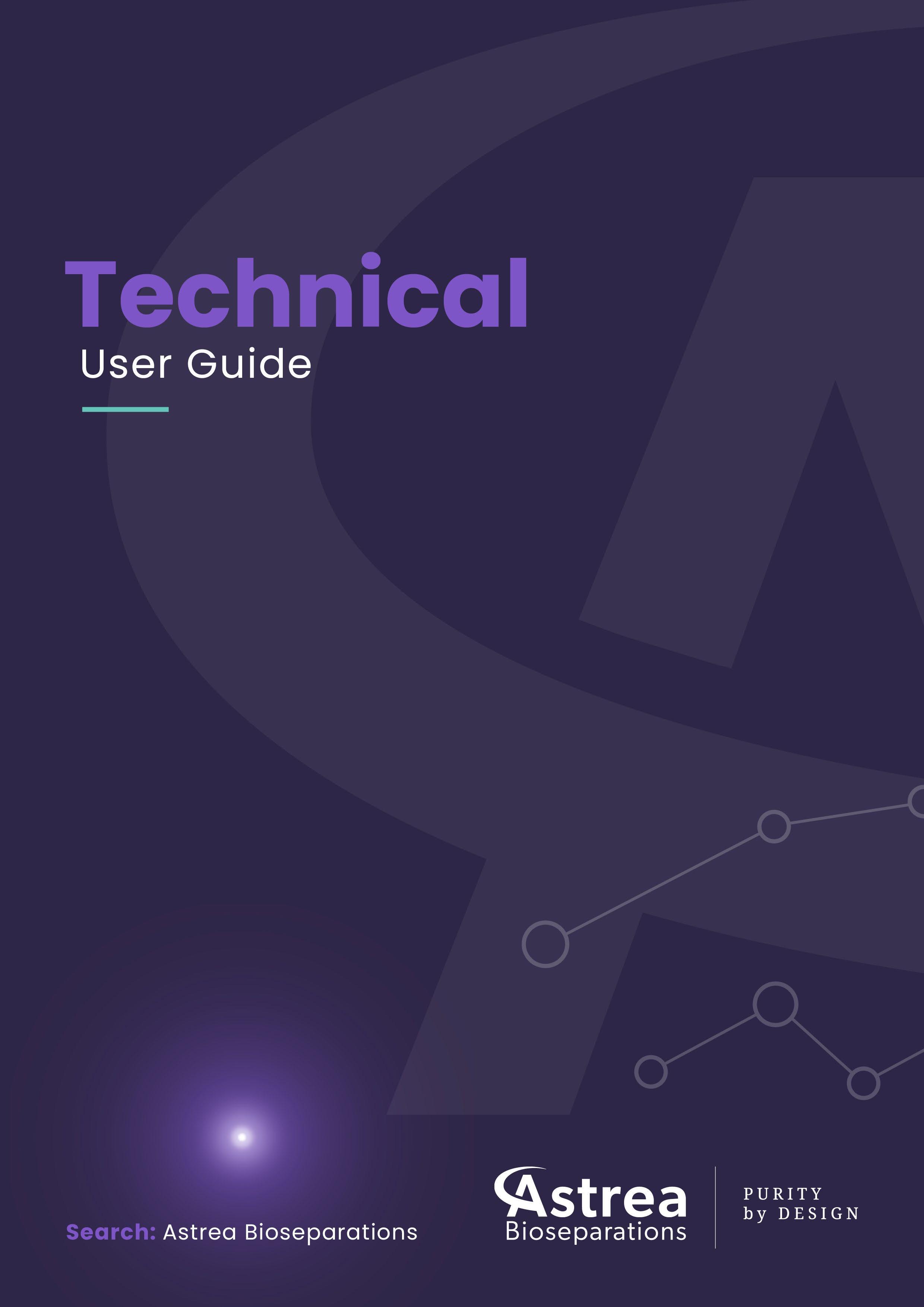
Refresh Kit: Guide to Replacing the Wetted Flow Path
Evolve® 450 mm Process Column
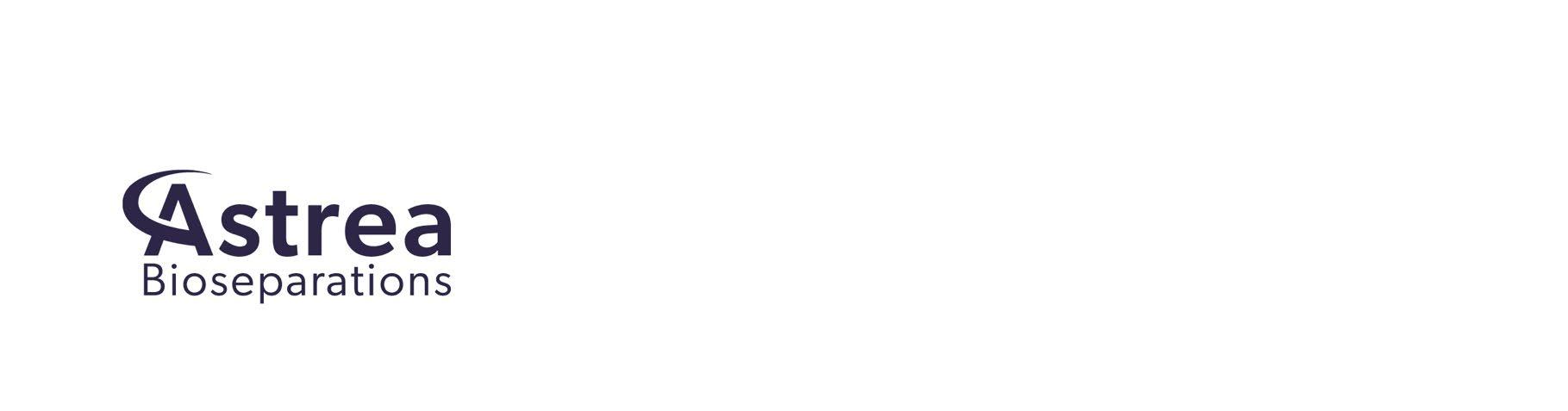
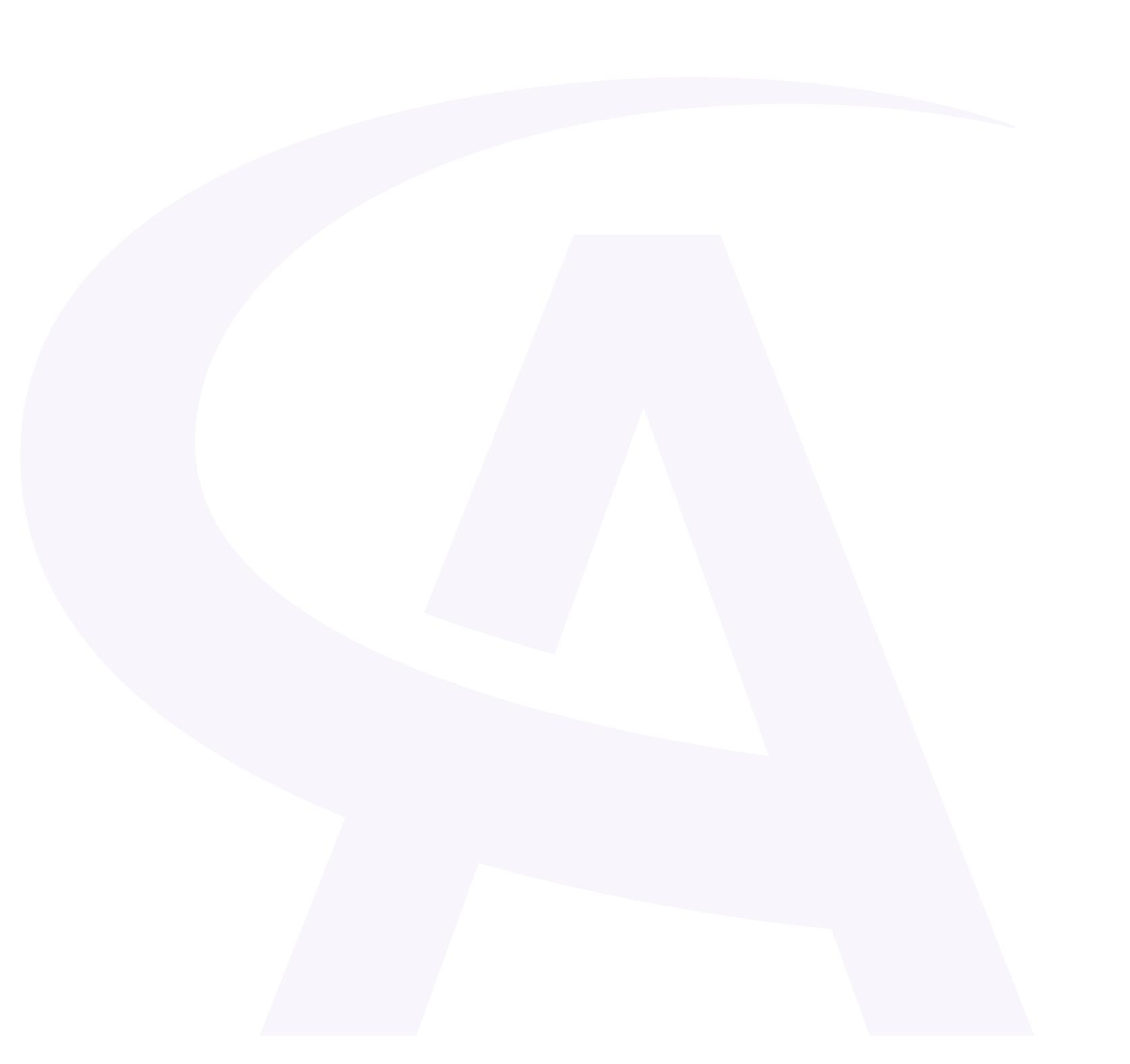
Refresh Kit: Guide to Replacing the Wetted Flow Path
Evolve® 450 mm Process Column
This manual describes the procedures necessary to replace the wetted flow path components in the Evolve® 450 mm Process Column using the Column Refresh Kit.
Figure 1: List of Refresh Kit components and column schematic.
Parts shown in red are the wetted flow path components
There are four main stages to refreshing the column by replacing the wetted flow path. The first three stages are based on the disassembly and reassembling each column sub assembly with new components, before the final stage of rebuilding and testing the complete column.
STAGE 1 – Refresh the Adjuster Assembly of the Evolve® 450 mm Process Column
STAGE 2 – Refresh the Tube Assembly of the Evolve® 450 mm Process Column
STAGE 3 – Refresh the Fixed Assembly of the Evolve® 450 mm Process Column
STAGE 4 – Rebuild and Test the Evolve® 450 mm Process Column
To disassemble and assemble the columns follow the instructions below. After reassembling the column, ensure that the column does not leak by performing a hydrostatic leakage test.
THESE PROCEDURES MUST BE PERFORMED USING AN OVERHEAD HOIST
NOTE: When assembling/dissembling attention should be paid to: -
1. Always use the correct size tools. A comprehensive tool kit is provided with the original column. See Table below.
2. Ideally components should be at approximately room temperature (approximately 20°C). If not, take particular care as thermal expansion or contraction may make components fit more tightly and thus more difficult to disassemble.
3. Dismantled assemblies should be rested on a clean, dry surface.
4. Pay particular care not to damage the edge of the flow cells.
5. When unpacking columns be careful not to scratch the inside of the column tubes
6. Be careful not to damage stainless steel surfaces by bumping, knocking or scratching.
7. Do not over-tighten components, and use correct torque settings as given in this guide.
8. Good engineering practices should always be followed and operations carried out in an approved and safe manner.
9. The components of the Evolve® 450 mm Process Column are heavy and large. Mechanical handling equipment or manual handling aids should be utilised to safely lift or move the column or its subassemblies. Provision is made for the use of a hoist as eye bolts are fitted or supplied. It is essential that ‘good practice’ is adopted regarding the use of appropriate slings and associated equipment. See original column manual for guidance.
10. All operations should be performed by two people.
The following tool kit is provided with the original column.
Tool
Allen Key Set
Allen key 14 mm Adaptor & Torque
Wrench 3/8" Drive & adaptor
Spanner 17 mm/13 mm AF
Spanner 19 mm/24 mm
Spirit Level
S/Driver with Wide Blade
Eye Bolt and Fixings
Where used
Various locations
Tie Bar fixing Bolts
Flow tube adaptor, Adjuster Flow tube, Column Feet
Flanges bolts Adjuster, Fixed and locking flow cell nut
Used to level the column
Removal of bed support retaining ring
Additional eye bolts to fit to tube unit during maintenance procedures
Alignment indicators are attached to the top flange, tube flanges, bottom flange and base plate. These should be used to assist the alignment and orientation of components.
Alignment indicators
1. Detach any pipework from the top sanitary clamp adapter.
2. Remove flange fixing bolts from the top column tube flange. Retain bolts, nuts and washers.
3. Check that adjuster seal is released by turning the seal actuation nut counterclockwise.
4. If necessary, remove the handles from the seal actuation nut if they interfere with the hoist slings.
5. Using a hoist lift adjuster unit out of tube unit
6. Move the adjuster along the hoist rail or move the remaining column unit so access to the lifted adjuster unit is possible.
7. Place the adjuster assembly so that the flow cell face is on the floor with the hoist still attached.
8. Identify the parts as shown in the schematic and photograph below.
9. Remove sanitary clamp adaptor using the 17 mm spanner and flow tube seal.
10. Remove the seal actuation nut and spacer (see Figure 5a)
11. Slowly, using the hoist, lift the adjuster flange This will cause the flow tube, seal setting tube and flow cell to slide out of the threaded rod (see Figure 5b)
12. Stand the flow cell on a flat surface (see Figure 5c)
13. Using “flats”, undo the seal setting tube and slide it upwards and retain.
14. Use the correct spanner to remove the flow tube and discard.
15. Discard the adjuster bed support, flow cell, bed support retaining ring and bed support retaining bolt (see Figure 5 d)
16. Lower the remaining components of adjuster assembly onto a flat surface.
17. Disconnect the hoist.
18. Refer to the table below and ensure the correct components are retained and discarded.
Wetted Flow Path Components DISCARD
Sanitary Clamp Adaptor
Flow tube seals x2
Flow tube
Adjuster bed support
Adjuster Flow cell assembly, including flow cell inlet, flow cell locking nut and gasket seal
Adjuster seal
Bed support retaining ring
Bed support retaining bolt
Non-wetted Components RETAIN
Seal Actuation Nut
Spacer
Stainless Steel Seal Adjust tube
Threaded central height adjust rod
Height adjust handle assembly
Adjuster Flange
Seal setting ring
Backing Plate
The adjuster flow cell is supplied as an assembled unit which simplifies adjuster assembly protocols. Replacement adjuster flow cells are provided with the flow cell adaptor fitted. Refer to photographs below to provide visual guidance through the procedure.
1. Place the adjuster flow cell on a flat surface (Figure 6a) and check the flow cell locking nut is located against the flow cell inlet (Figure 6b).
2. Carefully invert the adjuster flow cell.
All handling of bed supports should be performed by a user wearing gloves.
3. Locate the bed support into the bed support retaining ring. The smooth side (glossy side) of the bed support should be uppermost with the coarse side (dull in comparison to other side) in contact with the flow cell. (N.B bed support retaining ring shown as blue to highlight assembly – actual component black).
4. Fit the bed support retaining ring and bed support to the adjuster flow cell. Working around the retaining ring click it into position by locating the outer edge into the groove on the outside of the flow cell
Retaining Ring Adjuster Flow cell Bed Support
8: Location of bed support retaining ring onto the adjuster flow cell.
5. Locate the central bed support retaining bolt and secure, initially hand tight.
6. Carefully tighten the central bed support retaining bolt using the correct tool, keeping the tool perpendicular to the bed support (Figure 9). Incorrect use of the tool can cause damage to the bolt and ineffective tightening.
7. Locate the flow tube seal and fit the flow tube. Use the correctly sized spanner to tighten (see Figure 10a)
CAUTION – Do not over tighten as this may lead to failure of the component.
10 (a-d): Assembly stages of the Adjuster Assembly – Connection to back of Adjuster
8. Slide the stainless-steel central seal setting tube over the flow tube and connect to the flow cell inlet. Ensure that the tube is fully engaged, and no manual rotation can be achieved (see Figure 10b)
9. Move the flow cell locking nut upwards so it contacts the end of the seal setting tube (see Figure 10c)
10. Tighten the seal setting tube against the locking nut (see Figure 10d)
11. Fit the adjuster seal around the perimeter of the top flow cell.
12. Ensure eye bolts are fitted to the adjuster flange.
13. Using appropriate lifting slings, attach the hoist to the adjuster assembly and lift the unit high enough to allow the flow cell assembly to be fitted.
14. Move the adjuster assembly over the flow cell and lower so the flow cell assembly slides into the threaded height adjust rod/seal setting ring assembly (see Figure 11c). Ensure the adjuster seal is not trapped beneath the seal setting ring. (see Figure 11b)
15. Locate the spacer and fit the seal actuation nut (see Figure 11c)
16. Locate the flow tube seal and fit the sanitary clamp adapter.
CAUTION – Do not over tighten as this may lead to failure of the component.
17. The refresh of the adjuster assembly is now complete. Ensure the unit is firmly seated on the floor and detach the hoist.
1. Attach the spare set of eye bolts, provided with the original column, to the top tube flange.
2. Using appropriate lifting slings or equipment attach the hoist to the eye bolts.
3. Identify the components on the schematic shown in Figure 12.
Tube Unit Assembly
Wetted Flow Path components DISCARD Non-wetted components RETAIN
Tube (complete with scale label, Id labels)
Buffer seals
Bottom column flange
Top column flange
Tie bars and bolts
Bottom flange bolts, washers and nuts
4. Using the correct spanners, remove and retain the column tube bottom flange bolts, washers and bolts.
5. Lift the column tube unit and when suspended loosen the tie bar fixing bolts that are located in the bottom column flange.
6. Place the tube unit on a flat surface.
7. Remove and retain the tie bar fixing bolts from the top flange and remove the top flange.
14 (a-d):
8. Remove tie bars to allow the tube to be lifted out of the bottom tube flange. If the tube is difficult to remove from flange remove the lower buffer seal.
9. Discard the tube and buffer seals.
In the column refresh kit, the tube unit is partially assembled and is supplied with scale label and buffer seals in position.
1. Identify the replacement bottom tube flange. Turn and support on its side to allow the attachment of the tube support rods using the correct bolts and Allen key. Locate and secure tie bars on the bottom flange using the bottom fixing bolts. Initially hand tighten the bolts, working diametrically opposite. When complete, use the torque wrench (set to 50 Nm) tighten the tie bar bolts, working diametrically opposite.
2. When all rods are located and fixed, place the flange on a clean flat surface.
3. Locate the column tube seal into the groove in the flange.
4. Ensure the tube is orientated correctly; the orientation of the tube is shown by the fitted scale label.
5. The buffer seals should be in place on the outside diameter of the tube at a distance approximately 2 cm from the end of the tube.
6. Locate the acrylic tube in the bottom column flange. Ensure it is located centrally and push down to ensure correctly seated. This is a two-person operation
7. Using the hoist, lift the top column flange. A top column tube seal is provided, and although this seal is not process wetted it can be replaced. To do so, place the flange on a flat surface, remove lifting eyes, and invert. Remove existing column tube seal and replace. When complete, turn over the top flange and reattach lifting eyes. Reattach hoist and move over tube unit.
8. Place the flange over the tube unit so that the top fixing bolts can be engaged. Ensure alignment indicators are positioned correctly.
9. Lower the top flange and secure the bolts by hand but do not tighten the bolts.
10. Locate the upper and lower buffer seals into the bottom flange and underside of the top column flange.
11. Using the correct Allen key, tighten the tube support rod bolts located in the top column flange. Using the torque wrench (set to 50 Nm) tighten the tube support rod bolts located in the top column flange.
12. Use the hoist to lift the tube unit ready to assemble to column bottom fixed assembly.
13. Check the tube support rod bolts in the bottom flange and tighten if necessary.
1. To assist it is recommended that column feet are lowered to provide a stable base.
2. Identify the components on the schematic shown in Figure 16.
3. Using the correct size Allen key, remove and retain the pipe spool clamp top.
4. Remove the pipe spool elbow from the flow cell assembly.
5. Undo, remove and retain bottom flow cell bolts.
6. Remove the bottom flow cell from the backing plate and discard.
Sanitary Clamp Adaptor
Flow tube seal
Flow tube
Bottom Bed Support assembly
Bottom Cell fixing screw
Pipe spool clamp and fixing bolts
Backing Plate
Column Levelling feet
Bottom Flow cell Casters
Pipe spool elbow
Bottom Column Flange
Santoprene Ladish Seal
The fixed end flow cell is supplied complete with the process port in place.
1. Place the bottom flow cell on the backing plate using the alignment indicators to ensure flow cell is in the correct orientation.
2. Secure the flow cell to the column base plate using the bottom flow cell bolts.
3. Locate the bed support seal into the inner most groove on the flow cell.
4. Locate the fixed flange seal into the outer most groove on the flow cell.
5. Locate the bed support with the smooth side uppermost and secure using the bed support retaining bolt. When securing the bed support bolt ensure Allen key tool remains perpendicular to the bed support. Do not overtighten this bolt.
Note: Always use clean dry gloves when handling bed supports
6. Connect the pipe spool elbow to the flow cell and secure in place by refitting the pipe spool clamp top.
Reassembly of the column is the reverse of disassembly and starts from column bottom upwards. Each sub assembly is reassembled before attached to the column.
Assemble Tube Unit onto the Column Base and Bottom
Flow Cell
1. Attach appropriate lifting slings to the eye bolts located on the tube unit flange. Lift the tube unit.
2. Move the tube unit over the fixed end assembly.
Figure 18: Reassembly of Column - tube unit to fixed end.
3. Check that the O-ring seals are in the correct positions.
4. Align the tube unit using the alignment indicators.
5. Replace the bottom column flange bolts/washers in the tube unit.
6. Slowly lower the tube unit and use the column bottom flange bolts to align the tube unit onto the bottom flange.
7. When tube unit is in place on the column base, locate the column bottom flange nuts. Hand tighten, working diametrically opposite to ensure equal loading on the seal, then using the correct spanner work diametrically opposite to tighten.
8. Remove the eye bolts from the top flange and store with other column tools.
1. Attach appropriate lifting slings to the eye bolts located on the adjuster assembly. Lift the adjuster assembly.
2. Move the assembly over the column unit. Use alignment indicators to line up the adjuster. Slowly, position the adjuster unit into the column tube. Alignment pins located in the top flange are provided to assist positioning.
3. Care should be taken to ensure that when lowering the adjuster flange operators are clear of this area.
4. Locate the top flange fixing bolts/washers. Hand tighten, working diametrically opposite to ensure equal loading, then using the correct spanner working diametrically opposite to tighten fully.
The purpose of this test is to check that there are no leaks from the column and the column is ready to use.
Due to the materials of fabrication, when the column is initially exposed to pressure the column components will flex. It is important that the hydrostatic leak test is performed as outlined below following a multiple step operation.
1. Fill the column with WFI (water for injection) or high-quality water and position the adjuster at the operating bed height.
2. Ensure the adjuster seal is wetted with buffer or other suitable liquid prior to assembly. This helps ‘lubricate’ the seal to ensure correct seating.
3. Activate the adjuster seal.
4. Ensure all air is removed from the column and any connections.
5. Attach a calibrated pressure gauge to the top inlet of the column.
6. Open the valve and increase the pressure until 1 bar (15 psi) and close bottom inlet valve. Wait 15 minutes for the pressure to stabilize.
7. Release the pressure in the column.
8. Open the valve and increase the pressure until 2.5 bar (36.25 psi) and close bottom inlet valve. Wait 15 minutes for the pressure to stabilize.
9. Check the pressure and ensure pressure is 2.5 bar (36.25 psi).
Due the nature of materials it is possible there will be a small pressure drop, however, this should not exceed 0.2 bar.
The Evolve® 450 mm Process Columns are fitted with height adjustable feet and a spirit level is provided. This enables the column to be levelled and/or to increase ground clearance.
1. Ensure the column is in the final process position and the column has been disconnected from any overhead hoist.
2. Place the spirit level on the top surface on the column.
3. Locate the flat portion on the column feet bolt and, using the correct spanner, adjust so that the bubble is located centrally on the spirit level.
4. Turn the spirit level by 90 degrees and repeat.
To view our Evolve® Process Column User guides please visit: https://www.astreabioseparations.com/resources/hardware- user-guides
For further enquires please contact: sales@astrea-bio.com
Revision
Comments
Date
A Released Jan- 2021
B Updated to include Evolve® registered trademark status July 2021
C Updated manual handling guidance Feb 2022
D Torque values added to assembly of Tube unit July 2022
E Further Guidance provide on disassembly and reassembly May 2023
F Rebranding Apr 2024