
10 minute read
Ebroacero, una fundición de calidad para el sector minero
Área de pruebas donde cargadoras y dúmperes son probados para detectar posibles problemas o fallas antes de su despacho.
Zona de pruebas. Obsérvese la cargadora en la parte superior volteando el cazo y el dúmper subiendo por la rampa.
Advertisement
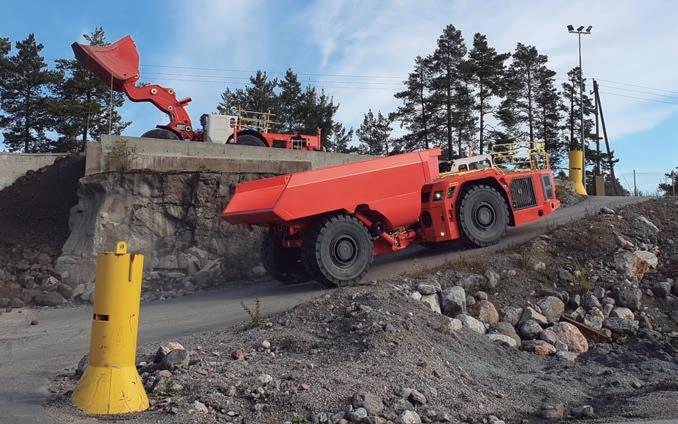
cuenta que cada máquina lleva su propia configuración en función del país y la tipología de trabajo que va a desempeñar.
Una vez terminada la fabricación, todos los equipos pasan un exhaustivo control de calidad, seguridad y funcionalidad para verificar que el equipo se encuentra apto para su entrega al cliente. Las instalaciones de Turku cuentan con una zona de pruebas diseñada para que tanto las cargadoras como los dúmperes sean llevados al extremo y así poder localizar cualquier falla tanto de materiales como de los procesos de fabricación. Una vez superadas dichas pruebas, los equipos se limpian y se repintan para su embarque y transporte a todo el mundo. En las instalaciones de Turku había decenas de equipos de todos los modelos esperando su despacho, estando la producción, tanto de cargadoras como de dúmperes, totalmente vendida. nes de onzas, actualmente con 1.100 trabajadores, 500 de ellos directos, y una capacidad de procesamiento de 2 millones de toneladas anuales, los procesos de automatización están siendo la clave. “Comenzamos las labores con dos cortas a cielo abierto y actualmente estamos con minería de interior, donde automatizamos todo lo posible los equipos y procesos. Al año realizamos alrededor de 200 cavidades y avanzamos unos 28 km, para lo que contamos con varios jumbos y bulonadoras automatizadas. El 85% de la perforación que realizamos se lleva a cabo de forma remota, en la que dos operarios trabajan al mismo tiempo con 4 equipos, y para el transporte tenemos intención de pasarlo también a autónomo en los próximos meses”, concluyó Näsi.
Otro ejemplo muy llamativo de automatización lo expuso Pat Boniwell, de la empresa Bynecut, un proveedor de servicios mineros en Australia, que cuenta con 100 trabajadores en 15 países y 50 clientes en todo el mundo. Anualmente desarrollan 130 km de galerías, extraen 32 millones de toneladas, realizan 3.000 m de perforación y proyectan 100.000 m3 de lechada de cemento.
“Estamos muy implicados en la automatización de nuestras cargadoras, perforadoras e incluso de los equipos de perforación ascendente para la realización de chimeneas, siendo la comunicación el aspecto más complejo. También es muy importante contar con una buena topografía de todo el interior de las minas y una fuerte implicación de los trabajadores y operarios de cada explotación”, explicó Boniwell.
Para ellos el gran problema se encuentra en la transmisión de datos. El 5G es el futuro. Los centros de gestión de los equipos autónomos se encuentran de media a 600 km de distancia de las explotaciones, llegando a una distancia máxima de 1.000 km, lo que puede llegar a ser un problema si no hay estabilidad en la señal. Además de la propia operativa de los equipos, el autodiagnóstico es otro aspecto fundamental en la transmisión de datos, algo que te
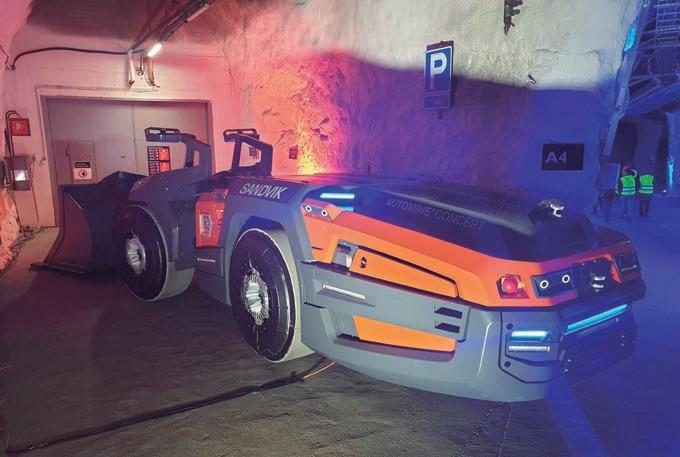
Prototipo de una perforadora totalmente autónoma con Automine.
permite conocer en todo momento cómo se encuentran los equipos.
Según Boniwell, para llevar a cabo una transformación de equipos convencionales a autónomos lo más importante es ponerse en manos de un profesional como Sandvik, contar con una planificación inicial y el compromiso de todos los trabajadores. Es fundamental transmitir a todos los implicados en las labores mineras qué se quiere hacer y porqué, lo que hace todo mucho más fácil a la hora de implantar el cambio.
“En España tenemos una gama de jumbos automatizados muy importante en el sector de la tunelización, algo que esperamos que se iguale en breve en las explotaciones mineras”, matizo Enrique Mota, director para España y Portugal de la división Sandvik Mining and Rock Solutions de Sandvik Española, S.A.
Con motivo del evento de Sandvik en Tampere, se presentó a Amelia, un jumbo de dos brazos totalmente automatizado, que con un diseño muy novedoso, el cual no incluye ya cabina, es capaz de trabajar de forma independiente. Se programa desde el exterior y ella misma elige el túnel, el recorrido (tiene cargada toda la topografía de la explotación minera) y el diseño de perforación. Se trata de un concepto futuro que ya está aquí y que únicamente hay que mejorar para que su implantación sea definitiva en los próximos años.
La presentación tuvo lugar en la mina experimental que Sandvik tiene dentro de sus instalaciones fabriles de Tampere, en Finlandia. Un complejo de varias galerías y cámaras en dos niveles, donde se experimenta con todo tipo de equipos.
INNOVACIÓN
El concepto de innovación se encuentra íntimamente ligado a los dos aspectos anteriores que se trataron en la convención de Sandvik, y prueba de ello fueron los diferentes testimonios que varios expertos mineros de todo el mundo trasladaron a los invitados.
Glenn Heard, director de minería de Barrick, comentó que la compañía cuenta con 240 equipos Sandvik y que solo en su explotación de Mali son 30 las máquinas operativas y que el comienzo no hubiera sido posible si tres técnicos de Sandvik no hubieran estado formado a sus trabajadores desde el arranque del proyecto.
Según Heard, “observando los datos que envía cada equipo se puede analizar cómo trabaja cada operador y así se le puede formar o corregir con idea de incrementar la productividad. Además, con la telemetría que envían los equipos y las correcciones a los operadores se cuidan mucho más las máquinas.
Los beneficios del estudio de los datos aportados por las máquinas permiten conocer en todo momento el comportamiento de los distintos operadores, la salud de los equipos, la competencia de los trabajadores y operarios de la empresa y la de-
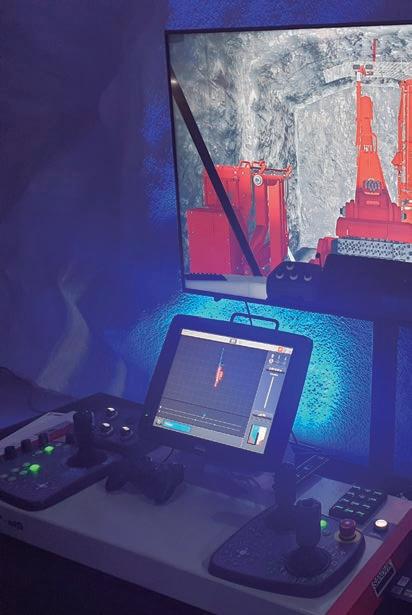
La utilización de simuladores es fundamental para la formación de los técnicos que posteriormente operarán los equipos a cientos de kilómetros de distancia.
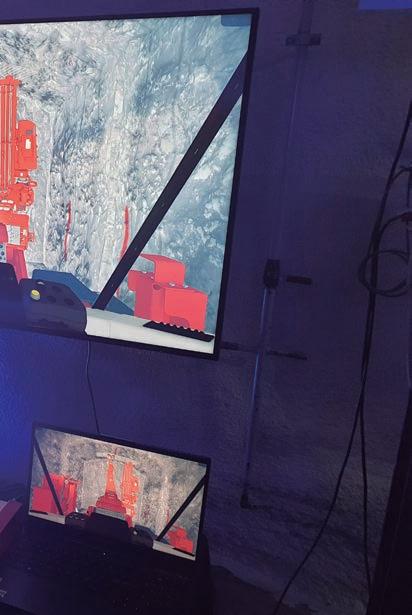
tección de los problemas con mucha antelación. El uso de los datos nos ha permitido conocer las horas de funcionamiento de cada equipo, sus problemas y hemos incrementado su uso, lo que nos ha llevado a aumentar la productividad”.
“Lo más importante es suministrar la información en tiempo real al operador, para que en todo momento sepa las infracciones que está cometiendo y así pueda corregirlas”, concluyó Heard.
Mick Radi, vicepresidente de Perenti Mining, un operador de servicios mineros que trabaja en 15 proyectos en 6 países diferentes, explicó cómo la innovación es fundamental para ellos. Están tratando de reducir los riesgos con un proceso de segregación de las actividades, como consecuencia de un accidente mortal que tuvieron. “Con respecto a la seguridad, no hay una receta perfecta. Cada empresa crea sus propias medidas de seguridad, las cuales obliga a que se respeten y se apliquen, consiguiendo resultados importantes. En cualquier caso, la implantación de la tecnología ha sido fundamental para la reducción de todo tipo de accidentes”, explicó Radi. Por su parte, Nikolay Kirov, ejecutivo de la empresa Dundee Precious Metals, compañía minera con sede en Canadá y minas en seis países, dedicada a la extracción de oro y todo tipo de metales preciosos, confirma que con el paso de los años han mejorado sustancialmente: han conseguido mantener la producción con menos personal, para lo cual ha sido fundamental la eficiencia de los equipos.
Sandvik envía diariamente la telemetría de cada equipo, “lo que permite verificar a nuestros técnicos el rendimiento de cada máquina y los posibles problemas que surjan, teniendo así capacidad de reacción. También permite conocer cómo trabaja cada operador, corrigiendo sus vicios y obteniendo lo mejor de cada uno de ellos”, aclara Kirov. Diariamente Dundee Precious Metals dispone de una recopilación de datos de cada máquina, que almacena, gestiona y analiza para obtener el máximo rendimiento de sus equipos. Otro ejemplo llamativo de automatización e innovación lo expuso Praveen Sharma, de la empresa india Hindustan Zinc, una compañía dedicada a la extracción de cinc y plata, que ha incluido recientemente equipos de baterías en alguna de sus explotaciones mineras.
Actualmente cuenta con una flota de 200 máquinas Sandvik, de las cuales están electrificando aquellas que por su tipología de proceso lo permite, además de automatizando todos los procesos, reconstruyendo parte de sus equipos y digitalizando todas las operaciones mineras.
Desde que comenzaron a trabajar en estos cambios, se han visto ya importantes mejoras en todo el proceso: un incremento del 15% en las operaciones de perforación, un 4% en el rendimiento de los equipos LHD, un 16% en los equipos de transporte, una mejora del 50% del tiempo de respuesta durante los atascos en
La gama de jumbos y bulonadoras de Sandvik se ofrece con distintos niveles de automatización.
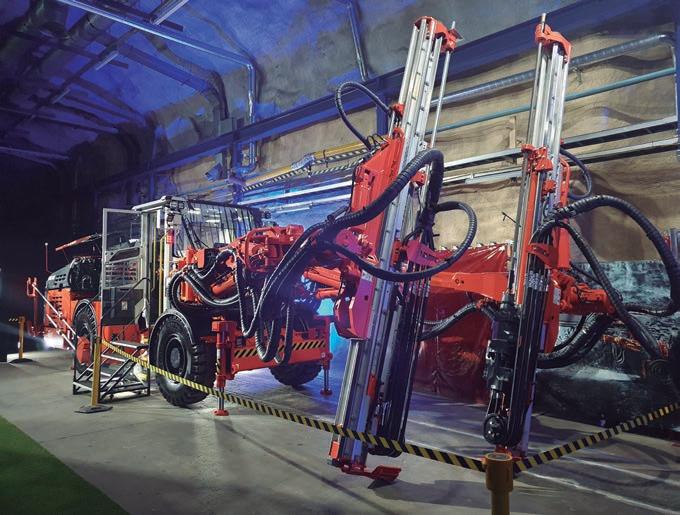
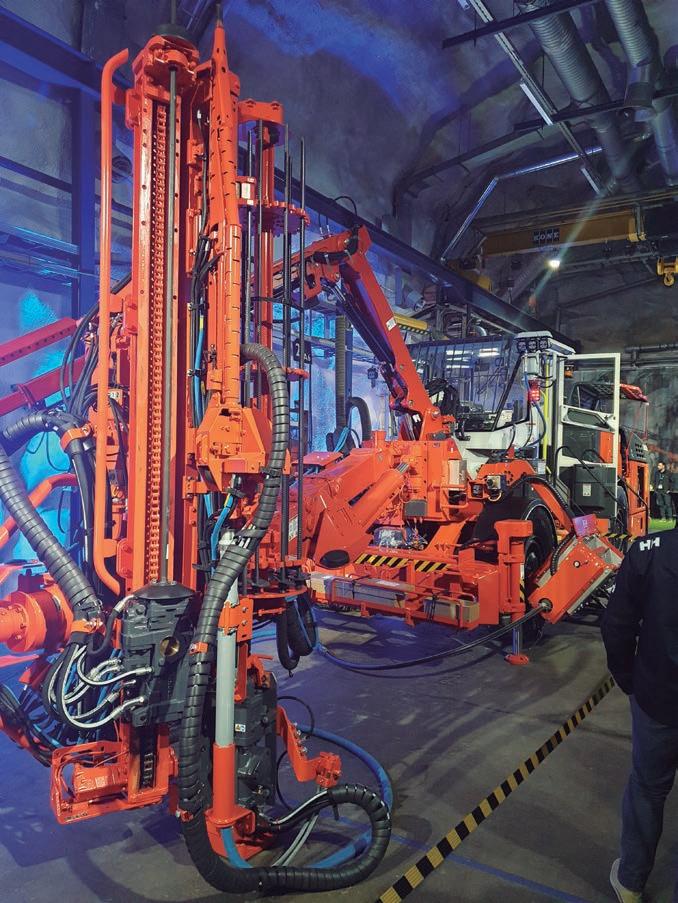
Prácticamente la gama completa de equipos de perforación de Sandvik se expuso en el interior de la mina experimental de Tampere.
rampa utilizando sistemas de visualización 3D y de monitorización, una mejora del 18% del factor de llenado utilizando básculas y sistemas de análisis de datos, etc.
Otro caso de éxito con equipos Sandvik es el de la empresa sueca Nordisk Bergteknik, AB. Su gerente Andreas Christoffersson explicó cómo parte del éxito de la compañía que dirige se debe a los equipos de Sandvik y a la excelente relación que hay con este proveedor. “Somos una empresa contratista de servicios de perforación, excavación, refuerzos de puentes y servicios subterráneos que lideramos la sostenibilidad porque creemos en ella y porque cada vez nos la exigen más nuestros clientes, para lo que contamos con los últimos y más modernos equipos que ofrecen los proveedores. Trabajamos con Sandvik desde la década de los 90, tanto en Suecia como en Noruega, y contamos con una relación extraordinaria con este proveedor, que nos permite tener todos nuestros equipos en perfecto estado, a nuestro personal muy formado e implantadas las últimas tecnologías. Contamos con varios equipos Sandvik eléctricos, con equipos automatizados en distintos niveles y también varios de ellos trabajando con Automine en 6 explotaciones mineras diferentes. En definitiva, los equipos Sandvik y la relación con esta empresa nos ha permitido estar a la vanguardia de la digitalización y la innovación de los equipos y procesos”, concluye Christoffersson. Los tres días del evento Innovaciones en Minería 2022 de Sandvik se completaron con las visitas a las instalaciones de producción de Tampere, donde se diseñan y fabrican las unidades de perforación, y a las de ingeniería y producción de Turku, donde las cargadoras y dúmperes tienen sus oficinas centrales.
Los mineros y operadores mineros que acudieron al evento pudieron corroborar cómo Sandvik lidera el cambio hacia un futuro basado en la electrificación, automatización e innovación, aspectos que van de la mano en un sector que evoluciona día a día, donde la interacción entre proveedor y cliente es más necesaria que nunca. Sandvik, conocedor de esta situación, busca siempre la máxima productividad de sus clientes, con unos equipos modernos, autónomos, conectados y cada día más electrificados.