
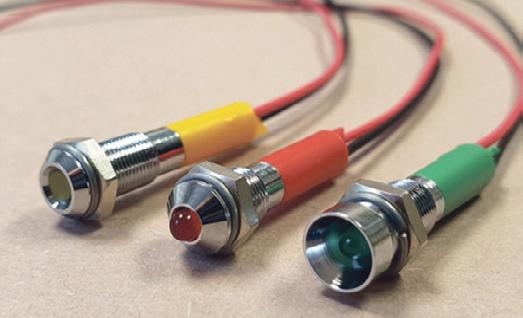
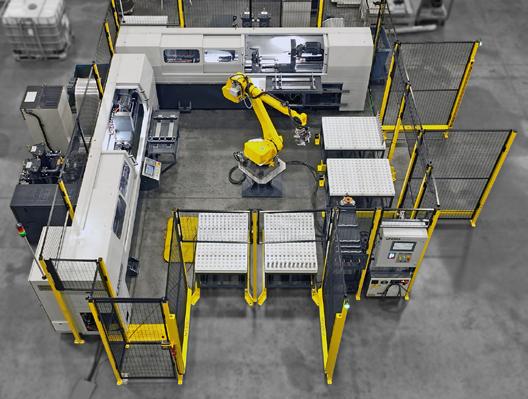
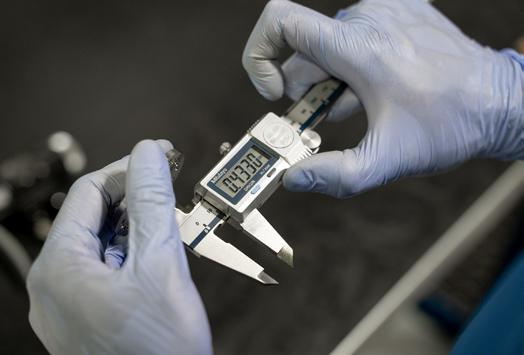
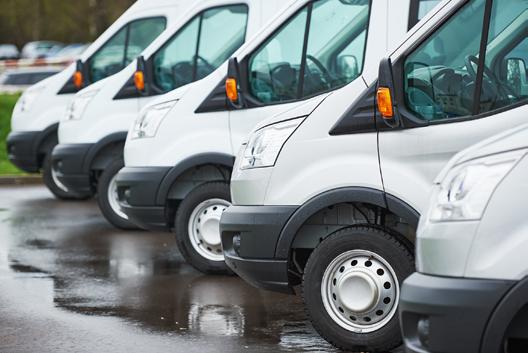
Gransden UK, formally known as Lock N Pop UK Ltd, is the sole UK and Ireland distributor of the Lock N Pop pallet stabilisation systems, primarily known for reducing plastic pallet wrap and enhancing pallet stabilisation. The UK based company has been supplying the Lock N Pop solution to customers across the industrial and food and beverage applications for over 25 years.
With the UK Government’s 2050 net-zero targets and a greater push towards the circular economy, all eyes are on sustainable best practices. With this in mind, Lock N Pop is seen as the sustainable solution of choice across the industry for the following reasons:
S Lock N Pop reduces the need for plastic pallet wrap
S Cost-effective under the new UK
CML IT continues to be the number one supplier of panel mount indicators, LED lamp replacements and LED
• Plastic and metal bezels with a wide range of options in stock.
• Development of custom solutions
• UK Manufacturing facility
• IPN40 and IP67 ratings
Plastic Tax (Plastic Packaging Tax PPT): introduced in April 2022
S The definitive environmentallyfriendly solution: Cold, waterbased and plastic-free
S Contains no hazardous, heated components or plastic consumables.
T 01728 726621 www.locknpop.co.uk
Gina Burton Editor
Welcome to our latest issue of Best Practice.
Multigrind Services Ltd is a leading specialist in precision grinding, and in this issue, we are pleased to feature them as our BP Spotlight Company. With an impressive history dating back to 1977, Multigrind has been offering a world-class service for nearly fifty years. In this article, we highlight the company’s industry-leading grinding capabilities as well as other notable services including the Extensive CNC Turning & Milling services like the Mazak Europe VCS 430A – offering world-leading precision. See them on page 7.
On page 22, we shine a spotlight on Abingdon Verification Instruments (AVi), a Test and Measurement company based in Oxfordshire specialising in the design and build of Automated Test Equipment (A.T.E.) solutions and general consultancy. We highlight the advantages of using their tailored A.T.E systems and AVi solutions designed to dramatically improve your product verification processes.
Publication Management
Thomas Reilly
Sales Manager
T 07539 070158 sales@bestpracticeuk.co.uk
Production
Robert Sharp
Production Manager production@businessandindustrytoday.co.uk
Accounts
Paul Whitaker
Accounts Manager T 0121 824 4742 accounts@bestpracticeuk.co.uk
Editorial
Gina Burton Editor gina@freshmedia-uk.co.uk
Other topics covered: Storage, Adhesives, Automation, Environmental, Air Control, Pumps, Oil & Gas, Business, Driver Safety & Deep Hole Drilling.
Have any news to share? Email: gina@bestpracticeuk.co.uk
In this issue of Best Practice, we are pleased to feature CML Innovative Technologies as our Lighting Technology Company of the Year.
Over the past decade, the United Kingdom has witnessed a significant decline in its manufacturing sector marking a substantial shift in the countrys economic landscape coupled with some of the recent additional pressures including those caused by global troubles there are still many positive reasons to remain optimistic.
CML IT has been designing and manufacturing lighting components and systems for over 90 years. We offer a wealth of experience of all types of lighting technologies in combination with advanced design capabilities. Our in-house test facilities and quality systems allow us to develop high quality solutions for a wide range of industries including Automotive, Medical and Aerospace Railroad and general Industry applications such as electrical control panels.
Our 3D CAD system incorporates highly advanced, interactive optical simulation software. This allows our Design Engineers to design, analyse, modify and optimise within a single CAD environment. Electronic designs are simulated prior to PCB design and layout. CML IT has extensive experience of designing LED driver circuits including microcontroller control of advanced functions such as dimming and colour mixing. Many of our designs have undergone rigorous EMC testing for use in the aerospace sector.
With Supply chains globally likely to face further uncertainty and undoubtably
A Grupo Antolin Company
pressurised with continued increases in costs of freight and distribution during 2025, there is once again a visible push to re shore or close sure manufacture or source product where possible. CML are focused and committed in association together with our authorised distribution partners to holding suitable levels of stock and to work ever closely with direct customers with planning and scheduling departments to help ensure continued supply making sure production lines are not put at risk.
After a highly successful year of New Product Introduction in 2024, the next 12 month looks set to be another bumper year of innovation with high levels of
expectation and saturation of product release. A new range of highly durable and well tested panel indicators with an expected release of some 260 SKUs have been initiated for high performance sealed both front facing as well as the rear for to achieve an IP67 standard. Withstanding high vibration and manufactured from a high grade of stainless steel helps make them ideal in demanding application areas such as construction, military, marine environments and also opening up new application possibilities including the ever growing food processing industry.
The new product introductions to be offered complement the existing product ranges perfectly, the general ranges allows for many customisation possibilities such as sealing arrangements, harness and cable options, wires and colour options and finishes of bezels, bespoke part numbering and marking options and of course as usual the options of colour illumination, our commitment to customisation has proven extremely popular and is another area of continued focus going forward.
T +44 (0)1284 714700 uksales@cml-it.com https://cml-it.com/en
The UNISIG 4-Spindle Gundrilling Cell with flexible automation simplifies rapid parts gundrilling. This system employs two UNISIG UNE20-21000-CR dual-spindle gundrilling machines, enabling 4x drilling of one part or 2x drilling of two different parts quickly and efficiently. These machines can drill up to 20mm diameter holes to a maximum depth of 1,000mm, while counter-rotating the workpiece for maximized hole concentricity.
In this cell, a 6-axis robot picks two parts at once to load or unload, utilizing dual parts staging stations to maximize spindle uptime. Laser verification technology assists the robot’s use of dual sets of pallets. UNISIG’s Automated Cell Controller (ACC) centralizes the controls for both machines, and a moveable inspection station allows for on-call part inspection. Variations of this manufacturing cell can be configured as needed.
The versatile UNE standard gundrilling machines balance highperformance components with a lower overall investment, making it easy for machine shops to bring their deep hole drilling operations in-house. Machine models have maximum drilling diameters ranging from 12 to 40mm and depths up to
meters, with the horsepower and coolant control to efficiently run indexable, brazed or solid carbide gundrills.
Twin spindle UNE machines can be configured as independent spindles,
allowing two drilling operations to be run on a single machine. Available counter-rotation of cylindrical workpieces minimizes hole drift and ensures drilling accuracy. Engineered for automation, these precision deep hole drilling machines bring next-level productivity to any shop floor. UNISIG UNE manufacturing cells with flexible automation combine precision, repeatability, and reliability for an unbeatable machining resource.
UNISIG applies decades of engineering expertise to create deep hole drilling solutions specific to its customers’ requirements. Browse: www.unisig.com to learn more about the realm of possibilities.
Link: https://unisig.com/news-andevents/technical-articles/gundrillingcell-with-flexible-automation
Further information on all machines of the UNE series and the complete UNISIG machine program is available at: www.unisig.de or follow the company on LinkedIn and Twitter (@UNISIG).
In this issue of Best Practice, we are delighted to feature Multigrind Services Ltd as our BP Spotlight Company.
Distinguished background
Multigrind Services Ltd is a leading specialist in precision grinding, through the complete manufacturing of parts and sub-assemblies: offering complete end-to-end solutions package including a subcontract grinding service in ferrous and non-ferrous metals and engineering plastics. Based in Rickmansworth, Hertfordshire, the company was established back in 1977 and now serves a customer base across the UK and further afield with a renowned ‘complete manufacturing package’ for niche and specialist work.
Next-level machinery
The state-of-the-art 10,000 sq. ft. facility is expertly equipped with over 30 advanced machines, including 13 CNC Lathes, 3 CNC Milling Machines, 4 CNC grinding machines along with numerous manual machines, built to deliver precise internal and external machining, including grinding, with tolerances down to 0.001mm. The manufacturer can deliver components from 1mm to 500mm in size, up to 1,500mm length on a ‘make complete’ or ‘grind only’ basis. The latest CAD/CAM technology ensures perfect accuracy every time, translating drawings
and 3D models directly into the machines. Furthermore, the ‘lights out’ production delivers impressive round-the-clock manufacturing.
Growing customer base
With an impressive history dating back to 1977, Multigrind has been offering a world-class service for nearly fifty years, with its unparalleled complete package service. From small batch work to one-off prototypes, to date, Multigrind has completed over 65,000 projects, working with over 1,269 clients, offering industry-leading solutions.
The growing diverse customer base stretches across many applications such as: aerospace, defence, oil & gas, automotive, motorsport (including Formula 1), food/scientific, medical and many others.
Complete package service
All equipment is maintained in strict accordance with their ISO 9001 QMS –for excellence every time, the complete package service includes the following:
S CNC Turning
S CNC Milling
S CNC Cylindrical Grinding
probing for close-tolerance results and a 4th axis for multiple operations in a single cycle, this machine is unbeaten in the field.
The range of Mazak Europe Quick Turn 250MSY’s have full C axis capabilities and the latest Smooth G controls enhanced by Hydrafeed Ltd Barfeeds.
Software innovation
S Centreless Grinding and Surface Grinding
S Various other services through supply chain partners including surface treatments/ plating, heat treatment, nondestructive testing (NDT), electrical discharge machining (EDM) and welding among others.
Meeting strict tolerances
Multigrind offers industry-leading grinding capabilities for all orders, from large volume to small batches. Since 1977, Multigrind has set itself apart from competitors, with meticulous measurements meeting the strictest tolerance requirements across stainless steel, aluminium, copper and plastics to name a few.
Unbeaten efficiency
Other notable services include the Extensive CNC Turning & Milling services, like the Mazak Europe VCS 430Aoffering world-leading precision. With in-built Renishaw UK & Ireland
What’s more, by investing in cutting-edge technology: PSL Datatrack Production Control software, Multigrind offers complete traceability at every stage. From the first quotation to last project dispatch, everything runs seamlessly. The software includes a fully functioning scheduling tool to optimise all manufacturing to meet delivery target dates, keeping customers happy every day.
Machinery maintenance and workers’ health
In the manufacturing sector, it’s important to take care of machinery to prolong longevity and reduce downtime. With many machines to manage, Multigrind invests in the best maintenance support.
For example, the large grinding machines in the facility create heat that quickly vaporises coolant. This runs the risk of oil mist entering the workshop atmosphere, causing hazards for workers.
With this in mind, Multigrind worked proactively with Oil Mist Filter experts: Filtermist International to employ The FiltermistXcel2 FX7000 large capacity oil mist filter to eliminate traces of oil mist in the air.
The Cincinnati 3EA is the largest centreless grinder on site, with capacity to grind a bar up to 150mm in diameter and 4m in length. The new FiltermistXcel2 FX7000 model brings next-level capacity, mitigating against the oil mist from the open-sided machine design.
By employing this level of maintenance expertise, Multigrind is prolonging machine life and simultaneously protecting its workers’ health.
If you’re interested in finding out more about Multigrind’s industry-leading services, please see below: T 01923 721011
must have policies and procedures to minimise risk – and that includes the recognised risks around driving. In the event of a serious incident, you could be asked to prove what you do to promote driver safety.
There are almost 40,000 injuries on Britain’s roads each year that involve someone who was driving for work.
Work-related road risk is the risk that an employee may be involved in a collision while driving for work, creating a risk to drivers and other road users. At its core, it’s about driver safety, but it can also put managers, directors and the organization itself at risk in the event of a serious crash, if they’re found to have not met their duty of care obligations.
If you want to ensure your employees are not part of the problem, or one of the casualties, it’s vital to set out the importance of driver safety – and the good practice standards you expect when your staff are driving for work.
Your organisation needs to do this for three reasons:
1) It’s the right thing to do. We all want our staff and other road users to get home to their families safe and well at the end of each day.
2) It makes good business sense. Poorly managed drivers will increase admin time, insurance costs, maintenance costs and fuel use. Good management brings improvements in all these areas and many more besides.
3) The law says you must do it. All companies
To communicate your commitment, and the required standards to drivers, you need a comprehensive, legally compliant and up-to-date driving for work policy.
What should be in the policy?
Your policy needs to include specific information in a concise and easy-tounderstand format.
Here’s a summary of what needs to be included.
A Policy Statement which explains to drivers why the policy exists and why it is important they follow it at all times. This should also include an authentic statement from a senior leader in the organisation explaining how important driver safety is and that absolutely everyone is included, from delivery drivers, right up to directors.
Before we even consider letting an employee drive for work, we need to check that they are eligible to do so, which means carrying out driver checks. We need to ensure that they have a valid driving licence and that the personal details they provided match those on file at DVLA. We need to know whether have any penalty points and whether they’re entitled to drive the class of vehicle we want them to.
Do they have an eyesight or medical condition that could affect their driving?
Do they have a history of collisions? And have they received appropriate training,
If you would like to know more, scan the QR code or please visit: www.drivingforbetterbusiness.com
When it comes to the transport industry, ever-changing legislation updates and DVSA regulations can be a real minefield for businesses of all sizes to stay on top of. If you’ve found yourself with a headache when it comes to managing your fleet effectively, you’re certainly not alone. At the end of the day it’s about safety you can have all the rules and legislations that you need but managing your fleet and your drivers safely is the priority. CheckedSafe, celebrating 10 years has the toolkit in place to help you manage all this through one unique platform. Gathering data via the award winning app to then fully managing via the back office platform. Using CheckedSafe to its fullest we can guarantee a compliant paperless solution managed in realtime.
1) Daily Pre-Use Check, Preventative Maintenance and Fleet Management Managing commercial vehicle fleets (including Grey Fleet Vehicles) comes with the legal responsibility of conducting regular checks to ensure vehicle safety and roadworthiness. We can supply you with the full toolkit from bespoke daily checks to full PMI’s, Schedules, we are also an Earned Recognition supplier (we can provide templates for ANY vehicle/ plant or machinery)
2) Verifying Driver Licences
We provide a full Driver Licence (DVLA) check service inc. DCPC and Tacho card checks all fully remote via our App our unique process that has been audited by DVLA can provide you the full remote package, If you have staff driving for work in company or private vehicles you are duty bound to ensure they licenced and fit to drive.
3) Fatigue Management (GB Domestic Hours) Do you manage driver fatigue? Are you
using Driver Hours Log Books? CheckedSafe have developed via the award winning app a GB Drivers Hours Module capable of capturing live data and reporting on such data including exception reporting no need to wait for you driver to hand in his book weekly it’s on the desktop and the driver can have a copy on his phone if anyone wishes to see the log book at any time, its real-time dynamic reporting so aside from complying with the GB Domestic Rules the system will assist you in managing driver fatigue as you can see in real-time the user driving/working hours daily.
Are you intrigued and looking for cuttingedge and innovative commercial fleet management solutions? Get in touch! T 01282 908429 info@checkedsafe.com www.checkedsafe.com
Rainbow Dynamics, the UK-based developer and manufacturer of robotic and automated materials handling solutions, has announced the appointment of Keith Gallant as its General Manager for the USA and Canada (pictured).
In his new role, Keith will be responsible for identifying growth opportunities and fostering the strategic partnerships that will enable Rainbow Dynamics to expand its presence within the US and Canadian intralogistics markets.
Prior to joining Rainbow Dynamics, Keith Gallant held a senior sales and marketing position with Dorabot – a robotics systems integrator. His CV also features Arobotic X, a company that represents manufacturers of a broad range of automation and robotics technology. The time spent at these two organisations has given Keith a unique insight into the logistics robotics sales process and the interplay between system integrators and OEMs.
His extensive experience and expertise includes the design and implementation of pallet and case-level AS/RS solutions, automated guided vehicles and robotic pick, pack and palletising applications for clients operating within diverse industry sectors. Keith Gallant’s appointment comes at an
exciting time for Rainbow Dynamics as the company continues to enhance its technology and product offerings and grow its global presence.
Rainbow Dynamics’ founder and CEO, Alfred Chen, commented, “I am thrilled to welcome Keith to the Rainbow Dynamics team. The USA and Canada play a pivotal role in our forecast growth trajectory and, with his proven track record in driving sustainable business development and spearheading commercial strategies, Keith Gallant a perfect fit.”
recent report by Texas-based SNS Insider forecasts that the US logistics automation and robotics market will be worth US $ 33.08 billion by 2032. According to the SNS Insider study, the growth is being fuelled by the increase in online shopping which is now thought to account for some 22% of US retail sales.
Keith Gallant said, “This is an incredible opportunity, and I am very excited to join Rainbow Dynamics at a time when the company’s growth is accelerating. My highest priority is to encourage open lines of communication between Rainbow Dynamics and its channel partners to ensure that the partners feel well-supported, respected and appreciated.”
There is huge demand among logistics companies across Canada and the USA for technology that will help improve the efficiency of their supply chain. Indeed, a
At Go True North, we specialise in helping organisations unlock their potential. We achieve this through Lean Innovation and Operational Excellence. By applying Lean Process Improvement principles, we streamline operations, reduce waste, and foster continuous improvement.
Whether you’re ready to take the next step in your business journey, transform your business or simply have a question, we’re here to help. Connecting with you is what drives us – so don’t hesitate to reach out.
Please visit gotruenorth.uk
Prefer to chat? Reach us directly at +44 (0)7488 899506 during our UK business hours.
“With consumers demanding next or even same-day delivery of their order, ecommerce retailers are under growing pressure to provide ultra-fast order fulfilment. As a result, investment in automation and robotics is now regarded as essential for any company looking to improve warehouse functions and boost order processing efficiency.” Keith Gallant added.
With its head office in the UK, Rainbow Dynamics offers a suite of agile robotic load handing solutions for logistics warehouses, manufacturing sites and e-commerce fulfilment centres.
https://rainbow-dynamics.ai
At Go True North we believe that efficiency is key to success. Drawing from our extensive experience in lean methodologies, we help businesses streamline operations, reduce waste, and achieve sustainable growth.
Lean efficiency in action
Recently, we worked in the water industry with a Regional Water Company. By applying lean principles, we improved their maintenance delivery, resulting in an increase in efficiency and 10% maintenance contract cost reduction.
Your path to success
Ready to optimise your operations?
Let’s work together to make lean efficiency the cornerstone of your business success. Visit our website or contact us today for a consultation.
T 07943 448605
neil.betts@gotruenorth.uk https://gotruenorth.uk
Nitrogen Oxides (NOx) are chief villains in the battle for climate control; belonging to a family of gases that are formed during the combustion of fossil fuels. When Nitric Oxide (NO) reacts with other gases, for example with Ozone, it forms Nitrogen Dioxide (NO2), which is considered highly toxic to human health.
The reaction with Ozone is also an indicator for why Nitric Oxide (NO) is considered a climate active gas, that interacts with Earth’s protective Ozone layer. Human exposure to high levels of Nitrogen Dioxide (NO2), but also Nitric Oxide (NO) can cause airway inflammation, susceptibility to allergens and exacerbate preexisting lung or heart conditions.
Nitric Oxide (NO) is a biological marker of inflammation and is also produced by cells involved in the inflammation process. It is typically used to diagnose allergic/eosinophilic asthma. Legal ambient air limit value (annual average value for the European Union) for Nitrogen Dioxide (NO2) concentrations is 40µg/m³. Maximum occupational exposure1 limit is 950µg/m³. Indoor air limit value for maximum exposure is 250µg/m³ but the precautionary value 80µg/m³. The WHO defines 40µg/m³ as precaution limit.
The Department for Environment, Food & Rural affairs (DEFRA) has also reported soil chemistry and biodiversity changes across many UK habitats, through gas (dry deposition) and precipitation (wet deposition.) Anthropogenic Nitrogen Oxides (NOx) influence tropospheric chemistry, which directly cause photochemical smog and concentrated levels of urban ozone.
ECO PHYSICS AG offer worldleading measurements of Nitrogen Oxide (NOx), through trailblazing chemiluminescence analysers. These innovative analytical solutions are unprecedented in speed and sensitivity, with a cutting-edge range of sensitivities from 1% down to 1 ppt (part per trillion). Chemiluminescence Analysers use a unique thermally-stabilised semiconductor photodiode, to measure light intensity produced by reactions between Nitric Oxide (NO) with Ozone (O3). The light intensity correlates to the proportion of Nitric Oxide (NOx) converted to Nitrogen Dioxide (NO2) by the reaction.
We caught up with Dr Grischa Peter Feuersänger, Head of Sales & Marketing, to find out more about ECO PHYSICS, “ECO PHYSICS was founded in 1990
through a management buyout, by co-founders Dr Matthias Kutter and Dr Werner Moser and we now operate from our base in Duernten, Switzerland. We offer innovative analytical solutions for measurement tasks in the fields of environment, health and process control. With our interdisciplinary research and development team, we are delivering customeroriented and tailor-made products and services. The initial know-how focus was centred on the principle of the chemiluminescence, thus developing and manufacturing analysers for the ambient pollution and emissions. We have
perfected analytical technique in speed and sensitivity. Today we are proud to claim world leadership in the fastest and most sensitive chemiluminescence analysers and the broadest commercially available range.”
This Swiss-based innovative company has EN ISO 9001: 2015 quality management and EN ISO 13485: 2016 medical devicescompliance, offering quality assurance to customers across many industries. There is a new range of gas analysers and boxed set gas analysers available: nCLD AL, nCLD AL2, nCLD AL3/8555, nCLD EL and nCLD EL2.
The nCLD AL3/8555 is a nextgenerational modular gas analyser, offering state-of-the-art simultaneous measurements of NO, NO2, NOx, NH3 and NOxAmines. Even lower detection limits can be detected through the newly designed reaction chamber, enhanced gas flow paths, improved pressure and temperature stability. This analyser is adaptable to non-standardised applications, with the unit calibration running smoothly on an automated basis.
Contact T +41 55 220 22 22 info@ecophysics.com www.ecophysics.com
Borger has launched a new cuttingbasket macerator that helps protect pumps and downstream equipment by consistently mashing solids.
Designed with pivoted cutting blades that adjust automatically, the OrbitGrinder operates at an even cutting speed, with its cutting basket’s blades arranged in a special star shape to maximise shredding.
Not only is flow through the OrbitGrinder’s cutting basket homogenous, but the baffle plate also ensures that the suction force of the pump is evenly distributed.
Compared to standard, round perforated disks, the circumferential speed of the Orbitgrinder’s blades is the same in every cutting point, delivering uniform macerating results. Macerators with round perforated disks also typically see excessive wear of the cutting plates’ outer edge, whereas the OrbitGrinder’s
design and durability provides a significantly prolonged service life.
The OrbitGrinder’s simple inlet and outlet can be positioned at different angles to suit, and with the top and bottom parts connected by standard screws, this highly effective new macerator can be easily integrated into any existing system.
As with all proven Borger equipment, the MaintenanceIn-Place design makes servicing much easier than laborious alternatives.
The OrbitGrinder benefits from a gas strut assisted quick-release cover. Impurities are sent into the debris collector.
Contact https://www.boerger.com/en_UK
Impact was asked to provide a welding and fettling extraction system for a British multinational consumer packaged goods company. The goal was to ensure the safety and protection of employees during the fabrication and repair of stainless-steel items. To meet this need, a comprehensive solution was designed, supplied, and installed.
An Impact 1,500x1,000mm downdraught bench was installed to effectively control airborne particulates generated during fettling processes. This bench also includes a containment bin to collect heavier particles and grindings, ensuring a clean and safe working environment.
Additionally, an Impact 2,000x1,000mm downdraught bench was provided for welding applications. This table is open on all four sides, offering excellent accessibility. The extraction outlet spigot can be positioned on either the right or left side to suit user requirements, and the table is equipped
with mild steel slats designed specifically for welding processes.
To enhance the system’s filtration capacity, an Impact ACF-T 130H cyclonic filter was installed. This unit combines cyclonic and cartridge filter technologies with a fully automatic compressed air cleaning system. It features a 72L dust collection bin and flame-resistant G105 cellulose/ polyester filter cartridges. The equipment is finished with a powdercoated enamel coating for durability and includes an 11kW backwardcurved centrifugal fan housed in an acoustic enclosure to minimise noise levels.
The system was commissioned by one of Impact’s P601/P604certified technicians, ensuring it met the required standards. Full documentation and a
commissioning report were issued in accordance with HSG 258 – Controlling Airborne Contaminants at Work. This installation highlights Impact’s commitment to delivering efficient, safe, and regulation-compliant systems for industrial applications.
You have a responsibility to protect your team, for your tailored solution, contact Impact’s technical sales team at: 0116 2448855 or email: enquiries@impactts.co.uk.
Bluewater, a world leader in innovative water purification and beverage solutions, has launched its innovative solution for highquality drinking water dispensers in the UK, the Bluewater Flow.
Already a smash hit in the USA with over 14,000 installations, the Bluewater Flow sets a new standard across the UK and Ireland for dispensing ondemand pure, greattasting water in offices, gyms, hospitals, and
schools that is free from potential contaminants such as toxic PFAS chemicals or waterborne germs.
The self-sanitising, free-standing Bluewater Flow indoor refill stations are designed for simple installation and connect to any potable water line within a 100 foot range for easy replacement of existing water fountains, water coolers, and large jug dispensers. Users can enjoy chilled or hot fast-flowing water that undergoes a revitalising process including the infusion of electrolytes, increased alkalinity, oxygenation, and trace minerals, providing a crisp, fresh, great-tasting hydration experience.
found in typical tap water. Offering reliable and eco-friendly access to clean water, the Bluewater Flow is a top seller in the United States at premium brands such as Red Bull, Apple, Marriott, and Google.
Bluewater key account sales manager Antonio Tedeschi describes the Bluewater Flow indoor station as ‘a game-changer for the UK and Ireland’s drinking water dispenser industry.’
Bluewater Flow 7 x Advanced Purification uses an existing water source and removes up to 99% of any impurities that can be
Contact T 07785 302694 david.noble@bluewatergroup.com www.mynewsdesk.com/bluewater www.bluewatergroup.com
On the 5th December last year, Alupro hosted policymakers, civil servants, industry leaders, NGO representatives and environmental experts at a special lunch reception in the House of Commons.
The event, kindly sponsored by Dr Rupa Huq MP, Labour MP for Ealing Central and Acton, celebrated progress in aluminium recycling and discussed the industry’s path to achieving a true circular economy in 2025.
Guests heard from Tom Giddings, executive director at Alupro; as well as Dr Rupa Huq MP; and Bob Blackman CBE MP, chair of the 1922 Committee and Conservative MP for Harrow East. Sam Jones, head of climate and sustainability at Coca-Cola Europacific Partners (CCEP), also took to the stage to discuss the pivotal role of aluminium in the UK’s packaging supply chain of the future.
In comment, Giddings said, “With members spanning the entire supply chain, Alupro acts as the voice of the aluminium packaging industry on issues of government policy and legislative development. While aluminium packaging recycling rates have continued to increase in 2024, maintaining positive policy progress is critical to further increasing collection volumes and material quality,
as well as helping the sector accelerate progress towards an economy that truly unleashes the circular economy power of aluminium.”
As part of the event, Alupro encouraged MPs to sign-up to its commitment to take action and support the industry towards circularity. The pledge consists of three points of action, from delivery of a worldclass Deposit Return Scheme in 2027 to implementation of a packaging Extended
Producer Responsibility system that encourages the use of the most recyclable materials as well as supporting UK recycling infrastructure through policies that encourage investment in domestic recycling facilities.
For more information about Alupro, or its work to fulfil the industry’s obligation to meet, and exceed, recycling targets for aluminium packaging, please: https://alupro.org.uk
IntraLogisteX exhibitor Element Logic has completed the installation of Slovenia’s first AutoStore (another IntraLogisteX exhibitor) system at the Intersocks warehouse in Kočevje.
This automated storage and retrieval solution will support Intersocks’ growing logistics needs as the company continues to scale its operations.
Intersocks, a manufacturer of technical sports socks, produces between 20 to 30 million socks annually, including about 2 million pairs of Crocs, which are distributed to more than 1,000 stores in Central and Eastern Europe and to 63 countries worldwide.
The new logistics centre in Kočevje will serve as a central hub for storage and distribution, allowing for faster and more efficient customer service.
The AutoStore system’s design has the ability to expand as needed and will allow Intersocks to adjust to future market demands. According to company, the new system will enhance order capacity, goods handling, and fulfilment speed, setting new standards in intralogistics for the company.
Joachim Kieninger, director of strategic business development in Element Logic Germany, said, “We are proud to have installed the first AutoStore project in Slovenia. This technology will optimally support Intersocks’ logistics requirements and support its growth in the long term.”
Join more than 11,000 industry leaders
Dematic has recently completed a modernisation of an AutoStore™ system for Manutan, Europe’s leading specialist in the distribution of equipment and supplies for enterprises and local authorities. With 25 subsidiaries across 17 European countries, Manutan selected Dematic to be the integrator of its existing AutoStore solution at its Gonesse logistics site, just outside Paris. The system utilises 60,000 storage bins and 68 robots.
Boosting productivity and efficiency
Following a 9,000-square-metre extension of its logistics centre in 2021, which included the installation of an AutoStore system and increased the total surface area of its warehouses to 50,000 square metres, Manutan wanted to
continue its transformation when it joined forces with Dematic to transform its AutoStore system by boosting site performance and sustainable practices at the location.
Results that align with customer CSR goals
The project adheres to Manutan’s corporate social responsibility (CSR) goals. With the optimisation of available warehouse space and the modernisation of its equipment, Manutan has initiated new processes and tasks to reduce any unutilised space and the use of unnecessary materials in product packaging. New settings for the carton closers and greater use of envelopes to replace parcels are helping to cut down on the overall volume of shipments. The transport optimisation, with a reduced number of trucks, directly contributes to Manutan’s FRET21 carbon neutrality objective.
For more information on Dematic, please visit: dematic.com and follow us on: LinkedIn, Facebook, and X.
at Robotics and Automation Exhibition on 25th-26th March 2025. Explore cutting-edge technologies, connect with peers and discover the latest innovations shaping the future of manufacturing, engineering, and logistics. Register now to secure your place at this premier event!
https://www.elementlogic.net/uk
Wieland Electric presents samos© PRO MOTION, a compact safety controller with integrated motion functionality
Wieland Electric is literally bringing movement to its safety portfolio: With samos© PRO MOTION, the technology company presents a new allin-one safety controller with integrated motion functionality. A total of six TÜV-certified motion function blocks ensure that up to 60% fewer modules are required and therefore more space is available in the control cabinet than with comparable providers. Among other things, the compact, programmable controller enables safe standstill monitoring, even with vertical and slow-moving axes, and also scores points with an anti-vibration toolbox for macro and micro vibrations
Whether mechanical engineering or intralogistics – wherever reliable
standstill, speed, direction and position monitoring is required, the compact safety controller from Wieland Electric with up to 70kHz motion inputs on the base module is suitable. The integrated motion function modules include safe standstill monitoring (SSM), which can be implemented with both a speed window and a position window. The limits of the position window or hysteresis can be defined very easily using intuitive configuration options, allowing vertical and slow-moving axes to be monitored reliably and continuously, for example in construction cranes, lifting platforms, high-bay warehouses or presses, T 01483 531213 www.wieland.co.uk
AdCo UK is one of the largest manufactures of shaped hotmelt adhesives and water-based adhesives for use in packaging and product assembly markets for over 21 years, from its Head Office and manufacturing facility in Liphook Hampshire with additional distribution facilities based in Leeds UK and a network of approved distributors based throughout the UK.
As well as supplying adhesives for all requirements, AdCo supplies a wide range of specialist applicators – from ProFlex industrial, heavy duty and professional glue guns to total melt, cartridge and bulk systems, we also manufacture and supply UF resins, PVA Adhesives, PU Adhesives, Tapes and much more
As part of our commitment to offer our customers the correct solution for their needs AdCo are continually investing in research and development along with new state of the art manufacturing equipment to ensure we continue to meet the ever changing needs of all types of industry.
Thanks to our unrivalled knowledge of adhesives and application techniques, our highly skilled technicians can offer a ‘find and supply’ service to all our customers. With a combined industry experience of over 120 years, our technicians can ensure that any bonding problem can be solved quickly and efficiently.
T 01428 751755 enquiries@adco.co.uk www.adco.co.uk
This is BASA’s 40th year of operation and we are still excelling in our mission to remain the umbrella organisation for UK adhesives and sealants manufacturers. Focussing on technical and legislative aspects and on promoting awareness of the industry and technology by providing guidance on technical and compliance issues, we create a variety of networking opportunities for members and provide a huge library of documents on the website.
BASA is the voice of the adhesives and sealants industry’s and is an information source for manufacturers and suppliers. The association advocates on behalf of its members and liaises with
Government regarding legislation and keeps Members well informed of UK, EU and International proposals and initiatives.
With the growing concerns around the environment and using sustainable products and raw materials, BASA is dedicated to helping its members minimise harmful chemical usage and educate the public on the industry’s drive for safer products. BASA members work hard to formulate innovative products that positively contribute to the sustainability agenda whilst maintaining performance and durability.
BASA hopes to continue to reach more potential members, looking at ways to support its manufacturers post Brexit and help them to navigate potential new legislation and trade rules.
Contact T 03302 233290 secretary@basa.uk.com www.basa.uk.com
Gransden UK, formally known as Lock N Pop UK Ltd, is the sole UK and Ireland distributor of the Lock N Pop pallet stabilisation systems, primarily known for reducing plastic pallet wrap and enhancing pallet stabilisation. The UK based company has been supplying the Lock N Pop solution to customers across the industrial and food and beverage applications for over 25 years.
The Lock N Pop pallet stabilisation solution simply saves money by removing the costs associated with palletised goods moving or collapsing in transit to endcustomers. The primary focus on streamlined production process efficiency and the end transit journey to high street shelf, distribution centre or even across international waters or airspace has been paramount and has afforded Lock N Pop goldstandard industry recognition.
Lock N Pop pallet stabilisation uses a cold, water based cohesive, that is carefully applied inline to the cases, bags, shrink-wrap trays etc. immediately before
palletisation. The cohesive has high shear strength characteristics which binds the products together, resulting in a stable pallet. However, the additional bonus is that the cohesive combines this high shear strength with a low tensile strength, meaning that the items can easily be separated.
For more information, contact Gransden UK Ltd: T 01728 726621
M 07516 683314
locknpop@gransden.org www.locknpop.co.uk
Oakway Storage, a leading provider of warehouse design solutions, is proud to announce the launch of its latest product: flexible warehouse protection.
This innovative solution prevents accidents and damage to people, racks, property and machinery. Above and beyond traditional steel-fabricated protection, the Oakway Storage solution returns to its original shape after impact, reducing shock and damage, whilst also increasing floor space through a cleverly designed minimal footprint.
According to the Health and Safety Executive (HSE), over 5,000 reported accidents involve workplace transport every year in the UK. This alarming statistic underscores the importance of implementing safety measures to prevent workplace accidents and injuries.
The new product features a flexible design that absorbs the impact of a forklift or other heavy equipment without causing damage to vehicles, floors or the
An innovative Pallet Live Storage installation can play a key role in supporting grocery retailers as they strive for market leading growth, according to Edward Hutchison, Managing Director of BITO Storage Systems.
Providing up to 50% more storage capacity than traditional racking on the same footprint, a Pallet Live Storage (PLS) system can contribute significantly to accommodating sufficient stock to help grocery retailers meet growing demand.
Supporting a retailer’s need to maintain customer service in tandem with achieving sales growth is one of the biggest challenges placed on a distribution centres (DC), particularly when it comes to handling the sheer volumes involved and fast turnaround required by everyday bulk stock lines, such as soft drinks.
Pressure intensifies when these lines experience peaks, such as during a hot summer – particularly in large cities or on the coast. If one store runs out of soft drinks on a very hot day, there’s a good chance that others in the region will experience a similar issue. All will want more but storage limitations mean there’s a chance that not every store will get the amount they require, which will impact negatively on the grocery retailer’s level of customer service.
Maximising the amount of storage that can fit within the constraints of a DC, to provide
efficient order fulfilment for retail stores, will help to avoid such situations. For those grocery DCs that need greater flexibility to meet a variety of demands from customers within a limited space, PLS offers a dense storage and order picking system that contributes to innovative, efficient and agile grocery logistics operations. On a relatively small footprint, pallets can be located ‘in the air’ on several levels of inclined roller lanes, with delivery lanes for pallet loads of bulk stock lines – such as soft drinks – on the ground floor. This provides dense storage and rapid access to orders.
The flexibility in such a design allows products that need to be sent immediately to stores to be picked directly from the flow lane and transported to Goods Out. If the ground floor delivery lanes are getting close to empty,
protection itself. This popular feature offers cost-effective protection over a longer period than traditional steel protection.
Oakway Storage offers a full range of warehouse fit-out solutions, including pallet racking, mezzanine floors, shelving systems and complete turnkey project management, with a reputation for delivering full warehouse fit-outs, fast.
For more information about Oakway Storage, including the flexible warehouse solutions, please visit the company’s website at: https://oakwaystorage.co.uk or call: 01604 792255.
then stock stored in the lanes above can be brought down and pushed through to the other side of the lane for order pickers to continue their pick.
Operating on the FIFO (First In First Out) principle, PLS ensures product rotation, which is important for grocery store replenishment, ensuring the first product sorted by the ‘best before’ date is picked. A further benefit is that PLS can accommodate seasonal items on the flow lanes in the upper levels, allowing the grocery DC to take advantage of quiet time to get those products out to stores early.
Gaining the capacity to stock items in sufficient quantities to avoid running out, thus allowing the DC to react on customer demands quickly and deliver straightaway irrespective of the amount ordered by a store, even when bulk products a hit, peak makes the investment in PLS well worth it. A PLS system supplier with an experienced team of experts should be able to work closely with the client to develop competitively priced, customised solutions and work around existing operations to deliver projects on time.
For further information on pallet live storage, please visit: www.bito.com
INDUS Engineering Services specialises in industrial maintenance for small to medium companies on the South Coast of the UK.
The company’s primary focus has always been to serve as an outsourced maintenance department for SMEs that lack the internal resources to manage their maintenance needs. They offer a service that bridges the gap between having a regular in-house maintenance team and the specialised expertise typically provided by original equipment manufacturer (OEM) technicians. This approach ensures that businesses can rely on expert maintenance without needing full-time staff, enhancing operational efficiency.
There have been positive changes for INDUS recently, in particularly over the last 18 months which has seen the company move premises, enabling them to expand their production capacity. This is part of an ongoing project aimed at further developing the facility by increasing floor space and creating specialised work areas to accommodate their diverse workload. These improvements are designed to enhance operational efficiency and support the company’s growth.
Over the years, INDUS has worked with several high-profile clients, consistently delivering on their requirements with efficiency and reliability.
When expanding business operations, general-purpose machinery may not always
meet specific needs. Assembly, handling, and testing processes often vary by industry, requiring specialised equipment that standard machines can’t provide, therefore, a custom solution may be essential to elevate business efficiency.
INDUS designs and manufactures bespoke machinery tailored to diverse industries. Their custom-built equipment streamlines operations and boosts productivity, helping businesses reach new levels of performance. Whatever the project, INDUS can deliver machinery that fits unique operational requirements.
From providing a comprehensive design, manufacture, or commissioning services for special purpose machinery, INDUS works with you from inception to implementation,
delivering a full turnkey solution tailored to your needs.
To guarantee an exceptional level of quality, INDUS combines high-grade materials with cutting-edge manufacturing techniques. Some of the special purpose machinery they have supplied in the past include automated production lines, rotary indexing tables, automated parts handling and orientating, control systems, assembly and testing equipment, welding and cutting equipment, manual workstations, and packaging and processing machines.
It can be challenging to trust a company to build special-purpose machinery because of the high stakes involved – businesses need tailored solutions that fit unique operational demands. At INDUS, they offer a comprehensive start-tofinish service, ensuring each step, from design to installation, is handled with expertise. After discussing requirements, they create detailed blueprints, either drawing from proven mechanisms or designing from scratch. Once approved, they move into manufacturing and fitting, with scheduled maintenance provided to ensure long-term reliability. This approach ensures confidence and smooth operation for years to come.
For more information, please see below: T 01202 942637 info@indusengineering.co.uk www.indusengineering.co.uk
SEMOTA is a hardware and software solution with a web-based application that enables the remote monitoring of any load cell, force, torque or pressure sensor, using our Wi-Fi enabled hardware.
SEMOTA Continuous Remote Monitoring provides dynamic dashboard views of your events, analysis and device control. Information can be captured and stored for review and in depth analysis. Linkage to common messaging systems deliver live alerts for device management. Tailor and build applications to suit your needs and devices. Read more below, then complete the form and we’ll arrange a demonstration.
THREE YEARS STORAGE
Whether your data is needed every day or every few seconds, SEMOTA is optimised to receive, compute, and return millions of data points across the globe.
LIVE DASHBOARDS
Using SEMOTA point-and-click application development tools, create real-time dashboards to analyse data and control devices. Visualize data with SEMOTA stock graphs, charts, tables, indicators, maps, metrics, and control widgets or
develop your own using the HTML canvas and your own code. Share your data through public links, or by embedding dashboards into custom web applications.
EVENTS ENGINE
Add conditional and complex business logic to your hardware with triggered webhooks for M2M communication, and SMS, Email, Telegram, and Slack alerts to keep operators on-the-ball and informed.
SYNTHETIC VARIABLES
Transform raw data into insights with Synthetic Variables that compute complex math formulas and statistical expressions.
With SEMOTA cloud software, you can build applications to best fit the operator’s needs. SEMOTA administrators can configure permissions and restrictions to any end user or operator who interacts with dashboards, devices, and/or events. Need a user to be able to oversee multiple organisations? Not a problem. You can optionally add more users or organisations to your account and we can configure your users to best suit your application.
T +44 (0)1344 776666 info@interface.uk.com www.interfaceforce.co.uk
Davies Turner is a well-established freight forwarding and logistics company based in the United Kingdom. Founded in 1870, Davies Turner has a long history of providing transportation and logistics services, making it one of the oldest independent freight forwarding companies in the UK.
Davies Turner was one of the first economic operators in Europe and has evolved to become a leading global powerhouse in the freight forwarding industry.
Davies Turner, a family-owned enterprise, boasts a network of 23 branches across the UK, several of which are equipped with expansive warehouses. Located in Coleshill, its headquarters serves as the epicentre of its operations. Recently, the company unveiled a state-of-the-art multi-user fulfilment centre and logistics hub in Atherstone, Warwickshire. This cutting-edge facility spans across four levels, each housing 35,000 square feet of space, and boasts an impressive capacity of 20,000 pallet locations. Additionally, the Rotherham site in South Yorkshire stands as a testament to the company's regional presence, featuring offices staffed by experienced professional’s under the adept leadership of Branch Manager, Andrew Ford.
“We specialise in the more awkward and out of gauge shipments that our competitors might not have the same experience with. Over the years, this has included vehicles and machinery of all shapes and sizes and even small rail engines. We can help with shipping anything out of the ordinary that may need a special licence and enjoy the challenge of shipping more unusual items!”
Davies Turner is the only freight forwarder running a regular dedicated rail import service from mainland China into the UK, which is a lifeline for many UK businesses. The express freight rail service departs weekly from Xian in Central China for groupage and full load
shipments. With concerns around the slower speed of ocean shipments and high cost of air freight, rail offers a cost-effective, reliable freight service. The LCL rail freight service takes just 19-23 days from terminal-to-terminal which is on average, 70% cheaper than air freight.
In alignment with the UK Government's ambitious 2050 Net Zero targets, businesses are urged to embrace transparency regarding their annual carbon emissions. Recognising the need for sustainable practices, Davies Turner is leading the charge towards a greener future. Leveraging the efficacy of rail transportation as a more environmentally-friendly alternative to air shipments, the company is committed to reducing its carbon footprint.
For instance, consider the stark contrast in emissions: A 40-ft container laden with 20 tons of cargo generates a mere 4% of the equivalent CO2 emissions when transported by rail compared to air shipment. Embracing this ethos, Davies Turner has embarked on a transformative journey, forging a partnership with Pledge to meticulously track and report all company carbon emissions.
This strategic collaboration not only underscores Davies Turner’s dedication to environmental stewardship but also empowers clients with a tangible means of quantifying and addressing carbon emissions across international supply chains. By embracing such initiatives, the company and its clientele are poised to make significant strides towards
achieving Scope 3 emission targets and fostering a more sustainable future.
With the ongoing conflict in Ukraine, disrupted shipping market in the Red Sea and Panama Canal, and sporadic port strikes, many businesses have faced huge shipping delays over recent months.
“With many volatile hot spots around the world currently, we monitor situations closely on behalf of our customers. Having a regular Chinese rail service that navigates deftly round the Red Sea Shipping crisis, keeps supply chains running across the world. To reiterate this point, last December a customer asked to trial a rail shipment with us from Shanghai to the UK, alongside a pre-existing ocean shipment from the same route with a different company. The results were conclusive: the rail shipment took 18 days terminal-to-door, whereas the ocean shipment took 45 days and also ran over the estimated time schedule,” said Andrew.
Davies Turner has built a strong reputation as a trusted partner for businesses seeking efficient and cost-effective logistics solutions in the UK and beyond. With a focus on sustainability, and its reliable and trusted customer service, it comes as no surprise that Davies Turner was named Number One Logistics Service Provider by Logistics Manager Publication in December 2023, in its annual list of the Top 50 UK logistics service providers. One of the key metrics for this decision was the 74.4% increase in turnover for the financial year, ending in 2022, with a record turnover of £350.6 million. Alongside the exclusive new opening of the £40 million stateof-the-art logistics hub in Atherstone, this is a very exciting time for Davies Turner.
For Air, Sea, Rail and Road freight quotations and further information, please see below: T 01709 529709 rotherhamsales@daviesturner.co.uk www.daviesturner.com/specialist/rotherhamspecialists
Oliver Twinsafe Trunnion Mounted valves and Floating Ball Valves have successfully been SIL certified at level 3. This new and important milestone provides operators with safety assurances at the highest level and has resulted from many months of engineering design, QA reviews, and audits.
A SIL (Safety Integrity Level) is a measure of safety system performance, in terms of probability of failure on demand (PFD). The higher the SIL level, the higher the associated safety level, and the lower probability that a system will fail to perform properly. SIL 3 is the highest rating that can be given to a valve.
High Integrity Pressure Protection Systems (HIPPS) and remotely located well-head manifolds are normally associated with SIL certification. Operators are to gain additional safety assurances from installing our ball valves, in that, when the valve is required to perform its fail-safe function, the probability of it not performing is extremely low.
SIL 3 certification has been awarded by Exida, a third-party safety assessment organisation. The certification covers our range of Single Isolate valves, and Double Block and Bleed valves comprising two separate isolates within the assembly. Bore sizes for Trunnion Mounted valves range from 1”–16” and 1”–3” on Floating Ball valves.
Contact www.valves.co.uk
Oliver Twinsafe is to supply Double Block and Bleed pipeline valves for use on Monoethylene glycol (MEG) injection pump systems. MEG is a widely used hydrate inhibitor designed to reduce the risk of hydrate formation in pipelines that could cause blockages.
The order includes a batch of 2 1/16” API 6A 5,000psi Double Block and Bleed valves in A182 F55 Super Duplex material that have been dynamically tested to meet the requirements of API 6A PSL level 3. In addition, the valve designs were pre-qualified to API 6A PR2 Appendix F, which involves multiple cycle testing at low, ambient and high temperature with zero leakage allowed across the valve seats throughout these cycles.
A number of Oliver instrumentation valves have also
been ordered, taking the total number of valves supplied for this offshore project overall to over 300 with more valves in the pipeline.
For information on how Oliver Twinsafe can provide pipeline valve solutions for your project, telephone: +44 (0)1565 632636 or visit our website at: valves.co.uk
A drone survey carried out by Lanes Group plc is helping a major manufacturer investigate the drainage system on one of its sites in readiness for future development.
The unmanned aerial vehicle (UAV) survey provided a highly detailed digital map of the factory site near Peterborough, which engineers can use to plot drainage assets with impressive precision.
It was carried out by Lanes Group Rail (LGR), Lanes Group’s rail division, in just one day when a conventional groundbased survey would have taken up to four days.
Significant cost saving
LGR Business Development Manager
Bill Waring said: “The aerial mapping surveys we carry out are fast becoming an essential element of site investigations across all sectors, including rail.
“In many cases, they can be carried out by a team of one, rather than the three or four operatives needed to work at height from ground level. It’s a significant cost saving, especially when time saved is factored in.
“Drone surveys also provide a hugely rich array of data that can be manipulated in many different ways to more accurately plot and understand the topography and built assets across large areas of land.
“They don’t just allow surveys to be carried out more quickly, more safely and with less site disruption. They also allow data
then be prepared more quickly and more flexibly for analysis.”
Eliminates site disruption
LGR’s drone survey unit holds the required Civil Aviation Authority commercial operating permission and is on the drone survey framework for Network Rail.
Lanes drone pilot and surveyor Adam Blakesley carried out the survey of the factory site that manufactures ground engineering infrastructure assets.
He flew a DJI Matrice M300 drone fitted with the latest 4K video camera to capture all the required data across an area covering 68,000m2. Esri Site Scan software was then used to process the images captured.
Adam Blakesley said: “We can stitch together many thousands of images taken during the drone flight into highly accurate orthomosaic images of the site. We can also create 3D models and point cloud images.
“These allow clients to view structures in very close detail without having to work at height, which may involve working from access platforms or erecting even more costly and disruptive temporary scaffolding.
“The advantages can be even more pronounced on rail networks. With the right precautions in place, drones can be flown over live rail assets with no disruption to services, negating the need to carry out surveys during engineering possession time.”
Flexible data analysis
The data gathered can be combined with other mapping software to plot assets across large areas with a great degree of accuracy.
This include WinCan drainage survey software used by Lanes CCTV survey teams, allowing data captured via drones to be merged with digital maps of underground drainage systems.
LGR has more than 30 years’ experience of working in the rail industry on national rail and Transport for London networks, while Lanes subsidiary UKDN Waterflow (LG) holds a Principal Contractor Licence (PCL) from Network Rail.
The ability to deliver drone surveys adds significant value to LGR’s capabilities and services, which include: conventional CCTV drainage surveys; track drainage and culvert cleaning and replacement; drain, sewer, and culvert lining; and vegetation control.
It also complements engineering services provided to the rail industry by Lanes Professional Services. They include drainage system investigation and design, and hydraulic engineering project management.
Talk to Lanes Group Rail about its drone survey service – for rail, commercial and industrial clients.
T 01708 528770
bill.waring@lanesgroup.co.uk https://www.lanesgroup.com
Automated Test & Measurement
Abingdon Verification Instruments (AVi), a Test and Measurement company based in Oxfordshire specialises in the design and build of Automated Test Equipment (A.T.E.) solutions and general consultancy.
Who we are
Established in 2021, AVi is an ISO 9001 accredited company that upholds high quality standards. As a small business, AVi always responds quickly to customer needs, offering exceptional customer service and project management support.
Industries served include Environmental Monitoring, Battery and EV Technology, Electronic Manufacturing, and Med-Tech industries. With emerging opportunities in aerospace and SME start-ups involved in new product development.
Benefits of using a tailored system:
S Significantly reduced development time and cost.
S Faster time to market.
S Quicker test set-up times & improved accuracy.
S User interface to eliminate operator error.
S Unattended testing with results stored locally.
S Better data acquisition & reporting.
S Scalable systems for evolving requirements and manageable equipment footprint.
Product validation is the cornerstone of product innovation, ensuring optimised performance, safety and the latest compliance with industry standards. An AVi solution dramatically improves your product verification processes through:
S Functional Testing: Ensure products perform as intended, using multiple simulated tests.
S Safety Testing: Safeguard risks to people, wildlife and the wider environment. BSI 9001 accreditation to oversee safety compliance.
S Environmental Testing: Assess products durability across a full range of factors including high temperatures or humidity, water ingress, shock and vibration and more.
Additional Electronics R&D services AVi also offers bespoke services in Electronics R&D, Embedded Systems Design, Schematic Capture, and PCB design and fabrication. Creating costeffective, flexible solutions for everyday products. These systems allow easy updates and enhanced functionality, reducing the need for costly hardware.
For tailored solutions to meet your business needs, contact us: T 01865 408352 sales@abvi.co.uk https://www.abvi.co.uk
UK machinery safety
Machinery safety is a top priority across all industries to safeguard safe working practices. Despite best safety practices, HSE reported that tragically 135 workers were fatally injured at work during 2022/2023 (RIDDOR), with construction, agriculture/ forestry/fishing and manufacturing reporting the highest fatalities. Machine hazards in manufacturing can range from machine guarding, electrical hazards, poor maintenance, mechanical hazards, to equipment malfunctions, and many more, with the onus placed on companies to become more stringent with the health & safety and regular inspections of machinery operations.
across many warehouse and distribution, manufacturing and food & beverage companies, freeing up staff to carry out other important tasks.
Introducing MachineSafe safety and compliance software
The MachineSafe safety and compliance software platform has been designed to fit a gap in the market for the inspection process by machinery safety engineers. With a rich background in conducting PUWER inspections, UKCA Marking, CE Marking and Machinery Risk Assessments, the MachineSafe engineers used this expertise to develop the platform.
The dreaded internal safety inspections
Automated assembly lines have now become standard practice
Contact T +44 (0)1793 547018 info@machinesafe.co.uk https://machinesafe.co.uk