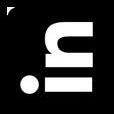
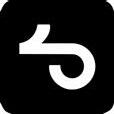
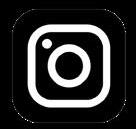
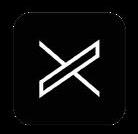
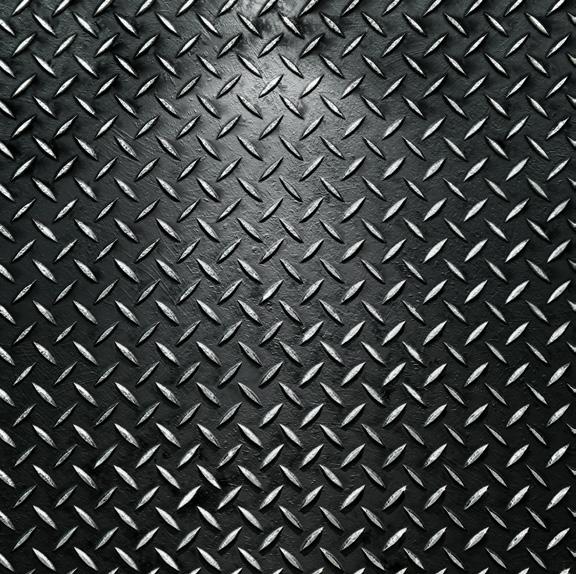
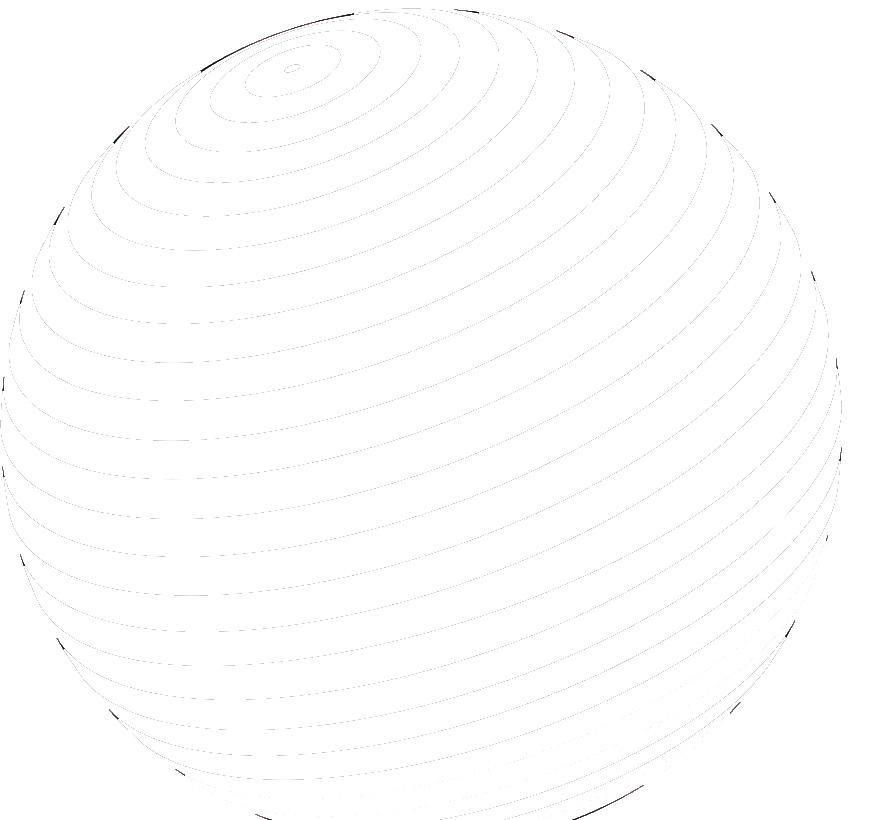
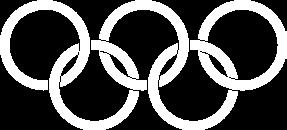

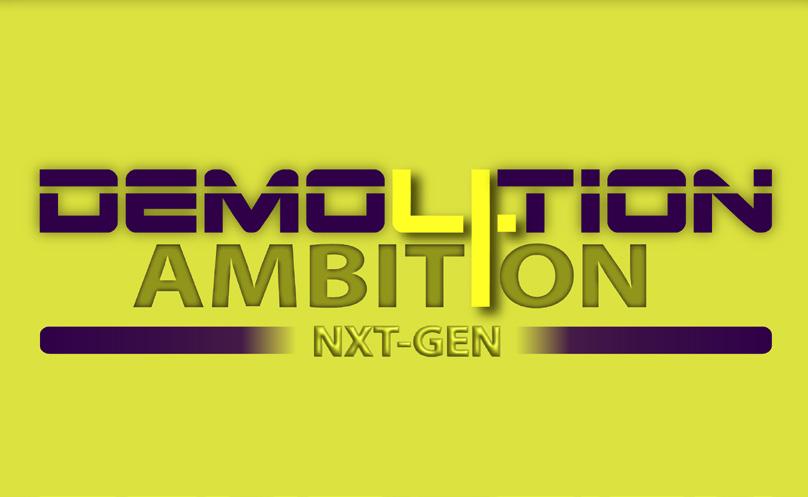
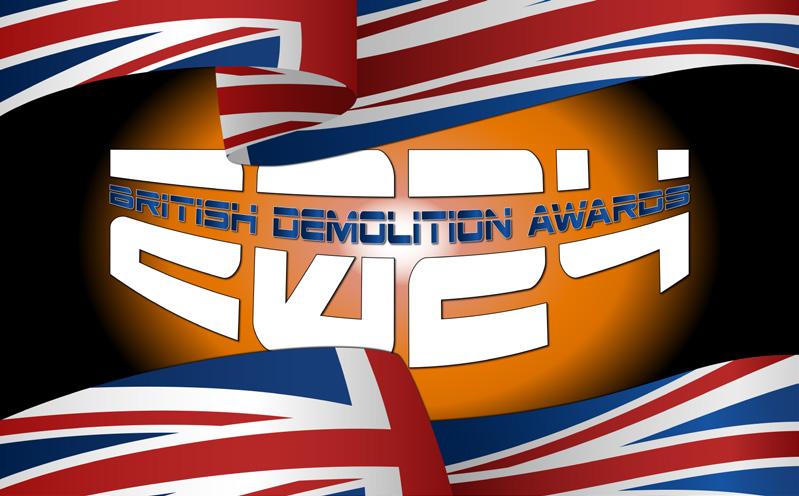
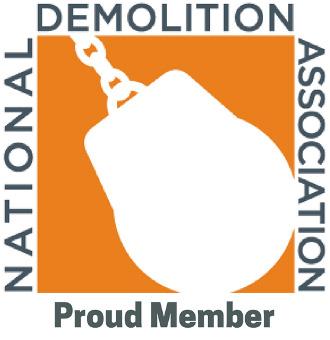


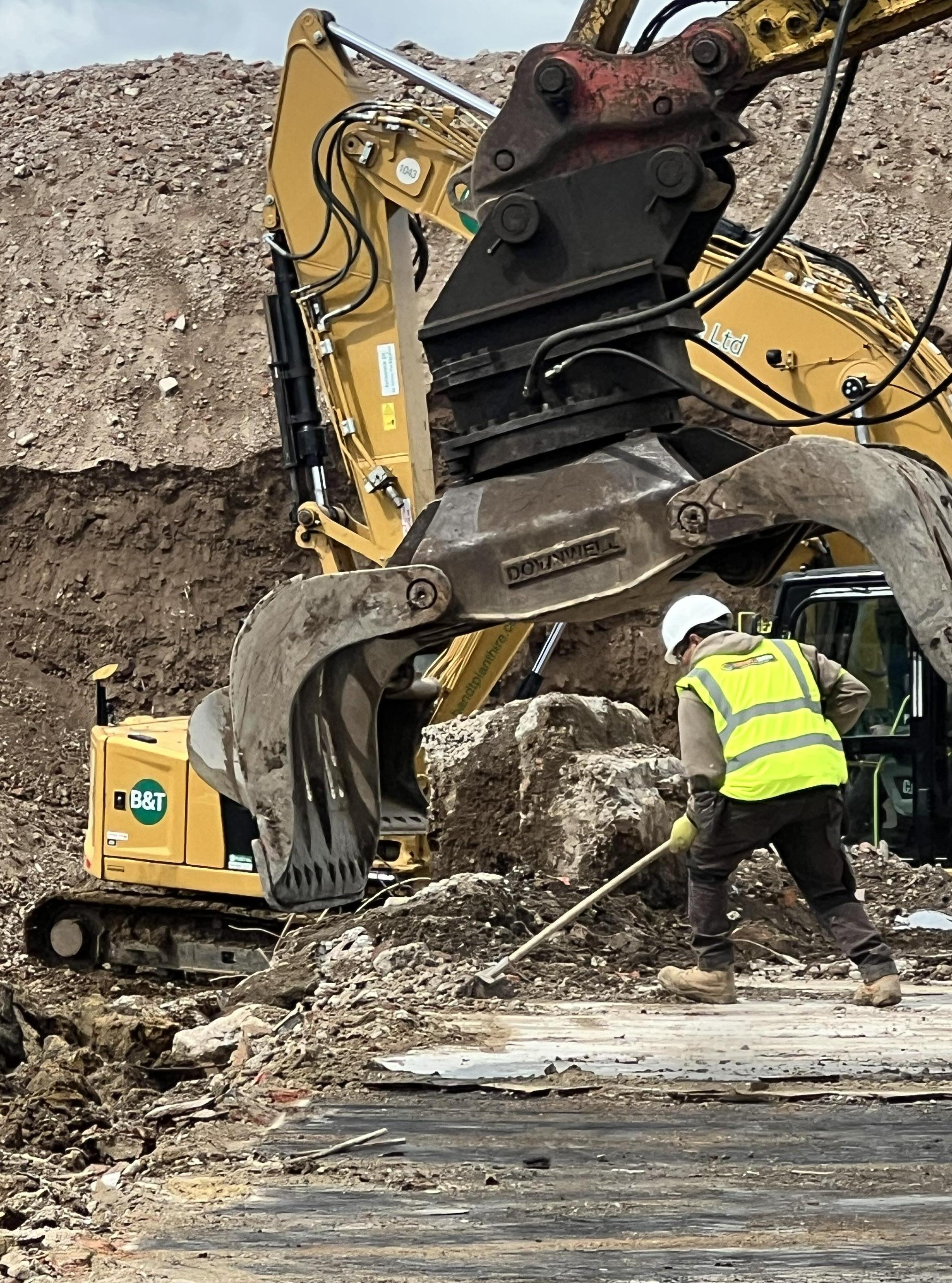
Welcome to issue #24 of Demolition Hub, marking our fourth anniversary as your indispensable bimonthly read for the demolition industry.
We might be tempted to pop some bubbly in celebration, but the whirlwind between issues means we’re already hard at work on the next edition. Plus, the sixth annual British Demolition Awards is just around the corner!
Recently, we’ve been busy promoting and attending events like the ‘NFDC Talks’ in collaboration with the IDE and HSE, as well as the Hillhead event, which, though recent, feels like ages ago.
I also attended the UKATA convention and toured numerous supplier premises across the country.
An attempted two-flight trip to Belgrade for my second EDA Convention ended with an unexpected overnight stay in Amsterdam (a true travel mishap, I assure you).
During this time, Demolition Hub joined the National Demolition Association, significantly expanding our North American readership and bolstering our international presence.
In addition, we’ve been setting up the PowerPlant Podcast in new London studios and I’m eager for some of you fascinating and outspoken individuals to join me in the studio soon. Read all about it inside – reach out and let’s chat!
Amid all this activity, I’ve hit the milestone of having attended 30 site visits so far in 2024, with the 31st just around the corner as I aim for 50 this year. This underscores our commitment to supporting and championing the demolition industry. A genuine thank you to all who have welcomed me on site.
We were also delighted to host a work experience placement for a week in which Annie came on board as a media student. Part of her week was out with me, and Downwell Enabling graciously showed Annie and me around their Twickenham demolition site. She has written a piece for this issue, for details see the contents page. Thank you Downwell Group, you certainly turned that young lady’s head towards demolition.
Annie’s enthusiasm for demolition has actually accelerated our plans. Originally slated for 2025 as another ambitious Demolition Hub campaign, we are excited to announce its launch right now – Demolition 4 Ambition: NXT GEN.
This initiative aims to inspire the next generation to join this fantastic industry and we need your support. Discover our plans inside.
Impressed with Annie’s skills, we’ve offered her a part-time junior writer role. She will also assist in this campaign, using innovative approaches to engage her demographic while continuing her college studies.
As we gear up for the British Demolition Awards, we are nearing full capacity. This year sees many contractors attending for the first time. My plea to you is to submit your entries – your great work deserves recognition. Enter now at BritishDemolitionAwards.com.
Oh and our socials continue to hit ridiculous numbers, so why not go have a look at them, in particular see our TikTok where more than 25,000 people watched me absolutely terrified as I was raised in a cage up 16-odd storeys.
Thank you for your continued support and enjoy this gold standard issue!
Publisher,
PUBLISHER
Ben Chambers ben@chambers.media 01903 952 648
EDITOR
Toby Wilsdon toby@chambers.media 01903 952 645
JUNIOR WRITER
Annie Davey annie@chambers.media
COLUMNISTS
Howard Button Richard Dolman Richard Vann Terry Lloyd Dr Terry Quarmby
ADVERTISING SALES
Ben Chambers ben@chambers.media 01903 952 648
Daniel Christmas dan@demolitionhub.com 01903 952 642
DESIGN
Nicki Chambers nic@chambers.media
Joe Bers joe@chambers.media
PRODUCED & PUBLISHED BY Demolition Hub Ltd Suites 5 & 6, Chapel House, 1-6 Chapel Road, Worthing, West Sussex BN11 1EX demolition@demolitionhub.com 01903 952 640
Demolition Hub is a proud member of the National Demolition Association
Demolition Hub is the media partner for the European Demolition Association and the Indian Demolition Association
Demolition Hub is published six times a year. The subscription rate is £60 per year. Subscription records are maintained at Demolition Hub Ltd, Suites 5 & 6, Chapel House, 1-6 Chapel Road, Worthing, West Sussex BN11 1EX
Articles and information contained in this publication are the copyright of Demolition Hub Ltd and may not be reproduced in any form without the written permission of the publishers. The publishers cannot accept responsibility for loss of, or damage to, uncommissioned photographs or manuscripts.
BRV holds annual conference in Vienna
Do you want to be part of the EDA Yearbook 2024?
EDA is part of the CEN/TC 350
Reflecting on a successful EDA Annual Convention in Belgrade
EDA signs collaboration agreement with ESS for CLR Expo 2024
EDI attends Asbestonomy in Madrid
EDI welcomes newest member, SEG UMWELTZSERVICE
Flesan joins EDA as a new member
Get to know the new RILEM Technical Committees
Exciting lineup of panellists for EDA Think Tank 2024
Grupo Mitre joins EDA as a new member
Impact of the circular economy on demolition industry
Dickson’s robots shine in assisting Bellevue 600 Project
Innovative use of protection screens manages debris at Nashville medical site
Walsh Group relies on Volvo excavators to remake downtown Chicago transit system
Cautious optimism by Robbie Blackhurst, Founder and Director of Black Capital Group
Opportunities for engagement by Viki Bell, Director of Operations, CEA
What a new government must change for companies like the Collard Group
Construction Plant-hire Association’s priorities for the incoming government
National Federation of Demolition Contractors
More uncertainty? by Richard Dolman
Striving towards a greener future by Terry Lloyd, Head of Vendor in the SME Lending Division at Paragon Bank
32
With Lee Rowbotham, Managing Director of DEMEX
Downwell Enabling Solutions: Soft strip and full mechanical demolition of Richmond College
MGL Demolition: Controlled asbestos removal and demolition of Castlegate Shopping Centre
DEMOLITION4AMBITION NXT-GEN – promoting demolition as an outstanding career choice for those leaving education
58
With Andy Leaver, Product Development Director at DIGGER GUARD®
Introducing the Powerplant Podcast
Adamo Group: Asbestos abatement and demolition of Eastland Shopping Centre 20 FINGER ON THE BUTTON by Howard Button 14
• Husqvarna
• Bobcat – RogueX2 Autonomous Loader Concept
• Brokk UK
• DEVELON
• Core-ect Diamond Drilling Ltd
The 2024 British Demolition (and Asbestos) Awards 2024
78
Getting on site with the best of Britain’s contractors
84
Snapshots of Ben and the Demolition Hub team’s activities between issues
90
• Casella
• Odour and Dust Solutions
• Bosstek
• Brendon Powerwashers
• Corgin
98
Laurini Officine Meccaniche: Bringing Italian innovation to the UK with Robustrack
Jocker wins Italian Demolition Recycling Award
Modified excavator for disabled workers: A triumph in accessible innovation
104
Exclusive new Cat® Track Wear Sensor provides remote, no-touch wear monitoring and alerts at key wear percentages
Liebherr premieres first large wheel loader with hydrogen engine
JCB powers into Monster Trucks
Komatsu unveils new cab for crawler excavators
Richard Vann: Should decommissioning experts have a voice in financial planning talks?
Michael Freeley: Could sustainability lead to the fall of the demolition industry?
Demolition Hub is the media partner for the European Demolition Association
We are pleased to share a highlight from the Austrian association, BRV. Its Annual Conference 2024 took place on 22 May at the Austria Trend Parkhotel Schönbrunn in Vienna. During the event it was presented the technical guide on Recyclable Construction and Demolition Materials, prepared by the European Demolition Association and the French C&D management system.
Under the theme New ways of recycling building materials in the circular economy, the conference gathered over 250 participants who explored innovative approaches to recycled building materials, circular tendering and the promotion of building material recycling. The event addressed key challenges of the circular economy within the construction sector, emphasising the
importance of tendering as a crucial lever for the adoption of sustainable and circular building materials.
With the EU Taxonomy Regulation demanding high recycling rates for various construction sectors and the EU Construction Products Regulation highlighting the recyclability and increased use of recycled building materials, the Austrian construction industry is proactively preparing to meet these requirements.
A notable moment of the event was the presentation of the EDA Guide on Recyclable Construction and Demolition Materials, which provided valuable insights into sustainable practices and advancements in the recycling of construction and demolition materials.
Do you want to be part of the EDA Yearbook 2024?
We are excited to announce that we are already hard at work on the EDA Yearbook 2024, which is set to be an invaluable resource, offering visibility and recognition to participating companies and professionals. Each edition is crafted with the participation of industry leaders, ensuring that the content is relevant, innovative and reflective of the latest trends and advancements in demolition, decontamination, and recycling.
The annual publication, renowned for its in-depth technical articles and insightful dialogues, will once again feature insights and expertise from our esteemed colleagues and members.
If you have valuable knowledge
or experience related to the demolition industry that you would like to share, we invite you to contribute a technical article. This is a fantastic opportunity to showcase your expertise and contribute to the collective knowledge of our industry.
To submit your article or discuss potential topics, please contact us at your earliest convenience. We are eager to collaborate with you and feature your contributions in this year’s edition.
Don’t miss the chance to be a part of this important industry
EDA’s commitment to advancing the circular economy in construction is evident through its involvement in numerous projects. With a dedicated Working Group on Circular Economy, EDA aims to establish and promote European standards and develop fundamental guidelines for sustainable practices in the industry.
Recognising the importance of setting standardised practices across Europe, EDA is part of the CEN/ TC 350, the Technical Committee responsible for developing standardised methods for the assessment of the sustainability of construction works. This move underscores EDA’s dedication to contributing to the development of standards that will guide the construction industry towards a more sustainable future.
The scope of CEN/TC 350/SC 1 is to standardise the field of circular economy in the built environment by specifying circular principles, guidelines and requirements to facilitate the transition to a more sustainable circular economy.
On 20 June, EDA participated in a crucial meeting focused on the sustainability of construction works. This meeting was part of the broader efforts of CEN/TC 350/SC 1 to discuss the principles and guidelines necessary for the circular economy in the construction sector.
As a member of CEN/TC 350, EDA will be in a strategic position to influence European policies and regulations related to the circular economy. This influence will ensure that the demolition and recycling sectors are adequately considered in
publication. We look forward to your participation. Stay tuned for more updates as we continue to work on bringing you the best insights and information in the sector.
For more information, visit the EDA Yearbook 2024 website and check out previous editions.
legislative developments.
This marks a significant milestone in EDA’s mission to lead the demolition, decontamination, and recycling sectors towards a sustainable future. By contributing to the development of European standards, EDA is not only supporting its members but also promoting a broader shift towards a circular economy in construction. The meeting on 20 June reaffirmed EDA’s commitment to this cause, setting the stage for impactful collaborations and advancements in sustainability practices.
After months of hard work, the EDA is pleased to reflect on the success of this year’s Annual Convention. From 13 to 15 June, more than 200 participants gathered in the Serbian capital Belgrade for a dynamic exchange of insights and innovations in demolition, decontamination, and recycling.
The convention also featured engaging panel discussions, workshops, and networking sessions, providing attendees with valuable opportunities to exchange knowledge and forge new partnerships.
One of the highlights of the convention was the presentation of the winner of the European Circular Economy Awards 2024 and we had the opportunity to learn about three exceptional projects, each recognised as finalists in their respective countries for their innovation and dedication to advancing the demolition and recycling sectors.
Thijs Noordhoek, representing VERAS Sloopaannemers, showcased a ground-breaking project that underscored new standards in high-quality reuse of materials in the building sector. His presentation highlighted innovative techniques.
Dr Ana Nadaždi from the Serbian Demolition Association (SDA) presented a project that demonstrated exemplary approaches to circular economybased model for assessing the sustainability of construction and demolition waste management. Her expertise and research are pivotal in setting benchmarks for industry best practices.
Raquel Arias, representing Association AEDED, shared
insights into a project focusing on the efficient recovery of material resources contained in construction and demolition waste based on advanced hyperspectral vision techniques. Her presentation emphasised the importance of sustainability and resource efficiency in shaping future industry trends.
Each project represented a commendable commitment to innovation and sustainability in our field, resulting in Ana Nadaždi winning this year’s award. Congratulations Ana, and thank you for sharing you inspiring project in the EDA Annual Convention 2024.
A further highlight of the convention was the Gala Dinner held at Belgrade’s White Palace, where attendees enjoyed an evening of cultural enrichment and entertainment. Traditional dancers and a talented cello quartet captivated the audience, making it an unforgettable experience.
Organising such a significant event presented challenges that were met with great enthusiasm and dedication. We extend our sincere appreciation to our co-organiser, the Serbian Demolition Association, SDA, whose expertise and collaboration were instrumental in ensuring the convention’s success.
As the convention drew to a close, participants left with renewed inspiration and a shared commitment to continuing advancements in demolition and recycling practices across Europe and beyond.
The EDA would like to extend its deepest gratitude to all sponsors of the event, whose generous support
contributed to its resounding success.
We were honoured to have the support of 23 sponsors across Gold, Silver and Bronze levels. They played integral roles in enhancing attendee experiences with their branded stands and special contributions, such as Caterpillar’s sponsorship of the Gala Dinner, INDECO’s welcome cocktail., Demarec’s delegate bags, Epiroc’s lanyards and KTEG’s materials in the conference bags.
We are thrilled to announce that the EDA Annual Convention 2025 will be held in Italy. We will have a comprehensive professional programme that will be announced soon. Highlights include the return of the prestigious European Circular Economy Awards, recognising best practices and innovative solutions in demolition and circular economy.
There will be the usual roundtables with industry experts, where relevant topics will be discussed and valuable insights shared. This is the perfect time to connect with colleagues, learn from industry leaders, and explore new collaboration opportunities.
Stay tuned to the event website for more updates and details about the programme. Don’t miss any updates!
See you in Italy in 2025!
The premium wheel loader and the essential crawler excavator are ready for any challenge.
We are thrilled to announce that we have signed a collaboration agreement with the Environmental Services & Solutions Expo (ESS) for their highly anticipated event: Contamination and Land Remediation Expo. As part of this exciting partnership, we invite all EDA members to register and participate.
The ESS Expo is set to take place at the Birmingham NEC from 11-12 September 2024. Registration is now open and a limited number of early-bird free tickets are available.
Don’t miss this opportunity to secure your spot at one of the
industry’s premier events.
ESS Expo brings together key industry events, including the Resource & Waste Management Expo, the Energy, Fuels and Decarbonisation Expo, the Water Resource Management Expo and the Contamination and Land Remediation Expo.
Partnered with the Environment Agency, the ESS Expo is expected to attract over 12,000 visitors. We encourage all EDA members to take advantage of this unique opportunity to network, learn, and
collaborate with industry leaders. Don’t miss out on your chance to be part of this event. We look forward to seeing you there!
For more information and to register, please visit the ESS Expo website.
The European Decontamination Institute, EDI, is pleased to announce its successful participation in Asbestonomy 2024, held in June in Madrid.
This event, dedicated to asbestos management and abatement, aligned perfectly with EDI’s mission to promote safe and effective decontamination practices across Europe.
Our attendance at Asbestonomy provided valuable networking opportunities and insights into the latest advancements in asbestos management technologies and best practices. These connections and knowledge will enhance our efforts to develop and disseminate guidelines that ensure the highest standards of safety in decontamination projects.
By engaging with industry experts and sharing knowledge, EDI continues to strengthen its role as a leader in the
decontamination sector, advocating for safer practices and fostering a collaborative professional community.
With more than 30 years’ experience, SEG UMWELT-SERVICE GmbH specialises in providing comprehensive environmental services, including hazardous waste management, soil decontamination, and asbestos removal.
Founded in Germany, SEG UMWELT-SERVICE GmbH has built a strong reputation for its commitment to environmental protection and sustainable practices.
The company employs a team
of highly skilled professionals who use cutting-edge technology and innovative solutions to address complex environmental challenges. Their expertise in handling hazardous materials and dedication to maintaining the highest safety standards make them a valuable addition to EDI.
SEG UMWELT-SERVICE GmbH involvement promises to enhance collaborative efforts within the institute, promoting the highest standards of environmental
safety and best practices in the decontamination industry.
We look forward to the valuable contributions that they will bring to EDI, furthering our mission to advance the decontamination sector across Europe.
Flesan, a leading company in the construction sector known for its diversified units specialising in demolition, public works, geotechnics, mining, infrastructure, industrial assemblies, machinery, environmental services and restorations, has recently become a member of the European
Demolition Association (EDA). The company was founded in 1981 and operates in Chile and Peru.
Flesan’s commitment to sustainability, innovation, and continuous improvement is evident in its comprehensive approach to construction projects. With a robust portfolio that spans various phases
The International Union of Laboratories and Experts in Construction Materials, Systems and Structures, RILEM, an international partner of EDA, is delighted
of construction and building, Flesan integrates cutting-edge technology and machinery to meet project requirements efficiently within agreed timelines and budgets.
to inform you about Technical Committees working on research topics related to waste and recycled materials.
• UMW: Upcycling Powder Mineral “Wastes” into Cement Matrices
• APD: Alternative Paving Materials – Design and Performance
• RCC: Rolled compacted concrete for pavement applications
Joining these TCs is free and industry participants are highly welcome. If you’re interested, please feel free to complete the Join a Technical Committee form.
This collaboration between RILEM and EDA is based on the common objective of fostering and promoting international cooperation through general access to advanced knowledge.
We are excited to present the panellists for the EDA Think Tank 2024, set to take place on 9 October in Brussels.
This year’s central theme is the newly updated Construction and Demolition (C&D) Waste Management Protocol and Guidance. The event will feature two insightful roundtable discussions with industry professionals who will share their ideas, best and worst practices and insights about the industry’s current state and future directions. Join us for this unique opportunity to gain valuable insights, network with industry leaders, and contribute to shaping the future of C&D waste management.
Debate session 1: New C&D Waste Management Protocol
• Liesbet Van Cauwenberghe, TRACIMAT
• Florian Flacheneker, European Commission
• Stefano Panseri, NADECO
• Katrin Mees, DEUTSCHERABBRUCHVERBAND
• Marco Camboni, RPA EUROPE
Debate session 2: Guidance for resource audits before demolition and renovation works
• Thomas Kasper, BRV
• Philippe Moseley, European Commission
• Johan D’Hooghe, TRACIMAT
• Duncan Rudall, NFDC
For more details and to register for the event, please visit our EDA Think Tank 2024 website. We look forward to welcoming you to Brussels.
The company was founded 39 years ago by Miguel Ángel Ippolito, who transitioned from auto mechanics to the demolition industry, setting a firm foundation for a business committed to triple impact: economic, social and environmental.
Thanks to the founder’s legacy and the company’s continuous evolution, Grupo Mitre has achieved significant milestones, including becoming the world’s first B Corporation demolition company. This certification highlights their positive impact on the environment and community.
With a strong dedication to the circular economy, Grupo Mitre stands out for its efforts to minimise landfill waste by recovering demolition aggregates and reintegrating as many building materials, such as doors and windows, back into the market.
In 2015, they further solidified their commitment to sustainability by incorporating their first on-site aggregate crusher, enabling the reprocessing of materials directly at the demolition site and reintroducing them into the construction production cycle. We at the EDA are proud to welcome Grupo Mitre as a new member, recognising their exemplary leadership in responsible demolition and recycling practices.
At the European Demolition Association we foresaw the rise of the circular economy and the accompanying legislation at national and member state levels. This prediction has now become a reality.
The circular economy is enhancing the relevance of our industry, particularly in demolition, decontamination, and recycling (DDR) activities, by creating new business opportunities. However, it also presents challenges.
The movement began in the UK, with calls from green organisations, media, the public and legislators to ban demolition and favour retrofitting existing buildings. This trend is now spreading across mainland Europe, posing significant challenges for our industry.
While we support a greener future, resource efficiency and product reuse, these goals must be pursued logically, practically and economically. Many of the calls for change come from well-meaning individuals outside the construction industry, who may not fully grasp
the practical implications, or from interested parties looking to benefit from recycled materials.
In response, we are developing a long-term strategy. At our recent convention in Belgrade, we emphasised the need to position our industry as part of the solution, not the problem.
We have identified an opportunity through the United Nations’ Urban Regeneration initiative, led by the Habitat Directorate. This initiative focuses
on improving urban spaces and reshaping communities by adapting the built environment.
Our goal is to ensure that the demolition sector contributes positively to the circular economy and urban regeneration efforts, aligning with environmental objectives while maintaining practical and economically viable practices. We believe that by working together, we can secure a sustainable future for our industry and the communities we serve.
Bellevue 600 – Phase 2 is one of the most unique and noteworthy projects NDA member Dickson Company has ever worked on. In the process of abating and demolishing this 10-storey, 40-m-tall building, the company encountered different challenges on all four sides that required creative problem-solving and specialised equipment to address.
Located in downtown Bellevue, Washington, this 21,000-m3 building, once home to the regional office of Honeywell, was set to be demolished to make way for a new office tower. The site had active uses tucked close in on all sides, most notably a crew working on the adjacent Bellevue 600 – Phase 1 project just five metres from the east wall, working 25 metres down preparing the foundation for a new neighbouring building.
During the bid process, the general contractor and its client made it clear that any debris entering the excavation was unacceptable. Dickson Company took this seriously and with a team of engineers and demolition professionals, the company decided
Demolition Hub is a proud member of the National Demolition Association
against relying solely on high-reach machinery to do the demolition. Instead, it formed a plan to demolish the building in two parts, first by using robotic demolition machines and support equipment to demolish the sections of the building closest to the transit hub to the south and the excavation to the east. Once the most critical parts of the building were demolished, the rest of the building was taken down using a 50-metre high-reach excavator.
Upon completion, Dickson Company was able to deliver the client a clean site, on time and under budget, with no injuries and no uncontrolled debris ever leaving the job site or entering the excavation.
Once hazardous materials were abated, Dickson Company used small equipment and demolition attachments to size, reduce and separate out all possible recyclable materials.
One of the additional efforts made on this project was to extract all acoustical ceiling panels prior to any demolition activities so they could be recycled rather than go into the landfill waste stream. Ninetythree percent of debris was reused or recycled.
This project presented a unique challenge for Dickson Company. The nearby excavation was an active worksite with construction personnel working continually for the duration of the project.
Dickson Company brought together a team of demolition professionals and engineers to come up with a plan that would enable it to meet the schedule and keep them safe. When the company concluded that using a traditional high reach approach for this demolition wasn’t feasible, it pivoted to a hybrid
approach that would allow it to demolish approximately one-third of the building, which was closest to the excavation, using remote control demolition equipment and small support equipment floor by floor. Only then did the company deploy high-reach equipment to demolish the less sensitive portions of the building.
• Occupied office building to the north
• Active roadway 15 metres to the west
• Transit hub and bus terminal 12 metres to the south
• Active excavation 4.5 metres from the east wall
Dickson Company was a 2024 Excellence in Demolition Category 2 Finalist for this project.
Demolition Hub is a proud member of the National Demolition Association
On the compact Vanderbilt University Medical Center (VUMC) campus in Nashville, Tennessee, crews were challenged to safely demolish the Oxford House, a 12-storey administrative building. The demolition was part of VUMC’s expansion of the Vanderbilt University Hospital, which includes the construction of a 44,000 m2 tower and connected parking structure.
NDA member Spirtas Worldwide based in St. Louis, Missouri, was awarded the demolition project.
VUMC is one of the busiest health systems in the mid-south, recording more than 3.2 million patient visits per year. It was critical that all demolition material from the Oxford House be safely contained and removed without impact to the nearby active work zones or the adjacent hospital.
To further complicate the effort, the Oxford House structure was built in the 1960s using a jack-slab or lift slab technique. In this method, each floor is cast on top of a previous slab and then raised by hydraulic jacks into position. Unfortunately, the steel
reinforcements within the Oxford House slabs had deteriorated over time, a weakness that had the potential to cause a slab to fail during demolition.
In addition, the compact site came with limited space to set up equipment and stage protective screening materials. In some areas, crews on nearby projects were only inches away. As planning progressed, it became clear that the screens would need to be delivered, installed and removed in stages as demolition progressed from floor to floor, requiring considerable coordination.
A tight timeline added another layer of complexity. All protection screens had to be designed and approved by the engineer-of-record and the first screens installed within two months.
While protection screens are most often associated with construction not demolition, Spirtas Worldwide found them to be the ideal safety solution for the Oxford House project.
“This demolition job does not provide any room for error,” said Chris Hancock, Project Manager for
Spirtas Worldwide. “We have hospital pedestrian and vehicle traffic incredibly close and, at times, under the building we are demolishing. Controlling material during the demolition process is essential to keep our workers and the public safe in a highly sensitive environment.”
Doka developed a protection screen solution that essentially climbs down, from top to bottom –not up, like the more familiar highrise screen systems. The screens were designed in 12-metre-long segments that could be lifted by the on-site crane then connected together to reach the required 30-metre height. Deliveries were often scheduled at night to minimise the impact on tradespeople working on-site during the day.
As a demolition contractor, Spirtas had limited experience working with formwork or protection screens. Doka experts facilitated hands-on training, guiding the Spirtas team through the step-bystep installation. Doka’s dedicated field supervisor continued to check in to support the crew as additional layers were installed and they became more familiar with the process.
By closely partnering with the Spirtas team, Doka was able to deliver an effective, efficient and high-performing solution that met the unique safety needs of the Vanderbilt University Medical Center job site.
Just north of downtown Chicago, Walsh Group is hard at work demolishing elevated train tracks and concrete decks as part of the largest rehabilitation job in the history of the Chicago Transit Authority.
The Red and Purple Modernization project replaces century-old structures that carry the “L” train – a name given by locals to the public transit system because most of the rail lines are elevated above city streets. And with well over 300,000 daily passengers and climbing, the upgrades are sorely needed.
This $2.1 bn (£1.6 bn) project will deliver improved infrastructure and ridership capacity along Chicago’s most used transit lines. In addition
to modernising century-old junctions and rebuilding worn-down stations, it calls for new bridges, support structures, tracks and 3.2 miles of signal system upgrades.
Because the job site sits near the centre of a major metropolitan area, space is incredibly limited. Rick Anderson and his team of about 50 people are relying on versatile excavators and wheel loaders that keep the job moving along while helping crew members and those living and working near the job site remain safe.
“There’s a lot going on, and everything’s tight,” says Anderson, general superintendent for Walsh Group. “For this demolition job, we’ve got sheet removal. We’re
breaking up concrete. Haul trucks are moving material in and out, plus there’s general cleanup. One of the biggest challenges is logistics –getting equipment in and out while trying not to affect the surrounding neighbourhood. People aren’t used to construction in their backyard.”
To manage the tight spaces and get the job done with minimal impact on the community around them, the Walsh team relies on a fleet of Volvo CE heavy equipment, including 13 ECR235 excavators, two EC355 excavators and four wheel loaders from L90s to L120s, all supplied by local Volvo CE dealer Alta Equipment Company.
“The decision about what equipment we needed was determined by the amount of space we have,” Anderson says. “Naturally, with excavators, you want the reach, and it would’ve been great to have massive machines in here to tear it up. But you can’t; it has to be sized for what will fit.”
Machine availability makes it happen
To get the right sized machines for the job, Walsh turned to Alta Equipment, which currently has a wide range of large and midsize excavators ready to go at a moment’s notice.
“We have an outstanding relationship with Walsh,” says Alyssa Van Baren, Alta Equipment Account Manager. “We like to sit down with
our customers, get a scope of the project and see exactly what they need. We look at the big picture so we’re prepared to give them the proper equipment, service and rentals at the exact time it’s needed. And that’s what we’ve done here.”
Anderson agrees. “Even with the bidding process up front, we have to make sure machines are available to provide an accurate price,” he says. “Alyssa and the Alta team have been outstanding at letting us know what’s available and getting us exactly what we need when we need it.”
“With this particular job, there are a lot of changes going on,” says Kevin Berger, Midwest Regional Equipment Manager for Walsh Construction.
“From the start, we were looking at buying a certain number of machines, but the job changed significantly and rentals became critical. It was all unplanned. That’s why we have about 17 excavators out here working right now. Alta helped make that happen.”
With so many machines running simultaneously, performance and safety have been paramount for the entire crew.
“It certainly does,” Anderson concludes. “If we ever get in a bind and need something quick, they go out of their way to help us. That’s something you just can’t put a price on.” Demolition
“I like to see exactly what’s going on, and the 360° camera and short tail swing on the ECR235 help me work more confidently,” says operator Nathan Lawyer. “And I like running Volvo equipment because my machine does exactly what I tell it to do. A lot of brands have a delay in the joysticks, but this machine is very smooth.”
Anderson says: “We also added tiltrotators so that our operators can angle the attachments and turn them easier while working in such cramped spaces. It helps us stay productive and prevent potential accidents.”
Anderson says Walsh is incomparable in their focus on safety, providing every possible avenue to create a safe working environment.
Exceptional manoeuvrability is only one of the advantages the Walsh team is experiencing with their machines.
“With demolition, you never know when machine service will be needed,” Anderson says. “And with Chicago traffic, it’ll likely take a while to get someone in. On this particular
job, we hired one of Alta Equipment’s mechanics on-site. He’s here every day, which takes the drive time and delays out. Not breaking down and keeping the job moving – that’s all that matters, and Alta’s support has been the difference maker.”
It’s this kind of out-of-the-box service and support that keeps the Walsh Construction team on task and on time.
“We have guiding principles here at Alta that are at the core of everything we do,” Van Baren says. “One team; mutual respect; invest in the best; and have a passion for excellence to create customers for life. I think we’re doing that with Walsh – and we’ll continue building long-term customer relationships just like this one. Uptime matters.”
by Howard Button
I recently returned from a lovely holiday in Newquay, where I haven’t been for what must be getting on for forty years. At least the old roads have been upgraded and the journey was far quicker than I can remember. But one thing that has not changed is that there are still plenty of caravans en-route. This got me thinking about electric vehicles, so I decided to do some research.
The Zero Emission Vehicle (ZEV) Mandate and CO2 Regulations, more commonly known as the Z mandate, is starting to kick in and like many others, I have taken the plunge and bought a hybrid car, side-stepping the range anxiety that full electric cars give.
The Z mandate, published in consultation form in March 2023, lays out some pretty tight restrictions for manufacturers of cars and vans. The objective is zero emissions vehicles, with a commitment to ending the sale of all new petrol and diesel cars and vans by 2030 and for all new cars and vans to be fully zero emissions at the exhaust by 2035.
We may all think we are ok, that’s a long way away, but the manufacturers need years to plan and develop new vehicles and sell old stock, while we struggle with a lack of charger station networks and many home owners wonder just how they will charge their ZEV from their home, which may be a terraced house with no driveway or a block of flats without any dedicated
resident charging points let alone a guaranteed parking spot.
Clause 24 of the Z mandate consultation document is a clear indication of how seriously the government is taking this proposal, with the possibility of huge fines for non-compliant manufacturers.
“If a manufacturer cannot meet their non-ZEV CO2 emissions standard after trading and/or the transfer of ZEVM allowances, they must make a payment equivalent to £86 per gram of CO2 per kilometre exceedance over the non-ZEV fleet multiplied by the number of vehicles. This is equivalent to the fine structure under existing UK CO2 emissions regulation.”
Taking all of this into consideration I move back to my original thoughts. Will the demise of petrol and diesel cars and vans also see the demise of caravans and trailers? I know my own hybrid car cannot be fitted with a tow bar as the battery pack takes up all of the rear end of the car and half the boot.
My local parish council recently purchased a new fully electric van for the village warden. This has already flagged up a battery issue as we cannot get as many tools and equipment inside and cannot fit a tow bar due to the size of the battery pack.
Will the Z mandate extend to vanderived pickup trucks and stop the practice of towing the mini digger to site for a small ground works job or
“Ending the sale of all new petrol and diesel cars and vans by 2030”
utilities road works gang?
These are all big questions that don’t seem to have been considered or included within the Z Mandate. Who knows which way successive governments will go with this legislation, but I doubt any will attempt to make significant changes. What next? Are we looking at zero emissions for our HGV fleets? Thankfully, many of the big engine manufacturers are working hard to achieve net zero. With names such as JCB developing hydrogen internal combustion engines, that might just be the fuel of the future.
Perhaps roads with no caravans is just as much of a dream as a motorway without roadworks and lane closures.
Happy holidays.
If you have something to say and would like to submit a column for publication in Demolition Hub, please email: toby@chambers.media
The UK wakes up to a new government after 14 years of Conservative rule. For the built environment, Labour’s return will be met with wary anticipation. While its manifesto pledges made a good read for a sector that has experienced ongoing skills shortages, rising costs and lacklustre growth, delivering on them will be another matter. Just think back to the success of the Conservatives’ new deal promise to “Build, build, build…”
Labour’s vowed rollout of a 10year infrastructure strategy to “end the chaos” of the UK’s “crumbling infrastructure” has some interesting, though not necessarily revolutionary, ideas. Delivering 1.5 million new homes in England sounds impressive, but there is already a backlog of 4.3 million homes. Regardless, it is a good starting point if Labour can overcome
the challenges faced by previous governments.
Housebuilding has long been stifled by planning policy, However Labour’s promise to slash red tape and give combined authorities much needed new powers are to be welcomed, though have yet to be tested by locals and environmentalists furious about green belt land being redesignated for development.
To meet its housing target, Labour must help the construction industry get back on its feet. Its first step will be addressing the ongoing skills crisis. The Apprenticeship Levy, for example, has not been fit for purpose for some time. Apprenticeship starts have severely declined and completion rates have plummeted.
Its replacement, the Growth and Skills Levy, will certainly prove very attractive for employers, who
“Labour has created a rod for its own back with promises to “hit the ground running”. It has inherited a very difficult challenge and must deliver”
have long complained they cannot spend their levy payments on apprenticeships. Given that UK employee investment has been falling, this levy, combined with the creation of the new Skills UK body, could be instrumental for the longterm health of the sector, attracting and retaining much needed new talent.
Labour has created a rod for its own back with promises to “hit the ground running”. It has inherited a very difficult challenge and must deliver, but if their ambitions are supported, our sector, the built environment, may experience the green shoots of recovery, sooner rather than later.
As the CEA, we are ready to engage actively with the new Labour Government to address the crucial challenges and seize the opportunities highlighted in our 2024 Manifesto. The commitment to decarbonisation, digital transformation and skills development outlined in Labour’s platform aligns closely with our industry’s goals.
Labour’s plans to introduce a new industrial strategy, developed in partnership with businesses through an Industrial Strategy Council, will leverage Britain’s strengths in life sciences, digital, creative industries, financial services and clean power. This collaboration will drive growth and innovation, benefiting the construction equipment industry and the wider economy.
The party’s promise to build 1.5 million new homes in England over the next five years is a remarkable initiative that will stimulate demand
The Construction Equipment Association (CEA) congratulates the Labour Party and the new prime minister, Keir Starmer on their historic election win. This significant change in leadership presents a unique opportunity to propel the UK construction equipment industry into a new era of innovation and sustainability.
in the construction equipment sector, a level of housebuilding not seen since the 1960s. This very ambitious target and reforms in housebuilding economics and bureaucracy will likely boost private sector participation, benefiting our industry significantly.
Decarbonisation remains a critical priority for us. Labour’s substantial investment of £23.7bn in green measures during the next parliament emphasises the central role of green policies in driving growth and prosperity. We anticipate robust support from the Labour government in advancing innovative technologies, including electric and hydrogen-powered machinery. Establishing a national alternative fuel infrastructure is essential and we look forward to contributing to these transformative efforts.
The party’s plan to allocate £1.7bn a year for the Great British Energy company aims to accelerate
the rollout of renewables and nuclear power, creating 650,000 jobs by 2030. This initiative will drive industrial renewal, lower energy bills, and ensure secure, clean energy supplies, promoting a stable environment for construction projects.
The digitalisation of our industry is another important area. We are ready to collaborate on harmonising digital legislation and enhancing cybersecurity measures. Addressing the skills gap is imperative for maintaining our competitive edge and we are eager to work with Labour to attract and develop the next generation of talent.
Lastly, we urge the new government to ensure regulatory stability and alignment with European standards, vital for maintaining our international competitiveness. Together, we can adopt a sustainable, innovative and prosperous future for the UK construction equipment sector.
What a new government must change for companies like the Collard Group
It’s been several weeks since the UK voted in a new government. Labour seems to offer benefits for our sector, but there are also opportunity gaps that must be prioritised.
Labour’s ‘Get Britain building again’ is a welcome priority for us at the Collard Group – as an enabling partner for construction works nationwide.
They’ve pledged to build 1.5 million homes over the next parliament, invest in crucial infrastructure, uncomplicate the planning process, and release ‘grey belt’ land for development. These are promising commitments.
In particular, their strategy to reform planning will hopefully streamline and speed up new development, unlocking building projects currently stuck in red tape.
We hope Labour will prioritise the construction sector’s significant skills and labour shortage. They could do that by equipping the unemployed with the right training and providing grants to help businesses upskill
“Labour’s ‘Get Britain building again’ is a welcome priority for us at the Collard Group – as an enabling partner for construction works nationwide”
their existing workforce or recruit additional employees.
With that in mind, seeing how things like Skills England affect our industry will be interesting. This initiative brings together companies like ours with education and training providers, unions, migration experts and the government to ensure we have people with the skills we need in this country. Having worked with Basingstoke College of Technology, for example, to attract students to our company, we’ve seen the value of partnership working, so there’s hope there.
Labour’s view on immigration isn’t always popular. However, any immigration strategy they introduce must help to plug the sector’s skills and labour gap.
At the Collard Group, we have a solid environmental purpose. We call this ‘recycling the past for the future’, where we demolish buildings, prepare land for development and process waste to make it useful again.
While the new government will favour businesses like ours with a serious sustainability agenda, we want this parliament to prioritise and better explain its commitment to reducing waste by moving to a circular economy.
Each year, we invest millions of pounds in fleet, plant, technology, and training to ensure we keep growing and innovating. In the past, the government has provided incentives to do this, for example, the ‘super-deduction’ initiative, where we could claim 130% capital allowances on plant and machinery investments. As a company keen to use greener, higher-performing and more fuel-efficient tools, we’re waiting to hear if the new government will prioritise something similar.
A change in priorities is on the horizon for our industry, and we’ve recently seen an increase in tenders arrive through our door, which may indicate developers are beginning to regain confidence now that inflation has stabilised. We’ll know soon whether the interest rate is lowered, too, as predicted [the Bank of England dropped the base rate to 5% on 1 August]. This should hopefully reinvigorate the economy, presenting even more opportunities for our sector.
At Romax Solutions, finding the best candidates is our driven desire and passion, we aim to meet the recruitment needs of a diverse range of clients within the construction & demolition industry, leaving them happy, everytime. Romax Solutions is also fully accredited by the Recruitment and Employment Confederation and the National Federation of Demolition Contractors.
With a depth of knowledge, our experienced and trusted staff are on-hand to deliver a bespoke service, supplying reliable and talented staff of all levels both nationally and locally. Specialising to demolition contractors to NFDC guidelines. As Members of the NFDC we offer Internal training to all our candidates whether starting their career in demolition or to help further their skill set.
Without the plant-hire industry, the UK’s construction sector cannot function. Contractors and subcontractors hire most construction equipment. Very few contractors own their own plant. CPA members operate and represent all the different types of construction equipment available.
The plant-hire industry also invests heavily in the workforce of the future. The sector is responsible for a vast array of apprenticeships within the industry and is a leader in the recruitment of young people and those looking for a major career change.
Offering long-term roles with the ability to train, progress and build a sustainable career, the plant-hire industry is playing its role in making construction a more attractive industry to have a career in.
Chris Cassley, Policy Manager of the Construction Plant-hire Association (CPA) said: “The new government must work with the construction industry in addressing critical issues such as decarbonisation and reaching net zero, improving productivity and
business investment, building the new homes that we desperately need, and renewing our ageing infrastructure.
“All of this requires a longterm vision and consistency from government in how policies are developed and implemented. Providing the stability and economic foundations needed for lasting economic growth comes only from engagement with industry in understanding the challenges companies face - and how they can be overcome. The CPA looks forward to working with the new government in achieving this aim.”
These are our core priorities for the next government.
Reinforce business investment and future house building programmes
Establish a credible timetable for the extension of the Full Expensing Allowance to every aspect of the construction plant-hire industry. When ‘fiscal conditions allow’ is too vague and undermines confidence in business investment decisions.
“Without the planthire industry, the UK’s construction sector cannot function”
Reforms to the planning system must be realistic and proportionate. Learning from past failures at both central and local levels are important if we are to build the future homes we need.
Decarbonisation of construction plant
There should be one single government department responsible for decarbonisation of construction plant. Current policies and roles are split between at least three government departments.
Temporarily reintroduce the rebate for Hydrogenated Vegetable Oil (HVO) to the construction industry for at least the next two years.
Develop a trial scrappage scheme for NRMM (Non-Road Mobile Machinery) businesses operating in Freeport zones, with a view to widening the scheme on a national basis.
Publish the Low Carbon Fuels Strategy as soon as possible and develop a road map for the decarbonisation of NRMM.
The position of construction minister must be solely dedicated to the sector and not split among a range of different ministerial responsibilities across different industrial sectors.
The current approach by the police on abnormal loads and embargo times are having an adverse effect on the efficient movement of construction plant – especially mobile cranes. Some companies are facing an existential threat. The government must get the Home Office and Department for Transport to work with the industry and police chief constables to outline concerns and ensure the current lack of flexibility amongst police forces is addressed.
Build on current work with the construction industry to grow the domestic skills base, improving both apprenticeship funding and retention rates amongst apprentices, while also making the industry an attractive career option for people already in the workforce. Realism is needed in recruiting from overseas, with the Migration Advisory Committee working with the construction sector in addressing current skills gaps.
The legislative impasse on the creation of Great British Railways (GBR) must be resolved as soon as possible. A growing rail plant and rail maintenance industry is at the heart of a successful rail sector. The current delays have undermined progress, with the supply of future work bank visibility fragile.
We support the new government’s commitment to sustainable development and commitment to provide a significant improvement in planning for new housing. We firmly believe that prioritising brownfield development is a critical step in protecting our green spaces and promoting sustainability.
By focusing on the redevelopment of brownfield sites, we can significantly reduce the need for new construction on greenfield locations, which will in turn preserve valuable agricultural land.
The demolition process plays a vital role in this, as it allows us to unlock and recycle materials that can be reused in the creation of new housing and infrastructure projects. This approach not only minimises the consumption of new resources but also enhances the overall sustainability of development projects.
We are enthusiastic about continuing our work with the Ministry of Housing, Communities and Local Government (formerly the Department of Levelling Up, Housing, and Communities) to support this cause by enhancing understanding of demolition’s role in sustainable development. Often misunderstood, the demolition industry is dedicated to sustainable practices that contribute to the efficient and responsible
redevelopment of our urban areas.
We also welcome Sarah Jones to her new role as Construction Minister in the Department for Business and Trade, alongside her role within the Department for Energy Security & Net Zero. We welcome the opportunity to collaborate with the minister and her team.
The NFDC looks forward to working closely with the government and other stakeholders to promote the benefits of brownfield development and to highlight the significant contributions of the demolition sector to a sustainable future.
“The NFDC looks forward to working closely with the government and other stakeholders to promote the benefits of brownfield development and to highlight the significant contributions of the demolition sector to a sustainable future”
By Richard Dolman
Are you feeling a little unsure of the market as we are in a period of political change?
At the time of writing this, a new government is being formed. So, what does this mean for us as business leaders, employees and the industry as a whole?
Whether we are in demolition, housebuilding, contracting or the wider construction industry, there are several factors that affect our ability to plan effectively and confidently, that impact our sales pipeline and directly influence our bottom line. Consumer confidence –that is confidence of the end users, confidence of contractors, main contractors and financers.
Political and economic changes hugely affect businesses, coupled with how our competitors react to
“There are several factors that affect our ability to plan effectively and confidently, that impact our sales pipeline and directly influence our bottom line”
these changes that impact your own business approach to pricing and sales mix. It has a domino effect. Arguably, this is completely understandable. Uncertainty changes our mindset. But in this latest wave of uncertainty, we knew an election was going to be called, then a date was set, then we entered purdah – the pre-election period of sensitivity.
According to The House of Commons Library, the period of pre-election purdah in which there is heightened sensitivity regarding decision making and publicity is not governed by law, but convention. Backbench and opposition MPs are not constrained by this, however, so why are we?
Convention has led to local authorities setting their own statutory guidance for purdah. In turn, when working with central government, we are also affected by these periods.
We’re all now waiting for the “what next”. What new policies are being implemented, which areas will have the greatest focus for the
incoming government, how will this affect our bottom line, ability to implement our own strategies, our labour supply and our orders? It all sounds very daunting, but does it need to be?
Policies are not usually implemented and actioned suddenly (unless as you read this we already have a new Act directly impacting us). Despite the inevitable declarations of change which will be implemented, it will take time. We have time to adapt with the potential changes, so why are we holding our breath? Wouldn’t it be better for us all to help instil confidence by sharing our plans and our (albeit considered) investments with our clients and the wider industry? This would show how we do still have plans for our businesses, we’re not shying away from progress because of political change, but trying to embrace it. Confidence drives consumer spending, and this is what we need. We all know this.
Let’s work together to keep our industry pushing forward. In recent years, the majority of us have overcome so many challenges, this is just another one. Change is inevitable. We shouldn’t be driven by the what ifs so significantly; we need to stand together to manage the next phase of change.
Lloyd, Head of Vendor in the SME
It’s been a busy few months for the industry. Like many in the sector we had been waiting in anticipation for the big event of the year – Hillhead. The Buxtonbased showcase is a great chance to catch up with friends and colleagues and to make new acquaintances.
It’s also a great opportunity to witness the constant innovation in the construction sector and see new technology emerging. There was everything from hydrogenfuelled equipment to autonomous machinery, showcasing the future of construction.
In addition to Hillhead, there has been another big event recently – the UK general election. It was evident that whoever won the election was going to need to do more for SMEs in the construction industry.
As previous columns have highlighted, it’s been difficult for
many in the sector over the past few years. External factors like supply chain difficulties, soaring labour costs and poor weather conditions affected the ability of many businesses to work to full capacity.
Therefore, it’s been a relief for many to hear policies announced so swiftly.
A welcome announcement has been the reintroduction of mandatory housing targets – this should be a huge support to all businesses operating in the construction sector. The focus on brownfield and greyfield sites is also a bonus as these will invariably require demolition skills.
Unfortunately, the previous removal of the housing targets was unhelpful for the industry as well as homebuyers. Therefore, the reintroduction of these targets and the pledge to deliver 1.5 million new homes over the next five
“It’s been a relief for many to hear policies announced so swiftly.”
years is encouraging.
In addition, there are wider signs that the economy is starting to bounce back. The ONS reported in July that there was 0.4% growth in GDP in May and the construction industry also reported an increase of 1.9%, a good sign after months of declining activity.
Further to this, the announcement of the National Wealth Fund – which has seen £7.3bn pledged to help drive investment in the UK and importantly unlock more opportunities in green energy will be welcomed by many in the industry as we continue to strive towards a greener future.
These new policies are encouraging positivity among those in the industry, however, we must hope that the new government continues to prioritise economic growth and see these policies through.
Our unique capability to repurpose virtually all construction and demolition waste from site helps our public sector, local authority, commercial and residential clients achieve zero-to-landfill targets.
Demolition
Structural alterations
Site clearance
Soft strip
Asbestos management
Remediation
Earthworks & civils
Temporary works
Demolition & Enabling Works Waste Management Aggregates & Concrete
Interviewee: Lee Rowbotham
Role:
Managing Director
Company: Demex
QSo how’s business?
I run Demex for the scrap metal merchants, CF Booth Group. They’re a family business with Demex as a subsidiary, but they leave me to run the Demex side of things. We’ve certainly been very busy.
We’re doing a job for Bradford College on one of the busiest streets in the centre of Bradford, taking down a four storey stone building. The building was full of asbestos so our licensed asbestos side has been in there for about 12 weeks. We did a basic soft strip to begin with, then they came in and removed all the asbestos. We then returned to do the final soft strip before we started demolition on Monday. We’re going
to salvage as much of the stone as we can for resale, it’s going well so far.
We’ve got a job demolishing a wing of a hospital in Harrogate, which is just a single storey building but it is attached to two other live sections of the building, so it’s separation then straightforward demolition.
Another inner city job attaches to a shopping centre right in the heart of Doncaster. Again that’s partly high reach work, partly lower level work. It’s got its own requirements including vibration, dust and noise monitoring.
We’re also taking down a large canopy outside of Rotherham
market and demolishing some buildings there, again city centre. And we’ve got a soft strip in a 23-storey student accommodation block in the centre of Leeds.
QTell us your own demolition story
If I’m totally honest, I wanted to be a policeman. So I stopped on at school and did some A Levels because I did quite well in my O Levels and was too young to join the police. When I did apply, I got to the final stages and went to London for my final interviews and medicals. I didn’t like those few days in London, so I decided not to join the police.
So suddenly, what next? My father was a contracts manager for a construction firm based in Sheffield, where I lived. They were after training up a civil engineer, putting them through college and university. So the first thing I said to my dad was, what’s a civil engineer?
They put me through the education, partly on the job, partly college and university and I became a civil engineer. I spent four or five years doing that and they made me a trainee site manager. My role was to do the civil engineering on the job and stop on to help run the site with the senior site manager to learn the ropes. They were clearing this housing estate of blocks of flats, so apart from the civil engineering, they asked me to keep an eye on the demolition company. I was just amazed at what they could do.
I was approached by a local demolition company. The contracts manager asked me to come in as a project manager, predominantly in charge of earthworks initially as that’s where my experience was but moving on to demolition. They showed me the ropes, estimating etc, and a few years in I became a project manager on the demolition side. I spent 12 or 13 years there and then I was offered a position as Contracts Manager with Demex, where I am now.
I was doing the Contract Manager’s role plus the estimating, pricing the work and method statements, spending six years here before being offered a role at a demolition company in Manchester. It was a lot larger firm and they specialised in nuclear, petrochemical and things like that, which I didn’t have a great deal of experience with – I wanted to spread my wings and learn it all.
So I went there for two years as Contract Manager and did various jobs around the country for them, including gas holder tanks in London, Peterhead power station, and then looking after a simple job at a nuclear plant, which gave me the ropes in the nuclear industry.
I’m a member of the Institute of
Demolition Engineers so I go to the annual seminar in Leeds and for a number of years I’d passed the time of day with a gentleman called Steve. When I’d got the nuclear project, I met Steve and dropped into conversation that I’d got a job starting there and it was a steep learning curve – I’d heard that getting RAMS, plans of works etc signed off with all stakeholders was quite difficult.
He laughed and said, “Believe it or not, I’m the health and safety officer there.” I said, “You’re joking. We’ve known each other for the last five or six years.” So he says, “You always make a beeline for me here, we have a chat and I really appreciate that, so I’ll return the favour. Come up and see me. I’ll spend a couple of days with you.”
That was the best two work days I’ve spent in my life. I went to the plant, met him and went through the job he was doing next. We sat down and literally wrote the RAMS together, so that went through fairly quickly – with nuclear jobs comments usually get passed back and forth and it might take three months before you get it signed off. So my employer thought, Lee’s good at this, he knows his stuff, and thanks to that two-day training on
how to present submissions they put me in charge of a few other nuclear jobs.
Then my old gaffer at Demex retired and the owner of the company rang me up and asked if I’d be prepared to come back and run it. I was more than happy where I was but the opportunity to go back and run a company I loved was a challenge I relished.
So for the last 12 years I’ve been back at Demex. Coming from civil engineering was a good foundation because appreciating how buildings are put together gave me the foundation on how to take buildings down. A lot of the time you’re just doing it in the reverse order.
I think the reason I’ve always loved demolition is that you’re always learning; anybody who tells you they know it all is a liar. Every job is different. It might look similar to the last job but it’s got different challenges and different approaches to how you’re going to demolish it. That’s what keeps me interested in the job.
QAnd what about the Demex story
The CF Booth group are scrap metal merchants based in Rotherham – once upon a time they were the largest family run scrap metal merchants. Obviously, they were having scrap metal brought in from all directions and they realised demolition people bring in a lot. So in 1976 they started Demex. We’ve got a licensed asbestos side and a recycling side, but predominantly we do demolition.
We don’t specialise in any particular type of demolition. It could be anything from a bungalow up to multi-storey blocks of flats, stadiums, ex-collieries etc. We have an abundance of excavators ranging from a 17-tonne rubber duck to 20 tonners, 30 tonners, 50 tonners. We’ve got a 32-metre high-reach and the largest of our excavators is a Hitachi 870, which is a 90 tonner that has an 11-and-a-half tonne shear on the end.
We’re not the biggest of companies but we do everything safely and get a good name for ourselves. We work for some blue chip companies but also for councils, Doncaster Council, Rotherham Council. Predominantly we’re the principal contractor, but we also work as a subcontractor.
QWhat kind of work culture do you like to foster?
The main thing is we work as a team, we all get on. I think you work a lot more efficiently like that. It’s a twoway street so they can come to me at any point and I listen to them and we help where we can. For instance, I might put a Method Statement together for a certain job, that goes out to the site manager, he cracks on with the job and then he might come back to me and say, “Do you think doing it like this might improve matters?” So I listen and if it’s true we’ll change it to suit.
One of the big issues at moment is mental health. We see each other as family, so we’re there to help each other, not just work with each other. That goes from me right down to the labourers on site.
Obviously, the most important thing is health and safety. It’s a must. If we need money to improve or maintain health and safety, then that is what it is, there’s no ifs and buts.
We must be doing something right because the average time spent at this company is probably 20 years plus. I’ve been here 12 years and I’m one of the newest members. We all know each other’s strengths and weaknesses, what makes each other tick.
QWhy choose Demex?
We’re the cream of the crop because we’re members of the National Federation of Demolition Contractors; we’ve been here since 1976, have very experienced, knowledgeable and well-trained staff and we’ve never failed at anything. We’ve done all types of work and the majority is done in house – if there’s asbestos on a job, it’s done in house,
all the transport is done in house. Where we do have to outsource, we know their health and safety standards are as good as good as ours.
We try and take all the weight off clients’ shoulders. Our attitude is, “You’ve given us the job, we’ll only involve you if and when it’s necessary. We’ll only contact you with a question, not a problem.”
We’re not one for advertising the company, it’s word of mouth – if we do a great job for people, they’ll pass that information on. You’re only as good as your last job so we say, let’s make that last job even better than the one before.
We don’t want upset clients, so we do a thorough estimate and are transparent in what we price. If that means that we don’t win the job because we are a little bit dear, then so be it.
Q
What certifications and accreditations do you have?
Demex is a member of the National Federation of Demolition Contractors, Constructionline Gold, SSIP and certain other things. Personally, I’m a full member of the Institute of Demolition Engineers, I’ve got my CSCS professionally qualified persons card in demolition; CCDO senior managers card (an NVQ 7); IOSH; UKATA licensed asbestos removal contracts and manager’s card.
I don’t have too much to do with the asbestos side of things but if I’m leading something I like to be knowledgeable in that field. So obviously back in the day, that’s when I went and got my UKATA contract manager’s certification, which I obviously annually review.
QHow do you bring new people on board?
It’s very difficult in our industry because the younger generation don’t want to commit to demolition because, well, it is hard work. So the NFDC and the industry are trying to bring younger people in through apprenticeships and things like that.
If we’ve got a young demolition labourer who’s keen, intelligent, ambitious, I’ll chuck all the money in the world at them to get them to the next level because it benefits us as a company. So willing people can go as far as they want in our company. But it is hard work getting the younger generation into the demolition world.
QDoes Demex have any engagement in the community?
We do. There’s a special needs school in Rotherham that can’t get funding to improve their buildings, which are really dilapidated. There’s a caretaker’s bungalow and some modular cabins that I’ve said we’ll demolish free of charge and remove from site.
Wherever we can help out, we do so. There are certain local charities that we’ve given to in the past and we sponsor a few youth football clubs. Whatever fundraising we do, we only give to children’s charities.
QWhere do you see things in terms of zero carbon machines?
We’ve not gone down that line yet as I don’t think the technology is there for your 30, 40 tonners that use a lot of power, but we certainly would do. But 50% of our company cars are electric. All our machines, our excavators and lorries are modern, we use HVO wherever we can, if we can get a supplier that supplies it locally to the job.
QWhere do you see Demex going over the next few years?
Offering what we offer now, keeping our good name and making progress within the industry. If we can grow, that’s brilliant, but what I don’t want to do is lose any quality.
I think we’re a nice size now and we can comfortably maintain that. We will try to get on board with any new techniques that emerge, especially if it saves time or makes life easier.
What do you do for fun?
Spend time with the family – my children are getting older and grandchildren are on their way
What would be your desert island (exile) luxury?
No mobile and internet reception
[No problem, that doesn’t just come as standard, it’s compulsory]
What gets you out of bed in the morning?
The love of my work, also knowing I will eventually be home to spend time with the wife and kids
When and where were you happiest?
Being present at all my children’s births
What’s the most expensive non-essential you’ve ever bought?
A Rolex
What’s your bucket list activity?
There is no dress rehearsal in life, so living it to its fullest, long enough to see my grandchildren grow into adults
M A XIMUM PERFORMANCE
LOWEST OPERATIONAL COSTS
HIGHEST RELIABILITY
Project (name/title): Richmond College
Structure: 1930s era school/college
Site area: Entire college
Scope of works: Soft strip, asbestos survey, full mechanical demolition including slab and foundation removal, crushing all hard arisings to 6F2 material for use within parmats on site, disconnection of services, asbestos removal, scaffolding
Contractor: Downwell Enabling Solutions
Client: London Square
Start date: February 2024
Completion date: Phase 1 completed soon with phase 2 commencing shortly
Future use: Affordable housing
A-Level student and budding journalist, Annie Davey experienced her first taste of demolition through a work experience placement with Demolition Hub. Accompanying Ben Chambers on a site visit to a Downwell Group project in Twickenham, she faced up to common preconceptions about the role of demolition in the human environment and society
I was fortunate enough to visit a demolition site for the first time as part of my work experience for college. Despite having very little knowledge of demolition before my visit, this experience was a real eye-opener for me and gave a great insight into the complex world of demolition. As a female college student with no family in the industry, I had previously only
been exposed to mainstream media’s mostly negative coverage of the industry and so naturally, as a media student, I wanted to get some first-hand experience and decide for myself what was fact and what was fiction about this, in my opinion, highly misunderstood industry.
My day was spent in Twickenham on Downwell Enabling’s demolition site where they are demolishing Richmond Upon Thames College to make room for new housing, with around 50% of the new homes being affordable for local people. We were greeted by the site managers, shown
around the site and talked through many of the processes taking place.
Working in demolition can be a dangerous job so unsurprisingly safety was clearly the number one priority on site, with all workers and visitors kitted out in high-visibility jackets, hard hats, steel-toed boots and with some even wearing masks and ear defenders. Fences surrounded the site, protecting members of the public, and metal barriers were placed throughout the site, showing where was safe/unsafe to go based on what machines were running and where.
The sheer scale of the site along with the numerous machines operating was, at first, slightly daunting to see but I soon grew used to it as I realised I was in safe hands.
My time on the demolition site provided invaluable insight into the fascinating world of demolition and allowed me to be fully immersed in it. I feel that I learned so much from the site visit and now have sufficient knowledge to form my own opinions and contribute to discussions around this industry with others, especially my peers, who may also not have much experience with demolition.
This site visit as well as this article have all been part of my work experience with Demolition Hub, who have been kind enough to offer me a placement for the week and arranged these great opportunities for me. I feel I’ve gained so much from this experience already that I can apply to both my studies but also in the future when I will hopefully be involved in the media industry further. I would like to say a big thank you to everyone at the company for being so helpful and accommodating during my time with them.
Three myths about demolition dismantled by my experience on site
by Annie Davey
Demolition is simple – it’s just destroying stuff
Demolition is just destroying buildings as quick as possible, right? Well, the site I observed yesterday immediately changed my perspective on this after I heard the timescale of the project; it started around
eight months ago and still had another two months left. Before any demolition even begins, the buildings must be prepped, with a soft strip to completely clear the insides of the building, as well as an R&D (refurbishment and demolition) service to check for any asbestos.
This lengthy process is necessary to maintain high safety standards and ensure that, whilst the aim is to destroy the building, it is done in a secure way with as few complications as possible.
From what I had heard before, I did not expect demolition projects to be so meticulously planned, with everyone having an important job to be doing and knowing exactly what it was. I quickly realised that the jobs were not just individuals ripping into buildings and tearing them down like I expected, but it was instead a team effort with an additional focus on prepping the area for future builds and keeping it safe for all workers.
This is the key myth I had heard about demolition and, while it can be an inconvenience with noise during working hours, I noticed the site I visited was very keen to prioritise the community. Until a few days before I visited the site, students were still attending the college (in those buildings that hadn’t yet been demolished), meaning the demolition had caused little disruption to their education. There was also a playground right behind the site that was mentioned to me as something that they also needed to bear in mind, keeping the park safe for the local children.
As for the belief that demolition causes lots of dust to be released into the neighbourhood’s air, since the dust can cause many diseases, Downwell and other contractors use many techniques to try and prevent this. One of the first pieces of machinery I was introduced to on the site was the DustBoss, which is used to keep the dust controlled. Many other techniques are also used alongside the dust monitoring equipment that is in operation all
day every day, if levels of dust rise above permitted HSE levels then the work stops. This dust control protects all aspects of the local community, both the people and the surrounding animals/wildlife, which seems especially important to Downwell, the self-styled ‘socially aware contractors’.
When an outsider thinks of demolition, they may think of losing things; losing buildings, losing houses, losing things to do in that area, losing profits and losing people. However, yesterday really demonstrated to me that there is a lot more to be gained from demolition rather than lost.
Learning that the college was being demolished to make room for more housing initially seemed a bit confusing to me, since I associated that with the children there losing an option for education. Upon further reflection, and on learning that a new college had already been built and opened in the area in 2020, I realised that the new, more affordable housing in this area of Twickenham will likely be a great gain for the area, aiding its redevelopment. More people moving in there will of course increase profits for business in that area, allowing the it to develop further than it has had the chance to in the past.
To keep the future for the redevelopment of this site at the forefront of the project, I was informed that Downwell is meeting with London Square (the housing provider/planner) weekly, ensuring the community’s wellbeing and safety continues to be the priority on the demolition site. The future of what is going to be known as Twickenham Square looks bright and will be sure to help Twickenham develop further.
Job title: Castlegate Shopping Centre
Contractor: MGL Demolition
Client: Stockton Borough Council
Structure type: 1970s multi-storey cast in-situ concrete framed structure
Start date: March 2022
Completion date: January 2024
Techniques: Controlled asbestos removal, part top down demolition, remote demolition through remainder of structures using high reach excavators. All hard arisings reprocessed on site for use in future development of the site
Future use: Social and leisure
MGL Demolition’s vital role in Stockton’s transformation Stockton is poised for an exciting transformation; a major regeneration programme is revitalising the town centre and waterfront. MGL Demolition, part of MGL Group, has played a crucial role in a landmark project led by Stockton-on-Tees Borough Council to breathe new life into the High Street and surrounding area.
Once a thriving retail hub, Castlegate Shopping Centre has been impacted by online shopping and out-of-town retail parks. Meanwhile, the former four-star Swallow Hotel has been derelict for over a decade. In 2019, the Council acquired both buildings and plans to redevelop the town centre were set into motion.
The sprawling 32,400 m² site footprint has been cleared, paving the way for the Stockton Waterfront development. The urban park and land bridge structure will reconnect the High Street with the riverside
and create a vibrant community space. This is a trailblazer in the “levelling up” agenda and is a pivotal component of the government’s Build Back Better High Streets Strategy.
Mark Davison, Joint Chief Executive of MGL Group, said: “MGL Demolition is proud to contribute to the regeneration of Stocktonon-Tees. Our specialist team has worked tirelessly to clear an area three times the size of Trafalgar Square. We’re not just removing structures; we’re clearing the path for brighter prospects and a thriving future for Stockton and its people. The new development will foster growth, create opportunities and build a sustainable legacy for future generations.”
Plans to transform Stockton High Street began with work on the five-storey car park. In March 2022, part of the car park was closed to enable pre-demolition surveys to be
undertaken. This included necessary works to divert existing services, including substations.
The 1970s structure featured a flat-slab design comprising concrete cast in situ, a standard construction method for high-rise buildings of that time. The reinforcement in the connections and cross walls served as primary framework support for the structure.
Following asbestos removal, demolition began at the south end of the car park in September 2022. Due to limited safe working space, detailed planning was required to coordinate road closures and traffic management. MGL Demolition’s skilled team of professionals employed modern techniques to demolish the car park quickly and safely using a Komatsu 350 and a 490 with a medium-reach (23-m) demolition arm.
The 10-storey Swallow Hotel formed part of the shopping centre
complex and was constructed using a reinforced concrete frame and flat-slab in-situ concrete floors. The external envelope consisted of glazed panels and brickwork featuring English Stretcher bond.
Following the extensive soft strip and removal of notifiable asbestos, the west end of the building was wrapped with scaffolding, and
floor-by-floor top-down demolition commenced in November 2022. This was necessary because of the proximity to the High Street.
The central and eastern sections of the Swallow Hotel were demolished using a Liebherr 954 with a 32-m high reach. All arisings were stockpiled for crushing and retained on site for reuse.
The Castlegate Shopping Centre opened in 1972 and it featured a distinctive two-storey food hall with a central concrete service elevator and a first-floor balcony leading to a rooftop car park. In recent years, it has become outdated and no longer attracts shoppers.
The second phase of the demolition programme spanned 220 m by 90 m and included a four-storey concrete framed structure. Careful planning was essential due to challenging site conditions. There was a 5.5-m height difference between High Street and Riverside Road, with a central retaining wall running its entire length, which will be preserved in the new development. The structure extended directly to the back of the High Street footpath, providing limited working space.
MGL Demolition’s fully trained in-house asbestos team removed extensive notifiable asbestos from the shopping centre, including the
Spencer Market Hall. Demolition commenced from the shopping centre’s south end, continuing north to the mall entrance. Removing the front glass atrium at the main entrance and dismantling its steelworks was methodically planned and carried out to tight timescales. The work was completed in the early hours of the morning to minimise disruption to the public. All materials were safely removed and disposed of, ensuring no safety
risks or compromises to the existing building.
Work to the north end beyond the glass atrium could only be carried out after June 2023 due to the relocation of the remaining tenants. To facilitate this process, various measures were implemented, including the installation of hoardings along the High Street and Riverside Road and the permanent closure of the Castlegate Shopping Centre and its
“This development will provide real transformational change and enhance the quality of life for residents and visitors”
rooftop car park.
MGL Demolition’s team eventually reached the iconic spiral ramp, known as the “Curly Wurly” by locals. This previously provided access to the rooftop car park and was demolished in August 2023.
Work continued towards Finkle Street on the High Street elevation. Due to the town centre environment, dust management was a priority. Water cannons were used to control the arisings, while high-pressure
hose attachments were used on the high-reach pulverising attachments.
80,000 tonnes of material from the demolition phase were processed to the required specifications for future onsite reuse. Successful waste minimisation and management strategies meant over 99% of non-hazardous waste was successfully diverted from landfill.
The project isn’t just about physical transformation; it’s also about fostering a positive social impact within the community. MGL Demolition developed a tailored social value programme, going above and beyond its core services. These initiatives included employee volunteering and contributions to a community group which supports diverse communities, and donations from the shopping centre going to a local school and a social enterprise charity aiding
local adults with learning disabilities and autism. In conjunction with Red Sky Foundation, the company donated a defibrillator to Stockon Riverside College, contributing towards healthier, safer and more resilient communities. These actions emphasise the positive impact on the local area.
Councillor Nigel Cooke, Cabinet Member for Housing and Regeneration at Stockton-on-Tees Borough Council, said: “This is an exciting time for the Borough and our partnership with MGL Demolition is a catalyst for ensuring our town centres are vibrant places which are economically successful, attracting investment and fit for future generations.
“This development will provide real transformational change and enhance the quality of life for residents and visitors, creating a
thriving and inclusive community hub. It will also allow us to showcase our fantastic events programme and provide flexible open spaces for families, play areas and market spaces on the site.”
Demolition was completed on time and within budget in January 2024, following 81,000 operativehours and no lost time incidents.
Construction of the urban park is underway, with the waterfront development on track for completion by the end of 2025.
Project: Eastland Shopping Center (Harper Woods, Michigan)
Structure: Shopping mall: structural steel, brick, concrete, universal waste
Site area: 121,000 m2
Scope of works: Asbestos abatement, building demolition, material separation, sorting and recycling
Contractor: Adamo Group
Client: Development company
Other stakeholders: Michigan Strategic Fund
Techniques: High-reach crane, front loader, magnetic sorter, atomised mist dust control cannons
Future use: Industrial distribution centre
by Michael Kelley, President BossTek
The creativity of architectural design at the time of construction can have a profound impact on demolition, since the recycling of construction and demolition material has become such an important part of the process. It is no secret that the demolition process releases dust emissions, but so can the separation of material for recycling. Projects with several materials can be a challenge as they retain and release different kinds of dust when they are demolished and separated into piles.
The Adamo Group is well aware of the issues associated with the demolition of different projects. Operating since 1964 and headquartered in Detroit, Michigan, the company has safely and expertly
demolished and cleared projects across the region. The company is very familiar with the wide variety of materials that can go into construction and a good example of this was its recent demolition of the Eastland Shopping Center in the town of Harper Woods, north-east of Detroit.
“Our business model is to employ the best practices for any project, which includes diligent recycling and effective dust control,” said Al Penrod, Equipment Manager of Adamo Group. “The basics of what it takes to complete a job successfully is talented people, high-tech facilities and a fleet of top-of-the-line equipment, and DustBoss® misting cannons are an integral part of that portfolio.”
Consistently updating operations using modern methods and equipment is at the core of why Adamo has been a top demolition contractor in North America. Expert engineering and management teams streamline projects, perform environmental testing and create hazard assessments using the latest tools and standards. Aggregated data frames how the property’s end-use is affected by a myriad of factors, from environmental to regulatory, helping better inform the next phases of the project including construction and environmental remediation.
With a $25m fleet of modern machinery, the company provides a wide range of services. Some large projects involve highway and bridge demolition, excavation and grading, utility installation and hazardous waste removal. Smaller projects require just as much expertise, including site decontamination, facility decommissioning, asset management and recovery, selective
demolition for facility renovation, asbestos abatement, recycling and industrial processing. Most, if not all, of these projects involve some sort of dust control.
Opened in 1957, the Eastland Shopping Center was considered one of J.L. Hudson Company’s most ambitious department store expansion projects. With waning occupancy over the past decade, the facility was purchased by a development company and retained roughly 10% occupancy by late 2021. The mall closed in early 2022 with the intention of building a $94m industrial distribution centre.
A collaboration with the Michigan Strategic Fund, the approved plan involves three commercial light industrial buildings totalling 121,000 m2. The proximity to the already established automotive infrastructure makes the location attractive for this type of development. In addition to the three buildings, the project will include 3,320 m2 of infrastructure
improvements, including sidewalk, curb and gutter improvements and road repair.
The entire demolition project from start to finish took eight months. After environmental testing and a meticulous hazard assessment, asbestos abatement was performed first. The building was also cleared of “universal waste”, a catchall term for batteries, mercury-containing equipment, lamps, and aerosol/ pressurised containers.
Once the toxic substances were removed, the taller structures were demolished first. Using several pieces of equipment in the fleet, including a mid-sized high-reach crane, front loader, magnetic sorter, etc, the Adamo Group dismantled the structure. An integral part of this was the DustBoss DB-60 misting cannon. Directed toward the activity area, the fine engineered mist raised the humidity of the area, preventing dust from becoming airborne and traveling into the surrounding community, as well as protecting
workers on site from hazardous dust.
Each material was separated for potential recycling, including:
• Structural steel
• Shredded material
• Brick block
• Concrete
• Other debris
A second DB-60 unit was used to reduce dust emissions from separating, piling, short-term storage, and disruption of the piles while filling transport canisters. “Materials were separated on site by mechanically picking or magnetised picking,” said Penrod.
“These structures collected over 60 years-worth of dust, so the separated materials can release a lot of emissions. The DustBoss really helped us control air quality so we could stay compliant.”
Different materials can produce and attract different particulates. Some are more regulated than
others. When regulators measure particulate matter (PM), they’re primarily looking for particles 10 microns (µm) in diameter or smaller. For perspective, dust is light enough to remain airborne on ambient air currents at 200 µm and becomes barely visible to the naked eye at 100 µm – approximately the cross section of a human hair.
The reason PM10 is regulated is because it can penetrate the body’s defences and enter deep into the lungs. Long-term exposure can irritate existing breathing problems and may lead to chronic lung diseases.
Crushed or broken concrete, for example, can release silica particulates, which are generally smaller than PM10. Silica is also present in brick and mortar as small as PM2.5.
Structural steel can have static or magnetic qualities that attract heavy metals and other hazardous dust particles, capturing them within recycling piles and shedding them in large quantities on windy days or when disrupted.
To capture small airborne particles, the droplets need to match the general size of the particles so that they can collide. The combined
mass causes them to drop to the ground. Droplets greater than 200 µm are large enough to sail through the air causing a slipstream current to move around them, which repels smaller particles, leaving them to remain airborne.
The traditional method of dust control is a worker holding a hose and spraying water toward the area. This activity has several drawbacks. One is that it puts workers in close proximity to the activity area and fall zone, which can be highly unpredictable. Hoses connect to hydrants, so they use between 380 and 2,000 lpm of water, causing a tremendous amount of wastewater runoff, mud and hazardous standing water.
To reach high up or across rubble towards active demolition requires high water pressure. So along with the water volume, the droplets produced by these hoses need to be large, approximately 200-1,000 µm, which is fine for surface suppression, but ineffective against airborne particulates.
In addition to the safety issues associated with hoses are factors such as the cost of labour, water bills, risk of complaints and air quality violations, all of which
combine to raise the overall cost of operation.
Automated mist cannons like the DustBoss DB-60 produce droplets approximately 50-200 µm from a misting ring in the front, which are propelled long distances by a powerful fan that pushes air through the rugged barrel. The droplets offer both airborne and surface suppression using only a fraction of the water required by hoses or sprinklers. This is why methods that rely on water pressure are being replaced with atomised mist cannons as the preferred method of dust control. They are more effective, cheaper to run over the long term and require no workers to operate.
The permit for the Eastland project did not specify the method of dust control beyond the fact that it must be water-based. Adamo Group purchased its first DustBoss unit in the original black colour over 15 years ago to provide better service to customers, retain high air quality and exceed compliance standards. The company was so impressed with the performance and low maintenance of the original unit
that they bought another one in the updated orange colour. Both have become an integral part of the operations.
The two DustBoss DB-60 cannons are BossTek’s mid-sized fan-driven designs. Each cannon is 2.06-m wide, 2.97-m long, 2.19-m tall and weighs 817 kg. Mounted on roadworthy wheeled carriages, the cannons can easily be moved to where they are needed by a pickup or vehicle equipped with a hitch.
The units have an adjustable elevation angle from 0-50°, with a throw distance of 60 m of fine mist propelled in a wide cone by a 25 HP fan running at 850 cubic metres per minute. When running with the optional 359° oscillation, each one can cover more than 11,600 square metres.
The cannons are equipped with a 38.10 mm cam-and-groove quick disconnect female hose coupling. Connected to municipal hydrants with variable pressure, the DB-60s require only 10 PSI of constant pressure. Water passes through an in-line 30 mesh 595-micron filtration system that captures any impurities in the water that might foul the lines. The water then enters a booster pump where the pressure is increased to the adequate level needed for the 30 specially designed nucleating nozzles attached to a brass mandrel to fracture the water into millions of minuscule droplets. The use of a booster pump allows the DustBoss to use a fraction of the water of hoses, only up to 100 lpm.
“They are standout pieces of equipment on the site,” Penrod said. “When the community drives by and sees the DustBoss units, they know that we’re serious about dust control.”
Positioning cannons on demolition sites
Understanding where the wind is blowing is the first step. As with any water-based application, adjusting for wind is a part of the dust control process. Prior to activity, workers
place the cannon upwind and allow the cone of mist to fill the area. The droplets will travel with the wind into the activity area where the crane attachment is operating, float with the particulates as they are produced and pull them to the ground.
There are units available that are designed for high-wind operations, but Adamo Group finds the standard misting units work for its current project needs. This is where the wheeled trailer is a large benefit. It allows the cannons to be wheeled around easily by a medium duty vehicle and positioned for precision dust control.
The water source is a consideration for any water-based solution, but most dust cannons also require a power source. Although there are options from BossTek that combine a mist cannon with a genset, allowing it versatility in places with limited access to power, Adamo chose standalone units for their smaller space requirement and easier manoeuvrability.
One benefit over spray hoses attached to hydrants is the low pressure requirement of the DustBoss units, which means the machines can be further from the water source. The reasonably low power demand means that access to alternative power sources such as
a power trailer or outlet-equipped machinery can operate the cannon.
The general rule for demolition dust is to avoid any situation that yields complaints from the public, as complaints regarding air quality submitted to the city or local EPA can trigger an inspection. Like most of Adamo Group’s projects, no complaints were lodged for the Eastland Shopping Mall demolition.
“Since we bought our first unit, we rarely receive dust complaints,” said Penrod. “With the addition of the second machine, the recycling piles are treated, so there’s little chance that dust leaves the site line.”
The addition of more robust dust suppression means that the company can have two units on large projects or split the pair between smaller projects as needed. This ensures that projects can keep operating in adverse conditions where dust may have been a problem in the past.
“Low maintenance is a standout trait for us. We position the unit, it turns on every time, and we walk away,” Penrod concluded. “BossTek has been great to work with and is always there when we need them, but we rarely do. I would recommend DustBoss to my colleagues.”
Our office was filled with youthful exuberance last week in the form of Annie, a work experience placement from one of the local schools. In all honesty, with our very busy office and me here there and everywhere this could have turned out to be a bit of a pain for us, and I’m happy to admit that.
However the move to ‘employ’ Annie for the week had such an impact on us that it forced our hands in pushing forward our scheduled late 2024 campaign plans due to what we all got out of the experience.
Therefore, a little earlier than planned, I want to introduce the British demolition industry to Demolition Hub’s latest campaign: DEMOLITION 4 AMBITION –NXT GEN.
This is us doing our bit, with our reach and tools we will now push to get the next generation into the working world of demolition, and this is how we are going to do it…
First things first, I want all those that want to be a part of this campaign to let us know, sign up for free, there will be no advertising costs assigned to this, just pure and simple helping contractors find talent and to educate school age and upwards individuals the benefits, the excitement, the career progression and quite frankly a fantastic industry to work within
and make a career from.
So, how are we going to do this?
You will message my team or me to register your company’s interest in DEMOLITION 4 AMBITION – NXT GEN and we will then schedule a call to briefly chat through it and identify schools, colleges and universities near your headquarters.
We will then contact the schools and if agreeable we will arrange to go into the school with you and talk to them.
We will present to them, and we ask that you prepare a presentation that can go alongside ours. Feel free to bring along who you want, but it may be a good idea to bring a current apprentice as well as someone who has worked in the industry for years, has a story to tell and can get these kids thinking about their futures.
We will introduce you and run the talk. There is no financial gain for us (nor you) and this does somewhat add to my and my colleagues already packed schedules, but it is vital that we make the move now to showcase your industry that this outsider has fallen in love with. Please do join us.
As an aside, we were so impressed with Annie that she has agreed to become a junior writer for us as well as to help us on this campaign.
Interviewee: Andy Leaver
Role: Product Development Director
Company: DIGGER GUARD®
Andy Leaver embarked on his journey in the plastics manufacturing industry as a trainee operator and draughtsman in 2008. Armed with an Honours degree in Product Design Engineering from Strathclyde University, he swiftly ascended to the role of Senior Design Engineer. His innovative problem-solving mindset propelled him to his
position as Product Development Director. Andy has spearheaded the design success story that is DIGGER GUARD®, disrupting the construction and demolition machinery marketplace with fresh ideas for security and safety solutions. Beyond work, he’s a devoted family man, balancing career, life, and daily fitness challenges.
Q
What is your core message to our demolition contractor readership?
There’s no room for complacency. Ask more from your suppliers and the products they’re making to help you get the job done.
Q
Give us some background on DIGGER GUARD
DIGGER GUARD designs and manufactures cutting-edge protective solutions for construction machinery including our awardwinning Vandal Guards and Polymer Handrail Systems aka ‘Boxing Rings’. Our products reduce downtime and maintenance while ensuring maximum durability, safety and efficiency on site. We solve problems through design innovation, advanced materials and manufacturing expertise.
Q
How did you personally start out in the industry, what attracted you to it and how has your career developed to where you are now?
After studying Product Design Engineering I joined a plastics
fabrication company, which allowed me to work in a variety of industries, from aerospace to subsea and everything inbetween. This experience in polymer engineering proved to be valuable when we founded DIGGER GUARD and has helped give me an alternative perspective on applications and solutions. Working in the construction industry has been great; while there have been some difficult technical challenges to overcome, the professional relationships we’ve formed and support from the extended community is something I haven’t experienced in any other industry.
QTell us about DIGGER GUARD’s products
DIGGER GUARD was born after we successfully developed and patented an innovative new security product – a vandal guard rooftop box system to protect heavy machinery cabs and windows.
Next, we created a unique patentpending polymer handrail to offer the first alternative to steel systems in the industry that is 75% lighter but
equivalent strength to steel.
We’re now gearing up to launch a new product for smaller equipment in the earthmoving and other ‘open’ vehicle market segments.
As our background lies in plastics fabrication, materials, manufacturing and precision engineering, we also provide bespoke polymer machining and fabrication services which includes design and prototyping, replacement, reverse-engineered, and precision parts. From polymer mechanical components to shatterproof replacement cab windows, we provide solutions to make sure your machinery stays operational.
QWhat is your message to contractors who don’t currently use DIGGER GUARD?
Our message is simple: Please take the time to look at the differences between the products you’re using now and the alternatives from DIGGER GUARD. We’re solving problems you hate and delivering benefits you’ll love.
And don’t hesitate to talk to us. We listen to learn. We believe
effective communication is paramount. There’s a lot to know and that we should pay attention to. Beyond universal industry drivers and challenges, not everyone’s goals, challenges, risks and concerns are always the same. Top down from OEMs to end-user operators there are perspectives to be heard that can help us do our job better.
QWhat makes DIGGER GUARD different?
DIGGER GUARD designs and manufactures parts and products that enhance the security, safety and productivity of heavy machinery and their operators. We do this through problem-solving design innovation, advanced materials, manufacturing excellence and sustainable
continuous improvement.
Simply put, we’re making protective products for the demolition and construction machinery industry better.
Complacency can creep in where there’s limited competition. We’re different because we have the desire and energy to disrupt the status quo and drive forward. And with our vast manufacturing experience and capabilities, we have the skills and resources to do just that.
QTell us about your team and working culture
We have a multi-disciplinary team of people with decades of experience and knowledge across multiple industrial processes, including plastic fabrication, thermoforming, precision engineering, materials technology and of course design and innovation.
I think we approach things differently from a lot of other suppliers in the industry. It’s in our DNA to constantly think in terms of continuous improvement, not just in terms of our own operations and processes, but from our customer’s perspective – we start every new relationship seeking to understand their challenges and opportunities.
QAre there any standout contracts or projects from DIGGER GUARD’s history?
There a quite a few to choose from, but I’ll tell you about our entry point into the heavy machinery industry following an invitation to work with Hitachi Construction Machinery UK (HCMUK).
We were tasked with designing and testing a new prototype for a vandal guard to protect excavator cab and windows. It was great to get to work so closely with a market leading OEM and gain deeper knowledge about the various challenges and issues with previous suppliers’ offerings. We were given the freedom to explore new ways of doing things.
Our design team talked to a variety of contractors and end-users to better understand the problems
with their existing vandal guards and what mattered most to them. We started with a blank sheet to design something very different that would deliver a complete solution.
The result was the first cab protection system to securely enclose the protective panels in a lockable rainproof rooftop box. Our solution solved multiple problems.
It removed the need for a metal cage where loose panels can get wet and dirty – our rooftop box also stops water ingress that can drip on the operator – a point of irritation that got flagged up to us repeatedly.
We solved another significant concern for operators – noise pollution from loose panels rattling around overhead. We mitigated this issue by securely housing the panels inside our rooftop box.
To protect the resale value of the machine, we designed the first hang and lock system that avoids destructive drilling of holes into the cab. This design feature also reduces initial system installation time to under 45 minutes, and then it’s on or off in under five minutes.
Since 2021 we’ve made further advances in keeping with our continuous improvement mindset. Our Vandal Guards are now 27% lighter than alternatives. And we’ve eliminated the problem of rust as all metal fixtures are stainless steel – hence our slogan “ROBUST AND NO RUST”.
QHow has the scope of DIGGER GUARD®’s business developed over time and are you in the process of developing your range or OEM partners?
We’re looking back at over five or so years here – similar to the timeline of when Demolition Hub came to life!
At the outset we were immersed in intensive market and product research and development, I suppose you would call it DIGGER GUARD’s start-up phase. Development work ran throughout the pandemic resulting in our Vandal Guards being awarded a patent in 2021.
Collaboration with the amazing team at Hitachi Construction Equipment (HCMUK) was an essential part of our early success. Our confidence grew as we developed our brand and found our feet in the heavy plant industry, first with the successful launch of our flagship awardwinning Vandal Guards and then with the path-beating decision to introduce a polymer alternative to steel handrails. Following trials and approvals by HCMUK – DIGGER GUARD’s range of Polymer Handrails was launched into the market.
Our Polymer Handrails have equivalent strength to steel while being 75% lighter, so we’re seeing a steady increase in the number of leading OEMs and dealerships field testing and adopting our system. Feedback has been extremely positive, given the multiple problemsolving benefits of our handrail design and materials.
Our turnkey in-house design, prototyping, manufacture and materials supply means we can make just about any polymer part or ancillary product for the OEM market. We’ll continue to work with leading OEM partners to drive forward the supply of premium solutions.
QWhat technological developments do the DIGGER GUARD products depend on? What do you envisage will be the future game changers?
Our products aren’t technology reliant, for now. As an industrial manufacturer we have expertise in integrating a wide range of materials and technical features to enhance performance and functionality.
However, we have extended our Vandal Guard product range to feature streamlined, integrated LED safety lighting systems. We came up with this idea to tackle the issue of raised beacons being more easily damaged and to solve the downtime issue that can present.
We’re staying on top of the latest technological advancements,
environmental demands, safety regulations and efficiency-boosting solutions to ensure our products continue to offer the best protection for machinery and operators.
We’ll embrace change and adapt to whatever the future brings.
QHow do you spread the word about your services?
In person contact with industry is essential. We network via trade organisations, exhibit at and visit shows including Hillhead, Plantworx and Scotplant.
We’ve raised our profile winning the Plantworx Innovation Award for Best Security Initiative for our Vandal Guards in 2023. Direct marketing and digital media campaigns have delivered strong results. And PRwise, we’ve had great exposure in industry media.
Social media is a key communications channel for the demolition and construction industry. In particular, end-user operators have engaged positively and given us helpful feedback. One of our favourite comments about our Vandal Guards was: “They’re the best thing since sliced bread!”
People who love working with your products talk about it. Word travels sideways and upwards in this industry. As our brand is becoming better known, we’re enjoying a higher level of engagement across different groups.
QHow do you see the outlook for the demolition plant sector generally?
We know the demolition industry’s performance runs in tandem with commercial and residential construction trends and the wider economy.
As a supplier of both essential and non-essential products and parts for plant equipment in the UK, we’re encouraged to see the industry’s gradual recovery reflected in a steady rise in our enquiries and orders.
Despite the fallout of a variety of factors including Brexit, the
pandemic and geopolitical tensions, we’re hoping hesitancy will lessen further and we’ll see a bounceback in demolition project starts and procurement in 2025.
QHow do you envisage DIGGER GUARD in 5 to 10 years?
DIGGER GUARD is poised for continued growth. We’ve got a receptive ready market, superior niche products and a committed team.
Moving forward, our plan is to broaden our UK footprint. In the longer term we’ll explore the potential of introducing our flagship products to the global construction and demolition plant market.
I think I can safely say on behalf of my colleagues, we’re extremely rewarded by all that DIGGER GUARD has brought to us in terms of job satisfaction. There are many reasons for this, not least the enjoyment of feeling part of the demolition and construction industry and working across all tiers of the supply chain.
The people we’ve met in this exciting and challenging industry have energised new thinking in our business and helped to create opportunities. We’ll keep driving forward, innovating to be disruptive wherever we come across complacency that underserves our customers and their industry.
QTell us about one of your key demolition-relevant products
Our Polymer Handrail System was the second product we developed after we became aware about problems with steel handrails. From knowledge and experience of other industry applications for polymer rails, we had a eureka moment and thought, this is going to work.
As I’ve already highlighted, HCMUK gave us the opportunity to develop new prototype designs for their handrail systems – it was a
project that led to what we believe is the first application of polymer handrails on excavators in the UK market.
Our handrails have been tested, deployed and welcomed by end customers including demolition contractors. We’re designing handrail systems for leading heavy machinery manufacturers as well as responding directly to contractor enquiries for various types and models of plant equipment.
QOutline the key functions/ specifications of the product Handrails are critical to the safety of operators using excavators and other types of heavy machinery. Demolition work is already filled with enough challenges, no one needs
the extra headache of dealing with rusty, fatigue-weakened handrails. We set ourselves the challenge to create a handrail system that not only matches the safety of steel but also offers unique advantages. A solution that extends lifetime in use.
We devised a unique lightweight polymer handrail system that is 75% lighter with equivalent strength to steel. The patent-pending design dampens vibration fatigue to limit failure points.
Polymer also packs a punch in terms of electric and thermal nonconductivity and its transparency to electromagnetic waves – a critical safety issue when using 3D mapping systems. And it doesn’t corrode or need painting, reducing maintenance costs and downtime.
What would you be in an alternative life?
Pro snowboarder
Who is your favourite artist?
The American director, Wes Anderson
Who do you most admire? My wife – for putting up with me
What would be your desert island (permanent exile) luxury? A solar powered laptop so I could keep doing the job I love. [Sorry, no comms allowed]
What gets you out of bed in the morning? The need to get shit done
What do you do for fun? CrossFit (yes, it’s a cult)
When and where are you happiest? Saturday morning, on my armchair, coffee in hand
What’s the most expensive non-essential you’ve ever bought? A wedding
What’s your bucket list activity? Marathon du Médoc
What would you do for a company excursion, money no object? Would have to be CONEXPO-CON/AGG (all on the company card)
What’s your favourite food/cuisine? Salt ’n’ chilli chips
What’s your tipple of choice? Can’t beat a cold pint of Tennent’s
Our publisher has gone rogue and decided to pitch himself out there as the next Joe Rogan. Well he does sport the hair for it these days.
But yes, it’s true Ben has decided to drag us kicking and screaming into the 21st century by introducing a brand-new video podcast for the demolition, construction and asbestos removal industries and most which promises to be packed full of personality.
Direct from our newly sourced London Studios “The PowerPlant Podcast” will see presenter Ben Chambers interview an array of popular, (in)famous and wellrespected industry professionals in the fields of demolition, construction and asbestos removal.
Relaxed, unscripted and informal, it is filmed on three broadcast quality cameras and professionally edited and produced so you, the viewer, can experience an hour of engaging conversation
from our guests on their industry, life, beliefs, opinions and whatever else Ben can squeeze out of them whilst all participants enjoy their tipple of choice in our fully licensed studio.
This series of podcasts aims to provide our guests an opportunity to showcase exactly what they do, have done and plan to do while we take them away from business and discover what excites, frustrates and captivates them, showcasing their personality and the real person behind the role.
Debuting podcast host Ben Chambers, publisher of titles
Episode #1 coming very soon.
including Demolition Hub Magazine will bring “The PowerPlant Podcast” to his network as well as being shared by all magazine brands on X, LinkedIn, Instagram and TikTok.
You will also be able to watch via our fleet of debuting PowerPlant social media platforms including Spotify and YouTube.
This off the cuff series of interviews aims to bring out the best from the very best individuals we have working within these closely related sectors, all whilst broadcasting to a large and pertinent audience directly from London.
To put yourself or a colleague forward for guest consideration or for advertising enquiries please contact us in private via: ppp@chambers.media | 01903 952 640
The PowerPlant Podcast – Digging Deeper!
Conversation | Industry | Personality
If you need a demolition machine capable of dismantling virtually anything, anywhere – with impressive speed and precision – a Husqvarna DXR demolition robot is a good choice in your fleet. The DXR range includes four models with different specs in power and weight.
Since the first launch in 2009 we’ve refined every detail to make our DXR more powerful, durable and responsive than ever. If you haven’t tried it yet, you have an exciting experience ahead of you.
Raw power in a smart packaging Why work manually when a robot can do the job for you? With raw power and admirable precision, one DXR and one operator can outperform most of the setups you see on demolition sites –while reducing labour costs and increasing safety.
Many customers agree that investing in a demolition robot is
a smart way to improve profitability. A DXR is also much more compact than an excavator in the same weight class, so it’s superb for carrying out demolition in confined spaces. Thanks to its low weight and zero direct operating emissions, Husqvarna DXR can also be very useful for carrying out precise demolition work in sensitive areas like hotels, hospitals and laboratories.
A wide range of powerful demolition robots and tools
Husqvarna DXR demolition robots and tools are developed for efficient demolition and dismantling jobs. Typical applications include work that
is too heavy for manual labour. DXR can also be used in fragile, hazardous or confined, hard-to-reach areas.
You can choose from many different versions of Husqvarna DXR demolition robots to meet your power preferences and weight restrictions. You can equip your Husqvarna DXR to match your needs with a wide range of attachable demolition tools and optional features.
Husqvarna DXR demolition robots are known for their high impact force and long reach. The solid chassis provides impressive stability, making it a powerful platform for a wide range of attachable tools.
The DXR’s low weight, compact dimensions and good climbing capability make it highly versatile and useful in many applications, from deep-down digging in narrow gold mining tunnels to demolishing tall factory chimneys while hanging from a crane.
• Compact design: The narrow width allows the DXR to pass through door openings. The low height provides good visibility above the machine. The outriggers have an extra wide span for superior stability and high workload.
• Wireless remote: The remote control is easy to use and read, with intuitive controls, displays and menus. The individual radiolink 2.4 GHz provides a reach up to 300 metres, enough to keep the operator at a safe distance from any hazard.
• Easy to service: All key service points are easy to access, making the daily checks and adjustments
easy to perform at the job site. This ensures the highest possible uptime and productivity.
Your Husqvarna DXR can be equipped with additional feature packages designed to complement the extensive range of standard features for even better precision, performance and protection.
• Hydraulic function: Allows the operator to control one extra hydraulic function, such as axial rotation of grapplers and shearer, with speed and precision. Also includes protection shields for the outer hydraulic cylinders. Available for all DXR models.
• Enhanced cooling: Allows the DXR to work continuously with full power in higher ambient temperatures. This enables higher productivity in various applications such as cement kilns and steel factories. Available for DXR 270/275, DXR 300/305 and DXR 310/315.
• Heat protection: Allows the DXR to be used for deslagging in hot melting plants and similar applications. Protects vital parts from damage caused by radiant heating as well as conduction heating. Available for DXR 270/275, DXR 300/305 and DXR 310/315.
The DXR 95 is our lightest and most compact demolition robot ever. Made to fit inside an ordinary van, the DXR 95 brings all the demolition power and precision you need to the most confined spaces, narrow doorways and steep inclines.
Bobcat unveiled the new RogueX2 autonomous loader concept at Intermat 2024, the second iteration of the original RogueX system.
The RogueX2 loader has been developed from the RogueX concept presented at the Conexpo show in Las Vegas over a year ago. RogueX2
is an all-electric and autonomous concept machine that produces zero emissions, and features a lithiumion battery, electric drive system and electric actuated lift and tilt kinematics with no hydraulics.
Specifically designed and built without a cab, the RogueX2 and RogueX concept machines address the challenges of workforce shortages by eliminating the need for an operator. They also provide the blueprint for how work machines of the future can be designed and optimised for new technologies and enable an entirely new work experience.
In RogueX2, the internal combustion engine (ICE) is replaced with an electric powertrain for power and drive. This machine also eliminates 100% of the hydraulics, including all connectors, hoses, tubelines and fittings that are common failure points. The absence of hydraulics and fluids in its design not only reduces ICE emissions but also minimises noise pollution and the risk of all environmental pollution.
The original RogueX was designed with tracks and it uses advanced workgroup kinematics to offer unique functionality that combines verticalpath, radial-path and variable-path lift capabilities in one machine. In contrast, RogueX2 is designed with wheels instead of tracks to optimise the electric battery run time. It also features axial flux motors, which give the machine incredible tractive effort. The machine delivers greater power output for demanding applications like grading, digging or powering attachments for heavy duty work.
Together, the RogueX and RogueX2 concept loaders have garnered many new patents pending. “These patents represent more than new features on a machine – they signify how we are breaking rules to define a new work experience,” said Joel Honeyman, Doosan Bobcat Vice President of Global Innovation.
Brokk is the world leader in remote controlled demolition robots, committed to innovation and excellence in the demolition industry. As well as selling and servicing the Brokk range of demolition robots, within the group portfolio we also supply Aquajet hydrodemolition robots, which are used in difficult cleaning and demolition environments; Darda attachments and tools; Bricking Solutions rigs, ramps and cages; Ahlberg Cameras systems; and the Firstgreen EV powered skidsteer and tracked loader ranges.
Our range of robotic demolition machines runs from the smallest
B70+ (560 kg), through to our B900 (11.5 T), with a vast range of attachments available across all robots.
The Brokk B70+ is a testament to the technical advancements of Brokk over the last decade. It takes Brokk’s signature expertise in bringing maximum power into a small package to the smallest demolition robot in the world. Fitting through the narrowest doorways, it can be transported in an ordinary passenger elevator.
Enhanced with a seamlessly integrated hydraulic system, the newest generation Brokk 70+ boasts unparalleled power within its compact frame. The Brokk 70+ emerges as the ultimate solution for secure and efficient demolition within tight quarters, revolutionising the landscape of confined space demolition. With new state-of-the-art features, the Brokk 70+ redefines
possibilities within the construction industry and beyond thanks to an increase in uptime and consistent power delivery over time. Expertly engineered to combine superior power, compact dimensions, and feather-light weight, the Brokk 70+ opens up opportunities for demolition in areas once deemed inaccessible.
• Increase in uptime and more power over time
• Smart sensors and a sophisticated two-way communication system
• Ergonomically designed control box weighing less than 3 kg and tilted joysticks
• 9.8 kW Brokk SmartPower+ electrical system
• Powered with only 16-A fuse
• Weighs less than 560 kg
Our B70+ also provides superb stability in a small package, ensuring safe climbing of stairs, superb
manoeuvrability and features our new Smartpower+ system. This seventh generation redefines the joy of operating by introducing a new and improved control box that features a shifted centre of gravity, tilted joysticks and faster dual charging for a more comfortable and efficient operating experience. Quick switches and intuitive settings result in an improved operating experience making it easier than ever to operate a Brokk robot, and in turn, easier to find and train operators.
In addition to an optimised operating experience, SmartPower+ robots also offer unmatched endurance by increasing operational uptime with consistent power delivery, resulting in fewer unwanted shutdowns. Engineered with rugged components, Brokk’s latest generation is resistant to shock, temperature and vibrations – not to mention that all new robots and control boxes are dust and water protected – leading to outstanding performance regardless of the weather and site conditions.
SmartPower+ is optimised for future over-the-air upgrades and continuously updated to be at the forefront of the industry. Brokk’s SmartPower+ generation also includes a noteworthy 87% reduction in cables and connectors, facilitating servicing and troubleshooting, which in turn increases the lifespan of the robot.
This new generation elevates the operator-machine interaction, focusing on added intelligence. Visual status updates through incremental light indicators allow the operator to focus their attention on the demolition work at hand and learn to better understand the needs of the robot.
A two way communication system communicates the status back to the operator in real time, while customised features enhance the experience, fostering a deeper connection with the robot. Brokk’s SmartPower+ generation is much
smarter too, alerting the operator about the power supply and any unwanted or unplanned machine statuses for increased uptime. Fast and simple settings, an increase in sensors, as well as tool presets contribute toward a more userfriendly operator interface for improved connectivity and longevity.
But here at BrokkUK, we do not limit our innovation to our robotic range, we deliver new ways of improving safety on all our clients’ worksites. Our Brokk Vacuum Excavator range extends from the B120D, through the B520D to our B900D. The revolutionary remotecontrolled no-dig vacuum excavation solution sets new standards for efficiency and safety in debris removal.
At its core, the Brokk Vacuum Excavator streamlines excavation processes with unparalleled precision, while significantly reducing the risk of damaging hidden services. Whether you’re working on road projects, railway maintenance or even disaster relief sites, the Brokk Vacuum Excavator is your versatile companion, ensuring swift and precise excavation in any scenario.
Compact and operator-friendly, the Brokk Vacuum Excavator boasts a small equipment footprint, making it perfect for residential areas and other locations where space is limited. Its remote-controlled operation not only enhances safety but also ensures maximum efficiency, allowing you to tackle excavation tasks with confidence and ease.
With power comes precision control and connectivity. Brokk Connect 2.0 is the next step for the online platform for connected Brokk robots and delivers several new features. These include a sophisticated always-on geofencing functionality that helps Brokk owners keep control of their fleet of machines and assists the owner in case of theft or unauthorised use.
It is now also possible to customise the online platform to your own preference. And there is a whole new weekly status report over your fleet of Brokk robots to keep you up to date if there is anything that needs attention.
Brokk Connect is available on all new Brokk robots but can also be retrofitted on older models. This way BrokkUK customers can get their entire Brokk fleet connected, maximising usage and performance on our clients’ jobs.
So whether clients choose our most powerful pound for pound robot, the B70+, through the ever versatile B110, the class leading B170, rugged B200 or B300 models, or scale up to the performance and innovation setting B500 and B900 ranges, all of which are available with Smartpower+ industry leading control systems and a huge range of attachments, our clients know that our products and our BrokkUK service and maintenance support will always partner with their ambition and deliver performance, power, safe sites and margin to their bottom line.
DEVELON first demonstrated the latest update to the company‘s unique Concept-X automated construction equipment at Intermat 2024.
Concept-X was unveiled in 2019 as the world’s first automated construction solution. At a demonstration of Concept-X in Korea, attendees witnessed autonomous construction equipment performing everyday jobsite tasks. The latest Concept-X 2.0 version demonstrated at Intermat included the following updates:
• New dozer added to autonomous equipment lineup
• Autonomous driving and blade control based on global
navigation satellite system (GNSS)
• Automated 3D grading with tiltrotator accessory
• Enhanced machine-learningbased auto digging and loading
• Integrated work planning algorithm applied
• Advanced E-Stop safety technology
The Concept-X 2.0 autonomous construction equipment involved in this latest iteration includes the DD100-CX dozer and DX225-CX crawler excavator. Both machines feature a new cabless design and a linear core design language.
Concept-X integrates technologies related to ICT and AI, to revolutionise the construction machinery industry and create sustainable customer value. Concept-X includes automated construction site solutions, surveying tasks using drones, unmanned automation of equipment and remote control based on 5G communication to increase productivity and reduce costs and risks based on accurate, fast work at the construction site.
The core of Concept-X is X-Center, which is a control system that enables the user to view equipment at the construction site and worksite at a glance. It surveys the terrain of the worksite through scanning using drones, and the data collected from various sites are analysed to instruct unmanned equipment and manage the equipment in an integrated manner.
DEVELON also implements autonomous solutions, equipment with an unmanned, automated solution that can perform work accurately and quickly based on analysed data from X-Center. Prognostics and Health Management (PHM) is implemented to allow future equipment to diagnose its own condition and alert users of possible
failure in advance, managing risk factors in advance by forecasting the remaining life through the checking of the status change history of each part as well as the overall status at the time.
DEVELON aims to contribute to customer convenience with differentiated competitiveness by implementing the worksite business model with maximised efficiency and productivity through Concept-X, a solution optimised for the future construction site.
Concept-X 1.0 is a project that combines cutting-edge technology with a focus on human connection to create power that improves all lives. The excavator in this project is unique because it does not have a cabin and is designed to re-imagine the relationship between humans and machines
through AI technology. Concept-X 2.0 is the successor to Concept-X 1.0 and takes autonomous smart constructions to the next level. This technology provides outstanding work efficiency with a new 3D MC algorithm resulting in impressive 13% improvement, allowing for more detailed and complex operations.
The Concept-X 2.0 Dozer has advanced safety technology with its 180° detection range and interlocked machine control, and LED integrated into machine operations provide a non-verbal language to understand the equipment’s status safely. The relationship between humans and machines will continue to strengthen as technology advances, and DEVELON’s Concept-X 3.0 technology will bring improved and optimised workflows and effective interactions between people. The opportunities lie ahead, and Concept-X 2.0 is designed to take us there.
Core-ect Diamond Drilling is a specialised concrete cutting business renowned for its precision, efficiency, advanced technology and commitment to safety, environmental stewardship and customer satisfaction through a combination of expertise and stateof-the-art equipment.
The company provides a range of concrete cutting and drilling services, catering to construction, renovation and demolition projects across various industries. It was established in 2021 by Glenn Joszko, a professional with extensive experience in the construction and demolition industry.
By continuously innovating and adapting to the evolving needs of the construction and demolition sectors, Core-ect ensures it remains at the forefront of reliable and efficient concrete cutting solutions, growing from a small local service provider to a leading name in concrete cutting nationwide.
Our services
• Robotic demolition
Precision demolition techniques to remove specific sections of structures without causing damage to surrounding areas. Applications include renovation projects, selective structural modifications, and interior demolition.
• Concrete cutting
Precision cutting of concrete structures using diamond-tipped saws and blades. Applications include roadways, bridges, floors, walls and other concrete structures requiring modification or removal.
• Core drilling
Drilling cylindrical holes in concrete, masonry and other hard materials using diamond drill bits. Applications include installing utility conduits, plumbing, HVAC systems, and structural testing.
• Wall sawing
Cutting vertical or inclined surfaces using wall-mounted saws. Applications include creating openings for doors, windows, and ducts; precise cutting of reinforced concrete walls.
• Wire sawing
Using a wire embedded with diamond segments to cut through large and thick structures. Applications include demolition of large concrete structures, such as bridges and piers, where other methods are impractical.
• Floor sawing
Cutting horizontal surfaces with walk-behind saws. Applications include cutting expansion joints, trenching for utilities, and removing damaged pavement sections.
Swantest can provide a wide range of test solutions for all aspects of a project. This can include structural tests on the superstructure, substructure and geotechnical tests on the substrate of any project. Our range of structural tests include:
Load Capacity Tests: Used for determining the load capacity of various structures, fixings and materials. We can load test structural slabs, marine structures, lift beams, pile foundations and more.
Anchor Tests: We can carry out pull tests and shear tests on all types of bolts, fixings and fasteners. From small fixings supporting a few kilograms up to large diameter bolts supporting significant loads.
Geotechnical Tests: In-situ site tests for verifying pile mats, formation layers, subgrades and other materials. These include; Plate bearing tests, CBR tests, shear vane tests, dynamic cone penetrometer test and light drop weight tests.
Balcony and Barrier Tests: Various types of horizontal load tests to check and verify the safe use of; Balcony handrails, balustrades, insert panels, sports ground barriers, bridge parapets, edge protection systems and more.
For more information call us on 0370 950 7707 Website: www.swantest.co.uk Email: info@swantest.co.uk 52-54 St. John Street, Farringdon, London, EC1M 4HF
I often look back fondly to 2018, when my colleagues and I embarked on an ambitious independent project: planning the UK’s first independent and open-to-all awards event for the demolition industry. At that time, we had been growing increasingly close to this remarkable field.
Our inaugural event was a modest affair at The Belfry in Sutton Coldfield, with just under 200 professionals joining us.
Despite some nerves and a few hiccups, it was a decent success and recognised as a good and respectable event.
The following year in Manchester came around a bit too quickly. Despite our best efforts, we weren’t as prepared as we should have been.
Technical issues, a few overly enthusiastic attendees and some disorganisation made it a bit of a
letdown. We seriously considered pulling the plug.
However, lockdown gave us the opportunity to rethink and strategise, with the British Demolition Awards at the top of our list. The additional year, coupled with the freedom and enthusiasm of our newly formed Demolition Hub Magazine and brand, allowed us to make the third staging the best yet. Hosting the awards close to home at Brighton & Hove Albion’s stadium in 2021 set the gold standard for us.
To enter this year’s awards please go to:
www.britishdemolitionawards.com
Since then, we’ve built on that success, making the awards better each year.
For 2024, we’ve sold more tables than ever before and secured excellent sponsorships. While it’s bittersweet for a sports fan like myself to move away from a stadium setting, we’ve secured
To attend please contact me: ben@chambers.media
a wonderful venue at a beautiful hotel in the heart of London.
I look forward to welcoming you all on the evening of 6 September.
Ben Chambers, Founder British Demolition (& Asbestos) Awards
Job name: Whitworth Building
Location/Client: Loughborough University
Expected duration: 24 weeks
Equipment used: Two Brokk 90s attached with breakers with Bobcat S70 clearing rubble
Job name: Richmond College
Location/Client: London Square
Equipment used: LiuGong 924F, Komatsu PC210
Job name: Jerome Tower
Location/Client: Acton Gardens, London
Expected duration: 24 weeks
Equipment used: Two x three-tonne excavators, 180-tonne crawler crane, CAT 340 high reach
Snapshots of Ben and the Demolition Hub team’s activities between issues
Exposure to silica dust (Respirable Crystalline Silica) is a well-known hazard in the construction and demolition sectors. Each year, an estimated 600,000 workers are exposed to the dust which can cause incurable and sometimes deadly respiratory diseases such as silicosis, chronic obstructive pulmonary disease and kidney disease. Regulations exist to protect
workers from the dust, which can be created when materials are cut, broken down, crushed, ground or drilled. The Control of Substances Hazardous to Health (COSHH) requires assessments of workplaces to be made to ensure that they are below the Workplace Exposure Limits (WELs), which are defined as 0.1 mg/m3 (milligrams per cubic metre) over a period of eight hours. The responsibility of preventing overexposure to dust sits with employers, however there are still people dying
from dust related illnesses, including around 300 a year from silicosis.
Employers in the construction and demolition sectors need to take proactive measures to monitor and control dust on site and the surrounding areas. Harmful dust affects workers on site at a much higher concentration than it does to neighbouring communities. Despite this, plumes of dust that escape the boundaries of the worksite can still cause respiratory irritation to those around the source, especially if they already suffer from a respiratory ailment such as asthma.
Monitoring and suppressing this dust can eliminate this risk, improving relationships with locals and complying to environmental and safety regulations.
Like any industrial working environment, once a potential risk has been identified, it is imperative that a risk assessment is conducted to conclude the nature and level of the risk present. According to the International Labour Organization (ILO), occupational surveillance involves active programmes to anticipate, observe, measure, evaluate and control exposures
to potential health hazards in the workplace. Environmental surveillance is used to document potential exposure to contaminants for a group of employees, by measuring the concentration of contaminants in the air, in bulk samples of materials, and on surfaces.
Risk assessments should be conducted routinely to identify the physical and chemical agents and the level at which they are present through objective measurement of dust present.
Investing in monitoring equipment allows employers to find the exact concentration of dust employees will be subject to. Remote boundary monitoring set up at strategic points that consider wind direction and activity location ensures companies remain compliant with regulatory limits and are not at risk of action from the local authorities. In densely populated cities site monitoring is of great benefit to the neighbourhood. For example, in London construction and demolition activity is responsible for up to 15% of air pollution.
However, although helping to comply with regulatory limits and conducting surveys is beneficial, personal monitoring is required to calculate an individual worker’s exposure to harmful dust and thus safeguard their future health. In personal monitoring a pump and filter are used to accurately measure the amount of dust inhaled by the worker. Once these samples are collected and analysed, measures can be put in place to minimise exposure and reduce concentration levels to below the WEL as far as is reasonably practicable, getting to a level that is only just below the WEL is not acceptable.
The usual hierarchy of control is applied to ensure that people cutting items that might expose them to silica or other dusts, prevents exposure. This may be extraction at the tools for example. Other controlling measures such as dust
suppression for silica may be an option or be necessary to prevent exposure of those around site or people surrounding the site.
Dust suppression systems exist in a variety of forms – for silica dust, it is widely accepted that water solutions are often the best for dust control. Water is sprayed towards the source of the dust during operation of the machinery or tool. To be totally effective a continuous stream is necessary as grinding, cutting and destruction will surpass the damp surface and generate dust.
The solution selected will depend on the size of the site and the working activities present as suppression units exist in a variety of capacities and sizes. Additionally, for medium to heavy duty dust, standard water misting is preferred but fan assisted misting could be required when fine water particles are required to be dispersed across a large area.
When it comes to dust suppression, the health of the worker and public should be the employers’ number one concern, not least because COSHH regulations stipulate that it is a duty to adequately protect
these groups. Besides this, excessive dust on site can damage equipment and reduce visibility which increases other risks and can increase maintenance costs.
Silica is an especially dangerous hazard that causes progressive illnesses meaning that measures to monitor and control the dust should be implemented with the highest consideration. If you are unsure about an effective dust monitoring and control process, consult an expert.
Casella is dedicated to reducing occupational health and environmental risks through a core competence in dust, noise and vibration monitoring. Casella’s core purpose is to create technology aimed at improving the working environment of employees while providing robust data and equipment platforms to enable organisations to remain compliant with health and safety regulations. The company is expert in the integration of sensor technology and data management systems that further improve productivity and overall safety in the workplace.
From fog cannons to sprinklers or even small mini-mist units, Odour and Dust Solutions offers a complete service. We supply units for purchase or for hire and even build bespoke systems for specific jobs.
The Control of Substances Hazardous to Health Regulations
2002 (COSHH) cover activities that may expose workers to construction dust and with new regulations in place and growing awareness of health issues, we can offer a dust and noise monitoring service to ensure the correct working conditions for your employees.
The HPW-DUST high pressure dust suppression system is the most innovative dust control system for mobile machinery in demolition, quarrying and crushing. The system produces targeted water mist straight to the dust source and prevents the emissions from spreading to the environment.
The Rino is a new fog making machine from Idrotech, designed to maximise droplets through increased water flow. Used in the demolition, quarrying and mining industries, it has proven a great success in helping to fight dust problems.
The Rino is one of several models, including the Elefante and Giraffe, designed to be used in larger areas. All units come with low or high pressure settings, automatic running and oscillation features. Electric controls are fitted in stainless steel cabinets, which are aesthetically pleasing and supplied at below market prices.
Mobile atomiser systems are the perfect way to deal with odour and dust problems indoors and out. The mobile atomiser is produced as a selfcontained unit and fitted with parts including pressure pump, atomiser, fan casings and electrical controls, all sourced in the UK.
Our trailers are fitted with quality diesel generators, allowing the unit to be moved to remote areas while still being fully functional. The mobile atomiser tank holds 1,100 litres allowing the machine to spray from 8 to 24 hours without refill.
In response to input from customers across the demolition industry, the leader in atomised mist technology has introduced a new model in its lineup of powerful dust control cannons. The DustBoss® DB-45 Surge from BossTek features an innovative pressurised centre nozzle paired with the industry-proven fan and misting ring system to suppress both surface dust and airborne particulates.
With three remote-controlled stages and precision oscillation for optimum command over water volume and coverage area, the DB45 Surge delivers the dependability of atomised mist along with J2P (jet-to-plume) nozzle technology that drives the dust-trapping mist more than 60 metres, even in troublesome windy conditions. The result is an easily manoeuvrable, autonomous
solution for outdoor operations in all weather. With a 60-m throw, those customers are now well-served by the new model.
Demolition contractors often experience turbulent winds high above the ground. In those situations, dust is lifted into the atmosphere and carried beyond the site line over long distances, which can lead to permit violations. Operators often mitigate particulate emissions using sprinklers or hoses to saturate a material’s surface – often at rates of 1,135 lpm or more.
The DB-45 Surge combines the power of a 19 kW industrial fan, misting ring and heavy-duty barrel with the extended reach of a central high-pressure spray nozzle. The misting ring introduces millions of tiny droplets into a target area for proven dust suppression. The pressurised spray resists wind shear and uses the force of the wind to further fragment droplets, enhancing its dust suppression capabilities. This is achieved with a maximum of 372 lpm and as little as 77 lpm when using only the misting ring and fan. The cannon also features a VFD (Variable Frequency Drive), which allows the unit to operate more efficiently at lower supply pressures.
The unit’s three stages are easily managed by a touch screen system, which can be specified in a
sealed NEMA 4 cabinet or controlled by a heavy duty hand-held remote with a 300-m range. Stage one is highly effective on calm days and uses the powerful 850 cubic-metresper-minute fan and misting ring for wide area coverage. For moderately windy days, stage two features a pressurised stream delivered by the J2P nozzle to pinpoint the source of the dust. During high-wind conditions, operators can choose stage three to engage the fan, misting ring and centre nozzle for maximum coverage.
Fed by a standard 50-mm hose with a cam-and-groove quick disconnect coupling, the powerful booster pump delivers as much as 500 PSI to the centre nozzle. The coverage area is extended with the customisable 260° horizontal oscillation range and 0° to 50° vertical throw angle. Mounted on a heavy duty roadworthy trailer for towing at highway speeds with a standard ball hitch, it can be placed by a pickup truck, skid steer or lift truck wherever dust suppression is needed.
Other options are already available, including tower mounting for permanent locations. The cannon is also available as part of the company’s popular Fusion lineup, pairing the DB-45 Surge with a trailer-mounted generator to alleviate the need for a nearby power source. With a 11 kW booster pump, the unit only requires a 45kW generator, which most demo contractors already have in their equipment arsenal.
“The entire DustBoss lineup is known for its rugged quality and long service life, often described as one of the most reliable and lowmaintenance pieces of equipment on any job site,” Michael Lewis, Vice President of Sales concluded. “Our three-year or 3,000-hour warranty is evidence of our confidence in the products. The DB-45 Surge is designed with that same philosophy: it’s built to last.”
With concerns for site staff, neighbours and the public, all sites now have a duty of care for those around us. During the summer dust becomes a problem quickly after a few dry days and looking to the autumn and winter mud is then your enemy.
So Brendon supplies solutions for this ongoing issue with our range of dust suppression units and power washers. But rather than having several units for the same task we can supply a single Bowserwasher that can dampen your dust and wash those wheels whatever the weather.
The Brendon bowsers come in both diesel and increasingly attractive petrol units. A batterypowered unit is in development and will be available from spring 2025 onwards. This means there is something for everyone’s sites issues.
When combined with our range of dust suppression accessories such as our DT400 misting cannon, spray-bar and whale tail water spreader, all powered from our power-washer units with no additional power source required,
the Brendon Bowser becomes a single site solution.
Our dust control units have proven popular the world over with two recently being used on a tunnel break-trough in Sydney, Australia.
From small and restricted access demolition jobs to much larger sites a Brendon can help win the battle
with mud and dust. Established for approximately 35 years, Brendon Powerwashers is a UK manufacturer with a reputation for supplying long lasting, heavy duty machines designed for the rigours of the rental, construction and mining industries throughout the UK, Europe, the Middle East and the rest of the world.
Fugitive dust is widely acknowledged to be a nemesis of the demolition industry. It’s impossible to carry out demolition works without creating it, yet ever-tightening legislation and public scrutiny are increasingly putting the spotlight on it. Many a project manager is left wringing their
hands, wondering how on earth they can possibly complete the job on time and within budget, without alienating regulators, neighbours and other sensitive receptors along the way.
Thankfully, help is at hand.
Corgin is a well-established, leading provider of dust suppression
solutions to the demolition sector. With possibly the largest hire fleet of mobile dust suppression units in the UK, we pride ourselves in responding quickly to the dynamic needs of demolition contractors. Our friendly team are always happy to give you the benefit of their experience, being willing to visit site to evaluate your requirements where needed.
We’ve found that the industry typically favours self-contained, fully portable dust suppression units and products like MistCannon Ranger and DustLayer are the result of many years of listening to our clients.
In response to a video clip of one of our products being posted on social media recently, the manager of the featured demolition site lodged an impromptu comment: “Great piece of kit, first class service as well from Corgin.”
As any successful business knows, the best form of marketing is when your clients become your mouthpiece.
There’s only one place you’ll find the heavy hitters of concrete and masonry this January: Vegas, baby — at World of Concrete 2025, the largest and only annual international event dedicated to your business. Be here to mix with industry giants. Get your hands on the latest technologies revolutionizing safety, performance and speed. And learn what it takes to not only claim a piece of our industry’s massive projected growth but dominate the field. Join the power players of concrete and masonry.
EXHIBITS: JANUARY 21-23, 2025
EDUCATION: JANUARY 20-23
LAS VEGAS CONVENTION CENTER
In the world of demolition, pipeline and infrastructure construction, Italian engineering stands tall, celebrated for its precision, reliability and innovative design. Leading this charge is Laurini Officine Meccaniche, a company that has been at the forefront of earthmoving machinery and equipment manufacturing since 1955. As Laurini continues to expand its global footprint, we are thrilled to announce that Robustrack Ltd has been appointed as the official UK agent, bringing Laurini’s state-ofthe-art machinery and engineering expertise closer to the British market.
Founded in the heart of Italy, Laurini has built a sterling reputation over nearly seven decades. Known for their quality and innovative equipment, Laurini specialises in bespoke, custom built machinery. Their product range includes pipeline padding machines, crushing and screening equipment, pipe carriers, demolition machines, tracked dumpers and various support machines, all designed to meet the rigorous demands of modern construction projects.
• Vulcano 2.0: A versatile machine designed for efficient ground preparation around pipelines.
• Vulcano Smart: Combines advanced technology with user-friendly operations for optimal performance.
• Selfloading Superscreen: Self-propelled and self-loading vibrating screen suitable for big pipeline projects.
• Hammer Crusher: Ensures proper granulation and separation of materials onsite.
• Grub: Remote controlled crushing machine, suitable for working at the bottom of the trench in pipeline projects.
• Muletrax 3000: A crawler carrier with hydraulic foldable saddles for pipe carrier.
• Jocker: A versatile and efficient tunnelling machine designed to mill entire tunnel vaults in a single pass.
To better serve the UK market, Laurini has partnered with Robustrack, a company renowned for its dedication to providing high-quality equipment and exceptional customer service. As UK agents, Robustrack will serve as the gateway to Italy, ensuring that British customers have direct access to Laurini’s cutting-edge machinery and comprehensive
• Laurini has adapted its robust technology to meet the needs of the demolition sector, providing machinery capable of handling the toughest demolition projects. Their machines are designed to maximise efficiency and safety while minimising environmental impact.
• Their design and builds include tilting cabs, camera systems, variable gauge undercarriages, interchangeable demolition arms, telescopic extensions, quick coupling double hydraulic pin systems, water pumps and automatic greasing systems.
• Adaption of current machines and commission of custom builds available.
• SETTANTA: A Laurini Demolition Machine with the best weight/performance ratio in the market.
• MRT-30R/MRT-330R: A series of innovative and hi-tec rotary dumpers on rubber tracks, with Caterpillar C7.3 engine.
support services.
Marco Laurini, CEO of Laurini Officine Meccaniche, commented on the partnership: “We are excited to collaborate with Robustrack to bring our innovative solutions to the UK. Their commitment to excellence and customer service aligns perfectly with our values and we are confident that this partnership will greatly benefit our UK customers.”
Davide Cerca, Director of
Robustrack Ltd, added: “Laurini is a leader in the industry, and we are proud to represent their products in the UK. Our Anglo-Italian team is ready to provide exceptional support and tailored solutions to meet the diverse needs of our clients, ensuring seamless communication and service.”
Robustrack has established itself as a leading supplier of hydraulic attachments in the UK. Known for its extensive range of high-quality products, Robustrack serves a wide array of industries, including construction, demolition, and infrastructure. Their expertise and dedication to customer satisfaction have made them a trusted partner for many UK businesses. Notably in this market, Robustrack is a supplier of Simex, MB Crusher and Trevibenne demolition attachments, which are highly compatible with Laurini machines, providing a comprehensive solution for full-spec demolition equipment.
Davide emphasised the significance of this partnership: “We are excited to add Laurini’s exceptional machinery to our portfolio. Our experience in the
supply of hydraulic attachments, including Simex and Trevibenne demolition attachments, will enable us to provide comprehensive solutions to our clients, enhancing their operational efficiency and project outcomes.”
The partnership between Laurini and Robustrack marks a significant milestone for the UK’s demolition, construction, pipeline, tunnelling and infrastructure sectors. British companies can now benefit from:
• Direct access to Laurini equipment: The full range of Laurini’s innovative machinery, including their adapted demolition machines, will be readily available in the UK,
• UK-based contact: Robustrack will provide dedicated customer service and support,
• Tailored solutions: With Robustrack’s devotion to customer support and Laurini’s engineering excellence, UK businesses can expect customised solutions that meet their specific project needs, whatever they may be,
• Bilingual communication:
“Our Anglo-Italian team is ready to provide exceptional support and tailored solutions to meet the diverse needs of our clients”
The ability to communicate in both English and Italian ensures seamless interactions and better customer service,
• Comprehensive equipment solutions: Robustrack’s experience and supply of demolition attachments ensures that customers can source both the machine and the attachments from a single, trusted provider.
Laurini Officine Meccaniche’s entry into the UK market, facilitated by Robustrack, is poised to revolutionise the construction, demolition, pipeline, tunnelling and infrastructure construction landscape. Combining Italian innovation with British service excellence, this partnership promises to deliver unparalleled efficiency, reliability, and performance.
Laurini’s internationally patented Jocker tunnelling machine has won the Italian Demolition Recycling Award for Best Innovation of 2024 in the Machinery and Equipment for Controlled Demolition category, presented during The GIC Italian Concrete Days Fair.
The innovative feature of this machine lies in its ability to perform scarification, specifically milling the vaults of tunnels, with higher productivity and greater safety compared to existing market solutions. This capability reduces maintenance and restoration times for concrete vaults prone to surface crumbling.
Marco Laurini explained: “In
May 2022 one of Italy’s leading highway maintenance companies commissioned us to design and build a new scarifying machine. In five months our engineers completed the design and in the following nine months we constructed and tested a fully innovative prototype capable of automated, remote controlled operation, ensuring safety without the need for an expert operator.”
Named Jocker, this machine has already begun operations in several highway tunnels and industry professionals have recognised its qualities and advantages, prompting orders for additional units.
In an inspiring story from Italy, a worker who lost the use of his legs in an accident has been able to return to work thanks to a specially modified excavator by Laurini. This groundbreaking machine, equipped with an innovative cabin designed for accessibility, allows him to operate a 25-tonne excavator from his wheelchair.
The project, completed in 2023, was commissioned by CGT –Compagnia Generale Trattori and took place in Milan. The Easy Access Cabin is the first system in the world capable of lowering the excavator’s pilot cabin to the ground, allowing the operator to access the controls from a wheelchair. Thanks to the hydraulic system, once inside, the cabin can be raised again and rotated, returning it to the front command position. The system operates even when the engine is off and can be activated by a remote control, ensuring ease of use and reliability.
The cabin was custom-designed using a Caterpillar 323, but the system can be easily replicated on excavators of other models and brands.
The project came to life
through the combined efforts of a passionate team. It began with a worker determined to continue his career despite his disability, an empathetic employer and Marco Laurini, a visionary always ready to tackle new challenges. Laurini was deeply moved by the employer’s commitment to the young man and saw the project as an opportunity to make a significant impact on someone’s life.
Gianni, the worker for whom the machine was commissioned, was overwhelmed with joy upon seeing the modified excavator for the first time. This development signifies a major step in accessibility and inclusivity within the sector and is a testament to Laurini’s innovative engineering.
With 120 years of undercarriage experience, Caterpillar continues to innovate, so customers get the most from their investment. Exclusive to Cat machines and undercarriages, the proprietary Cat Track Wear Sensor (CTWS) remotely monitors undercarriage wear to better predict wear out, plan maintenance and increase machine uptime.
Monitored within the Cat Wear Management System, the new CTWS wirelessly communicates critical track link wear information from the machine to the dealer for monitoring. Timed alert intervals – a 40% wear alert for possible bushing turns, 70% to signal for measuring and replacement part ordering, and 100% for required replacement –improve inspection scheduling and streamline ordering of replacement parts. The real-time track wear status enables no-touch track link measurements, increases fleet coverage by automating inspections, provides visibility to track wear when operating in remote locations and allows for prioritised timing of service visits by helping optimise manual inspections.
Field tested for proven reliability throughout the expected track life, more than 2,000 Cat machines have been shipped with the innovative sensor technology. The
small electronic sensor installs in a customised pocket in the track link for protection. Each link assembly includes a smart link, resulting in two sensors on a machine, one on each side. The CTWS survives high frequency shock loads and meets sensor functional and environmental tests. Subject to operating conditions, sensor battery life has been shown to last up to seven years.
The wear sensor is standard on new Cat D5, D6 and D8 dozers, and 953 and 963 track loader models in select regions with planned expansion to models in the dozer line in the future. It can be retrofitted on eligible dozer undercarriages.
Save
Make remote management straightforward
Slash admin archiving time
View onsite checks as they happen
Eliminate paperwork
Available for iPads and Android tablets
At a trade event at the Liebherr plant in Bischofshofen in Austria, the world’s first large wheel loader with a hydrogen engine was recently presented to high ranking representatives from politics and business.
The event included a series of talks on the topic of alternative drives. However, the focus was on Liebherr’s impressive machine show, where the hydrogen wheel loader was demonstrated for the first time in practical use.
At the same time as this world première, the first hydrogen filling station in the state of Salzburg was inaugurated, representing an important milestone in the use of hydrogen as a sustainable energy source. “To make progress in hydrogen research, we need to have access to hydrogen. We built this filling station to further advance our goals for decarbonising construction machinery,” says Dr Herbert Pfab, Chief Technical Officer of Liebherr Bischofshofen.
The L 566 H is the world’s first prototype large wheel loader with a hydrogen engine. Following extensive studies, this groundbreaking technology was identified as the optimal solution for operating large vehicles that are difficult to electrify without CO2 emissions. For smaller vehicles up to about 15 tonnes, battery-electric solutions
are often suitable. However, the situation is different with larger machines with an operating weight of up to 40 tonnes and high energy requirements. Hydrogen reciprocating piston engines prove to be ideal in this case.
These hydrogen engines are manufactured at the engine plant of Liebherr’s Components product segment in Bulle in Switzerland. They enable not only zero emissions of
greenhouse gases and almost no nitrogen oxides, but are also highly efficient. Another advantage is that the interfaces are comparable to those of a diesel engine – thermally and mechanically. This represents a significant step forward in the development of sustainable largescale machinery.
Another highlight of the show was a MAN truck, also with a hydrogen engine. This shows that hydrogen technology is not only feasible in wheel loaders but is already used in construction site trucks.
As part of the development of the hydrogen wheel loader, Liebherr Bischofshofen opened its own hydrogen filling station – the first of its kind in the entire state of Salzburg. An important strategic partner in this project is Maximator Hydrogen, which is not only the manufacturer of the newly opened filling station, but also a research partner of Liebherr. Together, they are working on mobile filling facilities so that machinery can be refuelled directly at the construction sites. This is particularly important for remote
construction sites and machines that are not very mobile.
Another reliable partner is MPREIS, which ensures the supply of green hydrogen. This is important because only through emission-free production – using wind, hydroelectric or solar energy – can hydrogen play a key role as a sustainable and climate-friendly energy source.
“We built this filling station to further advance our goals for decarbonising construction machinery”
The iconic JCB brand has been given a big boost by the arrival of a new JCB monster truck called DIGatron at events run by the American organisation Monster Jam. Inspired by the legendary JCB backhoe loader, DIGatron made its European debut last month in front of a large crowd at the London Stadium in Stratford.
JCB has partnered with Monster Jam and the company’s equipment is now being used to create the special monster racing circuits when they are installed at famous stadiums around the world. Two distinctive DIGatron trucks – each inspired by the legendary JCB backhoe loader –have been produced to the standard Monster Jam specification with one based in America and the other in Europe.
The instigator of the DIGatron project has been eight-year-old Otis Bamford – the grandson of JCB Chairman Lord Bamford. He was inspired by a model monster truck and his enthusiasm spread to his
mother Alice and then on to Lord Bamford.
The JCB Industrial Design team lead by Ben Watson worked with Monster Jam engineers to produce the DIGatron. It weighs 5,443 kg and is approximately 3.2 metres high, 3.8 metres wide and 5.2 metres long.
Power is supplied by a 1,100-kW purpose built, methanol fuelled and supercharged Monster Jam engine. Complete with nitrogen charged shock absorbers, the truck rides on four specially designed BKT tyres that are each 1.7 metres tall by 1.1 metres wide and are inflated to an optimal tyre pressure of 23 psi.
The driver of DIGatron, which has a ‘symbolic’ loader at the front and a backhoe arm at the rear, is Tristan England from Paris, Texas. He first arrived in Monster Jam working on his dad’s truck, Big Kahuna.
Tristan England attended the Monster Jam University and subsequently won his first tour championship in 2018. Now he is
the 2023 Monster Jam World Finals Racing champion.
JCB is now the official heavy equipment partner of Monster Jam and a number of its excavators, backhoe loaders, wheel loaders and compact tracked loaders were used to create the dirt track with all its exciting jumps at the London Stadium. A JCB Fastrac 8330 iCON high speed tractor with a towed LGP2000 Major water bowser from TRU Plant was used during the event for dust suppression.
As well as the monster trucks, the audience at the London Monster Jam also saw a display of the famous JCB Dancing Diggers. This show utilised not only four 3CX backhoe loaders but also two 531-70 Loadall telehandlers and two 270T compact tracked loaders.
There were three separate heats in the London Stadium for the drivers of the DIGatron, Grave Digger, Megalodon, Black Panther, The Amazing Spider-Man, El Toro
Loco, Iron Man and Thor monster trucks. Tristan England in DIGatron won the Racing and Skills heats. But during the final Freestyle heat DIGatron, like several other trucks in the competition, toppled on to its side.
Tristan England was unhurt and subsequent righting of DIGatron saw more conventional JCB kit in action. This was because the event’s recovery squad utilised one of their two JCB wheel loaders – a 437 and a 457 – each equipped with special lifting arms.
The London Stadium Monster Jam event saw the start of a special long-term partnership between JCB and the musician Joe Walsh’s charity Vets Aid (which helps American military veterans). His song “Dig It” (with brother-in-law Ringo Starr on drums) was played loudly as the JCB DIGatron dramatically entered the arena in Stratford for the first time.
Driven by extensive customer feedback and a deep-rooted commitment to operator wellbeing and productivity, Komatsu introduces a significant upgrade to its crawler excavator operator cab.
This upgrade reflects a clear understanding from Komatsu that operator comfort is key to jobsite efficiency. “We already provide our customers with highly productive and efficient machines,” says Vince Porteous, Product Manager at Komatsu Europe. “With the new operator cab, we’ve taken a significant step forward by increasing operator comfort and ergonomics.”
The new Komatsu operator cab prioritises first-class user experience from the moment an operator enters the machine.
High-visibility Komatsu yellow handrails on both the exterior and interior enhance safe access even in low light conditions, while a strategically placed Komatsu logo reinforces brand recognition. A new, chrome- finished exterior door handle provides a stylish and easyto-grip surface.
Komatsu’s long-standing commitment to operator safety is evident throughout the new cab design. Vince Porteous elaborates, “We’ve added new safety features to the new cab, such as the new toolless mirror for easy manipulation, a new additional door handle for easy closing, new highly
visible handrails, and new coming home lights that remain on for 30 seconds after the ignition key is removed.”
Once inside, the operator is greeted by a refined and ergonomic workspace. Inspired by high-end automotive design, the interior features a premium dark colour scheme with a plush floor mat, adding a luxurious touch that is also easy to clean.
The new cab prioritises clear visibility during operation. The front roller blind’s relocated position
increases visibility by blocking the sun without obstructing the operator’s view. Upgraded LED lighting, both above the seat and in the rear of the cab, ensures illumination regardless of the time of day.
For operator comfort and reduced fatigue, the new cab also features a UV-protective rear window tint that minimises sun exposure and helps maintain a cool working environment.
A new document holder on the right side of the operator seat keeps essential jobsite documents organised and easily accessible, keeping the workspace clutter free.
Besides the standard upgrades, Komatsu also offers optional features to further enhance the operator environment.
A premium seat option automatically adjusts its position based on the weight of the operator, providing the highest level of
personalised comfort throughout the workday.
New wide armrests with multipositional locations allow for an optimal working posture. New operation control levers are designed to comfortably mould to any hand size or shape, reducing strain and fatigue over long shifts.
The new-generation Komatsu operator cab goes beyond comfort to offer potentials of unlimited customisation possibilities.
A robust, multifunctional utility bar allows operators to seamlessly add accessories that suit their individual needs, including water bottles, monitors and tablets for digital enhancement.
Furthermore, for easy mobile device charging and data transfer, the cab features dual USB ports at the rear, including both USB-A and C format.
Building upon its well established reputation for exceptional operator protection, the new cab retains the iconic Safe SpaceCabTM design. This tubular structure, specifically engineered for hydraulic excavators, provides superior protection even in the event of a most extreme rollover accident.
Designed and manufactured at Komatsu UK, the new operator cab embodies Komatsu’s longstanding tradition of customer-centric design and commitment to quality.
“The approach to the new cab was completely in the spirit of creating value together – we went to many jobsites, listened to the needs of customers and brought those requirements back to our development teams. Concepts were then born, checked with customers, refined, checked again, and by continually listening and innovating we now come to market with a new cab that is full of customer value,” says James Venerus, General Manager Product Marketing at Komatsu Europe.
The new cab is available on all crawler excavator models from 17 tonnes to 49 tonnes, with the exception of the PC228USLC.
by Richard Vann, Managing Director RVA Group
Given the tough financial backdrop many industries are experiencing, asset owners are rightfully cautious about the cost of decommissioning projects. But there’s no room for corner cutting when it comes to ensuring safety, efficiency and environmental responsibility on site. And who could be more qualified to relay that rationale to stakeholders than the decommissioning
professionals undertaking the project?
From methodology and environmental health to safety compliance, resource planning, project scheduling and more, there’s much for decommissioning engineers to consider. So why would these professionals want to add more to the list? Because when it comes to the mothballing,
rationalisation, or clearance of an industrial site they understand the importance of communication. Specifically, they know the value of the engineering acumen they can bring to the finance table.
Leveraging engineering expertise for controlled costing
Some front-end engineering services – such as a costings study for example – might be deemed one of the least hands on elements of a decontamination, dismantling or demolition project by some. In reality, leveraging detailed knowledge and experience of highhazard assignments is essential for securing a safe, commercially viable and environmentally sound outcome.
This costing information serves as the foundation for compiling sanction-grade estimates, preparing funding applications, projecting cash flows and determining the programme and duration of works. It also establishes financial milestones crucial for ongoing cost control during project execution.
In conducting these rigorous cost assessments, direct expenses such
as contractor fees are scrutinised alongside broader considerations like potential plant resale values, market dynamics and the impact of regulatory changes. Site-specific factors are also taken into account to ensure comprehensive evaluation.
These costings also play a critical role in long-term liability planning for sites. In fact, the information is required under international financial provisioning standards such as FAS143 in the USA and IAS 37 in Europe. These standards ensure the owner has maintained accurate reporting to shareholders and adequate financial provisions for future decommissioning even if physical work doesn’t occur for several years.
Given the increasing frequency of asset transfers, variations of these longer-term liability studies serve as essential due diligence tools for prospective buyers and sellers. As well as providing clarity on the legacies that will remain with the site, they indicate any costs that will materialise over time.
Of course, regularly scrutinising these numbers every five years or so is crucial. This periodic review accommodates any changes in asset conditions as well as waste and scrap rates, inflation figures and regulatory updates and it ensures a comprehensive understanding of site liabilities. A fluid and reconfigurable spreadsheet should therefore lie at the heart of any longer-term costing studies.
Interestingly, more and more people are recognising the importance of this early dialogue. Ideally collaboration between the decommissioning and finance professions should begin before a facility has even been built. That way the cost of ownership of an asset over the full lifecycle, including eventual decommissioning, can be outlined from day one. In fact, this information is often demanded by funding institutions, landlords and other involved parties so the true risk exposure of involvement in a project can be assessed.
Planning for decommissioning
during the inception of a facility may seem premature. However, there will come a time when an asset reaches its natural end of life. And, as with most undertakings, the quality of input in the earliest stages of a decommissioning project usually dictates the level of success that can be achieved in the longer term. That doesn’t just include financial benefits but environmental ones too – promoting the circular economy through the reuse of resources later down the line.
In many cases, fiscal stakeholders may seek indicative financial provisions, acknowledging the inherent uncertainties that come with planning so far in advance. Nonetheless, the involvement of experienced decommissioning professionals adds significant value, ensuring informed decision-making and effective project management from inception to closure.
If you have something to say and would like to submit a column for publication in Demolition Hub, please email: toby@chambers.media
The demolition versus retrofit debate still looms large. As the construction industry continues to seek ways to reduce its carbon emissions, refurbishment frequently wins the sustainability argument.
Demolition is often portrayed as the environmentally unfriendly option, which in time could see the demolition market decline in a similar way to how the coal industry has since the 1980s.
But is this demise a realistic prospect and is it fair to label demolition as unsustainable?
The argument in favour of refurbishment hinges on concerns about embodied carbon and the belief that demolition, combined with the redevelopment that follows, causes serious damage to the environment.
The proposed demolition of Marks & Spencer’s flagship store on Oxford Street London is a case in point. When the plans were
announced, the backlash and public inquiry that followed illustrates both sides of what is often a complex argument.
M&S wants to replace a 1930s building with a 10-storey office and retail block pledging that 95% of the materials would be recovered, recycled or reused. Objectors to the scheme have called for the building to be retrofitted instead and for this type of demolition to be reconsidered to help the UK achieve its net zero objectives.
The plans were blocked by the then Communities Secretary Michael Gove, but in March 2024, the High Court quashed the government’s refusal.
Although the true impact of this decision is not yet clear, the ruling demonstrates how important it is to evaluate a building’s lifecycle when considering the sustainability impact. To ensure a balanced judgement, the input from heritage experts and other specialists should not be underestimated either.
Demolition, by its nature, will always have an environmental impact, but the industry has been working hard to mitigate the effects.
There has already been significant progress in terms of the recycling and reusing of demolition materials. For many years, the National Federation of Demolition Contractors (NFDC) has guided members on how to maximise the recycling, reusing and repurposing of demolition materials, including timber, steel, iron and concrete. The NFDC also encourages all members to switch to low-emission, lowcarbon fuel where possible.
The next leap forward will likely come from advancements in heavy plant machinery. The major plant manufacturers, many of which are associate members of the NFDC, are working closely with contractors as part of a concerted effort to make our industry greener.
Electrically powered equipment is already in use for smaller tasks and
with the right technology, we think it is only a matter of time before we see electrical heavy plant with sufficient battery life and recharging capabilities. JCB is also progressing the development of hydrogen powered machinery, which could result in a significant breakthrough for our industry, bolstering its green credentials.
Although the demolition industry faces greater environmental scrutiny, its role remains indispensable for many projects, especially where safety is the primary concern.
Take the public sector for example, which faces the significant challenge of buildings constructed with Reinforced Autoclaved Aerated Concrete (RAAC) and/or asbestos. This is an issue not only affecting hospitals across the NHS, but schools and universities. While refurbishment may be feasible for some structures, many will inevitably require demolition.
The same principle applies to a growing number of high-rise residential buildings that have been constructed with flammable cladding or have other serious design flaws.
The industrial sector is another area where demolition can be crucial. A considerable amount of J Freeley’s work is with clients operating in chemical and food manufacturing. The processes behind these operations are evolving rapidly which can leave the associated plant obsolete. Often the most viable solution is to demolish and rebuild otherwise the building will be left to deteriorate.
More complex refurbishment projects will create opportunities for demolition contractors too. These often require specialist skills for tasks such as temporary works and retaining facades. J Freeley has been involved in several projects of this nature including the listed NHS building, Cobbett House in Manchester. This saw our team carry out internal demolition works,
including the installation of a complex propping system to load bearing walls.
Looking ahead, the question whether to demolish or not shows no signs of going away. But this shouldn’t be seen as bad news for our industry.
Demolition contractors’ skills and adaptability will continue to play a vital role in managing and modernising the built environment. These qualities combined with ongoing efforts to adopt greener practices will ensure the demolition industry remains strong and can contribute to sustainable development now and in the future.
If you have something to say and would like to submit a column for publication in Demolition Hub, please email: toby@chambers.media