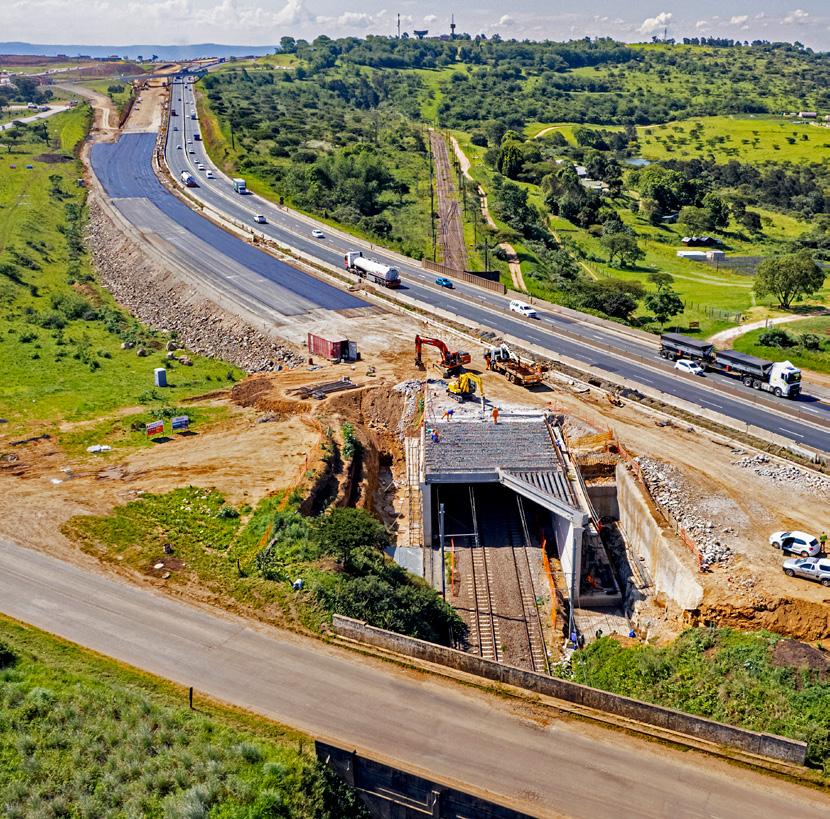
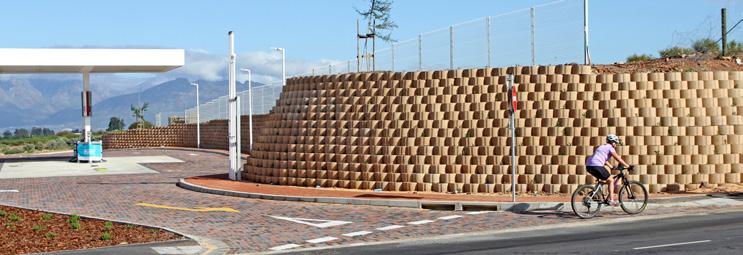








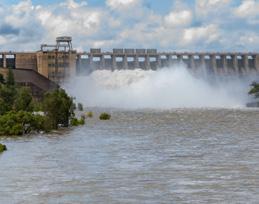
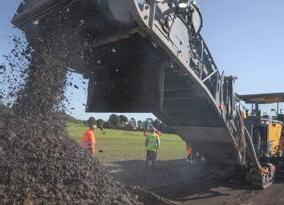


In 120 years, environmental exposure will be more aggressive. We have the solution, today.
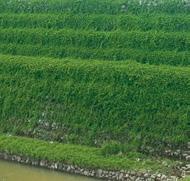

In 120 years, environmental exposure will be more aggressive. We have the solution, today.
New PoliMac® polymer coating for Gabions, Reno Mattresses and Rockfall protections designed to last
• Longer Life
• More Abrasion resistance
• More UV resistance
• More Chemical resistance
•
MANAGING EDITOR Alastair Currie
SENIOR JOURNALIST Kirsten Kelly
JOURNALIST Nombulelo Manyana
EDITORIAL COORDINATOR Ziyanda Majodina
HEAD OF DESIGN Beren Bauermeister
CHIEF SUB-EDITOR Tristan Snijders
CONTRIBUTORS Nezar A Eldidy, Sibusiso Mjwara, David Prinsloo
PRODUCTION & CLIENT LIAISON MANAGER
Antois-Leigh Nepgen
GROUP SALES MANAGER Chilomia Van Wijk
DISTRIBUTION MANAGER Nomsa Masina
DISTRIBUTION COORDINATOR Asha Pursotham
SUBSCRIPTIONS subs@3smedia.co.za
ADVERTISING SALES
KEY ACCOUNT MANAGER Joanne Lawrie
Tel: +27 (0)11 233 2600 / +27 (0)82 346 5338
Email: joanne.lawrie@3smedia.co.za
Whether it’s a power ship, green hydrogen, nuclear, solar, wind or coal fired energy, South Africa needs to bring everything to the table right now. Last year, government, industry and the public in general endured a record level of load-shedding. It was collectively referred to as a power crisis, but it’s well beyond that now as we enter unprecedented territory as a country.
PUBLISHER Jacques Breytenbach
3S Media
Production Park, 83 Heidelberg Road, City Deep Johannesburg South, 2136
PO Box 92026, Norwood 2117
Tel: +27 (0)11 233 2600 www.3smedia.co.za
ANNUAL SUBSCRIPTION: R600.00 (INCL VAT)
ISSN 0257 1978 IMIESA, Inst.MUNIC. ENG. S. AFR.
© Copyright 2023. All rights reserved.
IMESA CONTACTS
HEAD OFFICE:
Manager: Ingrid Botton
P.O. Box 2190, Westville, 3630
Tel: +27 (0)31 266 3263
Email: admin@imesa.org.za
Website: www.imesa.org.za
BORDER
Secretary: Celeste Vosloo
Tel: +27 (0)43 705 2433
Email: celestev@buffalocity.gov.za
EASTERN CAPE
Secretary: Susan Canestra
Tel: +27 (0)41 585 4142 ext. 7
Email: imesaec@imesa.org.za
KWAZULU-NATAL
Secretary: Narisha Sogan
Tel: +27 (0)31 266 3263
Email: imesakzn@imesa.org.za
NORTHERN PROVINCES
Secretary: Ollah Mthembu
Tel: +27 (0)82 823 7104
Email: np@imesa.org.za
SOUTHERN CAPE KAROO
Secretary: Henrietta Olivier
Tel: +27 (0)79 390 7536
Email: imesasck@imesa.org.za
WESTERN CAPE
Secretary: Michelle Ackerman
Tel: +27 (0)21 444 7114
Email: imesawc@imesa.org.za
FREE STATE & NORTHERN CAPE
Secretary: Wilma Van Der Walt
Tel: +27 (0)83 457 4362
Email: imesafsnc@imesa.org.za
All material herein IMIESA
Stage 8 and perhaps Stage 16 are being mooted. It’s an unimaginable scenario that requires a herculean response that fully embraces public and private sector participation among South Africa’s top leaders. It’s a time for unity and a tremendous opportunity to show the world that South Africa has the will, expertise and innovation to turn the situation around in the shortest time possible through a major ramping up in independent power producer (IPP) capability.
This responsibility will now officially be spearheaded by the Minister of Electricity, Dr Kgosientsho Ramokgopa. This follows President Cyril Ramaphosa’s decision to sign a proclamation in May 2023 that “transfers to the Minister of Electricity certain powers and functions entrusted by the Electricity Regulation Act (No. 4 of 2006).” This refers specifically to Section 34(1) and Section 34(2) of the Act, which deals with new generation capacity.
South Africa is committed to a Just Energy Transition. But the reality is that fossil fuels will be with us for many years to come, while in parallel renewables at scale steadily begin to dominate as a national power security solution. That process is gaining rapid momentum as business invests heavily in solar as an essential process in helping to balance base load requirements.
However, for energy-intensive sectors like manufacturing – a core component of the construction materials supply chain – the only way at present to sustain operations is by running on diesel during blackouts. That erodes margins and can led to ‘job shedding’, something we need to avoid at all costs.
Either way, one of the most pressing concerns is the need for smarter grid stability, which incorporates transmission network upgrades and investments in municipal microgrids. Transmission has always been the backbone to energy supply, but it’s now also the essential market for IPPs selling, or wheeling, power to the grid and end-users.
This will be the key to unlocking groundbreaking initiatives like the City of Cape Town’s recent release of a 500 MW dispatchable energy tender, which includes proposals like battery storage, and gas-topower, with successful IPPs awarded 10-year power purchase agreements.
Power is what drives our society and economy. It’s also the foundation for intelligent connectivity and the smart cities of the future – designed, operated and managed in the cloud. However, to operate effectively, cloud-based systems need fully functioning data centres, and network towers require sustained energy to ensure interrupted transmission for e-services. This will be a major priority as South Africa enters the winter months, with the prospect of higher levels of load-shedding.
In the end, though, solving our power woes is a collective responsibility. To underscore this, at the end of December 2023, around R56.3 billion in unpaid bulk electricity supply was owed to Eskom by municipalities. In addition to poor revenue collection, a key contributor is non-payment for services rendered. Prepaid metering is part of the solution because, unless consumers qualify for indigent services, going forward everyone needs to contribute to maintaining and upgrading our transmission network.
Novus Holdings is a Level 2 BBBEE Contributor: novus.holdings/sustainability/transformation
Secure your stand now and have the opportunity to:
• present your company, products and services to a target audience
• gain industry insight and meet potential partners, suppliers and clients
• interact with key decision-makers and industry peers
25-27 October 2023 86 TH IMESA Conference
BOARDWALK HOTEL Gqeberha (Port Elizabeth)
NOW
Sponsor a unique aspect of the conference and enjoy great benefits such as:
• free exhibition stands
• complimentary delegate registrations
• brand representation at the event, promotion of your company in the conference proceedings magazine and online
• free entry for guests at the social evening and much more.
t: +27 (031)266 3263
e: conference@imesa.org.za
marketing@imesa.org.za
www.imesa.org.za
Within any town or city, municipalities are expected to serve as a catalyst for positive socio-economic development. Their mandate is to maintain and enable ongoing infrastructure development to support private sector investment, which in turn generates the rates and taxes needed to run municipal programmes. Sounds straightforward, and it should be, assuming the requisite finances and technical skills are in place.
However, for municipal officials – and especially for municipal engineers spearheading service delivery implementation – it’s often a mammoth task. Aside from the issues of maladministration being tackled by the Auditor-General’s office, one of the overwhelming issues is the bureaucratic burden imposed by wellintended legislation like the Preferential Procurement Regulations.
The situation is compounded when there’s a lack of professional capacity to execute acceptable outcomes. This in turn puts tremendous strain on a shrinking pool of skilled personnel within municipalities, with the risk that they end up leaving the public sector.
The knock-on effect is that municipalities will increasingly struggle to attract graduate engineers and young professionals unless the operational environment is modern and forward-thinking. The upside is that some municipalities are well advanced along this path, but we need everyone to be on board.
As IMESA, we are committed to supporting our members – both candidate engineers and registered professionals – in terms of training and knowledge transfer.
At a higher level, IMESA is also a participant at the National Science and Technology Forum (NSTF), which represents more than 100 stakeholder entities spanning the private and public sector. But we also appreciate the urgent need to engage with schools at grassroots level to ensure that there’s an understanding and appreciation of the importance of studying in the fields of science, engineering and technology (SET) in a rapidly advancing high-tech world. It’s imperative that we have a pipeline of new talent coming through that will be responsible for designing, building and maintaining our smart cities of the future.
The key concern though is whether our schools are adequately equipped to
prepare our future engineers if our literacy levels keep declining. This viewpoint is based on the findings of the 2021 Progress in International Reading Literacy Study (PIRLS), which – despite being a statistical snapshot – shows a concerning trend, because numeracy and literacy are interlinked and vital for SET success.
Compared to 2016, South Africa’s mean achievement score dropped from 320 to 288 – the international average being 500 – with Singapore in the lead with a 587 rating. Breaking it down further, 81% of South Africa’s grade 4s and 56% of its grade 6 learners did not reach the low international benchmark category threshold of 400 points upon assessment. The latter is defined as ‘can read to locate and retrieve explicit information’. In comparison, the high international benchmark (550-624) category requires learners to ‘make intricate connections between events in the text; identify crucial features and make generalisations; and interpret complex text and tables.’
While the South African government is trying its best to turn this around, there’s a great deal of work to be done at preand primary school level if we’re going to fulfil the objectives of 5IR (people and machine inclusivity) in harnessing 4IR advances like digitalisation. The intention has never been for artificial intelligence to take over.
In the meantime, it’s crucial that we pool the skills and experience we have in South Africa to ensure the implementation of world-class infrastructure, as well as allied projects like renewable energy that will keep us globally competitive. Public and private sector collaboration is key.
That the sheer scale of the project places immense pressure on local aggregates suppliers is no overstatement but, with two strategically located quarries in the area, AfriSam is rising to the challenge.
Part of the 62 SIPs gazetted as part of the Infrastructure Investment Plan approved by Cabinet in 2020, the N3 national route upgrade –which focuses on an 80 km section from Durban to Pietermaritzburg – comprises 14 packages estimated to be in excess of R20 billion.
Aimed at strengthening the logistics and transport corridor between South Africa’s main industrial hubs, Johannesburg and Durban, the project will also improve access to Durban’s export and import facilities and raise efficiency along the corridor.
Work on the very first package of the project, the
stretch between the Dardanelles Interchange and the Lynnfield Park Interchange, is continuing apace. The project entails upgrading of the existing four-lane dual carriageway to an eightlane dual carriageway by widening to the median and outer shoulders over a 6.4 km distance, as well as the construction of associated bridges and interchanges.
The massive scale of the project presents both opportunities and challenges for local aggregates producers. AfriSam’s Umlaas Road Quarry, located right at the doorstep of the current project, has seen a massive sales boom in the past two years. Kovid Singh, works manager: Umlaas Quarry, AfriSam, confirms that the operation more than doubled its preCovid volumes in 2021, maintaining the same volumes in 2022.
Despite being located some 30 km away from the current project, AfriSam’s Pietermaritzburg Quarry – providing backup supply to Umlaas Road Quarry – has had a fair share of the
project volumes, largely supplying sub-base material such as G2, G4 and G5. Consequently, the operation has enjoyed a welcome increase in sales over and above the base load normally supplied into the Pietermaritzburg market, confirms Ernest Sebeelo, works manager: Pietermaritzburg Quarry, AfriSam.
However, supplying aggregates to a project of this magnitude is not without its challenges. From the onset, explains Theolan Govender, regional manager: Construction Materials KZN, AfriSam, production planning was a challenge due to the uncertainty related to the commencement of the projects and the associated volumes.
“When we initially provided our tender proposals for the various road packages, we had to work on indicative production volumes and timing for supply. Once the volumes materialised, we had to progressively ramp up, thus changing strategy to balance production and maintenance,” Govender explains.
AfriSam had to make use of its existing infrastructure within the group. To more than double capacity at its Umlaas operation, the company mobilised two existing trains of mobile crushers and screens to site, one from Johannesburg and the other from its KZN-based Verulam Quarry.
Upgrades include an eight-lane dual carriageway, median and out shoulders, as well as the construction of bridges and interchanges
A steady supply of quality aggregates from AfriSam is playing a key role in ensuring unhindered progress on one of government’s Strategic Integrated Projects (SIPs) – the N3 national route upgrade between Durban and Pietermaritzburg.
The AfriSam Umlaas Quarry team had to strategically produce and maintain both the mobile and fixed plants, running extended shifts to meet supply demands. Plant availability, stresses Singh, is key to meeting the project’s aggregates requirements.
Given the nature of the mobile machines, AfriSam had equipped the mobiles with the necessary internal and external resources to cater for maintenance and the availability of the equipment. As a result, the team has managed to drastically improve the mobile plant’s availability, providing increased uptime and volumes.
Having a mobile plant on-site has not only helped boost production capacity, but also allows the team at the AfriSam Umlaas Quarry to keep producing during load-shedding, which is a challenge in Mkhambathini Local Municipality, says Singh.
“Load-shedding is a big setback for us in this area,” says Singh. “We have between four and six hours of power blackouts per day, which puts us on the back foot in terms of production. To minimise downtime on our fixed plant, we now switch it off just before load-shedding to avoid crusher blockages. Bringing a mobile plant has also helped us minimise the impact of load-shedding on our ability to meet our project requirements.”
AfriSam takes pride and care in producing quality aggregates to its customers timeously. “We have a laboratory on-site to ensure that
we produce quality products within the required specification with the right consistency, which is key to the success of the road contractors,” says Govender.
Producing the new Class 1 specification products, says Sebeelo, has come with the challenge of setting the operational processes to produce at lower tonnages as opposed to the more common specification materials. However, the AfriSam Pietermaritzburg Quarry team has managed to effectively plan and change modes to optimise on uptime. Some of the new Class 1 spec products include the 7.1 mm concrete stone and the 5.1 mm unwashed sand, which are not easy to produce, explains Sebeelo.
Govender says effective management of resources and equipment have been crucial to keeping up with the increased aggregates demand, especially at Umlaas Road Quarry where the site team is ‘doing more with less’.
“We have successfully transformed this quarry to meet the needs of the market. We have further managed to double our capacity while maintaining an effective, but optimal structure,” he adds.
“Throughout, the teams at Umlaas Road and Pietermaritzburg have maintained an impeccable safety record with no lost-time injuries recorded in the past two years. This feat would not be possible without the commitment of our employees who have successfully upheld AfriSam’s values of people, performance and planet,” Govender concludes.
Nationwide blackout
Botswana suffered a countrywide electricity blackout, leaving many households and businesses without electricity. Botswana Power Corporation (BPC) – the stateowned company responsible for electricity generation, transmission and distribution – blamed the blackout on a ‘grid disturbance’, the cause of which is unknown.
The ‘disturbance’ affected a transmission line connecting Botswana to South Africa, and caused a total breakdown of units at the coal-fired Morupule Power Station, which supplies most of Botswana’s electricity.
British water signs MoU
A memorandum of understanding (MoU) has been agreed on between Egypt and the UK’s leading water sector trade association to establish a framework for bilateral cooperation on water projects for 27 governorates and the new cities across Egypt.
The units were later restarted and taken online – a process that can take days. Botswana imposed power cuts, and homes and businesses did not have electricity for up to eight hours a day. The country has a large coal reserve and almost all its electricity comes from coal-fired power stations. companies. We have 40 new cities under development including a new capital city – this is a huge area of development, requiring extensive water and sanitation infrastructure, technologies and services,” says Dr Sayed Ismail, deputy minister: Infrastructure in the Egyptian Ministry of Housing, Utilities & Urban Communities.
The MoU will make it easier for the UK water industry to participate in the opportunities in Egypt, and for Egyptian companies to access UK knowledge and experience.
“Egypt’s water and sanitation sector is undergoing a huge transformation and we need the expertise of British
Among the 40 new cities is the new administrative capital of Egypt – which has a planned population of 10 million inhabitants and will feature green spaces, as well as separate residential and industrial sectors.
Another new city – New Alamein – is
one of the most ambitious of Egypt’s smart cities, covering 50 000 acres and with a proposed population of three million. Styled as Egypt’s ‘Gate to Africa’, it will be made up of separate tourist, residential, industrial and historic sectors.
While undertaking such rapid expansion, the Egyptian government wants to build the capacity of employees in the water and sanitation sector, specifically in areas like facility management and service delivery.
“We are particularly interested in working with British companies on two key technologies – desalination and sludge-to-energy. We want to close the loop by generating energy and increasing water reuse while minimising costs,” says Ismail.
Investment in desalination is critical to Egypt’s plans for a more sustainable water future. There are plans for around 20 new desalination plants across the country, which the Egyptian government seeks to build in collaboration with the private sector.
“The River Nile is the main source of water – and the main source of life – for all Egyptians. At the moment, 90% of our water is taken from there, but we need to diversify our other resources, especially in coastal areas, the north of Egypt and the eastern borders near the Red Sea. This is where we see desalination playing a significant role,” he concludes.
1 500 km long railway works resumes
Construction works on East Africa’s ambitious standard-gauge railway line linking the port of Mombasa to Kampala and Kigali could soon be revived, following a deal inked between Uganda and Turkish firm Yapi Merkezi.
Yapi Merkezi is the same company contracted for the Tanzania Standard Gauge Railway.
The planned 1 500 km long railway from Mombasa to Kigali had fallen behind schedule, with only Kenya having completed the initial phase of the project from Mombasa to Nairobi.
It is not yet clear when construction works are set to begin, but Uganda has completed the feasibility and designs for the 273 km long line between Malaba, in Kenya, and Kampala. The Ugandan section is estimated to cost US$2.3 billion (R44.5 billion).
Rwanda, on the other hand, earlier indicated that it had completed the preliminary engineering design of the new line from Kampala to Kigali, through Mirama Hills.
The standard-gauge railway from Kampala to Kigali is part of the Northern Corridor infrastructure project designed to connect Mombasa to Malaba on the border with Uganda, and onward to Kampala, Uganda’s capital, and eventually Kigali in Rwanda, with a branch line to Kisumu, and another line to Juba in South Sudan through Kasese and Pakwach.
In March 2022, heavy rains caused nearly 500 people to flee their flooded homes, while making roads impassable and cutting off electricity supplies.
Fortunately, Beira will soon be better equipped to deal with floods with the construction of an approximately 100 hectare retention basin. To reduce persistent flooding in the city, the Ministry of Public Works, Housing and Water Resources is also considering the construction of spillway control stations equipped with gates, the Estoril outfall and its outlet channel to the mouth of the Maria River. Bridges and service roads will be built along the new drainage channels. About 13 km of existing drainage network will also be rehabilitated to support the new system.
The project, which will benefit other towns in Sofala province, will also establish an early warning system for disaster management, as well as build institutional capacity for the operation and maintenance of the future infrastructure. It is scheduled for delivery in 18 months.
Mozambican authorities are also announcing the restoration of the dune belt that protects the city with vegetation, the protection of coastal sections with rocks, the construction of a concrete protection wall (Mangal area in Praia Nova), the repair and reinforcement of the old wall (Mangal area in Praia Nova), and the construction of Clay Dique (in the Regulo Luis area, Estoril).
Financial support has been received from the Netherlands and the World Bank.
When designed and constructed by experienced professionals, gabion systems can easily last 50 years or more in land-based and riverine environments. However, that is interdependent on the quality of the wire specification and materials used, which must comply with recognised industry benchmarks, say Louis
Aleading gabion manufacturer with a 17-year track record, Gabion Baskets has always placed major emphasis on quality control. This extends to its design, project management and training services for industry.
“However, the best design can still fail if the wrong products and construction techniques are employed, which is well demonstrated by some of the retaining wall failures we’ve been called out to assess in the eThekwini region, which was hard hit by the 2022 floods,” Cheyne explains.
“We’ve completed a number of reinstatement projects to date, alongside our own ongoing works, where we’ve had an opportunity to demonstrate best-in-class construction methodologies, as governed by SANS 1200 DK:1996.”
As with the correct construction approach, having set standards for gabion systems is equally important, and prior to the introduction of SANS 23-3:2020 in August 2020, this was determined by SANS 1580:2010. The latter defined the correct manufacturing specifications for gabions and revet mattresses assembled using hexagonal steel wire mesh. However, there were industry concerns regarding the two specific SANS 1580:2010 tests that products needed to pass, namely the twisted-wire pull-apart test and the panelto-panel joint-separation test.
“The view from industry was that these tests were unrealistic and not clear in terms of ensuring consistent laboratory results. On the twisted-wire pull-apart test, for example, the criteria were too complex, which meant it was near impossible for manufacturers to comply,” Cheyne explains.
The adoption of SANS 23-3:2020 has established an industry-accepted and practical approach based on EN 10223-3:2013 – the European standard, as well as the internationally accepted benchmark. Both cover the requirements for hexagonal steel wire mesh products for civil engineering purposes and, unlike SANS 1580:2010, go into more detail on elements like dimensions, coatings, test methodology and delivery conditions of steel wire mesh products.
“For us, it’s a vital part of our business, both in South Africa and Africa to be compliant with SANS 23-2:2020. Contractors, consulting engineers and clients increasingly demand guaranteed quality assurance, and the updated standard ensures that our products can be tested with confidence at an accredited laboratory,” Cheyne explains, adding that all
Gabion Baskets’ products tested to date by SANS-accredited entity Metallurgical Testing Labs have passed with flying colours.
Where required, Gabion Baskets can also submit its welded mesh panel line for testing according to SANS 462:2005 (Ed. 1.00). Welded mesh is proving increasingly popular in the architectural field for applications like building and interior cladding, as well as for freestanding feature walls.
As part of its turnkey solutions, Gabion Baskets ensures that every element of the system supplied for a specific project meets the specification, including the geotextiles and rock fill material that form an essential and integral part of the structure.
“We pride ourselves on providing a valueengineered solution, working with the client’s consulting engineer and contractor to make
sure that the final works are functional and sustainable over their envisaged design life,” Cheyne continues.
Two recent projects in KwaZulu-Natal underscore best practice. The first entailed the reconstruction of a gabion wall system for a property owner in Cowies Hill, Pinetown.
Gabion Baskets’ KwaZulu-Natal branch, based in Pinetown, was asked to conduct a site inspection on the works, which had been executed by a local contractor in September 2022. It was noted that the materials used were substandard and, to compound the problem, the design was for a revetment wall, when it should have been for a mass gravity retaining wall.
“Our first suggestion was to replace the whole structure but, due to client budget constraints, this was not possible, so the existing materials were used wherever practical for the redesign and reinstatement,” Cheyne explains.
The main concern was the toe of the gabion structure, which had slid forward, affecting the stability at the top of the wall embankment. As an out-of-the-box solution, Gabion Baskets’ team proposed a method to secure the toe, which was accepted by the client. This entailed digging down 1 m in front of the wall to establishing a 1 m deep gabion footing. To provide added integrity, Y20 rebar was placed through this first gabion row at 1 m intervals. The latter ties in with the gabion mattress foundation on which the stepped-back gabion retaining wall was re-established. (See Diagram 1 for the design details.)
“Following completion, our site team carried out a series of inspections, and the reinstated wall is holding exceptionally well, with the recent inclement weather ‘testing’ the design on more than one occasion during subsequent heavy downpours,” says Cheyne.
The second project showcased involved the design proposal, product supply and project management for an L-shaped wall that serves as a retaining and feature wall. The latter varies in length from 16 m to 21 m, with heights from 1.5 m to 3 m, and has a 6-degree batter against the embankment. The client’s engineer approved Gabion Baskets’ design proposal. Since the ground on which the walls are built is relatively hard sandstone, the team had to utilise a skid steer for the major excavations and only excavated to the final measurements by hand. At the client’s request, the facing rows are filled with brown rock to create an aesthetic effect. The result is a masterpiece in soil retention.
“What these projects underscore is the importance of a professionally competent design, the right materials and expert installation experience,” adds Cheyne.
“Plus, the key advantage of gabions is their design flexibility and ability to blend in and enhance the natural environment, in addition to combatting the widespread problem of soil erosion in urban and rural areas,” Cheyne concludes.
EVENT: 86TH Imesa Conference
DATES: 25-27 October 2023
VENUE: Boardwalk Hotel, Gqeberha (PE)
THEME: Resilience is the future
Reinforced Earth was founded on a patented suite of mechanically stabilised earth (MSE) technologies by Henri Vidal in 1963. Ever since, his pioneering vision in this field has provided a standard for best practice in environmental and geotechnical engineering worldwide.
From a historical perspective, Vidal’s vision, as an architect and engineer, led to the development of a new composite material using earth as a raw material. The sectors in which the material finds application include Road and Rail – retaining walls and bridge abutments; Mining – headwalls to crushing plants, storage bunkers and reclaim tunnels; Hydraulic infrastructure – dams, reservoirs, canals, quays, jetties, river training, groynes and breakwaters; Oil and Gas – bund walls; Urban development – retaining walls and foundation slabs; and Waste management –landfill containment.
In South Africa, the company celebrates 48 years in 2023, with managing director Louwtjie Maritz now at the helm with over two decades of service and the responsibility for taking the business forward in the local and greater sub-Saharan region. Baseline services include structural design, the supply of specific components, and training provision for contracting teams.
“Essentially, Reinforced Earth® consists of engineered backfill that is reinforced with a range of application-specific elements –typically geosynthetics or steel strips and grids – interconnected with facing elements composed of precast or steel panels, or wire mesh,” explains Maritz.
The key purpose of Reinforced Earth’s facing panels is to ensure structural stability, as well as erosion protection for the reinforced backfill. Additionally, the facing design of the panels can be customised to optimise the aesthetic effect.
The technology suite comprises the following key solutions, namely the original Reinforced Earth®, TerraLink™, T-Wall®, TechWall®, TechSpan® and TechBox®
The TerraLink™ shored MSE wall solution is ideal when constructing retaining walls in geometrically narrow sites. Installation is carried out in front of a stable existing structure such as a stabilised slope or retaining wall.
“T-Wall® is a recent product acquisition that is proving popular in the USA for railway projects and we’re considering introducing it to the South African and African market, with a number of proposals submitted to various clients to date,” says Maritz.
The system enables the construction of a ‘T’ shaped gravity-type retaining wall built by assembling modular precast concrete units together with granular backfill. The perpendicular stems allow for internal stability, providing pull-out resistance against the lateral earth pressures exerted on the back of the facing. These are large-scale structures, with each T-Wall unit measuring 2 m in height and 4 m in width.
For challenging conditions, TechWall® delivers. This precast retaining wall system presents the design advantages of counterforts acting as cantilever beams resisting lateral earth pressure. Because the counterforts are optimally reinforced, the moments in the facing panel are minimised and a relatively thin, fullheight concrete facing panel may be used.
For transportation and mining projects, TechSpan® and TechBox® are further
examples of Reinforced Earth’s ability to design products that are modular and easy to install. Their applications include tunnels and underground structures, buried bridges, box bridges and culverts.
“Our objective is to employ these technologies to optimise structural soil interaction as part of a turnkey solution. This includes our design service – provided by professionally registered in-house engineers – which has always been provided at zero cost to the client. We work with the client’s engineers and the contractors to perfect and deliver the best solution. Each project is unique, requiring a custom design, so innovation is always top of mind,” says Maritz. As part of the global Reinforced Earth group (trading as Terre Armée in French), the South African operation has access to the full product suite, either manufactured locally, supplied from one of the group’s factories worldwide, or sourced via externally appointed suppliers. In many parts of the world, the precast elements are manufactured and supplied by Reinforced Earth. However, given the logistics challenges in Africa, the South African arm is one of the only group companies worldwide that rents its precast panel moulds as one of the options available to the contractor, so they can manufacture on-site. However, Reinforced Earth retains its oversight role in terms of strict adherence to quality control.
To support the final design elements, Reinforced Earth also manufactures precast top-outs that integrate with its retaining walls.
These include precast traffic barriers, trims and copings, and parapets.
“When it comes to tie-back reinforcing systems, geosynthetics are ideal for aggressive backfills. A current example is a Reinforced Earth project in Oranjemund, Namibia, where the contractor is using seawater for compaction with well-graded materials for the construction of an extensive retaining wall at a local mine,” Maritz explains.
For this project, Reinforced Earth is employing its new Geocore® reinforcement, tying into TerraClass® precast facing panels.
However, Reinforced Earth’s mainstream choice is the employment of galvanised steel strip or grid systems for retaining walls. Manufactured in South Africa, their durability is legendary in the right conditions. They can also be employed for foundation reinforcement, particularly in areas prone to settlement or seismicity.
Their integrity can also be tested over time thanks to in-built steel sacrificial strips that can be removed after a predetermined period – say 5 to 10 years – to check for loss of strength due to corrosion.
“On projects we’ve completed on the N3 in South Africa, we’ve gone back and pulled out strips on walls that are some 20 years old and they’re still 100%,” says Maritz.
Another innovation is TerraTrel®. This is a wire-faced MSE wall system, consisting of inextensible high-adherence steel reinforcing strips or ladders with a bolted connection to a wire mesh facing, as opposed to a precast facing. Backfilling the facing with rock provides a similar finish to a gabion system.
Over the past 48 years, Reinforced Earth has completed a broad range of projects that in more recent times include mega ones like the Gautrain Rapid Rail Link, and the Mbabane Bypass project in Eswatini.
Opened to traffic on 8 May 2009, the Mbabane Bypass was considered the ‘missing link’ in the MR3 highway connecting the Ngwenya/ Oshoek border post to Manzini. The 11 km highway section has a height differential of some 1 000 m between the start and end, with unstable founding conditions.
Overall, the project presented a number of key challenges and entailed the design and supply of materials for the construction of 5 600 m² of bridge abutments, 6 700 m² of retaining walls and 29 000 m² of tiered fills all with steel reinforcing strips. Africon (now Zutari) undertook the detailed design of all bridges on the project.
“The most notable component of the designs are the four tiered fill structures, which were designed as an alternative to incrementally launched bridges,” explains Maritz, adding that the Esitibeni, Qabalembadada and Mangwaneni tiered fills –with heights ranging up to 33 m on centreline – were originally designed as incrementally launched bridge structures.
The Gautrain project presented its own unique set of challenges, requiring some 80 Reinforced Earth structures on 38 sites that were constructed between 2007 and 2010. These comprised retaining walls (both
supporting and alongside the tracks), bridge abutments, and first-span viaduct abutments.
Reinforced Earth’s design was undertaken in conjunction with the Bombela CJV and several of its consulting engineer subcontractors. Notably, Reinforced Earth’s solution catered for vibration loadings, seismic accelerations of 0.3 g, and a service life of 100 years.
In most cases, steel reinforcing strips were used throughout except in those areas where DC currents could pose a corrosion risk due to electrolysis. In these instances, GeoStrap® and GeoMega® geosynthetic strips were employed.
Currently, Reinforced Earth is extensively involved on infrastructure projects within Southern Africa, as well as in the West African region for a number of mining operations. Works in South Africa include the Govan Mbeki Interchange project in Cape Town, where the TerraClass® precast panel system is being employed along with Reinforced Earth’s Geocore® geosynthetic connection system. The total area is around 2 300 m2.
Further afield, Reinforced Earth is supplying its TerraTrel® system with steel connection for the N3 Lynnfield-Ashburton upgrade being undertaken by SANRAL. Covering an area of some 10 000 m², works are now virtually complete. Reinforced Earth is also employing
Reinforced Earth’s TerraTrel® system (approximately 2 350 m²) is being employed for a section of the Polihali Access Road Western Section, forming part of Phase II of the Lesotho Highlands Water Project
the same system is being utilised along with steel connections.
65 million m2 and counting
“Globally, the group has completed some 65 million m² of Reinforced Earth® walls, which underscores the tremendous success of the technique. The advantage for South African and African customers is that we can draw on this expertise in terms of design recommendations and technical training to complement our own unique understanding of the local market,” adds Maritz.
“It’s clear that the benefits of MSE are well proven. Reinforced Earth has taken this a step further, constantly evolving our systems to execute durable structures that become one with the environment,” Maritz concludes.
the same system for SANRAL’s N3 Dardanelles to Lynnfield upgrade, now underway.
Outside South Africa, projects include the supply of the TerraTrel® system (approximately 2 350 m²) for a section of the Polihali Access Road Western Section, forming part of Phase II of the Lesotho Highlands Water Project.
In parallel are works that include the Mbudzi Interchange project in Zimbabwe, where the TerraClass® panels are being cast on-site (total area: 4 714 m²), and the Kampala Flyover Lot 1 development for the Uganda National Roads Authority (2 320 m²), where
The scale of South Africa’s plastic pollution problem came to the fore during the April 2022 floods in KwaZulu-Natal, when mountains of waste ended up on Durban’s beaches. It’s a worldwide problem and one being addressed across the globe by a multitude of stakeholders and organisations, ranging from beach clean-ups to manufactured interventions.
By Alastair CurrieCRDC’s ‘The Bag that Builds’ programme is one of the key sources of its production waste materials
CRDC’s focus from the onset has been on protecting the environment by creating a productive use for non-recyclable plastic waste (resins 1 through 7) that would otherwise be incinerated, disposed of at landfills or end up as general litter, threatening our rivers and oceans. Worldwide, CRDC research indicates that only 9.5% of plastic waste is being recycled. In South Africa, the figure is around 21% out of an estimated 1.5 million tonnes produced annually, which underscores the importance of CRDC’s initiative.
Foremost among the plastic waste pioneers is the Center for Regenerative Design & Collaboration (CRDC Global), founded in 2018 by Donald Thomson initially as a small non-profit community outreach programme in a fishing village in Costa Rica that has subsequently spread its wings to become a construction materials innovator. Today, CRDC Global has operations in Australia, Costa Rica, Hong Kong, Mexico, New Zealand, Samoa, the UK, USA and South Africa – with the latter operation established in 2019.
“Their breakthrough is RESIN8™, a patented lightweight plastic eco-aggregate for concrete, which is rapidly gaining ground in the world of construction,” says Abraham Avenant, CEO, CRDC South Africa (CRDC SA). “Based on a CRDC study, if the world as a whole were to use just 2.8% RESIN8 in all concrete products, the planet’s plastic pollution problem could be solved.”
A seasoned civil engineer and business leader, Avenant immediately saw the benefits for the local market. “The whole concept of sourcing the materials for RESIN8 is what makes the process unique,
CRDC SA’s RESIN8 manufacturing plant in Blackheath, Cape Town
CRDC Global’s focus from the onset has been on protecting the environment by creating a productive use for non-recyclable plastic waste (resins 1 through 7) that would otherwise be incinerated, sent to landfill or end up as general litter
because it entails partnering with communities, general industry, waste companies, waste pickers and municipalities to find a very viable alternative. Along the way, the environment wins, jobs are created and cost-effective structures are built,” he explains.
“Plus, the collection process is greatly simplified by the fact that our solution accepts all types of mixed or dirty plastic waste, so separation at source is not required. The one proviso is that our manufacturing process can absorb up to 10% contamination,” Avenant continues.
Virtually indistinguishable from standard construction aggregates, RESIN8 is designed to be used as a natural aggregate replacement in all structural and non-structural concrete products. Typically, 2% to 10% of natural aggregate can be replaced with RESIN8 in structural concrete applications and up to 50% in non-structural applications.
Significantly, concrete formed using RESIN8 exceeds ASTM international standards, as well as SANS standards. Another plus is that concrete containing RESIN8 can be safely crushed and recycled without any associated environmental risk – an example being microplastic contamination.
The manufacturing process is waterless and begins with the shredding of the waste plastic. The mixed waste is then pre-conditioned with proprietary mineral additives to eliminate all pathogens and odours. Then during the heat extrusion phase, the pre-treated mixture melts and becomes a completely inert construction material. The bulk RESIN8 is then granulated
RESIN8 is granulated into the size, shape and gradation required by standard concrete mix designs for both precast and cast-in-situ (wet mix) applications
This M190 concrete block looks identical to a standard product made from cement and stone aggregate; however, some 10% of the standard aggregate has been replaced with RESIN8 eco-aggregate without compromising the block’s performance in any way
into the size, shape and gradation required by standard concrete mix designs for both precast and cast-in-situ (wet mix) applications.
“The rough and open-cell structure of RESIN8, combined with mineral additives, enhances both the mechanical and chemical adhesion with the cement paste,” Avenant explains. “This results in exceptional performance properties in terms of compressive strength – equally comparable with standard concrete – along with maintained fire resistance, best-in-class thermal values and acoustic suppression.
“A further plus is that concrete made using RESIN8 is lighter than standard concrete, with obvious benefits in terms of product transport and design, due to the fact that RESIN8 is approximately 3.5 times lighter than natural aggregates. So, as an alternative building
system, it ticks all the right boxes. RESIN8 is green and highly cost-effective.”
In 2020, CRDC SA set up a pilot plant in Blackheath, Cape Town, in preparation for its commercial launch, with over 100 different plastic waste streams tested in collaboration with various waste management and FMCG entities. The global business case has already been proven – backed by more than US$2 million (R38.2 million) worth of research and development by CRDC Global – but South African companies new to the RESIN8 concept still needed to be convinced.
The waste collected during this engagement enabled the production of more than 85 t of RESIN8 (up to 500 kg/day being produced
by the pilot plant), which was supplied to local concrete product manufacturers and universities for trial product development and analysis.
These tests were highly successful. Concrete products such as kerbs, channels, bricks, blocks, pavers, pipes and toilet structures were manufactured within the requirements of the various SANS and ASTM specifications. RESIN8 was also successfully tested for castin-situ applications such as foundations and floor slabs.
Bitprop, a Western Cape-based affordable housing developer, was one of the early RESIN8 adopters, applying a combination of precast and cast-in-situ applications for the construction of its two-storey buildings in township communities designed to accommodate six 18 m2 units.
CRDC SA specified a 2.5% RESIN8 composition for the foundations and ground floor slabs, while the 14 MPa masonry bricks have a 10% component. For each 108 m2 building, that equates to some 6.2 t of plastic being absorbed.
“Our engagement has extended to include all built environment professionals in the public and private sector – ranging from architects and consulting engineers to housing practitioners and road and stormwater specialists,” Avenant explains.
Positive market feedback subsequently led to CRDC SA securing funding for the upscaling of the pilot facility to a full-scale RESIN8 plant during 2021. Some 70% of the capex and opex has been funded by Polyco, and the remaining 30% by Alliance to End Plastic Waste (AEPW) – a global nonprofit organisation.
“We have now received our waste management licence and, with the acquisition of the required equipment, we expect to start production in June 2023, ramping up progressively as market demand increases,” says Avenant.
By October 2023, the target is to process some 610 t/month of plastic waste, equating to around 725 t of RESIN8. The factory setup is designed so that production can easily be doubled by adding additional extruders.
In parallel, the pilot phase provided the ideal opportunity to introduce CRDC’s ‘The Bag that Builds’ (TBTB) programme, a social initiative that also provides an income.
“The concept is simple and a key part of the RESIN8 concept globally, where everyone
at all levels of society can make a difference, alongside the sustainable waste streams being supplied by industry and municipalities. In terms of the TBTB programme, anyone can fill our recycled plastic bags with all types of plastic waste, which is especially significant for waste pickers that at present cherry-pick saleable recyclable waste and randomly dispose of non-saleable, non-recyclable waste in the general environment,” Avenant explains, adding that general households and schools are being incentivised to participate in a pilot programme funded by AEPW.
In collaboration with various waste collection partners, CRDC has so far managed to incorporate TBTB into 18 collection hubs across the Cape Peninsula. This has enabled CRDC to collect 85 t (53 000 bags) of plastic waste through TBTB since November 2022.
“Going forward, we see huge potential for RESIN8 in the South African construction sector, and for TBTB to be rolled out nationally, supported by the manufacturing industry, municipalities and general society, to eradicate non-recyclable plastics from our environment and create a market for an eco-aggregate that adds real value from a sustainability and job creation perspective,” Avenant concludes.
RESIN8TM is the only material made from plastic waste (Resins 1-7) to improve the performance of structural concrete products and earn acceptance from the construction industry. Concrete applications using RESIN8 exceed SANS standards as the national benchmark for material performance. In hot mix tests done internationally, RESIN8 improves the stiffness and mechanical properties of the asphalt mix. RESIN8 is fully circular at the end of its concrete life.
Judging by the number of complaints received by the Concrete Manufacturers Association (CMA), it is apparent that many construction professionals still believe that the SABS is the custodian of South African national standards, as well as the country’s only certification provider.
There is widespread confusion as to what constitutes a national standard for precast concrete products, who is the custodian of these standards, and who is accredited to certify that the standards are being met in the production process,” says Henry Cockcroft, director, CMA.
“We have been alerted by our members and our certification body, CMACS (CMA Certification Services), to numerous instances in which tender documents display this confusion. A typical example often occurs in the specification of precast concrete culverts. Instead of declaring that culverts comply with SANS 986:2019 – the national culvert standard – it states they should carry SABS certification or be SABS compliant,” he continues.
There are 16 precast concrete standards, which are all SANS (South African National Standards) and not SABS standards, and they all fall under the jurisdiction of the Department of Trade, Industry and Competition (DTIC).
“Therefore, any tender document that specifies a national standard should either name the specific SANS standard or, failing that, should call for SANS compliance. There should be no mention of the SABS in any tender document because there is no
longer any such thing as a SABS standard,” Cockcroft explains.
The South African Bureau of Standards is a state-owned enterprise with two predominant divisions, namely the Standards Division and SABS Commercial. The former is involved in the creation and updating of SANS standards on behalf of the DTIC, while the latter is a private company, run as a business concern and involved in the testing and certification of products in compliance with the DTIC’s SANS specifications.
Cockcroft point out that although SABS Commercial is one of the bodies accredited to certify precast concrete products to SANS standards, it is no longer the country’s sole certification auditing body as it once was.
After the introduction of the Standards Act (No. 8 of 2008), the custody of South Africa’s national standards was transferred from the SABS to the DTIC. And since then, any organisation can apply to become a standards certifier, provided they are accredited by the South African National Accreditation System (SANAS).
SANAS accredits businesses concerned with product certification in terms of section 22(2)(b) of the Accreditation for Conformity
Assessment, Calibration and Good Laboratory Practice Act (No. 19 of 2006). CMACS was first accredited to certify precast concrete products in 2017 and since then – as is legally mandated – CMACS is audited annually and gets reaccredited by SANAS as an accredited certification body every three years.
“Tender documents that state that a product should be SABS certified are not only misleading but are flouting the law and the Competitions Act (No. 89 of 1998). Because specifying who the certification body should be – be it CMACS, the SABS or any other certification body – precludes those companies that have used alternative certification auditors from tendering,” Cockcroft stresses.
“This practice, whether through ignorance or intention, limits opportunity to specific suppliers, promoting favouritism, collusion and price-fixing. Therefore, precast concrete producers should make sure that their consultants – i.e. engineers, architects and other professionals – are conversant with certification practice,” Cockcroft concludes.
By harnessing precast concrete technology, South African municipalities are building reservoirs of a very high quality at a fraction of the time and cost.
Previously, only a few local contractors had the skills, experience and capacity to undertake these projects using traditional in-situ construction methods. This previously restricted greater participation in these Municipal Infrastructure Grant-funded projects.
However, there are now a growing number of new entrants to the market that are embracing the benefits of precast to build enduring structures. These include Selby Construction, Anita Building Construction, Mako Projects and Trading, and Morata Building & Civils. Each has already successfully completed precast concrete reservoirs of varying sizes up to 30 Mℓ with the support of Corestruc, a turnkey precast concrete contractor with a specific focus on water infrastructure, including pump stations, water treatment works and water towers.
Corestruc’s expertise spans the entire value chain from the design of precast concrete systems through to the logistics and rigging capacities that are required to transport and integrate the various prefabricated elements on site. Manufacture of the systems are undertaken by approved prefabrication companies located throughout the country.
The ease and speed at which these reservoirs are constructed and their performance to date have substantiated Corestruc’s method.
Selby Construction, for example, was able to shave as much as two-thirds off the construction schedule of a 30 Mℓ reservoir by using Corestruc’s precast concrete reservoir system.
Meanwhile, the precast concrete roof and wall of a 25 Mℓ reservoir were erected by Anita Building Construction in only three months, while working alongside Corestruc.
In turn, Morawa Building & Civils was able to complete a 10 Mℓ reservoir, including posttensioning, in only four months. This also provided significant savings in construction costs for the client. Using in-situ construction methods, it can take up to nine months to complete a reservoir of a similar capacity.
The precast concrete reservoir system accelerates the construction programme by enabling the various trades to work simultaneously. While earthworks and site terracing, as well as the construction of the roof column bases are underway, Corestruc manufactures the precast concrete wall and roof in preparation to integrate them on-site.
The roof is erected first – starting with the roof columns – which are connected to the holddown bolts in the column bases. Suspended precast concrete beams are then connected to the dowels that protrude from the precast concrete columns. Thereafter, hollow core slabs are connected to the stirrups protruding from the precast concrete beams.
Steel reinforcing is placed into the cores of the hollow core slabs and these voids are then filled with in-situ concrete. By forming a composite mechanism with the infill concrete, the stirrups act as mechanical interlocks.
Once the inner portion of the roof is in place, the construction of the in-situ floor slab starts, followed by the ring beam for the precast concrete wall. The first wall panel is supported on the ring beam by a push and pull prop.
For temporary stability, the wall is braced back to the roof structure. The steel brackets assist in holding the panels together and, therefore, eliminating the need for extensive propping to free up space.
Once all the panels have been placed, unbonded cables are pushed through the polyvinyl sleeves in the panels. They are then grouted monolithically with the joints of the panels.
Thereafter, a grout is poured continuously in between the wall panels and horizontal
cable sleeves. It is a high-strength and -flow grout with an extended pot life so that it does not segregate and set too early. These characteristics are achieved by manipulating the water-to-cement ratio of 0:37 with the use of admixtures.
The water temperature is also reduced and controlled to act as a chiller in the mix. In addition, only cement, including an unhydrated type that reacts with water to seal possible leaks, is used in the concrete mix.
The cables are stressed to 75% when the grout has cured to a strength of 80 MPa. This is undertaken via precast concrete buttress panels that have been spaced along the perimeter of the reservoir. Larger reservoirs have four buttress panels and the smaller structures two.
The wall is then pinned by casting a 200 mm to 250 mm high reinforced kicker on the wall footing on both sides of each panel. Joints between the panels are grouted with a highflow and strength grout and post-tensioning renders them in compression to achieve water tightness.
Corestruc uses a ‘slide-and-pinned’ system. Post-tensioning is undertaken when the wall is not yet fixed to the ring footing and it is, therefore, allowed to slide on a steel bearing or locating plates. The coated, post-tensioned cables are not bonded to the grout, with the reservoir designed to maintain a residual compression of a minimum of 1 MPa in all directions.
Horizontal reactions to the wall base are transferred to the ring foundation through the second phase cast-in-situ kicker. This is where the ring tension in the base is also activated to resist the reaction. Additional post-tensioning of the lower part of the wall reduces the amount of rebar required in the cast in-situ ring footing.
As part of the final aspects of the build, the concrete floor slab is completed and the hollow core slabs that make up the outer portion of the roof structure connected to the precast concrete beams. A grout topping is then placed over the hollow core slabs to form a single monolithic structure, with a precast concrete coping installed around the perimeter of the roof to provide an aesthetic finish.
Given the quality of the precast elements, these structures will provide a designed life of 100 years with routine maintenance. A key ingredient is their precision fabrication.
In this respect, self-compacting concrete is used to manufacture elements that contain significant reinforcing and where conventional vibrating pokers cannot be used effectively. In this environment, the perfect dosages of admixtures are also ensured. This avoids overdosing that may delay early strength development, which is imperative for uninterrupted production. Another significant focus in the factory is to maintain the perfect water-tocement ratio to ensure concrete strength. Aggregates from suitable suppliers are also graded appropriately to avoid early concrete shrinkage. The prefabricated elements are inspected
Corestruc’s expertise spans the entire value chain – from the design of precast concrete systems through to the logistics and rigging capacities that are required to transport and integrate the various prefabricated elements on-site
and approved for dispatch to ensure the accuracy of the placement of the cast-in components. Reinforcement bar size and placement are also verified as part of the quality control procedures at the factory.
These steps are complemented by the checks and balances introduced by Corestruc ahead of mobilising to site to commence erecting the structure. Corestruc manages the settingout and installation of the column anchors for the precast concrete roof. By confirming the dimensional accuracies before erection, the company ensures that the beams of the roof structure fit the first time round. The precast concrete wall panels are placed and positioned in a similar manner with the assistance of permanent locating plates that are fixed to the ring foundation.
Thanks to this partnership between Corestruc and the contractor, consistent and excellent results have been achieved for each project completed. For this reason, Selby Construction, Anita Building Construction, Mbako Projects and Trading, and Morawa Building & Civils are especially proud of the high quality of their precast concrete reservoirs.
Comments Willie de Jager, MD of Corestruc: “We are very proud to be a strong partner to these enterprising construction companies that are revolutionising the way in which we construct essential water infrastructure.”
New advances in concrete and waterproofing technology now make it possible to use the world’s oldest building material for spectacular, unprecedented designs and a variety of applications that promote sustainability.
Concrete tiling, for example, is an exceptionally durable roofing system where the tiles can be moulded into a variety of shapes and finished with various textures and colours. Allied to this is the employment of shingles, which can be produced to mimic traditional roofing materials such as slate or clay.
The other conventional approach is the employment of cast-in-situ techniques for flat or low-sloped roofs to create seamless and monolithic surfaces, as well as the use of precast concrete panels.
Once constructed, the major benefit of
www.cemcon-sa.org.za
concrete roof systems is their ability to withstand harsh weather conditions and remain intact for many years without needing repairs or replacements.
“In fact, a building envelope can be designed to accommodate a variety of functions over its lifespan. For example, a flat concrete roof design could allow for further storeys to be added later as the need arises, or funds become available, to further optimise the use of well-located land and existing services,” explains Bryan Perrie, CEO of Cement & Concrete SA (CCSA).
Perrie says the incorporation of roof gardens is now also increasingly common,
helping to offset the carbon footprint by reclaiming potentially lost green spaces.
“If properly designed and detailed, concrete roofs can also significantly improve thermal insulation inside a building. This can be particularly beneficial in areas with extreme temperatures, where air-conditioning and heating costs are high,” Perrie continues.
“Furthermore, concrete is a noncombustible material with excellent fire resistance. A concrete roof can prevent fires from spreading to other parts of a building and help protect the structure from damage,” he concludes.
Sika’s commitment to supporting local communities recently led it to partner with charity, Ironman 4 the Kidz, to help build a swimming pool for the Khayalethu Child and Youth Centre in Gqeberha, Eastern Cape.
At Khayalethu, children between 6 and 21 are given a safe and nurturing home, with physical, emotional and intellectual support. Many of them have previously
been in dangerous environments, surrounded by crime, abuse and poverty, but they now have another chance to reach their true potential.
In addition to donating some of the concrete and construction chemicals required for the project, Sika’s team provided expert advice. Solutions included Sika Form Oil, an emulsionbased shutter release agent, and Sika Cemflex, a universal waterproofing and bonding agent.
SikaTop Armatec-110 EpoCem bonding primer and reinforcement corrosion protection was also applied as a wet-todry bonding agent, where required, while SikaGrout-212 was used to grout around the weir boxes and do small repairs.
Led by contractors CHC-SA Concrete Flooring – the champions of the initiative – and supported by a host of generous individuals and companies, the project was completed in just 25 working days, an incredible achievement by all involved.
The use of crusher or manufactured sand in concrete mixes has become common practice as a costeffective alternative to natural sand. There have, however, been issues with grading, which often prompts contractors to supplement with natural sand from sources such as rivers and dunes.
“This is where the challenges lie, with less availability of natural sands – which increases costs – as well as the presence of clays, which means that less of this material can be used or it has to be excluded completely,” explains Patrick Flannigan, technical manager: Concrete Business Unit, Chryso Southern Africa.
As Flannigan points out, sands that contain swelling clays tend to absorb newer-generation plasticisers, preventing them from delivering benefits such as water reduction or slump retention –areas addressed by the development of Chryso Quad Clear (Clay Enabling Admixture Response).
Chryso Southern Africa also offers the quick and innovative Chryso Clear Test to identify where these swelling clays could present a problem for concrete users. Where they are identified in the source material, Chryso Quad Clear can then be added as a liquid to the relevant plasticiser.
Fines issues
Another important development for the construction and concrete manufacturing sectors is Chryso Quad Graft (Gap Gradation Fixing Technology). This can solve the problem of an excess or lack of fines in source material, which often occurs in crusher sand.
“The industry is seeing the environmental benefit of moving away from natural sand and more toward crusher sand, but this product often has varying levels of fines. In the past, this could have compromised the performance of concrete, but Chryso Quad Graft now solves this challenge,” Flannigan concludes.
Because sands are unique, Chryso offers tailor-made solutions for both an excess and lack of fines
So far, two projects have received this award, namely the Salamanca Hospital in Spain for 2021, and the Dubai Silicon Oasis mixedused development for 2022. Both demonstrate the advantages of using Terraforce’s proprietary precast concrete systems to create distinctive engineered structures that make profound architectural statements that enhance the built environment.
Since its entry into the market in 1984, Terraforce – headquartered in Cape Town – has expanded its international network to most corners of the world, including the Middle East, with Dubai being a focal point from the 1990s onwards. Since then, Terraforce systems have continued to form part of landmark projects that
include the Palm Island developments, completed around 2007, as well as more recent examples like the Dubai Silicon Oasis technology, commercial, retail and residential hub.
Dubai Silicon Oasis’ landscape architectural design incorporates up to 6 m high Terraforce L16 rock-face retaining walls that were skilfully installed by Al Aamal Construction. The retaining walls were necessary due to the
Client: Dubai Silicon Oasis Authority
Engineering consultant: KCE Consulting Engineers
Main contractor: Water in Motion
Subcontractor: Al Aamal Construction
Terraforce-licensed manufacturer, Dubai: Consent Concrete Products
substantial differences in levels on-site, and to provide access to a leisure area on ground level, with access stairs and ramps leading to the residences at top level. In total, 41 100 Terraforce L16 and 2 000 Terraforce 4x4 Step Blocks were installed.
Comments Sinan Awad from Al Aamal Construction: “The site consists of set-back and vertical walls, as well as 90-degree corners that were achieved
In 2021, Terraforce started the Best Terraforce Project of the Year Awards to recognise the excellent workmanship and manufacturing standards of their licensed partners and clients from around the world.The highly creative integration of Terraforce multilevel corner details, inset planter boxes, ramps with rails, and grand 4×4 Step Block staircases constructed at Dubai Silicon Oasis Beautiful landscaping finishes off the site
90-degree corners were achieved by carefully cutting the Terraforce L16 rock-face blocks
by carefully cutting the Terraforce L16 rock-face blocks. For additional stability, the blocks were concrete-filled and reinforced with rebar, and we used double block rows with the rock-face finish facing outwards on either side for some of the vertical walls adjoining the two grand staircases and ramps. Where the walls joined other structures, dowels were used to secure the connections.”
Client: Salamanca City Council, Spain
Project manager: Excelentísimo Ayuntamiento de Salamanca
Main contractor: Ferrovial Construcción
Subcontractor: Obre Tecnicas Y Medioambiente Terraforce-licensed manufacturer, Spain: Prensagra Prefabricados
For the Salamanca project, four Terraforce L16 rock-face finish walls were installed by Obre Tecnicas Y Medioambiente, a Spanish environmental engineering company specialising in the construction of reinforced soil structures. Featuring a distinctive wave design, they cover a surface area of some 2 300 m² and reach a maximum height of 7.86 m in places.
Miguel Seller, civil engineer at Obre Tecnicas Y Medioambiente, expands on the key elements, which were designed using Terraforce’s Maxiwall Pro software. “The main wall supports a new access road to the hospital, and in some sections special consideration had to be given to the placement of geogrids due to the presence of a large drainage pipe (2.5 m in diameter) near the visible face of the wall,” he explains.
Another unique challenge was that the contractor had to adapt the slope of the wall to meet another vertical wall. As Seller explains, it was very complex from a topographical point of view. Since part of the wall was also located in a floodplain, permeable soil was used as the reinforced soil to achieve improved geotechnical characteristics.
The final results are exceptional, with the additional coping blocks, the steel fencing along the top, as well as the large rock strip lining the foot of the retaining wall adding eye-catching visual elements.
“The durability and functionality of our precast systems are legendary, as is the ability of landscape architects and design engineers to create urban masterpieces. It’s not easy to choose a winner when the standard is so high, so those who won in 2021 and 2022 are truly deserving of recognition, as will be the 2023 project as the year unfolds,” Rust concludes.
Overall, the fantastic multilevel corner details, inset planter boxes, ramps with rails and grand 4x4 Step Block staircases make a notable visual statement and create effective breaks in what could have been a sheer and vast grey surface. “It’s a prime example of engineering excellence and design innovation,” says Holger Rust, founder and head of Terraforce.
Client: Engen
Consulting engineer: BVi Consulting Engineers
Main contractor: Ruwacon
Landscaping: Landscape Garden Co.
Terraforce block supplier: Brick Solutions
Terraforce block manufacturer: Klapmuts Concrete
The use of Terraforce smooth face concrete retaining wall blocks has provided a landscaping and structural solution for Engen’s recently commissioned Engen fill-up station and Quick Shop in Worcester, Western Cape.
Two long retaining walls were needed to support the cut and fill slopes on-site, with BVi Consulting Engineers specifying the extensively tested and proven Terraforce block system. This was expertly installed by Ruwacon, under the watchful eye of Pierre Coetzee, construction manager.
Says Coetzee: “A total of 12 160 L11 Terraforce blocks were installed, in combination with a stormwater conveyance and retention system to be used for irrigation of the water-wise planting in the blocks and elsewhere on-site. Also, the lower wall was designed as a double-skin installation to handle the expected heavy traffic loads above.”
The new Engen station was officially launched on 3 April 2023 and, once the planting by Landscape Garden Co. is well established, the walls will blend effectively into the surrounding environment.
The Johannesburg Development Agency (JDA) is steering the construction of the Selby Rea Vaya bus rapid transit (BRT) depot, with the third and final phase now in progress. This entails the refurbishment of an existing administration block.
The depot will provide major and minor maintenance services for two Rea Vaya BRT operating companies, with the setup designed to accommodate up to 270 buses.
Included in the scope of works completed to date are extensive alterations, refurbishments and additions to an existing workshop building. Allied to this is the construction of a new refuelling building, a new double-volume wash bay facility, two new refuse buildings, plus ancillary works.
Mokgema Mongane, CEO at the JDA, says the Selby depot forms part of the JDA’s accelerated delivery programme, with a priority focus on social and economic infrastructure.
“Once complete, the Selby BRT depot will be fundamental for the Rea Vaya Phase 1C operations to include the trunk route from Sandton to Alexandra along Rivonia Road and Katherine Drive, and the trunk route from Parktown to Alexandra along Louis Botha Avenue,” Mongane concludes.
Gabions and River Mattresses
Hexagon Wovenmesh
Square Weldmesh
Gabion Tool Sets
Biodegradable Soil Blankets
Soil Bioengineering
Gabion Rocks
Geotextiles
Sandbags
Gabion Barriers
Gabion Barrows
In the realm of the global construction industry, which was valued at US$11.1 trillion in 2018, building information modelling (BIM) has emerged as a gamechanging innovation, driving cost savings and efficiency. Yet, in South Africa’s construction sector – valued at R430 billion the same year – BIM adoption lags, despite its proven benefits.
This disparity, amid a five-year decline in the South African architecture, engineering, and construction (SAAEC) industry, presents a compelling case for investigating the progression of BIM adoption in South Africa.
BIM is a process that uses computer-aided design (CAD) technology to integrate all building design information into a virtual 3D model. It enhances design visualisation and collaboration among project team members. This improved communication helps to alleviate many issues currently plaguing the construction industry, such as late and costly design changes, and delay claims, all of which negatively impact project delivery. However,
despite these advantages, the construction industry has experienced little productivity change over the past 50 years, as resistance to technological innovation in the industry seems to remain prevalent.
The benefits of BIM adoption and implementation (A&I) are numerous, including improved project performance and quality, enhanced productivity, waste reduction, faster delivery, and lower construction costs. Despite this, several barriers impede its adoption, including a steep learning curve, lack of skilled personnel, high implementation costs, lack of government support, and concerns about data ownership and legal issues.
Globally, BIM has found success in countries like Australia, Brazil, China, Canada, the UK, USA and Europe (as seen in Figure 1), yet in South Africa, BIM adoption rates fall far behind. While countries that have actively adopted BIM for decades have seen significant progress,
those without government support, like South Africa, have not. This disparity underscores the necessity of national leadership in implementing BIM strategies.
The South African studies conducted up until 2021 on BIM in the SAAEC industry have been limited in scope and size, focusing on various locations across the country. These studies have, however, indicated an increasing trend of BIM adoption over time, with usage primarily in the planning and design phases. Contractors were found to have the lowest awareness of BIM, with little utilisation during the construction phase. The main barriers to BIM adoption in South Africa echo those found in international literature and other countries in the early stages
of BIM adoption. These include a lack of awareness and skills, high setup costs, lack of demand, and poor support from policymakers. However, one emerging driver of BIM adoption is the increased competitive pressure among organisations to keep pace with advances in technology. The study aimed to determine if South Africa’s BIM A&I aligns with an innovation diffusion model in an attempt to provide a valuable forecast about future BIM A&I in the SAAEC industry.
The study combined a mixed-methods approach to investigate the rate of A&I of BIM in the SAAEC industry. The research utilised primary data from 283 survey respondents, enriched by secondary data from interviews and an extensive review of relevant literature, providing a comprehensive understanding of BIM awareness, use, collaboration, drivers and barriers.
Initial results show that BIM awareness in the SAAEC industry is commendably high, with 73% of respondents acknowledging familiarity with BIM. This suggests that efforts to popularise BIM as a key tool for the construction industry are on the right track, but the findings also reveal a disparity between BIM awareness and application. While 57% of participants reported using BIM, only 27% said they regularly employ it for collaboration purposes. This gap highlights a disparity in the maturity of BIM A&I; most users are at the basic usage level, with full collaborative capabilities yet to be harnessed across the industry.
Another key part of this study was the identification and analysis of the top 10 drivers and barriers to BIM A&I, as these factors play a crucial role in shaping the industry’s progress. The top drivers, as per previous research, were improved collaboration and enhanced project and design visualisation. These drivers were consistent across all disciplines and both public and private sector organisations. However, new drivers emerged, including easier access to information, the role of a new generation of tech-savvy professionals in pushing BIM implementation, and increased competitiveness among organisations. In particular, young professionals were found to be key to driving BIM adoption in their respective teams, often initiating BIM awareness and championing adoption efforts.
Barriers to BIM A&I, however, have not seen much change, with skill shortages, organisational resistance to change, and high setup costs remaining the primary obstacles. Interestingly, BIM awareness climbed up as a barrier, suggesting an issue with converting awareness into practical application.
A key finding was the comparative analysis between private and public
sector organisations, revealing that private sector organisations lead BIM A&I, pioneering ahead and not waiting for government initiatives. Public sector organisations were shown to have extremely low BIM A&I, and largely attribute this to lack of government support. Yet, there is significant potential for government intervention to expedite BIM A&I, a gap currently not sufficiently addressed. Figures 2 and 3 indicate the disparity between public and private sector organisations’ BIM use and skill levels.
The study also modelled South African BIM A&I rates, revealing a good fit with the standard diffusion model S-curve. If the current trend continues, it is estimated that BIM usage will reach approximately 80% by 2026 and 90% by 2028. However, the current trend also suggests that BIM collaboration will lag, presenting an area for targeted intervention. Figure 4 shows current and projected BIM use and collaboration rates over time.
The study highlights that BIM awareness has risen impressively since the inaugural 2014 research on BIM in the SAAEC industry. However, while familiarity is high, it is clear that there is a significant difference between awareness and application. Just a quarter of respondents reported using BIM for collaboration, suggesting a gap between understanding and practical use. This distinction is particularly clear among contractors, who show lower BIM usage rates compared to consultants, likely due to on-site skills shortages on construction sites.
A striking finding of this research is the stark contrast between BIM A&I rates in private and public sector organisations. Private sector organisations are leading the charge, with higher rates of BIM use, skill levels and collaboration compared to their public sector counterparts. The private sector is proving to be the primary driver of BIM A&I in the SAAEC industry, independently tackling barriers and pioneering adoption without waiting for government support. Conversely, public
sector organisations, crippled by the lack of governmental support, show alarmingly low BIM usage and almost zero collaboration.
When benchmarked against international standards, South Africa’s BIM A&I rates reveal a concerning lag. South Africa trails seven to eight years behind the international average of 11 developed countries, as shown in Figure 5, many of which have mandated
BIM use on public projects and have governmentissued national BIM standards. This clear lack of government support is posited as a major factor contributing to South Africa’s lagging BIM A&I rates.
In terms of drivers and barriers to BIM A&I, the research identified improved collaboration and enhanced project and design visualisation as the top two drivers. However, the industry is still grappling with persistent barriers, including skill shortages, organisational resistance to change, and high setup costs, which have remained largely unchanged over the past decade. The inability to overcome these obstacles poses a real threat to future progress in BIM A&I in the SAAEC industry.
The implications of these findings are clear: robust government support and policy intervention are critical to advancing the industry’s BIM A&I. Strategic policy implementation, including mandating BIM use on all public projects and publishing a national set of BIM standards, could act as a catalyst for BIM adoption, accelerating current implementation rates and closing the gap with international standards.
These findings offer vital insights for professionals in the industry as well as policymakers, providing an impetus to drive legislative changes to eliminate barriers and enhance BIM usage. Future research can extend this knowledge by employing larger surveys to improve result validity and by investigating the gap between private and public sector organisations, further enriching the understanding of BIM A&I in the SAAEC industry.
By harnessing the power of BIM, South Africa’s infrastructure engineering sector can look forward to a future of improved collaboration, efficiency and competitive advantage.
The vision of the BIM CoDE•SA
(Convention for a Digital South Africa) is to commence with the process of developing a BIM policy, by the South African AEC industry, for adoption by the Cabinet of the Republic of South Africa. The policy should define the road map for meaningful implementation of BIM in the built environment of South Africa, for the benefit of its citizens. We invite you to join us and help define the policy.
www.bimcommunity.africa/bimcodesa
Without a credible register of indigent people, municipalities will be spending on free basic services that they cannot account for or producing bills for accounts that will never be paid. It’s an area of key concern and one being addressed in their jurisdiction by iLembe District Municipality.
The initiative forms part of the Vuthela iLembe Local Economic Development Support Programme (Vuthela Programme), which is contributing to the improvement of the municipality’s economic future through sustainable growth opportunities, as well as the creation of more inclusive employment and income generating opportunities.
Within this framework, the establishment of a credible indigent register is essential to help iLembe budget accurately for revenue, free basic services and associated expenses.
“Municipalities are expected to look after those households who battle to
make ends meet by providing them with free basic services as determined by the Municipal Indigent Policy Framework,” says Zama Soji, a public finance management expert for the Vuthela Programme.
These free basic services for indigent people may include, among other necessities, sufficient water, basic sanitation, refuse removal in denser settlements, environmental health, and healthcare. Examples of indigent relief can include 50 kW of free basic electricity and 6 kℓ of free water.
Information gaps
The Vuthela Programme is presently aligning indigent policies and registers across the district. The next phase will involve the automation of these registers to produce a credible indigent register for each local municipality.
“We have observed that district municipalities often battle to develop such registers, as they depend on the information shared by the local municipality, yet in terms of powers and
function, they provide water as a basic service across the district,” Soji explains.
“Already, while completing a consolidated indigent register, it has been found that while Ilembe District Municipality should have 28 900 beneficiaries, only 2 000 were on record. The verification of the registers from municipalities also uncovered several discrepancies, which included people who were in the service of the state, deceased, employed and those who do not meet the criteria in terms of the council’s policy for relief,” Soji continues.
To combat this, the process of registering indigent beneficiaries in future will be done on the system and no longer on paper, following an automated process of verification and approval. Since applicants will be vetted, only those who qualify will benefit.
“With frequency of verification, municipalities will also be able to identify those beneficiaries whose situation changes during the year and remove those who no longer qualify from the system,” Soji concludes.
Everyone is aware of the challenges in the Northern Cape specifically – a major region for solar projects. A lot of that is driven by the fact that our grid is old infrastructure, and really designed around big base-load technology,” explains Janice Foster, MD: Energy at Zutari. In terms of load distribution, she says the focus is on the main urban centres in the north-east, where the main coal supply is located.
“The more distributed parts of the network are therefore not as strong, so there are limitations in terms of volume.” Foster uses the analogy of a water pipe, explaining it can hold only a certain volume of water. “Similarly, an electricity cable can only carry so much current, and at the moment that is at capacity in the Northern Cape.”
Commenting on the Renewable Independent Power Producer Programme (REIPPP) – where Zutari has played a leading role in the bulk of the successful bids –Foster says most Bid Window 4 projects are online and operational. In addition, most Bid Window 5 projects have closed and are entering the construction phase. “There have been some preferred bidders for Bid
Window 6, but that is where we saw the first impact of the grid constraints.”
The Zutari Energy team is under immense pressure at present, as every new project that connects to the grid requires a completed grid study in terms of integration and optimisation. “We carry out a lot of early-stage strategic advisory type work where we strive to understand client loads, their energy requirements and how they can best address these,” explains Foster.
This can include a mix of potential on-site renewable generation and storage, balancing this against the grid, or taking advantage of new regulations that have enabled clients to buy directly from independent power producers (IPPs) and wheel through the grid.
Energy transition: pros and consa “Essentially, we are moving away from one big generator as an off-taker to multiple variations of how these projects are procured, constructed and how the entire solution is packaged,” says Foster.
“Historically, generation comprised massive capital investment projects. As that has evolved, the opportunity for smaller private players to be involved is more real.”
Foster warns that privatisation has its pros and cons. “We have seen in parts of the world where separate transmission, distribution and generation entities have worked well, and other parts where the model has not. However, I think an independent system operator is important, irrespective of how the balance of the system is owned and operated,” she continues.
“The other side of the coin is that private investment comes with significant levels of due diligence. From what we have seen in the renewables space, the majority of projects run on time. Any overspend is carried by the investors as they already have a tariff locked in, so there is high pressure on coming in on budget as well,” says Foster.
On the technology front, South Africa’s
With winter looming, bolstering the grid is the key to enabling the faster roll-out of distributed renewable energy projects to counter an anticipated escalation in Eskom power outages.
Independent Power Producers Procurement Programme Office released an RFP for battery energy storage systems (BESS) in March, with that bid date closing in July. It encompasses five to seven sites predominantly in the Northern Cape to support grid strengthening. “We are seeing projects from small scale up to utility scale considering storage as part of that solution,” notes Foster.
Meanwhile, in terms of other energy options, Foster says that while there is a huge amount of interest and investment in green hydrogen, it is early days yet. “It is not going to have a major impact in the short term. It remains to be seen when we will see any projects of scale coming online.”
Looking at e-mobility, which takes advantage of the growing distributed energy network, Foster says it is mainly focused on the bus and larger commercial vehicle segment. Uptake in the passenger vehicle market is being driven by the more affluent, largely due to the tax structure around importing electric vehicles.
However, Foster cautions that both the UK and Europe have committed to halting the production of internal combustion engine vehicles by 2030 and 2035, respectively. This could propel South Africa into a quicker roll-out than it is experiencing at present as new vehicle production lines globally switch to electric vehicles. In Africa, Kenya is an example of a market where e-vehicle adoption is well ahead of South Africa, mainly due to a different tax environment for vehicle importation.
In terms of the Just Energy Transition (JET) and South Africa’s push for renewables and decarbonisation of major industries, Foster says the short-term focus “must be to address load-shedding, because that impacts the poor much more than the wealthy.”
“Anyone who can afford to is starting to look at a plan and what that plan can look like to create energy security in a personal or private capacity. Those unable to do that, especially individuals and small businesses, are suffering and will continue to suffer the most. In terms of social impact, and not just from the perspective of the JET, it has to be an absolute priority,” Foster concludes.
Utility-scale battery storage is growing in leaps and bounds, with the US Energy Information Administration estimating it will reach 30 GW by 2025. This is a strong indication of the successful uptake of the technology to mitigate both shortterm and intraday imbalances in renewable power generation.
“To work effectively though, utility-scale battery storage requires a sophisticated energy management system (EMS) to provide insight into daily usage, provision, supply and so forth,” explains Dwibin Thomas, cluster leader: Digital Automation, Schneider Electric.
“The hardware includes battery modules, battery racks, protection devices and inverters that convert the direct current (DC) of the battery into the alternating current (AC) of the coupled power grid. In turn, the key software components are the EMS, the battery management system (BMS) and a supervisory control and data acquisition system (Scada).”
As Thomas points out, the EMS acts as a higher-level operating system, which integrates to external systems and manages the response to changes in demand and supply. Meanwhile, the function of the BMS is to monitor the performance data of the battery modules and to regulate their charging and discharging. In turn, the Scada controls and monitors all the processes of the battery system in real time while collecting data on the system’s performance, such as voltage, current and temperature, and provides alerts if there are any issues.
“Lastly, and this is a key benefit, battery storage can provide power to the grid in a matter of seconds, allowing for a seamless switchover between distributed energy resources – thereby providing stable supply to users,” Thomas concludes.
South Africa has the potential to become a major exporter of green hydrogen. Kirsten Kelly interviews Thomas Roos, senior research engineer at the CSIR, about the green hydrogen industry.
TR Green hydrogen is created by the electrolysis of water using renewable electricity. The electricity must be green (wind, solar, biomass or geothermal).
Green hydrogen is new, but South Africa has been making hydrogen for decades. Sasol has been using both coal and natural gas while PetroSA has been using solely natural gas to make hydrocarbons.
The primary driver is climate change.
Achieving the Paris Agreement target of keeping the global temperature rise to below 1.5°C requires a fundamental transformation of the global energy mix. Green hydrogen can play a key role in this transformation as a sustainable, carbon-neutral fuel. Furthermore, green hydrogen is expected to play a key role in achieving the Green Deal objective of making the EU climate-neutral – with net-zero greenhouse gas emissions – by 2050. In order to protect their industries, the EU have implemented the Carbon Border
The cost of desalination of saline or non-potable water makes up a near-negligible fraction (1%) of the hydrogen production cost
Adjustment Mechanism Regulation that requires importers of certain carbon-intensive goods to pay a levy on their imports. This motivates these importers to decarbonise their production processes and green hydrogen can assist in certain cases.
The secondary driver is the drop in the prices of renewable energy. Over the past few years, the price of photovoltaics and wind power has decreased dramatically.
The third driver is the growing market for green hydrogen imports. Japan and Germany are two such countries that plan to import green hydrogen in bulk:
Japan plans to import hydrogen in bulk from 2030, at a target cost delivered to Japan of US$3/kg (R58/kg), but only requires the imported hydrogen to be carbon-free from 2040 onwards. Japan is a major net energy importing country, ranked in the top four global importers of the three main fossil fuels: coal, natural gas and oil. Having signed the Kyoto Protocol on 28 April 1998, Japan has climate obligations. The Fukushima nuclear disaster in 2011 significantly reduced public acceptance of nuclear power, constraining the decarbonisation options available.
As an industrial powerhouse, Germany is dependent on large volumes of energy,
Thomas Roos, senior research engineer, CSIRand their natural gas supply has been compromised by the Russia-Ukraine war. Germany is expected to need an annual volume of hydrogen of between 90-110 TWh (2.7-3.3 Mt) by 2030. However, domestic generation will be insufficient to cover all the expected new green hydrogen demand, so most of the hydrogen needed will have to be imported. Germany aims to systematically develop green hydrogen production sites in partner countries within the GIZ that offer great renewable energy potential. South Africa meets both of these requirements.
With our renewable energy resources (sunshine and wind), we have the ability to export green hydrogen at a better rate than Europe. A recent report by PwC estimated that South Africa could potentially export 7 Mt of green hydrogen a year, with a local market of 2 Mt.
What industries are best positioned to use green hydrogen?
It is important to note the best and most economic and efficient decarbonisation solution is to use renewable energy directly wherever possible. Creating hydrogen has a conversion loss, where approximately 50% of electrical energy translates into chemical energy and hydrogen and the electrolyser to make hydrogen is capital intensive.
However, green hydrogen is ideal for two sectors: long-distance heavy transport (maritime shipping, commercial aviation, rail and long-distance heavy trucking) as well as certain manufacturing industries (steel, cement, plastics, ammonia).
The mining industry (platinum and gold) is interested in using green hydrogen to power trucks and specialised equipment, as well as the use of a dual-fuel engine that can run on both diesel and hydrogen.
Extra water and extra renewable energy. The German National Hydrogen Strategy states that the generation of hydrogen in partner countries for export to Germany must not result in a decrease in renewable energy available in that country. The high capital costs of an electrolyser and intermittent supply of renewable energy (wind and sun) can drive up the price of green hydrogen. Therefore, it is important to oversize renewables to make maximum use of the electrolyser. This would provide an opportunity at times to sell the excess electricity that is not needed to make green hydrogen back into the grid,
providing a viable solution as the South Africa battles with power generation and electricity availability.
If South Africa exported 10% of the world’s hydrogen requirements, our 40 GW grid would need to be upgraded to a 600 GW grid. Provinces and metros could use this opportunity to build transmission lines and substations, and attract further investment. The more renewable energy that is added to the grid, the cheaper the electricity.
Furthermore, for hydrogen to qualify as sustainable, the water source must be sustainable. This means that using water for fuel production must not negatively affect communities, agriculture or the environment. This is a particular concern under the German National Hydrogen Strategy, which states “the sustainable supply of water in arid regions of these countries must not be impaired by the production of hydrogen”.
Fortunately, the cost of desalination of saline or non-potable water makes up a near-negligible fraction (1%) of the hydrogen production cost. This is because it costs 50 KWh of energy to make 1 KWh of hydrogen, but it only takes 3 KWh to make 1 000 kg of desalinated water. Desalination is an expensive water source for most industries – except green hydrogen.
This means that it is entirely possible to make a policy where green hydrogen producers oversize their desalination plants as part of their licence to operate. A desalination plant could then sell water to a water utility only at the electricity price.
The Port of Saldanha Bay and Port of Coega Two are considered attractive for the manufacture of hydrogen for export.
The Port of Saldanha Bay is attractive for shipments to Europe, as it is South Africa’s deepest port and is on the western seaboard. It has a 365 m long tanker berth for liquid bulk cargo with a permitted draught of
21.25 m alongside. It is also geographically close to good combined solar and wind resources. It is within the Berg catchment that is severely affected by water stress.
The Port of Coega makes most sense for shipments to Japan and South Korea, as it is an underutilised deep-water port designed to accommodate vessels of 14 m draught on the eastern seaboard. While it is close to good wind resources, the local solar resources are not strong; however, it may be connected to good solar regions via the national electricity grid.
The German KfW Development Bank has provided roughly R400 million in grant funding to support the development of South Africa’s green hydrogen economy and bolster its transition to renewable energy. The CSIR and Meridian Economics are appointed by KfW to help it identify and evaluate highpotential projects for implementation.
We have identified six projects to be implemented by the Industrial Development Corporation (IDC) and KfW.
Government has gazetted nine potential hydrogen projects as Strategic Integrated Projects (SIPs). This means that the projects will follow an expedited path to delivery with stipulated and shorter timeframes for all necessary approvals.
Sasol and the IDC have concluded a memorandum of cooperation to jointly develop and shape an enabling environment to advance South Africa’s green hydrogen economy. The South African Hydrogen Society Roadmap has also been published.
The Western Cape and Northern Cape provinces have signed a memorandum of understanding to develop a green hydrogen corridor and hub. While the Northern Cape has the wind and sun resources, the Western Cape is home to the key Port of Saldanha Bay.
Within the global context, South Africa’s road network ranks in the top 10 in terms of size, and in parts is widely regarded as being of world-class standard, particularly along the national routes managed by Sanral. However, in general, there’s a growing maintenance backlog – well illustrated by the National Department of Transport’s Vala Zonke pothole repair programme. Managed by Sanral, it aims to stem the deterioration of secondary and rural roads at provincial and municipal level. Funding support comes from various sources, a key one being the Provincial Road Maintenance Grant (PRMG).
“It’s a fact with asset management that if you don’t catch it at the right time, then the remedial cost increases exponentially. So, the first priority is to routinely maintain our existing roads, keep asset registers up to date, and ensure that the right materials and technologies are employed, both from sustainability and durability perspectives,” explains Kevin Govender, technical executive: Transportation at Naidu.
In this respect, Naidu closely follows international
asphalt trends to investigate what works best in practice for the South African environment. Tried and tested products include high-modulus asphalt (EME), which has been proven globally over the past 30 years or so for its performance under extreme traffic loading. “That’s an increasing factor in South Africa given the major shift from freight rail to truck haulage along our main commercial routes,” says Govender.
Another tried and tested technique is the employment of crumb rubber binders in asphalt to improve fatigue and durability performance. Since the rubber is sourced by recycling used tyres, there’s an added environmental benefit from a circular economy perspective.
“Rubber bitumen has not been prominent locally in recent years. However, it’s beginning to resurface, with plans in the pipeline to incorporate it as part of bitumen rubber asphalt on current Sanral upgrades,” Govender continues.
“The bitumen rubber will be part of the opengraded design, which will have the added advantage of excellent surface drainage to prevent the risk of aquaplaning across four to five lane carriageways, as well as the added benefit of noise dissipation, meeting the SANS threshold specification of 55 decibels.”
While the construction of flexible asphalt pavements is traditionally highly mechanised, there is increasing scope for elements of labourintensive construction (LIC). Examples include pothole repair programmes, in addition to general maintenance, plus the construction of low-volume roads.
Naidu is a pioneer in LIC practices and has received industry recognition that includes a National SAICE 2018 Award for project D1613. The latter also received a Commended Award at the 2018 KZN Premier’s Service Excellence Awards.
Completed for the KZN Department of Transport, the scope entailed the upgrading of a district road, using a combination of LIC and plant-based construction techniques. However, over 36 000 m³ of material was moved by hand. A key element of Naidu’s out-of-the-box design was the employment of geocells that were filled with batched concrete to form a functional low-volume road.
All of Naidu’s geometric designers have completed the firm’s CETA-accredited NQF 7 course on LIC, which is also offered to the industry, along with an NQF 5 programme aimed at contractors and construction monitoring.
Forming part of an integrated transportation system, roads are an essential socio-economic conduit for any country, with ongoing maintenance and upgrading key to enabling safe and efficient travel.
Alastair Currie speaks to engineering leaders at Naidu Consulting (Naidu) about their role in promoting best practices in design and construction, harnessing the latest digital tools.The Tugela River Bridge with its 40 m spans
“We understand the need to create jobs at the ‘coal face’ of the roads industry, which starts with optimising LIC at the design stage,” Govender explains.
Naidu currently undertakes design and construction monitoring responsibilities for a range of clients nationally.
The firm’s flagship project is the N3 Ashburton to Murray Road upgrade (Package K), where construction commenced in March 2023. The works contract value is approximately R2.4 billion and involves widening the existing two-lane freeway to four or five lanes in each direction over a distance of approximately 5 km. The construction programme is scheduled to run over four years.
In today’s environment, how projects are designed and executed is increasingly influenced by advances in digitalisation. The Covid-19 years – with their enforced remote way of working –accelerated its adoption, particularly in the field of building information modelling (BIM) as defined by ISO 19650.
“We decided that the timing was right to move with the rest of the world to BIM and to motivate the advantages of BIM over a road project’s life cycle to the clients we work with. One of our projects at the time was the realignment of Section 27 on the N2 at the Umhlali and Umvoti river bridges. We thought this would be an ideal opportunity to run a BIM pilot study, with the Umvoti southbound carriage section selected for this purpose. This was supported by Sanral,” Govender continues.
The Umvoti southbound section was converted into a 3D model in order to create a digital twin, importing all the relevant engineering and quality control data into a BIM cloud repository. “It was a great learning curve for us, the client and the contractor to see the elements come together in near real time, and to be able to interrogate the process within a common data environment.”
Naidu’s design engineers have now all made
the shift from 2D to 3D software, with Philani Mkhize, the then senior technologist and now regional manager: Gauteng, spearheading the shift to 3D design across Naidu’s Roads & Highways Design Unit. Philani was also part of the BIM pilot team on the Umvoti project.
“One of the key benefits of BIM is multiple stakeholder collaboration to design, cost, construct and maintain infrastructure assets over their lifespan via a virtual hub. From my experience, the speed and ease of project delivery are vastly improved. It’s also amazing to see the BIM model develop as a live rendition of what is happening on the construction site via successive reporting updates,” Mkhize explains.
When it comes to connecting economies and communities, bridges are one of the essential elements in transportation design, for both road and rail. This is a core part of the integrated offering provided by Naidu and headed up by Josh Padayachee, technical executive: Bridges & Buildings. A key focus is on ensuing that structures are functional and climate-change resilient.
“Most clients in South Africa have adopted Sanral’s drainage manual, but there’s an unprecedented frequency of severe flood events that requires industry to collectively revisit future implications. Sometimes it’s a non-engineered response, like ensuring the eradication of
alien vegetation, which reduces the hydraulic capacity of rivers and especially bridge openings,” says Padayachee.
In KwaZulu-Natal – which experienced some of the worst floods in South Africa’s history during April 2022 – infrastructure repair work is ongoing. One of Naidu’s projects in the design phase is the Illovo River Bridge for clients Prasa and Transnet. During the floods, the approach embankments were washed away, compromising the integrity of the steel truss bridge, which is more than 70 years old and past its design life. Options being proposed by Naidu include a new incrementally launched bridge across the estuary aimed at minimising any environmental impact.
On the N2 Umshali Bridge, a similar scenario was experienced, where debris had dislodged the bridge deck. Naidu is currently implementing a solution that entails jacking the bridge horizontally and then vertically back into place. This ensures that the existing bridge does not have to be demolished.
“Road asset management is important, but it’s crucial for bridges,” Padayachee continues, adding that Naidu recently won a tender via competitive bid to inspect all of eThekwini Municipality’s approximately 400 bridge structures. “We’re also inspecting bridges in the region for Sanral and the KZN Department of Transport in the wake of the 2022 floods.”
Allied to this, Naidu has developed an in-house app for bridge inspections, aligned with TMH 19, which greatly speeds up data capturing and analysis. The same is true for the firm’s other purpose-designed apps for fibre routing, health and safety, pavement management systems, and water-loss management.
The bridge app generates a high-level budget on estimated repair costs, with structures listed in terms of their maintenance priority according to a condition index assessment. Asset owners
can then plan accordingly. These inspections must be completed by a Colto-accredited bridge inspector, with any immediate health and safety concerns identified and alerted to the client.
“An area we’re particularly proud of is our rural bridge programme, because these are so significant in changing the lives of communities previously cut off by raging river crossings from reaching schools, markets, jobs, health facilities and entrepreneurial activities,” says Padayachee.
“Another aspect is that many of the contractors involved are emerging SMMEs without extensive experience in bridge construction. It’s a great opportunity for us to make our contribution to boosting empowerment and capacitation through alternative design approaches. On top of this, our staff on-site go way beyond supervising the project: we provide practical training in areas like fixing steel reinforcement, setting out shutters and the process required for concrete placement,” he continues.
A classic example of a successful project is the Tugela River Bridge, measuring 210 m
in length. This was intentionally designed as a modular composite structure to facilitate its on-site installation in a relatively remote rural setting.
The construction programme was undertaken by a historically disadvantaged contractor together with 11 emerging contractors. The project won a National SAICE Award for Technical Excellence and a Highly Commended Award in the Community Based Category. At the SAICE KwaZulu-Natal Branch Awards, it also won the Community Based Award and the Technical Excellence Award.
It was one of the first projects in the history of South Africa to show that a project could be very technical, while still enabling community participation and varying contractor skills levels. Naidu’s design minimised the risk to the contractor because there was no need for scaffolding in the river. The 40 m truss spans were lifted into place by crane and topped with a concrete deck.
“Transportation and social infrastructure projects in general are vital elements of South Africa’s economic reconstruction and recovery initiatives. And wherever possible, we need to enable employment and build capabilities. In this respect, it’s clear that both high- and low-tech design and construct techniques can deliver great results. Plus, they can all come together within the BIM domain,” Padayachee concludes.
A digital rendition of a section of the N3 Ashburton to Murray Road upgrade (Package K) projectCommemorated annually on 28 April, the World Day for Safety and Health at Work initiative provides an important opportunity to reflect on the health status of the South African construction industry – one of the key enablers of socio-economic development and service delivery.
The event was launched by the UN’s International Labour Organization in 2003 to promote the prevention of occupational accidents and diseases across all industries. For Professor John Smallwood, professor: Construction Management at Nelson Mandela University, it’s a vital rallying point, and one that he believes should be extended to include an emphasis on wellbeing in general.
To date, the performance track record for health and safety (H&S) in South African construction is mixed. “Our industry continues to receive unfavourable media coverage due to trench collapses, building, support work and slab collapses, fatalities, injuries, disease, and damage to public property,” he explains.
“Therefore, in many cases, there’s a need to move from the ‘Basic’ stage (i.e. ‘Little interest in H&S – doing the minimum to get by – and exposed to significant H&S issues’) to the ‘Compliant’ stage in terms of the H&S journey model. From there, the next phase is the ‘Proactive’ stage, and then the ultimate ‘Resilient’ stage (i.e. ‘Worldclass H&S performance – creating a process of continuous improvement/innovation’),” he continues.
Historically, Smallwood says the focus in terms of H&S has been guided by thinking such as ‘the manifestations of safety-related failures are immediate’, and ‘the manifestations of health-related failures are long-term.’
“Regrettably, despite legislation existing in the form of the Occupational Health and Safety Act (No. 85 of 1993), there’s evidence of a ‘safetyitis’ trend – a ‘disease’ that, among others, militates against affording
occupational health (OH) the status it deserves,” he continues.
The Ergonomics Regulations amplified the need to address ergonomics, which is directly related to OH. Furthermore, Smallwood says enlightened construction stakeholders have expanded the H&S agenda to include primary health (PH), including, among others, PH promotion. An increasing focus on mental health further expands the agenda and is in line with international research.
This is well illustrated by last year’s World Day for Safety and Health at Work media release, which presented the key findings of an exploratory study. This was undertaken by Working Commission W123 ‘People in Construction’ (PiC) of the International Council for Research and Innovation in Building and Construction.
The top five research priorities included: mental health (1=), workforce engagement (2=), H&S (2=), and workforce well-being
(4=). The top five research gaps included: mental health (1=), workforce engagement (2=), workforce well-being (2=), and human rights (4=). Overall, the top five issues – based on the mean of the percentage responses, research priorities and research gaps – were mental health, workforce wellbeing and workforce engagement.
“Clearly, sound mental health is the key. In construction, compressed project schedules, the physically demanding nature of the work, exposure to hazards and risks, long hours and being separated from family and friends on remote sites, all increase the stress burden. This amplifies the need for industry, organisational and project-level interventions,” Smallwood adds.
“Appropriate project durations, a ban on weekend work, and the inclusion of mental health and well-being in the Construction Regulations and H&S programmes constitute minimum interventions,” he concludes.
Located at the toes of Drakensberg mountains, Ladysmith has experienced flooding for over 170 years. In modern times, the situation has been exacerbated by climate change, the most recent example being in January 2022 when the town experienced flooding on three different occasions, resulting in extensive loss of life and property damage. By Dr Nezar A Eldidy, Pr Eng*
The town’s location is part of the problem, as it is situated on the floodplain of the Klip River in the Thukela catchment area, with its central business district (CBD) and a large part of its residential areas situated within the river's flood basin.
Relocating the town is not an option, though, chiefly due to its places of historic and cultural interest, with at least 21 sites situated adjacent to the N11 route passing through the town. These include Later Iron Age sites, Anglo-Boer War period sites, homesteads, farmsteads, public buildings, one memorial, and two contemporary places of worship.
One of the interventions in subsequent years was the construction of the Qedusizi Dam in 1996 on the Klip River. The dam has a 32 m high wall, which was designed to manage flood peaks and delay floodwater from the upper region of the Klip River's catchment area. It has two openings without gates that allow a discharge of 450 m3/second, limiting large-scale damage and providing an adequate evacuation warning period.
However, it was meant to work in tandem with the nearby Windsor Dam, which was built to retain floodwater exceeding a flow of 700 m3/second. However, the dam was decommissioned in 1998 due to siltation and a lack of maintenance of the meanders of the Klip River.
As a result, during severe floods, Qedusizi Dam comes under major pressure. To illustrate the point, historical data suggests a 70% probability of a flow of about 1 000 m3/second every f years upstream of the Qedusizi Dam,
while a flood of about 1 500 m3/second may occur every 100 years.
On top of this, a study of the cross-sectional capacity of the Klip River’s meander reveals that the average carrying capacity has decreased to less than 50% of the maximum discharge from the Qedusizi Dam, and some areas have only 23% of their original carrying capacity.
Since sections of the river winding through the town are situated at higher elevation above the CBD, when the banks are breached the stormwater heads towards the CBD’s lowest point.
The situation is compounded by the underlying geology, which forms part of the Vryheid
Formation of the Ecca group. It consists of shales, mudstones and fine-grained sandstones, intruded by doleritic sills and dykes of Jurassic age.
On top of the sandstone/shales subsoil lies a layer of loamy clay. These clay-rich soils have the largest pore space, and hence the highest water retention capacity, which is not conducive for stormwater dispersion.
The typical coefficient of seepage for such soil is 0.8 m3/hour, which is an average value for this type of soil. In contrast, the estimated seepage into the soil from the meander and the surface of the CBD is 1 700 m3/hour and 1 800 m3/hour, respectively.
Another factor to consider is groundwater. Investigations in the vicinity of Ladysmith, where the soil has the same structure, show groundwater level fluctuations and a rainfall variation of about 3.2 m and 15%, respectively. In general, the response of groundwater levels to changes in rainfall across the province has a lag time of two to four months, so extensive surface water build-ups add to the drainage challenge.
The existing drainage pipes convey stormwater from the CBD into the Klip River through a system of duckbill check valves. However, in a post-flood inspection, 11 out of the 24 check valves were either damaged or completely pulled out.
Although these are manufactured as nonreturn valves, in practice, they come under passive pressure during floods. Turbulence occurs at the outlet, which leads to valve damage.
These and other findings formed part of the detailed step-by-step analysis needed to design a sustainable mitigation solution. That included gaining an understanding of how past flood events panned out.
Typically, the records show that during storm events, water gradually rises behind Qedusizi Dam. As momentum builds, the discharge from the dam increasingly raises the level of the Klip River. At peak discharge, the water level can reach up to 9 m in height, with the following ripple effects:
Water backflows through the drainage system: the current drainage pipe outfalls located above the riverbed have diameters of 900 mm to 1 200 mm. During a rain event, the duckbill valves discharge water from the CBD drainage gravity line (under active pressure). At the same time, the water level in the river will continue to rise until it exceeds the top of the pipe or the upper tip of the valve.
When the water level in the river exceeds the level of Forbes Street (one of the CBD’s lowest points), water flows back into the drainage system and into the CBD, resulting in a backflow that can reach 72 000 m3/hour.
This can put the lowest area in the CBD under approximately 2 m of water within
3.5 hours of reaching the high water level in the river due to pressure difference.
Water overflowing the banks: when water flowing from Qedusizi Dam reaches its maximum discharge of 450 m3 /second and is joined by a discharge of 50 m3/second from the Flagstonespruit, the water will breach the banks of the meander and pour at a rate of about 350 m3/second towards the CBD due to the reduction in carrying capacity of the meander/river cross section. The run-off of the CBD: it contributes about 60 000 m3/hour during the storm, but the controlling factor is the level of the Klip, and its backflowing into the CBD.
Slow drainage through the soil: as discussed above, the loamy clay retains water and takes considerable time to drain, which increases the surface run-off through the town.
The reality is that even with all the infrastructure solutions installed to date, Ladysmith – and its 250 000 plus inhabitants – will always be exposed to flood risks because of the town’s location.
Three solutions were investigated, namely:
• partial dredging and lining of the channel
• construction of an aqueduct for water transfer from upstream to downstream. The first solution was the most practical and attainable with the support of national government funding.
The recommended route is as follows:
• the dredging of about 1 million m3 of silt and deposits from the river to enlarge and deepen the cross-sections
• the installation of a pump station on Queen Street – the station will host three pumps of about 1 m3/second discharge and a head of not less than 10 m
• the building of a discharge and calming lagoon with gabions and lined with geotextiles to discharge water downstream of the CBD
• replacement of the duckbell valves with automated sluice gates or with flap valves
• the installation of an additional 900 mm collector pipeline with concrete chambers – the pipe will be at a higher level than the current drains
• the installation of two 600 mm steel pipelines to evacuate water from the pump station to the discharge lagoon.
Conclusion
Selecting the appropriate equipment for the drainage system can help prevent flooding, but the need for yearly maintenance of the river channel is crucial. In this respect, combatting silt build-up behind the Qedusizi Dam wall is an essential part of this process.
Established in 2001, Johannesburg Water is owned by the City of Johannesburg (CoJ) and is tasked with the operation and maintenance of the water and sewer network.
• Operational regions: 6
• Regional depots: 10
• Electromechanical depots: 4
• Wastewater treatment works
(1 043 Mℓ): 6
• R115 billion infrastructure replacement cost
• Average revenue: R12 million
• Staff: 2 786 (June 2022)
• 12 560 km water network
• 11 861 km sewer network
• 75 pump stations
• 129 reservoirs and towers
• Average daily water demand: 1 621 Mℓ
• Sewage treatment: 909 Mℓ/day
Johannesburg Water has 765 pressure management zones within its entire water reticulation network. Only 22 are smart-controlled. According to the WC/ WDM (water conservation and demand management) strategy, a further 177 new pressure management zones will be established over the next 10 years. This will be done in a prioritised format to ensure the most beneficial zones are established first. A total of 37 of the new PRV (pressure-reducing valve) zones will be smart-controlled pressure management stations that will be either time- or flow-based.
Over 5.7 million people live in CoJ, and this population increases by 2.49% a year. This means that next year, roughly 141 000 more people will move into the metro.
Currently, there are approximately 1.8 million households.
The number of informal settlements in Joburg rose from 179 (2012) to 312 (2022). These informal settlements must have water and sanitation services.
As the biggest potable water consumer out of the Vaal River Catchment, CoJ accounts for 40% of water consumption volumes out of the Rand Water Supply System.
Partnerships with the private sector are of extreme importance to Johannesburg Water. This is because we need further investment into our infrastructure to meet increasing water demand. Our rate of investment into infrastructure is smaller than the rate of deterioration. For example, we would like to replace 925 km of pipes in the next five years (185 km/annum); we can only replace 117 km with our current funding. Water losses have increased from 24% in 2019 to 31% in 2022. The lack of capital investment has continued to have an impact on the infrastructure failure rate. The increase in the infrastructure failure rate has resulted in an increase in physical losses.”
Derrick Kgwale, COO, Johannesburg Water
Johannesburg Water’s infrastructure assets have a current replacement cost of R115.4 billion. Its asset management plan dictates that a renewal rate of 2% per annum is required. Current expenditure patterns indicate an average renewal rate of 0.92% is achieved with current. Alarmingly, 25% of the asset base has a remaining useful life of less than 10 years.
As the custodian of quality in its sector, the Southern African Plastic Pipe Manufacturers Association (SAPPMA) continues to advocate the importance of maintaining the highest standards in the production of thermoplastic products.
The purpose and mission of SAPPMA are to create absolute customer confidence in the plastics pipe industry, thereby ensuring long-term sustainability and dynamic growth in this allimportant sector. To this end, SAPPMA is a voluntary, self-regulating, nonprofit association that represents approximately 80% of the plastic pipe manufacturers and other stakeholders in the Southern African market, and is recognised by design engineers and customers as the quality control gatekeeper.
“Plastic piping is used across the complete spectrum of many industries, including mining, civil, irrigation, industrial, telecommunications and building. Around 150 000 tonnes of pipe (PVC and HDPE) are produced annually in South Africa, representing many thousands of kilometres,” says Jan Venter, CEO of SAPPMA.
“The integrity of these networks, built up over many years, is of critical importance, serving the water supply and sewage disposal needs of many millions of people. This clearly highlights the need for a responsible, ethical and quality-conscious industry,” he continues.
In terms of its Code of Conduct, SAPPMA monitors its own members in terms of product quality and full adherence to all relevant national standards, based on international best practice. SAPPMA members also commit to independent and unannounced factory audits, along with sample testing.
The reality is that South Africa is a dry country and, given the rising demand for clean drinking water and inconsistent rainfall, it’s clear that current pipeline leakages – estimated at around 40% on average – can no longer be tolerated. That makes quality a top priority for any product or systems designed to support sustained potable water supply, with the added need for optimum life-cycle utilisation.
“HDPE and PVC pipes answer this call with distinction. In addition, they are highly suitable for the rehabilitation of old pipelines,” adds Venter.
“So, plastic is clearly no longer an alternative pipe material. It has grown to a dominant position in piping systems worldwide, with an estimated share of more than 50%.
This is supported by independent market surveys in South Africa, which indicate similar dominance in sizes up to 1 000 mm diameter,” Venter concludes.
Sizabantu Piping Systems was established in 2002 as a Marley Pipe Systems BBBEE initiative to focus on the marketing and distribution of plastic piping solutions in Southern Africa. IMIESA catches up with Don Coleman, managing director of Sizabantu Piping Systems.
Sizabantu Piping Systems has recently celebrated its 20th anniversary. What has changed in piping systems over the past 20 years?
DC The Southern African piping industry has undergone many changes. Original, larger traditional manufacturers in the plastic pipe industry, or founding members, have been slow in repositioning and adapting their operations to meet the rapidly changing market dynamics. They have been further hampered by their costly corporate structures that reduced their competitiveness. Other factors influencing the industry has been easy access to lowcost manufacturing equipment, which lowers
the barrier to entry and encourages leaner newcomers to enter.
The traditional customer base in certain markets has also changed with the introduction of the government procurement policies. There has also been the development and introduction of new piping technologies. Plastic pipes can now be manufactured with larger diameters and this has allowed the plastic pipe, for the first time, to compete against traditional piping materials. Higher nominal working pressure bulk water piping can now be produced locally.
What trends have you observed around piping systems?
There is a constant improvement in the quality and durability of plastic piping products to better withstand the harsh weather conditions and extreme temperatures that are often present in South Africa. Additionally, there is an increasing interest in the use of plastic piping for industrial and agricultural applications, such as irrigation and wastewater management.
Sizabantu Piping Systems can assist consulting engineers and civil contractors to check and scrutinise their designs and to ensure that the correct product is used for the correct application
This is supported by a high level of investment and continuous development to ensure that engineering, user and environmental needs are continually being addressed.
What are some of your popular products, and why?
We have introduced the Molecor PVC-O (orientation) technology, which has positioned the plastic pipe to compete against the large bore with medium pressure and traditional pipe materials. This range offers both the specifier and user all the benefits of a non-corrosive, user-friendly, proven and dependable piping system that can be fit for purpose.
What is Sizabantu’s recipe for success?
Sizabantu Piping Systems has attracted a team of enthusiastic, competitive entrepreneurs, with an ownership option. The team is focused on the markets we serve and is continually reviewing and being alert to any changing market trends. We are continually challenging ourselves, to ensure that the market has access to the latest and most appropriate products for their applications.
During a recent road upgrade project in Silkeborg, Denmark, the deployment of a Wirtgen W 380 CRi cold recycler demonstrated the efficiencies of insitu rehabilitation as a cost-effective and sustainable solution.
With conventional asphalt paving methods, the work would have involved milling off the entire road surface in several stages and then widening and repaving from the ground up. In contrast, with in-place cold recycling, the contractor was able to use the existing asphalt material to produce a new bitumen-stabilised material (BSM) base layer.
Leading the paving train, the Wirtgen W 380 CRi cold recycler first milled off the existing asphalt surface to a depth of 15 cm and then added foamed bitumen and cement to directly produce the new mix in the machine’s milling and mixing chamber. Around 300 tph (tonnes per hour) of BSM was transferred to the Vögele
Super 2100-3i road paver following behind, which then established the new 5.5 m wide and 12 cm deep pavement profile – all in a single pass.
The cold recycling train worked its way forward along the 3 km section at a rate of 4 m/min. Then as soon as the rollers had taken care of the final compaction, the road was able to be temporarily reopened for local traffic.
According to lead contractor Arkil A/S, the costs were 30% lower than for a conventional rehabilitation project. Here, savings on materials played the biggest role in the reduction of the overall project costs.
Thanks to foamed bitumen technology from Wirtgen, considerably less bitumen needed to be added as a binding agent when compared to the production requirements for a new asphalt mix. During the project, hot bitumen was delivered to site and automatically injected in place during the milling and mixing process via
Wirtgen’s Vario injection bar system. The latter automatically matches the feed volume to the travel speed and ensures the homogeneity of the mix transferred directly to the Super 2100-3i paver.
Another advantage of this technology is that the final asphalt surface layer can be paved thinner. In this case, only 3 cm of high-quality surface layer material was used, instead of the usual 4-5 cm. This also helped to reduce the construction costs.
Lower transportation costs led to further cost savings. The recycling area of over 12 000 m2 produced almost 4 000 t of material that did not have to be removed from the site. This in turn helped to lower CO₂ emissions with the elimination of some 400 truckloads of material to and from the site that would otherwise have been required.
Some 3 800 t of fresh hot-mixed asphalt would also have been needed for the base layer in the case of conventional asphalt paving. This clearly underscores the cold recycling approach as a far more efficient and environmentally friendly method.
The versatility and durability of BSM have been proven on decades of projects around the globe. The required minimum thickness for a sustainable BSM base layer is 10 cm; in Silkeborg, the Super 2100-2i paved the material with a thickness of 12 cm
AECOM siphokuhle.dlamini@aecom.com
AFI Consult banie@afri-infra.com
Alake Consulting Engineers lunga@alakeconsulting.com
ARRB Systems info@arrbsystemssa.com
Asla Construction (Pty) Ltd johanv@asla.co.za
BMK Group brian@bmkgroup.co.za
Bosch Projects (Pty) Ltd mail@boschprojects.co.za
BVI Consulting Engineers marketing@bviho.co.za
CCG puhumudzo@ccgsytems.co.za / info@ccgsystems.co.za
Corrosion Institute of Southern Africa secretary@corrosioninstitute.org.za
Dlamindlovu Consulting Engineers & Project Managers info@dlami-ndlovu.co.za
EFG Engineers eric@efgeng.co.za
Elster Kent Metering Mark.Shamley@Honeywell.com
EMS Solutions paul@emssolutions.co.za
ERWAT mail@erwat.co.za
ESCONGWENI BPH ENGINEERS (PTY) LTD info@escbph.co.za
Gabion Baskets mail@gabionbaskets.co.za
GIBB marketing@gibb.co.za
GIGSA secretary@gigsa.org
GLS Consulting info@gls.co.za
Gorman Rupp Cordeiro@gormanrupp.co.za
Gudunkomo Investments & Consulting info@gudunkomo.co.za
Hatch Africa (Pty) Ltd info@hatch.co.za
HB Glass Filter Media info@hardybulkinglass.com
Herrenknecht schiewe.helene@herrenknecht.de
Huber Technology cs@hubersa.com
Hydro-comp Enterprises info@edams.co.za
Infrachamps Consulting info@infrachamps.co.za
INFRATEC info@infratec.co.za
IQHINA Consulting Engineers & Project Managers info@iqhina.co.za
iX engineers (Pty) Ltd hans.k@ixengineers.co.za
JBFE Consulting (Pty) Ltd issie@jbfe.co.za
JG Afrika DennyC@jgafrika.com
KABE Consulting Engineers info@kabe.co.za
Kago Consulting Engineers kagocon@kago.co.za
Kantey & Templer (K&T) Consulting Engineers ccherry@ct.kanteys.co.za
Kitso Botlhale Consulting Engineers info@kitsobce.co.za
KSB Pumps and Valves (Pty) Ltd salesza@ksb.com
KUREMA Engineering (Pty) Ltd info@kurema.co.za
Lektratek Water general@lwt.co.za
Loshini Projects muzi@loshini.co.za
Makhaotse Narasimulu & Associates mmakhaotse@mna-sa.co.za
Mariswe (Pty) Ltd neshniec@mariswe.com
Martin & East gbyron@martin-east.co.za
M & C Consulting Engineers (Pty) Ltd info@mcconsulting.co.za
Mhiduve adminpotch@mhiduve.co.za
MPAMOT (PTY) LTD mpumem@mpamot.com
Mvubu Consulting & Project Managers miranda@mvubu.net
Nyeleti Consulting naidoot@nyeleti.co.za
Odour Engineering Systems mathewc@oes.co.za
Prociv Consulting & Projects Management amarunga@prociv.co.za
Rainbow Reservoirs quin@rainbowres.com
Re-Solve Consulting (Pty) Ltd maura@re-solve.co.za
Ribicon Consulting Group (Pty) Ltd info@ribicon.co.za
Royal HaskoningDHV francisg@rhdv.com
SABITA info@sabita.co.za
SAFRIPOL mberry@safripol.com
SAGI annette@sagi.co.za
SALGA info@salga.org.za
SAPPMA admin@sappma.co.za / willem@sappma.co.za
SARF administrator@sarf.org.za.co.za
SBS Water Systems marketing@sbstanks.co.za
Silulumanzi Antoinette.Diphoko@silulumanzi.com
Siroccon International (Pty) Ltd admin@siroccon.co.za
SiVEST SA info@sivest.co.za
Sizabantu Piping Systems (Pty) Ltd proudly@sizabantu.com
Siza Water (RF) Pty Ltd PA@sizawater.com
Sky High Consulting Engineers (Pty) Ltd info@shconsultong.co.za
SKYV Consulting Engineers (Pty) Ltd kamesh@skyv.co.za
Smartlock jp.alkema@smartlock.net
SMEC capetown@smec.com
Southern African Society for Trenchless Technology director@sasst.org.za
SRK Consulting jomar@srk.co.za
Star Of Life Emergency Trading CC admin@staroflife.co.za
TPA Consulting roger@tpa.co.za
V3 Consulting Engineers (Pty) Ltd info@v3consulting.co.za
VIP Consulting Engineers esme@vipconsulting.co.za
VNA info@vnac.co.za
Water Institute of Southern Africa wisa@wisa.org.za
Wam Technology CC support@wamsys.co.za
Wilo South Africa marketingsa@wilo.co.za
WRCON ben@wrcon.co.za
WRP ronniem@wrp.co.za
Zutari Rashree.Maharaj@Zutari.com
The foundation for Wacker Neuson’s success story was laid by Johann Christian Wacker in 1848 when he set up a blacksmith’s shop in Dresden, Germany. Since then, the company’s research and development (R&D) initiatives have continued to lead with innovative product solutions for the construction market.
Examples include the introduction of an electric rammer in 1930, and the development of an internal vibrator for concrete consolidation around 1934. The company also set a new benchmark for soil compaction with the production of the first reversible vibratory plate. In parallel, Wacker Neuson has forged ahead with key R&D advances within its compact machine line-up.
The zero-emission success story
Wacker Neuson broke new ground in 2014 with the introduction of its zero-emission series. The initial electrically powered machines and equipment were two batterypowered rammers and the WL20e battery-powered electric wheel loader. Since then, the portfolio has steadily expanded. It now includes electric vibratory plates, excavators, wheel and track dumpers, and soon electric telehandlers.
In recent years, digitalisation has also played an important role in the development of machines. A case in point is Wacker Neuson’s new EW100 wheeled excavator, which incorporates an intelligent attachment management system and a human machine interface. This assists the operator in changing attachments via the 10-inch touchscreen display.
These are just some of the examples of modern-day advances in functionality and efficiencies that will continue to establish Wacker Neuson as a trendsetter for future generations.
Keeping
with production demands, a Eurotec
The project’s Japanese contractor was already familiar with the ECO60, as it has been using the same model with confidence on previous projects. So, when a new plant was needed for the port extension, it was an easy choice to purchase the same model – designed and manufactured by leading OEM Lintec & Linnhoff – owner of the Eurotec brand. Producing up to 60 m3/h of readymix concrete in 1 m3 batches, plant owners can customise the number of aggregate bins (ranging from three to six inline bins) according to a project’s requirements. In the case of the Japanese contractor, both units are fitted with five aggregate bins to handle more complex concrete mix designs, such as those employed at Toamasina.
A key feature of the Eurotec ECO60 is its
twin-shaft mixer – 100% manufactured in Italy. Located at 90-degree intervals, the doublemixing spiral paddle structure is said to deliver greater abrasion resistance and production performance when compared to conventional mixers. This is a valuable advantage when blending materials with particle sizes from 120 mm to 150 mm.
On the go, the consistency of the mix is ensured by the weighing and batching systems, which are metered using load cells. This is managed with Eurotec’s own in-house ECS process control system software, which runs on Windows OS for fully automatic operations.
On the Toamasina project, the ECO60’s modularised structure enabled fast installation and easy maintenance with the plant producing consistently on the various stages assigned to the contractor, who’s scope of works was completed in July 2022. The feedback indicates exceptional plant availability and downstream readymix quality, so crucial for enabling sustainable infrastructure projects.
In the meantime, other phases of the port upgrade are ongoing. To date, port handling capacity has risen from just 60 t per day to 2 500 t per day. In addition, bottlenecks that would see full containers languishing for an average of 20 days has been eliminated.
Today, Toamasina handles 90% of Madagascar’s container traffic and more than 80% of all the country’s trade traffic, making it a leading regional hub with connections to Africa, Asia, Europe and the Gulf states.
pace
ECO60 concrete batching plant has played a key role in ensuring sustained readymix supply for phases of Madagascar’s Toamasina Port Development Project (Phase 2).The Eurotec EC060 concrete batching plant used by a Japanese contractor for phases of the Toamasina Port Development Project in Madagascar
High performance crystalline waterproofing admixture that enables concrete cracks to self-heal and therefore block water, even when under extreme hydrostatic pressure. It will continue to reactivate whenever water is present.
KEEPING WATER OUT:
■ Basements
■ Habitable basements
■ Parking garages
■ Utility/plant rooms
■ Tunnels
www.sika.co.za
KEEPING WATER IN:
■ Swimming pools
■ Water retaining structures
■ Dams
■ Water structures
■ Waste water treatment structures
Lintec and Eurotec brands of concrete batching plants are perfect for ready-mix and precast concrete applications. They are recognised for providing customers with solutions for all their jobsite needs. Our premium Lintec concrete batching plants are built in 100% ISO certified sea containers, boasting fast installation and dismantling.