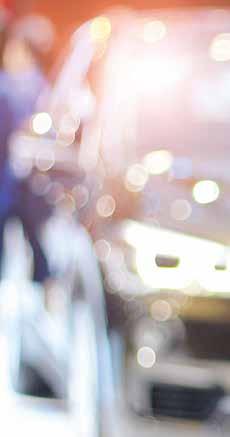
33 minute read
Competitividad a través de digitalización integral Competitiveness through comprehensive digitization
DIRECTIVOS TÉCNICOS DE CUATRO PROVEEDORES DE AUTOMOCIÓN INTERACTÚAN CON EL EXPERTO EN SOFTWARE DE GESTIÓN INFOR.
TECHNICAL MANAGERS FROM FOUR AUTOMOTIVE SUPPLIERS INTERACT WITH MANAGEMENT SOFTWARE EXPERT INFOR
AutoRevista organizó, el 2 de noviembre, una mesa redonda con el patrocinio de Infor, un especialista global de máximo nivel en software de gestión en la que se debatió como la tendencia hacia mayores niveles de digitalización integral pueden revertir en mejores índices de competitividad. En el encuentro participaron Jesús Fernández. director de Desarrollo Corporativo y Transformación Digital de Fagor Ederlan, Diego Mallada, IT Digital Director de Gestamp, Jorge Pérez Velasco, Manager Industry 4.0 de Gonvarri, y Germán Arias, director técnico de Michelin en Valladolid. Debatieron con Sebas Alsina, y Eladio Valencia, director de CloudSuite Automotive Solution y responsable de Ventas en Infor Iberia, respectivamente. / On 2 November, AutoRevista organised a round table with the sponsorship of Infor, a top-level global specialist in management software, in which how the trend towards higher levels of comprehensive digitisation can lead to increased competitiveness indices was discussed. Participating in the meeting were Jesús Fernández, Director of Corporate Development and Digital Transformation at Fagor Ederlan; Diego Mallada, IT Digital Director at Gestamp; Jorge Pérez Velasco, Manager Industry 4.0 at Gonvarri; and Germán Arias, Plant Technical Manager at Michelin in Valladolid. They held discussions with Sebas Alsina, and Eladio Valencia, director of CloudSuite Automotive Solution and head of Sales at Infor Iberia, respectively.
POR L.M.G. / FOTOS-PHOTOS: FAGOR EDERLAN, GESTAMP, GONVARRI, INFOR Y MICHELIN / TRADUCCIÓN-TRANSLATION: EIKATRAD SCP
Diego Mallada (Gestamp) comentó que “Gestamp lleva años apostando por la transformación digital. Contamos con un área de Industria 4.0 y de Fabricación Avanzada. Dentro de ese ecosistema disponemos de un área de IT para configurar plataformas, arquitecturas, desarrollos relacionados con los ámbitos de IoT, Big D iego Mallada (Gestamp) commented that “Gestamp has been committed to digital transformation for years. We have an Industry 4.0 area for Advanced Manufacturing. Within this ecosystem we have an IT area to configure platforms, architectures, developments related to the fields of IoT, Big
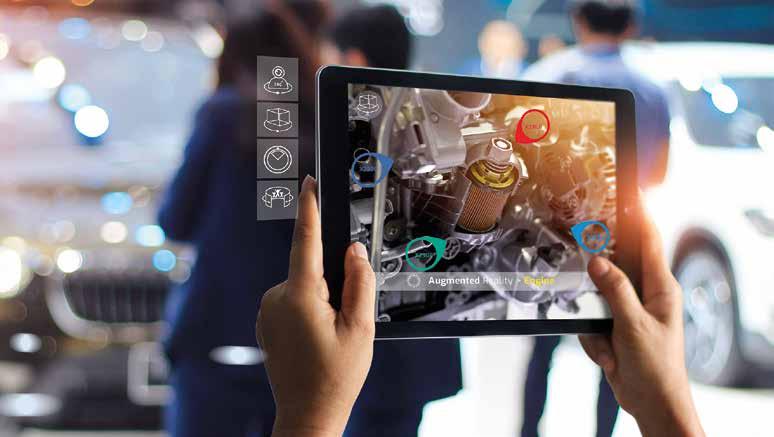
Data, inteligencia artificial, usabilidad y experiencia de usuario”. Jesús Fernández (Fagor Ederlan) señaló que, en su empresa, parte de Mondragón, “hemos iniciado, desde hace dos años y después de una etapa basada en proyectos de digitalización más tradicionales, una nueva etapa en la que estoy al frente de un proyecto de transformación digital de la compañía, interpretando el paradigma de Industria 4.0 más allá de lo que pueda ser la fábrica. La reflexión estratégica que condujo a la elaboración del Plan Digital 2021-2024 coincidió con la llegada de la pandemia, pero seguimos trabajando hasta su conclusión”. Jorge Pérez (Gonvarri) destacó, entre otras cosas, el trabajo en cooperación con Gestamp, al pertenecer al mismo grupo empresarial. Además, explicó que “lideró el equipo de Industria 4.0 de la compañía, un departamento creado con el objetivo de dar respuesta al entorno cambiante mediante la gestión a nivel corporativo todo tipo de iniciativas tecnológicas y de transformación digital aportando valor en tres ejes: eficiencia de nuestro proceso productivo, calidad del producto que fabricamos y seguridad de las personas que trabajan en nuestro entorno industrial”. Germán Arias (Michelin) detalló que “en torno a 2016, Michelin decidió dar el paso a la Industria 4.0, buscando implementar estas tecnologías de la forma más eficaz posible a escala global en la compaña. Se Data, artificial intelligence, usability and user experience”. Jesús Fernández (Fagor Ederlan) pointed out that at his company, part of Mondragon, “two years ago we started, after a stage based on more traditional digitization projects, a new stage in which I am in charge of a project of digital transformation to be, interpreting the Industry 4.0 paradigm beyond what the smart factory can be. Reflection strategy that led to the elaboration of the Digital Plan 2021-2024 has coincided with the arrival of the pandemic, but we have continued working until its conclusion”. Jorge Pérez (Gonvarri) highlighted, among other things, the work in cooperation with Gestamp, as they belong to the same business group. In addition, he explained that “I lead the company’s Industry 4.0 team, department dreated with the aim of created with the aim of responding to the environment changing through level management corporate all kinds of technological and digital transformation initiatives contributing in three areas: efficiency of our production process, quality of the product we manufacture and the safety of the people who work in our industrial environment”. Germán Arias (Michelin) explained that “in around 2016, Michelin decided to move to Industry 4.0, seeking to implement these technologies in the most efficient way possible on a global scale in the company.
Tenemos nuestra propia línea de producto de software, nuestro propio marketplace interno de aplicaciones ligado, en determinados casos, a sistemas existentes en la compañía y con integración con otros miembros de la cadena de valor / We have our own line of software product, our own internal application marketplace linked, in certain cases, to existing systems in the company and with integration with other members of the value chain
Diego Mallada, Gestamp
estableció una estrategia de adopción que está dando buenos resultados en la incorporación en amplio espectro de muchas fábricas y mucho personal de las mismas. de las casi 70 fábricas de Michelin en el mundo, la de Valladolid es una de las que ha sido designada para desplegar la estrategia de transformación digital de la compañía, con responsabilidad en el sur de Europa”. Eladio Valencia (Infor) explicó que “para nuestra compañía, automoción es un sector estratégico con unos 600 clientes en el mundo. Estamos englobados en el Grupo Koch, que factura unos 120.000 millones de euros y en España somos unas 400 personas dedicadas a proyectos de transformación digital. Contamos con diferentes proyectos en diseño (design thinking) y desarrollo de nuevos modelos”. Sebas Alsina (Infor) destacó la proyección de la compañía en los últimos años en el continente asiático, tanto con constructores de vehículos como con proveedores de componentes y remarcó la “tendencia a elegir la solución MultiTenant con las ventajas de Cloud sin necesidad de customización. Consta de módulos para diferentes campos integrados en una única suite”. En relación a la evolución reciente y a la situación actual, Diego Mallada (Gestamp) matizó “la diferencia de necesidades de digitalización en las diferentes regiones del mundo. Llevamos unos cinco años en este proceso y antes del mismo ya existían sistemas como ERP, MES o una red de comunicaciones. Se trata de traccionar una evolución de esos sistemas hacia otros más flexibles, más interoperables, con características de Big Data e inteligencia artificial. Dentro de ese proceso de transformación, hemos ido desarrollando nuestras propias soluciones, creando nuestra propia estrategia de software en cooperación con buenos partners, pero construyendo una base de plataformas y soluciones propias. Todo teniendo en cuenta el nivel de estandarización y de interoperabilidad”. Jorge Pérez (Gonvarri) se remontó a finales de 2016 como año en el que dentro de Gonvarri “nos planteamos el reto de qué podía aportar la tecnología a nuesAn adoption strategy was established that is producing good results in the wide-ranging incorporation of many factories and many factory personnel. of the almost 70 Michelin factories all over the world. Valladolid is one of those that has been designated to deploy the company’s digital transformation strategy, with responsibility for southern Europe”. Eladio Valencia (Infor) explained that “for our company, the automotive industry is a strategic sector with some 600 customers around the world. We are included in the Koch Group, which has a turnover of about 120 billion euros and in Spain there are about 400 people dedicated to digital transformation projects. We have different projects in design thinking and development of new models”. Sebas Alsina (Infor) highlighted the company’s projection in recent years in Asia, both with vehicle manufacturers and with component suppliers and highlighted the “tendency to choose the MultiTenant solution with the advantages of the Cloud without the need for customisation. It consists of modules for different fields integrated into a single”. In relation to recent developments and the current situation, Diego Mallada (Gestamp) clarified “the difference in digitisation needs in different regions of the world. We have been going through this process for about five years and before it there were already systems such as ERP, MES and a communications network. It is about driving an evolution of these systems towards other more flexible, more interoperable systems with characteristics of Big Data and artificial intelligence. Within this transformation process, we have been developing our own solutions, creating our own software strategy in cooperation with good partners, but building a base of our own platforms and solutions. All taking into account the level of standardization and interoperability”.
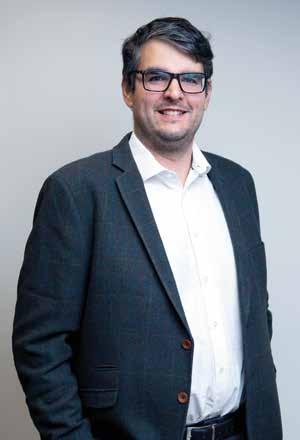
tro negocio. Tras un análisis interno y externo, constatamos que en un entorno cambiante donde la velocidad y la intensidad del cambio son elevados, la adopción de las tecnologías se convierte no solo en un reto sino en una obligación de cara a seguir manteniendo nuestra fuente de ventaja competitiva, sino para el futuro. A este hecho se suma que la aplicación de nuestros estándares de Lean Manufacturing nos ha ayudado y permitido alcanzar un nivel en nuestros resultados donde el siguiente salto vendrá apalancado en la aplicación de las tecnologías en nuestros procesos. Como consecuencia surge el proyecto estratégico Gonvarri 4.0, esponsorizado desde el top management de la compañía y al mismo tiempo involucrando a personas procedentes de nuestras plantas industriales siguiendo una estrategia bottom-up, ya que pensamos que el cambio resulta más fácil cuando las ideas que vienen de nuestros operarios se convierten en una realidad. Dentro del Gonvarri 4.0 comenzamos testeando un conjunto de tecnologías con la finalidad de proporcionar valores a los ejes de mejora de eficiencia operativa, calidad del producto y seguridad. También se persigue un cierto nivel de estandarización de procesos y la obtención de información en tiempo real. El siguiente paso ha sido crear sistemas software MES de gestión de activos y en los próximos años, nos centraremos en la homogenización y explotación del dato, para extraer su máximo valor”. Jesús Fernández (Fagor Ederlan) puntualizó que “es importante ver qué tecnologías se implementan en relación con medir un retorno económico que sea significativo, porque, en general, no se trata de soluciones con un resultado tangible a corto plazo. Desde que empezamos a hablar de inteligencia competitiva como un motor del crecimiento, ahora estamos en un escenario en el que, desde las nuevas posibilidades del mundo digital, podemos abordar proyectos en fábricas y en la gestión de la propia organización que antes eran impensables o eran económicamente inviables. El MES se ha convertido en el soporte básico para un nuevo sistema de control de la producción, en el que se centralizan datos que se gestionan en tiempo real en sistemas de computación en la nube y es la interfaz natural
Estamos evolucionando hacia un producto inteligente al que dotamos de servicio a nivel de datos y a unos procesos más flexibles / We are evolving towards a smart product to which we provide a data-level service and more flexible processes
Jorge Pérez (Gonvarri) looked back to the end 2016 as the year in which “we set onto Gonvarri the question of what technology could contribute to our business. After an internal and external analysis, we found that in a changing environment where the speed and intensity of change to which we are subjected are very high, the adoption of technologies becomes not only a challenge but also a obligation in order to continue maintaining our source of competitive advantage in the future. To this fact is added that the application of our Lean standards Manufacturing has helped us and allowed us to reach a level in our results where the next leap will be leveraged in the application of technology in our processes. Consequently, the strategic project Gonvarri 4.0 emerges, sponsored from the top management of the company and at the same time involving people from our industrial plants following a bottom-up strategy as we think that change is easier when the ideas that come from our operators become a reality. Inside Gonvarri 4.0 project we began by testing a set of various technologies to provide values to the axes of improvement of operational efficiency, product quality and safety. A certain level of standardisation of processes and obtaining information in real time is also being pursued. The next step has been to create MES asset management software systems and in the coming years, we will focus on data standardisation and exploitation to extract the maximum value from it”. Jesús Fernández (Fagor Ederlan) pointed out that “it is important to see what technologies are implemented in relation to measuring an economic return that is significant, because, in general, they are not solutions with a tangible result in the short term. Since we started talking about competitive intelligence
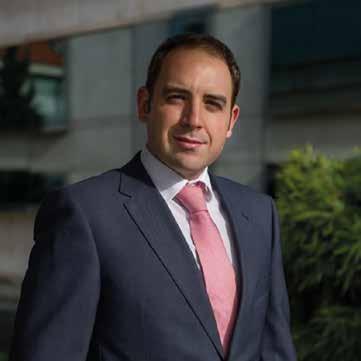
Nuestras soluciones Cloud se aplican en transacciones digitales, operaciones de producción, gestión de maquinaria, trazabilidad de los operarios y gestión de proveedores / Our Cloud solutions in digital transactions, production operations, machinery management, operator traceability and supplier management
Sebas Alsina, Infor
del operario en la máquina, entre otras muchas otras. Hemos empleado un año en diseñar nuestra estrategia de transformación digital que consta de cinco grandes bloques estratégicos: la fábrica inteligente; la eficiencia en los procesos no operacionales y la sostenibilidad de la actividad empresarial del mundo digital; la comprensión de cuál es o puede ser nuestro negocio digital, abarcando más allá de nuestra actividad esencial con diversas respuestas referentes a productos inteligentes y servicios integrales digitales; infraestructuras tecnológicas y funcionales; y gobernanza con un liderazgo estratégico que no es delegable, y que debe ser complementado por un liderazgo operacional, y en el que estamos trabajando”. Germán Arias (Michelin) se refirió a “un punto clave según el que la transformación digital que está basada en un 95% en las personas que hay detrás y en un 5% tecnología que hay que aplicar. Estamos ante un cambio de mentalidad enfocado a mejorar la dinámica de trabajo con un beneficio asociado, de una manera duradera y que sea coherente con quienes la tienen que llevar a efecto. En este sentido, hemos creado una infraestructura homogénea, una arquitectura operativa estándar sobre la que ir implementando los diferentes casos de uso de cada una de nuestras plantas de producción. Para ello, se invitó a participar a diferentes fábricas en la creación de soluciones que les aportaran valor y fueran el germen de un catálogo de casos de uso que, al final, se ha confeccionado con cerca de 50 de ellas. Todas utilizan de forma transversal para implementar las mejores prácticas. Hemos constatado que las mejores iniciativas parten de quienes están más cerca del producto. Actualmente estamos en una fase de convergencia y concentración de elementos comunes a todas las plantas con el apoyo de la inteligencia artificial, pero con la aportación decisiva del capital humano”. Teniendo en cuenta la importancia del software en la estrategia de los constructores de automóviles, Sebas Alsina (Infor) comentó las capacidades de “nuestras soluciones Cloud en transacciones digitales, operaciones de producción, gestión de maquinaria, trazabilidad de los operarios y gestión de proveedores. Todo ello a escala global gracias al concepto Multitenant, para as an engine of growth, we are now in a scenario in which from new possibilities of the digital world we can tackle projects in factories and in the management of the organisation itself that were previously unthinkable or were economically unviable. The MES has become the basic foundation for a new production control system, in which data is centralised, realtime managed in cloud computing systems and is the natural interface of the operator in the machine, among many others. We have spent a year designing our digital transformation strategy, which consists of five major strategic blocks: the smart factory; the efficiency of no operational processes; and the sustainability of business; the understanding of what our digital business is or can be, encompassing beyond our essential activity with diverse responses regarding intelligent products and digital services; technological and functional infrastructures: and governance with strategic leadership that cannot be delegated and must be complemented by an operational leadership on which we are working”. Germán Arias (Michelin) referred to “a key point according to which the digital transformation is based 95 to the people behind it and 5% technology that must be applied. We are facing a change in mentality focused on improving work dynamics with an associated benefit, in a lasting way and that is consistent with those who have to carry it out. In this sense, we have created a standardized infrastructure, a standard operational architecture on which to implement the different use cases of each of our production plants. For this, different factories were invited to participate in the creation of solutions that would add value and were the germ of a catalog of use cases that, in the end, has been made with about 50 of them. All are using it in a transversal way to implement best practices. We have found that the best initiatives come from those who are closest to the product. We are currently in a phase of convergence and concentration of elements common to all plants with the support of artificial intelligence, but with the decisive contribution of human capital”. Considering the importance of software in the OEMs
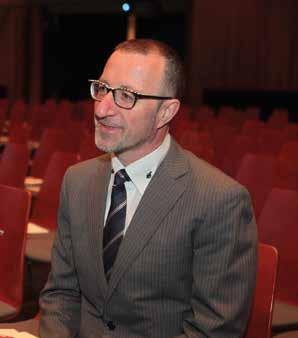
compañías con diferentes plantas en el mundo y con los mayores niveles de seguridad, que hemos puesto en marcha desde 2019”. Eladio Valencia (Infor) coincidió con el resto de participantes en que “si bien es cierto que el componente tecnológico cloud cada vez es más importante en la digitalización, el factor humano es fundamental en esta transformación digital. Por otro lado, estamos trabajando intensamente para medir el retorno de la inversión en estas tecnologías que en muchos casos estamos calculando en menos de tres años, teniendo en cuenta que la digitalización permite alcanzar objetivos que antes eran extraordinariamente complejos. En este proceso participamos en muchos consorcios con una proyección hacia toda la cadena de valor, lo que permite mejorar la competitividad. Favorecemos la comunicación entre proveedores y clientes mediante sesiones de Design Thinking para facilitar la colaboración entre las empresas en un mundo cada vez más interconectado”.
CADENA DE SUMINISTRO
En relación con la gestión de la cadena de suministro y relación con proveedores, Diego Mallada (Gestamp) comentó que “primero, es importante ver en interno los flujos logísticos propios para enlazarlos con los ciclos de vida del producto desde un enfoque de fabricación flexible. Este concepto responde tanto a la tendencia de customización como a los escenarios de complejidad y dificultad como los que ha sufrido la cadena de suministro en los últimos tiempos. Para la relación con la cadena de valor son muy importantes la interoperabilidad, la creación de consorcios y equipos de trabajo strategies, Sebas Alsina (Infor) commented on the capabilities of “our Cloud solutions in digital transactions, production operations, machinery management, operator traceability and supplier management. All this on a global scale thanks to the Multitenant concept, for companies with different plants in the world and with the highest levels of security, which we have implemented since 2019”. Eladio Valencia (Infor) agreed with the rest of the participants that “although it is true that the cloud technology component is increasingly important in digitisation, the human factor is essential in this digital transformation. We are also working hard tomeasure the return on investment from these technologies that in many cases we are calculating in less than three years, taking into account that digitisation allows us to achieve objectives that were previously extraordinarily complex. In this process we participate in many consortia with a projection towards the entire value chain, which allows us to improve competitiveness. We promote communication between suppliers and customers through Design Thinking sessions to facilitate collaboration between companies in an increasingly interconnected”.
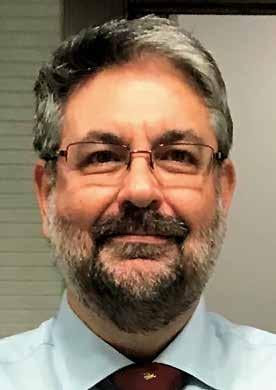
SUPPLY CHAIN
Regarding supply chain management and relationship with suppliers, Diego Mallada (Gestamp) commented that “first, it is important to the internal logistics flows to link them with the product life cycles with a flexible manufacturing approach. This concept responds both to the customisation trend and to complex and difficult scenarios such as those that the supply chain has suffered in recent times. Interoperability, the creation of consortia and work teams in the value chain are very important for the relationship with the value chain. With this in mind, we have recently joined Indesia, where we are working on the sharing of robust, accurate and interoperable data that allows scaling, considering faster and more adjustable product cycles”. Before addressing the point of the value chain, Jorge Pérez (Gonvarri) agreed with Germán Arias
Una iniciativa reciente nos ha llevado a formar parte de Catena X, plataforma en la que hemos planteado varios proyectos de servicios digitales enfocados al desarrollo conjunto con un OEM / A recent initiative has led us to become part of Catena X, a platform through which we have proposed several digital service projects focused on joint development with an OEM
en la cadena de valor. En este sentido,, recientemente nos hemos incorporado a Indesia, donde estamos trabajando en la compartición de datos robustos, veraces e interoperables que permitan escalar, teniendo en cuenta ciclos de productos más rápidos y ajustables”. Antes de abordar el punto de la cadena de valor, Jorge Pérez (Gonvarri) coincidió con Germán Arias (Michelin) en “la relevancia de generar ideas desde distintas plantas de la compañía canalizadas a través de una estrategia centralizada proyectada en plantas piloto que ejecutan pruebas de concepto que han de ser validadas a nivel corporativo de forma técnica y económica antes de hacer un roll out a toda la organización. A partir de esta base, ya estamos mirando al exterior para la solución de problemas tanto con clientes como proveedores, en nuestro caso tanto de relacionados con trazabilidad tanto de materia prima como de producto terminado. Estamos evolucionando hacia un producto inteligente al que dotamos de servicio a nivel de datos y a unos procesos más flexibles, a la vez que desarrollamos una relación ‘always online’ con clientes y proveedores”. Jesús Fernández (Fagor Ederlan) manifestó que “pensamos que va a haber una tendencia más intensa a trabajar en proyectos de codesarrollo e integración de la cadena de suministro en todos los ámbitos, algo que se está acelerando en los últimos meses. Hemos desarrollado un portal colaborativo con proveedores de utillaje, pero aún tenemos que trabajar en temas de eKanban para para la gestión del suministro desde el consumo real. Por otro lado, estamos sufriendo cambios muy acusados en la predicción de la demanda, situación que va a persistir hasta que no logremos un grado mucho más relevante en cuanto a transparencia de la cadena de suministro. En ese sentido, prevemos que va a haber un desarrollo de nuevos servicios que van a tener que ser necesariamente colaborativos. Una iniciativa reciente nos ha llevado a formar parte de Catena X, plataforma en la que hemos planteado varios proyectos de servicios digitales enfocados al desarrollo conjunto con un OEM, que pueden acabar siendo un estándar que implante el constructor. Debemos entender la cadena de suministro como un sistema que tiene que ser eficiente como sistema y no eficiente como cada una de sus partes”. Germán Arias (Michelin) comentó que “nuestra central de Compras lleva tiempo trabajando sobre plataformas compartidas para el suministro de materiales, gracias al cual hemos llegado a un nivel aceptable de automatización de pedidos y gestión de necesidades. A medio plazo, estamos tratando de conectar con nuestros ERP con estas plataformas para conseguir una gestión más integrada, sobre todo, cuando se dan problemas en la cadena de suministro como los que se están viviendo actualmente”. Sebas Alsina (Infor) intervino al hilo de la opinión del directivo de Michelin, apuntando que “la necesidad de (Michelin) on “the relevance of generating ideas from different company plants channelled through a centralised strategy designed in pilot plants that carry out tests of concept that have to be validated at the corporate level in a technical and economic way before rolling out to the entire organisation. From this base, we are already looking abroad to solve problems with both customers and suppliers, in our case, related to traceability both raw materials as finished product. We are evolving towards a smart product to which we provide a data-level service and more flexible processes, while at the same time developing an ‘always online’ relationship with customers and suppliers”.
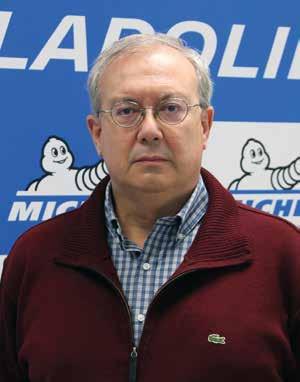
Operamos con una arquitectura estándar que se ha instaurado en todas y cada una de las de las fábricas del grupo en la cual se introducen todas las señales que capturamos de las máquinas para su análisis en tiempo real / We operate with a standard architecture that has been established in each and every one of the group’s factories in which all of the data that we capture from the machines are entered for analysis in real time
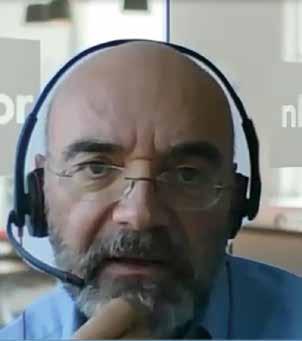
Participamos en muchos consorcios con una proyección hacia toda la cadena de valor, lo que permite mejorar la competitividad / We participate in many consortia with a projection towards the entire value chain, which allows us to improve competitivenessM
Eladio Valencia, Infor
implementar alertas y de cohesionar tanto los flujos de aprovisionamiento a cliente, como la logística interna y el abastecimiento de proveedores de forma coordinada con herramientas de software especializado”. German Arias (Michelin) estuvo de acuerdo, si bien comentó que “el grado de incertidumbre actual es de tal magnitud que incluso con ese tipo de sistemas es complicado hacer frente a determinadas situación como las que recientemente están afectando a las cadenas de suministro”. Eladio Valencia (Infor) comentó que “contamos con soluciones de gestión de proveedores, con monitorización de la trazabilidad de los productos en un marco de partenariado entre cliente y proveedor”.
HOJAS DE RUTA
En cuanto a la opción de disponer de una estructura o plataforma de software única, una matriz de software que soporte toda la gestión de una compañía, Diego Mallada (Gestamp) habló del desarrollo de una hoja de ruta que “ha desembocado en nuestra propia línea de producto de software, nuestro propio marketplace interno de aplicaciones ligado, en determinados casos, a sistemas existentes en la compañía y con integración con otros miembros de la cadena de valor. Eso implica una tendencia a la estandarización, teniendo en cuenta que hay requerimientos diferentes en las distintas partes del mundo. Para lograrlo, en nuestro caso, es la aplicación de metodologías nuevas, siendo ágiles en Jesús Fernández (Fagor Ederlan) stated that “we think there is going to be a more intense tendency to work on co-development and supply chain integration projects in all areas, something that has been accelerating in recent months. We have developed a collaborative portal with tooling providers, but we still have to work on eKanban issues for the supply management from consumption in real time. In addition, we are undergoing very marked changes in demand prediction, a situation that will persist until we achieve a much more substantial degree of supply chain transparency. Along these lines, we foresee that there will be a development of new services that will necessarily have to be collaborative. A recent initiative has led us to become part of Catena X, a platform through which we have proposed several digital service projects focused on joint development with an OEM, which may end up being a standard implemented by the manufacturer. We must understand the supply chain as a system that has to be efficient as a system and not efficient in each of its parts”. Germán Arias (Michelin) commented that “our purchasing centre has been working for some time on shared platforms for the supply of materials, thanks to which we have reached an acceptable level of order automation and needs management. In the medium term, we are trying to connect our ERPs with these platforms to achieve a more integrated management, especially when there are problems in the supply chain like the ones we are currently experiencing”. Sebas Alsina (Infor) intervened in line with the opinion of the Michelin manager, pointing out that “the need to implement alerts and to unify both the supply flows to the customer, as well as the internal logistics and the supply of suppliers in a coordinated way with tools of specialised software”. German Arias (Michelin) agreed, although he commented that “the current degree of uncertainty is of such magnitude that even with this type of system it is difficult to face certain situations such as those that have been recently affecting supply chains”. Eladio Valencia (Infor) commented that “we have supplier management solutions, with monitoring of product traceability within a framework of partnership between customer and supplier”.
ROADMAPS
Regarding the option of having a single software structure or platform, a software matrix that supports the entire management of a company, Diego Mallada (Gestamp) spoke about the development of a roadmap that “has led to our own line of software product, our own internal application marketplace linked, in certain cases, to existing systems in the company and with integration with other members of the value chain. This implies a trend towards
la publicación de nuevas características muy cerca de los usuarios finales. También apoyándonos en el inner sourcing, comunidad interna en la compañía, en la que cada división y región puedan contribuir. También es muy importante encontrar el talento adecuado para el manejo de estos nuevos sistemas a través de relaciones con partners, aproximación al ámbito startup y con programas propios de formación. También estamos generando un Datalake transversal, global y multientorno”. Jorge Pérez (Gonvarri) afirmó que “nosotros no entendemos esta estrategia hacia una solución que desemboque en una plataforma única. Hemos evolucionado desde un ERP con el que gestionábamos producción, mantenimiento, finanzas… a orientarnos hacia un ecosistema de aplicaciones digitales donde el ERP ocupa su lugar en gestión de clientes, proveedores, personas, finanzas…, mientras que los nuevos aplicativos que estamos desarrollando se centran específicamente en verticales como Gestión de la Producción, Mantenimiento, Sistemas de Control de Calidad, logística interna y externa…. Dos ejemplos claros son el MES de Gonvarri con el que monitorizamos la producción en tiempo real en todas nuestras plantas y el Sistema de Gestion de Activos y Mantenimiento. Sobre esos dos sistemas y nuestro ERP estamos dentro de 4.0 en el proceso de construir un conjunto de satélites de software integrados e interoperables. Un elemento clave para llevar a cabo todo este cambio requiere contar con el talento necesario con unas habilidades específicas que dentro de Gonvarri tratamos de atraer y de retener”. Jesús Fernández (Fagor Ederlan) detalló que, en cuanto a configuración del sistema de software, “hemos pasado por varias fases. Lo que actualmente estamos desarrollando en cuanto aplicativos de software de IT tradicionales como CRM, PLM, etc, lo hacemos con soluciones específicas que tratamos de estandarizar para todo el grupo. Si veo más complejidad en la estandarización en aplicaciones prescriptivas y predictivas por la necesidad de rediseñar algoritmos a la hora de transversalizar soluciones. A corto plazo no veo factible la aplicación de soluciones globales de inteligencia artificial en los procesos de fabricación y control. Tratamos de buscar estandarizaciones en el mundo OT, pero no es sencillo y estamos colaborando con startups en desarrollo de pruebas de concepto”. Enfatizó que “no se puede decir que un alto nivel de automatización y robotización sea igual a una cultura digital elevada en la que se extraiga el máximo valor a partir de estas nuevas tecnologías”. Añadió que “la situación de búsqueda de personas cualificadas se puede calificar prácticamente de dramática”. Germán Arias (Michelin) expuso que “operamos con una arquitectura estándar que se ha instaurado en todas y cada una de las de las fábricas del grupo en la cual se introducen todas las señales que capturamos de las máquinas para su análisis en tiempo real, de forma standardisation, taking into account that there are different requirements in different parts of the world. To achieve this, in our case, it is the application of new methodologies, being agile in the publication of new features very close to the end users. Also supporting us in the inner sourcing, internal community in the company, in which each division and region can contribute. It is also very important to find the right talent to handle these new systems through relationships with partners, alignment with startups and with its own training programs. We are also generating a transversal, global and multienvironment Datalake”. Jorge Pérez (Gonvarri) stated that “we do not understand this strategy towards a solution that leads to a single platform. We have evolved from an ERP with which we managed production, maintenance, finances… while the new applications that we are developing focus specifically on verticals such as Production Management, Maintenance, Quality Control Systems, internal and external logistics…. Two examples clear are the Gonvarri MES with which we monitor production in real time in all our plants and the Asset and Maintenance Management System. About those two systems and our ERP we are within 4.0 in the process of building a set of integrated and interoperable software satellites. A key element to carry out everything This change requires having the necessary talent with specific skills that within Gonvarri we try to attract and retain”. Regarding the configuration of the software system, Jesús Fernández (Fagor Ederlan) explained that “we have gone through several phases. What we are currently developing as traditional IT software applications such as CRM, PLM, etc., we do with specific solutions that we try to standardise for the entire group. I see more complexity in standardisation in prescriptive and predictive applications for the need to redesigning algorithms when it comes to mainstreaming intelligence solutions on manufacturing and control processes. In the short term, I do not see the application of global solutions based on artificial intelligence as feasible. We try to look for standardisation in the OT world, but it is not easy and we are collaborating with startups in the development of proofs of concept”. He emphasised that “it cannot be said that a high level of automation and robotisation is equal to a high digital culture in which the maximum value is extracted from these new technologies”. He added that “the situation of finding qualified people can be described as practically dramatic”. Germán Arias (Michelin) explained that “we operate with a standard architecture that has been established in each and every one of the group’s factories in which all of the data that we capture from the machines are entered for analysis in real time and combined
combinada con aplicaciones que ya existían. Respecto al tema del talento y la evolución de este tipo de tecnologías en nuestro personal, abordamos la cuestión mediante una doble vertiente: la externa para apoyarnos en competencias que no tenemos, y la interna para el desarrollo de personal propio que ha mostrado interés en esta evolución tecnológica. Actualmente nos apoyamos en torno a un 80% con personal interno. Desde hace ya cuatro años, tanto con la estrategia de la casa matriz como con las iniciativas de las plantas, hemos definido perfiles como el ingeniero, analista o administrador de datos analista que existen en cada una de las fábricas con la responsabilidad de dar un uso valioso al dato para su utilización posterior”. Sebas Alsina (Infor) apuntó la importancia de fortalecer el control de estructuras globales cada vez más complejas con la evolución en automoción en países como China, India y Brasil. Eladio Valencia (Infor) añadió que “contamos con clientes que tienen todos sus sistemas de gestión informático con Infor, mientras que otros apuestan por un formato mixto, canalizando determinados campos de gestión con otras compañías. Pensamos que ambos entornos son posibles. De hecho, tenemos casos en los que, partiendo de un entorno desarrollado por otra compañía, hemos implementado una solución de software de ámbito financiero en tres años, 1.000 días, que es un tiempo récord para un cliente de gran tamaño. Apostamos por procesos colaborativos, en los que las personas son muy importantes. En nuestro caso, estamos potenciando mucho la creación de perfiles muy cualificados para dar respuesta a la escasez existente. Contamos con grupos que está trabajando en entornos de inteligencia artificial configurando escenarios de innovación”.
CAMPOS PRIORITARIOS
En cuanto a los campos prioritarios para la digitalización, Diego Mallada (Gestamp) mencionó “eficiencia energética, logística, intralogística, monitorización… desde un enfoque de digitalización del conocimiento” y Jorge Pérez (Gonvarri) apuntó “el control de calidad en línea, la trazabilidad unitaria y la analítica predictiva tanto para la gestión de la producción como del mantenimiento” como ejes prioritarios. Jesús Fernández (Fagor Ederlan) puso el foco “en la calidad del producto y del coste”, para añadir que “si aumentamos la transparencia en la cadena de suministro, se pueden hacer proyectos muy interesantes”. Germán Arias (Michelin) señaló “la calidad, el mantenimiento y control de máquinas y la gestión de flujos de la fábrica” Sebas Alsina (Infor) resumió las posibilidades en una “implementación global, sencilla, económica y segura”, visión que Eladio Valencia (Infor) complementó “indicando la tendencia a implementar soluciones Cloud en calidad, gestión de mantenimiento, mejoras en procesos de fabricación y medición del retorno de inversión, con el consiguiente incremento de competitividad”. with applications that already existed. Regarding the issue of talent and the evolution of this type of technology in our staff, we approach the issue through two aspects: the external one to support us in competences that we do not have, and the internal one for the development of our own personnel who have shown interest in this technological evolution. Currently we support around 80% with internal personnel. For four years now, both with the strategy of the parent company and with the initiatives of the plants, we have defined profiles such as the engineer, data analyst and data administrator that exist in each of the factories with the responsibility of making data valuable for later use”. Sebas Alsina (Infor) pointed out the importance of strengthening the control of increasingly complex global structures with the evolution of the automotive industry in countries such as China, India and Brazil”. Eladio Valencia (Infor) added that “we have customers that have all their IT management systems with Infor, while others opt for a mixed format, channelling certain management fields with other companies. We think that both environments are possible. In fact, we have cases in which, starting from an environment developed by another company, we have implemented a financial software solution in three years, 1,000 days, which is a record time for a large customer. We are committed to collaborative processes, in which people are very important. In our case, we are greatly promoting the creation of highly qualified profiles to respond to the existing shortage. We have groups that are working in artificial intelligence environments setting up innovation scenarios”.
PRIORITY FIELDS
Regarding the priority fields for digitisation, Diego Mallada (Gestamp) mentioned “energy efficiency, logistics, intralogistics, monitoring ... with a focus of digitalization of the knowledge”. Jorge Pérez (Gonvarri) pointed out “online quality control, unit traceability and predictive analytics for both production management and maintenance”as priority axes. Jesús Fernández (Fagor Ederlan) focused “on product quality and cost”, adding that “if we increase transparency in the supply chain, very interesting projects can be carried out”. Germán Arias (Michelin) pointed out “the quality, maintenance and control of machines and the flow management of the factory”. Sebas Alsina (Infor) summarised the possibilities in a “simple, economical and safe implementation”, a vision that Eladio Valencia (Infor) complemented indicating “the trend to implement Cloud solutions in quality, maintenance management, improvements in manufacturing processes and measurement of return on investment, with the consequent increase in competitiveness”.