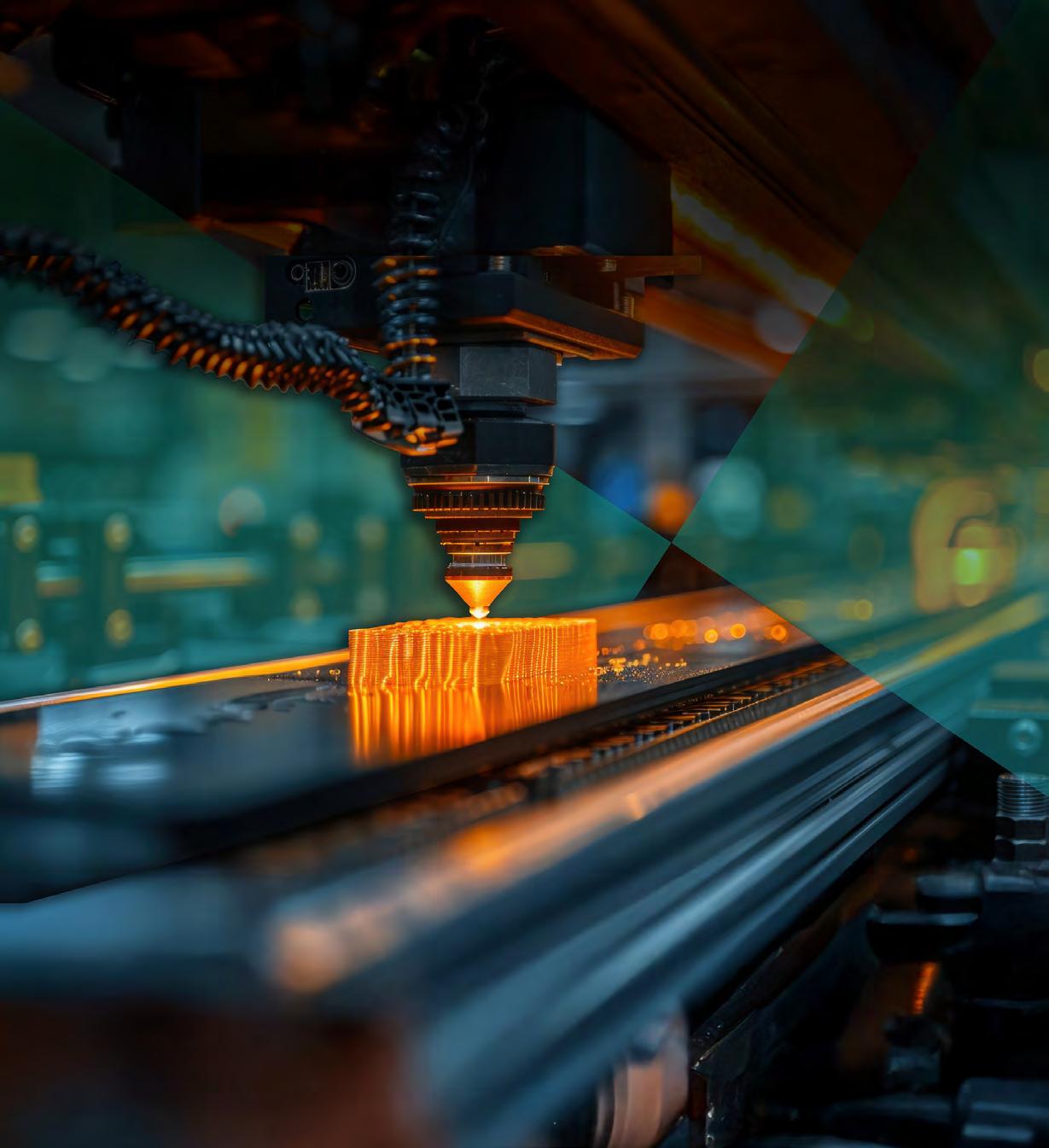
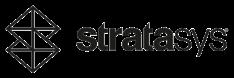
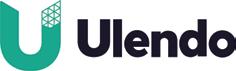
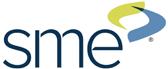
Additive manufacturing is rapidly emerging as a transformative force in solving some of today’s most urgent challenges—mass customization, fractured global supply chains, sustainability pressures, and volatile material costs. At the forefront of this evolution is “Vibe Manufacturing,” a pioneering approach that combines additive manufacturing with the power of artificial intelligence to unlock unprecedented speed, precision, and design freedom.
Imagine a world where a $100 part can be printed in-house for just $1. This isn’t science fiction—it’s the future we’re accelerating toward with Project DIAMOnD as evidence of member Air & Liquid Systems doing just that. To get there, manufacturers must fundamentally rethink their business models. The reliance on large capital expenditures will need to give way to a more agile, IP-driven mindset—one rooted in creativity, adaptability, and digital fluency.
Equally critical is preparing the workforce for this seismic shift. As automation and AI evolve, the human element remains irreplaceable. Skills like creativity, critical thinking, and complex problem-solving will define success in this new paradigm. Training and upskilling our workforce isn’t optional. It’s essential.
To explore these pressing topics, Automation Alley convened a roundtable of the brightest minds in additive manufacturing and advanced industry. Their insights form the foundation of this Integr8 Playbook, offering forward-thinking perspectives on where we are and where we’re headed.
Topics covered include:
• Vibe Manufacturing and how it is a natural fit for additive manufacturing
• How AI impacts additive manufacturing scalability
• How manufacturers align their workforce and workflow to be prepared for this new reality.
These topics address the critical intersection of emerging technology and practical implementation in manufacturing. Understanding the timing and nature of AI-driven additive manufacturing enables organizations to strategically plan for future disruptions and opportunities. Delving into AI’s role in enhancing scalability, repeatability, and quality uncovers its true potential to move additive manufacturing from niche applications to mainstream production.
We are proud to serve as a trusted partner for objective, original insight. Thank you to all our members and contributors who made this Playbook possible. Together, we are defining the next era of manufacturing.
Tom Kelly Executive Director & Chief Executive Officer Automation Alley
Roundtable Attendee List: Sponsors, Supporters and Participants
Main Feature: The Rise of IP Over Process-Driven Manufacturing
Expert Insights: How Additive Manufacturing Will Help Industries Navigate New Economic and Geopolitical Realities in 2025 Stratasys
Expert Insights: The Gap Between Hype and Reality in Additive Manufacturing Ulendo
Industry Pulse: Ecosystem Insights at a Glance
Future Trends: Designing the Future with AI and Human Ingenuity
Industry Insights: SME and RAPID + TCT: Advancing Additive Manufacturing for the Future of Industry SME
Case Study: Additive Manufacturing a Boost for Speed and Quality at Champion Plastics
Key Takeaways: Main Points from Integr8 Additive Manufacturing Roundtable
State and National Resources: Helpful Resources for Small- and Medium-sized Manufacturers
Sources
SPONSORED BY: Stratasys and Ulendo
Josh Boggess - VP of Sales, Stratasys
Amanda Hallock - Director of Marketing, Stratasys
Chinedum Okwudire - Founder/CTO, Ulendo Technologies, Inc.
Brenda Jones - CEO, Ulendo Technologies, Inc.
SUPPORTED BY: SME and Michigan Economic Development Corporation
ADDITIONAL
Pavan Muzumdar - COO, Automation Alley and CEO, Project DIAMOnD
Rick Bovensiep - Engineering Manager, H.O. Trerice Co, Inc.
John Bucknell - CEO & Founder, Virtus Solis Technologies
LaTricia Clark - CEO, EduVation
Xavier Fajardo - Founder & President, ACCUFACTURE LLC
Steven Gormley - Assistant Professor, Delta College
Steve Helminen - I4.0 Program Manager, Michigan Manufacturing Technology Center
Robert Joyce - Founder, FibreTuff
Josh Kolcan - Applications Engineer, Designfusion
Gary Krus - VP of Business Development and Operations, Hirotec America
Lisa Lehman - Manager, Wipfli, LLC
Michael Luzi - Vice President of Strategic Partnerships, BenePro/HRPro
Ray Putz - Senior Business Development Representative, Oakland County
Eric Raphael - President, Fixitopia
Cody Schaub - Economic Development Director, Office of Congresswoman Haley Stevens
Tom Schneider - President, HA Industries
Robert Scipione - Manufacturing Services Manager, Michigan Manufacturing Technology Center
Thomas Sommer - Director of Corporate and Foundation Relations, Lawrence Technological University
Marcus Stackpoole - CEO, Synergy Prototype Stamping, LLC
Rob Stipek - Additive Manufacturing Account Manager, Designfusion
Edward Tate - CTO, Virtus Solis Technologies
Shai Terem - CEO, Markforged
Chad Varney - Director of U.S. Operations, Designfusion
Maurice Wiggins - CEO, Wiggins Roofing
Additive manufacturing has arrived at a tipping point — not of hype, but of hard questions. No longer a futuristic curiosity, 3D printing is now a strategic tool being shaped by engineers, entrepreneurs, and policymakers alike. Across industries, the shift is unmistakable: major manufacturers are scaling investments, while nimble startups find inventive ways to tap into its transformative potential. But just as the process of additive manufacturing builds layer by layer, so must our understanding of how to fully unlock its value — and what’s standing in the way.
From the promise of AI-optimized designs and distributed production to the pressing realities of regulation, cybersecurity, and workforce gaps, this playbook brings together a diversity of voices to map both the terrain and the road ahead.
To start things off on a positive note, there’s a lot to be excited about with regards to additive manufacturing. Opportunities in 3D printing exist for virtually every sector, but especially manufacturing, healthcare, and construction. The technology has matured beyond its initial limitations to offer unprecedented design freedom and material efficiency. Here are three promising areas worth focusing on in the years ahead:
The integration of AI with additive manufacturing presents unprecedented possibilities. Smart algorithms can optimize design parameters in ways human engineers simply cannot match, reducing material waste. Predictive maintenance systems powered by machine learning can anticipate equipment failures before they occur, potentially saving manufacturers millions in downtime costs. AI-powered waste disposal systems stand to massively cut commercial waste by reducing overall transportation distances by as much as 36.8%
“
At the forefront of this evolution is ‘Vibe Manufacturing,’ a pioneering approach that combines additive manufacturing with the power of artificial intelligence to unlock unprecedented speed, precision, and design freedom.
Tom Kelly CEO Automation Alley “
“Vibe manufacturing is already happening, but it’s limited. We know it’s coming, which is why we’re all in this room. AI is doing good work, but there’s still a lot to be done. We believe AI-integration can be instrumental in helping additive manufacturing cross the chasm.”
Josh Bogess Vice President of Channel Sales
This evolution mirrors a trend in software development known as “vibe coding,” where AI tools translate natural language into working code. Just as software teams are adjusting to new collaborative workflows with AI, manufacturers are learning to co-create with intelligent systems that extend human creativity and precision.
“Vibe manufacturing is already happening, but it’s limited,” said Stratasys Vice President of Channel Sales Josh Bogess. “We know it’s coming, which is why we’re all in this room. AI is doing good work, but there’s still a lot to be done. We believe AI-integration can be instrumental in helping additive manufacturing cross the chasm.”
Ulendo CEO Brenda Jones agreed. “Vibe manufacturing is here, but we recognize we don’t yet have all the software tools we need to make it fully functional,” Jones said. “We need to integrate AI into those tools.”
Meanwhile, AI-enabled generative design tools are revolutionizing product development cycles. What once took months can now be accomplished in days or even hours. Companies like Autodesk report their customers achieving 2050% weight reduction in parts while maintaining or improving performance specifications.
Synergy Molding Technologies CEO Clay Stevens has a similar experience in deploying AI and additive manufacturing in his operations. “When quoting injection molding projects, we start by uploading the plastic part data into AI-DfAM software to first optimize the part for moldability. Then, without leaving the AI-powered DfAM software, we automatically generate the core and cavity injection mold data to form the optimized plastic part,” Stevens said. “Once we have the mold halves created, again staying in the same software, we are able to light-weight our tooling, add lattice structures, and add conformal cooling channels for better thermal optimization of the molding process. Once the modified tool data is
completed, the same AI-software optimizes that injection mold data for 3D printing by taking into account the additive equipment used, material to be printed, printed part orientation, and our internal cost structure to generate multiple simulation options for our designer to choose from.”
The end result is Synergy Molding Technologies is able to reduce design time anywhere from 25% to 75%, he added.
“For example, a project that would have conventionally required around 100 hours of design could be instead completed in 50 hours or less.”
“Vibe manufacturing is here, but we recognize we don’t yet have all the software tools we need to make it fully functional. We need to integrate AI into those tools.”
Brenda Jones CEO, Ulendo
Distributed manufacturing networks represent perhaps the most transformative potential of additive technologies. Rather than centralized production facilities shipping finished goods globally, we’re witnessing the emergence of interconnected printing hubs positioned strategically near end users. This model drastically reduces shipping costs, carbon emissions, and delivery times.
Artificial intelligence plays a crucial role in optimizing distributed additive manufacturing by enabling real-time decision-making across decentralized networks. AI algorithms can predict demand patterns, automate print queue scheduling, and optimize material usage across geographically dispersed 3D printers. With AI-driven analytics, manufacturers can dynamically allocate print jobs based on factors like printer availability, proximity to end users, or urgency of the order— bringing a new level of intelligence and adaptability to distributed manufacturing systems.
“AI will help with scalability, and scalability comes down to data. With larger companies like Strata-
sys or Markforged, sharing data between printers and AI can help everyone scale in the additive manufacturing industry,” Accufacture President Xavier Fajardo said.
The U.S. Marine Corps has already implemented this approach with their X-FAB (expeditionary fabrication) units, mobile facilities capable of 3D printing replacement parts in forward operating locations. Similarly, companies like SyBridge Technologies and Xometry are building commercial networks of manufacturing partners, creating what amounts to an Airbnb of manufacturing capacity.
Industry experts project an increasingly large portion of finished goods will be produced closer to their final destination tomorrow compared to today. This shift promises not only logistical advantages but also enhanced supply chain resilience against disruptions like those experienced during recent global crises.
According to industry analysts, the DED segment is projected to grow to USD 7.3 billion by 2033, outpacing several other additive manufacturing methods.
Direct Energy Deposition (DED) is being increasingly recognized for its potential in both expanded and new production lines. Jeff Robertson, director of business development at manufacturing giant Hexagon, recently said it’s one of their perceived “brightest spots” and largest areas of focus.
DED works by depositing metal powder or wire directly onto a substrate while simultaneously melting it with a focused energy source like a laser or electron beam. This allows for the creation of large, complex metal components with exceptional structural integrity. The technology excels particularly in repair applications, where damaged parts can be restored rather than replaced, offering significant cost savings for industries like aerospace and defense. According to industry analysts, the DED segment is projected to grow to USD 7.3 billion by 2033, outpacing several other additive manufacturing methods.
Despite promising advancements, significant hurdles remain in the full realization of additive manufacturing.
Regulatory frameworks often struggle to keep pace amidst technological advancement. Questions about intellectual property protection when AI generates novel designs remain largely unresolved. Who owns an AI-created innovation? The software developer? The manufacturer? These legal gray areas create hesitation among potential adopters.
Updates will come from regulatory bodies like the FDA, FAA, and international standards organizations. These agencies are beginning to develop specialized frameworks for additive manufacturing certification, but progress remains uneven across sectors. The FDA’s guidance on 3D printed medical devices represents a step forward, yet many industries still operate in regulatory uncertainty.
A part designed in Germany, printed in Singapore, and installed in Brazil may encounter three different regulatory environments.
Cross-border considerations further complicate matters. A part designed in Germany, printed in Singapore, and installed in Brazil may encounter three different regulatory environments. This regulatory fragmentation creates significant compliance costs and risks for global manufacturing operations. Industry consortia are advocating for harmonized international standards, but achieving consensus among competing national interests proves challenging.
Near-instantaneous, remote, and versatile production is great, but it comes with caveats. Prime among them? Data security. By taking operations digital, organizations expose themselves to new vulnerabilities. The digital files containing proprietary designs become valuable targets for industrial espionage and cybercriminals. A single compromised file could lead to counterfeit production or intellectual property theft on a massive scale.
A 2025 IBM security report recently ranked manufacturing as the top industry targeted by cyberattacks for the third year in a row. The distributed nature of additive manufacturing networks
expands the attack surface exponentially. Each node in the network – from design studios to production facilities – represents a potential entry point for malicious actors.
This is an issue that will not only affect progress in embedding 3D printing into the manufacturing industry, but getting Industry 4.0 off the ground as a whole. Businesses will only invest in digital transformation if they believe their intellectual property and operational data remain secure. Yet current efforts may already be working; according to the 2024 Gartner CIO and Technology Executive Survey, 80% of CIOs plan to increase spending on cyber/information security in 2024.
Everyday consumers aren’t alone in wanting unique, one-of-a-kind products. Beyond personalized mugs and keychains, large companies require parts customized for specific machines, particularly challenging operating environments and experimental designs. Only in their case, the final product needs to be commercial grade. Additive manufacturing has the potential to help, but only if deployed in an operationally realistic way.
Cost Prohibitive Equipment - Industrial-grade 3D printers capable of producing commercial-quality parts can cost anywhere from $100,000 to over $1 million, putting them out of reach for many small to mid-sized manufacturers.
Material Limitations - While the range of printable materials continues to expand, many specialized applications require specific material properties that current additive technologies cannot reliably reproduce.
Production Speed - For high-volume manufacturing scenarios, traditional methods still outpace additive manufacturing by orders of magnitude, creating bottlenecks in supply chains.
Quality Consistency - Ensuring uniform quality across batches remains challenging, with variables like temperature fluctuations and material inconsistencies affecting final product reliability.
Certification Hurdles - Regulatory approval processes for critical components in aerospace, automotive, and medical industries remain lengthy and complex for additively manufactured parts.
The shifting landscape of additive manufacturing demands new skill sets from workers. Traditional machining expertise must now be complemented with digital literacy and data analysis capabilities. According to a Deloitte study, 1.9 million manufacturing jobs could go unfilled by 2033 if this and related issues continue to go unaddressed.
“We need to hire and upskill the workforce,” Bogess said. “Students should be encouraged to use AI. Companies need to reinvest in their employees when it comes to AI. We can’t resist it—we must embrace it, and let employees lead the new AI initiatives. On the flip side, AI can be a powerful tool for workforce upskilling.”
Educational institutions are racing to develop curricula that address these needs, but the pace of technological change often outstrips academic program development. Industry-academic partnerships, like those between America Makes and community colleges, or between non-profits and local governments like Automation Alley and Oakland County’s Project DIAMOnD, offer promising models for workforce development that remain responsive to evolving industry demands.
This mirrors what’s happening in the software world, where engineers are learning to work with AI-powered “vibe coding” tools—rapidly prototyping solutions using natural language inputs. In manufacturing, the equivalent shift means workers must guide, refine, and interpret AI-generated outputs, from part designs to predictive models, while understanding the broader context in which those outputs are applied.
“AI is here, but it’s still important that people have job-specific knowledge—especially in design. AI helps most with iteration. It learns from it,” Fajardo said.
We need to hire and upskill the workforce. Students should be encouraged to use AI. Companies need to reinvest in their employees when it comes to AI. We can’t resist it—we must embrace it, and let employees lead the new AI initiatives. On the flip side, AI can be a powerful tool for workforce upskilling.
“
Josh Bogess
Vice President of Channel Sales Stratasys
One of the most pressing educational needs lies in teaching Design for Additive Manufacturing (DfAM) — a discipline that goes far beyond simply exporting a CAD file to a printer. Additive manufacturing enables geometries and internal structures that traditional manufacturing cannot replicate, but to capitalize on that potential, engineers and designers must think differently from the outset.
DfAM training focuses on optimizing part orientation, minimizing support structures, and utilizing topology optimization and generative design. It also includes understanding material behaviors specific to additive processes, such as thermal distortions in metal prints or layer adhesion in polymers. Without this foundational knowledge, companies risk underutilizing their machines or producing subpar parts that fail to deliver on the promise of AM. As DfAM becomes more central to production, expect to see an increased demand for mechanical engineers who are fluent in both design theory and real-world print limitations.
Recognizing this skills gap, a growing number of credential programs and certifications are emerging to equip the workforce with industry-aligned AM knowledge. Organizations like SME, ASTM International, and America Makes have rolled out tiered certifications that address everything from fundamental machine operation to advanced design strategies and quality assurance in regulated industries.
These credentials offer more than just technical know-how — they signal to employers that workers are equipped to thrive in high-tech, Industry 4.0 environments. For small and midsized companies that might not have the resources for on-the-job training, hiring workers with additive credentials is a fast-track solution to building AM capabilities. In the long run, widespread credential adoption may also help harmonize talent pipelines across regions and sectors, providing a shared baseline of additive manufacturing competence.
Michigan’s Project DIAMOnD, spearheaded by Automation Alley, is a standout example of workforce innovation. Originally launched to distribute 3D printers to small and mid-sized manufacturers across Southeast Michigan, the initiative recently expanded to include a new training component: the Project DIAMOnD Academy.
This academy pairs hands-on learning with cloud-connected production practices, preparing manufacturers to work in real-time distributed networks. Like vibe coding’s emphasis on lowering technical barriers in software development, the DIAMOnD Academy trains participants to approach manufacturing tasks as hybrid human-AI collaborations—turning prompts, data, and feedback into production-ready outputs. With practical training modules and expert-led guidance, the Academy is helping future-proof Michigan’s manufacturing workforce.
Pairing a tech-savvy young professional with an experienced engineer who holds deep institutional knowledge creates a powerful synergy within the manufacturing industry. The seasoned engineer brings decades of practical insights, process understanding, and historical context, while the younger professional contributes fresh perspectives, digital fluency, and a strong grasp of emerging technologies like AI, automation, and data analytics.
“New talent is being trained in AI, while seasoned workers hold deep institutional knowledge. We discussed the concept of paired programming—two people with different skill sets working together,” Jones said. “Imagine pairing a newly minted engineer with someone who’s been in the organization for years. You get cross-training in both directions. If your company can support this, it’s a powerful way to grow talent and foster knowledge transfer.”
Together, they can bridge the gap between legacy systems and next-gen solutions, accelerating innovation without losing sight of operational realities. This cross-generational collaboration not only supports smoother digital transformation but also fosters knowledge transfer, succession planning, and a more agile, future-ready workforce.
The road to widespread additive manufacturing isn’t without obstacles — but each challenge is also an invitation. An invitation to innovate, collaborate, and rethink what’s possible across the entire product lifecycle. Whether it’s reimagining logistics through distributed production, reducing waste through AI-driven design, or cultivating the next generation of digitally fluent workers, the path forward is being forged by those willing to confront complexity head-on. Additive manufacturing is no longer about proving what’s possible — it’s about building what’s next. And the future won’t be built in isolation, but together.
Additive manufacturing isn’t evolving in isolation. Much like software development’s shift toward vibe coding—where human creativity is amplified by AI-generated outputs—the future of making things is becoming faster, more collaborative, and deeply influenced by natural language workflows. Embracing this transformation doesn’t diminish the value of human expertise; it elevates it. The organizations that adapt, reskill, and reimagine their roles in this ecosystem will be the ones that shape its future.
Josh Boggess Vice President Americas Channel Sales
The global manufacturing landscape is entering a new era—defined not just by technological change, but by a dramatic shift in economic and geopolitical realities. With new tariffs already in effect under the returning administration, the U.S. is actively pursuing a protectionist trade strategy, signaling a definitive break from decades of globalization. These tariffs, aimed at reducing dependency on foreign-made goods, are already impacting the cost and flow of products across borders. While some industries scramble to adapt, others are turning to a powerful enabler of resilience and agility: additive manufacturing (AM), commonly known as 3D printing.
At a time when manufacturers face rising costs, fragile logistics, and mounting pressure to reshore production, AM offers more than just a workaround. It presents a fundamental shift in how we design, produce, and deliver products. From decentralizing supply chains to accelerating time-to-market, additive manufacturing is helping companies not just weather today’s storm, but future-proof their operations.
As of early 2025, newly imposed tariffs—particularly those targeting imports from China and other major manufacturing economies—are reshaping sourcing and procurement strategies across industries. According to U.S. Customs data, more than two-thirds of Chinese imports are now subject to higher duties, with additional tariffs extending to critical sectors like automotive components, electronics, and industrial equipment.
These measures have sent shockwaves through global supply chains, raising prices and lengthening lead times for manufacturers reliant on international suppliers. But even beyond China, geopolitical instability—from the war in Ukraine to tensions in the South China Sea—is pushing countries to reevaluate their industrial dependencies. Add to that inflationary pressures, persistent labor shortages, and residual post-pandemic logistics strain, and it’s clear that businesses need more resilient, localized, and cost-effective solutions.
Enter additive manufacturing.
With tariffs driving up the cost of imported goods, manufacturers are looking inward—and AM is accelerating the shift toward domestic production. Unlike traditional manufacturing, which often requires complex, global sourcing of parts and raw materials, AM enables companies to produce finished components locally, using digital files and minimal physical infrastructure.
During the COVID-19 pandemic, this shift was already underway. Stratasys’ Origin® One P3™ printers were used to produce millions of nasopharyngeal swabs domestically, scaling up to 190,000 swabs per day when overseas supply chains failed. That response foreshadowed today’s reality: supply chain resilience isn’t a luxury, it’s a requirement.
Now, with tariffs compounding existing risks, more companies are investing in additive manufacturing to insulate their operations from external shocks. By decentralizing production, businesses can reduce dependency on international freight and raw material imports, protect against cost spikes, and improve supply chain visibility.
The impact of tariffs isn’t limited to raw material costs—it also affects pricing competitiveness and margin control. Traditional manufacturing methods involve high setup costs, expensive tooling, and large minimum order quantities, all of which become harder to justify in a high-cost trade environment.
AM helps companies stay competitive by reducing material waste, eliminating tooling costs, and enabling low-volume production without sacrificing profitability. Northrop Grumman offers a compelling example. In its solid rocket motor program, the company adopted AM to replace traditional tooling used to mold propellant within motor casings. The result? Tooling lead times were slashed from months to weeks, and the company was able to iterate faster and at lower cost.
In an era when every dollar matters, additive manufacturing provides a leaner, smarter way to manufacture—one that aligns perfectly with the demands of a protectionist economy.
While cost savings are a major driver of reshoring, industries like aerospace, medical, and defense also demand extreme precision and strict quality control. AM excels in these environments by enabling production of high-performance parts with complex geometries that traditional methods struggle to achieve.
A case in point: Spanish aerospace supplier Indaero used 3D printing to reengineer a critical assembly tool for an Airbus NH90 helicopter. The traditionally manufactured aluminum tool was heavy, difficult to handle, and time-consuming to produce. By switching to AM, Indaero delivered a tool that was nine kilograms lighter, reduced manufacturing time by 66%, and cut tooling costs by 50%.
As more companies look to bring production home in response to tariffs and trade volatility, AM makes it feasible—not just in theory, but in practice. The ability to produce specialized, flight-ready, or medical-grade components domestically is a game-changer for U.S. industry.
One of the less obvious consequences of global tariffs is the strain they place on logistics and warehousing. Higher import costs and port congestion force manufacturers to hold more inventory domestically, tying up capital and increasing overhead. Additive manufacturing turns this model on its head.
With digital inventory systems, companies can store product designs in the cloud and print parts on demand—eliminating the need for large physical stockpiles. This justin-time approach saves money and space while allowing for greater responsiveness to market demand.
Fathom, a U.S.-based advanced manufacturing provider, illustrates this perfectly. As an early user of the Stratasys Continuous Build 3D Demonstrator, Fathom helped Intel produce more than 9,700 parts for “Spider Bots” featured at its developer conference. The project was completed in just five weeks—at a fraction of the traditional cost—demonstrating the power of AM to scale quickly without bloated inventory or production delays.
Fathom’s integration of AM into its operations reduced inventory by 93% and lead times by up to 75%, freeing up resources to focus on innovation and customer responsiveness.
Trade restrictions often limit access to international partners, technologies, and suppliers. But that doesn’t mean innovation has to slow down. Additive manufacturing empowers companies to take control of their R&D and prototyping processes, enabling rapid iterations without external dependencies.
Instead of waiting weeks or months for overseas tooling or parts, engineers can now go from concept to prototype in a matter of days. That speed gives businesses a critical edge—not just in getting to market faster, but in being able to respond to customer feedback in real time.
In an economy defined by volatility, that kind of agility isn’t just nice to have—it’s essential.
The new tariffs in 2025 are more than a policy change — they’re a catalyst for industrial reinvention. While the return to protectionism introduces new challenges, it also creates an opportunity to rethink how we manufacture, where we manufacture, and why.
Additive manufacturing stands out as one of the most effective ways to adapt. It supports domestic production, reduces exposure to global volatility, lowers operational costs, and unleashes a new level of design freedom. Whether you’re building aerospace components, healthcare devices, or industrial tools, AM helps you do it faster, smarter, and closer to home.
As manufacturers recalibrate for the realities of today’s trade environment, one thing is clear: additive manufacturing isn’t just a response to disruption — it’s a strategy for long-term growth and resilience.
Stratasys is leading the global shift to additive manufacturing with innovative 3D printing solutions for industries such as aerospace, automotive, consumer products, and healthcare. Through smart and connected 3D printers, polymer materials, a software ecosystem, and parts on demand, Stratasys solutions deliver competitive advantages at every stage in the product value chain. The world’s leading organizations turn to Stratasys to transform product design, bring agility to manufacturing and supply chains, and improve patient care.
To learn more about Stratasys, visit www.stratasys. com, the Stratasys blog, X/Twitter, LinkedIn, or Facebook. Stratasys reserves the right to utilize any of the foregoing social media platforms, including Stratasys’ websites, to share material, non-public information pursuant to the SEC’s Regulation FD. To the extent necessary and mandated by applicable law, Stratasys will also include such information in its public disclosure filings.
Brenda Jones CEO
What are some of the barriers to faster adoption of additive manufacturing? Which types of companies are playing a role in this dynamic, with a specific emphasis on Michigan-based enterprises?
Additive Manufacturing (AM), often touted as a revolutionary force in modern manufacturing, has experienced a reality check over the past 10 years. The initial hype during 2009 to 2023 was triggered by patent expirations and media attention. This led to a flood of printers onto the market with rapid growth in the number of companies offering printers, with specific impact in the FDM desktop space. This hype peaked from 2013 to 2015 driven, in part, by a comment made by President Barack Obama in his State of the Union speech, “3D printing has the potential to revolutionize the way we make almost everything.” Investor interest increased and stock prices of the major additive manufacturing players skyrocketed.
But then reality began to set in around 2015 as companies encountered challenges associated with high costs, low speeds and inconsistent quality. For example, vibrations caused when operating an FDM printer
at high speeds led to the high expense of failed parts due to quality issues such as ringing, ghosting and layer shifting. A similar quality situation plagued metal laser powder bed fusion (LPBF) printers whereby heat-induced deformation and stress in metal parts led to the time-consuming process of trial-and-error selecting the least problematic scan path heuristic (e.g., island, spiral, in and out) and the need to address subquality parts with extensive post-processing such as annealing, stress relief heat treatment, laser/shot peening as well as CNC milling or grinding.
During the post-COVID industrial rebound, Special Purpose Acquisition Companies (SPACs) emerged as an attractive alternative to traditional Initial Public Offerings (IPOs) to enable several key AM companies to obtain rapid capital infusion. Unfortunately, some of the residual hype for the industry led to high valuations that could not be supported by company operations. This caused investor disappointment, company closures, depressed prices in M&A, the shuttering of some companies and delisting from public stock exchanges. One can watch this busi-
ness drama play out on the tradeshow floor where key additive players are channeling their limited marketing investments away from generalized additive manufacturing events to those more narrowly focused on end user industries and specific applications. Additionally, some additive manufacturing OEMs and resellers have turned to contract manufacturing to provide a new revenue stream and assist their end customers in addressing peaks in demand without adding additional printers.
Although there has been movement toward building solutions around specific industrial applications to achieve higher quality and efficiency, manufacturers still remain cautious about capital expenditures in this area due to continued poor part economics, scalability challenges, limited materials, lack of materials standards and stringent qualification/certification requirements. We have recently entered a period of market shakeup and consolidation that, in this author’s opinion, will continue for the majority of this decade.
The economies of scale affect not only the investment in printers, but also the expertise and skills necessary to reliably produce high quality additively manufactured parts.
However, there are positive developments that are inching us closer to realizing the expectations of decentralized supply chains, plummeting inventory costs and parts being produced locally on demand. One such development is the growth of contract additive manufacturers such as Azoth3D in Michigan. The AM services offered by companies like Azoth3D, provides small to medium-sized manufacturers (SMBs) the ability to integrate parts made with 3D printers into their process without the upfront investment. In fact, some of these SMBs utilize the services of contract additive manufacturers to explore the applicability and suitability of additive, thereby derisking and building an internal case for investing in the technology at a later time. Whereas a specific small manufacture might eventually utilize only four to five printers in their facility, a contract additive manufacturer can leverage economies of scale by using hundreds or even thousands of printers in “farms” to provide additively manufactured parts for many different companies. The economies of scale affect not only the investment in printers, but also the expertise and skills necessary to reliably produce high quality additively manufactured parts. These contract additive manufacturers can also temporarily offload the lengthy and complex certification and qualification process. For an SMB that requires multiple 3D printer types/technologies, a contract additive manufacturer can more cost effectively operate a much larger variety of printers. Similarly, a contract additive manufacturer can provide a full suite of post-processing services, the cost of which can be spread over multiple clients.
The experience of producing high quantities of parts begets increased knowledge about the effective way to deploy and use additive manufacturing machines; e.g., specialized and scarce knowledge required for design-for-AM (DfAM) principles, material science and process optimization can be then transferred to SMBs when they are ready to embark on their own additive journey. Contract additive manufacturers are
on the “front lines” solving some of the difficult technical challenges and developing best practices that raise the “additive manufacturing IQ” of others.
In addition to 3D printer OEMs, 3D printer resellers are also providing contract manufacturing services to their clients. Similar to the OEMs, these resellers are helping their clients manage through periods when demand outstrips their capacity. Instead of purchasing new machines (which may be out of the question from a cost perspective) or just turning away business they cannot handle in a timely manner, they call on their reseller partner to provide capacity. Additionally, for some of the more complex printers like laser powder bed fusion (LPBF), knowledgeable team members at some resellers are providing the purchasers of LPBF printers with build files to more quickly get them started on extracting value out of their LPBF investment. Resellers are also providing software upgrades to significantly expand the capacity of machines they have already sold to clients. One Michigan-based example is Rev1 Technologies, the exclusive after-sales support provider for CreatBot across the U.S., is offering a software upgrade that can QUINTUPLE the speed of the F430 model without sacrificing quality.
And then there are companies that are focusing on solving specific issues standing in the way of increased adoption of additive manufacturing. Let’s take the problem of vibration in FDM printers, both desktop and industrial models. In the case of desktop printers being used for non-industrial purposes, a vibration compensation method called “input shaping” is increasingly being used to reduce the effects of vibration so that a printer can be operated at high speeds without sacrificing quality. However, the method used in “input shaping” to compensate for vibration brings with it quality issues such as corner rounding. For industrial application, this suboptimal print quality would not be sufficient. That is where early stage and nimble companies like Ulendo Technologies, Inc. provide software
solutions to address vibration problems at the level required for industrial applications. The company’s Ulendo VC (vibration compensation) product predicts when the printer is going to vibrate and makes adjustments to the movement of the print head to avoid the quality problems that would be introduced into the part by that vibration.
Once an FDM printer can start to print at lightning speed, extrusion issues start to pop up. This is where companies such as Slice Engineering in Florida come in. Slice specializes in parts and accessories that can be added to an existing printer to enhance its speed and quality; e.g., their patented high performance hot ends that adapt the extrusion process to handle the increased speed of the printer. In addition to hardware that can be added to an FDM printer as an “aftermarket” product, software upgrades can be applied to the printer’s controller firmware to improve the quality and speed of its operation. For example, Ulendo’s Calibration-as-a-Service® is a hosted software solution that replaces the traditional by time-consuming, manual and error-prone recalibration process of printing and measuring parts and then manually entering numbers into equations.
In metal 3D printing, Ulendo provides a software solution for the heat-induced deformation and stress that plagues laser powder bed fusion printers. Their patent-pending Ulendo HC (heat compen-
sation) innovation optimizes the path of the laser to cut mean deformation by 50% and stress by 88%. Moreover, with the integration of intelligent software and high-performance accessories, new life can be breathed into 3D printers that are already in the field, thereby providing increased quality and throughput for SMBs at low cost.
On the materials side, companies like 3DXTech in Michigan continue to offer an increasingly diverse and innovative range of options. One of their latest materials, Obsidian™ PA6+CF serves as a cost-effective alternative to a more expensive filament, Obsidian™ combines PA6 copolymer with high-modulus carbon fiber. This blend ensures excellent performance and appearance, offering users a significant cost saving without compromising quality.
It is understandable that an SMB manufacturer might hesitate to introduce additive manufacturing into their operations given the learning curve and expense. Fortunately, there are several avenues to ease these concerns. Automation Alley’s own Project Diamond program provides entry-level FDM 3D printers and relevant training to qualified manufacturers. Complementary to Project Diamond is The Digital Transformation Center in Auburn Hills, MI, a facility that provides companies access to industrial 3D printing equipment and training with the support of experienced additive manufacturing professionals at Geofabrica, a Michigan-based business that specializes in the development of custom 3D printing systems and processes for industrial applications. Another example is Detroit-based LIFT (Lightweight Innovations for Tomorrow), a nonprofit, public-private partnership between industry, academia and government. LIFT’s in-house experts and partners across industries, serves as a trusted advisor for SMB manufacturers to help them transition to advanced technologies like advanced manufacturing machines.
Acknowledging the challenges of the adoption of any new technology is the first step in being able to address those challenges and develop hardware and software to overcome them. Organizations like Automation Alley have charted a mission to bring together members of an ecosystem to tackle these problems as a team.
Thoughtfully and surgically inserted AI techniques are also another way to bridge the gap between hype and reality. For example, New York-based Senvol leverages its proprietary machine learning software, Senvol ML, to analyze the intricate relationships between AM process parameters and resulting material properties. This data-driven approach enables rapid optimization of AM processes, reducing reliance on costly and time-consuming trial-and-error methods. Predictive maintenance is another obvious example. Imagine the cost and time savings for the end user if they can detect in advance that a printer will fail or fall out of calibration before an issue affects the quality of a part or, worse yet, results in a failed part. Ulendo is building such an infrastructure as part of its Calibration-as-a-Service® (CaaS) platform described above. By performing AI-driven analytics on the vibration behavior of printers connected to CaaS, Ulendo can predict printers that are out of spec and need maintenance. Also leveraging its CaaS platform, the company is developing an AI-driven recommender system that can supply an end user with the best speed and acceleration to print a part to achieve optimal print quality. This removes the time-consuming trial and error process often involved in selecting optimal process parameters for AM.
We polled leaders in industry, academia and government for their input on these questions many face. Here’s what they said: Do you anticipate further consolidation in the AM market?
What is additive manufacturing primarily used for in your facility?
Process discipline will be replaced with Design excellence
Traditional manufacturing requires strict discipline in the process. As 3D printing makes the process more versatile and less expensive, the fixation will shift to design. The question will not be, How to manufacture? It will be, What am I manufacturing?
Capex will be replaced with Intellectual Property portfolios
Under the old manufacturing model, physical assets are capital intensive. With the focus changing to AI-based design and 3D printing, Intellectual Property will become more important on the balance sheet. If anyone can 3D print, what makes you different is your ideas.
Factors that hold back distributed manufacturing today like Identity management, IP tracking, smart recipes and traceability, can be solved by AI data monitoring and analysis. Once these values are quantified and optimized, distributed additive manufacturing will be one step closer to being realized.
AI + 3D Printing will open a vast array of opportunities and democratize and disrupt manufacturing further
AI will take design into places never imagined because it doesn’t have restrictions and is able to conceive of geometries based on engineers’ descriptions. It will radically change the design process through rapidly taking ideas and mak8ing them a reality. Engineers will become ten times more effective as AI becomes an integral part of the workflow.
manufacturing will be replaced by distributed parallel manufacturing
As predictability and reliability between 3D printers increases, scalability surges. The ability to print massive amounts of product in large networks is where the industry is headed.
For more than 90 years, SME has been a champion of North American manufacturing. As the nonprofit that represents the entire industrial ecosystem, elevating manufacturers, academia, and their communities, SME is committed to accelerating widespread adoption of manufacturing technologies and building the industry’s talent and capabilities. Its purpose is to advance manufacturing to ensure a resilient future for the industry.
That focus on the future is why SME has also been a champion of additive manufacturing’s potential since its earliest days. The first paper on additive manufacturing (AM) was presented at an SME research conference, introducing industrial 3D printing to the engineers and academics who have grown it into a key technology for modern manufacturing.
Since then, SME has invested heavily in nurturing AM throughout its evolution from laboratory prototypes to the once unthinkable number of applications it has today. One of the ways SME has supported the robust additive community is its creation and continued expansion of the RAPID + TCT annual conference and exhibition for 35 years. RAPID + TCT, produced in
partnership with Rapid News Group, is North America’s premier event for AM and industrial 3D printing. It remains a must-attend platform for manufacturers from around the world to showcase the latest innovations and applications of the technology and for industry experts to share their knowledge across a variety of sectors.
“SME is committed to removing barriers to AM adoption,” said Angie Szerlong, SME group director, AM Series. “From the very start, when the idea was presented at our North American Manufacturing Research Conference, all the way up to today where a community of thousands connect at RAPID + TCT, SME’s belief in the potential of AM to transform the manufacturing ecosystem has never wavered.”
The RAPID + TCT conference, which is the largest ever in 2025, featured more than 140 sessions over eight different tracks and offered attendees access to information on new developments as well as guidance on evaluating, adopting and optimizing AM technology for applications from consumer goods to mobility to health care.
“The conference is unmatched in terms of the knowledge and the insight manufacturing professionals are provided with to stay current with what’s happening with AM,” said Szerlong. “We rely on our RAPID + TCT Event Advisors, volunteers from across the industry, to ensure presentations and speakers deliver the most relevant, educational content. We are forever grateful for our community of dedicated volunteers.”
Many of the event advisors are part of SME’s AM Technical Community, a group of passionate industry experts dedicated to unlocking the full potential of AM, who dive deep into the technologies and processes that transform product development to bring innovative ideas to market quicker and more cost-effectively.
SME also facilitates a Healthcare Additive Manufacturing Technical Advisory Team who identify challenges, develop resources and facilitate changes in support of anyone using AM for medical and/or biomedical applications. Both groups present lively panel discussions at the SME Theater on the RAPID + TCT show floor.
For those just starting out to the additive world, SME’s AM Emerging Professionals Committee hosts an annual career forum and hands-on networking session at RAPID + TCT, designed for emerging professionals eager to build meaningful industry connections, share knowledge, and unlock new opportunities.
Open to all on the Main Stage at RAPID + TCT, the Executive Perspectives Keynote Series features curated discussions among panels of industry experts and thought leaders in the AM space who explore industrial 3D printing’s present and future impacts across a variety of sectors.
“Part of serving this community is making sure that we provide a forum for industry leaders to offer their thoughts and what they’re thinking about when it comes to the future of AM,” said Szerlong. “The Executive Perspectives series offers exactly that: the perspectives of executives who are driving the technology forward.”
“Part of serving this community is making sure that we provide a forum for industry leaders to offer their thoughts and what they’re thinking about when it comes to the future of AM.
“
Angie Szerlong SME Group Director AM Series
Opportunities to learn are around every corner at RAPID + TCT, including a course covering the foundations of AM followed by the Certified Additive Manufacturing Fundamentals (CAMF) exam. With a passing score of 70% or higher, individuals will be officially certified and may use the CAMF designation. Many students will get their first glimpse at modern manufacturing at the event, through the SME Education Foundation’s Bright Minds Student Summit. From guided show-floor tours and technology demonstrations, to keynote presentations and an interactive challenge, the experience fosters conversation between students and exhibitors, and validates student knowledge.
SME recognizes achievements in the field of additive manufacturing with its annual AM Awards, which are presented at RAPID + TCT each year. All awards celebrate the outstanding accomplishments of individuals, teams, and companies that have had a significant impact on commercializing AM. They represent more than two decades of SME recognition of notable, innovative leadership in the additive space.
“These awards recognize great minds in AM who are solving problems through implementing or deploying their achievements in production,” said Szerlong. “We also have our annual AM Pitchfest, where we give entrepreneurs, startups and academic spinoffs the opportunity to pitch their emerging technology, products and applications to an expert panel with the chance to win exhibit space and bring their idea to market at next year’s event.”
For 35 years, SME and RAPID have defined the crucial role of additive manufacturing and empowered the establishment of an industry that continues to conceive, test, improve and manufacture new products at a faster, more cost-efficient pace. For users and suppliers alike, the event is a destination for those who provide technology and those who need to understand, explore and adopt 3D printing, AM, 3D scanning, CAD/CAE metrology and inspection technologies.
Additive Manufacturing, or 3D Printing, has many uses in the parts production industry. It is used for prototyping, molding, and creating custom parts and tools. According to Fortune Business Insights, it has become nearly a $20 billion industry in the United States, with an expected growth of more than $101 billion by 2032.
Champion Plastics of Auburn Hills, Michigan, doesn’t use 3D Printing to create production parts but incorporates the technology to improve efficiency. “We use it as an auxiliary tool,” said Jeff Ignatowski, co-owner and president. “We use it to check fixtures for quality checks.”
The results have been positive, as his company consistently hits the 100% on-time delivery mark with zero quality defects and has received quality awards from General Motors and Harley-Davidson. They serve more than 30 customers in the automotive and motorcycle industries while meeting the needs of other firms in the industrial and consumer markets. At least 20 different types of parts come off the production line daily, and the team develops 30 to 40 new parts each year.
Before implementing 3D printing, creating gauges and fixtures was outsourced and expensive, and the turnaround took weeks. Now, they have results overnight.
Champion Plastics also uses 3D Printing to examine potential new tight-tolerance products. Ignatowski said a client might send a CAD file to develop a part, and his
engineers will print a version ten times the designed size to examine it better and evaluate its critical characteristics. “3D printing has been extremely helpful for development and quality inspections,” he said.
The technology also benefits quality control. The company uses a Keyence measuring device to inspect parts for dimensional accuracy. If a part doesn’t have the proper orientation, 3D printers create a fixture to align it to ensure proper measurement. Go/No Go Gauges checks are used to check parts without measuring the pieces. Gauges are printed to physically restrict a part from passing or rejecting inspection of certain features. “Our speed to market is the biggest impact” of in-house 3D Printing, Ignatowski said.
Champion Plastics’ most recent use of Additive Manufacturing has been for its End-of-Arm Tools (EOAT), which grab parts off the production line and package them for shipping. The three- and six-axis robots used for this work use grabbing tools that fit products with different geometries and require custom-made ends to fit specific parts. 3D Printing quickly creates the needed tools.
As a small business, they must remain current on Industry 4.0 trends. “We need to manage (growth) with technology,” Ignatowski explained. “We need to deal with these issues and not just throw people at it. We want to use our labor for skilled activities and not mundane tasks.”
The average employee has been with the company for ten years, and some have required reskilling and upskilling as technology has changed. Ignatowski and his partner, Vice President of Operations Matt McDermott, worked closely with their workforce to determine where new skills were needed and used grants from the State of Michigan to help fund the training. The employees embraced the opportunity. “They loved it,” Ignatowski said. “There may have been some anxiety when they were uncertain of what was needed in their positions, but this gave them the knowledge to be more comfortable.”
Champion Plastics has 25 employees without middle management, and that intimacy has created a positive work culture and fostered a healthy communication stream between ownership and the workers on the floor. “We ask employees for their ideas,” Ignatowski said. “We want to know what they think. That dialogue is crucial.”
Champion Plastics uses AI for clerical purposes, such as developing job descriptions, and plans to research its use for parts inspections. Operators are trained to identify flaws but cannot examine every piece that comes off the production line. Once taught, AI can provide that level of inspection.
“You have to teach it what to look for,” Ignatowski said. “What’s exciting is AI learning to look for flaws and defects. If I can ensure a customer their parts have been 100% inspected, that’s a big deal.”
The two owners get their “hands dirty,” Ignatowski said, by working the production line to see what’s working and what needs improvement. Ignatowski said Champion Plastics has experienced “historic growth” of 2530% over the past few years by developing a positive work environment and embracing technology such as additive manufacturing, which improved product quality and increased customer delivery time. He expects that trend to continue.
Champion Plastics, Inc. is located in Auburn Hills, Michigan. They have been supplying the automotive, industrial and consumer markets for more than 40 years.
They have injection molding machines ranging from 85 tons to 300 tons combined with value added assembly capabilities. Their team is dedicated to supplying products and services in the most cost effective, safe, and environmentally conscious manner. They are ISO 14001: 2015 and IATF 16949: 2016 certified with 100% on-time delivery and 0 PPM.
The shift toward localized, on-demand production through distributed additive manufacturing networks reduces carbon emissions, logistics costs, and supply chain vulnerabilities — with examples ranging from Project DIAMOnD and U.S. Marine Corps to commercial hubs like Xometry.
3D printing is no longer a novelty — it’s a strategic tool being embraced across industries. Major manufacturers are scaling investments, and startups are finding inventive ways to leverage this technology’s potential.
AI-driven tools like generative design and predictive maintenance are enabling faster, more efficient, and more sustainable production processes. Vibe Manufacturing mirrors the “vibe coding” trend in software where AI turns natural language into working outputs.
AM makes it feasible to produce complex, custom parts tailored to specific machines or environments — from aerospace components to personalized medical devices. However, scalability depends on overcoming current limitations in cost, material diversity, speed, and certification.
Despite its promise, additive manufacturing faces hurdles such as inconsistent regulatory frameworks, heightened cyber threats to digital design files, and barriers in cost, material limitations, and production speed that hinder mass adoption.
Manufacturing workers must now merge traditional skills with digital fluency, AI collaboration, and Design for Additive Manufacturing (DfAM). Credential programs and workforce development initiatives like Project DIAMOnD Academy are crucial to meeting this need.
The additive revolution is as much about cultural transformation as it is about technological change. Success depends on embracing collaboration between humans and AI, industry and academia, and organizations large and small to drive innovation at scale.
Michigan Industry 4.0 Grant: The Michigan Economic Development Corporation (MEDC) offers an Industry 4.0 Technology Implementation Grant that provides 50% reimbursement—up to $25,000—for small and medium-sized businesses investing in advanced technologies such as Additive Manufacturing. Businesses must meet eligibility requirements to apply.
Michigan Emerging Technologies Fund: In partnership with the Small Business Development Center, MEDC also supports innovation-focused companies through the Michigan Emerging Technologies Fund. This initiative helps expand access to federal innovation R&D funding, supporting tech-based business development across the state.
State of Michigan Business Resources: The State of Michigan offers a variety of support services to help businesses grow, including resources for expansion, capital access, workforce recruitment, and international market engagement.
Project DIAMOnD Digital Transformation Center: Companies participating in Project DIAMOnD can now access industrial 3D printing equipment and expert support at the Digital Transformation Center (DTC) in Auburn Hills, MI. The center enables companies to explore new applications and revenue streams using polymer and metal additive manufacturing.
U.S. Small Business Administration: The U.S. Small Business Administration (SBA) offers tools, loans, and guidance to help small businesses start or scale operations, including funding to upgrade Additive Manufacturing infrastructure and connect with potential investors.
SME Additive Manufacturing Certification: The Certified Additive Manufacturing Fundamentals (CAMF) certification from SME is a key credential for individuals pursuing careers in AM. Covering core topics like AM technologies, safety, and terminology, it’s ideal for professionals and students preparing for industry roles in sectors like automotive, aerospace, and healthcare.
National Institute of Standards and Technology (NIST): NIST leads national efforts in researching Additive Manufacturing materials, technologies, and processes. The organization also provides key benchmarks, standards, and conferences that shape the future of the AM industry.
Automation Alley is a nonprofit technology business association and Digital Transformation Insight Center focused on driving the growth and success of businesses in Michigan and beyond through innovation and automation. With a global outlook and a regional focus, we foster a vibrant community of manufacturing and technology innovators, entrepreneurs, and business leaders through opportunities for collaboration and learning. Our programs and services help businesses develop the skills and expertise needed to effectively jumpstart or accelerate digital transformation. By bringing together industry, academia, and government, we aim to create a dynamic ecosystem that drives innovation and growth across Michigan.
At Automation Alley, our mission is to help businesses thrive in the rapidly changing digital economy. We equip them with the knowledge, insights, and tools to develop a software-first mindset that leverages the power of automation, AI, and other cognitive technologies. We believe that by working together, we can build a stronger, more innovative, and more competitive economy for the future.
Wealth, prosperity and equality through technology.
To find out more about Membership visit: automationalley.com
National Library of Medicine - Artificial intelligence for waste management in smart cities https://pubmed.ncbi.nlm.nih.gov/37362015/
Autodesk - Celebrating innovation, achievement, and sustainability https://adsknews.autodesk.com/en/stories/celebrating-innovation-achievement-and-sustainability/
Advanced Manufacturing (SME Media) - AM Stabilizing Shows Promise Across Industries https://www.advancedmanufacturing.org/technologies/additive/am-stabilizing-shows-promise-across-industries/article_093e822a-e2da-4d4b-8724-f1d8e09f0f65.html
Business Research Insights - DIRECTED ENERGY DEPOSITION (DED) PRINTER MARKET OVERVIEW https://www.businessresearchinsights. com/market-reports/directed-energy-deposition-ded-printer-market-121026
FDA - Technical Considerations for Additive Manufactured Medical Devices https://www.fda.gov/regulatory-information/search-fda-guidance-documents/technical-considerations-additive-manufactured-medical-devices
IndustryWeek - IBM X-Force Threat Intelligence Report https://www.industryweek.com/technology-and-iiot/cybersecurity/article/55043740/manufacturing-is-1-in-cyber-attacks-for-third-straightyear-what-can-be-done
Gartner - Gartner Forecasts Worldwide IT Spending to Grow 8% in 2024 https://www.gartner.com/en/newsroom/press-releases/2023-1018-gartner-forecasts-worldwide-it-spending-to-grow-8-percent-in2024#:~:text=In%20the%202024%20Gartner%20CIO,for%20organizations%2C%E2%80%9D%20said%20Lovelock
Deloitte - US Manufacturing Could Need as Many as 3.8 Million New Employees by 2033 https://www2.deloitte.com/us/en/pages/about-deloitte/articles/press-releases/us-manufacturing-could-need-new-employees-by-2033.html
Fortune Business Insights - 3D Printing Market Size, Share & Industry Analysis https://www.fortunebusinessinsights.com/industry-reports/3d-printing-market-101902
Publication Credits
Editorial: Nicole Kampe, Dennis Burck and Joseph Gray
Graphic Design: Laura Gearhart
Photography: Sean Healey and Corey Sims
Made possible in part through ongoing support from the