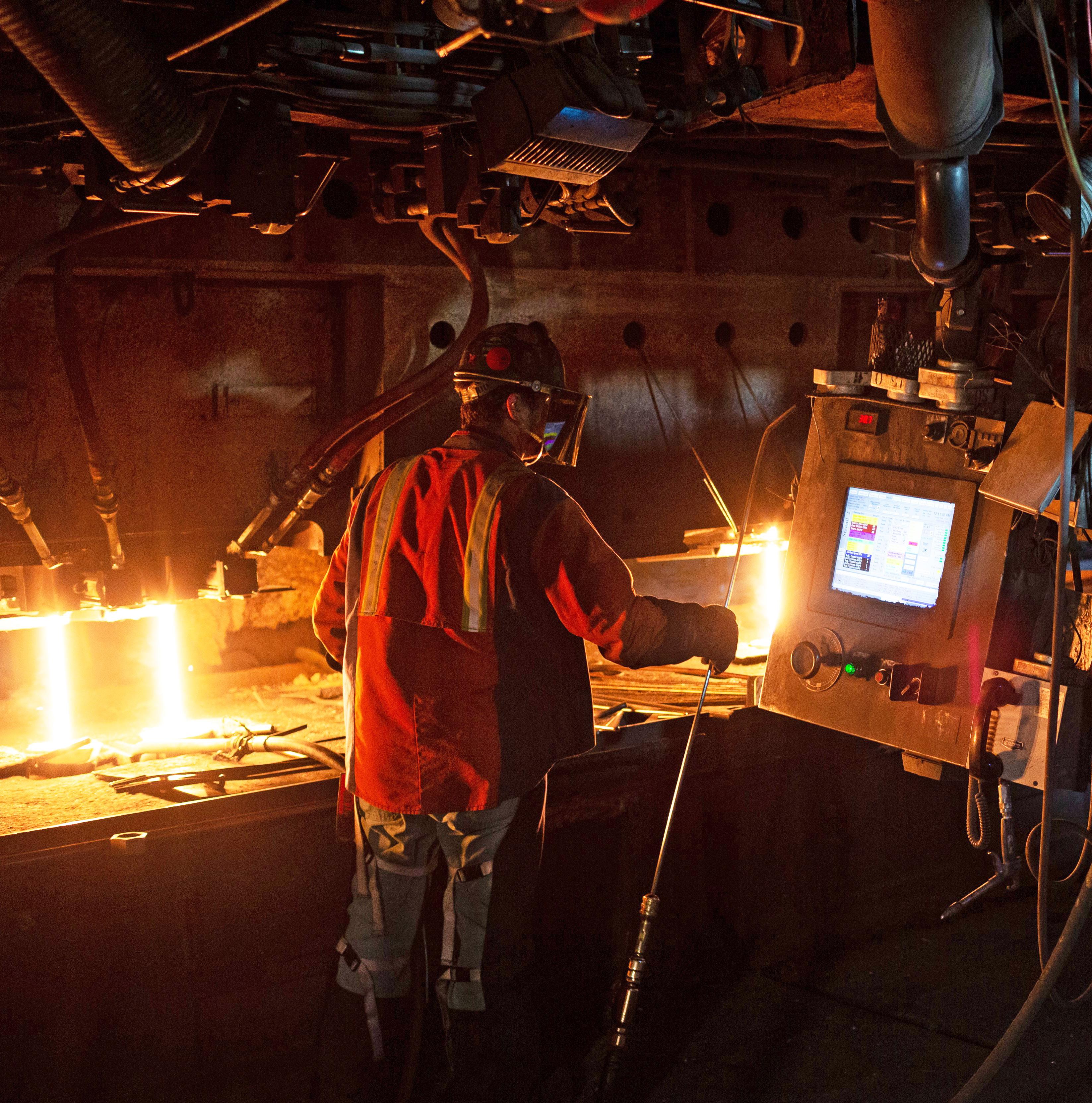
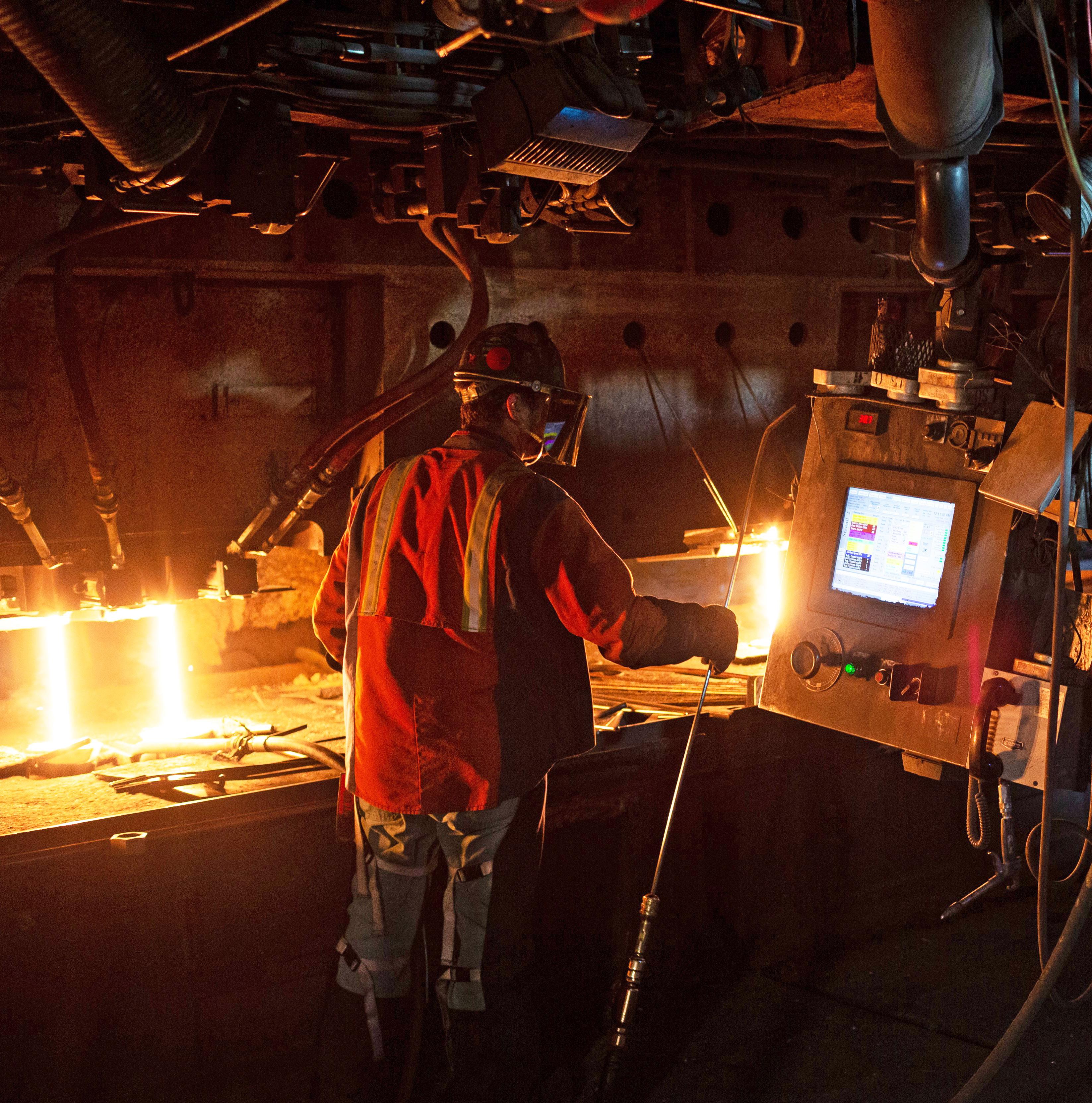
Cleaner power for a brighter future
At Entergy Arkansas, we’re powering a brighter future by investing in clean, reliable energy to keep you safe and comfortable while fueling our economy.
Building clean power generation
We’re the largest solar power provider in Arkansas. By the end of 2024, we will have at least 7,100 acres of solar arrays currently operating or under development. Together, our facilities will provide enough clean power to energize more than 130,000 homes.
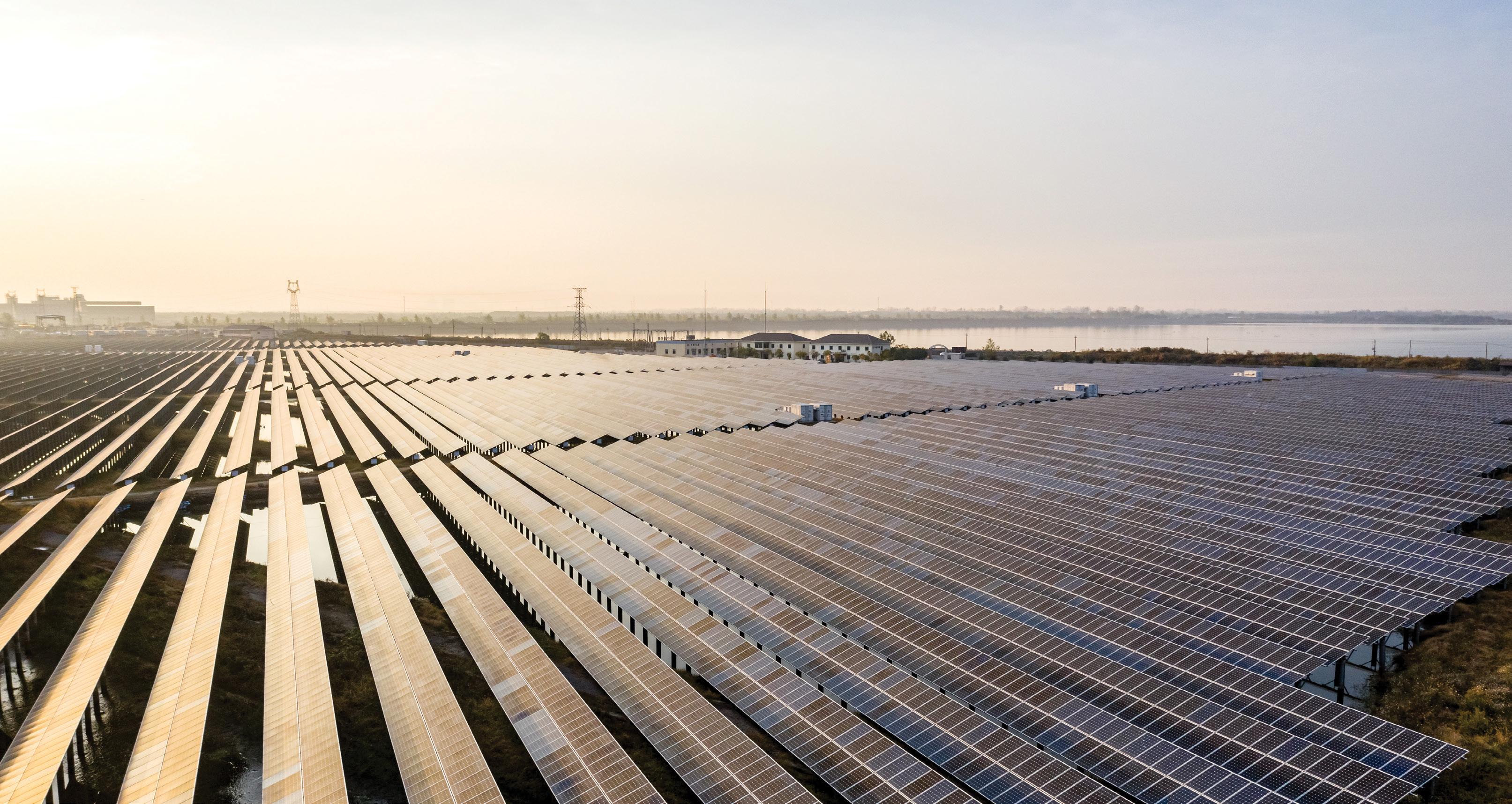
Modernizing the grid
We’re improving reliability and customer service by upgrading our critical infrastructure and have installed new advanced meters – giving you more confidence and control at your fingertips.
Supporting our communities
We’ve been serving Arkansans for over a century, with nearly 2,800 employees and over 728,000 customers. We’re honored to have been named a Top Economic Development Utility by Site Selection magazine.
Learn more at entergyarkansas.com/brightfuture
BROOKE WALLACE Publisher brooke@arktimes.com
EDITORIAL
DWAIN HEBDA Editor
MANDY KEENER Creative Director mandy@arktimes.com
MIKE SPAIN Art Director
ADVERTISING

PHYLLIS A. BRITTON Sales Director phyllis@arktimes.com
ACCOUNT EXECUTIVES LEE MAJOR lee@arktimes.com
KAITLYN LOONEY kaitlyn@arktimes.com
TERRELL JACOB terrell@arktimes.com
PRODUCTION
WELDON WILSON Production Manager/Controller
ROLAND R. GLADDEN Advertising Traffic Manager
GRAPHIC DESIGNER Sarah Holderfield
OFFICE STAFF
ROBERT CURFMAN IT Director
CHAROLETTE KEY Billing/Collections
JACKSON GLADDEN Circulation Director
PUBLISHED BY ALAN LEVERITT Publisher alan@arktimes.com
©2023 ARKANSAS TIMES LIMITED PARTNERSHIP 201 E. MARKHAM ST., SUITE 150 LITTLE ROCK, AR 72201 501-375-2985
Dear Reader:
If you’re reading this, Congratulations! You’ve just taken the first step toward a rewarding career in the skilled professions. We’re glad for your interest.
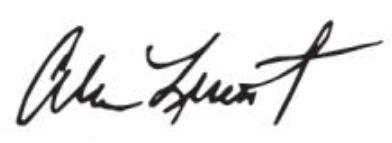
For years leading up to the pandemic, Arkansas companies — as well as those across the country — have been desperate to attract and retain enough trades craftspeople to build infrastructure, service homes and businesses and keep our factories running. COVID-19 only made matters worse as some 8 million skilled workers were displaced in 2020, according to the U.S. Department of Labor. Three years later, only half of those jobs have been refilled, making a difficult situation even more of a national emergency.
Blueprint was created to help address the shortage of skilled workers in Arkansas by providing timely, up-to-date and factual information about the opportunities that exist for people who learn a trade. Inside, we provide the latest pay scales, education options, in-demand jobs and real-life stories of people who are building a career and providing for their families in jobs ranging from electrician, advanced manufacturing and plumbing, to welding, information technology and allied health fields.
In this year’s edition, we are pleased to spotlight two Arkansas industries offering outstanding career options: defense and aerospace companies in Camden and the steel industry in Blytheville. We also salute one of the biggest manufacturing success stories in The Natural State right now with an in-depth look at Nucor-Yamato Steel and Nucor Steel Arkansas, which are transforming lives and economies in northeast Arkansas.
Whether you’re a high schooler pondering your future or an underemployed worker looking for a fresh start, there’s a good chance you’ll find what you’re looking for in a skilled job. As you build your career, you will earn the additional satisfaction of knowing you’re also building America’s strength through Arkansas grit.
Thank you for picking up Blueprint!
Alan Leveritt Publisher Arkansas Times/BLUEPRINT MagazineHELP WANTED!
Arkansas Companies Desperate for Skilled Labor
There’s never been a better time to be a skilled worker in Arkansas.
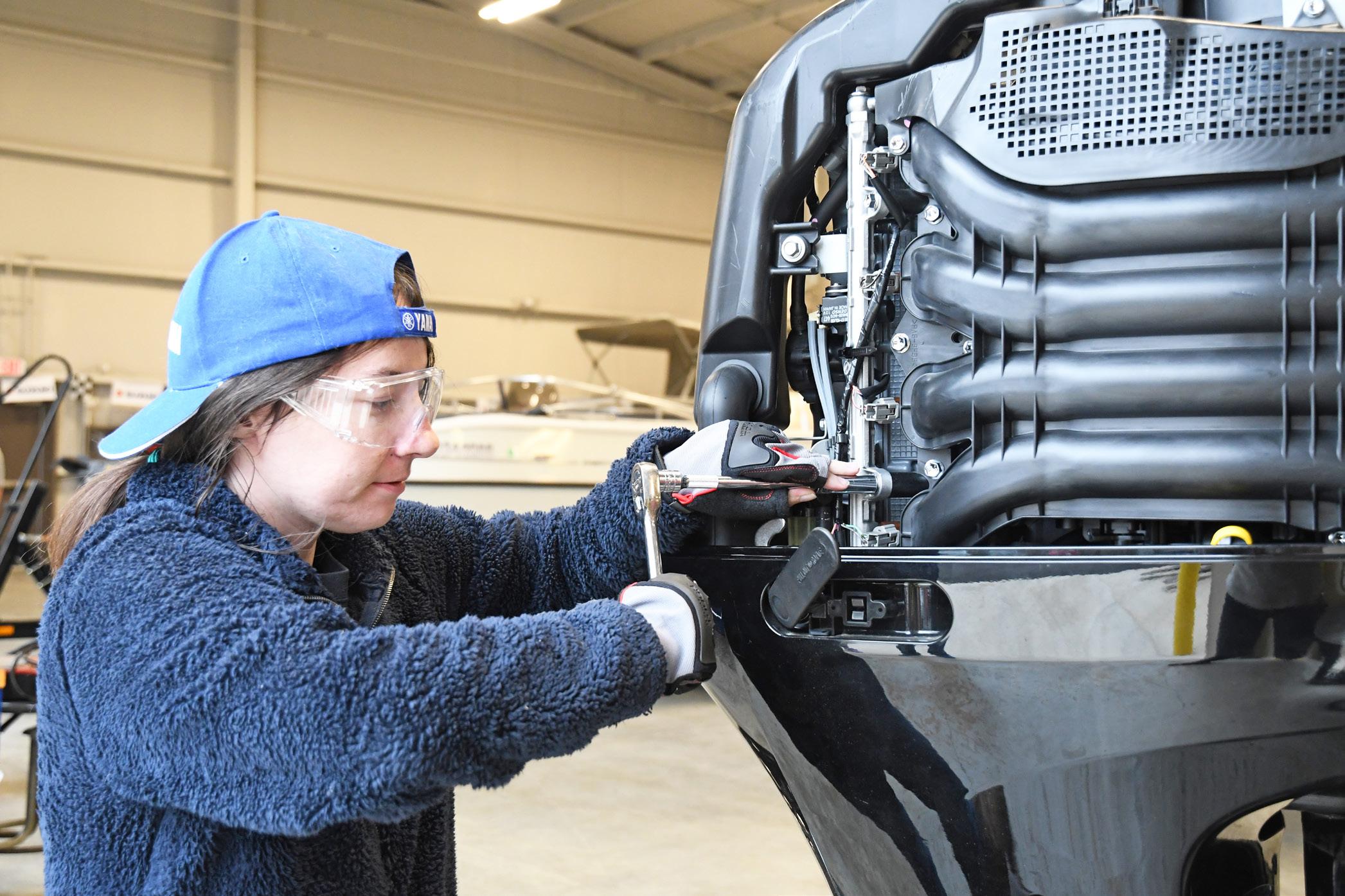
Skilled labor — also known as “the trades”— is in short supply in The Natural State, and Arkansas’s not alone. Skilled workers have been declining in numbers nationwide for decades as not enough young people have gone into jobs such as electricians, plumbers, construction, welding and a variety of manufacturing fields to help companies keep up with growth.
Contributing to the situation are the millions of existing skilled workers looking to retire and companies struggling to catch up with hiring after COVID. About 10,000 baby boomers reach age 65 every day, according to the U.S. Census Bureau, and by 2030 all members of this generation will be at least 65 years of age. This has reduced the boomer labor force by an average of 2.2 million workers each year since 2010, or about 5,900 workers daily, according to analysis by Pew Research Center.
The COVID-19 pandemic further complicated things by driving millions out of the trades overnight. According to the U.S. Bureau of Labor Statistics, nearly 8 million skilled labor jobs were eliminated during the pandemic, only about half of which have been refilled since.
But perhaps the most stubborn problem facing skilled careers has been an image problem 40 years in the making. Beginning in the 1980s, parents and guidance counselors preached to young people a four-year degree was the only path to long-term career success. Working with one’s hands, meanwhile, was often portrayed as low-skill, low-tech, dead-end work
that was hot, dirty and dangerous. Many high schools even did away with shop and ag classes altogether, reinforcing the negative stereotypes about skilled careers.
However, as many high school graduates found out the hard way, four-year colleges are not for everyone, causing many to drop out before attaining a degree, limiting job prospects (but not before racking up considerable student loan debt).
Fortunately, things are starting to turn around in Arkansas as more and more kids are being exposed to skilled careers at younger and younger ages. Community colleges across The Natural State have strengthened partnerships with local school systems to offer training classes during a student’s high school years. This allows more students to get at least part of their training out of the way before high school graduation.
Companies in need of skilled workers have also stepped up to the plate, with high wages; clean, safe working conditions; and career pathways that give employees looking to advance something to work toward. And, the nature of blue-collar jobs themselves has changed, with much more technology in play than ever before. As with every other area of life today, computers and digital technology are everywhere on the job site and in the factory, requiring a new generation of skilled workers to operate them and keep them running.
The future of skilled careers is one of immense opportunity, and while the shortage of skilled workers won’t be solved overnight, there are signs things are headed in the right direction. That’s good for companies, good for workers and great for the state of Arkansas.
HAROLD HOUNWANOU
Engineer
Little Rock Water Reclamation Authority
Home country: West Coast of Africa
Age: 35
BLUEPRINT: You’re from West Coast of Africa?
HAROLD HOUNWANOU: Yes, I grew up in a small town on the West Coast of Africa to the west of Nigeria. We speak French over there. I aspired to come to the United States because of the water access and sanitation issues we have in my country. Those are issues we face on a daily basis, and that inspired me to want to learn more.

In 2012, I moved here and went to Henderson State University where I learned English, then moved to North Carolina State University and earned a master’s in environmental engineering before moving back to Arkansas.
BP: You joined LRWRA as an engineer then?
HH: I’ve climbed the ladder. I started in 2017 as a utility worker, which is in the field doing manhole work, sewer line work, all kinds of repairs. It gave me the opportunity to learn about the field and what we do to provide sewer service to our customers in the city. It was somewhat of a foot into the door to get that exposure and learn what we do. After doing that for about 18 months I moved to the engineering department.
BP: Are there similar job opportunities there now?
HH: Over the last 18 months, we’ve had 12 retirements in my department alone, and when you have retirements you have to replace those people. People also get promoted and vacancies are created.
The entry level positions, the utility worker position where I started, right now we still have a few vacancies we are trying to fill. We have some commercial driver positions and it’s difficult to find drivers now.
BP: What are the most important skills you look for in a candidate?
HH: I like to call them human skills because ultimately we are in the business of developing relationships with people. Attendance, respect of others, the way you handle yourself and your work are all huge. You can teach hard skills; we have to make sure the employees that we hire are in alignment with our values.
JARRED MARTINEZ
Equipment Operator
Little Rock Water Reclamation Authority
Hometown: Bauxite
Age: 25
Years with LRWRA: 4
BLUEPRINT: How long have you been with the company?
JARRED MARTINEZ: This is going on my fourth year. I’ve been an equipment operator for almost a year now.
BP: What’s your background?
JM : My dad owns his own tile company and I worked for him in high school. I went to college to play baseball, and when that didn’t work out, I kinda didn’t know what I was going to do. I ended up joining the National Guard after one semester of college and then I just worked and did my Guard stuff.
The military helped me grow up a little bit. It also has multiple career paths you can do, and it ended up leading me into a good group of friends that helped me get this job.
BP: What’s your typical day like?
JM: When I get to work, I meet up with my crew leader and we go over the plan for the day. We get the supplies we need and we restock our truck. I operate a 3030 Cat trackhoe and we dig up sewer lines and line mains. We do mains that are located in front yards and backyards or out in the woods, so we can be anywhere digging two-and-a-half feet deep on a six-inch main to 15 feet deep on a 22-inch main.
BP: What training have you received to improve your skills?
JM: When I first got here, I didn’t have my commercial driver’s license and the company paid for me to get that. I also got hands-on training with heavy equipment so now I can operate anything from forklifts to front-end loaders to skid steers and trackhoes. I’ve done an internal class on shoring safety and trenching; every year we complete multiple safety classes that really help you understand what can go wrong and what to look out for to keep everybody safe.
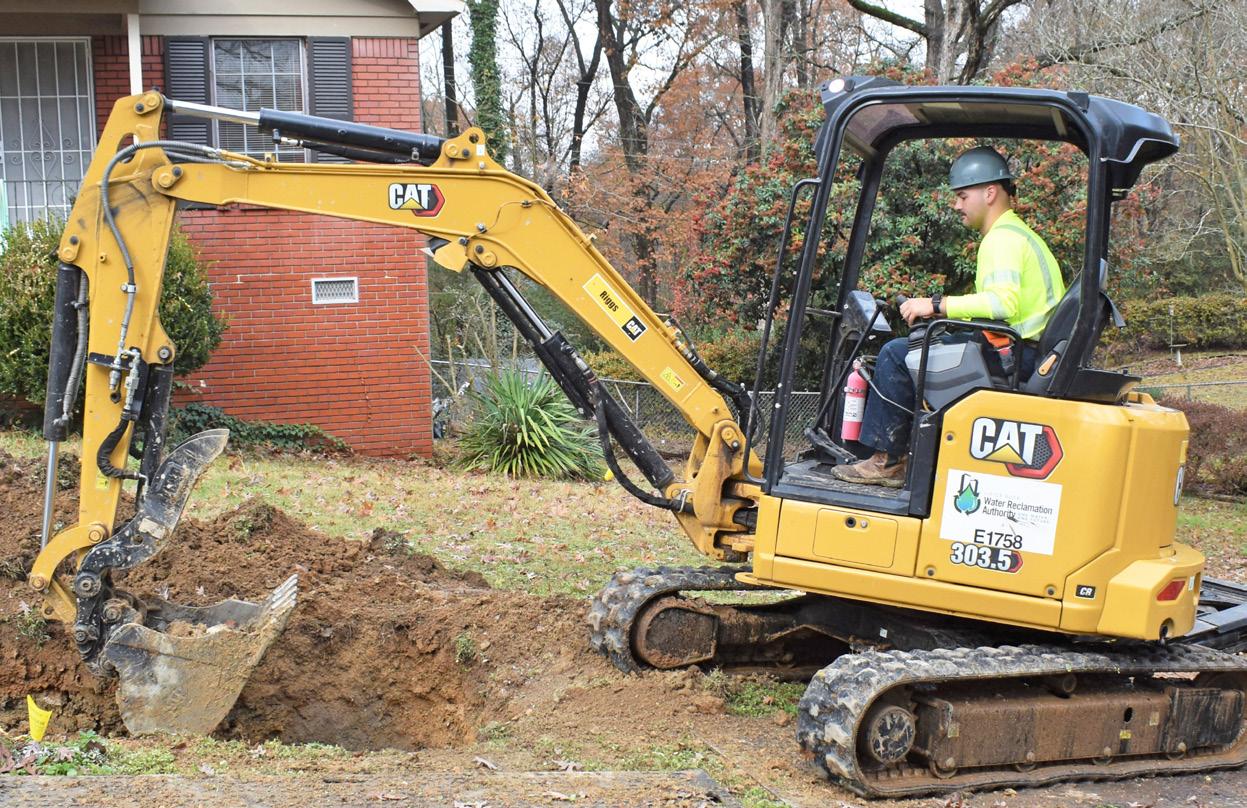
BP: If you could go back to your high school and talk about what it takes to be successful on the job, what would you tell students?
JM: What I’d really like to tell them is they need to have a good work ethic and they need to be able to adapt and overcome differences because no one you’re going to work with is going to be exactly like you. You have to be open-minded and make sure that you can work well together and listen to instructions.
TRAINING FOR THE JOB OF YOUR DREAMS
One of the most appealing things about a skilled career is the relatively short time it takes to train for these high-paying jobs. You generally don’t have to have any background or experience to land an entry-level position these days — although it helps — as more and more companies are willing to pay for your training.
The following are the most common training program pathways to a career track position in the trades.
TWO-YEAR COLLEGES AND UNIVERSITIES
Formerly known as trade schools or vocational-technical (vo-tech), two-year colleges have always been the backbone of skilled career education. These institutions of higher learning provide classes in a wide range of career fields from diesel mechanics and drafting to advanced manufacturing and allied health roles. Depending on the program, students can train for a career in as little as one semester (nine weeks).
Tuition costs at two-year schools are typically lower than four-year institutions as is the time it takes to complete a degree. Many two-year schools also have agreements with area high schools that allow students to take college-level courses while still attending high school. These classes, called concurrent college courses, are often available free or at greatly reduced cost.
DID YOU KNOW?
Concurrent classes can be extremely useful in helping a student get a jump on what’s next after high school. Some students work hard enough at concurrent classes to graduate with an associate degree at the same time they receive their high school diploma. This matters because the less time you spend in a college classroom, the lower your overall educational costs and likely the less debt you will pile up. Check with your guidance counselor to learn about concurrent courses in your area.
Two-year colleges usually have great relationships with local employers, making it easier to find a job after graduation. And many two-year degrees stack with other university programs, giving you a head start on finishing your bachelor’s degree in the future, if you so choose.
APPRENTICESHIPS
Another very popular route to a skilled career is the apprenticeship, an education model combining on-the-job training and classroom instruction.
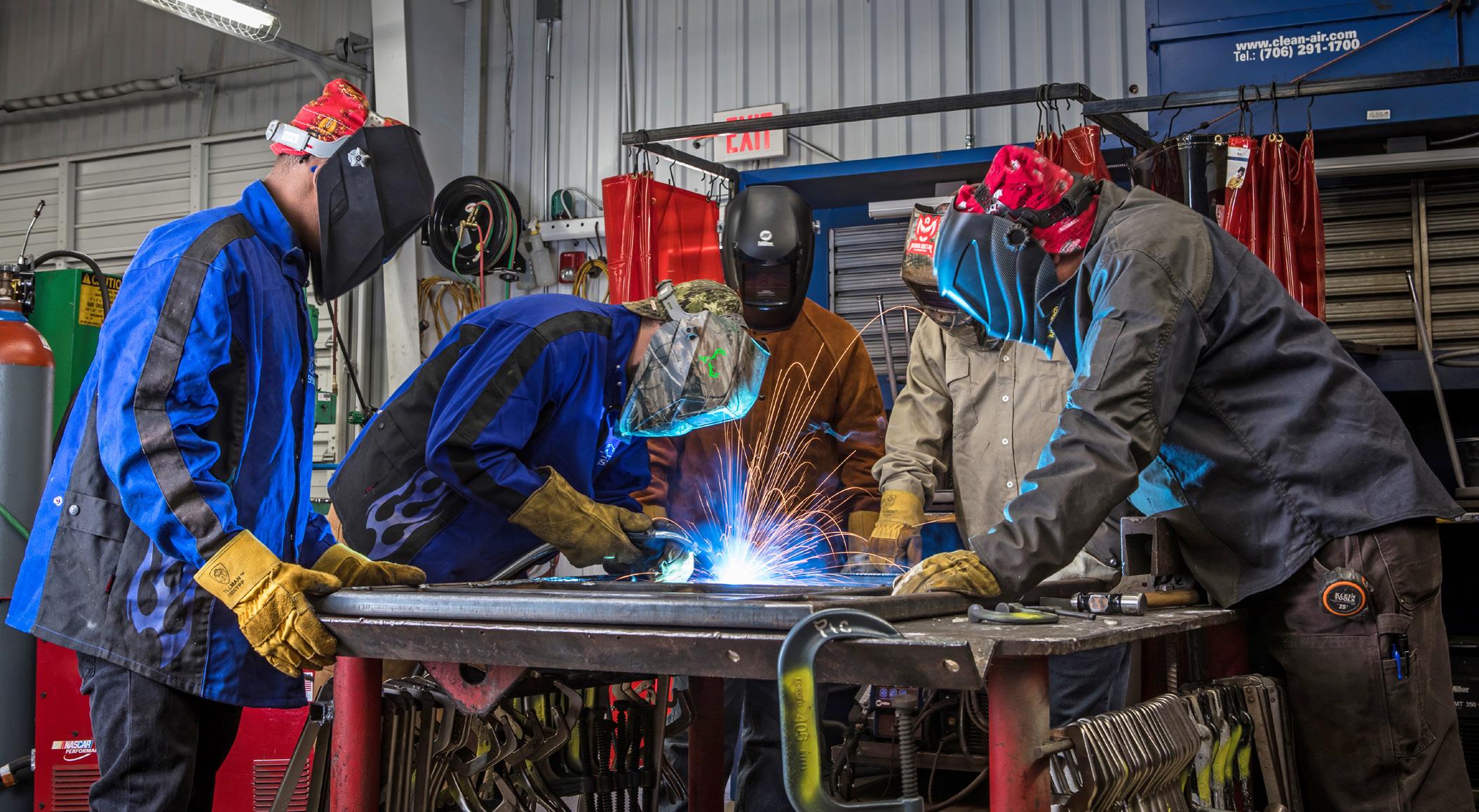
Many companies today will hire people with little to no skills background and enroll them in an apprentice program, which is kind of like work-study. As an apprentice, you will work for your company during the day under the supervision of an experienced employee and attend class a few nights a week where you’ll learn new concepts and practice your skills.
CONTINUED ON PAGE 10
Skilled
Source: explorethetrades.org
careers provide great pay and many companies provide generous bonus packages as well. The average starting pay for apprentice plumbers, HVACR technicians and electricians is just under $40,000. A fully trained technician makes an average of just under $69,000 per year, and moving into managerial roles boosts pay even more.National Park College's welding program is among the state's very best training.
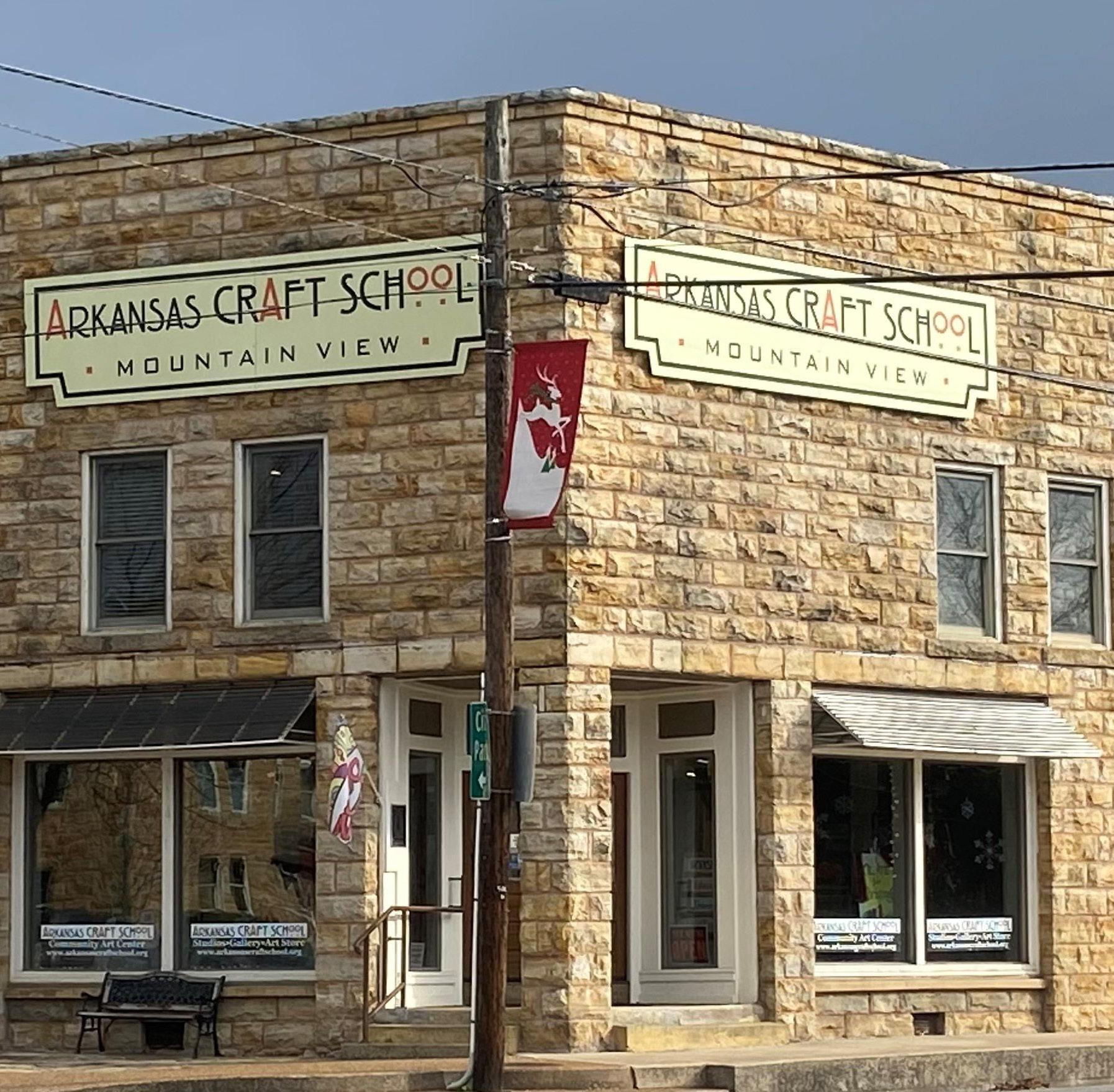

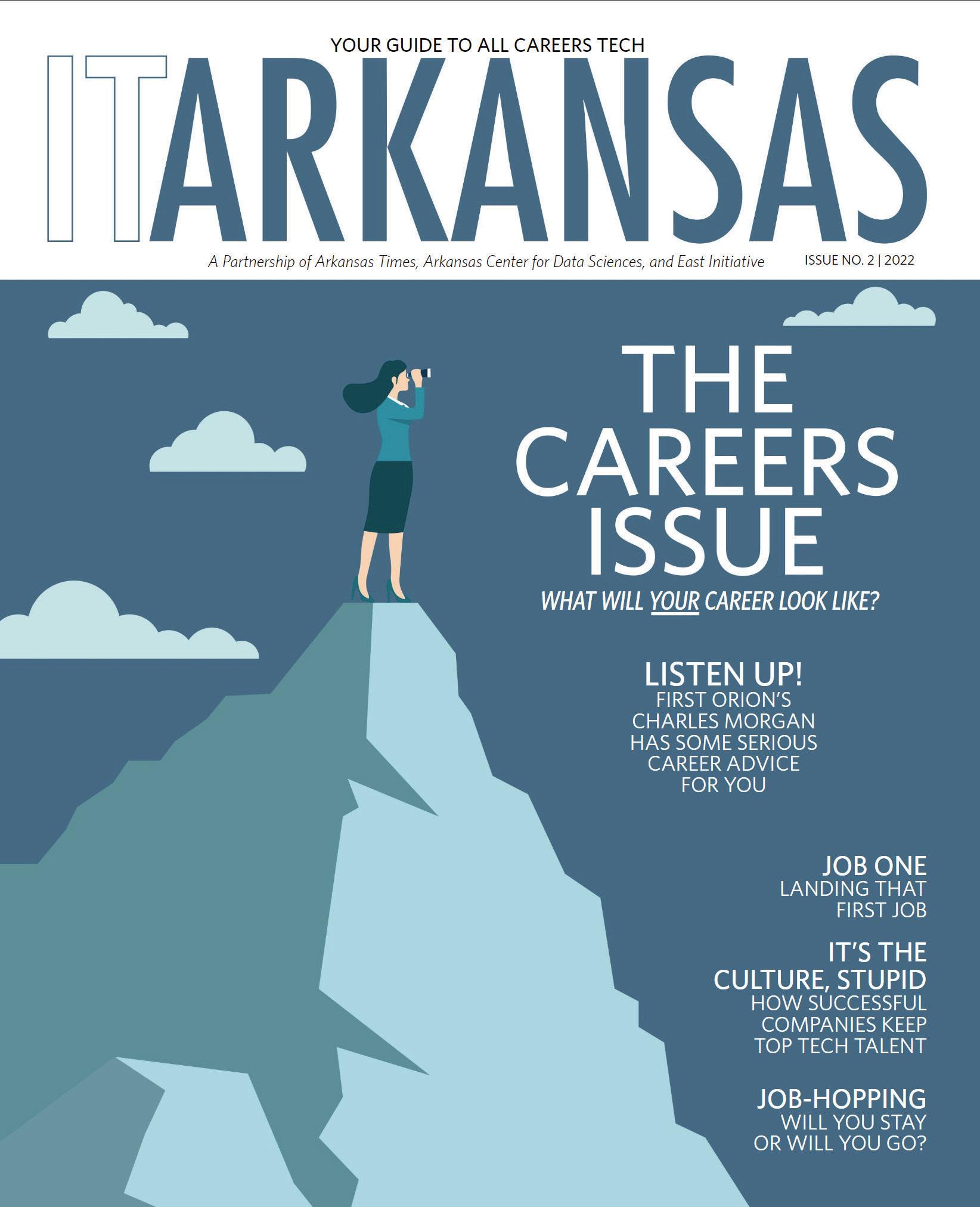
CONTINUED
Apprenticeships generally take anywhere from two to four years to complete, which means it’s some of the most comprehensive skills training there is. Depending on the company, apprenticeships are completed through organizations specifically set up to conduct this training or in some cases the apprenticeship training is all done in-house. Other apprenticeship programs are conducted by trade unions.
Completing an apprenticeship program provides several big advantages over other types of training. First, you earn while you learn because you’re drawing a salary from your employer. Second, the cost of the apprenticeship is usually paid for by the company you work for. Third, companies tie fixed pay increases to your apprenticeship, meaning the better you do in your studies and skills development, the more money you’ll make along the way.
ON-THE-JOB TRAINING
On-the-job training is a given for this list because success in any career requires constant improvement and refinement of skills. That’s why it is a good idea to ask questions about internal training during your employment interview; the more organized and intentional those programs are, the more you will learn.
© ROBERT KNESCHKSTOCK.ADOBE.COM / FOR ILLUSTRATION ONLY
The basics of some skilled jobs can be learned in months, not years.
Soft skills: a secret weapon in the workplace
I
“Soft skills are things that translate to any job field, whether it’s the lab or working at a bank or working at Walmart,” said Rebecca Burkman, director of environmental affairs for Little Rock Water Reclamation Authority. “We do soft skills-related training for both our hourly staff and our salaried staff, including one on conflict resolution and one on diversity and inclusion.”
DID YOU KNOW?
n addition to job-specific abilities, many hiring managers say soft skills are what separate one employee from another when it comes time for raises and promotions. Soft skills are a category of work and personal attributes that enhance a skill set such as being on time, working well with others and the ability to communicate effectivelyBurkman said technical skills for most entry level positions come down to on-the-job training. But what can’t be taught are the kinds of skills that stem more from an employee’s attitude than their aptitude.
“Most people are worried about the technical skills and what’s on their resume,” she said. “But as someone who hires those entry level positions, when I look at interviewing people, I already have their resume in front of me. I’ve already read it, so what I’m looking for in interviews are those soft skills and how well they would fit with the dynamic of the existing team.
The average cost of a technical education is about one-fifth that of a four-year degree. The average cost of a two-year public trade school education is just over $21,400 while the average cost of a four-year public college degree is $109,400. That’s a savings of more than $88,000, and with tuition reimbursement programs offered by many employers, your actual cost could be even less.
Source: explorethetrade.org
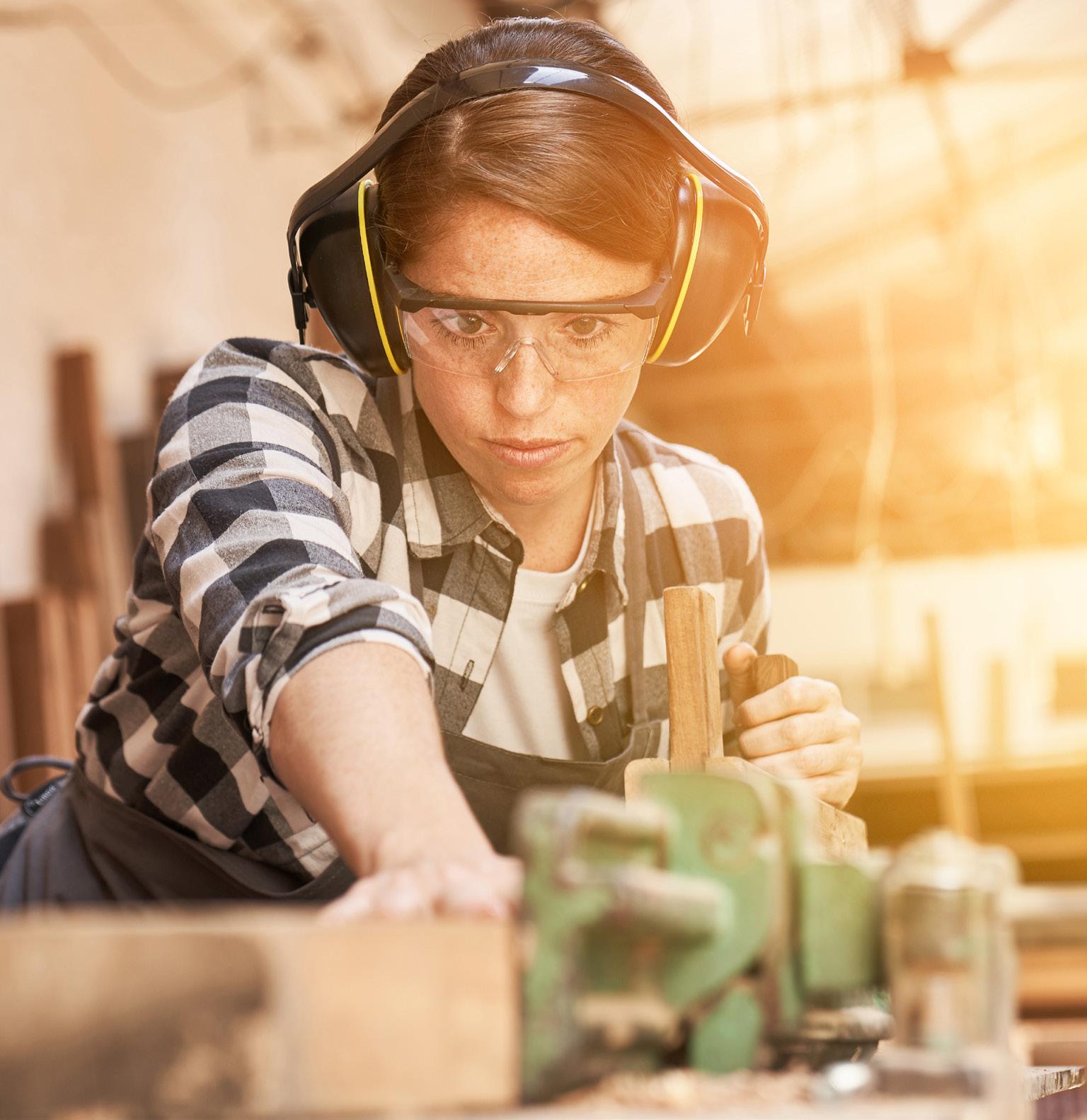
REBECCA BURKMAN
Director of Environmental Affairs
Little Rock Water Reclamation Authority
Hometown: North Little Rock
Age: 31
Time with the organization: 5 years
BLUEPRINT: How did you decide to join LRWRA?
REBECCA BURKMAN: I was in college and I got a bachelor’s in biology and then I didn’t really know what to do with that. I started applying at different lab jobs and I saw an advertisement for a lab tech position at a utility in North Carolina. I started working in a lab there and I applied for a job here, back home, because I was trying to move home.
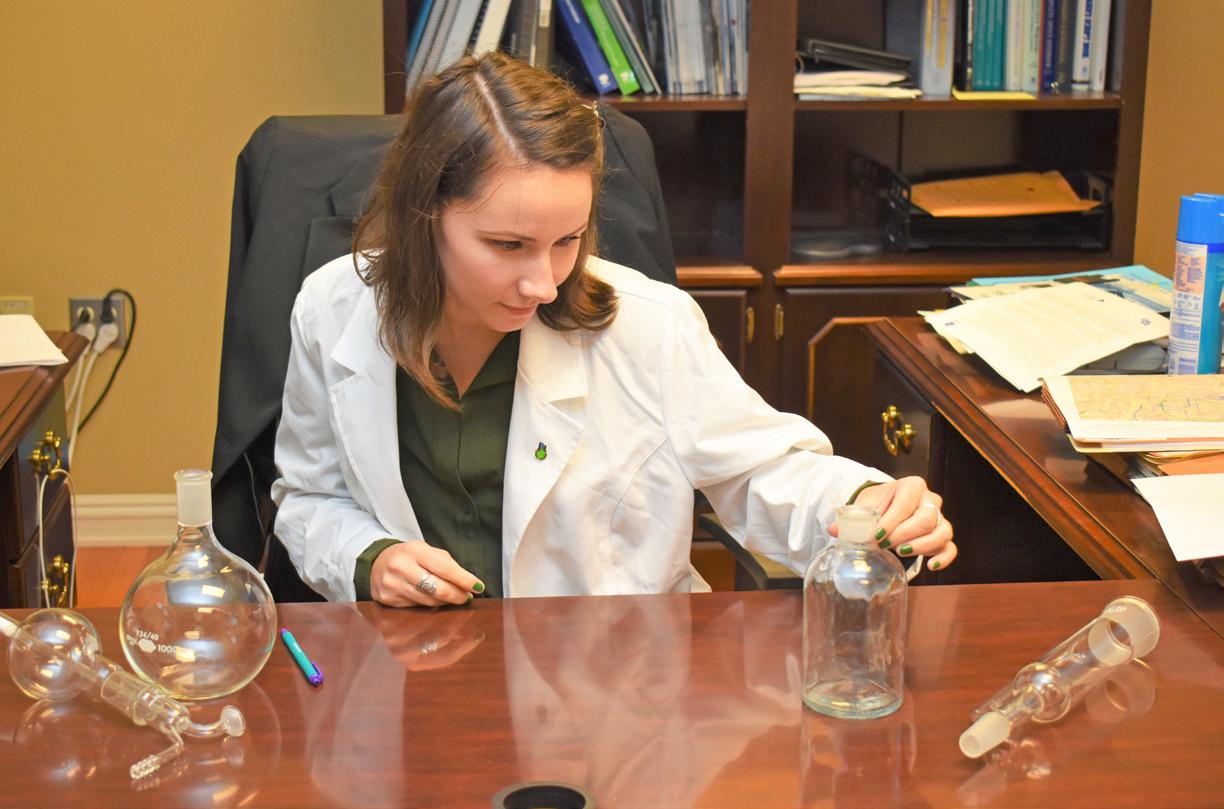
I started at entry level as a lab tech and in five years I went from entry level to executive.
BP: What are the opportunities for people who don’t have a four-year degree, who may have an associate degree or come right out of high school?
RB: Our company has a wide range of different types of jobs. If you like working with your hands, we’ve got a position for that. If you like working with numbers, we’ve got a job for that. We’re very competitive with our pay and we’ve got amazing benefits.
There are people who have worked 30-plus years with the utility because it’s really a good career field for any type of work. Baby boomers are retiring, so a lot of vacancies are going to be coming up and that means a lot of opportunities for young people.
BP: If you could address a room full of young people about what you like most about your career, what would your message be?
RB: I grew up learning about the natural world and it became my passion. That’s why I really love the mission of our company. We take something that is considered waste, we clean it, and we return it back to the environment. I love the mission of what we do, and I love the work environment. It’s full of great people and that’s something that I think is undervalued. It’s hard to put a price tag on working with great people.
DESI HUNTER
Senior Coach/Field Mentor, Entergy
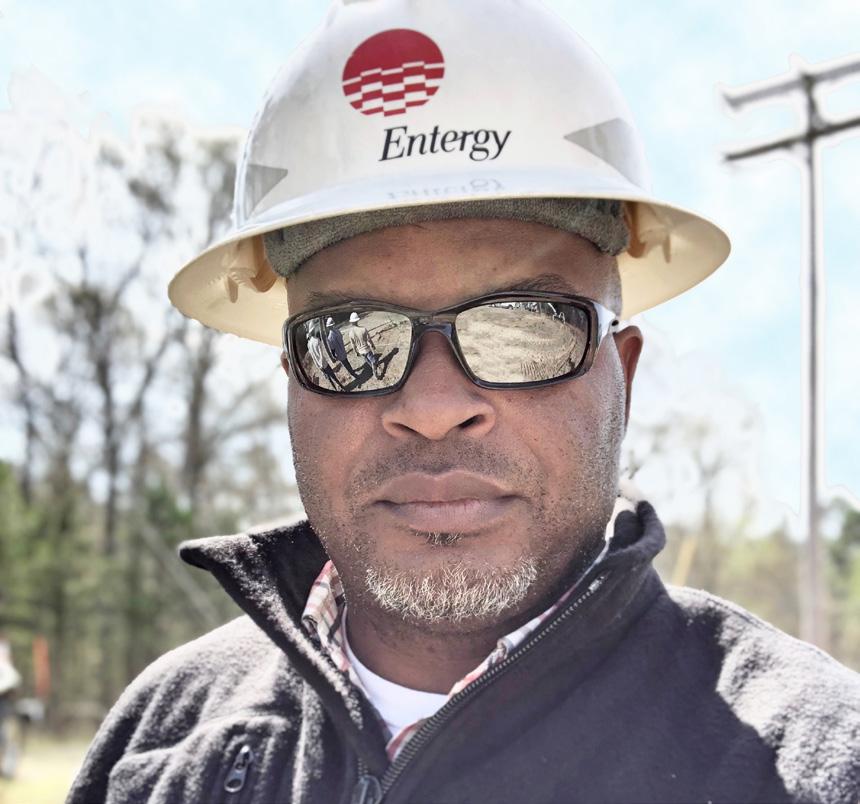
Hometown: Stephens
Age: 51
Years with Entergy: 23
BLUEPRINT: As a designated coach and mentor, why is it still difficult to get kids to consider a skilled career?
DESI HUNTER: When I grew up in the 1980s it was just pounded into your head you have to go to college. I grew up working in my grandfather’s gas station, changing oil and changing flats. I had those skills, but I was told I’ve got to go to college. So I went and it was not my thing. I lasted about three semesters and knew I didn’t want to do that. I enrolled in SAU Tech and got my airframe and powerplant license to work on aircraft.
We’re still forcing kids through college and they get out with a degree in accounting or business where they’re a dime a dozen. I try to tell kids, I’m not knocking a college education, but you can learn a trade like plumbing, welding or electrician, or work as an apprentice for a few years, and do well.
BP: How did you land here at Entergy?
DH: I found out about Entergy from a guy I knew who was looking to get on with the company. The more he talked, the more I thought, “Man, I’d love to do that.” So I went through the interview process and got hired even though I didn’t know anything about electricity.
BP: How did you learn what you needed to know?
DH: Entergy sends you to boot camp in Clinton, Mississippi. They teach you how to climb. They teach you wire sizes and wire connections and how to do CPR and things like that. That’s the basics you learn at boot camp, which is about 12 weeks. The rest is just on-the-job training.
BP: What do young people need to know about success in the working world?
DH: One thing is, they need to look at something like a career. Nowadays, I think kids look for a job and then they’re on to the next thing whenever they get tired of it. I remember when I got this job at Entergy, my parents were so proud. They were like, you have a great job with a great company that will give you a long career. That’s how you need to think of it, long term. That’s the first thing
What I always tell people is the two things you need are attitude and effort. I tell people if you have a good attitude and put forth the effort, you can be taught and trained to do anything you want to do.
Companies strive to build racially and gender-diverse workforce
Most people who work at Little Rock Water Reclamation Authority understand the critical role their work plays in the daily quality of life in the community. But few understand it as deeply as Harold Hounwanou, engineer. For Hounwanou, the work the company does every day has special significance.
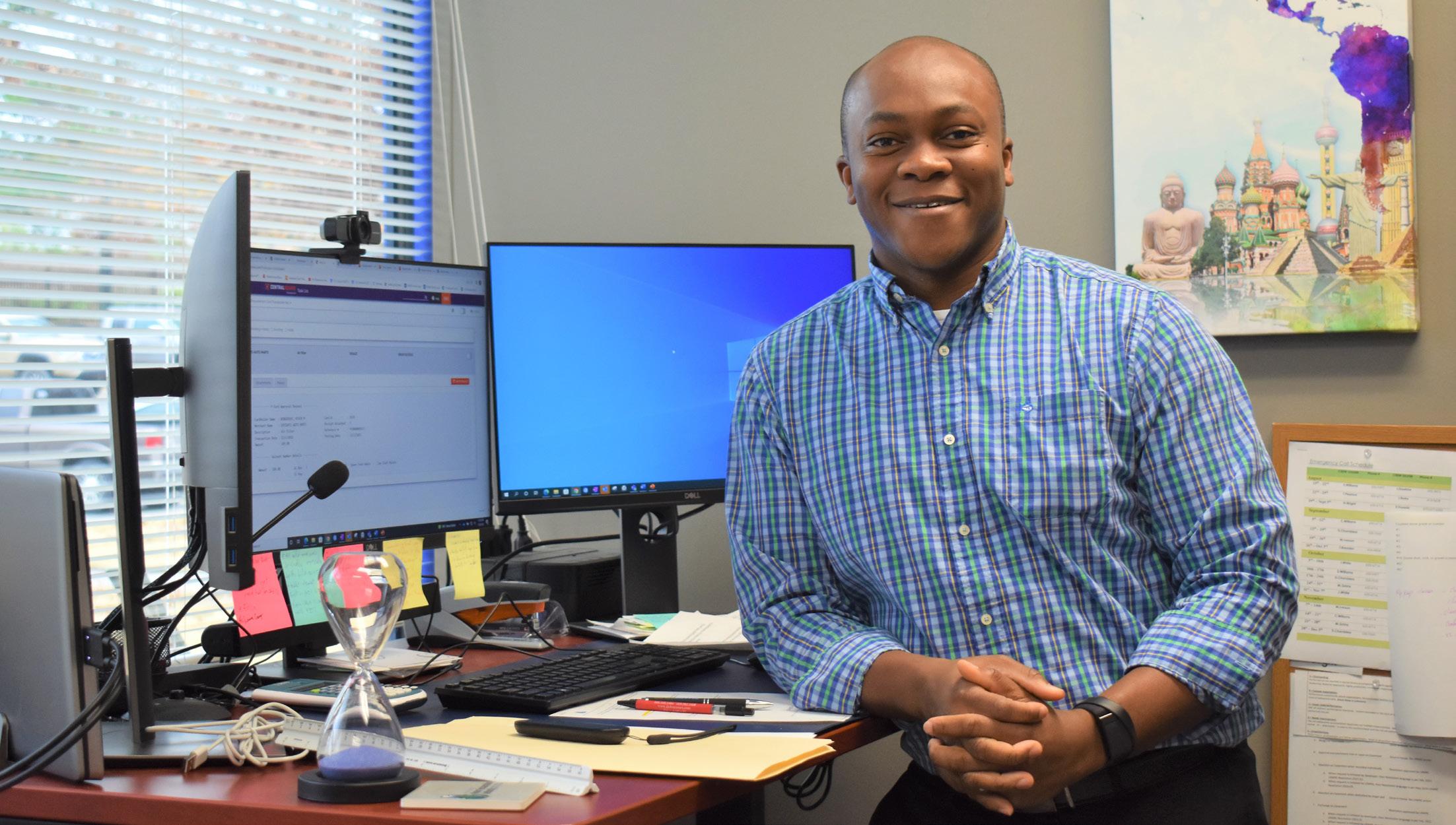
“I am originally from a small town on the West Coast of Africa, west of Nigeria,” he said. “To give you an example of what reality looked like growing up in my country, we had rolling outages, not just of power but also of water. We’d have a week on and a week off and sometimes that extended to a month, so you had to plan very well. We had to dig wells to be able to have ground water, which we boiled and stored for the times when we didn’t have running water. You opened the faucet and there’s nothing coming out. You had to plan for those days because water is life.”
Living that reality into his 20s left its mark on Hounwanou, so much so that when he came to the U.S. to attend college, he couldn’t believe the conveniences his American classmates all took for granted.
DID YOU KNOW?
Of
“Growing up, on Saturday morning I had to get up and wash clothes by hand, and to do that you needed water. You had to store the water and have it ready,” he said. “The first week I was here in the U.S. I took a bucket and went outside to wash my clothes by hand. A student stopped me and asked what I was doing, and in the broken English that I could speak at the time, I told them I’m going outside to wash my clothes. They said no, let me show you something.
“They took me to the basement and showed me all the washing machines and I started crying. I called my father and told him, ‘You would not believe the machines that they have here. They have a machine that washes your clothes and they have one that dries them, too.’”
More than a poignant story, Hounwanou’s lived experiences also illustrate the value of a diverse workforce as it brings many different perspectives to bear on the work at hand.
Much attention has been paid to diversity in the workplace over the past decade or so, efforts that are starting to pay off in many organizations. But as Lyndsey Hall, pretreatment sampling
CONTINUED ON PAGE 14
Source: U.S. Department of Labor
the 25 occupations with the lowest female representation, 21 of them are in skilled labor jobs. The bottom five include plumbers, pipefitters and steamfitters (1.4%), electricians (1.8%), carpenters (1.9%), automotive service technicians and mechanics (2%) and first-line supervisors in construction (3%).Harold Hounwanou, engineer for Little Rock Water Reclamation Authority. COURTESY LITTLE ROCK WATER RECLAMATION AUTHORITY
TERRIAN TYLER
Engineer, Little Rock Water Reclamation Authority
Hometown: Blytheville
Age: 28
Years with LRWRA: 1
BLUEPRINT: A lot of people think a skilled career is all about the technical aspect. What is the most important soft skill a person can have, in your opinion?
TERRIAN TYLER: No matter how smart you are, it doesn’t mean a thing if you can’t communicate. With what I do for example, I don’t spend all my time working with other engineers. I spend a lot of time explaining engineering concepts to non-technical people, covering different science concepts so they better understand what is going on. It’s all about having patience and it’s all about truly understanding the purpose of what you’re doing.
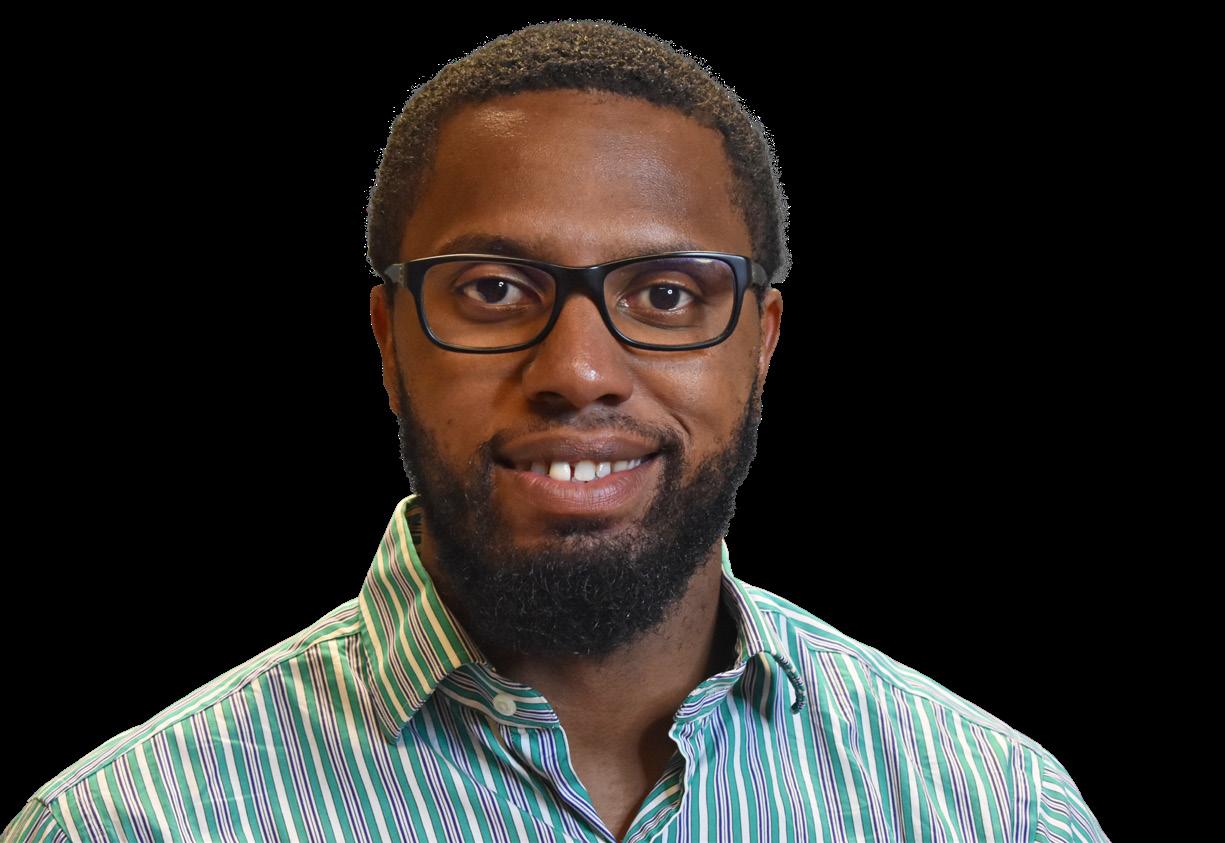
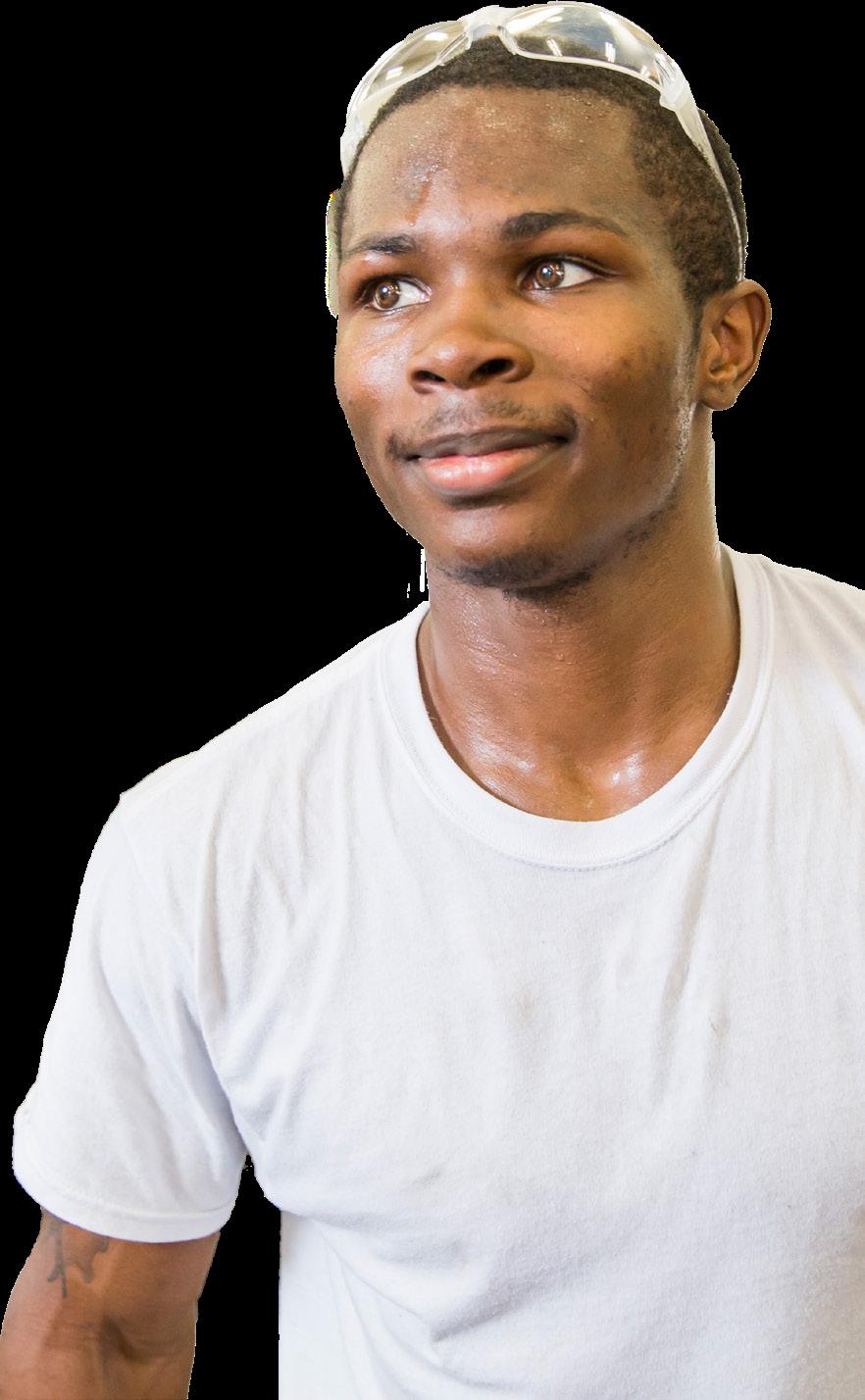

BP: Is a four-year degree mandatory for a fulfilling career at LRWRA?

TT: We have several project administrators who do not have a fouryear degree. We have inspectors who don’t have four-year degrees. If you didn’t want to work on my team specifically but you still want to get in the Water Reclamation, you can do it.
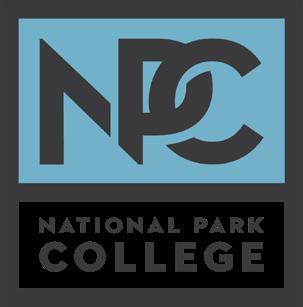
I think it’s important to point out, however, that while we have water treatment plant operators and several other individuals who don’t have a degree, they do have an education. If you want to work at the plant, for example, you take your wastewater operator’s test and get your license, which this is a process that may take a couple months. But you get your Class 1 and you’re working. If you go on to your Class 4, you can make a really great living.
I don’t want to say it’s easy, but it is not as hard as going to school for four years without knowing what you’re going to do at the end of it.
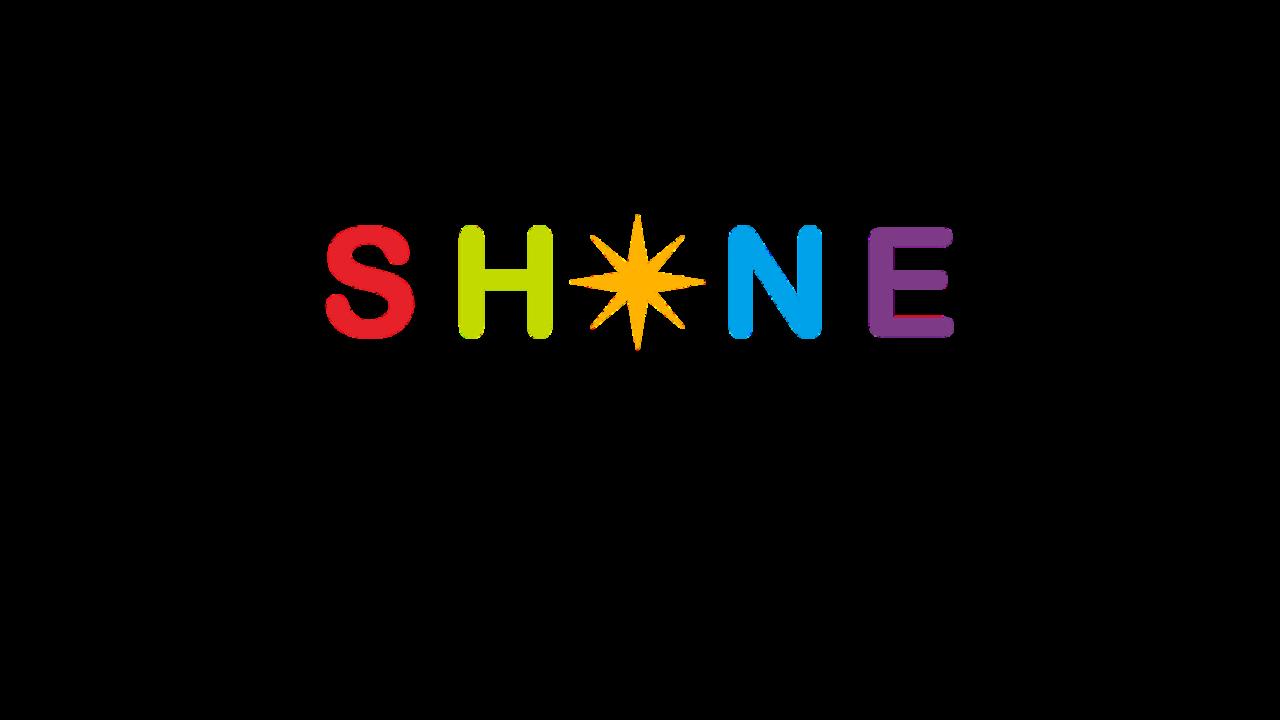
BP: How did you choose LRWRA to build a career?
TT: When I went to school, I focused on biological engineering, which is food, water and energy. Water stuck with me because it was one of those things everyone needs and it’s constantly a problem, either too little or too much.
The Authority does water reclamation, we reclaim the water that comes out of your house, and I wanted to work in a public utility because I feel like that’s where you can have the most impact with the general public. I worked for private companies where it was profit over everything, and so it’s nice to have a role where it’s safety first, the public first, the people first.
CONTINUED FROM PAGE 12
specialist with Little Rock Water Reclamation Authority, notes, there’s still a long way to go.

“No, there’s not a lot of females in this industry, at all,” she said. “I think one problem is that women don’t know about the opportunities here. They might think they can’t do the work because the job requirements are heavy lifting or that kind of stuff. But women can do it.
“In fact, at our utility we have a WOW program, which is Women of Waste Water. We try to meet once a month for an hour or so, all the women of the utility, and socialize and interact with each other and empower each other.”
Desi Hunter, who’s worked for Entergy for 23 years, said he’s seen the level of diversity in the trades rise and fall in that time. That tells him that the message of job opportunities and skilled careers for all must constantly be reinforced.
“Over the last two or three years what I’ve tried to do, I’ve been getting into Black churches. I’ve gone to Cinco de Mayo,” he said. “I’ve gone to different places to try to tell people about Entergy, things they might not know otherwise. When I grew up, I saw that serviceman come home to my neighborhood in his truck every night, a Black serviceman. I was like man, I want to do that someday. That’s pretty cool.”
DID YOU KNOW?
Minorities are highly underrepresented in the trades. Only 6.3% of construction workers are Black and 32.6% are Hispanic.
In the skilled trades overall, women comprise less than 10% of workers, even though they comprise half of the national workforce. Only 11% of people who completed an apprenticeship in 2020 were women.
Sources: Contractormag.com, U.S. Department of Labor
SHERREE BYNUM
Safety Specialist, Little Rock Water Reclamation Authority
Hometown: Little Rock
Age: 38
Years with LRWRA: 4 years
BLUEPRINT: How did you come to work here?
SHERREE BYNUM: I was always interested in science; my mom taught science for 46 years. I remember touring one of the [LRWRA] plants when we were in junior high, and I came away thinking, “This is not the place for me.” Years later an opportunity presented itself and after doing some research it looked like it was going to be a good fit for me. It’s just interesting how life circles back.
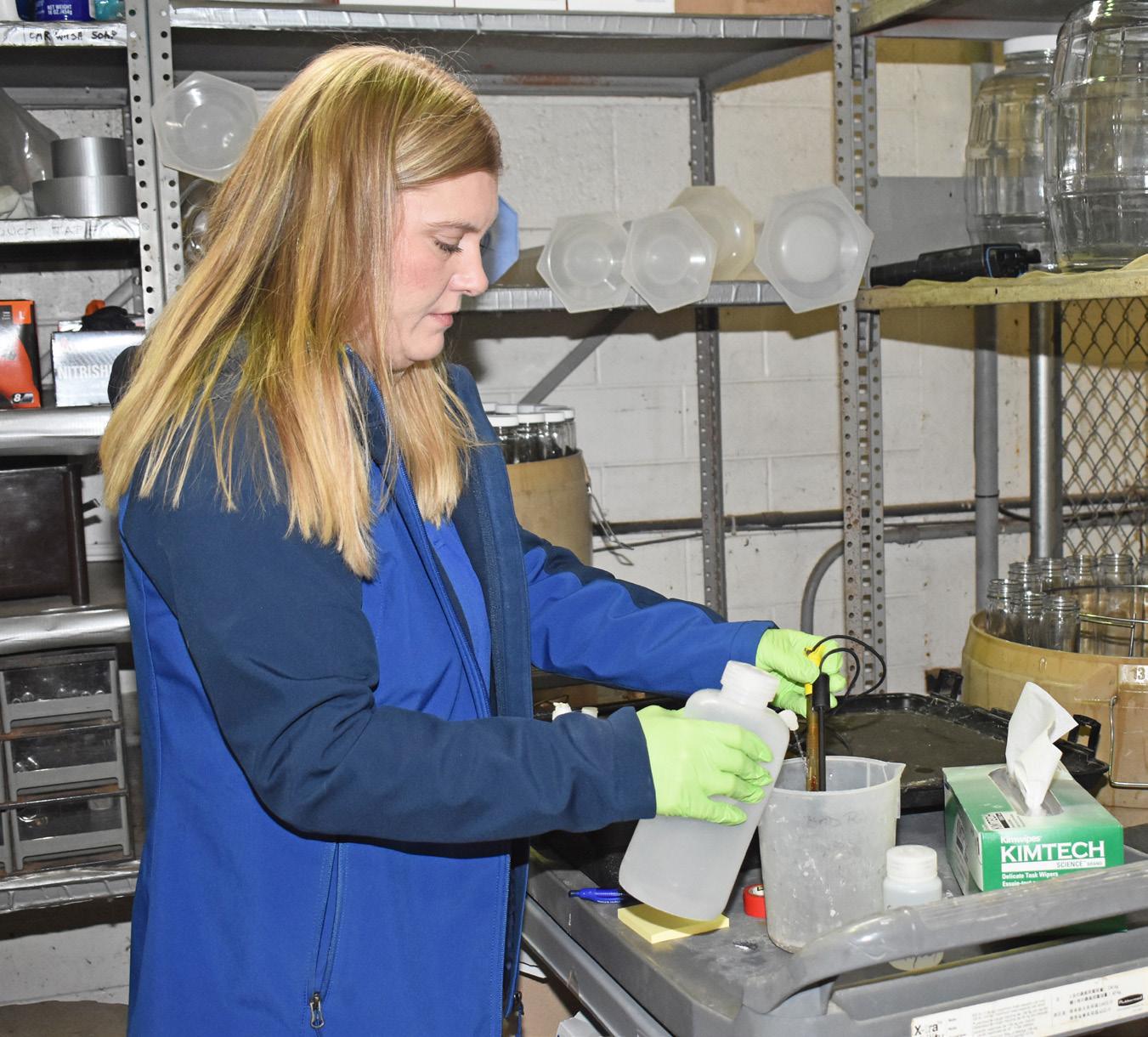
BP: What is your education?
SB: I graduated from Parkview Arts and Science Magnet High School and I have a Bachelor of Science in health science.
BP: What do you do in your role as safety manager?
SB: We do monthly safety trainings with our employees. Prior to COVID, we were meeting in a group session and we’re looking to restart that in 2023. Employees can also go online at their discretion and complete it.
BP: Do you get out of the office and go into the field to meet with employees in person?
SB: Typically at least two or three times a week I’m out at the plants, our treatment facilities, and then I get to go out and visit our crews that work around the city of Little Rock doing repairs onto our pipelines.
I go out and make sure they have safety protocols set up correctly, follow proper procedures and also make sure they have everything they need. Sometimes it’s just catching up, having the opportunity to talk to them, hear their concerns or questions about things.
BP: What do you like best about your job?
SB: There are so many things; it’s family oriented, it’s not such a big work environment. You can get in some jobs and you have thousands of employees, but here I get the opportunity to really get to know the people I work with. I think that is a plus in working here.
The work varies from day to day, it just really kind of depends on what’s going on. I can sometimes schedule myself for different things and it will not go that way depending on what they may have going on out in the field. We always have projects going on and they may call and say, “Sherree can you come out? We’re at this location.” I’ll go out and assist if there’s questions on safety issues they may have run into. We’re always available to assist.
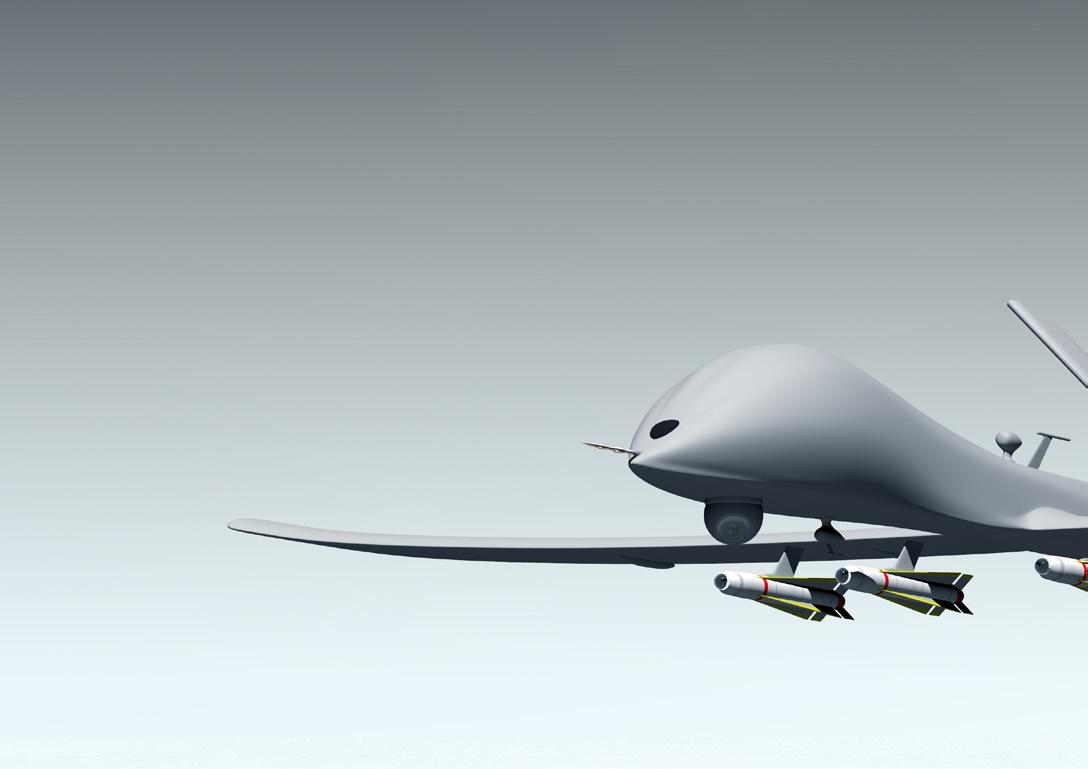
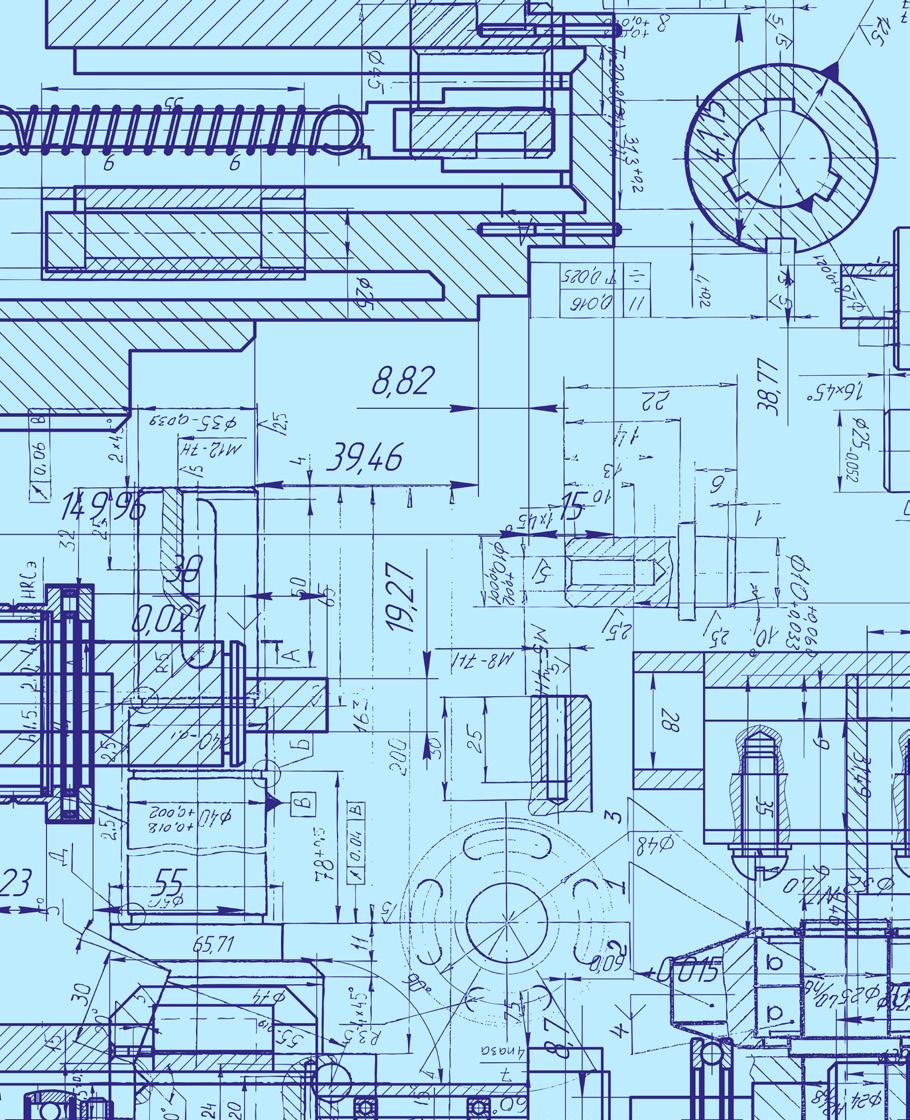
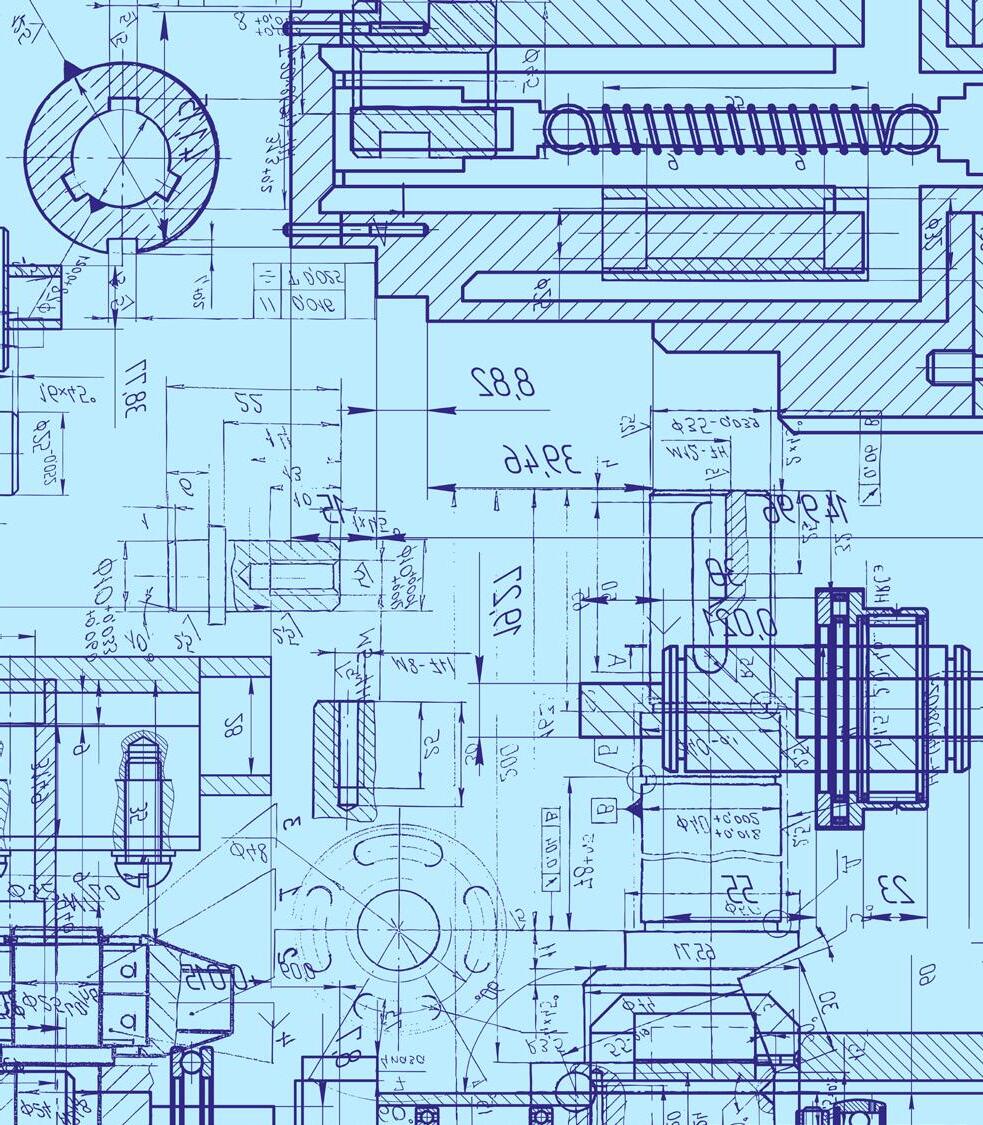
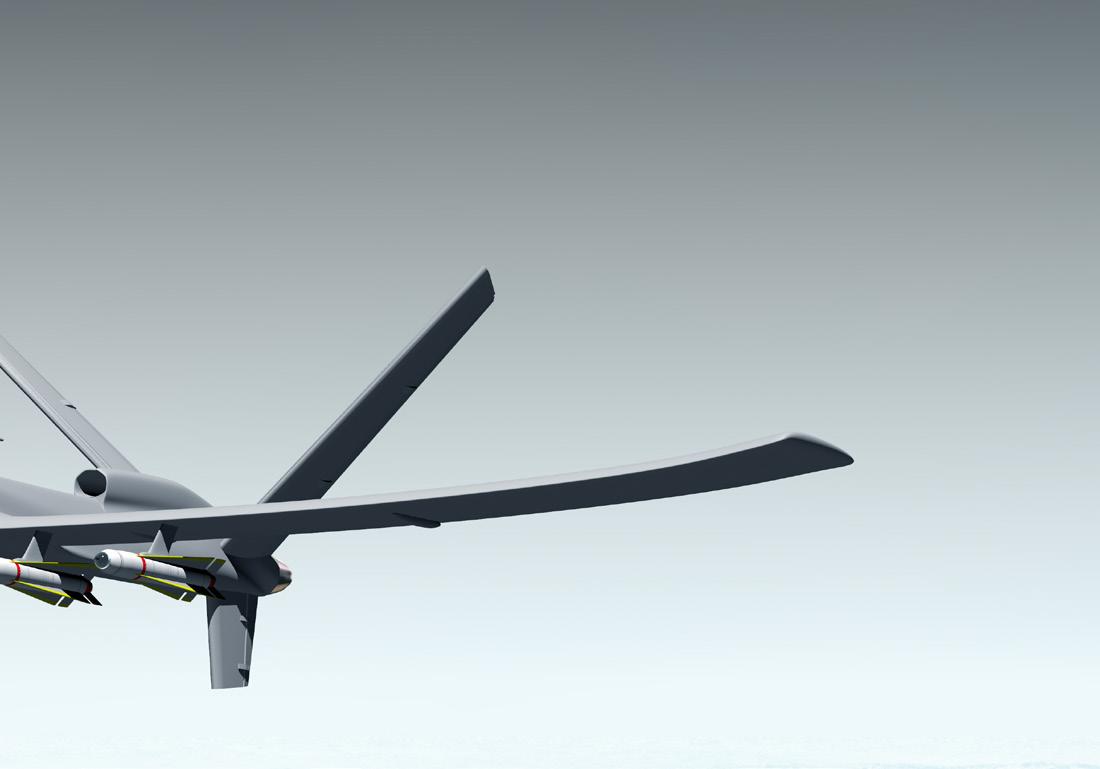
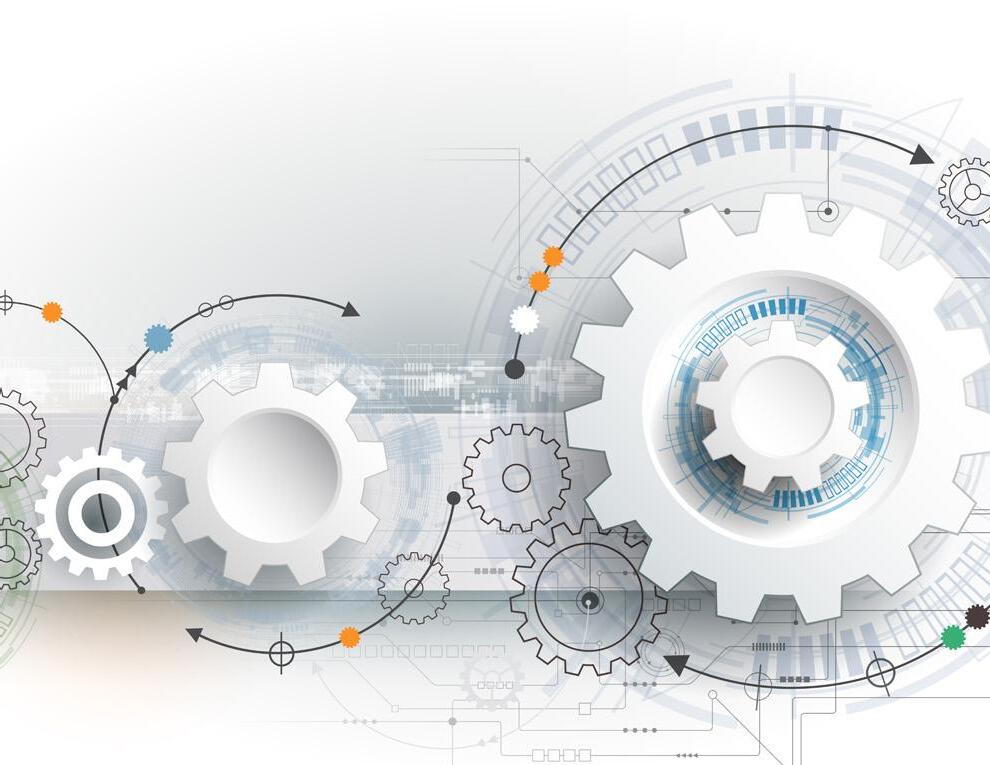
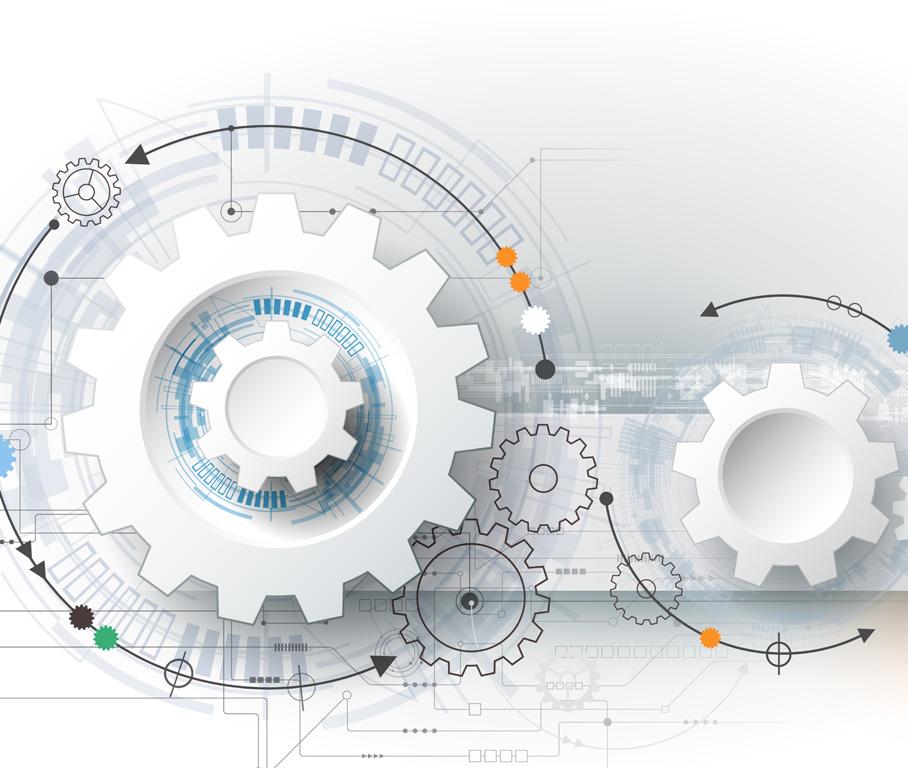
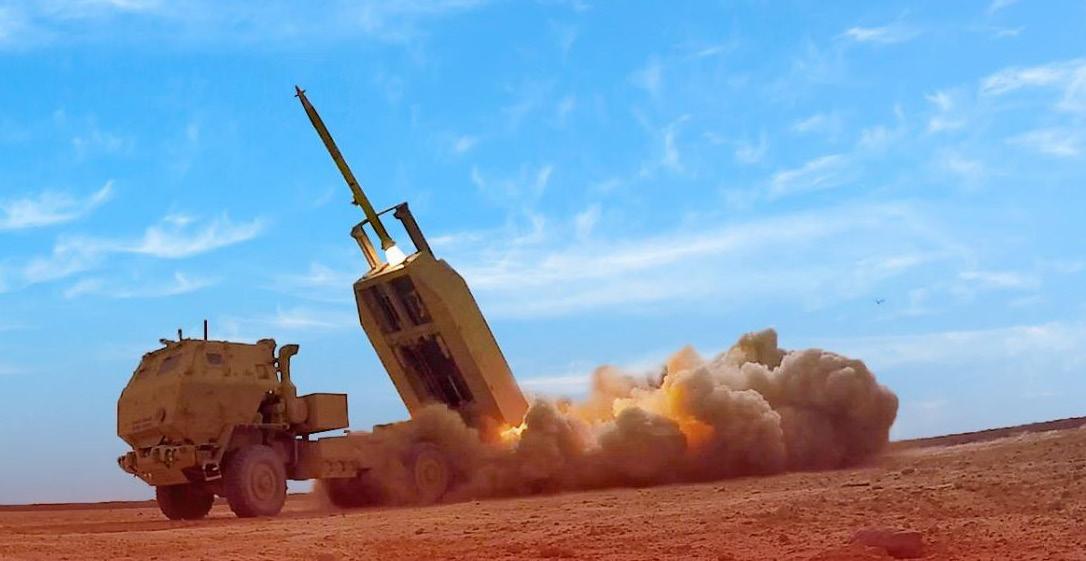
Things are Booming in Camden
At first glance, Camden, Arkansas, appears as just another charming small town. People still smile and greet you here, chat over coffee at the local cafe or wave as you drive along. It’s the kind of place you can immediately feel at home, enjoy a nice dinner out or just take in the local natural scenery.
But Camden is more than just good food and good brews (check out Native Dog Brewery while you’re there). It’s also one of the biggest manufacturing centers in Arkansas and a hub for the country’s aeronautics and defense industries.
And times, like the explosives being made here, are booming.
“We have multiple opportunities and openings available in the aerospace and defense industry,” said James Silliman, executive director for the Ouachita Partnership for Economic Development. “The companies have been here 40-plus years, and they continue to make investments in their facilities and equipment here, which means the job market here is very stable.
“Aerospace and defense industries provide well-paid, career-track positions to people of all skill levels. It’s a wonderful place to start and build a career.”
Camden’s history in the defense and aeronautics industry is a long one. Highland Industrial Park, the industrial district where many of the companies are located, began as Shumaker Naval Ammunition Depot during World War II. This provides the companies located here with ample production space as well as specialized facilities required for the manufacture and testing of ordnances.
For those who don’t know, an ordnance is anything our military men
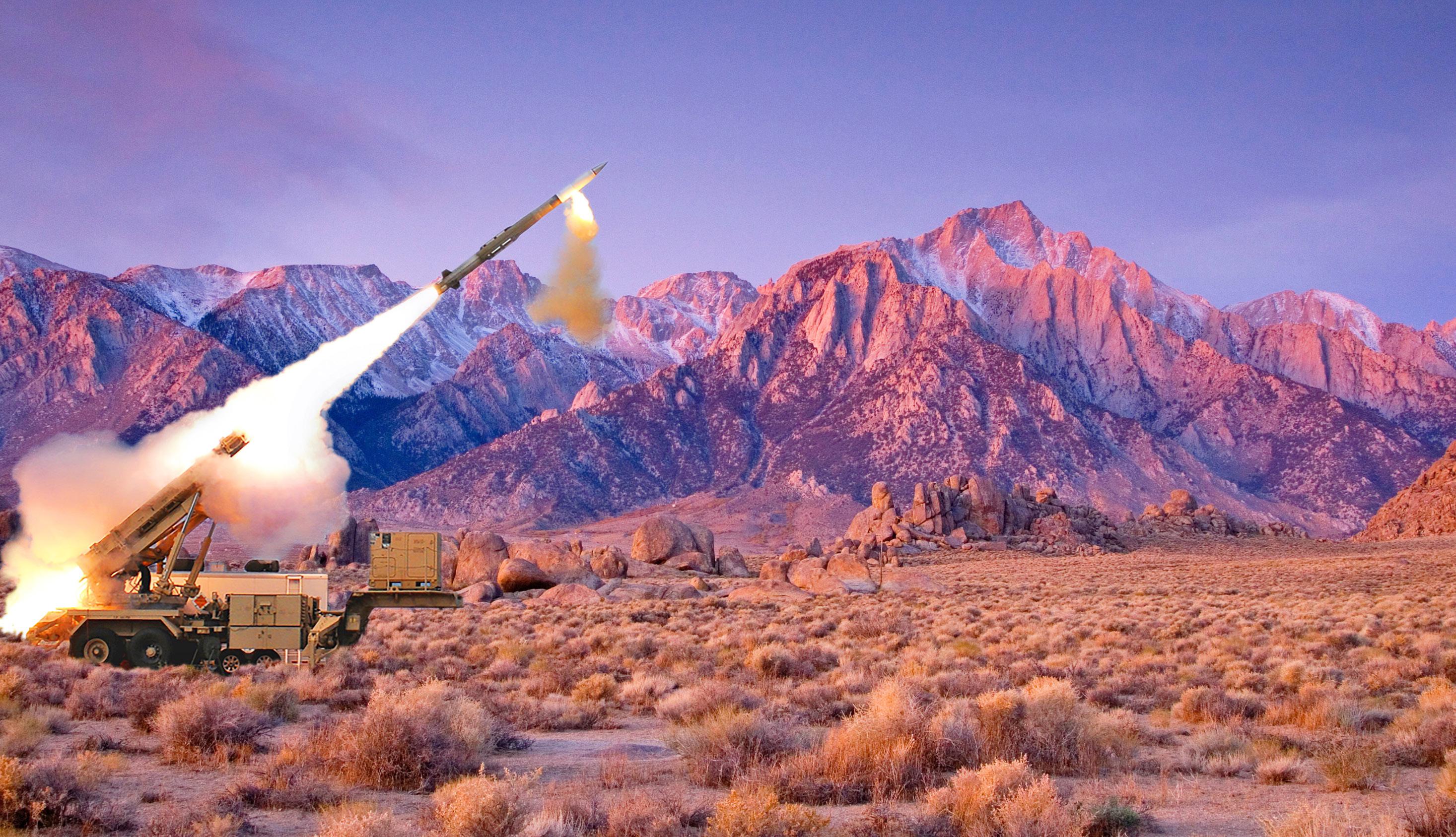
and women deploy that goes boom, such as hand grenades, missiles and various other tools for defeating terrorism and defending freedom around the world.
“Over time, we’ve evolved and been able to use the physical assets here in the park as far as facilities that are specially designed for manufacturing of ordnances as well as buildings where we can store ordnances safely,” said John Schaffitzel, president of Highland Industrial Park.
“We have 639 earth-covered storage bunkers in the park, and the manufacturing facilities are designed in a special way with structural concrete walls and really thick foundations. Those big, heavy-duty structural elements are the key element that we offer. We also own 18,780 acres of land, which is important. When you’re building ordnances, you want to be able to spread out and not be too close to one other.”
Skilled careers of all types are in heavy demand here, in companies of all sizes. Not only do global defense giants Aerojet Rocketdyne and Lockheed Martin operate here, but they are supported by dozens of smaller vendors located in Camden and nearby communities, all of which are in near-constant hiring mode. Companies work closely with the local college, Southern Arkansas University Tech, to help ensure training programs prepare students to excel in the workplace.
“It takes a whole mix of the workforce to make this place happen,” Schaffitzel said. “It takes all types of workers and skill sets. The key thing to know is advanced manufacturing now is different than what the old manufacturing line looked like, it’s much more high-tech than people think. And safety is priority number one for every one of these companies.”
Highland Industrial Park
Formerly
Shumaker Naval Ammunition Depot, the site was used by the U.S. Navy to develop, manufacture, test and store rockets from 1944 to 1957.
In 1968, the property became an industrial park and today, Highland Industrial Park is one of the largest of its kind in the United States, with 5.4 million square feet spread out among more than 1,000 buildings on 18,780 acres.
Now, 2,800 employees come to work here every day among the park’s 30 tenants. Such household names as Raytheon, Lockheed Martin, General Dynamics, Aerojet Rocketdyne and Armtec Defense all call the park home, as does Southern Arkansas University Tech.

Camden: Small-town vibe, big-city opportunity
TYRIS MORRIS
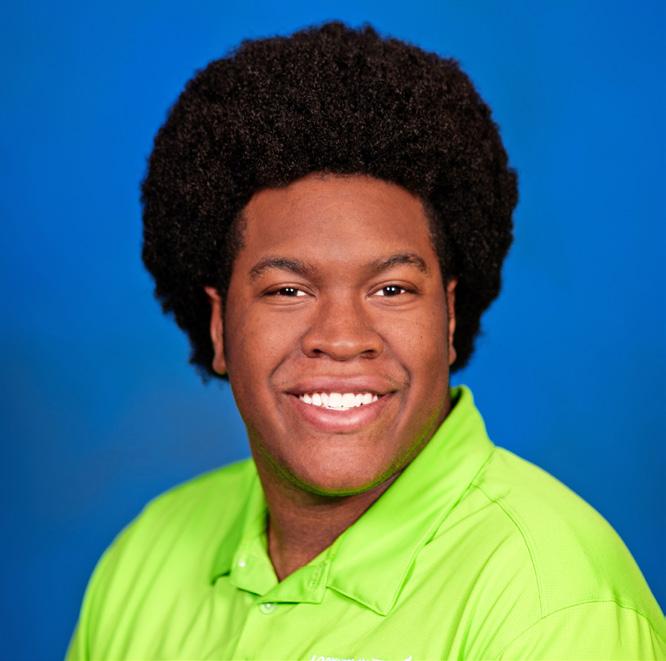
Inspector Senior, Lockheed Martin
Hometown: Camden Age: 25
Years with Lockheed Martin: 2.5
BLUEPRINT: When you started your career, what was the most surprising thing to you about the industry?
TYRIS MORRIS: I was surprised with the amount of technology that goes into the products that we build. We have semi-robotic processes, and we work with robots as well.
BP: Do you work in a team environment for the job you have now?
TM: I’m mixed because I work with a team of manufacturers that build the product, but then I have to go behind and make sure that they’re doing it right, and I’m the only one who does that.
I perform audits and do reports, I check the product that we build and make sure it is up to standard for our customer. I have to be very self-sufficient in what I do.
BP: What are some of the most important soft skills related to your job?
Acareer
isn’t all about where you work, it’s also about the quality of life where you live. Camden offers a slower pace, friendly people and loads of natural beauty and recreation to help you make the most of your off-time.
“If you enjoy small town life, Camden’s a good place to live,” said James Silliman, executive director for the Ouachita Partnership for Economic Development. “We have some nice amenities and restaurants and outdoor recreation. Hunting down in this part of the state is always a big recreational sport.”
With an extensive parks system and well-kept trails, outdoor activities are plentiful in this community. Several new businesses are breathing life into downtown spaces too, led by the award-winning Native Dog Brewery, which shares the community with one of the oldest continually operating eateries in Arkansas, the White House Cafe. While not the oldest restaurant in Arkansas, it is believed to hold the oldest liquor license in the state.
“Having moved here from a similar-sized town in Oklahoma, I can tell you Camden has the key things covered,” said John Schaffitzel, president of Highland Industrial Park. “You’ve got places you can go out to dinner. You’ve got places that you can go for entertainment or to watch college sporting events. The hospital system is a county-based hospital system, which is great. The basics that you need are here. It’s a great quality of life.”
CAMDEN AT A GLANCE
Population: 10,400
Median Home Value: $79,800
• Median Age: 36
• Median Household Income: $31,059
Median gross rent in 2019: $508 • Average Commute: 19 minutes
Cost of living index: 77.1 (low, U.S. average is 100)
Sources: U.S. Census Bureau, city-data.com
TM: You have to have good oral communication or business communications skills. You have to know how to talk to people in different circumstances. Another important skill to have, especially in the department that I’m in with inspection, you have to have a good eye for detail. You have to be very attentive to what you’re doing.
BP: Did you know what you wanted to do for a career when you were in high school?
TM: In high school I really didn’t know. I just knew that college was the norm so I went to school not knowing what I wanted to go to school for. I started working for another company out here and I was there for two years. Then I made the jump over to inspection for Lockheed Martin.
BP: Is there a lot of opportunity in the aerospace and defense industries?
TM: Oh my gosh, yes. There are a lot of jobs to be had here in southern Arkansas, more than people actually know. There’s a lot of defense plants here in the Highland Industrial Park. If you want to work here for a while and move, that’s also an opportunity that’s open for you, moving within the company.
The amount of money that you can make is good. Just because you’re in manufacturing does not mean you’re not making money.
BP: A lot of people think manufacturing and they think hot, dirty and dangerous. What’s the reality where you work?
TM: I’m inside all the time. When I got this job I said, “Do y’all have air conditioning in the building?” They were like, “Yes, there’s nothing to worry about.” So, yes, it’s inside and climate controlled. It’s good.
Rise of the Machines
If you think manufacturing, construction job sites and other skilled trade areas are stuck in the analog age, think again. Today’s skilled careers are as much about bits and bytes as they were about wrenches and hammers a generation ago. And while the ability to use hand tools of every description is still important to the finished product, there’s a lot more computerization at work in a typical factory than ever before.
“We are exploring opportunities to streamline our processes through automation, control systems, simulations, visual working aids and other new technologies,” said Jerry Bever, manufacturing engineering senior manager with Lockheed Martin in Camden. “Digital transformation initiatives such as robots, collaborative robots known as cobot systems, virtual reality and augmented reality are pillars in transforming the way we work.”
There are various factors driving the rapid advancement of technology into the skilled workplace and job site. For one, the marketplace is demanding products faster than ever before, a fact driven home by the
supply chain issues of the past couple of years.
Second, rising costs and global competition have manufacturers of all sizes seeking every efficiency advantage it can get. And third, ironically, is the shortage of skilled tradespeople itself, which has forced companies to look to automation in order to do more with fewer people.
The result, Bever said, is a demand for employee skills that were once unheard-of in manufacturing. Not only do the manufacturing workers of tomorrow have to know how to operate these new machines, demand for on-site programmers and IT troubleshooters has never been higher.
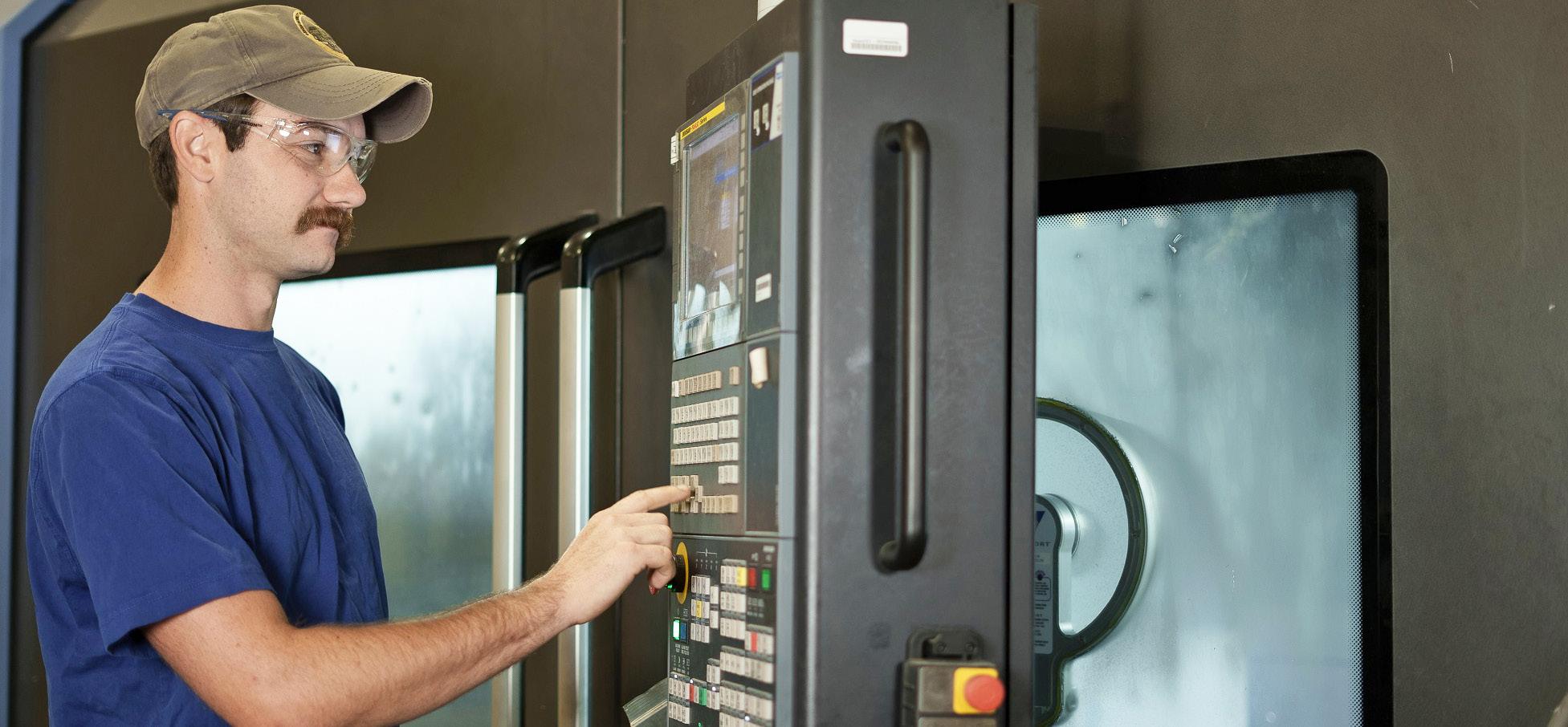
“A general knowledge of computer skills is essential for anyone working in our industry,” he said. “An employee’s skill in working with Microsoft Office, SAP, Apriso and other programs is important in our manufacturing environment.
“Beyond that, proficiency in mathematics, physics, robotics, electronics, CNC programming and operation and computer programming and gaming simulation are all useful and at work in today’s factories.”
TRANSFORMATIVE TECHNOLOGY
Three advanced technologies currently at work in factories from one end of the state to the other, each requiring employees with knowledge and aptitude to operate and maintain systems:
1. ROBOTICS
Cheaper, smarter and more efficient than ever, robots are used in a variety of manufacturing settings and tasks.
Once cost-prohibitive to all but the largest manufacturers, robotics are now typically within reach of mid-sized and smaller companies.
2. THE INTERNET OF THINGS (IOT)
IoT in manufacturing uses sensors to collect production data, giving operators valuable insights on how to run machines at peak efficiency, cutting
cost, waste and production time.
The technology also allows for remote operation and monitoring of certain processes, which allows one employee to do more, even from afar.
3. CLOUD COMPUTING
Another technology not associated with manufacturing until recently, cloud computing helps teams in different divisions and even separate locations work together efficiently.
Cloud computing is also essential for companies to connect with external audiences, such as integrating vendors within the supply chain or studying consumer buying and product utilization habits.
Source: Fingent.com
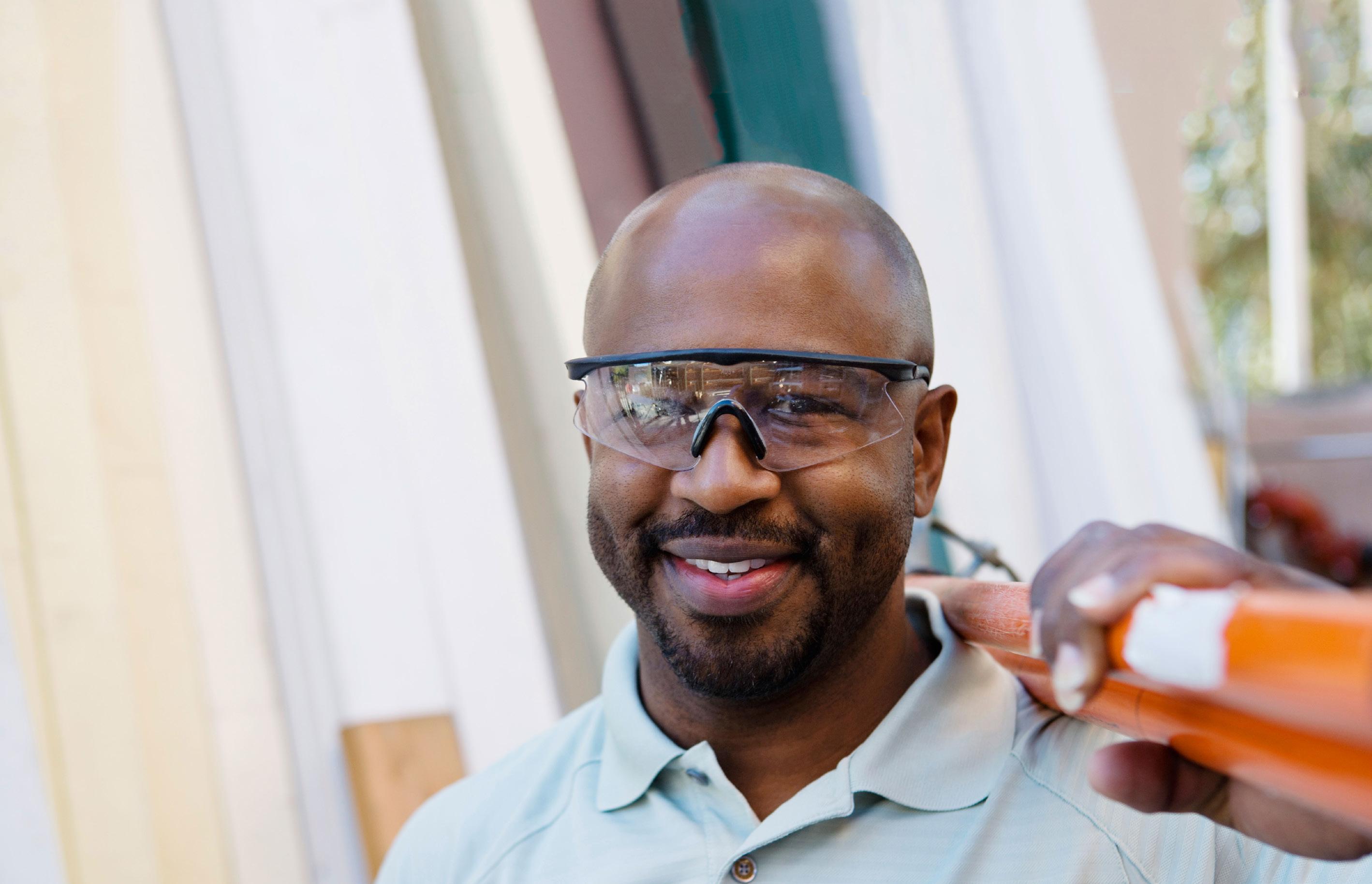
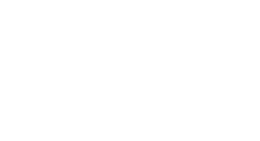
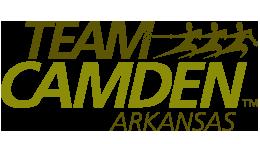
Diversity equals opportunity in Arkansas manufacturing
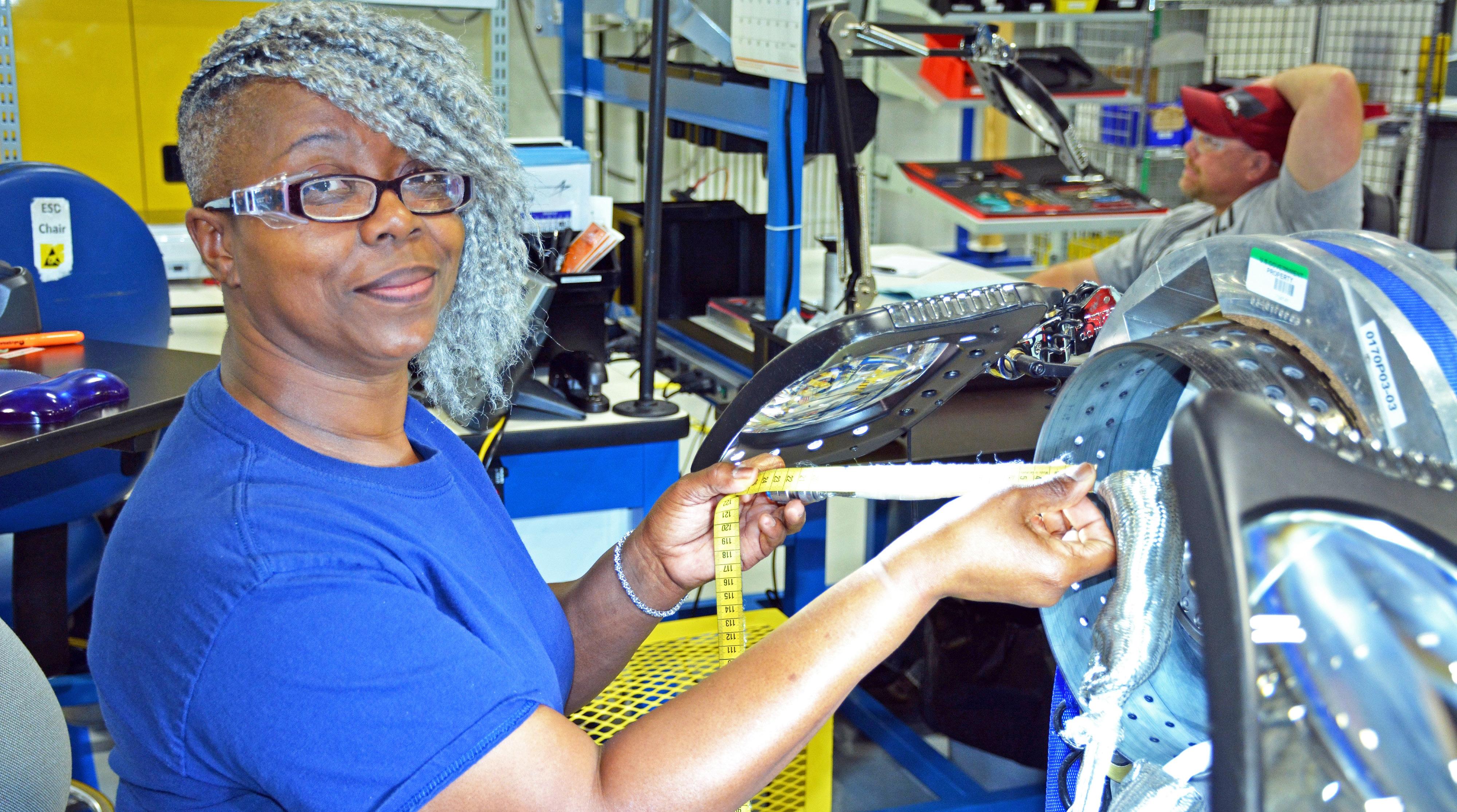
Clark Lewis likes to say that he first went to work in manufacturing at age 6. The Camden native came along with his father, who provided janitorial services at the local industrial park, at a very young age.
“I started at the age of 6,” said Lewis, now production manager with Lockheed Martin. “I then got recruited by a local diaper plant when I was 15 years old. I went to school in the day, and during basketball season I went to the graveyard shift. That’s when I was in high school.”
After the diaper plant shut down, Lewis would eventually find his way to the defense contractor. In less than a decade, he’d work his way to a position of great responsibility in the plant.
“I manage day-to-day production duties,” he said. “This requires a lot of communicating and planning from all the functions that drive and support the operations of the plant. I have over 100 employees in my organization, and I have hired over 90% of the existing workforce that’s working right now.”
Having done that much hiring, Lewis is well-acquainted with the company’s drive to maintain a diverse workforce. He said from his own experience through to today, providing equal employment and advancement opportunities has been a top priority at Lockheed Martin. He estimated the total plant was about 45% female, for instance, and in his own department, six out of 10 employees were women.
“They really look at diversity here; we have several groups here that really push that,” he said. “I’m on three diversity teams now. We take a really broad view of people to make sure we’re being consistent from all functions.”
Across the country, manufacturing is attracting large numbers of women into roles traditionally dominated by men. According to the U.S. Census Bureau, about 30% of manufacturing jobs are held by women, roughly three times the percentage of women in all trade jobs combined. Even more tell-
ing is one in four management positions in the manufacturing industry are women and women in manufaturing earn on average 16% more than the national median annual income earned by all women in the workplace overall.
Stacia Gentry, manager of manufacturing engineering operations integration with Aeroship Rocketdyne in Camden, said her work there leveraged the skills and experience she accumulated while in the military.
“My favorite part of military life was building relationships with people from different backgrounds,” the Army veteran said. “In my role here, I manage individual program integrators across multiple programs. We work to ensure seamless communication between the customer, the site leadership team, program managers and any other supporting department or vendor.
“Part of my team’s responsibility is to establish work standards to create work efficiencies and facilitate any needed functions and support in order to produce a safe, quality product. In leading this effort, I use the skills I learned from military service every day.”
Gentry acknowledged the difficulties many veterans face after their military careers are over. She said the supportive environment she’s found at Aerojet Rocketdyne helps the process of transitioning from military to civilian life.
“Civilian life requires more self-motivation than military life; being self-motivated is critical,” she said. “I would suggest choosing a career that allows a veteran to utilize the skills they’re obtained during their military service, such as team building, organization and collaboration, which are highly transferable to the civilian sector.
“A career in the [defense] industry is ideal for that. It also prepares you to build products that help defend and protect freedom here and abroad. That’s one of the main reasons why I joined the military in the first place.”
and) my family.
Working at Lockheed Martin comes with life-changing benefits. After serving as a funeral home director for 11 years, I joined Lockheed Martin's apprenticeship program. Through hands-on classroom training and intentional mentorship, I now perform manufacturing inspections using certified skills on both ground and flight electronic assemblies. For the first time, I have the opportunity to easily save for retirement, go back to school and advance my career. Explore career opportunities today at lockheedmartinjobs.com/camden-operations
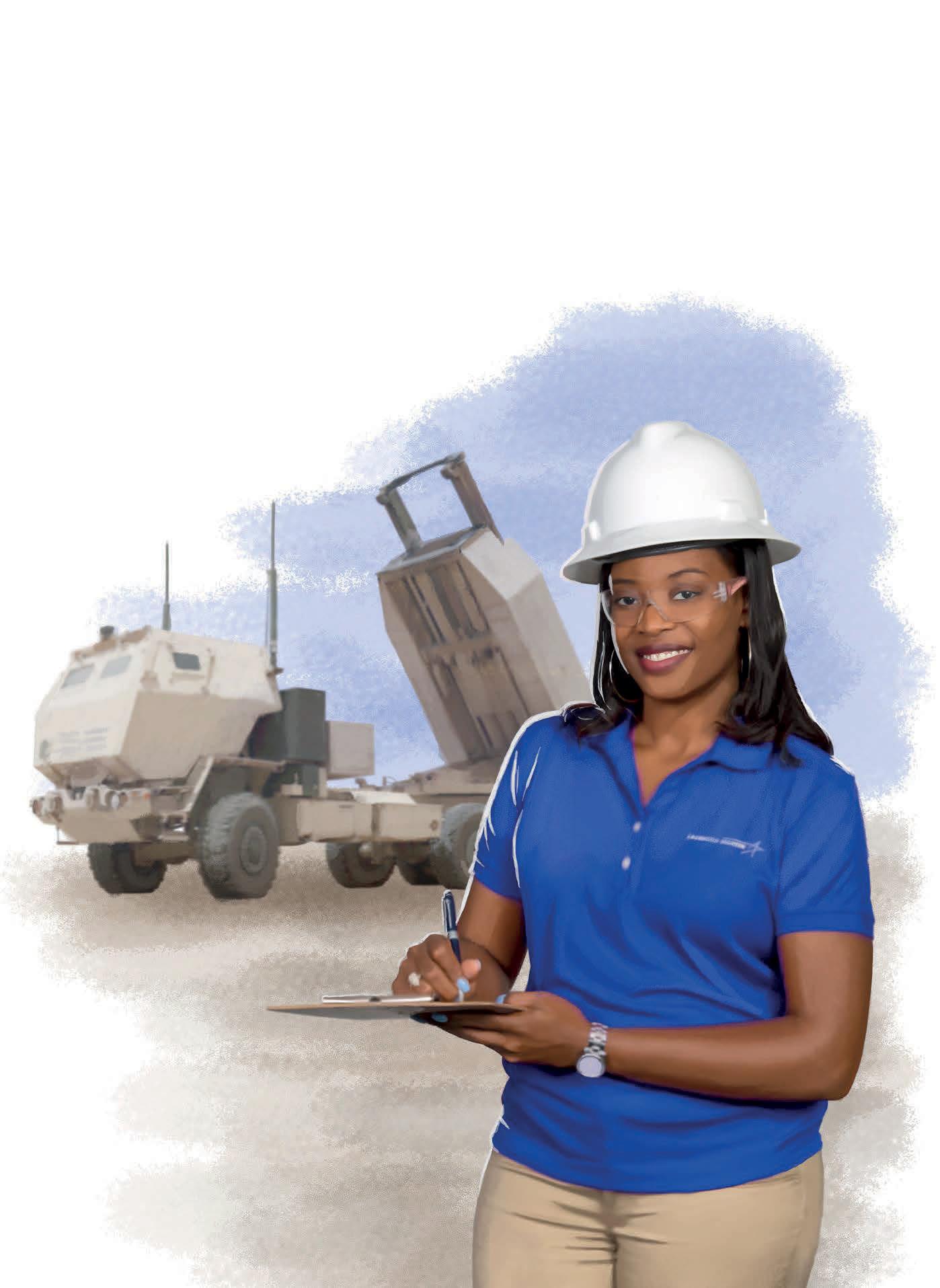
Only here can I turn on-the-job training into a brighter future for (meKEITH EVERHART Assembly Senior Specialist, Lockheed Martin
Hometown: Camden
Age: 38
Years with Lockheed Martin: 14
BLUEPRINT: Did you know about the manufacturing in your hometown growing up?
KEITH EVERHART: Unfortunately, in my high school, Harmony Grove, it wasn’t really explained how much opportunity we had right down the road. Because of that, I went to college like all my other friends without really knowing what I wanted to get into. I went three and a half years to a local college, have no degree and I had a boatload of student loans to pay back. If I could do it all over again, it would have never happened to me.
It was in college, however, that I actually started working in the plants around the area and working for the local electric company. When college didn’t pan out, I got an awesome opportunity to start with Lockheed Martin.
BP: How have you grown since you’ve been here?
KE: Pneumatic tools are everywhere at Lockheed Martin, and I will be honest, I wasn’t even sure what that was back in high school. Now, I don’t know how to live without them.
I have also grown in my leadership ability. With this new role that I’ve recently taken took on, I have grown in how to be a co-worker but also an authority figure without the actual title. It’s very hard to be friends and a boss. That has been a challenge but I’m getting there.
BP: People have a certain vision of what a manufacturing work environment is like. What’s the reality?
KE: It’s nothing like the stereotype about manufacturing. At Lockheed here, it’s clean. We pride themselves on “clean-as-you-go” because we have 100 percent foreign object debris prevention, and one of the ways to do that is by cleaning up as you go and not making a mess in the first place. People think the conditions in a plant are uncomfortable but there is heat in the winter, air conditioning in the summer; you’re not in the elements all day. I have been in other plants that didn’t do that, so I know how good it is here. If it’s raining or snowing, the hardest part you’ll face is walking from your car to the front door.
BP: Sounds like you’re very happy with where you are and what you’re doing.
KE: Yes, sir. I came out here not knowing much about anything. I’ve made the most of every opportunity I’ve been given and I’ve learned a lot. I come to work, I have great attendance and do what my boss asks me to do. I can’t wait to see what’s next.
Quality Engineering Lead, Aerojet Rocketdyne
Education: Southern Arkansas University, Magnolia
Major: Engineering/Computer-aided Design (CAD) modeling
BLUEPRINT: Describe your transition out of high school or college.
TREY GEER: The independence and ability to learn with hands-on experience was the most rewarding part of transitioning to a full-time career.
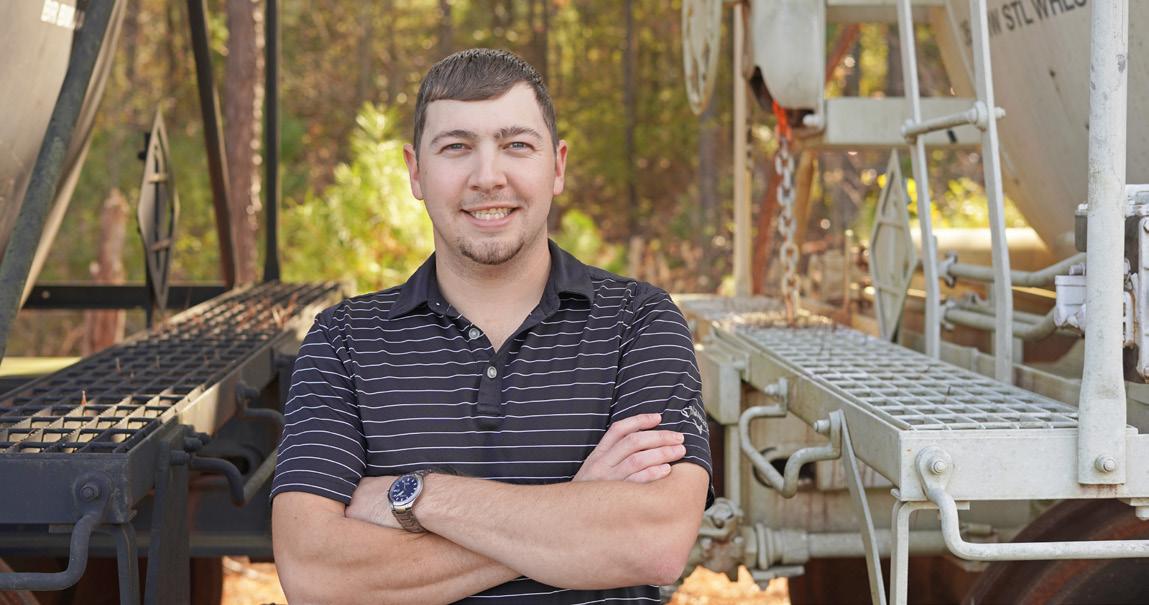
BP: How do the skills you learned in school help you in your role at your current organization?
TG: College developed the fundamental thought process of understanding problems and investigating and determining solutions.
BP: How does Aerojet Rocketdyne support recently graduated employees?
TG: AR supports recently graduated employees by instituting a phased training approach. This allows a recently graduated new employee such as myself to learn from experienced peers, but also to develop independence and provide personal input.
BP: What’s your favorite part about your job?
TG: Achieving a common goal with a dedicated team such as developing new processes and solving engineering problems.
BP: What advice do you have for high school or college graduates who are preparing to transition out of school?
TG: I’d definitely advise them to find a career occupation that inspires them to learn something new every day.
BP: Related to that, why should students consider a career in this industry?
TG: The aerospace standard is one of the highest standards in any industry or field. Once an employee has been exposed to that standard, it is easier to carry that expectation and mindset to any future career opportunities or even into your personal life. I would recommend it to anyone.
HOT JOBS!
INSPECTOR
WHAT DOES THE JOB DO?
Inspectors use various measurement and/or calibrated devices to inspect the products assembled at the Camden facility. They are also responsible for rejecting and generating quality notifications for hardware that fails to meet product specifications and assisting quality engineers with functions such as stock purges, product containment and nonconformance documentation.
WHY IT’S IMPORTANT:
Inspectors ensure that we provide the best product to our customers that will work right the first time, every time.
ESSENTIAL SKILLS AND ATTRIBUTES:
The most successful inspectors possess the ability to interpret product specifications and/or drawings or blueprints, use calibrated inspection equipment to validate dimensions, and pay strong attention to detail. It is also desired for them to have strong teamwork and communication skills as well as the integrity to uphold the highest possible quality standards.
WHAT MAKES THIS POSITION IN HIGH DEMAND?
Inspection of the quality of our products ensures it adheres to the Lockheed Martin standard and the product specifications as part of our ongoing commitment to our customers.
HOW DO I LEARN MORE? lockheedmartinjobs.com

HOT JOBS!
CHRISTA WORD
Engineering Aide, Lockheed Martin
Hometown: Camden
Age: 30
Years with Lockheed Martin: 2.5
BLUEPRINT: What made you want to embark on a manufacturing career?
CHRISTA WORD: My background is a little different. I graduated from high school and went to occupational therapy assistant school for my bachelor’s degree in that. I’ve actually been an occupational therapist for nine years and I still do that on Fridays and occasionally on the weekends, just to keep my license up.
When COVID hit and shut the schools down, it stopped much of the patient traffic coming into the hospitals for therapy. That took away my job and left me with a 1-year-old and no paycheck for six months. I came out here and started as a quality inspector. I did that for a little over a year, then I took this job and am about to start on my second promotion.
BP: Tell me about the company benefits.
CW: I work four 10-hour days, which is a benefit because you work four days a week and then you have three days off every week. You also have paid overtime after 40 hours; it’s time and a half, and if you work on a Sunday or a holiday it’s double time. Some people don’t count that as a benefit, but if you’re really struggling for money, that helps.
The retirement plan out here is like nothing I’ve ever heard of. They put in a percentage of your base salary, then if you put in up to a certain percent, they’ll match that. You also have your normal health, vision and dental insurance and they also offer a health savings account. We can withhold money from our paycheck to go onto a health card that can be used just for health expenses, and that money is not taxed.
BP: Has the company helped you with your technical education?
CW: Yes, all of it. If the company can benefit from you obtaining a degree, they’ll pay for it if you maintain a C average or better. I will soon graduate with my bachelor’s degree from Southern Arkansas University in Magnolia. Prior to that I had three associate degrees.
BP: Anything else?
CW: I would say the biggest perk, besides the retirement, is the paid time off that we get. I get paid vacation time and I get paid floating time and I get paid shutdown time and we get certain holidays off, too. Lockheed takes a lot of pride in their people enjoying their family and life. They know if employees get to be with their families and do those things that bring them happiness, then they’re going to stick around.
ASSEMBLER
Company: Lockheed Martin
WHAT DOES THE JOB DO?
Assemblers perform a variety of tasks ranging from repetitive to nonrepetitive production assembly operations on mechanical assemblies and subassemblies, such as running automated equipment and applying touch-up paint. An assembler also works from diagrams and drawings following detailed planning, and uses hand and/or power tools, jigs and saws. They may also disassemble, modify, rework, reassemble and test experimental or prototype assemblies and subassemblies according to specifications and under simulated conditions.
All Camden assemblers participate in the Camden Manufacturing Apprenticeship Program, a nationally recognized apprenticeship program, to provide them with the knowledge and hands-on experience to successfully and consistently assemble quality products for customers.
WHY IT’S IMPORTANT:
This position is the backbone of ensuring all products are completed with the highest quality and able to be delivered to the customers on time.
ESSENTIAL SKILLS AND ATTRIBUTES:
At minimum, an assembler must possess a high school diploma or GED equivalent, the desire and/or ability to use hand tools, ability to read and interpret assembly drawings or instructions. The ability to operate equipment and understand mechanical assemblies as well as strong teamwork, communication and problem-solving skills are also highly sought after.
WHAT MAKES THIS POSITION IN HIGH DEMAND?
This position makes up the majority of employees at the Camden facility who are responsible for completing their tasks accurately and in a timely manner to ensure product success.
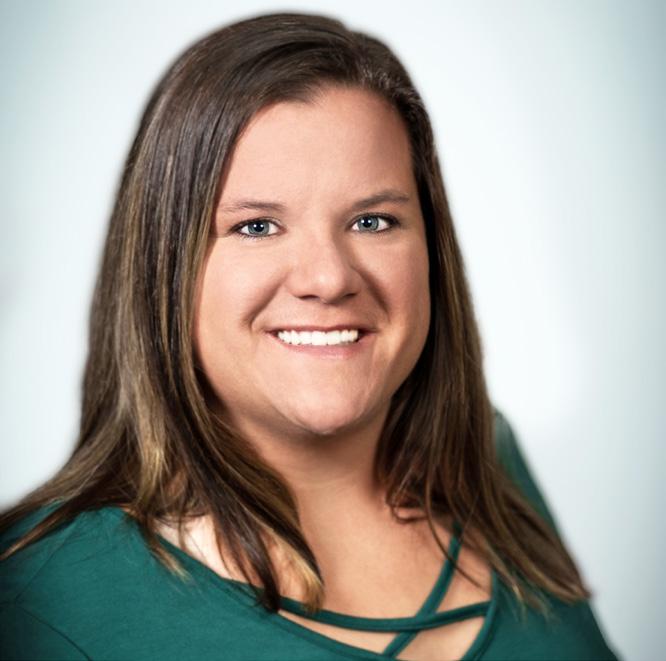
HOW DO I LEARN MORE? lockheedmartinjobs.com
MANUFACTURING EXPEDITER
WHAT DOES THE JOB DO?
A manufacturing expediter supports production work in a fast-paced environment by expediting, routing and dispatching materials and parts in accordance with production schedules and commitments.
A person in this role also reviews master production schedules to determine shortages and alert proper authorities of potential problems, keeps records of completed orders, schedules in-house material transportation, assists with work orders and prepares DOT paperwork as required.
WHY IT’S IMPORTANT:
These individuals track all product flow and use their skills to keep production on track and assure that we meet customer commitments and product deliverables.
ESSENTIAL SKILLS AND ATTRIBUTES:
At minimum, a manufacturing expediter must possess a high school diploma or GED equivalent and forklift driving experience. They are even more successful in their position if they also have SAP and inventory experience, knowledge of the manufacturing environment and excellent communication skills.
WHAT MAKES THIS POSITION IN HIGH DEMAND?
This position ensures we uphold the commitments made to our customers so we are able to retain our excellent customer service and world-class production reputation.
HOW DO I LEARN MORE? lockheedmartinjobs.com
POWER THE FUTURE WITH
NOT JUST A JOB. For more than 40 years, our team in Arkansas has delivered important defense propulsion that helps protect our war ghters, our nation, and our allies.
INNOVATION. Camden is Aerojet Rocketdyne’s Solid Rocket Motor Center of Excellence, where our team produces 75,000 solid rocket motors a year to power critical defense systems.
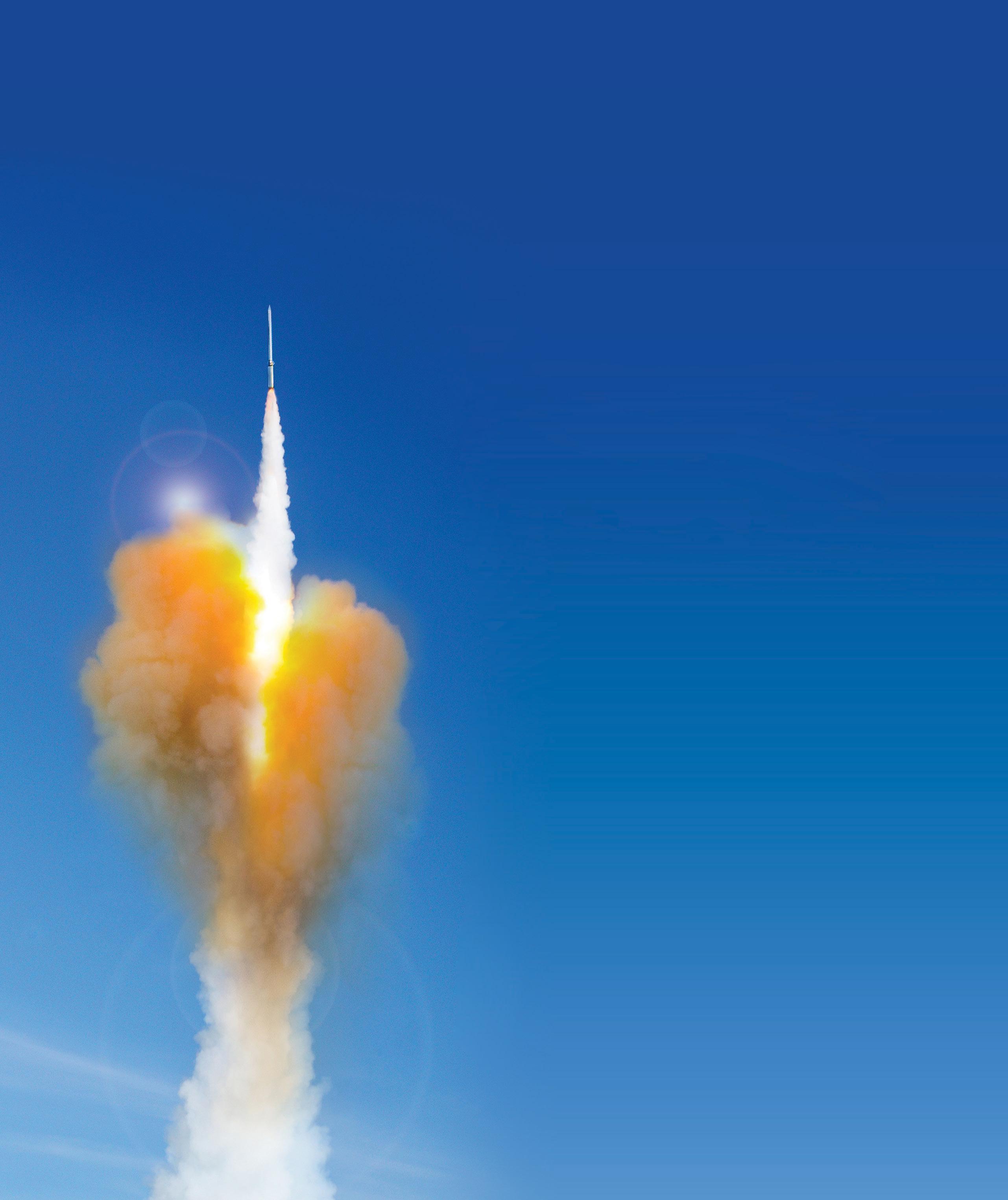
FLEXIBLE WORK SHIFTS. While employees generally work a 4/10 schedule, with Fridays off, alternate shifts are available.
COMMUNITY. Employees work together professionally and personally. Volunteer-led employee resource groups enhance a culture where everyone belongs.
COMPREHENSIVE BENEFITS. Highly competitive pay, employee stock program, 401k with match, paid vacation, tuition assistance, health and wellness programs and more.
GROWTH AND OPPORTUNITY. Our team has skyrocketed 70% over the past 7 years, and we continue to grow. Apply now at rocket.com / careers or scan QR code
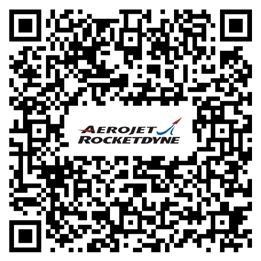
CyberLearn sets the bar for cybersecurity education in Arkansas
Looking to address a worker shortage statewide, the University of Arkansas at Little Rock has unveiled an innovative new cybersecurity curriculum and educational consortium. The program, called CyberLearn, will provide cutting-edge training in this rapidly growing field.
“We’ve put together a consortium of seven UA System schools, and in this consortium we’re sharing instructional resources,” said Dr. Erin Finzer, associate vice chancellor for academic affairs. “We’ve got a number of stackable certificate programs that range from six to 24 credit hours and these are all designed in partnership with our industry partners.”
The program rolled out in Fall 2022, offering students at each participating institution of higher learning the ability to work toward a certificate of proficiency in cybersecurity fundamentals. Additional certificates and degree programs will be added in spring 2023.
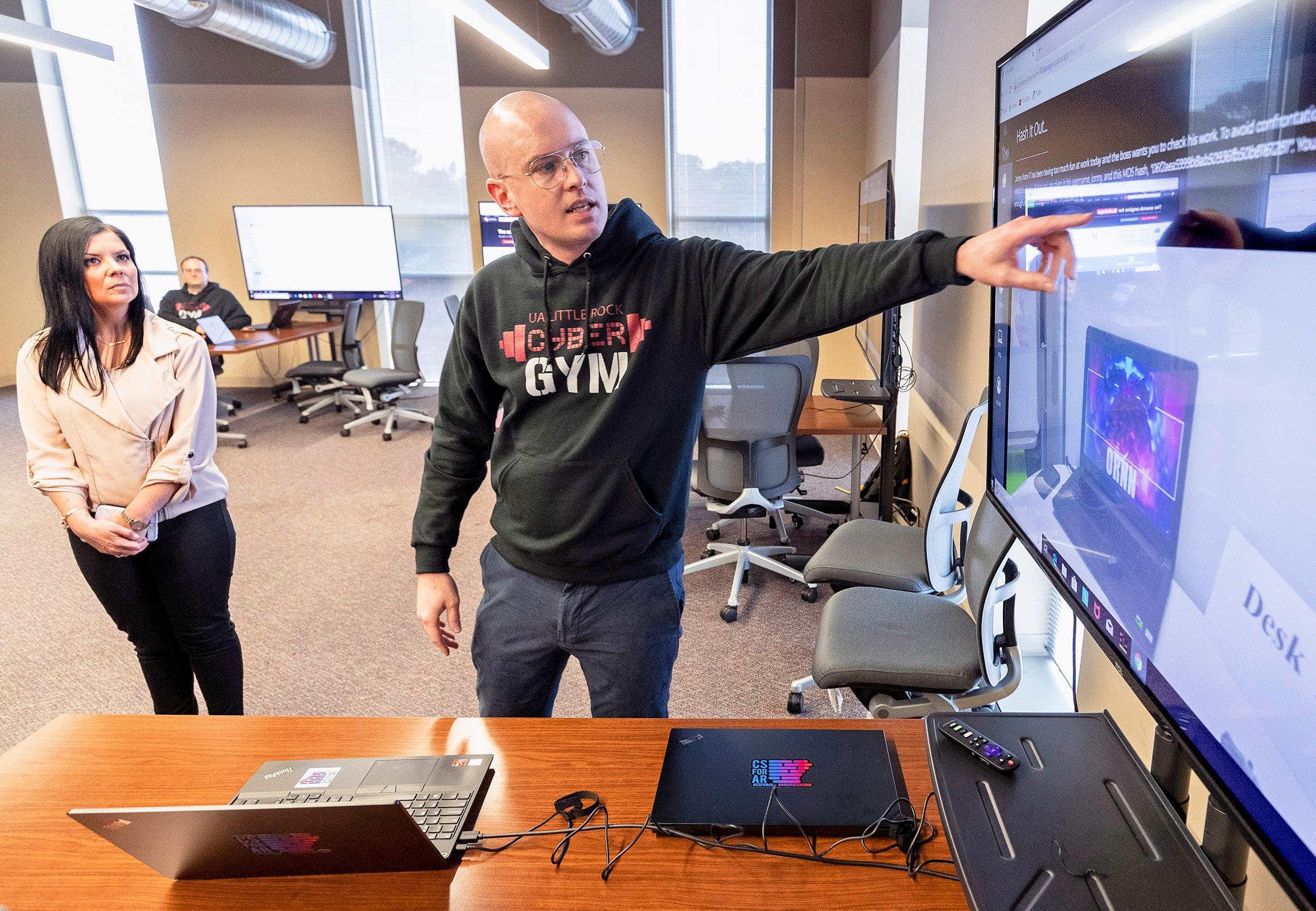
DID YOU KNOW?
Besides UA Little Rock, partner institutions in the consortium include UA Pine Bluff, UA-Pulaski Technical College, UA Cossatot, UA Hope-Texarkana, UACC Batesville and UACC Morrilton. The Forge Institute, the Arkansas Center for Data Sciences, and SmartResume are also collaborating on the initiative, which plans to roll out additional training modules starting next year.
CyberLearn comes at a time when the demand for people with this training is at an all-time high. According to The 2021 (ISC)² Cybersecurity Workforce Study, there are 2.7 million unfilled cybersecurity jobs worldwide and 467,000 open cyber jobs in the U.S. In Arkansas alone, there are nearly 3,100 cybersecurity vacancies, per UA Little Rock, part of a total of 20,000 IT-related unfilled jobs in The Natural State.
Meanwhile the problem of cybercrime continues to worsen. A recent survey of IT decisionmakers across eight countries by Center for Strategic and International Studies found 82% of
CONTINUED ON PAGE 28
Demand for skilled jobs is expected to grow faster than many white-collar jobs over the next several years. The Bureau of Labor Statistics forecasts plumbing jobs will grow 18% in 2028 compared to 2018; electrical jobs will grow 10% and HVACR jobs will be up 13% over that time period. All other industries combined are only expected to grow an average of 7% over the same decade.
Source: explorethetrade.org
DARION LAWS
Apprentice Lineman, Entergy
Hometown: Fayetteville
Age: 22
Years with Entergy: 1
BLUEPRINT: What made you want to work in utilities?
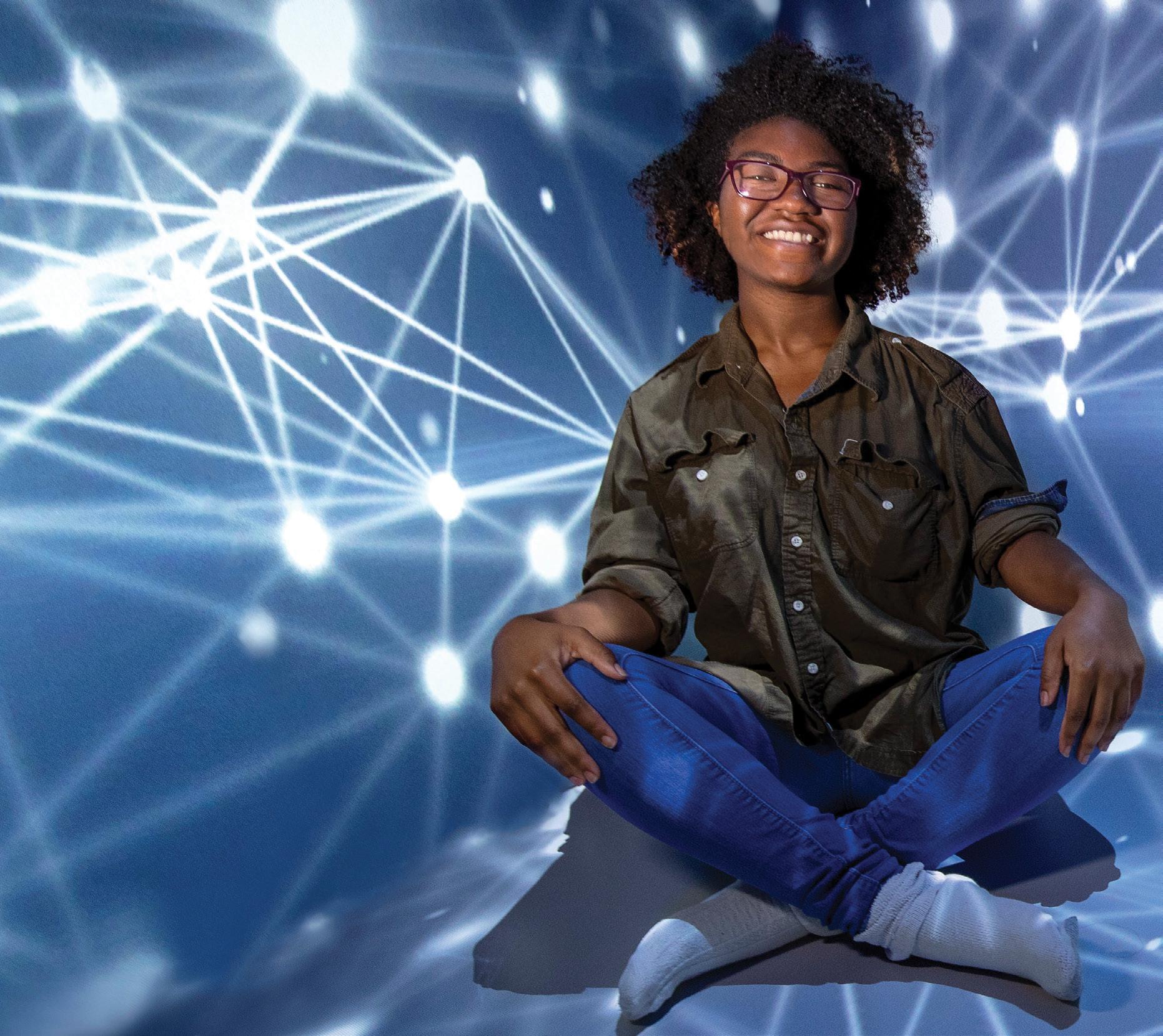
DARION LAWS: I’ve always seen lineworkers as being first responders to the community during a storm. I really enjoy helping others, and what we do really helps people in their time of need.
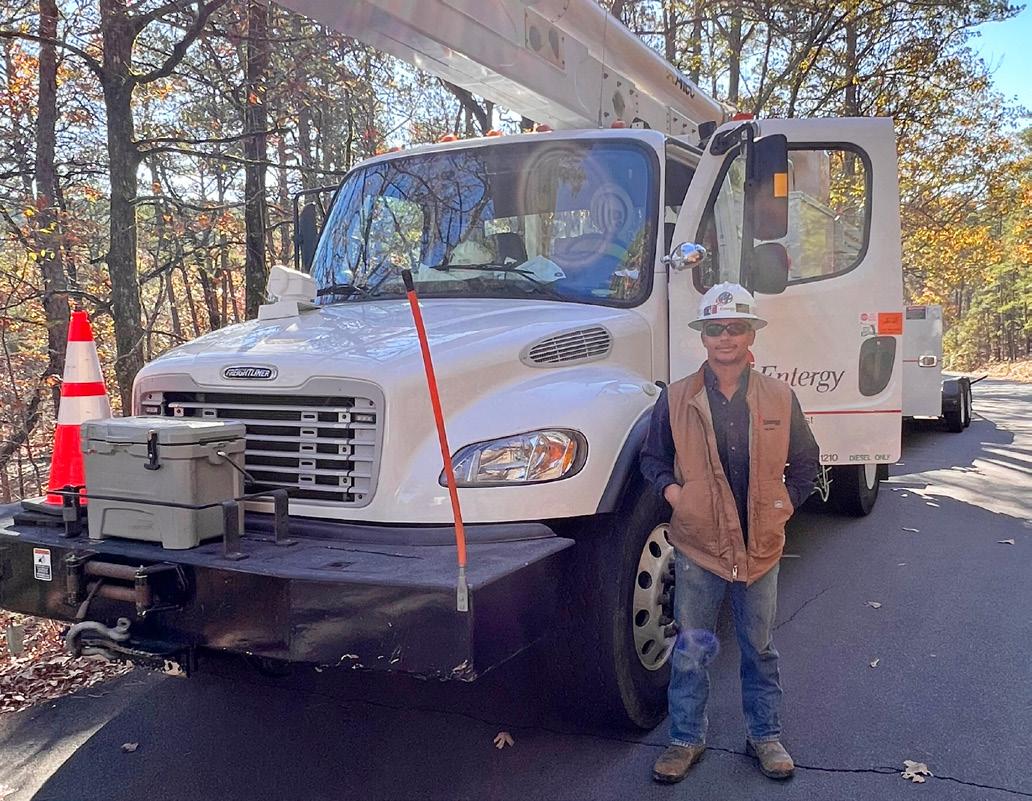
BP: How did you come into this job?
DL: I have a military background and Entergy Arkansas looks to hire veterans. I had a chance encounter with an Entergy employee at a car wash who talked about the brotherhood among lineworkers and he encouraged me to apply. Coming from the Marine Corps, that meant a lot, and it was true. There’s a brotherhood here, so this was a natural fit for me.
BP: Were you always good working with your hands growing up?
DL: I’ve always had a passion for learning about how different things work, and I consider myself a jack of all trades. I’ve completed a lot of on-the-job training, including building poles, working the bucket and hanging power lines and how to splice underground wires.
In Hot Springs, our crew does both underground and overhead lines, and we troubleshoot. My favorite things are hands-on stuff, figuring things out and climbing.
BP: This can be dangerous work; how have you learned to deal with that aspect of your job?
DL: It’s important in my job to learn leadership skills and how to teach. Helping newer apprentices — even teaching them what I’ve learned so far about paying attention to detail and safety — is critical. Anybody can make mistakes, so everyone is empowered to stop work if things don’t look right.
BP: You recently graduated as best overall performer in your Lineworkers Boot Camp class. How did that make you feel?
DL: It was humbling. These guys are like my family, and I learn something new every day. Working for Entergy Arkansas has come to be a true passion.
BP: If someone were reading this and weighing the possibility of following in your footsteps, what would you want that person to know?
DL: If you want to learn how to be a good human being — hard-working with a good work ethic, leadership, going above and beyond — and have a reliable job with great financial stability, definitely consider Entergy Arkansas.
CONTINUED FROM PAGE 26
employers report a shortage of cybersecurity skills, and 71% believe this talent gap causes direct and measurable damage to their organizations.
All of that adds up to robust career opportunities for people with the right skills. UA Little Rock reports entry-level salaries in cybersecurity can range from $40,000 to $130,000 nationally, depending on experience. The university also notes the average salary for cybersecurity jobs in Arkansas is $91,119, and the median starting salary for such jobs in Little Rock is $66,017.
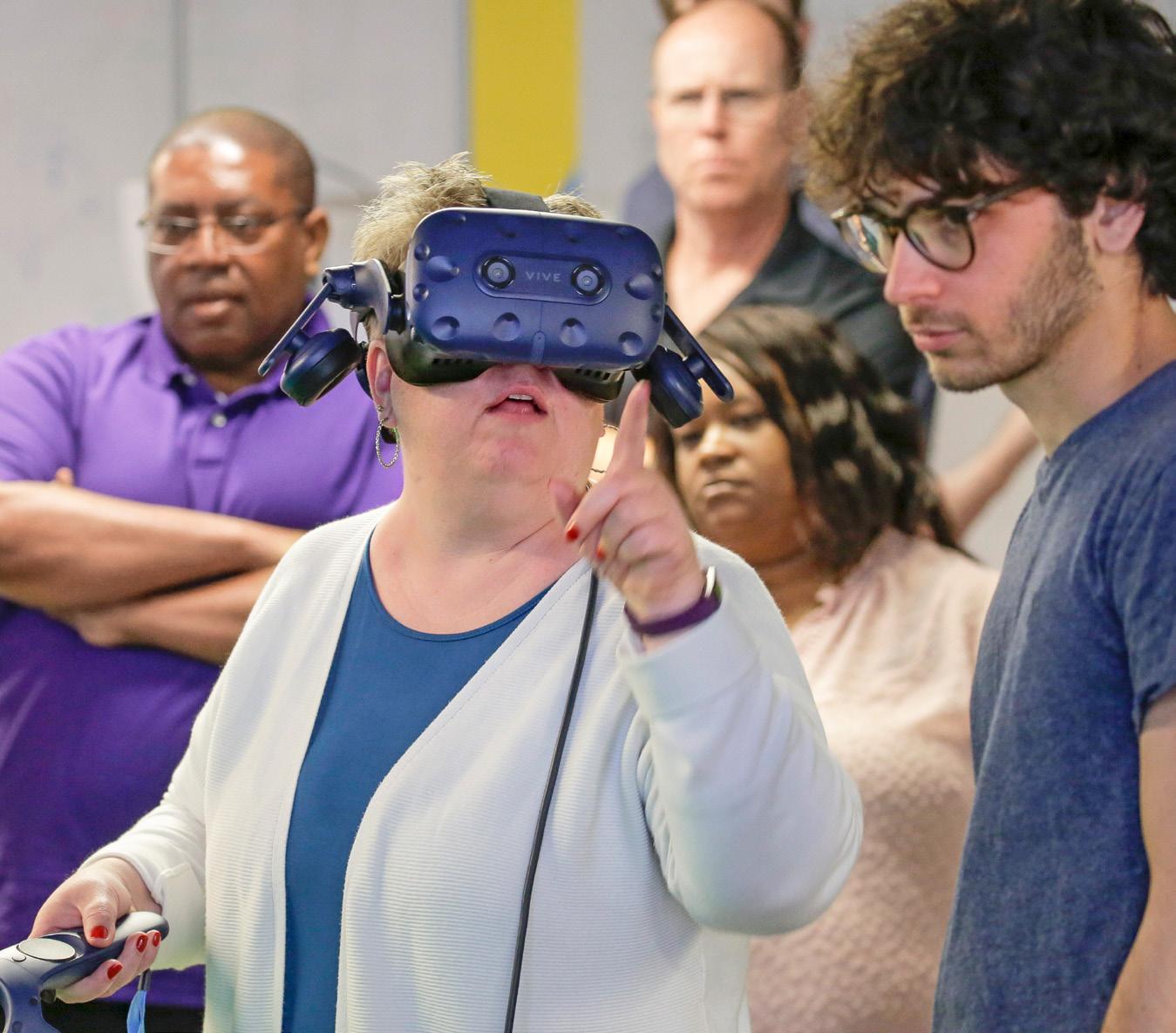
Finzer said as with all skilled careers, the technical side of the job is just one component of success.
“Our partners stress the need for workers with strong communication skills, critical thinking and problem-solving ability and curiosity to continue learning,” Finzer said. “They value individuals who come from academic disciplines and life experiences outside of computer science, individuals who bring the creative and critical thinking which lend themselves well to continuous learning in a rapidly evolving field.
“For this reason, the Cybersecurity Fundamentals Certificate of Proficiency was designed for learners of any background as a supportive entry into cybersecurity.”
For more information on the CyberLearn program, please visit cyberlearnarkansas.org.
WHAT I’VE LEARNED
LYNDSEY HALL
Pretreatment Sampling Specialist
Little Rock Water Reclamation Authority
Hometown: Toole, Utah
Age: 39
Years with LRWRA: 9
BLUEPRINT: What do you like most about your job?
LYNDSEY HALL: I feel very rewarded at the end of the day knowing that I’m doing my part for protecting the environment, working for the utility. The utility has been great as far as opportunities and continuing my education. The people are awesome and the benefits are great.
BP: What are some of the primary benefits of working here?
LH: One of the big benefits of the utility is a tuition reimbursement program. They will pay up to a certain dollar amount per year for you to get a degree or finish a degree. And they offer plenty of training hours or licensing programs to obtain a wastewater license.
BP: How did you find this career?
LH: I was always interested in science, so I knew I wanted to be in a field like that. I earned my bachelor’s in environmental management and I got an opportunity to get hired on as a lab tech at the Fourche Creek location. That’s how I got started here.

Growing up in Utah, water was very scarce out there. I knew I always wanted to do something to help with that, so when that opportunity arose, I jumped on it.
BP: What soft skills are important there?
LH: Communication is a big one. We monitor the industrial users that discharge into our treatment plant. Communication is key as far as keeping up with the industry and communicating with operations to let them know what could be coming into the plant that could cause a problem. Teamwork is another one. There’s three people in the pretreat area which I work in, and teamwork is key for these roles. One person could be busy doing something else while you might need a member of your team to go look into someone doing some discharging.
BP: What would you tell a young person still looking for a career path about working for LRWRA?
LH: You can go as far as you want to in the water and wastewater fields. As a young person, you don’t really think about the impact of not having any water one day. Knowing that we all need water, having a career in this field means being almost guaranteed to always have a job.
You’ve got to have a good work ethic. You’ve got to want to come to work every day. You’ve got to find something that makes you happy, that you’re willing to wake up and go do because if you don’t enjoy your job, you’re not going to want to give it your all.
— Jarred Martinez, Little Rock Water Reclamation AuthorityUA Little Rock's CyberLearn course employs various IT tools.
Guide to Apprenticeship Programs for Technical Careers
ELECTRICIAN
AEAP INC. (ANDERSON ELECTRIC)
Pine Bluff 870-534-2672
ARKANSAS COLLEGE OF ELECTRICITY
Rogers 479-636-2633
ARKANSAS NORTHEASTERN COLLEGE
Blytheville 870-838-2934
ASU-HEBER SPRINGS ELECTRICAL PROGRAM
Heber Springs 501-352-1384
B&D ELECTRICAL
Stamps 870-533-4408
BLACK RIVER ELECTRICAL
Paragould 870-239-0969
CABOT ELECTRICAL SCHOOL
Conway 501-796-8925
CONWAY AREA APPRENTICESHIP
Conway 501-450-4888
EL DORADO ELECTRICAL APPRENTICESHIP JATC
El Dorado 870-639-3781
FIVE RIVERS PLUMBING/ POCAHONTAS ELECTRICAL
Pocahontas 870-248-4180
FORT SMITH ELECTRICAL JATC
Fort Smith 479-709-9604
FULMER ELECTRICAL TRAINING
Conway 501-796-8925
IBEW/JATC
Jonesboro 870-932-2114
LITTLE ROCK ELECTRICAL JATC
Little Rock 501-565-0768
MCGEHEE ELECTRICAL
Elkins 870-222-3808
MCGREW SERVICE CO.
Hot Springs 501-760-3440
NATIONAL PARK COLLEGE/QTI ELECTRICAL APPRENTICESHIP
Hot Springs 501-767-9314
OTC ELECTRICAL
Malvern 501-337-5000
RUSSELLVILLE APPRENTICESHIP – ELECTRIC
Russellville 479-857-8105
SOUTH ARKANSAS COMMUNITY COLLEGE/ ELECTRICAL PROGRAM
El Dorado 870-864-7193
UAM COLLEGE OF TECHNOLOGY
Crossett 870-364-6414
VILONIA ELECTRICAL SCHOOL
Conway 501-796-8925
PLUMBER
ASU-HEBER SPRINGS PLUMBING PROGRAM
Heber Springs 501-250-5788
CENTRAL ARKANSAS APPRENTICESHIP TRAINING COMMITTEE
Little Rock 501-231-6471
CONWAY AREA APPRENTICESHIP Conway 501-450-4888
FIVE RIVERS PLUMBING/ POCAHONTAS ELECTRICAL
Pocahontas 870-248-4180
GARLAND COUNTY PLUMBING
Hot Springs 501-623-4562
JONESBORO AREA PLUMBING ASSOCIATION (JAPA)
Jonesboro 870-974-1205
NCA PLUMBING/TWIN LAKES PLUMBING INC.
Mountain Home 870-425-6298
NORTHWEST TECHNICAL INSTITUTE/NWA PLUMBING SCHOOL
Springdale 479-790-4623
NWACC - WESTERN ARKANSAS APPRENTICESHIP
Bentonville 479-986-4084
PLUMBERS & PIPEFITTERS APPRENTICESHIP TRAINING OF AR
Little Rock 501-562-4482
RICH MOUNTAIN COMMUNITY COLLEGE/PLUMBING PROGRAM
Mena 479-394-7622
SOUTH ARKANSAS COMMUNITY COLLEGE/ PLUMBING PROGRAM
El Dorado 870-862-8131
SOUTHEAST ARKANSAS PLUMBING/ ROGERS PLUMBING
Monticello 870-793-5253
WHITE RIVER PLUMBING/BINGHAM ENTERPRISES
Sulphur Rock 870-793-5253
INDUSTRIAL & CONSTRUCTION
ARKANSAS CONSTRUCTION EDUCATION FOUNDATION (ACEF)
Little Rock 501-372-1590
ASSOCIATED GENERAL CONTRACTORS (AGC)
Little Rock 501-375-4436
NABHOLZ CONSTRUCTION CORP.
Conway 501-505-5800
SHEET METAL
ARKANSAS SHEET METAL WORKS JATC
Little Rock 501-372-5150
JATC OF ARKANSAS
Little Rock 501-372-5150
PAINTER
INTERNATIONAL UNION PAINTERS AND ALLIED TRADES LOCAL 424
Little Rock 501-353-2957
NATIONAL APPRENTICESHIP TRAINING FOUNDATION
Arkadelphia 870-246-0320
UA FACILITIES MANAGEMENT
Fayetteville 479-575-5470
CENTRAL ARKANSAS BUILDING & CONSTRUCTION TRADES COUNCIL
Heat and Frost Insulators
Local 10 206 Ave Two SE Atkins, AR 72823
Jeramy McCoy, Business Agent
(P) 479-307-1701
(F) 479-307-1702
(M) 479-641-0772
awl10@insulators.org
International Brotherhood of Boilermakers Union
Local 69
4515 W. 61st St. Little Rock, AR 72209
Rodney Allison, Business Manager
(P) 501-565-0059
(F) 501-556-0112
bmlocal69@sbcglobal.net boilermakers.org
Bricklayers and Allied Craftworkers Union
Local 5 OK/AR
212 NE 27th St. Oklahoma City, OK 73105
Ed Navarro, President
(P) 800-579-9555
(F) 405-528-0165
ed@baclocal5.com baclocal5.com
Carpenters Union
Local 690
3920 Wall St. Little Rock, AR 72209
William White
(P) 501-568-2500
(F) 501-568-2522
carpenters690@prodigy.net ubclocal690.com
Carpenters Union Local 1836
1407 S. Knoxville Ave. Russellville, AR 72801
(P) 479-968-1724
(F) 479-967-5878
Dewayne Young, Business Representative
Jeremy Hughes, Business Representative dwyoung2002@yahoo.com
Jhughes@cscouncil.net centralS.carpenters.org
International Brotherhood of Electrical Workers Local 295
7320 S. University Ave. Little Rock, AR 72209
Will French, Business Manager
(W) 501-562-2244
(M) 501-291-9949
Ibew295.org
International Brotherhood of Electrical Workers
Local 1516
P.O. Box 577 Jonesboro, AR 72403
Kirk Douglas
(P) 870-932-2114
(F) 870-932-6707
ibewlu1516@sbcglobal.net
Elevator Constructors Union
Local 79
P.O. Box 2081
Little Rock, AR 72203
Mike Campbell, Business Manager
(P) 501-944-6970
(F) 501-372-2172
iuec-local79@sbcglobal.net
Iron Workers Union Local 321
1315 W. Second St. Little Rock, AR 72201
Johnny Wilson, Business Manager
(P) 501-374-3705
(M) 501-730-2607
Laborers International Union of North America (LIUNA)
Local 360
5 Colonial Square Clarksville, AR 72830
Tanif Crotts, Business Manager
(P) 479-754-1015
(F) 479-647-3909
tanif.c@liunalocal360.com
International Union Operating Engineers Local 624
202 Katie St. Richland, MS 39218
Brett Daniels, Business Agent
(P) 501-422-8109
brett@iuoe624.com
International Union of Painters & Allied Trades
District Council 80/Local 424
10112 Chicot Road, Suite 218
Little Rock, AR 72209
James McAlister, Business Representative
(P) 501-353-2957
(M) 501-772-6885
jmacftidc80@gmail.com www.iupatdc80.org
Plasterers & Cement Masons Union
Local 908
815 Enterprise
Cape Girardeau, MO 63701
Guy “Tom” Schwab, Business Manager
(P) 573-334-2729
(F) 573-334-5451
op908@clas.net
Plumbers & Pipefitters Union
Local 55
1223 W. Markham
Little Rock, AR 72201
Ricky Jeu, Business Manager
(P) 501-374-4943
(M) 501-529-3131
SMART Sheet Metal Union
Local 36
415 W. 12th St.
Little Rock, AR 72202
Danny Graves, Business Manager
(P) 501-372-5150
(M) 501-326-4777
smw361@sbcglobaI.net
www.smart-local.org/smart-sheet-metal-local-36
UA Local 669
Sprinkler Fitters
P.O. Box 400
Abita Springs, LA 70420
Tony Cacioppo, Business Representative
(P) 985-809-9788
(F) 985-809-7802
cacioppo.669@att.net
sprinklerfitters669.org
United Union of Roofers, Waterproofers & Allied Workers
Local 20
6301 Rockhill Road, No. 420
Kansas City, MO 64131
Jim Hadel, Business Representative
(P) 816-313-9420
(F) 816-313-9424
rooferslocal20.com
UBC Millwrights
Local 216
1407 Knoxville Ave.
Russellville, AR 72802
Matthew Nowling, Business Representative
(P) 479-967-0639
HEAVY METAL
HIGH INCOME CAREERS IN THE NORTHEAST ARKANSAS STEEL INDUSTRY
LEARN THE HOT JOBS IN DEMAND
HOW TO PREPARE FOR A CAREER IN THE STEEL INDUSTRY
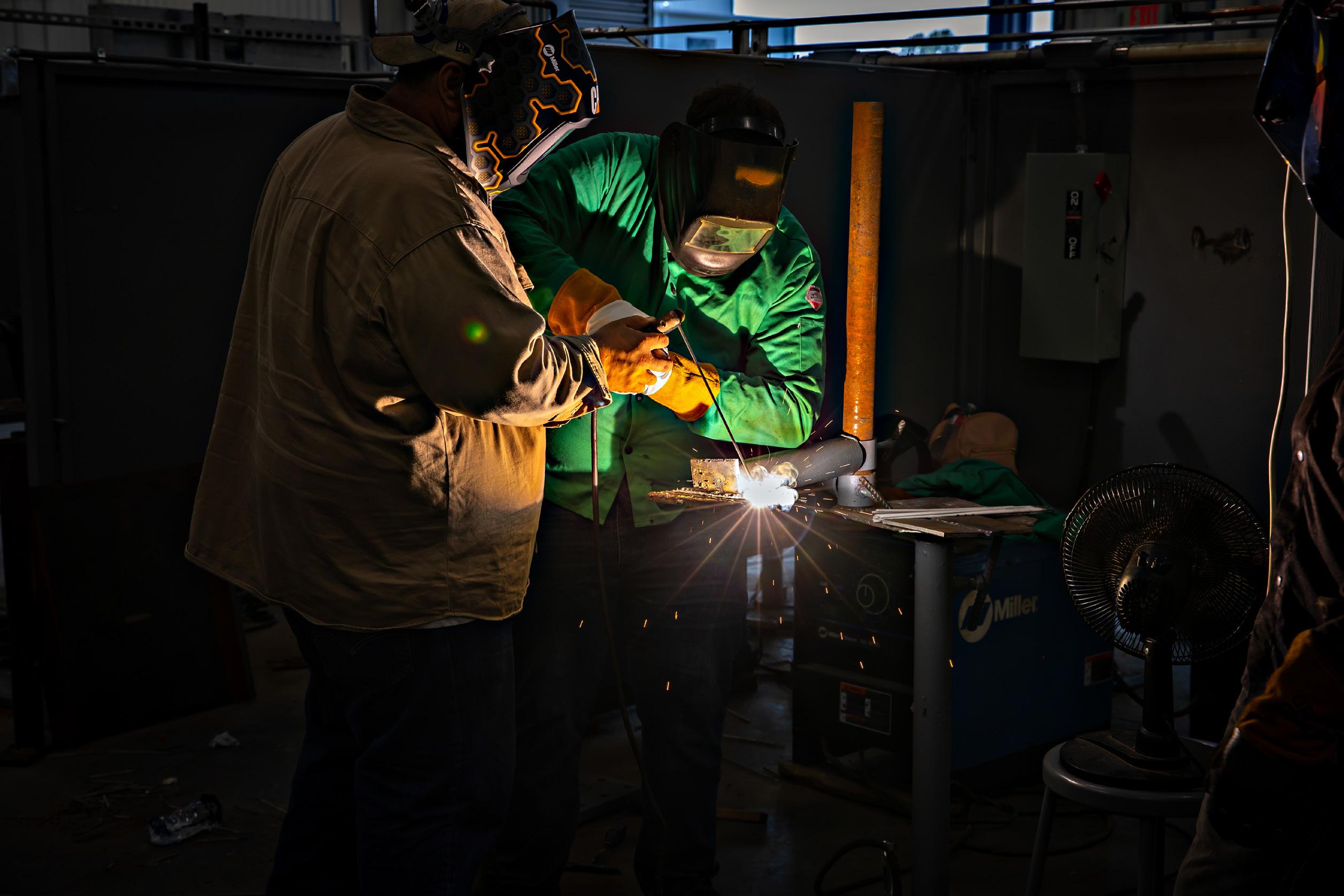
SPONSORED BY MISSISSIPPI COUNTY STEEL INDUSTRY
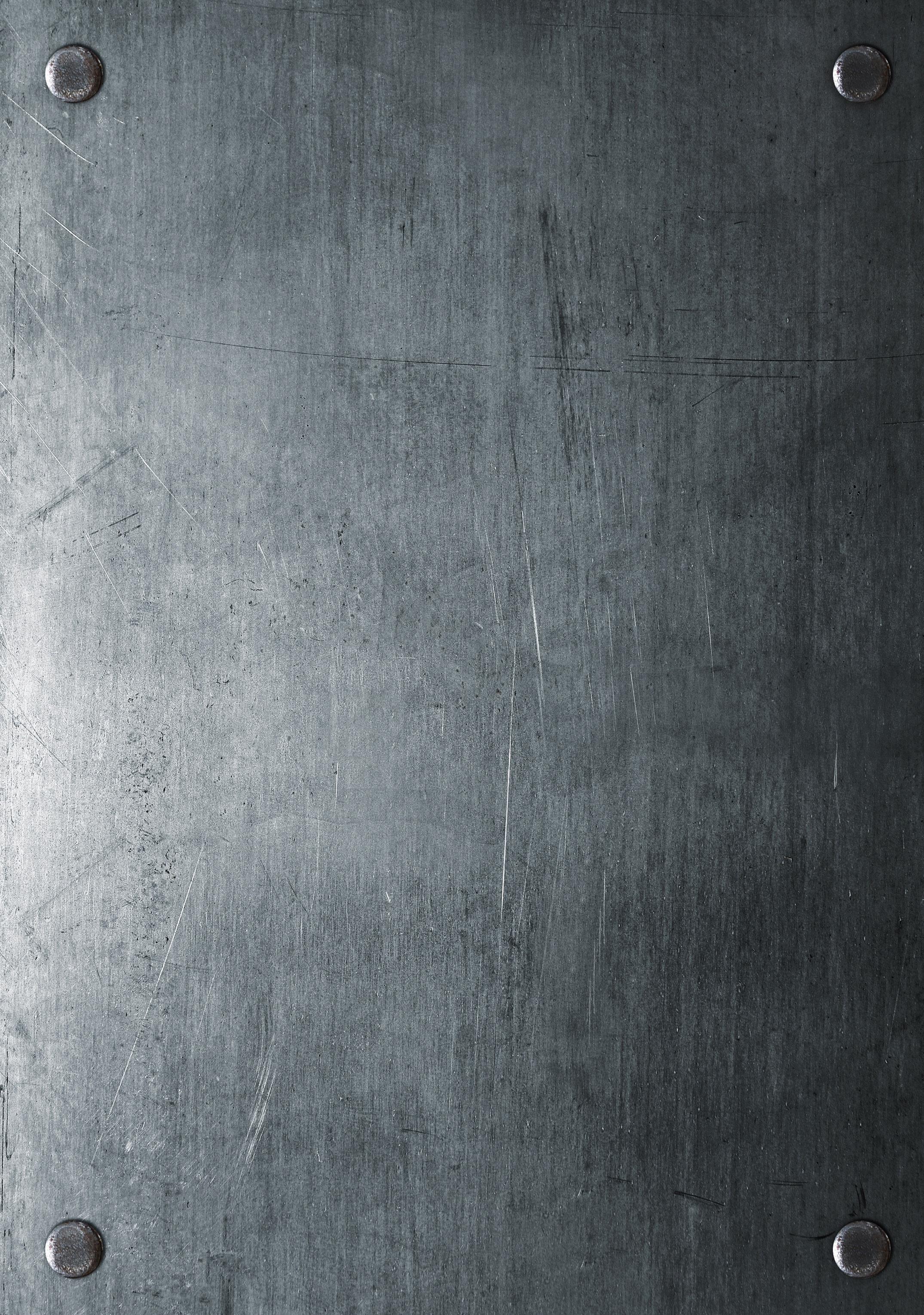
Boom Town
Blytheville Sets the Pace in Arkansas, Thanks to Steel
There was a time when America’s steel industry ruled the industrialized world as the unquestioned leader in steel production. And while the industry took its lumps through the 1970s and 1980s, resulting in the so-called Rust Belt across the upper Midwest, a shiny new chapter is bringing the luster back to the U.S. steel industry. And this time, it’s happening in Arkansas.
When much of the rest of the nation’s steel industry was grinding to a halt, visionary entrepreneurs were quietly laying the foundation in northeast Arkansas for what is today considered one of the most important steel centers in the entire country. And with this new growth has come thousands of jobs paying top dollar to workers in any number of skilled positions.
Arkansas Northeastern College has been an integral part of the steel industry’s success. Not only has the school invested heavily in cutting-edge equipment and instruction, it’s been banging the drum for the opportunities that exist in the trades be it in construction or manufacturing, especially steel.
“Our steel technology program has a couple different pathways,” said Dr. Jamie Frakes, associate vice president for workforce development and allied technologies. “When we look at steel industry technology, you can study the electrical side of the business and be heavily involved in that or you can be involved in the advanced manufacturing piece, the production side. Our students are literally learning the science of manufacturing production and everything that goes into producing steel.
“I think another important piece to the steel industry technology credentials that we offer is we also have an internship program that has been highly successful in recent years. That’s another opportunity for us to immerse our students in that environment while they’re earning
their credentials and attending class. That’s a model that, quite frankly, is a best practice for us. We’ve been doing that for some time now and we’ve become a model for other institutions.”
Steel first came to this part of the state in 1987 when Nucor-Yamato Steel built its first mill. That plant was followed by Nucor Steel Arkansas in 1992, which was expanded in 1998. The mills specialize in various types of steel used in production of automobiles, appliances, agricultural equipment and other industries.
In 2017, Big River Steel opened, converting scrap to flat-rolled steel. Additional ventures and expansions by Atlas Tube, Zekelman Industries and Majestic Steel all kept expanding the industry and attracting dozens of companies providing services to the bigger mills. Finally, in January of this year, U.S. Steel announced it would be entering the area, bringing with it 900 jobs and a $3 billion mill loaded to the brim with the latest in technology.

These expansions have upped demand for skilled workers in all fields exponentially, Frakes said.
“At Arkansas Northeastern College, we have a technical center which offers a number of programs to high school students, and those high school students get the opportunity to study computer information systems, aviation, industrial technology, office management and industrial technology, along with health sciences courses,” he said.
“We market those programs to our area high schools, letting them know of these options. The partnerships we have with our high schools are just phenomenal as far as opening doors for these students. Getting the word out earlier is important to our efforts and that’s where we’re seeing a lot of better numbers in that regard. There’s a ways to go, but we are getting better in meeting the demand.”
HOT JOBS!
PIPE FITTER
Company: The Systems Group
Starting Salary: Up to $29/hour
WHAT DOES THE JOB DO?
Plans the installation of piping system components, cuts pipe to lengths as determined by isometric drawings using a portable bandsaw, cutting torch and pipe cutting machine.
Threads pipe, mounts pipe hangers and brackets on walls and ceilings to hold the pipe, assembles and installs pipes and pipe fittings. Observes and complies with all safety, project rules and company policies and procedures.
WHY IT’S IMPORTANT:
Pipe fitting is important because pipe fitters build and maintain complex piping systems in refineries, energy plants and steel mills. The piping system carries a range of substances such as steam, oil and chemicals.
ESSENTIAL SKILLS AND ATTRIBUTES:
Pipe fitters need to be able to read blueprints, use advanced math and be able to operate industrial tools safely.
WHAT MAKES THIS POSITION IN HIGH DEMAND?
Pipe fitters are in demand because of the lack of training available and little public knowledge about this craft. There are very few training programs for pipe fitting in Arkansas technical colleges and schools.
HOW DO I LEARN MORE? www.tsg.bz
PIPE WELDER
Company: The Systems Group
Starting Salary: Up to $29/hour
WHAT DOES THE JOB DO?
Weld metal piping systems composed of pipe and tube as specified in blueprints and isometric drawings, follow welding procedures to ensure a quality weld.
WHY IT’S IMPORTANT:
Metal piping is used in almost every factory, industrial plant and shipyard in the country. Because piping is used in so many industries, pipe welders are vital to the building and maintaining of manufacturing facilities that support our way of life.
ESSENTIAL SKILLS AND ATTRIBUTES:
Experience in the use of various types of electric arc welding equipment, good hand-eye coordination, attention to detail and the ability to read a tape measure. A good attitude, patience and a willingness to work are important.
WHAT MAKES THIS POSITION IN HIGH DEMAND?
Pipe welding calls for a high degree of technical skill, manual dexterity and strong hand-eye coordination. The training to become a pipe welder is extensive.
HOW DO I LEARN MORE? www.tsg.bz
GAYLON NICKERSON
Auto Buckler, Tenaris
Hometown: Osceola
Age: 53
Tenure with Tenaris: 7 months
BLUEPRINT: What does your job entail at Tenaris?
GAYLON NICKERSON: The line I work on, we put all the markings and couplings on the pipe, and we do the threading. And that’s the beginning of the line, the threading. I’ve been doing that for about three months.
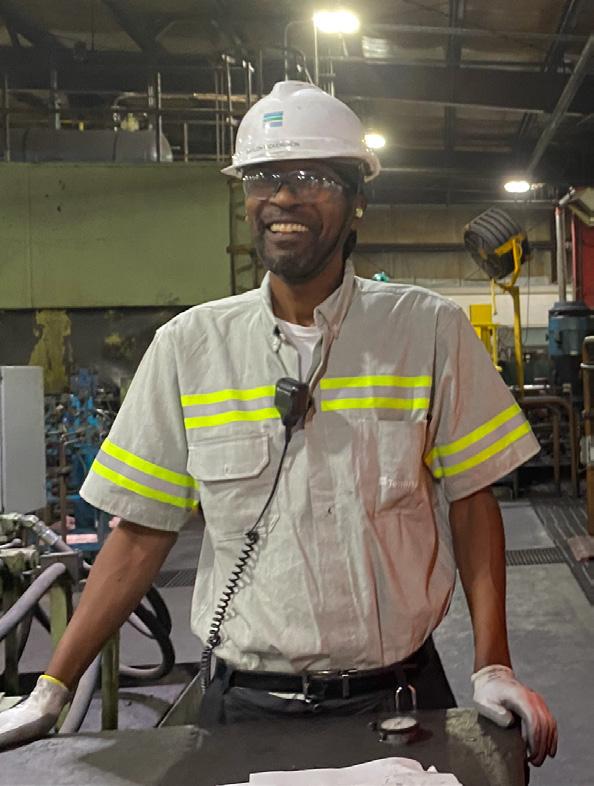
BP: What got you interested in joining Tenaris? Did you have family members working there?
GN: It was a career change. I didn’t know anybody who worked here personally, but I’d heard about it. When there’s a strong company in town, a lot of people know about it. There was a lot of talk about Tenaris being a good place to work.
BP: What emphasis is put on the safety program there?
GN: We have a safety meeting every morning before we start work. Every safety meeting always starts off by asking if anybody has anything they want to say about something they experienced on the production floor. I appreciate having the opportunity to give that input. There are also procedure books at all the workstations; if you follow the procedures, you can’t go wrong.
If something does happen, Tenaris has a program where they look into the incident thoroughly as far as what happened, why it happened, how it happened and what could have been done differently. They record it and if it’s not already in the safety manual, they will make changes right away to make the working environment better.
BP: What do you like best about working at Tenaris?
GN: I am a former NBA player, and our team is like a basketball team; you depend on your teammates. Your success relies on how well you work with and help your teammates. The better you are as a team, the more successful you will be.
That’s the same thing with Tenaris. Everybody has the same goal and that’s to put out good quality pipe. For that to happen, everybody has to do what they’re supposed to do. It’s a great team atmosphere. We work as a team and that makes you feel safe. It’s a good place to work.
BP: What would you tell high schoolers about working at Tenaris, and what would you tell them about what it takes to be successful?
GN: I would tell the kids that it’s a great career. I’d also tell them to prepare by learning some math. Pick up some kind of mechanics course, auto mechanics or some kind of mechanical work. Do that, you’ll be great for Tenaris.
DUSTIN DICKENS
Base Maintenance Group Supervisor, Tenaris
Hometown: Campbell, MO
Age: 25
Years with Tenaris: 6
BLUEPRINT: You are an electrical worker by trade, how did you train for that job?
DUSTIN DICKENS: You do four years on the job and then four years in a trade school where it’s one day a week. Then you have to have so many on-the-job hours. Two years of that training was at my previous job, an industrial contracting company. Those two years carried over when I came to Tenaris.
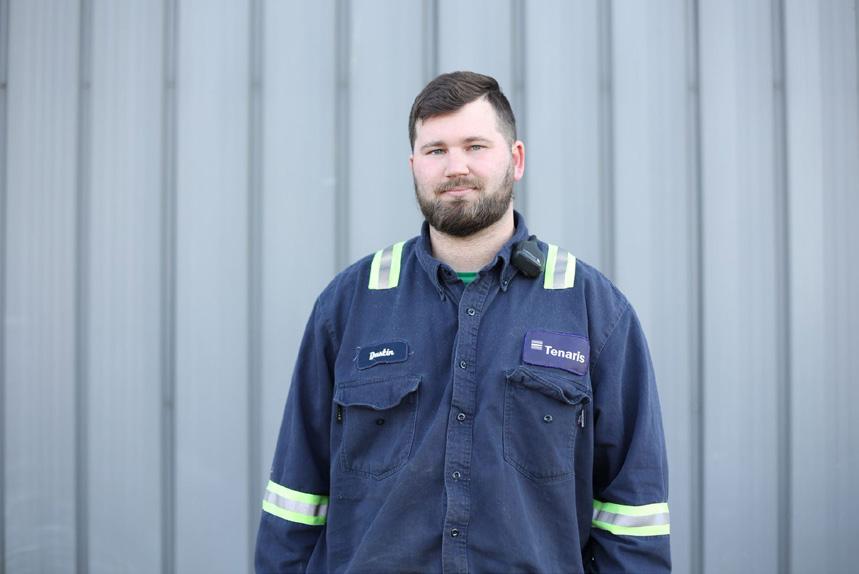
I’m now a journeyman electrician and I’m waiting on my affidavit to test as a master electrician.
BP: How did you decide on this particular career path?
DD: Almost everybody in my family has some sort of skilled trade. I have people in my family who are roofers, construction workers, electricians. I knew this type of work was what I wanted to do through working with my family and seeing the kind of benefits they saw from it.
BP: Do you typically work by yourself on issues or are you typically part of a team?
DD: There’s hardly ever a time when you don’t have a team with you out here. Primarily I’m with a group of six guys. We have production goals we’re supposed to meet, we have preventative maintenance activities we do where we go around and look at the equipment, talk to operators, look at possible downtimes we’ve had and look for solutions to fix them.
BP: What does your work week look like?
DD: It’s five days a week, minimum 10 hours a day. Normally it’s 50 hours but if the line’s down, I stay until it’s fixed. My set shift is 7 a.m. to 5 p.m., Monday through Friday. But, of course, I can get called in throughout the night, as needed.
BP: If you could talk to a roomful of young people about the things it takes to be successful in this job, besides the technical skills, what would you say is most important?
DD: I think just dedication. I think anybody can learn the job, it’s just the dedication and willingness to learn. Understanding that you are not above doing anything, that’s the biggest thing. You may think that you understand something, but when somebody else has a different point of view, that’s not necessarily wrong, it’s just a different way of looking at it. Being able to take that into account and learn together is the mark of a really great employee.
LANA SMITH
HVAC Student, Arkansas Northeastern College
Hometown: Blytheville
Age: 41
BLUEPRINT: What inspired you to go back to school?
LANA SMITH: I have been in or around the HVAC industry for the past 16 years. Never in a technical capacity, always clerical or management. Currently I am the office manager for a national HVAC manufacturing company in Blytheville. The company is rapidly expanding and we’re taking on more manufacturing from our home office, which is in Europe.

With that increase in manufacturing brings an increase in employees both skilled in HVAC as well as manufacturing. For me, if I’m going to operate a manufacturing facility, it was important for me to understand what my employees’ job duties are.
BP: So, the goal is not necessarily to start doing installs, but to understand the process and identify how to maintain quality control for employees and customers, right?
LS: Absolutely. There are times that I’ve gone out to the steel mills here in Mississippi County and I’ve gone out to see areas where HVAC systems are needed. I was there just to observe at that time, but I absolutely intend to take the knowledge that I get from this course. I intend to use that to go to our customer sites and be knowledgeable while I’m there of what I’m seeing and what their needs are.
BP: What technical skills did you bring into the educational program? LS: Prior to me deciding to do this, my technical background was very limited. We do manufacture here in our facility, so I don’t spend 100% of my time in my office. I am out in the warehouse, I am out on the floor. I fill parts orders for our company. So, I’m aware of what components the equipment takes.
Prior to taking this course, I also had a little knowledge on how an HVAC system operates, how it works. But as far as being able to go out and put my hands on a piece of equipment and diagnose it, I had no prior knowledge.
BP: What’s the job market like for someone who graduates from the program you’re currently in?
LS: The job market is very lucrative at this time. For a while now, the trade industries have kind of been shunned or pushed aside so everyone who’s currently in the industry is getting older. They’re retiring and we’re having trouble finding new technicians because we’re just not getting enough interest in the trade industries. Right now in the trade industries, for HVAC especially, the market for jobs is just wide open.
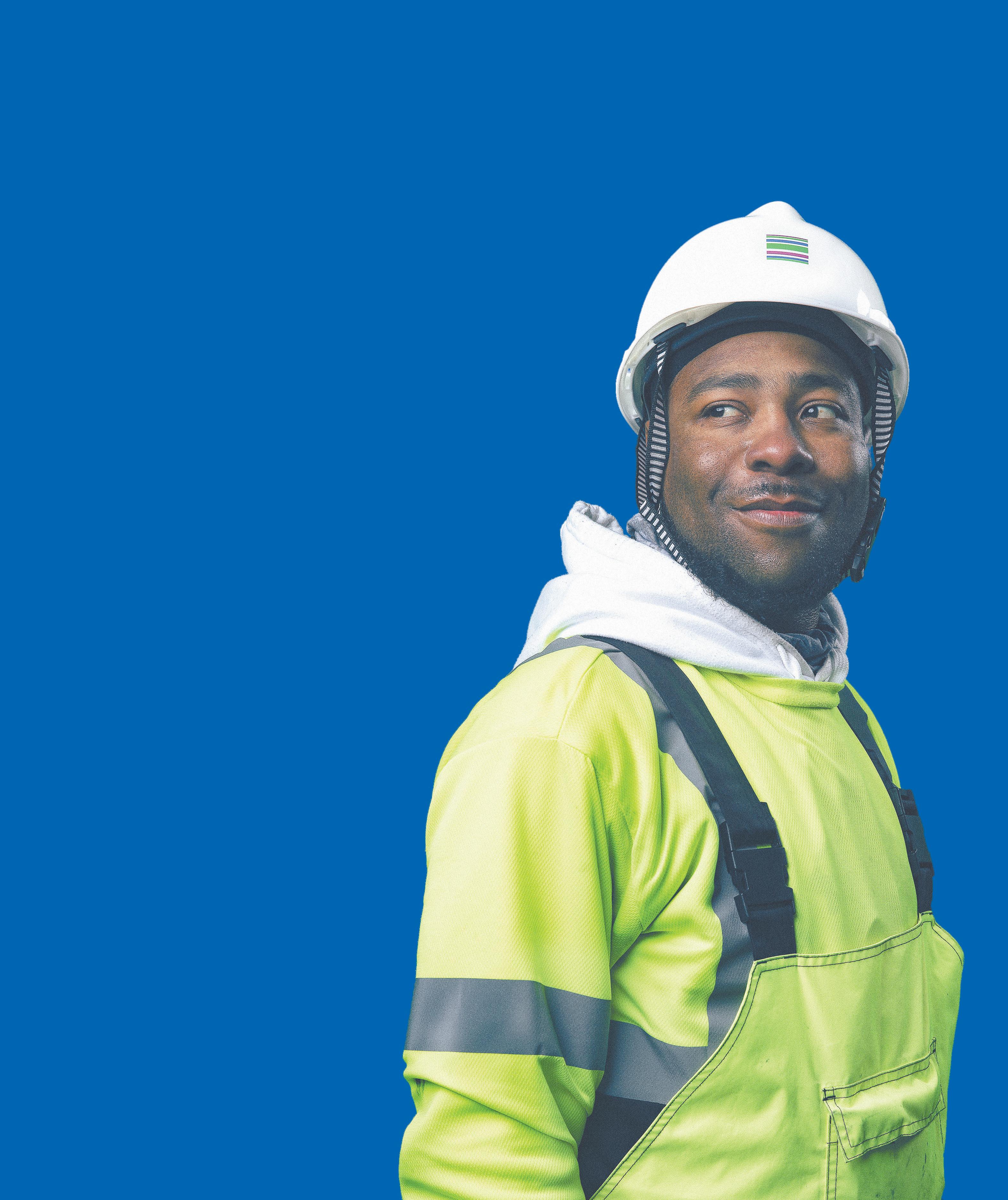
Student, aviation program
Arkansas Northeastern College
Hometown: Clinton
Age: 19
BLUEPRINT: What’s the job market like for a graduate of this program?
SAM APPLEBY: I’m actually employed right now, at age 19, by Midcontinent Aviation up in Hayti, Missouri, which is just 20 miles up the interstate from the college. What I do from 8 a.m. to 3 p.m. is I work on airplanes. I’m slotted to take over the body shop within a year or two.
BP: How did you get interested in this career field?
SA: I got into repairing vehicles, and later airplanes, by helping my grandpa keep his farm truck running. It was a 1978 Dodge and it always had issues. I got into aviation because my grandma, aunt and my other grandfather all worked in aviation maintenance. My mom’s dad was in the Air Force for aviation maintenance; when he was about my age, he was given the option of either going to jail or join the Air Force, so he joined the Air Force and spent 22 years being a C-130 mechanic. My dad’s mom and his sister both worked for Falcon Jet in Little Rock in the late 1990s and early 2000s. Grandma worked quality control and I’d been to work with her a couple times to see what it was like.
BP: What classes or experience in high school helped prepare you for this course of study in college?
SA: At my high school, and most high schools in Mississippi County, you have the ability to go to ANC on the high school side and take certain trade classes like welding, criminal justice, construction and aviation maintenance.
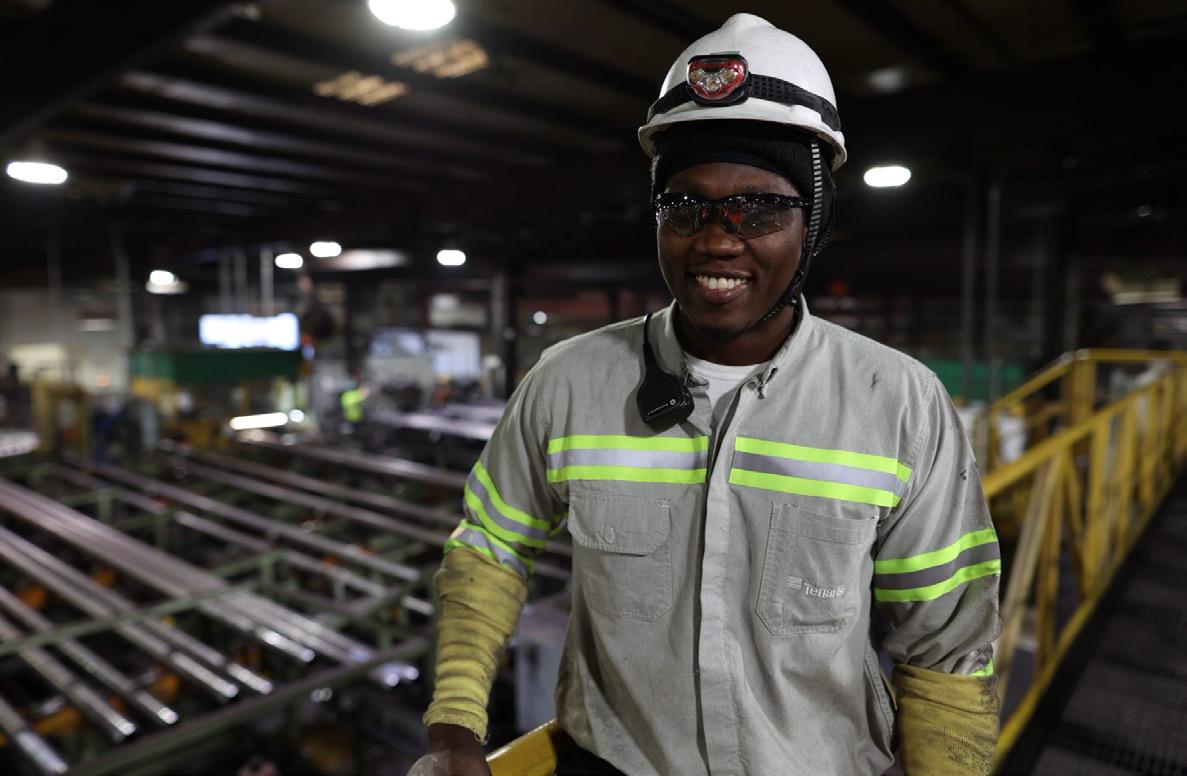
BP: Are there other classes high schoolers can take that will help them get a leg up on their college coursework?
SA: Take ag classes or shop classes; anything dealing with maintenance or motors or bodywork or sheet metal will get you into the routine of what I currently do every day. For anybody who’s concerned about their skills background, most personal airplanes are really just redesigned car motors put on a stainless steel chassis and wrapped in aluminum. There’s really not much difference between a car motor and an aviation motor until you get into jets and turboprops. Plus, if you can do body work on a car, you can do body work on an airplane. It’s not very different at all.
FERRIEL HARVEY
Team Leader PMC, Tenaris
Hometown: Blytheville
Age: 45
Years with Tenaris: 21
BLUEPRINT: Describe the personal growth you’ve experienced working for Tenaris.
FERRIEL HARVEY: The biggest thing that has changed over the years, I would say, is being open-minded and being patient. In the beginning, I really didn’t have a lot of patience. I felt like things weren’t coming fast enough and, on a few occasions, I almost wanted to quit.
It was a few guys who really took me under their wing and really coached me up. That allowed me to see things a lot differently. I began to understand every job is important no matter if you’re at the bottom entry level or the top as a supervisor or general manager. Every job is important.
BP: How did you wind up working here?
FH: I didn’t graduate high school, actually. I went to the 12th grade, but I got into some trouble and it caused me not to finish out my last year of school. I was kind of bouncing around, wasn’t sure if I wanted to stay here in Arkansas or move to Chicago. I’ve got family there.
I decided I needed to try to get a job but there was no job really trying to hire me at the time because I didn’t have a diploma. So, I went back to get my GED and, at the time, one of my dad’s friends was telling me it’s possible I could get on here at Tenaris.
The thing was, when I interviewed, every time they asked me a question, I went blank, like clockwork. At the end, I knew I’d bombed out, but the guy who was training us was a really nice guy. I guess he could tell that I wanted to work, because when a slot became available, he decided he was going to allow me to fill that slot. By the grace of God, he saw something in me. I kid you not.
BP: Now that you’re in a role that manages others, how do you invest in their success?
FH: Our new hires, we try to be patient when we’re training them. Like I said, a couple guys took me under their wing and that’s what I try to do for the people on my team now.
Being successful is a learning curve. When I first came into the field, I was kind of like, “Man, I wouldn’t do that.” The day I decided I wanted to be different from that type of mindset and accept doing what was asked of me, I found out being openminded opened so many doors.
MAKING WORK FASTER, SAFER, AND EASIER with Ergonomic Manual Materials Handling Solutions
NOW HIRING!
Southworth is THE WORLD’S LEADING SUPPLIER of hydraulic scissor lift tables. If you need a lift table, we have the broadest product line, largest inventory of stock models, the most flexible range of modifications and most experienced designers. This site contains detailed information and specifications for all of our lift tables and lift table accessories. Our well known Backsaver™ series of hydraulic lift tables are available in over 1,000,000 configurations so they are suitable for a wide variety of applications.
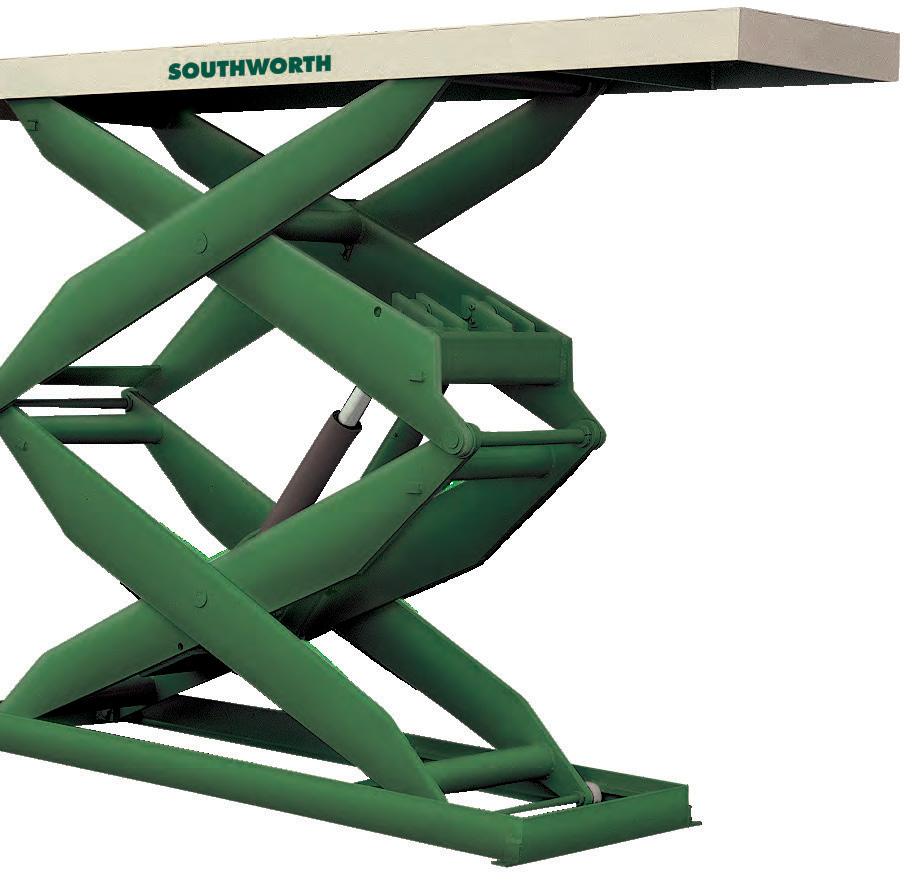

Our lift table family includes:
Hydraulic Lift Tables
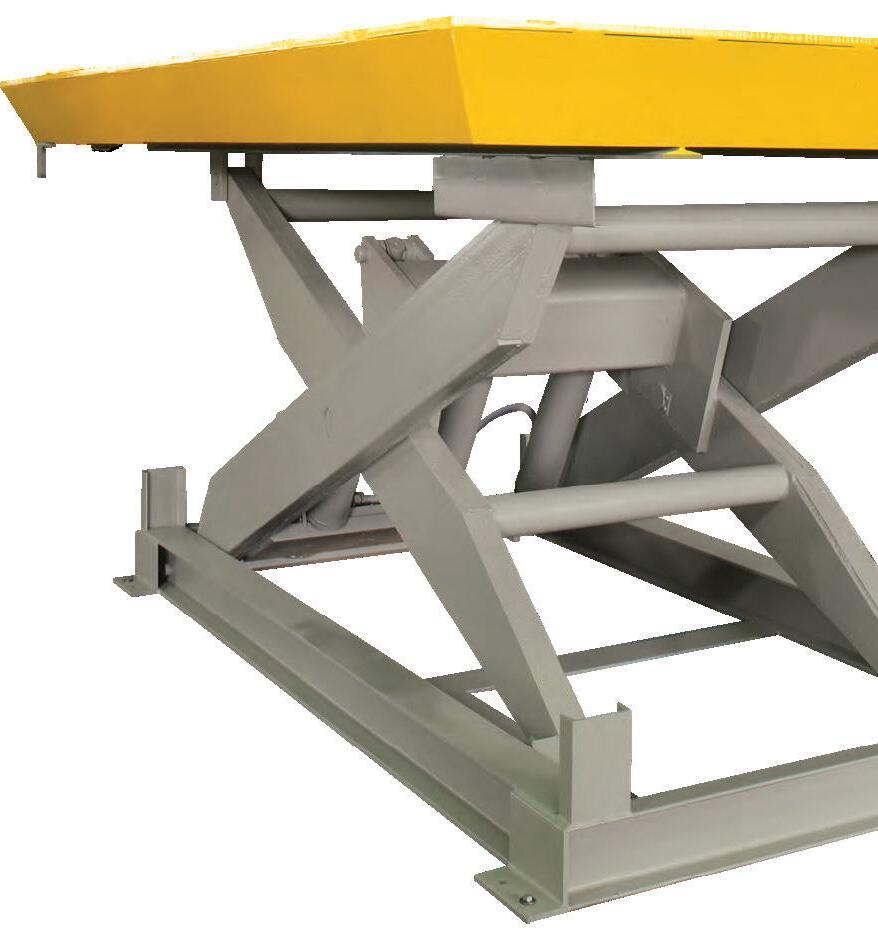
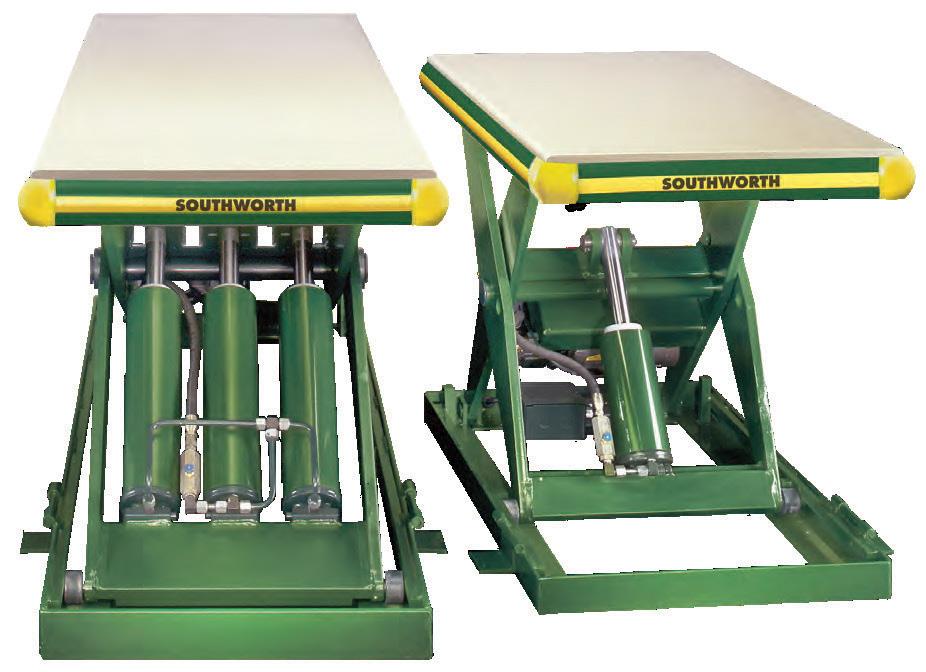
Pneumatic Lift Tables
Floor Height Lift Tables
Pallet Lift Tables
Portable Lift Tables
Compact Lift Tables
Turntable Lifts
Lift and Tilt Tables
High Rise Lift Tables
Tandem Lifts
Heavy-Duty Lifts and more
Honoring the Craft
In-house or on-campus, technical training takes center stage
For generations, a young person’s primary source of technical education was through a parent or family member or perhaps a random shop class in high school.
Today, however, cutting-edge technical training is more accessible than ever as two-year colleges and employers invest considerable time and big bucks to develop the workforce of tomorrow. And, through partnerships, these organizations are even more effective in reaching their intended audience.
“The partnerships we have helps get the word out earlier to our high schools and through our high school partners, letting students know that there’s more than one pathway to success,” said Dr. Jamie Frakes, associate vice president for workforce development and allied technologies at Arkansas Northeastern College in Blytheville.
“Once they get here for a tour, they are completely wowed by what we offer here at Arkansas Northeastern College. Our allied technologies building is state of the art; when you go through it, you see our welding lab, our HVAC lab. Our construction technology program is on the rise.
“On top of that, there are all of these computer labs and amenities that we offer through this building and through our credentials here at this college. I think it really impresses these students and it’s letting them know that the future is now.”
ANC has distinguished itself in many technical areas, from welding to plumbing to electrical training, not to mention an advanced steel technology program that’s the envy of the country. The college partners with Nucor-Yamato Steel to offer an intensive two-year internship program that can and does lead to permanent employment. And, there’s more.
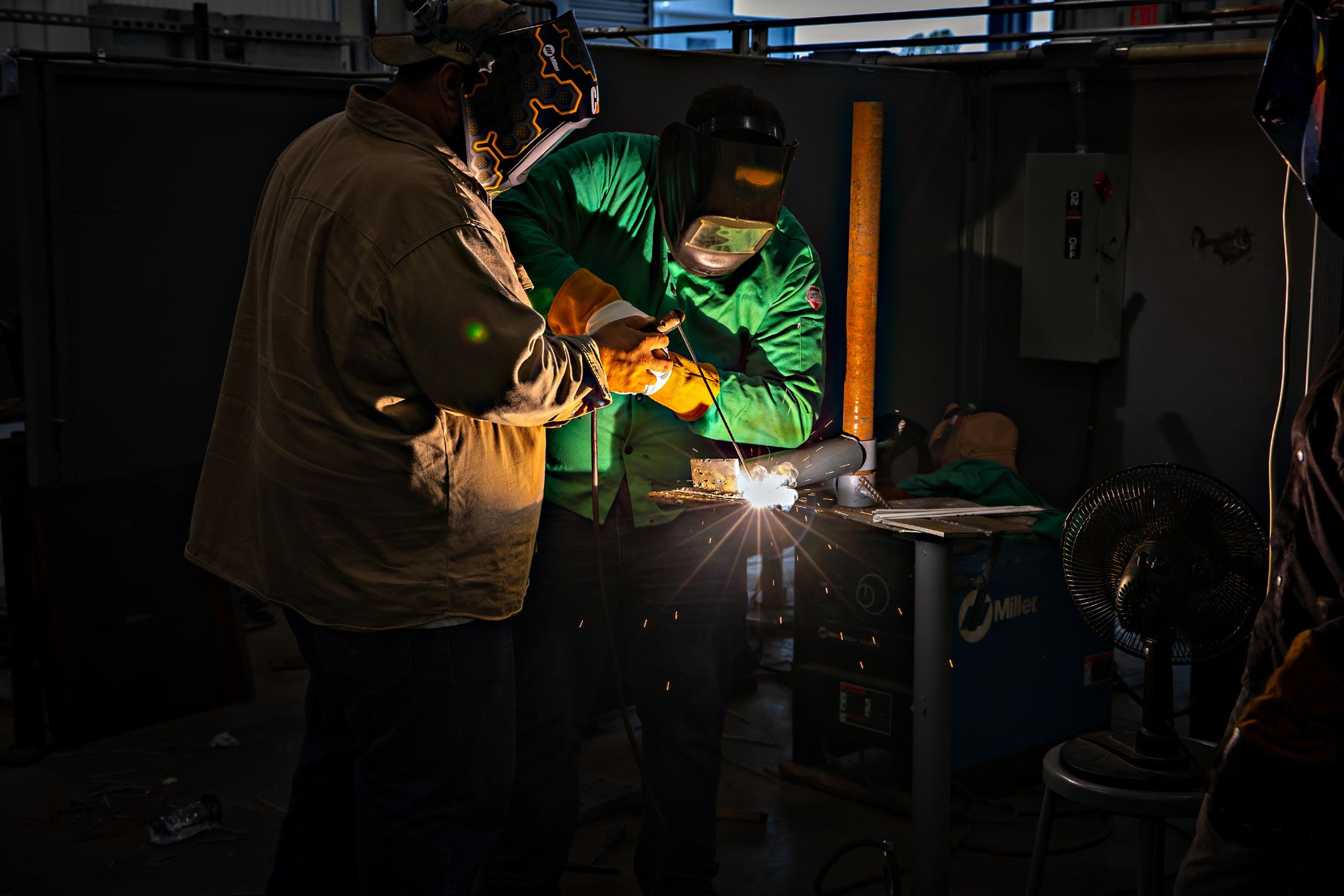
“One thing we have rolled out recently is a certificate of proficiency in entrepreneurship. That’s something we’re really focused on right now,” Frakes said. “We’ve been able to push that as a post-secondary credential and it’s something that current and prospective small business owners are interested in.”
ANC’s focus on skilled careers results in workplace-ready graduates who enjoy higher wages than their peers, including those with four-year degrees. Arkansas Northeastern grads earn an average salary of $55,000, which is $7,100 more on average, than graduates from second-place University of Arkansas. Five years after graduation, ANC graduates are still making more than graduates of any other school in the state.
Combine that with ANC’s lower tuition and a shorter time required to earn a degree and the economics lie heavily in ANC’s favor.
“First and foremost, Arkansas Northeastern delivers low cost and a high return for students when they get a job,” said Dr. Stacey Walker, dean for customized training. “We’re not talking about pennies, we’re talking about thousands of dollars’ difference. Plus, we have excellent job placement services here. We help you find your first job and if needed, you can come back and we’ll help you find another job.”
Walker also said in addition to the latest in technical training, the curriculum at ANC also strives to polish students’ soft skills, the intangible qualities that employers are clamoring for.
“We have a class called Workplace Essentials and it hits every one of the soft skills that industry has deemed important for an entry-level worker,” she said. “That includes time management, conflict resolution, team building and things that you would do in the workforce. We prepare the whole student for success.”
TRAINING DOESN’T END AT GRADUATION
Companies have to keep up with changing equipment, shifting regulations and rapidly expanding technology, and they need a workforce that is willing and able to consistently keep up. Blueprint talked to Scottie Smith, training manager with The Systems Group in Blytheville, to get a better sense of the training demands for that company.
BLUEPRINT: What’s the minimum skills education you prefer in new hires?
SCOTTIE SMITH: We prefer a new employee have a certificate or certification in the craft they are being hired for. However, if they are hired as a skilled helper for us and they want to learn a craft, we will train them in that craft using our internal training programs.
BP: What are some examples of internal training employees can access?
SS : All of our employees attend safety training, which we conduct throughout the year at each job site and fabrication shop. We also have a welding training program and a pipefitting training program for our employees. These programs are designed to upskill current workers or train employees who want to learn a craft but have little to no experience in them.
BP: What technical classes would you recommend a high schooler take to give them a jump on their career?
SS: We recommend students attend any type of shop class exposing them to working in an industrial craft. Students should also learn good safety habits, know how to read a tape measure and be able to add and subtract fractions.
METAL
FABRICATOR
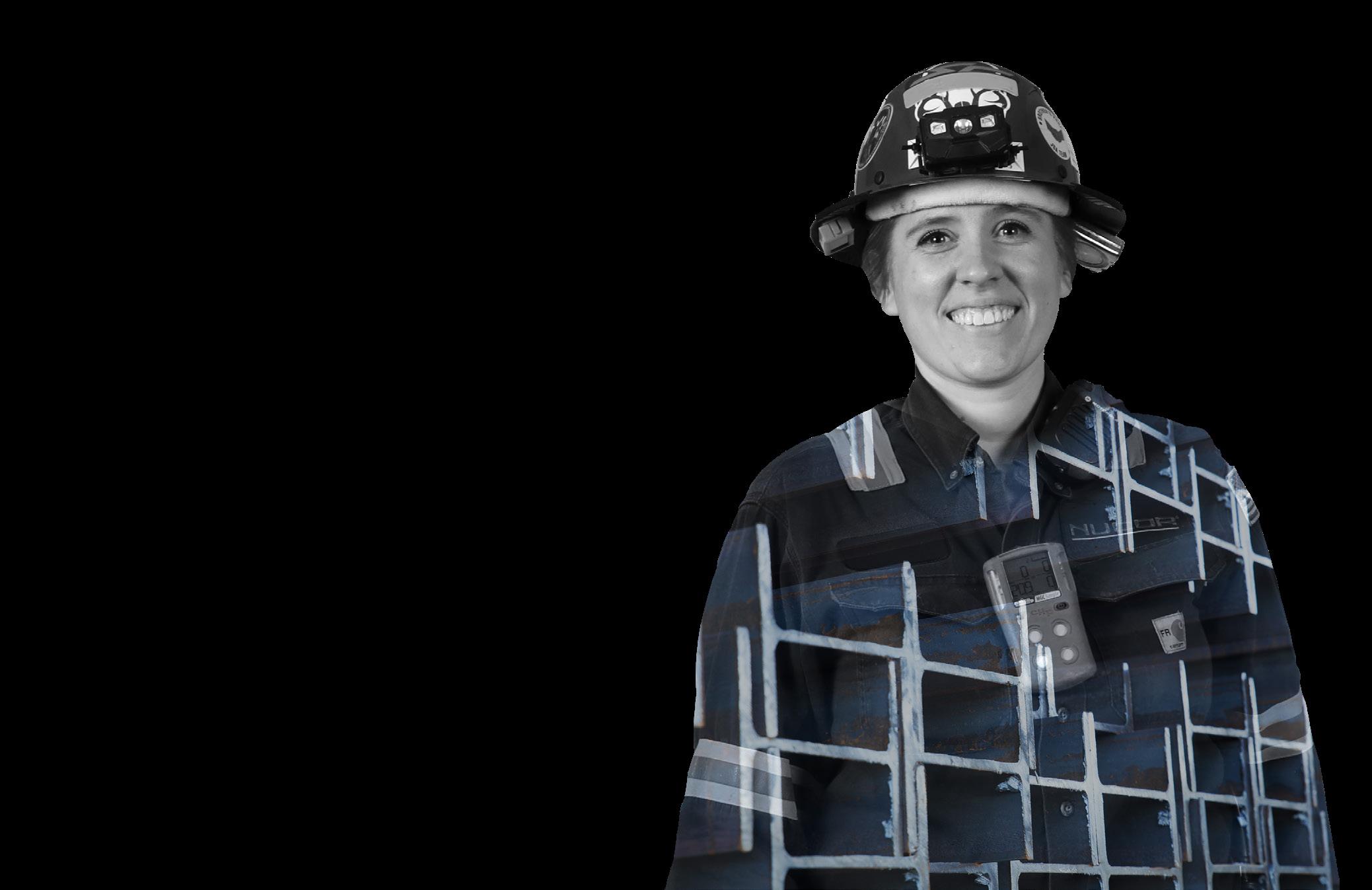
Company: The Systems Group
Starting Salary: Up to $29/hour
WHAT DOES THE JOB DO?
Layout, fabrication and assembly of angle iron, I-beams and various other shaped metals.
Repair products by dismantling, straightening, reshaping and reassembling parts using a cutting torch and other hand tools.
WHY IT’S IMPORTANT:
Anything made out of metal was built by a metal fabricator. Metal fabricators build our world and all of the things in it.
ESSENTIAL SKILLS AND ATTRIBUTES:
Welding skills using various arc welding processes, plus the ability to read blueprints and understand weld symbols.
WHAT MAKES THIS POSITION IN HIGH DEMAND?
Metal fabrication is a demanding job requiring patience and attention to detail. There are very few high-quality fabrication training programs available.
HOW DO I LEARN MORE? www.tsg.bz
COME ONE, COME ALL
Lana Smith, HVAC student at Arkansas Northeastern College in Blytheville, is a unique sight in her classes. Smith, who works in an office role for a local HVAC company, is one of few women in her classes. But, as she’s quick to point out, she’s not the only woman here, which she takes as a sign of progress.
“In our company, we have two technicians who are male and we recently hired a new apprentice who is female,” she said. “She is in the last part of the HVAC program with me here in school, which I was very excited about. I was afraid I was going to be the only female, but there are actually two other females in my class.”
Despite making up half of the labor force, women are vastly underrepresented in skilled professions, with particularly low percentages of women among plumbers, electricians and carpenters, according to U.S. Department of Labor statistics.
However, the loss of trades workers through retirement and COVID in recent years has driven up pay and benefits to where more women are looking into skilled careers. The National Association of Women in Construction reported women represent 11% of the construction workforce, higher than the average of all skilled professions, which is closer to 8.9%.
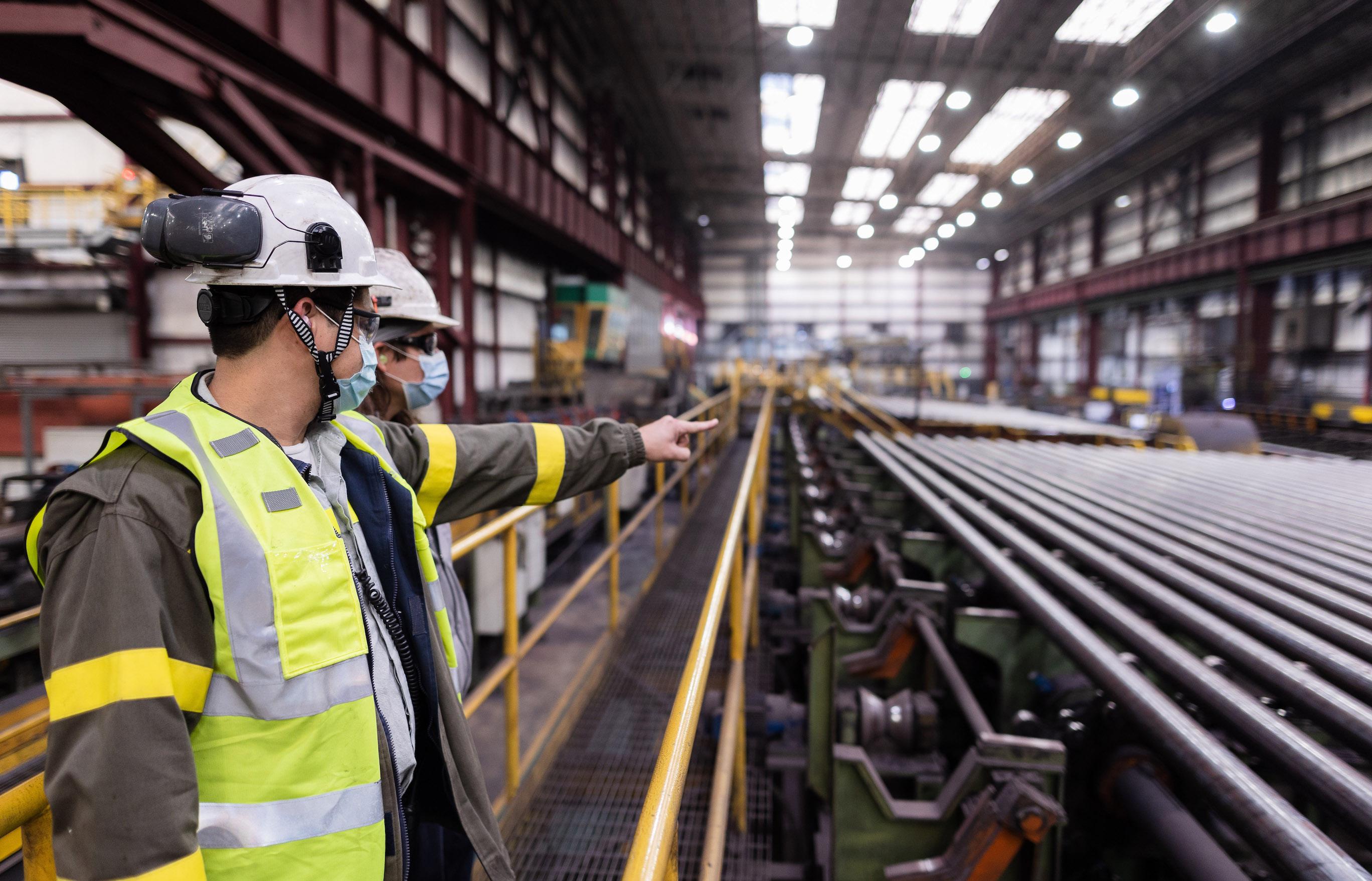
And a recent career survey by the National Kitchen & Bath Association found among high school students, the percentage of females interested in a skilled career is approaching that of their male classmates. Experts said the survey showed interest among high school girls in remodeling and renovation work is particularly strong.
Smith said more women should consider the trades as a lucrative career option, especially HVACR, which stands for heating, ventilation, air conditioning, cooling and refrigeration.
“This industry is absolutely open to females,” she said. “There are females out there who don’t see themselves sitting in an office every day. There are females who like to work with their hands and who like the challenge of having to figure out wir-
ing issues. This is absolutely an industry that females can do well.”
In fact, Smith said, women often make better technicians than men in many ways. “Females make excellent HVACR technicians and installers because attention to detail is very important in our industry,” she said. “Your customer’s issue may come down to a small wire connected in the wrong place. A lot of times, I find women are much more detail-oriented than men.”
Minority trade workers outnumber women, meanwhile, but still only account for 40% of the skilled labor population. As the worker shortage drags on and companies sweeten pay and benefits, however, it’s attracting more Black and Hispanic employees looking for a rewarding job and advancement.
“I didn’t have a clear-cut direction on what I wanted to do,” said Ferriel Harvey, who has 20 years with Tenaris. “But I did look to some of my family members who had a trade. My dad worked in a mill for the majority of his life, and I really did look up to him. I know what he did and how hard he worked and how it paid the bills and took care of us.
“When I came in to Tenaris, I came in at an entry level. Now, I’m a team leader on the PMC side.”
Harvey credits the company culture not only for a source of livelihood, but for helping him grow up, take constructive criticism and bide his time for advancement opportunities. He said that development was invaluable to his long-term development and it’s what he tries to pass down to the people he manages today.
“You’ve got to take time with employees, the new hires, and talk them through things sometimes,” he said. “I understand that now, after being employed here for a few of years. This is more of a family atmosphere where you get to know people.
“I had a couple of guys take me under their wing, coached me up on the do’s and the don’ts. A lot of this plays a part in the growth that has to happen in a person if they want a career in this type of industry.”
In today’s skilled labor market, there’s opportunity (and room) for everybodyWorkers of all races, colors and genders have a place in the trades. TENARIS
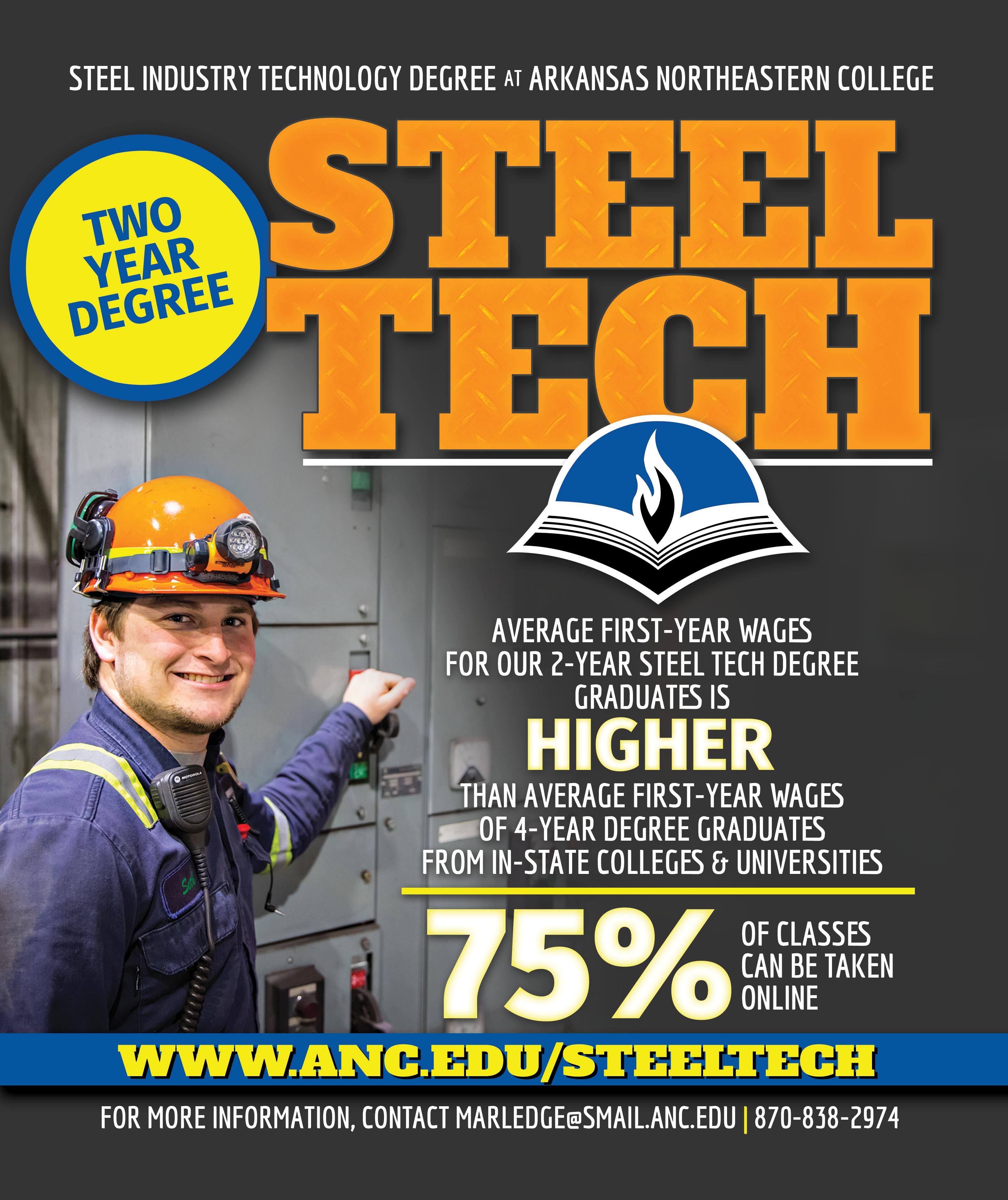
ORAN JOHNSON
Team Leader/Mill 6, Tenaris
Hometown: Manila
Age: 26
Years with Tenaris: 5
BLUEPRINT: What’s the length of your workday and how many hours do you put in during a typical work week?
ORAN JOHNSON: We’re working about 60 hours a week; we do five 12-hour shifts Monday through Friday. That’s pretty much year-round, 60 hours a week. A lot of my teammates have an hour drive one-way to and from work, so it can be a pretty long, demanding day.
BP: What does your day consists of as a team leader?
OJ: The team leader’s responsibilities are to manage the line itself. I’m responsible for making sure we’re producing quality pipe, making sure everybody’s being safe and following procedures. Any issues we have, I’m the guy to go try to fix those. I’m in kind of a relief position, you might say. I fill in vacancies when people take vacation or have to miss work.
BP: Sounds like you’re pretty versatile.
OJ: I have to be. I have to know how to run every piece of the process that we have here.
BP: What kind of training have you gone through over the past five years to build up that kind of skill set?
OJ: The company has training set up for us and that gets us certified for whatever job or task that we’re doing. I not only have to do that for myself, but as a team leader I have to make sure that everyone on my team gets the training they need.
BP: What’s the transition been like from a team member to a team leader? How did you learn the skills you needed to lead others?
OJ: I’d say having good leadership skills helps me out a lot as far as being respectful with my teammates. We all treat each other with respect. That and communication helps us out a lot out here. In fact, my favorite thing about my job is to sit down with my coworkers. It’s just like a family up in here. I have no issues coming to work. I love being here.
DEMOND JONES
General Foreman, The Systems Group
Hometown: Blytheville
Age: 46
Years with The Systems Group: 20
BLUEPRINT: Where did you start off with The Systems Group, job-wise?
DEMOND JONES: I started off as a welder and then I progressed to pipe fitter, which led to me being a lead man and then to fore man and general foreman.

BP: When did you first get interested in welding as a career?
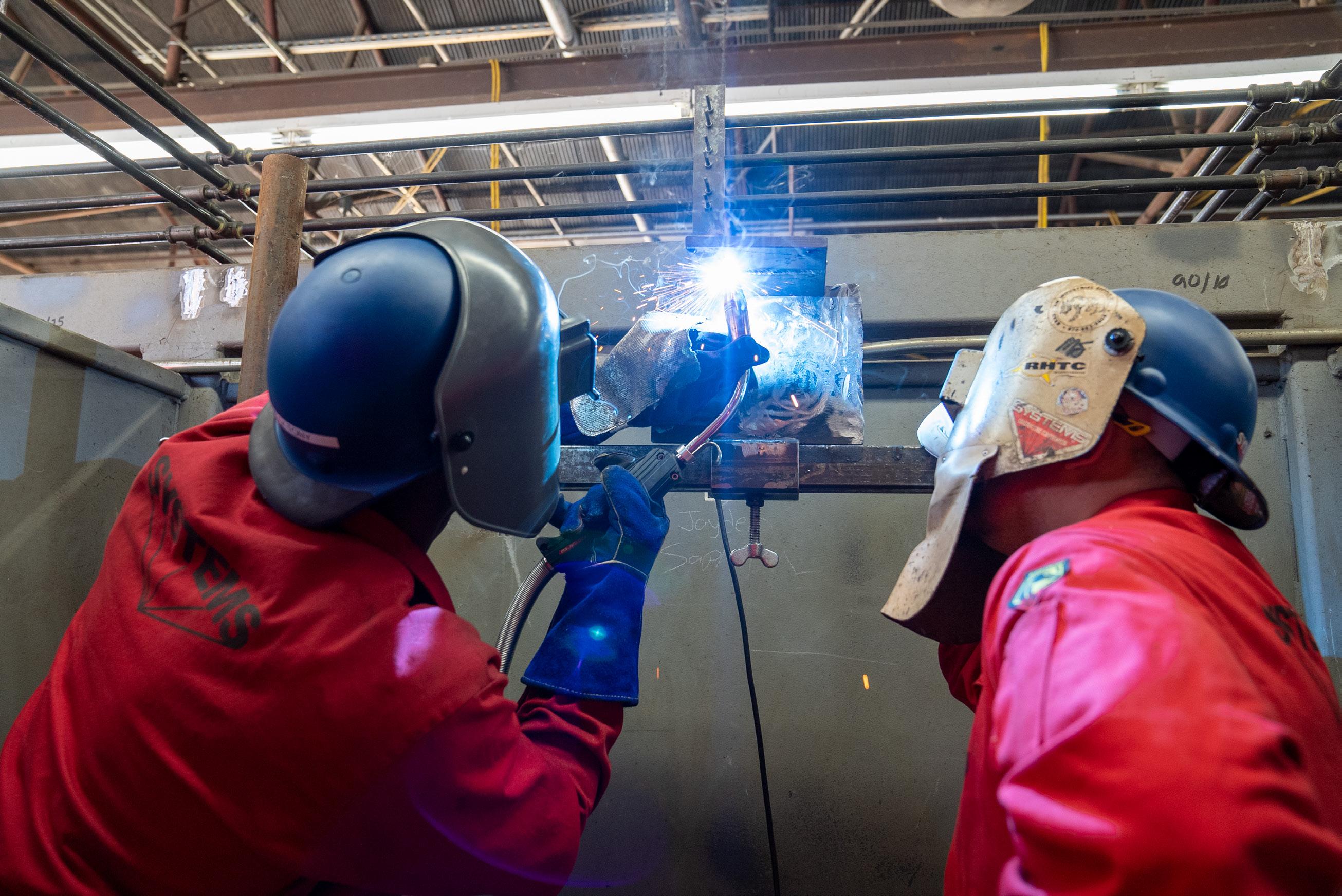

DJ: I worked at other factories before, and my work shut down unexpectedly. My wife and my mother-in-law were looking in the paper one day and they saw “Welders Needed.” So, my wife came to me and said, “Why don’t you do this; they’re always needing welders.”
So, I decided to enroll in welding school and things took off from there. I owe all the credit to my wife and mother-in-law, though, for introducing me to the trade. And I had no idea that I would be that good at welding or I would really like it.
BP: As general foreman, how big of a crew are you responsible for?
DJ: It varies with the size of the job. With the job I have now, I’m like second in command and I’m over a lot of area. For one job I may need three guys. If it’s a bigger job, I’ll have anywhere from six to eight guys.
BP: What’s your workday like and where does your work take you, location-wise?
DJ: I’ve always had pretty much just a set schedule. It’s been 10 hours a day pretty much, five days a week. You can get overtime if you want. The hours are out there for you. I’ve worked all the different hours, but for the most part Monday through Friday, 10 hours a day.
We’re a contractor and we have a set area where we actually work out of. We’ll build everything in that area, and as they go down to where we can install it, we’ll install it. But we’ve got different areas set up at this site and we’ve got different crews in different areas.
BP: As a foreman, you get the chance to assess applicants and hire for the team. Are you generally looking just at experienced welders, or can someone hire on and learn the trade on the job?
DJ: The Systems Group is now set up where they do apprenticeships. In fact, they just finished one and those folks are being put to work now. That’s something new that the company is doing; they’re advertising now to train people to come in to get in this field.
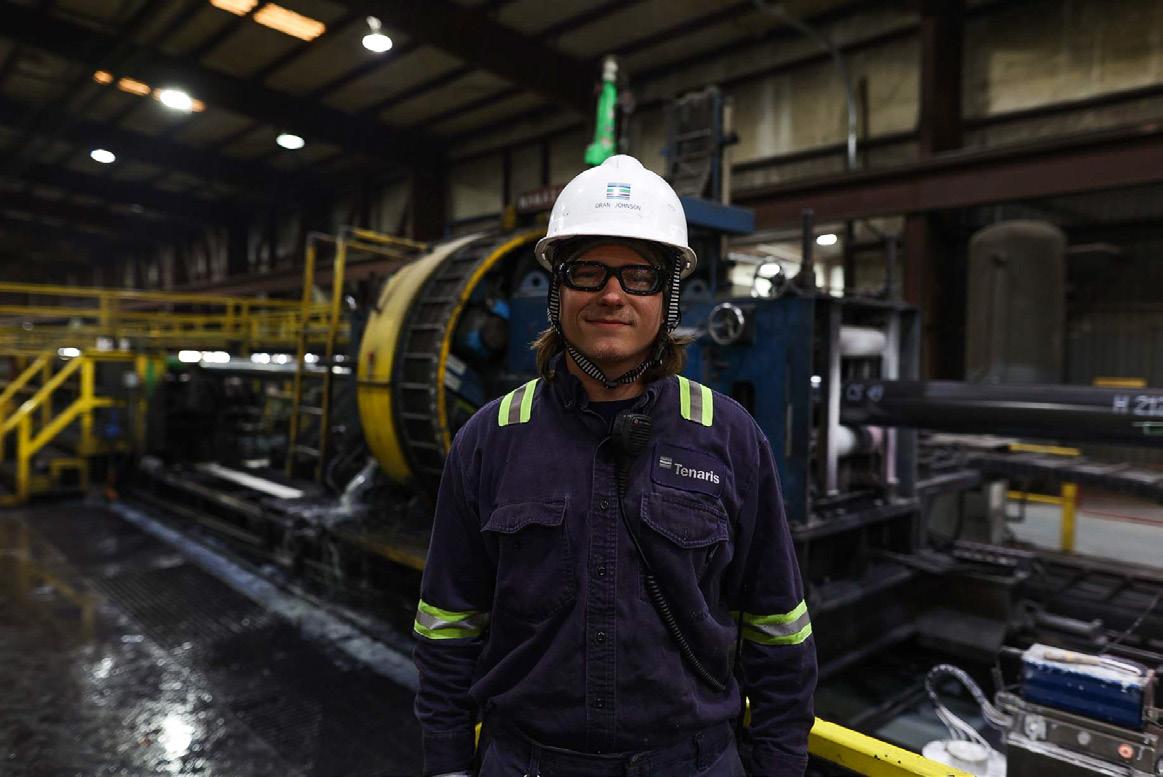
PAID
THE SYSTEMS WELDING PROGRAM GROUP

To meet the growing need for skilled craftsmen and women in the steel industry, The Systems Group has started a training program to develop current and newly hired employees. Our training program focuses on training new employees in structural GMAW welding, while up-skilling current employees in multiple welding processes. The training will occur during normal work hours. Trainees will receive their regular pay while participating in the program. Our training will be a mix of classroom and shop time. Classroom time will teach technical aspects of welding, while shop time will be a mix of weld booth time and on-the-job training. Once the trainees understand the fundamentals of welding, they will be in the fab shop working in their assigned areas with the welding instructor. Our training program is led by our welding instructor, Alex Ford.
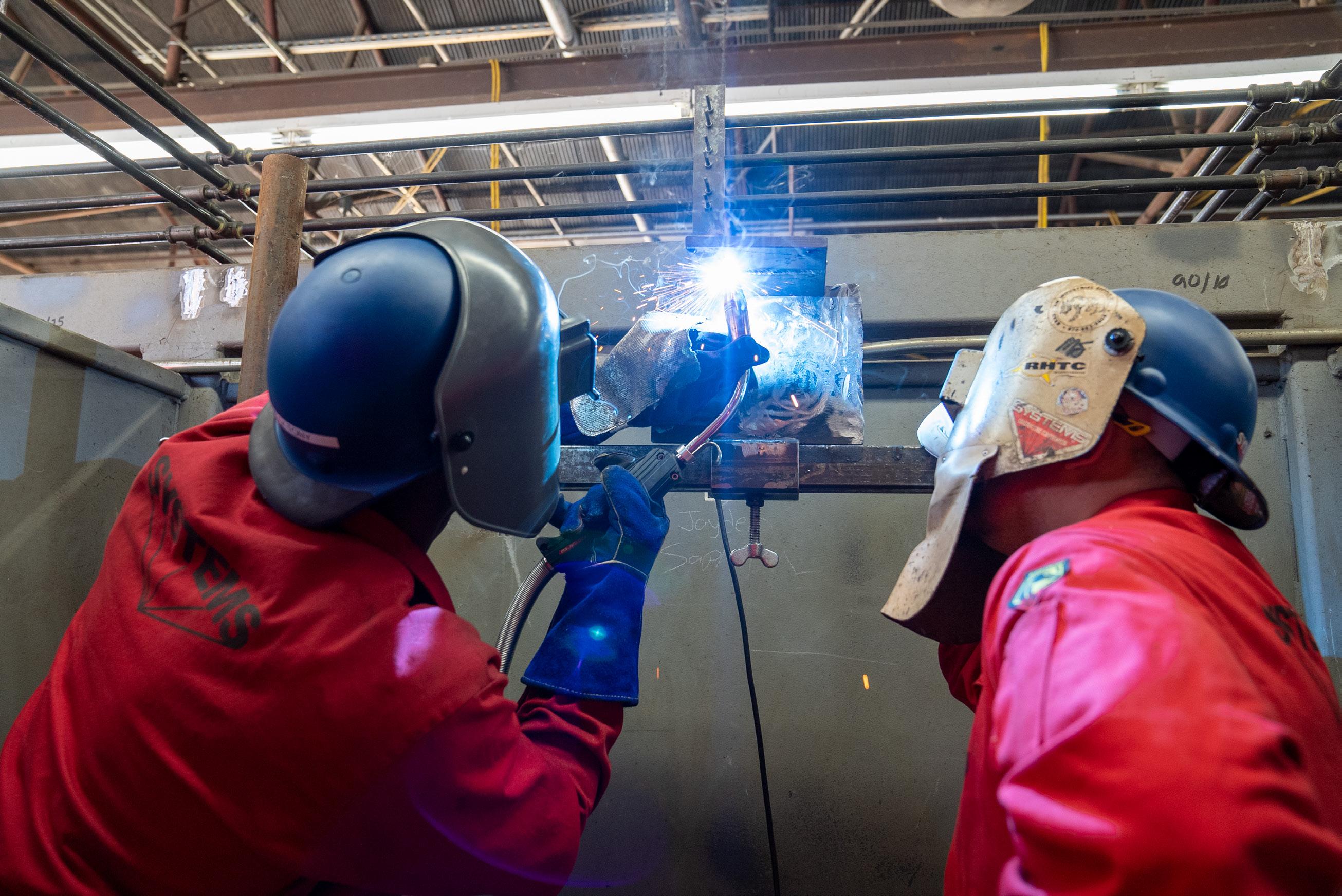
For more information, go online at careers.tsg.bz or call a recruiter at 1.800.501.1315.
FAB & MACHINE
I would most definitely recommend this course for other people. It is a learning experience and it can probably change your life.
-Tyler JohnsonVICTOR THOMPSON
General Foreman, The Systems Group
Hometown: Dyersburg, TN
Age: 54
Years with The Systems Group: 13
BLUEPRINT: Where did you get your start with the company?
VICTOR THOMPSON: I came on in 2010 with 75 men on site. I was a journeyman fitter and welder and I was the lowest paid journeyman out of all of them. I started on the bottom.
BP: What did you do to improve your skills and advance your career?
VT: I came in and worked real hard. I noticed who the qualified tradesmen were in the field, out in the mill or wherever, and I kept a keen eye on them all the time to learn what they knew, and what knowledge they had that I could get. I worked hard to make sure that whatever was out there to learn that I could learn it and advance up and move forward.
BP: Did you come from a family who was big into the trades?
VT: No, this is something I reached on my own. When I started back in the late 1980s I could not read a tape measure. Everything I learned, I learned on the job. Once I got into the pipe fitting trade, I learned about the National Center for Construction Education, and I jumped into that and got all the book knowledge I could off of it.
With Systems here, they allow you to advance yourself as far as you want to go. I hold 10 national certifications outside of my trade, from boilermaker to carpenter to basic rigger to advanced rigger to crane operator. I hold all those because the company gives me the time to advance myself and advance the company.
BP: What advice do you have for someone who’s just starting, right out of high school?
VT: If you’re still in school, seek out an ag shop, trade shop, in-school welding, whatever it might be. Get into that and see if it’s for you. Once I found out the trades were for me, I would find a good reputable company, and I would hire in. Hiring in on the bottom side these days doesn’t pay bad money, it really doesn’t.
BP: Did you ever find an older co-worker who didn’t want to help you when you were starting out?
VT: The people who have been doing it for years, if they see a young individual who’s willing to apply themselves and learn — male, female, doesn’t matter – they’re going to give them all the knowledge they possibly can. That’s where I picked it up, watching other guys.
JAMIE WEEKS
Construction Superintendent, The Systems Group
Hometown: Warren
Age: 51
Years with The Systems Group: 26
BLUEPRINT: What jobs have you held leading up to construction superintendent?
JAMIE WEEKS: I’ve done everything from pipe fitter, welder, foreman, general foreman, maintenance superintendent for 13 years and now construction superintendent. I’ve been in this role for six months.
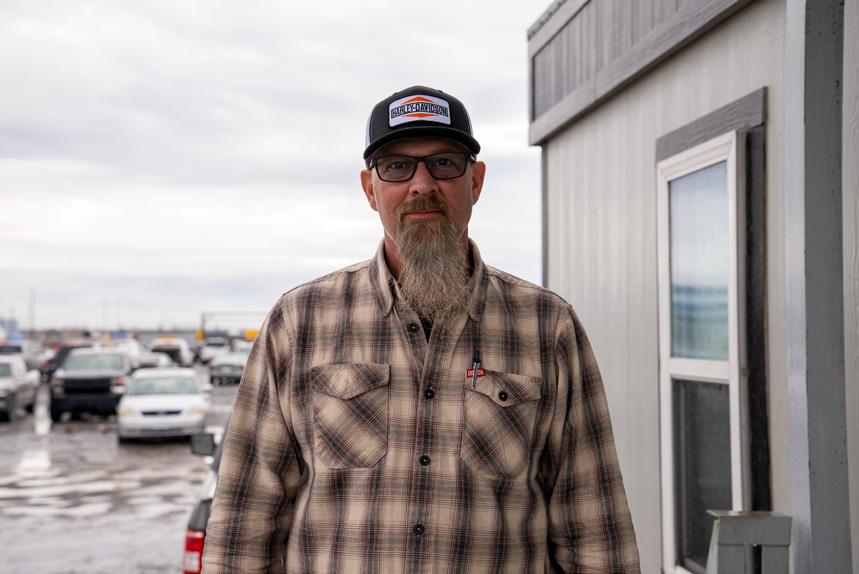

BP: How did you get started on this career path?
JW: My father worked for the company, got me a job and it’s progressed from there. I got a job as a welder’s helper, worked my way up to welder and just kept going.
BP: What’s a welder’s helper? What does that job do?
JW: I’d grind, cut, clean, carry the tools, whatever they needed done. That’s a job that’s still around; on the construction side, we try to hire as many helpers as we can. It helps with our cost per hour, but we also find people who are trainable, we mentor them and help them grow.
BP: Did you grow up working with your hands? How did you get your start?
JW: My cousins were drag racers, so I’ve been working on vehicles since I was 10 or 12 years old. When I got to The Systems Group, the only training I got at this level was on-the-job experience.
Today, we’re doing a pipe fitting apprentice program and a welding program. They’re just getting that started now, hiring some welding instructors and pipe fitting instructors. We’re trying to bring in younger workers, teaching them and trying to help them develop, make more money, become a journeyman.
BP: What soft skills are important for working there?
JW: Being dependable, being here on time when you’re scheduled. To me, that’s about as important as anything. And being willing to learn. Some of the younger generation come from these welding schools and they think they already know everything. Some of them don’t like to take direction. That’s something we’ve just got to work through.
BP: If you could talk to a roomful of those young people – high schoolers, let’s say – what would you say to them about a career in the trades, specifically at The Systems Group?
JW: Our company is very serious about safety, that’s one of the most important jobs we have is teaching safety, enforcing safety and making sure it’s followed through. Our management is really dedicated to that too, making sure everything is right and we have what we need to do the job so no one gets hurt and everyone gets to go home at night. That’s how I know our company cares about their employees. They’ve always cared for me and treated me right. To me, this company’s like a big family. It’s just a great place to work.
A REVOLUTION IN STEEL
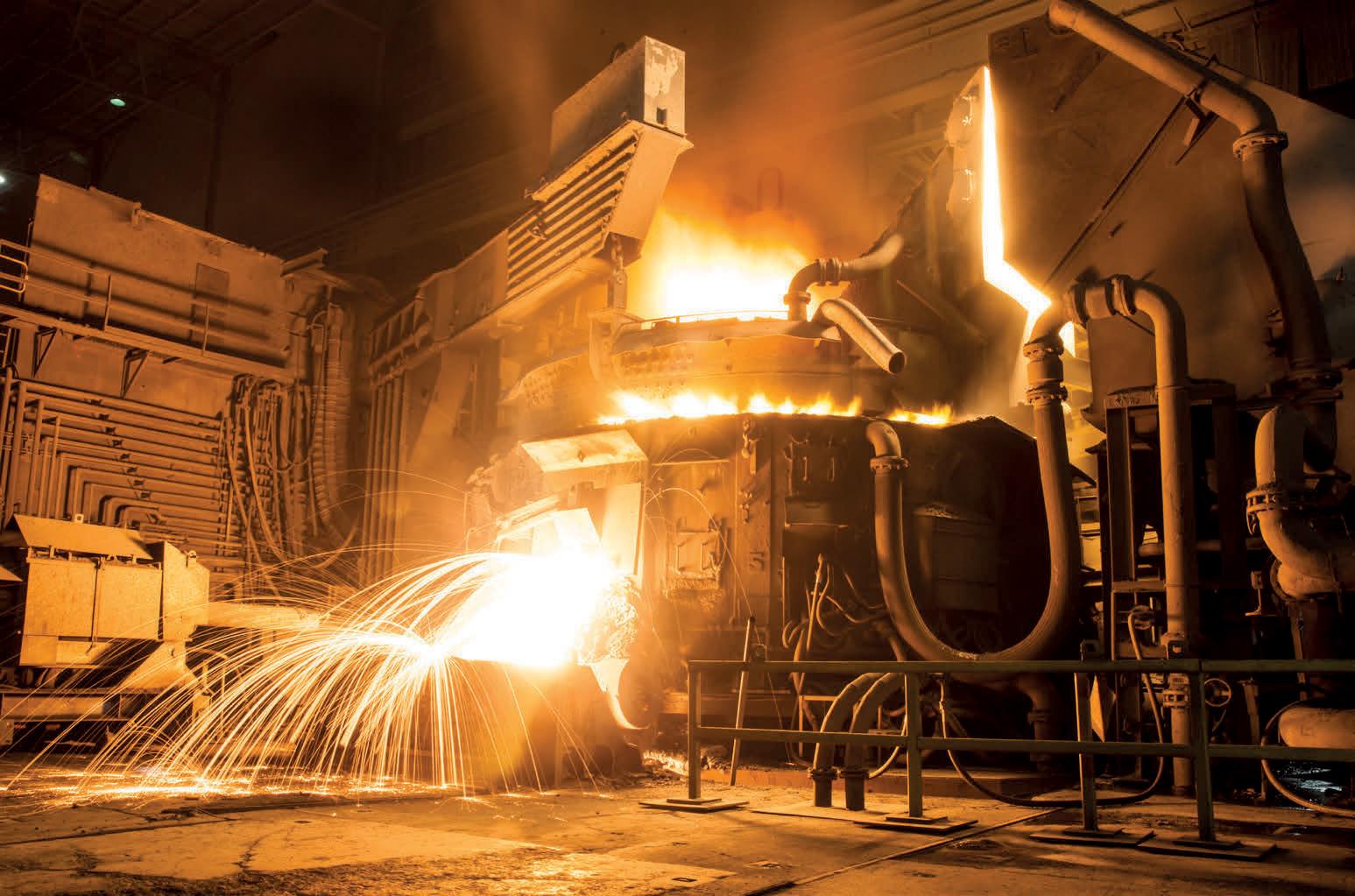
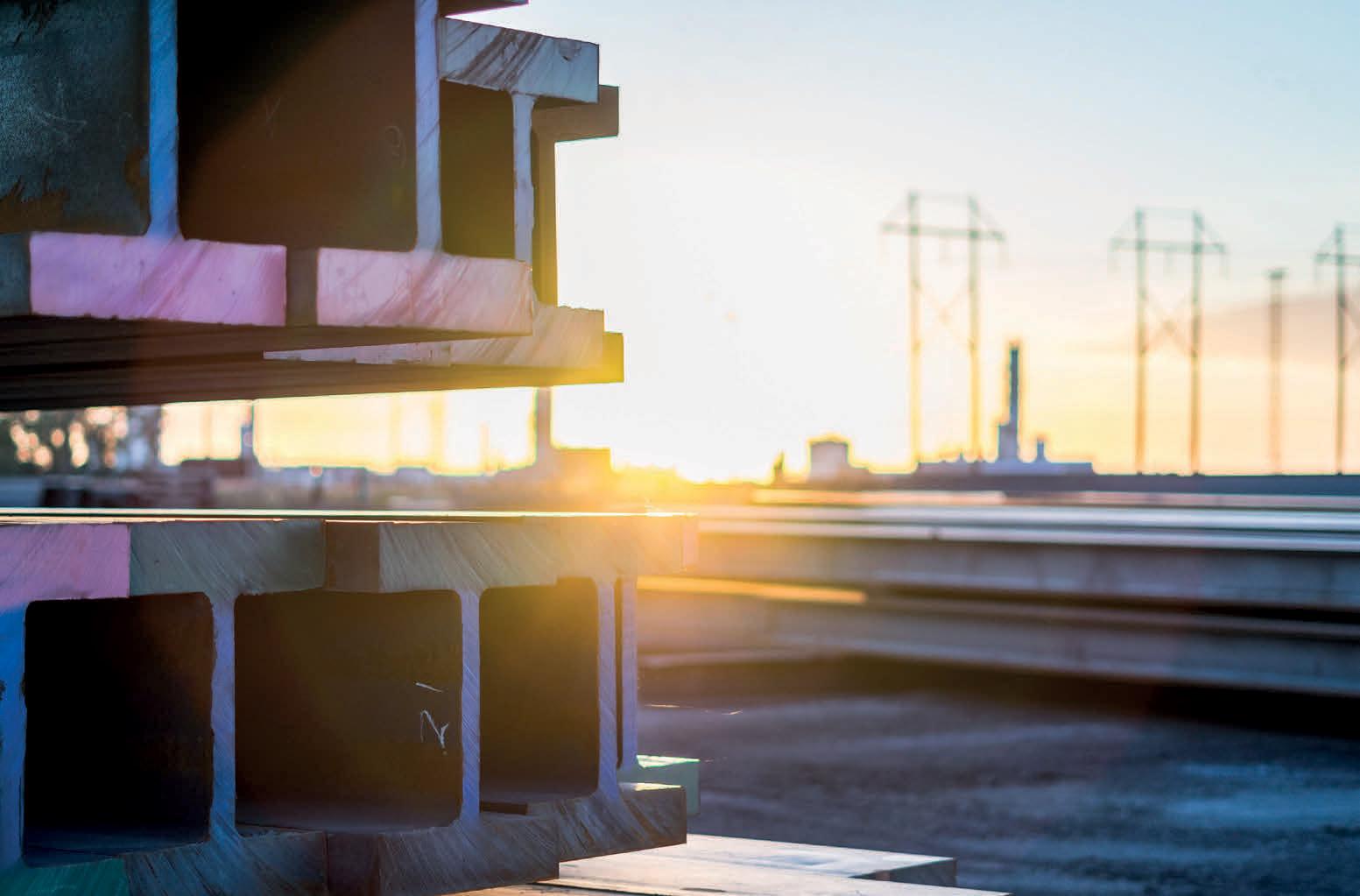
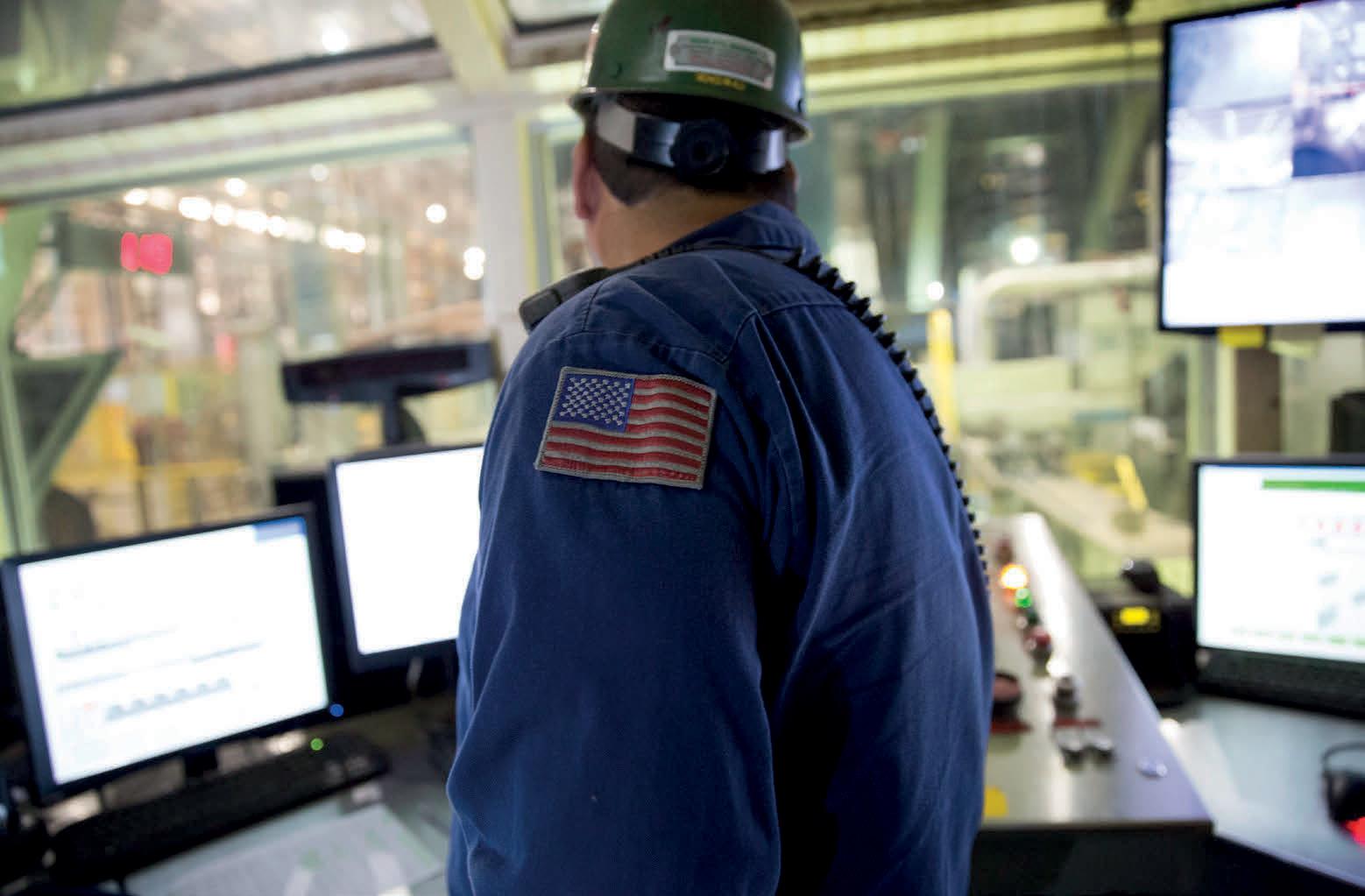
DISCOVER THE OPPORTUNITIES
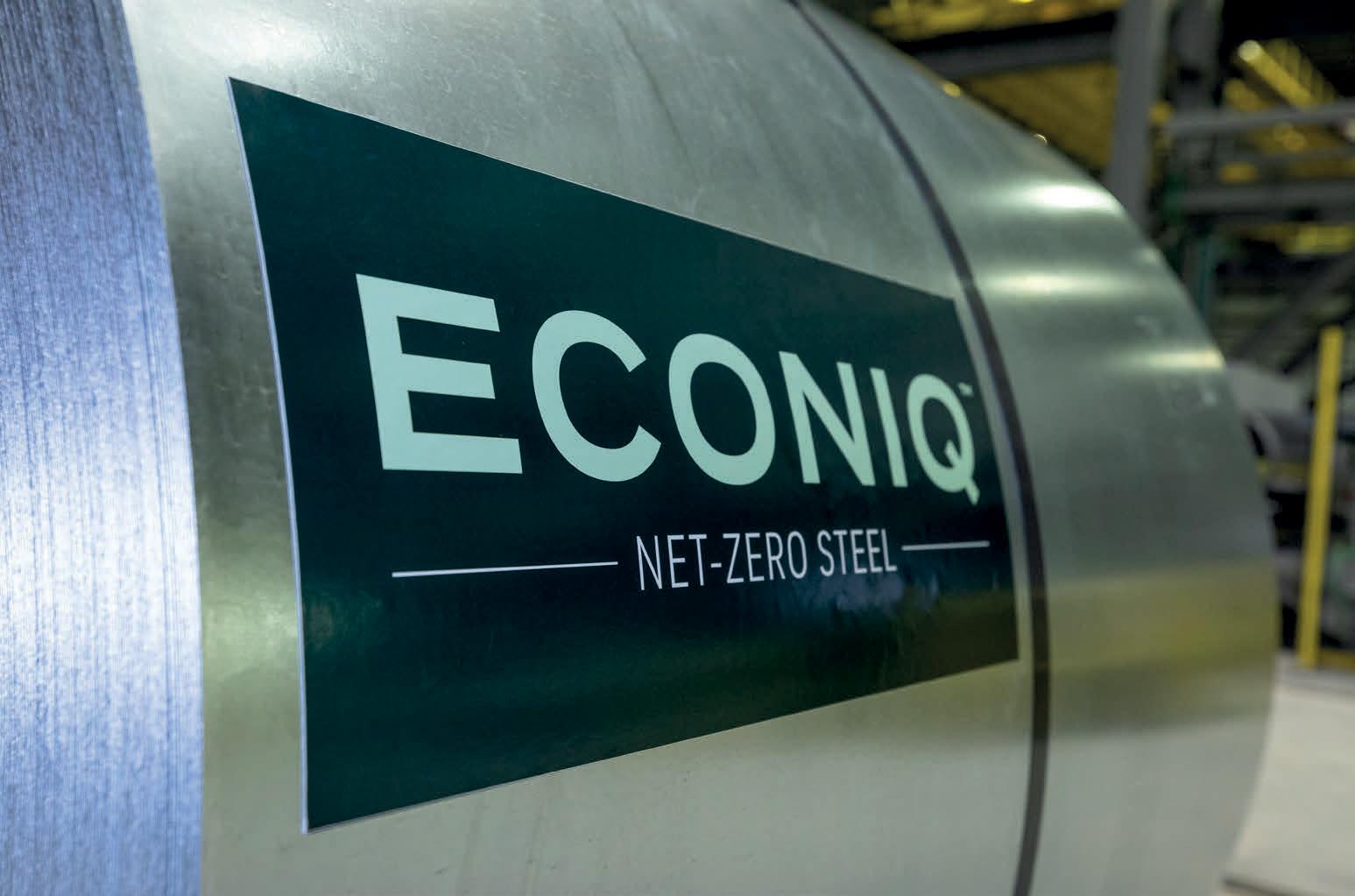
LEARN YOUR TRADE
• MAKE THE TEAM
• BUILD YOUR CAREER
NUCOR: A REVOLUTION IN STEEL

NUCOR STEEL MILLS – TRANSFORMING ARKANSAS’S MANUFACTURING LANDSCAPE
A REVOLUTION IN STEEL STEEL APPEAL
Northeast Arkansas is home to the second-largest steel producing county in the entire country, Mississippi County. As the U.S. enjoys a manufacturing boom that shows no signs of slowing, the steel industry in the U.S. – and in Mississippi – will continue to grow.
The industry got its start in northeast Arkansas back in 1987 when the Nucor-Yamato Steel Company (NYS) began operating a mill that produces steel beams used to build skyscrapers and other structures. Five years later, in 1992, sister division Nucor Steel Arkansas began producing steel sheet used to make cars, appliances and other products. Since then, these two Nucor mills have invested billions of dollars to grow, creating thousands of high-paying jobs with generous benefits and plenty of opportunities for teammates to advance their careers.
Nucor’s two Arkansas steel mills are some of the biggest and most technologically advanced manufacturing facilities in the country. They each have developed innovative high-strength, lightweight steel products for the construction and automotive industries, and they are both world leaders in sustainable steel production. All Nucor mills recycle scrap metal into new steel products, which makes the company a world leader in low-carbon steel production. And the company continues to find ways to lower its environmental footprint. It has made a commitment to reduce its greenhouse gas emissions intensity by another 35%, is supporting the development of renewable and other clean energy sources, and recently introduced the world’s first line of net-zero carbon emission steel products, called Econiq.
Today, Nucor’s plants are the model for the steel industry and the company is one of the most important corporate citizens in The Natural State. This advertising section in Blueprint will highlight the company’s many benefits, as told directly by the teammates of NucorYamato Steel Company and Nucor Steel Arkansas, who are building their futures as they help build America.
NUCOR BY THE NUMBERS
• 2,300 – Nucor Steel Jobs in Arkansas
• $100,000 – Median pay for Nucor teammates, excluding executives

• $36 billion – Net sales in 2021
• 23 million – Tons of ferrous scrap recycled into new steel annually
• $4,000 – Annual scholarship amount available to each Nucor teammate and their dependents
NUCOR LEADS THE PACK
• Largest steel and steel products producer in North America
• Largest recycler of any type of material in the Western Hemisphere
• #1 Most Admired Metals Company (Fortune Magazine, 2021)
• Named one of Fortune Magazine’s 20 Best Large Workplaces in Manufacturing and Production, 2021
TEAMMATE SPOTLIGHT
A REVOLUTION IN STEEL
WILLIAM SANDERS
EAF Helper, Nucor-Yamato Steel
Hometown: Memphis
Age: 32
Years with Nucor: 7.5
BLUEPRINT: What is your educational background and what were your career plans?
WILLIAM SANDERS: I went to the University of Arkansas at Pine Bluff and received a bachelor’s degree in industrial technology management as applied to engineering. I wanted to apply for a job in manufacturing and Nucor was offering an internship through UAPB. It was the perfect opportunity to put my educational skills to work.
BP: Why manufacturing? Do you enjoy working with your hands?
WS: Yes, I learned to work on cars, build fences and work on houses with my dad and uncle when I was younger.
BP: Was there a big learning curve once you joined the company?
WS: We get a lot of training on the job both directly for our role here and for other jobs, such as cross training. Nucor also offers educational reimbursement for college courses we may be interested in to continue learning.
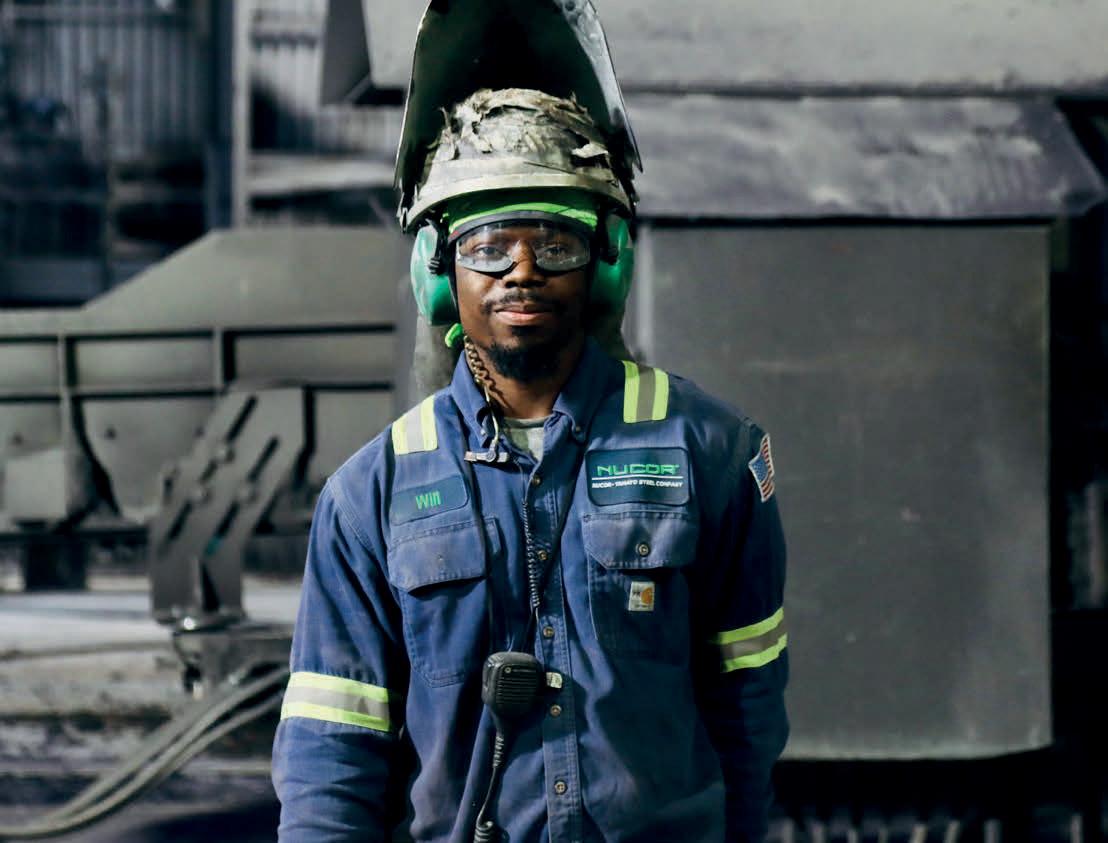

BP: What is your schedule like?
WS: I work twelve-hour shifts, four days on and four days off, rotating shifts from days to nights, seven days a week.
BP: What do you like best about working for Nucor?
WS: The pay and the benefits that come with the job are great! I really enjoy the people I work with and know they are looking out for my safety. We refer to each other as teammates because we get to know each other and form a real bond.
DISCOVER THE OPPORTUNITIES
• LEARN YOUR TRADE
• BUILD YOUR CAREER
NEAR PEER PROFILE TEAMMATE SPOTLIGHT
A REVOLUTION IN STEEL
BETH WREN
Safety Coordinator, Nucor Steel Arkansas
Hometown: Brookland, AR
Age: 42
Years with Nucor: 23 years
BLUEPRINT: What’s your background?
BETH WREN: Before Nucor-Yamato, I was a nutritionist for a hospital. I started as a contractor doing diabetes education and health and wellness programs for health and safety, and it ended up turning into a full-time position.
BP: What does your job entail now?
BW: I work with the new-hire processing, training them for the safety department.
BP: Are there opportunities for new teammates to have an immediate impact on safety?
BW: The new teammates bring in a new set of eyes. If they see something unsafe, Nucor culture lets them ask the question, ‘Why are we doing that? Can we do this differently?’ It empowers and helps new teammates to know they are just as much a part of our safety culture as teammates who’ve been here for 30 years.
BP: What have you learned by working for Nucor that everyone should know?


BW: The career possibilities are endless.
BP: What would you say to someone who thinks they lack the training for a job at Nucor?
BW: Nucor really wants to be proactive instead of reactive when it comes to training. Using our department as an example, we train new hires with a 10-hour class. After they are hired, we continually train people to meet the needs of the business. We just got certified in mental health first -aid because we have seen mental health as a growing issue. We also have first responder training; we have multiple teams for emergency response and high-angle rescue, and we do that training onsite. That training is a huge opportunity for teammates because when we get these certifications it’s not just a Nucor certification, it’s something teammates can take with them for the rest of their career.
DISCOVER THE OPPORTUNITIES •
What I tell people is yes, the pay is wonderful, but what you gain from here and how you grow here is even more valuable.
MAKE THE TEAM
LEARN YOUR TRADE • BUILD YOUR CAREER
ALL FOR ONE
NUCOR TEAMMATES FIND THEIR PLACE IN MANUFACTURING
One of the most important aspects of having a vibrant, healthy, productive and satisfying workforce is to ensure its diversity: diversity of background, diversity of thought, diversity of experience and diversity of ability.
Companies across the country are paying greater attention than ever to the makeup of their labor force, motivated by a combination of public relations, a response to the increased labor shortage, and customer demands.
At Nucor Steel Arkansas and Nucor-Yamato Steel (NYS), the production floor and offices are populated by men and women of various ages, races, ethnic backgrounds and countries of origin. In short, they reflect the communities of which they’re so proud to be a part. Their common denominator – what binds them all together – is a desire to build a career, look out for the safety of their fellow teammates, and support the company that makes it possible.
“As far as diversity goes, I see a lot of people of color here,” said Tyrone Dodd, who joined Nucor-Yamato Steel right out of high school last summer. “We all want to do a job and be safe doing it. It doesn’t really matter where you come from or what you look like -we’re all just one team.”
Nucor’s success in recruiting from a diversity of backgrounds has become almost self-sustaining, with members of our vibrant Arkansas community attracted to the company based on what they see in the faces of Nucor teammates.
Henderson, Safety Coordinator with Nucor Steel Arkansas. “When I think about the dynamics in this area, I think about leadership. You’ve got to have people of all backgrounds in leadership positions, which I’m proud to say we do. That way, students and people in the community see these people and know there’s a pathway for them.”
Nucor teammates know, once a new teammate joins the company, they will have an incredibly broad range of people in varying departments stepping up as mentors to assist in fulfilling career goals.
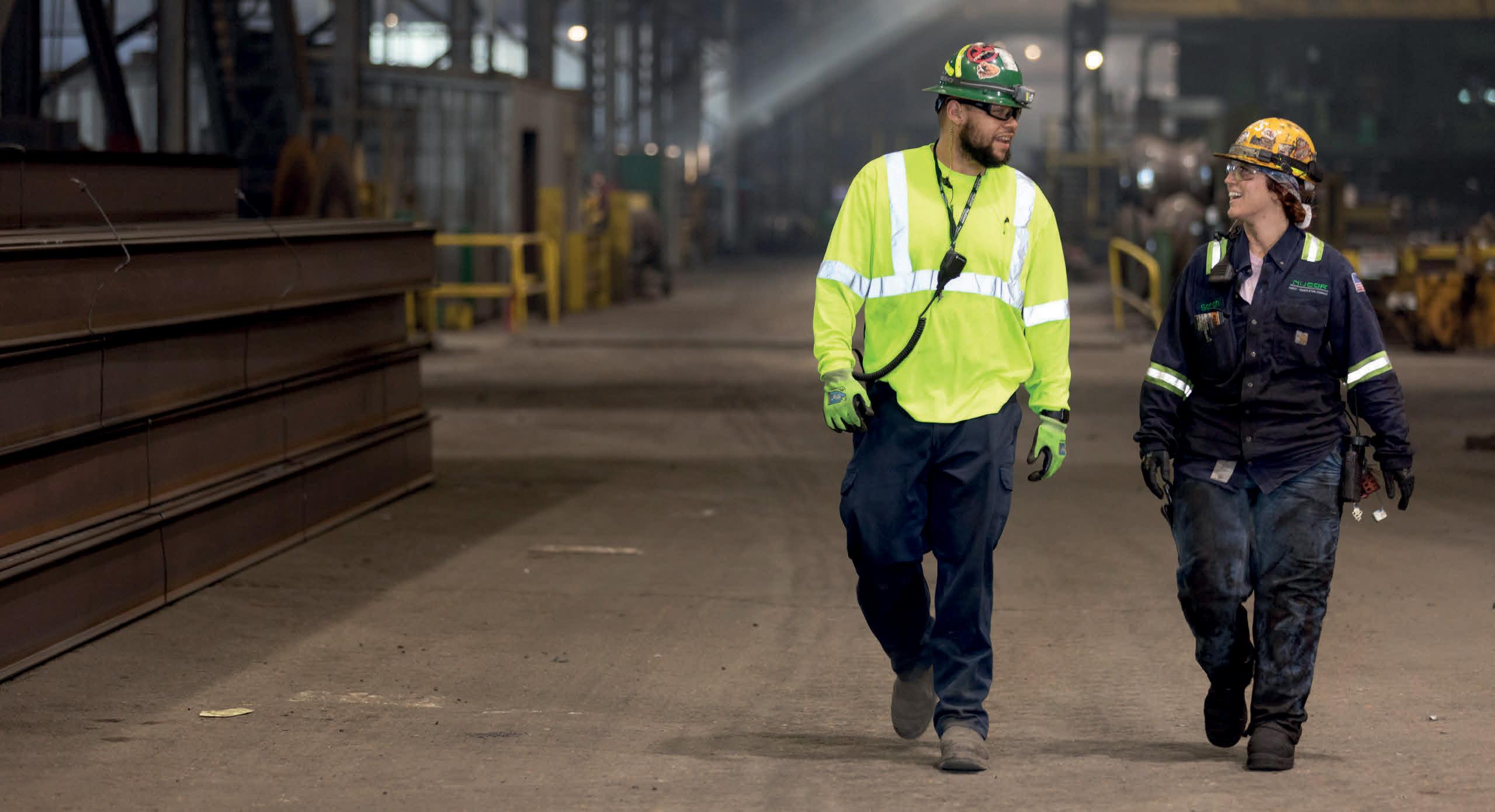
“I was blessed with the way things worked out for me here,” said James Jones, a lab crew leader who has worked at Nucor-Yamato Steel for 13 years. “Nucor runs on the abilities of its teammates more than anything. We have people who have worked here a long time, people who helped me move up at an accelerated rate. I was always well-received and was taken under someone’s wing to teach me how to be part of the Nucor leadership team.”
DISCOVER THE OPPORTUNITIES
LEARN YOUR TRADE
“I think it’s like the old saying, ‘You can’t be what you can’t see,’” said Randy
• MAKE THE TEAM
• BUILD YOUR CAREER
Almost everyone at a Nucor mill has a story about how the working environment and all-for-one mentality elevated their work life and inspired them to want to move past a job into a career. Despite being on the job less than a year, Mayra Gonzalez, a single mother of two originally from Mexico, has one such story. “I am a coil wrapper and handler; I prep the coils according to their packaging code and ship them out either by rail or truck,” she said. “My advice for others is to never give up. Everything is possible if you set your mind to it. I never really had a role model, so I became one to my daughters.”
TEAMMATE SPOTLIGHT
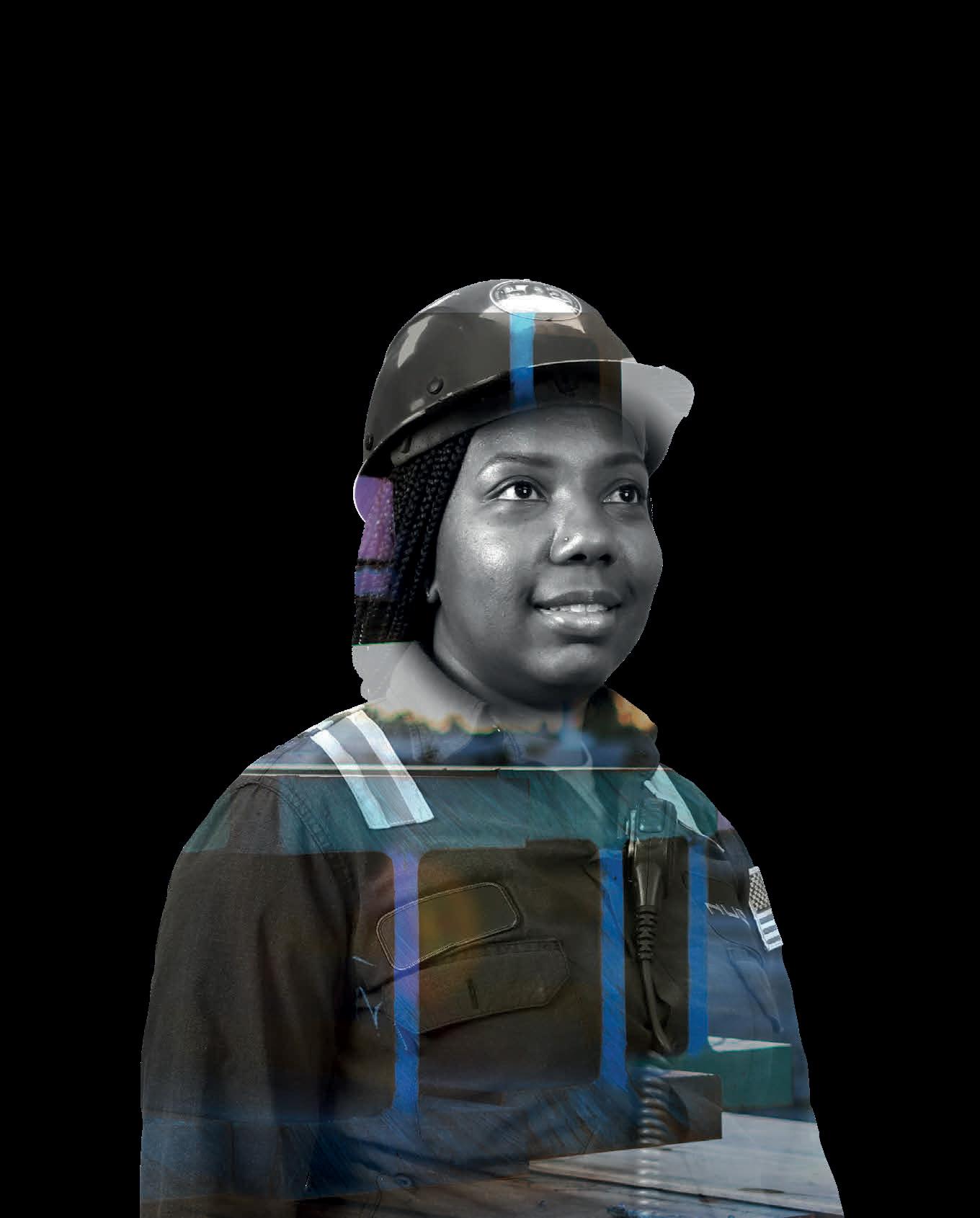
FRENZEL MORALES
PC Tech, Nucor Steel Arkansas
Country of Origin: The Philippines
Age: 27
Tenure with Nucor: 9 months
BLUEPRINT: How did you get interested in your career field?
FRENZEL MORALES: Growing up, I leaned toward technology, and I was a very curious person. Any toy I had, I broke it apart just to see how it functioned and how it worked. I took my first phone apart to see how it worked.

BP: What would surprise people about the level of technology at work in the steel plant?
FM: At Nucor, our biggest thing is safety. Some of the technology we’ve engineered works to take a person out of a dangerous position. Some of what we do is baseline work, but there’s a lot that’s more complicated. Last week I had to work on a computer that had specialty software just for that specific manufacturing area.
BP: Is all your work on PCs or do you work with the manufacturing equipment?
FM: We do a lot of what’s in-between, depending on where the equipment is out at the mill. It could be a computer, it could also be a printer, it could be a label printer that we print out labels to put on finished coils. If any of this equipment isn’t working, we swap it out and change it. And we have to work fast to get back up and running so it doesn’t stop production.
BP: What do you like about working at Nucor?
FM: Where do I start? I have a great team and my team always has my back. We’re working in an environment where there’s a lot of hot metal, and it can be somewhat dangerous. But at the same time, it’s all well thought out.
TEAMMATE SPOTLIGHT
A REVOLUTION IN STEEL
BLUEPRINT: How did you learn about opportunities at Nucor?
TYRONE DODD: During my senior year at school, I was selected for a Nucor pilot program, NuPath, that offers graduating Seniors the opportunity to interview for an entry level job at one of the Nucor Arkansas divisions. It was a great opportunity. After going through the interview process and graduation, I got hired on and learned even more while I was in training. I’ve learned something every day since I’ve been here.

BP: Now that you’re working at Nucor, what are your long-term goals?
TYRONE DODD
Buildings & Grounds, Nucor-Yamato Steel
Hometown: Blytheville
Age: 19
Tenure with Nucor: 6 months
TD: Right now, I am working with the building and grounds crew for a year to familiarize myself with the steel mill. After that, I can bid on an open job in another department where I want to work. So, I can go to the melt shop, shipping, anywhere I think I want to go.
BP: In your job today, is it a lot of solo work? Do you have a mentor? Do you work on a crew?
TD: The building and grounds crew consists of five people – me, three other men and our supervisor. They’re all my friends, they take care of me and have from day one. They are my mentors, teaching me everyday skills needed for my job. I see NYS as a diverse place to work. Everybody’s nice, everybody treats everyone the same, and everybody is a teammate on the same team.
DETERMINES EVERYTHING. WITH THE RIGHT ATTITUDE, NUCOR OFFERS UNLIMITED POSSIBILITIES." —RANDY HENDERSON
BLUEPRINT: Does working on heavy equipment run in your family? How did you get to work a crane?
JULIE PELTS: I originally set out to work in the office, but one day my manager encouraged me to get a feel for what is available at Nucor, so I rode in the crane for a bit and watched the guys run it. I thought, maybe I could do that.
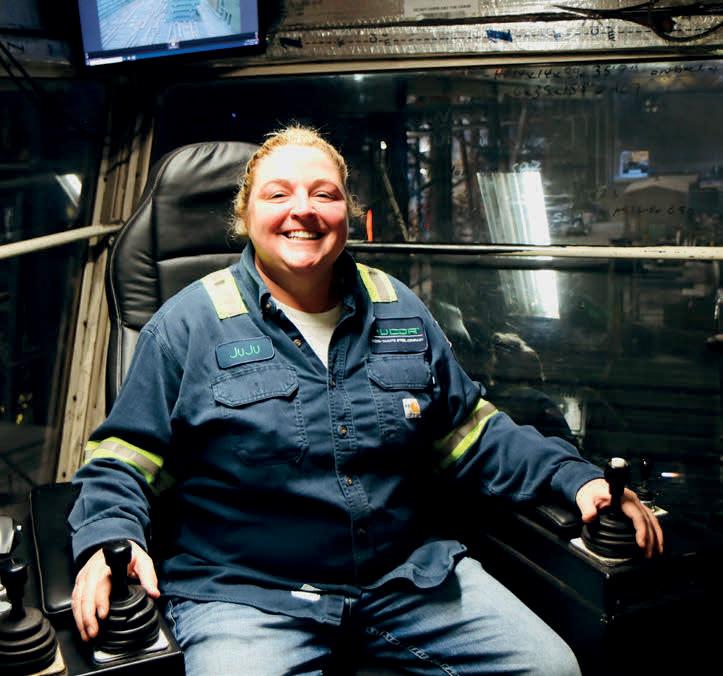
BP: What’s the formal training like?
JP: Training runs between 60 and 90 days. You get in the crane, and you have a trainer in there with you to explain everything about how to operate the crane. They eventually let you run for a little while, but they are always in the crane with you.
JULIE PELTS
Crane Operator, Nucor-Yamato Steel
Hometown: Cooter, Missouri
Age: 45
Years with the Company: 16
BP: What do you do during a typical shift? In the bloom yard we stack the steel. We cast it, we pick it up and put it in the yard and then we give it back to the roll mill for them to reheat and roll it.
BP: Have you had the opportunity to mentor other women in the same job?
JP: We have had a few other women come over here and I trained them. We also have Bloom Yard I and Bloom Yard II cranes and there have been women over there that I’ve helped train.
BP: Is it unusual for women to be crane operators? How were you accepted early on?
JP: Actually, at the time I started, we had quite a few women crane operators. And there’s another woman on our crew right now. In fact, I’ve been doing this for 13 years now. The guys were great and still are.
"ATTITUDE
JAMES JONES
BLUEPRINT: You have quite the connection to the Nucor plant, don’t you?
BP: What has been your experience working at Nucor?
A REVOLUTION IN STEEL
Lab Crew Leader, Nucor-Yamato Steel
Hometown: Blytheville
Age: 42
Years with Nucor: 13
JAMES JONES: My dad was one of the first people who helped to implement the design of the Nucor plant in Blytheville; he was a fabricator. When Nucor came to town my dad was one of the people who reviewed the plans and made the adjustments for real-time operation.
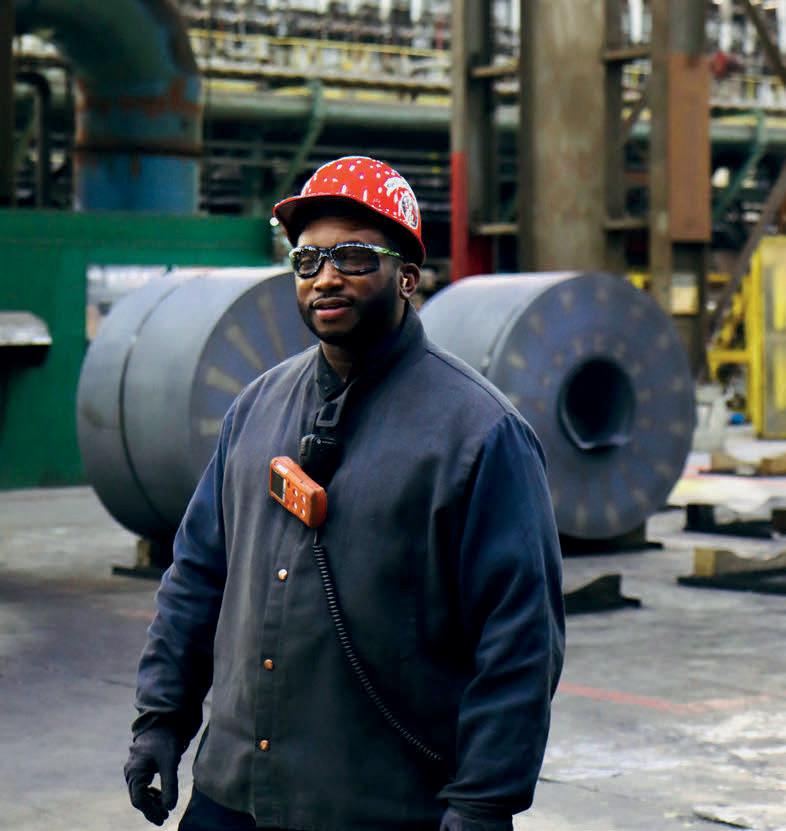
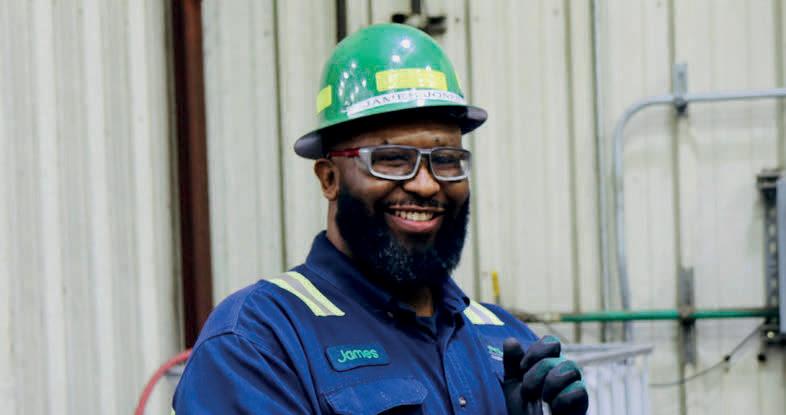
My dad was one of the first teammates at Nucor Yamato Steel. From the very beginning, he was able to provide our family with a good living and provided us with a lot of things that he could only dream of.
JJ: The people here care about you and treat you well in times of need. When my father was dying, my team said, “You do what you’ve got to do, and we’ll take care of everything else. You don’t have to worry.” I was able to spend time with him during his last days. Nucor wrapped me in an envelope of friendship and family so that it didn’t hurt as bad when I went back to work. So, yes, I have a little bit of heritage with this company and working here, it’s a personal thing for me.
RANDY HENDERSON
Safety Coordinator, Nucor Steel Arkansas
Age: 53
Years with the company: 26
BLUEPRINT: Where did you grow up?
RANDY HENDERSON: I was born and raised in Mississippi County, Arkansas.
BP: What brought you to Nucor?
RH: Like some in this area, I had a strong work ethic and limited skills. Nucor was willing to take a chance on me. I was hired in an entry level position, and I basically worked my way up from the bottom. Once I established myself within Nucor, my manager began to help push me out of my comfort zone to help me grow.
BP: Where did you start your career at Nucor?
RH: I started out as a shipper loader in the shipping material handling department. Before I knew it, 26 years had passed. I have held many different positions within Nucor, each a step up from where I started. I have also been involved in promoting and recruiting for Nucor within our hometown, as well as at many twoand four-year colleges. I am where I am today because Nucor allowed me the opportunity to grow, not only as a person, but as a leader for Nucor and our state.
BP: What helped you advance over that time?
RH: First and foremost, I had great Nucor mentors, people who took the time to help me and provide guidance. Second, the company presented me with a clear pathway to getting an education and reimbursing me for college courses. I went back to school and got my Associate of Art degree in technology and then, a year later, I got my undergraduate degree in technology. When I graduated, I had zero college debt; Nucor funded that 100 percent.
BP: Now that you’re a supervisor, what are some pieces of advice you give to new teammates about working here?
RH: I tell them the most important thing is your attitude. Attitude determines everything. With the right attitude, Nucor offers unlimited possibilities. That’s part of the Nucor brand, and I talk about that all the time. That is what I think makes Nucor stand out from the rest!
MAYRA GONZALEZ
Coil Wrapper/Handler, Nucor Steel Arkansas
Country of Origin: Mexico
Age: 38
Tenure with Nucor: 5 months
BLUEPRINT: Tell me about your background. MAYRA GONZALEZ: I’m a 38-year-old single mother of two teenage girls. I was born and raised in Mexico, but I have been living in Missouri for the last 23 years.
BP: What did you do before you joined Nucor?
MG: For 12 years I worked as a case manager for a federally funded nonprofit through the Department of Labor. One day I decided that I no longer had the passion for it and resigned. Shortly after that, a contractor company was needing a toolbox person to work during outages at various steel mills and keep inventory of tools. I obtained the job and worked my way to learn the proper tool names and got familiar with the steel mill environment.
BP: What do you like about Nucor?
MG: I like the learning opportunities. The company pays for your training and pays you while you train. In a short period of time with Nucor, I’ve taken advantage of the training and opportunities the company provides. I became a First Responder and a cab crane operator, and I got the opportunity to visit two Nucor plants in Kentucky for a Redline Audit.
BP: What would you tell someone looking to forge a career at Nucor?
MG: My advice for others is to never give up. Nucor encourages you to explore other jobs within the plant and move up and if you want to relocate to a different plant on another state, that is an option too.

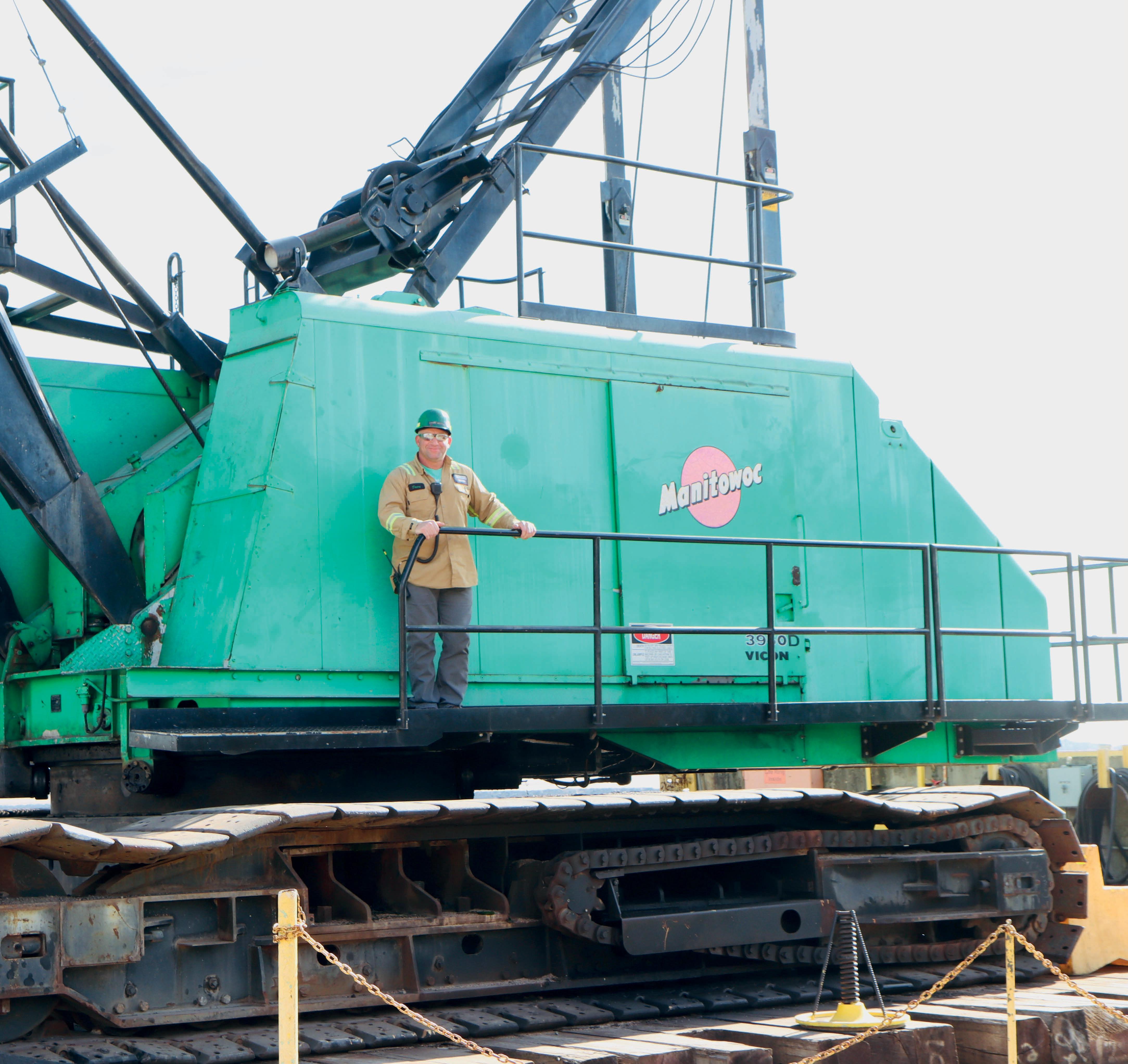
A REVOLUTION IN STEEL HOT JOBS!
PORT CRANE OPERATOR
DIVISION: Nucor-Yamato Steel and Nucor Steel Arkansas
AVERAGE STARTING SALARY: $83,000+
WHAT DOES THE JOB DO?
A port crane operator is responsible for port activities including river barge loading, equipment and port car repairs and oversight of all port personnel.
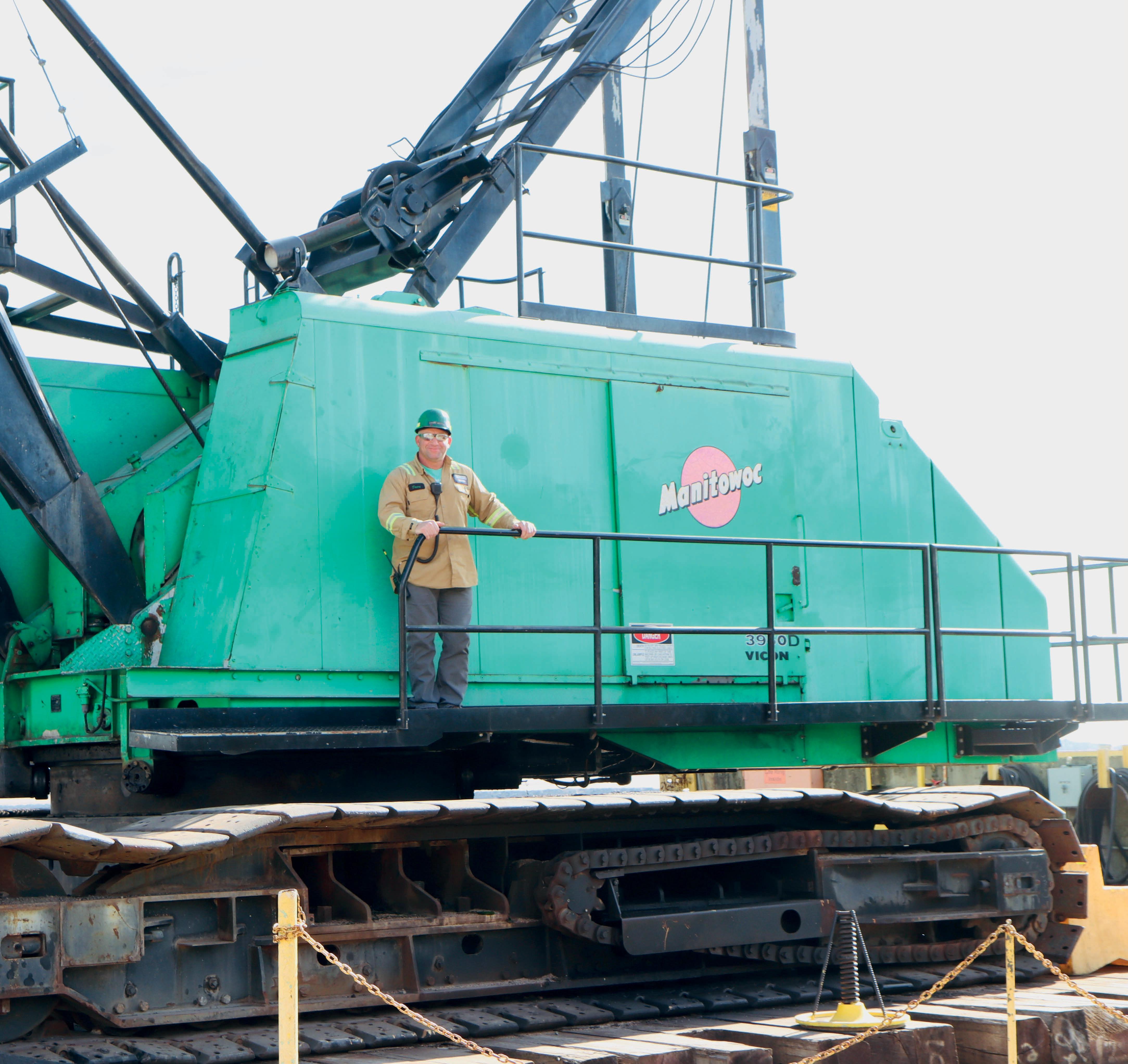
WHY IT’S IMPORTANT: Port crane operators are responsible for operating a crane to lift and move heavy objects in and out of barges. They are often tasked with moving large pieces of equipment or materials into place, but they may also be called upon to remove debris or clear an area of any obstructions that might get in the way of their work. Successful crane operators have extensive knowledge of how the crane operates, how to inspect the equipment for safe operations, as well as an understanding of hoisting mechanisms, rigging and load control. This includes knowing how to operate all of the various components as well as how these components interact with one another during normal operations. Most importantly, the port crane operator is responsible for the safety of the individuals within his or her area of operation.
SKILLS, EXPERIENCE AND ATTRIBUTES: Skills for success in this role include experience working a crane over the river, loading and unloading barges, rail cars, and/or trucks and previous rigging experience. Successful applicants must pass a depth-perception test.
WHAT MAKES THIS POSITION IN HIGH DEMAND?
The scarcity of crane operators with experience loading and unloading barges on the river makes this job in very high demand.
HOW DO I LEARN MORE? Please visit Nucor.com/careers to learn more about this opportunity.
PROCESS CONTROL
DIVISION: Nucor-Yamato Steel and Nucor Steel Arkansas AVERAGE STARTING SALARY: $110,000+
WHAT DOES THE JOB DO?
Process control engineers and technicians are highly trained maintenance personnel tasked with making the steel manufacturing process as efficient as possible. This means they help Nucor make steel safer, faster, at a lower cost and with higher quality.
WHY IT’S IMPORTANT: Making the steel process more efficient allows the company to sell steel to customers at a lower price. In the competitive steel market, having the lowest cost is essential for doing business. Accelerating the process automation helps make on-time deliveries.
SKILLS, EXPERIENCE AND ATTRIBUTES: Some of the skill sets for success in this role include database work, control systems, web development and mathematical modeling.
WHAT MAKES THIS POSITION IN HIGH DEMAND? Level II and Level III skill sets are exceedingly rare. Most of these positions are held by electrical engineers or technicians with equivalent experience. There are plenty of positions in this job area that require only a two-year degree, and with Nucor’s policy of promoting from within and its programs to assist teammates with education and skill development, these jobs often lead to rapid advancement.
HOW DO I LEARN MORE? Please visit Nucor.com/careers to learn more about this opportunity.
Nucor promotes continuous skills learning for teammates.
LEARN TO EARN TRAINING PROGRAMS SET UP TEAMMATES FOR SUCCESS TODAY, ADVANCEMENT TOMORROW
Few manufacturing jobs in Arkansas carry as many perks and benefits as working for Nucor Steel Arkansas or Nucor-Yamato Steel (NYS). From high pay to generous benefits, the compensation offered here is well known. But ask anyone who works here, and they will also point to the personal growth and skills development they have achieved as a result of the company’s mentality of continuous improvement.
“They are eager to send you to training and that’s probably one of my favorite things about working here,” said Ethan Green, an industrial electrician who’s been on board for 18 months. “If you want to learn something, they are willing to teach it or send you to a place that will teach you.”
Like a lot of new hires, Green didn’t have well-developed technical experience coming out of high school. But thanks to a steel tech internship, an educational partnership between Nucor and Arkansas Northeastern College in Blytheville, he was able to learn quickly.
“My internship definitely helped a lot, plus working out here in the mill,” he said. “The stuff in the book is great, but you can’t really do much with it until you apply it out there in the field. I worked with the day guys and the shift guys seeing what their job roles were. They helped me with questions I had from school and showed me what the job was really like.”
Tyler Avery, project electrical automation technician for NYS, knows the value of the internship well. A decade ago, the 28-year-old was the very first electrical intern to go through the program.
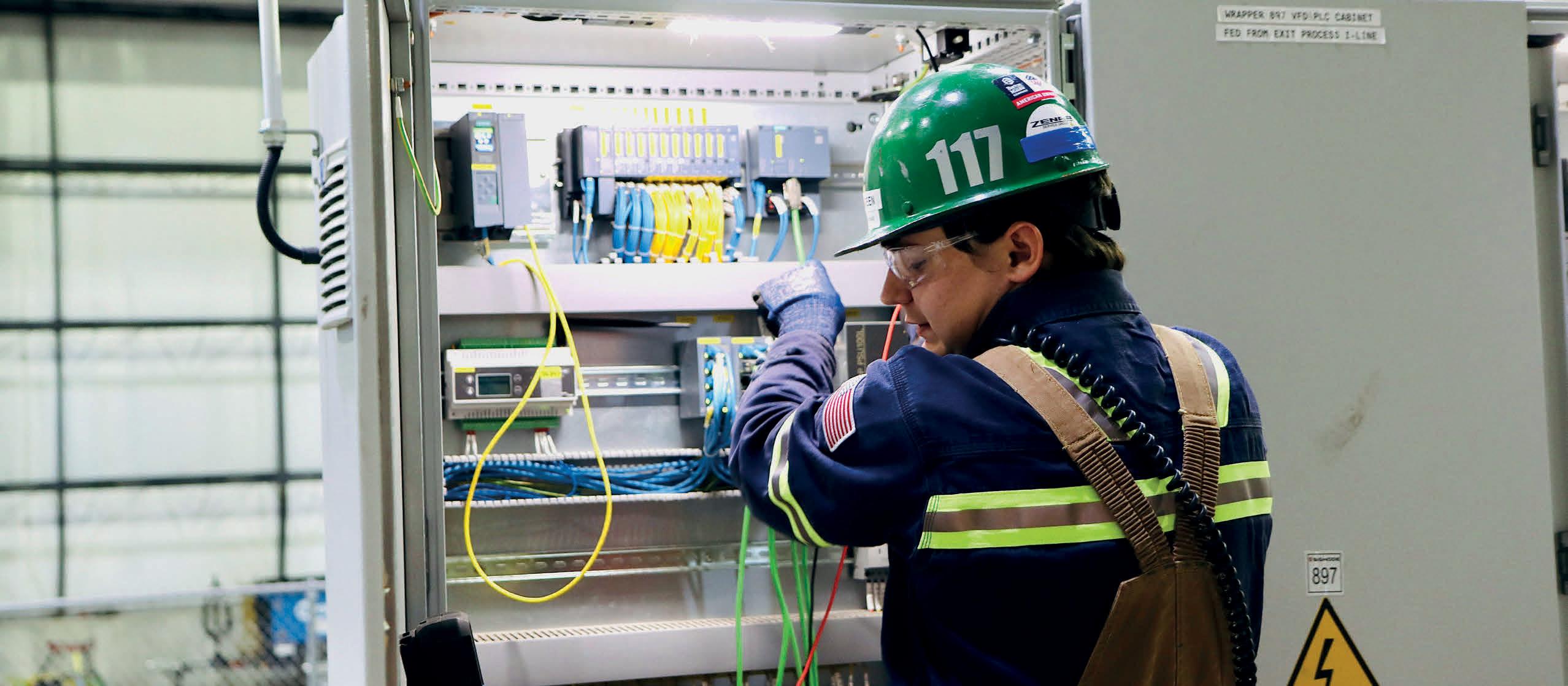
Avery said he’s not anti-college; in fact, he’s gone back to school to finish his degree, paid for by Nucor.
“Now that I’m mature enough to take it seriously, Nucor is paying for me to go back to school to get my four-year education,” he said. “I’ve done the electrical side, I’ve done the automation side and now I’m getting into the supervision side, so I’m learning about leadership roles. That’s definitely given my career a head start.”
As robust as the formal training programs are here, some of the best training comes outside the classroom, shared on the job and handed down from one generation of Nucor teammate to another. Charles Casey, Cold Mill 2 Supervisor at Nucor Steel Arkansas and a 31-year veteran of the company, said it’s been this way for as long as he can remember.
“Our guys on the floor are really good about taking their time to train newer folks and show them what needs to be done, how to work safely,” he said. “How we approach and talk to our leads out on the floor, that is us extending a helping hand to our new guys. There’s a lot of mentorship.
When a new teammate shows up, before they do the job that they’re hired to do, they work with a veteran teammate who’s doing that job, and they will not be released to do that job on their own until their mentor thinks they’re ready to go.
DISCOVER THE OPPORTUNITIES
“When I was in high school, I knew college wasn’t for me,” he said. “So, I chose to get a skilled trade and with Nucor’s help, I’m doing right now what an electrical engineer typically does.”
LEARN YOUR TRADE
• MAKE THE TEAM
“I tell young people all the time that Nucor is a place where what you’ve got to do is have a desire to come to work and put your head down and work hard and work safe. You are in control of your entire career here. If you’re here on time and do a good job, the sky is the limit for you.”
• BUILD YOUR CAREER
TEAMMATE SPOTLIGHT
BLUEPRINT: Did you have an idea of what you wanted to do when you were growing up?
A REVOLUTION IN STEEL
ETHAN GREEN: My father and my grandfather were industrial electricians, and my dad actually works at the Nucor-Yamato steel mill. So, I did have a pretty good idea., I just wasn’t sure how I was going to get into it. I heard about the steel tech program at Arkansas Northeastern College, and I decided to do that. I landed an internship and here I am.
BP: Did you do any advanced training when you were still in high school knowing you wanted to get into electrical work? Or did it all start in college?
ETHAN GREEN
Industrial Electrician, Nucor Steel Arkansas
Hometown: Gosnell
Age: 21
Years with Nucor: 1.5
EG: Not so much electrical. I was taking some welding classes at the college, but that was it. I just kind jumped into electrical when I got into the steel tech program.
BP: How did you combine what you learned in the classroom with what you were learning on the job?
EG: I worked with the day guys and the shift guys seeing what their job roles were. They would help me with questions I would have from school, and I would get to work alongside with them and troubleshoot, go on calls and kind of see what was going on and what life was like at the steel mill.
BP: What are your job responsibilities, generally speaking?
EG: My responsibility as a shift electrician is to take care of the line, make sure it stays running. We do anything from wiring all the way to the programming.
BP: How have you, as a new employee, gotten up to speed quickly?
EG: Working alongside my teammates and just putting my hands on the equipment were the biggest things. I get to work with mechanics and other electricians and production folks, and we work as a team be really effective.
ASHLEY KROLL Environmental Coordinator Management Rep/Nucor-Yamato SteelHometown: Manila, AR
Age: 30
Years with Nucor: 12
BLUEPRINT: You started with Nucor at a pretty young age. How did that come about?

ASHLEY KROLL: I started when I was 18 in a two-year steel industry technology internship with Nucor, a month after high school graduation. An engineer from Nucor came to talk to our physics class during my senior year. I was undecided about what I wanted to do, and when she told us about the internship program, I was like, sign me up.
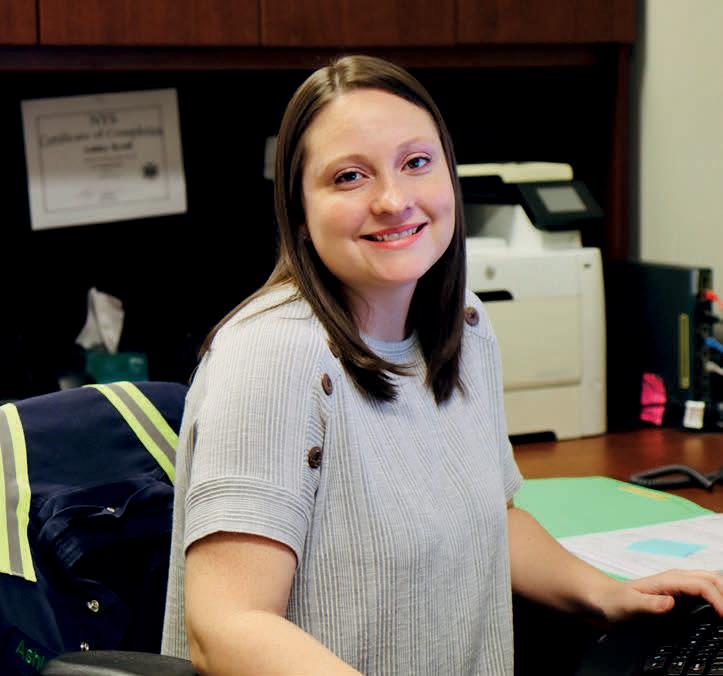
BP: Was college an option for you at that point?
AK: I was definitely not looking forward to racking up debt. I was struggling to figure out how I was going to make college work. I wanted to have a good career and start my life.
BP: How did that internship help you make that happen?
AK: I worked part time while I was going to college. The internship required that you had to keep good grades, to be at work on time, to have a positive attitude and most importantly, to make sure you were following the safety rules and doing your job duties as well. At the end of the two years, they offered me a full-time job.
BP: Did you have any experience in manufacturing or the trades prior to getting this internship?
AK: No, and honestly, I did not know a thing about the steel industry. When I stepped foot out here for the first time – and this place is huge, a lot of moving equipment, so many cranes and Taylor forklifts – I was just astonished and a little intimidated. It was amazing.
BP: You must be very proud of what you accomplished.
AK: I am extremely proud. And I’ll tell you this: I think Nucor is proud too. The teammates I work with, I think they’re proud of where I started and how far I’ve come. A lot of them have helped me along the way. I would say my hometown of Manila, AR, is very proud to have produced a young woman from that small town and that small high school who has accomplished so much.
DISCOVER THE OPPORTUNITIES • MAKE THE TEAM LEARN YOUR TRADE • BUILD YOUR CAREER
“IF YOU WANT TO LEARN SOMETHING, THEY ARE WILLING TO TEACH IT, OR SEND YOU TO A PLACE THAT WILL TEACH YOU.” —ETHAN GREEN
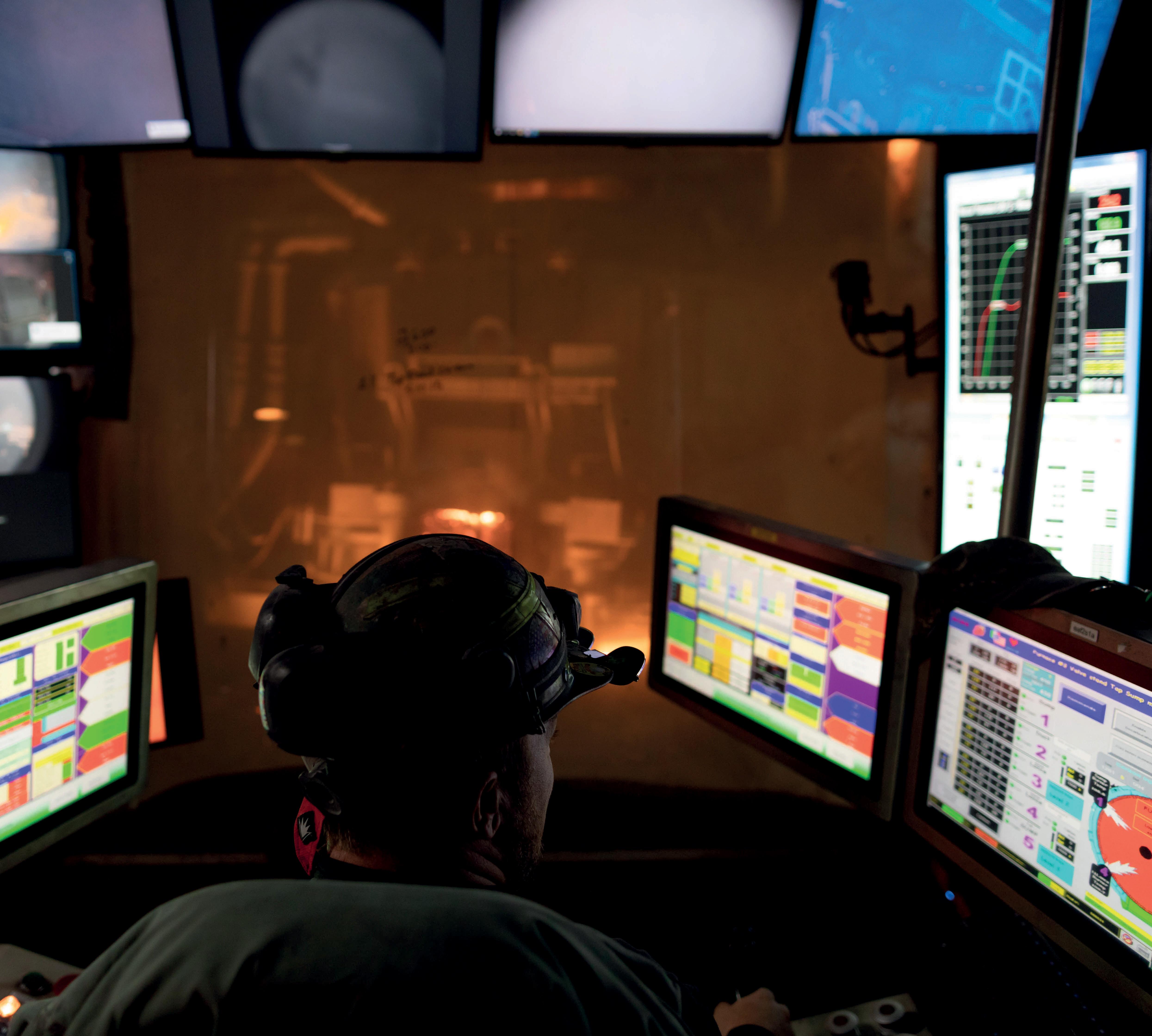
TEAMMATE SPOTLIGHT
A REVOLUTION IN STEEL
JOSH PAYNE
Cold Mill Electrician Lead, Nucor Steel Arkansas
Hometown: Senath, Missouri
Age: 39
Years with Nucor: 11 years
BLUEPRINT: Growing up, did you have a good idea of what you wanted to do?
JOSH PAYNE: My story is a little different than many of my teammates. I went to college to study early childhood education. But after I graduated with a bachelor’s degree, I realized education was not really what I wanted to do. I wanted to come to work for Nucor. They offered me an electrical apprenticeship; it’s a two-year program, and I finished it in eight months.
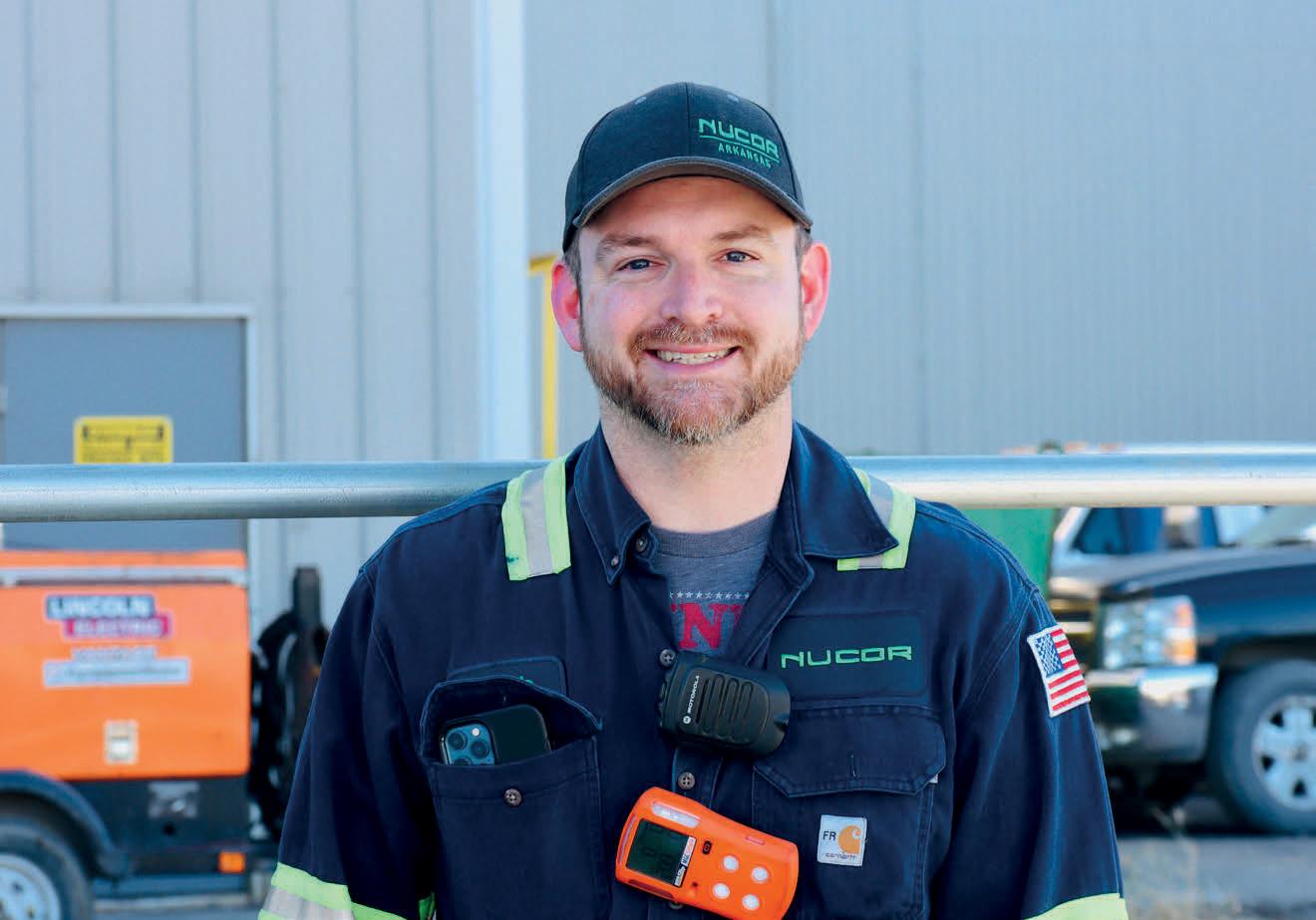
BP: What did that program entail?
JP: In the electrical apprenticeship program, they put me to work, and they moved me around to different departments. I worked in the cold mill, then the metal shop, the caster deck, and then with the electrical team. They were training me and teaching me on the job at the same time I was taking college classes that Nucor paid for.
BP: What was that like?
JP: I worked areas that were completely foreign to me. It was all new. The guys I worked with were all veteran electricians, and they were able to help me pick up on things and learn the electrical aspects of it.
BP: What advice do you have for a young person who doesn’t have a plan for what they want to do?
JP: I did the same thing. I got here having process knowledge that I could apply enabling me to troubleshoot things, because I knew what the equipment was supposed to do. I use my background in the education field every day to train people, to talk to people and to help people understand.
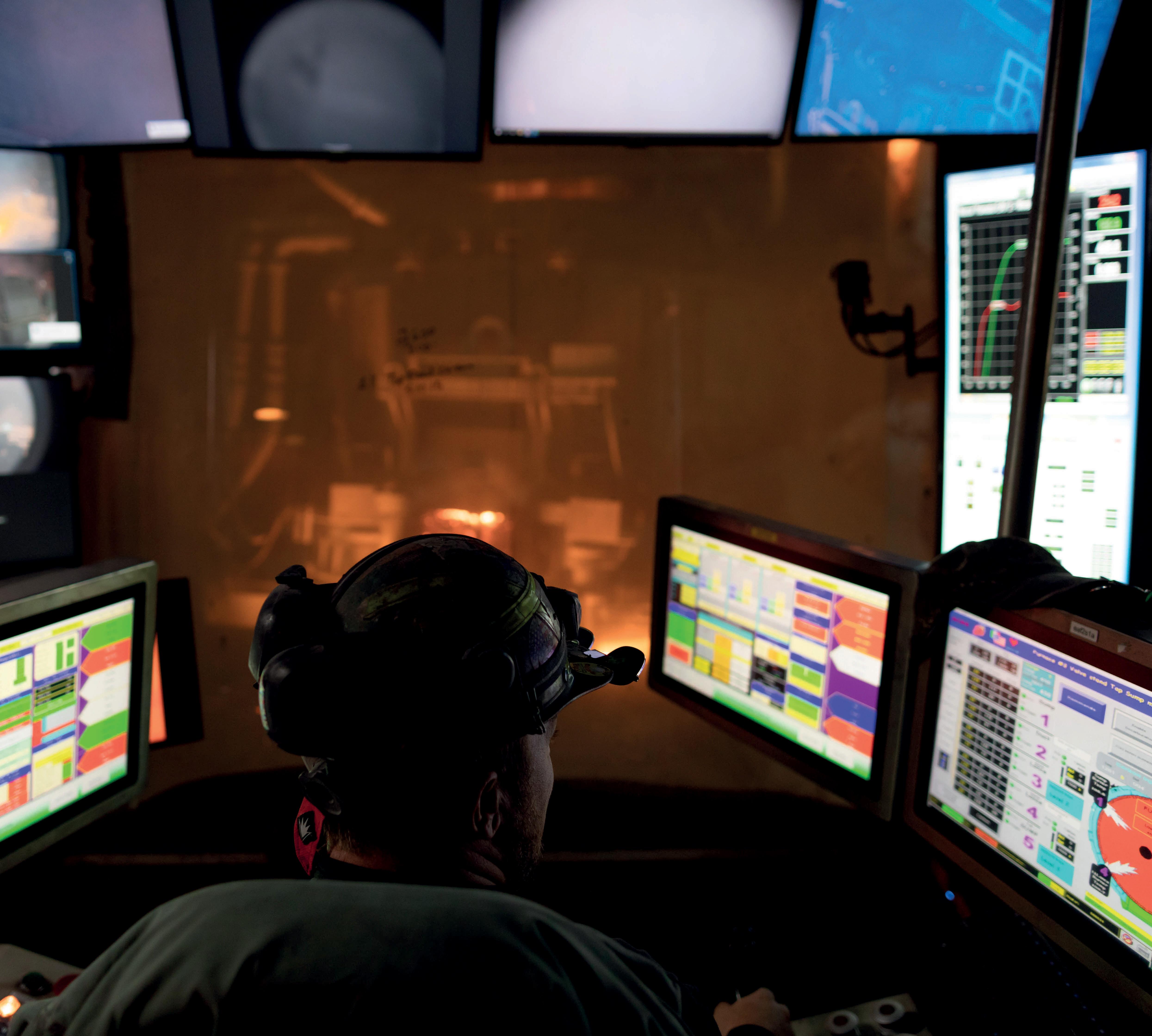
BP: Why would you recommend Nucor?
DISCOVER THE OPPORTUNITIES
JP: Coming into Nucor, you have the opportunity to move in any direction you want. If you want to do something at Nucor, everything is laid out and it’s there for you to go and get it.
LEARN YOUR TRADE
• MAKE THE TEAM
• BUILD YOUR CAREER
NUCOR: A REVOLUTION IN STEEL
NUCOR: A REVOLUTION IN STEEL
HOT JOBS!
HOT JOBS!
ENVIRONMENTAL ENGINEER
ENVIRONMENTAL ENGINEER
A REVOLUTION IN STEEL
DIVISION: Nucor-Yamato Steel and Nucor Steel Arkansas
DIVISION: Nucor-Yamato Steel and Nucor Steel Arkansas
AVERAGE STARTING SALARY: $64,000+ based on experience
AVERAGE STARTING SALARY: $64,000+ based on experience
WHAT DOES THE JOB DO? Support safety, environmental compliance and outreach efforts while promoting the mission of the organization within the division and community. Implement and manage the ISO 14001 Environmental Management System.
WHAT DOES THE JOB DO? Support safety, environmental compliance and outreach efforts while promoting the mission of the organization within the division and community. Implement and manage the ISO 14001 Environmental Management System.
• Build relationships with governmental, industry and community organizations.
• Build relationships with governmental, industry and community organizations.
• Oversee internal and external audits.
• Oversee internal and external audits.
• Ensure environmental objectives are met.
• Ensure environmental objectives are met.
• Develop and conduct environmental training.
• Develop and conduct environmental training.
• Facilitate community outreach programs.
• Facilitate community outreach programs.
• Engage the plant-wide team to identify and assist in continual improvement initiatives.
• Engage the plant-wide team to identify and assist in continual improvement initiatives.
• Take a lead role in safety initiatives.
• Take a lead role in safety initiatives.
• Maintain required emergency contingency plans.
• Maintain required emergency contingency plans.
WHY IT’S IMPORTANT: There are many environmental laws that govern industry and businesses, laws created to protect our air, water and land. Environmental engineers design, build and operate equipment and systems that give industry the ability to operate while staying within environmental laws. Some of the equipment and systems used in industry are wastewater treatment plants, baghouses, fume exhausts, fume
WHY IT’S IMPORTANT: There are many environmental laws that govern industry and businesses, laws created to protect our air, water and land. Environmental engineers design, build and operate equipment and systems that give industry the ability to operate while staying within environmental laws. Some of the equipment and systems used in industry are wastewater treatment plants, baghouses, fume exhausts, fume
SYSTEMS/NETWORK ENGINEER
SYSTEMS/NETWORK ENGINEER
DIVISION: Nucor-Yamato Steel and Nucor Steel Arkansas
DIVISION: Nucor-Yamato Steel and Nucor Steel Arkansas
AVERAGE STARTING SALARY: $70,000 + based on experience
AVERAGE STARTING SALARY: $70,000 + based on experience
WHAT DOES THE JOB DO?
WHAT DOES THE JOB DO?
Design, configure, secure, maintain and troubleshoot networks and networking systems. Work with users in full life-cycle software development including gathering requirements, designing solutions, developing full-stack applications and supporting those applications in production. Collaborate with individuals both in IT and across the organization
Design, configure, secure, maintain and troubleshoot networks and networking systems. Work with users in full life-cycle software development including gathering requirements, designing solutions, developing full-stack applications and supporting those applications in production. Collaborate with individuals both in IT and across the organization
WHY IT’S IMPORTANT:
WHY IT’S IMPORTANT:
Advancements in technology enable manufacturers to safely streamline production processes, innovate at a faster pace, reduce cost and deliver higher-quality products to meet customer demand. Systems and network engineers are crucial to installing, configuring, maintaining and securing the technology that enable these processes to run.
Advancements in technology enable manufacturers to safely streamline production processes, innovate at a faster pace, reduce cost and deliver higher-quality products to meet customer demand. Systems and network engineers are crucial to installing, configuring, maintaining and securing the technology that enable these processes to run.
SKILLS, EXPERIENCE AND ATTRIBUTES FOR SUCCESS:
SKILLS, EXPERIENCE AND ATTRIBUTES FOR SUCCESS:
1. Experience in an IT environment administering and supporting systems and network infrastructure or a bachelor’s degree in information systems, computer science, TSM or related field.
1. Experience in an IT environment administering and supporting systems and network infrastructure or a bachelor’s degree in information systems, computer science, TSM or related field.
scrubbers, thermal and catalytic oxidizers, cooling towers and landfills. An environmental engineer applies the correct technology to ensure compliance with state and federal environmental laws.
scrubbers, thermal and catalytic oxidizers, cooling towers and landfills. An environmental engineer applies the correct technology to ensure compliance with state and federal environmental laws.
SKILLS, EXPERIENCE AND ATTRIBUTES:
SKILLS, EXPERIENCE AND ATTRIBUTES:
• Bachelor’s degree in environmental engineering, related discipline or equivalent experience.
• Bachelor’s degree in environmental engineering, related discipline or equivalent experience.
• Previous experience in environmental engineering or equivalent field.
• Previous experience in environmental engineering or equivalent field.
• Environmental compliance experience.
• Environmental compliance experience.
• Permitting experience (Title V, PSD, NPDES).
• Permitting experience (Title V, PSD, NPDES).
• Knowledge of pollution control equipment, CEMS, drinking/ wastewater systems and ISO 14001 Environmental Management Systems.
• Knowledge of pollution control equipment, CEMS, drinking/ wastewater systems and ISO 14001 Environmental Management Systems.
• Experience with ISO 14001 or related systems.
• Experience with ISO 14001 or related systems.
WHAT MAKES THIS POSITION IN HIGH DEMAND?
WHAT MAKES THIS POSITION IN HIGH DEMAND?
Environmental laws are becoming increasingly more stringent because protecting the environment is even more of a priority in society. At the same time, there’s a worldwide demand for more complex products. The technology used in the environmental field is therefore becoming more complex, and new technologies are being created every day to minimize and control waste. Environmental engineers are at the forefront of creating and operating these new technologies.
Environmental laws are becoming increasingly more stringent because protecting the environment is even more of a priority in society. At the same time, there’s a worldwide demand for more complex products. The technology used in the environmental field is therefore becoming more complex, and new technologies are being created every day to minimize and control waste. Environmental engineers are at the forefront of creating and operating these new technologies.
HOW DO I LEARN MORE? Please visit Nucor.com/careers to learn more about this opportunity.
HOW DO I LEARN MORE? Please visit Nucor.com/careers to learn more about this opportunity.
4. MCSA certification or equivalent.
4. MCSA certification or equivalent.
5. Net+, CCNA certification or equivalent.
5. Net+, CCNA certification or equivalent.
6. Experience in the following areas:
6. Experience in the following areas:
• Cisco switches, firewalls and wireless LAN controllers
• Cisco switches, firewalls and wireless LAN controllers
• VMWare • PowerShell scripting
• VMWare • PowerShell scripting
• VPN technologies
• VPN technologies
• VOIP technologies
• VOIP technologies
• Microsoft PowerApps
• Microsoft PowerApps
• Fiber optic termination
• Fiber optic termination
• SharePoint administration
• SharePoint administration
• SAN administration
• SAN administration
7. Project management experience8. Customer support/help desk experience.
7. Project management experience8. Customer support/help desk experience.
WHAT MAKES THIS POSITION IN HIGH DEMAND?
WHAT MAKES THIS POSITION IN HIGH DEMAND?
Systems and network engineers play an essential role in any organization. Due to the growth and expansion of Nucor, this position is even more essential to support not only the existing and expanding infrastructure, but to provide the tools and technology to help the company become the safest steel manufacturer in the world.
Systems and network engineers play an essential role in any organization. Due to the growth and expansion of Nucor, this position is even more essential to support not only the existing and expanding infrastructure, but to provide the tools and technology to help the company become the safest steel manufacturer in the world.
DISCOVER THE OPPORTUNITIES
2. Knowledge of TCP/IP, sub-netting and VLANs.
2. Knowledge of TCP/IP, sub-netting and VLANs.
LEARN YOUR TRADE
3. Experience managing Active Directory, DNS, DHCP and Windows servers.
3. Experience managing Active Directory, DNS, DHCP and Windows servers.
• MAKE THE TEAM
•
BUILD YOUR CAREER
HOW DO I LEARN MORE? Please visit Nucor.com/careers to learn more about this opportunity.
HOW DO I LEARN MORE? Please visit Nucor.com/careers to learn more about this opportunity.
TEAMMATE SPOTLIGHT
A REVOLUTION IN STEEL
TYLER AVERY
Project Electrical Automation Technician, Nucor-Yamato Steel
Hometown: Blytheville
Age: 28
Years with Nucor: 9
BLUEPRINT: You were part of the Nucor internship program, is that correct?
TYLER AVERY: I was the very first electrical intern in the Nucor internship program between Nucor and Arkansas Northeastern College. I was kind of like a guinea pig. Now that internship program is one of the most successful programs with Nucor and ANC.
BP: Did you have any role models in the skilled careers growing up?
TA: I knew about skilled trades from the get-go. My dad is a welder and I’ve always worked with my hands with carpentry, working around the house, helping my dad. I ended up wanting to be an electrician.
BP: There are a lot of stereotypes about skilled careers. What’s the reality?
TA: As long as someone is willing to work, willing to challenge themselves, the opportunities at Nucor are endless.
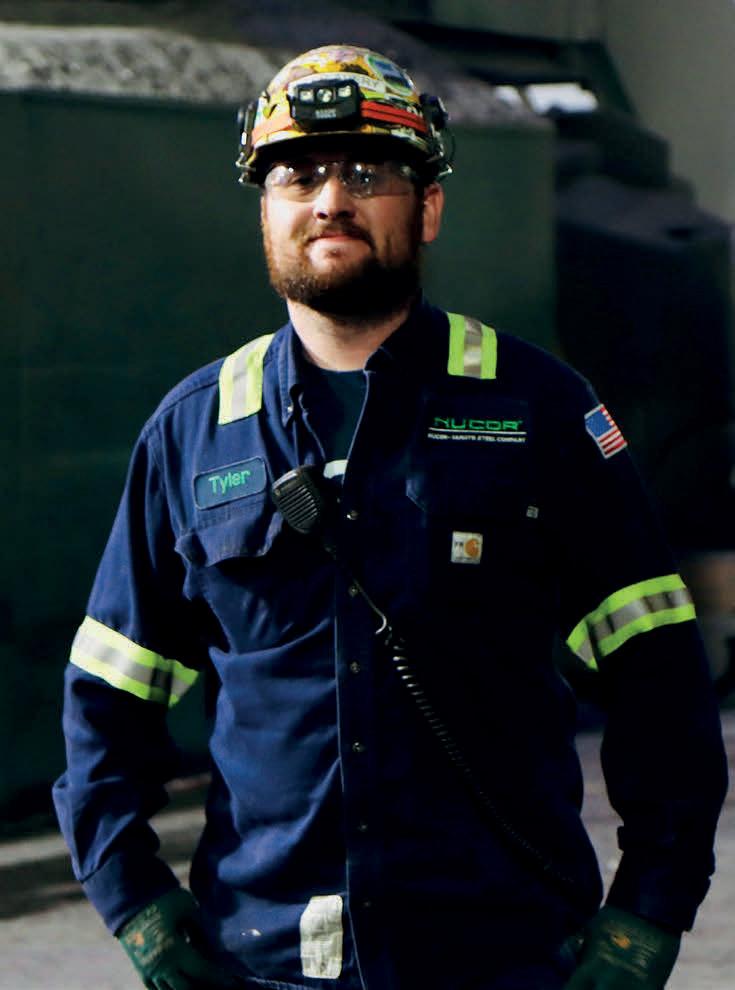

CHRISTIAN WILLIAMS
Melt Shop Mechanic, Nucor Steel Arkansas
Hometown: Paragould
Age: 20
BLUEPRINT: What’s a typical day like?
CHRISTIAN WILLIAMS: On a typical day I check my emails, do my inspections, and walk around the mill and make sure everything is running well. I talk to my operators and then I’m on call for anything that goes wrong. I assist with mechanics, helping them with their projects.
BP: What’s your schedule?
CW: I work four-on/four-off rotating nights and days. I work 12-hour shifts and during that 12-hour shift I’ll be on call. If our boss needs us, we’ll go in and take care of what we need to do.
BP: What do you like about your job?
CW: It’s something different every day.
BP: What soft skills are most important?
CW: Being on time and communication skills are important, but safety is the number one factor.
DISCOVER THE OPPORTUNITIES • MAKE THE TEAM
LEARN YOUR TRADE • BUILD YOUR CAREER
TECHNOLOGY FORWARD
TECHNOLOGISTS IN DEMAND AS COMPUTERS POWER TODAY’S STEEL MILLS, MANUFACTURING
A couple of generations ago, working in a steel mill was among the dirtiest, most physically demanding and potentially dangerous careers a person could have. But times have changed, as has the steel industry itself.
Today’s mills bear little resemblance to the fire-breathing factories of old, as computerization, robotics, artificial intelligence, and the Internet of Things help to run the show.
It’s a bold new chapter in manufacturing, demanding that employees with wide-ranging skill sets operate, troubleshoot and maintain high-tech equipment and the network backbone behind it.
Logan Nielsen, IT Leader for the Software Development team with NucorYamato Steel, has been with the company for five years.
“The software my team writes generally creates dashboards and interfaces for users to work with data,” he said. “Our customer is everyone out in the mill. I get a request every week for an application that needs to be written to display data or work with data to make the job out there easier.
“We create analytics and program a lot of reporting applications to show how well a crew is working, and if there were any issues or downtime. Probably the most fun part of my job is creating interfaces and dashboards that are easy to use as well as useful.”
Katie Behrendt, Sales Metallurgist with Nucor Steel Arkansas, said the massive amount of data captured continuously in the mill feeds even more sophisticated technology to keep the plant running at peak proficiency, right down to individual machines.
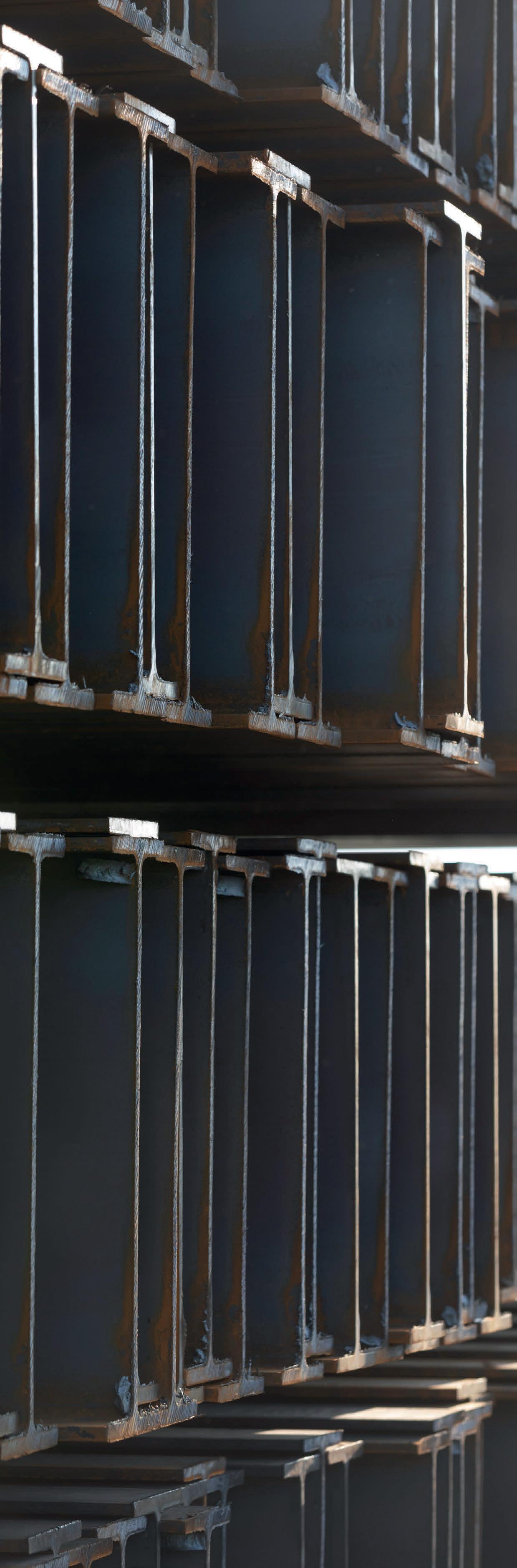
she said. “That could be something like an electric vehicle company needing a higher-strength steel or a thinner steel to build a new car. We can use the data we’ve collected from our mills here to design and develop new processes and new materials to meet our customers’ needs.”
Technology is also leveraged throughout the plant to help the company maintain its strict safety standards in an environment featuring furnaces that reach almost 3,000 degrees Fahrenheit, said Damilola Balogun, Plant Metallurgist for Nucor-Yamato Steel.
“We use a lot of robots in safety,” he said. “We don’t want teammates close to the furnace while working. I don’t have to go to the front of an electric arc furnace to take temperatures, we have a robotic hand that goes into the steel, takes temperatures and comes out.”
Managing this new, highly advanced workplace requires a different set of skills than steel teammates of the past might have had, but it’s not all keyboards and coding that Nucor leadership is looking for. Soft skills, such as the ability to work as a team and the ability to communicate well, are equally critical.
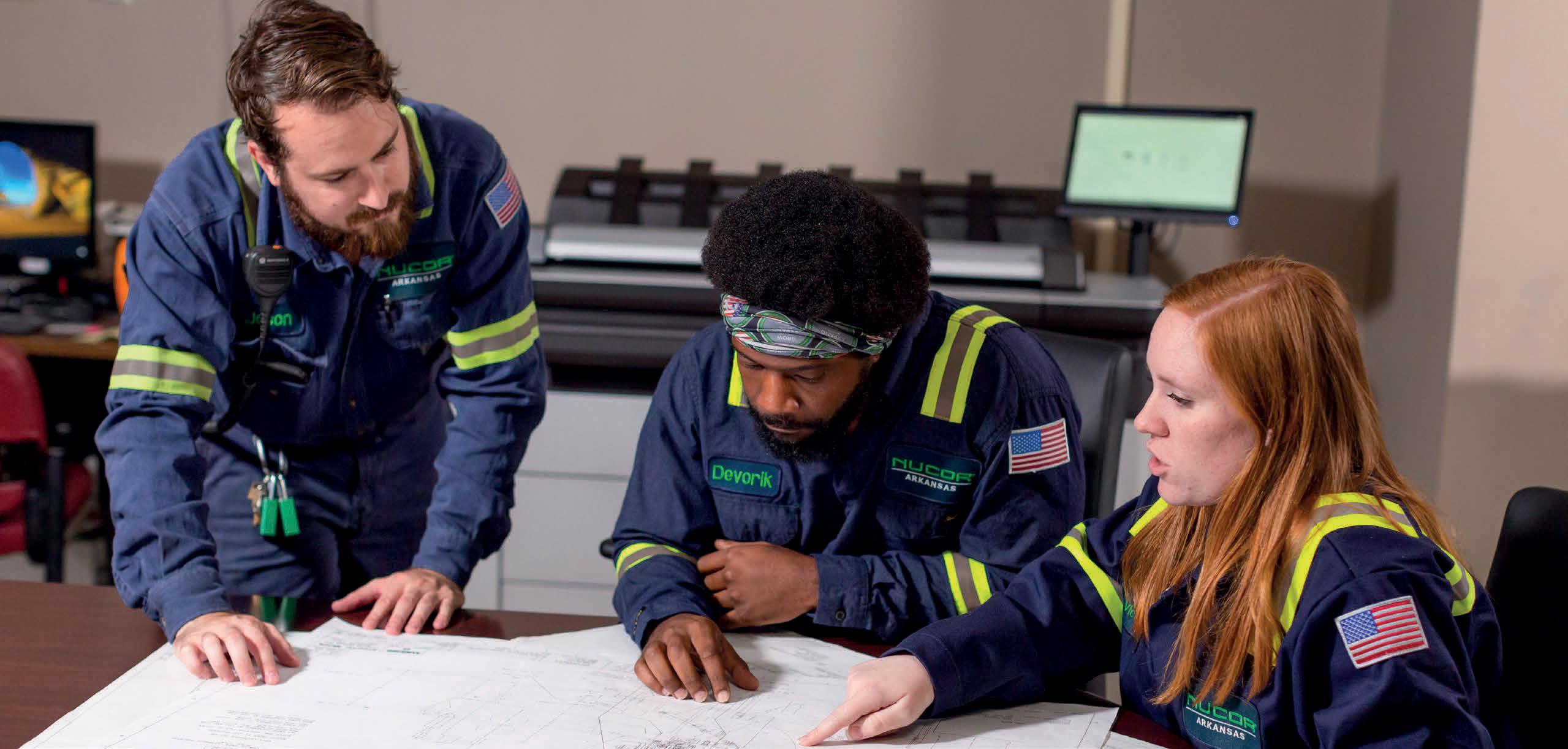
DISCOVER THE OPPORTUNITIES
LEARN YOUR TRADE
“The big things in technology we’re using and trying to make more use of are data analysis, machine learning and advanced automation techniques,”
• MAKE THE TEAM
• BUILD YOUR CAREER
“The old stereotype of the IT person sitting and typing away on a keyboard doesn’t exist here,” said Nishant Varadachari, IT Lead for business process for Nucor-Yamato Steel. “We get requests all the time from the mill, and we have to be able to follow up on that and ask questions so whatever we’re producing makes their lives easier. At every stage, our teammates have to be able to communicate, both in-person and over the phone, to ask questions, gather feedback and explain things. “In our company, skills can be taught, but it’s those natural communication skills and people skills that are truly valuable. They are what’s at the heart of Nucor.”
TEAMMATE SPOTLIGHT
A REVOLUTION IN STEEL
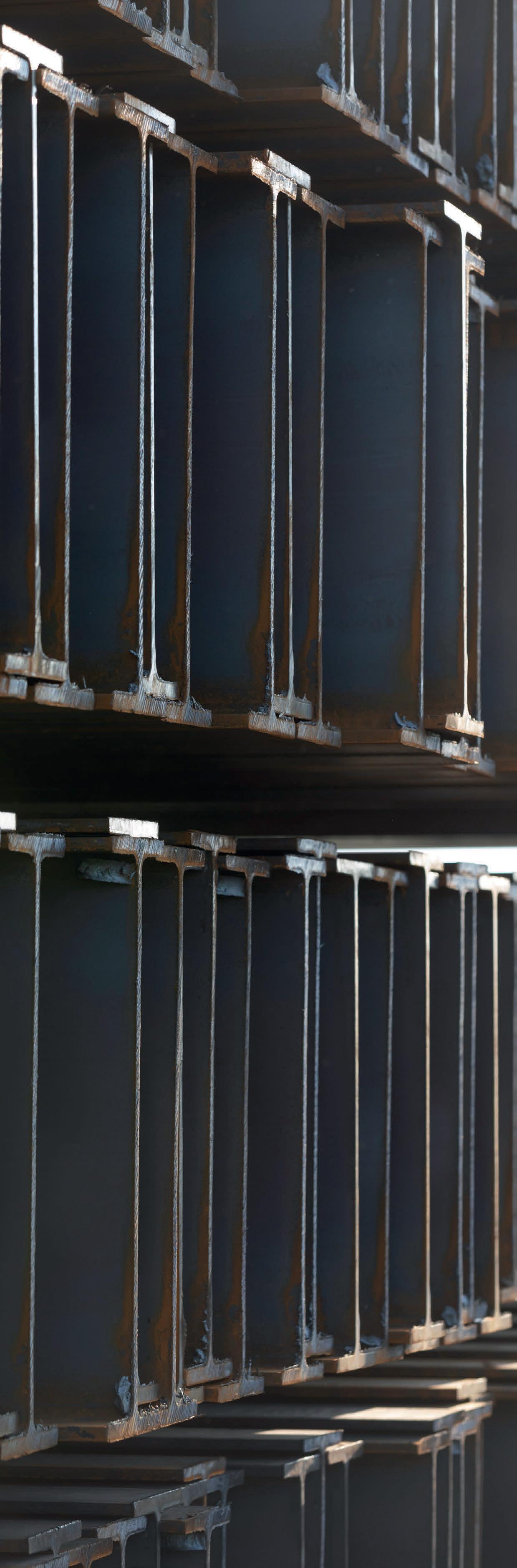
DAMILOLA BALOGUN
Plant Metallurgist, Nucor-Yamato
Home Country: Nigeria
Age: 26
Work Tenure: 6 months
BLUEPRINT: How did your professional journey lead you to Arkansas?
DAMILOLA BALOGUN: I have been in the United States for four years. I went to school at Missouri University of Science and Technology in Rolla, Missouri to obtain my doctorate in Metallurgy.
I’ve always wanted to work in a very big steel mill. Nucor is the largest steel manufacturer in the United States and our division, Nucor-Yamato Steel, is the largest manufacturer of beams in the United States.
BP: What do you like best about working at Nucor?
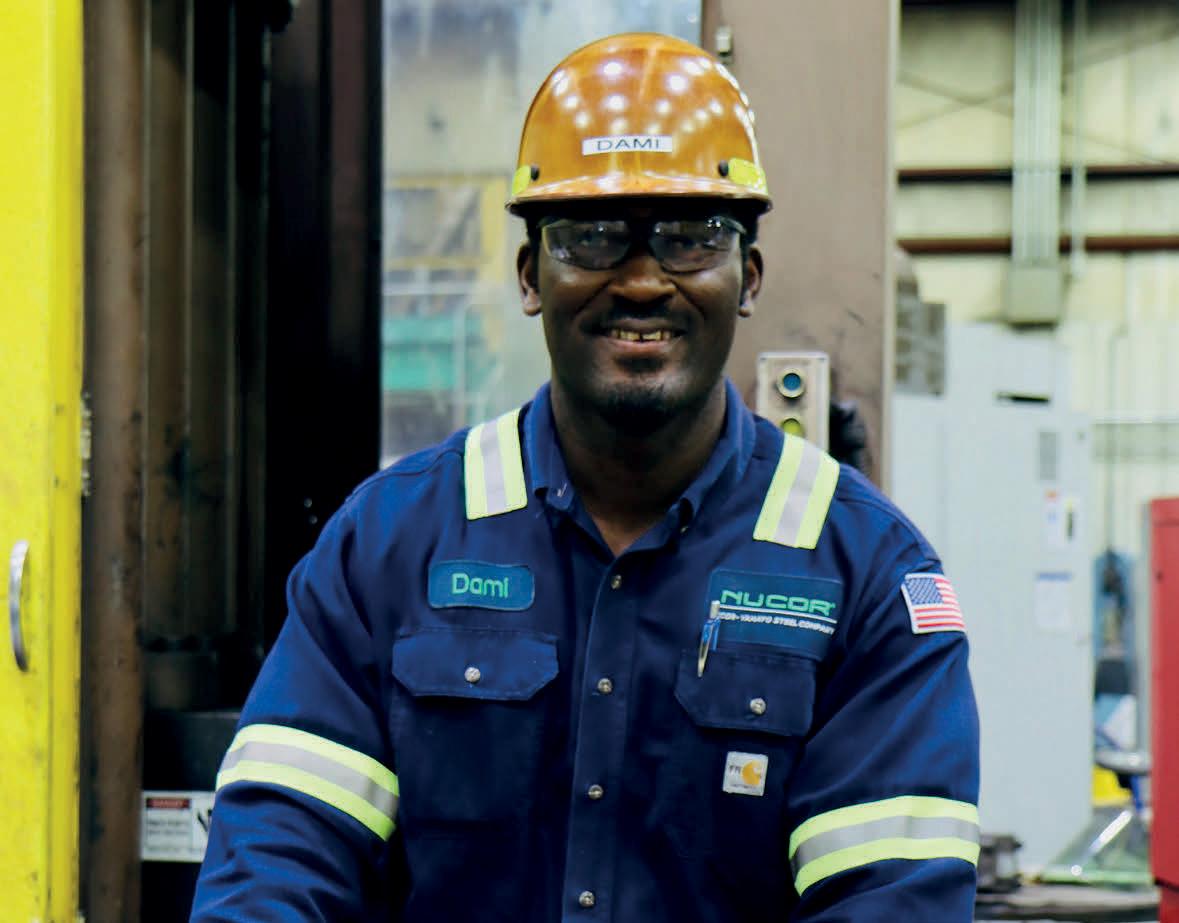
DB: Nucor is a company that really takes care of teammates. We are not even called employees, we are called teammates, we are called family. I have seen Nucor go out of their way to take care of their teammates. That’s why teammates typically always give their all to make sure everything runs smoothly.
Another very good thing about Nucor is that there is no hierarchy. What I’m trying to say is, you can start from entry level and end up as the CEO.
BP: What have you found to be important skills aside from your technical skills and how have you developed those?
DB: One of our challenges as a steel company is to be the world’s safest. To do that, we are held accountable in how we perform our work. To do that you need excellent communication skills.
DISCOVER THE OPPORTUNITIES • MAKE THE TEAM
In the six months since I joined Nucor, I have improved my communication skills thanks to training that involved going out into the plant to ask my teammates questions and get to know them on a deeper level.
LEARN YOUR TRADE • BUILD YOUR CAREER
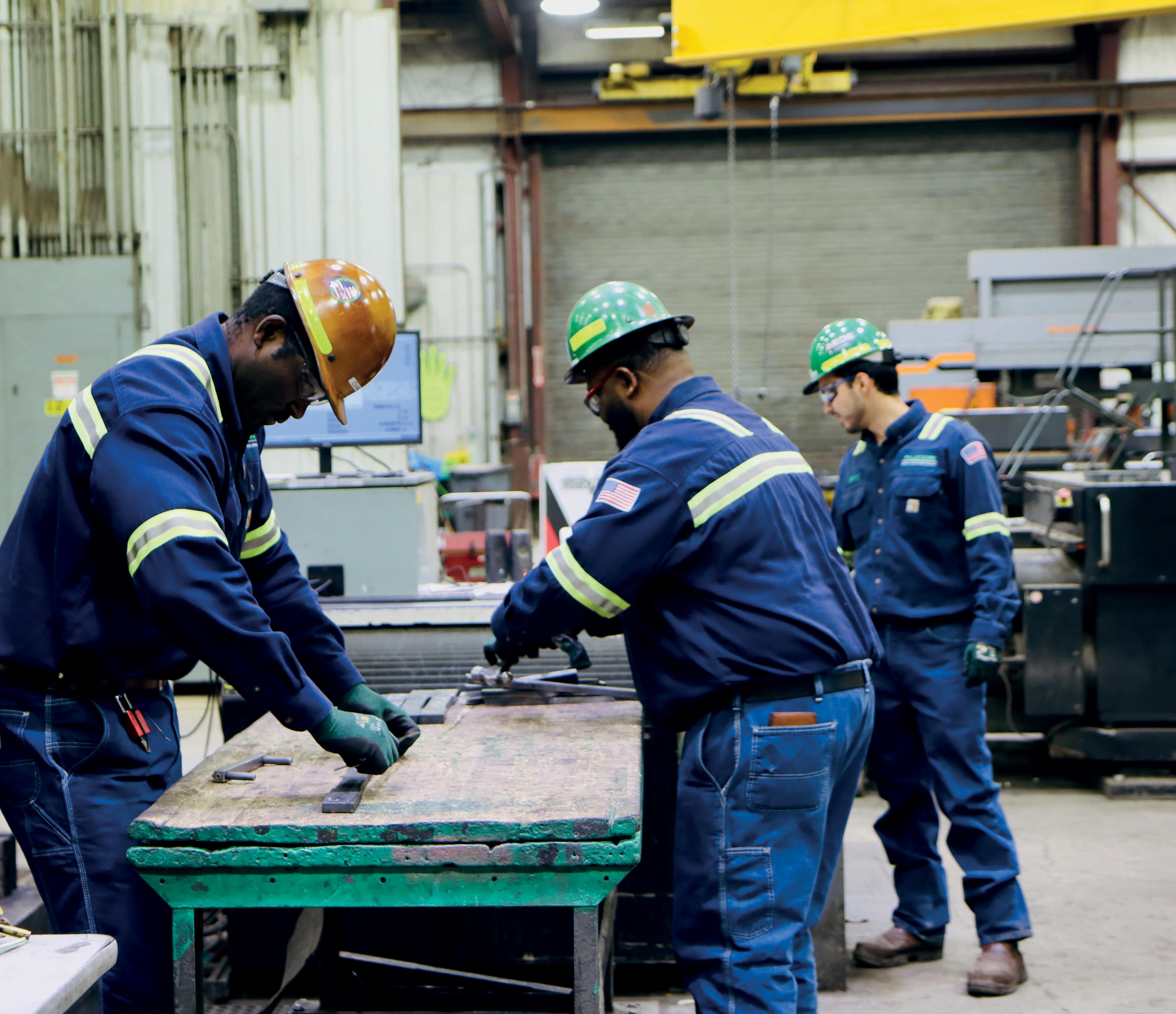
HOT JOBS!
A REVOLUTION IN STEEL METALLURGIST
DIVISION: Nucor-Yamato Steel and Nucor Steel Arkansas
AVERAGE STARTING SALARY: $80,000-$100,000 based on education and experience
WHAT DOES THE JOB DO?
A metallurgist is a highly sought-after manufacturing professional who can work in many different industries, including steel, aluminum, petroleum, automotive, aerospace and more. A metallurgist’s duties include:
• Review steelmaking and rolling processes to improve their metallurgical characteristics, yield and cost.
• Provide technical expertise for process development and continuous improvement of steelmaking processes.
• Engage in new product and grade development through analysis, experimentation and implementation of new raw materials, chemistries, equipment and manufacturing practices.
• Utilize engineering, physical metallurgy and steelmaking knowledge to help the company optimize process variables and improve the quality of its products, lower production costs, improve mechanical properties of low carbon steels and improve process efficiency.
• Implement and monitor testing practices as per required specifications so metallurgical requirements are met.
• Review, purchase and install new metallurgical equipment for upgrading of in-house testing capabilities.
• Provide support in the maintenance and proper operation of testing and analytical instruments.
• Utilize statistical process control tools to direct continuous improvement activities.
• Develop, revise and update standard operating procedures for special manufacturing projects.
• Develop and coordinate quality and safety training programs for operations, maintenance and quality-assurance laboratory teams.
• Review and process customer claims, which requires providing metallurgical technical support to the company’s sales and marketing departments.
WHY IT’S IMPORTANT: A metallurgist is responsible for the success of the company’s efforts to continue its development of innovative steel products, improve existing steel production practices which creates a safer product for our customers, and continuing efforts to make operations greener.
SKILLS, EXPERIENCE AND ATTRIBUTES: A metallurgical engineering degree from an accredited university is highly desirable as is prior work experience in the field of metallurgy. Data acquisition and analysis skills are also key to this position.
WHAT MAKES THIS POSITION IN HIGH DEMAND? Metallurgists are in scarce supply as there are currently only a small handful of universities in the United States offering a degree in metallurgical engineering. Metallurgical engineers are therefore in high demand; a newly graduated metallurgical engineer will typically command as many as a dozen job offers.
HOW DO I LEARN MORE? Please visit Nucor.com/careers to learn more about this opportunity.
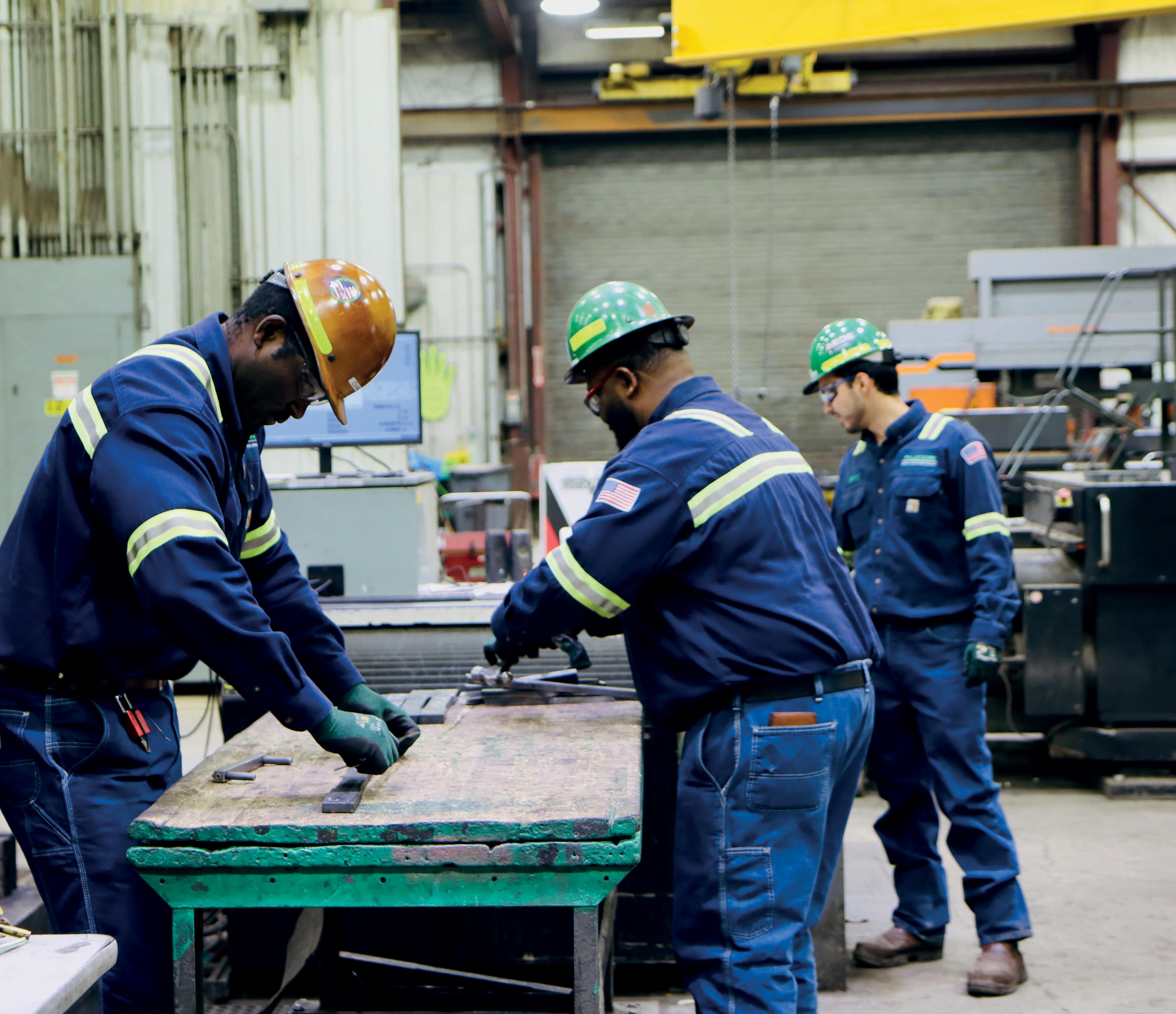
DISCOVER THE OPPORTUNITIES • MAKE THE TEAM LEARN YOUR TRADE • BUILD YOUR CAREER
TEAMMATE SPOTLIGHT
A REVOLUTION IN STEEL
BLUEPRINT: What misconceptions do people, including people in IT, have when it comes to technology and steel mills?
NISHANT VARADACHARI: If you’re looking from the outside, you’re thinking, “Okay this company just makes steel, so it probably doesn’t involve a lot of technology and computers.” That is absolutely wrong!
personal experience, a degree is good and it will be really helpful, but it’s not like you have to have a degree.
NISHANT VARADACHARI
Information Technology Lead/Business Process, Nucor-Yamato Steel
Country of Origin: India
Age: 38
Years with Nucor: 6
This technology was what I was used to seeing in my graduate studies and the places that I worked in California prior to coming to work for Nucor. When you go from school to the workplace and then come to Nucor, you see that the technology here is advanced. If you really have an interest in computer science, yes, you can make a good living at Nucor.
BP: Does it require the kind of college degrees you have in order to find opportunity at Nucor?
NV: Definitely not; there’s a home for pretty much anyone at Nucor. Speaking from
Being in IT in Nucor, you are mostly customer service. We are supporting the teammates out in the mill, because they are the ones who are actually rolling and casting and making the things with steel. So, if you come in with that mentality, there’s a place for you here.
BP: There’s a big focus on diversity across the board in workplaces, something IT has traditionally lacked. What’s the Nucor workplace like in terms of diversity?
NV: We have men and women from all different ethnicities. NYS’ IT department consist of 16-17 people; consisting of males and females, older and younger, as well as different ethnicities; everybody is really happy working, getting along. And, if you go around in the mill, it’s a pretty diverse environment out there as well.
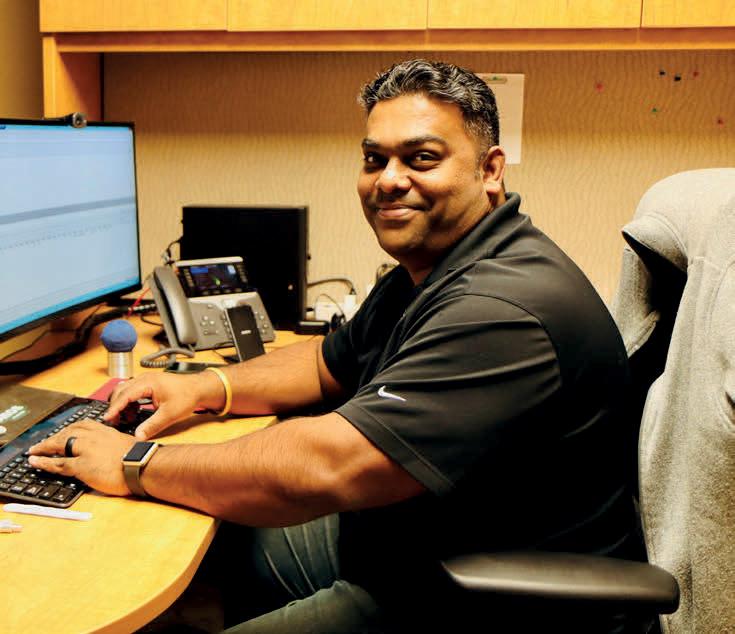
KATIE BEHRENDT
Sales Metallurgist, Nucor Steel Arkansas
Hometown: Waukesha, WI
Age: 36
Years with Nucor: 3
BLUEPRINT: What does a sales metallurgist do?
KATIE BEHRENDT: I’m part of Nucor’s tech services group. I help our sales team and our customers who have new inquiries for the mill, asking if we can make this or that. I help ensure we understand what they need and that we’re giving them what they need. And then, if they have issues, of course I’ll get involved as well.
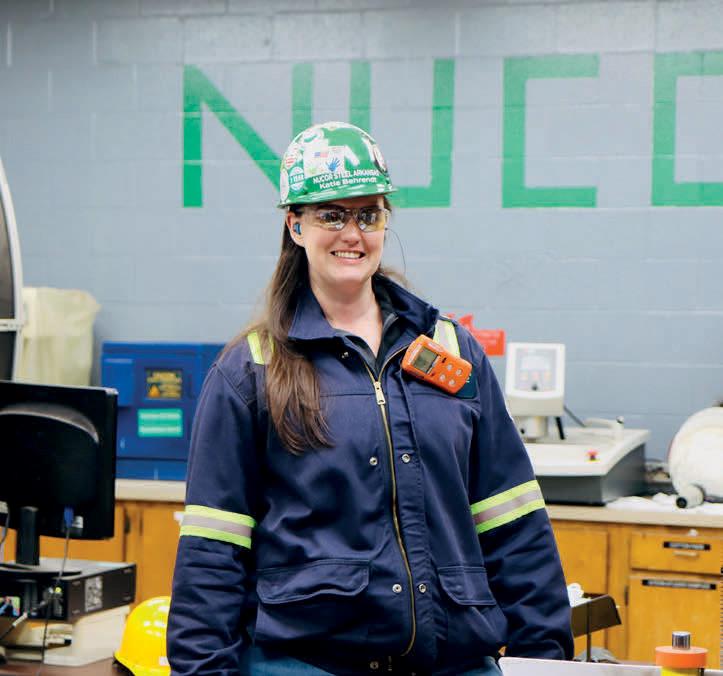
BP: Did you come to Nucor straight from college?
KB: Right before here I was at a U.S. Steel mill outside of Detroit. Right out of college I started in a wire mill in Milwaukee, and I was there for eight years.
BP: What is something about this job that might surprise someone?
lot of math and science, and I wouldn’t want anyone to think that they can avoid that, but I don’t think that’s required to become an engineer or a technological leader. I think it’s really just curiosity; it’s liking to take things apart and put them back together, it’s wanting to understand how things work. If people have that mindset, if they just have the curiosity and desire to understand, we can work with people and give them the technical part.
BP: What’s one characteristic that’s essential in this field?
KB: Being someone who asks, “Why? Why does this happen?” and then asking, “Why not? Why can’t we do it differently? Why can’t we do it better?” Those are really the people we’re looking for.
DISCOVER THE OPPORTUNITIES • MAKE THE TEAM
KB: I think that a lot of people have this view that being an engineer or getting into a technological field starts with being really good in math and science. We definitely use a
LEARN YOUR TRADE • BUILD YOUR CAREER
“IT’S REALLY JUST CURIOSITY ... LIKING TO TAKE THINGS APART AND PUTTING THEM BACK TOGETHER.” —KATIE BEHRENDT
BLUREPRINT: You have a degree in computer science which can be applied in a lot of places. Why work at Nucor?
BP: What opportunities are in your department for someone without a four-year degree?
A REVOLUTION IN STEEL
LOGAN NIELSEN: Nucor-Yamato has a good relationship with Missouri University of Science and Technology, where I went to school. They did a recruiting event on campus one spring, and I applied for a co-op when I was a secondsemester junior.
LN: We have a position called a technical analyst and they do a lot of things;, they’re the jack-of-all-trades in IT. A technical analyst is the frontline to our IT department, interfacing with customers a lot more than a software engineer. They are always on call.
LOGAN NIELSEN Information Technology Lead, Nucor-Yamato Steel
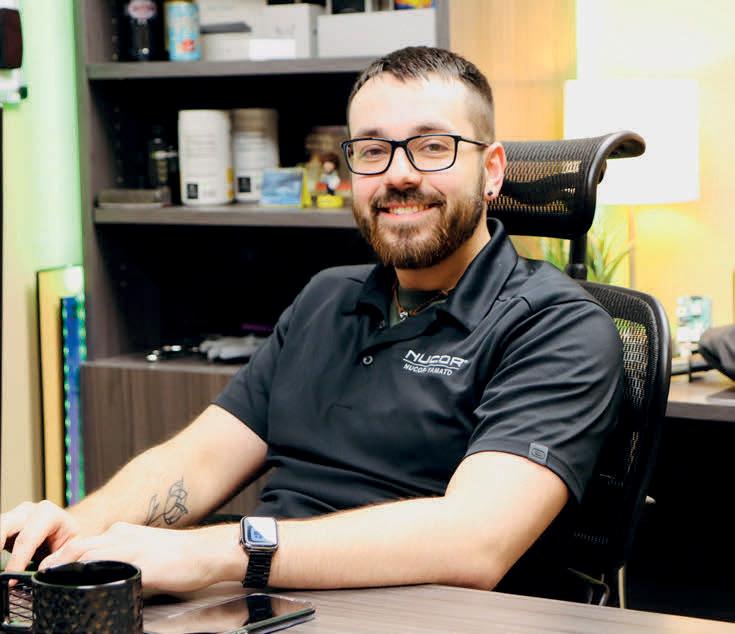
Hometown: Rapid City, South Dakota
Age: 27
Years with Nucor: 5
I did a seven-month co-op with the IT team and fell in love with everybody here. And really fell in love with the idea of development in the manufacturing world as opposed to the tech industry. I got a full-time offer before I finished my co-op contingent upon successful completion of my degree, and I accepted it.
BP: What’s the difference between a co-op and an internship?
LN: Generally, an internship lasts over the summer; Nucor’s co-op spans a summer and a semester, so you get an extra four or five months, which also allows you additional time to learn and work on your own.
If somebody calls our IT hotline, they’re the people who answer the call. That’s critical because if a monitor goes out in the middle of a crane, someone has to go replace that because they use those screens to keep people safe. If there are administrative issues – the technical analyst handles it; if there’s access right issues – the technical analyst handles that. That’s a job you only need an associate degree for, but it is really one of the most important jobs that we have in IT because it interfaces with customers all over, all the time.
BRIAN ABBOTT
Hot Mill Process Control
Lead/Nucor Steel Arkansas
Hometown: Steele, Mo.
Age: 45
Years with Nucor: 15
BLUEPRINT: What classes did you take in high school that prepared you for a career in manufacturing?
BRIAN ABBOTT: I went the vocational route. I took shop and electronics classes at a vocational-technical school my junior and senior year.
BP: Knowing what you know now, what classes would you recommend someone take to prepare for a career like yours?
BA: Physics and any type of programming class like Python, C++ would be helpful. Also, PLC programming classes would be very beneficial.
BP: What’s been your career progression at Nucor?

BA: I was originally hired as a shift electrician and then moved on to the process control group where we complement what the electricians do. We look at quality, reliability, performance, things like that. Basically, I’ve taken ownership of an area, the hot mill. I get
calls all the time. I’m on call 24/7 if something breaks. I’m kind of the last line of defense; if the electricians can’t fix it, they call me
BP: What are you most proud of in your career thus far?
BA: In our manufacturing process, material goes through the mill and is supposed to run up and make a nice, pretty coil. But if something happens in the process where it doesn’t make it to that, we call that a mill wreck. Part of what a process control engineer does is you investigate, get down to the root cause, define what happened, and then implement solutions to keep that from happening again.
The process control group, since I’ve been here, has reduced those from 500 to 600 a year down to 50 a year or less. That’s something I’m really proud of.
DISCOVER THE OPPORTUNITIES • MAKE THE TEAM LEARN YOUR TRADE • BUILD YOUR CAREER
“I WENT THE VOCATIONAL ROUTE. I TOOK SHOP AND ELECTRONICS CLASSES AT A VOCATIONAL-TECHNICAL SCHOOL MY JUNIOR AND SENIOR YEARS.” —BRIAN ABBOTT
NUCOR: A REVOLUTION IN STEEL
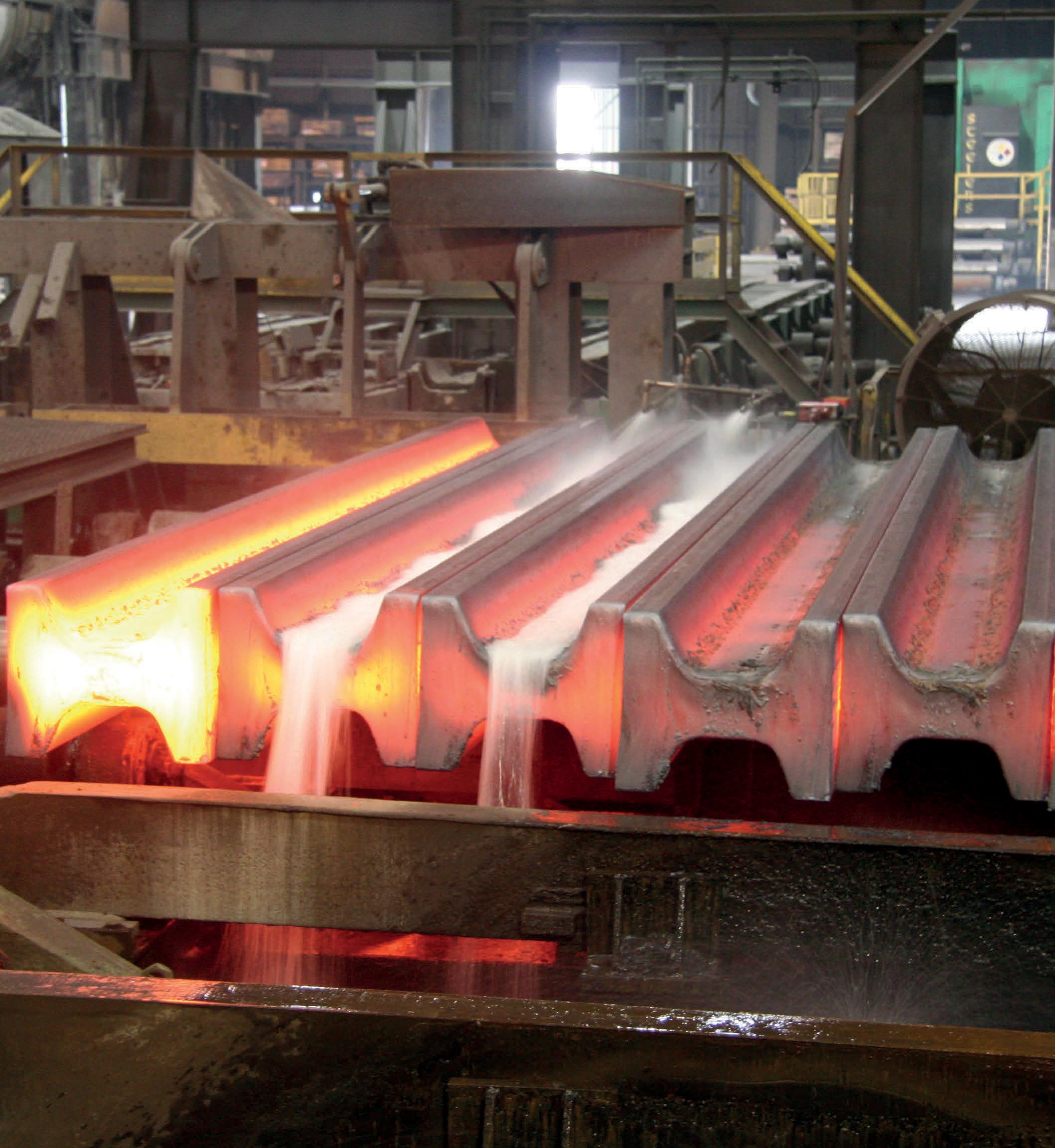
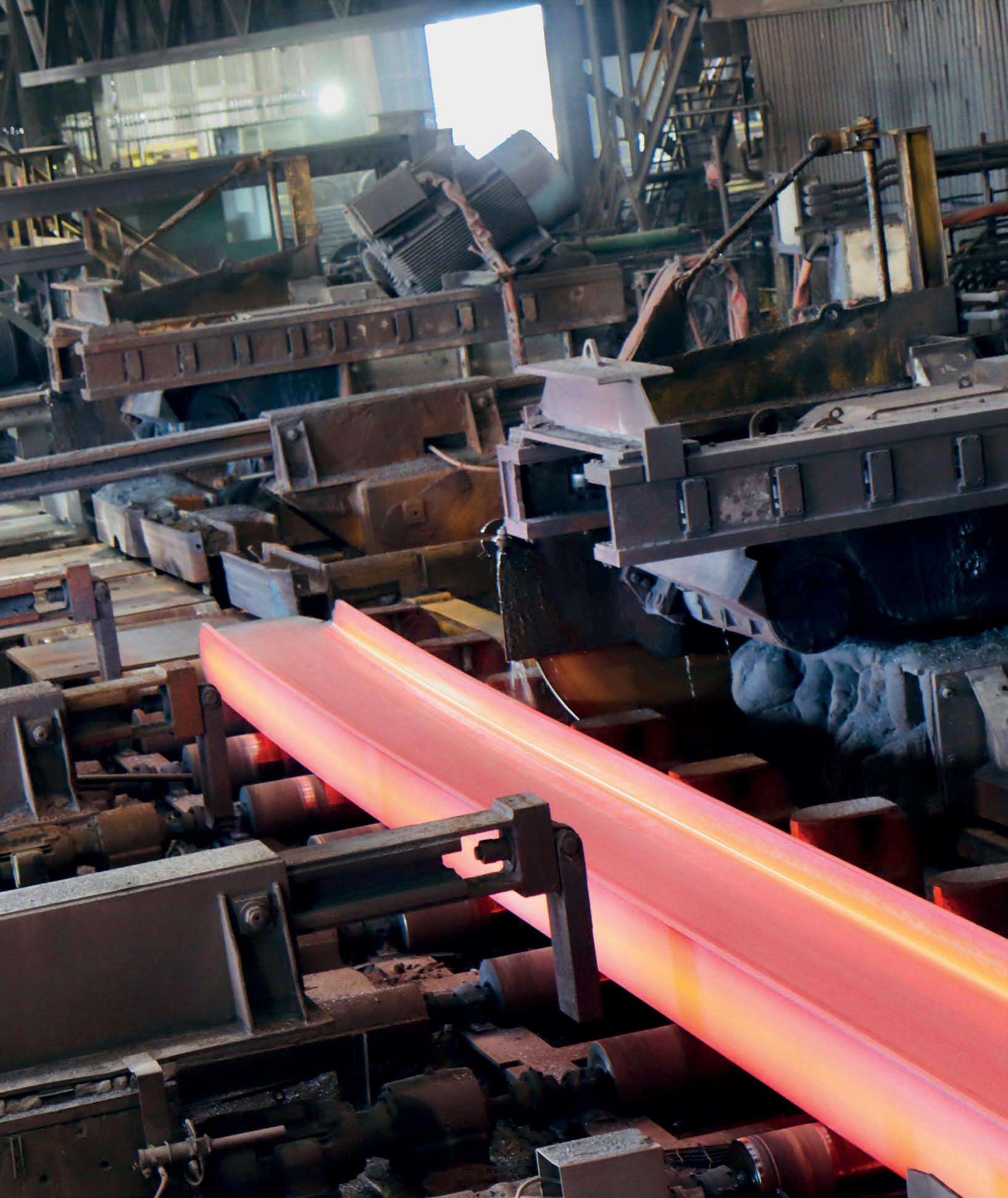
TEAMMATE SPOTLIGHT
A REVOLUTION IN STEEL
CODY MACE
Roll Mill 1 Lead, Nucor-Yamato Steel
Hometown: Goshen
Age: 31
Years with Nucor: 10
BLUEPRINT: What was it like the first time you walked into the steel mill?
CODY MACE: I remember the first day like it was yesterday – walking in and being overwhelmed. Everything was so big, the equipment, the atmosphere.
BP: Where did you get your start at Nucor?
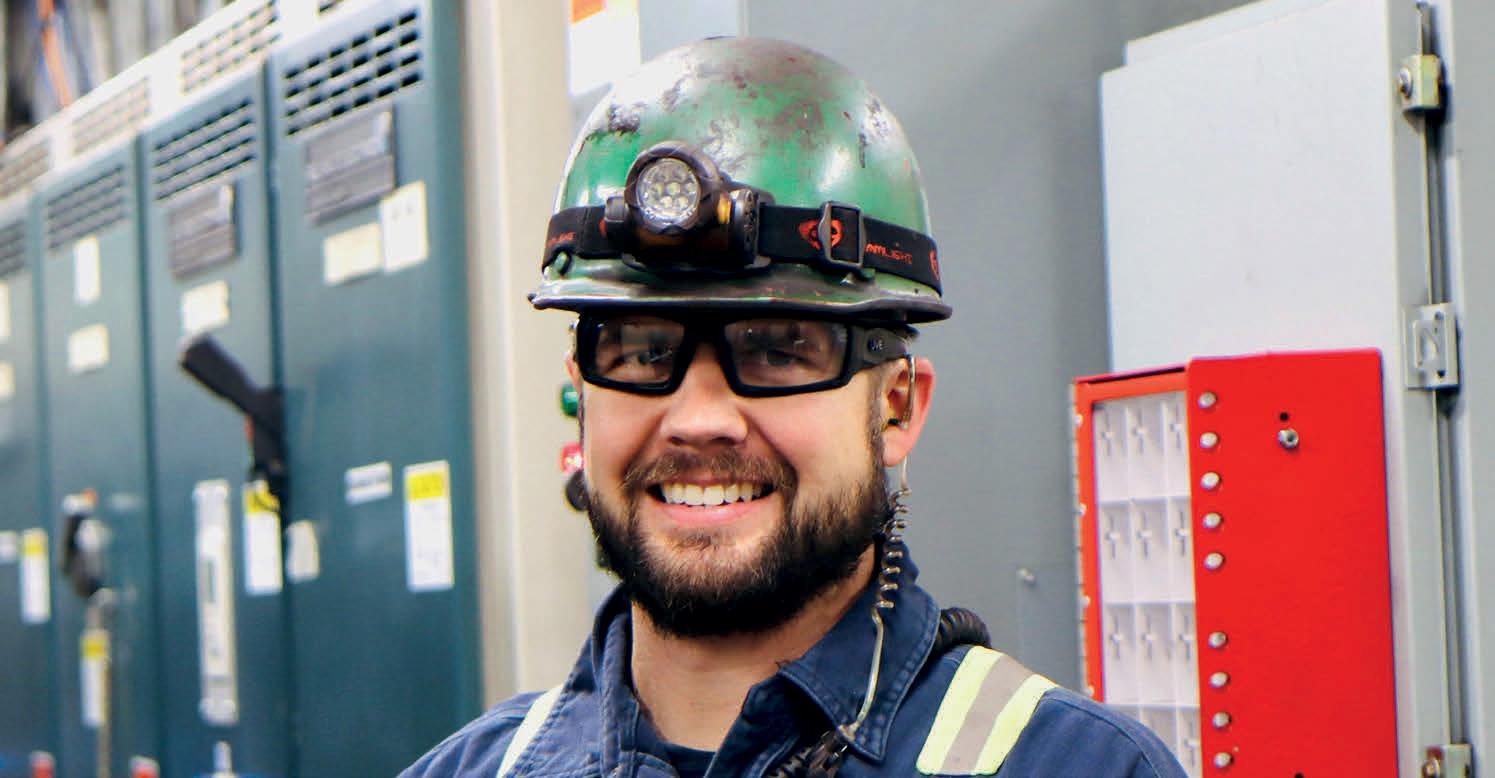
CM: I started in shipping, learning how to load rail cars, run cranes and run a tailer a little bit. Then I moved on to work in safety and in finishing steel in a roll mill a little bit as well. In finishing, you’re actually working on the inspection bin where the steel goes across the bed, and you look for any kind of defect.
BP: You were part of the steel tech internship program. What did that teach you?
CM: The great thing about being an intern is that every day you do something different. You may go, for instance, to the finishing bay or pulpit where you’re in the hot saws and you cut the steel, or you stack steel. It’s a great opportunity when you’re 18 or 19 years old to go in there and get an idea of what you really want to do as a full-time employee. And you make good money while you’re there.
BP: Did you have any mentors along the way?
CM: Mentoring happens every day out here, and it’s happened to me multiple times. I’ve got two or three guys I go to all the time with questions and any issues at all. That’s one of the things I like best about this place, the relationships you can build and the people you can trust.
BP: What do you like about the job you’re doing now?
CM: What I like about it is every day I come in and do something different. Some days are slower and other days are faster, but there’s always something going on.
BP: What’s your best advice for the next generation of workers?
CM: Stay hungry and stay motivated every day you’re out there. Never let up. If you’re an intern and people see you coming in on time every day, they see you take direction and see you’re willing to learn and they see that you like to work hard, supervisors will fight over you. Maintain that can-do attitude; positivity goes a long way out here.
DISCOVER THE OPPORTUNITIES
LEARN YOUR TRADE
• BUILD YOUR CAREER
TEAMMATE SPOTLIGHT
A REVOLUTION IN STEEL
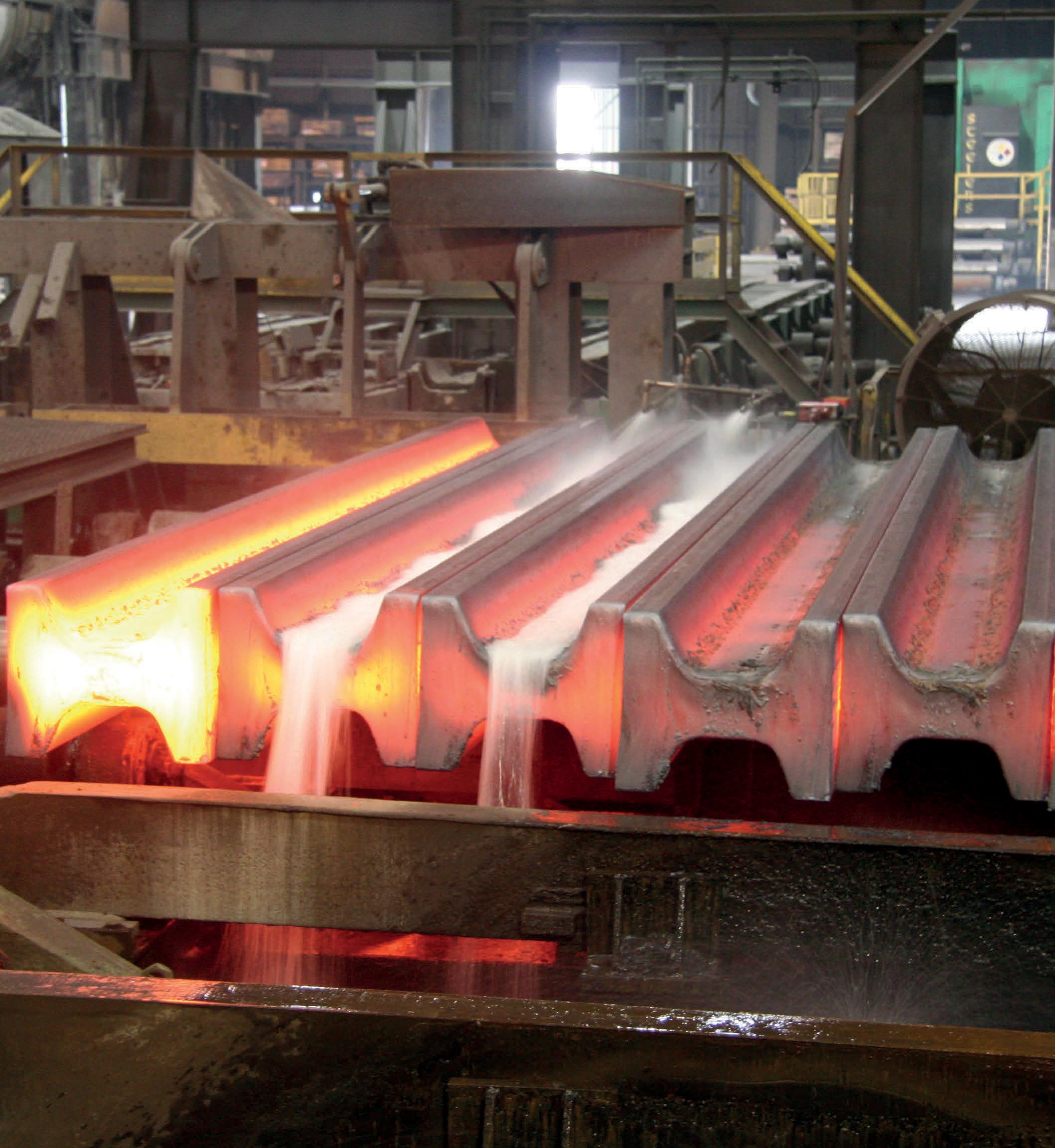
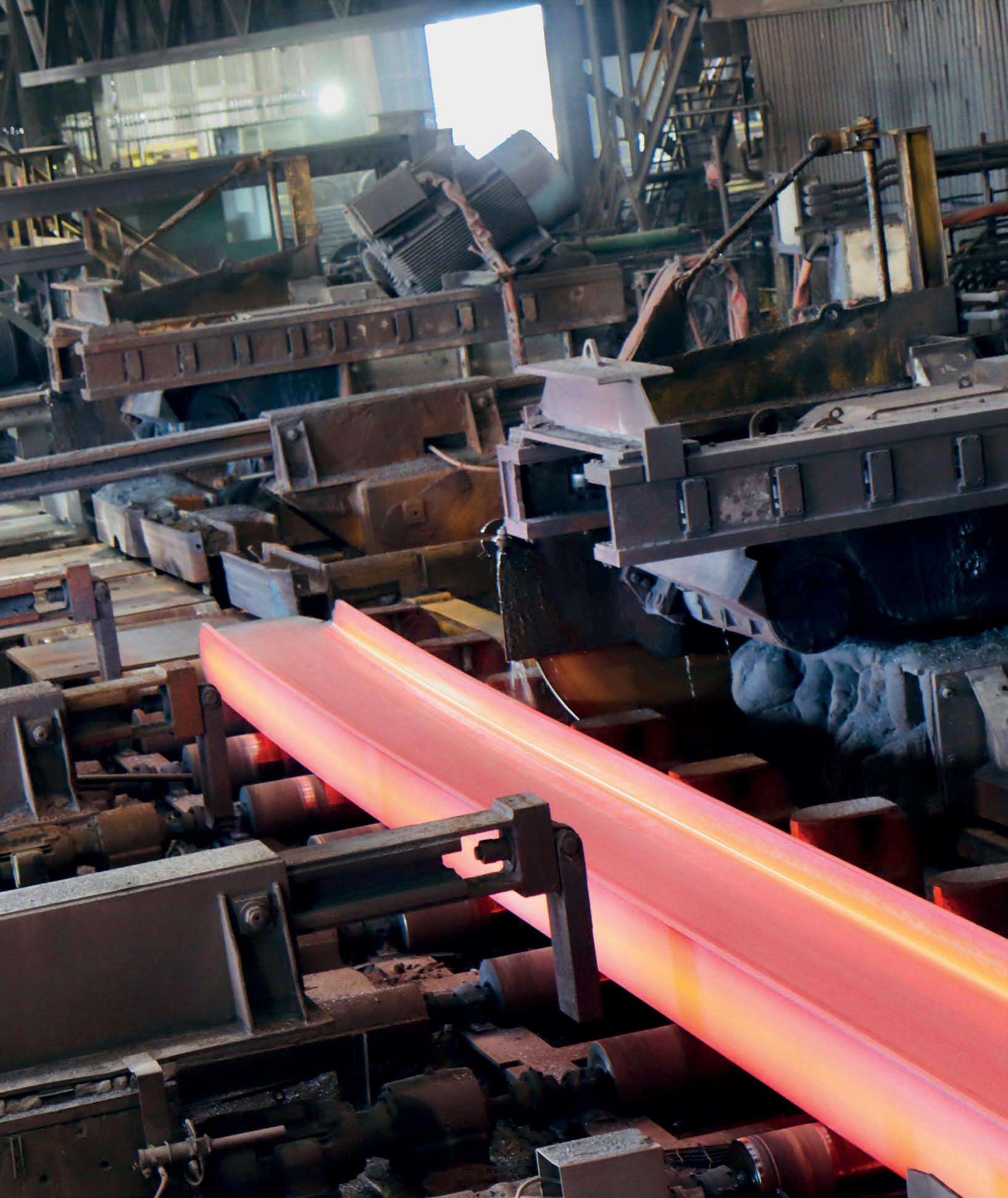
BARBARA HOPKINS
Traffic Clerk, Nucor-Yamato Steel
Hometown: Blytheville
Age: 47
Years with Nucor: 14
BLUEPRINT: When you were in high school, what was your goal career-wise?
BARBARA HOPKINS: My mind was pretty much made up that I wanted to be a secretary, working in an office. Two weeks after my high school graduation, I moved to Dallas and enrolled in Executive Secretarial College for legal assisting and that’s where my corporate career took off. From 1994 to 2007 I was in Dallas until the company I was working for started outsourcing and that was my opportunity to come back home to Arkansas.
BP: How did you get on with Nucor?
BH: Nucor was hiring a clerk; I came in with the quality department as a temp and six months later I was offered a position in the finance department as a temp. I did that for a couple of years, and then I got hired on.
BP: How have you improved your skills over the time you’ve worked at Nucor?
BH: I’ve had plenty of opportunities to do a little bit of everything. I started in finance, then went to the metal shop. The metal shop clerk position is something that is totally different from a finance clerk. And I was in the melt shop for almost seven years and that was brand-new for me.
Nucor gives you the opportunity to cross-train and learn the process. They can teach you everything you need to know if you’re willing to learn.
Nucor has also allowed me the opportunity to continue my education beyond the training they offer. Nucor reimburses you for college courses taken to improve yourself; this allows you to grow as well as help the company grow as you learn and share your knowledge.
BP: What’s something you want people to know about working at Nucor, especially young people just starting out?

BH: Nucor isn’t a cookie-cutter organization. They want you to bring in your own ideas to improve things or to make your job better. When I went through course certification in Human Resources and payroll, I’d pick up new training. I realized, OK, this is something useful.
BP: What’s the best advice you have for a new teammate?
DISCOVER THE OPPORTUNITIES
BH: The main thing is don’t be afraid to step up and try something different. When you say “manufacturing,” you think big machines, but there’s so many other intricate parts that make a finished product. Don’t be afraid to ask questions. Sometimes we don’t know what we really want until someone tells us about it.
• MAKE THE TEAM
LEARN YOUR TRADE • BUILD YOUR CAREER
NUCOR:
A REVOLUTION IN STEEL
HOT JOBS!
HOT JOBS!
SAFETY COORDINATOR
SAFETY COORDINATOR
A REVOLUTION IN STEEL
DIVISION: Nucor-Yamato Steel and Nucor Steel Arkansas
DIVISION: Nucor-Yamato Steel and Nucor Steel Arkansas
AVERAGE SALARY: $67,000+ based on experience
AVERAGE SALARY: $67,000+ based on experience
WHAT DOES THE JOB DO?
WHAT DOES THE JOB DO?
• Work closely with Nucor Steel Arkansas teammates, contractors and leadership to drive continuous improvement in Nucor’s safety culture, performance and safety systems.
• Work closely with Nucor Steel Arkansas teammates, contractors and leadership to drive continuous improvement in Nucor’s safety culture, performance and safety systems.
• Have knowledge of and participate in OSHA compliance, safety management system, workers compensation and ergonomic compliance.
• Have knowledge of and participate in OSHA compliance, safety management system, workers compensation and ergonomic compliance.
• Perform field industrial hygiene monitoring, as necessary.
• Perform field industrial hygiene monitoring, as necessary.
• Work with the team to develop and administer safety training.
• Work with the team to develop and administer safety training.
• Participate in and or lead safety focus groups.
• Participate in and or lead safety focus groups.
• Maintain safety, health and incident records.
• Maintain safety, health and incident records.
• Establish safety policies to promote team member safety at all levels.
• Establish safety policies to promote team member safety at all levels.
• Track safety data and use analytical tools to identify opportunities for improvement.
• Track safety data and use analytical tools to identify opportunities for improvement.
• Work with the team to maintain Safety Management System, programs and compliance issues
• Work with the team to maintain Safety Management System, programs and compliance issues
• Interact with all teammates to ensure plant-wide understanding of and compliance with federal, state and local regulations.
• Interact with all teammates to ensure plant-wide understanding of and compliance with federal, state and local regulations.
• Develop, organize and deliver safety training.
• Develop, organize and deliver safety training.
• Conduct safety inspections and audits.
• Conduct safety inspections and audits.
• Compile, review and report injury and illness statistics and OSHA 300 logs.
• Compile, review and report injury and illness statistics and OSHA 300 logs.
• Assist with the coordination of first responders and emergency response teams.
• Assist with the coordination of first responders and emergency response teams.
• Audit and monitor contractor safety programs.
• Audit and monitor contractor safety programs.
• Spend time in the mill to obtain understanding of production operations.
• Spend time in the mill to obtain understanding of production operations.
workplace not only means taking care of our team but it also creates financial stability by limiting our costs. The safety coordinator focuses solely on taking care of team members and regulatory compliance, making it one of the most important positions in the company.
workplace not only means taking care of our team but it also creates financial stability by limiting our costs. The safety coordinator focuses solely on taking care of team members and regulatory compliance, making it one of the most important positions in the company.
SKILLS, EXPERIENCE AND ATTRIBUTES:
SKILLS, EXPERIENCE AND ATTRIBUTES:
• Associate degree in related field or 4+ years’ experience in a safety position managing and presenting safety training and programs.
• Associate degree in related field or 4+ years’ experience in a safety position managing and presenting safety training and programs.
• Knowledge of OSHA, NFPA, ANSI and other regulatory standards.
• Knowledge of OSHA, NFPA, ANSI and other regulatory standards.
• Ability to prioritize and organize several projects effectively.
• Ability to prioritize and organize several projects effectively.
• Ability to analyze data and think strategically.
• Ability to analyze data and think strategically.
• First responder and EMT certification or willingness to obtain.
• First responder and EMT certification or willingness to obtain.
• Industrial hygiene and behavior-based safety experience.
• Industrial hygiene and behavior-based safety experience.
• Safety training experience and certifications.
• Safety training experience and certifications.
• OSHA Voluntary Protection Program experience.
• OSHA Voluntary Protection Program experience.
WHAT MAKES THIS POSITION IN HIGH DEMAND? Safety coordinators are in high demand partially due to their overall impact on teammates and the business. Successful individuals in this position have a desire to serve by taking care of others. The safety field’s technical needs are wide as far as standards and policies are concerned. It takes someone with a breadth of knowledge, an interest in researching and understanding multiple laws and regulations, as well as the ability to translate that information for individual teams and the company as a whole.
WHAT MAKES THIS POSITION IN HIGH DEMAND? Safety coordinators are in high demand partially due to their overall impact on teammates and the business. Successful individuals in this position have a desire to serve by taking care of others. The safety field’s technical needs are wide as far as standards and policies are concerned. It takes someone with a breadth of knowledge, an interest in researching and understanding multiple laws and regulations, as well as the ability to translate that information for individual teams and the company as a whole.
HOW DO I LEARN MORE? Please visit Nucor.com/careers to learn more about this opportunity.
HOW DO I LEARN MORE? Please visit Nucor.com/careers to learn more about this opportunity.
WHY IT’S IMPORTANT: Safety is a core part of our business; having a safe
WHY IT’S IMPORTANT: Safety is a core part of our business; having a safe
MECHANIC
MECHANIC
DIVISION(S): Nucor-Yamato Steel and Nucor Steel Arkansas
DIVISION(S): Nucor-Yamato Steel and Nucor Steel Arkansas
AVERAGE STARTING SALARY: $97,000 +
AVERAGE STARTING SALARY: $97,000 +
WHAT DOES THE JOB DO?
WHAT DOES THE JOB DO?
Our team is expected to demonstrate safety-minded support of our entire maintenance team while seeking to provide world-class reliability for our customers. We support our maintenance and production teams via mechanical and some electrical troubleshooting in a given area of the mill. Our team is responsible for interpreting drawings and manuals for the installation, repair and maintenance of complex equipment systems and machinery such as pumps, valves, cylinders, compressors, conveyors, overhead cranes, etc. Our department uses various pieces of equipment such as forklifts, man lifts, mobile crane, etc. in order to safely operate during routine mechanical operations. Troubleshoot and repair water systems, hydraulic systems, alloy systems, DRI system and mechanical components, plus participate and lead in all preventive and predictive maintenance programs. Mechanics are responsible for the continuous process of steel manufacturing. These highly trained technicians are responsible for complex hydraulic/pneumatic systems and installing and maintaining industrial precision equipment.
Our team is expected to demonstrate safety-minded support of our entire maintenance team while seeking to provide world-class reliability for our customers. We support our maintenance and production teams via mechanical and some electrical troubleshooting in a given area of the mill. Our team is responsible for interpreting drawings and manuals for the installation, repair and maintenance of complex equipment systems and machinery such as pumps, valves, cylinders, compressors, conveyors, overhead cranes, etc. Our department uses various pieces of equipment such as forklifts, man lifts, mobile crane, etc. in order to safely operate during routine mechanical operations. Troubleshoot and repair water systems, hydraulic systems, alloy systems, DRI system and mechanical components, plus participate and lead in all preventive and predictive maintenance programs. Mechanics are responsible for the continuous process of steel manufacturing. These highly trained technicians are responsible for complex hydraulic/pneumatic systems and installing and maintaining industrial precision equipment.
SKILLS, EXPERIENCE AND ATTRIBUTES: Skill sets for success in this role include knowledge of welding, cutting, hydraulic, pneumatic, alignment, big hammers, print reading, boilers, gear boxes and bearings. This position also requires excellent troubleshooting skills and the ability to make timely decisions to meet company goals.
SKILLS, EXPERIENCE AND ATTRIBUTES: Skill sets for success in this role include knowledge of welding, cutting, hydraulic, pneumatic, alignment, big hammers, print reading, boilers, gear boxes and bearings. This position also requires excellent troubleshooting skills and the ability to make timely decisions to meet company goals.
• Experience using engineering and maintenance principles
• Experience using engineering and maintenance principles
• Industrial mechanical maintenance experience
• Industrial mechanical maintenance experience
• Experience interpreting drawings and manuals for complex equipment and machinery
• Experience interpreting drawings and manuals for complex equipment and machinery
• Formal mechanical maintenance training and/or degree
• Formal mechanical maintenance training and/or degree
• Metal fabrication skills
• Metal fabrication skills
• High school diploma or GED equivalent
• High school diploma or GED equivalent
DISCOVER THE OPPORTUNITIES
WHY IT’S IMPORTANT: Maintaining the large industrial machinery at a steel manufacturer is essential for safety, productivity and efficiency. Keeping machinery running smoothly allows Nucor to meet production deadlines and work at top efficiency.
WHY IT’S IMPORTANT: Maintaining the large industrial machinery at a steel manufacturer is essential for safety, productivity and efficiency. Keeping machinery running smoothly allows Nucor to meet production deadlines and work at top efficiency.
WHAT MAKES THIS POSITION IN HIGH DEMAND? Industrial mechanics have a larger array of skill sets than a mechanic, welder, machinist or lubricator. It takes a well-rounded knowledge of all the listed trades. The good news is, individuals can begin a highly rewarding career in this job area with as little as a high school diploma and advance as they add to their education, experience and job skills.
WHAT MAKES THIS POSITION IN HIGH DEMAND? Industrial mechanics have a larger array of sets than a mechanic, welder, machinist or lubricator. It takes a well-rounded knowledge of all the listed trades. The good news is, individuals can begin a highly rewarding career in this job area with as little as a high school diploma and advance as they add to their education, experience and job skills.
MAKE THE TEAM
HOW DO I LEARN MORE? Please visit Nucor.com/careers to learn more about this opportunity.
HOW DO I LEARN MORE? Please visit Nucor.com/careers to learn more about this opportunity.
TEAMMATE SPOTLIGHT
A REVOLUTION IN STEEL
BLUEPRINT: What jobs have made up your career at Nucor?
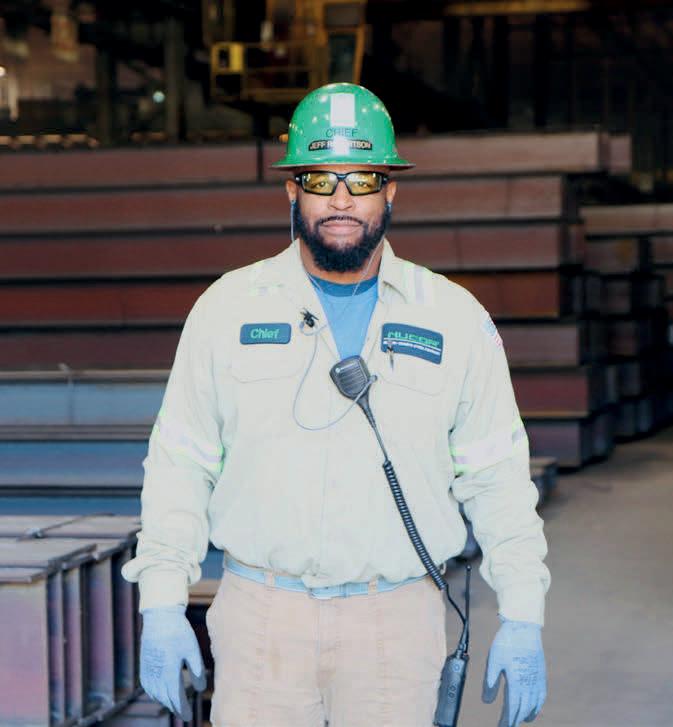

JEFF ROBERTSON: I’ve been with the company for over 27 years, and all of my time has been in shipping.
BP: What attracted you to Nucor in the first place?
JR: What originally attracted me to this company was the pay. I come from a not-so-rich family, raised by my grandparents. I had an opportunity once I got out of college to come out here to interview. I wanted to provide for my family in the way that I didn’t have when I was growing up. I saw this as a great opportunity to do that. I was planning for my future.
BP: As someone who worked from the bottom up, what advice do you have for young people looking to get on here, or who are just starting out with Nucor.
JR: Don’t be afraid to step out of your comfort zone. Make a plan where you can see yourself five years from now. Set some goals, both short term and long-term, things that are attainable. I know at 17, 18 years old you are not always thinking that way, but you’ve got to get your game plan together.
BP: How have things changed since you were that new hire?
Hometown: Wilson
Time with the Company: 27 years
JR: It takes a little more coaching to get new teammates in the right mode. We do set expectations once you’re hired. We set expectations of what we require, and we give evaluations every 30 days to let new hires know where they’re at, where they stand and where we think they need to be or where they should be. This is a great company with lots of opportunity, if you’re willing to learn and work for it.
Intern Supervisor, Nucor Steel Arkansas
Country of Origin: East Africa
Years with Nucor: 1.5
BLUEPRINT: What brought you to the United States?
KENNEDY OGWAMBO: I came to the United States in 2006. I went to Union University in Jackson, Tennessee, and then I transferred to Williams Baptist in Walnut Ridge, Arkansas.
BP: How did Nucor enter the picture?
KO: It was something different, a different opportunity. It’s a great industry to work in and a great company to work for.
BP: Where did you start with Nucor?
KO: I started out working in shipping and receiving. My role was getting the trucks in, unloading trucks, making sure my area was clean, that everybody was safe. After about three or four months they gave me another opportunity with the maintenance department. My new role was trying to see if we could save money by doing more maintenance ourselves, so we did a lot of construction.
BP: Did you have a background in that kind of work already?
KO: I worked for myself for a while on houses and I have a few rental properties. I had to teach myself quickly and figure out how to do what I needed to get done. I learned as I went, building stuff up.
BP: Even though you’re relatively new, is there something about Nucor that stands out to you?
KO: I’ve worked in different factories, and they talk about safety, but it’s just talk. When I was interviewing here, everybody was speaking the same language and I thought, “This sounds scripted.” But now I’m speaking the same language too. Safety, man, safety is really, really big. And that, to me, means that someone cares. I’m not just a number. I’m a person.
I mean, the money is great, but making sure you go home to your family, that’s just the biggest thing. I preach that now; even when I’m at home, I’m thinking about safety.
BP: What’s your advice for new people thinking about applying here?
KO: You have to be positive. Be positive and humble and hungry and everything else will fall into place. There are so many opportunities here, you just have to have the right direction and the right people around you to push you. I have great mentors and great leaders around me and those are the people who I listen and talk to, every day.
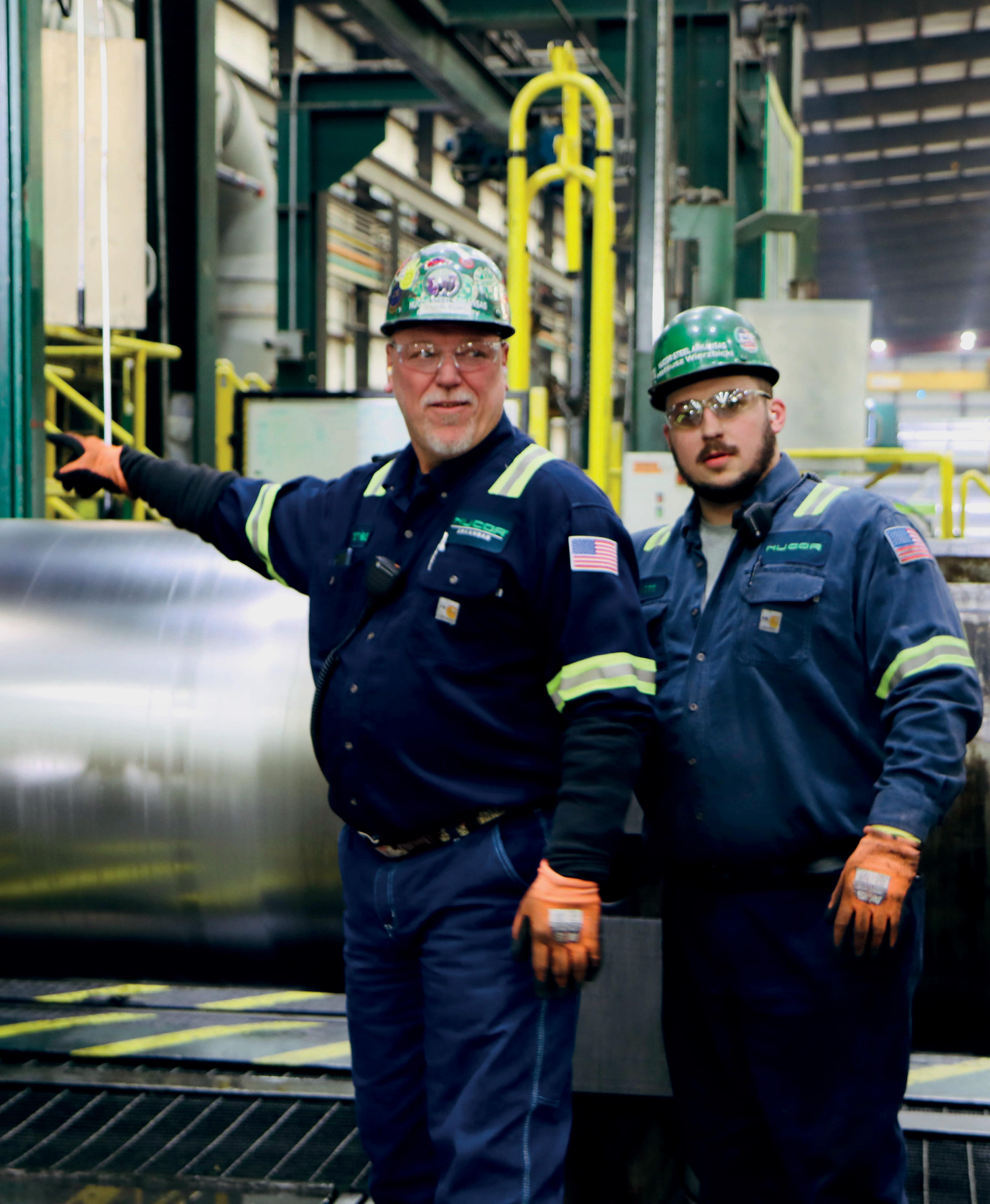
A GOOD LIFE
NUCOR TEAMMATES SHARE THEIR SECRETS TO A LONG AND SUCCESSFUL CAREER
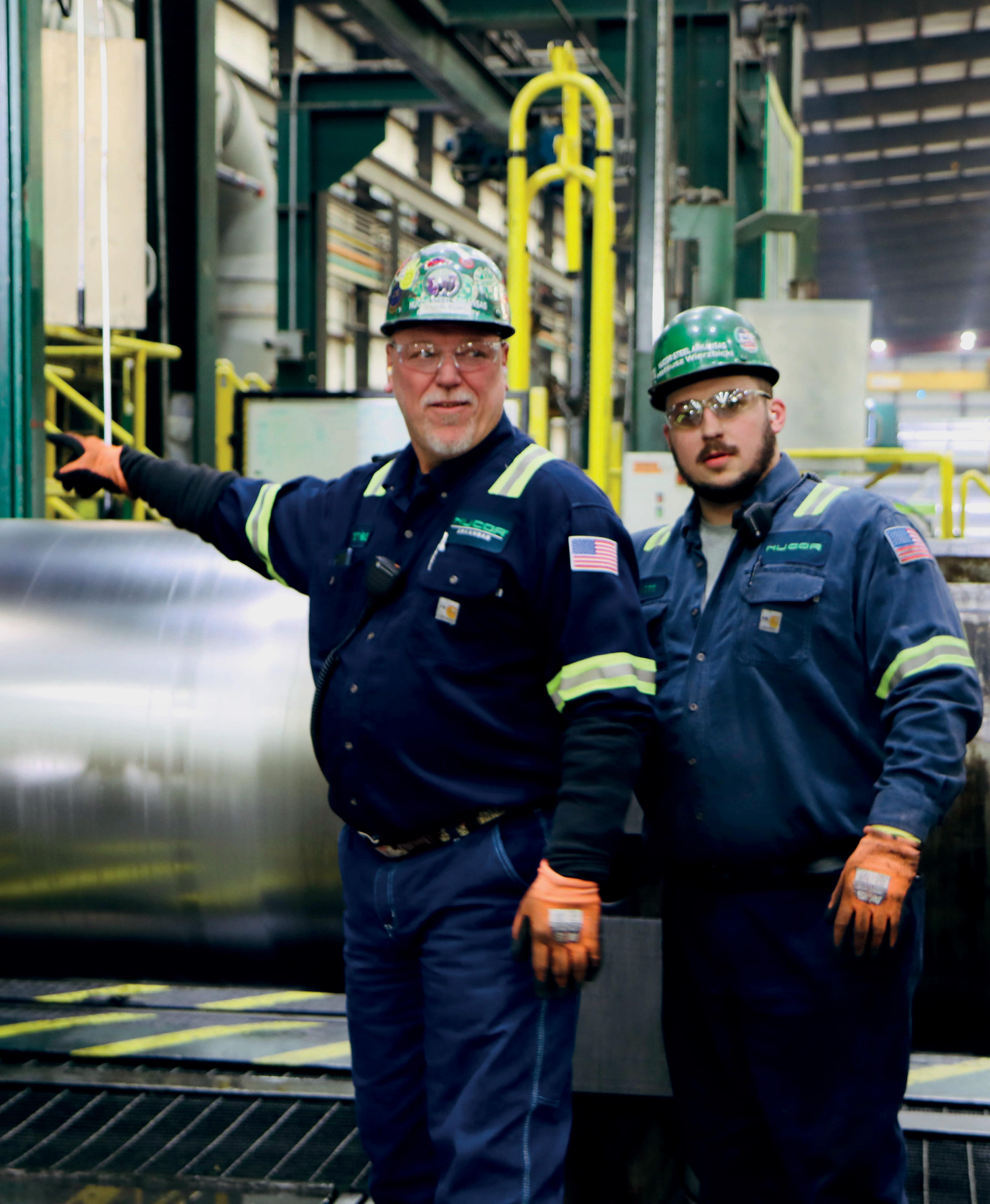
Shortly after his 18th birthday, Jim Shelton was hired for an entry-level job at a Nucor steel mill in Utah. He landed in Arkansas in 1988 as a roll mill operator, and today he’s the roll mill manager for Nucor-Yamato Steel (NYS). He has done it all on hard work, company training, and the can-do attitude embodied by every teammate at Nucor.
As impressive of a career as his has been, Shelton said the longevity in his work life comes down to a few simple elements.
“Integrity, teamwork, optimism, those are Nucor’s core values,” he said. “I can’t imagine working for anybody else, and a lot of that is because of the opportunities offered here. We empower our teams. We encourage them to make decisions, because the men and women on the floor make things happen more efficiently. It’s not necessarily the manager or the supervisor that makes things happen, it’s the teammates on the floor.”
“Limitations are often what teammates place on themselves; those who are preparing and really taking advantage of the opportunities, see the payoff when the opportunities come.”
Nucor’s corporate culture moves intentionally to help teammates map out a career plan while preparing them for the next step through training and feedback.
“I started off as a temporary employee. I was hired as an entry level production teammate in the hot mill,” said Sammy Sanchez, Nucor Steel Arkansas Cold Mill 1 Coil Bay Supervisor at Nucor Steel Arkansas. “In six months, I got a promotion to a Burner Bander and then I got another promotion to a Furnace Tech and another promotion to a Coiler Tech and then I did an Interim Lead role in the Hot Mill.
“Everybody here is striving to be better and always looking for the next step. I was in production, then I bid on an entry-level Maintenance Utility position, figuring if I have two backgrounds, two skill sets, maybe that’ll set me up for a supervisor role.”
Sanchez said at each step of his 16-year career, teammates and training opportunities helped him master new skills and develop a broader view of the overall work process. But like Shelton, he said the fundamentals of building a career don’t change, even if job titles do.
“When you have goals, are energetic, have the right attitude and mindset, and are eager to learn, the leadership team sees it,” he said. “They see you have a passion to get better. Those are the teammates they look to for promotion.”
Ashley Kroll is another example of a teammate who has leveraged her opportunities over 12 years with Nucor-Yamato Steel, where she’s recently been promoted to Environmental Coordinator Management Representative. From being the only woman in her steel tech internship to tackling every professional challenge placed in her path – including relocating for work to Texas for nine months with a small child in tow –Kroll has taken “can-do” to another level.
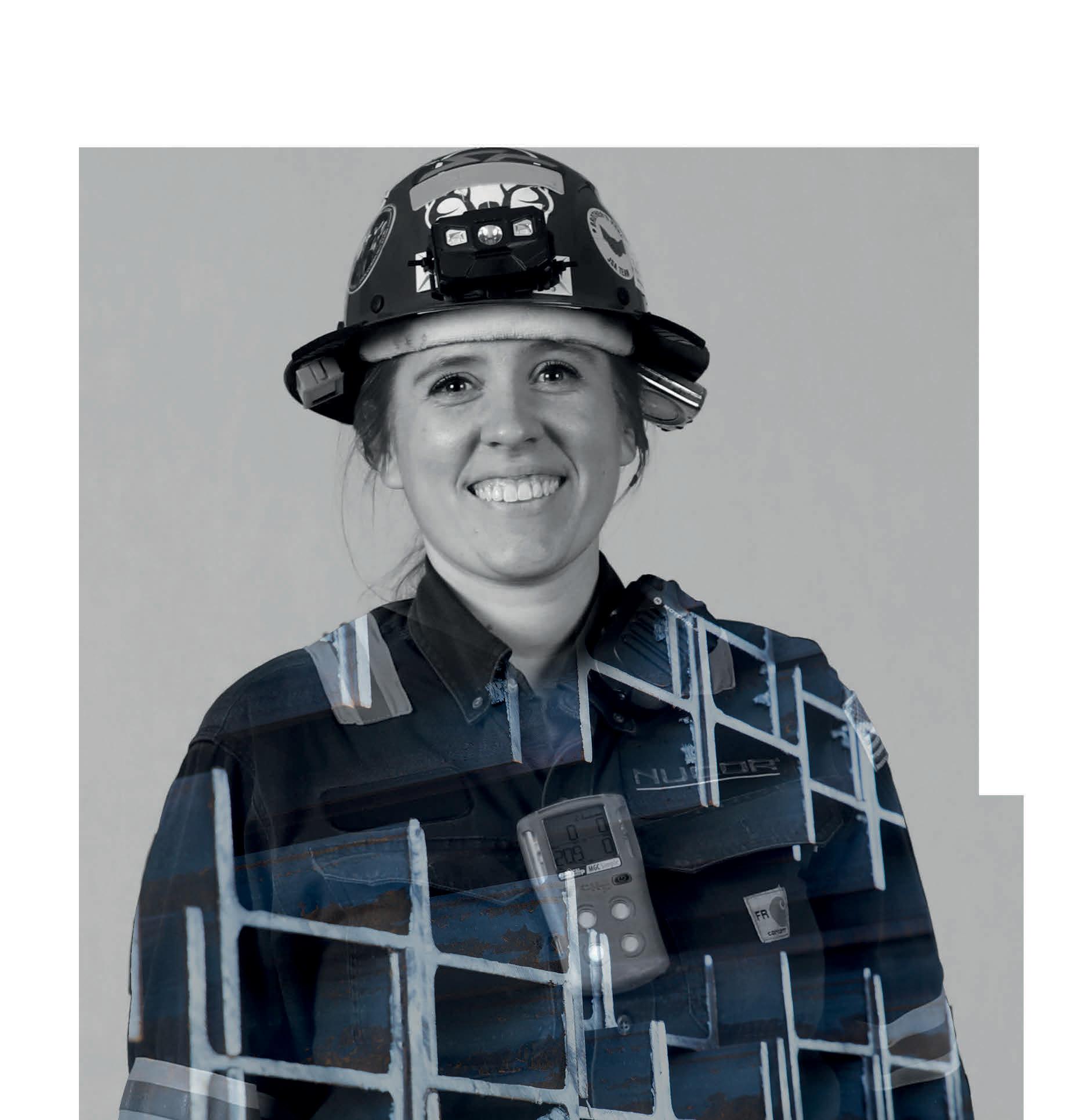
“Don’t be scared. Don’t be intimidated,” she said as advice to the next generation. “I didn’t know how to work a Microsoft Excel spreadsheet when I came here. Nucor paid for the class and I came back knowing how to work Excel, Microsoft Word and Microsoft Project. The point is, there’s always someone here ready to help, but you’ve got to be willing to figure out what you want to do and then give it your all to go do it.
“Be coachable, be open-minded and have the drive. Because if you have the drive and are coachable, that’s going to lay the foundation for everything else.”
TEAMMATE SPOTLIGHT
A REVOLUTION IN STEEL
BLUEPRINT: Did you grow up working with your hands?
SAMMY SANCHEZ: All my life, I’ve always worked with my hands. In Chicago my family had a mechanic shop, so I was always around tools. My dad was always working on trucks or fixing things. I love doing those type of things. I love fixing things.
In school, I took wood shop. I also took mechanics because I wanted to know how to troubleshoot problems with equipment and the tools used to fix them. Also, in the summer when I was growing up, I’d work at the golf course running the tractors, front-end loaders, backhoes.
BP: How have you improved your skills since you have been at Nucor?
Hometown: Chicago
Age: 39
Years with Nucor: 16
SS: Out here, you learn skills that you wouldn’t think you would use. I learned how to weld from teammates who are certified welders.
I took classes and learned how to operate heavy equipment.
BP: What’s the Nucor culture like?
SS: Continuous improvement is promoted here. It doesn’t matter who you are; you make your own career path. It’s here if you want it. If a teammate has that drive to advance, we help them with leadership, help them with public speaking, with business acumen to help on the business side, dealing with new teammates and hiring teammates. We put them through the courses to help them get better.
BP: What’s the best advice you could give to someone looking to follow in your footsteps?
SS: This is a great company. If my kids wanted to come here and work, I would promote that because I would want another generation of my family to work here. It takes drive and it takes effort, but your career is all up to you.
“YOU MAKE YOUR CAREER PATH. IT’S HERE IF YOU WANT IT.” —SAMMY SANCHEZ
BLUEPRINT: Where did you grow up?
CHARLES CASEY: I grew up right here in Armorel. I can look out the door and see the patch of woods where our house sat years ago. I ride on the same roads to work that I rode on the school bus as a kid.
BP: Do you have a college background?
CC: I have training from technical school in machine experience, CNC machines and others like that.
BP: What made you want to come work at Nucor?
CHARLES CASEY
Cold Mill 2 Supervisor, Nucor Steel Arkansas
Hometown: Armorel
Age: 57
Years with Nucor: 31
CC: Nucor-Yamato was built in ‘85 or ‘86, and I graduated in ’84 so I had heard about Nucor. When I got out of school I went into a vocational/technical school to learn how to be a machinist – which was a highly sought-after opportunity for people. I got into that kind of work and one thing led to another as far as my machine experience.
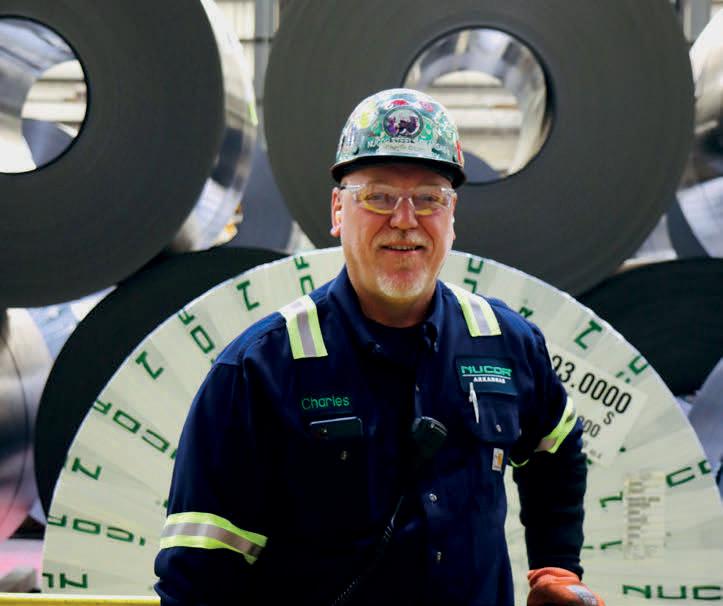
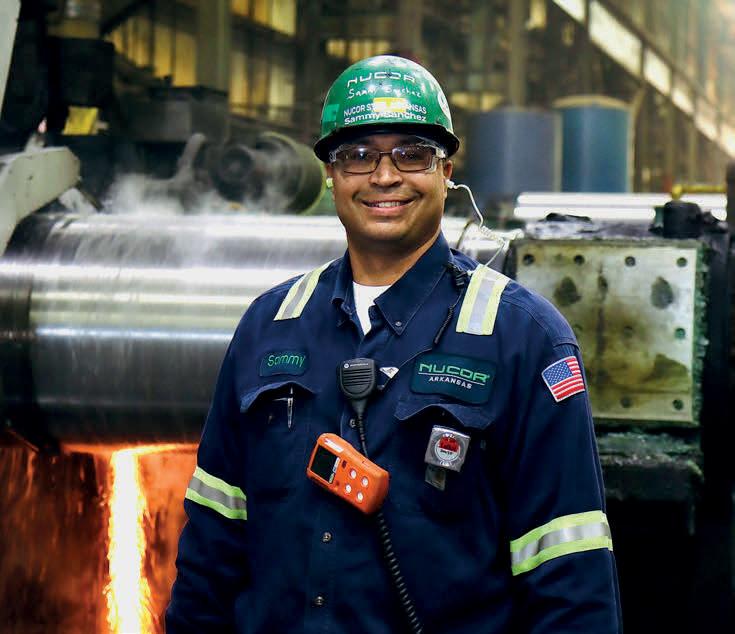
I worked for Milwaukee Tool, and they sent me to CNC training. I left there and went to BorgWarner and made car parts there, and then I got a call and was asked if I would be interested in interviewing here at Nucor Hickman. I came in for an interview and they offered me a job a few days later. The rest is history. I’ve done very well at Nucor for my family.
BP: Have other family members followed in your footsteps?
CC: Since I’ve been at Nucor, two of my sons came to work for Nucor. One is in shipping at Nucor-Yamato Steel (NYS) and the other one works in the mill. My oldest son works at Atlas right next door. We’re all in the steel business.
TEAMMATE SPOTLIGHT TEAMMATE SPOTLIGHT
A REVOLUTION IN STEEL
JIM SHELTONRoll Mill Manager, Nucor-Yamato
Steel
Hometown: Belleville, IL
Age: 55
Years with Nucor: 37
BLUEPRINT: What is your background?
JIM SHELTON: My uncle used to work for a steel company in California that closed down, and when Nucor Utah was built, he was recruited. We used to visit my uncle every year, and the steel industry just interested me. I started with Nucor 15 days after I turned 18. I worked at one of our other divisions in northern Utah for three years and then transferred to Nucor-Yamato Steel (NYS) in 1988 when this division was built.
BP: How did you learn the job skills you needed, starting that young?
JS: Nucor invests time in training new teammates, they are our most important resource. You are not just put out on the floor to figure it out on your own. I had a lot of folks along the way who taught, coached and mentored me throughout my career. We have a training calendar at our division so that the team has access to training that is available. Some training is required annually to make sure everyone is refreshed on certain topics.
Nucor also offers tuition reimbursement for teammates and their spouses who have an interest in furthering their education. We have several different safety ownership teams to get involved with that have different subject matter and offer team building and leadership opportunities without a title.
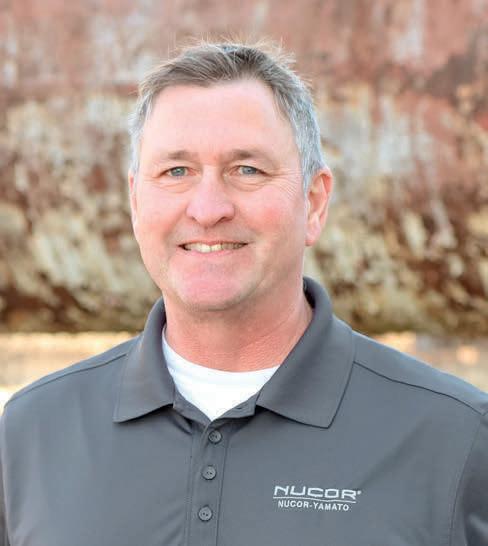
We also offer cross-training in different areas. If a teammate has an interest in an area, and maybe wants to learn more about it, they sign up on their days off to work in a different area which gives them a look at what it’s like in other areas of the mill and gives that area a look at the teammate. There are a lot of opportunities at Nucor, the sky is the limit, you just need to take advantage of the opportunities when they are available.
BP: What other skills do people need to be successful at Nucor?
JS: To me, attitude, the ability to learn, and getting along with others, those are things you start with. Those are fundamental traits to build a successful Nucor teammate from. From a leadership standpoint, it’s having the ability to create relationships, having the courage to have tough conversations on the front end, and understanding your team.
BP: How does it feel to have created such a long and successful career?
JS: I can’t imagine working for anybody else. We empower our teams at the floor level to be creative and look for safer and more productive ways of doing the things we do. It’s not the manager or the supervisor who makes things happen, it’s the teammates on the floor. You don’t have to have a position in management to be a leader at Nucor. It is very fulfilling to see new teammates join Nucor and watch their careers develop and be successful long-term teammates.
SHANNON WOOLSEY
Inside Sales Representative, Nucor-Yamato Steel
Hometown: Blytheville, AR
Age: 37
Years with Nucor: 3 years
BLUEPRINT: Did you start out to go into manufacturing?
SHANNON WOOLSEY: I earned an associate degree from Arkansas Northeastern College in 2009. From there I went to Arkansas State University Tech Center for a cosmetology and cosmetology instructor licenses. I owned a salon and then worked for a salon for a few years.
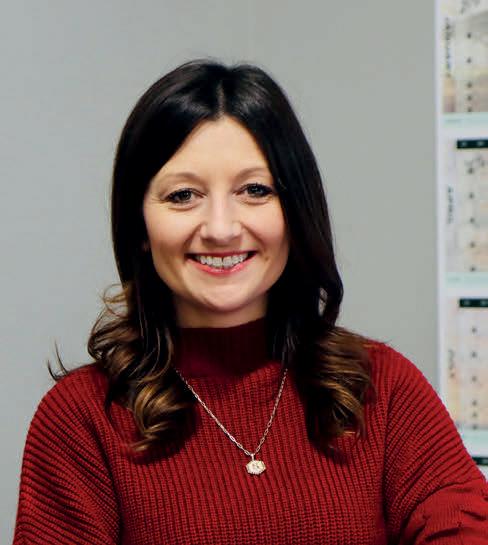
BP: How did that turn into a career in the steel industry?
SW: As a cosmetologist, I had a lot of clients who worked at Nucor. I had never been out to Nucor, didn’t even know where it was located. I had this one customer in particular who said, ‘I think you would be a good fit for Nucor.’ I enjoyed what I was doing, and the schedule, but one door led to another and before I knew it, I was at Nucor to interview and was hired.
BP: What’s the best thing about working at Nucor?
SW: Something I’ve really enjoyed about Nucor is the chance for advancement. If you’re open to new possibilities, there’s someone there who’s going to push you along and help you along the way. Internal advancement has always been preached and practiced here at Nucor.
BP: What have been some ways you have improved your overall skillset?
SW: I was part of the group that started Toastmasters at Nucor Yamato. I was also part of the Blytheville Leadership Institute which helped me learn more about what northeast Arkansas has to offer. I have completed the company’s Seven Habits of Highly Successful People class and I’m currently going through the Extreme Ownership program.
BP: What advice do you have for the next generation?
SW: Be respectful of leadership and other teammates, be a hands-on teammate, be willing to jump in and help and avoid saying, ‘That’s not my job.’ Be humble and willing to take the trash out if it needs to be taken out.
Communication is another important thing. We do a lot of coaching on communication skills. Someone in New York probably does not have the same personality or mindset that I have as a Southern girl. I have to know how to communicate with customers all over the United States.
HOT JOBS!
HOT JOBS!
SHIFT ELECTRICIAN
SHIFT ELECTRICIAN
DIVISION(S): Nucor-Yamato Steel and Nucor Steel Arkansas
DIVISION(S): Nucor-Yamato Steel and Nucor Steel Arkansas
AVERAGE SALARY: $88,000+
AVERAGE SALARY: $88,000+
WHAT DOES THE JOB DO?
WHAT DOES THE JOB DO?
Our team is expected to demonstrate safety-minded support of our entire maintenance team while seeking to provide world-class reliability for our customers. We support our maintenance and production teams via electrical and mechanical troubleshooting in a given area of the mill. Our team is responsible for planning, installation, programming, testing and troubleshooting of electrical machinery and automation systems. The person in this role must diagnose process and equipment problems and take appropriate measures to resolve issues. Shift electricians are responsible for the continuous process of steel manufacturing. These experienced industrial automation systems technicians are responsible for planning, installing, programming, testing and troubleshooting of electrical machinery.
Our team is expected to demonstrate safety-minded support of our entire maintenance team while seeking to provide world-class reliability for our customers. We support our maintenance and production teams via electrical and mechanical troubleshooting in a given area of the mill. Our team is responsible for planning, installation, programming, testing and troubleshooting of electrical machinery and automation systems. The person in this role must diagnose process and equipment problems and take appropriate measures to resolve issues. Shift electricians are responsible for the continuous process of steel manufacturing. These experienced industrial automation systems technicians are responsible for planning, installing, programming, testing and troubleshooting of electrical machinery.
WHY IT’S IMPORTANT: Electrical interruptions in the steel-making process can be costly. Shift electricians are the first defense against avoidable downtime. They rely on their years of experience and training to solve complex troubleshooting issues, which is essential for an efficient steelmaking process.
WHY IT’S IMPORTANT: Electrical interruptions in the steel-making process can be costly. Shift electricians are the first defense against avoidable downtime. They rely on their years of experience and training to solve complex troubleshooting issues, which is essential for an efficient steelmaking process.
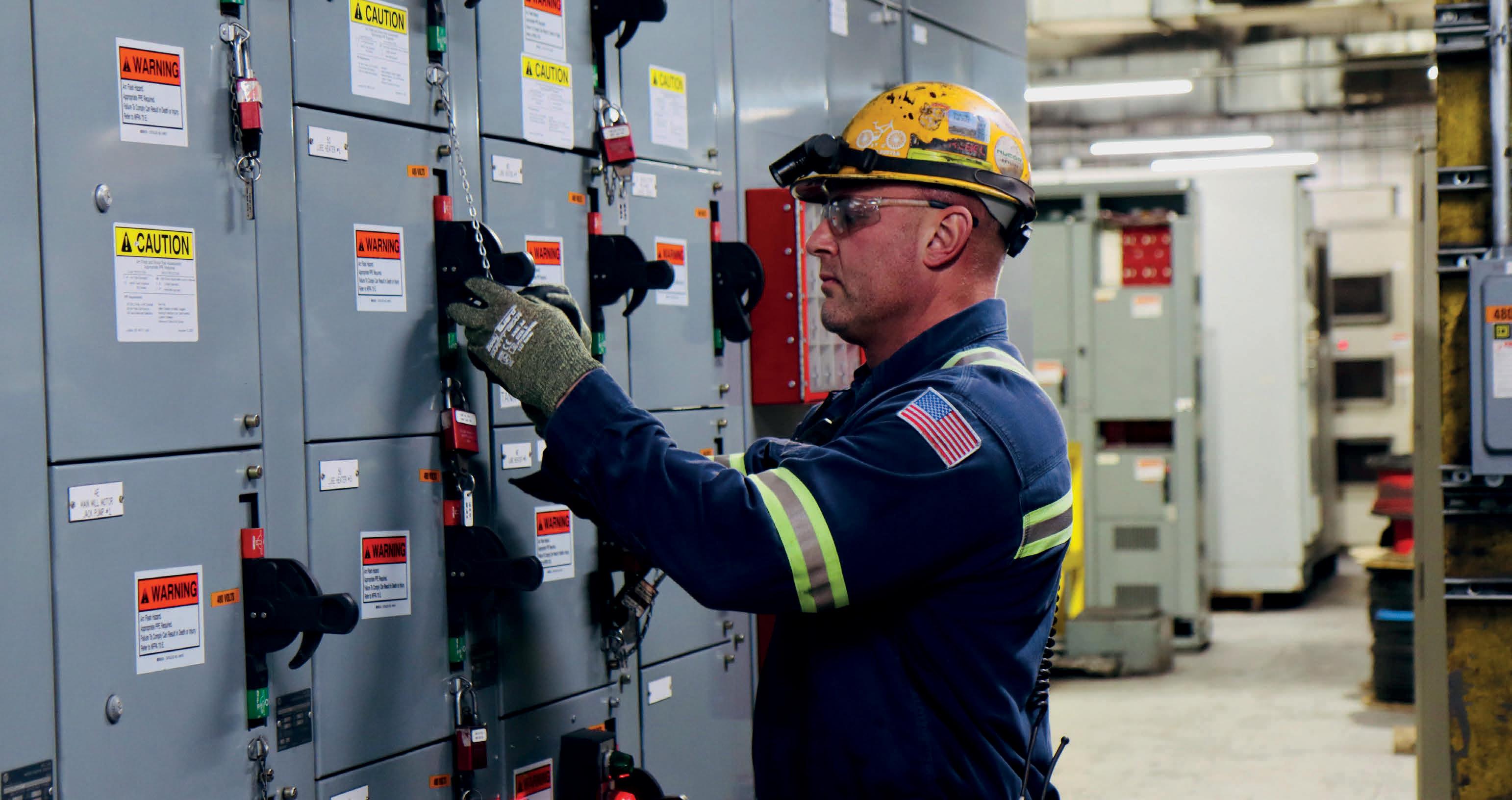
SKILLS, EXPERIENCE AND ATTRIBUTES: Some of the skill sets for success in this role include understanding of electrical theory, process instrumentation, ability to read electrical schematics, troubleshooting skills, programming experience and control systems.
SKILLS, EXPERIENCE AND ATTRIBUTES: Some of the skill sets for success in this role include understanding of electrical theory, process instrumentation, ability to read electrical schematics, troubleshooting skills, programming experience and control systems.
• Understanding of electrical theory, process instrumentation and control systems
• Understanding of electrical theory, process instrumentation and control systems
• Ability to read electrical schematics
• Ability to read electrical schematics
• Ability to troubleshoot electrical systems and equipment
• Ability to troubleshoot electrical systems and equipment
• Proficient in the use of electrical test equipment
• Proficient in the use of electrical test equipment
• Related industrial maintenance and automation experience in a manufacturing facility OR equivalent electrical training OR equivalent military experience
• Related industrial maintenance and automation experience in a manufacturing facility OR equivalent electrical training OR equivalent military experience
• Experience with medium-high voltage
• Experience with medium-high voltage
• Usage and limitations of various electrical troubleshooting tools and instruments
• Usage and limitations of various electrical troubleshooting tools and instruments
Experience with:
Experience with:
• PC, PLC, PID control and visualization programming
• PC, PLC, PID control and visualization programming
• AC motors and drives/maintenance and control of DC motors
• AC motors and drives/maintenance and control of DC motors
• Electrical, pneumatic and hydraulic LOTO
• Electrical, pneumatic and hydraulic LOTO
• Hydraulic and pneumatic troubleshooting
• Hydraulic and pneumatic troubleshooting
• Industrial motor starter circuit layout and troubleshooting
• Industrial motor starter circuit layout and troubleshooting
• Industrial instrumentation
• Industrial instrumentation
WHAT MAKES THIS POSITION IN HIGH DEMAND?
WHAT MAKES THIS POSITION IN HIGH DEMAND?
Industrial shift electricians require experience or equivalent technical training. Individuals with this skill set are in high demand and are being heavily pursued by all industrial facilities. Nucor also offers many job opportunities in this area where people of various skill levels can start potentially leading to high-level career positions.
Industrial shift electricians require experience or equivalent technical training. Individuals with this skill set are in high demand and are being heavily pursued by all industrial facilities. Nucor also offers many job opportunities in this area where people of various skill levels can start potentially leading to high-level career positions.
HOW DO I LEARN MORE? Please visit Nucor.com/careers to learn more about this opportunity.
HOW DO I LEARN MORE? Please visit Nucor.com/careers to learn more about this opportunity.
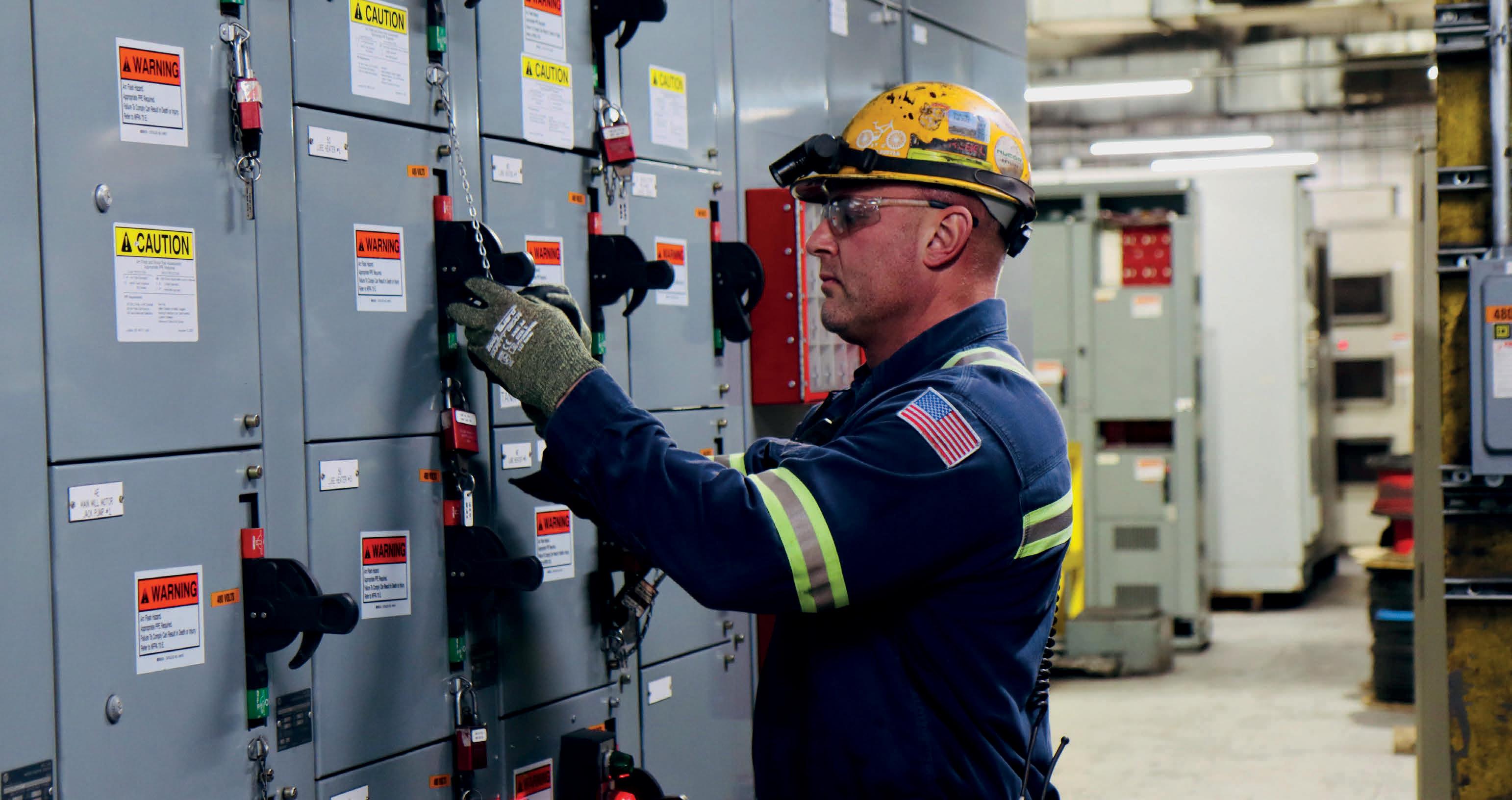
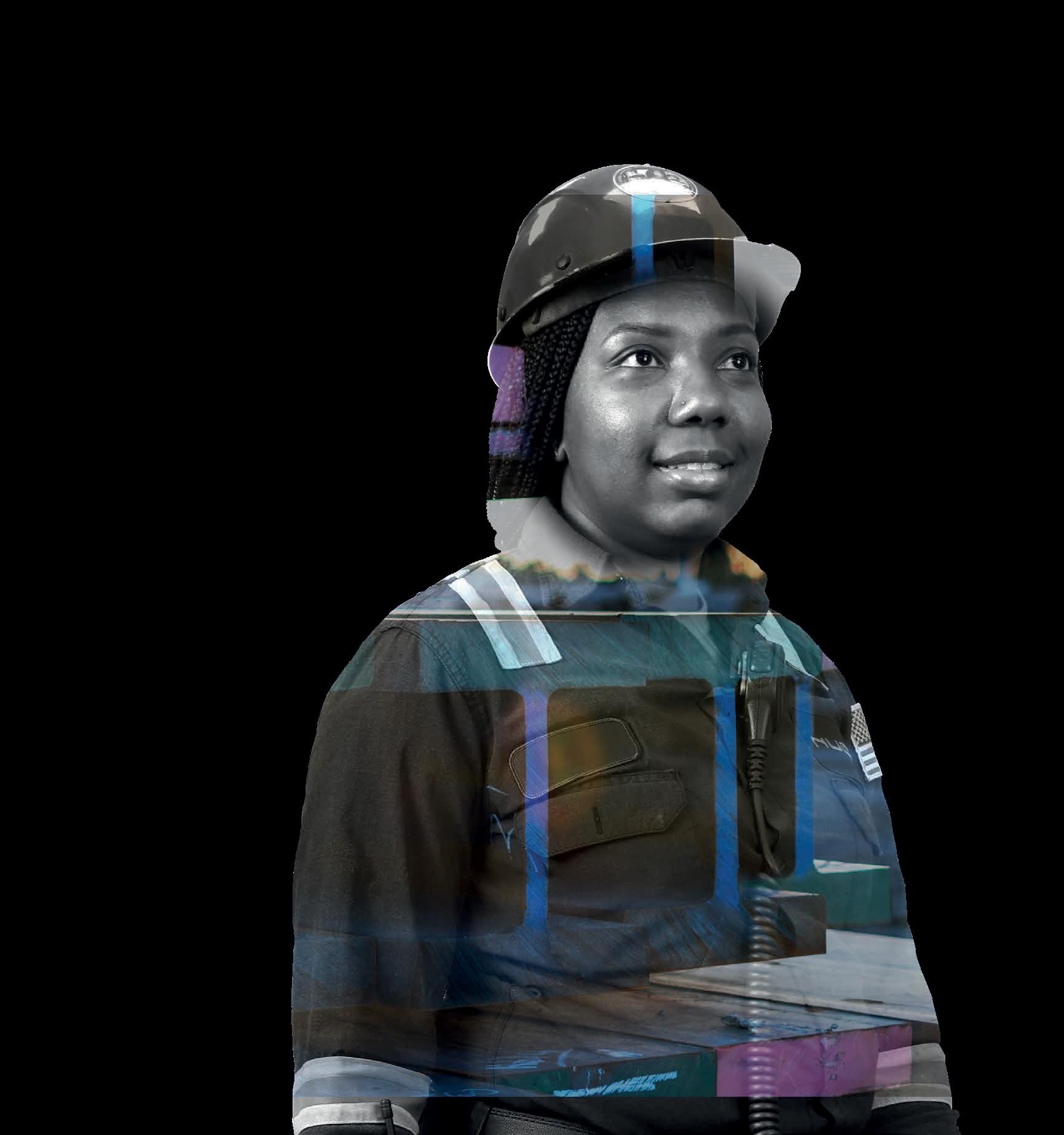
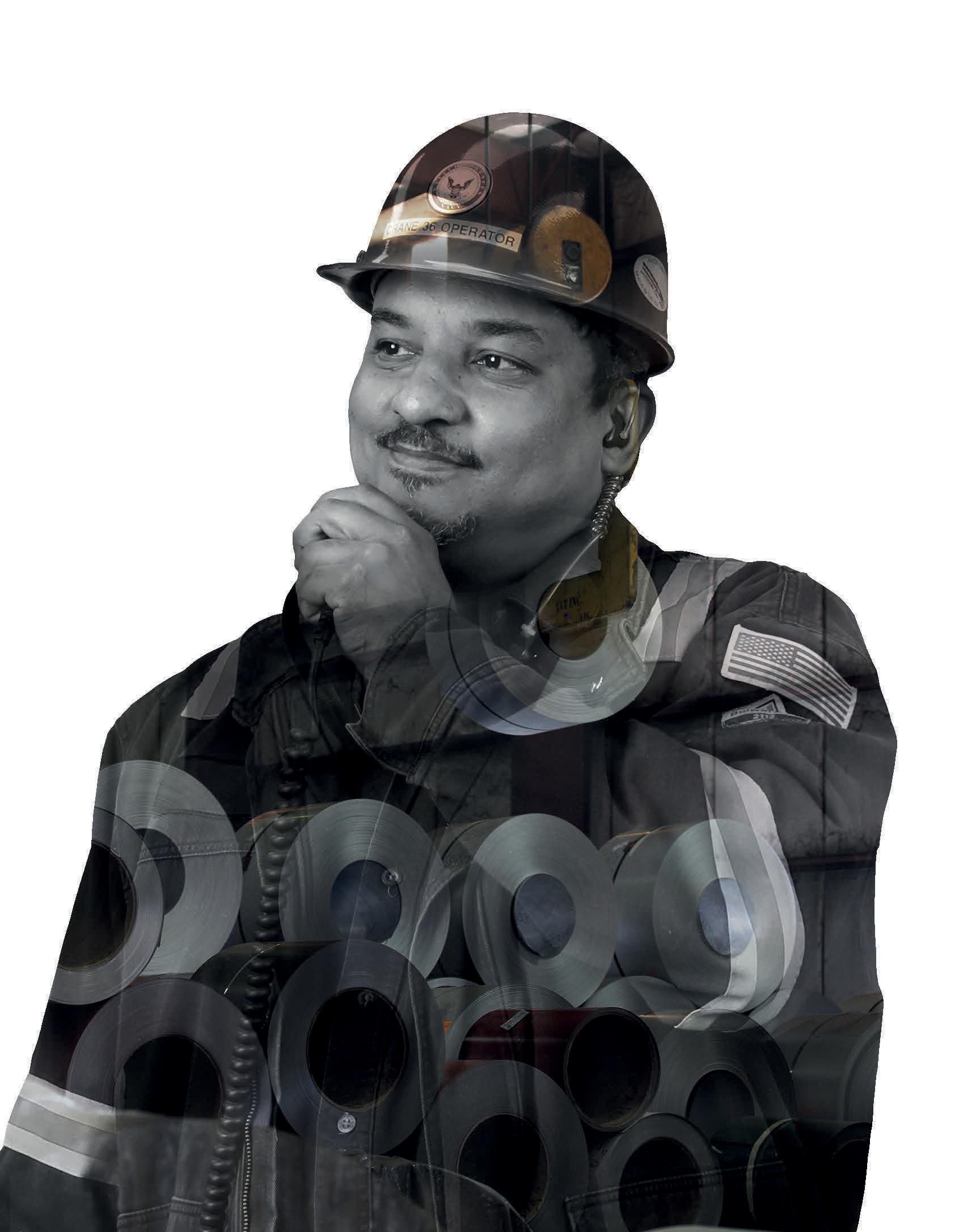
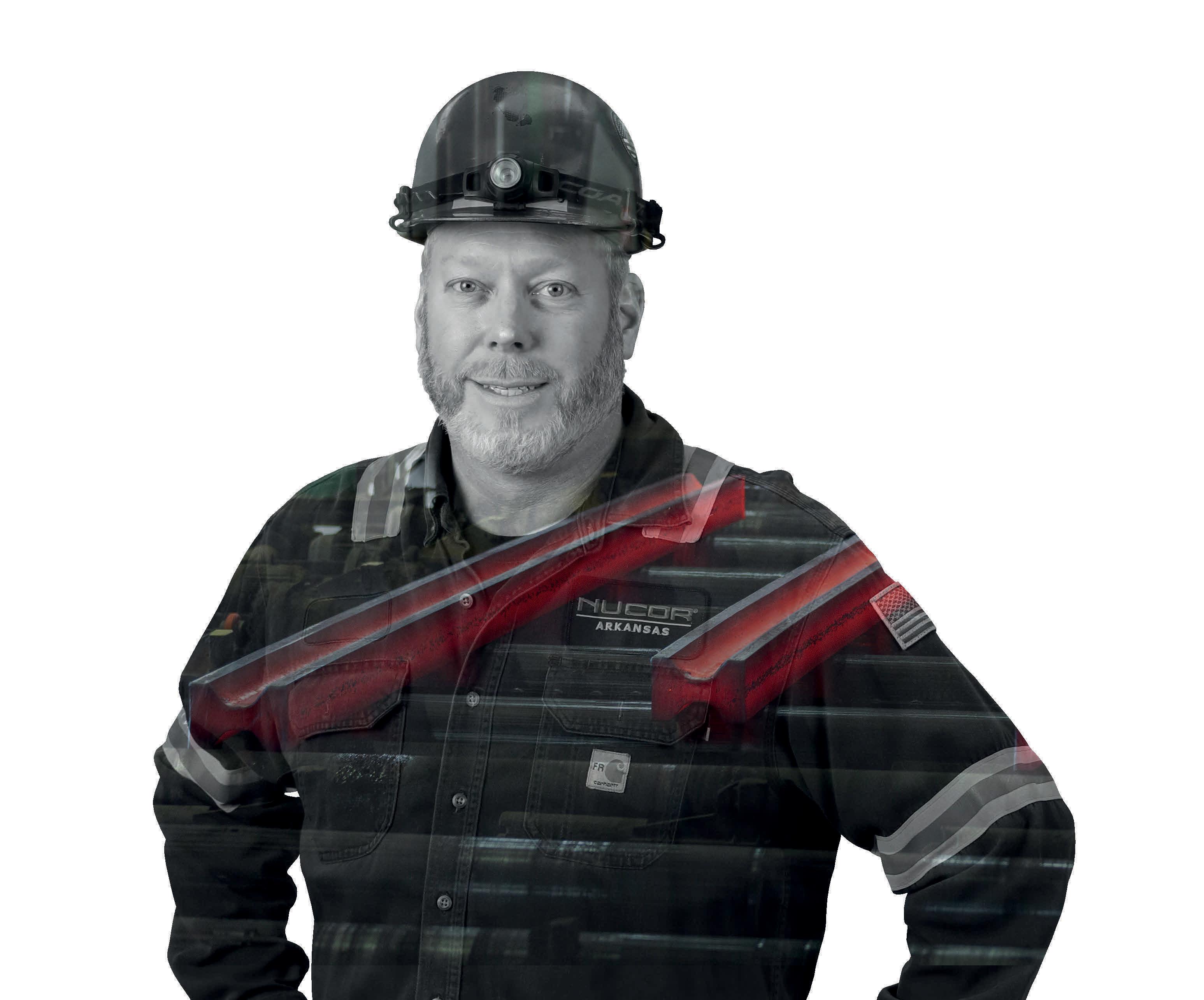
After a bumpy few years that saw some operators scaling back their operations, agri-timber is back in a big way in Arkansas. Since 2015, investment is up, demand is running high, and the need for workers is nearly constant. For people with the right skills and a good work ethic, the agri-timber industry provides a solid career choice.
WHAT DOES AN AGRI-TIMBER WORKER DO?
Agri-timber involves the management of forest resources, harvesting of trees in an environmentally responsible manner and processing the wood into a variety of products that consumers and other industries rely on every day. These final products range from lumber for the construction industry to paper products, to processed building products such as plywood and veneers. The types of careers available in this field include:
Logging equipment operators
• Use tree harvesters to fell trees, shear off limbs and cut trees into desired lengths.
• Drive tractors and operate machines called skidders, or forwarders, which drag or push logs to a loading area.
Log graders and scalers
• Inspect logs for defects and measure the logs to determine their volume.
• Estimate the value of logs or pulpwood.
• Often use hand-held data collection devices to track forest and specimen data.
Diesel techs
• Diesel engines power many industrial vehicles and machines.
• Diesel engines are increasingly sophisticated, with onboard electronics and telematics.
• Skilled diesel techs are required to keep such machines running at peak efficiency.
Just like any other manufacturing facility, sawmills and paper/pulp mills are dependent on a variety of skilled professionals, such as computer programmers/coders, electricians, plumbers and industrial maintence workers.
WHAT’S NEW?
Advanced manufacturing
Sawmills and paper/pulp mills have a long-standing reputation for being hot, smelly and unpleasant places to work. However, many of today’s mills rely on advanced manufacturing techniques, which harness the power of technology and automation to process raw timber. This results in a cleaner, safer and more comfortable workplace, greater yield and efficiency, and more responsible handling of waste products.
WHERE DO AGRI-TIMBER PROFESSIONALS WORK?
Generally speaking, logging crews spend their time outdoors in the woods, working in all types of weather. Factories and processing plants tend to be located within a reasonable distance of where the trees are harvested to help contain logistical costs.
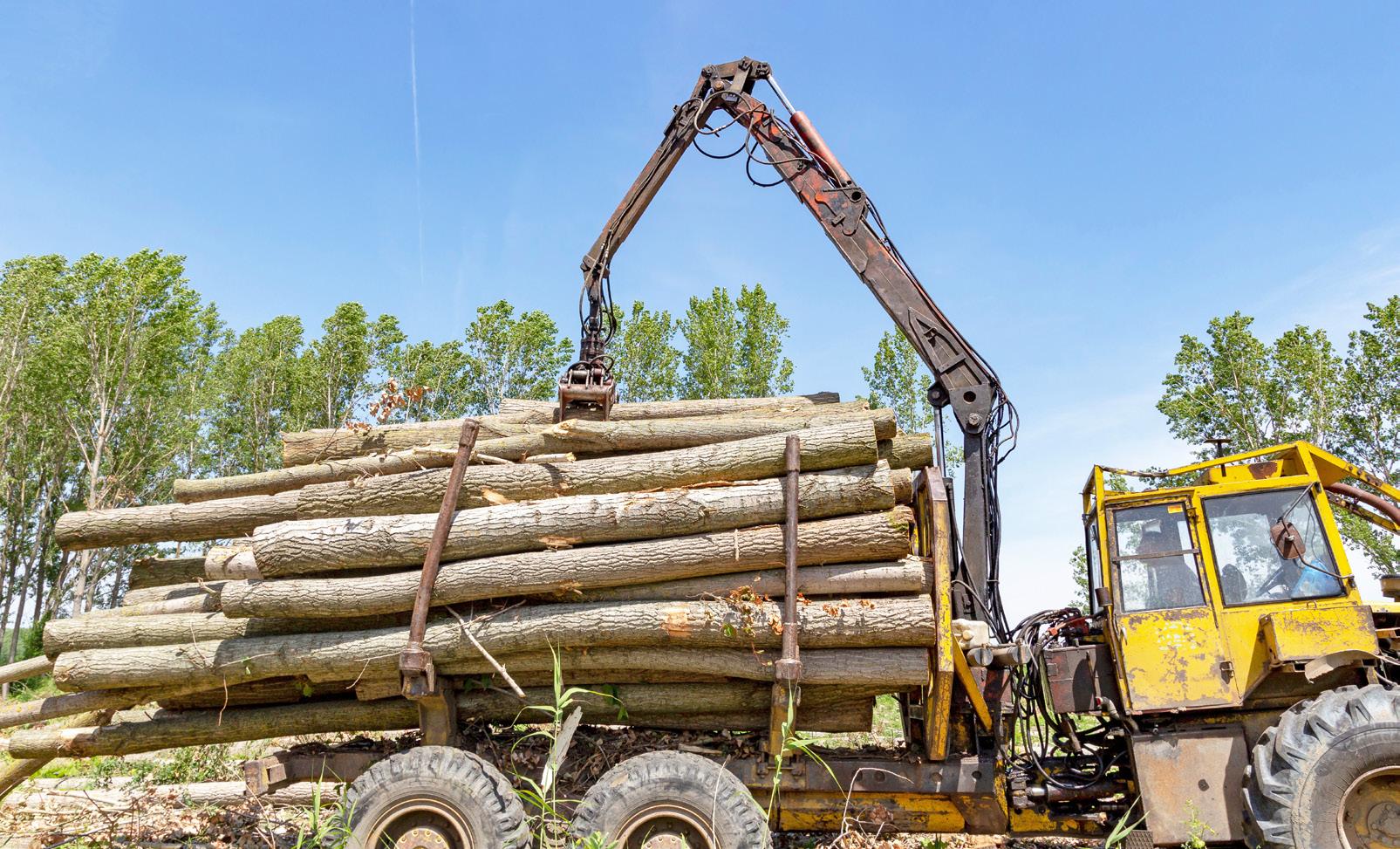
Arkansas’s timber processing plants are scattered throughout the state, with many of them clustered in the southwest corner, extending from Fort Smith diagonally to Arkansas City on the Mississippi River and to the Louisiana and Texas state lines.
WHAT’S THE JOB OUTLOOK?
Logging graders and scalers is a growing field in Arkansas. Forecasters predict the field will increase by 6% over the next few years, better than the national average. The number of logging equipment operators in the state is expected to drop slightly, down 3%, which is on par with national numbers.
HOW
MUCH CAN I MAKE?
• Lower range wages (bottom 10%) — $23,620 annually/$11.36 per hour
Middle range wages (median) — $46,750 annually/$22.48 per hour
• Higher range wages (top 10%) — $61,270 annually/$29.46 per hour
Log Graders and Scalers
• Lower range wages (bottom 10%) — $29,890 annually/$14.37 per hour
• Middle range wages (median) — $37,360 annually/$17.96 per hour
Higher range wages (top 10%) — $47,880 annually/$23.02 per hour
WHAT DOES IT TAKE TO BE SUCCESSFUL?
Communication skills
• Must communicate with other crew members to perform work efficiently and safely.
• Must be able to work as part of a team.
Computer skills
• Able to operate and adjust digitally controlled factory equipment or handheld devices.
Detail oriented
• Must watch gauges, dials and other indicators to determine if equipment and tools are working properly.
HOW DO I LEARN THE CRAFT?
A high school diploma is all that’s required for most logging jobs.
• Most industry-specific training comes on the job.
• Some community colleges offer associate degrees or certificates in forest technology.
• A few community colleges offer education programs for logging equipment operators.
• Many state forestry or logging associations provide training sessions for logging equipment operators. Training often takes place in the field, where trainees can practice various logging techniques and use specific equipment.
• Logging companies and trade associations may also offer training programs for workers who operate large, expensive machinery and equipment.
• Such programs often culminate in a state-recognized safety certificate from the logging company.
Did you ever notice how many people work in a hospital, clinic or even the office of your family doctor? The fact is it takes many trained people working together to deliver health care in the United States, and only a fraction of them have ever set foot inside a nursing or medical school. If you have an interest in the medical field, but don’t see yourself becoming a doctor or nurse, there’s a job waiting in the allied health field that’s got your name on it.
WHAT DOES AN ALLIED HEALTH PROFESSIONAL DO?
Allied health is a broad category of careers within the health care field. The number, variety and range of these jobs is vast — some estimates say up to 60% of all jobs in the health care field are classified as allied health professions. Many of these positions do not require a four-year degree, which allows people to start a career quickly.
Allied health professionals are the support staff at the doctor's or dentist’s right hand; they work in the pharmacy, the medical lab or the rehabilitation room, and they are the personnel trained to operate diagnostic medical equipment.
WHY SUCH HIGH DEMAND?
• People are living longer, thanks to advancements in medicine, technology and healthy habits.
• The increase of certain chronic conditions, such as diabetes and obesity, which have more complications and require more care.
• Gerontology (senior citizen care) is exploding with the aging of the baby boomers.
A SAMPLE OF ALLIED HEALTH JOBS
The website careerprofiles.info compiled a list of the fastest-growing allied health care jobs in the United States. The list includes medical assistants, cardiovascular technologists and technicians and respiratory therapists Medical assistants perform clinical and administrative duties for doctors, surgeons, chiropractors and other medical specialists.
• Typical job duties: Answering phones, greeting patients, maintaining medical records, scheduling patient appointments and handling patient billing.
• Education: Generally includes a certification or associate degree that takes 1-2 years to complete.
• Job Growth: Job demand is expected to grow 17% over the next few years, slightly higher than the national average.
• Pay: In Arkansas, the annual pay range for medical assistants is between $25,000 and $38,000.
Cardiovascular technologists and technicians help doctors diagnose and treat heart and vascular problems.
• Typical job duties: Prepare patients for heart procedures, such as balloon angioplasties, cardiac catheterizations and even open-heart surgery. They monitor heart rate and blood pressure and notify doctors after detecting abnormalities.
• Education: Most earn at least an associate degree at a community college; others complete a fouryear degree.
• Job Growth: Job demand is expected to grow 6% over the next few years, on par with the national average.
• Pay: In Arkansas, the annual pay range for cardiovascular technologists and technicians is between $30,000 and $76,000.
Respiratory Therapists assess, treat and assist patients with cardiopulmonary and other breathing problems.
• Typical job duties: Assess, treat and assist patients; oversee respiratory therapy, administer diagnostic tests and provide therapy.
• Education: Respiratory therapists generally hold an associate degree.

• Job Growth: Job demand is expected to grow 23% over the next few years, much faster than the national average.
• Pay: In Arkansas, the annual pay range for respiratory therapists is between $45,000 and $75,000.
WHERE DO ALLIED HEALTH PROFESSIONALS WORK?
Most allied health professionals work in a medical setting, such as a doctor’s office, dental practice, clinic or hospital. Some may be mobile, bringing therapies to homebound patients or performing other duties.
Many allied health jobs are an extension of the physician and frequently have close contact with patients.
Not all allied health professionals act as front-line support for medical procedures, however. These professionals maintain patient records and coordinate with insurance carriers for payment, among other tasks. Except for the fact they work at a clinic or doctor’s office, their work isn’t much different than clerical tasks in any other office.
For more information on these and other allied health professional jobs and to find training programs, visit www.careeronestop.org.
Aviation comes in all shapes and sizes, from crop dusters and private planes, to small corporate jets, to commercial airliners. Arkansas has a little bit of everything when it comes to this field, as it is home to aircraft manufacturing companies, airports and fixed-base operations. It’s a growing field in need of talented, skilled employees.
WHAT DO AVIATION TECHNICIANS DO?
Aviation technicians perform a wide variety of duties on private and commercial aircraft. The actual job duties vary, depending on which area of the industry one chooses.
Airframe
• Perform inspections of aircraft frames, mechanical components and electrical systems to locate wear, defects and other problems.
• Test aircraft functions using diagnostic equipment to ensure proper performance.
• Repair or replace components using hand or power tools.
• Technicians may specialize in a certain category of aircraft, such as passenger jetliners, propeller-driven airplanes or helicopters.
• Technicians may also focus on different systems such as engines (also known as the “powerplant”) or hydraulics.
Avionics
• Specialize in aircraft electronics, which includes a range of job types.
• Responsible for all the electronics onboard an aircraft, as well as the wiring that connects components to the electrical system.
• Run cables, mount antennas and connect instruments for navigation and engine monitoring.
• Test onboard equipment to ensure it’s working properly.
WHERE DO AVIONIC TECHS WORK?
Some specific types of businesses that employ aircraft technicians include:
Fixed-Base Operations
At most airports, private companies called FixedBase Operations (FBO) provide a number of services to smaller aircraft, such as corporate jets and private planes. Aviation technicians provide maintenance services for aircraft using the FBO.
Airlines
Commercial airlines have a lot of planes they need to keep operational if they are going to stay on schedule and deliver their passengers safely. Aircraft and avionics technicians are a key element of their success.
Shipping companies
Not all airplanes deliver people; some deliver millions of pieces of freight and consumer mail or packages every day. Retailers rely on companies like FedEx, UPS and the U.S. Postal Service to deliver orders to their customers, and these shipping companies rely on their planes to make that happen.
Flying Services
Flight schools, crop-dusting operations and air charter companies all need technicians to keep their machines in top shape and operating safely.
WHAT’S THE JOB OUTLOOK?
Arkansas’s demand for aircraft mechanics and service technicians jobs is expected to grow 13% over the next few years, more than double the national average. Avionics technician jobs in the state are also expected to grow, albeit more slowly, at 5%.
HOW MUCH CAN I MAKE?
Aircraft Mechanics and Service Technicians
Lower range wages (bottom 10%) — $36,900 annually/$17.74 per hour
• Middle range wages (median) — $56,100 annually /$26.97 per hour
• Higher range wages (top 10%) — $76,300 annually/$36.69 per hour
Avionics Technicians
• Lower range wages (bottom 10%) — $37,160 annually/$17.87 per hour
Middle range wages (median) — $59,950 annually/$28.82 per hour
• Higher range wages (top 10%) — $102,220 annually/$49.14 per hour
WHAT DOES IT TAKE TO BE SUCCESSFUL?
• Equipment Maintenance and Repairs
• Troubleshooting/Quality Control Analysis
• Critical Thinking
• Complex Problem Solving
HOW DO I LEARN THE CRAFT?
Aviation technicians typically have some training after high school, taken at a community college or specialized aviation technical school. Be sure to select a program that is FAA approved.
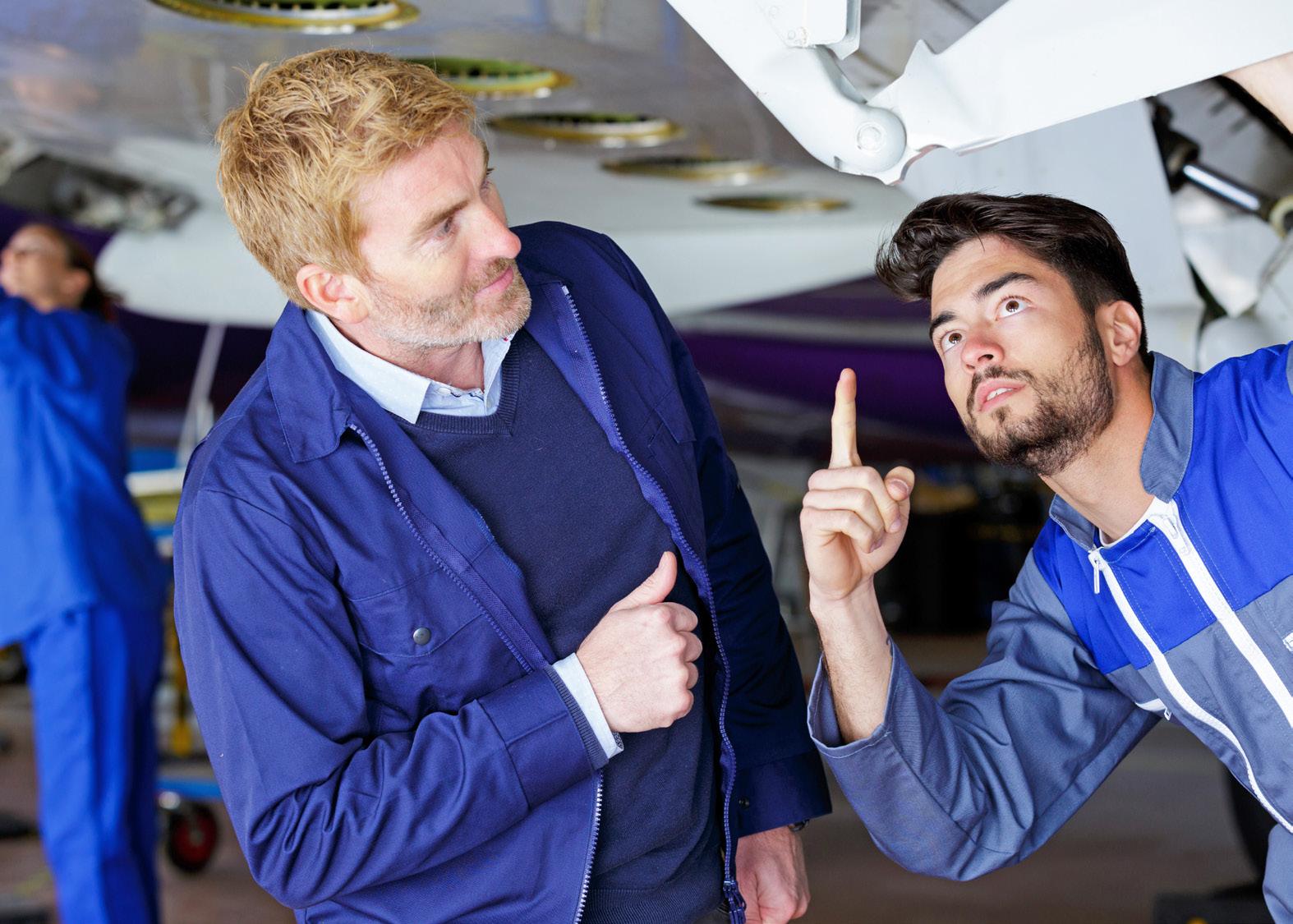
At the completion of this training, technicians take an exam administered by the FAA to obtain certification in their chosen field. Technicians can also expect to take continuing education classes or attend seminars or training sessions to stay current on new parts, regulations, technology and flight systems.
Once a technician receives an associate degree, they can opt to complete a four-year degree, which opens up a number of other job opportunities and greater earning power.
Computer-aided design/computer-aided manufacturing drafters create 2D and 3D drawings that are used to manufacture products. Drafters also design and make parts for use in a number of machines that are part of the manufacturing processes.
WHAT DOES A CAD/CAM DRAFTER DO?
Computer-aided design (CAD) and computer-aided manufacturing (CAM) are two computer-aided technologies. Starting in the 1980s, CAD/CAM programs have been used to make customized metal and plastic parts with computer-controlled machining.
The drafter (sometimes called a CAD operator) creates a technical drawing that contains all the dimensions for the part, much like a blueprint shows the dimensions of a house or building.
In addition to being faster than hand drawings and human-operated cutting or milling machines, CAD systems can also produce parts much more accurately. These machines have such precise measurements, they are accurate to 1/1,000 of an inch, one-third the width of a human hair.
WHAT’S NEW?
CAD is used in the design, development and manufacture of all kinds of products. CAD is widely used to produce parts for machines, in the design of manufacturing tools, and in designing residential and commercial buildings. CAD is especially important in microelectronics, providing lower development costs for newer, smaller and more powerful devices in a much shorter time frame. Drafters also work with CAD to create BIM drawings. BIM stands for building information modeling and is widely used in construction to produce highly accurate digital models of buildings and machines.
WHERE DO CAD/CAM DRAFTERS WORK?
Architectural drafters
Draw architectural and structural features of buildings for construction projects.
• May specialize in a type of building such as residential or commercial.
• May also specialize by the materials used, such as steel, wood or reinforced concrete.
Civil drafters
• Work with engineering firms, highway construction firms or within city planning departments. Prepare maps used in municipal construction projects, such as highways and bridges.
Electrical drafters
• Prepare wiring diagrams that construction workers use to install and repair electrical equipment and wiring in power plants, residential and commercial buildings.
Employed by a wide range of companies, including construction, electrical firms and manufacturers.
Electronics drafters
• Produce wiring diagrams for circuit boards.
• Produce layout drawings used in manufacturing and installing and repairing electronic devices and components.
Mechanical drafters
• Prepare layouts detailing a wide variety of machinery and mechanical tools and devices.
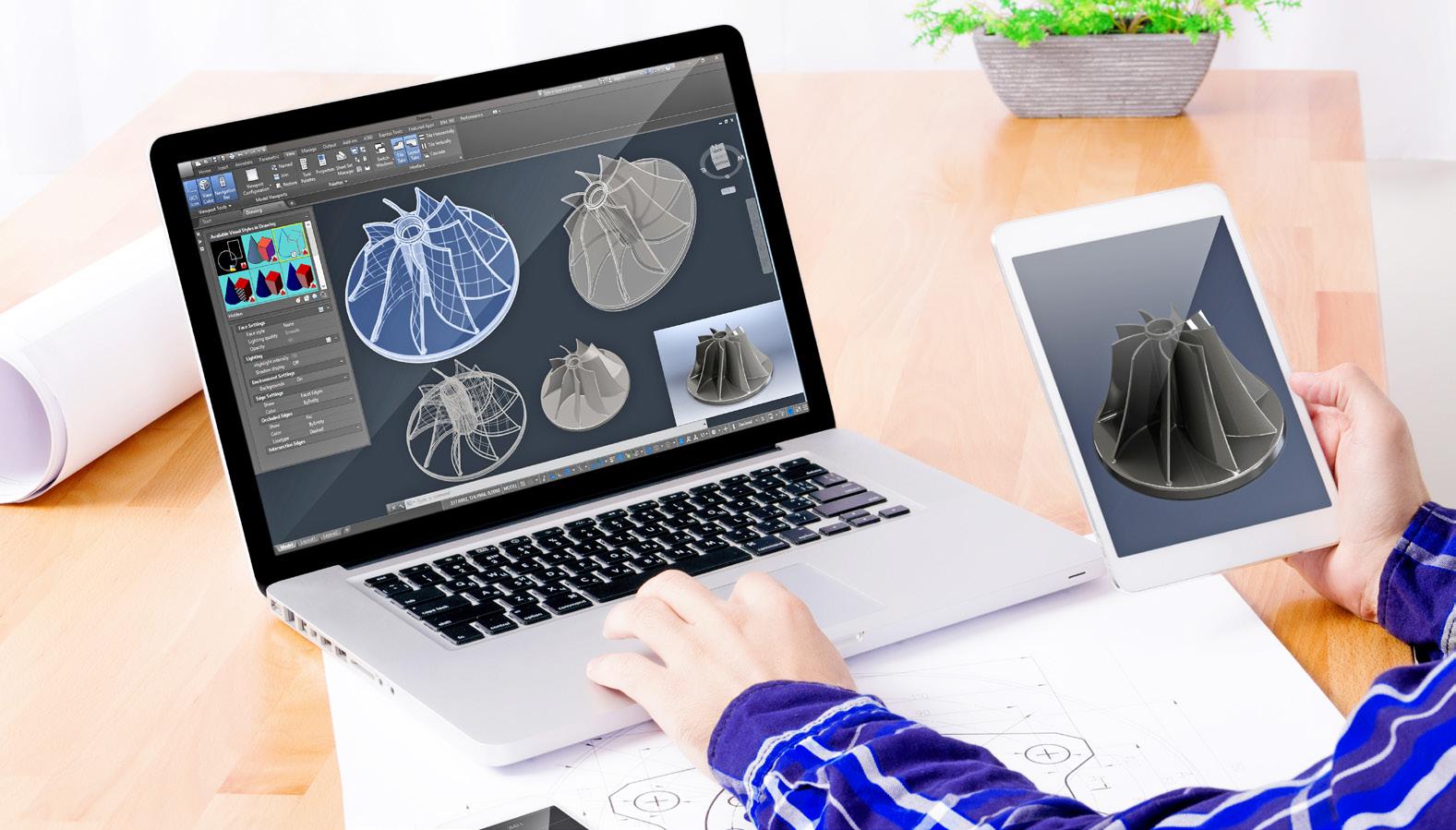
• Mechanical drafters also sometimes create production molds.
• Employed in a wide variety of manufacturing companies.
WHAT’S THE JOB OUTLOOK?
All categories combined, drafters in Arkansas held more than 1,000 jobs in 2018. More than half of those positions were in the architectural or civil fields. Most drafters work full time, spending the majority of their working hours in an indoor office setting. According to the U.S. Department of Labor, projected job growth for drafters overall is 2%. That may not sound like much, but it’s several percentage points above the national growth rate expected in these jobs.
HOW MUCH CAN
I MAKE?
Architectural/Civil Drafters
• •Lower range wages (bottom 10%) — $36,900 annually/$17.74 per hour
• Middle range wages (median) — $49,320 annually/$23.71 per hour
• Higher range wages (top 10%) — $74,170 annually/$35.66 per hour
Electronics Drafters
• Lower range wages (bottom 10%) — $36,900 annually/$17.74 per hour
• Middle range wages (median) — $46,840 annually/$22.52 per hour
• Higher range wages (top 10%) — $76,600 annually/$36.83 per hour
Mechanical Drafters
• Lower range wages (bottom 10%) — $31,750 annually/$15.27 per hour
• Middle range wages (median) — $47,130 annually/$22.66 per hour
Higher range wages (top 10%) — $72,580 annually/$34.89 per hour
WHAT DOES IT TAKE TO BE SUCCESSFUL?
• Creativity
• Detail oriented
• Interpersonal skills such as communication
• Math/technical skills
• Time-management skills
HOW DO I LEARN THE CRAFT?
Drafters generally need to complete a two-year associate degree from a community college. Drafters do not generally complete an apprenticeship like other trades do. Community colleges offer programs that lead to an associate of applied science in drafting or a related degree. The types of courses offered will vary by institution; some institutions may specialize in only one type of drafting. The American Design Drafting Association (ADDA) offers certification for drafters. ADDA certification shows you have invested extra time and effort into your craft and is sometimes required by your employer. It can also sometimes result in higher pay. Certifications are offered for several specialties, including architectural, civil and mechanical drafting.
Of all the skilled professions, carpentry is the oldest and arguably the most widely recognized. A skilled carpenter makes a positive, even life-changing impact on the people — and quality of life — in their community.
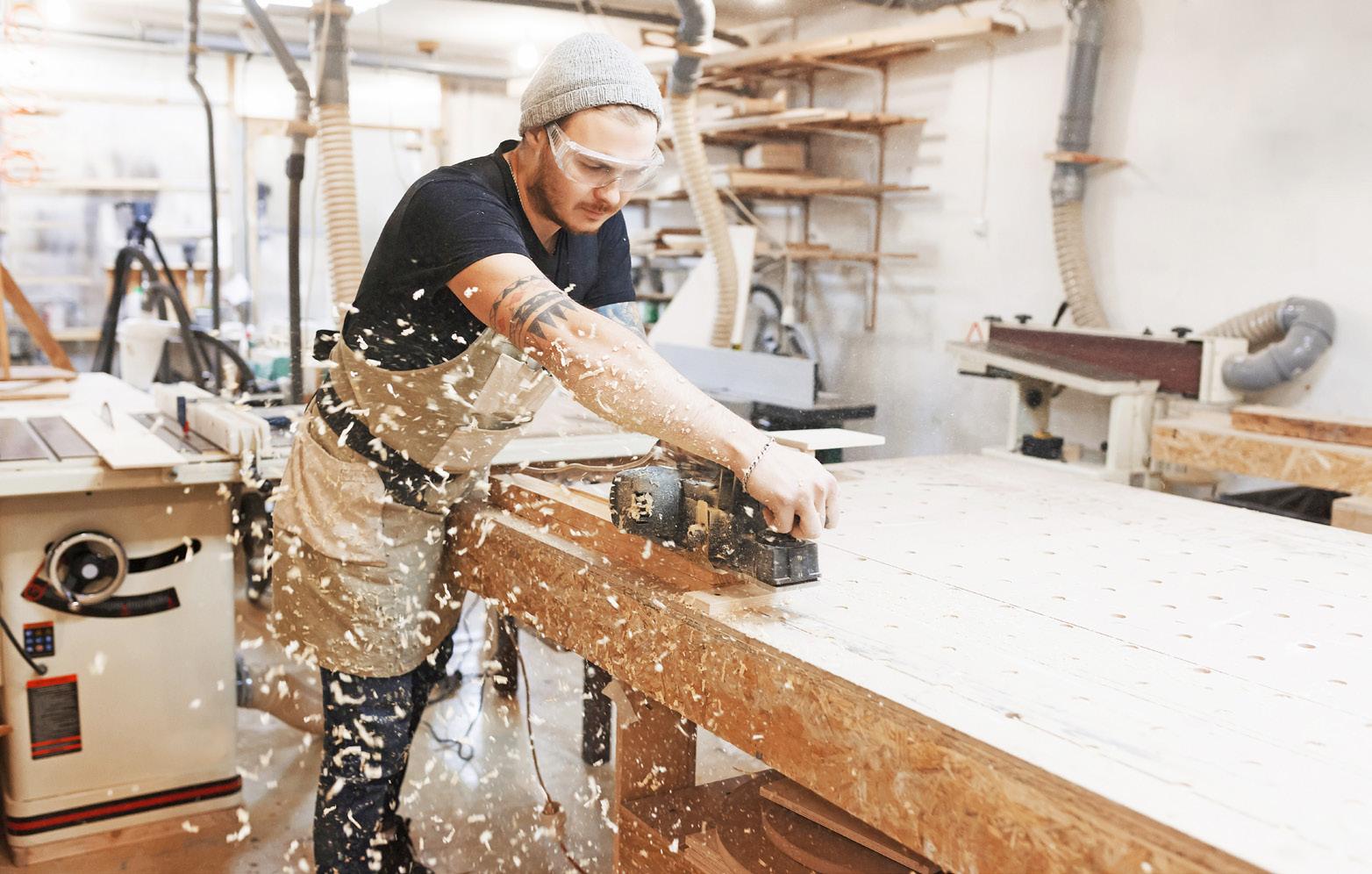
WHAT DOES A CARPENTER DO?
Carpenters construct, repair and install building frameworks, remodel and rehab existing buildings, and perform the finishing work made from wood and other materials.
Carpentry is a versatile occupation in the construction industry, with craftsmen and women generally proficient in a variety of tasks. Some carpenters are more specialized, such as those who insulate office buildings and/or install drywall or kitchen cabinets in homes.
The following are examples of types of carpenters:
Construction carpenters
• Construct, install and repair structures and fixtures.
• Use hand tools and power tools to complete their work.
• Construct building frameworks, such as walls, floors and doorframes.
Rough carpenters
• Build rough, temporary wooden structures, such as concrete forms and scaffolds.
• May also build tunnels, bridges or sewer supports.
• They use hand tools identical to that of construction carpenters.
WHAT’S NEW?
Cloud Computing/Apps
Visit a construction site and you’ll see more iPhones and iPads than paper blueprints. Being skilled in the trades means knowing how to quickly store and retrieve plans, documents and schematics, and that’s exactly what the cloud does for today’s carpenters and their clients.
If you choose to go into business for yourself, you will find apps that help you keep everything straight, from bidding new work to billing finished projects and everything in between.
BIM
Bulding information modeling allows architects, engineers, contractors and other construction professionals to create virtual plans. BIM also provides onboard tools for coordinating the many craftspeople who are scheduled to work on a building.
Changes can be made easily in the building specs with-
out having to lug around paper plans or waste a lot of time and manpower running back to the contractor’s office.
It also provides a work structure for the tradesmen and women in their proper order and coordinates the delivery of materials such as lumber, concrete, roofing materials or drywall.
Drones
Unmanned aerial vehicles are playing a larger role in the construction industry. Drones equipped with cameras can access remote locations, collect data, complete safety inspections, capture project progress and more. Surveyors also use them to create 3D mapping.
WHERE DO CARPENTERS WORK?
Carpenters work indoors and outdoors on many types of construction projects, from highways to kitchen remodels. Working outdoors subjects them to variable weather conditions, and there are times when conditions are such that a carpenter cannot work at all.
Most carpenters work full time, which may include working evenings and weekends. This includes self-employed carpenters, particularly in the early stages of starting a business.
Safety equipment, such as boots, hardhats and harnesses (when working high off the ground), is required when working for a general contractor or in an industrial setting.
WHAT’S THE JOB OUTLOOK?
The Department of Labor predicts the number of carpenter jobs in Arkansas will grow slightly in the next few years. About a third of carpenters are self-employed and one in five works in residential construction. As with other construction jobs, carpenters are at the mercy of the economy, and when a slowdown occurs, building projects are sometimes postponed or even canceled. When that happens, workers get laid off.
HOW MUCH CAN I MAKE?
• Lower range wages (bottom 10%) — $28,830 annually/$13.86 per hour
• Middle range wages (median) — $38,130 annually/$18.33 per hour
• Higher range wages (top 10%) — $54,580 annually/$26.24 per hour
Your actual earnings depend on your experience, any specialties you might have and even the part of the state where you live.
WHAT DOES IT TAKE TO BE SUCCESSFUL?
• Business skills
• Detail oriented
• Dexterity
• Math skills
• Physical strength/stamina
• Problem-solving skills
HOW DO I LEARN THE CRAFT?
A high school diploma is generally all that’s required to start a career in carpentry. High school courses in math, mechanical drawing and general technical training classes, such as wood shop, can be helpful starting points. Carpenters typically learn their craft on the job and through apprenticeships. Individual businesses, unions and contractor associations may sponsor apprenticeship programs, which can take two to four years to complete. Apprentices learn carpentry basics, blueprint reading, mathematics, building code requirements, and safety and first-aid practices.
Apprentice carpenters learn by working with more experienced co-workers and through classroom training. An apprentice typically begins doing simpler tasks, such as measuring and cutting wood, and works up to more complex jobs, such as reading blueprints and building structures.
There are also some community colleges that teach carpentry skills, which may or may not qualify as an apprenticeship.
All carpenters must pass the Occupational Safety and Health Administration (OSHA) 10- and 30-hour safety courses.
WHAT DOES A CNC PROGRAMMER OR OPERATOR DO?
CNC stands for computer numerical control, and it refers to a category of machines used to precision-produce metal and plastic parts.
A CNC operator is a specially trained technician who sets up and operates these machines to cut, shape and form metal and plastic materials or pieces.
A CNC operator’s job also includes studying blueprints or other instructions to determine equipment setup requirements. CNC operators conduct test runs of production equipment and make adjustments as necessary.
CNC machines work from special designs produced by computer-aided manufacturing (CAM) or computeraided design (CAD) systems. For this reason, CNC operators are sometimes cross-trained on CAD/CAM systems.
CNC programmers create the instructions for the computer to tell the machine what to do during the production process. In some cases, one employee performs both jobs.
WHAT’S NEW?
Computer-controlled equipment represents a quantum leap forward in the industry, as these machines are able to cut, mill or shape parts much faster and with far more accuracy than parts created by hand. The technology works in much the same way as the software that powers 3D printers in a lab.
CNC technology is a relatively recent invention and continues to evolve at a rapid pace.
Machines can form and shape a part from multiple angles at once. Some have the ability to flip the component over during the machining process.
CNC machines perform fully automated cuts or drill multiple holes with tremendous precision.
WHERE DO CNC OPERATORS WORK?
Most CNC operators today work in jobs in manufacturing facilities producing fabricated metal products, plastics and rubber products, transportation equipment, primary metal and machinery.
CNC is a cornerstone technology of advanced manufacturing, which is a much cleaner and safer form of
CNC OPERATORS/ PROGRAMMERS
Have you ever wondered where the parts come from to create new machines or to repair or upgrade existing machines? That’s the role of CNC operators and programmers, specially trained individuals who design precision parts, then program and operate computer-driven machinery to make those parts, which are used in all kinds of industries and to help bring new manufacturing technology to life.
manufacturing and provides a much more comfortable workspace. Employees of companies that use advanced manufacturing generally work in an indoor, climate-controlled workplace.
However, CNC operators must observe basic safety rules that may include wearing protective equipment. This equipment may include such things as safety glasses, earplugs and steel-toed boots. You may also have to wear a respirator to guard against fumes or dust, particularly when working with plastics.
WHAT’S THE JOB OUTLOOK?
CNC operators and programmers are the latest generation of a long line of machine operators and setters that have evolved with changes in technology in manufacturing. As more companies adopt systems that are considered “lean manufacturing,” CNC technology will continue to be an important part of production, and the demand for skilled CNC operators is likely to remain strong.
Combined, experts predict the number of these jobs to grow 26% in the coming years, most of that increase in the programming area. Most metal and plastic machine workers are employed full time. Overtime is common, and because many manufacturers run their machinery for extended periods, evening and weekend work is also common.
HOW MUCH CAN I MAKE?
With experience and expertise, workers can become candidates for more advanced positions, which usually include higher pay and more responsibilities. Experienced workers with good communication and analytical skills may move into supervisory positions.
CNC Programmers
• Lower range wages (bottom 10%) — $30,410 annually/$14.62 per hour
• Middle range wages (median) — $57,130 annually/$27.47 per hour
• Higher range wages (top 10%) — $85,270 annually/$41.00 per hour
•
CNC Operators
• Lower range wages (bottom 10%) — $30,060 annually/$14.45 per hour
• Middle range wages (median) — $41,250 annually/$19.83 per hour
• Higher range wages (top 10%) — $50,090 annually/$24.08 per hour
With experience and expertise, workers can become candidates for more advanced positions, which usually include higher pay and more responsibilities. Experienced workers with good communication and analytical skills may move into supervisory positions.
WHAT DOES IT TAKE TO BE SUCCESSFUL?
• Computer skills
• Mathematics
• Physical stamina/strength
• Design
• Mechanical skills
HOW DO I LEARN THE CRAFT?
Machine operator trainees usually begin by watching and helping experienced workers on the job. Eventually, these workers develop the skills and experience to set up machines and perform a full range of tasks.
CNC machine tool programmers typically need to complete courses beyond high school. CNC operators generally do not complete an apprenticeship like other trades.
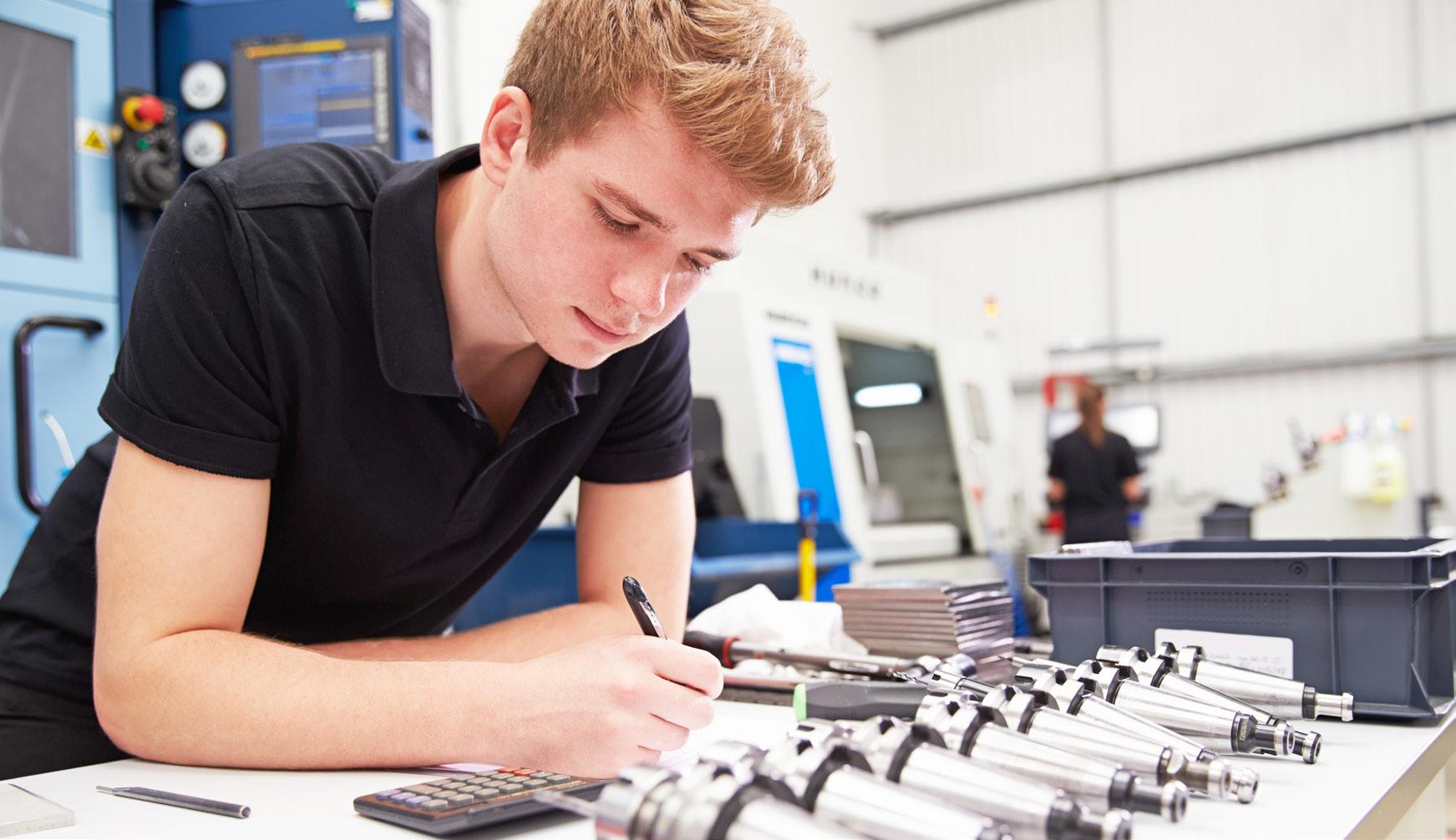
Some operators are trained on basic machine operations and functions in a few months, while computer-controlled machine tool operators may need up to a year to become fully trained in their craft.
Community colleges and other schools offer courses and certificate programs in operating metal and plastics machines that involve CNC programming.
Stop and think for a moment about everything in our world that runs on computer chips. Better yet, try to think of something that isn’t controlled by a computer or an app. The fact is, nearly everything we do is impacted in some way by technology — technology that’s configured at some stage by a computer programmer.
WHAT DO COMPUTER PROGRAMMERS AND COMPUTER CODERS DO?
Even though computer programmers and computer coders are in the same job family, there are important differences to consider.
Computer coders write the computer language (or code) for software programs that tell machines what to do. This software acts as the brains behind many of our “smart” devices (smartphones, smart cars, etc.) Coders may also develop websites or apps for the companies they work for.
Computer programmers do the same thing as computer coders, but they are also responsible for managing the overall project of designing, producing and testing a new software product, or designing a network system.
WHAT’S NEW?
Consider: Just 10 years ago, few people even knew what an app was, and look where we are now. Technology moves so fast, just about anything we could list under the heading “What’s New” is likely to be replaced by something faster and smarter within a very short period of time. Some emerging trends in the industry include: Virtual Reality (VR)/Augmented Reality (AR)
Technologies that provide the user the ability to experience a 360-degree digital environment.
• Some applications include giving a client a look at a building before it is built, conducting flight training or producing a safety course that simulates fire or other emergency.
Robotic Process Automation (RPA)
• RPA is the use of software to automate repetitive tasks that people used to do.
• About 60% of occupations can be partially automated; less than 5% can be completely replaced by technology.
• While this technology would affect, and potentially eliminate, some positions, it would also create new ones.
Machine Learning
• Machine Learning is a subset of artificial intelligence whereby computers are programmed to learn to do something they are not programmed to do. Computers “learn” by discovering patterns and insights from data. In general, there are two types of learning: supervised and unsupervised.
• Machine Learning is rapidly being deployed in all kinds of industries, creating a huge demand for skilled professionals. Machine Learning applications are used for data analytics, data mining and pattern recognition.
• Jobs in this area rank among the top emerging jobs on LinkedIn, with almost 2,000 job listings posted.
WHERE DO COMPUTER PROGRAMMERS AND CODERS WORK?
Most programmers and coders work full time in offices, but the nature of the work allows many to work from home. Programmers may work alone or they may work as part of a team, depending on the size of the project.
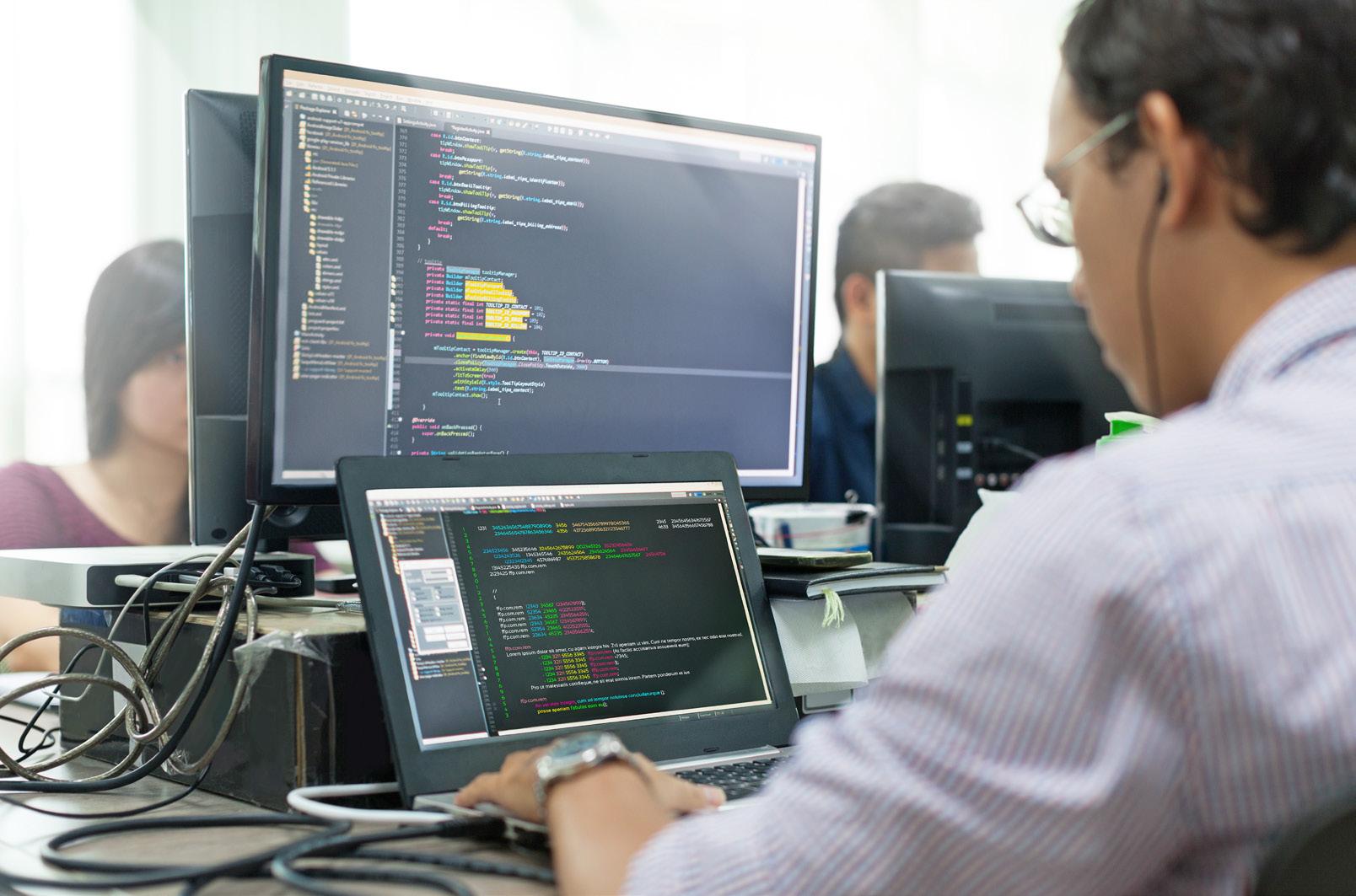
WHAT’S THE JOB OUTLOOK?
Expert predictions are mixed as to the future job outlook. Computer programmers and coders are part of a much larger group of jobs under the category of information technology. Programmers who have general business experience may become computer systems analysts. With experience, some programmers may become software developers. With the right education and experience, the career options in information technology are nearly endless.
HOW MUCH CAN I MAKE?
Computer Programmers
• Lower range wages (bottom 10%) — $49,340 annually/$23.72 per hour
• Middle range wages (median) — $80,290 annually/$38.60 per hour
Higher range wages (top 10%) — $128,880 annually/$61.96 per hour
Your actual earning power depends on the company you work for, your level of experience and certifications, your years of experience and, in some cases, the part of the state where you work.
WHAT DOES IT TAKE TO BE SUCCESSFUL?
• Analytical skills
• Thinking creatively
• Detail oriented
• Problem-solving
HOW DO I LEARN THE CRAFT?
If you attend high school in Arkansas, you already have access to beginning coding classes. In 2015, the state legislature passed a law requiring all Arkansas schools to provide computer science classes that included coding and other IT subjects as a way to give students a jump on the careers of the future. Arkansas was the first and, at the time, only state in the country to require schools to offer such classes.
Diesel engines are the workhorses of the road and job site. Machines, from over-the-road trucks to bulldozers, to industrial and farm equipment run on diesel engines, which are known for their reliability and toughness. Diesel techs keep these machines rolling and running — on the road, the job site and in factories.
WHAT DO DIESEL TECHS DO?
Diesel technicians inspect, diagnose, repair and maintain any machine with a diesel engine. A few examples include:
• Aircraft support equipment.
• Farm equipment, including tractors, harvesters, dairy and irrigation systems. Marine equipment, ships and yachts.
• Over-the-road trucks (semis).
• Buses and dump trucks.
• Earth-moving equipment, such as bulldozers, loaders, backhoes and graders.
• Road construction/highway paving equipment.
• Industrial/factory machines, including cranes, pumps and drilling equipment.
A diesel technician is similar to a diesel mechanic, because both use tools and training to diagnose problems, make repairs and perform necessary maintenance. A diesel technician is different from a diesel mechanic, generally speaking, in that:
• Diesel technicians are trained to handle onboard electronics (computer systems) of the modern diesel engine.
• Diesel mechanics are primarily trained to repair mechanical (moving parts) components of an engine. Typical day-to-day job duties of diesel technicians include:
• Make major and minor engine repairs by repairing or replacing parts and components.
• Perform routine and preventative maintenance.
• Work on a vehicle’s electrical and exhaust systems to comply with pollution regulations.
• Test drive vehicles to diagnose malfunctions or to ensure that they run smoothly.
WHAT’S NEW?
Diesel machinery has enjoyed major advances in technology, creating a growth in the need for skilled technicians.
Between safety regulations, environmental controls and insurance guidelines, the trucking industry has a lot of rules by which it must abide. To help stay in compliance, trucking companies rely on the technology that’s built into their fleet.
It’s not unusual for a new truck to have multiple computers on board regulating everything from speed and location to fuel consumption. Some trucks are sophisticated enough to monitor their own systems and alert the operator when a problem is detected.
Older trucks that didn’t have these computers installed when they were built are often overhauled with the new technology to help bring them up to speed.
Farm technology is another fast-growing area where technicians are needed. Modern farm equipment can map out a field, test soil samples from different areas and apply the precise mix of fertilizer or minerals for each area. Harvesting equipment comes equipped with auto-steer, can track yields in real-time and utilizes GPS to minimize harvest guesswork.
WHERE DO DIESEL TECHS WORK?
Diesel techs are employed by (among others):
• Manufacturers.
• Trucking companies.
• Equipment dealerships.
• Farm operations.
• Cities and counties. Some techs may also work as inspectors to make sure equipment meets government regulations.
The work environment for diesel technicians is in a repair, maintenance or garage-type facility. Some are mobile and must travel to the site of a breakdown or job site to provide service. In these instances, you may be required to work outside, sometimes in inclement weather.
The majority of diesel techs work full time. Some companies require on-call, night and weekend hours. Working hours may depend on your specialty; you may work on trucks as they come in for service, respond to emergency calls as they happen, or you may be responsible for the regular maintenance of a fleet of vehicles and equipment.
WHAT’S THE JOB OUTLOOK?
The Department of Labor expects the number of diesel technician jobs in Arkansas to grow by 6% in the coming years, slightly ahead of the national average.
HOW MUCH CAN I MAKE?
Diesel Technician
• Lower range wages (bottom 10%) — $29,530 annually/$14.20 per hour
• Middle range wages (median) — $42,700 annually/$20.53 per hour
• Higher range wages (top 10%) — $60,150 annually/$28.92 per hour
WHAT DOES IT TAKE TO BE SUCCESSFUL?
• Physical skills
• Physical strength
• Technical skills
• Computer knowledge
• Soft skills
HOW DO I LEARN THE CRAFT?
Many technicians, like mechanics, learned their trade on the job, but these days many employers prefer to hire technicians who have formal education in the field. As a result, several two-year colleges in Arkansas provide educational courses ranging from six months to about two years to complete.
In addition, many diesel technicians are also required to have a commercial driver’s license (CDL), which allows them to test-drive the vehicles they work on. Employers may also send experienced technicians to special training classes conducted by manufacturers and vendors to learn about the latest diesel technology, techniques and equipment.
Some employers may require (and pay for) their techs to be certified by the National Institute for Automotive Service Excellence (ASE). Diesel technicians may be certified in specific repair areas, such as drivetrains, electronic systems and preventative maintenance and inspection.
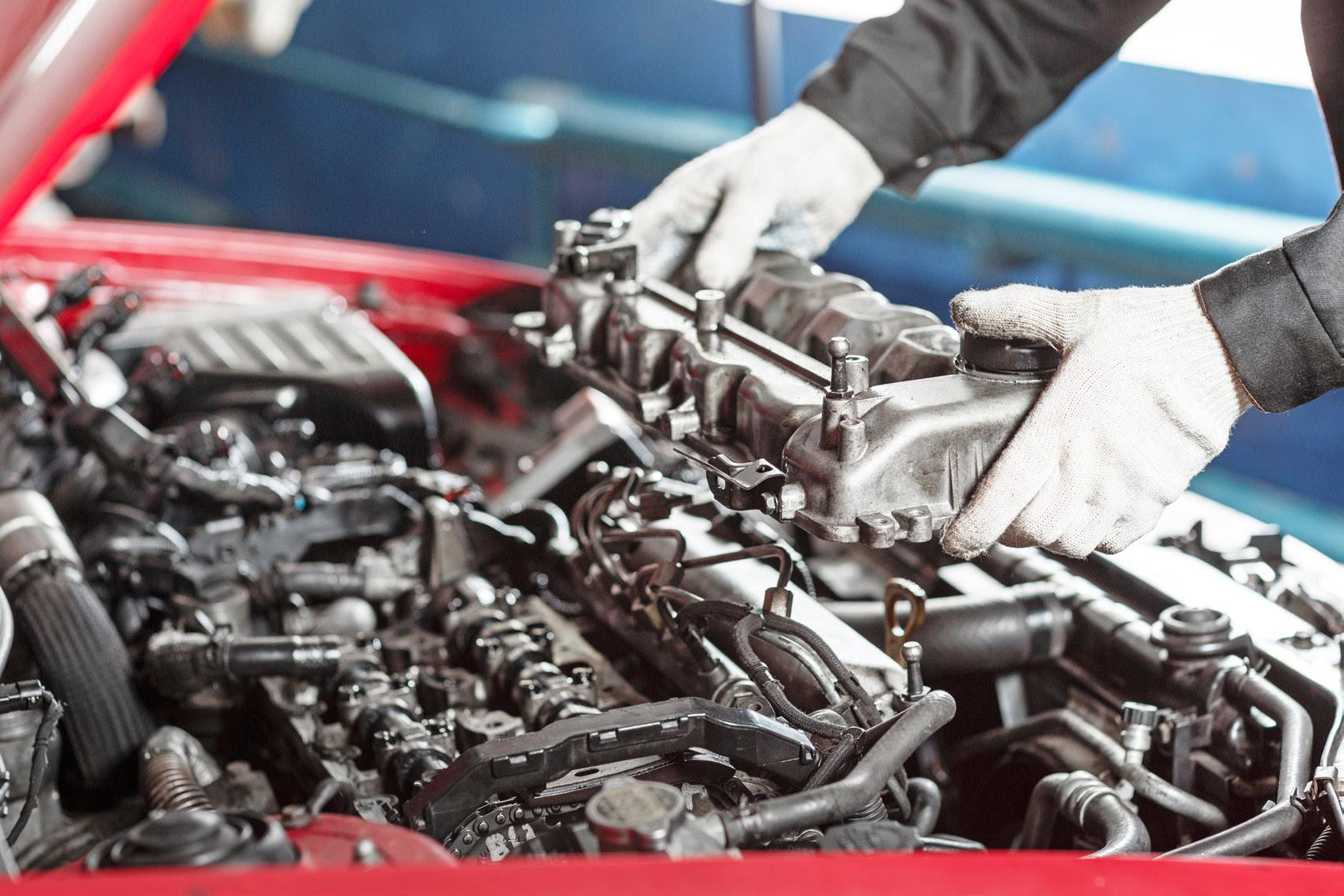
Electricians bring electrical power to homes and factories in every city and town in America. It is a steady occupation that is expected to grow rapidly in the coming years and is evolving with new levels of technology. You can choose to work for an electrical contractor, be on staff in a factory or own your own business, with the right license. All in all, it’s an exciting profession that’s always in demand.
WHAT DOES AN ELECTRICIAN DO?
Electricians install and maintain electrical power, wiring, communications, lighting and control systems in homes, businesses and factories. They work in accordance with rules and regulations to ensure that buildings operate in a way that is safe to residents and occupants.
Electricians’ general day-to-day responsibilities include:
• Ensure businesses and factories operate safely and efficiently through scheduled maintenance and upgrades to their electrical systems.
• Repair control systems, large and small motors and other equipment in factories; install electrical machines in factories.
• Read blueprints and install electrical wiring and systems in new residential and commercial buildings under construction.
• Access, test and upgrade older systems during remodeling projects. Find and replace faulty or aged wiring that could pose a safety hazard.
• Plan the layout and installation of wiring through an entire building or series of buildings. Add, maintain and replace circuit breakers, fuses and wires.
• Review the work other electricians do, making sure it meets the safety standards and building codes.
Electricians can be divided into four general categories:
Residential Wiremen
• Install and maintain electrical wires that go into people's homes.
• Install new electrical equipment, such as light fixtures, ceiling fans, dimmer switches and outlets.
Inside Wiremen
Place and maintain electrical wires in office buildings, factories, airports, schools and hospitals.
• Maintenance or repair of assembly line machinery or motors.
Telecommunications Electricians
• Lay cable (including fiber optics) needed for all forms of communication, including phone and computers.
• Install systems that run telephones, intercoms, computer networks, security and fire alarms.
Outside Linemen
• Work atop telephone poles or alongside the road.
• Work to restore power after storms and floods.
WHAT’S NEW?
Green Energy
• Green energy includes solar panels and wind turbines to generate power.
• Electricians handle special storage units called high-efficiency photovoltaic cells to collect energy. They also install and service power converters, which take the energy generated by the sun or wind, convert it to electricity and download it into the electrical system.
Smart Electrical Grids
• New technology that regulates the flow of power to users, detects malfunctions in the grid, and maintains service to homes and businesses.
• Electricians keep smart grids running at peak performance.
Home-Powered Roof Shingles
Roof shingles that collect sunlight and convert it into energy that powers the building. The shingles could potentially present a lower-cost option than conventional solar panels.
Electricians are needed to wire the solar shingling system into the building’s electrical systems.
WHERE DO ELECTRICIANS WORK?
Electricians work indoors and outdoors, at homes, businesses, factories and construction sites. Many electricians work alone, but sometimes they collaborate with others. At larger companies, electricians are more likely to work as part of a crew. During scheduled maintenance or on construction sites, electricians can expect to work overtime.
Work schedules may include evenings and weekends and may vary during times of bad weather, which may require working in rain, wind or snow.
WHAT’S THE JOB OUTLOOK?
The majority of electricians in Arkansas work for electrical contractors and nearly all electricians work full time. The U.S. Department of Labor projects electrician jobs in The Natural State to grow by 9% in the coming decade, ahead of the national average.
HOW MUCH CAN I MAKE?
• Lower range wages (bottom 10%) — $29,590 annually/$14.22 per hour
• Middle range wages (median) — $46,180 annually/$22.20 per hour
• Higher range wages (top 10%) — $61,420 annually/$29.53 per hour
Your actual earning power depends on the company your work for, your level of experience and licensing, your years of experience and, in some cases, the part of the state where you work.
WHAT DOES IT TAKE TO BE SUCCESSFUL?
• Intellectual ability
• Skills in math, algebra, reading, writing
• Troubleshooting
• Mechanical ability
• Business/interpersonal skills such as time management and communication
• Physical skills
HOW DO I LEARN THE CRAFT?
Most electricians learn their trade in a combination of classroom education and on-the-job training. Some twoyear colleges also offer courses in electrical fields. Generally, a high school diploma is sufficient to get started. The most common way electricians learn is through an apprenticeship program; think of these programs as “electrician school.” Apprenticeship programs take four or five years to complete and are often paid for by your employer. Some schools are also offered by trade groups and labor unions.
Since most apprentices are already employed, they work during the day where they are supervised by more experienced, licensed electricians and attend class at night. Upon completion of apprentice school, you can test for your journeyman’s license, which allows you to work unsupervised on most tasks.
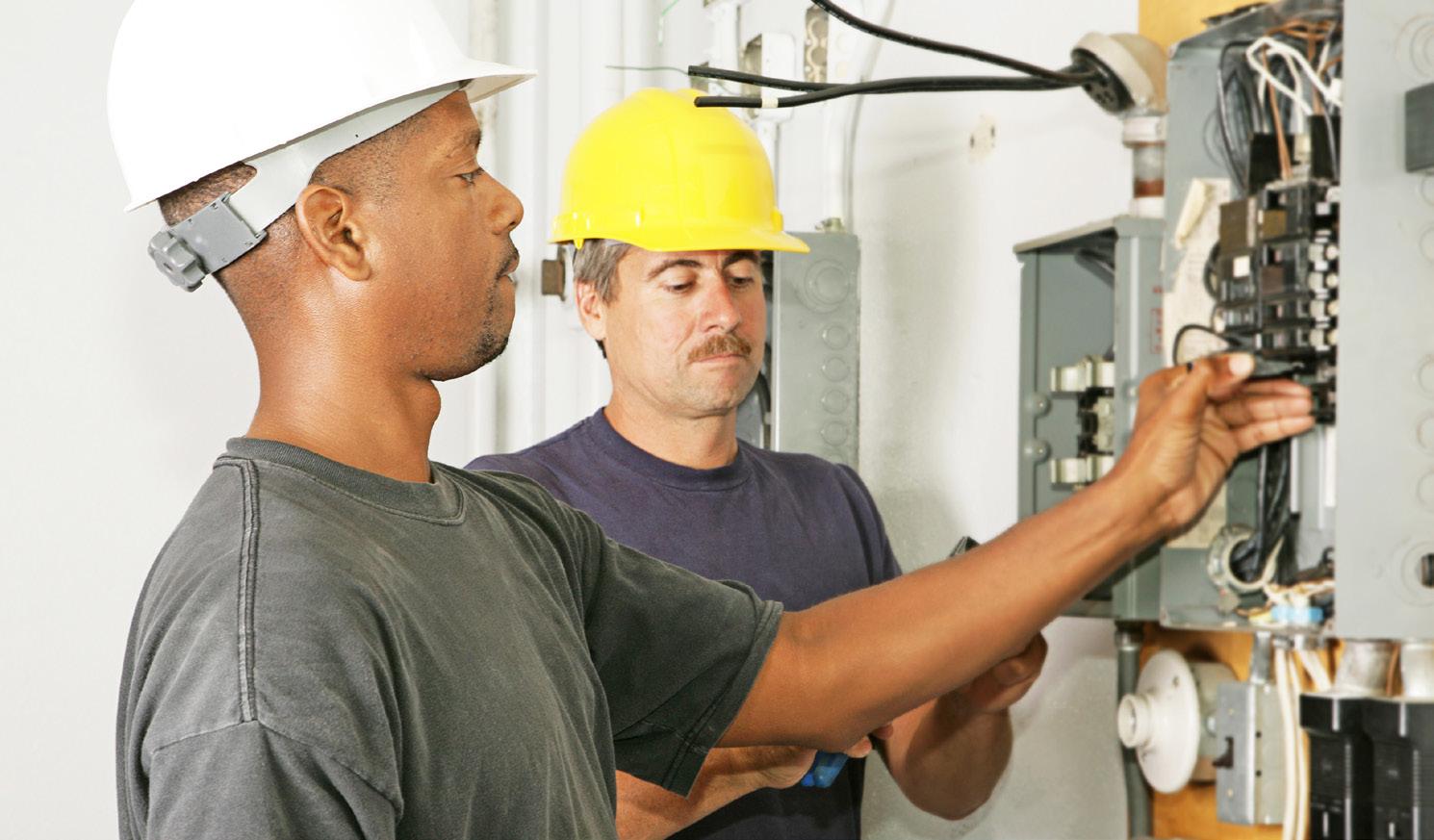
You can stay a journeyman electrician as long as you want, but many electricians choose to test for the highest license, a master electrician. You are eligible to test for your master’s license after being an electrician for five years, at least one of which must be at the journeyman level. The benefits of becoming a master electrician is more money and they may open their own electrical business.
Electricians may be required to take continuing education courses by their employers. These courses are usually related to safety practices, changes to the electrical code and training from manufacturers on specific products.
If it can push, pull, pump or lift material, rolls on tires or crawls on tracks like a tank, it’s where the heavy equipment operator calls home. On virtually all construction projects, these employees are the first workers on the job and the last to leave. Their work is essential to a smooth-running construction project.
WHAT
DO HEAVY EQUIPMENT OPERATORS DO?
Operators drive, maneuver or control a variety of heavy construction equipment. “Heavy equipment” is a blanket term for numerous machines including:
• Cranes
• Bulldozers
Front-end loaders
• Backhoes
• Graders
• Dredges
• Excavators
• Hoists
In addition to operating these machines, heavy equipment personnel also do the following:
• Clean and maintain equipment. Make basic repairs.
• Drive and maneuver equipment.
• Coordinate with other craftsmen on the job site. Some of the most common job titles within this category include:
Operating engineers (sometimes called hoisting or portable engineers).
• Work with excavation and loading machines equipped with scoops, shovels or buckets that dig sand, gravel, earth or similar materials.
• Includes bulldozers, trench excavators, road graders.
• Includes industrial trucks or tractors equipped with forklifts or booms for lifting materials.
Paving and surfacing equipment operators
• Control machines that spread and level asphalt or concrete for roadways or other structures.
• Includes asphalt spreaders, concrete paving machine operators and tamping equipment.
Pile-driver operators
• Use large machines mounted on skids, barges or cranes to hammer piles into the ground.
• Piles, made of concrete, wood or steel, support retaining walls, bridges, piers and building foundations.
WHAT’S
NEW?
Internet of Things (IoT)
• A sensor, or group of sensors, installed for collecting and transferring data. Whenever a product
carries the term “smart” or “intelligent” (smartphone, intelligent building) it’s considered part of this new group of products.
• Heavy equipment includes a wide range of sensors that automatically provide information, including diagnostics, fuel usage, machine hours and more. More workers are also wearing safety sensors to monitor air quality and biometrics at the worksite.
• Radio frequency identification (RFID) tags are commonly used to track materials and tools.
Designed Multifunctionality
• Construction companies are always looking for ways to get the most out of expensive equipment.
• Multifunctional equipment can adapt a machine to a variety of tasks, such as backhoes that double as loaders through the use of interchangeable attachments.
Telematics
• Used for years by trucking companies, telematics keep track of the location, condition and operation of machines on the road or the job site.
• The feature uses global positioning to determine where and how equipment is being used.
WHERE DO HEAVY EQUIPMENT OPERATORS WORK?
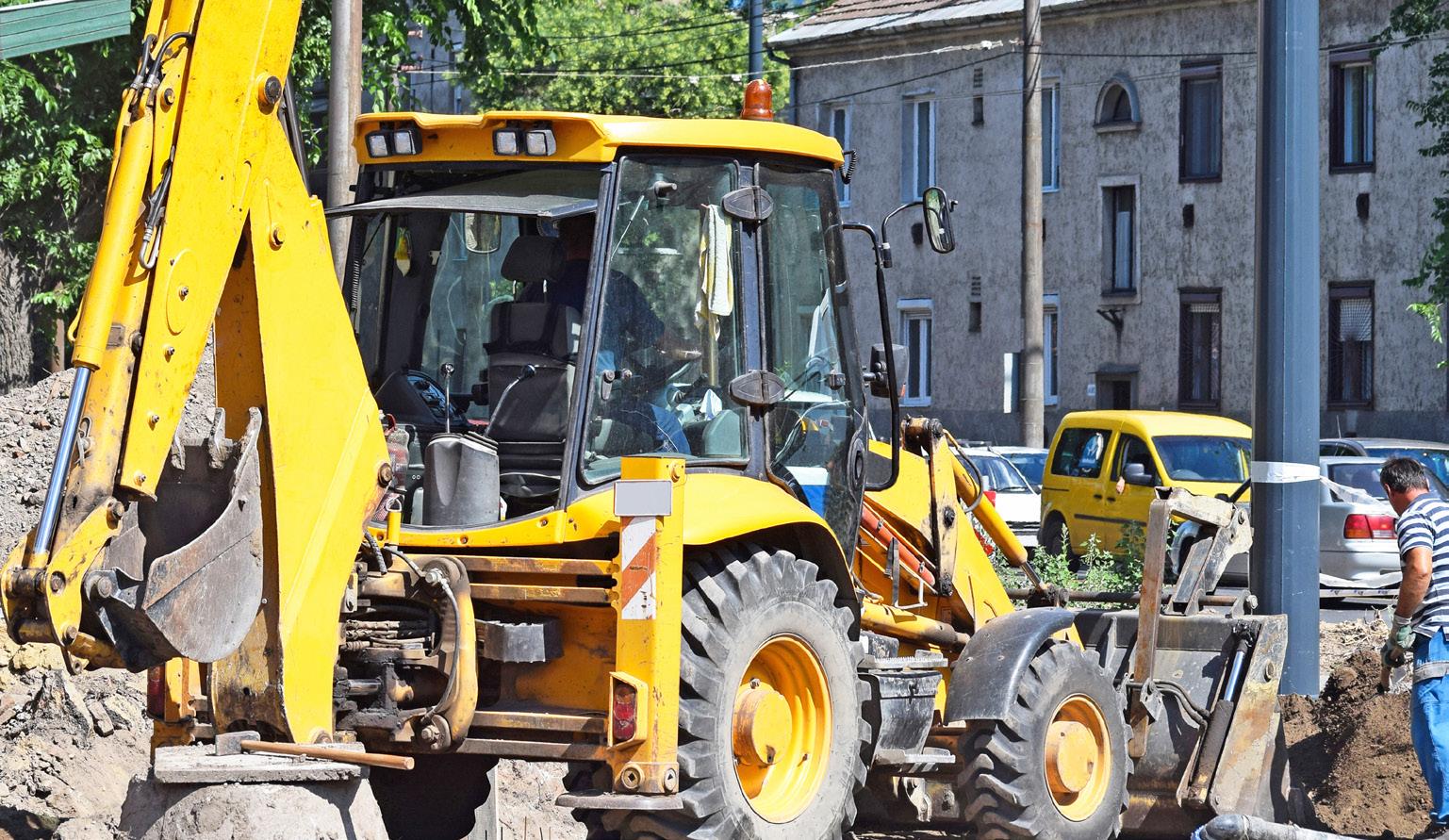
The majority of construction equipment operators work full time, in nearly every type of weather conditions. Like all jobs that work outdoors, there is the potential to get dirty, greasy or muddy on the job site. Some operators may also work in remote locations and have irregular schedules to match round-the-clock production or work that must be done late at night.
WHAT’S THE JOB OUTLOOK?
In Arkansas, the number of heavy equipment operator positions is expected to grow 6% in the coming years, slightly ahead of the national average. Heavy equipment operators who are versatile with several different types of equipment will find themselves more in demand than those who are proficient with only one kind of rig.
HOW MUCH CAN I MAKE?
• Lower range wages (bottom 10%) — $28,960 annually/$13.92 per hour
• Middle range wages (median) — $37,460 annually/$18.01 per hour
• Higher range wages (top 10%) — $48,850 annually/$23.49 per hour
WHAT DOES IT TAKE TO BE SUCCESSFUL?
• Hand-eye-foot coordination
• Mechanical skills
• Physical strength
• Comfortable with heights
• Building and construction
WHERE DO I LEARN THE CRAFT?
Many workers learn equipment operation on the job after earning a high school diploma or equivalent, while others learn by attending a two-year college.
Among two-year colleges, some may specialize in a particular brand or type of construction equipment, while others may incorporate sophisticated simulator training into their courses. This allows beginners to familiarize themselves with the equipment in a virtual environment before operating real machines.
Heavy equipment operators do not generally complete an apprenticeship program as workers in other trades do. In some cases, training is provided by equipment manufacturers, a trade union, industry groups or private companies.
New operators or operators-in-training may operate light equipment under the guidance of an experienced operator before moving up to heavier equipment such as bulldozers. Some construction equipment with computerized controls requires greater skill to operate. Operators of this equipment may need additional training and some understanding of electronics.
Construction equipment operators often need a commercial driver’s license (CDL) to haul equipment to job sites and may need special licenses for operating specific pieces of equipment.
HVACR technicians ensure people’s comfort by installing and maintaining heating, ventilation, air conditioning and refrigeration systems for homes and businesses. It’s a career field that demands a variety of skills of its technicians, and as long as summers are hot, winters are cold and food needs to be refrigerated, it’s a job that will never be out of demand.
WHAT DOES AN HVACR TECHNICIAN DO?

HVACR (sometimes written as HVAC-R) stands for heating, ventilation, air conditioning and refrigeration. HVACR technicians are specially trained individuals who install, service and maintain heating and air conditioning systems in homes, businesses and multi-unit residential.
HVACR technicians work with systems such as oil burners, boilers, heat pumps, central air conditioning and hot-air furnaces. They also work with components and appliances such as commercial grade ice makers, refrigerators and freezers. Some day-to-day duties include:
• Perform annual inspections and servicing.
• Replace old, outdated technology with more energy-efficient, greener models.
• Maintain ductwork that carries air from the heating or air conditioning unit to various parts of a building. Repair systems when they break down.
WHAT’S NEW?
Thermal-driven air conditioning
• Uses solar energy, backed up by natural gas on cloudy days or at night.
• Solar panels generate high enough temperature to drive a double-effect chiller.
• Provides a low-cost alternative to conventional air conditioning units.
Ice-powered air conditioner
• Another low-cost alternative to conventional air conditioning.
• Freezes 450 gallons of water in a tank overnight, provides cooling for up to six hours.
• Once ice melts, system switches to backup air conditioning unit.
Geothermal heat pump
Makes use of heat from the earth by way of looped piping placed into the ground.
• Fluid in this piping loop absorbs heat, which is carried back indoors to provide heating.
• Can also be used to supply cooling.
• Advertised to be up to four times more efficient than traditional systems. Smart thermostats
• Whole-house control systems that monitor and maintain climate control. Device “learns” owner preference and automatically adjusts rooms to those settings.
• Turns itself off when room is unoccupied; provides Wi-Fi enabled remote monitoring.
WHERE DO HVACR TECHNICIANS WORK?
A tech might work for a company that is appointment-based, going from home to home installing and maintaining cooling systems. Or, in industrial or commercial settings, techs might report to the same job site all day long for weeks at a time. Often, a HVACR tech’s van or truck is their office and workshop rolled into one.
HVACR techs may work full time, regular hours or they may be assigned at least part of the time to on-call to handle emergencies. These calls come in during business hours, on weekends and holidays, or in the middle of the night. After storms or blizzards and the normal changing of the seasons are almost guaranteed to generate a lot of overtime.
WHAT’S THE JOB OUTLOOK?
Demand for HVACR technicians and installers in Arkansas is expected to grow 6% in the coming years, per the U.S. Department of Labor. Arkansas’s job growth is expected to exceed that of the national average. To understand job growth, remember even the best HVACR system has a practical operating life of about 15 years. Imagine how many houses, apartments and commercial buildings are built or remodeled every year; that’s about how many systems need replacing.
HOW MUCH CAN I MAKE?
• Lower range wages (bottom 10%) — $29,010 annually/$13.95 per hour
• Middle range wages (median) — $38,440 annually/$18.48 per hour
• Higher range wages (top 10%) — $59,380 annually/$28.55 per hour
WHAT DOES IT TAKE TO BE SUCCESSFUL?
• Soft skills
• Active listening
• Communication
• Customer service
• Critical thinking/troubleshooting
• Mechanical/construction skills
• Physical skills/stamina
HOW DO I LEARN THE CRAFT?
HVACR technicians require specialized training and licensing. The level of complexity of today’s systems means most employers prefer to hire workers who have received specialized instruction after high school, either through a community college or a 3- to 5-year paid apprenticeship. Apprentices acquire their skills both in the classroom and on the job, with the cost of the training often paid for by the employer. In Arkansas, HVACR technicians are also required to hold one or more licenses, depending on job responsibilities. Following your formal training, you must sit for an exam to earn your license.
If you’re someone who likes a different challenge every day — and who enjoys being multifaceted enough to meet those challenges — then Industrial Maintenance may be the field for you. These skilled professionals are the go-to in any factory or industrial facility, trained to handle a number of situations. They are key players in keeping machinery rolling and the production schedule on time.
WHAT DOES AN INDUSTRIAL MAINTENANCE TECHNICIAN DO?
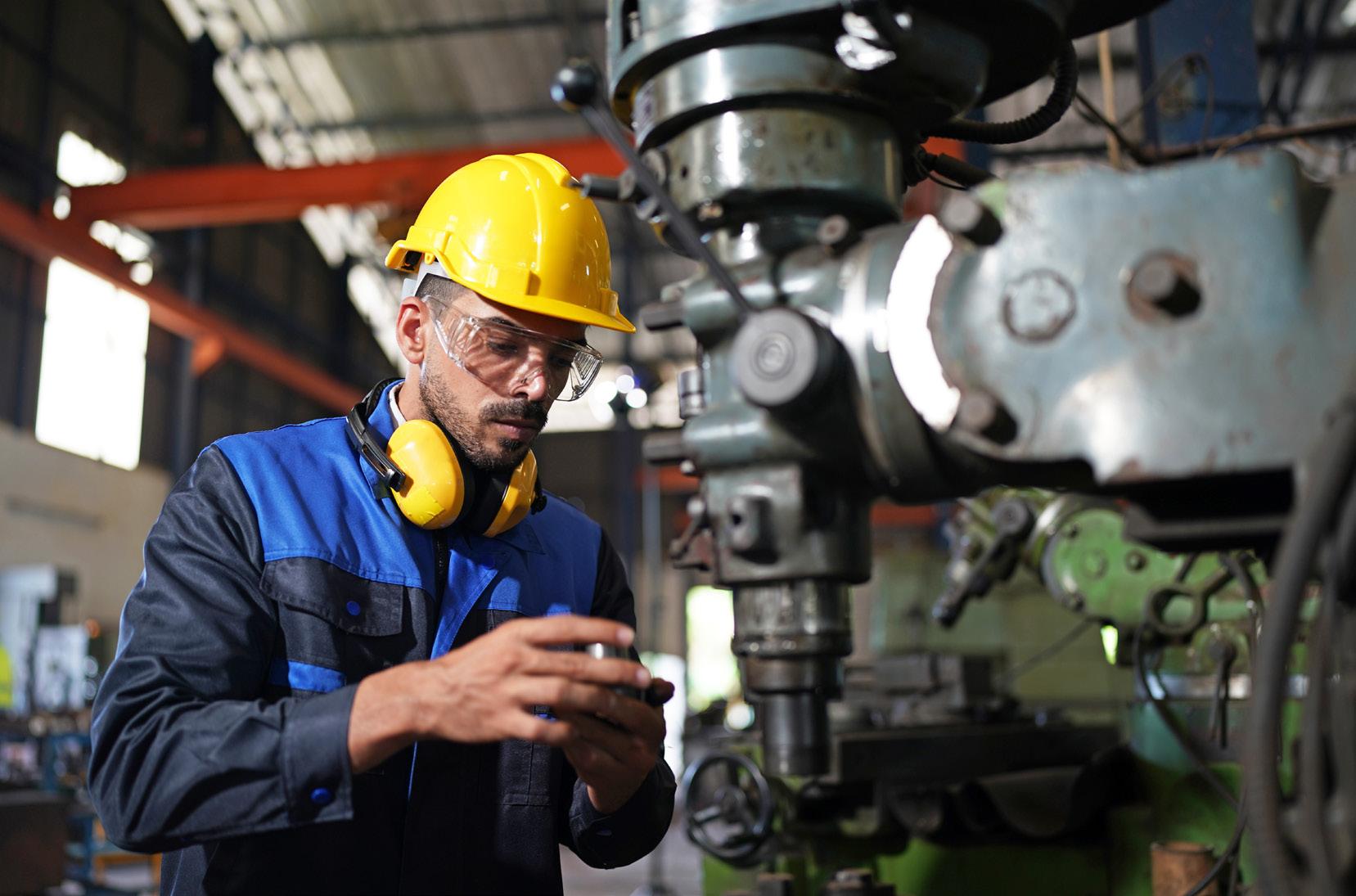
Industrial maintenance personnel are the mechanical experts in any manufacturing facility, trained to assemble, repair and service expensive equipment. They have a wide skill set that allows them to adapt to various situations.
Examples of machines they may work with are robotic welding arms, automobile assembly line conveyor belts, hydraulic lifts, production machinery and packaging equipment. Companies often consult with their industrial maintenance personnel before purchasing new equipment.
The industrial maintenance field can be broken down into the following job titles:
Industrial machinery mechanics
• Detect and correct errors before the machine damages itself or the product.
• Use technical manuals, understanding of industrial equipment and observation to determine the cause of a problem.
• Utilize computerized diagnostic systems and vibration analysis techniques to determine the cause of malfunctions.
• Disassemble malfunctioning machines, repair or replace parts, reassemble, then test.
• Work with hand tools; also utilize lathes, grinders and drill presses. Welding skills are often required.
Machinery maintenance workers
• Perform basic maintenance and repairs on machines.
• Clean, lubricate, perform basic diagnostic tests, check performance, test damaged machine parts.
• Following machine specifications and adhering to maintenance schedules, they also perform minor repairs.
• Use a variety of tools from screwdrivers and socket wrenches to hoists.
Millwrights
• Install, maintain and disassemble industrial machines.
Perform repairs, including replacing worn or
defective parts of machines.
• May take apart entire machines to relocate them or make room for new equipment.
• Disassemble, categorize and package each part of the machine. These projects can take a few hours or can take several weeks.
WHERE DO INDUSTRIAL MAINTENANCE TECHNICIANS WORK?
The vast majority of these skilled professionals work in a manufacturing or industrial plant. A small percentage work for companies that specialize in industrial repair and maintenance. Most of these technicians are employed full time during regular business hours, but they may also serve on-call, night or weekend shifts. The majority of work is typically performed indoors.
Workers must follow safety precautions and usually wear some form of protective equipment, such as hardhats, safety glasses, steel-toed shoes, gloves and earplugs.
WHAT’S THE JOB OUTLOOK?
The outlook for this job sector is bright. Across three main job groups, job growth is forecast at 17% over the next several years, growing much faster than the national average in each field. Industrial machinery mechanic jobs are expected to grow 26%; machinery maintenance workers are expected to grow by 146% and millwrights will grow to 10% in the coming decade.
HOW MUCH CAN I MAKE?
Industrial Machinery Mechanics
• Lower range wages (bottom 10%) — $35,380 annually/$17.01 per hour
• Middle range wages (median) — $48,390 annually/$23.27 per hour
• Higher range wages (top 10%) — $76,600 annually/$36.83 per hour
Machinery Maintenance Workers
• Lower range wages (bottom 10%) — $29,780 annually/$14.32 per hour
• Middle range wages (median) — $46,420 annually/$22.32 per hour
Higher range wages (top 10%) — $59,850 annually/$28.78 per hour
Millwrights
• Lower range wages (bottom 10%) — $37,590 annually/$18.07 per hour
• Middle range wages (median) — $48,060 annually/$23.11 per hour
• Higher range wages (top 10%) — $61,050 annually/$29.35 per hour
WHAT DOES IT TAKE TO BE SUCCESSFUL?
• Mechanical skills
• Production/processing methods
• Math skills
• Repair/maintenance skills
• Operation monitoring
• Troubleshooting/diagnosis
HOW DO I LEARN THE CRAFT?
Most workers in this field have at least a high school diploma and, depending on the position, may complete some post-secondary education up to an associate degree. Industrial maintenance programs are generally offered through community colleges and may include courses such as welding, mathematics, hydraulics and pneumatics.
Industrial machinery mechanics may receive more than a year of on-the-job training and often receive some college coursework as well.
Most millwrights go through an apprenticeship program that lasts about four years, after which they can usually perform tasks with less guidance. Employers, local unions and contractor associations typically sponsor apprenticeship programs.
Imagine someone invents a new machine that will revolutionize the way a certain product is manufactured. Have you ever wondered where parts, instruments and components come from to build that machine? Machinists are industrial technicians that provide the solution and also produce parts and components for existing machines.
WHAT DOES A MACHINIST DO?
Long before anyone had ever heard of a “maker space,” there were machinists, trained craftspeople who produced parts and instruments using a variety of mechanical and computer-controlled machines. Machinists set up and operate a variety of computer- and mechanically controlled tools to fashion raw materials like metal and plastic into precision parts and instruments.
Many machinists today must be able to use both manual and computer numerical control (CNC) machinery. Workers may produce large quantities of one part, small batches or one-of-a-kind items. Parts range from simple steel bolts to titanium bone screws for orthopedic implants.
Because most machinists train in CNC programming, they may also write basic programs and often modify programs. These modifications, called offsets, fix problems and improve efficiency by reducing manufacturing time and tool wear.
WHAT’S NEW?
Remote smart operations
• The Internet of Things incorporates smart, connected devices, including smart sensors to improve control over equipment and deliver more insights.
• Various machines can operate autonomously, requiring human input or oversight only when something goes wrong.
• When there is a problem, IoT offers much better diagnostic capabilities helping technicians pinpoint and correct problems.
Laser-beam machining
• A thermal process for chip or material removal, also known as laser micromachining (LBM).
• A high-energy laser beam focuses on a component and the thermal energy transfers to the targeted surface.
• Laser beam machining is more widely adopted in manufacturing, particularly for carbon-fiber materials and more durable composites.
3D printing
• 3D printers can create products and components from a variety of raw materials, including concrete, wood, steel and an increasing range of metals, alloys, ceramics and metal-matrix composite materials.
• Hybrid machining incorporates both traditional CNC machining and 3D printing solutions to improve product development.
• Manufacturers have much more control over the goods they create. Materials and components can be printed right at a job site with an unlimited range of customization. Automated finishing systems
• Robotic-powered finishing systems are revolutionizing the quality and output of the machinist industry.
• Robotic abrasive blasting systems offer unmatched improvements in quality, efficiency, versatility and safety.
WHERE DO MACHINISTS WORK?
The vast majority of machinists work in manufacturing industries and independent machine shops. Maintenance machinists work in most industries that use machinery in manufacturing plants. Most machine shops are relatively clean, well-lit and ventilated, and many computer-controlled machines are partially or totally enclosed. Exposure to noise, debris and lubricants are greatly minimized. Workers must follow safety precautions, including wearing safety glasses and earplugs.
WHAT’S THE JOB OUTLOOK?
The outlook for this job is good. The U.S. Department of Labor predicts job growth of 9% in Arkansas, well ahead of the national average.
HOW MUCH CAN I MAKE?
• Lower range wages (bottom 10%) — $29,490 annually/$14.18 per hour
• Middle range wages (median) — $43,960 annually/$21.14 per hour
• Higher range wages (top 10%) — $80,300 annually/$38.60 per hour
Individual wages can fluctuate by industry, experience and skill level. Machinists can advance in their careers in several ways:
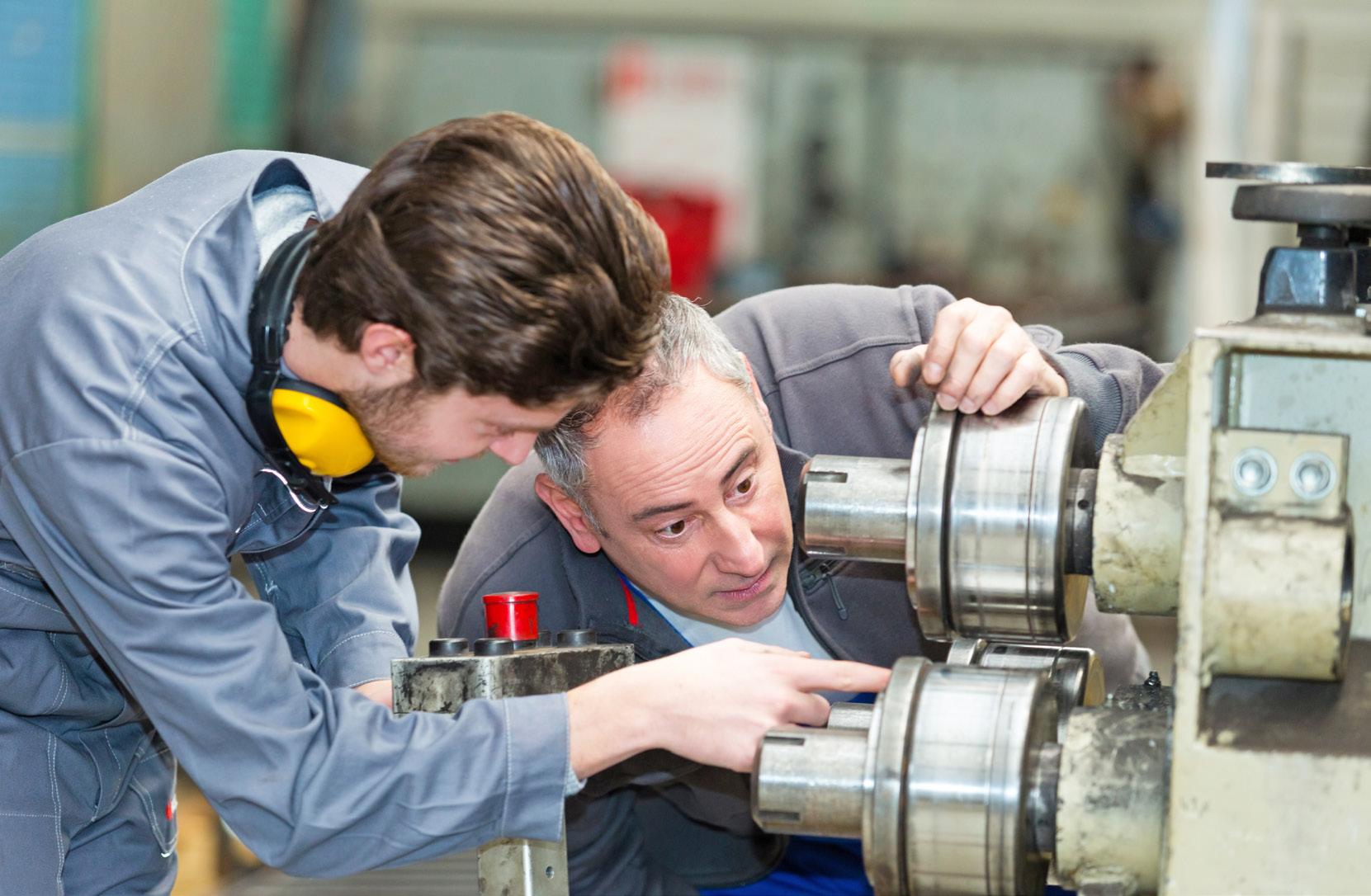
• Become CNC programmers.
• Become tool-and-die or mold makers. Be promoted to supervisory or administrative positions.
• Open your own machine shop.
WHAT DOES IT TAKE TO BE SUCCESSFUL?
• Physical strength/stamina
• Analytical and mathematical skills
• Attention to detail
• Mechanical/technical skills
HOW DO I LEARN THE CRAFT?
After earning a high school diploma or equivalent, some machinists learn entirely on the job. Others acquire skills in a mix of classroom and on-the-job training.
Formal training programs, typically sponsored by a union or manufacturer, are an excellent way to learn the job.
Training programs are often a combination of paid shop training and related classroom instruction and, depending on the program, can take months or years. Two-year college programs range from a couple of months to two years.
In Arkansas, machinists don’t generally serve an apprenticeship like other trades do.
WHAT DO PLUMBERS DO?
Plumbers build and maintain piping systems that are responsible for moving liquid, steam, natural gas, liquid fuel or waste from one place to another.
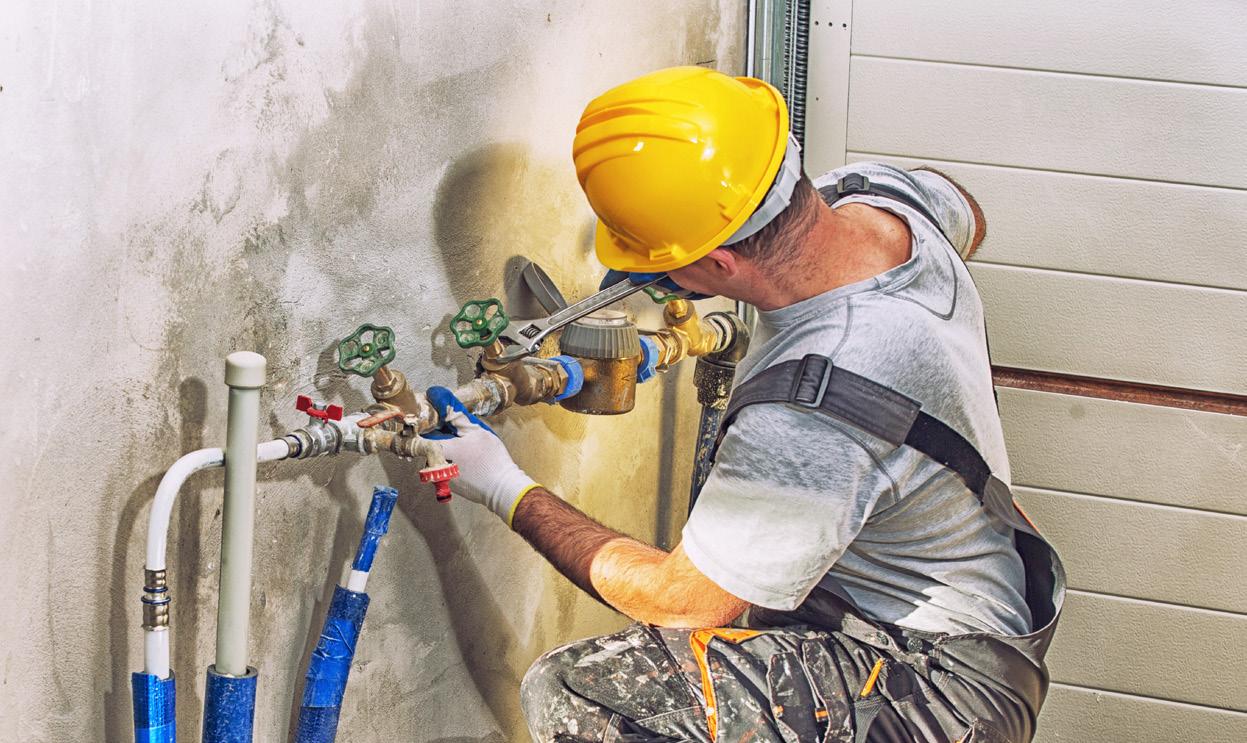
Day-to-day work activities include:
• Install and connect piping and fixtures, including welding metal components.
• Develop blueprints to plan pipes and fixtures within a structure.
• Make connections between the city’s water supply and homes and businesses.
• Install bathtubs, showers, sinks, toilets, dishwashers and water heaters.
• They may help design where the plumbing fixtures should go within the building.
• In industrial settings, they perform inspections, maintenance and new installation, handling fuel, wastewater and water used as a coolant, such as in nuclear power plants.
• Perform minor carpentry to repair or reconfigure systems, such as cutting holes in walls to access pipes or hanging supports to hold pipes in place
• Install and service septic systems.
• Perform functions related to gas lines, including installation, maintenance and replacement and proper installation of gas appliances.
Related jobs that utilize the same basic plumbing skill set while performing additional specialized work include:
Pipelayers
• Provide the major framework for outside plumbing systems by installing the pipe to build these systems.
• Construct oil and gas lines by soldering, welding or cementing them in place.
Pipefitters and steamfitters
The primary difference between pipefitters and steamfitters is pipefitters specialize in pipe systems that move liquids, while steamfitters specialize in pipe systems that move high-pressure liquids or gases.
• Pipefitters and steamfitters work with both high-pressure and low-pressure systems and install automated controls to regulate industrial systems.
Sprinklerfitters
A highly specialized plumber who installs and maintains automatic fire sprinkler systems in office buildings, manufacturing and industrial plants and multiunit residential properties.
• They may also work for landscape companies installing in-ground sprinkler systems.
Few skilled labor jobs provide as many different opportunities or are in as consistently high demand as plumbers. Whether working in new construction, industrial settings or running their own business, plumbers have the potential to earn very good wages over a long, successful career.
WHAT’S NEW?
“Brain Pipes”
• Smart home automation plumbing systems that allow the homeowner to conserve natural resources and reduce their water footprint.
• Smart pipes can monitor an entire home or building, sending the property owner an alert to any breaks or leaks.
Green Plumbing
• High-efficiency components designed to reduce water usage.
• Includes faucets, shower heads and toilets with lowflow flush capacity.
Smart Appliances
• Self-monitoring dishwashers, washing machines, water heaters and toilets.
• Computer chips control everything from wash settings and water temperature to water conservation modes and automated cycles.
• Appliances sync with smart devices to be controlled remotely.
Greywater Recycling
• Systems capture water from bathroom sinks, showers and washing machines that may contain traces of dirt, food or cleaning products.
• Systems redirect this water for use in watering residential yards and gardens or landscaping and flower beds outside corporations and office buildings.
WHERE DO PLUMBERS WORK?
With so many applications for a plumber’s skills, they can work in a wide range of environments:
If you work for a plumbing business that serves residential clients, or if you work for a manufacturing firm, you may work primarily daytime hours.
If you work for a company that does work in new construction, you could work outdoors in remote locations or put in overtime to keep up with production schedules.
Plumbers who are self-employed have some flexibility to determine their own schedules, but it takes a lot of work and “extra mile” service to get a business off the ground. Nearly all plumbers work “on call” at some point in their career, providing late-night and weekend emergency service.
There’s no denying that some of the material plumbers work with is unpleasant, particularly in the case of wastewater, backed-up toilets or malfunctioning septic systems. But that’s only one part of the plumbing industry. Plumbers who work for manufacturers and power plants often work in climate-controlled conditions. Building new
piping systems is no more or less uncomfortable than any other craft at a job site.
WHAT’S THE JOB OUTLOOK?
Demand for this fundamental skilled job is growing, especially compared to other states. The U.S. Department of Labor predicts job growth of 6% in Arkansas, three times the national average.
HOW MUCH CAN I MAKE?
• Lower range wages (bottom 10%) — $29,010 annually/$13.95 per hour
• Middle range wages (median) — $45,660 annually/$21.95 per hour
• Higher range wages (top 10%) — $63,420 annually/$30.49 per hour
Some things that impact your earning potential include your license level (apprentice, journeyman, master) and any additional training or certifications you earn. For master plumbers who choose to start their own business versus working for an established firm, potential earnings are limited only by your skill, customer service and work ethic.
WHAT DOES IT TAKE TO BE SUCCESSFUL?
• Mechanical ability
• Building and construction expertise
• Design skills
HOW DO I LEARN THE CRAFT?
Plumbers begin their journey in an apprenticeship program. Apprenticeship training schools are specialized education centers sponsored by trade associations, unions, as stand-alone institutions and some two-year Arkansas colleges.
Apprenticeships range from 4- to 5-year programs and, typically, you are sent to apprentice school by your employer after hiring on with a company. What this means is, you work during the day, learning your craft under an experienced plumber, and attend class one or two nights per week for classroom instruction. It also means that your education is paid for by your employer.
After you complete your apprenticeship, you test for your journeyman’s license. A journeyman level plumber can work unassisted on most projects and can generally handle more advanced projects than an apprentice. Some people choose to test for their master’s license. Master plumbers represent the highest level of plumbers and therefore command the highest pay.
Have you ever taken part in a process and thought, “There has to be a better way to do this.” That’s the daily motto of process technicians, employees whose job it is to figure out better ways to produce items through manufacturing. Process technicians help companies make better products in ways that are safer, more efficient and therefore more profitable.
WHAT DOES A PROCESS TECHNICIAN DO?
Simply put, process technicians look for ways to build or produce things better. They are trained to look for inefficiencies in production and find ways to improve the process. By assisting industrial engineers, process technologists help integrate workers, machines, materials, information and energy to make a product or provide a service. They prepare machinery and equipment layouts, plan workflows, conduct statistical production studies and analyze production costs.
Process technology can be broken down into two main categories:
Chemical technician
Chemical technicians use laboratory instruments and techniques to help chemists and chemical engineers research, develop, produce and test chemical products and processes. Among their job duties are:
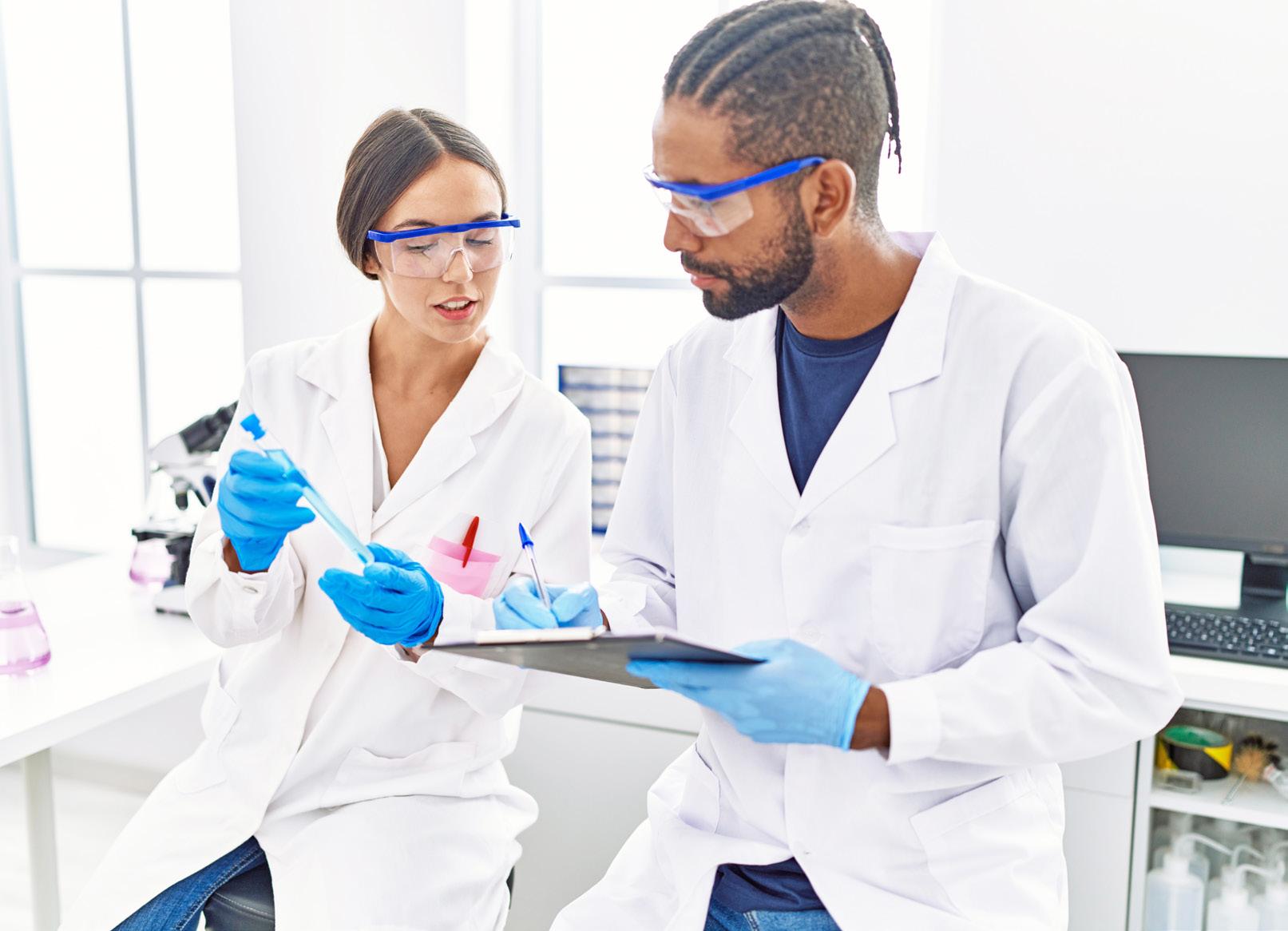
• Monitor chemical processes and test the quality of products to make sure they meet standards and specifications.
• Set up and maintain laboratory instruments and equipment.
• Troubleshoot production problems or malfunctioning instruments. Prepare chemical solutions.
• Conduct, compile and interpret results of chemical and physical experiments, tests and analyses for a variety of purposes, including research and development.
• Prepare technical reports, graphs and charts, and give presentations that summarize their results.
Industrial engineering technician
Industrial engineering technicians assist industrial engineers in devising efficient systems to make a product or provide a service. Industrial engineering technicians typically do the following:
• Suggest revisions to methods of operation, material handling or equipment layout.
• Interpret engineering drawings, schematic diagrams and formulas.
• Confer with management or engineering staff to determine quality and reliability standards.
• Prepare charts, graphs and diagrams to illustrate workflow, routing, floor layouts, how materials are handled and how machines are used.
• Collect data to assist in process improvement activities.
• Study the time and steps workers take to do a task through time and motion studies.
WHERE DO PROCESS TECHNICIANS WORK?
Process technicians typically work full time and inside, either in a factory, a lab or some other kind of manufacturing setting. They generally work regular business hours; however, some overtime may be required to meet project deadlines. Process technicians may also work irregular hours to monitor laboratory or plant operations during second and third shifts.
WHAT’S THE JOB OUTLOOK?
According to the U.S. Department of Labor, process technology jobs as a general category are expected to grow 9% in the coming years, almost double the national average. Your actual earning power depends on the company your work for, your level of experience and licensing, your years of experience and, in some cases, the part of the state where you work.
HOW
MUCH CAN I MAKE?
Chemical Technologist
• Lower range wages (bottom 10%) — $29,510 annually/$14.19 per hour
• Middle range wages (median) — $38,560 annually/$18.54 per hour
• Higher range wages (top 10%) — $62,660 annually/$30.12 per hour
Industrial Technologist
• Lower range wages (bottom 10%) — $35,440 annually/$17.04 per hour
• Middle range wages (median) — $47,860 annually/$23.01 per hour
• Higher range wages (top 10%) — $128,610 annually/$61.83 per hour
WHAT DOES IT TAKE TO BE SUCCESSFUL?
CHEMICAL:
• STEM concepts
• Critical thinking
• Information ordering
• Monitoring
• Deductive/inductive reasoning
INDUSTRIAL:
• Mechanical skills
• Engineering/technology concepts
• Production/processing concepts
• Mathematics
• Design
• Complex problem-solving
Products aren’t much good if they can’t get to customers and that’s where the trucking industry comes in. From over-the-road long-haul truckers driving coast to coast, to delivery drivers that bring goods to your door, everything you eat, wear or use has at some point in the supply chain been hauled on a truck.
WHAT DO TRUCK DRIVERS DO?
Truck drivers do just what their title says — operate heavy-duty trucks to transport loads from Point A to Point B. Truckers run on time schedules, with specified deadlines when loads have to be delivered, and they balance that with road conditions, speed limits and various other regulations to ensure the driver is operating in a manner that’s safe for themselves and other motorists.
But while the name itself is pretty self-explanatory, there are differences within the industry to consider. This article will focus on over-the-road (OTR) truck drivers, which can be divided into various categories:

Flatbed Truckers
• Flatbed trucks deliver freight secured to a trailer with no walls (hence “flatbed”) hauling such things a military vehicles, large machine parts or lumber.
Dry Van Truckers
• Dry van truckers drive what most people think of when they think of a semi — an enclosed trailer hauling nonperishable products and dry goods.
Tanker Truckers
• Tanker truckers transport liquids, which is one of the more difficult trucking operations, from food-grade loads like milk to fuel, chemicals or even hazardous waste.
Freight Haulers
• Freight haulers deliver goods that are not covered by dry van drivers. Freight haulers often transport liquids, oversized loads, hazardous goods, automobiles and logs on specially modified rigs.
Refrigerated Freight Drivers
• Refrigerated freight truckers deliver food, medical products, meat, body products and other highly perishable goods in temperature-controlled trailers.
WHAT’S NEW
The basics of trucking haven’t changed — deliver goods on time, safely — but as with every industry, technology has advanced, making trucks more comfortable, more fuel-efficient and loaded with various
computerized systems from navigational GPS to monitors that ensure drivers don’t exceed speed limits or their allowable daily mileage.
The regulatory climate for trucking companies is also changing as states push to reduce emissions and air pollution caused by gasoline- and diesel-powered engines. California and New York, among other states, have mandated that trucking companies replace their existing fleets with electric vehicles over the next couple of decades, which is controversial considering electric truck technology is not yet suited for long hauls, nor are charging stations readily available nationwide.
WHERE DO TRUCK DRIVERS WORK?
Over-the-road truck drivers may follow a set territory or they may go anywhere in the lower 48 states, plus Canada and Mexico. Truck routes range from a few days out and back to cross-country runs that keep drivers out for several weeks at a time.
The truck itself is both the driver’s home and office while they are on the road, as most rigs are outfitted with a sleeper compartment. In some cases, drivers will work in two-person teams, which allows for covering more miles per day than driving alone. It also provides companionship and assistance while out on a run.
WHAT’S THE JOB OUTLOOK?
Truck driver jobs in Arkansas are expected to grow 8% in the coming decade, twice the national rate for the coming decade.
HOW MUCH CAN I MAKE?
• Lower range wages (bottom 10%) — $25,700 annually/$12.36 per hour
• Middle range wages (median) — $47,990 annually/$23.07 per hour
• Higher range wages (top 10%) — $72,810 annually/$35.01 per hour
It should be noted that earning power varies widely with the type of loads you can handle, as some drivers have earned special certifications and therefore command more money. Also, the current shortage of drivers has driven up wages all over the country, with some companies offering handsome sign-on and retention bonuses to keep their fleets running.
And, unlike in past generations, trucking companies today also provide a full slate of benefits for drivers that rival anything to be found in a white-collar job. For example, Arkansas-based J.B. Hunt, one of the largest trucking and logistics companies in the world, advertises medical, dental, vision and prescription coverage, various types of life, accident and disability insurance, a company-matching 401(k) plan, paid vacation and various bonus programs.
WHAT DOES IT TAKE TO BE SUCCESSFUL?
• Mechanical skills
• Attention to detail
• Record-keeping
• Problem-solving
• Physical strength and stamina
HOW DO I LEARN THE CRAFT?
Learning to operate a semi generally happens at schools set up for that purpose, although some community colleges also offer this instruction. On average, trucking school takes three to five weeks to complete while two-year schools’ programs can be completed in a semester or two.
Once training is completed, drivers must pass a test to get their commercial driver’s license (CDL), required to operate semis, buses and other heavy, oversized vehicles. In Arkansas, 18-year-olds can drive commercial motor vehicles within state lines. Drivers must be 21 to drive commercial vehicles across state lines, haul hazardous materials that require placarding or operate a vehicle with double or triple trailers.
The welding profession is one of nearly unlimited opportunity. Welders work in a wide range of industries and work environments, are in high demand, command good wages and even launch their own businesses. For a person with the right skills and work ethic, welding is one of the most stable skilled professions one can have.
WHAT DOES A WELDER DO?
In the simplest terms, welders are skilled professionals who join two pieces of metal using heat and gas in order to seamlessly and permanently bond them.
The type of welding used on any given job depends on the materials. Welding is the most durable way to join two parts, using electrical currents to create heat and bond metals together. In all, there are more than 100 different processes that a welder can use, four of the most common being:
GMAW (Gas Metal Arc Welding)
• More commonly known as MIG (metal inert gas) welding, this type is among the most easily mastered type of welding.
• Acceptable for fusing mild steel, stainless steel and aluminum.
Arc Welding
• Arc welding is also known as SMAW (shielded metal arc welding) or stick welding.
• The most basic type of welding.
• Commonly used in manufacturing, construction and repair work.
FCAW (Flux-Cored Arc Welding)
• Developed as a lower-cost, high-speed alternative to stick welding.
• Known for being easy to learn.
• Commonly used to bond iron and steel; used in manufacturing, construction and repair work.
GTAW (Gas Tungsten Arc Welding)
• Commonly known as TIG (tungsten inert gas) welding.
• Delivers a superior finish without requiring a lot of finish sanding or grinding.
• Very complex process, requiring a welder with a lot of experience to perform well.
WHAT’S NEW?
Most people have at least a general idea of what a welder is and what he or she does. But did you know there are two related processes that perform many of the same functions as welders, but use different tools and bonding elements? These jobs aren’t new, exactly, but most people outside the industry haven’t heard of them.
Cutters
• Utilize heat from an electric arc, plasma stream or burning gases to cut and trim metal objects to specific dimensions.
• Cutters also take apart large objects such as ships, railroad cars, boilers and aircraft using special highstrength cutting materials. Solderers/brazers
• Use heat to join two or more metal objects together.
• Soldering and brazing are similar, except that the temperature used in soldering is lower.
• Soldering is used to make electrical and electronic circuit boards, such as computer chips.
• Brazing is used to connect cast iron and thinner metals that would warp under the high temperature of welding.
WHERE DO WELDERS WORK?
As the most common and most permanent way of joining pieces together, welding is a trade that performs work as a stand-alone component of larger projects or is used within another trade.
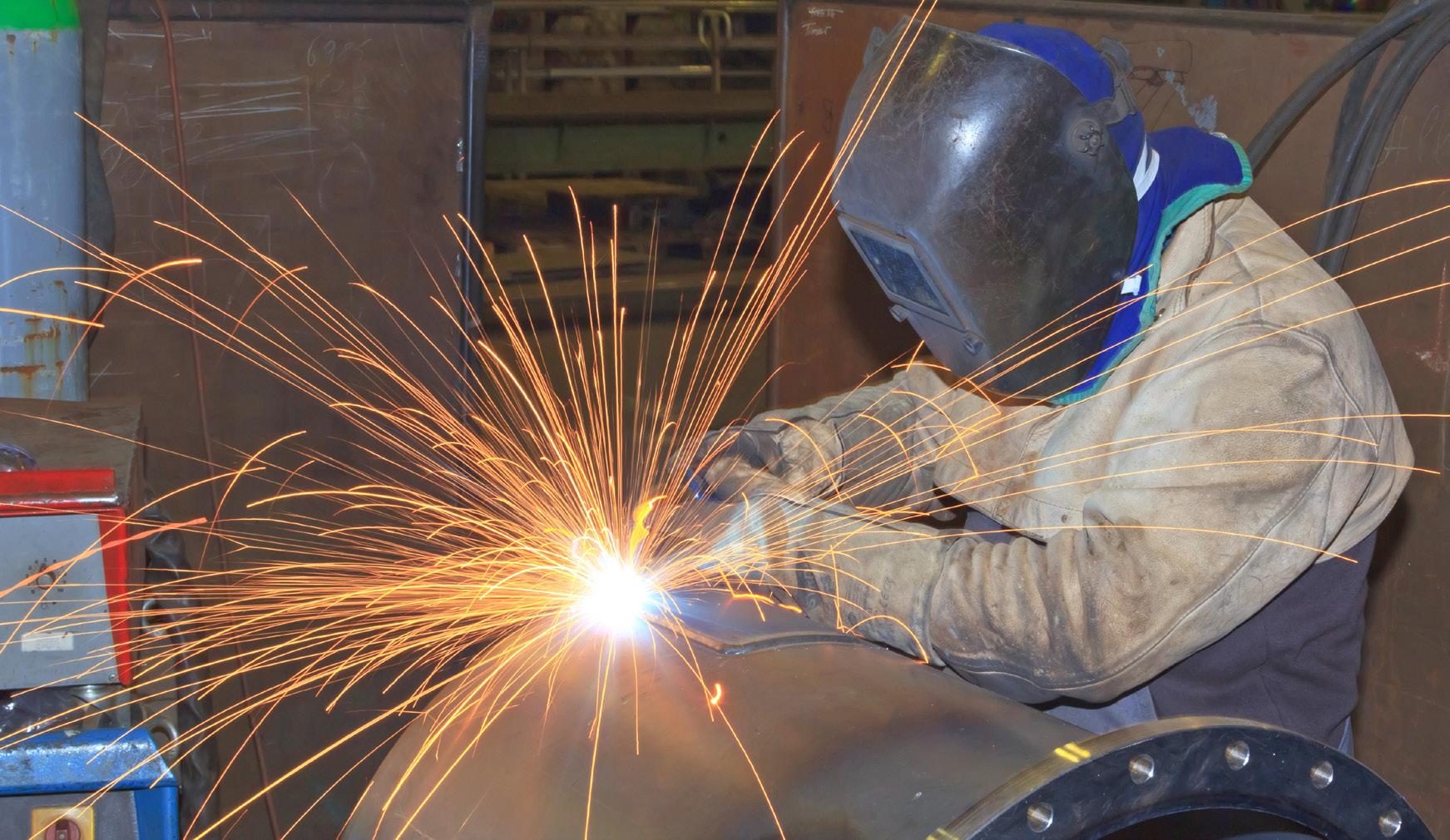
Plumbers are generally trained in the basics of welding in order to perform pipefitting tasks. Other industries use welding as part of their overall operations, including body shops, sheet metal, shipyards and boilermaking operations.
A welder may work on a building or bridge construction site (either indoors or outdoors), which exposes them to working in all kinds of weather. They may also be required to work several stories above the ground on steel building structures or bridges.
Other welders work in a metal shop or garage-like area, which is generally climate controlled. Still other welders work in a factory or industrial setting where they handle maintenance and fabrication tasks as they come up. Welders generally work full time and it’s not uncommon for them to work a lot of overtime to stay ahead of production schedules, particularly in construction. In some industrial settings, welders may be employed on overnight shifts.
WHAT’S THE JOB OUTLOOK?
As one of the most versatile skilled careers out there, welders are facing a bright future when it comes to job security. According to the U.S. Bureau of Labor Statistics, welding jobs in Arkansas are expected to grow by 10%, five times the national average. This makes Arkansas an excellent place to build your career.
Some welders move from construction job to construction job, meaning a general slowdown in building projects can mean periods of unemployment. The more mobile a welder is, the more easily he or she may find additional projects.
HOW MUCH CAN I MAKE?
Lower range wages (bottom 10%) — $29,190 annually/$14.04 per hour
• Middle range wages (median) — $37,760 annually/$18.16 per hour
• Higher range wages (top 10%) — $50,450 annually/$24.26 per hour
WHAT DOES IT TAKE TO BE SUCCESSFUL?
• Physical strength and dexterity
• Vision
• Attention to detail
HOW DO I LEARN THE CRAFT?
Some high schools have beginner welding programs as part of automotive or shop classes, which can give students a head start on their education.
Most welders have a high school diploma or equivalent and a professional certification, which can be earned through a community college, a private training program or welding courses sponsored by industry groups or trade unions.
Welding programs can be a few months long or they can be an apprenticeship lasting four or five years. They can be full-time classes like any other college curriculum or, in the case of many apprenticeship-type training programs, are held one or two nights a week while the student works full time for a welding company, thereby also learning on the job.
Another advantage of the work-study nature of apprenticeship programs is most employers pay for the training as an employee benefit.
RECLAMATION AUTHORITY FUELING TECHNICAL CAREERS
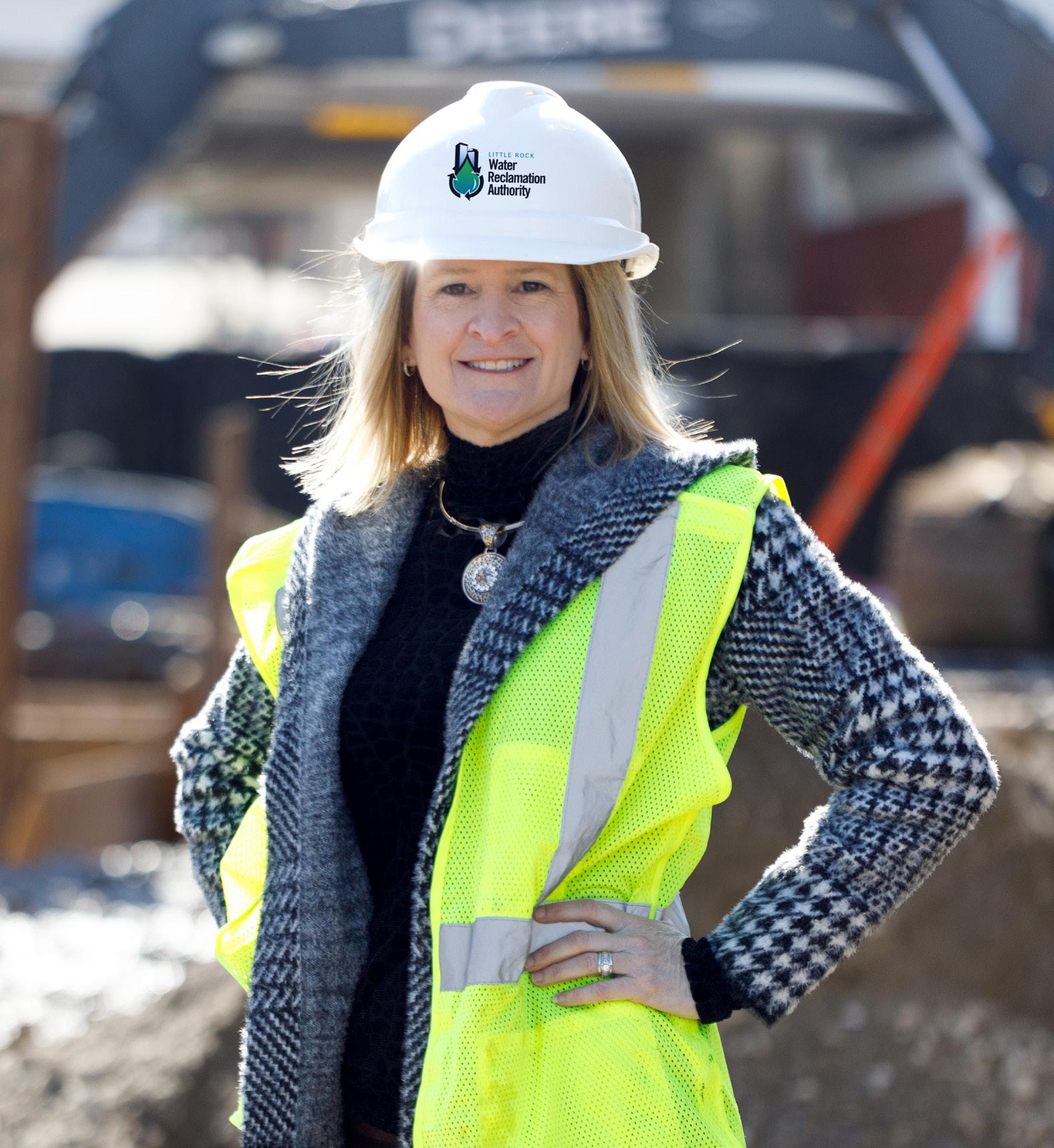
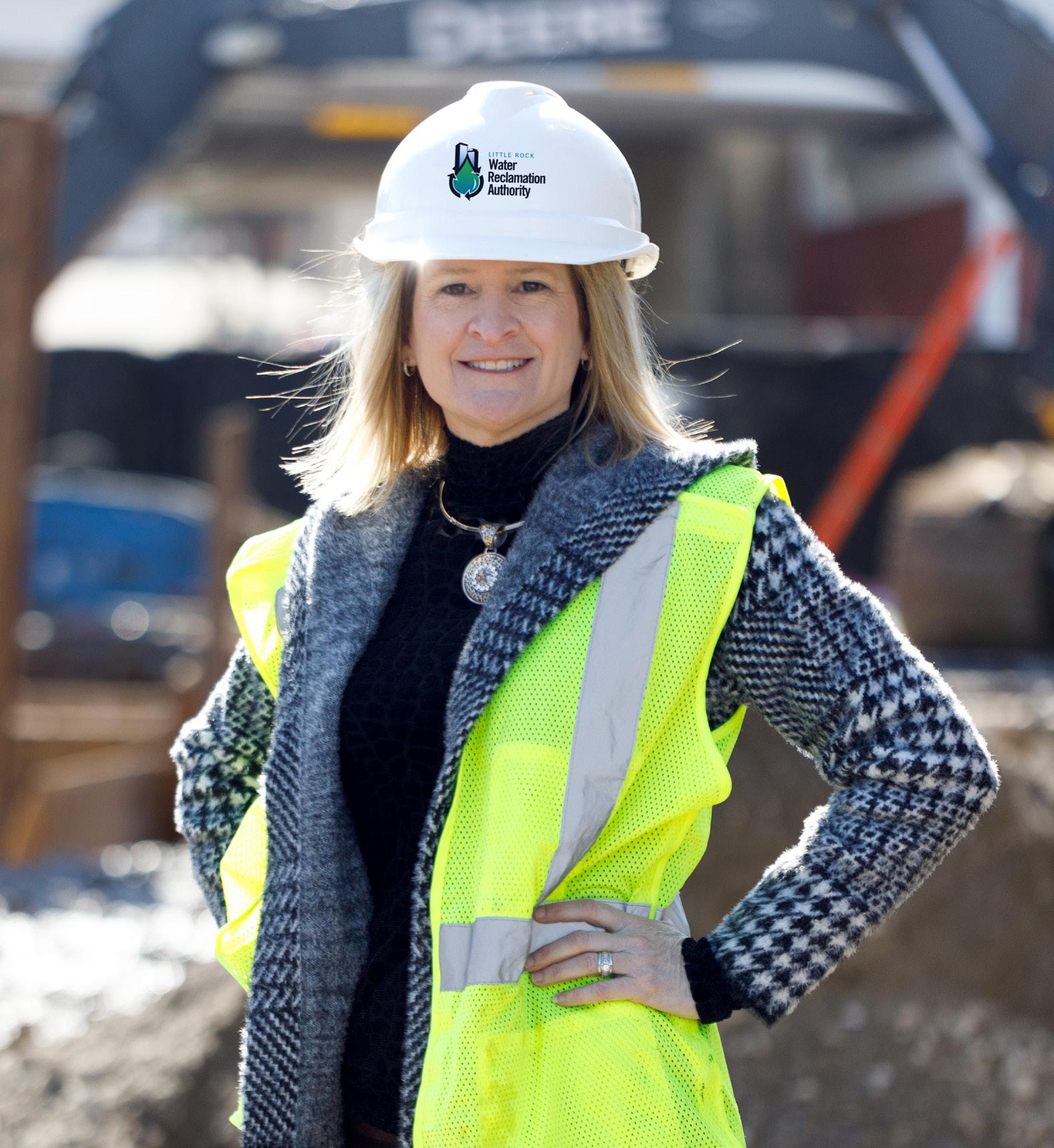
FUELING TECHNICAL CAREERS
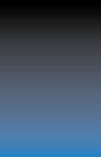
Little Rock Water Reclamation Authority offers job opportunities across diverse fields including plumbing, mechanics, HVAC maintenance and more. Through specialized training, we improve our team’s skills so we can protect public health, the environment, and help our city thrive.
Little Rock Water Reclamation Authority offers job opportunities across diverse fields including plumbing, mechanics, HVAC maintenance and more. Through specialized training, we improve our team’s skills so we can protect public health, the environment, and help our city thrive.
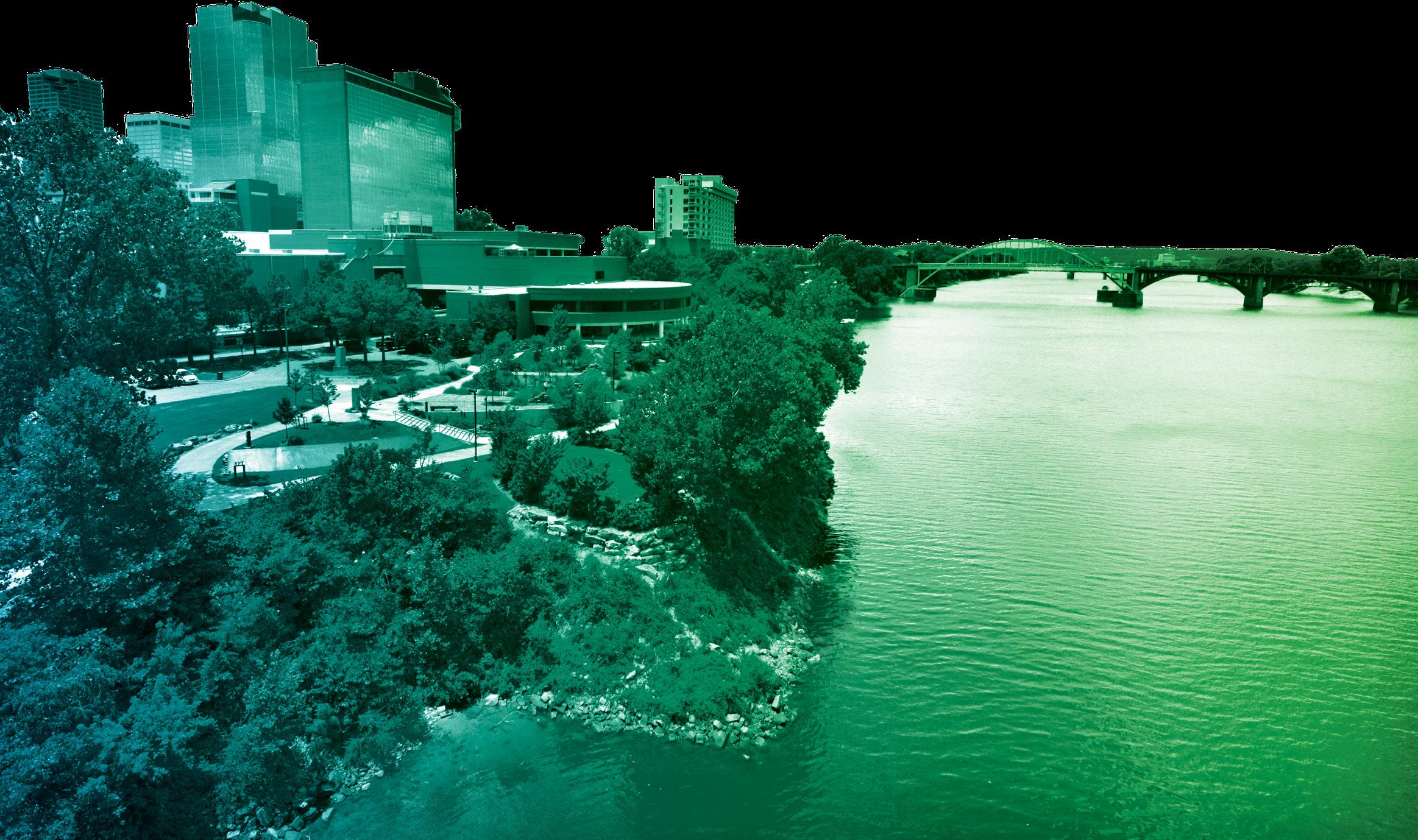
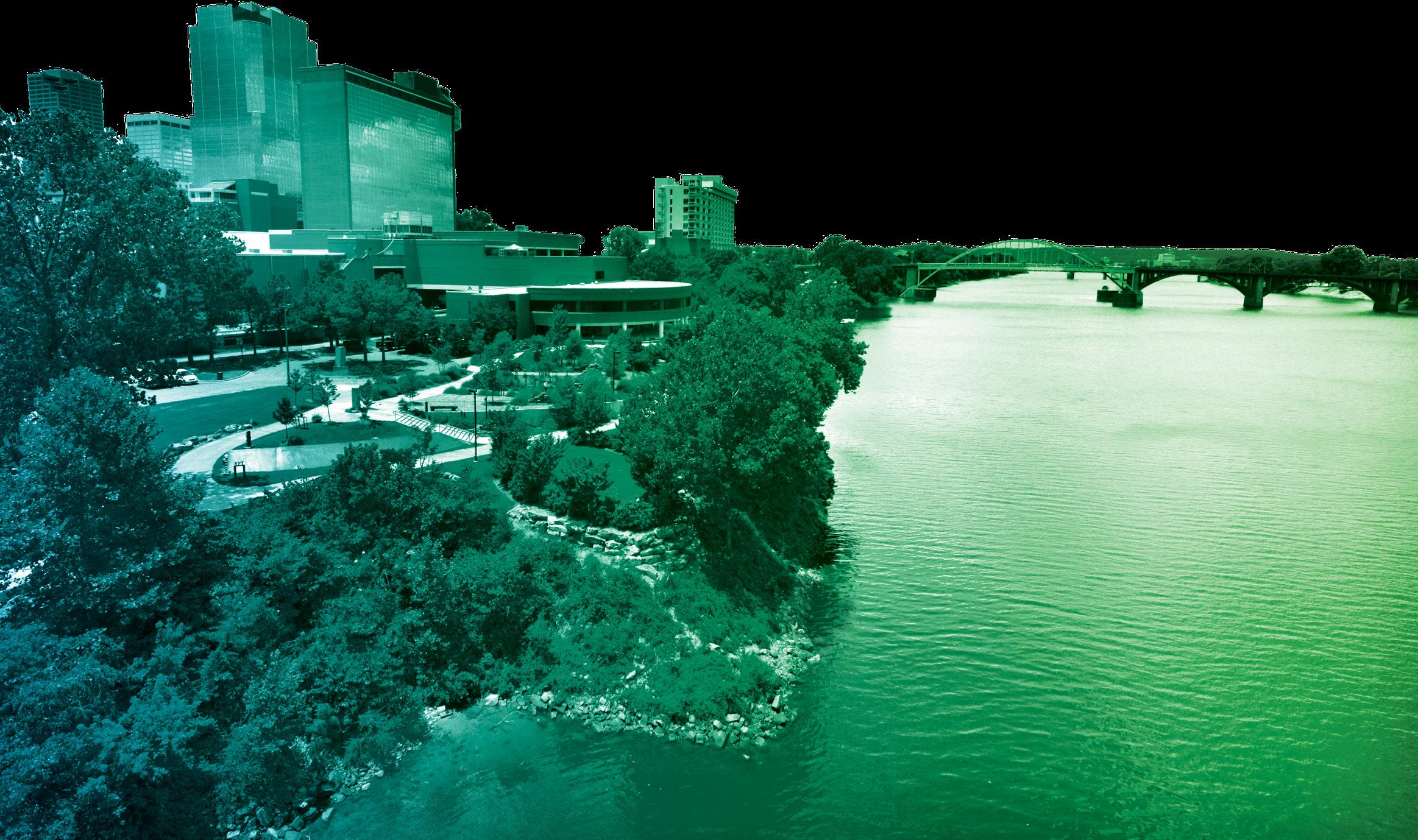
Scan the QR Code or visit lrwra.com/careers to learn more about our technical careers.
Scan the QR Code or visit lrwra.com/careers to learn more about our technical careers.
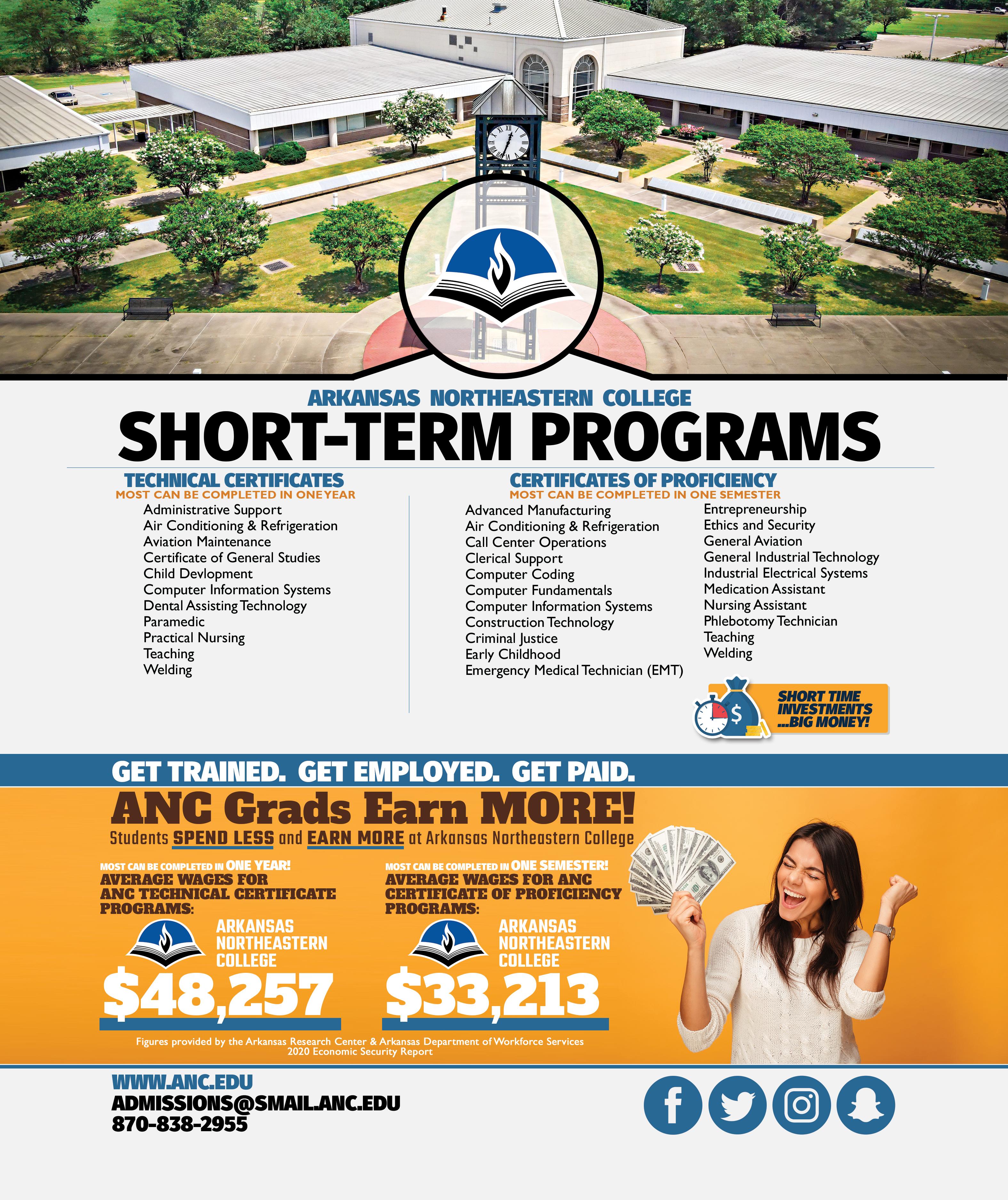