DemolitionHub.com

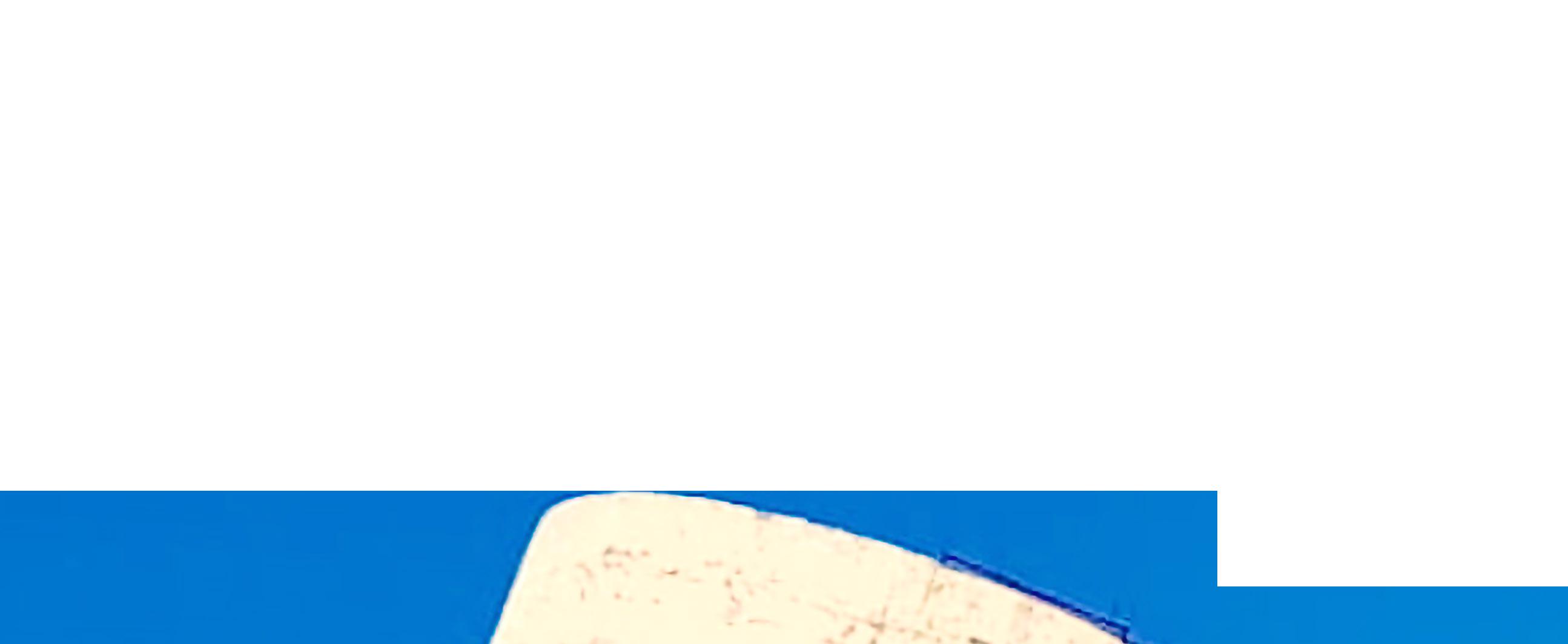
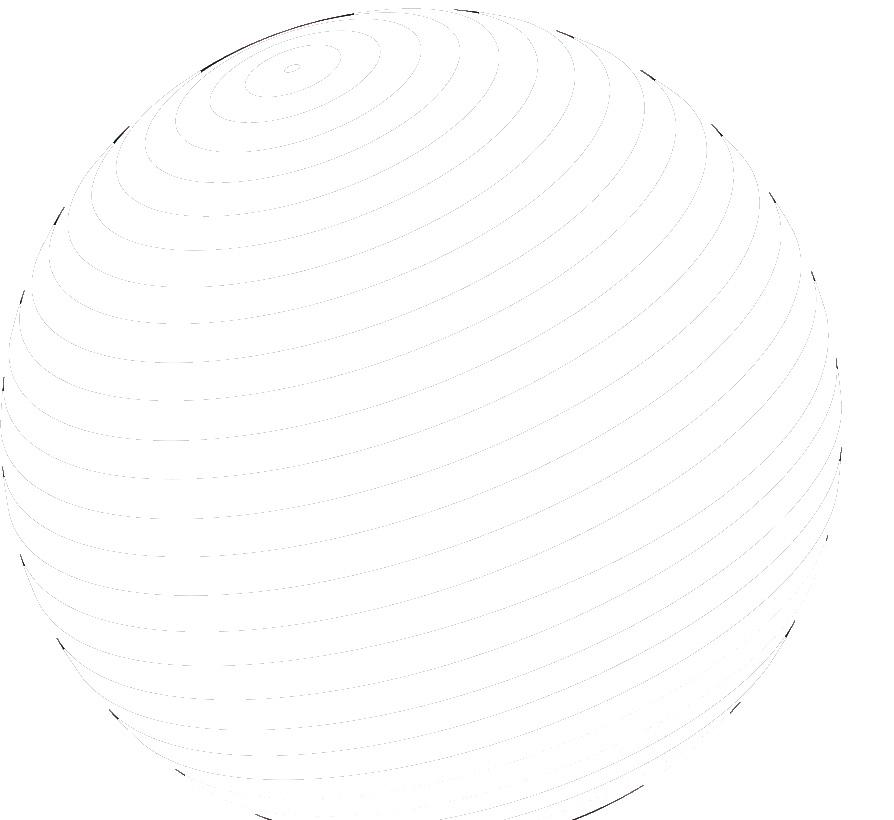
METROPOLITAN ELITE
Michael Hirst is the subject of the DEMOLITION DISCUSSION
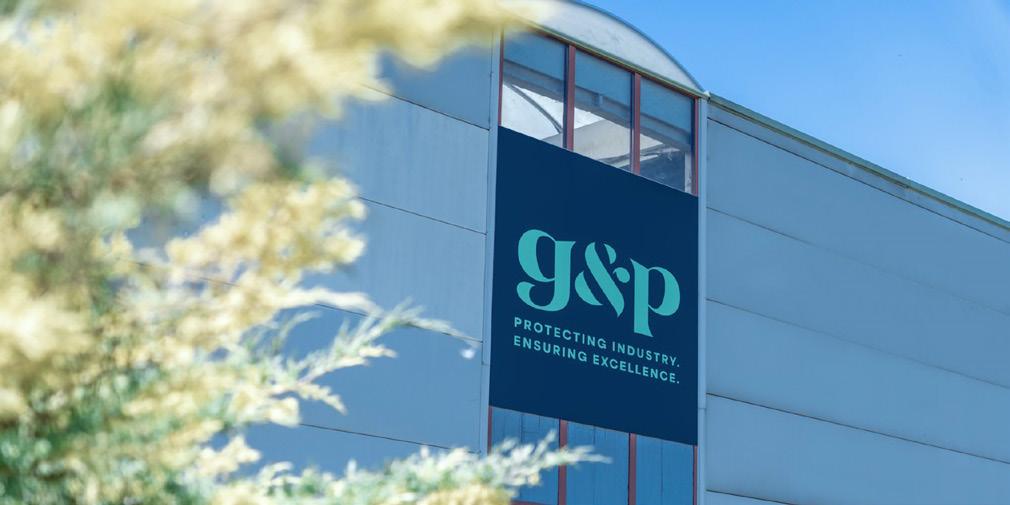
SUPPLIER TALK
30+ years’ experience of quality management services from G&P
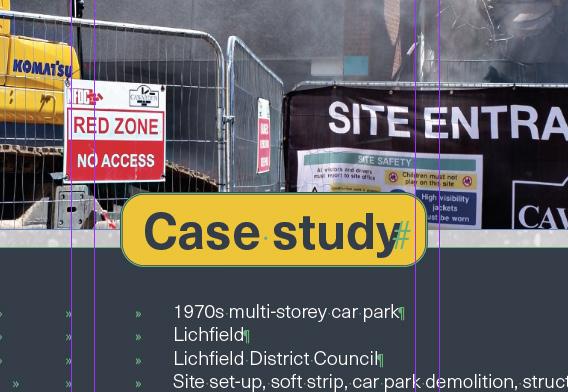
CASE STUDIES
All your projects, techniques and innovation inside
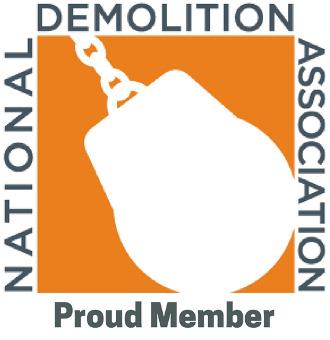

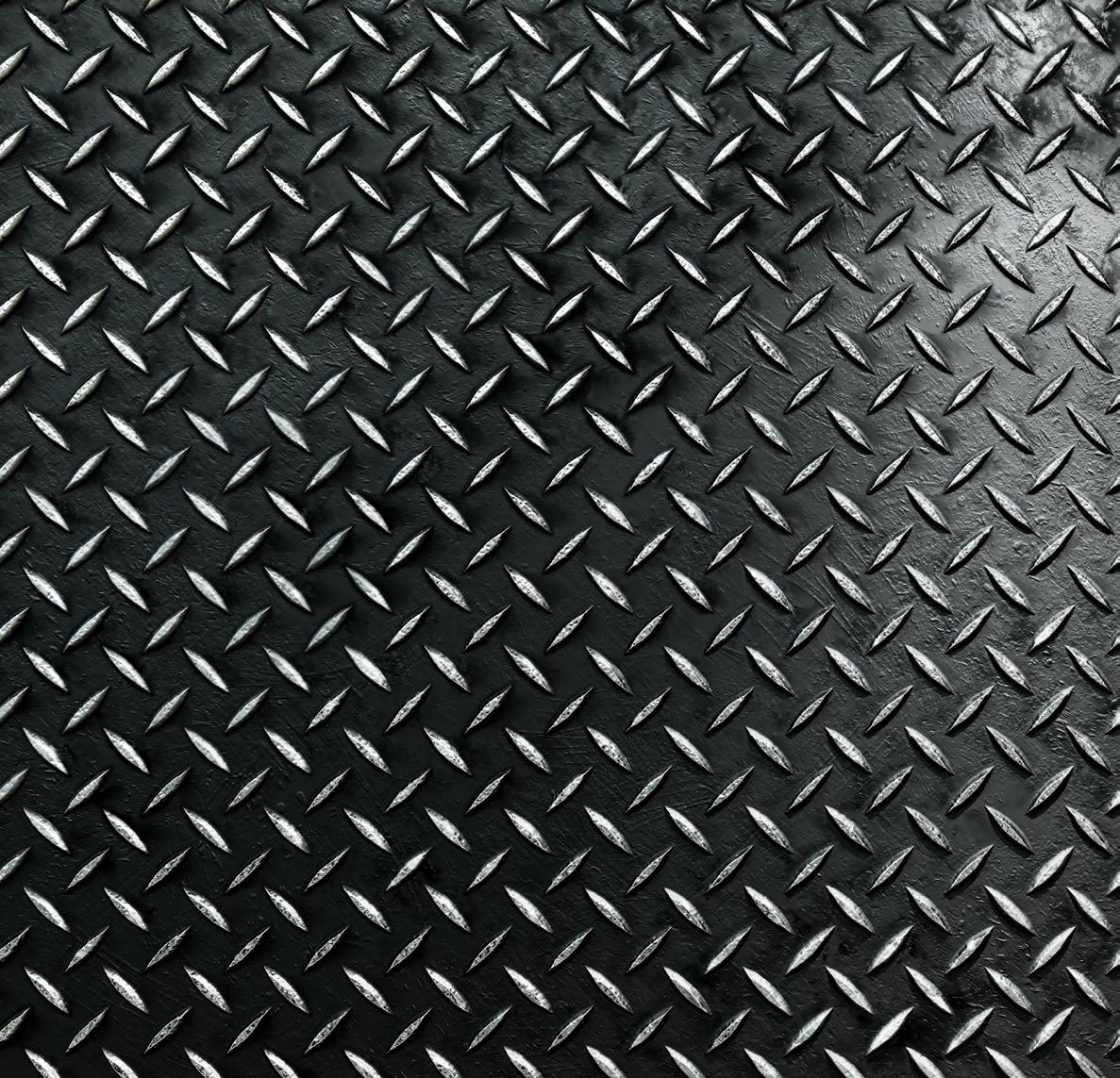
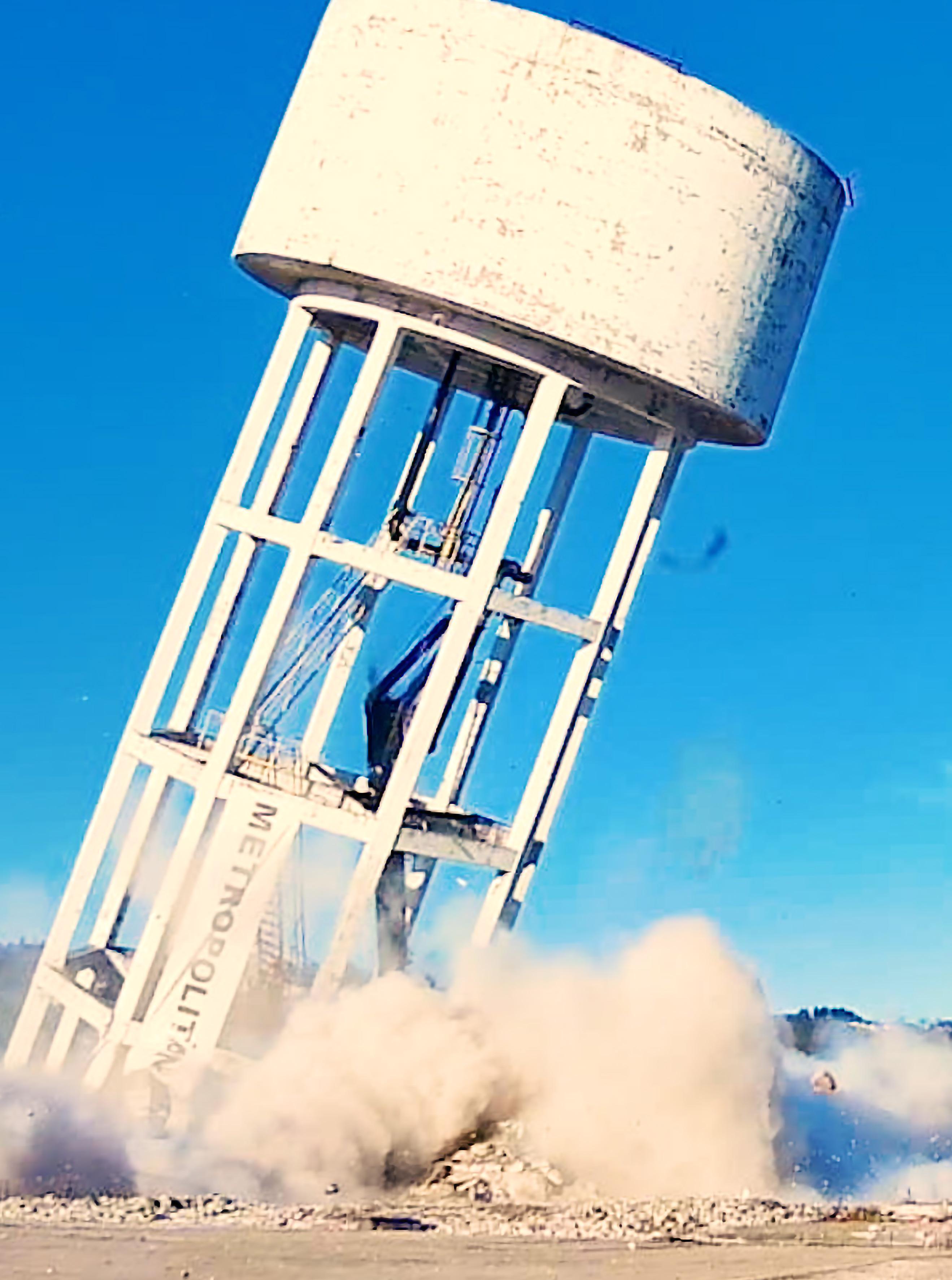
DemolitionHub.com
Michael Hirst is the subject of the DEMOLITION DISCUSSION
30+ years’ experience of quality management services from G&P
All your projects, techniques and innovation inside
Spring has certainly sprung and with it comes the season of transformation, renewal and fresh beginnings. There’s never been a more fitting time for British demolition to embrace change. As we welcome longer days and warmer weather, the demolition sector is undergoing a powerful revitalisation of its own.
In a significant move, Duncan Ruddell, CEO of the NFDC, has announced that he will be stepping down during this issue’s life. This marks the beginning of a new chapter for the federation, which also saw Adrian Corrigan stepping up as the newly appointed President at the recent AGM, taking over from John Lynch. Adrian, a longstanding and highly respected figure in the industry, brings with him a wealth of experience and a future-focused mindset, setting the stage for an exciting new era of leadership within the NFDC.
But the winds of change don’t stop there. The IDE is also embracing a shift in leadership. Vernon Watson has completed his term as President and the mantle has been passed to Armac’s Adrian McLean.
As the demolition sector continues to evolve, we eagerly anticipate the new directions these leaders will guide the industry towards, bringing fresh perspectives and renewed energy. We are here to support them and, just as importantly, to ensure that their voices are heard. Our door is always open, ready to assist in promoting their actions, ideas and the incredible work of their members to the widest audience possible.
Change isn’t just happening within these organisations – it’s happening here, too. We’re excited to announce that we’ll be doubling down on our commitment to showcase the stories, people and projects that define British demolition. We’re taking things to the next level, investing more time and energy than ever before to tell these important stories and give them the focus they truly deserve.
While we don’t want to give away too much just yet, we can’t help but tease some big things on the horizon. In a nutshell, we’re going to work harder than ever before to highlight and champion British demolition.
Get ready for an exciting video announcement on our social media, where we’ll reveal some of our upcoming plans. We’re on a mission to celebrate and support this incredible industry in every way possible and we’re thrilled to have you with us as we take this journey forward.
Stay tuned for more, because one thing’s for certain –#ChampioningDemolition has never been more important!
supporting partner for
PUBLISHER
Ben Chambers ben@chambers.media 01903 952 648
EDITOR
Toby Wilsdon toby@chambers.media 01903 952 645
COLUMNISTS
Richard Dolman
Terry Lloyd
We wish Howard Button a continued recovery
PHOTO CONTRIBUTER
Sky Revolutions
ADVERTISING SALES
Ben Chambers ben@chambers.media 01903 952 648
DESIGN
Joe Chambers joe@chambers.media
PRODUCED & PUBLISHED BY Demolition Hub Ltd Suites 5 & 6, Chapel House, 1-6 Chapel Road, Worthing, West Sussex BN11 1EX demolition@demolitionhub.com 01903 952 640
for
the
Demolition Hub is published six times a year. The subscription rate is £60 per year. Subscription records are maintained at Demolition Hub Ltd, Suites 5 & 6, Chapel House, 1-6 Chapel Road, Worthing, West Sussex BN11 1EX
Articles and information contained in this publication are the copyright of Demolition Hub Ltd and may not be reproduced in any form without the written permission of the publishers. The publishers cannot accept responsibility for loss of, or damage to, uncommissioned photographs or manuscripts.
NFDC welcomes Adrian Corrigan as new President
DEMOLITION DISCUSSION
With Metropolitan Demolition's Michael Hirst
DEMOLITION HALL OF FAME: Calling all demolition leaders 12
CASE STUDIES
Clifford Devlin: Kew Biothane Plant
Cawarden: From multi-storey to community impact
Hughes and Salvidge: In the Kingdom of Saudi Arabia 24 SUPPLIER TALK
Demo Temps, part of City Site Solutions
Number 8 Group
Romax Recruitment
The Labour Desk
Elite Consultancy Network 38 ATTACHMENTS FEATURE
Hill Engineering
MB CRUSHER
Ulrich Attachments 44 OUT
Snapshots of Ben and the Demolition Hub team’s activities between issues 46 SAFETY
Safety in demolition and the role of technology by Jonathan Davies of Finning UK and Ireland
48
EVENTS
bauma
• Hyundai hydrogen excavator digs in
With G&P's Rupert Musgrove 28 RECRUITMENT FEATURE
• JCB Powertrain ready to partner in clean power
• Komatsu on the pulse of the industry
• LiuGong product information
FACHTAGUNG ABBRUCH – Europe’s biggest demolition conference 8
• CASE Construction Equipment unveils the future of construction
• Develon Unveils Next Generation ‘-9’ Excavators
• Hyundai scoops innovation prize with HW155H
NDA's Demolition New Orleans – Safety, skills and shared lessons
The path to profitability by Keith Armishaw of Aquajet
Fuelling the future with Certas Energy:
Rebecca Redmond of Clifford Devlin to run 2025 London Marathon
Kaziwe Kaulule, Holcim UK: Why CDM and collaboration are key to sustainable growth
Terry Lloyd, Paragon Bank: Spring has sprung Richard Dolman, AR Demolition: Where are we at the close of Q1?
Join EDA and EDI’s new WhatsApp channel
Take part in the EDA Yearbook 2025
Inside FACHTAGUNG ABBRUCH 2025
EU targets for demolition waste recycling in 2025 XPLOSAFE joins EDA to strengthen safety in demolition
EDA incorporates LAURINI OFFICINE MECCANICHE
Make your brand shine at the EDA Convention
Priestly Demolition: Deconstruction at the Cameco Conversion Facility
The Workplace Advisors: Using AI to create flexibility for production jobs
Seyfarth Shaw: Potential changes at OSHA during second Trump administration
The latest demolition jobs from Romax Solutions
The National Federation of Demolition Contractors is proud to announce Adrian Corrigan’s appointment as its new President. His appointment marks a continued commitment to innovation, collaboration and excellence within the federation and the wider demolition industry.
Adrian, a long-standing and respected figure within the sector, brings with him a wealth of experience and a future-focused mindset. As Director at GBM Demolition, Adrian has played a pivotal role in driving operational excellence and innovation in
demolition practices across the UK. His extensive hands-on experience, combined with a strategic vision, positions him as an ideal leader to guide NFDC through the evolving demands of the industry.
A proud Member of the Institute of Demolition Engineers (IDE), Adrian has consistently championed the importance of professional development, safety and innovation. His commitment to upholding the highest standards aligns seamlessly with NFDC’s mission to elevate professionalism and integrity across all facets of demolition.
During the recent Annual General Meeting, Adrian honoured the outgoing President, John Lynch, by presenting him with the Outstanding Contribution Award – a heartfelt tribute to John’s dedication and impactful leadership. In doing so, Adrian not only paid homage to the progress made during John’s tenure, but also expressed his intention to build upon the fantastic trajectory, values and momentum established by his predecessor.
Speaking on his appointment, Adrian said: “It is a true honour to serve as President of the NFDC. I step into this role with gratitude, optimism and a clear intention to build on the strong foundations laid
by my predecessors. The demolition industry is evolving rapidly and I am committed to leading with transparency, inclusivity and a focus on the future. Together, we will continue to raise standards, embrace innovation and showcase the vital work our members do across the UK and beyond.”
Adrian’s presidency signals a new chapter for NFDC – one that promises progressive leadership, technological advancement and a renewed emphasis on collaboration while staying rooted in the strong values that have guided the Federation to date. His energy and forward-thinking approach are sure to resonate with both long-standing members and the next generation of professionals.
The NFDC Board and wider membership welcome Adrian to this esteemed position and look forward to supporting his vision as he takes the helm.
We are excited to announce the creation of a Selection Committee for an expanded 2026 Demolition Hall of Fame as we continue to honour the outstanding individuals who have made significant contributions in particular to the British demolition industry.
We are seeking passionate, experienced professionals including contractors, suppliers and association members to join the committee responsible for selecting the next group of demolition legends to be honoured within this fantastic industry.
If you have a deep understanding of the demolition sector, a commitment to recognising
excellence and a desire to help shape the future of our industry, we want to hear from you.
Who we’re looking for
• Industry professionals with extensive experience in demolition,
• Thought leaders, innovators and advocates who have shaped the industry,
• Those with a passion for recognising the pioneers and game-changers of the sector.
What you’ll be doing
• Reviewing and evaluating potential nominees for the Hall of Fame,
• Contributing to the selection process of industry trailblazers,
• Helping to preserve and celebrate the legacy of those who have made a lasting impact on demolition,
• Assisting in a buffed-up catalogue of categories in a rapidly evolving event.
If you’re interested in joining this exciting initiative email us via: HOF@chambers.media
More info on the Demolition Hall of Fame from DEMOLITION HUB can be found here: www.britishdemolitionawards.com/ hall-of-fame
Interviewee: Michael
Hirst
Role: Director
Company: Metropolitan Demolition Ltd
QWhat is your earliest demolition memory?
Seventeen years ago, aged 16, being awarded my first demolition contract. This was the asbestos removal and demolition of the former tram sheds in Ossett (near Wakefield), which was a £50k contract for a local house builder, programme 10 weeks.
QHow did you start out in the demolition industry?
I began by restarting the family business in 2008, which had run throughout the 60s, 70s, 80s and into the early 90s before being closed down.
We had two machines and one skip loader completing small demolition jobs around West Yorkshire to a multi-millionpound turnover business working nationwide for Tier 1 construction companies, major developers and well recognised project management companies providing Asbestos removal, demolition, decommissioning, remediation and crushing services.
QHow has your career progressed to where you are now?
My career has tracked a lot quicker than expected; I never expected to
be running such a well-established and recognised nationwide demolition company. Things really started to grow in 2022 when we were awarded the £4 million demolition contract at the Yodel National Distribution Centre near Oldham. All the other major projects just seemed to follow on from this, although we had completed some great projects previously, just not on the scale we are today.
QTell us about your team and working culture. Is there a fundamental company philosophy or ethic?
There is me and Gerard Jackson
at the helm, backed by a great office team and site-based teams. Most of the staff members here stick with the company long term. Our main philosophy is to provide hands-on service from a director level to provide out clients with an exceptional service throughout there project.
QWhat kind of projects do you work on most frequently? Do you have any particular specialisms?
Projects range from large scale industrial sites to inner city high-rise demolition and we have also worked on many chemical and COMAH
interview
sites nationwide. We are currently working on a lot of DFE projects for the replacement of schools across the country. Metropolitan has been very fortunate to work all sectors of demolition but now with more explosive demolition projects, which we are keen to do more of with our supply chain.
Q
What are the standout projects from Metropolitan’s history?
Ilford multi-storey car park was a particularly challenging project due to close proximity of the Network Rail assets and TFL depot adjacent. The project was a great success for
“Investment in our staff and new equipment has always been our number one priority, to get the job done to the best industry standards”
the company as it was our first multistorey car park demolition; hopefully we will use our experience from this to win similar projects in the future.
QWhat makes Metropolitan different?
We are always striving to be the best in the business to provide what our clients have seen and been told about us. Investment in our staff and new equipment has always been our number one priority, to get the job done to the best industry standards.
QTell us about the marketing and tendering process
There is only one main marketing process at Metropolitan and it is recommendation by word of mouth. Our great reputation keeps us as the successful company we are today.
QWhat memberships or accreditations do you or the company have?
Accreditations are something we are proud to uphold, the main one being the NFDC, NFDC, CHAS GOLD, Construction line GOLD, ISO9001, FORS, ACCLAIM and SSIP.
QWhat engagement does Metropolitan have in the community?
Metropolitan is engaged in many community and social events. Recently, working with our client Artisan Real Estate on an Edinburgh site, we donated PPE for school trips to keep the children safer.
Also recently, Gerard Jackson and Mick Love undertook school visits in Bradford to talk about the demolition industry followed by a Q&A while we completed the demolition of York House, a block of 120 flats on the Thorpe Edge estate.
QWhat measures is Metropolitan taking in regard to the climate crisis and sustainability? How do you foresee this developing both for your company and the industry in general?
Metropolitan is committed to running the latest trucks and vans and heavy plant to keep up with new emissions regulations. We have also been implementing HVO fuels as per our clients’ policies.
QHow do you see the demolition industry developing over the next few years? Do you foresee different demands in the medium term? We will always move with the times, but no major changes for us. We don’t want to reinvent the wheel.
QHow do you envisage Metropolitan in five to ten years?
I see the company over the next 10 years carrying as the great success it is today, we have no plans to be the biggest, just the one of the best at what we do.
QAnd what about you in a few years?
I will always carry on working with my co-director and best friend Gerard on a daily basis, dealing with the great clients we have now and in the future.
In the last few years I have been concentrating on expanding our commercial property business, but demolition is in the blood and will always be a big part of my career with many years left in the industry.
Tele Radio’s Panther PLd systems are the clear choice for duties that require high performance levels. Both our T19-2 and T29-12 meet Performance Level d (PLd), Category 3, equivalent to Safety Integrity Level (SIL) 2 – certifi cates independently awarded by notifi ed bodies. Whatever the job at hand, our stop function never fails.
Tele Radio offers a variety of radio remote control products, adaptable to a multitude of applications, throughout many industries like Agriculture & Forestry Equipment - Cranes & Material Handling - Mobile Hydraulic Machinery –Emergency & Recovery Vehicles - Industrial Doors & Gates – Propane and Tanker Trucks – Construction Equipment & Machines – Pumps & Aggregates, PLC Control – Recycling Machinery and more…
Title: Kew Biothane Plant
Structure: Sewage treatment/ Biothane production
Location: Kew, west London
Contractor: Clifford Devlin
Client: Elysian/CPC
Other significant stakeholders: Harlington School – Hayes
Site area: 8,000 m2
Scope of works:
Asbestos removal, demolition and clearance of structures, removal of foundations to two metres depth, and over 4,000 tonnes of soil, site preparation for future construction
Start date: August 2024
Completion date: January 2025
Techniques used: Traditional demolition using large excavators with modifications such as protective cab enclosures. Specialised demolition attachments included rotating hydraulic shears for precise cutting of metal frameworks, pulverisers for crushing concrete and separation from reinforcement, breakers to effectively fragment hard materials. Collectively, these adaptations ensured a safer and more efficient demolition process.
Future use: Residential care home
Clifford Devlin was awarded a significant demolition contract in west London by a new client. The project involved the complete demolition and clearance of structures, removal of foundations and over 4,000 tonnes of soil, and site preparation for future construction and installation of a TBS (Temporary Building Supply) base. The team was also responsible for managing debris, recycling materials and coordinating with third-party service providers for disconnections.
The project began with predemolition preparations, including the erection of hoardings to secure the site and the safe removal of any asbestos-containing materials. Service disconnections were arranged by third parties, with electrical supplies terminated by UK Power Networks and gas services disconnected outside the site boundary.
Once the site was secured, demolition commenced. Structures
were dismantled down to ground slab level, followed by the removal of foundations and hard standings to a depth of two metres. The team cleared all arising debris and transported it to licensed disposal and recycling facilities. On-site material crushing reduced the need for imported aggregates, promoting sustainability.
The final phase involved groundworks and site preparation. Pile probing was carried out to locate underground obstructions and piles were identified and marked for future construction. The site was levelled and a piling mat installed, along with the construction of a TBS base to support the next phase of development.
During the works, unexpected below-ground obstructions and service positions were encountered. To ensure safety, Explosive Ordnance Disposal Engineers (EODE) were brought in to deliver UXO (Unexploded Ordnance)
Safety and Awareness briefings to the workforce and project management team as needed before any intrusive works. They also provided an Operational UXO Emergency Response Plan (ERP).
Additionally, a live water hydrant was discovered on site and retained for use, reducing the need for external water sources. Electrical and gas disconnections were effectively managed through coordination with third-party providers, ensuring safety and preventing project delays.
To minimise the project’s environmental footprint, we reused all of the concrete on site (900 tonnes), which was crushed and laid for a piling mat. All other arisings were carefully segregated and recycled in line with Clifford Devlin’s commitment to sustainable practices and our carbon reduction plan. This meant that 17.2% of the total waste from site was reused on site and the remaining 82.8% was recycled. We were even able to help our client uplift some of its BREEAM credit ratings, specifically on PO 7.7 – Anti Bribery as well as MCE 4.1 – Construction, demolition and excavation waste.
Throughout the project, the team maintained clear communication with residents. Regular updates were provided and any concerns were promptly addressed. By adhering to the agreed schedule and minimising disruption, the project was carried out smoothly and with minimal impact on the surrounding community.
Structure: 1970s multi-storey car park
Location: Lichfield
Client: Lichfield District Council
Scope of works: Site set-up, soft strip, car park demolition, structural alterations, site levelling, drainage, landscaping, street furniture
Contractor: Cawarden
Other significant stakeholders: Harlington School – Hayes
Start date: March 2024
Completion date: February 2025
Techniques used: High reach, bay by bay and remote controlled demolition
In May 2024, a six-level multi-storey car park on Birmingham Road in Lichfield closed its doors after more than 50 years of operation, marking the first visible step in an ambitious urban redevelopment project. The demolition of the car park along with four retail units in Three Spires Shopping Centre was the first stage and a significant step in the transformation of the area, paving the way for an exciting new public space and connecting this to the cinema and plaza development in the city centre.
Cawarden was appointed by Lichfield District Council to deliver this integrated project, which included demolition, civil engineering and groundworks while delivering on our promise to give back to the area.
The demolition phase involved safely and efficiently dismantling the existing car park and shops to prepare the site for the new development. Our civil engineering team then executed comprehensive works, including site levelling,
drainage installation and landscaping – to ensure a solid foundation for future construction. Throughout the project, Cawarden remained dedicated to positively impacting the local area. Initiatives included engaging with local stakeholders, creating job opportunities and delivering environmental benefits.
The demolition and site preparation were executed over a structured 26week programme, including:
• Site setup: Established a selfcontained site compound with safety-first measures including a timber hoarding featuring a bespoke design and public viewing panels,
• Soft strip: Removed all nonstructural materials from shops,
• Demolition: Controlled demolition of the multi-storey car park and four retail units to create access for public space
development. The demolition methodology used a bay-by-bay approach and a combination of equipment including one of our high-reach demolition machines and a remote-controlled Brokk to complete the demolition of the car park’s stairs. To ensure safety, the adjacent footpath was closed to the public and scaffolding was installed to shield the neighbouring theatre from dust,
• Structural alterations: Separated retained shops.
Following the demolition works, the project moved to the civils and groundworks phase, ensuring a solid foundation for future development and to make the public realm enhancements, including pedestrianfriendly spaces with durable and aesthetically pleasing surfacing.
• Site levelling: Utilised recycled material from the demolition
process to create a stable base ready for paving and turf installation works,
• Drainage installation: Excavated and installed a new drainage system, incorporating attenuation crates and connecting to the existing STW infrastructure. Additionally, implemented a series of channel drains to effectively manage water runoff,
• Landscaping: Pruned existing trees and implemented a comprehensive planting scheme designed to enhance the landscape while deterring unauthorised access around the newly opened green space. Installed bespoke steel planters and shrubbery, complemented by hard and soft landscaping, including bound gravel surfaces, topsoil, turf and diverse planting to create a visually cohesive and inviting environment,
• Street furniture: Installed foundations for gates and benches across the scheme to enable the area to be utilised by all.
How Cawarden made a difference
As the main contractor, we ensured seamless project execution through a self-delivery model, maximising
efficiency and quality by keeping all works in-house.
• Greater control: Direct oversight of demolition, groundworks and civils ensured adherence to timeliness and quality standards,
• Cost efficiency: Minimising subcontractor reliance reduced costs and streamlined logistics and programme, creating maximum value,
• Expertise in action: In-house teams brought specialist knowledge, maintaining flexibility to adapt to challenges in real time.
Understanding that strong local engagement is key to a successful project, the team took a proactive approach to connect with stakeholders, ensuring transparency, coordination and lasting social impact. Through a series of targeted initiatives, we fostered meaningful relationships with the community, supporting local businesses, and contributing to broader social value commitments. Key engagement efforts included:
• Drop-in sessions: Creating open channels for discussion, allowing residents and stakeholders to learn about the project’s impact first hand,
• Business coordination: Maintaining ongoing dialogue with neighbouring businesses, particularly the theatre, to minimise disruptions and align logistical schedules,
• Social value commitments: Supporting the client’s regeneration strategy by delivering 13 community-driven initiatives under key themes –Confident Communities; Green Communities; Prosperous Communities; and, Active Communities. These efforts included job placements via the Job Centre, litter picks, food bank donations and sponsoring a local dance group.
By prioritising engagement, the team not only ensured smoother project execution but also left a positive and lasting impact on the local community.
Sustainability was at the core of the project, ensuring minimal environmental impact.
• Dust, noise, and vibration control: Advanced dust suppression systems and continuous monitoring maintained compliance and minimised disruption,
• Maximising recycling potential: Over 99% of the
demolition materials were recycled, with concrete and brick hardcore crushed into 6F2 aggregate for future construction use,
• Material reuse: Structural components such as slates, bricks, roofing elements and metal beams were salvaged and repurposed,
• Investing in green infrastructure: Contributing to sustainable landscape management and demonstrating a proactive approach to ecological restoration.
• Urban constraints: Working within a dense city centre required strategic planning to minimise disruption to surrounding businesses and residents,
• Logistical coordination: Heavy deliveries and site access had to be carefully scheduled to avoid conflicts with local refurbishments at the theatre and peak hours,
“Cawarden are professional, happy to go above and beyond to deliver the project and provide excellent customer service. Very satisfied with the work that was completed and would not hesitate to appoint Cawarden again for future projects.”
Karen Higgins, Lichfield District Council Projects Officer
• Environmental compliance: Maintaining air quality and noise control while executing the demolition required advanced dust suppression and monitoring systems to be put into place.
With the completion of the project, the city moves closer to unveiling a dynamic, open-air public plaza that will serve as a cultural and social hub. By prioritising sustainability, community engagement and meticulous planning, Cawarden has not only made way for future development but also leaves a
“Sustainability has been at the heart of Cawarden’s business for almost four decades, with a strong commitment to recycling materials. As a multi Green Award-winning organisation, we continue to lead the way in sustainable demolition and environmental responsibility. Our approach to the demolition of Lichfield’s multistorey Car Park has embraced our company ethos and we are proud to report an impressive 99.8% recycling rate on this project. We also continuously invest in new plant and vehicles with the latest fuel-efficient, low-emission engines, while embracing emerging technologies to drive our journey toward net-zero.”
Jonathan Groves, Quality Director – Cawarden
lasting positive impact on the local environment and economy. This case study showcases how our expertise can drive urban regeneration while maintaining a commitment to sustainability and community wellbeing.
“Thorough pre-planning was key to the project’s success – from detailed RAMS and method statements to seamless coordination with our project partners, including our structural engineers, particularly around the lift slab. Understanding how the structure was built ensured a smooth transition to site, allowing us to deliver the demolition efficiently and without a hitch. This project is a testament to our expertise and professionalism of the entire Cawarden team from start to finish.”
Malcolm Lowes, Demolition Director – Cawarden
Project: S-Chem Polystyrene Production Plant
Location: Al Jubail, Kingdom of Saudi Arabia
Contractor: Hughes & Salvidge
Client: S-Chem
Start date: October 2023
Completion date: June 2024
Techniques used: Mechanical demolition, high reach demolition, saw cutting, materials segregation and processing
Hughes & Salvidge was appointed principal contractor for the demolition and dismantling of S-Chem Polystyrene Production Plant in Al Jubail, Kingdom of Saudi Arabia in the last quarter of 2023.
With six areas, the project was bordered by a live substation and sump system, a live main site pipe rack and by the live Teal plant and ground flares, with sections also adjacent to a live road to the wider S-Chem site.
Where practical, track mat and or road plates were installed to provide ground protection and safe positioning of the excavator. All live manholes in the area were covered with steel plates to avoid any damage.
All excavators worked while facing the structures being demolished
or dismantled, positioned at a minimum distance of a 2:1 ratio, so any falling debris dropped to ground level safely without incurring any danger to the plant operator.
All materials were segregated and processed by a dedicated excavator for environmental checks and subsequent processing.
This area contained approximately half the length of the main pipe rack, the utilities and the unit furnace and incinerator.
Works commenced with the separation of the pipe rack; a portal frame with steel framed upper section and concrete lower section. The separation was carried out following a scaffold screen being erected
parallel to the live substation.
Operatives either cold cut the steel (via a reciprocating saw) or unbolted each section, while a crane suspended the load. Operatives worked at waist height to ensure they weren’t below the load at any time. Once separated, the crane to lowered it to ground level. This operation was carried out on all horizontal beams working top down.
The demolition of the main process plant (styrene filters/treaters, MRU, north–south pipe rack, rubber syrup system) were carried out using high reach excavators. Standard excavators were then employed for the lower level works, including
the dismantling of pipe bridges and smaller vessels, which were demolished on site mechanically to expand the working area for high level operations.
This area consisted of the HIPS Line, GPPS Line, central pipe rack and palletiser building. These four areas were split into phases to maintain safe control of the area.
The HIPS structure ranged from three to five storeys, was of steel-framed construction with fire protection coating up to halfway between the third and fourth floors. The structure was 10 metres wide by 60 metres long by 17.7 metres high for floor five and 11.6 metres high for floor three. Pipes spanned at varying heights along its full length.
The first floor contained various drums and heaters along with associated pipework. On the second floor were the bottom sections of the 70-tonne reactors, along with various drums, vessels and associated pipework, while the third floor housed the tops of the three reactors and two devolitisation chambers, along with the devolitisation water static mixer, the zinc stearate static mixers and manifold stations.
There were three uninsulated overhead condensers, three agitator package skids and three uninsulated air drums associated with the three reactors on the fourth floor. On the fifth floor were pipes and the continuation of the HIPS/GPPS tubular plug flow reactor Section 1 and the top floor had some manifolds and the insulated
HIPS/GPPS tubular plug flow reactor
Section 2.
All of the above plant and equipment underwent enabling works allowing it to be safely removed by mechanical means, the equipment was either cut in situ using a rotational shear attachment or removed from its position whole to be processed at ground level.
Within the HIPS structure there were four vessels needing special attention:
• Prepoly reactor,
• First-stage reactor,
• Second-stage reactor,
• Tubular plug flow reactor
Section 1.
The vessels were still removed mechanically, however Hughes & Salvidge installed additional ground protection, installing a protection area of rubber tyres at the base, then a 27-mm steel plate on top of the tyres and bulk timber (Ekki Mats) on top of the plate.
The demolition was sequenced working top down, bay by bay. The structure was a steel portal frame with plant and equipment on all levels and with the reactors centrally within the bay. The reactors were hung from the top by four connection points bolted to two supporting steels that ran between the bays. An excavator fitted with a rotational shear attachment began by removing the external cable tray and pipework from the face of the structure.
To ensure a safe and effective dismantling process, the 89-tonne excavator was positioned securely on the south end of the pipe rack in a stable location with sufficient clearance for movement and reach, cutting away the pipework and associated equipment from the top of the reactor.
Hughes & Salvidge then removed the cross members at first and second floor level to allow
them to remove any remaining obstructions around the reactor. This left the supporting steel in situ, so the reactor was still secure.
The excavator then cut the supporting bracing in front of the vessel before pulling the reactor from the framework on to the ground protection. As dismantled sections of pipelines and steel frame components accumulated they were segregated into waste streams and loaded into waste haulage lorries.
The excavator tracked to the next set of bays to shear through the upper steel frame structure, allowing the displaced steel section to be carefully lowered onto the footprint of the pipe rack area.
This step by step procedure was followed while ensuring the stability of temporary retained structures to ensure a successful and responsible dismantling of overhead pipelines supported on the steel frame structure.
The GPPS Line was demolished the same way and contained nearly the same equipment, so the procedure was followed with the installation of protection for the heavier reactors.
The GPPS Line had manifolds, pipework and small equipment running its entire length adjacent to the site boundary road. To ensure the boundary was protected, this element of works was demolished by a secondary excavator bay by bay to allow full sight of the material during demolition.
The next phase was the demolition of the palletiser building, entirely by mechanical means. An excavator fitted with a shear demolished the structure in a top down sequence, working bay by bay.
The structural report highlighted that the high level support bracing should remain for as long as possible; for this reason Hughes & Salvidge worked from south to east
as the bracing was located in the east and west elevations.
The excavator started by removing the cladding from the southern elevation, allowing the operator clear vision for the demolition of the roof section and internals of the structure. It removed internal equipment from the exposed floors before the floors themselves. The side elevations remained in situ as it included the wind bracing supports. Once exposed, the excavator carried out the same procedure with the back bay.
This methodology continued until the building was demolished to ground level while keeping the structural stability during the works.
The rubber dissolvers building was a tall steel structure, containing loading machinery such as the rubber bale loading robot, conveyor, chopper and exhaust blower. The first floor was dual level, with a lower section featuring an electrical room.
The structure’s northern section housed four-metre diameter by ten-metre high insulated rubber dissolvers. Pumps had been removed, leaving concrete bases, pipework, mixers and motors on top.
The warehouse was a steel framed structure adjacent to the dissolver building, measuring 31 by 14/24 by 8 metres. It was fully clad and had a concrete block facility. The two-storey, 11-metre high additives structure was 5 metres wide by 47 metres long with a steel clad roof.
The first floor contained pumps, pipes, lifting beams and an initiator feed room, while the top floor contained manifolds and filters. The additives structure had additive tanks, carbon drums and a connecting pipe rack to the HIPS/ GPPS Lines in Area 3.
The structures were dismantled mainly by remote mechanical means and the works were organised to suit the demolition phasing plan and involved small teams of demolition operatives/ plant.
The following distinct stages were followed to achieve the above:
• Draining residual material incoming pipe/support from Areas 2 and 3,
• Physical separation works incoming pipe/support from Areas 2 and 3,
• Demolish structures by mechanical means,
• Demolition of concrete bund/ upstands
This area contained product tanks
pipe rack, the additive and mineral oil tanks, and the product and feed tanks. All the five tanks in this area had a layer of bit sand under the bases.
The size of redundant tanks demolished or dismantled in the area were:
• Styrene tank: 10.7-metre diameter by 13.7-metre height,
• Recovery toluene tank: 7.7-metre diameter by 11.9-metre height,
• Mineral oil feed tank: 7.7-metre diameter by 11.9-metre height,
• Crude distillate tank:
12.2-metre diameter by 13.10-metre height,
• Additive feed tank: 5.45-metre diameter by 10.4-metre height,
• Pipelines, racks and structural frame support,
• Ancillary motors and pumps.
The tank demolition process followed the sequence below:
• Remove or strip tin corrugated sheeting and insulation,
• Punch entry holes in the tank wall,
• Shear and cut down the tank wall progressively,
• Shear through the roof structure from the eaves,
• Dismantle and remove internal roof support,
• Pull partly displaced section on to the tank footprint,
• Shear and cut the tank progressively in a clockwise or anticlockwise direction,
• Separate demolition arisings into various waste streams and remove from site,
• Progressively cut through and shear the base of the tank,
• Remove scrap arising to a processing area,
• Repeat the sequence until the tank is demolished.
The peroxide storage building was approximately 17 metres long by 10 metres wide by 10 metres high and was made of steel frame construction with external sheet cladding. There was a live fire water feed so Hughes & Salvidge installed protection by means of sand bags around the perimeter, ensuring that the clearance was a minimum of 150 mm, before installing 20-mm steel plate on top.
www.hughesandsalvidge.co.uk
0808 250 7086
Interviewee: Rupert Musgrove
Role: UK Managing Director
Company: G&P
Rupert Musgrove is an experienced leader with 25 years’ expertise in enhancing customer experience, product quality and operational excellence in both the automotive industry at Jaguar Land Rover and in consumer electronics at Dyson.
His key achievements include improving customer experience and product reliability at Dyson, reducing warranty costs and advancing vehicle quality at Jaguar Land Rover. In 2024, Rupert became the UK Managing Director at G&P, specialising in delivering quality management services across the off-highway, automotive, aerospace, defence and household goods sectors.
What is your core message to our demolition contractor readership?
In the complex demolitions manufacturing industry, effective quality management is essential to reducing costs, preventing defects and ensuring efficient production. Without robust oversight, qualityrelated expenses can make up a significant proportion of sales
revenue, driven by failures in prevention, appraisal and defect resolution.
Addressing quality earlier in the supply chain minimises risks, prevents costly recalls, and enhances overall operational efficiency. Poorquality components, inadequate process control and insufficient traceability remain common challenges that, if left unchecked,
can disrupt production, damage reputations, and result in financial loss.
To meet these challenges, the industry must prioritise proactive quality management throughout its entire supply chain. This includes deploying skilled professionals to inspect and rectify nonconformances, using real-time data to track and trace quality issues, and
“At our core, our success lies in building long-term partnerships with our clients by embedding skilled professionals within their operations”
implementing safeguards to prevent defects from reaching final assembly.
Strengthening supplier quality capabilities, investing in process control and fostering crossfunctional collaboration will help manufacturers to reduce costs, improve reliability, protect brand integrity and ultimately, increase profitability.
Give us some background on G&P G&P was founded in 1994 to provide quality management services to the automotive industry. Over the years, we’ve expanded our expertise to support the demolition, off-highway, aerospace and defence sectors, working with OEMs and tiered suppliers to ensure high-quality, zero-defect manufacturing.
Now operating in more than 250 manufacturing facilities across the UK, Europe, and China with more than 1,000 employees, we have established ourselves as a trusted partner in delivering agile and effective quality management.
We focus on managing, controlling and eliminating
disruptions throughout the development, production, launch and aftersales process and manufacturing supply chains.
We pride ourselves on our proactive approach to quality assurance and we offer the type of hands-on support that enables manufacturers to maintain efficiency and vastly improve their supply chain reliability.
How did you start out in the industry, what attracted you to it and how has your career developed to where you are now?
I began my career as a graduate engineering trainee at Land Rover after completing a Bachelor of Engineering in Manufacturing Engineering at the University of Birmingham.
What attracted me to the industry was the opportunity to work in an environment where product quality, engineering excellence and customer experience are at the heart of everything.
Over the years I moved from engineering roles to leadership
positions, first in the automotive sector at Jaguar Land Rover and then in consumer electronics at Dyson.
My career has developed through roles focused on improving operational excellence, quality management and customer experience.
At Dyson, I led teams to achieve exceptional reliability in product launches, while at JLR I successfully reduced warranty costs and improved customer satisfaction.
Today, I am the UK Managing Director at G&P, where I continue to lead quality management services, drawing on my extensive experience across industries to deliver top-tier results.
Tell us about the services you provide and how your relationship with clients works
At G&P we offer a comprehensive range of quality management services, including inspection, containment, rework, engineering support and supplier development. These services help manufacturers maintain production efficiency
and meet increasingly stringent quality standards. As such, we also provide Quality Management System (QMS) certification support, ensuring compliance with standards like ISO, TS and AS.
At our core, our success lies in building long-term partnerships with our clients by embedding skilled professionals within their operations, acting as an extension of their existing teams.
This collaborative approach ensures that quality challenges are addressed at the root cause, preventing disruptions and driving continuous improvement.
By offering both longterm managed services and rapid deployment for urgent requirements, we can provide flexible solutions tailored to the specific needs of our clients.
Our proactive approach to quality management truly sets us apart from the rest. Rather than simply reacting to defects, we focus on preventing issues before they even occur, ensuring a smooth and efficient manufacturing process.
By deploying highly-skilled technicians and engineers on site, we can offer immediate and effective problem resolution while driving long term quality improvements across the entire supply chain.
Another key difference is
our proprietary digital quality management system, “QTrak”. This provides real time data and analysis, allowing clients to monitor supplier performance, track inspections and identify trends that help them make more informed decisions.
Through the convenience and transparency that QTrack provides, combined with our decades of deep industry knowledge and a commitment to zero-defect manufacturing, we can offer a truly unique and value-driven service for our customers.
us about your team and G&P’s working culture
G&P’s success is built on the expertise and dedication of the team. We carefully select professionals with technical ability, problem-solving skills and a serviceoriented mindset, who are not only highly skilled but also adaptable and committed to delivering exceptional quality management.
We work hard to foster a culture of continuous improvement, collaboration and professionalism. With a strong emphasis on training and development, we are able to ensure our people stay ahead of industry advancements, and by embedding our team directly into client operations, we’re able to encourage a hands-on, partnershipdriven approach that prioritises efficiency, trust and long term success.
How has the scope of G&P’s business developed over time and are you in the process of developing your range of services?
Originally focused on the automotive sector, we have expanded our expertise to the off-highway, aerospace and defence industries, responding to the growing demand for high-quality, defect-free manufacturing. We also now operate in multiple countries across Europe and Asia and have strengthened our presence within the supply chains of leading OEMs and tiered suppliers both domestically and internationally.
Always striving to continuously evolve to meet industry needs, we’ve expanded our service offering to include technical rework, supplier capacity validation as well as talent recruitment through our G&P Talent division. Throughout, we always remain committed to innovation, exploring new technologies and processes to enhance our capabilities and better serve our clients.
Tell us about any apprenticeships or trainee schemes. How can any labour supply issues be dealt with?
At G&P, we recognise the growing skills shortage across manufacturing industries and actively invest in talent development. As such, we collaborate with academic
institutions, industry associations and training providers to support apprenticeships and trainee schemes that bridge the gap between education and practical industry experience.
To help address labour supply challenges, our G&P Talent division specialises in recruiting skilled personnel, offering both temporary and permanent workforce solutions. By leveraging our deep industry experience, we’re able to select the right candidates and maintain a database of highly-qualified personnel so we always have a strong pipeline of talent ready to meet the peaks and troughs of industry demands.
Do you undertake ongoing training or Continuous Professional Development?
Training and development are at the core of G&P’s philosophy. As such, we provide ongoing technical training, leadership development and industry certifications to ensure our team remains at the very cutting edge of quality management.
This emphasis on expertise strengthens our value proposition, allowing us to differentiate ourselves as the leading provider of highlyskilled, highly-qualified personnel. This means our clients can benefit from a team that’s continuously improving, making the service offering uniquely more attractive and valuable in a competitive space.
What are the biggest technological developments you have seen in your industry and what do you envisage will be the future game changers?
Advancements in automation, Artificial Intelligence and digital quality tracking have transformed manufacturing quality management. New tools such as digital twin technology and predictive analytics using AI are enabling manufacturers to prevent defects before they occur, improving efficiency and reducing waste.
Looking ahead, we expect the further integration of AI-driven defect detection, autonomous quality control systems and smart manufacturing technologies to absolutely revolutionise the industry.
How do you see the outlook for the demolition plant sector generally?
The demolition plant sector is rapidly evolving with a stronger focus on sustainability, efficiency and safety. As environmental regulations become stricter, manufacturers must adopt cleaner and more efficient processes, increasing demand for high-quality machinery and components.
At G&P, we play a key role in ensuring that demolition equipment meets stringent quality and performance standards – by supporting manufacturers with quality assurance and rework
solutions, we help the sector adapt to these changing industry demands.
How do you envisage G&P in five to ten years?
We aim to expand our international footprint while continuing to innovate and improve our quality management solutions. With strong foundations in the UK, Europe and China, we’re looking to further strengthen our presence across the UK and enter exciting new markets.
To help achieve this, investment in new technologies, digital solutions and workforce development will be our key drivers of growth. Ultimately, our mission is to be the quality management partner of choice for manufacturers worldwide.
In the long term, G&P will continue strengthening its existing services while exploring new opportunities in quality assurance and digital transformation, leveraging our recent successes and expanding senior leadership team to adapt to evolving industry needs and grow our client base.
By staying agile and responsive to the evolving demands of the market, we will remain at the very forefront of quality management, continuing to provide industry-leading solutions that help manufacturers to achieve zero-defect supply chains.
City Site Solutions Ltd is not just another recruitment agency, it’s a company built on a foundation of integrity, quality and innovation.
Since its inception in 2000 the firm has grown from a team of two directors and a single consultant operating in London Bridge to a thriving nationwide recruitment company. With six offices across the UK, over 40 dedicated staff members and a commitment to ongoing professional development, City Site Solutions has established itself as a recruitment agency with a difference.
The company was founded on the belief that recruitment should be about more than just filling vacancies, it should be about creating lasting, trusted relationships with both clients and candidates. The company set out to build a business that focused on understanding the unique needs of each client and providing a top-tier service to candidates. Whether working with large construction firms or individual tradespeople, City Site Solutions has always prided itself on its transparent, honest and personalised approach.
The company’s integrity quickly made it stand out in the crowded
recruitment market. It wasn’t just about placing candidates in jobs, it was about finding the right fit for both the client and the worker, ensuring long-term success for all parties involved. This relationshipdriven approach has been key to City Site Solutions’ success and growth over the years.
Each office operates with its own dedicated manager, consultants and resourcers, allowing for a localised, tailored recruitment experience for clients and candidates. The company’s expansion has been powered by its core team of experts, many of whom specialise in the construction industry. The team’s deep understanding of the sector combined with City Site Solutions’ commitment to quality has made the agency a go-to partner for construction companies in need of top talent.
From site managers to skilled tradespeople, City Site Solutions provides an unmatched recruitment service that ensures its clients have the right people in place to deliver successful projects. As the company continues to grow, it remains committed to its employees’ development, ensuring
that every consultant, resourcer and manager is equipped with the tools and knowledge they need to succeed.
Each staff member is encouraged to pursue further professional development, with many going on to become face fit testers, mental health first aiders and more. This ongoing commitment strengthens the company’s overall expertise, allowing it to continue providing exceptional service to its clients.
In 2024, City Site Solutions expanded its offerings even further with the creation of a specialised Demolition division, named Demo Temps. Recognising the unique demands of the demolition sector, the company launched this dedicated division to cater to the increasing need for skilled workers in the industry.
Since its launch, Demo Temps has proven to be a success, already supplying over 70 operatives across 14 different demolition sites. This specialised division allows City Site Solutions to offer even more targeted recruitment services, helping demolition companies find the right operatives for their specific needs while maintaining
the same high standards of service and professionalism that the company is known for.
The creation of Demo Temps also highlights City Site Solutions’ ability to adapt to changing market demands and respond with innovation. By focusing on specific sectors like demolition, the company has been able to diversify its service offerings and provide even greater value to its clients.
As City Site Solutions celebrates 25 years in the recruitment industry, the future looks bright. The company’s commitment to quality service, innovation and staff development has set it up for continued success in the years to come. With its ongoing
expansion into new sectors, such as demolition, and its focus on creating strong, long-lasting relationships with clients and candidates, City Site Solutions is poised to remain a leader in the recruitment industry.
In the ever-changing world of recruitment, City Site Solutions continues to set itself apart by remaining steadfast in its commitment to honesty, integrity, and personalised service. Whether you’re looking for skilled tradespeople, experienced consultants or a specialised solution for your business, City Site Solutions offers a recruitment experience that truly makes a difference.
Should you need a recruitment specialist that takes the time to understand your needs and requirements, that has the knowledge and expertise to offer solutions in a rapidly moving market, please get in touch today.
Hiring in temp labour to manage varying workforce requirements is now the accepted norm in construction and demolition as well as a multitude of other sectors. However there is still an underlying perception in some quarters that the use of temp workers is a convenient breach of compliant commercial practice to avoid tax and employment status issues. Without doubt there are businesses that push these boundaries however it is impossible to comprehend a workable solution that provides the flexibility and efficiency of a managed workforce that does not include access to temp workers via an agency.
Unfortunately not all agencies are created equal and many intentionally operate in the shadows of these adverse perceptions where ethics and compliance have no place. This is where the sole objectives are profit at any cost for both the labour supplier and user and in many cases the collateral damage falls on the temp worker as a result of exploitation or even abuse.
So the big question is “Should we care about how our temp labour is resourced and whether the suppliers of this labour should operate ethically and provide a genuinely compliant service?” Or is it ok to bury our heads and turn a blind eye to the obvious and
what in many cases falls outside the published standards of most organisations. There is no doubt that there are often personal and commercial benefits to both individuals and the businesses involved that can complicate or even halt any genuine attempt to eradicate substandard practices.
At Number 8 Resourcing we have made the very clear decision to establish and maintain a focus on providing a compliant and ethical service to both our clients and the workers we engage with. This at times has been commercially detrimental when ultimatums or conditions have been imposed that ultimately impact our supplier status. However, we have managed to grow and build strong relationships with clients and workers who value our standards and have confidence in the way we operate.
For Number 8, ethical practice goes well beyond just avoiding the “brown envelope” culture. The insidious presence of exploitation and human trafficking is an unfortunate reality where the potential financial benefits are so large. The signs can often be hard to spot so vigilance and a zero tolerance approach to the telltale signals that point to potential exploitation, is critical.
Right to work is also an area that often gets conveniently pushed
to the background in a pursuit to resource sites with labour that is notoriously hard to find or even just to cut costs. Again, detecting fraudulent activity is difficult and even for the most vigilant can prove complicated at times. Number 8 employs a best practice approach that generally picks up any obvious breaches however at times the sophisticated capabilities available to the desperate can make it difficult to detect false documents. If breaches occur our focus is on immediately mitigating any impact on us but more importantly our clients.
Thankfully ethical practice is not all about avoiding fraudulent or even criminal activity. Our ethical approach at Number 8 has opened a number of doors where we can focus on positive, socially responsible resourcing opportunities. As traditional labour pools have been reducing we have been able to gain trust and establish very strong working relationships inside the Ministry of Justice and with a number of category C and D prisons, with a long term view to promote career opportunities in demolition that will ultimately provide ex-offenders a strong platform to turn their lives around.
We are currently partnering with the NDTG to provide CCDO and other related training opportunities
inside the prisons in preparation for release as well as post release training with the assistance of the Department for Work and Pensions.
The NFDC and NDTG have also joined the initiative and will be actively promoting the use of ex-offenders to all members. Brian Carroll and team at NFDC HQ are motivated to use this initiative to promote a career in demolition to a resource pool desperate to make positive life changes and avoid the temptations or influences that took them down a path that led to imprisonment.
We have spent many hours inside a number of prisons talking to people who just want a chance to prove to society and themselves that they are better than what ultimately led to their incarceration. Working with progressive contractors like Clifford Devlin. We are confident that with the support and commitment of all NFDC members we can continue to attract quality new blood into the industry.
Number 8 Resourcing wants to be known as the labour supplier with a commitment to providing an ethical and compliant service to clients and workers. We want to continue to push boundaries and expectations that focus on socially responsible initiatives. Our future targets will be to attract
more women into entry level roles that have traditionally been dominated by men. We have also identified a number of roles that could offer physically challenged workers an opportunity to work in a progressive and socially aware industry. We hope that all demolition businesses will be open to some or all of these initiatives and want to join us and the NFDC/ NDTG on this rewarding journey.
Since being established in 2012, Romax Solutions has set a high standard when it comes to recruitment. Finding the best candidates is our driven desire and passion, we aim to meet the recruitment needs of a diverse range of clients within the construction industry.
Being based just outside of London gives us easy access to service all clients throughout Essex, London, Kent and surrounding areas while also having the capabilities to support and service nationwide projects and clients. With a depth of knowledge, our experienced and trusted staff are on hand to deliver a bespoke service to each and every client, supplying reliable and talented staff of all levels both nationally and locally.
Romax Solutions is fully accredited by the Recruitment and Employment Confederation and the National Federation of Demolition Contractors. These accreditations have enabled us to work alongside other NFDC members to meet their scope of needs on multiple projects. These projects range from small scale strip outs to large scale power station decommissions.
We are also always keen to add new talent to our current pool of candidates nationwide. These include those from management level downwards, including skilled demolition operatives and even those just starting out their demolition careers. We work effortlessly to ensure all candidates are fit for purpose, including using accredited training providers to upskill our operatives.
Romax Solutions Ltd is a principal supplier to some of the biggest construction and demolition contractors in the UK. We constantly look to recruit workers with a good attitude to work and experience in the construction industry and provide long term work for the right candidates depending on reliability and willingness to work.
In demolition, timing, safety and having the right people on site make all the difference. That’s where The Labour Desk comes in. As a trusted NFDC Industry Service Provider, we specialise in providing reliable, qualified demolition operatives across the UK – quickly, compliantly and with minimal hassle for our clients.
We’re proud to work with some of the leading names in the industry. These longstanding relationships are built on one thing: consistently delivering the right people, at the right time, with the right qualifications.
We know demolition inside out From Green Card CCDO labourers to black card managers, we provide all levels of demolition labour. Our workforce includes burners, bobcat operatives and high-reach excavator drivers – all fully vetted and certified for demolition work. Every operative we supply meets industry standards and is ready to hit the ground running.
We’re not just filling roles; we’re solving problems. Whether you need last-minute cover, a full team for a strip-out, or senior site leadership, our team
delivers experienced personnel who understand the demands and pace of demolition.
NFDC-approved and fully accredited
Our approval from the NFDC is more than a badge – it’s a benchmark. It confirms our commitment to high standards and our understanding of the demolition world.
We also hold CHAS Advanced, Constructionline Gold and SSIP accreditations, giving clients complete confidence in our approach to health and safety, compliance, and due diligence. As a business, we’re also proud members of the Recruitment and Employment Confederation (REC).
For clients, that means no grey areas: our labour is fully compliant, insured and ready to work safely on day one.
We know that getting labour to site is just as important as having the right people. That’s why we run our own fleet of cars, people carriers and minibuses to transport workers directly to your project. Whether your site is central or remote, we make sure the full team arrives on
time and together, ready to go.
This transport solution is a game-changer for our clients. It reduces delays, increases attendance reliability and takes one more headache off your plate.
Investing in the next generation
Demolition needs a future workforce and we’re helping to build it. We actively run outreach programmes in prisons and youth sectors, creating pathways into the industry for those who may not have had the opportunity otherwise. We believe in second chances, fresh starts and developing people who are eager to work and grow.
This proactive approach means we’re always growing our candidate pool with fresh, motivated talent, helping tackle the skills shortage head on and giving our clients access to a wider, stronger workforce.
• Trusted by top names within the demolition industry,
• Full range of CCDO-certified operatives supplied,
• NFDC Industry Service Provider – demolition-
specific standards met,
• Transport provided – cars, minibuses, people carriers,
• Compliance guaranteed – CHAS Advanced, Constructionline Gold, SSIP,
• Proactive recruitment –outreach to attract new talent. We understand demolition better than most – not just the roles but the pace, the pressure and the risks. Our service has been designed to meet the real-world challenges our clients face every day.
At The Labour Desk, we’re only as good as our last supply – and that’s exactly how we like it. If you’re looking for a responsive, experienced, and forward-thinking labour supplier who genuinely understands demolition, let’s talk. Whether you need a single operative tomorrow or a full crew next week, we’re ready.
www.thelabourdesk.co.uk
Since 2002, we’ve been at the forefront of delivering unparalleled recruitment services to the Construction Equipment sectors. Our success rests on a foundation of recruitment expertise and extensive industry knowledge across hire and rental, equipment dealers and manufacturers and cranes and powered access.
At Elite Consultancy Network, we put people first. Our consultants are dedicated to offering a first-class service to job seekers, candidates and clients who are looking for roles in sales, engineering, or operations. We have an “inch-wide, mile-deep” philosophy that goes beyond traditional recruitment.
Combining sector specialists with functional experts, we deliver a unified approach to helping clients build, assess and advance their senior teams and emerging leaders. Together, our team brings targeted insight and expertise that empowers clients to make strategic and impactful talent decisions.
Over the last two decades, we have built an extensive network of clients and candidates and partner with some of the world’s leading brand names. Working across both the UK and internationally, we have developed long-standing and trusted relationships with key players across our sector that other recruiters simply do not have.
Whether you’re looking for your dream job, a better opportunity, a step up or just a new challenge, we can help. We can put you in touch with decision makers across a wide range of industries and in a number of destinations in the Heavy Construction machinery Equipment sector.
Few industries are as inherently challenging as the demolition industry, involving as it does complex procedures and heavy plant machinery that, if not managed correctly, can lead to problems during the contract.
The demolition sector is one of the toughest and most challenging sectors for any plant but attachments from Hill Engineering were built with that standard in mind. Hill’s Tefra and Titan attachments were engineered for endurance, with robustness and performance built-in to guarantee efficiency, minimum downtime and above all, site safety.
The UK manufacturer has worked with many demolition specialists over the years and the expertise and experience it has gained has produced product innovations that add value to any demolition project, backed by its 360 Support programme that means operators can depend on maximum productivity from their equipment.
Since 2009, when Hill pioneered the award-winning Tefra hydraulic quick coupler, the company has continued to innovate, and now its
Tefra Connect sets new standards in site efficiency.
Tefra Connect is a revolutionary new concept that combines the ability to connect any hydraulic work tool safely and automatically, from the operator’s seat, with the versatility and functionality of the Tefra pin grabber coupler.
With a Tefra Connect-equipped excavator of 13 to 45 tonnes, operators can maximise machine use and reduce and even eliminate the need for other machines on-site, reducing machine costs, fuel consumption and transport movements.
For additional durability, Hill’s HDX Bucket, Riddle Bucket and Ripper models exploit the superb qualities of high tensile, wearresistant steels such as Hardox , Weldox and Hi-Tuf. These HDX models have a minimum 35% high-strength steel content and can be designed to suit specific applications.
A unique feature of the Titan HDX Bucket is its full-width internal secondary beam, located inside the box beam head section for extra strength and improved torsional rigidity. This bucket sports a
greater use of wear bars and drop forged wear plates to create added strength and durability.
The Tefra coupler also features this additional durability, as OEMs including Hitachi, JCB, Komatsu, Volvo and Caterpillar will testify. Hill also works closely with hire companies and end users to continually develop and improve its products to work smarter and safer, focusing on quality, innovation, reliability and safety.
Demolition’s Health and Safety record has been significantly improved in recent years by advancements in technology, with modern machinery equipped with safety features that reduce the risk of accidents.
This workplace safety was Hill’s other major consideration when designing its plant attachments. Products such as the Tefra Connect coupler enable the safe connection and disconnection of hydraulic tools such as hammers and grabs from the safety of the operator’s cab. This is particularly useful in top-down demolitions where the size of the working area can be compromised.
Complementing all of these
attachments for demolition is Hill’s 360 Support programme, which like its products, is unique in the industry. This kicks in from the moment a customer makes contact, with the Hill team using its in-depth knowledge and experience to ensure they have the right solution for their needs, and the flexibility to create bespoke options if necessary.
The Hill team then keeps the customer fully updated throughout the order and delivery process, with its strict quality control standards meaning the customer can rely on their Hill equipment to be built to award-winning standards, in addition to being durable, costeffective and safe.
Once the customer has taken delivery, the Hill after-sales team is there to keep them operational, around the clock and around the world, whether they need spares (up to 90% stock availability, with same-day delivery available), an engineer on-site, or technical advice. 360 Support is designed to minimise downtime and maximise productivity – a particular requirement for demolition.
The construction and demolition industry is radically transforming, and MB Crusher is leading the charge. With its easy-touse crushing and screening solutions, MB Crusher is turning demolition waste into a valuable resource, redefining efficiency and promoting sustainability. Give a new life to bricks, concrete and mixed demolition debris and earn from it!
Crushing the barriers to efficient material recycling
Traditionally, demolition and construction waste have been viewed as an expensive and inconvenient byproduct, requiring costly transportation and disposal in landfills. This approach strains budgets and harms the environment by increasing carbon
emissions and depleting landfill space. MB Crusher offers a gamechanging solution – crushing and recycling materials on site, right where they are generated.
By integrating MB Crusher attachments with loaders, excavators and backhoe loaders, contractors can process materials immediately, reducing reliance on external crushing facilities and haulage services. This results in significant cost savings, enhanced efficiency and a reduced environmental footprint.
Smart solutions for every job site
Whether on large demolition sites, roadworks or urban redevelopment projects, MB Crusher attachments adapt seamlessly to various working conditions. These solutions offer
multiple benefits, including:
• Cost savings: Reducing transport and disposal fees by recycling materials on site,
• Sustainability: Minimising landfill use and lowering CO2 emissions,
• Operational efficiency: Processing materials immediately, keeping job sites productive,
• Profitability: Turning waste into reusable aggregates, reducing the need for virgin materials.
MB Crusher’s machines come in different sizes and models, ensuring that businesses of all
scales can benefit from their revolutionary technology. Whether working in compact urban spaces or on vast construction sites, MB Crusher attachments are designed to deliver power and precision.
One of MB Crusher’s recent success stories comes from a demolition contractor working on a large-scale urban renewal project. The challenge was clear – managing tonnes of concrete and brick debris while minimising environmental impact. Instead of hauling waste off site, the contractor used an MB Crusher bucket to crush materials directly at the job site.
The result? A massive reduction in hauling and disposal costs, faster project completion and the ability to reuse crushed material for backfilling and new construction. This approach not only improved the project’s profitability but also aligned with the growing demand for sustainable building practices.
MB Crusher equals innovation
With years of industry expertise, MB Crusher has built a reputation for developing cutting-edge technology that meets the evolving needs of the construction and demolition sectors. The company’s commitment to research and development has led to innovations that optimise performance while ensuring durability and ease of use.
Demolition waste should not be viewed as a burden but as a resource that can be reused efficiently.
The construction industry is shifting towards more sustainable and cost-effective solutions and MB Crusher is at the forefront of this evolution. As global regulations tighten around waste management and environmental responsibility,
companies are seeking smarter ways to handle demolition debris. MB Crusher’s technology enables it to stay ahead of the curve by providing on-site recycling solutions that reduce waste and maximise resource efficiency.
The company’s range of crusher buckets, screening buckets and drum cutters ensures that businesses can find the perfect fit for their operational needs. These attachments are built to withstand even the most demanding conditions, making them an ideal investment for contractors looking to optimise their workflow.
Why choose MB Crusher?
• Versatility: Compatible with various types of heavy equipment,
• Durability: Built for highperformance crushing and screening in tough conditions,
• Eco-friendly: Reduces the need for raw materials, minimising environmental impact,
• Global reach: Trusted by contractors and businesses worldwide and available throughout the UK.
MB Crusher continues to push the boundaries of material processing technology, offering solutions that transform waste into opportunity. Whether you deal with road construction, urban development, or large-scale demolition, MB Crusher provides the tools you need to work smarter and more sustainably.
To maintain, or not to maintain, that is no question by
Doug Arnold, Aftersales Manager, Ulrich Attachments
Advances in technology and materials mean plant machinery is expected to last longer than ever these days. But while this means plant owners and operators are consequently being more proactive about maintaining those machines, sadly the same cannot necessarily be said for the attachments without which their carriers are superfluous.
A plant attachment should be able to last the lifetime of its carrier, say five to ten years, but in reality, often lasts less than half of that. Yet the repercussions of a
lack of attachment maintenance can be expensive in both downtime and parts, not to mention if the attachment failure impacts on the performance of its carrier.
Twice daily (or before and after use) maintenance of say a high tip bucket, or one with hydraulic rams, costs only a few hundred pounds a year in grease and lubricants for the pivot points. Neglecting it to the point where it needs complete refurbishment will cost anything from £3,000 to £8,000. The maths really does add up!
So why are so many plant owners/operators not embracing this aspect of their investment and identifying wear and tear before it becomes a major issue?
In today’s increasingly competitive environment, many businesses seem to operate in firefighting mode, where maintenance of their assets can get overlooked. This includes their plant operators as much as the plant itself.
You can grease a pivot joint, pin or bushing until the cows come home but if a less experienced operative is not cleaning the areas
around them before applying lubrication, dirt could become trapped, causing friction and premature wear. Hoses also need checking for leaks and fittings for loosening.
Less experienced operatives need to be aware that overloading the attachment, using it at an inappropriate angle or in an incompatible application (climate, material or terrain), could potentially lead to cracks and structural failure, with all the health and safety issues that poses.
Plant that is used by multiple operatives, rather than one consistent one, tends to suffer most. We see this particularly in sectors where operatives also work longer hours.
One way of avoiding all of this is to use attachments from a manufacturer that offers site inspections. These can be carried out by mobile engineers at intervals agreed between the manufacturer and the owner, at a cost of just a few hundred pounds. The fee covers technical measurements of the moving parts, and if necessary, replacement of worn parts quickly and effectively to keep downtime to
a minimum and machines up and running.
Manufacturers based in the UK with 100% availability of spare parts and next-day deliveries; an attachment hire fleet; trusted welding service for custom repairs or reinforcements; and refurbishment/remanufacturing and custom capabilities will complement this.
But the match point also comes at the point of purchase, so serious consideration should be given to high-quality attachments that are built to withstand heavy use and offer better durability. While they may cost more upfront, they often require less maintenance and have a longer lifespan.
Manufacturers with sales teams that look beyond the sale itself are also invaluable. These teams will drill their customers down on what the attachment is expected to do, how frequently and for how long, in what kind of environment, and whether they need features like
reinforced edges or wear-resistant coatings.
Back that up with the establishment of a regular lubrication schedule based on usage frequency which will optimise the longevity of the attachment the operator is buying. Comprehensive online and printed product guides or manuals should be regularly referred to.
Best practice is regular checks, including the replacement of hydraulic filters and fluid at regular intervals to avoid contamination. Low hydraulic fluid on attachments like quick couplers can damage seals, cylinders and motors. And just like cars, plant attachments need washing, drying and even the application of a protective coating or lubricant to metal surfaces prone to corrosion.
Storage off the ground in a covered dry area away from extreme weather conditions will also help minimise rust, corrosion and other degradation, and protect hydraulic fluids and other lubricants.
We recently saved a longstanding client the cost of a new high tip bucket by repairing their existing one. Work included shot blasting; replacing pins, bushes, bosses, cylinders and hoses; strengthening the hockey stick corner support; installing new bolts on the cutting edge plate; and hydraulic testing. All this at the fraction of the cost.
Did we take him to task about maintenance? We are pleading the Fifth!
www.ulrich.co.uk
Snapshots of Ben and the Demolition Hub team’s activities between issues
by Jonathan Davies, Industry Manager Industrial & Waste and Paving at Finning UK & Ireland
Anyone working in demolition will have seen safety improvements over the years. Increased awareness of the risks for those working on site combined with more stringent regulations have played a role. However, the application of technology both within machines and on site looks set to radically reduce accident rates. In this article Jonathan Davies explains the cutting-edge technology that will make the future demolition site safer, and why training and engagement remain the most important factors.
Safety remains a number one priority in the demolition industry. Along with our governing bodies we do all we can to ensure safety on site, however, the unique environment of demolition sites mean they are fundamentally a relatively dangerous place to ply your trade. According to the Health and Safety Executive (HSE) the construction industry sees more accidents than other sectors because of the unique challenges that come with working on site, including the risk of overturning machines, falling objects and moving vehicles – all common hazards on the demolition site.
The demolition industry is increasingly benefiting from technological advancements to reduce risks to workers. Drones are now used to survey sites, reducing the need for personnel to enter areas where height or instability might pose risks. Technologies like virtual reality are also being used for training and simulation, helping to plan and execute demolition work more safely and effectively. The most widely used innovations though are to be found in and around the heavy plant machinery.
Studies have shown that 55% of work site hazards go undetected
by those working on site. New technology added to modern heavy plant machinery now enables operators to identify hazards before they turn into dangerous situations.
The Cat® Detect system is a great example of this, enabling operators to set an exclusion zone around the machine. Using sensors and an audible alarm, the system warns the operator instantly if anybody strays into the zone.
Active Stability Monitoring is another safety feature developed by Caterpillar and is recommended for excavators used in demolition. It measures altitude and positioning
of the boom, together with load on the tool in real time and delivers both audible and visual alerts to the operator reducing the risk of the machine overturning and helping it to operate efficiently by maintaining optimal stability.
While remote control technology like Cat Command takes the operators out of harm’s way altogether. This enables machine operation with line of sight from up to 400 metres away, or with the use of cameras and a virtual cab from literally anywhere. Remote control has enormous benefits for operator safety particularly when the machine is working in inherently hazardous environments. Semi-autonomous machines are already working in the mining and docking industries for example and could play a role in deconstruction projects where working floor-by-floor involves unacceptable risks for operators.
Of course, any technology is only as good as the people using it and there is no substitute for workers taking ownership of their own safety and that of others. Remote control has huge potential for improving safety but also comes with the need for completely new safety protocols, enforced by watertight education and onsite management.
Technologies like Cat Detect and
Active Stability Monitoring need operator knowledge and compliance to access their full safety benefits. Operators must build the habit of engaging fully with the detection system from the second they enter the cab, as the most likely time for a collision is within the first few seconds of operation. They must learn to accept and trust stability alarms over their own judgement, understanding that they are responsible not just for avoiding their machine overturning, but also for reducing the statistical probability of any machine ever overturning to as close to zero as possible.
Backoffice oversight also has a role to play as telematics unlocks
the possibility to monitor everything from seatbelt use to how operators work with and respond to alarm systems. At the end of the day keeping people safe on a demolition site will always be about having the right procedures in place and making sure everyone from top to bottom cares about it enough to make sure these are followed through. If the industry can achieve that, then these new technologies have the potential to help reduce accident rates to zero.
Hyundai Construction Equipment’s HW155H hydrogen fuel cellpowered wheeled excavator concept was working on the demonstration area throughout this year’s bauma exhibition. The pre-production machine, which was first seen as a static exhibit at the last bauma in 2022, will demonstrate to customers how hydrogen could contribute to
future carbon-free operation on construction sites across Europe.
A hydrogen fuel cell uses a chemical reaction between hydrogen that is carried on board and oxygen in the atmosphere, to generate electricity, with the only emission being water vapour. The fuel cell delivers power on demand to drive the machine, either though electric motors, or
via electrically-driven hydraulic pumps.
The project to develop a fuel cell for the HW155H has been a cooperation between Hyundai Construction Equipment and Hyundai Motor Company, which has a range of powertrain solutions available in the passenger car and utility vehicle markets. Two cells have been
designed, creating 30kW and 50kW of power, with the HW155H using a combination of fuel cells to provide 70-100kW of power. These fuel cells would suit a range of machines, including the 15-tonne wheeled excavator, fork lift trucks and emergency generators.
The HW155H is a 15-tonne wheeled excavator that combines on and off-road capabilities, making it an ideal choice for hydrogen power. The machine uses the fuel cell to power an electric motor, that then drives the hydraulic system. The hydrogen storage on-board has the capacity to allow a full eight hours of operation, with refuelling taking between 10-20 minutes.
Hydrogen is a safe fuel, with an auto-ignition temperature that is higher than petrol of diesel. As it is 14 times lighter than air, it also disperses harmlessly into
the atmosphere. Hyundai has developed a world-first, innovative low pressure hydrogen storage solution, that offers high density storage for extended operating autonomy.
This will make the use of hydrogen an acceptable solution for infrastructure, civil engineering and building projects across the world. Hyundai’s high-density, solid state storage system will double the capacity of a conventional hydrogen tank, using a considerably lower filling pressure. This will optimise space within the machine, reduce fill times and improve safety on site.
The HW155H will meet the needs of a wide range of construction customers, delivering an operating speed and power similar to that of a conventional diesel-powered excavator., with all-day useability.
The construction industry is facing growing pressure to reduce its environmental impact and Hyundai Construction Equipment will demonstrate the feasibility and viability of hydrogen use within its machinery, paving the way to a more sustainable future. This has to include infrastructure and the Bauma demonstration will show a mobile refuelling solution, that would make the use of hydrogen on European construction sites in the near future a real possibility.
Hyundai Construction Equipment’s HW155H is in the running for a place among the top three nominees for Bauma 2025’s Innovation Awards, in the Climate Protection category.
www.hyundai-ce.eu
Gnat UK
One-Stop-Shop Selective Demolition Specialists for Main Contractors
• BROKK Robotic Demolition
• Aquajet Robotic Hydro Demolition
• Diamond Drilling & Concrete Cutting
• Abrasive Cold Cutting in Volatile Areas
Precision. Safety. Nationwide.
With cutting-edge Robotic Technology and unrivaled expertise, we deliver tailored solutions for complex demolition projects across the UK.
JCB Powertrain will demonstrate its leadership in the hydrogen sector with a stand built around this rapidly developing technology at the Bauma equipment fair in Munich, 7-13 April.
JCB is the first construction equipment company to develop a fully working combustion engine fuelled by hydrogen and a team of 150 engineers has been working on the exciting £100 million development for over three years.
JCB has already produced more than 130 evaluation engines which are powering backhoe loaders, Loadall telescopic handlers and generator sets. The hydrogen engine will also be suitable for applications across many industry sectors and to highlight this opportunity it will now be shown on the stand in Hall A4.115.
The company will also show a complete JCB Powertrain
model, a full assembly of diesel engine, transmission and axles. This complete driveline package, based around the company’s popular 448 Stage V engine, is available to original equipment manufacturers (OEM) as a single unit, or as individual components, to suit their specific machine requirements.
A team of engine and driveline experts from JCB Powertrain will be available throughout the
show, to discuss individual manufacturer and customer needs, from both an engineering and a sales standpoint.
JCB has also cleared significant hurdles in its development of the world’s first hydrogen combustion engine after securing landmark rulings from 11 licensing authorities across Europe allowing it to be used commercially in machines. Real-world testing of JCB’s hydrogen equipment on customers’ sites is now at an advanced stage and progressing well.
www.jcb.com
Among Komatsu’s 13 premieres is the all-new, PC220LCi-12.
Building upon Komatsu’s decade of experience and millions of operating hours in integrated machine control technology, this excavator offers customers new, completely unique, iMC 3.0 features. In addition to setting new standards of productivity and efficiency, the machine benefits from a completely new cab design focused on maximising operator comfort, and seamless connectivity solutions make digital jobsite transformation even easier.
Another highlight was the new Dash 11 wheel loaders WA47511 and WA485-11, developed by Komatsu Ltd. and manufactured at Komatsu Germany GmbH –Construction Division (Hannover). These two new models are packed with unmatched power and fuel efficiency, enabled by a powerful, high-torque engine with
an HMT transmission. The wheel loader also features significantly increased payload and bucket capacity, meeting EU Stage V emissions standards with a longlasting diesel particulate filter. The cabin is spacious and ergonomic, equipped with adjustable controls, and an air-suspended seat.
Looking at larger class wheel loaders, after a decade of development the reinvented WA700-8 was on show. Komatsu promises that this gentle giant will excite any operator with its comfortable cabin, unparalleled levels of safety, unrivalled power and stability, substantial load capacity and bucket volume, and impeccable environmental credentials.
Also presented were a new four-tonne skid steer loader and five-tonne compact track loader. Both machines deliver one of the highest operating capacities in the
category, merged with superior lifting capacity, breakout and traction force, meeting the evolving needs of our customers.
Every Komatsu machine comes with absolute peace of mind for their customers thanks to the comprehensive support solutions that ensure you get the most out of your investment. From proactive maintenance through service agreements and personalised support via the CARE program, to extended warranties and the availability of genuine parts, lubricants, and GET (Ground Engaging Tools), Komatsu offers a complete suite of services. Visitors learned more about costeffective REMAN components, the predictive power of KOWA oil analysis, and specialised undercarriage solutions for tracked models.
A lineup of electric machines, including the proven performer PC33E-6 as well as the preproduction PC20 Electric and PC26 Electric, was in live demo show ins Hall C6. Sharing the spotlights were the market pilots PC138E-11 and PC210LCE-11, joined by a few cutting-edge concept machines. With the indoor live demo featuring exclusively electric machines, customers can
perfectly experience the benefits of the electric drivelines: quiet, low vibrations and zero emissions.
Komatsu understands that integrating electrified machines into your workflow can bring new considerations. That is why Komatsu joins forces with industry leaders, including at bauma 2025 to showcase cutting-edge electric charging solutions, powering the future of construction. This is a great opportunity to connect with Komatsu’s electrification experts and explore how their innovative technologies can support your green transition.
As the industry has come to expect, Komatsu is synonymous with technology and customers will have the opportunity to experience their latest software and hardware innovations in
Komatsu’s dedicated space to digitalisation, where Smart Construction, Smart Quarry, and a full suite of telematics solutions will be showcased. By offering scalable and adaptable digital solutions, Komatsu continues to set the benchmark for innovation in these sectors, ensuring that businesses of all sizes can optimise performance with data-driven decision-making.
Smart Construction took centre stage, introducing several products designed to improve site operations. One of the key highlights will be the expanded compatibility of the 3D Machine Guidance system. Smart Construction will also present their 2nd generation Edge, featuring a refined object removal function with artificial intelligence.
Another major highlight was Smart Quarry, an OEM-agnostic solution to follow-up and manage the entire quarry operations.
Developed in partnership with MHI Group in Germany, the first installation is currently being deployed on a mixed fleet of machines.
Their telematics experts will also be present and are happy to provide attendees on how to leverage machine data to maximise equipment potential and optimise operations. From realtime monitoring and predictive maintenance to advanced analytics, Komatsu’s telematics solutions provide valuable insights that drive productivity, reduce downtime, and improve efficiency.
And for the first time at bauma, Komatsu showcased how they are tackling some of the world’s most demanding environments, from the depths of the ocean to the vastness of space.
www.komatsu.eu/en
Reinforcing its position as an industry pioneer at BAUMA 2025, LiuGong presented groundbreaking products designed to enhance efficiency, sustainability and performance in the toughest applications, unveiling cutting edge advancements in batteryelectric vehicles (BEVs), next generation T-Series wheel loaders and intelligent total solutions. Among these innovations was the world’s first 24-tonne electric surface motor grader, the 4280DE, a machine that redefines sustainability in the earthmoving sector and exemplifies LiuGong’s leadership in BEV technology.
LiuGong showcased 13 models across five product lines – wheel loaders, excavators, mining trucks, dozers and graders, including five new battery-electric models. Machines were tailored to address key application sectors of quarry and mining and demolition and recycling.
The world’s first 24-tonne surface all-electric motor grader, the 4280DE is designed for quarry haul road maintenance with an 8–10hour runtime from its 423 kWh battery. Developed in conjunction with customer feedback, this machine is optimised for power, precision and sustainability, seamlessly integrating into electric fleets.
The 870HE is a groundbreaking electric wheel loader, setting new
standards in sustainable heavy machinery. With its 423 kWh battery, operators can achieve 7-9 hours of uninterrupted zeroemission performance, making it a game-changer for demanding applications. Fast-charging technology enables a 20-100% charge in just 90 minutes, ensuring minimal downtime and maximum productivity.
The mining truck DR50CE delivers exceptional efficiency with its direct-drive electric motor, which reduces transmission losses and maintenance costs while maximising productivity. With a 45,000 kg payload and a 35m3 heaped capacity, it ensures near zero energy consumption on 6-8% gradients downhill hauling, thanks to regenerative energy recovery.
The new electric excavator 924FE, equipped with a highlift cab, brings Liugong’s proven performance in demolition, waste and material handling into the electric era. Unlike tethered cable systems, this battery-electric excavator delivers 7–10 hours of zero-emission power per charge – making it ideal for waste sorting barns and environmentally sensitive sites without compromising on strength, reach or productivity.
The 9018FE is a compact electric mini excavator designed for
internal demolition and urban applications, reducing carbon emissions and noise pollution. Despite its compact size, it packs a powerful lithium iron phosphate battery, delivering up to 4.5 hours of normal-duty operation, making it an essential tool for lowemission job sites.
T-Series loaders, designed by and for European customers LiuGong, recognised as the global leader in wheel loader production, unveiled its next generation T-Series Wheel Loader range, a product of six years of customer feedback and refinement. This new lineup is built to meet the evolving needs of European operators, delivering unmatched efficiency, durability, and operator comfort.
As the flagship model of the T-Series, the 890T has undergone over 20,000 hours of rigorous testing, ensuring exceptional reliability and efficiency. With a load capacity of 10,500 kg and a 5.4 m3 bucket, it offers enhanced fuel efficiency, increased operator comfort, and total maintenance access, making it the ideal choice
for demanding mining and quarrying applications.
The 842T is a versatile, nextgeneration wheel loader designed for construction, waste management, and agriculture. It features an advanced operator interface, programmable attachment settings and an integrated weight-load system. Over-the- air software updates further optimise performance, ensuring maximum efficiency in demanding applications.
A heavy-duty 75-tonne class excavator, the 975F has been tailored to the needs of European customers, offering unmatched durability, efficiency and operator comfort. It features LiuGong’s latest F-Series cab, enhancing visibility and control, making it an industry powerhouse in demolition and quarrying applications.
Tough applications need tough equipment: Demolition focus LiuGong strengthened its leadership in the demolition sector, unveiling factory-ready solutions that deliver unmatched power, precision and efficiency. Designed for high reach, precision and safety, LiuGong’s demolition lineup showcased industry-first innovations.
The upgraded excavator 909ECR series-2 has been designed to optimise performance for European operators. It has 30% increased hydraulic flow for improved multi- functioning in demanding applications. The two-piece boom enhances loading performance and versatility, while an extended undercarriage and an additional 350 kg counterweight provide stability for tilt-rotators and heavy attachments.
A powerful machine for demolition, the 933F DM features an 11.3-m pin height, making it ideal for high-reach applications. The factory-fitted tilting cab, capable of 30-degree tilt, provides enhanced visibility and control, while F-Series upgrades such as an improved seat, 10” display, 360° lighting, and DAB radio further enhance operator comfort.
A dominant force in quarrying and demolition, the 995F weighs in at just over 95 tonnes and has been widely adopted across Europe, with over 10 units already in operation with demolition customers, working on bridge and power stations projects. Known for its exceptional power, high-reach capabilities and tough performance, it is a top choice for processing applications and largescale demolition projects.
A concept machine designed to gauge market interest, the 9017F DM brings tried-andtested remote control technology to demolition and hazardous environments. With both batteryelectric and diesel solutions available, LiuGong is actively refining this technology through customer feedback, aiming for market introduction within the next two years.
www.liugong-europe.com
At Bauma 2025 CASE Construction
Equipment is introducing a range of products designed to meet the evolving needs of today’s job sites. With over 180 years of industry experience, CASE is pushing the boundaries, to deliver machines that improve operator comfort, increase productivity, and drive sustainability.
“Innovation is our foundation,” states Fabrizio Cepollina, Vice President CE EMEA Region & Global Alliances. It’s ingrained in our DNA. Since 1842, innovation has been our driving force, ensuring our continued vitality. For CASE, innovation means delivering practical, impactful solutions, products and services, that directly enhance our customers’ businesses.”
For customers seeking a reliable, versatile wheel loader, the CASE 421G is a game changer. Perfect for material handling and construction tasks, this 72 kW machine combines impressive power with operator comfort, to make even the toughest jobs easier.
The operator’s cab features a large, glazed area, a low front console and a standard rearview camera, offering exceptional visibility and improved safety. Seat-mounted controls and an ergonomic design reduce
fatigue during long shifts. The driveline features a ‘shift-on-fly’ transmission, specially designed for industrial machinery that requires a high tractive effort with a seamless transition between ratios.
The CASE 1021G+ X-DRIVE represents the next generation of large wheel loaders, combining the new “G+” Series operator cabin upgrades and a Continuously Variable Transmission (CVT) to optimise fuel efficiency, productivity and safety.
The CVT reduces fuel consumption and operating costs, while maintaining high performance. The machine’s intuitive touchscreen display and adjustable traction force allow operators to customise performance for every task boosting efficiency. A new premium seat, with heating, ventilation and a three-point seatbelt, rear object detection system, heated and electrically adjustable rear-view mirrors, along with new Click&Dig automation features, minimise operator fatigue and maximise comfort and productivity.
The CASE 580SV Evolution backhoe loader is designed for customers who need power,
speed and precision in a compact, versatile package. Built for versatility and performance, it boasts advanced features that improve operator comfort and efficiency.
New features include an automatic Direct Drive transmission, that locks the power of the engine output directly to the transmission, for increased gradeability and acceleration, while providing lower noise levels in the cab. A comfort steering system requires minimum operator effort, reducing fatigue over the working day. In addition, a new brake enabled idle function mirrors travelling with a cruise control system. The machine also features faster travel speed and new Power Boost and Power Lift functions, to maximise productivity. Improved radiator access allows easier cleaning and maintenance.
The new CX38D, the 20th model in an impressive range, is the perfect solution for customers looking for precision and versatility in a compact excavator. Whether working on residential projects or commercial sites, the CX38D delivers the ideal balance of power and comfort. The compact design allows for precise movement and great manoeuvrability in tight spaces, making it perfect for urban work. Electro-proportional
auxiliary controls and Hemisphere Machine Guidance make the CX38D incredibly adaptable, ensuring a wide range of tasks can be tackled with ease and precision. Hemisphere’s GNSS technology provides real-time positioning and machine tracking, helping optimise job progress and minimise material waste.
CASE offers a range of zeroemission electric models. These machines provide the same high performance as their diesel counterparts, but with no tailpipe emissions, reduced noise and fast recharging times. Electric drivelines provide instant torque, for superior operating power, with up to eight hours of autonomy. Fastcharging capabilities ensure all day productivity can be achieved. Electric machines can be operated in noise-sensitive zones, such as residential areas, schools, hospitals and during night time hours
and they can help customers to tap into new markets, qualifying for zero-emission tenders and earning environmental credits that enhance a business’s reputation.
The CX210ZQ, built in cooperation with MOOG, is a full-size electric excavator. Using an innovative ZQUIP modular battery system allows rapid battery swapping, to keep the excavator operating with minimal downtime and delivering powerful performances. This would allow operators to maintain working patterns throughout the day, boosting productivity on a range of job sites.
The service and product offerings we showcase at Bauma 2025 combine innovative tech solutions developed by our R&D team with the expertise provided by Raven and Hemisphere companies.
Our collaboration with MOOG, for advanced electric battery
systems, and GRAVIS ROBOTICS, for cuttingedge digitalisation and automation technologies, including autonomous heavy vehicle development, shows our commitment to delivering practical, future-ready machinery. These companies focus on electrification, digitalisation and automation.
Tailored solutions with Sampierana Special Applications CASE has developed a Special Applications division within Sampierana. Here, the company can build tailor made machines to meet specific customer requirements. This includes the CX135E XRD, the world’s most compact, high-reach demolition excavator. Capable of operating with a 700 kg crusher at a height of 13 metres, the machine has a retractable undercarriage and is able to operate in the tightest site conditions.
The division has also created a CX24D mini excavator with two-piece boom, also present on our bauma stand. This delivers superior lift capacity and extended digging capabilities, without compromising the overall compact dimensions of the machine. This machine will further enrich CASE portfolio, the widest mini and midi two-piece boom excavator range in the world.
At bauma, Develon is revealing two new -9 smart heavy crawler excavators at a special ceremony on the company’s stand. The 23 tonne DX230LC-9 crawler excavator is part of the static display and the 26 tonne DX260LC-9 model is showing its paces in the demonstration area throughout bauma.
With the -9 range, Develon is aiming to set a new standard for future products and technologies in construction equipment. Like all -9 models, the DX230LC-9 and DX260LC-9 models achieve this goal by combining 10 groundbreaking technologies and will redefine and set new industry levels of Productivity, Safety, Operator Convenience and Sustainability. The -9 range not only endorses the company’s forward-thinking vision but also underscores Develon’s unwavering dedication to innovation and excellence in the construction equipment sector.
Develon has integrated cuttingedge innovations into every aspect of the new -9 models, refining both overall product design and essential functionalities. These advancements enhance daily operations with significantly increased performance, reduced fuel consumption, and ensure industry-leading uptime. The improvements can be categorised into four key areas:
• Safety and smart features
• Operator convenience and cab comfort
• Increased productivity and efficiency
• New product design
Safety and smart features
The Smart All-Around Viewing Monitor (SAVM) is an AI-based Object Detection technology to effectively identify both moving and stationary individuals in close proximity to the machine. Upon detection, the system promptly alerts operators through a combination of visual signals and audible alarms on the monitor, ensuring a heightened awareness of the surrounding environment.
The Advanced Lift Assist system provides clear and immediate visibility of the machine’s tip-over possibility, serving to mitigate accident risks and keep the operator focused on driving.
The innovative E-Stop and Virtual Wall functions prevent accidents the operators are not aware of. To help ensure safety, the area surrounding the machine is clearly defined into specific zones: a yellow warning zone (Zone 2) and a red danger zone (Zone 1).
The SAVM and E-Stop system utilise 6 cameras and 3 radars and work in 3 stages with a detection range of 13 m and 330°:
• People detection from 13 m range,
• Warning and slowing down the speed from 6 m,
• Stopping the machine from 3 m (swing and reverse).
The E-Stop is an essential safety
feature designed to control or halt a machine’s movement, such as driving or swinging, in cautionary or dangerous areas, thereby ensuring operator safety.
The Virtual Wall feature significantly enhances operation by allowing users to confine the machine’s movement within predefined areas where the risk of collision may be heightened. This is especially useful in tight urban or underground sites with obstacles like wires and pipes, ensuring safer operations.
The -9 machines feature an ergonomically designed user interface that enhances ease of use. It includes a thoughtfully arranged keypad, a jog shuttle and a monitor that is easily accessible, among other features. One standout aspect is the wide and intuitive 12.8-inch monitor, available in dual configurations for diverse needs. Additionally, the machine comes with a comfortable seat that has a built-in cooling function, as well as a cab designed for improved visibility, providing operators with best-in-class convenience.
Develon provides customised solutions through its FEH (Full Electric Hydraulic) system on the -9 models. The operation and control of these machines can be fine-tuned, according to the unique characteristics of different workspaces and user preferences. This personalisation maximises
both efficiency and comfort, allowing operators to access optimised settings even when multiple individuals utilise the same equipment.
Operators have tuning options and can customise joystick sensitivity and more to match their driving habits and job site needs. Develon’s solutions ensure a comfortable, precise, and efficient machine handling experience for a variety of attachments and work styles.
One of the standout features of this service is the Digital Key, a sophisticated Bluetooth combined with high speed Ethernet network (5G) communication-based tool that empowers users to unlock the cab door, ignite the engine and adjust the air conditioning settings from the MY DEVELON app, all without the need for a physical key. This remote-control functionality allows for efficient management of the machine from a distance.
Furthermore, the platform enables users to view and analyse operational history, aiding efficient equipment management, especially in fleet or rental scenarios.
Compared to the previous -7 models, the new -9 machines provide a 12% increase in productivity and an 8%
reduction in fuel consumption. This enhancement is primarily attributed to the powerful output of Develon’s self-developed engine, which significantly boosts digging power and lifting capacity.
The incorporation of a Full Electric Hydraulic (FEH) control system—featuring electronic pumps, electronic Main Control Valves (MCV), and electronic Relief Control Valves (RCV)—has resulted in fuel savings of between 1700 l (for the DX230LC-9) and 2700 l (for the DX260LC-9) for every 1500 hours of operation compared to earlier models. In addition, the new -9 generation machines offer unparalleled lifting capacity and machine stability within their categories.
The implementation of Develon’s cutting-edge, in-house developed technologies, such as 2D Machine Guidance and Smart Control functions, enhances productivity by helping operators perform their tasks more easily and safely, reducing both time and costs. Additionally, these features are designed specifically for Develon machines, delivering economical and effective solutions.
The innovative Breaker Assist technology prevents blank firing, which helps protect the excavator and its components while minimising operator fatigue, leading to increased productivity.
Additionally, the Auto Breaker function allows operators to perform breaking seamlessly without the need for continuous button pressing, further reducing operator fatigue.
The Weighing Assist system is designed to accurately monitor production levels and manage volume, ensuring that dump trucks are loaded to their appropriate capacities. By effectively addressing the problem of overloading, the system enhances road safety and streamlines the operational processes previously required for weight compliance, ultimately leading to increased productivity.
The new -9 models are equipped with Develon’s advanced Prognostics and Health Management (PHM) technology. This technology continuously monitors key components like hydraulic oil, engine oil, pumps and motors, enabling timely predictions and proactive maintenance.
The external design truly encapsulates Develon’s vision of SMART construction equipment. Notable features include the industry’s first welcome light, strategically placed horizontal beacon lamps at the four corners of the cab’s upper surface, and signature lighting that adapts to the work environment by changing colour.
Additionally, the counterweight in the new design powerfully embodies a straight line, the Linear Core, serving as a design element that reflects Develon’s heritage of being both ‘refined and dignified’ as well as ‘stable and reliable’ to the company’s customers. www.eu.develon-ce.com
Hyundai Construction Equipment Europe has been awarded second place in the coveted bauma 2025 Innovation Award in the Climate Protection category. The award recognises the potential environmental contribution of Hyundai’s HW155H hydrogen fuel cell powered wheeled excavator concept, which was a stand-out
star throughout the show in Munich in April.
The HW155H provides a clear direction of travel for construction machinery powered by clean hydrogen fuel cell technology. Developed in cooperation with Hyundai Motor Company, a leader in the fuel cell field, the machine is equipped with a single fuel cell
that generates 90 kW of electrical energy. This powers an electric motor that in turn drives the machine’s hydraulic system.
As well as demonstrating how a hydrogen fuel cell can be used to power construction machinery, Hyundai unveiled a groundbreaking high-density metal hydride solid hydrogen storage
system. This low-pressure storage solution provides the machine with up to 12 hours of operating autonomy and can be refuelled in a similar time to a conventional diesel tank.
Alongside the HW155H, Hyundai also demonstrated a hydrogen refuelling solution, based on a hydrogen fuel-cell powered road going truck. Capable of refilling multiple construction machines at the same time, this mobile refueler showed customers how the technology could be easily adopted on remote construction projects.
The construction industry is facing growing pressure to reduce its environmental impact and, with the HW155H and its refuelling solution, Hyundai Construction Equipment has demonstrated the feasibility and viability of hydrogen use within its machinery, paving the way to a more sustainable future.
Peter Sebold, Product Manager at Hyundai Construction Equipment Europe said: “We are delighted that the bauma judging panel has recognised the potential of our hydrogen fuel cell technology and the part that the
HW155H and other machinery will be able to play in delivering a zerocarbon solution for construction sites across Europe.
“To actually have the HW155H and the hydrogen refuelling truck operating on our stand at the bauma fair was a massive attraction for visitors, while customers and dealers were fascinated to see how this emerging technology could play a vital role in the construction equipment of tomorrow.”
www.hyundai-ce.eu
The National Demolition Association (NDA) welcomed more than 1,300 attendees to Demolition New Orleans, held from 5 March for four days of networking, industry innovation and top-tier professional development. Among the packed agenda of events, a standout component was the robust lineup of education sessions, reflecting NDA’s ongoing commitment to promoting safety, workforce development and industry excellence.
Three sessions in particular highlighted the depth and diversity of NDA’s educational programming – ranging from technical insights to cultural shifts within the demolition workforce. Here’s a closer look at those sessions and what attendees took away.
In a powerful session, Colleen Loredo, CIH, CHMM, CPESC, Director of Environmental Services and Occupational Health at Independence Excavating
Inc., offered a crash course on the foundational principles of Industrial Hygiene (IH) tailored to demolition professionals. Loredo walked attendees through a five-part approach to safeguarding workers’ health on the job site:
• Anticipation: Proactively identifying potential hazards – like asbestos, lead and PCBs –based on building materials and site history,
• Recognition: Performing thorough inspections to uncover visible and hidden risks,
• Evaluation: Using tools such as air sampling and biological monitoring to assess worker exposure and inform mitigation strategies,
• Control: Applying the hierarchy of controls – from elimination and engineering controls to PPE – to manage risk effectively,
• Confirmation: Routinely verifying the effectiveness of these controls through monitoring and worker health surveillance.
The session reinforced that industrial hygiene isn’t just a compliance issue; it’s a cornerstone of safety culture. Loredo’s message was clear – an effective IH programme can significantly reduce health risks and help ensure a safer environment for workers and surrounding communities.
One of the most impactful sessions of the conference was also one of its most personal. The “Lessons Learned” panel brought together demolition professionals from different companies to talk candidly about mistakes, missteps, and the valuable safety lessons those experiences yielded. Panellists included Frank Bodami of Total
Wrecking and Environmental LLC; Doug Thomas of Independence Excavating Inc.; Cassie Dumoulin of Burns and McDonnell; and John Satterwhite of ROMCO Equipment Co. and Chair of NDA’s Safety Committee.
Openness matters: The demolition industry benefits when companies break down competitive silos and openly share safety challenges and learnings,
• Changing the narrative: Admitting to mistakes doesn’t indicate weakness – it signals growth, maturity and a commitment to continuous improvement,
• Powerful real-world stories: Panellists shared raw, honest accounts of projects that didn’t go as planned. These stories resonated deeply with the audience, reinforcing how quickly things can go wrong –and how much can be learned in the aftermath,
• Mentorship through storytelling: Sharing lessons learned isn’t just about peer learning; it’s a key method of training the next generation,
• A call to action: The session concluded with a powerful challenge – speak up. Every demolition professional has a story that can help someone else stay safer.
In a field where safety is paramount, this session underscored the importance of creating a culture of vulnerability, reflection and shared responsibility.
NDA education highlights
This session served as both a tour and a testament to NDA’s growing suite of educational programmes,
designed to meet the needs of professionals across every career stage. As speakers noted, with no university programmes [in the US] dedicated to demolition, NDA’s training is filling a critical gap. Speakers included Steve Schwartz of H&K Group Inc., Greg Menen of Mendil Enterprises Inc. and Brian McKinney of Gayanga Co. Attendees were introduced to several cornerstone programmes:
• Hands-On Equipment Maintenance Course: A half-day programme aimed at field technicians, focusing on practical equipment maintenance and best practices,
• Superintendent Boot Camp: An intensive, pre-convention, one-day course covering everything from preplanning and documentation to communication and equipment management,
• Foundations of Demolition Management Certificate Programme: A four-course, 40hour programme that includes training in estimating, project management, cost tracking and risk management – with upcoming sessions scheduled
for April and autumn 2025 in Washington DC.
• NEW: Demolition Methods, Planning and Design Course: A one-day course launching in June that introduces the engineering concepts behind demolition, from structural behaviour to safe planning practices – offering CE credit and a strong educational foundation (though not a replacement for engineering licensure).
The session not only walked through the logistics of each course but emphasised why these programmes exist – to elevate the professionalism of the demolition industry, reduce risk and open doors for new talent.
The educational sessions at Demolition New Orleans highlighted how NDA is leading the charge when it comes to workforce development, technical expertise and safety in demolition. Whether through sharing hard-earned lessons, mastering IH fundamentals or engaging with new training opportunities, attendees left New Orleans with valuable knowledge – and a renewed commitment to their craft.
Europe’s biggest demolition conference brings together 114 exhibitors and over 1,200 attendees events
Over many years, FACHTAGUNG ABBRUCH has established itself as the most important event in the demolition, recycling and pollutant decontamination industry. Once again the event, organised by the German Demolition Association (DA), featured an impressive industry exhibition, renowned speakers and countless networking opportunities. More than 1,200 attendees from across the industry made their way to the STATION-Berlin. The event attracted not only national but also international experts, who were inspired by the latest innovations and trends.
In his opening speech, DA Managing Director Andreas Pocha warmly welcomed the attendees and expressed his delight at the once again exceptional response. This year, the entire conference programme was held under the central theme of “Quality in demolition”. Pocha emphasised that high quality standards are essential in all areas of the demolition industry today. “Quality standards in new construction are always preceded by equivalent quality in demolition. We know how to do it,” concluded the DA Managing Director.
Twelve professional lectures by leading industry experts shaped the programme of this year’s event and offered attendees in-depth insights into current trends and challenges. Kristina zur Mühlen, TV presenter and physicist, hosted the entire lecture programme. After each presentation, attendees had the opportunity to ask speakers questions via an online tool.
Wolfgang Grupp, the keynote speaker at this year’s conference and owner of
TRIGEMA, is an impressive example of entrepreneurial success and is known for his clear and unambiguous words. Attendees were eager to hear his perspectives on the topic of “Quality in Germany – responsibility and performance of entrepreneurs in Germany” and they were not disappointed. He argued that the personal responsibility of entrepreneurs and the liability of decision-makers must be brought back into focus. Especially in difficult times, Grupp said, it is crucial for entrepreneurs to act as role models for their employees and to always safeguard the workplace. With personal insights from his own history, including memories of competitive challenges, Grupp made it clear that long-term success and quality can only be achieved through consistent responsibility, hard work and above average quality standards.
Markus Rost from Constructre GmbH then gave a presentation on the importance of good preliminary planning and emphasised why this can make a significant contribution to minimising risk in demolition projects. Rost presented new tools that have been further developed for the creation of demolition planning and showed how a systematic approach can increase efficiency and safety in the demolition process.
Another progressive presentation dealt with the topic of “LEAN Construction”, a project management approach that promotes a culture of collaboration in (re)construction projects. The focus is on an efficient organisation in which everyone involved works closely together to optimise processes and make the demolition
of buildings and facilities smooth and resource-efficient. Using the BMW engine plant in Munich as a practical example, speakers Gregor Scherleitner and Stepan Steinberger from PORR Becker Abbruchtechnik GmbH presented the process.
How to find a qualified demolition company was discussed by Dr Klaus Konertz from Umtec, noting that the cheapest provider is not always the best. Demolition companies should be selected according to criteria such as professional competence, membership of demolition associations and possession of the RAL quality mark, as these characteristics indicate a high level of quality.
Targeted material flow management, as Louis Delker from LD Umwelt GmbH concluded in his presentation, can unleash enormous potential and lead to a more sustainable use of resources. Thomas Mandrysch from PreussenElektra GmbH shed light on the challenging topic of power plant dismantling. In these projects, it is essential for demolition companies to work with the utmost precision and care, similar to the operation of a nuclear power plant.
When summing up the Recycling Congress, which was recently held on the initiative of the DA, Michael Weiß, Chairman of the Recycling and Waste Management Committee, came to the conclusion that recycling works – but only if the regulatory obstacles are removed. The criticism of popular but ineffective niche solutions from politicians was clear. The industry itself must become active to increase the recycling rate in real terms and not just on paper.
Another important item on the agenda was the handling of materials containing asbestos. Andreas Fricke from Balance Ingenieur – und Sachverständigengesellschaft drew particular attention to the need for appropriate health care in connection with the Hazardous Substances Ordinance and waste legislation in order to ensure the safety of workers. According to Fricke, the obligation to initiate work in the Hazardous Substances Ordinance is indispensable and its deletion is to blame for the fact that clients are now left alone with the risk assessment.
In an exciting presentation on the blast of the power plant in Ensdorf, it became clear that the key to success lies in cooperation. Blasting can only be carried out successfully and safely if everyone involved works hand in hand. This was emphasised by Janina Frias from Arcadis Germany GmbH, Clarissa Rapps from Wölfel Engineering GmbH and Michael Schneider from Richard Liesegang GmbH.
Dieter Schnittjer from the German Construction, Environmental and Mechanical Engineering Association (VDBUM) emphasised in his presentation how important it is for contractors and customers to have the same level of knowledge. Targeted further training can help project managers in public administration in particular to build up skills. This contributes significantly to the promotion of efficient construction processes
The more homogeneous the demolition, the higher the recoverability – this was the conclusion reached by Christian Pöppel from KRO Kiesgruben Rekultivierung Oberbayern GmbH
in his presentation on New opportunities for RC recycling thanks to the new DIN 1045-2.
Which blasting variant is used for which wind energy plant? Johannes Hubrich from Regrata Abbruch und Recycling GmbH answered this question in his presentation, concluding with a presentation on the theory and practice of such blasting demolitions and highlighting the advantages and disadvantages of this dismantling method.
The conclusion was clear. The best solutions are created when all those involved work together, contribute their expertise to the joint process and focus on high quality standards at all stages. The presentations at the FACHTAGUNG ABBRUCH 2025 showed that the challenges of the industry can be mastered through innovation, cooperation and responsibility – for a safe and sustainable future in demolition and recycling.
After an intensive day, the dialogue evening was the perfect opportunity for the conference participants to reflect on the day. The event was accompanied by videos of the sponsors and initial photo impressions of the day. In a relaxed atmosphere, there was another opportunity to make contacts and exchange ideas with potential business partners, with the trade exhibition remaining open.
The impressive number of trade visitors illustrates the importance of the conference and the growing interest in the latest developments presented here. The atmosphere was characterised by lively exchanges, exciting discussions and a variety of networking opportunities, which provided participants with new perspectives and valuable contacts.
FACHTAGUNG ABBRUCH 2026 will once again take place at STATION-Berlin on March 13, 2026.
www.fachtagung-abbruch.de/en.
The path to profitability – Gain a competitive edge with efficient, state-of-the-art hydrodemolition technology
by Keith Armishaw, Business Development Manager, Aquajet
Technology is constantly changing and at an accelerated pace. It no longer takes centuries or decades for new advancements; sometimes, technology is out of date in mere years or even months. Think of buying a new car, for example.
Today’s models have a list of new features, such as built-in wireless cellphone networks and automatic lane changing. These features weren’t even thought of by the average consumer a few years ago.
The same holds true for hydrodemolition equipment. Contractors are no longer going against jackhammers and hand lances, but rather the latest hydrodemolition advancements. While older models still run and are faster and more effective than handheld tools, new hydrodemolition technology offers far more functionality. And the benefits are anything but trivial. Recent advancements shave off time and provide better results, which ultimately gives contractors who adopt new technology a strategic opportunity for growth, innovation and improved results.
On the surface, it may not seem like significant changes have been made to new equipment, but what is the cost of not knowing? By embracing the latest hydrodemolition technology, contractors can unlock a new level of productivity, precision and profit. Rather than just keeping up with the competition, they can set the pace of their industry. Modern machines open the door to a superior standard of work, allowing contractors to confidently take on new projects.
Many contractors worry about making the leap to new technology, but with user-friendly features and an intuitive design, today’s hydrodemolition robots are easier than ever to operate. Dedicated support and training are also
available to ensure the entire crew feels confident and capable. Older machines, which have fewer automated functions, tend to require more operator experience and intuitive understanding to initially get the settings right. Modern machines’ settings paired
with a supportive manufacturer make it far easier for an operator with basic training to confidently run equipment.
With a state-of-the-art operating system, users can set parameters tailored to the specifications they need to remove concrete and save those presets for future use. Storing these parameters also provides a good point of reference for reviewing the machine’s production after a job and where potential adjustments could be made. Should the machine’s parameters require any tweaks, it can be as simple as fine-tuning the settings. With older systems, some changes required an operator with years of experience who knew how to make small, nonspecific adjustments.
Some new machines also allow users to say goodbye to manually keeping maintenance logs. Modern machines present clear, easy-to-understand error messages should a problem occur, slashing potential troubleshooting time.
Implementing any change to an equipment fleet will have a learning curve, but thankfully, modern technology is designed to make the transition as seamless as possible. With user-friendly interfaces, preset parameters and easily accessible training materials, contractors and their teams can quickly adapt, turning the challenge into an opportunity for growth and development.
For most of the hydrodemolition industry’s 30-plus years, simply being able to execute hydrodemolition was enough to qualify as cutting edge. Controlling a water jet through mechanical means was a safer, faster, more sophisticated way
to remove concrete compared to a jackhammer or hand lance.
Fairly recently, manufacturers introduced robots with a new lance movement to the market. They harness the benefits of both the oscillating and rotating lance movements. The result is a water jet that moves back to front and right to left. If the lance was holding a pen rather than shooting water, it would create a figure of eight, or infinity, pattern.
The infinity pattern creates constant oscillation speed that results in greater production. Furthermore, it creates a rough but even result and virtually eliminates pipe holes, leaving behind the ideal bonding surface. Creating the perfect profile for superior bonding strength results in repairs that can last up to three times longer. This will please project engineers and prevent the job from being held up by subpar results.
Users can also adjust the machine to fluctuate speeds in different zones of the work area for deeper or more shallow removal where needed. This is another
efficiency-enhancing feature, allowing operators to complete the removal in a single pass. For example, if the job requires removal 10 cm deep for the first half of the pass and 5 cm for the other section, the operator can set zones to accomplish this in one go. Operators can also set new machines to cut in a variety of shapes. So, the triangle shape left over from something like a bridge joint no longer needs to be removed manually by jackhammers or hand lances.
When an operation implements a machine that uses the infinity pattern, they’re making the most efficient use of all the force at their disposal. Contractors using equipment with an infinity pattern will typically increase efficiency by 15 to 20%, depending on the scope of the work. With the proper settings and depending what settings are changed, that number could increase to 50%. This can save significant time and money for things such as fuel if contractors can complete the project that much faster.
This represents state-of-theart engineering with precision and control previously thought unattainable. Contractors and their crews can take pride in knowing they are using the most advanced, efficient and powerful tools available to set a new standard in their industry.
Modern hydrodemolition machines’ components have more functionality for improved performance. For example, today’s hydrodemolition robots have a sensor in their hoist systems to set the height of the hood, eliminating the need for operators to manually check. While some may think additional elements increase the likelihood of breakdowns, that isn’t the case. Components in new machines are designed to last and require less attention. Rollers, for example, had to be tightened daily on old machines. Today’s rollers use more components, are preset and much more durable, allowing operators to approach them with a set-it-and-forget-it mentality.
It took time for the sensors equipped on new hydrodemolition robots to catch on and be more accepted, but they’ve made great strides in terms of reliability. They’re well-sealed mechanisms and handle stress from operation well, meaning far less upkeep. Previously, if a sensor was tied to a cable and the cable needed to be replaced, the sensor did, as well. With optimised sensors, one can simply replace the cable and get back to work. New and improved components in today’s equipment give contractors a competitive advantage by helping minimise downtime and keep projects on track.
Speaking of tracks – those can impact a project’s quality and efficiency. Take a bridge job, for instance. Sometimes, operators will have to drive the machine up to a 100 metres to the work area. New track systems allow the hydrodemolition robot to travel 50 metres per minute opposed to 30 with an older machine. The modern track systems also provide a smoother ride, reducing wear on the machine and increased stability during operation.
Adopting new technology seems like a significant step, but it’s important to consider the long-term benefits of reduced
maintenance costs, more reliable equipment, faster project turnaround times and an easier route to profitability.
Modern machines produce optimum results
Investing in new technology can seem unnecessary if you have equipment that still gets the job done. But hydrodemolition contractors are no longer competing with jackhammers and hand lances. They are competing with new hydrodemolition technology that is rapidly building on yesterday’s advancements, allowing those who invest to achieve better results faster and easier. Upgrading to today’s
equipment isn’t just about staying with the pack, it’s about paving the way and becoming a leader in the field. Contractors adopting the latest technology invest in their team’s success and company’s future by maximising their potential.
Keith Armishaw is the business development manager for Aquajet’s North American subsidiary. He has more than 25 years of industry and leadership experience.
keith.armishaw@brokkinc.com 001 418 928 9638 www.brokk.com
At a time when the construction sector faces unprecedented pressure to maximise efficiency while minimising environmental impact, one energy partner has consistently risen to the challenge. Certas Energy, the UK’s largest independent distributor of fuels and lubricants, has established itself as the go-to supplier for construction professionals who demand reliability, innovation and sustainability.
With a nationwide infrastructure of depots, tankers and staff, Certas Energy has quietly become an indispensable partner to demolition and construction firms across the country.
But what’s the story behind the distributor, and why are so many contractors choosing them to help keep their on-site machinery and vehicles running?
Certas Energy’s journey began over 40 years ago, evolving through strategic acquisitions and organic growth to become the formidable presence it is today. Operating under its current name since 2013, the company was formed when DCC Energy consolidated
several regional fuel distributors under one cohesive brand.
This consolidation created an organisation with unparalleled geographical reach and technical expertise. Today, Certas Energy delivers over six billion litres of fuel annually across the UK, with a significant portion serving the construction and demolition sectors.
“Our heritage in construction fuels goes back decades,” explains Peter Cronin, Commercial Marketing Manager for Construction at Certas Energy. “We’ve grown alongside the industry, adapting our services to meet the evolving needs of contractors. That institutional knowledge is invaluable – we understand the pressures construction firms face because we’ve been working with them through every market cycle.”
This experience has proven crucial in building trust with customers. In an industry where downtime can cost thousands of pounds per hour, Certas Energy has established itself as a partner that understands the critical nature of fuel supply.
The demolition industry presents
unique challenges that demand specialised fuel solutions. Certas Energy has built a formidable reputation in this high-pressure sector over the past decade, supporting some of the UK’s most complex demolition projects.
Demolition requires machines that operate consistently at peak power, often in challenging environments where refuelling access is restricted. The financial implications of machine downtime during critical demolition phases can be severe, with schedule delays cascading through entire project timelines.
“Demolition contractors operate in a different reality compared to general construction,” notes Peter. “Their machinery is pushed to maximum capacity for extended periods. Fuel quality is non-negotiable, and delivery windows are often tight and inflexible. We’ve tailored our service model specifically to address these requirements.”
This specialisation has paid dividends. Since 2015, Certas Energy has increased its market share in the demolition sector by also being one of the largest suppliers of HVO. The sector is demanding a sustainable
alternative to standard diesel and HVO is perfect for the sector. A drop in fuel with no need for modification.
While many still think of Certas Energy simply as a fuel supplier, the company has evolved far beyond this limited definition. Today, it offers a comprehensive suite of energy solutions tailored specifically for construction and demolition applications.
Its product range includes standard white diesel alongside premium fuels like GTL (Gasto-Liquid) Fuel, which offers significant environmental and performance benefits for construction machinery. The company also provides lubricants, AdBlue, and fuel management services that help contractors optimise their energy usage.
“What sets Certas Energy apart is our consultative approach,” notes Peter. “We don’t just deliver fuel; we work with clients to understand their operational challenges and develop bespoke solutions that address their specific needs. We are now a one-stop-shop for our customers.”
This approach is exemplified by their fuel management systems, such as Certas Energy’s FuelWise telemetry system, which allow firms to monitor consumption in real-time, identify inefficiencies, and prevent theft – a persistent problem on construction sites, as well as reduce overall fuel costs.
Perhaps nowhere is Certas Energy’s impact more evident than in its work supporting major demolition projects. One standout example involves the company’s partnership with a leading demolition specialist dismantling a 22-storey tower in central London.
The project presented numerous challenges: restricted access, strict noise and emission regulations, tight deadlines and the highprofile nature of working in a congested urban environment.
Certas Energy developed a tailored delivery schedule, providing out-of-hours fuel deliveries to minimise disruption to the surrounding area. They also supplied GTL Fuel, which significantly reduced local emissions and noise levels from the high-reach
demolition excavators – a crucial factor in obtaining continued local authority approval for the work.
The fuel quality was critical given the technical demands of high-reach equipment. Any machine stoppage at height presents serious safety and logistical challenges. Certas Energy understood the stakes and delivered a solution that kept our machines running continuously throughout the 14-month project.
The project was completed ahead of schedule, with the client estimating that Certas Energy’s reliable fuel supply and technical support prevented at least seven days of potential downtime –representing significant cost savings on a project of this scale.
Certas Energy has also distinguished itself in supporting the specialised world of explosive demolition.
When one of the UK’s foremost explosive demolition contractors undertook the controlled implosion of a former power station in 2021, they turned to Certas Energy for the critical fuel supply.
The operation involved months of preparation followed
by an extremely time-sensitive execution phase. Any delay would have significant regulatory, safety and financial implications. Certas Energy established dedicated fuel reserves exclusively for this project, guaranteeing supply regardless of wider market conditions.
“Explosive demolition is all about precision and timing,” explained Peter. “Certas Energy created a fuel security plan that gave us absolute confidence that our preparatory work wouldn’t be compromised by supply issues. They understood that this wasn’t a standard construction project where a day’s delay might be manageable – we had a non-negotiable deadline.”
The implosion was executed perfectly, with all machinery performing as required through the critical preparation phase – a testament to the reliable fuel supply and machinery performance.
As the demolition industry grapples with increasing pressure to reduce its environmental footprint, Certas Energy has positioned itself at the
forefront of the transition to cleaner fuels and more sustainable practices.
Their range of alternative fuels includes HVO (Hydrotreated Vegetable Oil), a renewable, drop-in replacement to diesel that can reduce greenhouse gas emissions by up to 90% compared to conventional diesel. They’ve also invested in Carbon Offset Fuel options, allowing companies to offset the emissions associated with their fuel use through verified carbon reduction projects.
For demolition contractors specifically, Certas Energy has pioneered the “Sustainable Demolition” programme, which helps firms transition to loweremission fuels while maintaining the power output of their heavy machinery demands. This initiative has been particularly successful in urban demolition projects where air quality concerns are paramount.
“The industry is changing rapidly,” said Ollie Bradshaw, Certas Energy’s Sustainability Manager for Liquid Renewables. “Demolition firms are increasingly required to demonstrate their environmental
credentials to win contracts. We’re helping our customers navigate this transition by providing practical, accessible alternatives to conventional fuels, like HVO.” This focus on sustainability extends to Certas Energy’s own operations. The company has invested in a modern, efficient delivery fleet and implemented route optimisation technology to reduce the carbon footprint of their distribution network.
In a competitive market, what factors have driven Certas Energy’s success in the demolition sector?
• Supply security: With a nationwide network of terminals and depots, Certas Energy offers unmatched reliability – a critical factor for demolition projects where fuel shortages can cause costly delays and safety concerns.
• Technical expertise: The company employs specialists with deep knowledge of demolition applications,
allowing them to recommend the optimal fuel and lubricant solutions for specific equipment and operating conditions.
• Flexible delivery options: From emergency same-day deliveries to scheduled out-ofhours service, Certas Energy adapts to the unpredictable nature of demolition work. Their emergency response protocol guarantees delivery within four hours in critical situations.
• Account Management: Dedicated account managers with demolition industry experience provide a single point of contact, simplifying the procurement process and ensuring consistent service levels.
• Innovation: Certas Energy consistently brings new products and services to market, helping demolition contractors stay ahead of regulatory changes and efficiency challenges.
As the demolition industry evolves, Certas Energy is positioning itself to lead rather than follow. The
company is investing heavily in its alternative fuels infrastructure, while continuing to supply conventional diesel for businesses at a different stage of their energy transition.
They’re also expanding their digital capabilities, developing more sophisticated fuel management tools that integrate with demolition firms’ broader equipment monitoring systems. These innovations promise to deliver even greater efficiency and cost control for contractors.
“The next decade will bring transformative change to how demolition sites are powered,” predicts Certas Energy’s Peter Cronin. “We’re already working on solutions that will help our customers navigate the transition to more sustainable fuels like HVO and GTL for the next 20 years. Eventually, we will see the introduction of improved hybrid and electric machinery, while continuing to optimise their use of liquid fuels where they remain the practical choice.”
This forward-looking approach appears to be resonating with demolition firms increasingly
focused on future-proofing their operations. Many report that Certas Energy’s willingness to discuss long-term energy transition strategies has strengthened their partnership beyond mere transactional relationships.
As the demolition industry continues to evolve, the importance of reliable, innovative energy partners has never been greater. Certas Energy has established itself as not just a supplier but a strategic partner to demolition firms across the UK.
Through its combination of nationwide infrastructure, technical expertise specifically tailored to demolition applications, and forward-thinking approach to sustainability, Certas Energy has earned its position as the foundation upon which many of the country’s most important demolition projects are built. As the industry continues its journey toward greater efficiency and sustainability, Certas Energy appears well-positioned to fuel the way forward.
Rebecca Redmond, Clifford Devlin’s Business Development Manager is running the 2025 London Marathon for the National Federation of Demolition Contractors.
Team NFDC are running for the charity Sue Ryder. Sue Ryder is dedicated to ensuring that everyone facing the end of life or coping with grief has access to the care and support they need. There is no onesize-fits-all approach to dealing with grief or the end of life, but with Sue Ryder’s compassionate assistance, no one has to face these difficult times alone. They are there when it matters most.
Any donation will be greatly appreciated.
To donate to Rebecca, you can scan this QR code
by Kaziwe Kaulule, Managing Director – Aggregates, Holcim UK
The UK demolition industry stands at a critical crossroads. As pressures mount to meet net-zero commitments, deliver cost-effective solutions and reduce embodied carbon in construction, there has never been a more urgent need for joined-up thinking between demolition, aggregates and construction sectors.
At Holcim UK (formerly Aggregate Industries), we believe that Construction Demolition Materials (CDM) are not just a by-product of demolition, they are a crucial resource to unlock a circular construction economy. As someone with a global perspective on sustainable materials, I’ve seen firsthand how integrated approaches can transform industries. Now,
working within the UK market, I’m convinced that greater collaboration with demolition professionals is essential to scaling circularity and creating shared value.
Historically, demolition materials have been seen as waste –something to dispose of rather than something to reuse. Thankfully, that perception is shifting. CDM now accounts for nearly 90% of total construction waste generated in the UK, and with almost 60 million tonnes of materials processed annually, it represents both a challenge and an enormous opportunity.
At Holcim UK, we are on a mission to triple our use of recycled
materials from 7% to 20% of our total aggregates output by 2030. This is a bold goal and we know we can’t achieve it alone. We need the demolition sector as a critical partner – bringing forward quality, consistent feedstock that allows us to produce certified, high-performing recycled aggregates that meet modern construction standards.
To ensure quality and trust, we have invested heavily in our ECOCycle range. This offers externally verified, certified recycled aggregates, shifting the conversation with customers from “cheaper” to “higher value and lower carbon.” Our customers now ask how we can help them meet embodied carbon targets, not just what we can deliver. And much of that value begins with demolition.
Demand for sustainable materials is accelerating fast. From public infrastructure projects like HS2 to private sector regeneration schemes, customers are demanding lowcarbon alternatives. And yet, the UK faces a material supply challenge, particularly when it comes to new sources of virgin aggregates. Yet, recycled demolition materials can help close that gap, but only if we have robust systems to capture, process and certify them at scale.
At Holcim UK, we’ve already made significant strides, including:
• Developing CDM ‘super hubs’
near major urban centres to process demolition materials close to their source,
• Becoming the first UK supplier to launch certified blended rail ballast, using 50% recycled content – a direct result of reprocessed demolition arisings,
• Leveraging our Glensanda superquarry and a growing portfolio of recycling operations to provide flexible, large-scale solutions.
But to truly scale circular construction, we need to overcome key barriers that demolition professionals are only too familiar with – inconsistent specifications, uneven market demand, and lingering perceptions of recycled materials as inferior.
Here’s where I believe the demolition sector has an incredible opportunity to lead; not just as an end-of-life service, but as a vital enabler of a circular economy.
Our teams are actively working to build these circular partnerships. In this vein, I would encourage demolition firms to engage with us to not only co-design processing and quality standards that ensure demolition materials meet end-user needs, but also support our call for consistent national specifications for recycled aggregates, replacing the patchwork approach we see today. This way, we can identify new revenue streams for high-quality
recycled content, helping demolition firms demonstrate added value to clients and policymakers.
Of course, industry collaboration alone won’t solve all the challenges. We need policymakers to support this circular shift. The National Infrastructure Commission, Environment Agency and planning authorities all have a role in embedding circular economy principles into procurement and permitting.
For example, mandating minimum recycled content in public projects, or streamlining the permitting process for CDM processing could unlock enormous latent capacity in the demolition sector. I strongly believe Holcim UK’s voice, combined with demolition’s on-the-ground expertise, would be powerful in driving these changes.
Another crucial piece of the puzzle is data. As an industry, we need to be able to more effectively track material flows and carbon savings from demolition through to construction. Our teams are investing in digital platforms and AI-driven tools that enable better traceability and certification.
For demolition firms, partnering with us on these innovations means:
• Being able to demonstrate the circular and carbon value of the materials they supply,
• Helping customers report on
Scope 3 emissions reductions,
• Participating in pilot projects that set the standard for the future of low-carbon construction.
Bringing new talent to the table
As we pursue this circular revolution, we need to bring new people into the industry. I believe circularity and digitalisation offer a way to do that.
Across the Aggregates business unit of Holcim UK, we are working to redefine the role of the modern quarry and recycling operator, embracing technology, AI and sustainability. I see an opportunity for a similar evolution in the demolition sector, attracting a new generation of digital, environmentally focused talent who want to be part of the climate solution, not just an end-of-life service.
The demolition sector holds one of the keys to unlocking circular construction in the UK. But to make the most of that opportunity, we must work together to align supply chains, standards and innovation. If you share this vision, I would welcome a conversation. Together, we can redefine what’s possible for the demolition and aggregates industries and build a truly sustainable future.
holcim.co.uk.
01291 318 630
by Terry Lloyd – Head of Vendor in the SME Lending division at Paragon Bank
As the days get warmer you can almost hear a sigh of relief from the construction and demolition industry – no more site closures, no more delays, spring has officially arrived.
The warmer weather is something many of us enjoy on a personal level. But for businesses operating in the construction and demolition industry, it’s a time when business owners can sleep easier knowing that it’s unlikely their project will be delayed due to harsh weather conditions. Many in the industry will now be looking forward to a busy six months while the good weather continues.
But while the days are longer and brighter, spring also brings the Chancellor’s Spring Statement, which many in the sector are nervously anticipating, but also hoping for a ray of light when it comes to recruitment.
After the last major fiscal event – the dreaded October Budget –business owners are still feeling uneasy, especially with the National Insurance hike on the horizon.
What many in the industry are hoping for, whether that is in the Spring Statement or in another form, is some support for the construction industry when it comes to recruitment.
There is a severe shortage of construction workers in the UK, which impacts the amount of work that can be undertaken across the sector. A recent survey by the Recruitment and Employment Confederation (REC) and Lightcast showed that there were over 117,000 job postings in the construction industry in February 2025, an increase of 4.7%.
Housebuilding remains a priority in the UK, with 1.5 million homes to be built in five years but recent reports showing a decline in building rather than an increase. In addition
to large infrastructure projects, such as HS2, the government must take some measures to support the industry.
Many in the construction industry would like to see more apprenticeships being offered –which seems like a sensible solution to an issue that has been worsening over the past few years.
What we do know, is that the current construction workforce is not large enough to support all the projects that the government is pledging to undertake and while this problem goes unsolved, it will continue to grow as those towards the end of their career take retirement.
So, while we look forward to the spring months and the busy diaries that come with it, unless we address the looming recruitment crisis in the sector, it will become increasingly challenging for the industry to service work and for the government to achieve its infrastructure and housing ambitions.
If you would like to be featured in our Opinion section, please contact toby@chambers.media
by Richard Dolman
As we end the first quarter of 2025, the demolition industry is facing a year of mixed signals. While there’s cautious optimism, the reality on the ground is that confidence in the economy is still fragile. I’ve seen first hand how this uncertainty is impacting the sector, particularly in terms of funding and project delays. But amid these challenges, I remain focused on a core issue – upskilling our workforce.
At AR, we understand that a strong, skilled workforce is the foundation of a successful demolition operation. That’s why I helped develop the foundation and master’s degree courses in Demolition Management, ensuring we have the next generation of leaders equipped with the right knowledge and skills to drive our industry forward. Education and training are fundamental to addressing the increasing complexity of projects and safety regulations.
But it’s not just about looking ahead – it’s also about the here and now. We are committed to continually supporting our current staff by helping them complete their NVQs and invest in their continual personal development. It’s critical that we ensure our people have
the skills needed to meet industry standards and stay ahead of emerging challenges. Whether it’s new environmental regulations or advances in demolition technology, the importance of ongoing development cannot be overstated.
The industry as a whole is struggling with several pressures. Delays in project starts and ongoing planning holdups have become commonplace. The broader economic slowdown has affected funding for both public and private sector projects, leading to postponed or cancelled initiatives. For the industry, this has translated into a slower start to 2025. This creates a ripple effect, creating gaps in our work schedule and forcing us to plan with even more caution.
Confidence is at the heart of this issue. As the GfK Consumer Confidence Index showed in early 2025, while there’s a slight improvement in household sentiment, the overall outlook remains cautious. The rise in inflation has also put added pressure on project budgets, with costs rising across materials, labour and operational expenses. These factors are all feeding into a cycle of uncertainty, which has had a direct
knock-on effect on our industry.
Despite these challenges, I remain convinced that the way forward lies in building a robust and skilled workforce. The emphasis on cost-cutting, which is so prevalent in the tendering process, may get projects through the door, but it’s not a sustainable model. Our industry must focus on delivering high-quality work and maintaining safety standards.
Looking to the future, we know that a skilled workforce will be the key to overcoming some of these challenges. The importance of investing in training and education for the demolition sector cannot be overstated. By equipping our teams with the right skills today, we are setting the foundation for success tomorrow. The economic uncertainty we face in 2025 may continue to cause disruption, but by investing in people, we can ensure that the demolition industry as a whole— emerges stronger in the years ahead.
Demolition
Demolition Hub is the media partner for the European Demolition Association
In the European Demolition Association and European Decontamination Institute, we are committed to keeping our community informed. This is the reason why we have created an official WhatsApp channel, which will allow our members to receive all the news from the Association in real time.
Through this channel, we will
share relevant information such as:
• News and official statements from the EDA and EDI,
• Events of all kinds so you will not miss any opportunity,
• Training and courses with details about our initiatives
• Important updates in the industry and about the EDA and EDI’s work.
With this new channel, we want to be sure that the information gets to you quickly, directly and without having to search for it on different platforms. With one click you will be up to date about everything that happens in the EDA.
Join now and be part of our community.
We are thrilled to announce that preparations for the EDA Yearbook 2025 have officially begun. Our annual publication will once again feature contributions from key players in the demolition industry, in-depth technical articles and insightful dialogues. Save your space and become a sponsor.
This year’s publication is set to be an invaluable resource, offering visibility and recognition to participating companies and professionals. As with all of our Yearbooks, this year’s edition will include technical and informative content, updates from the National Associations that are part of the EDA, news, events, interviews and relevant information for anyone interested in demolition.
Available in hard copy and digital format, the publication will be distributed among all the EDA members, partners and other
trade organisations related to the construction sector. Additionally, the EDA Yearbook 2025 will be present at the most relevant events of the sector, organised by EDA, its national associations and other entities.
Becoming a sponsor is a great opportunity to gain daily exposure
for your brand. Different sponsorship options allow all companies to participate.
The sponsorships are limited, so do not miss the chance to become a sponsor and book your space in our prestigious publication.
The FACHTAGUNG ABBRUCH 2025, held recently in Berlin, proved to be a success, attracting more than 1,200 representatives from the demolition industry and related sectors. The event showcased 114 exhibitors, offering attendees a comprehensive look at the latest products and services in demolition, pollutant remediation and recycling.
The EDA was present at this remarkable event, with members of the Board of Directors and several publications, such as the EDA Yearbook, High Reach Demolition Guidelines, Guide about Recyclable C&D materials. All these publications are available in the Library section of the EDA website.
This year’s congress centred around the theme “Quality in Demolition,” which served as the framework for all expert lectures.
The accompanying trade exhibition complemented the presentations, providing valuable insights into industry innovations. The congress concluded with a dialogue evening, allowing participants to network and exchange ideas in a relaxed setting.
The European Demolition
Association could not miss this event, one of the most relevant in the industry in Europe, and continue the excellent relationship with the German Demolition Association, DA, which is part of EDA.
The European Union has announced new policies to transform the construction and demolition sector, focusing on waste management and recycling, which means that the whole industry must be aware of the requirements in demolition practices.
Also, by the end of 2025, EU member states must increase recycling and material recovery of non-hazardous construction and demolition waste to a minimum of 70% by weight, as established in The Waste Framework Directive.
The new requirements could be summarised in three key points:
• Promoting selective
demolition to enable the safe removal of hazardous substances and facilitate high-quality recycling,
• Implementing waste reduction strategies in construction processes, encouraging sustainable materials use,
• Encouraging green public procurement practices for construction projects at local and regional levels.
These measures underscore the EU’s commitment to leading global efforts in sustainable construction practices and circular economy principles. Also, they aim to reduce
the environmental impact of the construction sector, which currently generates nearly a third of all EU waste.
The European Demolition Association is currently involved with the European Commission’s initiative that aims to define the End-of-waste criteria for mineral construction and demolition waste, and given that waste management legislation differs among EU member states, EDA has been holding meetings with national associations to discuss these criteria and their perspective. Stay tuned about this topic in the EU Construction and Demolition Waste Management Protocol.
The European Demolition Association (EDA) is pleased to welcome a new member: XPLOSAFE AS specialised in manufacturing unbreakable explosion-proof windows for construction machinery. This collaboration reinforces XPLOSAFE’s commitment to enhancing demolition and construction industry safety standards, in line with the company’s vision: SAFETY FIRST. Their products provide superior protection against all types of impacts. Using the most qualitative materials on the market and the use of single panes to avoid glare, reflection, icing and dust between
The European Demolition Association (EDA) is pleased to welcome LAURINI OFFICINE MECCANICHE, the Italian leader in the design and manufacture of innovative machines and equipment. Their Business Unit goes from pipeline, to demolition, tunnelling, sheet piles, and engineering.
They outline their role as game changers because they have
double panes, while ensuring clear visibility for operators. The panes replace traditional metal grating OPG level 2, greatly improving the operator visibility without compromising on safety.
Designed and produced in Norway, XPLOSAFE’s windows meets rigorous industry standards, including CE, EN and ISO certifications. Moreover, their testing includes exposure to extreme conditions, such as explosions falling objects, to guarantee durability.
The company looks forward to engaging with industry leaders and advancing innovation in demolition safety.
changed the rules of the game in several construction sites. More than 1,000 machines have been sold in 50 countries and the production area has increased by 900% since 2000.
LAURINE OFFICINE MECCANICHE projects begin with careful listening to the client’s needs to focus on the objectives and technical specifications required, followed by an in-depth analysis of the needs to guide the best technical and economic solution, ensuring that the proposal is perfectly aligned with the client’s requirements.
The Annual Convention is an incredible opportunity to make contacts and to show the world what you do. How? It is easy, become a sponsor and make your brand shine in Venice from 12 to 14 June.
All companies have the opportunity to be sponsors of the event. It means brand visibility in all the event materials before, during and after the Convention. Moreover, sponsorship also opens the door to making valuable networking connections with decision-makers and CEOs of leading companies in the industry.
Meet the marketing opportunities
EDA provides three sponsorship levels, Gold, Silver, and Bronze, which include valuable benefits like brand exposure, conference and Gala Dinner tickets, inclusion in the official programme and much more. Companies can further boost their visibility with exclusive options that include sponsoring conference materials, lanyards and delegate
bags. All the gold sponsorships, the Welcome Cocktail and the Gala Dinner are sold out, but some incredible options are still available, so get yours now.
Sponsorship opportunities are limited and allocated on a first-come basis. Do not miss your chance to leave a lasting impression at EDA AC25 and become a sponsor For more information, contact the EDA Secretariat at info@europeandemolition.org or call (+34) 602 250 893.
Meet some of the EDA Annual Convention speakers
The countdown to the EDA Annual Convention 2025 has begun and we can now announce the experts and industry leaders who will participate as speakers this year.
Conference Session 1
• Sustainable deconstruction of industrial structures at the port of Buenos Aires – Maximiliano Mauriño, GRUPO MITRE
• Asbestos removal in power plants demolition projects –Rui Silva, INTERAMIANTO
Conference Session 2
• Controlled demolition of the Michelangelo Hotel – Stefano Panseri, DESPE
• The Chorium (VI) regulatory paradox (colourful into the lungs) – Markus Sommer, KAVARMAT
Conference Session 3
• A first for DDM: Europe’s first suspension bridge dismantling – John Patist, DDM DEMONTAGE BV
• Can a small company work on nuclear projects? – Wesley Princen , AANNEMINGSBEDRIJF PRINCEN NV
• Conference Session 4
• Demolition of the La Salle Causeway Bridge – Ryan Priestly, PRIESTLY DEMOLITION
• Two Months in ten seconds:
The untold story of explosive demolition –
Alex Hadden, BAM BROWN AND MASON GROUP
Accommodation searching app for the Convention
The EDA Annual Convention 2025 will take place in Venice from 11 to 14 June, so attendees will need to find accommodation. Because of that, this year EDA offers several alternatives to find the perfect hotel for everyone at Lido Island.
The Hotel Excelsior Venice Lido Resort will be the meeting point for all leisure activities and special rates are available for attendees.
However, the Lido Hotel Consortium has prepared a specific application showing the availability of other hotels of different categories for the dates and number of people you choose.
But how do you do that search? That is easy, using the accommodation search app, available on the EDA Convention website.
How to use it
• Go to www. europeandemolition.org/ activities/eda-annualconvention-2025 and scroll down to the accommodation section,
• Insert arrival and departure dates and number of people
• Click “find accommodation”
• Once you have done that, it will be display a list of different hotels in the surroundings that can match your preferences.
by Connie Clearwater, Vice President of Marketing, Communication and Business Development for Priestly Demolition Inc
The deconstruction and dismantling of Cameco’s UF6 Plant, commonly known as Building 27 (B27), was an abandoned processing facility, heavily contaminated with radiological and chemical material. It consisted of two, two-storey building sections and a central seven-storey tower section with a total footprint of 72,800 square feet. Originally, work was planned to commence in June 2019 (with a completion date of 2021), but when the Covid-19 pandemic hit, the number of people on site had to be reduced, and the project was delayed until September 2021. Initially, Priestly Demolition Inc. (PDI) was contracted to demolish the B27 tower down to the fourth floor, but this plan was later revised so that the entire structure would be demolished.
This undertaking is known as the Vision in Motion (VIM) project, a unique and timely opportunity that was made possible because of the Port Hope Area Initiative (PHAI). The PHAI Port Hope project was undertaken by Canadian Nuclear Laboratories (CNL) and included the construction of a Long Term Waste Management Facility (LTWMF) in Port Hope. PHAI made 150,000 cubic metres of space available for the site to dispose of the eligible legacy waste (pre-1988). This is what drove the VIM schedule.
The first step was to establish a waste processing area on the ground floor of B27 where demolished materials from other areas of the building could be processed, including interior contents (equipment, steel, piping, ducting fixtures, etc.). All materials were assumed to be contaminated and were required to meet the Waste Acceptance Criteria (WAC). Contents were then packaged as required for shipment to the LTWMF. In general, materials had to be cut into small pieces to minimise void spaces. Large pipes had to be split down the middle and then efficiently packed into the Cameco-supplied hazardous waste PacTec bags (Super Sacs) before they could be loaded into the supplied IP2 shipping containers and shipped to the LTWMF.
Large equipment slated for demolition was also cut to fit
into hazardous waste bags at the workface; no equipment was removed whole. The bag labelling procedure was highly detailed and extremely important to ensure materials were identified correctly.
Upon removal of the interior building contents, all building surfaces within the building were thoroughly HEPA vacuumed to remove any remaining loose contamination. At the completion of this stage, only the interior structural steel (including flooring) and the fully intact building envelope remained.
Thorough HEPA vacuuming of the interior surfaces was the main control used to guard against the potential of contamination release into the environment. In subsequent steps, localised containment techniques were required to prevent a Loss of Primary Containment (LOPC).
The use of water to clean surface contamination was avoided when possible because the additional effluent material would need to be captured and transported to the water treatment circuit. Also, any water treatment requirements had to first be identified for Cameco approval.
In addition, a fixative coating was applied to all interior surfaces prior to any siding removals to “lock down” any remaining contaminants and provide a secondary means of preventing contamination release into the environment.
A radiological survey of the
building was completed after the completion of interior cleaning and HEPA vacuuming. This was to confirm contamination levels before proceeding with the tower demolition activities.
The tower floors were removed one by one (including transite siding and structural steel), starting at the top and proceeding to the ground. Because debris and equipment were not permitted to leave the footprint of the building before being packaged, the team created an opening in the lowerlevel roof to crane the super sacs and structural steel down from the building for further processing.
The extensive scaffolding setup and tower section had to be enclosed while asbestos transite siding and structural steel were being removed; additionally, a mobile crane was used in tandem to lift the cut structural steel and transite siding from the tower floors to the ground.
To add another level of complexity, water could leave the footprint of the building even once it was open to the elements. All the water had to be collected in totes and sent for evaporation.
An extensive ventilation system was installed, including 48 negative air machines with HEPA filters and ducting throughout the building. Emissions were modelled and monitored throughout the project with daily filter changes and air flow checks. The team used full-face respirators as well as powered air-purifying respirators throughout the demolition process.
Upon completion of the tower
demolition, the remainder of the building, excluding the cylinder prep, was demolished to slab on grade, including the generator room and tote bin room. Once the building was fully decommissioned, the ground floor slab was prepared for future renovation activities.
Cameco’s Port Hope Conversion Facility plans to refurbish the B27 building and slab and use it as a warehouse facility.
This was a hugely successful project for both Cameco and PDI. These two companies were fully dedicated to the safety of the team and the environmental controls that were required to ensure the success of the project.
Unique solutions were required for this project as it developed, and both teams are extremely proud of the work that was performed on site.
“Cameco was pleased to contract Priestly Demolition to remove the redundant UF6 building at the Port Hope Conversion Facility; however, it was clear this was to be no normal demolition,” says George Trotter, Programme Manager at Cameco Corporation. “Due to the nature of its former operation and the legacy wastes stored over the decades since, new procedures had to be developed to ensure radiological, conventional and environmental safety.”
The Cameco Corporation is a world leader in uranium production and is a major supplier of uranium processing services required to produce fuel for the next generation
of clean energy. The PHCF produces uranium hexafluoride and uranium dioxide. These operations are based in Blind River, Cobourg and Port Hope, Ontario, and are collectively referred to as the Fuel Services Division.
The PDI team greatly appreciates the opportunity to be a partner in the progress of this challenging project. We have built a strong and trusting relationship with Cameco as a result and continue to perform decommissioning work on the Port Hope site and the Vision in Motion project.
“I commend PDI’s willingness to adapt to change, ability to develop solutions and their unwavering commitment to doing it all safely. The entire team should be proud of what was accomplished,” says Andrew Turk, P.Eng, Senior Project Engineer at Cameco Corporation.
by Claudia St. John, President and CEO of The Workplace Advisors
I recently had the opportunity to speak at a conference on the topic of employee retention and workplace flexibility. One attendee asked me how it was possible to create flexibility in a manufacturing environment where schedules are highly structured and production must be done on site. His point was valid; you can’t offer hybrid or work-from-home options when the job requires operating machinery at a worksite.
But that doesn’t mean creating flexibility in shift work is impossible. It just requires a bit of out-ofthe-box thinking. And perhaps a little help from technology.
In today’s dynamic manufacturing landscape, managers are increasingly turning to artificial intelligence (AI) to revolutionise shift scheduling and enhance workplace flexibility for non-exempt hourly workers. This technological shift is not only improving operational efficiency but also boosting
employee satisfaction and retention. Here are a few of the ways our clients are using AI to transform the manufacturing workplace and provide flexibility for shift workers.
AI-powered scheduling tools are at the forefront of this transformation, offering managers powerful and often free solutions to optimise workforce allocation and accommodate employee preferences. AI algorithms can generate optimised and customised shift schedules by considering multiple factors simultaneously and quickly. To prove this point during my presentation, I created a sample work schedule that took many variables into account, such as:
• Employee availability and preferences,
• Required skills and qualifications,
• Production demands and forecasts.
By processing a complex web of variables such as these, AI was able to create a balanced schedule that met both operational needs and worker preferences in a fraction of the time it would take a human operations manager.
One of the key advantages of AI-driven scheduling is its ability to adapt to changes in real time. When unexpected absences or
production changes occur, the system can quickly recommend the most suitable replacements or shift adjustments. This agility ensures that manufacturing operations remain smooth while also providing workers with opportunities for additional hours or shift swaps when desired.
In addition, the free AI platform I was working with was able to quickly and easily ensure a fair distribution of desirable and less desirable shifts among employees – taking into consideration some factors that I hadn’t even thought of like childcare needs and commuting times. Moreover, the AI tool offered an impartial approach to scheduling that could create flexible opportunities while also reducing perceived favouritism.
Beyond basic scheduling, AI is enabling manufacturers to offer unprecedented levels of flexibility to their hourly workers. AI systems can manage flex day requests and time-off applications with ease. By analysing historical data and current staffing needs, certain AI tools can automatically approve or suggest alternatives for employee requests without compromising production targets.
Additionally, AI can easily facilitate non-traditional arrangements such as split shifts, job sharing or part-time positions. This flexibility allows employees to balance work with personal commitments while
ensuring production maintains optimal staffing levels. Workers can post shifts they want or need to give up, and the system can identify and notify qualified colleagues who might be interested in picking up extra hours.
We all know those employees who are eager to work as many shifts as possible to earn extra money and those who are happy to give up a few hours to accommodate their pursuits. AI can help facilitate those swaps within the constraints that their managers put in place, such as limiting overtime exposure, etc.
To successfully implement AIdriven flexibility in manufacturing settings, it’s important to select an AI scheduling tool that integrates well with existing ERP and HR systems. Look for solutions that you
can customise to align with your specific manufacturing processes and workforce needs. You may also want to consider implementing a self-service portal or mobile app that allows workers to view their schedules, request changes and manage their availability preferences, which can both empower them and reduce the administrative burden on managers.
And, by ensuring the right workers are in the right place at the right time, AI-driven scheduling can significantly boost productivity and increase employee satisfaction by giving them the flexibility enjoyed by non-production employees.
But let me be clear, while AI offers tremendous potential for enhancing workplace flexibility, it’s not without its weaknesses and challenges. Introducing AI-driven scheduling could face resistance from employees and managers
accustomed to traditional methods and despite the goal to add flexibility, it could be perceived as impersonal, which is the opposite goal. And while AI can handle complex scheduling tasks, human oversight remains essential. AIgenerated algorithms might make mistakes and miss the mark in significant ways. There will always be the need for judgment calls and out-of-the-box thinking – a uniquely human capability. While AI is an amazing tool, it does not replace managers and schedulers who know what works and what doesn’t.
Bottom line: In the right hands with the right mindset and oversight, AI can be an awesome tool to create more efficient, fair and flexible work environments that benefit both the organisation and its employees.
by Adam R Young
As we try to anticipate the shifts of a second Trump administration, supported by a Republicancontrolled Congress (albeit with very slim margins), these are some of our projections on what the future may hold for employers on the Occupational Safety and Health Administration (OSHA) front during the second Trump administration.
From the first Trump administration, we know that the number of OSHA inspectors and OSHA inspections dropped significantly. During the Obama administration (2008-2016), the number of OSHA inspectors fluctuated but generally stayed above 900, rising to 1,059 inspectors
from 2009 to 2011, then declining to 943 from 2011 to 2015, then rising again in 2016 to 952 inspectors. However, by the close of fiscal year 2020, the last year of the first Trump administration, that number had fallen to 790. By the end of 2023, there were 878 inspectors at OSHA, representing an 11% increase from fiscal year 2020. Those numbers are likely to fall below 800 again, if not further.
We also know that the regulatory legal landscape is very different now than it was during the first Trump administration due in large part to the Supreme Court’s decision in Loper Bright Enterprises v. Raimondo, No. 22-451, 603 U.S. 369 (2024). There, the Supreme Court held that courts, not agencies, are best situated to interpret ambiguous statutory provisions, even in areas of agency expertise. In doing so, the Supreme Court has reined in agencies like OSHA from effectuating their enforcement agenda based on the agency’s own interpretations of its regulations.
Against that background, and consistent with President Trump’s stated goal of a more limited federal government, including less federal government involvement in the workplace, we can expect:
During the first Trump administration, OSHA faced initial years of flat budgets, and OSHA
had a difficult time competing for safety professionals with private industry when trying to hire compliance officers. The agency will very likely face the same pressures again during the second Trump administration. We also anticipate fewer new OSHA regulations, fewer OSHA Emphasis Programs focusing enforcement on specific hazards and industries and less programmed inspection activity.
The Biden administration invested significant resources in bolstering OSHA’s and the Department of Labor’s whistleblower investigation programs. We anticipate a rollback of those efforts and the potential return to a more business-friendly Voluntary Protection Program (VPP) and cooperative compliance programmes over time.
OSHA published its proposed Heat Injury and Illness Prevention in Outdoor and Indoor Work Settings and began accepting public comments in the summer of 2024. The rule would apply to all employers and be triggered when employees are exposed to temperatures of 80°F (27°C) for more than 15 minutes in any given 60-minute period. The public comment period closed on 30 December 2024. Republican
elected officials recently have expressed opposition to heat illness protection, with the Texas and Florida governments passing laws preventing municipal rules relating to water breaks. Given the antiregulatory orientation of a second Trump administration OSHA, we anticipate OSHA bringing the heat illness rule-making process to a screeching halt. OSHA still uses the General Duty Clause to address the heat illness prevention rule.
On 1 April 2024, the Federal Register published OSHA’s final rule revising its regulations regarding whom employees can authorise to act as their representative(s) to accompany compliance officers during on-site OSHA inspections. The revised regulation clarifies that employees have the right to designate a nonemployee, third party to be their representative during the physical walkaround. In doing so, OSHA has effectively indicated non-unionised employees can look to unions for support during an OSHA inspection.
The rule is currently the subject of litigation in Texas; a coalition of business associations has filed a lawsuit against OSHA, captioned Chamber of Commerce of the United States of America, et al. v. OSHA, et al. Even if the Chamber of Commerce does not prevail, a Trump-controlled Department of Labor could choose to withdraw the new rule. The rule already passed the period for withdrawal by Congress under the Congressional Review Act.
During the Biden administration, the Department of Labor was led by individuals with pro-labor ties
– Boston Mayor and former union leader, Marty Walsh; and Julie Su, the former head of California’s Labor and Workforce Development Agency and civil rights lawyer. OSHA was led by Doug Parker, who began his legal career as a staff attorney at the United Mine Workers of America. President Trump is likely to nominate an Assistant Secretary of Labor for OSH with ties to the business community rather than organised labour.
Employers will recall, though, that OSHA went without a confirmed head of the agency during the entire first Trump administration after President Trump nominated Scott A Mugno, formerly the Vice President of Safety, Sustainability and Vehicle Maintenance at FedEx Ground, for the role. His nomination never received US Senate approval, and Deputy Assistant Secretary of Labor Loren Sweatt remained in charge of the agency until the Biden administration.
In a somewhat surprising move, President Trump has proposed Republican Congresswoman Lori Chavez-DeRemer as Secretary of Labor. Chavez DeRemer, who was defeated by her Democratic opponent in November, is known as a relatively pro-labor Republican and past supporter of the PRO Act, a legislative effort during the Biden administration to protect union organising rights. While ChavezDeRemer may face opposition in the Senate, we anticipate she would be more open to union policy agendas, including maintaining the OSHA Walkaround Rule discussed above. At the time of writing, President Trump has not yet nominated an Assistant Secretary of Labor for OSH; the choice of nominee may further clarify the agency’s enforcement agenda for 2025.
Focus on egregious and wilful offenders, limiting penalties for first-time offenders and small businesses
While President Trump has occasionally distanced himself from Project 2025, many believe it contains a reasonable forecast of policy goals for the second Trump administration, including with respect to OSHA. Chapter 18 of the plan, which focuses on the Labor Department and related agencies, refers to OSHA in this way: (1) Congress and the DOL should “exempt small business, first-time, non-wilful violators from fines issued by the Occupational Health and Safety Administration”; (2) the DOL should clarify that a home office is not subject to OSHA regulations; (3) federal labour agencies should use their discretion under the law to “exempt small entities from regulations where possible”; and (4) OSHA’s focus should be on health and safety inspections on egregious offenders.
While we foresee Trump administration support for a rule limiting OSHA penalties to small businesses receiving their first OSHA citation, we do not anticipate that OSHA will exempt small general industry and construction employers from most OSHA standards.
Adam R Young is a Partner in the Workplace Safety and Environmental Group in the Chicago office of Seyfarth Shaw LLP
Since being established in 2012, Romax Solutions has set a high standard when it comes to recruitment. Finding the best candidates is our driven desire and passion, we aim to meet the recruitment needs of a diverse range of clients within the construction industry. Being based just outside of London gives us easy access to service all clients throughout Essex, London, Kent and surrounding areas while also having the capabilities to support and service nationwide projects and clients.
With a depth of knowledge, our experienced and trusted staff are on hand to deliver a bespoke service to each and every client, supplying reliable and talented staff of all levels both nationally and locally. Romax Solutions
is fully accredited by the Recruitment and Employment Confederation and the National Federation of Demolition Contractors. These accreditations have enabled us to work alongside other NFDC members to meet their scope of needs on multiple projects. These projects range from small scale strip outs to large scale power station decommissions.
We are also always keen to add new talent to our current pool of candidates nationwide. These include those from management level downwards, including skilled demolition operatives and even those just starting out their demolition careers. We work effortlessly to ensure all candidates are fit for purpose, including using accredited training providers to upskill our operatives.
(Cat B Non-licensed asbestos removal)
Wandsworth, south-west London
Role: CCDO Operative with Cat B, for demolition works
Rate: £17 – £19 p/h
Requirements:
• CCDO Green/Red qualification
• Cat B Non-licensed asbestos removal
• Full PPE
• Minimum of two years’ experience in demolition
• Good timekeeping and willingness to work
What we offer:
• Ability to work through CIS / self-employed
• Weekly payments
• Assistance in regard to progression within construction
• Ongoing labourer work for the right candidate
For more information and to work on this project please contact the account manager of this specific job on 07557 196 353
Romax Solutions provides long term work for the right candidates depending on reliability and willingness to work.
Role: CCDO Operatives, work involves demolition, soft strip, long term works.
Rate: £16 – £18 p/h
Requirements:
• CCDO Green/Red Card
• Full PPE
• Minimum of two years’ experience within construction as a CCDO
• Good timekeeping and willingness to work
What we offer:
• Ability to work through CIS / self-employed
• Weekly payments
• Assistance in regard to progression within construction
• Ongoing work for the right candidate
For more information and to work on this project please contact the account manager of this specific job on 07557 196 353
Role: 360 Operator (D90) required for a demolition breaking works
Rate: £21 – £22 p/h
Requirements:
• Blue CPCS (NVQ Level 2) + D90 ticket
• Full PPE
• Minimum of three years’ experience as a 360 Operator and in demolition
• Good timekeeping and willingness to work What we offer:
• Ability to work through CIS / self-employed
• Weekly payments
• Assistance in regard to progression within construction
• Ongoing work for the right candidate
For more information and to work on this project please contact the account manager of this specific job on 07557 196 353
Romax Solutions provides long term work for the right candidates depending on reliability and willingness to work.
Role: CCDO Burner for burning works taking down structural steel works
Rate: £20 – £22 p/h
Requirements:
• CCDO/ CSCS card
• Oxy Fuel Cutting qualification
• Full PPE
• Minimum of three years’ experience within construction as a CCDO Burner
• Good timekeeping and willingness to work
What we offer:
• Ability to work through CIS / self-employed
• Weekly payments
• Assistance in regard to progression within construction
• Ongoing labourer work for the right candidate
For more information and to work on this project please contact the account manager of this specific job on 07557 196 353