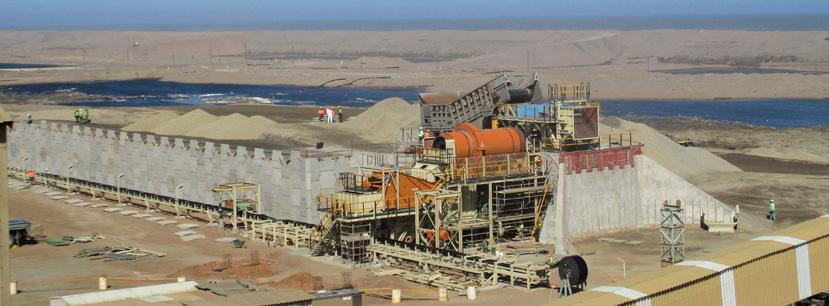
6 minute read
LEADING SOIL REINFORCEMENT IN SOUTH AFRICA AND AFRICA FOR 48 YEARS
from IMIESA May 2023
by 3S Media
Reinforced Earth was founded on a patented suite of mechanically stabilised earth (MSE) technologies by Henri Vidal in 1963. Ever since, his pioneering vision in this field has provided a standard for best practice in environmental and geotechnical engineering worldwide.
From a historical perspective, Vidal’s vision, as an architect and engineer, led to the development of a new composite material using earth as a raw material. The sectors in which the material finds application include Road and Rail – retaining walls and bridge abutments; Mining – headwalls to crushing plants, storage bunkers and reclaim tunnels; Hydraulic infrastructure – dams, reservoirs, canals, quays, jetties, river training, groynes and breakwaters; Oil and Gas – bund walls; Urban development – retaining walls and foundation slabs; and Waste management –landfill containment.
Advertisement
In South Africa, the company celebrates 48 years in 2023, with managing director Louwtjie Maritz now at the helm with over two decades of service and the responsibility for taking the business forward in the local and greater sub-Saharan region. Baseline services include structural design, the supply of specific components, and training provision for contracting teams.
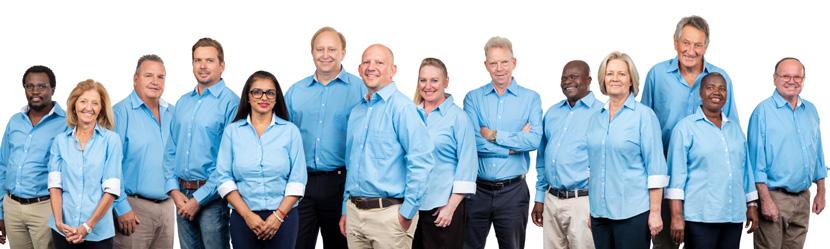
“Essentially, Reinforced Earth® consists of engineered backfill that is reinforced with a range of application-specific elements –typically geosynthetics or steel strips and grids – interconnected with facing elements composed of precast or steel panels, or wire mesh,” explains Maritz.
The key purpose of Reinforced Earth’s facing panels is to ensure structural stability, as well as erosion protection for the reinforced backfill. Additionally, the facing design of the panels can be customised to optimise the aesthetic effect.
Key techniques
The technology suite comprises the following key solutions, namely the original Reinforced Earth®, TerraLink™, T-Wall®, TechWall®, TechSpan® and TechBox®
The TerraLink™ shored MSE wall solution is ideal when constructing retaining walls in geometrically narrow sites. Installation is carried out in front of a stable existing structure such as a stabilised slope or retaining wall.
“T-Wall® is a recent product acquisition that is proving popular in the USA for railway projects and we’re considering introducing it to the South African and African market, with a number of proposals submitted to various clients to date,” says Maritz.
The system enables the construction of a ‘T’ shaped gravity-type retaining wall built by assembling modular precast concrete units together with granular backfill. The perpendicular stems allow for internal stability, providing pull-out resistance against the lateral earth pressures exerted on the back of the facing. These are large-scale structures, with each T-Wall unit measuring 2 m in height and 4 m in width.
For challenging conditions, TechWall® delivers. This precast retaining wall system presents the design advantages of counterforts acting as cantilever beams resisting lateral earth pressure. Because the counterforts are optimally reinforced, the moments in the facing panel are minimised and a relatively thin, fullheight concrete facing panel may be used.
For transportation and mining projects, TechSpan® and TechBox® are further examples of Reinforced Earth’s ability to design products that are modular and easy to install. Their applications include tunnels and underground structures, buried bridges, box bridges and culverts.
Turnkey approach
“Our objective is to employ these technologies to optimise structural soil interaction as part of a turnkey solution. This includes our design service – provided by professionally registered in-house engineers – which has always been provided at zero cost to the client. We work with the client’s engineers and the contractors to perfect and deliver the best solution. Each project is unique, requiring a custom design, so innovation is always top of mind,” says Maritz. As part of the global Reinforced Earth group (trading as Terre Armée in French), the South African operation has access to the full product suite, either manufactured locally, supplied from one of the group’s factories worldwide, or sourced via externally appointed suppliers. In many parts of the world, the precast elements are manufactured and supplied by Reinforced Earth. However, given the logistics challenges in Africa, the South African arm is one of the only group companies worldwide that rents its precast panel moulds as one of the options available to the contractor, so they can manufacture on-site. However, Reinforced Earth retains its oversight role in terms of strict adherence to quality control.
To support the final design elements, Reinforced Earth also manufactures precast top-outs that integrate with its retaining walls.
These include precast traffic barriers, trims and copings, and parapets.
Tie-back systems
“When it comes to tie-back reinforcing systems, geosynthetics are ideal for aggressive backfills. A current example is a Reinforced Earth project in Oranjemund, Namibia, where the contractor is using seawater for compaction with well-graded materials for the construction of an extensive retaining wall at a local mine,” Maritz explains.
For this project, Reinforced Earth is employing its new Geocore® reinforcement, tying into TerraClass® precast facing panels.
However, Reinforced Earth’s mainstream choice is the employment of galvanised steel strip or grid systems for retaining walls. Manufactured in South Africa, their durability is legendary in the right conditions. They can also be employed for foundation reinforcement, particularly in areas prone to settlement or seismicity.
Their integrity can also be tested over time thanks to in-built steel sacrificial strips that can be removed after a predetermined period – say 5 to 10 years – to check for loss of strength due to corrosion.
“On projects we’ve completed on the N3 in South Africa, we’ve gone back and pulled out strips on walls that are some 20 years old and they’re still 100%,” says Maritz.
Another innovation is TerraTrel®. This is a wire-faced MSE wall system, consisting of inextensible high-adherence steel reinforcing strips or ladders with a bolted connection to a wire mesh facing, as opposed to a precast facing. Backfilling the facing with rock provides a similar finish to a gabion system.
Milestone projects
Over the past 48 years, Reinforced Earth has completed a broad range of projects that in more recent times include mega ones like the Gautrain Rapid Rail Link, and the Mbabane Bypass project in Eswatini.
Opened to traffic on 8 May 2009, the Mbabane Bypass was considered the ‘missing link’ in the MR3 highway connecting the Ngwenya/ Oshoek border post to Manzini. The 11 km highway section has a height differential of some 1 000 m between the start and end, with unstable founding conditions.
Overall, the project presented a number of key challenges and entailed the design and supply of materials for the construction of 5 600 m² of bridge abutments, 6 700 m² of retaining walls and 29 000 m² of tiered fills all with steel reinforcing strips. Africon (now Zutari) undertook the detailed design of all bridges on the project.
“The most notable component of the designs are the four tiered fill structures, which were designed as an alternative to incrementally launched bridges,” explains Maritz, adding that the Esitibeni, Qabalembadada and Mangwaneni tiered fills –with heights ranging up to 33 m on centreline – were originally designed as incrementally launched bridge structures.
Gautrain
The Gautrain project presented its own unique set of challenges, requiring some 80 Reinforced Earth structures on 38 sites that were constructed between 2007 and 2010. These comprised retaining walls (both supporting and alongside the tracks), bridge abutments, and first-span viaduct abutments.
Reinforced Earth’s design was undertaken in conjunction with the Bombela CJV and several of its consulting engineer subcontractors. Notably, Reinforced Earth’s solution catered for vibration loadings, seismic accelerations of 0.3 g, and a service life of 100 years.
In most cases, steel reinforcing strips were used throughout except in those areas where DC currents could pose a corrosion risk due to electrolysis. In these instances, GeoStrap® and GeoMega® geosynthetic strips were employed.
Current projects
Currently, Reinforced Earth is extensively involved on infrastructure projects within Southern Africa, as well as in the West African region for a number of mining operations. Works in South Africa include the Govan Mbeki Interchange project in Cape Town, where the TerraClass® precast panel system is being employed along with Reinforced Earth’s Geocore® geosynthetic connection system. The total area is around 2 300 m2.
Further afield, Reinforced Earth is supplying its TerraTrel® system with steel connection for the N3 Lynnfield-Ashburton upgrade being undertaken by SANRAL. Covering an area of some 10 000 m², works are now virtually complete. Reinforced Earth is also employing
Reinforced Earth’s TerraTrel® system (approximately 2 350 m²) is being employed for a section of the Polihali Access Road Western Section, forming part of Phase II of the Lesotho Highlands Water Project the same system is being utilised along with steel connections.
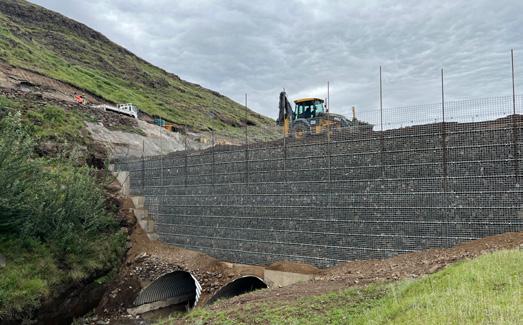
65 million m2 and counting the same system for SANRAL’s N3 Dardanelles to Lynnfield upgrade, now underway.
“Globally, the group has completed some 65 million m² of Reinforced Earth® walls, which underscores the tremendous success of the technique. The advantage for South African and African customers is that we can draw on this expertise in terms of design recommendations and technical training to complement our own unique understanding of the local market,” adds Maritz.
“It’s clear that the benefits of MSE are well proven. Reinforced Earth has taken this a step further, constantly evolving our systems to execute durable structures that become one with the environment,” Maritz concludes.
Outside South Africa, projects include the supply of the TerraTrel® system (approximately 2 350 m²) for a section of the Polihali Access Road Western Section, forming part of Phase II of the Lesotho Highlands Water Project.
In parallel are works that include the Mbudzi Interchange project in Zimbabwe, where the TerraClass® panels are being cast on-site (total area: 4 714 m²), and the Kampala Flyover Lot 1 development for the Uganda National Roads Authority (2 320 m²), where
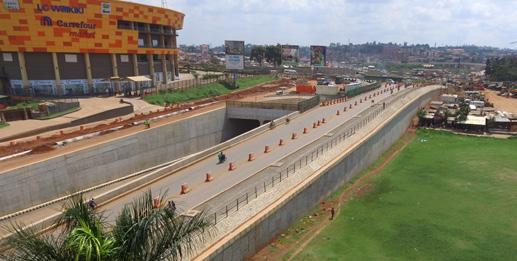
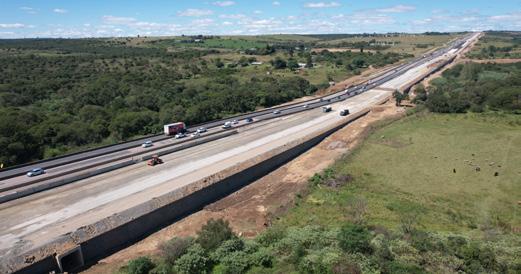
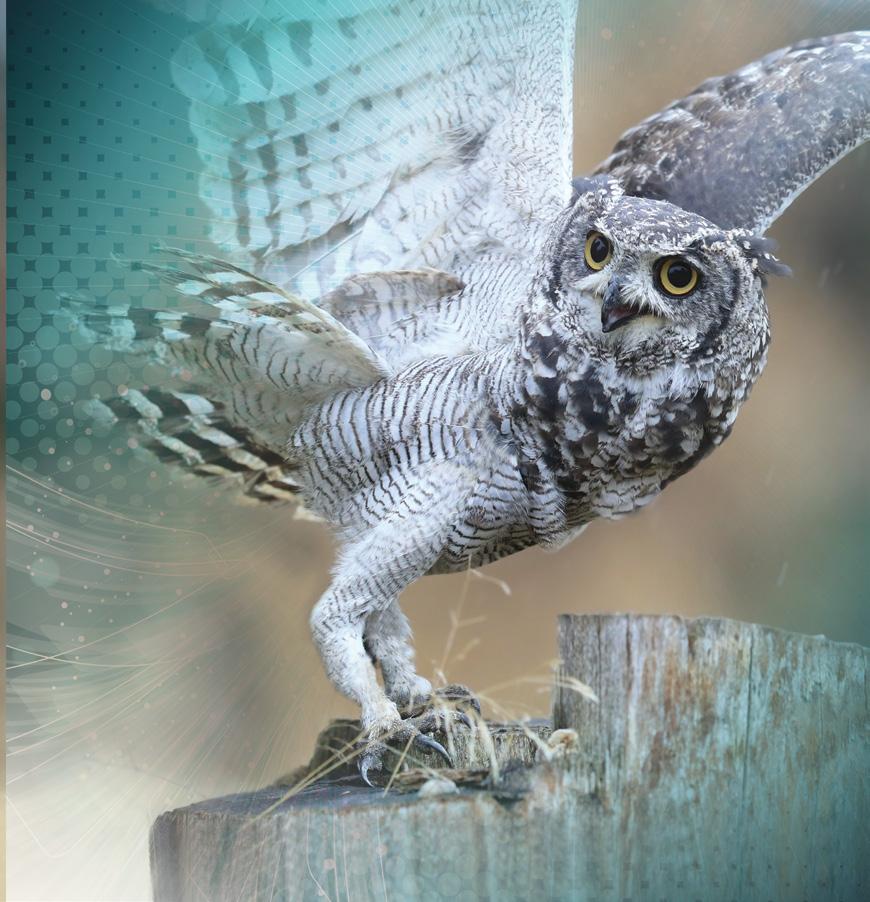