MODERN PERMANENT MAGNETS
Edited by John J. Croat
Naples, Florida, (USA)
John Ormerod
JOC LLC, Loudon, Tennessee, (USA)
Woodhead Publishing is an imprint of Elsevier 50 Hampshire Street, 5th Floor, Cambridge, MA 02139, United States The Boulevard, Langford Lane, Kidlington, OX5 1GB, United Kingdom
Copyright © 2022 Elsevier Ltd. All rights reserved.
No part of this publication may be reproduced or transmitted in any form or by any means, electronic or mechanical, including photocopying, recording, or any information storage and retrieval system, without permission in writing from the publisher. Details on how to seek permission, further information about the Publisher’s permissions policies and our arrangements with organizations such as the Copyright Clearance Center and the Copyright Licensing Agency, can be found at our website: www.elsevier.com/permissions.
This book and the individual contributions contained in it are protected under copyright by the Publisher (other than as may be noted herein).
Notices
Knowledge and best practice in this field are constantly changing. As new research and experience broaden our understanding, changes in research methods, professional practices, or medical treatment may become necessary.
Practitioners and researchers must always rely on their own experience and knowledge in evaluating and using any information, methods, compounds, or experiments described herein. In using such information or methods they should be mindful of their own safety and the safety of others, including parties for whom they have a professional responsibility.
To the fullest extent of the law, neither the Publisher nor the authors, contributors, or editors, assume any liability for any injury and/or damage to persons or property as a matter of products liability, negligence or otherwise, or from any use or operation of any methods, products, instructions, or ideas contained in the material herein.
British Library Cataloguing-in-Publication Data
A catalogue record for this book is available from the British Library
Library of Congress Cataloging-in-Publication Data
A catalog record for this book is available from the Library of Congress
ISBN: 978-0-323-88658-1
For Information on all Woodhead Publishing publications visit our website at https://www.elsevier.com/books-and-journals
Publisher: Matthew Deans
Acquisitions Editor: Kayla Dos Santos
Editorial Project Manager: Leticia M. Lima
Production Project Manager: Surya Narayanan Jayachandran
Cover Designer: Greg Harris
Typeset by Aptara, New Delhi, India
3.5 Industrial fabrication routes
3.6 Recycling efforts, recovery, and reusability in production line
3.7 Applications of hexaferrites: present and perspectives
4 Modern Sm-Co permanent magnets
Jinfang Liu, Michael Walmer, Melania Jasinski
4.1 Introduction
4.2 Manufacturing process of Sm-Co magnets
4.3 High (BH)max Sm2Co17 type permanent magnets
4.4 Temperature compensated Sm-Co magnets
4.5 Ultra-high temperature Sm-Co magnets with small reversible temperature coefficient of Br
4.6 Performance of Sm-Co magnets in special environments
4.7 Laminated Sm-Co magnets
4.8 Additive manufacturing
4.9 Small magnets
4.10 Sm-Co nanoparticles and nanoflakes for nanocomposite magnets
5
Masato Sagawa, Yasuhiro Une
5.1 Introduction
5.2 History of the development of Nd-Fe-B
5.3 Compositions of the NdFeB sintered magnets and their magnetic properties
5.4 Production process for sintered NdFeB magnets
5.5 Progress in the microstructure investigation
5.6 Development of HRE-Free and reduced HRE magnets
5.7 Ultimate NdFeB sintered magnets for EV traction motors
6
6.1
6.2
6.3
6.4 Anisotropic hot deformed NdFeB
6.5
7
Thomas
7.1
7.2
Yutaka Yoshida, Norio Yoshikawa
Contributors
Alberto Bollero IMDEA Nanoscience, Madrid, Spain
J.M.D. Coey Trinity College, Dublin, Ireland
Steve Constantinides Honeoye, New York, United States
John J. Croat Naples, Florida, (USA)
Roderick G. Eggert Colorado School of Mines and Critical Materials Institute, Golden, Colorado, (USA)
Takahiko Iriyama Daido Steel Co., Ltd., Nagoya, Japan
Melania Jasinski Electron Energy Corporation, Landisville, PA, USA
Jinfang Liu Electron Energy Corporation, Landisville, PA, USA
Alexander H. King Iowa State University, Ames, Iowa, (USA)
Kalathur Narasimhan P2PTechnologies, Moorestown, NJ
John Ormerod JOC LLC, Loudon, Tennessee, (USA)
Ester M. Palmero IMDEA Nanoscience, Madrid, Spain
Masato Sagawa Daido Steel Co., Ltd., Nagoya, Japan
Thomas Schliesch Max Baermann GmbH, Bergisch-Gladbach, Germany
Yasuhiro Une Daido Steel Co., Ltd., Nagoya, Japan
Michael Walmer Electron Energy Corporation, Landisville, PA, USA
Yutaka Yoshida Daido Steel (America) Inc., Victoria, BC, Canada
Norio Yoshikawa Daido Electronics Co., Ltd., Nakatsugawa, Gifu, Japan
The history of permanent magnets
John J. Croata, John Ormerodb aNaples, Florida, (USA), bJOC LLC, Loudon, Tennessee, (USA)
1.1 Introduction
Modern permanent magnets are now a quintessential component in a wide spectrum of electomechanical devices including motors, generators, sensors, loudspeakers, instruments, traveling wave tubes, bearings and clutches that are used in a wide range of products ranging from automobiles to missiles. Rare earth permanent magnets have become a critical part of many high-tech products, including personal computers, MRI, high-capacity hard disk drives (HDD), wind power electric generators and hybrid and electric vehicle drive motors. In addition, high performance permanent magnets have allowed the miniaturization of many products such as laptop computers and other consumer electronic products. In fact, modern rare earth permanent magnets now play an increasingly important role as an enabler and driver of technology. Without NdFeB permanent magnets such products would not have developed or would not have developed nearly so rapidly. This book provides an overview of all of the commercially important families of permanent magnets that are currently manufactured. Although permanent magnets are now used in large quantities, the development and use of permanent magnets was a relatively slow process. The first permanent magnets known to humans were naturally occurring lodestones which are created when bolts of lightning struck deposits of the mineral magnetite (Fe3O4). Although there are reports about the magical attractive properties of lodestones that date to as early as the sixth century BC, it was not until about the 11th century AD that they were first used in compasses, the first practical use of a permanent magnet. Although the properties of lodestones are comparatively poor, it was not until the mid18th century that the first permanent magnets were produced with higher properties and it was not until the 1930s and the development of alnico magnets that magnetic properties increased to the point where engineers were able to use permanent magnets in electomechanical devices like motors and generators. Prior to this, permanent magnets properties were so low that engineers were forced to use electromagnets for these devices. It was not until the mid-20th century and the development of ferrite magnets that permanent magnets began to be used in significant quantities.
The increasing use and importance of permanent magnets has been driven largely by a significant increase in magnetic properties. This is shown in Fig. 1.1, which displays the chronological development of the various families of permanent magnets over time and presents a very graphic picture of the evolution that has occurred in permanent magnets in the last century. This chronology is expressed in terms of maximum energy product (BH)max, which is the figure of merit most frequently used to
https://doi.org/10.1016/B978-0-323-88658-1.00004-2
Fig. 1.1 The chronological development of permanent magnets since 1917.
rate and compare the various families and grades of magnets. This number is proportional to the energy stored in the magnet and, therefore, the work that can be done by the magnet. As seen in this figure, between about 1917 and 2000 the maximum energy product increased by about fifty times. Over the same time, intrinsic coercivity levels have increased by an almost 100 times, from about 250 Oersted to as high as 25,000 Oersted. The 1950s and 1960s saw the development of sintered ferrite magnets, one of the most important discoveries in the history of permanent magnets. These magnets are still the most commonly used in terms of volume, a testament to their unparalleled economic efficiency and chemical stability. In 2020, an estimated 900,000 tons of sintered ferrite magnets were produced. Another major step in the evolution of permanent magnets was the discovery of Sm-Co magnets in the 1960s and 1970s. The discovery of Sm-Co magnets stimulated a great period of basic research which eventually led to the discovery of NdFeB magnets. As seen in Fig. 1.1, between 1970 and 1990, energy products increased by a factor of 12 compared to those obtained by the best ferrite magnets. The last 50 years has also seen the development of various grades of bonded magnets produced by compression and injection molding techniques. The status and recent developments in all of these families of magnets are presented in the following chapters. Also included are four chapters of general interest. Chapter 2 provides a discussion of the fundamental properties of permanent magnets so that the non-specialist readers can more easily follow the discussion of the various families of magnets. In addition, Chapter 10 provides an overview of the situation regarding critical material used in magnets, including rare earths and cobalt. Today you will find many articles in the news about how important key materials are for many high technology products and permanent magnets are no exception. Since coating are required for most rare earth based permanent magnets, a review of current coating
and coating evaluation technology is provided in Chapter 11. Finally, a chapter on the markets and major applications for the various families of permanent magnets is provided in Chapter 12.
1.2 Lodestones: the first permanent magnets
As previously mentioned, the first permanent magnets known and used by humans were lodestones, which are naturally occurring magnetized pieces of the iron mineral magnetite (Fe3O4) (Mills 2003; NASA 2020). Lodestones typically contain small amounts of titanium or other elements which slightly increase the coercivity of the magnetite and make them less susceptible to demagnetization over time. It appears that unless these elements are present the magnetite does not have the properties necessary to become or stay permanently magnetized. Lodestones are believed to become magnetized when lightning strikes the surface of magnetite deposits. It is well known that there is a magnetic field associated with a bolt of lightning and the prevailing theory is that fragments of the magnetite rock are ejected from the deposit and these pieces become instantly magnetized by the lightning strike. The typical lodestone has relatively poor magnetic properties with a coercive force of about 50 Oersted and an energy product well below 1 MGOe (7.9 kJ/m3), too low to be included on the chart in Fig. 1.1. However they strongly attract other iron objects as shown in the photograph in Fig. 1.2. Since this is a natural process, lodestones are still being produced in magnetite deposits around the world. Lodestones also served another important role as the means by which the first steel magnets were magnetized. It is not known when humans first discovered the propertied of lodestones. One place where lodestones were commonly found was in the prefecture of Magnesia in the Greek province of Thessaly and the name magnet or magnes comes from this
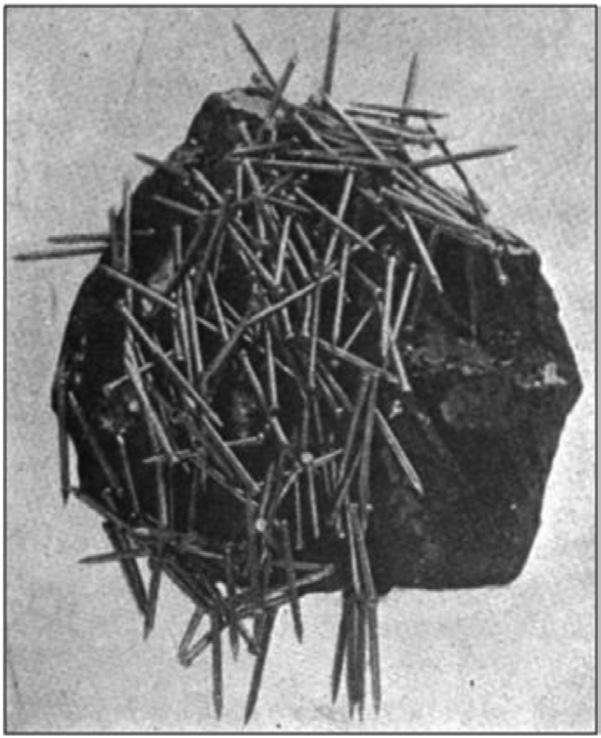
Fig. 1.2 A demonstration of the ability of loadstone to attract iron objects (Annet 1921).
region. The earliest known written reference to them was made by the sixth century BC Greek philosopher Thales of Miletus who reported on the ability of the lodestone to attract pieces of iron and other lodestones. Lodestones are also referred to in early Chinese chronicles that date to as early as the fourth century BC. Most historians credit the Chinese with the development of the first compasses but when they actually did this is still being debated. The first incontestable reference to the use of a magnetized needle for navigation appears in the Dream Pool Essay written by Song Dynasty writer Shea Kua in 1086 CE. This essay also describes how an iron needle was magnetized by rubbing it against a lodestone and then used in a compass by suspending it from a single silk thread. This was probably the world’s first practical use of a permanent magnet (Needham 1962; New World Encyclopedia 2020).
At this time historians are unsure if compass technology spread to the rest of the world or was independently discovered. Many historians believe that the technology was probably transferred to both Europe and the Islamic world from China by traders traveling down the Silk Roads. The earliest European reference to the compass used for navigation is found in the book De naturis rerum (on The Nature of Things) written by the English scholar Alexander Neckam in about 1190. However, he refers to the compass as a common navigation tool, an indication that it was being used somewhat earlier. One argument used for an indigenous European discovery is that the earliest European compasses had sixteen basic divisions whereas early Chinese versions had twenty-four In the Islamic world, the earliest reference to the use of a compass for navigation is found in The Book of the Merchant’s Treasure, written by Baylak al-Kibjaki in about 1282. However, the author describes having witnessed the use of a compass on a ship some forty years earlier. By the late-12th century the compass became widely used for navigation and is believed to have resulted in a significant increase in world trade.
1.3 Early permanent magnet studies
Humans had long recognized that there appeared to have two distinct poles on lodestone magnets and came to call them south-seeking and north-seeking poles. They also tried to find a magnetic monopole by cutting the magnets in two. Of course, they simply produced two new magnets that seemed to have weaker properties. For some time scholars and navigators did not understand why the magnet rotated into a north-south direction and some, including the Italian explorer Christopher Columbus, speculated that the magnets were being oriented by the north star, which they believed must be a giant celestial magnet. The first serious study of permanent magnets was carried out by the English physician and scholar William Gilbert near the end of the 15th century. Gilbert had a great interest in magnets and the strange directional properties of the compass needle. Some of his early discoveries were that the magnetic strength of lodestones could be increased by adding iron tips or keepers and reported that doing so could increase the weight of iron that could be lifted by a lodestone by a factor of five. He also discovered that the magnetism of a lodestone could be destroyed by heating to high temperature. He also reinvented the method of magnetizing iron needles by
rubbing them with lodestone, a practice first used by the Chinese. Gilbert was also the first to recognize that the best artificial magnets were produced from “hardened iron” which contained higher levels of carbon as opposed to “soft iron” which contained lower levels of carbon. Of course, the higher carbon levels resulted in slighter higher coercivity, enabling the magnet to retain its magnetization.
One of his most important experiments was to trace the magnetic field of a spherical piece of lodestone with a compass. He discovered that magnetic flux lines extended from the poles and were circular in shape and from this he eventually made his most important discovery, that the earth itself was a great magnet with a north and south pole. For the first time it was known why a compass aligned itself in a north-south direction. He published his extensive work in the book De Magnete, Magneticisque Corporibus, et de Magno Magnete Tellure (On the Magnet and Magnetic Bodies and on That Great Magnet the Earth) (Gilbert 1600). This book became the most influential book on magnetism for the next two centuries and shattered many popular myths and theories that were prevalent at the time. These included the widely held belief that a magnetic field could cure common diseases and that garlic, goat’s blood or diamonds could counteract a magnetic field. In an age when much that was written about permanent magnets was little more than superstition, Gilbert’s work stands out as one of careful scientific inquiry.
The Relationship between Magnetism and Electricity: Gilbert also had an interest in the properties of static electricity. He carefully observed the attraction between two pieces of amber that had been rubbed to build up a charge of static electricity but concluded that this force was different than that between two magnetized bodies. Among his observations was that the electric force was a surface phenomenon whereas the magnetic force was a property of the entire body of the magnet. He also noted that the electric force (the spark of electricity) became dissipated when transferred to another body but the magnetic force remained constant when interacting with another iron body. He was the first to use the terms “electric force” and “electric attraction” to describe the attraction between the two pieces of amber. To describe this electric attraction he coined the word electricus which means “like amber” from the Greek word elektron for amber. Albert’s book De Magnete would provide the first tentative studies of both magnetism and electricity and he sensed that they were somehow connected. However, it would be almost two centuries after publication of this book before scientists would discover the close relationship between electricity and magnetism.
One of the most important events leading to this discovery was the development of the first battery by the Italian physicist Alessandra Volta in the year 1800. His-early batteries consisted of two dissimilar metals immersed in an electrolyte. Although he investigated many different combinations, his best results were obtained using plates of zinc and copper with either a weak sulfuric acid solution or salt brine electrolyte. The importance of the development was that it allowed the production of a continuous electric current for the first time. All previous electricity studies were carried out on static electricity obtained by rubbing an object like amber. In 1820 the Danish physicist Hans Christian Oersted discovered that electricity passing through a conductor produced a magnetic field by observing that the flowing current deflected the
needle of a compass. This demonstration would not have been possible without the development of the battery by Volta. Later in the same year the French physicists Jean-Baptiste Biot and Felix Savant discovered that a current-carrying wire exerts a magnetic force that is inversely proportional to the distance from the wire. This was a very important discovery because it demonstrated for the first time the possibility that electricity and magnetism could be combined to do work. Also during the 1820s, the French physicist Andre-Marie Ampere measured the force between two current carrying conductors and developed Ampere’s Law, the first mathematical equation establishing the relationship between electricity and magnetism. This law provided a way to calculate the magnetic field that is produced as a result of an electric current moving through a wire of any shape, including a solenoid.
These early discoveries eventually led to the invention of the electromagnet by the Englishman William Sturgeon in 1824. The invention of the electromagnet was one of the most important developments in the history of magnetism because it led to the development of the first important electromechanical devices, including the first practical electric motors. A rendering of Sturgeon’s first electromagnet from a paper that he gave to the Royal Society in London in 1824 is shown in Fig. 1.3. Sturgeon activated the electromagnet by turning on the current from a batter through a switch which consisted of a small cup of liquid mercury. We see again how important the development of the battery was to the future understanding of electricity. Without the battery to provide a steady current, Sturgeon’s and other experiments involving the study of electricity could not have taken place.
In combination these pioneering discoveries led to the first primitive electomechanical devices, including electric motors and generators. Although the electric motor resulted from the combined inventions and innovations of many different scientists, credit for the first working motors go to the Prussian scientist Moritz Jacobi in 1834 who built a motor rated at 15 W to power a boat. In the same year the
Fig. 1.3 A rendering of William Sturgeon’s first electromagnet (Henry 1824).
American team of Thomas Davenport and Orange Smiley built a motor rated at 4.5 W. Their motors could rotate at 1000 rpm and were used to power a number of devices, including a printing press. Although these early electric motors used both steel bar magnets and electromagnets for their magnetic circuit, the permanent magnets did not have the strength to provide high performance and were soon replaced entirely by electromagnets. It was not until the discovery of alnico magnets in the 1930s that permanent magnets once again came to be used in motors. Of course, today electric motors are by far the largest single application for permanent magnets, accounting for an estimated 45 percent of the production of all types of magnets by volume.
1.4 The era of steel permanent magnets
Compound Steel Magnets: The first commercially available permanent magnets were compound steel magnets produced by bundling together a number of small iron rods or needles that were magnetized by rubbing them unidirectionally with a lodestone magnet. These magnets were referred to as “artificial magnets” and there were a number of techniques used to produce them. One of the most effective was placing one end of the iron rod in contact with one pole of a lodestone and then repeatedly rubbing along the length of the iron rod or needle. The rubbing is believed to slightly heated or vibrated the iron rod, causing the domain walls to move more easily and magnetize the iron. Evidence for this is that if oil or other lubricant was applied to the iron before the rubbing, the magnetization achieved was much reduced. Although artificial steel magnets were produced by this technique in many different regions, notably France and Russia, it was in England that the technology reached its zenith and London eventually became the center for the world’s first permanent magnet industry. This would have been near the start of the Industrial Revolution which is usually considered to have begun in England and Scotland in about 1750.
The first person to produce large compound magnets by bundling together a number of smaller iron magnets was the Englishman Servinton Savery in the 1730s (Savery 1730). Savory used lodestones to magnetize small iron rods measuring about 1.25 mm (1/20 inch) in diameter x 70 mm (2–¾ inch) in length. He then assembled 37 of these small rods in rectangular shaped bundles. To increase the holding power of his magnets, Savory attached soft iron keepers to the ends in the same manner as Gilbert. He then used these large bundles to magnetize larger solid iron bar magnets by what he referred as the “divided touch” method. This method, involved positioning two of these bundled magnets with opposing polarity over the iron bar to be magnetized and then drawing the two magnets apart. A small gap was left between the two poles of the magnets as shown in the drawing in Fig. 1.4(a). Because of the high permeability of iron, the magnetic field produced by the two magnet bundles would not penetrate very deeply into the iron bar being magnetized, greatly limiting the thickness of the iron bars that could be fully. magnetized. However Savory is reported to have produced iron bar magnets measuring as large as 400 × 19 × 19 mm (16 × 3/4 × ¾ inch) by his divided touch technique and that these magnets had substantial holding power.
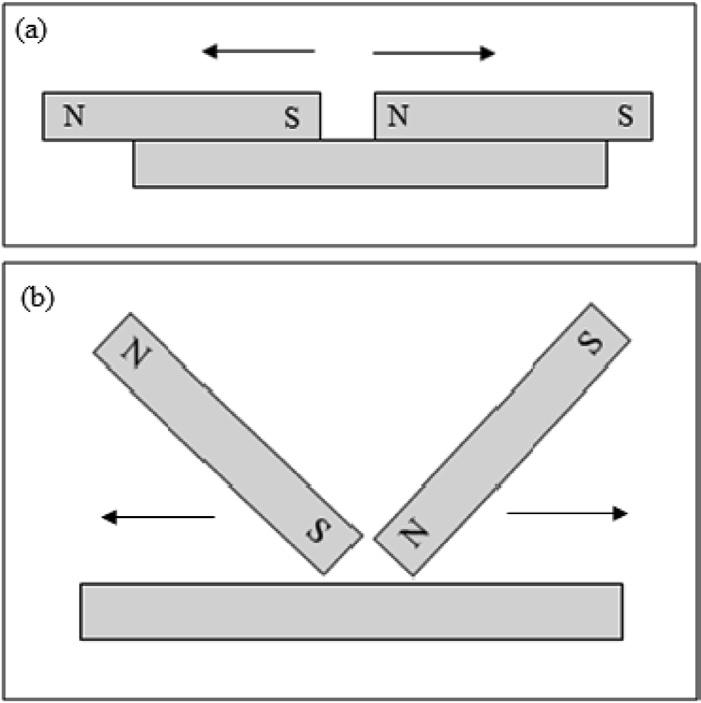
Fig. 1.4 (a) The divided touch method used by Servinton Savery. (b) The modified divided touch method used by Gowin Knight.
Another Englishman who became particularly renowned for the manufacture of large magnets from hardened steel was Gowin Knight (1713–72) (Knight 1744). Like Savory, he produced large magnets by bundling together smaller magnets that were also magnetized by the divided touch method. However, he developed a modification of Savory’s technique which involved positioning two bundled magnets at an angle relative to the surface of the bar to be magnetized. This technique is shown in Fig. 1.4(b). Knight used this technique to produce quite powerful bar magnets typically measuring 38 × 1.27 × 0.635 cm (15 × 1/2 × ¼ inch) which he sold for 10 guineas each, a considerable sum in 18th century England. These iron bar magnets were quite powerful and one is reported as being able to lift 28 times its weight of iron. Knight actually kept this technique a secret during his working life but it was revealed by an associate following his death in 1772. Although Knight produced very powerful bar magnets for the time, he was most renowned for building very large compound magnets by bundling together his bar magnets. His-largest was a magnet measuring 1.6 × 0.15 × 0.1 m (5 foot 4 inches x 6 inches x 4 inches). This magnet was comprised of 480 separate bar magnets and was eventually used by Michael Faraday for some of his experiments involving magnetism. Gowin eventually became wealthy by manufacturing not only large magnets but also high quality compasses for sailing ships, particularly for the British Royal Navy.
Steel Alloy Magnets: An important step in the history of permanent magnets was the development of the first steel alloy magnets during the 19th century. This development was made possible because metal workers were finally able to build furnaces that could exceed 1,538 °C (2,800 F), the melting point of iron. The first of these steel alloy magnets were tungsten magnets containing about 0.6 wt. percent carbon and 5.0 to 5.5 wt. percent tungsten. Magnets with Hci = 70 Oe (5.6 kA/m), Br = 9.5 kG (0.95 T) and BHmax = 0.39 MGOe (3.1 kJ/m3) were obtained. These magnets, which were developed in Germany and Austria between 1883–85, were the first important alloy magnets. By about 1885 chromium steel magnets contained about 6.0 wt.
percent Cr, were also developed. These magnets became particularly popular during World War I when the supply of tungsten became limited.
The next important steel alloy magnet development took place in Japan where physicist Kotaro Honda invented KS steel permanent magnets in 1917 (Honda and Saitô 1920). The typical composition of these steel magnets was 0.4–0.8 wt. percent carbon, 30–40 wt. percent cobalt, 5–9 wt. percent. tungsten, 1.5–3 wt. percent chromium with the balance iron. The cast magnets were tempered by heating at 950 °C and then quenching in heavy oil. Magnets with a cobalt content of 30 percent achieved Hci = 250 Oe (20 kA/m), Br = 9.0 kG (0.9 T) and (BH)max = 0.94 MGOe (7.5 kJ/m3). The coercivity values achieved were roughly three times those obtained with tungsten steel magnets. KS magnets were the first permanent magnets developed with an energy product close to 1 MGOe and is the first permanent magnet with an energy product high enough to be included on this chart in Fig. 1.1. These permanent magnets are those designated KS-Steel, where KS stands for Kichizaemon Sumitomo, who was the head of the family that provided financial support for the research leading to the invention. The development of KS steel magnets would be the first in a long list of permanent magnet discoveries by Japanese scientists that occurred during the 20th century.
1.5 The discovery of alnico permanent magnets
One of the most historically important families of permanent magnets are Alnico magnets, which are iron alloys containing Al, Ni and Co. They are characterized by high magnetic remanence but low coercivity. Because of the low coercive force, they are subject to demagnetization and must be used in a closed magnetic circuit or with a high length/diameter ratio. Alnico alloys have some of the highest Curie temperatures of any magnetic material, around 800 °C (1,470 F), although the maximal working temperature is normally limited to around 525 °C (975 F). Until the discovery of Sm-Co magnets in the 1970s they were the strongest permanent magnets available and were the first magnets used in large amounts in electromechanical devices like motors and sensors. The first alnico magnets were produced by the Japanese metallurgist Tokushichi Mishima in 1932 (Mishima 1932). His-first magnets were cast, isotropic alloys containing 25 at. percent nickel, 10 at. percent aluminum with the balance Fe. These alloys achieved an energy product of about 1 MGOe and a coercive force of about 400 Oe (32 kA/m), which was almost twice that of the best steel magnets available at that time. These are the MK-Steel magnets referred to in Fig. 1.1 where MK is an acronym for Mitsujima ka magnetic, ‘Mitsujima ka’ being the name of Mishima’s childhood home. These magnets were greatly improved by adding cobalt, which substituted for part of the iron, and the addition of Cu and other additive like Ti and Nb to improve the coercivity. By the end of the 1930s Alnico magnets with energy products between 1.5 and 1.8 MGOe (12 and 14.3 kJ/m3) were being produced on a commercial basis.
In 1938, a major advancement in these materials occurred when it was discovered that anisotropic alnico magnets could be produced by annealing the alloys in a magnetic field (Oliver and Sheldon 1938). This discovery led to the development of
permanent magnets with energy products that were up 5 MGOe (40 kJ/m3). These anisotropic magnets eventually became known as Alnico 5 through 9 grades of magnets. Further improvements to these anisotropic magnets was made by directional cooling of the cast alloys before annealing in a magnetic field. Energy products as high as 11 MGOe (87 kJ/m3) were produced and these are the magnets designated Columnar-Alnico in Fig. 1.1. Continued development eventually led to alnico magnets with energy products as high as 13 MGOe (103.5 kJ/m3) with Br = 11.5 kG (1.15 T) and Hci = 1.5 kOe (119 kA/m).
Most alnico magnets are produced by casting in sand molds. After removing from the molds the magnets are first given a high temperature solutioning treatment at about 1,250 °C . The magnets are then slowly cooled (1–1.5 °C/min.) from about 850 to 750 °C in a magnetic field of about 1,500 Gauss. The magnets are then given a hear treatment to improve coercivity. This varies between manufacturers but a typical hear treatment might be to hold for 2 h at 625 °C, then cool over a period of 6 h to 560 °C and then hold at 560 °C for 16 h. In some instances a chill plate is added to the bottom of the molds during the casting process to achieve a degree of directional cooling. This is one means by which columnar alnico magnets are produced. These magnets have the highest Br values of the various grades of alnico magnets
The hard magnetic properties of alnico magnets rely on the shape anisotropy associated with a two phase nanostructure comprising ferromagnetic Fe-Co needles in a matrix of weakly magnetic Al-Ni. A TEM of the typical anisotropic microstructure that forms when these materials are annealed in a magnetic field is shown in Fig. 1.5. The micrograph is for an Alnico 8 type alloy with a composition of 36.2 wt. percent cobalt, 14.0 wt. percent nickel, 6.6 wt. percent aluminum, 5.0 wt. percent titanium and 3.0 wt. percent Co after annealing in a magnetic field of 1,500 Gauss. The average width and length of the needles are about 50 nm (0.05 μm) and 500 nm (0.5 μm), respectively. It is this high L/D ration which provides the high shape anisotropy and the source of the coercive force in these type materials. The coercivity mechanism in
Fig. 1.5 TEM of the microstructure that forms in an alnico magnet when the alloy is annealed in the presence of a magnetic field (Iwama and Takeuchi 1974).
these materials is based on highly anisotropic rods which are isolated from each other by the Ni-Al phase. This isolation decreases exchange interaction between the rods and increases coercivity. This two-phase microstructure forms by a spinodal reaction, which is a type of solid state reaction where a single phase alloy transforms into two alloys with different compositions by a diffusion process. This is distinct from a eutectoid reaction where two different phases form from a single phase by a nucleation and growth process.
Although few alnico magnets are produced today, the discovery and development of these materials was a very important step in the evolution of permanent magnet materials. Before their discovery, the use of permanent magnets was limited to a few applications such as the compass. With its introduction, however, it became possible to replace electromagnets with permanent magnets and the use of permanent magnets started to become widespread in devices such as loudspeakers, electric motors, micro- phones, sensors, gauges and traveling wave tubes. The air core gauges used for the speedometer and fuel gauges in automobiles used alnico magnets for decades. However, the discovery of rare earth cobalt magnets starting with SmCo5 in the 1970s greatly impacted sales of alnico magnets and today they comprise a relatively small share of the magnet market. For this reason, no separate chapter highlighting this historically important family of permanent magnets has been included in this volume.
1.6 The discovery of hard ferrite magnets
Clearly, one of the most important families of permanent magnets ever developed are hard ferrite or ceramic magnets. Discovery of the first ceramic magnet is credited to Yogoro Kato and Takeshi Takei of the Tokyo Institute of Technology in 1930. This discovery eventually led to the founding of the TDK Corporation in 1935. However, these first ferrite magnets were based on compounds with the general formula MFe2O4 where M can be a divalent metal ion like Mn+2, Ni+2, Co+2, Cu+2 and Fe+2 and often a combination of these metal ions. The ferrite magnets developed by the Tokyo Institute of Technology used cobalt as the metal ion and these are the magnets listed as Co-Ferrite in Fig. 1.1. These cobalt ferrite magnets were also named OP magnets after Ookayama, the name of the town where the Tokyo Institute of Technology is located. The properties of these early cobalt-ferrite magnets, however, were fairly poor with energy products of only about 1 MGOe. For this reason very few appear to have been produced.
Modern ferrites magnets are M-type ferrites produced from the hexaferrite structure represented by the formula MFe12O19. This structure is highly anisotropic with the easy magnetic direction along the c axis. Credit for the discovery of these materials is generally given to the Phillips Research Laboratories in the Netherlands in the 1950s (Went et al., 1952). The first ferrite magnets produced by Phillips were based on barium hexaferrite (BaFe12O19) which was found to develop a coercivity as high as 2,100 Oersted (~170 kA/m). Phillips began marketing barium ferrite magnets under the trade name Ferroxdure in 1952. Because the material combined good magnetic properties with low cost, there was a rapid increase in sales. In the 1960s Phillips
Permanent Magnets
introduced an improved ferrite magnet based on strontium hexaferrite (SrFe12O19). A key advantage of strontium ferrite is that the magnetocrystalline anisotropy is about 10 percent higher than for barium. Energy products of up to 4 MGOe (31.8 kJ/m3) were achieved and these two grades of permanent magnets soon came to dominate the world market for permanent magnets. In the last several decades strontium ferrite magnet have been further improved with additions of La and Co. Commercial magnets with Br as high as 4,500 Gauss (0.453 T) and Hci as high as 5,500 Oe (537 kA/m) are now being commercially produced. Despite the much higher magnetic properties of modern rare earth magnets, hard ferrite magnets still constitute over 90 percent of worldwide permanent magnet production by volume, a testament to their unsurpassed cost efficiency. Another key advantage of ferrites is their unparalleled chemical stability in all kinds of environments. In 2020 roughly 900,000 tons of sintered ferrite magnets were produced for a wide variety of applications. The largest single application is automobiles where they are used in millions of brush-type motors that are used for, among others, environmental, window lift and seat adjust features. Other major automotive applications include actuators for features such as door locks and fluid level indicators. Modern automobiles contain on average a total of about 35 electric motors and actuators. An update on this important family of permanent magnets is provided in Chapter 3: Recent Advances in Hard Ferrite Magnets.
1.7 The discovery of Sm-Co permanent magnets
It is generally agreed that the history of rare earth-transition metal permanent magnets began with the discovery by Karl Strnat in 1967 of the extremely large magnetocrystalline anisotropy of ~ 130 kOe (10,345 kA/m) for YCo5 (Hoffer and Strnat 1966; Strnat, Hoffer and Ray 1966). This work was carried out at the Wright Patterson Air Force Base in Dayton, Ohio and their experimental results on a single crystal of YCo5 are shown in Fig. 1.6. Because the highest field that they had available was 45 kOe,
Fig. 1.6 Easy and hard magnetization curves of the YCo5 intermetallic compound from which the magnetocrystalline anisotropy HA was experimentally determined (Hoffer and Strnat 1966).
the magnetocrystalline anisotropy was determined by extrapolating the hard axis data until it crossed the easy axis curve. It is often said that these magnets were the first truly modern magnets, owing to their much higher magnetic energies and because the origin of the coercive force is the magnetocrystalline anisotropy of the rare earth ions. For the rare earths with unpaired 4f electrons, spin-orbit coupling results in highly anisotropic wave functions. In regard to permanent magnets, these wave functions are the most important characteristic of the rare earths since they are the origin of the coercive force in rare earth-transition metal compounds.
Prior to the 1960s, there were few studies of rare earth-intermetallic compounds because of the limited availability of pure rare earth metals. This lack of availability resulted from the fact that the rare earth are found in nature intimately mixed together and their physical properties made it virtually impossible to separate them by normal chemical or metallurgical techniques. However, techniques were developed in the late 1950s to separate the rare earths from each other using an ion exchange process Following this, extensive research work began on determining the properties of all of the pure rare earths and eventually rare earth intermetallic compounds. Researchers soon found that the rare earths have a remarkable disposition to form a wide variety of stable phases with well-defined stoichiometric ratios between the two elements. This is believed due to the large difference in their ionic sizes, resulting in a wide variety of possible arrangements for filling space. Today several thousand rare earth compounds have been reported and these compounds are found to have a wide range of properties, including magnetic and transport properties. Of this early research, investigations involving combinations of rare earths with the magnetic transition metal elements Fe, Co, Ni and Mn were of the most interest for the future development of rare earth permanent magnets, although this was not initially recognized. The first pioneering studies of rare earth-3d transition metal compounds, particularly the magnetic 3d transition metals Fe and Co, are believed to have begun with the studies by Nesbitt, Wernick and Corenzwit (1959) and Nesbit, Williams, Wernick and Sherwood (1961, 1962) at the Bell Laboratories, Murray Hill, New Jersey. This was shortly followed by similar studies by Hubbard, Adams and Gilfrick (1960) at the Naval Research Laboratories in Washington DC and Nassau, Cherry and Wallace (1960) at Carnegie Mellon University in Pittsburg. These studies found that it was possible to produce compounds which were ferromagnetic or ferrimagnetic and with Curie temperatures greater than 200 °C.
Although it was known that the rare earths had large magnetic moments and magnetocrystalline anisotropies, their ordering temperatures were found to be regrettably low because of the weak 4f-4f interaction: the highest Curie temperature for the rare earth metals is only 16 °C for Gd. The reason that the 4f-4f interaction is so weak is that the 4f wave functions are deeply embedded in the nucleus of the rare earth ions and interaction occurs via indirect exchange with the conduction electrons. However, early researches immediately saw the possibility of raising the ordering temperature of the rare earths by combining them with these 3d transition metals which have strong 3d-3d exchange interaction and, therefore, much higher Curie temperatures. It is the electric field from the neighboring 3d transition metal ions acting of these 4f orbitals that give rise to the large magnetocrystalline anisotropies in rare earth-3d
transition metal compounds. In summary, in the rare earth ions, the moment is from the 4f elections, but the exchange interaction is mediated via the conduction electrons, while in the 3d transition metals, the conduction electrons are the source of both the magnetic moment and the exchange interaction. In this sense, the transition metal sublattice in the R-TM compounds provides both a higher Curie temperature and stabilizes the anisotropy at a higher temperature.
SmCo5 Permanent Magnets: Very soon after the publication of the results shown in Fig. 1.7, Velge and Buschow (1968) at the Phillips Research Laboratories in the Netherlands reported producing a SmCo5 magnet with an energy product of 8.1 MGOe (64.5 kJ/m3) and an intrinsic coercivity of 5.2 kOe (413.8 kA/m). This magnet, which was produced from SmCo5 powder that was aligned and compacted in a magnetic field, appears to have been the first SmCo5 magnet ever produced. In 1969, Buschow, Naasterpad and Westendorp (1969) reported producing a SmCo5 magnet with an energy product of over 18 MGOe (143 kJ/m3) and an intrinsic coercivity of 5.2 kOe. In the same year Das reported producing a SmCo5 magnet with an energy product of 20 MGOe (159 kJ/m3) while working at the Raytheon Corp. in Waltham, Massachusetts (Das 1969). The team of Benz and Martin at the General Electric Research Center in Schenectady, New York were the first to produce SmCo5 magnets using the important liquid-phase sintering technique, which became the standard process for all types of Sm-Co magnets, and later for sintered Nd-Fe-B permanent magnets (Benz and Martin 1970). They were also the first to extensively study the mechanism of the liquid phase sintering process and the first to achieve an energy product between 24–25 MGOe (191–199 kJ/m3), which is the typical energy product of early SmCo5 production magnets.
This liquid phase sintering process involved starting with an homogenized SmCo5 alloy containing a small amount of the lower melting Sm2Co7 phase. This alloy was
Fig. 1.7 (a) Hexagonal unit cell of the SmCo5 intermetallic phase (adapted from Kirchmeyer and Burzo 1990). (b) Rhombohedral unit cell of the Th2Zn17 structure (Herbst et al., 1982).
ground to a fine particle size between 5 and 10 μm and compacted while applying as strong a magnetic field as possible. The green compact was then sintered in an argon atmosphere at a temperature between 1,100 and 1,150 °C for about one hour. At these temperatures the lower melting Sm2Co7 phase creates a liquid or near liquid phase at the grain boundaries between the SmCo5 grains. This liquid phase accelerates the consolidation of the individual SmCo5 grains, resulting in an almost 100 percent dense magnet with greatly reduced porosity and improved temperature aging properties. This process soon became the standard for the production of all SmCo5 type permanent magnets and is also used today to produce sintered NdFeB magnets.
As mentioned, the rare earth in combination with transition metals have a remarkable disposition to form a wide variety of stable phases. The Sm-Co alloy system is an excellent example of this, forming a large number of intermetallic compounds which include Sm2Co17,SmCo5, Sm2Co7, SmCo3, SmCo2, Sm9Co4 and Sm3Co. Buschow and Van der Goot (1969) were the first to systematically study the complete Sm-Co alloy system and reported the first tentative phase diagram, which showed all of the existing intermetallic compounds and the crystal structure of all but the Sm9Co4 compound. They reported that all of the rare earths except La, Eu and Tb form the same CaCu5 structure as YCo5. Fig. 1.7(a) shows this important hexagonal structure which forms for all of the RCo5 intermetallic compounds. The unit cell of this structure has only one rare earth site (1a), but two Co sites (2c and 3 g). There are two different layer types: the base consists of both R (1a) and Co (2c) atoms while the mid- layers consist exclusively of Co atoms on the 3 g sites. Fig. 1.7(a) also highlights the hexagonal rings which surround each of the Sm atoms and which forms exclusively from the Co (2c) atoms.
All of the rare earths except La, Eu and Yb also form the R2Co17 compounds. These compounds are isomorphic with the Th2Zn17 (space group R3m) structure for R = Y, Nd, Pr, Sm, Gd and Tb and the Th2Ni17 (space group P63/mnc) structure for R = Ho, Er, Tm and Lu. Fig. 1.7(b) shows the hexagonal (tripled rhombohedra) unit cell of the Th2Zn17 structure which consists of a six-layer repeat unit with only one rare earth site but four crystallographically distinct transition metal sites: c, d, f and h types, whose whole number of equivalent positions are 6, 9. 18 and 18, respectively. All of the rare earth atoms occur in three layers at z = 0.0, 0.33 and 0.66. The two structures are closely related and the Sm2Co17 structure forms from the RCo5 structure by the ordered substitution of one third of the Sm atoms in the SmCo5 structure with pairs (dumbbells) of Co atoms which reside on the 6c sites. One such dumbbell is shown in position over the Sm that it displaces in Fig. 1.7(a). These Co dumbbells are important structural components in that they are responsible for the strong planar magnetic anisotropy of the Co sublattice in R2Co17 intermetallic compounds. There are also structural similarities between the Th2Zn17 and the Nd2Fe14B structure.
Sm2Co17 Based Permanent Magnets: Shortly after the development of SmCo5 permanent magnets in the early 1970′s, researchers turned their attention to the Sm2Co17 intermetallic phase. This compound had all of the fundamental requirements needed for possible development into a permanent magnet, notably a hexagonal crystal structure with uniaxial symmetry, a high saturation magnetization of 1.25T, a high Cure temperature of 917 °C and a magnetocrystalline anisotropy of ~ 60 kOe (Strnat 1972).