4 minute read
Designing and constructing HIGH-PERFORMING GABIO N SYSTEMS
from IMIESA May 2023
by 3S Media
Next Article
When designed and constructed by experienced professionals, gabion systems can easily last 50 years or more in land-based and riverine environments. However, that is interdependent on the quality of the wire specification and materials used, which must comply with recognised industry benchmarks, say Louis
Cheyne, managing director of Gabion Baskets.
By Alastair Currie
Aleading gabion manufacturer with a 17-year track record, Gabion Baskets has always placed major emphasis on quality control. This extends to its design, project management and training services for industry.
“However, the best design can still fail if the wrong products and construction techniques are employed, which is well demonstrated by some of the retaining wall failures we’ve been called out to assess in the eThekwini region, which was hard hit by the 2022 floods,” Cheyne explains.
“We’ve completed a number of reinstatement projects to date, alongside our own ongoing works, where we’ve had an opportunity to demonstrate best-in-class construction methodologies, as governed by SANS 1200 DK:1996.”
As with the correct construction approach, having set standards for gabion systems is equally important, and prior to the introduction of SANS 23-3:2020 in August 2020, this was determined by SANS 1580:2010. The latter defined the correct manufacturing specifications for gabions and revet mattresses assembled using hexagonal steel wire mesh. However, there were industry concerns regarding the two specific SANS 1580:2010 tests that products needed to pass, namely the twisted-wire pull-apart test and the panelto-panel joint-separation test.
“The view from industry was that these tests were unrealistic and not clear in terms of ensuring consistent laboratory results. On the twisted-wire pull-apart test, for example, the criteria were too complex, which meant it was near impossible for manufacturers to comply,” Cheyne explains.
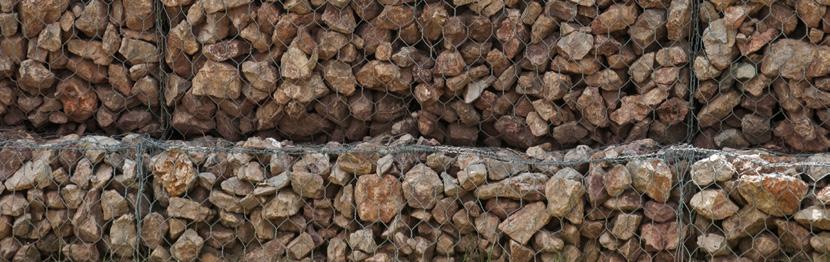
Updated standard internationally aligned
The adoption of SANS 23-3:2020 has established an industry-accepted and practical approach based on EN 10223-3:2013 – the European standard, as well as the internationally accepted benchmark. Both cover the requirements for hexagonal steel wire mesh products for civil engineering purposes and, unlike SANS 1580:2010, go into more detail on elements like dimensions, coatings, test methodology and delivery conditions of steel wire mesh products.
“For us, it’s a vital part of our business, both in South Africa and Africa to be compliant with SANS 23-2:2020. Contractors, consulting engineers and clients increasingly demand guaranteed quality assurance, and the updated standard ensures that our products can be tested with confidence at an accredited laboratory,” Cheyne explains, adding that all
Gabion Baskets’ products tested to date by SANS-accredited entity Metallurgical Testing Labs have passed with flying colours.
Where required, Gabion Baskets can also submit its welded mesh panel line for testing according to SANS 462:2005 (Ed. 1.00). Welded mesh is proving increasingly popular in the architectural field for applications like building and interior cladding, as well as for freestanding feature walls.
Construction in practice
As part of its turnkey solutions, Gabion Baskets ensures that every element of the system supplied for a specific project meets the specification, including the geotextiles and rock fill material that form an essential and integral part of the structure.
“We pride ourselves on providing a valueengineered solution, working with the client’s consulting engineer and contractor to make sure that the final works are functional and sustainable over their envisaged design life,” Cheyne continues.
Two recent projects in KwaZulu-Natal underscore best practice. The first entailed the reconstruction of a gabion wall system for a property owner in Cowies Hill, Pinetown.
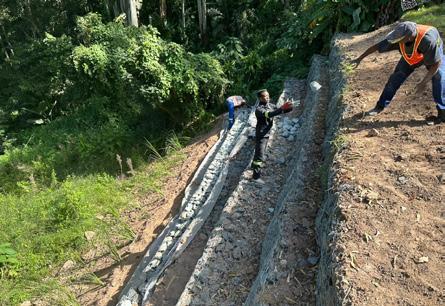
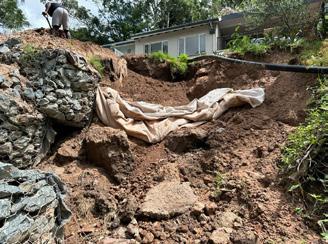
Gabion Baskets’ KwaZulu-Natal branch, based in Pinetown, was asked to conduct a site inspection on the works, which had been executed by a local contractor in September 2022. It was noted that the materials used were substandard and, to compound the problem, the design was for a revetment wall, when it should have been for a mass gravity retaining wall.
“Our first suggestion was to replace the whole structure but, due to client budget constraints, this was not possible, so the existing materials were used wherever practical for the redesign and reinstatement,” Cheyne explains.
The main concern was the toe of the gabion structure, which had slid forward, affecting the stability at the top of the wall embankment. As an out-of-the-box solution, Gabion Baskets’ team proposed a method to secure the toe, which was accepted by the client. This entailed digging down 1 m in front of the wall to establishing a 1 m deep gabion footing. To provide added integrity, Y20 rebar was placed through this first gabion row at 1 m intervals. The latter ties in with the gabion mattress foundation on which the stepped-back gabion retaining wall was re-established. (See Diagram 1 for the design details.)
“Following completion, our site team carried out a series of inspections, and the reinstated wall is holding exceptionally well, with the recent inclement weather ‘testing’ the design on more than one occasion during subsequent heavy downpours,” says Cheyne.

Cato Road, Kloof
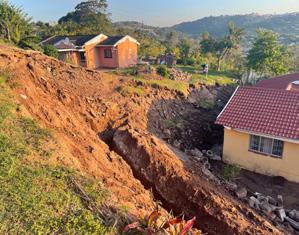
The second project showcased involved the design proposal, product supply and project management for an L-shaped wall that serves as a retaining and feature wall. The latter varies in length from 16 m to 21 m, with heights from 1.5 m to 3 m, and has a 6-degree batter against the embankment. The client’s engineer approved Gabion Baskets’ design proposal. Since the ground on which the walls are built is relatively hard sandstone, the team had to utilise a skid steer for the major excavations and only excavated to the final measurements by hand. At the client’s request, the facing rows are filled with brown rock to create an aesthetic effect. The result is a masterpiece in soil retention.
“What these projects underscore is the importance of a professionally competent design, the right materials and expert installation experience,” adds Cheyne.
“Plus, the key advantage of gabions is their design flexibility and ability to blend in and enhance the natural environment, in addition to combatting the widespread problem of soil erosion in urban and rural areas,” Cheyne concludes.
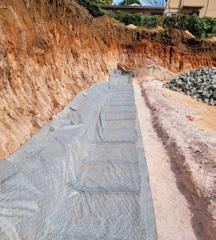
DIAGRAM 2: CATO ROAD, KLOOF, KWAZULU-NATAL
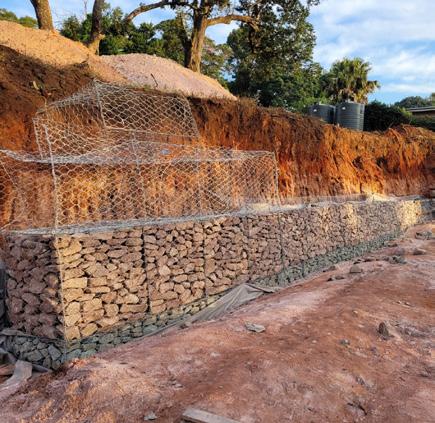
EVENT: 86TH Imesa Conference
DATES: 25-27 October 2023
VENUE: Boardwalk Hotel, Gqeberha (PE)
THEME: Resilience is the future