Specialising in stainless steel and its applications
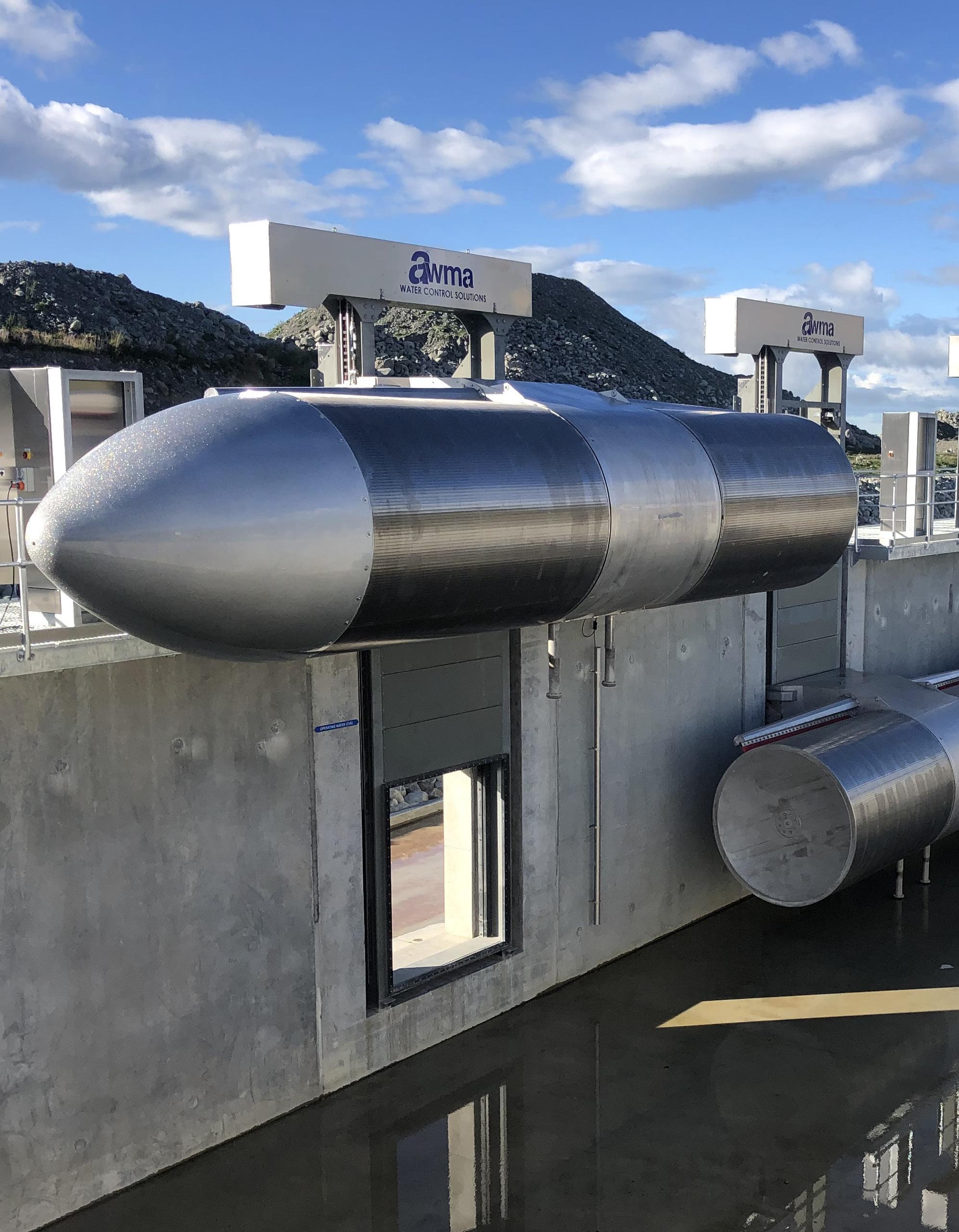
For the past six years, ASSDA Member and Accredited Fabricator AWMA Water Control Solutions have been a proud partner of Rangitata Diversion Race Management Ltd (RDRML) in delivering one of the world’s largest fish-friendly water extraction facilities using stainless steel.
The Rangitata Diversion Race (RDR) plays a crucial role in extracting water from the Rangitata River in New Zealand’s South Island, serving irrigation, stock water, and hydropower generation needs year-round. However, the environmental impact on native fish populations was a concern for RDRML.
To address this challenge, AWMA was awarded the design and construct contract to deliver an environmentally sustainable diversion screen solution that would allow the required flows while ensuring the safe passage of sporting fish, such as salmon and trout, as well as various native fish species back into the river system.
Over a period of five years, RDRML collaborated with consultants, ecologists, regulatory authorities, and other stakeholders to conduct extensive research and identify the most effective and viable screen solution available worldwide. This involved overseas visits to operational screening facilities, and discussions with water regulators, scientific specialists, and equipment manufacturers to gain firsthand knowledge of established screening practices. The comprehensive research led to the selection of physical, selfcleaning, wedge-wire screening systems, proven through decades of successful performance and compliance with industry guidelines.
The innovative solution designed by AWMA for the RDR project featured a stainless steel screening structure that was not only self-cleaning and fish-friendly but also delivered reliable water flows with a low whole-of-life cost. It complies with fish screening guidelines, meets client requirements, and sets a new standard for innovation in intake screen design.
Three main design characteristics prioritised for the fish protection screens were aperture size, approach velocity, and self-cleaning functionality. The aperture size of the screens was tailored to meet the specific aquatic life present, considering fish species and breeding patterns. Low approach velocities prevent entrainment and impingement
of debris and fish through low, even flow distribution across the entire screen area, as well as reducing head loss. The self-cleaning functionality of the screens eliminated the need for manual cleaning, minimising operational risks and increasing flow reliability. AWMA’s solution incorporates internal and external brush cleaning mechanisms to efficiently remove debris, algae, and weed while maintaining fish protection and optimal flow.
AWMA’s design for the RDR project required seven Cylindrical T-Screens, a Flat Panel Screen, and a LayFlat Gate, all fabricated using stainless steel. The screens, fabricated from stainless steel wedge wire, offer superior self-cleaning capability when complimented with an internal and external brush cleaning system.
The use of Australian-made stainless steel wedge wire as the screen medium further enhances the durability and maintenance-free nature of the screens. The precision construction of wedge wire, with resistance welded triangular profile wires onto support rods, ensures a robust structure and maintains accurate slot dimensions throughout the 50+ year asset life expectancy in fresh water. With a smoother outer surface and easy clean characteristics, the wedge wire screens facilitate efficient brush cleaning and remain unaffected by biofouling.
The combination of high-quality stainless steel materials and innovative infrastructure design has resulted in an environmental solution that delivers unparalleled outcomes, including native fish protection, high-quality water output, reduced energy consumption, and reliable flow delivery.
AWMA invested 6,300 labour hours into this project, utilising custom-designed tooling for the efficient handling, processing, fabrication, fit-out, testing and inspection of the screen elements. Over 55 tonnes of stainless steel in various grades and surface finishes were used for the manufacture and successful implementation of the project, with the majority of stainless materials supplied by ASSDA Member, Vulcan.
The self-cleaning intake screen solution designed for this project comprises seven T-screens (14 cylinder screens) and a 30m long Flat Screen. The flat screen was required towards the end of the bypass channel where space was restricted by the tapered design of the channel.
The 14 cylinder screens were fabricated from grade 304 stainless steel wedge wire screen mediums, measuring 2.1m in diameter and 3.0m in length. 140m of grade 316 stainless steel wire rope cables, complete with stainless turnbuckles and fittings were supplied by ASSDA Member and Accredited Fabricator Arcus Wire Group for the purposes of lowering and raising the intake screens within the AWMA retrieval systems.
The seven, 8.75m high retrieval systems were each fitted with headstocks consisting of grade 304 stainless steel headstock covers to protect the grade 316 stainless steel drive shafts that were 100mm in diameter. The 8-tonne stainless steel flat panel screen measured 30m x 3.5m (105 –––sqm).
Approximately 1.8 tonnes of stainless steel was used to fabricate the LayFlat Water Control Gate utilised at the end of the bypass channel as a fish-friendly, overshot gate for water regulation and control.
ASSDA Member Akras Industries was also engaged during the fabrication stage in a semi-automated butt fusion welding process to ensure high strength and single-welded seam joints. Prior to installation, a pickling surface treatment was performed on all stainless steel components by AWMA using pickling spray supplied by ASSDA Member, Midway Metals.
Stainless steel has ensured the durability, performance and longevity of the water extraction facilities while maintaining the project’s commitment to environmental sustainability. Completed in late 2022, this world-class project showcases the quality and diversity of Australia’s stainless steel materials, industry expertise and manufacturing capability.
The successful collaboration between AWMA and RDRML demonstrates a partnership commitment to sustainable water management and the protection of aquatic ecosystems. The RDR project stands as a testament to the effectiveness of advanced stainless steel screening technology in balancing water extraction needs with environmental preservation.
This Australian-made stainless steel wedge wire is durable and maintenance-free, with a 50+ year asset life expectancyAWMA’s Engineering Manager Lachlan Mathers accepting the 2022 ASSDA Fabricator Project of the Year Award (Process Industries) for this project.
For years, the plumbing industry has been dominated by materials such as galvanised mild steel, copper, and plastic. However stainless steel is quickly emerging as a standard construction material in various water supply applications.
Stainless steel offers a multitude of benefits, including corrosion resistance, hygienic properties, strength, long-term performance, excellent hydraulic conductivity, and the ability to withstand high pressure and temperature requirements. It has found its place in diverse applications, from desalination plants and reverse osmosis water treatment systems to water supply for high-rise buildings and domestic tapware. Stainless steel provides a safe and sustainable solution throughout the entire lifespan of the product.
The history of water supply dates back to ancient times when stone fluidity paths were used, predating the use of pipes. The Romans discovered that lead could be easily formed into pipework, although their decline has been partly attributed to lead poisoning from their water supply (although wine stored in lead containers is a more likely cause). Lead continued to be used for centuries, particularly in areas with hard or inhibited waters, notably in the United States. However, Australia took a different route, relying on galvanised steel as the default material for pipework from the late 19th century until after World War II. Unfortunately, the zinc coating dissolved in softer oxygenated water supplies, leading to taste and colour issues even before leaks occurred. Additionally, galvanised steel corroded from the outside when exposed to corrosive soils. These rust challenges, coupled with the wide availability of copper and its alloys, led to the adoption of copper pipework after World War II.
concerns prompted reductions in lead levels. Lead was detected in the first flow from cast copper base tapware after extended stagnant periods or due to leaching from dead legs. Increasingly sensitive test methods and concern about any ingested lead increased pressure to curtail any available lead. The Australian Building Codes Board (ABCB) has extensively consulted on this matter, and as of 2025, the National Construction Code (NCC) mandates a maximum lead content of 0.25% for alloys in contact with potable water, although some advocate for a complete prohibition of lead in contact with potable water despite potential casting challenges.
Compared to copper pipe and tube, stainless steel is stronger, has negligible leaching in potable waters and allows higher flow rates especially in hot water.
The cost of copper and the availability of affordable polymers led to a surge in plastic pipework in low and medium-rise buildings. Polymers such as PVC, polyethylene (PE of various densities), ABX, cross-linked PEX, and polypropylene (PP) gained popularity, with polybutylene (PB) being an exception as it is banned for potable water use in North America. Plastic pipework is found in applications in domestic and commercial buildings, as well as some chemical plants. Composite pipework, especially for larger-diameter applications in chemical plants, also gained a niche.
While there was a marketing push for stainless steel in potable water pipework during the 1980s, it faced challenges due to its reliance on silver soldered joints. Plumbers preferred the soldered or compression fittings used with copper or the solvent or electro-fusion couplings used for polymer pipework.
Copper offered advantages such as lightness, ease of bending, handling, and joining. It took some time to eliminate lead from the solders used in copper pipework. Copper alloys, including valves, fittings, and taps, could be easily manufactured as castings that were chemically compatible with copper pipework. Initially, lead was included in casting alloys (typically brass or gunmetal) to facilitate flow, but health
High-rise buildings encountered a significant challenge in terms of pressure ratings, necessitating the use of either separate low and high plant rooms on different circuits or stronger materials. Polymers are adequate for a single rise, while copper, although stronger than polymers, only possesses a yield strength of approximately 25% compared to stainless steel grades 304 or 316, and about 12% when compared to duplex grades. In some cases, existing high-
rise buildings with copper risers that were on the edge were upgraded in situ by replacing them with short sections of stainless steel, coupled using Victaulic joints. Standard joining systems, such as mechanical press-fit couplings onto a polymer ring, silver soldered capillary couplings, and compression fittings, are employed for stainless steel installations. Although both stainless steel and copper exhibit similar pressure loss due to pipe friction, there is a substantial contrast in erosion resistance. Copper can handle only about 10% of the velocity limit of austenitic stainless steels (304 or 316) in cold water, and less than 5% of the flow limit in hot water, i.e., greater than about 65°C. While pump power requirements and noise considerations often restrict the exploration of the upper end of the stainless steel velocity range, this discrepancy implies that turbulence and metal loss at corners and junctions pose no issues in stainless steel systems, unlike copper-based designs. Mixed metal and polymer systems are commonly utilised for mains and final distribution, which is generally satisfactory for cold water applications. However, the growing trend of recirculating hot water systems to minimise water wastage while waiting for hot water to flow has led to problems such as copper dissolution from copper pipework, especially at higher temperatures, and the leaching of stabilisers from polymers, resulting in potential cracking. Such issues have prompted litigation across Australia and other regions. Stainless steel, on the other hand, exhibits dissolution rates typically below 5% of the health limits, and the presence of metal ions is frequently undetectable
Furthermore, during the COVID-19 and SARS outbreaks, significant emphasis was placed on using copper alloy handles or metalwork to prevent the transfer of infections through splashes or droplets. This concept then extended to the belief that using a copper alloy in potable water systems would release copper ions on the surface, thereby inhibiting microbial growth, while an inert stainless steel surface would promote colonisation and growth, especially in warm water. This argument assumes that the water supply lacks sufficient disinfectant, typically chlorine (although chloramine is used in two Australian capital cities to maintain biological control at the end of the distribution system). Australia’s extensive distribution networks and generally soft, non-scaling water have necessitated additional chlorine dosing in the network beyond the treatment plant’s dose. In the past, when remote dosing was uncommon, chlorine could be absent at residences located 50km or more away from the water treatment plant. Under such conditions, as well as in remote tank systems utilising “fresh” rainwater, microbial activity was found to dissolve copper, causing blue water, an unpleasant taste, and staining of porcelain or plastic fixtures. This issue is now well understood, and chlorine levels are routinely monitored and controlled across the networks through multiple dosing points.
In conclusion, stainless steel, polymers, and copper all have their roles in potable water systems, driven by historical usage and inherent properties. However, as the trend toward a sustainable economy and the use of reusable materials gains momentum, there will likely be shifts in priorities and preferences.
Leaching metal ions Ni and Cr <5% of European limits even hot Plasticisers can leach causing embrittlement
At 20oC equilibrium
Cu+ rises from ~0.4ppm at pH7 to ~5ppm at pH3
Hot water No effect 0oC to steam
Depends on polymer but leaching worse especially if hot
Cu+ ions can embrittle polymers in some systems and cause failure
Water for injection Yes, with specific finishes No No
Formable/ joining Readily formed, welded Mechanical or solvent Solder or mechanical
High temperature Steam to chilled waters
Softens depending on material Lower velocity limits when flowing
Velocity limits 40m/s any temperature Depends on polymer
Microbial effects Smooth and limited colonisation
Surface defects allow colonisation
Sulphides Not usual in potable water No effect
3 or 1.5m/s for cold and hot (60oC) respectively
Stagnant with low chlorine at pH>7 can cause blue water from microbial corrosion
Sulphides form
Stainless steel is versatile and, despite its initially higher cost, its durability provides significant life-cycle cost benefits in pure water delivery.This article was written by Dr Graham Sussex, Technical Specialist, Australian Stainless Steel Development Association (ASSDA) in consultation with ASSDA Member Gentec Australia.
ASSDA Member Fabmetal Specialists has added a touch of luxury to Melbourne City’s latest residential landmark by delivering an exquisite package of geometric stair soffit and balustrade cladding, crafted from coloured stainless steel.
Spanning an expansive 12,000m2 site and set to become Victoria’s largest residential development, West Side Place elegantly connects Spencer and Lonsdale Streets in Melbourne’s CBD. The iconic project boasts an array of mixed-use spaces, including residential apartments, recreational facilities, retail, and dining arcades, and is also home to the prestigious Ritz-Carlton and Dorsett Hotels.
With its world-class design and a commitment to offering unparalleled luxury in urban living, every element of West Side Place demanded exceptional materials and craftsmanship. A notable feature on the ground floor of Tower 1, a striking freestanding staircase seamlessly guides guests to the first level, serving as an architectural masterpiece in its own right. The captivating geometry of the stair soffit, adorned in radiant “gold” stainless steel, effortlessly captures attention.
During the design stage, Fabmetal Specialists collaborated closely with the various stakeholders involved, elevating the original specification of 2mm brass sheets with a clear protective coating to the superior choice of stainless steel.
To bring their vision to life, the team selected grade 304 TiVox stainless steel, using 1.2mm sheets with a No.4 gold satin (slight brush) finish and an anti-fingerprint coating.
This exceptional material was supplied, expertly fabricated, and seamlessly installed by the Fabmetal Specialists team.
Fabmetal Specialists’ TiVox range is renowned for its signature coloured stainless steel panels. Achieved through a Physical Vapour Deposition (PVD) process, this innovative technique involves ionising titanium and zirconium within a high-temperature vacuum chamber, depositing a thin and durable coating onto the steel’s surface. The resulting coloured finish offers exceptional resistance to abrasion, scratches, corrosion, and requires minimal maintenance.
Forty bespoke stainless steel sheets, each measuring 4000x1500mm, were supplied to ensure seamless integration and smooth joint lines in the stair soffit cladding, meticulously meeting the architects’ vision. To maintain optimal flatness, the sheet panels were supported by a lightweight aluminium backing board, while every panel edge was expertly V-grooved, delivering a sharp and flawless finish. Fabmetal Specialiats’ patented Fablok system, renowned for its precision column assembly, was employed to seamlessly clip the panels together, eliminating visible fixings and caulked joints.
Fabmetal Specialists’ contribution to West Side Place showcases their commitment to excellence and their ability to transform architectural concepts into breathtaking realities using stainless steel.
Australia’s only dedicated stainless steel conference event
pacrimstainless.com
Registration opens in July!
Brought to you by ASSDA, PacRim Stainless is the premier annual event bringing together Australia’s stainless steel industry and colleagues from abroad in an exclusive networking environment.
Program overview:
Two half-day conference sessions with an exceptional line-up of speakers covering topics to discuss:
• Local and global stainless steel trends, outlooks and challenges
• Sustainable design and the clean energy revolution
• New and disruptive technologies and digital tools
• Next generation leadership Case studies: Innovation and life-cycle assessment
Australian Industry Stainless Steel Supplier and Fabricator Awards
Supported by:
SAVE THIS DATE: ASSDA Young Professionals Network function – 17 October 2023
PLATINUM MEMBERS:
GOLD MEMBERS:
Stanch Stainless Steel Co., Ltd.
Stoddart
YC Inox Co., Ltd.
AUSTRALIAN STAINLESS MAGAZINE
SILVER MEMBERS:
Acerinox \ Aqseptence Group \ Arcus Wire Group \ AusPress Systems \ Austral Wright Metals \ Amity Pacific \ Australian Stainless Distributors \ B & R Enclosures \ Callidus Welding Solutions \ Ching-Hann Industries Co., Ltd. \ Dalsteel Metals \ Fagersta Steels \ HH Stainless Pte Ltd \ Industrial Tube Manufacturing \ Metal Centre Australia \ Prochem Pipeline Products \ Sanwa \ Sefar \ Stainless Bar & Wire Company \ Stainless Steel Wire & Mesh \ Stirlings Performance Steels \ Yue-Seng Industrial Co., Ltd.
MORE INFO: Enquiries or further information on any material presented in this publication should be directed to ASSDA: Level 6, 200 Adelaide St, Brisbane Qld 4000 \ +61 7 3220 0722 \ assda@assda.asn.au \ assda.asn.au
EDITORIAL: Contributions of story ideas specialising in stainless steel and its applications are welcome from Members of ASSDA.
ADVERTISING: Advertise in the only publication that reaches a targeted group of 5000+ in the Australian stainless steel industry. Rates available at www.assda.asn.au.
CONTACT: Lissel Pilcher, Editor: lissel@assda.asn.au