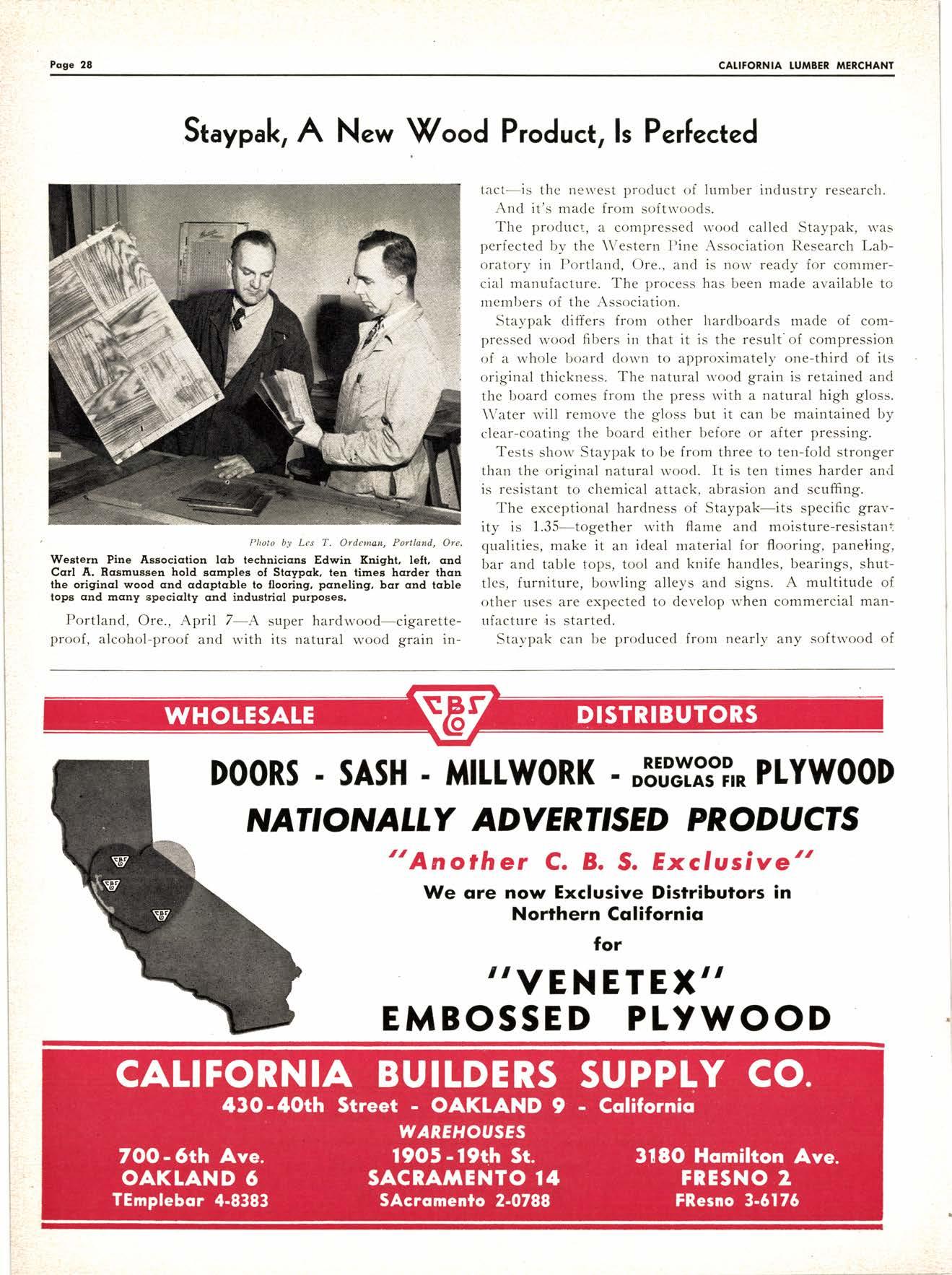
5 minute read
StaypaL, A N"w \(/ood Product, ls Pefiected
tact-is thc neu'est procluct of lumber industry research. And it's made from softu'oods.
The product, a compressecl wood called Staypak, u'as perfected by the Western I'ine Association Research Laboratory in Portland, Ore., and is no\\r ready for commercial manufacture. The process has been made available to members of the Association.
Staypak cliffers from other hardboards made of compressed wood fibers in that it is the result'of compression of a whole board dou'n to approximately one-third of its original thickness. The natural 'ivood grain is retained and the board comes from the press with a natural high gloss. \Vater rvill remove the gloss but it can be maintained by clear-coating the board either before or after pressing.
Tests shor,v Staypak to be from three to ten-fold stronger than the original natural rvood. It is ten times harder and is resistant to chemical attack, abrasion and scuffing.
Portland, Ore., April 7-A super hardtvood-cigaretteproof, alcohol-proof and with its natural wood grain in-
The exceptional hardness of Staypak-its specific gravity is 1.3S-together with flame and moisture-resistant qualities, make it an ideal material for flooring, paneling, bar and table tops, tool and knife handles, bearings, shuttles, furniture, bowling alleys and signs. A multitude of other uses are expected to develop when commercial mannfacture is started.
Staypak can be produced from nearly any softu'ood of low resin content. Experiments conducted with White Fir, a lumber species in plentiful supply throughout the rvestern states, have been outstandingly successful. Engelmann Spruce and Western Red Cedar can also be used.
Initial rvork on Staypak rvas done at the Forest Products Laboratory in Madison, Wis., but the problem of end and edge expansion after pressure had been removed prevented its economical manufacture. At this stage the project $'as taken on by the Western Pine lab where a press rvas ultimately developed to prevent the moisture loss during compression which caused the boards to later pick up atmospheric moisture and expand after release.
Lab engineers describe the process by 'ivhich Staypak is made as essentially one of compression and heat. A boarci subjected to a pressure of 1500 pounds per square inch at a temperature of 325 degrees Fahrenheit within the press. It remains there for a relatively short time.
No bonding agent is used to hold the board to its com-pressed size. The natural lignin in the wood flows under heat and acts as the cementing agent. Once pressed, the board will not'lose its shape under subsequent moisture or atmospheric conditions.
A piece of Staypak feels as hard and heavy as a smooth piece of slate. Any mark or design cut into the wood before pressing is still visible although not perceptible to the touch after processing. Designs may be impressed into the wood by applying resin-impregnated colored paper prior to pressing. The paper becomes part of Staypak in the press.and forms a continuous smooth surface with the rest of the piece.
But very probably the majority of manufacturers wrll prefer to market the product in its natural state. l'Manufacturers of other materials often try to make their products look like wood," a lab spokesman said. "We already have that appearance in Staypak-and we'd like it to stay that uray."
Staypak can be installed by gluing or rvith screws inserted through pre-bored holes. Metal-cutting or carbide tools are used to shape it. It has a stability far greater than any other natural wood, hard or soft. Staypak can be laid as flooring either in strips or like tile and can bc either stained or left natural. Although not fireproof, tests have demonstrated it to be extremely slow in kindling.
Staypak will act as an agent toward greater forest conservation, too, by furnishing another use for White Fir which occupies an increasing proportion of the nation's timber resources.
tilew Wholesqle Lumber Concern
Asher-Barker Corporation, fnc., wholesale lumber dealers, recently opened ofifices at 309-11 De Young Building, 690 Market Street, San Francisco 4. Their telephone number is YUkon 6-6330.
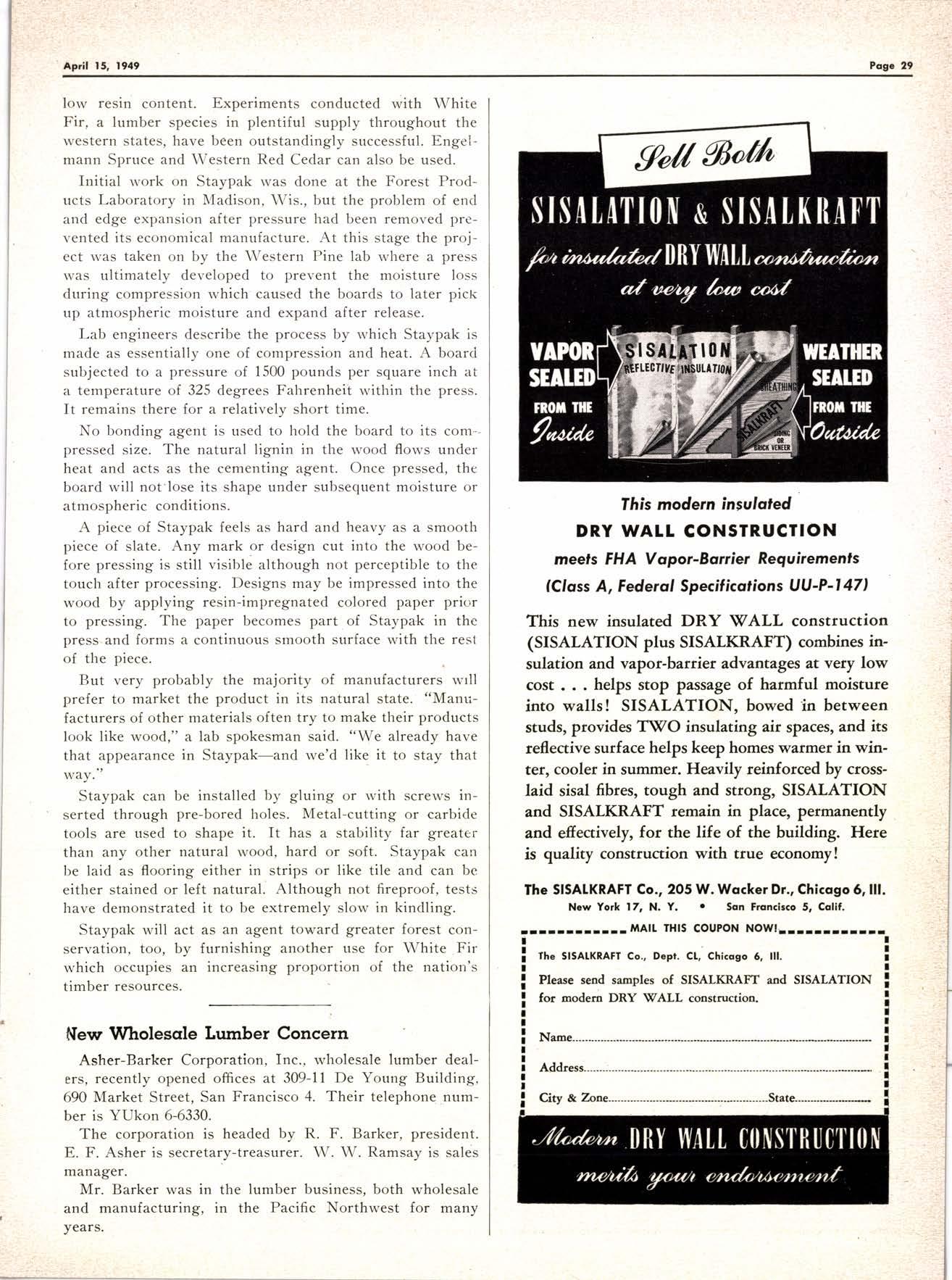
The corporation is headed by R. F. Barker, president. E. F. Asher is secretary-treasurer. W. W. Ramsay is sales manager.
Mr. Barker was in the lumber business. both wholesale and manufacturing, in the Pacific Northwest for many years.
This modern insuloted DRY WALI CONSTRUGTION rneets FHA Vopor-Borrier Requiremenfs (Closs A, Federal Specificofions UU-P-|47)
This new insulated DRY \$VALL construction (SISALATION plus SISALKRAFT) combines insulation and vapor-barriet advantages at vety low cost . helps stop passage of harmful moistute into walls! SISALATION, bowed ln between studs, provides T$fO insulating air spaces, and its reflective surface helps keep homes warmer in winter, cooler in summet. Heavily teinforced by crosslaid sisal fibres, tough and strong, SISALATION and SISALKRAFT remain in place, perinanently and efiectively, for the life of the building. Hete is quality construction with ttue economy!
The SISAIKRAFT Co., 205 W. Wqcker Dr., Chicogo 6,lll. Ncw York t7, N. Y. r Son Frunclrro 5, Colif. _r_----rr--- MAIL THIS COUPON NOWI-_-_--r-rr!r
! rm StSnxfAFt Go,, Depr. Cl, Chiccgo 6, lll. ! ll ! Please send samples of SISALKRAFT and SISALATION : ! for modern DRY VALL construction. i
Dinner at Eureka Honors Veteran Hammond Employees
A dinner at the Eureka Inn, Eureka, March 5, honored 60 employees of the Hammond Lumber Company, who have had 25 years or more service with the company.
Earl Birmingham, general manager of the Redwood Division, presented Hamilton gold wrist watches to each of the 60 veteran employees as a token of 25 years or more service. The total number who received watches was 169, made up as follows : Los Angeles, 100; Samoa and Eureka, 60; San Francisco office, 6; Portland office, 2; and Watsonville, 1.
George B. Mcleod, president of the Elammond Lumber Compbny, San Francisco, was present at the dinner.
The names of those who received watches in the Redwood Division are as follows:
Harry Sherman, Oscar B. Nordquist, James A. McArthur, Elmer E. Abrahamson, Wesley R. Dean, Frank B. Genzmer, Alvin L. Raines, Alfred M. Cabral, Patrick Kane, Edward G. Carter, Thomas B. Jordan, Edward J. Cox, llenry C. Domeyer, Ralph L. Hill, Cyrus L. Atwood, William L. Fredricks, Herm4n F. Heitman, August NI. Elam, Louis A. Bernier, Lloyd M. Snook, George D. Garvey, Robert A. Young, Henry Ohlendick, Pietro Frediani, Patrick Gallagher, Elmer H. Nordquist, Oscar E. Nelson, George A. Fisher, Filberto Carranco, William J. Early, Otto Johnson.
Oswald Anderson, Stanley Godden, Kenneth Cole, Andy Kovacovitch, Otto T. Nessier, Walter G. Rask, John Sta- nich, Joe Souza, Alexander Mason, Joe V. Gomes, Harvey Wiebke, Bartul Supe, Dewey Rimby, Stanley A. Hill, Jesse J. Brown, Mirko Crnich, Henry Eresberger, Ole I\I. Jordfald, John V. Malm, Oscar Siikarla, John P. Gallagher, Edrvard R. Marsh, Leonard Carlson, Manuel Rodrigues, Joseph N. Romero, Clarence P. Crocker, Dominick P. Vallerga, Pete F. Vallerga, Frank N. Jalonen.
Oregon Division (Portland Office)
W. H. Pancoast, H. C. Patton.
San Francisco Division
M. Ethel Emery, Anne M. Larkin, George B. Mcleod, S. Leonard Rea, W. S. Burnett, R. E. Caldwell, Homer Stewart (Watsonville).
President George B. Mcleod has 58 years' service, having joined the Hammond organization in 1891.
In the Redwood Division Robert A. Young started to work for Hammond in 1902; Harry Sherman began his service in 19O3, and Henry Ohlendick started in 1905.
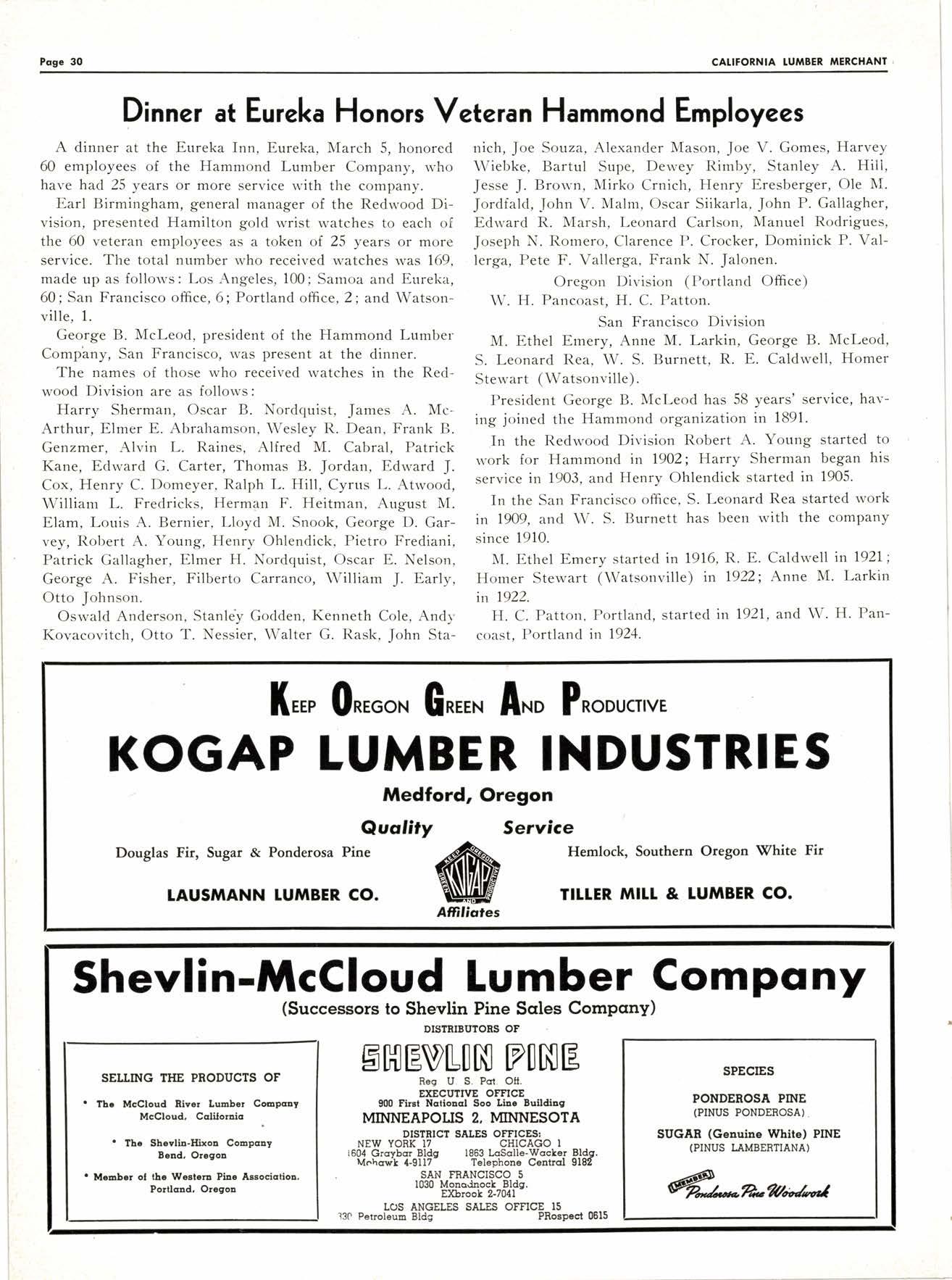
In the San Francisco office, S. Leonard Rea started work in 1909, and W. S. Burnett has been with the company since 1910.
M. Ethel Emery started in 1916, R. E. Caldwell in l92L; Homer Stewart (Watsonville) in l9Z2; Anne M. Larkin in 1922.
H. C. Patton, Portland, started in 192!, and W. H. Pancoast, Portland in 1924.
TILTER MItt & LUIVIBER CO.
Fir
Olympic Develops Labor Saving Device For Application of Sidewall Shakes
A simple but very useful device which makes the application of Olympic pre-stained Perfect Fit side'rvalls considerably easier, is the sidewall shake. This simple jack can be made on the job from a few undercourse shingles and a short piece of shiplap, and is very helpful as a platform for the Perfect Fits and the undercoursing. and elirninates the necessity of picking up from the ground or the staging each individual shake or shingle.