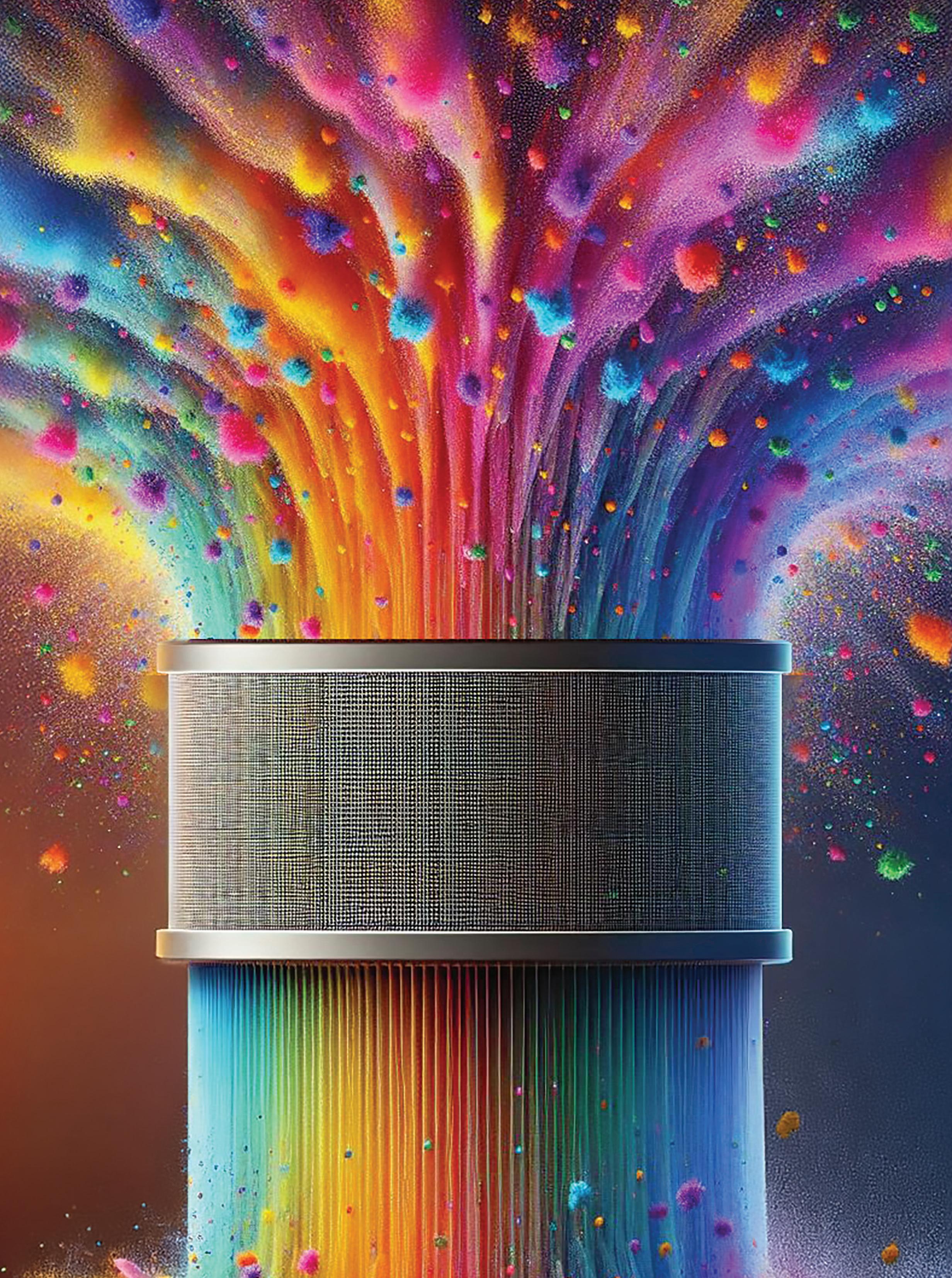
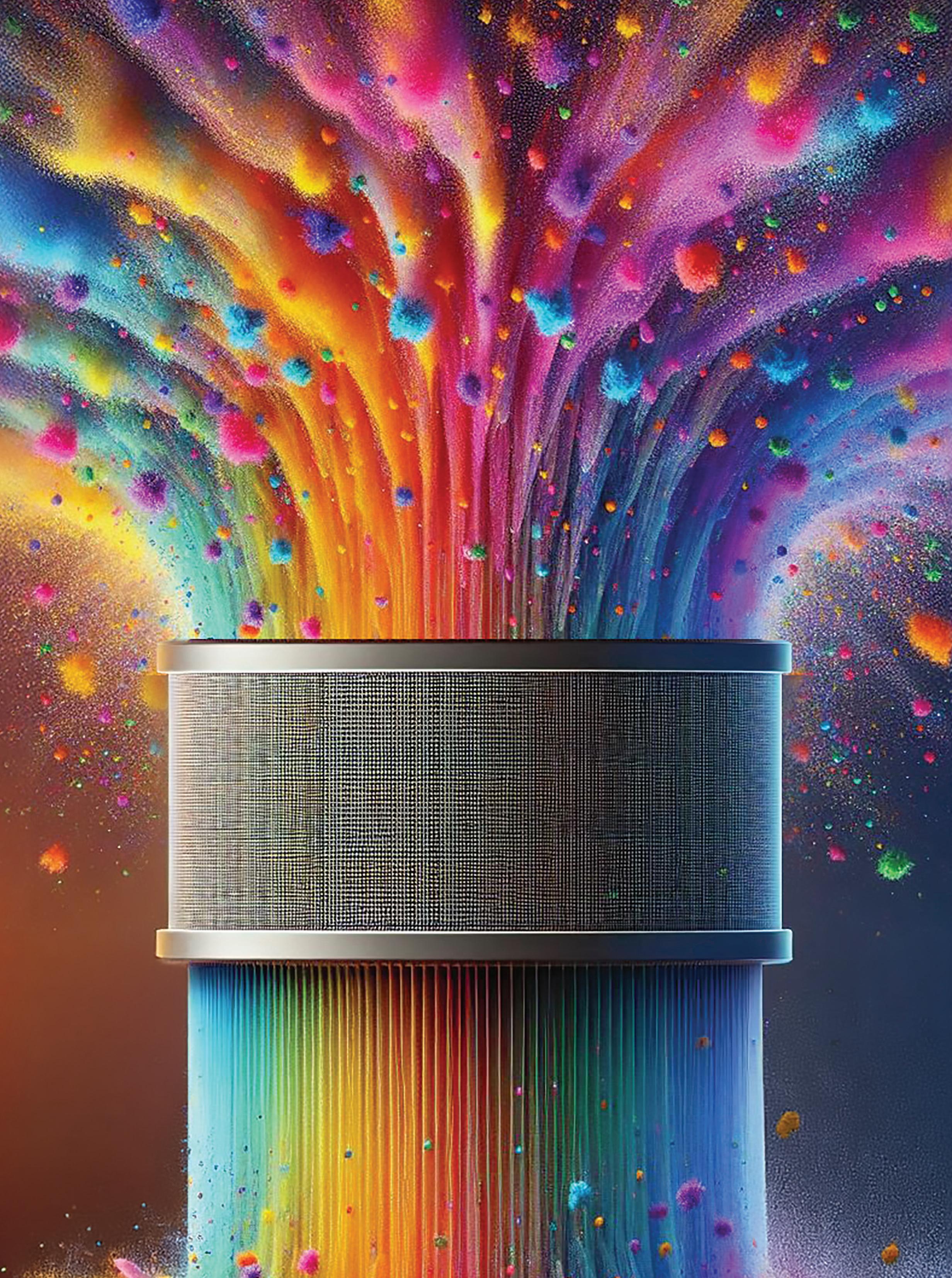
Filtering Innovation
Spiral Weld Tubes
At Beverlin, we’re at the core of innovation. Spiral weld tubes have several applicationspecific benefits compared to traditional straight seam welds.
Enhanced roundness and straightness
360-degree filtration flow
Larger outer diameters without specialized equipment To
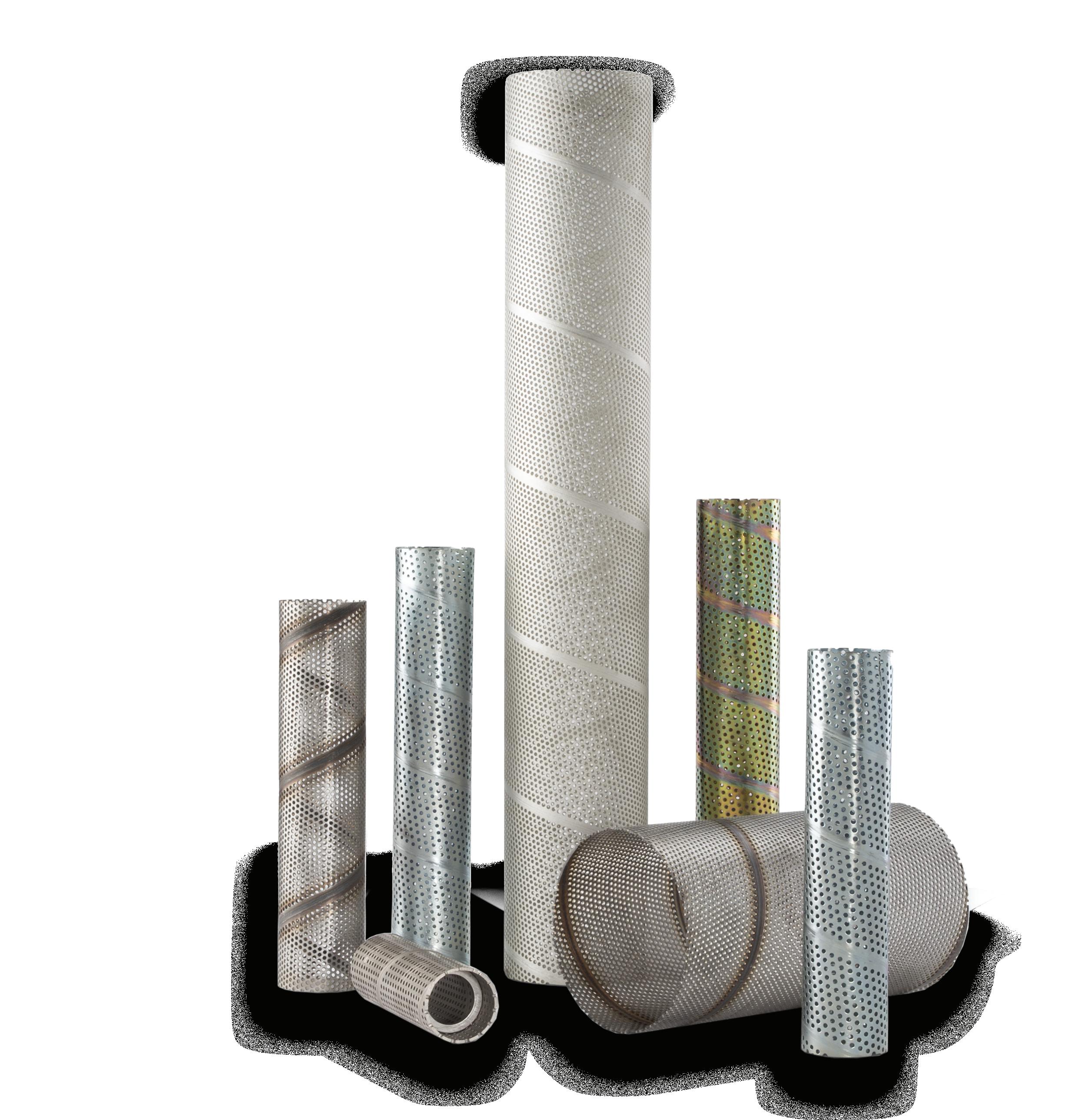

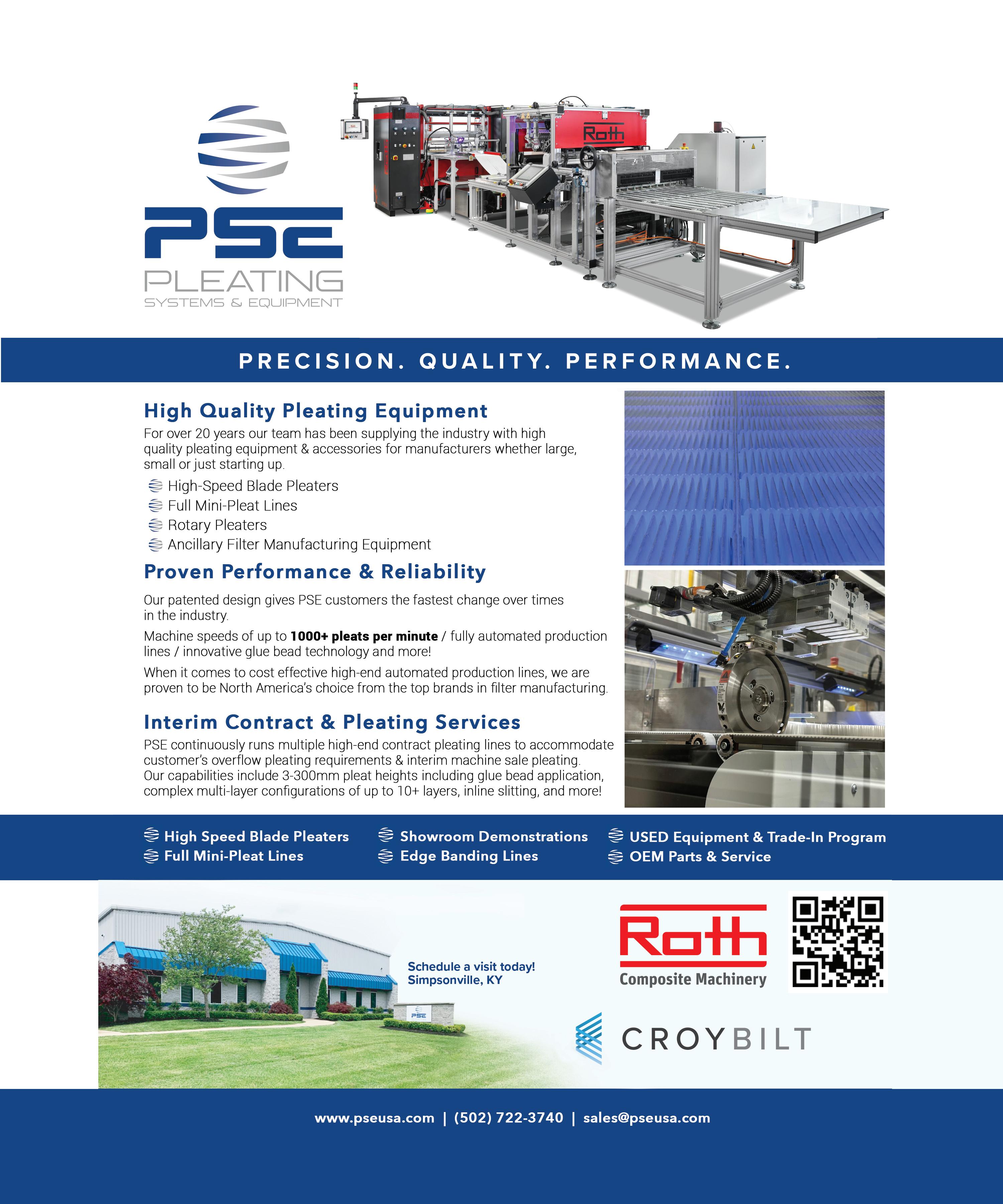
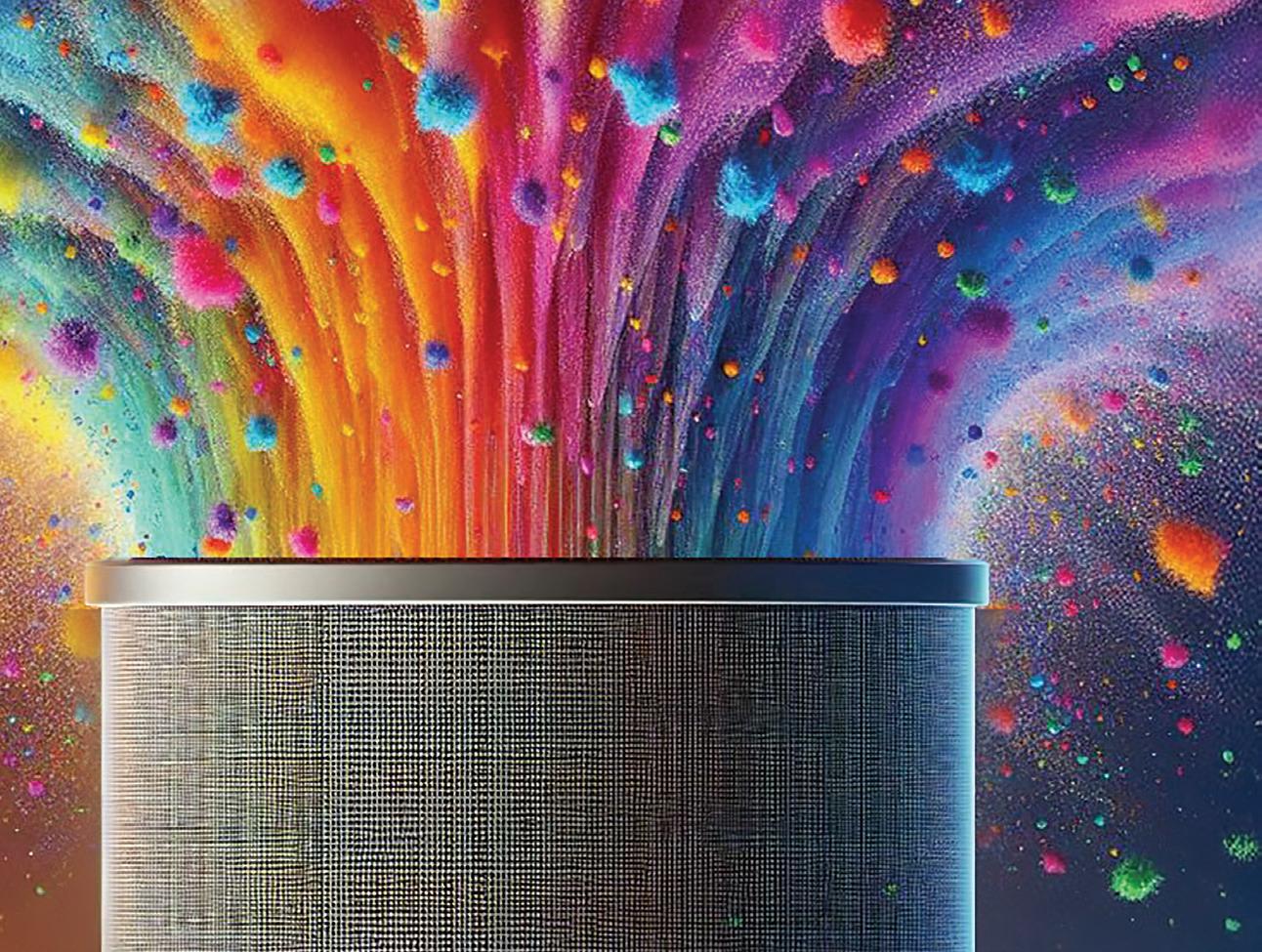

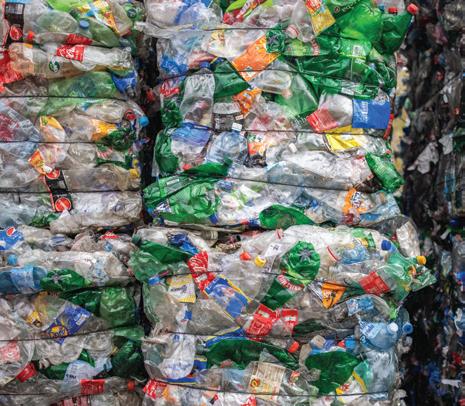

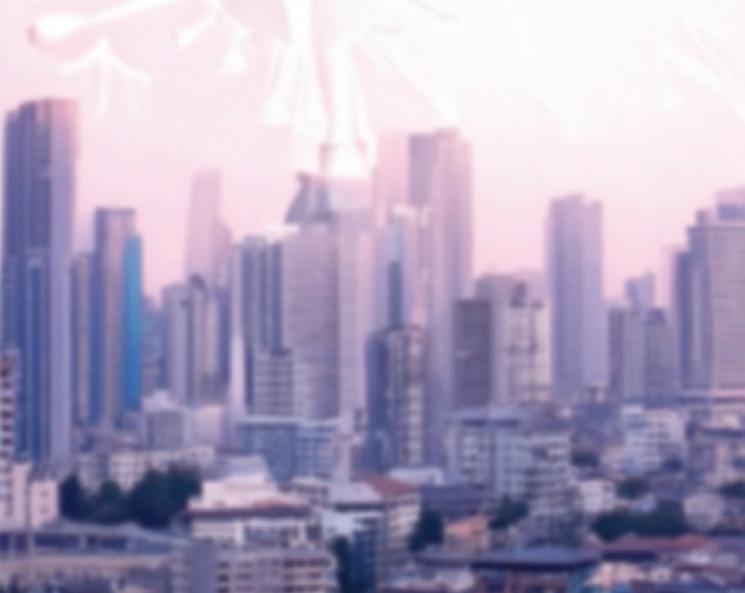



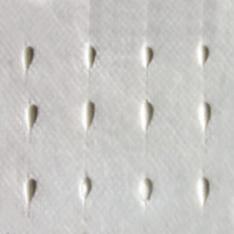
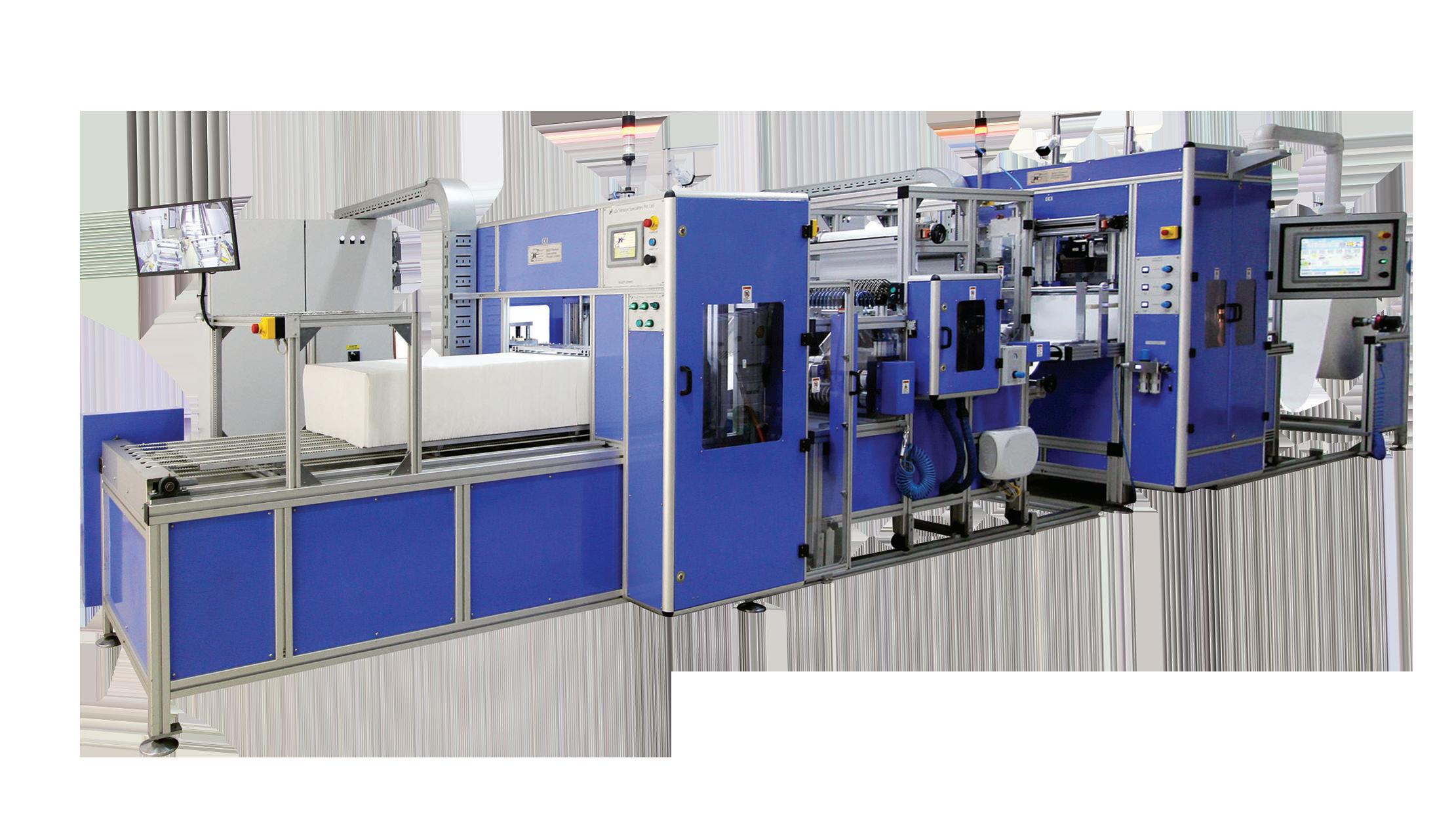
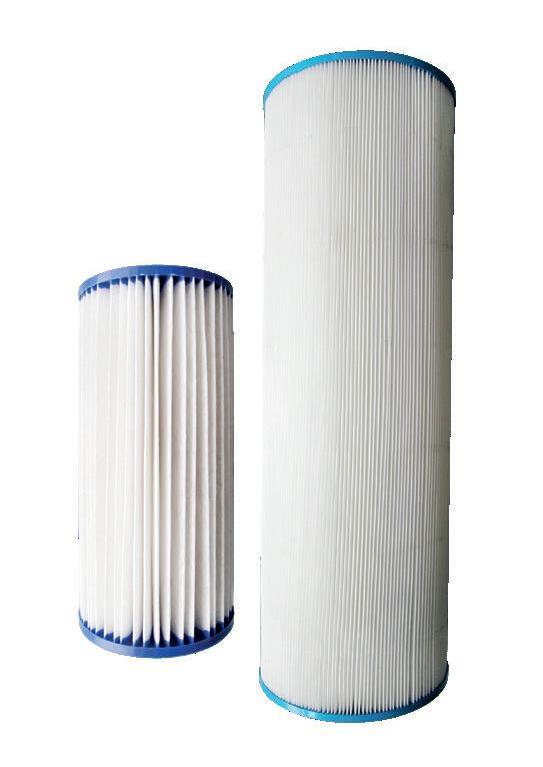
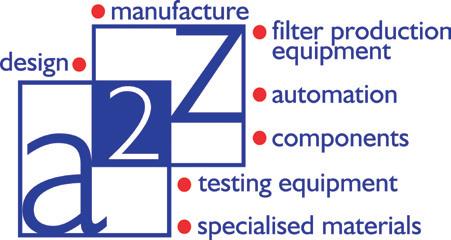

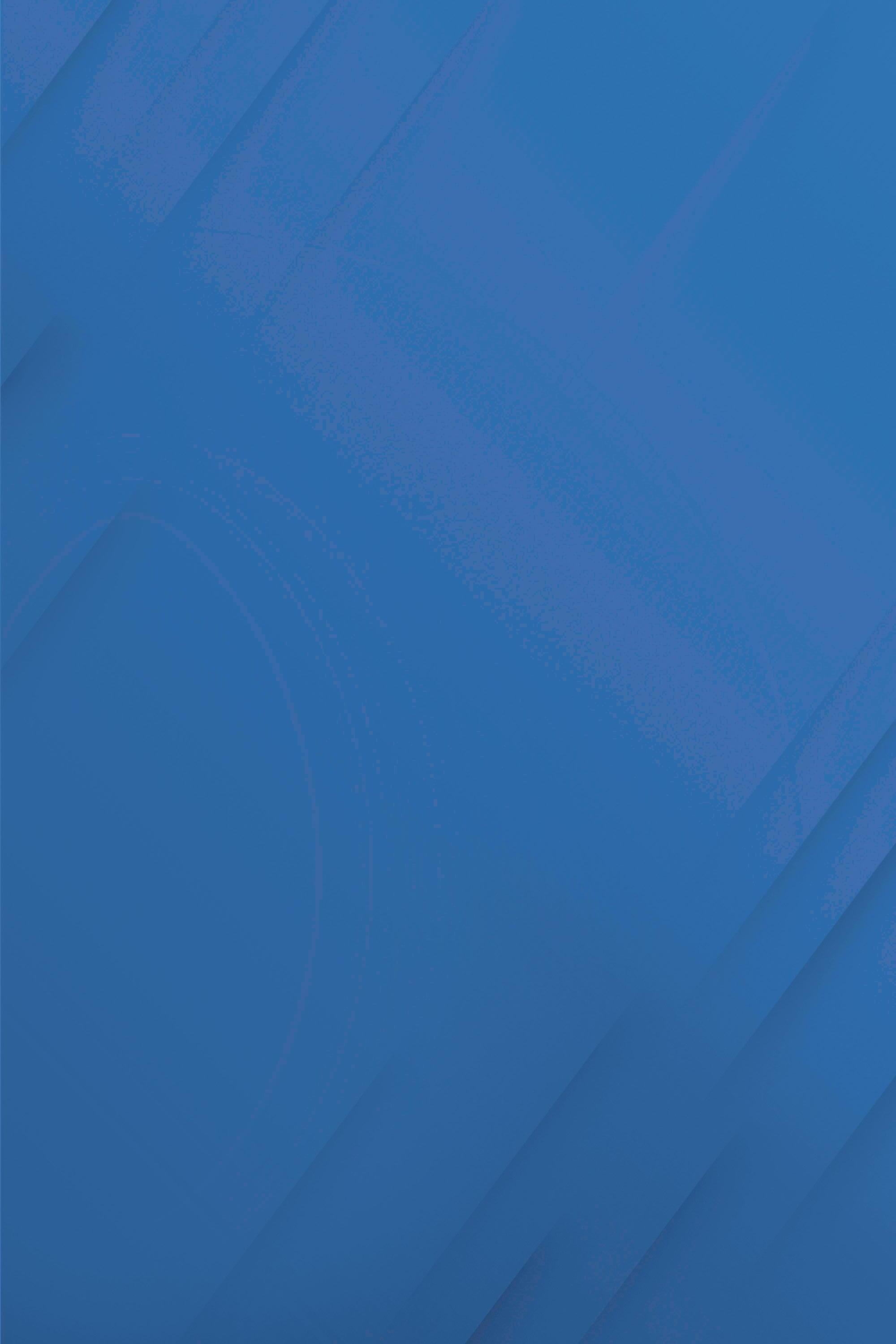

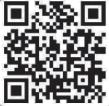
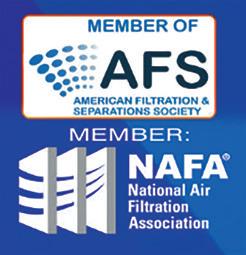



Caryn Smith
Chief Content Officer & Publisher, INDA Media csmith@inda.org
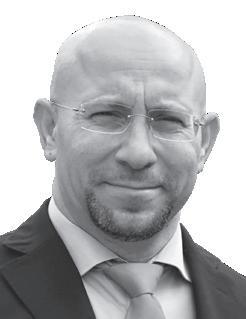
Dr. Iyad Al-Attar
Visiting Academic Fellow School of Aerospace, Transport, & Manufacturing, Cranfield University i@driyadalattar.com
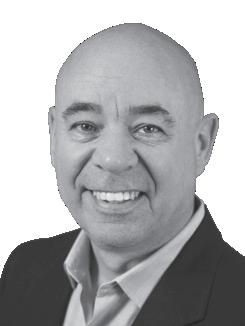
Jürgen Lobert Director of AMC Technology Entegris, Inc. www.entegris.com
2025 CALL FOR CONTRIBUTORS
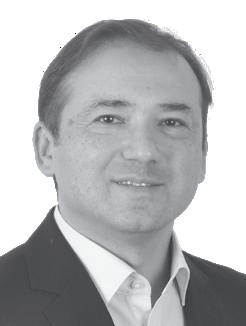
Serhat Oezeren
Global Vertical Market Manager – Chemicals, Polymers and Plastics Recycling Pall Corporation www.pall.com
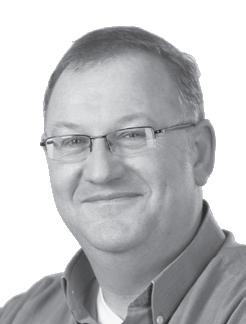
John Davies
Environmental, Health & Safety and Quality Manager EMEA, Filtration & Energy Solutions Division
Parker Filtration Group www.parker.com
Have you got something to say?
We are looking for individuals with their finger on the pulse of the marketplace. International Filtration News is seeking contributed technical, educational, and thought leadership articles from qualified industry professionals and those allied to the filtration industry. Contact Caryn Smith at CSmith@inda.org to pitch an idea or receive our 2025 Editorial Calendar. Represent your marketplace in our pages!

With our extensive knowledge in production of the innovative SOLTECH “Mini Pleat” Systems, and over 20 years of contract pleating with our revolutionary glue bead technology. SERVICES
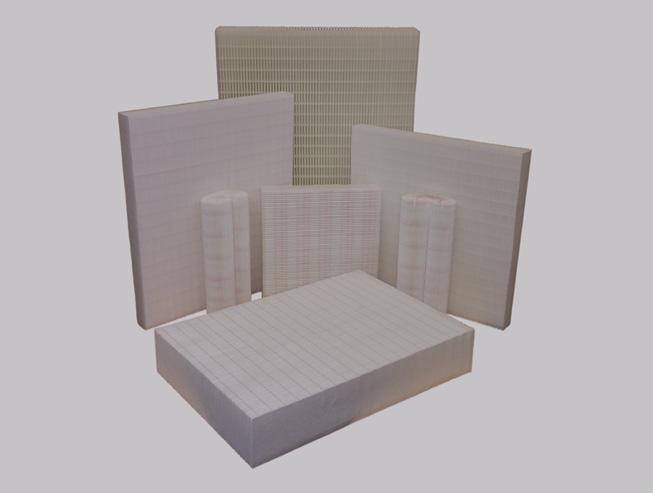

We offer the following services to our customers:-
MINI-PLEAT-GLASS
Mini-Pleat: H.E.P.A., ULPA & ASHRAE
Pleat heights 1/2” to 12” upto 39” wide. Interrupted beads, many configurations.
MINI-PLEAT-SYNTHETIC
Mini-Pleat: H.E.P.A. & ASHRAE
Pleat heights 3/4” to 4” upto 25” wide. Interrupted beads, many configurations.
We can incorporate the following features in your elements: Edge Seal - allowing economical frame sealing Slitting/Perforating - multiple packs
New for 2025! The American Filtration & Separations Society (AFS) is partnering with INDA to create a world-class FiltXPO™ conference program.
The two-day FiltXPO conference program will share technical insights in filtration innovations and technologies from industry professionals all over the world. Conference program details will be released in the fall of 2024.
Immerse yourself in the next generation of filtration technologies and innovations. Discover the latest developments from world-class exhibitors. Gain new intelligence on what is driving the filtration market.
Unlock business opportunities, gain exposure to new products, and build connections with key players in the filtration industry. Your next success story starts here.
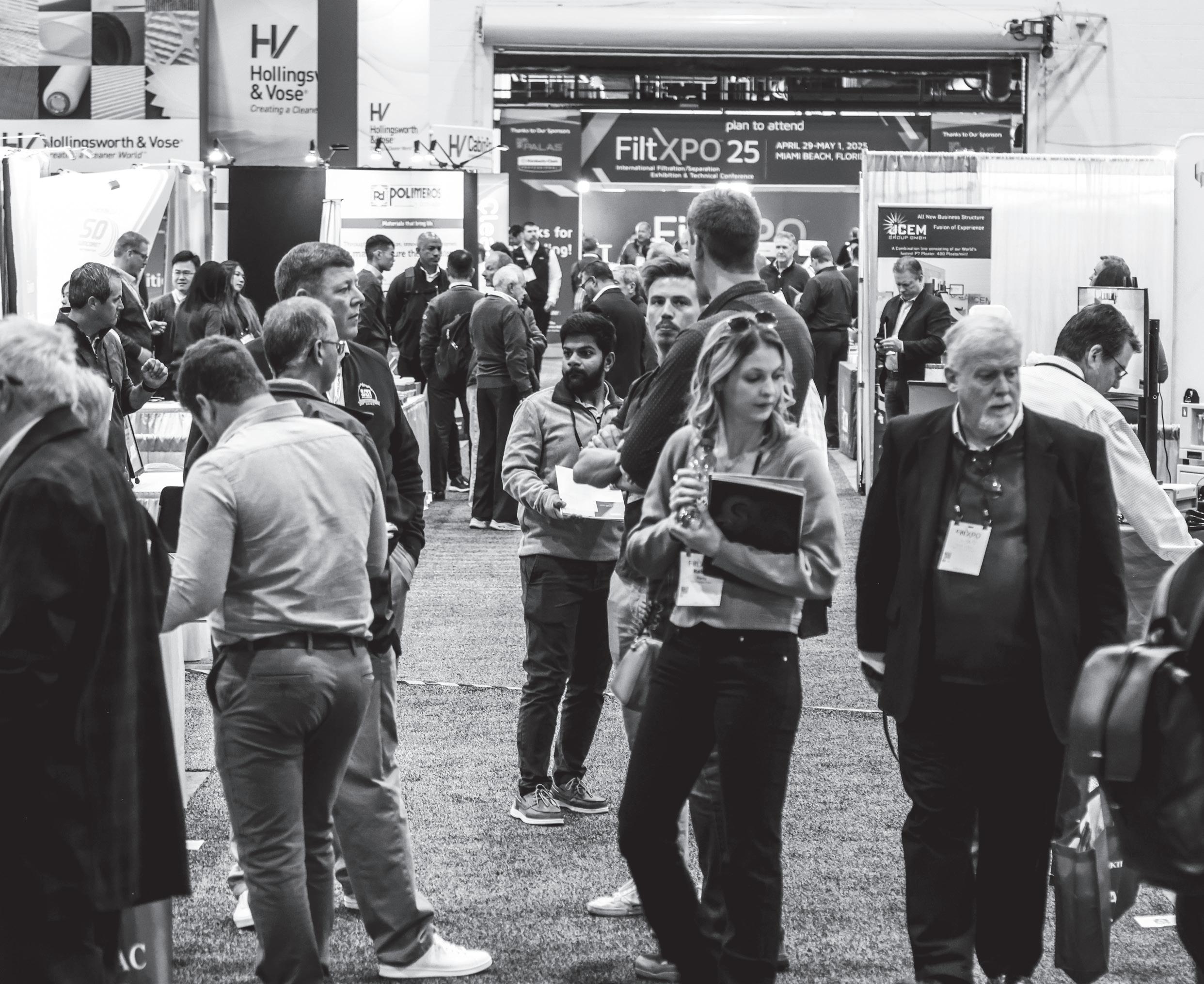



CSMITH@INDA.ORG +1
VIEWPOINT
Game Changing Innovation
“Innovation distinguishes between a leader and a follower.” — Steve Jobs
Every month, our team delves into reporting on progressive ideas and developments that are transforming the world of filtration, and if there’s one thing I’ve learned, it’s this: innovation isn’t just about thinking big; it’s about making an impact for the longterm.
Steve Jobs once said, “Innovation distinguishes between a leader and a follower.” In our industry, where health, efficiency, and sustainability depend on what we filter and how we filter it, leadership means staying ahead of not only the current demands but future ones, as well. The exciting ideas featured in IFN ’s Annual “Innovation in Action” Roundup on page 18 underscores how true innovation is taking shape right now in filtration. From new supply chain strategies to advanced technologies making filters more durable and eco-friendly, these developments aren’t just responses to today’s needs – they’re leading us toward tomorrow’s breakthroughs.
As you dive into “Innovation in Action,” keep in mind that innovation isn’t isolated to technology alone. True progress involves asking hard questions, especially when it comes to Environmental, Social, and Governance (ESG) practices. On page 36, the case study from Parker Hannifin explores how sustainable practices are increasingly at the forefront of industry leadership. With growing awareness around environmental impact, filtration industry companies are engaging
their workforce to ensure they’re making responsible choices that benefit people and the planet alike.
Finally, I encourage you to read “Revisiting the Pandemic: What (Filtration) Lessons Aren’t We Learning?” on page 39. There are still so many lessons to learn regarding filtration governance and the importance of indoor air quality (IAQ) for built environments and building envelopes. We still have room for improvement and innovation. Reflecting on our pandemic responses can sharpen our approach to future challenges and, once again, set the stage for true industry leadership.
Innovation is both a mindset and a responsibility. By seeking out better solutions today, we’re paving the way for a healthier, safer world tomorrow. So, let’s keep asking, exploring, and innovating – and let’s lead the way forward.
Lastly, the IFN team is now scheduling “IFN Discovery Meetings” to share with you how your company can leverage our reach and influence to 15,000 industry professionals worldwide. Some opportunities are even at NO COST! Please download the 2025 Media Kit at www.filtnews.com/ advertise. Email me to schedule a meeting at csmith@inda.org! ... Talk Soon!
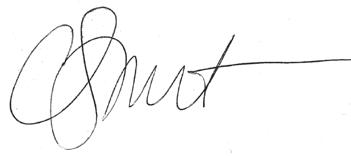
Caryn Smith Chief Content Officer & Publisher, INDA Media, IFN
International Filtration News Editorial Advisory Board
R. Vijayakumar, Ph.D., Chair
AERFIL
Tel: +1 315-506-6883
Email: vijay@aerfil.com
Tom Justice, CAFS, NCT
ZENE, LLC Filtration
Tel: +1 757-378-3857
Email: justfilter@yahoo.com
James J. Joseph
Joseph Marketing
Tel/Fax: +1 757-565-1549
Email: josephmarketing120@gmail.com
Wenping Li, Ph.D.
Agriltech Research Company
Tel: +1 337-421-6345
Email: wenpingl@agrilectric.com
Rishit R. Merchant
Parker Hannifin
Tel: +1 805-604-3519
Email: rishit.merchant@parker.com
Thad Ptak, Ph.D.
TJ Ptak & Associates
Tel: +1 414-514-8937
Email: thadptak@hotmail.com
UTILIZE YOUR EXPERTISE TO HELP SHAPE THE INDUSTRY!
We are Now Accepting Applications for 3 Open Seats on the IFN Editorial Advisory Board
Consider applying for the IFN Editorial Advisory Board.
As a member of this prestigious group, we value your insight into trends, innovations and story ideas, as well as your thought leadership. This board meets up to four times a year to discuss the state of the industry, and the IFN coverage of these important topics.
Send an email to Caryn Smith at csmith@inda.org for consideration.
SPOTLIGHT TECH
Removing “Forever Chemicals” From Water to Be Used in Renewable Batteries
Technology developed at The University of Queensland can remove harmful “forever chemicals” –known as PFAS – from water so they can be used in renewable batteries.
Researchers at The University of Queensland ’s Australian Institute for Bioengineering and Nanotechnology have made a filter which quickly and cleanly captures per- and polyfluoroalkyl substances (PFAS). The filter contains a patented sorbent solution that uses an ion-exchange technique to isolate and remove the PFAS particles as the water passes through it.
Dr. Cheng Zhang, a polymer chemist at the university, said fluorine-based materials can be harvested from the filter and he’s working on using them to improve clean energy technology.
“People are increasingly aware of the risks that PFAS poses to human health, and how long these chemicals persist in the natural environment,” he said.
“Not only does our filter technology remove harmful particles from water, those captured chemicals are available to be repurposed to help decarbonize the planet.
“The increasing demand for high-performance rechargeable batteries means manufacturers are constantly searching for new materials that improve the energy density, safety and cycling stability of batteries. Recycled PFAS has excellent properties for this purpose,” he said.
Pilot Testing
Having successfully tested a prototype of the PFAS filter in a laboratory, Dr. Zhang and Professor Jianhua Guo from UQ’s Australian Centre for Water and Environmental Biotechnology will at a later date start pilot testing in Brisbane and the U.S. with $1 million backing from the Advance Queensland Industry Research Projects program.
Testing is being planned for a range of sites including the Luggage Point Sewage Treatment Plant with water management company GHD, project management firm OCTA, and the Queensland Department of Environment, Science and Innovation.
Scheduled for the second year of the project, an additional pilot site will be established to scale up testing.
“These demonstrations will be pivotal to scaling up our filter technology for use in industrial water infrastructure,” Dr. Zhang said. “If this testing goes as we believe it will, we hope to reach commercial production within three years.”
History of PFAS
PFAS are synthetic chemicals used in consumer and industrial products because of their ability to resist heat, stains, grease and water but they persist in the environment and have been linked to a range of potential human health problems.
Much work has been done globally to eliminate PFAS from consumer and industrial products after government agencies and researchers began to take a closer look at the


chemicals some 30 years ago. Awareness of potential health issues related to PFAS began surfacing in the 1970s, and even in the 1950s there were some concerns. In January 2024 the Environmental Protection Agency (EPA) in the U.S. finalized a rule that prevents companies from starting or resuming manufacturing of certain PFAS without an extensive EPA review.
Companies have made great leaps in finding replacements for PFAS in consumer and industrial goods. In addition, there are several processes and filters on the market that seek to remove PFAS from drinking and other bodies of water, where much of the PFAS end up, causing potential health issues for people.
For more information visit The University of Queensland, Australia: uq.edu.au
Polymer chemist Dr. Cheng Zhang at the University of Queensland doing research on PFAS chemicals for use in better battery technology.
Photo courtesy of The University of Queensland
PFAS chemicals extracted from contaminated water by the filter. Photo courtesy of The University of Queensland
NOTES TECH
DuPont Launches Digital Tool to Estimate Sustainability Impact from the Use of Water Treatment Technologies

DuPont recently introduced the Water Solutions Sustainability Navigator, the first digital tool designed to help users estimate key sustainability indicators when using various water treatment technologies, whether from DuPont or from other manufacturers.
The Water Solutions Sustainability Navigator enables users to compare how different potential water treatment scenarios impact sustainability indicators, including carbon emissions, chemicals used, wastewater generated, solid waste generated and footprint needed – with all calculations and indicators validated by a third-party verification performed by LRQA, a global assurance provider.
Carbon emission calculations are in conformance with ISO 14020:2001 and 14021:2016, and chemical, footprint, wastewater and solid waste calculations are in conformance with ISO 14020:2023 and ISO 14021:2016 + A1: 2021.
“While there are many factors that can influence the design and selection of water treatment technologies, the Water Solutions Sustainability Navigator will help users better understand the interconnection of sustainability-driven choices and the cost of operations,” said Jeroen Bloemhard, Vice President and General Manager, DuPont Water Solutions.
Currently, the tool allows users to input four different water treatment technologies – reverse osmosis (RO), ultrafiltration (UF), ion exchange resins (IER) and membrane bioreactors (MBR) – used alone or in combination. www.dupont.com
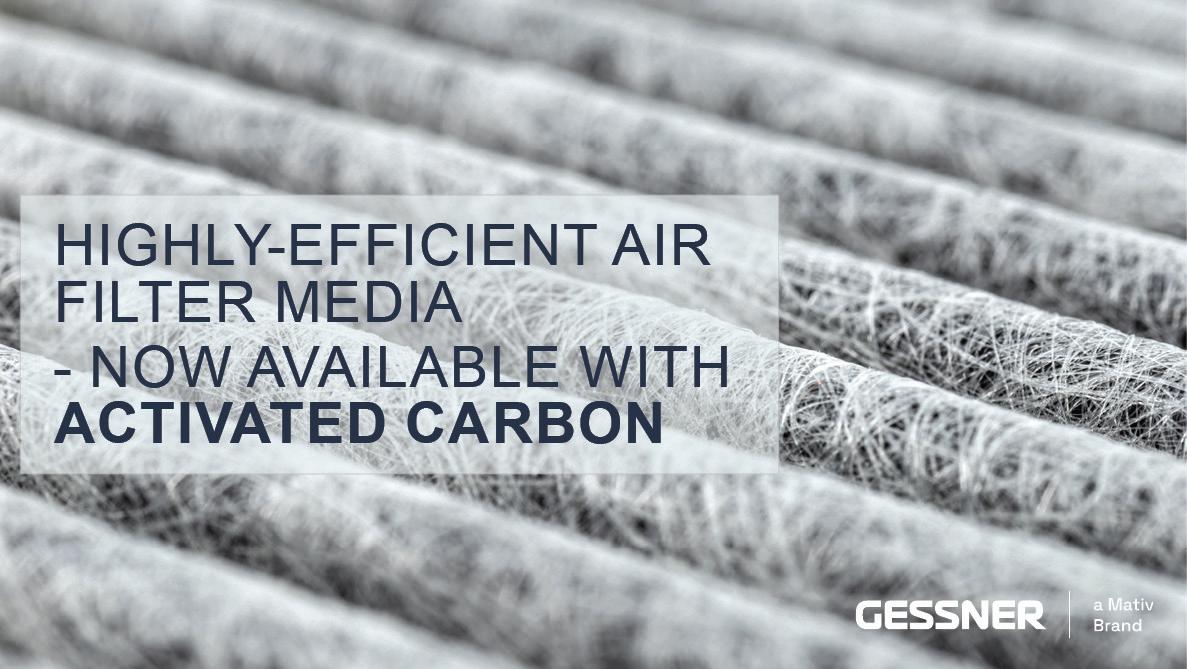
Gessner Adds Activated Carbon to Electrostatic Air Filter Media
GESSNER now offers their Alphastar™ tribo-electric nonwoven and NeenahPure™ meltblown nonwoven with an activated carbon layer for pleatable and bag filters. These high-efficiency, electrostatic filter media can be developed meeting individual requirements from high efficiency filtration to standard requirements.
The activated carbon layer captures and neutralizes a wide range of impurities, including volatile organic compounds (VOCs), odors, and other contaminants. Depending on the customers’ needs GESSNER develops the activated carbon layers for each individual application.
Alphastar™ triboelectric filter media provides superior filtration performance with high dust holding capacity, low resistance to airflow, and high removal efficiency. The NeenahPure™ product range is their highly charged meltblown media solution for pleatable and bag filters in HVAC, air purification and air pollution control applications to provide clean indoor air for a better protection.
With a range from highest to standard efficiency, covering efficiencies from MERV 8 – MERV 16 (ASHRAE) and from ePM10 – ePM1 (ISO 16890) and the technical possibilities to customize the activated carbon layer as well as the particle layer, GESSNER engineers filter media tailored to the specific requirements of each customer. www.gessner-filtration.com
Cleanova Launches Groundbreaking Carbon Capture Filtration Tech
Cleanova recently announced the launch of its new filtration technology designed for carbon capture, utilization and storage (CCUS) applications. By capturing carbon dioxide (CO2) from various sources, CCUS is set to play an important role in achieving global Net Zero emission targets.
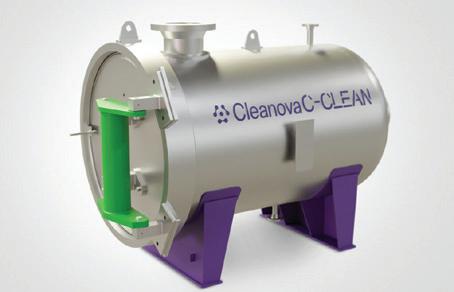
To ensure that CO 2 is free from both solid and liquid contamination, filtration technology is used to separate the captured gases from each other.
“Filtration technology plays a pivotal role at every stage in the carbon capture process, from the arrival of the feed gas, through chemical absorption to final storage and transportation,” explained Chris Nixon, Engineering and Products Director at Cleanova.
Each filtration solution has to be tailored to specific conditions such as CO 2 concentration, the nature of the emission source, the presence of other contaminants, temperature and pressure.
The Cleanova.C-CLEAN technology suite includes UNIQ-MAX High Capacity Filters, which prevent absorb plugging by removing high quantities of suspended particles from feed gases.
This is in addition to liquid/gas coalescers to ensure solvent purity, activated carbon filters to eliminate hydrocarbons and contaminants and oil mist eliminators to ensure clean exhaust air, stated the company. www.cleanova.com
Gessner’s carbon filter.
Metso Expands Polishing Filtration Product Family

Metso is expanding its polishing filtration product family with the addition of the GM (Glass Media) filter.
The Metso GM filter is designed to remove insoluble organics in battery metals processes by utilizing very efficient and patented coalescing media. With its cost-effective and modular design, the GM filter increases the recovery and recycling of valuable process chemicals.
“The GM filter is an ideal choice when insoluble organics need to be removed and recovered. Thanks to its efficient coalescing media for hydrometallurgical applications, the GM filter can perfect the removal and recovery of insoluble organics at a much higher velocity than the traditional coalescing media. In applications where an Active Carbon (AC) filter needs to be used for dissolved organics adsorption from the process, the AC filter’s efficiency and media lifetime can be improved by utilizing a GM filter in front of it,” said Mika Vuorikari, Director of Industrial Filtration at Metso.
The Metso GM filter is designed for variable sizes of process streams and its modular design makes it easy to expand to meet plant process requirements. It also optimizes back washing with filtered process liquid and circulates back to the process, ensuring that water consumption is kept to a minimum. The low pumping pressure of the filter also results in lower energy consumption.
Together with the Dual Media (DM) and Active Carbon (AC) filters, Metso has a complete filtration portfolio for SX-electrowinning and -crystallization processes. Strong know-how and experience from the hydrometallurgical industry allows Metso to design industry-leading filtration solutions for battery minerals processing. Metso has delivered more than ninety DM and AC filters to metallurgical SX processes globally. www.metso.com
Camfil USA Introduces Megalam® ES – Filters for Life
Sciences
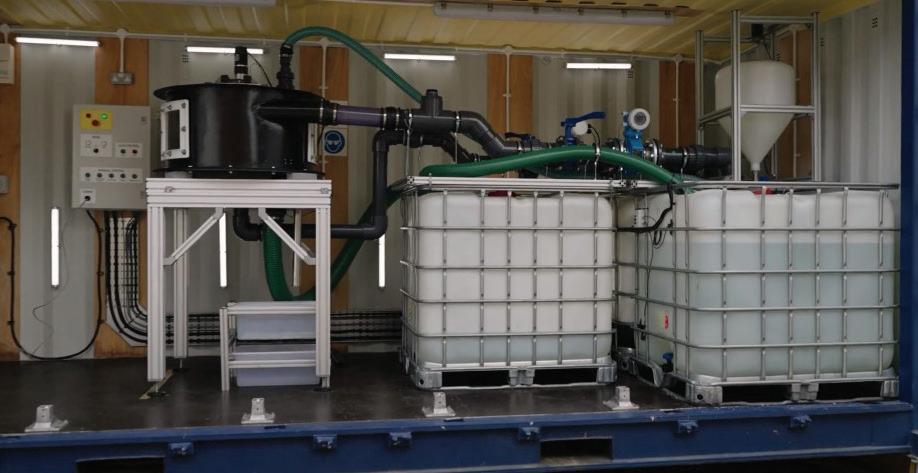
Capture Technology for Textile Manufacturing
British climate-tech company Matter has launched its new microfiber capture technology, Regen™, during the New York Climate Week. Regen, developed in collaboration with Paradise Textiles, is a self-cleaning filtration system designed to prevent microfibers from entering waterways by capturing them during the wastewater filtration process. The partnership will see Regen installed in Paradise Textiles’ new textile facility in Egypt next year.
Paradise Textiles, the material science arm of the Alpine Group – a major manufacturer of materials and apparel for brands such as The North Face, Lululemon, American Eagle Outfitters, and Puma – helped in developing the application of the technology for the textile industry. It provided insights into textile manufacturing processes, funded early research, and helped shape Matter’s Microfibre Assessment Program (MAP) to maximize fiber capture. Matter also raised $10 million in their 2023 funding round, and is backed by investors including S2G Ventures, SOUNDwaves, and Regeneration.VC.
The microfiber technology is designed to tackle the estimated 120,000 tonnes of microfiber emissions generated from textile production each year.
Microfibers are a large contributor to microplastic pollution in water, air, soil, and food sources, and recent studies have warned against the alarming health concerns to which microplastics have been linked. www.matter.industries
Camfil USA, a global leader in air filtration and clean air solutions, announced the launch of the Megalam® ES ePTFE HEPA filter, a next-generation filtration solution for the life sciences industry. This innovative filter provides unprecedented durability, superior energy savings, and reduced risk of contamination, making it the ideal choice for critical applications like pharmaceuticals, clean rooms, and biotech facilities.
The Megalam® ES sets itself apart from traditional glass fiber HEPA filters with its multi-layer ePTFE media, providing exceptional strength while maintaining low airflow resistance. Its heavy-duty anodized aluminum frame, featuring Camfil’s exclusive Klip-Lok™ mechanism, ensures easy installation and longlasting corner integrity, further enhancing the filter’s reliability and robustness. www.camfil.com
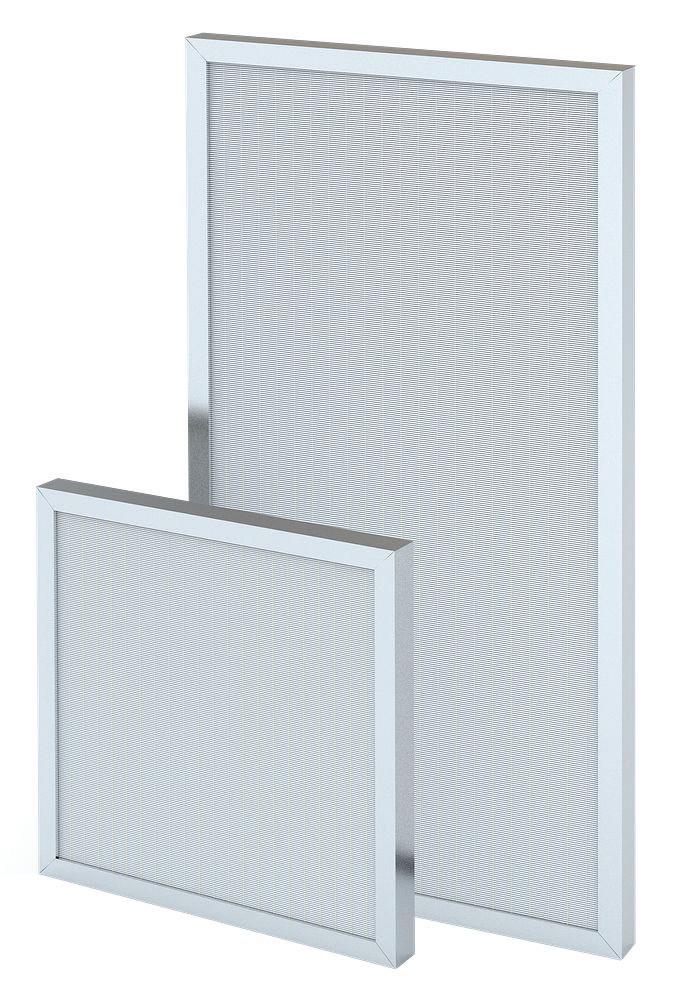
Microfiber
Evonik Introduces High-Capacity Biogas Membrane
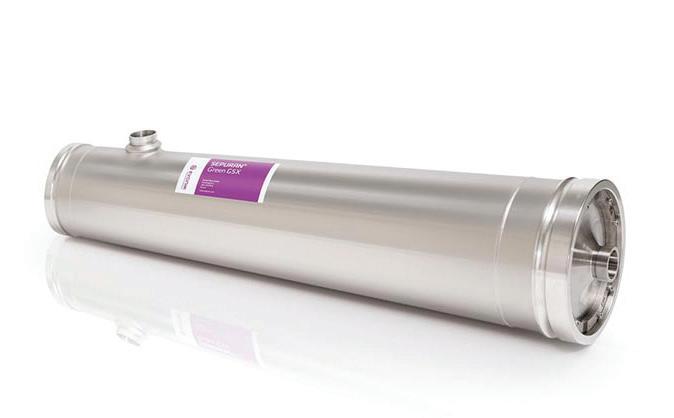
Evonik recently unveiled its latest biogas membrane, the SEPURAN ® Green G5X 11“, featuring the highest capacity of its kind currently on the market. Specifically designed for upgrading biogas to renewable natural gas (RNG) in large landfill, agricultural, organic waste, and wastewater treatment projects, the membrane is specifically engineered for maximizing sustainability and efficiency gains in biogas upgrading projects.
“The launch of this product addresses the growing demand for our membranes among large-volume biogas upgrading projects in landfills and other large RNG projects,” said Jennifer Doerper, global director of biogas membranes at Evonik. “The market-leading capacity of our SEPURAN® Green G5X 11” makes it the ideal choice for customers looking to boost their cost efficiency.”
The SEPURAN® Green G5X 11” is designed with double the capacity of the SEPURAN® Green G5X 6”L, and is ideal for large flow projects among landfills. Used in Evonik’s 3-stage configurations, which are patented in the U.S., it excels in maximizing methane recovery rates and enabling high onstream times.
Additionally, Evonik’s SEPURAN® Green G5X 11” offers more compact systems, less piping connections and welding time, and is easy to operate due to its ability for precise monitoring.
Scheduled to enter production later this year, the new SEPURAN® Green G5X 11” was on display at the Evonik booth during the RNG WORKS trade show in September in Nashville, Tennessee.
Evonik launched its first membrane product – SEPURAN® Green, for efficient upgrading of biogas – on the market in 2011, laying the foundations for future business in membranes. This was followed by further membrane products for nitrogen, helium, hydrogen, natural gas, and nanofiltration applications. Today, Evonik’s membranes are in service in 200 biogas installations in North America, and more than 1000 worldwide. www.evonik.com
Personal Breathing Unit from Martech
Metso Introduces Upgraded Larox® PF 60 Series Pressure Filter
Metso introduced the upgraded Larox® PF 60 series pressure filter at the opening ceremony of the new machining unit at the company’s Filtration Technology Center in Lappeenranta, Finland, on September 11, 2024.

“The new version of the Larox ® PF 60 series filter marks a step change in the technological development of tower filters. It significantly improves safety, process efficiency and dewatering capacity in mining and other process industry applications, thanks to its novel technological solutions. This upgraded model is fully automated to enable flexible operation for process variations and is future-ready for different plate pack configurations to provide consistent and homogenous filter cake with efficient solids wash,” said Jussi Venäläinen, Vice President of the Filtration business line at Metso.
The Larox® PF 60 series filter is part of Metso’s Planet Positive offering, thanks to its advanced features that decrease water and oil usage by up to 90% and 75%, respectively. In addition, it can reduce the need for installed electric power by 25%. The filter has a compact and open design, which translates to less floor space required and a significant improvement in ease of maintenance. The structure has also been upgraded to meet the latest seismic standards. To ensure optimized lifelong performance, Metso offers a comprehensive service portfolio including remote support.
“The investment into a new machining unit at our Filtration Technology Center in Lappeenranta goes hand in hand with the development of the Larox® PF 60 pressure filter and our ambition to offer our customers the best and most responsible filtration technology available. The highly automated machining unit significantly increases our manufacturing capacity and enables the production of high-quality filter components in a safer, more environmentally friendly manner,” explained Tero Tiainen, Director for Filters Manufacturing at Metso. www.metso.com
The topic of Carbon Capture and Utilization (CCU) and Direct Air Capture (DAC) has the potential to make a significant contribution to climate change and at the same time represents an important building block in the future economic system. That is why Hengst Filtration is proud to present the first CCU/DAC system for capturing carbon dioxide (CO2) from the air and then utilizing the carbon.“With this technology, we are fully committed to our vision of “purifying our planet,” because we adsorb the pollutants from the air and then make them available for other processes,” said Jens Röttgering, owner of Hengst Filtration. Carbon Capture and Utilization refers to the filtration, transport and subsequent use of CO2. Direct Air Capture refers to the extraction of CO2 from the air. Dr. Rolf Gausepohl, Head of the TechCenter Filtration at Hengst, commented: “Our CCU unit is fully developed and works in the daily process. We are now looking for suitable partners to further develop the technology and adapt it to real-life conditions.” www.breathingsystems.com
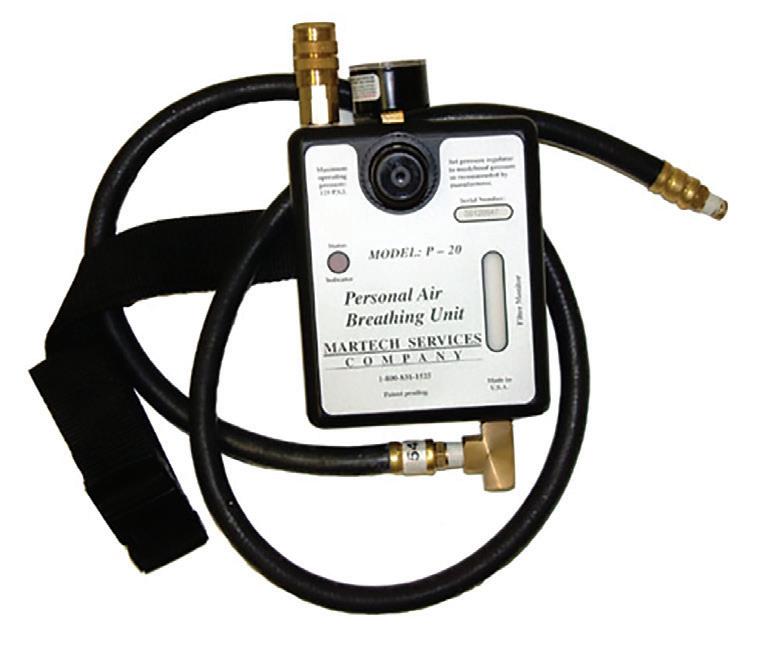
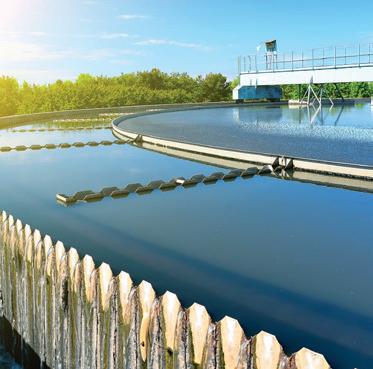
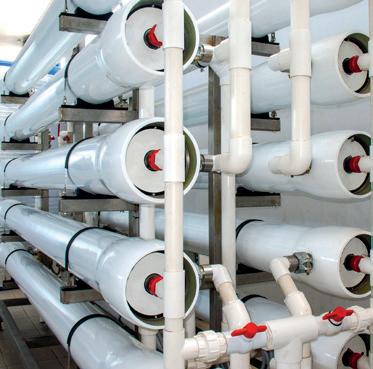
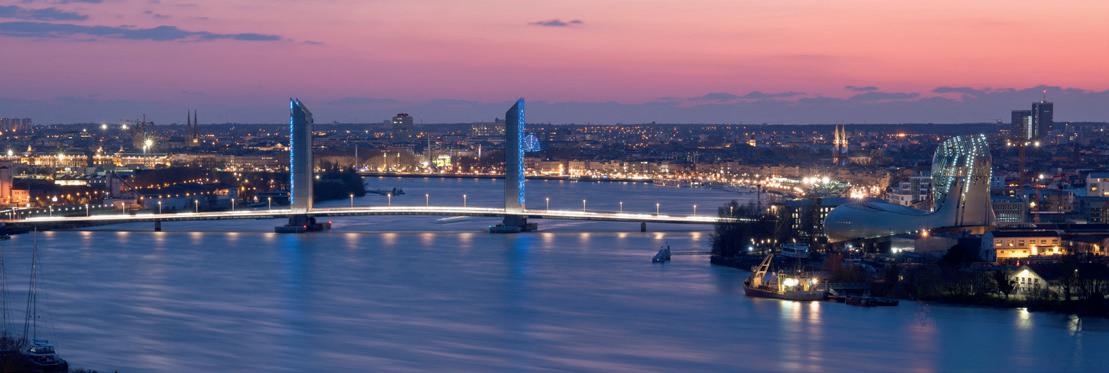
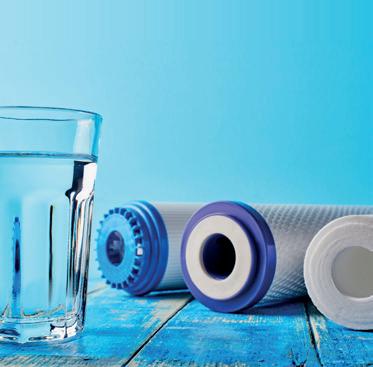


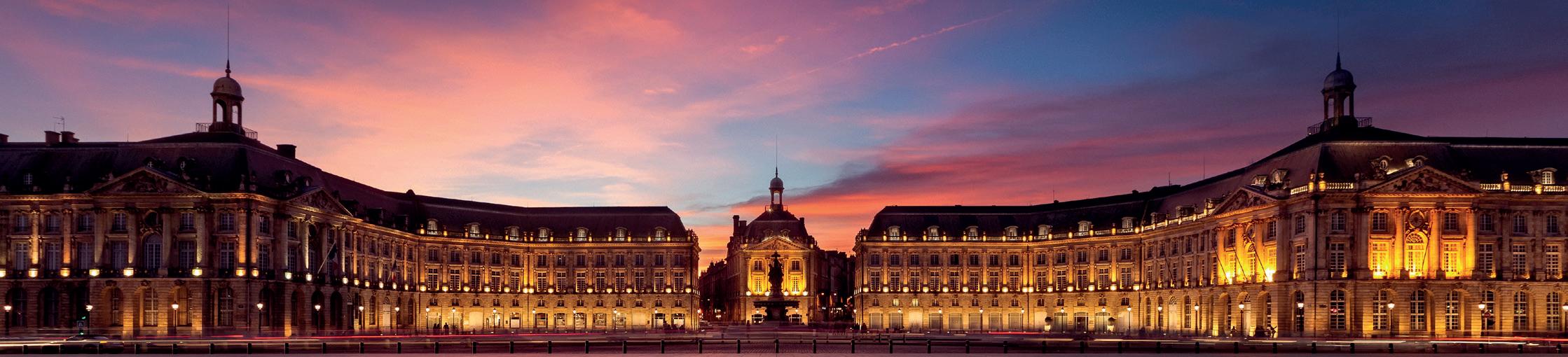

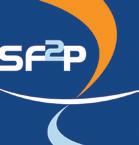

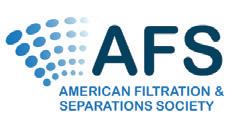
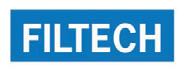
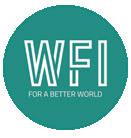
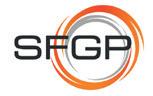
EMERGENCE
Compiled by Caryn Smith, IFN Chief Content Officer
IInternational Filtration News Explores Trending Innovation
n this new feature, IFN highlights significant research from universities and institutions around the world. If you are a part of a project you would like to highlight, email csmith@inda.org. Please write “IFN Emerging Research Submission” in your subject line in order to apply. Please send a completed press release and/or summary of the research as you would want it to be printed, a link to the university online story (if applicable), and all high resolution photographs/charts/graphs, short researcher bio(s). All selections could be edited for length.
MASSACHUSETTS INSTITUTE OF TECHNOLOGY
New Filtration Material Could Remove Long-Lasting Chemicals From Water
By David L. Chandler
Water contamination by the chemicals used in today’s technology is a rapidly growing problem globally. A recent study by the U.S. Centers for Disease Control found that 98 percent of people tested had detectable levels of PFAS, a family of particularly long-lasting compounds also known as “forever chemicals,” in their bloodstream.
A new filtration material developed by researchers at MIT might provide a nature-based solution to this stubborn contamination issue. The material, based on natural silk and cellulose, can remove a wide variety of these persistent chemicals as well as heavy metals. And, its antimicrobial properties can help keep the filters from fouling.
The findings are described in the journal ACS Nano, in a paper by MIT postdoctoral Yilin Zhang, professor of civil and environmental engineering Benedetto Marelli, and four others from MIT (Yilin Zhang, Hui Sun, Yunteng Cao, Maxwell J. Kalinowski, Meng Li, Benedetto Marelli).
PFAS chemicals are present in a wide range of products, including cosmetics, food packaging, water-resistant clothing, firefighting foams, and antistick coating for cookware. A recent study identified 57,000 sites contaminated by these chemicals in the U.S. alone. The U.S. Environmental Protection Agency has estimated that PFAS remediation will cost $1.5 billion per year, in order to meet new regulations that call for limiting the com-
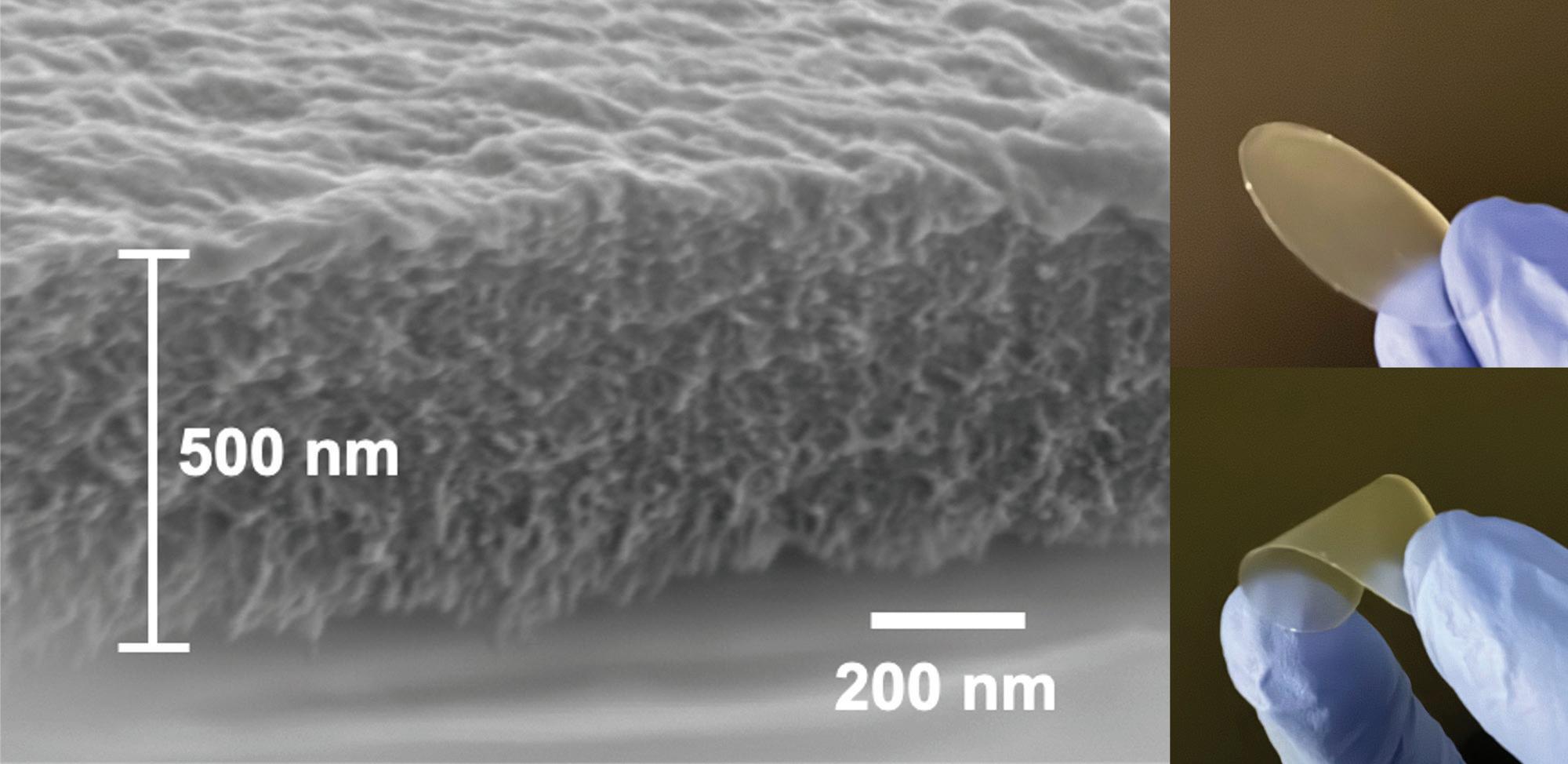
pound to less than seven parts per trillion in drinking water.
Contamination by PFAS and similar compounds “is actually a very big deal, and current solutions may only partially resolve this problem very efficiently or economically,” Yilin Zhang says. “That’s why we came up with this protein and cellulose-based, fully natural solution,” he says.
“We came to the project by chance,” Marelli notes. The initial technology that made the filtration material possible was developed by his group for a completely unrelated purpose – as a way to make a labelling system to counter the spread of counterfeit seeds, which are often of inferior quality. His team devised a way of processing silk proteins into uniform
nanoscale crystals, or “nanofibrils,” through an environmentally benign, water-based drop-casting method at room temperature.
Zhang suggested that their new nanofibrillar material might be effective at filtering contaminants, but initial attempts with the silk nanofibrils alone didn’t work. The team decided to try adding another material: cellulose, which is abundantly available and can be obtained from agricultural wood pulp waste. The researchers used a self-assembly method in which the silk fibroin protein is suspended in water and then templated into nanofibrils by inserting “seeds” of cellulose nanocrystals. This causes the previously disordered silk molecules to line up together along the
By integrating cellulose into the silk-based fibrils that could be formed into a thin membrane, and then tuning the electrical charge of the cellulose, the researchers produced a material that was highly effective at removing contaminants in lab tests. Pictured is an example of the filter. Courtesy of the researchers.
seeds, forming the basis of a hybrid material with distinct new properties.
The electrical charge of the cellulose, they found, also gave it strong antimicrobial properties. This is a significant advantage, since one of the primary causes of failure in filtration membranes is fouling by bacteria and fungi. The antimicrobial properties of this material should greatly reduce that fouling issue, the researchers say.
“These materials can really compete with the current standard materials in water filtration when it comes to extracting metal ions and these emerging contaminants, and they can also outperform some of them currently,” Benedetto Marelli says. In lab tests, the materials were able to extract orders of magnitude more of the contaminants from water than the currently used standard materials, activated carbon or granular activated carbon.
While the new work serves as a proof of principle, Marelli says, the team plans to continue working on improving the material, especially in terms of durability and availability of source materials. While the silk proteins used can be available as a byproduct of the silk textile industry, if this material were to be scaled up to address the global needs for water filtration, the supply might be insufficient.
Study Reveals Membrane Behavior Impacting WaterPurification Performance
Desalination can help provide muchneeded freshwater to communities lacking access, but the process can be difficult at scale. Now, scientists have discovered one of the reasons behind that difficulty.
Roughly 80% of the world’s desalination involves the use of reverse osmosis –a water-purification process utilizing a semi-permeable membrane to separate water molecules from other undrinkable substances. Engineers and scientists around the world have leveraged essential thin-film-composite reverse-osmosis membranes for more than 40 years.

Also, alternative protein materials may turn out to perform the same function at lower cost.
Initially, the material would likely be used as a point-of-use filter, something that could be attached to a kitchen faucet, Zhang says. Eventually, it could be scaled up to provide filtration for municipal water supplies, but only after testing demonstrates that this would not pose any risk of introducing any contamination into the water supply. But one big advantage of the material, he says, is that both the silk and the cellulose constituents are considered food-grade substances, so any contamination is unlikely.
“Most of the normal materials available today are focusing on one class of contaminants or solving single problems,” Zhang
A multi-institutional research team from the UCLA Samueli School of Engineering, the University of WisconsinMadison, Yale University and the University of Connecticut has recently published a study investigating the behavior of the membranes as governed by their viscoelastic properties.
Published in the Journal of Membrane Science, the study looked at the compaction (the process by which the polymer membranes increase in density under pressure) and relaxation (the corresponding decrease in density when pressure is relieved) involved in reverse osmosis.
The researchers found that by increasing the crosslinking-degree, or density of polymers in the polyamide layer, the membrane will exhibit decreased compaction and increased relaxation, thereby improving water permeability and salt
says. “I think we are among the first to address all of these simultaneously.”
“What I love about this approach is that it is using only naturally grown materials like silk and cellulose to fight pollution,” says Hannes Schniepp, professor of applied science at the College of William and Mary, who was not associated with this work. “In competing approaches, synthetic materials are used – which usually require only more chemistry to fight some of the adverse outcomes that chemistry has produced. [This work] breaks this cycle! ... If this can be massproduced in an economically viable way, this could really have a major impact.”
The research team included MIT postdoctorals Hui Sun and Meng Li, graduate student Maxwell Kalinowski, and recent graduate Yunteng Cao PhD ’22, now a postdoctoral at Yale University. The work was supported by the U.S. Office of Naval Research, the U.S. National Science Foundation, and the Singapore-MIT Alliance for Research and Technology.
Read: https://news.mit.edu/2024/new-filtrationmaterial-could-remove-long-lasting-waterchemicals-0906
Paper: https://pubs.acs.org/doi/full/ 10.1021/acsnano.4c07409
rejection. Polyamide, known for its use as a versatile material, is a type of synthetic polymer composed of long chains of molecules linked together by specially arranged atoms known as an amide group.
Findings from the research have the potential to alleviate some operational challenges of the desalination industry by highlighting the importance of developing new reverse-osmosis membrane materials with enhanced compaction resistance to improve long-term desalination performance.
Eric Hoek, a professor of civil and environmental engineering at UCLA Samueli, and Ying Li, an associate professor of mechanical engineering at the University of Wisconsin-Madison, are the co-corresponding authors.
“Mechanistic studies like this one can provide practical insights not just about
The team plans to continue working on improving the material, especially in terms of durability and availability of source materials. iStockphoto
UCLA SAMUELI SCHOOL OF ENGINEERING
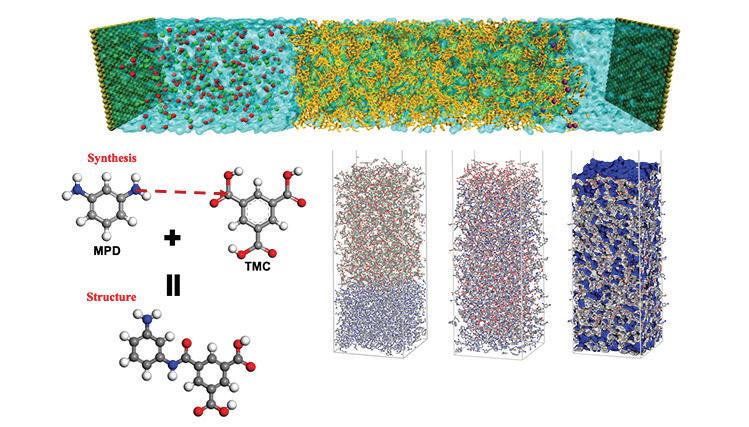
UNIVERSITY OF MISSOURI
Designing a Better Water Filter
Mizzou researcher Maryam Salehi is developing a fabric-like filter to remove tiny plastics and lead from drinking water.
Water filters on the market today can remove some contaminants, but they’re not designed to capture microplastics. In fact, some of them may actually add small plastics into drinking water during the filtration process. What’s worse is these microplastics can cause inflammation, increase the risk of cancer and act as carriers for harmful chemicals that trigger other health problems.
how a reverse-osmosis membrane can be damaged at high applied pressure, but also how new membrane materials might be designed to withstand such harsh operating conditions,” says Hoek, who directs UCLA’s Nanomaterials & Membrane Technology Research Laboratory, which explores membrane formation and application for water treatment.
To examine the polyamide layer’s role in compaction, the team created five reverse-osmosis membranes with varying degrees of crosslinking in the polyamide film. These membranes, all supported by identical base layers, demonstrated that higher crosslinking resulted in lower water permeability, higher salt rejection, less compaction and better recovery of permeability when pressure was reduced.
The study’s primary authors are Jishan Wu – postdoctoral researcher in Hoek’s lab – and Jinlong He of the University of Wisconsin-Madison. Other paper authors are members of Hoek’s lab – postdoctoral researchers Derrick Dlamini and Javier Alan Quezada, graduate students Xinyi Wang and Minhao Xiao, as well as undergraduate students Kay Au, Kevin Guo and Jason Le. They are joined by Hanqing Fan, Kevin Pataroque and Menachem Elimelech from Yale University, as well as Yara Suleiman and Sina Shahbazmohamadi from the University of Connecticut.
Xiao recently received a fellowship from the American Membrane Technology
Association and the U.S. Bureau of Reclamation for his membrane-related research in innovations for water treatment.
The study was funded by the National Alliance for Water Innovation through the U.S. Department of Energy’s Industrial Efficiency and Decarbonization Office, the UCLA Samueli School of Engineering and the UCLA Sustainable LA Grand Challenge.
An announcement of this study was first published by Water Desalination Report and adapted for this story.
Read: https://samueli.ucla.edu/study-revealsmembrane-behavior-impacting-water-purificationperformance/ © Copyright 2024 UCLA Samueli School Of Engineering
University of Missouri researcher Maryam Salehi and collaborators are coming up with a new way to trap those tiny invaders – and protect the public –through a fabric-like filter.
“The idea is to design a filter that can be attached to a faucet so it can remove microplastic and lead at the same time from tap water,” says Salehi, an assistant professor of civil and environmental engineering in Mizzou’s College of Engineering. “We’re envisioning an inexpensive point-of-use filter that could connect to any faucet.”
The filter membrane is made from polyvinyl alcohol fibers, which are polymers currently used in biomedical applications. The team chose the material
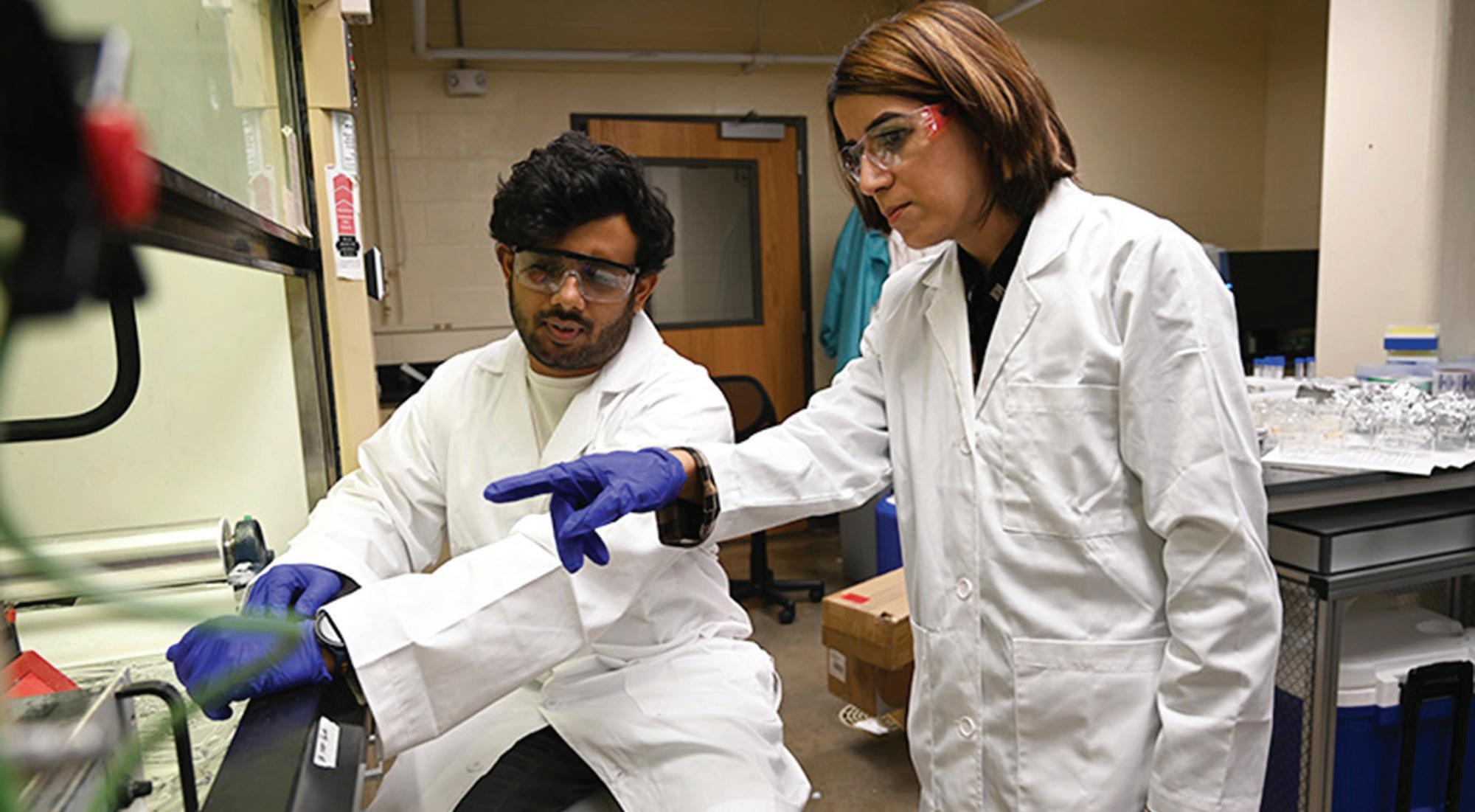
University of Missouri researcher Maryam Salehi and graduate student Anandu Gopakumar Nair investigate filter properties in her lab in Lafferre Hall. Zac Anderson
A schematic from a study investigating the compaction and relaxation behavior of composite reverse osmosis polyamide selective layers. Jishan Wu/UCLA
because it’s low-cost and biocompatible, meaning it’s not toxic to humans, animals or plants.
It’s also proving to be effective. In lab tests, the membrane was able to remove nearly 100% of larger microplastics and nearly 80% of the smallest microplastics, while at the same time removing about 70% of lead contamination.
“We still need to test the filter to see how it tolerates other conditions – such as disinfectant use in water – but the idea is to hopefully have something that can be commercialized and used to easily purify tap water,” Salehi says.
The team outlined their findings in a cover article published in Applied Polymer Science. Co-authors were Anandu Gopakumar Nair, a doctoral student at Mizzou, Alexander Ccanccapa, a postdoctoral researcher, and Kati Bell, an industry partner. The work is supported by Brown and Caldwell, as well as the National Science Foundation.
Salehi is a core researcher at the Missouri Water Center, which brings together stakeholders from academia, industry and government to advance water research.
Read: https://showme.missouri.edu/2024/designinga-better-water-filter/
JOHNS HOPKINS BLOOMBERG SCHOOL OF PUBLIC HEALTH
Filters and Digital Health Program
Reduced Participants’ Arsenic Levels by Nearly Half in American Indian Households Relying on Well Water
Acommunity-led water-testing project made up of households that rely on private well water with high arsenic levels saw on average a 47 percent drop in participants’ urinary arsenic levels after filters were installed and a digital health program was implemented, according to a new study led by researchers at the Johns Hopkins Bloomberg School of Public Health. Over the two-year study period, participating households were contacted to encourage use of the filter and remind users to replace the filter cartridge.
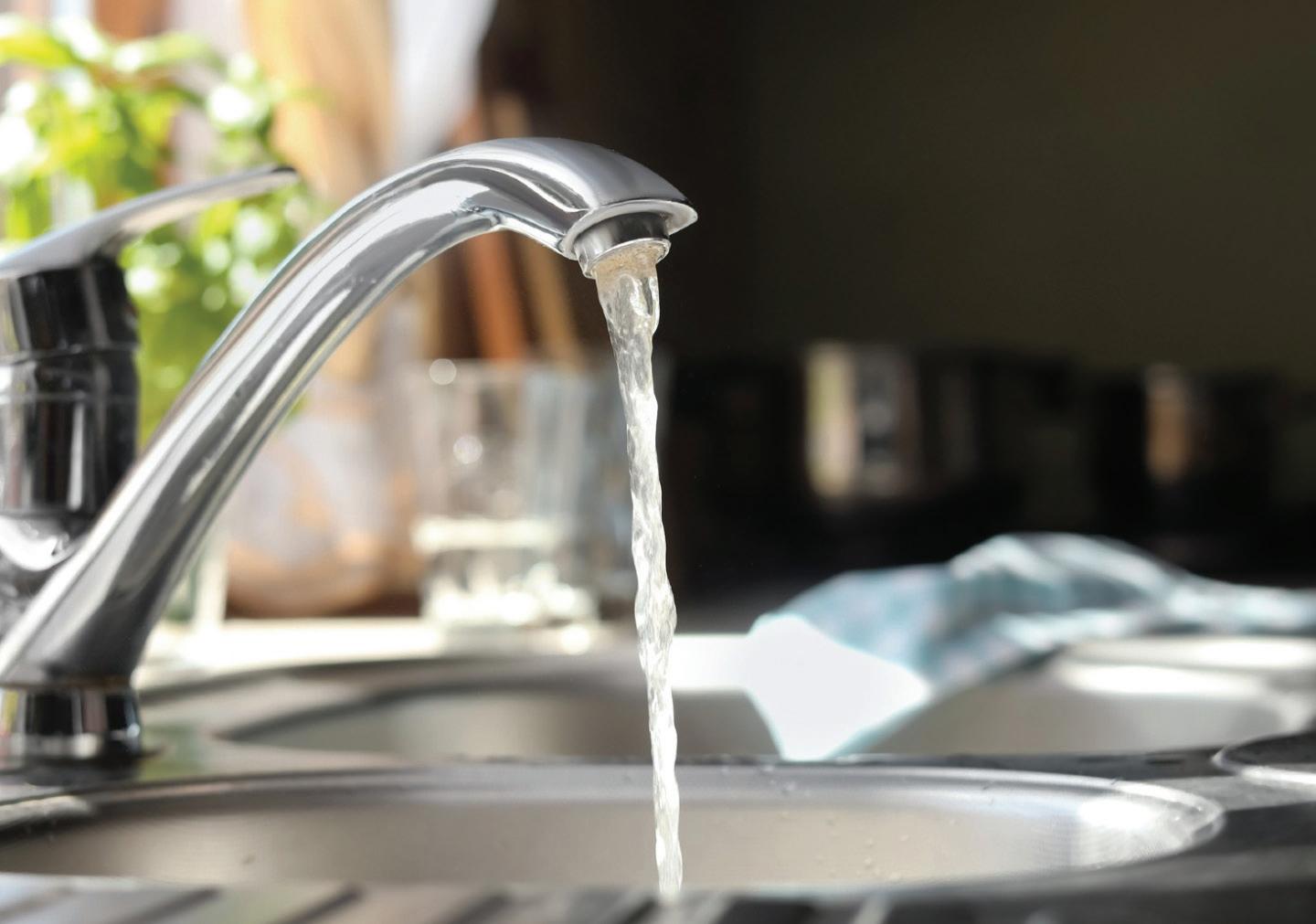
For the study – a randomized controlled trial in American Indian communities in the Northern Great Plains – socalled “point of use” arsenic filters were installed in households whose private wells had arsenic concentrations greater than the Environmental Protection Agency’s recommended limit of 10µg/L. Each of the study’s 50 participating household had two faucets on their kitchen sink: an arsenic filter faucet for drinking and cooking water installed by a community plumber for the study and the main kitchen faucet used for handwashing and washing dishes.
Study participants also reported a significant increase in their household’s exclusive use of arsenic-filtered water for drinking and cooking.
The researchers partnered closely with community members, tribal organizations, and the Indian Health Service throughout the program’s design and implementation to ensure the program suited the needs of the community and to address potential barriers to using the filters. The findings were published online March 27 in Environmental Health Perspectives.
“This trial shows the potential of digital health intervention programs like this to reduce environmental exposures, and may help alleviate costs associated with home visits for intervention delivery,” says
Christine Marie George, PhD, a professor in the Bloomberg School’s Department of International Health and the study’s cofirst author.
Around two million people in the U.S. use private wells with elevated arsenic levels, according to the Environmental Protection Agency. Rural and American Indian communities that rely on well water are disproportionately affected. Prior research has shown an association between arsenic exposure and the development of cardiovascular disease, diabetes, kidney disease, impaired lung function, and various cancers among American Indian communities.
For their randomized controlled trial, the researchers recruited households through a community-led water arsenictesting project that found arsenic levels above the EPA guideline in 29 percent of the 440 tested wells. Of these, 114 households met eligibility criteria to be enrolled in the study. Eighty-four participants from 50 of these 114 households participated in the study.
Participating households were divided into two study arms, with 51 participants in Arm 1 (27 households) and 33 participants in Arm 2 (23 households). Arm 1 consisted of the installation of a point of use filter with follow-up phone messages to encourage use of the filter. Arm 2 consisted of a point of use filter and
follow-up phone calls and texts, plus home visits from community members, supporting print materials, and videos of community testimonials in support of the filters.
The study was conducted between July 2018 and May 2021. Tracy Zacher, RN, field office director of the American Indian-owned Missouri Breaks Industries Research, Inc., and the study’s co-first author, led the study recruitment and evaluation activities and the arsenic testing.
Study participants’ arsenic levels were checked via urine samples collected at the beginning of the study and again after two years. Overall, there was a reduction in urinary arsenic levels on average by 47 percent during the two-year follow-up period, with no significant difference between the two study arms. Households reported exclusive use of arsenic-safe water to prepare food and drinks increased significantly from 11 percent at the start of the study to 42 percent of households
Study participants’ arsenic levels were checked via urine samples collected at the beginning of the study and again after two years.
by the study’s end. There also was no significant difference between study arms for this outcome.
“It is very exciting that the less intensive arm of the study that only provided phone calls and a filter worked just as well,” says George. “Additional studies are needed to evaluate this digital health approach in other arsenic-impacted settings in the U.S. and globally.”
The authors believe this is the first randomized controlled trial study of an arsenic mitigation program in the Americas. George credits much of the program’s success to the researchers’ collaboration with the impacted communities.
“Effect of an Arsenic Mitigation Program on Arsenic Exposure in American Indian Communities: A Cluster Randomized Controlled Trial of the CommunityLed Strong Heart Water Study Program” was written by Christine Marie George, Tracy Zacher, Kelly Endres, Francine Richards, Lisa Bear Robe, David Harvey, Lyle G Best, Reno Red Cloud, Annabelle Black Bear, Leslie Skinner, Christa Cuny, Ana Rule, Kellogg J. Schwab, Joel Gittelsohn, Ronald Glabonjat, Kathrin Schilling, Marcia O’Leary, Elizabeth D. Thomas, Jason Umans, Jianhui Zhu, Lawrence H. Moulton, and Ana Navas-Acien.
The research was supported by the National Institute of Environmental Health Sciences (NIEHS), National Institutes of Health (NIH R01ES025135).
Read: https://publichealth.jhu.edu/2024/filters-anddigital-health-program-reduced-participants-arseniclevels-by-nearly-half-in-american-indian-householdsrelying-on-well-water
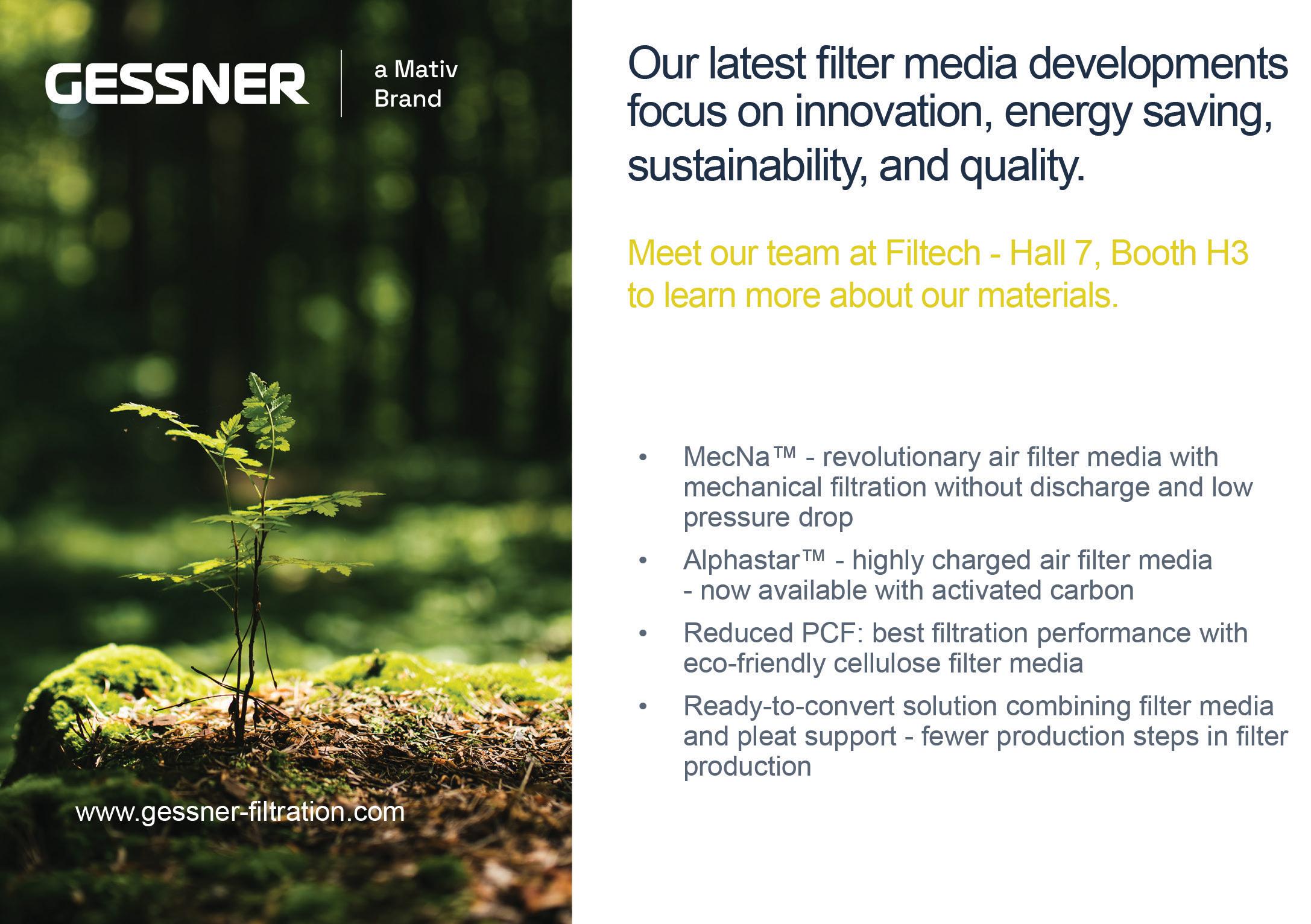
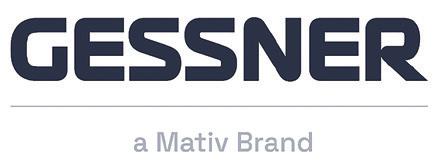
Superior Air Filtration
GESSNER’s High-Efficiency Electrostatic Air Filter Media is Now Available with Activated Carbon
In today’s world, where air quality is a paramount concern, innovative filtration technologies are more crucial than ever. GESSNER has therefore enhanced its high-efficiency electrostatic air filter media, which is now available with an activated carbon layer.
The Power of Activated Carbon
Activated carbon is celebrated for its exceptional adsorption capabilities. It effectively captures and neutralizes volatile organic compounds (VOCs), odors, and other contaminants, making it an essential component in advanced air purification. GESSNER’s activated carbon layers are specifically designed to meet individual application needs, offering flexibility and adaptability. The GESSNER world of activated carbon filter media includes Alphastar™, a tribo-electric nonwoven and NeenahPure™, a highly charged meltblown nonwoven.
ALPHASTAR™
Alphastar™ tribo-electric nonwoven filter media harnesses electrostatic forces to capture airborne particles, including dust and pollen. This filter media outperforms traditional non-electrostatic ones by trapping a wider range of pollutants with less energy usage. It exhibits an exceptional pressure drop efficiency ratio with very high dust-holding capacity,
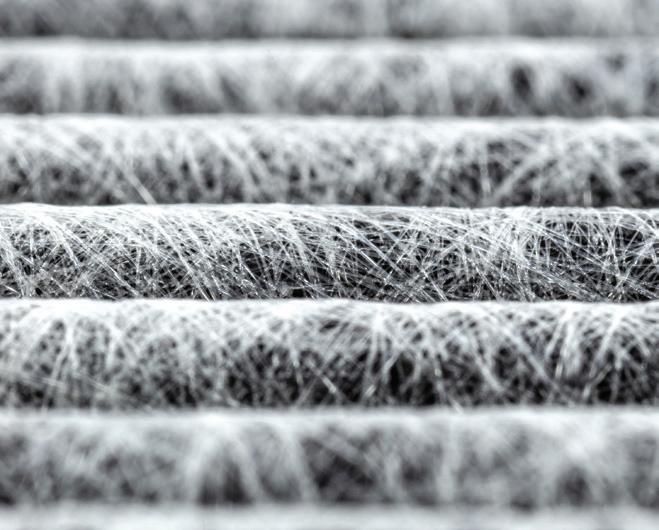
ultimately delivering superior filtration performance.
GESSNER’s Alphastar™ stands out with highest efficiencies, designed to deliver exceptional performance in air filtration. With MERV ratings ranging from 11 to 13, it effectively captures a wide range of airborne particles, ensuring a cleaner and healthier air quality. Additionally, this material’s energy efficiency cuts costs while offering superior air quality.
NEENAHPURE™
The NeenahPure™ product range is GESSNER’s highly charged meltblown media solution for pleatable and bag filters in HVAC, air purification and air pollution control applications to provide clean indoor air for better protection. A superior in-house charging technology allows the NeenahPure™ material to maintain
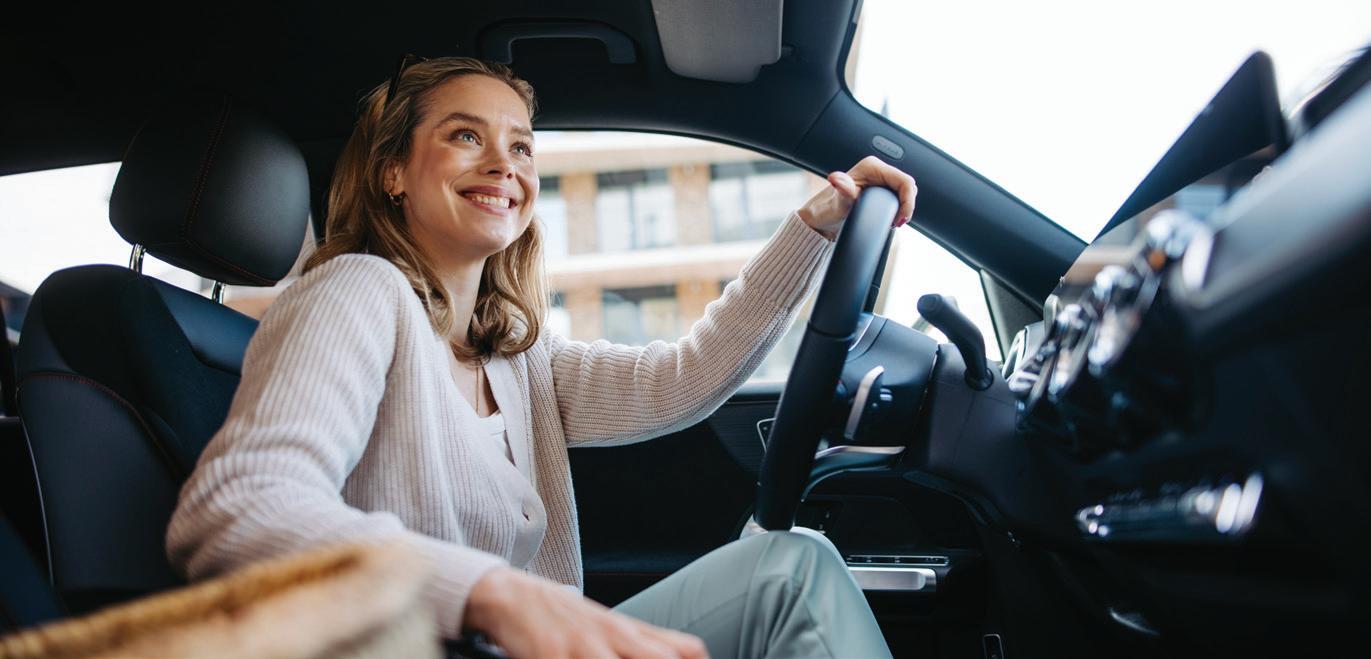
its charge over time, ensuring consistent filtration efficiency and low pressure drop.
The superior charging technology of GESSNER’s meltblown nonwoven delivers exceptional efficiencies of up to 99.9%, meeting ISO 16890 standards from ePM10 50% to ePM1 80%. Its energy efficiency not only reduces operational costs but also supports sustainable practices. For those seeking added protection, optional antimicrobial coatings provide enhanced safety, making the product the ideal choice for those prioritizing both efficiency and health.
Wide Range of Applications
Renowned for its remarkable ability to adsorb impurities and odors, activated carbon filter media has become an indispensable resource across various industries. Its versatility and effectiveness in improving air quality highlight its critical importance in ensuring cleaner and healthier surroundings.
The versatile filter media from GESSNER excels in multiple settings by effectively removing pollutants from HVAC, cabin air, and kitchen environments as well as in industrial applications. It not only cleans ventilation systems and eliminates odors in kitchen hoods and refrigerator filters but also purifies natural gas and exhaust air in industrial applications, ensuring cleaner and healthier air across all areas.
GESSNER’s highly efficient, electrostatic air filter media with activated carbon is a game-changer in ensuring cleaner, healthier air across various sectors. Explore the range of high-efficient air filter media and discover how innovative materials can enhance air filtration applications. www.gessner-filtration.com
Activated carbon filter media is used in various industries due to its versatility and efficiency.
GESSNER’S highly efficient air filter media with activated carbon.
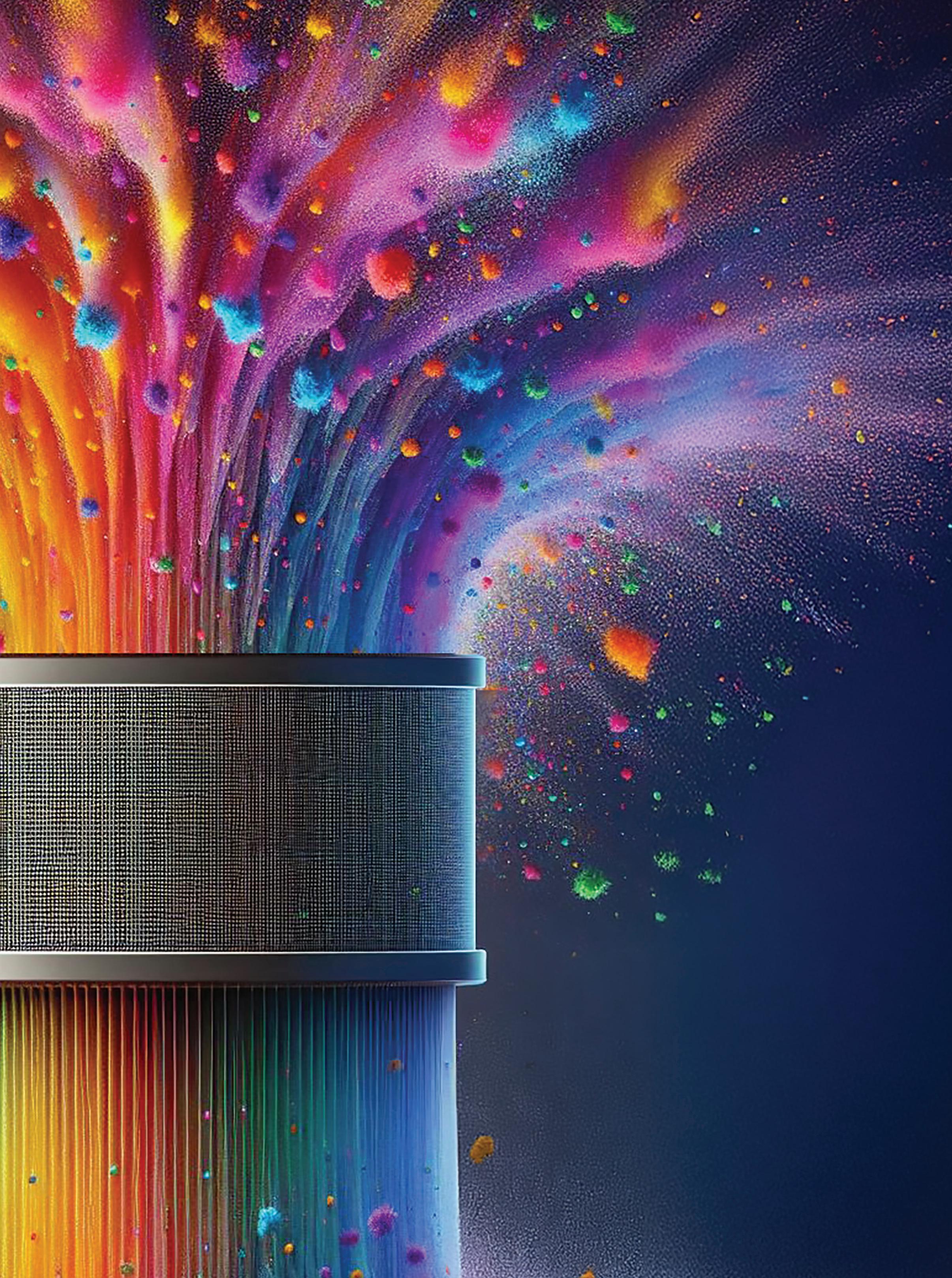
INNOVATION IN ACTION
Filtration for Today ... and tomorrow
Annual Showcase of Advancements Made for the Marketplace
Filtration industry companies are investing in research and development to bring new ideas to the world for enhanced filtration solutions and sustainability. Innovation requires intentional changes to generate long-term social and environmental benefits and improve the quality of solutions.
Innovations range from efficiency and effectiveness in design, to responsible sourcing with materials that are bio-based or feedstocks that draw on regenerative, and/or sustainable agriculture principles to advance circularity; to advancements that extend product life, and more. Needless to say, the supply chain is changing, and offering up new and improved solutions.
We asked companies to submit their most recent advancements and we are pleased to highlight the following companies and their achievements.
Artwork by April Bordeaux
AERO FRESCA DELIVERS UNPRECEDENTED AIR PURIFYING SYSTEMS Building Healthier Safer Workplaces for Enhanced Productivity
The Cirqulair patent was granted in the United States in August 2024. Cirqulair utilizes advanced technology and scientific principles to create air purification systems that exceed ISO Level 1 air quality standards for clean rooms and similar environments. Our patented technology integrates Newton’s Second Law of Motion and Van Der Waals’ Law of Force, along with innovative airflow designs and highly modified filtration methods, ensuring peak performance and efficiency. This system effectively eliminates 100% of particles as small as 1 nanometer (0.001 µm).
By applying Newton’s fundamental laws, Cirqulair drives effective air filtration and leverages Van Der Waals’ Law of Force to achieve an impressive 97.99999% removal rate for particles as small as 0.3 nanometers and complete elimination of 1-nanometer particles. This capability allows Cirqulair to target and eliminate viruses, volatile organic compounds (VOCs), gases like NOx and SO₂, carbon black, bacteria, and other harmful particulates. By harnessing the principles of force and motion, Cirqulair captures and removes airborne contaminants at an unprecedented level.
For asthma patients, Cirqulair provides a transformative experience, offering exceptionally clean air at home. Users have reported not needing to use their nebulizers throughout the night.
At Outlet of the Cirqulair
While existing standards for clean rooms typically focus on particles larger than 0.1 microns, this approach overlooks over 50% of ultra-fine dust particles that can carry viruses and bacteria.
Additionally, Cirqulair features a walkthrough system capable of detecting contagious airborne diseases, making it ideal for entry points at airports and cruise ships. This technology is known as QuBA.
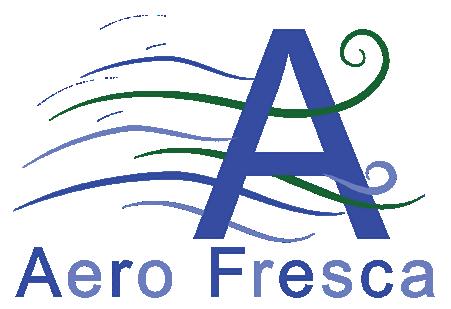
The Cirqulair technology was developed in the Netherlands by Van Wees Innovation while Aero Fresca Inc. is the exclusive distributor in North America. www.aerofresca.com


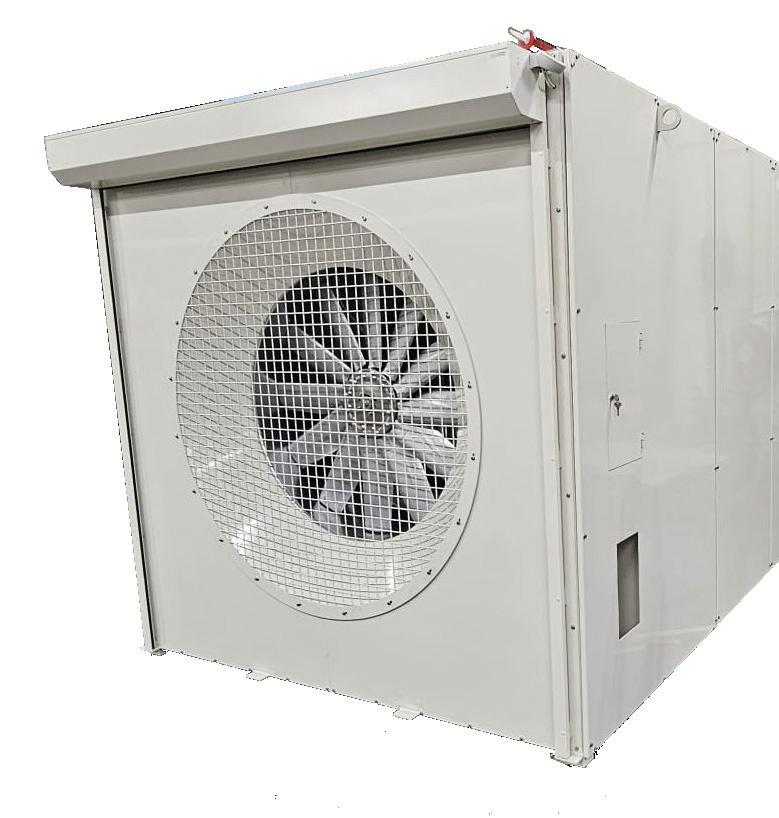
Circulair close-up and installation.
Total counts from 5nm up to 140 nm, (determined by SMPS settings) during 100 sec. Scan time: varying in 2 samples from 6 to 9 counts. Conclusion: The Cirqulair proves to be very effective in removing (nano) particles in size range up to 10 μ m as shown by CPC measurement 1 and in range of 5 to 140 nm. as indicated by SMPS measurement 2 and 3.
AqueoUS Vets® (AV®) EcoCarb Sustainable Carbon Water Filtration Medias
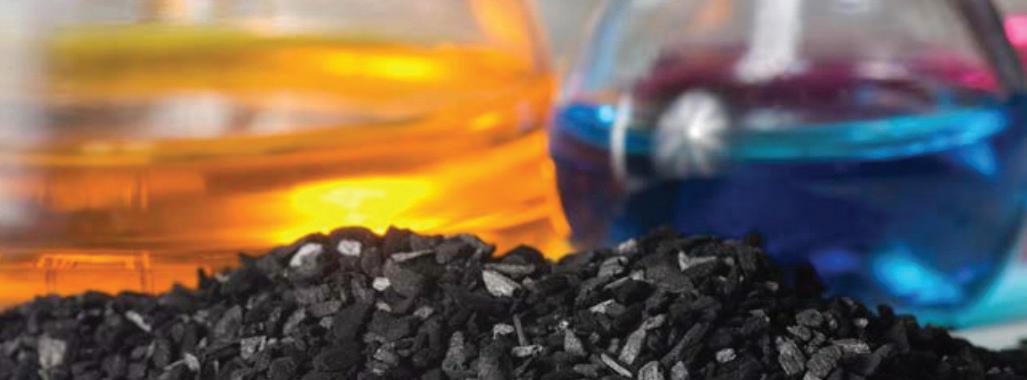
AqueoUS Vets® (AV®) EcoCarb media is environmentally friendly, produced from byproducts of other manufacturing processes. Minimal processing is involved which provides a lower overall carbon footprint. EcoCarb is friendly to the environment and offers equivalent performance, eliminating contaminants from drinking water. Each EcoCarb Media can be selected for the specific removal of contaminants based on water quality goals.

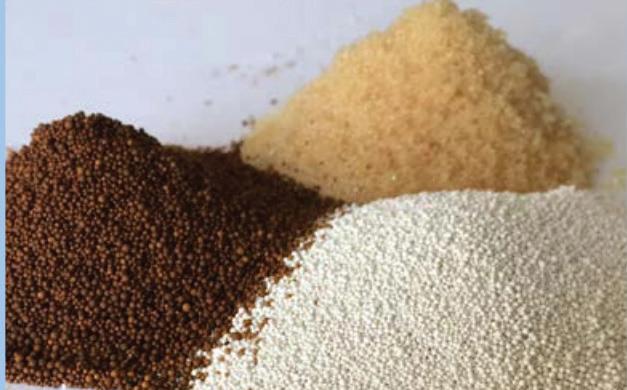
• EcoCarb 1240BA – Produced from bituminous coal sourced from remediated coal refuse sites.
• EcoCarb 1230C and 1240C – Produced from a renewable source, coconut shells, which remove CO2 from the atmosphere during the growing stage.
• EcoCarb 1240LDX and 830LDX – A low-density subbituminous coal byproduct extracted during the manufacturing process of a pigment. www.aqueousvets.com
CERAFILTEC: Advancing the Performance of Ceramic Membranes
By Julius Gloeckner, Chief Growth Officer
Si nce our founding, CERAFILTEC® has focused on advancing both the superior performance of ceramic membranes as well as their important advantages in the realm of sustainability. Regarding performance, ceramic membranes are known for their robustness and chemical and thermal stability, enabling reliable plant operation even in challenging feed water. They can withstand harsh cleaning processes without compromising their lifespan. With an expected service life of 15-20 years – far longer than polymeric membranes – they reduce the frequency of replacements and require less maintenance, significantly lowering operational costs and complexities. These characteristics also make them fully cost-competitive over polymeric membranes.
Our ceramic membranes also offer significant benefits regarding sustainability. They are reusable, and unlike polymeric membranes, generate no plastic waste. Typically made from aluminum oxide,
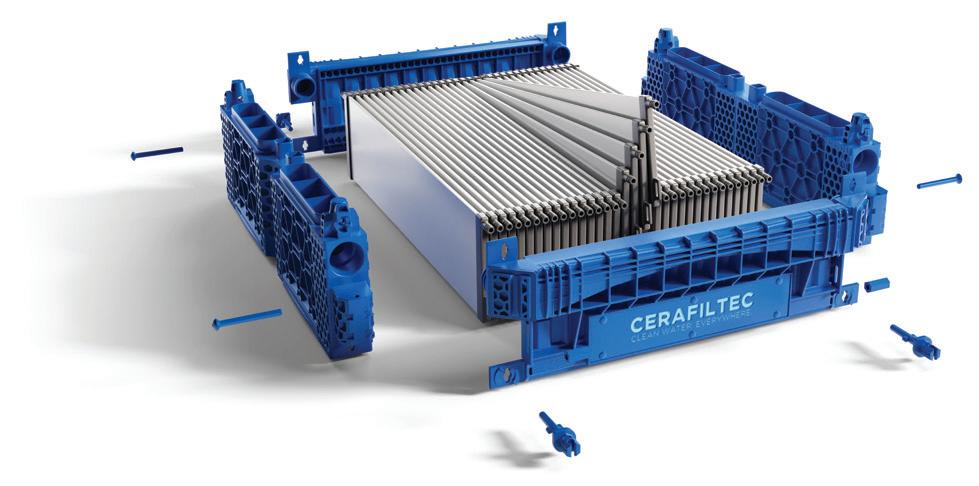

they present no PFAS-linked PVDF. Highly resistant to mechanical and chemical degradation, they are suitable for reliably treating water and wastewater of wide application ranges.
As CERAFILTEC continues to innovate, we are leading the shift from polymeric membranes to ceramic membrane technology. Our latest advancements include:
• Active Cake Layer Filtration (ACLF), a process combining adsorption directly with ultrafiltration that enables the removal of contaminants such as organics, microplastics/microfibers, and many other toxins.
• FLEXX-CAP® , which harnesses the power of enhanced fluid dynamics to significantly increase the performance of ceramic membranes in MBR systems.
FLEXX-CAP enables the first membrane technology that is unbreakable, always cleanable, and also movable.
• And most recently, CERApro®, the first advanced ceramic membrane projection tool. It enables engineers, plant owners, and designers to calculate, visualize in 3D, plan, and simulate the design and operation of plants using CERAFILTEC’s ceramic flat membranes.
CERAFILTEC is a global leader in ceramic ultrafiltration membrane technology, transforming water and wastewater treatment worldwide. Committed to a sustainable future, CERAFILTEC aims for CLEAN WATER. EVERYWHERE. www.cerafiltec.com
Modul Freisteller Explosion.
De Nora to Launch Line of Optimized SORB® FX Vessels for PFAS Removal
Industrie De Nora, an Italian multinational company listed on the Euronext Milan, specialized in sustainable electrochemical technologies and in the emerging green hydrogen industry, is actively engaged in addressing PFAS removal, one of the world’s fastest emerging and pressing water treatment problems. The company is announcing a new proprietary line of its SORB™ FX vessels to deliver enhanced PFAS removal, capable of treating flow rates ranging from 25 gallons per minute (5.7 m³/h) to 2,800 gallons per minute (636 m³/h). The improved features are based on the proven technology of this water decontamination mainstay. The launch took place in October at WEFTEC, a leading water quality event hosted by the Water Environment Foundation.
With over two decades of demonstrated effectiveness, the SORB line of contaminant removal systems from De Nora help solve environmental, regulatory and public health water treatment challenges for a wide range of contaminants of concern.
Removing PFAS from water and wastewater is emerging as a complex and potentially costly challenge. One important cost consideration is media life. Given the inevitability that media demand might soon outpace supply, it’s imperative that utilities, manufacturers and industrial operators get the absolute most life from their media.
The new line of SORB FX vessels employs the best available technology for PFAS removal, utilizing ion exchange, granular activated carbon, or a combination of both. De Nora’s patent-pending underdrain design merges two leading technologies: a ring design that simplifies tank inspection and media changeout, and the superior media utilization typical of header-lateral systems. The SORB OTTO underdrain features specially designed flexible strainer baffles, reducing media waste – “dead zones” – to below two percent. Additionally, an inlet distributor evenly feeds water across the entire top surface, maximizing media usage. Hydraulic modeling during the design phase ensures precise specification and calibration of this distributor, allowing De Nora customers to fully utilize the media, thereby extending its life and minimizing replacement costs by approximately five percent.
Pre-engineered systems offer a variety of standardized diameters, accelerating project design and installation. The inlet and SORB OTTO underdrain diffusers ensure optimal, balanced flow through the media, enhancing performance, extending media life, and reducing operational expenses (OPEX). Additionally, the SORB FX vessel can be fully serviced externally, eliminating the need for confined space permits.
The vessel’s compact, symmetric design simplifies installation and minimizes operating costs.
About De Nora
Industrie De Nora is an Italian multinational company listed on the Euronext Milan stock exchange, specializing in electrochemistry, a leader in sustainable technologies, and has a pivotal role in the industrial green hydrogen production chain.

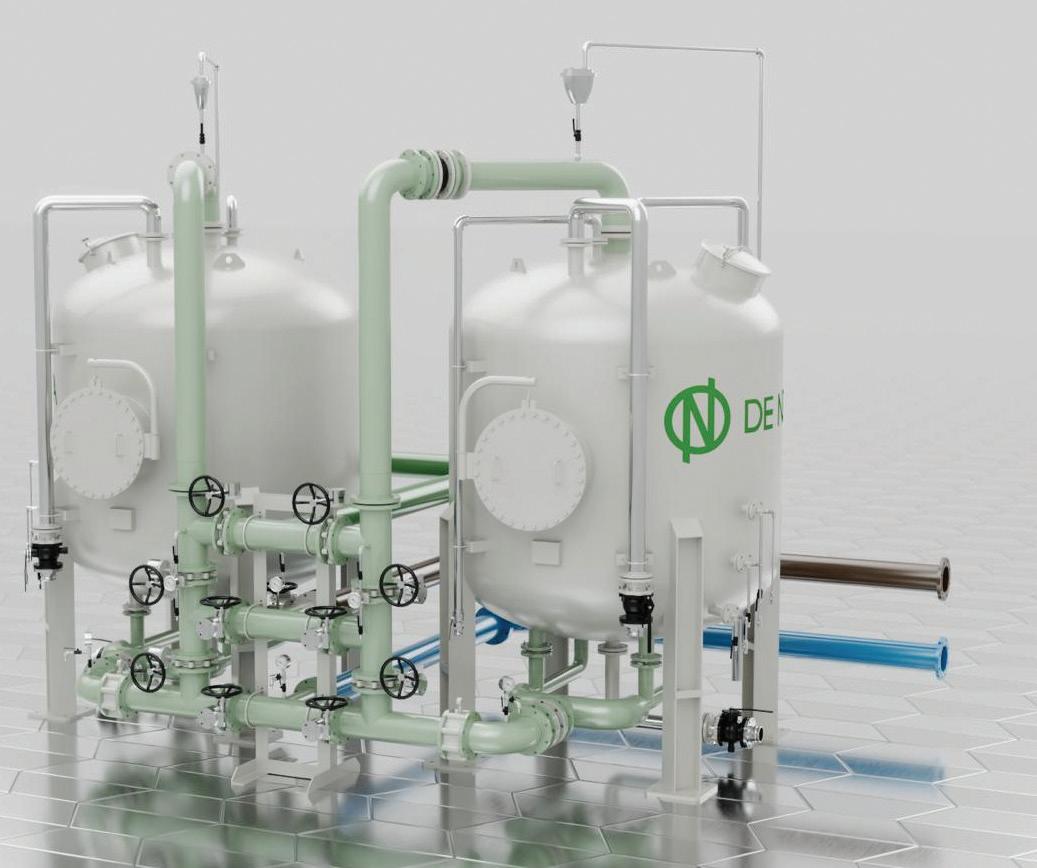
The company has a portfolio of products and systems to optimize the energy efficiency of critical industrial electrochemical processes and a range of products and solutions for water treatment. Globally, Industrie De Nora is the world’s largest supplier of activated electrodes (serving a broad portfolio of customers operating in the fields of chlorine and caustic soda production, components for electronics, and non-ferrous metal refining). Industrie De Nora is also among the world’s leading suppliers of water filtration and disinfection technologies (for the industrial and municipal sectors) and the world’s leading swimming pool disinfection components supplier.
Leveraging its well-established electrochemical knowledge, proven manufacturing capability, and a supply chain established over the years, the company has developed and qualified a portfolio of electrodes and components to produce hydrogen through the electrolysis of water, which is critical for the energy transition. In this sector, the company also holds 25.85% of thyssenkrupp nucera AG &Co. KGaA, a joint venture established with the thyssenkrupp group.
Founded in 1923, Industrie De Nora generated total revenues of around EUR 856 million and an Adjusted EBITDA of approx. EUR 171 million in 2023. The company’s growth process has developed organically through continued penetration of new markets and applications and through acquisitions in the U.S., Asia, and Europe. De Nora’s continuous innovation drives its growth, represented by its evolving intellectual property portfolio, which currently includes more than 280 patent families with more than 2,800 territorial extensions. The De Nora family controls the Group, which owns 53.3% of the company’s share capital. Snam S.p.A. is a minority shareholder with about 21.6% of the capital. www.denora.com

See It. Control It. Defining the Environment Before Deploying a Filtration Solution
By Jürgen M. Lobert, Director of AMC Technology, Entegris, Inc.
Many filtration solutions are deployed without accurately knowing the contamination challenges of the environment to be protected, either because no measurement has been done at all, or only qualitative evaluation methods like corrosion strips or generic particle estimates were used to define the state of contamination. In addition, many filter providers prefer to offer a few off the shelf products, rather than customizing the solution, in order to keep inventory and lead times low.
However, with sustainability becoming a strategic goal for most industrial operations, filter lifetime, cost of ownership and minimized waste streams are turning center stage of procurement and installation services. More importantly, processes, products and humans need to be better protected from contamination impact. Just like one would never use a simple MERV filter for a process needing ULPA filtration, one should not use a basic, off the shelf chemical filter with unknown capacity and removal efficiency for gas-phase contaminants.
Filter performance, as well as lifetime, can be optimized with the “See it. Control it.” paradigm, which is the most scientific, data-driven way to air filtration.
“The See It. Control It.” Paradigm
A proactive approach for contaminant removal is to choose the best filtration solution. Rather than using off the shelf products that might be cheaply and quickly available, the paradigm suggests to define the contamination first by characterizing the environment to be protected, and then finding or creating the most suitable solution for that specific environment.
The most important aspect of controlling gas-phase, airborne molecular contamination (AMC) and implementing filters is to define the contamination state of the environment to be protected. “The See it. Control it.” approach suggests to see the contamination through air analysis by a capable laboratory, which provides accurate gas phase analysis for any environment from the parts per million (ppm, 10-6) to the parts per trillion (ppt, 10-12) level.
The user can then control the environmental contamination more easily, as the filtration solution can be tailored exactly to that environment’s challenges and needs, as defined by the measurements. Some environments have an unusual mix of AMC classes and to prevent one portion of the filter being used up faster than others, filter vendors need to adjusts adsorbent mixes such that all adsorbents last about the same amount of time, based on the measurements of AMC in that environment.
What Is the Inkjet Cartridge Effect?
The idea of this approach is to avoid what we call the “inkjet cartridge effect,” referring to old style inkjet cartridges that held three equal amounts of magenta, yellow and cyan inks, but typically drained cyan first, forcing to discard a significant amount of yellow and magenta inks when replacing the cartridge. Applying our approach to this, we would determine first how much cyan, magenta and yellow is typically used up in a given amount of time, and then adjust the ink amounts accordingly such that all three are used up at about the same time (Figure 1).

Figure 1: The inkjet cartridge effect for AMC filters visualized. The bars indicate filter lifetime in months for the respective contaminant classes (example: acids, bases, organics), the relative adsorbent (“ink”) amounts are indicated as numbers above each bar. Equal adsorbent amounts yield different lifetimes. Unified lifetime is achieved by using different adsorbent amounts.
For real-world filter scenarios, commercial environments usually attempt to remove acidic, basic and organic contaminants from air streams. Each of those classes has their own adsorbent for optimized removal but each also has different concentrations in any environment.
The most common and economical filter type for these applications is the combined adsorbent filter, which contains a mix of all adsorbents in one set of (usually pleated, V-bank or loose fill) media. Adjusting adsorbent amounts for an equalized lifetime of all contaminant classes is easy, if the measurements are available. However, each contaminant class may also have different priorities or importance for the application and in some cases, lifetimes may become secondary to the priority of removing one contaminant class more efficiently.
For particulate contamination, one should not only determine the overall particle count, but also the size distribution to determine impact on the process. Larger particles are easy to remove with low rating MERV filters, but more advanced processes might need HEPA
and ULPA filters for best protection. Even those might still leave large numbers of very fine particles in the nanometer range to impact high technology processes. An understanding of these dependencies is important to define the best solution.
Filter Performance of Gas-Phase Filters
For gas-phase, chemical filters, the most critical performance characteristics are removal efficiency (RE) and capacity or remaining lifetime, but also pressure drop. Removal efficiency is defined as:
RE = (1 –Downstream) x 100(%) Upstream
With “Downstream” and “Upstream” being the contaminant concentrations up and downstream of the filter. Removal efficiency can be tracked over time to determine a practical end of filter life.
For AMC filters, removal efficiency is highest in the beginning and then decreases over time. Pressure drop does not appreciably change over time (AMC filters do not remove particles except for large dust). The RE curve over time follows a typical ‘S’ shape (essentially an inverted break-through curve, Figure 2):
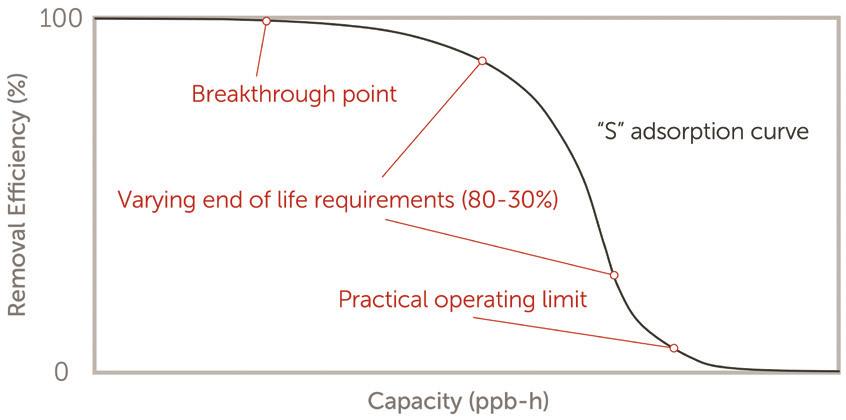
Filter Performance of Particle Filters
For particle filters, the performance of a filter can be measured with the log10 reduction value (LRV), which is the ratio of the levels of contamination before and after the filter process.
LRV = log (Challenge) Filtrate
Where Challenge and Filtrate are the upstream and downstream amounts of particles (in any one size class). An LRV increment of 1 corresponds to a reduction in concentration by a factor of 10.
Reporting this particle filter efficiency is usually standardized as a percentage of specific particle size ranges being removed. The Minimum Efficiency Rating Value (MERV), Efficiency, High Efficiency or Ultra Low Particle Air filter ratings (EPA, HEPA, ULPA) provide these classifications. MERV ratings 1 through 16 are described by ASHRAE standard 52.2-2017. The HEPA standard is now regulated by ISO standard 29463. In contrast to gasphase filters, particle filters become more efficient over time, they slowly clog up. As the filter pores close up, pressure drop increases and, with it, energy consumption. Both energy consumption and potential breakthrough will determine practical filter lifetime.
When Is a Filter Exhausted and Needs to Be Replaced?
The practical end of filter life depends on the minimum removal efficiency that still provides the application with a benefit and maintains the maximum contaminant concentration that the application can tolerate. This is a value that needs to be determined by experimentation, and by observing the application while monitoring concentrations.
Instead of using filter capacity values such as gram of contaminant per gram of adsorbent, we suggest a more user-friendly capacity that is expressed as ppb-h, the product of contaminant concentration (in parts per billion, ppb, 10-9) and time (in hours). Using this figure, an end user can measure the actual concentration in the application space, average that over time, and then plug it into the above curve to determine capacity in hours. An added benefit is that this process specific average does not have to be revealed to the filter manufacturer.
Filter performance characterization is guided by international standards. ISO standard 10121 describes test methods for air filtration media in part 1 and for devices in part 2.
For particle filters, this is an easier exercise, as in most cases, only the pressure drop needs to be monitored and filter life be cut off when the HVAC system’s capability or energy consumption is exceeded. Measurement frequency to prevent fine particles from breaking through is less critical than with gas-phase filters. Pressure drop is usually readily available from the air handling system, and flow capability is well defined for air handlers and fan filter units.
MERV filters are typically changed out every three to 12 months. Whereas HEPA and ULPA filters can last five or more years, life span depends on flow rate and air particle loading.
For chemical filters, the initial removal efficiency for AMC may not be 100% and largely depends on parameters like the adsorbent amount, the adsorbent nature, flow rate and temperature. Practical end of filter life for any one AMC filter application is defined as the point where ambient contaminant concentration can no
Figure 2: AMC filter capacity curve. Removal efficiency is largest early on, then decays in S-shape over time. Practical end of life values depend on application.
longer be maintained at the desired maximum level that is safe for the application.
Typical AMC filter lifetimes are weeks to years, depending on application, filter design and desired removal efficiency. Two of the biggest impact parameters are AMC challenge concentrations and air flow rate. Higher concentrations use up available active adsorbent sites faster and higher flow rate reduces residence time on the adsorbent and with that, the overall removal efficiency. Figure 3 shows a typical performance curve for the removal of organic contaminants for two flow scenarios, low flow at 0.5 m/s face velocity and high flow at 2.5 m/s, using the same filter media.
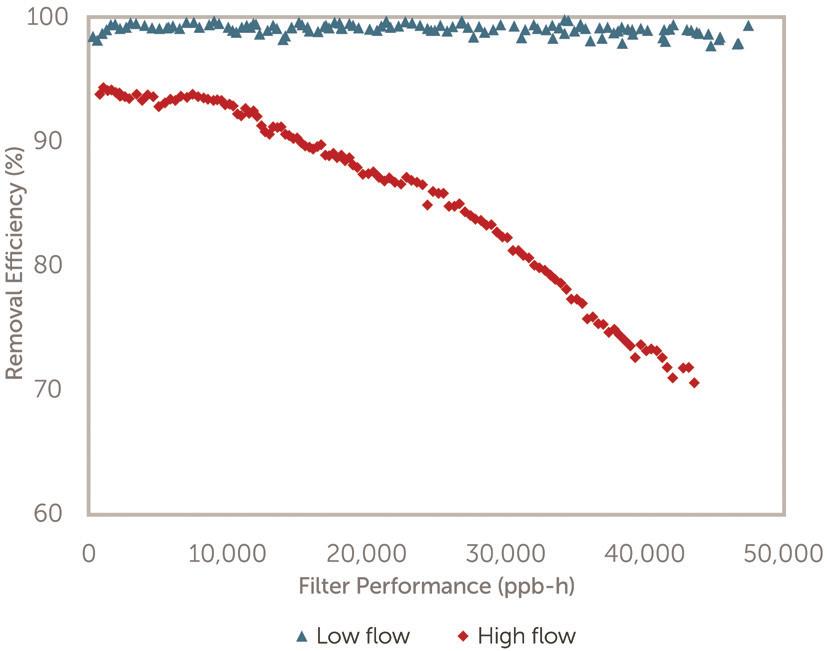
How to Optimize Filter Lifetime?
The described “See it. Control it.” approach helps to define and understand individual applications and put analytical as well as filter performance results in proper context by knowing contaminants, their concentrations, the filter’s removal efficiency and lifetimes and considering process impact. This leads to minimizing cost of ownership and maximizing the performance with optimized filtration solutions.
In addition, monitoring contaminants over time not only defines the application’s contamination state better, but also reveals gradual environmental changes, which may require filter solutions to be adjusted to that change. Having a commercial analytical service to measure AMC or particles onsite is a critical necessity.
Measurement Accuracy Is Important
The cost of analytical evaluation typically scales with performance. In order to get enough insight into the contamination state of a space, measurements must be specific, selective and accurate. For gas-phase contaminants, corrosion strips, micro balances or
other semi-quantitative means can be inexpensive, but are limited to qualitative answers at best, these systems do not provide accurate concentrations or identification of contaminants. Meaningful gas phase contamination should identify/speciate each contaminant, but also measure its concentration accurately with sufficient, statistically derived detection limits, ideally by an ISO 17025 accredited laboratory.
Semiconductor plants that operate at ppt concentration levels cannot be characterized with a local laboratory specializing in EPA type ambient air quantitation at the ppm level. Likewise, a product sensitive to submicron particle intrusion and protected by ULPA filters cannot be characterized with inexpensive particle counters that are made for PM 2.5 monitoring. A competent filter supplier should be able to help with the analytical evaluation as well as with putting data into the application’s context.
A Case Study
A semiconductor customer wanting to utilize AMC filters followed our “See it. Control it.” approach. As a first step, they characterized their cleanroom environment by measuring ammonia, a common contaminant that affects semiconductor circuitry, throughout the 40000 square foot large manufacturing space. Measurements were done in eight rows of four paths for a total of 32 measurement points. The idea was to find out how much the concentration of ammonia varied throughout the space, which, surprisingly, was between 4 and 20 ppb of ammonia (Figure 4) for an average of about 18 ppb. A single measurement might have not defined that average well enough.
The second step then was to install AMC filters, which were maximizing the removal of ammonia, while also reducing organic contamination in the same space (a minor concern). Once that formulation was established, the customer used the performance curve of the filter as provided by the product sheet of the filter manufacturer, which shows removal efficiency of ammonia as a
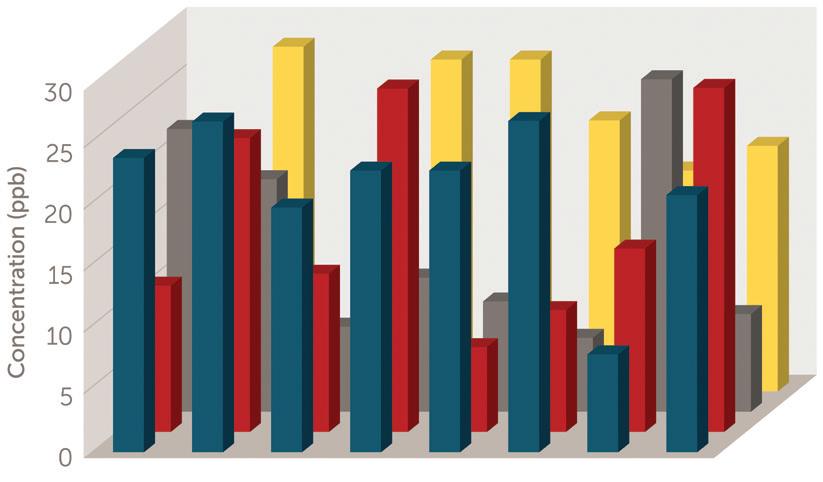
Figure 3: AMC filter performance as a function of flow rate. Notice how high flow not only significantly diminishes the lifetime, but also the initial removal efficiency.
Figure 4: Concentrations of ammonia in ppb, measured throughout a large manufacturing space. A large variability could be observed despite a uniform air supply.
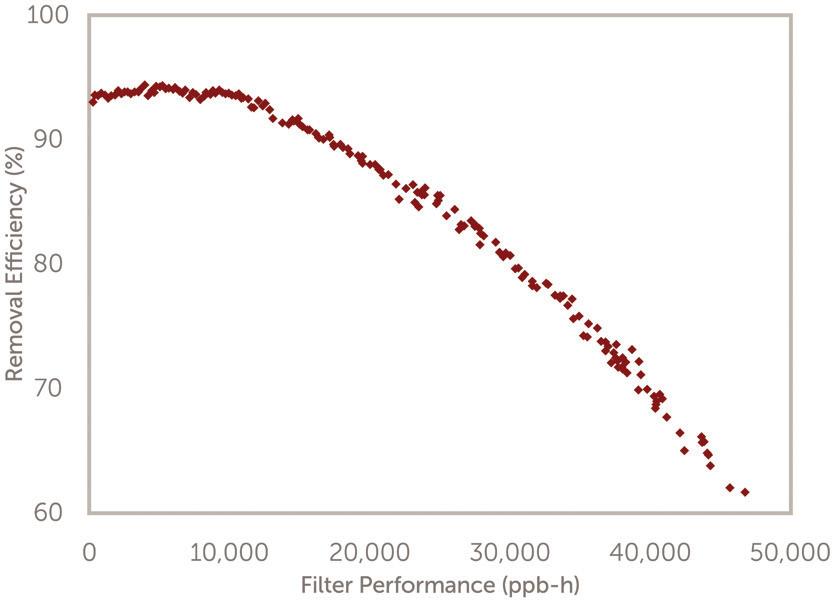
function of capacity (in ppb-h). This provided a reference point to calculate lifetime (Figure 5).
Once the filters were installed, ammonia concentrations were monitored over time. As Figure 6 shows, ammonia concentration successfully diminished as a function of the filter installation from an initial average of about 18 ppb to eventually level off at about 3.5 ppb.
Any concentration below 4 ppb was considered safe for the process at the time. The reason why concentration did not drop to zero is the fact that human bodies – the employees of that plant – naturally produce ammonia and emit it to the surrounding air. The leveled concentration was an equilibrium between ammonia production and removal.
When the average concentration trend exceeded the threshold of 4 ppb, defined by the process sensitivity, the contamination production exceeded its removal and the filter no longer protected the process. That is the time when the filter needed to be changed. Measurements need to be frequent enough to detect changes to avoid endangering the process, but also ensure to detect an upward trend, without relying on a single data point to make filter change decisions that could be very costly.
Iterating between that found lifetime (in this case: about one year) and the performance curve of the filter will yield the targeted removal efficiency of the installation. At an average AMC challenge of 7 ppb (from measurements taken upstream of the filter) and the determined one year lifetime (8700 hours) to filter exhaustion provides a value of about 60000 ppb-h capacity. Plugging that into Figure 4 would provide an
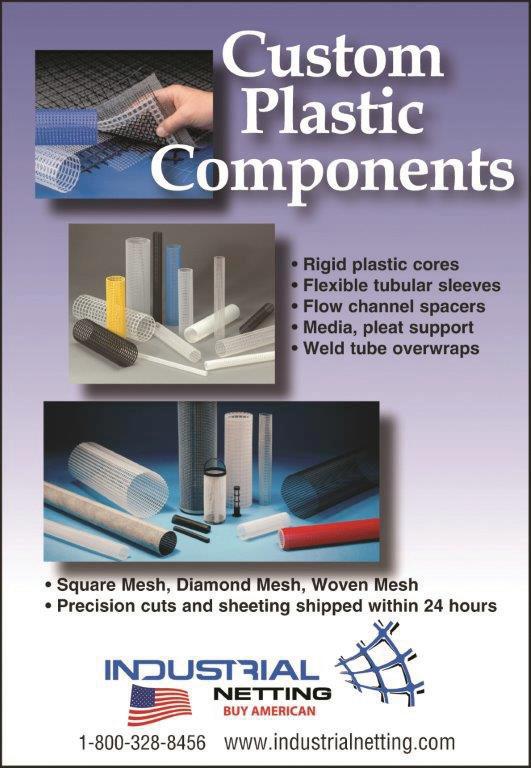
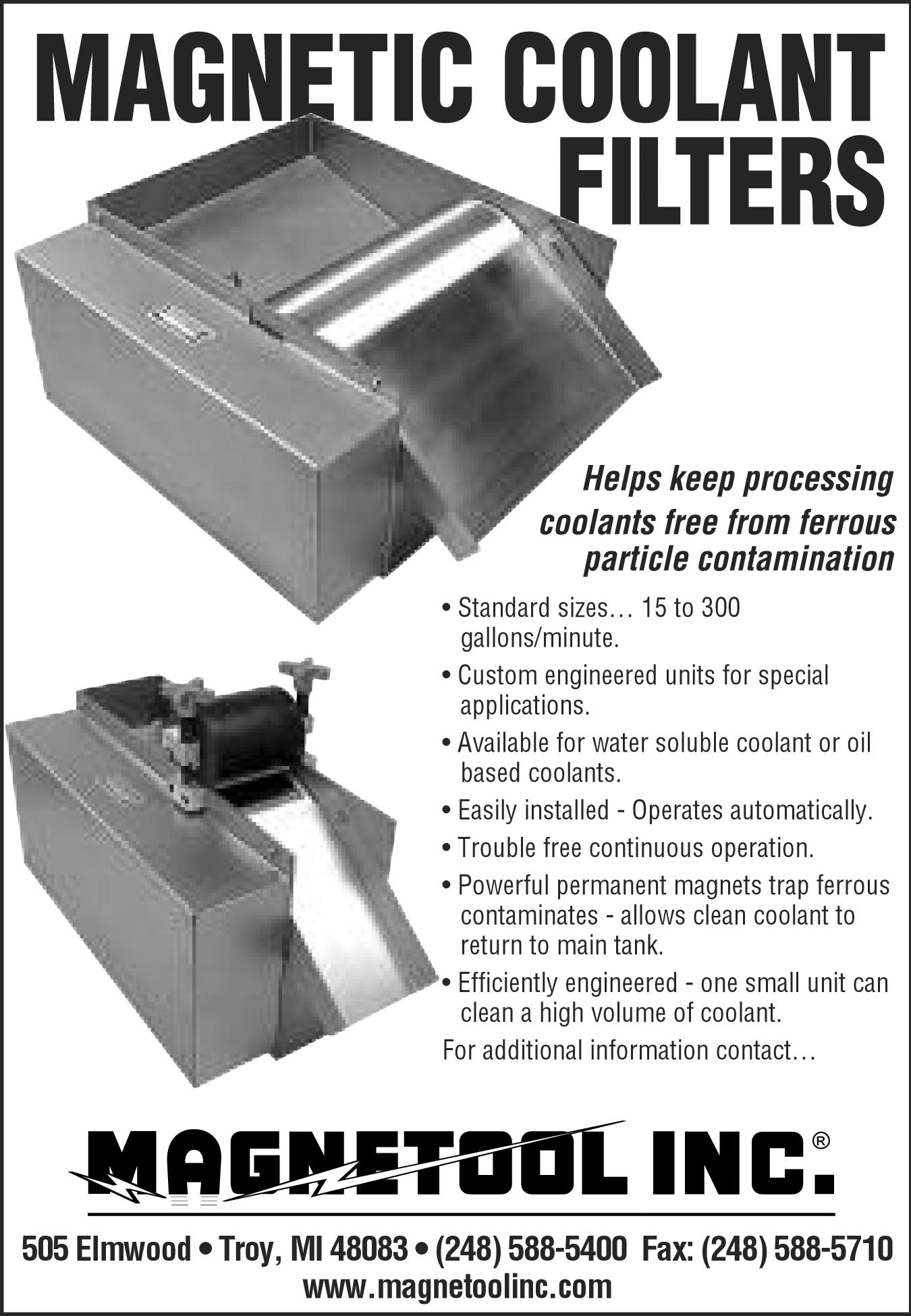
Figure 5: Filter performance curve for the removal of ammonia at high flow.

Figure 6: Manufacturing plant environmental ammonia concentration observed over time. Once concentrations exceed the safe threshold (red data), filters need to be changed out.
end of life removal efficiency of 50%. That is what the customer established as the future lifetime definition. For subsequent installations, they only measured filter removal efficiency occasionally, rather than weekly. Once the filters approached 50% RE, new filters were ordered for replacement.
By working together to get analytical expertise, evaluate filter performance and to put those data into context, the customer was able to extend filter lifetime until the threshold was determined below which the process was no longer affected, and the maximum tolerable lifetime of the filter and optimized cost of ownership. It is that iterative process that needs to be done initially, before a simple end of life definition can be adopted.
Limitations
Limitations to the shown paradigm apply if an industrial environment maintains many different spaces with very different contamination states and impacts. For example, a factory might have multiple assembly lines all using different chemicals, different amounts of employees with different air circulation flows an varying process sensitivities. Creating optimized solutions for each of these individual sub-space would lead to high inventory, longer lead times and higher cost for
References
1. Airborne Molecular Contamination (AMC) Solutions for Commercial Operations. Entegris white paper, September 2024. https://www.entegris.com/content/dam/shared-product-assets/ vaporsorb/brochure-airborne-molecular-contamination-solutions-for-the-microelectronics-industry-10092.pdf
2. Standard ISO 10121, Test method for assessing the performance of gas-phase air cleaning media and devices for general ventilation, International Standards Organization. https://www.iso.org/ search.html?PROD_isoorg_en%5Bquery%5D=ISO%2010121
3. Standard 52.2-2017, Method of Testing General Ventilation AirCleaning Devices for Removal Efficiency by Particle Size (ANSI Approved), ASHRAE. https://store.accuristech.com/ashrae/ standards/ashrae-52-2-2017?gateway_code=ashrae&product_ id=1942059
smaller purchase quantities and involved installation regimes. In these cases, purchasing a single filter for all environments will provide a better cost and lead time with simple inventory and installation routines, but will reduce applicability as the filters would be made to serve the least common denominator, instead of being optimizing for each sub-environment.
Another limitation is found in rapidly changing environments, where not only concentrations but also contaminant types change quickly over time. This would obsolete the best tailored solution quickly and demand a switch to a new solution in order to protect the process, increasing cost and not allowing to use filters up until their designated end of life. The same limitation applies here to any solution that tries to accommodate all contamination scenarios over time with less targeted contaminant removal.
Conclusions
We have shared and explained that the “See it. Control it.” approach to contamination control is well suited to optimize a filtration solution for longest filter lifetime, best performance and lowest cost of ownership. Accurate and competent analytical characterization as well as optimized filtration solutions are both required segments for this approach. We have shown how this applies to different filtration regimes and illustrated it with a real world case study. Some limitations apply to this scenario, but for most practical purposes, it is a valid and useful tool for contamination control management. www.entegris.com

Jürgen Lobert is a Director of AMC Technology at Entegris, Inc. with more than 20 years of experience in the measurement and filtration of gasphase (molecular) contamination. For another 20 years prior to that, he studied atmospheric chemistry and various sources and sinks for air pollutants and building advanced measurement technologies. Jürgen is the author of more than 60 publications on air chemistry and contamination control and he is a member of standards committees for SEMI and the IRDS.
4. Standard ISO 29463, High efficiency filters and filter media for removing particles from air, International Standards Organization. https://www.iso.org/search.html?PROD_isoorg_ en%5Bquery%5D=ISO%2029463
5. Standard ISO 5725, Accuracy (trueness and precision) of measurement methods and results, International Standards Organization. https://www.iso.org/standard/69418.html
6. Targeted Removal Assures Purity in Advanced Materials, Entegris, Inc., https://www.entegris.com/content/dam/web/ resources/pictograms/pictogram-targeted-removal-assurespurity-in-advanced-materials-12335.pdf
Dry Impregnation Solutions: An Innovative Cleantech for Better Performance
Fibroline is an engineering company specialized in technology transfer based in France near Lyon. It also has an entity in the United States, in North Carolina. The company has developed and patented several dry powder impregnation solutions, intended to provide efficient and environmentally friendly techniques to functionalize porous structures, and filter media in particular for gas capture such as CO2 or war gases and water treatment, including arsenic removal.
Indeed, these technologies have shown several innovative features that lead to numerous key competitive advantages in different sectors. The principles behind this technology give it capacities unmatched by common liquid impregnation solutions. Using dry impregnation leads to drastic reductions of all clogging effect and significantly increasing performances of impregnated products. An environmentally friendly process, it also leads to significant reductions in energy consumption and waste reduction with the complete removal of effluents.
The Leading Principles Behind Dry Impregnation Solutions
Dry impregnation consists in the distribution of powders in any form into porous structures by the use of high intensity alternating electric fields.
These technologies are available in several configurations, depending on customers’ needs in terms of targeted materials and production characteristics. Using repulsion of particles grants the capacity to impregnate in an extremely homogenous way, occupying all of the available space within the given material. It also allows to deposit active porous particles in various ratios, in very large quantities, but also in very small amounts with results that cannot be obtained with conventional liquid impregnation solutions.

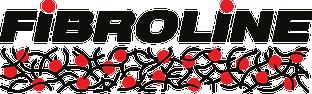
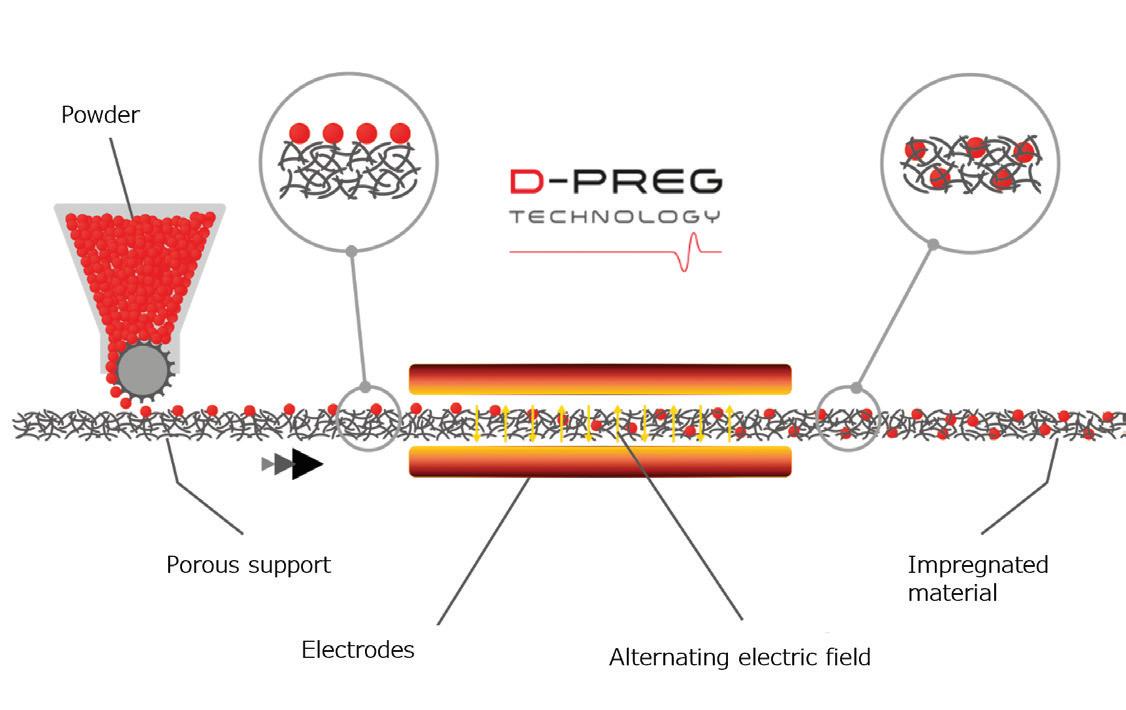
Within Fibroline’s technology portfolio, D-Preg is the one that is most used for the technical textile applications and therefore the filtration and separation sector. It is greatly appreciated for its flexibility and adaptability, working with material’s width ranging from 0,15 to 5m wide.
Dry impregnation solutions also allow for pattern deposition. Within the filtration sector, the manufacturer can pick preferred impregnation areas and decide where and how much to spread the powder on desired media. This grants capacity to concentrate functional actives exactly where needed, depending on the air or liquid flow. “Pattern deposition is especially a strong feature of Fibroline’s S-Preg solution, widely used in the medical and biomedical sectors, and can pave the way to new products in the filtration industry,” Léa Monin said, as a R&D project manager in charge of Filtration development at Fibroline.
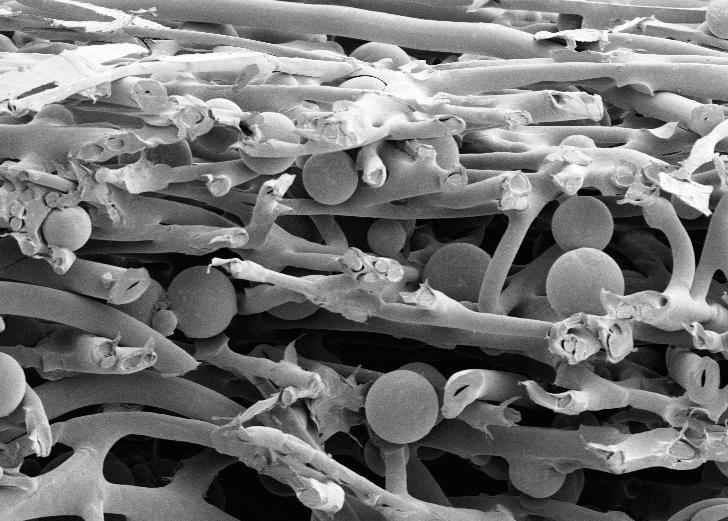
The use of dry impregnation favors the homogenous distribution of particles.
This description shows the basis behind D-Preg technology, the first dry impregnation solution used by Fibroline. Others have been developed to respond to various needs.
Clogging effect is greatly reduced as shown here in this impregnation process of SAP within NT2.

How These Principles Lead to Improved Performances
Because these technologies are based out of dry impregnation, they do not require any liquid binders, leading to the reduction of clogging effect. Therefore, active in powder form is fully available and this results in much higher efficiency of impregnated products overall. For instance, tests have shown that in the case of liquid impregnation of zeolite, 40% of active surface area got clogged with only 12% rate of latex binder impregnated. Fibroline’s dry impregnation solutions can reduce clogging to less than 7%.
Moreover, the use of actives in powder form also grants capacity to increase the specific surface area of the materials used by the manufacturers. Indeed, by using very thin powder instead of beads or pellets, the product benefits from a much wider active surface, and can therefore provide higher adsorption capacity and faster adsorption and desorption kinetics. A recent study on the capture of organosulfur compounds demonstrated a 105% raise of the adsorption kinetic using 30 microns zeolites instead of 2mm diameters beads at the same loading level.
With powder consisting in porous particles of controlled geometries, it also enables the trapping of targeted molecules selectively, and also increases the active filtration area. This makes Fibroline’s dry impregnation solutions perfectly suited for the use of MOFs, which are continuously growing in use with more and more applications being developed from them.
All in all, thanks to bigger specific surface area compared to beads or pellets and the removal of liquid binders that drastically reduces clogging effect, dry impregnation solution results in higher filter efficiency than conventional methods.
The Notable Features of Dry Impregnation Solutions as Cleantech
Other pros of dry impregnation technologies reside in their characteristics as distinguished cleantech with several environmentally friendly features. This
Not only does it make for simplified production lines, but it diminishes risks on industrial sites as it eliminates hazardous situations.
generates both greater sustainability and major savings for its users.
Replacing technologies that require solvents, these solutions have also eliminated VOCs emissions. For instance, for a recently transferred automotive interior applications, there were 100 time less VOCs emissions using dry impregnation solutions as compared to those of wet impregnation. As these emissions are immensely reduced, the quality of products is greatly improved with the removal of unsafe gases which can be a key benefit for specific applications in dealing with ever more constraining regulations.
Another key strategic aspect of the removal of solvents results in the simplification of industrial production processes. Not only does it make for simplified production lines, but it diminishes risks on industrial sites as it eliminates hazardous situations. They are therefore in accordance with safety regulations worldwide, such as SEVESO norms in Europe.
Using dry impregnation instead of liquid solutions also results in better energy efficiency and cost savings for its users. Since the technology does not need energy intensive drying, it can greatly reduce energy consumption. As an example, a 4m long and 1,50m wide unit running at 20m/min, impregnating up to 2T/h material requires less than 15kW. Instead of having to use large ovens to evaporate solvents, dry impregnation solutions can be combined with short thermal treatments resulting in space savings and increased productivity. These savings can be added to those from the complete elimination of effluents in dry impregnation solutions, making the latter all the more attractive.
Conclusion
Dry impregnation solutions bring several key innovations and competitive advantages to manufacturers. The use of alternating electric fields at its core is an innovation that results in improved performance of impregnated products. It is also a cleantech, as it greatly significantly liquid waste and VOCs emissions.
Fibroline does not build and prepare machines, but rather transfers its technologies by application sector. It accompanies its customers to secure a project from the initial idea to the industrial implementation of the solution. Said technologies are protected by numerous patents worldwide, and are continuously extended to new industries. www.fibroline.com
Flexible Ceramics – Pushing the Limits of Filtration
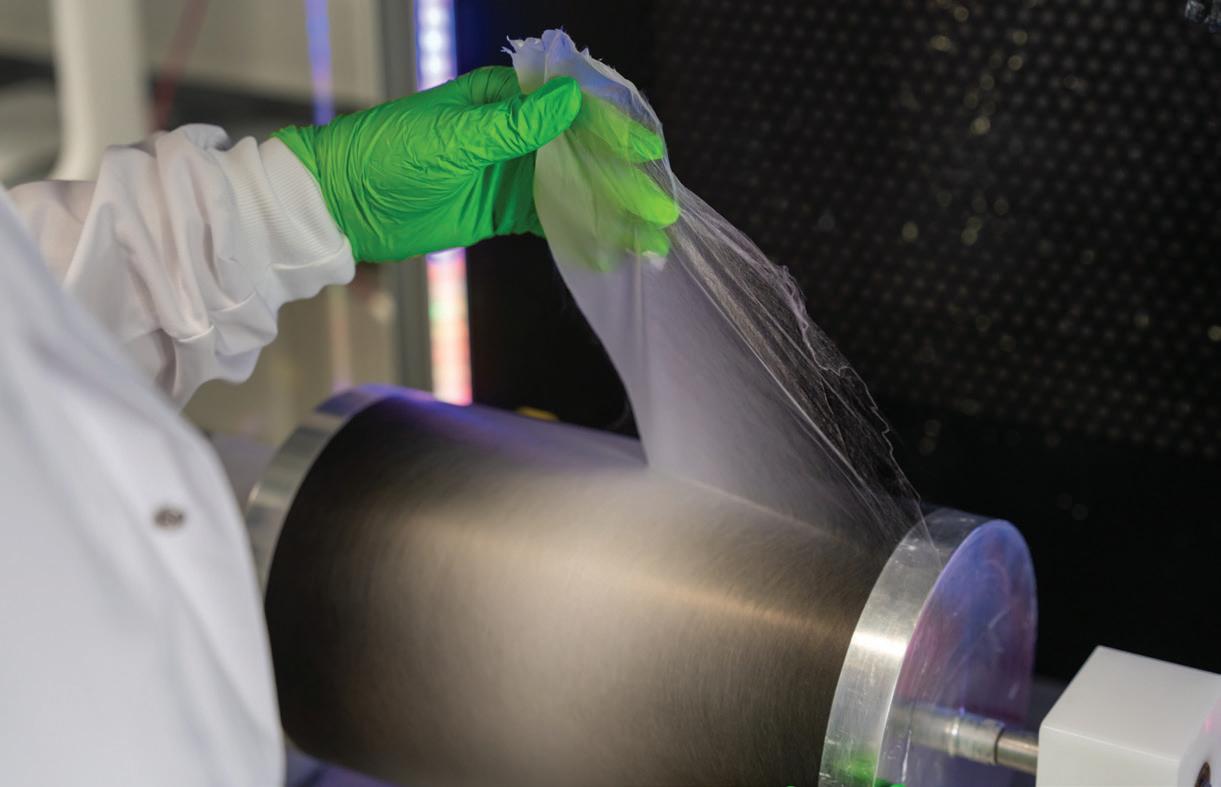
Recent advancements in material science have facilitated the development of flexible ceramic microfiber non-woven material, representing a significant innovation that combines the hightemperature stability and chemical resistance of ceramics with the flexibility and processability characteristic of non-woven material. This material can function either as standalone filtration media or, more significantly, as performance-enhancing layers within multi-layer filtration systems, potentially improving separation efficiency and system durability.
Key characteristics include a highly porous structure (>90%) and an ultrathin profile (130 micron), which enable efficient filtration with minimal pressure drop. The narrow pore size distribution improves the capture of fine particulates, making this material suitable for specific filtration applications. Their flexibility allows for processing into pleatable, complex shapes, ideal for space-constrained environments and lowpressure filtration systems.
The material exhibits high thermal stability, enabling reliable operation at temperatures up to 800°C without compromising structural integrity, while its chemical resistance enhances functionality in demanding environments, such as hot gas filtration, mist filtration, and aggressive gas separation. Additionally, the surface properties can be tailored through the application of sizing agents, allowing for targeted modifications to optimize performance when integrated as functional layers within comprehensive filtration systems.
The potential for catalytic coatings further extends the applicability of this material in scenarios where filtration and catalytic action are both required, for example in process filtration and industrial furnaces.

This adaptability, combined with the ability to modify key parameters such as pore size and surface characteristics, positions the material as a versatile, high-performance component across various filtration contexts.
By integrating flexibility, high porosity, thermal resilience, and options for surface modification, this ceramic microfiber nonwoven material establishes a highly adaptable platform for advanced filtration systems. With its unique properties, this material is a promising candidate for enhancing existing filtration solutions, particularly in high-temperature environments that demand customized filtration performance.
www.flexiramics.com
Custom Converting Equipment
•Unwinds / Rewinds
•Pocket filter machines
•Slitters (Ultrasonic, Laser or Conventional)
•Laminators (Ultrasonic, Thermal and Adhesive)
•Traverse and Spiral winders
•Membrane / Hollow fiber lines
•Festooners
•Accumulators
•Ultrasonic sewing machines
•Pleat welders
•Ring Welders
•Custom assembly machines
We employ our 70 years of web handling experience to benefit our customers. Contact Chase Machine today for your equipment needs!
Newly Available Multipass Test Bench for Hydraulic and Lubricating Oil Filtration: ISO-Compliant with Cyclic Flow and Vibration Testing
IFTS, Research and Testing Center, located in France, has launched a new version of a multipass test bench to qualify fluid power, lubricating oil and fuel filters in terms of filtration efficiency and dirt holding capacity. This version is designed to be as close as possible to the working conditions of filters (cf. figure 1).
IFTS proposes to combine cyclic flow variation, mechanical vibration and on-line particle counting from 1.5 to 70 µm(c) (using 2 light scattering and 2 light obscuration APCs in total). The principle of the bench is to clog the filter under test with standardized silica test dust (Arizona test dust as specified as per ISO 12103-1) up to a given ∆P increase in steady or cyclic flow conditions under vibrational fatigue and to monitor on line the instantaneous particulate filtration efficiencies.
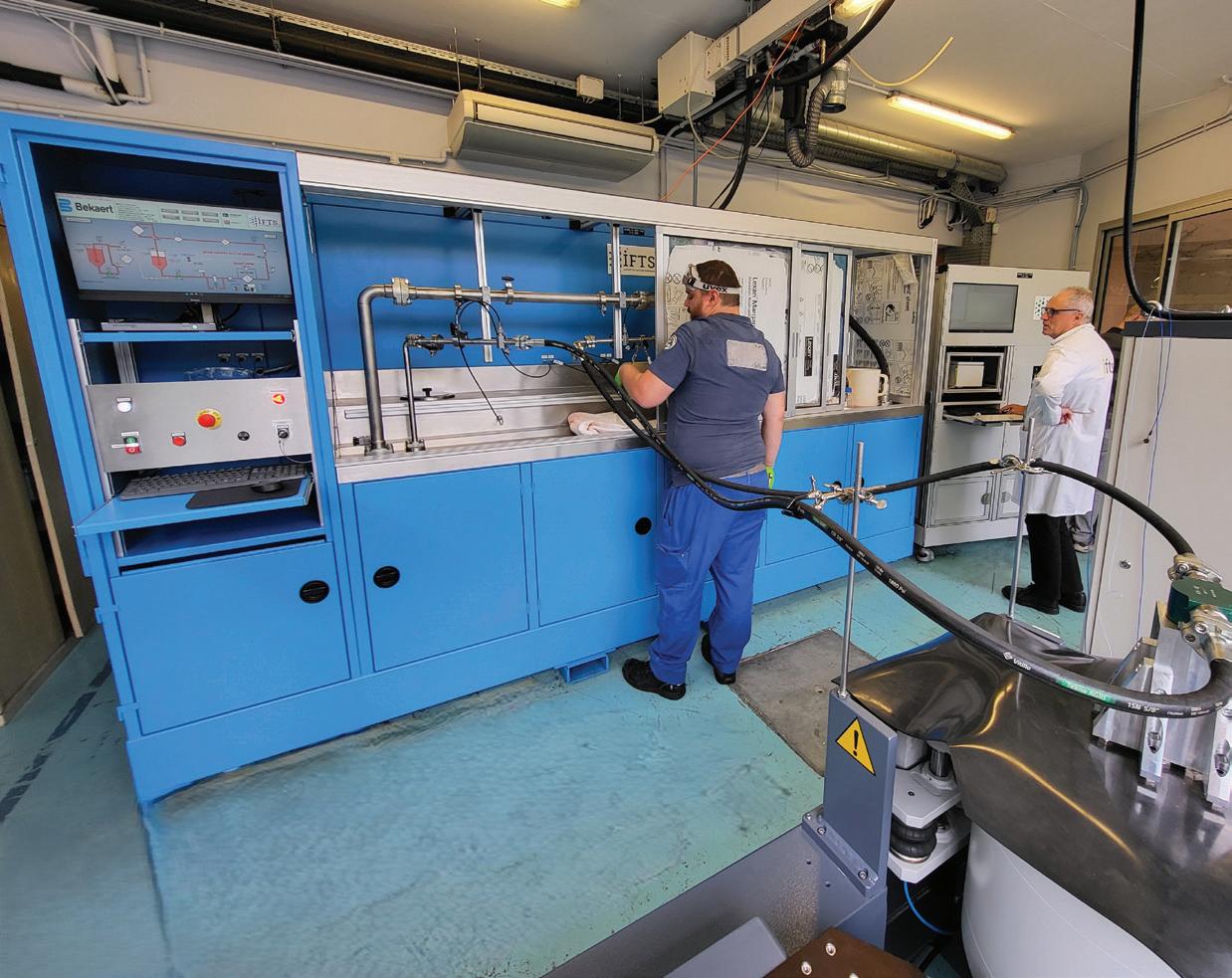

These combinations of working conditions will allow the users to discriminate filters from each other’s. The cyclic flow variation has usually a negative impact upon filtration efficiency (cf. figure 2) but the mechanical vibration could exhibit a significant filtration efficiency decay of the filter (cf. figure 3).
The vibration could generate particles release on preloaded filter which leads to negative filtration efficiency (See enclosed Table 1 based on Figure 3).
The outstanding working capacities of the bench that IFTS allows to meet conditions often found in fuel applications (5 L/min and 1 Bar of P) but also those exceptionally found in fluid power applications (200 L/min – and up to 60 Bar of P) (see table 2).
www.ifts-sls.com
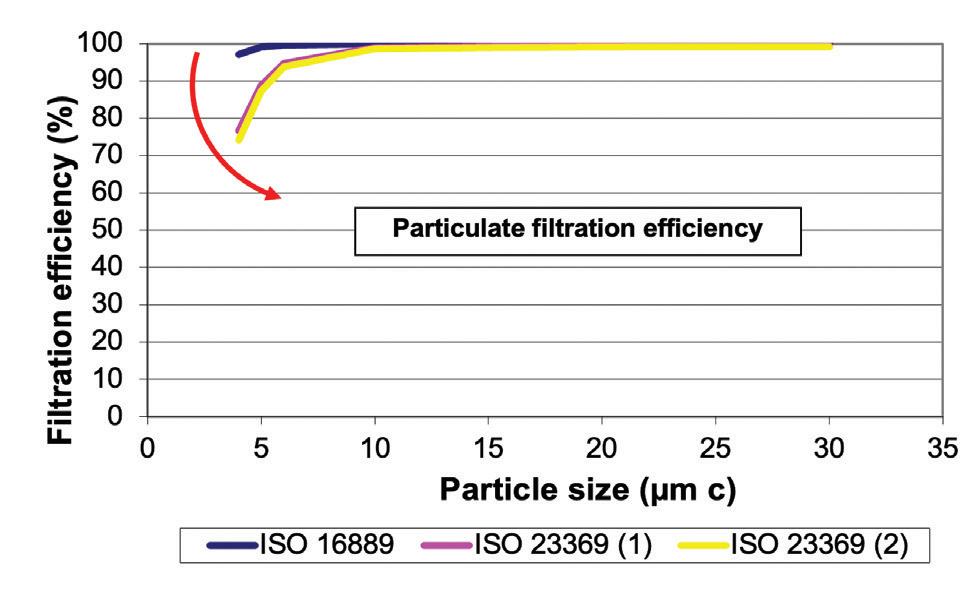
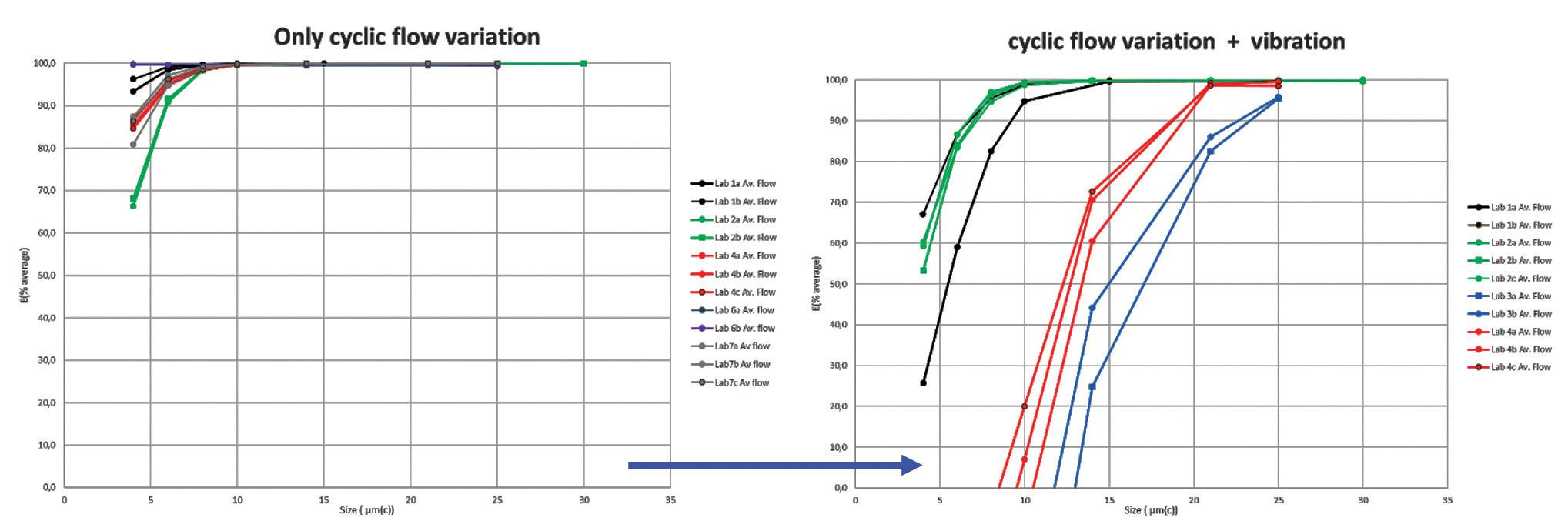
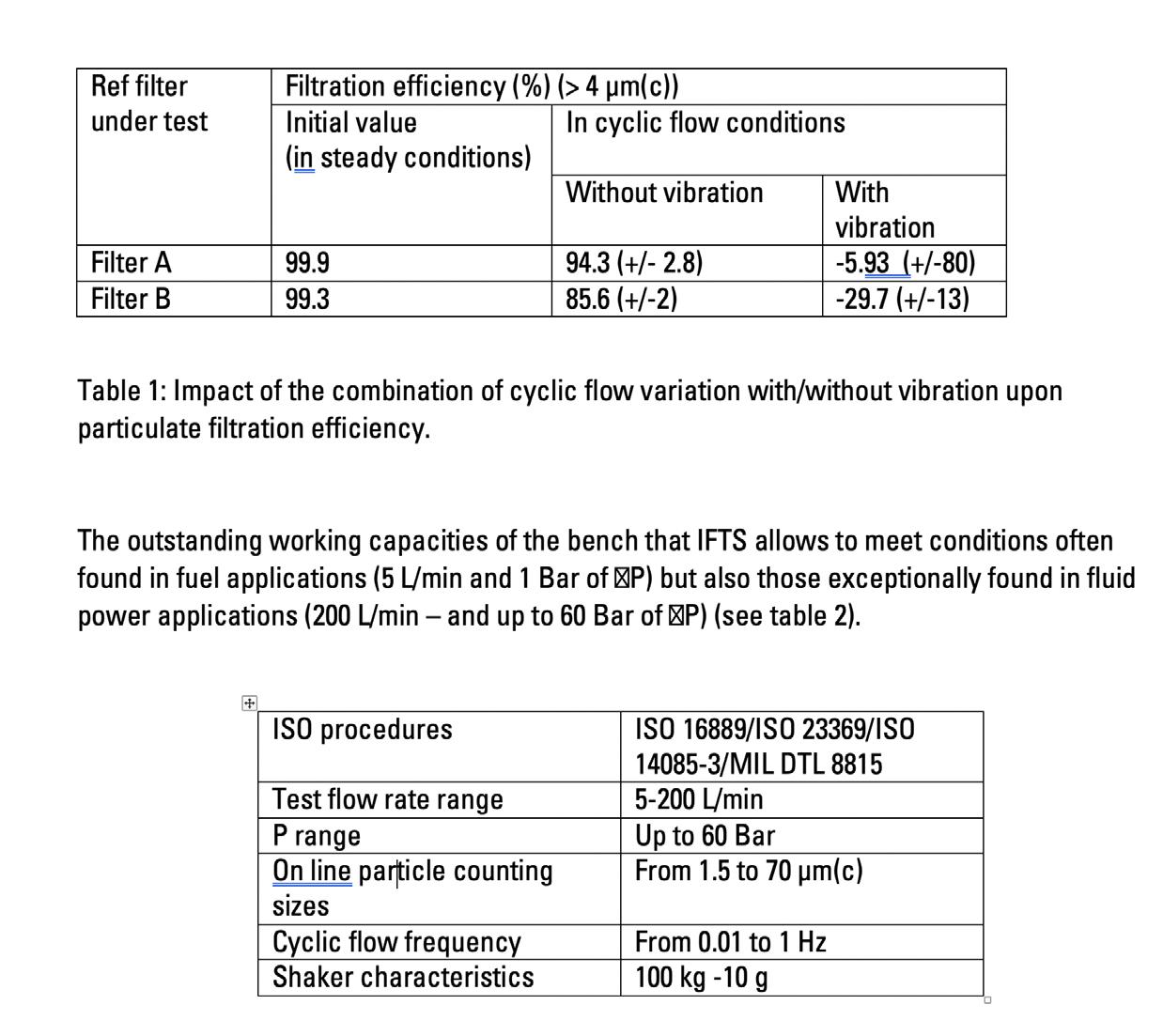
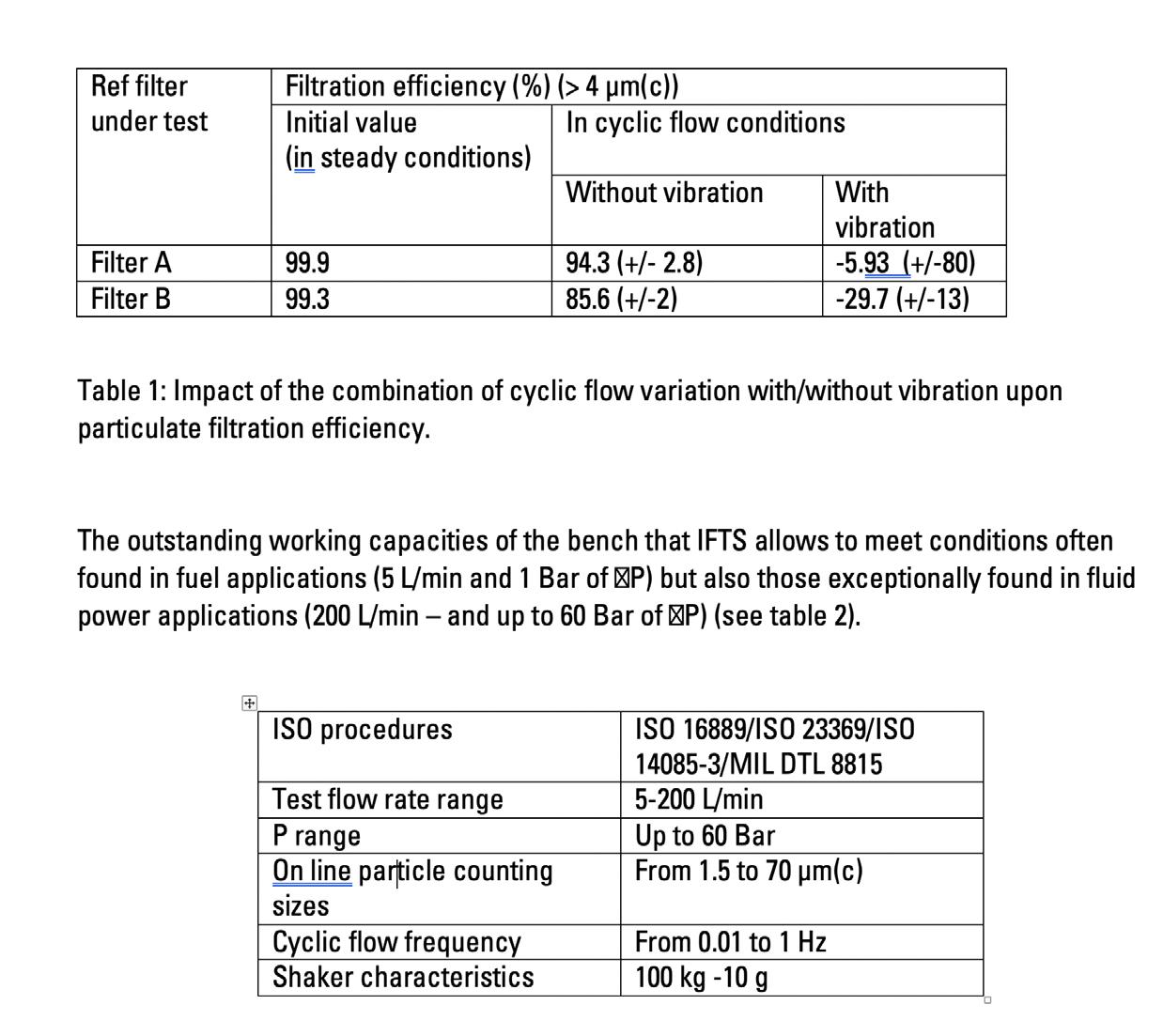
Figure 1: New equipment designed and proposed by IFTS.
Table 1: Impact of the combination of cyclic flow variation with/without vibration upon particulate filtration efficiency.
Table 2: Working characteristics of the new equipment supplied by IFTS.
Figure 3: Impact on the combination of the vibration with cyclic flow variation.
KM Pathogen Defense Introduces NanoFense: Revolutionary Antimicrobial Technology for Enhanced Air Filtration
KM Pathogen Defense LLC was formed to execute on an exclusive worldwide license for production of a disruptive antimicrobial technology [NanoFense], developed for protective air filtration applications. The U.S. patented formulation provides unparalleled, high performance against transmission of harmful pathogens, mold, and infectious diseases.

NanoFense is an antimicrobial silver nanoparticle formulation which has demonstrated remarkable efficacy against a broad spectrum of viruses, bacteria, and fungi. The formulation acts as a destructive adsorbent when applied or “coated” on existing filter media and has been validated to deliver this performance at multiple independent BSL-3 laboratories. Highly successful “real-world” testing results have been achieved against the Avian influenza virus (H9N2), Human Influenza A virus, Haemophilus Influenzae (H-flu), Rhinovirus, Swine Influenza virus (H1N1), Staphylococcus aureus including the viral MRSA strain, and Streptococcus pneumoniae.
and Pathogen Defense
range of viruses and bacteria. Treated media ensures that the filter cannot become a site for collected active virus particles or bacterial colonization which can lead to unintended self-contamination.
Earlier this year, a highly successful production run was carried out to verify the commercial scalability of this disruptive air filtration enhancement (the extremely uniform particle size results with virtually

no outliers ensure an effective, consistent protective treatment to virtually any air filtration application).
The NanoFense formulation is a suspension material that can be applied directly to filter media creating an additional level of protection by eradicating a wide
The transition from a laboratory scale ‘formulation’ to verified production scale capability positions this innovation as a viable enhancement for major consumer air filtration market segments (disposable facemasks, room air purifiers, airline cabin air systems, subways, etc.).
www.kmpathogendefense.com
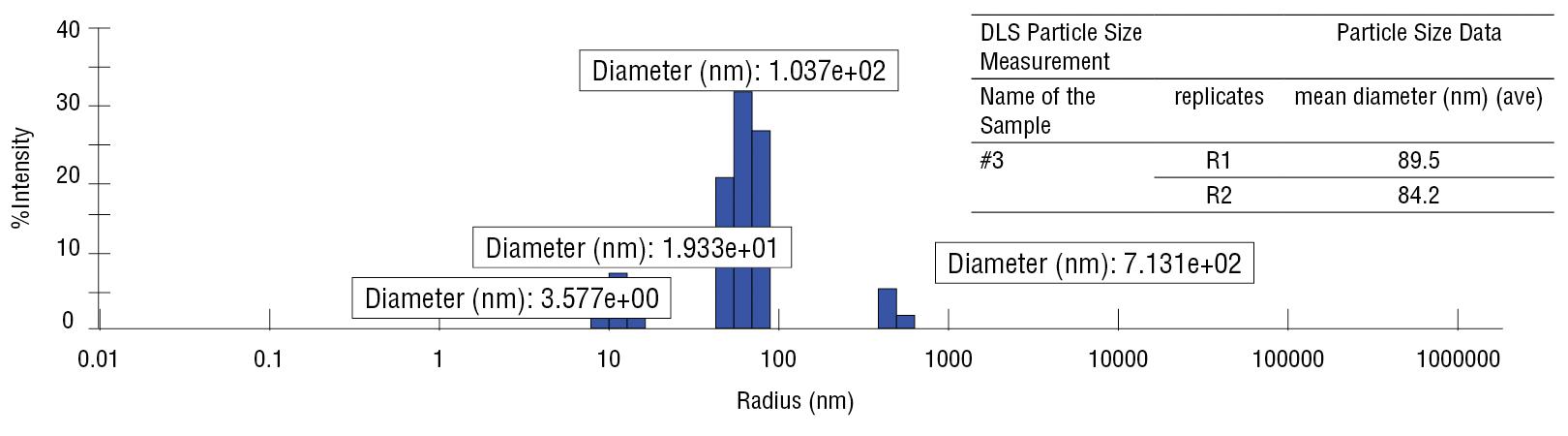

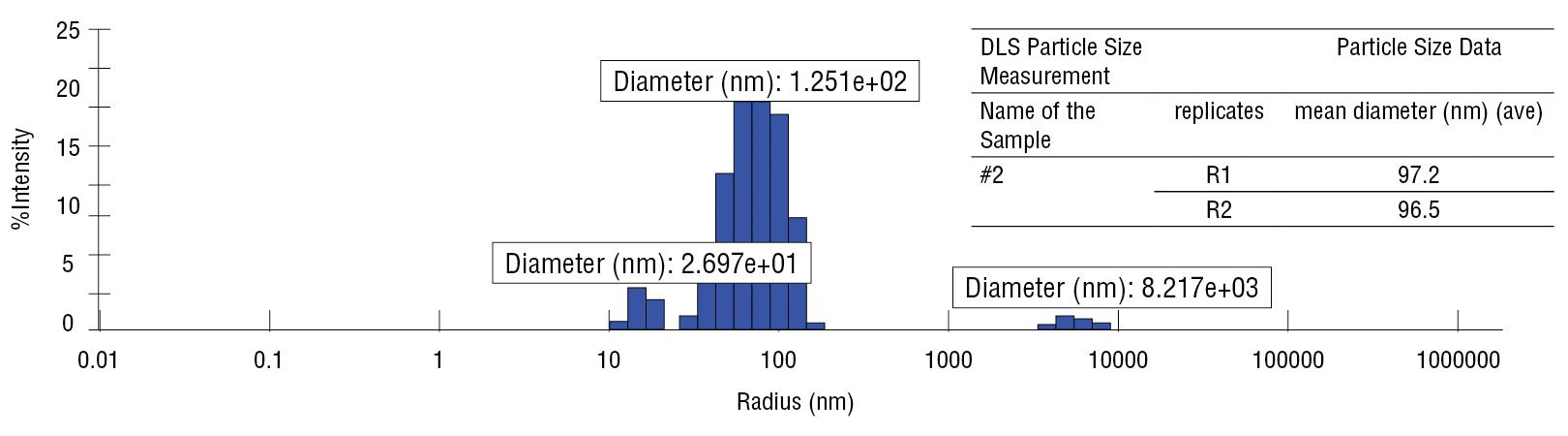
Treated media ensures that the filter cannot become a site for collected active virus particles or bacterial colonization which can lead to unintended self-contamination.
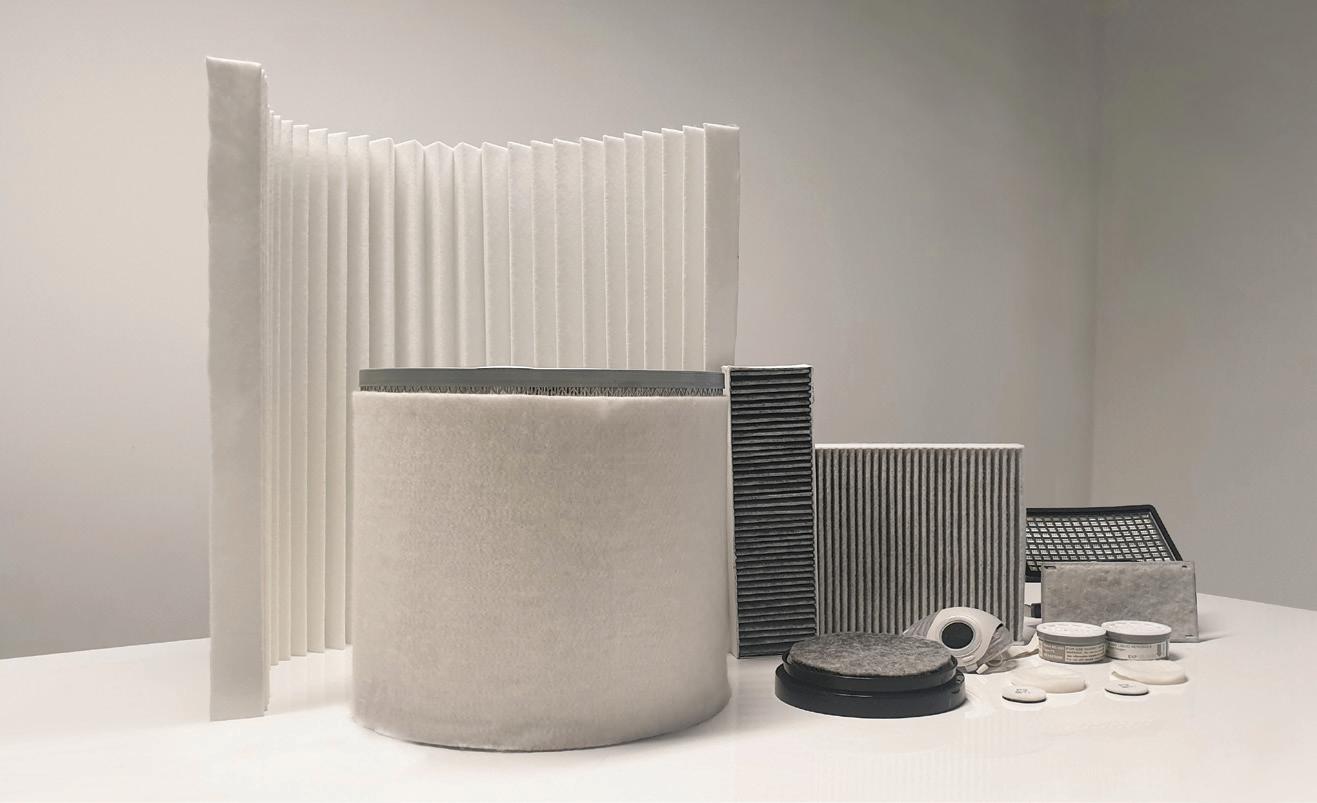
Lanaco, a New Zealand-based filtration technology leader, continues to redefine the air filtration industry with its groundbreaking product, EcoStatic®. This innovative wool-based filter media delivers unmatched filtration efficiency, low resistance, and eco-consciousness, providing an advanced solution for today’s most pressing air quality challenges.
Unmatched Performance, Naturally
EcoStatic® harnesses the natural electrostatic properties of wool to capture a broad spectrum of contaminants, including particulate matter, allergens, and volatile organic compounds (VOCs). The result is superior indoor air quality, with an ultra-low pressure drop that optimizes energy efficiency, making it ideal for high-performance HVAC, healthcare, and appliance applications.
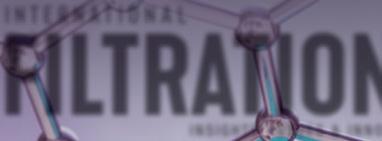


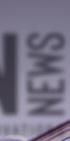
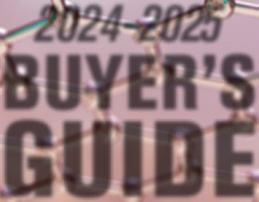
Commitment to Sustainability
A core principle of Lanaco is sustainability, and many EcoStatic® products are USDA Certified Biobased as part of the USDA BioPreferred® Program. Sourced from the proprietary Astino® sheep breeding program, Lanaco’s wool is produced using regenerative farming methods that ensure a renewable and traceable material supply chain. Every EcoStatic® product embodies a closed-loop philosophy – being bio-based, it is on a pathway to full biodegradability, contributing to the circular economy.
Innovation and Collaboration
In 2024, Lanaco achieved another milestone by partnering with Blueair to produce the world’s first wool-based electrostatic filter for consumer air purifiers. This collaboration combines Lanaco’s natural materials expertise with Blueair’s leading-edge technology, setting a new trend in air purification.
Looking Ahead
Lanaco is partnering with global leaders and innovators to push the boundaries of biomaterials, maximizing the potential of natural and renewable resources. By continuously enhancing EcoStatic® and collaborating to commercialize sustainable solutions, Lanaco is committed to making natural possible in air filtration. As EcoStatic® evolves, Lanaco continues to lead the transition to sustainable filtration by merging natural materials with advanced technology. www.lanaco.co.nz
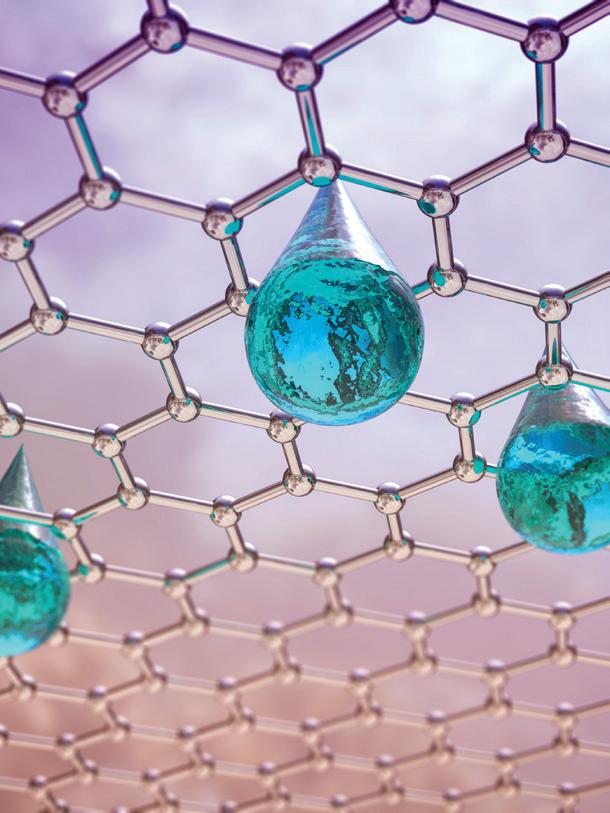
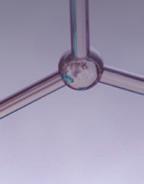
NanoMeld’s High E1™ Filter Media
The COVID-19 pandemic highlighted the importance of healthy indoor air.
Traditional HVAC air filters have been satisfactory at capturing larger E3 particles (>3,000 nm) like pollen, pet dander, and dust. However, they have been quite ineffective in their ability to ameliorate two major limitations:

1. Trapping smaller E1 particles, like those that carry the COVID-19 virus and other harmful microorganisms; and,
2. Minimizing the undesirable pressure drop with its associated higher air resistance that leads to increased energy costs for the consumer.
NanoMeld manufactures nanofiber-enhanced composites (high E1TM) that, after being incorporated into filters, can overcome those deficiencies.
When nanofibers – small, fibrous materials less than 1,000 nm in diameter – were applied to ASHRAE 52.2 - 2017 rated substrates, the porosity of those substrates decreased. Subsequently, those newly created composites were converted into filters alongside untreated substrates. Testing revealed that the previously lower MERV-rated (MERV 8 & MERV 10) filters with
the composite applied became capable of both catching potentially dangerous E1 particles and exhibiting a more advantageous pressure drop than conventional filters currently on the market.
Poor indoor air quality (IAQ) has been stronglylinkedtoavarietyofhealthproblems rangingfromfatigue,chronicheadaches,anddizziness torespiratorydifficulties,cardiovascularissues,and cancer.Children,theelderly,andthosewithchronic medical conditions are particularly vulnerable to contaminatedindoorair.Thefactthatmanypeople spendmostoftheirdaysinsidefurtheremphasizesthe importanceofhealthyairinresidentialandcommercial environments.
NanoMeld’sHighE1TM filtermediaismosteffective atcapturingairborneillness-causingparticleswithout damaging HVAC systems and without increasing consumers’energycosts.Healthierindoorairthat canhelptoimprovefamilies’overallhealthathome, increasestudentperformanceatschoolandboost employeeproductivityatworkisnowareality.
Bertrina L Scott, bertrina@nanomeld.com, (803) 810-6063

Chart Notes
B – MERV 8 Media without nanofiber coating
B-NF1 – B with 1 layer of nanofiber coating
B-NF2 – B with 2 layers of nanofiber coating
Pyrolysis - A Vital Ally in the Fight Against Plastic Waste
By Serhat Oezeren, Global Vertical Market Manager – Chemicals, Polymers and Plastics Recycling, Pall Corporation
As countries look to translate the recent global plastics treaty negotiations into action, it is vital that governments consider optimal pathways to advancing circularity through a combination of reduction, re-use and recycling strategies. Chemical recycling through pyrolysis (often referred to as ‘advanced recycling’) has emerged as an important piece of the puzzle, serving as a powerful complement to mechanical recycling due to its great versatility in processing different types of plastic waste.
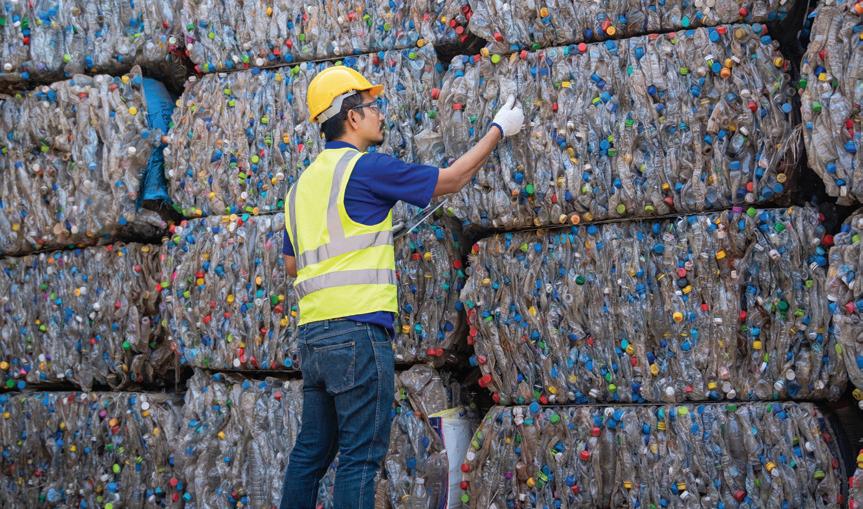
There are, however, numerous technical hurdles associated with the pyrolysis process, particularly when it comes to contamination. Numerous types of plastics and non-polymeric sources are combined in mixed plastic waste feedstocks. Those feedstocks contain coarse to fine particles (e.g. filler, flame retardants, etc.) and other materials which are detected in the oil downstream in the pyrolysis process (e.g. coke). Besides the particulate matter, a variety of additional contaminants such as organic gels, dissolved metals and dispersed liquids are found as a side product in pyrolysis oil. The complex mixture of those contaminants needs to be extracted from the oil.
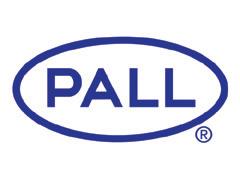

However, using depth filtration is an efficient and cost effective way to remove harmful contaminants and reduce the contamination levels of plastic waste pyrolysis oils to the thresholds accepted for crude naphtha feed in steam crackers.
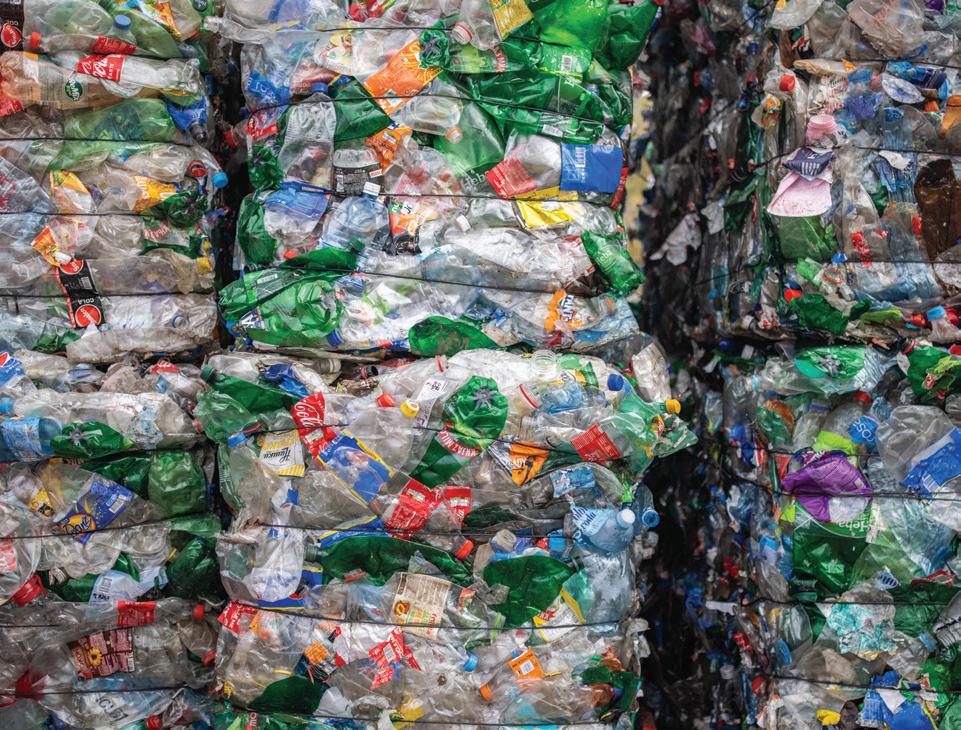
Appropriate filtration media and coalescer technologies are key at various stages of the process to remove particles and separate water from pyrolysis oil or liquids from gas. The retention and separation of contaminants not only purifies the oil and gas, making them more suitable for downstream processing, but also helps prevent equipment fouling and unnecessary maintenance downtime.
To further refine the pyrolysis oil for use as fuel or feedstock to produce plastic again, it must be transferred to a steam cracker to convert the oil into lighter olefins. The presence of particles and metal contaminants in crude plastic waste pyrolysis oils may have significant negative impacts on the steam cracker‘s furnace and recovery section such as furnace run-length reduction due to coking increase.
It is imperative that international governments more strongly acknowledge the crucial role of chemical recycling in advancing the circularity of plastic production and reflect this through supportive policy measures and greater investment. This will allow the technology to scale up to a level that significantly enhances the circular economy and disincentivises the production of virgin plastic from fossil fuels. We must use all the tools at our disposal to ensure a greener future. www.pall.com

Serhat Oezeren is Global Vertical Market Manager – Chemicals, Polymers and Plastics Recycling for Pall Corporation, a proven partner providing filtration, separation and purification solutions to meet the demanding needs of customers around the globe.
Pyrolysis Oil Filtration.
Getty Images
Discover Confidence in Respirator Integrity with the 8119A Leak Tester
In environments where respiratory protection is critical, whether in healthcare, industrial settings, or other safety-focused industries, the integrity of your equipment is non-negotiable. The 8119A Respirator Leak Tester, designed as an essential accessory for the Automated Filter Tester 8130A, offers a reliable solution to verify the effectiveness of your respirators.
Versatility in Testing Applications
The 8119A is designed for a broad range of testing applications, making it indispensable for professionals who need to ensure the integrity of personal protective equipment (PPE). It can be used to assess eyepieces, inhalation valves, voice emitters, and cartridge threads, as well as detect general physical damage that could compromise a respirator’s performance. This versatility allows for thorough post-maintenance inspections and routine checks, ensuring respirators consistently meet the highest safety standards.
An Evolution in Respirator Leak Testing
The 8119A Respirator Leak Tester is a next-generation advancement, continuing the legacy of its predecessor,
the 8119 accessory, which was widely used with the previous Automated Filter Testers 8127 and 8130. This evolution reflects a commitment to enhanced precision and reliability, providing users with peace of mind. By ensuring that respirators remain in optimal condition, the 8119A helps safeguard workers in demanding environments.
Why Precision Matters
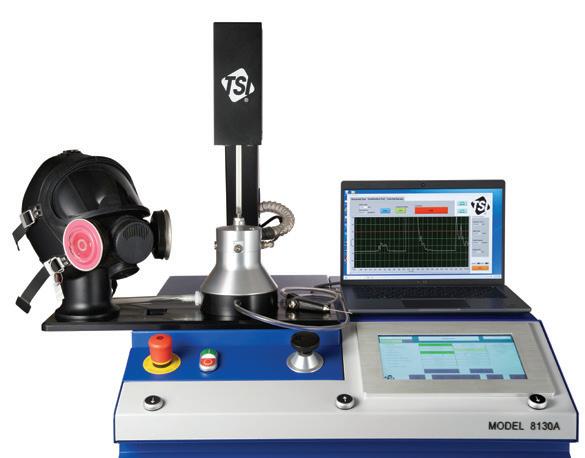

When it comes to worker safety, there is no room for compromise. Respirators play a vital role in protecting individuals from hazardous airborne particles, and regular testing with the 8119A ensures that these devices perform as intended. Incorporating the 8119A Respirator Leak Tester into your testing protocol will help you maintain the highest standards of safety and protection.
With the 8119A, you can trust that your respirators are reliable, keeping your team safe and your operations running smoothly. www.tsi.news/3myizmi

8119A Respirator Leak Tester.
Building in
By John Davies
Putting an ESG strategy in place is relatively straight forward. The hard work comes during the process of accurately tracking performance metrics and building the corporate structures necessary to empower and encourage change. Parker Hannifin’s John Davies, EHS & Quality Manager for the Filtration & Energy Solutions (FES) division - Altair Business Unit, outlines their approach to delivering on ESG.
ESG That Meets Goals
It’s a fairly safe bet that every single one of the world’s biggest companies – and many small and medium enterprises too – have an Environmental, Social, and Governance (ESG) strategy in place. However, for an ESG strategy to become more than an exercise in advanced green washing and bring about real corporate change requires much more than simply establishing the policy. A key process on the road to becoming responsible corporate citizens is setting challenging performance targets against rigorous benchmarking and demanding consistent improvement.
As part of an enhanced ESG strategy, air filtration experts at Parker Hannifin, for example, set out an ambitious target of achieving carbon-neutral operations by 2040 and cutting emissions from operations by half by 2030. The ESG program thus compares favorably to industry standards. In the UK, for instance, the UK government has set a net zero target a full decade later, in 2050.
Crucially, as part of this overarching strategy, Parker Hannifin created performance metrics around each individual division. The Parker Hannifin FES division has already succeeded in slashing emissions by 28% in just the first five years under its enhanced ESG plan. Furthermore, while the company’s FES division has already realized significant reductions in emissions it also continues to meet or exceed a challenging target of a 3% year-on-year reduction in CO2e production set against a 2019 benchmark. This emissions reduction target of 3% was established in 2022. However, in only the first year of implementing its latest emissions reduction plan, the division achieved a 13% cut in net direct emissions.
Policy in Action
These reductions have been achieved through the implementation of dozens of individual carbon reduction projects at various
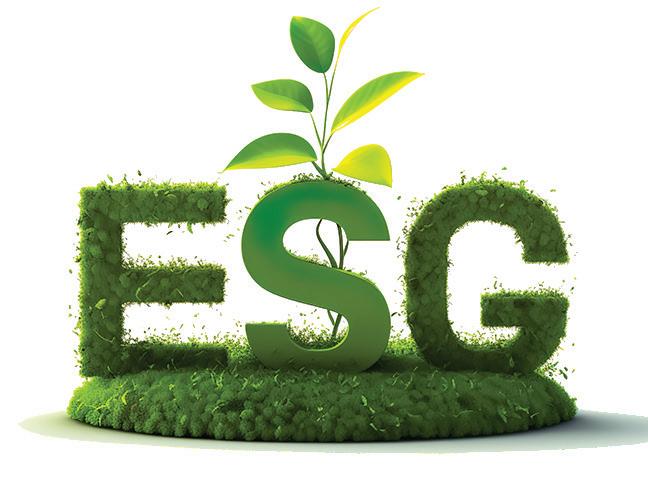

locations globally. For example, installing an updated efficient roof at the Parker Hannifin manufacturing facility in Alton, UK, the division significantly reduced gas and energy consumption, improving the building's energy efficiency by adding this secondary layer to the existing roof design.
In addition, the ongoing 3% target has prompted continuous improvement initiatives. One example of this policy in action is the inclusion of regular ‘energy treasure hunts’ in which threeday events are undertaken at each location to identify energy efficiency opportunities across the company. For the FES division, energy efficiency improvements implemented so far include switching to LED lighting and using PIR detectors, finding and addressing compressed air system leaks, and lowering the set point on air compressors so that they work optimally. More fundamentally, improvements in the actual filter manufacturing process have also made a substantial contribution. Often these improvements are relatively simple to achieve. For example, by tightly controlling temperatures for glue points and using automatic timers rather than working 24 hours a day, as was the case previously, energy is saved.
Delivering Actionable Data
A commitment to gathering information that can be used to enact future measures is another critical part of achieving results from an ESG strategy. At Parker Hannifin energy monitoring and data loggers are deployed across the distribution system that allow the company to identify where further savings may be achieved and the FES division has initiated supply chain reporting too. The ESG program has been concentrating on Scope 1 and Scope 2 emissions so far, but the company is currently engaged in evaluating and reducing Scope 3 emissions as well.
Data is captured across all sections in Benchmark Gensuite, a comprehensive environmental health and safety (EHS), sustainability, and ESG reporting software solution that helps companies
New roof adds to efficiency. Parker Hannifin

and investors analyze and report on investment-grade ESG data. Parker Hannifin uses this tool to track all waste streams which include general, recycled, hazardous waste and metal waste. In the UK, for example, nothing goes to landfill. General waste goes to energy recovery while other wastes and metals are recycled. The company also continues to not only prioritize minimizing waste sent to landfills but also conserving water across manufacturing sites.
Tracking waste and utility usage and converting that data into a CO2e figure gives actionable data that can inform goals and key performance indicators year-on-year. Having completed many on-site carbon reduction projects, including lighting retrofits, and HVAC system upgrades among others, the data reveals that while the emissions baseline in 2019 was around 946,000 kg’s of CO2e across the FES division, since the policy was introduced in mid-2022 and for the first full year that figure was already down to 823,000 kg’s CO2e.
Beyond the “E” of ESG
Parker Hannifin with more than 60,000 employees across the company, also prioritizes the health and safety and social aspects of its ESG commitments, which have resulted in a 45% reduction in the Recordable Incident Rate and a 33% reduction in the Lost Time Incident Rate over the last five years. This level of performance ranks Parker Hannifin in the top quarter of its peers.
service. In the UK-based FES division, this year’s local designated charity is the Hampshire and Isle of Wight Air Ambulance Service, for example, but other local projects are supported too. Currently, the FES division is engaged in providing refurbishment services for a specialized special needs children’s college and the Phyllis Tuckwell Hospice, which receives donated clothing and other items that are high on their needs list. UK employees also recently donated chocolate Easter Eggs to the local food bank. A key part of a successful strategy is to empower staff members to drive positive change and enabling local initiatives is an important element to gain traction and buy-in from employees.
Empowerment also comes from knowledge and training, and all Parker Hannifin FES division employees are given environmental awareness training delivered through an online platform. An internal group has also been formed with participants from all areas of the business. This group meets every other month to review ideas, explore current results and discuss future goals. While governance is specifically handled by corporate headquarters and individual division controllers, several audits and questionnaires are required on an annual basis.
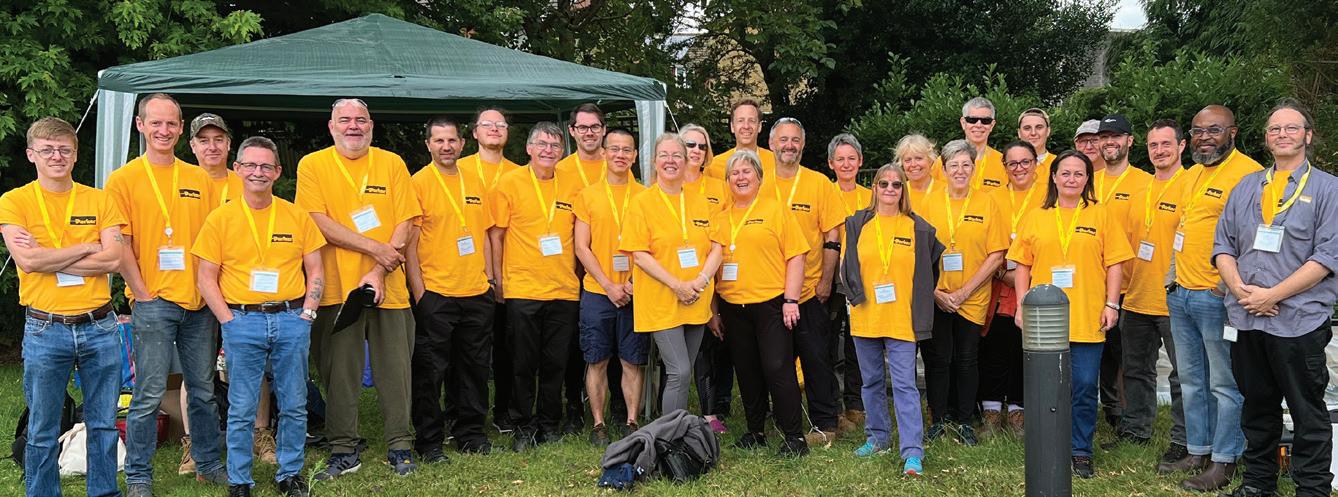
Employee well-being is also supported by having outside providers for mental health, and health surveillance programs. For example, mental health first aiders are on-site at the UK Alton site to support employees as needed.
In addition, in the 2023 financial year, the company focused on increasing diversity across the business, particularly in leadership positions and there is also compulsory code of conduct training for all Parker Hannifin employees annually. This reminds employees of the importance of diversity and inclusiveness, while training progress is tracked through the year. Beyond the immediate workforce, numerous outreach program are supported by employees. This ties in with wider Parker Hannifin Foundation initiatives which contributed more than $9 million to charities that helped strengthen communities around the world last financial year. The majority of these contributions supported causes that align with the Foundation’s three areas of focus – STEM education, community needs, and sustainability.
However, other, more local initiatives are also encouraged. An employee engagement team in each part of the business works to identify opportunities for employee well-being and community

Beyond that, the Atlon site is ISO14001 certified. ISO 14001 is an internationally agreed standard that sets out the requirements for an environmental management system that can support organizations to improve their environmental performance through more efficient use of resources and waste reduction While this means an environmental management and stewardship scheme is in place, ISO 14001 includes the need for continual improvement of an organization’s systems and approach to environmental concerns. The standard was recently revised to ISO 14001: 2015 with key improvements such as the increased prominence of the environment in the strategic planning processes. Certification also ensures that the Alton site is externally audited to confirm improvements in the environmental aspects and impacts on the local environment. Indeed, many of Parker Hannifin’s FES division customers require that certification.
Beyond Parker Hannifin
The FES division’s commitment to sustainability and environmental stewardship is yielding results, but Parker Hannifin also has an obligation to the wider world. This goes beyond the conventional supply chain concerns though. By supporting
Treloar’s College refurbishment team. Parker Hannifin
Treloar’s - Altair Business Unit manager at work.

improved energy efficiency in gas turbines, Parker Hannifin’s technology plays a very large role in protecting the environment far beyond the factory gate. A core element of this is a strong commitment to R&D to support continued performance improvements and in the last financial year, more than 40% of Parker Hannifin’s research and development was dedicated to expanding a clean technology portfolio, with a focus on electrification and the emergence of alternative fuels such as hydrogen and sustainable aviation fuels.
For the FES division, this R&D focus supports the development of filtration systems tailored for specific environmental conditions, such as damp coastal regions or dry and dusty deserts. These systems improve turbine performance and efficiency but also reduce differential pressure across the filtration system, increasing output and reducing operating heat rates. These are not one-time events but rather a continuous improvement in business processes both internal and external. It’s not without challenges including return on investment (ROI) calculations that are required to justify capital expenditure. Within Parker Hannifin’s FES division, all of the energy efficiency or CO2 reduction improvements identified
through energy treasure hunts have been implemented.
Looking to the future, the strategic goals for any ESG programme must continually evolve to meet emerging environmental, social, and governance challenges but the obligation to support a more sustainable tomorrow must remain constant. The key to success though is to empower the company to make positive change through actionable data, leveraging best practices, demanding targets, and dedication to that goal.
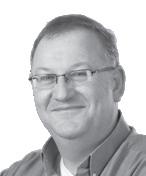
John Davies, Environmental, Health & Safety and Quality Manager EMEA, Filtration & Energy Solutions Division, Parker Filtration Group. He has spent over 17 years in the gas turbine filtration industry in a variety of Engineering, Quality and EHS roles. He’s been a product development engineer, looking at conceptual air filter designs and validation. He moved to the Altair Quality manger, to improve on established product and service processes, which he has overseen for the last 15 years. In tandem to Quality management, he has undertaken the role of EHS lead which he has done for the last 5 years.

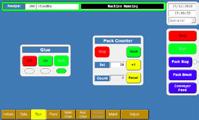
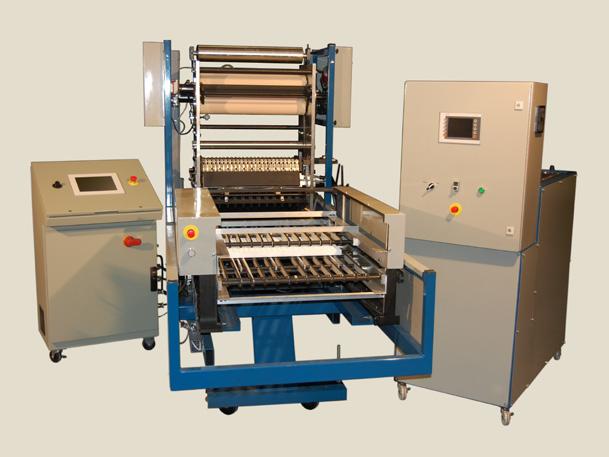
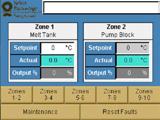
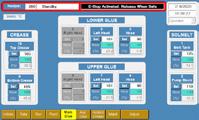
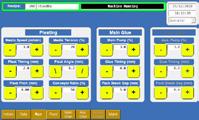
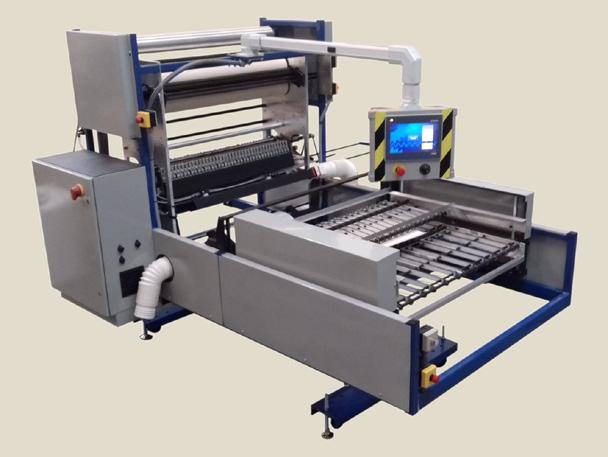
Charity Air Ambulance.
Revisiting the Pandemic
The Importance of Air Quality Governance in Poising Future Virus Transmissions for Defeat.
Dr. Iyad Al-Attar
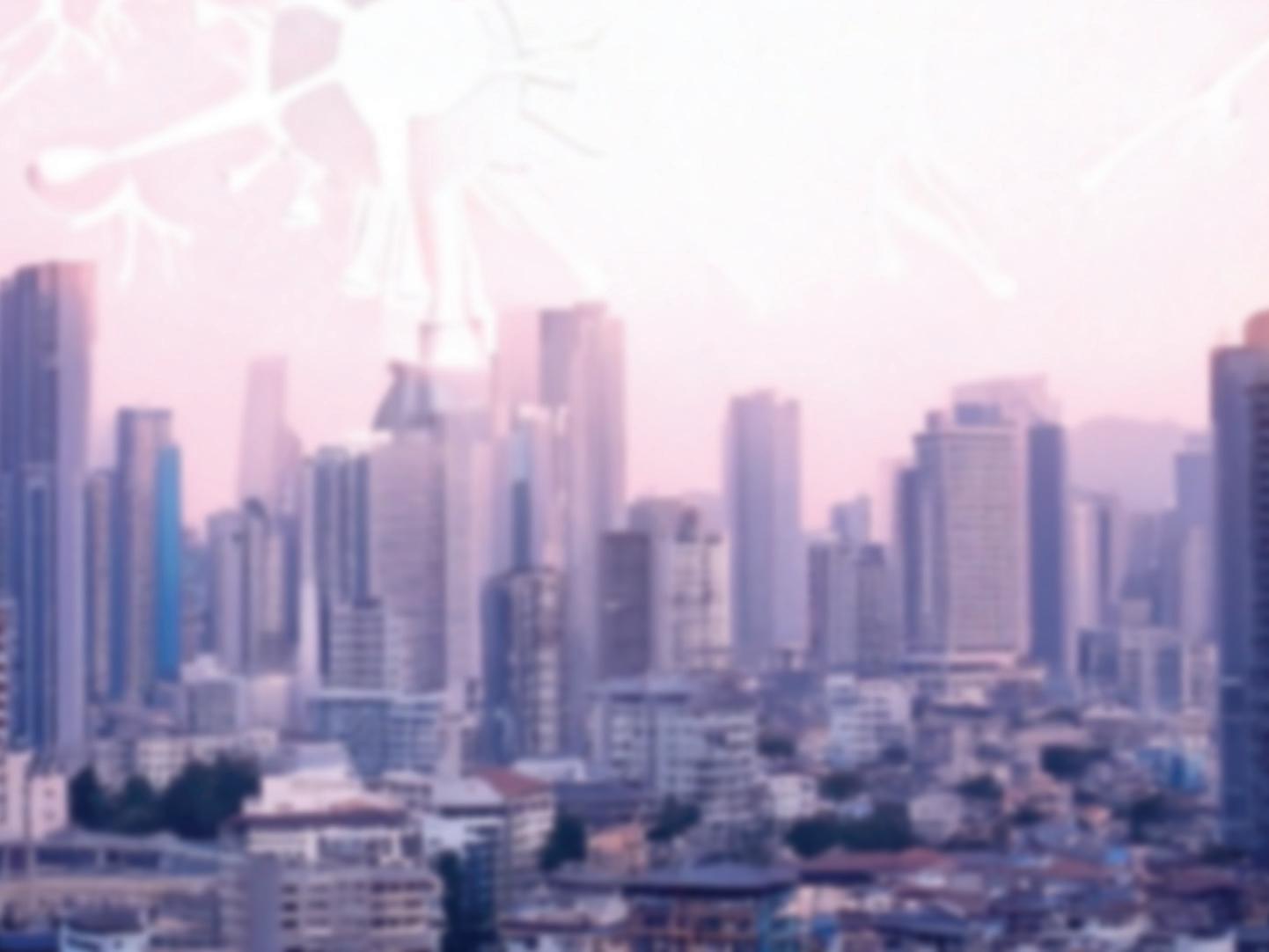
What (Filtration) Lessons Aren’t We Learning?
Air quality is crucial for urban sustainability, affecting public health, the environment, and the economy.
Managing air quality has become a significant challenge for cities due to increasing urbanization and industrial activities. The recent pandemic has highlighted the importance of Indoor Air Quality (IAQ) for built environments and building envelopes. Safeguarding the well-being of human occupants is essential for sustainable and healthy living in buildings. Therefore, incorporating air quality considerations from the beginning of any sustainable urban development is crucial for designers and occupants. To ensure fresh and clean air delivery to building envelopes, governance must be established using available technologies in HVAC, filtration, and air quality monitoring. Governing IAQ involves policies, regulations, and strategies designed to monitor and manage pollutants’ existence and concentration indoors.
The COVID-19 pandemic has emphasized the importance of IAQ in public health, highlighting the crucial role of filtration technologies in maintaining healthy indoor environments. As the airborne transmission of pathogens became a primary concern, advanced filtration systems gained prominence for their effectiveness in removing ultrafine particles, biological contaminants, and Volatile Organic Compounds (VOCs). The pandemic sent a clear message that a strategy is needed to investigate the capabilities of existing filtration systems in capturing all types of pollutants and protecting human health and well-being.
Poor IAQ has a significant impact on public health due to inconsistent adherence to standards, lack of awareness, and
legislation that does not deal with the root causes of poor IAQ. Air quality governance emphasizes the importance of protecting the well-being of city dwellers and occupants from various health issues, such as respiratory diseases and cardiovascular conditions. Obviously, protection comes to the forefront when considering the transmission of airborne viruses such as Corona. An increase in medical care and hospitalization represents a substantial cost for governments to accommodate the increased demand for such services. Research has shown that improving IAQ can lead to fewer respiratory issues, decreased asthma rates, and reduced absenteeism in schools and workplaces1. When cities make their built environments healthy and safe, they can reduce health-related costs and re-allocate resources to promote economic growth.
Sufficient evidence succinctly highlights the critical need to regulate IAQ through codes and standards and through their professional implementation and compliance2. This can be done by appropriate ventilation, efficient filtration, and contaminant control. Air quality governance can facilitate an implementation platform to reduce the concentration of harmful pollutants, aiming to avoid their accumulation on HVAC equipment, ducts, and the indoor environment. Governance frameworks help set limits on these pollutants, ensuring that building designs, HVAC systems, and ventilation practices adhere to standards that maintain safe indoor environments.
The pandemic has presented new challenges for filtration technologies, HVAC equipment, and building standards for which they were unprepared. It has highlighted the need to adapt practices to fully realize the benefits of technologies and
It is essential to note that individual behaviors play a significant role in developing respiratory issues and incurring healthcare costs compared to the quality of the built environments. Social change through public awareness, education, and community engagement is not just important but also essential. It is the key to bridging the gaps between legislation and implementing HVAC, filtration, and building standards governing IAQ. standards for enhanced IAQ. We live in a fortunate era. Decades ago, minimal technology existed in buildings, limited to public telecommunications utility and a pneumatic control system for the HVAC system. Today, technologies influence the design of the built environment where automated processes automatically control buildings’ operations including HVAC, lighting, security, and other systems. Technologies will continue to drive innovations in building design, construction and operation in the future, and certainly in the way we manage and control IAQ. While IAQ gained significant attention during the pandemic, it did not fully define buildings or constitute a common dominator in the grand scheme of building safety metrics. Achieving optimal ventilation rates, filter selection and configuration is difficult due to the dynamic nature of living and working in buildings, as simulating these dynamics is rather complex. The demand for fresh, clean, and sustainable air has led to new building standards for ventilation and filtration. However, we must acknowledge that we have yet to tailor ventilation rates, filtration efficiencies, and configuration for each application. There is a great deal to learn, particularly when addressing the reliance on conventional maintenance measures and simply committing to meeting the thermal comfort commitments. To enhance our health and wellbeing, we need individuals who can think systematically and grasp the essential IAQ
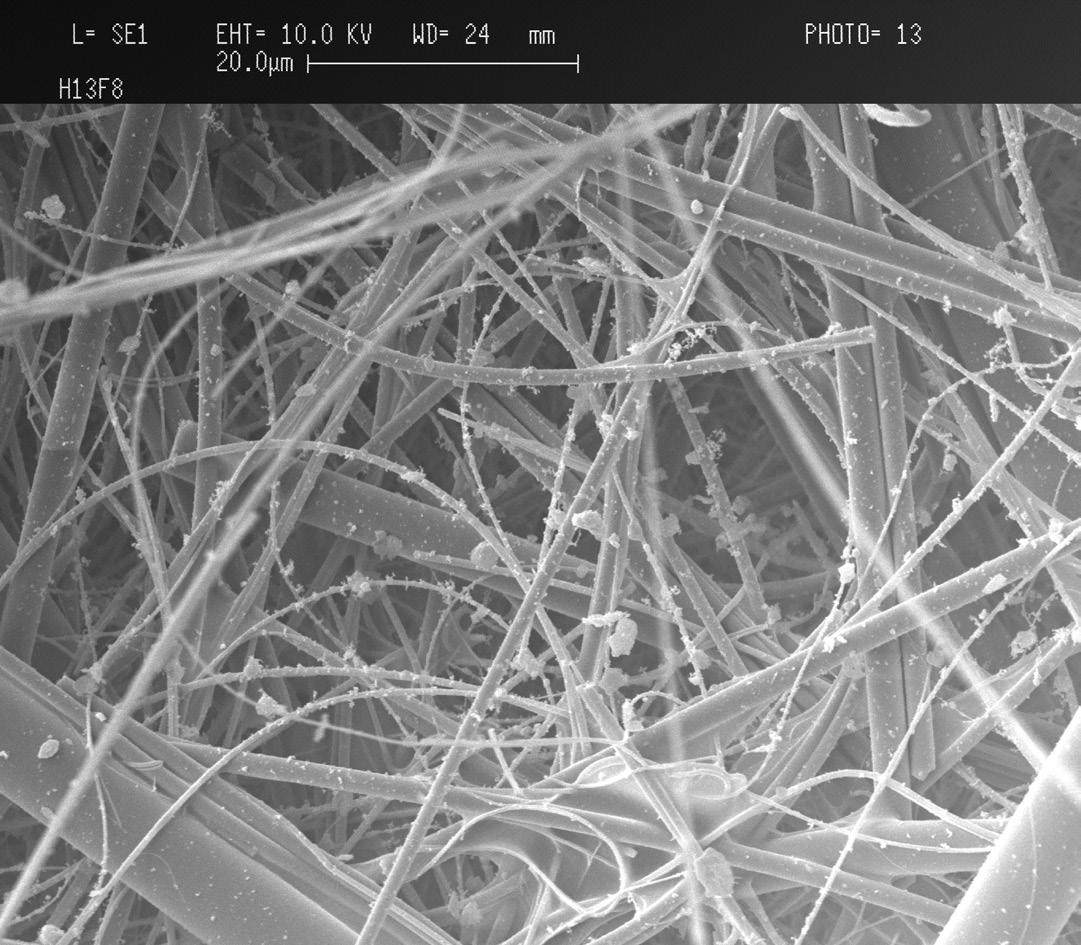
initiatives and concepts connected to the operation of buildings as integrated systems. By giving precedence to IAQ, we can position HVAC and filtration systems to adjust to fluctuations in air quality driven by data-informed feedback loops of indoor pollutant concentrations.
A primary challenge in advancing air quality governance is the fragmentation of authority between local, national, and international bodies. Each level of governance may have different priorities and resources, leading to inconsistencies in implementing air quality standards. Additionally, there is often a need for more public awareness regarding the importance of IAQ in virus transmission. As a result, regulatory bodies face challenges in enforcing policies that require costly upgrades to infrastructure, such as
retrofitting HVAC systems in schools and office buildings. Financial institutions can play a role in funding the retrofits necessary for building owners to undertake their IAQ obligation, where governments can monitor the IAQ outcomes afterward.
Moreover, standardization of measurement protocols is critical. While multiple studies underscore the need for improved IAQ3,4 the lack of standardized methods to measure viral particles in the air complicates enforcement. Governance frameworks should address these deficiencies by establishing universally accepted IAQ metrics and monitoring technologies that enable real-time air quality assessment in enclosed environments. Clearly and most importantly, no one can enhance IAQ without characterizing airborne pollutants’ physical and chemical characteristics. Moreover, continuous and reliable air quality monitoring sets the stage for a future outlook of buildings beyond thermal comfort, particle capture, and a simple thermostat displaying current ambient temperature.
The governance of air quality has significant socioeconomic implications. Implementing strong IAQ regulations often requires substantial investment in infrastructure upgrades, especially for small businesses and public institutions. However, the long-term economic benefits of reducing viral transmission, minimizing healthcare costs, and ensuring public safety far
Figure 1: Scanning electro microscopic image illustrating the capture of fine particle on HEPA filter media (H13-EN1882). Dr. Iyad Al-Attar
outweigh the initial expenses. Studies, such as those by Milton et al. and Wang et al.5,6 suggest that improved IAQ can lead to lower absenteeism, enhanced productivity, and cognitive function. Therefore, governments must balance short-term financial considerations with the long-term benefits of reducing the transmission of airborne pathogens.
Investing in air quality governance leads to healthier living and working environments and supports broader societal and environmental goals. These goals revolve around enhancing public health by reducing respiratory diseases and virus transmission while maintaining energy-efficient operations by integrating smart HVAC systems and IAQ initiatives. Ultimately, air quality governance can help ensure equitable access to clean indoor air, especially for vulnerable populations, and safeguard their health and wellbeing. However, it is essential to note that individual behaviors play a significant role in developing respiratory issues and incurring healthcare costs compared to the quality of the built environments. Social change through public awareness, education, and community engagement is not just important but also essential. It is the key to bridging the gaps between legislation and implementing HVAC, filtration, and building standards governing IAQ. This emphasis on public awareness and education should make all feel empowered and integral to reaching the desired IAQ outcomes.
Controlling IAQ in places like schools and hospitals can be challenging due to the simultaneous impact and exposure of multiple parameters and the influx of visitors. Managing IAQ can be complicated due to its dependency on various factors, such as the coexistence of particulates, gases, and bioaerosols, some of which are difficult to measure. Furthermore, fluctuating human occupancy indicated by carbon dioxide present in the building envelope emphasizes the need for demand-controlled ventilation systems, which are also intertwined with filtration systems. Additionally, the transient performance of air filters and
their premature clogging further complicates the maintenance of IAQ. Inconsistent air quality throughout the year, particularly in buildings without standardized regulations, and especially those that sustain massive infiltration leave occupants vulnerable to poor IAQ and accelerating the aging of facilities, including HVAC equipment and systems.
Air quality governance also addresses environmental impacts. Ensuring air quality regulations align with sustainability and climate goals promotes the use of low-emission building materials, reduces reliance on energy-intensive ventilation systems, and encourages the attainment of green building certifications. By managing indoor air quality to complement environmental objectives, governance frameworks can contribute to more sustainable urban development and help combat climate change by reducing carbon footprints.
Governance is expected to play an increasingly significant role in safeguarding the well-being of city dwellers and occupants. The benefits of improved IAQ will likely drive the implementation of more stringent regulations relevant to employing appropriate ventilation, efficient filtration, and contaminant control. However, social change is imperative to realize the fullest potential of current technologies, as smart buildings require responsible users to interact with the indoor environment. Therefore, we need to sharpen our tools and make the most of available technologies to achieve this.
As Abraham Lincoln suggested, "If I had eight hours to chop down a tree, I would spend the first six of them sharpening my axe." Air quality governance requires dedicated professionals and an informed community ready to diligently work toward providing sustainable, fresh, and clean air.
1. Niza, I.L., de Souza, M.P., da Luz, I.M. and Broday, E.E., 2024. Sick building syndrome and its impacts on health, well-being and productivity: A systematic literature review. Indoor and Built Environment, 33(2), pp.218-236.
2. Morawska, L., Allen, J., Bahnfleth, W., Bennett, B., Bluyssen, P.M., Boerstra, A., Buonanno, G., Cao, J., Dancer, S.J., Floto, A. and Franchimon, F., 2024. Mandating indoor air quality for public buildings. Science, 383(6690), pp.1418-1420.
3. Huang, J., 2023. Developing Disinfection Strategies for Controlling Human Norovirus Sars-Cov-2 and Clostridioides Difficile Endospores in Long-Term Care Facilities (Doctoral dissertation, Clemson University).
4. Alegbeleye, B.J., Akpoveso, O.O.P. and Mohammed, R.K., 2020. Coronavirus disease-19 outbreak: barriers to hand hygiene practices among healthcare professionals in sub-Saharan Africa. Int J Sci Adv, 1(1).
5. Milton D.K., Glencross P.M., & Walters M.D. (2000). “Risk of sick leave associated with outdoor air supply rate, humidification, and occupant complaints.” Occupational and Environmental Medicine.
6. Wang, C.C., Prather, K.A., Sznitman, J., Jimenez, J.L., Lakdawala, S.S., Tufekci, Z. and Marr, L.C., 2021. Airborne transmission of respiratory viruses. Science, 373(6558), p.eabd9149.
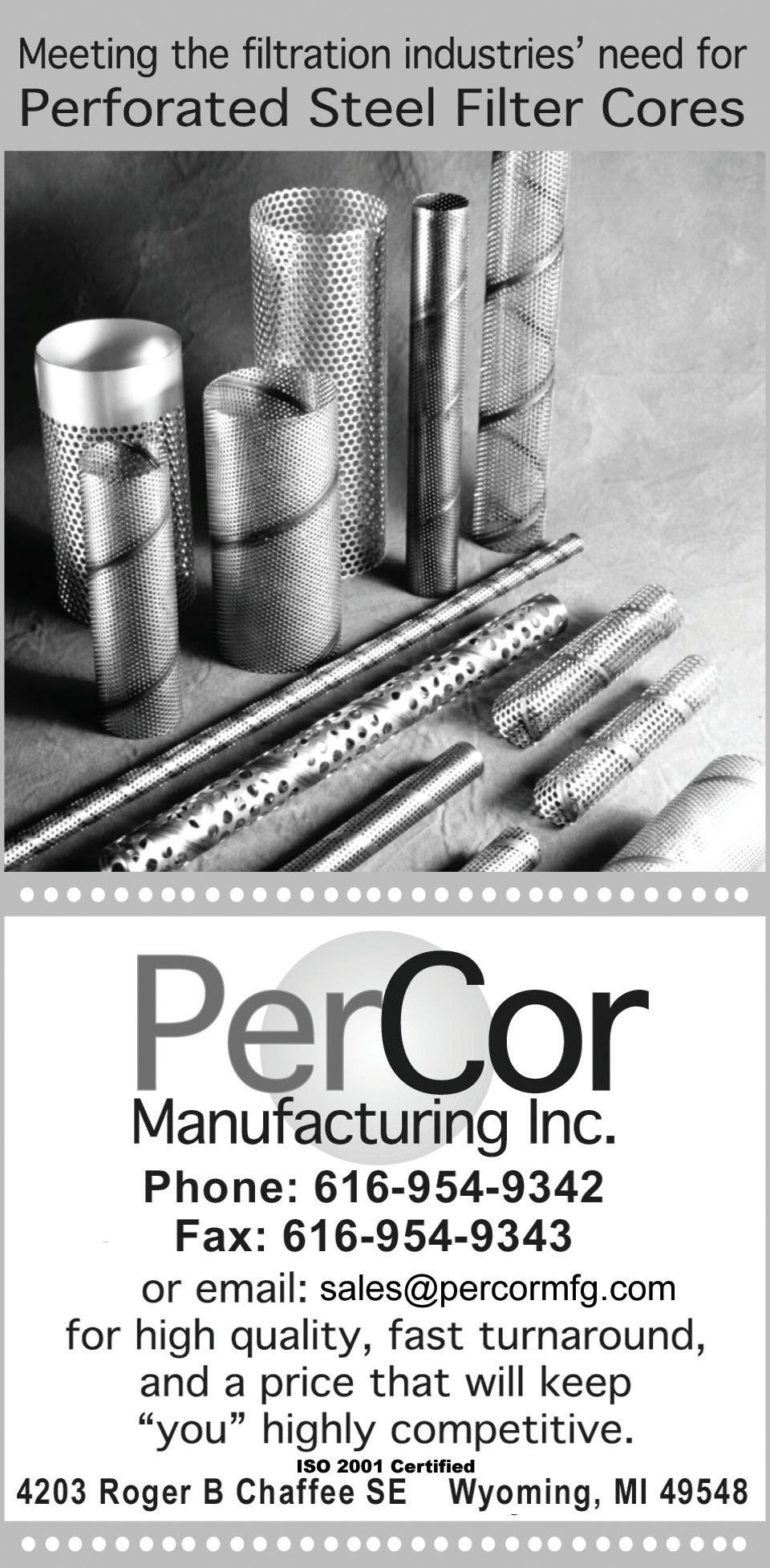
Nephros Delivers Critical Disaster Response After Hurricanes
Helene and Milton
Nephros, Inc., a leader in advanced filtration technology, has leveraged its significant disaster and emergency response capabilities to the Southeastern United States after recent hurricanes Helene and Milton. Nephros has provided crucial water filtration solutions to multiple healthcare and nursing care facilities affected by the storms, ensuring a safe supply of water to patients and staff amid recovery efforts.
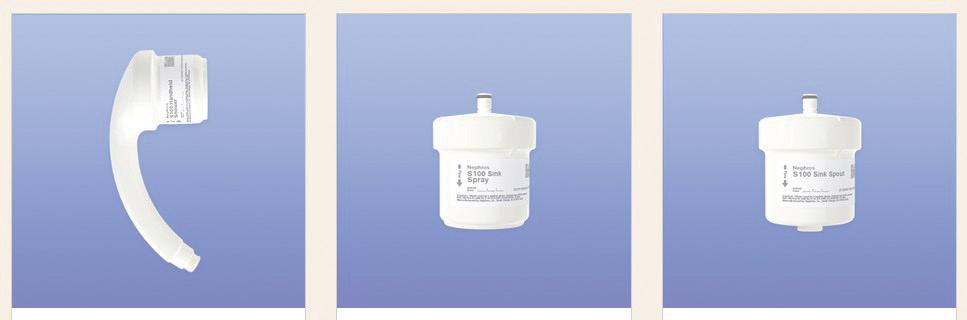
ously installed, facilities were prepared and protected when the hurricanes hit.
• Across North Carolina, Nephros pointof-use filters provided immediate protection against bacteria to get nursing and care facilities back up and running.
Water Filtration Systems Deployed to the Asheville Area
Christian relief ministry Samaritan’s Purse has expanded its relief efforts in western North Carolina after hurricane Helene, with the deployment of community water filtration systems to the town of Swannanoa and other hard-hit areas. Designed by a Samaritan’s Purse team of engineers, each water system can provide up to 50,000 liters of clean water daily –enough for 10,000 people.
Following natural disasters, access to clean, safe water is paramount for healthcare facilities, where contaminated water may severely compromise patient care and operations. The deployment of Nephros’ advanced filtration products enables and ensures reliable access to purified water during the most critical situations.
In recent weeks, Nephros has shipped a significant number of filters, responding after hours and delivering next day to both federal and local disaster response partners. To date, Nephros solutions have been deployed across multiple states within a variety of facility types.
For instance:
• Throughout Florida in hospitals where Nephros in-line filters had been previ-
BOFA Rebrands as Donaldson BOFA
PNephros’ ability to act quickly and provide essential filtration solutions for disaster response and emergency preparedness underscores its commitment to clean water access. Nephros infection control products are vital to the delivery of purified water for drinking, dialysis, surgical operations, and general facility hygiene, and offer an effective alternative to typical emergency water sources.
Critical to the company’s mission is the ability to provide high-quality water filtration in both routine and crisis situations. The speed and efficiency of the Nephros team allows for continuity of services in both everyday circumstances and compromised water events. www.nephros.com
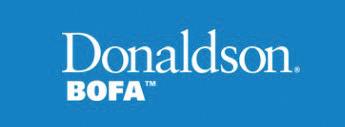
ortable industrial fume and dust extraction company BOFA, in Poole, Dorset, UK, announced a name change to Donaldson BOFA. The rebranding is said to reflect a closer alignment with its parent company, Donaldson. Additionally, the company announced the merger of BOFA International and BOFA Americas into Donaldson Filtration (GB) and Donaldson Company Inc, respectively.
Donaldson BOFA, with offices in the UK, U.S., and Germany, said it’s eyeing growing market opportunities thanks to the parent company’s presence in more than 40 countries. It has access to over 100 technical laboratories, and an R&D spend standing at more than $78m.
With this resource, Donaldson BOFA is able to test new materials and processes more cost effectively and anticipates potential reductions in the time for new products and system evolutions to reach the market.
Although Donaldson BOFA products are already sold to customers in 120 countries around the world, this closer alignment opens up new market opportunities for the business across a broader range of industries and applications. www.donaldsonbofa.com
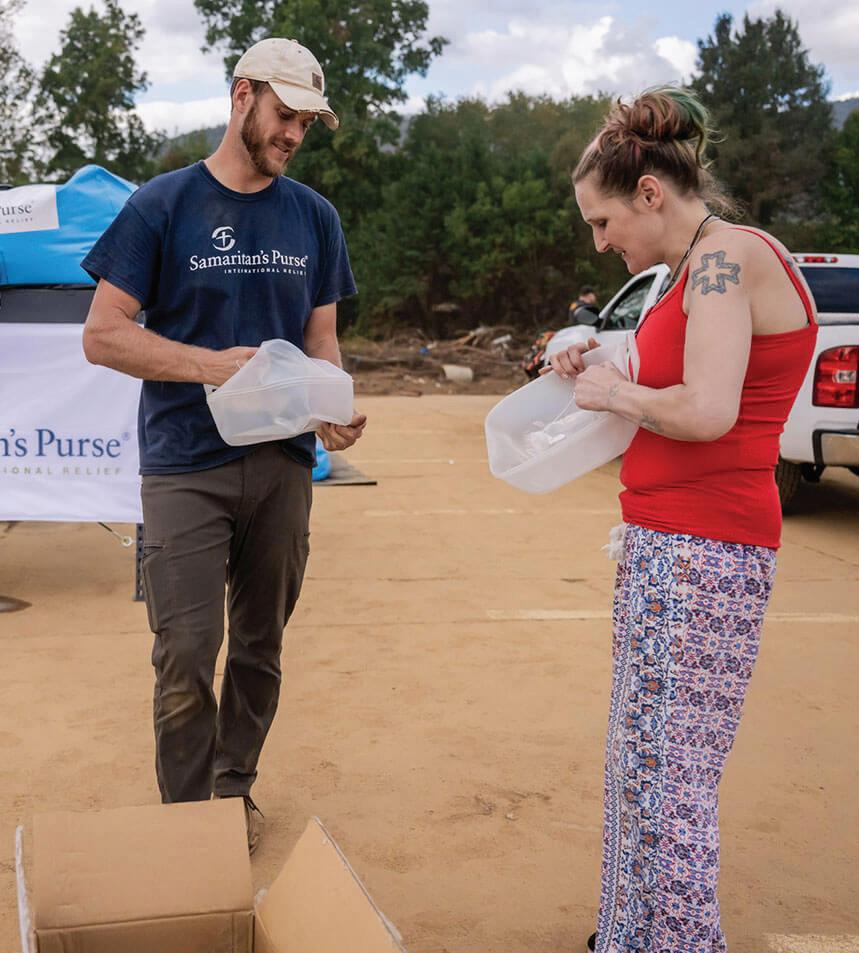
These units will serve as resources to communities including Swannanoa where the water pipeline network was destroyed during Hurricane Helene. They will help fill the gap as Buncombe County works to restore essential services such as water.
“We designed these systems to use overseas – and they work so well – but now the need is in our own backyard,” said Franklin Graham, president of Samaritan’s Purse. “We are airlifting supplies, mudding out homes, removing trees, and doing so much more and we’re thankful for everyone who is helping make it possible. We want to remind each person that we help that God loves and cares for them and hasn’t forgotten them.”
In addition to providing clean water, Samaritan’s Purse has flown supplies on 19 helicopter operations – sling loading emergency relief supplies to areas that have been cut off from basic necessities. They have airlifted infant hygiene kits, food, water, and medical supplies to fire departments, nursing homes, and some of the most isolated and hard-hit communities. www.samaritanspurse.org
Donaldson Announces New Distribution Center to Serve its Mobile Solutions Aftermarket Filter Business
Donaldson Company, Inc., a leading worldwide provider of innovative filtration solutions, announced the opening of its newest distribution center in Olive Branch, Mississippi. This new facility will further strengthen Donaldson’s ability to meet growing customer demand in the mobile solutions aftermarket business, including the heavyduty trucking, construction, mining, and agricultural equipment sectors.
The Olive Branch distribution center, located in the Memphis, Tennessee metropolitan area, will provide an additional 200,000 square feet of warehousing space to Donaldson’s distribution center footprint. Adding this new facility will provide the necessary room for the growth of the business while also providing the opportunity to further enhance the capabilities at the primary distribution center in Rensselaer, Indiana. The combined capabilities will enable more responsive service to customers and reinforce Donaldson’s commitment to operational excellence and customer satisfaction.
“Our industry-leading fill rates have been a cornerstone of Donaldson’s success in serving the mobile solutions aftermarket,” said Angela Zurick, vice president, mobile solutions aftermarket. “The addition of this new distribution center further enhances our ability to deliver products with speed and reliability, ensuring that our customers experience minimal downtime and maximum productivity. We are building on our reputation for unparalleled product availability, ensuring that our customers continue to receive the parts and filters they need, when they need them.” www.donaldson.com
Aquastill Acquires SolarSpring Membrane Distillation
Aquastill, one of the leaders in modular membrane distillation technology (using waste heat powering desalination of sea water and industrial wastewater), announced the acquisition of SolarSpring assets in the field of Membrane Distillation, following the insolvency proceedings of SolarSpring GmbH.
The assets acquired consist of the Intellectual Property (IP), laboratory equipment and selected R&D projects, which will be transferred to Aquastill BV in the Netherlands.
SolarSpring’s key people Rebecca Schwantes and Kirtiraj Chavan will support the transition and stay connected as advisors helping Aquastill to bring Membrane Distillation to the next level of technology readiness. www.aquastill.nl
Parker Hannifin is strengthening its position in the air filtration sector with the development of a comprehensive new testing program designed for advanced gas turbine filtration systems. Decades long experience and an extensive research and development has led Parker to creating an even more effective filtration systems for the future through this initiative.
At the center of the program is the clearcurrent Assure TriDustPlus filter, engineered specifically for the latest gas turbines. Parker’s newly developed testing regime goes beyond standard industry requirements to include additional investigations like hydrophobic and oleophobic tests, preventing contaminants
like saltwater and oil from entering the turbines.
The company has also pioneered an ice rejection test designed to assess filters’ performance in extreme conditions.
Aquaporin Enters Strategic Partnership with Brenntag
Aquaporin A/S, an innovative water technology company dedicated to rethinking water filtration with biotechnology, announced that Aquaporin has signed a distributorship agreement with Brenntag in APAC and in Turkey. The first membrane element order has already been shipped from Aquaporin to Turkey.
Brenntag has offices in more than 70 countries and works across many different industries, including water treatment. The global market leader in chemicals and ingredients distribution is driven by innovative technology and has decided to add Aquaporin’s CLEAR products to its portfolio.
Aquaporin is enthusiastic about the opportunities that this new strategic partnership with Brenntag will bring. This partnership is set to open new doors and significantly expand Aquaporin’s reach in the industrial element business. Already contributing to revenue numbers in 2024, Aquaporin expects this collaboration to contribute to a double-digit growth in 2025 in this segment.
Brenntag has an extensive line of water and wastewater treatment products and has the expertise to assist with many aspects in a broad spectrum of applications. www.aquaporin.com

The full suite of tests is focused on a single goal – ensuring that the filters still perform and achieve their primary function of dust removal and rejection under all conditions while minimizing disruptions to operation. Designed purposely within Parker for their products, these investigative techniques form part of a complete platform of
Gas turbine filtration systems
comprehensive tests that put their filters on a quantifiable performance footing. The outcomes of the test program were fed back into the development of the clearcurrent Assure TriDustPlus filter and guarantee its unmatched performance in the most challenging of conditions.
www.parker.com
Parker Hannifin Enhances Testing Capabilities
Reach Key Buyers & Decision-Makers in the Filtration Marketplace
Are you looking to position your company as a leader in the latest trends in the filtration industry? Do you want to connect with key decision-makers in your sector to improve and advance their filtration requirements?
Look no further than International Filtration News! IFN covers the topics, technologies, materials and equipment that shape the future of filtration and separation.
IFN is the leading source for dialogue, debate and innovation across the full spectrum of filtration and separation applications and processes. It is time to ramp up your reach!
CLASSIFIED MINI MART
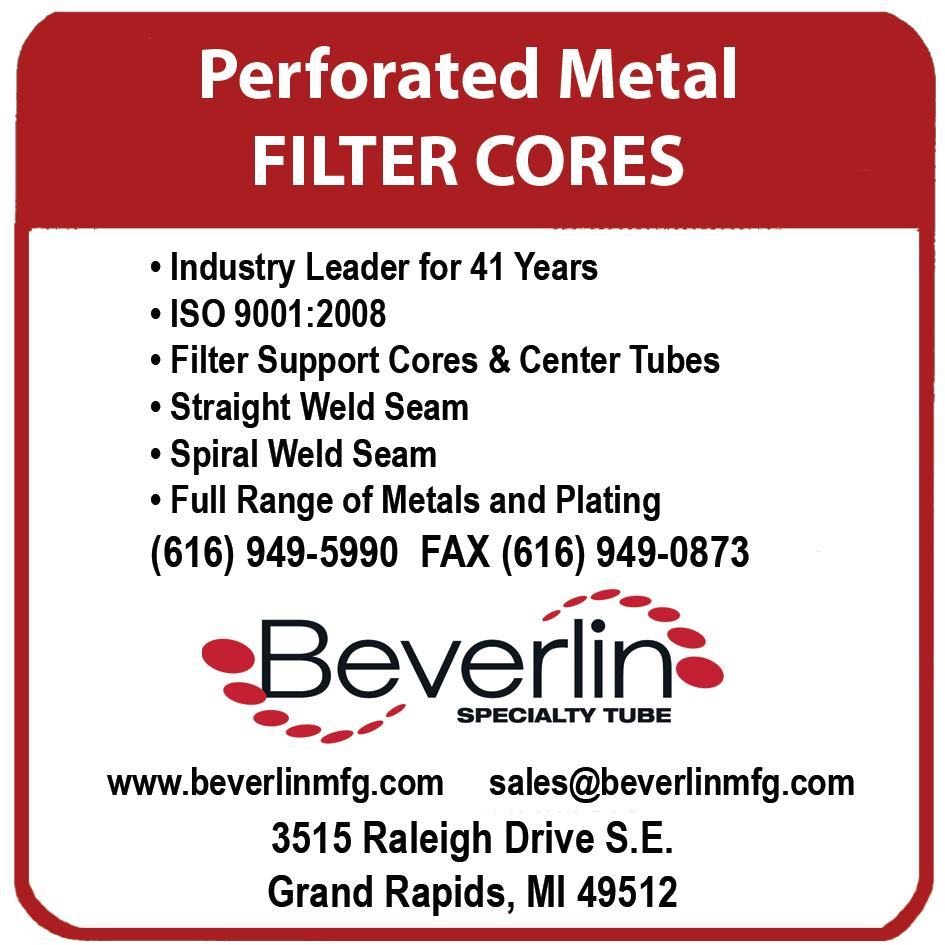
ADVERTISER INDEX
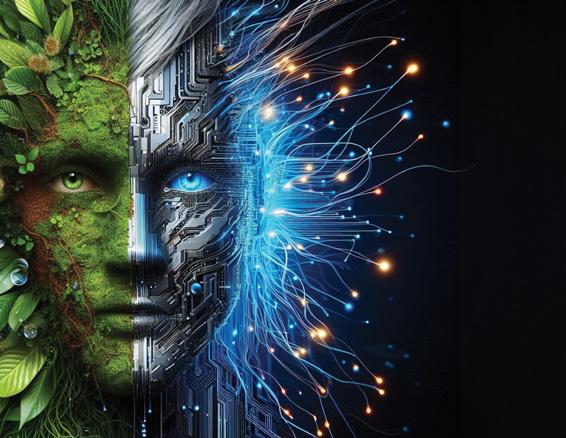

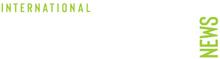
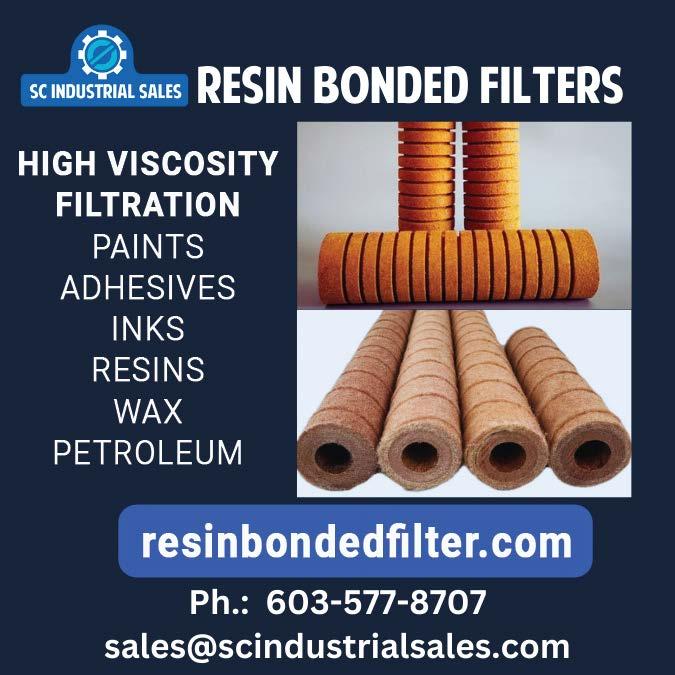
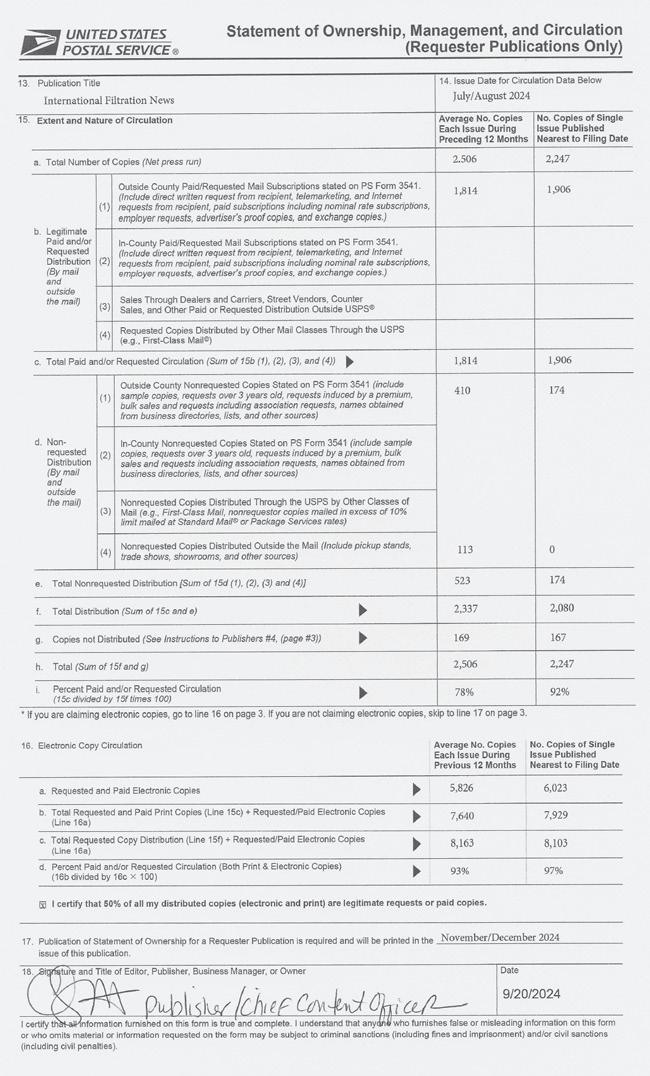


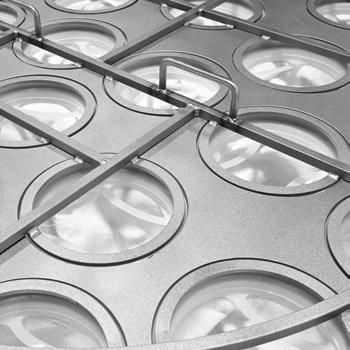
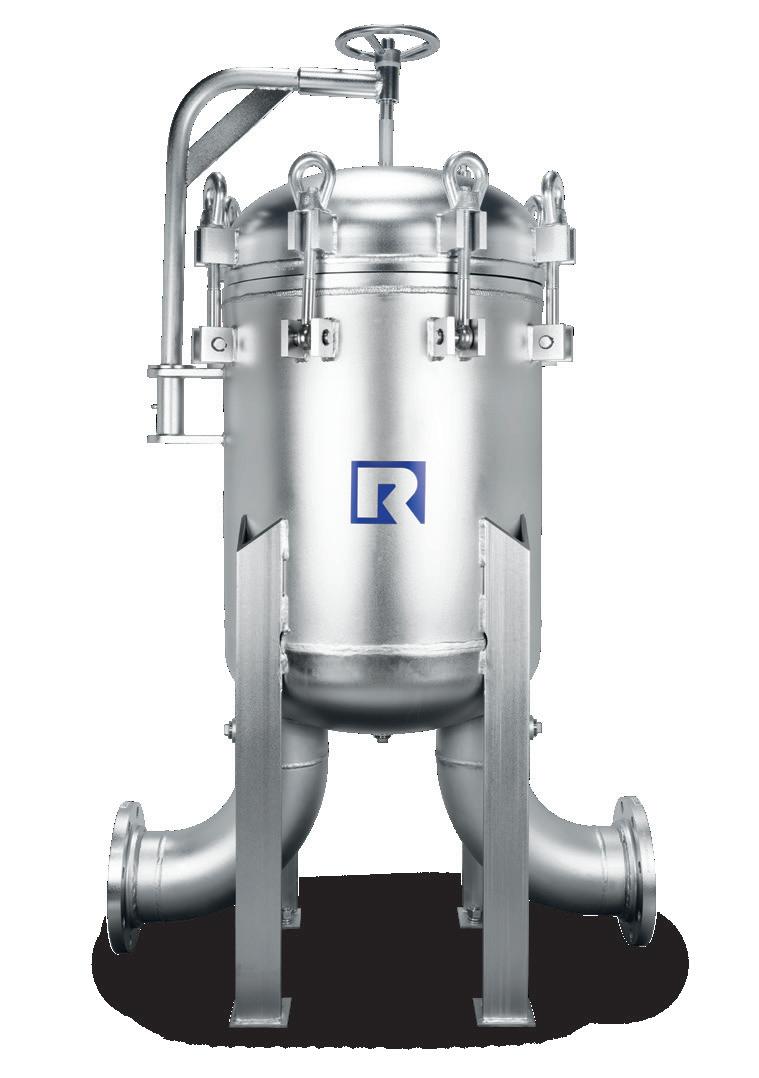
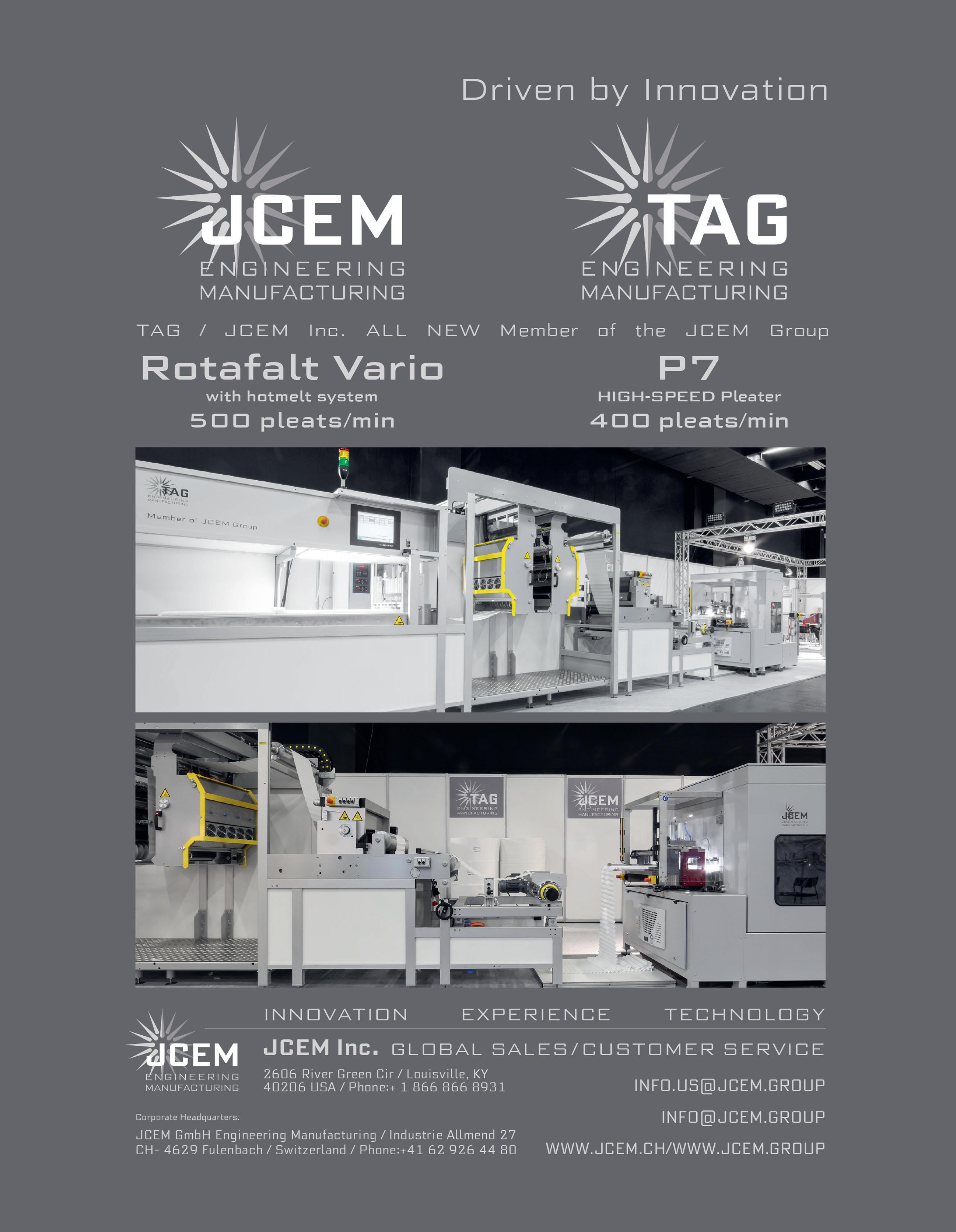