REACHING NEW HEIGHTS
INNOVATION, EXPANSION, AND TEAMWORK HELP THE CIANBRO COMPANIES SOAR
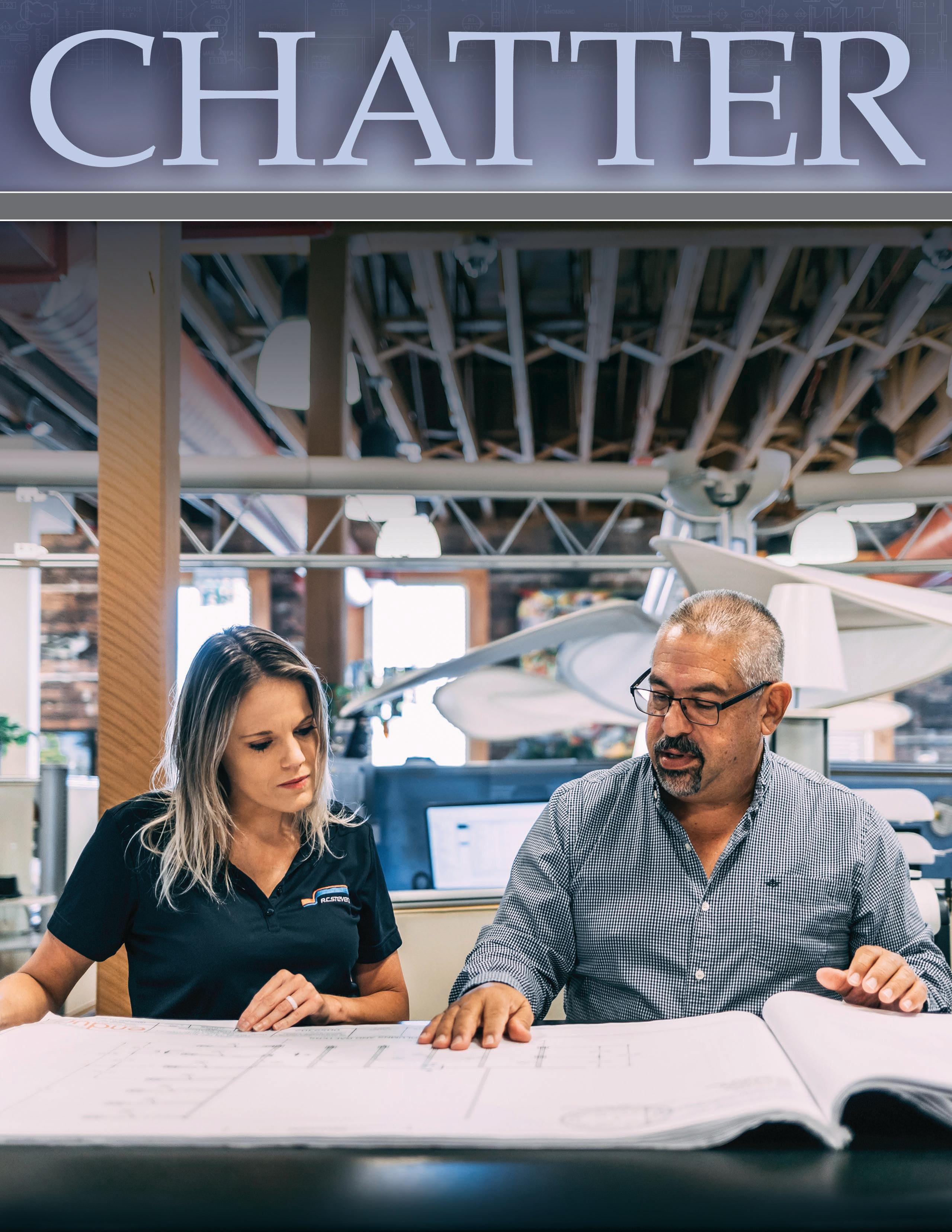
INNOVATION, EXPANSION, AND TEAMWORK HELP THE CIANBRO COMPANIES SOAR
Growth, innovation, and perseverance. These are the words that come to mind immediately when reflecting on the Company’s achievements in 2022. However, no word more accurately represents our accomplishments over the past year than “teamwork.”
Without our team coming together and working collaboratively, we would never achieve the innovation or perseverance necessary to successfully complete our projects. Without our team, none of this would have been possible.
The Cianbro Companies grew substantially in April 2022 with the acquisition and integration of the R. C. Stevens Construction Company, in Winter Garden, Florida. This is our third significant acquisition in recent history, following Starcon International in 2010 and A/Z Corporation in 2019. Collectively, these entities give Cianbro broad reach in many diverse business markets across the United States. Geographic and market diversity is a critical factor to
Cianbro’s growth and success, and it remains a strategic objective. To fulfill this strategy, philosophical and cultural alignment between the companies is paramount.
Growing the company strategically goes far beyond new markets, regions, and opportunities. We have welcomed hundreds of new team members into the Cianbro family over the last decade. In joining a 100% employee-owned company, it is important that we all help our new team members understand when they join The Cianbro Companies it’s all about people. As a company, we come from humble beginnings. The foundation of our success was built upon treating people with dignity and respect. Though we’ve seen significant growth by adhering to our core culture of treating people right we have also seen unprecedented success by working together with common goals.
As you look through these pages, you’ll find stories of incredible feats, well-deserved awards and honors, and most importantly, our people working together. It is, after all, teamwork that will help us continue to reach new heights. As you celebrate all of our incredible feats from 2022 just imagine what we will accomplish together in the years to come.
Let’s go for it!
Similar to last year’s edition of The Chatter, some stories contain bar-code-like squares called QR codes. If you’ve never used a QR code before, you can hover your smartphone over them and they will direct you to additional content, like videos. Here’s how it works:
• Go into your smartphone – whether it’s an iPhone, Android or Google Pixel – and open the camera app.
• Once it’s open, point your camera at the QR code.
• You’ll see a pop-up on your phone asking if you want to open the link within the QR code. Tap on that notification.
• From here, you will be directed to the supplemental material!
If you have any issues using the QR codes, please reach out to Cianbro’s IT Helpdesk at 207-679-2411.
ON THE FRONT COVER:
R. C. Stevens Construction Company joined The Cianbro Companies in April 2022. As their office grows in Winter Garden, Florida so does their commitment to integrity, innovation, and quality. Their culture of teamwork thrives on these core principles as well as providing a guide to how they do business with clients and the community.
Left to right: Christina Cole and Jaime Vargas.
ABOVE PHOTOS:
A team effort with help from technology - Safety Director Levi Ivey (top), prepares a drone for a flyover of West Lakes Health and Wellness Center (Page 8). Team members Susan House (from left, middle photo), Keith Wheaton, and Chris Lee review Procore project documents for long-time client, Peace River Citrus Products (Page 4). Steve Hesson (left, bottom photo) and Levi Ivey check the daily safety log while on-site at one of the many R. C. Stevens healthcare projects.
Partnerships are worth their weight in gold (or, in this case, oranges) for the team at R. C. Stevens. One of the first markets R. C. Stevens worked in goes back to the 1930s and ‘40s during the rise of frozen orange juice concentrate production in Florida. Raymond C. Stevens, the company’s founder, had excellent relationships with citrus owners, which resulted in major industrial design-build work in the citrus canning, processing, and bulk storage industry. That work included the first commercially operating citrus concentrate plant for Vacuum Foods (later Minute Maid, now Coca-Cola North America) and Kraft Foods.
Today, R. C. Stevens continues to work with several of those same companies that have stood the test of time and have proven loyal over several decades. Most recently, what started out as Project Eagle included two long-time clients, Peace River Citrus and Coca-Cola North America. Knowing the processes and management of both companies, and their long project history, made R. C. Stevens an excellent designbuild contractor of choice.
Peace River’s world-class citrus operations at the Bartow, Florida, plant has the capacity to produce up to 8 million boxes of grapefruit, mandarin, and orange varieties annually for concentrate and pasteurized juice products. Along with Coca-Cola’s market strategy and capabilities, they continue their decades-long partnership with a new facility that manufactures select juice beverages, including Minute Maid, for food service customers.
R. C. Stevens provided pre-construction, design-build,
R. C. Stevens provided pre-construction, design-build, construction, and project management services for Peace River and Coca-Cola’s new 360,000-square-foot juice beverage production facility.
construction, and project management services for their new 360,000-square-foot juice beverage production facility. Construction turnaround was 24 months, with completion in December 2021. The facility includes loading docks, cold storage, freezer, ambient/dry storage, palletizing area, process lines, ammonia compressors, electrical room, blending processing area, water treatment, tank farm, boiler, lab, control room, secured employee entrance, and parking.
In 2018, the Cianbro team began construction to replace the nearly 70-year-old bridge over Lake Champlain connecting North Hero and Grand Isle, Vermont. The North Hero-Grand Isle bridge had recently required several costly repairs, and the Vermont Agency of Transportation (VTrans) determined that the best course of action would be to update it with an entirely new structure that will last for roughly 100 years.
The North Hero-Grand Isle bridge is vital to commuters coming to and from southern Vermont and is the only vehicular movable bridge in the state. The bridge also sees frequent boat traffic on the lake throughout the summer. With a potential detour of more than 70 miles for vehicular traffic, the project team needed to build a temporary movable bridge using an Acrow bridge and trestle approach. However, as the project moved on to demolishing the existing
bridge in 2019, the team discovered contaminated soil, setting the timeline back by a year.
Once the team addressed the soil issue and the COVID pandemic had subsided, construction on the new bridge began in late 2020. The new bridge consists of two bascule piers constructed of concrete that make up the main structures on the project. Each pier is essentially a three-story building with electrical, mechanical, and storage rooms; and a control house for the bridge operator and bathroom.
Work on the new bridge began with an estimated 1,200 cubic yards of tremie placements and rock anchors for these piers. As the concrete came up, 3-foot-thick exterior walls soared out of the cofferdams built by the Cianbro team. Once the roofs of the piers were cast in place, the structural steel for the bridge, provided by Cianbro Fabrication & Coating and G&G Steel, began to be erected. This was no small feat, as the team had to ensure boats could pass through the channel unimpeded by a restricted channel width. The team worked six days a week and multiple night shifts to complete the work.
One unique feature of the new North Hero-Grand Isle bridge is the hydraulic cylinders, four on each leaf, which
make the bridge operate smoothly. The hydraulic piping and electrical work took place from 2021 through 2022. Many bridges contain a submarine cable, however, due to the site’s contaminated soil, the team installed a wireless system to operate both leaves of the bridge from the control house. Both bascule decks are half-filled concrete grid deck systems and were completed in the summer of 2022. The project progressed through earthwork and paving with a fall opening of the bridge in 2022.
Many of the team members on the North Hero-Grand Isle project were on the project from the beginning of construction. Our team has had a tremendous impact on the surrounding communities, and the dedication to the project throughout the years was impressive. Our team members and trade partners on this project are part of history for the state of Vermont, and we are proud of the team who made this bridge come to life.
Hear how our team overcame some of the challenges on the project.✔ 273,928 Project Safe Hours
R. C. Stevens is proud to be a part of an all-important project for the residents of The Communities of West Lakes. The community is made up of several historic Orlando neighborhoods, rich in African American heritage, that have come together with the help of LIFT Orlando.
LIFT was founded by business leaders working with residents committed to strengthening their community by building an economically viable area to live, learn, work, and grow. LIFT has helped amplify voices throughout the community by supporting them as agents of change. As part of these efforts, LIFT commissioned the Polis Institute to discover what assets the community already had and what residents thought could benefit their community the most. One of the areas of need was access to healthy foods and preventive healthcare.
To meet this need, the new 30,000-square-foot Heart of West Lakes Health and Wellness Center was planned, designed, and is now in its final months of construction. R. C. Stevens celebrated the building’s top-out in May 2022 with a luncheon for all on-site team members, and in July, with community/LIFT employee hardhat tours.
Before starting the construction, R. C. Stevens and LIFT Orlando hosted an online community forum for residents and local subcontractors. The project overview introduced the project, its impact on the surrounding area, and subcontract opportunities, especially for minority- and women-owned business enterprises.
The health and wellness center’s design facilitates connectivity and community engagement through open spaces, gardens, and walking paths. It also emphasizes its outdoor areas and green spaces in a setting that evokes feelings of familiarity and comfort.
The first phase of construction included the core and
tilt wall shell, site work, foundation, storefront, stairwells, elevators, and MEP. As the outside of the building is currently being completed, tenant buildouts are beginning to take shape, along with finishes for common corridors, exterior landscaping/greenspace, and an asphalt parking lot.
When complete, the Class A building will provide residents of the area with centralized primary care services, a fitness center, a co-working space, food services, and ultimately a sense of place and trust. Facilitating a holistic approach to wellness, the center will provide patients and visitors an opportunity to learn about nutrition, improve access to healthy foods, and provide the tools needed to develop positive lifestyles that ultimately increase quality of life.
In 2022, Cianbro’s IDM team in southern New England was awarded a fire water system upgrade project for a client in southeast Massachusetts.
The project encompasses the construction of a 250,000-gallon fire water tank and pump house building. The fire water tank will supplement the town’s water supply in case of a fire or emergency on-site. The pump house building next to the tank will house a fire suppression plumbing and electrical system, with a diesel pump driving the system. The team is installing a high-density polyethylene waterline from the existing waterline to the pump house, feeding the water into the tank’s inlet. The team is also installing an additional waterline at the tank outlet to tie into the fire loop to support the rest of the property, as well as roughly 5,000 feet of underground electrical conduit that will tie into the existing control room building.
Due to unforeseen delays before mobilization, the team has been continuously working at getting back on schedule and reducing the cost impacts that the early delays caused. One major time-saving solution was having the tank and masonry subcontractors work simultaneously. In addition, communication is key throughout the project to ensure all team members remain safe, especially because of the small gap between the tank and pump house building.
The team braved the challenging weather this fall and winter to keep the project on track, taking caution to ensure that all materials operate under the required temperature range. Additional heaters and blanketing have been needed for the concrete and CMU grout. All in all, the team has come together to ensure they deliver a quality product for the client.
With the shell completed, inside build-out work will commence for the community assembly area, café, and Florida Blue office.Taking a stroll down Plant Street in historic downtown Winter Garden, Florida, is special for many reasons. The historic fabric of the city, which is listed on the National Registry of Historic Places, remains largely intact, with several turn-of-the-century buildings still being used commercially. Worthy of continuous preservation efforts, these buildings link the old and new. The Exchange, built by R. C. Stevens, is an excellent example of combining the two; a new building that feels like it has always been there, seamlessly fitting into Plant Street’s historic character.
A lot of effort went into making a new building look old. Since the project fell within the Winter Garden Historic District, it emulates the type of commercial architecture cited in the Design & Standard Guidelines Manual published by the city of Winter Garden. The city’s vision was for The Exchange to look like several buildings from different time periods throughout the early 20th century.
A historical design consultant familiar with the vernacular was brought on to the team to provide authentic detailing of the era. His recommendations provided much of the massing and detailing, making the project feel as if it was “always
there.” These elements include window detailing, trim elements, brick details, building massing, and color palate. In addition, the team incorporated more contemporary elements in the style of an older building that has been sensitively remodeled over the years.
The 52,000-square-foot design-build, three-story building features modern office space on the second and third floors, with a mix of restaurants and small shop retail users on the first floor. The interior includes:
• State-of-the-art finishes.
• Millwork on the first floor.
• Crown molding in the elevator lobbies lending an old-style look.
• Floors that were designed with large column spacing, allowing tenants ranging from 2,500 square feet up to 14,000 square feet per floor.
The site design provided for and encouraged a range of pedestrian-oriented activities, with outdoor spaces that are harmonious with the surrounding downtown architecture and create an exciting streetscape. Site design elements such as seating areas, colorful/textural paving materials, street furnishings, art, water features, landscape structures, and lighting were encouraged to provide a multi-dimensional visitor experience.
Besides the new building, a pocket park (Monarch Butterfly Sculpture Park) was constructed adjacent to The Exchange and features downtown’s first sculpture, a copper butterfly standing 10 feet tall and 8 feet wide among the park’s trees, greenery, and benches.
The park’s artificial turf can withstand continuous foot traffic along with a compass rose to guide the way.
R. C. Stevens is located just a few blocks from The Exchange, and many of our team members live in Winter Garden and visit the downtown district daily. For our team, this project was not only special but personal.
In November, Cianbro completed the Bay Bridge 5kV electrical improvements project, a massive system upgrade for the Maryland Department of Transportation. The project created a dependable electrical system for the east- and westbound bridges spanning the Chesapeake Bay in Baltimore. Not only was the work scope a massive undertaking, but the team also encountered two significant challenges they tackled head-on: Lane closures and weather conditions. These challenges directly affected access to our work areas, and both persisted for the project’s duration. Nevertheless, the team persevered and developed contingency plans to ensure they completed the work on time.
The scope of work included the installation of new structural steel supports for the 5kV and 480V cable, 23 new platforms for electrical equipment, directional boring on the east and west abutments, roughly five miles of new 5kV and
480V cable on land and the bridge, new concrete pads for the electrical equipment, a pre-fabricated precast building, new generator, new integrated SCADA (supervisory control and data acquisition) system, cable relocation on the west-bound bridge (north bridge), and the demolition of the existing 5kV electrical cable and equipment.
During the installation of the new supports for the 5kV/480V cable, the team encountered multiple design issues, which led to modifying and re-installing the supports three times. While installing the medium voltage switches, the team had to plan and execute the operation carefully due to the switch’s size and the space between the steel members on the bridge. Once the team hoisted the switch, they had to finish assembling the platform before setting the switch in its final resting position. Upon review of the new electrical system, MDTA/EOR discovered a weak point within the
system, and MDTA granted a change order to replace roughly two miles of 5kV cable on the west-bound bridge, which extended the contract another year.
Due to the complexities of the new electrical system, multiple design issues were discovered, however, the project team, our subcontractors, the MDTA, and the engineer of record worked tirelessly in unison to solve and overcome each challenge.
This job presented several unexpected hurdles and logistical troubles, but it was completed successfully thanks to the dedication of our team members and their commitment to provide quality work while collaborating to ensure each other’s safety. Due to their focus on safety, our team completed the project without any incidents.
On September 28, many travelers heading south on Interstate 95 in Maine got a glimpse into Cianbro’s past, as a truck carried a near-pristine 1934 Ford dump truck down the highway. The dump truck, with the classic Cianchette Bros. Inc. displayed on both doors, turned a lot of heads that day, but none more important than that of Cianbro co-founder Kenneth Cianchette, who was celebrating his 98th birthday.
The dump truck, the 100th piece of equipment owned by Cianbro, was purchased by the company around 1950. Initially bought for the Loring Air Force Base project in Limestone, Maine, the truck had been in storage in Newport, Maine, for several years. While the body held up well over that time, the engine was inoperable. Howard Lynds, Rental Manager for Cianbro Equipment, took the initiative and identified the correct individuals to repower the truck so the historic dump truck would run again.
The project is part of a bigger initiative to restore multiple pieces of equipment from Cianbro’s early days. In addition to the dump truck, the team has supported the restoration of a
1940s cement mixer and a 1946 Jeep CJ2A. The team has also completed some engine and paint work on the Kenneth C., a newer-model push boat named in honor of Ken Cianchette, before it returned to the water at the Portsmouth Naval Shipyard.
“This work goes beyond restoring equipment,” says Doug LaCroix, Cianbro Equipment Manager. “Sure, we all enjoy seeing these historical pieces back in action, but what’s most
important is that it’s connecting new team members with our beginnings as a company. Team members can see the equipment that the brothers had purchased and utilized, which gives them a better appreciation of how equipment and vehicles have evolved over time. The Cianchette brothers’ vision and can-do attitude from 1949 will continue to inspire all of us for many years to come.”
While the dump truck was No. 100, the Jeep – the first Jeep model available for civilians to purchase – was No. 3. Carl Cianchette, one of the founding Cianchette brothers, bought it brand new, and it stayed in service with the company right up until the early 1980s.
“I remember riding in that Jeep when I was a kid,” recalls Charlie Cianchette, Vice President. “We towed trailers with it, threw hay on it, towed airplanes around. I’m happy to see it out of storage and on display.”
Another artifact from Cianbro’s history, a six-bag cement mixer, is now proudly on display outside of Cianbro’s Equipment office in Pittsfield, Maine. Though less is known about this piece of Cianbro’s history, it serves as yet another reminder of the company’s humble beginnings.
“Stay tuned to see what may be restored next,” adds LaCroix. “We’ve seen a lot of equipment come through the company after more than 70 years in business. However, without a doubt, it will be something that has helped us get to where we are today.”
As Cianbro Chair Pete Vigue pulled up to surprise Ken on his birthday, dump truck in tow, Ken was elated to see a piece from his past. As Pete chatted with the team members present, he got an idea. It was time to give this dump truck its first test drive in a long time. He hopped into the driver’s seat, started it up, and took it for a couple of short laps.
“Not bad for nearly 90 years old,” Pete said as he parked the dump truck.
Watch the team in Baltimore install one of the modules within a baghouse.
Visit Page 2 for directions on how to scan QR codes.
Every morning, travelers on Interstate 95 in central Maryland witness the sunrise behind the silhouette of the Baltimore skyline. One iconic feature of this landscape is the massive exhaust stack featuring a bold-lettered “Baltimore” written down the side. It’s a landmark for residents and commuters alike, and over the past year, the city’s skyline has been looking a little different. The luffing jib of a Cianbro Manitowoc 16K now casts its silhouette next to the “Baltimore Smoke Stack” in the morning light over the city. That machine and the Cianbro team on site are gearing up to perform the last of three major overhauls as part of a larger upgrade project at the WIN Waste Wheelabrator Baltimore facility.
The purpose and goal of the project is to reduce the net air emissions produced by the 64.5MW waste-to-energy incinerator. The project involves demolishing the existing Electrostatic Precipitators (ESPs) on each facility’s three incinerator boilers and retrofitting with three new, state-ofthe-art Hitachi Zosen-Inova fabric filter baghouses.
Each unit requires the erection of more than 2,000 tons of structural steel, and each new fabric filter baghouse is modularized to streamline construction. The upgrades include the construction of three new electrical rooms on deep pile foundations to provide power and control for the new fabric filter baghouses. In addition to the modular baghouse compartments for each unit, Cianbro will also construct a new inlet duct, which feeds the boiler exhaust air through the existing scrubbers into the new fabric filter baghouses, and a new outlet duct, which ties the exhaust side of the fabric filter baghouses to the induced draft fans flowing air to the stack. The scope also includes the installation of various mechanical piping, electrical, instrumentation, and monitoring/control systems for each unit.
Another significant project component is the construction and retrofitting of a new Automatic Selective Non-Catalytic Reduction (ASNCR) system, in which urea is injected into the furnace to react and reduce the NOx emissions from the boiler. This portion of the project includes the installation of urea distribution skids, boiler injection nozzles and bent tubes, purge water system, and compressed air system to tie into the facility’s existing metering equipment before
demolition of the existing SNCR systems on each unit.
Our client’s goal is to provide cleaner air to the community in Baltimore. Cianbro and our trade partners are proud to have had the opportunity to participate in that.
The project is being constructed by unit to maintain facility operations during demolition and construction.
The projected timeline for the WIN Waste Wheelabrator facility in Baltimore includes:
• Unit 3’s demolition began in March 2022 and achieved mechanical completion by the end of June 2022.
• Unit 2’s demolition commenced in August 2022 and achieved mechanical completion at the beginning of November 2022.
• Unit 1’s demolition is scheduled to begin in March 2023, with anticipated project completion by July 2023.
Right in the heart of Baltimore, our team works to upgrade the WIN Waste Wheelabrator facility.
Last year, The United Way of Kennebec Valley sought to inspire the central Maine community using a massive work of light-up art that reads: “Hopeful.” The piece, which is 25 feet long and 7 feet tall, had to be erected at 339 Water Street in downtown Augusta, before a lighting ceremony on September 20. United Way sponsor Drew Sigfridson, Managing Director of The Boulos Company and a Cianbro board member, knew just who to contact.
“Drew contacted Peter Vigue asking for help, and Pete put us in touch,” said Doug LaCroix, Cianbro’s Equipment Manager.
The challenge the team faced was to erect and install the artwork five stories in the air at a 60-foot radius from a lane closure on a downtown street. Additionally, all eyes were on the crew, as the cameras were rolling and cellphones were snapping photos. The question in the back of our team members’ minds was: “How do we install this safely without breaking even one of the 111 light bulbs?”
“A lot of planning led to the proper execution of the project,” said LaCroix. “We conducted a site visit about a week before to identify anything that might interfere with our plan. We built a wooden frame so we could transport the artwork upright and selected a 30-ton boom truck to make the pick. We had team members on an adjacent roof to perform the rigging and a 125-foot bucket truck for access to perform the mechanical installation. I was confident in the plan, and it went like clockwork.”
The team included Howard Lynds, Andrew Bisol, Ryan Graves, Chad Burgess, Todd Folsom, Mike Bishop, Dave Korb, Bob Meckley, and Von Weese.
“Thank you to everyone who contributed to the successful installation of the ‘Hopeful’ artwork in Augusta,” added LaCroix. “I couldn’t be prouder of our team’s efforts during the planning and execution of this project.”
The United Way of Kennebec Valley’s lighting ceremony went off without a hitch (or broken bulb) on September 20 to kick off their fundraising season themed “Hopeful! United for a Stronger Community.” The “Hopeful” artist Charlie Hewitt attended the event.
“Hopeful is not a passive work—it’s a challenge and a responsibility,” says Hewitt. “To be hopeful requires action, it requires commitment, it requires opening your eyes, it requires being part of something. It requires being passionately in love with your country, passionately in love with your family and passionately in love with everyone in your community.”
Located just down the road from Cianbro’s corporate headquarters, Maine Central Institute (MCI) is a semi-private high school with a rich academic, athletic, and art history that branches out beyond the borders of central Maine. Boarding students journey from as near as Philadelphia and as far as Germany or Vietnam to study at Maine Central Institute alongside their peers from local communities.
At the heart of Maine Central Institute is Founders Hall, the oldest building on MCI’s 23-acre campus that was listed on the National Register of Historic Places in 1980. Built in 1868, the school had renovated Founders Hall throughout the years, specifically focusing on taking small strides to modernize the building over the last 20 years. However, in spring 2021, following a robust fundraising campaign by the school, Maine Central Institute awarded Cianbro a full modernization of Founders Hall, which the team completed in December 2022.
“Going into this project, our team was well aware of how much Founders Hall means to the community,” says Lee McConnell, Senior Project Manager. “It’s a piece of history here in Pittsfield. Generations of students have graduated from Maine Central Institute having learned within these walls, and we wanted to ensure that the building was prepared for the next generation of students.” The scope of work included:
• Rebuilding the north and south stair halls with new steel stairs.
• Installing new entrances, new interior doors, and firerated corridors allowing egress.
• Reconfiguring all offices and public spaces in the first floor.
• Restoring Powers Hall, the performing arts space within Founders Hall, and installing new theatrical lighting, sound system, audiovisual equipment, including the ability to record and stream events.
• Installing an elevator linking all floors, including the basement.
• Adding a new ADA-accessible entrance to the building at the southwest corner entry.
• Adding air-conditioning in the first floor Core and Powers Hall, as well as code-mandated fresh air ventilation in all classrooms.
One of the primary catalysts for the renovation was to ensure the building was brought up to ADA standards. Though constructing the elevator was part of the original renovation design, the layout of Founders Hall created challenges to housing the elevator indoors, which the team worked with architect Tim Archibald from Midwest Architecture Studio to remedy.
In addition to classrooms and offices, Founders Hall is home to Powers Hall, where the school’s internationally renowned Bossov Ballet Theatre troupe rehearses. The renovation and updates to Powers Hall will not only help MCI recruit top pre-professional dancers and artists from all over the world, but will also bring the community together for a variety of performances throughout the summer.
“The team on this project was incredible,” says Archibald, who was not only the architect on the job, but is also an MCI graduate, Class of ’84. “Cianbro was a huge collaborator and partner with MCI on this project, both at the leadership level and the project management level. In addition, Norbert Young represented the MCI Board as the Owner’s Representative and provided expertise and countless hours to the project over several years. This project was very important to MCI and the community, because Founders Hall is the heart of our campus. It’s a 150-year-old building that needed a rebirth, and we have made it a modern facility for education.”
In early 2023, the work on Founders Hall earned Maine Central Institute a Maine Preservation Honor Award.
In December 2022, Cianbro finished the modernization of Maine Central Institute’s Founders Hall while maintaining the historic exterior. Built in 1868, Founders Hall is the heart of the 23-acre campus, located in Pittsfield, Maine.
INFRASTRUCTURE MARKET
On April 22, as the clock counted down to 7 p.m., a sense of anticipation was palpable among the team on the Veranda Street Bridge replacement project in Portland, Maine. Their task over the next two and a half days was to close down one of the busiest stretches of road in Maine, demolish the existing structure along Interstate 295, and install the new bridge using remote-controlled self-propelled modular transporters (SPMTs). This would be the first time this method of accelerated bridge construction was used in the state of Maine.
“At the beginning of this job, we knew we had a challenge,” said Mike Franck, Safety Manager on the Veranda Street project. “At the kick-off meeting, we got together with the management team, and we said, ‘for this to fly, we’ve got to have everybody buy in.’ And by buy-in, I mean attitudes. It’s not subcontractors, it’s not Cianbro, it’s a team.”
It was a tall task with a tight deadline. Cianbro set the expectation that traffic would be driving over the new stretch of Interstate 295 before 7 a.m. Monday. Senior Project
“Teamwork was very important on this project, between Cianbro, Shaw Brothers, Mammoet, and other major trade partners,” said Senior shortly after the new bridge was successfully rolled into place. “All in all, we’ve had hundreds of people help us get to where we are today, from planning and building the abutments and bridge decks, to the work we did throughout the road closure weekend.”
The need for the project was evident. The existing bridge over Veranda Street had significantly deteriorated since it was erected in 1961. In 2017, the Maine Department of Transportation determined it was structurally deficient. In addition, Veranda Street itself had become notorious for car accidents below the bridge due to a confusing traffic pattern. Though the bridge replacement over Veranda Street required the lion’s share of work, the team also constructed a safer intersection on lower Veranda Street.
When Cianbro was awarded the project, they were presented with two options on how they wanted to execute the bridge replacement. The first was a lateral slide technique using slide jacks, but the team opted for the second, a
novel approach using SPMTs to roll the bridge into place. This allowed the bridge to be built closer to the ground and farther from active traffic, enhancing safety for team members and motorists.
For that, Cianbro brought in Mammoet, an international leader in heavy lifting and transporting oversized objects. Cianbro had previously worked alongside Mammoet to transport modules weighing up to 384,000 pounds on the Motiva refinery expansion project. Though Cianbro has tackled similar bridge replacements in the past, Chet Muckenhirn, Senior Project Manager for the Veranda Street shutdown, said not only was this an innovative and complex bridge changeout in a short period of time, it also involved more trade partners than usual.
“To plan for a closure like this, you have to plan the work, and work the plan, and truly understand what’s going to happen every hour,” said Muckenhirn. “Everyone was part of a team, and everyone had their script that they had to follow to make sure it all happened successfully.”
With the closure of this section of Interstate 295 in place for the bridge move, the team decided to take advantage of the situation by tackling work on two other bridges near Exit 8. The demolition and reconstruction of four separate bridge joints within the weekend outage eliminated the need for extended periods of night-time lane closure work.
“I look back on this weekend and think about all the preparation and attention to detail that went into every
aspect of this work,” said Cal Senesac, Assistant Project Superintendent. “Everyone played a critical role in making this project successful and it wouldn’t have been possible without the efforts given from the team leading up and through the outage. It’s impressive what we accomplished, and everyone should take pride in that.”
The team sprang into action as soon as the clock hit 7 p.m. Friday. Seventeen excavators converged on the existing structure and began demolition. Sixty hours later, just after the sun had risen over Casco Bay on Monday morning, traffic began flowing across the bridge over Veranda Street. Not only did the team finish the project, but they did it four hours before the deadline.
“It’s a great feeling. Hey, we did it,” added Franck. “But it doesn’t stop here. It goes to the next project. Then the next one. That’s what we’re all about.”
Cianbro’s Power & Energy team has seen tremendous growth in 2022, working with new clients in the South East and taking on milestone projects that break new ground for Cianbro. In May, the team was awarded a 100 kV rebuild in North Carolina and the company’s first project for Central Electric Cooperative in South Carolina. Later in the summer, Cianbro was awarded its first 230 kV bundle job for a client in Virginia. To wrap up the year, the team was awarded Cianbro’s first-ever 500 kV transmission line project.
“This has certainly been an exciting year for our team,” says Josh Gale, General Manager for Cianbro’s Transmission, Distribution, and Substation group. “Our team has tackled complex Power & Energy projects, remaining committed to delivering quality outcomes to our clients, both familiar and new. They’ve done great throughout 2022, and we’re excited to see what 2023 has in store for us.”
The existing line was built in 1930 utilizing lattice tower structures and 4/0 copper conductor. Cianbro is rebuilding 11.3 miles of the single circuit line with a mix of 42 lattice tower structures and 39 concrete monopoles. To date, this is our largest transmission job for this particular client.
Construction began in a dense residential area in central North Carolina with several primary road crossings and a railroad crossing, which required extensive planning and preparation. The project is broken up into three phases. Phase 1 is 7 miles, Phase 2 is 2.5 miles, and Phase 3 is 1.8 miles. Cianbro just recently completed the first 5 miles of phase 1. As of February, the team has installed 29 new concrete monopole structures, 24 new lattice tower structures, and approximately 300,000 feet of new wire, fiber, and static.
This project consisted of two greenfield line taps, one in Horry County and the other in Anderson County, South Carolina. Exit 27 Tap consisted of approximately .2 miles of single circuit 100kV transmission line, with four direct embed monopole structures and two direct embed three-pole dead-end structures. Crews began construction on Exit 27 on August 21 and completed it on September 4, 2022. Red Hill Tap consisted of approximately .4 miles of single circuit 115kV transmission line with one fiber and six monopoles on pipe pile foundations. The team began construction on September 18 and completed it on October 9. While working on the Red Hill portion of the project, due to the location, Cianbro transmission crews were on standby for public utility company Santee Cooper in South Carolina during Hurricane Ian.
Under a critical outage schedule, the team executed the first 1.5 miles of the 230 kV bundle project in just under 14 weeks, finishing the first 1.5 miles just before Thanksgiving. Currently, the team is working on the project’s second phase, which encompasses 16.5 miles of the rebuild. The project’s
overall scope included demolishing 142 wood H-Frame structures and 471,000 feet of existing single conductor and replacing it with 139 new steel H-Frame structures and 480,000 feet of new bundled conductor. The team also had to devise a safe and efficient plan to pull in two fiber communication wires while one remained active. Cianbro and its subcontractor partners also installed 18 miles of temporary access to all structure locations, which included two complex river crossings where specialty Emtek floating mats were utilized to access those structure locations.
In the fall, Cianbro’s Power & Energy team embarked on its first-ever 500 kV transmission line project outside of Greensboro, North Carolina. The team is rerouting roughly three miles of an existing 500 kV line around a major building project, then connecting it back to the existing line.
With a 500kV transmission line, the team is working with larger lattice towers that are relatively uncommon in the region. Everything is magnified by the voltage class, including the conductor size and the hardware. The team began the project in October and anticipates completing the work in the spring.
“It’s a feather in the cap for Cianbro,” says Nate Lancaster, Project Manager. “I know we have a lot of team members who were excited to say that they’ve worked on 500 lines, and a lot of transmission line workers who wanted to be part of this project.”
enable the client to demo the previous plant and feed power up the hill to the new substation, which will serve as the main switching station.
When one of Cianbro’s Power & Energy substation teams was wrapping up a couple of jobs in Florida, Cianbro just happened to have picked up another substation project in North Carolina scheduled to begin in October 2021. Sure enough, when the jobs were finished, most of the Florida team decided to pack up, head north, and re-team on the 100 kV switching station.
“The timing was perfect because when we demobilized from those Florida jobs, the team was able to pick right up where they left off in North Carolina,” says Nate Lancaster, Project Manager. “Having that continuity among our team was key because we had a familiar rapport. We knew that each of us was committed to delivering quality work safely and on time, and we also knew our personalities and strengths.”
The client chose to build this new substation to support the decommissioning of a power plant just down the road from the new substation. Installing the new substation will
The project consisted of two major scopes, and the team knew that meeting deadline was critical. At its peak, there were 35 team members on the job site, and while one part of the team was constructing the substation itself, the others were working on a new high-security fence around the station’s parameter.
Though getting materials on time proved one of the most significant challenges, the team also had a few bouts with Mother Nature.
“We experienced a significant amount of rain in a short period of time,” says Lancaster. “That set us back and muddied up the facility and the sites pretty good. Ultimately, it was a minor challenge that the team overcame, and in true Cianbro fashion, we kept moving forward.”
The team finished the project in April 2022.
✔ 41,215 Project Safe Hours
Cianbro’s team who worked for more than a year and a half on the P-310 Dry Dock Super Flood Basin watched as the 5,338-ton concrete structure left Cianbro’s Ricker’s Wharf facility in Portland, where it was built, down Fore River to its permanent home at the Portsmouth Naval Shipyard. It was a proud moment in the summer of 2021 for the team and the company, but those moments of pride seem to keep coming. In the fall of 2022, the project earned ENR New England’s Best Airport/Transit project, and was a finalist for ENR’s Project of the Year. Additionally, the project earned an Eagle Award from the Massachusetts Chapter of Associated Builders and Contractors (ABC MA) and an Excellence in Construction Award from Associated Builders and Contractors of Connecticut (CT ABC).
Awarded in December 2019 by the Naval Facilities Engineering Systems Command (NAVFAC), the entrance structure is just a small portion of the overall modernization project. The ultimate goal is to create a navigation lock system to reduce tide dependency for submarine movements in and out of Portsmouth Naval Shipyard’s Dry Dock 1.
In early April 2022, the shipyard reached a milestone, successfully docking the USS Cheyenne into Dry Dock 1 without the assistance of buoyancy tanks for the first time ever. Cianbro’s work on the project has helped support the
U.S. Navy’s mission of returning critical assets back to its fleet.
“Cianbro takes on a number of challenging and complex projects, and this one was no exception. Projects like this are a once-in-a-lifetime experience for many of our team members,” says Brendan Scully, Project Manager. “Receiving these awards is a feather in our cap, not only for the company, but for each team member who put in the work on the super flood basin. We’re all proud of our team’s work, and this reaffirms that we accomplished something great.”
QA/QC
n By Jeffrey Lerch, QA/QC ManagerCianbro Corporation’s core quality program complies with ISO 9001, which is the standard for the codification of sound principles that help promote an effective quality management system and help provide uniformity and consistency across industries.
One component within this program is the expectation that organizations ensure qualified personnel are in place to complete necessary tasks. In addition, there is a litany of certifications within the construction industry, often required by a governing code, standard, or jurisdictional source.
These certifications can be as apparent as operating a crane to as obscure as training and testing individuals for hand excavation adjacent to existing buried gas piping.
Managing these certifications for an organization of our size and across such a broad scope of industries in which we operate can be challenging. Until recently, there has not been an effective way to get this information into the hands of those directly overseeing the work. In most instances, it has fallen on our human resources team members, quality control personnel, and operational leaders to ensure appropriately qualified personnel are available when needed. While this will always be the cornerstone of getting the right team members in the right place at the right time, there is a new program that can help with the effort.
The F.A.C.T.S. app, an acronym for Field Application for Certifications, Training and Safety, is an innovative tool that allows frontline supervisors, or any interested party, to quickly check and verify our training and certification level team members.
After a few clicks, you will reach the option of either scanning a tag on the team member’s hardhat or entering their team member ID. Either method quickly produces access to the team member’s records of qualifications, licenses, and certifications. In addition to verifying the qualification of an individual, this app also provides the status of certifications, whether current or expired.
Welding is one of the more critical construction activities at Cianbro. The ramifications of even a single weld failure could be catastrophic, have long-lasting effects on our reputation and potentially injure those relying on the integrity of the weldment. To prevent failures, Cianbro implements welding in accordance with appropriate industry welding
requirements, as specified by Welding Codes such as the American Welding Society, Structural Welding Code (AWS D1.1), the American Society of Mechanical Engineers, Welding Code for Boilers and Pressure Vessels (ASME Section IX), or others. All welding codes require a qualified welding procedure specification (WPS) and that welding be performed by qualified welders. Welders must follow the written WPS as qualified by their performance testing. Depending on specific variables established by testing, a welder establishes limits that must be adhered to in production. Variables such as pipe diameter, material thickness, joint details, etc., are established by performance testing. Those test results, and the allowable range a welder may vary from the actual test are recorded, and become the basis of qualification for the welder. While we have robust tools for tracking all the detailed information and variables related to welding qualification, the F.A.C.T.S. app can act as a bridge between these programs and supervisory personnel.
The F.A.C.T.S. app is yet another demonstration of Cianbro’s commitment and ability to continuously improve our manner of performing business.
Headquartered in Worcester, Massachusetts, Saint-Gobain Abrasives (SGA) is the world’s leading manufacturer of abrasives. The facility consists of three plants. In recent years, SGA has been working to modernize those plants, where roughly 1,200 team members work to produce superabrasive materials and bonded products like grinding wheels.
As part of the ongoing renovations, SGA awarded A/Z as the design-build partner to replace the existing central steam plant with a new combined cooling, heating, and power system (CCHP). A/Z completed the design services, construction management, and self-performed the civil/ structural/architectural, mechanical, fabrication/insulation, electrical, and telecom scopes of work.
The new system includes a natural gas-fired turbine generator, and a supplemental natural gas-fired heat recovery steam generation (HRSG), enabling it to generate electricity and steam to power the SGA Abrasives Plant. The turbine has a net electrical capacity of 4,600 kW at 13.8 kV.
The CCHP was designed to supply the maximum energy load of the production plant while minimizing purchased power. It also supplies SGA with cleaner, more reliable, and more efficient power and steam for the facility. The team also grid-connected the CCHP to allow for energy export during periods of lowered plant demand but will have the capability to ‘island’ the facility as needed. In addition, a standby generator provides auxiliary startup power allowing the plant to operate with no connection to the utility grid.
“Throughout the project, one of our biggest challenges was supply issues,” says Jason Brown, Project Manager. “However, where it was a design-build, we were able to seek alternatives, which allowed us to keep moving forward. We got it done, and there was a lot of collaboration, which was necessary to see this job through.”
Cianbro’s growth throughout our more than 70year history could be best described as deliberate and thoughtful. Since our beginnings, our team has found ways to better serve clients by diversifying our offerings while expanding our geographical footprint.
“Growth is about becoming a more dynamic company,” says Cianbro CEO Andi Vigue. “We don’t just measure growth as an increase in our volume. We focus on creating opportunities for our team
members to personally grow so that we can provide a broadening line of services to our customers.”
In 2021, Cianbro’s senior leadership journeyed south to Winter Garden, Florida, to learn more about the R. C. Stevens Construction Company and the services they offer. A connection between the parties was instantly developed, all centered around the companies’ shared values and culture.
Each company had developed and maintained a reputation for performing quality work in their fields of expertise all while treating people with dignity and respect. As time passed, the relationship continued to solidify, and it became apparent that the two companies would better serve their customers as one. The acquisition was finalized in April 2022, adding approximately 50 new employeeowners to The Cianbro Companies and officially expanding our offerings in Florida. “I am elated for our team members here at R. C. Stevens and what the future holds,” says R. C. Stevens President Tim Keating. “Cianbro is a well-respected and well-run organization. There is no doubt they care about their team members. Having their ongoing support for our growth strategy will enhance the offerings to our clients as well as create career growth opportunities for team members.”
Today, including the addition of R.C. Stevens, The Cianbro Companies has team members working all over the country in a variety of markets. By understanding and leveraging the strengths of every team member, The Cianbro Companies enhances the services offered to clients. As employee-owners, each team member is directly motivated to work as a team to safely put work in place.
“We have a lot of talented individuals within this organization, all unified by the belief that “No One In This Room Is Smarter Than All of Us” says Cianbro Chair Pete Vigue. “None of us can achieve greatness alone. Our company has thrived because we work together as a team, we focus on the long-term health of the company and we care about every team member. Continuing to do so will allow us to reach new heights. I guarantee you that.”
Founded in 1926 by builder/architect Raymond C. Stevens, R. C. Stevens is widely regarded as one of the southeast’s leading contractors. Some notable clients include Orlando Health, Coca-Cola Beverages, and Kraft Foods.
Specializes in design/ build projects for the healthcare, process/industrial, and commercial industries, with extensive, specialized food and beverage knowledge with many repeat clients.
R. C. Stevens is located in Winter Garden, Florida, about 20 minutes outside Orlando. They are the first of The Cianbro Companies to be based in the southeast.
“None of us can achieve greatness alone. Our company has thrived because we work together. If we continue to do that across The Cianbro Companies, we will reach new heights. I guarantee you that.”
– Pete Vigue, Cianbro Chair
In 2006, the Westover Air Reserve Base in Chicopee, Massachusetts, was chosen as one of the three bases in the United States to service the entire C-5M Super Galaxy fleet of jets. To keep technicians out of the elements while conducting maintenance and to expand the base’s capability to fit a whole C-5M cargo jet, federal officials approved a new $46 million indoor hangar. In September 2021, Cianbro and A/Z were awarded a joint-venture contract for constructing the new 105,000-square-foot hangar, projected to span two years.
In addition to demolishing the previous building, the team is installing concrete foundations, floor slab, and metal sandwich panels on the hangar area, electrically operated hangar doors, fire protection and alarm systems, and utilities. Due to the size of the C-5M Galaxy cargo ships, which are 65 feet tall and have a wingspan of 222 feet, the hangar doors are roughly 70 feet tall, and the project requires more
than 300 concrete piers, each made up of 600 cubic yards of concrete. Similarly, the building’s trusses weigh up to 98,000 pounds, are almost 300 feet long, and are placed roughly eight stories in the air.
“This is the greatest single-span truss facility we are building as a joint venture,” says Mark Caccio, A/Z Senior Project Manager. “Coordination is one of the biggest challenges on this project, which involves massive structural steel, metal-panel siding, and roof components. These pieces must be modeled before you even start erecting the building.”
Once completed in 2023, the hangar will be a state-ofthe-art facility at the Westover Base, which is the largest employer in Chicopee.
“This team, made up of Cianbro and A/Z team members, is a well-oiled machine right now,” adds Caccio. “The collaboration between team members has been great, and one of the best parts of this job is just watching the steel go up. It’s amazing because of its massive size. It’s not something you see every day.”
As our company continues to expand, remaining focused on our core values and culture of safety remains at the forefront of our growth. Nothing is more important to The Cianbro Companies than taking every step to ensure our team members return home in better condition than when they arrived at work. In this spirit, safety leadership from A/Z, Cianbro, R. C. Stevens, and Starcon came together for three days in July 2022 to discuss, improve, and combine our safety management systems. Combining the four safety management systems into a single system allows us to learn from each other’s best practices and improve the process. It also allows for superior trending to boost preventive safety measures. As a result of the safety leadership’s meeting, The Cianbro Companies have begun transitioning to ProCore for site safety auditing and injury management, which helps improve tracking of safety hazard recognition all the way to correction.
A second event that took place in 2022 was the return of the in-person Safety Specialist Professional Development, which didn’t take place in 2020 and 2021 due to COVID. In September, roughly 50 safety team members from Cianbro, A/Z, Starcon, and R. C. Stevens, gathered in Pittsfield, Maine, and split into two groups for a two-and-a-half-day education event. During the sessions, the teams focused on networking, sharing best practices, improving our safety systems, technical
sessions, and developing interpersonal skills to provide a supportive, effective, safety-driven working environment.
A significant part of the safety specialist development was ensuring our team members have a solid foundation supporting the mental wellness of every team member. Cianbro remains focused and dedicated on being an industry leader in suicide prevention and the growing mental health crisis that exists in construction. With the rollout of the Cianbro-customized version of the Relaxx app, the construction industry now has another tool to help team members.
As we look forward to 2023, our safety teams remain excited about leveraging the strengths from all our safety programs and ideas. We thank all our team members for remaining dedicated and proactive in keeping our company one of the safest.
teams, and multiple senior leader discussions from Pete and Mike on why we must always focus on the people at The Cianbro Companies.
n By Mark Brooks, Chief Security Officer/Cianbro Leadership CoordinatorOne universal truth for any reputable organization operating today is that they are interested in developing their team members. Moreover, these organizations understand how important it is to develop their talent to carry the organization and the industry into the future. Unfortunately, most organizations are so busy focusing on day-to-day operations that they lose sight of those long-term goals, and the next generation is thrust into leadership roles without adequate preparation.
Thankfully at The Cianbro Companies, that is not the case.
Pete Vigue, Cianbro Chair; Andi Vigue, President and CEO; and Mike Bennett, Cianbro Vice President, have set goals for The Cianbro Companies that encourage further development of our leaders through a course of education we call the Cianbro Advanced Leadership Initiative (CALI).
In designing this course, we have deliberately combined learning styles such as theory, reading, experience, projects, team building, and opportunities for personal growth to better prepare leaders for ever-increasing roles and responsibilities. CALI builds on themes from other professional development programs, including Fundamentals of Supervision (FoS), Engineer Development Program (EDP), Cianbro Leadership Initiative (CLI). CALI builds upon the foundation of these courses – our principles of “it’s all about People,” “no one is smarter than all of us,” and “our word is our bond” – and instills them in a more advanced fashion.
CALI began on June 14-16, 2022, at Acadia National Park’s Schoodic Institute. These three days focused on team building, advanced leadership theory with Dr. George Manning, assignments to be applied with their respective
On October 10-14, 2022, we switched to an experiencebased model for learning. The CALI Team assembled in Gettysburg, Pennsylvania, where we explored part of our nation’s history at the Battle of Gettysburg. The team members specifically learned how decisions made by key leaders on both sides changed the course of history.
CALI team members read the book Killer Angels and watched the movie Gettysburg in preparation for the trip. Again, Pete and Mike spent the entire session with the team members and covered topics on sacrifice, re-emphasizing the reasons “it’s all about the people” must remain at the heart of Cianbro’s decisions.
Other topics covered by licensed Battlefield Guides, National Park Rangers, and other staff were: communication, transformational leadership, seizing the objective, and loving the people you lead.
Each topic was taken from a lesson on the battlefield, which the participants applied to their current roles.
Throughout the two-year program, Andi Vigue assigned CALI team members a strategic objective to work on over the course of a year. Andi asked the team members to work in pairs to identify enhancement opportunities to advance the company. Their goal is to study and frame the problem and seek innovative solutions to these complex problems.
The CALI group will assemble again at Cianbro’s Rainbow Lake property in Maine in the summer of 2023 as they finalize their projects and present their findings, ideas, and solutions.
The Cianbro Companies knows that there is more to developing the leaders of tomorrow than merely talking about it. Instead, Cianbro is taking the initiative to continually improve our legacy leadership programs, even developing new, robust programs like CALI for our future!
As I was finishing up my sophomore year at the College of Business at Husson University, I applied for a summer internship with Cianbro on a whim. As a sophomore, I thought it was unlikely that they would offer me a position, seeing as I wasn’t a junior or senior in addition to the scarcity of quality HR internships available. However, I was familiar with Cianbro because my uncle had been a team member for more than 20 years, and aware of the company’s reputation for putting people first. Needless to say, I was surprised when I got the call from the recruitment team offering me a summer internship.
On May 19, I joined the majority of the 36 summer interns hailing from 17 colleges and universities across the country at the Cianbro Institute in Pittsfield, Maine. The interns represented schools such as the University of Maine, The Ohio State University, Virginia Tech, and Harvard.
Together, our intern class worked alongside seasoned professionals in various business units and markets, with a broad focus on engineering, contracts, human resources, information technology, and more. While my internship in HR was based primarily in the office setting, one of the common threads between many other interns was a desire to get out into the field.
Megan Fuller, a mechanical engineering major in her third
year at the University of Maine, worked on the Hampden Bridge Bundle project in Hampden, Maine, this summer. “I wanted hands-on experience. I wanted to be working with the crews in the field,” said Megan. “I also wanted to apply some of the knowledge I’ve learned in the classroom.”
Travis Nadeau, a senior at UMaine majoring in business information systems and business administration, wanted to get a different type of experiential education in information technology. Travis had the opportunity to work on various projects, most notably helping improve efficiency with tool tracking. It’s Cianbro’s culture, however, that most impressed Travis.
“It really is what everyone says,” said Travis. “The people make all the difference.”
As the interns reconnected for our closeout presentations in early August 2022, we had the opportunity to reflect on our time at Cianbro and evaluate how we will use the tools we’ve learned from this summer moving forward in school and our future careers. Some of the seniors even accepted full-time positions with Cianbro.
“It’s true what they say in orientation: ask questions!” said Andrew Haining, a senior at Maine Maritime Academy majoring in international business and logistics. “Everyone is ready and willing to help.”
Personally, when we welcome a new crop of interns in May 2023, my advice to them will be to take advantage of your resources. Cianbro’s summer internship truly is what you make it, and there’s a lot you can learn and gain if you put in the effort.
of the significant features include the following:
n By Jason Higgins, Finance LeaderIn recent years, Cianbro Fabrication & Coating Company (CFCC) embarked on renovations at its facility in Pittsfield, Maine, including the acquisition and installation of a new blast room, which is a critical part of the shop’s operations. The old blast pit was built in 1987, and after more than 30 years in service, it had reached the end of its useful lifespan. The team spent much of 2021 readying the foundation, finishing the canopy roof, and building a small annex to prepare to install the blast room.
The multi-year renovation project was completed throughout 2022 and included the state-of-the-art abrasive blast room and system that measures 18 feet tall, 24 feet wide, and 60 feet long, used to prep steel for coating, a steel plate duplicator and related building enclosure, and reclaimed fabrication floor space.
Since its installation, the new blast room and system have drastically improved throughput time, reduced annual maintenance costs, eliminated equipment breakdowns, and provided a safer work environment for team members. Some
• Full heavy-duty floor constructed of grating to reclaim blast media.
• Continuous flow in and out.
• Adjustable lighting wall/ceilings.
• A superior dust collection system.
• Floor rating of 10,000 pounds per square foot.
• A fall protection system to allow for work at elevated heights.
“The new blast room’s innovative technology enhances vision inside the booth and maintains cleaner airspace for our team members through its dust collection system, keeping safety at the forefront of this renovation,” says Ryan Graves, Safety Manager. “The new blast room also contains recessed light fixtures and an automatic grit cut-off system that also minimizes the grit accidentally released from the hose.”
“The modernization and upgrades have allowed us to perform our fabrication indoors, which is a much safer environment,” adds Craig Chambers, Fabrication Superintendent. “In addition, we have gained capacity and control over our production schedules, significantly reduced equipment main-
tenance and downtime, minimized the need for third-party subcontractors, and eliminated additional material handling, all adding value to our customers.”
The reclaimed fabrication floor space was completed in September and is divided into two work areas totaling 2,500 square feet, each with overhead cranes. New energy-efficient overhead lights brighten the work area, and large bay doors provide access to material handling equipment and outside air. Storage racks on the work area’s sides store frequently used welding equipment and supplies.
Key renovation tasks included demolition of the old blast pit, removal and disposal of used blast media, backfilling the pit with aggregate, installing rebar, and pouring concrete to complete the new floor. The team also installed bulk shielding gas distribution lines and other utilities before moving on to exterior wall framing for the bay doors, each of which has a new approach apron. For its final task, the crew installed the new exterior blue siding.
“The facility upgrades have greatly improved our shop flow,” says Mark Hansen, Project Manager. “We have less downtime due to equipment issues and can keep more work in-house and in our control. These factors, combined with the added fabrication space, allow us to get more work out the door and meet aggressive schedules, which helps improve our customer’s satisfaction.”
“This project was born out of concern for the health and
well-being of team members who, day in and day out, show up to perform a very difficult job,” says Ted Swenson, Sales and Estimating Manager. “Making the numbers work financially presented challenges that needed to be overcome. In the end, the team rolled up their sleeves and figured out a way to not only make it work, but to add value to the bottom line.”
CFCC has performed significant work to advance Cianbro’s jobs at TimerHP GoLabs, P-381 Tri-Venture, and more. By providing high-quality fabricated steel, eliminating defective parts, and offering other value-added services such as industrial coatings and detailed modeling for these critical projects, Cianbro was able to meet the owners’ project schedules.
Additionally, CFCC and Cianbro Equipment and Logistics have teamed up to repair and paint nearly 50 flexifloats. Previously, a third party performed this work because the old blast pit’s floor had deteriorated, and the room only had one entry/exit door. In the new blast room, the trailer is driven through using the yard truck.
“The investment that The Cianbro Companies has made in CFCC’s facilities and equipment is a clear message of confidence in our team,” says Mark McLean, Director of Operations. “With the help of the CEL properties team, we have accomplished these upgrades with little impact on our everyday operations. Thank you to all those involved!”
When Hurricane Fiona made landfall in Nova Scotia and Atlantic Canada on September 23, 2022, it ravaged communities, damaging homes and businesses and leaving hundreds of thousands of Nova Scotians without power.
Shortly after the storm subsided, Cianbro’s Distribution team mobilized, with 32 team members departing Maine on September 26 to assist with power restoration in Nova Scotia. The line workers, digger operators, and support staff worked 15 days clearing trees, setting poles, and installing wire. The residents of Nova Scotia were welcoming and understanding, given that many had been without power for several days. Our team saw just how grateful the residents were that Cianbro was there to assist in restoring power, with encouraging social media posts, comments, and the occasional delivery of homemade treats and meals as a thank you to our crews.
In late December, the team also responded to back-toback storms that carried through the holidays. In all, Cianbro had more than 40 lineworkers, operators, and support staff working through Christmas to restore power to the people of Maine and New Hampshire.
Here are just a few of the kind words Cianbro received
from Nova Scotia residents about our team’s hard work and commitment to helping our neighbors to the north: Lisa from Nova Scotia:
“My complete and utter appreciation to your linesmen who traveled to NS and hooked up my power after nine days.” Chance from Pictou County, Nova Scotia
“I am writing to say how pleased I was with one of your utility repairs crews here in Nova Scotia to help put back together our electrical grid in the aftermath of Hurricane Fiona. In particular, I refer to the crew led by Ryan here in Pictou County.
Ryan and his crew were repairing downed lines in our area over the past week. Ryan went out of his way to put back a bent mast on my summer home. Without his efforts, I would be waiting months to repair that service. Today he and his crew repaired it.
Thank you to Ryan and his crew. Great guys, very friendly, very helpful.”
Victor, Client Rep
“Hurricane Fiona was an unprecedented storm that impacted Northern Nova Scotia quite heavily. We were faced with a herculean task for the restoration of power in a safe and timely manner. Without the help of numerous contractors and other utilities NS Power would have been months to restore power to their customers. Most of our feeders were in a desperate state with multiple broken poles,
broken crossarms, trees buried in trees buried in trees, wire down everywhere, services completely ripped off houses, etc. I have been through Hurricane Juan and this was a lot worse. The damage was unthinkable and the task at hand was truly unimaginable.
Corey and his crew landed with myself. I wanted to reach out and express our gratitude to Cianbro for lending those crews to us and to the crews themselves for the work and commitment they put forth. Corey and the crew were extremely professional and committed to the task at hand. They came to work every day with a full plate ahead of them with an eagerness to get to work and turn some lights on. They worked very safe and efficiently and were true professionals in their trade. I pride myself in being a very capable Powerline Technician and Corey and his crews proved to be the same. I knew I could hand Corey a task and it would be done as safely, efficiently, and professionally as possible no questions asked. We would not be where we are today without the help of crews like Corey’s. We are extremely grateful to have neighbors like Cianbro and I just wanted to reach out and express our gratitude.
I am a firm believer in giving credit when credit is due and Corey and his crew deserve as much credit as I can throw their way. Please extend my thanks to those crews and let them know just how much their hard work and dedication was appreciated. Also know that the customers of Cianbro are in very capable and loyal hands when it comes to hard work, commitment and professionalism related to building, maintaining and reactive restorations on their powerlines and related equipment. There are no words to express how much Nova Scotia appreciated their support!”
As part of our commitment to our communities, The Cianbro Companies are mindful of assisting the next generation on their journey into construction, education, and leadership.
Each year, The Cianbro Companies Scholarship Program awards financial support to students of active team members. The program’s mission is to assist students with exceptional academic performance who display leadership inside and out of the classroom. These students must be pursuing an education at a post-secondary institution.
Awards are determined based on academic achievement, extracurricular activities, work ethic, leadership, community involvement, and the content of the essay. Scholarships are announced each year in May, and awarded to the college or university in the student’s name. In 2022, a total of 40 scholarships were awarded to students of team members across The Cianbro Companies.
In 2021, the company began The Cianbro Companies Intern Scholarship Program to recognize top performing interns. The scholarship gives students an opportunity to earn financial relief toward their post-secondary education.
In addition, R. C. Stevens is a proud member of the Central Florida Builders’ Exchange (CFBE) Scholarship endowment fund, which provides annual scholarships to the University of Florida M.E. Rinker, Sr. School of Construction Management. Six long-time CFBE member firms contribute to this scholarship opportunity for Upper Division and Graduate Construction students who live in the Central Florida area and show financial need. They also provide a letter to CFBE regarding their character, CM experience, and future goals in construction.
For years, Starcon’s facility in New Lenox, Illinois, predominantly consisted of office space, with more than 15,800 square feet for offices, meeting rooms, cubicles, computers, monitors, staplers, and more. However, the need for office space has recently waned, and Starcon saw an opportunity to develop the facility’s other purposes, specifically its fabrication operations.
To better serve clients, Starcon chose to renovate the New Lenox office, increasing its fabrication space from 1,200 square feet to 8,010 square feet, reducing the amount of office space to 8,870 square feet, and warehouse space to 10,700 square feet.
“We have several customers that we’re working with regularly, and this gives our team an opportunity to enhance our business with them in an efficient manner,” says Bentley “Bud” Hatteberg, North Region Operations Manager. “It’s safer and more productive having more than 8,000 square feet of fabrication space where we can measure out piping replacement projects, fab them right here in our shop, and
then have a crew install it on the site.”
While the team was doing some fabrication work before the renovation, they couldn’t handle several projects at a time because of the limitations of the workspace. Additionally, it was challenging to sell customers on the team’s original fabrication services simply because they couldn’t envision the work being done within only 1,200 square feet. Now, the team is lining up the fabrication work for Starcon’s customers and exceeded their financial goals for 2022 before they even hit November.
“More than anything, the renovated space is something we can all be proud of,” says Hatteberg. “Long-term team members are now walking through that door, and the atmosphere is livelier and more energetic than it’s ever been. They’re excited. Having the offices right next to the warehouse and fabrication space has also helped everyone feel more connected to the work that we do every day.”
Last spring, the Cianbro team mobilized for a monthlong shutdown at Woodland Pulp in Baileyville, Maine. The team of more than 200, including Cianbro team members and subcontractors, spent May rebuilding the Woodland #3 Recovery Boiler. The initial scope of work included:
• Demobilizing and replacing the entire floor of the boiler.
• Modifying the primary, secondary, and tertiary air systems.
• Installing a new quaternary air system.
Cianbro also installed new black liquor guns and smelt spouts, modified the startup burner system, and moved the load burner.
Proper planning and coordination were essential to completing the work within the 30-day outage while continuing to work safely within a tight site. The team’s biggest challenge was flying the floor panels into the boiler and completing the welds to facilitate the rest of the interior boiler work. Cianbro’s temporary design team was able to design a shoring tower system to fly the floor panels over and between existing piping and ductwork.
When working on boiler tubes, quality is essential. Our team completed over 700 tube welds with a greater than 96 percent pass rate.
The teams working on the air, black liquor, and smelt spout systems also did a great job modifying ductwork,
cutting new openings into the boiler, and installing new equipment efficiently. The team was able to coordinate effectively, completing all the work without interrupting each other.
Additionally, to help fine tune the skill sets of our team members and subcontractors on this project, the Cianbro Institute worked with QA/QC and the operations team, to establish a hands-on simulation of the window welds and buddy weld portion of this work. This simulation included a bend test to verify the quality of the participant’s welds. The Institute team was thrilled to hear about the quality welding performance that took place on this project.
“Our team worked safely and efficiently within a short span of time, delivering quality work for our client,” said Charles Tapley, Project Manager. “I’m proud to say that with the many potential hazards that come with working in a boiler house, our team was able to plan and complete the outage with 55,000 safe hours.”
The team worked over and under other team members, with hundreds of welds, many floors of scaffolding, rigging equipment, and working on existing systems that needed to be locked out properly. Cianbro spent weeks planning and reviewing the protocols to ensure these issues were addressed. Overall, this project was another successful project of many Cianbro has performed on the Woodland Pulp/St. Croix tissue site.
CIANBRO EQUIPMENT AND LOGISTICS
n By Nathaniel Picard, Operational Excellence ManagerIn 2021, Cianbro Equipment and Logistics (CEL) introduced The Marketplace, an online resource where team members can search for small tools, consumables, and bulk items. In August 2022, the team expanded the Marketplace offerings to include rental options for all CEL inventory, including all pieces of equipment. The Marketplace has also added several functions to provide a more efficient ordering experience, including order history, order templates, and wishlists. You can use order history to pull up all your past orders for reference or to duplicate a new order.
Order templates are great for repeat jobs, turnarounds, and maintenance accounts where you know you’ll need the
same orders repeatedly. Order templates have already been created for Industrial & Manufacturing, Infrastructure, and Starcon.
Wishlists let you build a list of items without filling up your cart, so you can prep an order and then share it with someone else right through The Marketplace.
The future for The Marketplace continues to look even brighter. As we focus on the next improvements, we will link tool and equipment certifications, inspections, registrations, manuals, and more. The CEL team’s goal is to create one site where you can find everything you need, and we’re dedicated to continuous improvement and getting you what you need. Based on team member feedback, we’re currently developing the capability of initiating returns through The Marketplace. The Marketplace team, led by Pam Dunphy and Doug LaCroix, continues to focus on our customers’ needs in our efforts to provide value and service to the job sites.
BUILDING MARKET
n By Bill Grover, Senior Project EngineerWhen IDEXX a global leader in developing, manufacturing, and distributing veterinary products, which also has water testing and Livestock, Poultry and Dairy diagnostics businesses was looking to expand its footprint into Scarborough, Maine’s Innovation District, Cianbro’s team knew just what was ahead of them. Headquartered in Westbrook, Maine, IDEXX has locations and laboratories worldwide, from The Netherlands and France to Brazil and Australia. With this in mind, Cianbro understood the new facility, named the Horizon Center, would have to be nothing short of state-of-the-art.
The team kicked off construction in March 2022, with the 114,000-square-foot building facility scheduled to open in summer 2023. When complete, the Horizon Center will provide IDEXX additional space for its Water manufacturing, Water and Livestock, Poultry and Dairy engineering, and product support departments that currently operate out of the corporation’s global headquarters.
The Horizon Center contains several specialized spaces that require complicated mechanical designs and specific systems to control cooling, freezing, humidification, and dust collection. All told, 25 major subcontractors are working on
IDEXX’s Horizon Center.
In addition to several key Cianbro team members, A/Z Corporation, one of the Cianbro Companies, is the designbuild partner responsible for the mechanical, electrical, plumbing, and fire suppression design. Cianbro is working with architects from Ci Design, structural engineers from E2 Engineers, and civil engineers from Gorrill Palmer. Constant communication has been critical during the design-build process, especially when working for a client whose needs are ever-changing.
The Horizon Center project certainly is not IDEXX’s first rodeo and, throughout the project, they brought numerous ideas to the table, challenging the team to innovate and find solutions for inefficiencies IDEXX discovered in their existing operations. The clear and prompt communication between all teams throughout design and construction has helped keep the project on schedule. As a result, the team is confident in turning over a building that meets IDEXX’s needs.
Though the final product will be a state-of-the-art facility for our client, there are some design and construction elements end-users might be interested in knowing about:
• Due to a high water table and sandy soils, the building’s subgrade had to be reinforced with stone aggregate piers. The building required 4,085 piers 18 inches wide, 30 feet deep, and spaced 6 feet apart.
• Nine truck bays will handle the shipping and receiving operations.
• The project scope includes relocating a nature trail for the Town of Scarborough. An existing trail segment was cleared and utilized for this project, so when the team nears completion, Scarborough officials will assist in locating a new route that will reconnect the trail ends further back in the wooded area behind the building.
Located on the banks of the Thames River in New London, Connecticut, the U.S. Coast Guard Academy is a reflection of those who call it their alma mater – brimming with excellence and pride. However, in 2017, the USCGA Alumni Association Board of Directors determined that one of the buildings on campus, decades-old Pine Hall, no longer met the Academy’s academic, leadership, athletic, recruiting, and boat maintenance needs. After the Board conducted a preliminary feasibility study, they reached out to alumni, parents, and friends to see if they would provide the financial support needed to construct the new Maritime Center for Excellence to take the place of Pine Hall. There was overwhelming support from all, and especially the alumni, making this the largest alumni funded capital project to date.
In May 2021, after overcoming many challenges, the USCGA Alumni Association awarded A/Z the $18.2 million construction contract for the Maritime Center for Excellence. For Don Ross, A/Z’s Director of Integrated Facilities Management and Program Management Services, the project means more than just delivering a new, stateof-the-art facility. A 1977 graduate of the USCGA, Don also served for four years as a civil engineer instructor and rowing coach at the Academy. Don played an important role in the project’s preconstruction phase, having not only an in-depth knowledge of the USCGA’s expectations and mission needs, but also A/Z’s relevant experience and abilities to successfully deliver this project.
“For me, this is the pinnacle of my career at A/Z, and I’ve been here for more than 26 years,” says Ross. “The USCGA take their motto, ‘Semper Paratus-Always Ready,’ to heart, and our project team has adopted that mindset. I’m proud of the team we have, and I’m equally proud of this facility.”
The Maritime Center for Excellence faces true north right along the Thames River, serving as the Academy’s ”maritime front door” for visitors traveling by water and a gateway for sailing, ocean engineering, and environmental courses. Constructing a project like this next to the water
can present a number of challenges, and among those is environmental protection and stewardship. The team developed and implemented a comprehensive Stormwater Pollution Prevention Plan (SWPPP) to ensure the river was protected from hazardous runoff and silt from the job site. In addition, the wind coming off the river was often fierce and the temperatures were bone chilling, but the team kept the environmental controls in place so work could continue uninterrupted through the harsh winter.
“I would say we’ve been lucky to have the team that we’ve had,” says David Bible, Senior Project Manager. “The level of their engagement and the determination to get the job done, and to do it well, has been second to none.”
The upper deck features a multipurpose welcome center, conference room, offices, and a large open viewing area down to the lower deck boat maintenance shop. The lower level also houses everything needed to keep the USCGA waterfront training fleet in peak operating condition — engineering and science labs, workshops (carpentry, paint/
fiberglass, electronics, and engine), and parts storage. The large, environmentally controlled Boat Bay can also hold two L44 sailboats, unlike the old Pine Hall, which could only hold one.
Additionally, the SmithGroup design features a sweeping stainless steel roof framed by large spans of curvilinear glue-laminated (glulam) timbers. Tall glass curtainwall panels and wooden decks wrap around the structure. The building is designed to achieve LEED Gold certification. The unique design of the roof, which emulates the shape of a boat hull, is a feature that challenged the team with hundreds of coordinates to ensure the roofline was properly constructed.
“The team has proven that no matter what is put in front of us, we can overcome it,” adds Ross. “We’ve worked with tough site conditions and the building’s challenging geometry, but everybody is enthusiastic about seeing this project through. There won’t be another building like this on the USCGA grounds, at least not in our lifetime. It will be around for over a hundred years, I’m sure.”
In the spring of 2021, deep within the hills of Clifton, Maine, Cianbro’s Industrial & Manufacturing team was hard at work erecting five 384-foot-tall Vestas wind turbines that would generate 20 megawatts of renewable energy, enough to power roughly 3,500 homes.
Though Cianbro has worked on several similar projects in the past, Silver Maple was unique in that it required pouring the largest wind tower foundation the company has ever completed at 900 cubic yards. In October 2021, the team
began pouring the first of five foundations, completing all five by the end of November. Throughout 2021, the team also completed crane roads, pad sites, underground and overhead collectors, and a new switchyard.
In June 2022, the team began accepting delivery of the tower components, erecting the first turbine tower in July. Finishing the fifth tower in August, the project underwent the mechanical completion checklist and Vestas’ commissioning to start running the turbines. The collector substation was also completed, providing necessary backfeed power to the turbines in early August.
“Our partners at Starcon provided key personnel during the erection phase of the project,” says Ben Blodgett, Project Superintendent. “Also, MJ Guyette, QA/QC Manager, did an outstanding job directing her team on a successful installation. The documentation required to develop the turnover books can be overwhelming, and this phase of the project went incredibly smoothly.”
• ATS switches and power monitoring.
• Unit substations.
• Incorporating battery energy storage system (BESS).
Just over a decade ago, Superstorm Sandy swept through the Northeast, devastating the region and leaving more than 8 million without power, some for more than a week. In response to Superstorm Sandy and anticipation of possible future weather events, New Jersey partnered with the federal government to launch the state’s first Energy Resilience Bank (ERB) in 2014, to focus on the condition and resilience of New Jersey’s energy infrastructure.
Leveraging the ERB program, RWJBarnabas Health, one of the largest healthcare networks in New Jersey, began exploring an electrical upgrade, implementing a 1.5 MW combined cooling and heat and power (CCHP) facility at the Robert Wood Johnson University Hospital Somerset. The primary power generator uses natural gas to help reduce the burden on the state’s electrical grid, which will help minimize the impacts of future major power outages.
A/Z is providing oversight on the system design review and requirements. The components required for the project include:
• CHP equipment, main breaker, and protective relays.
“One of our biggest challenges is that our project site is also an active hospital that has to remain operating throughout construction,” says Steve Williams, Operations Manager for the Mid-Atlantic Region. “We are coordinating with hospital staff to ensure we are on the same page, and it will also involve a lot of off-hours work. Additionally, many of the hospital’s systems are older, and we will have to retrofit equipment to fit those old systems.”
Then, there’s the logistics of getting the equipment into the facility, as the generators and other equipment often are too large to fit through the facility’s entrances. The team has had to get crafty, finding and sometimes creating ways to transport some items to their intended destination within the hospital.
“Overall, the team has come together and is performing well on this job,” adds Williams. The team is doing so well, in fact, that it has lined up additional CCHP work at other RWJBarnabas Health sites as they work toward substantial completion on the UHS campus later this year.
The Dow Chemical Company - Texas Operations held their 2021 Awards and Recognition Ceremony for Contractor Safety Performance on Wednesday, August 31, 2022, at the Dow Academic Center in Freeport, Texas. At this annual event, Dow shows their appreciation to contractors for their hard work and safe performance with a formal ceremony and dinner.
Starcon supervisors John Brooks and Julian Reeves kicked off the evening for the company by receiving the Supervisor Safety Excellence Award. To be considered for this honor, contractor supervisors must be top performers in site safety processes, including iCare observations, near miss reporting, low injury rates, and a low percentage of unacceptable safety observations within their crews.
Later in the evening, Starcon became one of 32 contractors to receive the Safety Sustainability Award. The award recognizes contractors who have worked over 20,000 hours in 2021, were involved in site safety processes, and maintained an injury rate less than that of the overall TXO site. Starcon exceeded the requirements for this honor, having finished 2021 with approximately 90,000 hours.
Starcon was then one of only 12 contractors to earn the Dow Safety Excellence Award. To achieve this, a contractor must be a top performer in site safety processes, have zero recordable injuries, have been on-site for more than one year, and have worked over 50,000 hours.
Five finalists competed for the prestigious Dow Eagle Award to cap off the night. To be considered for the Eagle Award, a contractor must have the following:
• Multiple years of presence on site with sustained safe performance.
• Be a top performer in site safety processes.
• Have zero recordable injuries.
• Be an active member of the Texas Operations Contractor Alliance for Safety (TOCAS).
• Have received both the Safety Sustainability and Safety Excellence Awards.
Though Starcon was not ultimately selected as this year’s Eagle Award winner, achieving these criteria to be in the running is an honor that takes sustained performance and commitment from the entire team.
The Starcon team at Dow TXO in Freeport, Texas, has been on-site since 2014 and has worked over 1.1 million hours without a recordable injury. The team has proven to be a valuable resource for Dow in various sectors including turnaround, construction, capital and maintenance projects.
In 2022, Starcon marked its 20th year on-site at Marathon Petroleum Corporation’s refinery in Canton, Ohio. Starcon got its start at the facility, which was then owned by Marathon Ashland Petroleum, on what was called “the crude blending project” in 2002. The crew of approximately 15 team members played a key role in acquiring the maintenance contract, and many of those team members are still with Starcon today.
Over those 20 years, the team on-site has grown tremendously, performing mechanical, tank, insulation, scaffold, civil, HVAC, and support work like planning and operating in routine maintenance, capital projects, and turnarounds. The Starcon team in Canton is looking forward to another 20 years at the refinery!
Pages 50 through 57 honor our active team members who have one or more years of service
53 Years
Peter G Vigue
44 Years
Charles Cianchette
Thomas Stone
42 Years
Jeffery Carr
Michael Crider
William Hadlock
Steve Hesson
Brent Kirby
Gregory Wing
41 Years
Cindy Clark
William Dusty
Alan Goepner
Perry Lorenz
Robert Lynch Jr
Nathan Weston
40 Years
Mona Evy
Alan Fisher
Ronald Oliver
39 Years
Scott Clements
Douglas Dow
David Saucier
Ernest Selberg Jr
38 Years
Timothy Keating
37 Years
Paul Belanger
Jerome Humphrey
36 Years
William Annibalini
Dennis Beisaw
Neal Dawes
Craig Holmquist
James Richards
Kevin Violette
35 Years
Anthony Ayotte
Anthony Ayotte
Shawn Bickford
Kevin Curry
Joseph Friant
Jean Gantnier
Patricia Laas
Ernest Long
Thomas Meunier
Ronald Nickerson
Dale Smith
34 Years
Richard Beliveau
O’Neil Boivin
Trent Clukey
Mark Cochrane
John Gamage
Michael Hilton
Howard Lynds
Darin Merrifield
Elbridge Watson
Thomas Wozniak
33 Years
Philip Dube
Richard Fish
Brian Hartness
Daniel Wyman
Mark Zagrobelny
32 Years
Kellie Duplisea
Dann Hayden
James Heist
Brian Ohlendorf
Shawn Ramsay
31 Years
Thomas Hamel
Bentley Hatteberg
James Rossi
Kimberly Sieber
George Tapley Jr
Matthew Velte
William Woodward
30 Years
Duane Boissoneault
Charles Brower
William McLeod
Jonathan Sacks
Robert Seegmiller
Charles Tapley
Peter Vigue
Max Wahl
29 Years
Mark Blanchard
Thomas Carranza
Kevin Crowell
Greg Frantz
Eric George
Tim Gorham
Jack Guarnaccia
Jeffrey Hinchman
Rick Leonard
Charles Schroeder Jr
Michael Stevens
Cory Thompson
Andrew Tower
James Zimmerman
28 Years
Tara Coffin
Jon Collins
Milton Cruikshank II
Dawn Erb
Paul Franceschi
Yves Gagnon
Kevin Grass
Todd Hoffa
Brent Luce
Timothy Pushor
Amy Webber
Von Weese
Michael Zemla
27 Years
Chris Alexander
Michael Bennett
Michael Bishop
Jason Butler
Thomas Cooper
Jason Curry
Lincoln Denison Jr
Thomas Dewey
Chester Dolloff
Todd Folsom
Joseph Hyde
Scott Knowlen
Kevin Kokotovich
Kirk Maenhout
Thomas Mahar
Joseph Orlando
James Peakes
Sandra Perreault
Patrick Slawek
Raymond Therrien
Troy Twitchell
Daniel Williams
Kenneth Woodcock
26 Years
Michael Berry
Andrew Bowden
Patti-Lynn Brann
Ruben Casillas
Ralph Clukey
Robert Costine
Wayne Enman
John Farnham
Roy Fitzmaurice
Timothy Flewelling
Charles Hall
Brent Haskell
David Hibbard
Steven Lusi
Donald Ross
Keith Ryder
Christopher Scott
Larry Snowman Jr
Jennifer Turcotte
Bradley Vanadestine
Brian Wheeler
Todd Whitehead
25 Years
Craig Alexander
David Bousquet
Allyn Brice
Michael Brodeur
Barry Brooks
Joshua Brown
Craig Chambers
John Coon Jr
Christopher Downs
Chaderick French
Maurice Gould
Jeffrey Hetzer
Dale Kolashuk
Douglas LaCroix
Todd Lambert
Leonard Lasecki
Laurette Laverdiere
Keith Mazzarese
Randy Morin
Mark Nelson
Thomas Noble
Robert Peters
Juan Salazar
Kelly Shank
Jeremy Sherman
James Sowders Jr
Aaron Walsh
24 Years
Scott Alexander
Christopher Bagley
Esteban Bernal
Shawn Bickford
Benjamin Blodgett
Richard Brescia
Anthony Carr
John Clark
Bobbi Collins
Troy Dziecinny
Alexander Ferguson
Kelvin Friend
Jeffrey Gillespie
Gary Guindon
Thomas Levandowski
Novak Nedic
Jeffrey Parrish
Shawn Super
Michele Toothaker
Jason White
23 Years
David Bolduc
Richard Bonick
Aron Ceglarek
Jeffrey Cooper
Adele Diodato
Jacob Dionne
Shawn Doran
Neil Dupont
Michael Edwards
Luke Finley
Langis Gagnon
Matthew Gendron
Ryan Graves
Scott Hepworth
Eric Herrman
Mark Hutchins
Scott Jackson
Donna Jacques
Eric Lane
Jeremy Lane
Jose Luna Torres
James Lyons
Jeremy Mace
Ryan Marcotte
Gary Mason
Garrett McVaney
Russell O’Neal
Richard Preble
Shawn Reid
Susan Roberts
Jason Rourke
Francisco Salazar
Gary Smith
Kerry Swallow
Donald Swanson
Jeremy Whitney
Walter Willard
22 Years
Ernest Adams
Hunter Anderson
Ronald Ayres
Jason Batchelder
Maurice Batchelder
Christopher Brann
Scott Bumps
Eugene Carini
Ulicer Castro
Linwood Charette
Joshua Clark
Roland Clark
Jose Rey
Alexis Reyes
Percy Richardson III
Kate Riley
Damien Robinson
Angel Rodriguez
Esteban Rodriguez Jr.
Jorge Rodriguez
Brent Russell
Chad Russell
John Russell
Victoria Salinas
Pristine Jo San Miguel
Johnathan Sanchez
Gavin Sanders
Benjamin SanMartin
Matthew Sargent
Joseph Schelling
Kristine Sconyers
Mark Selig
Anthony Shaw
Brian Sherman
Erica Short
Jesus Silva
Suzanne Sinclair
Thomas Sloan
Joel Soucie
Shawn Soucie
Justin Stanciel
Matthew Stearns
Jesse Steorts
Philip Strouth
Joshua Swanson
Joshua Sweedler
Gardner Swenson
Jacob Sylvestre
Douglas Taylor
Wade Thurlow
Chalmes Tillman
Callie Toothaker
Thomas Trader
Elizabeth Traphagen
Emmanuel Trejo
Bobby Troupe
Carlos Trujillo
Noah Tuttle
Cory Tyler
Emmanuel Ugarte
Kymberly Valero
Noe Valladares
Edgar Valles
Jair Valverde Palacio
Cole VanEnkevort Heid
Yoshfrank Vargas
Alberto Vega Sr.
Jose Vega
Juan Vega Padilla
Ryan Veilleux
Edward Velez
Frederick Viano Jr.
Edwardo Villarreal
Jesse Villarreal Jr.
Joel Villarreal
Melissa Walker
Craig Waterman
Brandon Watson
Justin Watts
Michael Weiand I
Though Cianbro’s Building market has developed a reputation for taking on complex and sizable projects, the team in the Mid-Atlantic region recently delivered a small but significant 1,520-square-foot weigh station to Maryland’s Department of Transportation in Conowingo, Maryland.
Cianbro served as a general contractor for the weigh station under the broader site contract awarded to Allen Myers.
While the building was significantly smaller than a typical Cianbro project, it wasn’t without its challenges. Like most recent projects, the Conowingo Weigh Station experienced material lead-time issues, which delayed the start of the six-month project. That postponement created a domino effect, and construction went far deeper into winter than the team had anticipated. In addition, the delay with storefront windows slowed the ability to close up the building to create conditioned space, pushing back work such as drywall, millwork, and flooring.
Another challenge was working around the changing site conditions and maintaining consistent access to the building structure.
In the face of all these challenges, Project Manager Stacey Lioreisis and her team maintained their composure and worked through it all. She worked closely with Allen Myers and Maryland’s Department of Transportation for the six months it took to complete the project.
“It was a pleasure working with the team from Allen
Trenten Welch
Matthew Weldon
Keith Wheaton
Roger Whiteneck Jr
Erik Whitmer
Krystal Wiley
Stephen Wilkins
Stephan Williams
Douglas Wilson
Benjamin Wolf
Marcus Worster
Patrick Wright
Markus Ybarra
Stanley Yellowhair
Tab Yellowhair
Ford Zehner
Steven Zigler
Myers, Maryland DOT, and of course, our subcontractors who executed the project so well,” says Lioreisis. She adds that although the building was a relatively simple structure, it houses four state troopers and provides them with offices, a lobby, a data room, a kitchen, and bath and shower rooms for the inspection crews.
The following team member have each devoted a quarter-century of service to The Cianbro Companies.
Mike began his career at Cianbro during a summer break at school on the Beverly-Salem Bridge project in Massachusetts, and became an ironworker on several projects. Today, Mike is a Lift Superintendent for Cianbro Equipment & Logistics and is known as a well-respected and knowledgeable team member.
Patti has worked with Cianbro’s Power & Energy team for more than 10 years and has become known for being detail-oriented and her ability to plan. She takes new team members under her wing, is well respected by her team, and continually seeks to innovate or find efficiencies in processes.
Andy began at Cianbro as a fabricator helper and quickly enrolled in one of Cianbro’s first electrical apprenticeship programs. After completing his apprenticeship, he got his license, worked as an electrician, and showed the aptitude to become a foreman. He recently left the electrical group and is now a senior project estimator.
Ralph began his career in the civil trades and eventually found his passion for ironwork. Ralph is known to boost team morale on the job site and always goes above and beyond what is asked of him. Ralph is a hard worker who’s been a key team member on several industrial and infrastructure jobs.
First brought on to the Cianbro team as a structural welder for the Yankee Rowe Decommissioning Project, Bob has developed his skills as a welder, rigger, millwright, and equipment operator. He has worked throughout southern New England, and his experience and dedication to working safely has made him a sought-after crane operator within the company.
John’s background is diverse, and before he joined Cianbro, he already had building management and estimating experience. He began his career here estimating industrial work, even taking part in boiler shutdowns. Now, John is the senior estimating manager of both Industrial and Transmission & Distribution estimating.
Many people who have worked with Roy say he is one of the best carpenters they’ve ever had the pleasure of working with. Roy brings a great sense of humor to the job site and is always ready to work with his can-do attitude. When you’re working with Roy, you can guarantee that he will do the job right.
When Tim first joined Cianbro, he was known as “The Network Guy,” however, he quickly moved into application development and content management as Cianbro continued its online journey with company intranets and external sites. A true Cianbro entrepreneur and most often ahead of his time, Tim has embraced and suggested improvements to the ever-evolving world of software and technology.
Charles has championed Cianbro’s QA/QC process and has been one of the driving forces behind the program’s success. A self-starter, Charles has also been a critical team member in getting several design/build projects off the ground, has helped write quality-specific manuals, and has taken part in many boiler outages.
Brent has been a consistent part of the Substation group for over a decade and became a leader in multiple roles because of his civil/mechanical acumen. He’s been a mentor to several young team members, displaying patience while passing down his knowledge. Brent is also an excellent communicator on the job sites.
Keith’s dedication to Cianbro is second to none. Teams are always excited to have Keith on the job because they know he’s willing to step up to any challenge. As a general foreman, he’s emerged as a natural leader, overseeing morning meetings, safety talks, recognitions, and addressing any issues brought to his attention.
Todd Lambert
Todd has been a steady force and true craftsman, starting his career as an electrician. Todd has as built a loyal customer base. When assigned to projects, leadership would refer to it as pushing the “easy button.”
Leonard Lasecki
Over 25 years, Lenny has been tasked with incredibly diverse tasks, all of which he has accepted with optimism and enthusiasm. His unique combination of skills demonstrates competency and professionalism.
Keith Mazzarese
Jennifer Turcotte
Jen is an incredible administrative specialist for Cianbro Fabrication & Coating. She is attentive, ensuring everything is taken care of, sometimes even beyond the scope of her duties. She is dedicated to her Cianbro family, helps keep them on track, and is always willing to help when someone has a question or problem.
Bradley Vanadestine
Larry is a team player and goes above and beyond to ensure the team members on his job site work safely. As an assistant project superintendent, Larry always brings a positive attitude, which spreads among other team members. In addition, he encourages other team members to continue their learning and development so that they are ready for the next phase of their careers with Cianbro. A/Z
Keith’s 25 years of exceptional operational leadership have resulted in numerous repeat clients and a plethora of manufacturing/ process work. He delivers the same intensity to every project, regardless of size.
Robert Peters
Rob has been a cornerstone of the CSA Group. As a contributing factor to the company’s growth, his attitude and willingness to lend a helping hand make him one of the most desired team members on any project.
James Sowders
Jim is one of A/Z’s most reliable team members. His integrity is evident; he is known for being the first on the job site and the last to leave. He is an excellent welder and takes great pride in his craft.
Ruben Casillas
Michael Brodeur
An excellent boom truck operator, Brad has become known for his ability to quickly run through the Certification of Crane Operators course. Brad transitioned to the Cianbro Institute to teach, ultimately returning to the field as a friction crane operator. One thing is for sure, Brad tells it like it is. You’ll always know where you stand with Brad. Mike has embodied the “Whatever It Takes” motto, and A/Z has been so fortunate for his unwavering dedication for all these years. He continually demonstrates an unwavering work ethic, knowledge, and respect.
Dale Kolashuk
Dale emerged through the ranks, beginning as a technician and spending many years at Pfizer in Groton, Massachusetts. His military background gives him a “never quit” mentality. He is an essential asset to some of our most demanding clients.
Ruben is an A Welder for Starcon and has experienced a lot of growth and changes at Starcon during his 25-year career. Ruben is also well versed in pipefitting and mechanical work, and is always willing to help out in any role. Ruben has been a valuable asset on various maintenance jobs as well as capital and turnaround construction in the Chicagoland area.
Chris Scott
Chris’ dedication to Cianbro, and more recently, Starcon, is extraordinary. Over the past 25 years, Chris has proven he’s willing to fulfill any role that is needed and is a trusted and well-respected leader across The Cianbro Companies.