
5 minute read
World-class reservoirs built with precast precision
from IMIESA May 2023
by 3S Media
By harnessing precast concrete technology, South African municipalities are building reservoirs of a very high quality at a fraction of the time and cost.
Previously, only a few local contractors had the skills, experience and capacity to undertake these projects using traditional in-situ construction methods. This previously restricted greater participation in these Municipal Infrastructure Grant-funded projects.
Advertisement
However, there are now a growing number of new entrants to the market that are embracing the benefits of precast to build enduring structures. These include Selby Construction, Anita Building Construction, Mako Projects and Trading, and Morata Building & Civils. Each has already successfully completed precast concrete reservoirs of varying sizes up to 30 Mℓ with the support of Corestruc, a turnkey precast concrete contractor with a specific focus on water infrastructure, including pump stations, water treatment works and water towers.
Corestruc’s expertise spans the entire value chain from the design of precast concrete systems through to the logistics and rigging capacities that are required to transport and integrate the various prefabricated elements on site. Manufacture of the systems are undertaken by approved prefabrication companies located throughout the country.
Fast and efficient
The ease and speed at which these reservoirs are constructed and their performance to date have substantiated Corestruc’s method.
Selby Construction, for example, was able to shave as much as two-thirds off the construction schedule of a 30 Mℓ reservoir by using Corestruc’s precast concrete reservoir system.
Meanwhile, the precast concrete roof and wall of a 25 Mℓ reservoir were erected by Anita Building Construction in only three months, while working alongside Corestruc.
In turn, Morawa Building & Civils was able to complete a 10 Mℓ reservoir, including posttensioning, in only four months. This also provided significant savings in construction costs for the client. Using in-situ construction methods, it can take up to nine months to complete a reservoir of a similar capacity.
Precast methodology
The precast concrete reservoir system accelerates the construction programme by enabling the various trades to work simultaneously. While earthworks and site terracing, as well as the construction of the roof column bases are underway, Corestruc manufactures the precast concrete wall and roof in preparation to integrate them on-site.
The roof is erected first – starting with the roof columns – which are connected to the holddown bolts in the column bases. Suspended precast concrete beams are then connected to the dowels that protrude from the precast concrete columns. Thereafter, hollow core slabs are connected to the stirrups protruding from the precast concrete beams.
Steel reinforcing is placed into the cores of the hollow core slabs and these voids are then filled with in-situ concrete. By forming a composite mechanism with the infill concrete, the stirrups act as mechanical interlocks.
Once the inner portion of the roof is in place, the construction of the in-situ floor slab starts, followed by the ring beam for the precast concrete wall. The first wall panel is supported on the ring beam by a push and pull prop.
For temporary stability, the wall is braced back to the roof structure. The steel brackets assist in holding the panels together and, therefore, eliminating the need for extensive propping to free up space.
Once all the panels have been placed, unbonded cables are pushed through the polyvinyl sleeves in the panels. They are then grouted monolithically with the joints of the panels.
Thereafter, a grout is poured continuously in between the wall panels and horizontal cable sleeves. It is a high-strength and -flow grout with an extended pot life so that it does not segregate and set too early. These characteristics are achieved by manipulating the water-to-cement ratio of 0:37 with the use of admixtures.
The water temperature is also reduced and controlled to act as a chiller in the mix. In addition, only cement, including an unhydrated type that reacts with water to seal possible leaks, is used in the concrete mix.
The cables are stressed to 75% when the grout has cured to a strength of 80 MPa. This is undertaken via precast concrete buttress panels that have been spaced along the perimeter of the reservoir. Larger reservoirs have four buttress panels and the smaller structures two.
The wall is then pinned by casting a 200 mm to 250 mm high reinforced kicker on the wall footing on both sides of each panel. Joints between the panels are grouted with a highflow and strength grout and post-tensioning renders them in compression to achieve water tightness.
Slide and pinned
Corestruc uses a ‘slide-and-pinned’ system. Post-tensioning is undertaken when the wall is not yet fixed to the ring footing and it is, therefore, allowed to slide on a steel bearing or locating plates. The coated, post-tensioned cables are not bonded to the grout, with the reservoir designed to maintain a residual compression of a minimum of 1 MPa in all directions.
Horizontal reactions to the wall base are transferred to the ring foundation through the second phase cast-in-situ kicker. This is where the ring tension in the base is also activated to resist the reaction. Additional post-tensioning of the lower part of the wall reduces the amount of rebar required in the cast in-situ ring footing.
Final elements
As part of the final aspects of the build, the concrete floor slab is completed and the hollow core slabs that make up the outer portion of the roof structure connected to the precast concrete beams. A grout topping is then placed over the hollow core slabs to form a single monolithic structure, with a precast concrete coping installed around the perimeter of the roof to provide an aesthetic finish.

Long service life
Given the quality of the precast elements, these structures will provide a designed life of 100 years with routine maintenance. A key ingredient is their precision fabrication.
In this respect, self-compacting concrete is used to manufacture elements that contain significant reinforcing and where conventional vibrating pokers cannot be used effectively. In this environment, the perfect dosages of admixtures are also ensured. This avoids overdosing that may delay early strength development, which is imperative for uninterrupted production. Another significant focus in the factory is to maintain the perfect water-tocement ratio to ensure concrete strength. Aggregates from suitable suppliers are also graded appropriately to avoid early concrete shrinkage. The prefabricated elements are inspected
Corestruc’s expertise spans the entire value chain – from the design of precast concrete systems through to the logistics and rigging capacities that are required to transport and integrate the various prefabricated elements on-site and approved for dispatch to ensure the accuracy of the placement of the cast-in components. Reinforcement bar size and placement are also verified as part of the quality control procedures at the factory.
Precision engineering that is fit for purpose
These steps are complemented by the checks and balances introduced by Corestruc ahead of mobilising to site to commence erecting the structure. Corestruc manages the settingout and installation of the column anchors for the precast concrete roof. By confirming the dimensional accuracies before erection, the company ensures that the beams of the roof structure fit the first time round. The precast concrete wall panels are placed and positioned in a similar manner with the assistance of permanent locating plates that are fixed to the ring foundation.
Thanks to this partnership between Corestruc and the contractor, consistent and excellent results have been achieved for each project completed. For this reason, Selby Construction, Anita Building Construction, Mbako Projects and Trading, and Morawa Building & Civils are especially proud of the high quality of their precast concrete reservoirs.
Comments Willie de Jager, MD of Corestruc: “We are very proud to be a strong partner to these enterprising construction companies that are revolutionising the way in which we construct essential water infrastructure.”
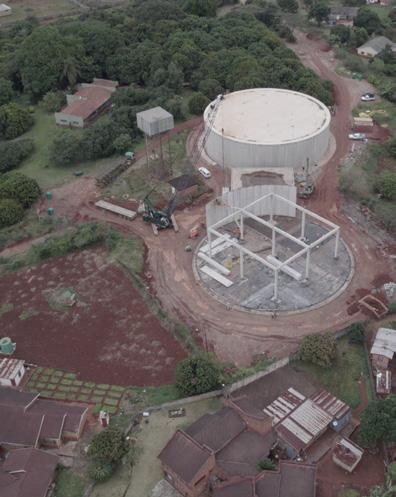