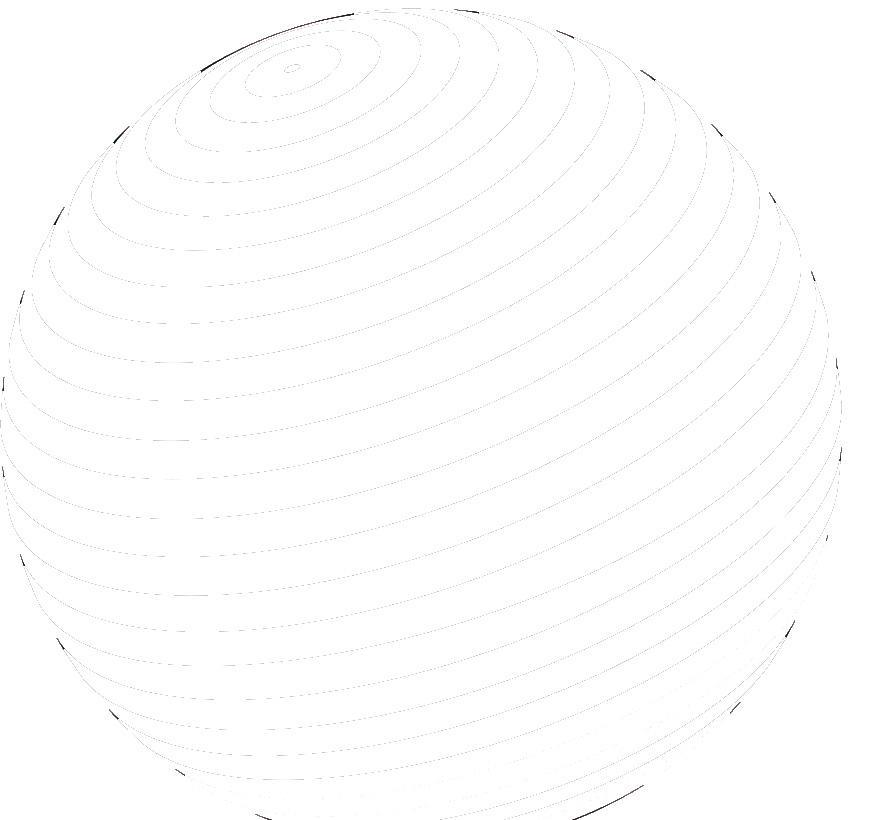

SUPPLIER TALK
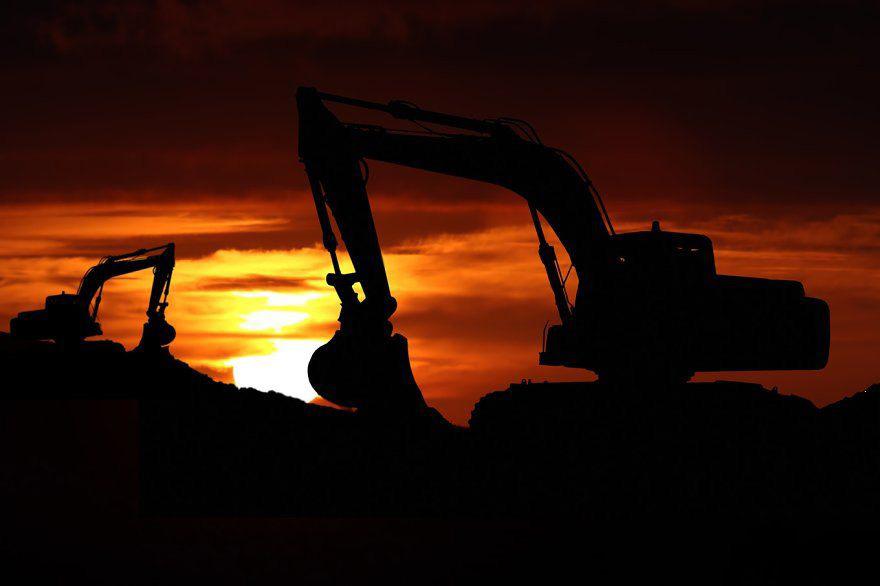
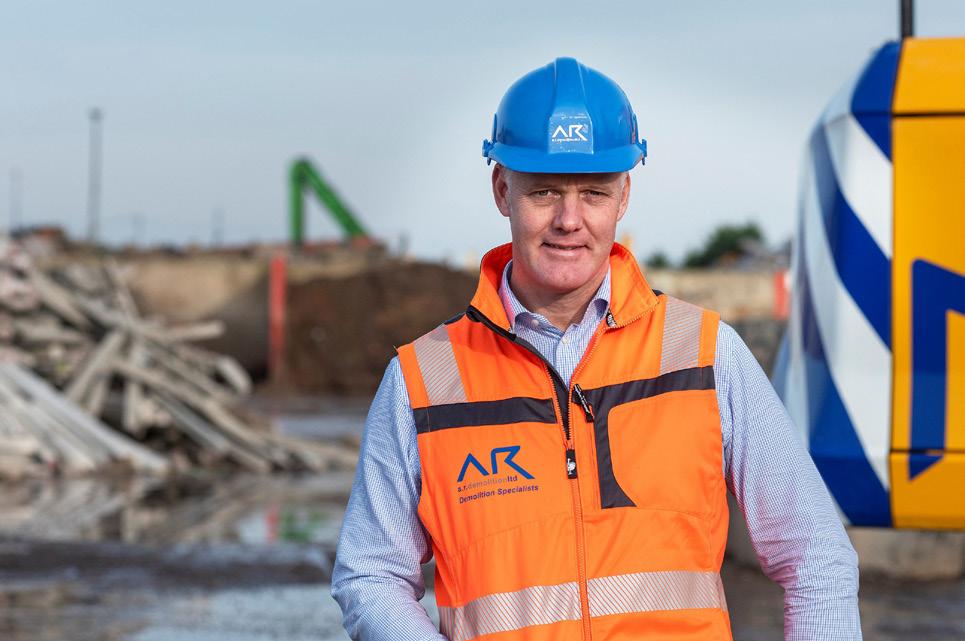
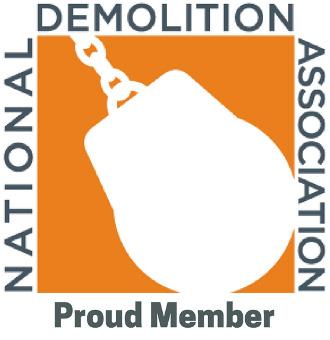

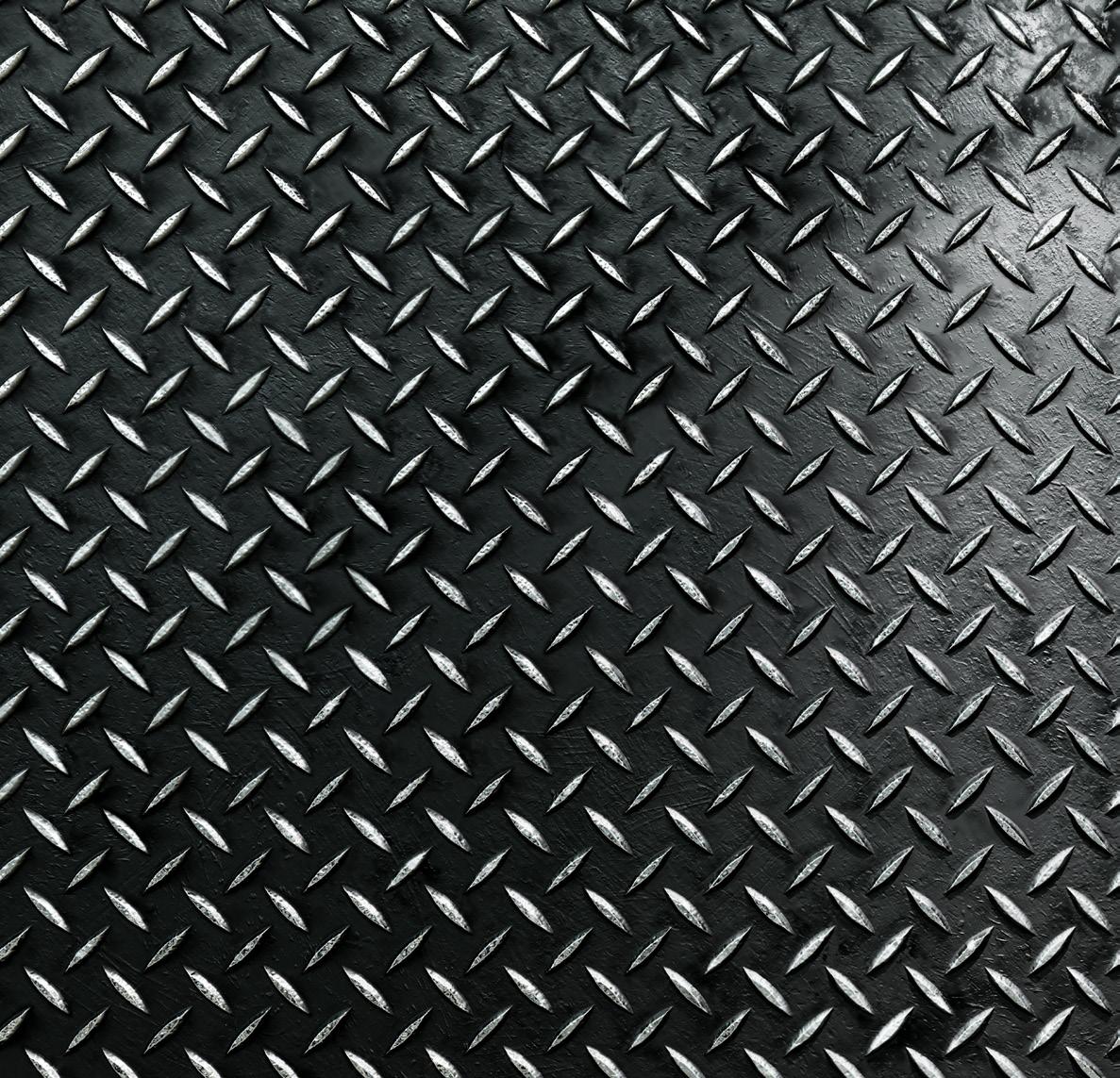
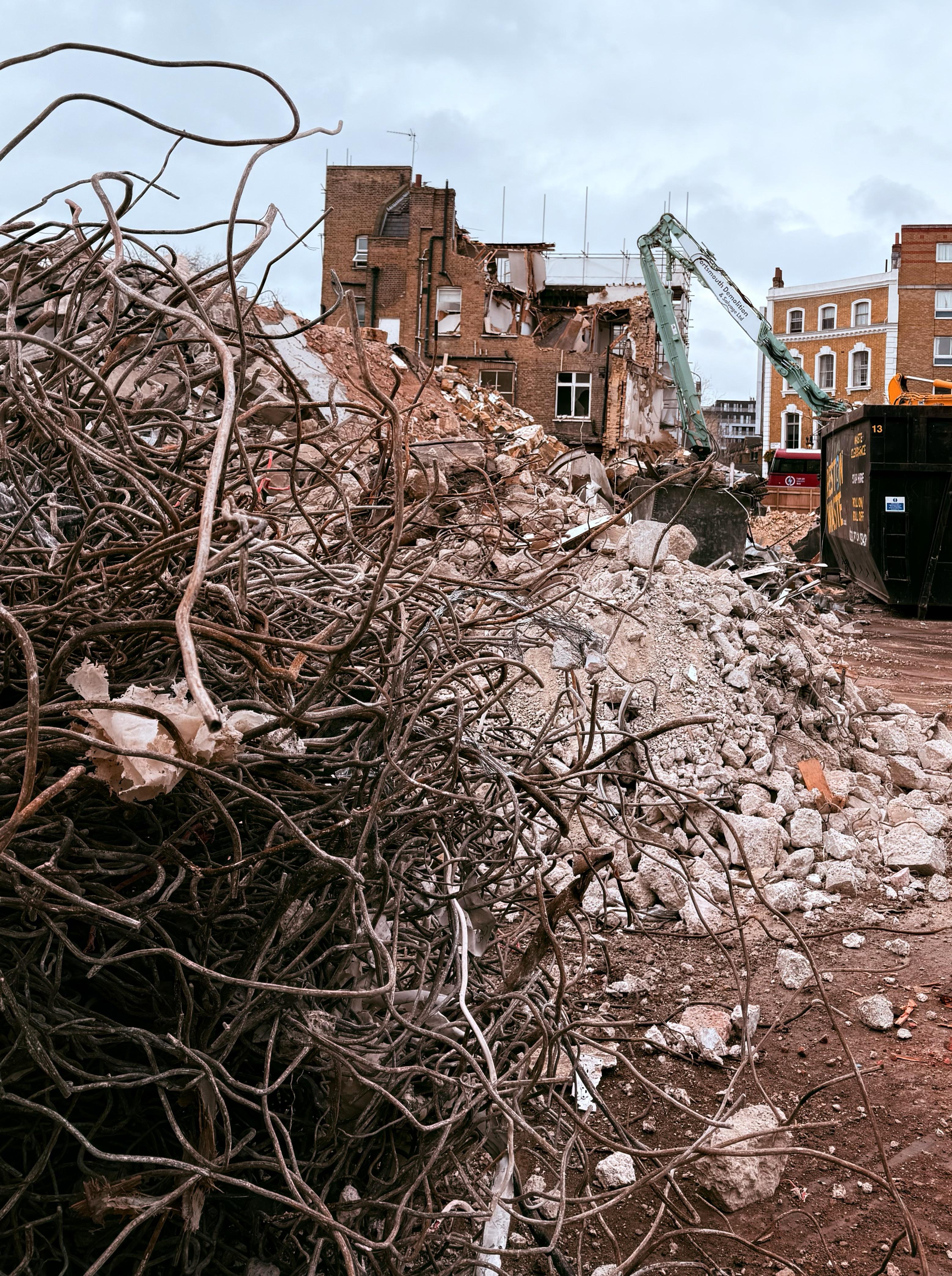
Hello and welcome to the first Demolition Hub magazine of the year. We celebrate five full years in September, with 2025 marking our sixth calendar year. We say magazine, but Demolition Hub is so much more. We’re your ongoing industry publication with personality, news, case studies and interviews, and we’ve evolved beyond the six issues we produce each year, delivered straight to your inbox, socials, and letterbox.
Our investment in the industry has enabled us to grow the British Demolition Awards to become the largest attended global demolition event, celebrating the work you do on a daily basis. Our socials continue to thrive, regularly hitting six figures on TikTok and Instagram, with original content posted almost daily.
Contractors obviously also benefit. In 2024, we conducted 33 ‘On-site’ visits with 25 different contractors, and we’re eager to continue showcase your challenging, impressive projects. We kicked off this year with Portsmouth Demolition in London – book a visit to show what you can do.
In short, we’ve become an approachable, likeable medium for services to communicate directly with the industry’s best. No turning back now – let’s continue this evolution together!
In this issue, we feature an insightful conversation with Emma Grant from CheckaTrade, who recently reconnected with us to discuss its push into the demolition sector.
We also present a long overdue chat with Richard Dolman of AR Demolition on his backstory, workforce training, the labour market and ethical standards in the industry.
Thanks to all who contributed. Next, we’ll be at the Executive Hire Show, join the IDE at the end of the month, and then head to New Orleans for the National Demolition Association’s convention.
Get in touch.
Ben Chambers Publisher, Demolition Hub
ben@chambers.media
PUBLISHER
Ben Chambers ben@chambers.media 01903 952 648
EDITOR
Toby Wilsdon toby@chambers.media 01903 952 645
COLUMNISTS
Howard Button
Richard Dolman
Richard Vann
Terry Lloyd
ADVERTISING SALES
Ben Chambers ben@chambers.media 01903 952 648
DESIGN
Joe Chambers joe@chambers.media
PRODUCED & PUBLISHED BY Demolition Hub Ltd
Suites 5 & 6, Chapel House, 1-6 Chapel Road, Worthing, West Sussex BN11 1EX demolition@demolitionhub.com 01903 952 640
is the media partner for the European Demolition Association and the Indian Demolition Association
Demolition Hub is published six times a year. The subscription rate is £60 per year. Subscription records are maintained at Demolition Hub Ltd, Suites 5 & 6, Chapel House, 1-6 Chapel Road, Worthing, West Sussex BN11 1EX
Articles and information contained in this publication are the copyright of Demolition Hub Ltd and may not be reproduced in any form without the written permission of the publishers. The publishers cannot accept responsibility for loss of, or damage to, uncommissioned photographs or manuscripts.
6 NEWS
Connecting talent and opportunity with globalbridge Search is on for the UK’s most promising plant apprentices
Lighthouse Charity supports record number of families in 2024
National Demolition Association releases advocacy agenda for demolition industry
12
DEMOLITION DISCUSSION
With AR Demolition’s Richard Dolman
18
DEMOLITION EXCAVATOR FEATURE
CASE
JCB Komatsu SENNEBOGEN DEVELON
Wacker Neuson XCMG
Case Study in Brief: Burke Demolition Collard Group: Harlington School redevelopment Round the Corner: Clifford Devlin
42 FINANCE FEATURE
Acquired Asset Finance Aldermore
JCB Finance
Paragon Bank
Kick Asset Finance
Construction Plant Finance
Ultimate Finance
52
With Emma Grant, Head of Trade Experience at Checkatrade 32
56 EVENTS
World of Concrete
FACHTAGUNG ABBRUCH 2025
UK Concrete Show bauma
Executive Hire Show
88
DEMOLITION HUB ON SITE
Getting on site with Britain’s contractors
Snapshots of Ben and the Demolition Hub team’s activities between issues
Richard Vann
Terry Lloyd
Richard Dolman
Sunward welcomes Warwick Ward on board Grantham Industries secures £500,000 from Paragon Bank to acquire Rutland waste site
Brokk Inc. named North American distributor for Darda
Aquajet expands hydrodemolition reach with new Support System
DEVELON increasingly popular in Czech Republic
Landmark for JCB as its hydrogen engine is approved for use
LEKATECH, the Finnish electric hammer revolutionary, joins the EDA
Venice to host EDA Annual Convention 2025
Growth returns to European construction sector
Study on technical requirements for non-road mobile machinery
EU Council approves Conclusions on Labour and Skills shortages
Scott Laird’s story of industry dedication
The logistics of luxury
Giving the gift of feedback
The latest demolition jobs from Romax Solutions
In 2025 the CEA is making significant strides with globalbridge, a platform designed to level the playing field for young people and redefine how new talent is discovered. With momentum already building, the goal remains clear: to ensure every young person has the chance to shine while every employer gains access to the diverse skills our industry urgently needs.
What is globalbridge?
globalbridge was born from a simple yet transformative goal: to provide every young person with a fair opportunity, regardless of the background that they came from or the connections they had.
The platform empowers students to showcase their skills and achievements beyond traditional grades. It enables them to create multimedia profiles that include projects, videos and personal highlights – offering a fuller picture of their talents.
This approach extends beyond students. globalbridge also delivers data-driven insights to schools, enabling them to refine their support programmes and identify what truly works. Employers benefit from an innovative opportunity-matching system, bringing the right talent directly to their doorstep while promoting inclusivity and diversity within their workforce.
This initiative underlines the CEA’s commitment to addressing the industry-wide skills shortage. By connecting employers with the next generation early, globalbridge creates a fairer, more inclusive approach to talent development. For young people, it’s a gateway to careers within construction equipment and other sectors, showcasing roles that might otherwise remain hidden.
Jacqui Miller-Charlton MBE, a key supporter of globalbridge and part of the Miller Groundbreaking dynasty, describes it as a “game-changer” for connecting young people with meaningful career opportunities. “We’re absolutely blown away by what the team has achieved so far,” said Jacqui.
As the first CEA member company to adopt the platform, Miller Groundbreaking is collaborating with globalbridge to create a seamless application system. At the same time, Jacqui is calling on employers to create more opportunities across the construction sector and beyond.
Viki Bell, Director of Operations at the CEA, added: “The skills shortage in our industry is a challenge we cannot ignore. globalbridge offers a practical and innovative solution
by connecting employers with young talent and giving students a chance to shine in ways that go beyond traditional grades. It’s an inspiring step forward for workforce development and we’re proud to support it.”
Shaping the future workforce
globalbridge goes beyond traditional recruitment by actively shaping tomorrow’s workforce. The platform introduces young people to the wealth of opportunities in industries like construction at an early stage. “Kids are always on their tablets and phones,” Jacqui notes. “globalbridge
leverages technology to connect with them directly, providing guidance, inspiration and a pathway to meaningful careers.”
globalbridge is already making waves across the construction sector and beyond. It is supported by influential partners and strongly focused on innovation. Collaborating with organisations like the CEA ensures that its message reaches educators, parents, employers and policymakers alike.
A vision for the future
Jacqui praises the platform for its originality and vision. “globalbridge is truly one of a kind. There’s nothing else out there that connects young people, educators and employers so seamlessly. It’s a platform that’s ahead of its time and the vision behind it is extraordinary… [it’s] a solution that not only opens doors for young people but also helps businesses find the next generation of talent in a smarter, more accessible way.”
Join us on 25 February 2025, 12.30-1.30pm, for a webinar exploring myglobalbridge, the platform transforming how young talent connects with industry. Featured guest Jacqui Miller-Charlton MBE will share insights on how globalbridge is helping employers engage with future talent and address the skills shortage.
thecea.org.uk/connectingtalent-and-opportunitywith-gb-webinar
A nationwide search is on for the most promising apprentices and trainees in the construction plant industry who, in the eyes of their employers, are likely to become tomorrow’s leaders of the sector.
The Construction Plant-hire Association (CPA) has opened entries for the CPA Stars of the Future Awards 2025. The awards are free to enter and open to both CPA members and non-CPA members. Nominations are welcome from all employers including planthire companies, manufacturers, contractors, suppliers and others operating in the construction plant sector with apprentices and trainees
in their workforce. Nominees need to be on an approved apprenticeship scheme or employer in-house learning programme.
To make a nomination, employers can download a nomination form from the CPA website at www.cpa.uk.net/skills-training/starsof-the-future and complete and return it to the CPA by the nomination deadline of 21 March.
The winners will be announced at a prestigious awards ceremony at the Heart of England Conference and Events Centre in Fillongley, near Coventry, on Thursday 10 July. The event will be hosted by construction industry journalist and vlogger Peter
Haddock.
Awards will be made for the well-established categories of Plant Mechanic of the Year (Level 2), Plant Technician of the Year (Level 3), Young Plant Operative of the Year, Plant Operative of the Year, Plant Installer of the Year, Lifting Technician of the Year, Hire Controller of the Year, Apprentice Mentor of the Year and College of the Year. All nominees are also eligible for special awards including the Judges’ Special Award and the Best Personal Statement Award.
In recognition of the growth of the awards over the last 12 years, a new awards category has been added for 2025 for Technical Support Person of the Year. This award is for apprentices or trainees who are in a role that has a plant technical focus and who are supporting other plant-focused operations of their business such as data handling and supply, hiring activities, sales and marketing activities, parts and/or resources/ equipment supply, machine/
equipment systems programming/ maintenance, site operational planning, supporting external customers, etc.
Steve Mulholland, CPA Chief Executive Officer said: “We urge employers – both small and large – to nominate apprentices and trainees who they see as being the industry’s future leaders, as it means the world to them to be nominated for an award. The awards are open to all employers across the industry, so nominating organisations needn’t be a CPA member to put someone forward.
“Stars of the Future is becoming more high profile every single year and last year’s winners received national recognition and won some fabulous prizes, including tool kits, machine training courses, iPads, an overseas trip to visit a Liebherr crane manufacturing plant in Germany, another overseas trip to one of Wolffkran’s manufacturing facilities in Luckau, Germany, and a VIP day courtesy of JCB. We know that many previous Stars of the Future winners have been fast-tracked to supervisory and management positions.
“At the CPA, one of our primary objectives is to encourage new blood into the construction plant sector and Stars of the Future helps us to achieve this. The standard of entries gets higher every year and last year we received 80 nominations from across the industry. We anticipate even more this year,” he added.
Stars of the Future has a two-tier judging process – the CPA selection panel and a panel of external judges from across the industry who decide the eventual winners of each category.
www.cpa.uk.net/skills-training/ stars-of-the-future lisa@lisacollinscommunications.co.uk
+44 (0)7968 840 390
National Plant Mechanic of the Year: Bethan Whittaker of KJ Services and Bridgend College
National Plant Technician of the Year: Morgan Wardle of Banks Plant Solutions and Askham Bryan College
Hire Controller of the Year: Millie Scott-Young of Sunbelt Rentals
Young Plant Operative of the Year: Josh Jones of L Lynch Plant Hire & Haulage
Plant Operative of the Year: Reece Stray of L Lynch Plant Hire & Haulage
Lifting Technician of the Year: Zac Bradshaw of Commhoist
Plant Installer of the Year: Hayden Chappell of Southern Hoist Services
Individual Apprentice Mentor of the Year: Steve Gwynn of Sunbelt Rentals
Group Apprentice Mentor of the Year: Dave Rogers of L Lynch Plant Hire & Haulage
Best Personal Statement Award: Shannon Weiss of Finning UK and Finning Academy
The Judges’ Special Award: Tom Williams of CBL and Bridgend College
Sponsorship opportunities are available for Stars of the Future 2025.
In 2024, the Lighthouse Charity was once again setting new records, reaching more people and delivering more support than ever before and the charity is in the unique position of being able to offer every aspect of emotional, physical and financial wellbeing support.
Last year the charity’s helpline advisors and caseworkers delivered an amazing £4.98 million* of charitable support to 5,695 families who reached out for help through the charity’s free and confidential helpline and live web chat service.
The charity also supplied 5,712 meals and provided 5,756 counselling sessions to our workforce.
Furthermore, their #MakeItVisible tour team continued to reach some of our industry’s most vulnerable workers, sharing the message of support with frontline trades. Last
year the charity’s team visited 572 sites and started conversations with over 28,000 site workers. This initiative introduced 88 workers expressing suicidal thoughts to the #MakeItVisible team. But through starting a conversation, those suicides have been prevented.
Reflecting on a year of positive impact, Sarah Bolton, CEO of the Lighthouse Charity said, “This support was delivered against another challenging year with the construction sector being one of the worst hit for company insolvencies. This, alongside continued increases in the cost of materials and the cost of living has added pressure on our construction community. The important thing is that people know about us and
are reaching out for help. Whether it’s supporting someone through illness or injury, making sure there’s a meal on the table for the family or simply offering a listening ear, the message is simple – if you’re struggling, help is here.
“To ensure that we are meeting the industry’s needs, we are continually improving and growing our charitable services, listening to our communities and extending our message of support beyond the boundaries of the workplace.
“But our work is only possible thanks to the support of the people in our construction community. Whether it’s organising fundraising days, becoming a company supporter, attending events, or helping us spread the message of support through their supply chains, all of this contributes to us being able to make a life changing and lifesaving impact. Our work is continuous and we are looking forward to extending our services and the support we offer even further in 2025.”
*Final and audited figures will be available later in the year in the charity’s 2024 annual accounts and Impact Report.
The National Demolition Association (NDA) has released its 2025 National Policy Agenda, which outlines a comprehensive advocacy agenda for the demolition industry. The policy agenda is a vital guide and resource for Members of Congress and the Trump administration as they tackle the country’s most pressing challenges.
James Milburn, President of NDA, said: “The demolition industry is deeply invested in America’s economic success and stands ready to partner with lawmakers and the new administration to implement policies that drive economic prosperity. We look forward to working together to create meaningful demolition jobs now and in the future.”
The 2025 NDA National Policy Agenda represents 11 different policy areas:
• Workplace Safety and Health
• Workforce Development
• Labour and Human Resources
• Tax Policy
• Environmental Stewardship
• Healthcare
• Disaster Response
• Procurement Transparency and Fairness
• Trade
• Infrastructure
• Electric Vehicles
Interviewee: Richard Dolman
Role: Director
Company: AR Demolition
Toby Wilsdon
What’s your earliest demolition memory?
Richard Dolman
When I was 20, in the early 1990s, I bought JCB 3CX, took a two-week course to learn how to drive one and went out on hire as an owner operator – quite different to the specialist contractor we are today.
My earliest demolition memory is of a project in Leicester where they were knocking down semi-detached houses to build new homes. I was on hire to Tarmac Homes, who were building the replacement houses, and I watched the adjacent demolition with interest.
I was doing bits of everything, light finishing off after the houses had been built – digging trenches, keeping the ground workers fed with gravel when they were putting drains in, carrying stone around the houses ready for slabbing and patios and forming driveways, that sort of thing.
TW
Tell us about your path into demolition.
RD
I started doing a few more hire jobs and gradually the occasional small groundworks job, driveways or site clearances, anything a JCB could do. I got a 13-tonne excavator,
which I used to hire out, and one day a customer said he’d bought a fuel station and could I knock it down for him. I said, “I can do that.” I did it, enjoyed it and made a few quid. I took a look at the demolition industry and thought, I’m going to have a go at this.
Did that include taking out the fuel tanks?
RD
Yeah. It was a near vertical learning curve. I got that bit right, actually, by talking to people. I learned how to talk to the local petroleum officer. I learned that you had to get the tanks degassed, which I did.
There was a lot more petrol in the tanks than anticipated and I remember the company that I’d got coming to foam fill them saying, “There’s too much petrol in there, that needs to go. If we can’t do this tank we’re going to have to leave and
“We believe in an honest profit but giving our customers a great job”
you’ll have to rebook us with a revisit charge.” It would have finished me before I’d even started.
So I said to them, “Are you able to pump the fuel out for me?” They said yes, so I told them, “Right, I’ll do the rest. I’ll put you all in a hotel for the night, see you back here early in the morning and we’ll get that fuel out.”
And then they foam filled the tanks.
TW
The confidence of youth. RD
I think naivety and stupidity, but one could argue it was a pivotal moment, because if I hadn’t have done that, I probably wouldn’t have got beyond the starting post.
So I did that job and then I’d go months without another demolition job and I realised that there weren’t a lot of people doing a lot of training. And so I went really hard at that, pushing it to potential customers that I’d got a trained workforce. And then somebody else would give me a job. There were a couple of people that gave me incredible breaks and that started it going.
People liked what we were doing because I was doing it a bit differently. I had a trained workforce; I wasn’t ever going out trying to charge customers extras. I was very much about, “That’s what it’s going to cost, I’ll do a fair honest job,” which
I did.
It got a lot of momentum so I asked my cousin Andrew to partner up with me. He was doing haulage and low loader work with his own lorry, and that’s where AR came from.
We pushed even harder at the training and the integrity and trying to do it differently from how I perceived the demolition industry to be. It accelerated fast and nearly went off a cliff face at one stage. If I’m honest, we’d not employed the right management and started to lose the core values. In about 2016 we worked out we needed a change to realign the business following huge growth, back to focusing on what we are all about – honesty, integrity and quality.
We’re back there now. It’s a controllable size; we’re not always the cheapest but what we do offer is great value for our customers. Our bottom line is that we believe in an honest profit but giving our customers a great job. If you’re doing your job how I like to do it, you never have to go back for more saying, “Oh, we didn’t allow for this.”
As I’ve already intimated, I think there are some out there who have the complete opposite attitude when it comes to how to win a job. That’s not where I want to be, where AR wants to be.
For many years I’ve talked about lessons learned. Everyone makes
“Don’t ever sell something that you can’t deliver”
mistakes but you’re often judged on how you fix it. Rather than trying to hide, put your hands up and say, “We’ve made a mistake. What can we do to fix it?” And it normally works out well.
TW Where did this attitude come from?
RD
My parents have always been about, “If you’re going to buy something, buy the best quality you possibly can.” Always know that you can lie straight in bed at night. My dad sold fishing tackle and shooting equipment and he’s always lived by, “Don’t ever sell something that you can’t deliver,” and he’s instilled that into me. What that means is, if you tell someone you’re going to do it, you do it, even if you lose out yourself. I’ve lived by that.
I believe in my workforce. We all love the big, shiny kit but it’s useless without the most vital component, the operator. And that’s not just machine operators, it’s everybody, whether they’re on the ground or site management, etc. I want them to buy into what AR is all about, I want them to buy into a job for life and when they retire say, “You know what, they really looked after me.” I’ve always been about the people because they’re the biggest asset we’ve got.
TW
Where does your passion for education and training come from?
RD
I just feel that the industry needs it. There are people in the industry who want to see it professionalised,
and I’ve just felt that there’s been something missing. There are aspects of the industry that I’m not a fan of. But there are other parts where I’ve got to acknowledge that the industry has been kind to me and my organisation. So I want to put something back and make it more sustainable and taken seriously, because quite often the demolition industry is not taken seriously.
It often gets, “Here we go again, the demo ops, brace yourselves.” And if I’m honest, particularly with some things that have gone on recently, it can sometimes deserve that reputation.
But there are people who really want to shake that reputation and that’s what I hope to be part of. I wouldn’t dream of thinking that I could single-handedly change it. But I’d like to think that I can contribute.
TW
People have wrecking balls in mind but they’ve probably never seen one.
RD
I’ve never seen a working wrecking ball and I’ve been associated with the industry for nearly 30 years. And then there’s explosives, a specialised field that most people rarely get involved in. There is that image of smash it up and go, whereas now it’s such an engineered industry. We’re asked to do a magic trick – “Make that building vanish and cause no impact on anybody else’s day-to-day work,” which great, but it requires an engineered approach.
The same with our investments. I remember reading Plant Trader, there would always be an ad for a beat-up old excavator saying, “Spares and repairs or good for
demolition.” Whereas now, what construction-related industry, invests like we do? Demolition has evolved from wrecking balls through a beat-up old excavator to incredible bespoke machinery. I challenge anybody to come up with a sector in construction that has bigger investment in plant and machinery.
TW
Are there any speciality projects for AR Demolition?
RD
I love the technically challenging ones. We dismantled some printing presses out of a building once and we made our own crane because we couldn’t get one in. We adapted that crane to turn it into an engineered shield, Big Blue, as we called it, for working next to a highway, or close to the public.
At Hams Hall Bridge (pictured
“We’re at the dawn of a new era”
above) last year, we couldn’t get a crane anywhere near due to the power lines, so we made our own gantry system to pick it out. I think we’ve carved ourselves into one of the go-to specialists for that.
We do quite a lot taking down redundant quarrying plant – we’re well recognised there. Traditionally, quarrying didn’t have good accident statistics, in particular demolition was bypassing procurement because it’s often metal based so a quarrying engineer would just get the local scrap man in and say, “Can you get rid of that?” But they didn’t have good incident statistics so they started to shake themselves up.
To this day the construction industry – and this is one of my worries with it – say, “We want this accreditation, we want you to work to this standard, be in this association,” all kinds of things. That comes with a cost, but the number
of times I hear, “We’re not going to award you this job because they were cheaper.” Often it can be a contractor that’s not got all the accreditation, is not doing all the training.
Our bottom line reflects us doing things the correct way. But what customers will do, particularly in construction because it’s so commercially driven, is talk themselves into the cheaper quote rather than looking at what they’re actually getting, which is fine until something goes wrong – waste goes somewhere it shouldn’t, or there’s an incident.
In quarrying they won’t entertain that. They say, “We want you to be this, we want you to be that way,” and they actually mean it. You wouldn’t get near a tender list if you hadn’t got the credentials. You get sectors like this, like the rail sector, the energy sector who mean it, they’re the type
of client that we want to work for.
Quite often, because a lot of clients don’t understand this, they put you in a reverse auction to the bottom, and that’s just not for me.
What was your experience of the presidency of the IDE?
There were a lot of things I wanted to do for the good of the industry but if I’m honest, I think some people stood in the way because it wasn’t their organisation involved, or their organisation’s idea.
I have a bit of an image in this industry that some people don’t like because I don’t quite fit the mould and I think that got in the way of me completing some really good things, which is disappointing. Associations and trade bodies aren’t about the competitive side, but it
interview
“Everything’s got a place but we’re focusing a little too much on electric”
does creep in.
I’m particularly proud of my involvement with the demolition foundation and master’s degrees and I think we’re at the dawn of a new era there, which is going to be really strong.
I did take a lot of good from it, I enjoyed it. My first year was during Covid, so it was pretty dormant for a year. The second year wasn’t and I met some incredible people, interesting people, and did some really good stuff. But disappointingly, because of different agendas, I probably didn’t get everything done that I’d have liked.
I’ve now completed my immediate post-presidency. I’m fortunate enough to have been voted on to the Council of Management again –I’m doing that because of my passion for the degree.
TW
What’s your take on the availability of labour?
RD
Really tricky, it’s very hard to get people of the standard that you’d like. I don’t blame the industry; I blame the education system as a whole. Not going to university or higher education is looked down upon. I absolutely wish the system was promoting that it’s a good thing to leave school and be a bricklayer, a plasterer, a plumber, demolition worker or hairdresser. With the workforce getting older, there’s less and less good labour.
When we were at school there were probably 30 jobs to choose from, that was about it. Now, there are incredible careers for people in all sorts of sectors, and rightfully so. I
just wish we’d promote people using their hands a bit more because the career opportunities in demolition are astonishing. I’ve seen people come into our organisation from the bottom, now having senior jobs.
TW
What involvement in the community does AR Demolition have?
RD
Corporate Social Responsibility is a big thing now and we do lots of jobs where it’s part of the criteria to win the job and we do it very willingly. We do things like charity events, going into schools and talking about the industry and my journey, off our own back.
TW
What are your thoughts regarding lower carbon power sources?
RD
Everything’s got a place but we’re focusing a little too much on electric. There are some basic principles I wonder about – where’s the power going to come from? What’s the environmental impact of the mining, what happens to the batteries at the end of their life?
I wonder where we would be now if we’d invested as much in fossil fuels as we have in electric, whether they could be a lot cleaner. And the people who are pushing us so hard to go electric today are the same organisations who told us 20 years ago that diesel was the way to go – and now diesel is the devil himself. If the tech is there, then that’s brilliant. We need to look at all angles, don’t we?
TW
Are there any other developments you can see in the industry?
RD
I think a mind-shift towards end of life of structures is probably the way. I have a real thing about old buildings. If we take down a building that is four or five hundred years old, we can easily reclaim all the materials, they can get reused and build another structure that might last another three, four or five hundred years.
Whereas modern materials are very efficient with regards to insulation and construction costs, but we seem to be taking them down within 30 years. So we’re now building structures that last less than a tenth of what many buildings did, and we’re seeing recycling rates come down because we can’t do anything with the material.
I think that greater engagement across sectors is needed to understand how we are designing and building things and what the end of life is.
That is a massive piece of work and one that we’ve all got a responsibility to be involved in.
“By no means am I talking about retiring”
TW
Have you got any interesting projects coming up?
RD
We’ve always got lots of projects that we’re looking at. There’s a nice technical one that we’ve been looking at that will be a real challenge. There’s lots of things in the energy sector that look pretty cool that we’re hoping to get involved in. We’re working more and more on the recycling side, our aggregates business has just invested in a wash plant.
We’re pushing more towards the technical projects because, as I’ve said, we don’t want to be part of this reverse auction as to who can do it this cheapest just to keep a yard full of big diggers busy.
TW
Would you move into power stations?
RD
We’ve looked at it. Didcot’s a taboo subject but I was very impressed with the guy that went in afterwards and brought it down – Roland Alford of Alford Technologies. The way he did it remotely and the tech he used to bring it down was incredible.
Alford Technologies are real pioneers in explosive technology who develop, design and manufacture their explosive demolition products. Because they designed the whole lot from scratch, they came up with something better.
We said, “We can hook up with this guy and use a different method,” but we weren’t big enough and well known enough at the time. But I think it’s really disappointing that no-one else snapped him up because I think that could have
changed that side of demolition, but it doesn’t seem to have changed too much yet.
TW
Where do you see yourself and AR Demolition in five or ten years?
RD
I think AR will hone itself more and more into the specialist sector. We’ve got some really good young people coming through who have got different ways of doing things from me but have the same ethics. So I think the right thing for me to do would be to make way for them – and hopefully they’ll tap me for a bit of experience.
By no means am I talking about retiring, but I want to make way for them and steer the organisation from the back room, if you like, and they can wheel me out when they want me.
I want to maintain the thing about integrity and doing things right and to size the business to the number of customers that that fits.
TW
Will you be retiring at some point or will you just keep on working?
RD
I think I’ll always do something just because of my nature. But I have learned in the last few years to level out the work life balance a bit, and I think the result is more productivity anyway.
If you would like to be featured in our Demolition Discussion or Supplier Talk interviews, please contact toby@chambers.media
Who or what would you be in an alternative life?
An F1 driver
Who is your favourite artist?
Brian Johnson of AC/DC
What do you do for fun?
Play with a traction engine
What would be your desert island luxury?
Good quality sausages
What gets you out of bed in the morning?
All of the great fun I have with my incredible friends and family
What’s the most expensive nonessential you’ve ever bought?
A traction engine
What would you do for a company excursion, money no object?
Tour every Grand Prix on the calendar (not sure would be everyone’s cuppa)
What’s your favourite food?
Sunday dinner
What’s your tipple of choice? Port
The CX210E-S – the Essential 20-tonne crawler excavator
CASE Construction Equipment’s second 20-tonne class crawler excavator in its E-Series lineup is the ‘Essential’ alternative to the regular CX210E. The CX210E-S retains all the performance and operator comfort as well as quality and reliability of the standard model but comes with a simplified offer at an increasingly competitive price point.
The machine is powered by an identical FPT NEF6 Stage V diesel engine and features the same outstanding Japanese technology, delivering equally impressive productivity and controllability.
The CX210E-S uses a heavyduty version of the lower frame, with an LC undercarriage with reinforced components. The track frames have a single-track guide, and triple grouser steel shoes are available in 600-mm heavy-duty, or 700-mm widths.
The excavators feature a heavy duty monoboom and a single, equally heavy-duty 2.94-m dipper arm option. The CX210E-S comes factory-fitted with standard quick coupler circuit and high-flow multifunction auxiliary hydraulics, with a low-flow circuit also available for enhanced versatility with all kinds of attachments.
The operator’s cab boasts a pneumatic and heated operator’s seat with suspended joystick consoles, 10-inch display with integrated A/C and five configurable buttons, a Bluetooth radio, an LED light package and a FOPS Level 2 top guard, thus offering the same degree of uncompromised protection and comfort to the operator as the current CX210E.
The E-S model tips the scales around 500 kg heavier than the CX210E, due to the heavy-duty
build of its front-end equipment, lower structure and undercarriage and it can be boosted by another 500 kg by selecting an optional counterweight to better manage heavier attachments. It boasts lifting capacity and drawbar pull virtually unchanged and the machine also delivers the very same breakout forces.
The ‘Essential’ model benefits from all of the existing services offered by CASE, including extended warranty and planned maintenance contracts, regular inspections, fluid analysis, maintenance kits and telematics. The CX210E-S is supplied as standard with the same bi-directional modem as other E-Series crawler excavators,
The 20-tonne sector remains one of the most highly competitive arenas in the European crawler excavator market. By offering a simplified configuration choice and even more competitive pricing, with no loss of performances, quality or reliability, the CX210E-S provides CASE dealers with an ‘Essential’ option for cost-conscious rental and contracting customers. www.casece.com
+44 (0)7581 054 354
An operator protection cage shields operators from falling material.
Certified to FOPS Level 2, it is designed to provide maximum protection with limited impact on visibility due to the design of the angled bars. The cage is platform mounted so can be easily replaced and does not immobilise the machine if damaged. Furthermore the complete front piece of the cage can open like a door allowing easy cleaning of the front glass.
Visibility and on-site safety can be further improved by standard rearview and optional side-view cameras, which provide uninterrupted rearward and sideward views on a large, landscape 7”-colour display.
All JCB XD demolition excavators feature a Side Impact Protection System (SIPS) designed to protect the fuel and hydraulic tanks, cooling pack and hydraulic pump bags. SIPS are fitted down both sides of the machine’s upper structure, bolted on
in two sections on each side for easy repair or replacement.
A 400% increase in thickness in underbelly protection from 2 mm to 10 mm guards vital machine components on the upper and lower structure. JCB also now has an external steel plate covering the tanks, which are set inboard for additional protection.
JCB XD models benefit from heavy duty dippers, with wear strips added to the underside of the dipper and a bolt of ram guard for the bucket ram with wear pads on the slide mechanism for extensive durability.
Twin track guides are fitted as standard on JCB XD models to protect the track chain of the machine when tracking in arduous conditions. Optional full-length track guides can be specified with the machine for even greater durability.
JCB also now fits a wide core radiator as standard and has options for a reversing fan and flyscreen
that is pleated in design with no detriment to the 55°C ambient cooling performance.
The bold new counterweight on the X Series is shaped to protect the asset too with dedicated strike points on the corners with the logo recessed to protect company branding. The counterweight also comes as red and white chevrons as standard on the XD model.
For ultimate attachment handling, JCB offers the option of Advanced Tool Select. On the display 10 attachments can be set up with desired flow and relief pressure, with customisable control curves for the proportional sliders allowing operators to fine tune the response. ATS monitors pressure changes and makes alterations to the system to maintain a constant and consistent flow to the attachment.
www.jcb.com
+44 (0)800 083 8015
MAXIMUM PERFORMANCE
LOWEST OPERATIONAL COSTS
HIGHEST RELIABILITY
Econ Group, a family owned and managed demolition business established in 1982, runs a fleet of Komatsu demolition excavators consisting of six machines, all built in the Komatsu UK factory in Birtley, County Durham. Each excavator (aside from the PC170LC-11) comes factory fitted with demolition spec features and is ready to work on delivery.
The demolition contractor is currently using them at a massive redevelopment scheme in north London, clearing the existing housing to make way for a new development. When a team from Marubeni Komatsu paid them a visit, they were demolishing 16 houses along with
three maisonette blocks at three stories high, with the material being crushed to be reused on site.
On site, the team found a PC490LCD-11 coming through the building with a selector grab. Rather than just knocking it down, the materials were being segregated –clean wood, general waste, iron, non ferrous metals, plastic windows each going into separate recycling waste piles. A PC290LCD-11 was working on the ‘munching pile’ pulverising the concrete to get the iron out so both could be recycled.
Why Komatsu?
Liam Moore, General Manager, explains: “Because it is a tough
industry one of the things that we were looking for is a machine that’s purpose built for the industry that we want to put it to work in. Komatsu is one of the only manufacturers out there, built in the UK, that come straight off the production line if you order it in demolition spec, with all the bells and whistles.
“Doing my research there are a number of competitors in our sector that are still continuing to run Komatsu Dash-7 and Dash-8 machines and that shows they are able to stand the test of time.
“We currently, typically look to run a machine between five to six years and then look to replace and that way we get the best value out
of the product. And of course more importantly at the back end, when you look to sell the product, you get a brilliant residual value.”
Liam continues: “We started our journey with Marubeni-Komatsu in 2020 when we purchased a single PC210LCD-11 and then when we came to look at continue to grow and renew the fleet in 2024 there was really only one front runner that stood out for us, and that was Komatsu.
“We looked at PC170LC-11, which is a unique machine in the UK market and is fantastic and very adaptable for all sorts of situations that we as a business face. We purchased an additional PC210LCD-11, PC290LCD-11, PC360LCD-11 and just last month we took delivery of the largest machine in the fleet which is the PC490LCD-11.
“All of those machines have been absolutely flawless, the service support and backup from Marubeni-
Komatsu has been exceptional with regular phone calls and fast responses.
“When we took delivery of each of the new machines we wanted to give the operators a sense that the machine was theirs as well as the business’s and we decided to name each and every one of them. So if you take ‘Bucktooth’ for example (PC290LCD-11) – it has a large pulveriser muncher on it that has a tooth that reminds them of a dinosaur – hence the name Bucktooth.”
Jamie O’ Donnell, Contracts Manager says: “By keeping one operator on one machine we find that it works better – they look after the machines better – they keep them clean, tidied and well maintained and then the operator also learns the capabilities of that machine.”
Concluding, Liam says: “I believe that Komatsu in the UK, with Marubeni-Komatsu supporting us and being behind us has a combination of a fantastic product
and brilliant customer service, bringing a winning combination. That’s why we continue to invest in Komatsu.”
Factory demolition specifications:
• ISO10262 Level 2 top and front guards
• EN356 Grade P5A high impact protective glass (front and top window)
• Roof window wash/wipe system
• Protected lamps
• Bucket cylinder guard
• Reinforced linkage
• 9-mm thick undercovers
• 15-mm thick side protection
• Two additional attachment lines
• Integrated attachment control system
• Drain line
www.marubeni-komatsu.co.uk
info@mkl.co.uk
+44 (0)3301 234 441
Demolishing buildings and industrial plants requires precision and skill. This is why the experts at Karl Group Deggendorf/Hengersberg rely on the SENNEBOGEN 870 E Demolition machine, which with a reach height of 36 metres and a load capacity of four tonnes, leaves nothing to be desired.
The Karl Group specialises in large and special demolitions, demolition of buildings of all types and sizes as well as remediation of contaminated sites. A current project is the demolition of the old factory
buildings of the former textile works in Deggendorf/Seebach, where the SENNEBOGEN 870 E Demolition is being used.
demolition
The SENNEBOGEN 870 Demolition with its three-part long front equipment is ideal for demanding demolition work at great heights and for handling heavy loads. With a maximum reach height of 36 metres, buildings with up to ten storeys can be safely demolished or dismantled. The machine
demonstrates its strengths in densely built-up urban areas in particular by precisely picking up building sections with the demolition shears or grapple and bringing them safely to the ground.
Comfort for the driver and during transport
A particular highlight of the demolition machine is the telescopic crawler undercarriage, which ensures a narrow transport width and high stability during operation. In addition, the elevating and tilting
cab provides an optimum view of the demolition object and the surrounding area.
The machine can be dismantled into its three units – basic machine, demolition equipment and counterweight – for easy transport. Thanks to the removable counterweight, the transport weight of the basic machine can be reduced by an additional 26 tonnes, making transport easier and more cost-effective.
With the SENNEBOGEN 870 E Demolition, the Karl Group relies on state-of-the-art technology to efficiently and safely dismantle old factory buildings.
www.sennebogen.com sebastian.loibl@sennebogen.de +49 (173) 6619014
DEVELON now offers a total of four specialised demolition machines with operating weights up to 71 tonnes and a reach of up to 31 metres. The models in the range are the DX140RDM-7, DX245DM-7, DX380DM-7 and the top-of-therange DX530DM-7.
All models meet the Stage V emission standard, while varying in size, weight and range. They have a maximum payload capacity of up to three tonnes at the boom and are powered by engines with outputs of up to 294 kW. All four machines offer perfect flexibility thanks to their
modular boom design and hydraulic locking mechanism.
A cab tilt of up to 30 degrees is available for better operator visibility. The DX140RDM-7 can be supplied with either a monolithic or interchangeable boom on request.
The DX245DM-7, DX380DM-7 and DX530DM-7 always have an interchangeable boom, which not only increases the machines’ availability but also significantly simplifies transport.
This is also facilitated by the low transport width of the machines from 2.5 metres thanks to the extendable chassis. The customer can thus choose from a range of solutions depending on the project they need to handle.
Even more choice in the new DX140RDM-7
Like the three larger models from 31 to 61 tonnes, the new DX140RDM-7 22.5-tonne demolition excavator offers multiple configurations to choose from, providing the customer with a range of solutions depending on the project to be completed, including a multipurpose version that can be used for other applications on site as well as demolition.
In fact, the DX140RDM-7 offers even more choices, starting with a ‘Monolithic’ variant unique to this model that features only a demolition arm without any possibility of interchangeability.
Alternatively, like the larger machines, the DX140RDM-7 is also available in a dual format
utilising a modular boom design and hydraulic lock mechanism, allowing the user to change between different arms for demolition and digging using the same machine.
In the fixed ‘Monolithic’ version of the new DX140RDM-7, the impressive working range allows the machine to work with a demolition attachment to a maximum height of 16 metres. The recommended maximum tool weight in this mode is 1,450 kg. In common with the other models in the demolition excavator range, the DX140RDM-7 offers high visibility and a tiltable cab, particularly suited to high reach demolition applications and providing a 30-degree tilting angle.
In the dual purpose version of the DX140RDM-7, the pin height and maximum tool weight are 14 m and 1450 kg, respectively (with a two-metre extension as an option). All the components such as the undercarriage, the tilting cab and
the shoes remain the same as in the fixed version, only the modular boom design and hydraulic lock mechanism are different, allowing the user to swap between the demolition and digging arms.
The innovative design ensures it is a simple process to change between a demolition boom and an earthmoving boom to accomplish different types of work on the same project. A special stand is provided to facilitate the boom changing operation, which is based on quickchange hydraulic and mechanical coupler connections. A cylinderbased system is used to push the locking pins into place to help complete the procedure.
The multi-boom design also allows the earthmoving boom to be mounted in two different ways, which with the demolition boom, provides further flexibility with a total of three different configurations for the dual purpose base machine.
The DX140RDM-7 has a hydraulically adjustable undercarriage, which extends to a maximum width of 3.7 metres to provide optimum stability when working on demolition sites. The width of the undercarriage can be retracted hydraulically to 2.5 metres in the narrow width position, which is ideal for transporting the machine. The mechanism is based on a permanently lubricated, internal cylinder design which minimises resistance during the movement and helps to prevent damage to the components.
ET42 and EZ50 tracked excavators for more efficiency on construction
High performance, compact dimensions, comfortable operation – these demands are being put on excavators of the four to five-tonne class. With the tracked conventional tail excavator ET42 and the tracked zero-tail excavator EZ50, Wacker Neuson offers the ideal combination of these requirements and as an expert optimiser, supports the efficient construction site.
The powerful drive allows customers to deploy the machines for demanding tasks as well. Both excavators are impressive for their high lifting and digging power for quick work cycles and the three-point kinematics for more break out force, insertion depth and dumping height.
www.wackerneuson.com
uk.orders@wackerneuson.com
+44 (0)1785 785 700
XCMG, a global leader in construction machinery manufacturing, ranks in the top half of China’s top 100 manufacturing companies. With export revenues exceeding $1.6 billion, the company’s reputation continues to grow worldwide.
In the UK, XCMG is based in High Wycombe, operating through a robust network of distributors to sell and service their innovative machines. Among these, the XCMG XE380E crawler excavator has emerged as a standout product, receiving widespread acclaim from operators and industry professionals alike.
Unmatched performance for heavy-duty applications
The XCMG XE380E, with its impressive specifications, is built to tackle some of the most demanding tasks in mining, municipal engineering and infrastructure construction. With an operating weight of 39 tonnes, a maximum digging reach of 11,244 mm, and a maximum digging depth of 7,423 mm, it offers unparalleled capability for large-scale and deep excavation work. At its core is the powerful Cummins L9 engine, delivering 252 kW at 1,800 RPM, ensuring efficient and reliable performance in any condition.
• Operating weight: 39/38.6 t
• Max digging reach: 11,244 mm
• Max digging depth: 7,423 mm
• Engine power: 252 kW at 1,800 RPM
• Engine model: Cummins L9
Superior design and operator comfort
One of the key highlights of the
XE380E is its newly designed cab. Featuring a spacious, luxurious interior with centralised operating buttons, it offers an upgraded driving experience. The ergonomic layout ensures that operators can work comfortably for extended periods without fatigue.
Feedback from operators has been overwhelmingly positive, with comments like, “More powerful than the previous machine” and “Smoother hydraulics than what we’ve used before,” highlighting the machine’s exceptional performance.
The XE380E comes equipped with advanced features to boost productivity and precision. The
PTO pump, included as standard, independently controls the rotary pipeline, ensuring precise flow control during operations. Additionally, its full-size reinforced chassis structure provides superior stability even under the strain of heavy digging force, making it a reliable choice for complex construction tasks.
A trusted choice in the UK market
XCMG’s partnership with Mervyn Lambert Plant has further strengthened the XE380E’s presence in the UK. Managing Director Peter West and Alan Sam shared their positive experience with Mark Hewitt during the handover of the machine. The XE380E has proven itself as a trusted choice for operators, who
praise its power, efficiency, and smooth hydraulics.
The XCMG XE380E combines cutting-edge technology, unmatched performance and operatorcentric design. Whether it’s for mining, municipal engineering or infrastructure construction, the XE380E continues to set new benchmarks in the industry.
For those seeking a machine that delivers exceptional power, reliability and comfort, the XCMG XE380E stands out as an unbeatable choice in the world of crawler excavators.
www.xcmguk.com info@xcmguk.com
+44 (0)1494 413 340
Description of works
Burke Demolition was appointed to carry out the internal stripout and demolition of the numerous mezzanine floors from the 24,000 m² former BooHoo National Distribution Centre.
• Stripout of office areas
• Removal of MEP throughout (high and low level)
• Demolition of 12,000 m² of racking and mezzanine systems
Challenges
Due to the fast programme associated with the refurbishment of the commercial property for immediate future use, Burke Demolition was appointed to carry out the stripout works and mezzanine floors demolition of the 24,000 m² using 20-tonne demolition excavators fitted with shears / rotating grabs / magnets,
while other trades worked near to our increased exclusion zones.
How Burke demolition made a difference
We delivered on programme with only 0.03% of the waste streams going to landfill. Noise and dust monitoring was undertaken regularly with exclusion zones expanded in nosier periods to help protect other trades. No complaints were raised by neighbouring properties, businesses, or individuals.
Independent site safety inspections by an external safety services consultancy were conducted weekly and the average site report was communicated as “very good” with some weeks “exceptional”. Any actions were addressed immediately.
Approximately 175 fire extinguishers were saved for reuse.
Recycling and reuse
Burke Demolition undertook a pre-demolition audit including our recycling methodology which helped develop and contribute to the principal contractor’s site waste management plan (SWMP), which was implemented, monitored and reviewed throughout the project using the BRE SmartWaste online database software. For our stripout and demolition phase 99.97% was diverted from landfill and transported to local permissioned facilities.
Title: Harlington School
Structure:
Large secondary school buildings
Site area: 18,000 m2
Scope of works: Demolition and asbestos removal of the existing school building; removal of all foundations and hardstandings; cut and fill to formation level for enabling package
Contractor: Collard Group
Other significant stakeholders: Harlington School – Hayes
Start date: April 2024
Completion date: August 2024
Techniques used: Demolition, asbestos removal, soft strip, enabling, cut and fill
Future use: New educational facility and football pitch
When Collard Group was awarded the demolition and enabling works package at Harlington School, Middlesex, it marked the beginning of a transformative project that would not only reshape the school’s physical landscape but also demonstrate the company’s expertise in sustainable demolition practices. The project spanned two phases, each with its own unique challenges and opportunities, but both underscored Collard Group’s commitment to precision, safety, and environmental responsibility. Here, we explore the key elements of the works carried out, the hurdles overcome and the innovative solutions that ensured a smooth and efficient process.
Area demolished, including original buildings and later extension
Site enclosure
Access route, away from active school buildings, main entrance and residential road
Duration: 12 weeks
Scope: Asbestos removal, soft strip, demolition, earthworks
Plant used: 49-tonne Komatsu and Hitachi excavators and other specialised machinery
The first phase of the Harlington School redevelopment involved the complete demolition of the existing school building, thought to have been constructed in 1977.
The building occupied a significant portion of the site, housing key facilities including the library, dining room, gym and lecture theatres, as
well as several classrooms. In 1997, an additional larger section had been added to the east and south, which included more modern steelframed construction.
The scope of work required the removal of both the older, traditional structure and the later extension, creating a clear site for the development of a new educational facility.
Collard Group’s scope of works included structural demolition, asbestos removal and the soft strip of the building’s internal materials. Specialised machinery and techniques were employed throughout the process, with remote mechanical demolition
conducted by 360-degree excavators equipped with hydraulic demolition grapples and shears, in line with the guidelines set forth by BS6187.
A crucial aspect of the project was the removal of hazardous materials. Asbestos was identified in several areas of the school building, requiring careful and meticulous removal to ensure the safety of all workers and minimise environmental impact. Asbestos removal was carried out by our in-house team Amiante STR, with full compliance to all regulatory requirements, using fully certified operatives and appropriate control measures.
Given the site’s proximity to an active school environment, safety and disruption minimisation were paramount. Collard Group worked closely with the client, to ensure daily operations did not interfere with the school’s ongoing activities. To mitigate risks, a full site enclosure was maintained at all times, complete with appropriate signage and security measures. The site gates remained locked and visitors were strictly monitored, ensuring no unauthorised access during the demolition works.
Another significant challenge was working in and around a live electrical substation located in the western part of the site. This presented a risk to workers, which Collard Group addressed by installing robust hoarding, crash decks and maintaining clear emergency access routes at all times. Coordination with site and electrical teams was crucial to ensure the safety of both personnel and equipment.
Environmental responsibility
Collard Group demonstrated a strong commitment to sustainability throughout Phase 1, with waste management at the forefront of the operation. Non-ferrous metals, including copper wiring and aluminium, were securely removed and sent for recycling. Meanwhile, materials such as concrete and brick were crushed on-site and processed, ensuring that hardcore materials could be reused in subsequent works.
Client testimony
“Great progress on the superstructure demolition by Collard Group at Harlington School. Thank you to Sam Tunnicliff, John Nuttall and the team for your efforts.”
Project Director
Duration: Four weeks
Scope: Cut and fill to formation to engineered specification and installation of drainage
Plant used: Tracked excavators, D5 dozers, site dumpers, Bomag 120 roller
Following the success of the demolition works, Collard Group was entrusted with the enabling package, which involved extensive earthworks in preparation for a new football pitch. The second phase required significant alterations to the landscape, as approximately 3,000m³ of material was excavated and removed to create the correct formation levels for the new pitch.
The earthworks included the installation of a 400-mm engineered fill layer, which would serve as the foundation for the pitch. Collard’s team ensured that the material placement met the specified levels and compaction criteria, with CBR tests carried out to guarantee the strength and stability of the subbase. Additionally, the installation of surface water drainage was required to ensure proper water management for the new pitch area, which was a critical aspect of the works.
Before any excavation work began, Collard Group conducted a comprehensive CAT survey to ensure the absence of underground services in the working area. Excavation was carried out using a combination of tracked excavators, dozers and rollers. The site was cleared of all anthropogenic materials and subsoil materials were imported and graded to achieve the specified formation levels.
Drains were laid out to manage surface water efficiently. A network
of 80-mm drainage pipes was installed to facilitate water flow, ensuring that the pitch would be sustainable and operational yearround. After drainage works, a separation membrane was applied over the formation, with a minimum 300-mm overlap to ensure proper ground protection before further construction.
As with Phase 1, sustainability remained a key focus throughout Phase 2. The waste materials generated during the excavation were reused wherever possible and Collard Group worked to reduce the environmental impact by limiting material wastage and optimising the recycling of on-site materials.
Health and safety protocols
Safety was a primary consideration, particularly given the scale and
complexity of the enabling works. Collard Group staffed the site with qualified professionals holding certifications such as CPCS, SMSTS and CCDO, ensuring that all operatives had the necessary training and qualifications. A robust health and safety plan was in place, with site-specific inductions, daily briefings and method statement reviews conducted at the start of each shift.
Exclusion zones were strictly enforced, and site access was controlled to minimise risk. Special permits were issued for tasks such as hot works and excavation and safety signage was posted to clearly delineate areas of restricted access.
The redevelopment of Harlington School provided Collard Group with the opportunity to showcase its expertise in demolition,
asbestos removal, earthworks and sustainable construction practices. From the complex demolition of an ageing school building to the preparation of the land for a new sports facility, the project highlighted Collard Group’s ability to deliver high-quality results while maintaining the highest standards of safety and environmental responsibility.
By working in close collaboration with the client, and ensuring that all works were completed on time and within budget, Collard Group has set a standard for excellence in both demolition and enabling works. The successful execution of both phases of the project reinforces Collard Group’s position as a leader in sustainable construction practices, capable of handling complex and high-profile projects with professionalism and expertise.
For booking forms and information regarding Exhibition space please contact info@ide.org.uk
Members and non-Members of the IDE are welcome to attend.
Clifford Devlin has successfully completed key phases at its west London project, including the decommissioning of tanks, careful vegetation removal, asbestos removal, demolition, hardstanding clearance and crushing. The project began in August 2024 and is expected to be completed end of January 2025.
Clifford Devlin is now entering the final phase of this project, which involves site levelling and the installation of the piling mat. After Clifford Devlin’s work is complete, the site will be handed over to the piling contractor to undertake the next phase of works preparing site for the new build construction.
To date the team has worked a total of 108 days with zero accidents or incidents. This exceptional safety record demonstrates that health and safety is always a priority on Clifford Devlin sites. For further details, see the full case study in the next issue of Demolition Hub magazine.
Unlocking financial opportunities for demolition companies
In the dynamic world of construction, demolition companies play a crucial role in paving the way for new developments. However, the financial challenges they face can be significant. From acquiring specialised equipment to managing operational costs, demolition companies often require substantial capital to thrive. This is where Acquired Asset Finance Ltd explores various financing options available to demolition companies, helping them unlock their full potential.
Understanding the financial needs of demolition companies
Demolition companies have unique financial needs that differ from other sectors within the construction industry. These needs include:
Equipment acquisition and maintenance: Demolition requires heavy machinery such as excavators and other plant. The cost of purchasing and maintaining this equipment can be substantial.
Operational costs: Daily operations, including labour, fuel, and safety measures require consistent cash flow.
Project financing: Large-scale demolition projects often require upfront capital to cover initial costs before payments are received.
Financing options for demolition companies
Equipment financing: Given the high cost of demolition equipment, equipment financing can be an attractive option. This type of financing allows companies to purchase or lease machinery without the need for a large upfront payment. The equipment itself often serves as collateral, making it easier to secure the loan.
Bank loans: Traditional bank loans are a common financing option for demolition companies. These loans offer competitive interest rates and flexible repayment terms. To secure a bank loan, companies typically need to provide detailed financial statements, a solid business plan and collateral.
Credit line: A credit line provides demolition companies with access to a predetermined amount of funds that can be used as needed. This flexible financing option is ideal for managing cash flow and covering unexpected expenses. Interest is only paid on the amount borrowed, making it a cost-effective solution.
Invoice financing: Invoice financing, also known as accounts receivable financing, allows demolition companies to borrow
against their outstanding invoices. This option provides immediate cash flow, enabling companies to continue operations while waiting for clients to pay their invoices. It’s particularly useful for companies with long payment cycles.
Government grants and loans: Various government programmes offer grants and loans to support small businesses, including demolition companies. These programmes often come with favourable terms and lower interest rates. Researching and applying for these opportunities can provide much-needed financial support.
Financing is a critical component for the growth and success of demolition companies. By exploring various financing options and implementing best practices, these companies can secure the capital needed to invest in equipment, manage operational costs and take on larger projects. With the right financial support, demolition companies can continue to play a vital role in the construction industry, transforming landscapes and making way for new developments.
gul@aafinanceltd.co.uk
+44 (0)7957 698 129
The sector is undergoing significant shifts driven by sustainability, economic pressures, supply chain challenges and the need for innovation. While challenging, these changes also present opportunities for companies to evolve, improve operational resilience and drive growth. Our latest SME Growth Index, based on research conducted by Opinium on behalf of Aldermore in April 2024, identifies four key ways the industry could transform.
Sustainability is increasingly important in demolition and construction, yet many companies have been slow to prioritise it. Currently, only one in five firms (22%) measure and reduce their carbon footprint and only a quarter (26%) have adjusted their supply chains for sustainability. However, this does leave a significant opportunity for growth in ‘green’ practices.
As environmental regulations tighten, demand for energy-efficient technologies and waste-reduction strategies will be better positioned to meet future demands. This shift can also improve market competitiveness, as clients and stakeholders are placing greater emphasis on sustainability in their projects and supply chains.
Adopting greener practices is not only good practice, but also helps firms comply with regulations and opens the door to new business opportunities. By collaborating with suppliers to use technologies that enhance energy efficiency, demolition companies can lead the way in decarbonisation and set themselves apart in the marketplace.
High inflation, rising energy costs and supply chain disruptions have had a significant impact on the industry with project delays and increased operational costs.
The reliance on international suppliers has exposed vulnerabilities in supply chains, especially during periods of economic uncertainty. To mitigate these risks, demolition companies can look at sourcing equipment locally and investing in regional capabilities.
This approach not only makes supply chains shorter and more reliable, but also reduces the risks associated with shifting international prices and shipping delays and can reduce carbon footprints.
Late payments remain a major hurdle for many, directly affecting cash flow and limiting growth potential. The total value of outstanding late payments for an average SME in the construction and demolition space is £75,200 and 55% of SMEs in the sector say the time they spend chasing late payments is ever increasing. For firms facing these challenges, delayed payments hinder their ability to invest in equipment, expand services and take on larger projects.
Addressing late payments is critical for unlocking further growth in the sector. Improved cash flow allows businesses to invest more confidently in innovation and free up management time to focus on core activities such as upskilling their workforce.
As demand for housing and public infrastructure grows, companies will have more opportunities to take on large- scale projects. For example, housing demand, particularly in urban areas, is expected to rise, creating new opportunities.
At the same time, companies should embrace innovation and digital tools to stay competitive, positioning themselves for longerterm growth.
The demolition industry is clearly set for transformation, driven by the need for sustainability, economic resilience, and technological innovation. By embracing sustainable practices, strengthening supply chains, improving payment processes, and focusing on infrastructure and innovation, companies can position themselves for success in an evolving market. These shifts will not only help the industry overcome current challenges but also open up new growth opportunities in the years ahead.
At Aldermore, we’re dedicated to getting you the assets your business needs to thrive. www.aldermore.co.uk/business-
As the industry faces increasing demand with the government’s strong focus on infrastructure and housebuilding, it is important that businesses have access to a finance partner that they can trust.
Using asset finance to fund plant, equipment and vehicles enables businesses to spread the cost of investment. This way of financing may also open up additional credit lines that may be independent from bank credit lines and is less likely to require additional security (other than the asset itself) compared to that typically required with a bank loan.
It is important that businesses find the best finance to fit their needs. JCB Finance Marketing Director, Paula Millward said: “We have been operating within the sector for a long time. As you’d expect from the JCB in-house finance company, our team have a wealth of knowledge, which is a real benefit when understanding the specific needs of our customers. Customers can be assured when dealing with JCB Finance, they come first.”
JCB Finance not only provide asset finance for UK businesses on the full JCB range, new and used, but are also able to finance other essential complementary plant, machinery, equipment, and commercial vehicles.
Paula added “We understand through over 50 years in the industry, one size does not fit all. One common deciding factor is whether you want to own the machine at the end of the agreement.
If the answer is yes, Hire Purchase (HP) could be the product for you.
HP offers accurate budgeting and the security of fixed repayments. We also have products that offer a payment holiday, giving businesses peace of mind if the unexpected happens.
You can also claim the Annual Investment Allowance and Corporation Tax full expensing relief on qualifying assets placed on Hire Purchase just as if you had paid cash; enabling you to preserve working capital, choose payment terms to suit your business and save the tax – even if only the deposit has been paid.
If ownership isn’t so important, and you’d like to benefit from lower payments due to value which remains unpaid by you, then leasing could suit your business and JCB Finance has a leasing facility for JCBs called JCB FlexiLease which gives customers the opportunity to earn from any profits achieved on disposal of the machine at the end of the lease – something that isn’t usually offered. Unlike HP which requires all VAT up front, VAT is payable with each instalment on a lease which can really help with cashflow too.”
JCB Finance support construction and demolition businesses across the UK, all and JCB Finance customers have a dedicated Relationship Manager. Customers also have access to JCB Finance Online, an online portal which allows you to manage your account and access help.
Paragon Bank is a leading specialist lender headquartered in Solihull. The FTSE 250 listed company has two main lending divisions, Commercial Lending and Buy-to-Let Mortgages. Through these divisions Paragon supports landlords and businesses to achieve their goals. The bank’s lending activity is funded via retail savings, with over £16 billion in deposits from UK savers.
In the Commercial Lending division, Paragon works to support small to medium businesses to grow their business. The division works with 40,000 customers, from SME businesses to larger corporate businesses, providing a range of financing options to suit different businesses’ needs.
Paragon’s Commercial Lending division is made up of four different areas: SME Lending, Development Finance, Motor Finance and Structured Lending.
Paragon’s SME Lending team works closely with the construction, demolition and associated industries, as well as other businesses across the UK to provide various forms of finance, predominantly asset finance.
The team is led by Managing Director John Phillipou, who has a wealth of experience, as well as being Chair of the Finance and Leasing Association (FLA). John and his team are passionate
about supporting SMEs to grow their business and want to help companies reach their potential.
SME Lending continues to be a priority division for Paragon, in December 2024 the company announced its full-year results and was able to confirm that the division saw a lending increase of 7.3% to £480.7 million in the 23/24 financial year. In addition, it grew its loan book by 7.9% to £817.5 million in comparison to £757.5 million the previous year, showing the growth in this division, as it looks to support more SME businesses.
Within the SME Lending division at Paragon there are three separate teams – Broker, Vendor, and Specialist Lending. The broker team works with intermediaries across the country to reach clients who are looking for asset finance. The vendor team supports manufacturers directly, to support their clients with suitable funding solutions, as well as individual businesses looking for a funding solution to support their business. The Specialist Lending team works across a range of funding options, including invoice finance, discount receivables as well as aviation finance.
Within the SME Lending division, Paragon offers a range of finance products, including, hire purchase, finance lease, operating lease and refinancing options for existing assets. More recently, Paragon has announced its approval to join the British Business Bank’s Growth Guarantee Scheme (GGS). Under the scheme, Paragon will offer asset finance and commercial loans, with facility sizes ranging from £25,001 to £2m per customer, subject to eligibility.
The Growth Guarantee Scheme is the successor to the Recovery Loan Scheme and was launched by the British Business Bank in 2024.
Following its acceptance to join the scheme, Paragon has expanded its range of green assets and equipment it looks to fund, supporting SME businesses on their path to sustainability.
In addition to its usual assets it will lend on, it will now consider and has approved a range of green assets such as solar panels, wind turbines, EV charging infrastructure, hydroelectric turbines and geothermal heat pumps. The bank will also consider battery energy storage systems, voltage optimisation systems, tidal and wave energy and more.
These different types of finance offer a wide range of solutions to businesses looking to purchase a new piece of equipment or raise some capital to grow their business.
The demolition industry is one of the cornerstones of construction, clearing the way for new developments and revitalised landscapes. Whether it’s dismantling towering structures, preparing industrial sites for regeneration, or managing complex site clearances, every project requires specialised equipment to get the job done efficiently and safely. However, acquiring this equipment can pose significant financial challenges. That’s where asset finance comes into play.
At Kick Asset Finance, we understand the unique demands of
demolition contractors. Our tailored financing solutions are designed to help you access the machinery and tools you need without disrupting your cash flow or compromising your budget.
Demolition businesses, whether established contractors or growing firms, often operate in a fast-paced environment where time is of the essence. Without reliable access to funding, critical equipment purchases can be delayed, leading to
potential project setbacks.
Our services cater to a wide range of businesses, from specialist demolition firms requiring bespoke machinery like high-reach excavators to contractors who need reliable transport and safety equipment. Regardless of your company’s size or scope, our goal is to make financing straightforward and stress-free, so you can focus on what you do best.
Demolition work demands an array of specialised machinery,
each playing a vital role in ensuring projects are completed efficiently. At Kick Asset Finance we provide funding for heavy equipment such as excavators, crushers and loaders; vehicles like low loaders and tipper trucks, which are essential for transporting materials and equipment to and from sites; and specialist attachments such as breakers, shears and crushers.
In addition, we recognise the importance of safety and technology in today’s demolition industry. Dust suppression systems, generators, fleet management tools and asset tracking software are just some of the additional items we can help you acquire. By spreading the cost over manageable payments, you can stay equipped with the latest tools while preserving your financial stability.
Financing equipment through asset finance offers numerous advantages for demolition contractors. One of the most significant benefits is the ability to keep cash flow consistent. Rather than making a large upfront investment, businesses can spread the cost of machinery over time, ensuring there’s capital available for other essential expenses.
Asset finance also removes the burden of high upfront costs, which can be especially beneficial for businesses managing multiple projects simultaneously. Additionally, financing arrangements often come with flexible terms, allowing businesses to align repayments with their project timelines and revenue streams.
Another key advantage lies in the potential tax benefits. Interest payments and depreciation on financed equipment may be taxdeductible, reducing the overall cost of ownership. These financial benefits, combined with the ability
to upgrade equipment as your business grows, make asset finance a vital tool for staying competitive in a dynamic industry.
At Kick Asset Finance, we pride ourselves on offering a seamless and efficient financing process. We understand that time is a critical factor for demolition contractors, which is why we’ve streamlined our application and approval process to minimise delays. From the initial consultation to securing funds, we’re committed to providing end-to-end support.
We partner with a network of trusted lenders to ensure you have access to competitive rates and flexible terms. By working closely with you to understand your specific requirements, we tailor solutions that meet the demands of your business, whether you’re purchasing new machinery or upgrading your fleet.
The demolition industry thrives on precision, reliability and innovation, and these values are at the core of what we do at Kick Asset Finance. Our mission is to be a trusted partner to contractors across the UK, helping businesses thrive by providing access to the tools and resources they need to succeed.
Whether you’re a seasoned contractor looking to expand your operations or a new business in need of essential equipment, we’re here to help. By combining industry expertise with a customer-focused approach we aim to make asset finance a straightforward and empowering solution for demolition professionals.
In a strategic move set to revolutionise financing in the construction sector, Steve Moody and Dawsongroup Finance Ltd have announced the formation of Construction Plant Finance. This joint venture combines Steve’s extensive experience in the construction finance sector along with Dawsongroup’s innovative approach to commercial asset financing, offering an independent and tailored solution for the UK’s construction industry.
Construction Plant Finance, headquartered in Hampshire, stands out as one of few independent finance companies dedicated solely to the construction plant and equipment sector. Having Dawsongroup Finance in place as the funder, they operate without ties to banks or manufacturers, ensuring unbiased and flexible financing options for clients.
The UK construction industry is poised for significant growth in 2025, driven by renewed housing targets and increased investment in repair, maintenance, and improvement work.
Steve Moody, Consultant of Construction Plant Finance, brings 40 years of experience in construction finance to the venture. He commented: “We are thrilled to launch Construction Plant Finance into the market. Our team understands the unique needs and opportunities of the industry and is committed to providing tailored financing solutions that empower businesses to access the right equipment for the right job, funded the right way.”
Kevin Wills, Managing Director of Dawsongroup Finance, added: “This partnership pulls the strengths
www.constructionplantfinance.co.uk
newbusiness@constructionplantfinance.co.uk
+44 (0)2382 352 506
of both Dawsongroup Finance and Steve Moody together to offer innovative and flexible asset finance solutions. Leveraging our years of experience at Dawsongroup in funding commercial assets, Construction Plant Finance can provide truly independent financing options that cater to the diverse needs of the construction industry.”
Construction Plant Finance will offer a comprehensive range of asset financing options, including Hire Purchase, Finance Lease and Operating Lease. These solutions
are designed to meet the varying requirements of businesses, from standard equipment like dumpers and excavators to specialised machinery such as cranes and vacuum excavators.
By combining Steve Moody’s deep-rooted expertise in construction with Dawsongroup Finance’s innovative asset financing capabilities, Construction Plant Finance is set to become a pivotal partner for businesses aiming to thrive in the evolving construction landscape.
The demolition sector is a dynamic but demanding industry, where having the right equipment can make all the difference between completing a project efficiently and facing costly delays. This is where asset finance facilities come into play as they provide a proven and flexible way to acquire the necessary equipment you need without having to cover hefty deposits of the full cost upfront, or even help boost cashflow by releasing the money tied up in the assets you already have.
Asset finance facilities are designed to help businesses acquire the essential equipment they need to succeed, or obtain funding from existing assets such as vehicles and machinery to help strengthen cashflow quickly. Options including hire purchase, lease financing and refinancing can cater to the diverse needs of demolition contractors.
Hire purchase helps to spread the cost of the equipment over a fixed period, with ownership of the asset(s) transferring at the end of the term.
Alternatively, lease financing enables businesses to use the equipment without the burden of ownership, with the flexibility to move onto a new asset at the end of the lease term.
With refinancing, businesses can access the money tied up in existing assets to boost cashflow when a quick injection of cash is most needed.
One of the key advantages of Asset Finance is the positive impact it can have on cashflow management. By spreading the cost of equipment
over time, demolition contractors can preserve working capital and invest it in other critical areas of their businesses such as overheads or supplier payments. This financial flexibility is especially crucial in an industry where project timelines and costs can sometimes be unpredictable.
Moreover, it can be structured to accommodate the cyclical nature of the demolition sector through manageable monthly repayments or even by offering a balloon payment option which sees smaller monthly payments offset by a larger sum due at the end of the facility, which can help alleviate pressures on working capital and provide breathing space to plan ahead to ensure your business maintains financial stability and focuses on delivering exceptional results for your customers.
The impact of asset finance solutions is best illustrated through the success stories of real businesses. Many demolition contractors have already leveraged Ultimate Finance’s funding to expand their operations, take on larger projects and enhance their competitive edge. For example, one client was able to finance a fleet of new excavators, enabling them to undertake a high-profile demolition project that would have been impossible without financial support. This not only boosted their business growth but also cemented their reputation as a leading contractor in the industry.
Asset finance offers a lifeline to contractors seeking to acquire essential equipment, manage cashflow and achieve their business
ambitions. For more information about how asset finance can help, it is advisable to consult with a financial broker, which can guide you to the right funding solution for your business.
Ultimate Finance, established in 2002, is a specialist asset-based lender that provides a wide range of flexible solutions that are tailored to business need to support the ambitions of UK businesses.
Part of international private investment company Tavistock Group, Ultimate Finance has teams across the length and breadth of the country with regional offices in London, Bristol, Lutterworth, Leeds and Edinburgh to help provide a localised and relationship-based approach to business funding.
Ultimate Finance currently supports more than 4,000 businesses with flexible funding solutions to help realise potential through unlocking working capital, funding the purchase of assets and supporting property developers and investors with short term funding, all designed to ease business cashflow challenges.
It provides asset finance facilities up to £500,000 per single asset and £2m per customer, with repayment terms from 12 to 84 months.
121 7757
Company: Checkatrade
QWhat is your core message to our demolition contractor readership?
My core message to demolition contractors is that Checkatrade is here to help you build trust with customers, grow your business and secure more work. We understand that the demolition sector requires a high degree of professionalism and safety. Checkatrade allows you to showcase your expertise, providing customers with verified reviews and giving them confidence in choosing your services.
Q
Tell us about your career up until now. What are the common threads and how do you see yourself in a work context?
I’ve always been passionate about connecting people and building communities that drive mutual success. My career has been a blend of customer experience,
product, marketing, partnership development and creating value driven programmes for businesses. My previous roles at eBay, Black & Decker, DeWalt and British Gas have given me a good background in marketplace, construction and service led businesses and I am bringing all of these experiences into my role at Checkatrade.
The common thread has been putting people at the centre of decision making, ensuring their needs are met in order to build trust and loyalty. In my current role I see myself as an enabler, ensuring tradespeople have the tools and support they need to thrive.
Q
What attracted you to Checkatrade?
What drew me to Checkatrade was its unwavering commitment to tradespeople and consumers alike. It’s a brand built on trust and
integrity, with a mission to raise standards across the trades industry. The opportunity to enhance trade experiences, build meaningful partnerships, and be part of a company that genuinely values its community was too good to pass up.
Q
Give us some background on Checkatrade and its journey from a local directory to nationwide presence today.
Checkatrade began as a local solution to tackle rogue trading after a storm caused widespread damage. It evolved into a trusted directory, providing verified, reliable tradespeople to homeowners. Over the years we’ve expanded nationally, combining rigorous vetting with customer reviews to create the gold standard for the industry. Today, Checkatrade is synonymous for homeowners with trust, and millions of homeowners rely on us to connect them with reputable trades.
QTell us about the services Checkatrade provides to its members. Is it more than a database? Is it possible to quantify the benefits for tradespeople?
Absolutely. Checkatrade is much more than a database. We provide members with a platform to showcase their credentials, receive verified reviews and access tools to grow their business. Our services include access to member benefits such as discounts on supplies and free business coaching. We aim to be a one-stop shop for tradespeople, helping them succeed in an increasingly competitive market.
In terms of quantifying the benefit, we know that on average our
trade population gets 30% to 40% of their work through Checkatrade and via our member benefits they can save up to £1,200 per year, using discounts that help them cut down on every day as well as business expenses such as fuel and food.
QThe online marketplace is enormous, with directories, consumer champions, comparison websites and ratings websites. What makes Checkatrade different for the tradesperson and consumer? For tradespeople, Checkatrade offers a unique combination of trust, visibility and growth opportunities. We rigorously vet all members, which means they are part of a trusted network that stands out from the competition. For consumers, Checkatrade provides peace of mind with verified reviews, a workmanship guarantee and a commitment to quality. It’s this dual focus on trust and transparency that sets us apart.
QYou employ more than 500 people. Tell us about your team and working culture. What’s it like to work there?
Our culture is built on collaboration, passion and a deep commitment to our customers. We’re all in this
together and that spirit is evident in everything we do. Checkatrade is a dynamic environment where everyone is encouraged to contribute ideas and challenge the status quo to deliver the best for our members and customers. We bring our customers into our internal meetings, we’ve had recent football matches with our trades and we do regular customer visits. We are on a journey and it is absolutely critical that we bring our customers into everything we do.
QCheckatrade has introduced a £1,000 guarantee scheme, clearly of great benefit to consumers. How does that work out for the contractors?
The workmanship guarantee scheme is a win-win. It reassures consumers that they’re protected, which builds trust in our members. For tradespeople, this trust translates into more job opportunities and a competitive edge in the marketplace. It’s part of our commitment to supporting both tradespeople and customers.
QCheckatrade commissions research and reports. Tell us about that.
We regularly commission research to understand market trends, consumer behaviour and the challenges facing tradespeople. These insights inform our strategies and help us develop solutions that address real-world issues, from skill shortages to customer expectations. We also use this research to inform government, pushing the agenda on behalf of our trades and making sure we make a stand on important issues that impact our industry.
QTell us about the supply of skilled labour in the UK as well as other issues affecting small to medium trades of the type found on Checkatrade. What are the issues and how can these be addressed?
The UK faces a significant skills shortage, particularly in the trades
sector. This is compounded by an aging workforce and a lack of young people entering the industry. At Checkatrade, we’re passionate about promoting trades as a viable, rewarding career path. We are pushing the agenda and developing new initiatives to attract new talent, provide training, and support apprenticeships.
QWhat technological developments do you envisage will be the future game changers?
AI and automation will play a big role in streamlining processes like job matching and customer communication. There is so much opportunity in the tools and services available to us to make our trades more efficient in order to try and shrink the skills gap a little. It won’t solve all of the skills gap problems but increasing efficiency of our trades unlocks more job opportunities and earning potential for them.
QConversely, the Checkatrade model still works for those without internet access –who may include those most vulnerable to rogue traders. How does Checkatrade continue to work offline?
We provide offline support through our distributed printed materials like the Checkatrade directory. The directory is useful for everybody, it’s the thing you put on your fridge
or in a draw to keep in case you need some work doing or you have an emergency. The directory is a huge part of our business and will continue to be a focus for us. It is of great value to our trades and homeowners alike, approximately 140 million directories are delivered every year.
QAnd speaking of paper, you’ve recently launched a Checkatrade magazine for members. How’s that going? Of course it’s not as established as Demolition Hub, but the magazine has been a huge success, providing members with valuable insights, tips and updates. It’s another way we connect with our members and offer them resources to succeed in their businesses. It also shows all of the great benefits and discounts that our tradespeople can take advantage of that they may not have looked at before.
Q
How do you envisage Checkatrade in five to ten years? And how about yourself? In five to ten years, I see Checkatrade as the definitive platform for tradespeople, offering unparalleled support, tools and opportunities to grow their businesses. I hope it becomes the partner for all trades in the UK, a tool that our tradespeople can’t live without. Personally, I aim to continue championing the trades, driving initiatives that empower them and ensuring Checkatrade remains at the forefront of the industry.
What would you be in an alternative life?
In an alternative life I would be a holiday tester. I would love to travel more, exploring new places, meeting new people and sharing stories on my return.
What would be your desert island luxury?
A year’s supply of chocolate. I can’t live without chocolate, it’s my go-to sugar rush item. Would need to be in a fridge somewhere though.
What do you do for fun?
I love doing up property. DIY is my happy place, from putting up shelves to knocking out an old kitchen or siliconing a bathroom.
What’s your ideal weekend?
A mix of relaxation and adventure, starting with a hike up a mountain then lunch in a fancy restaurant to a good film in the evening.
DXR REMOTE DEMOLITION ROBOTS
Husqvarna DXR demolition robots are known for their high-impact force and long reach. The solid chassis provides impressive stability, making it a powerful platform for a wide range of attachable tools.
The remote-controlled DXR works in various areas, keeping the operator out of harm's way.
INTRODUCING THE DXR 95, OUR COMPACT AND LIGHTWEIGHT DEMOLITION ROBOT WITH HIGH HITTING FORCE.
by Ben Chambers
In what was my eighth appearance at the Las Vegas Convention Center, I can confidently say, this is the show that has everything.
Now, I’ve got a soft spot for Las Vegas – I would happily call it home. For those of you who know me, that might raise an eyebrow or two, but I’ll stand by it. Yes, I get it – the neon lights, the 24/7 hustle and the buzz can sometimes cast a dark shadow over the place, but for me, that’s part of the charm.
Las Vegas is another world, one I could easily get lost in for weeks. It’s probably not the most sensible idea, but hey, it’s fun to dream. Fortunately, most of the time, I find myself in Sin City for one reason or another –usually, some kind of construction event. And, for me, this time was extra special because it was the global construction show I look forward to most every year: World of Concrete.
And let me tell you – this year did not disappoint.
Held from 20 to 23 January at the Las Vegas Convention Center, after 50 years World of Concrete (WoC) remains the event for those in the concrete and related construction industries. But don’t just take my word for it; ask anyone who attended.
The level of energy, innovation and global engagement is unmatched. Whether you’re a contractor, architect, supplier or just a concrete enthusiast (no judgment here!), WoC offered an invaluable platform for exploring the newest products, technologies and trends. The event isn’t just about seeing the latest gadgets – it’s about immersing yourself in the future of construction.
If you love getting your hands dirty and checking out new tools, you were in for a treat at WoC 2025. It didn’t just feature a typical exhibition – it was a tech-lover’s playground. Inside and outside the convention halls, industry-leading manufacturers and suppliers showcased their cutting-edge products and machinery. From advanced concrete pouring systems to new sustainable materials, there was no shortage of innovations.
My favourite part? The New Product Zone. This is where we got a sneak peek into the future of concrete and masonry. It’s like the tech section of a car show but with more power tools and a whole lot
of cement. If you’re a contractor or supplier looking to stay ahead of the curve, this zone is where you want to be. I had a blast talking with vendors about their latest products and trust me, the future looks cool.
One of World of Concrete’s best features is its incredible educational programme. Whether you’re looking to refine your skills or earn some industry certifications, the seminars and workshops cover all bases: concrete repair, safety standards, cutting-edge tech and of course, emerging trends.
These weren’t just run-of-themill presentations either – they were deep dives into topics that really matter. Concrete repair techniques that save you time and money? Yep. New safety standards that could save lives on the job? You bet. The event was packed with opportunities to learn, grow and gain real-world knowledge that can make you a more efficient, effective professional in an ever-evolving industry.
Of course, no event is complete without networking opportunities, and WoC 2025 didn’t disappoint. Whether you were sipping on coffee at a booth or enjoying a cocktail at one of the evening receptions, there was always someone to talk to, share insights with or simply swap stories. It’s not just about making business connections – it’s about sharing ideas and working together to solve the industry’s challenges.
I always walk away from WoC with a handful of new contacts and a deeper understanding of where the industry is heading. I think that’s what sets this event apart; it’s a melting pot of ideas and innovations, with professionals from all parts of the concrete industry working toward a common goal – to build a better future for our cities, our roads and our structures.
People from all corners of the world were represented at WoC, bringing their unique perspectives and solutions to the table. Whether it was contractors from Europe or suppliers from Asia, the diversity of ideas and experiences highlighted the global nature of the concrete sector.
We all face similar challenges –
sustainability, safety, efficiency –and it’s inspiring to see how professionals around the world are tackling these issues. It’s a rare opportunity to come together and not only learn from each other but also build bridges for future collaboration.
As much as I love soaking in all the exciting developments at WoC, I’m also always thinking about what comes next. The focus on sustainability, smart technology and safety is only going to grow and events like this are shaping the future.
What struck me most was the shared sense of optimism. Even as we face challenges – supply chain disruptions, workforce shortages, rising costs – the concrete and masonry industries are moving
forward with innovation and resilience. WoC isn’t just about looking at what’s new today; it’s about laying the groundwork for the advancements of tomorrow.
If you haven’t yet made your way to World of Concrete, let me tell you, you are missing out. WoC 2025 was a fantastic example of why this event is the heartbeat of the concrete industry. It’s where you go to see what’s cutting edge, learn from the best and meet the people who are shaping the future of construction. With each year, it gets bigger, bolder and even more exciting. I can’t wait for the 52nd WoC. In fact, I’ll be there again next year – cocktail in hand (even if it’s only after the conference wraps up).
I’ll see you in Vegas.
The DEUTSCHER ABBRUCHVERBAND (DA), the German demolition association, is making final preparations for FACHTAGUNG ABBRUCH 2025. This year the event will return to STATION Berlin on 14 March. After the success of the 2024 event, which attracted over 1,200 participants and 124 exhibitors, there is great anticipation for this year’s event.
Offering an excellent opportunity for professionals in the demolition and dismantling sectors to come together, this year’s theme is Quality in Demolition. What is more, the programme will also include several specialised presentations, each followed by discussions, fostering engaging dialogues among industry professionals.
Rates and registration
For those interested in attending, the congress fee is €420 (plus 19% VAT), with a reduced rate of €380 for DA members. This includes access to the lectures, exhibition, coffee breaks, lunch, and the Dialogue Evening, as well as free shuttle services.
Registrations must be completed online by 21 February, at the FACHTAGUNG ABBRUCH website.
The concrete industry is one of the most exciting sectors in construction; constantly evolving, innovating and trail-blazing – the opportunities for growth are significant. This year, the UK Concrete Show will return to Birmingham’s NEC from 26 to 27 February, offering a unique opportunity for professionals to network, share best practice and do business.
Located in Hall 17, it’s the only exhibition dedicated to the UK’s concrete sector and visitors will have direct access to the concrete industry’s biggest names and be introduced to many new businesses exhibiting for the first time. From admixtures and test equipment to pumps and volumetric trucks, there are 140 exhibitors under one roof.
The go-to networking facility for industry connections and support. This dedicated space showcases partner organisations including: The Concrete Society; Institute of Concrete Technology; ACIFC; Structural Concrete Alliance; Institute of Quarrying; British Aggregates Association; The Graphene Council; and the Drilling & Sawing Association.
Young talent is critical to ensure an inclusive, innovative and sustainable future for the industry. Join us to recognise the
achievements of those in the early stages of their careers in the sector, as we celebrate the top five individuals who have made a positive contribution to the industry.
This year’s show also introduces the New Product Hub, a feature gallery highlighting the latest and best releases from our exhibitors over the past 18 months. Use a token given to you as you enter the show to vote for your favourite product.
The theatre has been expanded to 30 speakers; broadcaster Susannah Streeter returns to host six sessions spanning over two days. Gain invaluable insights and join the debate with each session concluding with a panel and live Q&A with the audience.
Full seminar listings including timings can be found online at concreteshow.co.uk/seminars with a session preview below:
Wednesday 26 February
10:25–12:30 Sustainable concrete solutions for a greener tomorrow. This session explores key technologies driving decarbonisation across the UK cement and concrete sector; the importance of collaboration across the supply and contractor chain if targets are to be achieved;
and shines a spotlight on the latest research projects creating innovative solutions for a greener tomorrow.
13:00–14:00 Graphene in concrete: performance, sustainability and commerciality. Hosted by The Graphene Council and featuring the latest advancements in grapheneenhanced concrete technology. 14:00–14:25 Digitalisation spotlight. Digitalisation of readymixed concrete is now a reality with collaboration between the contractor and producer allowing optimisation of mix designs to meet performance criteria, while reducing the carbon value of the concrete. In this session, we will discuss the delivery of CEVO Digital and Tarmac’s first trial of MixAI with Getjar on a Mace project known as Belgrove House in King’s Cross. 15:00–16:20 Repair and maintenance, protecting our built heritage. From concrete scanning, structural applications and injection techniques to waterproofing systems and repair mortars, the management of concrete repair and maintenance is being increasingly driven by sustainability.
Thursday 27 February
10:30–11:30 Ready for the revolution – from drive-throughs to eMixers. The ready-mixed concrete sector is undergoing a revolution as innovation
Gnat UK
One-Stop-Shop Selective Demolition Specialists for Main Contractors
• BROKK Robotic Demolition
• Aquajet Robotic Hydro Demolition
• Diamond Drilling & Concrete Cutting
• Abrasive Cold Cutting in Volatile Areas
Precision. Safety. Nationwide.
With cutting-edge Robotic Technology and unrivaled expertise, we deliver tailored solutions for complex demolition projects across the UK.
delivers greater productivity and more sustainable, lower-carbon outcomes. Find out about the latest ‘drive-through’ technology that can offer more bespoke self-service solutions.
11:45–12:50 Spotlights Session. Developed by Imperial College, find out about Kiacrete – a new puddle-free pavement technology embracing the challenges of climate change; understand the benefits of using sophisticated liquid systems and attract new customers for your business with invaluable tips from a digital marketing consultancy.
13:00–14:00 Digital monitoring and measurement of fresh concrete. The adoption of digital measurement and monitoring can provide improved visibility and traceability to drive quality and
productivity improvements and associated cost reductions.
Reduction in plant/person interface adds safety benefits; reduced wastage and efficient use of resources bring sustainability benefits. These calibrated, digital systems may also be capable of adjusting concrete properties such as the addition of water or admixtures to correct consistencies.
14:10 – 15:30 Attracting and retaining talent: education, training, and the power of people/Emerging Talent Awards Presentation. How businesses can attract, train and retain the next generation of concrete professionals is essential for your business to prosper and successfully meet the growing challenges of sustainability and
digitalisation. The ICT provides an industry perspective on the training and qualifications available to enhance your career prospects. Culture Kick stresses the importance of creating the right culture for young people to thrive in. Finally, the opportunities available through the recently launched Student and Young Professional Network (ICT SYPro) are espoused.
Celebrate excellence in the use of concrete through a photographic display of the 2024 award-winning projects.
concreteshow.co.uk.
bauma, the world’s leading trade fair for construction machinery, building material machines, mining machines, construction vehicles and construction equipment will be held in Munich from 7 to 13 April. The event has been taking shape for some time now, with exhibitors as Liebherr, Peri and Wirtgen beginning to set up their booths in October.
In 2025, numerous well-known companies will once again use bauma as a showcase for themselves and their products. Returning companies include Volvo, Deutz, Liugong, CNH, Skyjack and JLG.
Around 150 new exhibitors will be at bauma 2025 as well, including such companies as Fortescue,
DSI/Sandvik, HG – 100% electric dumpers, EXiron AG, Gravis Robotics AG, Metso Oyj, rockrobot oy, Wabtec Corporation and WEICO GmbH.
Digitisation and sustainability will remain the buzzwords of the industry this year. As a result, they are also reflected in the five key topics that bauma will address: Climate neutrality, alternative drive concepts, networked construction, sustainable construction and mining challenge. From Monday to Friday, the bauma FORUM will focus on one of these key topics. The programme will consist of brief presentations, panel discussions and key notes. Exhibitors will also present products and innovations from these areas.
As part of changes for 2025, the area devoted to occupational health and safety will be centrally consolidated in Hall B4. This strategic placement offers visitors a comprehensive overview of developments and technological advances that will improve safety on construction sites.
Eleven research institutions will present innovative projects at the bauma Science Hub. Among other things, the Technical University of Munich will present autonomous solutions for bulk goods transportation and a paving robot. The University of DuisburgEssen will demonstrate a cable robot
“The
for precise use on construction sites and the Technical University of Dresden will present ways to avoid accidents by using a mobile excavator that can recognise human beings. Many other exciting projects await visitors directly at the exhibitors’ booths.
bauma 2025 will also offer young, innovative companies the opportunity to present their ideas. Almost 50 startups have registered to showcase their innovations and developments related to the main topics of bauma, including mobile robot technologies, the development of digital twins of construction sites, alternative drive systems, ultrasonic technology in concrete production,
autonomous crane solutions for digital construction sites in rough terrain as well as end-to-end and other software solutions that help companies in the office and on the construction site.
Another special attraction will be the VR Experience Zone 2025, a partnership between the Construction Future Lab (CFLab) and Messe München. The interactive exhibition will combine a museumlike character with innovative technology and shed light on key future topics in the construction industry. Interested visitors can experience demonstrations on such topics as construction robotics,
alternative drive technologies, additive processes and the digitalisation of machines and interfaces. The offer is supplemented by expert interviews and multimedia content. This experience will provide visitors with comprehensive and practical insights into innovations in the industry and bring futurerelevant developments to life.
Caterpillar will showcase a wide range of equipment, technologies, power options and services in Hall B6. Covering over 9,000 m2 , Caterpillar’s exhibit will feature 48 machines, including 17 new introductions or upgrades. These include enhancements to the battery electric lineup, expansions to the Next Generation lineup and additions to the demolition, waste handling, and recycling portfolios.
The Cat Performance Centre will take centre-stage, showcasing the possibilities when power, machinery, technology and autonomy work together. The display will focus on a range of solutions designed to support our customers be more successful on their respective jobsites, including helping increase performance, streamline efficiencies and achieve their sustainability goals.
Visitors will have the chance to simulate how upgrading their fleet with Caterpillar’s latest machine technologies can lead to significant reductions in fuel consumption and associated greenhouse gas (GHG) emissions.
Technology, connectivity and safety Experts will be on hand to demonstrate advancements to VisionLink®, an integrated Cat solution for equipment management, operations management and safety management. The expanded Cat Detect Portfolio, including People Detection, Seatbelt Monitoring, Driver Safety System (DSS), and Collision Mitigation, will demonstrate how technologies can maximise safety and performance.
Cat Command technology will enable remote machine operation from a safe distance, with a demonstration of machines operating remotely from sites across Europe including at the Caterpillar Demonstration and Learning Centre in Malaga.
Further introductions to the Demolition, Waste Handling and Recycling portfolios include the new 330 UHD Ultra High Demolition Hydraulic Excavator. Standard features include the Stability Monitoring System with light and sound indicators in the cab on the
ultra-high front, Cat Payload and Cat Grade Control with 2D for the retrofit front parts. Also joining the lineup is the introduction of the Variable Angle Boom option on the 340 VAB designed for demanding demolition sites.
The Cat Certified Rebuild Programs and Cat Certified Used products will highlight how end-of-life machines can be restored to like-new condition by skilled dealer technicians, who can also provide support beyond the standard machine warranty with Equipment Protection Plans. These offerings can reduce the cost of buying new equipment while also being a sustainable choice by reducing waste and consumption of raw materials.
A range of Caterpillar Industrial Engines that are compatible with renewable fuels such as 100% hydrotreated vegetable oils (HVO) will be on display in Hall A4, stand 336. The stand features the first showing of a series electric drivetrain, part of a growing electrification ecosystem of solutions
from Caterpillar; a hydrogen engine testing exhibit highlighting the ongoing fuels development work and a remanufactured C7.1. The C13D, C9.3B and C2.8 engines will also be featured in hall B6.
Providing reliable on-site power, Caterpillar’s range of EUV certified mobile XQP generator sets have been specifically designed to withstand the harsh conditions across many construction sites. The XQP115 genset, also compatible with HVO, will be on display outside hall B6.
The XES60 mobile battery energy storage solution (BESS) will be on display inside hall B6 within the power hub area. Since its launch, the XES BESS products have been a key piece of equipment on many construction sites with its rapid plug and play installation. It supports on-site battery electric machine charging and can be used with a combination of grid connection, generator sets using a variety of liquid and gaseous fuels, and renewable energy sources.
www.cat.com/bauma
Visitors to the Kobelco stand at bauma will experience an extensive lineup of innovative construction equipment, including mini and midsize excavators, conventional excavators and crawler cranes.
This year, Kobelco will emphasize its commitment to sustainable construction and advanced technology. The exhibit will highlight breakthroughs in emission reduction technology, remote operation, enhanced safety systems and stateof-the-art demolition equipment, underscoring the company’s dedication to developing solutions for the future of the construction industry.
Special attention will also be given to K-Dive® technology, which has been recognised as a finalist for the prestigious bauma Innovation Award in the digitalisation category. K-Dive is Kobelco’s advanced remote operation platform that enhances operator efficiency, safety and connectivity by enabling multiple excavators to be operated long distance and remotely, without loss of precision. This technology represents a significant step forward, offering groundbreaking solutions for hazardous environments and
improving overall productivity.
Makoto Kato, General Manager of Kobelco Construction Machinery Europe BV, shared his excitement about the event: “bauma is the ideal platform to demonstrate Kobelco’s cutting-edge advancements and commitment to innovation. This year, we are proud to present machinery and technology that not only enhance efficiency and safety but also contribute to a greener and more sustainable future. We look forward to connecting with our industry partners and customers to showcase our shared vision for the future of construction.”
More details on Kobelco’s participation at bauma 2025 will be unveiled during the pre-bauma press conference later in February.
A host of new products await visitors to Liebherr’s booth. Visitors can look forward to world exclusives in excavators, cranes, deep foundation machines and material handlers.
See for yourself in the InnovationLab
The central focus of the Group’s forward-looking technologies can be found in the InnovationLab in the outdoor area, booth 810. Visitors will have the chance to try out pioneering technological concepts first hand, whether on-screen or through interactive installations spanning numerous product segments.
Liebherr is showcasing the development and implementation of object identification by machines fitted with the necessary camera systems and sensors. These are the prerequisites to make advanced assistance systems, autonomous machine operations and predictive maintenance a real possibility.
Liebherr views digitalisation as an ongoing and forward-looking process, with artificial intelligence and the Internet of Things being integrated more heavily into machines and work processes. We will also forge ahead with the expansion of the cloud infrastructure to process the growing volumes of
data efficiently and to facilitate new data-powered business models.
There will be a particular focus on the aspects of intelligent machine controls, assistance systems and (semi-)autonomous processes, especially since they improve the communication between man and machine as well as between machine and machine, reducing the machine’s energy consumption and downtime.
Digital solutions fundamentally facilitate the collection of relevant machine data and process data. This ensures machine operations and maintenance based on cutting-edge technologies can be predicted with more precision and planned for more effectively.
The components product segment is also presenting its Energy Planner at bauma. This is a browser-based software for planning every aspect of a construction site’s power and energy requirements. For every construction phase, the tool calculates the energy requirements and charging phases of the specific machines.
Liebherr Connect is an intelligent interconnection between machines and systems, serving as a connectivity solution that not only facilitates time and cost savings, but also makes machines and systems
safer and easier to operate. It provides access to digital solutions and services, as well as extensive machine data and process data. This connects Liebherr machines with numerous products and applications that Liebherr makes available in the MyLiebherr customer portal and mobile apps and cloud applications.
To progress in decarbonising its machines, Liebherr keeps an open mind to alternative technologies, focusing its development work on more than just reducing CO2 emissions, with another three pillars being the technological maturity of alternative drive options, the infrastructure and the costs of the energy sources. Liebherr is making significant investments in research and development work in all areas of drive technologies, now and in the future.
With the new version of the Liduro Power Port (LPO) mobile energy storage system from series 100 and the prototype of a stationary energy storage system LPO 600, the components product segment is demonstrating the
opportunities for a zero local emissions energy supply for construction sites, coupled with electric machinery. The LPO 600 mobile charging station has a gross energy content of 564 kWh and can provide sufficient energy for large machines or fleets, even in terrains without the relevant infrastructure.
A highlight from the field of hydrogen technology is the first prototype of a Liebherr large wheel loader with a hydrogen engine. According to extensive studies on the subject, hydrogen is a highly suitable carbon-neutral alternative for powering large vehicles that are difficult to power with electricity. Liebherr is presenting the prototype in the outdoor area.
Liebherr Group is exploring a broad range of solutions including battery and mains-operated electric solutions, alternative fuels such as HVO as well as hydrogen or ammonia-based drives – some of which are on show at bauma.
On 12 and 13 February, the CBS Arena in Coventry will become the heart of the tools, plant and equipment hire industry. With all 145 stands booked, the stage is set for two unforgettable days of innovation, connection and inspiration.
Over nearly two decades, the Executive Hire Show has become a key event for the hire industry, bringing together suppliers and hirers to explore new ideas, discover practical solutions and support the sector’s growth.
As the industry sharpens its focus on sustainability and efficiency, this year’s show promises to deliver solutions for the challenges ahead. Attendees can expect to explore the latest electric and hybrid machinery advancements, alternative power options and sustainable site solutions. From fleet-transforming tools to software that streamlines operations, it’s a showcase of how innovation meets opportunity to futureproof the hire sector.
With independent hirers making up 86% of last year’s attendees, the event has proven its broad appeal across the industry. Whether you’re leading a national operation
or growing an ambitious startup, the Executive Hire Show provides the platform to learn, collaborate and thrive.
Chris Moore, Executive Hire Show Director, commented: “The Executive Hire Show has become an essential event for the hire industry. With a sold-out exhibition, exclusive deals and the Passionate Hire Awards at the Networking After Party, it’s the perfect opportunity to connect, celebrate and shape the future of hire. This year’s Innovation Trail will showcase groundbreaking products and services transforming
the sector, giving visitors a unique chance to explore cutting-edge solutions. It really is too good to miss.”
With more than 145 exhibitors, live demonstrations and actionable insights into challenges such as decarbonisation, Executive Hire Show 2025 promises to inspire and provide practical solutions for every hire business. Registration is free, visit www.executivehireshow.co.uk for fast-track entry and start planning your visit.
Here’s a small sample of what’s on offer:
The Electric Heating Company (EHC) has launched its innovative Mobile Boiler range, offering portable, compact and efficient temporary heating solutions for construction sites, renovations and light commercial uses. With models ranging from the 2-8 kW Comet PV to the 26 kW Mercury Combi, these boilers provide adjustable flow temperatures (20°C-85°C) and are perfect for tasks like screed drying or emergency heating.
Stand K41
KAESER’s new HPC MOBILAIR M44 compressor fills a key market gap, offering compact, highperformance, and eco-friendly portable compressed air systems. Powered by a Stage V-compliant Kubota diesel engine with optimised power management, it delivers 4.1 m³/min at 7 bar while ensuring exceptional fuel efficiency and minimal emissions. With features like anti-frost control, the Sigma Control Smart
system for precise pressure adjustments and a lightweight design under 750 kg, the M44 is ideal for applications ranging from pneumatic hammers to sewer robots. Optional extras include compressed air reheating and oil-free configurations for tailored solutions. Explore the innovative MOBILAIR M44 on the HPC’s Compressed Air Systems stand.
Stand K70
Dragon Equipment, renowned for its compact crushing machines, is raising the bar with the CR450 Diesel Crusher. Powered by the highly regarded Kubota D722 19 HP diesel engine, the CR450 offers higher torque and increased output, crushing through even the hardest materials for over 12 hours thanks to its 33-litre fuel tank.
With a 460 mm by 205 mm Hardox jaw and remote-control
capability, the CR450 is designed for maximum productivity and safety, perfect for tough-to-reach sites. All-terrain tracks and a compact 970-mm width improve on site stability, while its lightweight build ensures easy transport alongside an excavator. After its official launch in 2024, the CR450 Diesel Crusher will make its first in-person appearance at the EHS this year. Stand G12
JCB will unveil its new electric micro excavator – the 8008E CTS, sharing its structure, bodywork and dig-end with the diesel-powered 8008 CTS.
The 9.9-kWh battery delivers enough power for a full day’s shift while 110V and 230V charging suit construction use. Noise level at the operator station is 66 dB(A), while external noise is 80 dB(A), making it ideal for use indoors.
Maximum bucket tearout is 9.3 kN and dipper tearout is 4.6 kN. Also on the stand will be a range of sustainable equipment for the rental industry including the world’s first hydrogen combustion engine, the 16C-1 mini excavator, 1T-2 site dumper and HTD-5E electric Dumpster.
Stand: F40
Prolectric’s patented lighting tower technology will be officially showcased for the first time at the Executive Hire Show 2025. Adding to the excitement, Prolectric will reveal a prototype of the groundbreaking ProCharge – a revolutionary BESS product ahead of its 2025 launch. Featuring a
12-panel solar array, the ProCharge has already been saving one of the UK’s largest contractors over £200 a day. Designed to power site compounds, electric telehandlers, small EV vans, ATVs, mini diggers and dumpers, it’s set to transform on-site energy use.
Stand J10
SANY is bringing a showcase of innovative machinery tailored for the plant hire sector. Highlights include the popular SY26C mini excavator, a compact yet powerful machine with reduced tail swing, easy towing capability and a nextgeneration operator’s cab. The fully electric SY19E, with zero emissions
and a long-lasting LFP battery for faster, safer charging will also be displayed. The SY35U zero tail swing excavator, equipped with a Stage V YANMAR engine, advanced load-sensing hydraulics and safetyfocused features, rounds out the mini excavator lineup.
Stand C20
Bobcat will showcase its expanded product range including one of the most extensive lineups of compact machinery, material handling equipment, attachments and portable power solutions –all supported by Bobcat’s global dealer network.
Among the highlights are the latest PG40 and PG50 portable generators, which represent a leap forward in design and efficiency. Powered by Stage V D24 engines and Stamford alternators, these
models deliver increased power output and reduced fuel consumption compared to their predecessors.
The PG50 offers a true 50 kVA prime unit, while the PG40 delivers 40 kVA, both with sleek, compact designs and optional factory-mounted running gear for easy transportation. The new generators also feature ‘Liquid Heat,’ a low-load management system that reduces downtime and extends engine life. Stand A72
Atlas Copco will unveil its ZBP 120-120 portable, modular energy storage system, delivering 120 kVA power and 123 kWh energy storage, making it ideal for noisesensitive zones and emissions-free applications. Powered by highdensity lithium-ion batteries, the ZBP 120-120 supports standalone and hybrid operation, integrates with renewable energy inputs,
and reduces generator runtime by up to 70%. With over 40,000 hours of working life and minimal maintenance, it’s a cost-effective, sustainable choice for the hire industry.
Part of the Innovation Trail, the ZBP 120-120, highlights Atlas Copco’s commitment to efficiency and environmental performance. Stand B22
GroundGuards, a leading name in ground protection, is bringing two standout products to EHS 2025: ProMat and UltraTrack Pro. Designed with sustainability and performance in mind, both products are crafted from recycled materials, reducing environmental impact while delivering industryleading reliability.
ProMat: Offering exceptional value at just £98, ProMat is lightweight at 38 kg, yet durable enough for demanding conditions.
Made from 100% recycled highdensity polyethylene (HDPE), it’s an eco-friendly, cost-effective choice for hire companies and event organisers.
UltraTrack Pro: Built for largescale projects, UltraTrack Pro features oversized panels for faster setup and overlapping joints that create cleaner, safer work sites. Its heavy-duty durability and sustainable design make it ideal for high-demand applications.
Stand A52
Towmate Trailers, a British manufacturer of towable solutions for the construction and public utilities sectors, will showcase its innovative designs. Known for its modular approach, Towmate offers reconfigurable trailers to meet specific requirements, focusing on efficiency, reducing downtime, and minimising repair costs.
Featured products include the Rhino Plant Trailer, equipped with a pivot axle system to reduce tyre and axle damage, and LoadSentry, a strapless security system for securing diggers. Also on display will be the Raptor 125 Pipe Trailer, designed for laying coils of pipe for gas and water, featuring the latest customer-driven modifications. Stand F10
Western Global, a leader in fuel storage solutions, returns to the event, showcasing cuttingedge products designed for efficiency and reliability. Key highlights include the DEFCube and TransCube Global, offering advanced solutions for fuel and AdBlue storage.
Available in 500-L and 2,200-L capacities, the DEFCube provides innovative AdBlue storage with a poly inner and steel outer for temperature control. Features like forklift pockets, stackable design and lockable compartments
ensure mobility, security and space efficiency.
Known for versatility, the TransCube Global fuels multiple pieces of equipment simultaneously, extending run times and saving time and resources. Its transportable design makes it ideal for construction and rental applications.
For larger-scale needs, the TransTank and EnviroCube offer robust storage with durable designs and compatibility with fuel management systems.
Stand G22
Tufftruk will showcase the latest addition to its TRUXTA range, the EB800PTP “Mid Tip” Battery Powered Mini Dumper. This standon machine combines a 960-mm tipping height, hydraulic power tipping and zero-emissions design, offering unrivalled performance and versatility on site. Its articulated chassis and patented steering pivot system ensure maximum manoeuvrability, while the compact
design allows it to fit through standard doorways.
Attendees can also explore the new EB800PTCB Battery Powered Concrete Buggie, featuring TRUXTA’s iconic lime green Poly Skip, alongside the full TRUXTA range. Built for durability, safety and eco-friendly operation, Tufftruk’s innovative machines are designed to meet the needs of modern job sites. Stand I12
Hatz Digital Solutions is transforming engine management with real-time performance tracking and IoT technology. Designed to maximise efficiency, productivity and profitability, the system provides vital information such as engine performance, location, maintenance needs and error codes, all accessible via a browser-based dashboard.
With features like geopositioning, data transfer via SIM card and over-the-air
updates, Hatz engines become indispensable data providers for optimised planning. The technology is intuitive and powerful, offering structured information that improves profitability while ensuring availability and reliability. This solution is compatible with all electronically controlled Hatz engine applications, making it ideal for hire companies and construction professionals looking to enhance their operations.
Stand B23
Household names like Thwaites, Niftylift, Mecalac, MHM, Altrad Belle, Husqvarna UK, Makita, Genquip, Ammann and Toro will also be on the show floor, alongside 45 first-time exhibitors bringing fresh energy and ideas to the event. The diversity of exhibitors ensures something to inspire every visitor, whether exploring innovations, discovering sustainable solutions, or securing exclusive show-only deals.
W E A R E
C A W A R D E N
F o r m o r e t h a n 3 5 y e a r s , w e ’ v e b e e n a
t r u s t e d f a m i l y - o w n e d a n d o p e r a t e d
s p e c i a l i s t c o n t r a c t o r , c o n s i s t e n t l y
d e l i v e r i n g e x c e p t i o n a l p r o j e c t s
L e t o u r e x p e r t i s e a n d e x p e r i e n c e w o r k
f o r y o u
c a w a r d e n . c o m
Job name: Pharma/Nightclub
Location/Client: Borough High Street
Expected duration: 14 weeks
Equipment used: Kobelco High-Reach, Komatsu excavator, attachments Geith and Strickland.
Snapshots of Ben and the Demolition Hub team’s activities between issues
by Richard Vann
No matter how extensive your demolition planning techniques, you never truly know what’s around the corner. And with multiple variables at play, it’s impossible to control one single, specific route map. It would be naive to think this is the case. But that doesn’t mean you can’t be prepared for different outcomes.
Here, Richard Vann, Managing Director at global decommissioning consultancy RVA Group, explores why scenario planning is crucial when managing large-scale demolition projects – providing the knowledge and agility to react when the unexpected happens, while keeping safety, costs, and timelines at the forefront.
Demolition is a complex, often unpredictable process – one that involves far more than simply knocking down structures. Unlike construction, where precise plans are drawn up from blueprints and materials, demolition projects are full of unknowns. From structural complexities and outdated designs to hazardous substances that pose risks to human health, many of these may only become apparent once the work begins.
This is why feasibility and option studies are such powerful tools in our industry. They allow us to consider the different paths a project might take, each with its own variables and potential challenges, to anticipate different outcomes and create contingencies for each path. From the exploration of different asset divestment options and methodologies to resource planning and EHS considerations, this type of scenario planning empowers clients with intel, supported by evidence-based recommendations, to make informed decisions at every stage.
Such studies are even more value-adding when accompanied by live, adjustable spreadsheets that adapt financial projects as
external factors evolve. With a more dynamic approach, teams can confidently navigate any disruption without losing sight of the project’s end goal. Even with a comprehensive schedule of work in place, backed by a proficient project team equipped to execute the methodologies agreed, a plan should always remain flexible.
Every project holds surprises
Demolition projects, by their very nature, uncover unanticipated challenges all the time. And as the saying goes – you don’t know what you don’t know. So how can you plan for everything? And why would you execute every planning exercise in utmost detail if you aren’t yet clear on exactly what the detail will be?
Demolition doesn’t follow a blueprint
If you build a house, a quantity surveyor can use a design to calculate the quantity and type of materials required, as well as a project timeline, with a significant degree of accuracy. Even with this blank slate, unexpected challenges may arise along the way – so imagine the complexities when dealing with
decades-old infrastructure where documentation is incomplete, inaccurate, or often nonexistent.
Deconstructing an asset the size of a power station, which has stood for more than 60 years, brings a whole new level of complexity. Drawings are often incomplete – if not missing altogether – and the people who operated the plant may no longer be available to provide site-specific knowledge. Educated assumptions must therefore be made until surveys can be concluded and the structure is brought to a known state.
Structures and scenarios constantly change, so planning must remain dynamic at every stage of the demolition, adapting to developments as they arise. Planning only stops when the asset has been brought safely to the ground and prepared for its next phase, whether it’s repurposed or mothballed for future use.
Mindset is as critical as the plan
Mindset matters almost as much as
the quality of the initial plan itself. You can’t take your eye off the ball, as you don’t know what tomorrow will bring. And the ongoing progress and evolution of the plan should not – and cannot – remain the responsibility of just one party.
At RVA Group, we’ve long talked about the importance of a tripartite alliance between a client, contractor and an independent consultant like RVA. For a start, nobody knows everything. A contractor may be able to prove the capabilities of a new machine that could help complete the project quicker and safer, for instance. Or there may be advanced waste management experience that would strengthen the environmental credentials of a methodology.
Failing to include all three parties at the decision-making table increases project risk. In one instance, a client engaged RVA to draft a job specification, before terminating our involvement when the contractor was appointed. The client took the programme forward without ongoing impartial project management support, and there were two major incidents on site.
Some operators bypass independent advice altogether, relying on presumptions instead of evidence. But without detailed surveys, for instance, how can a contractor provide accurate quotes? Does the client understand the supply chain’s capacity or anticipate programme delays? Have isolation strategies been designed to ensure the safety of all stakeholders? And what about resale opportunities for dismantled assets versus the scrap market?
The planning considerations, of course, go on and on, but comprehensive planning answers a myriad of questions such as these.
To organisations rationalising their operations or mothballing a redundant site to limit their liability, demolition may seem like a straightforward task. A nuisance event to move past quickly. But this mindset invites trouble. Cutting corners in planning means you’re gambling on what lies ahead – and it’s better to prepare for the unexpected than to pay the price later.
by Terry Lloyd – Head of Vendor in the SME Lending division
As we enter the new year, many of us will be wondering what 2025 will hold for the industry. Will it be another year of change, or will things start to stabilise for the construction sector after a challenging 2024?
The good news is that the year is off to a positive start and the construction figures released on 16 January by the Office for National Statistics (ONS) were positive.
The figures showed a 0.4% rise during the month of November, following a decrease in October – a good sign that despite the colder weather, we’re still seeing an increase in construction output. Digging a little bit deeper into the figures, we can see an increase of 0.3% in new work as well as a 0.5%
increase in repair and maintenance. The increase in new work is particularly good as it indicates that the industry is growing and new projects are getting off the ground.
Furthermore, we saw an increase in the three months to November by 0.2% – so despite the reduction we saw in October, it’s promising to see that the downturn in construction output wasn’t prolonged.
The question is, what is driving the increase in construction output?
Is it perhaps Labour’s new focus on house building and the aim to get 1.5 million homes built in the next five years? From October to November, we saw an increase of 0.9% in new public housing –which is promising but there was a decrease in private homes being built, showing that there are still barriers to building these homes.
We are starting to see more changes introduced by Labour to reach this target, but only time will tell whether these new policies will make a bigger contribution to the 1.5 million homes the government wants to achieve.
It has come out swinging in the new year and Chancellor Rachel Reeves has made bold statements about getting building unlocked through adopting a tougher stance on organisations attempting to block schemes in the courts.
Likewise, the government has made clear it wants to see fewer infrastructure and commercial projects – significant contributors to construction output – bogged down in lengthy court processes.
Labour is also reportedly looking to remove some of the restrictions around environmental offsetting when new schemes are built. Instead of requesting this to be done in advance of projects, developers or contractors will instead pay into a new fund that will go towards offsetting these projects in the future.
The interventions are timely. We saw a slowdown in infrastructure works both month-on-month from October to November and yearon-year from November 2023 to November 2024. Hopefully, the resurgence of HS2 to Euston, amongst other large projects we have across the UK will support more new work in infrastructure over the coming year, in addition to some of the policies Labour is looking to bring in.
While we are unsure of the timeline for this potential change to the planning process, it could make a big difference to projects of all sizes, particularly large infrastructure projects. Like many in the industry, I’ll be waiting to hear more from the government on this announcement.
by Richard Dolman
As we enter 2025, the UK economy is showing signs of recovery, but with mixed signals for the construction and demolition sectors. Despite the challenges that marked 2024, including tax changes and a slowdown in economic momentum, a more positive outlook is emerging for the year ahead.
The Bank of England projects GDP growth of 1.5%, with the Office for Budget Responsibility (OBR) forecasting a stronger 2% rise. However, the demolition industry must carefully navigate this evolving landscape of opportunities and challenges to make the most of what 2025 has to offer.
According to the BCIS (Building Cost Information Service), construction output is predicted to recover through 2025, though the pace of recovery is not without its hurdles. While labour costs are currently slowing, they are expected to rise again by mid year, adding pressure to already strained budgets. This increase, combined with inflationary pressures on materials and other costs, may add to the challenges. At the same time, a decline in new orders suggests that the industry is facing a little uncertainty, but this may be in the short term.
Nevertheless, the UK government’s commitment to large-scale infrastructure and housing projects is a silver lining for the demolition sector. There is a clear push to increase affordable housing, with £5 billion earmarked for the development of new homes, alongside significant funding for projects like HS2, the TransPennine route, and brownfield land regeneration.
The focus on brownfield land release, with £80 million set aside for its development, is particularly noteworthy. As urban regeneration takes centre stage, demolition will play a crucial role in clearing derelict or underused sites for new residential, commercial and infrastructure projects.
Despite these positive trends, challenges remain. BCIS notes that the construction sector, including demolition, faces pressure from rising labour costs. Although this rise is predicted to slow early in the year, it will likely pick up again in the second half, potentially creating budgeting challenges.
Looking to the future, the impending Spending Review in June 2025 will be a key event for the industry. This review will provide further clarity on government
spending priorities, which could significantly impact demolition projects – both positively and negatively. If government investment in infrastructure and housing continues to rise, it could provide a much-needed boost to the sector. On the other hand, any cuts or delays to planned projects could dampen the outlook for the demolition industry, particularly if new orders continue to decline.
The challenges facing the demolition industry in 2025 are clear, but so too are the opportunities. With a recovery forecasted for construction output and increasing government spending on infrastructure and housing, we can expect some greater stability this year.
We are poised for growth, but it will require careful navigation of both challenges and opportunities. Considered planning and investing in skilled labour will help us weather the economic landscape we’ve become accustomed to.
One of Europe’s largest stockists and suppliers of new and used earthmoving and waste recycling equipment and spare parts has signed up with global machinery manufacturer Sunward to stock its comprehensive range of mini excavators.
Warwick Ward (machinery), which was founded 55 years ago and now has depots in the north, Midlands and south, not to mention its own Centre of Excellence, will break new ground, literally, with the partnership with Sunward.
Warwick Ward Executive Chairman Ashley Ward said the partnership would give the company, which also operates an extensive hire fleet for both long and short term hires, a fully-equipped workshop, and nationwide service
team and transport facility, access to new markets and a differentiated customer base.
Following many months of discussions, he said: “The new partnership with Sunward is one that is exciting. Their mini excavator range very much complements the other brands and products in the Warwick Ward portfolio and is a fantastic new addition to our product offering for 2025.
“The build quality and core components of the range are top quality and performance has been very impressive in testing. The products are competitively priced and being able to offer up to five years’ warranty is impressive and reassuring and demonstrates the confidence Sunward have in the quality of the product.”
He added: “Sunward has a European HQ and distribution hub in Belgium which is important to us in terms of optimum logistics and speed of movement of the products, and importantly spare parts in transit to the UK.
“We are impressed with the company’s approach and strategy and the discussions we have had with their senior leadership team, both in Belgium and in China, have been very positive and productive.”
Rick Still, Sunward’s Country Manager for the UK and Ireland, said: “We are delighted to bring Warwick Ward on board and welcome them to our ever-expanding dealer network. The very positive attitude and the ‘can do’ approach of the Warwick Ward senior management team has been very impressive.”
Lincolnshire-based waste management, earthmoving and demolition company Grantham Industries has secured a £500,000 finance facility from Paragon Bank’s SME Lending division to support the purchase of a commercial waste site in Rutland.
The £500,000 funding will also enable Grantham Industries to renovate the site, building the existing waste transfer station into a waste and recycling centre offering a broader package of services to the local area. The new site in Rutland has expanded the company’s geographical presence, building on its existing operations in Louth, Lincoln and Doncaster.
In addition to the funding facility, Paragon has also recently supported Grantham Industries with a £198,000 asset finance package to purchase a Volvo Wheel Loader for use on one of its current waste transfer sites, expanding its fleet of vehicles.
This deal has been led on behalf of Paragon’s SME Lending division by Henry Oakes, Business Development Manager in the Vendor team headed by Terry Lloyd.
Grantham Industries was started in 2001 by Managing Director Simon Grantham and his brother Andrew, offering a range of services under its GBM Demolition, GBM Plant Services and GBM Waste Management brands. The company employs more than 90 people and operates across the country.
Grantham Industries Finance Director Leanne Fairburn said: “We had a very specific requirement to purchase a waste site and were looking for a lender to support this
transaction. We were delighted that Paragon could support us with a funding facility, building on our existing relationship with the bank after purchasing equipment previously.
“Purchasing the site in Rutland will be a new opportunity for us to expand our footprint and proposition and we’re grateful to Henry and the Paragon team for all their help in making this a smooth process.”
Business Development Manager Henry Oakes added: “It’s been a pleasure to help Grantham Industries expand its business and purchase the site which will undoubtedly bring about new opportunities for them.
“At Paragon we strive to support clients with their business goals through various financing options, so we were thrilled to be able to arrange a funding facility for Grantham Industries.”
Brokk Inc., the North American distributor for Brokk demolition robots and Aquajet Hydrodemolition equipment has been named the North American distributor for Darda, the world’s leading manufacturer of hydraulic splitters and compact attachments, including concrete crushers, shears, multicutters and tank cutters. Darda, like Brokk and Aquajet, is owned by the Brokk Group, the global leader in advanced demolition equipment.
As the North American distributor, Brokk Inc. will be focused on building a Darda dealer network in North America and spreading awareness of the comprehensive range of products among end users in construction, demolition, mining and tunneling industries.
“We’ve long been champions of the Darda brand,” said Jeff Keeling, Vice President for Sales and Marketing at Brokk Inc. “Not only are we both part of the Brokk family, we have also paired Darda attachments with Brokk robots for decades. Now with the full range of Darda products, we’ll be able to reach an even larger audience with these high-quality, high-performance products.”
Darda, located in Blumberg, Germany, got its start in 1958 by producing simple splitting machines for the natural stone industry. A decade later, the company’s innovative hydraulic rock and concrete splitter revolutionised the demolition industry. By the late 1990s, Darda had evolved into producing carrier-operated attachments for compact machines such as mini excavators and demolition robots. Darda became part of the Brokk Group in 2006 and has dealers around the world.
Brokk Inc. was established in 2000 in Monroe, Washington to sell and service Brokk products
in North America. Over the last 25 years the company has built a sales force located throughout the United States and Canada and sold more than 2,000 Brokk machines. In 2017, Brokk Inc. became an Aquajet distributor, expanding its demolition solutions by offering hydrodemolition equipment for concrete removal. Known for outstanding service and support, Brokk Inc. has opened service centres in Stanhope, New Jersey; St. Joseph, Missouri; and most recently, Hamilton, Ontario.
“This is a strong partnership that will greatly benefit our customers in North America,” said Bernd Ströbele, Darda Sales Director. “Brokk Inc. is perfectly positioned to develop a robust distribution network for Darda products while promoting the full range of attachments and handheld tools.”
www.brokk.com/us
Aquajet, a global leader in the design and manufacture of innovative hydrodemolition technology distributed in the US by Brokk Inc, has introduced its new Support System designed to enhance the capabilities and flexibility of hydrodemolition robots in challenging environments.
The system centres around the upgraded Aqua Spine 3.0, an extendable rail system that attaches easily to any surface, providing a stable platform for the Power Head to move along during operation. The Ergo Climbers have also been upgraded to version 3.0, with new features that ensure seamless compatibility with the new system.
To better support the Aqua Spine and Ergo Climbers, Aquajet created the customisable Support System, providing more flexibility and adjustable setups for different projects. This whole system is ideal for a variety of hydrodemolition work and is compatible with both the Aqua Cutter 750V hydrodemolition robot and Ergo system.
Recognising that not all projects involve straightforward flatwork, this solution equips contractors with a highly adaptable, ready-to-use setup capable of tackling complex applications, such as tunnel, bridge, silo and dam wall repairs and refractory work.
Roger Simonsson, Managing Director of Aquajet said: “We noticed a pain point where contractors are still using hand lances for jobs that can be accomplished more quickly with a hydrodemolition robot, given the right setup. To make it easier to deploy hydrodemolition robots in even the toughest environments, we upgraded both
the Aqua Spine and Ergo Climbers and developed a fully customisable Support System with adjustable legs, brackets and rotatable joints. This allows contractors to purchase a system tailored specifically to their project needs, ensuring the right configuration for each job.”
The Aqua Spine 3.0 greatly expands range and flexibility for both on and offshore hydrodemolition applications, excelling in both linear work such as structure walls and power plants, and circular applications like tunnels and pillars. New passable mounts/brackets,
support legs, adapter plates and feet make up the Aqua Spine, providing users the option to build longer setups when needed, rather than having to repeatedly move a shorter setup along the removal area.
Passable mounts allow the Power Head to seamlessly move from section to section without the need to stop and reposition. The upgraded version is also lighter than the previous Spine and can handle a 60% greater load and 50% greater torque.
The Aqua Spine 3.0 is compatible with the Circular Power Head and Aqua Centralizer, a ring mounted to the Aqua Spine base used for work on pipes or inside tunnels. The curved roller beam is compatible with both the Climber and Spine system and can be easily constructed into a complete circle. All parts of the Spine system are assembled with M16 or M20 bolts, allowing contractors to easily assemble and adjust with few tools.
The updated Ergo Climber 3.0 features several improvements, such as beam brackets with adjustable height and angle, adjustable clamping screws allowing it to attach and move along both standard and curved scaffolding pipes or roller beams and be configured as a complete circle for pillars and pipes.
New passable brackets enable the Climbers to move the Ergo Power Head continuously along the scaffolding, making it possible to build infinitely long racks and increasing productivity without the need to stop and reposition.
Simonsson said: “With this new Support System, contractors can easily adjust the support legs to exact heights or angles, ensuring stability and optimal positioning for their hydrodemolition project, regardless of the surface or environment. The true value, however, lies in its reusability and scalability. If a future project requires
different specifications, the system can be reconfigured or expanded with additional components. This flexibility reduces the need for entirely new setups, saving both time and resources, while keeping contractors prepared for any challenge that comes their way.”
Aquajet’s new Support System is designed to deliver even more flexibility and stability when working with the Aqua Spine 3.0 or the Ergo, offering a customisable solution that adapts to the specific demands of each job. Whether working on floors, walls or ceilings, the system ensures that contractors can position their equipment with remarkable accuracy, adjusting the height and angle of the components to provide optimal stability in any environment.
The system consists of support legs, brackets and joints that are easily adjustable in both height and angle and can be assembled to allow the Aqua Spine to rotate
360 degrees – either manually or hydraulically. Featuring only nine parts, the Support System uses interchangeable CC80 hole pattern and M16 screws, enabling quick reconfiguration from one project to
Aqua Spine 3.0 with Support System and a curved roller beam makes usually challenging
the next. What truly sets this support system apart is its modularity. Contractors can select from light and heavy versions to meet the specific job needs. The light series is a lighter-weight, flexible system ideal
for the Ergo, while the heavy series is more stable and robust to handle a more powerful machine, like the Aqua Cutter 750V’s power head. These systems can be adapted to a wide range of industries to remove any number of materials. It adapts to various surfaces such as floors, walls or ceilings, allowing contractors to precisely adjust leg height and angle for optimal stability. Fully customisable for specific project requirements, the system’s reusability and scalability allow for future reconfiguration, saving time and resources by eliminating the need for entirely new setups.
Demolition is an important industry in the Czech Republic. In many towns and villages there are numerous brownfield sites – whether they are the remains of industrial or agricultural production, disused municipal buildings or large private buildings.
Small buildings such as houses can be dismantled using conventional construction equipment, however, as the height increases, special machinery must be used. DEVELON has offered a wide range of specialist equipment for many years and these now include a range of four new demolition machines.
The DX140RDM-7, DX245DM-7, DX380DM-7 and DX530DM-7 are available in the Czech Republic through its importer GARNEA a.s. The machines vary in size, weight and range with operating weights of up to 71 tonnes and a reach of up to 31 m. They have a maximum payload capacity of up to three tonnes at the boom and power outputs up to 290 kW, with all four meeting the Stage V emission standard.
These demolition excavators from DEVELON offer perfect flexibility thanks to their modular boom design and hydraulic locking mechanism and a cab tilt of up to 30° is available for better operator visibility.
The DX140RDM-7 is available with either a monolithic or interchangeable boom on request. The DX245DM-7, DX380DM-7 and DX530DM-7 always have an interchangeable boom, which not only increases the machine’s availability but also significantly
simplifies transport. This is also facilitated by the low transport width of the machines – from 2.5 m – thanks to the extendable chassis. The customer can thus choose from a range of solutions depending on the project they need to handle.
Jan Breburda, Product Manager for Special Applications at DEVELON said: “High reach demolition excavators have a firm place in the heavy equipment market thanks to their variability. The uniqueness of the DEVELON model range lies, among other things, in the fact that it offers more compact machines than is common. Customers can thus benefit from the advantages of this concept in a much wider range of demolition projects.”
DEVELON demolition machines have found their way to a number of Czech customers courtesy of GARNEA a.s. and its partners.
Develon
Demolition with a DEVELON DX380DM-7 machine has been carried out by PERENA Liberec on the site of a former Tesla factory. František Drešer, Managing Director of PERENA Liberec s.r.o. said: “The advantage of this excavator for us was especially its versatility. The excavator has a long boom with a reach of 23 m and if necessary, the boom can be easily replaced with a standard boom and the demolition machine can be used to load rubble and dismantled material from the demolition. Another reason for purchasing this excavator was the very comfortable operator’s cab,
easy operation and last but not least the availability of service and its expertise.”
The main requirement when choosing a demolition machine was its compactness, explains the Managing Director of Prodemi s.r.o., Dušan Mihalik: “We chose the DEVELON demolition excavator because it was the only brand that could offer this special machine in the weight category up to 30 tonnes.
“Thanks to its compact dimensions, the machine can be used on smaller demolition sites where large machines cannot fit, but conventional excavators would not be able to do the job safely and efficiently.
“Thanks to the variable boom, one machine can carry out demolition and then clean up after itself or load
straight into the crusher so there is no need for another machine on site for these operations. Meanwhile, changing the boom is a breeze for two people. After a short training session, our workers can do it in 40 minutes.”
The success of specialised excavators in the Czech demolition market would not be possible without perfect service. This is taken care of by the importer, GARNEA a.s., with its network of partners throughout the Czech Republic.
Vít Brůžek, Product Manager for DEVELON excavators at GARNEA a.s. said: “We provide our customers with round-the-clock technical advice and service vehicles with certified service technicians. The telematics system MY DEVELON also contributes to the most worry-free operation, thanks to which we can have a perfect overview of the machine even remotely.”
www.eu.develon-ce.com/en
JCB has cleared significant hurdles in its development of the world’s first hydrogen combustion engine after securing landmark rulings from licensing authorities allowing it to be used commercially in machines.
JCB is the first construction equipment company to develop a fully working combustion engine fuelled by hydrogen and a team of 150 engineers has been working on the exciting £100 million development for over three years.
Today JCB confirmed that 11 licensing authorities across Europe have now given permission for JCB’s hydrogen engine to be sold –with authorities in other countries set to follow suit with certification in 2025.
JCB Chairman Anthony Bamford, who has led the company’s hydrogen engine project, said: “This is a very significant moment for JCB. To start the New Year with certification in place in so many European countries bodes very well for the future of hydrogen combustion technology. JCB has proved in recent years that it is a proper zero emissions solution for construction and agricultural equipment.
“This formal type approval/ certification paves the way for the sale and use of hydrogen engines right across the UK and Europe. I couldn’t have hoped for a better start to the year. Most of all, I am delighted for our team of British engineers who have worked tirelessly to reach this stage.”
JCB confirmed that the Netherlands’ Vehicle Authority RDW was the first licensing authority to issue official certification, giving permission for the engine to sold in The Netherlands. Other licensing bodies across Europe have followed RDW’s lead by issuing the necessary
certification, including Great Britain, Northern Ireland, Germany, France, Spain, Belgium, Poland, Finland, Switzerland and Lichtenstein. Licensing authorities in other countries are set to follow with certification during 2025.
JCB has already produced more than 130 evaluation engines which are powering backhoe loaders, Loadall telescopic handlers and generator sets. Real-world testing of JCB’s hydrogen equipment on customers’ sites is now at an advanced stage and progressing well.
Tele Radio’s Panther PLd systems are the clear choice for duties that require high performance levels. Both our T19-2 and T29-12 meet Performance Level d (PLd), Category 3, equivalent to Safety Integrity Level (SIL) 2 – certifi cates independently awarded by notifi ed bodies. Whatever the job at hand, our stop function never fails.
Tele Radio offers a variety of radio remote control products, adaptable to a multitude of applications, throughout many industries like Agriculture & Forestry Equipment - Cranes & Material Handling - Mobile Hydraulic Machinery –Emergency & Recovery Vehicles - Industrial Doors & Gates – Propane and Tanker Trucks – Construction Equipment & Machines – Pumps & Aggregates, PLC Control – Recycling Machinery and more…
The European Demolition Association is pleased to welcome a new member, the Finnish company LEKATECH. Since its foundation in 2018 LEKATECH has revolutionised the world of breakers and hammers with its state-of-the-art advanced electric powered solutions.
Continuing its work in redefining the capabilities and benefits of hammers and breakers, LEKATECH was proud to unveil its latest development at Hillhead 2024, the new Electric Hammer LEKA Toras 35.
The development and introduction of LEKATECH electric hammer technology is seen by the breaking industry as game changing. The patented LEKATECH linear electric motor technology is the result of many years of dedicated research and innovation. Its development is now disrupting the traditional hydraulic impact hammer market as its electric technology produces high levels of performance, delivering huge benefits on urban
construction projects and in quarry or mine environments, above or below ground.
LEKATECH’s electric hammer technology is a major advance in hammer design and construction. Lightweight and high-power, LEKATECH hammers produce low vibrations and are built for operator comfort, economic use and high productivity. Electrically powered, LEKATECH’s linear electric motor produces low emissions and operating costs, and as such is transforming breaking globally.
The EDA is proud to welcome LEKATECH into our network and looks forward to fruitful collaboration in promoting the highest standards across the demolition sector in Europe. www.lekatech.fi
Everything is ready for the EDA Annual Convention 2025, taking place in Venice from 12 to 14 June. This is one of the most important events of the year and a must for the demolition and recycling industry.
It will include more than a dozen technical presentations aimed at professionals take place in locations across the city, with its narrow streets and iconic landmarks.
In addition to more than a dozen technical presentations aimed at professionals, the event will also include a leisure programme for accompanying persons, so EDA encourages attendees to come accompanied.
• The welcome cocktail will be in the magnificent Murano Glass Cathedral
• The Gala Dinner will take place at Pescheria Di Rialto, of the most famous places in the city
• The Convention Event will take place at the famous Palazzo del Casino, located at Lido Island, where the Mostra di Venezia festival celebrates its sessions.
The convention includes a leisure programme for participants and companions. The event, which will start with the EDA General Assembly, the Circular Economy Awards and the Welcome Cocktail, will also offer a leisure programme the following days for those who want to explore every corner of the city.
On 13 June, the leisure programme for companions will take place and is the perfect option to enjoy the city while the professional programme is taking place.
An intimate look at the city’s hidden gems with an expert guide will start with a private water taxi transfer from the Hotel Excelsior to St. Mark’s. The tour will end with a traditional Italian lunch followed by some shopping time, before returning to the hotel and getting ready for the gala dinner.
The following day, on 14 June, the leisure programme for all participants will be held. This tour is prepared for those who participate in the events that take place on 13 June and want to take some time to appreciate Venice. This special experience also includes a guided programme and makes the EDA Annual Convention not only a technical event, but a cultural one too.
EDA offers companies in the sector the opportunity to gain visibility before, during and after the event. Choose a marketing opportunity and make your brand stand out. The number of sponsorships is limited and assigned in order of request, so do not wait.
The convention is a profitable way to make the most of your brand. Options to choose from are Gold, Silver, or Bronze sponsorships. Each includes:
• Conference tickets
• Desk at the exhibition area
• Brand visibility
• Appearing on the programme
• Appearing in the conference book
• Appearing on the list of participants
• Gala dinner tickets
You can offer documentation or a promotional item in the conference bag as an extra or exclusive sponsorship is always a good choice. In this regard, you can choose to offer a lanyard, conference materials or a delegate bag to the public.
Another profitable option is being a sponsor at the welcome cocktail or at the gala dinner, which includes offering a welcome speech to the participants and displaying corporate material.
Although you can come by yourself, enjoying this event as a delegation will not only be more professionally enriching but also financially advantageous.
Benefits include the lowest rate being applied and simultaneous translation from English into your native language for 10 or more people registered for the professional programme.
EDA’s new Guide about Roles and Career Development in Demolition is finally out and openly available for consultation. The document aims to serve as a basis for developing training courses for the various roles involved in demolition activities.
The released document outlines their potential career paths, job descriptions and the educational and training requirements necessary to carry out these tasks safely and efficiently.
In addition, the guide is designed to serve as a foundation for developing training programmes in regions and countries where
the subject has not yet been fully developed. Moreover, it is intended to assist demolition and decontamination companies and organisations offering training courses within the sector by providing a comprehensive framework for professional development in the field.
The Guide about Roles and Career Development in Demolition was made by sharing knowledge in the EDA Working Group on
An ING report predicts that 2025 will be a good year for the European construction sector, which will experience a recovery thanks to positive indicators such as rising house prices.
It will be a slow process, but the sector will experience a 0.5% growth this year. A marginal growth that comes after a year of decline represents an optimistic sign.
In light of the report, several key points need to be addressed when analysing the cause of these good expectations:
• House prices are rising once more, which means that building new houses is now a more attractive proposition for project developers. Also, this enables them to cover the costs of increased building materials. The Netherlands is seen as the most attractive country
to buyers while Germany and Spain are lower on the list.
• The infrastructure approach to the economic cycle has improved, becoming more
resilient, especially by the investments made by local and central governments.
• Growth indicators in engineering developments.
The publication in November of the Study on technical requirements for the road approval of NonRoad Mobile Machinery brings good news for these machines in the European scenario.
The study, conducted by fka–TRL on behalf of the European Commission and presented during CECE’s November Technical Week, offers a crucial step for establishing a practicable framework for NRMM road approval. Take a look to the Study on Technical Requirements for the Road Approval of nonroad Mobile Machinery.
This means that the EU will adopt
common rules and regulations, as well as unify the national ones that are established in this term. A common set of rules and safety measures for harvesters and other non–road mobile machinery (NRMM) will be adopted by the EU.
Up until now, non-road mobile machinery has not had an EU-wide type approval system, with it being left to the member states to establish their own regulations. This has meant that there was no unified regulation, which caused an increase in costs in order for users to follow each state’s requirements.
EU Study on Technical Requirements for the Road Approval of non-road Mobile Machinery
op.europa.eu/en/ publication-detail/-/ publication/62061020-a23711ef-85f0-01aa75ed71a1
Addressing labour and skills shortages is one of the challenges for the European Union, with wide-ranging implications for its competitiveness, innovation capacity, and green and digital transitions.
Because of this, the EU Council has approved some conclusions and called on member states to prioritise training and education to tackle these shortages, especially by supporting individuals currently underrepresented in the labour market.
These efforts are seen as crucial for fostering sustainable and inclusive growth and also for strengthening social cohesion.
Driven by demographic changes, the increase in the demand for specialised skills, and poor working conditions, labour and skills shortages are on the rise in EU countries. Many working-age
Europeans remain economically inactive or underemployed, especially women, low-skilled workers, older workers, young people, ethnic minorities and persons with disabilities.
Bearing this in mind, the Council has urged member states to take concrete steps like providing targeted upskilling and reskilling programmes, eliminating barriers to labour market participation, or addressing the gender pay gap.
In addition, this call to action follows the European Commission’s publication of an action plan on labour and skills shortages on 20 March 2024. Employment and social affairs ministers have since debated the issue as part of the European Semester, underscoring the urgent need for coordinated efforts to ensure the EU workforce is prepared for future challenges.
The EDA plays an essential role in this. It is necessary to identify the main roles in demolition activities, their functions and the minimum education each should require.
The association Working Group on Education not only has been very useful to shed light on this regard but also in unifying the knowledge in the Guide about Roles and Career Development in Demolition.
Scott Laird has been a force in the demolition industry for decades, but his contributions were formally recognised when he was awarded the International Personality Award at the 2024 British Demolition Awards. A project manager and business development manager at Independence Demolition, Laird’s journey in the industry began by chance when his father’s construction company transitioned from fabrication to demolition.
Over the years, Laird has become known not only for his technical expertise but for his passion and dedication to the craft, mentoring younger generations and driving the industry forward.
In this Q&A, Laird reflects on his career, the evolution of demolition and what it means to receive this international recognition. He also shares insights on the challenges facing the industry today, from workforce shortages to safety and environmental responsibilities. Through his candid and heartfelt responses, Laird’s love for demolition and his unwavering commitment to the industry shine through.
What attracted you to the demolition industry, and what keeps you passionate about it? I came to the United States in 1980. I lived in Fort Worth, Texas, for about a year when I came here. My father
had a construction company in Northern California and I ended up going there to work with him. We were basically in the boilermakers; we did a lot of refinery work.
We had a client who we did some fabrication work for, and he came to us and said: “I need some buildings cleared off my property because I want to expand. Do you guys do demolition?” My dad had done some demolition in the past but never officially, but being the entrepreneur he was, he said: “Sure, we can do that.”
Lo and behold, we started to do that. We took those four buildings on, and then within six months of that, we were doing more demolition than fabrication. We ended up being a $15-million-a-year demolition company.
What was it like working with your father and learning the demolition trade from him? It was a great learning experience. I had no experience in demolition. Just because of who he was, my father became one of the best demolition guys I’d ever been around and have ever been around. He understood what it took and taught me what it took to be a demolition guy – that it’s not always just numbers and all that.
There’s a lot of feeling and a lot of understanding why a building’s going to fall. I started off as a labourer basically – a torch cutter, labour equipment operator – and learned the trade from the bottom up. I ended up sort of running his company, as he was semi-retired before we decided to part ways.
Demolition Hub is a proud member of the National Demolition Association
Can you tell me more about the challenges and rewards of transitioning from fabrication to demolition?
My father’s motto every day was “change the skyline.” If we change the skyline, we’ve done something well. We’ve moved a building, or we’ve taken a pile of scrap and moved it.
My passion is just the love of the industry. It’s understanding that every single task on every single day is different. And even sometimes those repetitive tasks are so rewarding because you know what you’re doing – if you’re doing precuts on a boiler, if you’re doing what they call a sit cut so something sits down properly, you know if you do it right, the building’s going to fall. You have overpowered this 20,000-tonne structure, or whatever it is, by your knowledge and by numbers.
How did you develop your expertise in demolition? Did you have a specific project or mentor who helped you along the way?
When I started, we didn’t do engineering. My dad’s favourite thing is he would run out and mark an X on the ground and say: “The building’s going to fall right here, son,” and I would say: “How do you know that?” He would say: “I just know.” The passion for me is in understanding where that building’s going to go and understanding what you have to do to accomplish that. Understanding that, once it’s on the ground, what do you have to do to be profitable? What do you have to do to move the steel?
And then it builds from that to relationships. You need to talk to people about how you move that steel, who you’re selling it to, what size they want it, or you’re talking to a client who wants to save the concrete. Every single day, I wake up and my saying is: “You can’t be
in demolition if you don’t love it.” Demolition is not easy. What we do is extremely difficult. What we do is extremely challenging. I’m in business development now; I’m not out in the field. I’m an office puke, as I call myself. But every day, even in the business development portion of this industry, I absolutely love it. I wonder who I’m going to talk to today, who may give me an opportunity to bid on their building, or who can I help in the demolition industry today.
Later today, I’ve got some calls with a couple of young men, high school students, who are here in Northern Colorado and are interested in finding out about demolition. I’m going to tell them what demolition is and what a great career it can be.
You’ve mentioned some big challenges in your career. What would you say was the most significant project that defined your career?
The guy who gave me my big break when I left my dad’s company was Trent Michaels. He let me take on a power plant. I’d never done a power plant, let alone a 100,000-tonne power plant. I had done some smaller stuff.
This gentleman gave me a chance to do the Moss Landing Power Plant, where, 40 feet from the boiler was the world’s largest marine mammal sanctuary in Monterey Bay. I would walk out of the boiler, walk out on at the low point there, and I could see whales breaching every single day.
Trent Michaels gave me a chance. I was learning on the go. I was taking what I had done in smaller portions of demolition and calling some friends who had done a little bit of demolition and then calling some people in NDA to get some help. Doing that job gave me confidence
and gave me the assurance. I finished that job with no injuries and no accidents. That made me think “OK, you can do this.”
What does being inducted into the British Demolition Awards Hall of Fame mean to you, and how did you feel when you received the news?
I got a LinkedIn message from Ben Chambers. I’m not a big LinkedIn guy; I don’t do a lot of checking on LinkedIn and stuff like that, but I got an email and I’m like: “What’s this?” It was a Friday afternoon and I clicked on it and, I’ll be very honest, I broke down. I burst into tears. I could not believe that somebody within our industry had seen the love, passion and value I bring. I was shocked, humbled and honoured.
I called Ben and I’m sure he wasn’t happy – it was probably close to midnight for him. I said: “Ben, there are 50 other people who deserve this more than I do.” He told me my service to demolition represents what the demolition industry is, especially what I had done for the NDA coming out of Covid-19 when we had to cancel. I was the convention chair following the worst thing that could ever happen. But Covid was not going to beat me, because we don’t allow anybody to beat us in the demolition industry. I went to Scott Homrich and said: “Listen, I want to be the convention chair. I know it’s your choice but if you consider me, I guarantee that you will get a return on your investment.”
He appointed me as convention chair. I got a bunch of the people back from New Orleans and had the best Convention Committee I could ever have. We went from being cancelled and postponed to going to the hardest place that we could ever have a convention in,
San Diego, where land is expensive, not available and everything costs two and a half times what it costs anywhere else to do. Just through pure love of NDA, we made it happen.
The morning we get there and we started laying it out, I was there with Tom Kephart in this field, and we both look down, and there’s a rattlesnake. The day before we started setup, they had a year’s worth of rain in one night in San Diego. That was bad enough. We ran out there and we got equipment stuck. We did all these things. Then we’re standing there and we’re like: “Oh my God, that’s a snake. That’s a real snake.” We killed the snake, but then what’s that challenge? We have to now go out and get the international sign for rattlesnakes to post up because we had people from out of the country there.
In my career and in being a volunteer, I’ve never been so proud of so many people who worked so hard to make that happen. I really, truly believe if we had failed and it hadn’t happened, I think the Live DEMOlition Event would have gone away. Since then, we’ve had amazing people who have come behind me,
like Karsten Pawlik and Jeff Sessler. These people are just absolutely superstars now and they’ve taken the playbook and expanded it to places that we hope will keep moving us forward. I’m so looking forward to what Andrew DiBiase is going to do in New Orleans.
When did you start getting involved with NDA?
Probably 25 years ago, but I took a long time off when I was working for another company. That was when I was general superintendent and they unfortunately didn’t see the value in me attending NDA.
When I was at my dad’s company, I pushed membership and went through his company. I dug deeply into NDA the year after Austin. Independence Demolition was a member, but they didn’t really participate. I convinced my boss at that time that it was good for us to be part of it.
The first convention we all really attended was Austin. Andrew DiBiase put on the first Live DEMOlition Event. There was horrendous rain, and he did an amazing job. One of my very good friends and mentors, Greg Menen, took over
and did Denver. Denver was right after Austin and that was a perfect fit for me at that time because I’m right here. I could be his guy on the ground. My real participation started in Denver around six years ago. The rest is history.
Our biggest challenge is the workforce. That’s why I’m having this conversation with the high schoolers this afternoon. If people get into this industry and put in the effort, you learn more things than you’ll ever learn.
We’re not knuckle draggers with big hammers that break things any more. It’s very technical. Engineering is extremely involved now. We’re very technologically advanced and advancing every day.
We have to attract the younger people. Leonard Cherry said something at that Denver convention that stuck with me forever. He said that whatever you put into NDA and the demolition industry, you get back tenfold. I’m living proof of that. If we can get the younger people excited about it and bring them in, I think we’re moving in the right direction. Obviously, safety is also extremely important and we have to work every single day and work harder than the day we did before to make sure it remains a priority. Industry accidents have got to stop. It’s better than it was but it’s nowhere near where it needs to be.
I think the other challenge is just being a steward of this world. We need to know about recycling; we need to know about the environment; we need to also know about the people. Mental health doesn’t get talked about enough but there are a lot of mental health issues within our industry.
Nestled amid the tranquil surroundings of Weston, Florida, the Bonaventure Resort and Spa once stood as a beacon of luxury and leisure. However, when the pandemic swept through the hospitality industry, the resort faced challenges that ultimately led to its closure in April 2022. The closure marked the end of an era but also paved the way for a new beginning.
Gables Properties of Atlanta/ Gables Residential planned to breathe new life into the property by developing a luxury apartment home community. However, before construction could begin, the existing structures of the Bonaventure Resort and Spa had to be carefully dismantled and cleared – a task that required the expertise of a demolition contractor capable of navigating the intricacies of such a significant project in a residential setting.
The right partner
In the search for a demolition contractor, Gables Properties of Atlanta/Gables Residential embarked on a meticulous selection process.
Among the contenders, NDA member Rapid Removal emerged as the clear choice, thanks to its proven track record of managing large-scale projects with precision and efficiency.
Time was of the essence and Rapid Removal was able to deploy its specialised demolition assets and crew to complete the job under the budgeted project duration. The project not only required specialised demolition expertise but also the ability to perform heavy demolition in a residential neighbourhood without disturbing the neighbours.
The demolition strategy
With the project greenlit, Rapid Removal wasted no time in mobilising its resources. On 12 December 2023 the demolition
operation commenced – a carefully choreographed dance of heavy machinery and skilled labour.
Dividing the property into manageable sections, Rapid Removal deployed specialised crews to systematically dismantle the structures, working from east to west.
“The buildings were spread out over a 23-acre property,” says James Carpenter Jr., Vice President and owner of Rapid Removal.
“Logistics and coordination with all assets on the project were instrumental to maximising production. Congregating the assets too closely together created congestion and slowed production. However, spreading the assets too far away made dust control and trucking more difficult to manage.”
Rapid Removal’s process involved dividing the total team into crews. Crew 1 worked on the four-storey structures that surrounded the property, working from east to
a proud
west. Crew 2 worked on the singlestorey spa and conference centre that were in the centre of the property, working east to west. Crew 3 followed behind the four-storey wrecking team to demolish and process the concrete slabs. Crew 4 followed behind the Crew 2 wrecking team, demolishing the concrete slabs and processing the concrete as well.
There were also crews assigned to move and sort debris to maximise recycling on the job.
One of the primary challenges encountered was the protection of the existing trees within the property. With stringent demolition permits in place, Rapid Removal had to devise innovative strategies to ensure minimal disruption to the surrounding greenery while maintaining progress on the demolition.
“The demolition permit was issued with some limiting restrictions: the landscape permit was not issued at the same time as demolition,” Carpenter says. “We were restricted to only demoing trees and vegetation within 10 feet of the structures.
In several cases, trees had to remain in places that were within five feet of four-storey structures. The technical ability of our team to drop these structures efficiently without damaging adjacent trees proved to be a key element in progressing the job on time.”
Carpenter continues: “Tree protection during demolition was at first a large limiting step. At times, this impacted demolition means and methods as well as hauling routes within the job site. However, we devised a plan in which we were able to mitigate
tree damage while performing the demolition in an efficient manner.”
Over the course of 96 days, Rapid Removal’s dedicated team worked tirelessly to complete the demolition project. Despite the scale of the endeavour, the crew remained focused on two key objectives: efficiency and sustainability. By prioritising recycling and onsite processing, Rapid Removal was able to minimise waste and reduce the environmental impact of the demolition. In total, 1m kg of steel were recycled and approximately 50,000 tonnes of concrete were repurposed, which truly showed the company’s dedication to sustainable practices.
Throughout the demolition process, Rapid Removal encountered various challenges, from logistical hurdles to regulatory requirements. However, its ability to adapt and innovate ensured that the project remained on track. By fostering open communication with stakeholders and prioritising safety at every stage, Rapid Removal not only met but exceeded expectations.
“Our number one priority is not only the safety of our team but also the safety of the general public,”
Carpenter says. “We completed the project safely, with no incidents. In addition, the project was completed in less time than the budgeted project duration. There were no complaints registered from the residents from the surrounding neighbourhood, nor were there any code violations or other violations issued by the municipality where the project took place.”
by Liz Whisler, Vice President of Leadership Development at The Workplace Advisors
Feedback is more than just a performance review tool; it’s a gateway to foster communication and trust within an organisation. Offering insights into both strengths and areas for improvement can empower employees to enhance their performance and reach their full potential. When managers provide
thoughtful, supportive feedback aimed at helping team members improve their work performance, they not only elevate morale but also strengthen team relationships.
Feedback as a gift Leaders should reframe their approach to feedback and
recognise that holding back on feedback deprives team members of valuable growth opportunities.
To overcome hesitation in providing feedback, start by acknowledging its importance in professional development. Most employees want feedback to improve their performance. Viewing feedback as a collaborative process rather than a one-way critique can make the experience more positive for both parties.
Constructive feedback aims to improve performance or behaviours. It allows employees to learn, grow and develop their skills in a supportive environment. Positive feedback identifies an employee’s strengths and accomplishments. It’s crucial for boosting morale and helping team members recognise where they excel. Often, managers provide a mix of positive and constructive feedback to give employees a holistic view of their performance.
One note of caution when considering feedback: Those ubiquitous “great job” or “atta girl/ boy” comments are often mistaken for positive feedback. While they may feel positive, this form of feedback is largely received longterm as insignificant, meaning it lacks
specificity and thereby does little to either reinforce positive behaviour or correct ineffective or poor behaviour. If you find yourself giving this sort of “great job” kind of feedback, take it a step or two further by specifying what behaviours you think are great and why they matter.
Timeliness is crucial. Providing input as close to the event as possible ensures that details are fresh and allows for prompt addressing of issues before they escalate.
Implementing quick, informal feedback sessions, such as brief daily check-ins, can be an effective way to maintain open lines of communication.
Be specific when providing feedback, using concrete examples and observable behaviours rather than generalisations to help employees understand exactly what they’re doing well or areas where they need to improve.
Solution-oriented feedback is more likely to lead to positive
change. Instead of simply pointing out problems, offer actionable suggestions for improvement and collaborate with the employee to develop an improvement plan.
We recommend using a goalsetting framework like SMART (Specific, Measurable, Achievable, Relevant, Time-bound) to structure these improvement plans effectively.
To truly harness the power of feedback, organisations must create a culture where it’s valued and actively sought. This starts with leadership setting the example by actively seeking feedback from their teams. Encouraging peerto-peer feedback can foster a more collaborative environment where learning and improvement are ongoing processes.
Integrating feedback into regular work processes, rather than reserving it only for annual reviews, helps create a culture of continuous improvement. And celebrating improvements made from received
“To truly harness the power of feedback, organisations must create a culture where it’s valued and actively sought”
feedback reinforces its value and encourages ongoing engagement with the feedback process.
Implementing a 360-degree feedback system can provide a more comprehensive view of employee performance and encourage multidirectional feedback. This approach helps create a more holistic understanding of each team member’s strengths and areas for growth.
Remember, feedback is indeed a gift – one that keeps on giving in the form of enhanced performance, stronger relationships and a more dynamic, successful organisation. Use these techniques to master effective practices in your organisation.
Since being established in 2012, Romax Solutions has set a high standard when it comes to recruitment. Finding the best candidates is our driven desire and passion, we aim to meet the recruitment needs of a diverse range of clients within the construction industry. Being based just outside of London gives us easy access to service all clients throughout Essex, London, Kent and surrounding areas while also having the capabilities to support and service nationwide projects and clients.
With a depth of knowledge, our experienced and trusted staff are on hand to deliver a bespoke service to each and every client, supplying reliable and talented staff of all levels both nationally and locally. Romax Solutions
is fully accredited by the Recruitment and Employment Confederation and the National Federation of Demolition Contractors. These accreditations have enabled us to work alongside other NFDC members to meet their scope of needs on multiple projects. These projects range from small scale strip outs to large scale power station decommissions.
We are also always keen to add new talent to our current pool of candidates nationwide. These include those from management level downwards, including skilled demolition operatives and even those just starting out their demolition careers. We work effortlessly to ensure all candidates are fit for purpose, including using accredited training providers to upskill our operatives.
(Cat B Non-licensed asbestos removal)
Wandsworth, south-west London
Role: CCDO Operative with Cat B, for demolition works
Rate: £17 – £19 p/h
Requirements:
• CCDO Green/Red qualification
• Cat B Non-licensed asbestos removal
• Full PPE
• Minimum of two years’ experience in demolition
• Good timekeeping and willingness to work
What we offer:
• Ability to work through CIS / self-employed
• Weekly payments
• Assistance in regard to progression within construction
• Ongoing labourer work for the right candidate
For more information and to work on this project please contact the account manager of this specific job on 07557 196 353
Romax Solutions provides long term work for the right candidates depending on reliability and willingness to work.
Role: CCDO Operatives, work involves demolition, soft strip, long term works.
Rate: £16 – £18 p/h
Requirements:
• CCDO Green/Red Card
• Full PPE
• Minimum of two years’ experience within construction as a CCDO
• Good timekeeping and willingness to work
What we offer:
• Ability to work through CIS / self-employed
• Weekly payments
• Assistance in regard to progression within construction
• Ongoing work for the right candidate
For more information and to work on this project please contact the account manager of this specific job on 07557 196 353
Role: 360 Operator (D90) required for a demolition breaking works
Rate: £21 – £22 p/h
Requirements:
• Blue CPCS (NVQ Level 2) + D90 ticket
• Full PPE
• Minimum of three years’ experience as a 360 Operator and in demolition
• Good timekeeping and willingness to work What we offer:
• Ability to work through CIS / self-employed
• Weekly payments
• Assistance in regard to progression within construction
• Ongoing work for the right candidate
For more information and to work on this project please contact the account manager of this specific job on 07557 196 353
Romax Solutions provides long term work for the right candidates depending on reliability and willingness to work.
Role: CCDO Burner for burning works taking down structural steel works
Rate: £20 – £22 p/h
Requirements:
• CCDO/ CSCS card
• Oxy Fuel Cutting qualification
• Full PPE
• Minimum of three years’ experience within construction as a CCDO Burner
• Good timekeeping and willingness to work
What we offer:
• Ability to work through CIS / self-employed
• Weekly payments
• Assistance in regard to progression within construction
• Ongoing labourer work for the right candidate
For more information and to work on this project please contact the account manager of this specific job on 07557 196 353