
27 minute read
Ferroviario
Nacional
Crónica de los Asesores del Ministro de Transporte y Obras Públicas
Advertisement
Ing. Luis Ceiter– Ing. Carlos González
Ing. María Magdalena Cerviño
Una visión global
El ferrocarril en Uruguay comenzó a operar en el año 1869 con el primer tramo de 17 km de extensión entre la estación Bella Vista en el departamento de Montevideo y la estación Las Piedras en el departamento de Canelones.
Se extendió a todo el país como medio de transporte principal en la última década de Siglo XIX, llegando a Paso de los Toros en 1878, a Paysandú en 1890 y a Rivera en 1892.
Los criterios básicos del diseño de la red ferroviaria fueron un trazado que evitara las zonas inundables, “por las cuchillas”, pendientes aceptables para el ferrocarril de máximo 0,15%, y diseño de puentes y estructuras que nunca se inundaban, siguiendo el patrón característico que a pesar de que los puentes viales se interrumpen con las lluvias intensas, en el caso del ferrocarril son casi inexistentes los eventos de puentes cortados por crecidas de los cauces de agua.
La modernización y mejora del eje central del ferrocarril en Uruguay significa oportunidades para el transporte de productos como granos, madera y sus derivados y contenedores, así como posibilidades para el desarrollo del transporte de pasajeros.
El Ferrocarril Central fue concebido como una respuesta adecuada del punto de vista de la logística para el transporte de la celulosa y los insumos de la Planta de UPM 2 pero, aún así, tendrá una capacidad ociosa disponible para transporte de otras cargas de dos millones de toneladas por año.
El ferrocarril está diseñado para 4 millones de toneladas por año, por lo que el remanente de capacidad de 2 millones genera oportunidades para el transporte ferroviario de otras cargas y la aparición de otros negocios asociados al ferrocarril. Ya se está evaluando la incorporación de otros operadores, de modo que puedan incorporarse al sistema, utilizando la nueva capacidad de carga de la línea.
El ferrocarril es el medio de transporte más seguro y amigable con el medio ambiente para el transporte de carga pesada de larga distancia por el medio terrestre. Uno de los objetivos del
Ferrocarril Central del Uruguay es la promoción de una nueva cultura de seguridad ferroviaria y de nuevos y competitivos niveles de servicio del modo.
Esta nueva línea del Ferrocarril Central es moderna, eficiente y está basada y construida sobre estándares europeos y aplicará las mejores prácticas en la industria. Un criterio adicional para el diseño de este ramal, es una entrada a Montevideo y su zona metropolitana en armonía con el estilo de vida existente, mejorando las interconexiones urbanas y aumentando la seguridad.
El Proyecto del Ferrocarril Central (FFCC) se extiende en el tramo de vía férrea desde el Puerto de Montevideo hasta la Planta de Celulosa UPM2 (273 km) ubicada al sur del Río Negro, en el departamento de Durazno.
Situación Actual de la Obra
El avance de la obra del FFCC en términos económicos está en el orden de un 90% y en términos físicos en un orden del 70%.
Restan tramos de obras complejos como el ingreso a Montevideo que se están manejando con la Intendencia y la sociedad contratista a los efectos de lograr soluciones armónicas de convivencia entre la ciudad, el tránsito y el transporte ferroviario. Otro tramo complejo es la solución al norte del Río Yi, que estuvo supeditada a la solución técnica para la adecuación del puente ferroviario patrimonial ahí existente, a los requerimientos del nuevo proyecto.
Se prevé la finalización de la construcción para el segundo semestre del presente año, de manera de comenzar el proceso de pruebas, el que una vez finalizado pondrá al sistema en condiciones de comenzar las operaciones de transporte ferroviario bajo las condiciones de diseño.
En referencia al mantenimiento de la vía y sus sistemas asociados, existe en los contratos un período de mantenimiento bajo la modalidad del contrato PPP (Participación Público-Privada) a cargo de la sociedad contratista y existe otro contrato adicional de mantenimiento por 7 años más que está a cargo de otra de las empresas del grupo que está llevando a cabo el proyecto. Todo eso lleva a que el mantenimiento estará bajo este esquema por un período de 22 años.
Con relación a la integración del resto del sistema ferroviario a la línea del Ferrocarril Central resulta necesario realizar acondicionamientos de varios tramos y de sus sistemas de señalización a efectos de hacerla compatible con los estándares de diseño de la nueva línea.
El ramal de Rivera ya ha sido objeto de acondicionamientos, por lo que se estará en condiciones iniciales de operar la línea Montevideo-Rivera aunque en este caso con las restricciones de peso por eje presente en ramal Rivera. El ramal Represa de Salto Grande, con el que se logra la conectividad con la República
Argentina, requiere de nuevas obras de mejoramiento, las que están en consideración del Ministerio de Transporte y Obras Públicas.
Sobre las obras de adecuación de nuevos tramos de la red ferroviaria, es de interés del gobierno que la empresa que tuvo a su cargo la provisión de los durmientes de hormigón para el Ferrocarril Central permanezca en operaciones en el país para la eventual provisión de durmientes para los nuevos proyectos, atendiendo a la conveniencia de mantener la capacidad de producción con estándares internacionales y a efectos de poder mantener las fuentes laborales en un campo de alta especialización.
La Dirección Nacional de Transporte Ferroviario como Unidad Ejecutora desde enero del 2023
Por las disposiciones de la Ley N° 20.075 de Rendición de Cuentas y Balance de Ejecución Presupuestal correspondiente al ejercicio 2021 se creó como Unidad Ejecutora la Dirección Nacional de Transporte Ferroviario (DNTF) del Inciso 10 “Ministerio de Transporte y Obras Públicas”, la que existía con rango de Dirección General dentro de la Dirección Nacional de Transporte, y se transfirieron las competencias de la Administración de Ferrocarriles del Estado (AFE) relacionadas a la gestión de la infraestructura y las operaciones ferroviarias a la nueva unidad ejecutora.
El ente autónomo AFE continuará asociado a las operaciones ferroviarias mediante su participación en el capital accionario de la empresa SELF, Servicios Logísticos Ferroviarios, la operadora estatal de trenes.
La nueva Dirección Nacional se está estructurando, desarrollando su organigrama y definiendo la dotación de personal y el proceso de capacitación al que tendrá que someterse la totalidad de los recursos humanos que pasarán a gestionar el sistema ferroviario nacional bajo su nueva organización.
Uno de los cometidos de esta Dirección es la de establecer y controlar el cumplimiento de los reglamentos, resoluciones e instrucciones necesarias para el correcto funcionamiento del modo ferroviario, y su correspondiente régimen de sanciones.
Se han ido generando en los últimos años una serie de Normas, Decretos y Reglamentaciones para lograr que funcione el Sistema Ferroviario Nacional bajo los nuevos parámetros técnicos.
Otro de los cometidos de la nueva Dirección es la Gestión Operativa del Centro de Control de Tráfico Ferroviario, el que será el responsable de la operación del sistema ferroviario, comprendiendo la planificación, regulación y gestión de la circulación por la red ferroviaria.
Dentro de los desafíos presentes de la nueva gestión de las operaciones ferroviarias se encuentra la compatibilización del sistema ferroviario de control de trenes que estaba instalando AFE, denominado AUV (Automatización de Uso de Vía), aún en proceso de puesta en operación, con el sistema tecnológico previsto para el Ferrocarril Central, denominado ERTMS (European Rail Traffic Management System). Las acciones a tomar responderán al objetivo de desarrollar las coordinaciones entre ambos sistemas para que se pueda dar la interoperabilidad entre redes. Ello implicará una adecuación del parque tractivo pre existente de SELF para hacerlo compatible operacionalmente con el nuevo sistema del Ferrocarril Central.
La complejidad operativa y las implicancias de la entrada en operación del nuevo Centro de Control de Tráfico Ferroviario hacen necesario que el inicio de las operaciones ferroviarias requiera la presencia de supervisión especializada en la materia, la que no existe en nuestro país, por lo que se está en un proceso de identificación de posibles candidatos extranjeros con experiencia en la materia para cumplir dicha función durante las fases iniciales de operación del nuevo sistema ferroviario.
Por otro lado, el modo ferroviario impone que, por razones de seguridad, se tenga que tener entidades independientes.
Por tal motivo está creado legalmente el Órgano de Investigación de Accidentes e Incidentes Ferroviarios (Decreto 67/021) el que va a tener representantes de la DNTF y profesionales de la Facultad de Ingeniería de la Universidad de la República que asesora al Poder Ejecutivo en la materia. A su vez, todo el personal que integre el nuevo OIAIF deberá pasar por un proceso de capacitación adecuado a las nuevas características del sistema.
Es un gran desafío a nivel país, “es poner en marcha nuevamente el modo ferroviario en el país“.
Un Ferrocarril de Primer Mundo
En los últimos 15 años el país ha vivido un intenso proceso de crecimiento, desarrollando y diversificando sus exportaciones. La carga doméstica transportada en el país mostró un crecimiento del orden de cuatro veces el volumen transportado al inicio de tal proceso. No obstante, el modo ferroviario no acompañó tal crecimiento, sino que vivió un proceso de declive de su participación en el transporte de carga.
Cuando toda la infraestructura del ferrocarril nacional esté lista y los ferrocarriles en movimiento, Uruguay tendrá en funcionamiento un sistema destacado de primer mundo, con volúmenes significativos de transporte de carga ferroviaria.

Al aparecer el Proyecto del FFCC se recuperó la sensación de “un modo de transporte deprimido“ del sistema ferroviario y a raíz del mismo es bastante intensa la cantidad de proyectos que surgen y que están a consideración del Ministerio de Transporte y Obras Públicas.
Las locomotoras que se están construyendo para operar en Uruguay en la línea del FFCC son de última generación y con la tecnología utilizada en Europa. Otro operador ferroviario está encargando la construcción de locomotoras con tecnología estadounidense de vanguardia para la operación en la línea del FFCC y en el resto de la red.
El FFCC está actuando como un catalizador; además es carga nueva que se adicionará al sistema.
Durante mucho tiempo estuvimos convencidos que la intermodalidad es muy cara para Uruguay, pero muchas empresas nos están mostrando que les conviene el sistema multimodal.
La mejora de la infraestructura logística del país, en un enfoque multimodal, significa el aumento en la competitividad exportadora del Uruguay.
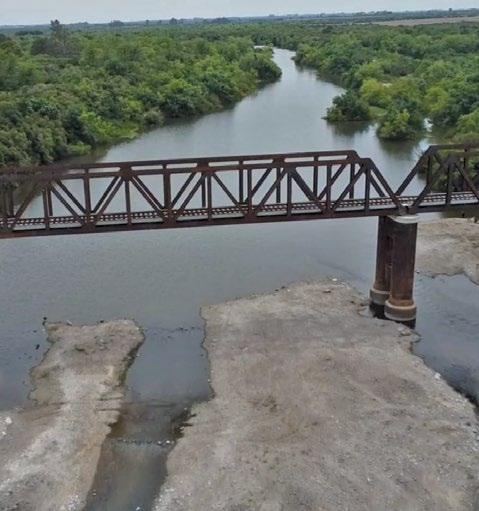
Estamos convencidos que en las próximas décadas habrá una erupción del Sistema Ferroviario Nacional generando un ambiente no conocido de vinculación intensa del sistema portuario nacional, a través del sistema ferroviario, con la región.
Referencias: https://www.afe.com.uy/ https://www.gub.uy/ministerio-transporte-obras-publicas/
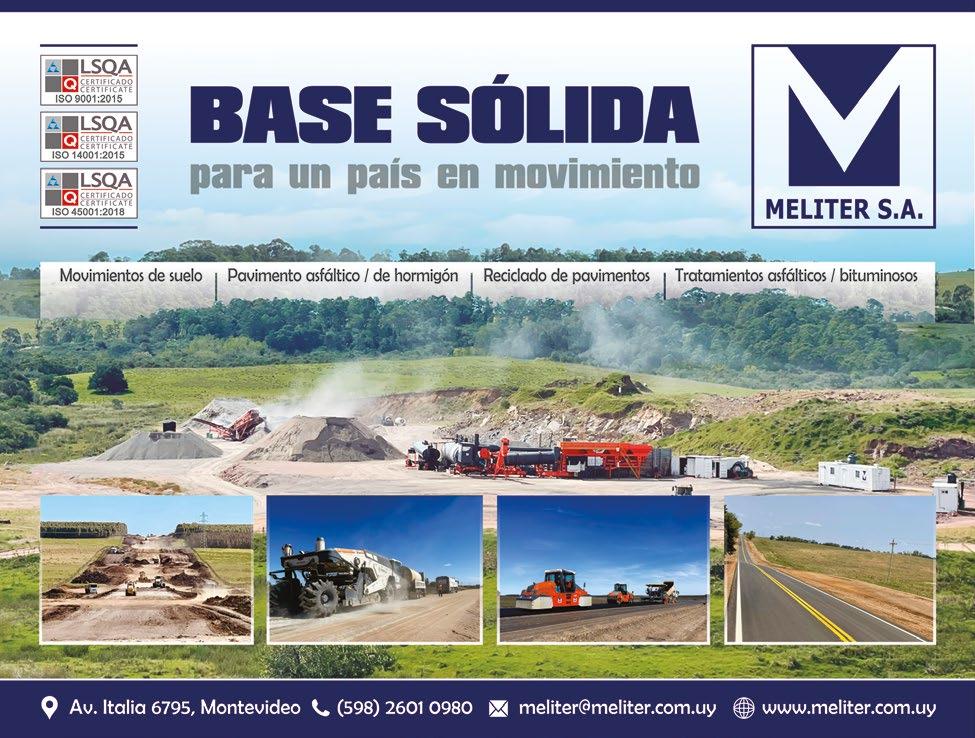
Ing. Nelson Pintos e Ing. Diego Nollenberger de CDS Ingenieros
¿En qué consiste la evaluación estructural de pavimentos?
La evaluación estructural de pavimentos consiste, en la determinación de la capacidad portante del sistema pavimento –subrasante de una estructura vial existente, en cualquier momento de su vida de servicio, con el fin de establecer y cuantificar las necesidades de rehabilitación.
Tradicionalmente, y con la finalidad de conocer las características estructurales, el ingeniero ha recurrido a sondeos de exploración directa, mediante los cuales obtiene muestras que son ensayadas en el laboratorio para conocer sus propiedades mecánicas, y posteriormente incorporarlas en el modelo del pavimento, con lo cual deduce las características estructurales del mismo. Esta metodología es discreta, costosa, lenta y de carácter destructivo.
La alternativa que se presenta es una propuesta con ensayos no destructivos realizada mediante FWD (Falling Weight Deflectometer), el cual es un equipo que mide la deflexión del pavimento, bajo la acción de una carga de impacto, simultáneamente en el centro del área cargada y en varios puntos alejados de la misma, a través de nueve sensores alineados longitudinalmente, lo que permite obtener el cuenco de la deformada bajo una carga dinámica, similar a la de un vehículo pesado.
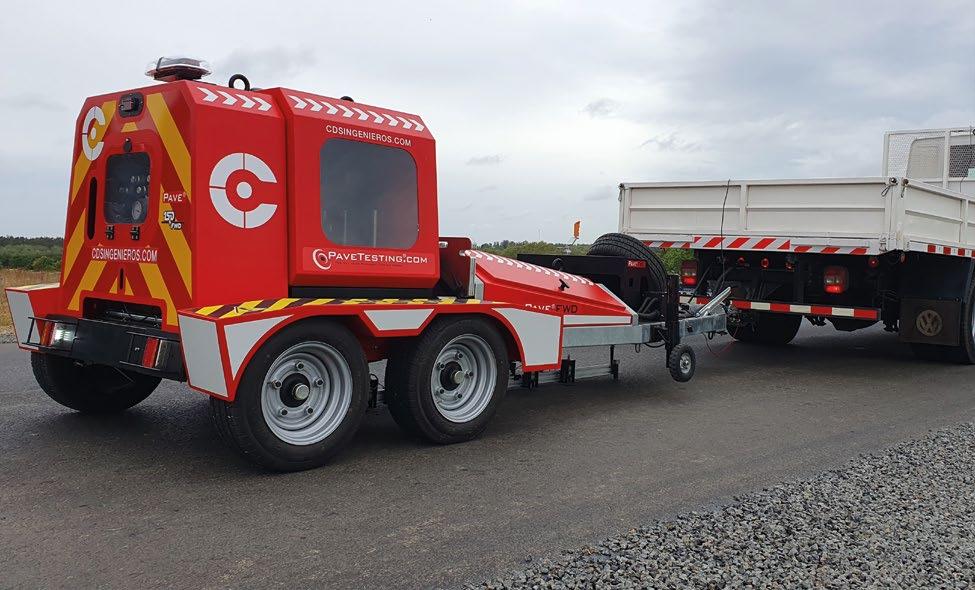
En la actualidad, los métodos no destructivos han adquirido gran importancia en la evaluación de pavimentos; debido a su rapidez, son económicos y no afectan a la estructura del pavimento; los cuales nos permiten obtener la capacidad estructural del pavimento a través del cuenco de deflexiones generado.
En tal sentido y en búsqueda de continuar a la vanguardia en la incorporación de nuevas tecnologías para la auscultación de pavimentos, CDS Ingenieros ha incorporado recientemente la más moderna tecnología en auscultación estructural de pavimentos, el Deflectómetro de Impacto Pave 150 FWD de la empresa inglesa PaveTesting.
¿Qué información recaba?
Mediante el deflectómetro de impacto tipo FWD se pueden obtener las deflexiones máximas y las áreas de los cuencos de la deformada, con las cuáles mediante procesos de retrocálculo, logramos obtener los módulos elásticos (de rigidez/resiliencia) asociados a las capas que constituyen la estructura de nuestro pavimento, así como llegar a determinar la vida remanente del mismo.
A la vez, las mediciones deflectométricas en sí mismas nos permiten determinar una serie de parámetros estructurales de nuestro pavimento que en forma cualitativa nos permiten realizar una evaluación de estado a diferentes profundidades de la estructura (capas superiores de pavimentos, a nivel de bases y subbases e incluso a nivel de la subrasante). Estos parámetros estructurales se basan principalmente en la forma del cuenco de deflexiones, la deflexión máxima, el área del cuenco y el índice de curvatura superficial.
Los factores que afectan en mayor medida a las deflexiones incluyen la carga, el clima y las condiciones del pavimento. Estos hechos deben considerarse cuidadosamente cuando se realizan las mediciones de campo ya que impactan directamente en los resultados obtenidos.
· Carga: La magnitud y duración de la carga influye considerablemente en las deflexiones de los pavimentos. Es recomendable que el equipo FWD sea capaz de aplicar una carga al pavimento, similar a la carga actual de diseño (por ejemplo 40 kN). Desafortunadamente, no todos los equipos comerciales que efectúan ensayos no destructivos pueden simular la carga de diseño, algunos lo hacen con la magnitud de la carga, pero no con su duración o frecuencia en forma normalizada. En tal sentido el deflectómetro de impacto FWD (Falling Weight Deflectometer) es aceptado como el equipo que permite simular la magnitud y duración de las cargas que circulan.

Temperatura: La temperatura y la humedad son dos condiciones climáticas que afectan la magnitud de las deflexiones. En los pavimentos asfálticos, las altas temperaturas producen el reblandecimiento de la carpeta asfáltica e incrementan las deflexiones no pudiéndose ser correlacionable su comportamiento viscoelástico. En el caso de los pavimentos de hormigón, la temperatura en forma de cambios globales del gradiente térmico representa una influencia muy importante en las deflexiones medidas cerca de las juntas o grietas. Las temperaturas altas provocan expansión en las losas, y por ende un acercamiento entre ellas; así, se incrementa la eficiencia de la transferencia de carga, y por consiguiente las deflexiones son menores. Es por ello, que debe de tenerse especial atención con la temperatura a la hora de las mediciones de campo.
· Condiciones del pavimento: Es evidente que las condiciones en que se encuentre el pavimento influyen en la magnitud de las deflexiones medidas. Para pavimentos asfálticos, las deflexiones obtenidas en áreas con agrietamientos y /o ahuellamientos serán mayores que las que se consigan en áreas sin deterioros. En los pavimentos de hormigón, las oquedades bajo las losas de concreto provocarán incrementos en las deflexiones; a su vez, la ausencia de deterioros de los dispositivos de transferencia de carga afectará a la deflexión medida en ambos lados de las juntas. Las deflexiones obtenidas cerca de una alcantarilla suelen ser mucho mayores; y para secciones en desmonte y en terraplén se presentan diferencias considerables en las deflexiones. Es importante considerar tales condiciones cuando se obtienen deflexiones en un tramo carretero, y más aún cuando se seleccionan las zonas de evaluación.
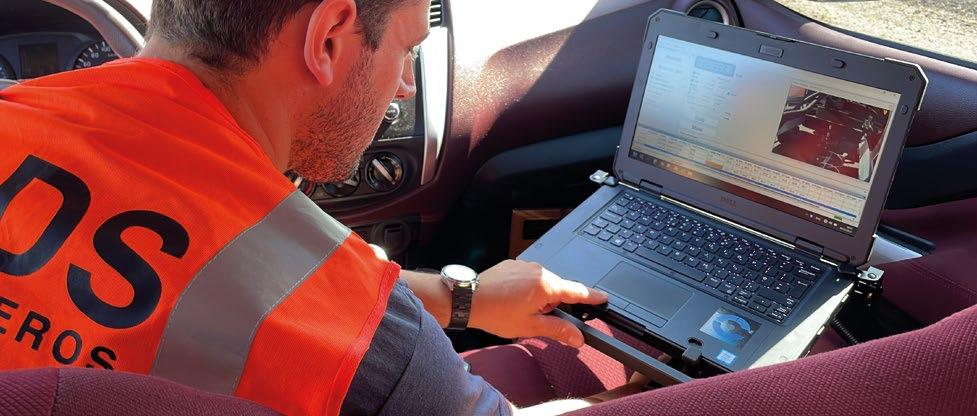
Aunque existan y se utilicen para la evaluación y proyecto de pavimentos equipos no destructivos, nunca deberán eliminarse los estudios geotécnicos tradicionales que permitan conocer las propiedades fundamentales de los materiales pues sirven para calibrar la información que se obtiene de equipos como el deflectómetro de impacto. Es por ello que se torna imprescindible acceder a información de antecedentes de la construcción del tramo que se esté evaluando, así como ciertas prospecciones geotécnicas que permitan mejorar los modelos a la hora de los ya citados retrocálculos.
Mantenimiento y rehabilitación de pavimentos
Los proyectos de rehabilitación de pavimentos son una necesidad que se impone debido a la importancia de la recuperación y mantenimiento del patrimonio vial construido.
Una parte fundamental en el diseño de rehabilitación de pavimentos es establecer la condición en la que se encuentra la estructura del pavimento existente.
Dado que gran parte de las carreteras construidas en Uruguay han sido construidas sobre la base de diseños realizados mediante métodos empíricos, es necesario realizar evaluaciones de estas estructuras usando este tipo de procedimientos, en programas computacionales con capacidad de simular las respuestas de los pavimentos a las cargas aplicadas, lo que permite establecer la modelización matemática por retrocálculo del comportamiento del pavimento en evaluación.
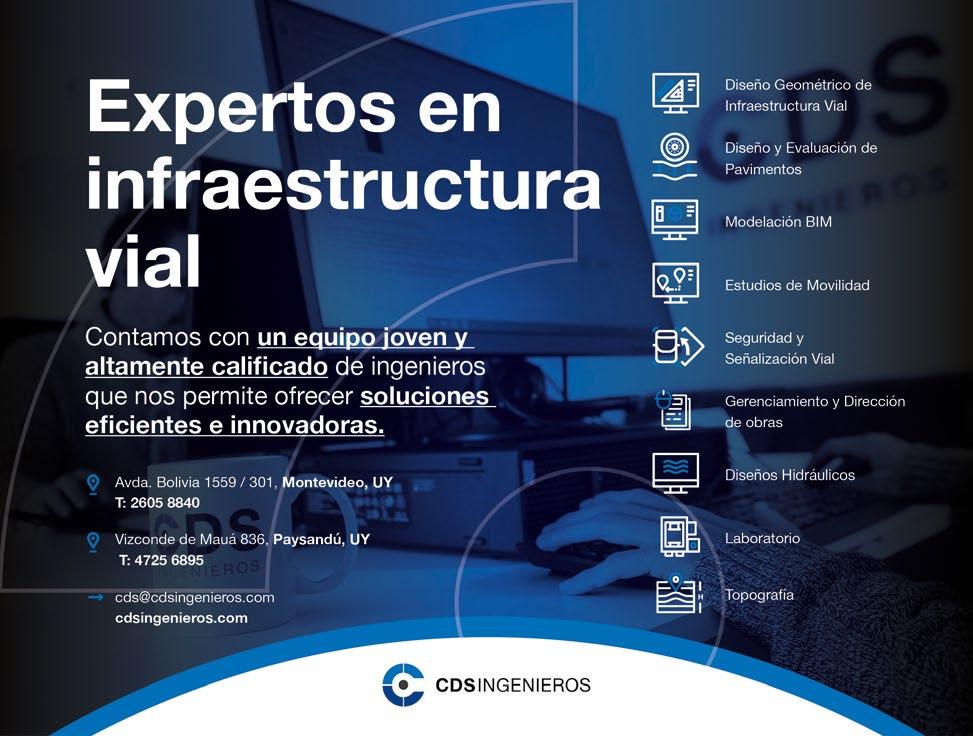
Conociendo el espesor y los módulos de las capas del pavimento, así como las cargas aplicadas, es posible por medio de la mecánica de los pavimentos determinar las tensiones, las deformaciones y los desplazamientos representados por la deflexión, con lo cual es posible realizar la evaluación y el diseño de las estructuras con vistas a su rehabilitación. En este sentido los métodos de retrocálculo permiten obtener los módulos en las condiciones de campo, con lo que se obtiene rapidez en la caracterización de los materiales minimizando en muchos casos la necesidad de toma de testigos o muestras.
Para el diseño de la capa de refuerzo en la rehabilitación de pavimentos existen varias metodologías empíricas-mecanicistas como la AASHTO o el método sudafricano (SAPEM), y softwares como el Backvide y DAPS, que permiten incorporar la información recabada mediante deflexiones en el diseño.
Infraestructura
Fehmarn Belt Fixed Link
El túnel sumergido que unirá Alemania con Dinamarca Trabajo desde Uruguay
Trabajos en el extranjero
En agosto del año 2020, Enginlabs comenzó a trabajar desde Uruguay, en uno de los proyectos de infraestructura más grandes que hay en el mundo en este momento, “The Fehmarn Belt Fixed Link”, el túnel sumergido más largo que se haya construido, conectará Alemania con Dinamarca y será una pieza clave dentro del corredor Escandinavo – Mediterráneo que conecta los países escandinavos con el resto de Europa.
El túnel tendrá 18 km de largo y conectará la isla de Lolland al Sur de Dinamarca, con la Isla de Fehmarn al Norte de Alemania, atravesando las aguas poco profundas del estrecho de Fehmarn. Se estima que el monto de inversión total de la obra ascenderá a 7.100 millones de Euros, de los cuales 700 millones corresponden exclusivamente a las obras de dragado y movimiento de suelos.
El túnel será de uso vehicular y ferroviario y se calcula que la obra bajará el tiempo de viaje desde Hamburgo a Copenhague de 5:00hs a 3:40hs. Estará compuesto por 89 elementos prefabricados de hormigón de 217m de largo, construidos en una fábrica ubicada del lado danés, armada exclusivamente para este proyecto. Los elementos del túnel se llevarán flotando hasta su ubicación en el mar y serán hundidos hasta su posición exacta, en el fondo de una trinchera de 12m de profundidad. Para generar la trinchera se excavará aproximadamente 19:000.000m3 de suelo que será utilizado para generar rellenos y ganar terreno al mar.
Enginlabs es contratado por el consorcio de Empresas formado por Boskalis y Van Oord, empresas encargadas de las obras de dragado y movimiento de suelos. La obra se encuentra actualmente en etapa de construcción y se espera su inauguración para el año 2029.

Diseño geométrico
Diseño geométrico y modelado 3D de la infraestructura en colaboración con Ingenieros Geotécnicos e Hidráulicos radicados en Europa, principalmente en Países Bajos.
El intercambio es un proceso dinámico y eficiente entre Europa y Uruguay, con reuniones de coordinación diarias en las mañanas, y revisión del trabajo en las tardes (horario uruguayo).
Coordinación
Coordinación y planificación del equipo de diseño geométrico, con los ingenieros de otras áreas y con los gerentes de proyecto radicados en Europa.
Coordinación con el departamento de topografía, ubicado a pie de obra y entrega de los modelos constructivos que serán cargados en las excavadoras y equipos de dragado.
Modelos de Maquinaria
Luego de completada la fase de diseño en detalle y previa aprobación por parte del cliente, se entregan los modelos constructivos. Estos modelos serán cargados en forma directa en los equipos de guía y control de maquinaria.
Otros trabajos en el extranjero
Actualmente EnginLabs también se encuentra trabajando en otros proyectos de relevancia a nivel internacional. Se destacan:
Constanta
Beaches,
renovación de 6 kms de costa en Constanta, Rumania. Nuevas escolleras y playas protegerán las zonas costeras pobladas de las olas del Mar Negro y, al mismo tiempo, impulsarán el sector turístico.
Revolution wind, construcción de molinos de viento y subestaciones marinas, ubicadas frente a Long Island en la costa Este de los Estados Unidos.
CREMAF Ruta 5
Tramo 1
69K000 - 95K350
Trabajos en Uruguay
Enginlabs se encuentra trabajando en el proyecto ejecutivo vial para el consorcio Lemiro Pablo Pietroboni - Berkes en el marco de la concesión CREMAF Ruta 5 Tramo 1.
El tramo de obra en la Ruta 5 se ubica entre la progresiva 69K000 y el empalme con la Ruta Nacional N°56 en el acceso a la ciudad de Florida, pasando por los pueblos Mendoza, Mendoza Chico y por los empalmes con las Rutas Nacionales N°76 y N°12. Se muestra la Planta de Ubicación del proyecto.
El proyecto duplica la Ruta 5, contiene dos puentes en su trayecto, 4 pasajes peatonales inferiores, pasajes de fauna y retornos particulares. El pasaje por Mendoza y Mendoza Chico son de especial cuidado.
El trabajo se hace en conjunto con profesionales de otras disciplinas y equipo técnico de LPPietroboni en coordinación.
Diseño geométrico
Duplicación de calzada de Ruta 5. Adecuación de la calzada actual (tramos a modificar para que verifiquen una velocidad de diseño de 90 km/h). Retornos y empalmes (geometría y ubicación).
· Atravesamiento de centros poblados. Obras de drenaje. Puentes y pasajes a desnivel.
· Obras complementarias (calzadas de servicio, cruces peatonales, sendas peatonales, paradas de ómnibus, entradas particulares, pasa fauna, etc.)
· Proyecto de costados de camino y medianas/proyecto de sistemas de contención.
· Señalización.
Modelos
Se realizó modelación de todo el proyecto, y dichos modelos se envían a obra para su construcción.
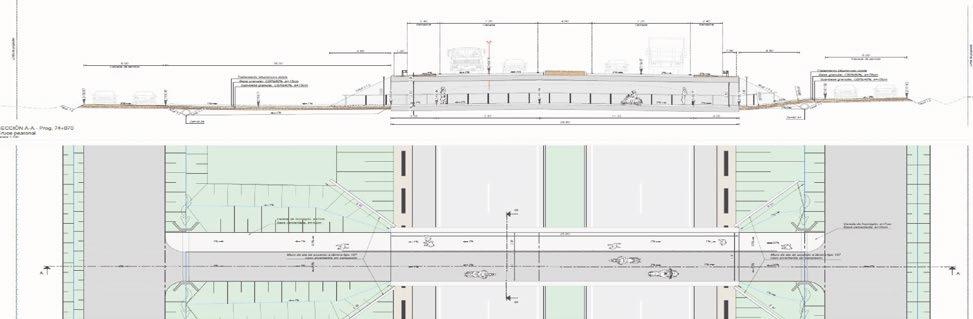
· Se realizaron modelos detallados de los pasajes peatonales.
Otros trabajos en Uruguay
Enginlabs se encuentra proyectando junto a DICA y Asociados 76 kilómetros en la Ruta 14 entre Lascano y Ruta 9, para la CND y la Intendencia de Rocha, en coordinación con el MTOP.
La empresa también se encuentra realizando la señalización y defensas del tramo de concesión de Ruta 5 de HyG desde el kilómetro 40 hasta el kilómetro 69.
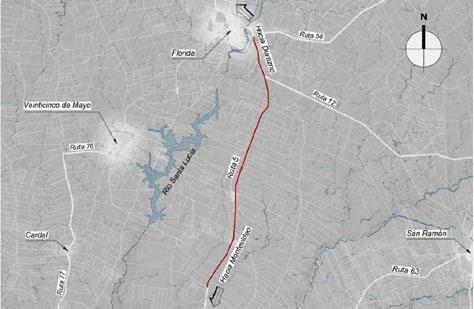
Infraestructura
Ruta 24: Rehabilitación mediante la
considera la resistencia residual que le confieren las macro fibras al hormigón, entre otros parámetros de diseño. De esta manera, el proyecto resultó en una capa de Hormigón Reforzado con Fibras (HRF) de 15 cm de espesor, con losas cortas de 1,8 m × 1,8 m, considerando además adherencia con la capa asfáltica, la cual luego de su tratamiento (fresado y texturizado) debía mantener un espesor remanente mínimo de 12 cm.
Fibras
Desempeño
Información proporcionada por Hormigones
Artigas
Introducción
La Ruta 24 pertenece a la Red Vial Nacional, y recorre la zona del litoral en la región Noroeste del país, enlazando las Rutas 2 y 3, de Fray Bentos a Paysandú, donde predomina el tránsito pesado agroforestal. Durante los años 1999 y 2000, se realizó la rehabilitación de la ruta, mediante la conformación de un paquete estructural, con 45 cm de material granular (base y subbases) más 15 cm de concreto asfáltico, que sirvió al tránsito pesado durante 10 años, y luego fue esencial al considerar el espesor remanente de la capa asfáltica para poder aplicar un novedoso método de diseño, en una nueva rehabilitación.
De esta manera, entre agosto de 2011 y marzo 2012 se construyó un primer tramo de la RN 24 de 21,6 km de longitud, desde el empalme con la RN 2 hasta el empalme con la Ruta 20, y en el año 2013 se amplió un segundo tramo de 27,3 km adicionales, alcanzando así una longitud total próxima a los 49 km.
El objetivo del presente trabajo es evaluar el desempeño de la ruta, y valorar el estado del hormigón, luego de 10 años en servicio al tránsito pesado.
Antecedentes
La edad de diseño para la rehabilitación de la ruta es la correspondiente a 15 millones de ejes equivalentes AASHTO, donde el MTOP, adoptó un novedoso método de diseño, el cual
Los requisitos establecidos para el HRF en el Pliego de Especificaciones Técnicas Particulares de la obra fueron: resistencia a compresión 35 MPa; módulo de rotura 5 MPa; y resistencia residual (fD150) 1 MPa (20 % del MR), todos ellos valores medios a la edad de 28 días. La Tabla 1 muestra la dosificación propuesta para cumplir estos requisitos, considerando los ajustes realizados por las condiciones estacionales. Las principales propiedades valoradas en el hormigón, durante el desarrollo del tramo I de la obra, se indican en la Tabla 2.
La obra fue ejecutada por la empresa constructora Grinor y el hormigón premezclado fue provisto por Hormigones Artigas.
Desempeño de los Tramos I y II
Se adoptó la restitución efectiva de losas que se han llevado a cabo como un indicador para evaluar el desempeño estructural de los TI y II de la ruta, donde la severidad de la fisuración de ancho mayor a 4 mm ha generado desprendimientos y la necesidad de reponer una losa.
El área intervenida en la reposición de losas, hasta el 30 de abril de 2021, por concepto de fisuras básicamente, consistió en 1.243 m2, de los 351.144 m2 construidos, lo cual representa el 0,35% del total de la superficie, que se compone en el TI con una tasa de bacheo de 0,64 % al cabo de 10 años y de 0,13 % en el TII al cabo de 8 años.
Prácticamente la mitad de las patologías que han merecido intervención se han dado en las losas próximas a los inicios o fines de las jornadas.
En relación con la regularidad superficial, el contrato exigió un IRI característico, con la implementación adicional de un premio o bonificación, por debajo de los umbrales de aceptación, que permitió evolucionar de 2,8 m/km a 2,4 m/km para la aceptación de cada km de senda construida, y simultáneamente la bonificación se pasó a aplicar a partir de valores de 2,2 m/km, hasta 1,8 m/km, de forma escalonada, según el IRI obtenido.
Los resultados obtenidos del valor promedio de IRI en cada km luego de la construcción del TI fue algo menor a 1,8 m/Km, en tanto que para el TII fue de 1,4 m/km.
Luego de 9 y 7 años en servicio de los TI y TII, todos los subtramos kilométricos cumplieron con la condición de mantenimiento de 3,5 m/km, y cada tramo individualmente con la condición de 3,2 m/km, obteniéndose un aumento de 0,5 m/km (de 1,8 a 2,3) en promedio para el TI y de 0,3 m/km (de 1,4 a 1,7) para el TII desde la construcción.
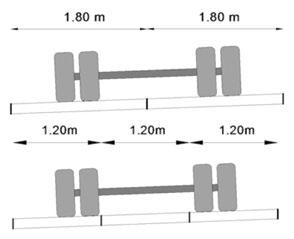
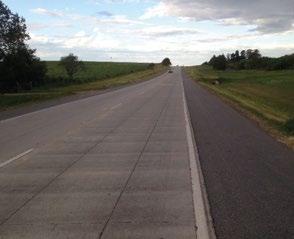
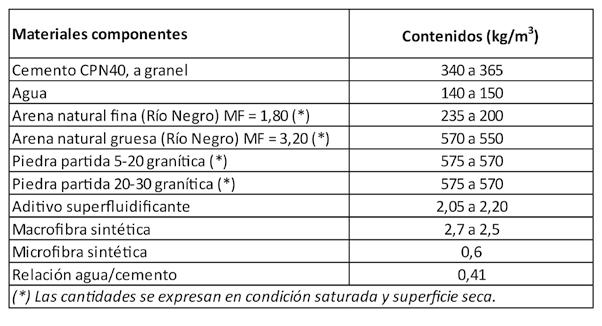
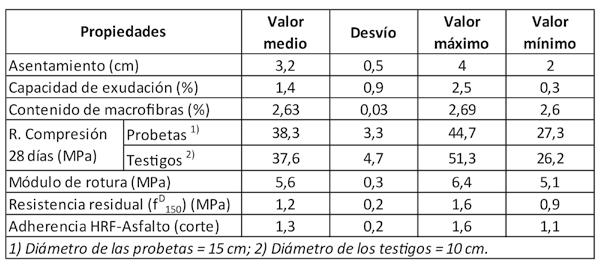
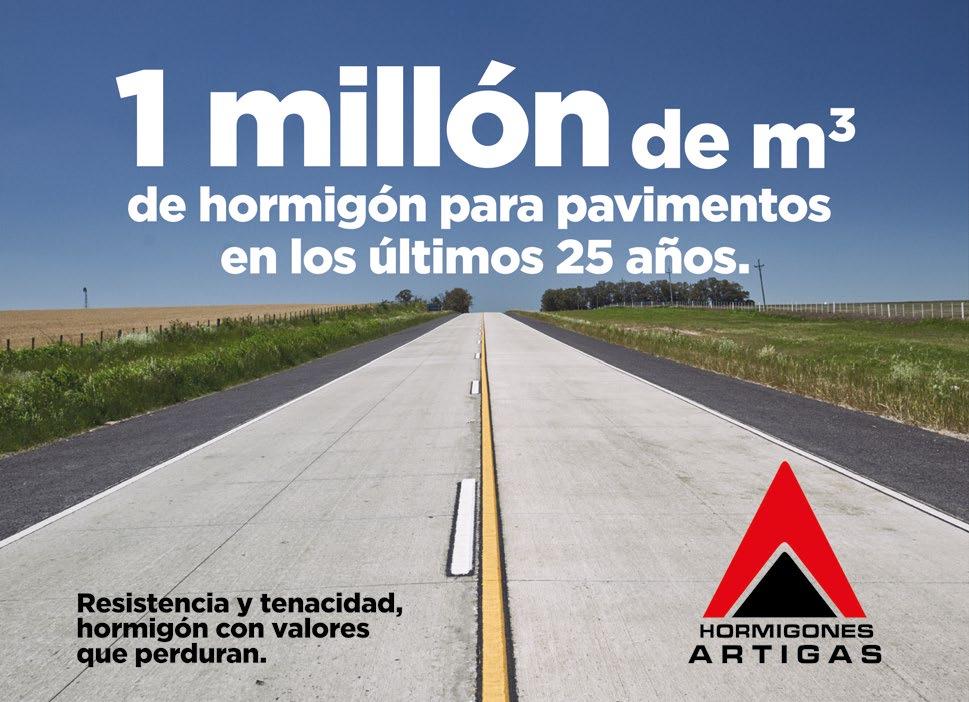
Se destaca que luego de dicho período en servicio al tránsito pesado, el 96% de los subtramos kilométricos aún seguían cumpliendo con la condición de aceptación fijada para el momento de la construcción.
Otra observación esperada del IRI obtenido, es la coincidencia de las zonas de mayor rugosidad del pavimento con las actuaciones de bacheo.
Por último, en lo que refiere a la evaluación de un tramo experimental de 500 m de longitud, con losas de HRF adherido, que fueron conformadas de 1,20 m × 1,20 m, y 12 cm de espesor, donde las ruedas típicamente circulan próximo a las juntas longitudinales, no se observó un mayor deterioro de las juntas respecto a la situación estándar, y tampoco se presentó una mayor evolución de daño en el pavimento (figura 1).

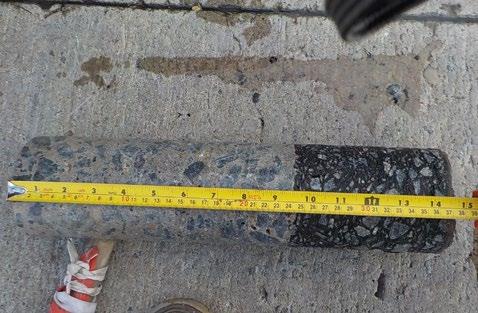
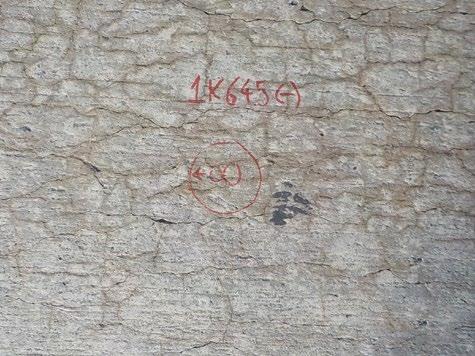
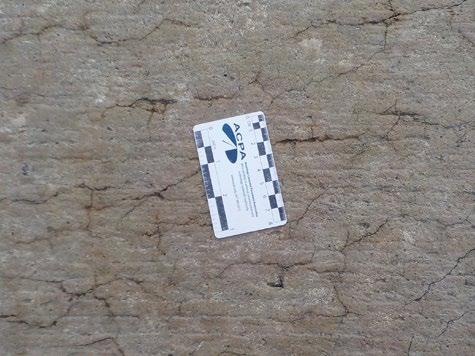
Consideraciones sobre el hormigón
A pesar de lo expuesto sobre el buen despeño del pavimento, a raíz de la presencia de un cuadro de fisuración generalizado en las losas, similar al que produce la Reacción Álcali Sílice (RAS), se decidió estudiar las posibles causas de estas fisuras mediante la evaluación de testigos de hormigón extraídos del pavimento durante el mes de junio de 2021.
Para el estudio del hormigón se seleccionaron dos zonas (A y B) correspondientes al tramo ejecutado en 2011, de la senda cargada y a 60 cm del borde de la calzada. Si bien, el cuadro de fisuración de la zona A es más benigno que el de la zona B, ambos sectores muestran el mismo patrón de fisuras (Figura 2). En las Tablas 3 y 4 se presentan los resultados obtenidos y las principales observaciones realizadas sobre los testigos.
En la Tabla 5 se informan la resistencia a compresión (f´c) y los índices de daño de la rigidez (SDI), índice de deformación plástica (PDI), índice de no linealidad (NLI), correspondientes al primer ciclo de carga; y también se incluyen SDI 2-5 y PDI 2-5, promedios en los ciclos 2 a 5.
En un estudio complementario, para comprobar la existencia de fenómenos asociados a la RAS, se procedió al examen petrográfico del hormigón sobre secciones delgadas de cuatro testigos, dos de la zona A y dos de la B. Los resultados indican un deterioro insignificante en los testigos 4, 5 y 10, con microfisuras, principalmente en el agregado grueso y algunas en la pasta de cemento. La presencia de relleno en las fisuras es escasa. Si bien el deterioro del testigo 8 es mayor, principalmente por el desarrollo de microfisuras en la pasta de cemento, tanto vacías como con productos de reacción, su nivel de daño es marginal a moderado.
Si bien, se observaron microfisuras en el agregado grueso, en general, no continúan hacia la pasta de cemento por lo que se interpretan como propias de la roca, previo a su incorporación en el hormigón, por ejemplo, producidas en el momento de explotación y trituración del árido.
Consideraciones finales

La diferencia en el desempeño de ambos tramos puede considerarse multicausal, ya que el Tramo I ha superado los 11.000.000 de Ejes Equivalentes, mientras que el tramo II alcanzó los 9.000.000 de EE, lo que representa un 20% menos de tránsito pesado, y esto coincide además con la construcción original de la calzada asfáltica que también la obra se dividió en dos etapas, con materiales de distintos orígenes en las capas granulares de base y subbase.
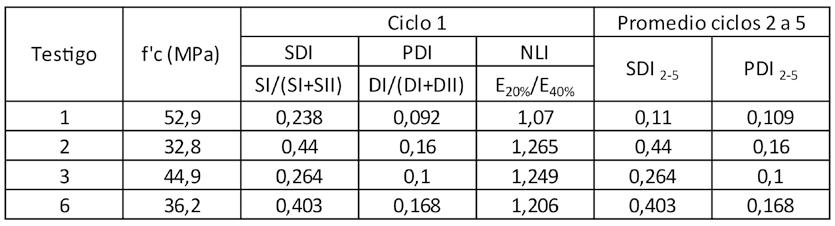
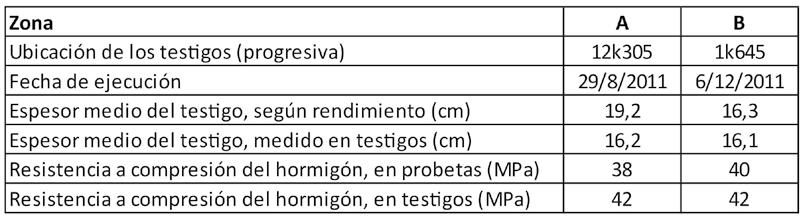
Además, la diferencia observada en la evolución del daño podría también vincularse al proceso constructivo y/o de elaboración de materiales, donde se apreciaron distintos valores de IRI obtenidos durante la construcción. Otra diferencia surge a partir del knowhow entre TI y TII.
En relación con el cuadro de fisuración que poseen las losas, el estado actual de servicio del pavimento, en el tramo de ruta analizado, es altamente satisfactorio, habiendo transcurrido cerca del 80 % de la vida útil de diseño. Por tratarse de un hormigón con fibras, aún con fisuras, es esperable que conserve una capacidad resistente residual. Si bien, el espesor medio medido sobre los testigos (≈ 16 cm) es similar para las dos zonas evaluadas (A y B), el espesor promedio del pavimento en la zona A (volumen de hormigón colocado/superficie construida = 19,2 cm), resulta superior al de la zona B (16,3). Esto, sumado al hecho de que la ejecución de ambos tramos se llevó a cabo bajo condiciones climáticas disímiles (zona A: invierno; zona B: verano), podría explicar, entre otros factores (grado de adherencia con la capa asfáltica), los diferentes grados de fisuración observados sobre la superficie del pavimento.
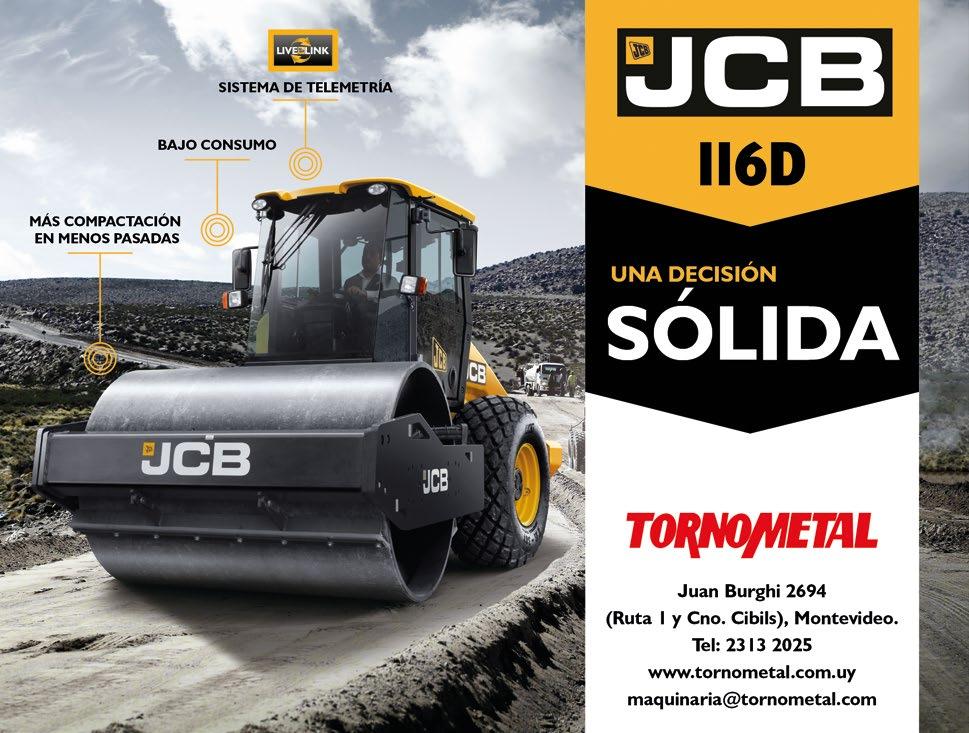
Si bien el examen microscópico mostró algunos signos localizados de RAS, el grado de deterioro de los testigos es marginal y su estado general es bueno. Dado que los signos despreciables de RAS detectados no guardan relación con la magnitud del deterioro del hormigón, es difícil hallar elementos de juicio que permitan atribuir el daño del hormigón a la RAS. En base a lo expuesto, es posible inferir que el deterioro observado en la respuesta mecánica del hormigón pueda ser atribuido a los efectos de fatiga del material (la estructura transita un período muy avanzado de su vida útil), combinados con posibles defectos generados durante la etapa constructiva, por ejemplo, vacíos de compactación, cambios estacionales del clima, etc., desestimando a la RAS como parte de este mecanismo.
Referencias (Autores)
- Fontáns David, Pastorini Magdalena, Pappalardi Mariano, “Desempeño de un tramo de carretera en Uruguay rehabilitado mediante ejecución de una capa adherida de hormigón reforzado con fibras” XVIII Congreso Argentino de Vialidad y Tránsito (2022).
- Milanesi Carlos A., Pappalardi Mariano, Marfil Silvina, Locati Francisco, Giaccio Graciela, Zerbino Raúl, Fontáns David, Pereyra María, Vila Patricia, “Consideraciones acerca del estado del hormigón del pavimento de la Ruta Nacional 24 (Uruguay) luego de diez años en servicio al tránsito” X Congreso Internacional y 24° Reunión Técnica de la Asociación Argentina de Tecnología del Hormigón (2022) 634-641.
INFRAESTRUCTURA
Viaducto en Rambla
Portuaria
Obra emblemática en la capital
Información proporcionada por Grupo Saceem
El Puerto de Montevideo ha marcado en gran medida el desarrollo tanto de la ciudad como del país desde hace ya 113 años. Se ha consolidado como el principal puerto de trasbordo regional, formando parte del corredor bioceánico Atlántico-Pacífico con la hidrovía Paraguay-Paraná.
Este crecimiento ha sido acompañado por el crecimiento de sus áreas vecinas, conviviendo en forma paralela con el principal acceso a la ciudad desde la zona Oeste del país.
Proyecto
El proyecto, denominado “Redefinición de la circulación en la rambla portuaria” inició sus obras en diciembre del 2019, y la construcción realizada por el Consorcio Saceem - Grinor demandó tres años de trabajo y una inversión de 135 millones de dólares.
Fue financiado por recursos propios de la ANP y con un préstamo del Fondo Financiero para el desarrollo de la Cuenca del Plata (FONPLATA).
Con el objetivo de acompañar el crecimiento del Puerto de Montevideo y de las nuevas necesidades del tránsito de la Ciudad, el equipo de Saceem-Grinor diseñó y presentó, en el año 2016, mediante el instrumento de Iniciativa Privada una serie de obras de infraestructura con el fin de:
• Separar el tránsito portuario del tránsito urbano de la ciudad.
• Disminuir el tiempo de entrada y salida a la ciudad desde el Oeste aumentando la capacidad de la Rambla Portuaria.
• Eliminar la futura interferencia que se generaría con el Ferrocarril Central.
• Ampliación del recinto portuario aumentando su capacidad de almacenamiento de contenedores, áreas de maniobra y circulaciones internas.
La construcción del Viaducto de 1.800 metros de longitud, diseñado para una velocidad de 75Km/h, a ocho metros de altura, aumenta un 50% la capacidad del tránsito pasando de dos a tres carriles en cada sentido. Permitió al Puerto ganar un área inmediatamente debajo de 16.000 m2 para una nueva vía de circulación en dos carriles en ambos sentidos, reordenando la circulación en el recinto portuario.
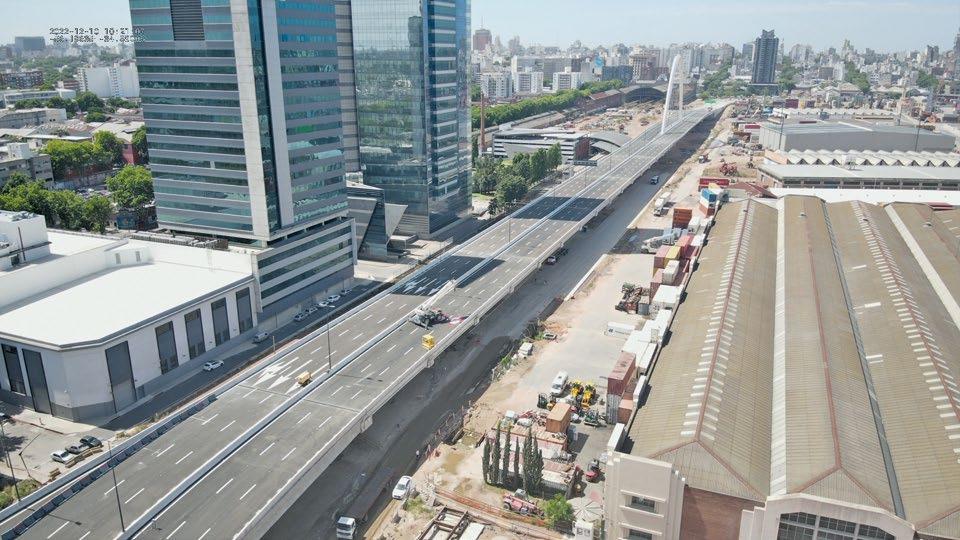
La construcción de un Puente en Arco, de 90 metros de luz libre, 160 metros de largo, y 50 metros de altura, permite el pasaje inferior de la vieja vía ferroviaria que ingresa al puerto, hacia la terminal de contenedores. Por sus características estéticas, el arco le dará un realce a la fisonomía de la zona, siendo un nuevo ícono referente de la ciudad.
A través de dos rampas principales de 200 metros de longitud, el viaducto se conecta a la rambla al sur a la altura de la calle La Paz, y al norte a la altura de la calle San Fructuoso.
Desde la calle Colombia a través de una rampa secundaria se puede acceder al viaducto, así como descender del mismo por otra rampa que conecta con la calle Francisco Tajes.
Un segundo Viaducto interno de 150 metros de largo dentro del recinto portuario, permitirá el pasaje a desnivel de la circulación interna de camiones, evitando la interferencia con el tren que ingresa a la terminal de UPM.

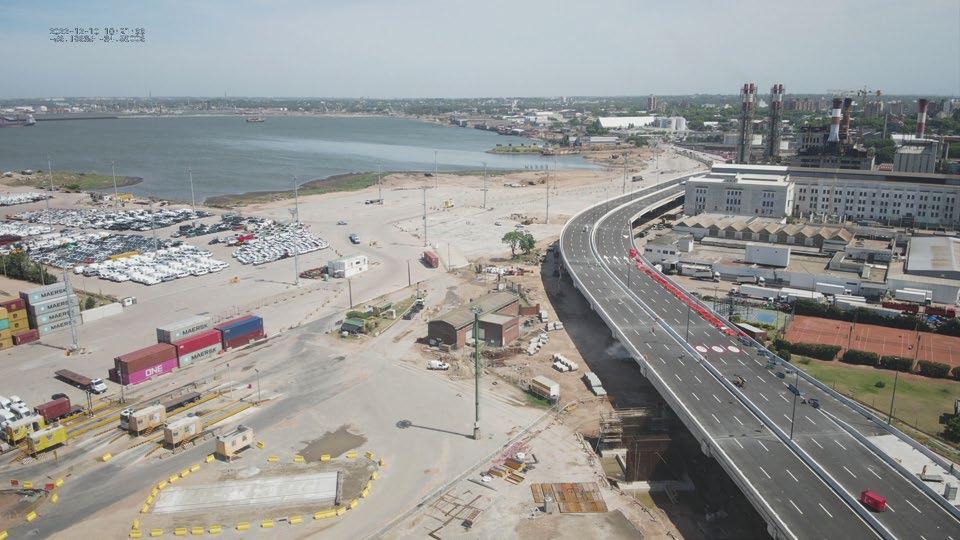
En cuanto al área operativa del puerto, se ejecutaron 90.000 m2 de hormigón compactado a rodillo de 43 cm de espesor, contando dicha nueva infraestructura con servicios de iluminación, agua potable, incendio, saneamiento y drenajes pluviales. Su capacidad de carga permite acopiar contenedores hasta 5 niveles.
Se amplió el recinto portuario desplazando la línea costera. Mediante el procedimiento de reclamación de tierras, se rellenó y acondicionaron más de 14.000 m2, conformando un área logística y de circulación, con capacidad de espera para 80 camiones. Entre el área ganada a la bahía, y acondicionamiento de otras áreas se pavimentaron 45.000 m2 con pavimento articulado de adoquines de hormigón.
Las vías de circulación internas, rampas de acceso, y reformulación de las calles anexas implicaron la ejecución de 54.000 m2 de pavimentos de hormigón de 20 cm de espesor y más de 11.500 m2 de veredas.
Puente en Arco
El Puente en Arco de 1.200 toneladas de acero total está formado por un cajón metálico de 1.000 toneladas y un arco de 200 toneladas, es una solución estructural que trasmite todas las cargas hacia los extremos, comprimiendo el arco que sostiene el tablero a través de las péndolas; en este caso nueve péndolas que sostienen el cajón metálico del arco sobre el que apoya un tablero de hormigón armado de 35 centímetros de espesor medio.
Las cargas descienden a través de las pilas en forma de “V” de hormigón armado hasta un gran cabezal de 850 m3 de hormigón que descarga sobre 16 pilotes de 1,50 metros de diámetro, en cada uno de los extremos. Esta solución además de ser muy atractiva permite lograr mayores luces que con otro tipo de solución. Ese objetivo fue buscado debido a la trayectoria con la que atraviesan las dos vías de tren que van a convivir en esa zona.
La parte metálica del Puente en Arco fue fabricada en Vigo, España, y transportado por vía marítima, en cinco tramos el tablero y en cuatro partes el arco. Se montó luego de terminadas parcialmente las pilas de hormigón en “V”, mediante apoyos auxiliares; el tablero se montó en tramos, y el arco se montó en tres partes con el uso de una grúa de 650 toneladas.
En total se prefabricaron a pie de obra 415 vigas pretensadas de 21 metros, 56 vigas postensadas de 40 metros y 22 dinteles. También se ejecutaron 4.500 unidades de prelosas de hormigón.
Se elaboraron 310 pilotes de aproximadamente 30 metros de profundidad, 52 pórticos formados por un cabezal, pila y dintel con un total de 250 m3 de hormigón cada uno. Las rampas se conformaron por muros de contención de hormigón armado rellenas de suelo compactado y terminadas con pavimento de hormigón.
En total se utilizaron más de 60.000 m3 de hormigón, 6.000 toneladas de acero, 100.000 m3 de rellenos de suelo, 90.000 m3 de rellenos para bases de pavimentos y 4.000 toneladas de mezcla asfáltica.
En materia de recursos humanos se utilizaron 1.600.000 horas hombre con un pico de 500 personas trabajando en la obra.
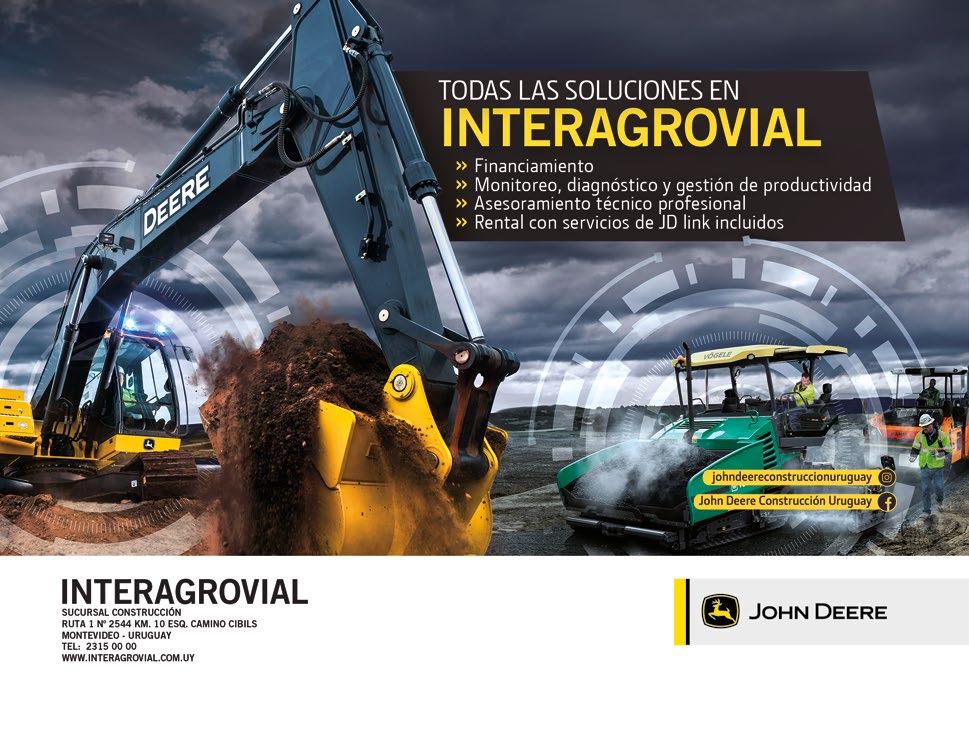