DFCI FUTURE CANCER HOSPITAL DESIGN-ASSIST
PARTNER
April 3, 2025
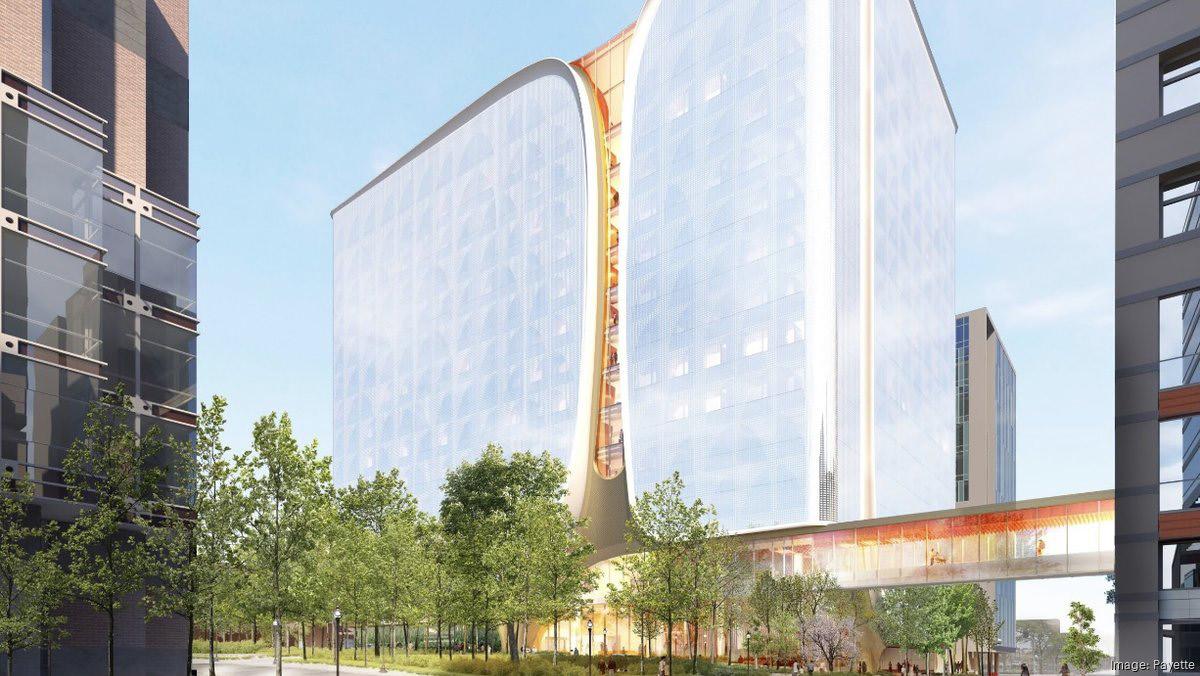
TRADE
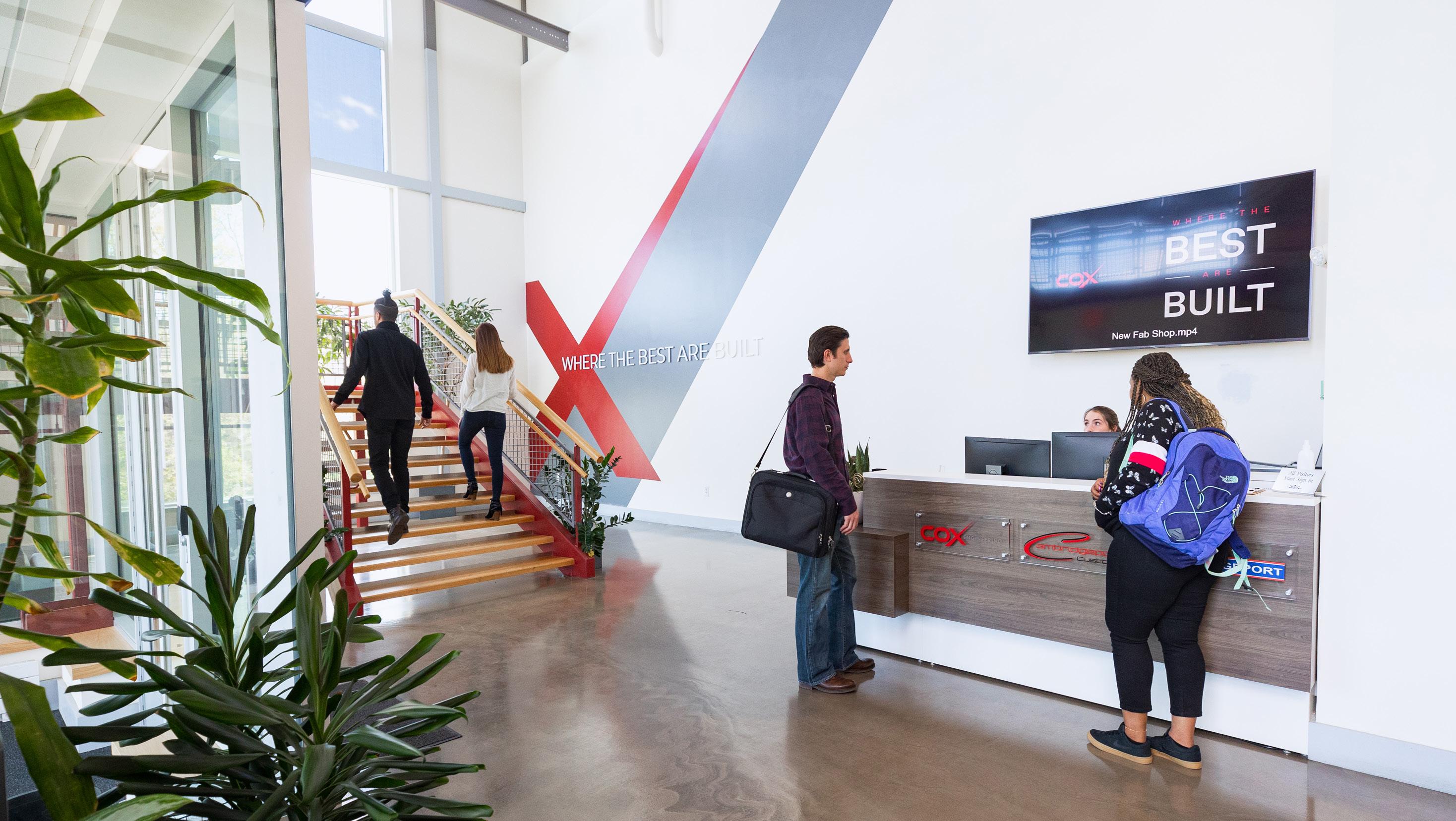

April 3, 2025
NEIL JOHNSON
President
Preconstruction Manager
RICH MOURADIAN
Vice President, Business Development
JEREMY STORM
Lead Mechanical Coordinator
Operations Manager
- $43M ($18M Core + Shell / $25M Fit-Out)
- 289,000 SF Total
- Field Labor Mgmt. (SM - 26) (Pipe - 20)
- Trade Partners Managed
• ATC / INS / TAB / RIG
- 9-story building with 3 levels underground parking
- Subcontracted on the fly to perform the entire fit-out in a Design Assist role.
- Worked simultaneously with separate crews for both C/S and multiple floors.
- $9.5M
- 2 floors / 59,000 SF each
- Field Labor Mgmt. (SM - 18) (Pipe - 20)
- Trade Partners Managed
• ATC / INS / TAB
- Design-Assist
- Cox assisted with the budget phases and helped Commodore establish and maintain the budget.
- Originally built for office space. Slab to Slab heights made it challenging for CAD dept to fit all of the mechanicals in the ceiling plenum.
- $9.9M - 51,000 SF
- Field Labor Mgmt. (SM - 20) (Pipe - 22)
- Trade Partners Managed
• ATC / INS / TAB / RIG
- $11M - 78,000 SF
- Field Labor Mgmt. (SM - 10) (Pipe - 12)
- Trade Partners Managed
• ATC / INS / TAB / RIG
- $28.2M
- 600,000 SF
- Field Labor Mgmt. (SM - 14) (Pipe - 20)
- Trade Partners Managed
• ATC / INS / TAB / RIG
- 14-story core/shell Life Science building with 2-story penthouse
- Suffolk Construction
- Prefab to accommodate build schedule
- Rig and install pipe, ducts, supports, and equipment
- $22M
- 42,000 SF
- Field Labor Mgmt. (SM - 14) (Pipe - 18)
- Trade Partners Managed
• INS / TAB / RIG
- Warehouse renovation to manufacturing center
- Accelerated schedule to bring equipment inside
- Coordination of supplemental steel support, including options for bottom-ofpipe and duct supports
- $35.5M
- 310,000 SF
- Field Labor Mgmt. (SM - 14) (Pipe - 18)
- Trade Partners Managed
• ATC / INS / TAB / RIG
- 12-story building housing lab, office, research, and development space
- Suffolk Construction - Complex coordination of equipment, high-pressure steam pipe installation
- Rigging large equipment to the roof
• Boston Medical Center
• Boston Children’s Hospital
• Massachusetts General Hospital
• Dana-Farber Cancer Institute
• Lahey Hospital & Medical Center
• Beth Israel Deaconess Medical Center
• St. Elizabeth Medical Center
• Newton Wellesley Hospital
• Brigham and Women’s
• Faulkner Hospital
• New England Baptist Hospital
• Mass Eye & Ear
LEAD COORDINATOR
PIPE COORDINATOR
DESIGN ASSIST TEAM PRIMARY CONTACTS
PROJECT EXECUTIVE
PRECONSTRUCTION
PIPE DETAILERS
DESIGN ASSIST TEAM SUPPORT
PRECONSTRUCTION
SHEET METAL DETAILERS
SHOP FAB MANAGER
TIM WALSH
GENERAL FOREMAN
SHAWN LALLY
PIPE SUPERVISOR
JASON RAFFAELO
PROJECT MANAGER
STEFFAN HERTER
ASST. PROJECT MGR
OWEN SULLIVAN
SHEET METAL FOREMAN
KEVIN CHAPLIN
SM SUPERVISOR
PAT SUGHRUE
PRECONSTRUCTION MGR
DOUG ROSE
ESTIMATORS
SM/PIPE ESTIMATORS
LEAD START UP TECH
TONY ELLISON
OPERATIONS MGR
SEAN BAYLES
VP CONST & BD
RICH MOURADIAN
CONST. EXECUTIVE
RYAN GOBBI
NEIL JOHNSON PRESIDENT
• Submitted RFl’s are always accompanied by proposed solutions.
• Cox will manage an issue log to limit RFI paperwork log jams.
• Cox Shop Foremen and Field Foremen are engaged to investigate prefabrication and modularization opportunities and provide constructability review.
• Consistent engagement / contact with the design team to eliminate unnecessary intent questions, confirmations, constructability issues.
• Provide Coordination support for spatial constructability.
• Target Value Design.
o Transparent budget control report management
o Value added solution option pricing validation
o Coordinate bidding, leveling, and presenting options for equipment and sub-trades within the budget.
o Vetting of early equipment release packages/Vendor engagement and management
• Site logistics, schedule validation support
• Field manpower loaded and cash flow schedules
• PVF Review: Ensure all services are covered in the CD Set and DA Process.
• Preliminary Point Loading
• Insulation Review: Verify that all services requiring insulation are addressed in the CD Set and DA process.
• HVAC Riser Layout: Confirm fit, spacing, supports, and coordination with structural layout. Provide formal drawings for slab openings and sleeving.
• Fuel Oil System:
o Confirm pipe sizing, containment, and insulation/wrap requirements.
o Coordinate with Waldman for equipment access and code clearance.
o Coordinate mechanical corridors with other trades.
o Confirm fuel oil fill boxes, venting layout, and flow diagram review.
• Equipment Piping Review: Provide feedback on details and clarifications to avoid RFIs.
• Flow Diagram Review: Address uncertainties to prevent RFIs for the CD Set.
• Rated space delineation / confirmation.
• Mechanical Skids
o Misc. equipment skids
o Pre-mounted pumps on concrete inertia bases poured at the fabrication facility with manifolded pump trim.
• Piping and Duct riser assembly modules (RAM’s).
• Penthouse/Mechanical Rooms (anything in a box!!)
• Modular multi-trade racks.
o Pipe and duct racks including all required valves, taps, insulation, ID’s (all pretested and certified)
• VAV/FPT/FCU terminal units with pre-piped coil connections/trim.
• Traditional piping spools and sheet metal manifolds.
• Pre-assembled and batched hangers, supports and supplemental steel.
• Sound attenuator and inlet/outlet fittings pre-mounted on terminal units.
• Coordination & Planning:
o Coordinate with the GC and trades for tower crane scheduling.
o Maximize prefab and manifold use to reduce picks and speed up installation.
• Strategic Rigging:
o Begin rigging mechanical rooms furthest from access points.
o Prioritize prefab duct and pipe for crane rigging; use hoists for smaller items.
• Key Considerations:
o Identify structural updates early (e.g., riser openings, steel changes).
o Plan leave-outs for shafts, knee walls, and overhead rigging steel.
• Process & Collaboration:
o Develop detailed sequences for each phase and share with the team.
o Work with riggers to plan efficient equipment transport.
• Equipment Review:
o The team will review equipment details to optimize loading and entry points (e.g., glory holes, curtain wall).
• Sequence of Installation: Present installation sequences to all trades to ensure smooth and efficient work, starting from the top down.
o Coordinate to avoid inefficiencies across all trades.
o Example: Use a coordination drawing as a sequence for installation.
• Prefab & Efficiency: Maximize prefabrication to reduce crane time and improve productivity.
o Prefabricate equipment skids and components to minimize congestion and streamline mechanical room installation.
• Early Collaboration: Collaborate early with the GC and other trades to identify supplemental steel for supporting multiple services in shafts.
o Identify systems for temporary heating/ cooling and create a BMS control plan.
• Long Lead Time Management: Identify longlead items early and place them in a “pack and hold” for smoother project flow.
• Quality Control: Use Cox Fabrication Facility’s QA/QC program to identify and resolve missing accessories.
• Lessons learned
• Cox Team Scheduled Reviews of DD Drawings & Specifications
• MEP EST software used to generate / populate drawings per DA progress and finalized designs
• Budget breakdowns and reviews as need to ensure transparency for the design team / owner
• Structural Gaps: Missing steel in shafts for MEP trades and prefabricated riser installations. Insufficient steel or slab reinforcement for heavy equipment in mechanical spaces.
• Scheduling & Crane: Inadequate tower crane duration affecting the schedule.
• VFDs: Generic VFD specs, but ULH drives required for lab/life science projects with significant cost differences.
• Insulation & Space Conditions: Unclear definitions of “conditioned space” affecting insulation and fire wrap scope.
• Coordination Issues: Mechanical equipment (e.g., electric heaters, heat trace) installed by electricians, requiring clear scope and P&ID info for BMS tie-ins.
• Control Systems & Inspections: Insufficient A/Vs and EPOs in mechanical spaces, causing delays during inspections.
• Electrical Coordination: Coordination of heat trace, AHU wiring, and electrical components (e.g., motor starters, VFDs).
• Other Issues: Scaffolding needs and location identified. Load/wind & vibration analysis expectations clearly defined.
• Early Procurement & Equipment:
o Procure long-lead items early (e.g., chillers, AHUs, energy recovery systems).
o Apply spray-on fireproofing in shafts early.
o Install curtain walls for water-tightness, enabling duct insulation and shaft closure.
o Use temporary roofing to support mechanical system installations and shaft work.
• Risers & Shafts:
o Coordinate and release fabrication for mechanical pipe and duct risers to enable early installation.
o Coordinate steel requirements and roof openings for mechanical equipment.
• Tower Crane Coordination: Plan crane use and sub-schedule for tower crane duration. Coordinate critical pick priorities with curtain wall crane use.
• Structural & Steel Work:
o Trimble and install bang its/hangers once decks are turned over.
o Install strongback and supplemental steel before equipment is set.
• System & Control Programming:
o Prioritize programming of critical systems (e.g., HW/CHW) for temporary or permanent heating/cooling.
DESCRIBE CRITICAL PATH SCHEDULE ACTIVITIES FOR ANALYSIS
• Fire & Life Safety: Identify EOR requirements for affidavits/TCO, including life safety systems, fire alarms, TAB expectations, startup, and commissioning.
• Shaft & Equipment Work: Prioritize shaft work and high pipe installations.
• Supplemental Structural Steel: Provide supplemental structural steel to support heavy pipe and equipment.
• STRATUS: When it comes to complex and time sensitive construction tasks its critical to the success of this project to utilize STRATUS. One of the many advantages of STRATUS is scheduling & time management (FAB to INSTALL)
• Safety Task List:
o Begin building during the DA phase.
o Highlight tasks for Safety Group discussions and plan of attack.
o Address tasks with historical safety issues and create plans for OSHA-approved Safe Work Authorized Procedures (SWAP).
• Shaft Work Coordination: High coordination needed for safety and efficiency during shaft work. Ensure shaft turnover occurs early for mechanical work.
• Floor Turnover Efficiency: Ironwork should be turned over floor-by-floor to avoid inefficiencies during Trimble/layout processes.
• Equipment Procurement: Identify critical long-lead equipment early to avoid delays.
• Slab Openings & Supports: Fabricate custom supports when slab openings in shafts don’t align with structural steel.
• Oversized Custom Plenums: Large AHU plenums require extended coordination and approval times.
• Boiler Exhaust Stacks: Confirm space for guy wires on the roof.
• Energy Recovery Systems: Follow flow diagrams and control drawings to ensure accurate fabrication.
• Rigging & Steel Additions: Ensure dunnage steel matches equipment structural supports.
• Cox aggressively works with our trade partners, Local 17 Sheet Metal Workers and Local 537 Pipefitters to source increased female and minority participation.
• Cox routinely supports sponsoring qualified candidates for apprenticeship.
• Additional diversity opportunities include subcontractor partners as follows:
o Duct and Pipe Insulation WBE/MBE
o Control electrical wiring WBE
Alternate #1 Include Full Coordination of a Single Patient Floor Add $163,072
Alternate #2 Include 16 hours for a Project Manager and 60 hours of a BIM coordinator to model relocation of existing utilities within the existing steam tunnels to facilitate the new tunnel point of connection on the Dana Farber side of Brookline Ave. Add $6,586