IMMERSIVE HORIZONS:
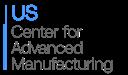

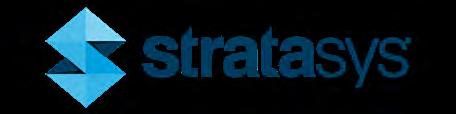

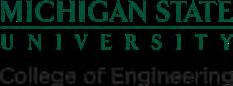
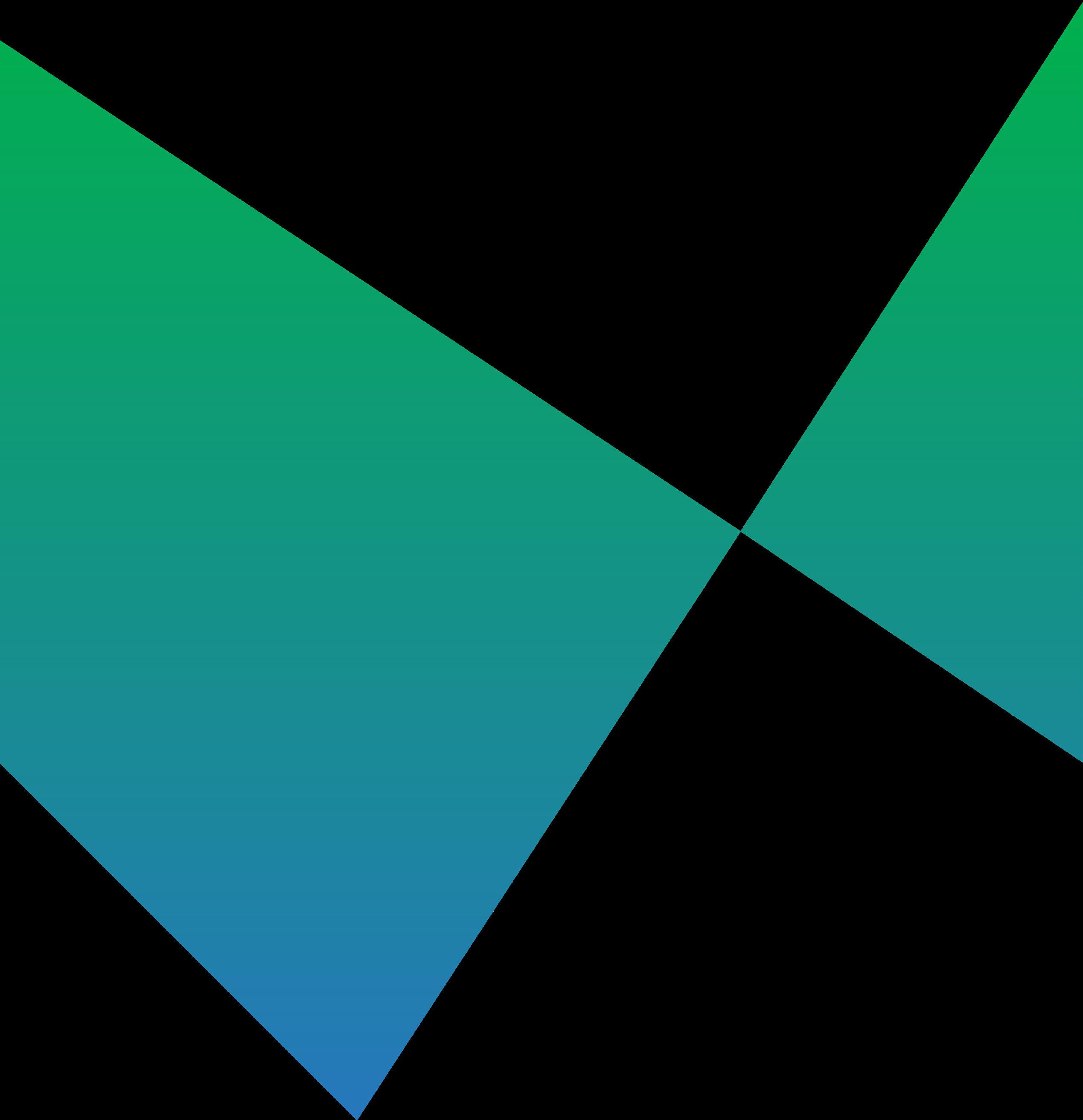
TOM KELLY EXECUTIVE DIRECTOR & CEO AUTOMATION ALLEY
Humans are vision-driven creatures, and the saying “seeing is believing” is not just another cliché. Eighty percent of all learning comes through vision. Therefore, it is no wonder that Augmented Reality and Virtual Reality (AR and VR) hold so much promise in the future of industries, whether it is for training purposes, collaboration across continents or understanding design changes in real time.
However, bridging the physical and digital world is no easy task. High development costs, technical limitations, and the need for more immersive and user-friendly experiences are significant hurdles facing the AR and VR market today.
These issues can cause businesses to be hesitant to adapt to AR and VR work due to unclear ROI. But a churning workforce may be just one case that pushes adoption over the edge.
Training with AR and VR provides a substantial fast-tracked and enhanced way to educate prospective employees in a safe setting with
negligible risk to themselves and the company. This way, the learning curve is not a learning cliff.
In an Airforce study on virtual reality training for avionic maintenance, AR/VR technology cut 20 days worth of traditional coursework off the syllabus for airmen to gain proficiency.
Furthermore, in design, AR and VR are providing new ways to collaboratively work on projects within the cloud across vast locations in real time.
Join us as we explore the future of AR and VR with thought leaders and innovators from across industries. Our experts will share insights on the latest advancements, discuss the challenges of integrating AR and VR into existing workflows, and examine how these technologies can drive innovation and growth.
We are at the cusp of a new era in humancomputer interaction. Let us embrace the possibilities of AR and VR as we shape the future together.
TOM KELLY EXECUTIVE DIRECTOR & CEO AUTOMATION ALLEY
GABY WALDMAN-FRIED INDUSTRY STRATEGY MANAGER, DESIGN & MANUFACTURING AUTODESK
RANDY NUNEZ MANAGING PRINCIPAL NUNEZ CONSULTING, LLC
LEAH CAPLANIS PRESIDENT BLUE
DR. KHALID MIRZA FOUNDING DIRECTOR, AUGMENTED REALITY CENTER OAKLAND UNIVERSITY
JESSE HACKER SOFTWARE ENGINEERING SUPERVISOR –SOFTWARE AND CENTRAL TECHNOLOGIES, RESEARCH AND ADVANCED ENGINEERING, CONTINENTAL
AMY SEYMOUR CHIEF TECHNOLOGY OFFICER INTERACTIVE TRAINING SYSTEMS
DEBORAH KIEFER PROJECT MANAGER, AUGMENTED REALITY CENTER OAKLAND UNIVERSITY
DAVID QUEVEDO DIRECTOR, ROBOT REBUILD, WARRANTY & QUALITY ABB INC.
ROGER BETTEN PRESIDENT MFP AUTOMATION ENGINEERING
GEORGE SINGOS STRATEGY & PARTNER OUTREACH, MICHIGAN MANUFACTURING TECHNOLOGY CENTER
MICHAEL LUZI VICE PRESIDENT OF STRATEGIC PARTNERSHIPS, HR BENEPRO
BEAU-JAMES ERION PRESIDENT BLITZ PROTO WAQAR (WB) HASHIM FOUNDER AND CEO
DAN STEWART RELATIONSHIP MANAGER AUTOMATION ALLEY
KATELYN KONTNY PROJECT MANAGER AUTOMATION ALLEY
By Dr. Khalid Mirza Founding Director
Imagine a world where training simulations feel as real as the job itself, designs come to life before your eyes, and customer experiences transcend the boundaries of physical reality. This is the transformative power of Augmented Reality (AR) and Virtual Reality (VR) in action. These technologies are revolutionizing various industries by offering immersive and interactive experiences that were previously unimaginable. AR and VR are not only enhancing existing processes but also creating entirely new opportunities across multiple sectors.
1. Training and Education: AR and VR create realistic simulations that allow students and trainees to practice skills in safe, controlled environments. For example, medical students can perform virtual surgeries, and pilots can practice flying in flight simulators. These technologies also enable remote training sessions, where participants can engage in
hands-on learning regardless of their location, making them particularly useful for large, geographically dispersed organizations.
2. Design and Prototyping: Designers and engineers can use AR and VR to visualize their creations in 3D, making it easier to spot design flaws and make improvements before physical prototypes are built. Virtual prototyping significantly reduces the time and cost associated with physical prototyping.
3. Manufacturing: AR can overlay instructions and guides onto physical equipment, aiding technicians in performing maintenance and repairs more efficiently. VR can be used for quality control by simulating production processes and identifying potential issues before they occur on the manufacturing floor. Continued on next page >>
4. Customer Engagement and Retail: AR and VR provide customers with interactive product demonstrations, allowing them to see and interact with products in a virtual space. This enhances the shopping experience and can lead to higher conversion rates. Retailers can offer virtual try-ons, where customers can see how clothes, accessories, or even furniture would look on them or in their homes without physically being there.
5. Entertainment and Media: VR enables immersive storytelling by offering new ways to experience stories, making viewers active participants rather than passive observers. This is already transforming film, gaming, and live events. Events such as concerts, conferences, and exhibitions can now be held in virtual spaces, reaching a global audience without physical constraints.
The boundless potential of AR and VR technologies lies in their ability to visualize and consume data in unique ways that were not possible before. These technologies can visualize data analytics in more accessible and understandable formats, leading to better data-driven decision-making. For example, business executives can explore sales data in immersive dashboards, and predictive models can simulate various scenarios, helping organizations plan and prepare more effectively.
Combining AR/VR with AI and machine learning can lead to smarter, more adaptive environments. AI can enhance VR training programs by adapting to the user’s learning pace and style. Integration with the Internet of Things (IoT) can bring real-time data into AR and VR environments, such as overlaying sensor data on machinery for maintenance or visualizing smart city data in an immersive format.
The increasing demand for AR/ VR and rapid advancements in technology are driving down hardware costs, and the availability of free and open software platforms can further reduce costs for custom immersive applications.
Deploying and implementing AR and VR technologies can present several challenges:
1. Cost: The initial investment in high-quality AR/VR hardware, such as headsets, sensors, and compatible computers, can be high. This can be a significant barrier for educational institutions and businesses. Software development for custom AR/VR applications requires specialized skills and can be expensive. However, the increasing demand for AR/VR and rapid advancements in technology are driving down hardware costs, and the availability of free and open software platforms can further reduce costs for custom immersive applications.
2. Technical Understanding: Many organizations lack in-house expertise to understand and implement AR/VR technologies effectively, leading to suboptimal usage and underutilization of the technology’s potential. Training staff and users to effectively use AR/VR systems requires time and resources, but educational programs and workshops in immersive technologies can greatly assist.
3. Evaluating Solutions: Organizations may need to experiment with multiple hardware and software solutions to find the best fit, which can be time-consuming and costly. Off-the-shelf solutions may not be sufficient, necessitating custom development that aligns with specific requirements. Publicly accessible spaces for evaluating various AR/VR hardware and software options can help organizations with limited resources. Ensuring that AR/VR solutions can scale to accommodate a growing number of users without compromising performance is also crucial and needs to be addressed in AR/VR hardware and software options.
4. Content and Experience Design: Developing high-quality, engaging content that effectively utilizes AR/VR capabilities requires a special skill set. Providing a variety of content to meet diverse needs and learning styles can be challenging. Interdisciplinary teams combining technology and design skills are best suited for developing highly visual and interactive immersive applications.
The future of AR and VR is poised for exciting advancements driven by emerging technologies and evolving trends. Improvements in accessibility, display technology, interaction methods, AI integration, and mixed reality applications are set to enhance user experiences and broaden the scope of these technologies. Innovations such as 5G, edge computing, spatial computing, and extended reality will further push the boundaries of what is possible in AR and VR, making these immersive technologies an integral part of various aspects of life and industry.
As these developments continue, AR and VR are expected to become more deeply embedded in our daily routines, professional environments, and entertainment experiences, driving a new era of digital interaction and immersion. The time is now to take the first step into this exciting future.
Realizing and maintaining the possibilities of Industry 4.0 will require ample human talent. The integration of augmented reality (AR) and virtual reality (VR) technologies into workforce training presents a promising solution to this challenge. These immersive technologies offer innovative ways to accelerate skill development, transfer knowledge from experienced workers to newcomers, and create engaging learning experiences that can attract and retain talent in the manufacturing sector. However, widespread adoption is still limited, and challenges remain that need to be addressed in order for these technologies to meet their full potential.
Our latest roundtable discussion explores the current state of AR and VR in manufacturing workforce training, the challenges faced in their adoption, and the potential they hold for reshaping the industry's future.
Anyone familiar with the manufacturing industry knows it’s in the midst of an unprecedented skills gap. The aging workforce, rapid technological advancements, and shifting economic landscapes have created a perfect storm, and the current situation is particularly dire. A joint study conducted by Deloitte and The Manufacturing Institute states that by 2030, the industry could face a shortage of up to 2.1 million workers. COVID-19 exacerbated this trend by causing 1.4 million job losses at the onset of the pandemic. Several years later, manufacturing companies have only recovered about 63% of those positions, leaving 37% of those roles, along with future job demands, still uncertain.
This shortage isn’t just a minor inconvenience; it’s a full-blown crisis threatening to derail productivity, stifle innovation, and inhibit the growth potential of manufacturers across the sector. Surveys of executives and managers in the manufacturing industry consistently show that the most significant hurdle is knowledge transfer—ensuring that seasoned workers pass their expertise to newer employees before retiring.
As Gaby Waldman-Fried, industry strategist at Autodesk, said, “The big topic was the cost of development of these AR experiences. Do you have to have an in-house developer to create them? What is the development time? The trending issue currently is how to minimize prototyping costs and save engineering time. We do that with virtual integration systems.”
AR and VR technologies offer a compelling way to bridge this knowledge gap. As older employees retire en masse, younger generations are showing less interest in traditional manufacturing careers. AR and VR offer a hands-on, immersive training experience that can compress years of learning into just a few months. New hires can be quickly brought up to speed using these technologies, which simulate real-world environments and processes with minimal risk to safety or productivity. A new manufacturing technician, for example, could use a VR headset to walk through a virtual factory, interact with digital twins of real machinery, and practice complex procedures before stepping onto the actual factory floor. This type of experiential learning offers more engagement than traditional training methods like PowerPoint presentations or shadowing experienced workers.
Continued on next page >>
Immersive learning is fast becoming a crucial component of workforce training in manufacturing. According to a 2022 survey by PwC, 60% of employees felt that AR/VR training provided a more effective learning experience compared to traditional methods, highlighting its potential for enhanced learning retention and engagement. However, even with this promise, 30% of older employees expressed concerns about the usability and effectiveness of these new technologies. This generational divide remains a critical challenge in the adoption of AR and VR in the workplace.
The potential of AR and VR extends beyond just workforce training. Khalid Mirza, ARC director at Oakland University, said it’s important to consider the long-term advantages of investing in these technologies. "In everyone’s mind, entering the AR/VR world may seem costly, but it's important to consider the long-term benefits. If you have digital prototypes, how quickly can you change the variations without needing the physical object? How about training? Remote training? It’s all possible with immersive technology," he said.
60% of employees felt that AR/VR training provided a more effective learning experience compared to traditional methods.
For manufacturers, the return on investment can be substantial. Mirza said remote collaboration and virtual prototyping are transforming how teams work, allowing global collaboration without requiring physical presence. "This platform offers opportunities to come together in a virtual meeting without being physically present. Instead of showing a video or talking about it for customer engagement, you can experience the product virtually and interact with it as if it was there, creating a very engaging experience,” he said.
Despite the clear benefits of AR and VR, several hurdles stand in the way of widespread adoption. Waldman-Fried said one of the most significant issues is cost. "The initial investment can be substantial. Headsets and software licenses often cost thousands of dollars per unit. That’s simply unrealistic for small and medium-sized enterprises," she said. The cost barrier, however, isn't the only challenge; the technology itself still has some limitations.
For instance, headsets can cause discomfort after prolonged use. "Headsets shift the center of mass forward and give you headaches," Waldman-Fried said. “The long-term effects of wear have not been studied at all. With the current tech, we’re essentially trading accuracy of the system for weight.” While accuracy remains a priority, the bulkiness of the equipment and the need for additional infrastructure, like stable Wi-Fi or Bluetooth connectivity, can be significant obstacles, especially in complex manufacturing environments.
Waldman-Fried also pointed to another key issue: the interaction between AR and the physical world. "The way that AR interacts with light and physical space is still not there yet, it’s not perfect," she said, emphasizing that hardware development is lagging behind software improvements. Furthermore, battery life is still a problem. "We don’t have a battery that can last eight hours that’s small and light enough to carry," she added. Until these hardware limitations are resolved, manufacturers may struggle to justify large-scale investments in AR and VR.
George Singos, strategy and partner relations manager at MMTC, sees generational differences as a potential barrier. “There is a generational divide in manufacturing companies,” Singos said. “We’ll see 20-year-olds adopt this technology seamlessly and 60-year-olds having some trouble. The question becomes: How do you encourage all people to adopt this technology?”
These divides can make it difficult to implement AR/VR solutions effectively across an entire workforce, particularly if older employees are resistant to using new technology. Moreover, disparate systems can create further challenges in integrating AR and VR into existing workflows. Singos said, “There are disparate systems in AR/VR, the ERP system, and the quality system. There are a lot of connectivity challenges that tie into the cost justification.”
Whether it’s remote assistance, virtual collaboration, or digital prototyping, AR and VR can significantly reduce training time and improve production efficiency.
Despite these obstacles, AR and VR technologies are improving, and companies that invest early stand to gain a significant competitive advantage. As Mirza noted, the industry is still at the beginning of this technological evolution: "It's gaining traction and momentum. You should be the first to embrace it, as you can offer a unique experience for customers," he said.
Waldman-Fried agreed but emphasized that progress needs to be faster. "Software is going much faster than developing hardware for these experiences," she said. This discrepancy between hardware and software development is something companies need to be aware of as they weigh the costs and benefits of adoption.
In the long run, as more companies invest in AR and VR, the costs are expected to decrease. "The biggest challenge is the cost. Do we need high-end computers, expensive headsets, and software tools? Yes, it is costly, but the prices are rapidly decreasing because more companies are now producing them, and more software is being developed," Mirza said.
These technologies are opening up possibilities that seemed unimaginable just a few years ago. Whether it’s remote assistance, virtual collaboration, or digital prototyping, AR and VR can significantly reduce training time and improve production efficiency. As Singos put it, “AR/VR provides a method to crash virtually before you take a big opportunity, which could cost tens of thousands of dollars if it wasn't calculated right.”
The integration of AR and VR into workforce training is just one facet of the ongoing industrial revolution known as Industry 4.0. While significant challenges remain—from costs and connectivity issues to generational divides—the potential to reshape workforce development and manufacturing processes is undeniable. As Mirza observed, "Most importantly, it’s the beginning of this technology, it’s gaining traction and momentum."
As these immersive technologies continue to evolve, manufacturers who embrace them early will not only bridge the skills gap but also position themselves at the forefront of the industry’s next transformation.
Before a full-scale roll out, implement AR/VR in a controlled setting to evaluate its impact on specific processes.
Augmented and virtual reality have existed for decades. However, it has only been more recently that technology has taken these systems from science fiction stories and video games and moved them into the heart of industry.
Today, many companies are harnessing the power of AR and VR to train employees on complex machinery operation and safety procedures, create and visualize products in 3D environments, detect issues in real-time and ensure product consistency, and provide customers with an immersive experience of their products.
For industry to effectively embrace these technologies, they must identify a use case, foster workforce training, and ensure data privacy and security
It’s important for companies to first outline specific objectives they wish to gain from AR/VR integration, such as reducing design errors, enhancing training efficiency, or improving maintenance procedures. Identifying a use case ensures focused efforts and facilitates measuring success. Before a full-scale roll out, implement AR/VR in a controlled setting to evaluate its impact on specific processes. Use insights from these pilot projects to refine the implementation plan and address potential challenges.
Next, select AR/VR devices and platforms that align with your manufacturing needs. Options range from head-mounted displays for immersive experiences to handheld devices for more straightforward applications. Ensure the chosen technology is compatible with existing systems to streamline integration.
Introduce AR/VR training programs to familiarize employees with these new technologies. Employee training, reskilling, and upskilling can be costly and time-consuming, but AR/VR technology can help reduce the strain on financial and workforce resources during the onboarding process.
AR/VR training simulations allow employees to train at their own pace and are customized for specific duties and situations. Workers can learn how to construct virtual products and experience real-world situations without using physical materials, which reduces waste due to faulty attempts. AR/ VR training provides added safety for industry trainees facing physical risks. Workers in these precarious situations can safely perform their duties multiple times until achieving a satisfactory level of confidence. Companies are seeing the positive outcomes of using AR/VR as part of the onboarding process, with companies reporting a 40% increase in employee retention and a 30% decrease in training costs.
Continued on next page >>
Beyond individual performance, AR/VR improves collaboration and team building. Companies can encourage collaboration between IT, engineering, and operations teams to integrate AR/VR solutions seamlessly. Such cooperation ensures that technological implementations are practical and aligned with manufacturing objectives across the organization.
Adapting new technologies always comes with cybersecurity risks. Companies must establish robust data protection measures to safeguard sensitive information utilized in AR/VR applications. This includes protecting proprietary designs and operational data from potential breaches.
Start by using role-based access controls (RBAC) to ensure that only authorized employees can access sensitive information. Data transmitted between devices and servers should be encrypted to prevent unauthorized access or interception.
Regular software updates and patches are essential for preventing vulnerabilities. Additionally, companies should monitor AR/VR systems in real time to detect suspicious activity and have an incident response plan in place to address potential security breaches. Compliance with relevant data protection regulations further ensures the privacy and security of both company and customer data.
Augmented and virtual reality are helpful tools for educators to capture their students' attention and improve outcomes through virtual lectures and collaborations, simulated learning, and sparking the imagination.
Academia is focused on developing highly skilled graduates who can enter the workforce and are prepared to not only contribute but to innovate industries. Today, students have access to ever-improving and more affordable technology in their private lives, forcing educators to find new and interesting ways of engaging their classrooms. Augmented and virtual reality are helpful tools for educators to capture their students' attention and improve outcomes through virtual lectures and collaborations, simulated learning, and sparking the imagination. Academia plays a critical role in AR/VR’s successful adoption into the manufacturing sector. For AR/VR to be effectively embraced by industry, academia should consider the development of specialized AR/VR curriculum, collaborate with industry on applied research, and establish AR/VR research hubs
Educators are finding more ways to introduce AR/VR learning into the classroom. Universities and technical colleges should create targeted programs that teach students how to design, develop, and implement AR/VR applications for manufacturing environments. This could include virtual prototyping, maintenance training, and immersive design simulation. In addition, academic institutions should offer continuous education opportunities on AR/VR for current manufacturing employees. This could involve online courses, certifications, and micro-credentialing programs that keep the workforce up-to-date with the latest AR/VR advancements.
Academia should prioritize partnerships between with manufacturing companies to conduct joint research on AR/VR technology. This collaboration can address specific challenges manufacturers face, such as improving worker training, enhancing design accuracy, or optimizing production processes through immersive simulations. Research could also explore how AR/VR technologies impact human-machine interaction, ergonomics, and cognitive load in manufacturing environments. This research can help design more intuitive systems that enhance worker productivity, safety, and well-being.
Universities should consider establishing interdisciplinary research hubs focused on AR/VR innovations, where experts in computer science, engineering, and manufacturing can collaborate. These hubs would focus on solving real-world problems, driving technology transfer, and accelerating AR/VR applications in manufacturing.
As AR/VR becomes more common in the classroom, more students must be trained to develop the technology. The skills required to be proficient in the technology include:
• Programming
• Software development
• 3D Modeling
• Game development
• Video
• Trigonometry
• Project management
• Writing
• Problem-solving
Tax credits, grants, or low-interest loans can ease the initial investment burden, making it more affordable for small- and medium-sized manufacturers who may lack resources to integrate AR/VR technologies.
As industries continue to embrace digital transformation, augmented reality and virtual reality (AR/VR) technologies are emerging as pivotal tools in revolutionizing manufacturing processes. Governments have a crucial role in facilitating this shift by implementing policies and programs that support the adoption and integration of AR/VR technologies in the manufacturing sector. By addressing key challenges and providing targeted assistance, governments can accelerate the widespread use of AR/VR, fostering innovation, improving efficiency, and enhancing workforce capabilities within industry. The following recommendations outline strategic actions that governments can take to support and advance AR/VR adoption in manufacturing.
Governments can encourage manufacturers to adopt AR/VR by providing financial incentives. Tax credits, grants, or low-interest loans can ease the initial investment burden, making it more affordable for small- and medium-sized manufacturers who may lack resources to integrate AR/VR technologies. By offsetting these costs, governments can accelerate the adoption of advanced technologies that improve efficiency, reduce errors, and enhance productivity.
Governments can establish regional innovation hubs and testbeds focused on AR/VR in manufacturing. These centers can serve as collaborative environments where manufacturers can test AR/VR applications without needing to commit to large-scale implementation upfront. By fostering public-private partnerships, these hubs can drive R&D and bring together industry experts, academics, and startups to innovate and refine AR/VR solutions tailored to the manufacturing sector.
Government investment in R&D can spur innovation in AR/VR technologies tailored to manufacturing. By funding research programs that focus on advanced applications—such as virtual factory simulations, real-time equipment monitoring, and AR-guided maintenance—governments can drive new breakthroughs that improve manufacturing processes. Supporting R&D efforts also ensures that AR/VR technologies evolve to meet the needs of the manufacturing industry. Continued on next page
Governments can play a critical role in developing and enforcing standards that ensure AR/VR technologies are compatible and secure. Clear guidelines and certification programs will help manufacturers choose trusted solutions and accelerate adoption by eliminating concerns over interoperability, cybersecurity risks, and technology scalability. This creates a stable environment for investment and fosters trust across the industry.
One of the key barriers to AR/VR adoption in manufacturing is the lack of trained workers. Governments can address this by funding education and training programs specifically designed for AR/VR applications in manufacturing. By partnering with universities, technical schools, and industry leaders, governments can help develop a workforce skilled in operating and maintaining AR/VR systems, ensuring a smooth transition to these technologies in the factory environment.
Automation Alley posted weekly polls in April and May 2024 for our LinkedIn followers of over 6,000 professionals in the technology and manufacturing ecosystem on the topic of AR/VR. This is how the industry responded at a glance.
Do you implement AR/VR in your business/company?
There are several common AR/VR headset choices on the market. Which one have you purchased or intend on purchasing for your business?
Addressing the Skills Gap: AR and VR technologies offer innovative solutions to the manufacturing industry's growing skills gap by accelerating training and knowledge transfer, particularly from retiring workers to new hires. This immersive training can significantly reduce learning time and enhance skill development.
Challenges in Adoption: High costs, hardware limitations, and a generational divide are key barriers to widespread AR and VR adoption. Headsets are expensive and uncomfortable for long-term use, and older workers are often more resistant to adopting the technology.
Long-Term Potential: Despite the challenges, AR and VR hold significant promise for the future of manufacturing. As the technology improves and costs decrease, these immersive tools will enhance remote collaboration, digital prototyping, and overall production efficiency, giving early adopters a competitive edge.
Government Support for AR/VR Adoption: Governments can accelerate the integration of AR/VR technologies in manufacturing by offering financial incentives such as tax credits, grants, and low-interest loans. These measures help reduce the financial burden on manufacturers, particularly small- and medium-sized businesses, encouraging them to adopt these advanced technologies to improve efficiency and productivity.
Focus on R&D and Workforce Training: Establishing innovation hubs, funding research and development (R&D), and supporting workforce training programs are crucial government actions. These initiatives foster innovation, create industry standards, and develop a skilled workforce, ensuring AR/VR technologies are effectively integrated into manufacturing processes.
Identifying Use Cases and Workforce Training: Companies must clearly define specific use cases for AR/VR technologies to ensure effective integration, such as improving training efficiency or reducing design errors. Implementing AR/VR training programs enhances employee skills while reducing training costs and increasing retention, allowing workers to practice in a risk-free environment.
Ensuring Data Privacy and Security: Robust data protection measures are essential when using AR/VR, as these technologies handle sensitive information like proprietary designs. Companies should implement role-based access controls, encryption, and regular software updates to safeguard against breaches and ensure compliance with data protection regulations. 1 2 3 4 5 6 7
Automation Alley is a nonprofit technology business association and Digital Transformation Insight Center focused on driving the growth and success of businesses in Michigan and beyond through innovation and automation. With a global outlook and a regional focus, we foster a vibrant community of innovators, entrepreneurs, and business leaders through opportunities for collaboration and learning. Our programs and services help businesses develop the skills and expertise needed to effectively jumpstart or accelerate digital transformation. By bringing together industry, academia, and government, we aim to create a dynamic ecosystem that drives innovation and growth across Michigan.
At Automation Alley, our mission is to help businesses thrive in the rapidly changing digital economy. We equip them with the knowledge, insights, and tools to develop a software-first mindset that leverages the power of automation, AI, and other cognitive technologies. We believe that by working together, we can build a stronger, more innovative, and more competitive economy for the future.
Wealth, prosperity and equality through technology.
Publication Credits
Editorial: Nicole Kampe, Dennis Burck, Joseph Gray
Graphic Design: Laura Gearhart
Photography: Sean Healey and Corey Sims
Optometrists - Guide to Vision and Learning Difficulties https://www.optometrists.org/vision-therapy/guide-vision-and-learning-difficulties/
Air and Space Forces Magazine - New Tech Helping Airmen Think Faster https://www.airandspaceforces.com/air-force-aetc-virtual-reality-cognition/
Deloitte - Creating pathways for tomorrow’s workforce today https://www2.deloitte.com/us/en/insights/industry/manufacturing/manufacturing-industry-diversity.html
U.S. Bureau of Labor Statistics - Employment recovery in the wake of the COVID-19 pandemic https://www.bls.gov/opub/mlr/2020/article/employment-recovery.htm
Vorecol - Integrating Virtual Reality and Augmented Reality in Training Management Strategies https://psico-smart.com/en/blogs/blog-integrating-virtual-reality-and-augmented-reality-in-training-managementstrategies-164931
ESS - Enhancing Onboarding With Virtual and Augmented Reality https://esoftskills.com/hr/enhancing-onboarding-with-virtual-and-augmented-reality/
Oakland Univesity - Augmented Reality Center https://oakland.edu/secs/labs-and-centers/augmented-reality-center/
Made possible in part through ongoing support from the