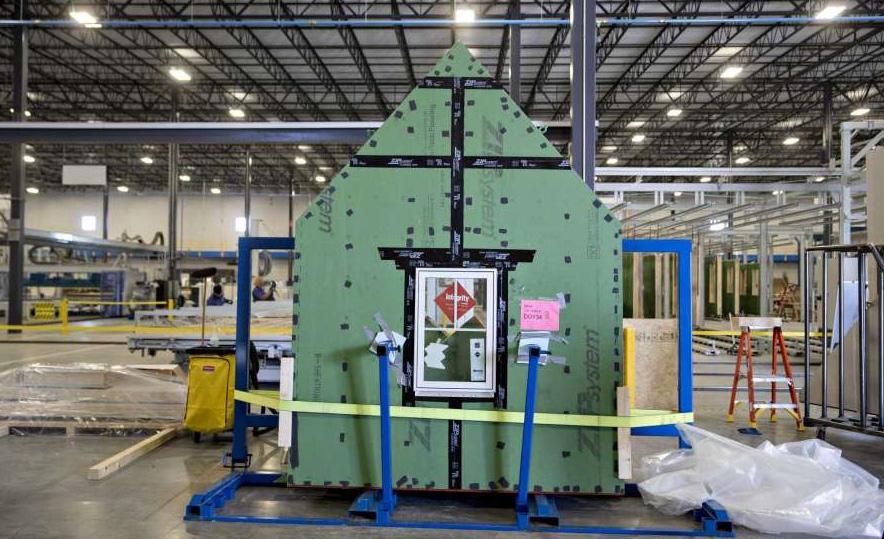
3 minute read
Construction Efficiencies
from 2020 US Department of Energy Solar Decathlon, 2nd Place, Mixed-Use Multifamily Division: HILLDING
AFFORDABILITY + FEASIBILITY
Construction in Philadelphia is typically a poorly coordinated process with frequent changes needing to be made in the field, often delaying the construction schedule and inevitably costing more. Our approach seeks to
Advertisement
address this in two ways: 1.The use of prefabricated assemblies 2.Embedded system coordination.
The use of panelized prefabricated elements dramatically cuts back material waste and completely reframes the construction schedule, fully assembling a mid-size house in as little as 5 weeks. Figure 45 - BluePrint Robotics Zip Assemblies
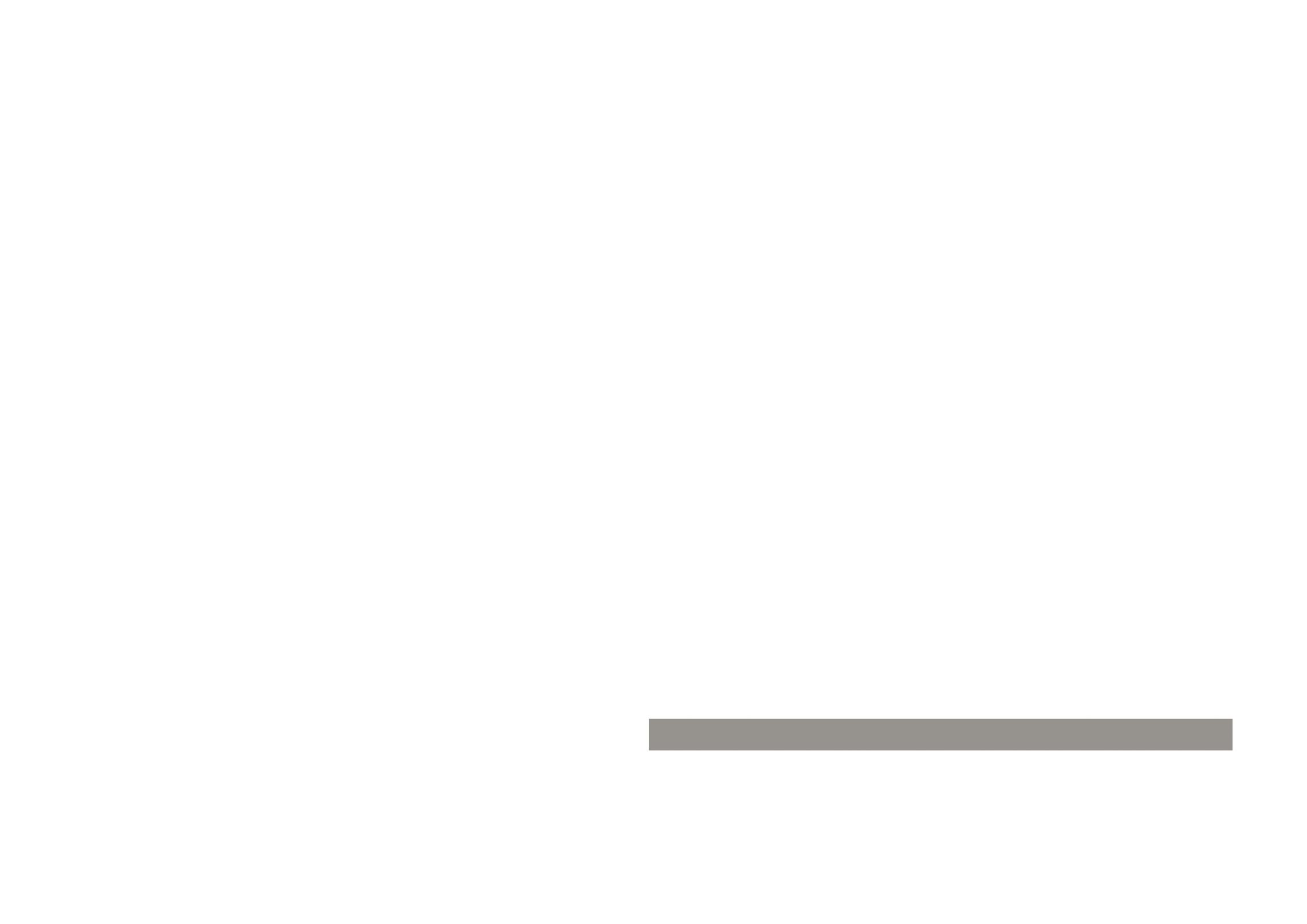
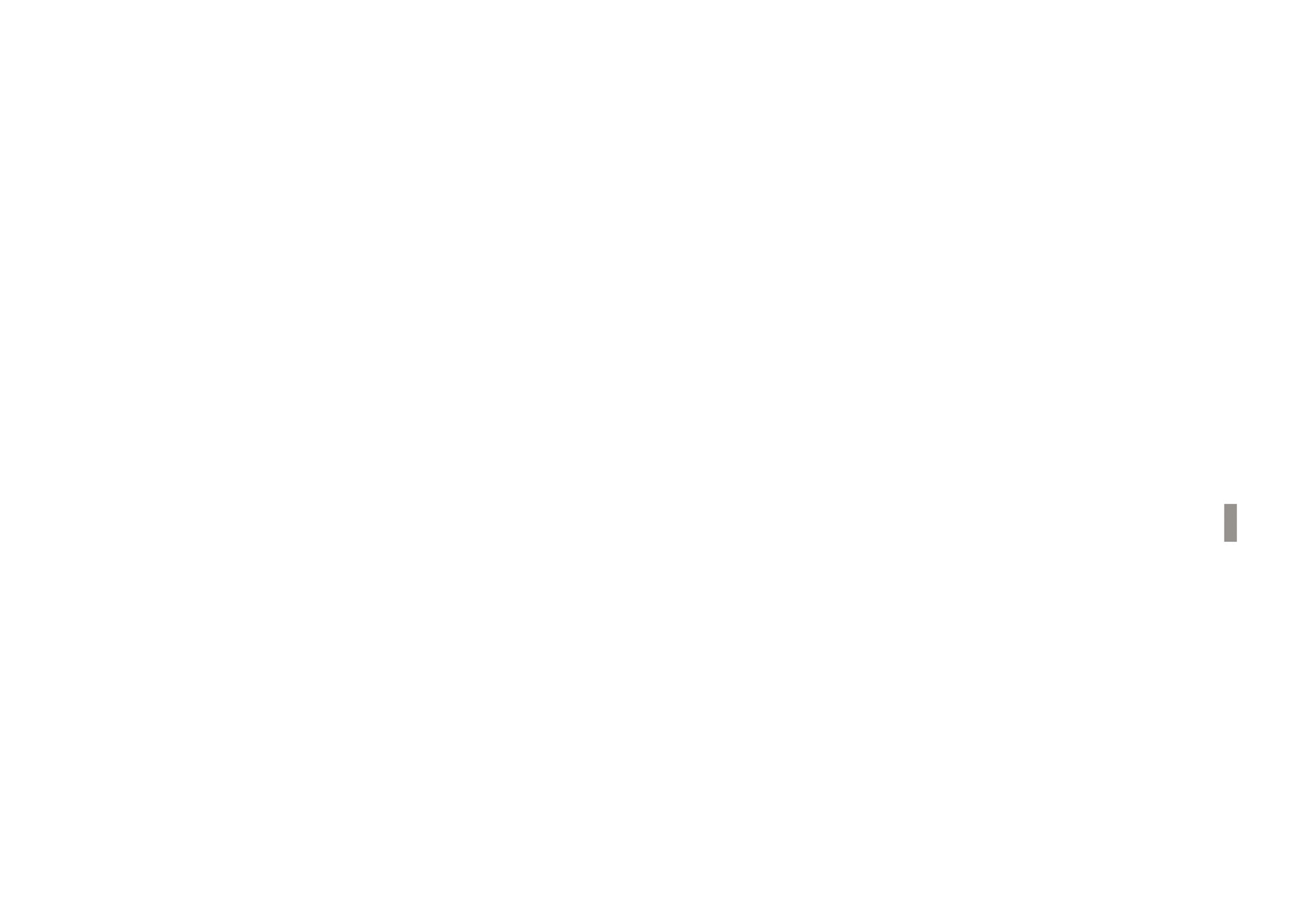
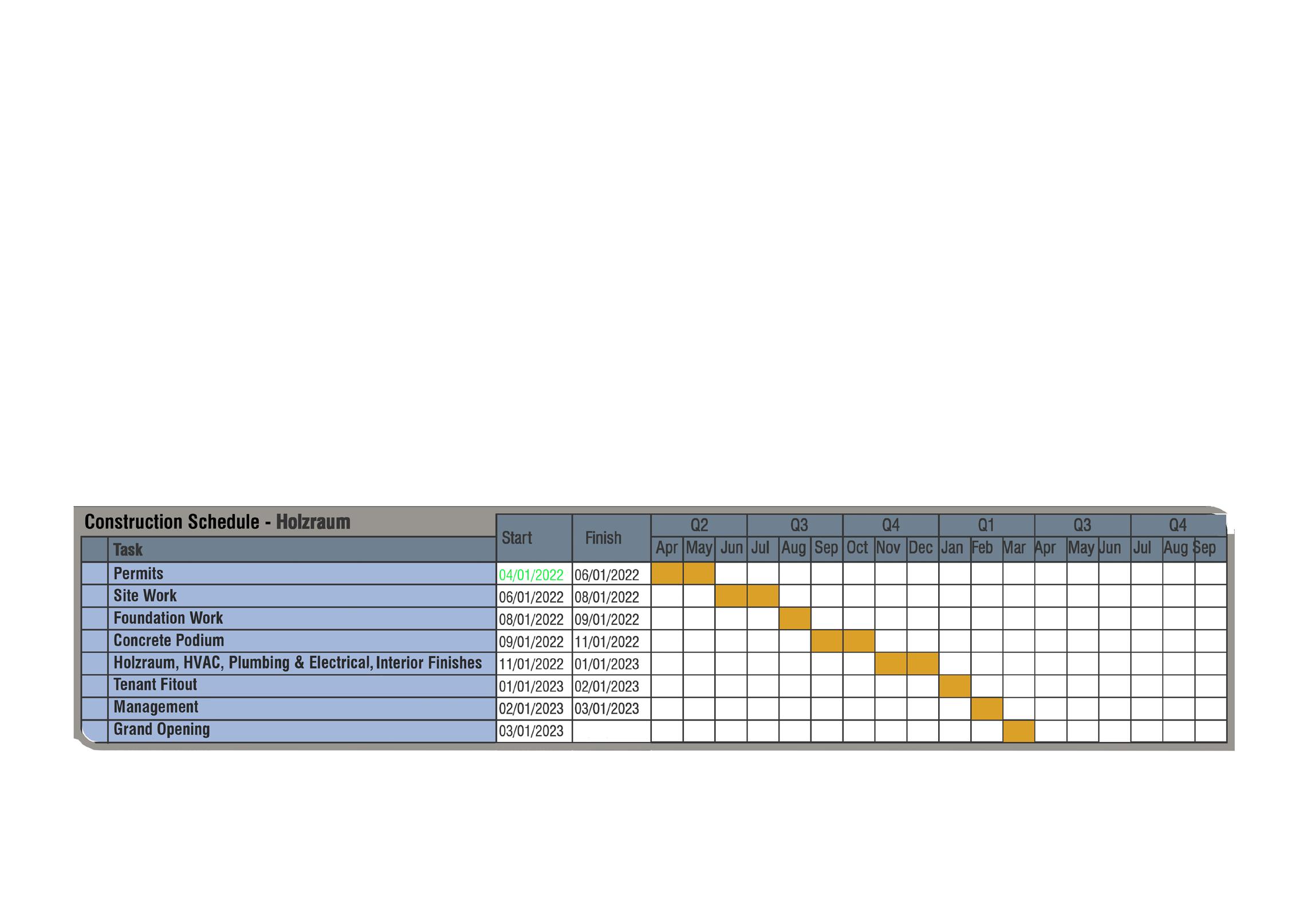
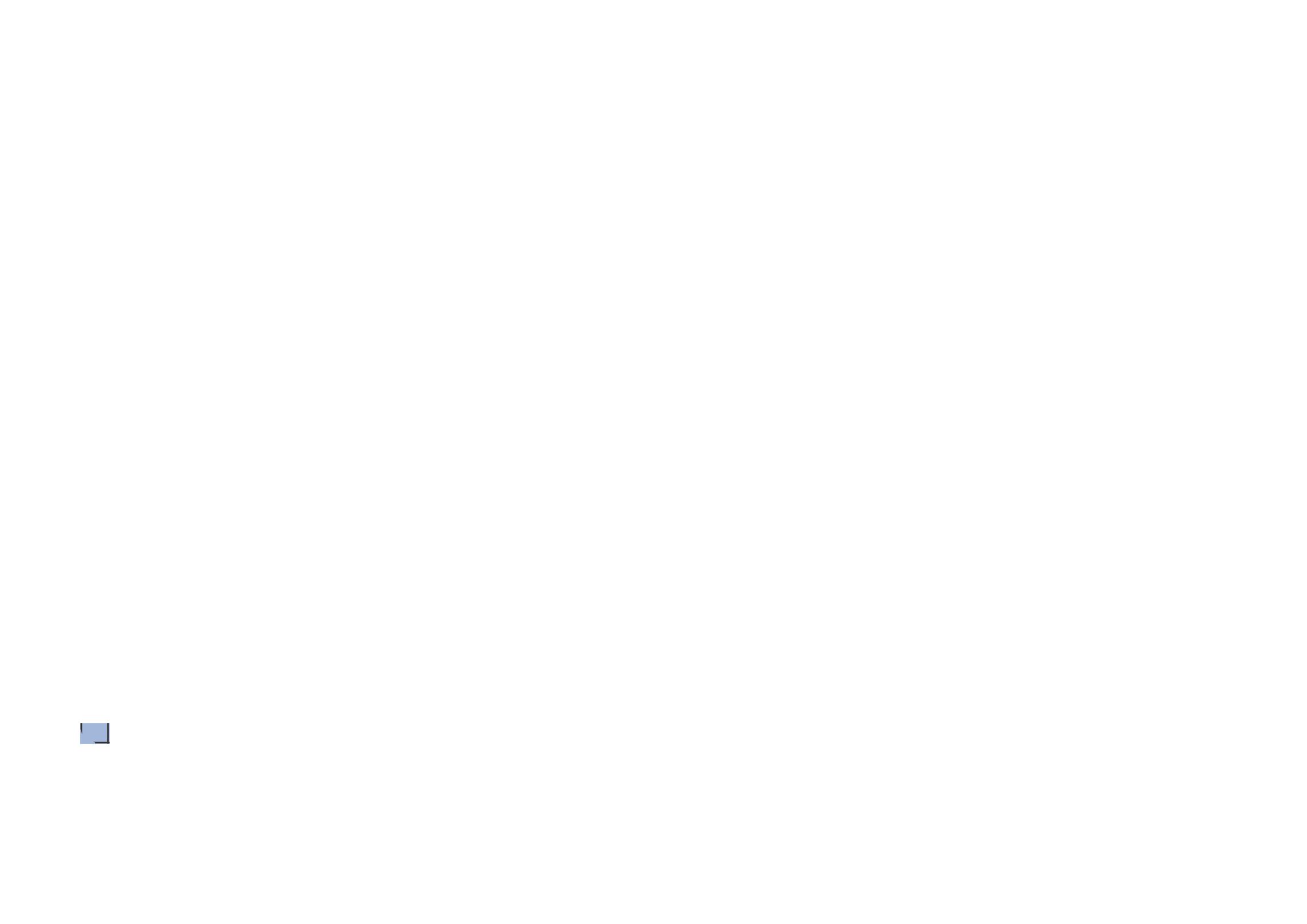
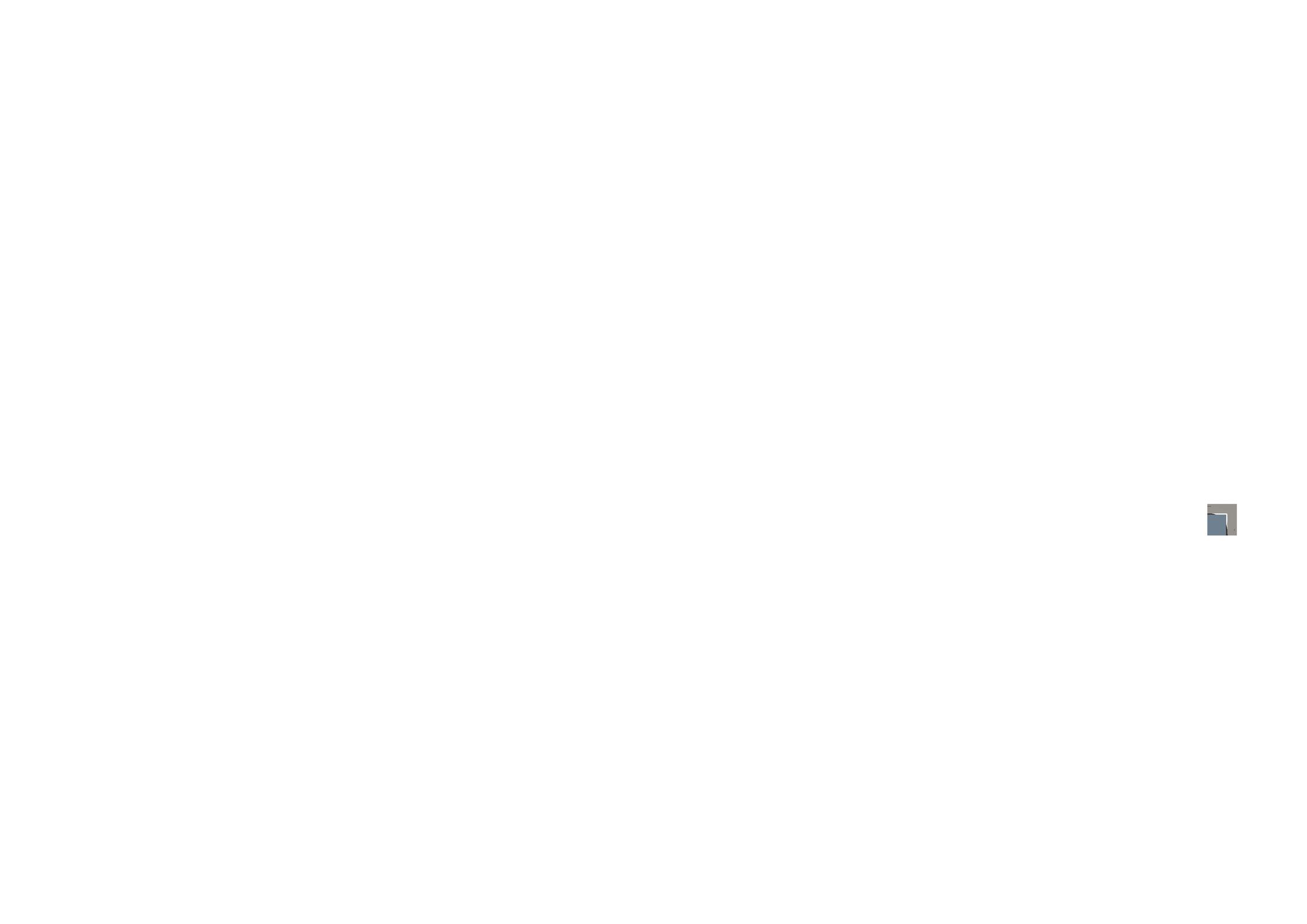


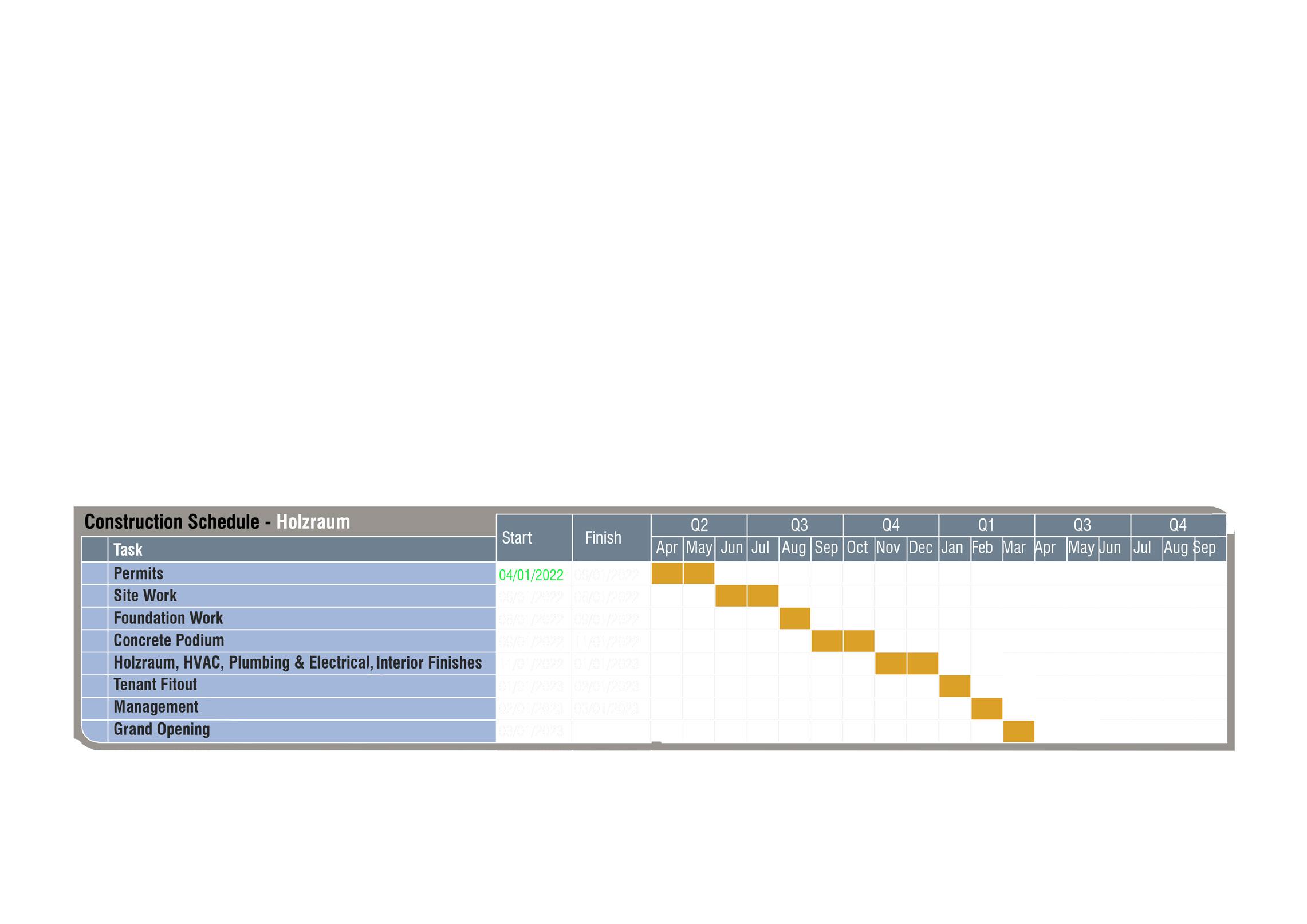
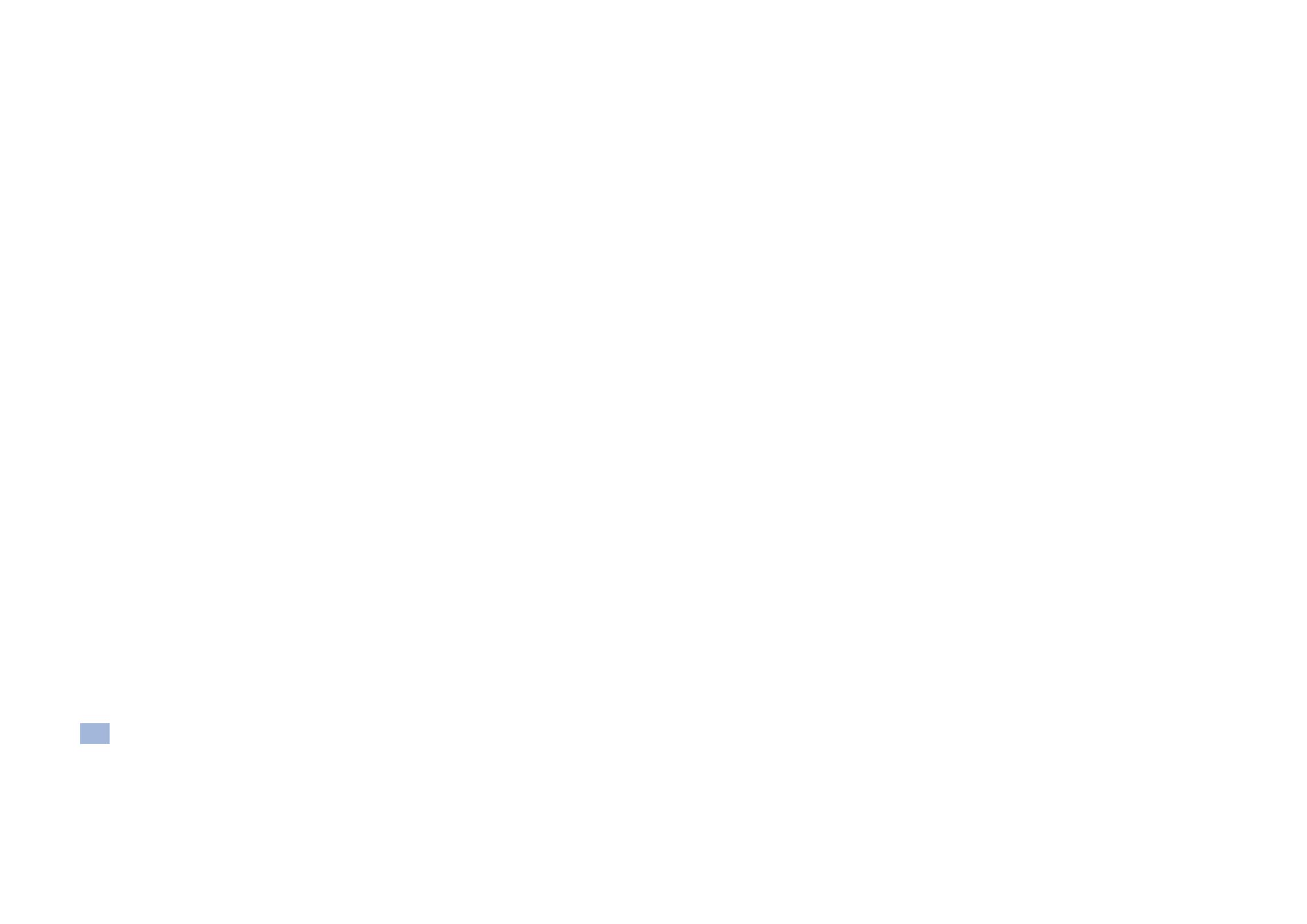
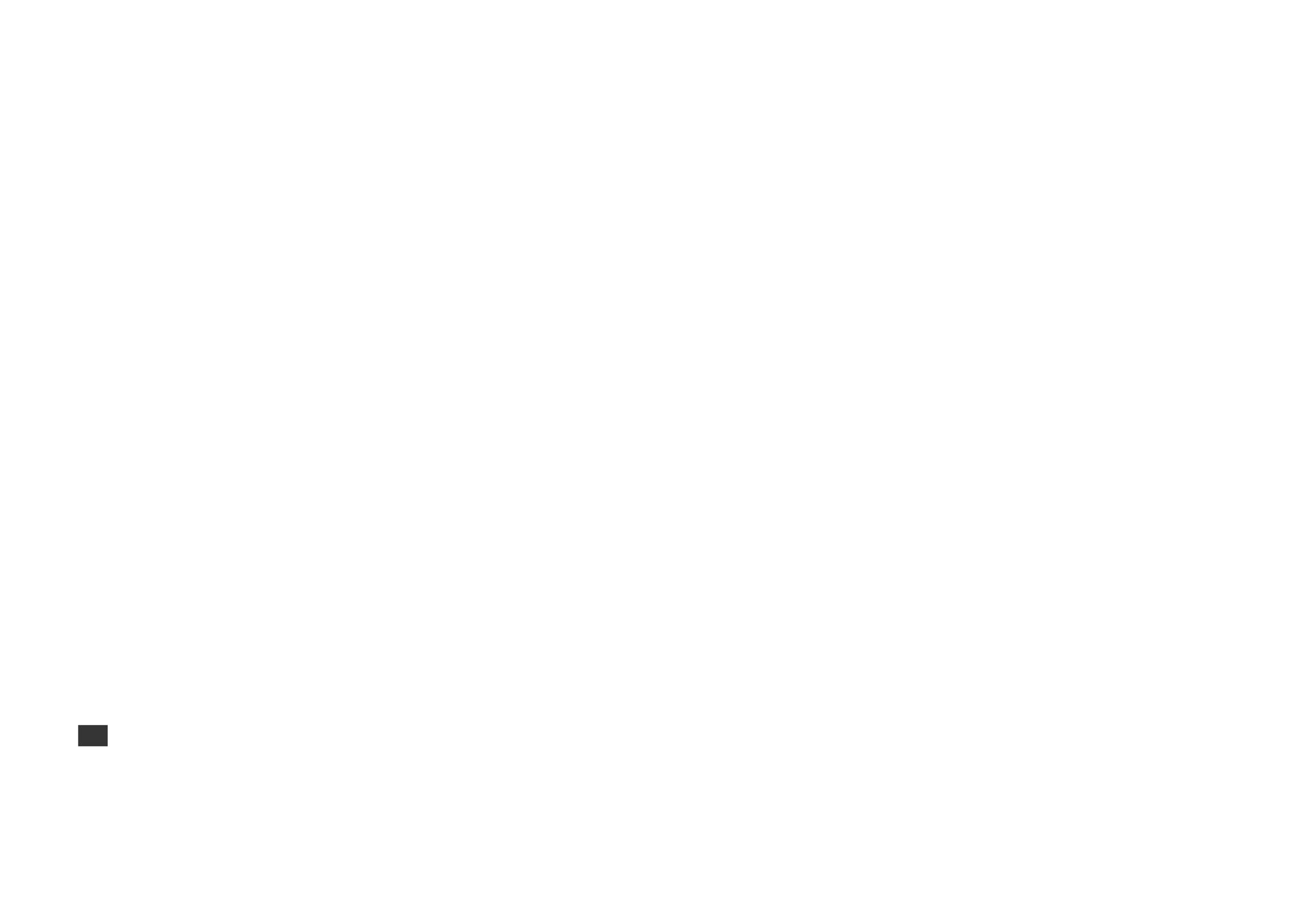
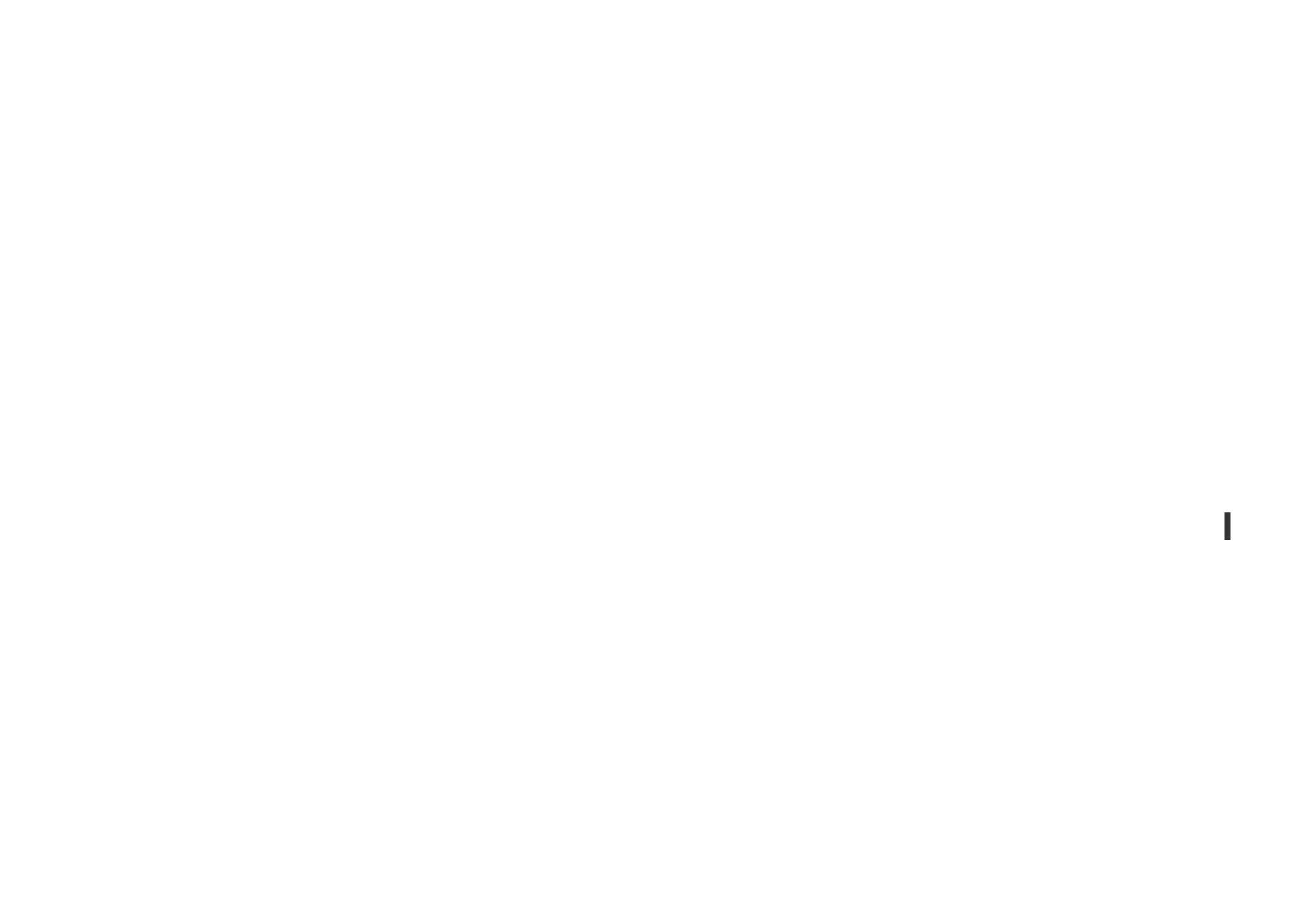


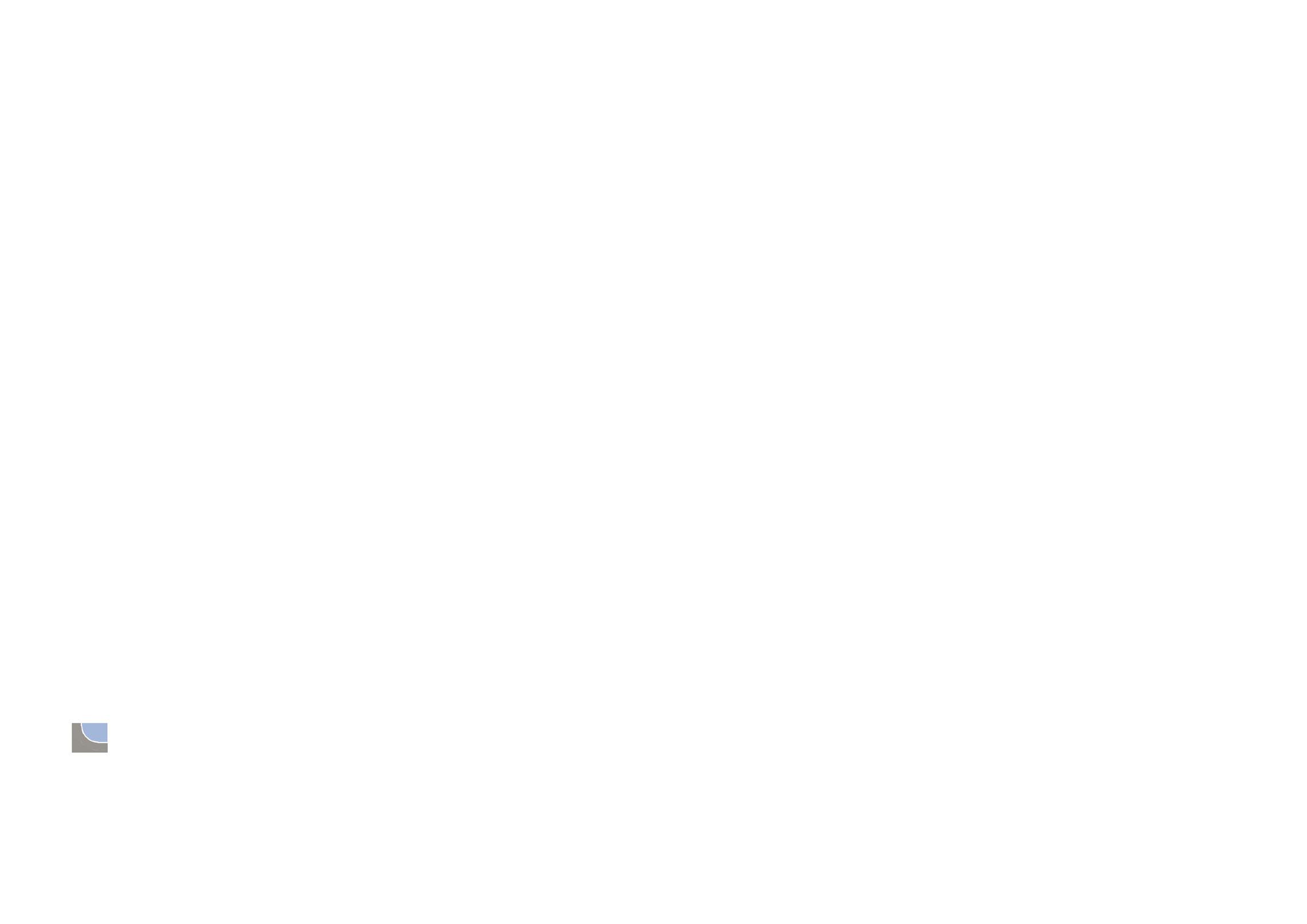

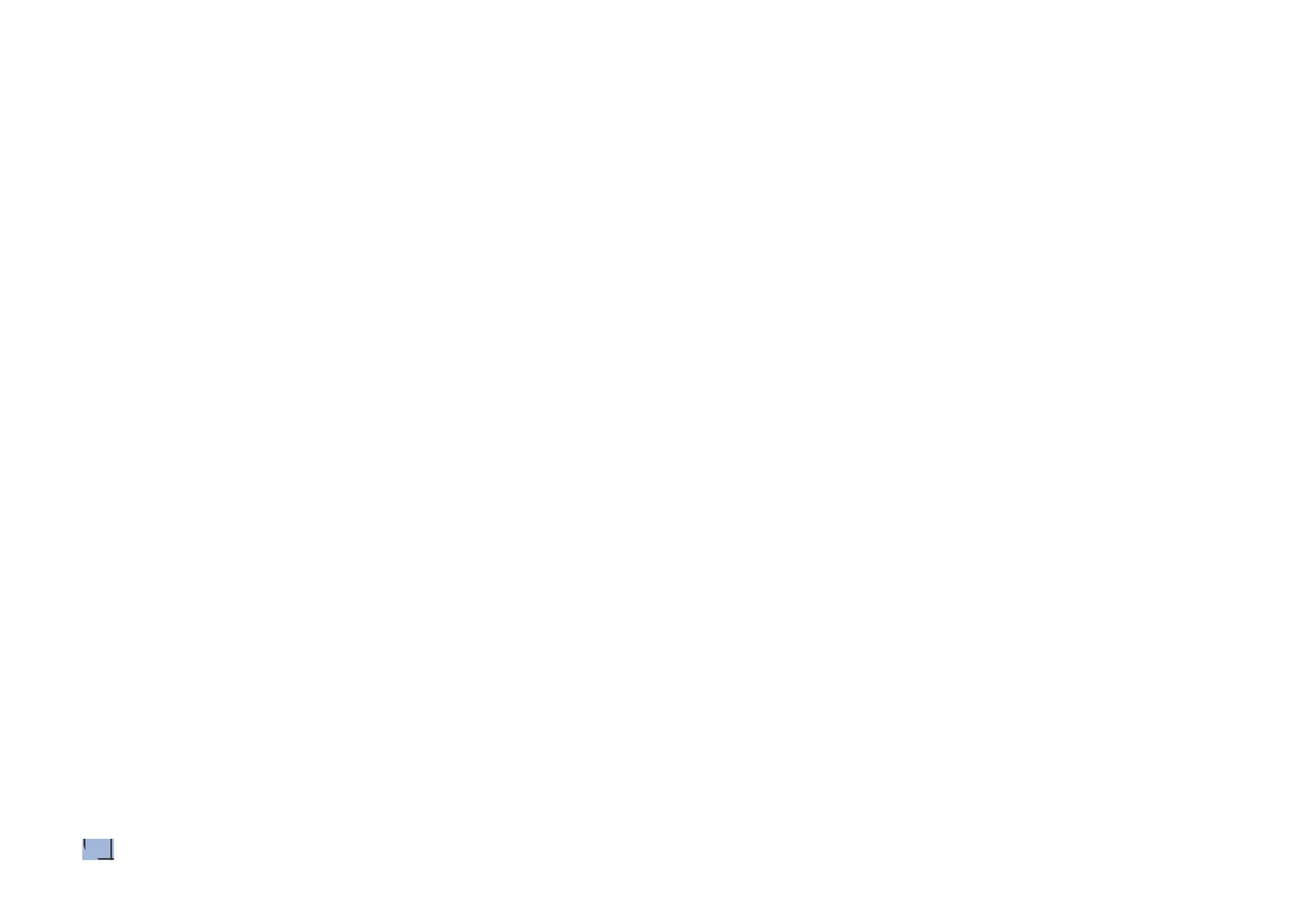
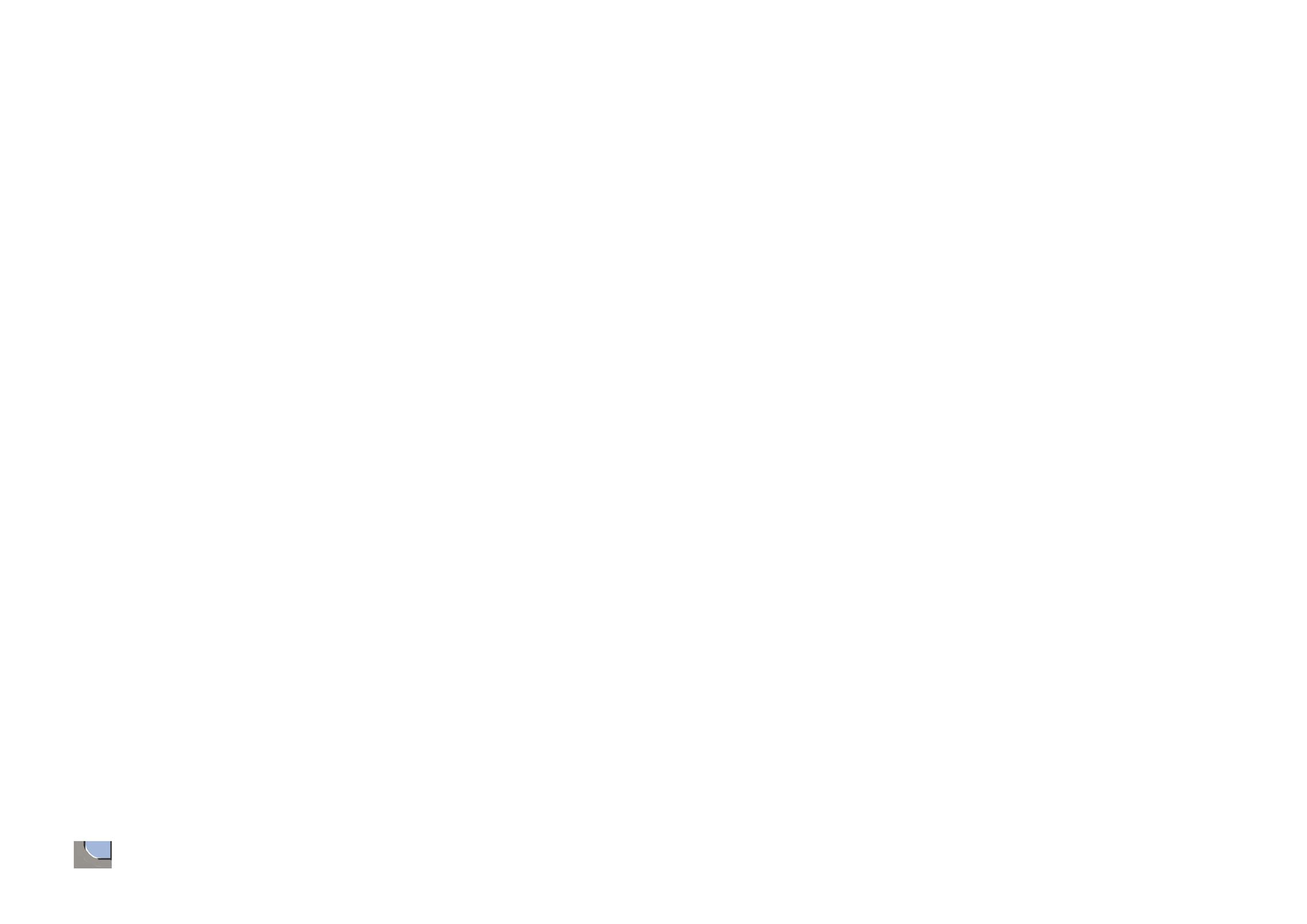
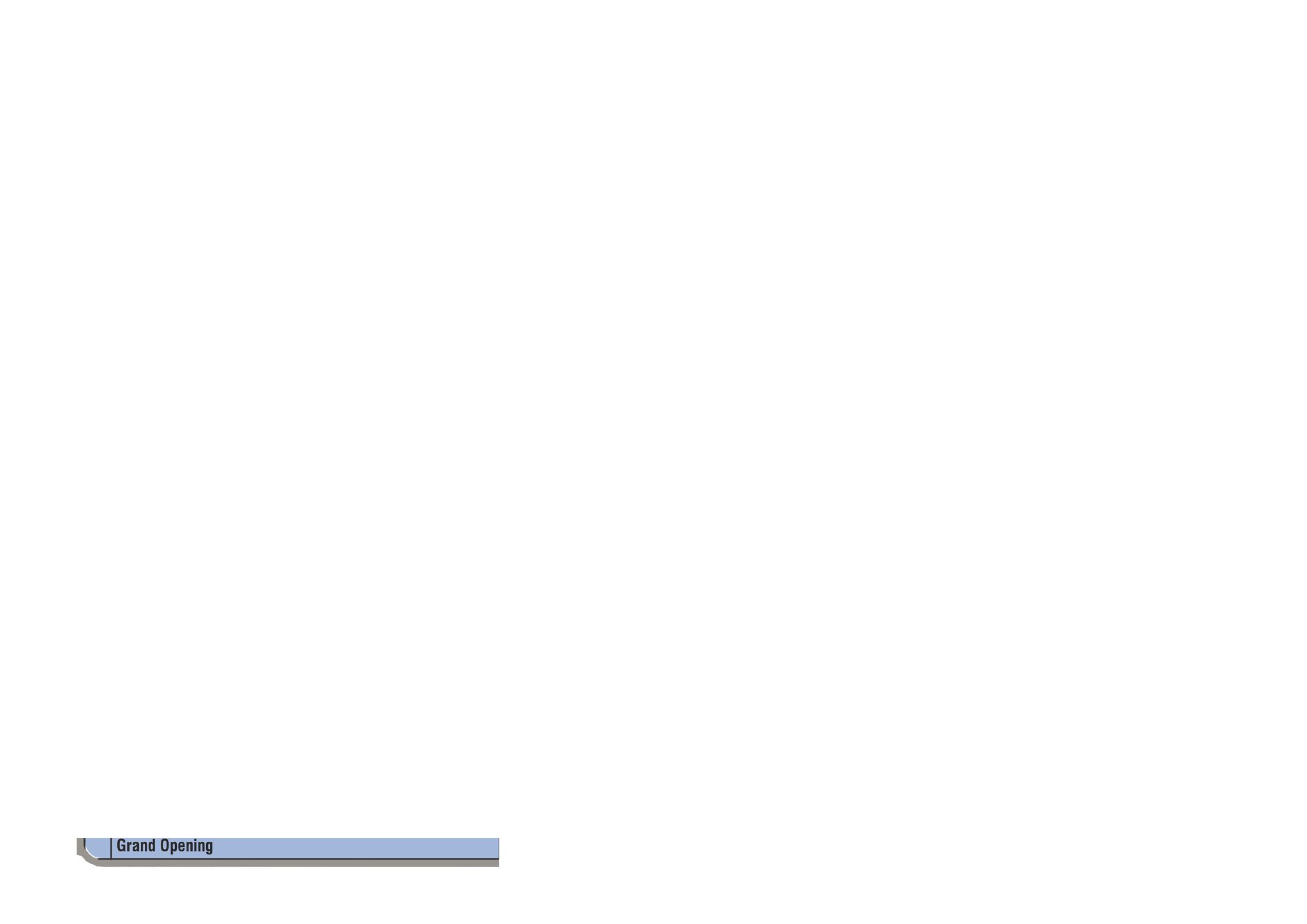
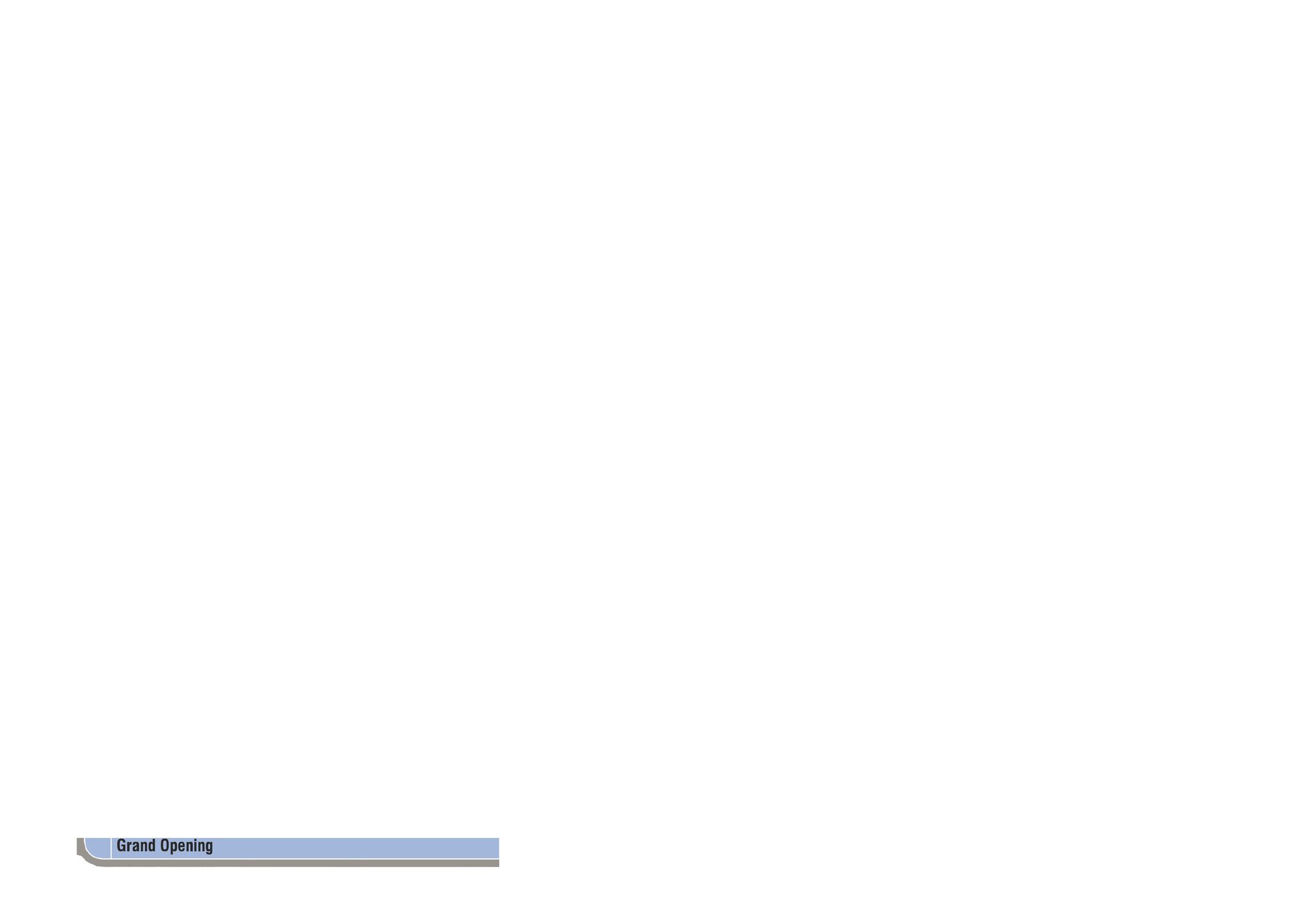
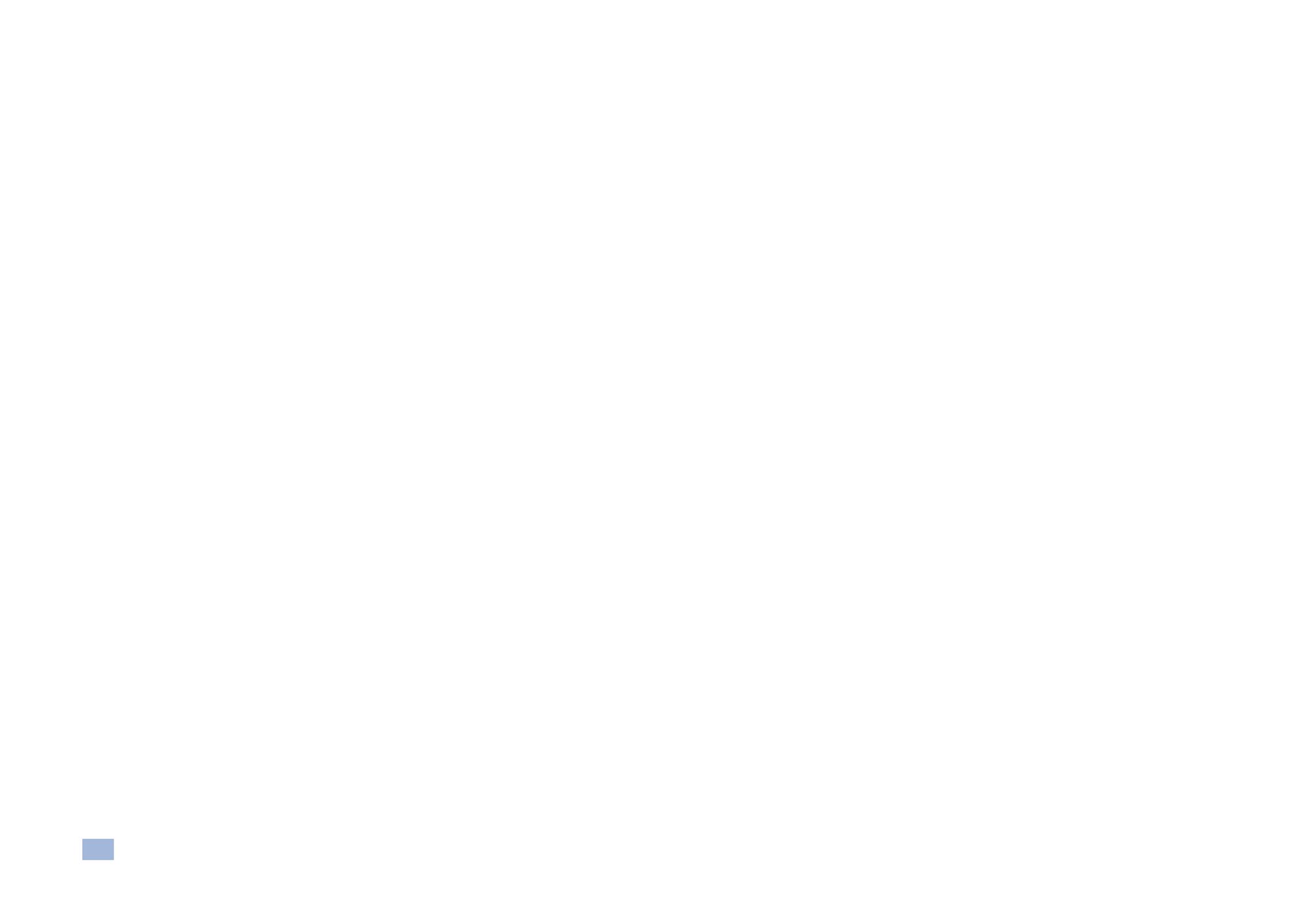
Figure 46 - Typical Construction Schedule vs. HolzRaum Schedule
PANELIZATION
Exterior and interior walls can be manufactured in assemblies as long as 10’ by up to 40’ panels, designed to fit on a flatbed. These panels can contain embedded system ducts, plumbing, and electrical; lining up at the build-site with high accuracy.
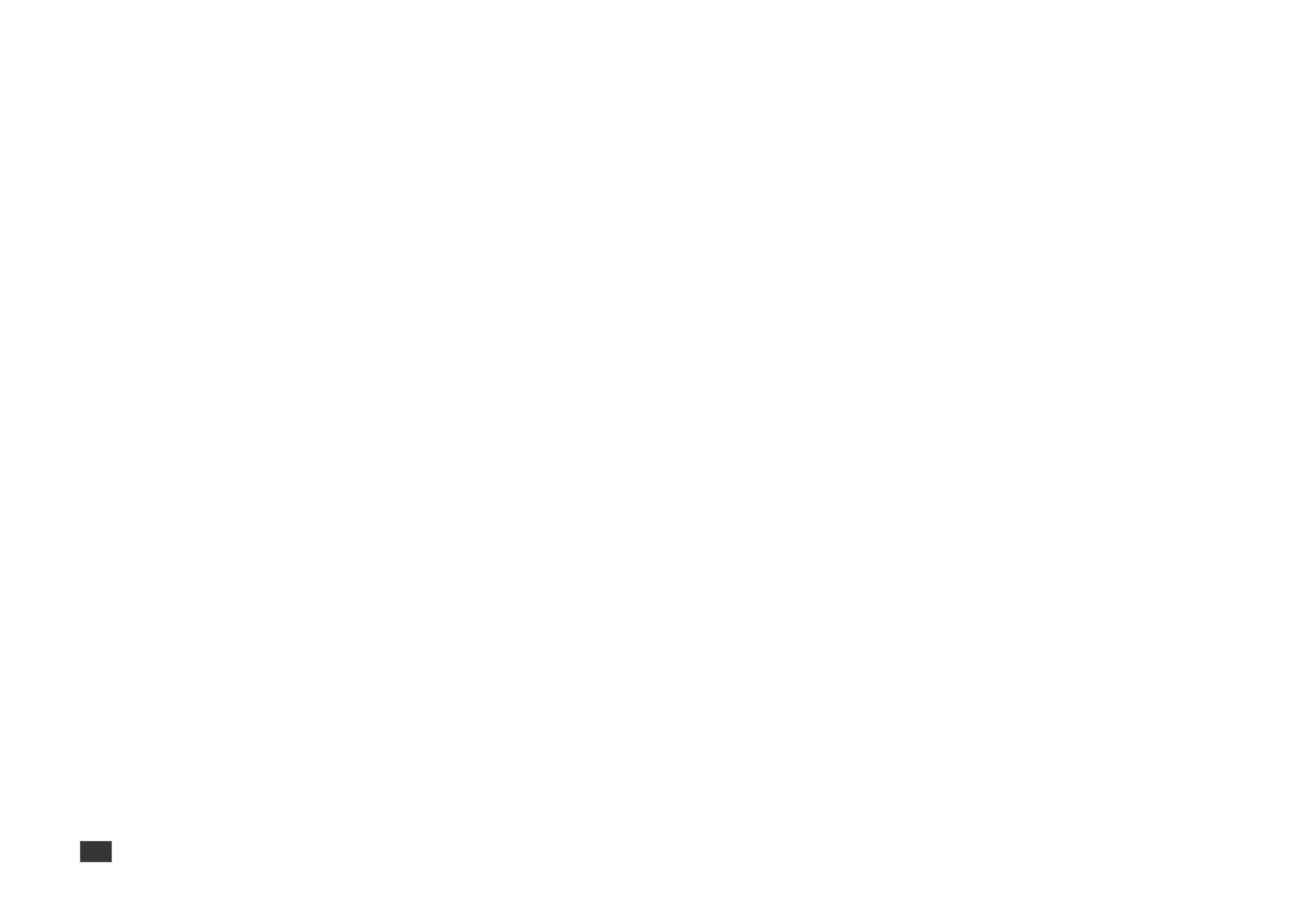
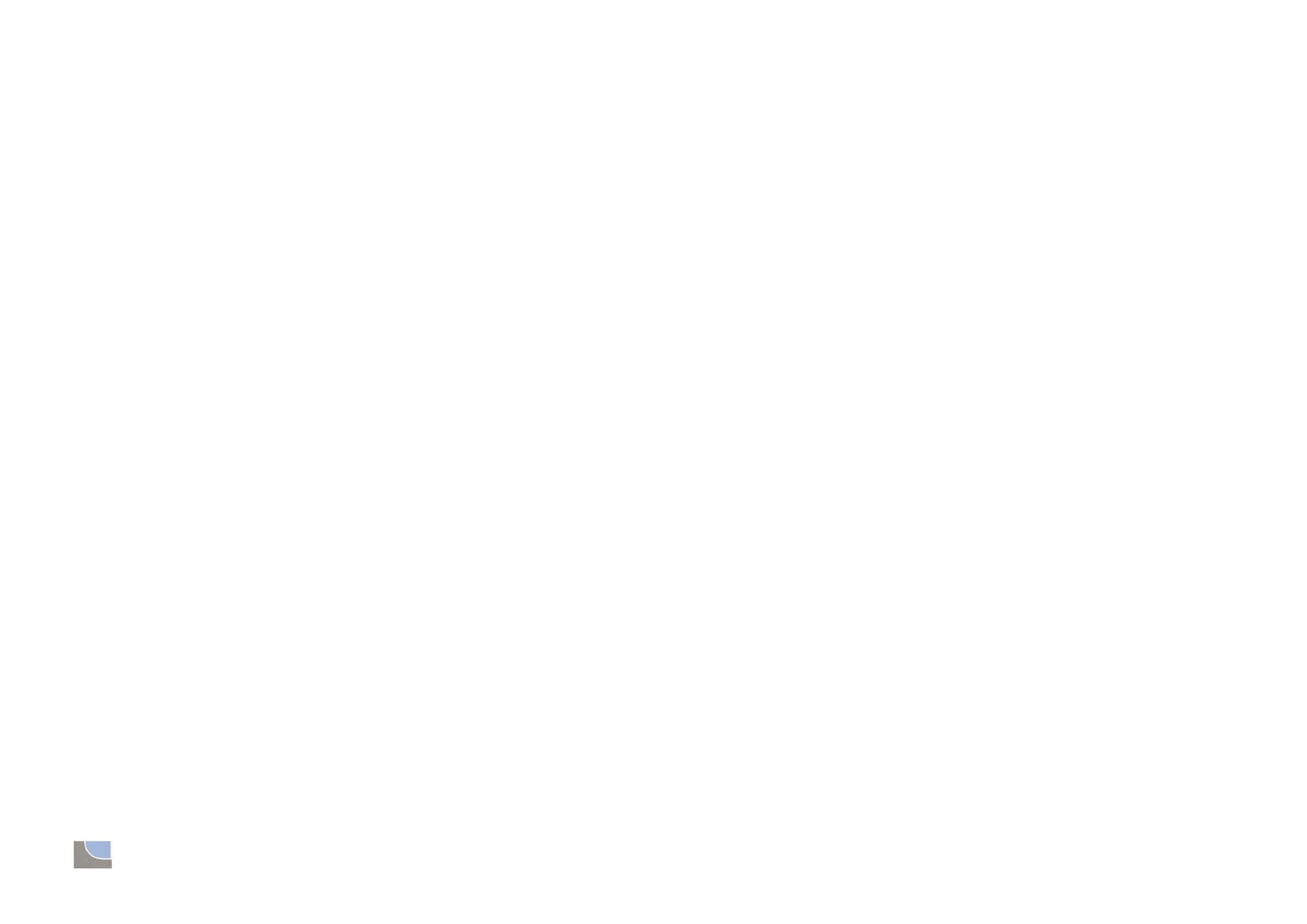

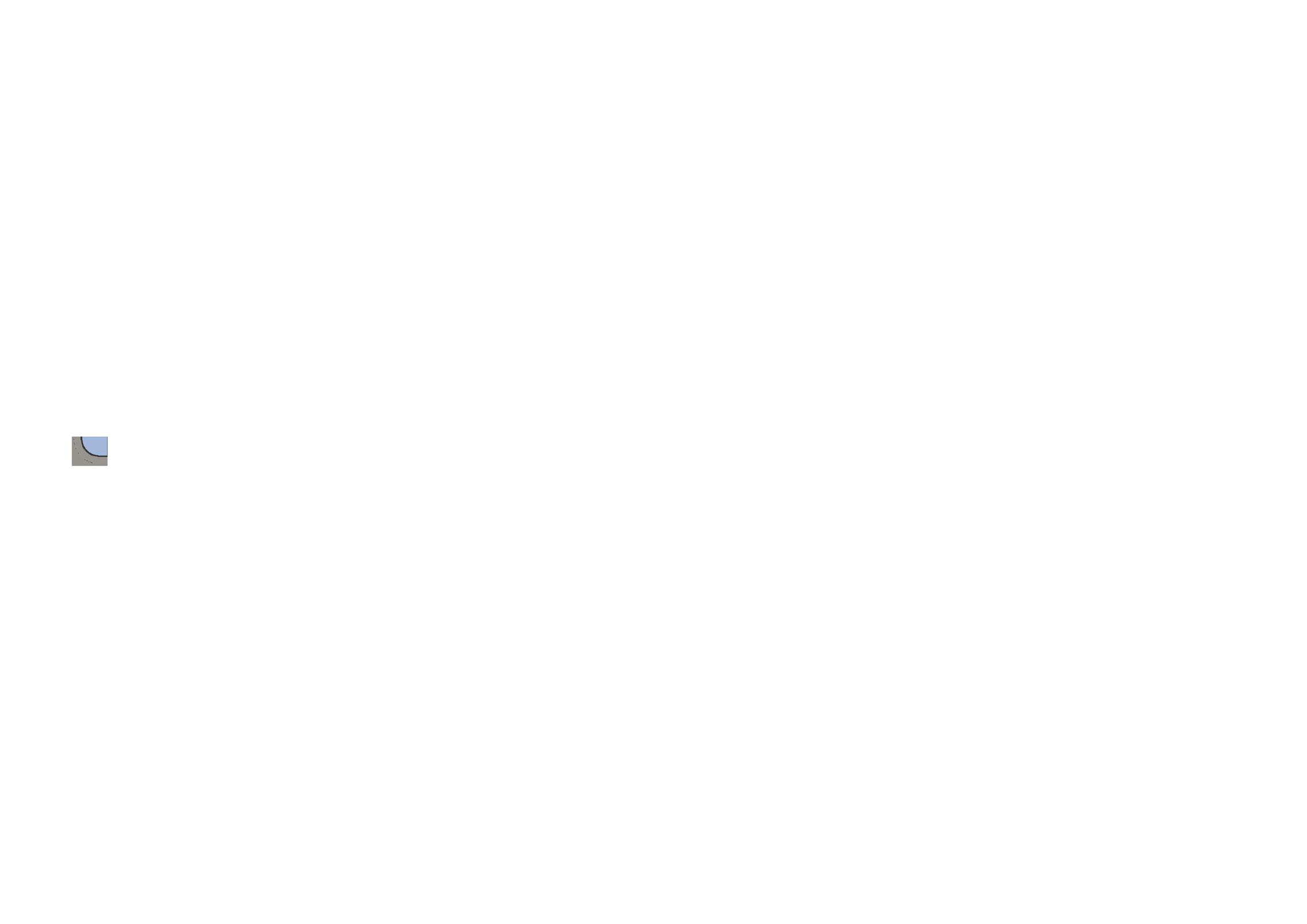


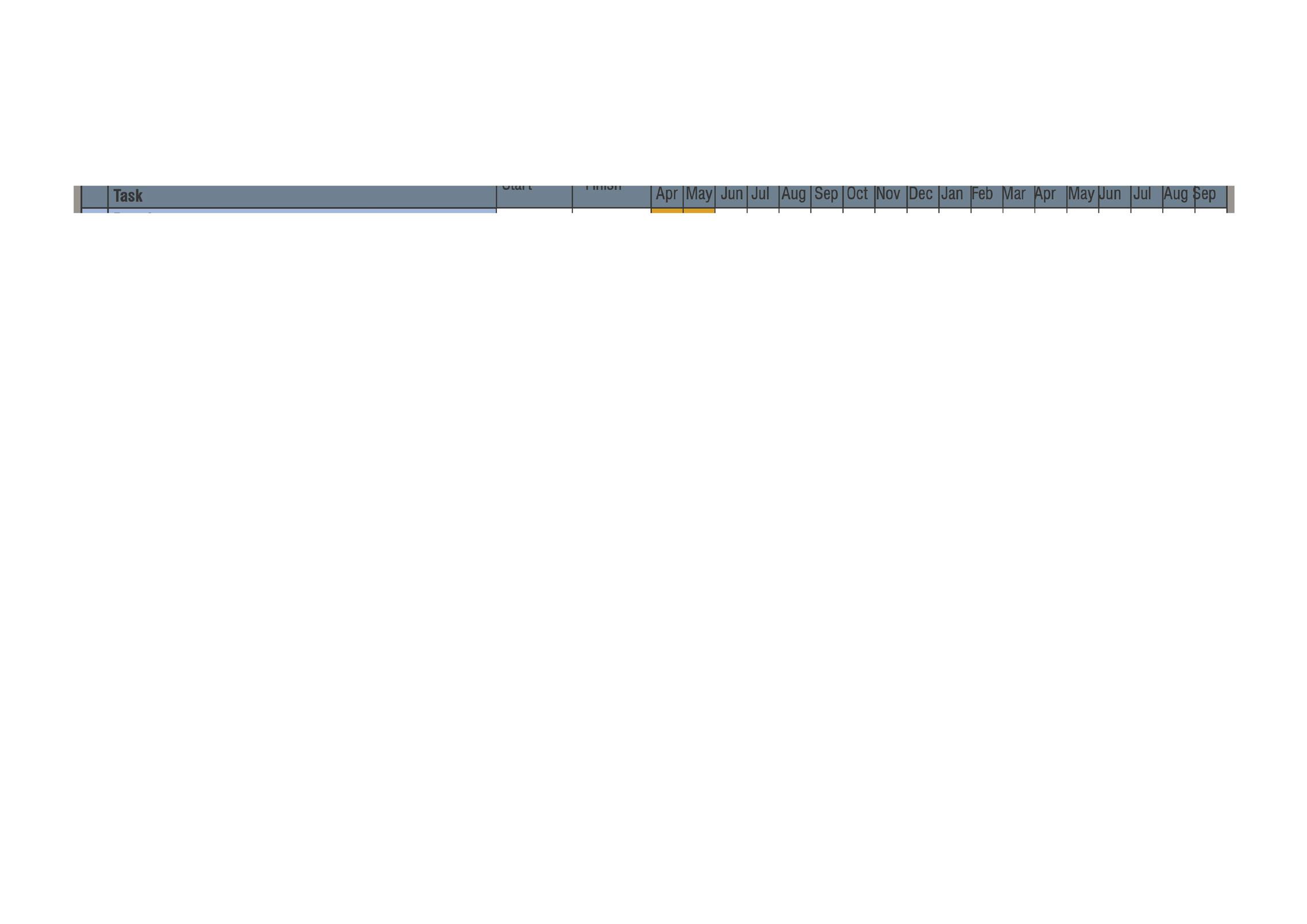
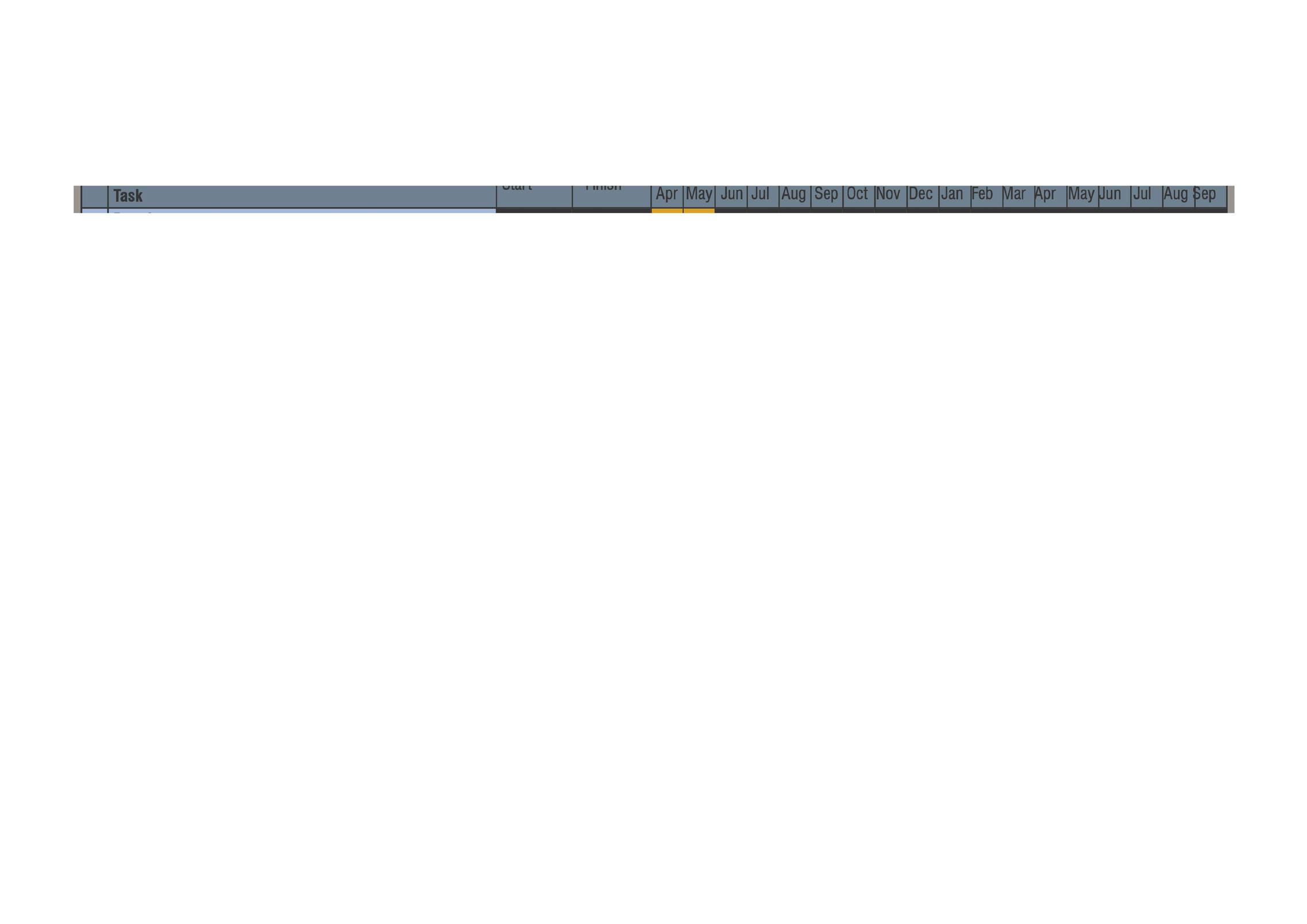
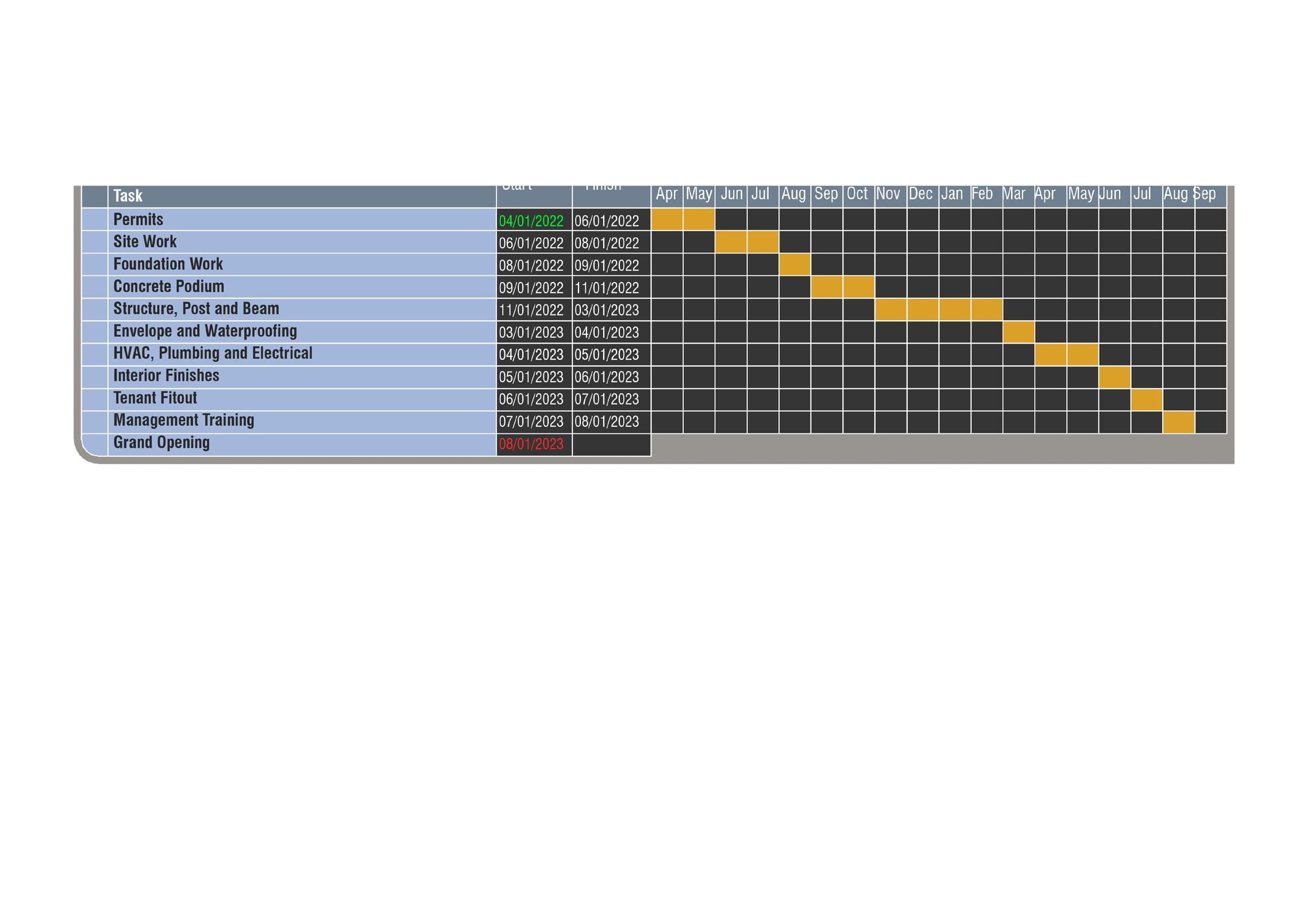
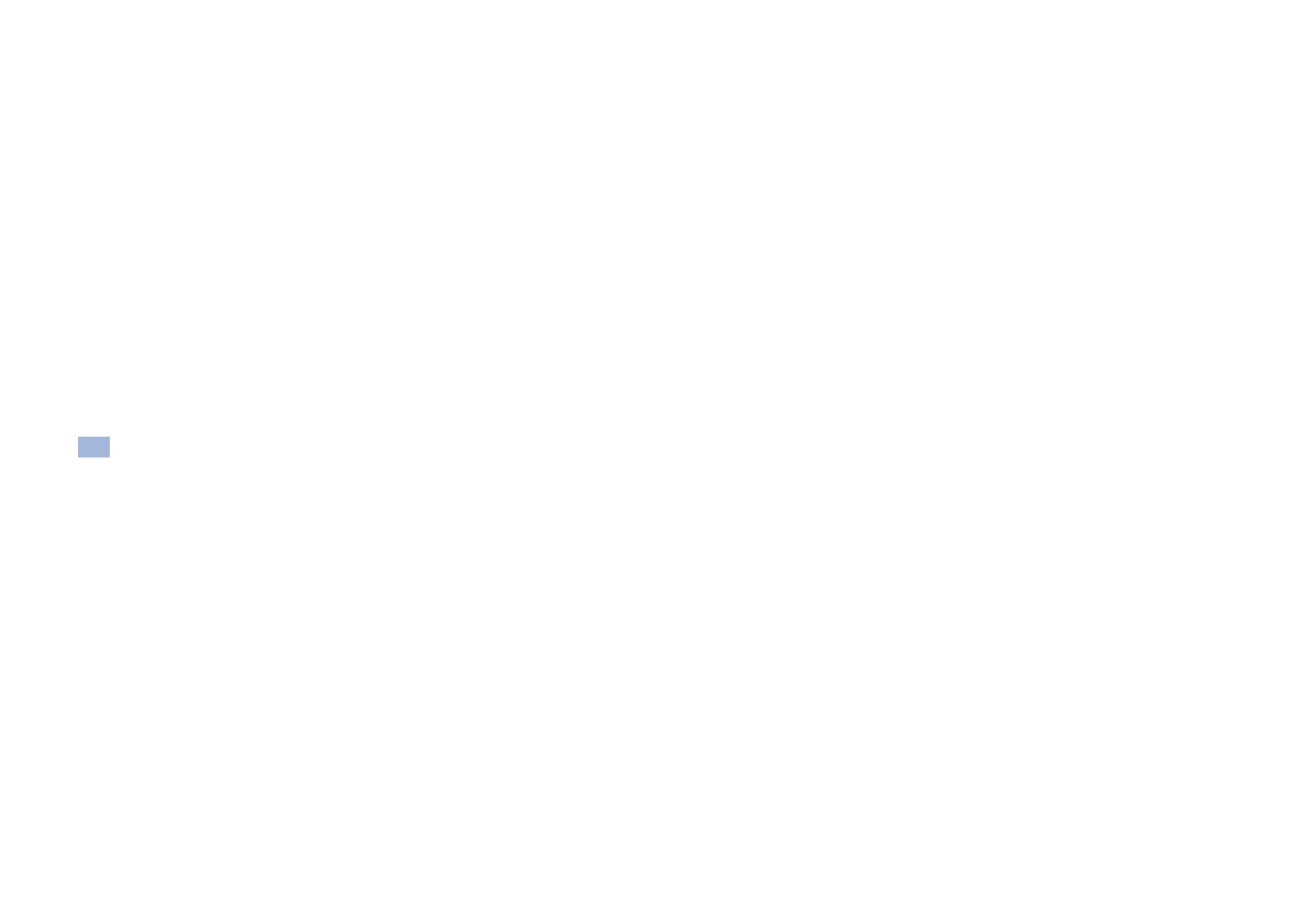


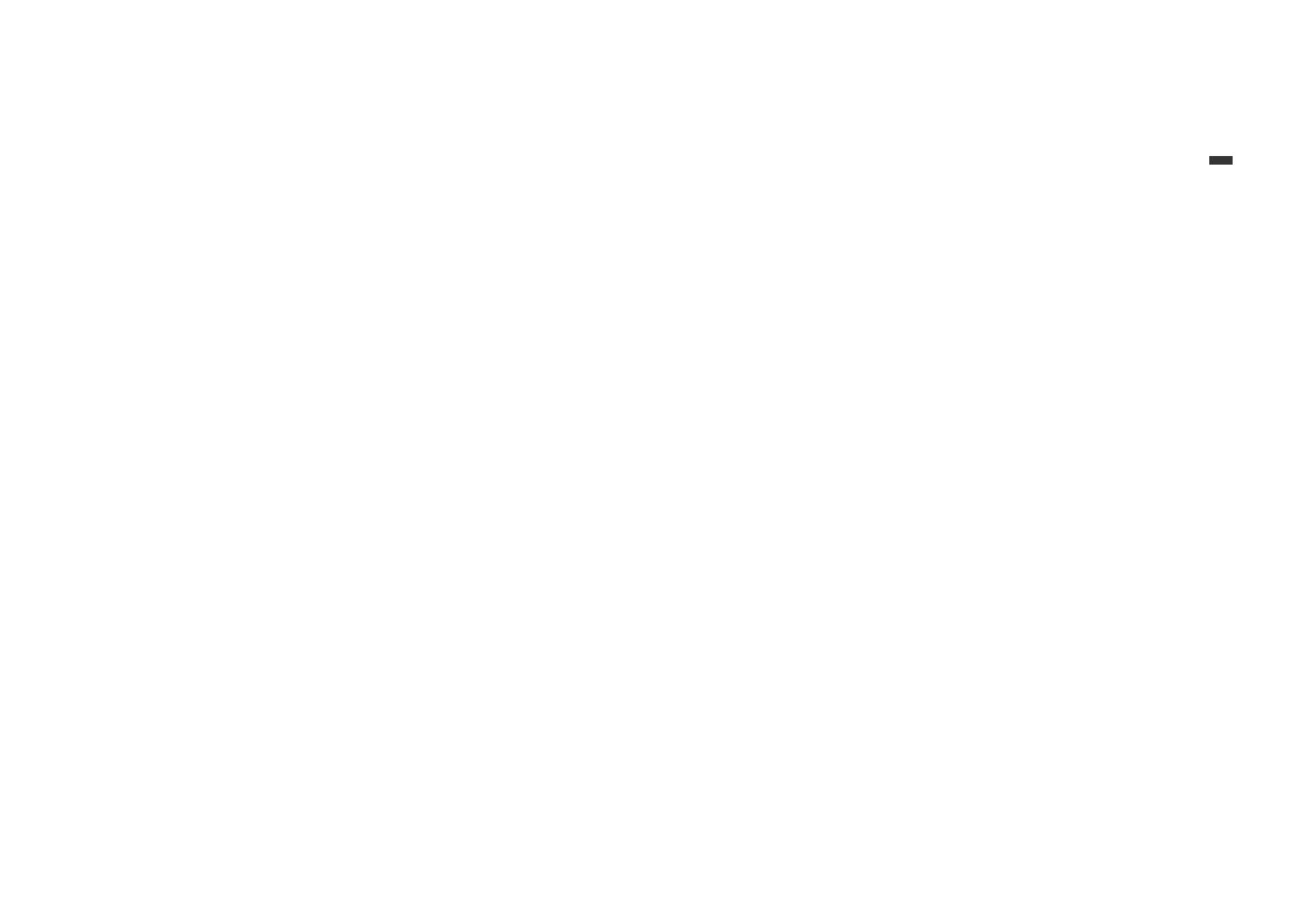
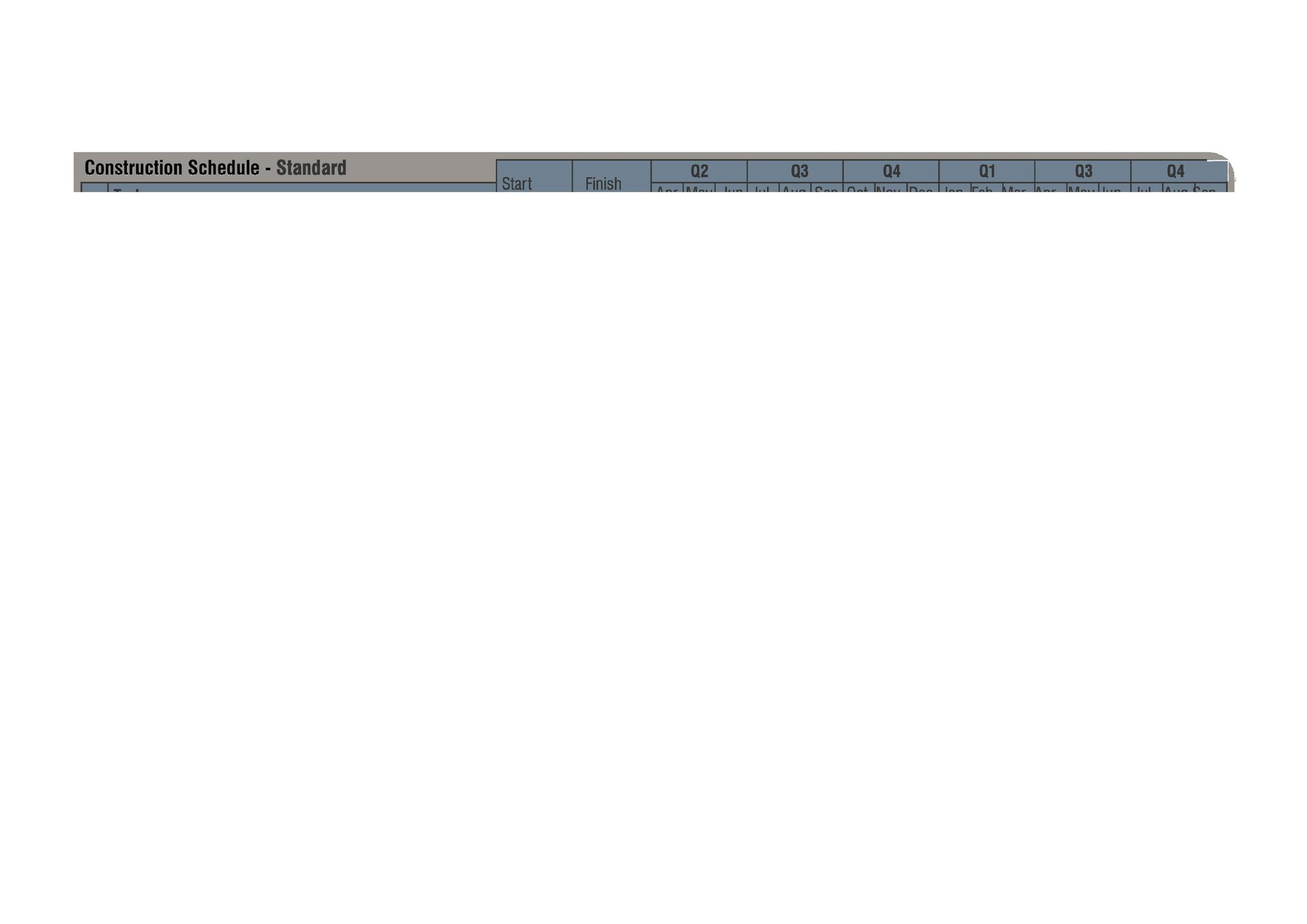
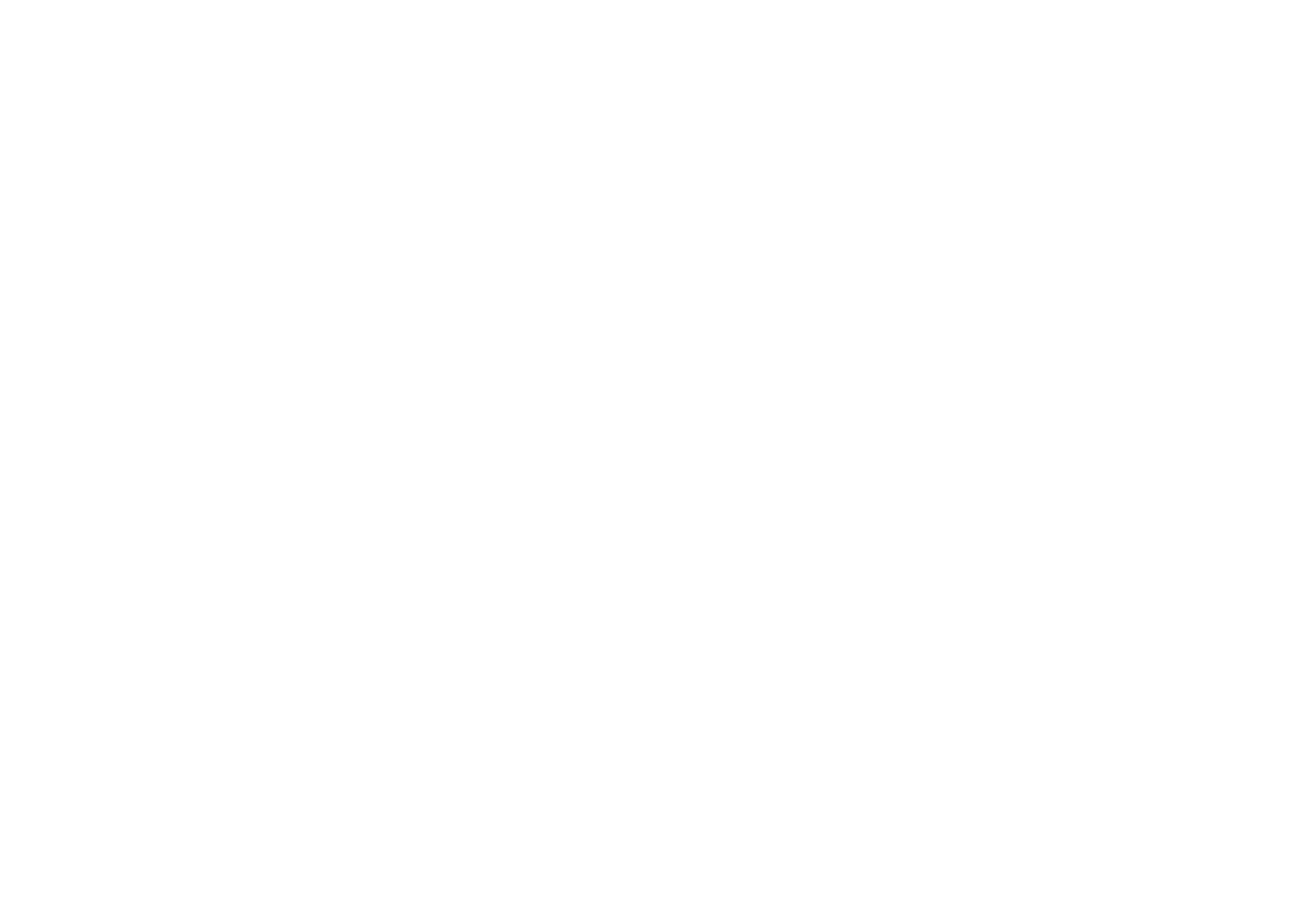
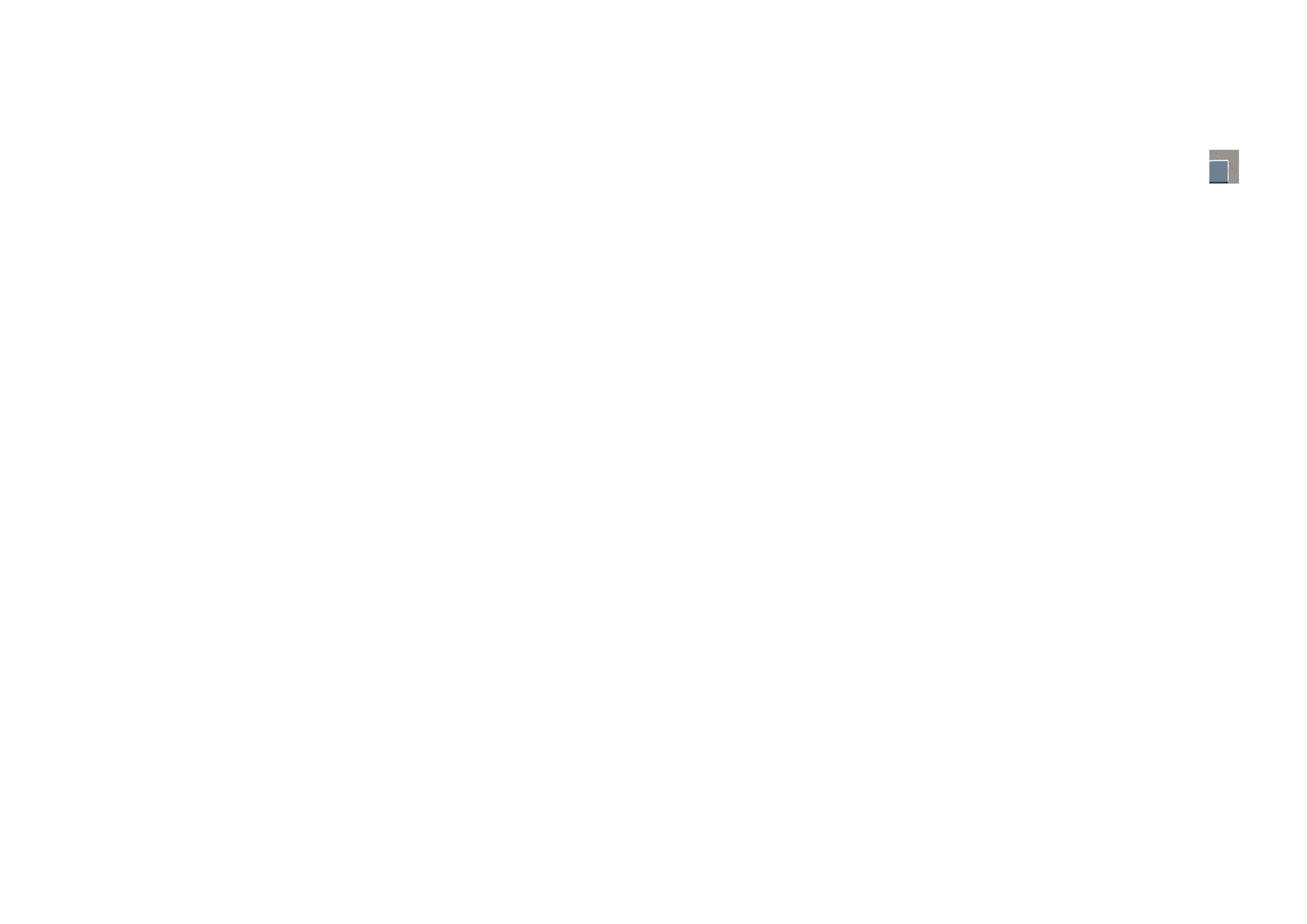

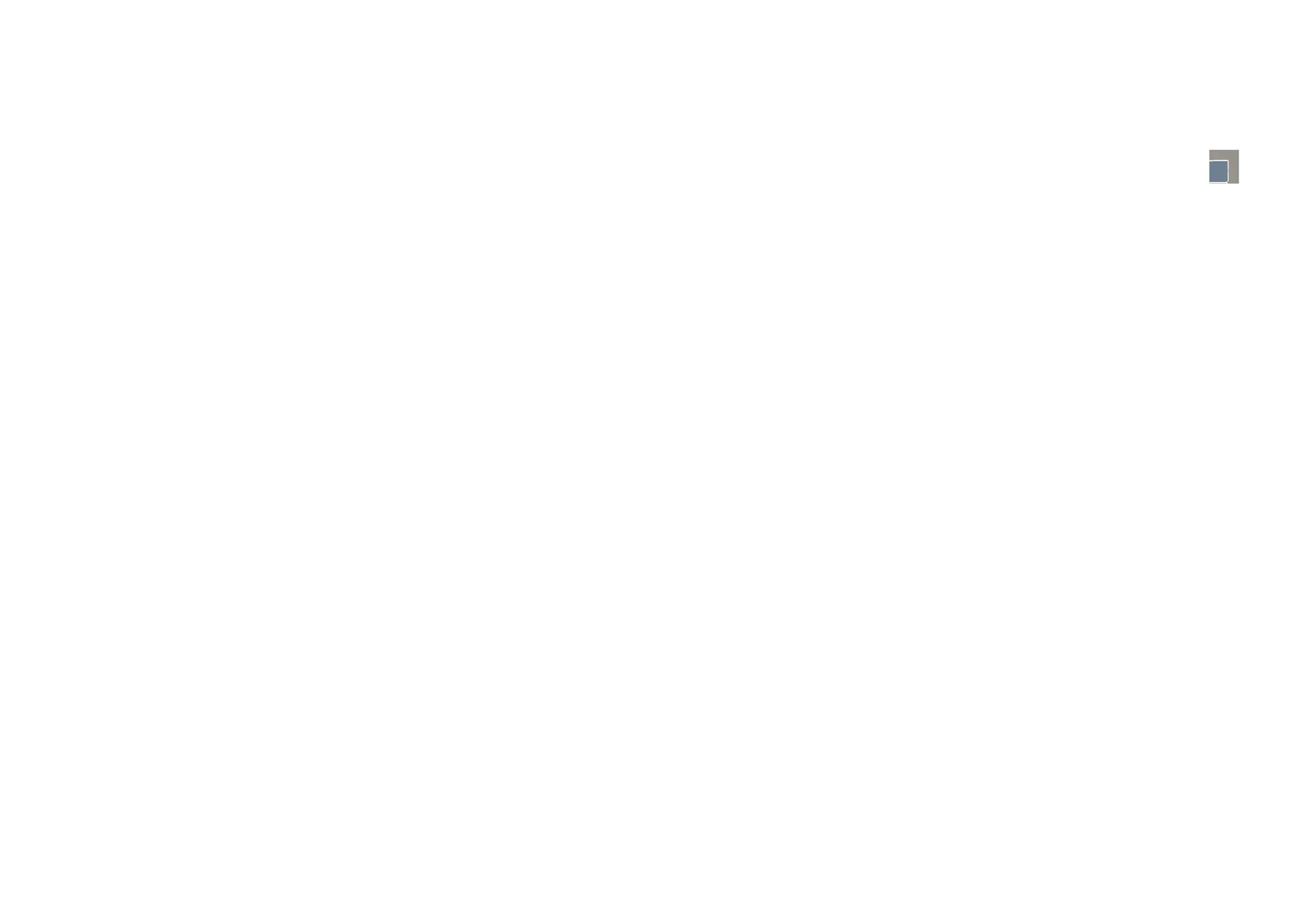
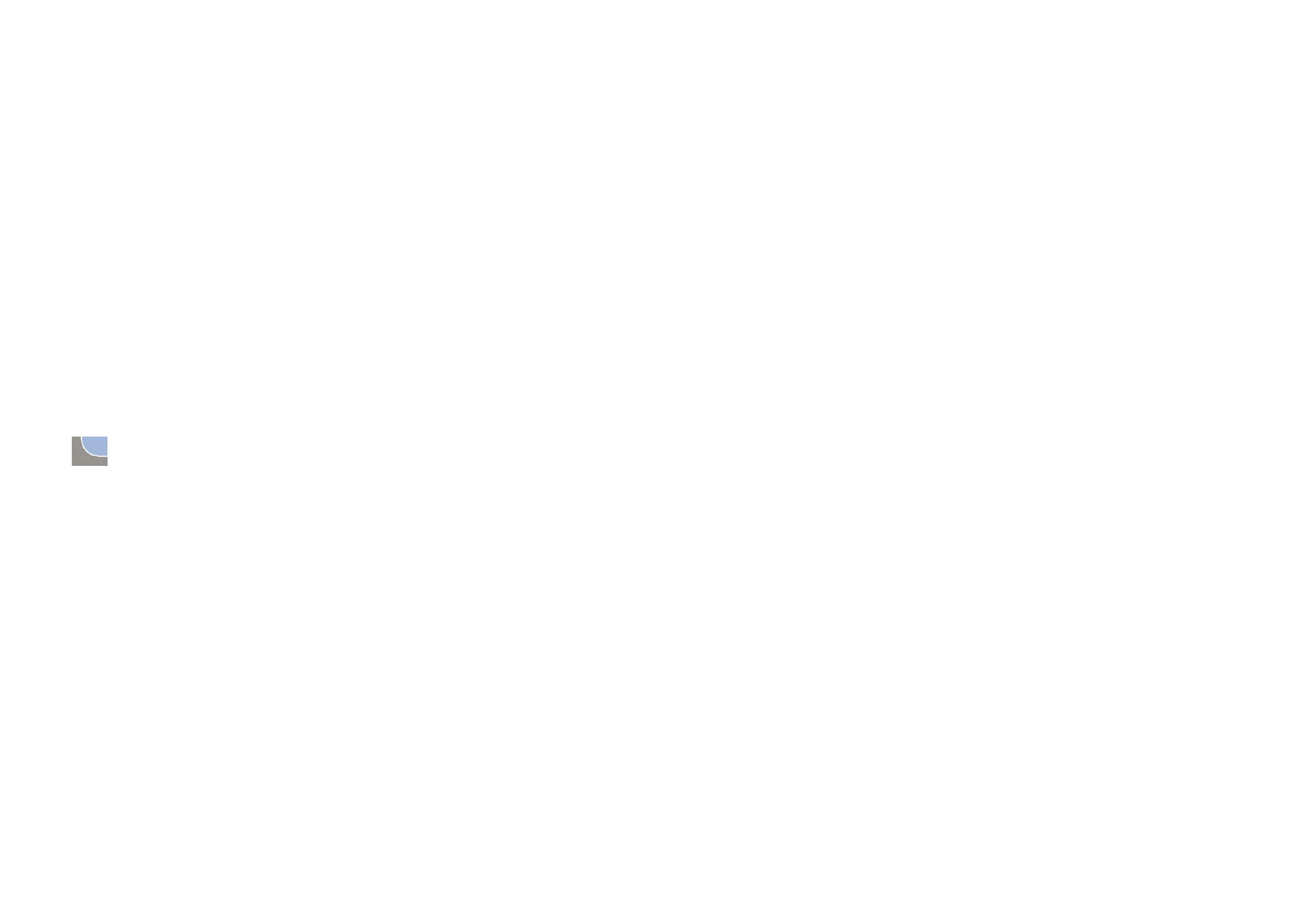
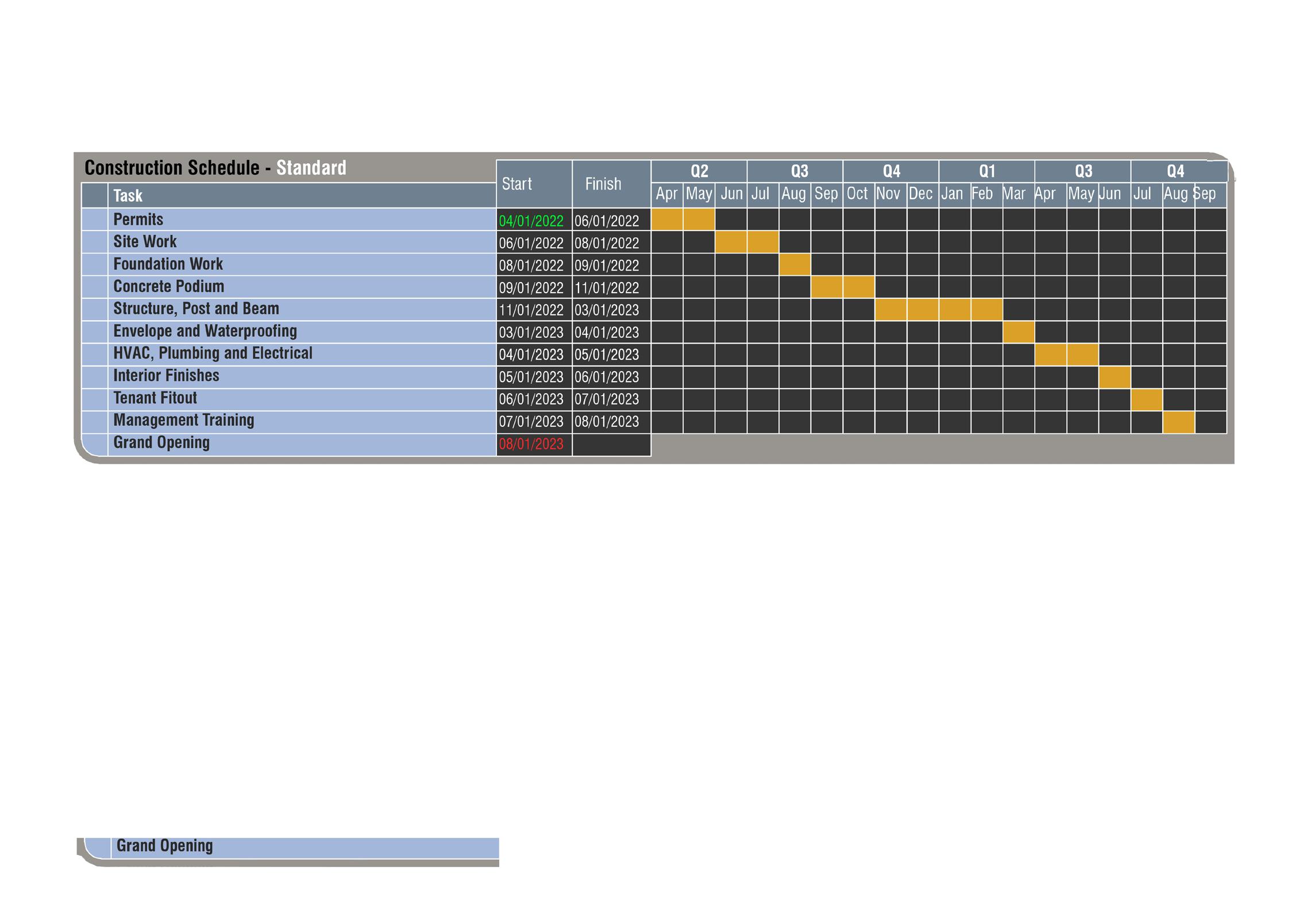
BLUEPRINT ROBOTICS
Large savings on labor come through is through the use of prefabricated elements, specifically the HolzRaum System manufactured by Blueprint Robotics in Baltimore, MD.
A standard construction schedule for a development of this scale lasts 17 months.
Since labor costs in large cities like Philadelphia are quite high, a shorter construction schedule translates into significant savings.
By using the prefabricated HolzRaum system, we are able to shorten our construction schedule by five months. These savings are invested in PassivHaus strategies and sophisticated water management, so that we are able to create a higher quality development for code-minimum costs, especially as facilities for prefabricated assemblies begin to open in Pennsylvania.