RISE OF THE MACHINES:

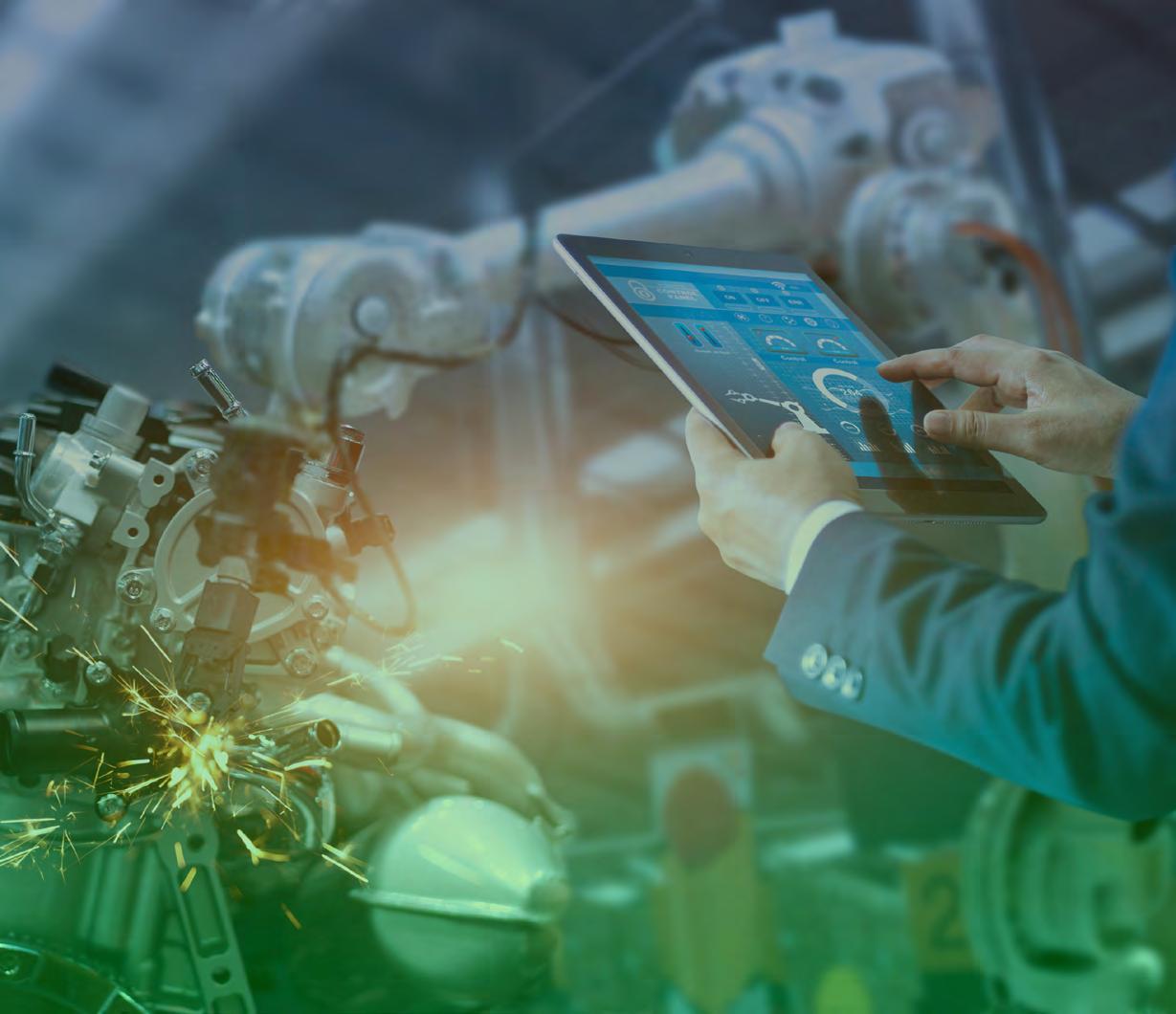
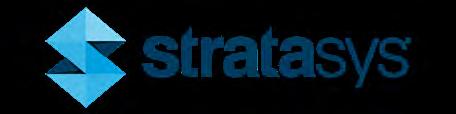
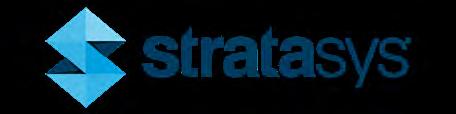
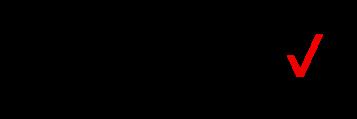
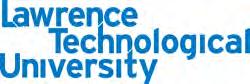
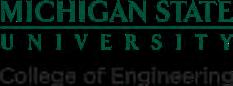
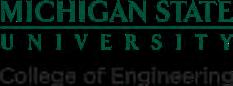

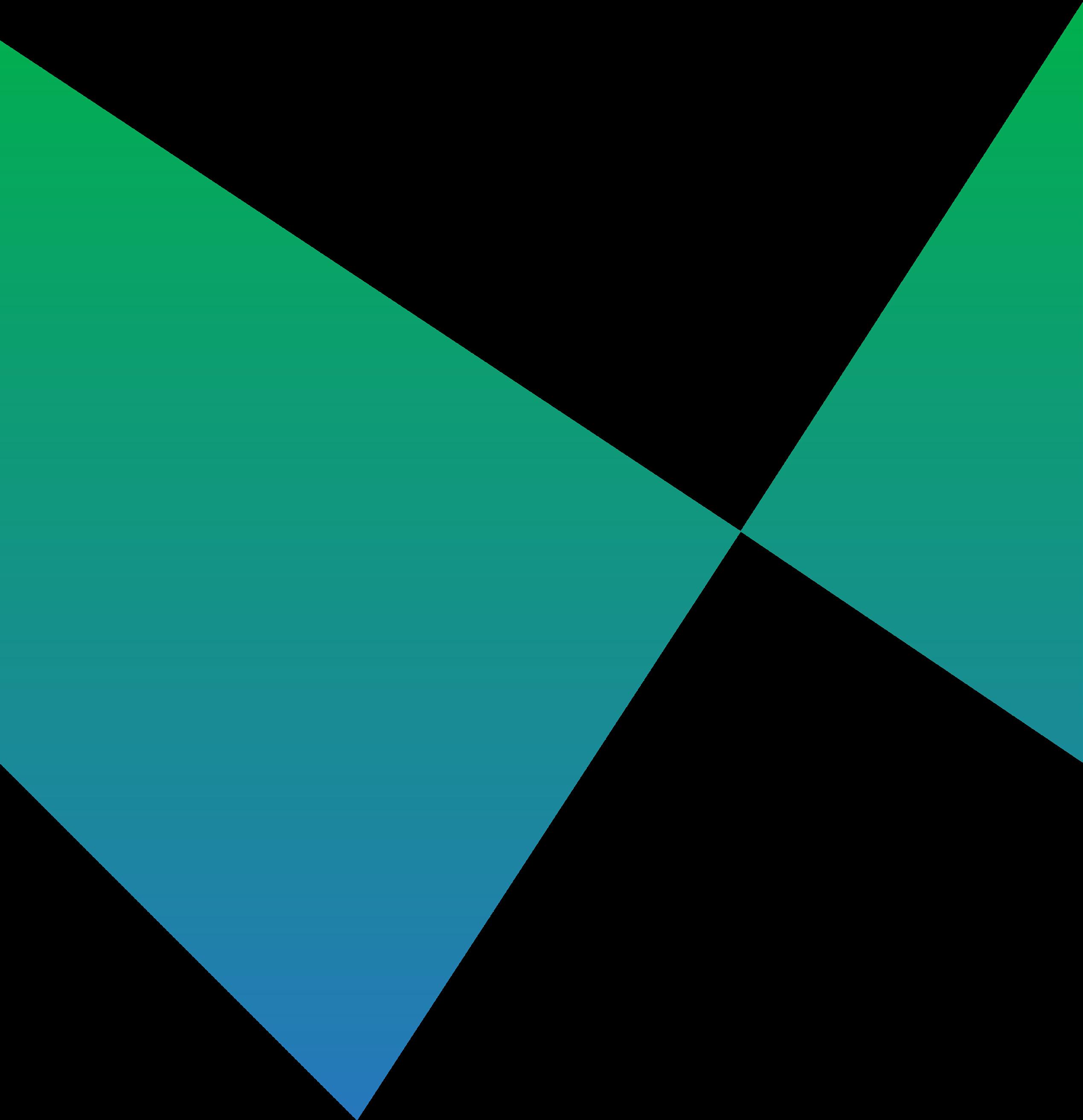
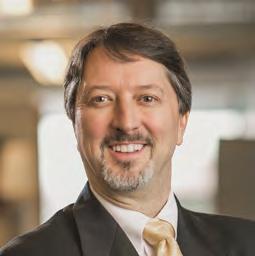
TOM KELLY EXECUTIVE DIRECTOR & CEO AUTOMATION ALLEY
TOM KELLY EXECUTIVE DIRECTOR & CEO AUTOMATION ALLEY
DR. ROYA SALEHZADEH ASSISTANT PROFESSOR
LAWRENCE
TECHNOLOGICAL UNIVERSITY
Five years ago, few would have believed we were on the brink of self-programming robots capable of learning assembly without human intervention. Yet today, the rapid advancements in AI place us at that precipice.
Google’s DeepMind exemplifies the potential of AI-driven robotics, with applications that could revolutionize our industry as this technology matures. While still in its infancy, these systems are mastering basic tasks—like fitting square pegs into square holes—entirely on their own, without human guidance in refining their decision-making. They are learning independently.
But today’s simple tasks raise an intriguing question: What will tomorrow hold? Will we witness robots that can design custom tooling simply by observing a part? Will they adapt in real time to shifting production lines? Only time and innovation will tell.
What’s clear is that we are in a pivotal era that will shape the future of automation and advanced robotics, fueled by the rapid integration of AI into our daily operations.
To navigate this landscape, we sought insights from our expert members on several critical issues and trends in robotics and automation:
DR. JAMES MYNDERSE, PHD ASSOCIATE PROFESSOR
LAWRENCE
TECHNOLOGICAL UNIVERSITY
Human-Machine Collaboration: How ready is our work culture to embrace collaboration with cobots? What synergies can emerge to address potential challenges?
Addressing Workforce Shortages: With 65% of manufacturers citing workforce shortages as their primary concern, can automation serve as a stopgap solution? Might it even lead to job creation in the long run?
Emerging Technologies: What new technologies are shaping the future of robotics and automation? How can we best support their development?
We are proud to present expert dialogue on these pressing questions, drawing insights from leaders in government, industry, and academia. Together, these sectors can drive meaningful change and illuminate the path forward amidst the challenges posed by emerging technologies.
We are living in an exhilarating time for robotics and automation. Let us unite as industry partners to navigate these transformative changes together.
DAN STEWART RELATIONSHIP MANAGER AUTOMATION ALLEY
INGRID TIGHE PRESIDENT MICHIGAN MANUFACTURING TECHNOLOGY CENTER
SRINIVAS KUPPA CHIEF TECHNOLOGY OFFICER SYMPHONYAI
JOSEPH DESANTO CRO LINCODE LABS INC.
DAN ROMAN DIRECTOR-INFRASTRUCTURE AND NETWORKS VERIZON
GEORGE SINGOS STRATEGY AND PARTNER OUTREACH MICHIGAN MANUFACTURING TECHNOLOGY CENTER
GARY KRUS VP OF BUSINESS DEVELOPMENT AND OPERATIONS HIROTEC AMERICA
DAN KENDALL EXECUTIVE VP / OWNER 313 INDUSTRIES INC.
DR. ROYA SALEHZADEH ASSISTANT PROFESSOR LAWRENCE TECHNOLOGICAL UNIVERSITY
BRADLEY PEIRSON PROGRAM DIRECTOR BAKER COLLEGE
SVEN NOWAK HEAD OF CYBERSECURITY AND FUNCTIONAL SAFETY TUV RHEINLAND OF NORTH AMERICA, INC.
RASMUS BENDVOLD MANAGING DIRECTOR, US WHEEL ME
KYLE BEARDMORE DIRECTOR HARCOURT
DR. JAMES MYNDERSE, PHD ASSOCIATE PROFESSORH LAWRENCE TECHNOLOGICAL UNIVERSITY
TROY NEVA VERTICAL SALES DIRECTOR SIEMENS
JAMES KLUMP DIRECTOR OF SALES BIZLINK ROBOTIC SOLUTIONS USA, INC.
JEROME FEIG FOUNDER AND OWNER MINOXY
TRAVIS PEITZ BUSINESS DEVELOPMENT MANAGER EXPORT CORPORATION
JOSEPH PETROSKY VICE CHANCELLOR FOR ECONOMIC & WORKFORCE DEVELOPMENT OAKLAND COMMUNITY COLLEGE
ROB STIPEK ADDITIVE MANUFACTURING ACCOUNT MANAGER DESIGNFUSION
RAJESH IYENGAR FOUNDER AND CEO LINCODE LABS INC.
DR. XIAOHONG (SHAWN) GAYDEN FOUNDER AND CEO INTECELLS, INC.
By Jennifer Artley Senior Vice President, 5G Acceleration
otivated by the need for faster, safer and more efficient operations – and concerned about persistent skilled labor shortages – business leaders and technology executives in a wide range of industries are making robotics and automation key components of their long-term digital transformation efforts.
At Verizon, we serve 99% of Fortune 500 companies, and these relationships give us unparalleled insight into how leaders in almost every industry – manufacturing, energy, retail, distribution and logistics, and even health care –are working to drive innovation and efficiency through robotics and automation.
Every day, in consultation with our customers, we see that advances in robotics – from AGVs and AMRs (automated guided vehicles and autonomous mobile robots) to “cobots” (collaborative human/robot applications) – are revolutionizing entire industries.
And every day, Verizon’s customers are seeing first-hand how advances in private wireless network connectivity and edge computing are transforming robotics and automation.
Connectivity is at center of IT/OT convergence
After years of media hype, we are at last witnessing the true convergence of so many breakthrough technologies – robotics, AI, IoT, AR and VR, to name a few. While these capabilities are wildly diverse in their form factors and uses, they all have one thing in common: they need reliable, high-speed, low-latency network connectivity to support near-real time data capture and analysis. Technology systems are only as performant as their slowest common denominator. Continued on next page >>
That’s why more and more companies are deploying private 5G networks at their facilities, and that’s why our research keeps finding that edge computing and private networks have become strategic priorities.
For example, in October 2023, Verizon sponsored an Enterprise Strategy Group (ESG) survey of 472 business leaders from multiple industries, asking about intentions and priorities for IT spending. The resulting report, “Going Beyond Digital Transformation,” showed that 54% of respondents said “becoming more operationally efficient” is their number one IT-related goal.
Further, 64% of ESG survey respondents said that learning to leverage edge computing is a “top 5” priority. And 71% reported that 5G would play a “critical” or “significant” impact on their ability to achieve their goals.
“As organizations deploy massive numbers of IoT devices, IP cameras, autonomous vehicles and artificial-intelligence-driven applications, they will likely find it challenging to collect, analyze, and act on the huge amount of data these devices yield,” the ESG report reads. “What’s becoming evident as organizations strive to be even more ‘data-driven’ is the need for a network design that provides the high speed, low latency, and edge computing power needed for real and near-real time decision-making and action.”
In April, 2024, Verizon sponsored an IDC survey of more than 1,100 IT and business leaders. Again showcasing the importance of robotics and automation, the resulting paper, “Private 4G/5G Networks Driving Operational and Strategic Gains for Enterprises,” finds that 34% of survey respondents say “increasing operational efficiency” is their second most important desired business outcome from IT investment. (“Improving customer satisfaction” was the number one goal, with 35%).
Private 5G connectivity, the IDC paper finds, “creates a framework for gaining mission-critical insight into customer preferences, enabling realtime, autonomous operations and realizing material improvements to the bottom line.”
A private 5G network is an exclusive, dedicated wireless 5G network within a customer location (like a corporate campus or a factory floor). It’s a costeffective, highly reliable, ultrafast, and secure solution, allowing companies to achieve a whole new level of operational efficiency, innovation, agility, and competitiveness.
Better still, private wireless can be integrated into existing network infrastructures, eliminating the need to “rip and replace.” Many of Verizon’s customers find that private 5G is just right for certain conditions, applications and use cases, and can augment existing Wi-Fi networks to continue to support low-latency and non critical applications
But because private 5G can provide coverage to tens of thousands of devices across hundreds of square miles – versus Wi-Fi’s limited reach measured in yards – private 5G requires fewer access points to manage, maintain and secure. This helps drive down operating costs and enhances overall network agility and resilience.
One of the more exciting robotic capabilities that many of our customers are evaluating and deploying involves the intersection of machine visioning, digital twins and predictive maintenance.
Meanwhile, edge computing puts processing power and storage where it’s most needed: at the edge of the network, close to where data is generated. Edge computing helps further reduce latency and, when coupled with 5G, makes access to remote servers vastly more efficient. An ultra-fast, lowlatency network and edge computing, for example, can enable robots to become fully integrated pieces of the Industrial Internet of Things (IIoT).
One of the more exciting robotic capabilities that many of our customers are evaluating and deploying involves the intersection of machine visioning, digital twins and predictive maintenance.
Robots equipped with cameras and sensors can inspect products for defects, leveraging AI to ensure only high-quality products proceed. Robots can even perform ultrasonic or X-ray inspections on manufactured components, identifying internal flaws without damaging the product.
With private 5G and edge computing, robots are also growing smaller and lighter, and moving them from points A to B becomes easier. With 5G and edge, less computing power is needed aboard a robot because complex functions can be performed on nearby servers, with negligible impact on machine responsiveness. This means clunky processors and giant batteries can be stripped from robots, reducing their form factors and drastically increasing their mobility.
In some cases, a piece of machinery that was previously tethered to an electrical outlet may be freed to move nimbly around the floor, often autonomously.
In board rooms, on factory floors, and in any one of Verizon’s many 5G innovation labs, our conversations with customers are no longer just about the “art of the possible.” Instead, together we are sharing insights and best practices about how – right now – our company and theirs are using private 5G, edge computing, robotics and automation to control costs, improve throughput, and increase revenue.
Many companies tell us that private wireless isn’t just solving today’s challenges; it’s inspiring plans for future innovation and business transformation.
It’s an exciting time to be on either end of these conversations.
The workforce is evolving. From sci-fi to commonplace, collaborative robots, autonomous ground vehicles and traditional robotic arms are augmenting the workforce. These intelligent machines, supercharged from the marriage of Artificial Intelligence and the Internet of Things, are reshaping factory floors as we know them.
With promises of increased productivity, improved safety, and greater flexibility, automation and robotics are at the forefront of the fourth industrial revolution. According to the International Federation of Robotics, 523,000 new robots were installed worldwide in 2023, bringing the total number of operational robots in industry to more than 4.5 million.
However, adopting robots is not without its challenges. Concerns about job displacement, ethical considerations, and the need for workforce retraining are key obstacles. As with any major technological shift, the transition to automated robotics requires careful planning and open dialogue between employers, employees, and policymakers.
Collaborative robots, or "cobots," are a key example of how AI, IoT, and automation intersect. Cobots are designed to work alongside human workers, not replace them. Equipped with advanced sensors and software, cobots can detect the presence of nearby humans and adjust their movements to ensure safe interactions.
While automation has long been a part of manufacturing, the current wave represents the latest stage in a centuries-long evolution. The first industrial revolution introduced mechanized production powered by steam and water. The second revolution, driven by electricity and mass production, further accelerated automation. The third revolution brought computers, electronics, and information technology to manufacturing. Now, with cyberphysical systems, Industry 4.0 is transforming the landscape once again.
A prominent feature of this transformation is the rise of Automated Guided Vehicles (AGVs) and Autonomous Mobile Robots (AMRs). These robots are now used in about 60% of automotive manufacturing facilities and 80% of e-commerce operations.
"Safety may not be the primary driver of why to adopt, but it is a benefit of adoption,” said Dan Roman, Director of Private Wireless Infrastructure at Verizon. “Language independence per robot plays an important part in adoption rates too."
Robotic Process Automation (RPA) is also contributing to innovation. Whereas older systems were limited to repetitive tasks, modern cobots possess capabilities that allow them to perform tasks alongside humans with remarkable efficiency. These machines are increasingly integrated into real-world workspaces, coexisting safely with human workers.
The benefits of robotic automation are clear, especially in terms of efficiency. Cobots allow human workers to focus on higher-level, valueadded tasks that require creativity and problem-solving. By leveraging the unique strengths of both humans and machines, operations can run more smoothly and productively.
Technological advancements have made the deployment of cobots more feasible. The rise of AI and reductions in market costs have enabled companies—large and small—to implement robotic automation more quickly than anticipated.
For example, in 2021, Procter & Gamble partnered with MassRobotics to explore how automation could improve time-to-market and operational efficiency. Meanwhile, a 2022 McKinsey Global Industrial Robotics Survey projected that automation and robotics will account for 25% of capital spending for industrial companies in the next five years.
Ingrid Tighe, President of the Michigan Manufacturing Technology Center, emphasized that cobots, robots, and other technology are becoming more accessible and manageable. “They are easier to use, more dynamic, and more affordable. So, we are seeing more and more companies able to adopt and use this technology. This is augmenting the workforce, and we are seeing the benefits, i.e., cobots aiding in surgery.’”
Roman also stressed that addressing workforce training is essential to maximizing the potential of robotics. "One of the key things we addressed is robotics workforce training. It has to be a continuous investment from the organization in order to enable the full potential of cobots in autonomous environments."
The rise of AI and reductions in market costs have enabled companies–large and small–to implement robotic automation more quickly than anticipated.
While the advantages of robotics are significant, there are challenges to widespread adoption. High costs, integration issues, and concerns from employees and leadership must be addressed.
"In addition to technical challenges, leaders need to address the cultural environment around automation and turnover," Roman explained. "To avoid distrust, sell the value to the partners in your organization instead of dictating it."
• How does the total cost of ownership for cobots (including initial investment, maintenance, and training) compare to labor costs over a five- to 10-year period?
• What new revenue streams or market opportunities could be unlocked by integrating cobots into production processes?
• How will cobot integration affect product quality and consistency? Can we estimate potential reductions in defects or waste?
• What are the projected impacts on workplace safety, and how can we quantify savings from reduced injuries or accidents?
• How will cobots improve employee job satisfaction and retention by taking on repetitive or physically demanding tasks?
While cobots handle many tasks, human skills like creative problemsolving, critical thinking, and emotional intelligence remain irreplaceable in manufacturing. For example, robots are not yet capable of troubleshooting complex, unforeseen issues, such as power disruptions, or optimizing production workflows on the fly. Furthermore, robots need ongoing maintenance, ensuring demand for skilled technicians who can repair and service these machines.
Roman also raised the question: "Another perspective shift is, should we look at automation as an RD functionality instead of an ROI functionality?" This shift in thinking may alter the approach many companies take when evaluating the value of robotic investments.
Education plays a crucial role in overcoming resistance to robots in the workplace. Companies must invest in training programs that allow workers to learn how to work alongside robots—whether it's learning to program, service, or simply coexist with them on the factory floor.
"Workforce re-skilling and training are essential," said Tighe. "Virtual training is now something companies can use with AR/VR. Community colleges are implementing mechatronic and PLC robotics programs."
Effective change management strategies, clear communication, and robust training programs will be essential in easing concerns and demonstrating that robots complement, rather than replace, human workers.
AI, IoT, and other emerging technologies have advanced at such a rapid pace that predicting the future of robotics in manufacturing is challenging. However, current trends provide some insight.
Sustainability is becoming a major priority for manufacturers, driven by both operational needs and consumer demand. Robotic automation can help companies achieve sustainability goals by optimizing material usage, reducing waste, and improving logistics. Robots are also more precise and consistent than their human counterparts, further reducing inefficiencies.
Roman highlighted the importance of data in improving robotics systems: "How do we enable robotics to be self-healing? To do this, we need to analyze the data pools to understand the line and automation as a whole."
The environmental impact of robots themselves is also being addressed. Many manufacturers are incorporating recyclable materials, modular designs for easier repairs, and energy-efficient components. For instance, AI-powered systems can automatically shut down non-essential equipment during off-peak hours to reduce energy consumption.
Looking ahead, the capabilities of cobots are expected to expand. Future cobots may be equipped with advanced sensors that allow them to perform delicate assembly tasks, identify microscopic defects, or handle complex material handling jobs. Machine learning algorithms will make cobots more autonomous and adaptable, improving their efficiency with use. In short, the future of robotics in Industry 4.0 is burning bright, and is already being accelerated by technology developing in partnership with it today.
Machine learning algorithms will make cobots more autonomous and adaptable, improving their efficiency with use.
Industrial facilities report an average monthly shutdown costs up to $125,000 per hour. By leveraging data and predictive analytics, manufacturers can extend equipment lifespan, decrease downtime, and improve resource allocation.
As robotics technology continues to advance, manufacturing companies must strategically consider how to integrate robotics and Industry 4.0 technologies to maximize productivity, address workforce challenges, and enhance competitiveness. Below are key recommendations for industry leaders seeking to successfully adopt robotics within their operations.
The rapid evolution of robotics—driven by advancements in AI, machine learning, and generative AI—is transforming manufacturing. Generative AI, for instance, now enables intuitive robot programming through natural language, allowing operators to adjust robot actions without needing specialized coding skills. This makes robotics more accessible to a broader workforce and reduces training time and cost. Moreover, robots equipped with machine learning capabilities can adapt to diverse tasks, making them valuable in dynamic, high-mix manufacturing environments.
Incorporating connected devices and predictive analytics through the Internet of Things (IoT) can help optimize production by providing real-time insights into machine health, inventory needs, and workflow efficiency. Predictive maintenance, enabled by AI, helps reduce unplanned downtimes, which can be costly. According to a 2023 study by ABB, industrial facilities report an average monthly shutdown costs up to $125,000 per hour. By leveraging data and predictive analytics, manufacturers can extend equipment lifespan, decrease downtime, and improve resource allocation.
Industry leaders should prioritize the following technological advancements to maximize robotics adoption:
• Mobile Manipulators (MoMas): These robots, which combine mobility with dexterous arms, can navigate complex manufacturing environments, perform material handling tasks, and handle equipment maintenance. This adaptability reduces bottlenecks and helps address labor shortages.
• Soft Robotics: Developing robots with flexible, damage-resistant materials improves safety and reduces wear on delicate parts and products.
• Enhanced Sensing Technology: Upgraded cameras, 3D guidance, and sensor arrays allow robots to perform precise tasks and improve their interactions with surrounding environments.
For smaller manufacturers, adopting robotics presents unique challenges, including cost, flexibility, and workforce considerations. However, advances in collaborative robots (cobots) and affordable automation solutions have made robotics adoption feasible even for SMEs.
To maximize the value of robotics in smaller operations, SMEs should:
1. Take a Holistic View of Automation: Robotics should enhance the entire production process, not just replace human tasks. Redesign processes as needed to fully leverage robotic capabilities.
2. Start Small and Expand Gradually: Begin with a single, simple automation project to build confidence and expertise within the team, then scale up based on successful outcomes.
3. Engage the Workforce in Automation Adoption: Introduce automation gradually, involving employees at each step to gain buy-in and foster a collaborative approach to change. Automation should be part of an ongoing change-management strategy.
4. Focus on Upskilling the Workforce: Automation can free employees from repetitive tasks, allowing them to focus on higher-level responsibilities. Providing training opportunities empowers employees to support, maintain, and improve robotic systems.
5. Leverage Available Resources and Funding: Many regions offer subsidies or grants to help SMEs implement automation. Exploring these options can significantly reduce the upfront cost of robotics.
As robots handle routine tasks, workers can focus on strategic roles, enhancing productivity and job satisfaction while supporting business growth.
Collaborative robots, or cobots, are designed to work alongside humans safely and efficiently. Cobots excel at repetitive or physically demanding tasks, allowing human workers to focus on complex problem-solving and innovation. However, successful human-cobot collaboration requires careful planning and adherence to safety protocols.
To create a safe and efficient environment for cobots, manufacturers should:
Prioritize Safety: Conduct thorough safety assessments, ensure cobots have sensors to detect human presence, and maintain clear boundaries around cobot work zones.
Implement Regular Maintenance: Routine inspections and preventive maintenance minimize the risk of mechanical failures, reducing safety hazards and avoiding costly downtime.
Provide Comprehensive Safety Training: Train all employees on cobot interactions and establish clear guidelines on safety practices.
Equip Cobots for Specific Tasks: Match cobots to appropriate tasks, such as handling heavy objects or performing precise assembly, to minimize strain on human workers and reduce injury risks.
Cobots also offer an opportunity to upskill employees, preparing them for roles that involve programming, monitoring, and maintaining robotic systems. Investing in employee training not only increases engagement but also builds a workforce skilled in managing advanced technologies.
Adopting robotics and Industry 4.0 technologies is not just about increasing efficiency—it’s a pathway to achieving a competitive edge. Industry leaders can use robotics to expand capabilities, improve production quality, and explore new markets. With robotics handling routine processes, manufacturers can shift focus to developing innovative products, exploring customization options, and enhancing customer experiences.
Some ways robotics can enhance competitiveness include:
Optimizing Throughput and Flexibility: Robotics can help manage complex, mixed-product manufacturing lines, increasing responsiveness to changing customer demands.
Reducing Operational Costs: Automation can decrease the cost of production over time, allowing companies to reinvest in research and development.
Enhancing Product Quality: Robots reduce human error in assembly, inspection, and packaging, resulting in consistent, high-quality products.
1. Upskilling and Reskilling Programs: As robots take on repetitive and physically demanding tasks, companies should focus on training employees for roles that require higher-level skills, such as robotics programming, troubleshooting, and systems maintenance. Offering training in data analytics, IoT integration, and AI programming can further enable workers to manage and optimize robotic processes effectively.
2. Collaborative Training Programs with Educational Institutions: Partnering with local colleges, trade schools, and technical training centers to develop robotics-specific programs ensures a steady pipeline of skilled workers. This partnership can also create internship opportunities, allowing students to gain practical experience and companies to identify potential hires.
3. Developing Career Pathways in Robotics: Defining clear career paths that integrate robotics expertise can boost employee engagement and retention. By mapping out pathways—from entry-level technician roles to advanced robotics engineer positions—companies can show employees a long-term future within the organization, supporting talent retention.
4. Employee Engagement in the Automation Process: To foster a culture of collaboration, companies should actively involve employees in the robotics adoption process. Gathering feedback, involving employees in initial rollouts, and encouraging team members to propose areas for further automation can build enthusiasm and trust in the new technology.
5. Cross-Training in Human-Robot Collaboration (Cobots): With the rise of cobots, training employees to work seamlessly with robots is essential. Cross-training allows workers to understand the safe handling and potential of cobots, enabling them to identify efficiencies and suggest further applications in daily operations.
Academia plays a critical role in the advancement of robotics and automation in industry. To address the rapid expansion of robotics and the adoption of advanced technologies in factories, academia and the private sector must collaborate to build a talent pipeline that meets current and future workforce demands. By creating strategic partnerships, integrating advanced technologies in learning environments, and fostering interdisciplinary studies, educational institutions can play a pivotal role in advancing the robotics sector and driving digital transformation.
Hands-on robotics projects offer students from elementary to higher education a progression of learning experiences—from basic programming to complex problem-solving, fostering essential skills like collaboration, communication, and critical thinking. As students advance, exposure to robotics encourages an early interest in STEM fields, laying the foundation for further studies in math, programming, and engineering.
Additionally, classrooms can leverage robotics to transform the educational landscape, providing personalized support for students with disabilities, assisting with complex tasks, and creating an engaging learning environment. Institutions should consider adopting assistive robots to support students with diverse needs, including vision and hearing impairments and physical disabilities. By integrating robotics into lessons, educators can provide dynamic learning experiences that improve engagement and outcomes for all students, particularly those with learning challenges.
Colleges and universities should emphasize STEM programs that support robotics innovation, with specialized curricula in fields such as advanced mathematics, engineering, computer science, and artificial intelligence. Robotics education also benefits from interdisciplinary approaches, combining technical skills with insights from environmental science, sociology, political science, and communication. This broader focus equips students to address the societal impacts of robotics, from resource management to public perception and regulatory considerations.
By fostering interdisciplinary programs, educational institutions can prepare students not only to develop cutting-edge technology but also to anticipate and manage the broader effects of robotics in society.
The private sector is instrumental in bridging the gap between academic training and industry needs, addressing challenges such as teacher shortages in STEM fields and the high costs associated with robotics programs. Companies can support educational initiatives by offering grants, scholarships, co-op programs, and expert-led workshops. Providing resources like parts, tools, and equipment enables institutions to maintain up-to-date robotics labs and support hands-on learning experiences.
Additionally, industry collaboration can shape workforce readiness by aligning academic curricula with evolving technology needs. Companies can engage with academic leaders to develop a workforce strategy that includes reskilling and upskilling, ensuring that students graduate with skills relevant to the current market. This alignment will provide students with a clear path to careers in robotics, fueling innovation and sustaining the industry's growth.
Industry collaboration can shape workforce readiness by aligning academic curricula with evolving technology needs.
Federal grants and funding programs are essential to enable companies, particularly small and medium-sized businesses, to innovate in robotics without financial barriers.
To support the growth of robotics in manufacturing and promote the digital transformation of industry, government agencies should focus on fostering innovation, establishing clear standards, and investing in workforce development. By implementing these strategies, government entities can help advance robotics technology and contribute to a robust talent pipeline, ensuring the industry remains competitive on a global scale.
Federal grants and funding programs are essential to enable companies, particularly small and medium-sized businesses, to innovate in robotics without financial barriers. Programs like the U.S. Small Business Administration’s SBIR (Small Business Innovation Research) and STTR (Small Business Technology Transfer) are critical, providing billions in funding to thousands of companies annually to advance new technologies. These grants enable the exploration and commercialization of robotics innovations, benefiting both the public and private sectors.
Maintaining and expanding these funding avenues will support research and development in robotics, allowing the U.S. to keep pace in the global race for technological leadership.
Investment in robotics today lays the groundwork for domestic production, efficiency gains, and economic growth in the years ahead.
With the increasing use of AI-driven robotics, the government plays a crucial role in establishing standards to ensure safety, fairness, and interoperability. Unified national regulations will help the robotics industry streamline compliance, fostering innovation while addressing public concerns about data privacy, security, and algorithmic bias. Federal standards that cover the collection, storage, and use of data generated by robots—as well as cybersecurity protocols—are essential to protect sensitive information and build public trust in robotic technologies.
Furthermore, governments can work closely with industry leaders, technology experts, and civil rights advocates to create regulations that balance technological advancement with ethical considerations. Safety standards specific to cobots (collaborative robots) used in manufacturing are particularly important to protect workers on the factory floor. National guidelines on payload capacities, maintenance requirements, and usage protocols will help minimize workplace risks, ensuring safe integration of robotics into manufacturing environments.
As the demand for robotics talent grows, government initiatives must focus on developing a skilled workforce ready to meet the needs of a technology-driven manufacturing sector. Governments can support STEM education in K-12 schools and fund specialized training programs at universities, including partnerships with private-sector robotics companies to facilitate internships, apprenticeships, and mentorships. By investing in talent development, governments can ensure a steady stream of qualified professionals equipped with the technical skills needed to design, operate, and maintain robotic systems.
Supporting initiatives to reskill and upskill existing workers will also be essential as automation becomes more prevalent. Workforce development programs should prioritize flexible, modular training opportunities that can be adapted to evolving technology, empowering workers to transition smoothly into new roles within the digital economy.
The robotics industry thrives on collaboration between government, academia, and private industry. Government-sponsored research partnerships can accelerate innovation by providing resources for projects that may be too costly or complex for companies to undertake alone. By facilitating partnerships between educational institutions and technology companies, the government can help align academic curricula with industry needs, creating a more relevant and effective training pathway for future workers.
Moreover, governments can incentivize private companies to contribute to public robotics initiatives by offering tax breaks, grants, or recognition programs for businesses that support education, training, or research in robotics.
As robotics technology continues to integrate into daily life and work, governments should prioritize transparent communication about its use and potential societal impacts. Public information campaigns can educate citizens on how robotics is used across sectors—from manufacturing and healthcare to public safety and environmental monitoring. Providing opportunities for community feedback on government robotics initiatives will help build public trust and allow for responsive governance.
By making information on robotics use, AI algorithms, and data management publicly available, governments can mitigate concerns around job displacement, surveillance, and data privacy. Regular evaluations on efficiency, safety, and ethical implications should be conducted, with results shared openly to foster a well-informed public.
By Ingrid Tighe, President Michigan Manufacturing Technology Center
obotics is having more than a moment in manufacturing. Humanoids are stealing the spotlight in pilot programs at Amazon warehouses and BMW and Mercedes plants, but enhancements to tried-and-true technologies are the developments making waves in our industry. Collaborative robots and vision systems are more versatile and accessible than ever— and many small- and mid-size manufacturers see them as a critical way to stay competitive and streamline their operations.
Collaborative robots have long been one of the most commonly adopted robotic technologies, and the advancements keep piling up. Just ten years ago, five manufacturers produced the world’s cobots, and applications trended toward palletizing and packing. Today, more than 30 cobot manufacturers exist, and capabilities have expanded and diversified, with cobots that feature single or multiple arms, precise end-of-arm tools and grippers, and scanners or other vision systems. Cobots take up limited floor space and have a smaller learning curve than many other emerging robotic technologies. With their ever-growing range of capabilities, they are a smart option for manufacturers seeking greater efficiency, enhanced quality, and the ability to compensate for workforce shortages and make production safer for human workers.
Advanced vision systems have been improving quality in many sectors for years by using cameras and sensors to gather data about the manufacturing process, identify risks and defects, and even perform tasks in response. Smart camera-based and compact systems are simpler, more affordable options for small- and mid-size manufacturers, but the capabilities of advanced vision systems run the gamut. The most common uses for vision systems in manufacturing include visual or sensor-based inspections that trigger automated repair. They can also be paired with a robotic arm for part location or bin picking, or with an AMR to navigate warehouses autonomously. Advanced vision systems have a variety of applications and entry points, and this versatility is making them increasingly popular among small- and mid-size manufacturers.
The impact of robotics on manufacturing is significant and growing, and collaborative robots and advanced vision systems are proving to be crucial entry points for smaller manufacturers. Small- and midsize manufacturers are using technology to save money, improve quality, enhance their supply chains, and reduce the impact of worker shortages—crucial actions to keep them competitive in an ever-changing global marketplace. Robotics is forever changing the way we do business and is the path of the future for Michigan companies.
Automation Alley posted weekly polls in August 2024 for our LinkedIn followers of over 6,000 professionals in the technology and manufacturing ecosystem on the topic of Robotics. This is how the industry responded at a glance.
On average, does deploying advanced robotics in your facility cut employees in your workforce?
The integration of robotics, AI, and IoT is reshaping industries, particularly on factory floors. Collaborative robots (cobots), autonomous vehicles, and robotic arms are augmenting human workers to increase productivity, improve safety, and provide greater flexibility. The total number of operational robots in industry surpassed 4.5 million in 2023, signaling widespread adoption.
Cobots are designed to work alongside humans, not replace them. They enhance human productivity by handling repetitive, physically demanding tasks, allowing workers to focus on higher-level duties requiring creativity and problem-solving. This collaborative model promotes efficiency and helps improve job satisfaction by reducing workplace injuries and stress.
While the benefits of robotics are clear, significant challenges remain, including high costs, technical integration issues, and employee concerns about job displacement. Successful adoption requires robust workforce training, change management strategies, and open communication to ensure workers can operate, program, and repair robots alongside traditional tasks. Organizations need to invest in continuous education and retraining.
Robotics is increasingly seen as a tool for achieving sustainability goals, reducing waste, optimizing resource usage, and enhancing energy efficiency. Looking ahead, the capabilities of cobots will continue to expand with advancements in AI and machine learning, enabling robots to perform more delicate tasks, improve operational efficiency, and contribute to environmental sustainability by using energy-efficient components and recyclable materials.
Emerging technologies like generative AI, machine learning, and predictive analytics are transforming robotics. These innovations allow for intuitive robot programming, making automation more accessible even for non-experts. For instance, natural language interfaces and AI-driven predictive maintenance are helping manufacturers optimize production, extend equipment lifespan, and reduce costly downtime. Robotics, equipped with soft materials and advanced sensors, can now perform a broader range of tasks, from delicate handling to dynamic, high-mix manufacturing.
To meet the growing demand for robotics talent, governments must invest in STEM education at the K-12 and university levels, as well as in specialized training programs for existing workers. Developing a skilled workforce through public-private collaborations, internships, apprenticeships, and reskilling initiatives will help ensure that workers are equipped to design, operate, and maintain robotic systems. By fostering these talent pipelines, governments can ensure that the workforce is prepared for the technological shifts brought about by automation and robotics.
Partnerships between academia and the private sector are essential to ensure that robotics education aligns with current and future industry demands. Companies can support educational initiatives through grants, scholarships, and providing resources like equipment and expertise. Collaborating with academic institutions also helps shape curricula that equip students with the skills needed to meet workforce requirements, ensuring that the talent pipeline remains strong and supports innovation in the robotics sector. 1 2 3 4 5 6 7
Automation Alley is a nonprofit technology business association and Digital Transformation Insight Center focused on driving the growth and success of businesses in Michigan and beyond through innovation and automation. With a global outlook and a regional focus, we foster a vibrant community of innovators, entrepreneurs, and business leaders through opportunities for collaboration and learning. Our programs and services help businesses develop the skills and expertise needed to effectively jumpstart or accelerate digital transformation. By bringing together industry, academia, and government, we aim to create a dynamic ecosystem that drives innovation and growth across Michigan.
At Automation Alley, our mission is to help businesses thrive in the rapidly changing digital economy. We equip them with the knowledge, insights, and tools to develop a software-first mindset that leverages the power of automation, AI, and other cognitive technologies. We believe that by working together, we can build a stronger, more innovative, and more competitive economy for the future.
Wealth, prosperity and equality through technology.
Publication Credits
Editorial: Nicole Kampe, Dennis Burck, Joseph Gray
Graphic Design: Laura Gearhart
Photography: Sean Healey and Corey Sims
Google - Deepmind
https://deepmind.google/discover/blog/shaping-the-future-of-advanced-robotics/
National Association of Manufacturers - Study: Manufacturing in U.S. Could Need Up to 3.8 Million Workers https://nam.org/study-manufacturing-in-u-s-could-need-up-to-3-8-million-workers-30626/
International Federation of Robotics - World Robotics - Industrial Robots https://ifr.org/wr-industrial-robots/
United Robotics Group - Embracing the next generation of manufacturing automation https://unitedrobotics.group/en/blog/article/embracing-the-next-generation-of-manufacturing-automation
Robotics 24/7 - MassRobotics Partners With Procter & Gamble to Explore Manufacturing Automation Advances https://www.robotics247.com/article/massrobotics_partners_with_procter_gamble_to_explore_manufacturing_ automation_advances