Specialising in stainless steel and its applications
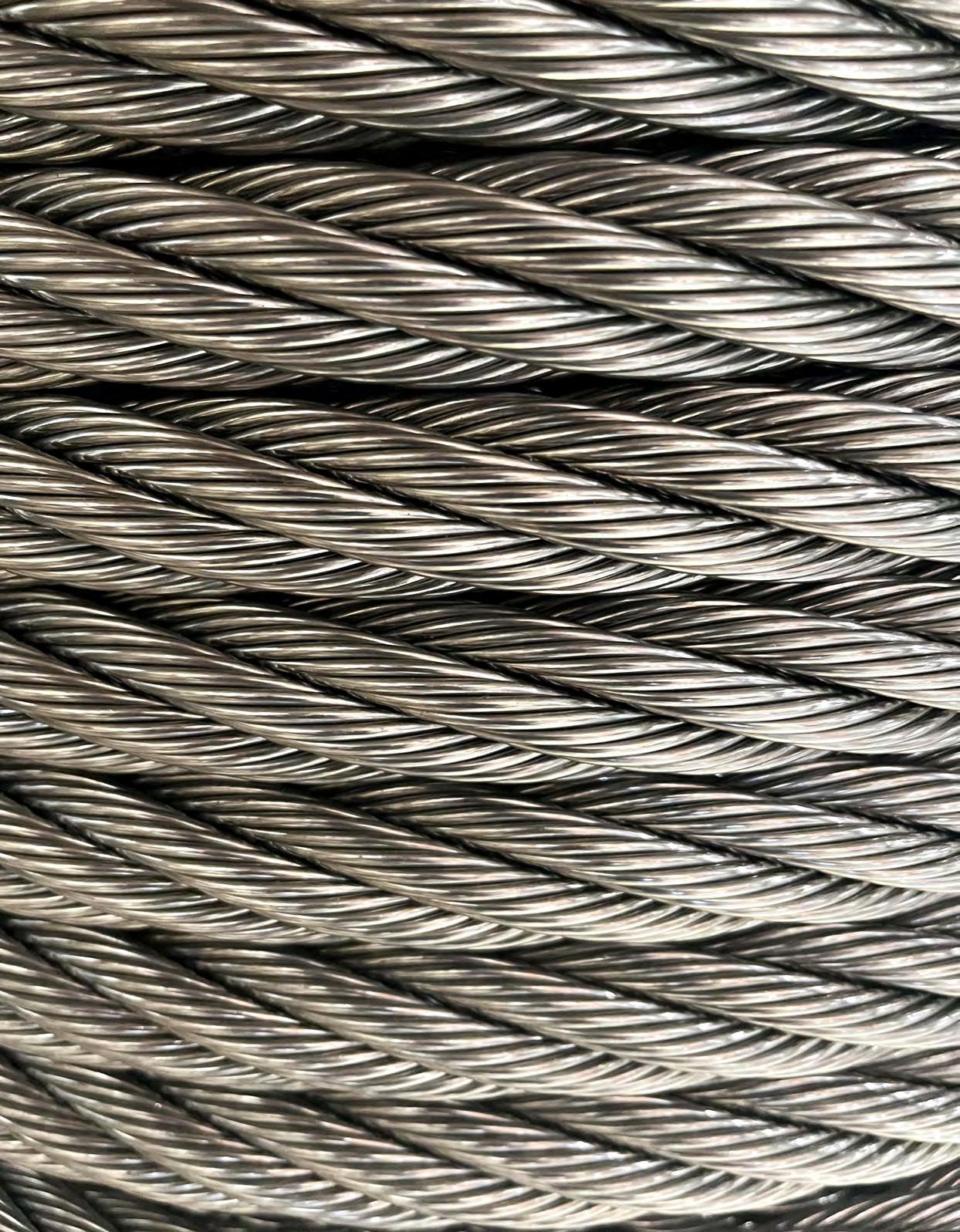
The 344MW Kokhav Hayarden pumped storage hydropower plant is located 120km northeast of Tel Aviv. The project is the first and largest of its kind in Israel, as well as the lowest of its kind globally. The powerhouse lies 275m below sea level and features two 3.1 million m3 reservoirs at different heights. Expected to be operational in early 2023, the hydropower station is designed to provide flexible backup power and stability to the national electricity grid of Israel.
Arcus Wire Group was engaged by GE Renewable Energy to manufacture and supply the cables to form part of a guiding system for the draft tube gates and stop logs for the lower surge shaft of the power station.
The original project brief specified eight identical wire ropes approximately 110m in length with a diameter of 35mm constructed of a half-locked coil with an internal core of large diameter wire, capable of a permanently applied load of 100kN in an underwater application. A long working life was a critical requirement as maintenance of the cables was not an option once in place.
The initial consideration of materials in order of preference was carbon steel (heavy zinc coating), austenitic stainless steel and duplex stainless steel. The water baseline data for the application during operating conditions were:
• pH value: Min 6.50 pH, max 9.00 pH
• Temperature: Min 2°C, max 33°C
• Total Dissolved Solids (TDS): Max 2,200mg/L
• Hardness: CaCO3 Max 960mg/L
• Alkalinity: CaCO3 Max 436mg/L
• Iron concentration: Max 320μg/L
• Chloride (CI ) ) concentration: Max 1,000mg/L
• Sodium (Na+) ) concentration: Max 504mg/L
• Magnesium (Mg2+) ) concentration: Max 144mg/L
• Silica and other hard particles with hardness >5 Mhos:
– Particle diameter >_ 50μm: Maximum concentration = 20mg/L
– Particle diameter >_ 1.5μm: Maximum concentration = 50mg/l
The cable guiding system required one part of the wire rope to be attached to an anchor embedded in concrete and permanently submerged in water exposed to highly corrosive conditions. The top part of the cable is connected to a posttensioned wire located above ground and exposed to air, with temperatures at a maximum of 45°C and humidity of up to 75%. Post-installation, the wire rope cables will not be accessible for maintenance for up to 30 years.
ASSDA was consulted during the design phase, and as the specification evolved, the client identified stainless steel as a more suitable and sustainable option than carbon steel wire ropes for the submerged application. Considering the maximum temperature and minimum pH level, grade 316 stainless steel would be at its limits, particularly with the crevices that are characteristic of wire rope. 2205 duplex stainless steel was recommended and ultimately chosen as the material of construction to reduce the risk of pitting and crevice corrosion, in addition to its tensile strength, longevity, and life-cycle cost-effectiveness.
The final design specification delivered alloy grades 1.4362, 1.4462 and 1.4501 duplex stainless steel wire rope cables, half-locked coil with an internal core of large diameter wires and a 30-year lifetime warranty.
The terminations proposed and subsequently selected for use were grade 2205 duplex stainless steel swage forks. They were designed specifically by the Arcus Wire Group team for the 26mm wire rope and a pin diameter of 40mm to allow connection to the anchor at the bottom and the post-tensioning system at the top.
Arcus Wire Group worked with its mill and manufacturing partners to produce and fabricate 970m of 26mm diameter 6x19 SL and IWRC construction 2205 duplex stainless steel wire rope and 20 units of 2205 duplex stainless steel fittings. Seale construction (SL) is a wire rope construction that offers excellent breaking load characteristics. It is used in a wide variety of applications and is resistant to wear and abrasion due to its larger outer wires. An independent wire rope core (IWRC) adds strength to the total length of the rope and reduces the amount of stretch during service.
Material testing was performed on the wire rope cables. This included destruction testing of a 3m sample cable to measure the breaking strain (breaking at 456.061kN as tested on a horizontal tensile testing machine calibrated to AS 2193: Calibration and classification of force-measuring systems), 10 rounds of cyclic loading to 100kN and unloading to 1kN of an 11m sample cable and loading up to 1.8 times the maximum working load of 180kN to determine elongation under the various conditions. All cables delivered conformed to EN 12 385-4: Steel wire rope.; EN 13411-8 Terminations for steel wire ropes –Safety – Part 8: Swage terminals and swaging; and EN 10088-3: Stainless steels – Part 3: Technical delivery conditions for semifinished products, bars, rods, wire, sections and bright products of corrosion resisting steels for general purposes.
The duplex stainless steel wire cables were assembled, swaged, tested, and quality certified at Arcus Wire Group’s facility on the Gold Coast, Australia, and shipped over 14,000km to the project site in Israel. The final delivery included 8 x hamma® 26mm diameter 2205 duplex stainless steel wire cables measuring 111.4m and weighing over 325kg each.
Arcus Wire Group has delivered Australian stainless steel innovation and service delivery at its best with the supply of its wire rope cable solution meeting the exacting demands, life-cycle and performance expectations of Israel’s new hydropower station.
2205 duplex stainless steel was chosen... for tensile strength, longevity and life-cycle cost-effectiveness
Stainless steels are almost universally used around indoor and exterior pools for railings around or into the water, fixtures, furniture, grills, etc. The finishes are bright and readily cleanable for hygiene and are resistant to staining or corrosion by the chemical treatments required for the maintenance of public health.
This article discusses the unexpected problem (and the solutions) that showed up in the 1980s because of the changing design and operation of indoor heated and chlorinated swimming pools when combined with the increased use of stainless steels as structural supports in ceilings over pools. The problem: 304/316 stainless steel rods/bolts/wires with surface tensile stresses cracked and broke in high-up, unwashed areas because of a previously unknown, ambient temperature stress corrosion cracking (SCC) mechanism – and, literally, several roofs fell into pools. There are multiple mitigating actions, but a certain solution is to use readily available higher alloys which do not suffer SCC at near ambient temperatures.
There were four factors and a lack of knowledge:
• More water vapour in the airspace because of demands for warmer water temperatures which overwhelmed the dehumidification of the air conditioning systems and increased the risk of condensation on cooler metal surfaces.
• Because of greater patronage, there are hygienic requirements for higher chlorine dosing and/or more shock dosing which increases the volatile content in the airspace which then dissolved in the condensed water films.
• In areas that were not washed (e.g. tension rods and bracing in the roof space, ceiling-mounted fans, air conditioning ducts, light fittings, suspended ceilings, signage, suspension wires), the condensed water film dissolved the volatile chlorides and became very aggressive with low (acidic) pH and high chloride concentration.
• An increasing use of stainless steel in load-carrying service. The knowledge gap was that the chloride-induced SCC of the common 300-series stainless steels was only considered to be a risk for temperatures above about 55oC, e.g. on the outside of leaking hot water systems or in the residual stress along welds or the water line of a hot water tank.
There was a basic assumption that there would always be components subject to surface tensile stress, so materials testing was required to select alloys resistant to SCC in the pool atmosphere environment. The Nickel Institute (NI) funded research work in the 1990s to identify the mechanism of failure and recommend suitable alloys and operating techniques to prevent recurrence. The results were published in Stainless steel in swimming pool buildings (NI 12010, 1995) and recommended 904L or 6% molybdenum alloys. It did not recommend 2205 duplex stainless steel because there was some pitting in the ferrite phase, although no cracking was observed. ASSDA published a technical alert in 2001 which was mainly based on the NI data. It included recommendations for resistant alloys, pool management and inspections to detect possible risks.
The 2003 German building code mandates using high molybdenum alloys listed below (the ~6% Mo austenitic alloys) for unwashed stainless steel applications. The codified alloys are listed in EN 13451-1:2011 –Swimming Pool equipment, Appendix G (see summary Table 1).
Table 1: Recommended stainless steel alloys for unwashed service in pool atmospheres
EN UNS Mo Ni Mn N Cu 1.4565 S34565 4 16 6 0.4 1.4547 S31254 6.5 18 0.2 0.7 1.4529 S08926 6.5 25 0.4 1
Notes:
1. Nominal compositions
2. 904L (1.4539) showed no attack in the NI test work and was recommended but the later EN has a limit to water supplies <250mg/L chloride, i.e., drinking water.
Euro Inox summarised these and further work in their 2013 publication, Safe use of stainless steel in swimming pool environments. There have also been multiple summary engineering papers including lists of readily washed components that can use high austenitic alloys with various molybdenum, nickel, and nitrogen content. Research continues into the use of duplex grades.
The message about alloy choice has had good penetration although those new to stainless steel for indoor chlorinated pools still suggest 316 bolts to support overhead spotlights, 316 bolts over heavily chlorinated wastewater tanks or 316 cables or struts to hang water slides. There were cases of fabricators substituting 304 hangers for the specified painted and galvanised hangers for pool lighting panels – which sagged when several broke as shown in the picture on the left.
When a high austenitic alloy is used for unwashable areas above warm, chlorinated pools. However, one state has satisfactorily used chloramines for potable water disinfection since the 1930s. This is probably because the required dose for disinfection at ambient temperatures is significantly lower than the inadvertent chloramine levels in the atmosphere above a warm pool overpopulated with unwashed bodies.
For external pools subject to wind and rain there is no potential for concentration of chloramines. This means 304/316 around external pools are not at risk from SCC although routine washing is recommended to maintain a bright stainless appearance. Higher grades such as duplex may be required in marine environments, especially for unwashed components such as fastenings of glass panels –simply to avoid tea staining.
The risk of SCC of low alloy stainless steels in the atmosphere only arises with warm chlorinated pools. Pools that only use ozone as a disinfectant are not at risk because ozone is readily reduced to oxygen and does not accumulate like chlorine or chloramines. However, if a shock or backup chlorination procedure is used, then the recommendations of this article should be followed.
In the vast majority of typical stainless steel components regularly drenched, or which aren’t under tensile stress, such as:
• Benches • Pool ladders
• Safety rails • Doors and windows
• Non-safety critical components that will be washed for aesthetics.
SCC has not been found to be a problem in these applications.
• Monitor and control pool chemical levels including chlorine and amines.
• Prevent excessive bathing loads – which may vary with monitoring results.
• Provide good shower and toilet facilities and clear instructions to patrons for use prior to entering the pool.
• Monitor and control air quality. This may require advice from the design and installation contractors.
• Institute a regular inspection and cleaning program – preferably biannual.
If not already identified, log items potentially at risk.
If a program has been established, review to check it covers possible new items, e.g. changed light fittings, signs or hangers.
• If records show consistent excursions from chemical control levels, review processes.
If the initial survey has identified low alloy stainless steel components in safety critical locations, then either replace them with high alloy components or arrange a close inspection.
• Clean surface debris with fresh water – not just a wipe with a cloth.
• If rust stains are present, consider replacement.
• If there are no stains, stress corrosion cracks can be very fine and require x10 examination or even dye penetrant assessment. Cracked components require immediate replacement.
• Clips and wires are normally under tension and should be flexed to determine their integrity.
Cautiously test fasteners by loosening and retightening to the same load.
When working with stainless steel assets, a lot of attention is put into getting the ‘pre-install’ aspects right. Design, specification, fabrication, and commissioning are all equally important, but how the stainless steel in these assets is cared for and maintained is just as critical for optimum life and performance.
ASSDA Member Kleanwell specialises in asset management through the provision of cleaning and maintenance programs. Their work focuses on products where stainless steel is predominant - lift and elevator cladding, facades, awnings, and ducts among many others.
Jessica Wehbe, Director of Strategic Relationships at Kleanwell, says there is a clear gap in awareness and communication between the pre- and postinstallation stages, where contractors “do not know how to maintain their assets and the client at the end of the day is left scratching their head”. Jessica strongly believes there is a need for “clear communication between all parties that are involved from the design, manufacturing and installation, and maintenance teams” at the very early stages. This presents opportunities to set strong specifications (properly aligned to desired maintenance budgets and plans), and expectations around future material performance.
The well-worn phrase “stainless steel is low maintenance, not NO maintenance” should be embedded as early as possible.
A recent project Kleanwell completed at Sydney Olympic Park involved major restoration works to 21 lift landing doors with 15 years of poor maintenance. The before and after images show a dramatic improvement, however, pit-like artefacts remain. A basic cleaning regime implemented post-commissioning would likely have resulted in better aesthetics and lower cost than the recent history shows.
According to ASSDA Technical Specialist Dr Graham Sussex, some useful things to remember are:
If an adjacent window needs cleaning, clean the stainless steel as well.
Regular planned washing preserves the stainless lustre.
Never use abrasives or bleach when cleaning stainless.
AFTER: Surface deep cleaned, rust removed. Surface is left clean. Unfortunately damage from pitting is visible.
BEFORE: Build-up of pollution and oil accumulated over 15+ years. Never been deep cleaned.
When you last snacked on some almonds, you may not have given much thought to how they were harvested and made ready for your consumption. However, like almost all food and beverages, on their journey to your snack bowl they encountered some stainless steel bearing equipment.
Australia is a dominant producer of almonds, with the Murray Darling region accounting for almost a third of production. Kooba, located a few kilometres south of Griffith in south-central New South Wales and off the Murrumbidgee River, is the site of a large almond orchard having received significant recent investment.
Irrigation is critical to growing almonds, and water usage can reach up to 14ML per hectare. ASSDA Member
Custom Built Stainless, through their sister company and installer Irribiz, was commissioned to fabricate a range of dam water delivery systems for the efficient growth of these almonds. The scope of works included on-site valve banks, pump stations and fertigation (a process of delivering dissolved fertiliser through irrigation supply) systems, with stainless steel featuring heavily as a material of construction.
ICI Industries’ (parent company of Custom Built Stainless and Irribiz) Engineering Manager Vernon Green said, “A key element of supporting the business case for using stainless steel versus PVC and Poly Ethelene was the long-term value, with other factors taken into consideration including the aesthetic appearance and environmental sustainability”.
Around 7 tonnes of grade 304 and 316 stainless steel pipe in sizes ranging from 50mm to 600mm diameter was supplied by fellow ASSDA Member A&G Engineering. Welding was completed in accordance with AWS D18.1: Specification for Welding of Austenitic Stainless Steel Tube and Pipe Systems in Sanitary (Hygienic) Applications and AS 4041: Pressure Piping Walkways were also manufactured from grade 316, with all stainless components pickled and passivated prior to installation.
As the world continues to work through severe drought conditions and water supply issues, projects being designed to be as efficient as possible in water use will continue to rely on the longevity, durability and life-cycle benefits of stainless steel.
The Australian Stainless Steel Development Association (ASSDA) was established in 1992 to address and harness stainless steel’s growth trend in Australia, and today this remains the Association’s core objective.
2022 marks ASSDA’s 30-year anniversary. It’s an important milestone and opportunity to reflect on our achievements, contribution to the Australian stainless steel market, the ongoing impact of our organisation, and the challenges and opportunities ahead.
The event aims to bring together all those connected to us over the last 30 years, including our valued Members, Board Directors (past and present), industry colleagues and other stainless steel champions.
Stanch Stainless Steel Co., Ltd.
Stoddart
YC Inox Co., Ltd.
CONTACT:
Acerinox \ Amity Pacific
Austral Wright Metals
Aqseptence Group
Arcus Wire Group
Australian Stainless Distributors
Ching-Hann Industries Co., Ltd.
assda.asn.au
Dalsteel Metals
Co.,
AusPress Systems
Callidus Welding Solutions
Fagersta