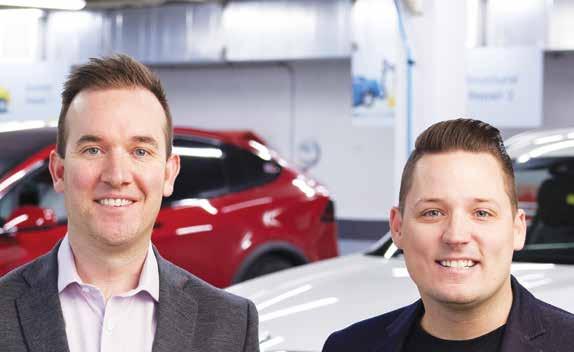

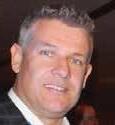
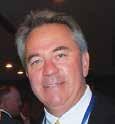

The smarter spray gun. Designed for the modern painter.
The first ever spray gun designed specifically to deliver top-of-the-line performance with revolutionary replaceable nozzle technology that saves you time. Experience faster cleanup, faster changeovers and faster cycle times. Bringing you the best of 3M Science, all packed into the smartest, lightest spray gun in the world.
The recent study by the Insurance Institute for Highway Safety (IIHS) casts a spotlight on the current state of partial driving automation systems, revealing a concerning gap in safety measures.
IIHS recently revealed the results of its tests on vehicles with semi-autonomous advanced driver assistance systems (ADAS). The safety advisory found that, out of 14 models tested, only one earned an acceptable rating to pass all IIHS tests. Two earned marginal ratings; 11 were rated poor.
After evaluating vehicle performance, the IIHS said there is “no evidence that these systems
Furthermore, recent statistics from Transport Canada’s National Collision Database (NCDB) for 2021 paint a sobering picture of road safety in Canada. With 1,768 reported fatalities and 8,185 serious injuries, the numbers barely reflect a decrease despite technological advancements aimed at making roads safer. This emphasizes the undeniable role of human error and the necessity for a multi-faceted approach to road safety, combining technology with improved driver education and awareness.
The IIHS study is a wake-up call, highlighting the urgent need for enhanced safety measures in vehicles equipped with partial automation. It
THE IIHS SAID THERE IS NO EVIDENCE ADVANCED DRIVER ASSISTANCE SYSTEMS HAVE ANY SAFETY BENEFITS.
have any safety benefits.” Notably, Dave Harkey, IIHS president reported that “while some drivers may feel that partial automation makes long drives easier, there is little evidence it makes driving safer,” and some high-profile crashes have illustrated that current ADAS technology “can introduce new risks when systems lack the appropriate safeguards.”
With only one out of 14 systems earning an acceptable rating, the findings signal a critical need for improvement in an industry racing toward automation.
These results have prompted IIHS to introduce a new rating program, designed to encourage automakers to incorporate more robust safeguards in partially automated driving systems. Despite the advancements in Advanced Driver Assistance Systems (ADAS)—such as automatic emergency braking and adaptive cruise control—the IIHS’s inaugural rating program underscores the complexities of ensuring safety in vehicles equipped with these technologies. The calibration and maintenance of these systems are paramount, especially after a collision to maintain their effectiveness and safeguard passengers.
reveals that while some systems show promise, many lack robust safeguards, effective driver monitoring, timely attention reminders, and appropriate emergency procedures to ensure driver and road safety.
As the automotive industry evolves with increasingly sophisticated ADAS technologies, the challenge of ensuring these systems are accurately maintained and calibrated grows. While ADAS can significantly reduce the risk of accidents, these systems have limitations and are not infallible. Understanding the need to maintain and calibrate ADAS technologies is crucial. Post-collision, professional checks and recalibrations are essential to ensure system accuracy and reliability and to prevent safety compromises.
PUBLISHER
Darryl Simmons publisher@collisionrepairmag.com
ASSOCIATE PUBLISHER
Orest Tkaczuk | orest@mediamatters.ca
EDITOR
Allison Rogers | allison@mediamatters.ca
ART DIRECTOR
Yvonne Maschke | yvonne@mediamatters.ca
ASSISTANT EDITOR
Sarah Perkins | sarah@mediamatters.ca
GRAPHIC DESIGN INTERN
Namra Ahmad | namra@mediamatters.ca
VP OF INDUSTRY RELATIONS & ADVERTISING
Gloria Mann 647.998.5677 | gd.mann@rogers.com
DIRECTOR OF BUSINESS SOLUTIONS
Ellen Smith 416.312.7446 | ellen@mediamatters.ca
INDUSTRY RELATIONS ASSISTANT
Wanja Mann 647.998.5677 wanjamann1@gmail.com
DIGITAL OPERATIONS MANAGER
Cassie Doyle | cassie@mediamatters.ca
MARKETING COORDINATOR
William Simmons | william@mediamatters.ca
CONTRIBUTORS
Stefano Liessi, Jay Perry, Bill Speed
SUBSCRIPTION
Single edition $7.99 One-year $39.95 ( 6 issues)
Collision Repair ™ magazine is published bimonthly, and is dedicated to serving the business interests of the collision repair industry. It is published by Media Matters Inc. Material in Collision Repair™ magazine may not be reproduced in any form without written consent from the publisher. The publisher reserves the right to refuse any advertising and disclaims all responsibilities for claims or statements made by its advertisers or independent columnists. All facts, opinions and statements appearing in this publication have been compiled and included with the permission, though not necessarily the endorsement, of the editor, or of independent columnist contributors, and are in no way to be construed as those of the publisher, or as endorsements of them.
PRINTED IN CANADA ISSN 1707-6072
CANADA POST CANADIAN PUBLICATIONS MAIL
SALES PRODUCT AGREEMENT No. 40841632
RETURN POSTAGE GUARANTEED
Send change of address notices and undeliverable copies to: 317 Reid St., Peterborough, ON K9J 3R2
“We acknowledge the financial support of the Government of Canada”
Collision Repair magazine is published by Media Matters Inc., publishers of:
When
•
•
•
•
Donald Hall has joined SATA Canada as a business development specialist for the Alberta region, he announced via LinkedIn in late January. Working in the industry since 2016, Hall delivers years of experience in relationship building and development, previously working with some of the largest collision networks in Canada. Regarding his new role, Hall said he is “excited to connect with valued SATA customers in the region, as well as developing new connections.”
CrashBay has announced the appointment of John Young as its new Chief Financial Officer (CFO). Young will also serve as an advisory board member for the company. A seasoned tech and startup executive, Young brings 25 years of experience, driving 12 successful exists, numerous acquisitions and raising more than $235 million in capital. CrashBay said Young’s extensive background in guiding disruptive, technology-driven companies; serving as a mentor to entrepreneurs and positive contributions to the growth and profitability of multiple ventures will make him a valuable addition to the team.
Certified Collision Group, Inc. (CCG) has announced the appointment of Michelle Sullivan as its new Chief Executive Officer. With a career spanning 30 years, Sullivan has successfully spearheaded strategic initiatives and achieved significant growth. Sullivan has also served as the U.S. Sales Director, East for AkzoNobel and has also held senior leadership positions in the PBE distribution segment. “I am honoured and excited to join Certified Collision Group as its CEO. I believe in the tremendous potential of this company, and I am committed to building on its legacy of success,” said Sullivan when she ascended her role.
The men and women of LKQ are passionate about parts and providing the best possible service to our customers. Our world-class product sourcing, recycling, and remanufacturing operations and our more than 20,000 North American employees are the difference between delivering a part that’s just OK and one that’s just right for the job.
Feel the passion and find your next replacement part at www.LKQcorp.com
What steps to take when it’s beyond a minor dent
Learn about the repair process to stay informed
Follow our 10 steps to get through a collision repair
Collision Repair magazine representatives recently had the opportunity to participate in an exciting Open House event at the AkzoNobel Ontario headquarters in Etobicoke, Ontario. The event showcased the latest innovations and developments in the collision repair industry. Attendees were given a demonstration of an Automated Dosing Machine, led by technical consultant Dave Woolley. Other topics included discussions on coatings specifically designed for ADAS-enabled vehicles and attracting youth to the industry. To conclude the event, John Cox, Canadian ACoat services manager, showed a demonstration of Carbeat, AkzoNobel’s interactive shop management tool.
Made
Axalta Coatings Systems has announced ‘Starry Night’ as its 2024 Global Automotive Colour of the Year. This latest edition marks the tenth year that Axalta has introduced its automotive colour of the year and the first time it has featured a shade of black. Dan Benton, senior manager, global colour at Axalta further noted that “black is the second most popular automotive colour globally. We’re excited to feature a black shade as our 2024 Global Automotive Colour of the Year. ‘Starry Night’ is a hue where black is bright and dark is distinguished.”
The fourth-quarter 2023 overall average length-of-rental for collision-related car rentals was 16.4 days–just over a halfday lower than Q4 2022’s average LOR. Of all the provinces, Ontario had the highest LOR at 18.1 days, followed closely by Alberta at 17.1 days. Comparatively, Prince Edward Island (P.E.I) had the lowest LOR record at just 13.9 days. When looking at national statistics for Driveable LOR, the country saw an average rate of 12.6 days or a 0.2-day increase from 2022. Once again, Ontario had the highest rate of Driveable LOR at 14 days followed by Alberta at 13.9 days. Here, Quebec had the lowest Driveable LOR at just 9.9 days.Non-driveable LOR across Canada, on average, saw a rate of 30.9 days and this is consistent with 2022’s data. For rentals associated with total losses, the length of rental periods for the country saw an average of 23.6 days, a 1.8-day decline from Q4 2022.
Joe Saputo, owner of CARSTAR Ancaster, CARSTAR Ancaster West and CARSTAR Guelph, was recently visited by Hamilton, Ont. news network CHCH, where he delved into the inner workings of the shop to promote his services in the local market. In the segment, Saputo shows off the floor at CARSTAR Ancaster, showing reporter Emily Vukovic the inner workings of the shop and services offered to customers. Saputo also covered paintless dent repair services, automotive refinishing–including the BASF 100 line, which Saputo was one of the first in Canada to incorporate into his shop.
As part of its partnership with the Stake Formula 1 (F1) Stake team, Fix Network World has revealed its logo on the updated C44 vehicle. According to a recent LinkedIn post made by Fix Network World, the C44 is “a result of collaborative innovation and cutting-edge engineering.” The vehicle features what the F1 Stake team refers to as an “aggressively redesigned” aerodynamic package and a switch from a push-rod to a pull-rod front suspension. In October 2023, the F1 Stake team first announced a partnership with the Fix Network team. Now, Fix Network World highlights the C44 as a “powerful synergy” culminating from the success of this partnership.
One major announcement to come out of BMW’s February Certified Collision Repair Centre (CCRC) conference was the OEM’s decision to expand its restricted parts program in Canada to include select aluminum and carbon fibre components. The decision is in line with BMW North America’s parts restrictions in the United States market, BMW Collision and Wholesale Manager Chris Castagna told Collision Repair mag. This move aims to ensure the highest standards of repair and maintenance for BMW vehicles, maintaining the brand’s commitment to safety, quality, and performance. By controlling the distribution of critical repair materials, BMW seeks to further enhance the integrity of repairs done within the CCRC network.
General Motors (GM) has issued a recall for 222,490 vehicles in Canada and over 300,000 vehicles worldwide due to tailgates that can spontaneously unlatch and spill cargo.The vehicles specifically affected include the Chevrolet Silverado and GMC Sierra from the 2020 to 2023 model years. Some heavy duty models from 2024 are also affected. The issue stems from improper sealing that can allow water to leak into the exterior tailgate switch, causing it to unlatch and open unexpectedly. To fix the issue, GM dealers will need to replace the exterior tailgate switch with a new material that improves resistance to “water intrusion.” Currently, GM has also ordered a stop-sale for current possibly affected trucks on dealer lots until they can be repaired. Owner letters for drivers with affected vehicles began arriving in mid March.
Cybersecurity research warns that hand tools with smart features can be vulnerable to cyber attacks. In its research, Nozomi Networks’ Labs found vulnerabilities in a Bosch Rexroth smart pneumatic torque wrench that the company says is commonly used on vehicle production lines. The wrench’s smart functions allow it to send activity data to a central server for logging, as well as to receive remote reprogramming for different torque settings. Because of this, it is also possible for outside entities to send signals to the tool, or even install new code, changing the tool’s function or hijacking it entirely. The company also noted that automating an attack of this kind would be easy, allowing a perpetrator to take down an entire production line and then try and ransom control back to the user.
The Bosch tool in question will however not remain vulnerable for long, as the company is reportedly rolling out a security update in the near future to prevent attacks.
Robotics startup Figure has announced a signed partnership with BMW Manufacturing to deploy its humanoid robots in the automaker’s facilities in the United States.This new partnership marks the first commercial deal that Figure has signed since it was first founded in 2022. While the company did not disclose how many robots BMW will be using, the partnership will start with small quantities and then expand if performance targets have been met, according to Brett Adcock, chief executive at Figure. Figure’s humanoid robots will be deployed in BMW’s manufacturing facility in Spartanburg, South Carolina for the trial run. Here, the robots will be integrated into manufacturing processes including the body shop, sheet metal and warehouse after being trained to perform specific tasks such as heavy manual labour. The robots are expected to be on the manufacturing floor in the next 12 to 24 months.
Insurance provider State Farm will pay a US$2 million settlement following a two-year investigation by the Montana State Commissioner of Securities and Insurance (CSI) into the insurer’s claims handling practices.The investigation revealed that State Farm had underpaid some drivers who had been in accidents with State Farm’s insureds from November 1, 2018, through April 15, 2022.The settlement and order also require State Farm to reevaluate all affected claims and pay any additional money that may be owed to Montana customers. If State Farm does not take corrective actions, CSI will fine the insurer an additional US$2 million. As a result of CSI’s investigation, State Farm reports that it has reviewed more than 2,436 Montana claims and made an additional US$1,182,927.43 in payments to Montana customers.
Engineers with the University of Nebraska’s road safety testing facility have discovered that electric vehicles are too heavy to be stopped by highway guardrails. In early February, engineers with the university released their initial crash test results in which a 2022 Rivian R1T—which weighs nearly four tonnes—was rammed into the same type of guardrails used along most American and Canadian highways. During the test, the Rivian R1T tore through the metal guardrail and continued until hitting a concrete barrier on the other side of the test lane. Road safety officials and organizations have weighed in on the issue and say that electric vehicles themselves appear to offer superior protection to their occupants, even if they, like other heavy vehicles, might prove dangerous to occupants of lighter vehicles in a crash.
“We knew it was going to be an extremely demanding test of the roadside safety system,” said Cody Stolle with the university’s Midwest Roadside Safety Facility. “The system was not made to handle vehicles greater than 5,000 pounds.
A new study from researchers at Stanford University has found that simply resting a lithium-metal battery can reverse degradation from charging and use. Currently, these batteries are not used in electric or hybrid vehicles, even though they offer higher energy density and output, and lighter weight than their lithium-ion counterparts. This is because, while more energy efficient, lithium-metal batteries have been found to rapidly degrade after just a few charge cycles. Researchers have found that when completely discharged and without any
running
it, a
actually begin to heal itself. Resting a battery for just an hour, researchers say, will begin the healing process by allowing any trapped energy to dissipate.
At the recent Ecar Expo in Gothenburg, Sweden, Volvo proudly showcased David Gustafsson’s fully functional, drivable 1:1 scale Lego Volvo wagon. Unlike most life-size Lego replicas that are just static displays, Gustafsson’s creation has a fully functional interior with turning climate control knobs, doors that swing open, and a working gear selector. It also features pivoting side mirrors and active headlights that follow the movement of the steering wheel. What sets Gustafsson’s Lego V70 apart is its ability to actually drive, all thanks to an electric motor and a battery pack. With the use of a remote control, the vehicle can start, move, steer and brake, but cannot reach high speeds.Gustafsson dedicated over a year on this project and used over 400,000 Lego pieces to complete the vehicle.
Essex County OPP say a 45-year-old driver from the Leamington area has been charged after police discovered the individual’s vehicle had a paper license plate. A member of the Essex OPP was on general patrol on Talbot Street West in the Leamington area on January 22 at approximately 1:30 a.m. when they ran a check on the vehicle’s plates. The check revealed that the license plate number was no longer valid and that the driver had a paper copy affixed to their vehicle instead of the Ministry of Transportation-issued plate.
Power up your skills in ADAS technology in only three days. This hands-on course is designed for Automotive Service Technicians or Collision Technicians, or apprentices in their 3rd or 4th year. Gain practical knowledge of ADAS sensor calibration techniques using the latest industry specific equipment.
Learn more at bcit.ca/adas EDUCATION FOR A COMPLEX WORLD.
ADAS instructor Russ Hunter sets up targets to calibrate windshield camera for lane departure warning system.Cousins Sean and Mark
McIntosh of Kirmac know collision repair is a matter of community, culture and compassion
In the collision repair industry, nothing is more important than attention to detail.
Noticing a dent or scratch in a vehicle can be the difference that makes or breaks a quality repair. Attention to detail is not only a marker of technical skill, but signals a drive for growth and a sense of compassion for both employees and customers alike.
For cousins Sean and Mark McIntosh, respective president and vice president of Kirmac Collision and Auto Glass in British Columbia, a lifetime journey in the collision repair industry has meant learning how an attention to technical, personal and communal details can create big changes. Collision Repair magazine sat down with the cousins to discuss how when it comes to the industry and the inner workings of a shop, the “culture is everything.”
Leaders of the second generation to take over the Kirmac Collision reins, Sean and Mark both professionally joined the family
business during and after high school, but can remember childhood weekends spent with their fathers at the shop.
Originally started by Sean’s father, Ian McIntosh, and Mark’s father, Ken McIntosh in 1973, and today, a 20-store outfit with more than 275 employees, Sean recalls going to the shop with his father and sisters in the early days “and just hanging around” as a child.
“I’m sure on top of getting many things accomplished for the business, it was probably an effort, to give my mom a break too,” Sean jokingly noted, “but being there, I would get to see the inner workings of the shop without completely realizing it.”
Despite this front row seat to the industry, Sean remarked that “at that moment in my life, if you had asked me what I wanted to do, it wouldn’t have been autobody.”
Instead, Sean’s position for the industry began with an initial foray into the world of
“A lot of effort has been spent trying to build a culture in the shops centred on an employee community. You spend more time at work than you do at home, so it’s important that you enjoy the team you work with.”
— Mark McIntosh, vice president, Kirmac Collision and Autoglass
racing where Sean spent the early part of his career living in the United Kingdom racing formula cars throughout Europe.
In between racing seasons, Sean would return to the business where he would begin learning everything from parts to production and customer service, and following his racing career, he began attending BCIT for business management.
Mark meanwhile, began working for the family business right out of high school and, like Sean, worked the front desk before continuing to develop his skills in other areas.
He commented that learning in this way was a good experience because it allowed him to get an intimate understanding of each level of the business.
“You don’t really realize when you start that you have a passion for it, and then as we started to learn the business, we realized that it was interesting and then it grew into what it is today.”
Mark also noted that he never experienced any pressure from his parents to work for the business and instead, was allowed to come to see it in his own time as an opportunity for something bigger.
The cousins further discussed how their fathers did a good job at preparing them for their current roles by developing a plan of strategic succession. This plan included a balance between focusing on the small things, as well as working on seeing the bigger picture.
“We reported to the president of the company at the time, John Kerschbaum. Before joining Kirmac, John worked for Future Shop and The Brick in finance. He brought experience and the disciplines you need running much larger organizations. As we progressed through the company, we never had direct reporting relationship with our parents and had to prove ourselves, which I think is healthy,” Sean said.
Mark said that John taught the cousins “things we never would have been able to learn from our fathers alone. We got the best of both worlds, financial management on one side from John and the relationships and the business side from our dads.”
In 2014, the family sold its 12 shops in Seattle, Washington, to Service King, something that for Mark was another step in the succession plan for Kirmac.
As a result, in 2021, along with Sean’s sisters Elisa—a member of Kirmac’s Leadership Team and its Director of Information and Technology and Lindsay, and Mark’s sisters
Leanne and Laura, the second generation purchased Kirmac from the first generation, marking the official transition. This is when Mark and Sean assumed their current roles at Kirmac.
“When we announced the transition to our stores, there wasn’t a huge change because we were already leading the day-to-day operations in the locations. We still have a lot to learn, but the strategic succession plan made the transition much smoother.”
As their families heed the business, Ian and Ken are enjoying retirement, but are always available to consultant on strategy or transfer a key relationship. They also drop in occasionally to visit with team members at the locations—something that is more than easy to do as Kirmac Collision continuously makes an effort to develop a positive sense of community culture.
With the company having the number of locations it does across British Columbia, Sean stressed that “success comes from trusting and relying on the team around us.”
“Sometimes we have to go into the weeds to solve a problem, but for the most part, you have to rely on your team.”
Many of Kirmac Collision’s current executive team members have also grown up in the industry alongside Sean, Mark and Elisa, moving through the ranks from apprentices or manning the front before climbing current roles as regional managers or trainers.
“A lot of effort has been spent trying to build a culture in the shops centred on an
employee community,” Mark said. “You spend more time at work than you do at home, so it’s important that you enjoy the people you work with.”
In focusing on these interpersonal details, Sean and Mark similarly encourage their shop teams to do events together as well as monthly lunches, and work to recognize birthdays and anniversaries. Just look to the Kirmac Collision’s Facebook page and you’ll see team members going to paintball, concerts, bowling and more.
Incredible value can also be seen in Kirmac Collision’s strong charity presence, with Kirmac Cares For Kids having donated more than $5 million to support children throughout B.C. since its inception in 2010.
Because the business is spread out across Metro Vancouver, the McIntosh family decided that they wanted to start a focused charity initiative that would allow them to help the various communities where their shops operate.
“It was important for us to focus on helping children because they’re often an undefended group. The initiative has grown into something way bigger than anyone thought in the beginning. Our primary brand is Kirmac Cares for Kids to many people,” Sean said.
Kirmac Cares for Kids primarily supports the B.C. Children’s Hospital but has also branched out and donates to the Surrey Memorial Children’s Health Centre, and the Boys Club Network.
“Supporting these great causes is our family’s way of making a positive impact on the communities that have supported Kirmac for more than 50 years,” Sean commented.
When asked where they see themselves heading in the next five years, Sean and Mark discussed, that along with growing location count, they always keep a close eye on changes in the industry because “you have to invest to stay ahead, especially in our industry’s rapidly changing environment. We’re always looking for new ways to assist our teams in delivering safe repairs to our customers.”
This mindset is especially true for Kirmac Collision when it comes to technology, with each of the company’s 20 shops being outfitted with Advanced Driver Assistance System (ADAS) calibration tech.
“It was a journey starting out,” Mark said. “We have changed our calibration strategy
quite a few times. It is so new; you have to be agile and adjust on the fly. I’m sure as ADAS technology develops, we’ll have to continue to look at how we do things.”
One of Kirmac Collision’s newest locations in Vancouver was also the first in the province and the second in Canada to feature a PPG Moonwalk paint mixing system.
Here, Sean noted that the system “automates the paint mixing process, allowing our technicians to focus on other value-add activities.”
In addition to a longstanding partnership with PPG since 1991, Kirmac Collision also has long-term partnerships with Lordco Auto Parts, 3M, GFS, Car-O-Liner and Bellini, among others.
As a result, while speaking about the collision repair technology and trends of 2011 in a previous issue of the magazine, Ian
McIntosh, featured in the volume ten printing of Collision Repair, originally said that “I’m really happy to be where I am right now. I wouldn’t have spent 38 years in the business if I didn’t love it.”
In this way, while technology may have continued to advance and the industry itself may have radically shifted from that first interview over 13 years ago, the sentiment of Kirmac Collision remains the same.
By focusing on the details of the industry from technology and partnerships to community and culture, for Sean and Mark McIntosh, one detail has come to stand out above the rest, and it is one that strongly echoes the Collision Repair conversations of the past:
“Ultimately, we love the industry and it’s been very good to our family. No matter what happens, we’re honored and happy to carry Kirmac on.”
Thirty years. Three stores. More than 60 staff members. Countless lives changed—both customers and industry friends alike. In 1994, Kelvin Campbell was handed the keys to Chapman Auto Body. Former owner Bob Chapman told him to “go and make something out of it.” So, that’s exactly what Kelvin did. Now, three decades later, Collision Repair magazine is celebrating Kelvin’s commitment to his business and the overall betterment of our industry.
Kelvin, 30 years is an incredible milestone! Your innovative spirit and unwavering commitment to excellence have set a benchmark for success in the automotive collision industry. Congratulations on this remarkable achievement!
While Kelvin hails from a family of bodymen, his own journey in the industry began soon after he saw an ad for a 20-week autobody course at the College of Cape Breton. After 12 weeks in the course, Kelvin was the sole student left—and he remained committed to his craft, receiving eight weeks of personal one-on-one instruction during the latter half of the program.
Once he had graduated, Kelvin’s skills as a painter at a local facility were noticed by Bob Chapman, the owner of Chapman Volvo in Halifax. Two years into his new career in Halifax, Chapman Volvo shut down the collision centre at the dealership. Kelvin wasn’t going to let that happen. He put in an offer to buy the shop. Thus began the journey of this Maritime MSO.
“Basically, we’d hit the ceiling at $4.5 million a year—and that was in a $3 million-a-year shop,” Kelvin told Collision Repair mag at the time he took on his second location. Under constraints at the original store, he was having to place his customers on a waiting list of four to six weeks.
When he decided it was time for an expansion, Kelvin set his sights on the suburb of Bedford, about a 15-minute drive from the Agricola St. space. Kelvin hired a design firm to realize his vision of a more efficient commercial space, and after three weeks of drafting, the builders were able to get to work.
Campbell drew particular inspiration from a trip he took to Europe in 2012, with his colleagues from the Collision Performance Group. The trip allowed him to put together a wish list of design features.
In 2021, Kelvin expanded again, taking over a shop from his trade school pal, Anthony Lewis.
“Anthony was running two facilities and decided it was time to take care of one instead of two. We’re good friends from way back, so it was just a great fit,” said Kelvin.
The Harbourside team hit the ground running with renovations.
“We’re doing major renovations, adding paint booths, tooling up and getting certified,” he told Collision Repair in 2021. “Our main goal is to increase the footprint on the property and drive up production.”
Today, the finished facility boasts 10,000 sq. ft. and a host of new tools.
Spray Gun.
The spray gun. Designed for the modern painter.
The first ever spray gun designed specifically to deliver top-of-the-line performance with revolutionary replaceable nozzle technology that saves you time. Experience faster cleanup, faster changeovers and faster cycle times. Bringing you the best of 3M Science, all packed into the smartest, lightest spray gun in the world.
“30 years ago, Bob Chapman handed me the ownership of Chapman Auto Body and said, ‘go make something out of it.’ Three shops later, with 65 employees—here we are, still standing and thriving.”
Happy 30th anniversary to Kelvin Campbell and the team at Chapman Auto Body
Thank you for your pioneering spirit and unwavering commitment to the BMW Group Canada Certified Collision Repair Network
California:
TIRESIZE RIMSIZE
P235/55R18 99V 18X7 1⁄2J
P235/55R18
99V 18X7 1⁄2J
SEATINGCAPACITY
Thecombinedweightofoccupantsandcargoshouldneverexceed
TOTAL 3 FRONT 3REAR 0
COLDTIREPRESSURE 303kpa 44psi
GVWR: WITH
TP
K
BYFORDMOTORCO.INU.S.A.
SRSSIDEAIRBAG
COUSSINGONFLABLELATÉRAL (SRS)
GVWR: WITHTIRESRIMS
REARGAWR: 1508KG P235/70R16SL 16X7.0J
PSI COLD RIMS PSI COLD F0085T0183
TOAVOIDSERIOUSINJURYORDEATH: •Donotleanagainstthedoor. •Donotuseseatcoversthat Seeblocksideairbagdeployment. owner’smanualformoreinformation.POURÉVITERDESBLESSURES GRAVESOUMORTELLES: •Nevousappuyezpascontrelaporte. •N’utilizezpasuncouvre-siège quipeutbloquerledéploiementdu Voircoussingonflablelatéral.lemanuelduconducteurpour deplusamplesrenseignements.
00000000000000000 AT 240 kPa/35
AVERTISSEMENT
CONFORMSTOALLAPPLICABLEFEDERALMOTOR STANDARDSIN DATEOF MANUFACTURE SHOWNABOVE.
DS0:
UA 13 3U51B
RC:
TP/PS R AXLE TR SPR
Californiaclass/stds: PC/ULEVqualified Group: FGMXV01.80111.2L
Evap:SFI/HO2S/TWCFGMXR0095805 , OBD:II
TIREANDLOADINGINFORMATION
REAR 2
FRONT 2
TOTAL 4
Thecombinedweightofoccupantsandcargoshouldneverexceed352kgor776lbs.
SRSSIDEAIRBAG COUSSINGONFLABLELATÉRAL
00000000
GP K 45 V DB F05 UTC
SEATINGCAPACITY
TIRE SIZE
FRONT REAR
SPARE 215/55R1697H215/55R1697HT125/85R1699
COLDTIREPRESSURE
240kPa,35PSI
CONTROLVEHICLEEMISSIONINFORMATION
Conformstoregulations: 2015
240kPa,35PSI420kPa,60PSI
SEEOWNER’S MANUALFOR ADDITIONAL INFORMATION
U.S.EPAclass/stds: LDV/TIER2
Fuel: Gasoline
Californiaclass/stds: PC/ULEVqualified Group: FGMXV01.80111.2L
Evap:SFI/HO2S/TWCFGMXR0095805 , OBD:II
Fuel: Gasoline ABZ
Norm Angrove, who most recently served as the director of Automotive Refinish for PPG Canada, has announced his retirement, effective April 1, 2024.
During his 35+ year career in the automotive refinishing sector, Norm has seen countless new product releases, shop openings, industry events, consolidation in both collision repair and distribution and overall market shifts i.e., Canada’s infamous shift to waterborne paints in 2009, among a plethora of others.
For Norm, a career in the refinish business was always natural. His father owned and operated a distribution company. In his teen years, he’d work the shop during summer holidays, later joining as a salesperson and eventually working his way to sales manager.
From there, Norm ran the company. Eventually, it was sold, and Norm joined the team with Bob Kirstiuk and First Parts, which later became Advantage Parts Solutions as we know it today.
Norm later crossed paths with Larry Jeffries, who was with a paint company at the time. Along with Sam Malatesta and Sam
Mercanti, the men launched the CARSTAR brand in Canada in 1995.
In the early 2000s, Norm returned to distribution and worked with James Maxwell and his organization as VP of sales. The organization built the largest ICI Autocolor distributor in Canada.
Norm first joined PPG in the spring of 2005 as the national manager of industry relations. He has held various roles of increasing responsibilities over his years in PPG’s automotive refinish division, including regional manager of central Canada; senior manager of value programs North America; national business development manager and Canadian collision manager.
He was appointed the director of automotive refinish, Canada in July 2015 and is the longest-ever serving Canadian director for PPG’s automotive refinish business.
As an individual with key insights on the past, present and future of our industry, Collision Repair asked Norm if he had any advice for collision repair centres as they navigate the future.
First—you must be “world-class.”
“You can be world-class among collision centres, but you need to be a world-class employer, doing world-class repairs, dealing with customers in world-class way— everything must be of that caliber.”
— Norm Angrove, collision and refinish industry veteran
“What’s big, for me, is the fact the Gen Z or Millennial workers—they’re not walking into your business and comparing you to other collision centres they could work. They are comparing you to other experiences in life. You can be world-class among collision centres, but you need to be a world-class employer, doing world-class repairs, dealing with customers in world-class way—everything must be of that caliber.”
He also stressed that, in the modern market, “speed is the new superpower.” “Speed of execution and sustainability will be the true winners”
“Speed is a game-changer today. Who can do it the best, who can do it the fastest. That’s who is going to win.”
He also stresses that anyone in business needs to be in-tune with relevant industry trends.
“I truly believe if you lose sight, you lose the fight”.
Please join Collision Repair magazine in congratulating Norm Angrove on his retirement, in addition to the utmost thanks for his extensive contributions to our industry.
Norm would like industry contacts to know he can best be reached at the email address normanangrove@gmail.com
The Saskatchewan Association of Automotive Repairers (SAAR) hosted its annual spring conference at the Temple Gardens in Moose Jaw on the first weekend of March, where industry participants gathered to discuss everything from future technology to how to effectively say no in a workplace.
The event kicked off with an Advanced Estimating Class run by Stefano Liessi, training and Curriculum Coordinator Color Compass University. Liessi worked with a group of over 30 attendees in a presentation that was both interactive and informative.
Saturday, March 2, 2024 was a full day of presentations starting off with a short Annual General Meeting where Joe Cardiff from Cardiff Collision was elected to the board of directors for SAAR. Here, Troy Kolish from SGI also presented special made lanyards from the First Nation’s company Feathers and Lace to SAAR President Terry Beattie and Tom Bissonnette. The lanyards were made to honour the Creator’s Story and were designed in SGI colors.
Ryan Taylor of Bodyshop Booster and AMP Bureau then gave a presentation on the potential value of artificial intelligence
(A.I.) in the bodyshop. Taylor specifically discussed the “coming storm of A.I.,” and how the technology can be used to streamline customer communication to ensure that shops are available to customers 24/7 by helping to organize phone, email and texting systems as well as early damage detection and the claims process. With the use of A.I., Taylor reported that admin time could be reduced by as much as 30 percent.
Scott Kucharyshen, Program Head and Shane Roset, Auto Body Collision Technician Program Head at Saskatchewan Polytechnic then gave an update on student numbers, stressing that there will be many graduates looking for jobs in the industry in the coming months. This year also saw Saskatchewan Polytechnic implementing a level four harmonization, and Kucharyshen and Roset noted that the school has developed an estimating and repair planning course to take place in April.
From here, Ryan Smith and Ciaran Downes with Saskatchewan Government Insurance (SGI) discussed the upcoming corporate transformation occurring at the beginning of April. This transformation will change the
computer system that SGI uses, something that Smith and Downes noted is the biggest change that SGI has ever undertaken. The goal of these changes is to help build consistency and efficiency between customers and partners, and the duo reminded attendees to not feel overwhelmed with the process because training and awareness sessions will be provided through a series of technical bulletins, Lunch and Learns and town hall meetings.
After lunch, Christie Hall, Area Manager of Operations, CARSTAR Canada, returned to give a detailed presentation on how to effectively say “no” in the workplace and why being able to do so matters. She stressed that “it’s not what you say, but how you say it” that matters. Following Hall, Theran Bloudoff, one of the last high school full-time autobody teachers at A.E Peacock Collegiate in Moose Jaw, Saskatchewan, reassured that the next generation of students are interested in cars so long as the industry knows how to properly market itself. He discussed how 80 percent of the work his students do is hands-on and that he makes sure that their learning is interactive since they are
a generation so used to the immediacy of technology.
Bloudoff ended his presentation by encouraging shops to reach out to their local high schools—especially those with automotive programs—because there is more than a fair chance that “a kid there is drawing cars on their notes and waiting to be exposed to the industry.”
Tom Julius, director of business development for Car-Part.com then outlined the importance of using green recycled parts in the automotive and collision industry both from an environmental and economic perspective. He was followed by Peter Wrong, representing 3M to discuss new products and innovations from the company, including the 3M Skills Development Centre in St. Paul, Minnesota. Some attendees at SAAR have even made the trip to the facility for training.
“We decided to heavily invest in a facility to complete [collision repair training] for you guys,” said Wrong. “So much so that this [15,000 sq. ft.] facility is off-site. The reason being—the type of training we’re doing here, we didn’t want it to be strictly
3M-based training. This is standard operating procedure-based training.”
Wrong also stressed that, while the Skills Development Centre is qualified for I-CAR in the United States, courses and certifications achieved at the facility are yet to meet I-CAR Canada qualifications; though they will be soon, he added.
Patrick Demers, key account manager for Progi, was up next to discuss the benefits of ProgiSync, which is used by 2,800 collision shops in Canada. ProgiSync was originally developed for the Alberta market and hail claims, said Demers.
“Once they saw the benefit of a dedicated calendar for estimate appointments, they started to use it for regular collision estimates, too, becoming a powerful first-notice of loss (FNOL) tool for insurers.”
The event ended with a one-on-one interview between Tom Bissonnette and John Abu-Ata from APT Auto Parts, who delved into his business story to conclude the speaking portion of the event.
The night continued—despite threats of a major snowstorm—with a banquet and acoustic performance by Jack Semple.
Scott Kucharyshen, Program Head and Shane Roset, Auto Body Collision Technician Program Head at Saskatchewan
Polytechnic gave an update on
student numbers, stressing that there will be many graduates looking for jobs in the industry in the coming months.
This year’s BMW Certified Collision Repair Centres (CCRC) conference, titled “Breaking Boundaries” was held in mid-February in Palm Springs, California, highlighting the network’s ongoing advancements and the collective drive towards excellence in automotive repair.
The event was marked by insightful contributions from industry experts, including a notable presentation by renowned industry expert and motivational speaker Mike Anderson. Anderson emphasized the immense benefits of the CCRC network, highlighting the critical role of networking in sharing visions and stories within the industry. His message underscored the importance of collaboration and communication among professionals to drive innovation and excellence.
A focal point of the conference for Canadians was BMW collision and wholesale manager Chris Castagna’s overview of the network’s past achievements and his outline of a roadmap for future growth. Castagna expressed gratitude towards previous director Michel Matte for his foundational work in building the CCRC program into the success it enjoys today. This passing of the torch highlighted the continuous effort and leadership that drive the network forward.
The conference also highlighted the significant role of Canadian CCRCs in the BMW repair ecosystem. Remarkably, Canada boasts one of the highest percentages of CCRCs performing BMW accident repairs, with about 40 percent of such repairs being carried out by certified centres. This statistic not only
reflects the trust placed in the CCRC network by BMW vehicle owners but also underscores the network’s expertise and capacity to deliver top-notch repair services.
Keith E. Jones was also announced as collision strategy and program manager for DEKRA, supporting the CCRC program in Canada.
Throughout the three-day event, the emphasis on collaboration, expertise and innovation
shone through. The Day At The Track was a key component, with attendees having the opportunity to test the mettle of the BMW fleet on an actual racetrack. Canadians claimed the first and third place spots on the track; Matt Pritiko of Burwell Auto Body took first, and Sean McIntosh of Kirmac Collision took third.
Plenty of our Canadian friends made the trek to sunny California for the meet up— check out our photos from the event.
Mitchell CSI Award — B&D Autobody
Autohouse KPI Award — B&D Autobody
Sam Piercey Memorial Award — CSN Heartland Collision
Western Canada CCRC of the Year — Dilawri Collision Centre Calgary
Central Canada CCRC of the Year — Pfaff Autoworks
Eastern Canada CCRC of the Year — Auto Bugatti
Overall Canadian CCRC of the Year — Dilawri Collision Centre Calgary
Originating as a revered and esteemed brand within the vibrant landscape of Quebec, ProColor Collision emerged as a paragon of excellence and innovation in the collision repair industry. With a rich history spanning decades, ProColor garnered acclaim and recognition for its unwavering commitment to quality, customer satisfaction, and industry-leading practices. As Fix Network embarked on its quest to expand its footprint and redefine industry standards, the acquisition of ProColor in 2019 represented a strategic milestone in this transformative journey. With a vision to complement existing offerings of the Fix Auto collision repair brand, whom the network is best known for, to addressing capacity challenges, and providing consumers with expanded choices without compromising the quality and service that Fix Network is known for, the network has propelled ProColor Collision onto the national (and international) stage, ushering in a new era of innovation, collaboration, and success.
In the bustling city of Charlottetown, two giants, Fix Auto and ProColor Collision stand shoulder to shoulder, united by a shared vision of excellence and a commitment to serving their community. Meet Chris Dalziel, the proud owner of ProColor Collision Charlottetown, whose family legacy spans over half a century in the automotive industry. As he reflects on the evolution of the collision repair landscape, Chris paints a vivid picture of transformation, collaboration, and mutual support.
In the earlier days, when the industry dynamics were vastly different, Chris recalls a time when insurance claims played a smaller role in their operations. “Ten to fifteen years ago, the landscape was not the same. Claims held much less sway in our business,” Chris reminisces, adding, “They now constitute the large majority of our workload.”
This shift signaled a paradigm change that demanded a strategic response.
Chris’s decision to join the network was influenced by a combination of factors deeply rooted in both familial legacy and strategic foresight. Having purchased the shop from his uncle in 2017, Chris inherited a business with a longstanding reputation for repair quality, yet one that was still grappling with challenges in maximizing claims acquisition. Reflecting on past opportunities, Chris notes that Steve Leal, president of Fix Network World, had originally approached his family’s business in 2012, but they weren’t yet prepared to make the leap. However, as market dynamics evolved, particularly amidst the challenges brought forth by the COVID-19 pandemic in 2020, Chris and his team recognized the need for a strategic shift. With insurance claims taking center stage in their business model, they embarked on a thorough exploration of network options. Among the contenders, ProColor stood out for its synergies within Fix Network and its broader ecosystem, offering a holistic approach to automotive repair that already encompassed collision repair services with reputable brand, Fix Auto, mechanical services through Speedy Auto Service and windshield repair and replacement via NOVUS Glass. This alignment with Fix Network’s comprehensive vision, coupled with their track record of success, made it the clear choice for Chris and his team as they embarked on a new chapter of growth and collaboration within the network.
Fix Auto Charlottetown, led by Dave Gaudet, whose father had once worked alongside Chris’ uncle before venturing out on his own, was once viewed as an opponent. “At one time, the sentiment between our businesses was ‘that’s competition, don’t share industry secrets,’” Chris reveals.
However, after joining the network, the winds of change brought forth new opportunities for collaboration and synergy.
Hurricane Fiona, a force of nature that swept through Charlottetown in September 2022, brought with it a deluge of insurance claims, challenging the capacity and resources of both ProColor Collision and Fix Auto. In a remarkable display of solidarity, the two brands rallied together, crossing traditional boundaries to support one another. “During the Hurricane Fiona fiasco, Fix Auto reached out to us, knowing that our shop had capacity and thought that since we were now a part of the same network, we could help each other out,” Chris explains.
Following their conversation, within a span of 72 hours, ProColor Collision Charlottetown had an additional 45 claims, alleviating the burden of antsy adjusters, and ensuring prompt and efficient service for their customers. This pivotal moment exemplifies the ideals of collaboration and cooperation that define the relationship between ProColor Collision and Fix Auto. They have also sent Fix Auto their own claims when they’ve needed that same support, and it has been back and forth since then. This also means that between the two brands, they are able to capitalize on the market share rather than the competition. “Now, if something comes up and one of the two shops has a problem or a question about a paint code, for example, we can text each other. It’s nice knowing we have that support under 3 kilometers away and someone to bounce ideas off of,” Chris affirms.
In a world where competition often reigns supreme, Chris advocates a philosophy of unity and collective progress. “We all have the same goal,” he asserts, “we need to be talking to each other rather than pushing the facade that ‘it’s me against everyone else.’”
In the heart of Ontario’s bustling automotive hub in the Greater Toronto Area, Azad Daya, the visionary owner of ProColor Collision Etobicoke North and ProColor Collision Guelph, stands as a testament to the transformative power of passion, innovation, and collaboration. With a keen eye for opportunity and an unwavering commitment to excellence, Azad and his team have emerged as a driving force behind the success of the ProColor brand, championing its growth and expansion across the province.
For Azad, the decision to join Fix Network was driven by a shared vision of excellence and a commitment to continuous improvement. “I joined Fix Network in 2021, drawn by their strong corporate structure and unwavering commitment to franchisee success,” Azad reflects. Through access to cutting-edge technology, comprehensive training programs, and unparalleled operational support, Azad and his team have unlocked new levels of performance and efficiency, setting a standard of excellence within the industry.
Azad underscores the brand’s pivotal role in addressing capacity concerns that collision repair shops have been experiencing across the nation and emphasizes
that how the brand chooses to position itself in these circumstances will be instrumental in forging its future and fostering brand growth.
Even this past year, as the demand for automotive repair services surged to unprecedented levels, particularly in key geographic regions like Toronto and Ottawa, Azad recognized the urgent need for a strategic response. “The biggest issue was that the Ottawa and Toronto areas saw a bottleneck with insurance claims, particularly with our national partner TD (Collision Repair Experts),” Azad recalls.
After some jestful remarks between Azad and a CRE operations team representative regarding load-levelling in the GTA, the serious opportunity to provide some aid to the Ottawa region was presented. In a remarkable display of resourcefulness and initiative, Azad seized the opportunity to address the capacity crunch head-on, leveraging the synergies within the Fix Network to support his fellow franchisees. Through collaborative efforts with Fix Network’s operations team and regional leaders, a seamless exchange of vehicles between ProColor Collision and other network brands was orchestrated, ensuring timely and efficient service delivery.
The impact of Azad’s intervention extended a lifeline to fellow franchisees grappling with these capacity challenges. “We were able to pick up and drop off 107 claims in a month,” Azad proudly declares. Even with the tremendous amount of damaged vehicles from the hail in Linsday, Ontario, where Fix Network did not have a facility, Azad’s team, as well as the Fix Auto and ProColor shops in Aurora and Pickering, were able to step in and tackle these claims to ensure this community was able to have their vehicles repaired in a timely manner. Azad’s spirit of collaboration and mutual support lies at the heart of the Fix Network ethos, empowering franchisees to overcome obstacles and thrive in a competitive marketplace.
As ProColor Collision continues to chart a course of expansion and growth, Azad remains steadfast in his commitment to the brand and its principles. With an eye towards the future, Azad is poised to lead the charge, seeking out new opportunities for growth and expansion wherever capacity issues arise within the Fix Network.
As we reflect on ProColor’s remarkable journey since joining the Fix Network family, it’s evident that growth has been a defining theme. In the past year alone, we’ve witnessed the expansion of ProColor Collision across Canada with the opening of several new shops, each of which meet the Fix Network growth criteria of adding capacity where needed and at the highest level of quality.
ProColor Collision Calgary North East
ProColor Collision Guelph
ProColor Collision Brampton East
ProColor Collision Thornhill
ProColor Collision BTech Edmonton East
ProColor Niagara Falls
As we celebrate the expansion of ProColor Collision across Canada, it’s clear that its journey has been guided by a steadfast commitment to excellence and innovation. With each new shop, they have strengthened their presence in key geographic regions, addressing capacity issues and offering consumers more choice while upholding the
exceptional service standards that Fix Network is known for. This growth not only benefits customers but also elevates the entire industry, setting new standards for quality and professionalism. From coast to coast, ProColor Collision continues to complement Fix Auto offerings, delivering top-notch repairs and exceeding expectations at every turn. As the brand looks ahead, they remain dedicated to their mission of providing unparalleled service and driving positive change in the automotive repair sector. Working in symmetry, the banners under Fix Network are shaping the future of collision repair and leading the way towards a brighter, more resilient industry.
PART ONE of what some of Canada’s collision leaders foresee for your future
If you’ve been to any conference, meeting or partook in any industry conversation as of late, you’ll be familiar with the sentiment that the automotive industry has seen more change in the last five years than the previous 20 years combined.
If you’re in tune with the industry in any way, shape or form, you also know that this is just the beginning. Things move fast in the modern world, and collision centres have no choice but to keep up.
In the face of these times, we are launching an exclusive executive opinion series. This is part one of a multi-issue series from Collision Repair magazine, featuring top-performing industry representatives from across North America. Read the first of our expert opinions on the following pages.
CRM: What do you foresee as the top trends this year?
MM: The evolution of the collision centre, OE and insurance company dynamic. Some call it the Bermuda Triangle, I just call it common sense. We have to fix cars properly and according to industry and OE guidelines. The challenge is that those making those guidelines (OEs), aren’t paying the repair bill. So there is a natural disconnect. Fixing that disconnect is a top priority.
Second—insurance companies and their supply chain strategy. Branded centres, dedicated capacity programs and OE certification segmentation are changing the landscape.
Supply and demand. Since the pandemic, we have seen a massive shift towards a material increase in cars to fix and not enough collision centres to fix them. Does that change throughout the year and shift towards fewer cars to fix and no capacity issues? Time will tell.
CRM: What is one thing you would advise collision centres to pay attention to?
MM: Profitability. This is the most important thing for me and our franchisees. Collision centres have to become more profitable. To attract talent, to fix cars right, to invest in equipment, to ensure sustainability of the environment, to grow and to deliver on customer, OE and insurer’s needs. It all depends on our sustained profitability across all stakeholders. CARSTAR has a 30-year legacy because of our owners and their resilience to endure the countless obstacles that get thrown their way, from; rising cost of materials, overhead, labour; technician shortages; complex manufacturer technology; even pandemics. Our reputation as premier industry-leaders are hard-earned by these remarkable owners. They know it’s important to pay attention to profitability and they take advantage of every support pillar we have to ultimately build a best-in-class business that our partners can count on to sustain the test of time.
MG: As we navigate through 2024, the need to address the nationwide shortage of repair capacity is a pivotal trend shaping our industry. This challenge affects all industry stakeholders but places most of the burden to find solutions on repairers. A long-term solution involves repairers making significant capital investment in both human resources and business expansion with no guaranteed return; repair businesses are footing the bill and taking all the risk.
From our vantage point of decades spent analyzing collision metrics, AutoHouse suggests instead that repairers look first at optimizing existing capacity. Once you’ve gained all the efficiency that can be squeezed out of your current resources, decisions around expansion may be very different, or at minimum, thoroughly evaluated.
Before making any substantial financial commitments, it is crucial to assess and optimize current operations. In our experience, maximizing efficiency requires being smart as well as busy. Many repairers have successfully increased their monthly repair volume and profitability without additional resources by anchoring their operations to some key metrics. If enhancing your repair count by 10-20 units a month could influence your strategic decisions, it’s time to take a closer look at some numbers.
Improving operational efficiency benefits everyone; it eases the industry’s capacity constraints by boosting a repairer’s throughput
CRM: What do you foresee as the top trends this year?
PP: Firstly, labour shortage. Repairers are still attempting to overcome service delays which are caused by increases in work, but not enough staff to support operations. Many organizations in the collision repair space, inclusive of Simplicity are taking matters into their own hands and making our workforce sustainability a strategic imperative. Organizations who are investing, committing resources to recruitment of top talent and emerging talent, are derisking their business for future success.
Capacity is still one of the largest challenges facing the collision repair space. It impacts customers negatively, puts downward pressure on collision centre margins and drives up costs for our B2B work providers. Although capacity is strongly linked to the talent shortage, I believe collision repairers will continue to revisit their operational model. Collision repairers will need to demonstrate our ingenuity, as we’ve done many times in the past and work on concepts just as Just-in-Time (JIT) inventory of vehicles and revisit processes to determine where is waste that can be removed in ordered to enhance capacity for your customers.
and increasing their profits. After that, contemplating investment in the next phase of business growth might seem a lot more straightforward. Below are some key metric comparisons provided by your colleagues at AutoHouse and please always reach out at www.autohousetechnologies.com with any questions.
CRM: What is one thing you would advise collision centres to pay attention to?
MG: Touch time is the overarching measure of efficiency but the three foundational metrics below drive successful operations.
1) Daily Output is the average hours produced/day (e.g. 100 hrs/ day averaged over 60 production days). Ideally, daily output will be consistent.
2) WIP Ratio is Current Hours onsite/Daily Output (e.g. 11.0:1). This equates to having 11 days of inventory on site or just over 1,100 Hrs in WIP. Faster inventory turnover equals more profit; just ask Walmart.
3) Performance by Repair Segment is Touch Time by Repair Size (hours are categorized into Xpress, Light, Medium and Heavy). Most repairers can significantly improve performance by processing smaller repairs more efficiently and using repair size to determine scheduling and workflow.
Finally, I believe we need to pay attention to the proliferation of environmental sustainability in the collision repair space. Although Simplicity is the pioneer in environmental sustainability, other members of the collision repair community are making their first steps into their net zero journey. This is exceptionally encouraging. I believe that not only work providers, but the end user wants to deal with an organization that considers all stakeholders, inclusive of their community. This will develop tremendous equity in the communities served.
CRM: What is one thing you would advise collision centres to pay attention to?
PP: One thing collision repairers should focus on—profitability. Without it, we can’t exist.
Collision repairers should visit their revenue and costs and set a one percent target/month. How do I increase my revenues by one percent per month, and how do I reduce my cost of goods sold (COGS) and operating expenses by on percent per month? This will drive substantial results and pave the way for further sustainability in our industry.
Sylvain Simard and Jean-Sébastien Simard
CARSTAR Chicoutimi Sud and Nord
We’re happy to be part of the brand because we feel the family spirit, which we also like our employees to feel. We can do our work with passion, while feeling heard and supported by the CARSTAR team.
Contact Collin Welsh to learn more about joining the CARSTAR family at cwelsh@carstar.ca
For the modern shop, good looks are just as important as a good repair
Beyond the layout of tools and equipment, a building’s design permeates every aspect of a collision repair shop, influencing everything from customer experience to workflow optimization.
While the old stereotype of the bodyshop as a dirty, dingy place may still exist in some
people’s minds, for today’s shops, good looks are a topic on the same par as a good repair. Collision Repair magazine recently reached out CSN 427 and CSN Avenue Collision in Ontario and Winnipeg’s Donvito Automotive Group, Collision and Glass to discuss how the aesthetic of a facility is more than just a coat
of paint or a well-placed tool rack—it can be the driving force behind a shop’s efficiency, profitability and long-term viability.
Read below to find out how strategic planning and innovative design elements are driving the industry forward, one meticulously crafted space at a time.
For Jessica D’Alessandro, Head of Marketing and PR for CSN 427 and CSN Avenue Collision, from the moment a customer walks into your shop, they are evaluating your brand. As a result, the teams at CSN 427 and CSN Avenue Collision work hard on and take pride in the consistent maintenance of both the interior and exterior of both buildings.
When asked about intentional design aesthetics, D’Alessandro noted that the goal of both shops is for CSN 427—located at 395 Evans Ave, Etobicoke, Ontario—and CSN Avenue Collision— located at 293 Macpherson Ave, Toronto, Ontario—to be as user-friendly as possible—both for employees and customers.
When thinking about interior layouts, D’Alessandro acknowledged that she frequently takes inspiration from coffee shops, lounges and cafes, and aims to create a modern look with a balance between providing both communal and private spaces. As a result, the shops feature areas for customers to sit and do work or relax as well as individual
pods for customer service reps to step away as needed.
The use of glass also helps the shops to create an open and transparent atmosphere, which D’Alessandro says can help build trust with customers, and is something she would like to include more of in both shops. For instance, the CSN 427 location features a large window so that customers can see into the back as cars are being repaired, showing them that CSN 427 trusts them to be a part of and engaged in the repair process.
For D’Alessandro, part of building a design rooted in openness and trust is in making the reception area a central point of design—something CSN Avenue Collision accomplishes by having the front desk be the first thing a customer sees when entering the building.
“It’s important to create a focal point for customers so that they feel welcomed into the space and know where to go for information,” D’Alessandro told Collision Repair magazine.
“Another key part of this is in having good
signage to help direct the flow of customers in the space.”
Still, in working to achieve areas of comfort, community, functionality and modern aesthetics, it’s also important to have room for fun and CSN 427 achieves this in part by providing bikes for employees to use to get around the 90,000 square footage shop.
In turn, D’Alessandro’s father, Lorenzo D’Alessandro can occasionally be seen traveling in style on an electric scooter sporting the CSN logo.
With these conscious design features in place, D’Alessandro spoke about how customers have responded positively to the decisions, complementing both shops on how comfortable, clean, and put together they are.
“Putting money into the look of a shop can be a last priority,” D’Alessandro said, “but it’s something that should be at the forefront. It benefits customers and staff, and it sends a message to potential employees. Having a clean, well-designed place to work gives employees a place to take pride in and want to return to.”
Similarly, for Rick De Dominicis, vice president of operations of Donvito Automotive Group, the design of a shop is all about creating a luxury experience for customers while also standing out from the competition.
When discussing specific design choices of Donvito Automotive Group’s collision and auto glass repair shop location—found at 1700 Sargent Ave. in Winnipeg—De Dominicis noted that the shop is certified in several luxury automotive brands, like BMW, Mini Cooper, and Tesla, and so the initial design goal was to “create a luxury look to match the luxury vehicles.”
While the longtime stereotype of the collision repair shop was a dingy place, De Dominicis hoped to buck the trend, and when the Winnipeg location was built in 2013, he hoped to make a positive lasting impression with its design.
“When we first built in 2013, we would hear comments everyday about how cool it was, with people wanting to know what we did there. Now, I hear comments less often, but we succeeded in leaving an impact and lots of people I talk to know exactly where our building is. I definitely think that the unique exterior design helped contribute to this. We’ve become a sort of landmark location.”
From here, De Dominicis has worked on ensuring that all of the Donvito Automotive Group’s collision and auto glass repair shop locations have transitioned to offering the feeling of luxury. This includes equipping each location with a customer lounge section and staying up to date on customer trends and needs.
Donvito Automotive Group, Collision and Glass also worked closely with BASF to ensure that the inside of the shop was built with a functional flow so that employees could easily navigate the space and have set workstations to improve output.
Moreover, when considering a shop’s design, De Dominicis further stressed the importance of learning from the automotive community. For Donvito Automotive Group’s collision and auto glass Winnipeg location in particular, De Dominicis told Collision Repair magazine how vendor partners and others in the industry have come to visit the shop to get ideas about design and to learn from the shop’s layout.
“More than just the design of a shop, it’s important to always be adapting to your customers,” De Dominicis said. “Visually, the shop is about making a difference, but
it’s also important to make sure that your customer service matches the look and feel of the building.”
To help communicate this sense of professionalism, De Dominicis discussed how the front of house staff maintain business casual attire, and the shop itself includes charging stations to ensure it is able to offer up-to-date customer service when it comes to the latest tech trends.
When asked about dream design details, De Dominicis explained how it would be nice to have more space to continue expanding future customer service resources.
“If I could add anything to the shop,” De Dominicis said, “I would love to be able to have more space for a supercharging station. Part of maintaining a shop’s design is in keeping up with customer needs and with
the increase in electric vehicles, it would be nice to be able to have more charging spaces.”
As such, while there are many approaches when it comes to a shop’s design, D’Alessandro and De Dominicis help demonstrate how the significance of design in a collision repair shop cannot be overstated.
By prioritizing elements such as layout, workflow optimization and customer interaction zones, a well-designed shop can not only attract more clients, but also contribute to their satisfaction and loyalty. A carefully crafted environment also fosters employee morale and productivity.
Ultimately, investing in design is not just about creating a visually appealing space. It’s about creating a functional and thriving ecosystem that sets a collision repair shop apart in an increasingly competitive industry.
“When we first built in 2013, we would hear comments everyday about how cool it was, with people wanting to know what we did there.”
— Rick De Domicis, VP of Operations, Donvito Automotive Group, Collision and Glass
BARCODE/RFID TECHNOLOGY — Using both barcodes and RFID tech to track and manage inventory more efficiently and accurately. Inventory information is stored in computer software.
JUST-IN-TIME (JIT) INVENTORY — Ordering and using parts precisely when they are needed.
VENDOR-MANAGED INVENTORY — Supplier-controlled inventory levels, where suppliers monitor and replenish parts based on autobody shop demand, reducing inventory management responsibilities.
CONSIGNMENT INVENTORY — Parts owned by suppliers but stored and used by the autobody shop, with payment made only when the parts are used in repairs.
ome shops have parts rooms that are set up like luxury grocery stores. Everything is in its place, polished to perfection, waiting to be picked off the shelves and thrust to their destiny. Other sites might refer to their parts storage areas as “the backrooms” or “the dungeon’; some might keep it out of mind entirely, opting for just-in-time strategies—or taking things in stride, if you will.
Each shop has its quirks. Regardless of how parts are kept, some things remain the same across the board: struggles with availability and, in many cases, incorrect or damaged shipments.
There are countless different parts ordering strategies adopted by collision centres across Canada. Deciding factors can depend on shop size, volumes, repair versus replacement preferences and much more. Everyone has their way of doing things—so we at Collision Repair asked shops to submit some basic facts on their strategies to better understand how different sizes of collision centres across Canada grapple with the ups and downs of parts supply and, inevitably, disruption.
Check out our survey stats on the following pages.
90.3 PERCENT OF RESPONDENTS WERE SHOP OWNERS/MANAGERS
54.8 PERCENT OF RESPONDENTS DESCRIBED THEIR SHOPS AS HIGH VOLUME
41.9 PERCENT DESCRIBED THEIR BUSINESSES AS AVERAGE/MEDIUM VOLUME
HOW MUCH MONEY DO YOU ESTIMATE IS INVESTED IN PARTS INVENTORY CURRENTLY PRESENT ON YOUR SHOP FLOOR?
— 3.2 PERCENT
6.5 PERCENT LESS THAN $10,000
9.7 PERCENT BETWEEN $11,000 AND $25,000
— 32.3 PERCENT BETWEEN $26,000 AND $50,000
29 PERCENT BETWEEN $50,000 AND $100,000
16.1 PERCENT BETWEEN $100,000 AND $250,000
BETWEEN $250,000 AND $500,000
MORE THAN $500,000
— 3.2 PERCENT
ACCORDING TO OUR SURVEY RESULTS, MOST RESPONDENTS KEEP BETWEEN $50,000 AND $100,000 OF PARTS IN THEIR SHOP (33.3 PERCENT); A FURTHER 26.7 PERCENT OF RESPONDENTS REPORTED BETWEEN $100,000 AND $250,000 OF PARTS ON THEIR PRODUCTION FLOORS.
HIGH VOLUME SHOPS:
50 PERCENT USE JUST-IN-TIME (JIT) INVENTORY
37.5 PERCENT USE RFID/BARCODE TECHNOLOGY VIA COMPUTER MANAGEMENT SYSTEM
25 PERCENT USE MANUAL INVENTORY MANAGEMENT (SPREADSHEET, ETC.)
6.25 PERCENT USE VENDOR-MANAGED INVENTORY
6.25 PERCENT USE CONSIGNMENT INVENTORY
AVERAGE/MEDIUM VOLUME SHOPS:
69.2 PERCENT USE MANUAL INVENTORY MANAGEMENT (SPREADSHEET, ETC.)
23 PERCENT USE RFID/BARCODE TECHNOLOGY VIA COMPUTER MANAGEMENT SYSTEM
15.4 PERCENT USE VENDOR-MANAGED INVENTORY
7.7 PERCENT USE JUST-IN-TIME INVENTORY
*Some respondents track inventory using multiple methods.
HOW DO YOU MANAGE PARTS INVENTORY?
43.8 PERCENT USE MANUAL INVENTORY MANAGEMENT (SPREADSHEET, ETC.)
12.5 PERCENT USE VENDOR-MANAGED INVENTORY
31.3 PERCENT USE JUSTIN-TIME (JIT) INVENTORY
33.4 PERCENT USE BARCODE/ RFID TECHNOLOGY VIA COMPUTER MANAGEMENT SYSTEM
HOW OFTEN DO YOU ENCOUNTER PROBLEMS WITH PARTS AVAILABILITY?
OFTEN — 83.9 PERCENT OCCASIONALLY — 16.1 PERCENT RARELY — 0 PERCENT NEVER — 0 PERCENT
HOW OFTEN DO YOU ENCOUNTER PROBLEMS WITH PARTS SHIPMENTS?
OFTEN — 45.2 PERCENT OCCASIONALLY — 51.6 PERCENT RARELY — 3.2 PERCENT NEVER — 0 PERCENT
We have adopted a system of ordering parts and booking the vehicle when they are delivered. It came to be during the pandemic, and as we continue to face backorders, we’ve kept it going. The only glitch in our system are [from] estimates generated by unqualified insurance appraisers from owner-supplied photos. Most of these result in additional parts being required and delays in the repair process—especially if there are additional backorders.”
“Like gaining experience through working
almost every make. Why can the OEMs keep selling vehicles they can’t supply structural parts for?!”
Manufacturers should be mandated to hold some parts in reserve for repairs, rather than just putting all of the parts into production. This is unfair for the consumer and the collision industry.”
“We’re always working towards just-in-time ordering and we find availability slowly improving.”
“Insurance wants X-approved parts; the OEM approves only OEM parts. Shops are stuck in the middle, watching our profit get eaten away by time wasted on a management system we have
For [our] brands and severities of damage, I am on the lookout for a better way to check parts and catalogues for inventory. Tracking and storage location for easier retrieves is very important, too.”
www.kecotabs.com
for the cleanest lateral tension possible designed to maximize the output without the risk of creating collateral damage. Multiple shoes give technicians flexibility and options for applying force to flat panels and body lines with both perpendicular and in-line configurations. For more information email Sales@keco.com or call 888-532-6822.
www.hunter.com
Opportunity doesn’t knock; it rolls: Vehicles need alignments and new tires, but you won’t know unless you look. Quick Check® Drive from Hunter Engineering is a fully autonomous inspection system that finds the opportunities you need. Twelve cameras and 32 laser sensors provide accurate alignment and tire tread measurements in seconds, displaying the easily understood results on the large Flightboard™ video monitor for convenient customer discussions. For more information visit www.hunter.com/vehicle-inspection/quick-check/
The SATA RPS (Rapid Preparation System) multi-purpose cup system performs four functions: mixing, painting, refilling, storing. The handling of SATA RPS is so easy because it consists of only three parts: cup, lid and sieve.
SATA RPS fits directly onto your SATA spray gun with QCC connector (Quick Cup Connector) without any adapters. It makes a technician's life much easier, considerably increases productivity and drastically reduces the consumption of cleaning solutions and solvents.
www.sata.com/sata-rps-multi-purpose-cup
Bendable – allows the painting of sill areas or wheel arches "overhead"
Stable – due to the screw connection between cup and lid, the cup always remains on the lid and gun even when touching obstacles. Easy removal of the lid in case of emergency – without soiling the working area.
Clean removal of the cup – by pressing the cup in, vacuum is created, which empties the material passage when pulling the trigger.
Constant material flow – helps the painter to achieve perfect coating results just like child's play.
Very quick colour change – cleaning becomes a minor matter
Available in 3 cup sizes: 0.3 l, 0.6 l and 0.9 l
Also available as UV version: 0.6 l
After nearly 30 years in teaching, I’ve never seen the situation more dire
As a retired high school autobody teacher, I spent my entire career trying to promote the automotive collision industry to my students by giving them real life experiences. These experiences varied from real world projects on live vehicles, field trips, co-op opportunities and competing in skills competitions at the local, provincial, and national levels.
Of my students that were interested in a career in our industry, I guaranteed that I would do my very best to find a job for them. For those that did find roles, they are currently working in the industry and are doing quite well. To my knowledge, many students don’t stay in touch. I have about a dozen former students working in the trade. I have a couple that did it for a few years and then transferred over to the construction industry. I retired in 2017, but I still have former students contacting me if they are looking to move or use me as a sounding board for their concerns.
In my 28-year teaching career, I can only recall one or two times where shops had called the school looking for young people to train as technicians. This is over and above those progressive shops that were involved in the co-op program.
During my time in the Toronto District School Board, I saw eight autobody programs shut down. As chair of the Skills Ontario Auto Body competition, I have seen many school boards stop competing in the autobody category because they no longer had a program running to support a competitor. The excuses I have heard for closing a program usually came down to how to deal with isocyanates in the paint products.
The federal and provincial governments have tried throwing money at the problem, but autobody repair is not one of the skilled trades that is getting any of this influx, from what I have heard. The Ontario Ministry of Education mandates one minimum credit in
technological education as part of the total credits to graduate high school. On the surface this sounds great, but the barn door has been closed after the horse has left.
In the 90s, the provincial government introduced Broad Based Technology courses. It was basically a smattering of curriculum from the technological education umbrella. Transportation, construction, communications, services, etc. If you took transportation as a course, it was supposed to cover land, sea, air and space travel.
This, in my opinion, was the cause of many tech programs to be shuttered or gutted. If you can teach everything in one classroom, you don’t need all the specialty rooms and the specialty teachers to teach them. The big problem with this thinking is that, depending on the teacher’s background, they will teach to their specialty and not provide the students necessarily what they may want.
In my retirement job, I have had the opportunity to be in shops on a regular basis. Nowadays, shops are consistently asking if I know of any technicians looking for work or to move. This is not the question to be asking. The question to be asking is what I can do as a shop owner to recruit young people to my business.
As mentioned previously, I only had a handful of shops reach out during my entire teaching career. When that did happen, I would ask if the shop knows of an autobody program in a high school in their area. Has the shop reached out to a local high school looking for a co-op student? Has the shop offered up an opportunity for local schools to come for a tour of their facility? Has the shop offered up a workplace opportunity for students to spend a day or two in the shop to see if this is the industry that the student may be interested in?
Sadly, I have more questions than answers, so I put a survey out to a number of my former students, former skills competitors and even a couple of shop managers/owners—I will conclude, for now, there.
The majority of survey answers, in a nutshell were:
Q1: Did you take an autobody course or co-op in high school?
A: YES
Q2: Did you take one, or both? (i.e. just auto class/just co-op, or both options)
A: BOTH
Q3: Did taking either course help you to decide to pursue a career in the trade?
A: YES
Q4: Would you have considered a career in the autobody industry, had you not been exposed to it in high school?
A: NO
Q5: Was your high school program similarly equipped to what you found in the workplace?
A: YES
Q6: Did your high school experience prepare you for the workplace?
A: YES
Q7: Did your teachers help you in your decision to pursue a career in autobody?
A: YES
Teacher guided me through various repair procedures and techniques for modern day repairs and restoration. Preparation and painting techniques. Given multiple projects to help me to identify what kind of technician I would like to become.
Q9: How, in your opinion, could the industry better support high school autobody programs to keep them alive, and be able to better prepare youth for the workplace?
More workshops for middle school students, where they can learn and try new tools and equipment.
Industry leaders should be more involved in course and curriculum development, as well as training opportunities for students. Shops/ manufacturers could donate equipment, materials and vehicles for training purposes. Workshops with bodyshops and manufacturers to have in-class speaking sessions about the industry as a whole.
Demonstrations of paintless dent repair, polishing, equipment demonstrations that may entice students.
Q8: What, if anything, would have helped you to be better prepared for the workplace?
Challenged me to be the best that I could be. Teacher paid attention to my strengths and weaknesses and helped me to turn my weaknesses to strengths.
More estimatingmultitasking; as a potential career path; more hands-on experience.
has been a licensed auto body and collision damage repairer since 1981 and previously taught autobody and collision repair with the Toronto District School Board for nearly 30 years. He has served as a national technical committee member for SkillsCanada Auto Collision competitions since 2006, acting as a WorldSkills expert for Canada for international competitions in 2017, 2019 and 2022.
Are you feeling a wee bit stunted in your growth? Interestingly, from recent inquiries, I have been told on multiple occasions that shops are booking weeks and even months out. This information tells me—a neighbourhood leader in analytics—that growth isn’t the problem; it is managing the growth and retaining some revenue from it.
My question to you: how much growth are you leaving on the table?
When processes get out of control, we throw good money after bad or leave the good money on the table. It is tough to say ‘NO’ to more work coming through your door; the fact is, if you are over your capacity, you are stunting your growth. Having a pile of vehicles that have yet to be repair-planned outside ‘waiting,’ is a waste of time. Anytime you are waiting for someone or something, you are wasting time.
Growth is more than just a bunch of jobs waiting in line; it is getting the revenue out of them and possibly reinvesting it. Ask yourself this, “do I have any vehicle in my shop waiting for a part or parts?” If you answer this with a yes, that vehicle is not growth but a cost. Now ask yourself this question; “how many of my stalls are without a tech?” or “how many techs have more than one stall?” You are stunting your growth if you do not have a tech per stall. It is physically impossible for a person to work on two vehicles at once. Studies show that every time you drop one task to begin another, it takes an average of 20 minutes to get back to the flow you were at on the first task when you come back to it. The argument has been presented that “my tech needs a second stall for reassembly or (my favourite) small jobs. If the shop has a dedicated reassembly area, then lovely. However, this decision needs to be part of your scheduling; this balances your KPIs, which, as you have heard me say before, many of you are held hostage by.
Let us say for a moment you could grow your business without investing a wad of cash and by reducing the intake to reflect your actual capacity. Yes, that is right, you read it here first for the umpteenth time ‘more OUT of less.’ This is NOT the same as ‘more FOR less’.
Repair planning is a crucial element, as is scheduling. These two processes go hand in hand. You ask why—well, because you create accuracy when you account for all the line items, parts, and processes upfront. This accuracy is what you need to have an accurate schedule to keep your actual capacity running smoothly. Missing an item or operation,
THE FACT IS, IF YOU ARE OVER YOUR CAPACITY, YOU ARE STUNTING YOUR GROWTH.
creates a bottleneck. This means waiting on something or someone. If you can have a tech in each stall turning through work that is correctly repair planned without delays, you will see exponential growth. The art of repair planning reduces supplements, increases touch time, reduces LOR, and improves cycle time, all of which are reflected in your bottom line because you are billing for the operations performed.
Yes, it is true that you will have to deal with some friction, but rationalizing the confirmation bias is also not the answer. Let’s clarify; accounting for all your line items will bring in more true revenue, needing less vehicles (more out of less). Leaving out line items is equal to discounting your work; ergo, you try to make it up on volume (or leaving
line items off the RO) means (more for less). A race to the bottom. A whole lot more of less is, a whole lot less.
Now, what you could do is buy more shops! Yes, great way to grow your business. Or is it? When the decisions are made based on true proper data that reflects reality, then yes, this could be very lucrative; however, if the shop[s] you are about to purchase rely on volume to make up revenue then you could be sliding down a very slippery slope. Recently, in an article in Collision Repair magazine, we learned of a large MSO that has gone into protection for bankruptcy. This is not an experience anyone wants to go through, and sadly it is a very vicious vortex once operations reach the point of no return. It may sound equivalent to, “you can make it up on the next one.” No, no you cannot. Why would I be able to make it up on the next one when I can’t make it on this one? It will never happen. Never has, never will. As I stated earlier, often people throw good money after bad, and unfortunately this occurs when they are leaving good money on the table. It only takes one hiccup for the ‘high-volume, low margin train’ to come to a stop.
Instead of buying up shops to grow your business from the outside, grow it from within first. Once you do this, you are better equipped to take on the outside revenue. Having all that money tied up in multiple operations with all of them leaving money on the table, sounds like a recipe for disaster, doesn’t it?
The most accessible place to gain growth is in front of you. There is no magic, no special equipment, no special training certificates, no Keebler Elves, just the simple operation of slowing down and accounting for everything. In my opinion, and you are all entitled to my opinion, correctly managing what you already have through proper repair planning will be more growth than you imagined. Anything after that is a fine wine. And a fine wine pairs nicely with a plate of tuna pasta.
The World’s Happiest Country List was recently released. It was nice to see we Canadians are at number 15 (overall) out of 147 countries listed. Our neighbours to the south are close at position 23. I still find it worth pondering why arguably the two richest countries in the history of humanity are not in the number one position. One significant factor is that the young, defined as those under 30, of our nation (and the U.S.) actually dragged the number down.
Our workforce is multi-generational obviously, and when we dissect the groups, we find that the younger generation, Gen X & Z, make up over 47 percent of that workforce. That could be an indicator that almost half of the workforce isn’t as happy as they could be.
This has me wondering how we can create happy employees in the workplace. We know the happier an employee, the more engaged they are in the operations of the company. So, in paying attention to what younger workers want in a career or job, we find from a 2022 study by Gallup that pay (and/or benefits) has risen on the scale to top position. This makes a lot of sense as it is the younger people that are experiencing inflation for the first time in their lives as well as facing the possibility of not having access to homeownership in their future. Financial stress is evident.
This fact cannot be remedied instantly. I feel that most leaders though, are not paying enough attention to the issue. It is not your
JAY PERRY
job as a leader to just give someone more money. It is your job to provide your people with a pathway to increasing their value to the company so that they can earn more money. Compensation is related to development, growth, reward and recognition. That takes foresight, planning and cooperation. This pathway (Career Pathing) is ignored by most companies, as very few have created, implemented and supported them.
Of course, there are other things on the list of what employees want and I think this is where it can get very interesting and even easier to provide. Things such as work-life balance—which includes flex-hours—creative approaches to where and when to work, experimenting with ideas (such as a four-day workweek) and more.
Another very important issue, at 58 percent of workers: an employee wants to do enjoy what they are doing, and that is their main responsibility. This requires understanding people at a deeper level, something we teach in our coaching practice. It can start very simply with leading recruits to a realistically achievable future. Remember career pathing?
Providing mentors, coaches—from staff or outside services—in addition to advanced training courses to help them increase personal value, and this fulfills a lot of what is needed from leadership. Many of you have heard me say, “assess don’t guess” when it comes to hiring. Still, I find few that do this, and it is truly one of the ways to stay the one who’s driving!
is the founder of Ally Business Coaching, a process improvement and leadership development firm, and co-author of the book Success Manifesto with Brian Tracy. Jay is also an education partner with California Coast University in Santa Ana, California.
He can be reached at jayperryally@gmail.com.
CARSTAR has announced that it is now an official sponsor of the BC Lions and will also serve as the official collision and glass sponsor of the 111th Grey Cup.
According to a recent press release, “in partnering with the Lions, CARSTAR will proudly support and attend the Lions ‘Play with the Pros’ and ‘Punt, Pass, and Kick events’ that are taking place across the province, providing new opportunities for CARSTAR owners to interact with their communities.”
As part of the partnership, CARSTAR will have branding throughout B.C. Place for the games and customers who visit a British Columbia CARSTAR facility in communities like Surrey, Hope, Chilliwack, Mission, Armstrong, Vancouver, Campbell River, Cranbrook, Kimberly and Parksville will have the opportunity to get in on the action with varying promotions happening in-store throughout the season.
Moreover, as the official gold level collision and glass sponsor of the Grey Cup, CARSTAR will be a part of the Grey Cup pre-game festivities with activities like the CARSTAR zipline to be held front and centre in the Grey Cup fan village.
“We are thrilled to have the opportunity to further connect with our B.C. community through this meaningful partnership with the Lions,” said Dave Foster, VP of Network and Promotion and Development, CARSTAR Canada.
A new study by the University of British Columbia (UBC) highlights how it is cheaper in some regions to drive an electric vehicle (EV).
In their study, researchers specifically analyzed how far people need to drive their electric vehicles in order to break even on the cost when considering factors such as the impacts of tax rebates and tax rates, charging costs, typical distance households travel in a region and electricity costs—all of which vary from region to region.
The study found that across Canada, Quebec has the biggest advantage in terms of consumer costs, followed closely by New Brunswick, Newfoundland and Labrador, Nova Scotia, British Columbia, and Prince Edward Island. Comparatively, Saskatchewan, the Northwest Territories and Nunavut are at the biggest disadvantage.
Bassam Javed, the study’s author and a PhD candidate at the Institute for Resources, Environment and Sustainability (IRES) at UBC noted that “in Quebec, an electric car owner must travel at least 46 kilometers per day to come out ahead in comparison with owning a traditional car. In Nunavut, this number rises to 180 kilometers.”
Javed further notes that the results of the study suggest that if a consumer is looking to make the switch to electric, choosing a smaller, more basic EV can lead to more savings than a luxury electric vehicle.
Dr. Amanda Giang, a professor in the department of mechanical engineering at IRES further noted that as the cost of switching to EVs will be higher in some places and for some households, targeted interventions will be needed to address the affordability gap.
The Insurance Bureau of Canada (IBC) reports that Alberta’s ‘good’ drivers are being forced to pay auto insurance premiums to subsidize high-risk drivers.
Using data from a Deloitte LLP report, the IBC has said that it discovered that the province’s worst drivers have been offered subsidized insurance rates for 20 years.
Notably, the agency says that under Alberta’s grid rating system, high-risk drivers are offered a cap on the amount of premiums they would be required to pay.
To collect its data, Deloitte LLP’s report looked at seven medium to large-sized insurers that make up approximately 80 percent of the private passenger vehicle auto-insurance market in Alberta and then investigated the demographic profiles of drivers capped by grid premiums. The IBC then analyzed the cost subsidy these drivers receive and the difference between an insurer’s premium and the grid premium when the latter was the lesser of the two.
As a result, the Deloitte LLP report found that ‘safe’ drivers are charged $180 million in auto insurance premiums—or $65 per person—to subsidize the premiums of high-risk drivers.
The report also found that Alberta’s worst drivers are being offered average annual subsidies of $9,859.
The IBC suggests that the grid system, first put in place in 2004 to help new drivers access affordable premiums, should be removed or “substantially reformed” to help reduce the number of drivers who the system was not designed to help.
Using a stepped point system ranging from -15 to +15 and above, grid steps correspond to the highest premiums that insurance companies can charge for mandatory coverage, the report notes. Drivers pay the lowest premium of that determined by the grid rate formula set by the Automobile Insurance Rate Board (AIRB) and by that of the relevant insurer’s internal risk classification network.
Alberta-based multi-shop operator (MSO) Collision Kings has launched a sale and investment solicitation process after the company sought and obtained protection under the Companies’ Creditors Arrangement Act (CCAA) pursuant to an order granted by the Court of King’s Bench of Alberta.
FTI Consulting Canada was appointed as Monitor for the CCAA proceedings, which will see the Collision Kings Group sell all or part of its business, property, assets and undertakings.
The Collision Kings Group operates 10 collision repair facilities and two CARSTAR branded intake centres and mechanical shops. The collision facilities are: CARSTAR Calgary Royal Oak, CARSTAR Calgary Sunridge, CARSTAR Calgary East Lake, CARSTAR Calgary Burnsland, CARSTAR Calgary Downtown, CARSTAR Lloydminster City Centre Auto Body, CARSTAR Grand Prairie Don Golden, Nick’s Collision and Glass Repair and Bunzy’s Auto Body; and the two intake centres and mechanical shops are: CARSTAR Calgary Inglewood Appraisal Centre and CARSTAR Calgary Foothills.
The sale and investment solicitation process will include an initial bid—a stalking horse bid—for certain assets of the Group to set a low-price limit for prospective bidders and ensure continuity of operations through the process.
The deadline to submit a binding offer to purchase was March 8, 2024.
https://www.collisionrepairmag.com/collision-kings-launches-sale-and-investment-solicitation-process-to-sell-all-or-part-ofalberta-based-mso/
Fix Auto Canada has proudly extended its footprint into Saskatchewan with the inauguration of Fix Auto Saskatoon East.
Gurveer Randev, an avid automotive enthusiast and owner of several Fix Auto shops in Calgary since 2019, is at the helm of Fix Auto Saskatoon East.
According to a recent press release celebrating the grand opening of the shop, Randev, recognizing the opportunity to carve out a distinct identity within the automotive aftermarket, with a passion for cars and dedication to the industry, saw the decision to enter the Saskatchewan market as an obvious choice.
Situated in two buildings covering more than 1,579 square metres (17,000 square feet), Fix Auto Saskatoon East features an on-site car wash, ample parking, and a fully equipped paint shop with a high clearance paint booth.
Recent upgrades also include a comprehensive renovation of the entire body repair shop so as to create a clean and inviting space for customers.
Beyond these improvements, Fix Auto Saskatoon East has further upgraded its facility to accommodate modern repair equipment and has optimized production flow. The shop takes pride in its teams’ knowledge and training, with several members being I-CAR Platinum Certified technicians, and the shop itself holding an I-CAR Gold Certification as well as accreditation by Saskatchewan Government Insurance (SGI).
“Cars have always been my first love, and having the opportunity to contribute to this industry is a no-brainer. For me, no other industry compares in the sense of the satisfaction you get from fixing the unfixable,” Randev said.
The Manitoba Public Insurance (MPI) Board of Directors have selected Satvir Jatana as the corporation’s new president and Chief Executive Officer (CEO).
Jatana currently serves as MPI’s vice president and chief customer officer, where she oversees product development, communications, government relations and efforts to expand the gathering and utilization of customer feedback across MPI.
Jatana takes over from Marnie Kacher, who recently acted as the corporation’s interim president and CEO from May 2023.
In her new role, Jatana will focus on setting a new corporate direction for MPI, informed by guidance and advice from government members, MPI’s Board of Directors and insight from the recent organizational review completed by EY, a recent press release further outlined.
“MPI is a strong organization full of talented and committed people, but it is in need of a reset,” said Carmen Nedohin, MPI Board Chair. “Satvir’s insight as a long-term employee, breadth of experience as a leader and strong desire to unite and engage MPI’s team makes her the right person to lead MPI into a new chapter.”
According to a recent study made by insurance comparison website, MyChoice, the 2022 changes to Ontario’s G license driving test has resulted in a 7.8 percent rise in accidents among new drivers.
In January 2022, Ontario first introduced significant alterations to the G road test in a move aimed at addressing the backlog of drivers waiting for their test as a result of pandemic restrictions.
These changes, made without formal safety evaluations or cabinet approval, involved removing elements from the test deemed duplicative such as emergency stops, three-point turns, parallel parking and driving in residential areas.
Two years after these changes were first enacted, MyChoice has conducted a study involving 4,800 Ontario G-licensed drivers to see the long term impacts on driving safety.
The company compared two groups, those who got their license at any point in 2022 with at least one year of driving experience; and those who got their license at any point in 2021 with at least one year of driving experience.
For each category in the study, 2,400 drivers were randomly selected from overall quotes completed on the MyChoice website. Here, the company specifically focused on the percentage of drivers involved in accidents for each period.
Initial findings reveal that after the test changes, the percentage of novice drivers involved in accidents increased from 9.59 percent to 10.34 percent, an overall increase of 7.82 percent.
In January 2022, Ontario first introduced significant alterations to the G road test in a move aimed at addressing the backlog of drivers waiting for their test as a result of pandemic restrictions.
Myers Automotive Group, which includes several CARSTAR Myers locations and several car dealerships in the Ottawa area, has recently donated $2.5 million to The Campaign to Create Tomorrow at the Ottawa Hospital.
To date, this is Myers Automotive Group’s largest philanthropic donation, but the company has a long history of charitable contributions.
With this most recent donation to the Ottawa Hospital, Rob Mews, co-owner of Myers Automotive Group alongside his brother Harry Mews commented that “it’s important for all businesses to help as much as they can, whether it’s donating money or donating time.
You know, all businesses rely on the community for their success. And this is just a means of giving back.”
On March 6, 2024 the School of Transportation at Centennial College hosted a hiring event to assist employers and students in connecting for future employment opportunities.
Specifically, the event was intended to help students reach out to potential employers and establish summer co-op opportunities as well as graduate employment for diploma students in the Automotive Service Technician, Parts and Service and Autobody programs.
The event saw approximately 103 co-op students and 150 graduate students and alumni in attendance with 38 vendors from across the industry there for networking.
Collision Repair magazine reached out to Shawna Barnes, Cooperative Education Advisor & College Professor who stated that the event’s highlights were “seeing employers and students coming together, networking, [performing] on the spot interviews, and all of the collaboration between the vendors and the up-and-coming technicians.”
The Ontario government is considering changing the threshold for Property Damage Only (PBO) collision reporting from $2,000 to $5,000.
This change, if passed, will more than double the damage value required before a crash must be reported to police.
Minister of Transportation Prabmeet Sarkaria originally told CTV News Toronto that the dollar threshold has remained stagnant at $2,000 since 2015.
“We’ve heard some challenges that people have with respect to getting to reporting centres,” Sarkaria said.
“As technology advances, as cars advance, we’ve also seen the price of vehicles increase, and many other factors that feed into that threshold of $2,000.”
Currently, if a driver gets into a collision involving damage to public or private property, but no bodily injury, and the damage is under the threshold, they do not need to contact or register the vehicle with authorities.
In considering changing the threshold value from $2,000 to $5,000, the province has cited factors such as inflation and the advancement of car technology.
Despite potential changes, drivers can always report a collision if the property damage is less than the threshold for mandatory reporting, the province stressed. The choice remains with the driver.
Tesla’s recent decision to cut Model Y prices by $4,000 in Canada could influence car-buying decisions in Quebec, as certain trim levels of the Model Y now qualify for a combined $12,000 rebate for Quebec-based buyers.
The Model Y rear-wheel drive (RWD), the base model of Tesla’s all-electric SUV, now starts at $53,990, qualifying for the federal rebate of $5,000, and this is combined with a Quebec Roulez vert program rebate of $7,000; the threshold for which covers vehicles at $65,000.
The Model Y is already the most popular EV, based on iZEV rebates in Canada. This new price reduction, combined with rebate qualification, could further drive demand in the province, especially considering how Quebec drivers prefer all-wheel drive vehicle variations and longer-range trim options.
According to the latest Plugged In: EV Collision Insights report from Q3 2023, Quebec already has the second-highest EV repairable claims frequency, with 4.11 percent of repairable claims being zero-emissions vehicles. In all of North America, Quebec has the thirdhighest frequency, behind British Columbia and California.
Auto Prévention, an occupational health and safety specialist for Quebec’s automotive industry, has announced a collaboration with the Provincial Council of Automotive Service Industry Party Committees (CPCPA) to launch a new electric vehicle (EV) safety certificate.
To develop the program, Auto Prévention is also in partnership with the province’s joint committees (CPAs) and the Labour Sector Committee (CSMO).
The program, launched in January, is part of Quebec’s Electric Vehicle Skills Program (EVSP) training curriculum, which aims to offer a structured training path and recognized electric and hybrid vehicle certification to industry workers in auto mechanics, body work and heavy road vehicles.
The goal of the new course is to help generate knowledge and awareness of the risks of high voltage automotive systems.
Specifically, the 14-hour course enables workers to locate and determine the potential danger of high-voltage components, learn safety rules and various safe intervention methods, how to safely diffuse systems and to update knowledge of basic electricity skills.
The training is subsidized and the training manual and class 0 gloves are provided free of charge.
For more information, visit https://competencesve.ca/en or contact your regional CPA.
The New Democratic Party (NDP) in Nova Scotia have recently called on the government to waive fees for vehicle permit renewals as well as reconsider vehicle inspection timelines.
Currently, vehicle permit renewals typically range between $150 and $300, and take place every two years depending on the type of vehicle plate. The NDP says that Nova Scotians deserves a break as they continue to face rising costs of living and are calling on the government to waive fees for vehicle permit renewals.
The NDP in Nova Scotia is also asking for the province to get rid of the fees for license renewal, basic identification cards and change of name or address requests and to change Motor Vehicle Inspections (MVI) to every five years instead of two.
In recent comments on the decision, many drivers in Halifax have welcomed the NDP’s suggestion, and say they’d like the province to reconsider the fees.
However, the Department of Public Works also originally pointed out in a statement to Global News that all fees collected in this way under the Motor Vehicle act are used to build and maintain the province’s highways.
Holland College in Charlottetown, P.E.I, is offering a short-term subsidy course in electric vehicle maintenance. The five-day course is recommended for experienced technicians and tuition is covered by the provincial government’s National College Fund.
Craig Roche, program manager, says the goal is to give technicians a greater comfort level in working with EVs. The course focuses on charging and cooling systems and identifies different battery types and their separations.
There is a six-hour online component module that must be completed before the 30-hour classroom/shop training period, according to Holland College’s website.
“Upon completion of this training, technicians will have the skills and confidence to help maintain and service the growing EV market on Prince Edward Island,” reads the college’s course description.
Registration for the course is open now; three classes of eight students each are slated for the end of March.
Midtown Auto Repair
The cliche most associated with spring— cleaning. Getting all the dust out; starting anew. Refreshing old ways of operating to try something new and fresh—who knows, maybe it’ll breathe new life into your profits. Busting out the duster to rid your production floor of the stagnant dust (and salt) brought in by the Canadian winter. Quite literally opening the bay doors to let some fresh air in—the metaphors write themselves.
Beyond the traditional act of tidying up our physical spaces, spring cleaning offers a valuable opportunity to target and address problem areas within any business, fostering improvement, efficiency, and ultimately, success. Best of all—if you’ve already failed your New Year’s resolution, spring and the general air of rebirth and regrowth brings you a perfect opportunity to renew them. You make the rules.
Let’s start with the basics and declutter that shop floor. You know that hill of “I’ll deal with it later” parts that has magically grown into a mountain? It’s time to conquer it! Clear out the clutter, organize your tools and bring some feng shui into the place. Remember, a tidy shop is a happy shop, and a happy shop gets things done in record time.
Now, let’s talk about those outdated processes that are holding you back like a rusty old bumper; it’s time to swap them out for shiny new ones. Take a close look at your workflows and ask yourself, “Is this the way we’ve always done it or the way it should be done?” Upgrade your tech—look up ways to lift the stress of the cost—streamline your operations, and watch your business soar like a freshly waxed sports car on the Autobahn.
Let’s not forget about the heart and soul of your business—your people. Spring cleaning is the perfect time to invest in your team’s growth and development. Send them to training sessions, and workshops and treat them to some spring merriment and teambuilding fun (psssst—take some hints from our cover stars!). Give them the tools they need to shine and watch them transform into a dream team that would make the Ninja Turtles jealous.
Speaking of superheroes, let’s tackle those villains lurking in the shadows of your company culture—the negative vibes, the gossipmongers and the grumps that bring the general juju down. It’s time to zap them with a burst of positivity and teamwork. Foster a culture of open communication. Encourage your team to share ideas. Celebrate wins. Foster a happy environment where people want to hang out.
Last but not least, let’s give your online presence a makeover that would make Instagram influencers jealous. Spruce up your website, update your social media profiles, and share some behind-the-scenes glimpses of the magic happening in your shop. Show the world that you’re not just another runof-the-mill collision repair business, but a vibrant, fun-loving team ready to tackle any dent, scratch or fender bender with a smile.
Perhaps my optimism is overwhelming to some; but, as true Canadians, you know that once the sun is out, it really feels like anything is possible. Let’s stride into spring with a… spring in our step? I’m out of similes and metaphors.
Let the April showers bring flowers for the rest of our days!
Local business owners are supported by a team of sales, operational and marketing professionals, and backed by proven tools and ongoing training programs.
ProColor Collision is committed to helping shop owners grow their business in their communities while leveraging strong established relationships with global insurers, suppliers and fleet companies.
Contact Amin Youssef at ayoussef@fixnetwork.com or visit the franchise page at Procolor.com to find out more.
With a waterborne basecoat that’s easy to mix, match and apply and that uses the same coat flash application you’ve already perfected, Cromax® EZ makes an exceptional finish feel effortless. Discover how easy an outstanding finish can be.