Driving cost, process, and operational efficiencies with Fabsorbent™ F1P HF
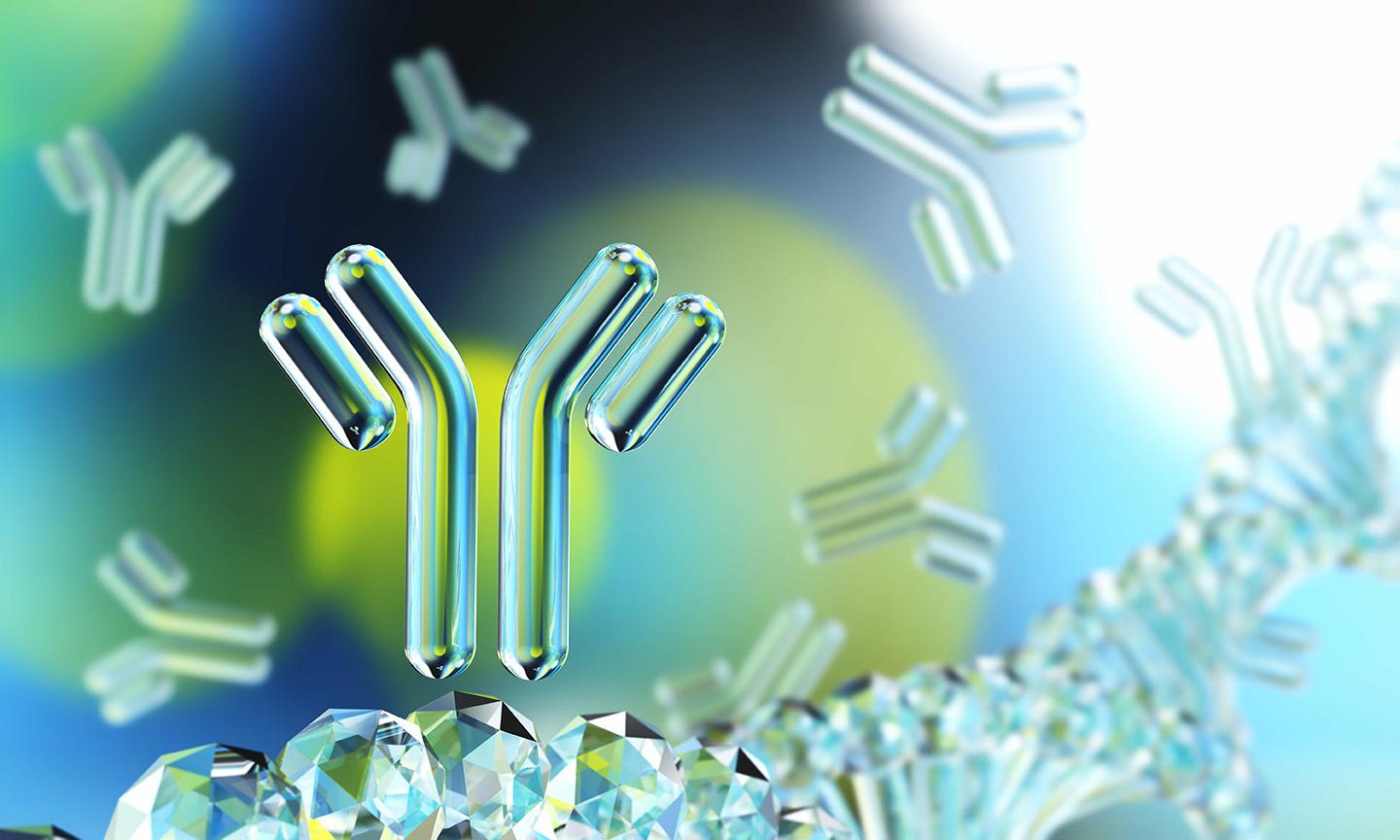
Efficiency is a defining priority in modern biomanufacturing, whe gains directly impact scalability and success. This white paper explores the critical role of purification efficiency, introducing Fabsorbent™ F1P HF as a compelling alternative to Protein L. Designed for antibody fragments and bispecific antibodies, Fabsorbent™ combines broad specificity, fast flow performance, and robust chemical stability to drive down costs and streamline downstream operations.
In the biopharmaceutical industry, purification remains one of the most critical steps influencing cost of goods (COGs), process efficiency, and scalability. As the therapeutic landscape continues to evolve toward more complex modalities like bispecific antibodies (bsAbs), the need for more adaptable and cost-effective purification platforms has never been more urgent. The drive toward lower manufacturing costs and improved process economics is forcing a re-evaluation of capture technologies.
F1P HF delivers cost-efficiency compared to market leading Protein L resin
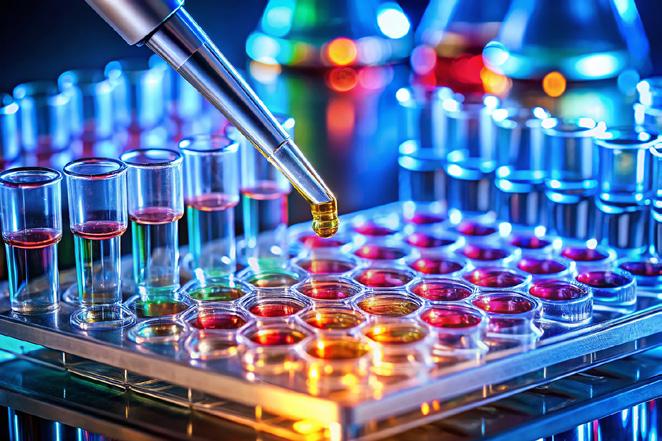
But cost-efficiency is just the beginning
• Lower resin cost per gram of product
• High recovery, higher purity
• Pay less, purify more
Efficiency in bioprocessing now encompasses several key performance categories, including cost, process, and operational efficiencies. Lowering the material cost per gram of purified product, along with minimizing expenditures on consumables, buffer solutions, and labor, can significantly impact overall cost, particularly in high-volume bioreactor settings or when using intensified processing strategies. By reducing resin costs, optimizing buffer usage, and limiting auxiliary requirements such as unique cleaning operations or storage infrastructure, organizations can reduce their COGs while improving predictability and financial control. Increasing throughput and yield, reducing processing time, and improving impurity removal are central to process efficiencies, especially for complex biologics which demand purification strategies that balance sensitivity and robustness. Resins that support fast flow rates and short cycle durations enable higher productivity and better product quality, supporting faster batch release and smoother regulatory alignment. A modern, efficient process is not only about throughput, however. It is also about establishing a reliable, reproducible, and scalable platform that can transition seamlessly from lab to commercial scale. Streamlining procedures, ensuring compatibility with stringent cleaning protocols, simplifying logistics, and maintaining high product consistency are essential for operational efficiency. This includes minimizing hands-on maintenance, using robust materials resistant to harsh chemicals, and selecting resins that perform consistently
• Comparable yield recovery, with higher impurity removal
• Ultra-stable ligand designed for robustness and reproducibility
• Simplified CIP with full stability in 1 M NaOH (unlike others limited to 0.1 M)
• Straightforward analytics compatible with standard LC/MS workflows
• Over 200 reuse cycles, with no need for cold storage
• No immunogenic leachables, making it ideal for sensitive biologics
Parameter
Ligand composition & stability
Reusability
Selectivity
Cleaning
Operational flexibility
Storage conditions
3.67 ppm HCP log clearange 1.84 ppm HCP log clearance
Synthetic ligand
Highly stable
100+ cycles
Broad selectivity, both kappa and lambda light chains
Stable to 1 M NaOH
Operates across a range of pH & salt conditions
Ambient
across manufacturing sites. These attributes reduce the risk of deviations in GMP production, simplify tech transfer, support single-use strategies, enable outsourced column packing, and allow integration with continuous processing platforms. This enhances organizational agility and accelerates timelines across all stages of development and commercialization.
As therapeutic formats shift toward more complex molecules such as asymmetric and fragmented bispecifics, conventional affinity resins like Protein L are increasingly strained by limitations in impurity clearance, elution conditions, and chemical stability. These challenges are especially pronounced in workflows requiring high throughput, scalability, or gentle processing conditions. Emerging alternatives such as Fabsorbent™ F1P HF offer a different approach, combining a synthetic triazine ligand with broad specificity for both kappa and lambda light chains.
In comparative studies on a model protein, Fabsorbent™ F1P HF achieved significantly higher host cell protein (HCP) clearance from an E. coli-derived Vk fragment feedstock (3.67 vs. 1.84 log ppm clearance) while maintaining comparable recovery (~77–78%) and enabling elution at a milder pH (5.0 vs. 2.5). Importantly, the cleaner your profile at the capture step, the easier and more cost-effective downstream polishing becomes. This sets the stage for simpler purification strategies and improved final product quality. Built on a high-flow 90-micron PuraBead® matrix, the resin also demonstrates strong mechanical and chemical resilience suited to both pilot- and commercial-scale use. These findings point to
Protein ligand, derived from bacterial sources
Less stable; leaching
10–20 cycles
Kappa light chains
Generally stable to 100 mM NaOH
Limited
Cold-stored
the value of re-evaluating affinity capture strategies for non-traditional antibody formats, especially when process efficiency and product quality are key drivers.
A cost comparison between Fabsorbent™ F1P HF and a leading market Protein L resin also demonstrated economic benefits. Based on process models involving a 2000-liter bioreactor with a 2 g/L titer, the calculated cost per gram of purified protein includes resin, buffer, and column packing expenditures. The resin cost per gram for the leading market Protein L resin was $9.57, whereas Fabsorbent™ achieved a slightly lower cost of $9.29. While the per-gram resin price difference may appear modest, when scaled across multiple batches, the savings stack up. Fabsorbent™ not only results in lower material costs, but also contributes to simplified operations and reduced consumable demand. Its chemical resilience allows the use of a single, robust cleaning protocol. In many facilities, this simplifies buffer preparation and reduces sanitization steps, resulting in shorter turnaround time between batches, a critical driver of facility productivity. Additionally, predictable buffer requirements help streamline raw material procurement and inventory management, minimizing overstocking or urgent procurement risks. These consolidated efficiencies ultimately reduce total cost of ownership and streamline overall process economics.
Fabsorbent™ F1P HF distinguishes itself through its robust operational profile. It demonstrates excellent chemical and pH stability, withstanding short-term exposure from pH 1.5 to 14.0, and maintaining long-term integrity between pH 3
to 13. These attributes allow the resin to perform reliably under stringent conditions, such as those required in GMP environments. Its compatibility with 1.0 M sodium hydroxide for clean-in-place procedures ensures ease of sanitization and compliance with microbial control requirements. This capability is particularly valuable in environments where strict regulatory oversight and routine sanitization are standard. This resin also supports platform standardization, enabling organizations to simplify cleaning validation and reduce the number of steps required for facility turnover. Fabsorbent’s fast cycle times are attributed to its high-flow PuraBead® matrix, which supports flow rates of up to 500 cm/h. This attribute allows for more cycles per day, contributing to greater productivity without requiring changes in existing infrastructure. Facilities can optimize their chromatography schedules and reduce idle time between unit operations. Process development studies involving design of experiments have confirmed Fabsorbent™’s flexibility across a range of pH and salt conditions. The optimal performance was identified in high pH, low-salt environments, with acetate buffers at pH 5.5 showing the best balance between elution strength and product purity. The resin consistently retained binding efficiency and selectivity, even when conditions deviated
slightly from the optimized setup, indicating robustness and broad applicability across different antibody fragment workflows. This process resilience provides manufacturing teams with operational headroom to accommodate feedstock variability, equipment constraints, or parallel platform integration. A summary of these benefits can be seen in Table 1.
Astrea Bioseparations brings additional value to Fabsorbent™ by offering vertically integrated manufacturing and supply chain capabilities. Central to this is our PuraBead® base matrix platform that serves as the foundation for Fabsorbent™ Fabsorbent™ base matrix is produced entirely in-house by Astrea Bioseparations, giving full control over a critical raw material supply. Astrea Bioseparations’ history as a trusted partner to global biopharmaceutical leaders, including its role as the contract manufacture for ThermoFisher’s CaptureSelect® product line, highlights its commitment to quality, innovation, and technical pedigree. Full control over resin development and base bead translates to greater security of supply, improved lead times, and better alignment with customer production schedules. By minimizing reliance on third-party suppliers, Astrea Bioseparations reduces the
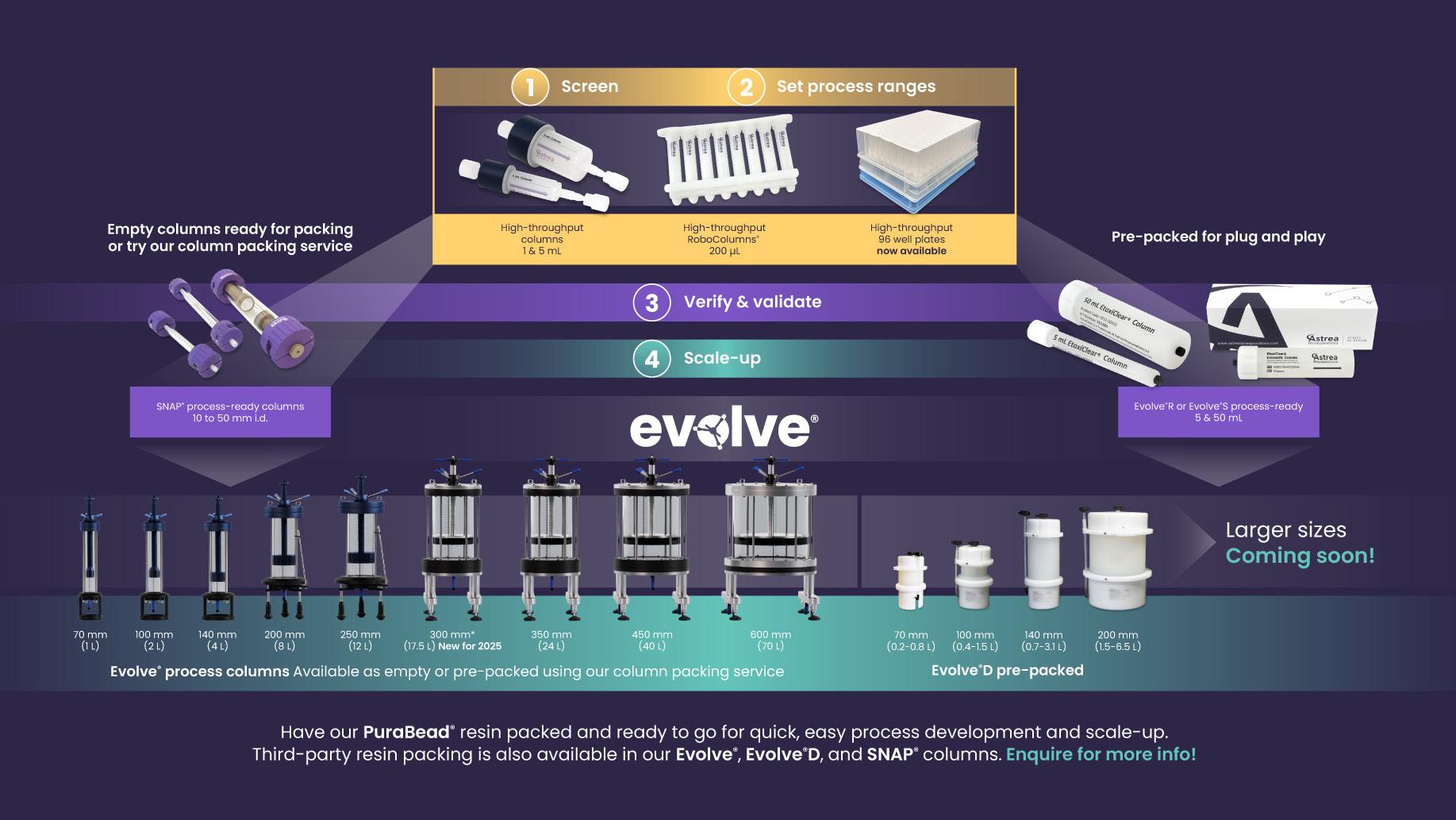
risk of disruption and enables more consistent quality across batches. This supports process robustness, eases regulatory documentation, and improves overall predictability in GMP workflows. For manufacturers using Fabsorbent™, these efficiencies collectively reduce the total cost of ownership and simplify tech transfer, scale-up, and long-term adoption.
Streamlining purification development often begins with the tools used during early-stage screening. Availability of chromatography resins like Fabsorbent™ F1P HF in multiple formats, from high-throughput screening plates (such as 96well formats) to pre-packed columns, enables more efficient method development and scale translation. These formats support rapid condition optimization and facilitate a more seamless transition from bench-scale experiments to pilotand manufacturing-scale operations. On the operational side, the use of pre-packed columns, such as those offered through platforms like Evolve® and Evolve®D, can significantly reduce in-house burden by eliminating the need for manual packing. This not only saves time and labor, but also helps mitigate variability in column performance, an important consideration during process validation. For organizations operating under tight timelines or within regulated environments, outsourced column preparation can simplify tech transfer, standardize performance across sites, and reduce the capital investment needed for packing infrastructure. Together, as shown in Figure 2, these development and operational tools can contribute to a more agile and reproducible downstream process, especially when scaling novel or sensitive biologic formats.
In addition to these tangible process and operational benefits, Fabsorbent™ offers a strategic advantage in the evolving landscape of biologics manufacturing. The industry’s shift toward modular, continuous, and intensified processing requires resins that can adapt to diverse production formats and maintain performance under demanding conditions. Fabsorbent™ meets these needs with its versatile ligand design, scalable matrix platform, and simplified operational profile. It is compatible with standard chromatography systems, supports straightforward analytical workflows such as LC/MS, and integrates seamlessly into both batch and continuous operations. These capabilities position it as a foundational technology for modern biomanufacturing.
Moreover, as regulators increasingly emphasize process robustness and data-driven quality assurance, the reproducibility and predictability of Fabsorbent™ further strengthen its value proposition.
As companies seek to improve margins, reduce time-tomarket, and align with global regulatory expectations, the selection of platform technologies becomes a key differentiator. Fabsorbent™ provides the confidence and control needed to meet these goals. It reduces financial risk by lowering overall process costs, improves technical reliability through chemical and mechanical robustness, and enhances supply security through in-house manufacturing and global distribution. Its synthetic construction eliminates many of the risks associated with biologically-derived ligands, and its consistent performance ensures that downstream processing is no longer a bottleneck but a strategic enabler. For forward-looking companies seeking to build efficient, scalable, and compliant biologics platforms, Fabsorbent™ offers a proven and versatile solution.
Fabsorbent™ F1P HF represents a step-change in resin technology for antibody light chain purification, which includes bispecific antibodies, fragments, and antibody drug conjugates. It combines economic efficiency, high performance, and operational simplicity in a platform that is ready for the challenges of modern biopharmaceutical manufacturing. Whether deployed in early-stage development or large-scale GMP production, it delivers measurable improvements in cost structure, process throughput, and regulatory confidence. Astrea Bioseparations supports this offering with the infrastructure, experience, and technical insight necessary to help customers succeed. In a market defined by complexity and competitive pressure, Fabsorbent™ offers a reliable and forward-looking solution as a compelling alternative to leading market Protein L products and a cornerstone of efficient, future-ready bioprocessing.
Specialized purification technologies will remain integral in improving manufacturing efficiency, enhancing product quality, and overcoming the unique challenges associated with antibody fragments and bispecific antibodies.
Discover how Fabsorbent™ F1P HF, HCPure™, and SP PuraBead® Edge can optimize your bispecific purification processes. For detailed insights into any of the resins in this paper, or to discuss your specific purification needs, visit our website astreabioseparations.com or reach out to us sales@astrea-bio.com.