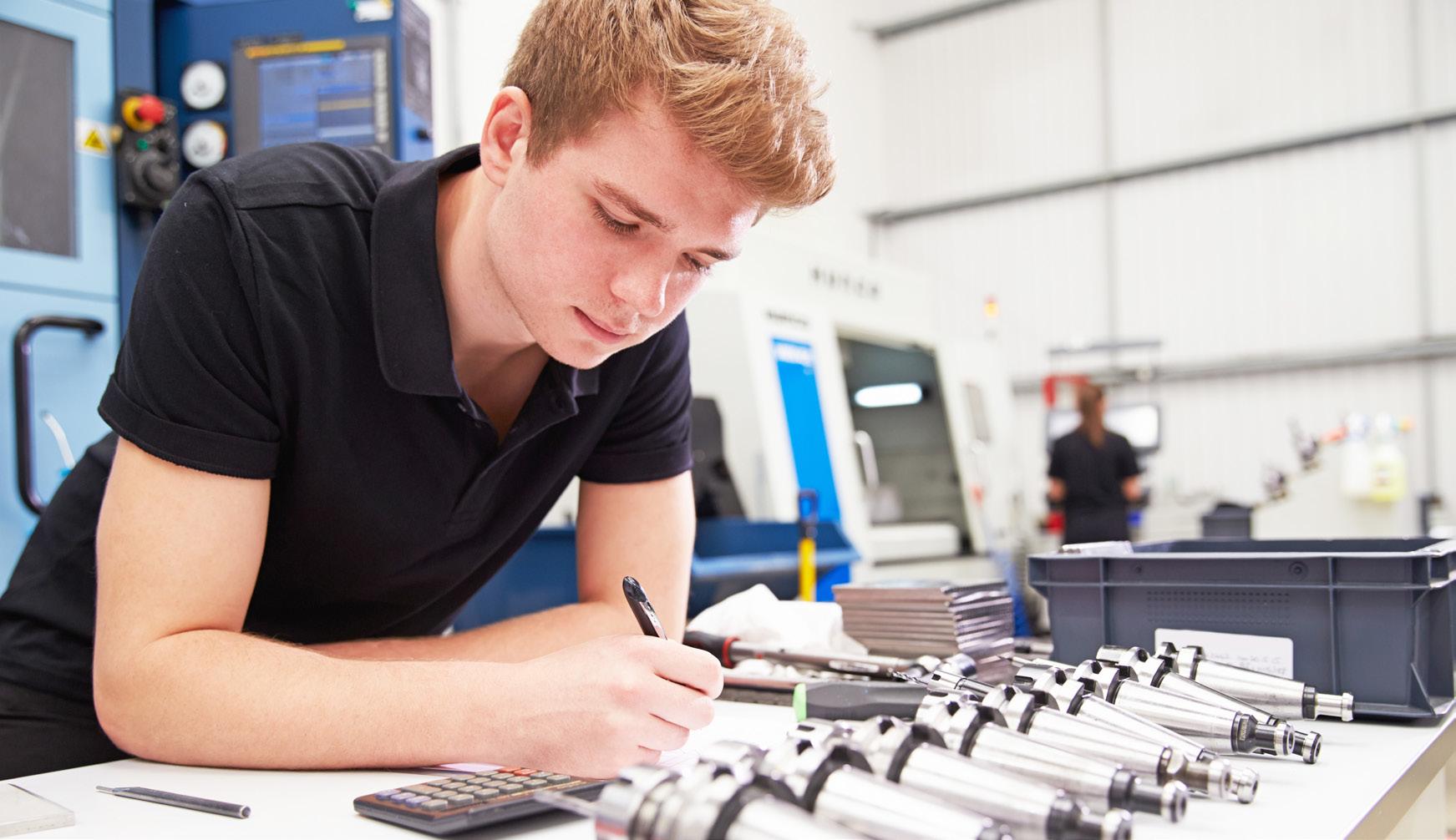
38 minute read
CNC OPERATORS/ PROGRAMMERS
from BluePrint 2023
Have you ever wondered where the parts come from to create new machines or to repair or upgrade existing machines? That’s the role of CNC operators and programmers, specially trained individuals who design precision parts, then program and operate computer-driven machinery to make those parts, which are used in all kinds of industries and to help bring new manufacturing technology to life.
manufacturing and provides a much more comfortable workspace. Employees of companies that use advanced manufacturing generally work in an indoor, climate-controlled workplace.
However, CNC operators must observe basic safety rules that may include wearing protective equipment. This equipment may include such things as safety glasses, earplugs and steel-toed boots. You may also have to wear a respirator to guard against fumes or dust, particularly when working with plastics.
WHAT’S THE JOB OUTLOOK?
CNC operators and programmers are the latest generation of a long line of machine operators and setters that have evolved with changes in technology in manufacturing. As more companies adopt systems that are considered “lean manufacturing,” CNC technology will continue to be an important part of production, and the demand for skilled CNC operators is likely to remain strong.
Combined, experts predict the number of these jobs to grow 26% in the coming years, most of that increase in the programming area. Most metal and plastic machine workers are employed full time. Overtime is common, and because many manufacturers run their machinery for extended periods, evening and weekend work is also common.
HOW MUCH CAN I MAKE?
With experience and expertise, workers can become candidates for more advanced positions, which usually include higher pay and more responsibilities. Experienced workers with good communication and analytical skills may move into supervisory positions.
CNC Programmers
• Lower range wages (bottom 10%) — $30,410 annually/$14.62 per hour
• Middle range wages (median) — $57,130 annually/$27.47 per hour
• Higher range wages (top 10%) — $85,270 annually/$41.00 per hour
•
CNC Operators
• Lower range wages (bottom 10%) — $30,060 annually/$14.45 per hour
• Middle range wages (median) — $41,250 annually/$19.83 per hour
• Higher range wages (top 10%) — $50,090 annually/$24.08 per hour
With experience and expertise, workers can become candidates for more advanced positions, which usually include higher pay and more responsibilities. Experienced workers with good communication and analytical skills may move into supervisory positions.
WHAT DOES IT TAKE TO BE SUCCESSFUL?
• Computer skills
• Mathematics
• Physical stamina/strength
• Design
• Mechanical skills
HOW DO I LEARN THE CRAFT?
Machine operator trainees usually begin by watching and helping experienced workers on the job. Eventually, these workers develop the skills and experience to set up machines and perform a full range of tasks.
CNC machine tool programmers typically need to complete courses beyond high school. CNC operators generally do not complete an apprenticeship like other trades.
Some operators are trained on basic machine operations and functions in a few months, while computer-controlled machine tool operators may need up to a year to become fully trained in their craft.
Community colleges and other schools offer courses and certificate programs in operating metal and plastics machines that involve CNC programming.
Stop and think for a moment about everything in our world that runs on computer chips. Better yet, try to think of something that isn’t controlled by a computer or an app. The fact is, nearly everything we do is impacted in some way by technology — technology that’s configured at some stage by a computer programmer.
WHAT DO COMPUTER PROGRAMMERS AND COMPUTER CODERS DO?
Even though computer programmers and computer coders are in the same job family, there are important differences to consider.
Computer coders write the computer language (or code) for software programs that tell machines what to do. This software acts as the brains behind many of our “smart” devices (smartphones, smart cars, etc.) Coders may also develop websites or apps for the companies they work for.
Computer programmers do the same thing as computer coders, but they are also responsible for managing the overall project of designing, producing and testing a new software product, or designing a network system.
WHAT’S NEW?
Consider: Just 10 years ago, few people even knew what an app was, and look where we are now. Technology moves so fast, just about anything we could list under the heading “What’s New” is likely to be replaced by something faster and smarter within a very short period of time. Some emerging trends in the industry include: Virtual Reality (VR)/Augmented Reality (AR)
Technologies that provide the user the ability to experience a 360-degree digital environment.
• Some applications include giving a client a look at a building before it is built, conducting flight training or producing a safety course that simulates fire or other emergency.
Robotic Process Automation (RPA)
• RPA is the use of software to automate repetitive tasks that people used to do.
• About 60% of occupations can be partially automated; less than 5% can be completely replaced by technology.
• While this technology would affect, and potentially eliminate, some positions, it would also create new ones.
Machine Learning
• Machine Learning is a subset of artificial intelligence whereby computers are programmed to learn to do something they are not programmed to do. Computers “learn” by discovering patterns and insights from data. In general, there are two types of learning: supervised and unsupervised.
• Machine Learning is rapidly being deployed in all kinds of industries, creating a huge demand for skilled professionals. Machine Learning applications are used for data analytics, data mining and pattern recognition.
• Jobs in this area rank among the top emerging jobs on LinkedIn, with almost 2,000 job listings posted.
WHERE DO COMPUTER PROGRAMMERS AND CODERS WORK?
Most programmers and coders work full time in offices, but the nature of the work allows many to work from home. Programmers may work alone or they may work as part of a team, depending on the size of the project.
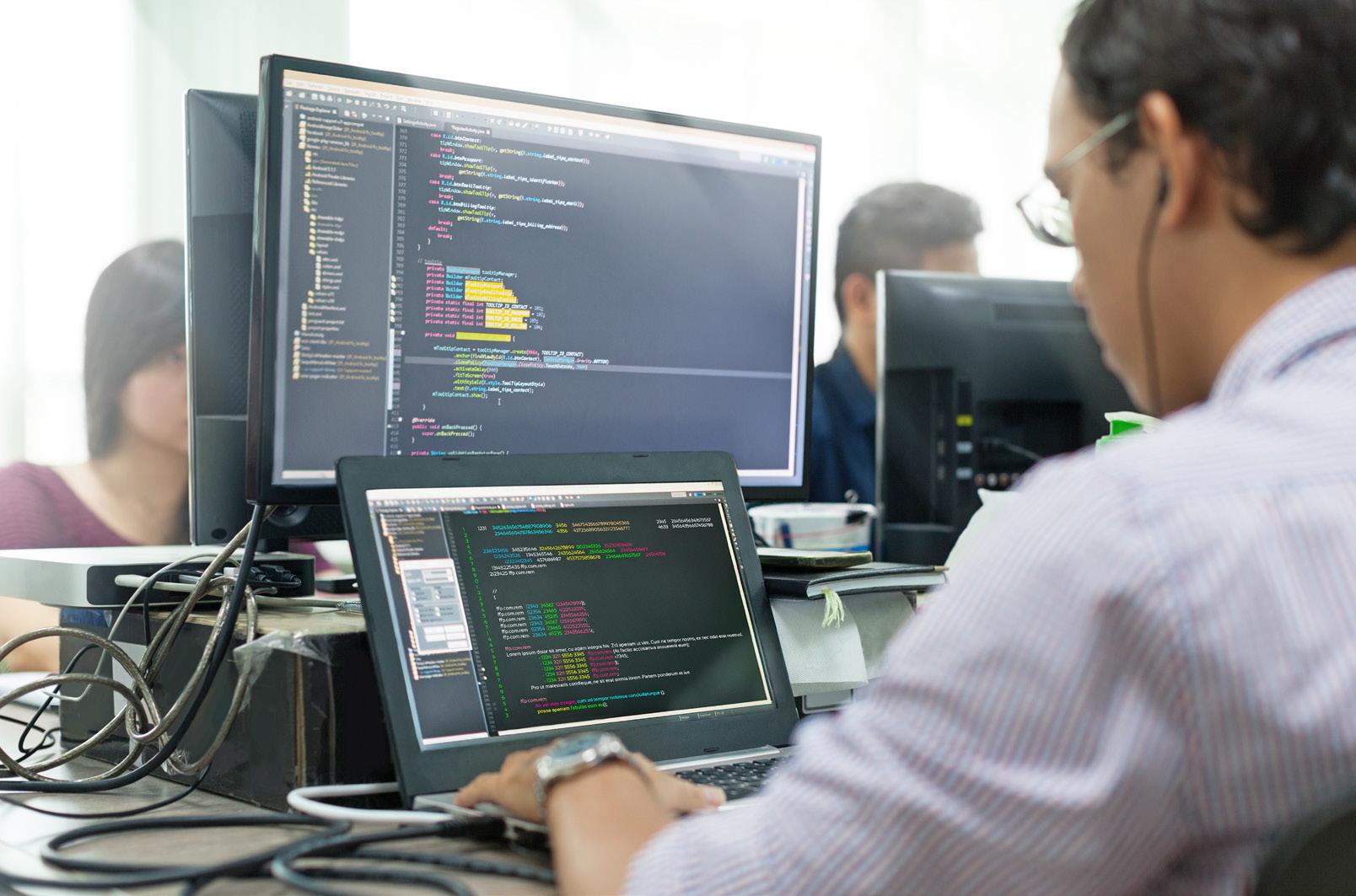
WHAT’S THE JOB OUTLOOK?
Expert predictions are mixed as to the future job outlook. Computer programmers and coders are part of a much larger group of jobs under the category of information technology. Programmers who have general business experience may become computer systems analysts. With experience, some programmers may become software developers. With the right education and experience, the career options in information technology are nearly endless.
HOW MUCH CAN I MAKE?
Computer Programmers
• Lower range wages (bottom 10%) — $49,340 annually/$23.72 per hour
• Middle range wages (median) — $80,290 annually/$38.60 per hour
Higher range wages (top 10%) — $128,880 annually/$61.96 per hour
Your actual earning power depends on the company you work for, your level of experience and certifications, your years of experience and, in some cases, the part of the state where you work.
WHAT DOES IT TAKE TO BE SUCCESSFUL?
• Analytical skills
• Thinking creatively
• Detail oriented
• Problem-solving
HOW DO I LEARN THE CRAFT?
If you attend high school in Arkansas, you already have access to beginning coding classes. In 2015, the state legislature passed a law requiring all Arkansas schools to provide computer science classes that included coding and other IT subjects as a way to give students a jump on the careers of the future. Arkansas was the first and, at the time, only state in the country to require schools to offer such classes.
Diesel engines are the workhorses of the road and job site. Machines, from over-the-road trucks to bulldozers, to industrial and farm equipment run on diesel engines, which are known for their reliability and toughness. Diesel techs keep these machines rolling and running — on the road, the job site and in factories.
WHAT DO DIESEL TECHS DO?
Diesel technicians inspect, diagnose, repair and maintain any machine with a diesel engine. A few examples include:
• Aircraft support equipment.
• Farm equipment, including tractors, harvesters, dairy and irrigation systems. Marine equipment, ships and yachts.
• Over-the-road trucks (semis).
• Buses and dump trucks.
• Earth-moving equipment, such as bulldozers, loaders, backhoes and graders.
• Road construction/highway paving equipment.
• Industrial/factory machines, including cranes, pumps and drilling equipment.
A diesel technician is similar to a diesel mechanic, because both use tools and training to diagnose problems, make repairs and perform necessary maintenance. A diesel technician is different from a diesel mechanic, generally speaking, in that:
• Diesel technicians are trained to handle onboard electronics (computer systems) of the modern diesel engine.
• Diesel mechanics are primarily trained to repair mechanical (moving parts) components of an engine. Typical day-to-day job duties of diesel technicians include:
• Make major and minor engine repairs by repairing or replacing parts and components.
• Perform routine and preventative maintenance.
• Work on a vehicle’s electrical and exhaust systems to comply with pollution regulations.
• Test drive vehicles to diagnose malfunctions or to ensure that they run smoothly.
WHAT’S NEW?
Diesel machinery has enjoyed major advances in technology, creating a growth in the need for skilled technicians.
Between safety regulations, environmental controls and insurance guidelines, the trucking industry has a lot of rules by which it must abide. To help stay in compliance, trucking companies rely on the technology that’s built into their fleet.
It’s not unusual for a new truck to have multiple computers on board regulating everything from speed and location to fuel consumption. Some trucks are sophisticated enough to monitor their own systems and alert the operator when a problem is detected.
Older trucks that didn’t have these computers installed when they were built are often overhauled with the new technology to help bring them up to speed.
Farm technology is another fast-growing area where technicians are needed. Modern farm equipment can map out a field, test soil samples from different areas and apply the precise mix of fertilizer or minerals for each area. Harvesting equipment comes equipped with auto-steer, can track yields in real-time and utilizes GPS to minimize harvest guesswork.
WHERE DO DIESEL TECHS WORK?
Diesel techs are employed by (among others):
• Manufacturers.
• Trucking companies.
• Equipment dealerships.
• Farm operations.
• Cities and counties. Some techs may also work as inspectors to make sure equipment meets government regulations.
The work environment for diesel technicians is in a repair, maintenance or garage-type facility. Some are mobile and must travel to the site of a breakdown or job site to provide service. In these instances, you may be required to work outside, sometimes in inclement weather.
The majority of diesel techs work full time. Some companies require on-call, night and weekend hours. Working hours may depend on your specialty; you may work on trucks as they come in for service, respond to emergency calls as they happen, or you may be responsible for the regular maintenance of a fleet of vehicles and equipment.
WHAT’S THE JOB OUTLOOK?
The Department of Labor expects the number of diesel technician jobs in Arkansas to grow by 6% in the coming years, slightly ahead of the national average.
HOW MUCH CAN I MAKE?
Diesel Technician
• Lower range wages (bottom 10%) — $29,530 annually/$14.20 per hour
• Middle range wages (median) — $42,700 annually/$20.53 per hour
• Higher range wages (top 10%) — $60,150 annually/$28.92 per hour
WHAT DOES IT TAKE TO BE SUCCESSFUL?
• Physical skills
• Physical strength
• Technical skills
• Computer knowledge
• Soft skills
HOW DO I LEARN THE CRAFT?
Many technicians, like mechanics, learned their trade on the job, but these days many employers prefer to hire technicians who have formal education in the field. As a result, several two-year colleges in Arkansas provide educational courses ranging from six months to about two years to complete.
In addition, many diesel technicians are also required to have a commercial driver’s license (CDL), which allows them to test-drive the vehicles they work on. Employers may also send experienced technicians to special training classes conducted by manufacturers and vendors to learn about the latest diesel technology, techniques and equipment.
Some employers may require (and pay for) their techs to be certified by the National Institute for Automotive Service Excellence (ASE). Diesel technicians may be certified in specific repair areas, such as drivetrains, electronic systems and preventative maintenance and inspection.
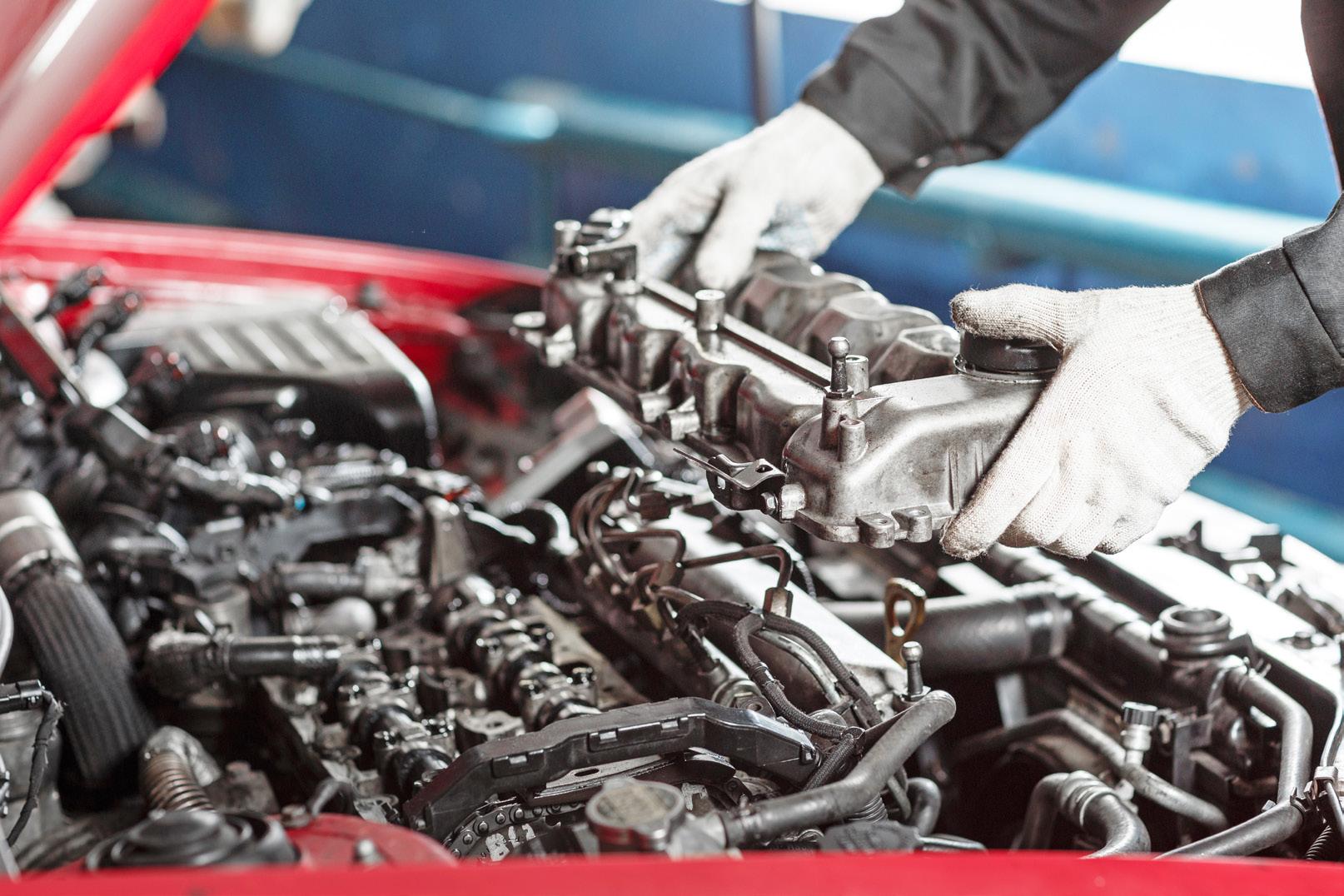
Electricians bring electrical power to homes and factories in every city and town in America. It is a steady occupation that is expected to grow rapidly in the coming years and is evolving with new levels of technology. You can choose to work for an electrical contractor, be on staff in a factory or own your own business, with the right license. All in all, it’s an exciting profession that’s always in demand.
WHAT DOES AN ELECTRICIAN DO?
Electricians install and maintain electrical power, wiring, communications, lighting and control systems in homes, businesses and factories. They work in accordance with rules and regulations to ensure that buildings operate in a way that is safe to residents and occupants.
Electricians’ general day-to-day responsibilities include:
• Ensure businesses and factories operate safely and efficiently through scheduled maintenance and upgrades to their electrical systems.
• Repair control systems, large and small motors and other equipment in factories; install electrical machines in factories.
• Read blueprints and install electrical wiring and systems in new residential and commercial buildings under construction.
• Access, test and upgrade older systems during remodeling projects. Find and replace faulty or aged wiring that could pose a safety hazard.
• Plan the layout and installation of wiring through an entire building or series of buildings. Add, maintain and replace circuit breakers, fuses and wires.
• Review the work other electricians do, making sure it meets the safety standards and building codes.
Electricians can be divided into four general categories:
Residential Wiremen
• Install and maintain electrical wires that go into people's homes.
• Install new electrical equipment, such as light fixtures, ceiling fans, dimmer switches and outlets.
Inside Wiremen
Place and maintain electrical wires in office buildings, factories, airports, schools and hospitals.
• Maintenance or repair of assembly line machinery or motors.
Telecommunications Electricians
• Lay cable (including fiber optics) needed for all forms of communication, including phone and computers.
• Install systems that run telephones, intercoms, computer networks, security and fire alarms.
Outside Linemen
• Work atop telephone poles or alongside the road.
• Work to restore power after storms and floods.
WHAT’S NEW?
Green Energy
• Green energy includes solar panels and wind turbines to generate power.
• Electricians handle special storage units called high-efficiency photovoltaic cells to collect energy. They also install and service power converters, which take the energy generated by the sun or wind, convert it to electricity and download it into the electrical system.
Smart Electrical Grids
• New technology that regulates the flow of power to users, detects malfunctions in the grid, and maintains service to homes and businesses.
• Electricians keep smart grids running at peak performance.
Home-Powered Roof Shingles
Roof shingles that collect sunlight and convert it into energy that powers the building. The shingles could potentially present a lower-cost option than conventional solar panels.
Electricians are needed to wire the solar shingling system into the building’s electrical systems.
WHERE DO ELECTRICIANS WORK?
Electricians work indoors and outdoors, at homes, businesses, factories and construction sites. Many electricians work alone, but sometimes they collaborate with others. At larger companies, electricians are more likely to work as part of a crew. During scheduled maintenance or on construction sites, electricians can expect to work overtime.
Work schedules may include evenings and weekends and may vary during times of bad weather, which may require working in rain, wind or snow.
WHAT’S THE JOB OUTLOOK?
The majority of electricians in Arkansas work for electrical contractors and nearly all electricians work full time. The U.S. Department of Labor projects electrician jobs in The Natural State to grow by 9% in the coming decade, ahead of the national average.
HOW MUCH CAN I MAKE?
• Lower range wages (bottom 10%) — $29,590 annually/$14.22 per hour
• Middle range wages (median) — $46,180 annually/$22.20 per hour
• Higher range wages (top 10%) — $61,420 annually/$29.53 per hour
Your actual earning power depends on the company your work for, your level of experience and licensing, your years of experience and, in some cases, the part of the state where you work.
WHAT DOES IT TAKE TO BE SUCCESSFUL?
• Intellectual ability
• Skills in math, algebra, reading, writing
• Troubleshooting
• Mechanical ability
• Business/interpersonal skills such as time management and communication
• Physical skills
HOW DO I LEARN THE CRAFT?
Most electricians learn their trade in a combination of classroom education and on-the-job training. Some twoyear colleges also offer courses in electrical fields. Generally, a high school diploma is sufficient to get started. The most common way electricians learn is through an apprenticeship program; think of these programs as “electrician school.” Apprenticeship programs take four or five years to complete and are often paid for by your employer. Some schools are also offered by trade groups and labor unions.
Since most apprentices are already employed, they work during the day where they are supervised by more experienced, licensed electricians and attend class at night. Upon completion of apprentice school, you can test for your journeyman’s license, which allows you to work unsupervised on most tasks.
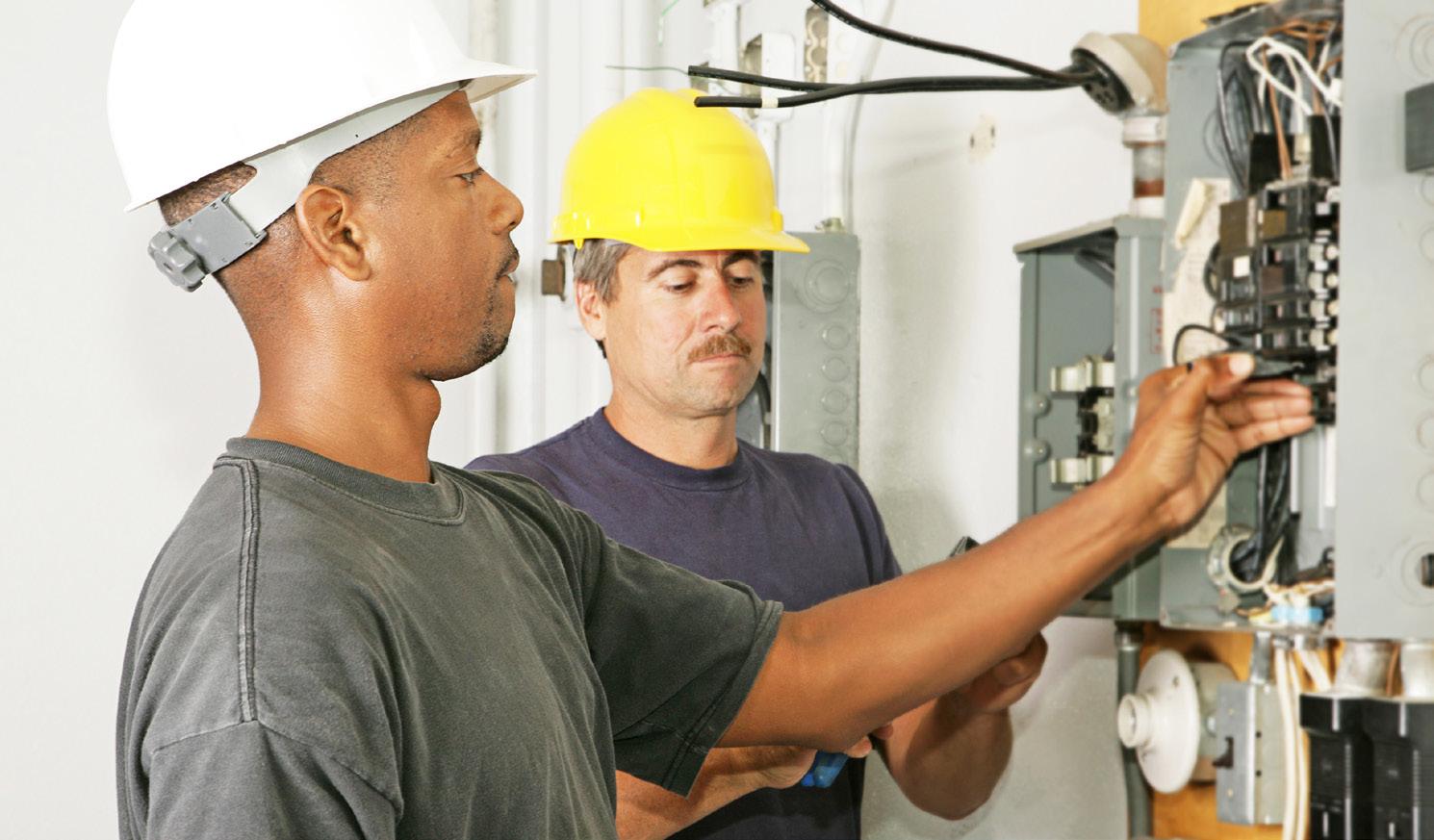
You can stay a journeyman electrician as long as you want, but many electricians choose to test for the highest license, a master electrician. You are eligible to test for your master’s license after being an electrician for five years, at least one of which must be at the journeyman level. The benefits of becoming a master electrician is more money and they may open their own electrical business.
Electricians may be required to take continuing education courses by their employers. These courses are usually related to safety practices, changes to the electrical code and training from manufacturers on specific products.
If it can push, pull, pump or lift material, rolls on tires or crawls on tracks like a tank, it’s where the heavy equipment operator calls home. On virtually all construction projects, these employees are the first workers on the job and the last to leave. Their work is essential to a smooth-running construction project.
WHAT
DO HEAVY EQUIPMENT OPERATORS DO?
Operators drive, maneuver or control a variety of heavy construction equipment. “Heavy equipment” is a blanket term for numerous machines including:
• Cranes
• Bulldozers
Front-end loaders
• Backhoes
• Graders
• Dredges
• Excavators
• Hoists
In addition to operating these machines, heavy equipment personnel also do the following:
• Clean and maintain equipment. Make basic repairs.
• Drive and maneuver equipment.
• Coordinate with other craftsmen on the job site. Some of the most common job titles within this category include:
Operating engineers (sometimes called hoisting or portable engineers).
• Work with excavation and loading machines equipped with scoops, shovels or buckets that dig sand, gravel, earth or similar materials.
• Includes bulldozers, trench excavators, road graders.
• Includes industrial trucks or tractors equipped with forklifts or booms for lifting materials.
Paving and surfacing equipment operators
• Control machines that spread and level asphalt or concrete for roadways or other structures.
• Includes asphalt spreaders, concrete paving machine operators and tamping equipment.
Pile-driver operators
• Use large machines mounted on skids, barges or cranes to hammer piles into the ground.
• Piles, made of concrete, wood or steel, support retaining walls, bridges, piers and building foundations.
WHAT’S
NEW?
Internet of Things (IoT)
• A sensor, or group of sensors, installed for collecting and transferring data. Whenever a product carries the term “smart” or “intelligent” (smartphone, intelligent building) it’s considered part of this new group of products.
• Heavy equipment includes a wide range of sensors that automatically provide information, including diagnostics, fuel usage, machine hours and more. More workers are also wearing safety sensors to monitor air quality and biometrics at the worksite.
• Radio frequency identification (RFID) tags are commonly used to track materials and tools.
Designed Multifunctionality
• Construction companies are always looking for ways to get the most out of expensive equipment.
• Multifunctional equipment can adapt a machine to a variety of tasks, such as backhoes that double as loaders through the use of interchangeable attachments.
Telematics
• Used for years by trucking companies, telematics keep track of the location, condition and operation of machines on the road or the job site.
• The feature uses global positioning to determine where and how equipment is being used.
WHERE DO HEAVY EQUIPMENT OPERATORS WORK?

The majority of construction equipment operators work full time, in nearly every type of weather conditions. Like all jobs that work outdoors, there is the potential to get dirty, greasy or muddy on the job site. Some operators may also work in remote locations and have irregular schedules to match round-the-clock production or work that must be done late at night.
WHAT’S THE JOB OUTLOOK?
In Arkansas, the number of heavy equipment operator positions is expected to grow 6% in the coming years, slightly ahead of the national average. Heavy equipment operators who are versatile with several different types of equipment will find themselves more in demand than those who are proficient with only one kind of rig.
HOW MUCH CAN I MAKE?
• Lower range wages (bottom 10%) — $28,960 annually/$13.92 per hour
• Middle range wages (median) — $37,460 annually/$18.01 per hour
• Higher range wages (top 10%) — $48,850 annually/$23.49 per hour
WHAT DOES IT TAKE TO BE SUCCESSFUL?
• Hand-eye-foot coordination
• Mechanical skills
• Physical strength
• Comfortable with heights
• Building and construction
WHERE DO I LEARN THE CRAFT?
Many workers learn equipment operation on the job after earning a high school diploma or equivalent, while others learn by attending a two-year college.
Among two-year colleges, some may specialize in a particular brand or type of construction equipment, while others may incorporate sophisticated simulator training into their courses. This allows beginners to familiarize themselves with the equipment in a virtual environment before operating real machines.
Heavy equipment operators do not generally complete an apprenticeship program as workers in other trades do. In some cases, training is provided by equipment manufacturers, a trade union, industry groups or private companies.
New operators or operators-in-training may operate light equipment under the guidance of an experienced operator before moving up to heavier equipment such as bulldozers. Some construction equipment with computerized controls requires greater skill to operate. Operators of this equipment may need additional training and some understanding of electronics.
Construction equipment operators often need a commercial driver’s license (CDL) to haul equipment to job sites and may need special licenses for operating specific pieces of equipment.
HVACR technicians ensure people’s comfort by installing and maintaining heating, ventilation, air conditioning and refrigeration systems for homes and businesses. It’s a career field that demands a variety of skills of its technicians, and as long as summers are hot, winters are cold and food needs to be refrigerated, it’s a job that will never be out of demand.
WHAT DOES AN HVACR TECHNICIAN DO?
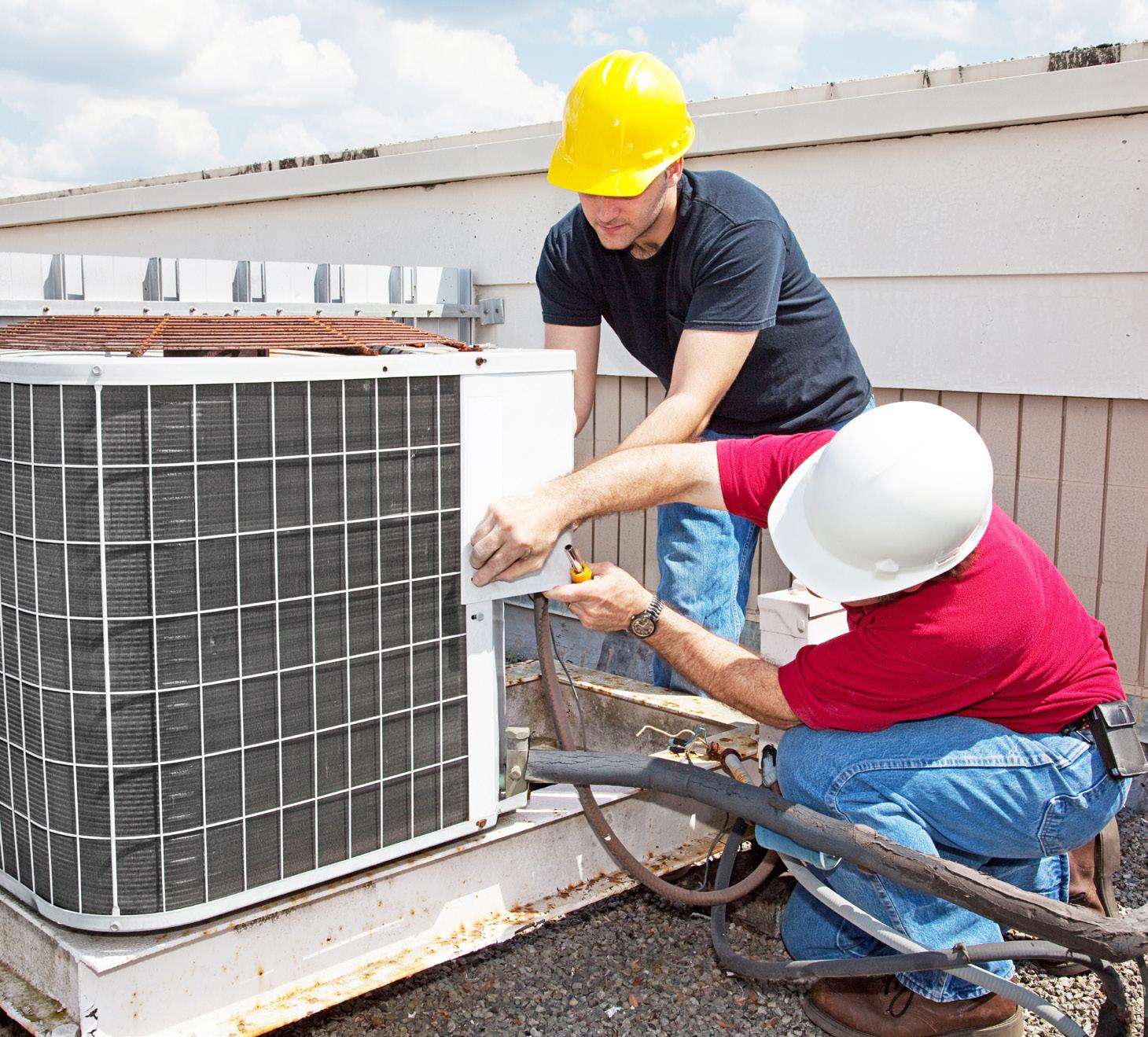
HVACR (sometimes written as HVAC-R) stands for heating, ventilation, air conditioning and refrigeration. HVACR technicians are specially trained individuals who install, service and maintain heating and air conditioning systems in homes, businesses and multi-unit residential.
HVACR technicians work with systems such as oil burners, boilers, heat pumps, central air conditioning and hot-air furnaces. They also work with components and appliances such as commercial grade ice makers, refrigerators and freezers. Some day-to-day duties include:
• Perform annual inspections and servicing.
• Replace old, outdated technology with more energy-efficient, greener models.
• Maintain ductwork that carries air from the heating or air conditioning unit to various parts of a building. Repair systems when they break down.
WHAT’S NEW?
Thermal-driven air conditioning
• Uses solar energy, backed up by natural gas on cloudy days or at night.
• Solar panels generate high enough temperature to drive a double-effect chiller.
• Provides a low-cost alternative to conventional air conditioning units.
Ice-powered air conditioner
• Another low-cost alternative to conventional air conditioning.
• Freezes 450 gallons of water in a tank overnight, provides cooling for up to six hours.
• Once ice melts, system switches to backup air conditioning unit.
Geothermal heat pump
Makes use of heat from the earth by way of looped piping placed into the ground.
• Fluid in this piping loop absorbs heat, which is carried back indoors to provide heating.
• Can also be used to supply cooling.
• Advertised to be up to four times more efficient than traditional systems. Smart thermostats
• Whole-house control systems that monitor and maintain climate control. Device “learns” owner preference and automatically adjusts rooms to those settings.
• Turns itself off when room is unoccupied; provides Wi-Fi enabled remote monitoring.
WHERE DO HVACR TECHNICIANS WORK?
A tech might work for a company that is appointment-based, going from home to home installing and maintaining cooling systems. Or, in industrial or commercial settings, techs might report to the same job site all day long for weeks at a time. Often, a HVACR tech’s van or truck is their office and workshop rolled into one.
HVACR techs may work full time, regular hours or they may be assigned at least part of the time to on-call to handle emergencies. These calls come in during business hours, on weekends and holidays, or in the middle of the night. After storms or blizzards and the normal changing of the seasons are almost guaranteed to generate a lot of overtime.
WHAT’S THE JOB OUTLOOK?
Demand for HVACR technicians and installers in Arkansas is expected to grow 6% in the coming years, per the U.S. Department of Labor. Arkansas’s job growth is expected to exceed that of the national average. To understand job growth, remember even the best HVACR system has a practical operating life of about 15 years. Imagine how many houses, apartments and commercial buildings are built or remodeled every year; that’s about how many systems need replacing.
HOW MUCH CAN I MAKE?
• Lower range wages (bottom 10%) — $29,010 annually/$13.95 per hour
• Middle range wages (median) — $38,440 annually/$18.48 per hour
• Higher range wages (top 10%) — $59,380 annually/$28.55 per hour
WHAT DOES IT TAKE TO BE SUCCESSFUL?
• Soft skills
• Active listening
• Communication
• Customer service
• Critical thinking/troubleshooting
• Mechanical/construction skills
• Physical skills/stamina
HOW DO I LEARN THE CRAFT?
HVACR technicians require specialized training and licensing. The level of complexity of today’s systems means most employers prefer to hire workers who have received specialized instruction after high school, either through a community college or a 3- to 5-year paid apprenticeship. Apprentices acquire their skills both in the classroom and on the job, with the cost of the training often paid for by the employer. In Arkansas, HVACR technicians are also required to hold one or more licenses, depending on job responsibilities. Following your formal training, you must sit for an exam to earn your license.
If you’re someone who likes a different challenge every day — and who enjoys being multifaceted enough to meet those challenges — then Industrial Maintenance may be the field for you. These skilled professionals are the go-to in any factory or industrial facility, trained to handle a number of situations. They are key players in keeping machinery rolling and the production schedule on time.
WHAT DOES AN INDUSTRIAL MAINTENANCE TECHNICIAN DO?
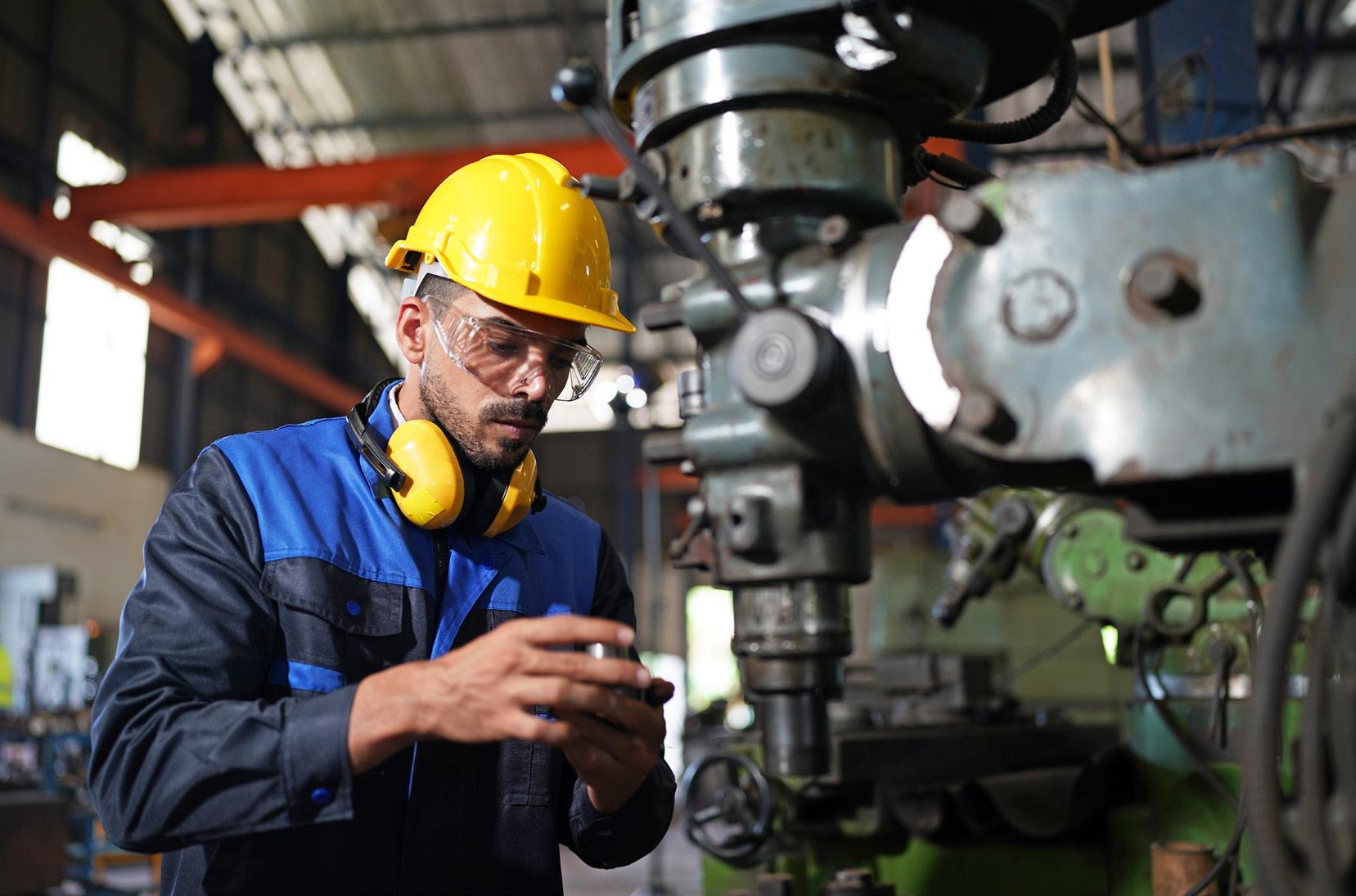
Industrial maintenance personnel are the mechanical experts in any manufacturing facility, trained to assemble, repair and service expensive equipment. They have a wide skill set that allows them to adapt to various situations.
Examples of machines they may work with are robotic welding arms, automobile assembly line conveyor belts, hydraulic lifts, production machinery and packaging equipment. Companies often consult with their industrial maintenance personnel before purchasing new equipment.
The industrial maintenance field can be broken down into the following job titles:
Industrial machinery mechanics
• Detect and correct errors before the machine damages itself or the product.
• Use technical manuals, understanding of industrial equipment and observation to determine the cause of a problem.
• Utilize computerized diagnostic systems and vibration analysis techniques to determine the cause of malfunctions.
• Disassemble malfunctioning machines, repair or replace parts, reassemble, then test.
• Work with hand tools; also utilize lathes, grinders and drill presses. Welding skills are often required.
Machinery maintenance workers
• Perform basic maintenance and repairs on machines.
• Clean, lubricate, perform basic diagnostic tests, check performance, test damaged machine parts.
• Following machine specifications and adhering to maintenance schedules, they also perform minor repairs.
• Use a variety of tools from screwdrivers and socket wrenches to hoists.
Millwrights
• Install, maintain and disassemble industrial machines.
Perform repairs, including replacing worn or defective parts of machines.
• May take apart entire machines to relocate them or make room for new equipment.
• Disassemble, categorize and package each part of the machine. These projects can take a few hours or can take several weeks.
WHERE DO INDUSTRIAL MAINTENANCE TECHNICIANS WORK?
The vast majority of these skilled professionals work in a manufacturing or industrial plant. A small percentage work for companies that specialize in industrial repair and maintenance. Most of these technicians are employed full time during regular business hours, but they may also serve on-call, night or weekend shifts. The majority of work is typically performed indoors.
Workers must follow safety precautions and usually wear some form of protective equipment, such as hardhats, safety glasses, steel-toed shoes, gloves and earplugs.
WHAT’S THE JOB OUTLOOK?
The outlook for this job sector is bright. Across three main job groups, job growth is forecast at 17% over the next several years, growing much faster than the national average in each field. Industrial machinery mechanic jobs are expected to grow 26%; machinery maintenance workers are expected to grow by 146% and millwrights will grow to 10% in the coming decade.
HOW MUCH CAN I MAKE?
Industrial Machinery Mechanics
• Lower range wages (bottom 10%) — $35,380 annually/$17.01 per hour
• Middle range wages (median) — $48,390 annually/$23.27 per hour
• Higher range wages (top 10%) — $76,600 annually/$36.83 per hour
Machinery Maintenance Workers
• Lower range wages (bottom 10%) — $29,780 annually/$14.32 per hour
• Middle range wages (median) — $46,420 annually/$22.32 per hour
Higher range wages (top 10%) — $59,850 annually/$28.78 per hour
Millwrights
• Lower range wages (bottom 10%) — $37,590 annually/$18.07 per hour
• Middle range wages (median) — $48,060 annually/$23.11 per hour
• Higher range wages (top 10%) — $61,050 annually/$29.35 per hour
WHAT DOES IT TAKE TO BE SUCCESSFUL?
• Mechanical skills
• Production/processing methods
• Math skills
• Repair/maintenance skills
• Operation monitoring
• Troubleshooting/diagnosis
HOW DO I LEARN THE CRAFT?
Most workers in this field have at least a high school diploma and, depending on the position, may complete some post-secondary education up to an associate degree. Industrial maintenance programs are generally offered through community colleges and may include courses such as welding, mathematics, hydraulics and pneumatics.
Industrial machinery mechanics may receive more than a year of on-the-job training and often receive some college coursework as well.
Most millwrights go through an apprenticeship program that lasts about four years, after which they can usually perform tasks with less guidance. Employers, local unions and contractor associations typically sponsor apprenticeship programs.
Imagine someone invents a new machine that will revolutionize the way a certain product is manufactured. Have you ever wondered where parts, instruments and components come from to build that machine? Machinists are industrial technicians that provide the solution and also produce parts and components for existing machines.
WHAT DOES A MACHINIST DO?
Long before anyone had ever heard of a “maker space,” there were machinists, trained craftspeople who produced parts and instruments using a variety of mechanical and computer-controlled machines. Machinists set up and operate a variety of computer- and mechanically controlled tools to fashion raw materials like metal and plastic into precision parts and instruments.
Many machinists today must be able to use both manual and computer numerical control (CNC) machinery. Workers may produce large quantities of one part, small batches or one-of-a-kind items. Parts range from simple steel bolts to titanium bone screws for orthopedic implants.
Because most machinists train in CNC programming, they may also write basic programs and often modify programs. These modifications, called offsets, fix problems and improve efficiency by reducing manufacturing time and tool wear.
WHAT’S NEW?
Remote smart operations
• The Internet of Things incorporates smart, connected devices, including smart sensors to improve control over equipment and deliver more insights.
• Various machines can operate autonomously, requiring human input or oversight only when something goes wrong.
• When there is a problem, IoT offers much better diagnostic capabilities helping technicians pinpoint and correct problems.
Laser-beam machining
• A thermal process for chip or material removal, also known as laser micromachining (LBM).
• A high-energy laser beam focuses on a component and the thermal energy transfers to the targeted surface.
• Laser beam machining is more widely adopted in manufacturing, particularly for carbon-fiber materials and more durable composites.
3D printing
• 3D printers can create products and components from a variety of raw materials, including concrete, wood, steel and an increasing range of metals, alloys, ceramics and metal-matrix composite materials.
• Hybrid machining incorporates both traditional CNC machining and 3D printing solutions to improve product development.
• Manufacturers have much more control over the goods they create. Materials and components can be printed right at a job site with an unlimited range of customization. Automated finishing systems
• Robotic-powered finishing systems are revolutionizing the quality and output of the machinist industry.
• Robotic abrasive blasting systems offer unmatched improvements in quality, efficiency, versatility and safety.
WHERE DO MACHINISTS WORK?
The vast majority of machinists work in manufacturing industries and independent machine shops. Maintenance machinists work in most industries that use machinery in manufacturing plants. Most machine shops are relatively clean, well-lit and ventilated, and many computer-controlled machines are partially or totally enclosed. Exposure to noise, debris and lubricants are greatly minimized. Workers must follow safety precautions, including wearing safety glasses and earplugs.
WHAT’S THE JOB OUTLOOK?
The outlook for this job is good. The U.S. Department of Labor predicts job growth of 9% in Arkansas, well ahead of the national average.
HOW MUCH CAN I MAKE?
• Lower range wages (bottom 10%) — $29,490 annually/$14.18 per hour
• Middle range wages (median) — $43,960 annually/$21.14 per hour
• Higher range wages (top 10%) — $80,300 annually/$38.60 per hour
Individual wages can fluctuate by industry, experience and skill level. Machinists can advance in their careers in several ways:
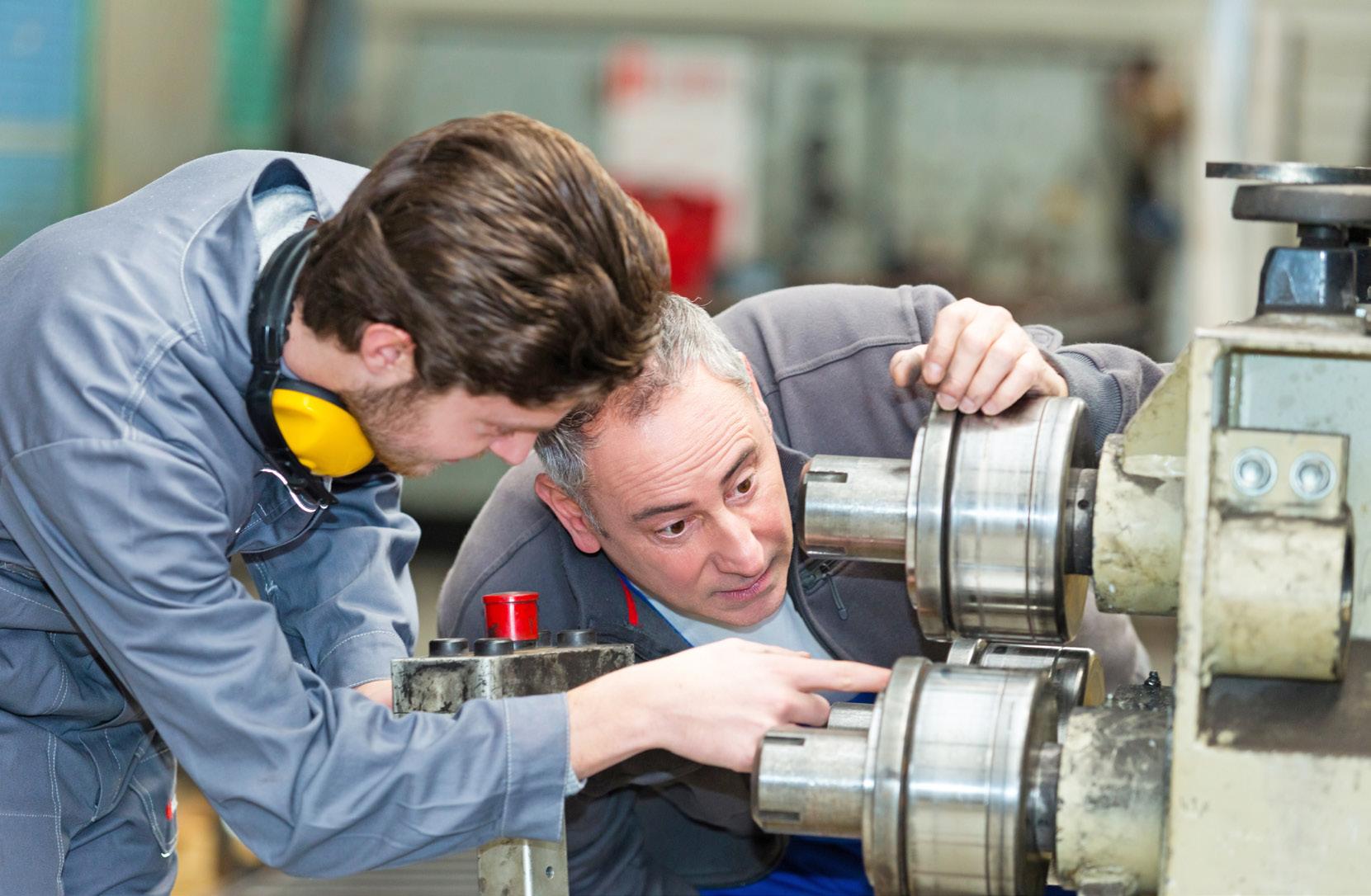
• Become CNC programmers.
• Become tool-and-die or mold makers. Be promoted to supervisory or administrative positions.
• Open your own machine shop.
WHAT DOES IT TAKE TO BE SUCCESSFUL?
• Physical strength/stamina
• Analytical and mathematical skills
• Attention to detail
• Mechanical/technical skills
HOW DO I LEARN THE CRAFT?
After earning a high school diploma or equivalent, some machinists learn entirely on the job. Others acquire skills in a mix of classroom and on-the-job training.
Formal training programs, typically sponsored by a union or manufacturer, are an excellent way to learn the job.
Training programs are often a combination of paid shop training and related classroom instruction and, depending on the program, can take months or years. Two-year college programs range from a couple of months to two years.
In Arkansas, machinists don’t generally serve an apprenticeship like other trades do.
WHAT DO PLUMBERS DO?
Plumbers build and maintain piping systems that are responsible for moving liquid, steam, natural gas, liquid fuel or waste from one place to another.
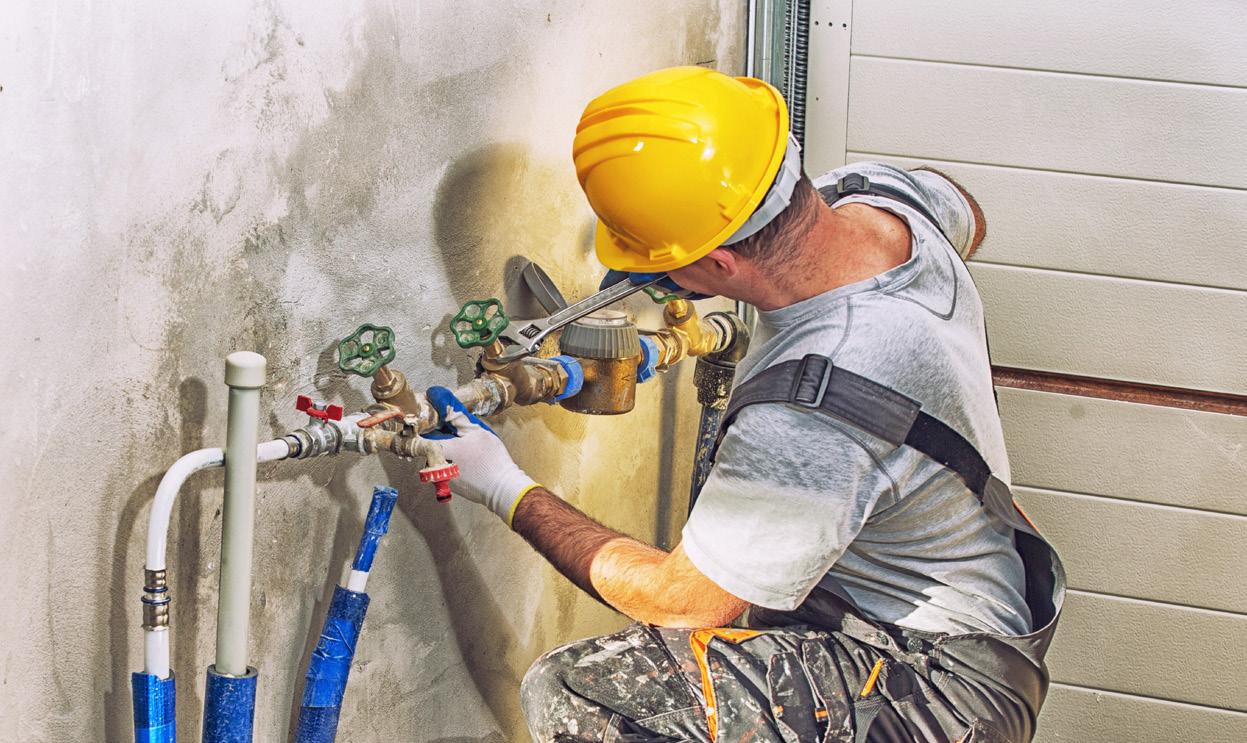
Day-to-day work activities include:
• Install and connect piping and fixtures, including welding metal components.
• Develop blueprints to plan pipes and fixtures within a structure.
• Make connections between the city’s water supply and homes and businesses.
• Install bathtubs, showers, sinks, toilets, dishwashers and water heaters.
• They may help design where the plumbing fixtures should go within the building.
• In industrial settings, they perform inspections, maintenance and new installation, handling fuel, wastewater and water used as a coolant, such as in nuclear power plants.
• Perform minor carpentry to repair or reconfigure systems, such as cutting holes in walls to access pipes or hanging supports to hold pipes in place
• Install and service septic systems.
• Perform functions related to gas lines, including installation, maintenance and replacement and proper installation of gas appliances.
Related jobs that utilize the same basic plumbing skill set while performing additional specialized work include:
Pipelayers
• Provide the major framework for outside plumbing systems by installing the pipe to build these systems.
• Construct oil and gas lines by soldering, welding or cementing them in place.
Pipefitters and steamfitters
The primary difference between pipefitters and steamfitters is pipefitters specialize in pipe systems that move liquids, while steamfitters specialize in pipe systems that move high-pressure liquids or gases.
• Pipefitters and steamfitters work with both high-pressure and low-pressure systems and install automated controls to regulate industrial systems.
Sprinklerfitters
A highly specialized plumber who installs and maintains automatic fire sprinkler systems in office buildings, manufacturing and industrial plants and multiunit residential properties.
• They may also work for landscape companies installing in-ground sprinkler systems.
Few skilled labor jobs provide as many different opportunities or are in as consistently high demand as plumbers. Whether working in new construction, industrial settings or running their own business, plumbers have the potential to earn very good wages over a long, successful career.
WHAT’S NEW?
“Brain Pipes”
• Smart home automation plumbing systems that allow the homeowner to conserve natural resources and reduce their water footprint.
• Smart pipes can monitor an entire home or building, sending the property owner an alert to any breaks or leaks.
Green Plumbing
• High-efficiency components designed to reduce water usage.
• Includes faucets, shower heads and toilets with lowflow flush capacity.
Smart Appliances
• Self-monitoring dishwashers, washing machines, water heaters and toilets.
• Computer chips control everything from wash settings and water temperature to water conservation modes and automated cycles.
• Appliances sync with smart devices to be controlled remotely.
Greywater Recycling
• Systems capture water from bathroom sinks, showers and washing machines that may contain traces of dirt, food or cleaning products.
• Systems redirect this water for use in watering residential yards and gardens or landscaping and flower beds outside corporations and office buildings.
WHERE DO PLUMBERS WORK?
With so many applications for a plumber’s skills, they can work in a wide range of environments:
If you work for a plumbing business that serves residential clients, or if you work for a manufacturing firm, you may work primarily daytime hours.
If you work for a company that does work in new construction, you could work outdoors in remote locations or put in overtime to keep up with production schedules.
Plumbers who are self-employed have some flexibility to determine their own schedules, but it takes a lot of work and “extra mile” service to get a business off the ground. Nearly all plumbers work “on call” at some point in their career, providing late-night and weekend emergency service.
There’s no denying that some of the material plumbers work with is unpleasant, particularly in the case of wastewater, backed-up toilets or malfunctioning septic systems. But that’s only one part of the plumbing industry. Plumbers who work for manufacturers and power plants often work in climate-controlled conditions. Building new piping systems is no more or less uncomfortable than any other craft at a job site.
WHAT’S THE JOB OUTLOOK?
Demand for this fundamental skilled job is growing, especially compared to other states. The U.S. Department of Labor predicts job growth of 6% in Arkansas, three times the national average.
HOW MUCH CAN I MAKE?
• Lower range wages (bottom 10%) — $29,010 annually/$13.95 per hour
• Middle range wages (median) — $45,660 annually/$21.95 per hour
• Higher range wages (top 10%) — $63,420 annually/$30.49 per hour
Some things that impact your earning potential include your license level (apprentice, journeyman, master) and any additional training or certifications you earn. For master plumbers who choose to start their own business versus working for an established firm, potential earnings are limited only by your skill, customer service and work ethic.
WHAT DOES IT TAKE TO BE SUCCESSFUL?
• Mechanical ability
• Building and construction expertise
• Design skills
HOW DO I LEARN THE CRAFT?
Plumbers begin their journey in an apprenticeship program. Apprenticeship training schools are specialized education centers sponsored by trade associations, unions, as stand-alone institutions and some two-year Arkansas colleges.
Apprenticeships range from 4- to 5-year programs and, typically, you are sent to apprentice school by your employer after hiring on with a company. What this means is, you work during the day, learning your craft under an experienced plumber, and attend class one or two nights per week for classroom instruction. It also means that your education is paid for by your employer.
After you complete your apprenticeship, you test for your journeyman’s license. A journeyman level plumber can work unassisted on most projects and can generally handle more advanced projects than an apprentice. Some people choose to test for their master’s license. Master plumbers represent the highest level of plumbers and therefore command the highest pay.
Have you ever taken part in a process and thought, “There has to be a better way to do this.” That’s the daily motto of process technicians, employees whose job it is to figure out better ways to produce items through manufacturing. Process technicians help companies make better products in ways that are safer, more efficient and therefore more profitable.
WHAT DOES A PROCESS TECHNICIAN DO?
Simply put, process technicians look for ways to build or produce things better. They are trained to look for inefficiencies in production and find ways to improve the process. By assisting industrial engineers, process technologists help integrate workers, machines, materials, information and energy to make a product or provide a service. They prepare machinery and equipment layouts, plan workflows, conduct statistical production studies and analyze production costs.
Process technology can be broken down into two main categories:
Chemical technician
Chemical technicians use laboratory instruments and techniques to help chemists and chemical engineers research, develop, produce and test chemical products and processes. Among their job duties are:
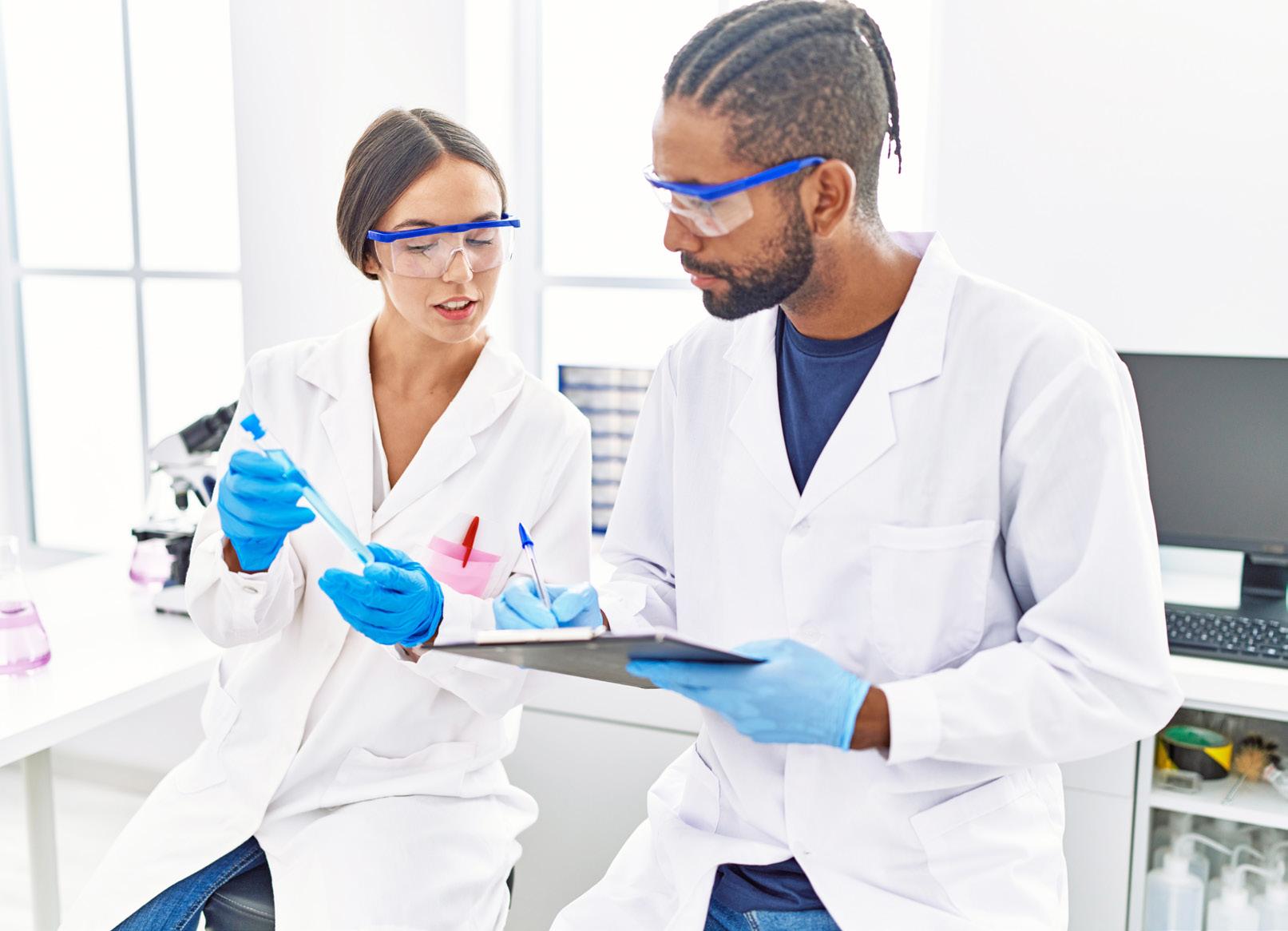
• Monitor chemical processes and test the quality of products to make sure they meet standards and specifications.
• Set up and maintain laboratory instruments and equipment.
• Troubleshoot production problems or malfunctioning instruments. Prepare chemical solutions.
• Conduct, compile and interpret results of chemical and physical experiments, tests and analyses for a variety of purposes, including research and development.
• Prepare technical reports, graphs and charts, and give presentations that summarize their results.
Industrial engineering technician
Industrial engineering technicians assist industrial engineers in devising efficient systems to make a product or provide a service. Industrial engineering technicians typically do the following:
• Suggest revisions to methods of operation, material handling or equipment layout.
• Interpret engineering drawings, schematic diagrams and formulas.
• Confer with management or engineering staff to determine quality and reliability standards.
• Prepare charts, graphs and diagrams to illustrate workflow, routing, floor layouts, how materials are handled and how machines are used.
• Collect data to assist in process improvement activities.
• Study the time and steps workers take to do a task through time and motion studies.
WHERE DO PROCESS TECHNICIANS WORK?
Process technicians typically work full time and inside, either in a factory, a lab or some other kind of manufacturing setting. They generally work regular business hours; however, some overtime may be required to meet project deadlines. Process technicians may also work irregular hours to monitor laboratory or plant operations during second and third shifts.
WHAT’S THE JOB OUTLOOK?
According to the U.S. Department of Labor, process technology jobs as a general category are expected to grow 9% in the coming years, almost double the national average. Your actual earning power depends on the company your work for, your level of experience and licensing, your years of experience and, in some cases, the part of the state where you work.
HOW
MUCH CAN I MAKE?
Chemical Technologist
• Lower range wages (bottom 10%) — $29,510 annually/$14.19 per hour
• Middle range wages (median) — $38,560 annually/$18.54 per hour
• Higher range wages (top 10%) — $62,660 annually/$30.12 per hour
Industrial Technologist
• Lower range wages (bottom 10%) — $35,440 annually/$17.04 per hour
• Middle range wages (median) — $47,860 annually/$23.01 per hour
• Higher range wages (top 10%) — $128,610 annually/$61.83 per hour
WHAT DOES IT TAKE TO BE SUCCESSFUL?
CHEMICAL:
• STEM concepts
• Critical thinking
• Information ordering
• Monitoring
• Deductive/inductive reasoning
INDUSTRIAL:
• Mechanical skills
• Engineering/technology concepts
• Production/processing concepts
• Mathematics
• Design
• Complex problem-solving
Products aren’t much good if they can’t get to customers and that’s where the trucking industry comes in. From over-the-road long-haul truckers driving coast to coast, to delivery drivers that bring goods to your door, everything you eat, wear or use has at some point in the supply chain been hauled on a truck.
WHAT DO TRUCK DRIVERS DO?
Truck drivers do just what their title says — operate heavy-duty trucks to transport loads from Point A to Point B. Truckers run on time schedules, with specified deadlines when loads have to be delivered, and they balance that with road conditions, speed limits and various other regulations to ensure the driver is operating in a manner that’s safe for themselves and other motorists.
But while the name itself is pretty self-explanatory, there are differences within the industry to consider. This article will focus on over-the-road (OTR) truck drivers, which can be divided into various categories:

Flatbed Truckers
• Flatbed trucks deliver freight secured to a trailer with no walls (hence “flatbed”) hauling such things a military vehicles, large machine parts or lumber.
Dry Van Truckers
• Dry van truckers drive what most people think of when they think of a semi — an enclosed trailer hauling nonperishable products and dry goods.
Tanker Truckers
• Tanker truckers transport liquids, which is one of the more difficult trucking operations, from food-grade loads like milk to fuel, chemicals or even hazardous waste.
Freight Haulers
• Freight haulers deliver goods that are not covered by dry van drivers. Freight haulers often transport liquids, oversized loads, hazardous goods, automobiles and logs on specially modified rigs.
Refrigerated Freight Drivers
• Refrigerated freight truckers deliver food, medical products, meat, body products and other highly perishable goods in temperature-controlled trailers.
WHAT’S NEW
The basics of trucking haven’t changed — deliver goods on time, safely — but as with every industry, technology has advanced, making trucks more comfortable, more fuel-efficient and loaded with various computerized systems from navigational GPS to monitors that ensure drivers don’t exceed speed limits or their allowable daily mileage.
The regulatory climate for trucking companies is also changing as states push to reduce emissions and air pollution caused by gasoline- and diesel-powered engines. California and New York, among other states, have mandated that trucking companies replace their existing fleets with electric vehicles over the next couple of decades, which is controversial considering electric truck technology is not yet suited for long hauls, nor are charging stations readily available nationwide.
WHERE DO TRUCK DRIVERS WORK?
Over-the-road truck drivers may follow a set territory or they may go anywhere in the lower 48 states, plus Canada and Mexico. Truck routes range from a few days out and back to cross-country runs that keep drivers out for several weeks at a time.
The truck itself is both the driver’s home and office while they are on the road, as most rigs are outfitted with a sleeper compartment. In some cases, drivers will work in two-person teams, which allows for covering more miles per day than driving alone. It also provides companionship and assistance while out on a run.
WHAT’S THE JOB OUTLOOK?
Truck driver jobs in Arkansas are expected to grow 8% in the coming decade, twice the national rate for the coming decade.
HOW MUCH CAN I MAKE?
• Lower range wages (bottom 10%) — $25,700 annually/$12.36 per hour
• Middle range wages (median) — $47,990 annually/$23.07 per hour
• Higher range wages (top 10%) — $72,810 annually/$35.01 per hour
It should be noted that earning power varies widely with the type of loads you can handle, as some drivers have earned special certifications and therefore command more money. Also, the current shortage of drivers has driven up wages all over the country, with some companies offering handsome sign-on and retention bonuses to keep their fleets running.
And, unlike in past generations, trucking companies today also provide a full slate of benefits for drivers that rival anything to be found in a white-collar job. For example, Arkansas-based J.B. Hunt, one of the largest trucking and logistics companies in the world, advertises medical, dental, vision and prescription coverage, various types of life, accident and disability insurance, a company-matching 401(k) plan, paid vacation and various bonus programs.
WHAT DOES IT TAKE TO BE SUCCESSFUL?
• Mechanical skills
• Attention to detail
• Record-keeping
• Problem-solving
• Physical strength and stamina
HOW DO I LEARN THE CRAFT?
Learning to operate a semi generally happens at schools set up for that purpose, although some community colleges also offer this instruction. On average, trucking school takes three to five weeks to complete while two-year schools’ programs can be completed in a semester or two.
Once training is completed, drivers must pass a test to get their commercial driver’s license (CDL), required to operate semis, buses and other heavy, oversized vehicles. In Arkansas, 18-year-olds can drive commercial motor vehicles within state lines. Drivers must be 21 to drive commercial vehicles across state lines, haul hazardous materials that require placarding or operate a vehicle with double or triple trailers.
The welding profession is one of nearly unlimited opportunity. Welders work in a wide range of industries and work environments, are in high demand, command good wages and even launch their own businesses. For a person with the right skills and work ethic, welding is one of the most stable skilled professions one can have.
WHAT DOES A WELDER DO?
In the simplest terms, welders are skilled professionals who join two pieces of metal using heat and gas in order to seamlessly and permanently bond them.
The type of welding used on any given job depends on the materials. Welding is the most durable way to join two parts, using electrical currents to create heat and bond metals together. In all, there are more than 100 different processes that a welder can use, four of the most common being:
GMAW (Gas Metal Arc Welding)
• More commonly known as MIG (metal inert gas) welding, this type is among the most easily mastered type of welding.
• Acceptable for fusing mild steel, stainless steel and aluminum.
Arc Welding
• Arc welding is also known as SMAW (shielded metal arc welding) or stick welding.
• The most basic type of welding.
• Commonly used in manufacturing, construction and repair work.
FCAW (Flux-Cored Arc Welding)
• Developed as a lower-cost, high-speed alternative to stick welding.
• Known for being easy to learn.
• Commonly used to bond iron and steel; used in manufacturing, construction and repair work.
GTAW (Gas Tungsten Arc Welding)
• Commonly known as TIG (tungsten inert gas) welding.
• Delivers a superior finish without requiring a lot of finish sanding or grinding.
• Very complex process, requiring a welder with a lot of experience to perform well.
WHAT’S NEW?
Most people have at least a general idea of what a welder is and what he or she does. But did you know there are two related processes that perform many of the same functions as welders, but use different tools and bonding elements? These jobs aren’t new, exactly, but most people outside the industry haven’t heard of them.
Cutters
• Utilize heat from an electric arc, plasma stream or burning gases to cut and trim metal objects to specific dimensions.
• Cutters also take apart large objects such as ships, railroad cars, boilers and aircraft using special highstrength cutting materials. Solderers/brazers
• Use heat to join two or more metal objects together.
• Soldering and brazing are similar, except that the temperature used in soldering is lower.
• Soldering is used to make electrical and electronic circuit boards, such as computer chips.
• Brazing is used to connect cast iron and thinner metals that would warp under the high temperature of welding.
WHERE DO WELDERS WORK?
As the most common and most permanent way of joining pieces together, welding is a trade that performs work as a stand-alone component of larger projects or is used within another trade.

Plumbers are generally trained in the basics of welding in order to perform pipefitting tasks. Other industries use welding as part of their overall operations, including body shops, sheet metal, shipyards and boilermaking operations.
A welder may work on a building or bridge construction site (either indoors or outdoors), which exposes them to working in all kinds of weather. They may also be required to work several stories above the ground on steel building structures or bridges.
Other welders work in a metal shop or garage-like area, which is generally climate controlled. Still other welders work in a factory or industrial setting where they handle maintenance and fabrication tasks as they come up. Welders generally work full time and it’s not uncommon for them to work a lot of overtime to stay ahead of production schedules, particularly in construction. In some industrial settings, welders may be employed on overnight shifts.
WHAT’S THE JOB OUTLOOK?
As one of the most versatile skilled careers out there, welders are facing a bright future when it comes to job security. According to the U.S. Bureau of Labor Statistics, welding jobs in Arkansas are expected to grow by 10%, five times the national average. This makes Arkansas an excellent place to build your career.
Some welders move from construction job to construction job, meaning a general slowdown in building projects can mean periods of unemployment. The more mobile a welder is, the more easily he or she may find additional projects.
HOW MUCH CAN I MAKE?
Lower range wages (bottom 10%) — $29,190 annually/$14.04 per hour
• Middle range wages (median) — $37,760 annually/$18.16 per hour
• Higher range wages (top 10%) — $50,450 annually/$24.26 per hour
WHAT DOES IT TAKE TO BE SUCCESSFUL?
• Physical strength and dexterity
• Vision
• Attention to detail
HOW DO I LEARN THE CRAFT?
Some high schools have beginner welding programs as part of automotive or shop classes, which can give students a head start on their education.
Most welders have a high school diploma or equivalent and a professional certification, which can be earned through a community college, a private training program or welding courses sponsored by industry groups or trade unions.
Welding programs can be a few months long or they can be an apprenticeship lasting four or five years. They can be full-time classes like any other college curriculum or, in the case of many apprenticeship-type training programs, are held one or two nights a week while the student works full time for a welding company, thereby also learning on the job.
Another advantage of the work-study nature of apprenticeship programs is most employers pay for the training as an employee benefit.