McCarthy Drives Piles for Solar Farm
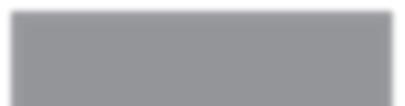
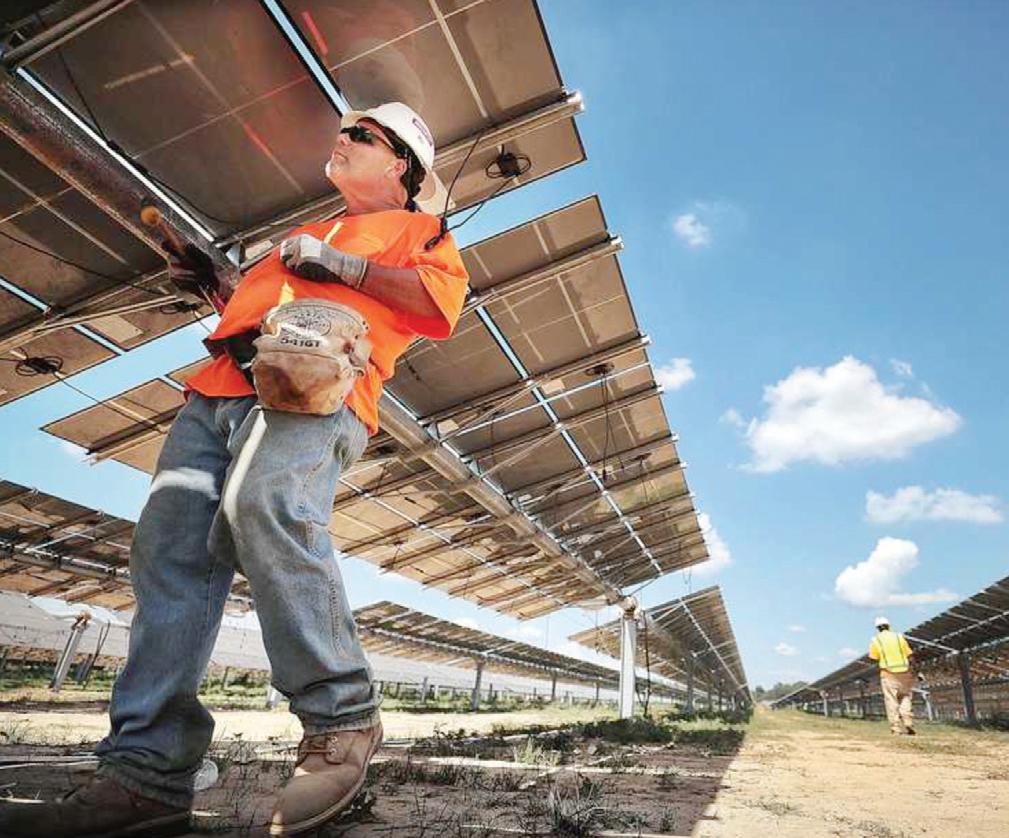
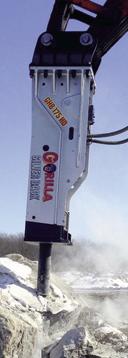




Solar power, like other renewable energy sources, is big news these days. But for it to be truly useful to the power grid, solar power needs to be more than panels on the rooftops of a few homes. Solar power needs to be harvested on a massive scale.
McCarthy Building Companies, Renewable Energy and Storage group is doing that nationally and recently began construction of a new utility-scale solar facility on 1,600 acres near Pearsall, Texas, 55 mi. southwest of San Antonio. The region is well-suited to solar farming as it has below average rainfall, enjoys some 250 days per year of sunshine and has a city close enough to use the power that is generated.
The project calls for 85,000 steel piles to be driven 4-to-5 ft. deep with 6-to-8 ft. protruding from the ground to support the solar module. McCarthy will self-perform the installation of the steel piles, tracking system and above ground electrical work to energize more than 780,000 solar modules. McCarthy has subcontracted some of the work such as the building of an electrical substation on the property.
Leeward Renewable Energy (LRE) contracted with McCarthy to be the project’s EPC (engineering, procurement and construction) contractor for the Horizon Solar project, which will be a 200-megawatt facility. The project will provide the renewable energy equivalent of powering 40,000 average Texas households. Horizon Solar will include components from leading American companies including mod-
“The Nation’s Best Read Construction Newspaper… Founded in 1957.”McCarthy is using Gayk machines for the Horizon Solar project in Pearsall. Workers drive the machine to the preloaded GPS coordinates, press the button and the machine drives the pile. The project began in August 2022 and is expected to be completed in a little more than one a year.
KSM’s Matt Jackson (L) talks with Brice Lockhart on a job site near Odessa, Texas. “Matt and Kirby-Smith have been great to partner with,” said Lockhart. “They have a huge inventory of machines and have been able to get us pretty much anything we needed. Service after the sale is very important to us and they have delivered every step of the way.”
Brice Lockhart doesn’t necessarily believe in the adage, “bigger is not always better.”
“We like jobs that involve really big pipe, especially ones with large quantities that need to be put in the ground,” said Lockhart, who owns and operates Lockhart Excavation LLC in Austin, Texas, with his wife, Melanie. “We’ve laid an up to 72-inch water line and we did a 30-mile, 24-inch water line in Hutto years ago. They are not always as big as those, but for the most part, our jobs are sizable. We strive for those.”
Lockhart added that experience plays a big role in Lockhart Excavation’s ability to complete such undertakings on time and on budget. He has been putting pipe in the ground for nearly 30 years and the majority of his staff has a similar level of expertise.
“I started doing utility work in 1994 and spent 20 years working for another contractor,” recalled Lockhart. “When it went out of business, I started Lockhart Excavation. October will be our eighth year in business. Several of the guys on staff worked with me in the past — probably 80 percent of them. I give them a lot of credit for our success. They just know how to get the job done.”
Lockhart Excavation started as an eight-man crew and within the first year, Lockhart added three more crews to meet growing demand. After a period where “things leveled out,” Lockhart Excavation experienced another rapid expansion during the last two to three years. Today, the company employs approximately 90 people and installs all types of wet utilities throughout the Austin area and West Texas.
In the Midland-Odessa area, Lockhart Excavation recently installed more than 22,000 ft. of water, sewer and storm pipe for a 152-home subdivision. Superintendent Daniel Torres said that’s been a fairly typical type of job in West Texas.
“Generally, we have two or three of those going at once out here, but back in Austin, we usually run 15 to 20 jobs,” Torres said. “Residential is our main market — putting in utilities for subdivisions and apartment complexes. We have work lined up in the area for a while, so it’s keeping us busy.”
Lockhart said residential projects are the company’s forte, but it occasionally takes on commercial and large public utility installs. The 30-mi. water line, which was an $18 million
The U.S. Department of Transportation recently announced more than $39 million to fund three projects in Texas to improve port facilities through the Maritime Administration’s Port Infrastructure Development Program. The funding, made possible by the Bipartisan Infrastructure Law and additional Congressional appropriations, helps improve supply chain reliability through increased port capacity and resilience, more efficient operations, reduced port emissions, and new workforce opportunities. Together, these investments will help get goods to shelves faster and lower costs for American families.
Creating a stronger and more resilient supply chain for the nation has been a key focus for the President who issued an Executive Order on Supply Chains in February 2021 and stood up a Supply Chain Disruptions Task Force, co-chaired by Secretary Buttigieg in July 2021. The Administration, supported by Secretary Buttigieg and the Department of Transportation has engaged in near-term actions to address supply chain disruptions and now, with investments like this one, are working to create the infrastructure for a stronger, more resilient supply chain for the long term.
“So many of the goods we all count on, from appliances to furniture to clothes, move through our nation’s ports on their way to us,” said U.S. Secretary of Transportation Pete Buttigieg. “Using funds from President Biden’s Bipartisan Infrastructure Law, this year we’re awarding record levels of funding to improve our port infrastructure, strengthen our supply chains, and help cut costs for American families.”
The Port Infrastructure Development Program (PIDP) supports efforts by ports and industry stakeholders to improve port and related freight infrastructure to meet the nation’s freight transportation needs and ensure our port infrastructure can meet anticipated growth in freight volumes. The program provides planning, capital funding and project management assistance to improve ports’ capacity and efficiency. The PIDP pro-
vides funding to ports in both urban and rural areas for planning and capital projects. It also includes a statutory set-aside for small ports to continue to improve and expand their capacity to move freight reliably and efficiently and support local and regional economies.
More than 60 percent of the awards will be benefitting ports in historically disadvantaged communities and several of the projects will help reduce emissions at the ports through electrification. Additionally, more than $150 million in awards include a focus on electrification of port equipment to reduce emissions and improve air quality. The awards also include nearly $100 million for port projects that will advance offshore wind deployment — in support of President Biden’s bold goal of deploying 30 GW of offshore wind by 2030, which is enough to power
10 million homes with clean energy, support 77,000 jobs and spur private investment up and down the supply chain.
“President Biden’s commitment to modernizing our infrastructure — from the beginning of his Administration — has resulted in
an unprecedented investment in all segments of our port infrastructure to enable us to move goods more quickly, strengthen supply chain resiliency and reduce the climate impacts of port operations themselves,” said Maritime Administrator Ann Phillips.
Texas grants include:
Location: Beaumont
This project includes two components: the “Lot 6 Project,” which involves the strengthening of a 400-ft. section of dock area to support heavy loads with the addition of a 400-ft. x 100-ft. pile-supported relieving platform and four monopiles for breasting barges; and the “Lot 14B Paving Project,” which includes the design and installation of a 26.14-acre container marshalling yard and hard-
Location: Harlingen
The project will renovate the Port of Harlingen’s main dock and related facilities. Work includes repairs to or replacement of the timber fendering system, timber rails, steel sheet pile bulkhead, steel anchor rods that hold the bulkhead in place, deteriorated concrete deck in multiple locations, mooring piles and related structures and a mechanical winch operator and cable. In addition, the project will demolish, excavate, dewater and re-compact critical uplands areas.
Location: Matagorda
The project funds the rehabilitation of the bulkhead and vessel berthing areas in Turning Basins 1 and 2, including the repair or replacement of approximately 5,600 ft. of bulkhead and installation of approximately 20 vessel-toshore power stations with multiple outlets to serve several vessels at once. The rehabilitation will make the facilities more resilient to the effects of natural disasters and sea level rise.
For a full list of FY22 PIDP award recipients and to learn more about the program, visit https://www.maritime.dot.gov/PID
(All photos courtesy of U.S. Department of Martime.)
Niece Water Towers deliver reliability and durability when you need fast mobile water service. With a 12” discharge tube it fills your tanks at a rate of over 1,000 gallons per minute. Offers removable power pack for security, fifth wheel tow hitch, professionally engineered and constructed.
It features (8) legs for stability
5th wheel set up for quick “tow and go.”
McCarthy Building Companies, Renewable Energy and Storage group recently began construction of a new utility-scale solar facility — Horizon Solar — on 1,600 acres near Pearsall, 55 mi. southwest of San Antonio.
To prepare the ground, workers had to remove the numerous gnarled mesquite trees on the property.
ules from First Solar and smart solar trackers from NexTracker.
The project began in August 2022 and is expected to be completed in a little more than one a year. LRE will own and operate the facility.
Some might picture this project as just another job of fence pole digging across a piece of Texas prairie. Of course, the job is much more complicated than that.
One of the first orders of business was to prepare the land, which will then be revegetated with native plants. McCarthy elected to subcontract the ground clearing scope of work. The subcontractor utilized a gigantic chain, one used in the shipping industry, with each link weighing 75 lbs. and weighted capacity of over one million pounds to help with the process.
John Messerli is the project manager of McCarthy on the job. He oversaw the team as they graded the land, getting it ready for the pilings.
“The project requires us to build roads for the delivery trucks to navigate the property for the installations and be able to return later for regular maintenance,” he said.
The rocky landscape is well suited for road building. Most road building projects require trucking loads of stone to a location for workers to create a solid surface able to bear the weight of heavy machinery. “The property has lots of rock similar to brown landscaping rock, so we can use that along with native materials on site to build the road,” said Messerli. “With that solid base our team compacted it and no longer need asphalt.”
The property formerly was cattle range with a pond for
TxDOT and Flatiron Dragados LLC (FDLLC) have executed a signed letter agreement that establishes the legal framework for resolving the safety issues identified in the design of the New Harbor Bridge Project.
The agreement affirms FDLLC’s responsibility to complete this work at FDLLC’s expense and to TxDOT’s satisfaction.
While this step is encouraging for moving the project forward, it is important to note that the Notice of Default remains in place.
There is still progress that needs to occur between TxDOT and FDLLC in order to finalize and approve the design changes required to address the safety issues identified by TxDOT and allow for an updated schedule to complete the project.
“TxDOT understands and very much shares in the frustration that the residents and businesses of the Corpus Christi region have felt over the delays associated with the work on this project,” Executive Director Marc Williams said in his remarks at the Texas House of Representatives Transportation Committee Hearing in Corpus Christi. “Our commitment remains to see this project through to completion in a manner that is: safe, responsible and expedited and to quickly provide the region with an updated sched-
ule as soon as the design changes are approved.”
Texas Department of Transportation officials and Flatiron/Dragados made an announcement during a tour of the incomplete north and south bridge approaches with local media outlets.
The project now has a tentative completion date of sometime in 2025, said Valente Olivarez Jr., TxDOT’s Corpus Christi District engineer. Officials said a more specific timeline would be provided when the design concerns are resolved.
“Flatiron/Dragados feels pretty confident that we are looking at a 2025 date with completion and opening, but … it depends on finalizing the (design) solutions,” Olivarez Jr. said while briefing media under the new bridge approach on North Beach.
TxDOT and Flatiron/Dragados’ engineer of record, Arup-CFC, resolved their design dispute concerning the bridge’s delta frames. The redesign, which Olivarez said was approved on, included additional steel to specific parts of the frame.
As a result, the work of precasting the
delta frames could resume at the developer’s Robstown precasting site, said Olivarez and Lynn Allison, a spokesperson of Flatiron/Dragados.
Still outstanding are the deficiencies in the bridge’s main span design, including elements of the bridge's foundation and stability in certain wind conditions and the specific crane placements during the construction process of the main span.
To validate the work, TxDOT hired an independent bridge engineering firm, SYSTRA International Bridge Technologies (IBT), in 2020, to provide a third-party review of the bridge design.
The safety concerns center around design issues, which include the foundations, load and weight capacity, structure and the future stability of the main stay bridge.
TxDOT formally raised these issues with FDLLC on April 29, 2022, through a notice of non-conforming work and then directed FDLLC to pause construction on July 15, 2022, to ensure further construction did not result in unsafe conditions.
.)
Construction Equipment Guide • Texas State Supplement • www.constructionequipmentguide.com • December 4, 2022 • Page 11
El Paso, TX 915-541-0066 San Antonio, TX 210-310-0066 Get an “A” with Hyundai Hyundai Construction Equipment is excited to announce the launching of our new A-series machines. Along with a new look, these machines are packed full of standard new features and benefits to get the job done efficiently. • Cummins Performance Series Engines Stage V emissions compliant engines • No EGR (Exhaust Gas Recirculation) Improved fuel consumption • Smart Power Mode 3-5% fuel savings in high load work • New engine hood design Enhanced visibility to rear of machine ©2022 Hyundai Construction Equipment Americas. All Rights Reserved.
San Benito, TX 956-361-0066 Laredo, TX 956-725-0066 More standard features. More value. www.hceamericas.com To learn more about the what the new Hyundai A-Series machines can offer your business, contact your Hyundai dealer today.
Corpus Christi, TX 361-289-0066 Victoria, TX 361-576-0066
Corpus Christi, TX 361-289-0066
Victoria, TX 361-576-0066
El Paso, TX 915-541-0066 Houston, TX 713-247-0066
San Antonio, TX 210-310-0066
Corpus Christi, TX 361-289-0066 Victoria, TX 361-576-0066
Houston, TX 713-247-0066
San Benito, TX 956-361-0066
Laredo, TX 956-725-0066
El Paso, TX 915-541-0066 Houston, TX 713-247-0066
San Antonio, TX 210-310-0066
job that Lockhart Excavation did as a general contractor, was in the latter category.
“It ran from Noack to Hutto and was the largest we have done so far,” said Lockhart. “We crossed varying terrain. The biggest challenge was boring under Brushy Creek. We had to dig a bore pit 40 feet deep. Those types of jobs are rare, but we can handle them. Mostly, we stick with the residential and right now there is plenty of that type of work to do.”
After expanding into West Texas, Lockhart Excavation needed more equipment. Lockhart contacted Kirby-Smith Machinery Inc. (KSM), which has helped Lockhart Excavation add more than 20 Komatsu excavators to its fleet. Matt Jackson, a KSM territory manager, assisted with the most recent purchases, which included Komatsu PC210LC-11 and PC360LC-11 excavators.
“The PC360s are good for large pipe and heavier work such as breaking rock and moving mass amounts of material quickly,” said Torres. “We use the
“It
lot of power, so I can get through any type of material quickly,” said Manuel Tores.
last. Reliability and longevity are very important to me. We put a lot of hours on our Komatsus and rarely have an issue. That’s extremely valuable when time is money and you have to get pipe in the ground as quickly as possible.”
Lockhart also appreciates KSM’s superior service.
“Matt and Kirby-Smith have been great to partner with,” stated Lockhart. “They have a huge inventory of machines and have been able to get us pretty much anything we needed. Service after the sale is very important to us and they have delivered every step of the way. For example, we had a minor issue with a machine, and they had it fixed within a few days. In our experience, other companies would have taken months.”
KSM tracks Lockhart’s newest machines with Komtrax for hours, so its service team knows when to perform scheduled services under the Komatsu Care program, which covers the first 2,000 hours or three years.
“They set it up during convenient times in order to minimize our downtime,” said Lockhart. “Because Komatsu Care is complimentary, it saves us money on those services. More importantly, it ensures they are done on time by trained technicians, and that keeps our machines in good working order so that we maintain productivity.”
Lockhart said that if the company’s recent workload is an indicator for the future, it’s on a good path. He can see Lockhart Excavation adding more crews and additional
excavator
“The PC360s are good for large pipe and heavier work.” said Daniel Torres, superintendent.
equipment within the next couple of years.
“Both the Austin area and West Texas continue to grow, so there has been plenty of work,” said Lockhart. “As customers got to know us and saw our quality of work, they asked us to do more for them. They also referred us to others. That’s how we got into West Texas. A friend of mine was doing work for a developer who needed some help. I had a crew that needed work, and we moved in. We have been there for six years now and we believe it’s going to stay busy for quite some time.”
Kirby-Smith Machinery.)
“The
is fast, so we can put pipe in quickly,” said operator Raul Arellano
has aOperator Manuel Tores digs a trench with a Komatsu PC360LC-11 excavator. LOCKHART from page 4
The Texas Department of Transportation (TxDOT) awarded the Extra Mile Awards at their annual Texas Transportation Short Course in College Station. The Extra Mile Award recognizes employees who have acted heroically to help a fellow Texan in need. An employee who receives this award has: saved someone’s life or attempted to save another life, while on the job or on the employee’s own time
or acted in a heroic manner to prevent injury to another person or to diminish a life-threatening situation.
This year recipients included 18-year veteran Jesus A. Garcia and 3-year-technician Cruz A. Hernandez of Terlingua, a substation of Presidio in the El Paso District.
It is their careful eye that is credited for saving a young woman’s life. The pair was called out at 5:30 a.m. to assist with debris removal. The call from the Brewster County Sheriff’s Office came after first responders saw large rocks from a rockslide on FM-170 12 mi. west of Lajitas that needed to be cleared.
Crews are used to clearing debris after a rockslide in that area and went on their way. Something was different this time though as they encountered a vehicle 10-to-12 ft. down a deep ditch on a curve 1/2 mi. east of Lajitas. It was a little bright light that caught the attention of Hernandez going around the curve in a dump truck. He called Garcia in the lead truck to stop and check. He found it was a young lady that was trapped in her car unconscious, bleeding and seriously injured. The crew called 911 and stayed with her until the ambulance arrived.
It turns out the young lady had left work in Terlingua at 1:00 a.m. and fell asleep on a curve, rolling her vehicle multiple times, just before she got home to Lajitas 16 mi. away. Her parents had been searching for her for hours, but it was the height from the dump truck, that gave Hernandez that life-saving view.
Medics told TxDOT employees that if it had been another hour, the young driver would not have made it. The victim’s injuries were so serious she had to be airlifted to Lubbock.
“These employees embody the selfless, caring, responsive demeanor we strive to achieve every day in our roles to serve others,” said TxDOT El Paso District Engineer Tomas Treviño. “They didn’t think twice about stopping to render aid and this was especially important in such a remote area of our District.”
The first Extra Mile Award was presented in 1983. Recipients are recognized publicly and receive a plaque.
This is not the first time staff from the TxDOT El Paso District have been recognized. Staff members were recognized in 2008, 2015 and 2018.
“These employees embody the selfless, caring, responsive demeanor we strive to achieve every day…”
Thomas Treviño TxDOT
The project calls for 85,000 steel piles to be driven 4-to-5 ft. deep with 6-to-8 ft. protruding from the ground to support the solar module
water. Although the area does not get much rain, the team will prepare the land to properly receive water so rain will not interfere with solar panel operation. Workers will create storm water retention ponds and seed the land so native grasses help hold the dirt in place when it rains.
With roads in place, workers will unload more than 25 semis of material each day, averaging two-to-five trucks of steel piles. Logistics are key in the project.
“It requires a lot of communication across the property to keep everyone working together,” Messerli said. “We have teams unloading the trucks and staging material in the areas. Other teams line up the machines that drive the piles into the ground.”
The steel piles are not one-size fits all. Different size piles are used because of uneven terrain and potential erosion.
McCarthy is using Gayk machines for pile driving. Workers drive the machine to the preloaded GPS coordinates, press the button and the Gayk drives the pile according to the predetermined elevation. It requires less than two min-
utes to drive each pile. In some areas, due to rocky sub surfaces, the Gayk machines may have difficulty achieving full embedment, which is considered refusal. In those instances, McCarthy has various plans to maintain the integrity of the pile. In some places the rock must be crushed so the piles will be accepted in the land.
The pilings will support a single-axis tracking system that will maximize solar capture by rotating to catch the morning sun in one position and the evening sunlight in another.
A key component of the project was the 300 workers needed, from entry-level to experienced. The job postings included laborer, operator, crew lead and electricians.
“We tried to emphasize hiring local workers and veterans,” said Messerli. “We train 10-to-20 people at a time based on their experience. We make sure they understand the tools being used and safety procedures. We show them how to build the units piece by piece.”
Lack of trained workers is a common challenge throughout the construction industry.
“Some people are not prepared for the rigors of working
outdoors,” he added. “But many others have handled the training well and understand what will be expected of them, and prefer to be outside working as opposed to in an office or building. Once a project completes, we work to retain those who were trained and take them to a new solar project where their skills are applied again and they have the opportunity to train others. For many, it’s been a rewarding and appealing career path.”
Scott Canada, executive vice president of McCarthy’s Renewable Energy and Storage team, agreed on the importance of worker training.
“With utility-scale solar construction jobs on the rise in Texas and around the country, we are continually working to help local skilled craft workers and veterans join our solar project teams and receive the training needed to develop rewarding careers in the growing renewable energy sector.”
Since 2010, McCarthy’s Renewable Energy and Storage group has built or is constructing nearly 80 utility-scale solar energy projects, delivering a combined capacity of more than 8.8 gigawatts of clean energy production and more than 775 megawatts of energy storage. CEG
(All photos courtesy of McCarthy.)
Dallas College has been awarded a $3.5 million Skills Development Fund grant from the Texas Workforce Commission (TWC) to train more than 1,500 employees in construction-related courses. The grant, announced at a special check-signing ceremony with TWC Commissioner Aaron Demerson, is aimed at expanding trainees’ current job responsibilities and increasing productivity for Texas employers.
In partnership with 18 Texas construction businesses, the grant will cover 100 percent of the tuition for all trainees participating in the project and there is no cost to employees or employers for instructional delivery, said Tim Samuels, senior director of corporate partnerships of Dallas College.
More than 1,000 of those workers are already employed by one or more of the companies, while other trainees will be new hires.
Dallas College will provide a broad range of customized training for employees under the grant, in eight Local Workforce Development Board areas, with a focus on the evolution of construction projects. The training includes programming for pipe lay-
ers, plumbers, installation and repair workers, construction managers, sheet metal workers, trade and extraction workers, surveyors, welders, mapping technicians and HVAC technicians.
“Careers in construction are critical for economic growth, no matter where you are and no matter where you live,” said Pyeper Wilkins, vice chancellor of workforce and advancement of Dallas College. “With this much-needed grant funding, Dallas College and our partners are forging key career paths for a workforce that is central to our region’s future. Employers who are looking for a workforce talent pipeline know this is a tough labor market, and construction is one of the sectors struggling most to fill open positions,” she added.
Workers who help construct buildings took home an average weekly wage of about $1,760 in Texas, according to the TWC.
“Thanks to the TWC and Dallas College ... thousands of Texans will receive valuable upskilling and training opportunities that will take their careers to the next level and support building and construction,” Texas Gov. Greg Abbott said in a statement.
The University of Texas Board of Regents gave final authorization for design, development and additional construction funding for the University of Texas at Tyler School of Medicine’s new Medical Education Building — approving a total project cost of $308 million for the facility. The UT Tyler School of Medicine will welcome its first cohort of students to campus in the summer of 2023 and the building is expected to be completed in March 2025.
“By approving the total project cost, design development and allocation of funds for the new Medical Education Building, the regents are taking the next pivotal step in launching the UT System’s 7th medical school — one that is specifically dedicated to benefitting Northeast Texas for generations,” said Kevin P. Eltife, chairman of the UT Board of Regents.
The Medical Education Building, a planned five-story, nearly 248,000-sq.-ft. facility, will support interdisciplinary education for graduate medical students, resident training, and nursing and aid as part of a medical education program expansion throughout the UT Health East Texas Health System. In addition, the Medical Education Building will provide outpatient and specialty clinical services with exam rooms, specimen collection/processing, and imaging facilities.
“This facility provides the physical cornerstone of UT Tyler’s plan to train physicians and meet health care needs across the state, while also growing workforce opportunities and economic development in the region,” said UT System Chancellor James B. Milliken.
The Medical Education Building will be built in Tyler’s Midtown District and will connect via skybridge to the UT Health East Texas Hospital — allowing for hands-on learning of residents in the adjacent hospitals. It is designed to have blended programming and clinical spaces for patient care, including women’s imaging, women’s health, diagnostic center, orthopedics and sports medicine, pulmonary and a surgery center to support medical residents in the graduate medical education programs.
“I am immensely grateful to the UT System Board of Regents, Chancellor Milliken and our community of supporters who have been instrumental in the efforts to enhance health education for East Texas,” said UT Tyler President Kirk A. Calhoun.
The UT Tyler School of Medicine will be the first in northeast Texas, offering aspiring doctors a chance to train and practice without leaving the region. Capital projects funded over the next decade, including the new Medical Education Building, will ensure the new medical school has the right environment in place to draw and retain exceptional medical school faculty and students and enhance biomedical research and core residency programs.
Associated Supply Company (ASCO), a provider of construction, agriculture and material handling equipment, announced that it has been awarded the Texas (and Oklahoma) sales and service territory for construction and mining equipment by Hitachi Construction Machinery Americas Inc. (HCMA).
With more than 60 years of experience, ASCO is well-established in Texas with 24 dealership locations supporting many other brands of equipment. With a proven track record of successful growth, ASCO has a clear vision for the potential of the HCMA products to strengthen their current relationships with customers and build new relationships with the world-renowned lineup of Hitachi construction and mining equipment.
“We are excited to combine Hitachi’s worldwide reputation as a premier manufacturer with ASCO’s commitment to providing excellent customer service, product knowledge and industry relationships to create new opportunities for both of us,” said Brax Wright, CEO, ASCO.
“ASCO looks forward to joining our Team with Hitachi, a world class manufacturer,” said Steve Wright President, ASCO. “Together, we will offer the customer a superior option in our market. We are excited about this new opportunity we have to
serve our customers with Hitachi”
ASCO’s other product offering includes CASE Construction Equipment, CASE IH, Doosan, Volvo Construction Equipment, Genie, K-TEC, Gradall, Sennebogen, as well as many other lines of well-known and respected agriculture, construction and material handling equipment.
ASCO was founded in 1960 as Associated Supply Company in Lubbock, Texas, by the late J.W. “Bill” Wright as a Towmotor lift truck dealership and U.S. Army surplus equipment store. The company is currently led by Bill and Corinne’s children, Brax Wright, Steve Wright and Paula Key. Three of the third-generation work in the company today, along with more than 600 other teammates.
For more information, visit www.ascoeq.com.
Hitachi Construction Machinery Americas, Inc. is a Japanese construction equipment company which is into the manufacturing, sales and service of construction machinery, transportation machinery and other machines and devices. It is a subsidiary of the Hitachi Group.
Mena Souliman, associate professor and the Ronald D. Brazzel Endowed Professor of Civil Engineering of The University of Texas at Tyler, has received a nearly $600,000 Texas Department of Transportation grant to enhance the asphalt currently being used in highway/road resurfacing projects for improved wet-weather driving.
The Texas A&M Transportation Institute will work with Souliman on the three-year project. Souliman and his collaborators will examine the current highway/road construction processes in the hopes to decrease crashes on wet resurfaced pavements. The 2021 “Weather Conditions for Crashes” report from TxDOT found that “rain” was the most repeated weather condition behind “clear/cloudy” in all reported crashes.
“The current design methodology for asphalt and seal coat surfaces is limited when considering safety aspects like friction and surface texture, also known as skid resistance,” said Souliman. “Our goal is to develop a laboratory-based, friction prediction system to select the pavement surface type and coarse aggregate types that will provide adequate skid resistance over the life of the pavement surface.”
Groups that will provide input for implementation of these research results will be selected from the Federal Highway Administration, Texas Asphalt Pavement Association and various material producer and construction associations, Souliman added.
“Investigation of better ways to mitigate automobile accidents is clearly important to society and is addressed by this project,” said Steven Idell, UT Tyler senior vice president of research. “This award is yet another strong testament to the very high quality of
work being done by Dr. Souliman and his collaborators in the area.”
Souliman studies pavement materials design, fatigue endurance limit of asphalt mixtures, field performance evaluation, maintenance and rehabilitation techniques and pavement management systems in the construction of roads and highways.
The professor joined the UT Tyler College of Engineering faculty in 2014. He holds a Master of Science and Ph.D. in civil, environmental and sustainable engineering from Arizona State University. He also directs the UT Tyler Texas Rural Transportation Research Center.
His participation in local, state and national projects includes work with the city of Tyler and the U.S. Department of Transportation. He has authored more than 100 technical publications, conference papers and reports in the field of pavement and aggregate testing, characterization and field monitoring.
With a mission to improve educational and healthcare outcomes for East Texas and beyond, UT Tyler offers more than 80 undergraduate and graduate programs to 10,000 students. UT Tyler recently merged with The University of Texas Health Science Center at Tyler (now known as UT Tyler Health Science Center). Through its alignment with UT Tyler Health Science Center (HSC) and UT Health East Texas, UT Tyler has unified these entities to serve Texas with quality education, cutting-edge research and excellent patient care. Classified by Carnegie as a doctoral research institution and by U.S. News & World Report as a national university, UT Tyler has campuses in Tyler, Longview, Palestine and Houston.
courtesy of TxDOT.)
“The current design methodology for asphalt and seal coat surfaces is limited when considering safety aspects like friction and surface texture, also known as skid resistance,” said Mena Souliman, associate professor and the Ronald D. Brazzel Endowed Professor of Civil Engineering of The University of Texas at Tyler.
DALLAS
FORT
TYLER