
3 minute read
ANNI 80: ARIA DI TURBO
ANNI 80: ARIA DI TURBO
Il 1° luglio del 1979 Jean-Pierre Jabouille vinceva sulla monoposto Renault mossa dal motore turbo EF1 il Gran Premio di Francia di Formula 1 . Per la prima volta una vettura con motore sovralimentato mediante turbocompressore vinceva un Gran Premio nella massima categoria del Motorsport. Quel giorno nacque l’”Era del Turbo” che dalla Formula 1 si riversò a cascata su tutti i costruttori di auto. Infatti negli anni successivi ogni casa automobilistica iniziò a proporre nei propri listini modelli sportivi di prestazioni elevate con motorizzazione turbo. Anche in Alfa Romeo si sperimentava questa soluzione. Tramite il Reparto Corse della Casa, l’Autodelta governata dall’ing. Carlo Chiti, già nel 1979 venne allestito un lotto di 400 Alfetta GTV 2.0 Turbodelta. Analogamente nel 1982 sempre presso l’Autodelta venne allestito un lotto di 361 Giulietta 2.0 turbo Autodelta. Queste vetture in tiratura limitata, oggi molto ricercate dai collezionisti, fornirono la base di sperimentazione per lo sviluppo della versione di serie del Bialbero sovralimentato. Parallelamente in quegli stessi anni si stava diffondendo, presso i centri di calcolo delle case automobilistiche, l’utilizzo di software specifici per la progettazione dei componenti delle auto. Il programma di calcolo che si impose fu il Metodo degli Elementi Finiti (FEM) che permette di simulare il comportamento reale del componente suddividendo la geometria del componente stesso in tanti piccoli elementi virtuali collegati in un reticolo (“mesh”). Una volta realizzato il reticolo, per ogni elemento occorre definire il materiale, le condizioni al contorno (temperature, flussi ecc.), le sollecitazioni (forze, pressioni ecc.). Il programma elabora queste informazioni e fornisce una simulazione del comportamento del componente (deformazioni, gradienti di temperatura, rotture ecc.).
Esempio di applicazione del Metodo degli Elementi Finiti su un componente del motore.
Anche in Alfa Romeo venne costituito un team dedicato al calcolo con questo software. L’adozione della sovralimentazione sul “bialbero” avrebbe imposto un aggravio delle sollecitazioni termiche e strutturali dei componenti, soprattutto della testa cilindri. Venne quindi realizzato uno studio della testa per verificarne il comportamento e la risposta alle maggiori sollecitazioni. La testa cilindri venne suddivisa in migliaia di piccoli elementi tridimensionali in modo da rispettarne la complessa geometria. L’utilizzo del software permise di verificare l’andamento delle temperature e il comportamento del materiale nelle condizioni più estreme.

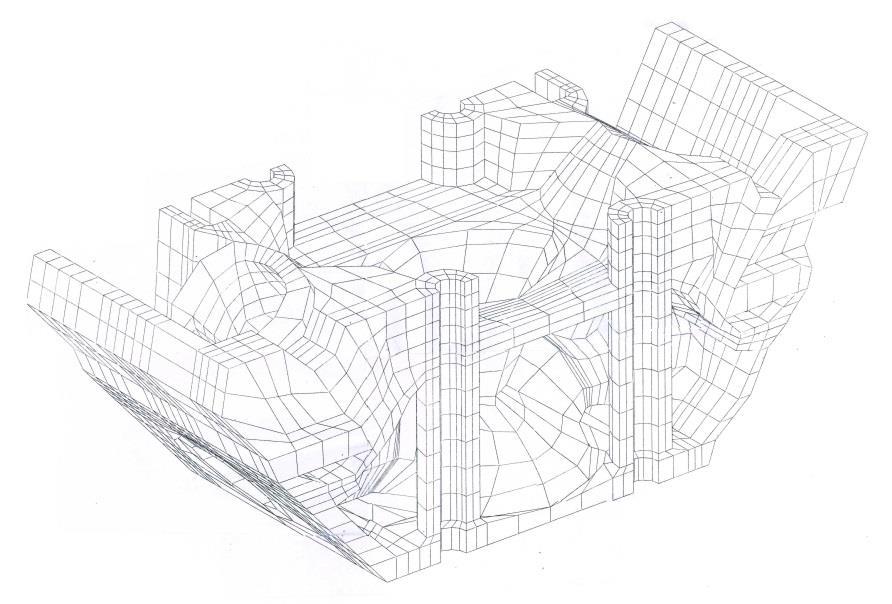
Sezione della testa motore in lega corrispondente a un cilindro e rappresentazione della “mesh” per la stessa sezione
Il risultato di questi studi fu la produzione in serie nel 1986 della motorizzazione 1.8 turbo per la Alfa 75. L’ormai glorioso Bialbero si arricchiva quindi di questa tecnologia, beneficiandone in termini di prestazioni e di immagine. La classica versione “1750” con cilindrata di 1779 cm3 raggiungeva ora i 155 CV di potenza. Il motore veniva così dotato di un gruppo turbocompressore che, mosso dai gas di scarico, comprimeva l’aria di aspirazione in modo da aumentare il “riempimento” del motore e quindi “bruciare” più benzina, aumentando le prestazioni. Un intercooler raffreddava l’aria a valle del compressore per aumentarne ulteriormente la densità.
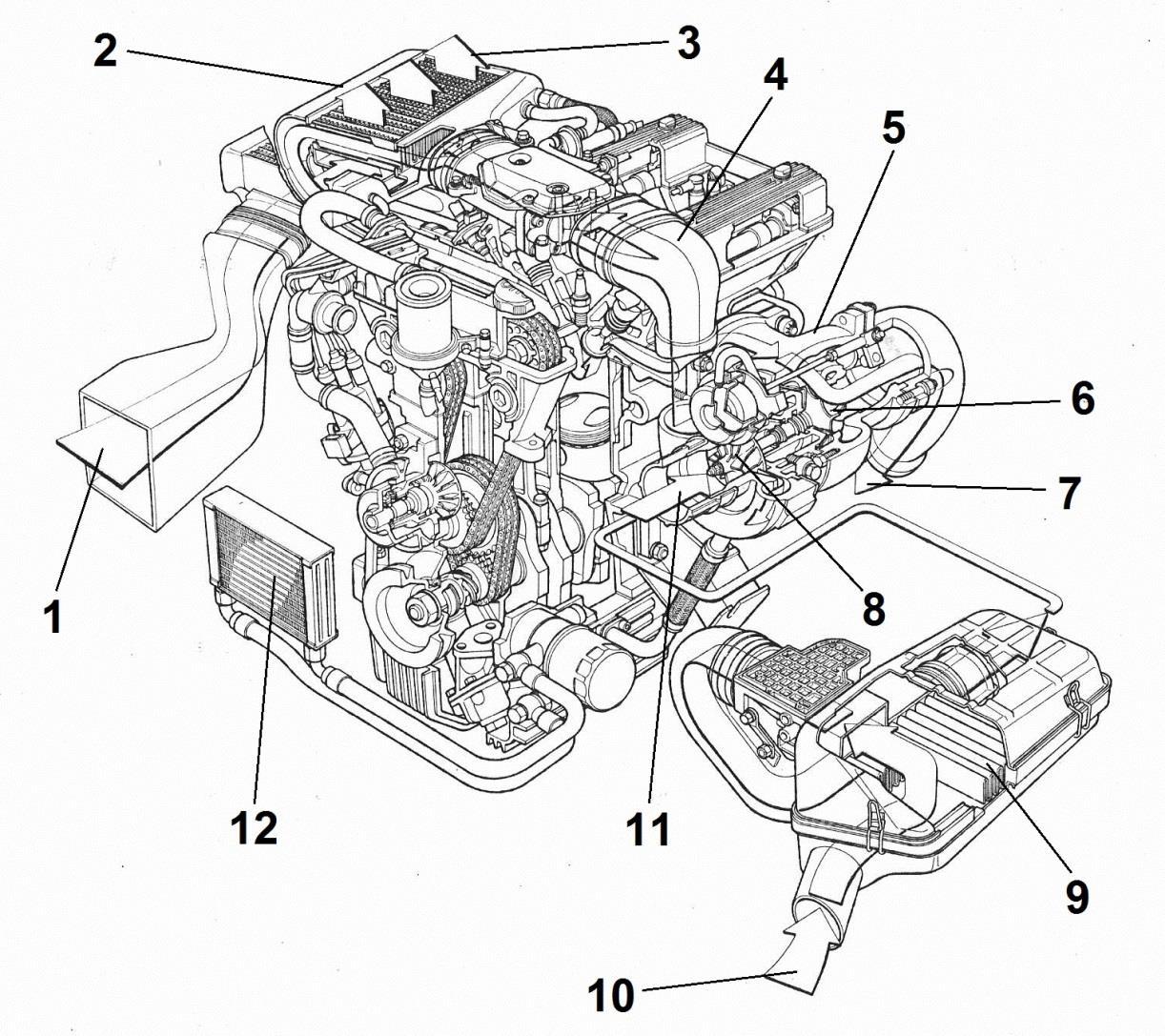
1. Ingresso aria per intercooler 2. Intercooler 3. Uscita aria intercooler 4. Condotto aria compressa tra compressore e intercooler 5. Gruppo turbocompressore 6. Turbina sui gas di scarico 7. Uscita gas di scarico 8. Compressore 9. Filtro aria motore 10. Ingresso aria motore 11. Ingresso aria compressore 12. Radiatore olio
Il propulsore era equipaggiato con un sofisticato sistema di controllo motore dotato di due centraline elettroniche. Una per la gestione della iniezione elettronica, l’altra per il comando dell’accensione e il controllo della pressione di sovralimentazione. Una serie di sensori fornivano alle centraline le informazioni sulle condizioni di funzionamento del motore in modo da attuare le migliori strategie di funzionamento in grado di ottimizzare prestazioni, consumi ed emissioni. Venne introdotto il sensore di detonazione, che informava la centralina nel caso di incipiente detonazione (“battito in testa”) in conseguenza delle condizioni di combustione più spinte. La centralina poteva così variare i parametri di accensione in modo da scongiurare questo dannoso fenomeno.
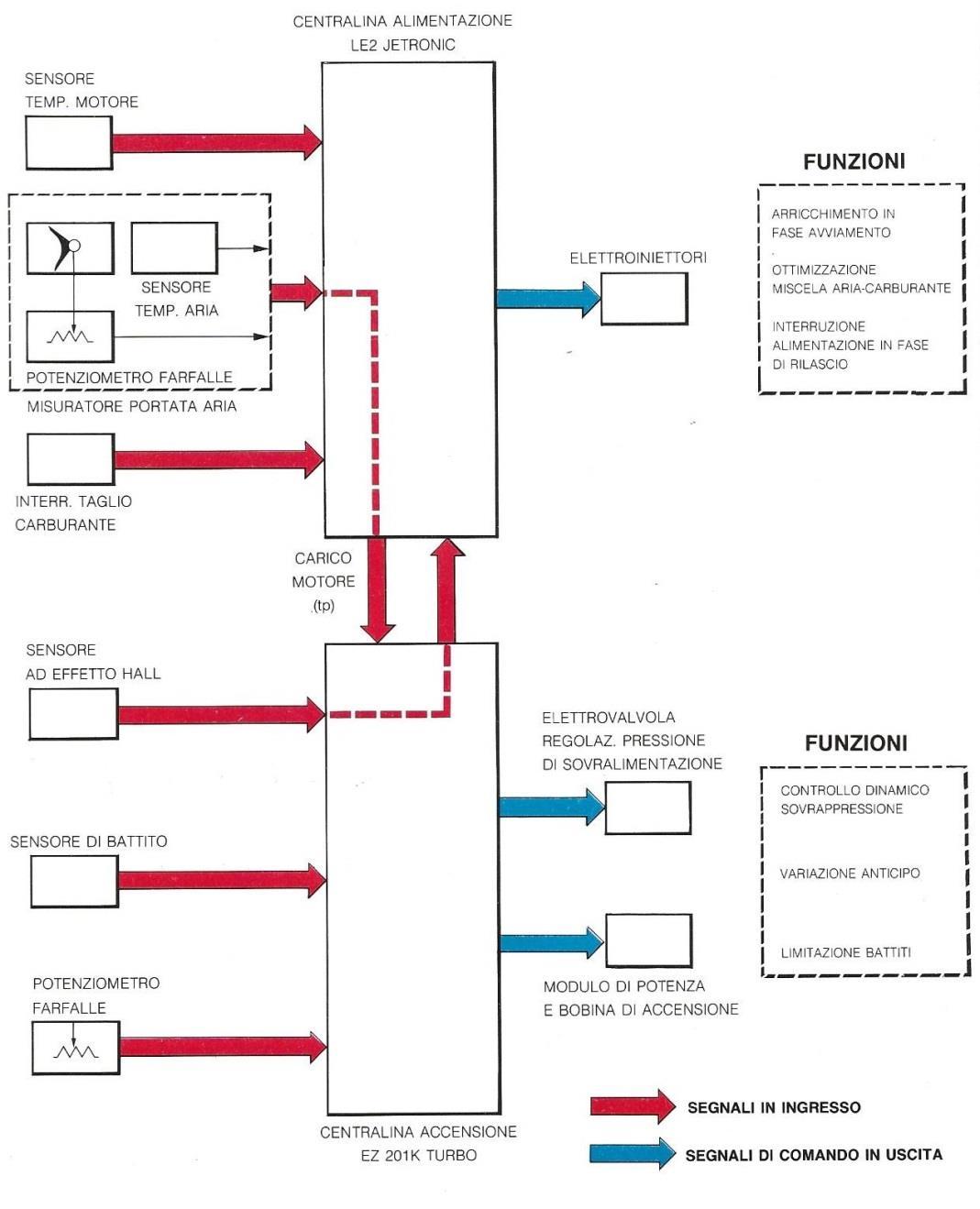
Schema logico del sistema di controllo motore