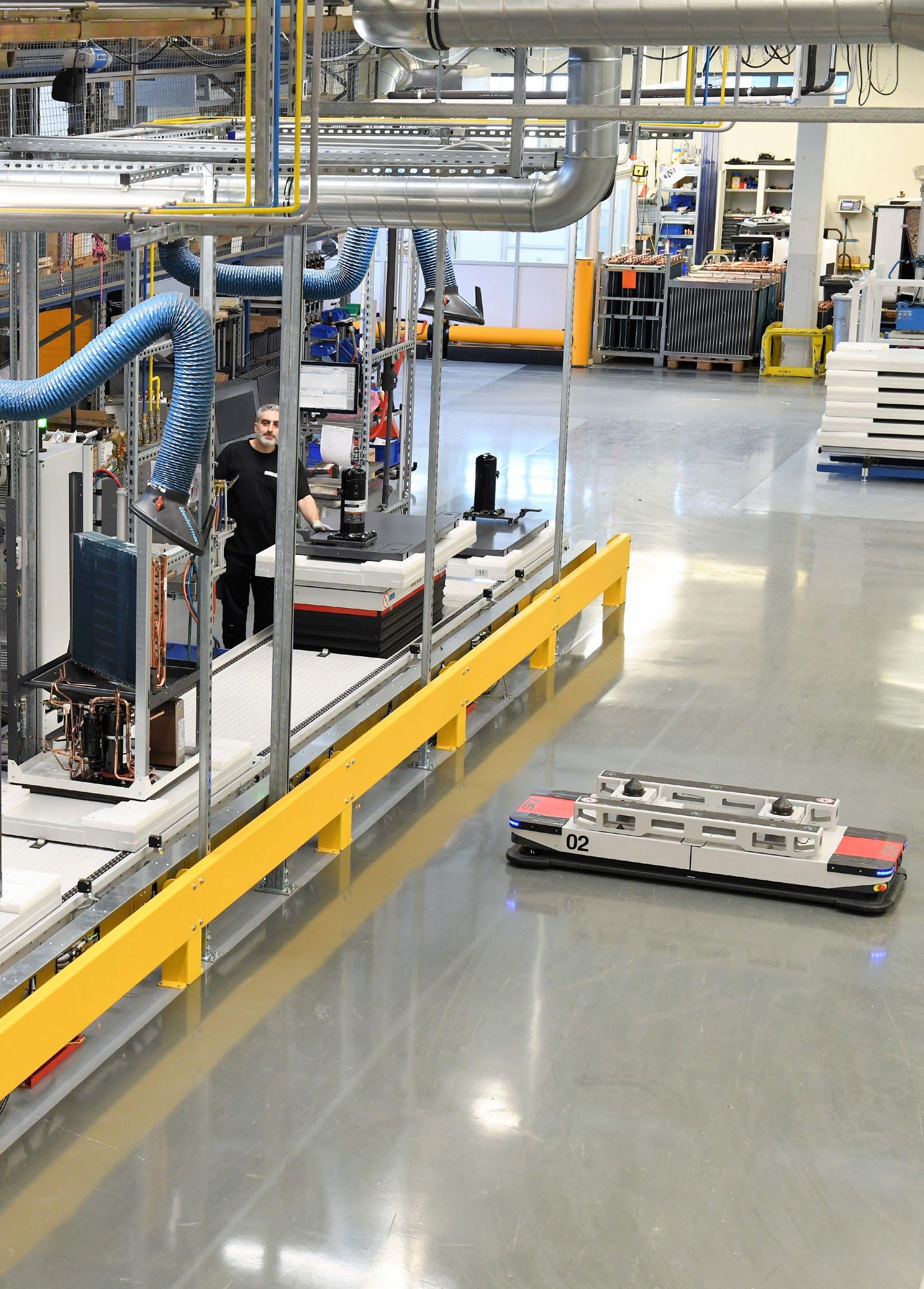
Chapter 1
Many manufacturers still operate with isolated IT solutions. However, an integrated process organization brings advantages, as can be seen especially in the cooperation between production and intralogistics.
SAP DM + SAP EWM
Chapter 2
To ensure that the right materials are in the right place at the right time, IT solutions need to interact with each other - this is how it is achieved.
Chapter 3
IGZ has increased its focus on the comprehensive control of material management. As a result, SAP DM has been given various functions to enable end-to-end process modeling for common integration scenarios.
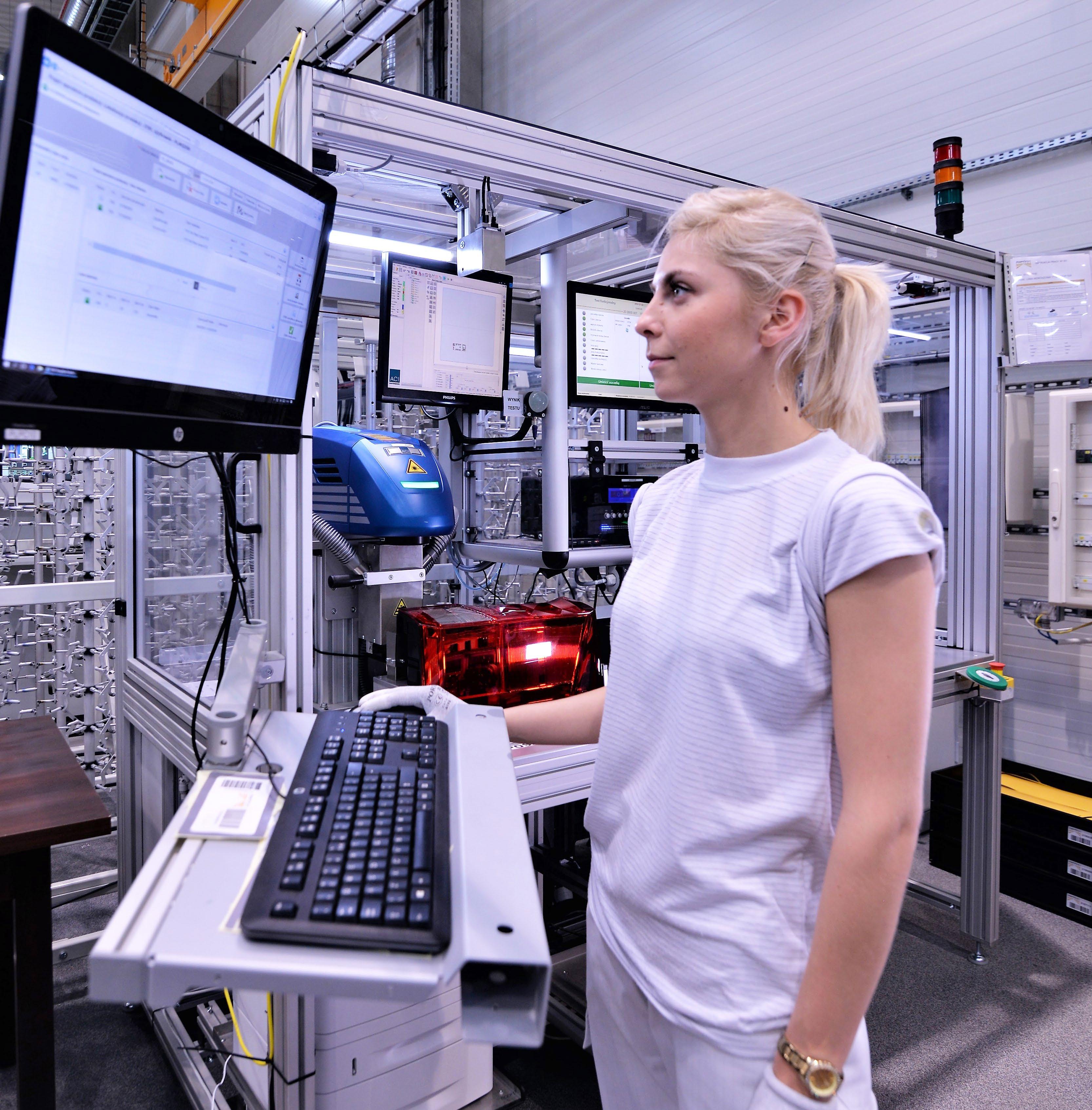
Given the challenging times we live in, integrated production logistics is an often underestimated factor for success. In this white paper, you will learn about the advantages of an integrated process organization (for example MES-triggered production supply) and how you can integrate and implement it with other SAP solutions.
The smart factory: from isolated solutions to a manufacturing platform
Fluctuating market demand, delivery bottlenecks from various suppliers and increased individualization of products – we are living in challenging times that are making it increasingly difficult for processes along the supply chain to run smoothly. One reason for this is the organizational structure of manufacturing companies as many manufacturers still focus too much on the set boundaries of their departments and operate with isolated IT solutions. The potential that remains untapped as a result and the advantages that an end-to-end process organization brings instead become particularly clear when it comes to collaboration between production and intralogistics.
END-TO-END PROCESS ORGANIZATION
Managing production and warehousing separately and operating them with two separate systems is still a common status quo. This contrasts with the concept of an intelligent factory, which is often referred to as a „smart factory“. This is because a smart factory is a concept in which a production facility produces almost automatically and continuously improves itself by the use of advanced technologies such as artificial intelligence, robotics, IoT and mass data analysis. Comprehensive automation creates advantages in terms of efficiency, flexibility, quality and safety and creates sustainable competitive advantages.
However, the basic prerequisite for this vision is the seamless interaction between production, logistics and IT as well as a high-performance IT infrastructure that enables large volumes of data to be analyzed quickly and reliably. This enables important and critical decisions to be made, which must not be restricted to specific departments, but should be exchanged between different systems through an open and standardized communication architecture and
reinterpreted in the respective context. Only in this way can process modeling be carried out end-to-end (E2E) and optimal coordination of processes from different departments be achieved. Ultimately, this is the goal of a smart factory, which subsequently leads to increased economic power of a manufacturer.
END-TO-END-PROCESS
An end-to-end (E2E) process is a process that includes all steps from the identification of a need or requirement to the final delivery or fulfillment. This allows cross-departmental and cross-system synergies and dependencies between the individual processes to be identified and utilized in order to achieve maximum efficiency.
WHY IS THE INTEGRATION OF PRODUCTION AND INTRALOGISTICS PROCESSES PARTICULARLY IMPORTANT?
Neither a company‘s production nor its intralogistics are independent of each other. Production and intralogistics are closely linked, as production relies on intralogistics to provide the materials and tools that are needed. Intralogistics relies on production to transport and store products within the factory. If this mutual dependency is not taken into account and the two departments act independently of each other, this can often lead to idle times and excess stock, resulting in higher costs of production and storage.
A PRACTICAL EXAMPLE IN THE CONTEXT OF „MATERIAL SUPPLY“:
THE CHALLENGE: PROBLEM DEFINITION:
Maximum material availability with minimum stock on the line
The problems that can arise due to silo thinking and isolated IT solutions become, among other things, clear in the context of „material supply“: while a company‘s manufacturing execution system (MES) supports the control of the production process and records consumption, the warehouse management software (WMS) is responsible for monitoring stock levels to ensure that the required materials are available at the right places in the plant. If the two systems do
not communicate with each other, either too much stock is stored at the production line or downtime is imminent because the required materials are no longer available before the WMS provides replenishment. Short-term changes to production planning exacerbate these risks, as changes to the production program are usually accompanied by different material requirements at the line, which often have to be provided within a very short period of time.

Central process control is achieved by integrating the three SAP systems for production, warehouse and business level.
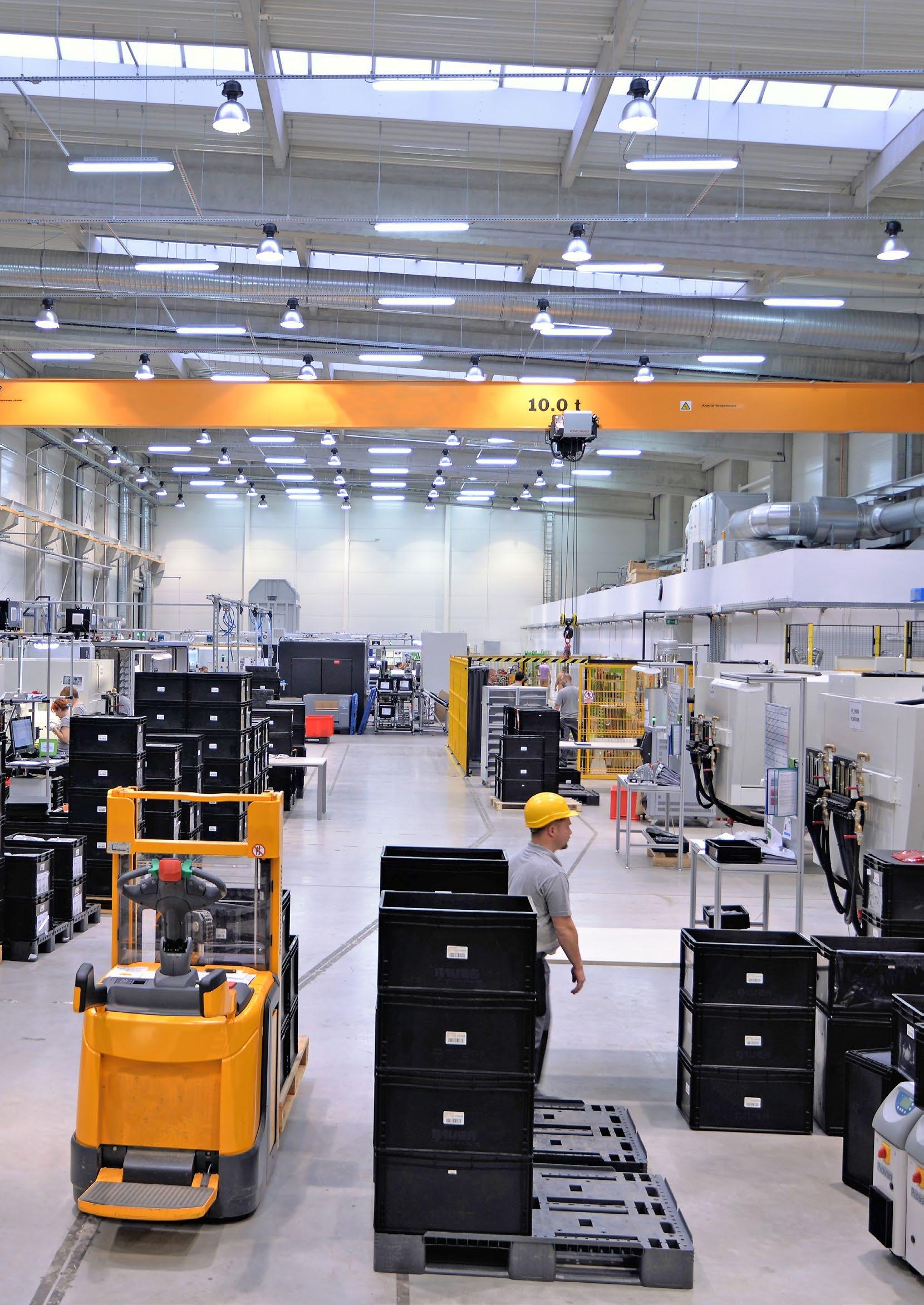
Pioneering work for interlinked warehouse and production processes
To ensure that the right materials are always available at the right workcenter at the right time during the production process, an interlocking system is required. IGZ recognized the central importance of this interaction at a very early stage. This is why the SAP engineers implemented the first highly integrated, cross-divisional SAP projects in production and logistics. The know-how built up in the process was implemented in the form of best-practice solutions based exclusively on SAP standard software, which have made a significant contribution to the functional scope of SAP standard products as we know them today.
HIGHLY OPTIMIZED ASSEMBLY WITH AUTOMATED PRODUCTION LOGISTICS
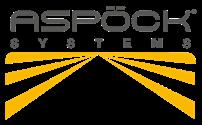
Aspöck Systems GmbH produces customized vehicle lighting systems for the European market. The manufacturer uses a fully SAP-based IT platform across several locations for process control. The solutions for production control (SAP MES), warehouse management (SAP EWM) and enterprise resource planning (SAP ERP) work together in an integrated manner. After the solutions had already led to significant savings at the main plant in Peuerbach they were also rolled out in Kluczbork, Poland. Due to the SAP strategy and the added value of an open IT platform, Aspöck decided to replace the proprietary and unsustainable production and warehouse management system and introduce SAP MES together with SAP EWM.
CONSISTENT PROCESS DATA IN THE SYSTEM
Central process control is achieved by integrating the three SAP systems for production, warehouse and administrative business level. All process and logistics data are available in the ERP system so that the manufacturer can enter production orders, including the work plan, directly from its main plant in Peuerbach for production at the Polish plant in Kluczbork. Online feedback on the production status of an order is provided ‚just in time‘, both from SAP MES and from SAP EWM to the SAP ERP system. For this purpose, the operating data is recorded at the worker terminals (PODs) and reported online. Stock levels are always kept up to date via standard interfaces. Production data acquisition (PDA) of process data at the worker terminal ensures traceability throughout the entire manufacturing process. In addition, each production step can be traced in order to identify the cause of a non conformant batch. QM inspection lots, data acquisition and quality management checks from SAP ERP were integrated for this purpose, which automatically trigger workflows in the MES system.
MINIMIZATION OF ERRORS THANKS TO IT-SUPPORTED RECORDING
The MES enables the company to prioritize production orders and define the sequence of individual work processes in the work plan. The configuration of the PODs makes it possible to display exactly the information that is important to each employee at the worker terminal. Workstation-specific information includes documents such as work instructions, circuit diagrams and product and component illustrations as well as packing specifications, which are integrated in the ERP system as links in a production order. In this way, the master documents remain centrally stored in SAP ERP.
In the background, an automatic version management ensures that employees always receive the current revision status of the associated documents. Thus is ensured that all documents are up-to-date and available automatically and electronically in the correct version and quantity. Today, the MES application controls all assembly workstations with the online recording of production data and without paper-based documents. Pending orders are displayed on touchscreens in form of an orderlist. When an employee is assigned an order, the material supply is automatically triggered via SAP EWM. The integration of SAP MES and SAP EWM therefore
ensures that the workers are always supplied with the right components from the warehouse for the current order and that the workflow continues seamlessly even at the start of a new order.
In addition, the intelligent SAP EWM and MES process interlocking, based on the work plans specified by SAP ERP, ensures that further processing at the subsequent workstation is blocked until all current production and inspection steps have been completed. Process interlocking prevents test and inspection steps from being forgotten and faulty parts from being passed on through the production stages. The potential for errors is reduced thanks to the largely automated recording and evaluation of process and logistics data, which is evident in the manual processes. For example, employees no longer have to enter data manually to print container labels. Thanks to the integrated MES solution, the information for labeling is automatically transmitted to the warehouse management software and the appropriate label is printed out without any further intervention. This prevents incorrect pallet or packaging labeling due to an incorrect QR or barcode.
LEAD TIMES & INVENTORY REDUCED BY 25%
A measurably successful project: by establishing a central IT platform for production and logistics and the associated optimization of processes, the throughput times of production orders were significantly reduced. The added value achieved through the highly integrated, cross-departmental switch to SAP standard software from IGZ can also be expressed in key performance indicators: for example, the lead time and material stock at the Peuerbach site were each reduced by 25 percent, while the workload for planning a production order was optimized by 50 percent. A further advantage is the system maintainability and the possibility created for Aspöck to expand the system itself, as the company will be able to draw on its own SAP expertise in future.
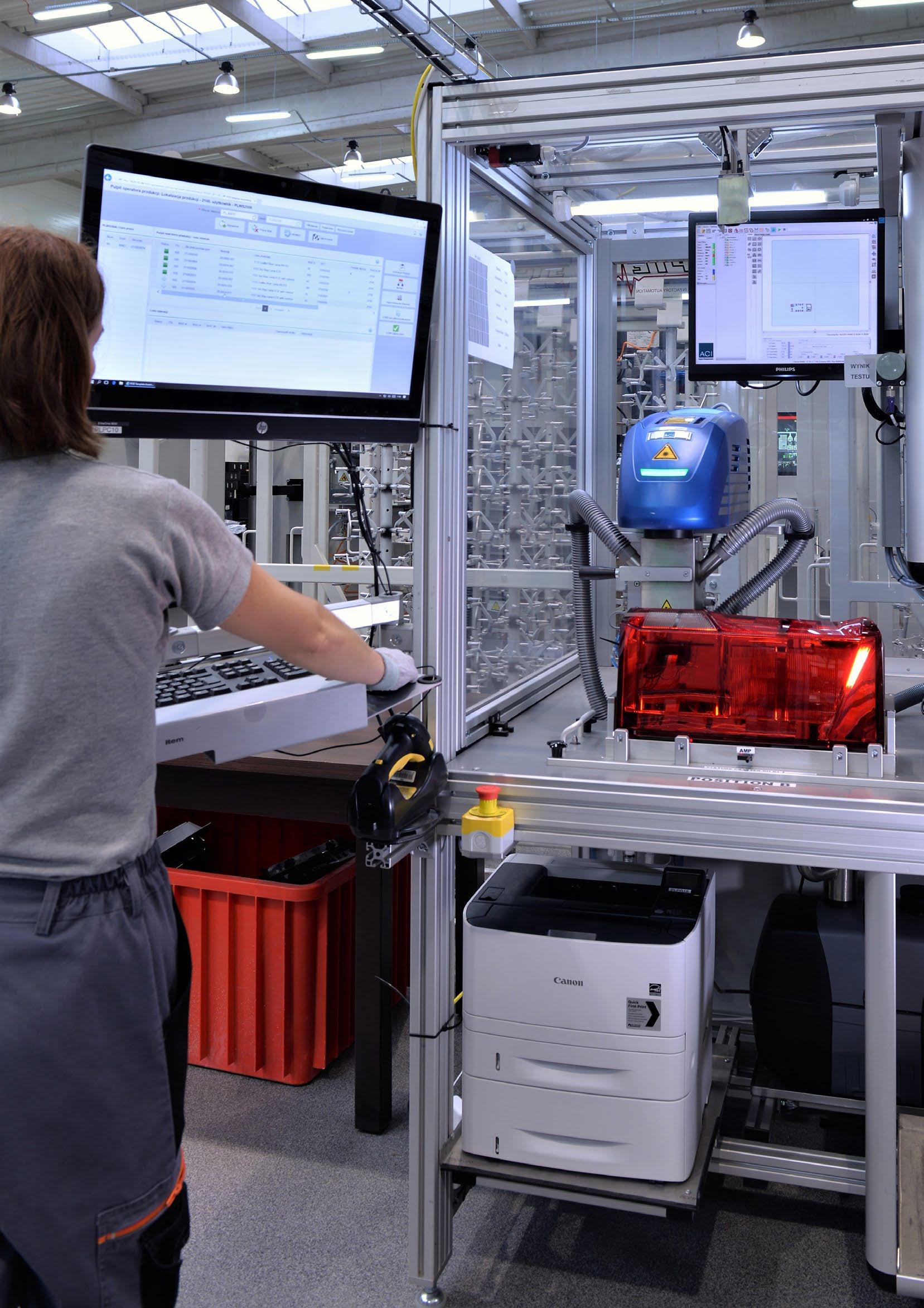
„
Production data acquisition of process data at the worker terminal ensures traceability throughout the entire manufacturing process.
FULLY CONNECTED PRODUCTION AND LOGISTICS PROCESSES
Dormakaba has also recognized the benefits of integrating MES and WMS and has taken an important step towards the „smart factory“ with the consolidated introduction of SAP Digital Manufacturing (SAP MES) and SAP Extended Warehouse Management (SAP EWM). For the Swiss manufacturer of safety solutions, batch size 1 is not a trend, but has long been a required reality. Around 95 percent of the products in Wetzikon are manufactured individually; there is virtually no warehousing of finished goods. More than 1,000 customer orders are processed every day. This results in over 3,000 production orders in the same period. These figures alone indicate the enormous challenges involved. Added to this are the customer-specific coding (permutation) and the variety of variants associated with „batch size 1“, which amounts to n x 100,000.
SAP STRATEGY REPLACES LEGACY SYSTEMS
To meet these challenging production requirements, dormakaba previously used several self-programmed solutions: an order and production platform with specialized MES support and a system for managing the production and distribution warehouses. Although these solutions led to more effective production processes, they had the disadvantage of creating a complex process and system landscape over time, which the company no longer considered sustainable.
The logistics and production functionalities mapped in the old individual systems could no longer be integrated into a new, group-wide process strategy based on the SAP ERP solution. In addition, it was difficult to integrate products and processes into the production and logistics IT. Following a deployment analysis, the recommended overall concept from IGZ was followed and the decision was made to introduce SAP MES and SAP EWM in phases.

SYNCHRONIZED SYSTEM COMMUNICATION BETWEEN
SAP MES & SAP EWM
In the first step of the cross-departmental project, SAP MES was implemented in the production areas without a direct connection to the existing warehouse system. This was implemented using web service technology and SAP Plant Connectivity (SAP PCo). As a result, the response time for data exchange between the plants and SAP MES was reduced to less than 200 milliseconds. At the same time, paperless production has already been implemented in the „Keys and Mechatronics“ area.
In the subsequent phase, the production control system was rolled out to all other sections and the previous warehouse management system was replaced by SAP EWM to enable direct and close online integration between SAP MES and SAP EWM. The supply and loading of the production lines in the fully automated key production is carried out intelligently via automated guided vehicles (AGV) directly via SAP MES. The migration to SAP standard software also offered the opportunity to optimize the „scrap and replacement process“ (SRP). This is a subsequent step required by rework, in which the re-production of order-specific components is initiated. These are now subjects to special control of the material flow with SAP EWM directly to the SRP station. However, the only front end for the operational employees is SAP MES; they have no contact with SAP EWM, as all material movements are automatically controlled via SAP MES in the background thanks to end-to-end process modeling.
This seamless end-to-end integration could only be realized through the close integration of the two SAP solutions (MES + EWM) and is a decisive step towards the „Smart Factory“ for dormakaba.
RESULT: PAPERLESS PRODUCTION AND MORE TRANSPARENCY
The implemented platform acts as a link between warehouse stocks, shopfloor and ERP, provides information in real time and controls paperless production in lot size 1 fully automatically. The transparency also ensures that faster and better decisions can be made in order to be able to intervene manually. Associated follow-up processes, such as the return of components that are no longer required due to a last-minute order change, are clearly defined and implemented fully automatically through cross-system communication.
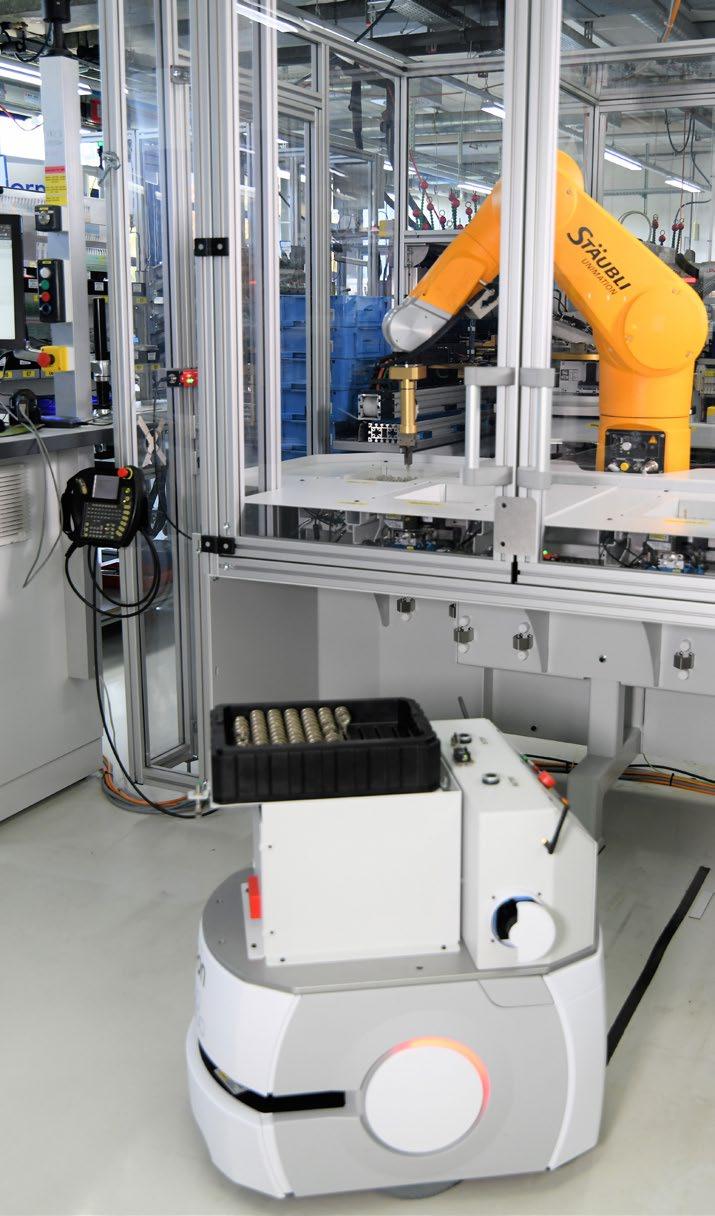
The interaction of production (SAP DM) and logistics (SAP EWM)
IGZ‘s pioneering project work has increased the focus on the comprehensive control of intrafactory material movements - and thus further expanded the functional scope of the corresponding SAP standard solutions. The functions have also been incorporated into the cloud-based MES solution „SAP Digital Manufacturing“. The crossindustry production control system already includes various functions „out-of-the-box“ to enable companies to implement end-to-end process modeling for common integration scenarios between production and logistics (in combination with SAP EWM).
PRODUCTION SUPPLY THROUGH MES-CONTROLLED STAGING
A classic example of the digital mapping of overarching processes at shopfloor level in combination with intralogistics is MES-triggered staging for production supply. In this scenario, users utilize SAP DM as the leading system for material staging in production. Thanks to deep integration and a linked data structure with the warehouse management software SAP EWM, material requirements, data on stocks and goods movements from production can be synchronized with those in the warehouse in real time.
Once the production order has been created and released in SAP ERP (ECC or S/4HANA), it is transferred to SAP DM. At the same time, material staging is triggered via the ERP system, which creates a production material requisition (PMR) in SAP EWM. Depending on the desired configuration, the warehouse management software then meets the demand in the next step by either fulfilling individual requests directly (single-order staging) or supplying several orders in one go (multi-order staging).
In the second scenario, the staging requirements are first consolidated in the warehouse and the respective outbound deliveries are optimized using wave management integrated in SAP EWM, taking into account various criteria such as the number of components to be provided. In this way, picking in the warehouse as well as the internal flow of goods and the associated transport workflows can be organized efficiently
at shopfloor level. By using a scanning process to link the production order and the components loaded for it in SAP EWM, the employee can also ensure complete traceability of all components used.
The actual delivery to the line can take the form of pallets and containers or be automated using automated guided vehicles (AGVs). As a result, all components of the requested production orders are provided in the sequence specified by SAP DM for subsequent assembly at the desired workstations and, if necessary, further provisioning requirements are also transferred to SAP EWM fully automatically.
iWAVE MANAGEMENT
A wave is a grouping of warehouse request items that are processed together in subsequent processes. This grouping is used to manage warehouse and intralogistics activities effectively, such as picking, transfer postings and the internal material flow.
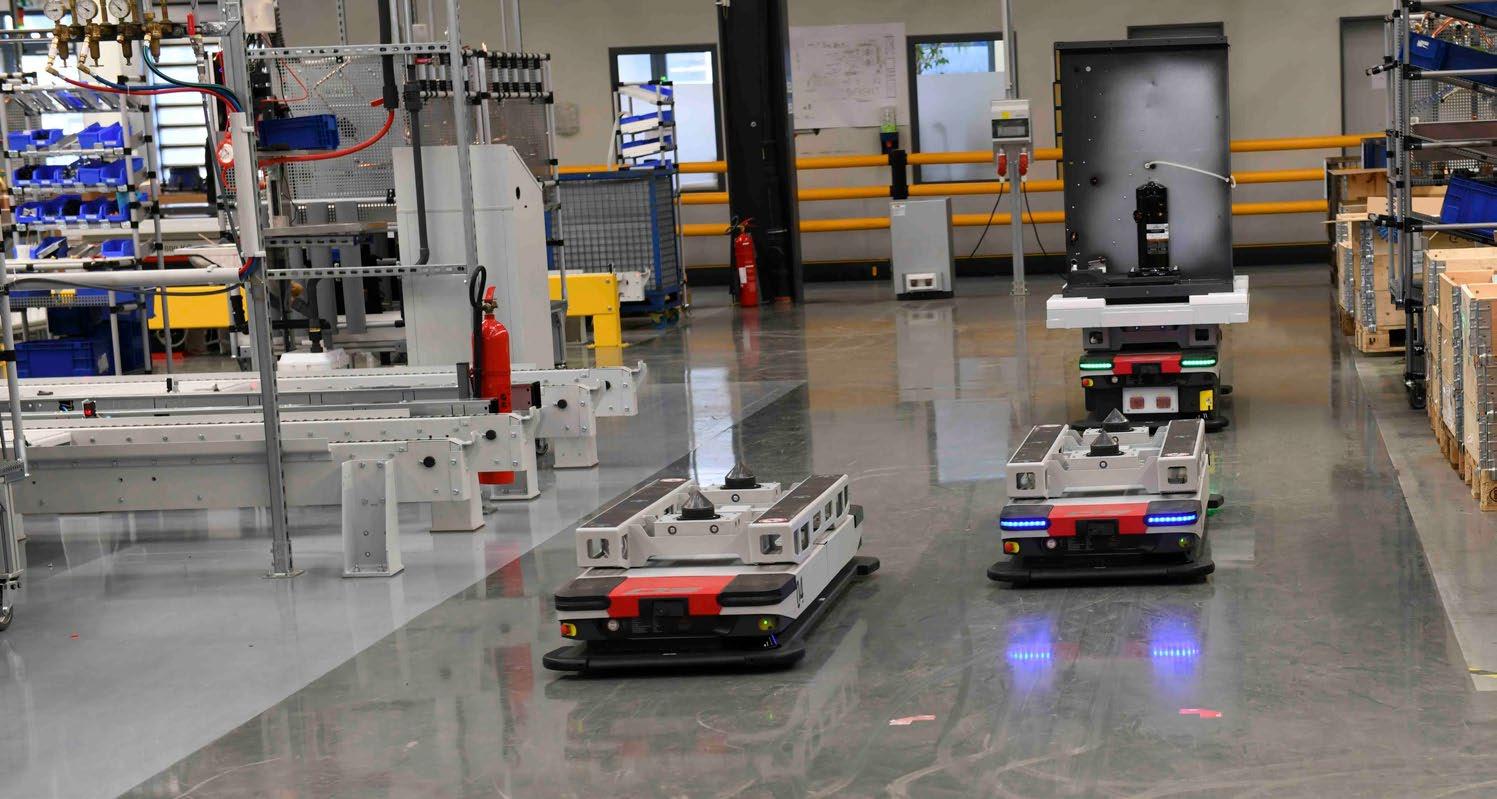
Production order is created and released
Order is triggered
Order is created
Production material request is created, staging method is retur ned
Order is updated
Staging request is created
Stock request is created
Wave management (optional)
Warehouse task is created
Transfer from EWM storage location to EWM production storage location
DM updates the staging request
DM creates stock/ updates this
PSA stock is ready
PRODUCTION SUPPLY THROUGH DYNAMIC STAGING
React as quickly as possible to unplanned events without affecting production performance: This is exactly what the integration of SAP DM to SAP EWM offers with the option of dynamic staging. The concept updates the staging request created by SAP DM continuouslyif necessary, taking into account the latest information such as the scheduling and distribution of orders – in particular the assignment of interrelationships between resources, work centers and production supply areas (PSA).
The „Scheduling and Monitoring“ application of the REO module can be used to flexibly reschedule the work center intended to carry out an order operation. Thanks to the integration between SAP DM and SAP EWM, the planned PSA of the components is automatically adjusted before the staging of SAP EWM is triggered.
Production order is created and released
Order is triggered
Order is created
Production material request is created, staging method is retur ned
Order is updated
Staging request is created If required: Change PSA (using SAP REO)
Stock request is created
Wave management (optional)
Warehouse task is created
DM updates the staging request
DM creates stock/ updates this Transfer from EWM storage location to EWM production storage location
PSA stock is ready

The interaction of production (SAP DM) and logistics (SAP EWM)
USE CASES
The main benefit of dynamic staging compared to the MES-triggered staging described above is the enhanced responsiveness. It enables flexible changes to the PSA to be supplied. When and how dynamic staging is adding value in practice is illustrated below using two examples in which dynamic staging comes into play:
2
SHORT-TERM ALLOCATION OF THE PROCESS TO SEVERAL RESOURCES
To carry out operation A, 90 pieces of a component are required. Initially, the execution of operation A was scheduled for work center A, which is why the supply of the required components has been scheduled in PSA A. If, for example, the delivery date to be met is postponed due to external circumstances, the current planning threatens to exceed the agreed delivery deadline. In this case, it is beneficial to prioritize the order and use other available capacities for the production of the order. For this scenario, the Dispatching and Monitoring (REO) application offers the functionality of dividing an operation into several „split operations“, which in total still comprise the quantity of the production order.
1
SHORT-TERM RESCHEDULING OF AN OPERATION TO A NEW RESOURCE
To carry out operation A, 90 pieces of a component are required. Initally, operation A was scheduled to be carried out at work center A with PSA A. However, due to an unscheduled event (malfunction of a machine, defect of a tool, etc.), work center A is unavailable, which is why operation A has to be rescheduled at short notice. Using the Dispatching and Monitoring (REO) application, operation A can be flexibly moved to and scheduled for resource B. The rescheduling of operation A within SAP DM also automatically adjusts the staging request so that the 90 pieces of the required component for operation A are now also automatically staged by SAP EWM in PSA B for work center B.

If the production manager splits operation A, the individual “split operations” can be scheduled to several available work centers (operation A1 -> work center A, operation A2 -> work center B, operation A3 -> work center C) and the production order can be completed earlier. Thanks to the bidirectional communication between the two SAP solutions (SAP DM + SAP EWM), this division and rescheduling also automatically adjusts the staging request so that the 90 pieces of the required component for operation A are now staged for the individual split operations as follows: 30 pieces in PSA A, 30 pieces in PSA B and 30 pieces in PSA C.



Summary of SAP DM + SAP EWM
In conclusion, the seamless integration of SAP DM and EWM makes it possible that cross-system processes such as MEStriggered staging can be mapped end-to-end. By automating complex, multi-faceted processes across multiple IT-systems, the efficiency of production can be significantly increased and, at the same time, human errors can be minimized through digital process management.
An extended integration scenario for even more flexibility is dynamic staging: reactive rescheduling, while taking all available capacities into account in real time, allows production managers to react faster to unforeseen events.

Would you like to find out more about SAP DM and SAP EWM and how they interact?
BENEFITS DUE TO THE INTEGRATION OF SAP DM + SAP EWM
Optimized production capacity utilization thanks to increased flexibility
Efficient order picking and demand-oriented staging
Automated staging based on MES planning data
„Single point of truth“: MES system is the leading system for material staging in production
Error reduction through consistent, cross-system processes based on SAP standard software
In-depth process and inventory transparency in warehouse and production
Maximum transparency of the staging process
Upgrade and release-compatible standard integration scenarios
For more information about SAP DM visit us online
For more information about SAP EWM visit us online:
CONTACT US FOR FURTHER INFORMATION!
Do you still have questions?
Or would you like more information on the topics of production and logistics?
If you are currently working on the digitalization of your production processes, please contact us. We will advise you and explain how we have already solved demanding challenges in the production environment based on SAP standard software together with our customers. We look forward to hearing from you!
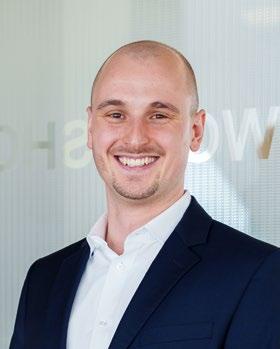
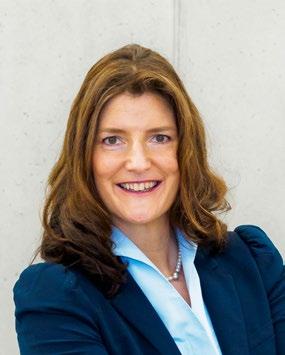
Copyright © 2023, IGZ Ingenieurgesellschaft mbH.
All rights reserved
Publisher: IGZ Ingenieurgesellschaft mbH
IGZ Ingenieurgesellschaft für logistische Informationssysteme mbH Logistikweg 1
95685 Falkenberg
Tel.: +49 9637 9292 - 0 | info@igz.com | www.igz.com