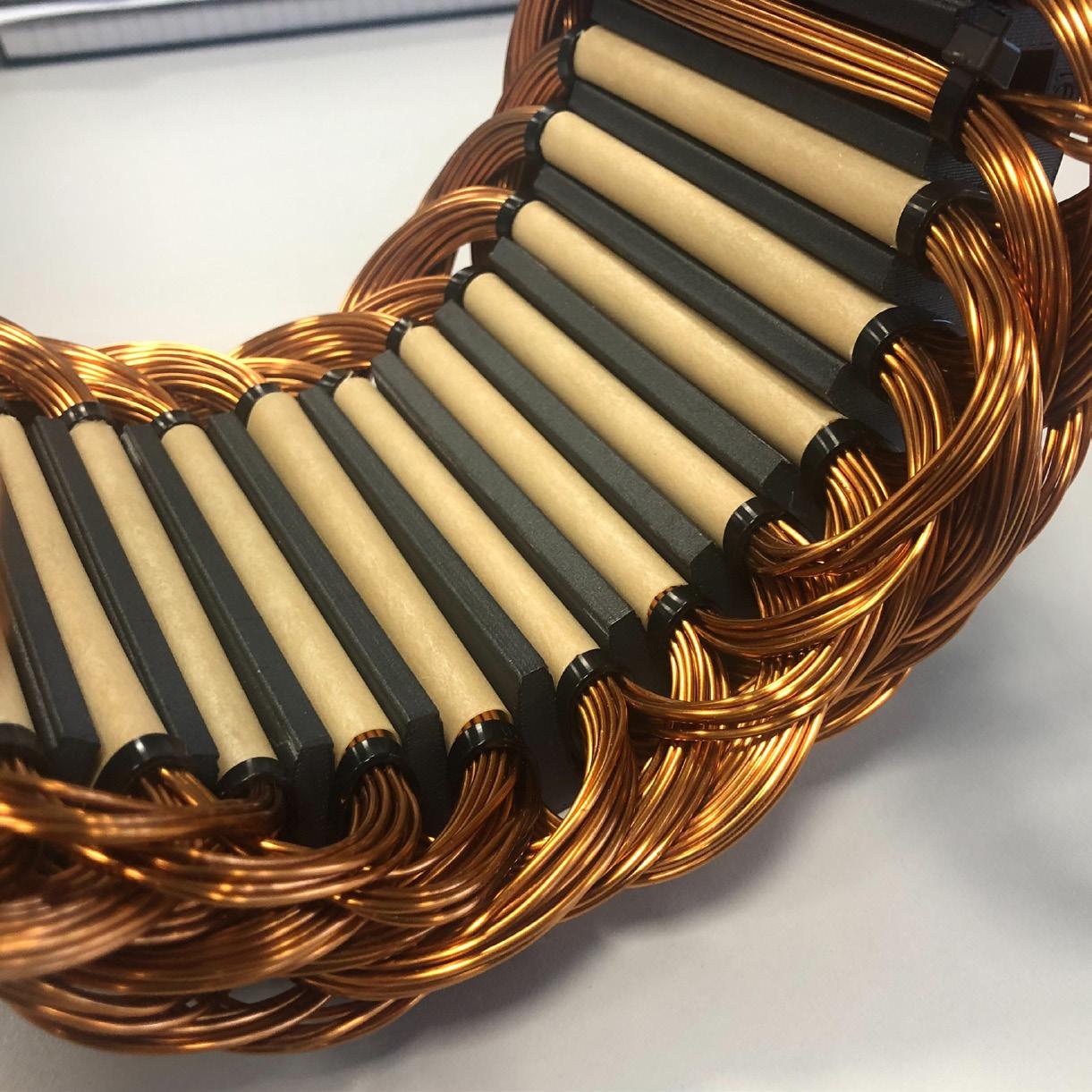
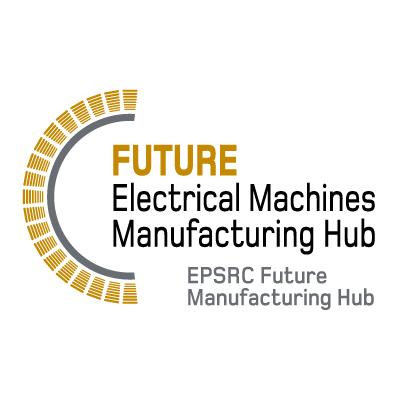
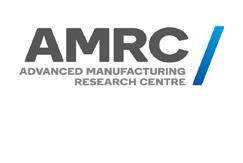
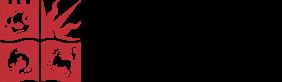
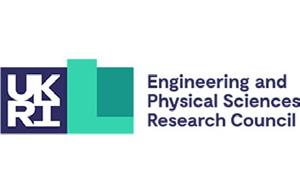
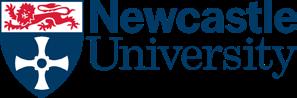
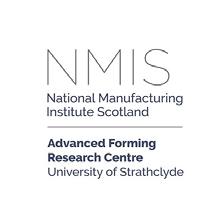
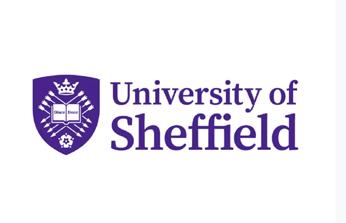
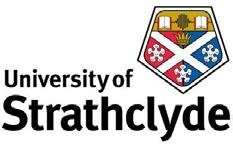

the future electrical machines manufacturing hub putting UK manufacturing at the forefront of the electrification revolution
the future electrical machines manufacturing hub putting UK manufacturing at the forefront of the electrification revolution
As will be evident from this our 2024 Annual Report, the 5th year of the Hub’s research activities has seen several important achievements, events and a continued evolution in the research being delivered by the Hub.
A notable milestone for the Hub this year was our successful EPSRC mid-term review in late April 2023. This major review involved both in-depth reports detailing our progress and a two-day visiting panel which looked at all aspects of our research and wider activities. This panel included discussions with our researchers at a poster session and with some of our industry partners. We were given a wealth of feedback, much of it very positive and supportive, alongside several recommendations for improvements against which we developed an action plan. As you will see from the report, this included reconfiguring our advisory boards and we remain grateful to the members of these boards for their time and valuable input. It was particularly gratifying that the review panel highlighted our efforts in Equality, Diversity and Inclusion and in training provision as exemplars of good practice. As with all such reviews, this success was achieved as a result of teamwork, but it would be remiss not to acknowledge the central role that Laura O’Keefe, our Hub manager, played in this review success.
As you will see from this report, we have evolved our research programme in line with the changes identified in our ‘Phase 2’ planning activities that were detailed in our 2023 Annual Report. This has included expanding the Hub consortium to bring in Bristol University’s activities in the additive manufacturing of electrical machine coils under the leadership of Nick Simpson. My colleague in Mechanical Engineering in Sheffield, Hassan Ghadbeigi also joined the Hub to add lamination blanking into the research portfolio and more broadly to enhance our capabilities in mechanics and materials. As you will see in this annual report, they have already delivered significant added value to our research outcomes and our collective capabilities for delivering multi-disciplinary research. The past year has seen the gathering of
pace on PhD graduations and numerous successes in promotions and external recognition for Hub team members.
The past year also saw our third and final call for feasibility studies which has resulted in 7 further projects being funded as detailed on page 70 of this annual report. This brings the total number of feasibility projects funded over the course of the Hub to 14, at 13 different Universities. It is particularly heartening that 8 of the 14 have been awarded to early and mid-career academics, including 5 of the 7 awarded in this third round where early-career applications were specifically encouraged. From the outset, a core feature of the Hub has been our efforts to extend the research community engaged with electrical machines beyond the long-standing mainstream electrical machines research groups. Not only have we achieved this within the main academic consortium itself with 3 manufacturing research groups but many of the feasibility awards have gone to groups for which this is their first foray into leveraging their expertise to electrical machines.
As we enter the last two years of the Hub’s 7-year funded programme, we are set fair to drive forward and draw together many of the complementary strands of research capabilities we have developed. In particular we are well placed to deliver one of the key goals set out in our original proposal back in 2018 which was to establish electrical manufacturing research as a research discipline of note and scale in the UK.
I hope you enjoy reading this latest annual report and please do contact us if you would like further information on any of our activities.
The FEMM Hub will address key manufacturing challenges in the production of high integrity and high value electrical machines in the following sectors: aerospace, energy, high value automotive, Premier consumer
1 2 3 4 5 6 7 8
To establish electrical machine manufacturing as a recognised research discipline in the UK with a critical mass of activity which is internationally leading.
To develop innovative manufacturing processes and technologies to improve the integrity and in-service reliability of high performance electrical machines.
To bring rigorous leading-edge manufacturing systems and digital manufacturing research into high value electrical machine manufacture with ultimate control and flexibility.
To embody the research findings in an array of hardware demonstrators and modelling tools to support Technology Readiness Level (TRL) scale up and wider industry/academic engagement.
To rapidly transition emerging technology through to industrial application by pulling proof of principle/concept manufacturing systems through to manufacturing research demonstrators prototypes for industry to work on alongside Hub researchers and develop for application.
To create an open and inclusive academic, innovation and industry communities around the Hub that provides supported access to the research outputs we develop and stimulates new collaborations.
To improve the UK skills base, including within partner companies, in the field of electrical machines and their manufacture.
To support UK manufacturing industry as electrical machines increasingly become core products in new sectors.
Our Executive Team is made up of the Director, Deputy Director, Hub Manager, representatives from each of our academic partners and an Early Career Representative.
Hub Director
Professor Geraint Jewell
The University of Sheffield
Deputy Director
Professor Ash Tiwari
The University of Sheffield
MANAGER
Dr Laura O'Keefe
The University of Sheffield
EARLY CAREER REPRESENTATIVE
Dr Xiao Chen
The University of Sheffield
UNIVERSITY OF
Dr Glynn Atkinson
Dr Jill Miscandlon
Dr Lloyd Tinkler
Dr Nick Simpson
Our Strategic Advisory Board was set up in 2023 following our midterm review and is committed to:
- Providing feedback on the progress and outcomes of the Hub’s research programme.
- To advise on the degree to which the Hub’s vision is being delivered.
- To provide feedback on whether the Hub’s activities are sufficiently aligned with industry projections and government policy.
- To advise on emerging topics or trends in academic and industrial R&D on electrical machines and their manufacture.
- To advice on opportunities for dissemination through means that would influence policy and industry practice and, where appropriate, help facilitate the realisation of these opportunities.
Our board brings together senior figures from the each of the FEMM Hub’s industry partners. They appraise and advise on the impact activities to maximise the opportunities for knowledge exchange and ensure the Hub delivers impact for UK industry. We would like to thank our industry board for all their input this year.
Our partners help us work towards our vision of putting UK manufacturing at the forefront of the electrical revoultion and have helped shape our current and future research programme. We are interested in the full spectrum of industry partners from large OEM’s through to SME’s in the supply chain.
If you are interested in becoming a hub partner, please email Hub Manager: Laura.Okeefe@sheffield.ac.uk.
The Future Electrical Machines Manufacturing (FEMM) Hub research team is made up of individuals from the Department of Automatic Control and Systems Engineering (ACSE) at the University of Sheffield; Advanced Manufacturing Research Centre (AMRC); University of Bristol; Department of Electronic and Electrical Engineering at the University of Sheffield; Department of Mechanical Engineering at the University of Sheffield; National Manufacturing Institute of Scotland (NMIS) and the University of Newcastle. More information on our team can be found on our website.
We actively promote a culture where the diversity of the staff involved in the Hub is positively valued and celebrated. We believe that diversity in all its forms delivers a greater impact to our research and enhances the experience of our staff, students and partners. The Hub’s commitment to EDI is demonstrated and promoted through our internal and external communications.
The FEMM Hub Equality, Diversity and Inclusion committee was set up to maintain a fully inclusive culture that is proactive in initiating change and driving forwards best practice in equality and diversity matters. The committee is made up from a representative from each of our partners as well as the FEMM Hub Manager.
This training session took place during a FEMM Hub QRM at the University of Strathclyde.
The two hour training session covered the basics of allyship, why it matters, and practical ways for becoming an effective ally to marginalised groups, with a particular focus on sexism and racism. Through interactive activities and group work, participants will build a solid foundation from which to develop their allyship.
Our team undertook mental health awareness training in February 2024 during our QRM in Newcastle. We felt this training was necessary to empower and equip our team members to improve mental health in the workplace. 1 in 4 adults have been diagnosed with a mental illness with it being the largest single souce of burden of disease in the UK. This session was designed to give us the very best chance of being able to spot a colleague in crisis, to know when and how it’s appropriate to intervene and understand how organisations can support people on their journey back to wellness.
The session covered:
- An introduction to Mental health
- How to spot the signs and symptoms of poor mental health
- Ways to support others with mental health illnesses
- Preventative methods for staying mentally healthy
- Resources that can be accessed for further support
The FEMM Hub started its 7-year programme of work on April 1st 2019. The original proposal for the Hub was required to include a programme of research for the first half or so of the 7-year period. With the remainder to be developed in consultation with our advisory boards. In February 2022 we began this process with a facilitated partner connect workshop which resulted in a report on the priorities, trends and opportunities identified by industry partners and the FEMM hub team. Using this report, the team formulated a list of 37 research topics with an emphasis on mapping these topics onto the outputs of the partner connect workshop. This list was then presented at a joint Industry and Scientific Advisory board meeting and they were given the opportunity to vote on this list. This list was then consolidated into the final research programme for years 5-7, which can be found below.
Grand Challenge 1: Manufacturing-led innovation in electrical machines
This theme is concerned with realising the dividends that come from much closer integration between innovation in electrical machine design and advanced manufacturing methods.
1.1: Realising novel machine design freedoms from innovative manufacture.
1.3. Manufacturing of light-weight and multi-functional structural components.
1.4. Manufacturing the novel and non-standard materials
Grand Challenge 2: Process innovation, monitoring and simulation
This theme is focused on the numerous processes that underpin electrical machine manufacture. The research will draw heavily on modelling and simulation to explore the influence of current and emerging processes on final machine performance.
2.2: Manufacturing high performance coils and ultimate control.
2.3: Manufacturing technologies for flexibility and customisation.
Cross cutting themes: A central thread of activity linking our research outputs
Cross cutting (X) themes underpin our Grand Challenge (GC) themes. Each GC theme incorporates elements each of the X themes in order to develop a deeper understanding and maximise FEMM Hub outputs.
X1: Sustainable manufacturing of electrical components for the circular economy.
X2: In-process tracking and tractability for zero-defect manufacture of electrical machines.
X3: Roadmapping and technology reviews
X4: Demonstrator
Aligned projects: A central thread of activity linking our research outputs
This theme is concerned with realising the dividends that come from much closer integration between innovation in electrical machine design and advanced manufacturing methods.
1.1: Realising novel machine design freedoms from innovative manufacture.
1.3. Manufacturing of light-weight and multi-functional structural components.
1.4. Manufacturing the novel and non-standard materials
Phase two of this work package has commenced with the appointment of two new Research Associates; Dr Luke Saunders, bringing industrial manufacturing experience to the project and Dr Yusuf Ugurluoglu, beginning his first appointment as a Research Associate following the successful completion of his Mechanical Engineering PhD. We are also adding two funded PhDs to the research later this year.
This project aims to increase the power density of electrical machines within the same thermal limits. This can only be achieved with changes to the machine design and construction methods. Modularisation of the machine enables greater access and control to the coil winding process, enabling a denser, more thermally conductive capable coil which can operate at higher loadings within its thermal limits. Further gains can be obtained by incorporating advanced thermal management into the module.
Modularisation does however pose a number of challenges; more components, mechanical, thermal and magnetic interfaces. This work package is investigating these aspects methodically to advance understanding and suggest manufacturing and design methods to minimise problems. Research is split into the following themes:
During phase two, more cross institute research is planned including Robotic winding of modules with the AMRC, Mechanical design and testing of modular stators with Sheffield and the development of the dry machine with NMIS/Strathclyde.
As a basis for experimental comparison between modular and non-modular machines, we have designed two machines to the Freedom Car specification: 50kW peak and 30kW continuous, up to 14,000rpm and at efficiencies exceeding 95%.
A distributed wound machine sets the benchmark as the “common manufacturing method” machine. A concentrated wound version allows direct comparison and is the intermediate step toward modularisation of the stator by a variety of methods. Experimental data will allow direct performance comparison between the various methods of construction.
The concentrated wound version of the machine is under construction and will begin testing toward mid 2024. The case is designed to be compact and cost-effective, allowing further use with different stators, including distributed wound and modular configurations. This is enabled by using two end caps for easy access inside the motor, and a stator assembly which can be slid into, and out of the case and locked in place with retaining rings. Thermal management is achieved via a spiral cooling jacket, which is slid over the stator case and sealed with o-rings. No direct fluid contact is possible with the stator, rotor or coils. The RM44 rotary magnetic encoder is selected to precisely measure shaft position and speed on electric motors. It can operate at high speeds of up to 60,000 rpm while maintaining accuracy within ±0.5°.
The mechanical interface between stator modules is a critical aspect of the design, particularly as it directly impacts the durability and operational efficiency of machines. Research focuses on how the modular interface and topology affect three key factors: noise, vibration, and wear. Noise and vibration are significant as they can affect the safety and performance of the machine’s operation. Through simulation and small prototype design and test we will identify designs that minimise these issues, leading to quieter and more robust modular design. The vibration test follows the standards set out in BS ISO 20816-3:2022 for mechanical vibration, ensuring that the results are in the defined range. Circumferential and axial segmentation will be considered and the findings will allow us to further develop one or two full modular stators for testing against the demonstrator benchmark machines.
The main argument for modular machines is the improved thermal performance achievable through a more controlled winding process, giving a higher slot fill and improved bulk thermal properties and contact with the tooth (figure 1). Greater control is possible due to the improved access of the winding machine to a single, segmented tooth, as opposed to the needle winding process necessary for a complete stator. Initial tests are being carried out on a traditional slot shape (figure 2), with slight modifications then applied to give a flatter slot surface (figure 3).
Initial tests will compare the thermal performance of the two tooth topologies. One set wound by a highly capable winding business, and a second set by robots at the AMRC. During robot winding, data will also be gathered for use in the other work packages.
In this investigation we will be manufacturing two different topologies of modular stator teeth and having them copper wire wound by robot or commercially standard winding. The tooth assemblies are then placed inside an environmental chamber at a set temperature and the coil energised. The resulting temperature profile of the coil is determined from the change in electrical resistance.
It is theorised that winding process, conductor position control and the coil-tooth contact surface will influence thermal performance, and this set of tests will help to highlight favourable modular topologies.
Measurements of the effect of surface roughness and pressure on the magnetic interface of a split core is being presented in ICEM 2024. The more processed interfaces exhibit lower loss, and the application of pressure did not have a significant effect on the interface gap length. These early results suggest stator modules require additional processing at the interface to minimise loss and reluctance.
One of the main streams of work for GC1.3 in the past two years has been the development of a methodology to fully integrate manufacturing constraints and opportunities with the machine design considerations. The novelty in this work includes material data specific to individual manufacturing process in the design of components. Not only does this reduce the risk of over-engineering components, it also allows for an assessment of when and where expensive materials and processing routes can be put to best use.
In 2022, the team working on GC1.3 published the paper “A Manufacturing Driven Design Methodology to Lightweighting of the Structural Elements of a Permanent Magnet Electrical Machine Rotor,” in IEEE Access [1]. This paper was the culmination of over a year’s work, optimising how the manufacturing requirements can be optimally integrated into the design stage of electrical machines components. Typically, electrical machines are designed with little or no input from a manufacturing production viewpoint, and this can often lead to cost increases and time delays as designs are iterated to accommodate for manufacturing limitations. This paper proposed a methodology to fully integrate the mechanical design and manufacturing process routes into electrical machine design, and illustrated the benefits of such a process within the context of lightweighting a permanent magnet rotor for an aerospace electrical machine.
Within the methodology proposed in this paper, several alternative configurations of rotor design were considered with appropriate manufacturing routes identified at the initial concept design. Different material and manufacturing constraints were identified in this paper, as well as the impact that the manufacturing process can have on the final component. These impacts were then embedded into the initial design procedures. The final section of the paper demonstrated an application of this methodology, and discussed the features which offer opportunities for achieving economically lighter weight design through the integration of manufacturing into the design procedure.
2: Schematics for the three different design options considered [1]
Figure 3:Comparison of mass of the spoked rotor hub design when manufacturing specific material data is used [1]
The case study in this paper presented three designs of a rotor hub and shaft, shown in Figure 2, and considered the effect on weight when manufacturing specific material data is used. The choice of manufacturing route can greatly affect the yield stress of the final component, and this was included in the modelling to highlight potential lightweighting potential by selecting an optimal method of manufacture, as shown in Figure 3. Work is now ongoing for the follow up to this paper, where a second paper will focus on more detailed modelling which will further highlight the benefits of introducing manufacturing considerations into the design of electrical machine components.
Last year a new stream of work was also launched, in conjunction with GC2.3, on understanding what a manufacturing system for small batch electrical machines would look like. The approach developed for the type and volume of machines considered in the FEMM builds on several manufacturing system ideas that have already been developed. Examples can be found in academia and industry of Dedicated Manufacturing Systems (DMS), Reconfigurable Manufacturing Systems (RMS), and Flexible Manufacturing Systems (FMS). A Flexible Manufacturing System is a manufacturing system in which there is some amount of flexibility built in that allows the system to react to a certain degree of change. Reconfigurable Manufacturing Systems (RMS) are designed for rapid changes in structure, hardware, and software, in order to quickly adjust its production capacity and functionality within a series of part families.
Manufacturing processes were generated for each of the four key elements of the machine: rotor, stator, coils, and non-actives. They were then ranked against each other based on a variety of drivers including process speed, process and tooling flexibility, and cost. The highest ranked manufacturing methods were then combined to produce a flexible factory option, which is shown in Figure 4.
Figure 4: Flexible factory set-up with a combination of flexible and reconfigurable cells, where blue and orange cells represent stator and rotor manufacture, respectively, and grey cells represent inspection, testing, and general assembly cells. Flexible and reconfigurable cells are shown with a designation of ‘F’ and ‘R’ respectively.
The net zero 2050 targets which have been set out by many countries across the globe will rely on the electrification of transport and energy sectors, which in turn will require an increase in the power density and volume of electrical machines. The key aim of this work is to understand how we ensure manufacturing solutions are flexible enough for future production challenges. This includes not only the ability to handle different machine topologies currently being manufactured, but also the ability to deal with radical design changes that might come with the need for ever increasing power density requirements. In 2022, the team working on GC1.3 also designing and delivered a training course for FEMM hub members “Manufacturing Opportunities for Future Electrical Machines”. This course was delivered by colleagues at the Advanced Forming Research Centre (AFRC) and the Advanced Manufacturing Research Centre (AMRC), and introduced novel manufacturing routes which could be utilised for the manufacture of non-active components in electrical machines. This course was well attended, with over 75 participants, and will be run again in future.
With a focus on the wind energy sector, Dr Abbas Mehrad Kazemi Amiri led a team of researchers to deliver the technology white paper “Design and Manufacturing Challenges and Opportunities for Offshore Wind Turbine Electrical Generators”. The main objective of this Technology White Paper, in which the existing and future challenges in cost-effective design and manufacturing of the next generation of direct-drive electrical generators in offshore wind turbine generator systems are identified, and corresponding opportunities to address those challenges are discussed. It has tried to contribute to finding answers to the following questions: a) what are the current manufacturing methods? b) what are the challenges with scale-up in size and number? c) what are the major differences between the direct-drive generator and the conventional ones for wind turbines that influence the manufacturing process?
Direct-drive permanent magnet generators are now dominating the offshore supply chain. In offshore wind farms, the overall cost of energy is pushing the turbine design to be larger in power and slower in rotational speed. Due to the high demands on wind energy as the major low carbon source of energy, significantly more wind turbines (particularly offshore) need to be designed, manufactured and installed. This white paper relies on the literature review, existing information in the public domain as well as interviews with experts, as the two former sources have been found to be quite limited. More information on this white paper can be obtained by contacting Dr Amiri or Dr Jill Miscandlon (both University of Strathclyde).
• Work stream 1: Continuation of current lightweighting design development, with methodology validation and prototype testing
• Work stream 2: Manufacturing-driven design of down-scaled wind turbine direct-drive generator
Work stream 1 will build on previous research and will produce high-fidelity finite element modelling and analysis of family tree design candidates presented in [1]. “A Manufacturing Driven Design Methodology to Lightweighting of the Structural Elements of a Permanent Magnet Electrical Machine Rotor” [1] set out a methodology for determining the optimal material and manufacturing route for specific electrical machines components. The next stage will involve stress and compliance analysis of the design candidates where the joint manufacturing and mechanical constraints are imposed, and the use of different metallic materials with the mechanical properties associated with the manufacturing process taken into account. Based on the results of the finite element modelling, a design will be chosen for prototype manufacture. Mechanical tests will then be conducted on the manufactured candidate design under operational loads. Shaft and hub mechanical strength tests will be conducted, including stress, deflection, tolerance, vibration measurements, and verification against the finite element analysis results.
Work stream 2 will follow on from the white paper “Design and Manufacturing Challenges and Opportunities for Offshore Wind Turbine Electrical Generators”. Downscaling, modelling, redesign and testing will be conducted in order to establish the comparison with the baseline design. An adaptation of the design and manufacturing methodology developed in [1] will be applied to the rotor of a direct-drive generator to create novel candidate design models. Finite element modelling will be utilised for a multi-material rotor design, which aims to utilise carbon fibre composite in the deflection hotspots in combination with a metallic structure for further lightweighting achievement in addition to the above. Focus will be given to the achievable tolerances, mechanical strength of the novel rotor design, and electromagnetic losses in the generator.
[1] Miscandlon et al., A Manufacturing Driven Design Methodology to Lightweighting of the Structural Elements of a Permanent Magnet Electrical Machine Rotor,” IEEE Access, vol. 10, pp. 117449-117468, 2022
[2] Global Wind Energy Council. Gwec - global wind report 2022. Technical report, Global Wind Energy Council, 2022
For the start of phase 2 of the FEMM hub, a new work stream was launched to focus on novel and nonstandard electrical machine materials. This work package is supported primarily by colleagues in NMIS and AMRC, and is focusing on two key areas:
1. Materials and manufacturing processes for low temperature operation
2. Advanced materials and manufacturing technologies for superconducting machines
Exciting developments over the past few years have included the design of traditional electrical machines for use in cryogenic environments- mainly for use in hydrogen powered aircraft- and the further development of fully superconducting machines. Both technologies are developing rapidly, but the manufacturing technologies that will be required for each- especially when larger volumes will be requiredare still unclear. One of the aims of GC1.4 is to assess the current state-of-the-art in design and material selection for low temperature applications, and link this to the manufacturing research that is already ongoing within the FEMM hub.
The first key task for this GC is to compare traditional machine topologies with those for low temperature operation, and understanding the crossover potential for standard materials and manufacturing routes. Although a lot of information is known about the performance of standard alloys (such as titanium, aluminium, and steel) at room and elevated temperatures, the mechanical and fatigue properties at cryogenic temperatures are not well understood. GC1.3 previously reviewed the yield stress of key materials in relation to various manufacturing routes (J. Miscandlon et al.: Manufacturing Driven Design Methodology to Lightweighting of the Structural Elements, DOI: 10.1109/ACCESS.2022.3214305), and GC1.4 aims to expand this work by reviewing the academic literature for data on the yield stress below zero degrees. Once this review has been completed and the gaps identified, GC1.4 will be conducting low temperature materials testing within the University of Strathclyde on selected materials, with an aim to publish the results in an academic paper.
GC1.4 is also engaging with the Lightweight Manufacturing Centre (LMC) at NMIS to advance the use of composite materials in future machine design. We are looking at opportunities for the wider use of composites in standard electrical machines for lightweighting purposes, but we are also investigating the performance of such materials in cryogenic environments. Understanding the strengths and limitations of a wide range of materials in temperatures ranging from -220°C to 250°C will be critical in fully optimising the design and manufacture of future machine topologies.
Once the material properties of metal alloys and composites are understood for low temperature operation, GC1.4 will down-select one or two materials for prototype testing. Working closely with the design team at AMRC and the manufacturing specialists at the LMC and the Advanced Forming Research Centre (AFRC), novel designs will be manufactured and tested for low temperature applications. Throughout the design process, the team will be focused on a range of factors, including material section, design for manufacture, component quality and performance, and sustainability. This integrated product development cycle is shown below. The prototypes that will be produced as part of this GC will also aim to be as lightweight as possible, while building in additional functionality where possible, which links with the aims of GC1.3. :Product development cycle, as used in the LMC (https://www.nmis.scot/what-we-do/lightweight-manufacturing-centre/our-capabilities/)
This theme is focused on the numerous processess that underpin electrical machine manufacture. This research will draw heavily on modelling and simulation to explore the influence of current and emerging processes on final machine performance.
2.2 Manufacturing high performance coils and ultimate control.
Bristol: Additive Manufacturing of High Performance Electrical Machine Windings
2.3 Manufacturing technologies for flexibility and customisation.
This Grand Challenge is concerned with manufacturing high performance electrical machine coils, with precision placement of conductors in the coil geometry, managed layer transitions and minimised end winding projections. The research is focussed on solid bar section bar conductors and hollow bar conductors, typically with a square crosssection or rectangular cross section with a small aspect ratio. An image of the solid bar conductor is shown (see right). A small duct through the centre of the hollow conductor allows for direct heat transfer, from the conductor to a fluid in the duct. Thus, a more robust insulation system can be employed which meets the electrical and mechanical requirements, since the dependency on heat transfer across the coil and the coil - stator core interface, through layers of electrical insulation, is removed. A hollow conductor thermal model and associated thermal test rig were established in Phase 1 of this Grand Challenge, along with an investigation of minimum bend radii, for both hollow and solid bar conductors. Further details can be found in the previous annual reports.
Bar conductors enable greater utilisation of the stator slot area, which provides scope to increase the coil current density and hence the power density or torque density of the electrical machine. However, a typical electric machine for an automotive traction application can operate at speeds up to 12,000rpm, which equates to a fundamental frequency in the region of 1kHz. Future generation machines for automotive and aerospace applications may require even greater operating speeds. The AC losses in the winding, resulting from Eddy current and proximity effects, can be significant and require thorough consideration.
The ongoing activities within Phase 2 of this Grand Challenge, are Multiple layer bar windings and high frequency characteristics of machines, focusing on AC loss modelling in bar windings in the first instance.
There are several manufacturing challenges in producing a coil from bar type conductors that don’t exist with stranded circular wire bundles of equivalent copper area, due to the fixed conductor geometry of the bar. These include managing layer changes, limitations on minimum bend radii, maximum tension,
increased stiffness, springback, additional complexity of in-plane bend forming and placement of the active region conductors such that slot utilisation is maximised. The objective of this activity is to develop methodologies of producing coils in bar conductor, to a specified geometry and with a high level of precision, primarily as an automated process. Accounting for springback and preserving the geometry of the cross-sectional area of the conductor present further challenges. Deformation of the conductor will affect heat distribution and losses within the conductor. In the case of the hollow conductors, deformation of duct will in result in greater pressure drop and thermal resistance to the fluid.
The proposed strategy to form multi-layer coils in bar conductor, is introduced in the 2023 annual report. The coil is produced by winding a series of turns onto a former, representative of the stator tooth, using a commercial winding machine adapted for this application. To maximise the slot area, the wire in the active region of the coil should remain parallel to the back of the slot and the side of the slot. To achieve this, and establish the required number of turns, to the specific width and depth of the coil design, an in-plane layer change feature is created in the conductor feed, at a controlled distance from the former, at each turn. This shifts the lateral position of the wire feed, relative to the side of the former and away from the preceding turn. Turns are accumulated in layers along the depth of the coil before incrementing by a radial layer, with respect to the stator tooth, if required, as per the coil design. The intention is that the jog created in the wire at each turn, facilitating the lateral layer changes, will nest in the end winding regions of the coil (see right). The precise location of the layer change feature in the wire feed, required to nest, will be achieved by rotary position control of the winding machine head.
Initial winding trials will be with a 4x4mm solid bar conductor and 4x4mm hollow conductor with a 2mm duct, each with a 0.5mm radius on the corners. Demonstrator machine designs have been used to determine representative target coil geometries, for each conductor, although the emphasis is on gaining an understanding of the underlying bend mechanics and developing techniques to produce multiple layer bar winding, with a flexible configuration.
The layer change feature will be pressed into the wire feed using a punch and die tooling set, creating an offset bend, with two equal and opposite bends and where the wire continues to run parallel prior to and following the inline jog, in one operation. A first iteration standalone press assembly, shown below was designed and manufactured in 2023.
The press comprises of a fixed baseplate and sliding plate, guided by a set of four linear ball bushings
mounted on hardened steel shafts, which are secured to the baseplate and a top support plate. The tooling to form a particular offset bend geometry has been produced as a set of two punch and die’s, in tooling steel for hardness. The lower die is secured to the baseplate and the upper die to the sliding plate. The punch - die sets are easily interchangeable, so that a range of bend angles can be investigated. The pressing force, for this iteration of the press, is provided by an RS electromagnetic actuator, capable of producing up to 4000N, over a stroke of 100mm. Fixed mechanical stops, appropriate to the 4x4mm conductor, limit forward travel of the sliding plate beyond the point where deformation of the actual wire profile would occur, other than sufficient travel to press the offset bend. PTFE inserts within the mechanical stops act as a wire guide to ensure the conductor is parallel to the die set and the press force is applied to the upper
and lower flat sections of the conductor profile. Trials of forming an offset bend into sample lengths of the 4x4mm solid and hollow bar conductors have been successful. However, whilst informative, the trials do not account for the additional complexities, in forming the offset bend, while the wire is under tension. Thus, the recent focus in this grand challenge has been to establish a forming rig that provides the necessary enhancements to the winding machine and facilitates the winding trails in bar conductor. A simplified schematic of the intended process, to directly produce a form wound multi-layer coil in bar conductor, is shown above. The trial coils will be wound on a Winding Technologies WT500 coil winding machine with requisite additional equipment, comprising of the press assembly and traversing former assembly, installed. The bespoke hardware for this forming rig is currently being manufactured and off-the-shelf components are being procured. The traversing former assembly mounts directly on the bedplate of the winding machine and makes use an existing T-slot for alignment with the face plate. The centre height of the former matches that of the winding machine spindle. Torque is transferred to the former via a ball spine shaft, sized appropriately for the predicted torque to overcome the required tension in the wire feed. One end of the shaft is secured in a tool holder centred on the faceplate of the winding machine head and the other supported by the former assembly, in a tailstock type arrangement. The axial position of the rotating former will be controlled via an electromagnetic actuator. A CAD image of the former is shown right. The central section, on which the coils is wound, is interchangeable to allow flexible coil geometries.
The press assembly has been modified to utilise existing linear guide rails on the winding machine frame, which are normally a base for the wire guides. This 2nd
iteration of the press has been altered to use a pneumatic actuator to achieve a more consistent force at the press tooling. The wire supply spool will be mounted on the winding machine tensioner, which provides a controllable braking force. During the winding process the tension is measured by a load cell. The wire straightening rollers and wire guides will be mounted in series with the wire feed tensioner and the winding machine.
To achieve a net coil geometry within acceptable limits of the design it is essential that the tension in the wire feed, as the coil is wound, is appropriate to the wire size. Insufficient tension will result in a coil that is loose on the former and result in additional conductor length. If the tension is excessive and / or beyond the limits of the material, the wire profile may deform, reducing the conductor cross-sectional area or indeed break.
An online calculator, recommended by several winding machine equipment manufacturers, suggests an optimum tension of 66kg for the 4x4mm solid bar conductor, based on a circular conductor of equivalent area. As part of this investigation, a mechanical FEA model has been established to predict the tension at which the wire profile will deform and a more optimised winding tension. The results of this modelling, for standard annealed copper, are shown below. Independent tensile testing of copper wire samples from the 4x4mm solid and hollow bar conductor stock, purchased in 2023, is underway.
By installing the layer change feature in the wire, the overall length of wire in the coil is increased. It is intended that this additional length of wire is drawn from the feed spool, without elongation of the wire, as the offset bend is pressed into the feed. Furthermore, as the coil is formed, the angles in the offset bend will tend to alter, since the wire is under significant tension. In order that the net shape of the layer change feature can be achieved consistently, knowledge of the relationship between offset bend angle and tension is crucial. An investigation is underway and mechanical FEA models of the 4x4mm conductors have been developed, with configurable offset bend geometries. Figure 6 shows predicted stress and plastic strain in the solid bar conductor, with a preinstalled 45° offset bend and a 6.54mm span between each bend, under a 61kg tension (600N).
An electrical machine, designed to exploit windings formed from 4x4mm hollow conductors, was designed in early phase 1 of this Grand Challenge, as a potential demonstrator machine for FEMM hub research. This machine design has provided the candidate coil geometry for some of the hollow conductor coil forming research within the FEMM hub and the active rotor component for the rotor lightweighting activity in Grand Challenge 1.3. The topology is a 30 slot, 10 pole permanent magnet machine, with an integer slot winding. The designed base speed of the machine is 10,000 rpm, with a 20% overspeed capability. The slot geometry has been devised for a 4x4mm hollow copper conductor winding, whilst maximising the slot utilisation. The duct in the hollow conductor is 2mm. The predicted peak electromagnetic torque of the machine is 315Nm, at a current density of 25A/mm2 in the winding, providing sufficient cooling can be achieved in the hollow conductor.
An investigation of AC losses in hollow conductors has been ongoing within this grand challenge, albeit as a background activity in recent years. Previously, FEA modelling techniques were developed to consider current distribution in hollow conductors, but progress was limited to a single conductor and a single slot of an electrical machine, at representative frequencies. More recently the FEA modelling capability has been expanded to include predictions of the AC loss contribution for each conductor position within a slot, the accumulation of AC losses over the full machine and a loss comparison with an equivalent stranded coil.
Predicted current distribution within the conductors are shown to the right, in a single slot, for a current density of 25A/mm2 and a rotor speed of 10,000rpm. The predictions illustrate the significant increase in AC loss that occurs in conductors located towards at the slot opening, explainable through slot leakage flux. The modelling enables an assessment of the frequency envelope, where hollow
conductors remain a viable solution for a winding, at the design stage. The table below presents a summary of predicted AC losses across the whole supposed hollow conductor demonstrator machine, as a function of the conductors’ radial position within the slot, at operating speeds of 5000rpm and 10,000rpm. The predicted DC loss component 2997W. The proportion of predicted AC losses that occur in the conductors located towards the front of the slot is evident in the results.
Predicted copper loss over the normal speed range of the machine design, at a current density of 25A/mm2, is shown (see right). Again, the predicted DC loss
component is 2997W. As expected, the AC loss in the hollow conductor is highly speed dependent. Once the speed exceeds 3100rpm, the predicted AC loss becomes the dominant component.
Modelling individual conductors in an equivalent stranded coil usually requires a significant investment in time, particularly given the range of available wire strand diameters and the potential to vary the strand diameters within the bundle. Thus, an automated approach has been employed to generate the stranded coils and integrate them into existing finite element models of the machine. A parametric model has been developed, which allocates a space envelope in the slot to each turn and can replace the bar conductor with a stranded equivalent with an accompanying circuit model. The scripting allows loss predictions in flexible winding configurations to explored. Figure 10 shows an equivalent stranded coil in the slot, representing a bundle of 25 strands of 0.78mm diameter wire (copper diameter 0.72mm), formed into the 8 turns. The slot area available for the winding is identical to that of the hollow conductor winding, shown in Figure 8, where the original locations of the hollow bar conductors can be seen. The circuit model is shown in Figure 11, where each line of the circuit represents a parallel conductor in the bundle, and 8 turns.
This work package is split across three key themes, all of which are associated with and enabled by the use of additive manufacturing. Each of these three strands – investigating electrical conductivity and associated temperature coefficient, practical insulation of additive conductors, and integration of value-add geometries and features – aim to improve electrical machine efficiency, increase machine temperature ratings, and extract heat more effectively. By doing this, step changes in machine performance can be achieved.
Experience has shown a wide variation in the resulting electrical properties (electrical conductivity and coefficient of resistivity) of AM components across copper and aluminium due in part to the broad range of manufacturing approaches and the number of influencing process parameters involved. Supplier estimates against in-house measurements show significant differences owing to different measurement methods (4wire DC or eddy current probe) and sample geometry. This work package aims to develop a measurement standard based on ASTM B193-16 Standard Test Method for Resistivity of Electrical Conductor Materials for AM components which enables efficient parameter development and confidence in the resulting material properties.
To establish the electrical properties of additively manufactured copper, standardised serpentine samples are produced, geometrically measured using a probing system, Fig. 1, and the electrical resistance (at room temperature) measured using a 4-wire method. This allows the electrical conductivity to be inferred. However, when developing the process parameters to produce high density and geometrically accurate
parts, small cubes are typically produced which do not lend well to a 4-wire measurement approach. An alternative method of measuring electrical conductivity is to use a calibrated eddy current probe, Fig. 4, however, as shown in Fig. 6, this method can be very sensitive to the orientation of the probe and to edge effects which places a limit on the minimum sample dimensions. This is compounded by the impact of surface roughness and porosity that is typically present, Fig. 7. This work package is developing guidelines and protocols for the accurate and repeatable measurement of electrical conductivity applicable to additive manufacturing researchers, practitioners and suppliers.
The geometric freedom of additive manufacturing can enable novel conductor geometries to be realised such as Litzpins which are a hairpin conductor with targeted transposition to minimise AC loss, Fig. 8. If these new geometries are to be adopted, their robust and repeatable electrical insulation must be demonstrated in representative operating conditions.
The electrical insulation coating is made challenging by the nature of the additively manufactured substrate which exhibits surface roughness, porosity, and a level of oxidation. This work package develops post-processing methods (electropolishing and etching) to minimise surface roughness and make the substrate compatible with the coating. Powder coating, liquid spraying and liquid dip coating methods are experimentally evaluated where additively manufactured samples are compared with commercially available electrical copper. The coated samples are then mounted, polished and subject to optical microscopy to measure the coating thickness and consistency, Figs. 10 and 11.
Ongoing work focuses on coating simple additively manufactured windings and subjecting them to High Voltage breakdown tests to assess the quality of the coatings as compared to commercially available equivalents. The results have informed Design for Additive Manufacturing (DfAM) rules such as the addition of radii on conductor edges to facilitate more uniform and robust coatings.
Additive manufacturing can allow value-add features to be included in windings such as voids for sensors, terminals, and cooling structures or channels. Several thermal management concepts have been developed, including end-winding heat exchangers and through-conductor cooling. These concepts have now been experimentally tested. In particular, a through-conductor cooling design is taken from an initial CAD model, through manufacturing, post-processing and electrical insulation coating and then assessed under DC conditions. Ongoing work includes these thermal management schemes in automated design tools to allow their application to concept motor and generator designs.
Grand challenges 2.3 focuses on developing more flexible manufacturing processes and the opportunities in machine design which this opens. Two key areas of research are remote laser cutting of electrical steels, and robotic winding.
Remote laser cutting (RLC) is proposed as an alternative to conventional laser cutting used for of laminations. RLC relies on the use of high-brilliance lasers to achieve power densities 10 7 –10 10 W/cm 2 and high-speed scanning optics to achieve surface speeds on the order of several meters per second whereupon material partially vaporised. This vaporised fraction ejects the molten material from kerf, progressively cutting through the sheet over multiple scans.
Research this year has continued to investigate the scale up of this process, producing the first complete stator by this method (see left) - the results of which were presented at E|DPC 2023 and published in conference proceedings2 . Research has also continued to investigate the influence of cutting parameters on cut edge and magnetic performance. Whilst these investigations have shown RLC to be highly productive and allow more complex features to be realised without compromising process times, investigations have yet to replicate the lower impact on magnetic performance reported in literature. Additionally scans of the top surface shown in Figure 2 shows greater variation in burr and surface roughness in the kerf than previously observed in cross-sections. Research is planned to address burr condition by a clean-up laser scan in the second phase of the Hub.
Preparations are currently being made for an upgrade the existing continuous wave laser module to pulsed laser which will significantly extend the process parameter space into more ablative regime with the hope of avoiding thermal damage. It is anticipated that this laser will be around 2 kW emitting pulses of tens of nanoseconds in the near infra-red range. In parallel to this activity, researchers at the AMRC and
1 L. Tinkler et al, Manufacturing processes for 2.5D laminated stacks, 2023 13th International Electric Drives Production Conference (EDPC)
University of Sheffield are also collaborating with researchers The Manufacturing Technology Centre (MTC) to investigate the influence of waterjet guided laser cutting on magnetic performance. A conference paper is currently being prepared for 13th CIRP Conference on Photonic Technologies.
Industrial robot manipulators can be adapted to a wide range of tasks applicable to electrical machines and have been demonstrated in magnet placement, coils insertion and lamination stacking. Such robots are therefore proposed as the basis of a flexible manufacturing system that can switch between these various tasks, affording the benefits of automation, such as improved quality and throughput, without the inherent inflexibility of dedicated automation. Here work has continued to develop the use of industrial robots as the basis of a flexible needle winding system which can accommodate a wide range of winding designs. The results of this research were presented at E|DPC 2023 and published in the conference proceedings. 2 This reported on the suitability of industrial robots for needle winding with experimental trials on accuracy, repeatability and stiffness. The work also characterised the angular dependence of the wire leaving the needle on the wire tension under static conditions. A model has been created to estimate fluctuations in wire tension during needle winding due to
this angular effect. Experimental trials are currently underway to measure these fluctuations by mounting the bobbin on a multi-axis load cell which will allow direct measurement of the magnitude and direction of the force imparted byd the wire. Thereafter research will focus on minimising these fluctuations by compensating through speed and tension control.
In phase II of the FEMM Hub the robotic winding cell will refocus on other electrical machines assembly task as well as investigating the disassembly through aligned research projects.
As report in the 2023 annual report, a desktop study was conducted into manufacturing processes for slinky stators. This is a technology highlighted on the Advanced Propulsion Centre’s Electrical Machines Roadmap to help improve material utilisation. This work estimated the material utilisation for different stator split ratios and observed a marginal benefit if the rotor lamination is also required. Several cutting processes were proposed and evaluated in terms of productivity and flexibility. The results of this work were presented as a poster at PEMD 2023 but were not published in proceedings to ensure open access to the work. A follow-up paper, bolstered with experimental results, is planned for 2024.
In the past year Hub researcher Dr Alexei Winter has lead projects funded through the High-Value Manufacturing Catapult well aligned with the FEMM Hub to develop coil winding processes included wet winding of complete coil chains to avoid need for global impregnation after winding, and to demonstrate winding process for hollow conductors developed by the hub.
Cross cutting (X) themes underpin out Grand Challenge themes. Each theme incorporates elements each of the X theme in order to develop a deeper understanding and maximise FEMM Hub outputs.
X1: Sustainable manufacturing of electrical components for the circular economy
X2: In-Process tracking and tracability for zero-defect manufacture of electrical machines
X3: Roadmapping and technology reviews
X4: Demonstrator
GC X1 is a cross-cutting theme within the FEMM hub focused on the sustainable manufacture of electrical machine components, with a view to implementing circular economy strategies. Sustainability is a key component of any future machine design, and as such, this Grand Challenge was updated to be a crosscutting theme of all FEMM hub work packages. This will ensure that a clear focus is given to the sustainability of future electrical machines. This work package aims to:
• Reduce use of finite materials in next generation of machines and enable recapture cycles to reuse materials
• Give consideration to energy efficient manufacturing
• Implement Design for Disassembly strategies for future electrical machines, including opportunities for reuse, recycle, remanufacture etc.
• Develop a circular economy approach for an electrical machine supply chain that uses data driven intelligence based on product data
Current electrical machines are manufactured using a linear economy model that takes raw material, transforms it into products, and then discards them to waste without considering the environmental consequences. The circular economy (CE), as shown below, is a systemic approach to economic development designed to benefit businesses, society, and the environment. Adopting circular economy approach does not dictate one solution to solve all the issues, but is an alternative way of approaching the problem, and provides many solutions that can be adopted.
Often, when “sustainability” is mentioned within the engineering community, the first response is often linked to recycling material. Although recycling of materials will be an important factor in the drive towards circularity, it should not be considered the first or only solution. The circular economy hierarchy is shown below, a ranked order with the most favourable solutions at the top, i.e. those that require less energy consumption and material usages, and the least favourable solutions at the bottom. This hierarchy doesn’t imply that activities such as recycling or remanufacture should not be included in a comprehensive circular economy strategy, but other strategies, such as redesigning components in order to reduce material waste and design for disassembly and repair, should be prioritised.
Grand Challenge X1, in conjunction with PhD student Leigh Paterson, has been looking at ways of quantifying the various issues around current production and through-life management of electrical machines. A paper has been accepted in the journal Sustainability entitled “The Juxtaposition of Our Future Electrification Solutions: A View into the Unsustainable Life Cycle of the Permanent Magnet Electrical Machine” [1], and will be published in early 2024. Electrical machines provide a cleaner alternative for fossil-based technologies across multiple sectors including transport and energy. However, the products are often manufactured in a way that does not take into account their end of life, with common disposal techniques including shredding, burning, and landfill disposal. For electrical machines to be a truly sustainable solution, improvements need to be made from material sourcing, through manufacturing, to design for disassembly. This paper summarises the current demand and challenges for electrical machines, and follows each component through their typical lifecycle. The key aim of this paper was to present the typical life cycle of permanent magnet electrical machine as it stands today, and to demonstrate the environmental issues associated with the current linear life cycle. Alternative practices have also been discussed in the paper, with the short term aim to ease the immediate environmental burden of these products, and the ultimate aim to design and manufacture fully sustainable electrical machines.
Continuing on the theme of a fully sustainable electrical machine, GC X1 has lead a cross-challenge work stream including all partners of the FEMM hub to understand how to design an electrical machine that has 100% value retention, i.e. a zero-waste machine. We began this work stream with a workshop using TRIZ (Theory of Inventive Problem Solving), which is a structured brainstorming tool used for early stage, conceptual idea generation. The first step was to identify key system components that could hinder the manufacture of a zero-waste machine, and determine the primary benefits that such a machine should possess. Potential solutions were then generated using a ‘9-box’ process that enables the mapping of any system in time and scale. In time includes before, during, and after use, i.e. manufacture, in-use, and end of life; and in scale includes sub-system, system, and super-system, i.e. materials, components or full machine, and wider system context (e.g. full vehicle/aircraft, or wider supply chain). This work led to identifying three work streams to take forward:
Theme 1- Interlocking meta-surfaces: how can mechanical interlocking or reversible assembly process be implemented in high value electrical machines
Theme 2- Injection over-moulded coil modules: can we use injection moulding to manufacture modular windings that are optimised for disassembly and repair
Theme 3- Case study comparing disassembly of different machines: how do we measure ‘success’, and how do different machine topologies compare.
These three work streams have now kicked off, and have representation from all grand challenges, and aim to answer some of the most challenging questions around the future sustainability of electrical machines. In 2023, the FEMM hub published its first roadmap that highlights the development requirements for electrical machines to achieve a net zero future [2]. This roadmap was well received within the community, and as a follow up, GC X1 is leading in the development and publication of a positioning paper on the circular economy of electrical machines. This paper will summarise information from key stakeholders in industry and research, highlighting the major challenges and opportunities for the UK to lead the way in manufacturing fully sustainable, high value electrical machines.
The FEMM hub team at NMIS hosted a masters student in 2022/23 in the area of electrical machine sustainability. Eilidh Pearce completed her masters thesis on “Sustainable Design of Generators for Offshore Wind: Life Cycle Comparison of Lightweight Rotor Structures” under the supervisions of GC X1 leader Dr Jill Miscandlon, and was supported by Dr Pablo Sola at Edinburgh Napier University. Dr Sola previously received funding from the FEMM hub for a feasibility study “CEDEMSARI- A critical evaluation of large scale direct drive wind turbine electrical machines manufacturing techniques considering sustainability aspects and recyclability issues”. The collaboration in previous years has led to Dr’s Sola and Miscandlon co-supervising a PhD studentship that will be filled in early 2024.
References
[1] Paterson, L., Miscandlon, J., Butler, D., The Juxtaposition of Our Future Electrification Solutions: A View into the Unsustainable Life Cycle of the Permanent Magnet Electrical Machine. Sustainability 2024 [2] M. Ward et al., FEMM Hub Roadmap, 2023, available online (accessed February 2024), https://www. electricalmachineshub.ac.uk/roadmap
The tracking and traceability of manufacturing processes allow for improved quality and cost savings within many industrial activities. These have recently been driven by digitalisation through sensors and other data capture means, and the integration of this data into high-fidelity models or ‘Digital Twins’. The manufacture of electric machines is itself a complex task, involving the synthesis of many traditional machining/forming and cutting processes interspersed with assembly, integration and test. As we move to phase two of the hub our research has looked to the continue the development of our sensorised workstations in coil winding and hot crimping processes with a focus on digital twin modelling and characterisation of these manufacturing processes. We have also looked to undertaken collaborative research with other partners such as the AMRC on high speed processes in electric motor (EM) manufacture, and sustainability with the cross cutting theme X1 on the circular economy of EMs.
The digitisation of processes in electrical machine manufacture has been the centre piece of this theme throughout the years. This has included research around monitoring of specific tools or processes such as additive methods like laser-based powder bed manufacturing or joining technologies, for example our work on the hot crimping of connections and terminations of coils. One of the other main processes, one Ishikawa-diagram representing a number of influences to the winding result.
that along with bearing failure impacts the life-time performance and failure rate the most is centred on coil winding and forming processes. The coil winding / forming process within electric machine manufacture includes several variable methods, from simple bobbin wound linear coil winding and needle fed winding, to the more common random wound and insertion techniques used in the automotive industry. In all instances, it is important to know the state of the wound coil, either for in-process monitoring or post-process assessment and characterisation. Past work focused on the capture and extraction of data or information from the coil winding process, for example the position and placement of individual wires as the coil is formed through the use of a deep neural network (DNN) semantic object detection. The next stage of this research has been on the development of a ‘Digital Twin’ model of the linear winding process, where features and image data extracted from our sensorised linear coil winding workbench can be fed in real-time to a model for capture, characterization and predictive processing.
This digital twin has several benefits, the ability to characterise in near real-time could allow us to undertake corrective measures if errors or defects seem likely or are predicted. It also allows manufacturers to simulate the effect certain process (wire speed, tension, bobbin design, winding pattern, etc) or material (wire gauge, insulation, friction coatings) parameters have on the performance and outcome of the formed coils. Some of these influences can be seen in the Ishikawa-diagram, and the incorporation of these influences and their underlying physics into this digital twin model are the focus going forward. The incorporation of data captured from machine vision and integrated sensors into the developed digital twin model can be used to characterise both the process and final result as seen below. One of the related challenges to this research as discussed previously is the tradeoff between speed and accuracy. Past efforts have understandably focused on accuracy, using computationally expensive finite element modelling methods, which require many hours to compute the linear winding process. We ourselves have also used Discrete Event Simulation (DES) modelling as a faster approach (1-10mins), providing us with estimations on the distribution of geometric (wire gaps, crossover etc) or material (elastic / plastic deformations) faults created, given the initial conditions. Our goal here is to explore real-time tracking of wire placement, and associated process factors (tension, plastic deformation, stress etc) on the coil as it is being formed through the use of ‘Edge’ compute devices. This has been something that has been highlighted from industrial stakeholders, where large cloud infrastructure may not be available, and the need for smaller, memory efficient models (DNN, analytical) can be employed. An outline of this research can be seen in figure 3, where we want to investigate across the different coil forming use cases, and levels of computational cost and fidelity in the digital twin models used.
Another area of research is in-process monitoring and inspection during the thermal or hot crimping process of making terminations. Hot crimping is achieved using a welding power supply and a weld head to deliver current and apply vertical force to remove insulation and fuse the wires and sleeve. This process removes the requirement of enamel removal before joining (as it combines the process steps of stripping and joining the wires) and therefore this process offers the benefits of short tact-times, cost-effectiveness,
and efficiency. However, it is prone to the generation of defects such as improper insulation melting and burnt wires resulting in the requirement for frequent setup processes. To understand the correlation between the machine and the process parameters and the onset of defects during the termination process we have developed a lab-based sensorised hot-crimping system as seen below. The hot crimping system is instrumented with an RGB vision system for monitoring the wear in the electrodes, and any visible defects in the termination such as the region of the burnt insulation outside the lug, the shape, size and location of footprint of the electrode on the lug, along with any deformity in the shape of the lug. An infrared camera (IR) was attached to capture the thermal profile of the joint during the crimping and the cooling cycle to identify any hidden defects that are not visible using vision systems. Different wire types with enamel coatings (polyurethane and polyamide-imide), and diameters (1-1.4 mm) were tested with different lug materials. A design of experiments was planned to understand the impact of process parameters (such as crimping cycle times, applied current, and applied pressure), and machine parameters (such as delay in electrodes touching the lug surface and electrodes heating cycle) on the quality of the termination. As the terminations were being made, visible inspection was carried out using images from RGB camera and thermal inspection was conducted by analysis of the IR profile of the joint. The results from inprocess observations were validated by conducting the following end-of-line quality tests (i) multi-meter connectivity tests on all the wires in a sample to check the number of connected and unconnected wires samples and (ii) force pull-out tests that measured the force, displacement of the crosshead, and time to determine the pull-out strength of the terminal.
The experimental results revealed that the crimping cycle time and the amount of current passed through the electrodes have a profound impact on the shape and size of the footprint of the electrode on the lugs, which is related to the mechanical strength of the lug (as determined from force pull-out tests) and the electrical goodness of the lug (as determined from connectivity tests). It was observed that with the choice of appropriate crimping cycle time and crimping current, the terminations reached good connectivity with more than 90% of the wires being connected (example shown below), and a firm
mechanical bonding was achieved with a pull-out force reaching over 1400N. This finding opens the path for in-process visual inspection, where the shape, size and location of the footprint of the electrode on the lugs can indicate the mechanical strength and electrical connectivity of the termination (see left). Similarly, the IR profile of the wires recorded during the process can highlight defective wires due to their temperature values being lower than other wires as shown below. This effect is caused either by no current flowing through (in the case of unconnected wires) or by increased resistance values. In addition to this, the crimping machine parameters such as the inherent random delay between the moment when the electrodes touch the lug and the moment when the electrodes heat up, have a significant impact on the type of defect induced in the termination. The current research is focussing on building a correlation matrix for the impact of various machine and process parameters on the generation of defects in the termination. The next steps for this research work, as investigated by a Ph.D. researcher, are defect quality assessment and classification to predict the defective state of a component with AI models through RGB images for surface and IR images for inner features. This includes training a Neural Network (NN) to identify areas of surface defects using RGB images.
Across the manufacture of electric motors there are several processes, or tools where the need for highspeed capture of data can provide useful information for tracking and traceability. This can be for example as discussed earlier the process of coil forming, or perhaps recent work in additive processes such as laser-based additive manufacture of components, to welding and terminations work. As discussed earlier, the move to phase two of the hub includes the focus on such high-speed processes, and with the recent purchase of an event-based camera, the early stages have involved data gathering and evaluation of this novel sensor technology. Event based cameras work on a completely different paradigm, capturing per-pixel data only when a sufficient threshold has been met. This provides some benefits, such as an extreme capture rate of around 10,000fps, a high dynamic range (120dB) and low light capture (0.08 lux). Supporting both DNN machine vision architectures and more biologically inspired spiking neural networks (SNN), the EVK4 camera provides new opportunities for tracking and traceability of high-speed processes. Some of this recent work can be seen below, where the influence of parameters on additive manufacture, in this case gas flow and composition have on the effects of ‘spatter’ or ejaculation of powder material, or the detection and tracking of enamel damage on copper wire. This research is still at an early stage and will begin to ramp up more in Q4 of 2024, however if you have high-speed processes you are interested in capturing feel free to contact us.
The move to a more green and sustainable economy will naturally revolve around the use of electric
vehicles and the manufacture of electric motors. This has been spearheaded by the X1 theme on “Sustainable Manufacturing of Electrical machine components for the circular economy”.
In collaboration with this theme and AMRC we are also looking to investigate the role digital technologies (sensors and machine learning) can play in helping to accelerate this field of research. This begins with extending our previous work on the manual assembly of coils and terminations, in particular the capture and modelling of Deformable Linear Objects (DLOs) to investigate methods for tracking human activities and actions. This work, undertaken by our new PhD student Junxi Zhang will look at machine vision and machine learning methods for understanding manufacturing activities and actions performed by human operators at both manufacture and the end-of-life cycle Re-X (remanufacturing, repair, reuse, recycle) processes. This is challenging as current approaches look typically at the early stages of manufacture, where activities, processes and actions are more controlled and understood, whilst at the end of the life cycle the product itself can through historical use and degradation lead to irregular states and non-deterministic processes in the Re-X pathways. The second collaborative piece of research between X1 and AMRC is to investigate sensorised platforms for the end-of-life inspection of electric motors and components. This will include research on multi-sensor, nondestructive testing methods to inspect and characterise the states, possible remaining useful life and Re-X pathways an electric motor can enter in the wider circular economy.
This research proposed the development of a hybrid computational framework for fault detection during the coil winding manufacturing process by using a combination of a Discrete Event Simulation (DES) model with a Supervised Machine Learning (SML) algorithm. The proposed methodology utilised a Knowledge Distillation (KD) approach to address the challenges associated with the technique and optimise the student model’s performance by employing architecture search and data augmentation. The random forest algorithm demonstrated superior performance due to its ability to handle complex data and identify the impact of interdependencies of process parameters on the final product quality. The method was validated by conducting physical experiments on a linear coil-winding machine, and the results indicated that the random forest algorithm could decrease simulation time from 2 minutes to less than a second. The multi-objective optimisation approach was explored that aimed to balance and optimise the tradeoff between coil-winding speed selection and defect rates leading to a reduction in production costs and the number of faults. The objectives of the process were not independent, but rather interconnected, and therefore making adjustments to one variable often resulted in changes in others creating a complex network of cause-and-effect relationships known as interdependencies. Understanding these interdependencies was crucial for the success of the multi-objective optimisation approach. Given the specific problem’s characteristics, NSGA-II emerged as the most appropriate algorithm for this research. The sensitivity analysis results highlighted how optimisation approaches impacted interdependency values within these models. Both the NSGA-II (DES) and NSGA-II (RF) models successfully reduced the interdependency value, enhancing the effectiveness of system management and optimisation. The NSGA-II (RF) model, in particular, demonstrated high-speed response, making it well-suited for real-time applications or time-sensitive decision-making scenarios in electric machine manufacturing.
The FEMM Hub has an aim of putting UK Manufacturing at the forefront of the electrification revolution. That electrification revolution is being accelerated by the global drive towards decarbonisation and the replacement of incumbent combustion based technologies for power generation and transportation with electrically powered alternatives. This transformation is the subject of legislation through the 2019 Climate Change Act, which mandates the transition to net zero by 2050 in the UK. In this document and the analysis which underpins it, the FEMM Hub investigators, researchers and industrial partners have aimed to explore what this transition to net zero means for future electrical machines manufacture, and to use this timebound driver as the end point of a roadmap. The transition to net zero creates a set of requirements on the electrical machines industry.
Through the FEMM Hub Roadmap and the analysis which underpins it, the FEMM Hub investigators, researchers and industrial partners have aimed to explore what this transition to net zero means for future electrical machines manufacture, and to use this time-bound driver as the end point of a roadmap. The transition to net zero creates a set of requirements on the electrical machines industry.
NEED 1: Make machines better so they perform better
NEED 2: Make manufacture more efficient
NEED 3: Secure supply of critical materials
NEED 4: Flexibility and scalability to meet demand
While it is clear that there are many uncertainties due to the development of future products, business models, and behavioural responses to the net zero challenge, we can begin to articulate a set of issues around material supply and demand and sustainability, which have been initiated by the hub and which need to be extended through future research.
• Post launch of the hub, a cross cutting theme on circular economy was initiated. It is essential that this focus is maintained and embedded across the programme.
• Identifying sector-based demand for electrical machines is subject to large sources of uncertainty, and therefore attempts to determine likely criticalities in terms of material supply is at least equally difficult. There would be value in instigating a focused activity with a view to providing a flexible / dynamic model material supply and demand based on available assumptions.
• Irrespective of the set of planning assumptions made, it seems inevitable that demand for high performance electrical machines is likely to increase aggressively in the coming years. Future manufacturing needs to be capable of dealing with this growth, and of being flexible and adaptable to the uncertainty in demand.
The FEMM Hub roadmap is built on an assessment of technical drivers for potential machine and manufacturing improvements.
The high level improvement factors are as follows:
- Power and torque density
- High efficiency operation
- High speed operation
- Reliability and robustness
- Sustainable lifecycle
- Cost
This analysis has allowed us to develop a combined future product and future factory model, and to track specific areas of current, planned and required research in a structured manner.
At the 2023 FEMM Hub Conference, Roadmap lead Professor Michael Ward discussed progress and next steps with delegates. Building on the roadmap we feel it is important to maintain focus and attention on some of the key risks on the journey to decarbonisation.
These include:
Materials and supply chain resilience
Jobs and prosperity (national and regional)
Technology leadership
Triple bottom-line for electrical machines
If you would like to be kept updated with the next steps, please get in touch via L.Okeefe@sheffield.ac.uk.
We are building a set of demonstrator machines which will allow us to compare experimentally a benchmark machine with sets of machines using the advanced manufacturing techniques the hub is investigating. With so many industrial partners involved in the hub, selecting the correct machine specification has promoted debate. Several partners would like to use their own specification but have understandable reservations on publishing commercially sensitive details. To overcome this, we have selected the well published USDA FreedomCar 2020 specification as our baseline for comparison. This also gives us the additional benefit of a wider body of research carried out around the FC2020 specification to compare our work to.
The FC2020 specification is for light electric vehicles operating at 30kW continuous and 50kW peak power and speeds of up to 14,000rpm. Efficiency needs to exceed 95% across a wide operating range. The major design points are shown in the table below. As a benchmark for experimental comparison, we are constructing two machines using standard techniques; a distributed winding and a single tooth (concentrated) winding version. We will then build variants of these using new manufacturing techniques and topologies. The stator and rotor are currently being manufactured by Midland Tool & Design. The liquid cooled case and shaft being are being manufactured at Newcastle University.
- EEE TUOS: From nominal core properties to in-service performance
- MEC TUOS: Influence of cut edge damage on mechanical and magnetic properties in electrical machine laminations
- FEMM Hub PHd Projects
- Feasibility calls
Edge damage effect on magnetic permeability of Cobalt iron due to laser cutting
To investigate the effect of heat treatment and laser cutting on the microstructural morphology and chemical composition of the Cobalt iron samples at the cut edge, a set of samples with shear cut edges and laser cut edges were hot mounted in conductive Bakelite. The samples were located to enable the analysis of the cut section. Standard metallography practice, ground and polished using P1200 and P2500 silicon carbide abrasive paper, followed by 6μm, 1μm, and 0.5μm diamond suspensions, was followed to achieve a mirror polish on the regions of interest. Subsequently, the polished samples were swab etched with 6% Nital solution (6% by volume nitric acid of concentration 68%, balance industrial methylated spirits). After etching the images were acquired using bright-field microscopy with a 20x objective and a ZEISS Axiocam 105.
The figure below shows the bulk microstructure of the material in the as-received condition (i.e. after the heat treatment) where grains with a diameter 13-150μm can be observed. The bright strips in the figure are cross section of the material moulded in Bakelite (the black region of the micrograph). The micrograph shows grains as large as 150μm surrounded by smaller grains due to variation of grain growth rate during the production cycles. The grain boundaries are revealed as narrow line in the strips as a result of the etching process. The microstructure of the shear and laser cut edges are shown in Fig. 2. While the applied cutting operations do not significantly alter the microstructural morphology at the vicinity of the cut edge, conventional features including roll over, shear and fracture zones and burr formation are visible in Fig. 2a. The highlighted region of the figure also demonstrates that although the localized shear bands are only visible to depth of about 50 microns, grains as deep as 100μm are affected by the rollover region. Fig. 2b shows that the laser cutting process results in a straight edge with no visible heat affected zone (HAZ), however, given the thermal energy input to the material a very narrow thermally affected zone is expected
that the associated investigations are out of the scope of this paper. Therefore, the effect of post shear cutting heat treatment and laser cutting on the microstructural morphology of the material was found to be negligible.
Fig. 2: Microstructural morphology of the cross section as the cut edge for (a) shear cut and (b) laser cut edges showing no significant alterations due to the cutting processes. significant alterations due to the cutting processes.
The cut edge topography of the samples was also investigated using Scanning Electron Microscope (SEM) micrographs and energy-dispersive X-ray (EDX) analysis was applied to determine the chemical composition of the material at various locations across the surface and cut edge. To measure the chemical composition before and after laser cut, 1cm2 samples with a shear and laser cut edge were produced by cutting with standard scissors. Samples were mounted on a 45° fixture such that the cut edge and top surface were visible. Several Energy Dispersive Spectroscopy (EDS) point spectra were acquired and the range of chemical elements were calculated for each case. Fig. 3 shows the SEM micrographs of the shear (Fig. 3a) and laser (Fig. 3b) cut samples where the relevant SEM imaging parameters are also indicated in the figures. The cut edge morphology for the shear cut sample clearly demonstrates shear and fracture zones with the flat and dimpled regions, respectively. The features on the cut edge of the laser cut sample, Fig. 3b, correspond to the kerfs of the laser cutting process that are spaced approximately 30-35μm apart.
Table 1 and Table 2 list the ranges of elemental compositions at the very surface for shear and laser cut edges, respectively, obtained by the EDX analysis. It was found that, although no HAZ was observed at the cross-section, laser cut samples are marginally depleted from main alloying elements of Fe and Co, probably due to the formation of other compounds on the surface during the laser cutting. The unexpected presence of aluminium may be due to contamination by the insulating panels used in laser cutting.
Table 1 Range of elemental compositions for shear cut edges.
Table 2 Range of elemental compositions for laser cut edges.
To validate the proposed model for the edge damage effect on magnetic permeability in the last annual report, a further 4 test-pieces were cut from the centre of 30mm wide strips of the same batch of Hiperco 50 (both rolling direction and transverse direction samples) and using the same laser cutting condition. These test-pieces were 8mm, 10mm, 12mm and 14mm wide strips which spanned the full length of the 300mm long strips from which they were taken, as illustrated in Fig. 4. The effective quasi-static magnetisation curves of these four rolling direction strips were measured in the single-strip tester and are shown in Fig. 5 alongside the corresponding characteristic for a 30mm wide reference strip from the same batch. In all cases, the B axis corresponds to the effective mean flux density. As will be apparent, there is a marked difference in the effective magnetisation curves of these 4 strips, which is indicative of different relative contributions to the net characteristic from damaged regions. As would be expected, the 14mm wide shows the least degradation in its overall effective magnetisation characteristic from the starting 30mm wide strip.
One-dimensional finite element models of each strip were established in which each strip was divided into 0.1mm wide layers in order to represent the spatial variation in permeability away from the cut edges. The resulting predicted net magnetisation characteristics are shown in Fig. 6 alongside the corresponding measured effective characteristics. As will be apparent, there is good agreement in terms of the predictions and measured behaviour of the strips, in particular that the model captures well the significant degradation introduced by laser cutting from the reference 30mm wide strip that has no cuts present.
It is worth noting that while the original pre-cut characteristic and the predicted characteristic from the edge damage model do not contain a reversible region by virtue of having been fitted using the knee adjustment curve-fit function in Altair Flux, the measured characteristic is the raw measured data which has undergone no such fitting. There is therefore a contribution to the discrepancies observed in Fig. 6 from the comparison of a fitted curve with an actual measured curve with an appreciable reversible region.
Given that the edge damage effect on the electrical conductivity of soft magnetic materials is negligible, and hence the eddy current loss is assumed not being affected by the edge damage. The excess loss component is typically much smaller than the hysteresis loss component, and thus the focus of this section is to investigate the edge damage effect on hysteresis loss variations.
To account for the change in the hysteresis loss density in the regions around the laser cut, a two-term exponential function is employed to represent the normalized hysteresis loss density after laser cut with respect to those before laser cut, as shown in (1).
(1)
Where P_hy (x,B) is the hysteresis loss density distribution over strip width after laser cut at a given distance from the cut edge x and flux density B, while P_hy0 (B) is the average hysteresis loss density before laser cut at a given flux density B. The α, β, γ, and δ are coefficients of the hysteresis loss density distribution function. x is the distance from the cut edge. The a-priori constraints imposed on the hysteresis loss edge damage function in (1) are:
(2)
When x →∞, the distance to the cut edge is infinite, at which there is no edge damage effect, and hence the Khy coefficient should be 1. Therefore, the coefficients β and δ have to be negative. The conditions of Khy (x ,B)>1 and (dK_hy (x,B))/dx<0 ensure an increased hysteresis loss after laser cut while its trend is a monotonic decay with the increase of the distance to the cut edge.
It is interesting to note that there is significant variation in the flux density across the strip widths, based on the model for the edge damage effect on magnetic permeability variations in the last section. By way of example, Fig. 7a shows the predicted variation in flux density across the 30mm wide rolling direction strips at 1T average flux density for 1-slit, 2-slit, 3-slit and 4-slit strips. It can be seen that although the average flux densities for all the four strips are 1T, their flux density distribution are very different due to their different numbers and locations of laser cut slits. It is important to recognise that this flux re-distribution effect is in addition to any changes in the localised loss behaviour when subjected to a specific level of excitation, i.e. edge damage causing a localised change in the core loss model coefficients. When modelling the localised change in the core loss model coefficients, the flux density re-distribution effect due to permeability variations resulting from edge damage should be taken into account, because the hysteresis loss distribution is a function of flux density as illustrated in (1).
The damage introduced into the cut edge of a material when producing the geometry required for rotors and stators can significantly decrease the efficiency and performance of the electrical machine. In this project, a number of edge cutting methods will be analysed to understand the physical influences that drive damage at the cut edge and strive to increase both manufacturing and machine efficiencies.
Over the past year, the influence of remote laser cutting has been investigated. Remote laser cutting is an alternative to traditional gas assisted laser cutting, where a high energy density beam vaporises material, cutting the sheet in several passes. This allows the beam to be driven with galvanometers, significantly increasing the speed of the cut, with a potential market in prototyping and low volume, high value manufacturing. Both the mechanical and magnetic performance were evaluated post laser cut for a 3.2% silicon steel, this investigation has helped guide the hub’s research in Phase 2 and a journal paper is now under review containing the broad result set obtained.
measurements showed increased hardness at the cut edge
The commercially preferred method of generating the complex rotor/stator geometries is by blanking, thanks to the short cycle time and low per part cost. The University of Sheffield recently procured a 500kN capacity eccentric cam press and associated tooling with funding from the Hub, allowing researchers to begin a set of feasibility studies for a number of novel modifications to the blanking process. Previously, research from the Manufacturing and Structural Integrity group at the UoS has linked magnetic performance to strain in blanking using a lab-scale, cross-section blanking tool with in-situ DIC over a variety of parameter sets. Additionally, a damage model has been developed for the same material that is applicable to blanking with the potential for coupling of “magnetic damage” thanks to the ability to calibrate on thin sheet geometries. The new press will facilitate further investigation, ensuring these lab scale investigations are validated for industrial parameter sets. New ultra precise instrumentation has been acquired from Micro-Epsilon to measure in-situ punch displacements with a resolution of four nanometres, at 5kHz, in order to detect the influence of tool defects and wear.
A collaborative project has been jointly funded by a Royal Society Grant and the FEMM Hub with TU Dortmund to investigate the influence of high speed blanking on the cut edge quality was carried out. This study highlighted the difficulty with tooling design for thin sheets, which is amplified by the extreme acceleration in high speed blanking, as difficulties with tooling reliability and damage prevented the investigation of multiple clearances. Nevertheless, it was shown that increasing the energy delivery to the punch did have a small positive effect on edge quality, in comparison with conventional blanking. These results will be presented at the IESSS conference in Aachen and may lead to further collaboration, particularly in the comparison of conventional and high speed blanking using the newly acquired press.
Cut edges were also compared with quantitative surface form and roughness measurements using white light interferometry. This was repeated for 4 sections spaced 90 degrees around a circular sample. This better helps researchers understand if material/punch orientation influences the cut, particularly as the tool wears or acquires defects.
Work has also begun to identify the route cause of magnetic performance loss in mechanical blanking. A novel experimental method has been devised to determine and control the main factor affecting the functional performance of electrical laminations after blanking. Samples with various properties including material, thickness and coating were tested in the Single Sheet Tester to determine the base magnetic properties, then a controlled and uniform plastic deformation was applied in each group and the SST was conducted on each sample to determine the effect of applied processing on the enhancement or reduction of the magnetic loss.
Specific loss measured before and after dimpling for a variety of samples. As expected, all samples showed an increased loss, with a proportionality decreased significance at higher inductions and frequencies.
Current studies have reported the performance of various image augmentation methods on the evaluation performance in classification and detection scenarios. Although the benefits of augmentation techniques are proven, the reasoning behind the choice of a particular augmentation technique remains unclear making it a trial-and-error process. Therefore, understanding the semantics of data augmentation becomes crucial for the ongoing research in this area. This research project focused on addressing this gap in knowledge by proposing a framework for choosing an appropriate augmentation method in various scenarios. This was achieved by investigating pixellevel transformations (blur, noise, grayscale and exposure) in the context of data augmentation to enhance the training performance of Quality Inspection models in scenarios with extremely limited training data. Firstly, the effects of four pixel-level transformations on YOLOv7 and SSD real-time object detectors were analysed by observing the patterns and linking them to either the semantics of each augmentation technique or to the detectors’ architecture. For example, YOLOv7 takes into account the meaning of the object in the image. The augmentation methods such as Blur, Noise and Exposure add or enhance the information while Grayscale deletes a majority of it.
Secondly, the augmentation effect transferability across dissimilar datasets was recorded. Image enhancement techniques showed similar qualitative results regardless of the dataset. Lastly, a framework was proposed for choosing the appropriate augmentation method in various scenarios. It should be noted that there is not one best method but a set of four that vary slightly – Blur, Noise, Exposure, and Grayscale. The criteria for choosing a method were the presence of background objects in the images, classification and detection loss minimisation, meanAP maximisation, and metrics convergence speed. The framework provided is backed by consistent results that show improvement in key metrics in all three datasets. Specifically, for the dataset ‘SpikeGood’ that contained images of electrical machine terminations, up to 35% improvement in meanAP was noticed while a significant reduction in the classification loss from 0.005 to 0.0025 and a reduction in the detection loss was achieved.
Reece’s project is concerned with developing an understanding in several aspects of the design, material selection and manufacturing processes for achieving ultra-high efficiency in MW rated electrical machines for aero-propulsion systems. Although performed largely within the context of MW machines, many of the findings should have sufficient generic value to smaller machines for e-taxi and smaller end of the regional aircraft sector.
Recent work within this PhD involves loss and resistivity testing of high performance soft magnetic materials which are used withing the aerospace sector. The data acquired will later be used in improved loss and performance analysis allowing models to be generated under different operating conditions, more representative of what would be seen during a machines use. Further work in design studies focussing on machine design parameters have taken place and may be the subject of a paper released in the future.
The focal point of Choong’s PhD is placed on high-performance and lightweight electrical machine rotors, using the combination of applicable magnetic materials with advanced carbon fibre composite technologies. The finite element 3D structural modelling aspects of this project have been carried out on a preliminary design concept 1, which was an evolution from a previously developed reference electrical machine. Design concept 1 incorporated a carbon fibre embodiment in the main structure, as well as a unidirectional carbon fibre reinforced polymer as an outer containment solution to accommodate for operational conditions. Design concept 2 is currently under development and is an iteration of design concept 1 with more innovative features to allow for even more lean design, such as the elimination of additional components to further improve power density. The anisotropic properties of carbon fibre composites were taken into account during 3D mechanical finite element modelling in all of the design concepts’ structures. This was carried out by assigning representative coefficients of thermal expansion, orthotropic elasticities, Poisson’s ratios, shear moduli, orthotropic stress limits and so on in the radial, circumferential(hoop) and axial directions. Electromagnetic finite element modelling and design iterations will take place following the mechanical finite element work packages.
John’s PhD involves taking advantage of the design and manufacturing freedoms afforded by the use of additive manufacturing of metals. Novel winding geometries were explored using an algorithmic data driven process, utilising a genetic algorithm and meta-models, coupled with a highly time efficient electromagnetic FEA based simulation model. The aim was to explore the design space and optimise a novel winding structure that could potentially outperform traditionally wound copper and aluminium windings.
Over 25,000 FEA simulations were conducted and around 300,000 algorithmic iterations were performed resulting in 46 concentrated and distributed winding designs. It was found that the resulting novel winding structures were around 6-7% more performant when compared to a default winding design, which represented a traditional wild wound winding configuration. It was also found that winding mass can potentially be optimised and reduced, resulting in less material usage, reduced cost, increased motor compactness and density.
A motorette sub-assembly model of one of the most performant additively manufactured winding designs was constructed from the additively manufactured winding parts. AC and DC tests were performed, and it was found that the RAC/ RDC value deviated by only 9.4% compared to the high precision 3D electromagnetic model of the constructed winding.
In order to achieve both global and national net zero targets, there has been a shift towards electrification for both transportation and energy generation. Whilst the use phase of the PMEMs within these products is generally carbon neutral, the manufacture and end of life is not. Considering the cradle-to-gate stage of a PMEM lifecycle - that is, from inception to assembled product ready for sale – there are many potential changes to be made which could reduce the environmental impact of the machine, increase the sustainability and move the entire lifecycle closer to net zero. Working with two IAB member companies, case studies have been ongoing assessing current and potential cradle-to-gate scenarios, against which, possible changes are analysed. This is used to evaluate the likelihood of reduction in environmental impact of PMEMs. The final analysis of this will present potential sustainability solutions for future PMEM manufacture as the output of this research.
In October 2023, Strathclyde welcomed a new PhD student Prithvi Bhagat, who is co-sponsored by FEMM hub member Protean Electric. The aim of Prithvi’s PhD is to demonstrate and focus on potential alternative methods of manufacture for a wheel mounted electrical machine, with a focus on light weighting opportunities sustainability. Current designs of this machine include a rotor and stator casing which account for approximately 28% of the total machine mass. The beginning of the PhD will look at a full review of a case study machine, with key areas highlighted for which alternative manufacturing methods or material choices could lead to lighter components or opportunities for more sustainable designs. One or two components will be selected for further analysis, with a full method of manufacture down-select activity and Life Cycle Analysis undertaken to systematically select optimal solutions based on key drivers. This PhD is closely linked to the ongoing work in GC X1, and will aim to provide cost effective alternative manufacturing routes for future sustainable electrical machines.
Hao’s PhD project was aimed at exploring the utilization of Fibre Bragg Grating (FBG) sensors in electric machine condition monitoring, with a particular focus on developing effective means of using real-time measured strain/vibration at some critical positions (e.g. endwindings, stator yoke and stator teeth) to indicate machine conditions and identify different machine faults. He is developing multi-physics-based condition monitoring techniques that exploit the capabilities of FBG to precisely measure thermal and mechanical information in a distributed manner throughout machine stator and endwinding. He is currently working on experimental validation of using FBG sensor to indicate machine vibration condition and capture characteristics of both electrical and mechanical faults.
Ji’s PhD focussed on the design and optimization of consequent pole (CP) permanent magnet (PM) machines for electrical vehicles. Based on the previous investigation of symmetrical and asymmetric pole shaping methods to reduce torque ripple, the influences of slot/pole number combinations and armature reaction are studied this year. It is validated that for the CPPM machines with an even slot number for one phase in a submachine, the asymmetric pole shaping method can contribute to lower torque ripple, while for other machines, the symmetrical pole shaping method tends to have lower computational complexity. Besides, it confirms that the armature reaction will lead to variations of fundamentals and harmonics in performances for all the CPPM machines, and CPPM machines suffer from weaker demagnetization withstand capabilities than SPM counterparts.
Dan’s PhD explored the containment process of the magnetic components of electrical machines. Research includes material selection based on material properties, whilst also investigating mechanical stresses of the containment sleeve. This includes a model comparing different interference fits of the sleeve on the rotor and this affects the stresses within the machine. In addition to mechanical stresses, the conductivity behaviour of electrical machines has also been explored with respect to the containment sleeve. This is being researched to reduce the eddy current losses within the machine without any significant loss to structural integrity or performance of the machine. Future focuses include looking into grooved sleeves and the benefits these may have to electrical machine operation.
Ze’s PhD focused on sensor fusion and its role in aiding process monitoring and anomaly detection for industrial processes such as our digitalised linear coil winder demonstrator. This has now been upgraded into the Siemens IoT hardware and software environment to allow us to capture more data at higher speeds and fidelity. Our goal is to investigate how new Deep Neural Network Transformer models can be adapted to this domain from their natural language processing origins. The attention mechanism capabilities of these models allow us to exploit multi sensor systems and learn the correlations and importance of sensor with regards to condition monitoring and remaining useful life (RUL). Our research has developed a number of transformer model architectures that showcase state-of-the-art in performance for a number of condition monitoring tasks through a novel transfer learning approach. This allows us to train a language model for sensor fusion tasks with substantially less data then would otherwise be possible and with a much-reduced need for feature engineering. In addition, we can exploit the attention mechanism to help us better understand how the model performs, for example identify which of the sensors is used most for inference for a particular condition monitoring task.
In November 2023, we awarded 7 Feasibility projects. A short summary of the successful calls can be found below, for more information on these projects please visit our website: https://www. electricalmachineshub.ac.uk/get-involved/third-feasibility-call
Hydrogen-powered aircraft are gaining momentum because they can achieve zero carbon emission in flight. The use of liquid hydrogen as a fuel source means that aircraft can also create a cryogenic environment in which to run the electrical motor propulsion system improving the power density and efficiency. This project aims to investigate use of additive manufacturing of stator windings for cryogenically cooled axial flux motors. The cryogenic test will provide insight into how additively manufactured stator windings and soft magnetic composite cores perform at cryogenic temperatures.
This project will demonstrate the feasibility of using aerosol deposition to manufacture ceramic insulated wire (both bare nickel-coated copper and as a top-coat of ceramic on polymer). Such ceramic insulated wire could either a) significantly increase the operating temperature of machine insulation or b) significantly increase the partial discharge endurance. The project will scale previous tests carried out on flat insulation samples that showed a ceramic layer could be deposited without harming the underlying insulation while delivering a 70x increase in lifetime under partial discharge. The work will examine the feasibility of placing these coatings onto round wire / hairpin samples.
PI: Dr Yongxin Pang
This project will augment the 500°C capable electrical insulation systems developed at Teesside University to achieve harmonic performance in thermal, dielectric, mechanical and manufactural aspects:
- Improving underachieved materials properties via wet chemistry - Enhancing process adaptability to current manufacturing practice
- Extending the technologies to insulate additively manufactured electrical components.
PI:
Dr Yongjing WangIt is projected that globally, there will be 31.6M electric vehicles (EVs) by 2027, up from 6.5M in 2019. The rise will be even more dramatic when countries like the UK mandate a full switch to EVs in the coming decade or so. These developments will, in turn, generate a step change in the quantity of electric motors that will reach the end of service life in their original platform. A solution is needed for the remanufacturing of those electric motors to achieve a sustainable circular economy. Disassembly is the first step in the remanufacturing of a product. The disassembly of end-of-life products usually must be performed by humans due to the difficulties associated with uncertainties in their conditions. To cope with the expected large numbers of electric motors available for remanufacturing, it is necessary to find ways to reduce the manual labour content in their disassembly.
PI: Dr Pedram Asef
We will use high-fidelity models and experiments to investigate the performance of additive manufacturing of Copper and Fe-Si for novel winding and stator/rotor manufacturing solutions operating at high speeds and temperatures. The novel parts will be utilised in an in-wheel double stator switched reluctance machine. The impact of this work will enable manufacturing of customisable electrified components for the aviation sector.
PI: Prof. Soran Birosca
- Demonstrating novel fabrication methods for Electrical Steel (ES) variants via metal 3D printing using in-situ steel lamination, in-situ alloying, and in-situ alloy treatment.
- Establishing the applicability of Electro Pulse techniques to modify and optimise microstructure of ES variants.
- Determining part quality and microstructure from feasibility trials for current ES and high Si ES using ‘standard’ parameters for AM of ES previously reported in the literature and development to novel process adjustments.
PI: Dr Halid Abu-Bakar
To comprehensively assess the opportunities and challenges posed by the Circular Economy (CE) within the Electrical Machines Manufacture sector, ensuring resource efficiency, sustainability, and alignment with global CE benchmarks and the BSI PAS 7770 framework.
Abstract: Electrification is increasing in prevalence due to the importance placed on it for achieving global net zero targets. This has led to the proliferation of electrical mobility, including the wide-scale production of passenger vehicles, personal mobility devices and recent announcements regarding electrically powered aircraft, as well as in energy production. Electrical machines provide a cleaner source of energy during operation in comparison to their traditional fossil-based alternatives. The uncertainty and lack of transparency hanging over these green credentials can be attributed to how these products are manufactured and then disposed of at the end of their life. For them to be a truly sustainable solution, improvements need to be made across their entire life cycle. With the projected increase in their numbers due to the advancement of electrification, this current life cycle is not sustainable, directly opposing the intention of these products. This paper will introduce the current demand and challenges. It will also present these motors broken down into their constituent parts and follow each through their typical lifecycle. This paper presents the typical current life cycle of permanent magnet electrical machines, demonstrating the environmental issues associated with the current linear life cycle, and proposing alternative practices, to ease the environmental burden.
https://doi.org/10.3390/su16072681
Abstract: Within aerospace and automotive manufacturing, the majority of quality assurance is through inspection or tests at various steps during manufacturing and assembly. Such tests do not tend to capture or make use of process data for in-process inspection and certification at the point of manufacture. Inspection of the product during manufacturing can potentially detect defects, thus allowing consistent product quality and reducing scrappage. However, a review of the literature has revealed a lack of any significant research in the area of inspection during the manufacturing of terminations. This work utilises infrared thermal imaging and machine learning techniques for inspection of the enamel removal process on Litz wire, typically used for aerospace and automotive applications. Infrared thermal imaging was utilised to inspect bundles of Litz wire containing those with and without enamel. The temperature profiles of the wires with or without enamel were recorded and then machine learning techniques were utilised for automated inspection of enamel removal. The feasibility of various classifier models for identifying the remaining enamel on a set of enamelled copper wires was evaluated. A comparison of the performance of classifier models in terms of classification accuracy is presented. The best model for enamel classification accuracy was the Gaussian Mixture Model with expectation maximisation; it achieved a training accuracy of 85% and enamel classification accuracy of 100% with the fastest evaluation time of 1.05 s. The support vector classification model achieved both the training and enamel classification accuracy of more than 82%; however, it suffered the drawback of a higher evaluation time of 134 s.
https://doi.org/10.3390/s23083977
ABSTRACT: Consequent pole permanent magnet (CPPM) machines can improve the ratio of average torque to PM volume, but suffer from more serious armature reactions. In this paper, the variations of electromagnetic performance of surface-mounted PM (SPM), conventional CPPM machines, and pole-shaped CPPM machines with armature reaction at currents up to 5 times overload are analyzed and compared. The flux densities, flux linkages, back EMFs, inductances, torque characteristics, and demagnetization withstand capabilities are analyzed by the finite element method (FEM) and frozen permeability method. It is validated that the third order harmonics in inductances for CPPM machines tend to be reduced as current rises since the saturation in iron pole is prone to reducing the saliency effect. But the armature reaction tends to result in the increase of torque ripple components for all the machines. It is also found that the overall torque ripple of asymmetric pole-shaped machine tends to increase significantly under overload conditions. On the contrary, the symmetrical pole-shaped machine can maintain a relatively stable torque ripple under overload conditions which is similar to the SPM counterpart. Additionally, due to the large armature reactions, CPPM machines suffer from weaker demagnetization withstand capabilities and weaker overload capabilities than their SPM counterparts. Four CPPM prototypes with and without pole shaping are tested to confirm the FEM analysis
HTtps://doi.org/10.3390/en16041982
Influence of slot/pole number combinations and pole shaping on electromagnetic performance of permanent magnet machines with unbalanced north and south poles
Abstract:The influences of slot/pole number combinations on electromagnetic performances, including flux linkage, inductance, and torque ripple harmonic components etc., resulting from unbalanced characteristics between north and south poles in concentrated winding permanent magnet (PM) machines with symmetrical and asymmetric rotor pole shaping methods are theoretically analysed and experimentally validated in this paper. It shows that for the PM machines with odd number of coils per phase per submachine, including consequent pole (CP) and surfacemounted PM (SPM) machines, the influences of unbalanced pole characteristics can lead to additional torque ripple harmonics due to additive effects in windings, but can be cancelled in other machines. Compared with symmetrical pole shaping method, asymmetric pole shaping method can result in lower torque ripple for CPPM machines with odd number of coils per phase per submachine, while symmetrical and asymmetric pole shapes have similar effects on torque ripple reduction for other CPPM machines and all the SPM machines. The findings have been validated by finite element analyses on 12-slot/8-pole, 12-slot/10-pole, 9-slot/6-pole, and 12-slot/14-pole machines, and by experiments with 12-slot/8-pole and 12-slot/10-pole CPPM prototypes.
https://doi.org/10.1049/elp2.12293
Abstract: To enable use of additively manufactured (AM) soft magnetic material in electric machines, large bulk cross-sections must be avoided as they allow large eddy currents, reducing efficiency. Fe6.5 wt%Si is an excellent soft magnetic material, but is brittle. In this study we exploit this inherent characteristic of the material to develop crack networks within the AM material to inhibit parasitic eddy currents. By manipulating the laser parameters and scan strategy to purposefully induce cracking, the effective resistivity of the material can be increased to 206 µΩ·cm, 250% of the materials’ already high resistivity of 82 µΩ·cm. Crack density is shown to increase with decreasing scan speed, and calculated electrical tortuosity shown to correlate with effective resistivity. Different scan strategies are shown to alter the orientation of the cracks, demonstrating that the crack orientation could be controlled in relation to the magnetic flux, providing high electrical resistance in the plane of the eddy currents, whilst maintaining magnetic properties. This method yields losses of 2.2 W/kg at 1 T, 50 Hz, similar to methods using air gaps, but with a much higher stacking factor of > 97%, outperforming other methods used in AM of soft magnetic material, showing promise for manufacturing stators of complex electric machines.
https://doi.org/10.1016/j.addma.2023.103555
Abstract: Additive manufacturing has enabled the processing of high silicon electrical steels which have excellent soft magnetic properties. In bulk form, core losses as a result of eddy currents would be too large to allow their use in high-frequency electrical machines, therefore strategies are needed to reduce eddy currents. Additive manufacturing affords high part complexity and provides the opportunity for cross sectional patterns within the material to limit eddy current generation. This study investigates several designs, including a novel hexagonal pattern which is shown to have the lowest eddy current loss coefficient of 0.0005, less than 25% of the bulk material which has an eddy current loss coefficient of 0.0021. Heat treatment is shown to increase the eddy current losses, demonstrating that for high-frequency machines, it may be beneficial to use the material in the as-built state. Physical samples were compared to their intended geometries, showing there are defects in these complex cross sections causing increased eddy currents when compared to simulations, but that geometrical accuracy can be improved by alternative design methodology which experimentally experiences smaller losses. These novel cross sectional designs may be implemented into an electric machine that has a 3D magnetic flux pathway enabled by additive manufacturing, affording more flexibility for electrical engineers to design new motor architectures in the pursuit of higher power density machines.
https://doi.org/10.1016/j.matdes.2023.112002
A model to account for magnetic permeability changes resulting from edge damage caused by laser cutting in a high performance cobalt-iron alloy
Abstract: Laser cutting is the mainstay of electrical machine stator core manufacture for prototyping and for high value, small and medium batch sizes. However, it can introduce localized damage into electrical steels, with reduction in magnetic permeability and increase in core loss in regions adjacent to the edge. These phenomena have been studied in Silicon-iron alloys, but there is little published data on Cobalt-iron. This paper presents experimental measurements on magnetic edge damage effect in Cobalt-iron alloys due to laser cutting. The paper then uses magnetic measurements for an increasing number of cuts in test samples to develop a model that represents the deterioration of magnetic permeability with distance from the cut edge, including cumulative damage effects from multiple cuts. The model is suitable for incorporation into finite-element models, either as a continuous function of position or to generate individual magnetization curves for discrete layers in finite-element mesh. The paper concludes by using the model to generate a series of magnetization curves which include the damage effect and in turn uses these to predict the net magnetic behavior of a series of rectangular strips. Good agreement is obtained between these predictions and measurements of samples from the same batch of Cobalt-iron.
https://doi.org/10.1016/j.jmmm.2023.171081
ABSTRACT: The electrification and hybridization of ground- and air-transport, in pursuit of Carbon Net Zero targets, is driving demand for high power-density electrical machines. The powerdensity and reliability of electrical machines is ultimately limited by their ability to dissipate internally generated losses within the temperature constraints of the electrical insulation system. As the electrical windings are typically the dominant source of loss, their enhanced design is in the critical path to improvements in power-density. Application of metal additive manufacturing has the potential to disrupt conventional winding design by removing restrictions on conductor profiles, topologies and embedded thermal management. In this paper, a modular endwinding heat exchanger concept is presented, which enables effective direct cooling without occupying valuable stator slot cross-section. In addition, this arrangement eliminates the need for a good stator-winding thermal interface, thereby allowing mechanical or other less permanent winding retention methods to be used, facilitating non-destructive disassembly and repair. A prototype winding is fabricated and experimentally tested to demonstrate the feasibility of the concept, yielding promising results.
https://doi.org/10.1109/TIA.2022.3209171
AbSTRACT: In this paper, a general analytical model is developed to analyze the cogging torque accounting for unequal north and south poles as well as pole shifting, which can be applied to consequent pole permanent magnet (CPPM) machines and other rotor PM machines. The optimal slot opening and optimal pole-arc to pole-pitch ratio with/without pole shifting for minimum cogging torque are then analytically derived and verified by finite element analyses and experiments. It shows that in contrast to conventional PM machines with equal north and south poles, of which the fundamental cogging torque order is the least common multiple (LCM) between slot number Ns and pole number 2 p , the fundamental cogging torque order for the PM machines with unequal north and south poles (as often the case in CPPM machines), is the LCM between Ns and p , which has been derived analytically. However, in the special case when the slot number in one submachine is even, the LCM between Ns and 2 p has the same value as the LCM between Ns and p.
https://doi.org/10.1109/TEC.2022.3221917
AbSTRACT: In this paper, a general analytical model is developed to analyze the cogging torque accounting for unequal north and south poles as well as pole shifting, which can be applied to consequent pole permanent magnet (CPPM) machines and other rotor PM machines. The optimal slot opening and optimal pole-arc to pole-pitch ratio with/without pole shifting for minimum cogging torque are then analytically derived and verified by finite element analyses and experiments. It shows that in contrast to conventional PM machines with equal north and south poles, of which the fundamental cogging torque order is the least common multiple (LCM) between slot number Ns and pole number 2 p , the fundamental cogging torque order for the PM machines with unequal north and south poles (as often the case in CPPM machines), is the LCM between Ns and p , which has been derived analytically. However, in the special case when the slot number in one submachine is even, the LCM between Ns and 2 p has the same value as the LCM between Ns and p.
https://doi.org/10.1080/17477778.2023.2202338
A full list of our publications can be found on our website https://www.electricalmachineshub.ac.uk/outputs/publications
Okorie, O., Charnley, F., Ehiagwina, A. , Tiwari, D., Salonitis,K. Towards a simulation-based understanding of smart remanufacturing operations: a comparative analysis. Jnl Remanufactur (2020). https://doi.org/10.1007/s13243-02000086-8
S. Khan, M. Farnsworth, R. McWilliam, J. Erkoyuncu. (2020). On the requirements of digital twin-driven autonomous maintenance. Annual Reviews In Control. 50, 13-28. https://doi.org/10.1016/j.arcontrol.2020.08.003
Prajapat, N., Turner, C., Tiwari, A., Tiwari D. et al. Real-time discrete event simulation: a framework for an intelligent expert system approach utilising decision trees. The International Journal of Advanced Manufacturing Technology, 110, 2893–2911 (2020). https://doi.org/10.1007/s00170-020-06048-5
Oyekan, J., Hutabarat, W., Turner, C., Arnoult, C. and Tiwari, A. (2020). Using Therbligs to embed intelligence in workpieces for digital assistive assembly. Journal of Ambient Intelligence and Humanized Computing, Springer, vol. 11, 2489–2503, ISSN: 1868-5137
Oyekan, J., Fischer, A., Hutabarat, W., Turner, C. and Tiwari, A. (2019). Utilising low cost RGB-D cameras to track the real time progress of a manual assembly sequence. Assembly Automation, Emerald, ISSN: 0144-5154, vol. 40, no. 6, 925-939.
Tiwari D, Farnsworth M, Zhang Z, Jewell GW, Tiwari A. In-process monitoring in electrical machine manufacturing: A review of state of the art and future directions. Proceedings of the Institution of Mechanical Engineers, Part B: Journal of Engineering Manufacture. May 2021. doi:10.1177/09544054211016675
Tiwari, D.; Miscandlon, J.; Tiwari, A.; Jewell, G.W. A Review of Circular Economy Research for Electric Motors and the Role of Industry 4.0 Technologies. Sustainability 2021, 13, 9668. https://doi.org/10.3390/su13179668
Izhar Oswaldo Escudero-Ornelas, Divya Tiwari, Michael Farnsworth, Ashutosh Tiwari, 'Modelling Interdependencies in an Electrical Motor Manufacturing Process Involving Deformable Material', Advances in Manufacturing Technology XXXIV, Vol.15, pp. 291 - 298. DOI: 10.3233/ATDE210051
R. Wrobel, R.J. MGlen, 'Heat pipes in thermal management of electrical machines – A review', Thermal Science and Engineering Progress, Volume 26, 2021, 101053,ISSN 2451-9049,DOI: 10.1016/j.tsep.2021.101053.
J. Oyekan, Y. Chen, C. Turner, A. Tiwari, 'Applying a fusion of wearable sensors and a cognitive inspired architecture to real-time ergonomics analysis of manual assembly tasks',Journal of Manufacturing Systems, Volume 61, 2021, Pages 391-405,ISSN 0278-6125,https://doi.org/10.1016/j.jmsy.2021.09.015.
Farnsworth, M., Tiwari, D., Zhang, Z. et al. Augmented classification for electrical coil winding defects. Int J Adv Manuf Technol 119, 6949–6965 (2022). https://doi.org/10.1007/s00170-022-08671-w
Clift L, Tiwari D, Scraggs C, Hutabarat W, Tinkler L, Aitken JM, Tiwari A. Implementation of a Flexible and Lightweight Depth-Based Visual Servoing Solution for Feature Detection and Tracing of Large, Spatially-Varying Manufacturing Workpieces. Robotics. 2022; 11(1):25. https://doi.org/10.3390/robotics11010025
R. Wrobel, 'Thermal Science and Engineering Progress, A technology overview of thermal management of integrated motor drives - Electrical Machines', Thermal Science and Engineering Progress, Volume 29, 2022, 101222, ISSN 24519049, https://doi.org/10.1016/j.tsep.2022.101222.
J. Qi et al., "Effect of Pole Shaping on Torque Characteristics of Consequent Pole PM Machines," in IEEE Transactions on Industry Applications, doi: 10.1109/TIA.2022.3156904.
J Qi, ZQ Zhu, L Yan, GW Jewell, C Gan, Y Ren, S Brockway, C Hilton, "Suppression of Torque Ripple for Consequent Pole PM Machine by Asymmetric Pole Shaping Method," in IEEE Transactions on Industry Applications, vol. 58, no. 3, pp. 3545-3557, May-June 2022, doi: 10.1109/TIA.2022.3159629.
D. Miller, B. Song, M. Farnsworth, D.Tiwari, F. Freeman, I. Todd, A. Tiwari, 'IoT and Machine learning for in-situ process control using Laser Based Additive Manufacturing (LBAM) case study', Procedia CIRP,Volume 104, 2021, Pages 1813-1818, ISSN 2212-8271, https://doi. org/10.1016/j.procir.2021.11.306.
Clift L, Tiwari D, Scraggs C, Hutabarat W, Tinkler L, Aitken JM, Tiwari A. Implementation of a Flexible and Lightweight Depth-Based Visual Servoing Solution for Feature Detection and Tracing of Large, Spatially-Varying Manufacturing Workpieces. Robotics. 2022; 11(1):25. https://doi.org/10.3390/robotics11010025
Igiri Onaji, Divya Tiwari, Payam Soulatiantork, Boyang Song & Ashutosh Tiwari (2022) Digital twin in manufacturing: conceptual framework and case studies, International Journal of Computer Integrated Manufacturing, DOI: 10.1080/0951192X.2022.2027014
J. Oyekan, Y. Chen, C. Turner, A. Tiwari,, 'Applying a fusion of wearable sensors and a cognitive inspired architecture to real-time ergonomics analysis of manual assembly tasks', Journal of Manufacturing Systems, Volume 61, 2021, Pages 391-405, ISSN 0278-6125, https://doi. org/10.1016/j.jmsy.2021.09.015.
Oyekan J, Farnsworth M, Hutabarat W, Miller D, Tiwari A. Applying a 6 DoF Robotic Arm and Digital Twin to Automate Fan-Blade Reconditioning for Aerospace Maintenance, Repair, and Overhaul. Sensors. 2020; 20(16):4637. https://doi.org/10.3390/s20164637
Prajapat, N., Turner, C., Tiwari, A. et al. Real-time discrete event simulation: a framework for an intelligent expert system approach utilising decision trees. Int J Adv Manuf Technol 110, 2893–2911 (2020). https://doi.org/10.1007/s00170-020-06048-5
M. Zhou, Z. Li, H. Assadi, I. Chang, C. Barbatti,'An accelerated three-dimensional coupled electromagnetic-mechanical model for electromagnetic pulse forming', Journal of Manufacturing Processes, Volume 72, 2021,Pages 240-251,ISSN 1526-6125,https://doi. org/10.1016/j.jmapro.2021.10.007.
Rafal Wrobel, David Reay, ‘Heat pipe based thermal management of electrical machines – A feasibility study’, Thermal Science and Engineering Progress, Volume 33, 2022,101366, ISSN 2451-9049, https://doi.org/10.1016/j.tsep.2022.101366.
Ward, Michael James and Miscandlon, Jill and Salamati, Mohammad and Butler, David and Uflewska, Olga and Fehring, Feline, A Wicked and Complex Problem Framework Applied to Engineering Research Effectiveness in Resource Efficiency and Decarbonisation. Available at SSRN: https://ssrn.com/abstract=4151603 or http://dx.doi.org/10.2139/ssrn.4151603
Jill Miscandlon, Abbas Kazemi-Amiri, Stephen J. Forrest, Xiao Chen, Daniel Harper, Alasdair McDonald, Geraint W. Jewell, "A manufacturing driven design methodology to lightweighting of the structural elements of a permanent magnet electrical machine rotor," in IEEE Access, 2022, doi: 10.1109/ACCESS.2022.3214305.
Ze Zhang , Michael Farnsworth , Boyang Song , Divya Tiwari , and Ashutosh Tiwari, 'Deep Transfer Learning With Self-Attention for Industry Sensor Fusion Tasks', IEEE SENSORS JOURNAL, VOL. 22, NO. 15, 1 AUGUST 2022
N. Simpson, G. Yiannakou, H. Felton, J. Robinson, A. Arjunan and P. H. Mellor, "Direct Thermal Management of Windings Enabled by Additive Manufacturing," in IEEE Transactions on Industry Applications, vol. 59, no. 2, pp. 1319-1327, March-April 2023, doi: 10.1109/ TIA.2022.3209171.
Zhu, Z.Q.; Liang, D. Perspective of Thermal Analysis and Management for Permanent Magnet Machines, with Particular Reference to Hotspot Temperatures. Energies 2022, 15, 8189. https://doi.org/10.3390/en15218189
Since 2020, each of our FEMM Hub project teams meet monthly. During these online hour long meetings, researchers give presentations detailing that months progress before spending time discussing next steps and gaining valuable advice from others on the call. These meetings are open to any member of staff belonging to our hub partners. There is no obligaton to attend these regularly, we welcome any opportunity to share our research progress.
If you would like to find out more about joining our meetings, please contact FEMM Hub Administrator Lindsey FarnsworthL.Farnsworth@sheffield.ac.uk.
1.1: Realising novel machine design freedoms from innovative manufacture.
1.3. Manufacturing of light-weight and multi-functional structural components.
1.4. Manufacturing the novel and non-standard materials
2.2: Manufacturing high performance coils and ultimate control.
2.3: Manufacturing technologies for flexibility and customisation.
X1: Sustainable manufacturing of electrical components for the circular economy.
X2: In-process tracking and tractability for zero-defect manufacture of electrical machines.
X3: Roadmapping and technology reviews
X4: Demonstrator
In addition to our monthly online meetings for each of our research projects, we meet collectively every quarter for a two-day research meeting. Each of our projects present a detailed update on their progress which is discussed as a group; we also undertake an element of training at each meeting.
On the 11th and 12th of July 2023, researchers from the FEMM Hub travelled to the Technology and Innovation Centre (TIC) at Strathclyde University to discuss the latest outcomes of their research with their peers. Each project was given the opportunity to present to the group, seek feedback and ask questions.
On the morning of day 2, academic members of the FEMM Hub visited one of their partners Tannlin at their site in Prestwich, Glasgow. The Tannlin Group supplies customers in aerospace, medical, defence, electronic and automotive industries; where Tannlin Technology designs and manufactures laser cutting systems, laser cut parts and is the home of the research and development group; and Tannlin UK designs and manufactures laser cut stencils and PCBA tooling. They have sites worldwide to allow them to work closely with their customers in 28 countries that they export to.
On the 11th and 12th of October, researchers from each of our hub partners joined together in Sheffield for the latest FEMM Hub Quarterly Research Meeting. The location of the meeting was AMRC Knowledge Transfer Centre, where we kicked off with a tour of AMRC’s impressive Factory of the Future and the Composites Centre.
Hub Director Professor Geraint Jewell then gave an update on overall FEMM Hub progress before we heard presentations from each of the FEMM Hub PhD’s. Following these presentations, the group undertook
“Self-awareness training” led by FEMM Hub Manager Dr Laura O’Keefe. In this training, the group touched upon ideas of their physical; emotional; and psychological self. By becoming more self aware, it has been found that our communication with others becomes more effective and we make more thoughtful and strategic decisions. The sessions included several exercises to idenfity their learning and communication styles which the team found useful.
Day 2 was hosted in the Mappin Building on the main University of Sheffield Campus. Dr Xiao Chen and Dr Jason Ede kicked off the day updating the group on their projects from nominal core properties to in-service performance and ended with Dr Hassan Ghadbeigi informing the group on Cut edge characterisation in advanced electrical alloy.
On the 28th and 29th February, we joined together at The University of Newcastle. Hub Director Professor Geraint Jewell welcomed the team gave an update on hub matters. He then passed over to Dr Glynn Atkinson to update on ‘Realising novel machine design freedoms from innovative manufacture’ . The team then heard updates from Steve Forrest from University of Sheffield on ‘Manufacturing high performance coils and ultimate control’ and Dr Alexei Winter from AMRC, University of Sheffield on ‘Manufacturing technologies for flexibility and customisation’. Following lunch, the team discussed the FEMM Hub Policy Paper led by Professor Michael Ward.
Day 2 began with a presentation from Dr Divya Tiwali and Dr Michael Farnsworth from The University of Sheffield on ‘In-process tracking and tractability for zero-defect manufacture of electrical machines’. Final presentations were given from Dr Xiao Chen on ‘From nominal core properties to in-service performance’; Dr Nick Simpson and Dr Anna Ermakova on ‘Additive Manufacturing of High Performance Electrical Machine’ and Luke Jones on ‘Cut edge characterisation in advanced electrical alloy’ before a final word from our Hub Director.
Our team have had a busy year!
VIsit our news page to keep upto-date through out the year
www.electricalmachineshub. ac.uk/news
British Science Week is a ten-day celebration of science, technology, engineering and maths which takes place between the 8th and 17th of March 2024. On Monday the 11th of March, 5 of the FEMM Hub team travelled to Charnock Hall Academy in Sheffield to deliver an interactive session.
Kicking off the event, FEMM Hub Director Professor Geraint Jewell delivered a presentation on “What is an engineer?” before the Hub Manager Dr Laura O’Keefe, Dr Lloyd Tinkler (Project lead - Manufacturing technologies for flexibility and customisation), Wei Liang Choong and Reece Eblet (FEMM Hub PhD students) delivered motor workshops to 120 pupils in Year 4 and Year 6. At the end of each workshop pupils had the opportunity to “Ask an Engineer” which proved very popular.
We’re excited to share two FEMM Hub videos that were filmed in March 2024. This promotional material will be suitable for both public and expert audiences to increase our role as an advocate for the case for high-value manufacturing and remanufacturing in the UK.
The first video is focusing on our research in X2, the use of advanced vision systems which featured Dr Divya Tiwari, Dr Michael Farnsworth and PhD student Ioan-Alexandru Herdea. The second looking at the research in project X1, circular economy of electrical machines led by Dr Jill Miscandlon and featured Professor Michael Ward.
Both of these will be live on the FEMM Hub website shortly!
On the 29th and 30th of November, FEMM Hub members Dr Lloyd Tinkler and Gianmarco Pisanelli travelled to Regensburg, Germany to attend the 13th International Electric Drives Production Conference (E|DPC). The conference attracted over 200 attendees from 16 different nations to share knowledge and insights in the field of electric drives production.
Gianmarco Pisanelli (top right) presenting his research titled “Flexible Manufacturing of High-value Low-volume Electrical Machines through Robotic Coil Winding” during the first session on Winding Technologies. Dr Lloyd Tinkler (bottom right) presented during the Soft Magnetic Materials session on day 2. His presentation titled “Manufacturing Processes for 2.5D Laminated Stacks” received great feedback and proved a great topic of discussion over the lunch break that immediately followed.
On the 28th of November, the FEMM Hub held its annual conference at IET’s Austin Court in Birmingham which was attended by 88 delegates. After an introductory presentation from Hub Director, Professor Geraint Jewell, conference delegates were delighted to hear from Prof. Dr.Ing. Jürgen Fleischer the Director of Machines, Equipment and Process Automation at Karlsruhe Institute of Technology in Germany. His keynote titled “Facing the Challenges in Electric Motor Production” covered Challenges and Trends in Development and Manufacturing; Flexible and Scalable Manufacturing Processes and Sustainability in Electric Motor Production.
Following the keynote, Dr Xiao Chen, Senior Lecturer at The University of Sheffield kicked off the first session of the conference on Electrical Machines Manufacture featuring presentations from Liz Scoffins from the Manufacturing Technology Centre and Lloyd Tinkler and Alexei Winter from AMRC.
The poster session followed which featured a poster from each of the FEMM Hub Projects as well as our PhD Students before we broke for lunch. Providing ample time for networking.
Professor Michael Ward opened the afternoon session with a presentation on the current progress of the FEMM Hub Roadmap and the planned next steps. The presentation provoked some interesting questions from the audience and we look forward to getting input from conference delegates in the upcoming months as the roadmap is developed.
Dr Jill Miscandlon welcomed presenters during her session on the Sustainable Manufacture of Electrical Machines. Both presenters, Wiktor Dotter from ZeBeyond and Stuart Bradley - Principal Engineer, WMG gave interesting perspectives on this topic.
The FEMM Hub recently closed its 3rd Feasibility Call and hub Director Professor Geraint Jewell was delighted to announce the successful applicants before the final session of the day on Emerging
Technologies. Dr Michael Farnsworth chaired the session which featured presentations from Alex Goodall - Materials Engineer, University of Edinburgh; Vicente Climente-Alarcon -Cryogenic Electrical Machines Engineer, GKN Aerospace before the final speaker of the day Lindsay Lee - Technical Fellow for Data Science, AMRC who presented on data-centric manufacturing.
If you have any questions about the FEMM Hub Conference please get in touch with FEMM Hub Manager Dr Laura O’Keefe - L.OKeefe@sheffield.ac.uk
The 2024 FEMM Hub Conference will take place on the 20th of November. If you would like to attend, please contact our Administrator Lindsey: l.farnsworth@sheffield.ac.uk
On the 7th of November, the FEMM Hub team travelled to Millenium Point in Birmingham to take part in the KTN 2023 Engage with...LIVE event. This in-person-only event brought together the Power Electronic, Machines and Drives (PEMD) community. The event was opened with a keynote from Dave Smith, the UK’s National Technology Adviser before presentations highlighting funding opportunities and career opportunities in electrification. A networking lunch allowed all participants a chance to visit the exhibition space and the FEMM Hub team enjoyed meeting with delegates.
On the 23rd and 24th of October members of the FEMM Hub travelled to Brussels to attend PEMD, an international conference on Power Electronics, Machines and Drives.
The two-day event kicked off with a Keynote speech by Dr.Ing Sigurd Øvrebø, Managing Director RollsRoyce Electrical Norway titled “From air to water and back again - 25 years of power electronics in different applications”. FEMM Hub Members Dr Lloyd Tinkler and Dr Alexei Winter both presented posters at the event, in addition to speaking to delegates on the AMRC stand.
Information about PEMD 2024 can be found by visiting: https://pemd.theiet. org/pemd-2024/
FEMM Hub Deputy Director has been honoured with one of the most prestigious awards in engineering. Professor Ash Tiwari has been elected to the Royal Academy of Engineering’s Fellowship in recognition of his outstanding contribution to engineering.
The Academy is one of the world’s leading engineering institutions. It brings together some of the best engineering researchers, innovators, entrepreneurs, business and industry leaders through its Fellowship, which elects new Fellows each year by peerreview in recognition of their outstanding and continuing contributions to the profession.
Professor Koen Lamberts, President and ViceChancellor of the University of Sheffield, said:
“ Engineering has always been a significant part of the University of Sheffield’s identity, and our academics are known around the world for their engineering research and expertise. I am delighted that the Academy has recognised the outstanding dedication, hard work and skills of our engineers, and the positive impact their research has on society.”
Professor Ashutosh Tiwari is internationally renowned for research in digital manufacturing and works in partnership with industry to develop new techniques and solutions for digitalisation, instrumentation, in-process monitoring and realtime simulation of skill-intensive manufacturing processes, such as wing manufacture and engine assembly. He holds a Royal Academy of Engineering / Airbus Research Chair in Digital Manufacturing, and has a strong track record of leading research and innovation projects across technology readiness levels. He serves on the Engineering and Physical Sciences Research Council (EPSRC) Strategic Advisory Team for Manufacturing and Circular Economy, is Deputy Director of the EPSRC Future Electrical Machines Manufacturing Hub, and Sheffield Lead of the Made Smarter Research Centre for Connected Factories. He is passionate about training people for manufacturing research.
IEEE International Conference on Industrial Informatics (INDIN 2023) hosted by Institute industrial IT of Technische Hochschule OstwestfalenLippe and Fraunhofer IOSB-INA took place in Germany from 17th - 20th July 2023. PhD student Mr Izhar Oswaldo presented his research work at the conference. His presentation titled ‘Hybrid Computational Framework for Early Fault Detection in Coil Winding Manufacturing Process Using Knowledge Distillation’ discussed the utilisation of the knowledge distillation approach to improve the performance of the discrete event simulation model for early detection of faults in the coil winding process during the manufacture of electrical machines. To achieve this, a hybrid model was developed using supervised machine learning algorithms that could maintain model accuracy while reducing simulation time. This work was co-authored by Divya Tiwari, Michael Farnsworth and Ashutosh Tiwari.
On the 21st of June 2023, the FEMM Hub was invited to present at the University of Sheffield’s Engineering research symposium.
On the 25th of May, Dr Glynn Atkinson travelled from Newcastle University to Helsingborg, Sweden to attend a Sustainability Day conference hosted by Alvier Mechatronics at their new sea front offices. Alvier Mechatronics, a FEMM hub partner and long time research partner with the Newcastle University Electrical Power Group, is a Höganäs-affiliated company, which develops electrical drive solutions to the automotive industry.
On the 27th of February, Dr Nick Simpson, Lead of The Electrical Machine Works, Associate Professor in Advanced Electrical Machine Design and Manufacture, UKRI Future Leaders Fellow travelled to the UK Atomic Energy Authority to discuss the potential for metal additive manufacturing of coils in the fusion sector. The unparalleled geometric freedom of metal Additive Manufacturing (AM) allows complex electromagnetic coils to be realised featuring targeted AC loss mitigation through spatially varying conductor shape and topology, embedded thermal management such as liquid cooling channels or extended surfaces, novel electrical insulation coatings, and value-add features such as integrated terminals and sensors. This talk will present the state-of-art in digital design, manufacture and test of such windings including the post-processing challenges in realising low surface roughness and robust electrical insulation, with a view to identifying opportunities for AM of active electrical components in your sector.
Our training sessions are available exclusively to our hub partners.
If you would like to be added to our mailing list - get in touch!
Wednesday 19th of July 2023
1-4pm
ABStract
This training course, led by Professor Geraint Jewell, started by providing an engineering focussed introduction to both hard and soft magnetic materials covering magnetic, electrical and mechanical properties. The course then described the numerous practical, design and manufacturing aspects of deploying magnetic materials in electrical machines. The interaction between magnetic properties and machine performance was explored through several design studies.
Professor Geraint Jewell is a graduate of the University of Sheffield (BEng 1988, PhD 1992) and has been a member of the academic staff since 1994. He served as Engineering’s first Faculty Director of Research and Innovation from 2008-2011 and as Head of the Department of Electronic and Electrical Engineering from 2013 to 2019. He served as Interim Head of the Advanced Manufacturing Group from 2022 and became Vice-President and Head of the Advanced Manufacturing Group in June 2023.
During his time on the academic staff, he held an EPSRC Advanced Research Fellowship (2000-2005) and a Royal Society Industry Fellowship at Rolls-Royce (2006-2008). He has been Director of the Rolls-Royce University Technology Centre in Advanced Electrical Machines since 2006 and Director of the EPSRC Future Electrical Machines Manufacturing Hub since 2019.
TUESDAY 20TH OF FEBRUARY 2024
1 - 3pm
Abstract
Electrical machines are widely used in conjunction with power converters which use high frequency witching devices to modulate machine terminal voltages in order to control the machine speed or torque. The high frequency switching produced by the power converter can cause high frequency parasitic currents flowing through the machine bearings, leading to deterioration of the lubrication film and surface damage to the rolling parts of the bearings. The training session explained the high frequency bearing current mechanism, review of bearing current modelling approaches, review of bearing current mitigation techniques, and our research activities on bearing currents.
Dr Xiao Chen joined University of Sheffield as a lecturer in 2019 and he is currently a senior lecturer in electrical machines. He is leading an EPSRC funded project on bearing currents and associated high frequency effects in permanent magnet machines, and also leading other projects on digital twins of electrical machines and Litz wire AC losses for electrical machines.
Daniele De Gaetano joined the University of Sheffield within the department of Electronic and Electrical Engineering in 2022 as a research associate. Currently, he is a research engineer within the University of Sheffield Advanced Manufacturing Research Centre (AMRC). His research interests include bearing currents, electrical machine high frequency analysis, multiphase electrical machines, high speed electrical machines for aerospace propulsion.
To find out more about our upcoming sessions, please visit: www.electricalmachineshub.ac.uk/femm-hub-training-sessions
https://www.linkedin.com/company/epsrc-future-electricalmachines-manufacturing-hub https://www.facebook.com/FEMMhub/
@FEMMhub