
4 minute read
PAID THE SYSTEMS WELDING PROGRAM GROUP
from BluePrint 2023
To meet the growing need for skilled craftsmen and women in the steel industry, The Systems Group has started a training program to develop current and newly hired employees. Our training program focuses on training new employees in structural GMAW welding, while up-skilling current employees in multiple welding processes. The training will occur during normal work hours. Trainees will receive their regular pay while participating in the program. Our training will be a mix of classroom and shop time. Classroom time will teach technical aspects of welding, while shop time will be a mix of weld booth time and on-the-job training. Once the trainees understand the fundamentals of welding, they will be in the fab shop working in their assigned areas with the welding instructor. Our training program is led by our welding instructor, Alex Ford.
For more information, go online at careers.tsg.bz or call a recruiter at 1.800.501.1315.
FAB & MACHINE
I would most definitely recommend this course for other people. It is a learning experience and it can probably change your life.
-Tyler Johnson
VICTOR THOMPSON
General Foreman, The Systems Group
Hometown: Dyersburg, TN
Age: 54
Years with The Systems Group: 13
BLUEPRINT: Where did you get your start with the company?
VICTOR THOMPSON: I came on in 2010 with 75 men on site. I was a journeyman fitter and welder and I was the lowest paid journeyman out of all of them. I started on the bottom.
BP: What did you do to improve your skills and advance your career?
VT: I came in and worked real hard. I noticed who the qualified tradesmen were in the field, out in the mill or wherever, and I kept a keen eye on them all the time to learn what they knew, and what knowledge they had that I could get. I worked hard to make sure that whatever was out there to learn that I could learn it and advance up and move forward.
BP: Did you come from a family who was big into the trades?
VT: No, this is something I reached on my own. When I started back in the late 1980s I could not read a tape measure. Everything I learned, I learned on the job. Once I got into the pipe fitting trade, I learned about the National Center for Construction Education, and I jumped into that and got all the book knowledge I could off of it.
With Systems here, they allow you to advance yourself as far as you want to go. I hold 10 national certifications outside of my trade, from boilermaker to carpenter to basic rigger to advanced rigger to crane operator. I hold all those because the company gives me the time to advance myself and advance the company.
BP: What advice do you have for someone who’s just starting, right out of high school?
VT: If you’re still in school, seek out an ag shop, trade shop, in-school welding, whatever it might be. Get into that and see if it’s for you. Once I found out the trades were for me, I would find a good reputable company, and I would hire in. Hiring in on the bottom side these days doesn’t pay bad money, it really doesn’t.
BP: Did you ever find an older co-worker who didn’t want to help you when you were starting out?
VT: The people who have been doing it for years, if they see a young individual who’s willing to apply themselves and learn — male, female, doesn’t matter – they’re going to give them all the knowledge they possibly can. That’s where I picked it up, watching other guys.
Jamie Weeks
Construction Superintendent, The Systems Group
Hometown: Warren
Age: 51
Years with The Systems Group: 26
BLUEPRINT: What jobs have you held leading up to construction superintendent?
JAMIE WEEKS: I’ve done everything from pipe fitter, welder, foreman, general foreman, maintenance superintendent for 13 years and now construction superintendent. I’ve been in this role for six months.
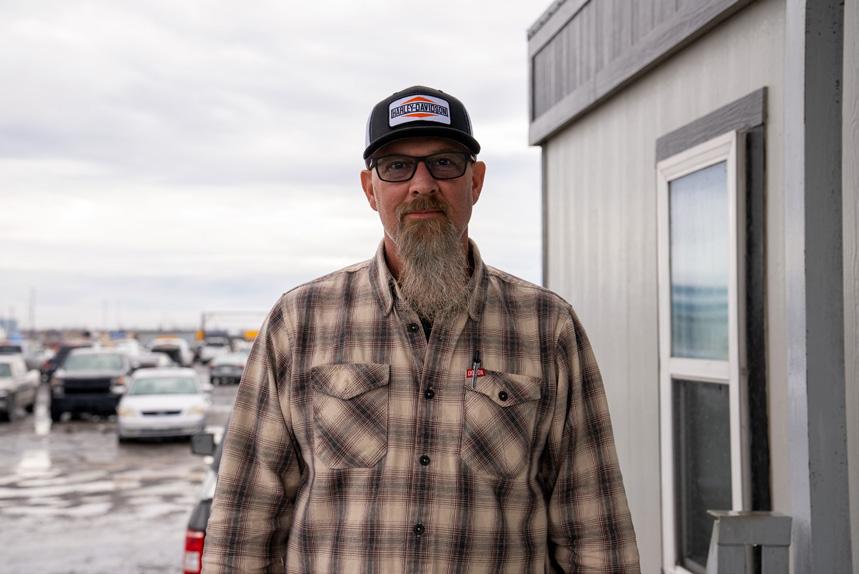

BP: How did you get started on this career path?
JW: My father worked for the company, got me a job and it’s progressed from there. I got a job as a welder’s helper, worked my way up to welder and just kept going.
BP: What’s a welder’s helper? What does that job do?
JW: I’d grind, cut, clean, carry the tools, whatever they needed done. That’s a job that’s still around; on the construction side, we try to hire as many helpers as we can. It helps with our cost per hour, but we also find people who are trainable, we mentor them and help them grow.
BP: Did you grow up working with your hands? How did you get your start?
JW: My cousins were drag racers, so I’ve been working on vehicles since I was 10 or 12 years old. When I got to The Systems Group, the only training I got at this level was on-the-job experience.
Today, we’re doing a pipe fitting apprentice program and a welding program. They’re just getting that started now, hiring some welding instructors and pipe fitting instructors. We’re trying to bring in younger workers, teaching them and trying to help them develop, make more money, become a journeyman.
BP: What soft skills are important for working there?
JW: Being dependable, being here on time when you’re scheduled. To me, that’s about as important as anything. And being willing to learn. Some of the younger generation come from these welding schools and they think they already know everything. Some of them don’t like to take direction. That’s something we’ve just got to work through.
BP: If you could talk to a roomful of those young people – high schoolers, let’s say – what would you say to them about a career in the trades, specifically at The Systems Group?
JW: Our company is very serious about safety, that’s one of the most important jobs we have is teaching safety, enforcing safety and making sure it’s followed through. Our management is really dedicated to that too, making sure everything is right and we have what we need to do the job so no one gets hurt and everyone gets to go home at night. That’s how I know our company cares about their employees. They’ve always cared for me and treated me right. To me, this company’s like a big family. It’s just a great place to work.