SUSTAINABLE FUTURES:
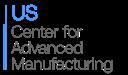


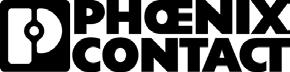

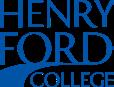
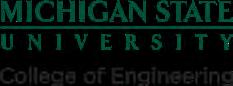
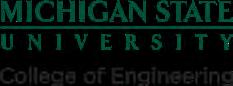

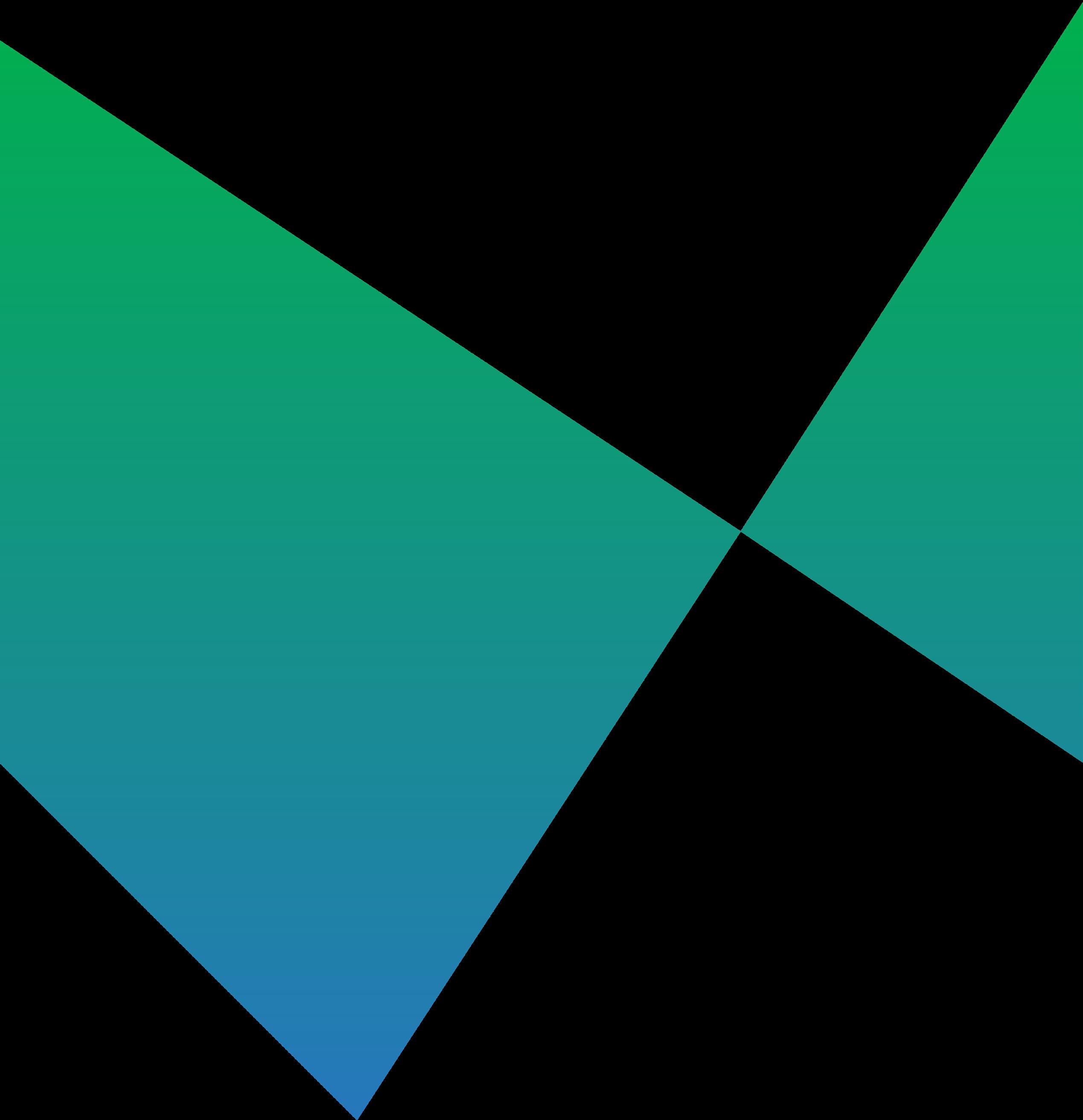
TOM KELLY EXECUTIVE DIRECTOR & CEO AUTOMATION ALLEY
We bear a profound responsibility in industry. Each year, industrial activities account for nearly 30% of U.S. greenhouse gas emissions, contributing significantly to the degradation of our environment. The question is, what are we doing to stem this trend? More importantly, how can our actions encourage other large contributors, such as the transportation and energy sectors, to embrace greener practices?
Addressing sustainability in industry requires a global perspective. Carbon emissions do not recognize national borders; they traverse continents freely, putting the entire planet at risk. This global challenge calls for a unified response from both industry and government. Together, they can collaborate to create fair and effective standards that incentivize sustainable practices.
Moreover, sustainability must be promoted across the entire product lifecycle, from design to disposal. This holistic approach ensures that environmental impact is minimized at every stage. With advancements in technology, such as cleaner manufacturing processes,
energy-efficient machinery, and smarter resource management, we are seeing promising innovations that could make industry more sustainable.
Our Integr8 roundtable on sustainability aimed to jumpstart this process by getting academia, industry and government in the same room to talk about sustainable implementations and the future of industry. Their findings are encapsulated throughout this playbook on the topic, and we are honored to curate their message.
Astronomer Carl Sagan once described our planet as a " pale blue dot," a fragile speck in the vastness of the cosmos. This image serves as a reminder of how small, yet precious, our world truly is. Beyond the lines on a map that separate nations, we share a collective duty to safeguard this planet.
As tenants of Earth and manufacturers, we must act with care and urgency, or risk being evicted by nature’s uncompromising laws. Let us embrace sustainability not just as an obligation but as an opportunity to reshape the future for generations to come.
TOM KELLY
EXECUTIVE DIRECTOR & CEO AUTOMATION ALLEY
EVAN D'SILVA FINANCIAL ADVISOR PRUDENTIAL
MAX NEVILLE COMMUNICATIONS SPECIALIST FORVIA
CHAN GILL
VERTICAL MARKET MANAGERFACTORY AUTOMATION PHOENIX CONTACT
ZOÉ BEZPALKO
SENIOR DESIGN & MANUFACTURING SUSTAINABILITY MANAGER AUTODESK
MILTON PUTMAN
CHIEF EXECUTIVE OFFICER AND FOUNDER COMPLETE IMAGE MANUFACTURING
OLUBUKOLA FAMUYIWA
MICHELLE HALSBAND OPERATIONS MANAGER FORWARD ENGINEERING
TODD WILLIAMS VICE PRESIDENT - INDUSTRIAL SYSTEMS LEIDOS
ASSOCIATE BUSINESS DEVELOPMENT ENGINEER DIGITAL - FACTORY NOW PHOENIX CONTACT MARY
NICHOLAS PASEIRO
IEMP COORDINATOR - CEM HENRY FORD COMMUNITY COLLEGE
ELIZABETH BERNHARD EXECUTIVE DIRECTOR MANUFACTURING GROWTH ALLIANCE
BEN WIXSON GROUP MANAGER - MICHIGAN ASA
By Chan Gill
Vertical Marketing Manager
Factory Automation
Sustainability means so many different things to many people, companies, and organizations. According to Webster’s Dictionary, sustainability is “capable of being sustained… of, relating to, or being a method of harvesting or using a resource so that the resource is not depleted or permanently damaged.”
We live in a complex world where sustainability is embraced by many and loathed by others. In business, the implementation of sustainable practices can be a difficult conversation, and tough decisions need to be made. What is the company’s position on sustainability? What do they know and understand about sustainability? How does a company start its sustainability or Net Zero journey? What is the government’s role and responsibility when it comes to sustainability?
So many questions and complexities. One thing is evident. Consumers are guiding the discussions with their
dollars and cents, supporting and investing in companies with public sustainability plans, Net Zero commitments, and actions supporting sustainability. They are using their buying power to send a message to all industries. Companies are driven every day by economic considerations, return on investment, and total cost of ownership. The adoption of sustainable practices, escalation of environmental trends, government programs, and investment are starting to drive sustainability in business in the United States.
The Inflation Reduction Act of 2022 earmarked $369 billion dollars for energy security and to address climate change. This is the single greatest investment in proclimate policy in our country’s history. For years, there has been discussion of environmental taxation being implemented, taxing companies (potentially individuals) on their carbon footprint.
Continued on next page >>
Europe has been embracing sustainability for several years. Now, they are driving it via Europe’s Corporate Sustainability Reporting Directive (CSDR). This year, the directive affects approximately 10,000 companies. In the future, it will affect more than 50,000. It’s not a secret that our U.S. policy is frequently influenced by that of Europe. Could a corporate sustainability reporting directive be on the horizon for the U.S.? Will it lead to a corporate carbon footprint tax?
We are learning that investment in sustainability has benefits. It can help companies grow their sales and client base, become more efficient, reduce their utility usage, and be more aware of their packaging materials and production waste. All this results in cost saving, better quality, a stronger, more positive corporate image, and helping to preserve our planet for future generations.
How does this tie in with Industry 4.0? Via data. Data is the new gold (as coined by either Clive Humby, British Mathematician, or… Salesforce).
Data is what we use to help us on our Net Zero journey; it is the starting point. We collect it, move it, analyze it, make decisions based upon it, create intelligence around it, and more and more importantly – we protect it (think cybersecurity).
Data helps us establish a baseline for our sustainability journey. We use this baseline to identify places in our business, operations, and production where we can:
• improve ourselves,
• become more efficient,
• understand our processes better,
• learn about producing quality parts and results,
• maintain our equipment better via condition-based monitoring,
• and understand the utilities we are using.
We then use our own human intelligence, along with artificial intelligence (AI) and machine learning (ML), to improve our operations and lessen our carbon footprint. The goal is to create a brighter tomorrow – a cleaner environment with renewable energy that is affordable for all.
This is the beginning of what will be the “All Electric Society.” We need to understand that we are borrowing the planet from the next generation. We owe it to them to do what we can to make this planet a better place. Yes, it can start with something as simple as recycling and eco-friendly packaging. But it must expand to include more than that. Companies need to examine not only their impact on the environment, but also their entire Product Environmental Footprint (PEF). PEF reflects the impact of a complete product on the environment from supply chain origination through its lifecycle. This will require transparency and trusting partnerships between the companies and people working together to adopt sustainable practices.
In closing, from the words of Jack Nehlig, President of Phoenix Contact USA: “We believe together, we can help create a more sustainable world, one based on our passion for technology and innovation. In the end, we want to power a smart, sustainable world for future generations to enjoy.”
The manufacturing industry is undergoing a seismic shift as sustainability becomes central to its future. As the environmental impacts of production become increasingly clear, manufacturers are tasked with balancing economic growth with environmental stewardship. Sustainable manufacturing aims to reduce resource consumption, minimize waste, and lower greenhouse gas (GHG) emissions, all while maintaining profitability.
Sustainable manufacturing refers to the process of creating products with minimal negative environmental impact, emphasizing energy efficiency, resource conservation, and a reduction in emissions. The U.S. Environmental Protection Agency (EPA) defines sustainable manufacturing as “the creation of manufactured products through economically sound processes that minimize negative environmental impacts while conserving energy and natural resources.” It goes beyond eco-friendly practices by focusing on the entire lifecycle of a product, from raw material extraction to end-of-life disposal or recycling.
What this exactly translates to in terms of an actionable manufacturing process is more complicated.
“We need a uniform understanding of what sustainability is across the board,” said Chan Gill, vertical marketing manager of factory automation at Phoenix Contact. “It means so many different things to different people, and there are different perspectives on it. We need to come to a consensus on what it means.”
What we can measure is manufacturing’s impact on the environment. The manufacturing sector is a significant contributor to greenhouse gas emissions, accounting for about 23% of global emissions, according to the EPA. Key sources of GHG emissions in manufacturing include the combustion of fossil fuels for energy, chemical reactions required to make products from raw materials, and the use of energy-intensive processes such as cement, steel, and chemical production.
To reach sustainability goals, many manufacturers are embracing commitments to ‘net-zero’ emissions. “One of the key phrases, especially in manufacturing, is net zero.” Gill said. “Essentially, it's a commitment to carbon neutrality, cutting your greenhouse gas emissions to as close to zero as possible, and then finding ways to offset the amount left over.”
Through its manufacturing process, Phoenix Contact supports six of the 17 United Nations Sustainable Development Goals (SDGs). However, there are significant challenges when striving toward a more sustainable manufacturing process.
Continued on next page >>
Cost of Transition: The most immediate challenge is the cost. Implementing energy-efficient technologies, shifting to renewable energy, and redesigning supply chains require significant upfront investments. However, Gill sees a broader trend: “Gen Z takes a lot of heat. They are also pushing companies across multiple industries to become more sustainable. How are they doing that? With their dollars and cents and what they buy.”
Technological Gaps: Despite advances in clean technology, manufacturers often face gaps between sustainable aspirations and available technological solutions. Zoé Bezpalko, senior design and manufacturing sustainability manager at Autodesk, stresses that “the challenge really lies in the 'how.' Technology is key to solving global challenges like climate change. Research shows that up to 73% of energy consumption in manufacturing can be avoided today using existing technology.”
Supply Chain Complexity: Manufacturers often operate within complex, global supply chains. Ensuring sustainability across every stage of production—from raw material sourcing to delivery—poses logistical and ethical challenges. Phoenix Contact is committed to making its entire supply chain sustainable, Gill added. “We have pledged to be net-zero through the entire supply chain. That means every little plastic bead, every ounce of silver, and every ounce of copper comes from sources that prove to us they are sustainable, and they have a sustainability plan for net zero by 2050.”
Consumer Expectations and Market Dynamics: While more consumers are demanding sustainable products, manufacturers must find ways to balance these market demands while maintaining profitability.
Manufacturers often operate within complex, global supply chains. Ensuring sustainability across every stage of production— from raw material sourcing to delivery— poses logistical and ethical challenges.
Several innovations are helping to move the needle on sustainability in manufacturing.
Industry 4.0 and Smart Manufacturing: The integration of digital technologies is transforming how manufacturers operate. According to Bezpalko, “AI and ML can be used to program machines, learn trends in energy and material usage, and shift the use of these resources to different times, optimizing sustainability.”
Renewable Energy Integration: Renewable energy adoption is a key strategy in reducing GHG emissions. Gill emphasizes the role of software in improving sustainability: “Software’s going to be a big piece of sustainability no matter how we look at it. One of the hottest things we see in the industry today is utility gear monitoring.”
Government regulations play a pivotal role in encouraging manufacturers to adopt sustainable practices.
Nicholas Paseiro, IEMP coordinator at Henry Ford Community College, highlighted the role of government support: “Government incentives obviously can help bridge the gap. With small companies, having energy independence helps them to have freedom and confidence in their decision-making.”
For large-scale change, infrastructure development is crucial. “The government needs to invest in infrastructure today to enable a circular economy,” Bezpalko noted. “How that, in turn, is going to make it easier for consumers to participate within the circular economy? Because it’s all about convenience.”
Achieving sustainability in manufacturing requires collaboration. “Collaboration is one of the challenges we see today, Bezpalko said. “How do we bring a pre-competitive collaboration, maybe by standardizing the workflows and processes, maybe by opening that black box of technology so that it's not something owned by a single company, but shared across the industry?"
Moreover, educational institutions have an important role. “Educational institutions can provide a space for students, CEOs, and governors to collaborate—spaces for different people within a community to work together,” Paseiro said.
Sustainability in manufacturing is no longer optional; it is an imperative driven by environmental, economic, and regulatory pressures. By adopting innovative technologies and practices, manufacturers can reduce their environmental footprint while maintaining economic viability. While the path to sustainable manufacturing is fraught with challenges, the opportunities for innovation, cost savings, and competitive advantage are substantial.
“Technology is key to solving global challenges like climate change,” Bezpalko said.
“Sustainability is a data problem; currently the data required is completely disconnected—across industries, stages of the product life cycle, and stakeholders. Connecting all of that is a real challenge.”
"Technology is key to solving global challenges like climate change,” and it will play a critical role in reshaping the future of manufacturing.
The World Economic Forum highlights that industrial waste, including waste from manufacturing processes, accounts for at least 50% of the global waste. Reducing waste is essential for both environmental impact and cost savings.
Achieving sustainability in manufacturing requires a holistic approach that integrates cutting-edge technology, efficient resource use, and collaboration across the supply chain. The transition to a circular economy—where waste is minimized and materials are reused— demands intentional planning and the adoption of Industry 4.0 technologies.
The World Economic Forum highlights that industrial waste, including waste from manufacturing processes, accounts for at least 50% of the global waste. Reducing waste is essential for both environmental impact and cost savings. By implementing waste audits, manufacturers can identify areas of inefficiency and improve recycling efforts. Some key steps to achieve this include:
Material Efficiency: Manufacturers should focus on minimizing the materials they use and finding opportunities to reuse or recycle production byproducts. This includes reducing packaging, switching to biodegradable materials, and designing products that use fewer parts and are easier to disassemble for recycling.
Energy Use Optimization: Energy-intensive industries can benefit from upgrading old machinery to more energy-efficient models. For example, air compressors, which can be significant energy drains, should be routinely inspected for leaks and maintained properly. Poorly maintained air compressors cost U.S. manufacturers $3.2 billion annually in wasted energy, according to the US Department of Energy.
Energy from Renewables: Installing commercial solar panels can reduce energy costs and reliance on fossil fuels. Research from Northeastern University shows that rooftop solar installations could meet 5-35% of U.S. manufacturing electricity needs The federal solar tax credit, available through 2034, provides an incentive for this transition
Building Design for Efficiency: Manufacturers can reduce energy use by designing or retrofitting buildings to incorporate natural light, upgrading insulation, and installing programmable thermostats and high-efficiency HVAC systems.
Industry 4.0 technologies—such as IoT, AI, and machine learning—offer manufacturers significant opportunities to monitor and optimize resource use in real-time.
IoT for Resource Optimization: IoT devices can track material usage and equipment performance, providing data that helps manufacturers streamline production, reduce waste, and anticipate supply chain disruptions. For example, real-time data from sensors can enable more accurate inventory management and prevent overproduction that leads to waste.
AI for Predictive Maintenance: Using AI to monitor machinery allows manufacturers to predict equipment failures and schedule maintenance before breakdowns occur. This approach extends the lifespan of machinery, reducing the need for new raw materials and minimizing production downtime. A study by Shell found that AI predictive maintenance reduced equipment failures and led to significant cost savings
Digital Twins: Digital twins create virtual models of manufacturing processes, allowing companies to simulate production scenarios and optimize resource use without physical trial and error. This technology can also simulate environmental impacts, helping manufacturers design more sustainable production lines and buildings
Sustainability isn’t achieved in isolation. Manufacturers must collaborate with their suppliers and logistics partners to reduce the overall environmental impact of their supply chains. Some strategies include:
Sharing Data: Supply chain transparency allows all stakeholders to better forecast material needs, avoid overproduction, and reduce waste. Open data platforms and IoT networks enable real-time information sharing about inventory levels and transportation routes, reducing inefficiencies.
Promoting Green Logistics: By adopting electric vehicles (EVs) for transport, optimizing shipping routes, and reducing redundant shipments, manufacturers can significantly lower their carbon footprint. AI and virtual reality (VR) can help predict disruptions, such as weather events, and allow logistics teams to plan accordingly.
Setting Common Goals: Manufacturers and their supply chain partners should commit to shared sustainability targets, such as reducing CO2 emissions or improving recycling rates. These collaborations can drive larger systemic change across industries.
To fully embrace a circular economy, manufacturers must consider sustainability from the product design phase. Products should be designed for durability, repairability, and recyclability. Key principles include:
Modular Design: Products made with fewer, standardized parts are easier to repair and recycle. Manufacturers can encourage consumers to repair products rather than discard them by offering repair kits and making disassembly simple.
Recycling-Focused Design: Avoiding mixed-material products and using easily recyclable materials can ensure that products stay within the circular economy longer. Including disassembly instructions or videos can encourage consumers to recycle components instead of discarding them
Design for Additive Manufacturing: Products designed for additive manufacturing use only the material needed, significantly reducing waste. This method allows for more efficient designs, incorporating complex geometries and reducing the need for multiple parts, while ensuring recyclability and resource efficiency.
The world is only 8.6% circular, down from 9.1% just two years ago, according to a February 2024 report from Circle Economy. With over 100 billion tons of materials consumed annually, it’s clear that new approaches are urgently needed. Academia plays a crucial role in this transformation by developing curriculum focused on sustainable materials, environmental impact, and sustainable engineering practices, while fostering partnerships with industry to pilot innovative technologies and approaches for a circular economy.
Colleges and universities must develop interdisciplinary programs that combine engineering, environmental science, data analytics, and social sciences. These programs can focus on sustainable materials, renewable energy, and waste reduction while teaching students how to design products and systems with circularity in mind. Courses should emphasize lifecycle analysis, closed-loop systems, and emerging Industry 4.0 technologies such as additive manufacturing.
Sustainability Engineer: Designs systems and processes that reduce environmental impact.
Circular Economy Specialist: Develops strategies to keep materials in use longer through recycling, remanufacturing, and sustainable sourcing.
Environmental Data Analyst: Uses data to forecast environmental trends and develop strategies to minimize industrial waste.
Green Building Architect: Designs energy-efficient, sustainable buildings.
Renewable Energy Engineer: Works on developing and implementing technologies like wind, solar, and geothermal systems.
To effectively train students for the future, academia should create deeper collaborations with industry. Establishing live projects where students work alongside professionals on real-world sustainability challenges—such as waste reduction, clean energy installations, or sustainable manufacturing innovations—will provide invaluable hands-on experience. Internship programs and cooperative education (co-ops) can inject fresh perspectives into companies while giving students opportunities to contribute to the circular economy through practical work.
Examples:
• Partnering with manufacturers to improve energy efficiency using IoT systems.
• Co-developing sustainable supply chains that prioritize material reuse and responsible sourcing.
Sustainability depends on advancing technology. Universities should prioritize hands-on experiences in renewable energy, smart manufacturing, and resource-efficient design. Encouraging innovation through tools like AI, VR, and 3D printing will help students build practical solutions. Virtual simulations of complex systems—such as geothermal extraction or energyefficient production lines—can expose students to the challenges and opportunities of sustainable engineering. Additionally, collaboration between departments like chemistry, engineering, and environmental science will foster interdisciplinary innovation.
Project Ideas:
• Install solar or wind energy systems on campuses, allowing students to track energy output and propose optimizations.
• Utilize VR to simulate material extraction and sustainability impacts in mining or drilling operations.
Internship programs and cooperative education (co-ops) can inject fresh perspectives into companies while giving students opportunities to contribute to the circular economy through practical work.
Governments can move the idea of a circular economy forward by setting policies and regulations related to sustainable manufacturing practices, offering financial incentives to invest in greener strategies and technologies, and supporting infrastructure development for recycling and waste management.
Achieving sustainability requires cooperation among many parties. The manufacturing, technology, shipping, aerospace, transportation, and shipping industries are among the dozens of sectors that must set objectives to create an effective and longlasting circular economy.
Each sector and its companies will establish their own goals and timetables to achieve those benchmarks, but governments can step in and help set a common path to a greener future.
Governments can move the idea of a circular economy forward by setting policies and regulations related to sustainable manufacturing practices, offering financial incentives to invest in greener strategies and technologies, and supporting infrastructure development for recycling and waste management.
To improve manufacturing practices, the government announced in an October 2022 report a National Strategy for Advanced Manufacturing, presented by the Subcommittee on Advanced Manufacturing Committee on Technology of the National Science and Technology Council.
Under the first objective, Develop and Implement Advanced Manufacturing Technologies, the U.S. government aims to enable clean and sustainable manufacturing to support decarbonization. The report states: "The United States has committed to 50-52% reduction of net GHG (greenhouse gasses) emissions below 2005 levels in 2030, and net-zero by 2050. The Inflation Reduction Act, signed into law in August 2022, in combination with the infrastructure modernization investments in the Bipartisan Infrastructure Law enacted in November 2021, will provide significant resources and incentives to help reach the climate and clean energy goals. These new resources, via the National Climate Task Force and the Executive Order on America's Supply Chains, will facilitate the efforts to advance clean energy and climate-aligned manufacturing across the U.S. Government."
The report offered the following recommendations to achieve the objective:
• Decarbonization of Manufacturing Processes: Develop and demonstrate advanced manufacturing technologies that increase energy efficiency, electrify industrial processes, employ lowcarbon feedstocks and energy sources in manufacturing, support new chemistries that avoid direct greenhouse gas emissions from industrial processes, capture and store industrial carbon dioxide, and create alternatives to GHG-intensive industrial products. Create and disseminate validation tools and processes to assist the integration of electrified and efficient technologies into manufacturing. Create transparency on advanced materials and processes with lower energy and carbon footprints.
• Clean Energy Manufacturing Technologies: Improve materials, manufacturing processes and product designs for clean electricity generation and storage; zero-emission transportation, buildings, and industry to enable a decarbonized economy. Enhance the manufacturing of devices and materials that enable more efficient power conversion and transmission with advanced conducting materials, processing technologies and machine development. Manufacture advanced batteries with high energy densities and secure novel sustainable materials for low- and high-voltage applications.
• Sustainable Manufacturing and Recycling: Develop economically viable manufacturing technologies that separate valuable materials from waste streams, as well as alternatives to energy - or pollutionintensive materials. Conduct R&D in the areas of sorting, purification, and deconstruction technologies. Scale up sustainable materials design and manufacturing, recycling and circular methods for multiple materials classes, and pilot programs and facilities. Improve data and methods to assess life cycle impacts and identify areas for improvement.
The report further discusses advancing greener initiatives by focusing on the bioeconomy. In 2022, President Joe Biden signed an executive order "on Advancing Biotechnology and Biomanufacturing Innovation for a Sustainable, Safe, and Secure American Bioeconomy." The order calls for a government-backed approach to "provide innovative solutions in health, climate, change, energy, food security, agriculture, supply chain resilience, and national and economic security."
Under this order, the federal government encourages industry leaders to find ways to incorporate biotechnology to use natural rubber, bioplastics, renewable chemicals, sugar, natural fibers, yeast, algae, and other sustainable materials in products.
Local, state, and federal governments can partner with industrial, technology, and supply chain leaders to examine fossil fuel usage and find ways to reduce it and implement renewable energy sources.
That spirit of cooperation can be implemented in other areas, such as using metals, lumber, and water conservation. Regulations for mining, deforestation, and industrial water use can be established to ensure minimal environmental impact and the preservation of soil and water sources.
Each level of government must collect data associated with using natural resources and manufacturing processes that impact the environment. A partnership between government officials and private sector leaders can create sustainable regulations that are achievable and allow businesses to implement them quickly and affordably.
Just 8.6% of extracted materials “make it back into the economy,” according to Forbes. The public and private sectors must address that low percentage. Forbes suggested ways to increase the amount of reused materials with strategies such as product-as-a-service, product life extension, and design for recycling, pointing out each strategy poses potential tax implications.
• Product-as-a-service (renting or leasing): The automotive industry has been leasing vehicles for decades, and that model is catching on in other areas. According to Forbes, "Stripe saw a 550% increase in the money spent on renting clothing, equipment, and tools in the first three quarters of 2022 compared with the same period in 2019." They noted that tax collection in the U.S. varies by state, and some cities impose their own lease taxes.
• Product life extension: In this model in which a business buys back products from customers and resells them at a discount to reduce the materials extraction needed to create new products. The tax concern is that taxes are collected for each resale. The European Union encourages reselling by eliminating its value-added tax if the product is resold at a cheaper price. Some EU countries reduce their VAT on repairs for resold products. In the U.S., taxing repair services varies by state.
• Design for Recycling: Design for recycling is aimed at "maximizing the recoverability of materials for use in new products. Despite clear environmental benefits of material reuse, products made from recycled materials are taxed in the same way as those made from newly extracted resources,” according to Forbes. They stated that businesses in the EU have asked for a reduction of value added tax for recycled products, but a study showed that those savings do not get passed on to buyers, so consumers' habits haven't changed. Another issue is categorizing products for tax reduction, which could make the incentive structure complex and ripe for misuse.
First, the federal government should work with state and local officials to unify rental and leasing rules and offer tax incentives at each level for companies renting or leasing products and equipment that meet the requirements to be considered "green."
Second, a price reduction price point for resold items should be determined to exempt them from sales tax. Also, allow repair costs, materials purchased, and tools and equipment to receive tax reductions or eliminations.
Third, establish classifications and reduce or eliminate taxes on products made using recycled materials. Work with industry leaders to find ways to promote those products and pass some of the savings on to their customers to encourage purchasing greener options.
Beyond reducing product taxes, governments can promote sustainable manufacturing through tax incentives to purchase more energy-saving equipment and environmentally friendly offices and facilities.
Some of the current incentive programs include:
1. The 179D Commercial Buildings Energy-Efficiency Tax Deduction offers a $5.36 per square foot deduction for building upgrades such as water systems, HVAC, insulation, heating, and lighting.
2. Commercial Clean Vehicle Credit makes certain electric vehicles eligible for credits of $7,500 for vehicles under 14,000 pounds and up to $40,000 for vehicles exceeding 1,4000 pounds.
3. Biodiesel Tax Credit allows businesses that power their vehicles with pure, unblended biodiesel (B100) up to a $1 per gallon credit. This incentive expires on Dec. 31, 2024.
4. Other tax credits are available, including hydrogen, fuel cells, and wind, as well as improved waste energy collection and storage.
5. ENERGY STAR, a voluntary U.S. EPA program, has a vital business component that aids in making commercial buildings more energy efficient. According to the ENERGY STAR website, "the program for commercial buildings and industrial plants helped businesses and organizations save 230 billion kilowatt-hours of electricity, avoid $14 billion in energy costs, and achieve 170 million metric tons of greenhouse gas reductions.” The program also offers certifications to the private sector.
The U.S. Department of Energy offers grants to finance research and technology improvements in renewables, nuclear energy, state programs, small business innovations, carbon management, and other clean energy and water initiatives.
There are billions of dollars available from all levels of government. The manufacturing and technology industries must take advantage of these funds to develop new sustainable policies and processes to extend product life, reclaim natural resources, improve energy efficiency, and reduce the economy's environmental impact, making it more circular.
The development of infrastructure to support sustainable manufacturing is critical for driving a circular economy in industry. Efficient recycling and waste management systems that focus on industrial waste streams, rather than just residential programs, are key to ensuring that valuable materials are reused in manufacturing processes. Governments can play a pivotal role by fostering infrastructure that supports the recycling of industrial byproducts such as metals, chemicals, plastics, and electronic waste, helping manufacturers reduce their environmental impact.
One strategy for achieving this is through industrial symbiosis, where the waste or byproducts of one manufacturing process serve as inputs for another. Governments can help facilitate this by creating regional industrial ecosystems that connect manufacturers, allowing them to exchange materials and reduce overall waste. For example, a byproduct from a metal fabrication plant could be repurposed as raw material for a chemical manufacturer. This type of collaboration can lower costs for manufacturers and reduce the burden on natural resources.
Additionally, governments should invest in sustainable manufacturing infrastructure that supports the adoption of advanced technologies aimed at reducing energy consumption, water usage, and emissions. This can include providing incentives for manufacturers to retrofit their operations with green technologies such as energy-efficient machinery, renewable energy systems, and carbon capture solutions. Investing in smart manufacturing systems that optimize resource use through data analytics and automation can further enhance sustainability efforts across the sector.
An essential tool for driving sustainability in manufacturing is life cycle assessment (LCA), which evaluates the environmental impacts of a product or process from "cradle to grave." This includes everything from raw material extraction to production, use, and final disposal. Life cycle data enables manufacturers to understand the full environmental impact of their operations and make informed decisions about material sourcing, product design, and process improvements.
Government support for continued LCA data collection, reporting, and analysis is crucial for setting sustainability goals and monitoring progress. The federal government can help by funding research and technology that aids industries in tracking their environmental footprint across the supply chain. Policies that incentivize transparency in reporting, such as requiring life cycle disclosures for certain products, can push the entire sector toward more sustainable practices.
The Solid Waste Infrastructure for Recycling (SWIFR) grant program, initiated under the Bipartisan Infrastructure Law, is a strong example of how government can support improved recycling systems. While this program currently focuses on general recycling efforts, its principles can be adapted to industry by encouraging the development of infrastructure that supports post-industrial material recovery and recycling at a larger scale. Grants and incentives for industrial recycling facilities that can handle complex manufacturing waste streams, such as electronics or chemical byproducts, can make a significant difference.
Building infrastructure for the recovery of raw materials from industrial waste streams is a critical component of a circular economy. Governments should invest in advanced recycling facilities and technologies that can handle the specific needs of manufacturers. These facilities should be equipped to sort, process, and return valuable materials like metals, rare earth elements, and polymers back into the production cycle, reducing reliance on virgin materials and lowering overall emissions from extraction and processing.
In partnership with industry leaders, the government can also establish material recovery zones in key industrial regions, where manufacturers can take advantage of shared recycling facilities. These zones would help create localized hubs of circular manufacturing, reducing transportation costs and supporting regional economic growth.
To drive sustainability in manufacturing, governments must focus on building infrastructure that supports industrial recycling, promotes life cycle assessment, and encourages the development of technologies that enable circular practices. Collaboration between public and private sectors is essential to ensure that the necessary infrastructure is in place to reduce waste, conserve resources, and lower the environmental impact of manufacturing processes. By prioritizing investment in sustainable infrastructure, governments can help lead the transformation toward a more circular and sustainable manufacturing future.
If Sustainability is Your Problem,
is Your Solution
By Zoé Bezpalko Senior Sustainability Strategy Manager, Product Design & Manufacturing, Autodesk
When I talk to manufacturers about sustainability, many of them are frankly scared.
The concern is understandable. By 2050, the demand for energy is expected to increase by 50 percent, with projected resource use doubling by that date. Companies that want to compete globally will need to comply with stringent carbon regulations such as those set by the Paris Agreement, the European Ecodesign Directive, and Digital Product Passport.
In fact, this shift toward sustainability represents an enormous opportunity—especially for U.S. manufacturers, who can access to millions of dollars in tax rebates and credits if they take proactive steps to reduce their carbon footprints. And the very thing they need to complete much of this work is already at their fingertips: data. According to the University of Cambridge , up to 73 percent of energy consumption can be avoided with current techniques, technologies, and know-how.
The real challenge is bringing all of this information together.
"This shift toward sustainability represents an enormous opportunity —especially for U.S. manufacturers."
Here’s a sampling of how our customers and partners have achieved extraordinary sustainability outcomes, largely using data that already lived in their environments.
Designing Leaner Products: Using the generative design features of Autodesk Fusion, the sports equipment manufacturer and retailer Decathlon created a diving fin that is twice as light as the market benchmark, with half the carbon footprint. Fusion leverages machine learning and artificial intelligence to iterate multiple design options based on user-defined constraints, which allowed the Decathlon team to take a “blank slate” approach to their new product design. The React fin, selected as one of the company’s best product innovations in 2023, also incorporates recycled materials, and it is made from a single type of plastic—simplifying end-of-life recycling.
Optimizing Energy Consumption: Using Autodesk Platform Services (APS), 20 consortium members from several European countries developed the ECO-innovative Energy FACTory Management platform (ECOFACT) at four demonstration sites across Europe. The initiative includes a digital twin platform that combines industrial digital twin models of production lines and machines with simulation and optimization tools into a single web environment, with the aim of better tracking and optimizing energy use. At one site, the effort cut thermal energy consumption and CO2 emissions each by 16 percent .
Research and development accounts for only around five percent of the total cost of most products, and yet around 80 percent of the environmental impact of products is determined at this early stage. The problem is that most companies lack an effective method for bringing together information from throughout the product lifecycle. Autodesk collaborated with our partner Pré Sustainability, and their flagship LCA software SimaPro to develop a lifecycle assessment application that enables designers and manufacturers to access bill-of-materials data early in the research and design stage—providing them with insights during the part of the process when this information can make the greatest impact.
For manufacturers overwhelmed by looming carbon requirements, the good news is that they likely already have much of the technology—and much of the data—they need to rise to this challenge. Currently, that information is spread out not only across the product lifecycle, but also among a wide array of different personas and even regions. To calculate the true environmental cost of production, a company might need to determine the carbon equivalent of a kilowatt-hour of energy produced in a specific country, or calculate the different carbon outcomes of running a CNC machine in Poland versus China.
Again, this information largely already exists—somewhere. By adopting digital tools and processes that bring their siloed sustainability data together in one place, manufacturers can not only avoid falling behind but they can position themselves as leaders in the sustainability space.
"By adopting digital tools and processes that bring their siloed sustainability data together in one place, manufacturers can not only avoid falling behind but they can position themselves as leaders in the sustainability space ."
Automation Alley posted weekly polls in June and July 2024 for our LinkedIn followers of over 6,000 professionals in the technology and manufacturing ecosystem on the topic of Sustainability. This is how the industry responded at a glance.
Which stage in the manufacturing value chain are renewed sustainability efforts needed the most?
How
Adopting Sustainable Practices: Manufacturers can achieve sustainability by reducing material waste, optimizing energy use, and switching to renewable energy sources. Key actions include improving material efficiency, upgrading machinery, and installing commercial solar panels to reduce reliance on fossil fuels. 1 2 3 4 5 6
Balancing Economic Growth with Environmental Stewardship: Sustainable manufacturing aims to minimize environmental impacts—such as reducing greenhouse gas emissions and conserving resources—while still maintaining profitability. This shift is essential as manufacturers face increasing pressure to balance growth with sustainability.
Technological Innovation as a Driver: Advances in Industry 4.0, smart manufacturing, and renewable energy are pivotal to achieving sustainability. Existing technologies, such as AI and machine learning, can optimize energy usage, while renewable energy adoption reduces emissions.
Collaboration and Policy Support are Crucial: Achieving sustainable manufacturing requires collaboration across industries and support from government policies. Incentives, infrastructure investment, and educational partnerships play a key role in enabling manufacturers to adopt sustainable practices.
Curriculum Integration for Circular Economy: Colleges and universities should develop interdisciplinary programs that incorporate sustainable materials, renewable energy, and waste reduction. These courses must emphasize lifecycle analysis and circular economy principles, preparing students to design sustainable systems using emerging technologies like additive manufacturing.
Collaborating Across the Supply Chain: Manufacturers must work with suppliers and logistics partners to achieve sustainability goals. Strategies include sharing data for better forecasting, promoting green logistics by adopting electric vehicles, and using AI to optimize routes and reduce environmental impact.
Automation Alley is a nonprofit technology business association and Digital Transformation Insight Center focused on driving the growth and success of businesses in Michigan and beyond through innovation and automation. With a global outlook and a regional focus, we foster a vibrant community of innovators, entrepreneurs, and business leaders through opportunities for collaboration and learning. Our programs and services help businesses develop the skills and expertise needed to effectively jumpstart or accelerate digital transformation. By bringing together industry, academia, and government, we aim to create a dynamic ecosystem that drives innovation and growth across Michigan.
At Automation Alley, our mission is to help businesses thrive in the rapidly changing digital economy. We equip them with the knowledge, insights, and tools to develop a software-first mindset that leverages the power of automation, AI, and other cognitive technologies. We believe that by working together, we can build a stronger, more innovative, and more competitive economy for the future.
Wealth, prosperity and equality through technology.
Publication Credits
Editorial: Nicole Kampe, Dennis Burck, Joseph Gray
Graphic Design: Laura Gearhart
Photography: Sean Healey and Corey Sims
EPA - Sources of Greenhouse Gas Emissions https://www.epa.gov/ghgemissions/sources-greenhouse-gas-emissions
The Planetary Society - A Pale Blue Dot https://www.planetary.org/worlds/pale-blue-dot#:~:text=Carl%20Sagan%20Unveils%20the%20Pale,the%20Voyager%20missions%20in%201990.
EPA - Sustainable Manufacturing https://www.epa.gov/sustainability/sustainable-manufacturing
Phoenix Contact - Sustainability https://www.phoenixcontact.com/en-us/company/sustainability
United Nations - The 17 Goals https://www.globalgoals.org/goals/
Circle Economy - Our world is now only 8.6% circular https://www.circle-economy.com/news/our-world-is-now-only-8-6-circular
World Economic Forum - How AI can solve manufacturing's waste problem https://www.weforum.org/agenda/2021/04/how-ai-can-cut-waste-in-manufacturing/
Northeastern University - Rooftop solar panels could power one third of US manufacturing sector https://ioppublishing.org/news/rooftop-solar-panels-could-power-one-third-of-us-manufacturing-sector/
Solar Learning Center - 30% Federal Solar Tax Credit Extended Through 2032 https://www.solar.com/learn/federal-solar-tax-credit-steps-down/
Shell - Shell Achieves Major Milestone: Scales Artificial Intelligence Predictive Maintenance to 10,000 Pieces of Equipment Using C3 AI
https://c3.ai/shell-achieves-major-milestone-scales-artificial-intelligence-predictive-maintenance-to-10000-pieces-of-equipment-using-c3-ai/
National Strategy for Advanced Manufacturing
https://www.whitehouse.gov/wp-content/uploads/2022/10/National-Strategy-for-Advanced-Manufacturing-10072022.pdf
Does Tax Policy Support The Circular Economy?
https://www.forbes.com/sites/aleksandrabal/2023/01/17/does-tax-policy-support-the-circular-economy/
179D Commercial Buildings Energy-Efficiency Tax Deduction
https://www.energy.gov/eere/buildings/179d-commercial-buildings-energy-efficiency-tax-deduction
Commercial Clean Vehicle Credit
https://www.irs.gov/credits-deductions/commercial-clean-vehicle-credit
Biodiesel Tax Credit
https://afdc.energy.gov/laws/396
Other Tax Credits
https://www.dsireusa.org/
Energy Star
https://www.energystar.gov/buildings/about-us#:~:text=ENERGY%20STAR%20is%20a%20voluntary,that%20commercial%20buildings%20use%20 energy.
The U.S. Department of Energy https://www.energy.gov/funding-financing
Solid Waste Infrastructure for Recycling (SWIFR) grant program https://www.epa.gov/infrastructure/solid-waste-infrastructure-recycling-grant-program
Made possible in part through ongoing support from the