions. The size distribution of smoke PM is vastly below 300 nm (PM <0.3 µm), and its composition is largely comprised of organic compounds (over 90%), followed by elemental carbon (roughly 5–10% by weight) and other inorganic elements. In addition, wildfires emit hundreds of volatile organic compounds (VOCs) such as formaldehyde, acrolein, and poly-aromatic hydrocarbons (PAHs), which can subsequently contribute to the creation of ozone and secondary organic aerosols.
Moreover, recent studies show that wildfire smoke supports the transport of bioaerosols, composed of fungi, bacteria, their metabolic byproducts, and even seeds and plant matter. Not surprisingly, most of the microorganisms in the smoke remain viable. After all, fires and smoke have been a natural phenomenon and an
important means for the spread of life on this planet for billions of years.
Such an array of complex pollutants capable of traveling long distances and infiltrating into buildings has dire consequences on human health. Indeed, multiple studies highlight the health risks associated specifically with exposure to wildfire smoke: increased respiratory morbidity, cardiovascular mortality, respiratory emergencies, hospital admissions, and out-of-hospital cardiac arrests. Emerging data further links wildfire smoke to reduced birth weight and increased systemic inflammation. Importantly, the adverse health effects of wildfire smoke is largely attributed to submicron smoke particles. Recent studies indicate that the toxicity of wildfire smoke PM can be higher than “conventional” PM2.5 originated from, for example, automotive and stationary emission sources.[1]
Current recommendations for wildfire smoke exposure are based on previously established guidelines for non-wildfire PM, specifically PM2.5, and their pollution levels are reported in terms of mass concentration, typically in µg/m3. During wildfire episodes, daily PM values can skyrocket to around 800 µg/m3 or more, a stark contrast to the EPA’s primary 24h PM standard of 35 µg/m3. Even though submicron particles dominate the wildfire smoke in terms of particle count, their mass contribution to PM2.5 becomes less prominent in the presence of larger particles.
Consequently, the significance and contribution of wildfire smoke submicron particles are poorly understood when
using a PM2.5-based air quality framework for assessing ambient and indoor air quality. Submicron particles may be more potent than larger particles on an equal mass basis. This may be due in part to a much higher particle count concentration and combined particle surface area. For submicron particles, at a given mass concentration, a decrease in size results in a steep increase in PM count and surface area per unit mass.
Recent research highlights that the sizeresolved PM characterization and their composition are important for identifying clear relations between smoke exposure and health effects. Smoke particles demonstrate highly reactive surface chemistry and adsorb many toxic organic compounds and reactive oxygen species. Their large surface area and ability to enter the bloodstream due to their small size are the two most significant characteristics that make them more toxic than larger particles. Given their large number and surface area, it is important to characterize their number concentration. Consequently, particle counts in the appropriate size range should be adopted more broadly.
Currently, HVAC filters are commonly used for PM removal in both residential and commercial indoor environments.
Their PM removal efficiency largely depends on the material properties of the filter media, followed by filter geometry and HVAC system configuration and runtime.
HVAC filters are tested using ASHRAE Standard 52.2 (or EN779 in Europe). ASHRAE Standard 52.2 classifies the single-pass particle removal efficiency of HVAC filters based on the minimum removal efficiency for three broad particle size bins (0.3–1, 1–3, and 3–10 µm) using inorganic salts, such as KCl or NaCl particles, in a laboratory test facility (ASHRAE, 2017). The minimum removal efficiency value among these three size bins is then used to assign an HVAC filter its efficiency rating, called the Minimum Efficiency Reporting Value (MERV).
In general, increasing MERV ratings lowers indoor PM concentrations. Specifically for wildfire smoke, MERV 11 or higher filters are typically recommended. Most MERV 11 and 13 HVAC filters in use today rely on electret filter media. These electret filters are electrostatically charged polymer-based filters that exhibit higher filtration efficiency (at least initially) and low airflow resistance compared to purely mechanical filters. Given the appropriate filter geometry, a filter manufactured with electret filter media provides cost and HVAC energy savings advantages, compared with pure mechanical filters.
But, can we rely on HVAC filters for protection against wildfire smoke?[2] Limited information existed about the size-resolved filtration efficiency of a filter media using a representative sample of wildland fuel smoke, e.g. pine needles or wood chips. A recent study on the subject tries to bridge the knowledge gap.[3]
Current MERV ratings do not account for PM < 0.3µm when evaluating particle removal efficiency and are thus far from representing the typical size distribution of wildfire smoke particles. Furthermore, the general knowledge of the filtration efficiency of submicron particles is based on laboratory studies using inorganic salts, dioctyl phthalate (DOP), or other analytes that are vastly different from smoke.
Based on the conventional understanding of particle filtration, the filtration efficiency of smoke particles should increase sharply below the 0.3 µm particle size range – the most penetrating particle size (MPPS) range of most filters – as illustrated in the test result in Figure 1 (gray trace, electret MERV 11 tested with KCl). It turned out, however, that the pine needle smoke (PN) – an analogous surrogate for wildfire smoke – filtration efficiency of electret media was significantly lower than expected based on its designated MERV rating (Figure 1, orange trace, MERV 11 tested with PN) and follows an almost zero linear trend for much of the relevant smoke particle size range.[3]
Recent research found that an application-specific, nano-architectured coating, when applied to the media, can stabilize the electret media charges in the presence of smoke and boost the smoke filtration efficiency of the base media by more than 3x (Figure 1, blue trace, MERV 11 coated with nano-architectured coating and tested with PN smoke).
Testing only the initial filtration efficiency misses an important parameter for assessing media performance over its useful life. This is an especially key consideration in the case of electret filters, as exposure to environmental factors can have a detrimental effect on their long-term performance. Recent studies demonstrate
that smoke loading (aging) leads to a significant decrease in filtration efficiency for most particle sizes, but especially in the relevant submicron range.
One study of air cleaners equipped with electret air filters found that the clean air delivery rate (CADR) for smoke was reduced by 95% after the deposition of only 10 mg of PN smoke on the filter.[2] In a recent study, when MERV-11 electret media was aged with PN smoke, its filtration efficiency against smoke was further reduced from the above-shown initial levels (Figure 1, orange trace, MERV 11 tested with PN).[3] In contrast, the same media with the nano-architectured coating improves filtration efficiency with smoke loading.
Smoke particles are characterized by a complex composition, including solid (e.g., black carbon) and a large fraction of liquid/oil-like organic phases (e.g., semivolatile organic compounds, SVOCs). The dynamics of the liquid and solid particle filtration differ significantly due to the differences in deposition modes (dendritic structures formed by solid particles vs. film formation by liquids), collision kinetics, and differences in the particle/fiber surface interactions.
Scanning Electron Microscopy (SEM) can provide insights into how different pollutants interact with the filter media (Figure 2). In the case of mostly inorganic, solid particles, the dendritic-type deposition morphology is commonly observed,
while in the case of smoke particles, the fibers’ surface is found to be covered with droplets resembling “beads on string” morphology. This type of morphology is frequently observed for liquid-phase organic aerosols.
The presence of oil in the particle causes a reduction in the media’s filtration efficiency in comparison to solid particles of the same size. Hence, solely relying on salt particles in standardized testing methods for evaluating the performance of filters is insufficient in the context of real-world HVAC systems challenged with environmental pollutants such as smoke particles.
Current recommendations for preserving good IAQ during wildfire smoke events include HVAC filter upgrades and the use of air cleaners. For HVAC systems, the correlation between MERV ratings and smoke removal efficiency is a key factor for improving IAQ solutions. These include accurate IAQ assessment and monitoring that considers both particle counts and mass concentrations across various size ranges and testing filters' filtration efficiency using smoke particles in a relevant, application-based context.
It is equally important to understand the mechanisms and interactions of smoke with filter media since they determine the filtration efficacy. The development of standardized measurements that are relevant for specific applications is necessary to promote better understanding and drive the innovation of solutions.
ranges, in combination with the assessment of relevant standards and guidelines, the corresponding energy impact of various filter media and filters are necessary for informing filter selection and recommendations for countering increasingly challenging real-world IAQ problems. Meanwhile, stand-alone, high-efficacy air cleaners can be an effective add-on solution, despite common drawbacks, including maintenance hassles and costs.
Dr. Tanya Shirman Ph.D. is a chemist and material scientist with over a decade of experience leading multidisciplinary R&D teams. Her expertise extends to nano-structured materials design and synthesis for catalytic and air-purification applications and extends to translating transformative technologies from lab to market. Tanya is co-founder and VP of Materials in Metalmark Innovations, PBC. - Harvard startup focuses on improving indoor air quality and balancing energy and climate goals through developing and integrating innovations in materials science, engineering, data analytics, and machine learning.
Sissi Liu is passionate about solving complex societal problems with cutting-edge technology. She has 20 years of experience in climate tech and sustainability, entrepreneurship, and venture investing. Sissi co-founded Metalmark Innovations, where she is CEO, to tackle the global air pollution crisis and climate change challenges.
In summary, a better appreciation and further research of filter media testing and rating, ambient pollution sources and levels of PM2.5 versus PM <300 nm measurement and reporting, and particle removal efficiencies of commercial filter media in these particle size
1. Aguilera, R. et al. “Wildfire smoke impacts respiratory health more than fine particles from other sources: observational evidence from Southern California.” Nat Commun 12, 1493 (2021).
https://doi.org/10.1038/s41467-021-21708-0].
2. A. L. Holder et.al. “Impact of do-it-yourself air cleaner design on the reduction of simulated wildfire smoke in a controlled chamber environment,” Indoor Air, vol. 32, no. 11, p. e13163, 2022, doi: 10.1111/ina.13163.
3. Shirman et al. “Evaluation of Filtration Efficiency of Various Filter Media in Addressing Wildfire Smoke in Indoor Environments: Importance of Particle Size and Composition” Atmosphere 2023, 14(12), 1729. https://www. mdpi.com/2073-4433/14/12/1729]
Energy and resource efficiency are crucial in the context of the energy transition. The building sector in particular is a major contributor to climate-damaging greenhouse gas emissions.[16] In order to reduce these emissions, a significant increase in energy efficiency in residential buildings is highly relevant.[24]
Ventilation systems with heat recovery have a big impact on reducing energy consumption of residential buildings. [24; 4; 5] Although controlled ventilation systems offer obvious benefits, such as high air quality and energy efficiency, there is still a lot of hesitation to install this systems in residential buildings.[4]
This is mainly caused due to the investment costs, space requirements, and noise emissions. However, promoting the increased use of these systems in residential buildings could make a decisive contribution to achieving the goals of the energy transition.
The HaLo-Filter (High-absorption Lowpressure-loss - Filter) research project is intended to increase the acceptance of energy-efficient residential ventilation systems. Essentially, ventilation systems consist of three main components, the fans, a heat exchanger and the air filters. The aim of the research project is to combine
The basis is an air-to-air heat exchanger developed by ProVentecs GmbH with the ability to transfer liquid condensate from the used to the fresh air (Figure 1).
The geometry of conventional heat exchangers, has to be adapted that liquids can be evacuated from the heat exchanger. With the heat exchanger developed by ProVentecs GmbH this adjustment is not necessary, which means that the geometrical dimensions can be significantly reduced while maintaining the same degree of heat transfer. However, to ensure a hygienic air transport, the heat exchanger has to be replaced at regular intervals.
Another of the three main components of a ventilation system has to be exchanged to a similar interval: the air filters. The combination of these two replacement components is intended to compensate for the disadvantage of replacing two components. This also leads to a significant reduction of space required for heat exchanger and air filters, allowing smaller, more inconspicuous ventilation units.
The requirements a fiber filter media has to meet to be integrated in a heat exchanger are contradictory. At first the pressure drop of the filter media has to be minimal to prevent excessive high increase in power consumption and noise
emission of the ventilation system.[14; 6]
On the other hand, the filter efficiency of the filter media has to meet the classification as a fine filter media.[6; 30] Conventional filter media reduce the pressure drop by increasing the filter surface based on the geometry used. Due to the integration of the filter media into the flow channels of the heat exchanger, it is not possible to increase the filter surface. The shape of the filter media has to be adapted to the geometry of the heat exchanger.
The requirements for the filter media are therefore not only determined by the filtration properties, but also by the geometrical dimensions of the heat exchanger and the available free flow cross-sections. The filtration properties of a fiber filter are mainly defined by two parameters, the fiber diameters and the porosity of the material, i.e. the ratio of solid to void fractions of the fiber filter. Fiber filter theories can be used to analyze the influence of fiber diameter, porosity, and flow velocity on filtration properties and pressure drop.[17; 8; 29; 19] All theories for fiber filter media are based on the basic separation mechanisms of aerosol particles from a gas on individual fibers (Figure 2).
The development of an analytical calculation program enables the determination of the required filter parameters. For classification as fine filter media, a minimum efficiency of 35% is required in relation to particles with an equivalent diameter of 0.4 µm.[12] The maximum pressure drop of the filter media generated should be in a range significantly below 50 Pa in order to keep the necessary energy and thus the power consumption of the ventilation system at a minimum value. The calculations show that a fiber filter media with fiber diameters of 0.9
µm at a porosity of 99.98% have to be achieved to meet the requirements of maximum pressure drop and minimum filter efficiency (Figure 3). In general, a fiber air filter that is energetically and separation efficient should be composed of fibers that are as fine as possible with low fiber compaction.[7]
The state-of-the-art in fiber filter media production are the nonwoven technologies such as meltblown, spunbond or staple fiber nonwovens.[17; 2; 20] In particular, the meltblown process enables the economical and process-reliable production of ultrafine fiber nonwovens with fiber diameters in the lower micrometer and upper nanometer range.[2; 20; 13]
Meltblown is a single-stage process in which a thermoplastic polymer granulate is melted in an extruder and fed directly into the spinnerets. The viscous polymer exits through fine capillaries, solidifies into fine fibers that are stretched and entangled by the turbulence in the free jet, and is deposited to form a nonwoven fabric. Besides the fiber diameters, the grammage of the nonwoven is the second decisive production-related parameter. It is an indicator of the porosity of the fiber media and thus also of the filter media. Conventional meltblown nonwovens typically range in grammages from 3 to 100 g/m².[2; 13] In order to integrate a nonwoven into the flow channels of the heat exchanger a grammage of < 0.1 g/m² has to be achieved for the required porosity.[2]
With the state of the art it is currently not possible to produce a nonwoven with the necessary filtration properties, which means that an alternative manufacturing process is required. Decoupling of the single-stage meltblown process is the basic idea of the manufacturing process for the HaLo filter media. In this approach, an endless microfiber multifilament yarn is first produced. The straight microfiber multifilament yarn has to be further processed to produce a voluminous semi-finished textile product that achieves a filtration effect. Applied and attached to the heat exchanger plates a deep air filter media with increased dust holding capacity and a low pressure
drop gradient, flowing longitudinally to the filter surface, is created (Figure 4).
To produce an endless multifilament yarn with fiber diameters in the lower micrometer range, the Island-in-the-Sea melt spinning process is preferred.[26] With this process a bicomponent yarn is spun in which the individual microfibers are embedded in a lost matrix. A polymer combination
(1) Interception
(2) Inertial Impaction
(3) Brownian Diffusion
of polyamide 12 (PA12) for the microfibers and a water-soluble polyvinyl alcohol (PVA) matrix component is used to produce the Island-in-the-Sea multifilament yarn for HaLo-Filter production.
Currently, no commercial Island-in-theSea multifilament yarn with the required microfiber diameters of < 1.0 µm and a water-soluble matrix component is available.[23; 31] Therefore, the development of the microfiber yarn was implemented
(5) Gravitation Settling / Sedimentation
(4) Interaction Between Interception and Diffusion
(6) Electrostatic Effects
within the research project. To date an Island-in-the-Sea multifilament yarn with microfibers of approx. 900 nm and a technical and textile strength of 61 cN/tex can be produced. Due to the mechanical and polymer properties the yarn can further be processed in technical and texturing processes (Figure 5).
The textile industry uses the process of texturing to increase the overall volume
and elastic elongation of synthetic fibers. This results in a three-dimensional, crimped yarn structure that achieves a filtration effect comparable to nonwovens fabrics.[21; 15; 25] To create a permanent fiber crimp, two main texturing processes are used.[21]
During the Bulked-Continuous-Filament (BCF) process, a multifilament yarn is forced in an expansion chamber by a hot gas stream to form a three-dimensionally crimped yarn plug. By subsequently cool-
ing the applied structure, which is a compose of semicircular arcs, is permanently fixed.[21; 18] The second main texturing method is the false twist texturing process (DTY). Within this process a multifilament yarn is twisted by a twist applicator, this structure is fixed by heating and cooling and then the yarn is twisted back again. A three-dimensionally crimp is applied to the multifilament yarn which leads to screw or helical turns.[21; 1]
• BCF PROCESS: Texturing of fibers with a minimum of 1.5 dpf; Corresponds to a fiber diameter of about 13 µm for PA12 fibers.[21]
• DTY TEXTURING: achieves titer per filament of just under 0.2 dpf; Corresponds to a fiber diameter of at least 4 – 5 µm for PA12 fibers.[1]
The microfiber yarn developed within the research project achieves a titer per filament of 0.007 dpf and is thus significantly below the currently minimum possible fiber titer. Using the entire Island-in-the-Sea yarn, including the lost matrix, during texturing allows the fiber diameter to be adapted to both the BCF and DTY process. In addition, microfiber breaks are avoided which ensures a reliable production.
The Crimp contraction (Chart 1), can be determined by the ratio of crimped and stretched length using standardized methods.[11] This parameter provides information about the increase in volume of the yarn due to texturing. This allows the evaluation of the two processes by the porosity applied to the filter media.
The maximum possible values of crimp contraction can theoretical be determined based on trigonometric relationships of the ideal crimp structures.[18; 21]
In order to determine and evaluate the crimp contractions of the two texturing processes according to the standard, various series of tests were carried out (Figure 6).
The BCF method results in significantly higher crimp contraction in all measurement series. The theoretically determined values and the assumption that DTY texturing achieves higher values in crimp cannot be confirmed by the measurements according to the standardized
method. Further measurements as well as optical analyses of the textured yarns suggest that the DIN standard results provide an inaccurate account of the texturing results.
By measuring the entire force-elongation curve of a crimped yarn the uncrimping work can be determine. This is the required energy to strecht the yarn to the point of complete decrimption.[18; 27] This allows a verfication of the DIN measurement results. Based on the uncrimping work, both the theoretical curvature and the crimp geometry of the textured yarn can be determined. This provides information about the number of arcs per length as well as the dimensions of the arcs such as arc radius, arc length or arc height.[18; 3] (at right).
Besides the uncrimping work this methode provides the determination of the total crimp contraction contained in the yarn (Figure 7).[18; 27] Particularly in case of fibers under 0.1 dpf, the crimp contraction value is determined insufficiently due to the measuring principle according to the DIN standard.
The evaluation of the theoretical curvature clarifies the different crimp structures of the texturing methods. Within BCF, many but plane bends are produced. This structure only leads to a very small increase in volume in the yarn, which means that the required high porosity in the filter material cannot be achieved. The DTY process produces structure of arcs with a high angle of curvature but a small arc number. The overarched curvatures achieved by the high crimping angles enable a high volume increase in the yarn and thus increased porosity in the filter media (Figure 7).
An ideal crimp for the use of the crimped yarn as a highly porous filter media would consist of a high number of arcs with high crimp angles and small arc dimensions. The crimp contraction alone does not allow a reliable statement about the suitability as a filter media, it is an indicator, but the crimp geometry has also to be determined. To create a high filter porosity high crimp angles are necessary and this can only be achieved be the DTY process. The process principle of BCF prevents this.
The crimp geometry applied by BCF is limited to the dimensions of the yarn itself. The theoretical considerations already clarified that the crimp angle by BCF can reach a maximum value of π assuming an ideal compose of semicircular arcs. [18; 3] If this is the case, the diameters of the fiber are in contact. Further compression of the fibers is not possible and the arc dimensions are defined by the dimensions of the fiber. The use of the Island-in-the-Sea yarn during the texturing process results in the limitation of the maximum curvature of the microfibers embedded in the PVA matrix to the dimension of the Island-inthe-Sea fibers. After removing the water soluble PVA Matrix the curvature applied leads only to a slight undulation of the microfibers due to the significantly small microfiber diameters. As a result, the
References:
1. [ATK 12] Atkinson, Colin; False Twist Textured Yarns; Elsevier; Woodhead Publishing Lim-ited; 2012.
2. [BAT 15] Batt, Till; Entwicklung eines Meltblow-Verfahrens zur Herstellung thermoplas-tischer FeinstfaserVliesstoffe; Universität Stuttgart; 2015.
3. [BAU 00] Bauer-Kurz, Ina; Fiber crimp and crimp stability in nonwoven fabric processes; Dissertation; North Carolina State University; 2000.
4. [BUN 22] Bundesverband der Deutschen Heizungsindustrie e. V. (BDH); Fachverband Gebäude-Klima e.V. (FGK); Beitrag der Wohnraumlüftung mit Wärmerückgewin-nung zur Reduktion fossiler Energien und Reduktion der CO2-Emissionen im Gebäudesektor 2022.
5. [BUN 22] Bundesverband der Deutschen Heizungsindustrie e. V. (BDH); Fachverband Gebäude-Klima e.V. (FGK); Stiefkind Wohnungslüftung mit Wärmerückgewin-nung? 2022.
6. [CEA 13] Ceasar, Thomas; Industrielle Luftfiltration; Moderne Industrie; 2013.
7. [DAU 12] Dauner, Martin; Batt, Till; Abschlussbericht NaBlo: Nano-Meltblown-Fasern für Filtermedien 2012.
8. [DAV 73] Davies, Charles Norman; Air Filtration; Academic Press; 1973.
9. [DIN 83] DIN 53840 - 1; Bestimmung von Kräuselkennwerten an texturierten Filamentgar-nen.
10. [DIN 83] DIN 53840 - 2; Bestimmung von Kräuselken-
high porosity required for the purpose of filtration cannot be achieved (Figure 8).
This limitation of the maximum angle of curvature is avoided by the crimping structure as helix curls of DTY, higher and overarched crimp angles can be achieved.
The final step to produce the HaLo-filter media involves the processing of the tex-
nwerten an texturierten Filamentgar-nen.
11. [DIN 06] DIN EN 14621; Prüfverfahren für texturierte und nicht texturierte Multifilament-garne.
12. [DIN 12] DIN EN 779; Partikel-Luftfilter für die allgemeine Raumlufttechnik.
13. [DRA 19] Drabek, Jiri; Zatloukal, Martin; Meltblown technology for production of polymeric microfibers/ nanofibers: A review 2019.
14. [FAI 99] Faist Wolfgang Dr.; Anforderungen an die Wohnungslüftung im Passivhaus 1999.
15. [FAL 81] Falkai, Béla von; Bonart, Richard; Synthesefasern; Verl. Chemie; 1981.
16. [PHI 20] Fraunhofer-Institut für Solare Energiesysteme ISE; Studie: Wege zu einem klima-neutralen Energiesystem 2020.
17. [GAI 18] Gail, Lothar; Gommel, Udo; Reinraumtechnik; Springer Berlin Heidelberg; 2018.
18. [GEI 69] Geitel, Karlheinz; Die Bogenzahl, eine notwendige Größe zur Beschriebung der Kräuselung? 1969.
19. [GOU 96] Gougeon, R.; Boulaud, D.; Renoux, A.; Comparison of Data from Model Fiber Filters with Diffusion, Interception and Inertial Deposition Models 1996.
20. [GRI 19] Gries, Thomas; Veit, Dieter; Wulfhorst, Burkhard; Textile Fertigungsverfahren;3., überarbeitete und erweiterte Auflage; Hanser; 2019.
21. [HEA 01] Hearle, J. W. S.; Hollick, L.; Wilson, D. K.; Yarn
tured Island-in-the-Sea multifilament yarn. First, the water-soluble PVA matrix has to be removed from the microfibers. Subsequently, the crimping of the microfibers is reactivated under the influence of heat. Applying temperature to the yarn causes shrinkage in the textured microfibers, maximizing the bulk and volume of the crimped microfiber yarn.[11; 3; 28]
Due to insufficient fiber crimp of the microfiber yarn, the goal of producing the highly porous HaLo-filter media could not yet be achieved. The goal after completion of this research project (in December 2023), is to submit a follow-up project in order to be able to optimize the microfiber crimp and to investigate the remaining open questions in more detail.
Lukas Herrmann M. En works an as a Research and Development Engineer at ProVentecs GmbH, specializing in ventilation systems and air filtration. He earned a Masters in Engineering from Bremen University of Applied Sciences, studying Engineering Sciences focused on futureproof energy systems. He is in final stages of his PhD at University of Bremen.He can be reached at Lukas.Herrmann@proventecs.de.
This was supported by the Federal Ministry for Economic Affairs and Climate Action, on the basis of a decision by the German Bundestag.
texturing technology; CRC Press/Woodhead Publ; 2001.
22. [HER 23] Herrmann, Lukas; Abbildungen ProVentecs GmbH. https://www.proventecs.de/. 27.10.2023.
23. [HIL 23] Hills Inc.; Fibers. http://www.hillsinc.net/ fibers/. 27.10.2023.
24. [JUG 21] Jugel, Christoph; Abschlussbericht denaLeitstudie Aufbruch Klimaneutralität 2021.
25. [KOS 97] Koslowski, Hans J.; Chemiefaser-Lexikon;11. Aufl.; Dt. Fachverl.; 1997.
26. [MUK 14] Mukhopadhyay, S.; Bi-component and bi-constituent spinning of synthetic poly-mer fibres; Woodhead Publishing Limited; 2014.
27. [REU 00] Reumann, Ralf-Dieter; Prüfverfahren in der Textil- und Bekleidungstechnik; Sprin-ger-Verlag Berlin Heidelberg GmbH; 2000.
28. [STR 16] Straovoytova, Diana; Analysis of Effect of Heat-Setting Temperatures on Crimp Parameters in Polypropylene Single-Fibres 2016.
29. [THO 17] Thomas, Dominique; Charvet, Augustin; Bardin-Monnier, Nathalie; Appert-Collin, Jean-Christophe; Aerosol Filtration; ISTE Press; Elsevier; 2017.
30. [VDI 18] VDI 6022; Raumlufttechnik, Raumluftqualität.
31. [WIL 23] Wilkie, A.; Multi-component Fiber Technology for Medical and other Filtration Applications. http:// www.hillsinc.net/assets/pdfs/multi-component-fibermedical.pdf. 27.10.2023.
Do You Want to Increase Your Company Exposure to Fiber & Filtration Professionals? YOU GET 3X EXPOSURE IN PRINT GUIDE, DIGITAL GUIDE + SOCIAL MEDIA!
Take advantage of this incredible way to be found among the best of the industry!
◗ For $495, Standard Company Listings receive:
• Up to 5 categories for a searchable listing + logo for 1 year in online guide
• Print listing + logo with categories listed in IFN or IFJ publication
• NEW: Buyer’s Guide link accessible from INDA.ORG website, increasing SEO
• NEW: Promotion of Buyer’s Guide on IFN & IFJ Social Media & in the Monthly E-Newsletter
• NEW: Digital Flipbook with clickable links on Home Page of IFN or IFJ websites
◗ For $995, Premiere Vendor Category Listings receive all the Standard Company Listings (listed left), with the additional value of:
• Up to 12 categories for a searchable listing + logo for 1 year in online guide
• NEW: New “Premiere Vendors” Buyer’s Guide landing webpage – only for this category –with clickable company logo.
• NEW: Two “Buyer’s Guide e-Promotions” with the logos of all “Premiere Vendors” (clickable) sent to IFN or IFJ promo lists
Choose from specialties in over 70 categories!
IFN Buyer’s Guide for International Filtration News is printed in the July/August issue (Vol. 4). The listing runs for an entire year on www.filtnews.com/buyers-guide. Listing Due by
The objective of this article is to explain the various arrangements for cleaning manufacturing-process-liquids. Most industrial applications use a closed loop concept. The closed loop concept recirculates the fluid so it can be reused and the cost of replenishment can be kept at a minimum.
The main feature of manufacturing systems is that the process continually sends contaminants into the fluid as it operates. This phenomenon is somewhat different than most other types of fluid cleaning applications, where the contaminant level is reduced as the fluid cleaning function operates.
In addition to the continual addition of contaminants, the system has another major difference. The fluid is exposed to contaminants from three sources.
• Direct result – contaminants that are purposely created by the process; i.e., grinding.
• Indirect result – contaminants which are generated as a byproduct of the process; i.e., fine particulates abraded off the sheet stock during a rolling mill operation.
• Foreign – contaminants which come from the environment of the plant; i.e., plant garbage, debris, tramp fluids.
Closed loop, with its constant recirculation, is the best way to cope with these. Manufacturing fluids do not have to be totally cleaned. The fluid must be just clean enough for the process to keep operating properly at the expected quality.
Due to the evolution of manufacturing jargon, it is important to define the meaning of the different terms used in this article. Hopefully this will minimize misunderstandings of the terms. Terms such as filtration, separation and clarification have become loosely used to a point where one title is found for more than one type of cleaning device. The goal is to guide the use of these terms so they refer to a specific device.
Clarifier is the general term for equipment which cleans fluids. These include both separators and filters.
Separator are cleaning devices which use a specific physical characteristic of the particulate to remove it from a liquid which also has specific physical features and takes advantage of how the two relate to each other.
• The solids may be heavier than the liquid so separation can be accomplished with settling
• The particulate may be lighter, then flotation can be used
• Magnetic material separation can use magnetic attraction
• Centrifugal which generate a greater force on the solids for effective separation
Filter is a device which provides a barrier to intercept the solids as the fluid flows through it.
Figure 1 shows the most popular arrangements of cleaning systems. The actual arrangements for manufacturing fluids are called “closed loop.” The most used arrangement, regardless of
installation size, is the full flow closed loop arrangement. The fluid in continuously recirculated so it can be reused.
The arrangement is called full flow when the flow to the device equals or greater than the flow rate going to the process. It ensures that all the flow passes through the cleaning device. The flow shows where the fluid is contaminated at the process and is sent to the dirty liquid reservoir. From there it is sent to the cleaning device at a flow rate which is slightly higher than the flow rate going to the process. The extra flow returns to the dirty reservoir as a second closed loop.
There are four major components:
• Process – the actual manufacturing operation which generates contaminant as it produces the product.
• Dirty liquid reservoir – the holding chamber for the contaminated fluid. It can also be fitted with a self-cleaning conveyer to remove settled solids. When a conveyor is added, the dirty liquid reservoir becomes part of the fluid cleaning component and works in conjunction with the cleaning device.
• Cleaning device – the main cleaning function. Fluid scan consists of one or more cleaning devices. All closed loop schematics show a cleaning device in each arrangement. The device can be any apparatus as described in the paragraph on definitions. The device in the schematic may not be just a single unit. For this discussion it may include many pieces of cleaning equipment combined to intercept the varied range of contaminants.
• Clean liquid reservoir – the tank or compartment which holds cleaned liquid ready to supply the process. It always has an excess flow rate to allow some of the liquid to flow back to the dirty liquid reservoir in an independent loop.
This arrangement was once called “bypass” but the title is not as popular because the term is now used for other system flow situations. It is often referred to as “kidney loop.”
It uses one main reservoir where the process and cleaning device flow from and to the same tank independent of each other. The flow rate to the cleaning device can vary depending on the flow rate and clarity levels needed for the process, and the size and efficiency of the cleaning device. Also, the main reservoir can be fitted with a self-cleaning conveyor so it contributes to the fluid cleaning function. The side arm arrangement’s main value is that it can be installed when there is no room or the installation is too complex for a full flow arrangement.
A batch arrangement is used when the plan is to remove all or a portion of the volume in the main reservoir on a routine schedule and send that liquid to a remote area where another cleaning system is set up to treat the fluid. This is a remote operation and often installed when there is no room for a full flow or sidearm arrangement close to the production facility. It is also used for a recovery
procedure: for the fluid or solids which may have a value. It works on the theory of volume turnover and is an effective rule.
The arrangement requires an effective procedure to transfer the fluid from the main reservoir to and from the remote unit. This usually is a piping loop or dedicated transfer tanks.
Any one of these arrangements can be used to reach the desired clarity levels as long as the selection of components in the arrangement meet the needs of the system,
Full flow is the best arrangement and satisfies the expectations of the operator since they see that all fluid flows into the cleaning device before the liquid is sent to the clean liquid reservoir The other arrangements have their place in a facility. They do not treat all the liquid as the full flow set-up, but they can reach the desired clarity levels to satisfy the needs of the process.
James J. Joseph is a consultant in industrial liquid filtration and is author of the book, Coolant Filtration 2nd Edition, Additional Technologies. He currently owns Joseph Marketing in Williamsburg, Virginia and can be reached at 757-565-1549 or via email at josephmarketing120@gmail.com@verizon.net. He serves on the editorial board of the International Filtration News.
Dr. Felix Swamidoss holds a prominent role as the Head of R&D at Spectrum Filtration India. With a doctorate in the field of air filtration, this has enabled him to secure more than seven patented innovations in nanofiber media for air filtration, underscoring his remarkable expertise in the field. One highlight is the development of “Piezoelectrically enhanced electrostatic nanofiber media,” which is of critical importance in the field. Also to note, Dr. Swamidoss groundbreaking work in pleat design and the development of progressive media using expanded polytetrafluoroethylene (ePTFE) has set new benchmarks for the latest air filtration innovations.
Particle deposition on fibers within loaded filters is a pivotal factor influencing the efficiency and overall performance of air filtration systems. This study delves into the intricate mechanisms governing particle deposition, placing a particular emphasis on the formation of dendrites observed on fibers. The exploration is centred around a specific scenario involving a single particle characterized by dimensions X and density Y. The objective is to scrutinize the trajectory of this individual particle as it traverses through the fibers, raising fundamental questions about its ultimate deposition location. As particles accumulate within a filter, they not only impact the filter’s structure but also exert a profound influence on both the pressure drop across the filter and its collection efficiency. Understanding the mechanisms of deposition and their consequential effects on filter performance is imperative for optimizing air filtration systems. However, this is a highly intricate process that remains an active area of research.
So, what are dendrites?
Dendrites, characterized by branch-like structures formed through the deposition of particles as seen in the below image, offer a visual representation of the dynamic interplay between particles and fibers. The formation of these dendritic structures is
intricately linked to the dominant deposition mechanism at play.
By focusing on the specific scenario involving a single particle, the study aims to shed light on the nuanced trajectory of particles through fibers, raising questions about the ultimate deposition location and, consequently, the structural alterations within the filter. This research seeks to unravel the complexities surrounding particle deposition, providing insights into the mechanisms that govern this phenomenon.
Brownian diffusion is a fundamental mechanism where particles collide with each other and the fibers due to random motion. This mechanism results in a uniform distribution of par ticles across the entire fiber surface, covering the overall fiber circumference. The interplay between particle size and Brownian motion determines the deposition pattern, and understanding this diffusion process is vital in pre dicting the formation of dendrites.
In interception, particles are captured on the leading surface of the fiber, follow ing the airflow path. This mechanism is influenced by the size of the particles and the geometry of the fi bers. The trajectory of particles becomes crucial, as those following the airflow path are more likely to be intercepted and deposited on the fibers. Explor ing the dynamics of interception sheds light on the preferential deposition sites and contributes to the understanding of dendrite formation.
Particles with higher inertia predominantly deposit near the front stagnation point of the fiber during inertial impaction. This mechanism follows a straight path, and particles settle solely on the fiber’s face.
Understanding
particle deposition mechanisms and dendrite formation is crucial for designing effective air filtration systems. Tailoring filter materials and configurations based on the characteristics of the particles and the filtration environment
can enhance filtration efficiency.
The size and velocity of particles play a pivotal role in determining the extent of inertial impaction. Investigating this mechanism is essential for comprehend ing how particle characteristics influ ence the formation of dendritic structures on fibers.
The investigation into the trajectory of a single particle with di mensions X and density Y involves considering the interplay of
all principal mechanisms of air filtration. The ultimate deposition location depends on the intricate balance between Brownian diffusion, interception, and inertial impaction.
Does the particle settle on the same side it encounters, or does it load to the opposite side? The answers lie in the dynamic interplay of these deposition mechanisms. Understanding particle deposition mechanisms and dendrite formation is crucial for de-
Bob McIlvaine is the president of The McIlvaine Company, which is helping filter suppliers understand the true cost of their products and the impact on the Serviceable Obtainable Market. He can be reached at rmcilvaine@ mcilvainecompany.com or +1 847.226.2391
The Potential Filtration/Separation Revenues Associated with Carbon Capture and Sequestration are More Than $13 Billion Per Year.
Apowerful new tool to combat climate change is carbon negative technology. CO 2 is removed from the ambient air and directed back to the underground reservoirs which once held coal, oil, and gas. There is already a big investment yp substitute wood pellets for coal and then sequester the CO2.
The split by process is:
• Bioenergy and Carbon Capture and Sequestration (BECCS)
• Blue Hydrogen
• Rare Earth Recovery
• Waste to Energy and other applications
This prediction will surprise advocates of green hydrogen who expect ultrapure water filtration systems for electrolyzers to be the biggest market.
According to IEA, bioenergy with carbon capture and storage (BECCS) involves any energy pathway where CO2 is captured from a biogenic source and permanently stored. Only around 2 Mt of biogenic CO2 are currently captured per year, mainly in bioethanol applications. Plans for around 20 facilities together capturing around 15 Mt CO2 per year of biogenic emissions have been announced since January 2022.
Based on projects currently in the early and advanced stages of deployment, carbon removal via BECCS could reach just under 50 Mt CO2/ year by 2030, which falls far short of the approximately 190 Mt CO2/year removed through BECCS by 2030 in the net zero emissions (NZE) by 2050 scenario. Targeted support for carbon dioxide removal (CDR), and BECCS in particular, will be required to translate recent momentum into operational capacity.
Filtration and separation can be divided into initial and liquefied gas quality. Precipitators and scrubbers, along with fabric filters are used for the initial treatment. They reduce particulate to 15 mg/Nm3 or less. This would meet air pollution standards but is not good enough for transporting CO2. A second set of filters such as is used ahead of air compressors is needed. In addition, mercury must be reduced to very low levels for corrosion purposes. Activated carbon is used but a new technology using ionic liquids is also being employed.
There has been a big development in carbon capture. MHI has developed a CO 2 absorber which with an efficiency of 99%.
If oil, coal, or natural gas is converted to hydrogen and the CO2 sequestered, it is considered blue hydrogen. The economics are favorable to frst gemerate ammonia which is hydrogen plus nitrogen and is easily transported. The hydrogen can be extracted at the point of use. This is particularly advantageous where there are long distances between the source and use. Ammonia is chosen as the most economical method to transport hydrogen. Yara has converted natural gas to ammonia in Australia and is committed to ship millions of tons to Japan for use in power generation.
A process called insitu rare earth recovery has been overlooked, but ironically it was well known to coal fired scrubber system suppliers in the 1970s. Many pre-scrubbers were employed to remove particulate and HCl.
These scrubbers ended up with rare earths leached out of the fly ash. The metals were considered
Recently the U.S. and China have realized that extracting rare earth from fly ash can be less expensive than natural ore mining. Hundreds of millions of dollars have been spent to prove that the extraction will be economical for many coals.
a contaminant and no attempt was made to use them.
Recently the U.S. and China have realized that extracting rare earth from fly ash can be less expensive than natural ore mining. Hundreds of millions of dollars have been spent to prove that the extraction will be economical for many coals. The big problem is the large amount of energy required to pulverize fly ash.
By contrast, the insitu accidental process not only avoids the need for pulverizing but also creates the leaching fluid at no cost.
There are 2700 waste to energy plants around the world and soon there will be 3000. They are en
closed in ski hills, golf courses and other attractive settings. The air emissions are very low thanks to efficient air pollution controls. These plants generate electricity while greatly reducing the waste volume to non combustible matter.
Several projects are under way to employ CCS. In the UK the government is building a CO2 pipeline throughout the country, so a WTE plant does not have to invest in its own pipeline.
Summary: Carbon capture and sequestration is an economical way to offset carbon emissions from sources which can not be controlled. The only other carbon negative technology is Direct Air Capture. This approach is very expensive and involves a carbon absorber 100 times larger than those used to capture CO2 from processes.
INDA, the Association of the Nonwoven Fabrics Industry, has named experienced sales and business development professional, Dan Noonan, as its new Director of Memberships and Business Development.
Noonan brings 20 years of experience leading sales teams across the U.S. at Localedge/ Hearst Media Services.
Noonan will be responsible for enhancing the value of INDA membership and its industry supporting programs. He will work with staff, leadership, and members to identify and expand opportunities to enhance INDA’s programs, services and relevance to the industry.
“We are pleased to have Dan on board at INDA. Dan will surface opportunities which boost the value of INDA membership while supporting our mission for industry growth,” said Tony Fragnito, INDA President & CEO.
“I’m excited to join the team at INDA. I’ve already found that this is an amazing group that is dedicated to both our members and the industry as a whole. I’m really looking forward to connecting with our membership to learn more about their individual needs and what role INDA can play in delivering value to them.”
Noonan holds a bachelor’s degree in marketing from Providence College. He may be reached at dnoonan@inda.org. www.inda.org
London, UK Mayor Sadiq Khan has announced plans to fit PM2.5 filters in 200 schools, aiming to improve air quality for children’s health, with potential for wider implementation if successful. The pilot is expected to cost £2.7m and forms part of the mayor’s 2024/25 budget. The funding will pay for the filters and their maintenance, school engagement, educational materials and monitoring the impact of the program, City Hall said. www.london.gov.uk
GEA is investing EUR 18 million (USD 20 million) in a technology center for alternative proteins in Wisconsin, USA. The new food tech hub will pilot microbial, cell-based and plant-based foods. GEA’s state-of-the-art technologies and a team of biotechnology experts form the basis for scaling new food for industrial production, which is increasingly in demand in the USA. Groundbreaking at the new GEA campus in Janesville is scheduled for spring of 2024, with the opening to follow one year later.
The USA is one of the countries promoting the development of sustainable food options through favorable regulation and openness to innovative food technologies. For example, the Food and Drug Administration (FDA) already approved cell-cultivated chicken meat in 2022 and last year confirmed that the use of precision-fermented milk proteins in foods is safe. www.gea.com
Filter King LLC, a leading manufacturer of HVAC home and business air filters, announced the opening of a new manufacturing facility in Miami, Florida. The 100,000-square-foot facility, which includes production, warehousing, and distribution, as well as the company’s corporate headquarters, was precipitated by surging demand for its premium quality air filters, and high growth expectations for 2024 and beyond.
Filter King’s products are sold through multiple channels, including, direct-to-consumer (D2C) e-commerce marketplaces and filterking.com, as well as commercial sales to condominiums, property management companies, schools, hospitals, government facilities, and HVAC service providers. www.filterking.com
SUEZ, a leading player in water management, recently signed a contract for the Buaran III Water Treatment Plant (WTP) project in Jakarta. The group will supply key equipment for the water treatment process and will provide technical advisory services for the installation and commissioning of the Buaran III utility. The new WTP in the Indonesian capital will enhance the resilience of the city’s water supply system to provide a safe, reliable, and long-term supply of water to local communities.
Currently, Jakarta’s WTPs can treat 1.47 million cubic meters daily, supplying 65% of urban areas with clean water. The city’s government is aiming for total urban clean water coverage of 100% by 2030, planning new WTPs to meet rising demand with an additional 960,000 cubic meters per day. The completion of the Buaran III WTP, expected in first half of 2025, will boost progress towards this goal. It will provide an additional 260,000 cubic meters of clean water per day to communities in Jakarta, accounting for approximately 28% of the incremental water capacity needed to meet the 2030 target. www.suez.com
Xylem Inc., a leading global water technology company dedicated to solving the world’s most challenging water issues, announced the appointment of Radhika Fox as Senior Advisor to the company.
“Radhika is one of the world’s most insightful and effective champions of water – a universally respected voice for solutions to society’s biggest water challenges,” said Matthew Pine, Xylem president and CEO.
DFox will provide strategic counsel to Xylem on evolving issues and opportunities in the water sector and provide advice on a range of matters to support the delivery of Xylem’s strategy. Fox most recently served as the Senate-confirmed Assistant Administrator for the US Environmental Protection Agency’s Office of Water, acting as chief advisor to the EPA Administrator and White House on water resources and water infrastructure in the United States.
Prior to joining the EPA, Fox served as the Chief Executive Officer for the US Water Alliance, a non-partisan network that unites diverse stakeholders on common-ground solutions to the nation’s pressing environmental, water, and climate challenges. Her career in water began at the San Francisco Public Utilities Commission – a public agency that provides water, wastewater, stormwater, and electric power services to over 2.6 million people in the San Francisco Bay Area. www.xylem.com
PuPont announced that FilmTec™ LiNEXD nanofiltration membrane elements, the company’s first offering dedicated to lithium brine purification, was named a finalist in the 2024 Edison Awards™ in the Resource Recovery & Environmental Conservation category.
Lithium brine purification is critical to producing batteries needed for electrification to help combat climate change. FilmTec™ LiNE-XD elements can help enable lithium production from resources such as salt lake brine, geothermal brine, and surface and subsurface clay. FilmTec™ LiNE-XD nanofiltration membrane elements are designed to withstand harsh conditions while also yielding high recovery of both lithium and water; requiring less energy than other methods.
The Edison Awards™ is an annual competition honoring excellence in new product and service development, marketing, human-centered design, and innovation. The gold, silver and bronze winners will be announced at the 2024 Edison Awards Gala in Fort Myers, Florida, on April 18, 2024. www.dupont.com
uraffinity, which develops precision technology for the removal of PFAS ‘forever chemicals’ across multiple water treatment applications, has won a $250,000 award from the Morgan Stanley Institute for Sustainable Investing.
In addition to the financial award, Puraffinity receives a yearlong collaboration with the Institute for Sustainable Investing which will help them grow and scale up their innovative solution.
Puraffinity, which is tackling the human health and environmental challenges of per-and polyfluoroalkyl substances (PFAS) has developed a suite of adsorbent materials, exhibiting high selectivity towards diverse PFAS compounds. These are adaptable for multiple applications. The company has a goal to provide one billion people with PFASsafe water by 2030. www.puraffinity.com
As of February 1, 2024, Filtration Technology Systems (“FTS”) has merged with Jewett Automation, LLC of Richmond, Virginia. This business merger is part of an ongoing efforts to be the leading filtration automation business by offering best-inclass standard products, unique custom automation solutions, superior customer service and dedicated aftermarket support, the company said. FTS will continue to operate as Filtration Technology Systems. www.filtrationtech.com